Procurement Quality & Supply Chain PQDR — User

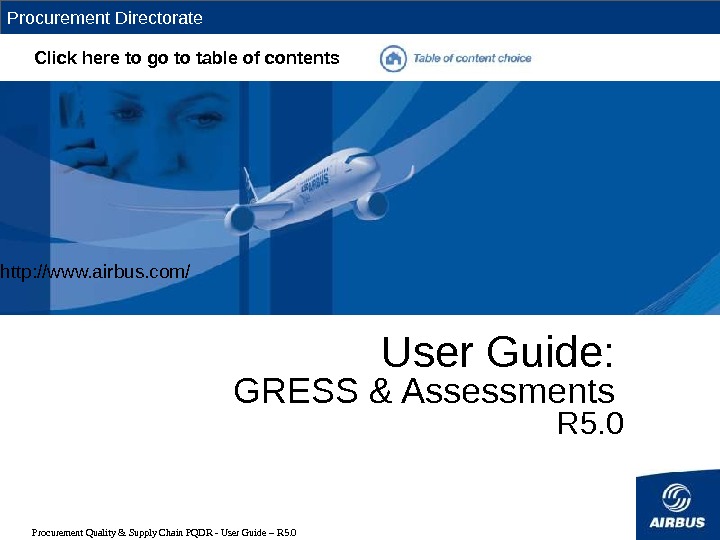
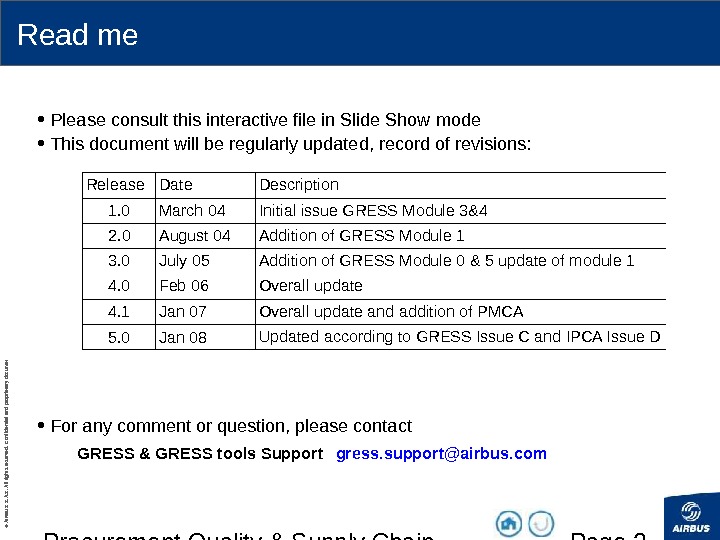

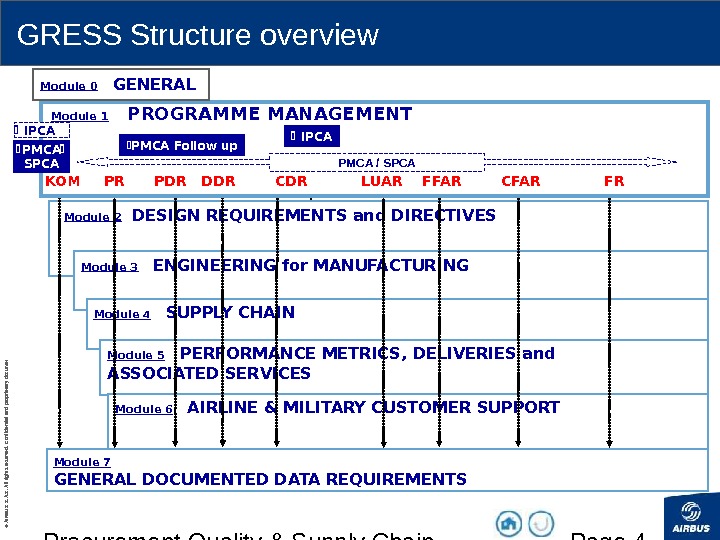




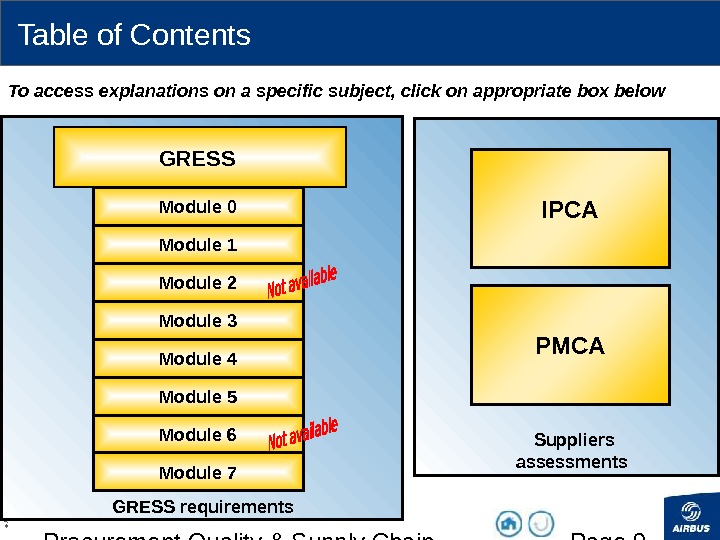
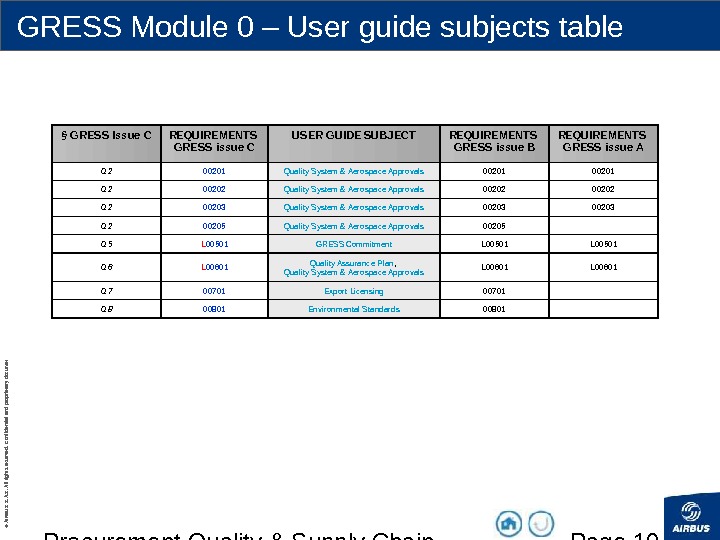
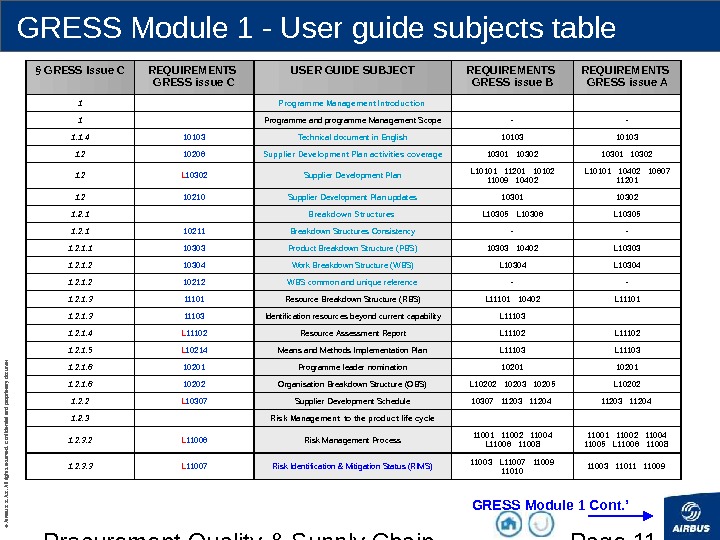
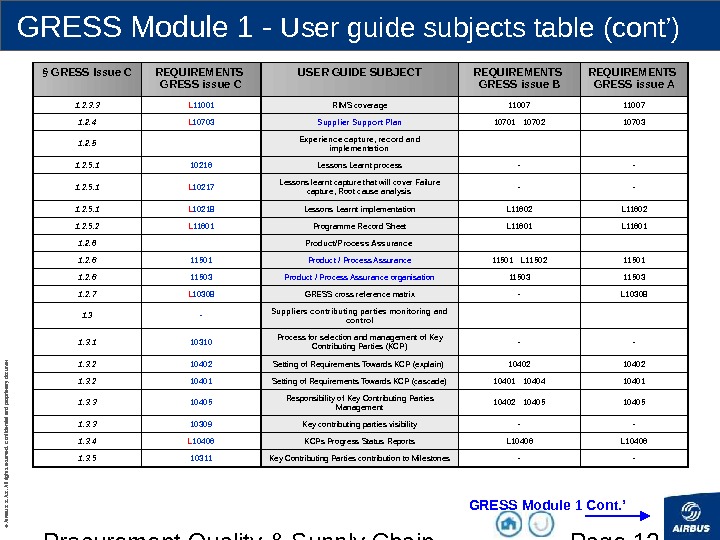
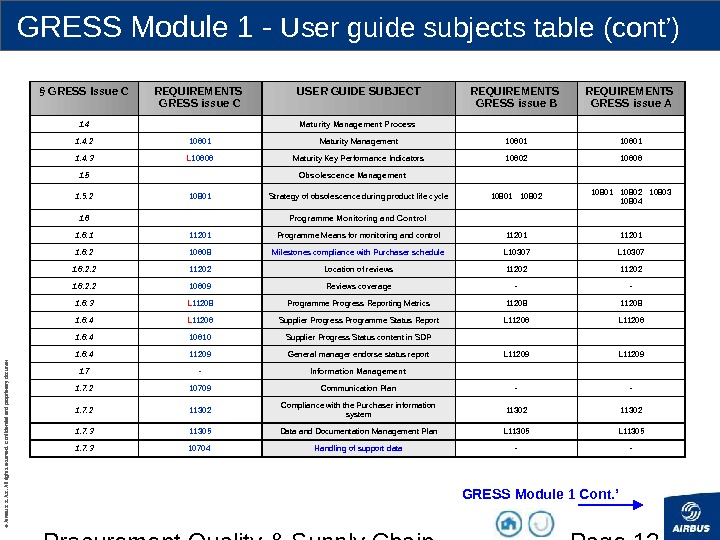
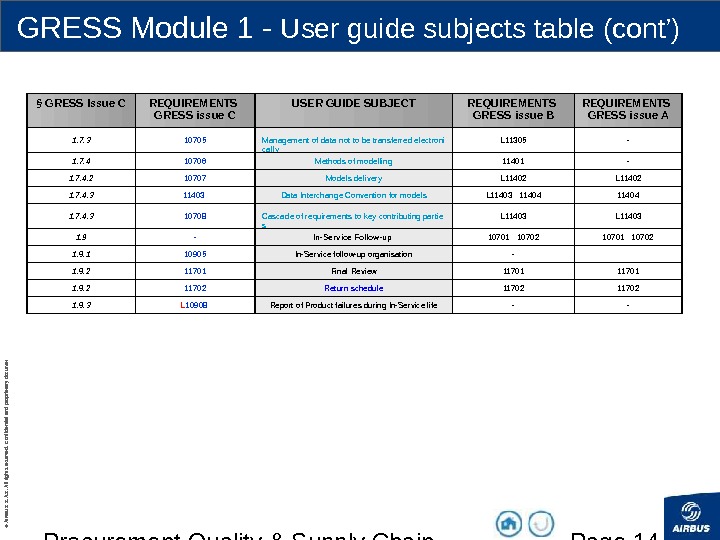
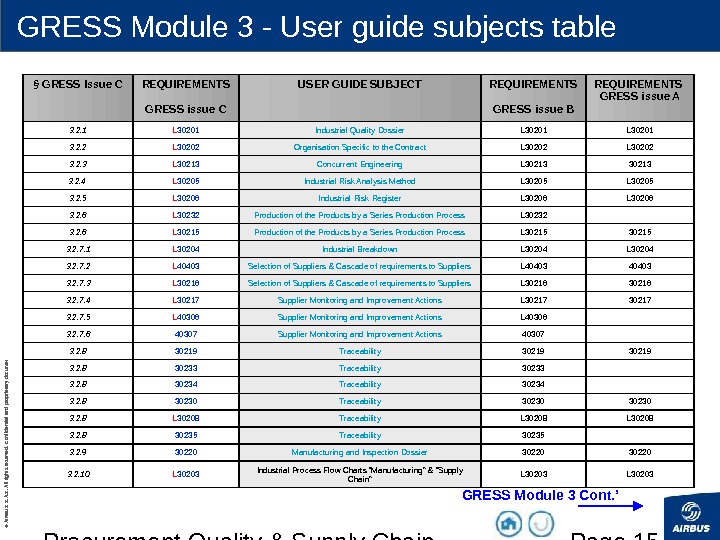
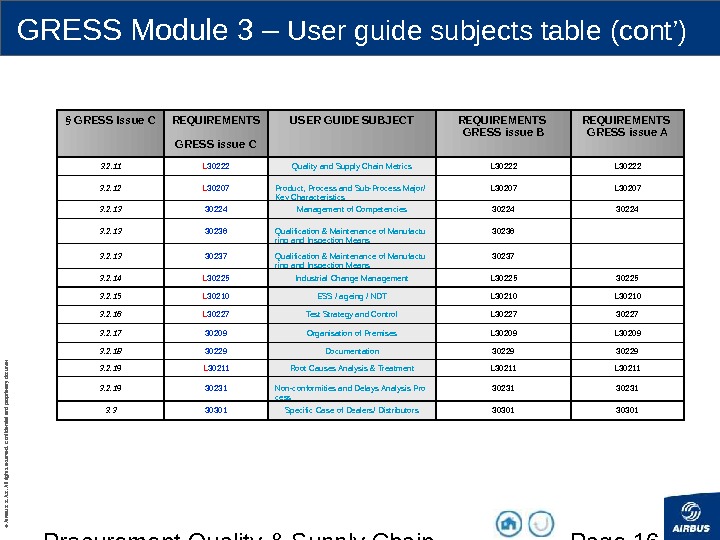
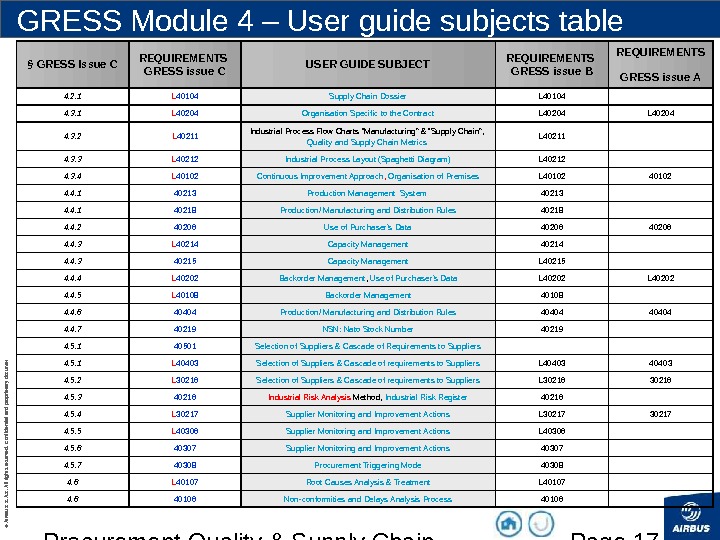
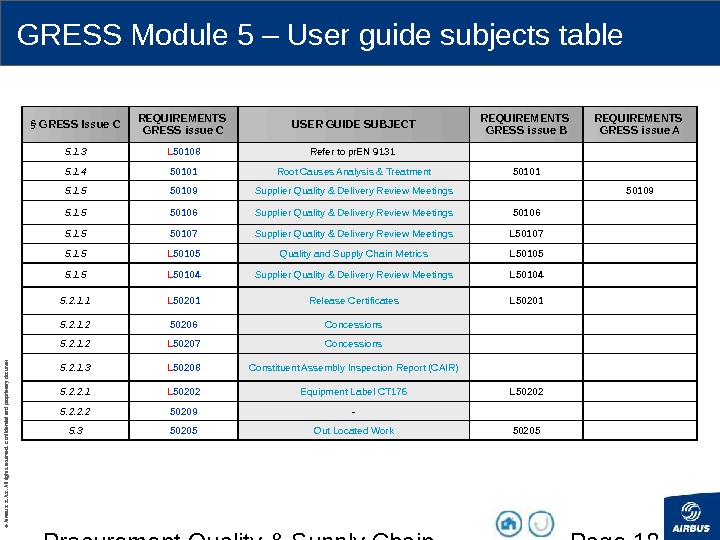
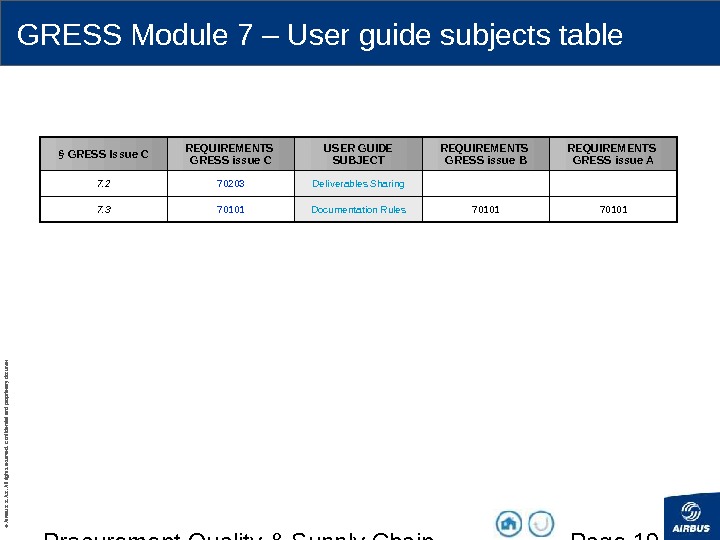
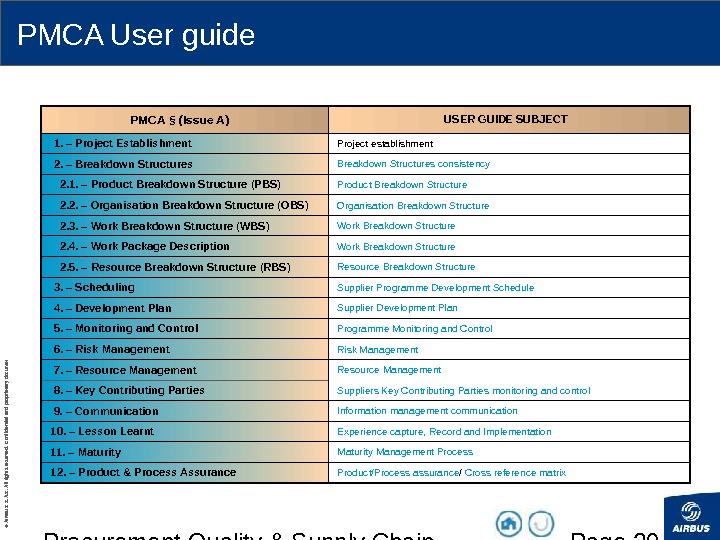
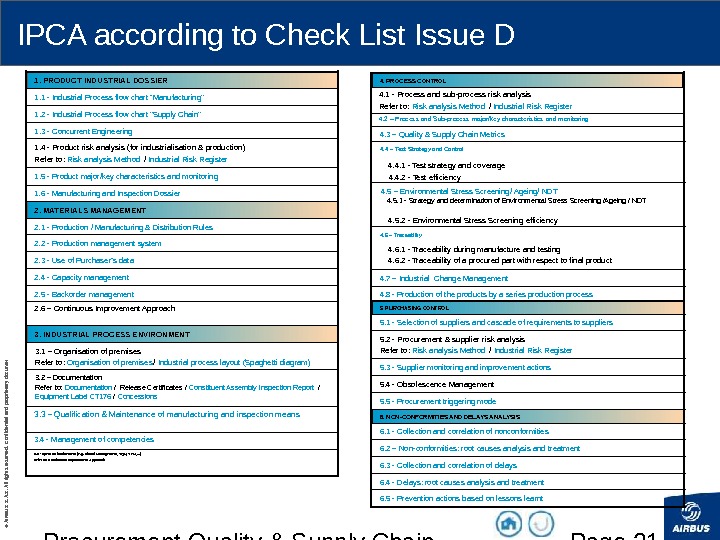
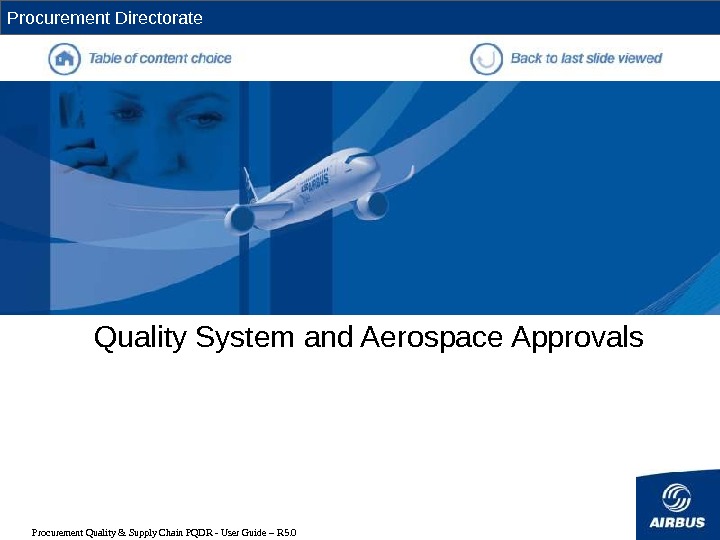
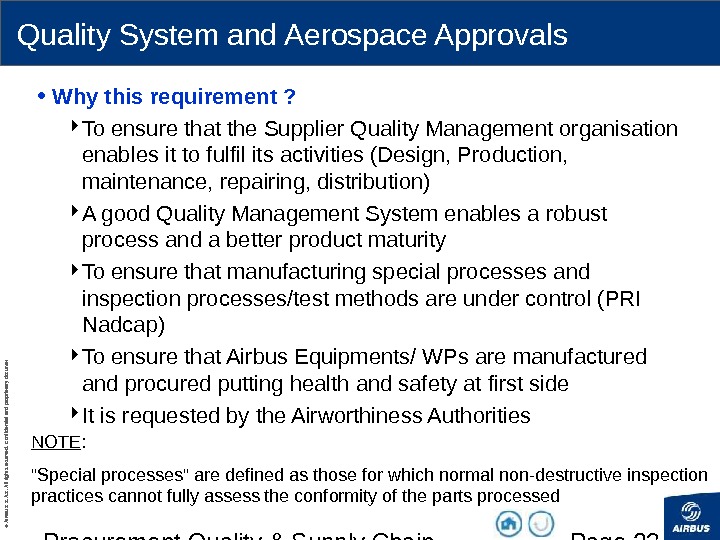
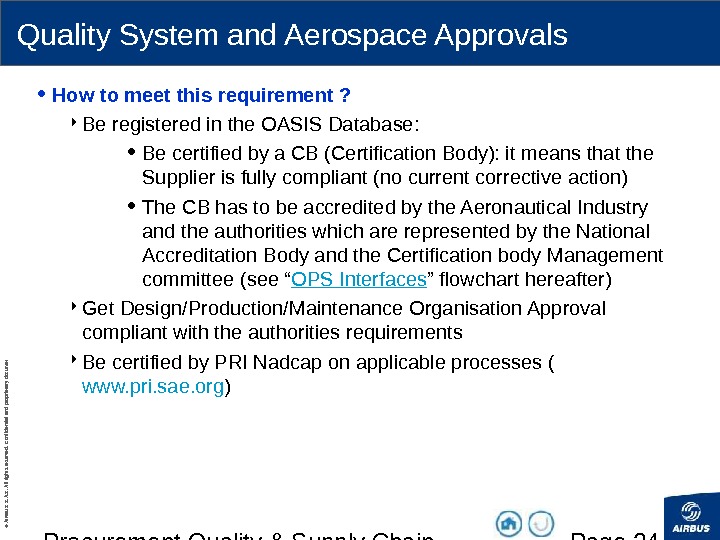
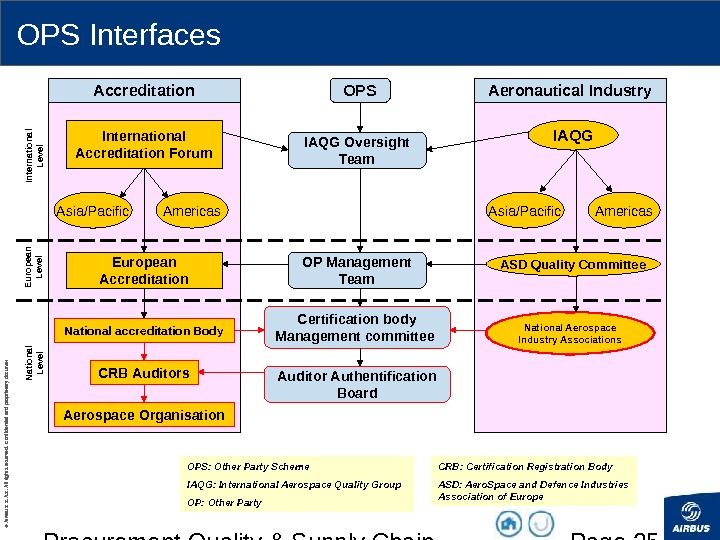
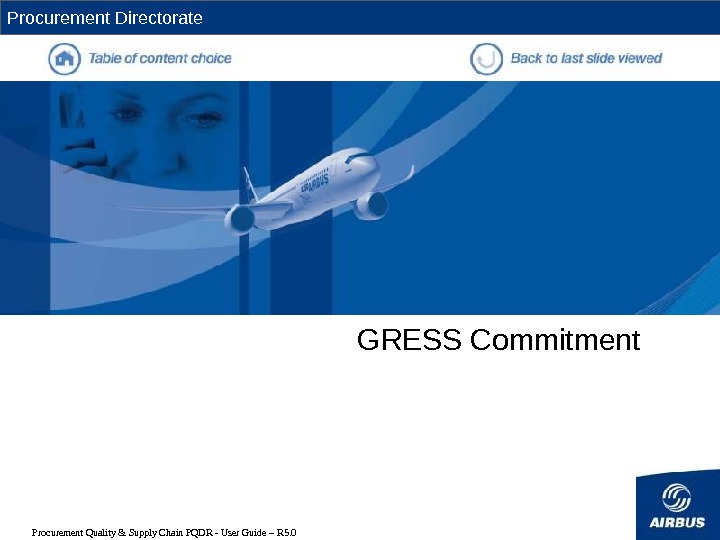
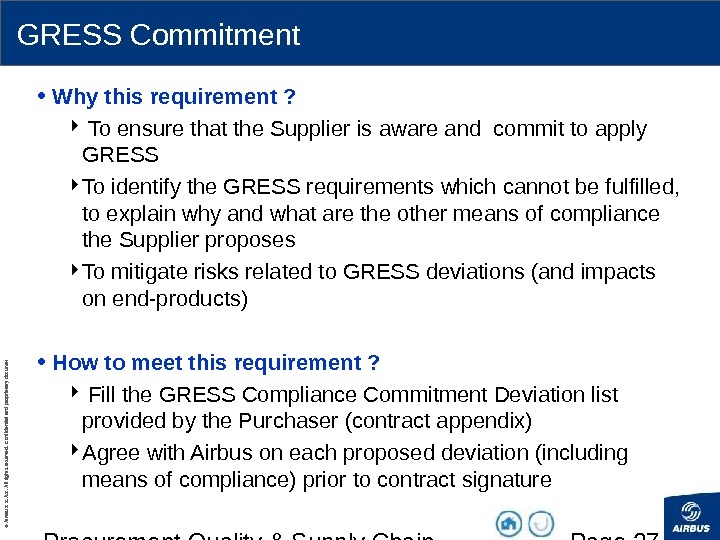
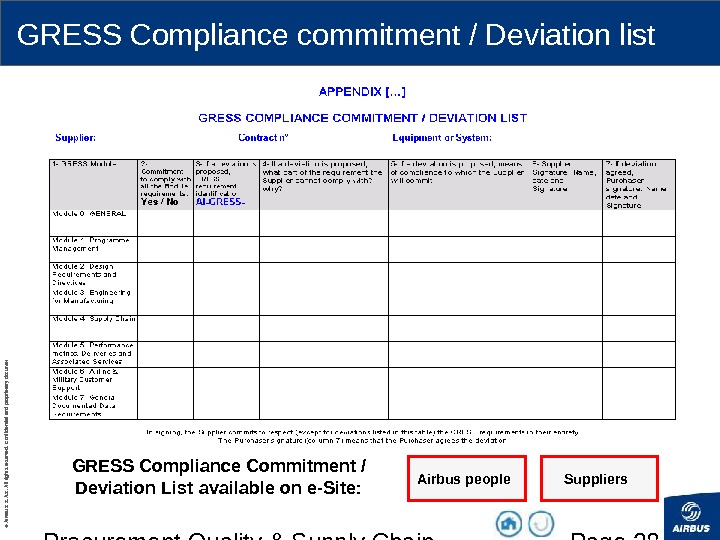
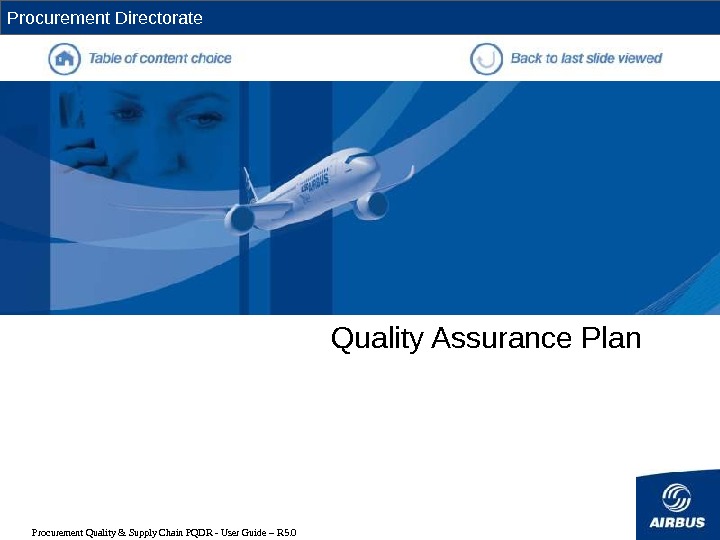
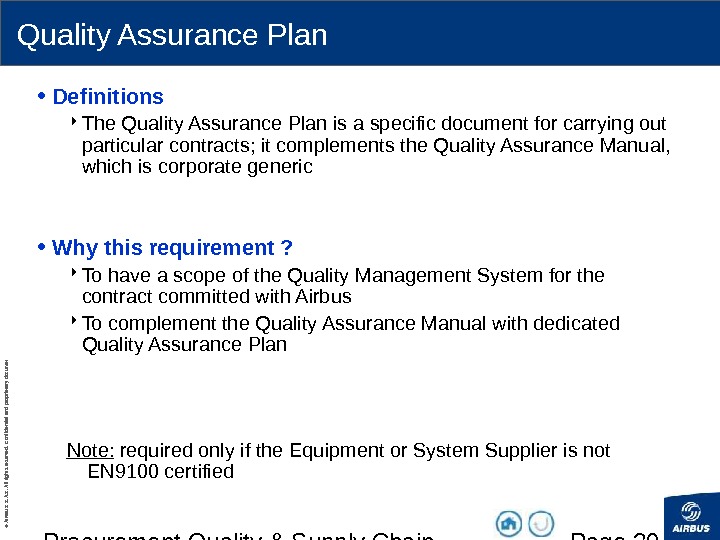
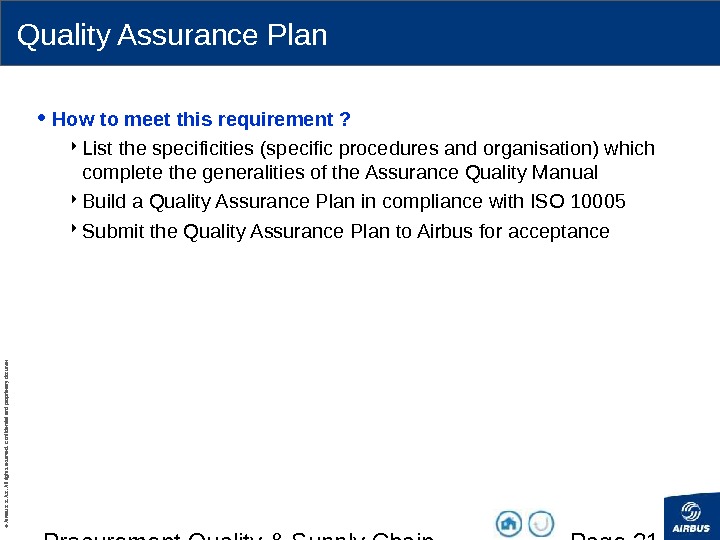
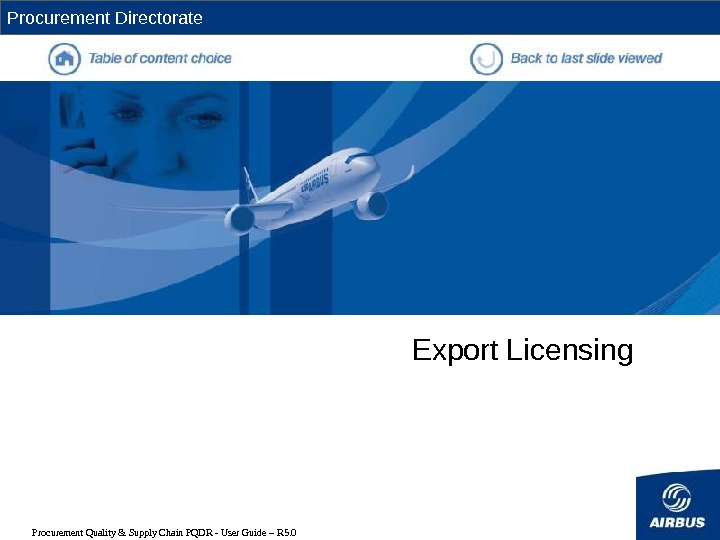

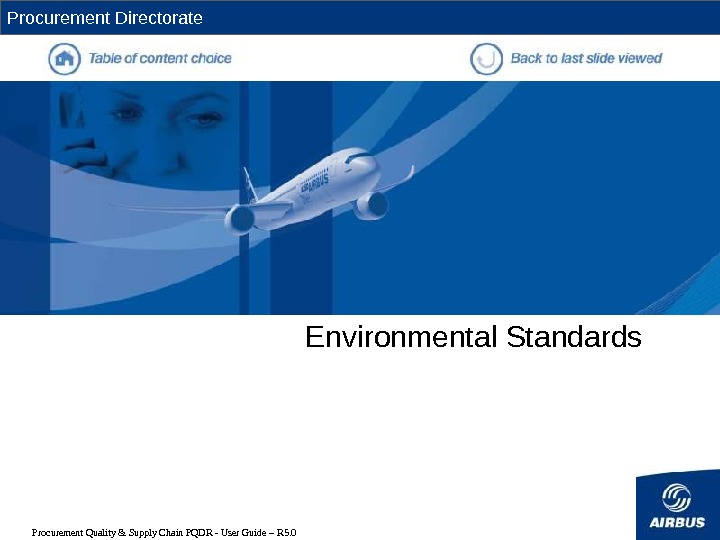
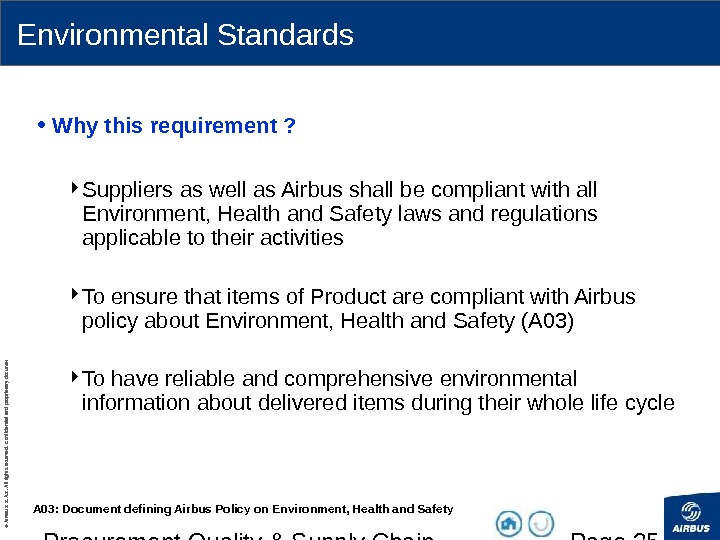
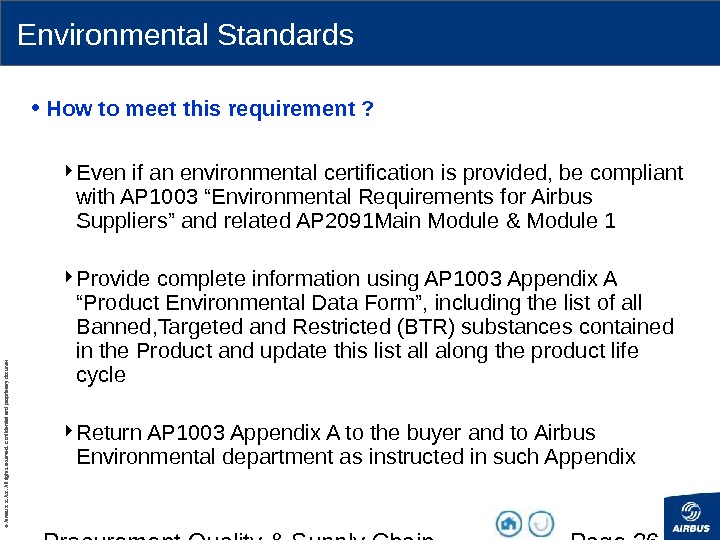
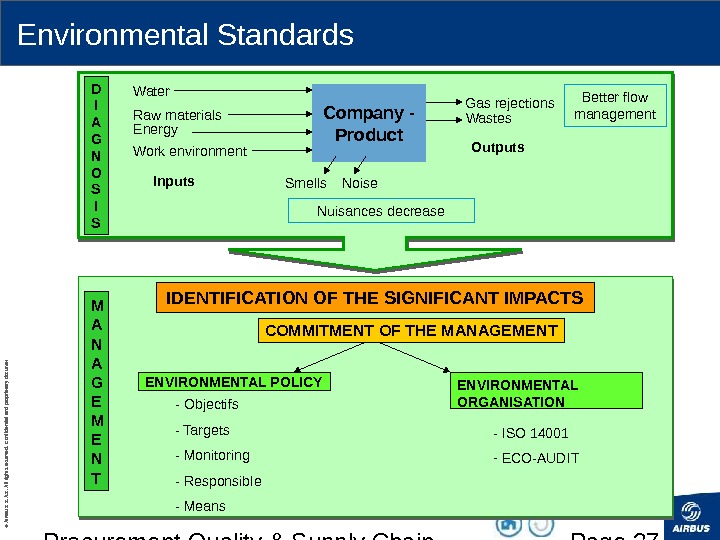
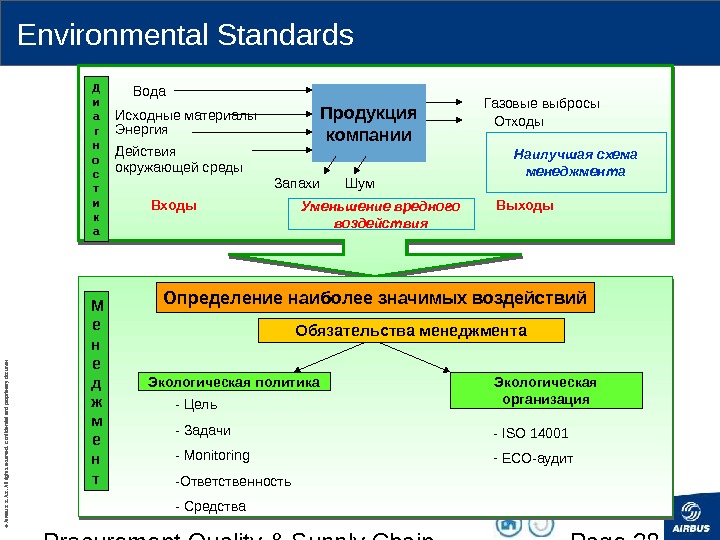
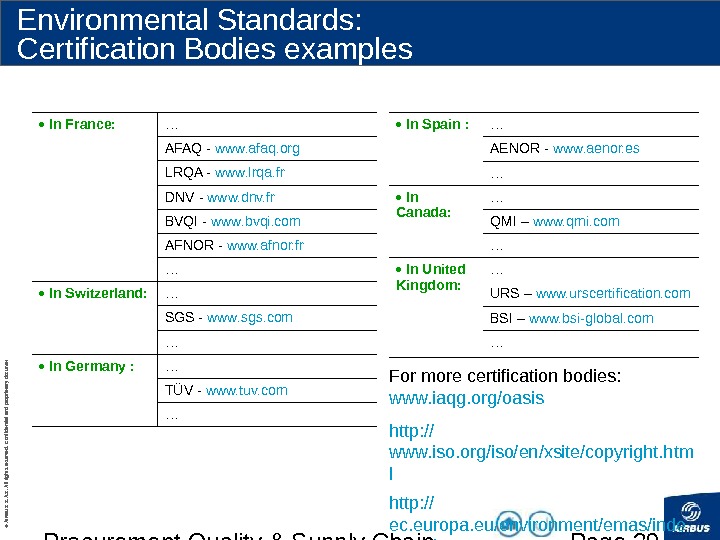
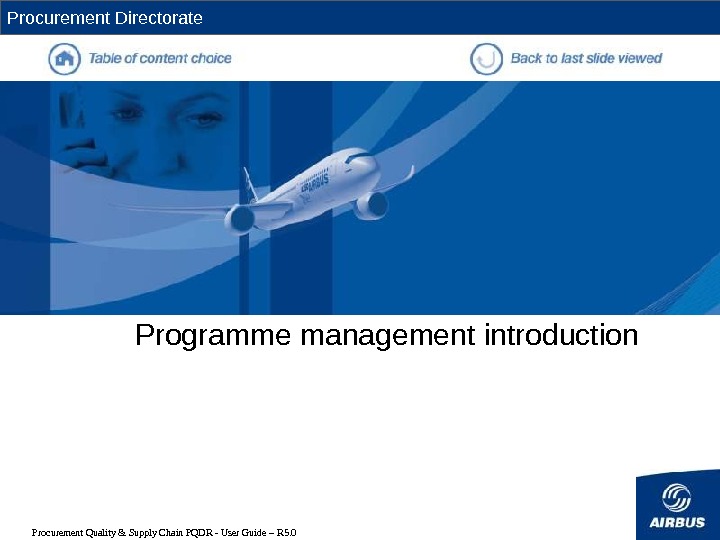
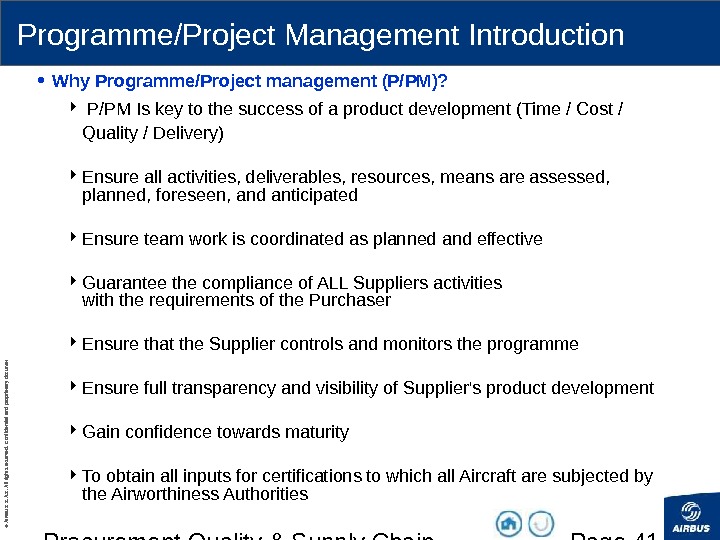

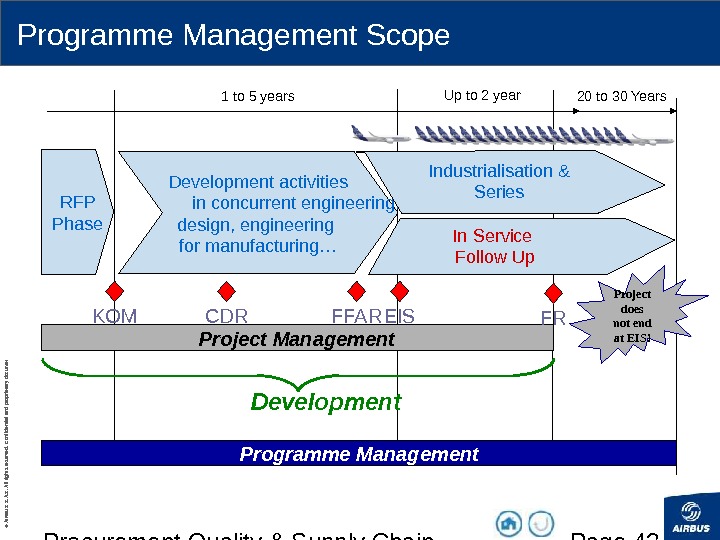
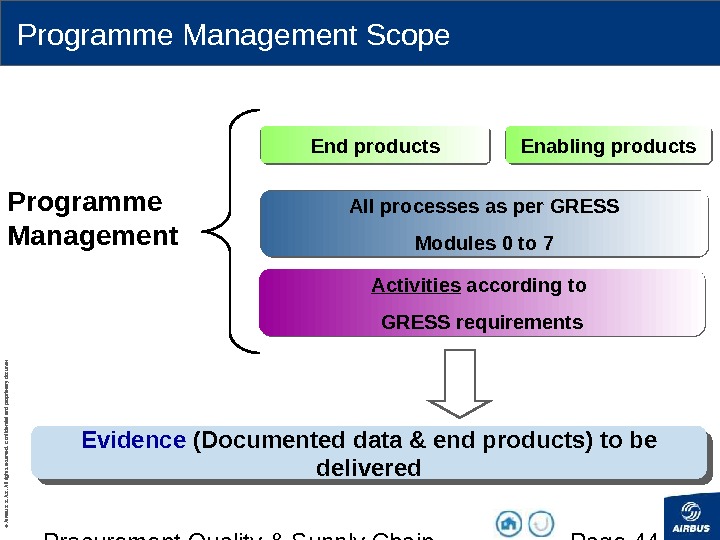
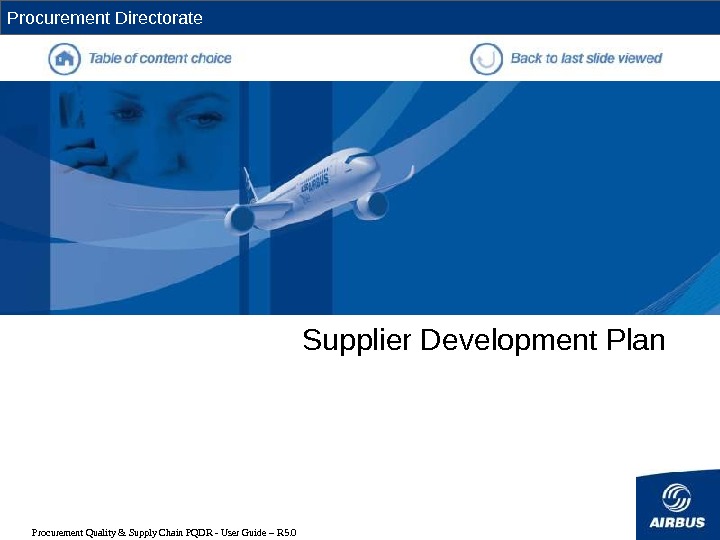


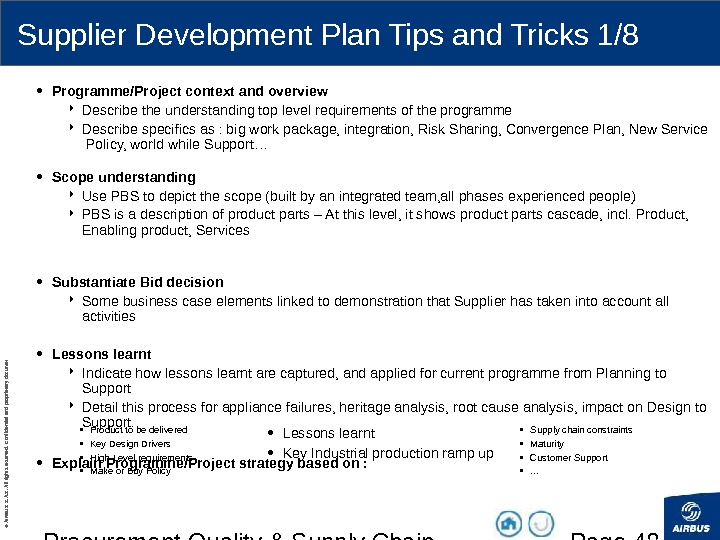
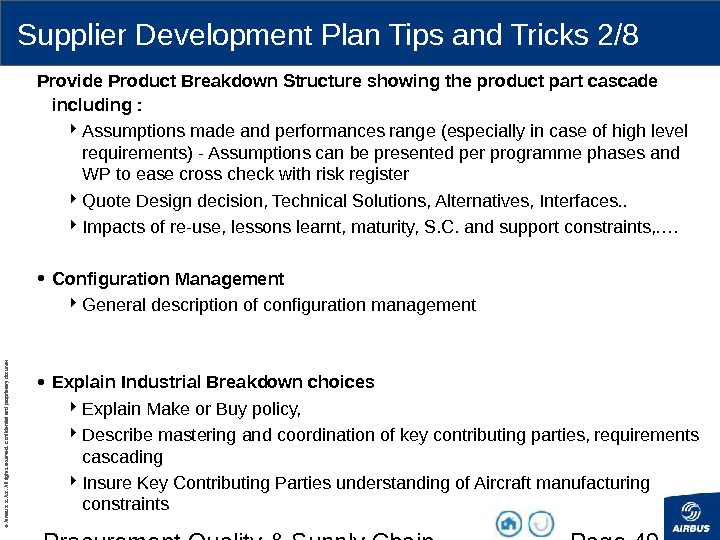
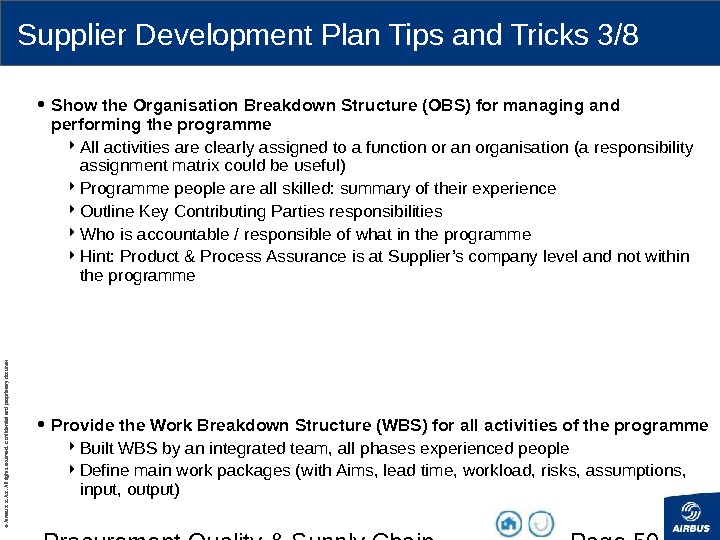
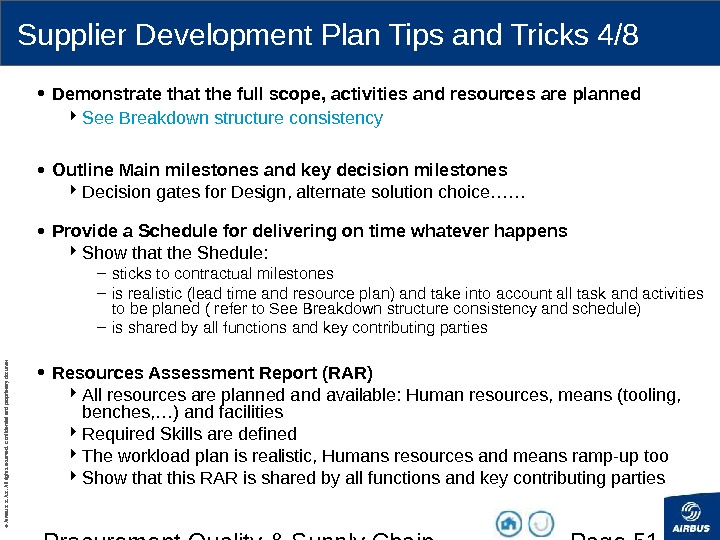

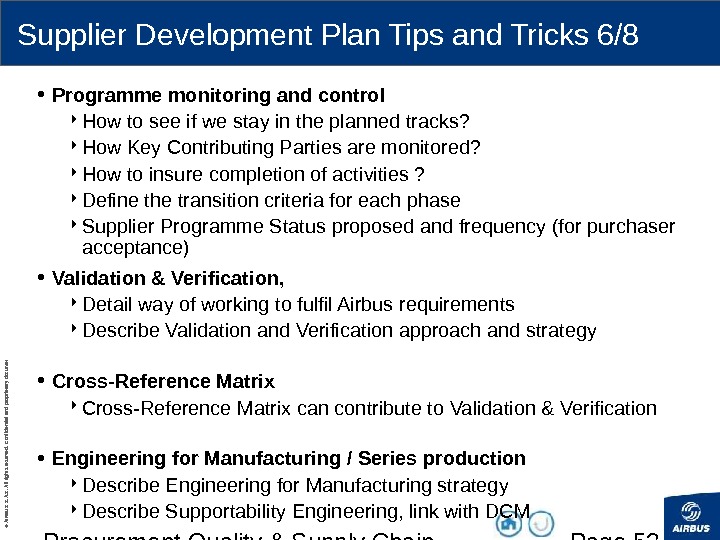


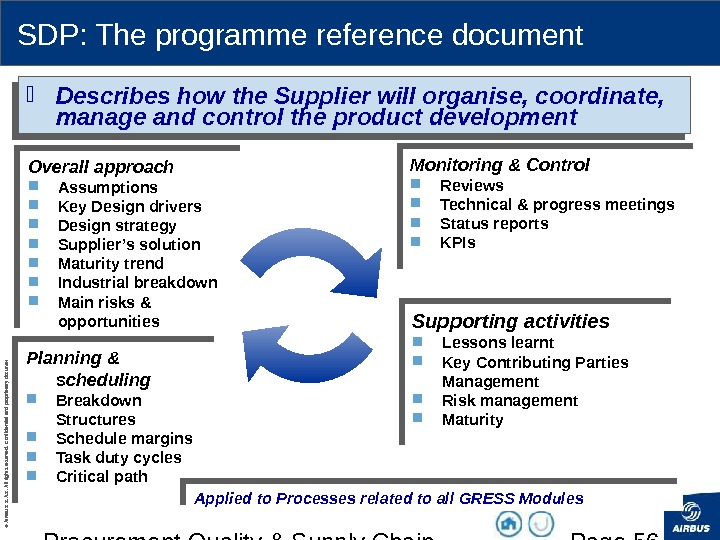
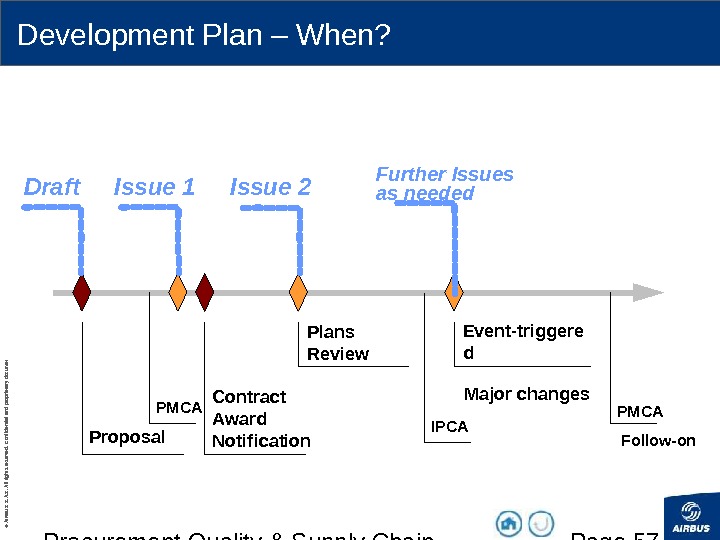
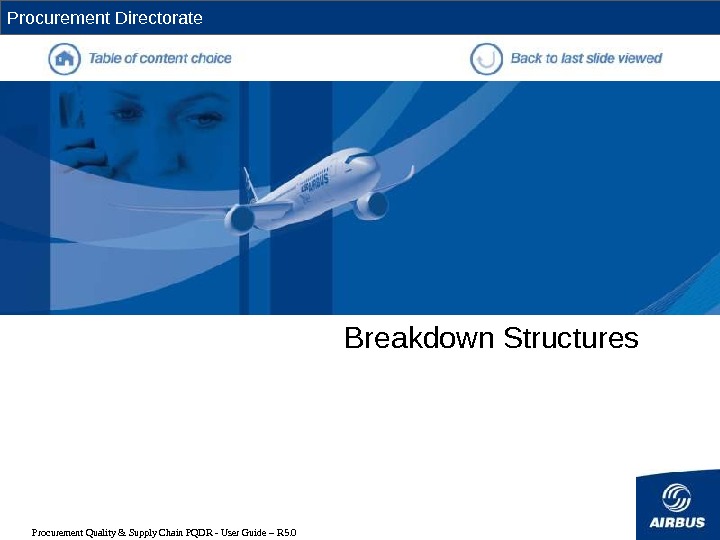
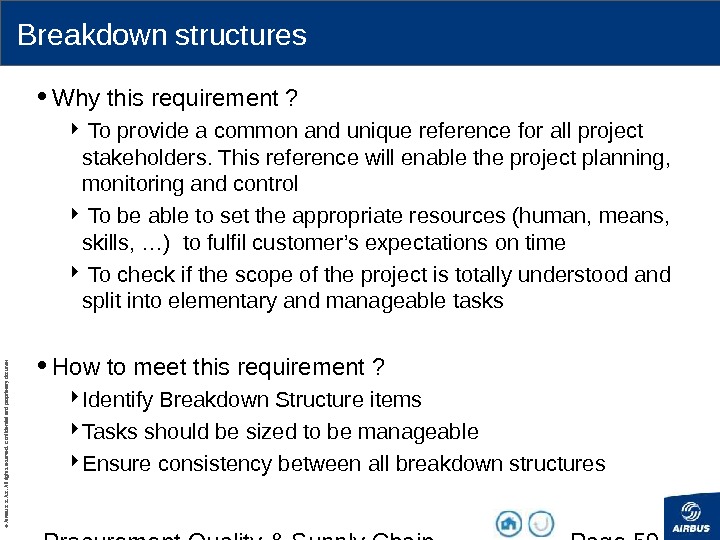
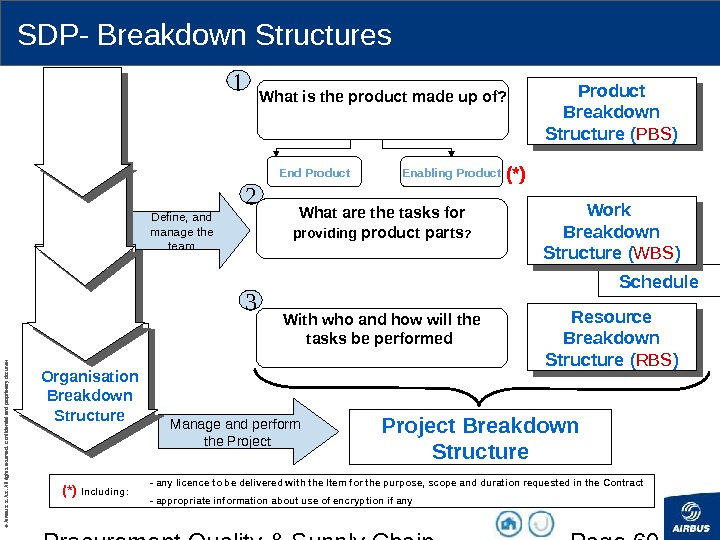
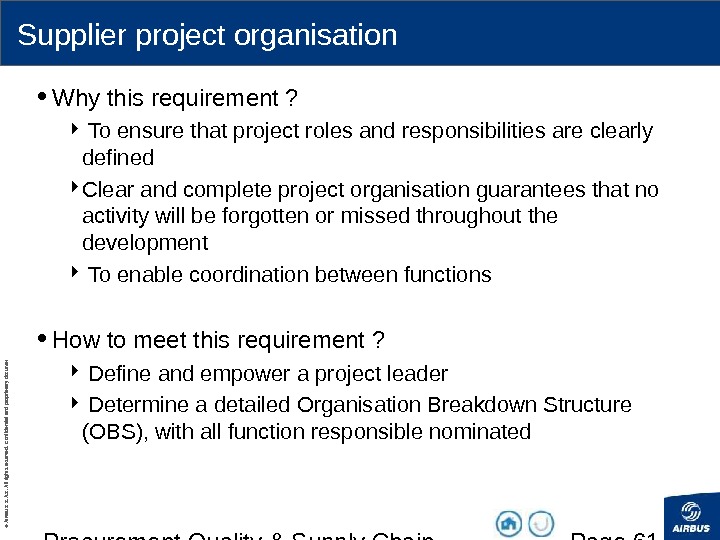
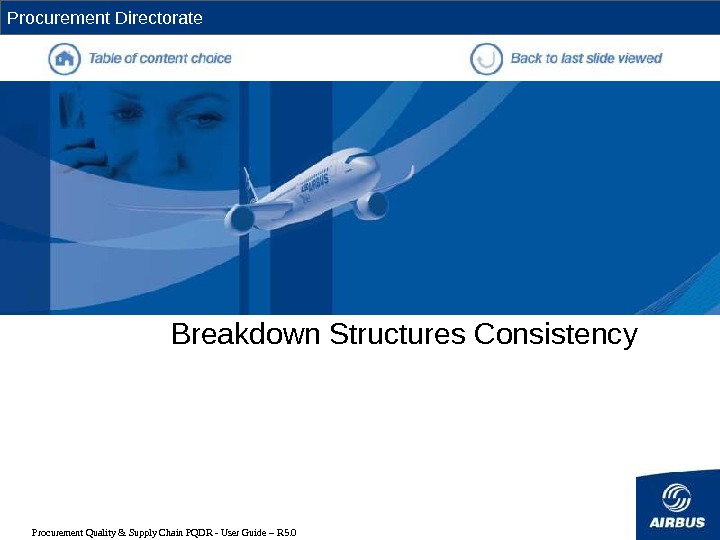
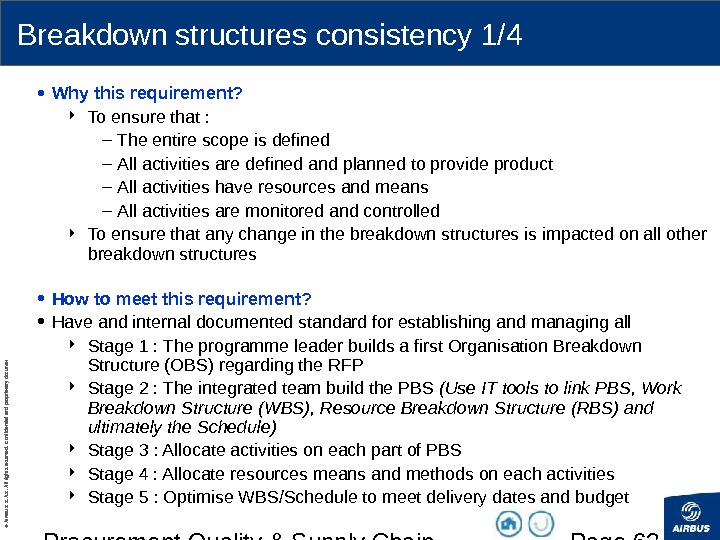

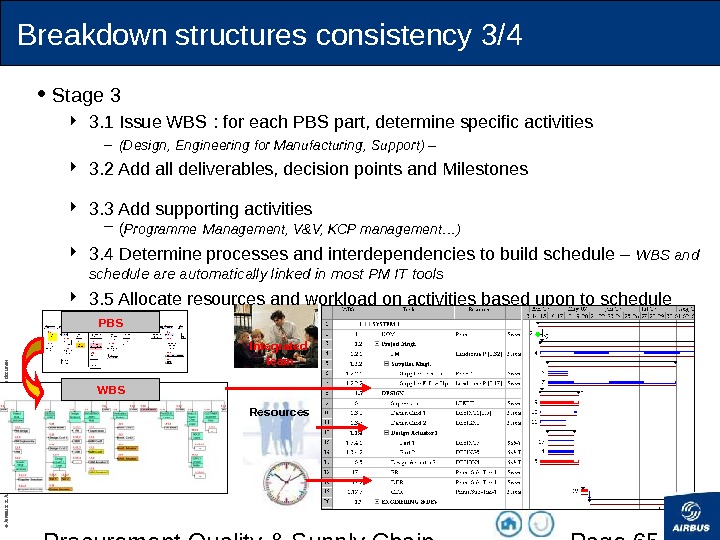

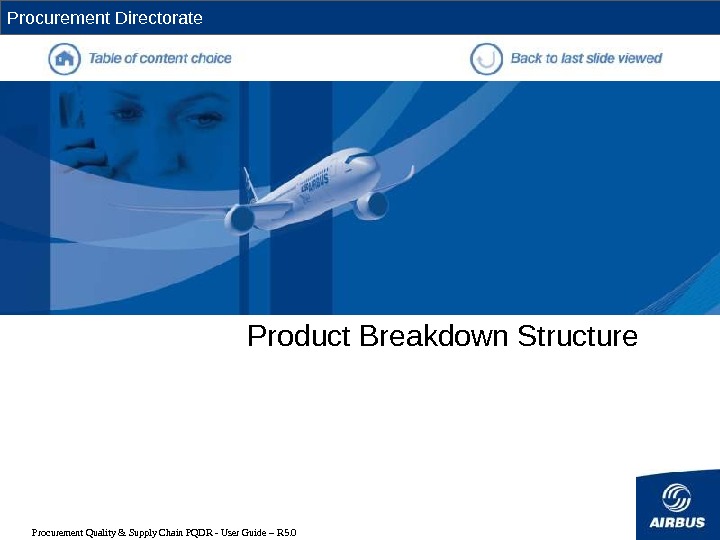
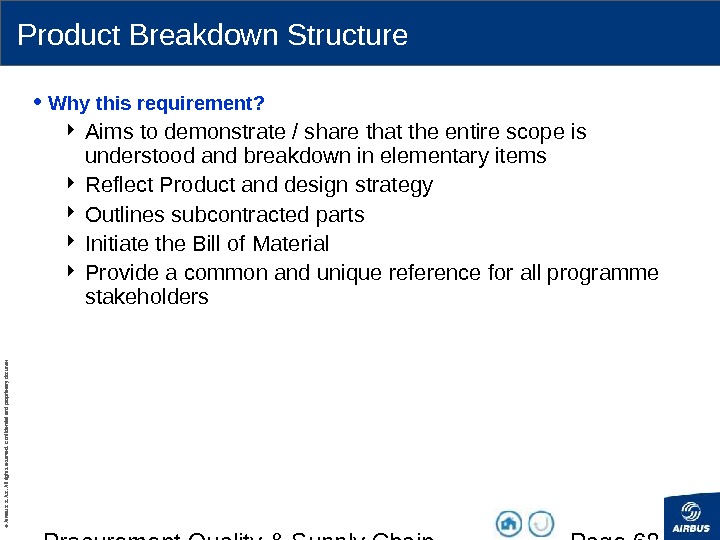

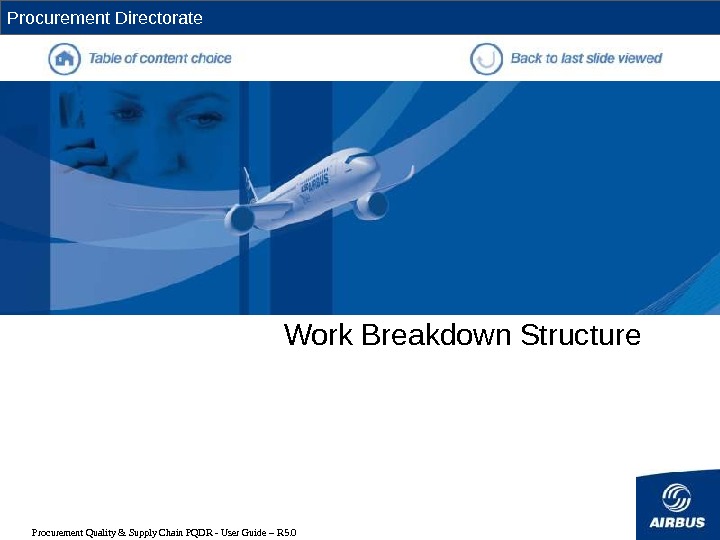

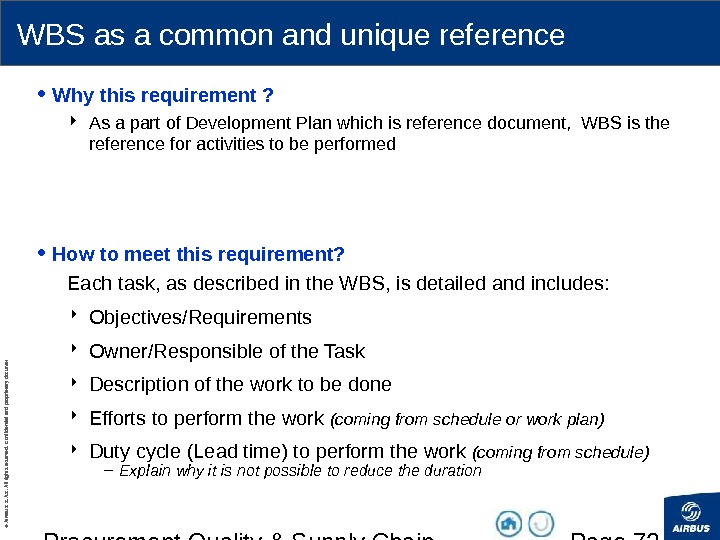
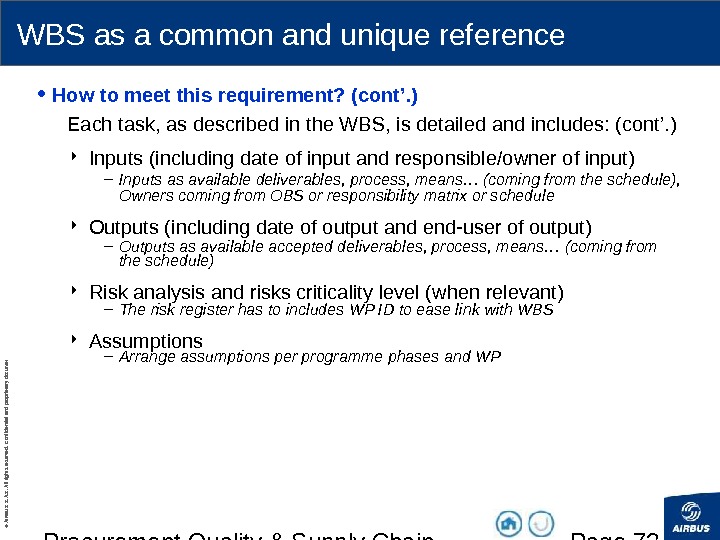
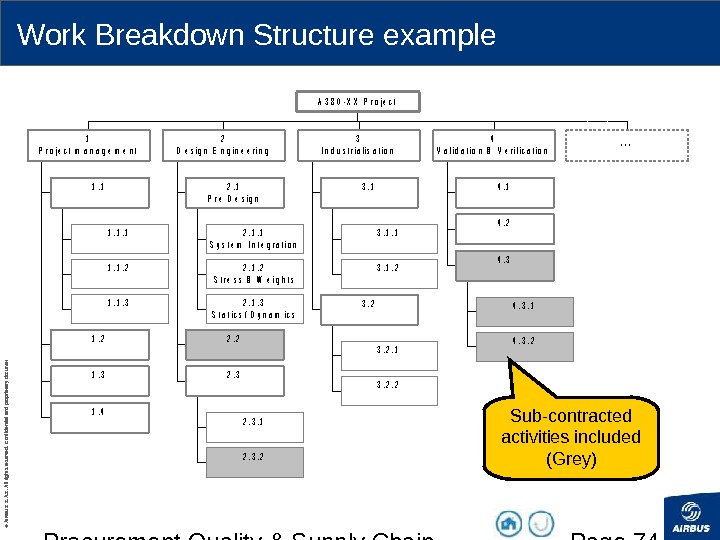
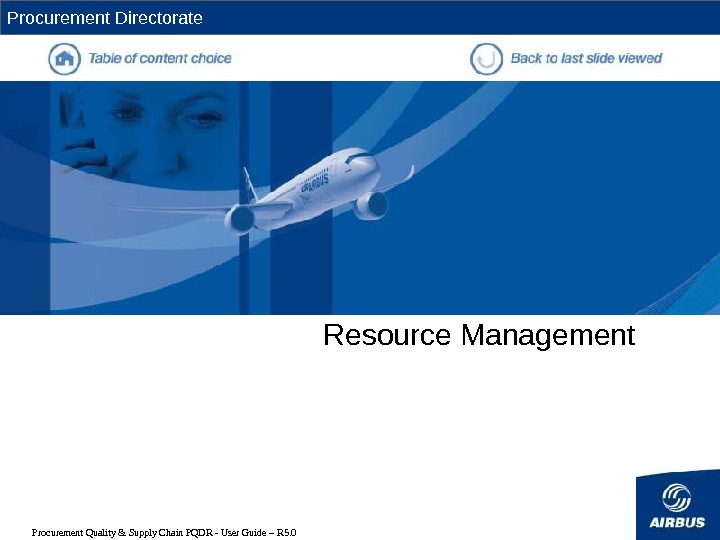
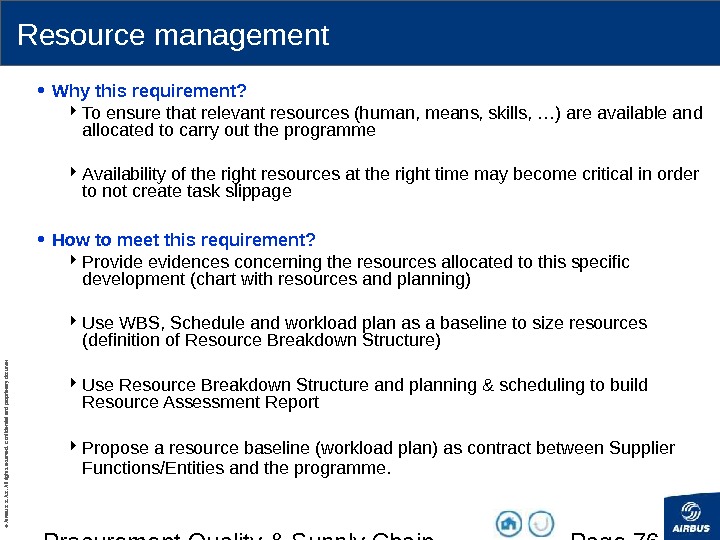
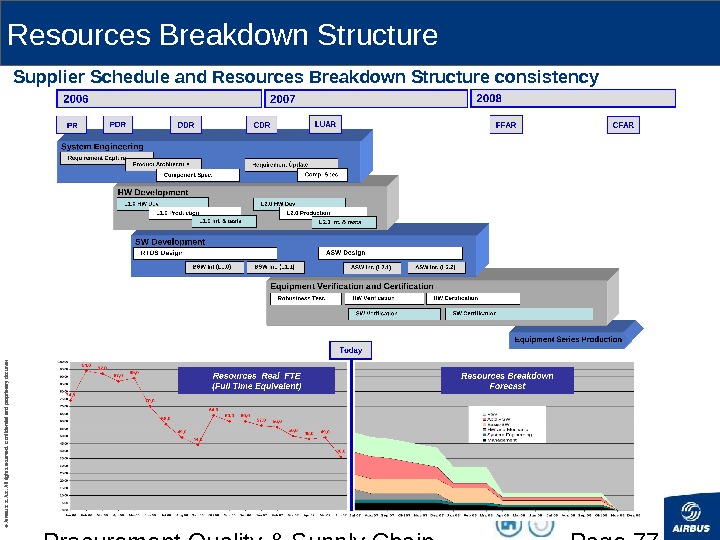
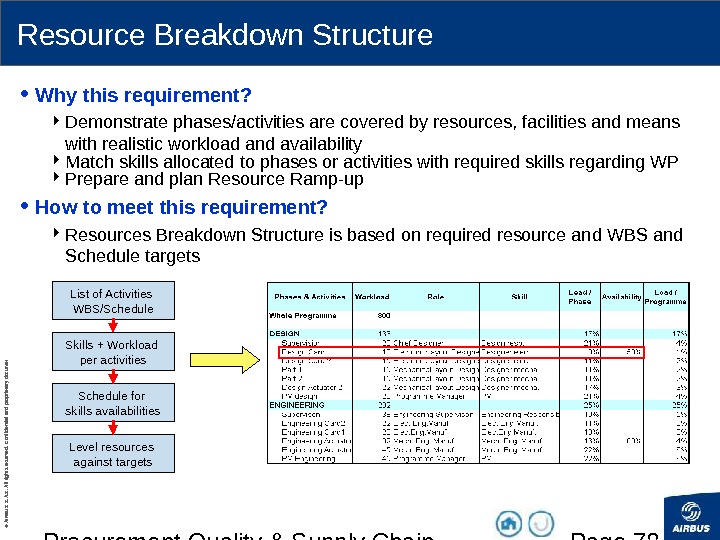

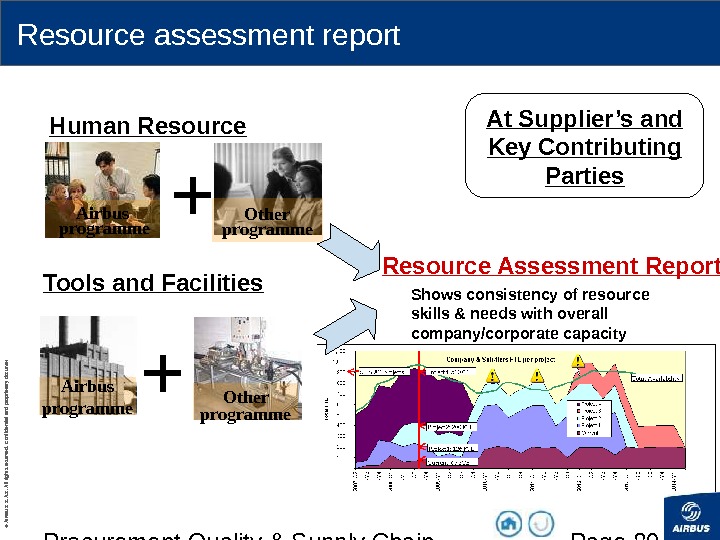
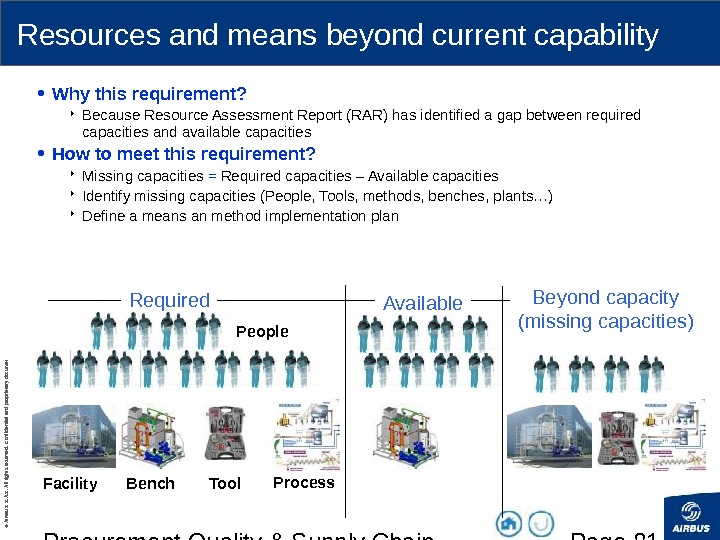
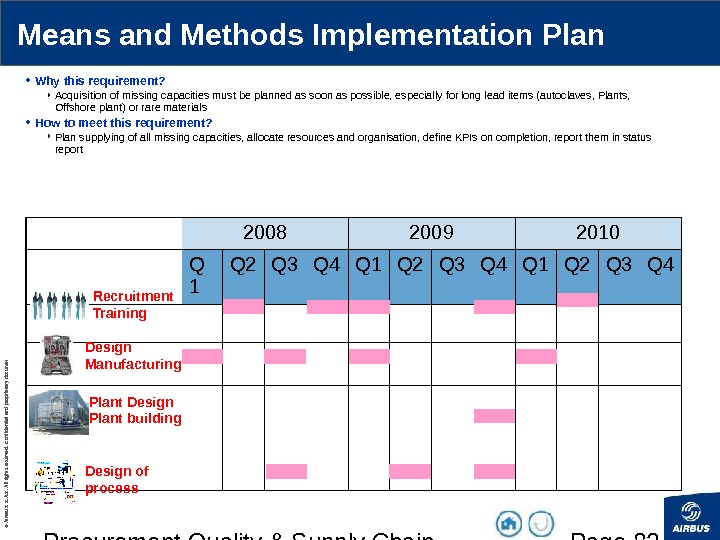

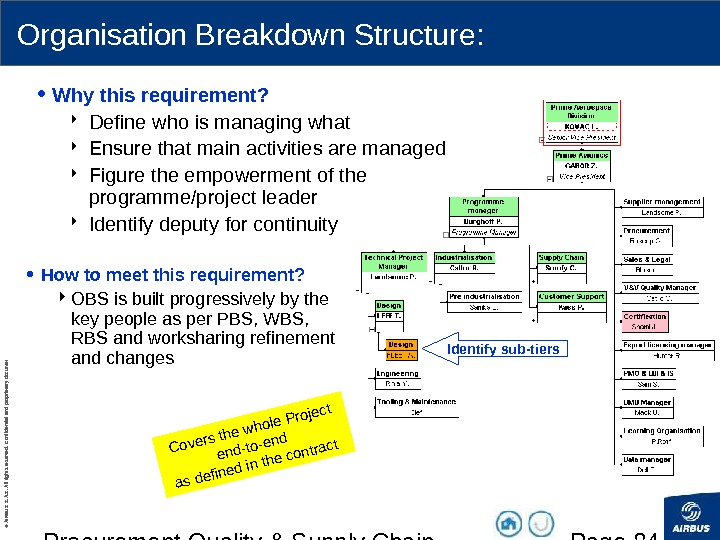
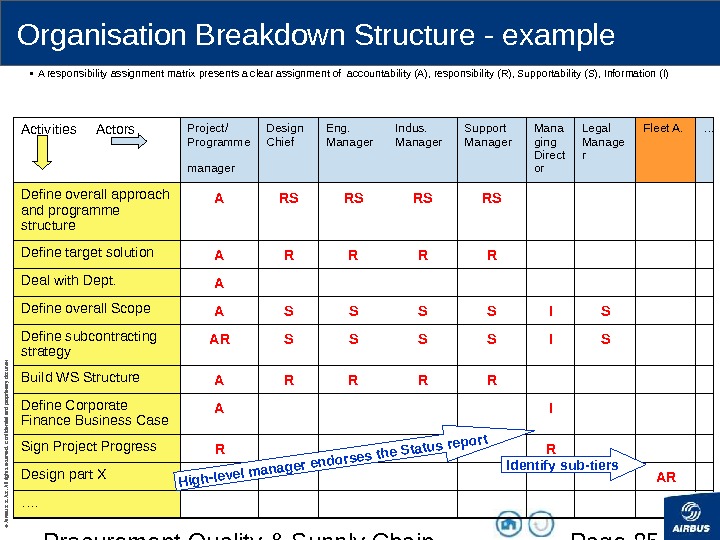
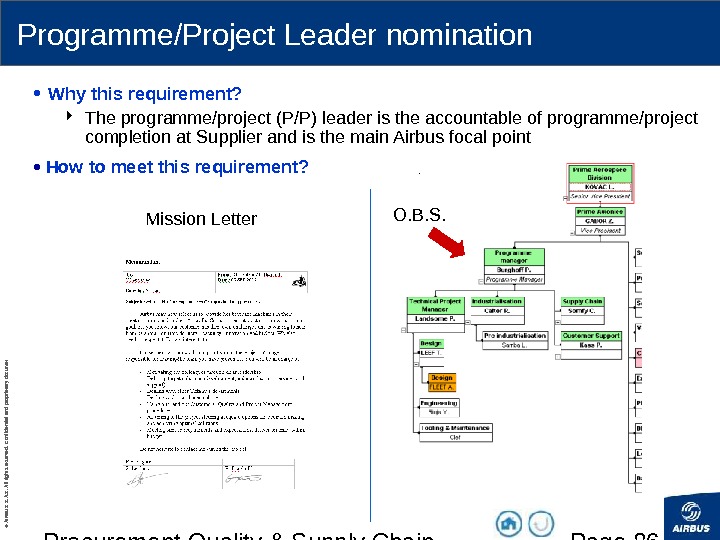

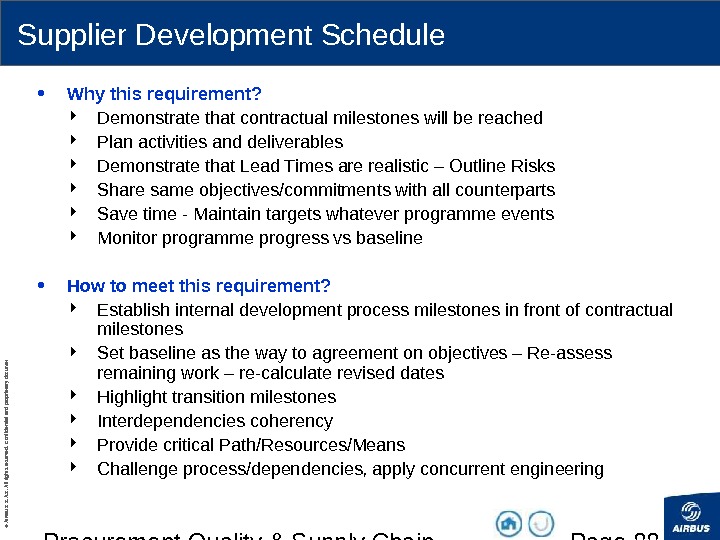
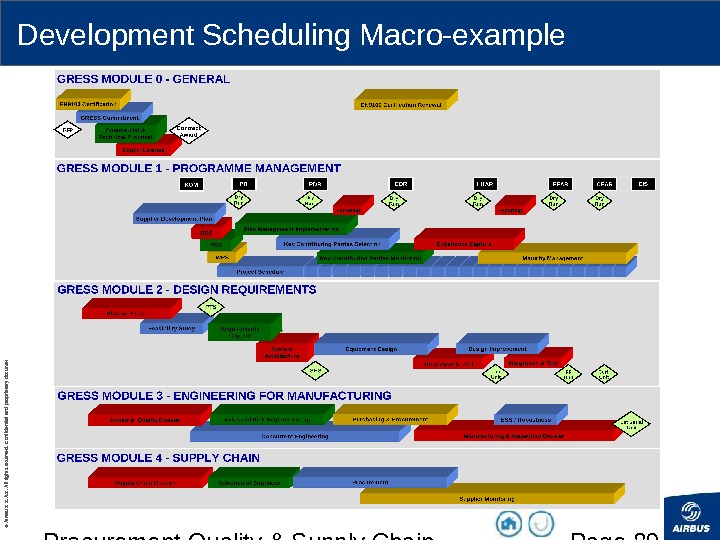
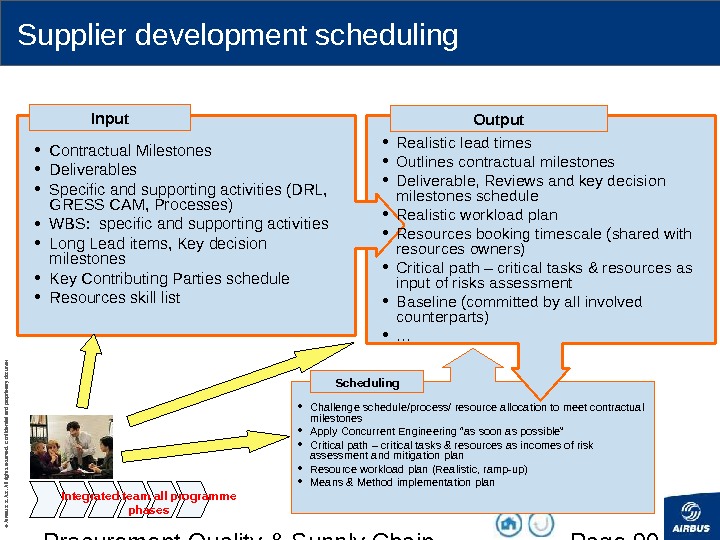
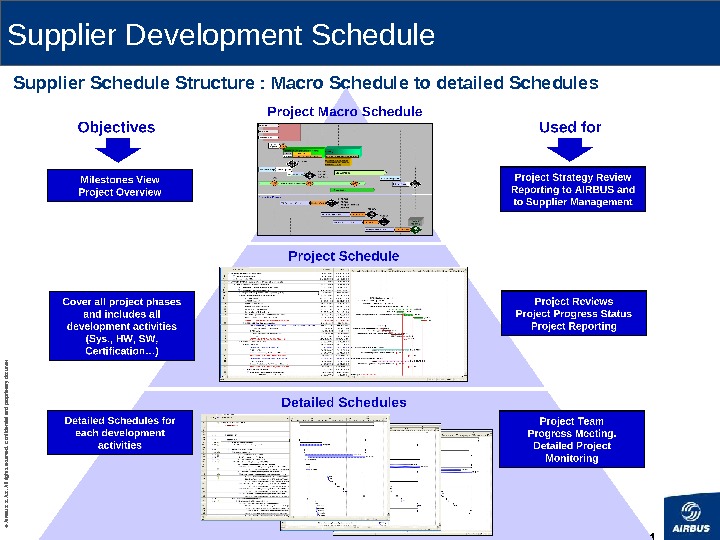
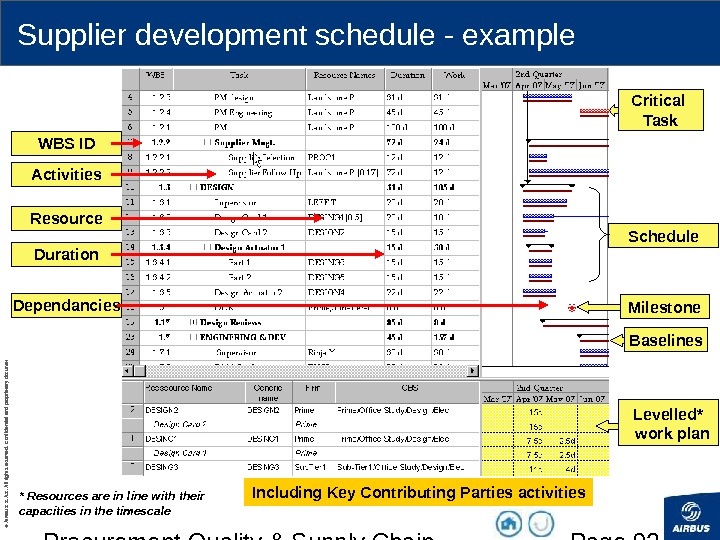

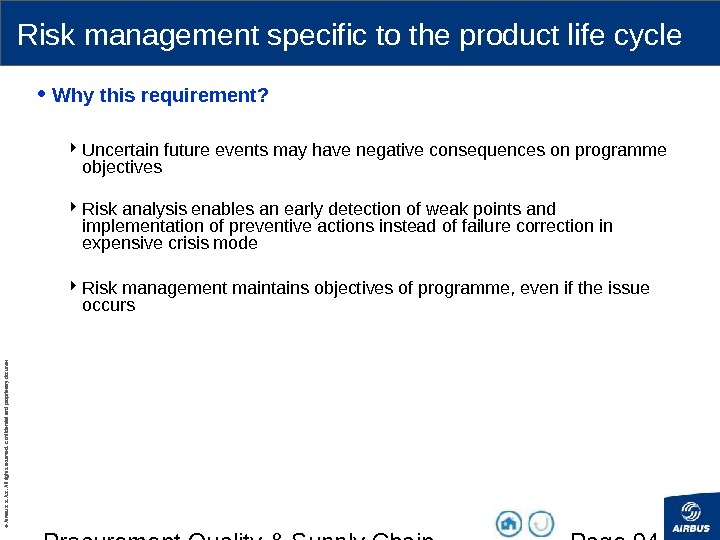
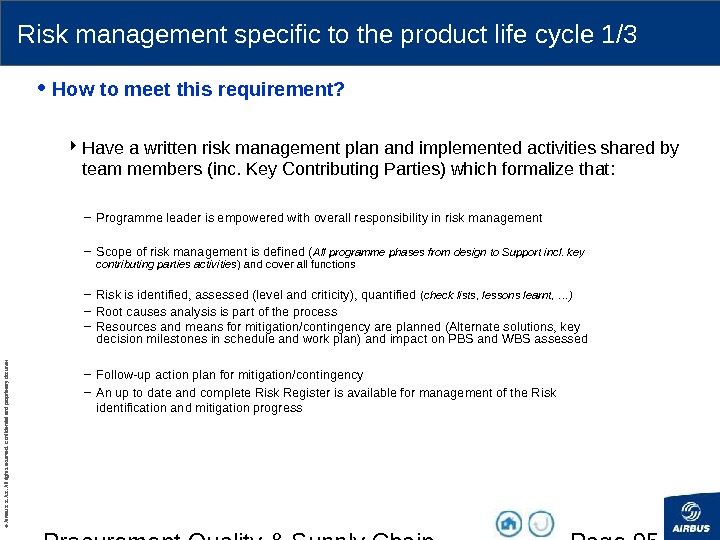
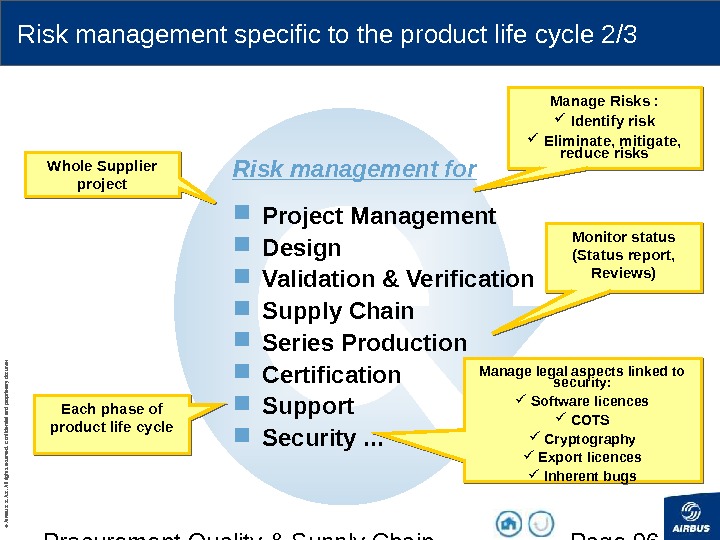

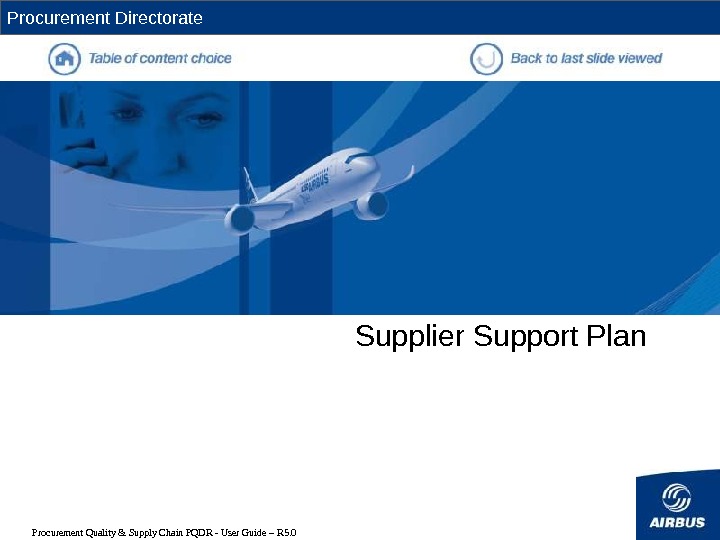
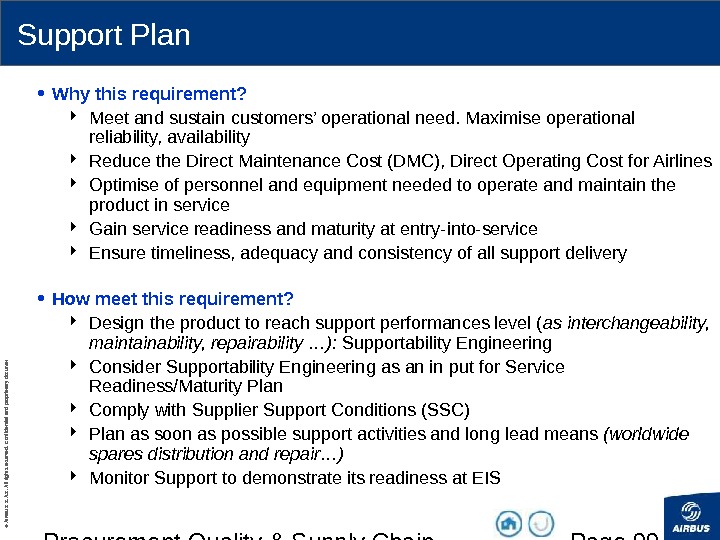
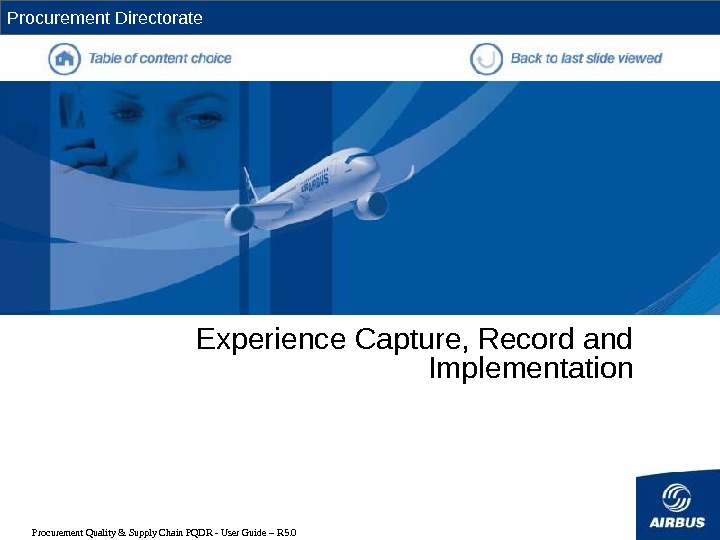

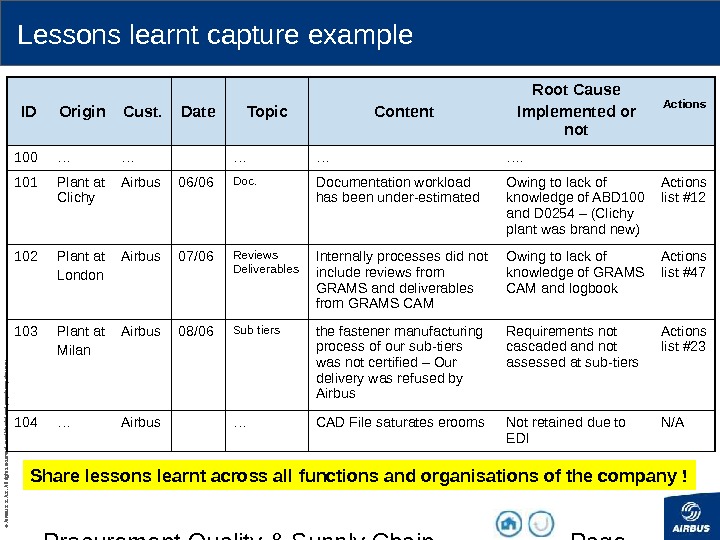
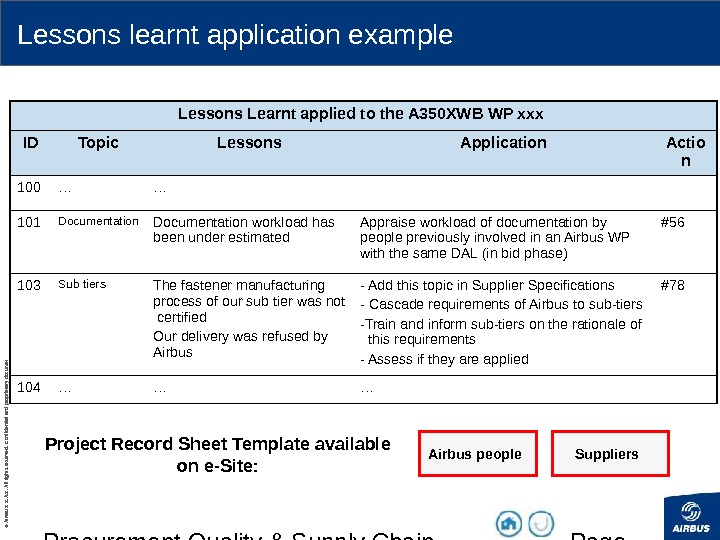
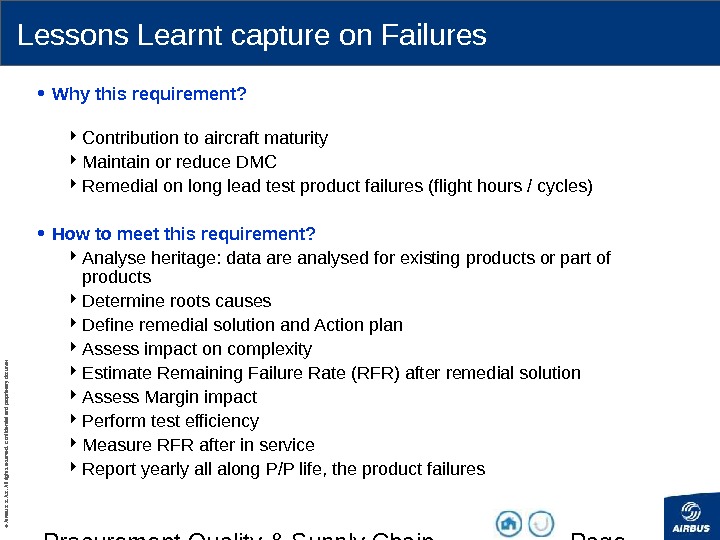
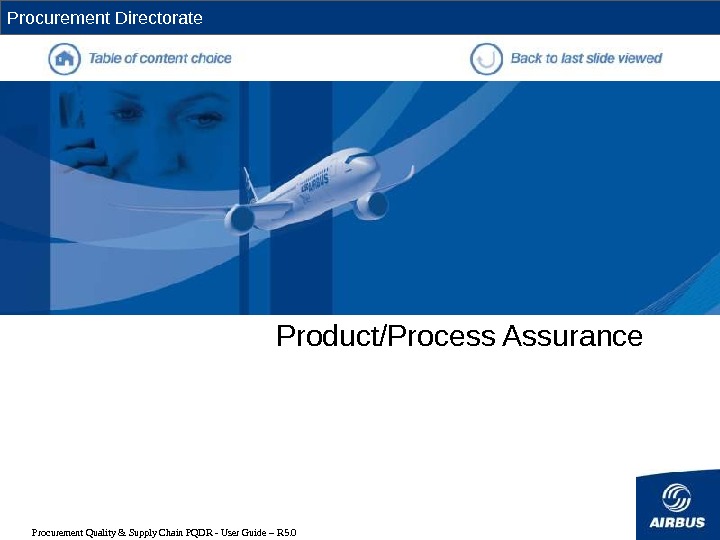

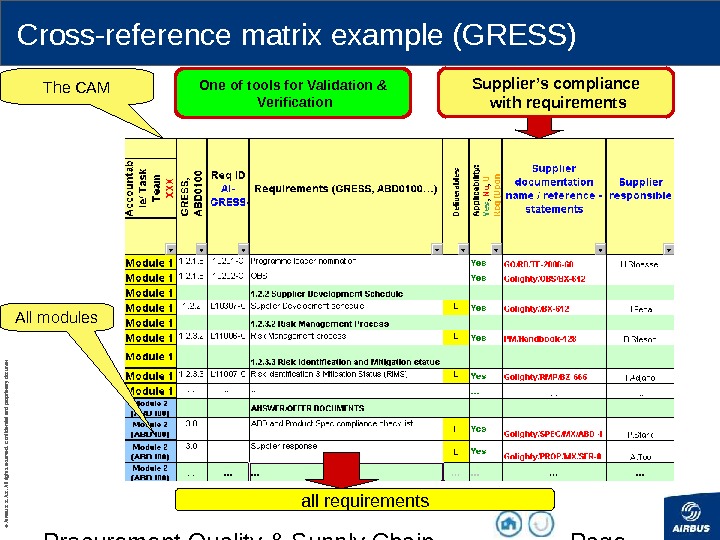
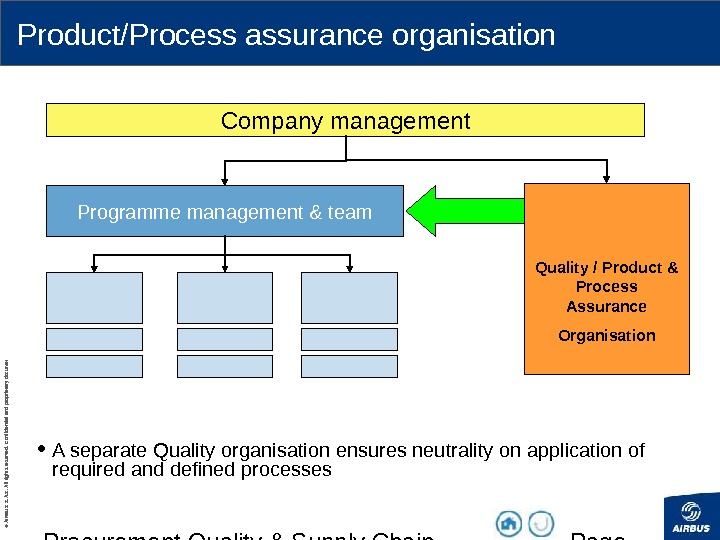
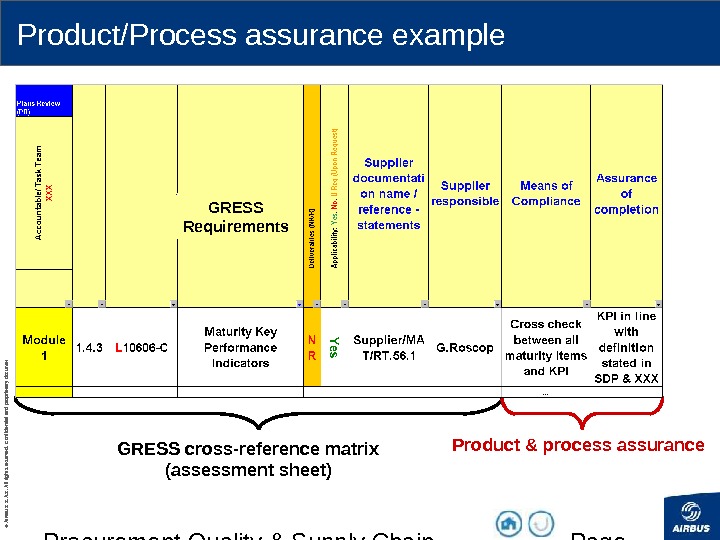
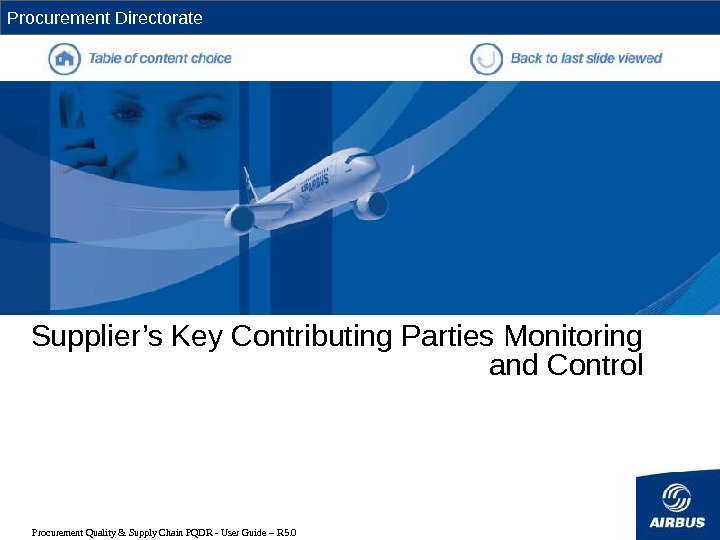
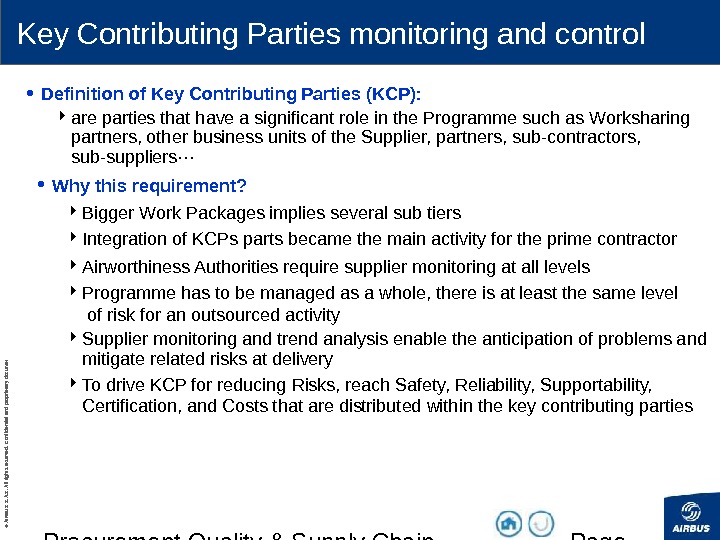

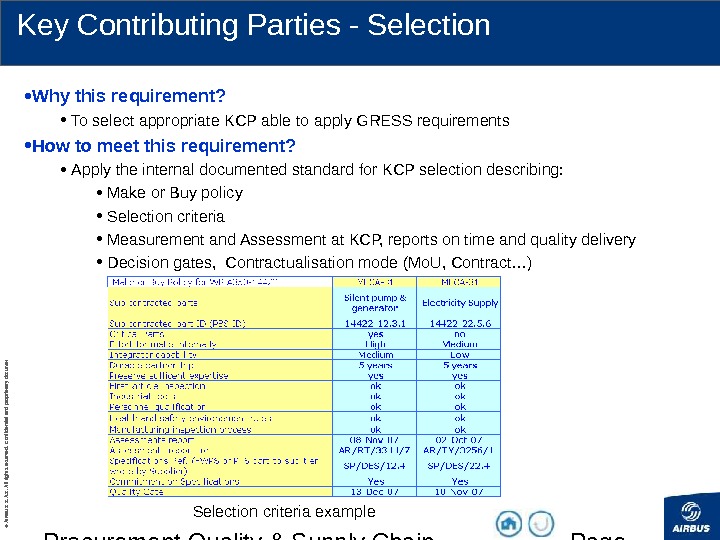

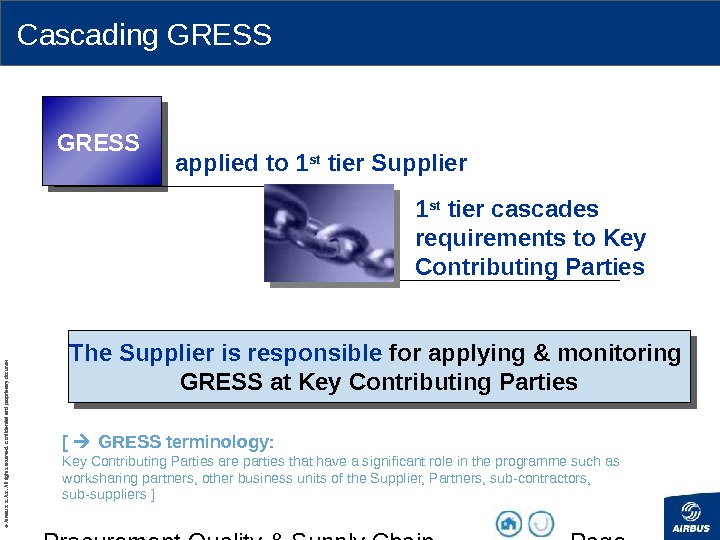
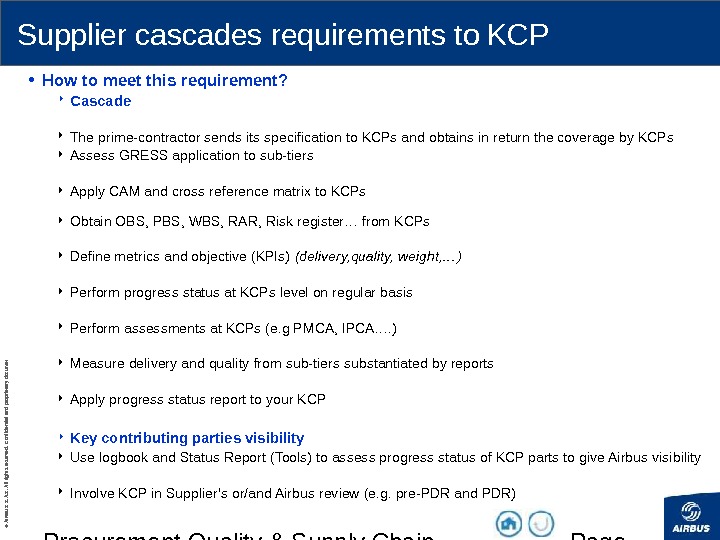
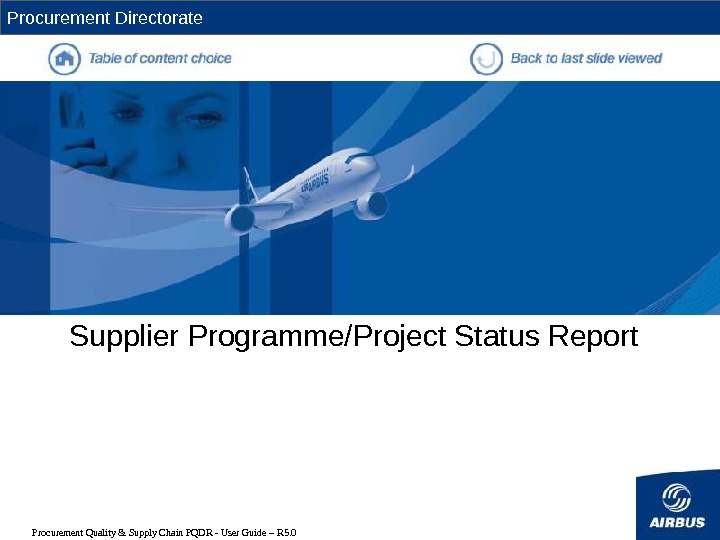
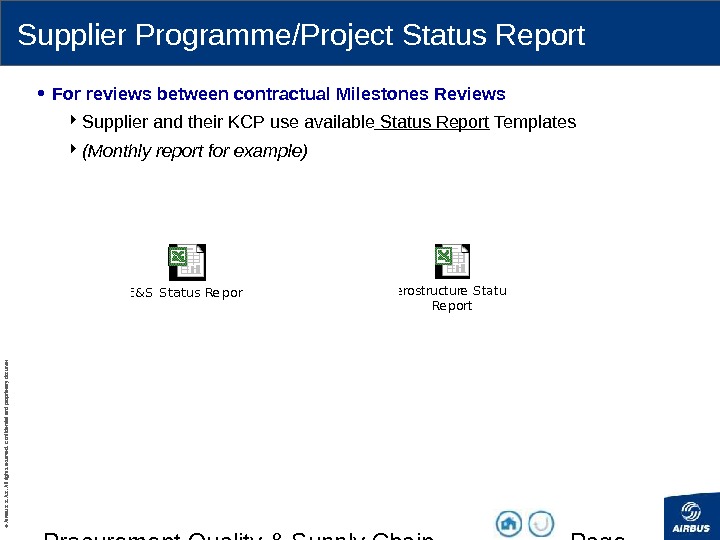
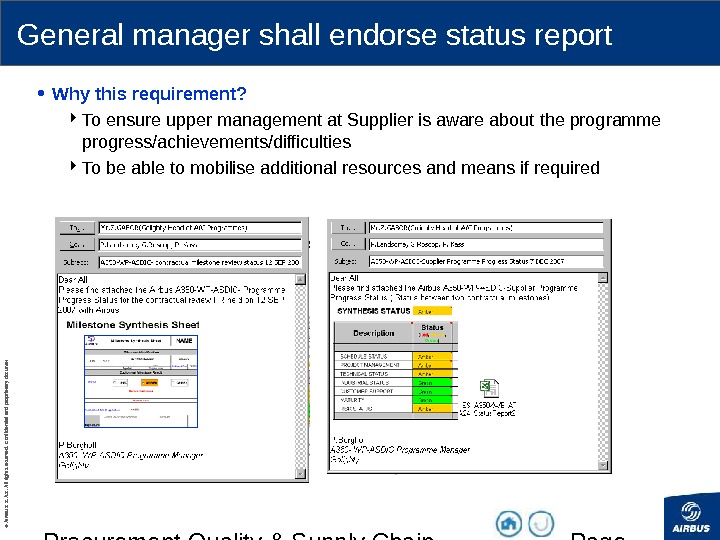
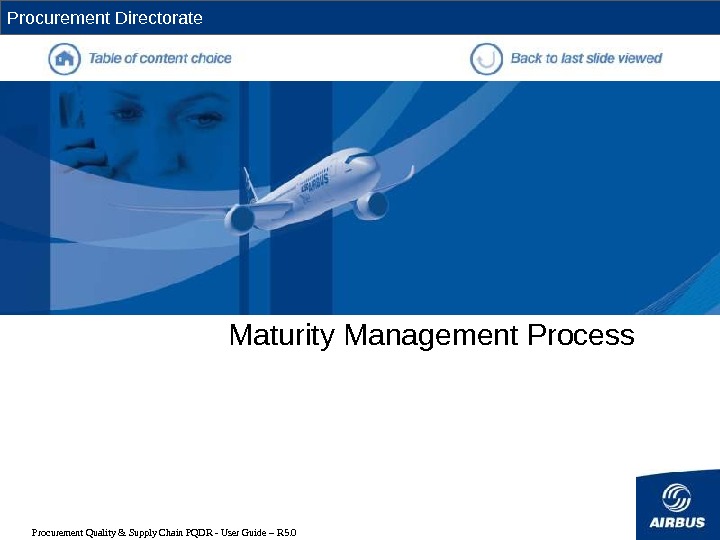
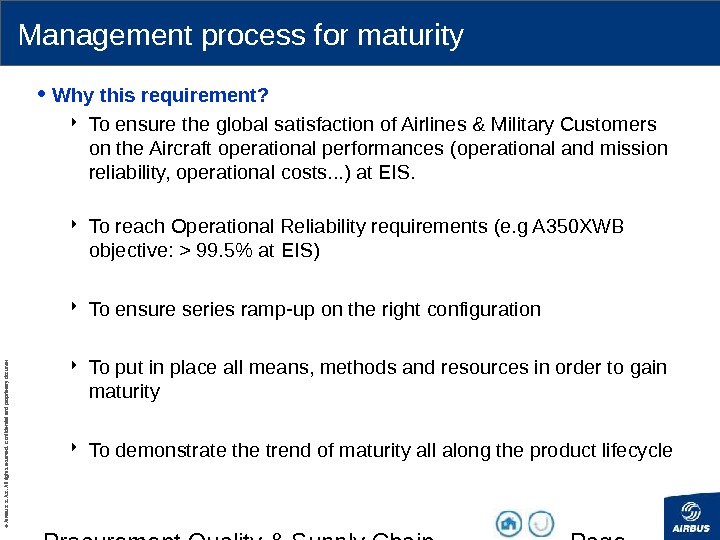
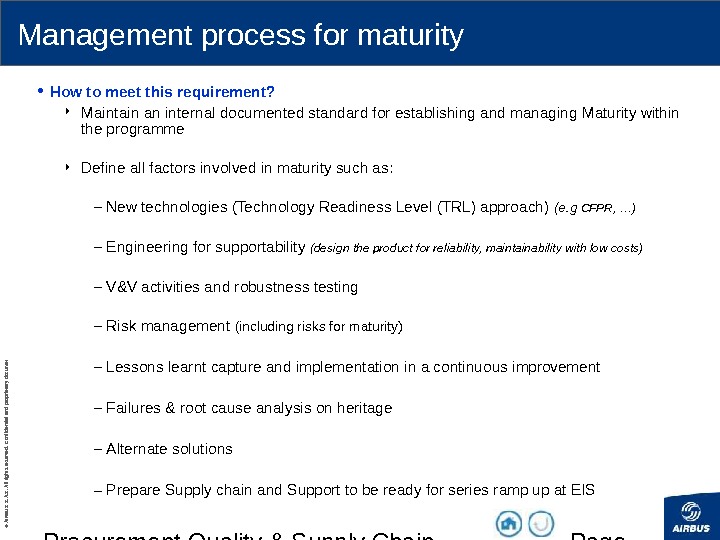
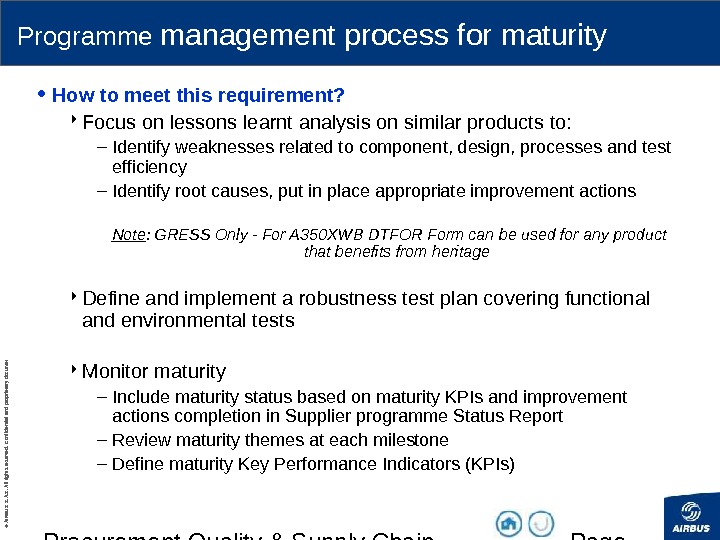

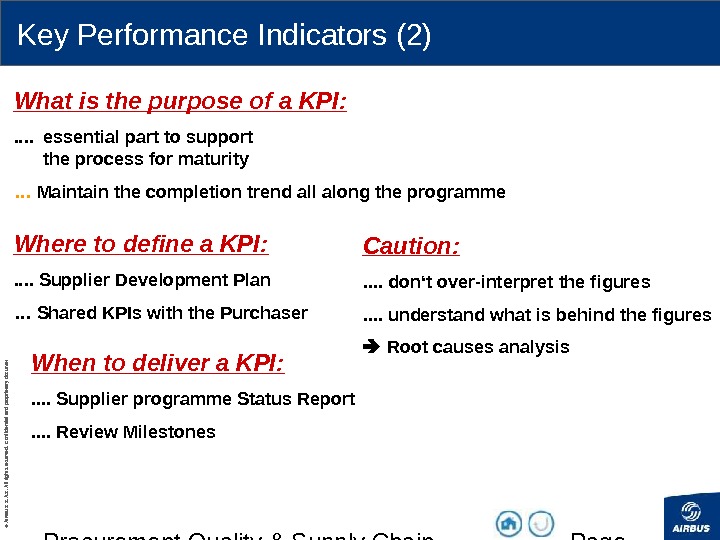
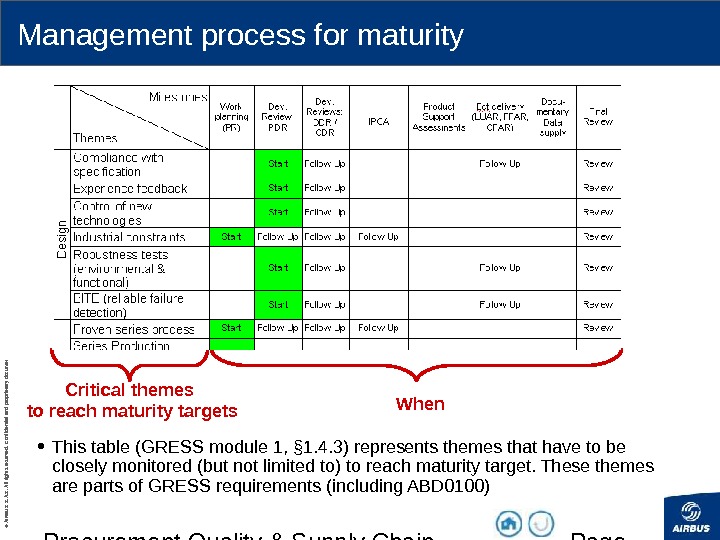
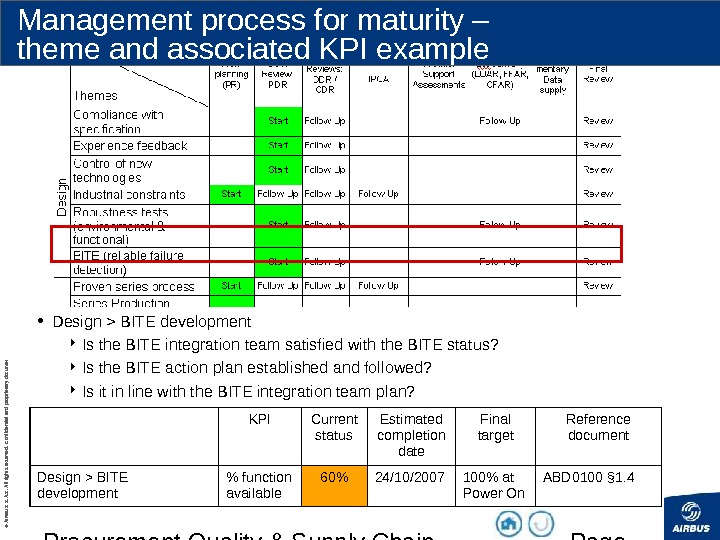
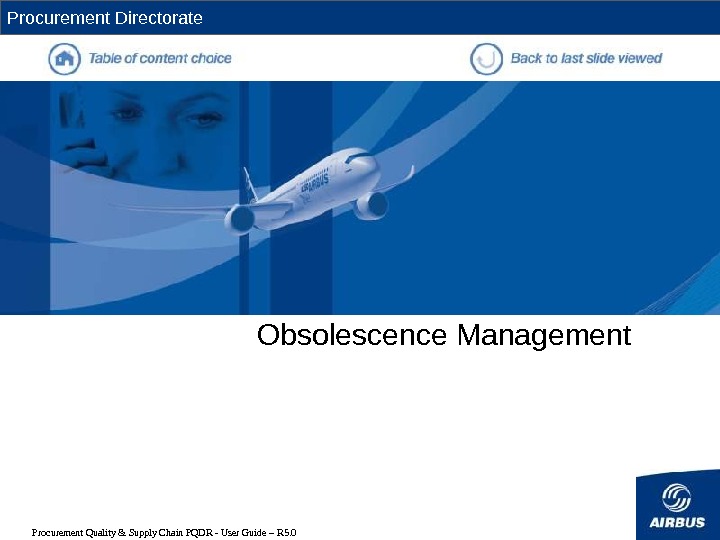
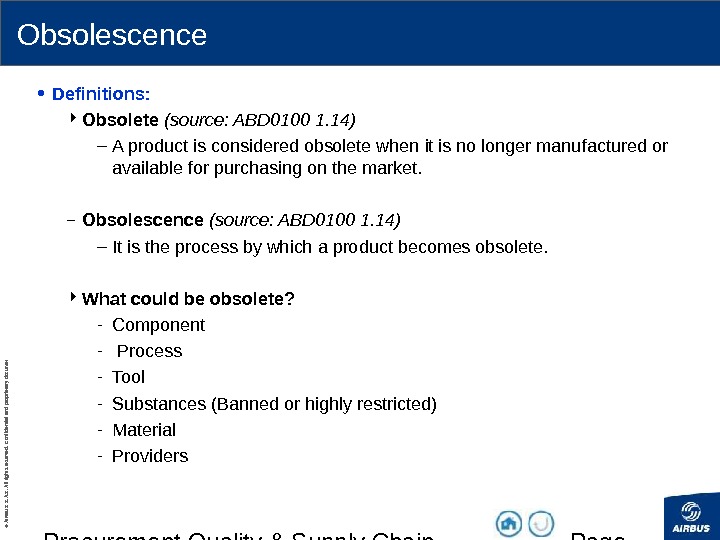
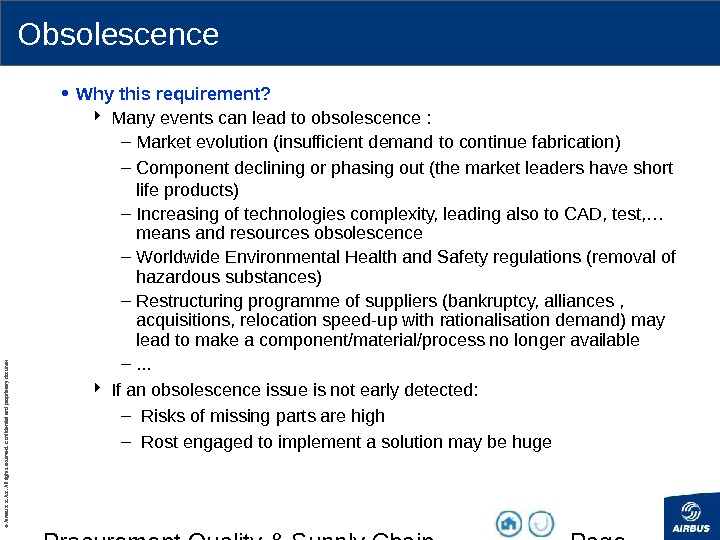
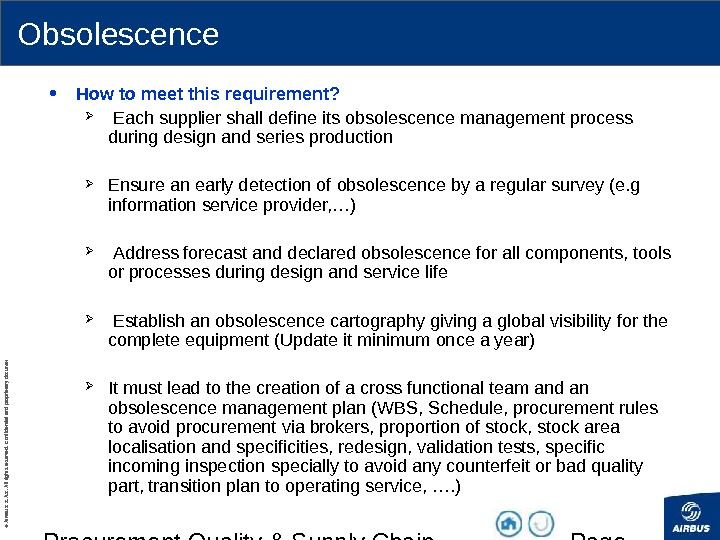
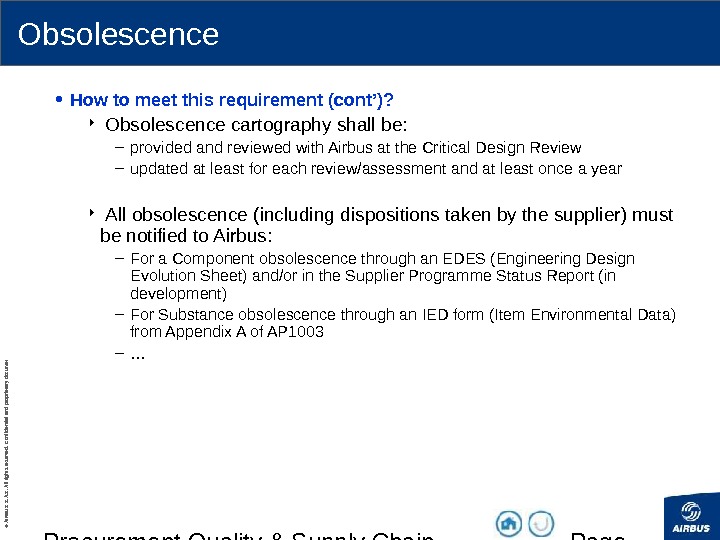
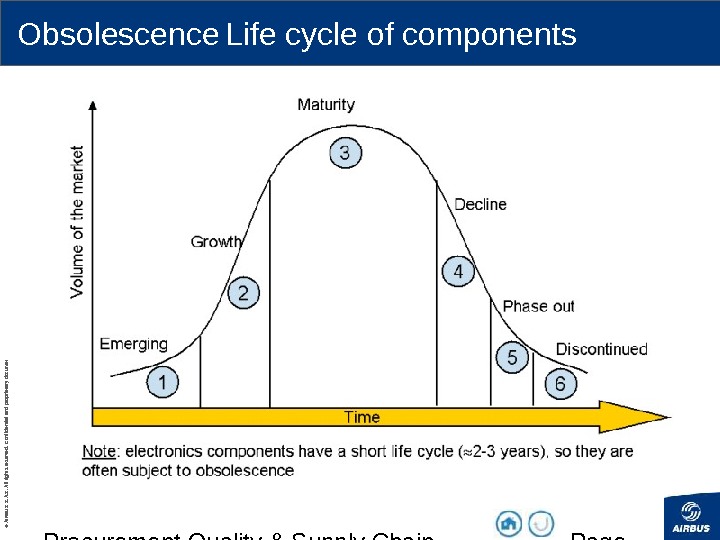
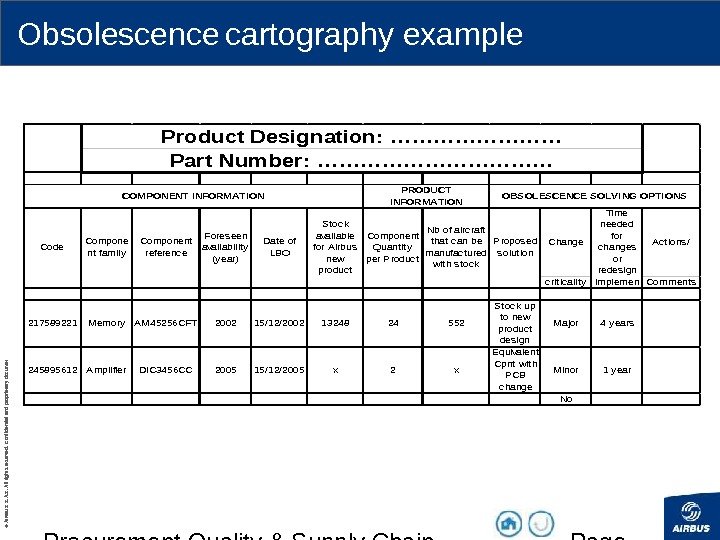
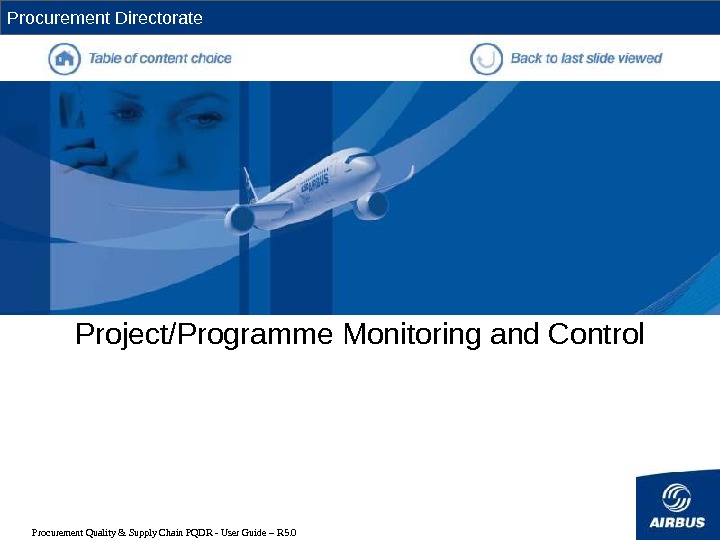
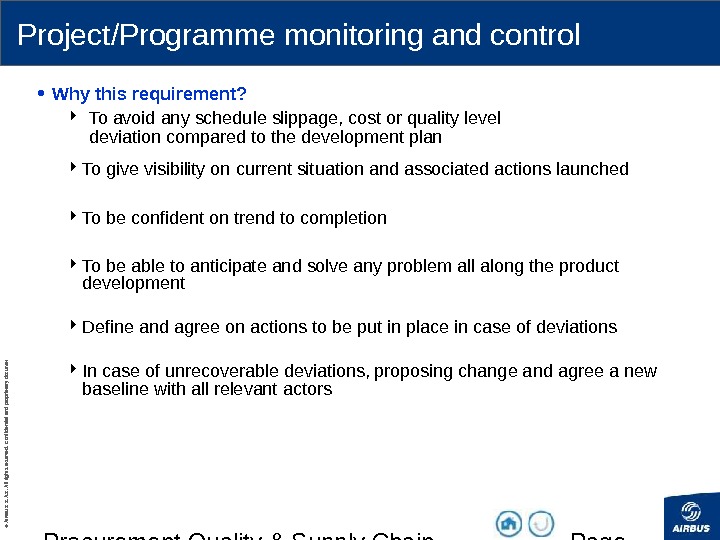
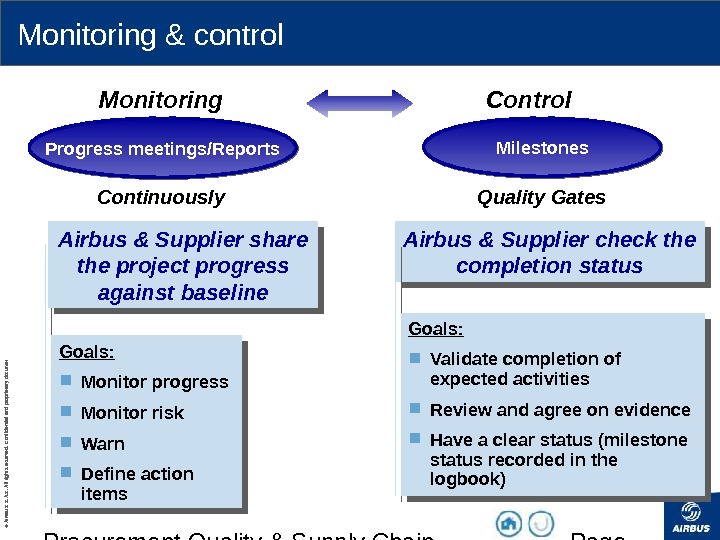
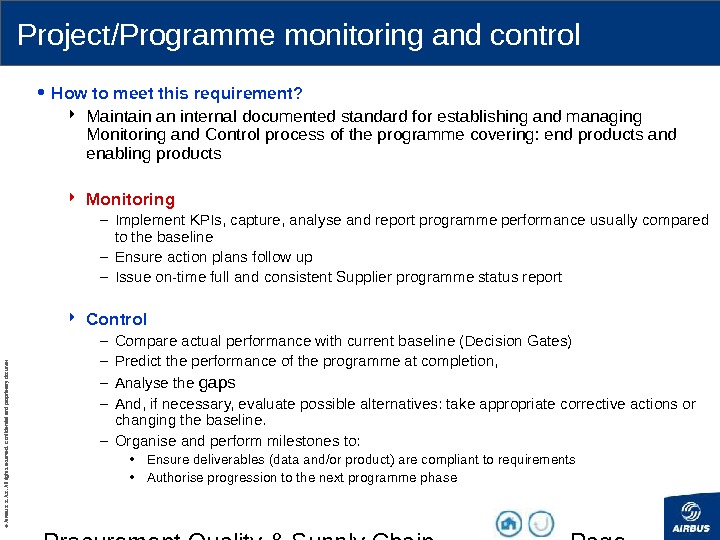
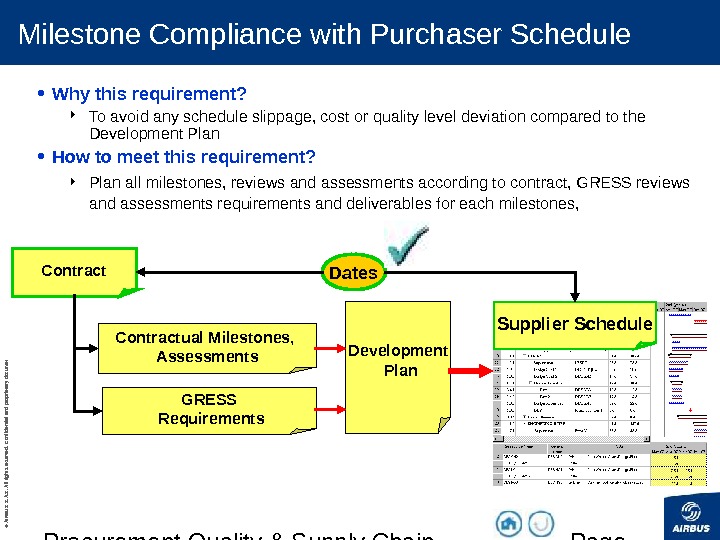
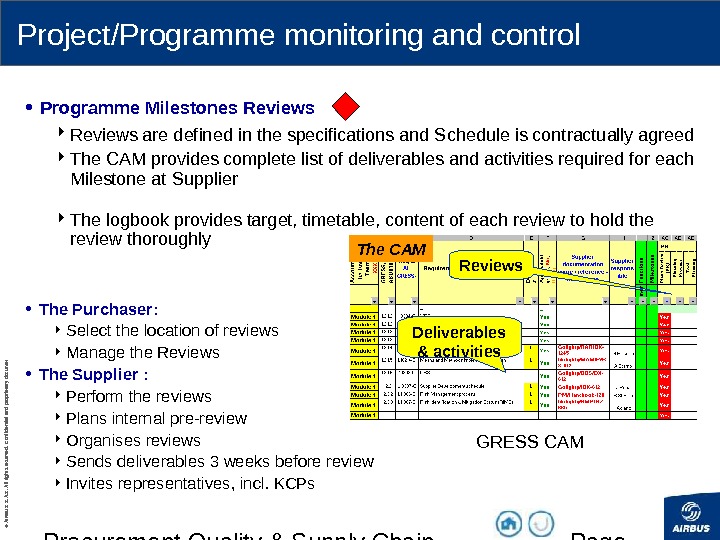
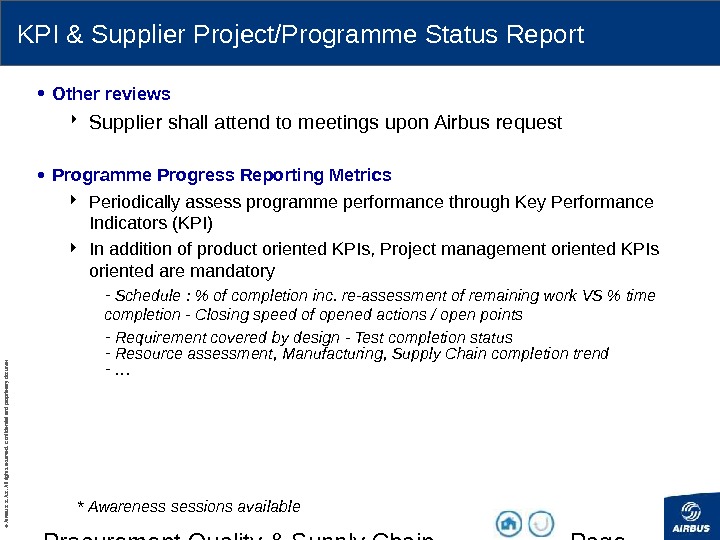
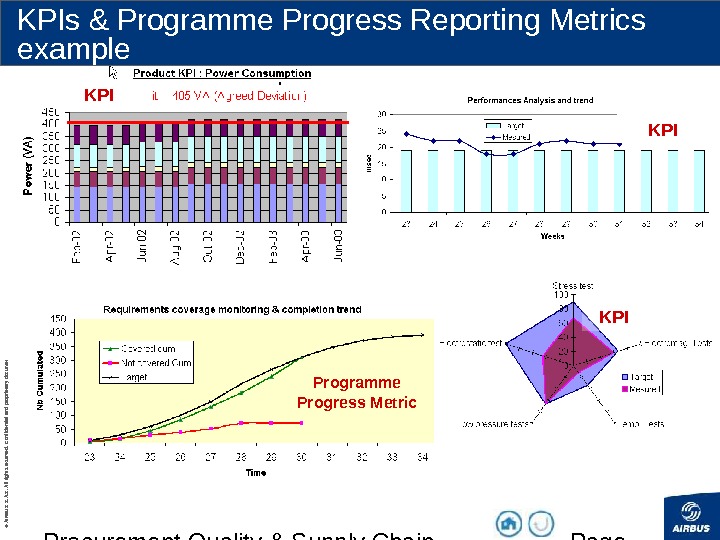
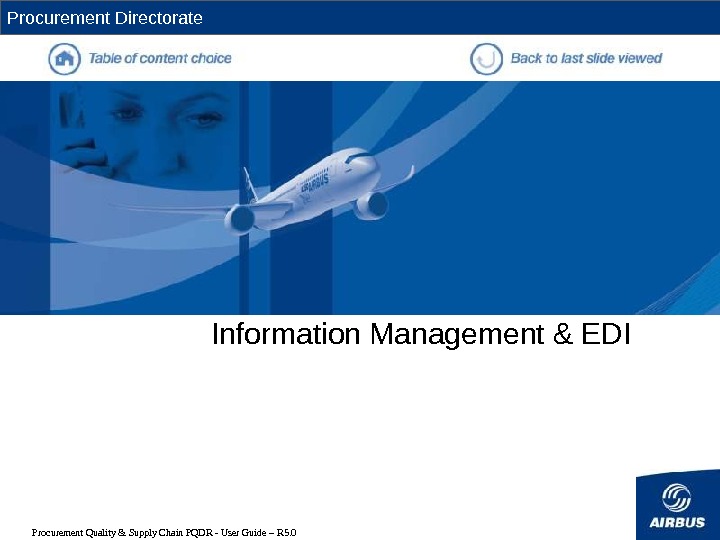
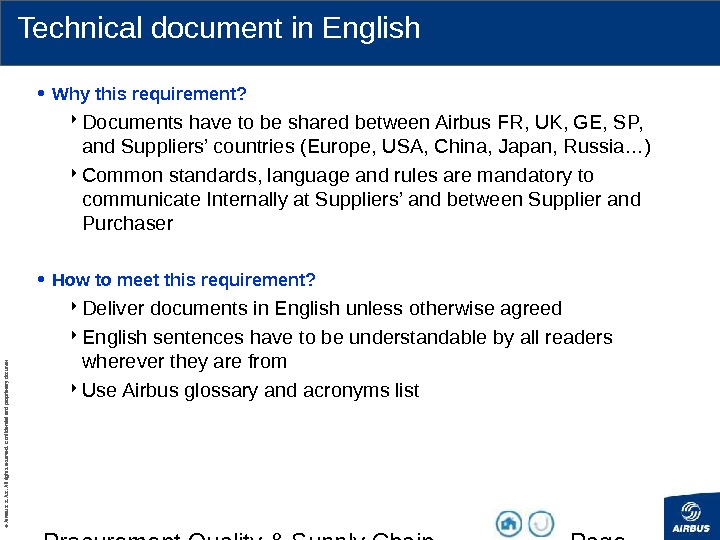

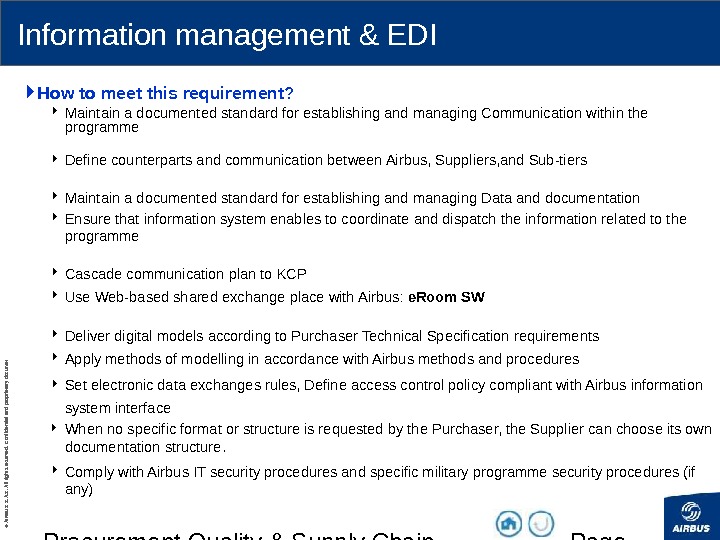
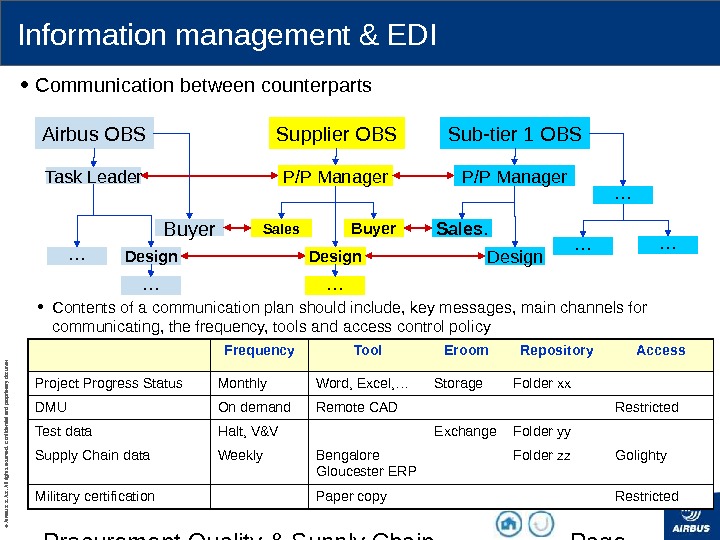
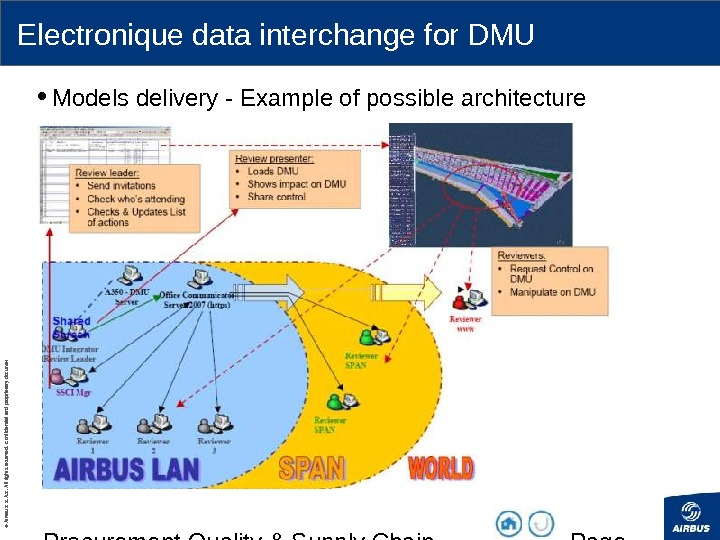
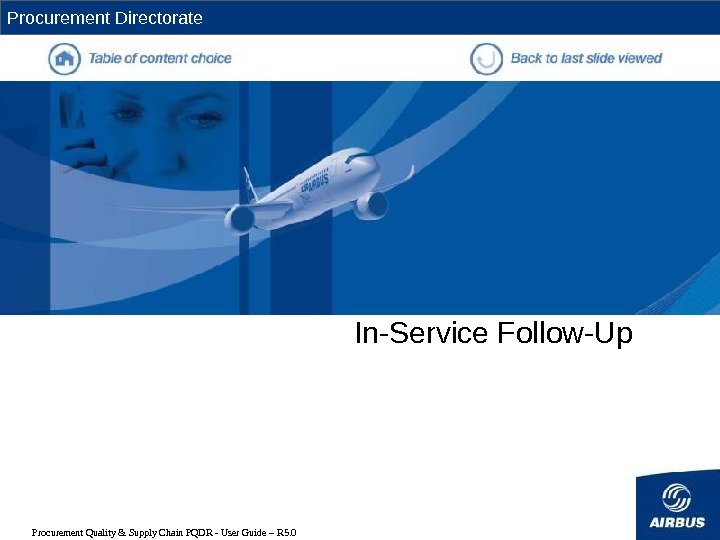

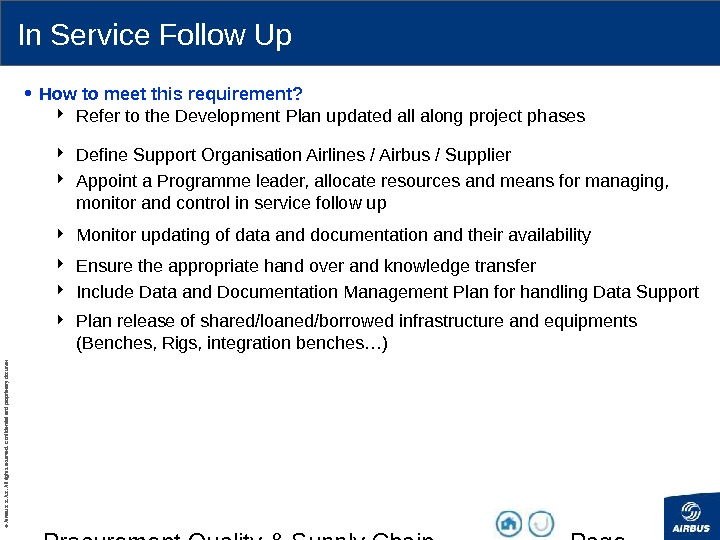
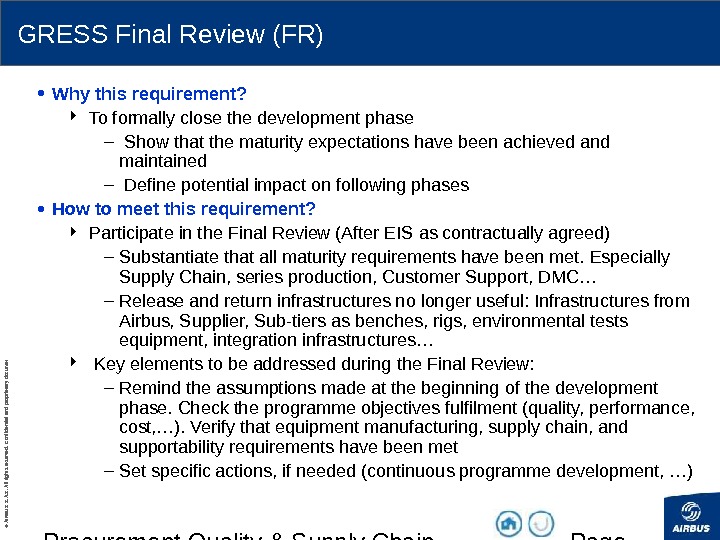
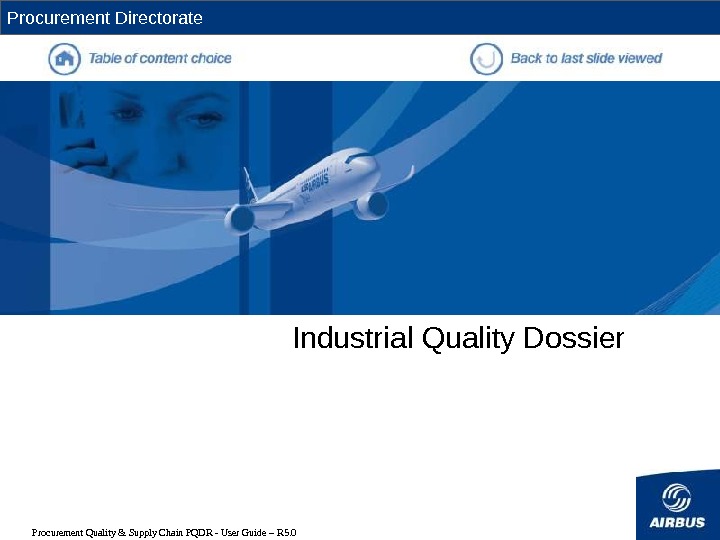
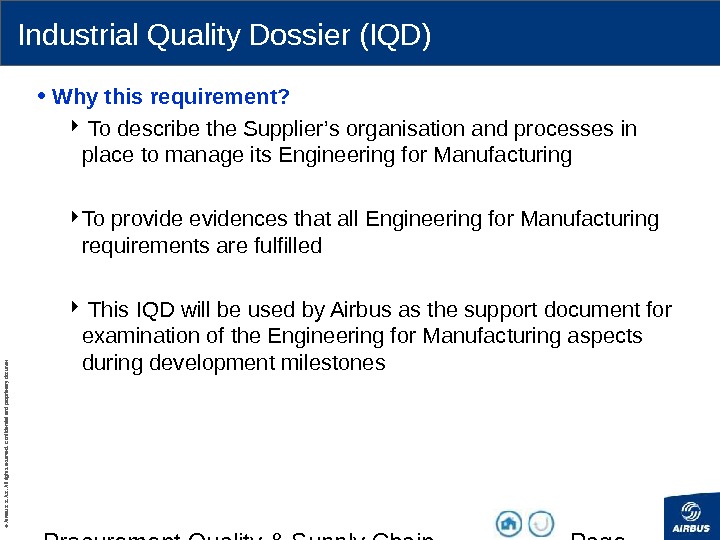
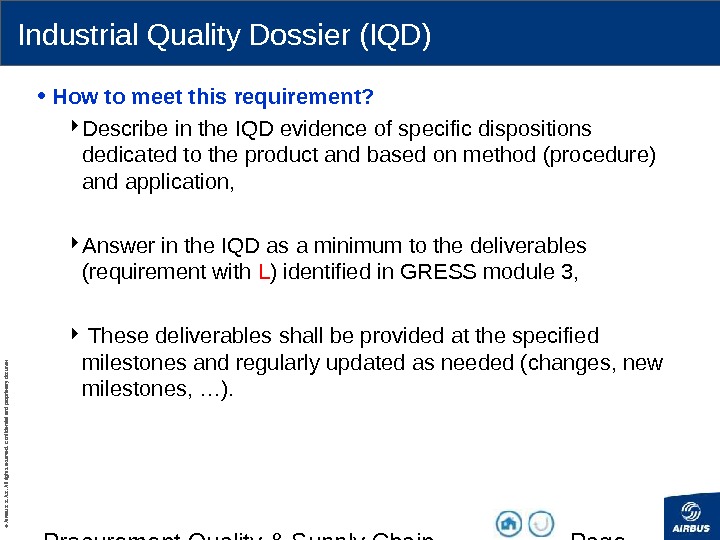

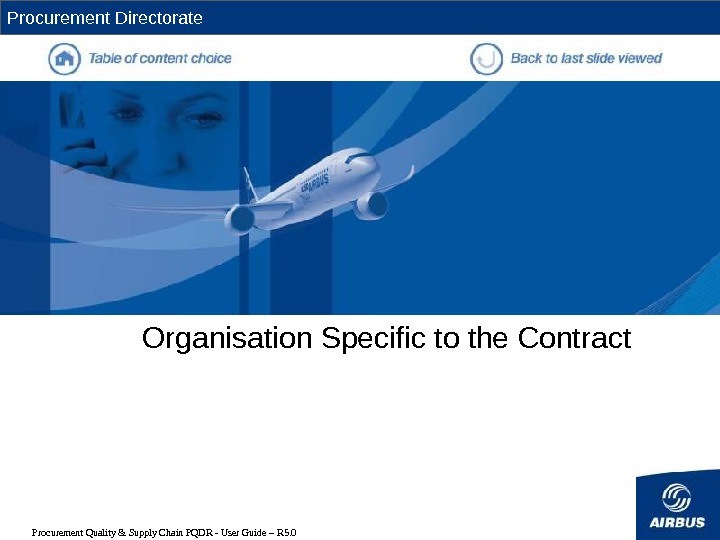
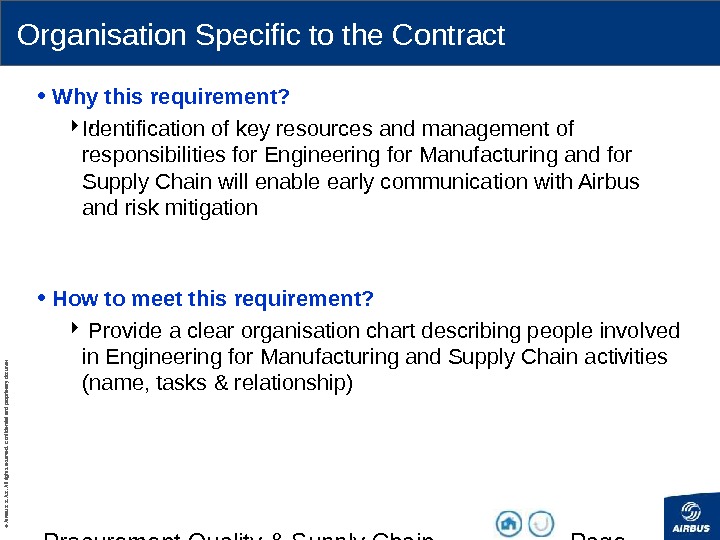
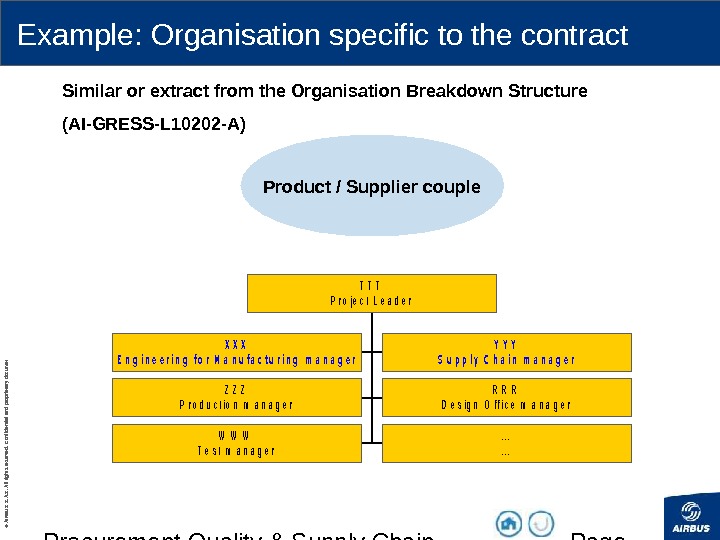
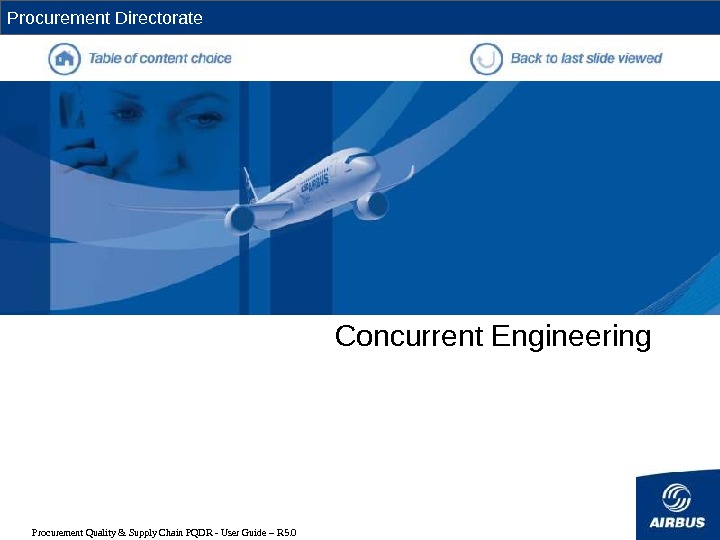
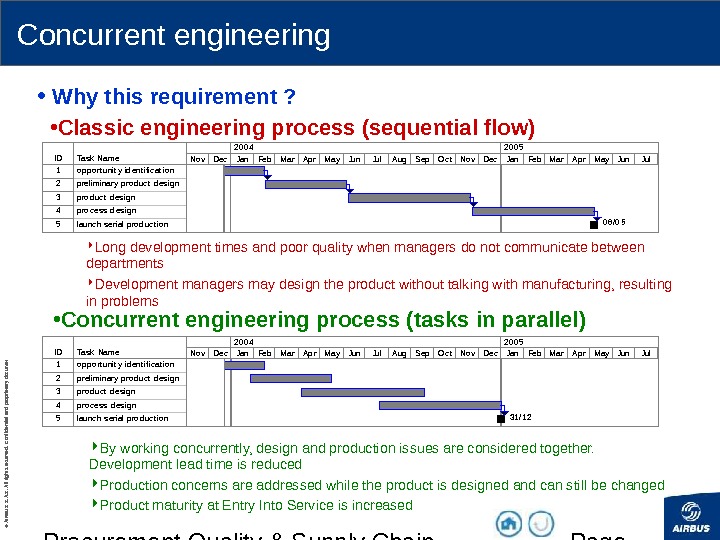
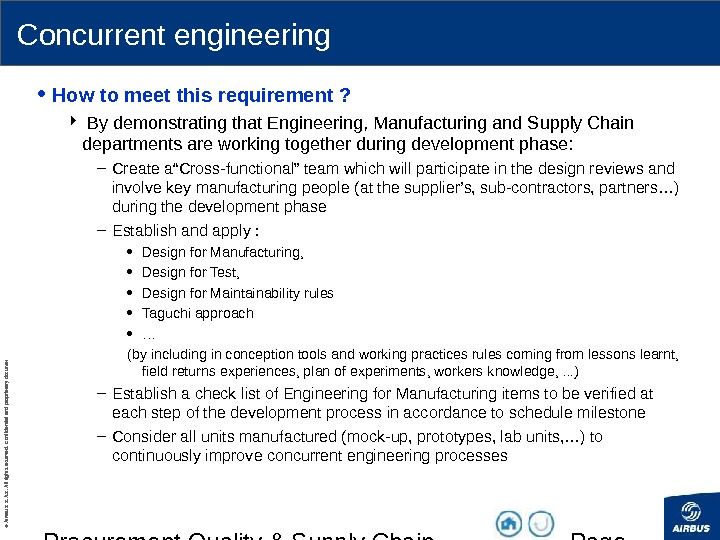

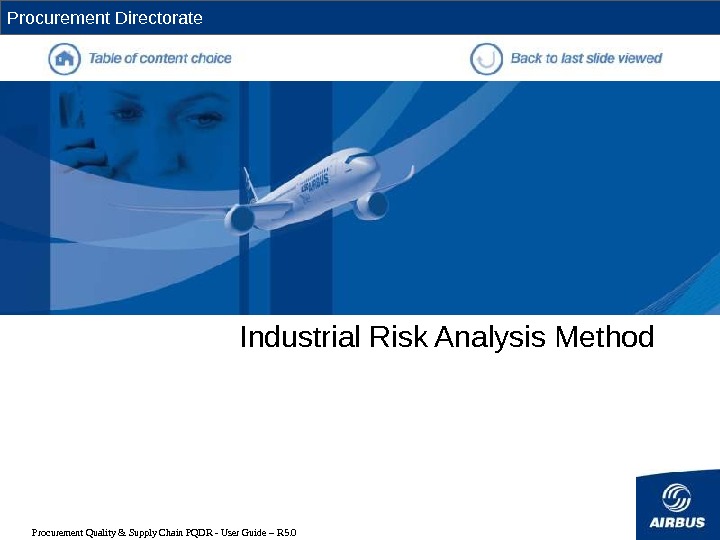
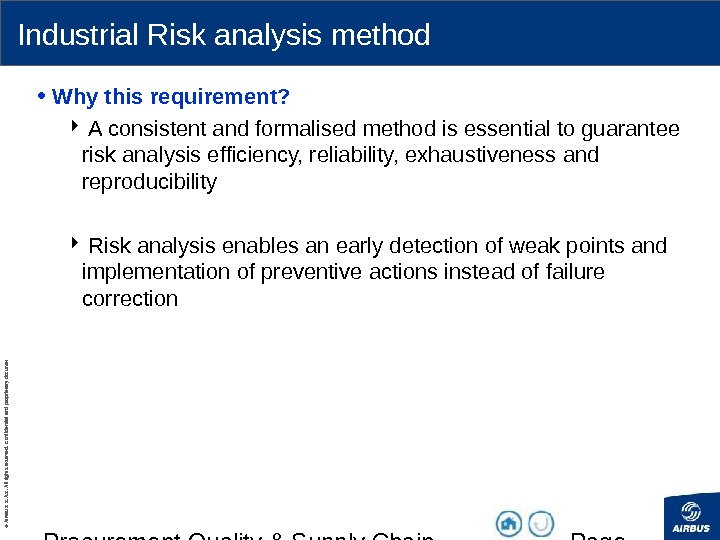
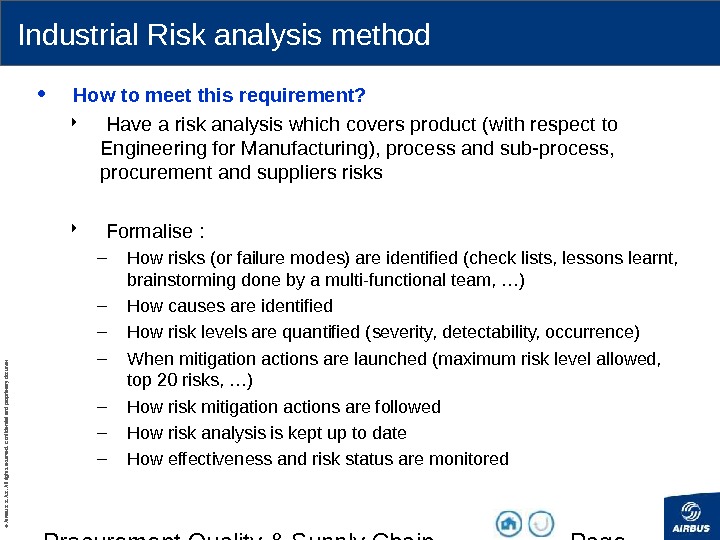
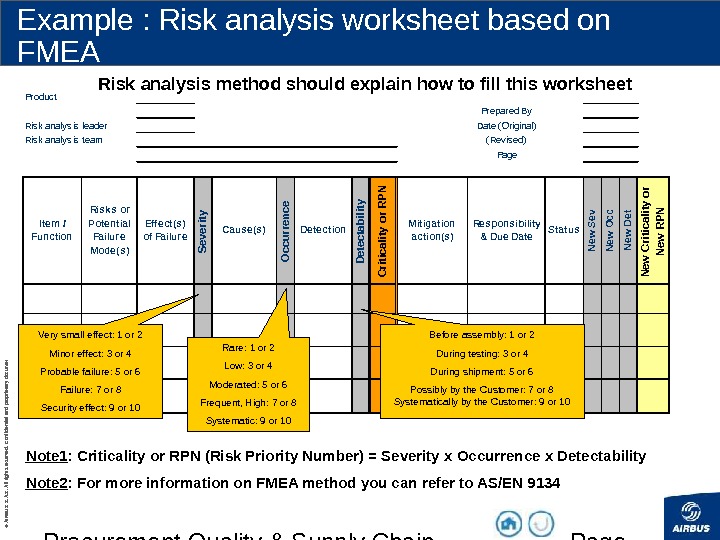
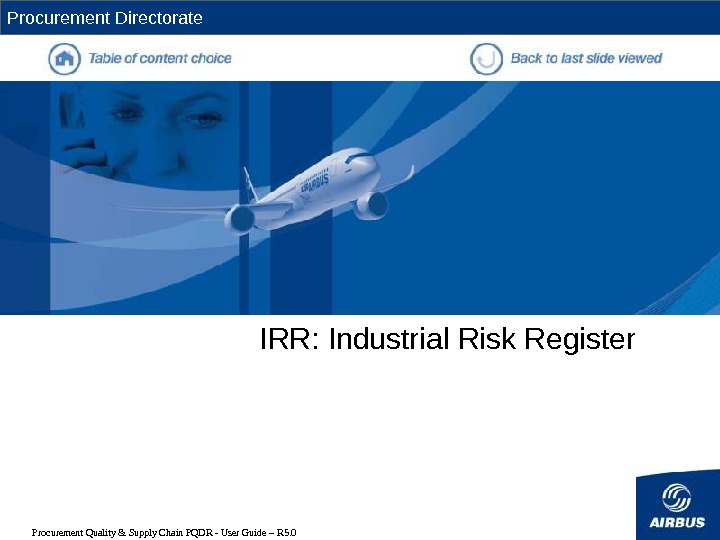
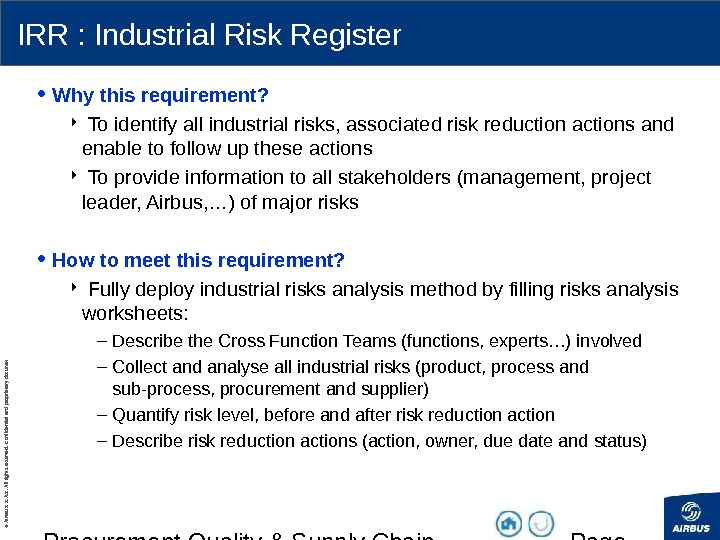
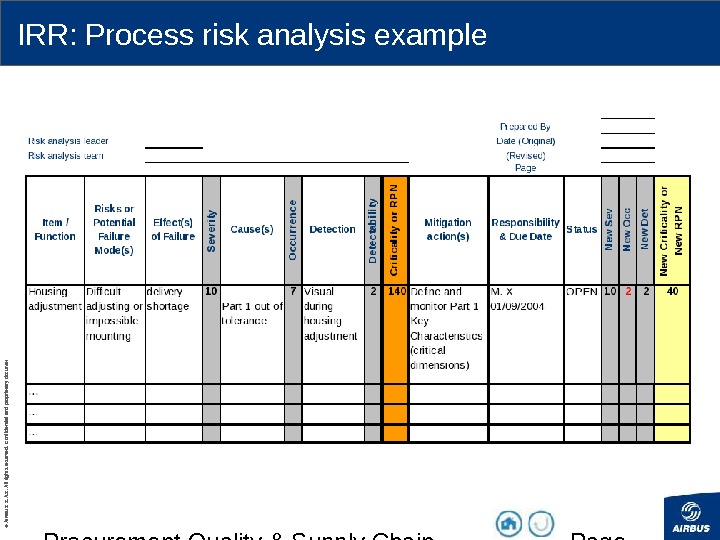
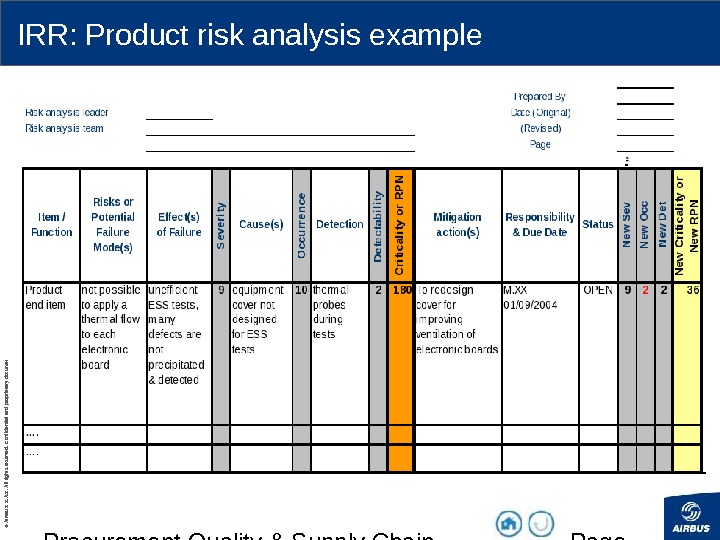


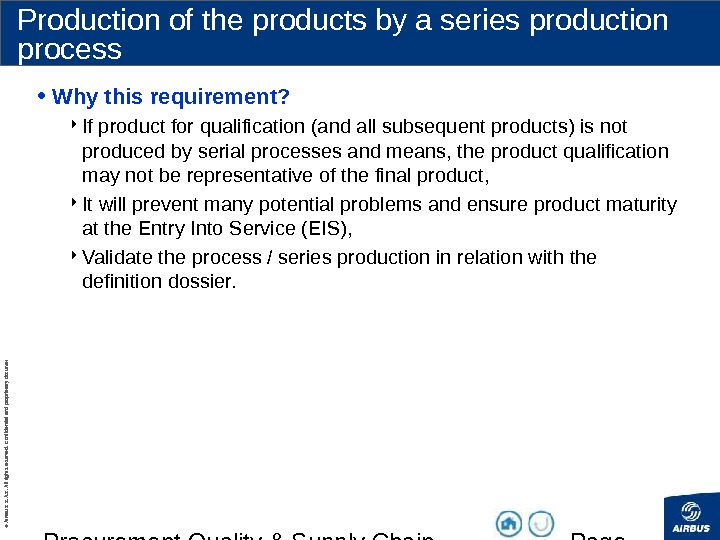
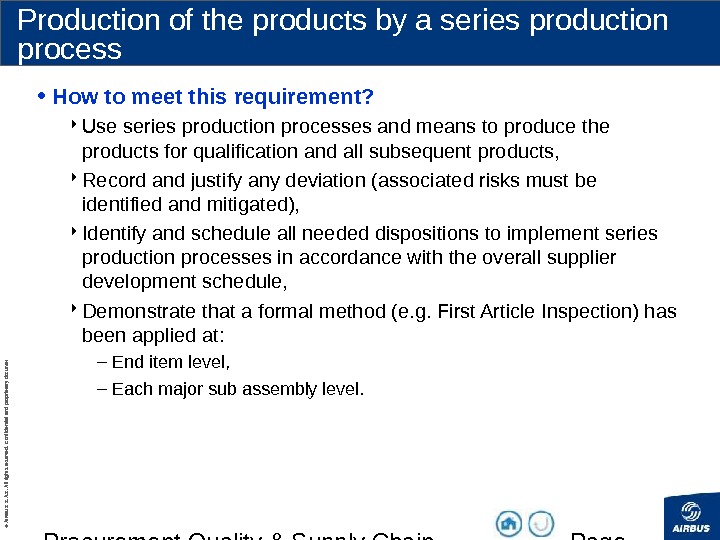


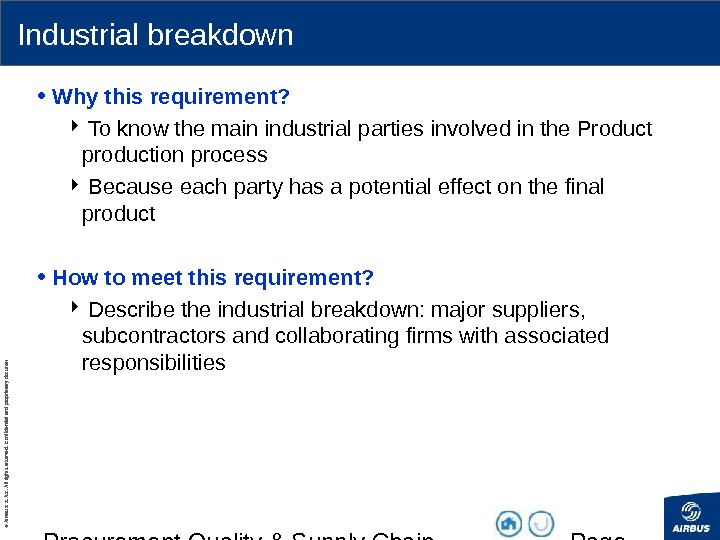
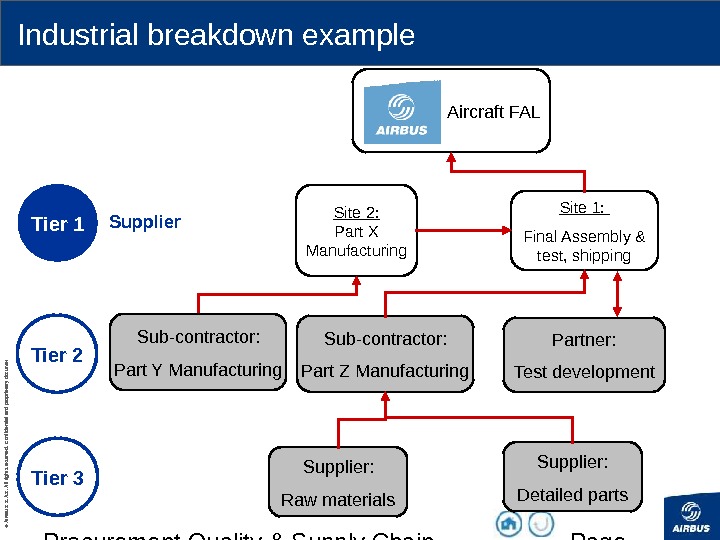
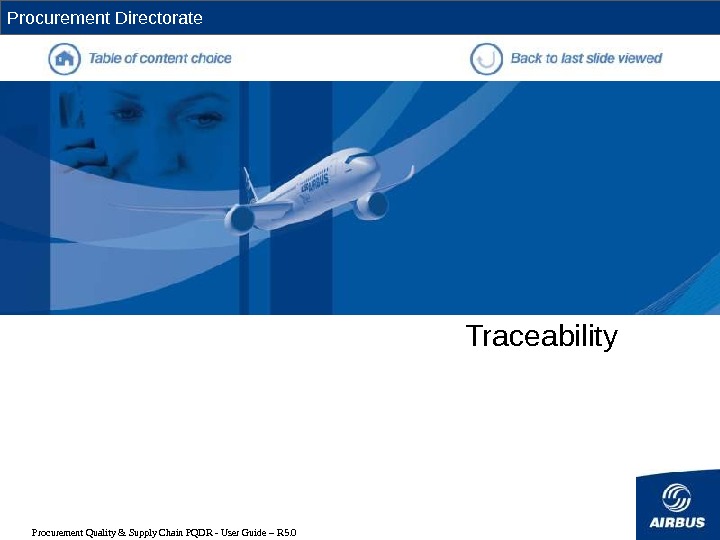
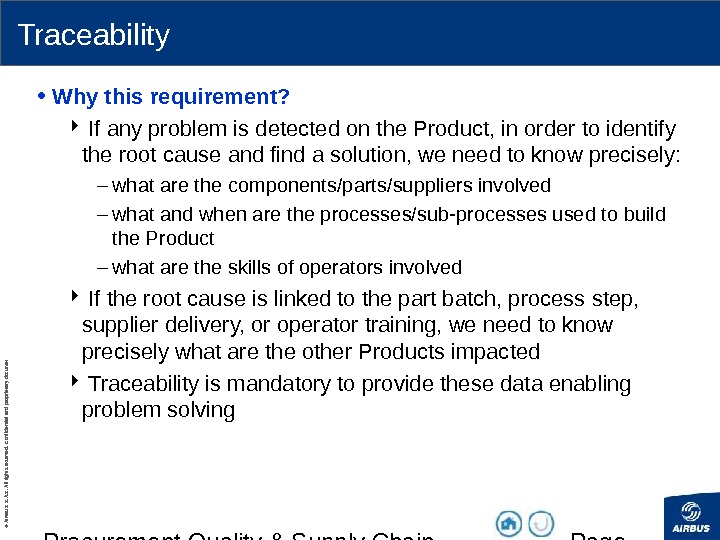
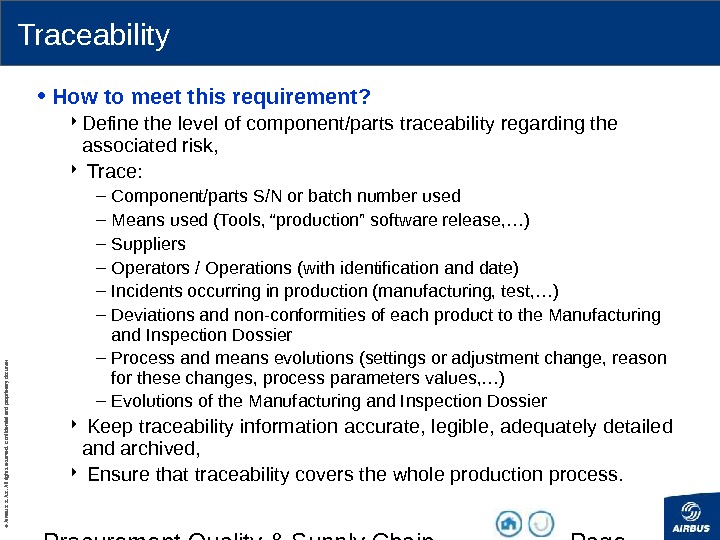

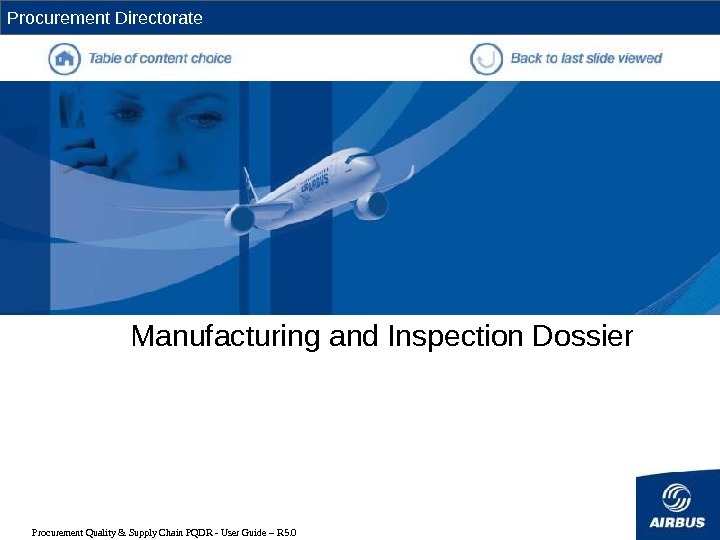

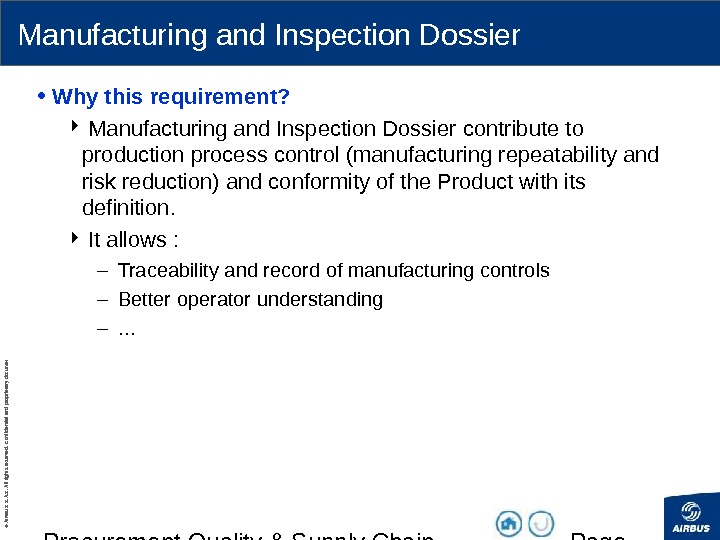

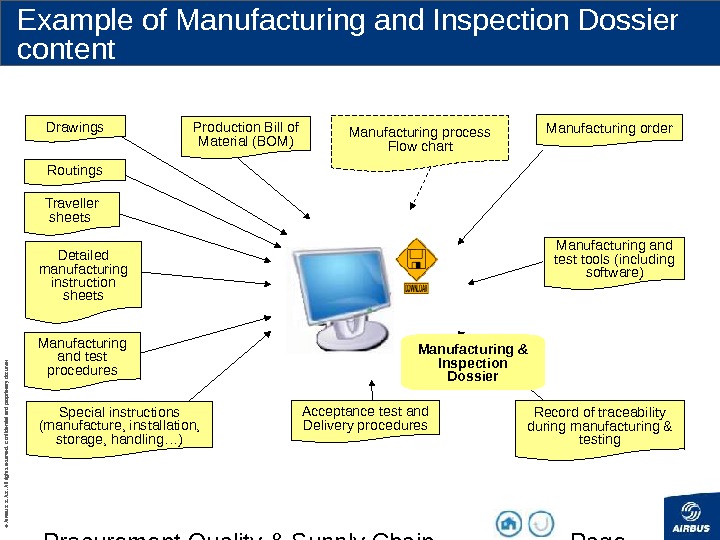
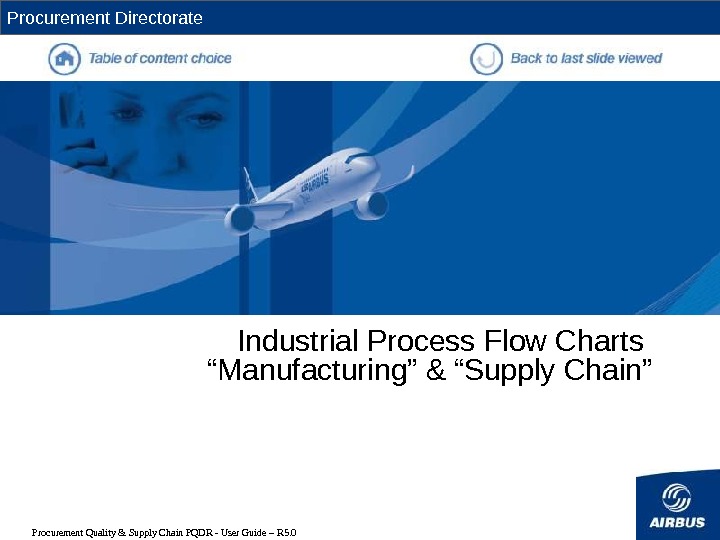
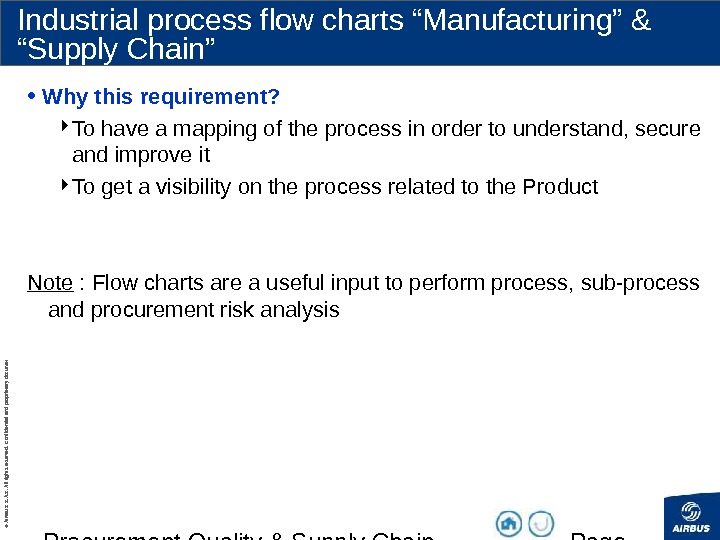
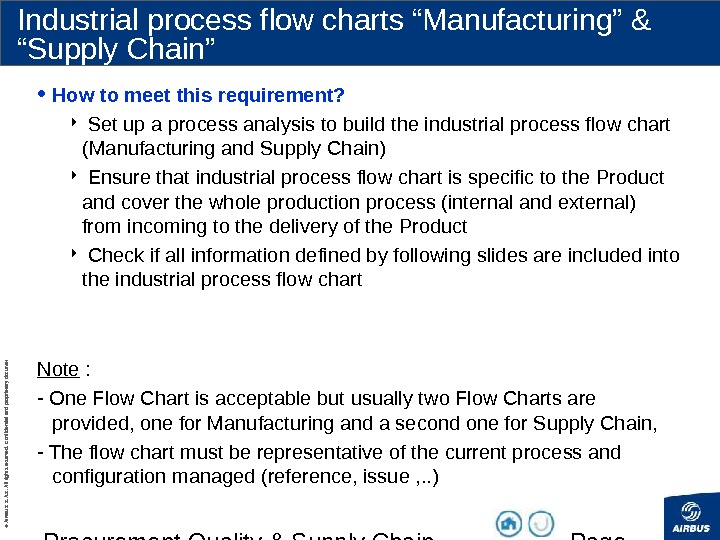


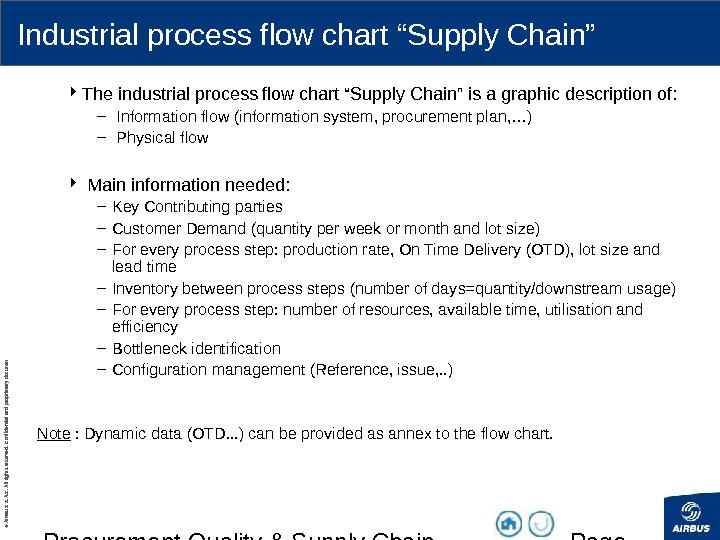

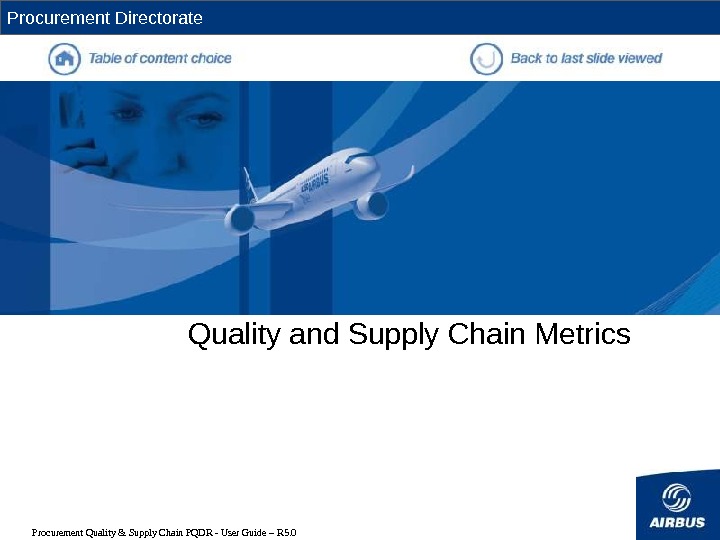
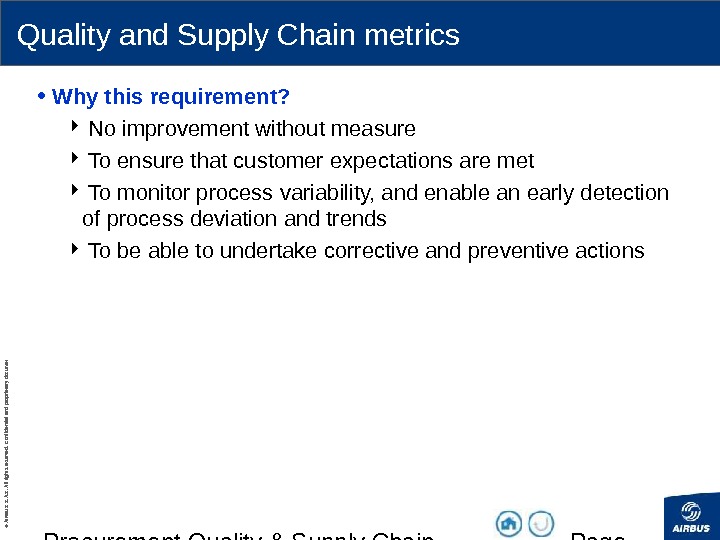

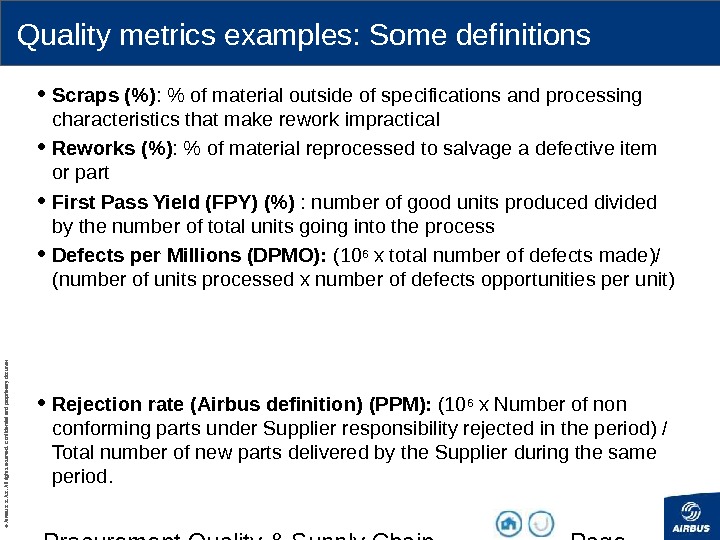
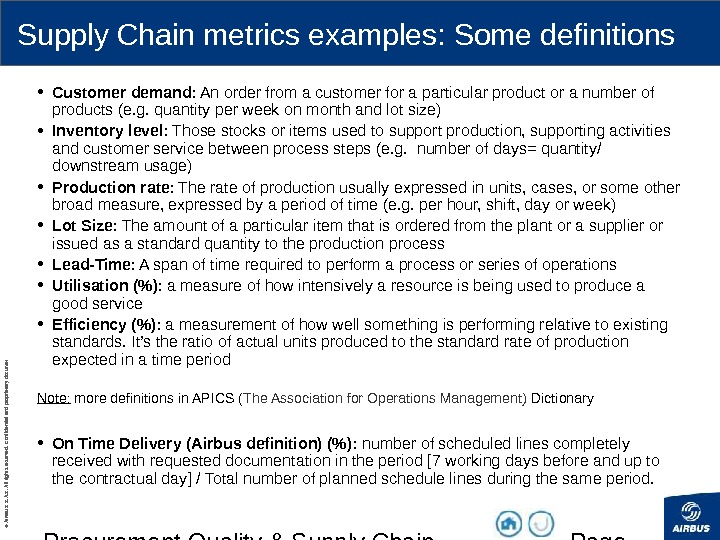
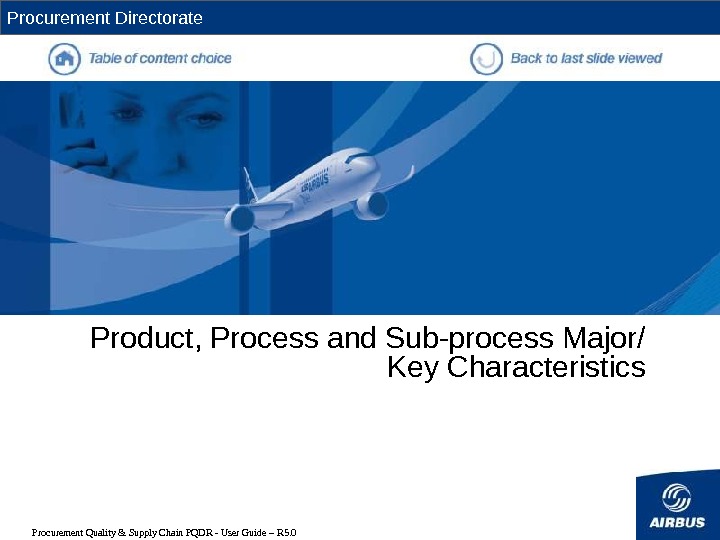
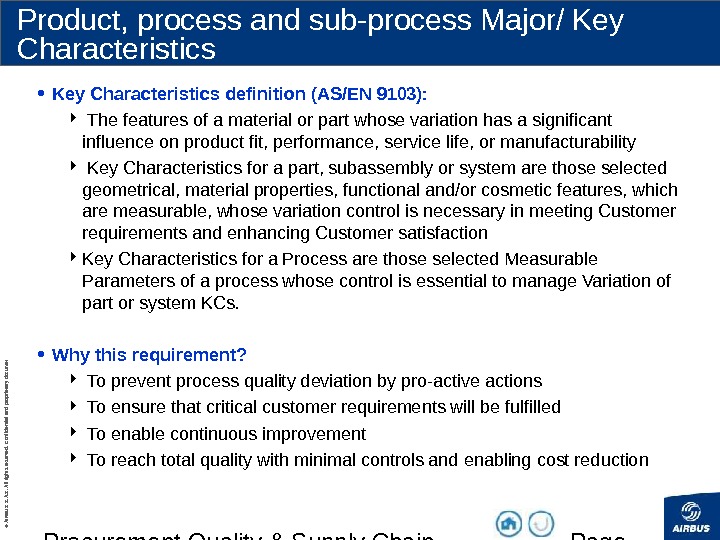
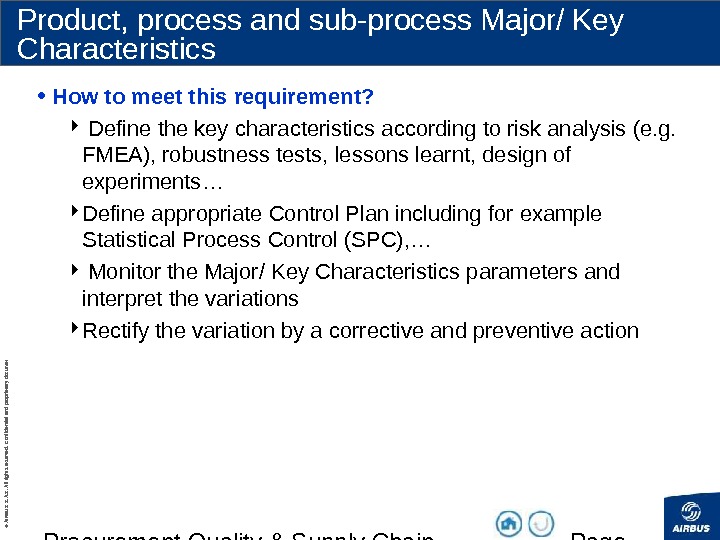
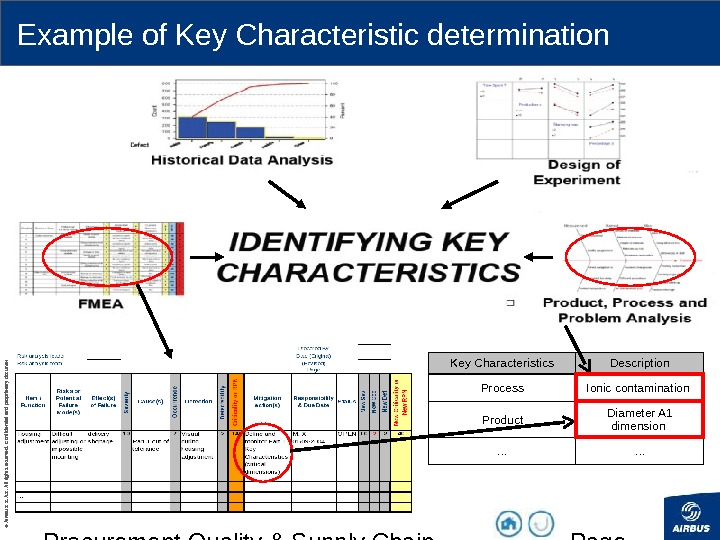


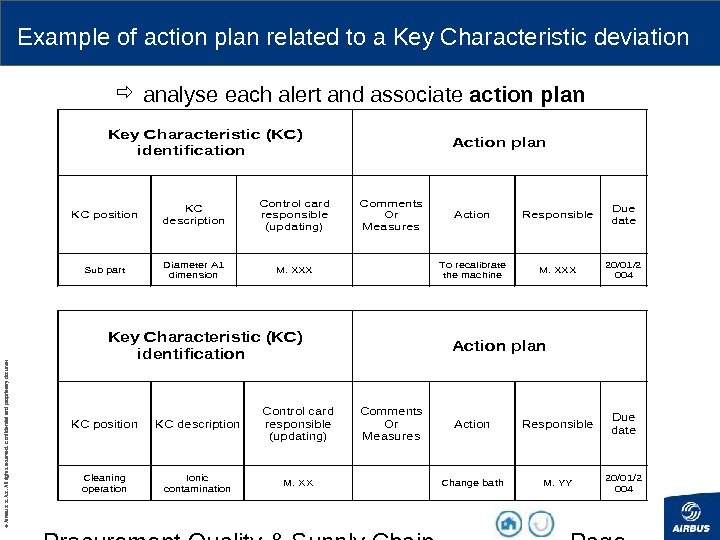
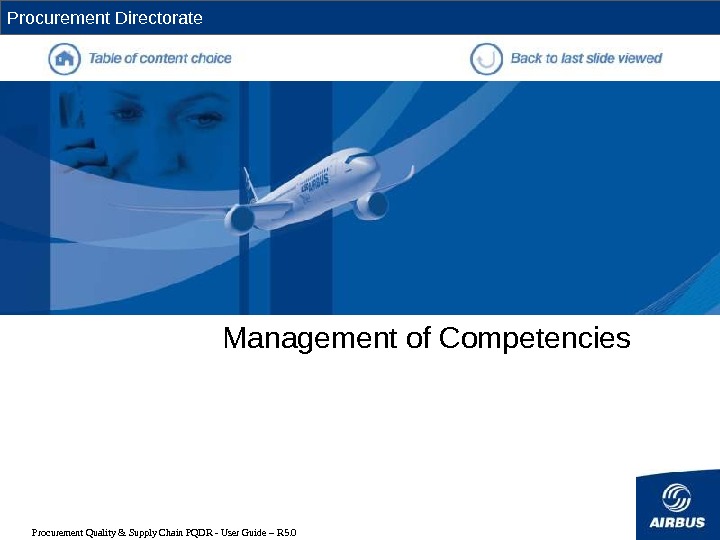
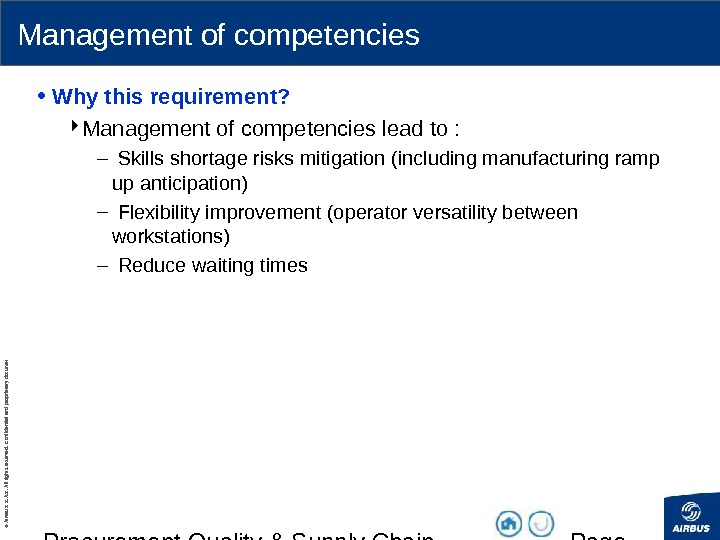
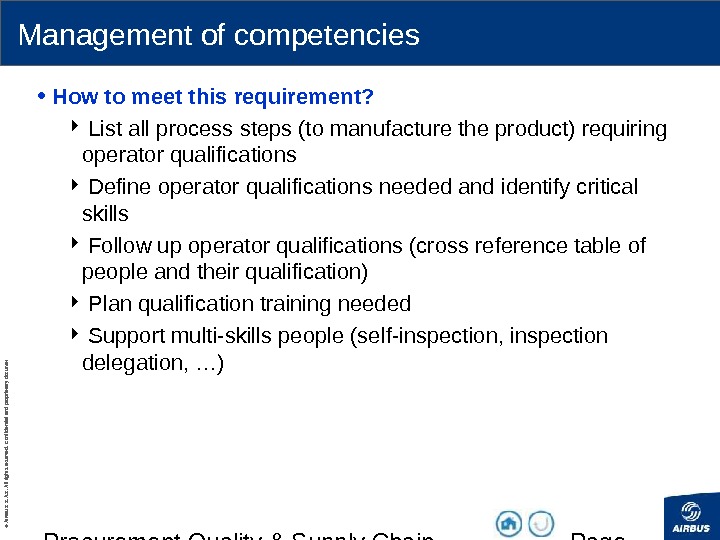

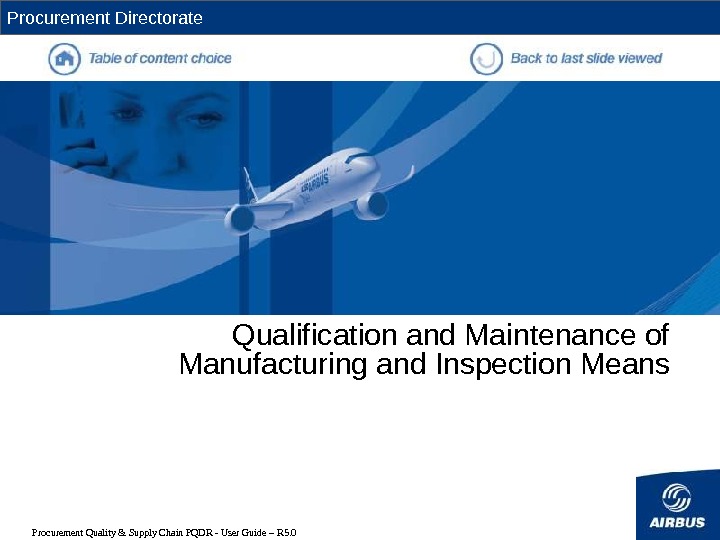
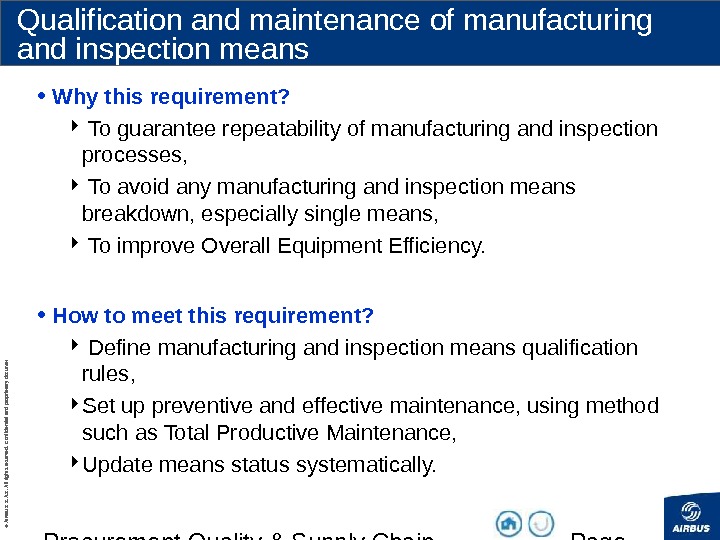
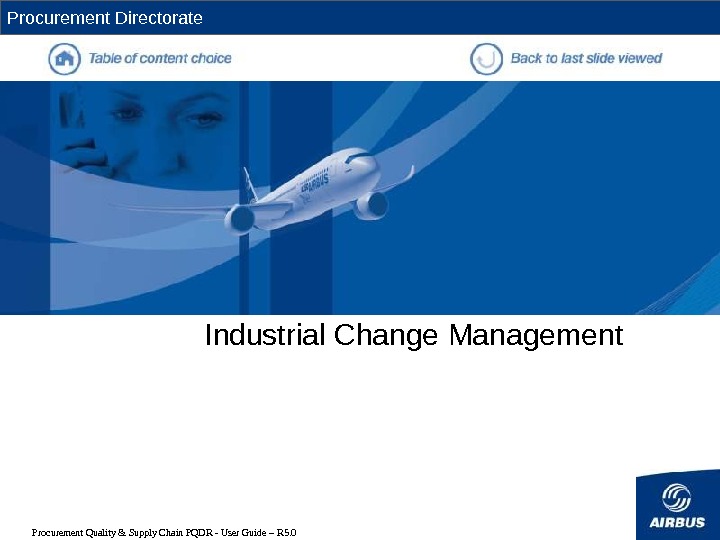
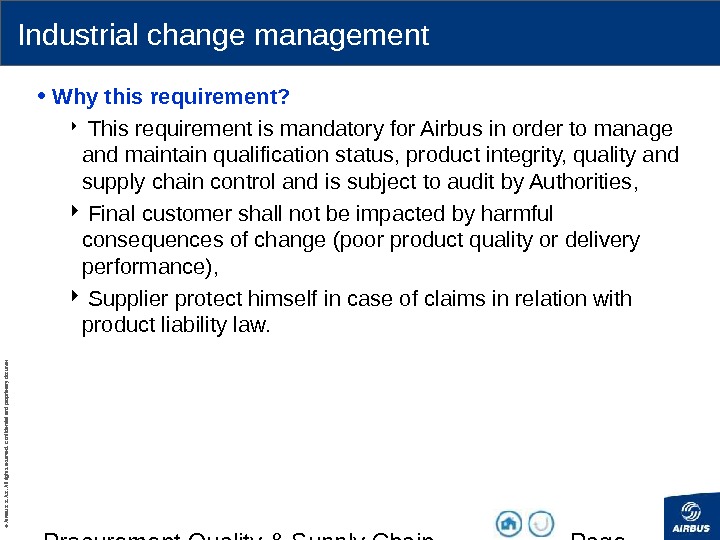
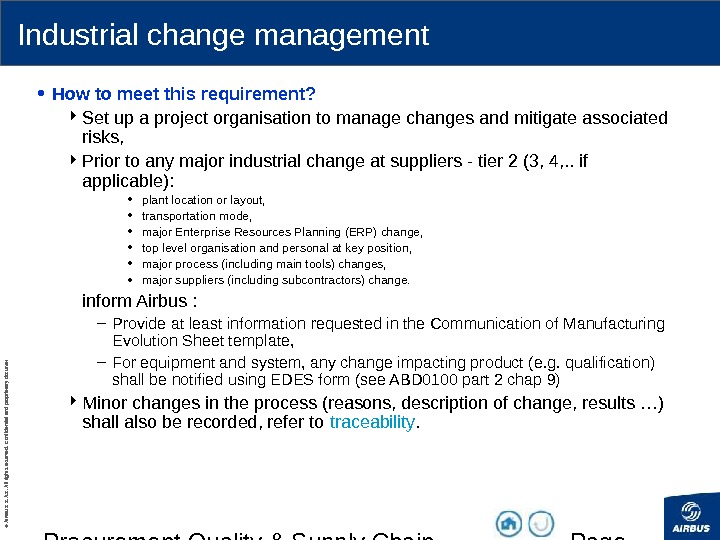
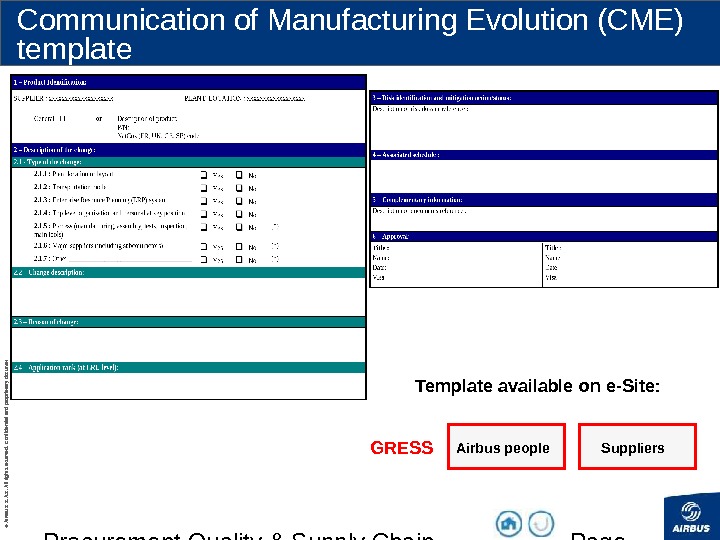
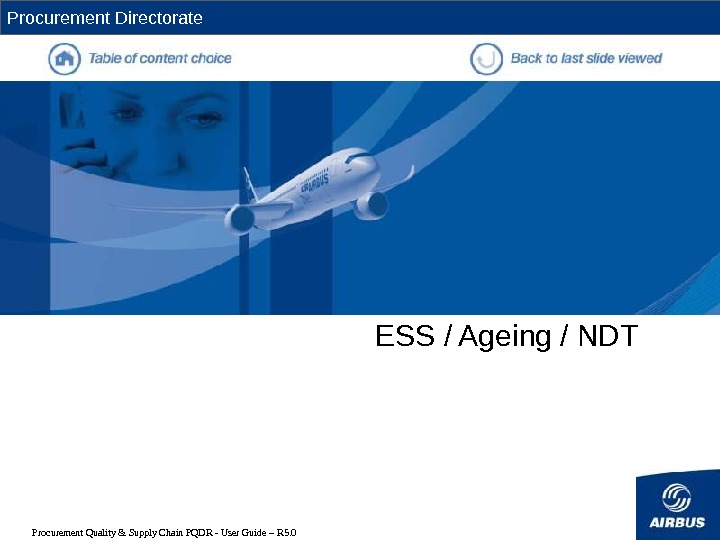
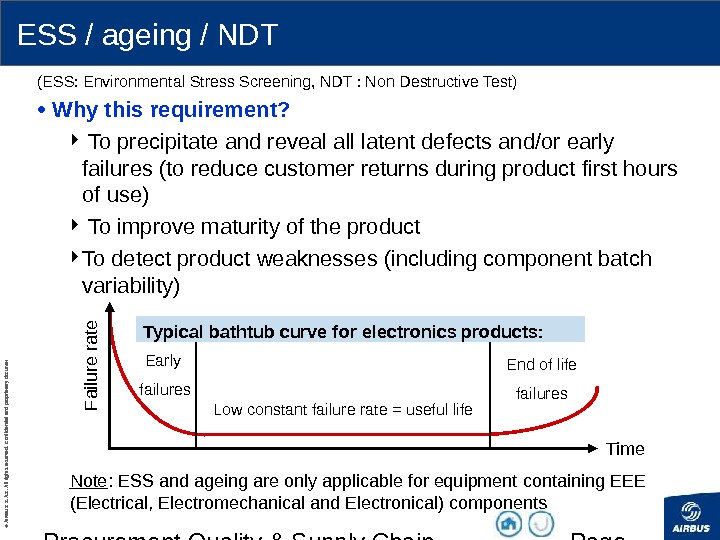
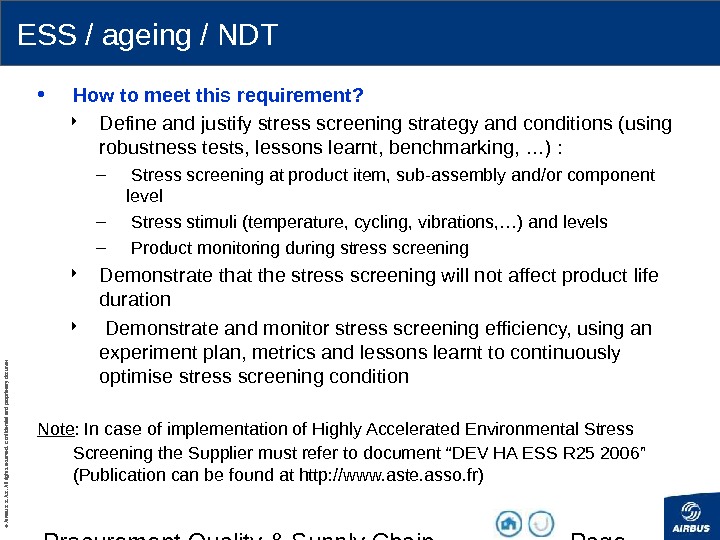
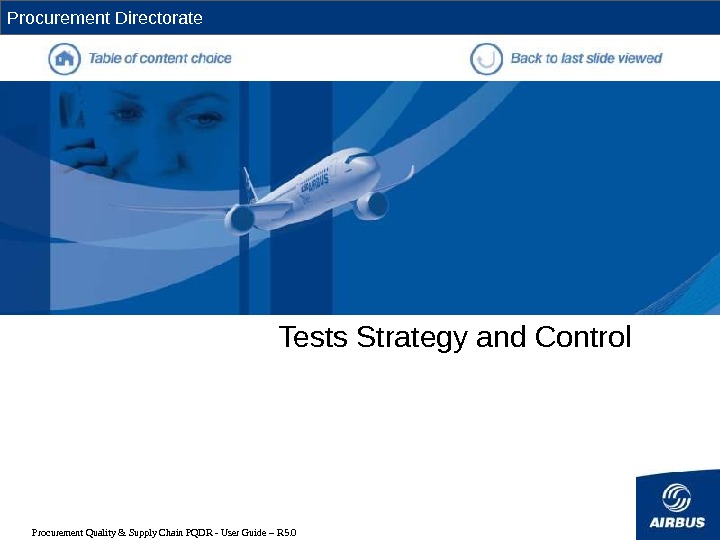
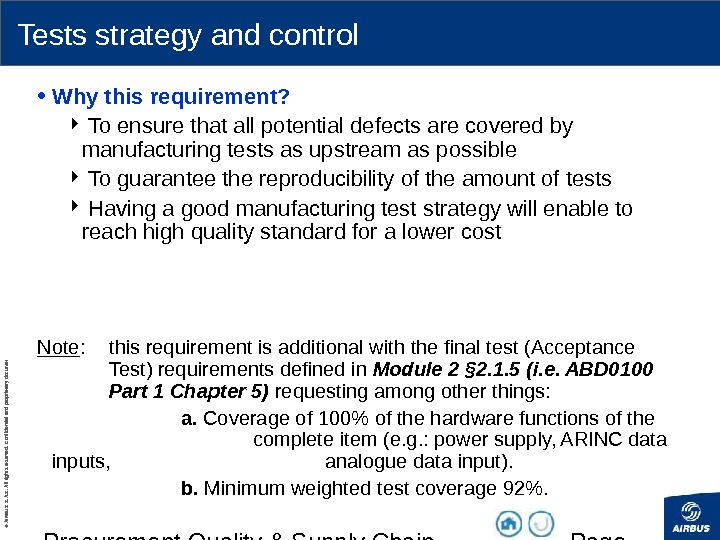

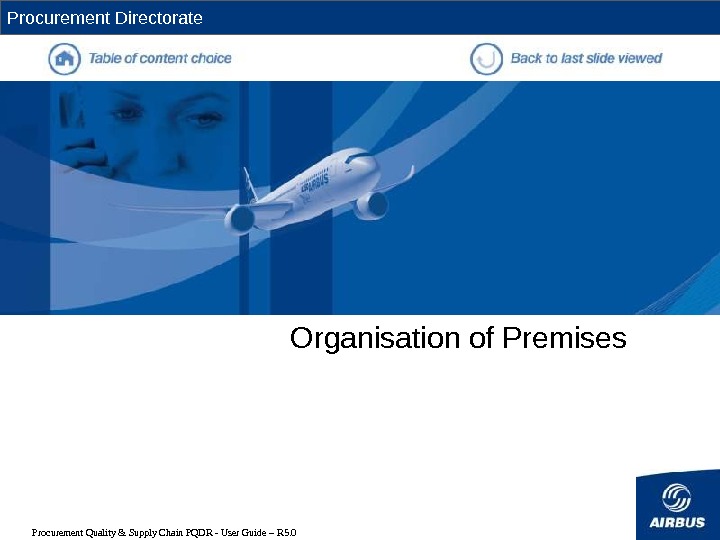
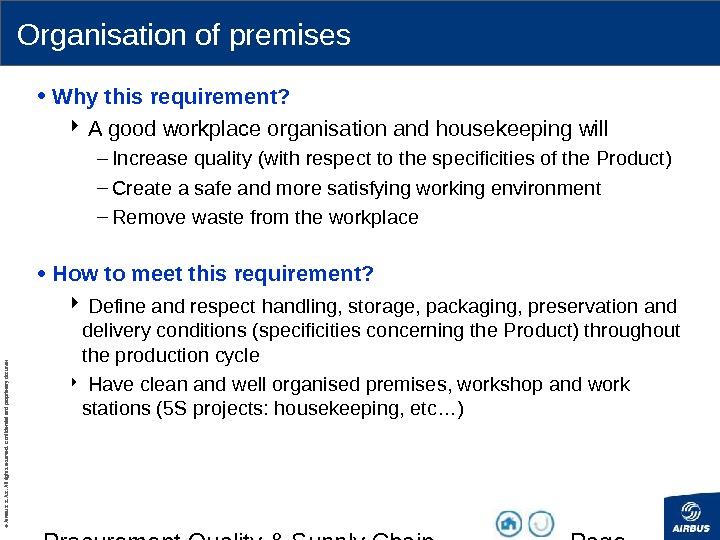
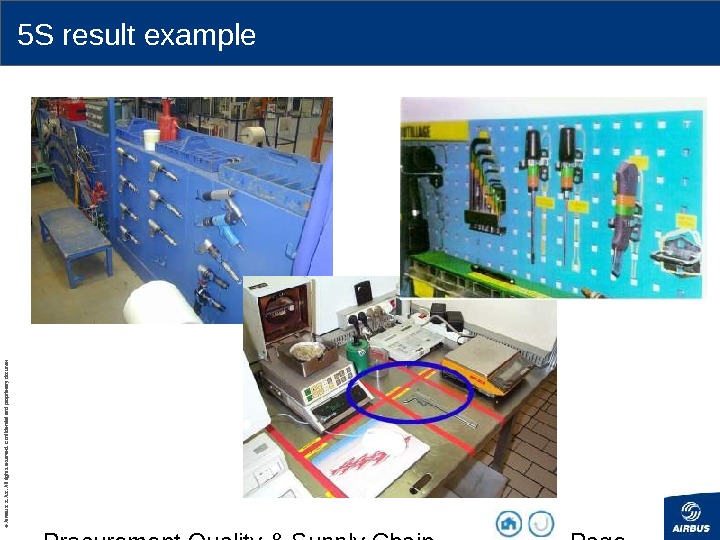
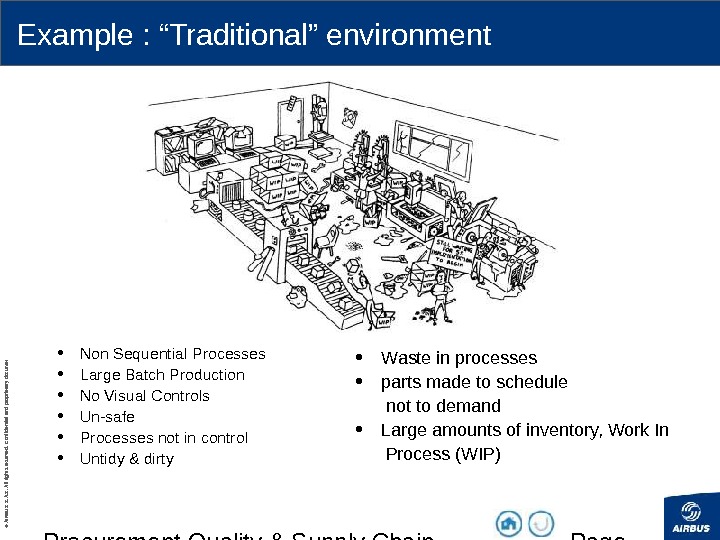
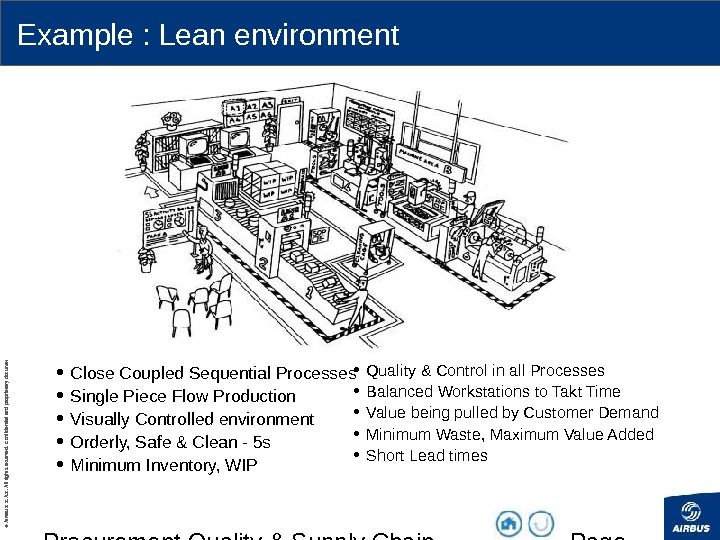

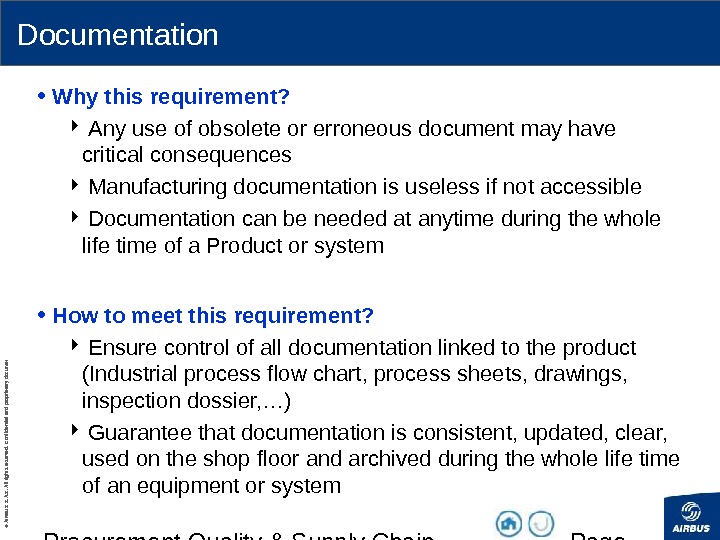
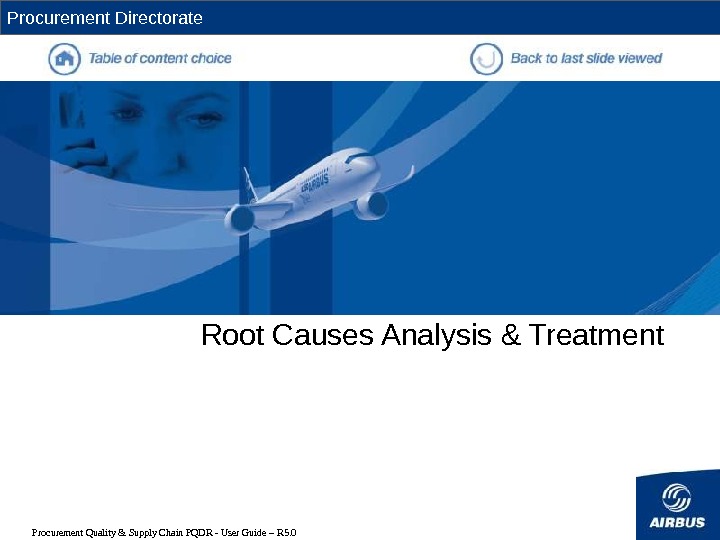
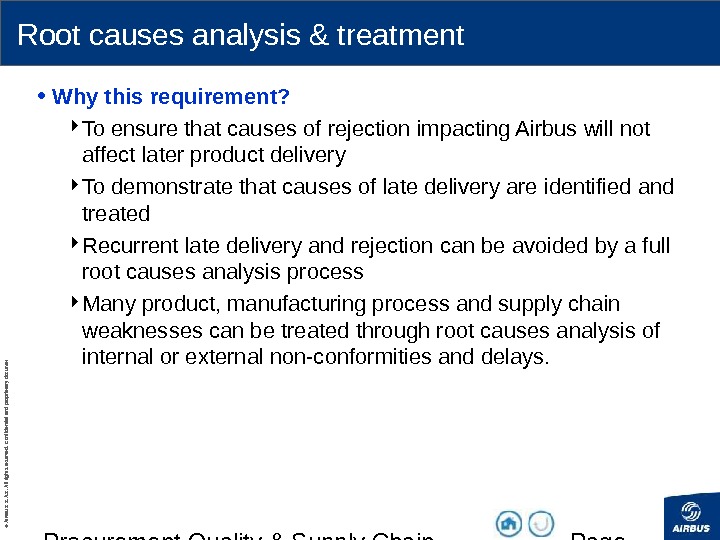
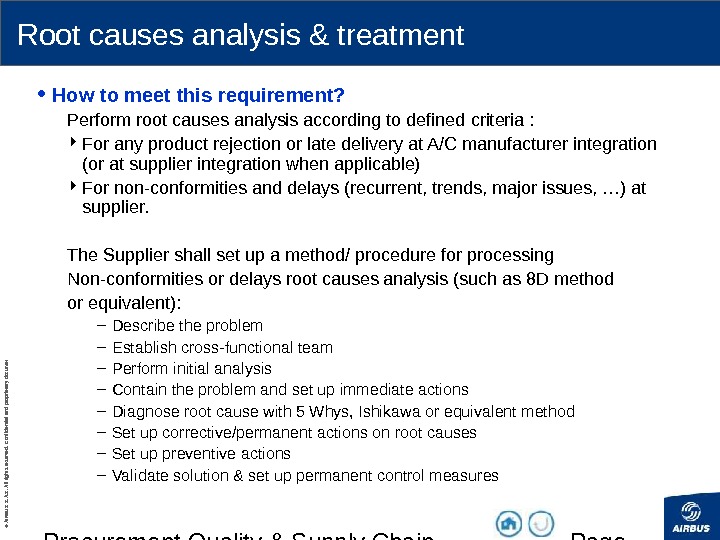
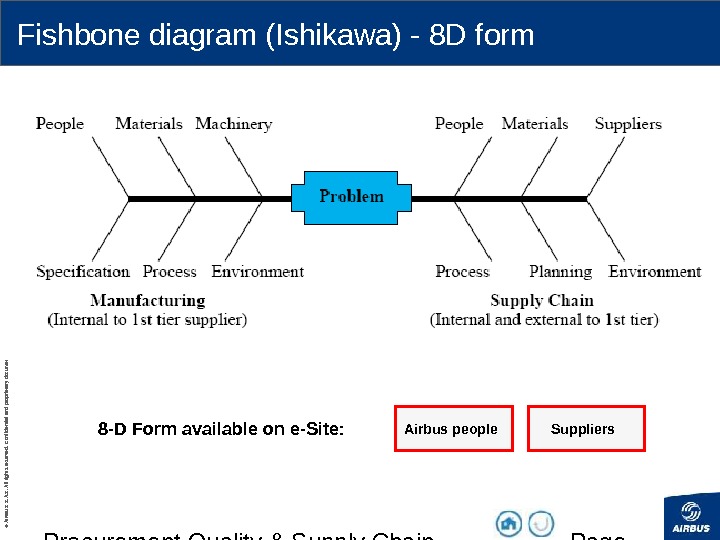
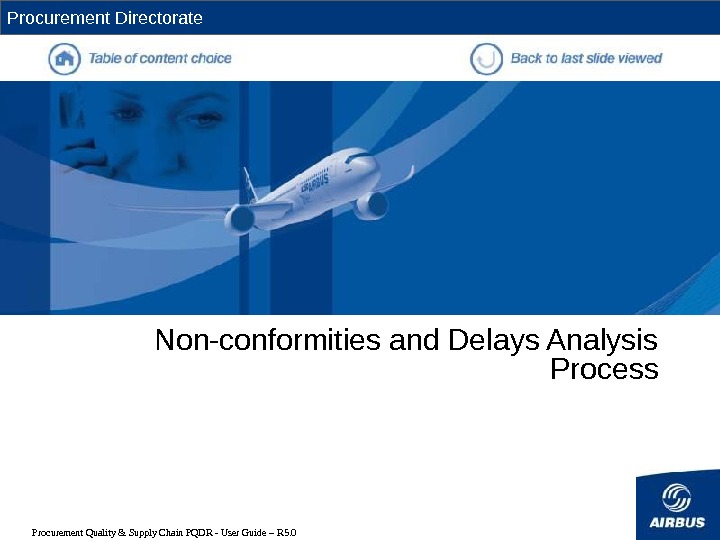

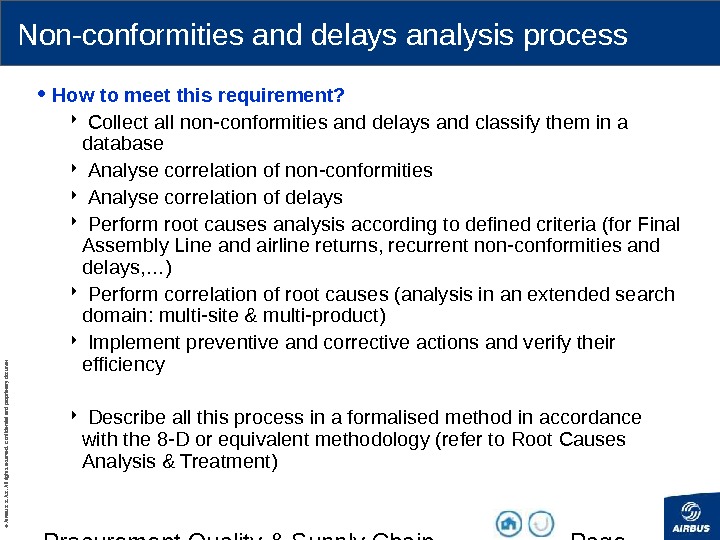


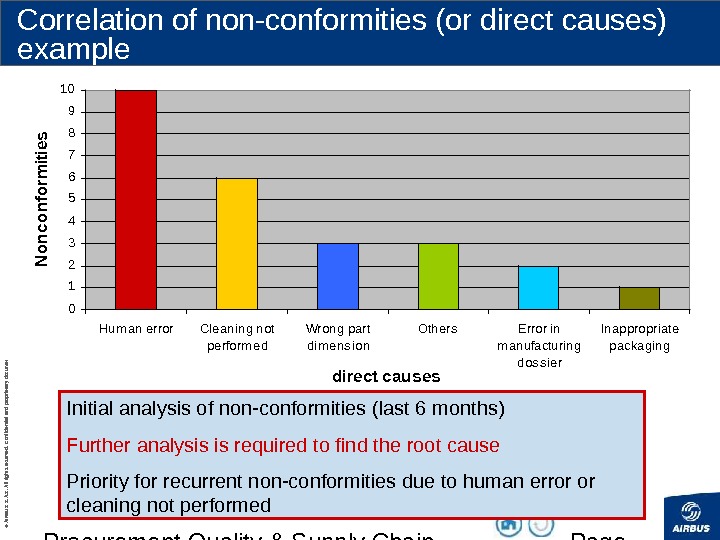
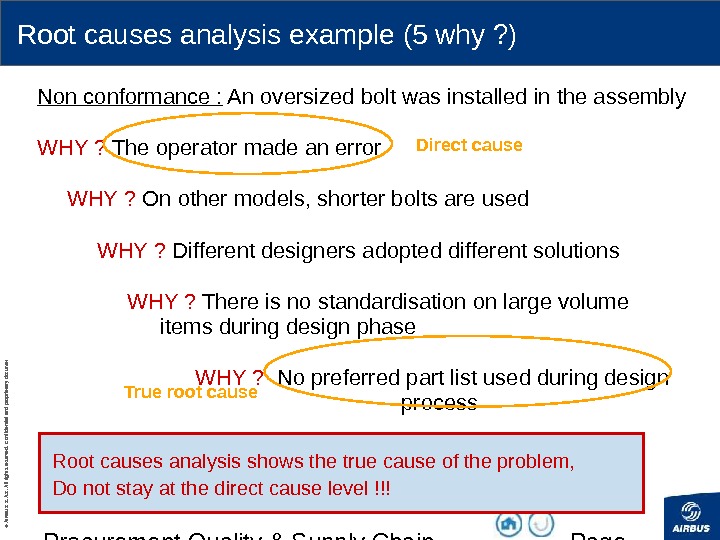
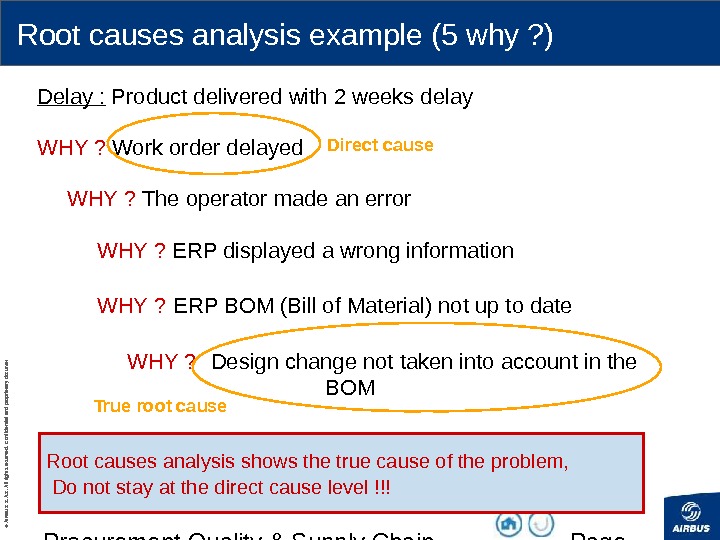
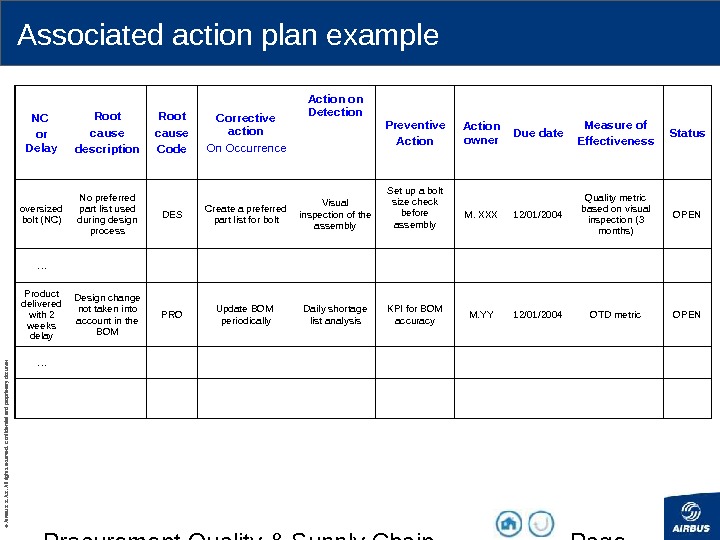
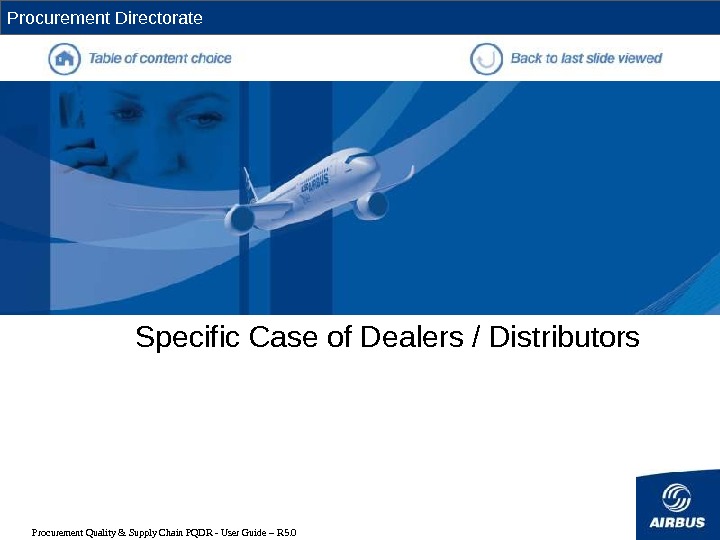
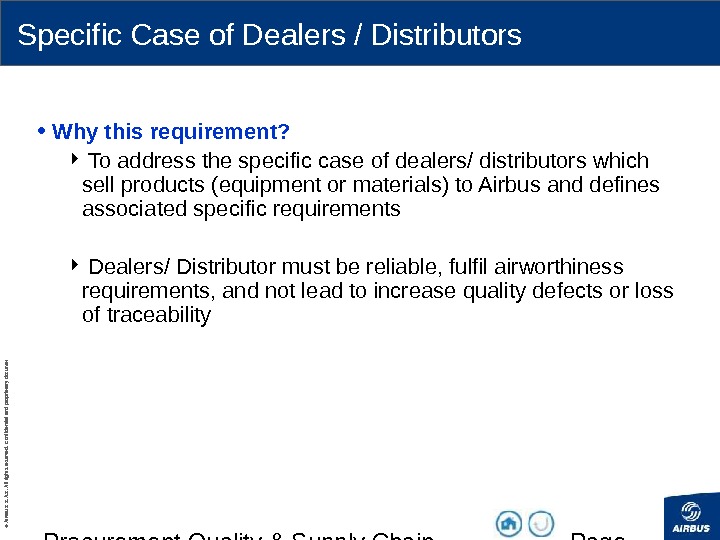
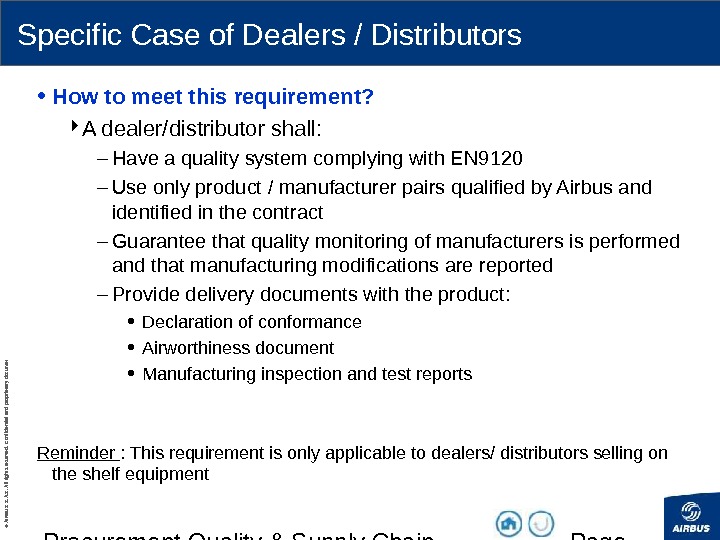
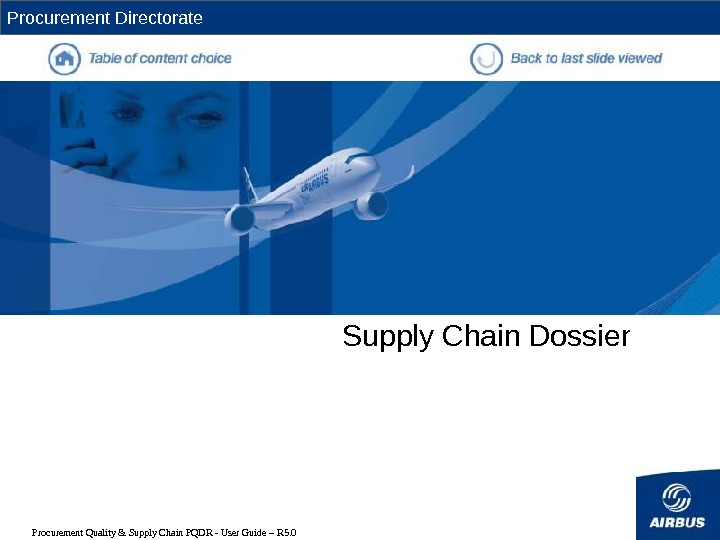
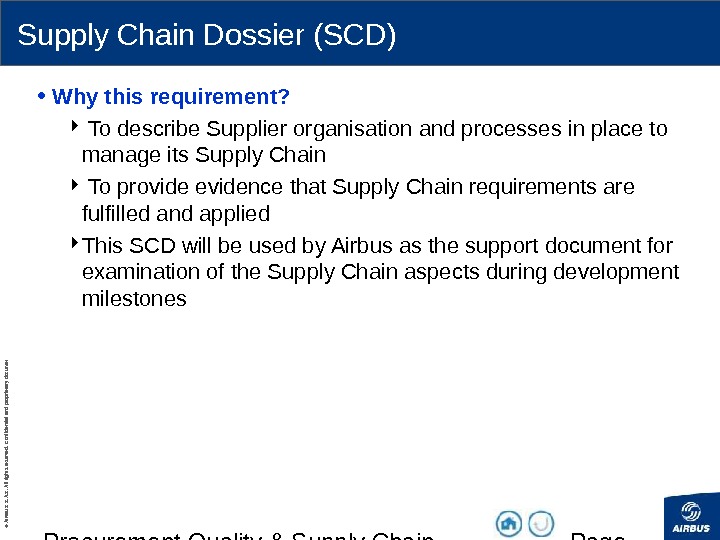
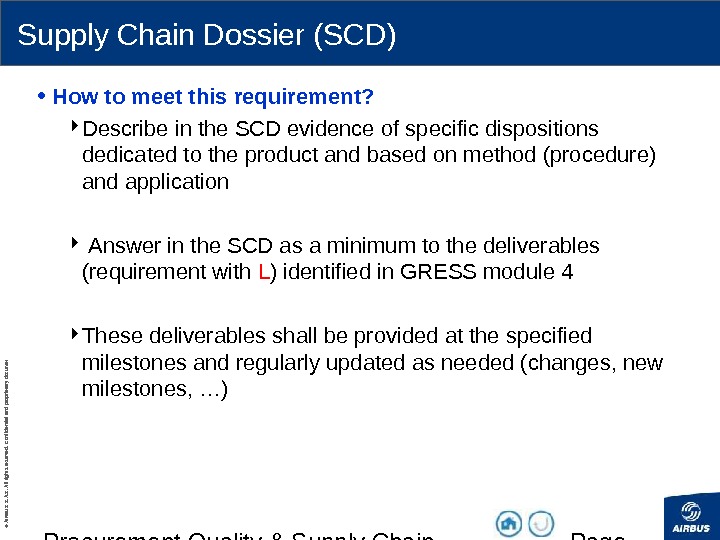
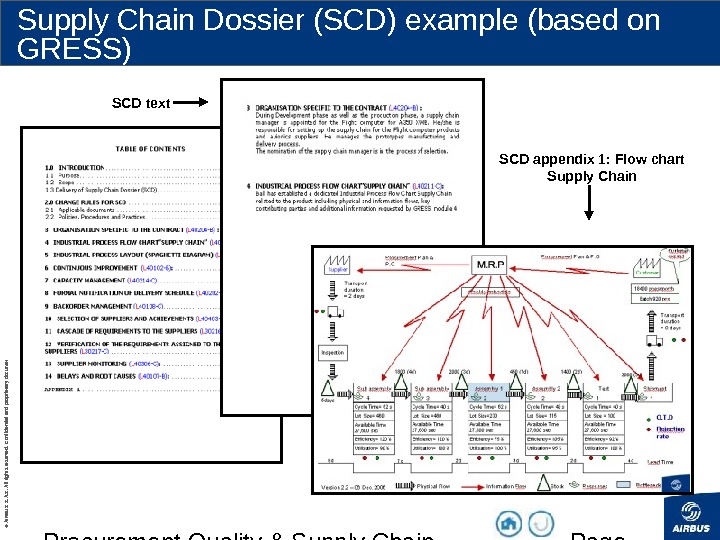
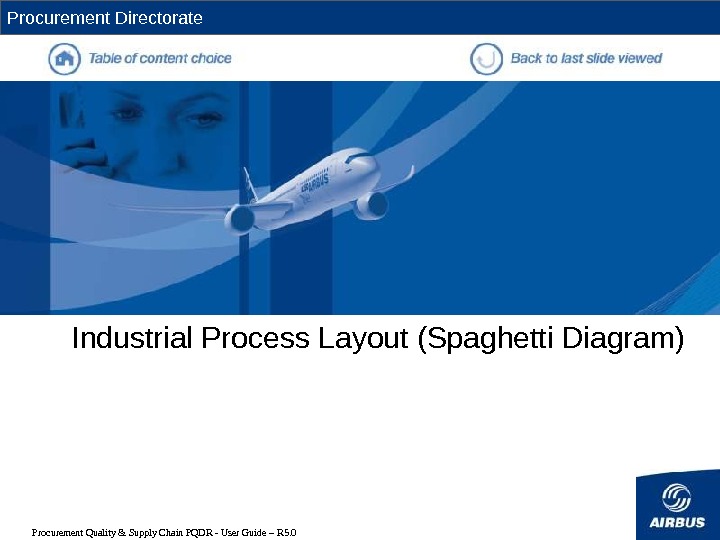
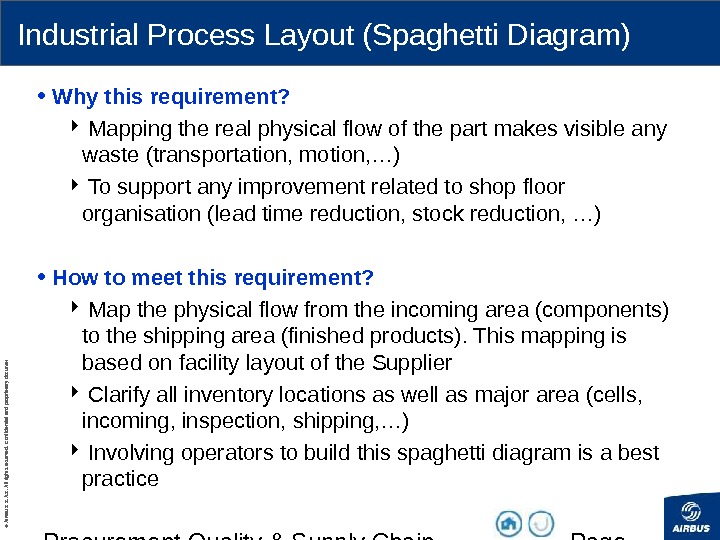
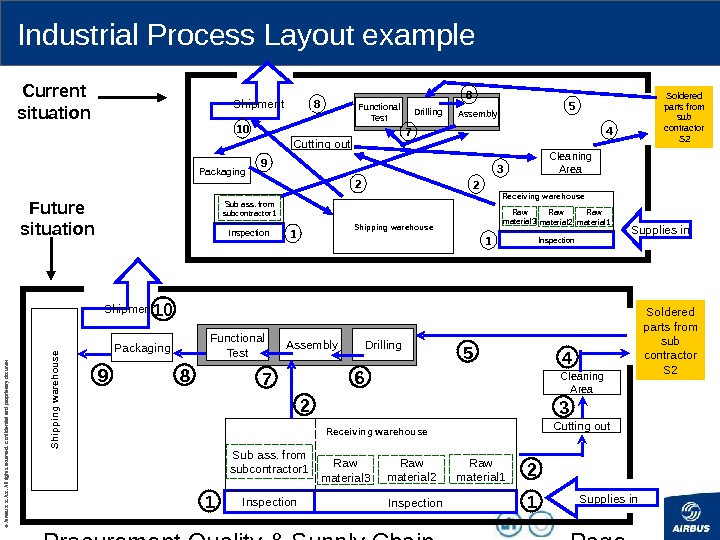
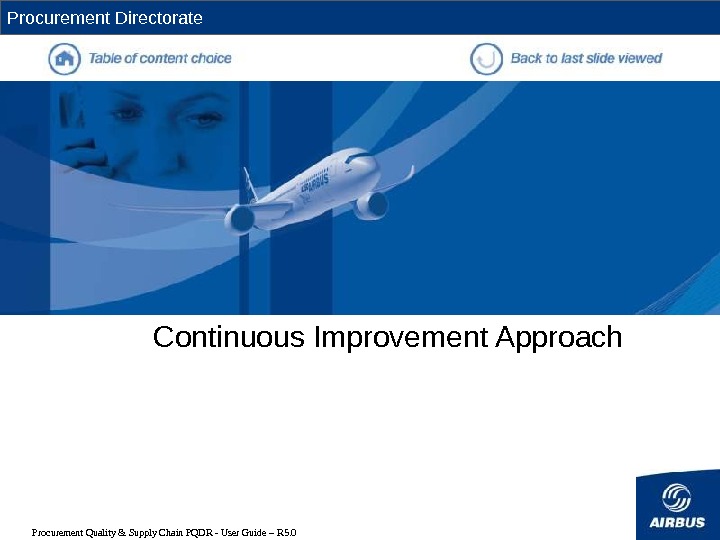
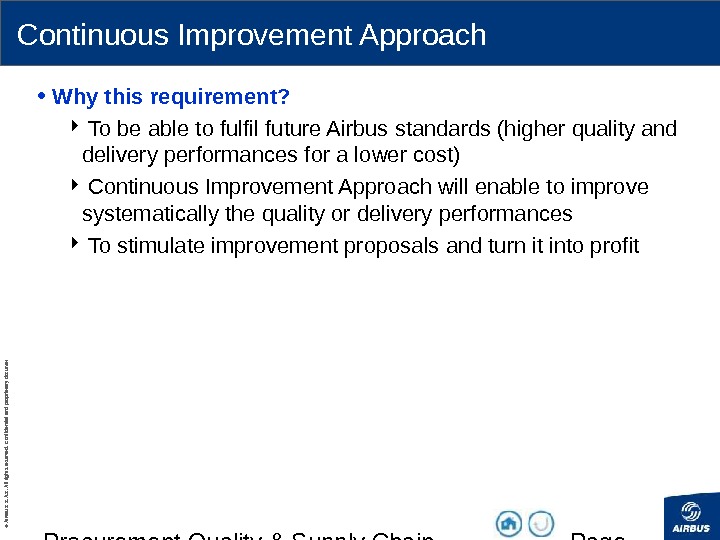
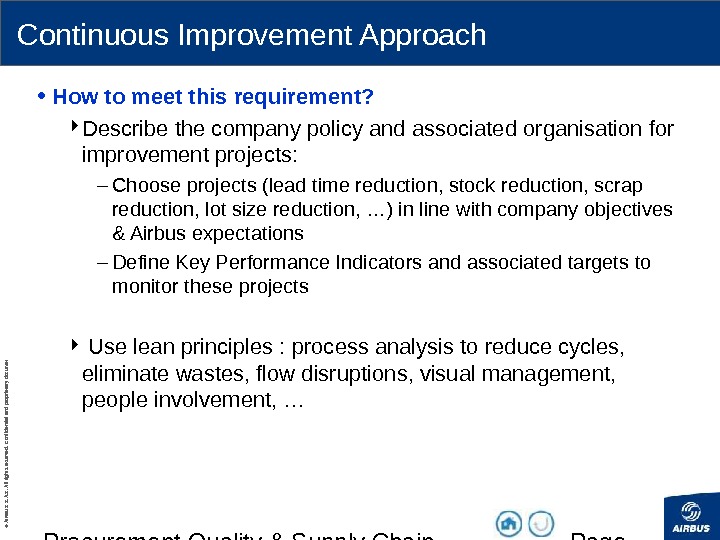

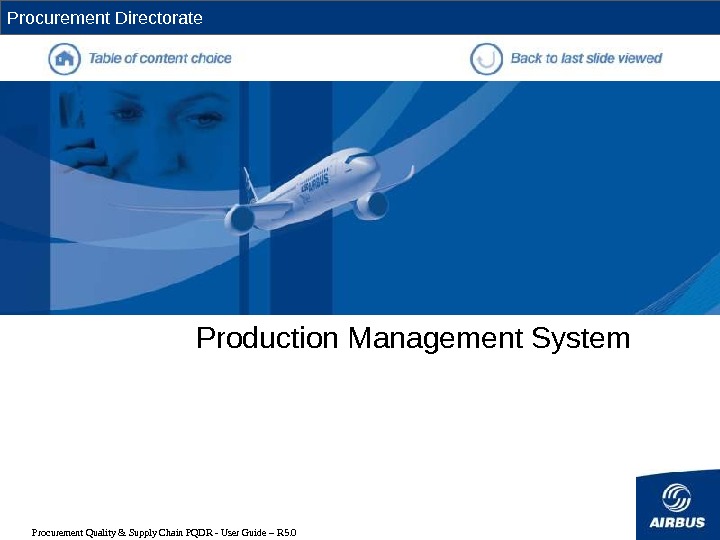
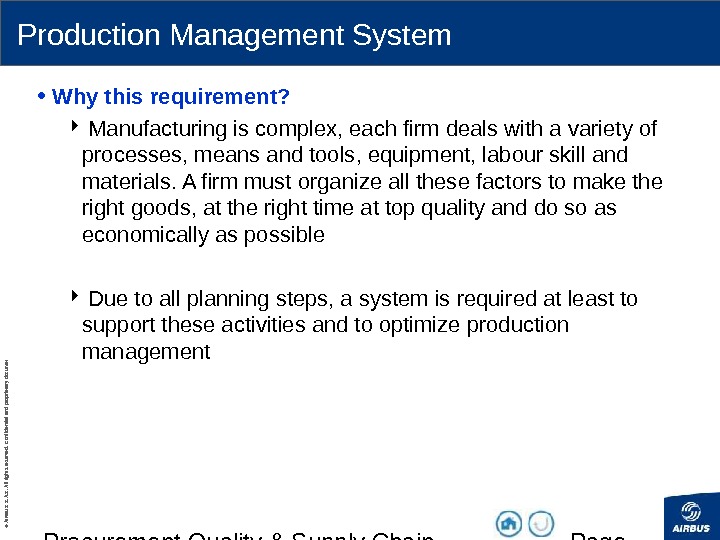
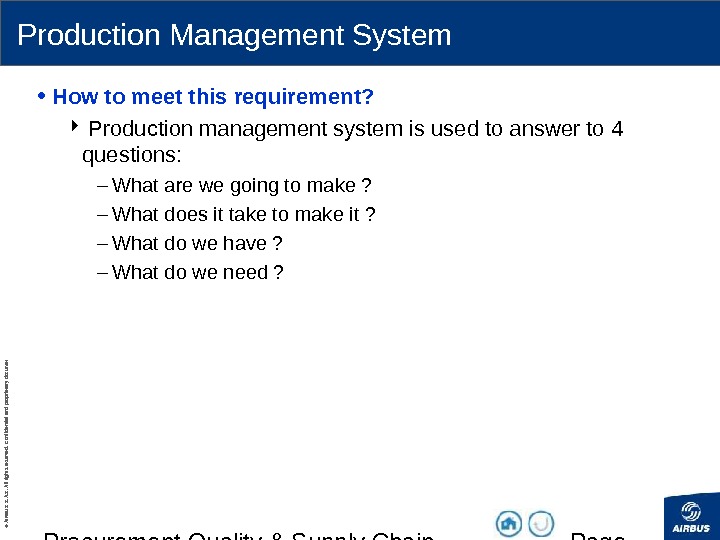

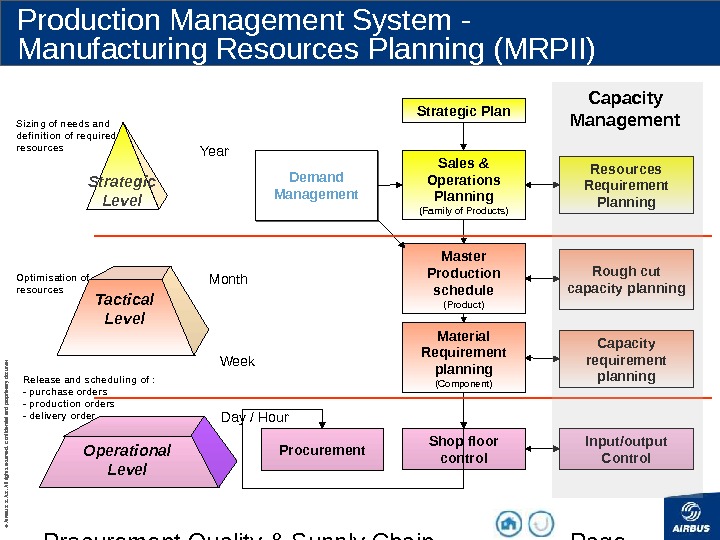
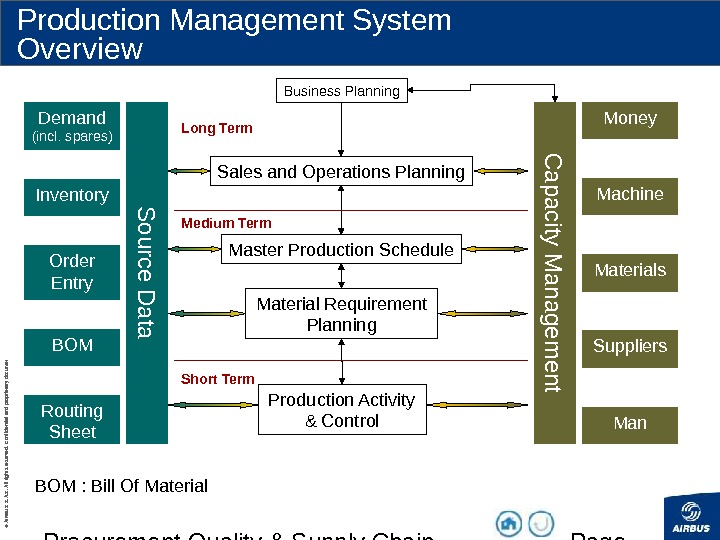
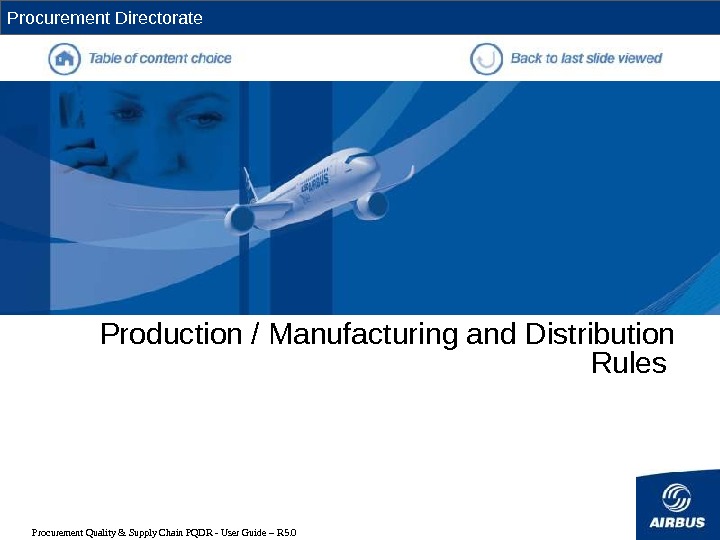
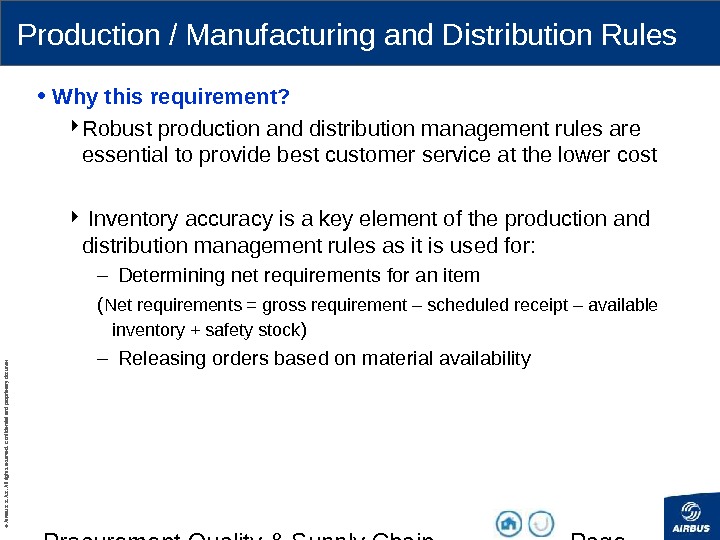
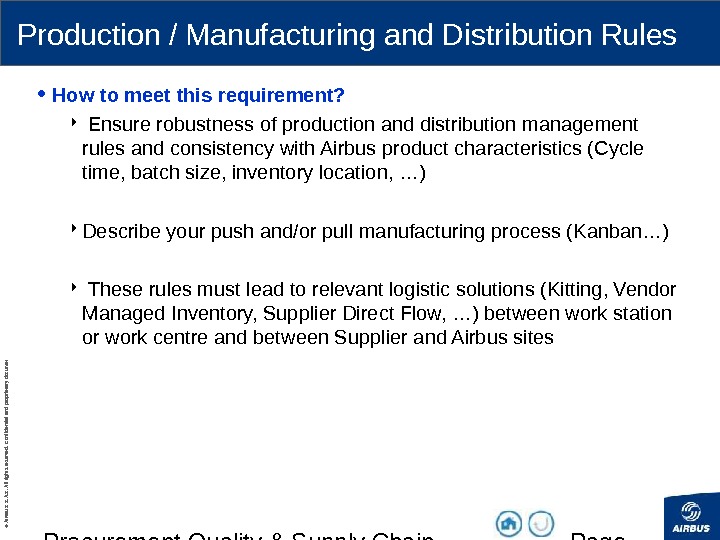
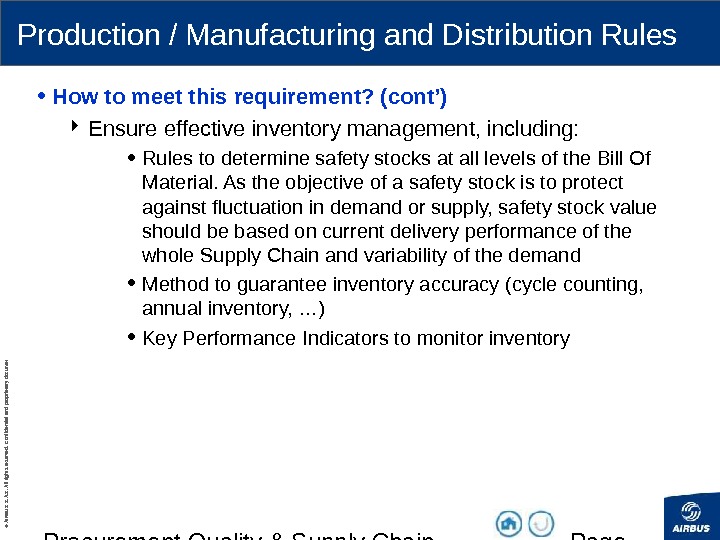


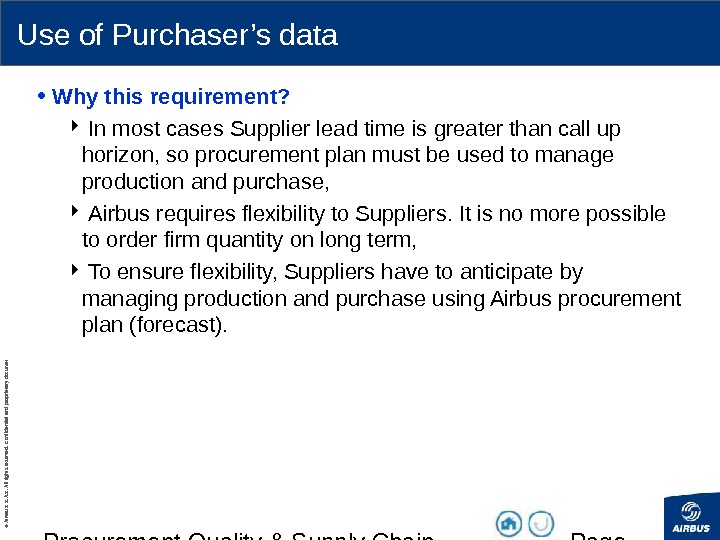
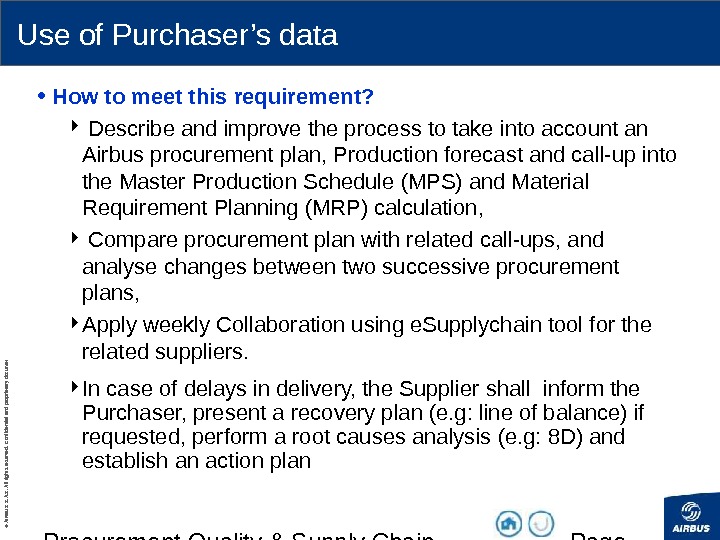
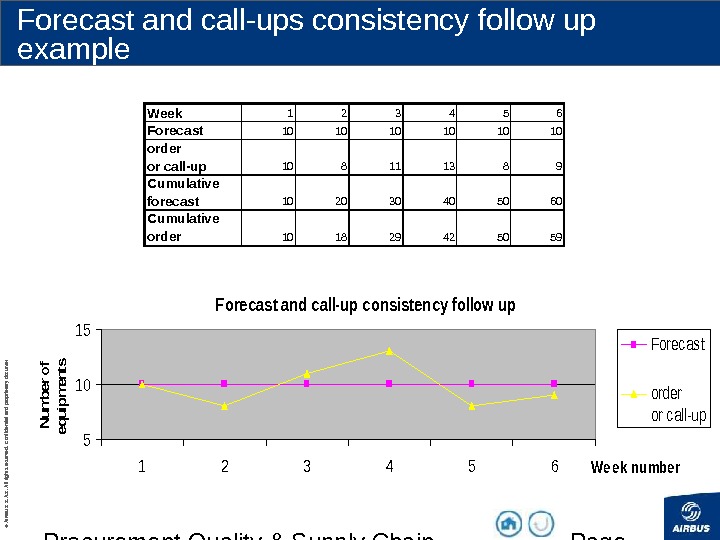
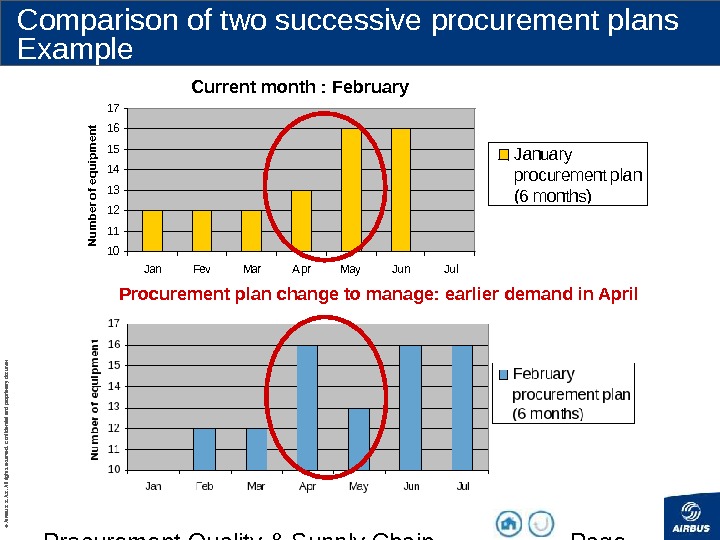
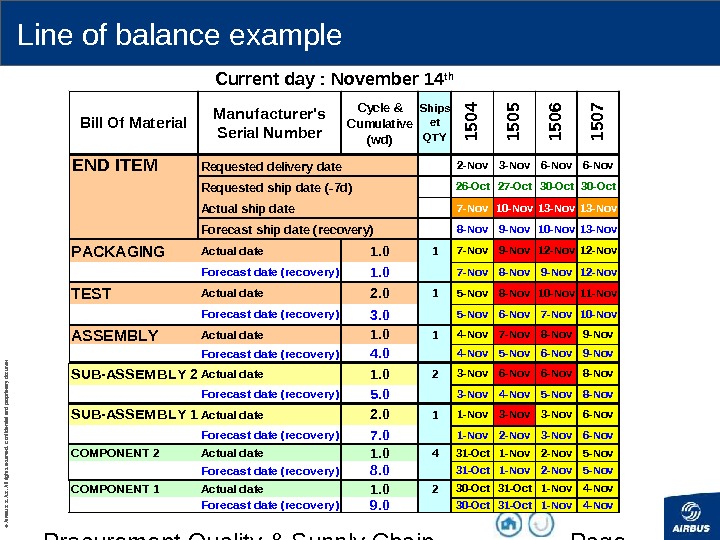
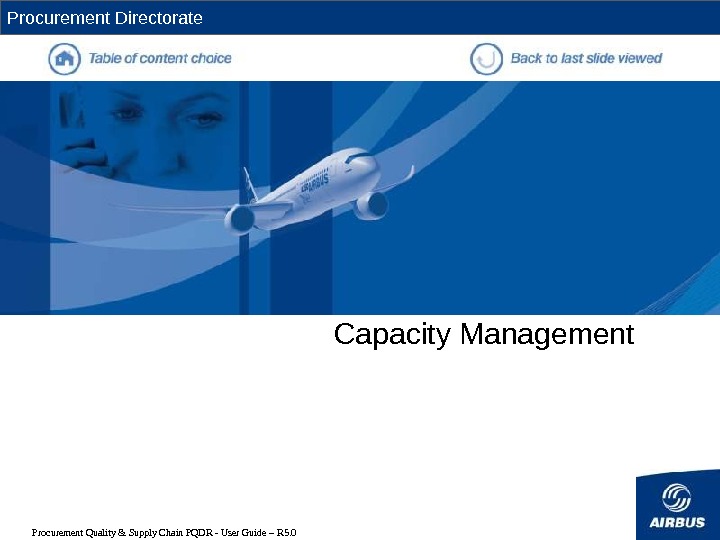
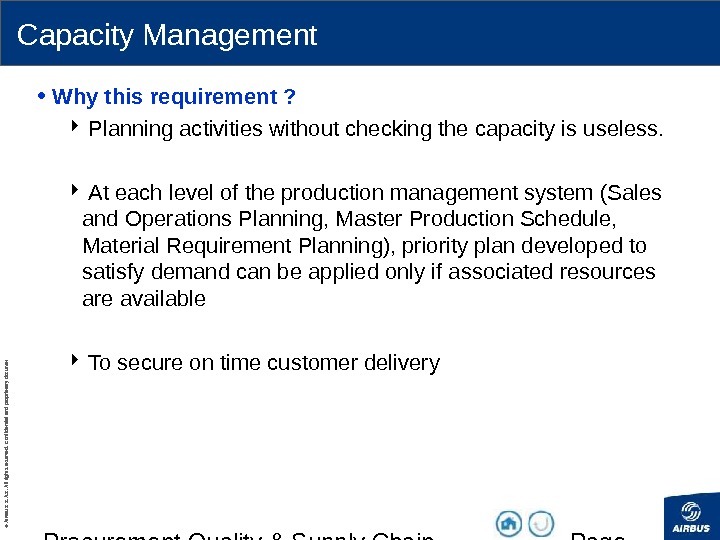
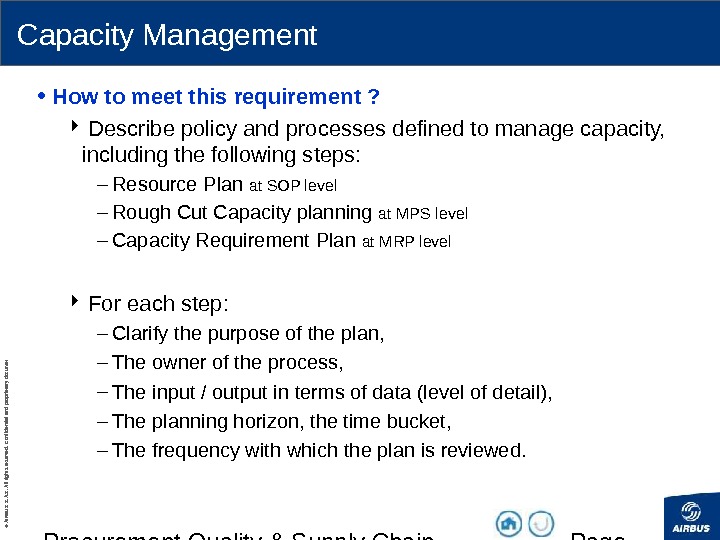
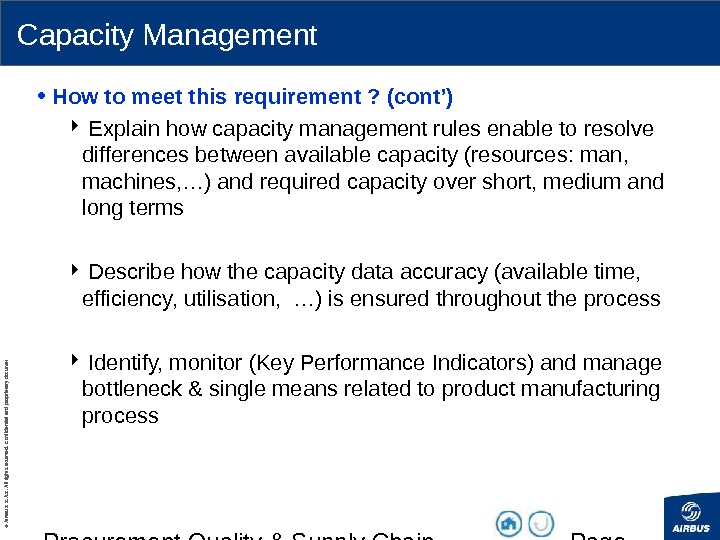



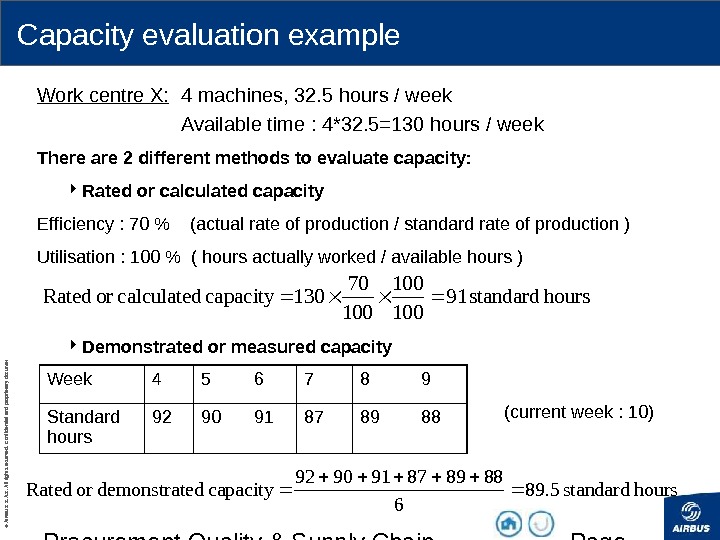
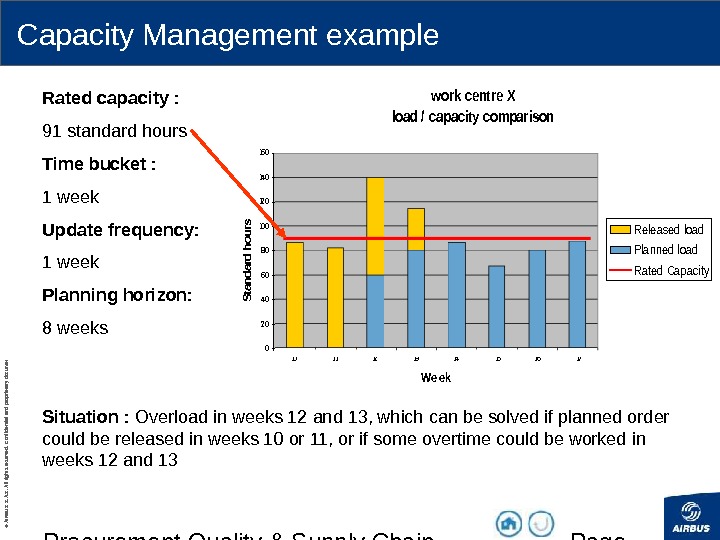
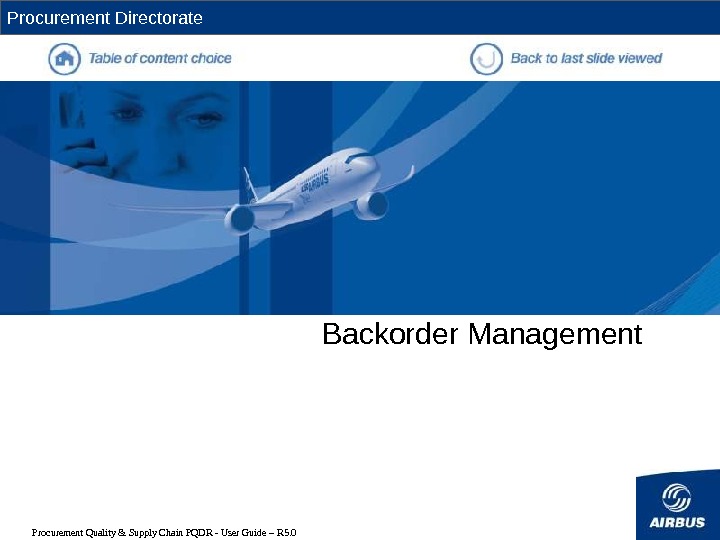
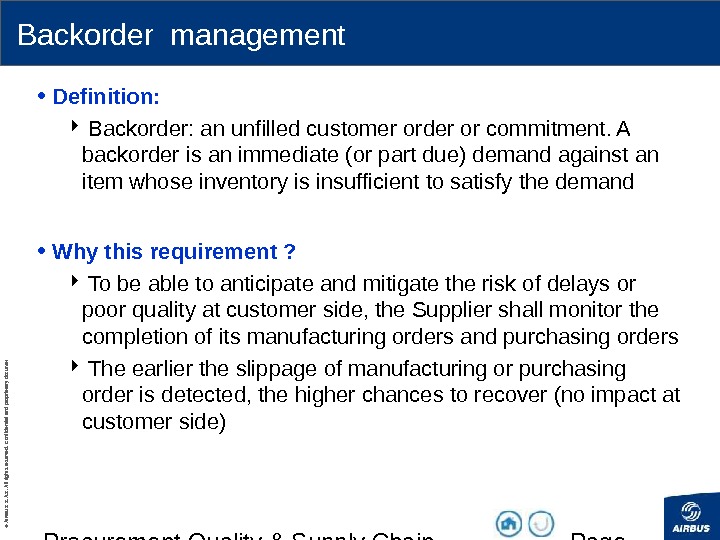
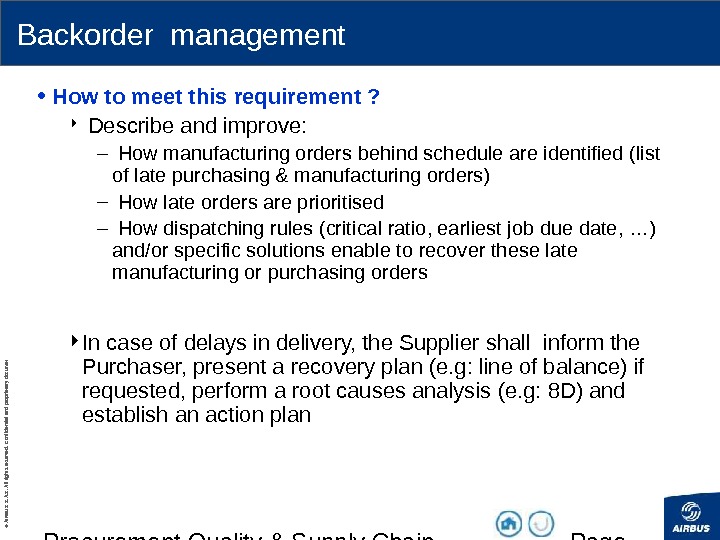
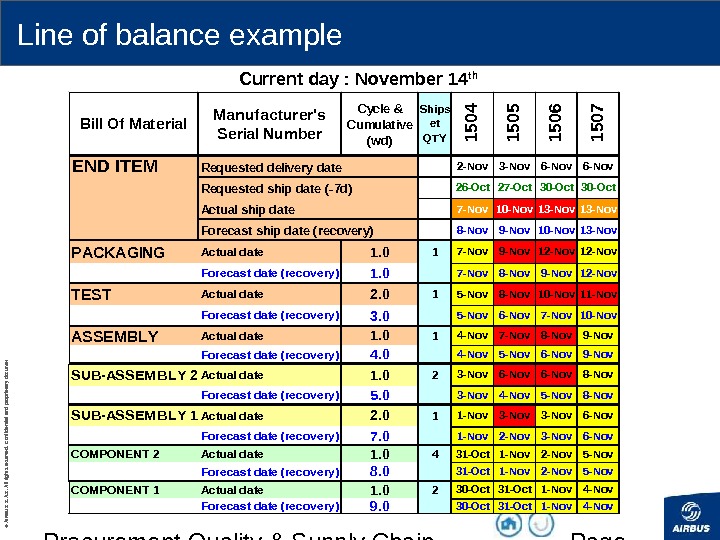
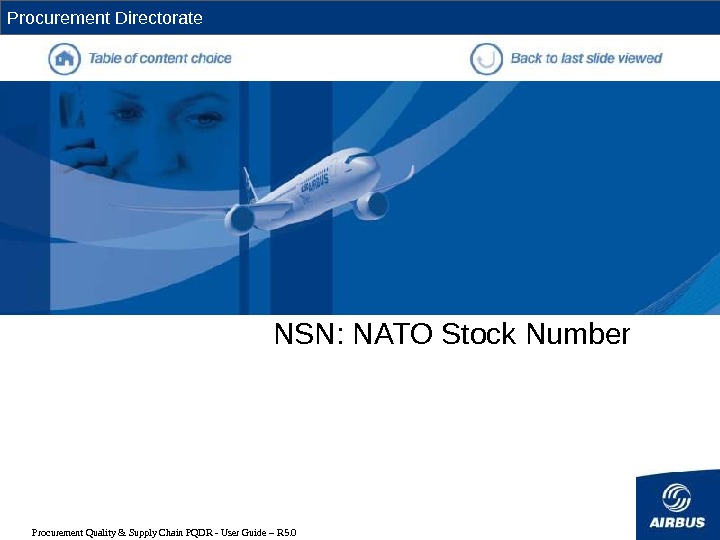
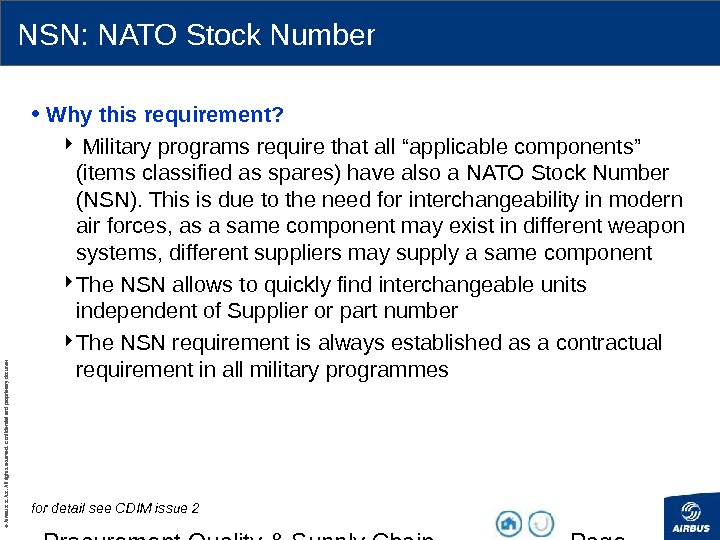
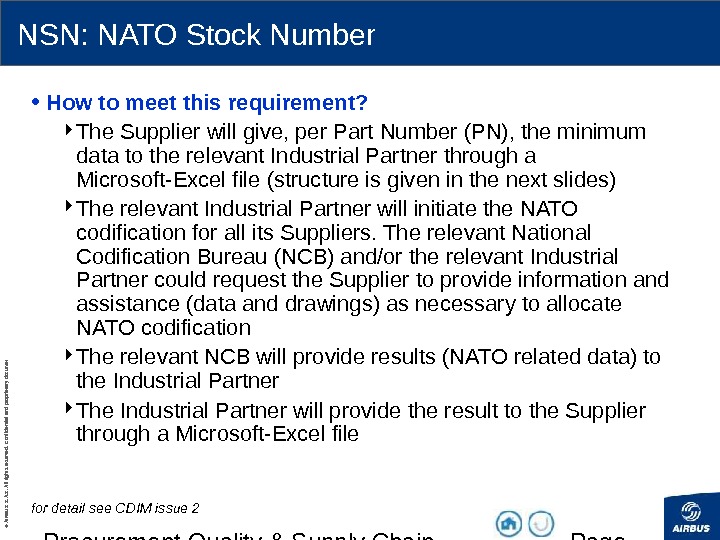
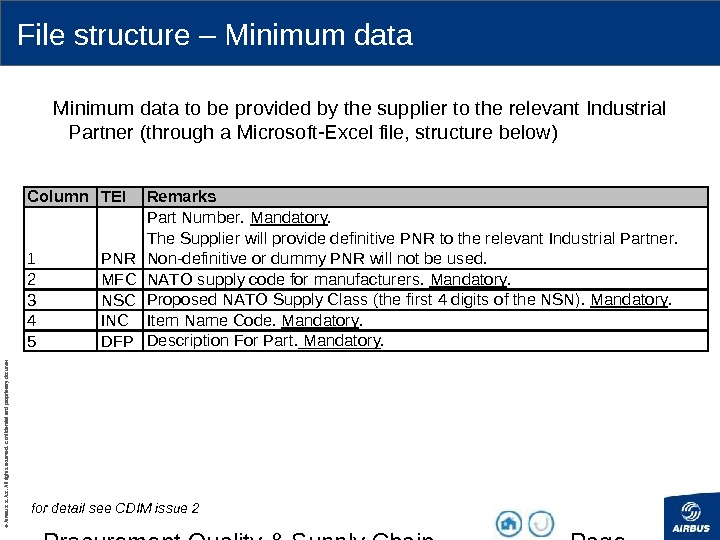
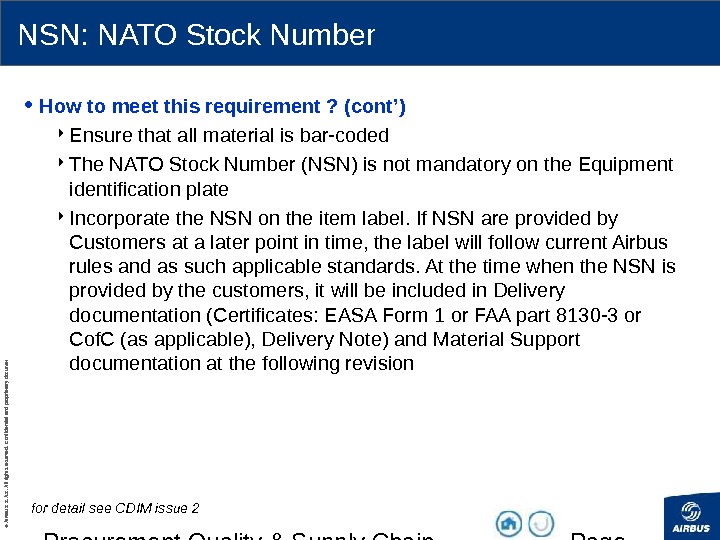
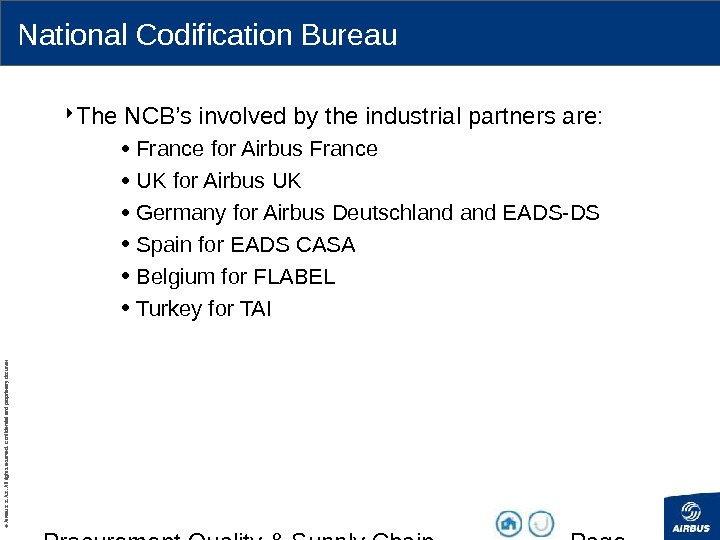
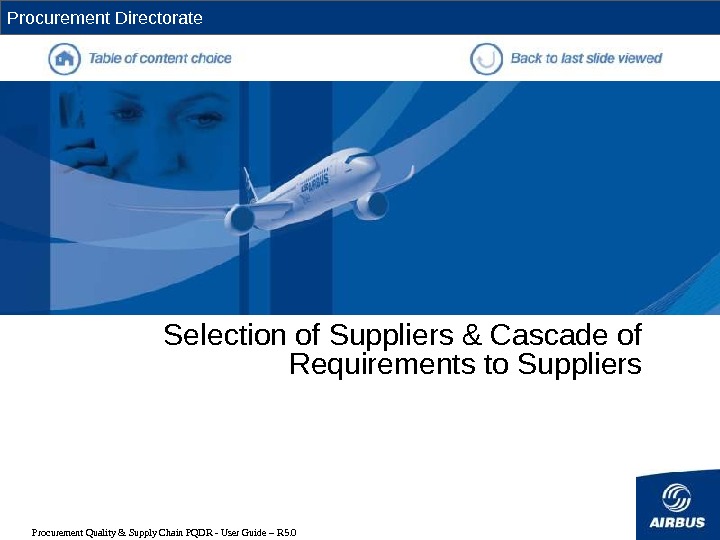
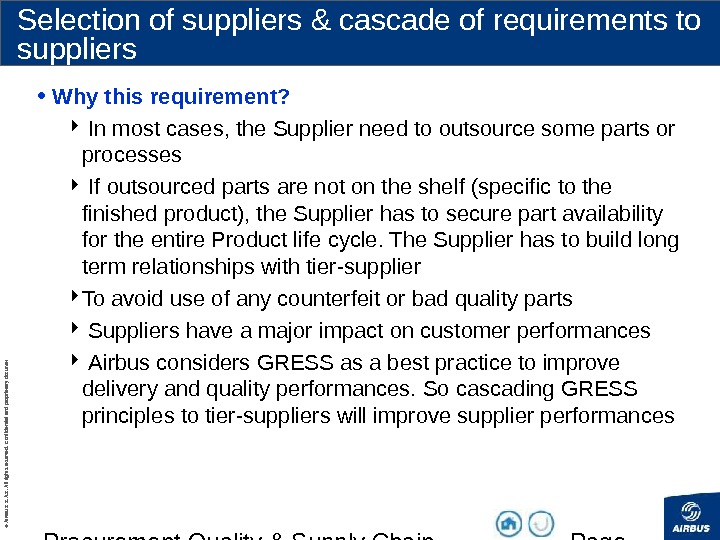
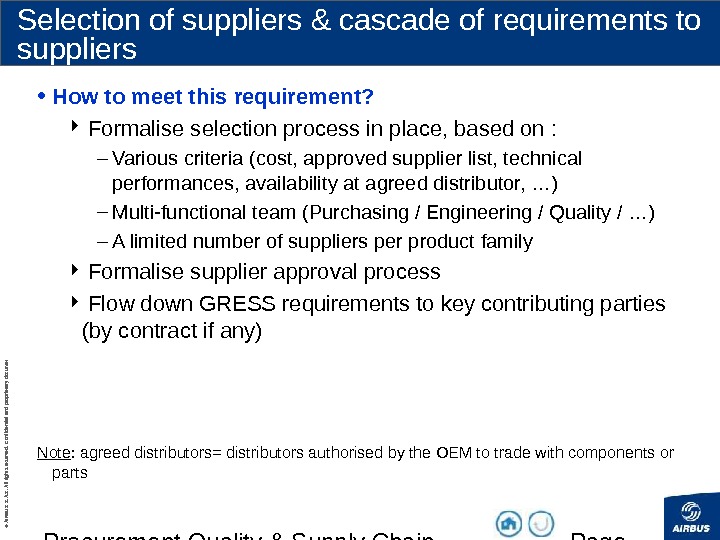
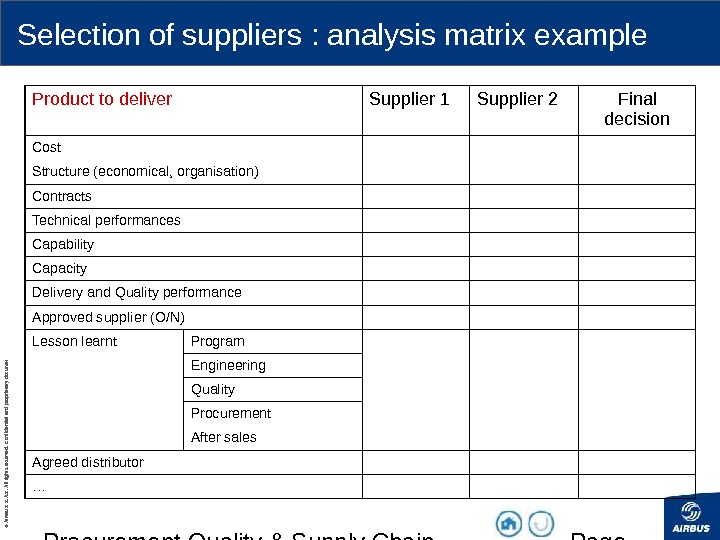
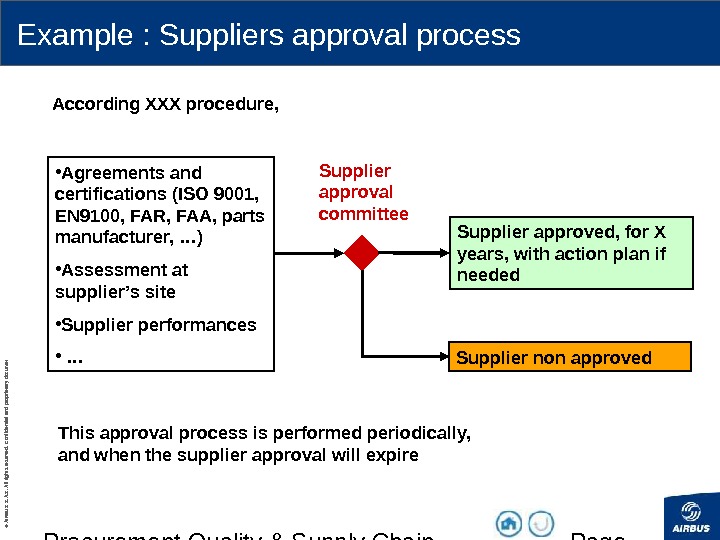
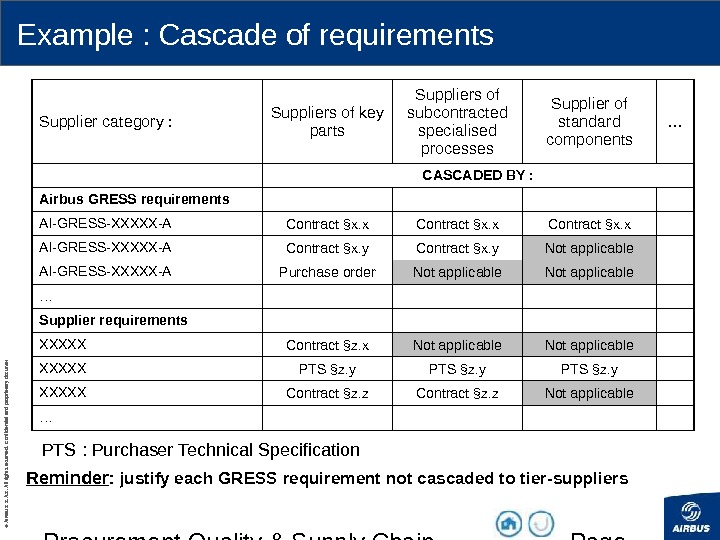
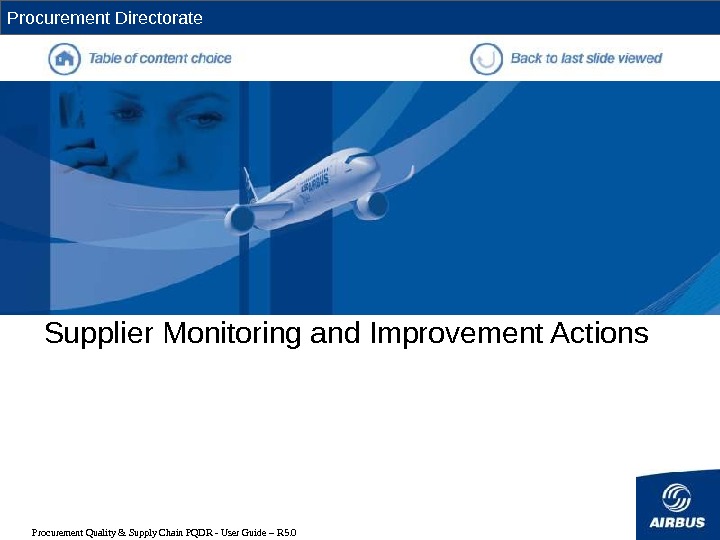
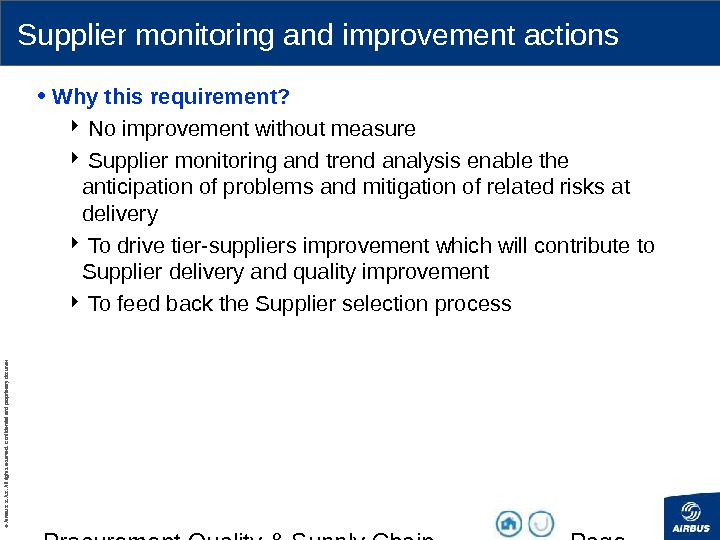
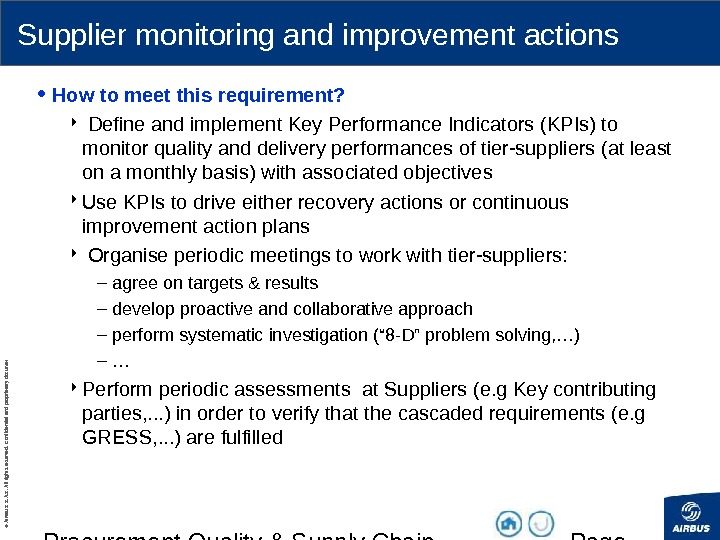
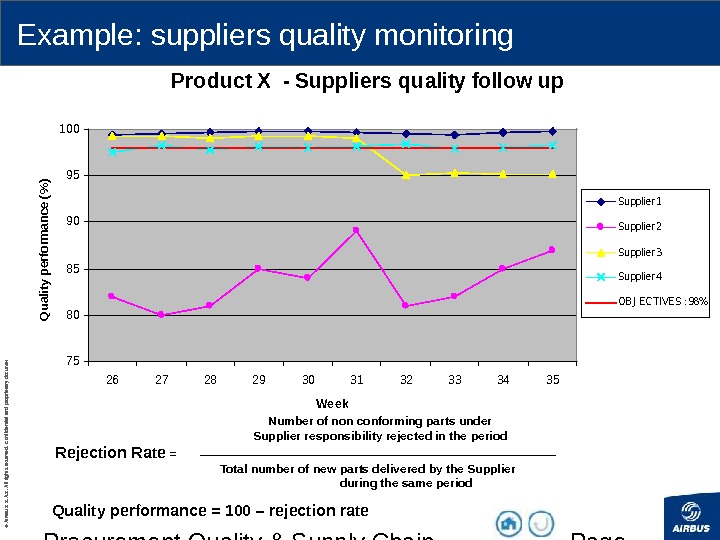
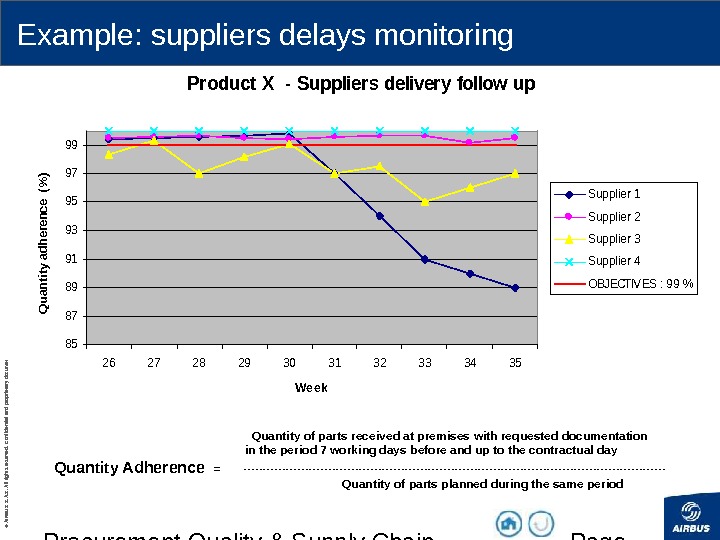
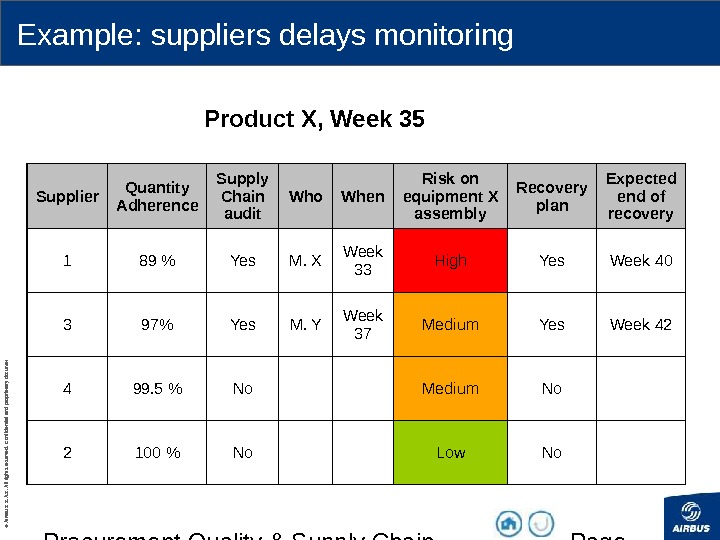
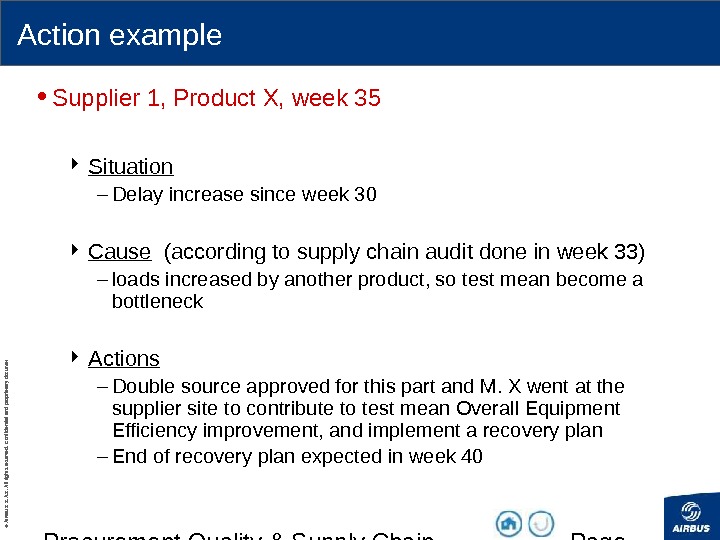
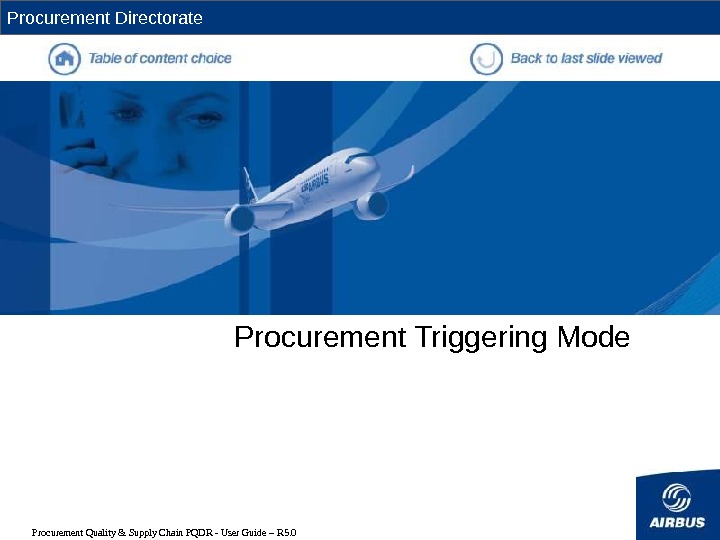
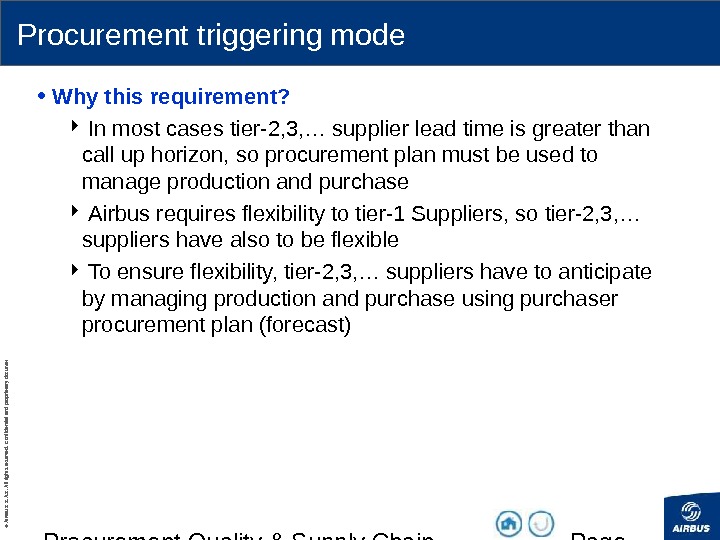
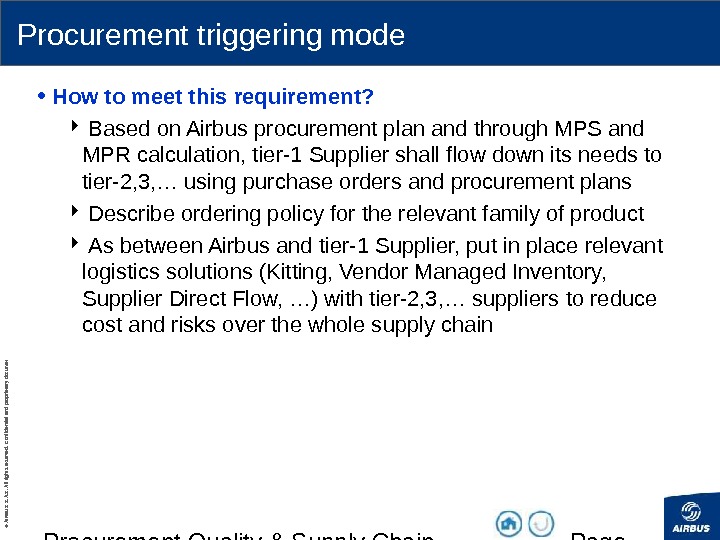
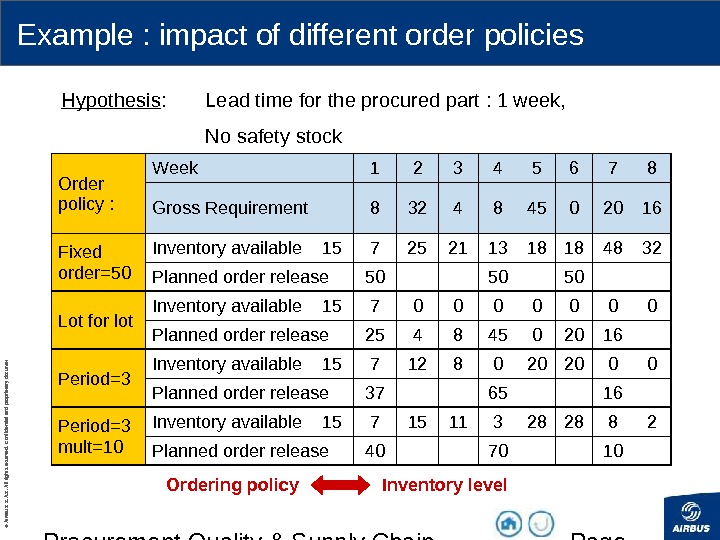
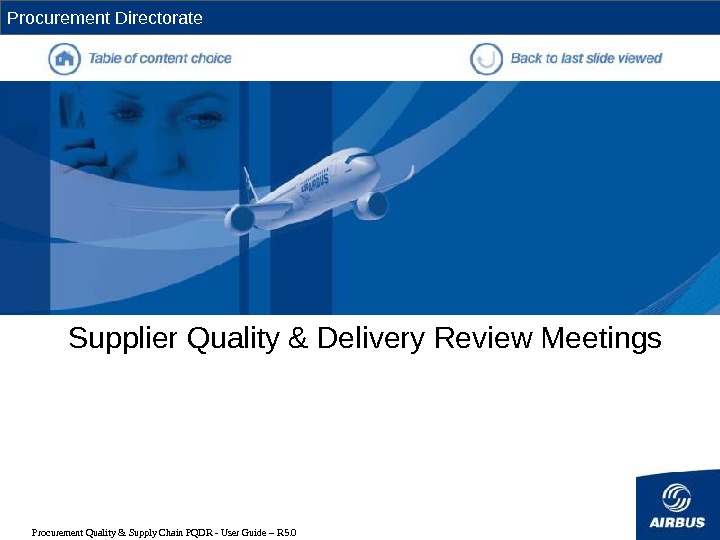
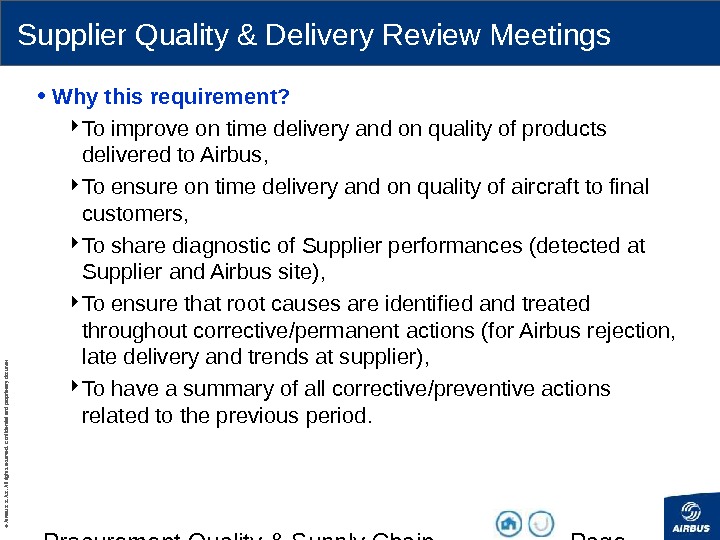
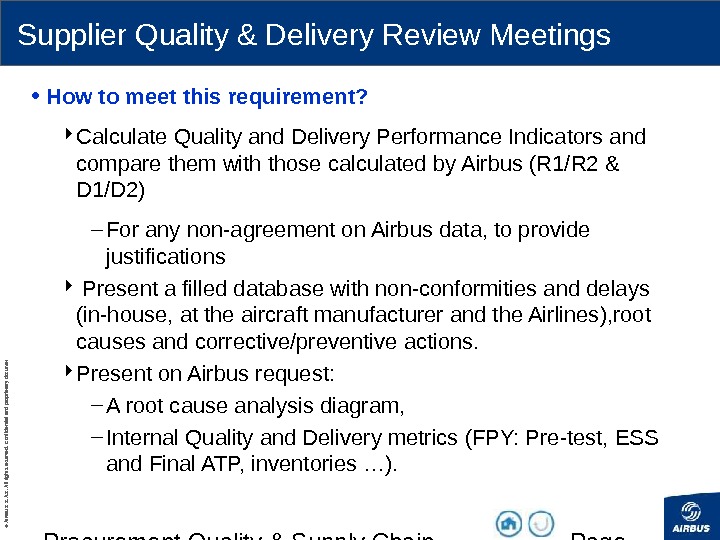

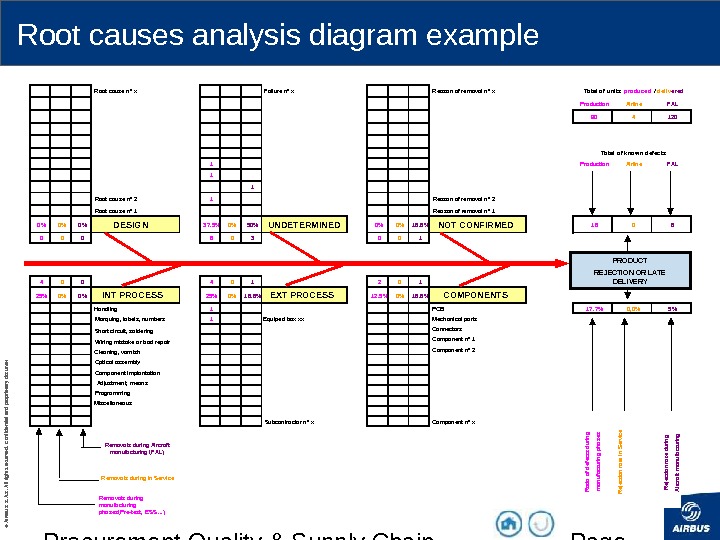

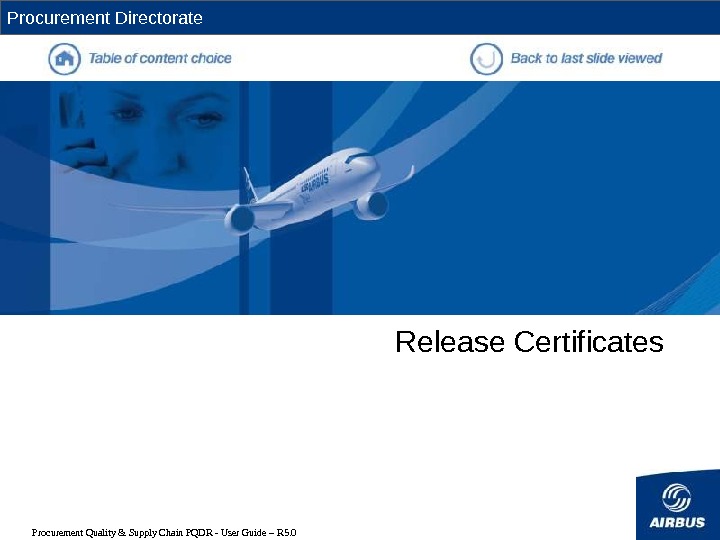
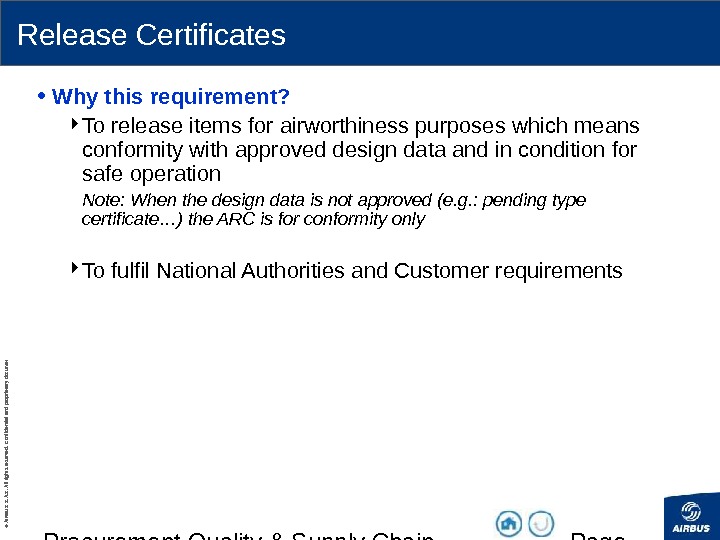
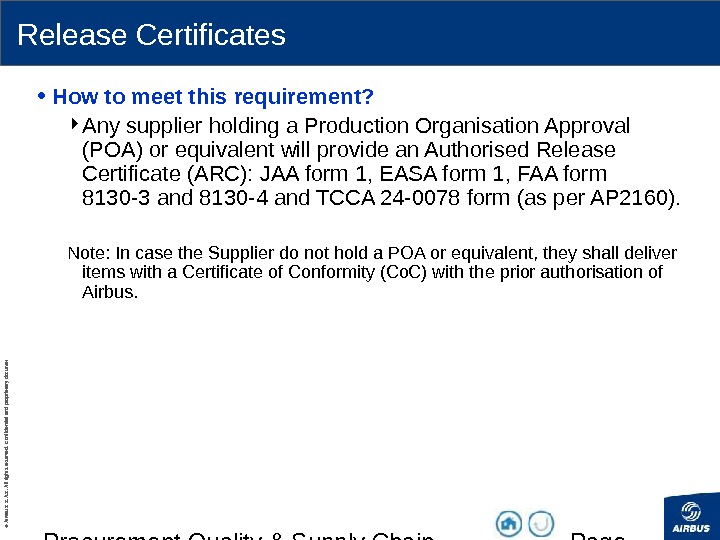
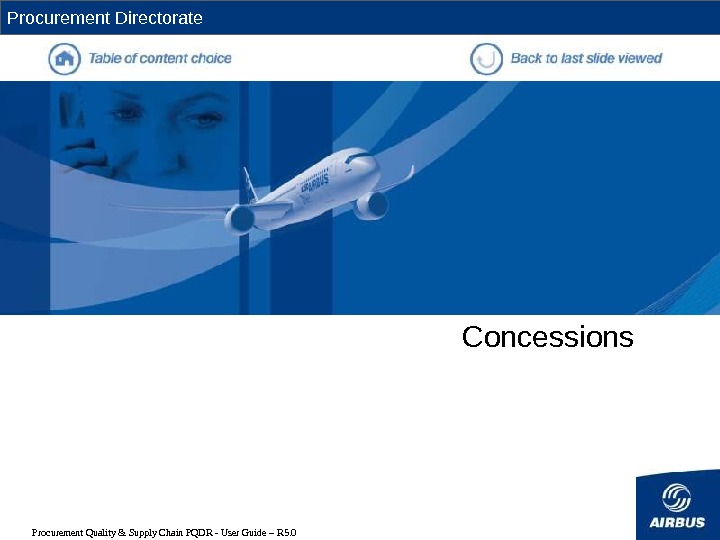
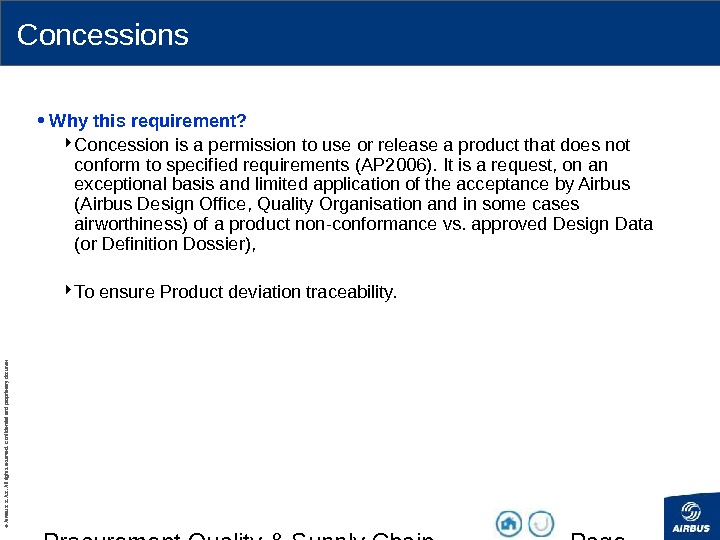
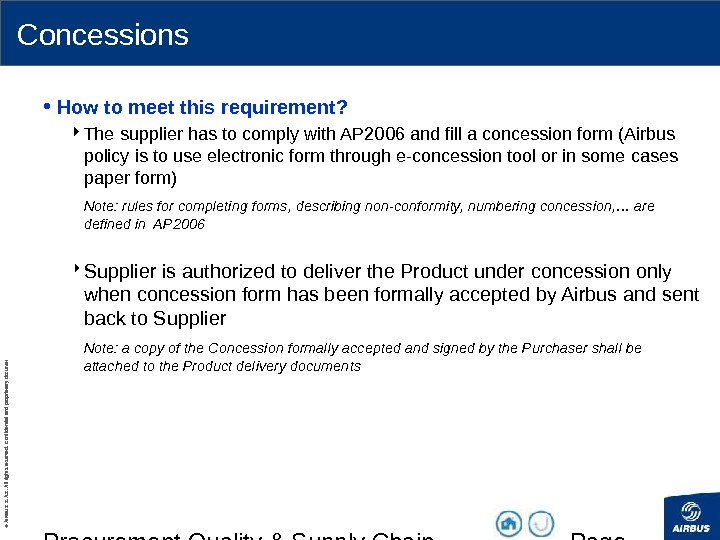
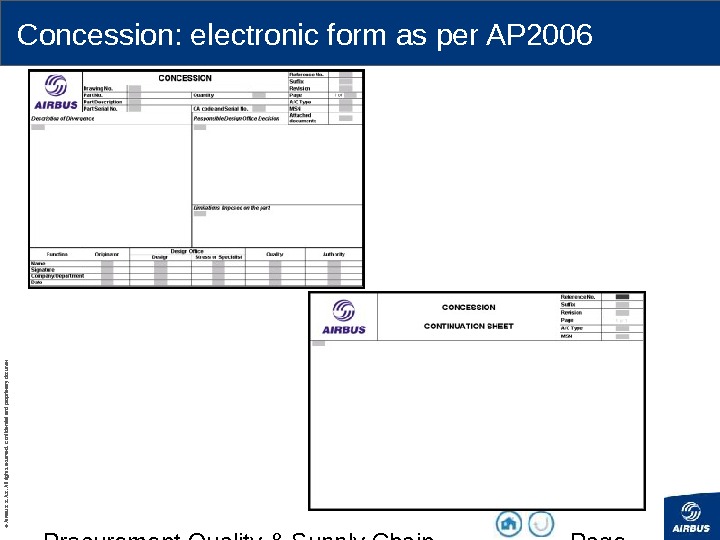
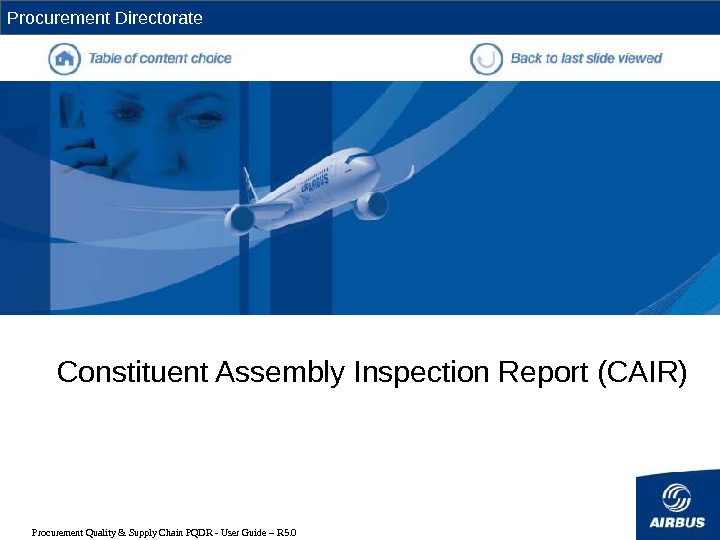
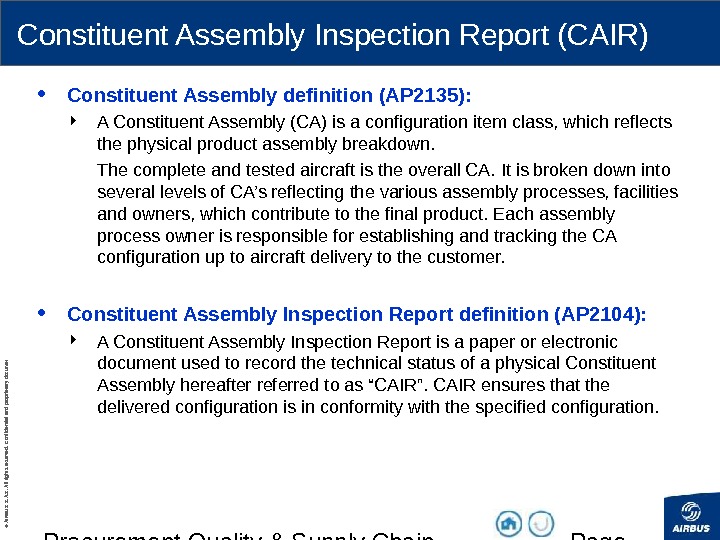

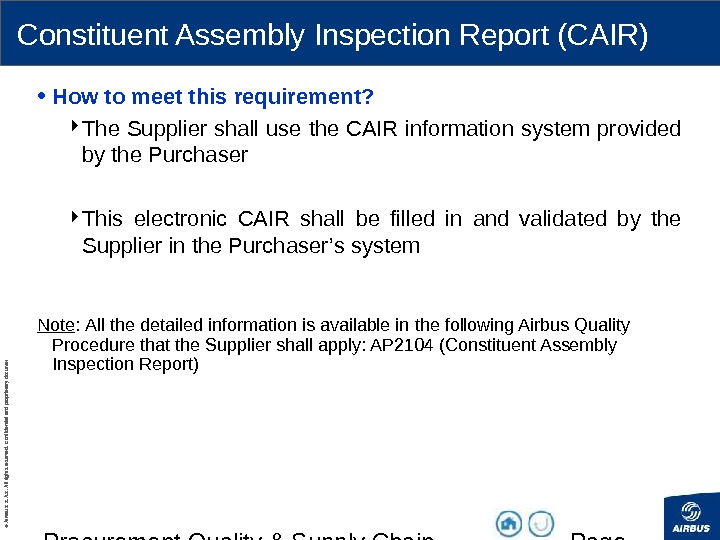
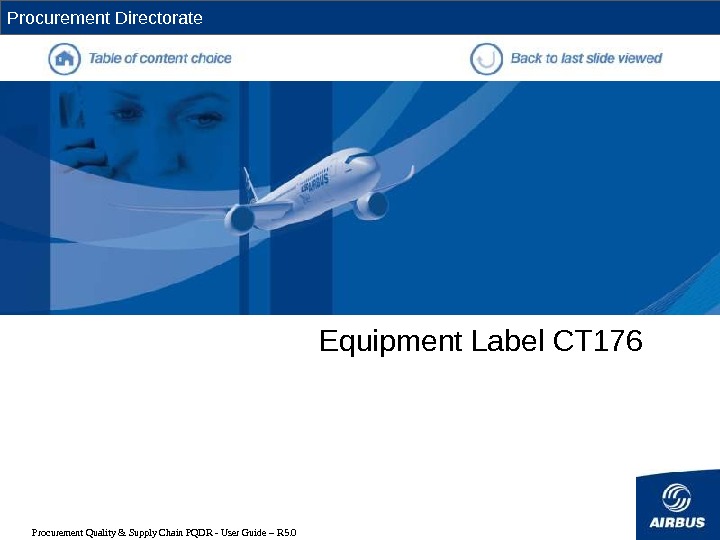
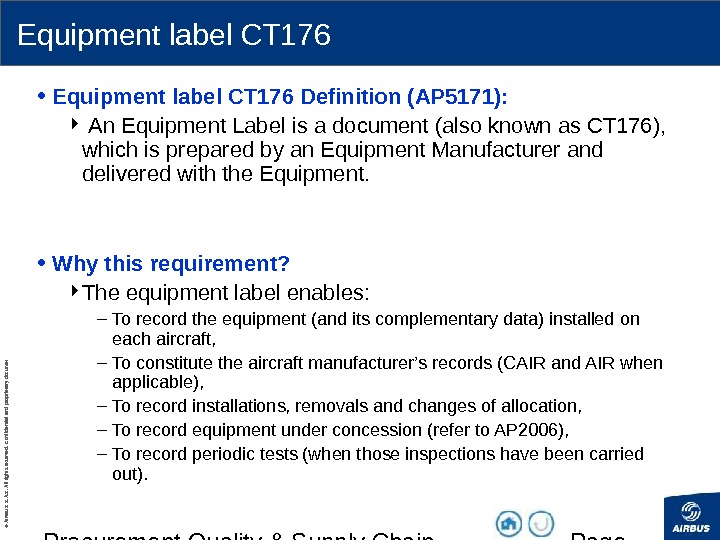
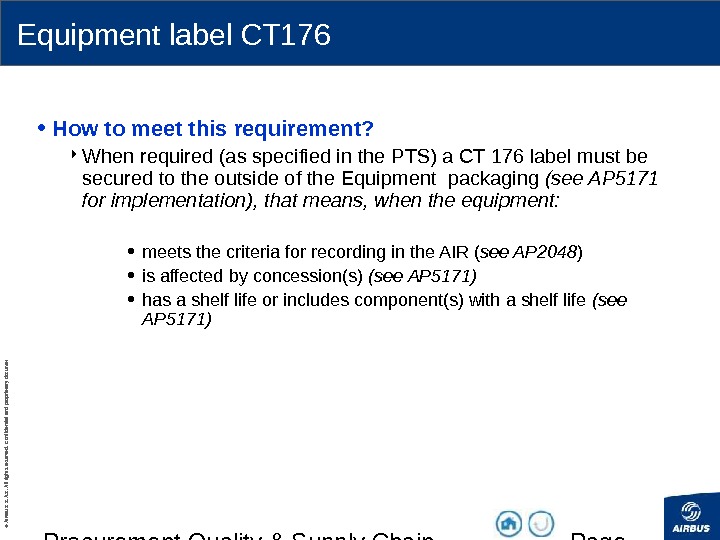
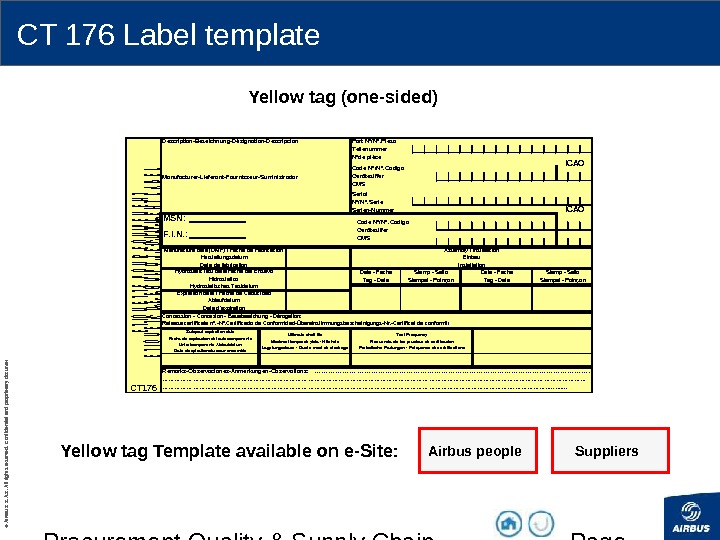
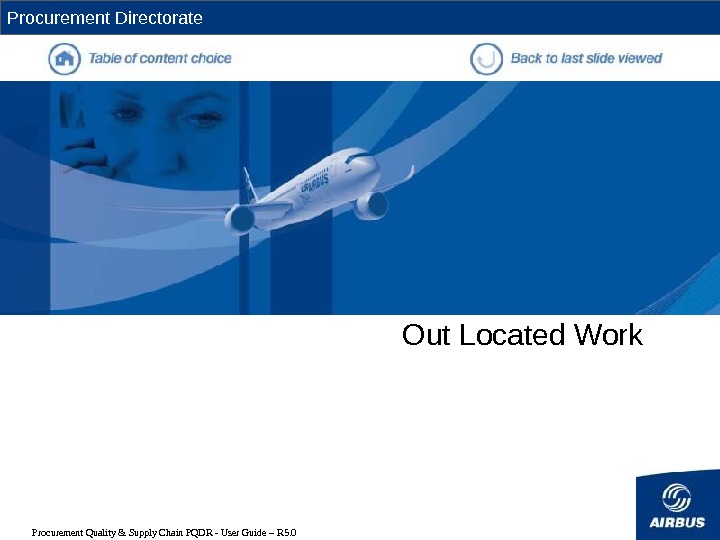
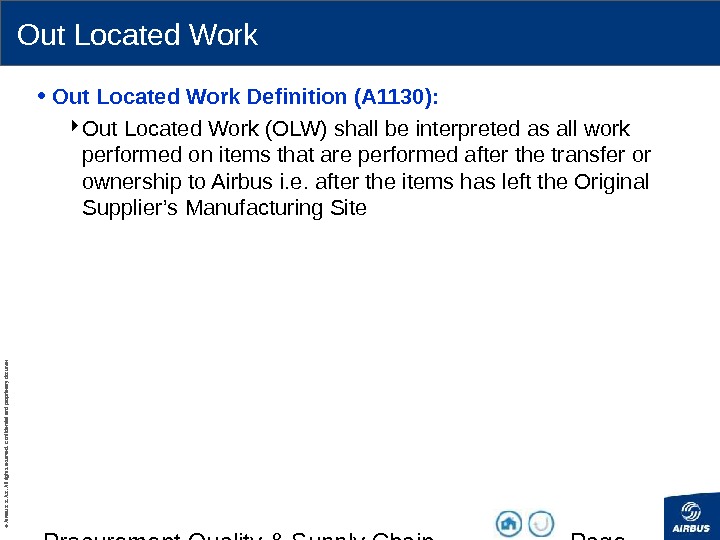
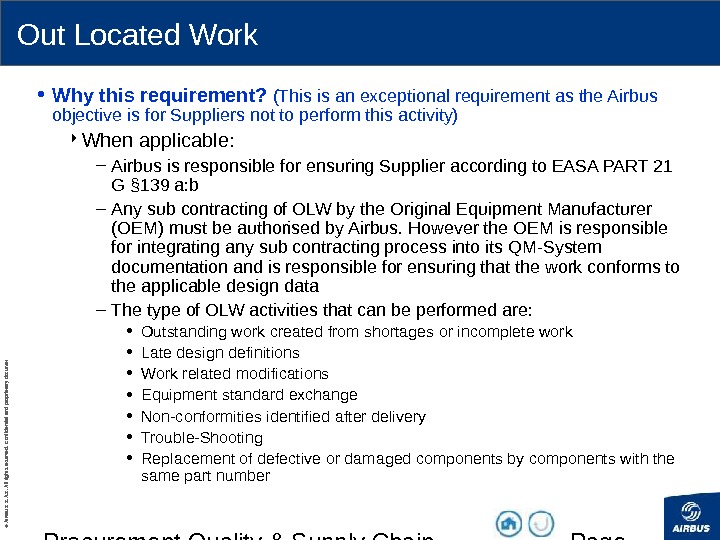

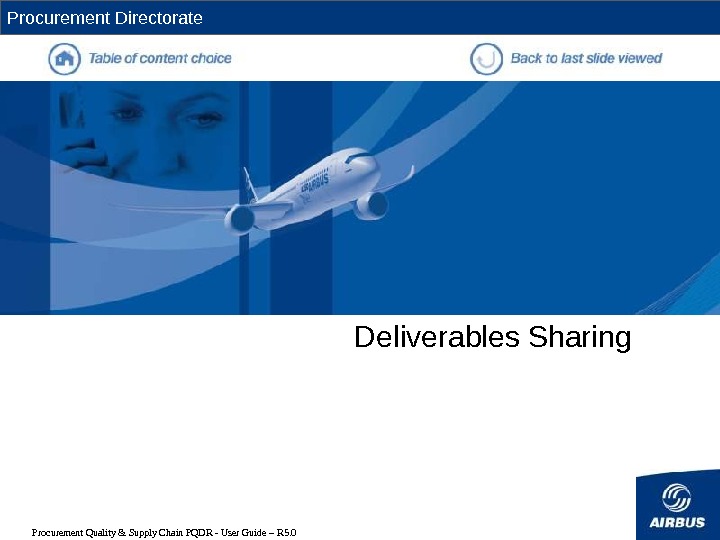
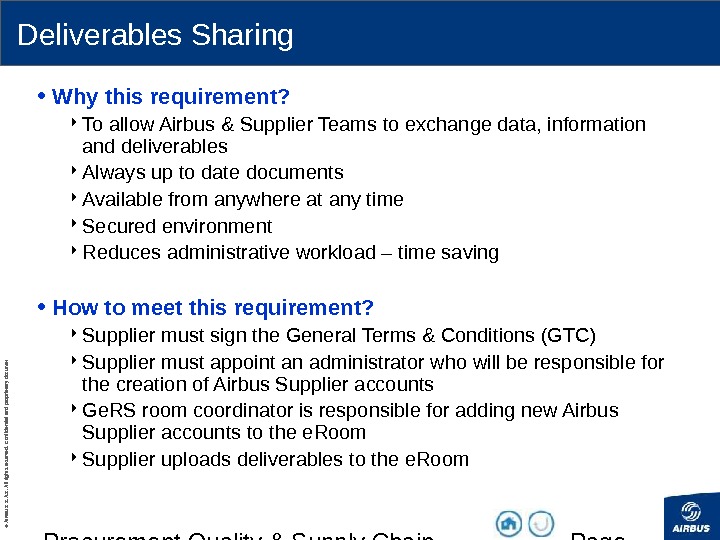
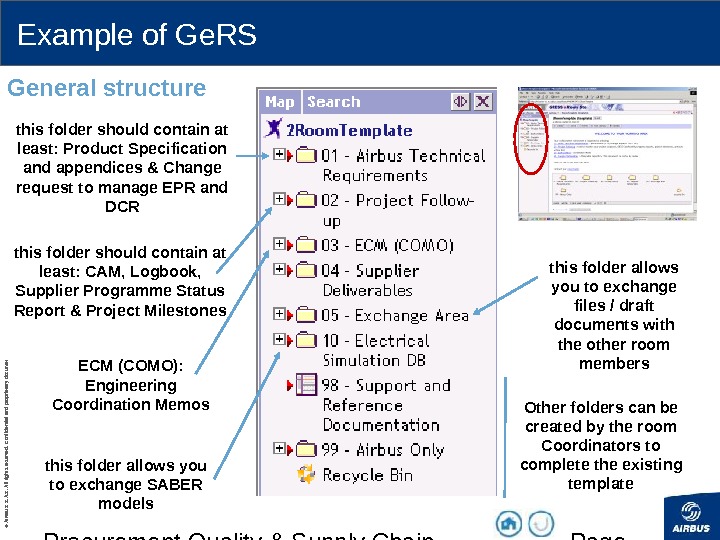
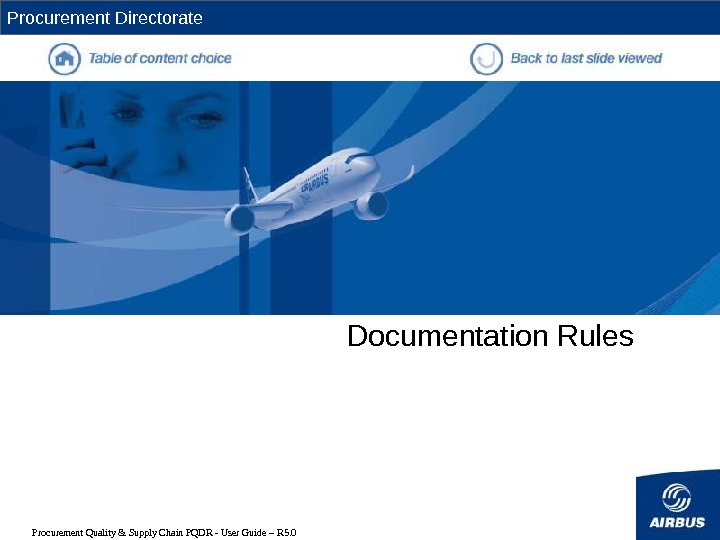
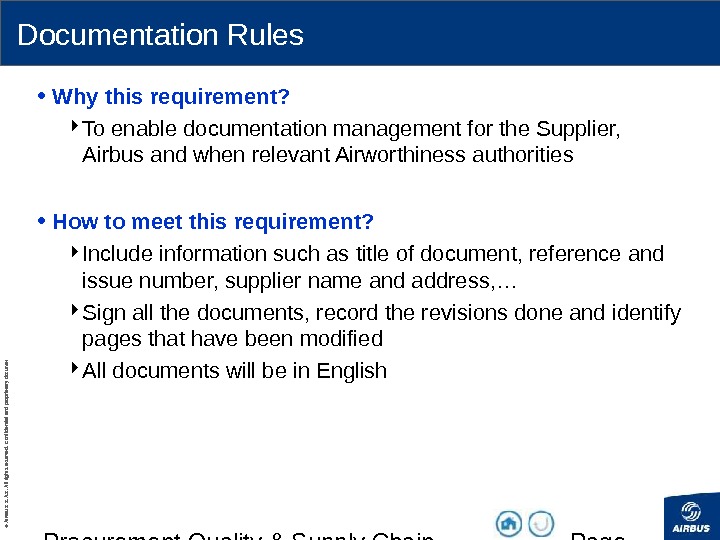
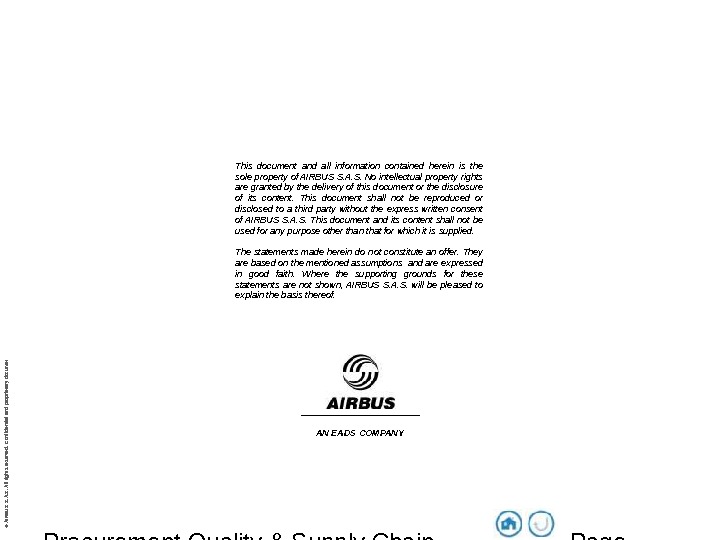
- Размер: 5.8 Mегабайта
- Количество слайдов: 341
Описание презентации Procurement Quality & Supply Chain PQDR — User по слайдам
Procurement Quality & Supply Chain PQDR — User Guide – R 5. 0 Procurement Directorate User Guide: GRESS & Assessments R 5. 0 Click here to go to table of contents http: //www. airbus. com/
Procurement Quality & Supply Chain PQDR — User Guide – R 5. 0 Page 2© AIRBUS S. All rights reserved. Confidential and proprietary document. Read me • Please consult this interactive file in Slide Show mode • This document will be regularly updated, record of revisions: • For any comment or question, please contact GRESS & GRESS tools Support gress. support@airbus. com. Release Date Description 1. 0 March 04 Initial issue GRESS Module 3&4 2. 0 August 04 Addition of GRESS Module 1 3. 0 July 05 Addition of GRESS Module 0 & 5 update of module 1 4. 0 Feb 06 Overall update 4. 1 Jan 07 Overall update and addition of PMCA 5. 0 Jan 08 Updated according to GRESS Issue C and IPCA Issue
Procurement Quality & Supply Chain PQDR — User Guide – R 5. 0 Page 3© AIRBUS S. All rights reserved. Confidential and proprietary document. Introduction to GRESS What is GRESS? • General Requirements for Equipment and System Suppliers (GRESS = AP 1013) Complete set of general requirements, for all functions at Suppliers Unique document for Airbus and any System or Equipment Suppliers • GRESS Genesis: June 2001: GRESS Issue A: – Applied for all Supplier’s System/ Equipment development on A 380 April 2004: GRESS Issue B: – Applied for all Supplier’s System/ Equipment development on A 400 M and A 380 System/Equipment Cabin Suppliers June 2007: GRESS Issue C: – Taking into account lessons learnt from A 380/ A 400 M and A 350 XWB needs Note : Jan 2006: GRESS Issue B + amendment 1 for A 350 (design 1 A)
Procurement Quality & Supply Chain PQDR — User Guide – R 5. 0 Page 4© AIRBUS S. All rights reserved. Confidential and proprietary document. GRESS Structure overview Module 5 Module 2 DESIGN REQUIREMENTS and DIRECTIVES Module 3 ENGINEERING for MANUFACTURING Module 4 SUPPLY CHAINModule 0 GENERAL Module 5 PERFORMANCE METRICS, DELIVERIES and ASSOCIATED SERVICES Module 6 AIRLINE & MILITARY CUSTOMER SUPPORT Module 7 GENERAL DOCUMENTED DATA REQUIREMENTS Module 1 PROGRAMME MANAGEMENT IPCA KOM PR PDR DDR CDR LUAR FFAR CFAR FR PMCA SPCA PMCA / SPCA IPCA PMCA Follow up
Procurement Quality & Supply Chain PQDR — User Guide – R 5. 0 Page 5© AIRBUS S. All rights reserved. Confidential and proprietary document. Introduction to IPCA — IPCA (Industrial Process Control Assessment) is used to assess the whole Supplier’s «Industrial Process» (both Quality & Supply Chain) with respect to a product and its production line -IPCA is used to check at Supplier’s sites if industrial process is stable, capable and under control related to the current design status -IPCA is used to get confidence & secure On Time Quality Delivery at Airbus by: • Identifying manufacturing quality and supply chain risks • Ensuring that the supplier set an action plan to mitigate the risks in a relevant time frame compared with Airbus deadlines • Monitoring the supplier’s action plan • IPCA is described in AM
Procurement Quality & Supply Chain PQDR — User Guide – R 5. 0 Page 6© AIRBUS S. All rights reserved. Confidential and proprietary document. Introduction to PMCA -PMCA (Project Management Capability Assessment) is used to assess the capability of Project Management at Suppliers with respect to a product. -PMCA is a Method that can be used pan-Airbus for all Programmes Systems & Equipment during: R&T phase (Capability for a development) Selection Phase (Preventive mode) Development Phase (Recovery Mode) Serial Production Phase (Recurrent problems, major changes e. g Transfer of Work…. ) -PMCA can also be used for improving the Maturity of the Supplier’s equipment or system development by launching a specific improvement plan based on the assessment’s results. -PMCA is based on best practices & lessons learnt from A 380, A 400 M, and legacy programmes. • PMCA is described in AM
Procurement Quality & Supply Chain PQDR — User Guide – R 5. 0 Page 7© AIRBUS S. All rights reserved. Confidential and proprietary document. User Guide – Generalities & Scope • GOAL ? User Guide is to provide general explanations for a better understanding of GRESS requirements and Suppliers Assessments (IPCA and PMCA) • FOR WHOM ? Any function involved in GRESS implementation ( Program/Project, Engineering, Procurement, Quality, Supply Chain, Customer support, …) and Suppliers Assessments For both Airbus and Suppliers • SCOPE: GRESS issue A, issue B and issue C Industrial Process Control Assessment (issue D) Project Management Capability Assessment (issue A)
Procurement Quality & Supply Chain PQDR — User Guide – R 5. 0 Page 8© AIRBUS S. All rights reserved. Confidential and proprietary document. User Guide — Content • User Guide explanations are available by subject (concurrent engineering, risk analysis method, …) • For each subject, you will find: Why this requirement ? What is the goal of this requirement, why applying this requirement is useful and will contribute to improvements How to meet this requirement? General way to deal with this subject and to answer to Airbus requirement Some examples if needed Note : examples are deliberately kept very simple, knowing that each user (internal or external) may take the initiative to go in depth by its own as required
Procurement Quality & Supply Chain PQDR — User Guide – R 5. 0 Page 9© AIRBUS S. All rights reserved. Confidential and proprietary document. Table of Contents To access explanations on a specific subject, click on appropriate box below GRESS Module 0 Module 1 Module 2 Module 3 Module 4 Module 5 Module 6 GRESS requirements IPCA PMCA Suppliers assessments Module
Procurement Quality & Supply Chain PQDR — User Guide – R 5. 0 Page 10© AIRBUS S. All rights reserved. Confidential and proprietary document. GRESS Module 0 – User guide subjects table § GRESS Issue C REQUIREMENTS GRESS issue C USER GUIDE SUBJECT REQUIREMENTS GRESS issue B REQUIREMENTS GRESS issue A 0. 2 00201 Quality System & Aerospace Approvals 00201 0. 2 00202 Quality System & Aerospace Approvals 00202 0. 2 00203 Quality System & Aerospace Approvals 00203 0. 2 00205 Quality System & Aerospace Approvals 00205 0. 5 L 00501 GRESS Commitment L 00501 0. 6 L 00601 Quality Assurance Plan , Quality System & Aerospace Approvals L 00601 0. 7 00701 Export Licensing 00701 0. 8 00801 Environmental Standards
Procurement Quality & Supply Chain PQDR — User Guide – R 5. 0 Page 11© AIRBUS S. All rights reserved. Confidential and proprietary document. GRESS Module 1 — User guide subjects table § GRESS Issue C REQUIREMENTS GRESS issue C USER GUIDE SUBJECT REQUIREMENTS GRESS issue B REQUIREMENTS GRESS issue A 1 Programme Management Introduction 1 Programme and programme Management Scope — — 1. 1. 4 10103 Technical document in English 10103 1. 2 10206 Supplier Development Plan activities coverage 10301 10302 1. 2 L 10302 Supplier Development Plan L 10101 11201 10102 11009 10402 L 10101 10402 10607 11201 1. 2 10210 Supplier Development Plan updates 10301 10302 1. 2. 1 Breakdown Structures L 10305 L 10306 L 10305 1. 2. 1 10211 Breakdown Structures Consistency — — 1. 2. 1. 1 10303 Product Breakdown Structure (PBS) 10303 10402 L 10303 1. 2 10304 Work Breakdown Structure (WBS) L 10304 1. 2 10212 WBS common and unique reference — — 1. 2. 1. 3 11101 Resource Breakdown Structure (RBS) L 11101 10402 L 11101 1. 2. 1. 3 11103 Identification resources beyond current capability L 11103 1. 2. 1. 4 L 11102 Resource Assessment Report L 11102 1. 2. 1. 5 L 10214 Means and Methods Implementation Plan L 11103 1. 2. 1. 6 10201 Programme leader nomination 10201 1. 2. 1. 6 10202 Organisation Breakdown Structure (OBS) L 10202 10203 10205 L 10202 1. 2. 2 L 10307 Supplier Development Schedule 10307 11203 11204 1. 2. 3 Risk Management to the product life cycle 1. 2. 3. 2 L 11006 Risk Management Process 11001 11002 11004 L 11006 11008 11001 11002 11004 11005 L 11006 11008 1. 2. 3. 3 L 11007 Risk Identification & Mitigation Status (RIMS) 11003 L 11007 11009 11010 11003 11011 11009 GRESS Module 1 Cont. ’
Procurement Quality & Supply Chain PQDR — User Guide – R 5. 0 Page 12© AIRBUS S. All rights reserved. Confidential and proprietary document. GRESS Module 1 — User guide subjects table (cont’) § GRESS Issue C REQUIREMENTS GRESS issue C USER GUIDE SUBJECT REQUIREMENTS GRESS issue B REQUIREMENTS GRESS issue A 1. 2. 3. 3 L 11001 RIMS coverage 11007 1. 2. 4 L 10703 Supplier Support Plan 10701 10702 10703 1. 2. 5 Experience capture, record and implementation 1. 2. 5. 1 10216 Lessons Learnt process — — 1. 2. 5. 1 L 10217 Lessons learnt capture that will cover Failure capture, Root cause analysis — — 1. 2. 5. 1 L 10218 Lessons Learnt implementation L 11602 1. 2. 5. 2 L 11601 Programme Record Sheet L 11601 1. 2. 6 Product/Process Assurance 1. 2. 6 11501 Product / Process Assurance 11501 L 11502 11501 1. 2. 6 11503 Product / Process Assurance organisation 11503 1. 2. 7 L 10308 GRESS cross reference matrix — L 10308 1. 3 — Suppliers contributing parties monitoring and control 1. 3. 1 10310 Process for selection and management of Key Contributing Parties (KCP) — — 1. 3. 2 10402 Setting of Requirements Towards KCP (explain) 10402 1. 3. 2 10401 Setting of Requirements Towards KCP (cascade) 10401 10404 10401 1. 3. 3 10405 Responsibility of Key Contributing Parties Management 10402 10405 1. 3. 3 10309 Key contributing parties visibility — — 1. 3. 4 L 10406 KCPs Progress Status Reports L 10406 1. 3. 5 10311 Key Contributing Parties contribution to Milestones — — GRESS Module 1 Cont. ’
Procurement Quality & Supply Chain PQDR — User Guide – R 5. 0 Page 13© AIRBUS S. All rights reserved. Confidential and proprietary document. GRESS Module 1 — User guide subjects table (cont’) § GRESS Issue C REQUIREMENTS GRESS issue C USER GUIDE SUBJECT REQUIREMENTS GRESS issue B REQUIREMENTS GRESS issue A 1. 4 Maturity Management Process 1. 4. 2 10601 Maturity Management 10601 1. 4. 3 L 10606 Maturity Key Performance Indicators 10602 10606 1. 5 Obsolescence Management 1. 5. 2 10801 Strategy of obsolescence during product life cycle 10801 10802 10803 10804 1. 6 Programme Monitoring and Control 1. 6. 1 11201 Programme Means for monitoring and control 11201 1. 6. 2 10608 Milestones compliance with Purchaser schedule L 10307 1. 6. 2. 2 11202 Location of reviews 11202 1. 6. 2. 2 10609 Reviews coverage — — 1. 6. 3 L 11208 Programme Progress Reporting Metrics 11208 1. 6. 4 L 11206 Supplier Progress Programme Status Report L 11206 1. 6. 4 10610 Supplier Progress Status content in SDP 1. 6. 4 11209 General manager endorse status report L 11209 1. 7 — Information Management 1. 7. 2 10709 Communication Plan — — 1. 7. 2 11302 Compliance with the Purchaser information system 11302 1. 7. 3 11305 Data and Documentation Management Plan L 11305 1. 7. 3 10704 Handling of support data — — GRESS Module 1 Cont. ’
Procurement Quality & Supply Chain PQDR — User Guide – R 5. 0 Page 14© AIRBUS S. All rights reserved. Confidential and proprietary document. GRESS Module 1 — User guide subjects table (cont’) § GRESS Issue C REQUIREMENTS GRESS issue C USER GUIDE SUBJECT REQUIREMENTS GRESS issue B REQUIREMENTS GRESS issue A 1. 7. 3 10705 Management of data not to be transferred electroni cally L 11305 — 1. 7. 4 10706 Methods of modelling 11401 — 1. 7. 4. 2 10707 Models delivery L 11402 1. 7. 4. 3 11403 Data Interchange Convention for models L 11403 11404 1. 7. 4. 3 10708 Cascade of requirements to key contributing partie s L 11403 1. 9 — In-Service Follow-up 10701 10702 1. 9. 1 10905 In-Service follow-up organisation — 1. 9. 2 11701 Final Review 11701 1. 9. 2 11702 Return schedule 11702 1. 9. 3 L 10908 Report of Product failures during In-Service life — —
Procurement Quality & Supply Chain PQDR — User Guide – R 5. 0 Page 15© AIRBUS S. All rights reserved. Confidential and proprietary document. GRESS Module 3 — User guide subjects table § GRESS Issue C REQUIREMENTS GRESS issue C USER GUIDE SUBJECT REQUIREMENTS GRESS issue B REQUIREMENTS GRESS issue A 3. 2. 1 L 30201 Industrial Quality Dossier L 30201 3. 2. 2 L 30202 Organisation Specific to the Contract L 30202 3. 2. 3 L 30213 Concurrent Engineering L 30213 3. 2. 4 L 30205 Industrial Risk Analysis Method L 30205 3. 2. 5 L 30206 Industrial Risk Register L 30206 3. 2. 6 L 30232 Production of the Products by a Series Production Process L 30232 3. 2. 6 L 30215 Production of the Products by a Series Production Process L 30215 3. 2. 7. 1 L 30204 Industrial Breakdown L 30204 3. 2. 7. 2 L 40403 Selection of Suppliers & Cascade of requirements to Suppliers L 40403 3. 2. 7. 3 L 30216 Selection of Suppliers & Cascade of requirements to Suppliers L 30216 3. 2. 7. 4 L 30217 Supplier Monitoring and Improvement Actions L 30217 3. 2. 7. 5 L 40306 Supplier Monitoring and Improvement Actions L 40306 3. 2. 7. 6 40307 Supplier Monitoring and Improvement Actions 40307 3. 2. 8 30219 Traceability 30219 3. 2. 8 30233 Traceability 30233 3. 2. 8 30234 Traceability 30234 3. 2. 8 30230 Traceability 30230 3. 2. 8 L 30208 Traceability L 30208 3. 2. 8 30235 Traceability 30235 3. 2. 9 30220 Manufacturing and Inspection Dossier 30220 3. 2. 10 L 30203 Industrial Process Flow Charts “Manufacturing” & “Supply Chain” L 30203 GRESS Module 3 Cont. ’
Procurement Quality & Supply Chain PQDR — User Guide – R 5. 0 Page 16© AIRBUS S. All rights reserved. Confidential and proprietary document. GRESS Module 3 – User guide subjects table (cont’) § GRESS Issue C REQUIREMENTS GRESS issue C USER GUIDE SUBJECT REQUIREMENTS GRESS issue B REQUIREMENTS GRESS issue A 3. 2. 11 L 30222 Quality and Supply Chain Metrics L 30222 3. 2. 12 L 30207 Product, Process and Sub-Process Major/ Key Characteristics L 30207 3. 2. 13 30224 Management of Competencies 30224 3. 2. 13 30236 Qualification & Maintenance of Manufactu ring and Inspection Means 30236 3. 2. 13 30237 Qualification & Maintenance of Manufactu ring and Inspection Means 30237 3. 2. 14 L 30225 Industrial Change Management L 30225 3. 2. 15 L 30210 ESS / ageing / NDT L 30210 3. 2. 16 L 30227 Test Strategy and Control L 30227 3. 2. 17 30209 Organisation of Premises L 30209 3. 2. 18 30229 Documentation 30229 3. 2. 19 L 30211 Root Causes Analysis & Treatment L 30211 3. 2. 19 30231 Non-conformities and Delays Analysis Pro cess 30231 3. 3 30301 Specific Case of Dealers/ Distributors
Procurement Quality & Supply Chain PQDR — User Guide – R 5. 0 Page 17© AIRBUS S. All rights reserved. Confidential and proprietary document. GRESS Module 4 – User guide subjects table § GRESS Issue C REQUIREMENTS GRESS issue C USER GUIDE SUBJECT REQUIREMENTS GRESS issue B REQUIREMENTS GRESS issue A 4. 2. 1 L 40104 Supply Chain Dossier L 40104 4. 3. 1 L 40204 Organisation Specific to the Contract L 40204 4. 3. 2 L 40211 Industrial Process Flow Charts “Manufacturing” & “Supply Chain”, Quality and Supply Chain Metrics L 40211 4. 3. 3 L 40212 Industrial Process Layout (Spaghetti Diagram) L 40212 4. 3. 4 L 40102 Continuous Improvement Approach , Organisation of Premises L 40102 4. 4. 1 40213 Production Management System 40213 4. 4. 1 40218 Production/ Manufacturing and Distribution Rules 40218 4. 4. 2 40206 Use of Purchaser’s Data 40206 4. 4. 3 L 40214 Capacity Management 40214 4. 4. 3 40215 Capacity Management L 40215 4. 4. 4 L 40202 Backorder Management , Use of Purchaser’s Data L 40202 4. 4. 5 L 40108 Backorder Management 40108 4. 4. 6 40404 Production/ Manufacturing and Distribution Rules 40404 4. 4. 7 40219 NSN: Nato Stock Number 40219 4. 5. 1 40501 Selection of Suppliers & Cascade of Requirements to Suppliers 4. 5. 1 L 40403 Selection of Suppliers & Cascade of requirements to Suppliers L 40403 4. 5. 2 L 30216 Selection of Suppliers & Cascade of requirements to Suppliers L 30216 4. 5. 3 40216 Industrial Risk Analysis Method, Industrial Risk Register 40216 4. 5. 4 L 30217 Supplier Monitoring and Improvement Actions L 30217 4. 5. 5 L 40306 Supplier Monitoring and Improvement Actions L 40306 4. 5. 6 40307 Supplier Monitoring and Improvement Actions 40307 4. 5. 7 40308 Procurement Triggering Mode 40308 4. 6 L 40107 Root Causes Analysis & Treatment L 40107 4. 6 40106 Non-conformities and Delays Analysis Process
Procurement Quality & Supply Chain PQDR — User Guide – R 5. 0 Page 18© AIRBUS S. All rights reserved. Confidential and proprietary document. GRESS Module 5 – User guide subjects table § GRESS Issue C REQUIREMENTS GRESS issue C USER GUIDE SUBJECT REQUIREMENTS GRESS issue B REQUIREMENTS GRESS issue A 5. 1. 3 L 50108 Refer to pr. EN 9131 5. 1. 4 50101 Root Causes Analysis & Treatment 50101 5. 1. 5 50109 Supplier Quality & Delivery Review Meetings 50109 5. 1. 5 50106 Supplier Quality & Delivery Review Meetings 50106 5. 1. 5 50107 Supplier Quality & Delivery Review Meetings L 50107 5. 1. 5 L 50105 Quality and Supply Chain Metrics L 50105 5. 1. 5 L 50104 Supplier Quality & Delivery Review Meetings L 50104 5. 2. 1. 1 L 50201 Release Certificates L 50201 5. 2. 1. 2 50206 Concessions 5. 2. 1. 2 L 50207 Concessions 5. 2. 1. 3 L 50208 Constituent Assembly Inspection Report (CAIR) 5. 2. 2. 1 L 50202 Equipment Label CT 176 L 50202 5. 2. 2. 2 50209 — 5. 3 50205 Out Located Work
Procurement Quality & Supply Chain PQDR — User Guide – R 5. 0 Page 19© AIRBUS S. All rights reserved. Confidential and proprietary document. GRESS Module 7 – User guide subjects table § GRESS Issue C REQUIREMENTS GRESS issue C USER GUIDE SUBJECT REQUIREMENTS GRESS issue B REQUIREMENTS GRESS issue A 7. 2 70203 Deliverables Sharing 7. 3 70101 Documentation Rules
Procurement Quality & Supply Chain PQDR — User Guide – R 5. 0 Page 20© AIRBUS S. All rights reserved. Confidential and proprietary document. PMCA User guide PMCA § (Issue A) USER GUIDE SUBJECT 1. – Project Establishment Project establishment 2. – Breakdown Structures consistency 2. 1. – Product Breakdown Structure (PBS) Product Breakdown Structure 2. 2. – Organisation Breakdown Structure (OBS) Organisation Breakdown Structure 2. 3. – Work Breakdown Structure (WBS) Work Breakdown Structure 2. 4. – Work Package Description Work Breakdown Structure 2. 5. – Resource Breakdown Structure (RBS) Resource Breakdown Structure 3. – Scheduling Supplier Programme Development Schedule 4. – Development Plan Supplier Development Plan 5. – Monitoring and Control Programme Monitoring and Control 6. – Risk Management 7. – Resource Management 8. – Key Contributing Parties Suppliers Key Contributing Parties monitoring and control 9. – Communication Information management communication 10. – Lesson Learnt Experience capture, Record and Implementation 11. – Maturity Management Process 12. – Product & Process Assurance Product/Process assurance / Cross reference matrix
Procurement Quality & Supply Chain PQDR — User Guide – R 5. 0 Page 21© AIRBUS S. All rights reserved. Confidential and proprietary document. IPCA according to Check List Issue D 3. INDUSTRIAL PROCESS ENVIRONMENT 3. 1 – Organisation of premises Refer to: Organisation of premises / Industrial process layout (Spaghetti diagram) 3. 2 – Documentation Refer to: Documentation / Release Certificates / Constituent Assembly Inspection Report / Equipment Label CT 176 / Concessions 3. 3 – Qualification & Maintenance of manufacturing and inspection means 3. 4 — Management of competencies 2. 6 – Continuous Improvement Approach 3. 5 — Operator involvement (e. g. Visual Management, TQM, TPM, …) Refer to: Continuous Improvement Approach 2. 5 — Backorder management 2. 4 — Capacity management 2. 3 — Use of Purchaser’s data 2. 2 — Production management system 2. 1 — Production / Manufacturing & Distribution Rules 1. 5 — Product major/key characteristics and monitoring 2. MATERIALS MANAGEMENT 1. PRODUCT INDUSTRIAL DOSSIER 1. 4 — Product risk analysis (for industrialisation & production) Refer to: Risk analysis Method / Industrial Risk Register 1. 3 — Concurrent Engineering 1. 2 — Industrial Process flow chart «Supply Chain»1. 1 — Industrial Process flow chart “Manufacturing» 5. 3 — Supplier monitoring and improvement actions 5. 2 — Procurement & supplier risk analysis Refer to: Risk analysis Method / Industrial Risk Register 5. 1 — Selection of suppliers and cascade of requirements to suppliers 5. PURCHASING CONTROL 6. 1 — Collection and correlation of nonconformities 6. NON-CONFORMITIES AND DELAYS ANALYSIS 5. 5 — Procurement triggering mode 5. 4 — Obsolescence Management 6. 2 – Non-conformities: root causes analysis and treatment 6. 3 — Collection and correlation of delays 6. 4 — Delays: root causes analysis and treatment 4. 7 – Industrial Change Management 6. 5 — Prevention actions based on lessons learnt 4. 6. 2 — Traceability of a procured part with respect to final product 4. 6. 1 — Traceability during manufacture and testing 4. 5. 2 — Environmental Stress Screening efficiency 4. 5. 1 — Strategy and determination of Environmental Stress Screening /Ageing / NDT 4. 4. 2 — Test efficiency 4. 4. 1 — Test strategy and coverage 4. 3 – Quality & Supply Chain Metrics 1. 6 — Manufacturing and Inspection Dossier 4. 8 — Production of the products by a series production process 4. 2 – Process and Sub-process major/key characteristics and monitoring 4. 1 — Process and sub-process risk analysis Refer to: Risk analysis Method / Industrial Risk Register 4. PROCESS CONTROL 4. 4 – Test Strategy and Control 4. 5 – Environmental Stress Screening/ Ageing/ NDT 4. 6 – Traceability
Procurement Quality & Supply Chain PQDR — User Guide – R 5. 0 Procurement Directorate Quality System and Aerospace Approvals
Procurement Quality & Supply Chain PQDR — User Guide – R 5. 0 Page 23© AIRBUS S. All rights reserved. Confidential and proprietary document. • Why this requirement ? To ensure that the Supplier Quality Management organisation enables it to fulfil its activities (Design, Production, maintenance, repairing, distribution) A good Quality Management System enables a robust process and a better product maturity To ensure that manufacturing special processes and inspection processes/test methods are under control (PRI Nadcap) To ensure that Airbus Equipments/ WPs are manufactured and procured putting health and safety at first side It is requested by the Airworthiness Authorities. Quality System and Aerospace Approvals NOTE : «Special processes» are defined as those for which normal non-destructive inspection practices cannot fully assess the conformity of the parts processed
Procurement Quality & Supply Chain PQDR — User Guide – R 5. 0 Page 24© AIRBUS S. All rights reserved. Confidential and proprietary document. Quality System and Aerospace Approvals • How to meet this requirement ? Be registered in the OASIS Database: • Be certified by a CB (Certification Body): it means that the Supplier is fully compliant (no current corrective action) • The CB has to be accredited by the Aeronautical Industry and the authorities which are represented by the National Accreditation Body and the Certification body Management committee (see “ OPS Interfaces ” flowchart hereafter) Get Design/Production/Maintenance Organisation Approval compliant with the authorities requirements Be certified by PRI Nadcap on applicable processes ( www. pri. sae. org )
Procurement Quality & Supply Chain PQDR — User Guide – R 5. 0 Page 25© AIRBUS S. All rights reserved. Confidential and proprietary document. OPS Interfaces Accreditation OPS Aeronautical Industry IAQG Oversight Team OP Management Team Certification body Management committee Auditor Authentification Board IAQG Americas. Asia/Pacific ASD Quality Committee National Aerospace Industry Associations. International Accreditation Forum Americas. Asia/Pacific European Accreditation National accreditation Body CRB Auditors Aerospace Organisation National Level European Level International Level CRB: Certification Registration Body ASD: Aero. Space and Defence Industries Association of Europe. OPS: Other Party Scheme IAQG: International Aerospace Quality Group OP: Other Party
Procurement Quality & Supply Chain PQDR — User Guide – R 5. 0 Procurement Directorate GRESS Commitment
Procurement Quality & Supply Chain PQDR — User Guide – R 5. 0 Page 27© AIRBUS S. All rights reserved. Confidential and proprietary document. • Why this requirement ? To ensure that the Supplier is aware and commit to apply GRESS To identify the GRESS requirements which cannot be fulfilled, to explain why and what are the other means of compliance the Supplier proposes To mitigate risks related to GRESS deviations (and impacts on end-products) • How to meet this requirement ? Fill the GRESS Compliance Commitment Deviation list provided by the Purchaser (contract appendix) Agree with Airbus on each proposed deviation (including means of compliance) prior to contract signature. GRESS Commitment
Procurement Quality & Supply Chain PQDR — User Guide – R 5. 0 Page 28© AIRBUS S. All rights reserved. Confidential and proprietary document. GRESS Compliance commitment / Deviation list GRESS Compliance Commitment / Deviation List available on e-Site: Airbus people Suppliers
Procurement Quality & Supply Chain PQDR — User Guide – R 5. 0 Procurement Directorate Quality Assurance Plan
Procurement Quality & Supply Chain PQDR — User Guide – R 5. 0 Page 30© AIRBUS S. All rights reserved. Confidential and proprietary document. • Definitions The Quality Assurance Plan is a specific document for carrying out particular contracts; it complements the Quality Assurance Manual, which is corporate generic • Why this requirement ? To have a scope of the Quality Management System for the contract committed with Airbus To complement the Quality Assurance Manual with dedicated Quality Assurance Plan Note: required only if the Equipment or System Supplier is not EN 9100 certified. Quality Assurance Plan
Procurement Quality & Supply Chain PQDR — User Guide – R 5. 0 Page 31© AIRBUS S. All rights reserved. Confidential and proprietary document. Quality Assurance Plan • How to meet this requirement ? List the specificities (specific procedures and organisation) which complete the generalities of the Assurance Quality Manual Build a Quality Assurance Plan in compliance with ISO 10005 Submit the Quality Assurance Plan to Airbus for acceptance
Procurement Quality & Supply Chain PQDR — User Guide – R 5. 0 Procurement Directorate Export Licensing
Procurement Quality & Supply Chain PQDR — User Guide – R 5. 0 Page 33© AIRBUS S. All rights reserved. Confidential and proprietary document. Export Licensing • Why this requirement? To ensure that the supplier and its subcontractors are able to export Equipment/ WP (including data and documentation) to Airbus and its customers throughout the world wide in a timely manner To ensure that Airbus’ business is conducted in a legal and compliant manner with respect to international trade regulations • How to meet this requirement? Apply for an export license, when necessary from the relevant national authority Ensure that the export licence(s) is obtained in time to allow delivery of the Item and that it does not infringe on the operator’s ability to utilise its aircraft Send the export form for export control classification and update it for CDR, LUAR, FFAR, CFAR and when Part Number (PNR) changes
Procurement Quality & Supply Chain PQDR — User Guide – R 5. 0 Procurement Directorate Environmental Standards
Procurement Quality & Supply Chain PQDR — User Guide – R 5. 0 Page 35© AIRBUS S. All rights reserved. Confidential and proprietary document. • Why this requirement ? Suppliers as well as Airbus shall be compliant with all Environment, Health and Safety laws and regulations applicable to their activities To ensure that items of Product are compliant with Airbus policy about Environment, Health and Safety (A 03) To have reliable and comprehensive environmental information about delivered items during their whole life cycle. Environmental Standards A 03: Document defining Airbus Policy on Environment, Health and Safety
Procurement Quality & Supply Chain PQDR — User Guide – R 5. 0 Page 36© AIRBUS S. All rights reserved. Confidential and proprietary document. Environmental Standards • How to meet this requirement ? Even if an environmental certification is provided, be compliant with AP 1003 “Environmental Requirements for Airbus Suppliers” and related AP 2091 Main Module & Module 1 Provide complete information using AP 1003 Appendix A “Product Environmental Data Form”, including the list of all Banned, Targeted and Restricted (BTR) substances contained in the Product and update this list all along the product life cycle Return AP 1003 Appendix A to the buyer and to Airbus Environmental department as instructed in such Appendix
Procurement Quality & Supply Chain PQDR — User Guide – R 5. 0 Page 37© AIRBUS S. All rights reserved. Confidential and proprietary document. Environmental Standards D I A G N O S I S Company — Product Gas rejections Wastes Better flow management Outputs Nuisances decrease. Smells Noise. Water Raw materials Energy Inputs M A N A G E M E N T IDENTIFICATION OF THE SIGNIFICANT IMPACTS COMMITMENT OF THE MANAGEMENT ENVIRONMENTAL POLICY ENVIRONMENTAL ORGANISATION — Objectifs — Targets — Monitoring — Responsible — Means — ISO 14001 — ECO-AUDITWork environment
Procurement Quality & Supply Chain PQDR — User Guide – R 5. 0 Page 38© AIRBUS S. All rights reserved. Confidential and proprietary document. Environmental Standards Д и а г н о с т и к а Продукция компании Газовые выбросы Отходы Наилучшая схема менеджмента Выходы Уменьшение вредного воздействия. Запахи Шум. Вода Исходные материалы Энергия Входы М е н е д ж м е н т Определение наиболее значимых воздействий Обязательства менеджмента Экологическая политика Экологическая организация — Цель — Зада чи — Monitoring — Отве тственн ость — Средств а — ISO 14001 — ECO- аудит. Действия окружающей среды
Procurement Quality & Supply Chain PQDR — User Guide – R 5. 0 Page 39© AIRBUS S. All rights reserved. Confidential and proprietary document. Environmental Standards: Certification Bodies examples • In France: … AFAQ — www. afaq. org LRQA — www. lrqa. fr DNV — www. dnv. fr BVQI — www. bvqi. com AFNOR — www. afnor. fr … • In Switzerland: … SGS — www. sgs. com … • In Germany : … TÜV — www. tuv. com … • In Spain : … AENOR — www. aenor. es … • In Canada: … QMI – www. qmi. com … • In United Kingdom: … URS – www. urscertification. com BSI – www. bsi-global. com … For more certification bodies: www. iaqg. org /oasis http: // www. iso. org/iso/en/xsite/copyright. htm l http: // ec. europa. eu/environment/emas/inde x_en. htm
Procurement Quality & Supply Chain PQDR — User Guide – R 5. 0 Procurement Directorate Programme management introduction
Procurement Quality & Supply Chain PQDR — User Guide – R 5. 0 Page 41© AIRBUS S. All rights reserved. Confidential and proprietary document. • Why Programme/Project management (P/PM)? P/PM Is key to the success of a product development (Time / Cost / Quality / Delivery) Ensure all activities, deliverables, resources, means are assessed, planned, foreseen, and anticipated Ensure team work is coordinated as planned and effective Guarantee the compliance of ALL Suppliers activities with the requirements of the Purchaser Ensure that the Supplier controls and monitors the programme Ensure full transparency and visibility of Supplier’s product development Gain confidence towards maturity To obtain all inputs for certifications to which all Aircraft are subjected by the Airworthiness Authorities. Programme/Project Management Introduction
Procurement Quality & Supply Chain PQDR — User Guide – R 5. 0 Page 42© AIRBUS S. All rights reserved. Confidential and proprietary document. Programme/Project Management Introduction • How to meet this requirement? Ensure that Supplier programme management takes into account end products and enabling products — (Based on Product Breakdown Structure) Provide programme management evidences, according to GRESS requirements – ( evidences are formal or non-formal proofs that activities have been performed) Ensure that programme management covers ALL GRESS modules Ensure activities covers phases from Selection phase to Serial production phase ( incl. Support ) Understand all the extent of the tasks to be realised for products related to an Aircraft and the requirements of the Airworthiness Authorities • Definitions reminder End Product: item of equipment or system that is delivered to Airbus and Airlines & Military customers to perform operational functions and performances Enabling Product: item that provides the means for: – Getting an end product into service, keeping it in service, or ending its service – E. g. Tests benches, Tooling, Delivery means, ground-support equipment…
Procurement Quality & Supply Chain PQDR — User Guide – R 5. 0 Page 43© AIRBUS S. All rights reserved. Confidential and proprietary document. Programme Management Scope RFP Phase Development activities in concurrent engineering: design, engineering for manufacturing… EISKOM FFARCDR Project Management FR Programme Management. Development 20 to 30 Years. Up to 2 year 1 to 5 years Industrialisation & Series In Service Follow Up Project does not end at EIS!
Procurement Quality & Supply Chain PQDR — User Guide – R 5. 0 Page 44© AIRBUS S. All rights reserved. Confidential and proprietary document. Programme Management Scope End products. Enabling products All processes as per GRESS Modules 0 to 7 Evidence (Documented data & end products) to be delivered Activities according to GRESS requirements Programme Management
Procurement Quality & Supply Chain PQDR — User Guide – R 5. 0 Procurement Directorate Supplier Development Plan
Procurement Quality & Supply Chain PQDR — User Guide – R 5. 0 Page 46© AIRBUS S. All rights reserved. Confidential and proprietary document. • Why this requirement? To enforce clear planning and resource allocation BEFORE contract award notification To provide the basis for (quantitative) measurement of the programme success To be sure that the Supplier has embraced all the scope and its associated work. To have an understandable summary of the supplier approach and way of working To establish a consistency between all parts of the programme : Requirements, Key Design Drivers, Risks, Engineering, Industrial breakdown, …production ramp-up, Customer support. . . Resources, and Programme monitoring To have a reference document about the programme – To trace main drivers and changes : assumptions, design drivers, alternate solution choice… – To ensure continuity of programme, even if team members change or leave. Supplier Development Plan
Procurement Quality & Supply Chain PQDR — User Guide – R 5. 0 Page 47© AIRBUS S. All rights reserved. Confidential and proprietary document. Supplier Development Plan • How to meet this requirement? Provide a complete and consistent Supplier Development Plan (SDP) which cover: All end products, enabling products, activities and processes Provide releases of Supplier Development Plan at the requested milestones (see CAM) Start with a synthesis on all Supplier Development Plan topics — give consistency, add links between all topics. Give confidence during reading – make SDP understandable by any newcomer • Guidelines Have a written process which describes how to manage SDP Describe the main Programme/Project goals, activities, strategies, constraints and requirements Consider the SDP as the reference on of Programme/ Project Management, design, engineering, industrialisation, Supply Chain and Support Ensure the consistency of transition phases (development to productions in series and support) Share the SDP with all key Programme/Project key members (incl. key contributing parties) Update the SDP parts in case of major changes …. • Hints : Build the SDP with key members of the Project (Design, Engineering for Manufacturing, Integration and Tests, Product/Process Assurance, Support…)
Procurement Quality & Supply Chain PQDR — User Guide – R 5. 0 Page 48© AIRBUS S. All rights reserved. Confidential and proprietary document. Supplier Development Plan Tips and Tricks 1/8 • Programme/Project context and overview Describe the understanding top level requirements of the programme Describe specifics as : big work package, integration, Risk Sharing, Convergence Plan, New Service Policy, world while Support… • Scope understanding Use PBS to depict the scope (built by an integrated team, all phases experienced people) PBS is a description of product parts – At this level, it shows product parts cascade, incl. Product, Enabling product, Services • Substantiate Bid decision Some business case elements linked to demonstration that Supplier has taken into account all activities • Lessons learnt Indicate how lessons learnt are captured, and applied for current programme from Planning to Support Detail this process for appliance failures, heritage analysis, root cause analysis, impact on Design to Support. • Explain Programme/Project strategy based on : • Product to be delivered • Key Design Drivers • High-Level requirements • Make or Buy Policy • Supply chain constraints • Maturity • Customer Support • … • Lessons learnt • Key Industrial production ramp up
Procurement Quality & Supply Chain PQDR — User Guide – R 5. 0 Page 49© AIRBUS S. All rights reserved. Confidential and proprietary document. Supplier Development Plan Tips and Tricks 2/8 Provide Product Breakdown Structure showing the product part cascade including : Assumptions made and performances range (especially in case of high level requirements) — Assumptions can be presented per programme phases and WP to ease cross check with risk register Quote Design decision, Technical Solutions, Alternatives, Interfaces. . Impacts of re-use, lessons learnt, maturity, S. C. and support constraints, …. • Configuration Management General description of configuration management • Explain Industrial Breakdown choices Explain Make or Buy policy, Describe mastering and coordination of key contributing parties, requirements cascading Insure Key Contributing Parties understanding of Aircraft manufacturing constraints
Procurement Quality & Supply Chain PQDR — User Guide – R 5. 0 Page 50© AIRBUS S. All rights reserved. Confidential and proprietary document. Supplier Development Plan Tips and Tricks 3/8 • Show the Organisation Breakdown Structure (OBS) for managing and performing the programme All activities are clearly assigned to a function or an organisation (a responsibility assignment matrix could be useful) Programme people are all skilled: summary of their experience Outline Key Contributing Parties responsibilities Who is accountable / responsible of what in the programme Hint: Product & Process Assurance is at Supplier’s company level and not within the programme • Provide the Work Breakdown Structure (WBS) for all activities of the programme Built WBS by an integrated team, all phases experienced people Define main work packages (with Aims, lead time, workload, risks, assumptions, input, output)
Procurement Quality & Supply Chain PQDR — User Guide – R 5. 0 Page 51© AIRBUS S. All rights reserved. Confidential and proprietary document. Supplier Development Plan Tips and Tricks 4/8 • Demonstrate that the full scope, activities and resources are planned See Breakdown structure consistency • Outline Main milestones and key decision milestones Decision gates for Design, alternate solution choice…… • Provide a Schedule for delivering on time whatever happens Show that the Shedule: – sticks to contractual milestones – is realistic (lead time and resource plan) and take into account all task and activities to be planed ( refer to See Breakdown structure consistency and schedule) – is shared by all functions and key contributing parties • Resources Assessment Report (RAR) All resources are planned and available: Human resources, means (tooling, benches, …) and facilities Required Skills are defined The workload plan is realistic, Humans resources and means ramp-up too Show that this RAR is shared by all functions and key contributing parties
Procurement Quality & Supply Chain PQDR — User Guide – R 5. 0 Page 52© AIRBUS S. All rights reserved. Confidential and proprietary document. Supplier Development Plan Tips and Tricks 5/8 • Means & Methods Implementation Plan Describe how not yet available resources (at the SDP writing time) will be provided • Give confidence by Risk Management for no surprise Risks are assessed from Design to Support Risks are assessed and mitigated by an integrated team including sub-tiers Mitigation plan is planned (alternate solutions, sourcing , resources…, schedule impact) Risk assessment is monitored on a regular basis • Data and Documentation & Communication Describe Data and Documentation management Describe Communication process, activities and means
Procurement Quality & Supply Chain PQDR — User Guide – R 5. 0 Page 53© AIRBUS S. All rights reserved. Confidential and proprietary document. Supplier Development Plan Tips and Tricks 6/8 • Programme monitoring and control How to see if we stay in the planned tracks? How Key Contributing Parties are monitored? How to insure completion of activities ? Define the transition criteria for each phase Supplier Programme Status proposed and frequency (for purchaser acceptance) • Validation & Verification, Detail way of working to fulfil Airbus requirements Describe Validation and Verification approach and strategy • Cross-Reference Matrix can contribute to Validation & Verification • Engineering for Manufacturing / Series production Describe Engineering for Manufacturing strategy Describe Supportability Engineering, link with DCM
Procurement Quality & Supply Chain PQDR — User Guide – R 5. 0 Page 54© AIRBUS S. All rights reserved. Confidential and proprietary document. Supplier Development Plan Tips and Tricks 7/8 • Supply Chain Describe Supply Chain strategy Constraints for ramp up and production rates • Performance Metrics, Link with maturity, monitoring, KPIs, Sub-tiers quality and on time delivery metrics • Deliveries and associated services , Describe how indicators are included as part of programme management • Customer Support Link with engineering for supportability — Drivers as DMC, operational reliability, link with maturity – Show that all task, activities resources, have bee planed and are monitored. Show Support will be mature at EIS (KPIs, completion trend…) • Supplier’s Key Contributing Parties Management Link with design strategy, work sharing, cascade of requirements, specifications, change request – transfer of work…
Procurement Quality & Supply Chain PQDR — User Guide – R 5. 0 Page 55© AIRBUS S. All rights reserved. Confidential and proprietary document. Supplier Development Plan Tips and Tricks 8/8 • Maturity understanding What is the Supplier’s understanding of maturity? How maturity is built since Design to Support? How to demonstrate that maturity completion will be reached all along the programme Define Key Performance Indicators (KPI) for all GRESS maturity themes • Obsolescence (see ABD 0100) Describe Obsolescence management • Information management Describe Information management: – Communication, Information System Management • Integration Describe integration strategy, activities and means
Procurement Quality & Supply Chain PQDR — User Guide – R 5. 0 Page 56© AIRBUS S. All rights reserved. Confidential and proprietary document. SDP: The programme reference document Describes how the Supplier will organise, coordinate, manage and control the product development Planning & scheduling Breakdown Structures Schedule margins Task duty cycles Critical path Supporting activities Lessons learnt Key Contributing Parties Management Risk management Maturity Applied to Processes related to all GRESS Modules Monitoring & Control Reviews Technical & progress meetings Status reports KPIs. Overall approach Assumptions Key Design drivers Design strategy Supplier’s solution Maturity trend Industrial breakdown Main risks & opportunities
Procurement Quality & Supply Chain PQDR — User Guide – R 5. 0 Page 57© AIRBUS S. All rights reserved. Confidential and proprietary document. Development Plan – When? Contract Award Notification Plans Review Event-triggere d. Issue 1 Proposal. Draft Issue 2 Further Issues as needed PMCA Major changes IPCA PMCA Follow-on
Procurement Quality & Supply Chain PQDR — User Guide – R 5. 0 Procurement Directorate Breakdown Structures
Procurement Quality & Supply Chain PQDR — User Guide – R 5. 0 Page 59© AIRBUS S. All rights reserved. Confidential and proprietary document. • Why this requirement ? To provide a common and unique reference for all project stakeholders. This reference will enable the project planning, monitoring and control To be able to set the appropriate resources (human, means, skills, …) to fulfil customer’s expectations on time To check if the scope of the project is totally understood and split into elementary and manageable tasks • How to meet this requirement ? Identify Breakdown Structure items Tasks should be sized to be manageable Ensure consistency between all breakdown structures. Breakdown structures
Procurement Quality & Supply Chain PQDR — User Guide – R 5. 0 Page 60© AIRBUS S. All rights reserved. Confidential and proprietary document. Manage and perform the Project. Organisation Breakdown Structure. SDP- Breakdown Structures What is the product made up of? End Product Enabling Product What are the tasks for providing product parts ? With who and how will the tasks be performed Project Breakdown Structure Product Breakdown Structure ( PBS )1 Schedule. Work Breakdown Structure ( WBS )2 Resource Breakdown Structure ( RBS )3 Define, and manage the team. Organisatio n Breakdown Structure (*) — any licence to be delivered with the Item for the purpose, scope and duration requested in the Contract — appropriate information about use of encryption if any (*) Including:
Procurement Quality & Supply Chain PQDR — User Guide – R 5. 0 Page 61© AIRBUS S. All rights reserved. Confidential and proprietary document. • Why this requirement ? To ensure that project roles and responsibilities are clearly defined Clear and complete project organisation guarantees that no activity will be forgotten or missed throughout the development To enable coordination between functions • How to meet this requirement ? Define and empower a project leader Determine a detailed Organisation Breakdown Structure (OBS), with all function responsible nominated. Supplier project organisation
Procurement Quality & Supply Chain PQDR — User Guide – R 5. 0 Procurement Directorate Breakdown Structures Consistency
Procurement Quality & Supply Chain PQDR — User Guide – R 5. 0 Page 63© AIRBUS S. All rights reserved. Confidential and proprietary document. Breakdown structures consistency 1/4 • Why this requirement? To ensure that : – The entire scope is defined – All activities are defined and planned to provide product – All activities have resources and means – All activities are monitored and controlled To ensure that any change in the breakdown structures is impacted on all other breakdown structures • How to meet this requirement? • Have and internal documented standard for establishing and managing all Stage 1 : The programme leader builds a first Organisation Breakdown Structure (OBS) regarding the RFP Stage 2 : The integrated team build the PBS (Use IT tools to link PBS, Work Breakdown Structure (WBS), Resource Breakdown Structure (RBS) and ultimately the Schedule) Stage 3 : Allocate activities on each part of PBS Stage 4 : Allocate resources means and methods on each activities Stage 5 : Optimise WBS/Schedule to meet delivery dates and budget
Procurement Quality & Supply Chain PQDR — User Guide – R 5. 0 Page 64© AIRBUS S. All rights reserved. Confidential and proprietary document. Breakdown structures consistency 2/4 PBS consistency is built by an integrated team PBS Tree shape view. OBS programme team
Procurement Quality & Supply Chain PQDR — User Guide – R 5. 0 Page 65© AIRBUS S. All rights reserved. Confidential and proprietary document. Breakdown structures consistency 3/4 • Stage 3 3. 1 Issue WBS : for each PBS part, determine specific activities – (Design, Engineering for Manufacturing, Support) – 3. 2 Add all deliverables, decision points and Milestones 3. 3 Add supporting activities – ( Programme Management, V&V, KCP management…) 3. 4 Determine processes and interdependencies to build schedule – WBS and schedule are automatically linked in most PM IT tools 3. 5 Allocate resources and workload on activities based upon to schedule WBS and schedule WBS Resources. PBS Integrated team
Procurement Quality & Supply Chain PQDR — User Guide – R 5. 0 Page 66© AIRBUS S. All rights reserved. Confidential and proprietary document. Breakdown structures consistency 4/4 • Resources Breakdown Structure (RBS) RBS comes from schedule using skills of resources and workload. WBS schedule and resources
Procurement Quality & Supply Chain PQDR — User Guide – R 5. 0 Procurement Directorate Product Breakdown Structure
Procurement Quality & Supply Chain PQDR — User Guide – R 5. 0 Page 68© AIRBUS S. All rights reserved. Confidential and proprietary document. Product Breakdown Structure • Why this requirement? Aims to demonstrate / share that the entire scope is understood and breakdown in elementary items Reflect Product and design strategy Outlines subcontracted parts Initiate the Bill of Material Provide a common and unique reference for all programme stakeholders
Procurement Quality & Supply Chain PQDR — User Guide – R 5. 0 Page 69© AIRBUS S. All rights reserved. Confidential and proprietary document. Product Breakdown Structure example 1. 1 e l e c t r o n i c 1. 2 m e c h a n i c 1. 3 s o f t w a r e E q u i p m e n t 1 2. 1 e l e c t r o n i c 2. 2 m e c h a n i c E q u i p m e n t 2 E q u i p m e n t 3 : b a t t e r i e s S y s t e m X X X Sub-contracted activities included (Grey)
Procurement Quality & Supply Chain PQDR — User Guide – R 5. 0 Procurement Directorate Work Breakdown Structure
Procurement Quality & Supply Chain PQDR — User Guide – R 5. 0 Page 71© AIRBUS S. All rights reserved. Confidential and proprietary document. Work Breakdown Structure • Why this requirement? Aims to demonstrate that all (specifics and supporting) activities for provide all product part are planned – Shows that responsibilities for producing each element are clearly identified. Breakdown corresponding to clearly identified products to generate. Shows the worksharing between sub tiers Note: A System is more than the addition of stand alone equipment or components. System integration shall be managed in order to deliver an integrated and verified System
Procurement Quality & Supply Chain PQDR — User Guide – R 5. 0 Page 72© AIRBUS S. All rights reserved. Confidential and proprietary document. WBS as a common and unique reference • Why this requirement ? As a part of Development Plan which is reference document, WBS is the reference for activities to be performed • How to meet this requirement? Each task, as described in the WBS, is detailed and includes: Objectives/Requirements Owner/Responsible of the Task Description of the work to be done Efforts to perform the work (coming from schedule or work plan) Duty cycle (Lead time) to perform the work (coming from schedule) – Explain why it is not possible to reduce the duration
Procurement Quality & Supply Chain PQDR — User Guide – R 5. 0 Page 73© AIRBUS S. All rights reserved. Confidential and proprietary document. WBS as a common and unique reference • How to meet this requirement? (cont’. ) Each task, as described in the WBS, is detailed and includes: (cont’. ) Inputs (including date of input and responsible/owner of input) – Inputs as available deliverables, process, means… (coming from the schedule), Owners coming from OBS or responsibility matrix or schedule Outputs (including date of output and end-user of output) – Outputs as available accepted deliverables, process, means… (coming from the schedule) Risk analysis and risks criticality level (when relevant) – The risk register has to includes WP ID to ease link with WBS Assumptions – Arrange assumptions per programme phases and WP
Procurement Quality & Supply Chain PQDR — User Guide – R 5. 0 Page 74© AIRBUS S. All rights reserved. Confidential and proprietary document. Work Breakdown Structure example 1. 1. 1. 2 1. 1. 3 1. 1 1. 2 1. 3 1. 4 1 P r o j e c t m a n a g e m e n t 2. 1. 1 S y s t e m I n t e g r a t i o n 2. 1. 2 S t r e s s & W e i g h t s 2. 1. 3 S t a t i c s / D y n a m i c s 2. 1 P r e D e s i g n 2. 2 2. 3. 1 2. 3. 2 2. 3 2 D e s i g n E n g i n e e r i n g 3. 1. 1 3. 1. 2 3. 1 3. 2. 2 3 I n d u s t r i a l i s a t i o n 4. 1 4. 2 4. 3. 1 4. 3. 2 4. 3 4 V a l i d a t i o n & V e r i f i c a t i o n. . . A 3 8 0 — X X P r o j e c t Sub-contracted activities included (Grey)
Procurement Quality & Supply Chain PQDR — User Guide – R 5. 0 Procurement Directorate Resource Management
Procurement Quality & Supply Chain PQDR — User Guide – R 5. 0 Page 76© AIRBUS S. All rights reserved. Confidential and proprietary document. • Why this requirement? To ensure that relevant resources (human, means, skills, …) are available and allocated to carry out the programme Availability of the right resources at the right time may become critical in order to not create task slippage • How to meet this requirement? Provide evidences concerning the resources allocated to this specific development (chart with resources and planning) Use WBS, Schedule and workload plan as a baseline to size resources (definition of Resource Breakdown Structure) Use Resource Breakdown Structure and planning & scheduling to build Resource Assessment Report Propose a resource baseline (workload plan) as contract between Supplier Functions/Entities and the programme. Resource management
Procurement Quality & Supply Chain PQDR — User Guide – R 5. 0 Page 77© AIRBUS S. All rights reserved. Confidential and proprietary document. Resources Breakdown Structure Supplier Schedule and Resources Breakdown Structure consistency
Procurement Quality & Supply Chain PQDR — User Guide – R 5. 0 Page 78© AIRBUS S. All rights reserved. Confidential and proprietary document. Resource Breakdown Structure • Why this requirement? Demonstrate phases/activities are covered by resources, facilities and means with realistic workload and availability Match skills allocated to phases or activities with required skills regarding WP Prepare and plan Resource Ramp-up • How to meet this requirement? Resources Breakdown Structure is based on required resource and WBS and Schedule targets List of Activities WBS/Schedule Skills + Workload per activities Schedule for skills availabilities Level resources against targets
Procurement Quality & Supply Chain PQDR — User Guide – R 5. 0 Page 79© AIRBUS S. All rights reserved. Confidential and proprietary document. Resource baseline contract between Supplier Functions/Entities and the programme/project • Why this requirement? To ensure resources availability on right time scale at company level and at key contributing parties level • How to meet this requirement? The contractual agreement includes: resource quantity, skills, hourly cost, arrival dates and duration of assignment The functions/entities are responsible for: – Providing the agreed quantity of resources – Ensuring a balance between internal headcount – Subcontracting resources, experienced staff and junior staff – Developing resources skills, tools and methods
Procurement Quality & Supply Chain PQDR — User Guide – R 5. 0 Page 80© AIRBUS S. All rights reserved. Confidential and proprietary document. Resource assessment report Shows consistency of resource skills & needs with overall company/corporate capacity. Resource Assessment Report Tools and Facilities + Other programme. Airbus programme + At Supplier’s and Key Contributing Parties Other programme. Human Resource Airbus programme
Procurement Quality & Supply Chain PQDR — User Guide – R 5. 0 Page 81© AIRBUS S. All rights reserved. Confidential and proprietary document. Resources and means beyond current capability • Why this requirement? Because Resource Assessment Report (RAR) has identified a gap between required capacities and available capacities • How to meet this requirement? Missing capacities = Required capacities – Available capacities Identify missing capacities (People, Tools, methods, benches, plants…) Define a means an method implementation plan Available Beyond capacity (missing capacities)Required Process Facility Bench Tool People
Procurement Quality & Supply Chain PQDR — User Guide – R 5. 0 Page 82© AIRBUS S. All rights reserved. Confidential and proprietary document. Means and Methods Implementation Plan • Why this requirement? Acquisition of missing capacities must be planned as soon as possible, especially for long lead items (autoclaves, Plants, Offshore plant) or rare materials • How to meet this requirement? Plan supplying of all missing capacities, allocate resources and organisation, define KPIs on completion, report them in status report 2008 2009 2010 Q 1 Q 2 Q 3 Q 4 Recruitment Training Design Manufacturing Plant Design Plant building Design of process
Procurement Quality & Supply Chain PQDR — User Guide – R 5. 0 Procurement Directorate Organisation Breakdown Structure
Procurement Quality & Supply Chain PQDR — User Guide – R 5. 0 Page 84© AIRBUS S. All rights reserved. Confidential and proprietary document. Organisation Breakdown Structure: • Why this requirement? Define who is managing what Ensure that main activities are managed Figure the empowerment of the programme/project leader Identify deputy for continuity • How to meet this requirement? OBS is built progressively by the key people as per PBS, WBS, RBS and worksharing refinement and changes Covers the whole Project end-to-end as defined in the contract Identify sub-tiers
Procurement Quality & Supply Chain PQDR — User Guide – R 5. 0 Page 85© AIRBUS S. All rights reserved. Confidential and proprietary document. Organisation Breakdown Structure — example • A responsibility assignment matrix presents a clear assignment of accountability (A), responsibility (R), Supportability (S), Information (I) Activities Actors Project/ Programme manager Design Chief Eng. Manager Indus. Manager Support Manager Mana ging Direct or Legal Manage r Fleet A. … Define overall approach and programme structure A RS RS Define target solution A R R Deal with Dept. A Define overall Scope A S S I S Define subcontracting strategy AR S S I S Build WS Structure A R R Define Corporate Finance Business Case A I Sign Project Progress R R Design part X AR …. Identify sub-tiers High-level manager endorses the Status report
Procurement Quality & Supply Chain PQDR — User Guide – R 5. 0 Page 86© AIRBUS S. All rights reserved. Confidential and proprietary document. Programme/Project Leader nomination O. B. S. Mission Letter • Why this requirement? The programme/project (P/P) leader is the accountable of programme/project completion at Supplier and is the main Airbus focal point • How to meet this requirement?
Procurement Quality & Supply Chain PQDR — User Guide – R 5. 0 Procurement Directorate Supplier Development Schedule
Procurement Quality & Supply Chain PQDR — User Guide – R 5. 0 Page 88© AIRBUS S. All rights reserved. Confidential and proprietary document. • Why this requirement? Demonstrate that contractual milestones will be reached Plan activities and deliverables Demonstrate that Lead Times are realistic – Outline Risks Share same objectives/commitments with all counterparts Save time — Maintain targets whatever programme events Monitor programme progress vs baseline • How to meet this requirement? Establish internal development process milestones in front of contractual milestones Set baseline as the way to agreement on objectives – Re-assess remaining work – re-calculate revised dates Highlight transition milestones Interdependencies coherency Provide critical Path/Resources/Means Challenge process/dependencies, apply concurrent engineering. Supplier Development Schedule
Procurement Quality & Supply Chain PQDR — User Guide – R 5. 0 Page 89© AIRBUS S. All rights reserved. Confidential and proprietary document. Development Scheduling Macro-example
Procurement Quality & Supply Chain PQDR — User Guide – R 5. 0 Page 90© AIRBUS S. All rights reserved. Confidential and proprietary document. Supplier development scheduling • Contractual Milestones • Deliverables • Specific and supporting activities (DRL, GRESS CAM, Processes) • WBS: specific and supporting activities • Long Lead items, Key decision milestones • Key Contributing Parties schedule • Resources skill list Input Output • Challenge schedule/process/ resource allocation to meet contractual milestones • Apply Concurrent Engineering “as soon as possible” • Critical path – critical tasks & resources as incomes of risk assessment and mitigation plan • Resource workload plan (Realistic, ramp-up) • Means & Method implementation plan • Realistic lead times • Outlines contractual milestones • Deliverable, Reviews and key decision milestones schedule • Realistic workload plan • Resources booking timescale (shared with resources owners) • Critical path – critical tasks & resources as input of risks assessment • Baseline (committed by all involved counterparts) • … Scheduling Integrated team all programme phases
Procurement Quality & Supply Chain PQDR — User Guide – R 5. 0 Page 91© AIRBUS S. All rights reserved. Confidential and proprietary document. Supplier Development Schedule Supplier Schedule Structure : Macro Schedule to detailed Schedules
Procurement Quality & Supply Chain PQDR — User Guide – R 5. 0 Page 92© AIRBUS S. All rights reserved. Confidential and proprietary document. Supplier development schedule — example WBS ID Activities Resource Duration Dependancies Including Key Contributing Parties activities Schedule Baselines Critical Task Milestone Levelled* work plan * Resources are in line with their capacities in the timescale
Procurement Quality & Supply Chain PQDR — User Guide – R 5. 0 Procurement Directorate Risk Management
Procurement Quality & Supply Chain PQDR — User Guide – R 5. 0 Page 94© AIRBUS S. All rights reserved. Confidential and proprietary document. • Why this requirement? Uncertain future events may have negative consequences on programme objectives Risk analysis enables an early detection of weak points and implementation of preventive actions instead of failure correction in expensive crisis mode Risk management maintains objectives of programme, even if the issue occurs. Risk management specific to the product life cycle
Procurement Quality & Supply Chain PQDR — User Guide – R 5. 0 Page 95© AIRBUS S. All rights reserved. Confidential and proprietary document. Risk management specific to the product life cycle 1/3 • How to meet this requirement? Have a written risk management plan and implemented activities shared by team members (inc. Key Contributing Parties) which formalize that: – Programme leader is empowered with overall responsibility in risk management – Scope of risk management is defined ( All programme phases from design to Support incl. key contributing parties activities ) and cover all functions – Risk is identified, assessed (level and criticity), quantified ( check lists, lessons learnt, …) – Root causes analysis is part of the process – Resources and means for mitigation/contingency are planned (Alternate solutions, key decision milestones in schedule and work plan) and impact on PBS and WBS assessed – Follow-up action plan for mitigation/contingency – An up to date and complete Risk Register is available for management of the Risk identification and mitigation progress
Procurement Quality & Supply Chain PQDR — User Guide – R 5. 0 Page 96© AIRBUS S. All rights reserved. Confidential and proprietary document. Risk management specific to the product life cycle 2/3 Project Management Design Validation & Verification Supply Chain Series Production Certification Support Security. . . Whole Supplier project Each phase of product life cycle Monitor status (Status report, Reviews)Manage Risks : Identify risk Eliminate, mitigate, reduce risks Risk management for Manage legal aspects linked to security: Software licences COTS Cryptography Export licences Inherent bugs
Procurement Quality & Supply Chain PQDR — User Guide – R 5. 0 Page 97© AIRBUS S. All rights reserved. Confidential and proprietary document. Risk management specific to the product life cycle 3/3 W ork package Risk ID Detection Date Program m e area Risk description Severity Occurrence Criticality Action description Owner Due date Status … … … 1. 2 10 15/10/0 7 Design Tailor-made eye glasses could be too heavy – weight out of range High Define alternate design solution based on titanium side-pieces Paul 15/11/07 Open 2. 4 11 20/10/0 7 Support Titanium stiffness does not allow customisation to final customer morphology Med. High side-pieces flexible mock up for modelling final product on customer Mar k 15/11/07 Open 3. 7 12 12/11/07 Supply Chain Supply chain delays from offshore sub-tiers … … … … … 1 3 6 9 120123456 time N um ber of R isk. Risk load along Programme life. Risk register and monitoring example
Procurement Quality & Supply Chain PQDR — User Guide – R 5. 0 Procurement Directorate Supplier Support Plan
Procurement Quality & Supply Chain PQDR — User Guide – R 5. 0 Page 99© AIRBUS S. All rights reserved. Confidential and proprietary document. Support Plan • Why this requirement? Meet and sustain customers’ operational need. Maximise operational reliability, availability Reduce the Direct Maintenance Cost (DMC), Direct Operating Cost for Airlines Optimise of personnel and equipment needed to operate and maintain the product in service Gain service readiness and maturity at entry-into-service Ensure timeliness, adequacy and consistency of all support delivery • How meet this requirement? Design the product to reach support performances level ( as interchangeability, maintainability, repairability …): Supportability Engineering Consider Supportability Engineering as an in put for Service Readiness/Maturity Plan Comply with Supplier Support Conditions (SSC) Plan as soon as possible support activities and long lead means (worldwide spares distribution and repair…) Monitor Support to demonstrate its readiness at EIS
Procurement Quality & Supply Chain PQDR — User Guide – R 5. 0 Procurement Directorate Experience Capture, Record and Implementation
Procurement Quality & Supply Chain PQDR — User Guide – R 5. 0 Page 101© AIRBUS S. All rights reserved. Confidential and proprietary document. • Why this requirement? Benefit from experience of previous programme Avoid recurrent errors Support people involved in the programme life cycle Provide a guideline for other programmes Enable maturity enhancement Enable future programme leaders to access information and lessons learnt • How to meet this requirement? Capture lessons learnt from former and current running programme, from all organisation, functions, business unit… Classify them per topic (design, programme management, Airbus programme…) Select lessons learnt to be applied, thanks to relevant people Provide example of lessons learnt applied to the current programme Outline main lessons applied in Development Plan Capture lessons learnt during the current programme lifecycle. Experience capture and record
Procurement Quality & Supply Chain PQDR — User Guide – R 5. 0 Page 102© AIRBUS S. All rights reserved. Confidential and proprietary document. Lessons learnt capture example ID Origin Cust. Date Topic Content Root Cause Implemented or not Actions 100 … … …. 101 Plant at Clichy Airbus 06/06 Documentation workload has been under-estimated Owing to lack of knowledge of ABD 100 and D 0254 – (Clichy plant was brand new) Actions list #12 102 Plant at London Airbus 07/06 Reviews Deliverables Internally processes did not include reviews from GRAMS and deliverables from GRAMS CAM Owing to lack of knowledge of GRAMS CAM and logbook Actions list #47 103 Plant at Milan Airbus 08/06 Sub tiers the fastener manufacturing process of our sub-tiers was not certified – Our delivery was refused by Airbus Requirements not cascaded and not assessed at sub-tiers Actions list #23 104 … Airbus … CAD File saturates erooms Not retained due to EDI N/A Share lessons learnt across all functions and organisations of the company !
Procurement Quality & Supply Chain PQDR — User Guide – R 5. 0 Page 103© AIRBUS S. All rights reserved. Confidential and proprietary document. Lessons learnt application example Lessons Learnt applied to the A 350 XWB WP xxx ID Topic Lessons Application Actio n 100 … … 101 Documentation workload has been under estimated Appraise workload of documentation by people previously involved in an Airbus WP with the same DAL (in bid phase) #56 103 Sub tiers The fastener manufacturing process of our sub tier was not certified Our delivery was refused by Airbus — Add this topic in Supplier Specifications — Cascade requirements of Airbus to sub-tiers -Train and inform sub-tiers on the rationale of this requirements — Assess if they are applied #78 104 … … … Project Record Sheet Template available on e-Site: Airbus people Suppliers
Procurement Quality & Supply Chain PQDR — User Guide – R 5. 0 Page 104© AIRBUS S. All rights reserved. Confidential and proprietary document. • Why this requirement? Contribution to aircraft maturity Maintain or reduce DMC Remedial on long lead test product failures (flight hours / cycles) • How to meet this requirement? Analyse heritage: data are analysed for existing products or part of products Determine roots causes Define remedial solution and Action plan Assess impact on complexity Estimate Remaining Failure Rate (RFR) after remedial solution Assess Margin impact Perform test efficiency Measure RFR after in service Report yearly all along P/P life, the product failures. Lessons Learnt capture on Failures
Procurement Quality & Supply Chain PQDR — User Guide – R 5. 0 Procurement Directorate Product/Process Assurance
Procurement Quality & Supply Chain PQDR — User Guide – R 5. 0 Page 106© AIRBUS S. All rights reserved. Confidential and proprietary document. • Why this requirement? Product assurance shall ensure that the product satisfies the specification requirements. If deviations they shall be justified and accepted. Process assurance shall provide documented evidence that plans are followed. (All activities that were planned have been performed. This requirement is required by Airworthiness Authorities) • How to meet this requirement? Have and internal documented standard for establishing and managing P&P Assurance Include: end product: enabling products and service in P&P Assurance Plan Include: Validation & Verification (incl. Traceability, Configuration Management, Certification, Assessments…) in Product Assurance Use GRESS requirement cross-reference matrix as a baseline Plan all tasks needed to ensure that Airbus requirements (including GRESS) are fulfilled (use PBS/WBS) Provide evidence of performed tasks. Product/Process assurance
Procurement Quality & Supply Chain PQDR — User Guide – R 5. 0 Page 107© AIRBUS S. All rights reserved. Confidential and proprietary document. Cross-reference matrix example (GRESS) all requirements. The CAM All modules Supplier’s compliance with requirements. One of tools for Validation & Verification
Procurement Quality & Supply Chain PQDR — User Guide – R 5. 0 Page 108© AIRBUS S. All rights reserved. Confidential and proprietary document. Product/Process assurance organisation • A separate Quality organisation ensures neutrality on application of required and defined processes Company management Programme management & team Quality / Product & Process Assurance Organisation
Procurement Quality & Supply Chain PQDR — User Guide – R 5. 0 Page 109© AIRBUS S. All rights reserved. Confidential and proprietary document. Product/Process assurance example GRESS cross-reference matrix (assessment sheet) Product & process assurance. GRESS Requirements
Procurement Quality & Supply Chain PQDR — User Guide – R 5. 0 Procurement Directorate Supplier’s Key Contributing Parties Monitoring and Control
Procurement Quality & Supply Chain PQDR — User Guide – R 5. 0 Page 111© AIRBUS S. All rights reserved. Confidential and proprietary document. • Definition of Key Contributing Parties (KCP): are parties that have a significant role in the Programme such as Worksharing partners, other business units of the Supplier, partners, sub-contractors, sub-suppliers Key Contributing Parties monitoring and control • Why this requirement? Bigger Work Packages implies several sub tiers Integration of KCPs parts became the main activity for the prime contractor Airworthiness Authorities require supplier monitoring at all levels Programme has to be managed as a whole, there is at least the same level of risk for an outsourced activity Supplier monitoring and trend analysis enable the anticipation of problems and mitigate related risks at delivery To drive KCP for reducing Risks, reach Safety, Reliability, Supportability, Certification, and Costs that are distributed within the key contributing parties
Procurement Quality & Supply Chain PQDR — User Guide – R 5. 0 Page 112© AIRBUS S. All rights reserved. Confidential and proprietary document. Key Contributing Parties — monitoring and control • How to meet this requirement? Maintain an internal documented standard for monitoring and control Key Contributing Parties Define dedicated organisation AND activities for Key Contributing Parties management Substantiate worksharing based upon a make-or-buy policy and PBS, WBS with sub-contracted parts/activities. Select Key Contributing Parties based on defined criteria and assessment Contract as soon as possible even in RFP phase Involve Key Contributing Parties in all programme phases (even in RFP phase) Define clear specifications of the outsourced work, including Airbus requirements – (GRESS, ABDxx, DOxx, qualification, certification doc. ) – Cascade and explain appropriate requirements to key contributing parties Embed PBS, WBS, RBS, Schedule, Risk, V&V plan… from KCP into the same documents of the Prime contractor
Procurement Quality & Supply Chain PQDR — User Guide – R 5. 0 Page 113© AIRBUS S. All rights reserved. Confidential and proprietary document. Key Contributing Parties — Selection • Why this requirement? • To select appropriate KCP able to apply GRESS requirements • How to meet this requirement? • Apply the internal documented standard for KCP selection describing: • Make or Buy policy • Selection criteria • Measurement and Assessment at KCP, reports on time and quality delivery • Decision gates, Contractualisation mode (Mo. U, Contract…) Selection criteria example
Procurement Quality & Supply Chain PQDR — User Guide – R 5. 0 Procurement Directorate Supplier Cascades Requirements to Key Contributing Parties
Procurement Quality & Supply Chain PQDR — User Guide – R 5. 0 Page 115© AIRBUS S. All rights reserved. Confidential and proprietary document. Cascading GRESS applied to 1 st tier Supplier 1 st tier cascades requirements to Key Contributing Parties The Supplier is responsible for applying & monitoring GRESS at Key Contributing Parties [ GRESS terminology: Key Contributing Parties are parties that have a significant role in the programme such as worksharing partners, other business units of the Supplier, Partners, sub-contractors, sub-suppliers ]
Procurement Quality & Supply Chain PQDR — User Guide – R 5. 0 Page 116© AIRBUS S. All rights reserved. Confidential and proprietary document. Supplier cascades requirements to KCP • How to meet this requirement? Cascade The prime-contractor sends its specification to KCPs and obtains in return the coverage by KCPs Assess GRESS application to sub-tiers Apply CAM and cross reference matrix to KCPs Obtain OBS, PBS, WBS, RAR, Risk register… from KCPs Define metrics and objective (KPIs) (delivery, quality, weight, …) Perform progress status at KCPs level on regular basis Perform assessments at KCPs (e. g PMCA, IPCA…. ) Measure delivery and quality from sub-tiers substantiated by reports Apply progress status report to your KCP Key contributing parties visibility Use logbook and Status Report (Tools) to assess progress status of KCP parts to give Airbus visibility Involve KCP in Supplier’s or/and Airbus review (e. g. pre-PDR and PDR)
Procurement Quality & Supply Chain PQDR — User Guide – R 5. 0 Procurement Directorate Supplier Programme/Project Status Report
Procurement Quality & Supply Chain PQDR — User Guide – R 5. 0 Page 118© AIRBUS S. All rights reserved. Confidential and proprietary document. Supplier Programme/Project Status Report • For reviews between contractual Milestones Reviews Supplier and their KCP use available Status Report Templates (Monthly report for example) E&S S tatus Re port Ae rostructure S tatus Re port
Procurement Quality & Supply Chain PQDR — User Guide – R 5. 0 Page 119© AIRBUS S. All rights reserved. Confidential and proprietary document. General manager shall endorse status report • Why this requirement? To ensure upper management at Supplier is aware about the programme progress/achievements/difficulties To be able to mobilise additional resources and means if required
Procurement Quality & Supply Chain PQDR — User Guide – R 5. 0 Procurement Directorate Maturity Management Process
Procurement Quality & Supply Chain PQDR — User Guide – R 5. 0 Page 121© AIRBUS S. All rights reserved. Confidential and proprietary document. • Why this requirement? To ensure the global satisfaction of Airlines & Military Customers on the Aircraft operational performances (operational and mission reliability, operational costs. . . ) at EIS. To reach Operational Reliability requirements (e. g A 350 XWB objective: > 99. 5% at EIS) To ensure series ramp-up on the right configuration To put in place all means, methods and resources in order to gain maturity To demonstrate the trend of maturity all along the product lifecycle. Management process for maturity
Procurement Quality & Supply Chain PQDR — User Guide – R 5. 0 Page 122© AIRBUS S. All rights reserved. Confidential and proprietary document. • How to meet this requirement? Maintain an internal documented standard for establishing and managing Maturity within the programme Define all factors involved in maturity such as: – New technologies (Technology Readiness Level (TRL) approach) (e. g CFPR, …) – Engineering for supportability (design the product for reliability, maintainability with low costs) – V&V activities and robustness testing – Risk management (including risks for maturity) – Lessons learnt capture and implementation in a continuous improvement – Failures & root cause analysis on heritage – Alternate solutions – Prepare Supply chain and Support to be ready for series ramp up at EISManagement process for maturity
Procurement Quality & Supply Chain PQDR — User Guide – R 5. 0 Page 123© AIRBUS S. All rights reserved. Confidential and proprietary document. Programme management process for maturity • How to meet this requirement? Focus on lessons learnt analysis on similar products to: – Identify weaknesses related to component, design, processes and test efficiency – Identify root causes, put in place appropriate improvement actions Note : GRESS Only — For A 350 XWB DTFOR Form can be used for any product that benefits from heritage Define and implement a robustness test plan covering functional and environmental tests Monitor maturity – Include maturity status based on maturity KPIs and improvement actions completion in Supplier programme Status Report – Review maturity themes at each milestone – Define maturity Key Performance Indicators (KPIs)
Procurement Quality & Supply Chain PQDR — User Guide – R 5. 0 Page 124© AIRBUS S. All rights reserved. Confidential and proprietary document. Key Performance Indicators (1) What is a KPI: … Measurement of product(s) key characteristics e. g. : Weight, Power consumption, Supply Shain readiness, Training capacities, response time of the Hot line What can be understood in a KPI: . . . Current technical performance and completion trend KPI Measure EIS Time programme start Margin Root Cause Analysis and Action plan TREND Today Requirement Target level. Example of KPI’s
Procurement Quality & Supply Chain PQDR — User Guide – R 5. 0 Page 125© AIRBUS S. All rights reserved. Confidential and proprietary document. Key Performance Indicators (2) Caution: . . don‘t over-interpret the figures. . understand what is behind the figures Root causes analysis. Where to define a KPI: . . Supplier Development Plan … Shared KPIs with the Purchaser What is the purpose of a KPI: . . essential part to support the process for maturity … Maintain the completion trend all along the programme When to deliver a KPI: . . Supplier programme Status Report. . Review Milestones
Procurement Quality & Supply Chain PQDR — User Guide – R 5. 0 Page 126© AIRBUS S. All rights reserved. Confidential and proprietary document. Management process for maturity • This table (GRESS module 1, § 1. 4. 3) represents themes that have to be closely monitored (but not limited to) to reach maturity target. These themes are parts of GRESS requirements (including ABD 0100) When. Critical themes to reach maturity targets
Procurement Quality & Supply Chain PQDR — User Guide – R 5. 0 Page 127© AIRBUS S. All rights reserved. Confidential and proprietary document. Management process for maturity – theme and associated KPI example • Design > BITE development Is the BITE integration team satisfied with the BITE status? Is the BITE action plan established and followed? Is it in line with the BITE integration team plan? KPI Current status Estimated completion date Final target Reference document Design > BITE development % function available 60% 24/10/2007 100% at Power On ABD 0100 § 1.
Procurement Quality & Supply Chain PQDR — User Guide – R 5. 0 Procurement Directorate Obsolescence Management
Procurement Quality & Supply Chain PQDR — User Guide – R 5. 0 Page 129© AIRBUS S. All rights reserved. Confidential and proprietary document. • Definitions: Obsolete (source: ABD 0100 1. 14) – A product is considered obsolete when it is no longer manufactured or available for purchasing on the market. – Obsolescence (source: ABD 0100 1. 14) – It is the process by which a product becomes obsolete. What could be obsolete? — Component — Process — Tool — Substances (Banned or highly restricted) — Material — Providers. Obsolescence
Procurement Quality & Supply Chain PQDR — User Guide – R 5. 0 Page 130© AIRBUS S. All rights reserved. Confidential and proprietary document. • Why this requirement? Many events can lead to obsolescence : – Market evolution (insufficient demand to continue fabrication) – Component declining or phasing out (the market leaders have short life products) – Increasing of technologies complexity, leading also to CAD, test, … means and resources obsolescence – Worldwide Environmental Health and Safety regulations (removal of hazardous substances) – Restructuring programme of suppliers (bankruptcy, alliances , acquisitions, relocation speed-up with rationalisation demand) may lead to make a component/material/process no longer available –. . . If an obsolescence issue is not early detected: – Risks of missing parts are high – Rost engaged to implement a solution may be huge Obsolescence
Procurement Quality & Supply Chain PQDR — User Guide – R 5. 0 Page 131© AIRBUS S. All rights reserved. Confidential and proprietary document. • How to meet this requirement? Each supplier shall define its obsolescence management process during design and series production Ensure an early detection of obsolescence by a regular survey (e. g information service provider, …) Address forecast and declared obsolescence for all components, tools or processes during design and service life Establish an obsolescence cartography giving a global visibility for the complete equipment (Update it minimum once a year) It must lead to the creation of a cross functional team and an obsolescence management plan (WBS, Schedule, procurement rules to avoid procurement via brokers, proportion of stock, stock area localisation and specificities, redesign, validation tests, specific incoming inspection specially to avoid any counterfeit or bad quality part , transition plan to operating service, …. )Obsolescence
Procurement Quality & Supply Chain PQDR — User Guide – R 5. 0 Page 132© AIRBUS S. All rights reserved. Confidential and proprietary document. • How to meet this requirement (cont’)? Obsolescence cartography shall be: – provided and reviewed with Airbus at the Critical Design Review – updated at least for each review/assessment and at least once a year All obsolescence (including dispositions taken by the supplier) must be notified to Airbus: – For a Component obsolescence through an EDES (Engineering Design Evolution Sheet) and/or in the Supplier Programme Status Report (in development) – For Substance obsolescence through an IED form (Item Environmental Data) from Appendix A of AP 1003 – …Obsolescence
Procurement Quality & Supply Chain PQDR — User Guide – R 5. 0 Page 133© AIRBUS S. All rights reserved. Confidential and proprietary document. Obsolescence Life cycle of components
Procurement Quality & Supply Chain PQDR — User Guide – R 5. 0 Page 134© AIRBUS S. All rights reserved. Confidential and proprietary document. Change. Actions/ criticality. Comments 217589221 Memory. AM 45256 CFT 200215/12/20021324824552 Stock up to new product design Major 4 years 245895612 Amplifier. DIC 3456 CC 200515/12/2005 x 2 x Equivalent Cpnt with PCB change Minor 1 year No Product Designation: ………… Part Num ber: ……………… Nb of aircraft that can be manufactured with stock Proposed solution Time needed for changes or redesign implemen COMPONENT INFORMATIONPRODUCT INFORMATIONOBSOLESCENCE SOLVING OPTIONS Code. Date of LBO Stock available for Airbus new product Component Quantity per Product Compone nt family Component reference Foreseen availability (year)Obsolescence cartography example
Procurement Quality & Supply Chain PQDR — User Guide – R 5. 0 Procurement Directorate Project/Programme Monitoring and Control
Procurement Quality & Supply Chain PQDR — User Guide – R 5. 0 Page 136© AIRBUS S. All rights reserved. Confidential and proprietary document. • Why this requirement? To avoid any schedule slippage, cost or quality level deviation compared to the development plan. Project/Programme monitoring and control To give visibility on current situation and associated actions launched To be confident on trend to completion To be able to anticipate and solve any problem all along the product development Define and agree on actions to be put in place in case of deviations In case of unrecoverable deviations, proposing change and agree a new baseline with all relevant actors
Procurement Quality & Supply Chain PQDR — User Guide – R 5. 0 Page 137© AIRBUS S. All rights reserved. Confidential and proprietary document. Monitoring & control Goals: Monitor progress Monitor risk Warn Define action items. Airbus & Supplier share the project progress against baseline Airbus & Supplier check the completion status Goals: Validate completion of expected activities Review and agree on evidence Have a clear status (milestone status recorded in the logbook)Monitoring Control Progress meetings/Reports Continuously Milestones Quality Gates
Procurement Quality & Supply Chain PQDR — User Guide – R 5. 0 Page 138© AIRBUS S. All rights reserved. Confidential and proprietary document. Project/Programme monitoring and control • How to meet this requirement? Maintain an internal documented standard for establishing and managing Monitoring and Control process of the programme covering: end products and enabling products Monitoring – Implement KPIs, capture, analyse and report programme performance usually compared to the baseline – Ensure action plans follow up – Issue on-time full and consistent Supplier programme status report Control – Compare actual performance with current baseline ( Decision Gates) – Predict the performance of the programme at completion, – Analyse the gaps – And, if necessary, evaluate possible alternatives: take appropriate corrective actions or changing the baseline. – Organise and perform milestones to: • Ensure deliverables (data and/or product) are compliant to requirements • Authorise progression to the next programme phase
Procurement Quality & Supply Chain PQDR — User Guide – R 5. 0 Page 139© AIRBUS S. All rights reserved. Confidential and proprietary document. • Why this requirement? To avoid any schedule slippage, cost or quality level deviation compared to the Development Plan • How to meet this requirement? Plan all milestones, reviews and assessments according to contract, GRESS reviews and assessments requirements and deliverables for each milestones, Milestone Compliance with Purchaser Schedule Supplier Schedule Development Plan. Contractual Milestones, Assessments. Contract GRESS Requirements Dates
Procurement Quality & Supply Chain PQDR — User Guide – R 5. 0 Page 140© AIRBUS S. All rights reserved. Confidential and proprietary document. Project/Programme monitoring and control • Programme Milestones Reviews are defined in the specifications and Schedule is contractually agreed The CAM provides complete list of deliverables and activities required for each Milestone at Supplier The logbook provides target, timetable, content of each review to hold the review thoroughly • The Purchaser: Select the location of reviews Manage the Reviews • The Supplier : Perform the reviews Plans internal pre-review Organises reviews Sends deliverables 3 weeks before review Invites representatives, incl. KCPs Deliverables & activities Reviews. The CAM GRESS CAM
Procurement Quality & Supply Chain PQDR — User Guide – R 5. 0 Page 141© AIRBUS S. All rights reserved. Confidential and proprietary document. KPI & Supplier Project/Programme Status Report • Other reviews Supplier shall attend to meetings upon Airbus request • Programme Progress Reporting Metrics Periodically assess programme performance through Key Performance Indicators (KPI) In addition of product oriented KPIs, Project management oriented KPIs oriented are mandatory — Schedule : % of completion inc. re-assessment of remaining work VS % time completion — Closing speed of opened actions / open points — Requirement covered by design — Test completion status — Resource assessment, Manufacturing, Supply Chain completion trend — … * Awareness sessions available
Procurement Quality & Supply Chain PQDR — User Guide – R 5. 0 Page 142© AIRBUS S. All rights reserved. Confidential and proprietary document. KPIs & Programme Progress Reporting Metrics example KPI KPI Programme Progress Metric
Procurement Quality & Supply Chain PQDR — User Guide – R 5. 0 Procurement Directorate Information Management & EDI
Procurement Quality & Supply Chain PQDR — User Guide – R 5. 0 Page 144© AIRBUS S. All rights reserved. Confidential and proprietary document. Technical document in English • Why this requirement? Documents have to be shared between Airbus FR, UK, GE, SP, and Suppliers’ countries (Europe, USA, China, Japan, Russia…) Common standards, language and rules are mandatory to communicate Internally at Suppliers’ and between Supplier and Purchaser • How to meet this requirement? Deliver documents in English unless otherwise agreed English sentences have to be understandable by all readers wherever they are from Use Airbus glossary and acronyms list
Procurement Quality & Supply Chain PQDR — User Guide – R 5. 0 Page 145© AIRBUS S. All rights reserved. Confidential and proprietary document. Information management & EDI Communication is a two-way process to ensure understanding of content by the recipient Bigger WP may involve several KCPs with team members dispatched in several countries Paper/physical information support exchange not efficient Security policy must encompass the whole supply chain • Why this requirement? Communication is about telling the right people, the right thing, at the right time, in the right way.
Procurement Quality & Supply Chain PQDR — User Guide – R 5. 0 Page 146© AIRBUS S. All rights reserved. Confidential and proprietary document. Information management & EDI How to meet this requirement? Maintain a documented standard for establishing and managing Communication within the programme Define counterparts and communication between Airbus, Suppliers, and Sub-tiers Maintain a documented standard for establishing and managing Data and documentation Ensure that information system enables to coordinate and dispatch the information related to the programme Cascade communication plan to KCP Use Web-based shared exchange place with Airbus: e. Room SW Deliver digital models according to Purchaser Technical Specification requirements Apply methods of modelling in accordance with Airbus methods and procedures Set electronic data exchanges rules, Define access control policy compliant with Airbus information system interface When no specific format or structure is requested by the Purchaser, the Supplier can choose its own documentation structure. Comply with Airbus IT security procedures and specific military programme security procedures (if any)
Procurement Quality & Supply Chain PQDR — User Guide – R 5. 0 Page 147© AIRBUS S. All rights reserved. Confidential and proprietary document. P/P Manager. Information management & EDI • Contents of a communication plan should include, key messages, main channels for communicating, the frequency, tools and access control policy. Airbus OBS Task Leader … Design … Supplier OBS Buyer Design …Sales Sub-tier 1 OBS P/P Manager Design … …Sales. … Buyer • Communication between counterparts Frequency Tool Eroom Repository Access Project Progress Status Monthly Word, Excel, … Storage Folder xx DMU On demand Remote CAD Restricted Test data Halt, V&V Exchange Folder yy Supply Chain data Weekly Bengalore Gloucester ERP Folder zz Golighty Military certification Paper copy Restricted ed
Procurement Quality & Supply Chain PQDR — User Guide – R 5. 0 Page 148© AIRBUS S. All rights reserved. Confidential and proprietary document. Electronique data interchange for DMU • Models delivery — Example of possible architecture
Procurement Quality & Supply Chain PQDR — User Guide – R 5. 0 Procurement Directorate In-Service Follow-Up
Procurement Quality & Supply Chain PQDR — User Guide – R 5. 0 Page 150© AIRBUS S. All rights reserved. Confidential and proprietary document. • Why this requirement? Customer Support Activities might last several 10 th of years Project activities occur during Support : – Continuous Product Development – Post-Type Certification, re-Qualification – Change of Supplier, Transfer of work, Offshore – Series Production changes related to Direct Maintenance Cost – Obsolescence, Re-industrialisation – Change request impacts, SB management, Concessions requests – Root causes failure analysis reported in agreed template Some product performances for maturity can only be measured after many hours of flight and have to be measured in Support phase People, Sub-tiers can change, the reproducibility of the Support performance have to be ensured. In-Service-Follow-Up
Procurement Quality & Supply Chain PQDR — User Guide – R 5. 0 Page 151© AIRBUS S. All rights reserved. Confidential and proprietary document. In Service Follow Up • How to meet this requirement? Refer to the Development Plan updated all along project phases Define Support Organisation Airlines / Airbus / Supplier Appoint a Programme leader, allocate resources and means for managing, monitor and control in service follow up Monitor updating of data and documentation and their availability Ensure the appropriate hand over and knowledge transfer Include Data and Documentation Management Plan for handling Data Support Plan release of shared/loaned/borrowed infrastructure and equipments (Benches, Rigs, integration benches…)
Procurement Quality & Supply Chain PQDR — User Guide – R 5. 0 Page 152© AIRBUS S. All rights reserved. Confidential and proprietary document. • Why this requirement? To formally close the development phase – Show that the maturity expectations have been achieved and maintained – Define potential impact on following phases • How to meet this requirement? Participate in the Final Review (After EIS as contractually agreed) – Substantiate that all maturity requirements have been met. Especially Supply Chain, series production, Customer Support, DMC… – Release and return infrastructures no longer useful: Infrastructures from Airbus, Supplier, Sub-tiers as benches, rigs, environmental tests equipment, integration infrastructures… Key elements to be addressed during the Final Review: – Remind the assumptions made at the beginning of the development phase. Check the programme objectives fulfilment (quality, performance, cost, …). Verify that equipment manufacturing, supply chain, and supportability requirements have been met – Set specific actions, if needed (continuous programme development, …)GRESS Final Review (FR)
Procurement Quality & Supply Chain PQDR — User Guide – R 5. 0 Procurement Directorate Industrial Quality Dossier
Procurement Quality & Supply Chain PQDR — User Guide – R 5. 0 Page 154© AIRBUS S. All rights reserved. Confidential and proprietary document. Industrial Quality Dossier (IQD) • Why this requirement? To describe the Supplier’s organisation and processes in place to manage its Engineering for Manufacturing To provide evidences that all Engineering for Manufacturing requirements are fulfilled This IQD will be used by Airbus as the support document for examination of the Engineering for Manufacturing aspects during development milestones
Procurement Quality & Supply Chain PQDR — User Guide – R 5. 0 Page 155© AIRBUS S. All rights reserved. Confidential and proprietary document. Industrial Quality Dossier (IQD) • How to meet this requirement? Describe in the IQD evidence of specific dispositions dedicated to the product and based on method (procedure) and application, Answer in the IQD as a minimum to the deliverables (requirement with L ) identified in GRESS module 3, These deliverables shall be provided at the specified milestones and regularly updated as needed (changes, new milestones, …).
Procurement Quality & Supply Chain PQDR — User Guide – R 5. 0 Page 156© AIRBUS S. All rights reserved. Confidential and proprietary document. Industrial Quality Dossier (IQD) example (based on GRESS) IQD text Appendix 1: procedure Appendix 2: application (Industrial Risk Register)
Procurement Quality & Supply Chain PQDR — User Guide – R 5. 0 Procurement Directorate Organisation Specific to the Contract
Procurement Quality & Supply Chain PQDR — User Guide – R 5. 0 Page 158© AIRBUS S. All rights reserved. Confidential and proprietary document. Organisation Specific to the Contract • Why this requirement? Identification of key resources and management of responsibilities for Engineering for Manufacturing and for Supply Chain will enable early communication with Airbus and risk mitigation • How to meet this requirement? Provide a clear organisation chart describing people involved in Engineering for Manufacturing and Supply Chain activities (name, tasks & relationship)
Procurement Quality & Supply Chain PQDR — User Guide – R 5. 0 Page 159© AIRBUS S. All rights reserved. Confidential and proprietary document. Example: Organisation specific to the contract. X X X E n g i n e e r i n g f o r M a n u f a c t u r i n g m a n a g e r Y Y Y S u p p l y C h a i n m a n a g e r Z Z Z P r o d u c t i o n m a n a g e r R R R D e s i g n O f f i c e m a n a g e r W W W T e s t m a n a g e r. . . T T T P r o j e c t L e a d e r Product / Supplier couple. Similar or extract from the Organisation Breakdown Structure (AI-GRESS-L 10202 -A)
Procurement Quality & Supply Chain PQDR — User Guide – R 5. 0 Procurement Directorate Concurrent Engineering
Procurement Quality & Supply Chain PQDR — User Guide – R 5. 0 Page 161© AIRBUS S. All rights reserved. Confidential and proprietary document. Concurrent engineering • Why this requirement ? ID Task Name 1 o p p o rt unit y id ent ificat io n 2 p reliminary p ro d uc t d es ig n 3 p ro d uct d esig n 4 p ro cess d es ig n 5 launch s erial p ro d uct io n 0 6 /0 5 No v D ec Jan Feb Mar Ap r May Jun Jul A ug S ep O ct No v D ec Jan Feb Mar Ap r May Jun Jul A ug 2 0 0 3 2 0 0 4 2 0 0 5 ID Tas k Name 1 o p p o rt unit y id ent ificat io n 2 p reliminary p ro d uct d es ig n 3 p ro d uct d es ig n 4 p ro c ess d esig n 5 launch serial p ro d uc t io n 31 /1 2 No v D ec Jan Feb Mar A p r May Jun Jul Aug S ep O c t No v D ec Jan Feb Mar Ap r May Jun Jul Aug 2 0 0 3 2 0 0 4 2 0 0 5 • Classic engineering process (sequential flow) Long development times and poor quality when managers do not communicate between departments Development managers may design the product without talking with manufacturing, resulting in problems • Concurrent engineering process (tasks in parallel) By working concurrently, design and production issues are considered together. Development lead time is reduced Production concerns are addressed while the product is designed and can still be changed Product maturity at Entry Into Service is increased
Procurement Quality & Supply Chain PQDR — User Guide – R 5. 0 Page 162© AIRBUS S. All rights reserved. Confidential and proprietary document. Concurrent engineering • How to meet this requirement ? By demonstrating that Engineering, Manufacturing and Supply Chain departments are working together during development phase: – Create a“Cross-functional” team which will participate in the design reviews and involve key manufacturing people (at the supplier’s, sub-contractors, partners…) during the development phase – Establish and apply : • Design for Manufacturing, • Design for Test, • Design for Maintainability rules • Taguchi approach • … (by including in conception tools and working practices rules coming from lessons learnt, field returns experiences, plan of experiments, workers knowledge, . . . ) – Establish a check list of Engineering for Manufacturing items to be verified at each step of the development process in accordance to schedule milestone – Consider all units manufactured (mock-up, prototypes, lab units, …) to continuously improve concurrent engineering processes
Procurement Quality & Supply Chain PQDR — User Guide – R 5. 0 Page 163© AIRBUS S. All rights reserved. Confidential and proprietary document. Example: internal review check list • Check list for internal review xxx: Engineering for Manufacturing • Manufacturing process flow chart identified • Make or buy strategy defined • Capability / capacity study • Key characteristics identified • … • Testability • Test strategy defined • Test means identified • … • Maintainability • Repair tools and process identified • … • Multi-functional team involved: ……Manufacturing team leader …… ……Design manager ……Test responsible ……Manufacturing planner ……Reliability ……Quality engineer …M. XPurchasing Date. Name. Function Review Attendees … … …Programme manager
Procurement Quality & Supply Chain PQDR — User Guide – R 5. 0 Procurement Directorate Industrial Risk Analysis Method
Procurement Quality & Supply Chain PQDR — User Guide – R 5. 0 Page 165© AIRBUS S. All rights reserved. Confidential and proprietary document. Industrial Risk analysis method • Why this requirement? A consistent and formalised method is essential to guarantee risk analysis efficiency, reliability, exhaustiveness and reproducibility Risk analysis enables an early detection of weak points and implementation of preventive actions instead of failure correction
Procurement Quality & Supply Chain PQDR — User Guide – R 5. 0 Page 166© AIRBUS S. All rights reserved. Confidential and proprietary document. Industrial Risk analysis method • How to meet this requirement? Have a risk analysis which covers product (with respect to Engineering for Manufacturing), process and sub-process, procurement and suppliers risks Formalise : – How risks (or failure modes) are identified (check lists, lessons learnt, brainstorming done by a multi-functional team, …) – How causes are identified – How risk levels are quantified (severity, detectability, occurrence) – When mitigation actions are launched (maximum risk level allowed, top 20 risks, …) – How risk mitigation actions are followed – How risk analysis is kept up to date – How effectiveness and risk status are monitored
Procurement Quality & Supply Chain PQDR — User Guide – R 5. 0 Page 167© AIRBUS S. All rights reserved. Confidential and proprietary document. Example : Risk analysis worksheet based on FMEA Product Prepared By Risk analy s is leader Date (Original) Risk analy s is team (Rev ised) Page Item / Function Risks or Potential Failure Mode(s) Effect(s) of Failure Severity Cause(s) Occurrence Detection Detectability Criticality or RPN Mitigation action(s) Responsibility & Due Date Status New Sev New Occ New Det New Criticality or New RPNRisk analysis method should explain how to fill this worksheet Note 1 : Criticality or RPN (Risk Priority Number) = Severity x Occurrence x Detectability Note 2 : For more information on FMEA method you can refer to AS/EN 9134 Very small effect: 1 or 2 Minor effect: 3 or 4 Probable failure: 5 or 6 Failure: 7 or 8 Security effect: 9 or 10 Rare: 1 or 2 Low: 3 or 4 Moderated: 5 or 6 Frequent, High: 7 or 8 Systematic: 9 or 10 Before assembly: 1 or 2 During testing: 3 or 4 During shipment: 5 or 6 Possibly by the Customer: 7 or 8 Systematically by the Customer: 9 or
Procurement Quality & Supply Chain PQDR — User Guide – R 5. 0 Procurement Directorate IRR: Industrial Risk Register
Procurement Quality & Supply Chain PQDR — User Guide – R 5. 0 Page 169© AIRBUS S. All rights reserved. Confidential and proprietary document. IRR : Industrial Risk Register • Why this requirement? To identify all industrial risks, associated risk reduction actions and enable to follow up these actions To provide information to all stakeholders (management, project leader, Airbus, …) of major risks • How to meet this requirement? Fully deploy industrial risks analysis method by filling risks analysis worksheets: – Describe the Cross Function Teams (functions, experts…) involved – Collect and analyse all industrial risks (product, process and sub-process, procurement and supplier) – Quantify risk level, before and after risk reduction action – Describe risk reduction actions (action, owner, due date and status)
Procurement Quality & Supply Chain PQDR — User Guide – R 5. 0 Page 170© AIRBUS S. All rights reserved. Confidential and proprietary document. IRR: Process risk analysis example
Procurement Quality & Supply Chain PQDR — User Guide – R 5. 0 Page 171© AIRBUS S. All rights reserved. Confidential and proprietary document. IRR: Product risk analysis example
Procurement Quality & Supply Chain PQDR — User Guide – R 5. 0 Page 172© AIRBUS S. All rights reserved. Confidential and proprietary document. IRR: Procurement and Supplier risk analysis example Obsoles cence Sole/Single source Unique Technology or complex component Long lead time Availibility of raw materials Supplier status Risk W eight 2 1 2 3 2 2 U 22279 H (c) H (b) L L L H (a) 22 — (a) run an industral audit — (b) research an alternate source — (c) redesign the product M. X 01/09/2008 M. Y 01/12/2008 M. Z 01/12/2009 OPEN 12 … … U 45688 … … …Supplier Y Status New Criticality or New RPNMitigation action(s) Supplier X Bill of material Criticality or RPN Responsibility & Due Date. Risks or Potential Failure Mode(s) Scoring 20 or greater requires mitigation action(s)L=Low risk (1 point) M=Medium risk (2 points) H=High risk (3 points) New criticality all risks are low (L) and the result is
Procurement Quality & Supply Chain PQDR — User Guide – R 5. 0 Procurement Directorate Production of the Products by a Series Production Process
Procurement Quality & Supply Chain PQDR — User Guide – R 5. 0 Page 174© AIRBUS S. All rights reserved. Confidential and proprietary document. • Why this requirement? If product for qualification (and all subsequent products) is not produced by serial processes and means, the product qualification may not be representative of the final product, It will prevent many potential problems and ensure product maturity at the Entry Into Service (EIS), Validate the process / series production in relation with the definition dossier. Production of the products by a series production process
Procurement Quality & Supply Chain PQDR — User Guide – R 5. 0 Page 175© AIRBUS S. All rights reserved. Confidential and proprietary document. Production of the products by a series production process • How to meet this requirement? Use series production processes and means to produce the products for qualification and all subsequent products, Record and justify any deviation (associated risks must be identified and mitigated), Identify and schedule all needed dispositions to implement series production processes in accordance with the overall supplier development schedule, Demonstrate that a formal method (e. g. First Article Inspection) has been applied at: – End item level, – Each major sub assembly level.
Procurement Quality & Supply Chain PQDR — User Guide – R 5. 0 Page 176© AIRBUS S. All rights reserved. Confidential and proprietary document. Series production deviation & schedule : Example Items, Means Identified deviation Justification Risk Action Date Product for qualification Serial product Front face board Flying probe tester In circuit test (available 3 months after the serial target product qualification) Definition must be finalized to engage the manufacturing of the test means (soft and tools) Lower coverage rate (components not tested by Flying probe tester) Untested components identified and tested by functional complementary tests 20/02/2006 … … ….
Procurement Quality & Supply Chain PQDR — User Guide – R 5. 0 Procurement Directorate Industrial Breakdown
Procurement Quality & Supply Chain PQDR — User Guide – R 5. 0 Page 178© AIRBUS S. All rights reserved. Confidential and proprietary document. Industrial breakdown • Why this requirement? To know the main industrial parties involved in the Product production process Because each party has a potential effect on the final product • How to meet this requirement? Describe the industrial breakdown: major suppliers, subcontractors and collaborating firms with associated responsibilities
Procurement Quality & Supply Chain PQDR — User Guide – R 5. 0 Page 179© AIRBUS S. All rights reserved. Confidential and proprietary document. Industrial breakdown example Supplier: Raw materials Sub-contractor: Part Z Manufacturing Site 1: Final Assembly & test, shipping. Site 2: Part X Manufacturing Aircraft FAL Supplier: Detailed parts Partner: Test development. Sub-contractor: Part Y Manufacturing. Tier 1 Tier 2 Tier 3 Supplier
Procurement Quality & Supply Chain PQDR — User Guide – R 5. 0 Procurement Directorate Traceability
Procurement Quality & Supply Chain PQDR — User Guide – R 5. 0 Page 181© AIRBUS S. All rights reserved. Confidential and proprietary document. Traceability • Why this requirement? If any problem is detected on the Product, in order to identify the root cause and find a solution, we need to know precisely: – what are the components/parts/suppliers involved – what and when are the processes/sub-processes used to build the Product – what are the skills of operators involved If the root cause is linked to the part batch, process step, supplier delivery, or operator training, we need to know precisely what are the other Products impacted Traceability is mandatory to provide these data enabling problem solving
Procurement Quality & Supply Chain PQDR — User Guide – R 5. 0 Page 182© AIRBUS S. All rights reserved. Confidential and proprietary document. Traceability • How to meet this requirement? Define the level of component/parts traceability regarding the associated risk, Trace: – Component/parts S/N or batch number used – Means used (Tools, “production” software release, …) – Suppliers – Operators / Operations (with identification and date) – Incidents occurring in production (manufacturing, test, …) – Deviations and non-conformities of each product to the Manufacturing and Inspection Dossier – Process and means evolutions (settings or adjustment change, reason for these changes, process parameters values, …) – Evolutions of the Manufacturing and Inspection Dossier Keep traceability information accurate, legible, adequately detailed and archived, Ensure that traceability covers the whole production process.
Procurement Quality & Supply Chain PQDR — User Guide – R 5. 0 Page 183© AIRBUS S. All rights reserved. Confidential and proprietary document. Example Company name: X Project: A 380 Product x Code : 1684654 MO 18596 Serial Number : 234 Issue 1 Part Code number Serial or batch number Part 2 4984654 524 Part 1 4985463 … Raw material 0015632 … Operation OP Date Visa Inspection raw material 020 25/06/2004 M. Z Cutting out 035 … Solder 040 … Solder inspection 045 … Drill 060 … Part 2 inspection 080 … Assembly 100 … Test 105 … Packaging / Shipment 120 …
Procurement Quality & Supply Chain PQDR — User Guide – R 5. 0 Procurement Directorate Manufacturing and Inspection Dossier
Procurement Quality & Supply Chain PQDR — User Guide – R 5. 0 Page 185© AIRBUS S. All rights reserved. Confidential and proprietary document. • Definitions (from Airbus Procedure 2080) – Manufacturing Dossier: Set of Data/Documents which allows, with reference to the Definition Dossier, the purchase, production, assembly and testing of an aircraft, or a product. – Inspection Dossier: Set of Data/Documents or a list of actions which allows, with reference to the Design Requirements and Definition Dossier, the verification of conformity of an aircraft or a product with its definition. Manufacturing and Inspection Dossier
Procurement Quality & Supply Chain PQDR — User Guide – R 5. 0 Page 186© AIRBUS S. All rights reserved. Confidential and proprietary document. Manufacturing and Inspection Dossier • Why this requirement? Manufacturing and Inspection Dossier contribute to production process control (manufacturing repeatability and risk reduction) and conformity of the Product with its definition. It allows : – Traceability and record of manufacturing controls – Better operator understanding – …
Procurement Quality & Supply Chain PQDR — User Guide – R 5. 0 Page 187© AIRBUS S. All rights reserved. Confidential and proprietary document. Manufacturing and Inspection Dossier • How to meet this requirement? Have a complete and detailed Manufacturing and Inspection Dossier Ensure consistency between Definition Dossier, Manufacturing and Inspection Dossier and the Product Formalise and/or improve the configuration management process
Procurement Quality & Supply Chain PQDR — User Guide – R 5. 0 Page 188© AIRBUS S. All rights reserved. Confidential and proprietary document. Example of Manufacturing and Inspection Dossier content Production Bill of Material (BOM)Drawings Routings Traveller sheets Detailed manufacturing instruction sheets Manufacturing and test procedures Special instructions (manufacture, installation, storage, handling…) Acceptance test and Delivery procedures Record of traceability during manufacturing & testing. Manufacturing and test tools (including software)Manufacturing order Manufacturing process Flow chart Manufacturing & Inspection Dossier
Procurement Quality & Supply Chain PQDR — User Guide – R 5. 0 Procurement Directorate Industrial Process Flow Charts “Manufacturing” & “Supply Chain”
Procurement Quality & Supply Chain PQDR — User Guide – R 5. 0 Page 190© AIRBUS S. All rights reserved. Confidential and proprietary document. Industrial process flow charts “Manufacturing” & “Supply Chain” • Why this requirement? To have a mapping of the process in order to understand, secure and improve it To get a visibility on the process related to the Product Note : Flow charts are a useful input to perform process, sub-process and procurement risk analysis
Procurement Quality & Supply Chain PQDR — User Guide – R 5. 0 Page 191© AIRBUS S. All rights reserved. Confidential and proprietary document. Industrial process flow charts “Manufacturing” & “Supply Chain” • How to meet this requirement? Set up a process analysis to build the industrial process flow chart (Manufacturing and Supply Chain) Ensure that industrial process flow chart is specific to the Product and cover the whole production process (internal and external) from incoming to the delivery of the Product Check if all information defined by following slides are included into the industrial process flow chart Note : — One Flow Chart is acceptable but usually two Flow Charts are provided, one for Manufacturing and a second one for Supply Chain, — The flow chart must be representative of the current process and configuration managed (reference, issue , . . )
Procurement Quality & Supply Chain PQDR — User Guide – R 5. 0 Page 192© AIRBUS S. All rights reserved. Confidential and proprietary document. Industrial process flow chart “Manufacturing” Main information needed: – main manufacturing, inspection and test phases of subassemblies and product – procurement (related to Key contributing parties), – identification of internal and external (sub-contracted ) activities (including reference of the related flow charts), – processes requiring qualified operator, – which and where Key characteristics are monitored, – which and where quality metrics are recorded, – configuration management (reference, issue, …), – …
Procurement Quality & Supply Chain PQDR — User Guide – R 5. 0 Page 193© AIRBUS S. All rights reserved. Confidential and proprietary document. Industrial process flow chart “Manufacturing” example R. A. : Risk Analysis (Sub Process ) SOP: Standard Operating procedure OMS: Operational Method sheet FT Functional Test Inspection Bottleneck. Quality Metrics: KC 2 FTCutting out (Mean X) SOP 1/OMS 2 R. A. dossier 85 Solder (Mean Y) KC 1 M 3 Drill (Mean Z) R. A. dossier 112 SOP 2/OMS 2 assembly Packaging / Shipment R. A. dossier 142 Cleaning. M 1 M 2 Sub assembly (Supplier 1) (flow chart ref: xxxx) M 1 Sub-contractor S 1 (flow chart ref: yyyyy) Soldering Process Ref. : zzzzzz is p. Raw material/ component External activity (Key contributing parties)Process under Qualified operator. Legend : Suppliers Rejection Rate(%) KC 1(ionic contamination) time 100 % FPY 90% 60% 30% TARGETFirst Pass Yield KC 2(power consumption) M 1 KC 2 M 2 Flow Chart : Metrics :
Procurement Quality & Supply Chain PQDR — User Guide – R 5. 0 Page 194© AIRBUS S. All rights reserved. Confidential and proprietary document. Industrial process flow chart “Supply Chain” The industrial process flow chart “Supply Chain” is a graphic description of: – Information flow (information system, procurement plan, …) – Physical flow Main information needed: – Key Contributing parties – Customer Demand (quantity per week or month and lot size) – For every process step: production rate, On Time Delivery (OTD), lot size and lead time – Inventory between process steps (number of days=quantity/downstream usage) – For every process step: number of resources, available time, utilisation and efficiency – Bottleneck identification – Configuration management (Reference, issue, . . ) Note : Dynamic data (OTD. . . ) can be provided as annex to the flow chart.
Procurement Quality & Supply Chain PQDR — User Guide – R 5. 0 Page 195© AIRBUS S. All rights reserved. Confidential and proprietary document. Industrial process flow chart “Supply Chain” example Customer demand Customer 18400 pces/month • • M. R. P Supplier • • Inspection Assembly 1 Shipment Batch 920 pcs. Procurement Plan & P. O 4 2 2 1 1 Physical Flow Information Flow Stock Resources Bottleneck. Utilisation= 90%Efficiency= 120%Available Time 27, 600 sec Lot Size= 460 Cycle Time= 62 s Sub assembly Utilisation= 100% Efficiency= 120%Available Time 27, 600 sec Lot Size =460 Cycle Time= 40 s Utilisation= 100%Efficiency= 75%Available Time 27, 600 sec Lot Size=230 Cycle Time= 62 s Utilisation= 95%Efficiency= 105%Available Time 27, 600 sec Lot Size= 115 Cycle Time= 40 s Utilisation= 100%Efficiency= 92%Available Time 27, 600 sec Lot Size = 100 Cycle Time= 40 s Test. Assembly 2 Sub assembly 3 (flow chart ref: yyyyy) 2 5 days 1800 (4 d) 2000 (3 d) 450 (1 d) 1400 (2 d) 2000 (3 d) 7 d 2 d 3 d 2 d 4 d 5 d Lead Time. Weekly schedule O. T. D Rejection rate. Transport duration = 2 days Transport duration = 8 days External activity (Key contributing parties)
Procurement Quality & Supply Chain PQDR — User Guide – R 5. 0 Procurement Directorate Quality and Supply Chain Metrics
Procurement Quality & Supply Chain PQDR — User Guide – R 5. 0 Page 197© AIRBUS S. All rights reserved. Confidential and proprietary document. • Why this requirement? No improvement without measure To ensure that customer expectations are met To monitor process variability, and enable an early detection of process deviation and trends To be able to undertake corrective and preventive actions. Quality and Supply Chain metrics
Procurement Quality & Supply Chain PQDR — User Guide – R 5. 0 Page 198© AIRBUS S. All rights reserved. Confidential and proprietary document. Quality and Supply Chain metrics • How to meet this requirement? Define relevant metrics at process steps where process variations can be detected (Key Points) Have metrics relevant/representative for Airbus product and use them to set up real actions Set metric objectives in compliance with overall delivery and quality performance goals. Objective should be SMART : – S pecific – M easurable – A chievable – R ealistic – with T imescale Assure continuous follow-up of metrics and set up recovery actions (e. g. root causes analysis, corrective action…) when objectives are not reached Note : all metrics must be visible in the “industrial process flow charts»
Procurement Quality & Supply Chain PQDR — User Guide – R 5. 0 Page 199© AIRBUS S. All rights reserved. Confidential and proprietary document. Quality metrics examples: Some definitions • Scraps (%) : % of material outside of specifications and processing characteristics that make rework impractical • Reworks (%) : % of material reprocessed to salvage a defective item or part • First Pass Yield (FPY) (%) : number of good units produced divided by the number of total units going into the process • Defects per Millions (DPMO): ( 10 6 x total number of defects made)/ (number of units processed x number of defects opportunities per unit) • Rejection rate (Airbus definition) ( PPM ) : ( 10 6 x Number of non conforming parts under Supplier responsibility rejected in the period) / Total number of new parts delivered by the Supplier during the same period.
Procurement Quality & Supply Chain PQDR — User Guide – R 5. 0 Page 200© AIRBUS S. All rights reserved. Confidential and proprietary document. Supply Chain metrics examples: Some definitions • Customer demand : An order from a customer for a particular product or a number of products (e. g. quantity per week on month and lot size) • Inventory level : Those stocks or items used to support production, supporting activities and customer service between process steps (e. g. number of days= quantity/ downstream usage) • Production rate : The rate of production usually expressed in units, cases, or some other broad measure, expressed by a period of time (e. g. per hour, shift, day or week) • Lot Size : The amount of a particular item that is ordered from the plant or a supplier or issued as a standard quantity to the production process • Lead-Time : A span of time required to perform a process or series of operations • Utilisation (%) : a measure of how intensively a resource is being used to produce a good service • Efficiency (%) : a measurement of how well something is performing relative to existing standards. It’s the ratio of actual units produced to the standard rate of production expected in a time period Note: more definitions in APICS ( The Association for Operations Management) Dictionary • On Time Delivery (Airbus definition) (%): number of scheduled lines completely received with requested documentation in the period [7 working days before and up to the contractual day] / Total number of planned schedule lines during the same period.
Procurement Quality & Supply Chain PQDR — User Guide – R 5. 0 Procurement Directorate Product, Process and Sub-process Major/ Key Characteristics
Procurement Quality & Supply Chain PQDR — User Guide – R 5. 0 Page 202© AIRBUS S. All rights reserved. Confidential and proprietary document. Product, process and sub-process Major/ Key Characteristics • Key Characteristics definition (AS/EN 9103): The features of a material or part whose variation has a significant influence on product fit, performance, service life, or manufacturability Key Characteristics for a part, subassembly or system are those selected geometrical, material properties, functional and/or cosmetic features, which are measurable, whose variation control is necessary in meeting Customer requirements and enhancing Customer satisfaction Key Characteristics for a Process are those selected Measurable Parameters of a process whose control is essential to manage Variation of part or system KCs. • Why this requirement? To prevent process quality deviation by pro-active actions To ensure that critical customer requirements will be fulfilled To enable continuous improvement To reach total quality with minimal controls and enabling cost reduction
Procurement Quality & Supply Chain PQDR — User Guide – R 5. 0 Page 203© AIRBUS S. All rights reserved. Confidential and proprietary document. Product, process and sub-process Major/ Key Characteristics • How to meet this requirement? Define the key characteristics according to risk analysis (e. g. FMEA), robustness tests, lessons learnt, design of experiments… Define appropriate Control Plan including for example Statistical Process Control (SPC), … Monitor the Major/ Key Characteristics parameters and interpret the variations Rectify the variation by a corrective and preventive action
Procurement Quality & Supply Chain PQDR — User Guide – R 5. 0 Page 204© AIRBUS S. All rights reserved. Confidential and proprietary document. Example of Key Characteristic determination Key Characteristics Description Process Ionic contamination Product Diameter A 1 dimension … …
Procurement Quality & Supply Chain PQDR — User Guide – R 5. 0 Page 205© AIRBUS S. All rights reserved. Confidential and proprietary document. Example of a Control Plan Part / Process No. Process Name / Operation Description Product/ Process / CNC — Progr. : characteristic’s f. inspection/ tolerance Evaluation, Measurement Tech. / device Sample, Size / Frequence 1 incoming inspectionscrew 1245 Draw ing no. Tref er to draw ingspecif ic toolsampling/ lot size 2 cleaning machinecleaning bath. Operation no. X / program no. X KC: ionic contamination. SPC run chartdaily 3 housing operationpart A 1 Operation no. Y / program no. Y KC: diameter A 1 dimension. SPC run chart 100% 4 f unctional test. End Item. Operation no. W / program no. W KC: pow er consumption. SPC run chart 100% CONTROL PLAN Control Pla n No. : Supplie r; Pla nt: Pa rt No. / la te s cha nge le ve l: Da te (Orig. ): Comme nts / Re ma rks Da te (Re v. ): Dra w ing no / cha nge le ve l. Qua lity Approva l Da te : Pa rt Na me / De scription: Engine e ring Approva l Da te : Note: There are other Variation Control methods such as Tooling, Control of Process Settings, Standard Processes, Mistake Proofing, …
Procurement Quality & Supply Chain PQDR — User Guide – R 5. 0 Page 206© AIRBUS S. All rights reserved. Confidential and proprietary document. Example of SPC monitoring Warning: Process deviation can be detected before being out of specification Alarm 10 11 128 97 Note : For low quantities SPC may be based on rolling months
Procurement Quality & Supply Chain PQDR — User Guide – R 5. 0 Page 207© AIRBUS S. All rights reserved. Confidential and proprietary document. Example of action plan related to a Key Characteristic deviation Key Characteristic (KC) identification Action plan KC position KC description Control card responsible (updating) Comments Or Measures Action Responsible Due date Cleaning operation Ionic contamination M. XX Change bath M. YY 20/01/2 004 Key Characteristic (KC) identification Action plan KC position KC description Control card responsible (updating) Comments Or Measures Action Responsible Due date Sub part Diameter A 1 dimension M. XXX To recalibrate the machine M. XXX 20/01/2004 analyse each alert and associate action plan
Procurement Quality & Supply Chain PQDR — User Guide – R 5. 0 Procurement Directorate Management of Competencies
Procurement Quality & Supply Chain PQDR — User Guide – R 5. 0 Page 209© AIRBUS S. All rights reserved. Confidential and proprietary document. • Why this requirement? Management of competencies lead to : – Skills shortage risks mitigation (including manufacturing ramp up anticipation) – Flexibility improvement (operator versatility between workstations) – Reduce waiting times. Management of competencies
Procurement Quality & Supply Chain PQDR — User Guide – R 5. 0 Page 210© AIRBUS S. All rights reserved. Confidential and proprietary document. Management of competencies • How to meet this requirement? List all process steps (to manufacture the product) requiring operator qualifications Define operator qualifications needed and identify critical skills Follow up operator qualifications (cross reference table of people and their qualification) Plan qualification training needed Support multi-skills people (self-inspection, inspection delegation, …)
Procurement Quality & Supply Chain PQDR — User Guide – R 5. 0 Page 211© AIRBUS S. All rights reserved. Confidential and proprietary document. 1212 Skill matrix example • Team/Area: • Team/Area Leader: • Date: • Skills/Tasks • Name • Dick • Developer • Coach • Skill Level Key • Un — Trained • Learner • Practitioner • Harry • Skills/Task • Score • Tom • • Drilling • • … • • Name • Score • … 11 24 3 12 14 24 10 24 8 12 8 5 12 4 12 7 12 35 72 • Team/Area: • Team/Area Leader: • Date: • Skills/Tasks • Name • Dick • Developer • Coach • Skill Level Key • Un — Trained • Learner • Practitioner • Harry • Skills/Task • Score • Tom • Cutting out • Drilling • … • • Testing • Name • Score • 11 24 3 12 14 24 10 24 8 12 8 5 4 12 7 12 35 72 Skill coverage of a process step O p e rato r q u alificatio n s
Procurement Quality & Supply Chain PQDR — User Guide – R 5. 0 Procurement Directorate Qualification and Maintenance of Manufacturing and Inspection Means
Procurement Quality & Supply Chain PQDR — User Guide – R 5. 0 Page 213© AIRBUS S. All rights reserved. Confidential and proprietary document. • Why this requirement? To guarantee repeatability of manufacturing and inspection processes, To avoid any manufacturing and inspection means breakdown, especially single means, To improve Overall Equipment Efficiency. • How to meet this requirement? Define manufacturing and inspection means qualification rules, Set up preventive and effective maintenance, using method such as Total Productive Maintenance, Update means status systematically. Qualification and maintenance of manufacturing and inspection means
Procurement Quality & Supply Chain PQDR — User Guide – R 5. 0 Procurement Directorate Industrial Change Management
Procurement Quality & Supply Chain PQDR — User Guide – R 5. 0 Page 215© AIRBUS S. All rights reserved. Confidential and proprietary document. • Why this requirement? This requirement is mandatory for Airbus in order to manage and maintain qualification status, product integrity, quality and supply chain control and is subject to audit by Authorities, Final customer shall not be impacted by harmful consequences of change (poor product quality or delivery performance), Supplier protect himself in case of claims in relation with product liability law. Industrial change management
Procurement Quality & Supply Chain PQDR — User Guide – R 5. 0 Page 216© AIRBUS S. All rights reserved. Confidential and proprietary document. Industrial change management • How to meet this requirement? Set up a project organisation to manage changes and mitigate associated risks, Prior to any major industrial change at suppliers — tier 2 (3, 4, . . if applicable) : • plant location or layout, • transportation mode, • major Enterprise Resources Planning (ERP) change, • top level organisation and personal at key position, • major process (including main tools) changes, • major suppliers (including subcontractors) change. inform Airbus : – Provide at least information requested in the Communication of Manufacturing Evolution Sheet template, – For equipment and system, any change impacting product (e. g. qualification) shall be notified using EDES form (see ABD 0100 part 2 chap 9) Minor changes in the process (reasons, description of change, results …) shall also be recorded, refer to traceability.
Procurement Quality & Supply Chain PQDR — User Guide – R 5. 0 Page 217© AIRBUS S. All rights reserved. Confidential and proprietary document. Communication of Manufacturing Evolution (CME) template Airbus people Suppliers. Template available on e-Site: GRESS
Procurement Quality & Supply Chain PQDR — User Guide – R 5. 0 Procurement Directorate ESS / Ageing / NDT
Procurement Quality & Supply Chain PQDR — User Guide – R 5. 0 Page 219© AIRBUS S. All rights reserved. Confidential and proprietary document. ESS / ageing / NDT (ESS: Environmental Stress Screening, NDT : Non Destructive Test) • Why this requirement? To precipitate and reveal all latent defects and/or early failures (to reduce customer returns during product first hours of use) To improve maturity of the product To detect product weaknesses (including component batch variability) Time F ailu re rate. Early failures Low constant failure rate = useful life End of life failures. Typical bathtub curve for electronics products: Note : ESS and ageing are only applicable for equipment containing EEE (Electrical, Electromechanical and Electronical) components
Procurement Quality & Supply Chain PQDR — User Guide – R 5. 0 Page 220© AIRBUS S. All rights reserved. Confidential and proprietary document. ESS / ageing / NDT • How to meet this requirement? Define and justify stress screening strategy and conditions (using robustness tests, lessons learnt, benchmarking, …) : – Stress screening at product item, sub-assembly and/or component level – Stress stimuli (temperature, cycling, vibrations, …) and levels – Product monitoring during stress screening Demonstrate that the stress screening will not affect product life duration Demonstrate and monitor stress screening efficiency, using an experiment plan, metrics and lessons learnt to continuously optimise stress screening condition Note : In case of implementation of Highly Accelerated Environmental Stress Screening the Supplier must refer to document “DEV HA ESS R 25 2006” (Publication can be found at http: //www. aste. asso. fr)
Procurement Quality & Supply Chain PQDR — User Guide – R 5. 0 Procurement Directorate Tests Strategy and Control
Procurement Quality & Supply Chain PQDR — User Guide – R 5. 0 Page 222© AIRBUS S. All rights reserved. Confidential and proprietary document. • Why this requirement? To ensure that all potential defects are covered by manufacturing tests as upstream as possible To guarantee the reproducibility of the amount of tests Having a good manufacturing test strategy will enable to reach high quality standard for a lower cost Note : this requirement is additional with the final test (Acceptance Test) requirements defined in Module 2 § 2. 1. 5 (i. e. ABD 0100 Part 1 Chapter 5) requesting among other things: a. Coverage of 100% of the hardware functions of the complete item (e. g. : power supply, ARINC data inputs, analogue data input). b. Minimum weighted test coverage 92%. Tests strategy and control
Procurement Quality & Supply Chain PQDR — User Guide – R 5. 0 Page 223© AIRBUS S. All rights reserved. Confidential and proprietary document. Tests strategy and control • How to meet this requirement? Consider manufacturing test strategy during design (design for testability) Define manufacturing tests strategy (test points, means, …) taken into account : – customer quality needs – risk analysis and key characteristics – detection of anomalies as early as possible Duly justify non tested part or manufacturing phase, and propose an action plan to mitigate the associated risks Demonstrate test efficiency by using metrics
Procurement Quality & Supply Chain PQDR — User Guide – R 5. 0 Procurement Directorate Organisation of Premises
Procurement Quality & Supply Chain PQDR — User Guide – R 5. 0 Page 225© AIRBUS S. All rights reserved. Confidential and proprietary document. Organisation of premises • Why this requirement? A good workplace organisation and housekeeping will – Increase quality (with respect to the specificities of the Product) – Create a safe and more satisfying working environment – Remove waste from the workplace • How to meet this requirement? Define and respect handling, storage, packaging, preservation and delivery conditions (specificities concerning the Product) throughout the production cycle Have clean and well organised premises, workshop and work stations (5 S projects: housekeeping, etc…)
Procurement Quality & Supply Chain PQDR — User Guide – R 5. 0 Page 226© AIRBUS S. All rights reserved. Confidential and proprietary document. 5 S result example
Procurement Quality & Supply Chain PQDR — User Guide – R 5. 0 Page 227© AIRBUS S. All rights reserved. Confidential and proprietary document. ‘ Traditional’ Environment. Example : “Traditional” environment • Non Sequential Processes • Large Batch Production • No Visual Controls • Un-safe • Processes not in control • Untidy & dirty • Waste in processes • parts made to schedule not to demand • Large amounts of inventory, Work In Process (WIP)
Procurement Quality & Supply Chain PQDR — User Guide – R 5. 0 Page 228© AIRBUS S. All rights reserved. Confidential and proprietary document. Example : Lean environment • Close Coupled Sequential Processes • Single Piece Flow Production • Visually Controlled environment • Orderly, Safe & Clean — 5 s • Minimum Inventory, WIP • Quality & Control in all Processes • Balanced Workstations to Takt Time • Value being pulled by Customer Demand • Minimum Waste, Maximum Value Added • Short Lead times
Procurement Quality & Supply Chain PQDR — User Guide – R 5. 0 Procurement Directorate Documentation
Procurement Quality & Supply Chain PQDR — User Guide – R 5. 0 Page 230© AIRBUS S. All rights reserved. Confidential and proprietary document. • Why this requirement? Any use of obsolete or erroneous document may have critical consequences Manufacturing documentation is useless if not accessible Documentation can be needed at anytime during the whole life time of a Product or system • How to meet this requirement? Ensure control of all documentation linked to the product (Industrial process flow chart, process sheets, drawings, inspection dossier, …) Guarantee that documentation is consistent, updated, clear, used on the shop floor and archived during the whole life time of an equipment or system. Documentation
Procurement Quality & Supply Chain PQDR — User Guide – R 5. 0 Procurement Directorate Root Causes Analysis & Treatment
Procurement Quality & Supply Chain PQDR — User Guide – R 5. 0 Page 232© AIRBUS S. All rights reserved. Confidential and proprietary document. Root causes analysis & treatment • Why this requirement? To ensure that causes of rejection impacting Airbus will not affect later product delivery To demonstrate that causes of late delivery are identified and treated Recurrent late delivery and rejection can be avoided by a full root causes analysis process Many product, manufacturing process and supply chain weaknesses can be treated through root causes analysis of internal or external non-conformities and delays.
Procurement Quality & Supply Chain PQDR — User Guide – R 5. 0 Page 233© AIRBUS S. All rights reserved. Confidential and proprietary document. Root causes analysis & treatment • How to meet this requirement? Perform root causes analysis according to defined criteria : For any product rejection or late delivery at A/C manufacturer integration (or at supplier integration when applicable) For non-conformities and delays (recurrent, trends, major issues, …) at supplier. The Supplier shall set up a method/ procedure for processing Non-conformities or delays root causes analysis (such as 8 D method or equivalent): – Describe the problem – Establish cross-functional team – Perform initial analysis – Contain the problem and set up immediate actions – Diagnose root cause with 5 Whys, Ishikawa or equivalent method – Set up corrective/permanent actions on root causes – Set up preventive actions – Validate solution & set up permanent control measures
Procurement Quality & Supply Chain PQDR — User Guide – R 5. 0 Page 234© AIRBUS S. All rights reserved. Confidential and proprietary document. Fishbone diagram (Ishikawa) — 8 D form 8 -D Form available on e-Site: Airbus people Suppliers
Procurement Quality & Supply Chain PQDR — User Guide – R 5. 0 Procurement Directorate Non-conformities and Delays Analysis Process
Procurement Quality & Supply Chain PQDR — User Guide – R 5. 0 Page 236© AIRBUS S. All rights reserved. Confidential and proprietary document. Non-conformities and delays analysis process • Why this requirement? Zero defect and zero delay are the performances we always try to reach Recurrent defect and delays can be avoided only by a full non-conformance non-conformities and delay analysis Many product, manufacturing process and supply chain weaknesses can be identified and corrected due to non-conformities and delay analysis
Procurement Quality & Supply Chain PQDR — User Guide – R 5. 0 Page 237© AIRBUS S. All rights reserved. Confidential and proprietary document. Non — conformities and delays analysis process • How to meet this requirement? Collect all non-conformities and delays and classify them in a database Analyse correlation of non-conformities Analyse correlation of delays Perform root causes analysis according to defined criteria (for Final Assembly Line and airline returns, recurrent non-conformities and delays, …) Perform correlation of root causes (analysis in an extended search domain: multi-site & multi-product) Implement preventive and corrective actions and verify their efficiency Describe all this process in a formalised method in accordance with the 8 -D or equivalent methodology (refer to Root Causes Analysis & Treatment)
Procurement Quality & Supply Chain PQDR — User Guide – R 5. 0 Page 238© AIRBUS S. All rights reserved. Confidential and proprietary document. Non-conformities and delays collection example Procurement Manufacturing process (including test phases) A/C manufacturer integration (e. g. FAL) INTEGRATED DATABASENon-confor mities & associated code. INTEGRATED DATABASE Delays & associated code In-service use (Airline returns)
Procurement Quality & Supply Chain PQDR — User Guide – R 5. 0 Page 239© AIRBUS S. All rights reserved. Confidential and proprietary document. Non — conformities or delays analysis process example Root causes ana lysis (5 Why, 8 D…)Correlation of direct causes • Action plan : Corrective and/or preventive remedial action. Follow up actions, check efficiency Collect of root causes analysis (codification)Collect of non-conf. , delays or direct causes (code) INTEGRATED DATABASE Correlation of root causes
Procurement Quality & Supply Chain PQDR — User Guide – R 5. 0 Page 240© AIRBUS S. All rights reserved. Confidential and proprietary document. Correlation of non-conformities (or direct causes) example 0 1 2 3 4 5 6 7 8 9 10 Hum an error. Cleaning not perform ed Wrong part dim ens ion Others. Error in m anufacturing dos s ier Inappropriate packaging direct causes N o n co n fo rm ities Initial analysis of non-conformities (last 6 months) Further analysis is required to find the root cause Priority for recurrent non-conformities due to human error or cleaning not performed
Procurement Quality & Supply Chain PQDR — User Guide – R 5. 0 Page 241© AIRBUS S. All rights reserved. Confidential and proprietary document. Root causes analysis example (5 why ? ) Non conformance : An oversized bolt was installed in the assembly WHY ? The operator made an error WHY ? On other models, shorter bolts are used WHY ? Different designers adopted different solutions WHY ? There is no standardisation on large volume items during design phase WHY ? No preferred part list used during design process Direct cause True root cause Root causes analysis shows the true cause of the problem, Do not stay at the direct cause level !!!
Procurement Quality & Supply Chain PQDR — User Guide – R 5. 0 Page 242© AIRBUS S. All rights reserved. Confidential and proprietary document. Root causes analysis example (5 why ? ) Delay : Product delivered with 2 weeks delay WHY ? Work order delayed WHY ? The operator made an error WHY ? ERP displayed a wrong information WHY ? ERP BOM (Bill of Material) not up to date WHY ? Design change not taken into account in the BOM Direct cause True root cause Root causes analysis shows the true cause of the problem, Do not stay at the direct cause level !!!
Procurement Quality & Supply Chain PQDR — User Guide – R 5. 0 Page 243© AIRBUS S. All rights reserved. Confidential and proprietary document. Associated action plan example NC or Delay Root cause description Root cause Code Corrective action On Occurrence Action on Detection Preventive Action owner Due date Measure of Effectiveness Status oversized bolt (NC) No preferred part list used during design process DES Create a preferred part list for bolt Visual inspection of the assembly Set up a bolt size check before assembly M. XXX 12/01/2004 Quality metric based on visual inspection (3 months) OPEN … Product delivered with 2 weeks delay Design change not taken into account in the BOM PRO Update BOM periodically Daily shortage list analysis KPI for BOM accuracy M. YY 12/01/2004 OTD metric OPEN …
Procurement Quality & Supply Chain PQDR — User Guide – R 5. 0 Procurement Directorate Specific Case of Dealers / Distributors
Procurement Quality & Supply Chain PQDR — User Guide – R 5. 0 Page 245© AIRBUS S. All rights reserved. Confidential and proprietary document. Specific Case of Dealers / Distributors • Why this requirement? To address the specific case of dealers/ distributors which sell products (equipment or materials) to Airbus and defines associated specific requirements Dealers/ Distributor must be reliable, fulfil airworthiness requirements, and not lead to increase quality defects or loss of traceability
Procurement Quality & Supply Chain PQDR — User Guide – R 5. 0 Page 246© AIRBUS S. All rights reserved. Confidential and proprietary document. Specific Case of Dealers / Distributors • How to meet this requirement? A dealer/distributor shall: – Have a quality system complying with EN 9120 – Use only product / manufacturer pairs qualified by Airbus and identified in the contract – Guarantee that quality monitoring of manufacturers is performed and that manufacturing modifications are reported – Provide delivery documents with the product: • Declaration of conformance • Airworthiness document • Manufacturing inspection and test reports Reminder : This requirement is only applicable to dealers/ distributors selling on the shelf equipment
Procurement Quality & Supply Chain PQDR — User Guide – R 5. 0 Procurement Directorate Supply Chain Dossier
Procurement Quality & Supply Chain PQDR — User Guide – R 5. 0 Page 248© AIRBUS S. All rights reserved. Confidential and proprietary document. Supply Chain Dossier (SCD) • Why this requirement? To describe Supplier organisation and processes in place to manage its Supply Chain To provide evidence that Supply Chain requirements are fulfilled and applied This SCD will be used by Airbus as the support document for examination of the Supply Chain aspects during development milestones
Procurement Quality & Supply Chain PQDR — User Guide – R 5. 0 Page 249© AIRBUS S. All rights reserved. Confidential and proprietary document. Supply Chain Dossier (SCD) • How to meet this requirement? Describe in the SCD evidence of specific dispositions dedicated to the product and based on method (procedure) and application Answer in the SCD as a minimum to the deliverables (requirement with L ) identified in GRESS module 4 These deliverables shall be provided at the specified milestones and regularly updated as needed (changes, new milestones, …)
Procurement Quality & Supply Chain PQDR — User Guide – R 5. 0 Page 250© AIRBUS S. All rights reserved. Confidential and proprietary document. Supply Chain Dossier (SCD) example (based on GRESS) SCD text SCD appendix 1: Flow chart Supply Chain
Procurement Quality & Supply Chain PQDR — User Guide – R 5. 0 Procurement Directorate Industrial Process Layout (Spaghetti Diagram)
Procurement Quality & Supply Chain PQDR — User Guide – R 5. 0 Page 252© AIRBUS S. All rights reserved. Confidential and proprietary document. Industrial Process Layout (Spaghetti Diagram) • Why this requirement? Mapping the real physical flow of the part makes visible any waste (transportation, motion, …) To support any improvement related to shop floor organisation (lead time reduction, stock reduction, …) • How to meet this requirement? Map the physical flow from the incoming area (components) to the shipping area (finished products). This mapping is based on facility layout of the Supplier Clarify all inventory locations as well as major area (cells, incoming, inspection, shipping, …) Involving operators to build this spaghetti diagram is a best practice
Procurement Quality & Supply Chain PQDR — User Guide – R 5. 0 Page 253© AIRBUS S. All rights reserved. Confidential and proprietary document. Industrial Process Layout example Supplies in. Raw material 3 Raw material 2 Functional Test Cutting out Shipping warehouse. Drilling Cleaning Area Raw material 1 Sub ass. from subcontractor 1 Assembly Inspection. Receiving warehouse. Shipment Soldered parts from sub contractor S 2 Packaging 2 45 6 789 10 32 11 Supplies in. Cutting out Shipping warehouse Cleaning Area. Functional Test Drilling Assembly Raw material 3 Raw material 2 Raw material 1 Inspection. Receiving warehouse. Shipment Soldered parts from sub contractor S 2 Packaging Sub ass. from subcontractor 1 Inspection 11 2 2 3 456 78 910 Current situation Future situation
Procurement Quality & Supply Chain PQDR — User Guide – R 5. 0 Procurement Directorate Continuous Improvement Approach
Procurement Quality & Supply Chain PQDR — User Guide – R 5. 0 Page 255© AIRBUS S. All rights reserved. Confidential and proprietary document. • Why this requirement? To be able to fulfil future Airbus standards (higher quality and delivery performances for a lower cost) Continuous Improvement Approach will enable to improve systematically the quality or delivery performances To stimulate improvement proposals and turn it into profit. Continuous Improvement Approach
Procurement Quality & Supply Chain PQDR — User Guide – R 5. 0 Page 256© AIRBUS S. All rights reserved. Confidential and proprietary document. Continuous Improvement Approach • How to meet this requirement? Describe the company policy and associated organisation for improvement projects: – Choose projects (lead time reduction, stock reduction, scrap reduction, lot size reduction, …) in line with company objectives & Airbus expectations – Define Key Performance Indicators and associated targets to monitor these projects Use lean principles : process analysis to reduce cycles, eliminate wastes, flow disruptions, visual management, people involvement, …
Procurement Quality & Supply Chain PQDR — User Guide – R 5. 0 Page 257© AIRBUS S. All rights reserved. Confidential and proprietary document. Lean principles example: TIMWOOD — 7 Wastes O verproduction O verprocessing 77 55 66 44 33 2211 W aiting time Waiting for: raw material, a machine to finish it’s cycle, maintenance/breakdowns, instructions T ransport Moving raw materials Moving parts between processes. D efects, scrap, rework, poor quality None of which add any value to the customer Doing more than the customer requires Plus, Waste no. 8. . Not using all the potential of people M ovement People having to move between operations I nventory and WIP Holding more parts or work in process than is needed!Producing too much or too early. . . Overproduction causes the other wastes!
Procurement Quality & Supply Chain PQDR — User Guide – R 5. 0 Procurement Directorate Production Management System
Procurement Quality & Supply Chain PQDR — User Guide – R 5. 0 Page 259© AIRBUS S. All rights reserved. Confidential and proprietary document. • Why this requirement? Manufacturing is complex, each firm deals with a variety of processes, means and tools, equipment, labour skill and materials. A firm must organize all these factors to make the right goods, at the right time at top quality and do so as economically as possible Due to all planning steps, a system is required at least to support these activities and to optimize production management. Production Management System
Procurement Quality & Supply Chain PQDR — User Guide – R 5. 0 Page 260© AIRBUS S. All rights reserved. Confidential and proprietary document. Production Management System • How to meet this requirement? Production management system is used to answer to 4 questions: – What are we going to make ? – What does it take to make it ? – What do we have ? – What do we need ?
Procurement Quality & Supply Chain PQDR — User Guide – R 5. 0 Page 261© AIRBUS S. All rights reserved. Confidential and proprietary document. • How to meet this requirement? (cont’) Describe policy and processes defined to manage the production planning activities related to the product. Explain owner of the process, inputs and outputs, planning horizon, time bucket, update frequency, … at least for the following steps : – Sales and Operation Planning – Master Production Schedule – Material Requirement Planning – Purchasing and Production Activity and Control Describe how data accuracy is ensured in production management system ( Bill Of Material, Inventory, …)Production Management System
Procurement Quality & Supply Chain PQDR — User Guide – R 5. 0 Page 262© AIRBUS S. All rights reserved. Confidential and proprietary document. Production Management System — Manufacturing Resources Planning (MRPII) Strategic Plan Sales & Operations Planning ( Family of Products ) Master Production schedule (Product) Material Requirement planning (Component) Shop floor control Resources Requirement Planning Rough cut capacity planning Capacity requirement planning Input/output Control. Demand Management Procurement. Strategic Level Tactical Level Operational Level. Sizing of needs and definition of required resources Optimisation of resources Release and scheduling of : — purchase orders — production orders — delivery order Month Week Day / Hour. Year Capacity Management
Procurement Quality & Supply Chain PQDR — User Guide – R 5. 0 Page 263© AIRBUS S. All rights reserved. Confidential and proprietary document. Production Management System Overview Business Planning Sales and Operations Planning Master Production Schedule Material Requirement Planning Production Activity & Control C a p a c ity M a n a g e m e n t Machine Materials Man. Money S o u rc e D a ta Inventory Order Entry. Demand (incl. spares) Routing Sheet Long Term Medium Term Short Term. BOM Suppliers BOM : Bill Of Material
Procurement Quality & Supply Chain PQDR — User Guide – R 5. 0 Procurement Directorate Production / Manufacturing and Distribution Rules
Procurement Quality & Supply Chain PQDR — User Guide – R 5. 0 Page 265© AIRBUS S. All rights reserved. Confidential and proprietary document. • Why this requirement? Robust production and distribution management rules are essential to provide best customer service at the lower cost Inventory accuracy is a key element of the production and distribution management rules as it is used for: – Determining net requirements for an item ( Net requirements = gross requirement – scheduled receipt – available inventory + safety stock ) – Releasing orders based on material availability. Production / Manufacturing and Distribution Rules
Procurement Quality & Supply Chain PQDR — User Guide – R 5. 0 Page 266© AIRBUS S. All rights reserved. Confidential and proprietary document. Production / Manufacturing and Distribution Rules • How to meet this requirement? Ensure robustness of production and distribution management rules and consistency with Airbus product characteristics (Cycle time, batch size, inventory location, …) Describe your push and/or pull manufacturing process (Kanban…) These rules must lead to relevant logistic solutions (Kitting, Vendor Managed Inventory, Supplier Direct Flow, …) between work station or work centre and between Supplier and Airbus sites
Procurement Quality & Supply Chain PQDR — User Guide – R 5. 0 Page 267© AIRBUS S. All rights reserved. Confidential and proprietary document. Production / Manufacturing and Distribution Rules • How to meet this requirement? (cont’) Ensure effective inventory management, including: • Rules to determine safety stocks at all levels of the Bill Of Material. As the objective of a safety stock is to protect against fluctuation in demand or supply, safety stock value should be based on current delivery performance of the whole Supply Chain and variability of the demand • Method to guarantee inventory accuracy (cycle counting, annual inventory, …) • Key Performance Indicators to monitor inventory
Procurement Quality & Supply Chain PQDR — User Guide – R 5. 0 Page 268© AIRBUS S. All rights reserved. Confidential and proprietary document. Logistic solutions example: A 380 Final assembly line Shop Floor Station. Bar-coded plates (Eqt) Supplier. Bar-coded parcel labels End of Line Stock Dispatch Centre Supplier Direct Delivery. WP, eqt, sub-asse-Call-up Supplier Direct Flow. WP, eqt Direct Line Feed. Distribution Platform Min / Max. Hardware, small parts Kitting VMIVMIAirbus Inventory Eqt, parts, materials (WP: Work package, eqt: equipment, sub-ass: sub-assembly, VMI: Vendor Managed Inventory)
Procurement Quality & Supply Chain PQDR — User Guide – R 5. 0 Procurement Directorate Use of Purchaser’s Data
Procurement Quality & Supply Chain PQDR — User Guide – R 5. 0 Page 270© AIRBUS S. All rights reserved. Confidential and proprietary document. • Why this requirement? In most cases Supplier lead time is greater than call up horizon, so procurement plan must be used to manage production and purchase, Airbus requires flexibility to Suppliers. It is no more possible to order firm quantity on long term, To ensure flexibility, Suppliers have to anticipate by managing production and purchase using Airbus procurement plan (forecast). Use of Purchaser’s data
Procurement Quality & Supply Chain PQDR — User Guide – R 5. 0 Page 271© AIRBUS S. All rights reserved. Confidential and proprietary document. Use of Purchaser’s data • How to meet this requirement? Describe and improve the process to take into account an Airbus procurement plan, Production forecast and call-up into the Master Production Schedule (MPS) and Material Requirement Planning (MRP) calculation, Compare procurement plan with related call-ups, and analyse changes between two successive procurement plans, Apply weekly Collaboration using e. Supplychain tool for the related suppliers. In case of delays in delivery, the Supplier shall inform the Purchaser, present a recovery plan (e. g: line of balance) if requested, perform a root causes analysis (e. g: 8 D) and establish an action plan
Procurement Quality & Supply Chain PQDR — User Guide – R 5. 0 Page 272© AIRBUS S. All rights reserved. Confidential and proprietary document. Forecast and call-ups consistency follow up example Week 1 2 3 4 5 6 Forecast 10 10 10 order or call-up 10 8 11 13 8 9 Cumulative forecast 10 20 30 40 50 60 Cumulative order 10 18 29 42 50 59 Forecast and call-up consistency follow up 5 10 15 123456 We e k numbe r Num ber of equipm ents Forecast order or call-up
Procurement Quality & Supply Chain PQDR — User Guide – R 5. 0 Page 273© AIRBUS S. All rights reserved. Confidential and proprietary document. Comparison of two successive procurement plans Example 10 11 12 13 14 15 16 17 Jan. Fev. Mar. A pr. May. Jun. Jul Num ber of equipm ent January procurement plan (6 months) Procurement plan change to manage: earlier demand in April Current month : February
Procurement Quality & Supply Chain PQDR — User Guide – R 5. 0 Page 274© AIRBUS S. All rights reserved. Confidential and proprietary document. Line of balance example Bill Of Material. Manufacturer’s Serial Number Cycle & Cumulative (wd) Ships et QT Y 1504 1505 1506 1507 END ITEMRequested delivery date 2 -Nov 3 -Nov 6 -Nov Requested ship date (-7 d)26 -Oct 27 -Oct 30 -Oct Actual ship date 7 -Nov 10 -Nov 13 -Nov Forecast ship date (recovery)8 -Nov 9 -Nov 10 -Nov 13 -Nov PACKAGINGActual date 1. 017 -Nov 9 -Nov 12 -Nov Forecast date (recovery)1. 07 -Nov 8 -Nov 9 -Nov 12 -Nov TESTActual date 2. 015 -Nov 8 -Nov 10 -Nov 11 -Nov Forecast date (recovery)3. 05 -Nov 6 -Nov 7 -Nov 10 -Nov ASSEMBLYActual date 1. 014 -Nov 7 -Nov 8 -Nov 9 -Nov Forecast date (recovery)4. 04 -Nov 5 -Nov 6 -Nov 9 -Nov SUB-ASSEM BLY 2 Actual date 1. 023 -Nov 6 -Nov 8 -Nov Forecast date (recovery)5. 03 -Nov 4 -Nov 5 -Nov 8 -Nov SUB-ASSEM BLY 1 Actual date 2. 011 -Nov 3 -Nov 6 -Nov Forecast date (recovery)7. 01 -Nov 2 -Nov 3 -Nov 6 -Nov COMPONENT 2 Actual date 1. 0431 -Oct 1 -Nov 2 -Nov 5 -Nov Forecast date (recovery)8. 031 -Oct 1 -Nov 2 -Nov 5 -Nov COMPONENT 1 Actual date 1. 0230 -Oct 31 -Oct 1 -Nov 4 -Nov Forecast date (recovery)9. 030 -Oct 31 -Oct 1 -Nov 4 -Nov Current day : November 14 th
Procurement Quality & Supply Chain PQDR — User Guide – R 5. 0 Procurement Directorate Capacity Management
Procurement Quality & Supply Chain PQDR — User Guide – R 5. 0 Page 276© AIRBUS S. All rights reserved. Confidential and proprietary document. • Why this requirement ? Planning activities without checking the capacity is useless. At each level of the production management system (Sales and Operations Planning, Master Production Schedule, Material Requirement Planning), priority plan developed to satisfy demand can be applied only if associated resources are available To secure on time customer delivery. Capacity Management
Procurement Quality & Supply Chain PQDR — User Guide – R 5. 0 Page 277© AIRBUS S. All rights reserved. Confidential and proprietary document. Capacity Management • How to meet this requirement ? Describe policy and processes defined to manage capacity, including the following steps: – Resource Plan at SOP level – Rough Cut Capacity planning at MPS level – Capacity Requirement Plan at MRP level For each step: – Clarify the purpose of the plan, – The owner of the process, – The input / output in terms of data (level of detail), – The planning horizon, the time bucket, – The frequency with which the plan is reviewed.
Procurement Quality & Supply Chain PQDR — User Guide – R 5. 0 Page 278© AIRBUS S. All rights reserved. Confidential and proprietary document. Capacity Management • How to meet this requirement ? (cont’) Explain how capacity management rules enable to resolve differences between available capacity (resources: man, machines, …) and required capacity over short, medium and long terms Describe how the capacity data accuracy (available time, efficiency, utilisation, …) is ensured throughout the process Identify, monitor (Key Performance Indicators) and manage bottleneck & single means related to product manufacturing process
Procurement Quality & Supply Chain PQDR — User Guide – R 5. 0 Page 279© AIRBUS S. All rights reserved. Confidential and proprietary document. Production Management System Closed Loop with Capacity Management Sales and Operations Planning Master Production Schedule Material Requirement Planning Capacity Ok ? No Yes Production Activity & Control. Purchasing Performance Measures Feedback Resource Requirement Plan Rough-Cut Capacity Plan Capacity Requirements Plan
Procurement Quality & Supply Chain PQDR — User Guide – R 5. 0 Page 280© AIRBUS S. All rights reserved. Confidential and proprietary document. Production Management System Closed Loop with Capacity Management (cont) • If the Capacity Management is not supported by the tool supporting the 3 main steps of the planning process (SOP, MPS and MRP), there is a risk of checking the capacity based on inaccurate data. To mitigate this risk, the supplier shall clarify: Interfaces between the Planning and the Capacity tools – List all the tools supporting either the Production Management System or the Capacity Management Process – Clarify all the interfaces existing between those tools (input / output, frequency of synchronisation, etc) Data to be shared by the various tools – List all the inputs requested by the Capacity Management Process and clarify which tool is managing those (actual order quantities, open shop orders, lead times, routing sheets, etc). – Clarify how the data synchronisation is ensured between those tools
Procurement Quality & Supply Chain PQDR — User Guide – R 5. 0 Page 281© AIRBUS S. All rights reserved. Confidential and proprietary document. Production & Capacity Management Systems Sample Mapping The mapping is a visual way to represent: • Interfaces between the Planning and the Capacity tools • Data to be shared by the various tools SAP SOP: not done MPS MRP Excel RRP: not done RCCP CRPPP, MM Every 1 st Monday of the month, manual process Each Monday, manual process Macro “xx” & “yy” Production plan, routings, time standards, lead times and work center files Planned order releases, open shop orders, routings, time standards, lead times and work center files
Procurement Quality & Supply Chain PQDR — User Guide – R 5. 0 Page 282© AIRBUS S. All rights reserved. Confidential and proprietary document. Capacity evaluation example Work centre X: 4 machines, 32. 5 hours / week Available time : 4*32. 5=130 hours / week There are 2 different methods to evaluate capacity: Rated or calculated capacity Efficiency : 70 % (actual rate of production / standard rate of production ) Utilisation : 100 % ( hours actually worked / available hours ) Demonstrated or measured capacity Week 4 5 6 7 8 9 Standard hours 92 90 91 87 89 88 (current week : 10) hours standard 5. 89 6 888987919092 capacity eddemonstrator Rated hours standard 91 100 100 70 130 capacity calculatedor Rated
Procurement Quality & Supply Chain PQDR — User Guide – R 5. 0 Page 283© AIRBUS S. All rights reserved. Confidential and proprietary document. Capacity Management example work centre X load / capacity comparison 0 20 40 60 80 100 120 140 160 1011121314151617 We e k Standard hours. Released load Planned load Rated Capacity Rated capacity : 91 standard hours Time bucket : 1 week Update frequency: 1 week Planning horizon: 8 weeks Situation : Overload in weeks 12 and 13, which can be solved if planned order could be released in weeks 10 or 11, or if some overtime could be worked in weeks 12 and
Procurement Quality & Supply Chain PQDR — User Guide – R 5. 0 Procurement Directorate Backorder Management
Procurement Quality & Supply Chain PQDR — User Guide – R 5. 0 Page 285© AIRBUS S. All rights reserved. Confidential and proprietary document. • Definition: Backorder: an unfilled customer order or commitment. A backorder is an immediate (or part due) demand against an item whose inventory is insufficient to satisfy the demand • Why this requirement ? To be able to anticipate and mitigate the risk of delays or poor quality at customer side, the Supplier shall monitor the completion of its manufacturing orders and purchasing orders The earlier the slippage of manufacturing or purchasing order is detected, the higher chances to recover (no impact at customer side)Backorder management
Procurement Quality & Supply Chain PQDR — User Guide – R 5. 0 Page 286© AIRBUS S. All rights reserved. Confidential and proprietary document. Backorder management • How to meet this requirement ? Describe and improve: – How manufacturing orders behind schedule are identified (list of late purchasing & manufacturing orders) – How late orders are prioritised – How dispatching rules (critical ratio, earliest job due date, …) and/or specific solutions enable to recover these late manufacturing or purchasing orders In case of delays in delivery, the Supplier shall inform the Purchaser, present a recovery plan (e. g: line of balance) if requested, perform a root causes analysis (e. g: 8 D) and establish an action plan
Procurement Quality & Supply Chain PQDR — User Guide – R 5. 0 Page 287© AIRBUS S. All rights reserved. Confidential and proprietary document. Line of balance example Bill Of Material. Manufacturer’s Serial Number Cycle & Cumulative (wd) Ships et QT Y 1504 1505 1506 1507 END ITEMRequested delivery date 2 -Nov 3 -Nov 6 -Nov Requested ship date (-7 d)26 -Oct 27 -Oct 30 -Oct Actual ship date 7 -Nov 10 -Nov 13 -Nov Forecast ship date (recovery)8 -Nov 9 -Nov 10 -Nov 13 -Nov PACKAGINGActual date 1. 017 -Nov 9 -Nov 12 -Nov Forecast date (recovery)1. 07 -Nov 8 -Nov 9 -Nov 12 -Nov TESTActual date 2. 015 -Nov 8 -Nov 10 -Nov 11 -Nov Forecast date (recovery)3. 05 -Nov 6 -Nov 7 -Nov 10 -Nov ASSEMBLYActual date 1. 014 -Nov 7 -Nov 8 -Nov 9 -Nov Forecast date (recovery)4. 04 -Nov 5 -Nov 6 -Nov 9 -Nov SUB-ASSEM BLY 2 Actual date 1. 023 -Nov 6 -Nov 8 -Nov Forecast date (recovery)5. 03 -Nov 4 -Nov 5 -Nov 8 -Nov SUB-ASSEM BLY 1 Actual date 2. 011 -Nov 3 -Nov 6 -Nov Forecast date (recovery)7. 01 -Nov 2 -Nov 3 -Nov 6 -Nov COMPONENT 2 Actual date 1. 0431 -Oct 1 -Nov 2 -Nov 5 -Nov Forecast date (recovery)8. 031 -Oct 1 -Nov 2 -Nov 5 -Nov COMPONENT 1 Actual date 1. 0230 -Oct 31 -Oct 1 -Nov 4 -Nov Forecast date (recovery)9. 030 -Oct 31 -Oct 1 -Nov 4 -Nov Current day : November 14 th
Procurement Quality & Supply Chain PQDR — User Guide – R 5. 0 Procurement Directorate NSN: NATO Stock Number
Procurement Quality & Supply Chain PQDR — User Guide – R 5. 0 Page 289© AIRBUS S. All rights reserved. Confidential and proprietary document. NSN: NATO Stock Number • Why this requirement? Military programs require that all “applicable components” (items classified as spares) have also a NATO Stock Number (NSN). This is due to the need for interchangeability in modern air forces, as a same component may exist in different weapon systems, different suppliers may supply a same component The NSN allows to quickly find interchangeable units independent of Supplier or part number The NSN requirement is always established as a contractual requirement in all military programmes for detail see CDIM issue
Procurement Quality & Supply Chain PQDR — User Guide – R 5. 0 Page 290© AIRBUS S. All rights reserved. Confidential and proprietary document. NSN: NATO Stock Number • How to meet this requirement? The Supplier will give, per Part Number (PN), the minimum data to the relevant Industrial Partner through a Microsoft-Excel file (structure is given in the next slides) The relevant Industrial Partner will initiate the NATO codification for all its Suppliers. The relevant National Codification Bureau (NCB) and/or the relevant Industrial Partner could request the Supplier to provide information and assistance (data and drawings) as necessary to allocate NATO codification The relevant NCB will provide results (NATO related data) to the Industrial Partner The Industrial Partner will provide the result to the Supplier through a Microsoft-Excel file for detail see CDIM issue
Procurement Quality & Supply Chain PQDR — User Guide – R 5. 0 Page 291© AIRBUS S. All rights reserved. Confidential and proprietary document. File structure – Minimum data to be provided by the supplier to the relevant Industrial Partner (through a Microsoft-Excel file, structure below) Column TEI Remarks 1 PNR Part Number. Mandatory. The Supplier will provide definitive PNR to the relevant Industrial Partner. Non-definitive or dummy PNR will not be used. 2 MFC NATO supply code for manufacturers. Mandatory. 3 NSC Proposed NATO Supply Class (the first 4 digits of the NSN). Mandatory. 4 INC Item Name Code. Mandatory. 5 DFP Description For Part. Mandatory. for detail see CDIM issue
Procurement Quality & Supply Chain PQDR — User Guide – R 5. 0 Page 292© AIRBUS S. All rights reserved. Confidential and proprietary document. NSN: NATO Stock Number • How to meet this requirement ? (cont’) Ensure that all material is bar-coded The NATO Stock Number (NSN) is not mandatory on the Equipment identification plate Incorporate the NSN on the item label. If NSN are provided by Customers at a later point in time, the label will follow current Airbus rules and as such applicable standards. At the time when the NSN is provided by the customers, it will be included in Delivery documentation ( Certificates: EASA Form 1 or FAA part 8130 -3 or Cof. C (as applicable), Delivery Note) and Material Support documentation at the following revision for detail see CDIM issue
Procurement Quality & Supply Chain PQDR — User Guide – R 5. 0 Page 293© AIRBUS S. All rights reserved. Confidential and proprietary document. National Codification Bureau The NCB’s involved by the industrial partners are: • France for Airbus France • UK for Airbus UK • Germany for Airbus Deutschland EADS-DS • Spain for EADS CASA • Belgium for FLABEL • Turkey for TAI
Procurement Quality & Supply Chain PQDR — User Guide – R 5. 0 Procurement Directorate Selection of Suppliers & Cascade of Requirements to Suppliers
Procurement Quality & Supply Chain PQDR — User Guide – R 5. 0 Page 295© AIRBUS S. All rights reserved. Confidential and proprietary document. • Why this requirement? In most cases, the Supplier need to outsource some parts or processes If outsourced parts are not on the shelf (specific to the finished product), the Supplier has to secure part availability for the entire Product life cycle. The Supplier has to build long term relationships with tier-supplier To avoid use of any counterfeit or bad quality parts Suppliers have a major impact on customer performances Airbus considers GRESS as a best practice to improve delivery and quality performances. So cascading GRESS principles to tier-suppliers will improve supplier performances. Selection of suppliers & cascade of requirements to suppliers
Procurement Quality & Supply Chain PQDR — User Guide – R 5. 0 Page 296© AIRBUS S. All rights reserved. Confidential and proprietary document. Selection of suppliers & cascade of requirements to suppliers • How to meet this requirement? Formalise selection process in place, based on : – Various criteria (cost, approved supplier list, technical performances, availability at agreed distributor, …) – Multi-functional team (Purchasing / Engineering / Quality / …) – A limited number of suppliers per product family Formalise supplier approval process Flow down GRESS requirements to key contributing parties (by contract if any) Note : agreed distributors= distributors authorised by the OEM to trade with components or parts
Procurement Quality & Supply Chain PQDR — User Guide – R 5. 0 Page 297© AIRBUS S. All rights reserved. Confidential and proprietary document. Selection of suppliers : analysis matrix example Product to deliver Supplier 1 Supplier 2 Final decision Cost Structure (economical, organisation) Contracts Technical performances Capability Capacity Delivery and Quality performance Approved supplier (O/N) Lesson learnt Program Engineering Quality Procurement After sales Agreed distributor …
Procurement Quality & Supply Chain PQDR — User Guide – R 5. 0 Page 298© AIRBUS S. All rights reserved. Confidential and proprietary document. Example : Suppliers approval process According XXX procedure, • Agreements and certifications (ISO 9001, EN 9100, FAR, FAA, parts manufacturer, …) • Assessment at supplier’s site • Supplier performances • … Supplier approval committee Supplier approved, for X years, with action plan if needed Supplier non approved This approval process is performed periodically, and when the supplier approval will expire
Procurement Quality & Supply Chain PQDR — User Guide – R 5. 0 Page 299© AIRBUS S. All rights reserved. Confidential and proprietary document. Example : Cascade of requirements Supplier category : Suppliers of key parts Suppliers of subcontracted specialised processes Supplier of standard components … CASCADED BY : Airbus GRESS requirements AI-GRESS-XXXXX-A Contract §x. x AI-GRESS-XXXXX-A Contract §x. y Not applicable AI-GRESS-XXXXX-A Purchase order Not applicable … Supplier requirements XXXXX Contract §z. x Not applicable XXXXX PTS §z. y XXXXX Contract §z. z Not applicable … Reminder : justify each GRESS requirement not cascaded to tier-suppliers. PTS : Purchaser Technical Specification
Procurement Quality & Supply Chain PQDR — User Guide – R 5. 0 Procurement Directorate Supplier Monitoring and Improvement Actions
Procurement Quality & Supply Chain PQDR — User Guide – R 5. 0 Page 301© AIRBUS S. All rights reserved. Confidential and proprietary document. • Why this requirement? No improvement without measure Supplier monitoring and trend analysis enable the anticipation of problems and mitigation of related risks at delivery To drive tier-suppliers improvement which will contribute to Supplier delivery and quality improvement To feed back the Supplier selection process. Supplier monitoring and improvement actions
Procurement Quality & Supply Chain PQDR — User Guide – R 5. 0 Page 302© AIRBUS S. All rights reserved. Confidential and proprietary document. Supplier monitoring and improvement actions • How to meet this requirement? Define and implement Key Performance Indicators (KPIs) to monitor quality and delivery performances of tier-suppliers (at least on a monthly basis) with associated objectives Use KPIs to drive either recovery actions or continuous improvement action plans Organise periodic meetings to work with tier-suppliers: – agree on targets & results – develop proactive and collaborative approach – perform systematic investigation (“ 8 -D” problem solving, …) – … Perform periodic assessments at Suppliers (e. g Key contributing parties, . . . ) in order to verify that the cascaded requirements (e. g GRESS, . . . ) are fulfilled
Procurement Quality & Supply Chain PQDR — User Guide – R 5. 0 Page 303© AIRBUS S. All rights reserved. Confidential and proprietary document. Product X — Suppliers quality follow up 75 80 85 90 95 100 26272829303132333435 We e k Quality perform ance (% ) Supplier 1 Supplier 2 Supplier 3 Supplier 4 OB J EC T IVES : 98%Example: suppliers quality monitoring Number of non conforming parts under Supplier responsibility rejected in the period Rejection Rate = ——————————————— Total number of n ew parts delivered by the Supplier during the same period Quality performance = 100 – rejection rate
Procurement Quality & Supply Chain PQDR — User Guide – R 5. 0 Page 304© AIRBUS S. All rights reserved. Confidential and proprietary document. Example: suppliers delays monitoring Quantity of parts received at premises with requested documentation in the period 7 working days before and up to the contractual day Quantity Adherence = ——————————————————- Quantity of parts planned during the same period Product X — Suppliers delivery follow up 85 87 89 91 93 95 97 99 26272829303132333435 We e k Quantity adherence (% ) Supplier 1 Supplier 2 Supplier 3 Supplier 4 OBJECTIV ES : 99 %
Procurement Quality & Supply Chain PQDR — User Guide – R 5. 0 Page 305© AIRBUS S. All rights reserved. Confidential and proprietary document. Example: suppliers delays monitoring Supplier Quantity Adherence Supply Chain audit Who When Risk on equipment X assembly Recovery plan Expected end of recovery 1 89 % Yes M. X Week 33 High Yes Week 40 3 97% Yes M. Y Week 37 Medium Yes Week 42 4 99. 5 % No Medium No 2 100 % No Low No. Product X, Week
Procurement Quality & Supply Chain PQDR — User Guide – R 5. 0 Page 306© AIRBUS S. All rights reserved. Confidential and proprietary document. Action example • Supplier 1, Product X, week 35 Situation – Delay increase since week 30 Cause (according to supply chain audit done in week 33) – loads increased by another product, so test mean become a bottleneck Actions – Double source approved for this part and M. X went at the supplier site to contribute to test mean Overall Equipment Efficiency improvement, and implement a recovery plan – End of recovery plan expected in week
Procurement Quality & Supply Chain PQDR — User Guide – R 5. 0 Procurement Directorate Procurement Triggering Mode
Procurement Quality & Supply Chain PQDR — User Guide – R 5. 0 Page 308© AIRBUS S. All rights reserved. Confidential and proprietary document. • Why this requirement? In most cases tier-2, 3, … supplier lead time is greater than call up horizon, so procurement plan must be used to manage production and purchase Airbus requires flexibility to tier-1 Suppliers, so tier-2, 3, … suppliers have also to be flexible To ensure flexibility, tier-2, 3, … suppliers have to anticipate by managing production and purchase using purchaser procurement plan (forecast)Procurement triggering mode
Procurement Quality & Supply Chain PQDR — User Guide – R 5. 0 Page 309© AIRBUS S. All rights reserved. Confidential and proprietary document. Procurement triggering mode • How to meet this requirement? Based on Airbus procurement plan and through MPS and MPR calculation, tier-1 Supplier shall flow down its needs to tier-2, 3, … using purchase orders and procurement plans Describe ordering policy for the relevant family of product As between Airbus and tier-1 Supplier, put in place relevant logistics solutions (Kitting, Vendor Managed Inventory, Supplier Direct Flow, …) with tier-2, 3, … suppliers to reduce cost and risks over the whole supply chain
Procurement Quality & Supply Chain PQDR — User Guide – R 5. 0 Page 310© AIRBUS S. All rights reserved. Confidential and proprietary document. Example : impact of different order policies Order policy : Week 1 2 3 4 5 6 7 8 Gross Requirement 8 32 4 8 45 0 20 16 Fixed order=50 Inventory available 15 7 25 21 13 18 18 48 32 Planned order release 50 50 50 Lot for lot Inventory available 15 7 0 0 0 0 Planned order release 25 4 8 45 0 20 16 Period=3 Inventory available 15 7 12 8 0 20 20 0 0 Planned order release 37 65 16 Period=3 mult=10 Inventory available 15 7 15 11 3 28 28 8 2 Planned order release 40 70 10 Hypothesis : Lead time for the procured part : 1 week, No safety stock Ordering policy Inventory level
Procurement Quality & Supply Chain PQDR — User Guide – R 5. 0 Procurement Directorate Supplier Quality & Delivery Review Meetings
Procurement Quality & Supply Chain PQDR — User Guide – R 5. 0 Page 312© AIRBUS S. All rights reserved. Confidential and proprietary document. Supplier Quality & Delivery Review Meetings • Why this requirement? To improve on time delivery and on quality of products delivered to Airbus, To ensure on time delivery and on quality of aircraft to final customers, To share diagnostic of Supplier performances (detected at Supplier and Airbus site), To ensure that root causes are identified and treated throughout corrective/permanent actions (for Airbus rejection, late delivery and trends at supplier), To have a summary of all corrective/preventive actions related to the previous period.
Procurement Quality & Supply Chain PQDR — User Guide – R 5. 0 Page 313© AIRBUS S. All rights reserved. Confidential and proprietary document. Supplier Quality & Delivery Review Meetings • How to meet this requirement? Calculate Quality and Delivery Performance Indicators and compare them with those calculated by Airbus (R 1/R 2 & D 1/D 2) – For any non-agreement on Airbus data, to provide justifications Present a filled database with non-conformities and delays (in-house, at the aircraft manufacturer and the Airlines), root causes and corrective/preventive actions. Present on Airbus request: – A root cause analysis diagram, – Internal Quality and Delivery metrics (FPY: Pre-test, ESS and Final ATP, inventories …).
Procurement Quality & Supply Chain PQDR — User Guide – R 5. 0 Page 314© AIRBUS S. All rights reserved. Confidential and proprietary document. Database example CMS PNR SER Removal or Late Delivery Date Reason for Rejection or Late Delivery Repair remedial Action Root cause description Root cause Code Corrective action On Occurrence Action on Detection Preventive Action Effectivity Date Or due date Product SER Effectivity Product SER Delivery date Repair/remedial actions Root cause description Root cause code Corrective action on occurrence Action on detection Preventive action Describe immediate containment action(s) launched and due date Fill in explicit description of the root cause. Airbus responsible person keeps the right to amend this field as appropriate Design DES Fill in description of actions to eliminate the cause of a detected non-conformity/late delivery or other undesirable non-conformity/late delivery in order to prevent its recurrence. Fill in description of actions to improve the detection of this non-conformity/late delivery (modification/addition of manufacturing procedures – inspections, ESS (Environmental Stress Screening), ATP (Acceptance Test Procedure…) Fill in description of action(s) to eliminate the cause of a potential non-conformity/late delivery or other undesirable situation in order to prevent its occurrence. Process PRO Purchase PUR No Fault Found NFF Undetermined UNDLegend:
Procurement Quality & Supply Chain PQDR — User Guide – R 5. 0 Page 315© AIRBUS S. All rights reserved. Confidential and proprietary document. Root causes analysis diagram example Root cause n° x Failure n° x Reason of removal n° x Total of units produced / deliv ered Production Airline FAL 90 4 120 Total of known defects 1 Production Airline FAL 1 1 Root cause n° 2 1 Reason of removal n° 2 Root cause n° 1 Reason of removal n° 1 0% 0% 0% DESIGN 37. 5% 0% 50% UNDETERMINED 0% 0% 16. 6% NOT CONFIRMED 16 0 0 0 6 0 3 0 0 1 4 0 0 4 0 1 25% 0% 0% INT PROCESS 25% 0% 16. 6% EXT PROCESS 12. 5% 0% 16. 6% COMPONENTS Handling 1 PCB 17. 7% 0, 0% 5% Marquing, labels, numbers 1 Equiped box xx Mechanical parts Connectors Short circuit, soldering Component n° 1 Wiring mistake or bad repair Component n° 2 Cleaning, varnish Optical assembly Component implantation Adjustment, means Programming Miscellaneous Subcontractor n° x Component n° x Ratio of defects during manufacturing phases Rejection rate in Service Rejection rate during Aircraft manufacturing Removals during Aircraft manufacturing (FAL) Removals during in Service Removals during manufacturing phases(Pre-test, ESS…) PRODUCT REJECTION OR LATE DELIVERY
Procurement Quality & Supply Chain PQDR — User Guide – R 5. 0 Page 316© AIRBUS S. All rights reserved. Confidential and proprietary document. Quality metrics example : pareto of defect Defects/Remov als per SRU* 0 1 2 3 4 5 6 7 SRU 1 SRU 2 SRU 3 SRU 4 SRU 5 SRU 6 SRU 7 SRU 8 Defects/Remov als per Phase 0 1 2 3 4 5 6 7 Integration. Pre test. Burn-in. ATPMechanical control Delivery Production Period: January-05 to May-05 Quantity produced: 90 * SRU: Shop Replaceable Unit
Procurement Quality & Supply Chain PQDR — User Guide – R 5. 0 Procurement Directorate Release Certificates
Procurement Quality & Supply Chain PQDR — User Guide – R 5. 0 Page 318© AIRBUS S. All rights reserved. Confidential and proprietary document. Release Certificates • Why this requirement? To release items for airworthiness purposes which means conformity with approved design data and in condition for safe operation Note: When the design data is not approved (e. g. : pending type certificate…) the ARC is for conformity only To fulfil National Authorities and Customer requirements
Procurement Quality & Supply Chain PQDR — User Guide – R 5. 0 Page 319© AIRBUS S. All rights reserved. Confidential and proprietary document. Release Certificates • How to meet this requirement? Any supplier holding a Production Organisation Approval (POA) or equivalent will provide an Authorised Release Certificate (ARC): JAA form 1, EASA form 1, FAA form 8130 -3 and 8130 -4 and TCCA 24 -0078 form (as per AP 2160). Note: In case the Supplier do not hold a POA or equivalent, they shall deliver items with a Certificate of Conformity (Co. C) with the prior authorisation of Airbus.
Procurement Quality & Supply Chain PQDR — User Guide – R 5. 0 Procurement Directorate Concessions
Procurement Quality & Supply Chain PQDR — User Guide – R 5. 0 Page 321© AIRBUS S. All rights reserved. Confidential and proprietary document. Concessions • Why this requirement? Concession is a permission to use or release a product that does not conform to specified requirements (AP 2006). It is a request, on an exceptional basis and limited application of the acceptance by Airbus (Airbus Design Office, Quality Organisation and in some cases airworthiness) of a product non-conformance vs. approved Design Data (or Definition Dossier), To ensure Product deviation traceability.
Procurement Quality & Supply Chain PQDR — User Guide – R 5. 0 Page 322© AIRBUS S. All rights reserved. Confidential and proprietary document. Concessions • How to meet this requirement? The supplier has to comply with AP 2006 and fill a concession form (Airbus policy is to use electronic form through e-concession tool or in some cases paper form) Note: rules for completing forms, describing non-conformity, numbering concession, … are defined in AP 2006 Supplier is authorized to deliver the Product under concession only when concession form has been formally accepted by Airbus and sent back to Supplier Note: a copy of the Concession formally accepted and signed by the Purchaser shall be attached to the Product delivery documents
Procurement Quality & Supply Chain PQDR — User Guide – R 5. 0 Page 323© AIRBUS S. All rights reserved. Confidential and proprietary document. Concession: electronic form as per AP
Procurement Quality & Supply Chain PQDR — User Guide – R 5. 0 Procurement Directorate Constituent Assembly Inspection Report (CAIR)
Procurement Quality & Supply Chain PQDR — User Guide – R 5. 0 Page 325© AIRBUS S. All rights reserved. Confidential and proprietary document. Constituent Assembly Inspection Report (CAIR) • Constituent Assembly definition (AP 2135): A Constituent Assembly (CA) is a configuration item class, which reflects the physical product assembly breakdown. The complete and tested aircraft is the overall CA. It is broken down into several levels of CA’s reflecting the various assembly processes, facilities and owners, which contribute to the final product. Each assembly process owner is responsible for establishing and tracking the CA configuration up to aircraft delivery to the customer. • Constituent Assembly Inspection Report definition (AP 2104): A Constituent Assembly Inspection Report is a paper or electronic document used to record the technical status of a physical Constituent Assembly hereafter referred to as “CAIR”. CAIR ensures that the delivered configuration is in conformity with the specified configuration.
Procurement Quality & Supply Chain PQDR — User Guide – R 5. 0 Page 326© AIRBUS S. All rights reserved. Confidential and proprietary document. Constituent Assembly Inspection Report (CAIR) • Why this requirement? It provides with: – a complete status of each Constituent Assembly at the moment of their first delivery to the Purchaser and their subsequent evolutions until Aircraft delivery to the Customers and at specific aircraft milestones – an up to date technical status to the Purchaser Thanks to the CAIR the Supplier attest the conformity and the configuration after each modification in the Constituent Assembly.
Procurement Quality & Supply Chain PQDR — User Guide – R 5. 0 Page 327© AIRBUS S. All rights reserved. Confidential and proprietary document. Constituent Assembly Inspection Report (CAIR) • How to meet this requirement? The Supplier shall use the CAIR information system provided by the Purchaser This electronic CAIR shall be filled in and validated by the Supplier in the Purchaser’s system Note : All the detailed information is available in the following Airbus Quality Procedure that the Supplier shall apply: AP 2104 (Constituent Assembly Inspection Report)
Procurement Quality & Supply Chain PQDR — User Guide – R 5. 0 Procurement Directorate Equipment Label CT
Procurement Quality & Supply Chain PQDR — User Guide – R 5. 0 Page 329© AIRBUS S. All rights reserved. Confidential and proprietary document. Equipment label CT 176 • Equipment label CT 176 Definition (AP 5171): An Equipment Label is a document (also known as CT 176), which is prepared by an Equipment Manufacturer and delivered with the Equipment. • Why this requirement? The equipment label enables: – To record the equipment (and its complementary data) installed on each aircraft, – To constitute the aircraft manufacturer’s records (CAIR and AIR when applicable), – To record installations, removals and changes of allocation, – To record equipment under concession (refer to AP 2006), – To record periodic tests (when those inspections have been carried out).
Procurement Quality & Supply Chain PQDR — User Guide – R 5. 0 Page 330© AIRBUS S. All rights reserved. Confidential and proprietary document. Equipment label CT 176 • How to meet this requirement? When required (as specified in the PTS) a CT 176 label must be secured to the outside of the Equipment packaging (see AP 5171 for implementation), that means, when the equipment: • meets the criteria for recording in the AIR ( see AP 2048 ) • is affected by concession(s) (see AP 5171) • has a shelf life or includes component(s) with a shelf life (see AP 5171)
Procurement Quality & Supply Chain PQDR — User Guide – R 5. 0 Page 331© AIRBUS S. All rights reserved. Confidential and proprietary document. CT 176 Label template Yellow tag (one-sided) ICAO Manufacturer-Lieferant-Fournisseur-Suministrador ICAO MSN: F. I. N. : Remarks-Observaciones-Anmerkungen-Observations: Part N°/N°. Pieza Teilenummer N°de pièce Description-Bezeichnung-Désignation-Descripcion ETIQUETTE POUR EQUIPEMENT ETIQUETA DE EQUIPO / EQUIPMENT LABEL GERÄTE-ANHÄNGER ……………………………………………………………………………………………. . . . CT 176 Code N°/N°. Codigo Geräteziffer CMS Manufacture date (DMF) / Fecha de Fabricacion. Herstellungsdatum. Date de fabrication. Hydrostatic test date/Fecha del Ensavo Hidrostatico. Hydrostatisches Testdatum. Serial N°/N°. Serien-Nummer. Expiration date / Fecha de Caducidad. Ablaufdatum. Date d’expiration Assembly / Instalacion. Einbau. Installation. Date — Fecha. Tag — Date. Stamp — Sello. Stempel — Poinçon. Date — Fecha. Tag — Date Release certificate n°. -N°. Certificado de Conformidad-Übereinstimmungsbescheinigungs-Nr. -Certificat de conformité n°: Concession — Concesion — Bauabweichung — Dérogation: ……………………………………………………………Sub part expiration date Fecha de expiracion del sub-componente Unterkomponente Ablaufdatum Date d’expiration du sous-ensemble Ultimate shelf life Maximo tiempo de yida — Höchste Lagefungsdauer — Durée maxi de stockage Test Frequency Frecuencia de las pruebas de verificacion Periodische Prufungen — Fréquence des vérifications Yellow tag Template available on e-Site: Airbus people Suppliers
Procurement Quality & Supply Chain PQDR — User Guide – R 5. 0 Procurement Directorate Out Located Work
Procurement Quality & Supply Chain PQDR — User Guide – R 5. 0 Page 333© AIRBUS S. All rights reserved. Confidential and proprietary document. Out Located Work • Out Located Work Definition (A 1130): Out Located Work (OLW) shall be interpreted as all work performed on items that are performed after the transfer or ownership to Airbus i. e. after the items has left the Original Supplier’s Manufacturing Site
Procurement Quality & Supply Chain PQDR — User Guide – R 5. 0 Page 334© AIRBUS S. All rights reserved. Confidential and proprietary document. Out Located Work • Why this requirement? (This is an exceptional requirement as the Airbus objective is for Suppliers not to perform this activity) When applicable: – Airbus is responsible for ensuring Supplier according to EASA PART 21 G § 139 a: b – Any sub contracting of OLW by the Original Equipment Manufacturer (OEM) must be authorised by Airbus. However the OEM is responsible for integrating any sub contracting process into its QM-System documentation and is responsible for ensuring that the work conforms to the applicable design data – The type of OLW activities that can be performed are: • Outstanding work created from shortages or incomplete work • Late design definitions • Work related modifications • Equipment standard exchange • Non-conformities identified after delivery • Trouble-Shooting • Replacement of defective or damaged components by components with the same part number
Procurement Quality & Supply Chain PQDR — User Guide – R 5. 0 Page 335© AIRBUS S. All rights reserved. Confidential and proprietary document. Out Located Work • How to meet this requirement? Comply with A 1130 Providing: • A completing the OLW Supplier Authorization Request form, (Appendix A attached to A 1130) • Demonstrate to Airbus how you comply to A 1130 (i. e compliance matrix) • A copy of authorised personnel list • Any supporting Data/ Documents in conjunction with Airbus (as necessary) Airbus reviews this information and either approves or rejects the Supplier request to perform Out Located Work process: – The Supplier shall contact Airbus Supply Chain Quality Procurement organisation to request (No work can be performed by the Supplier without Airbus written authorisation )
Procurement Quality & Supply Chain PQDR — User Guide – R 5. 0 Procurement Directorate Deliverables Sharing
Procurement Quality & Supply Chain PQDR — User Guide – R 5. 0 Page 337© AIRBUS S. All rights reserved. Confidential and proprietary document. Deliverables Sharing • Why this requirement? To allow Airbus & Supplier Teams to exchange data, information and deliverables Always up to date documents Available from anywhere at any time Secured environment Reduces administrative workload – time saving • How to meet this requirement? Supplier must sign the General Terms & Conditions (GTC) Supplier must appoint an administrator who will be responsible for the creation of Airbus Supplier accounts Ge. RS room coordinator is responsible for adding new Airbus Supplier accounts to the e. Room Supplier uploads deliverables to the e. Room
Procurement Quality & Supply Chain PQDR — User Guide – R 5. 0 Page 338© AIRBUS S. All rights reserved. Confidential and proprietary document. Example of Ge. RS Other folders can be created by the room Coordinators to complete the existing templatethis folder allows you to exchange files / draft documents with the other room members. General structure this folder allows you to exchange SABER modelsthis folder should contain at least: CAM, Logbook, Supplier Programme Status Report & Project Milestones ECM (COMO): Engineering Coordination Memosthis folder should contain at least: Product Specification and appendices & Change request to manage EPR and DCR
Procurement Quality & Supply Chain PQDR — User Guide – R 5. 0 Procurement Directorate Documentation Rules
Procurement Quality & Supply Chain PQDR — User Guide – R 5. 0 Page 340© AIRBUS S. All rights reserved. Confidential and proprietary document. Documentation Rules • Why this requirement? To enable documentation management for the Supplier, Airbus and when relevant Airworthiness authorities • How to meet this requirement? Include information such as title of document, reference and issue number, supplier name and address, … Sign all the documents, record the revisions done and identify pages that have been modified All documents will be in English
Procurement Quality & Supply Chain PQDR — User Guide – R 5. 0 Page 341© AIRBUS S. All rights reserved. Confidential and proprietary document. This document and all information contained herein is the sole property of AIRBUS S. A. S. No intellectual property rights are granted by the delivery of this document or the disclosure of its content. This document shall not be reproduced or disclosed to a third party without the express written consent of AIRBUS S. A. S. This document and its content shall not be used for any purpose other than that for which it is supplied. The statements made herein do not constitute an offer. They are based on the mentioned assumptions and are expressed in good faith. Where the supporting grounds for these statements are not shown, AIRBUS S. A. S. will be pleased to explain the basis thereof. AN EADS COMPANY