Презентация presentation Порошк мет-гия 766 слайдов

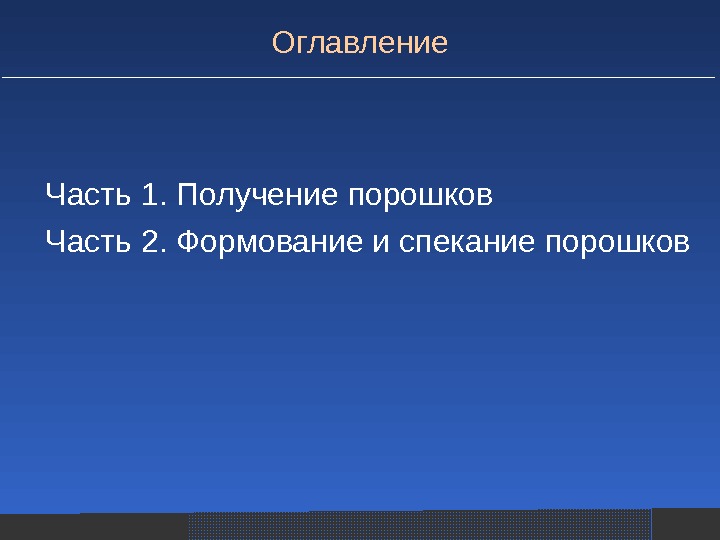

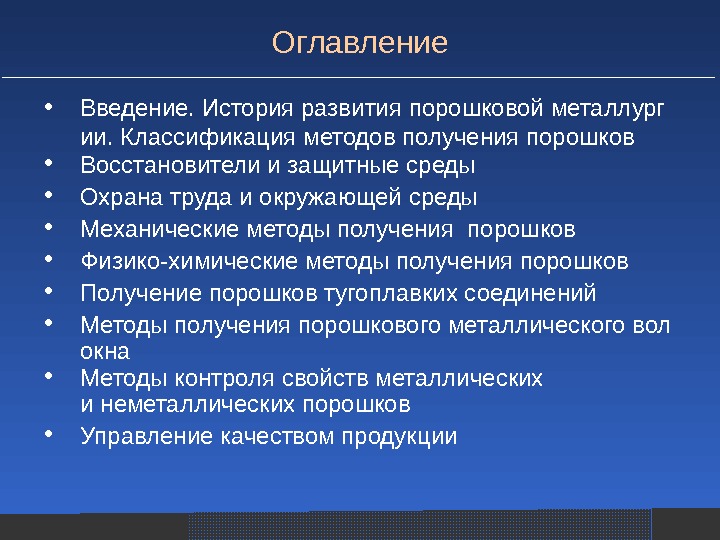
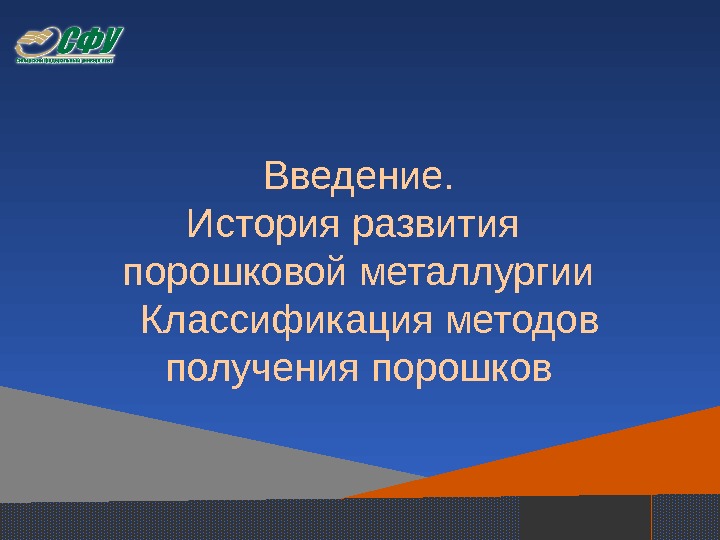

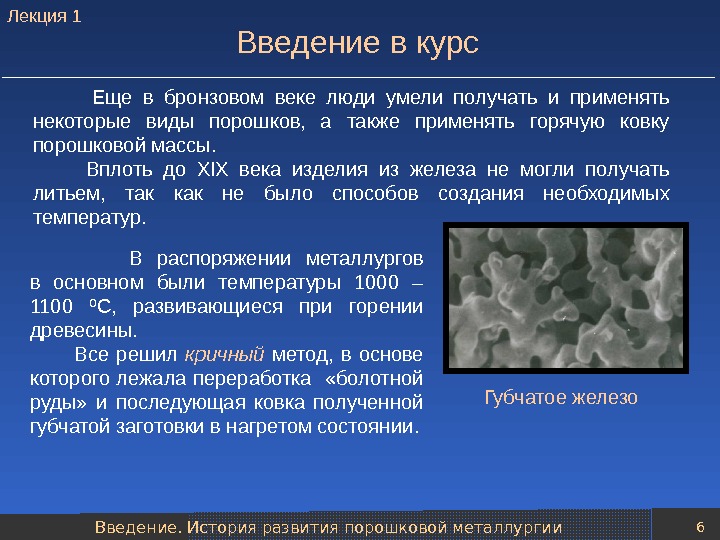
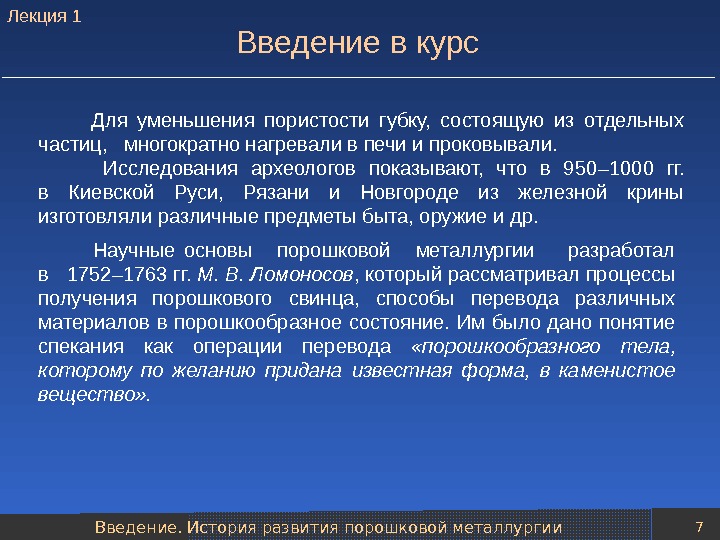
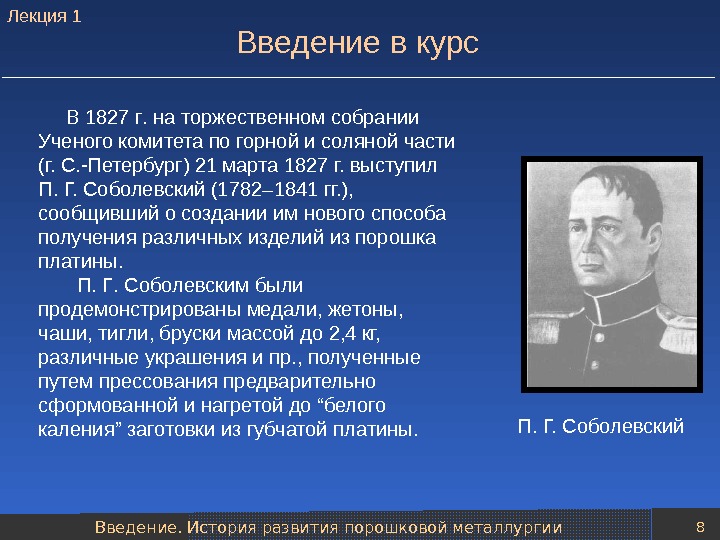
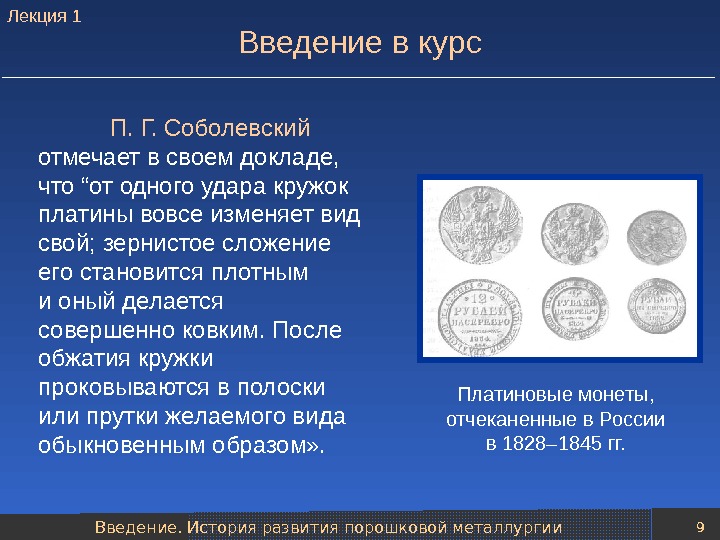
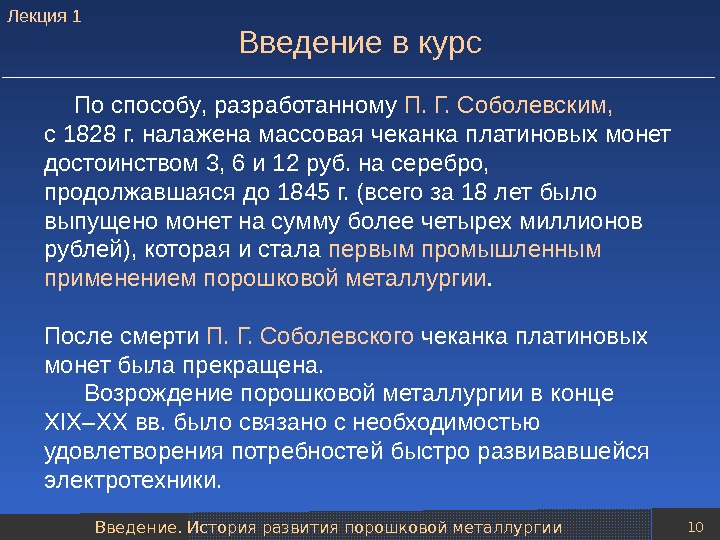
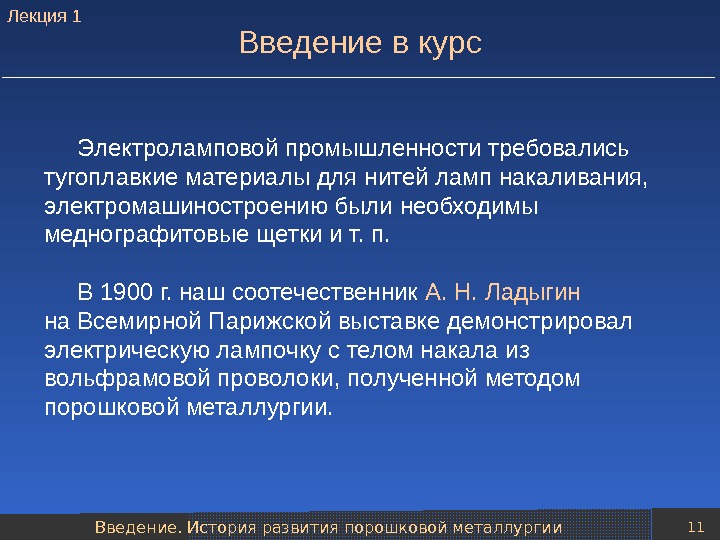
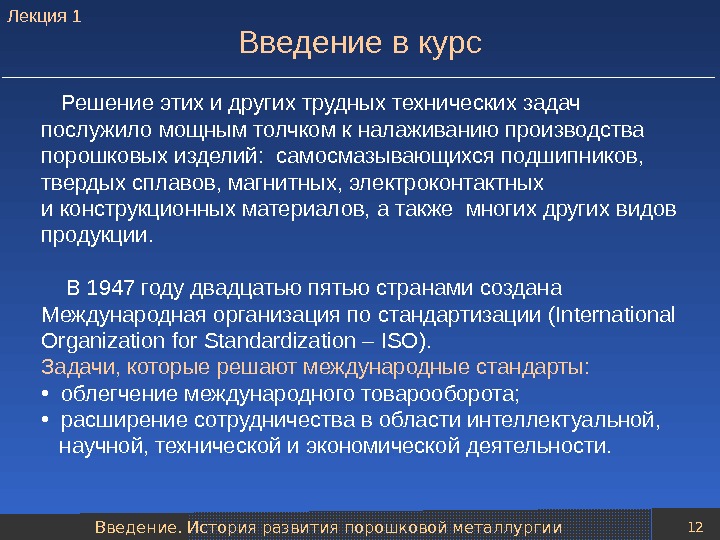
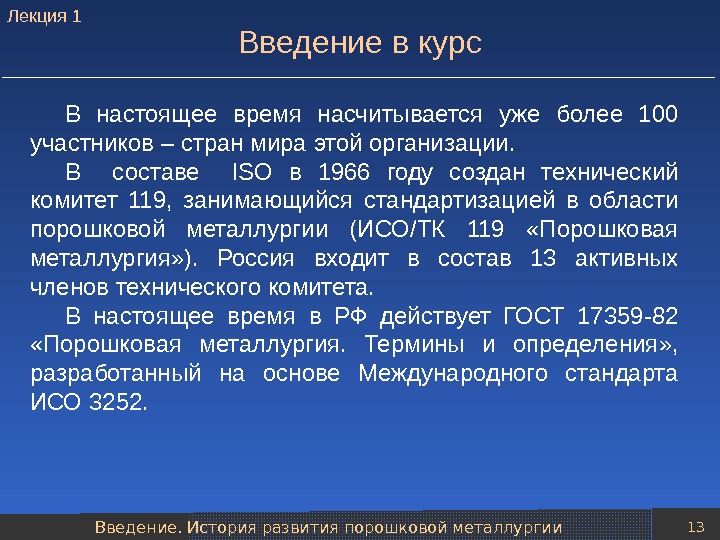
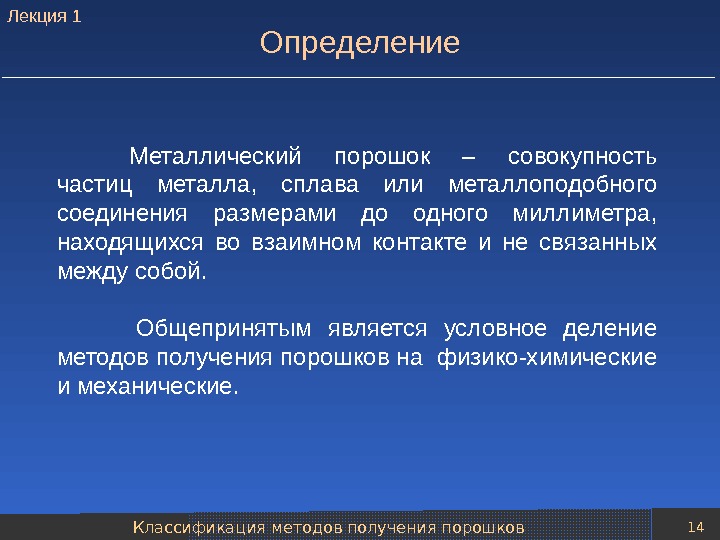
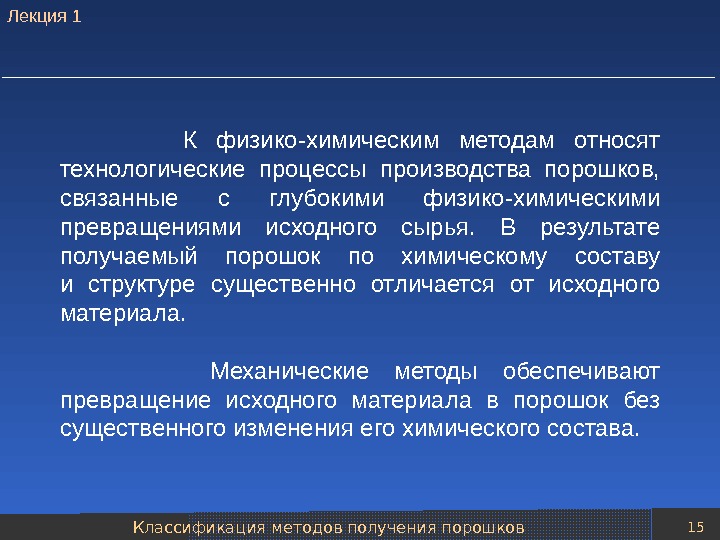
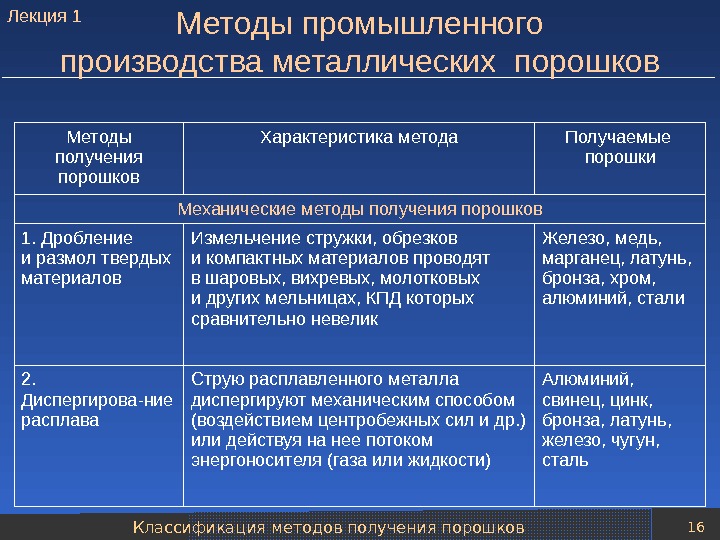
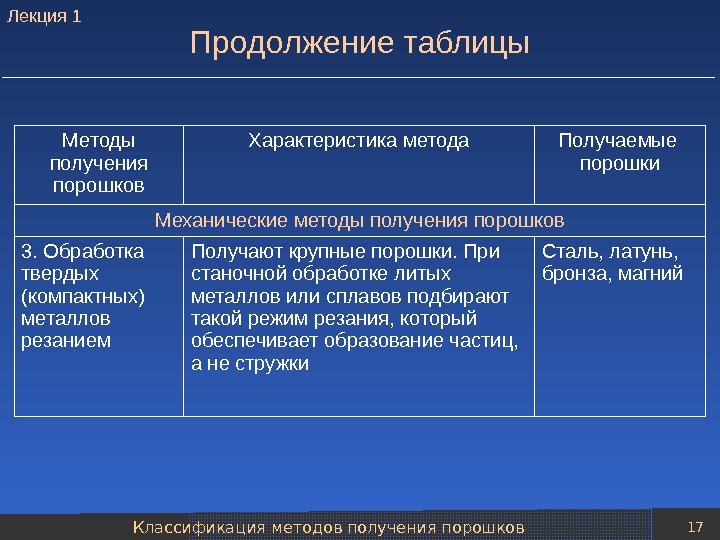

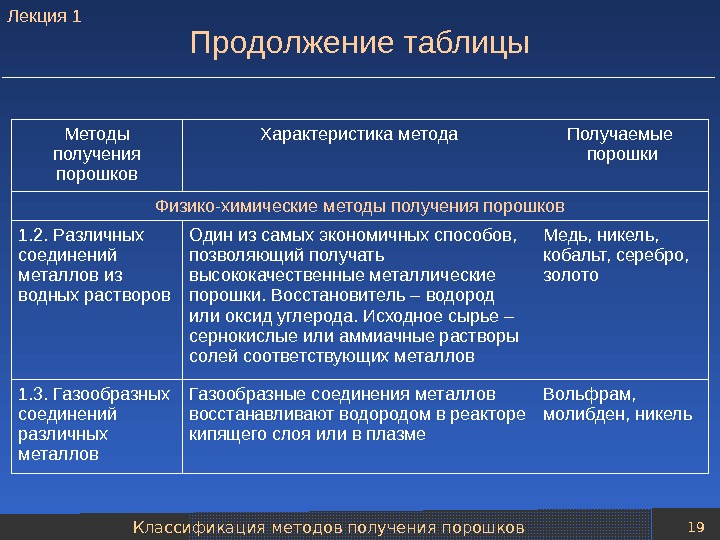
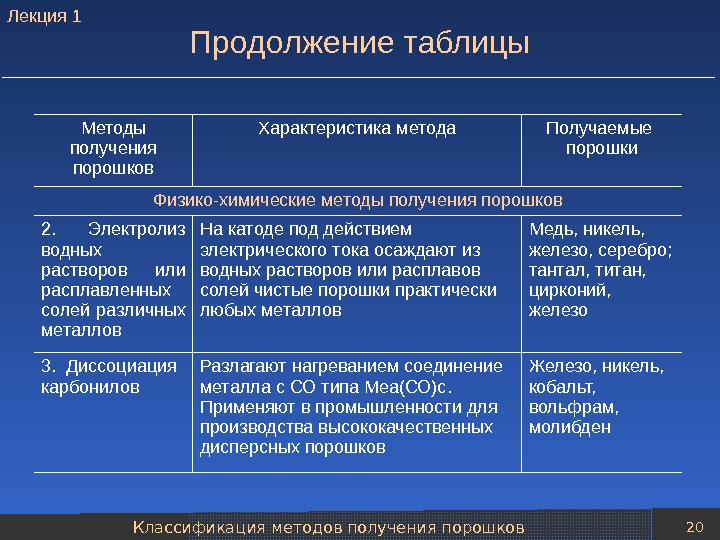
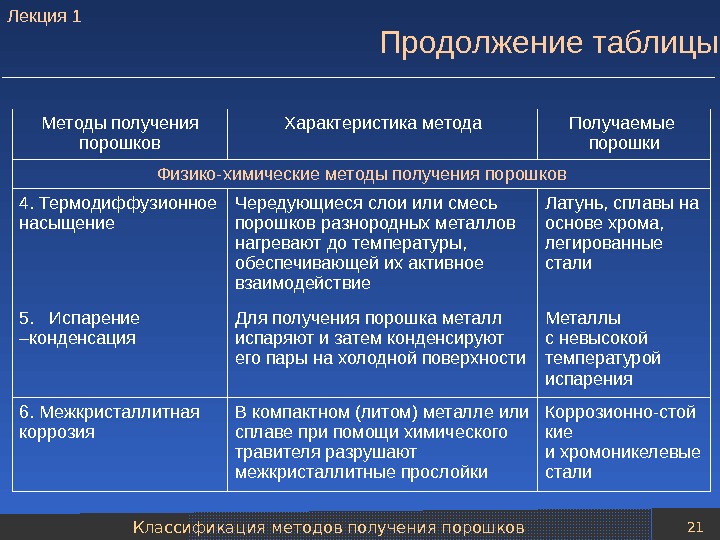
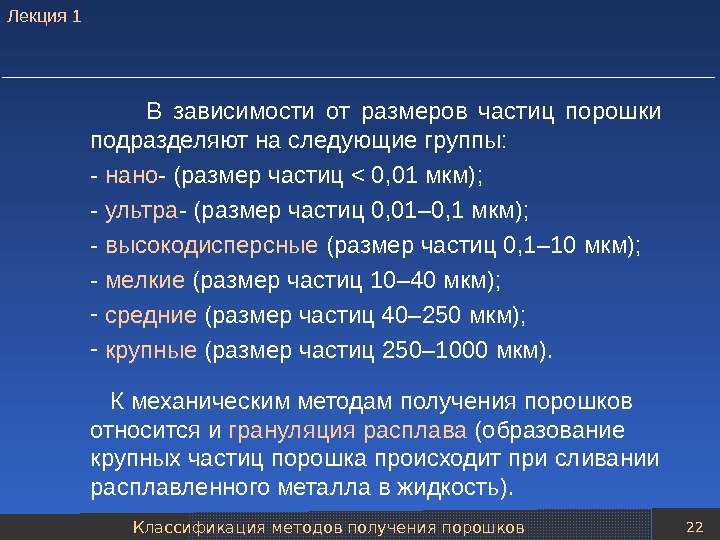
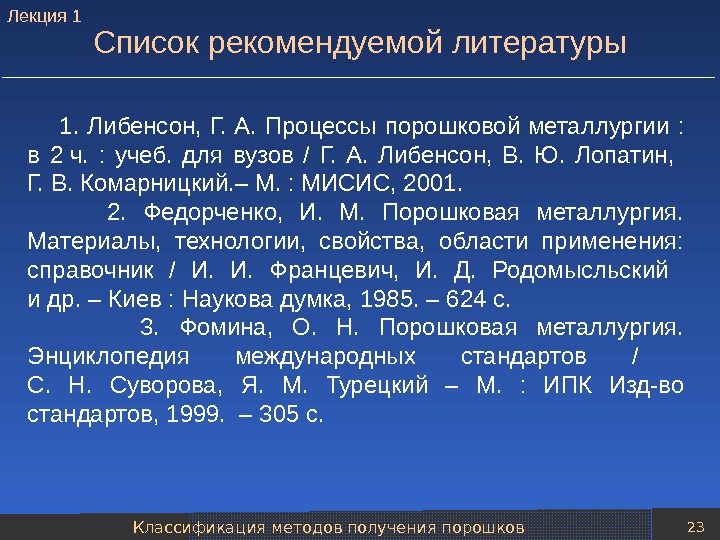
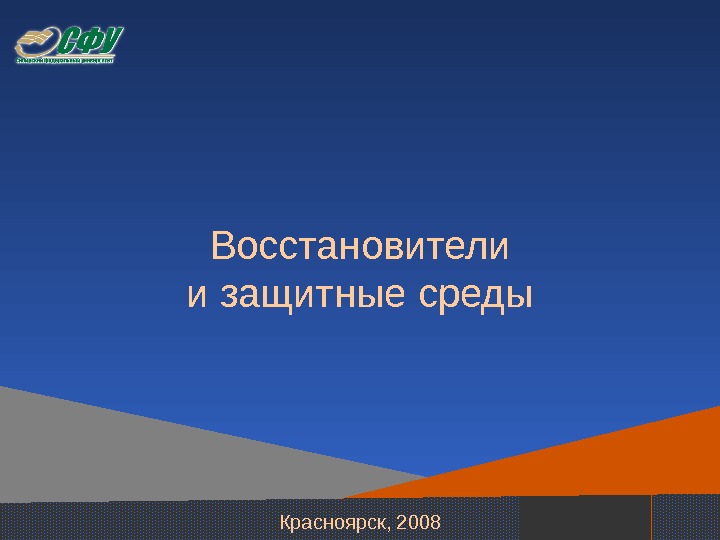
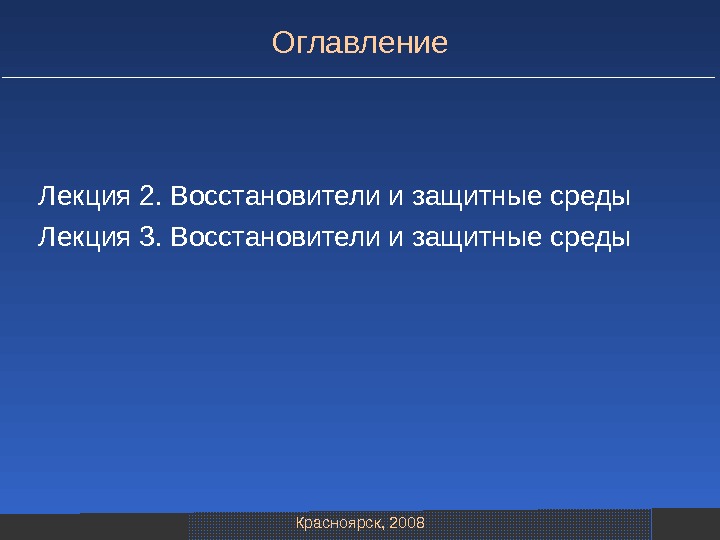

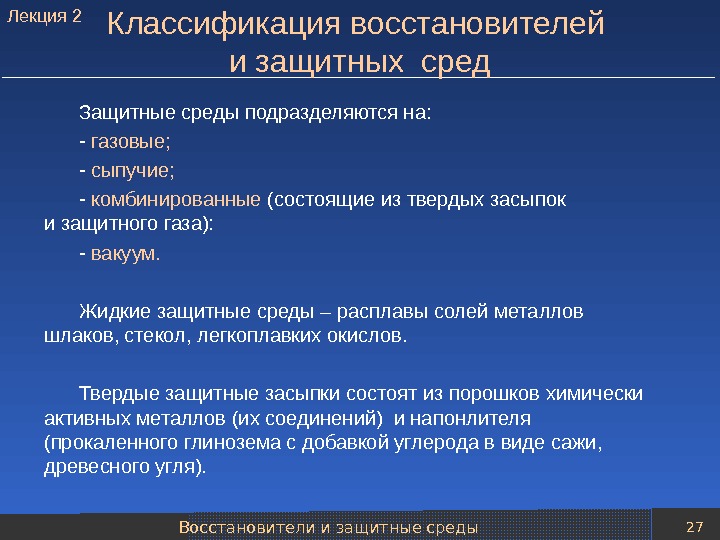
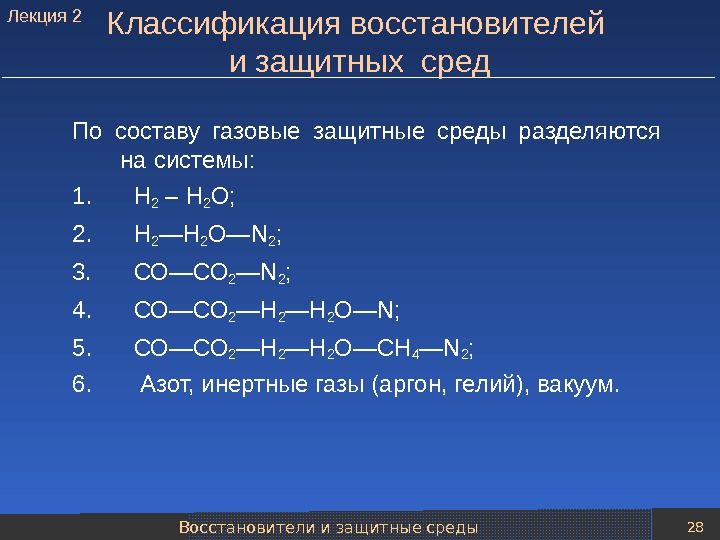
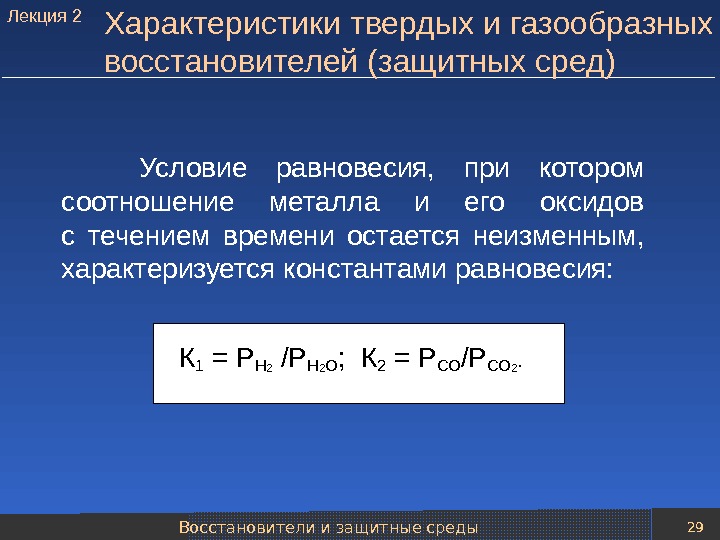

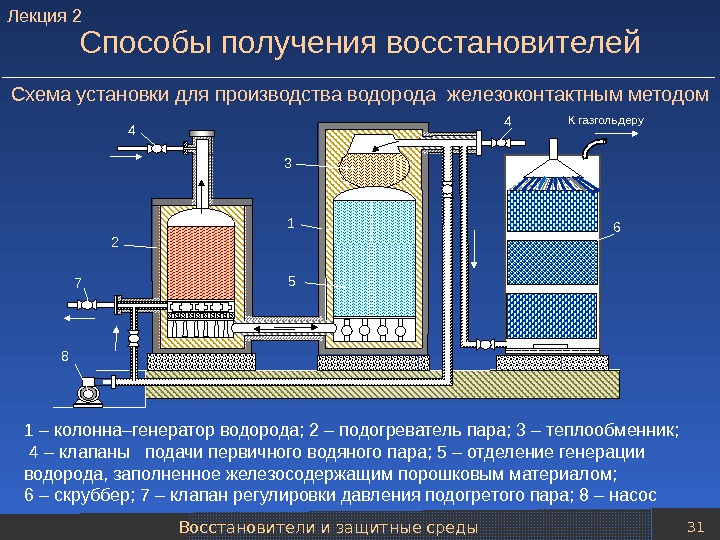
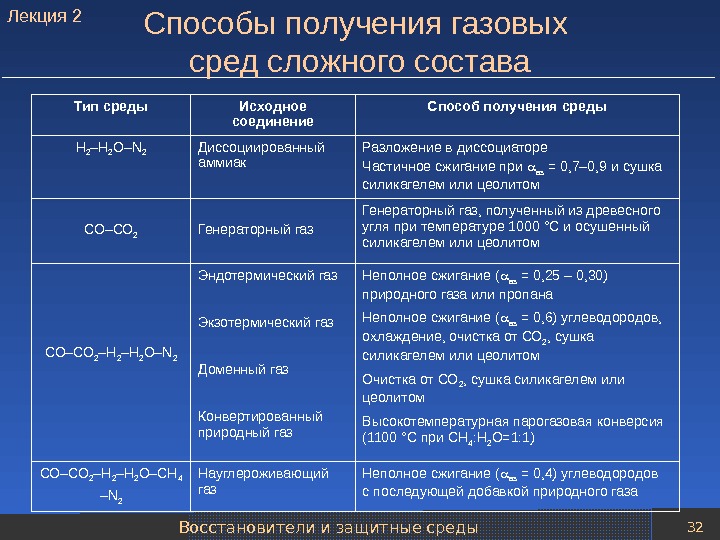
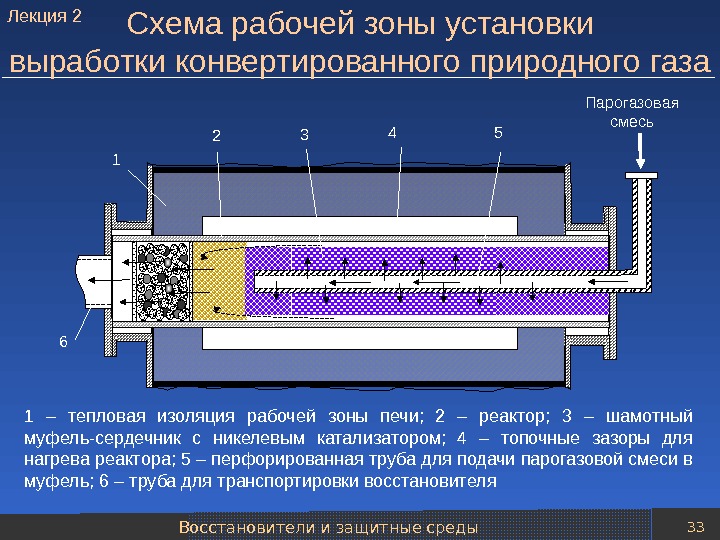

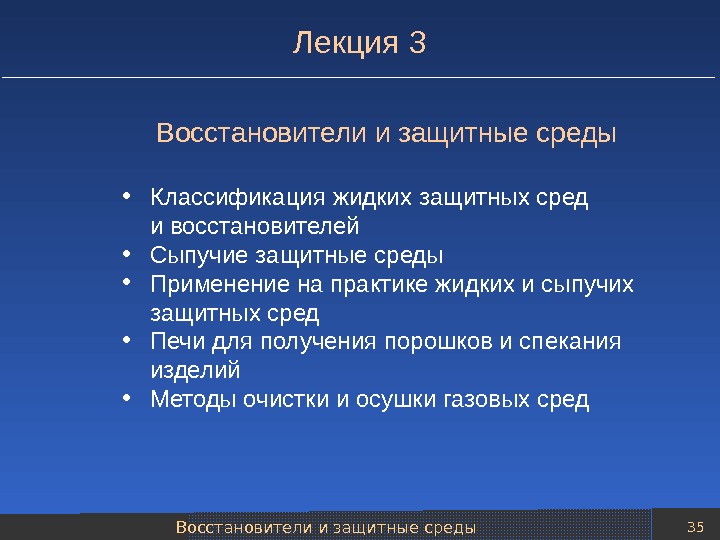


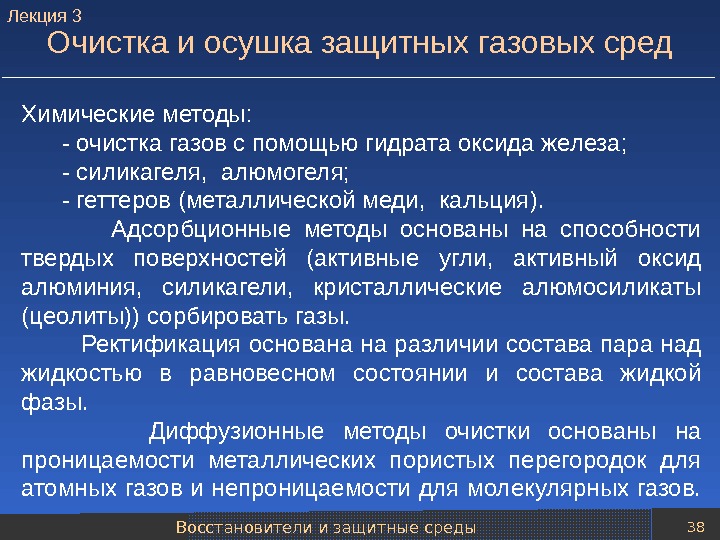
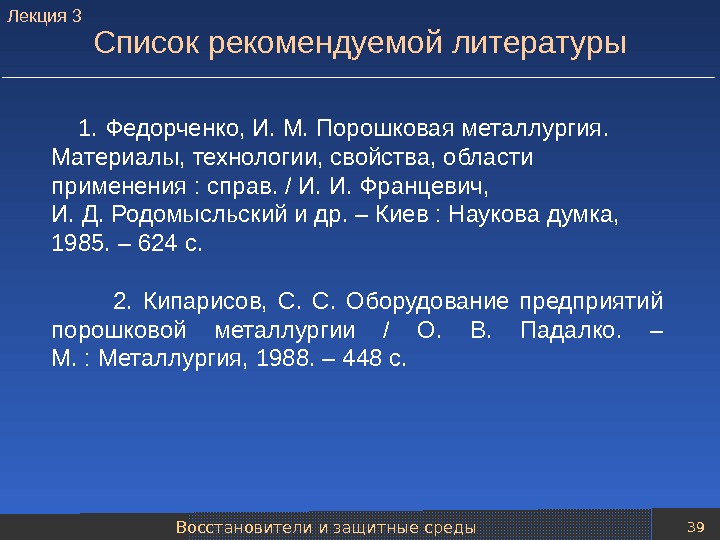
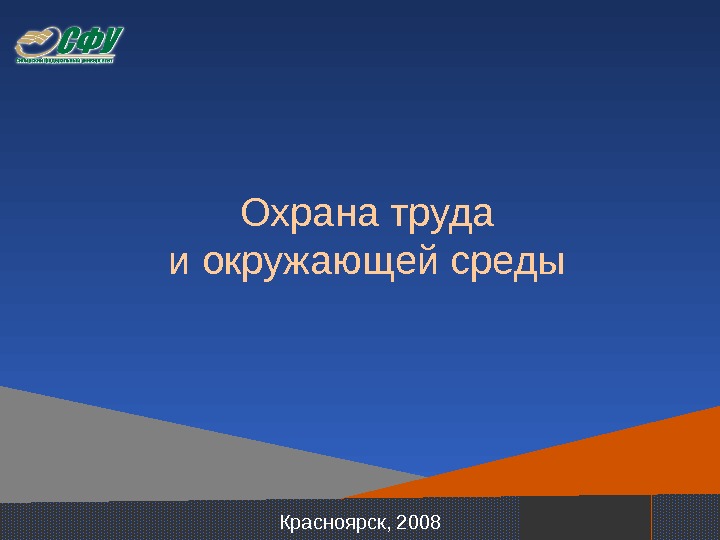
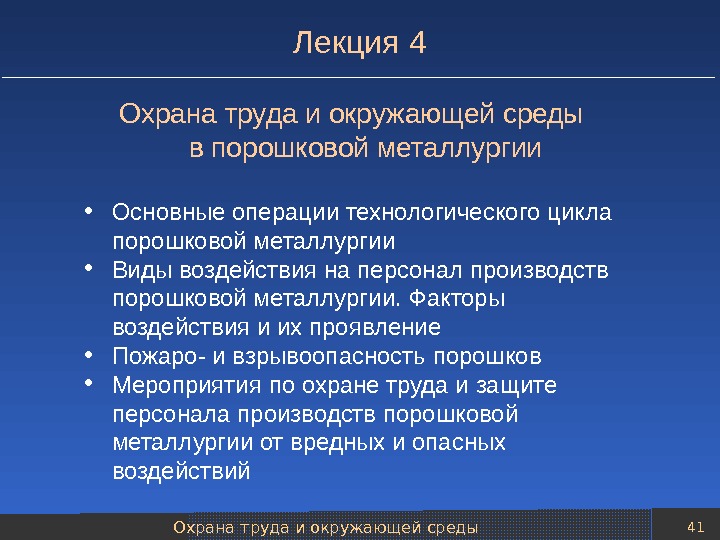


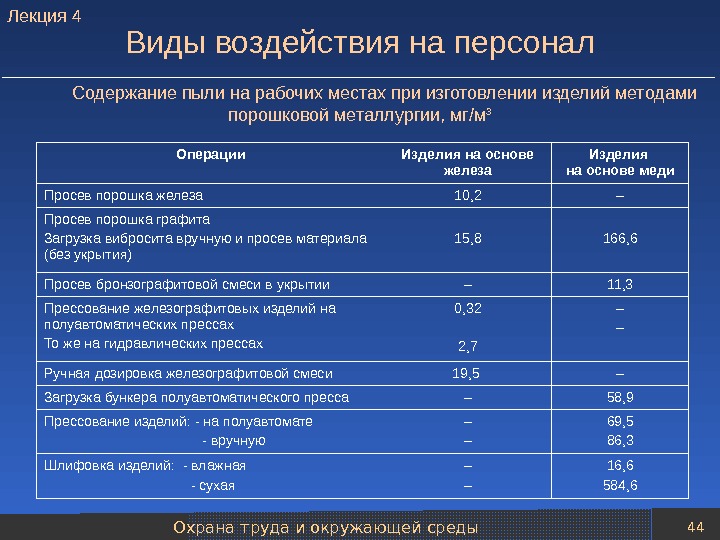
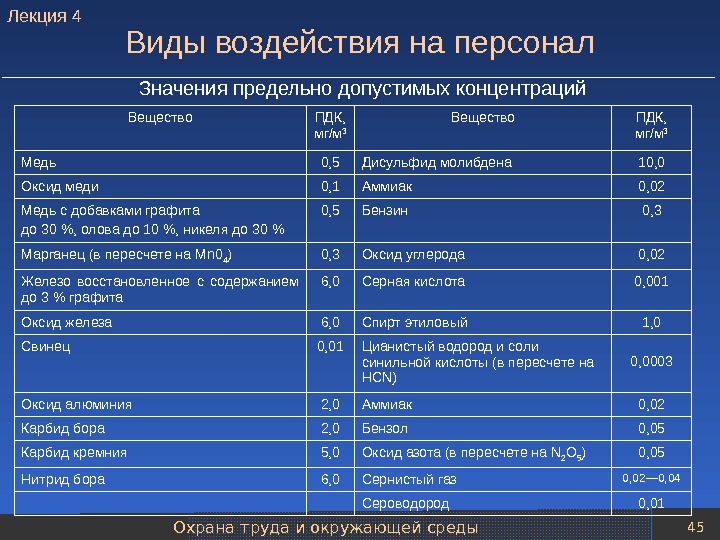
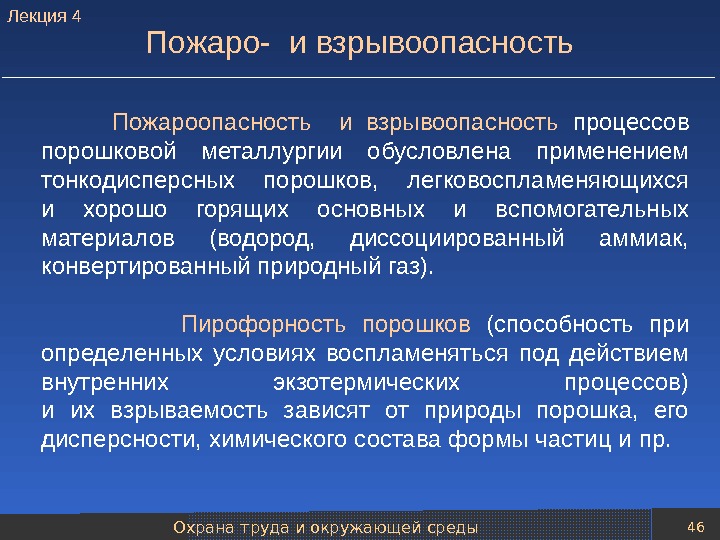
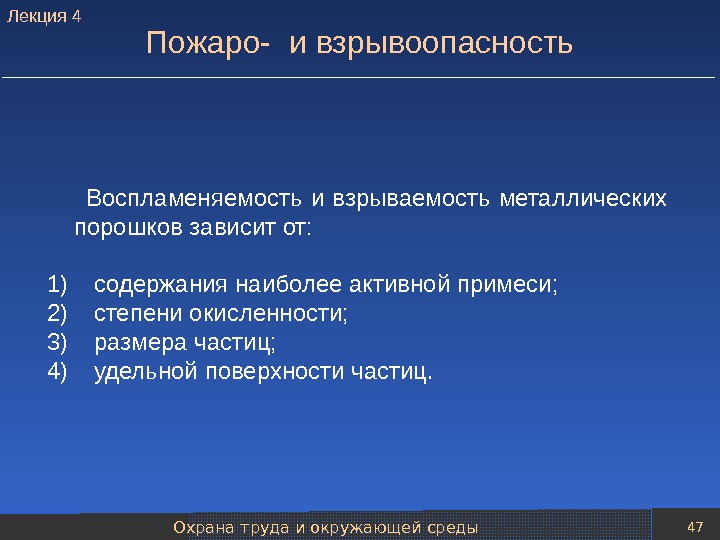
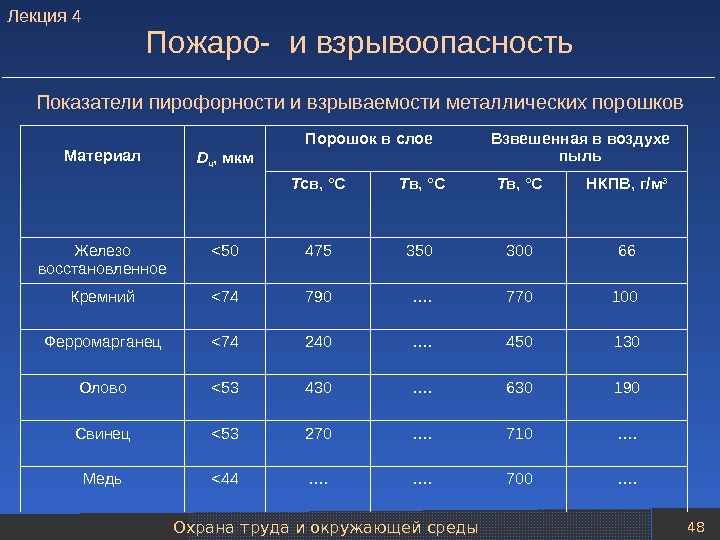
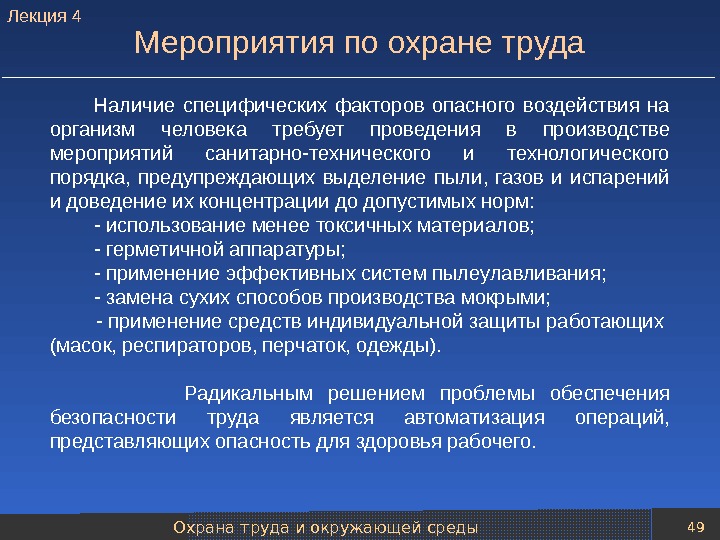
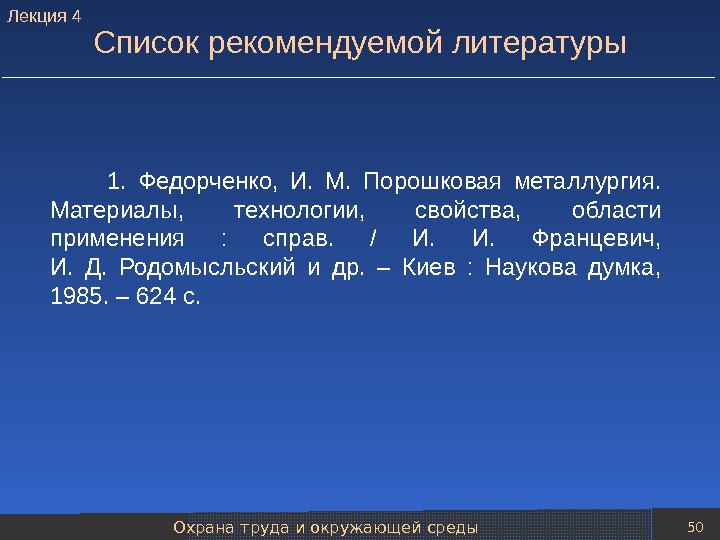
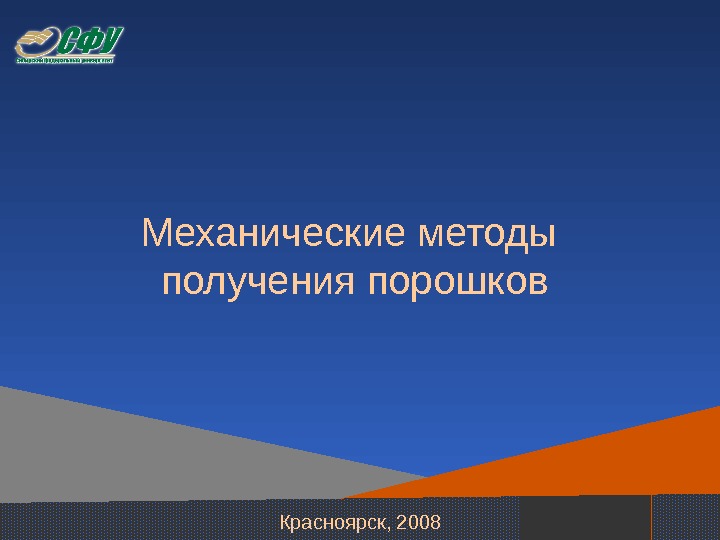
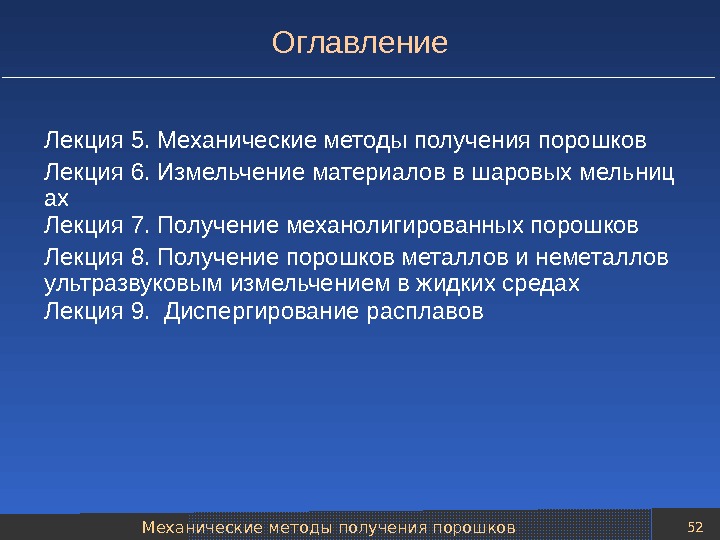

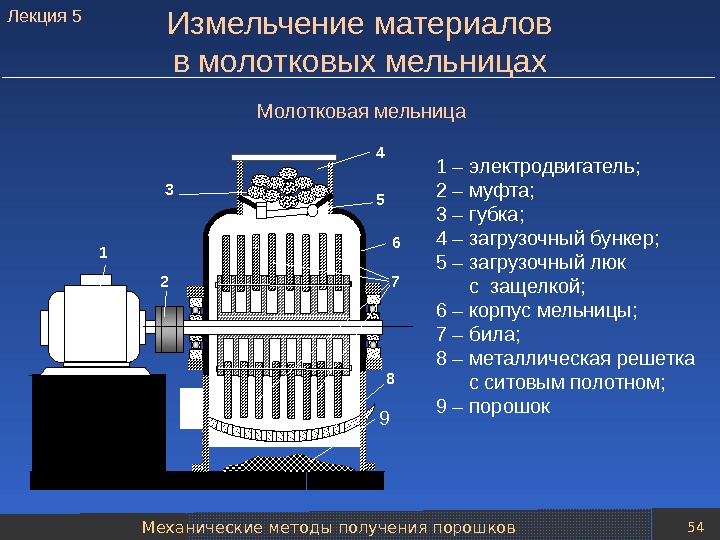
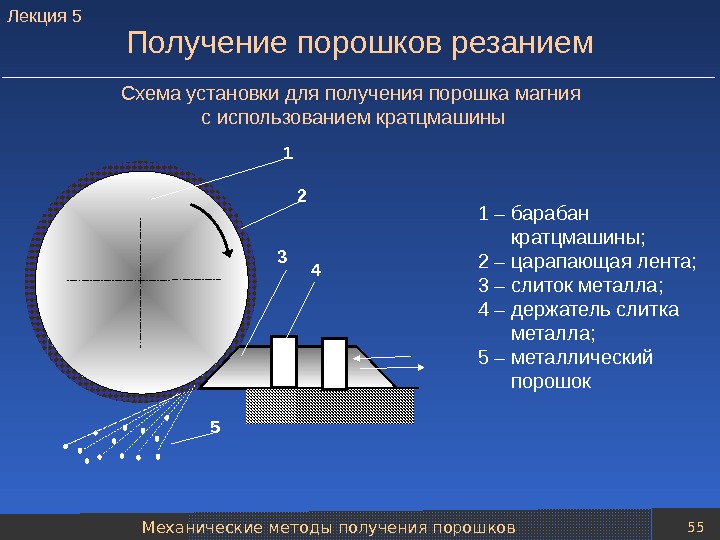
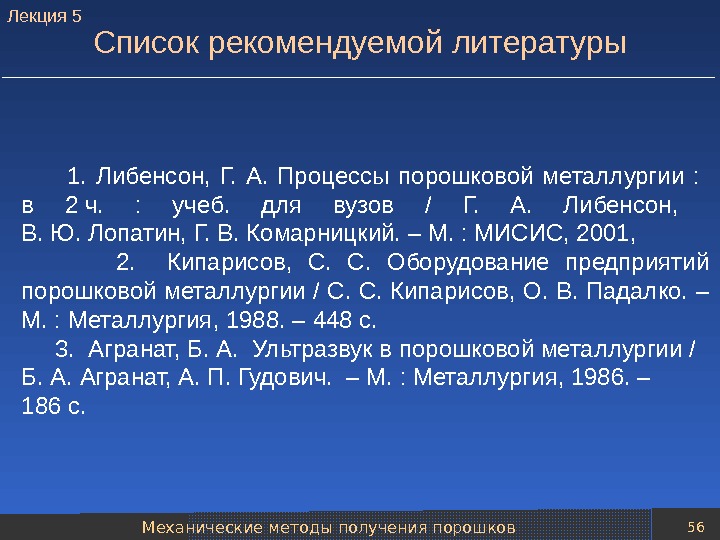
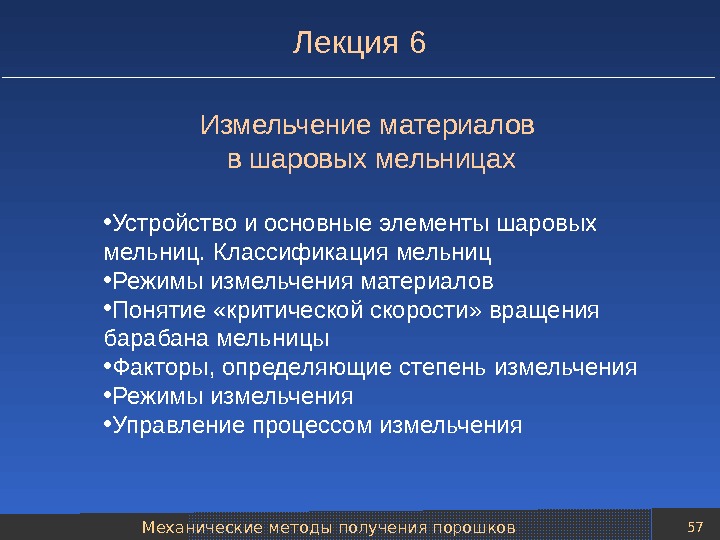
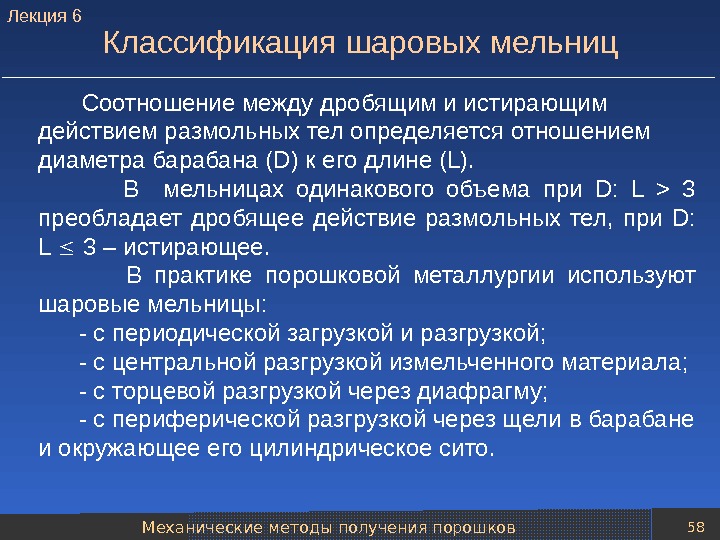

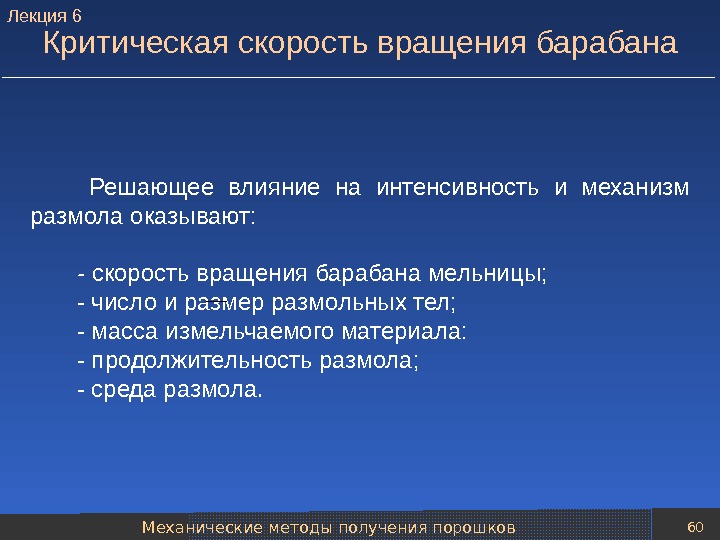

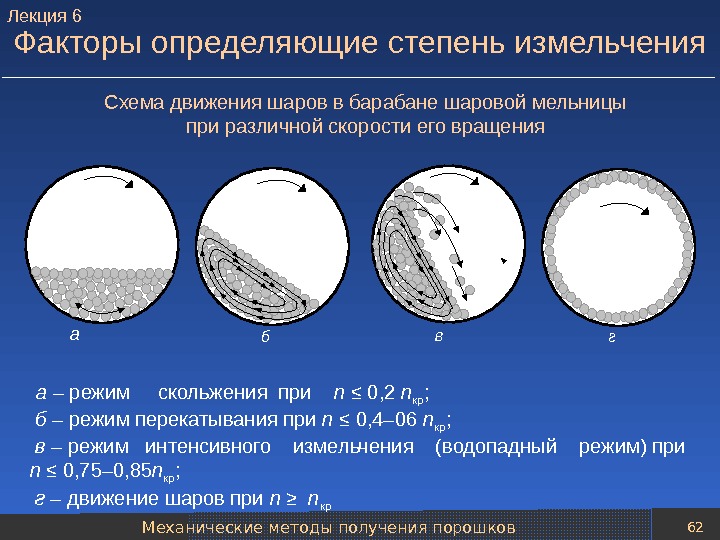
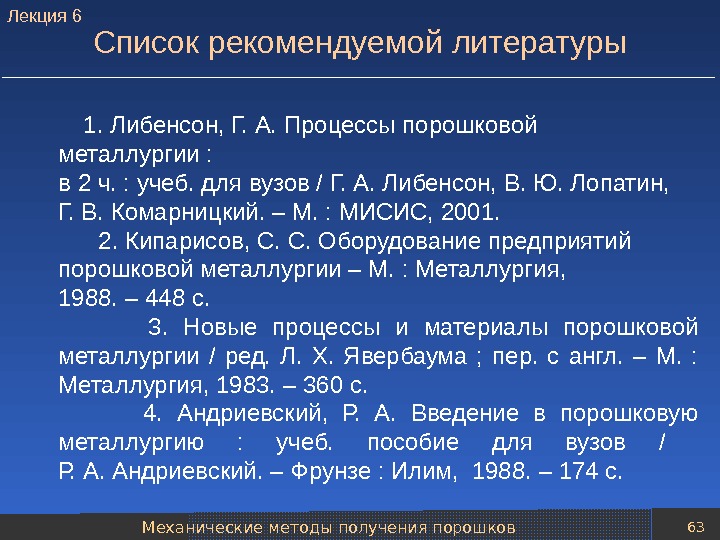
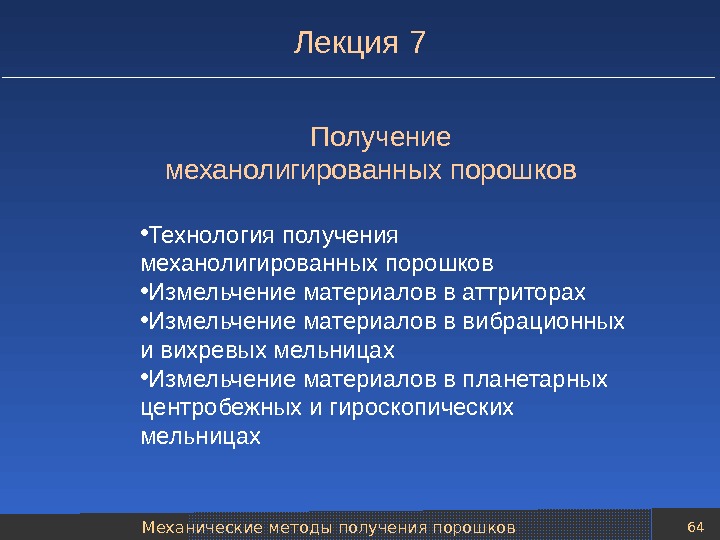
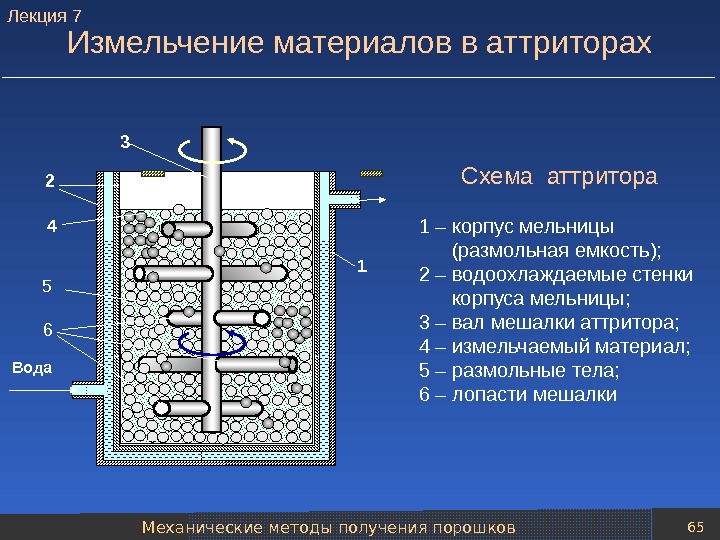
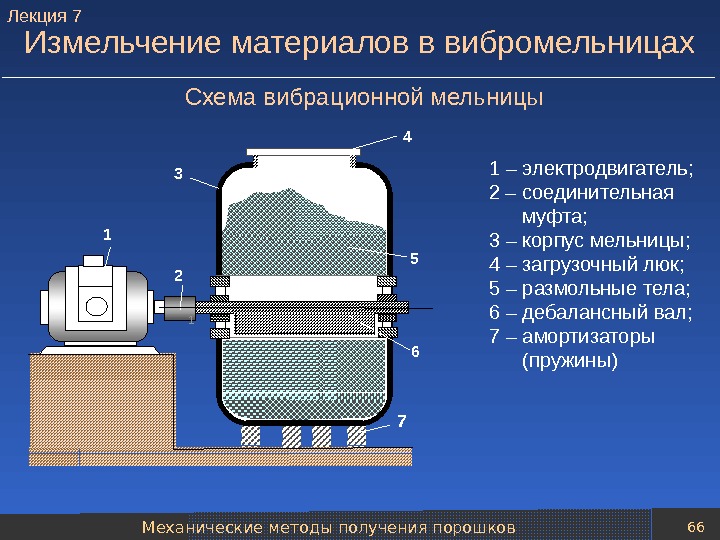
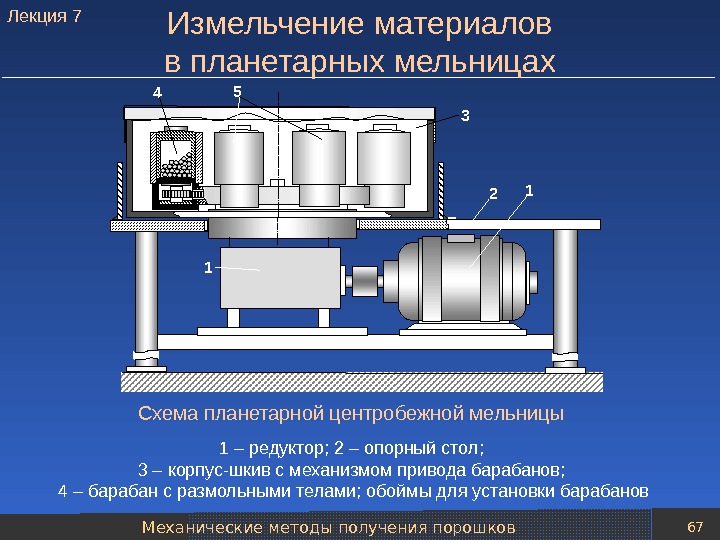
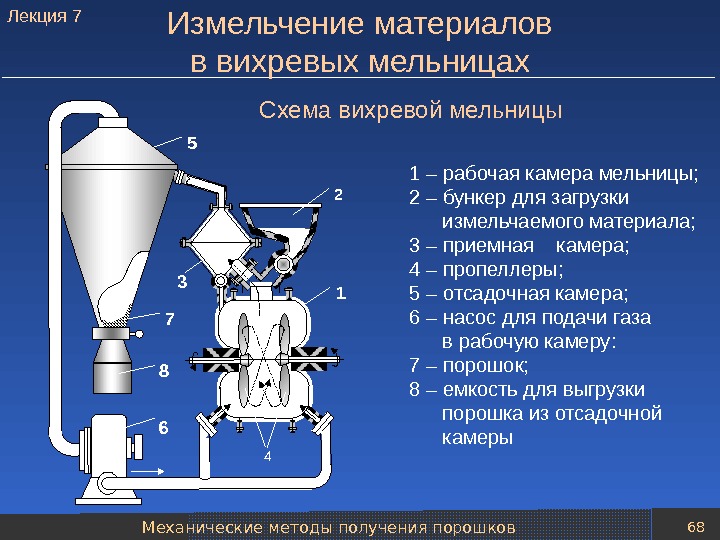
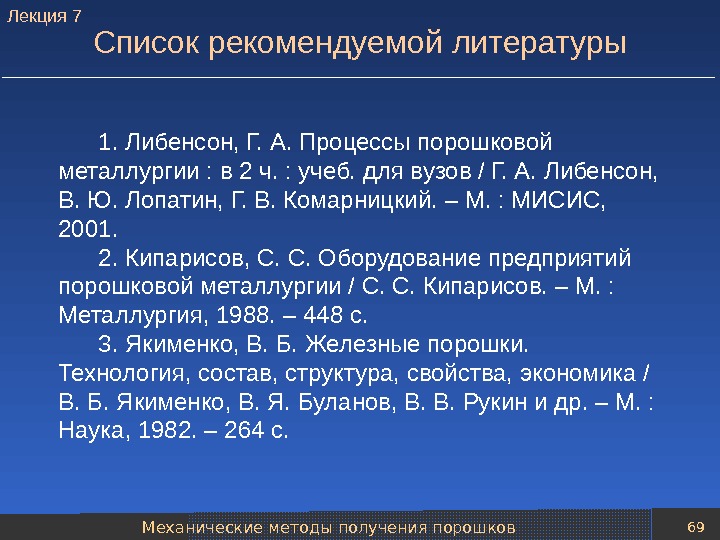
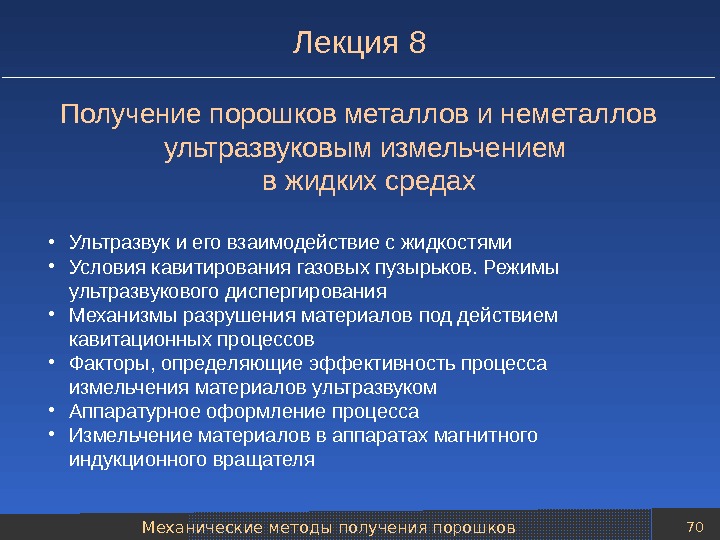

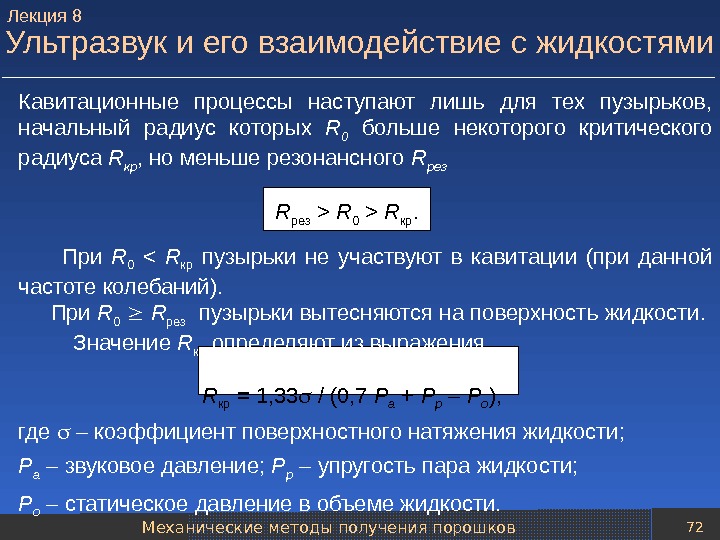
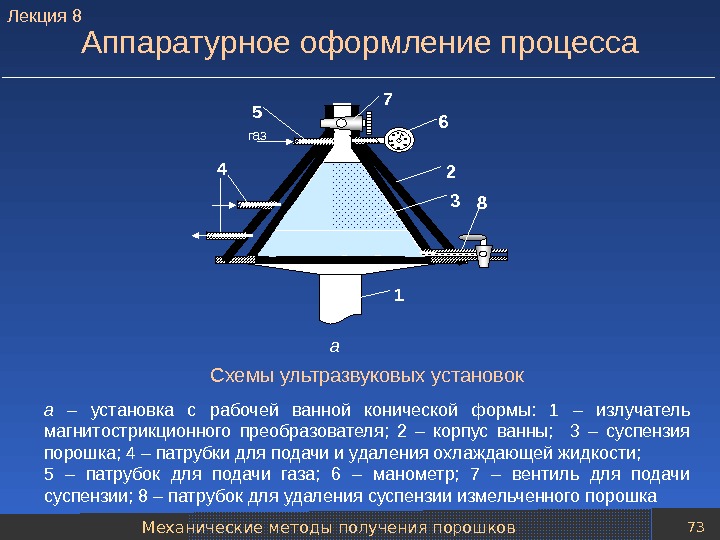
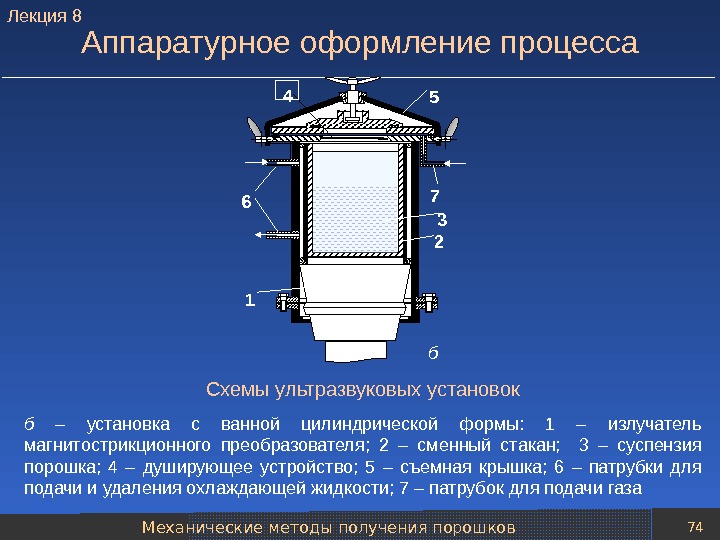
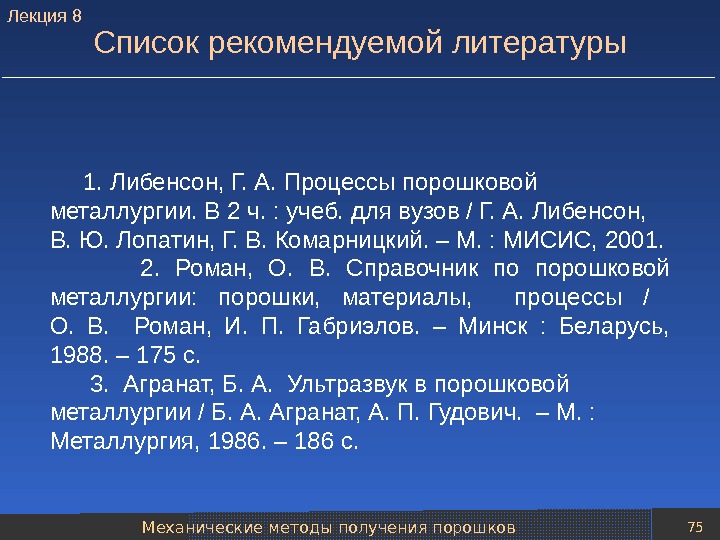
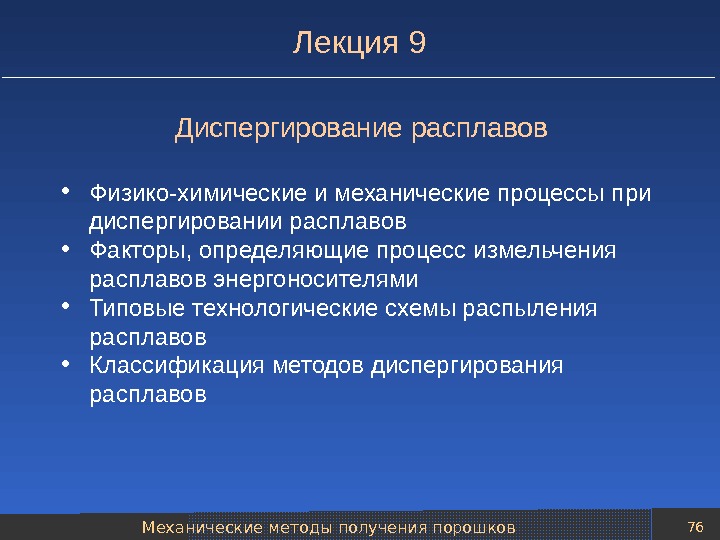
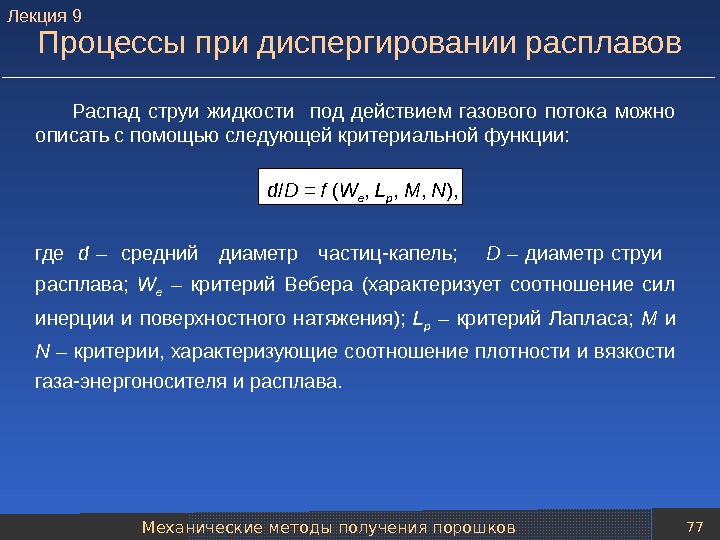
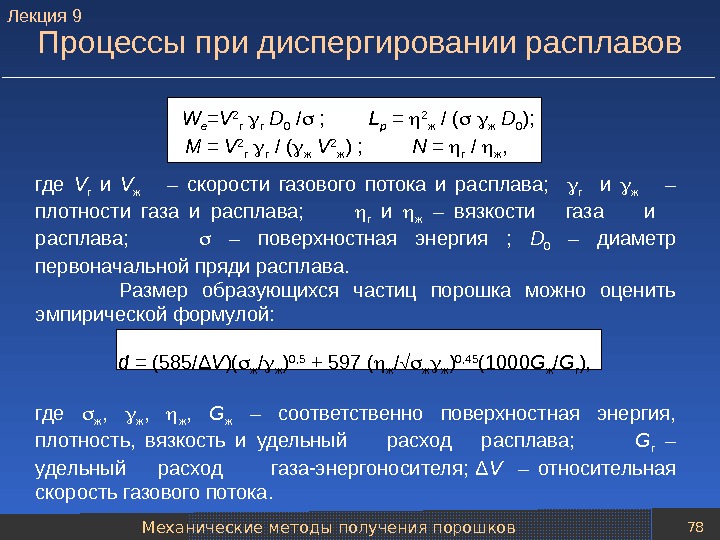
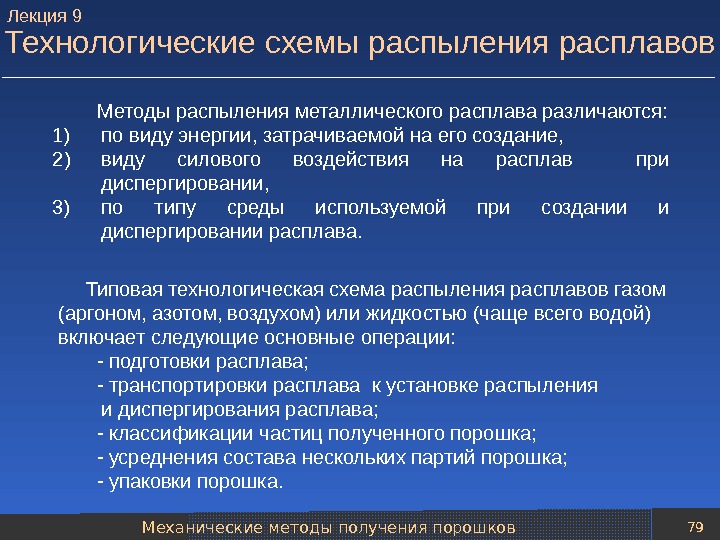
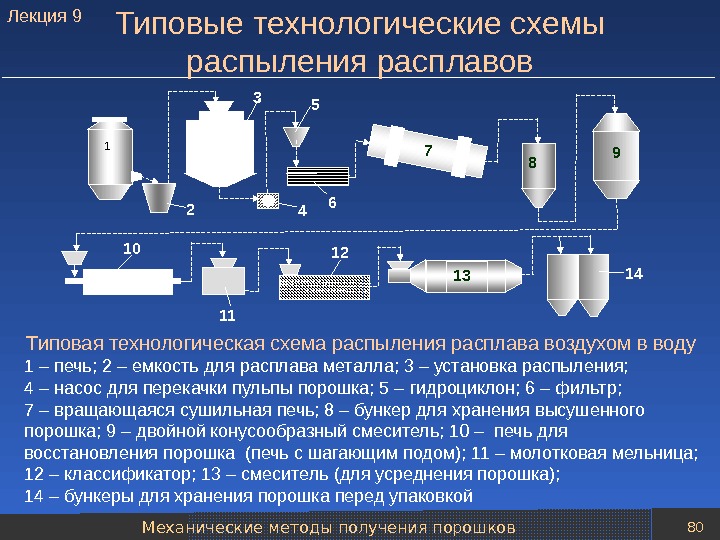
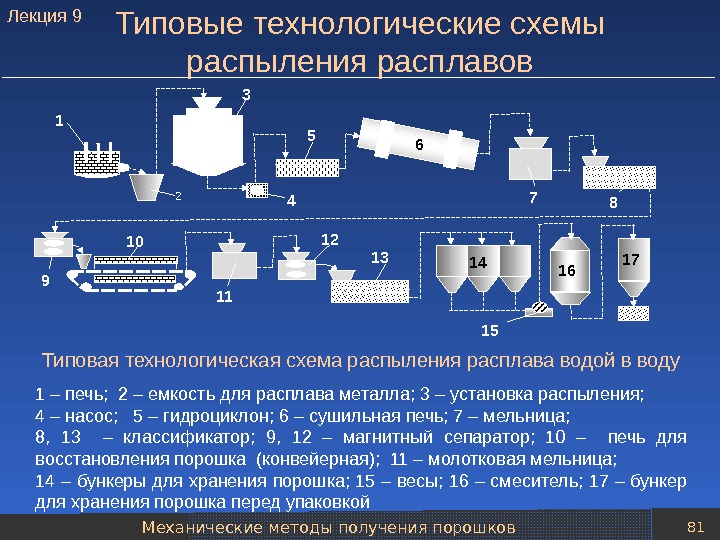
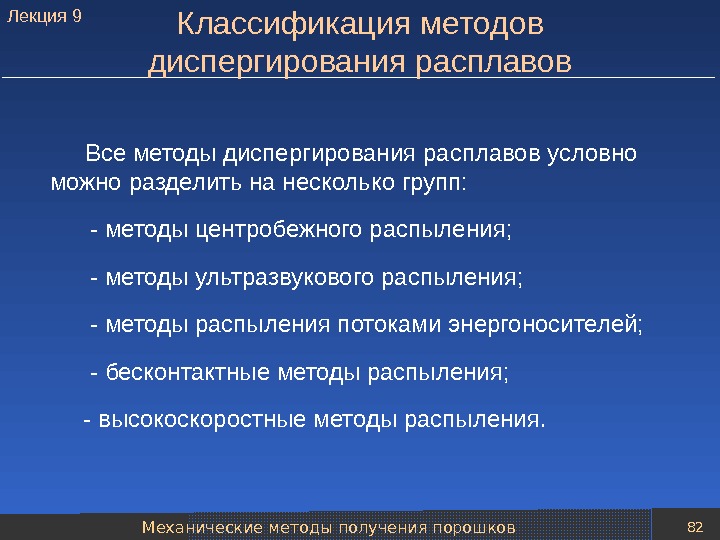

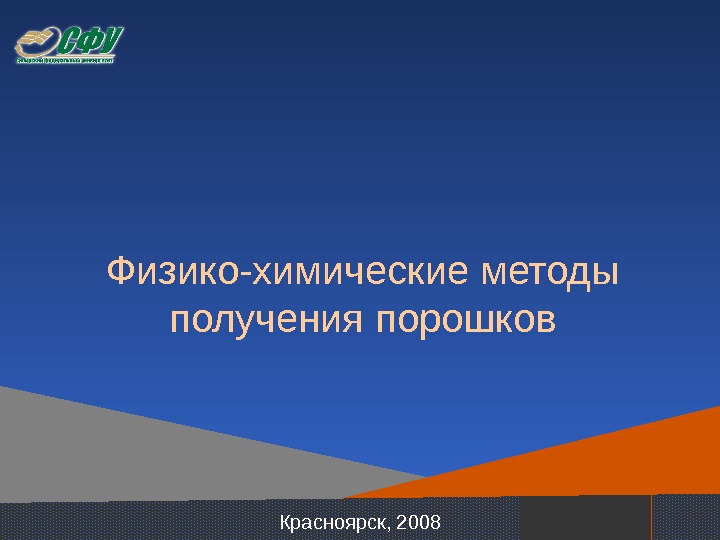
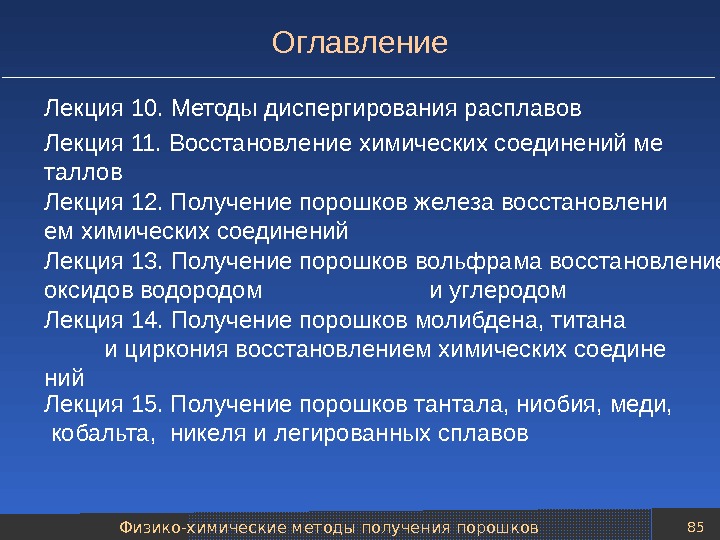
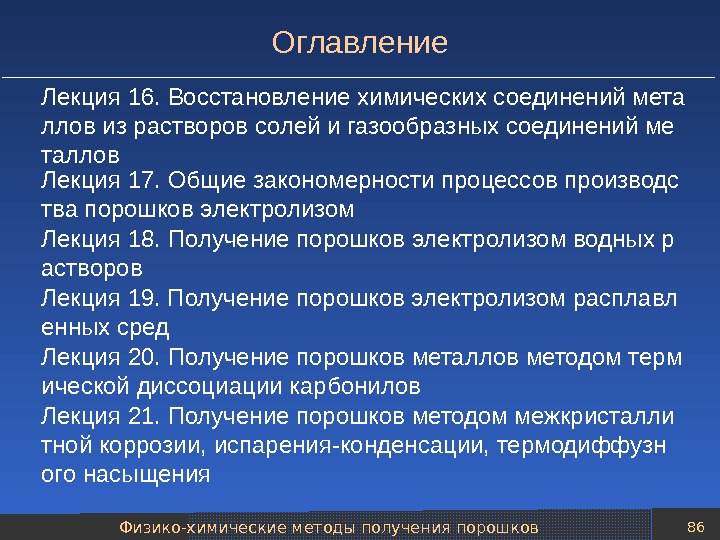
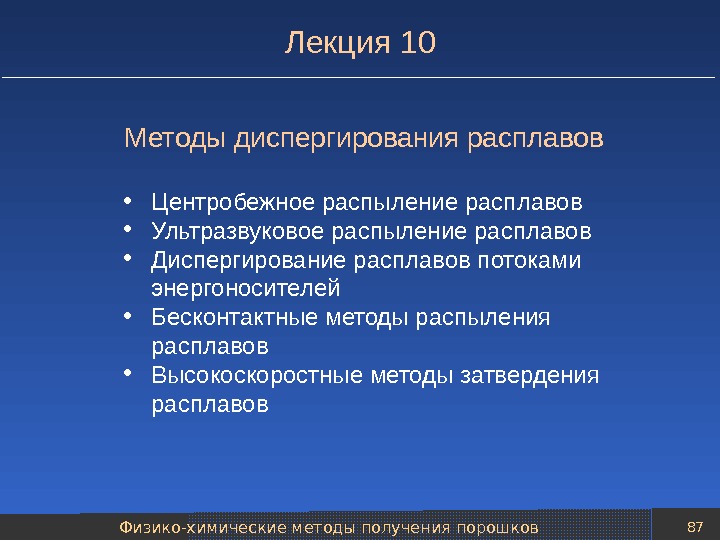

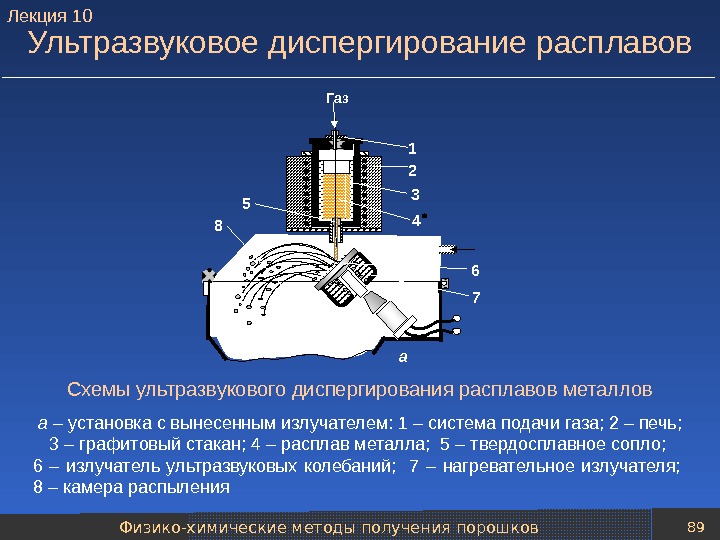
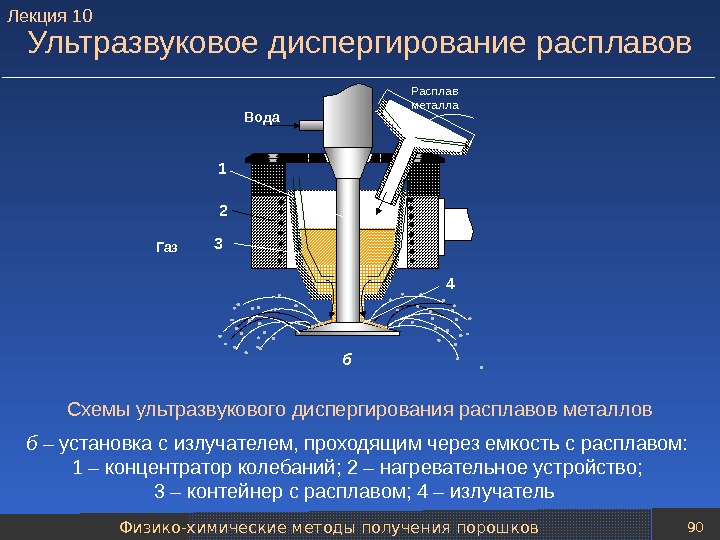
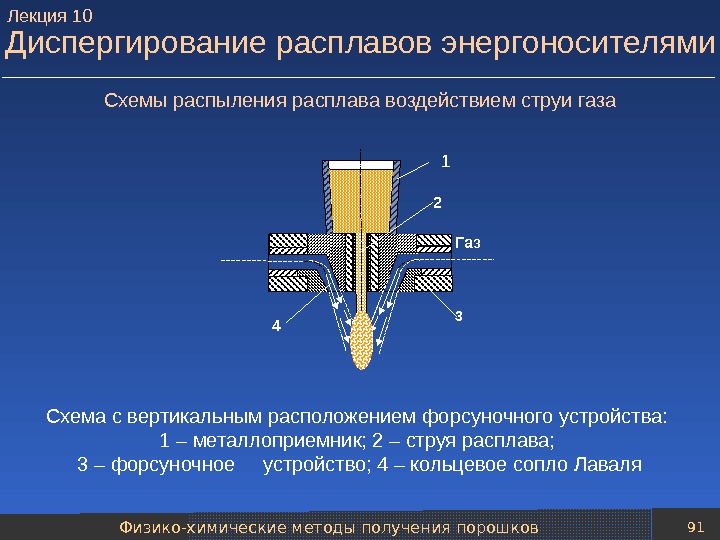
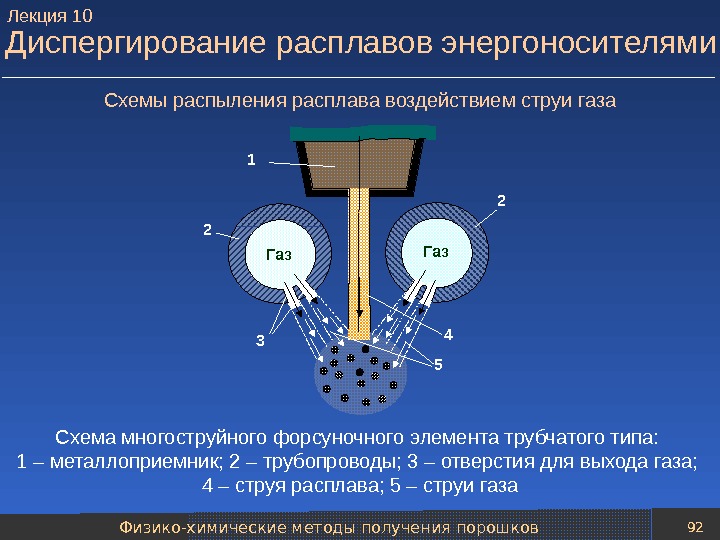

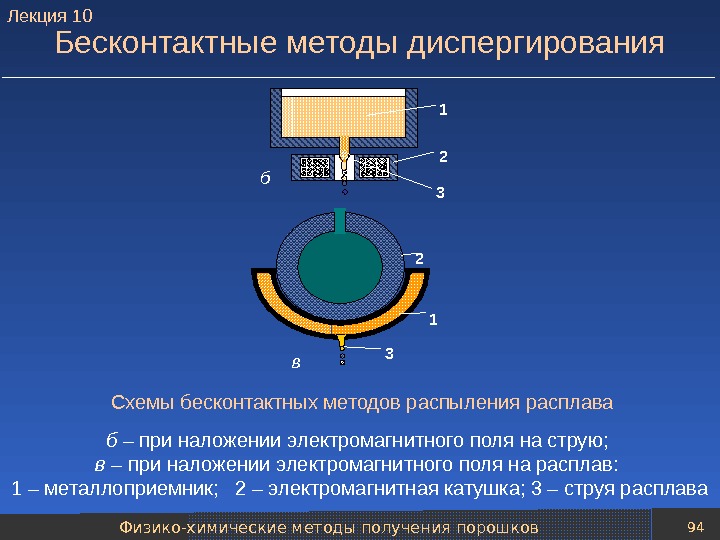
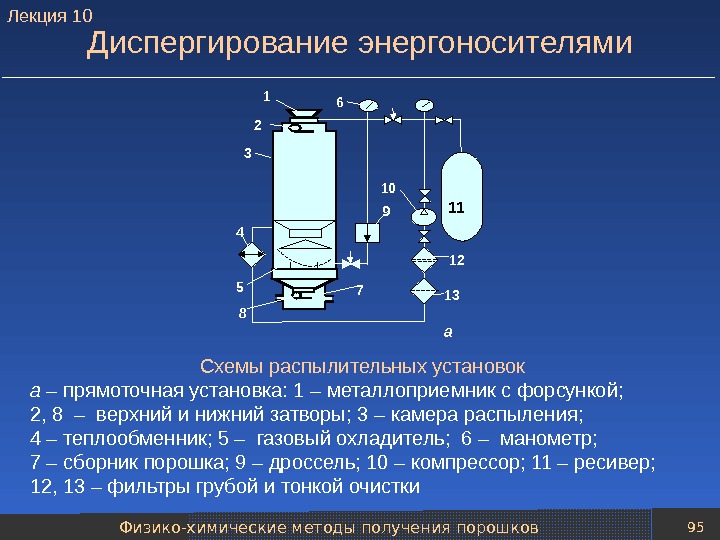
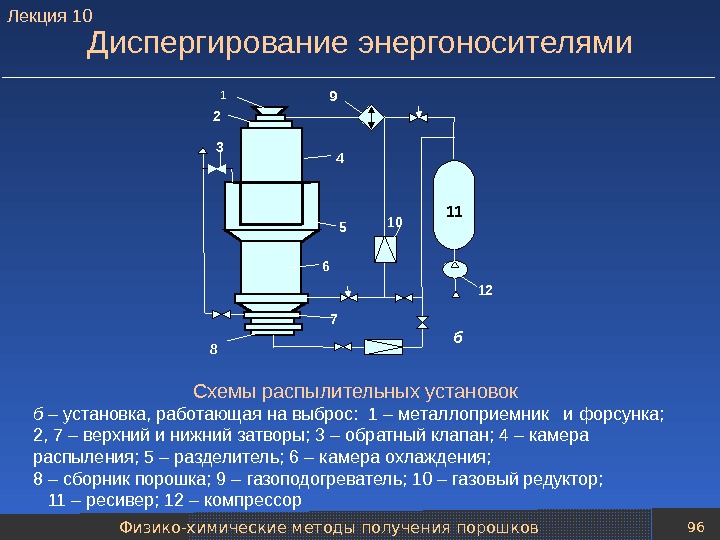
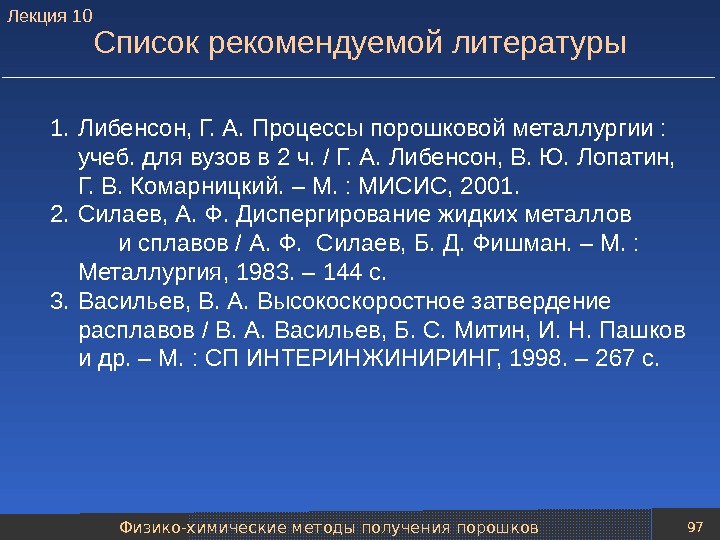
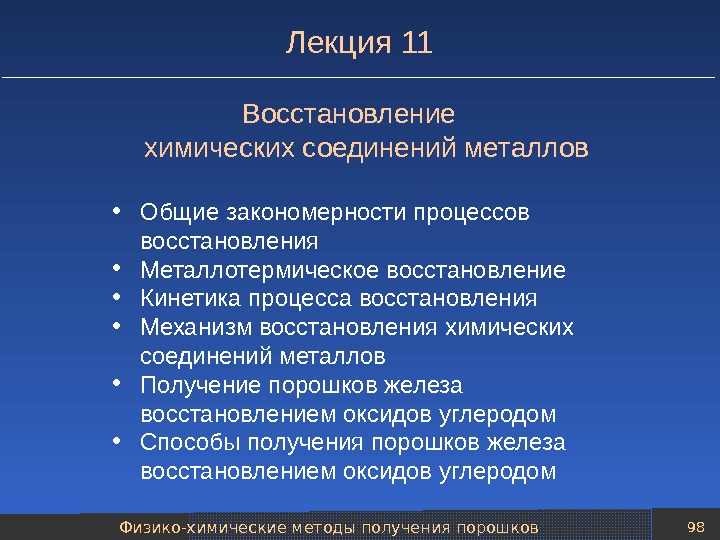
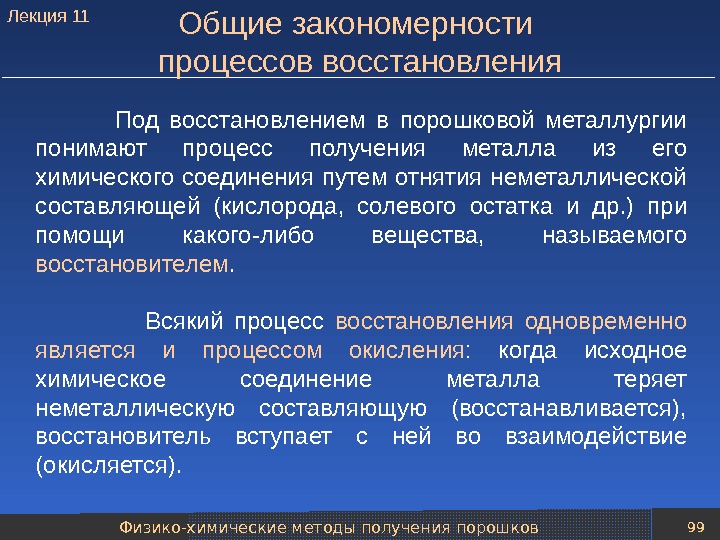
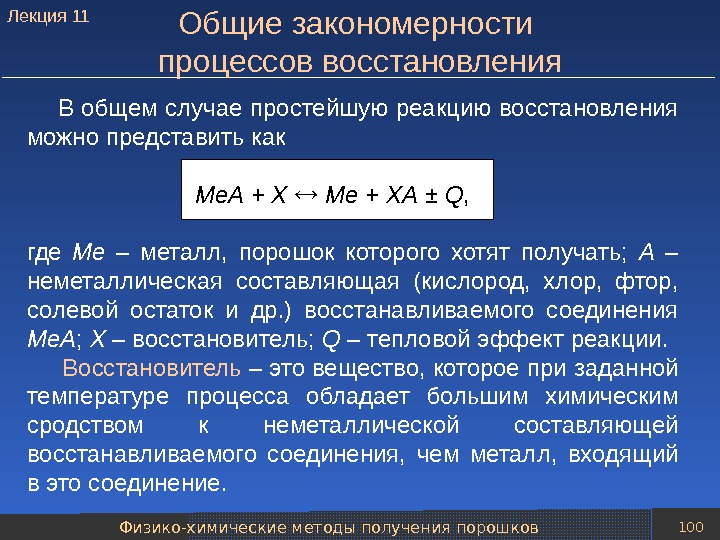
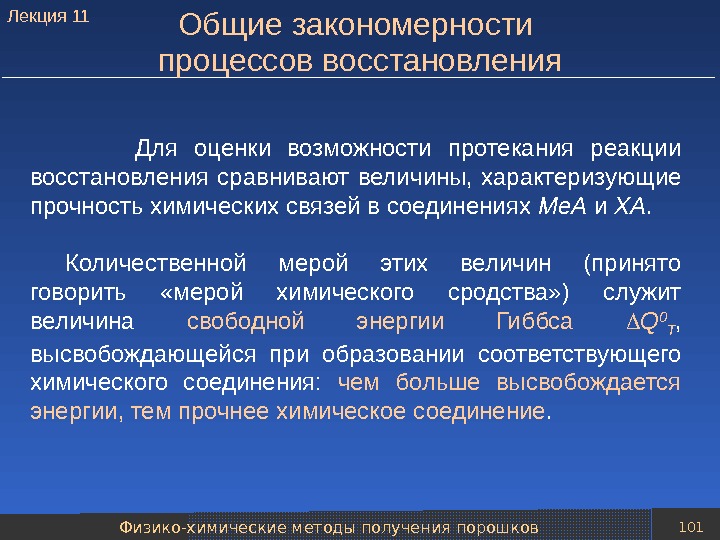
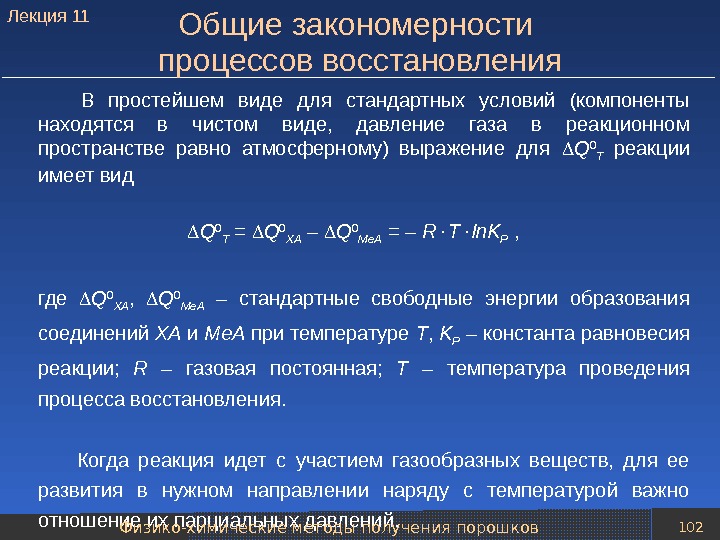
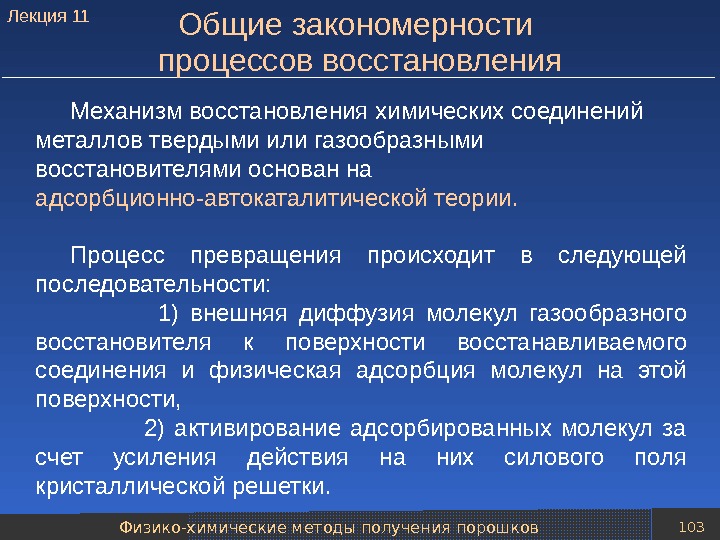
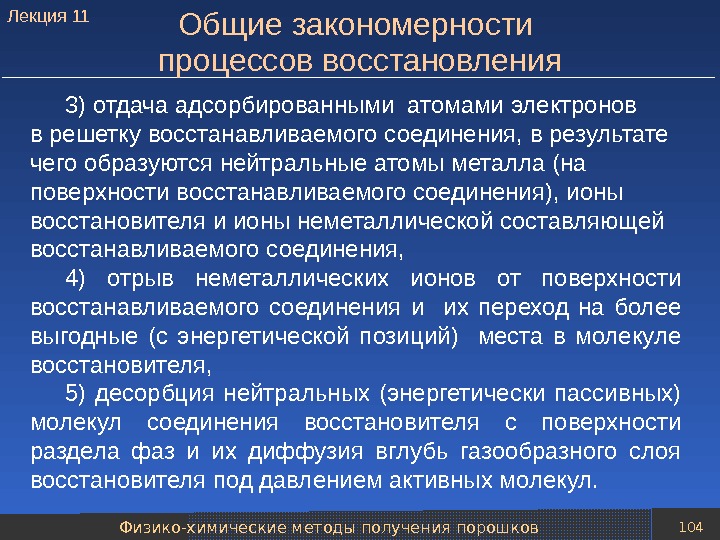
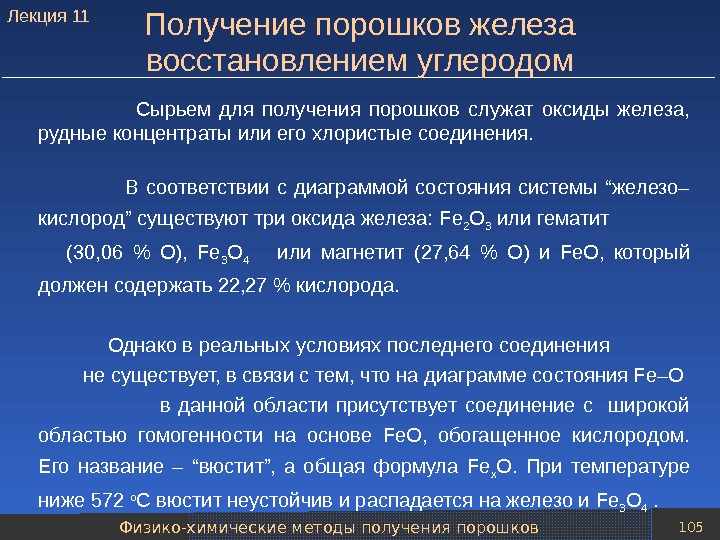

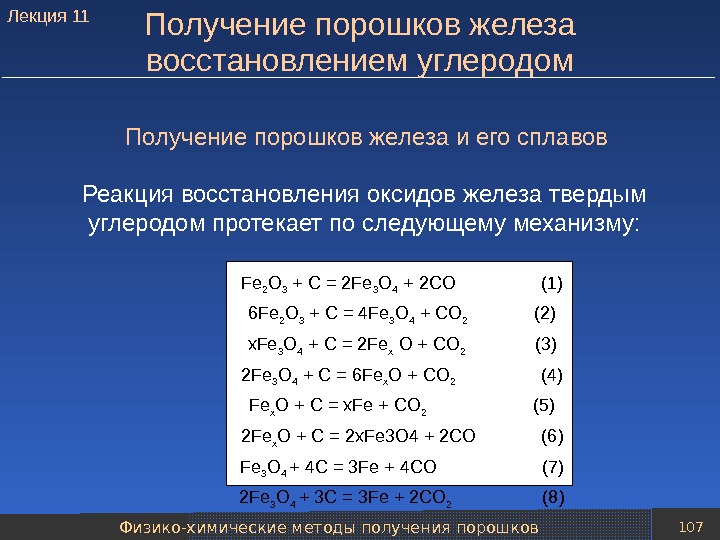
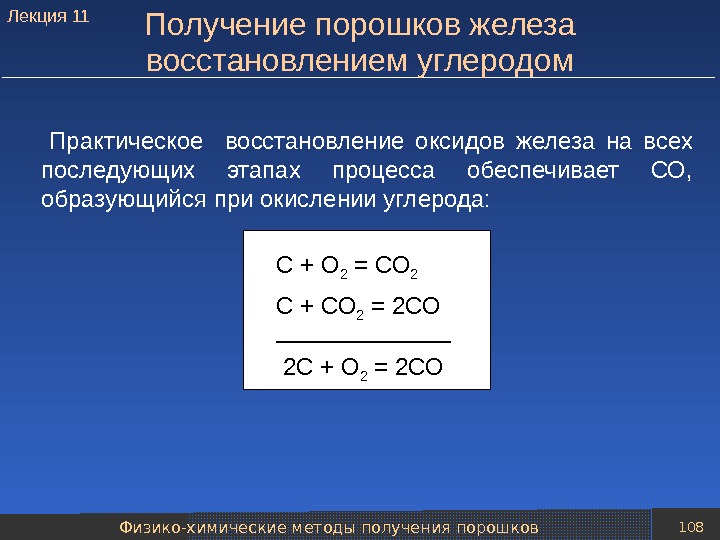
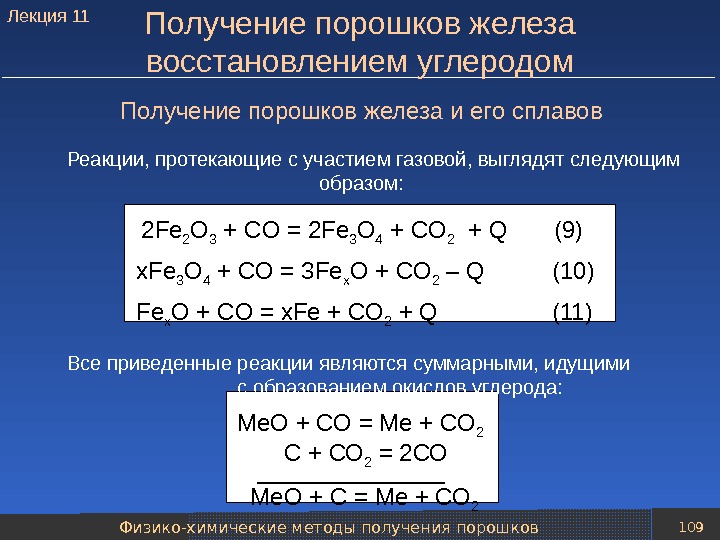
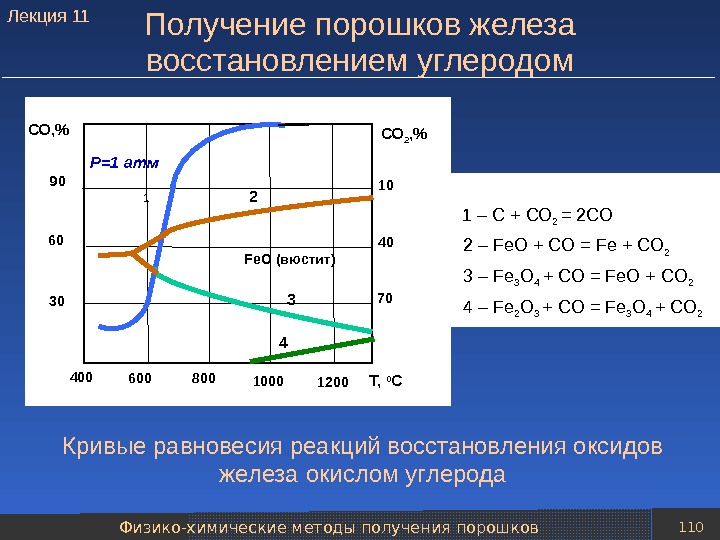

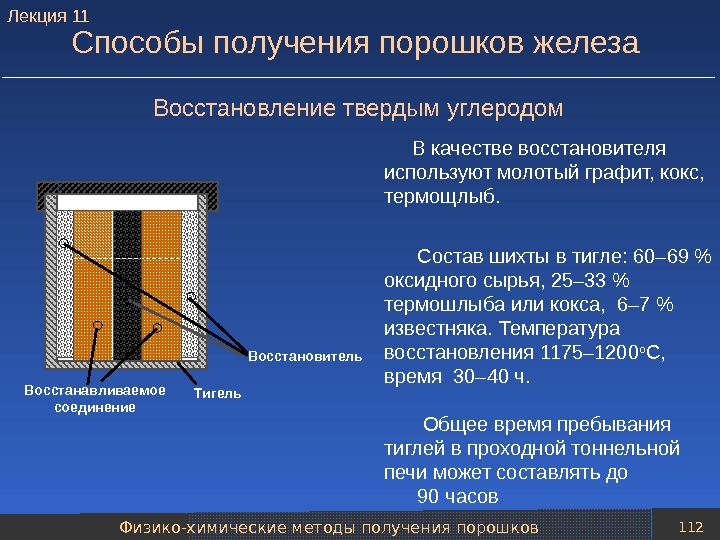
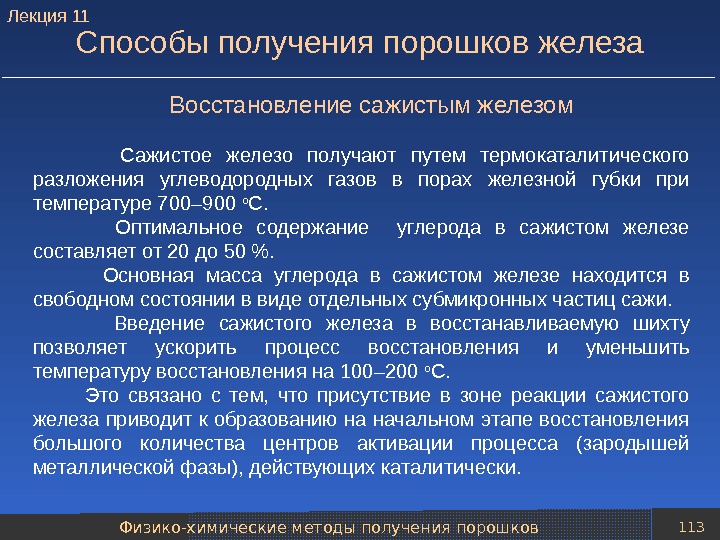
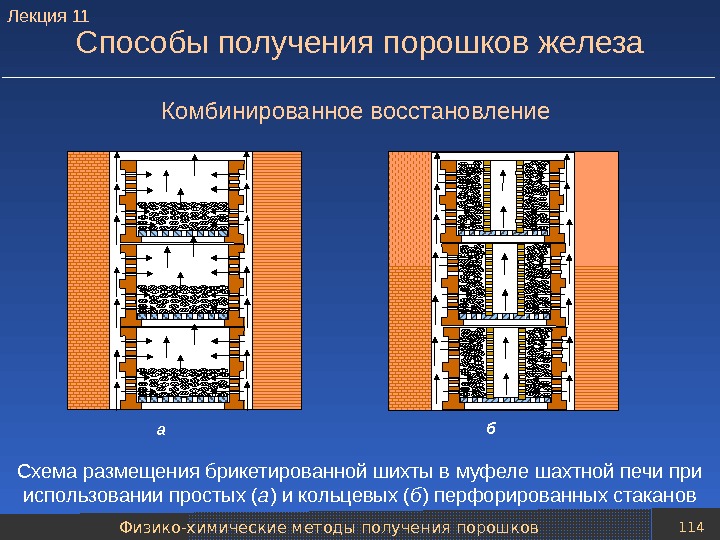
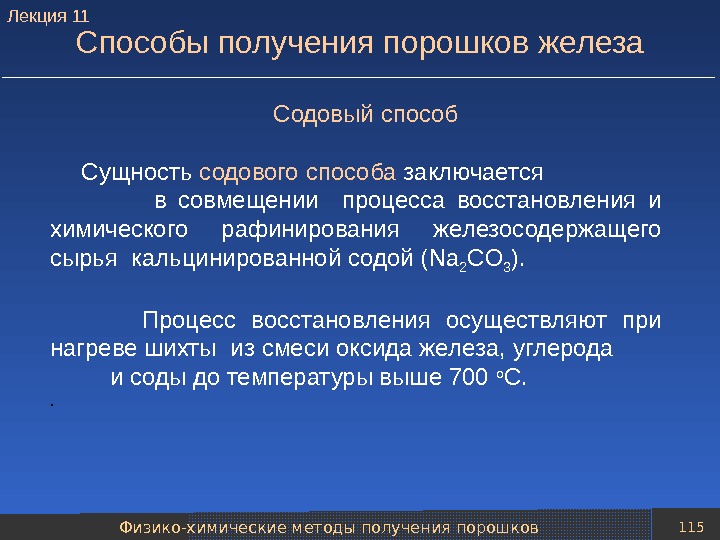

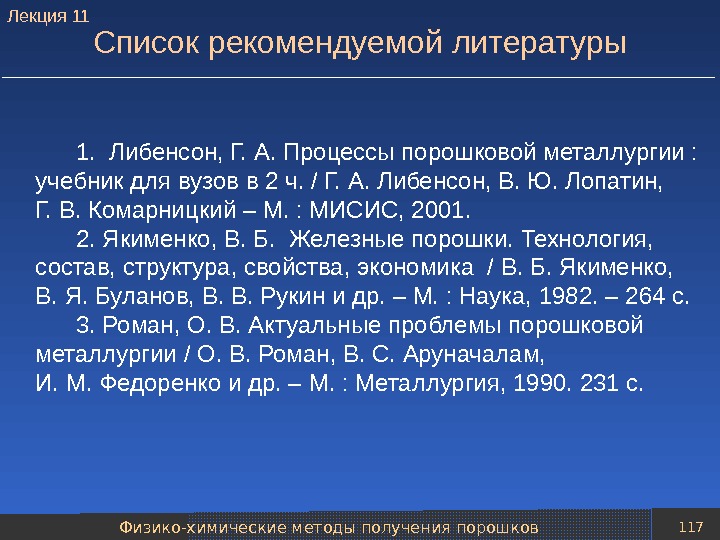
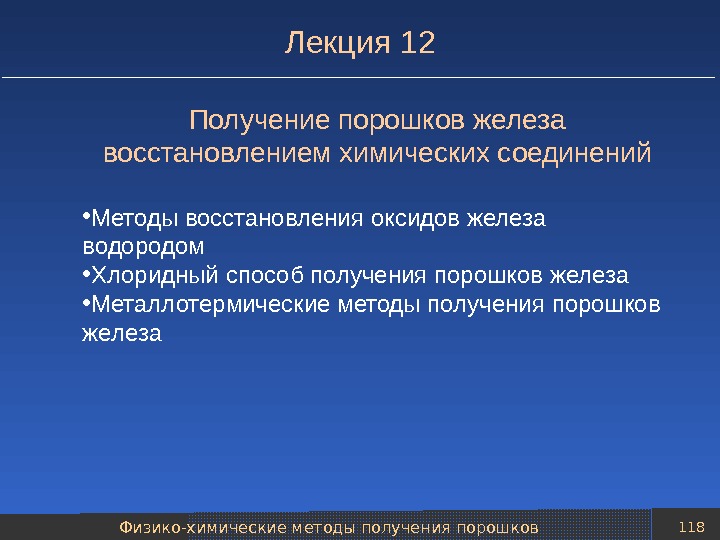
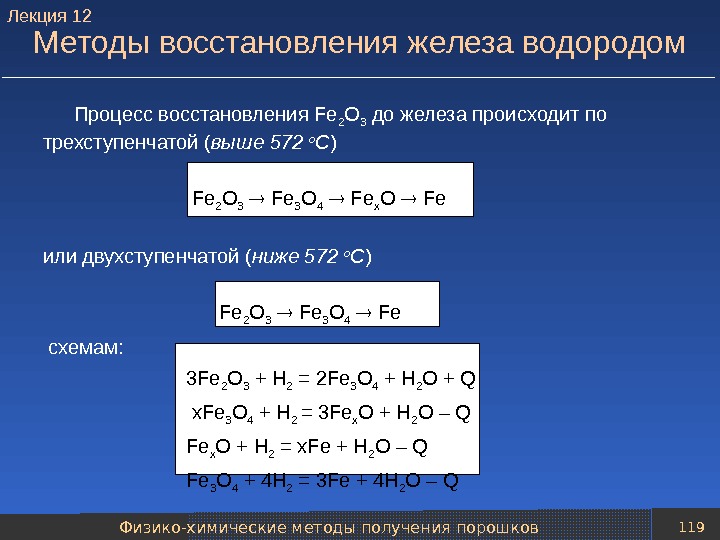
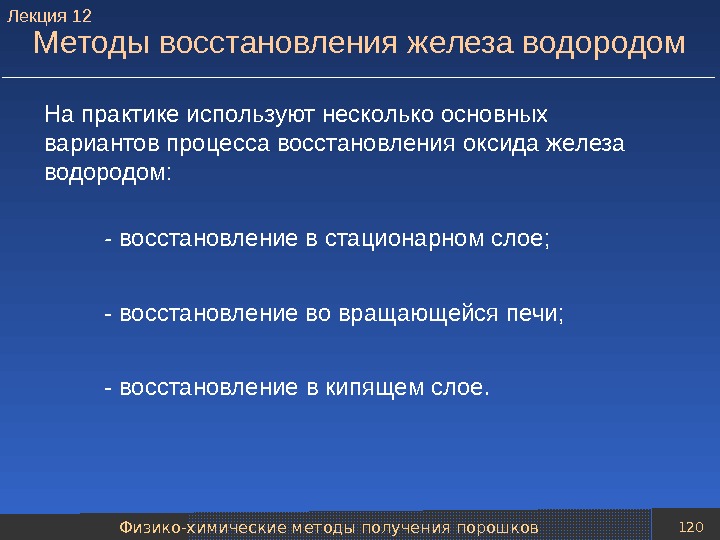
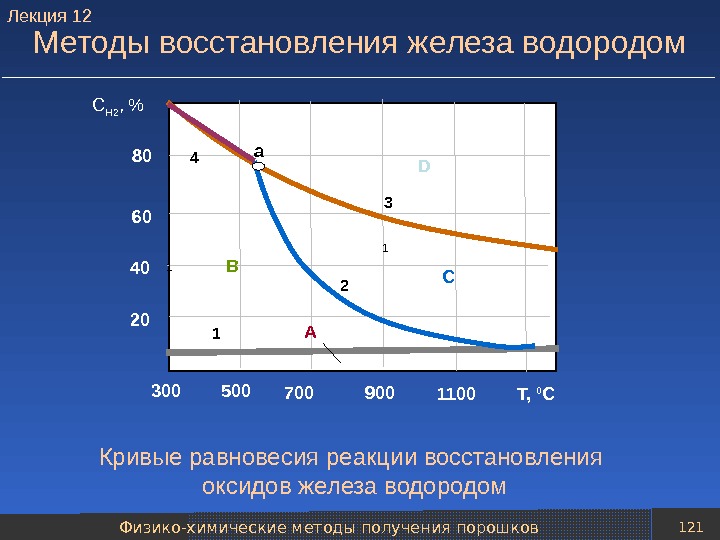
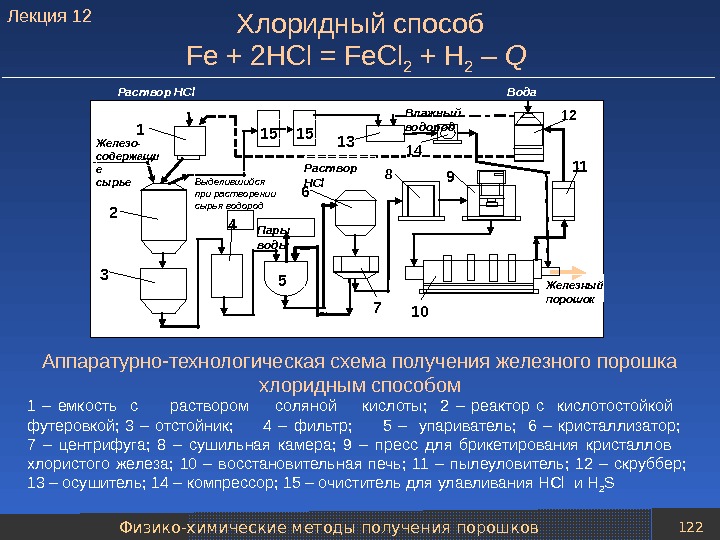
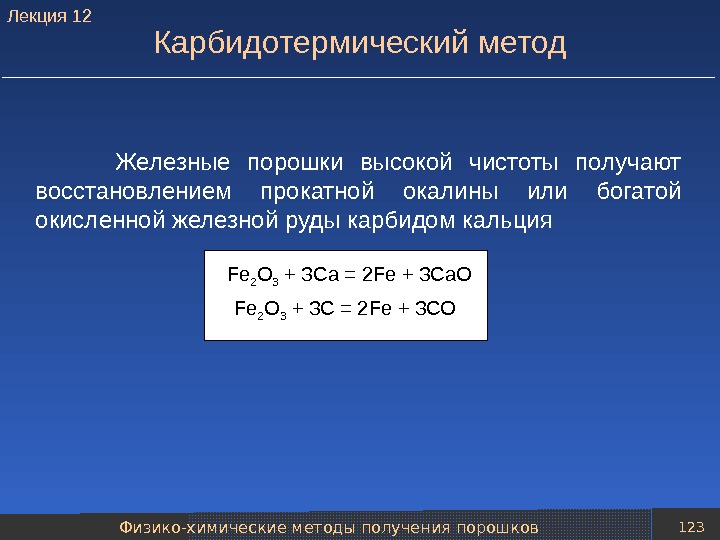
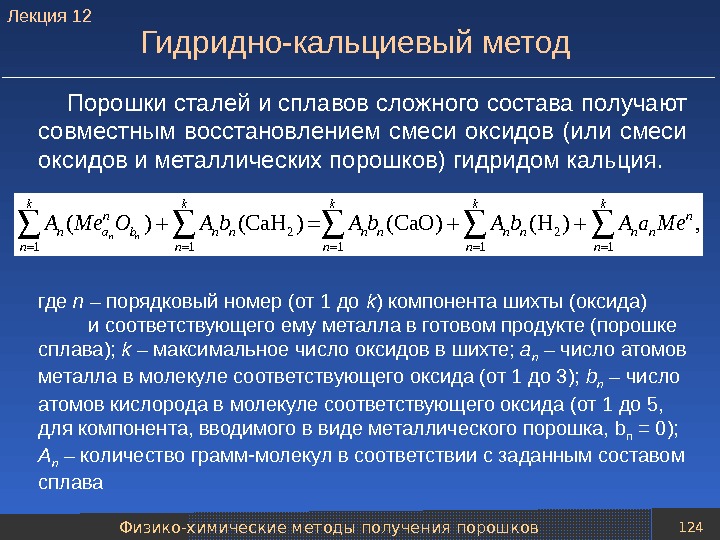
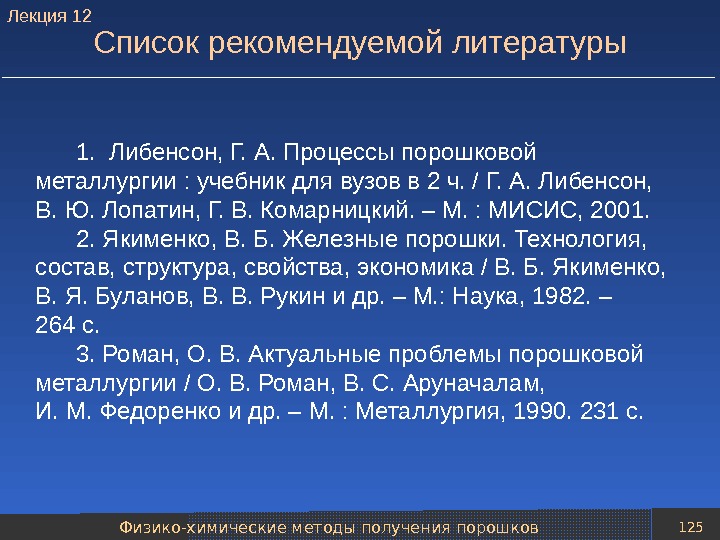
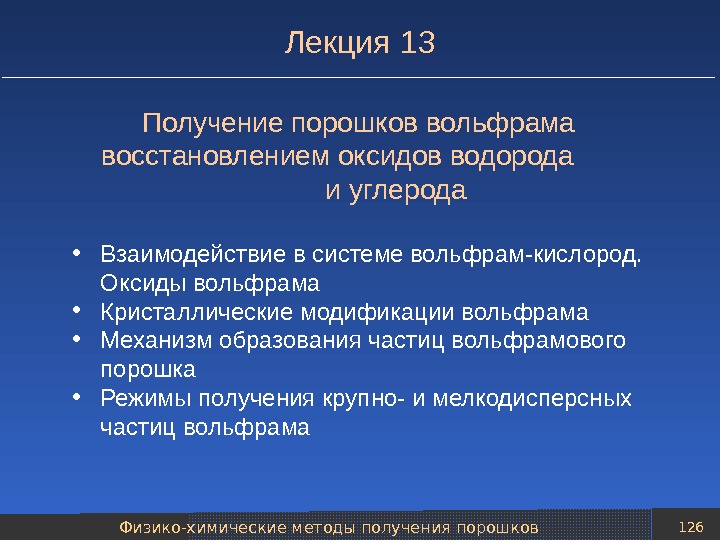
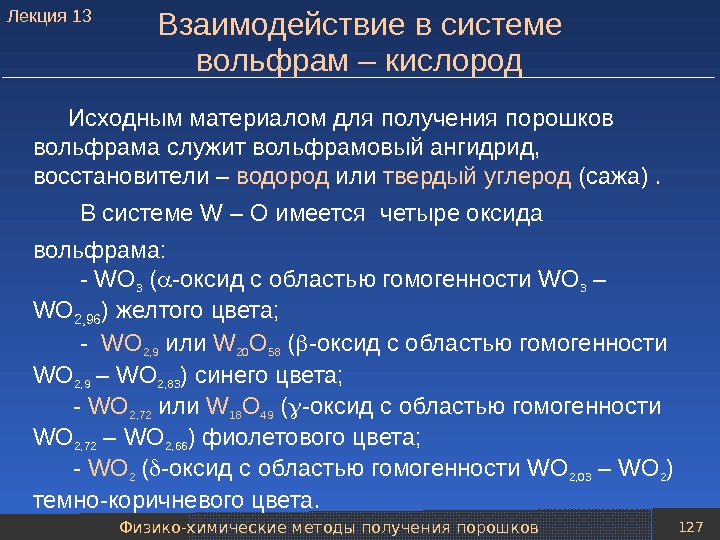
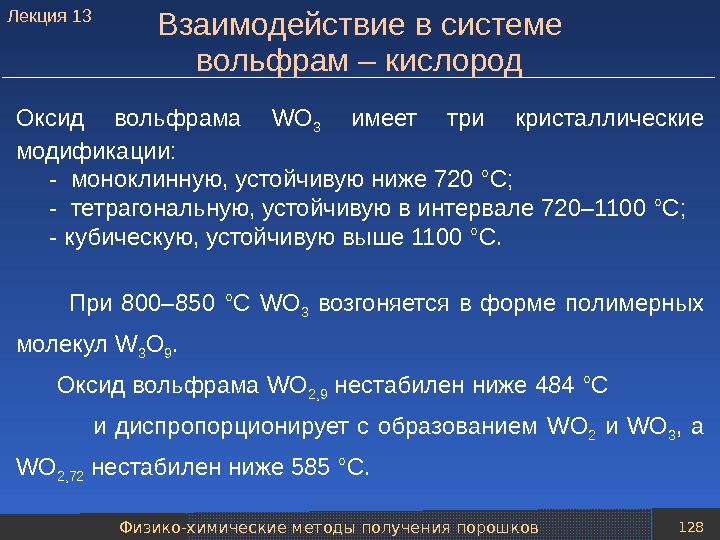
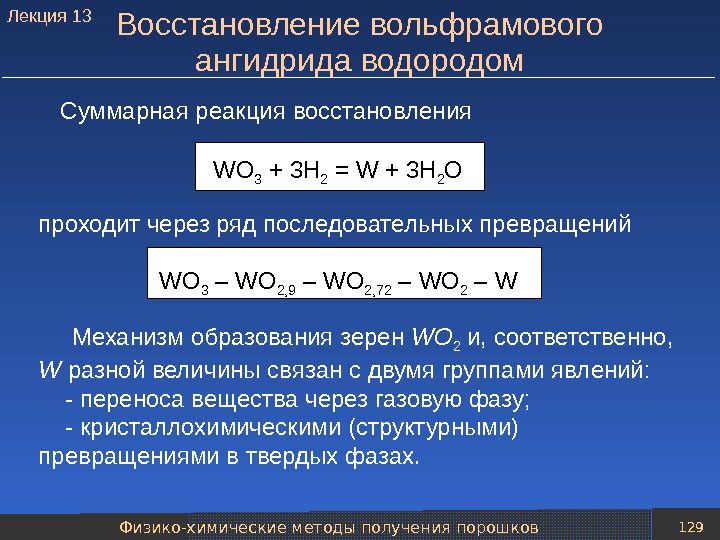
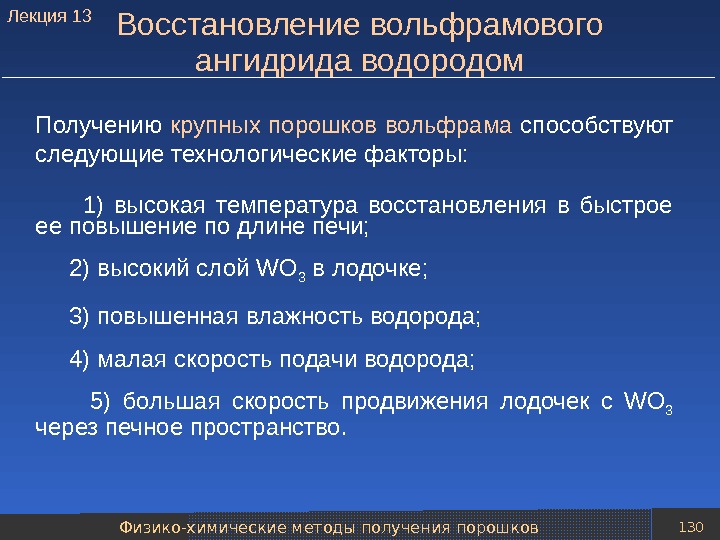
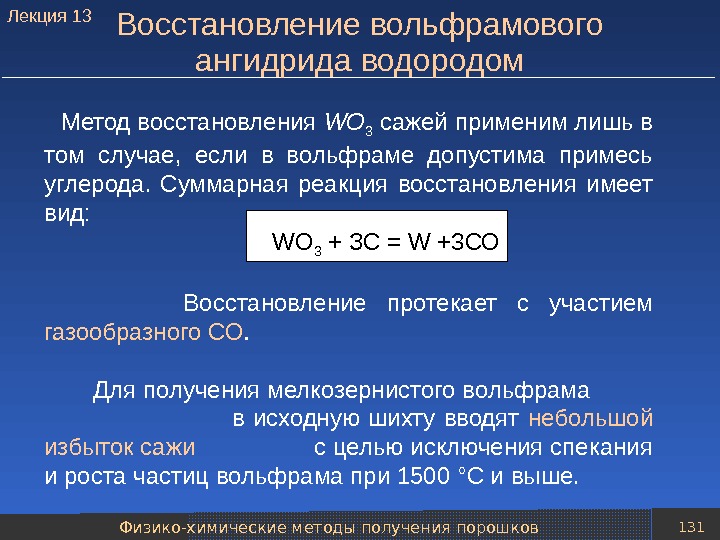
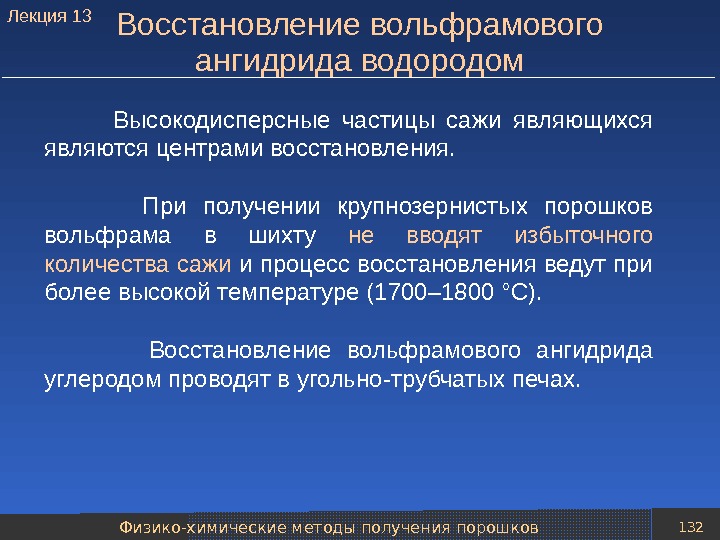
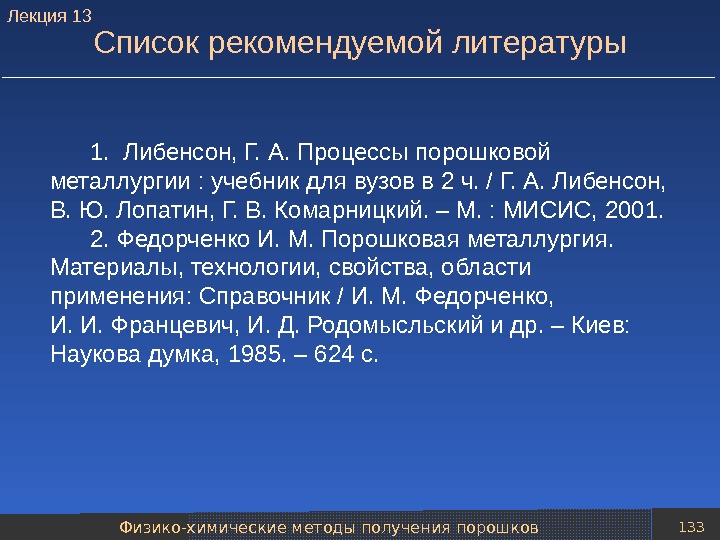
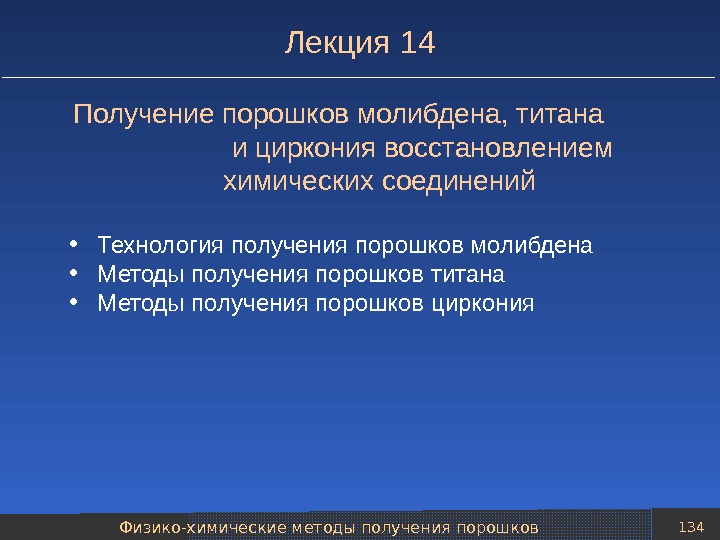
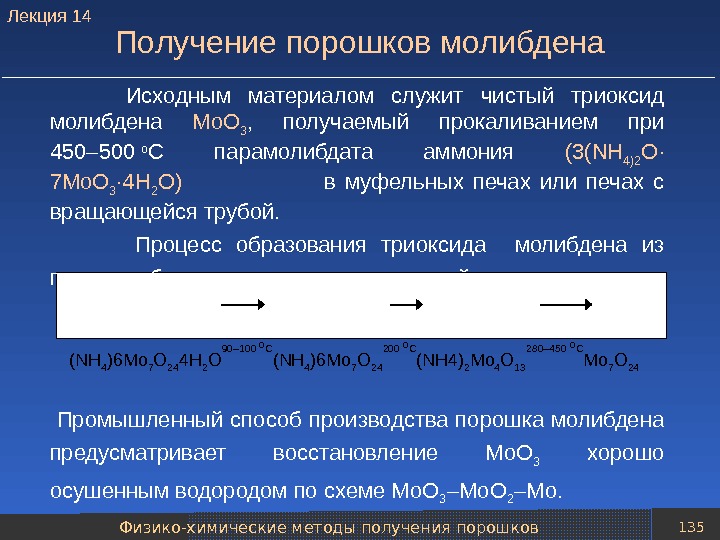

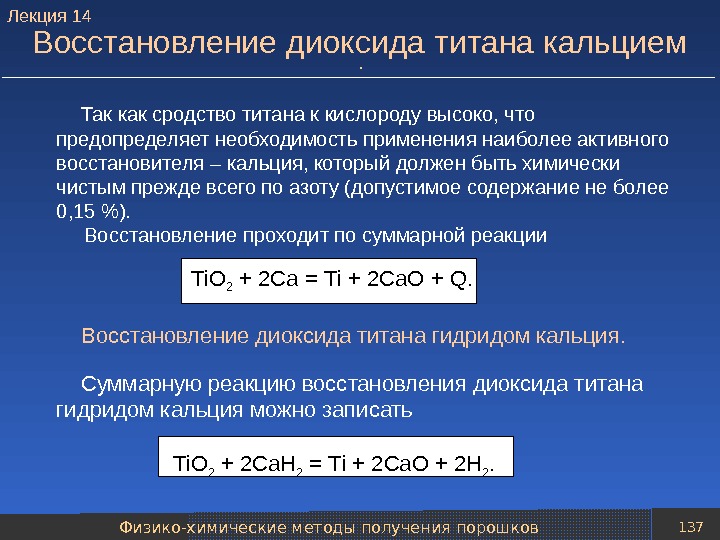

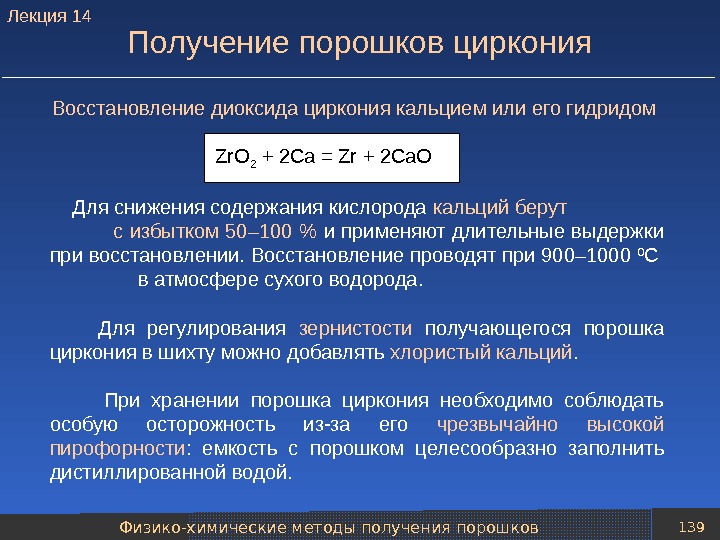
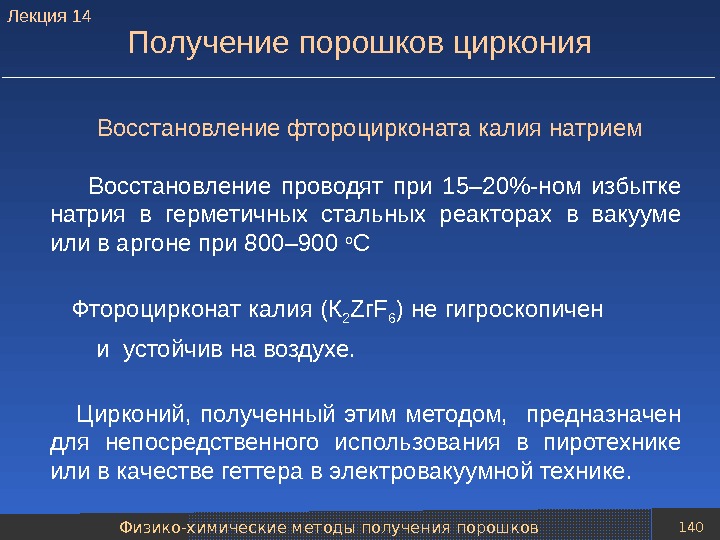
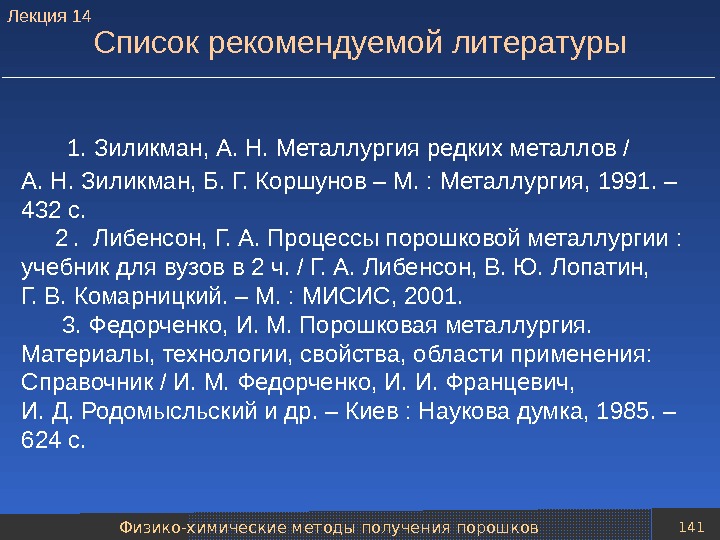
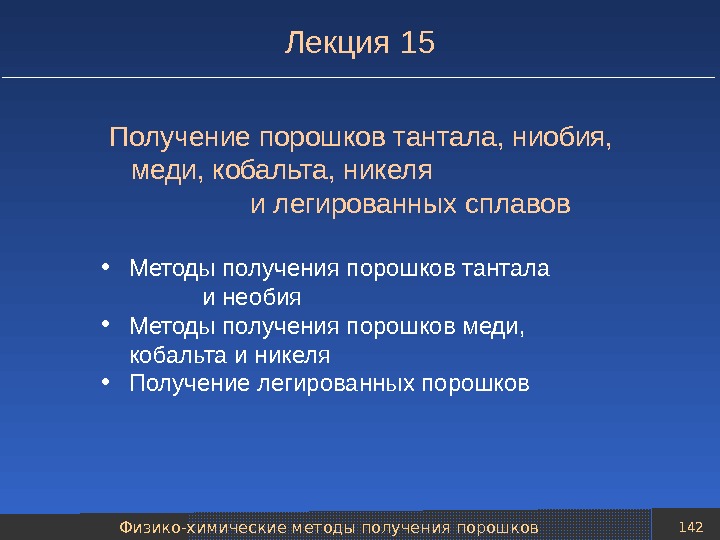
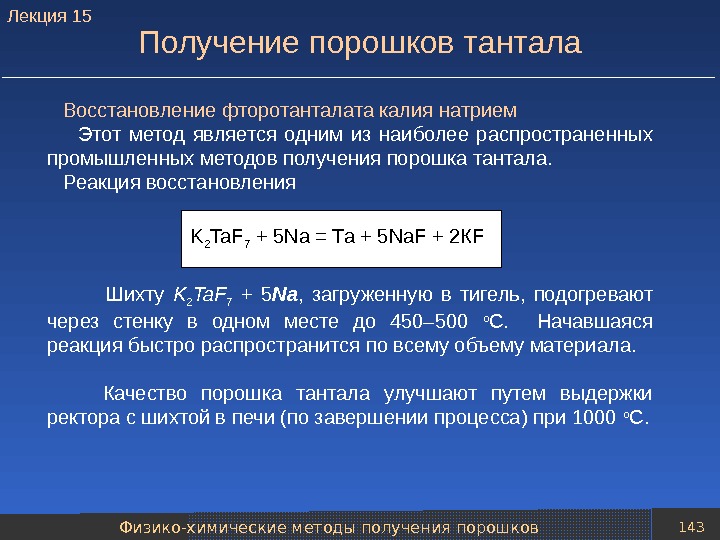
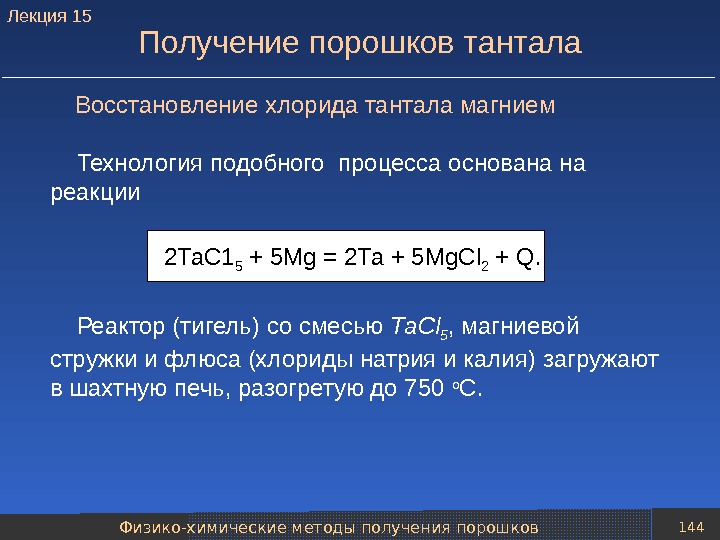
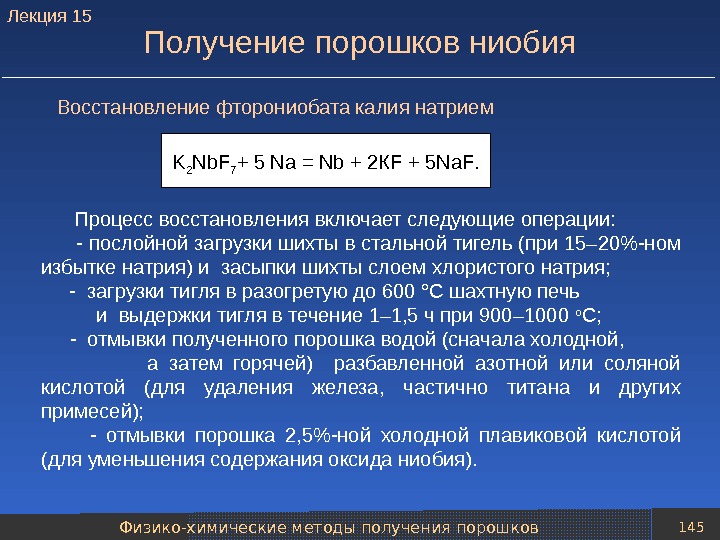
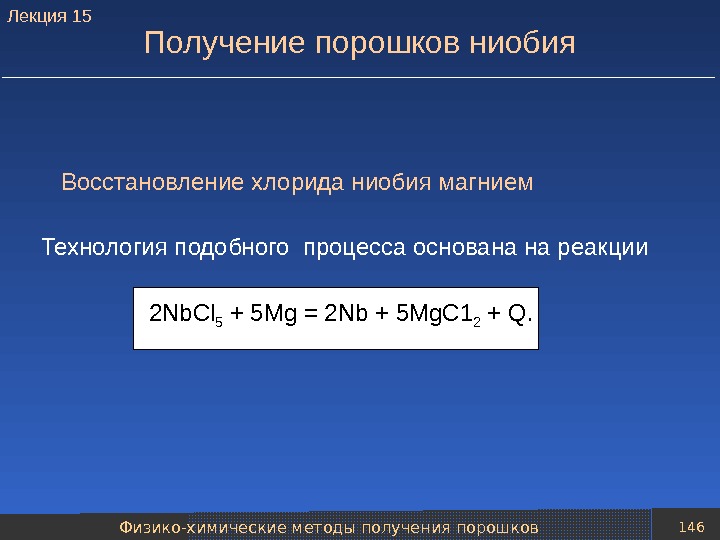
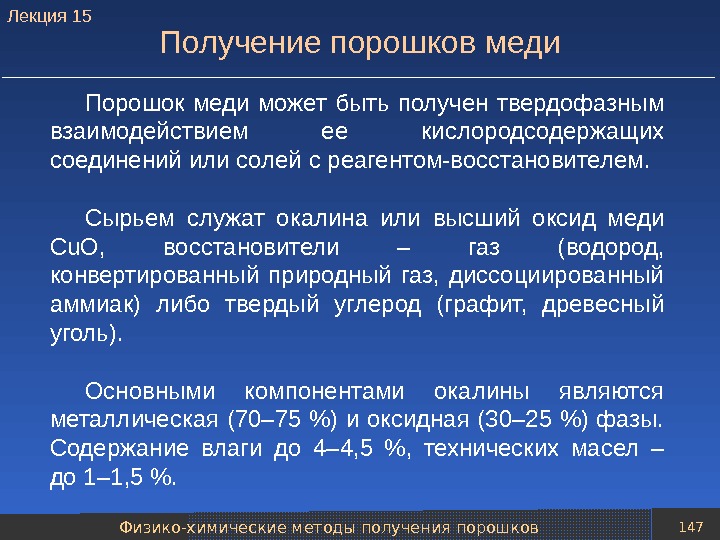
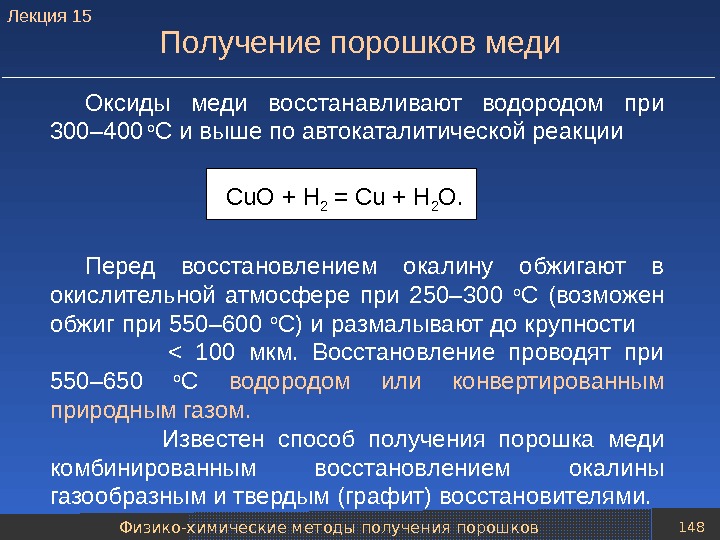
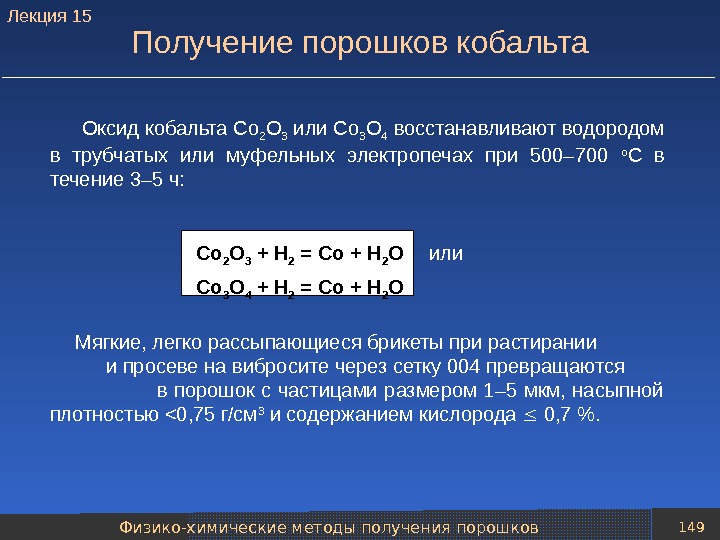
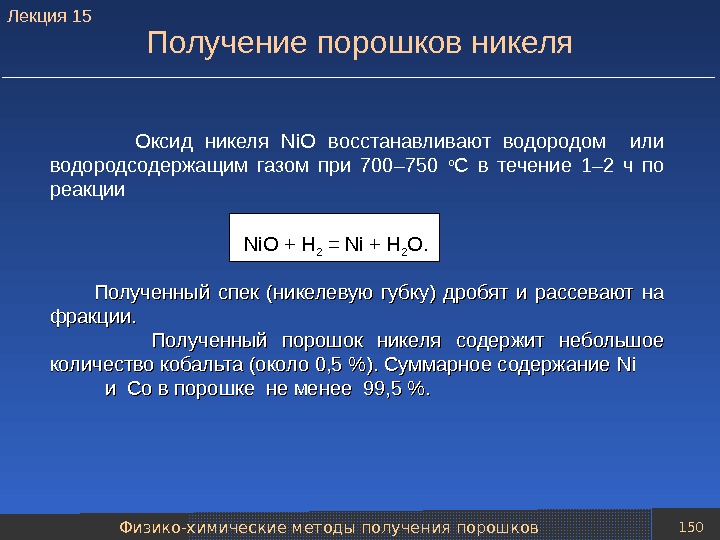
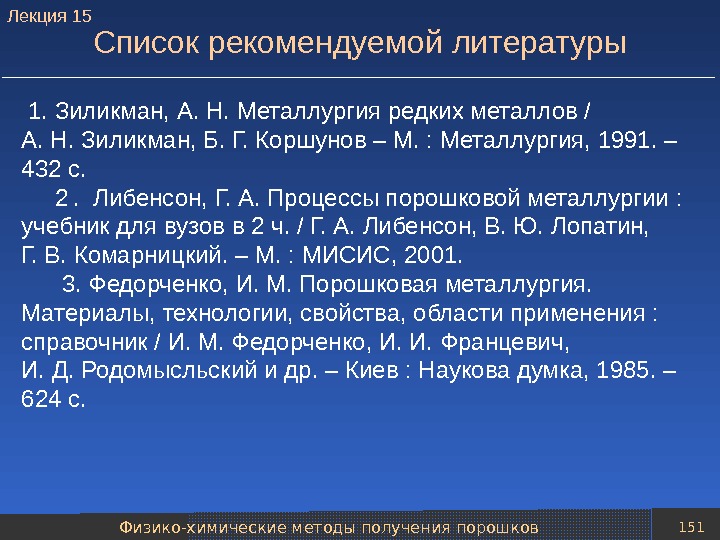
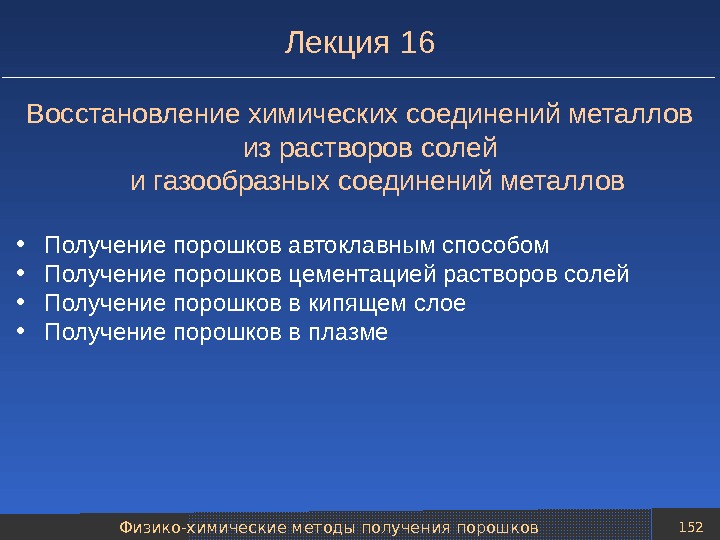
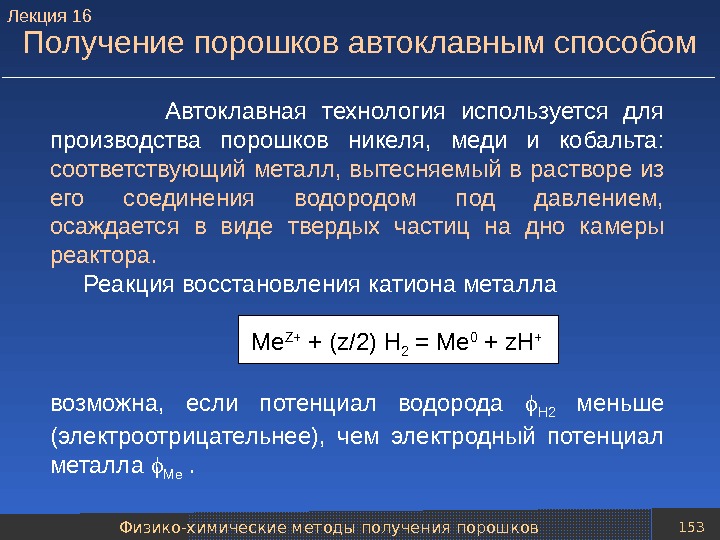
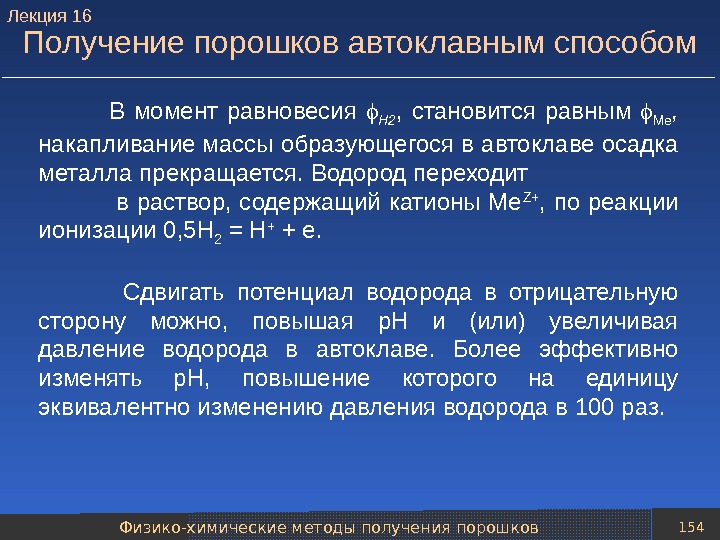
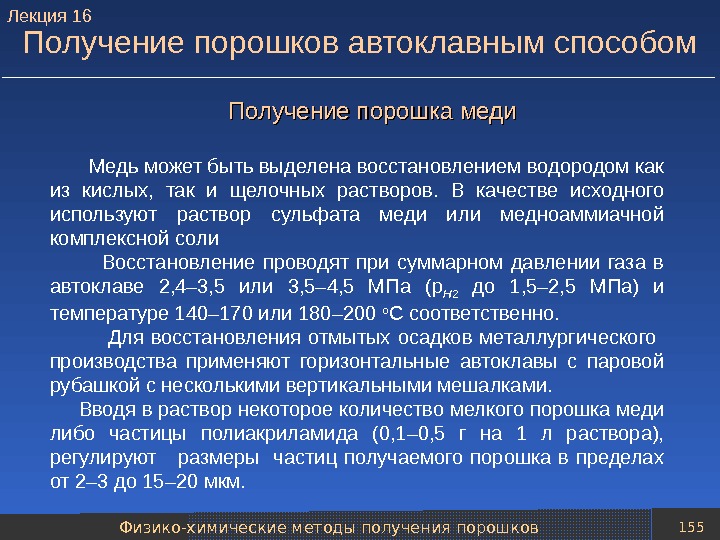
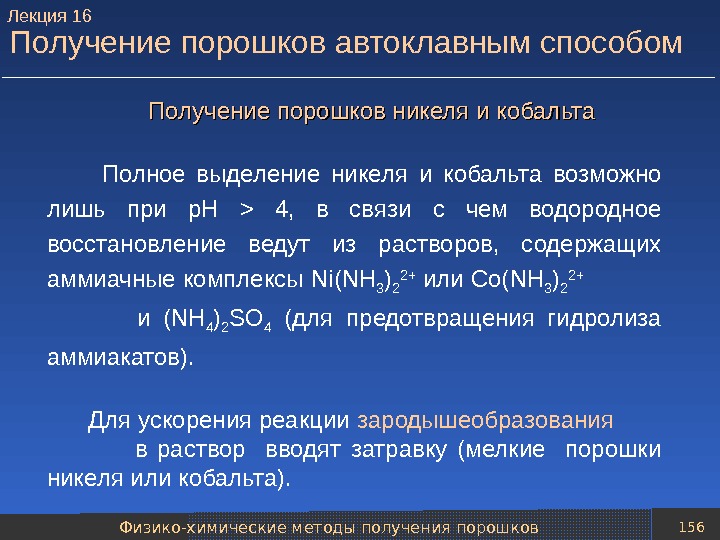
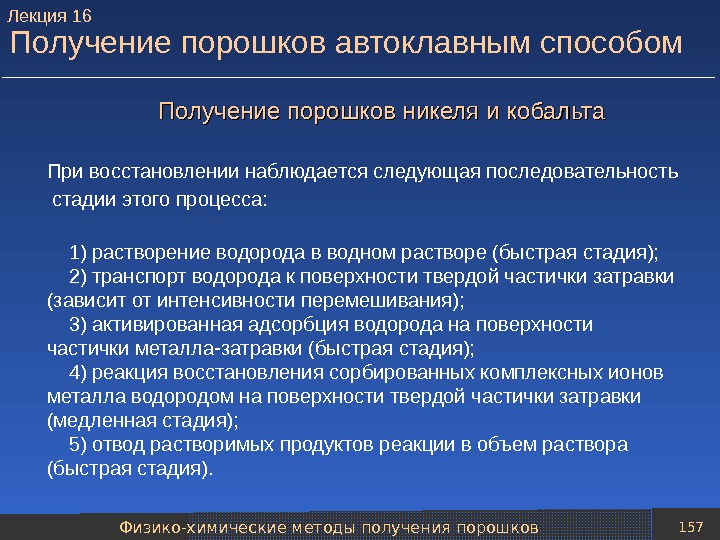
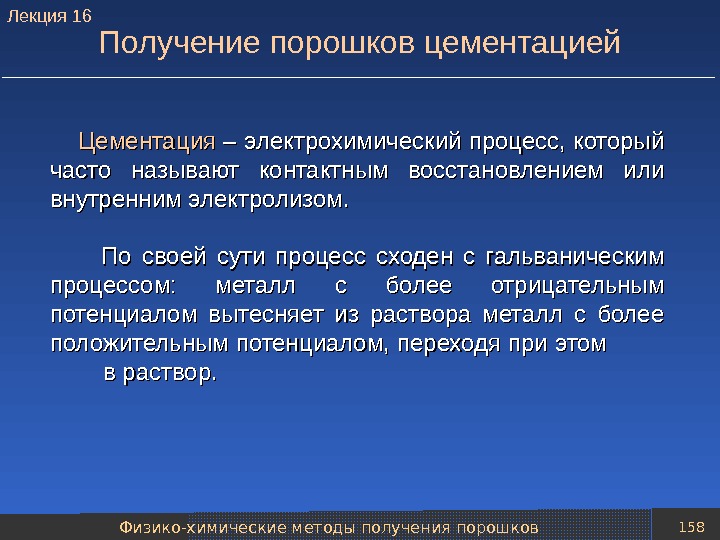
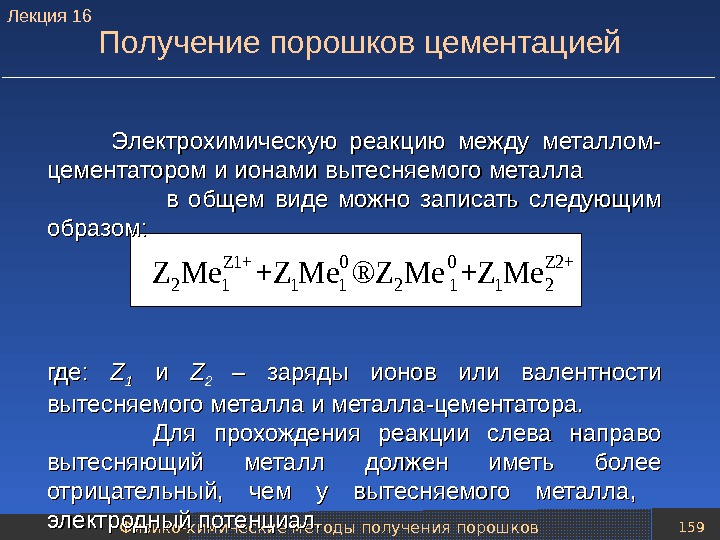
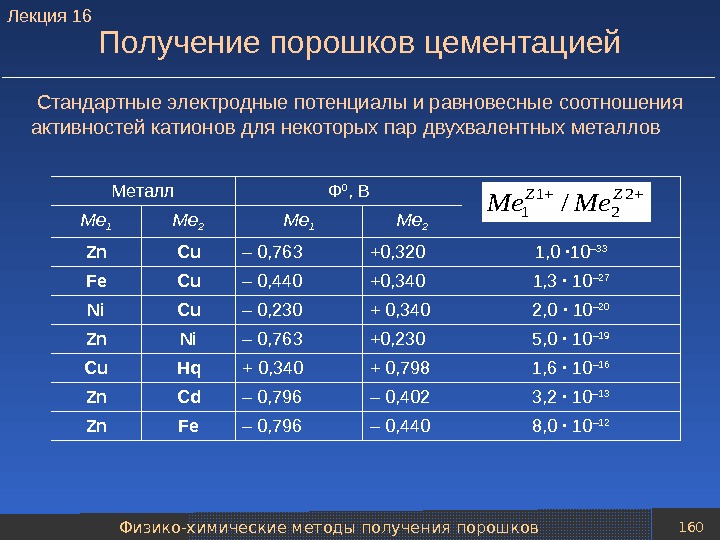
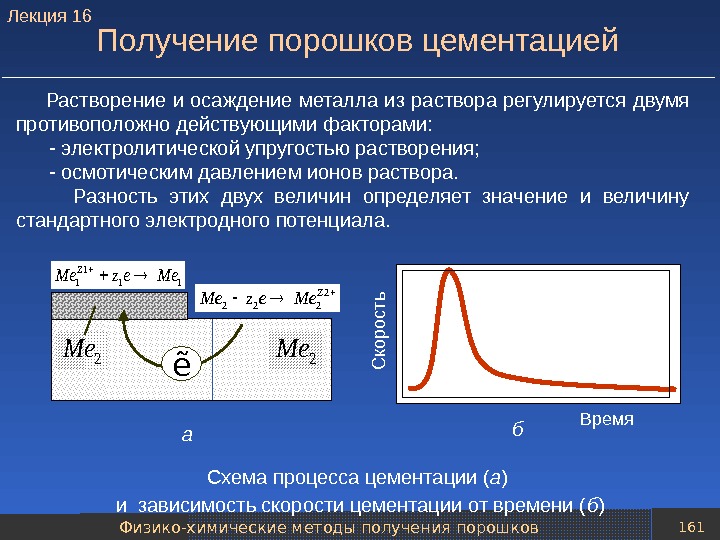
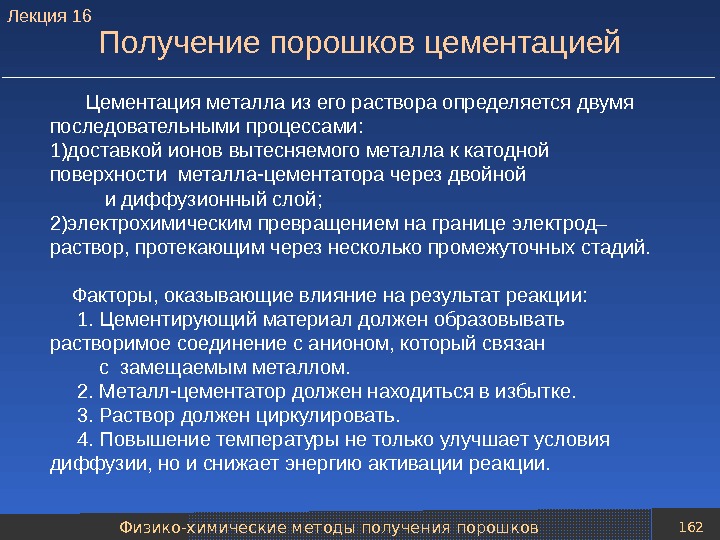
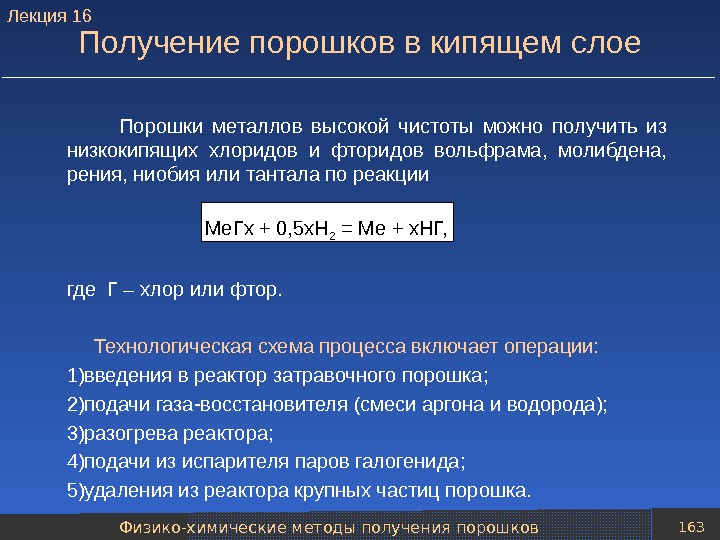
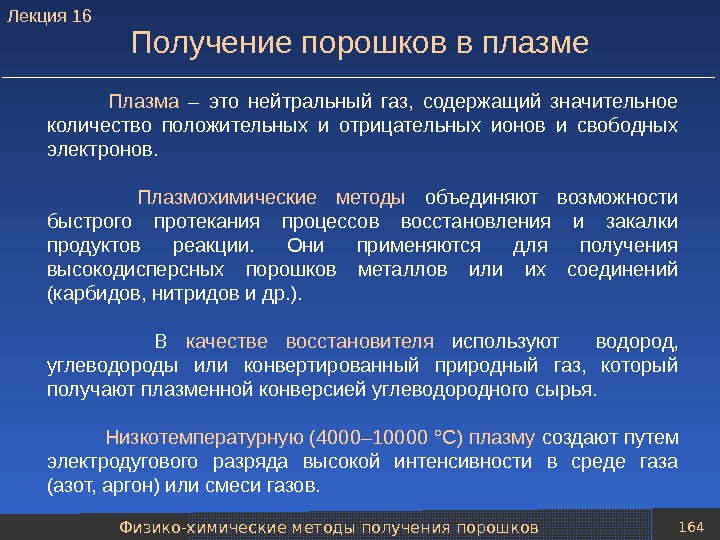
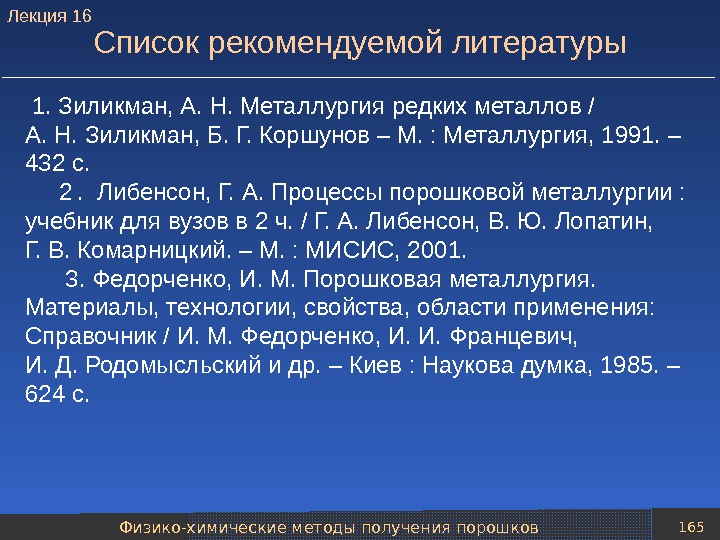
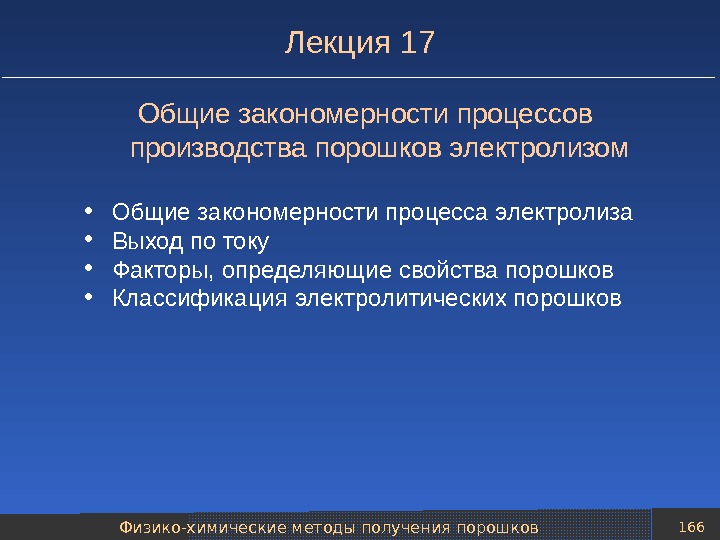
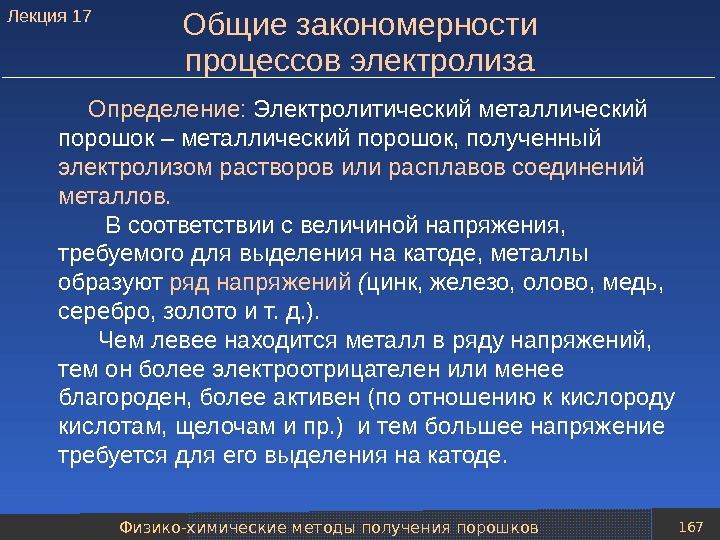
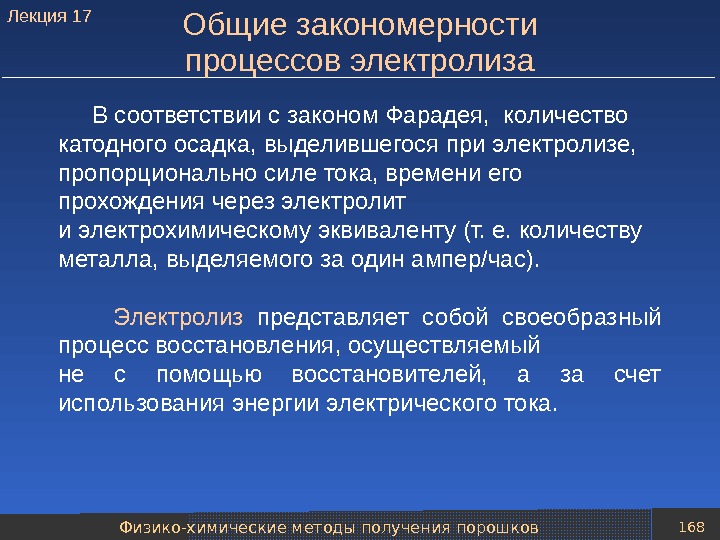


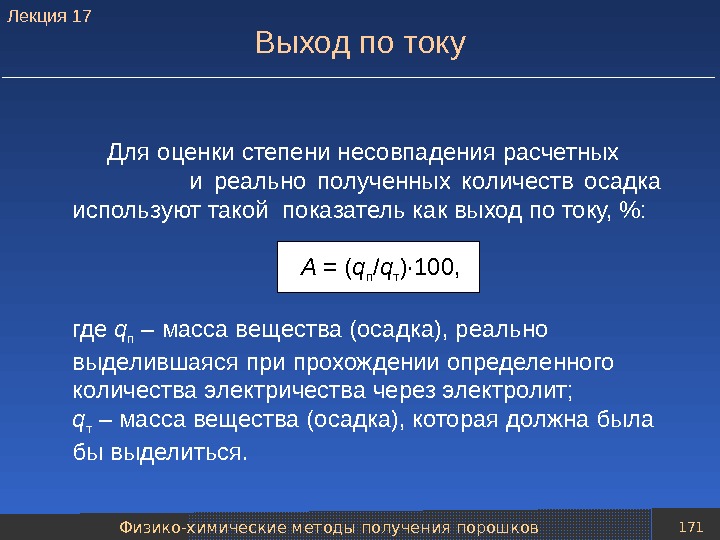
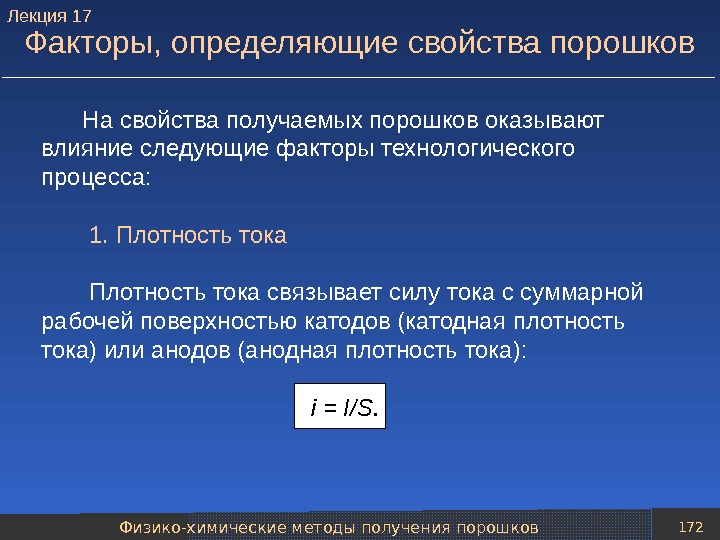
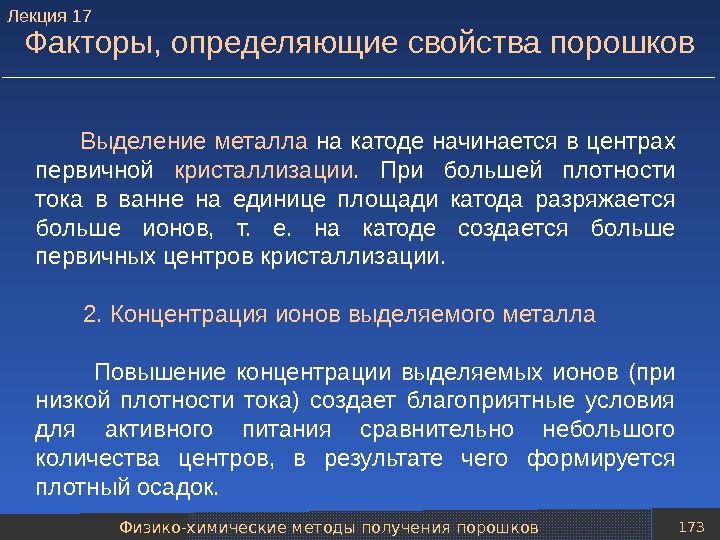
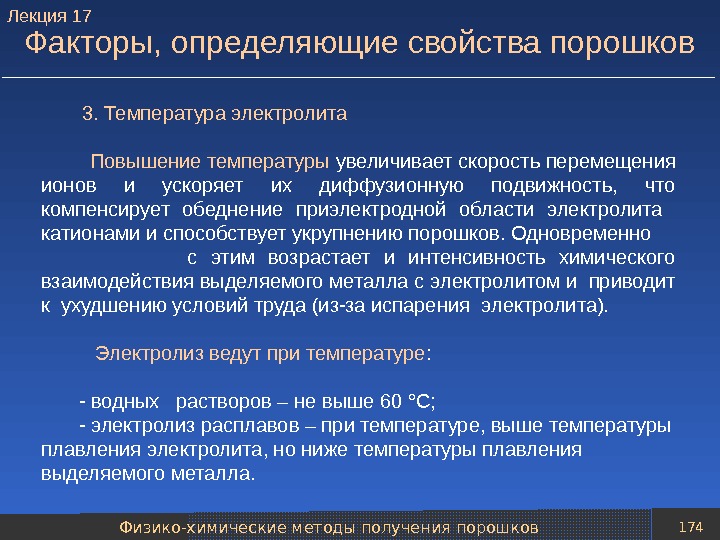
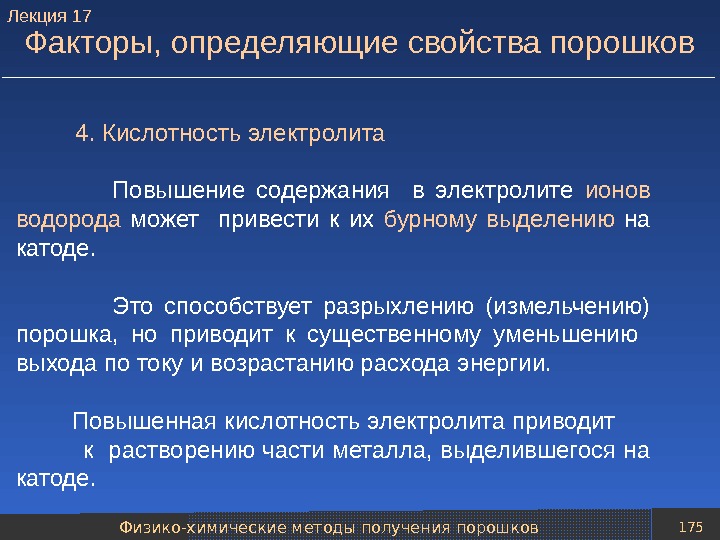
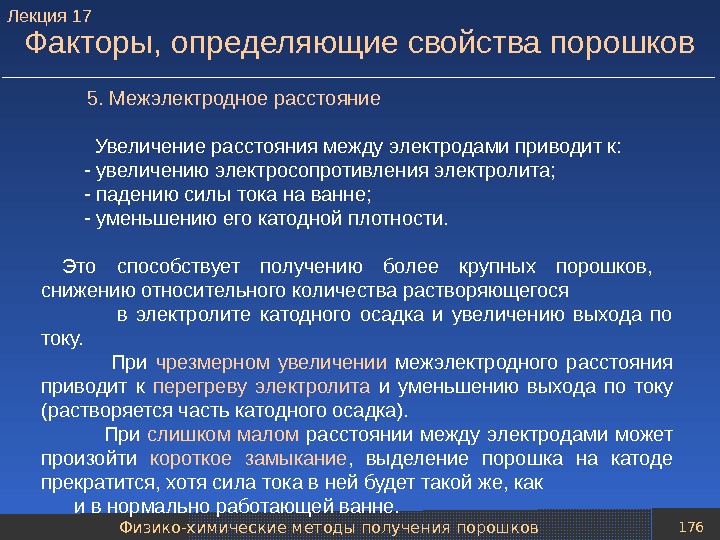
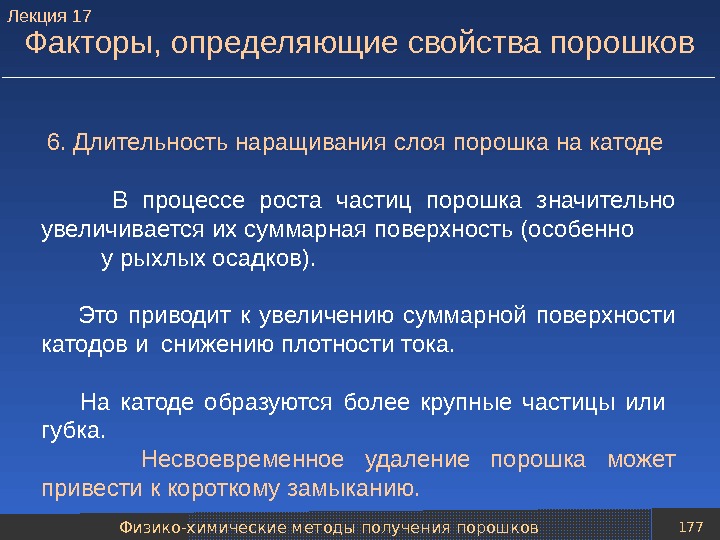
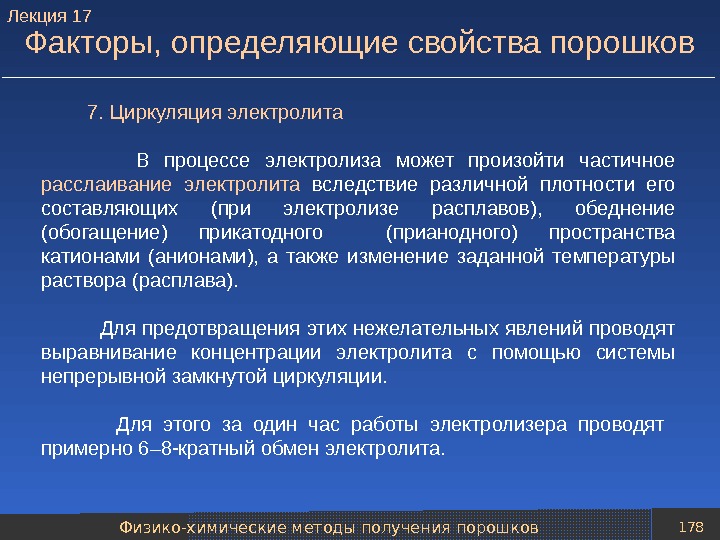
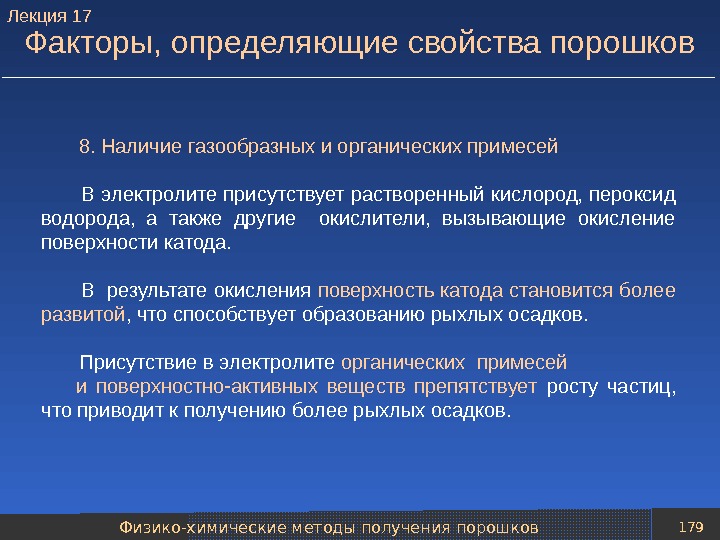
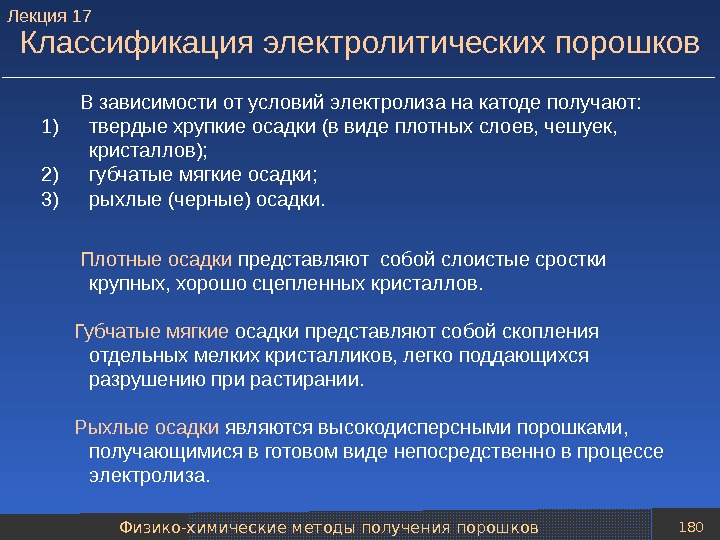
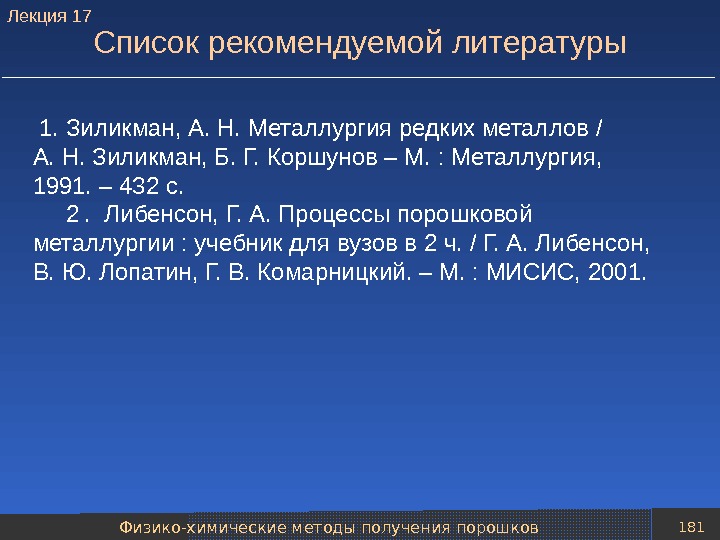
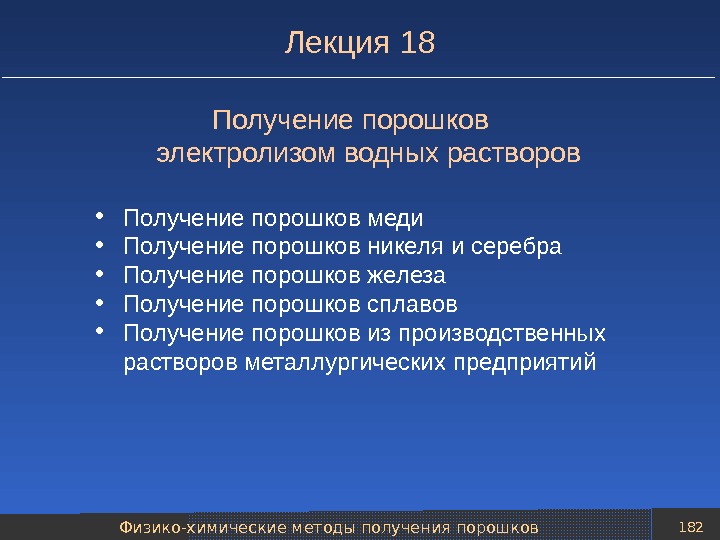
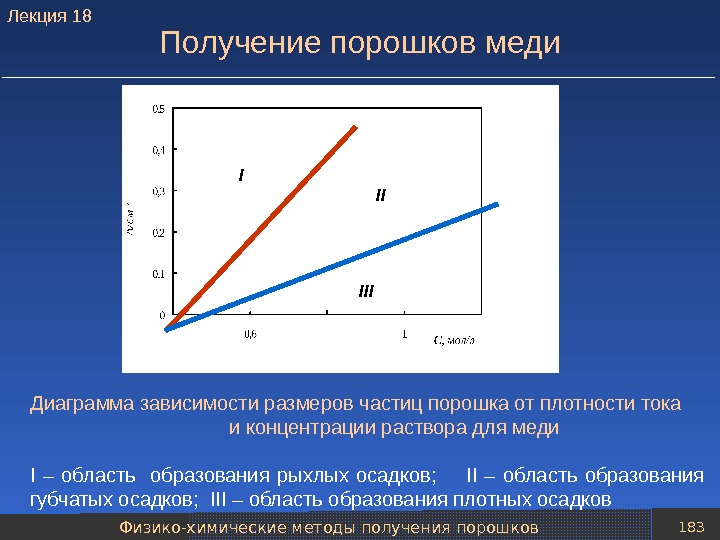
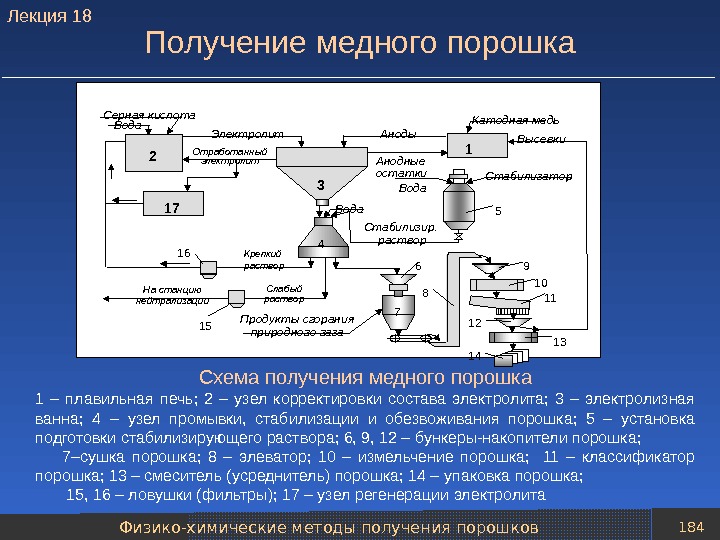
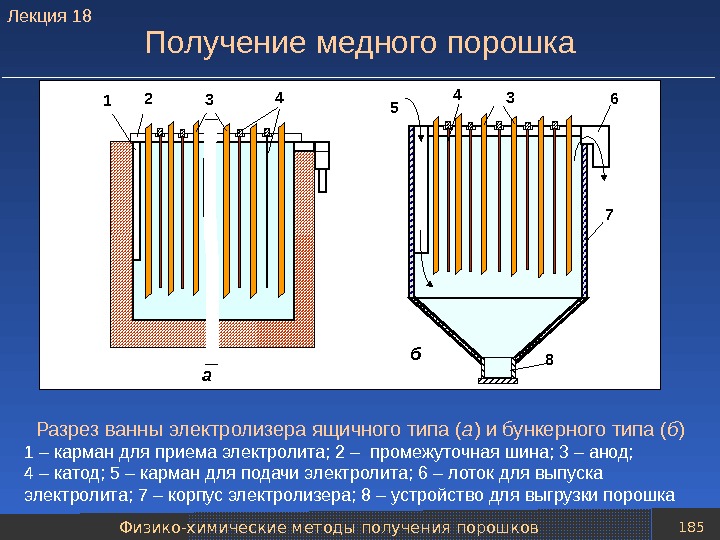
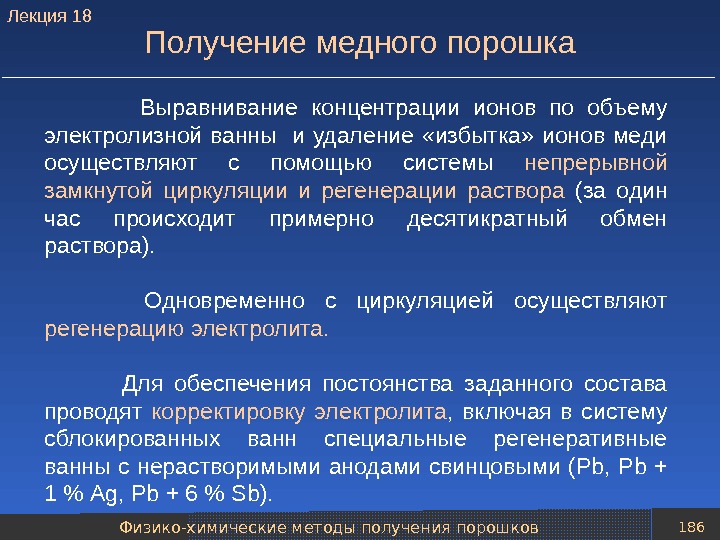
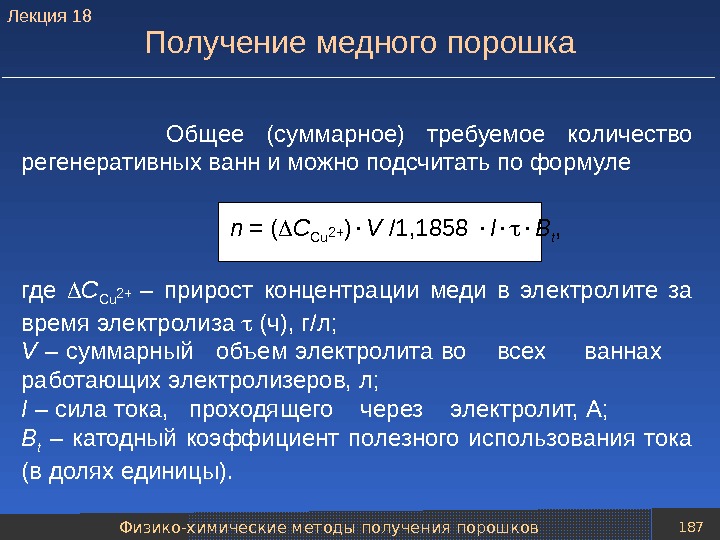
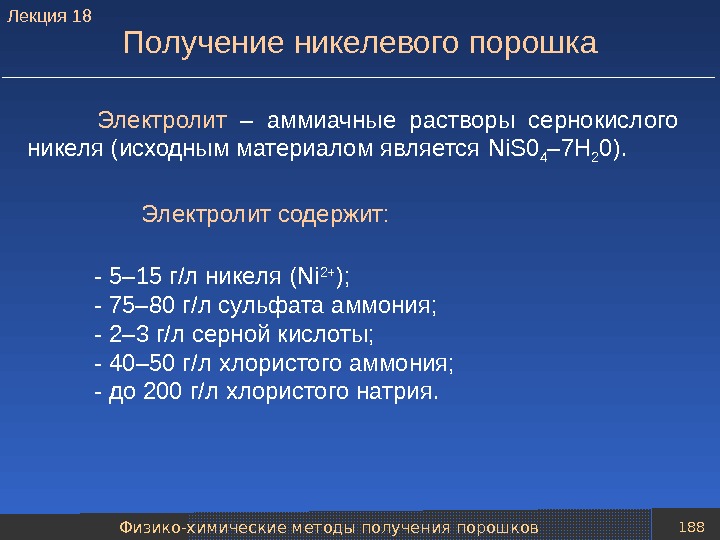
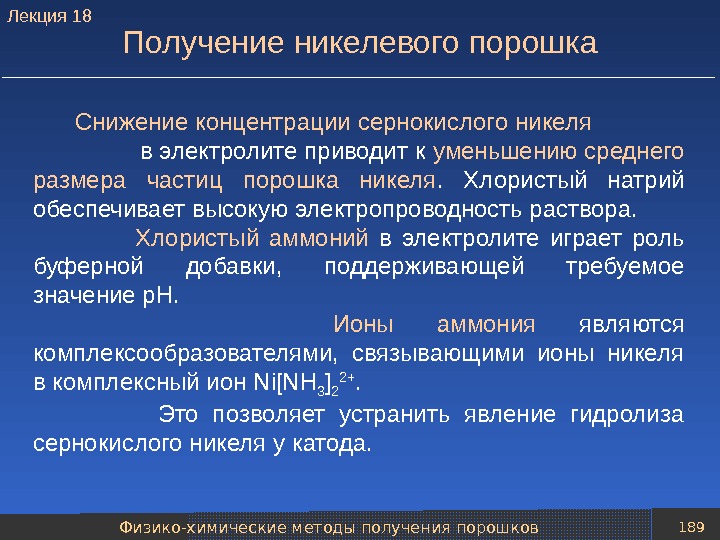
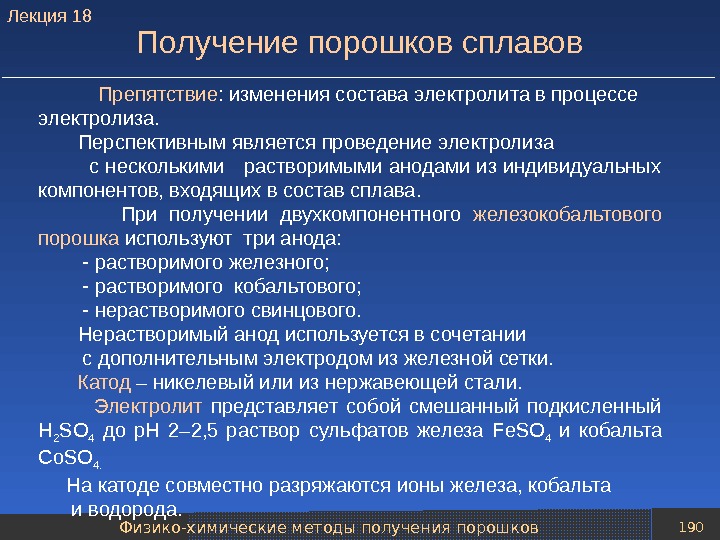
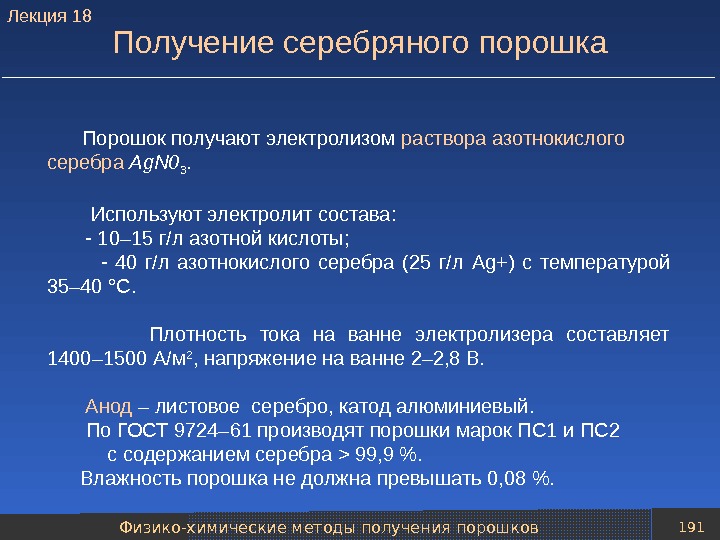
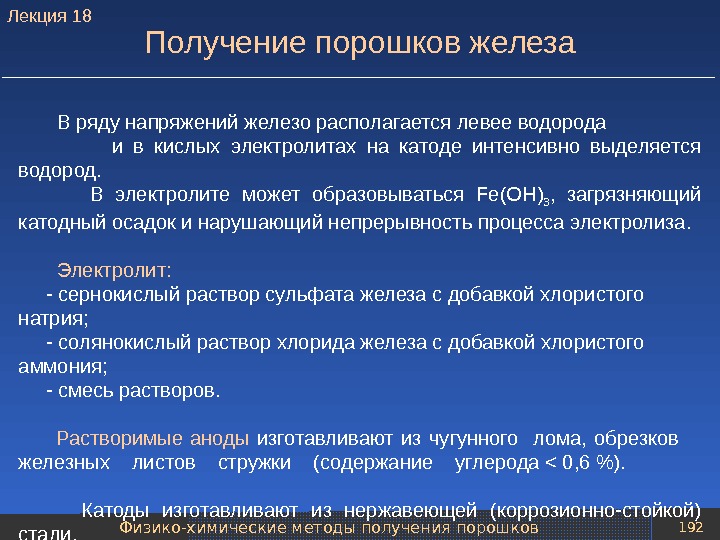

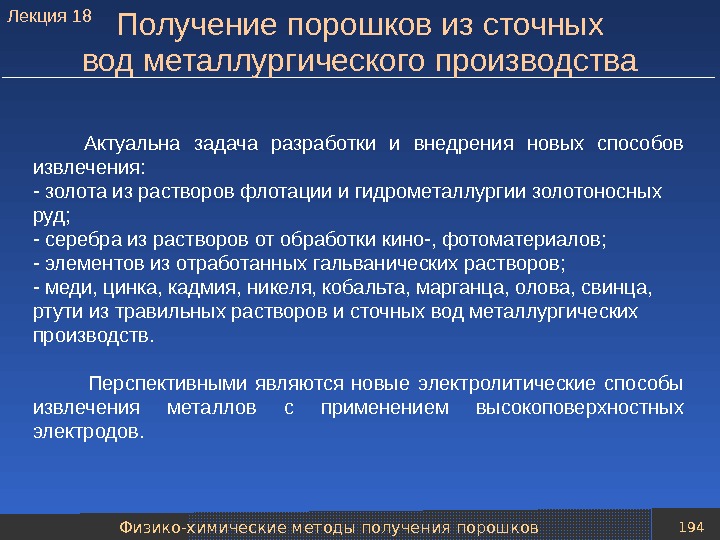
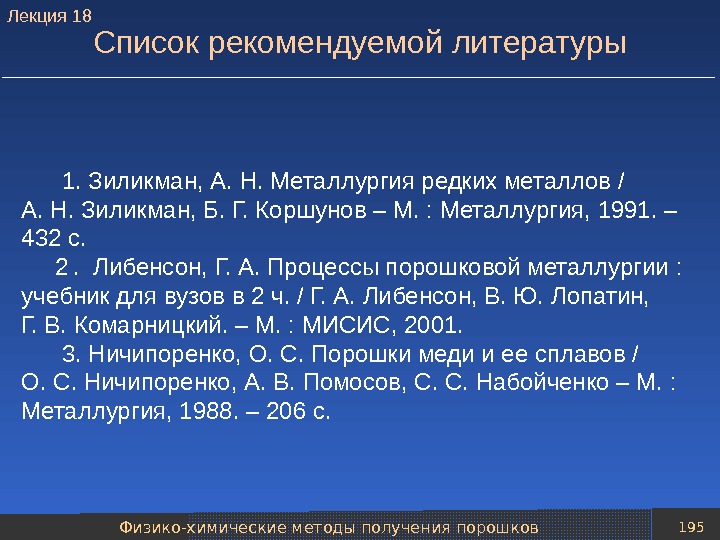
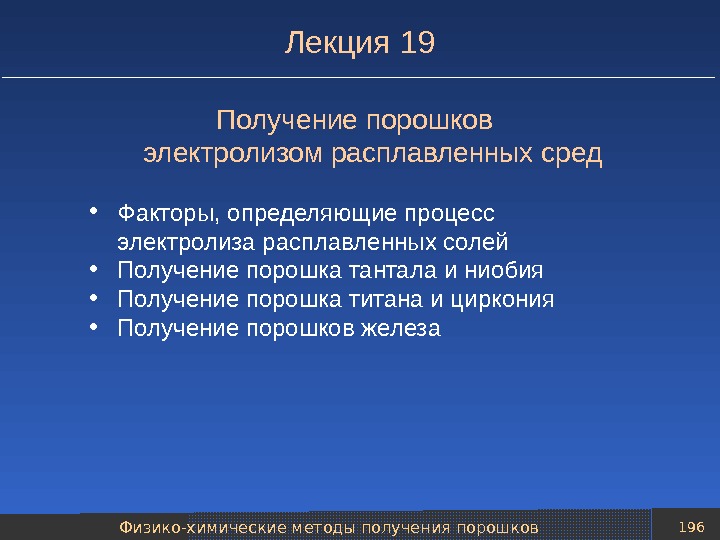
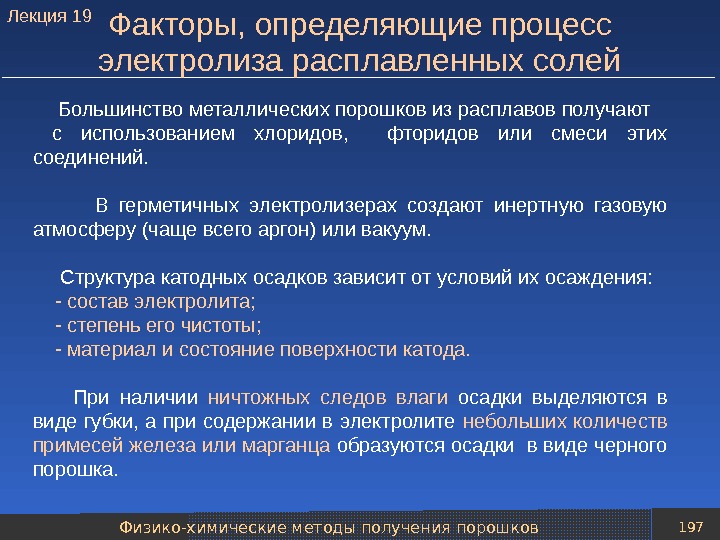
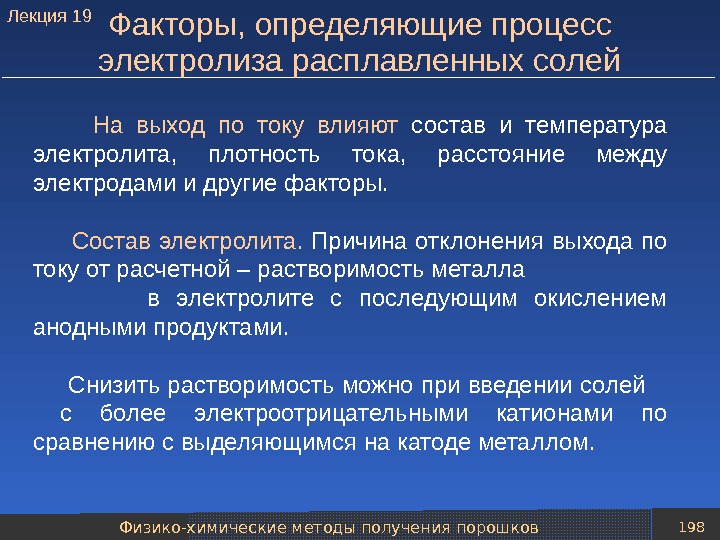
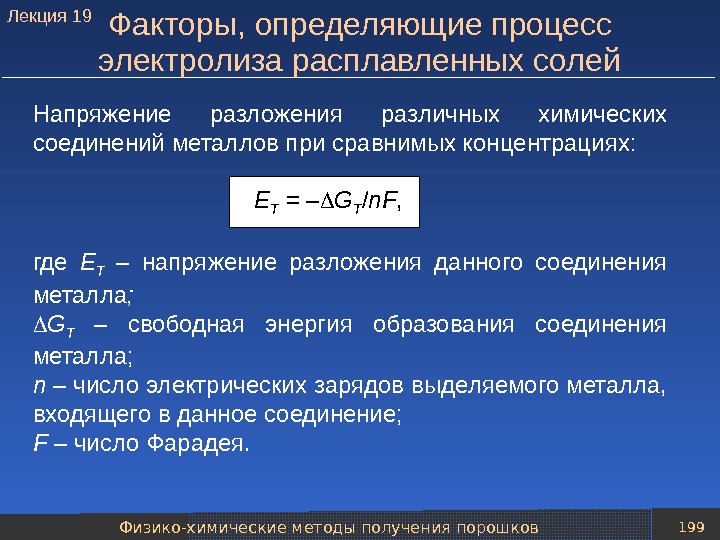
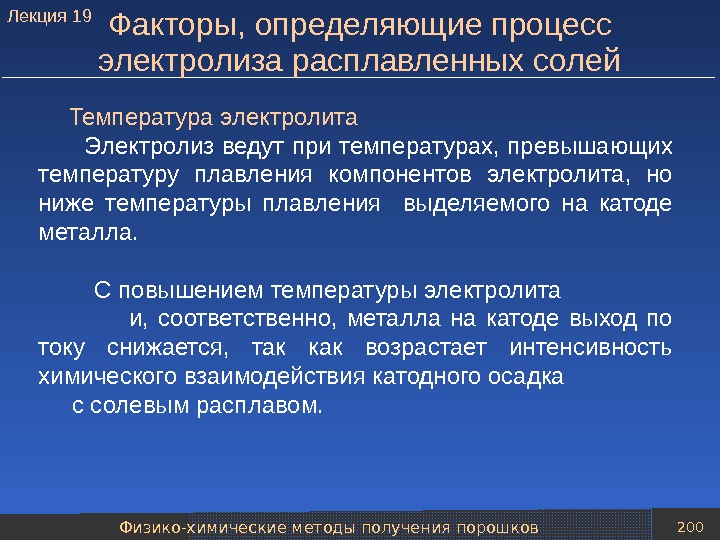
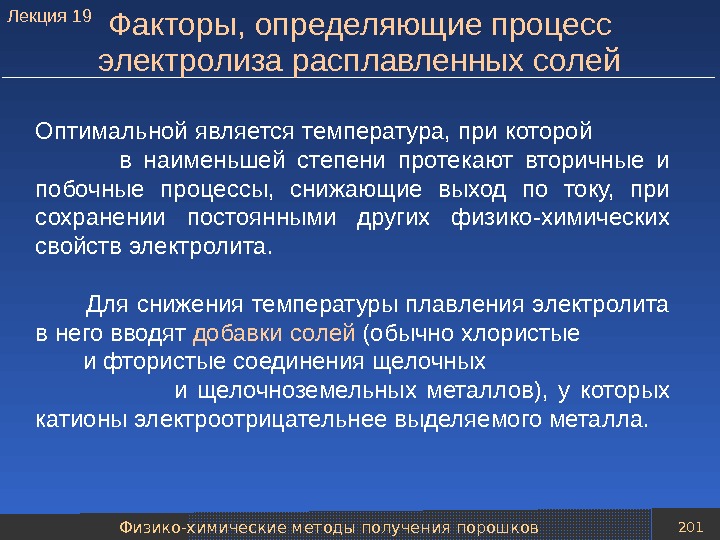
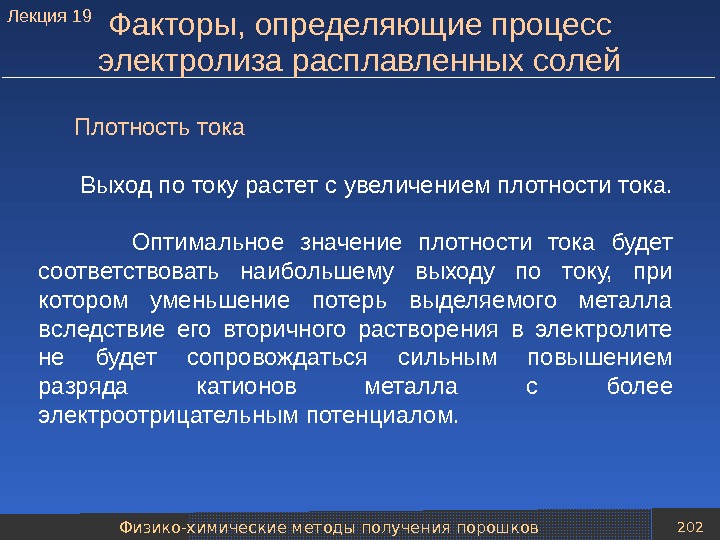
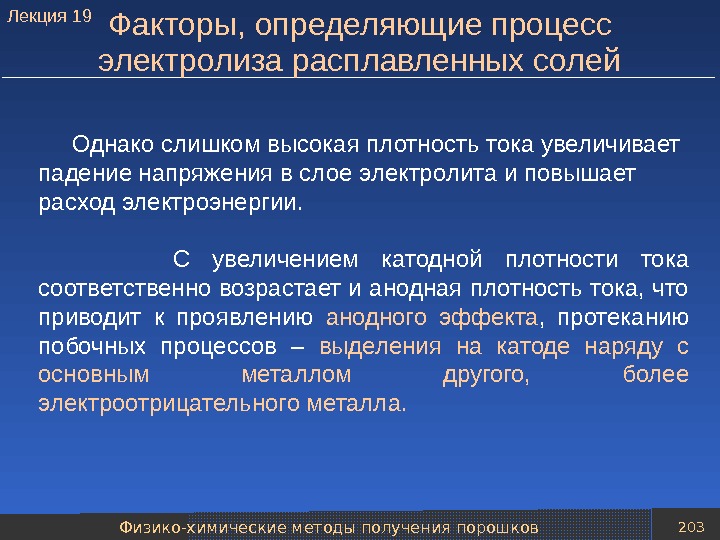
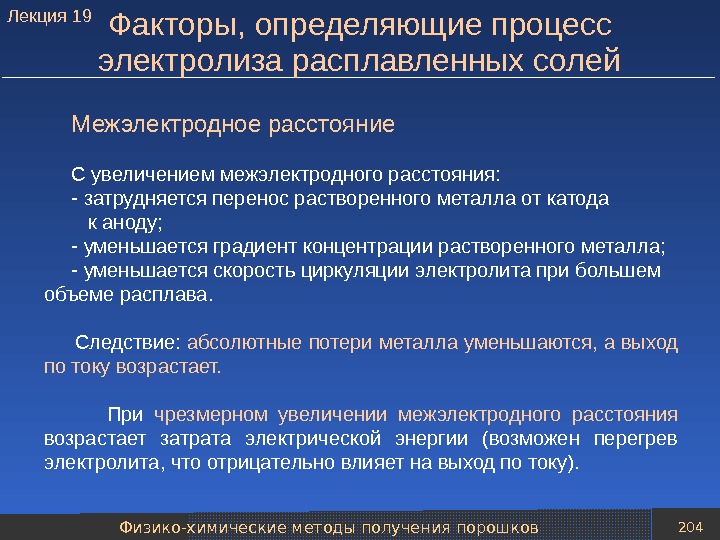

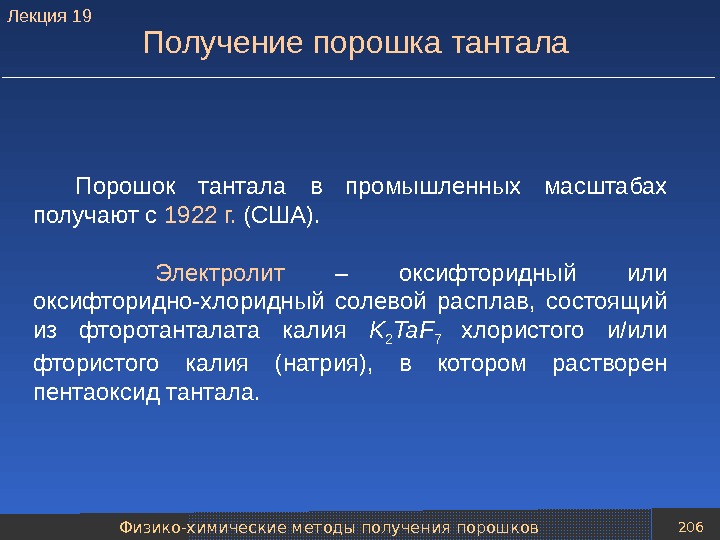
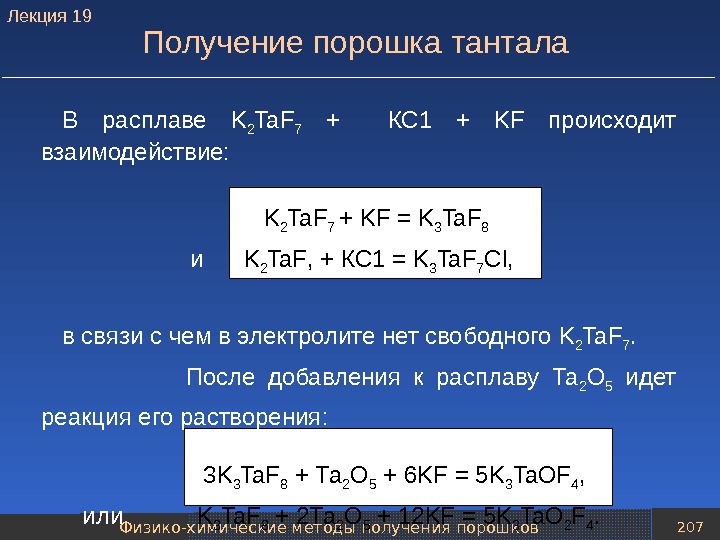
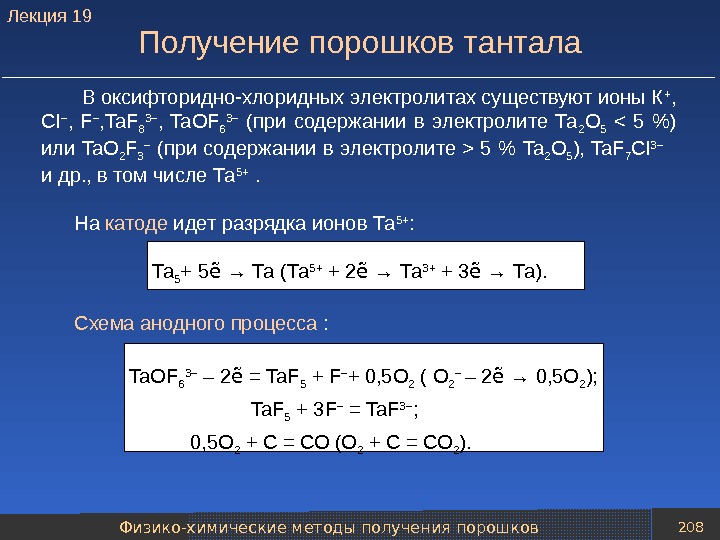
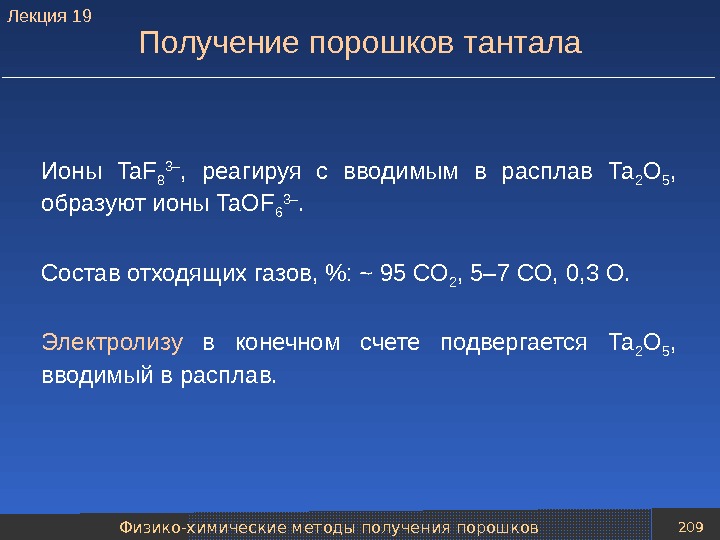
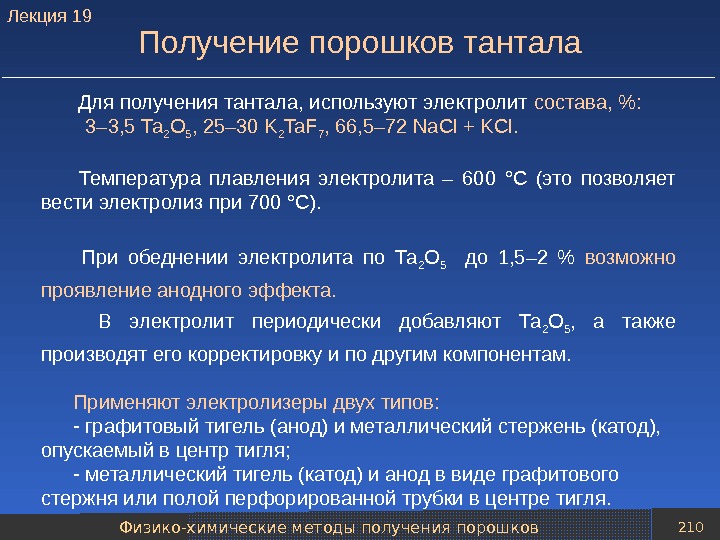
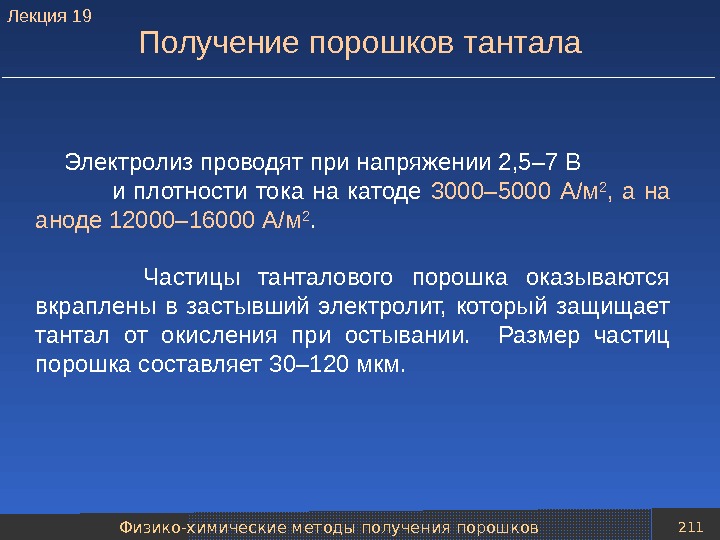
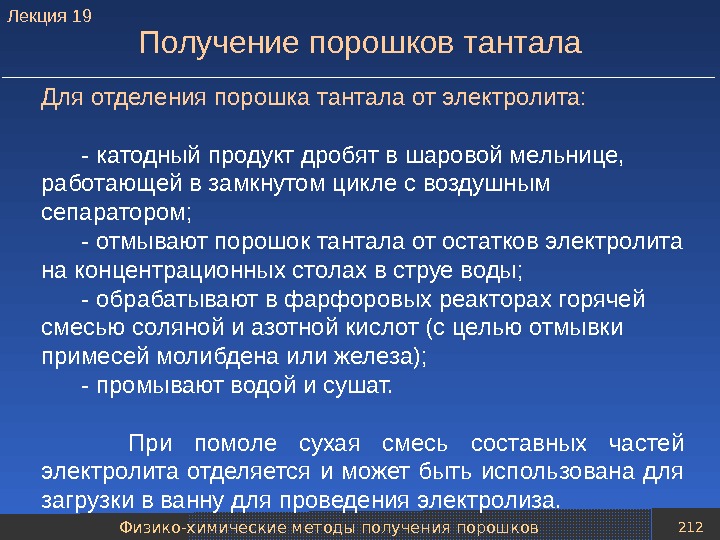
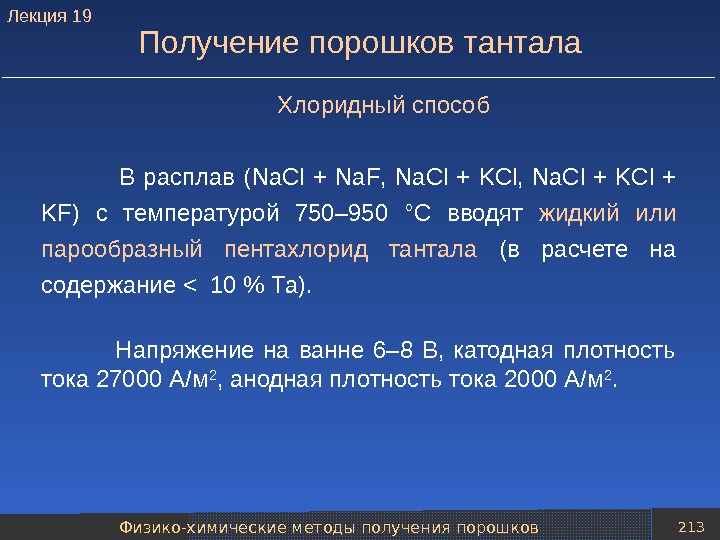
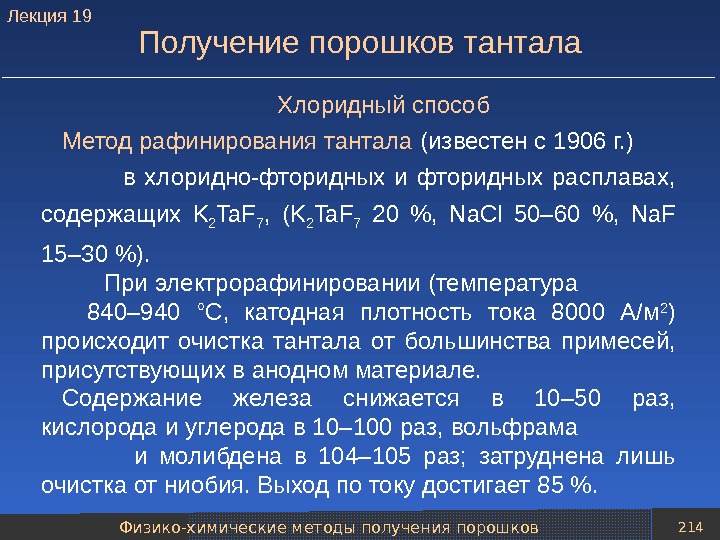
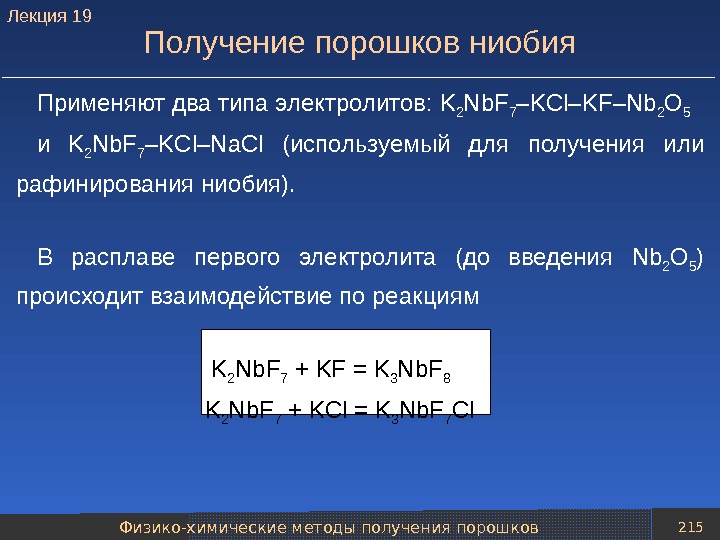

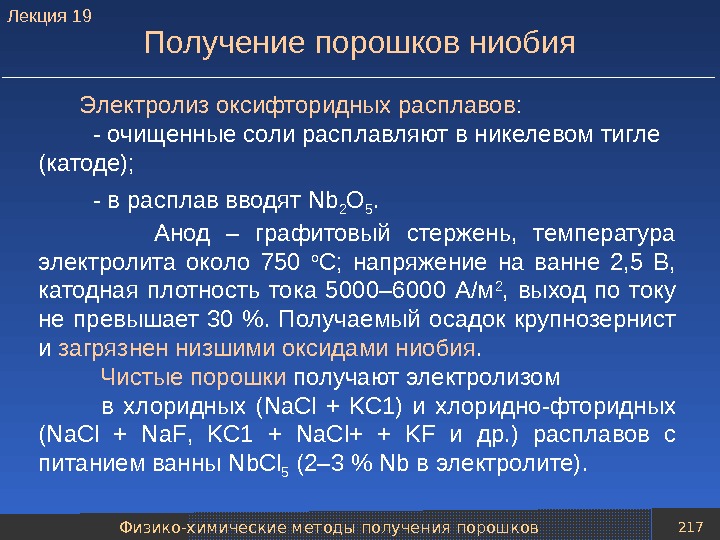
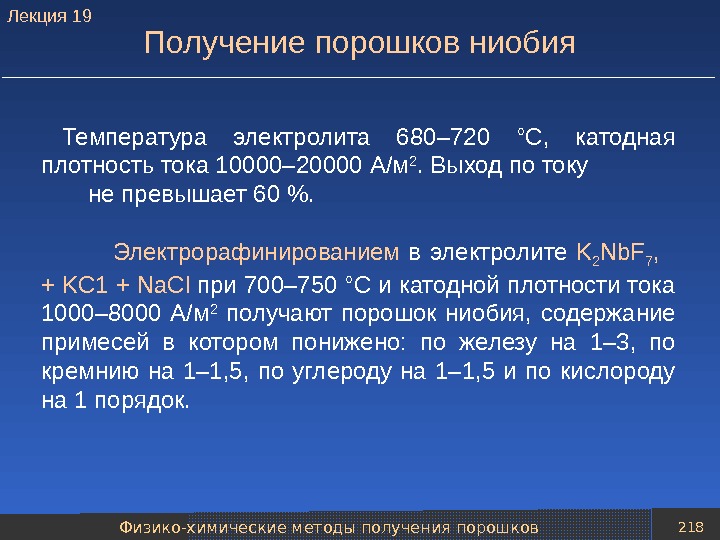

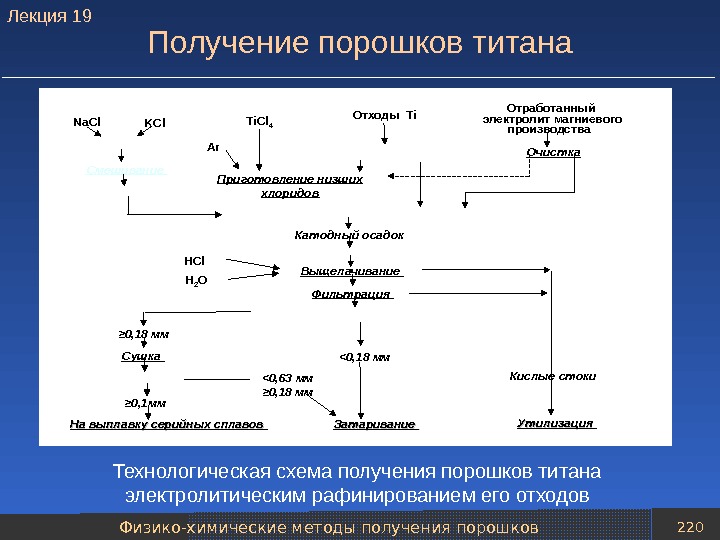
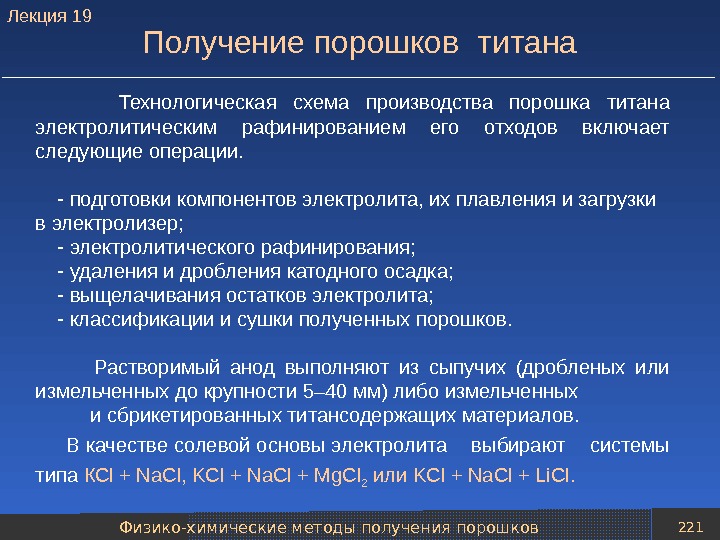
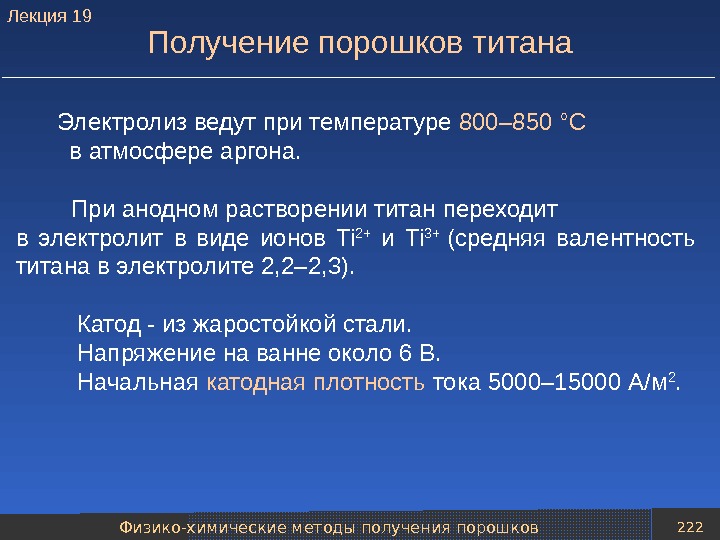
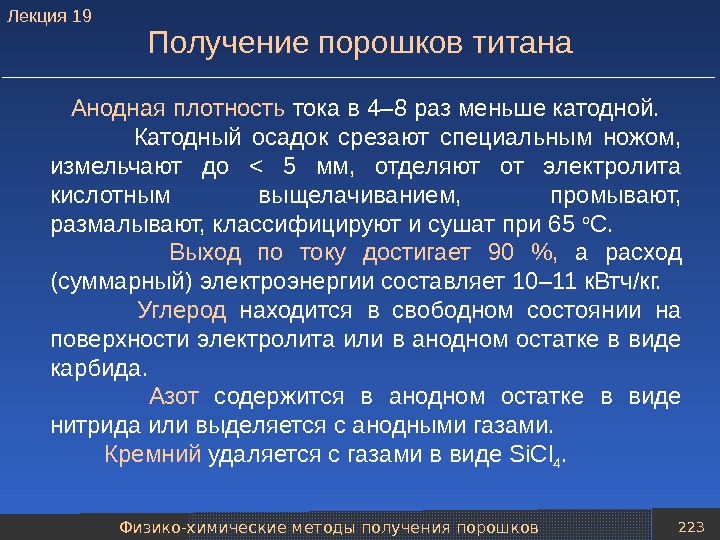
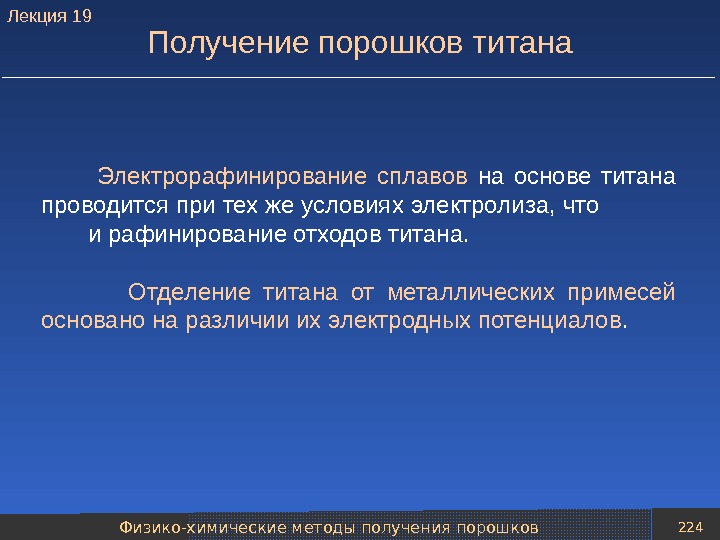
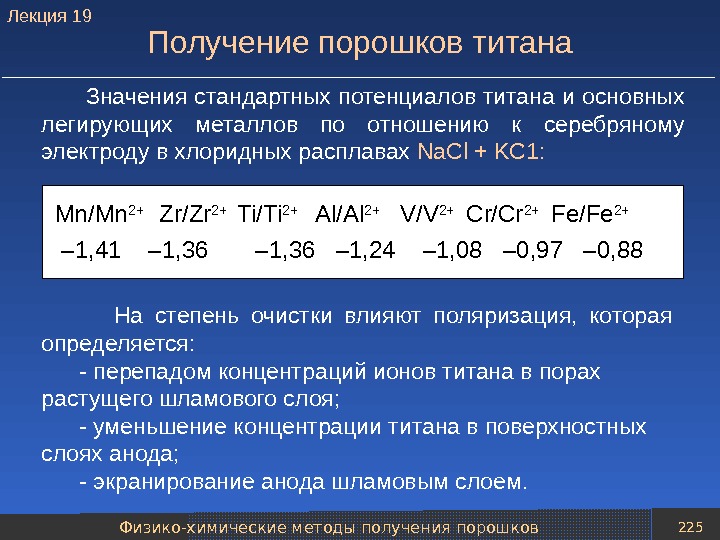

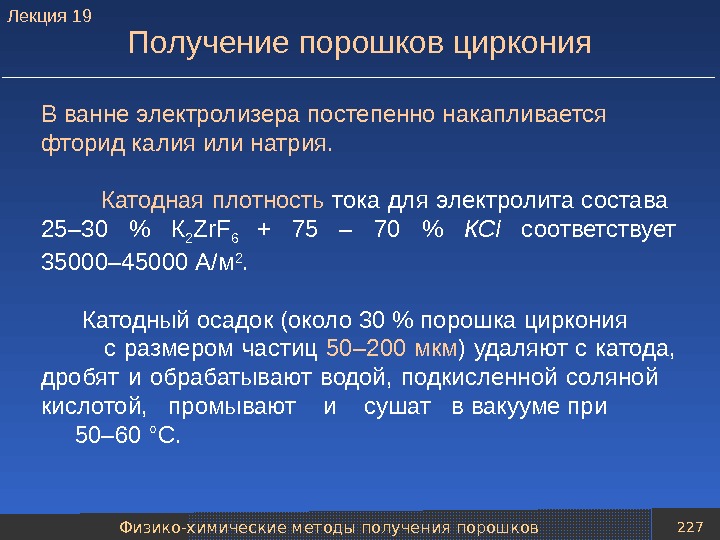
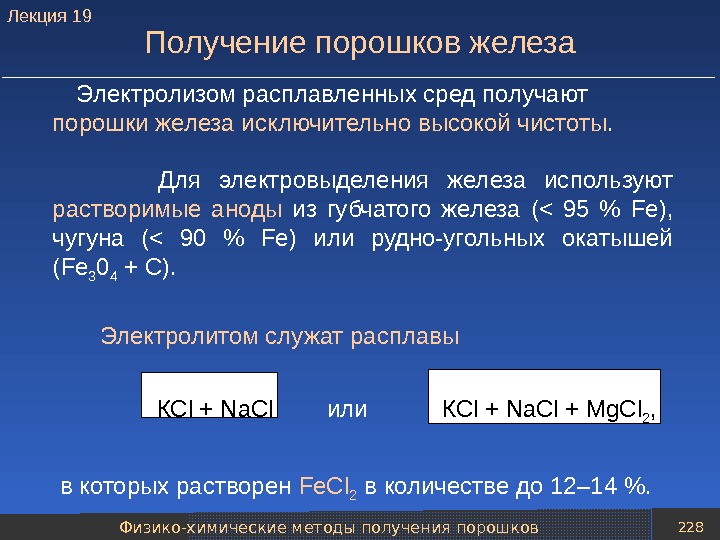
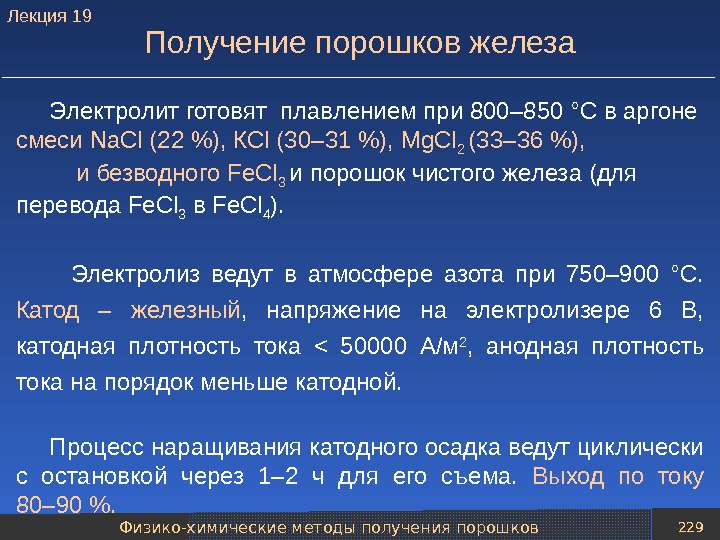
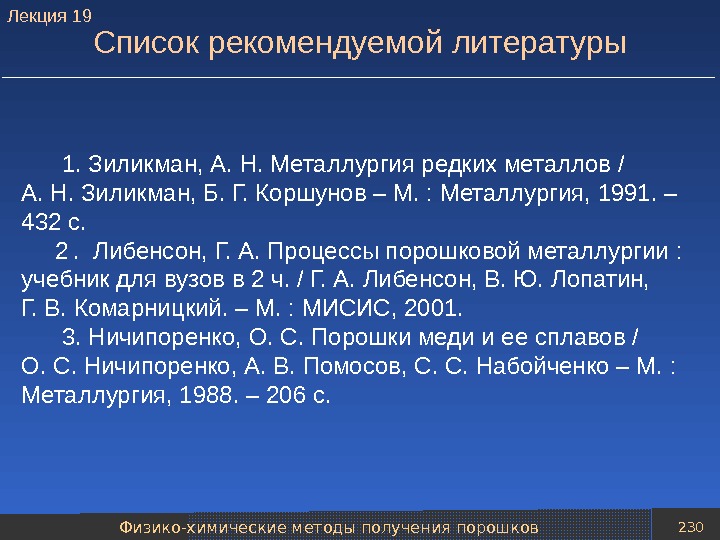
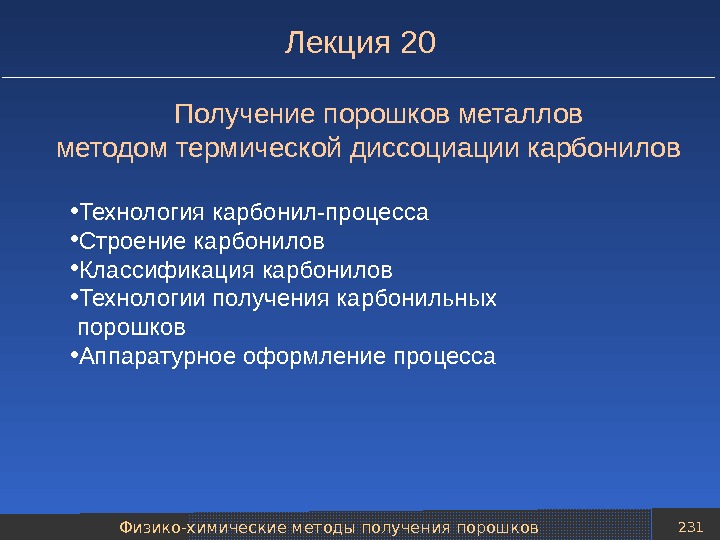
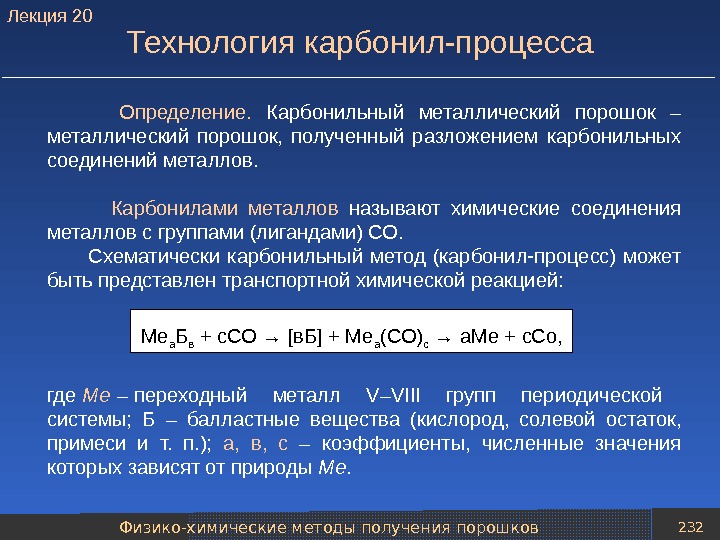
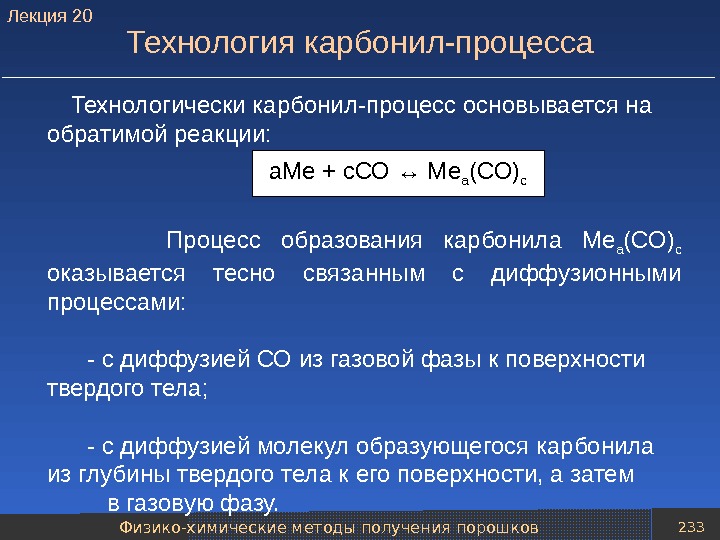
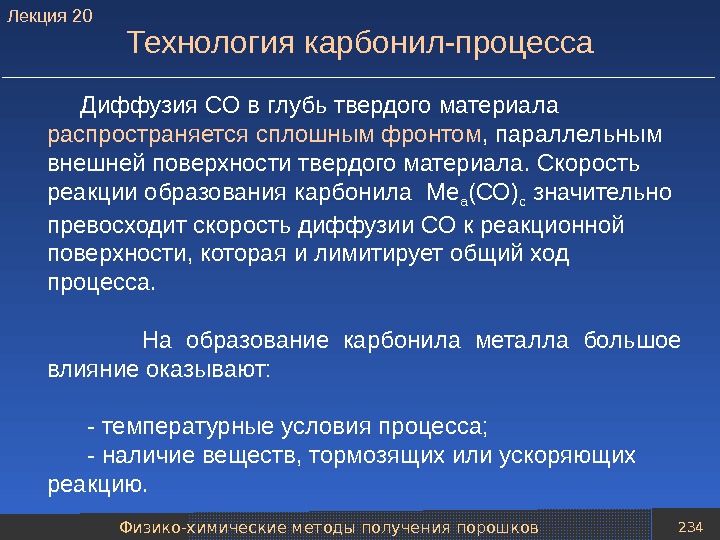
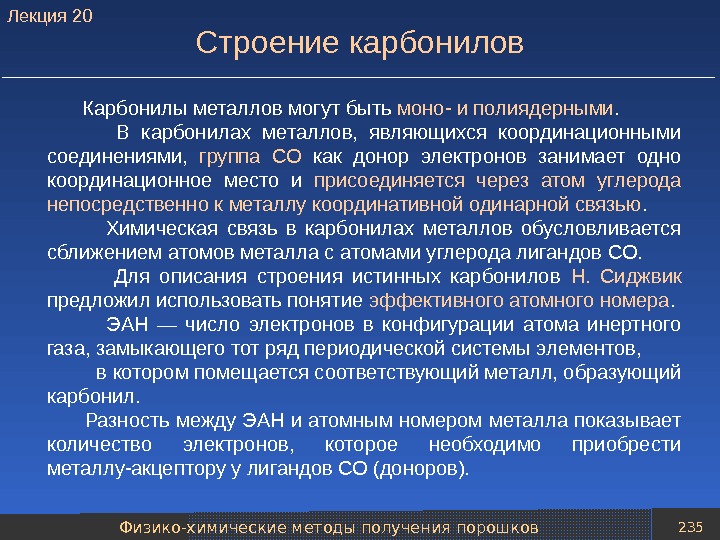

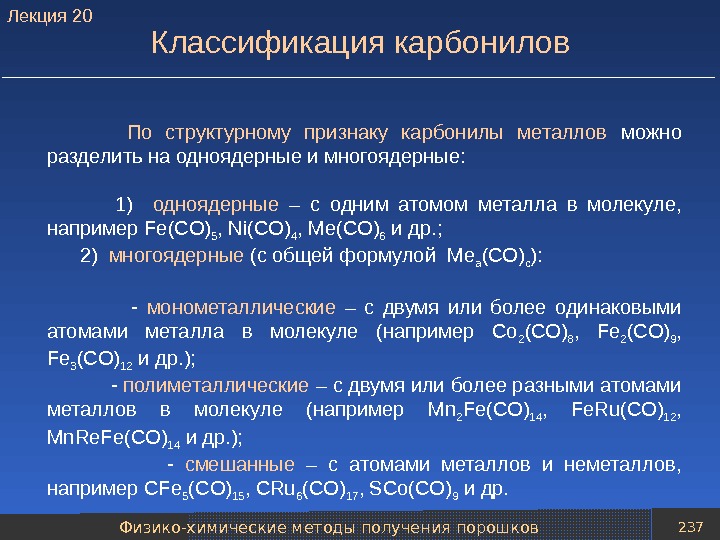
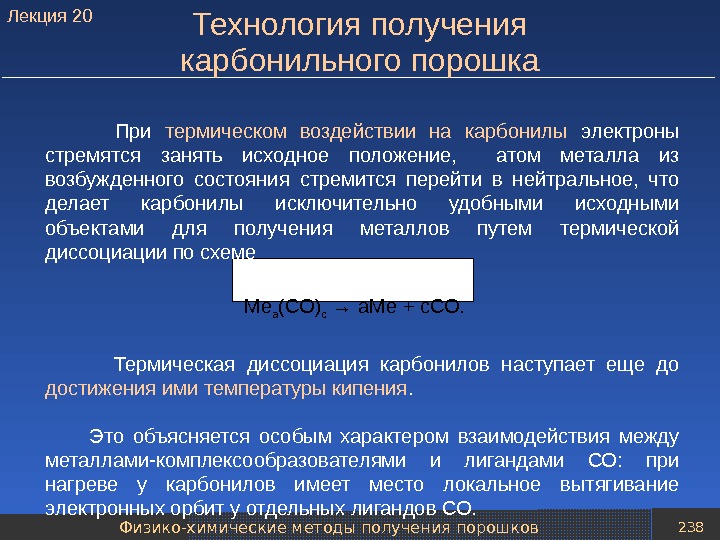
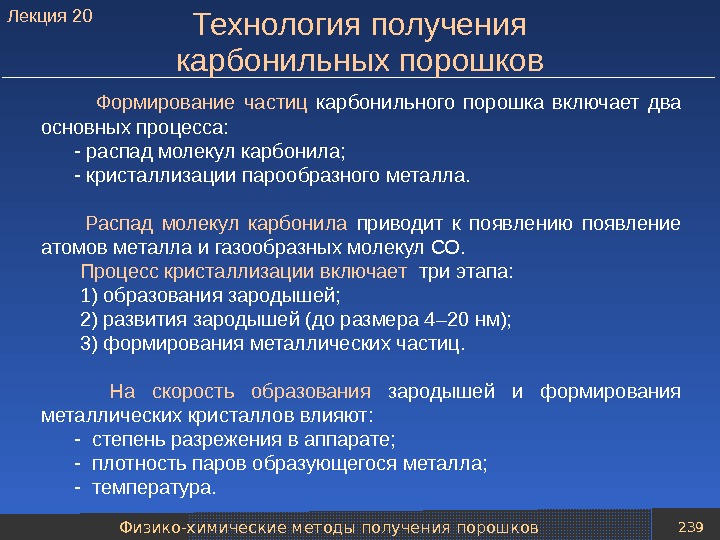

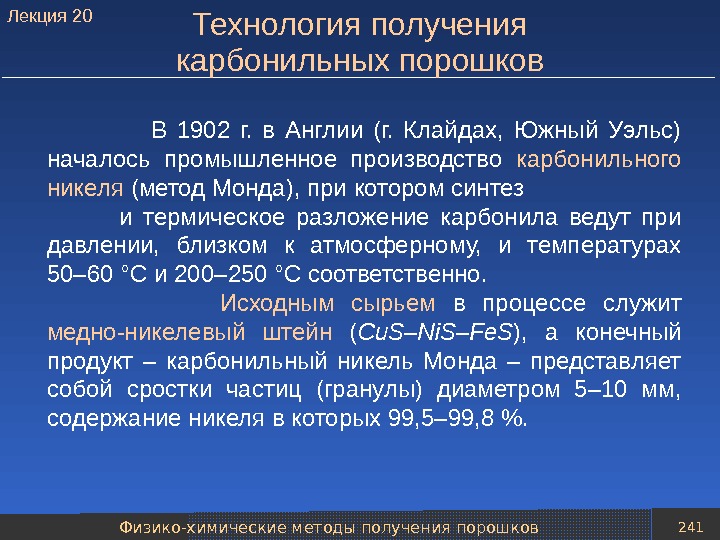
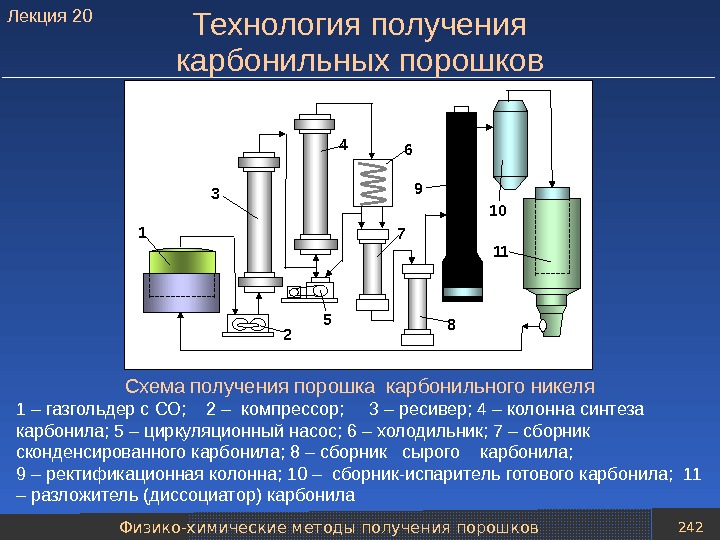
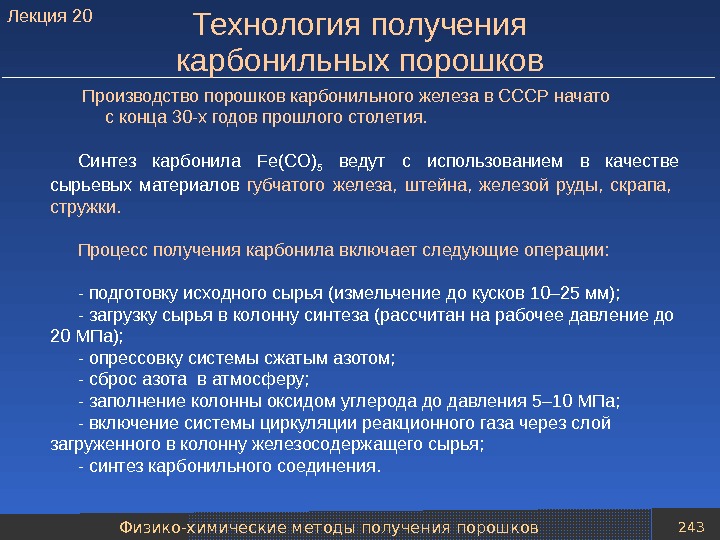
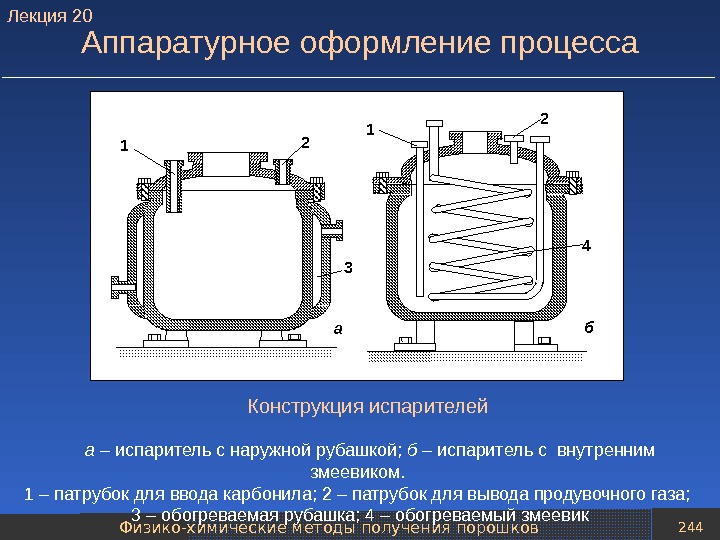
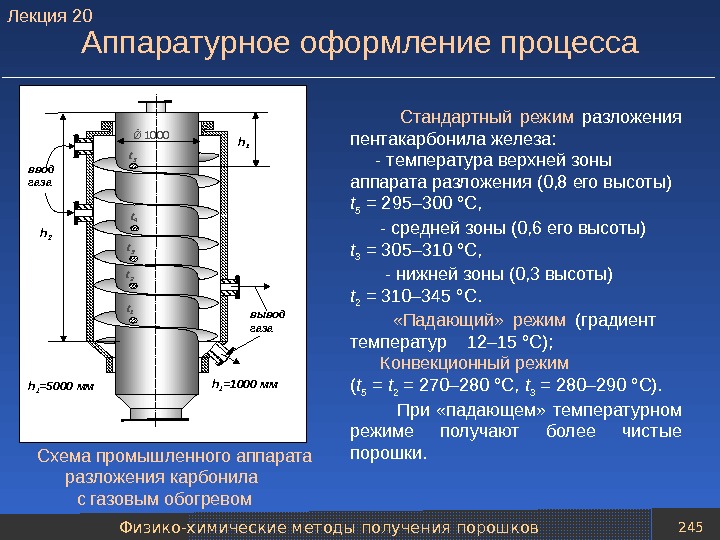
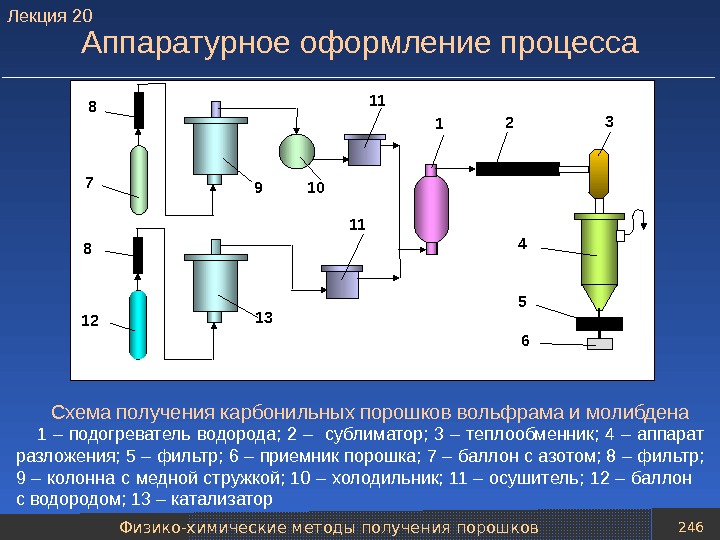
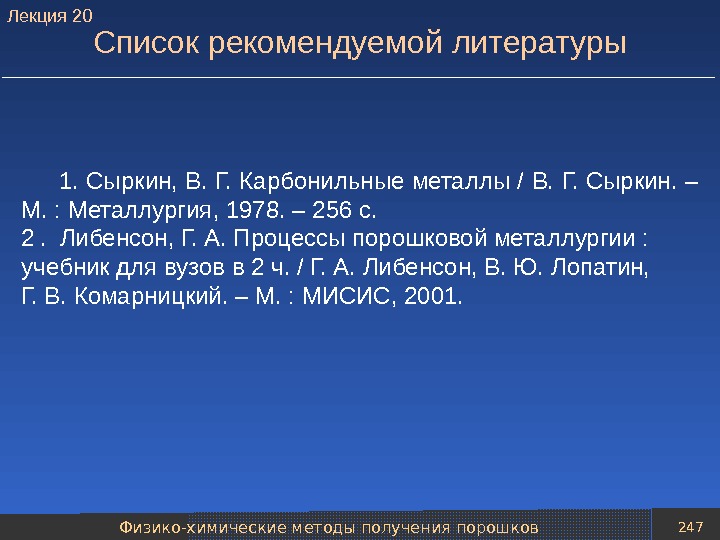
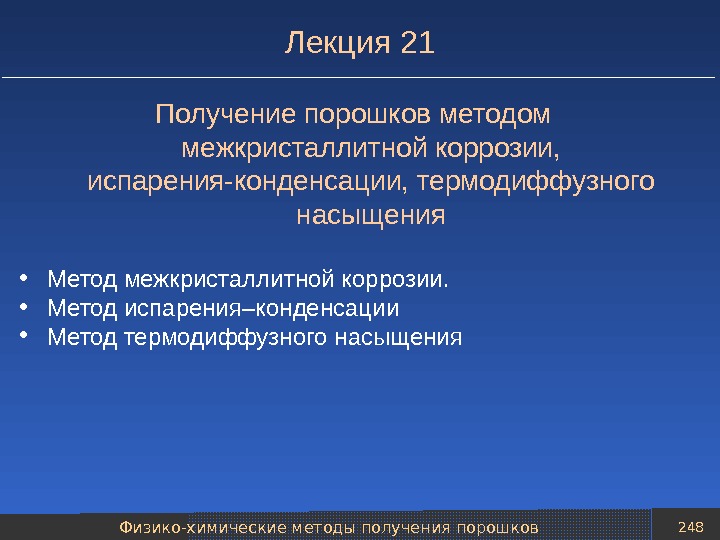
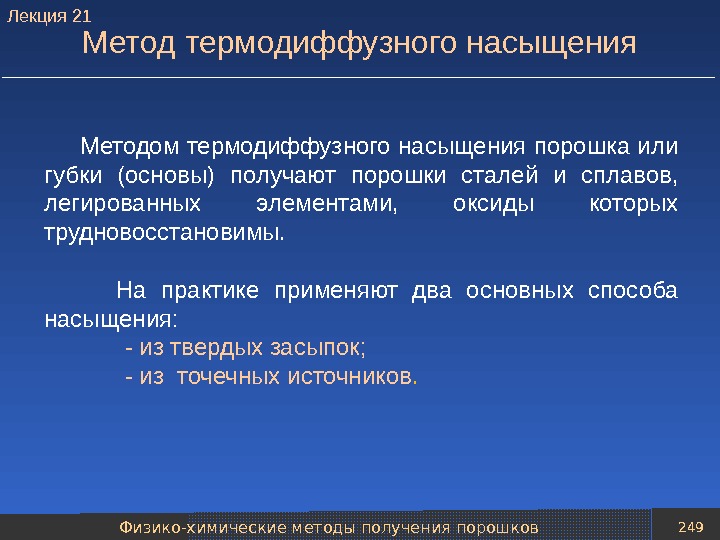
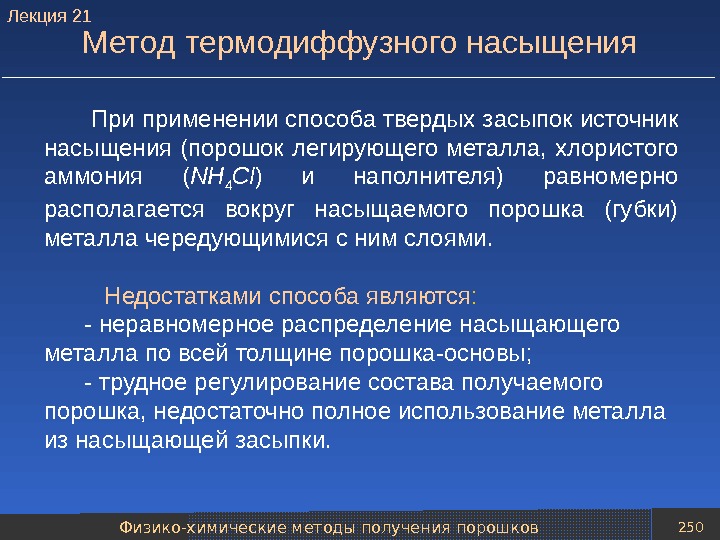
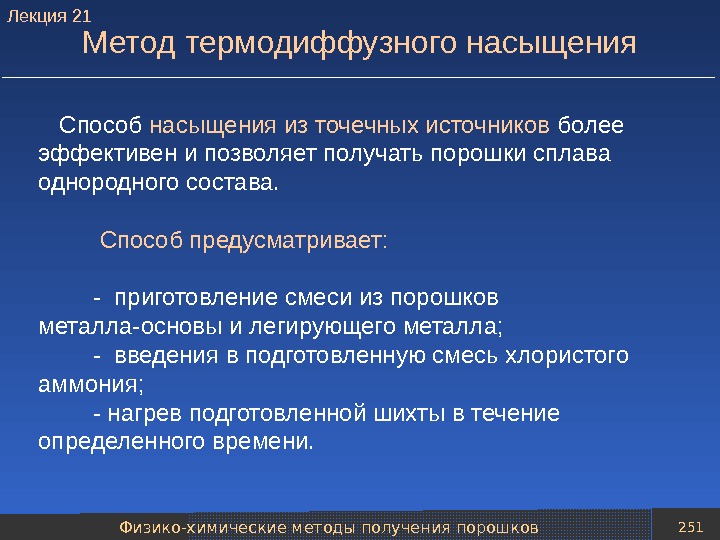
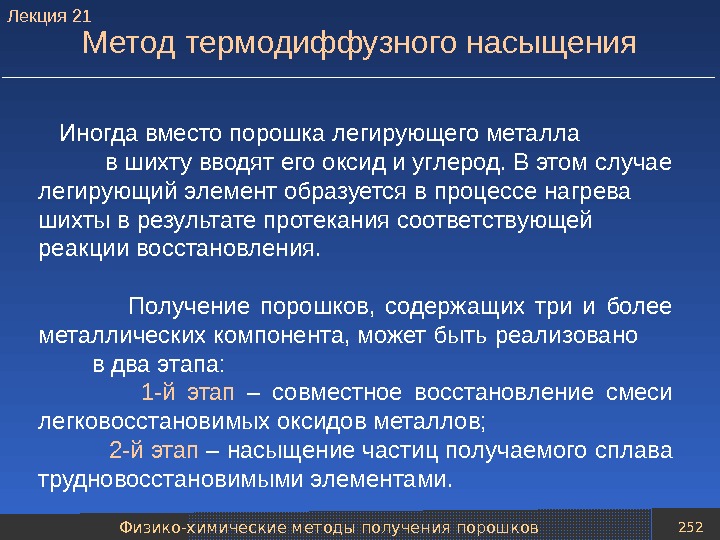
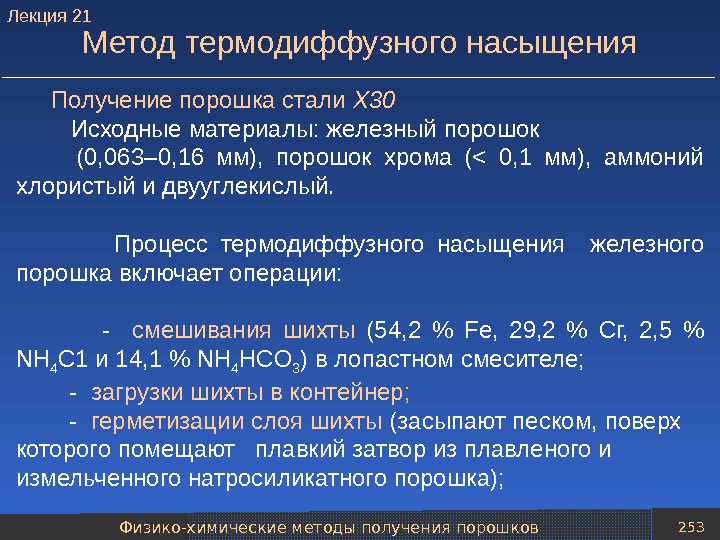
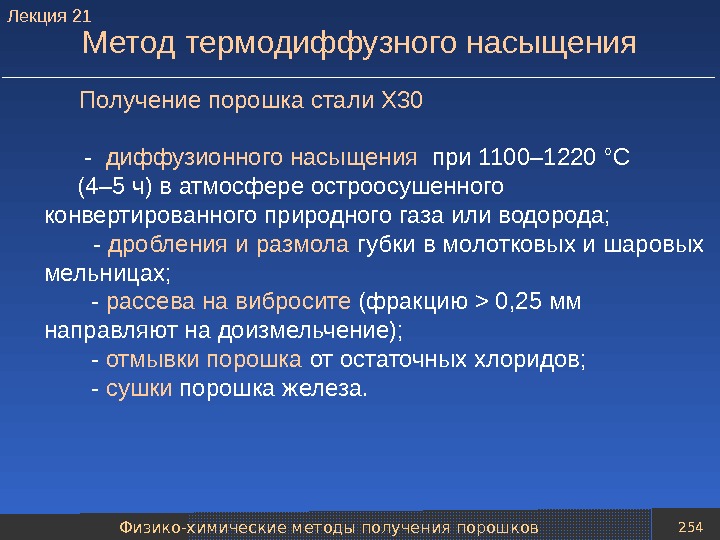

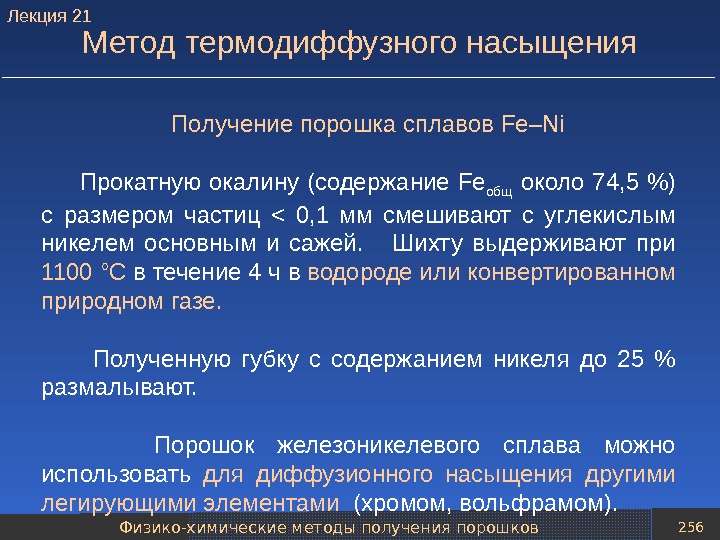
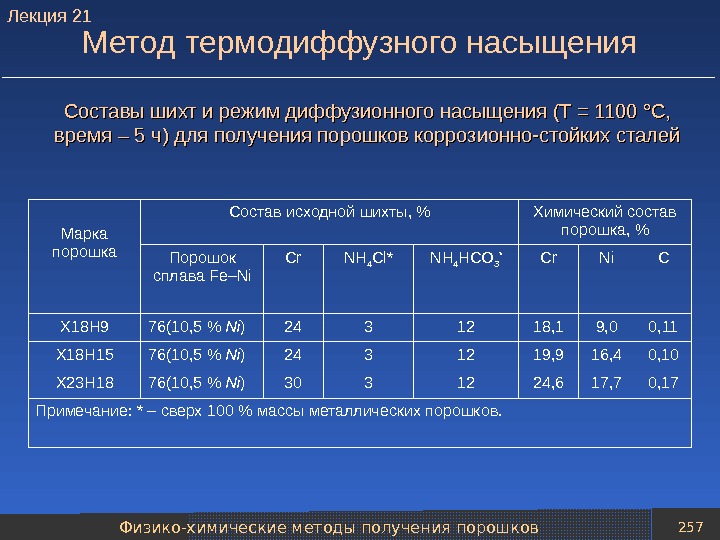
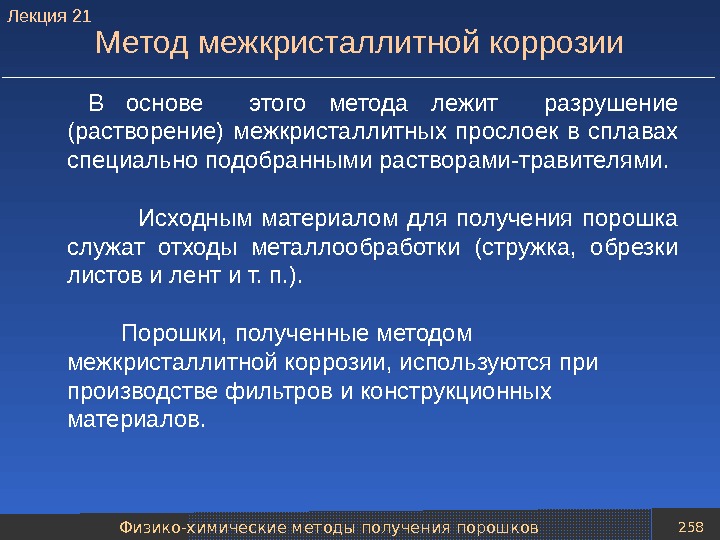
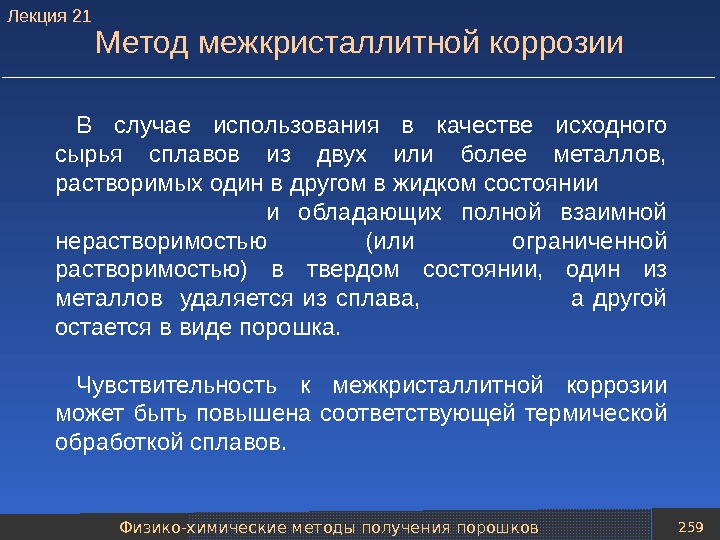
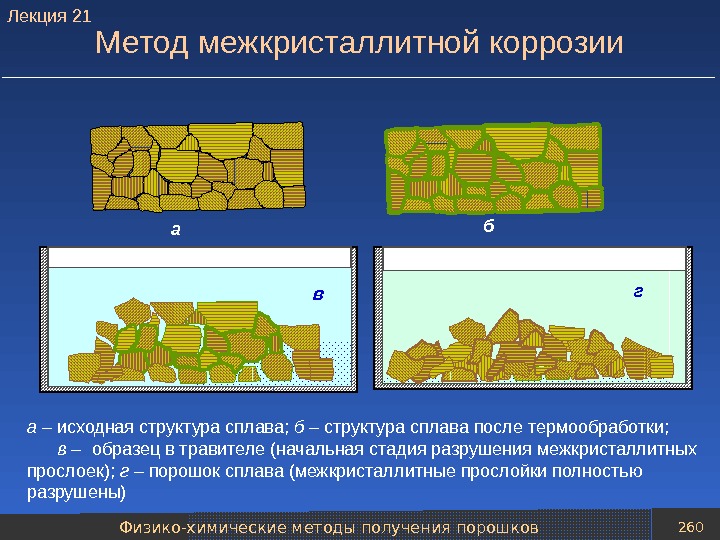
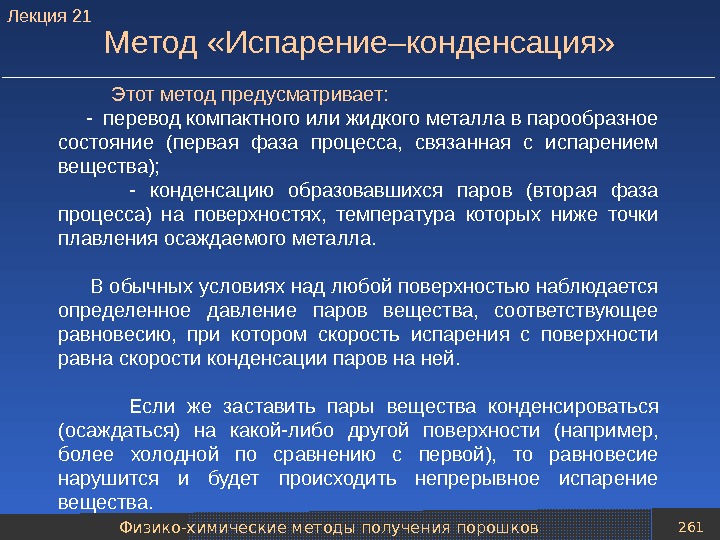
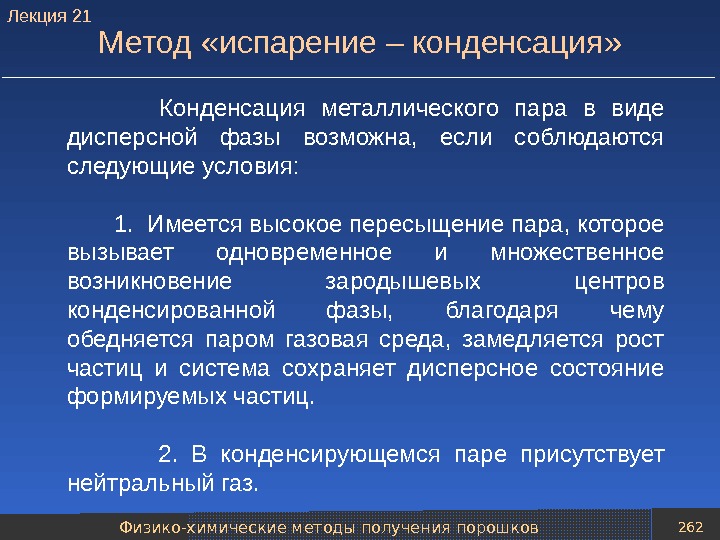

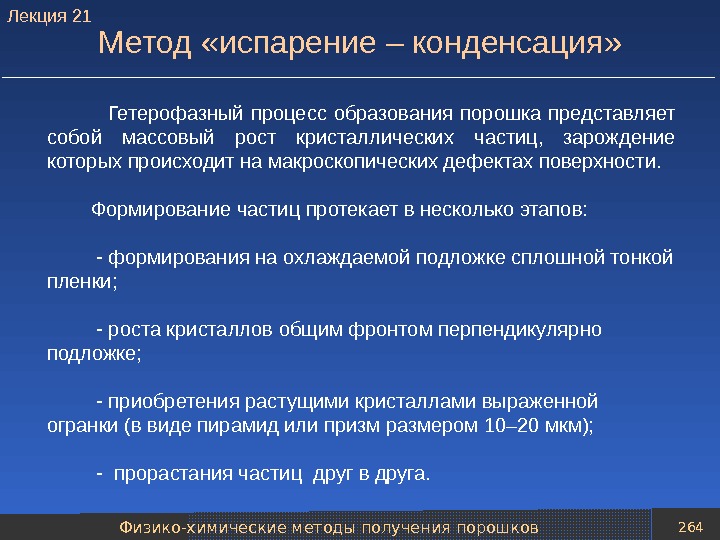
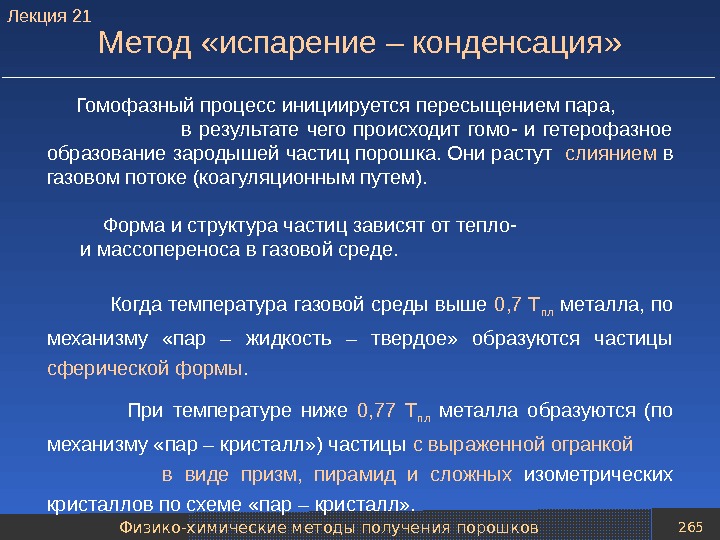


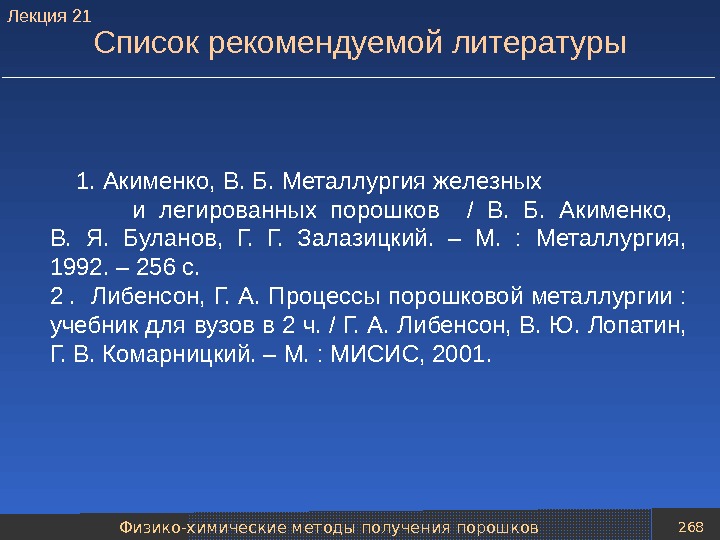
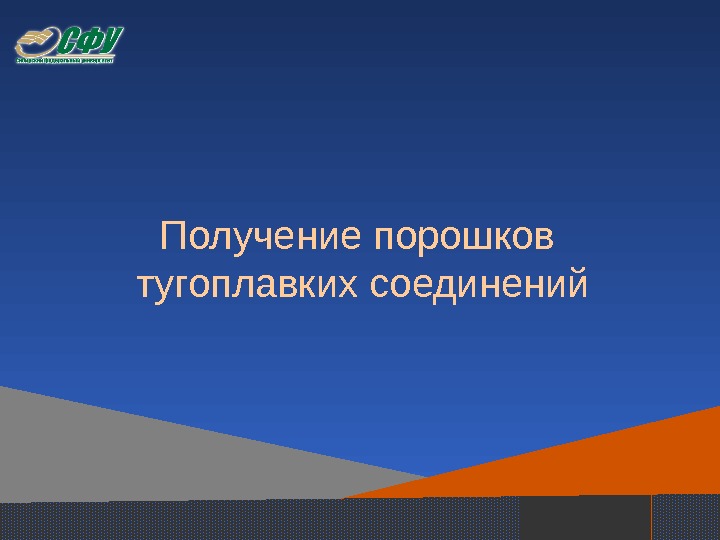

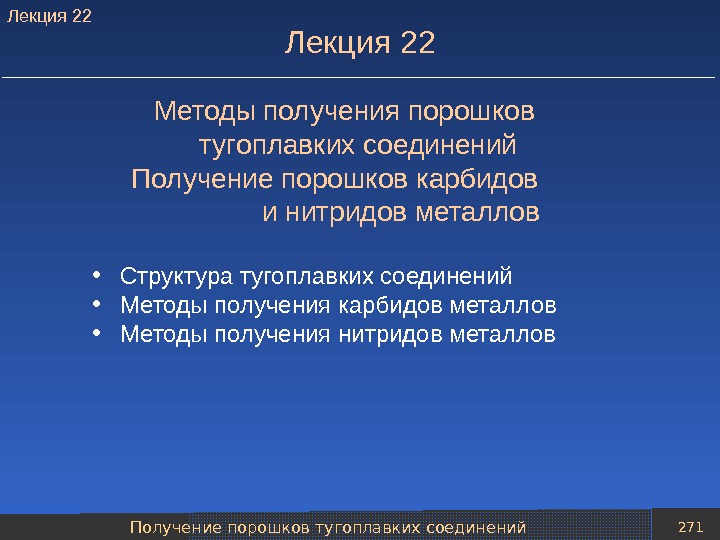
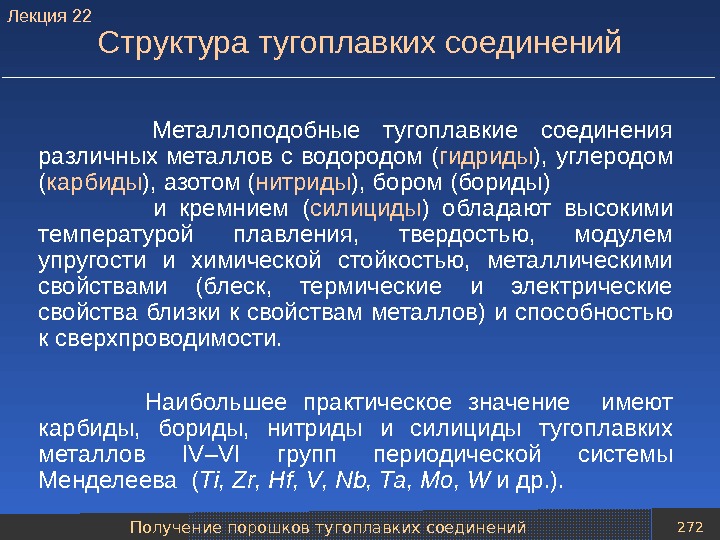
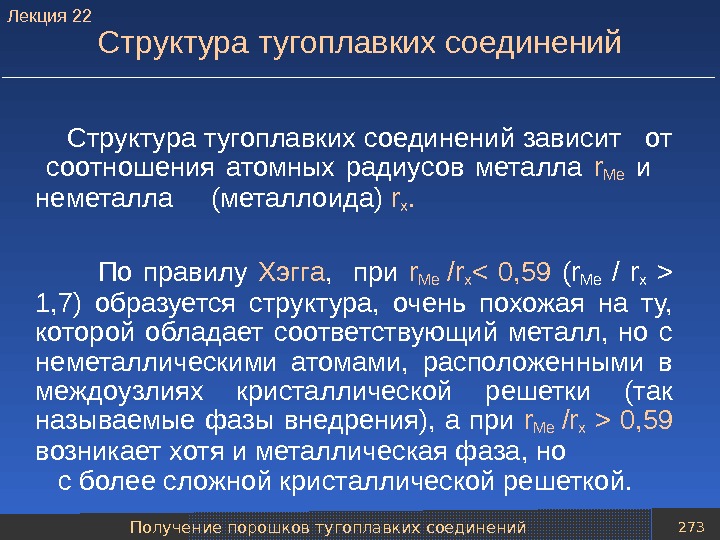
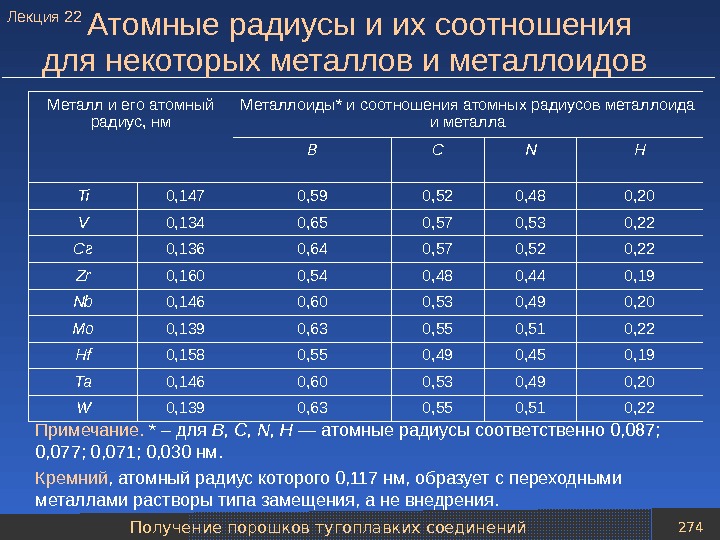
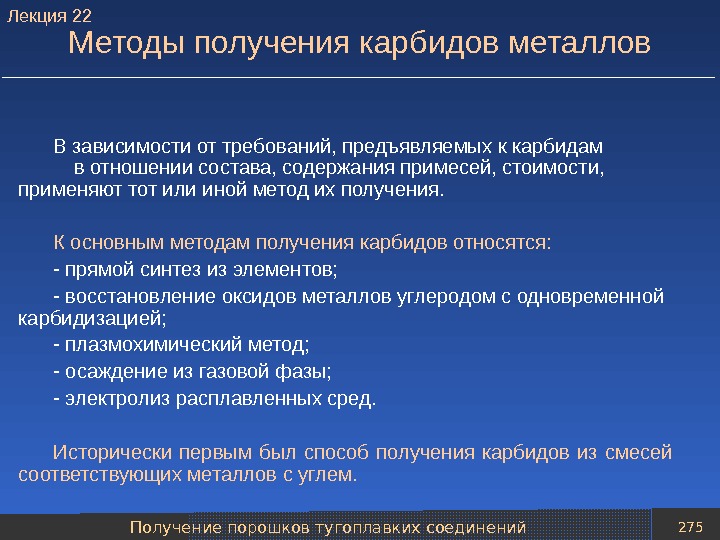
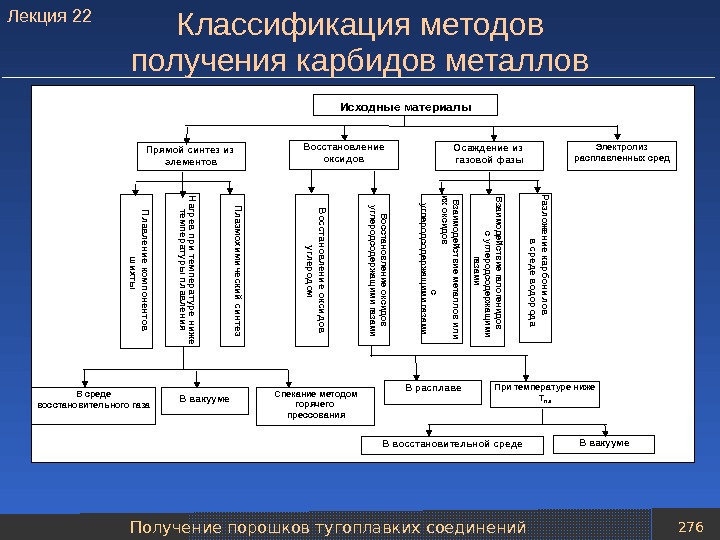
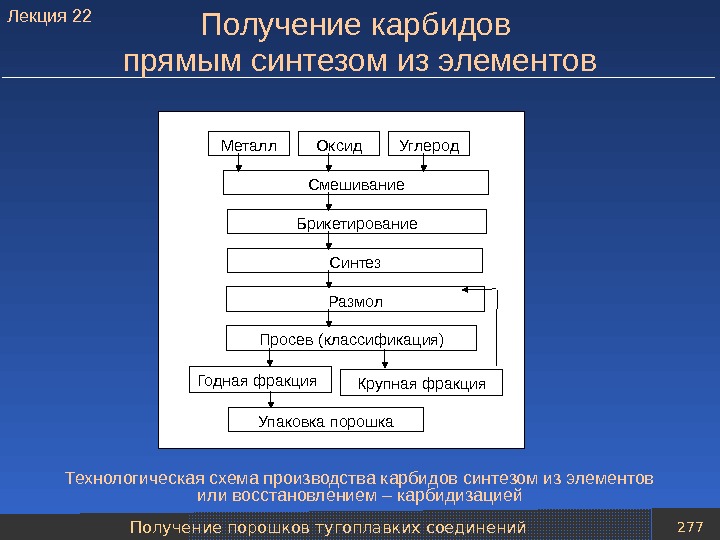
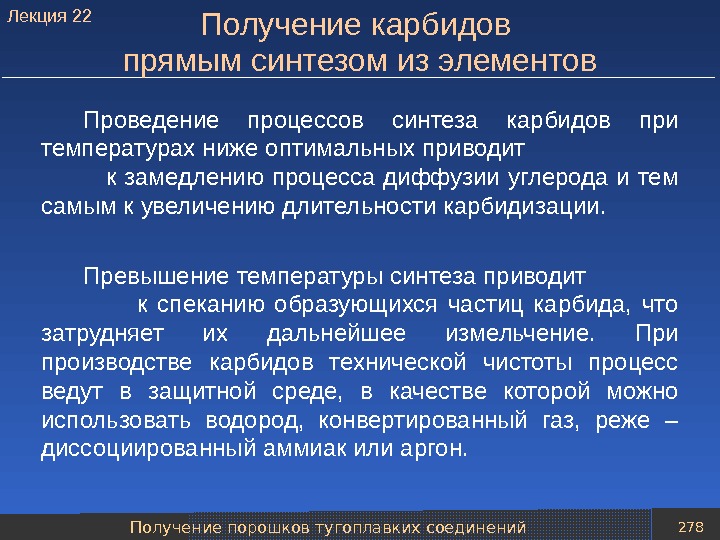
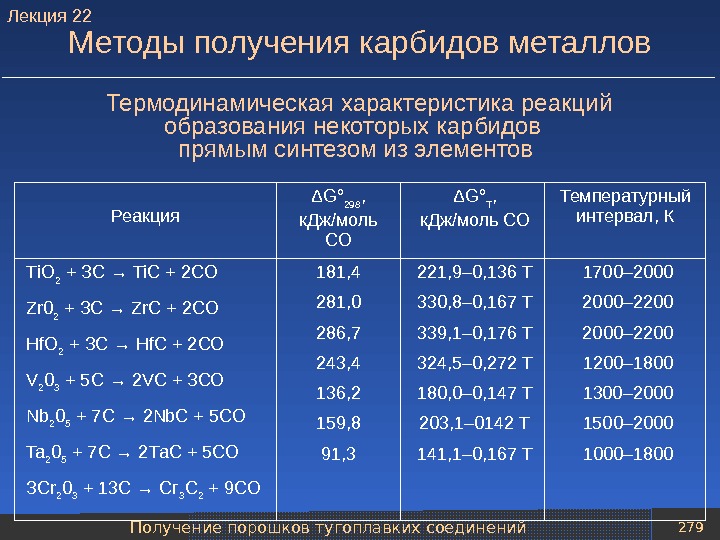
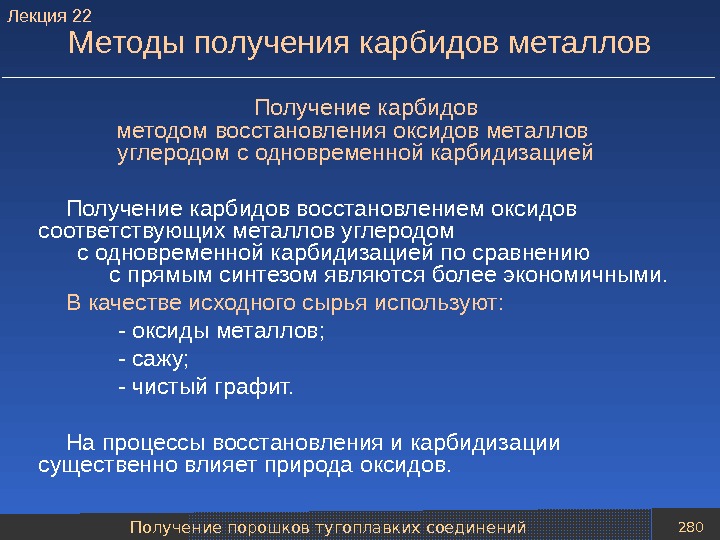
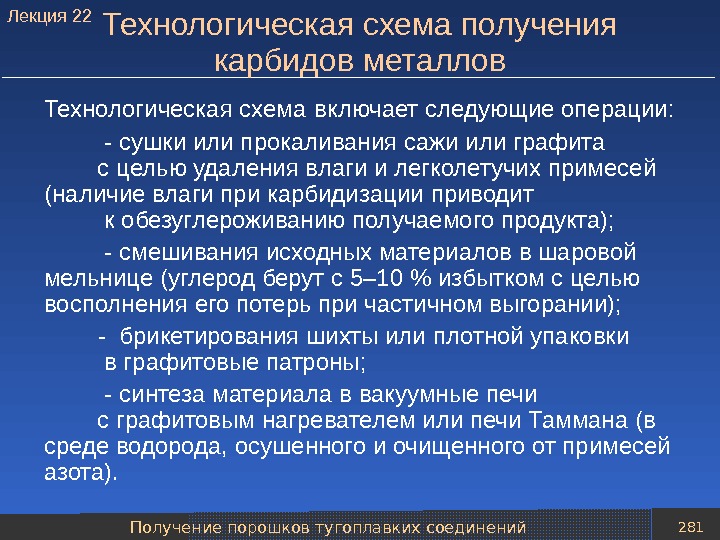
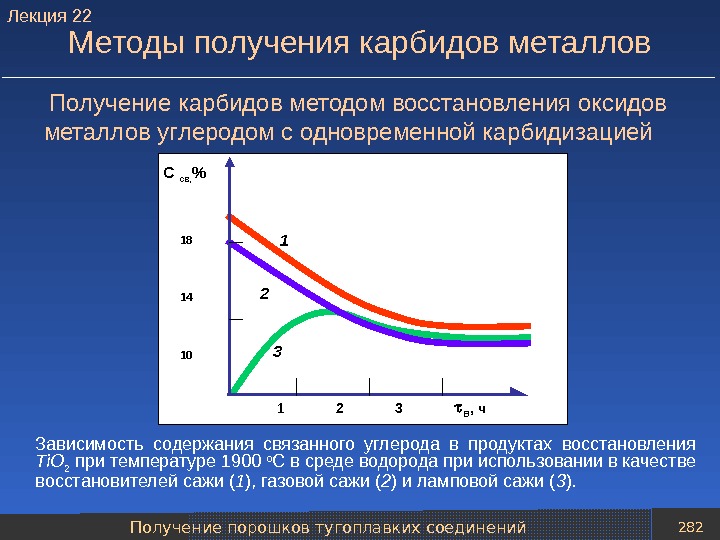
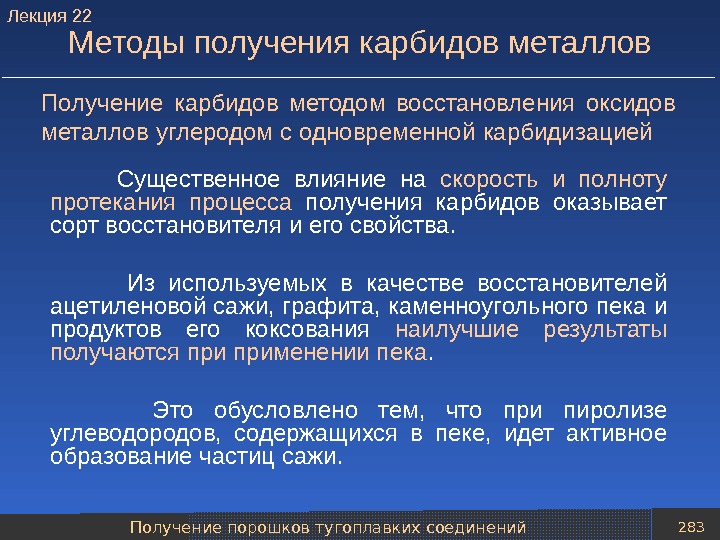
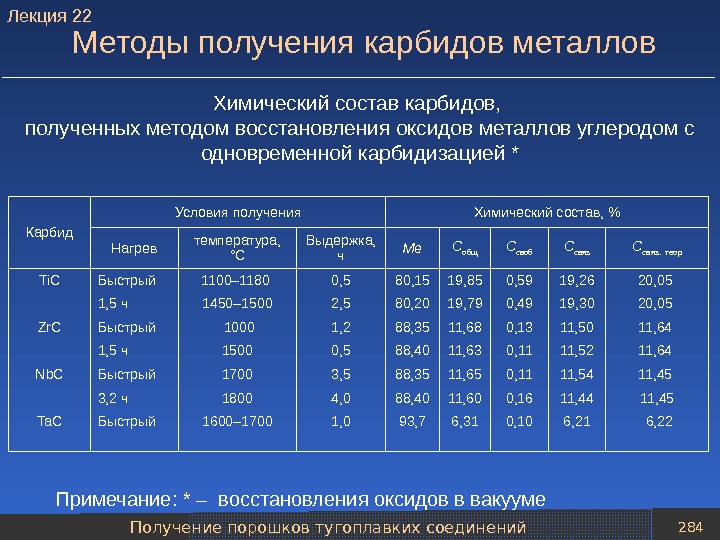

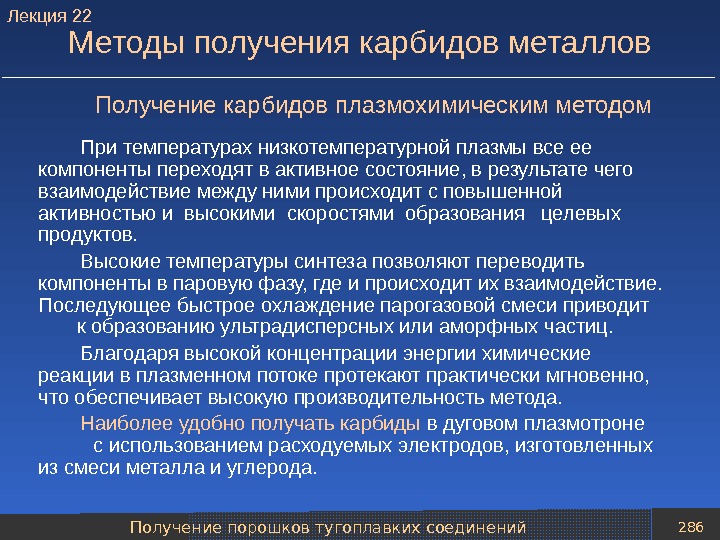
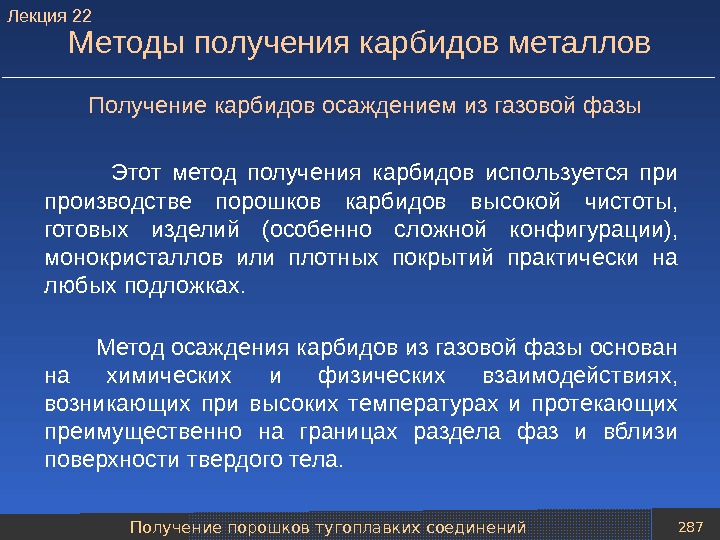
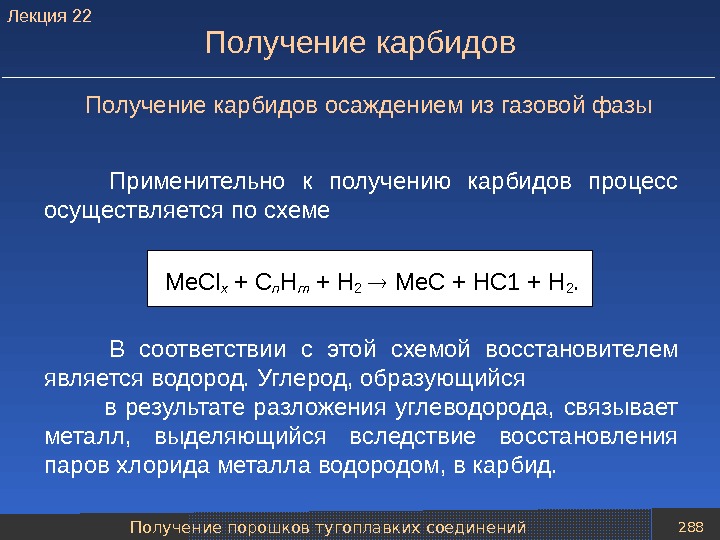

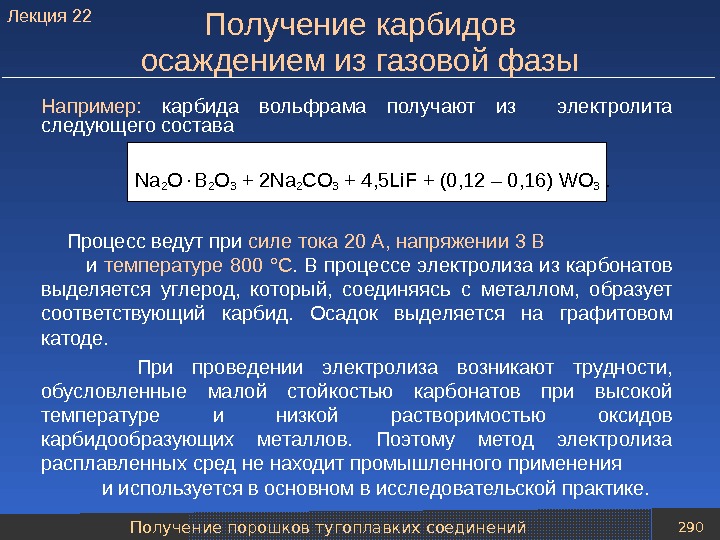
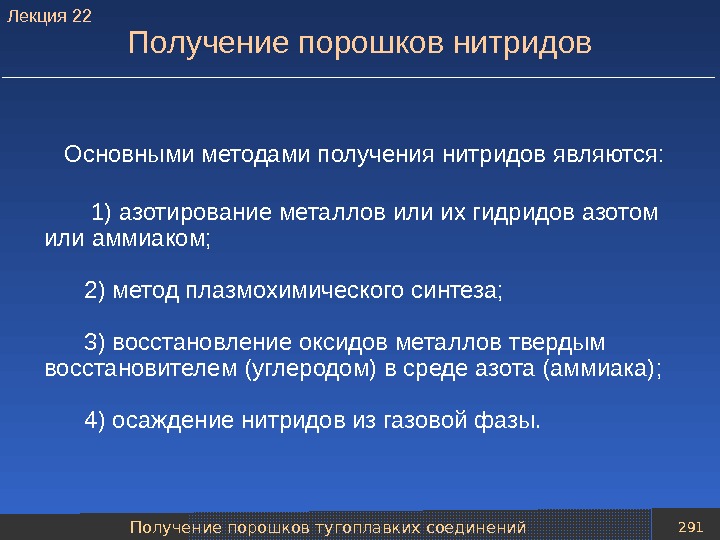
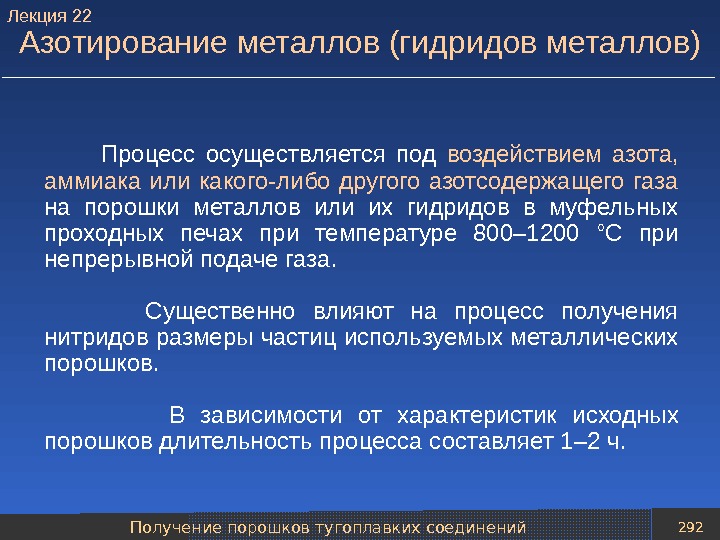


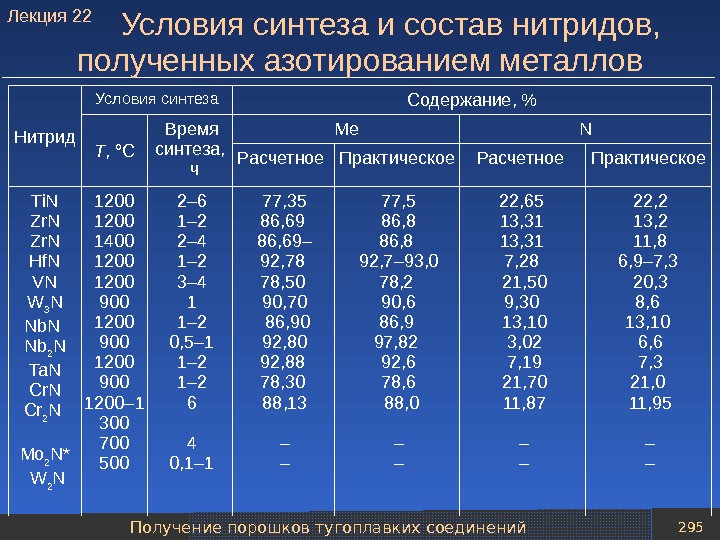
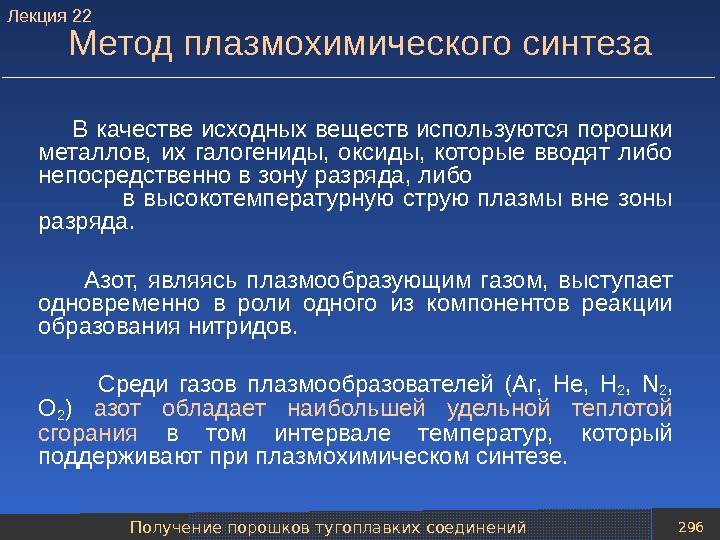
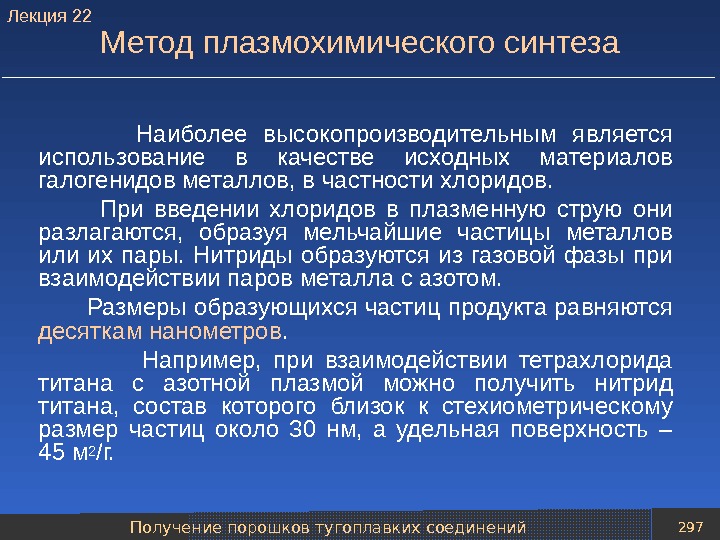
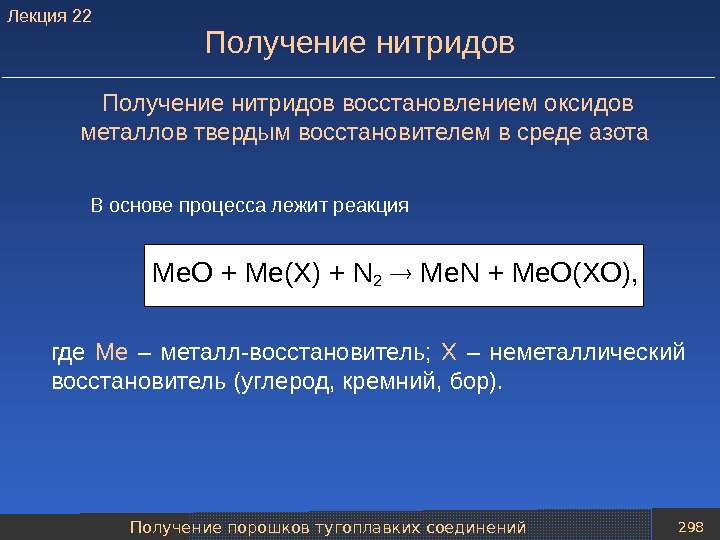
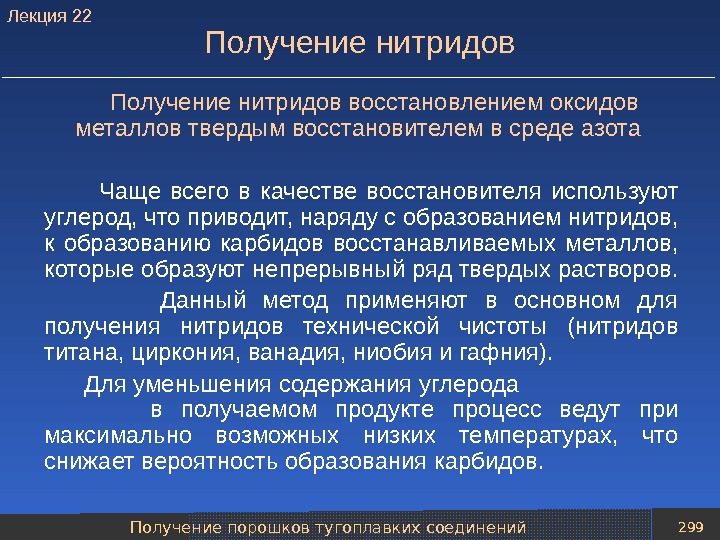
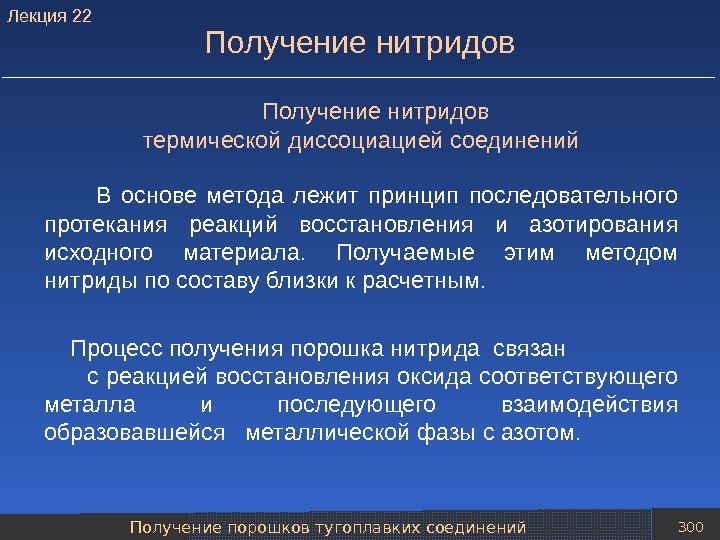
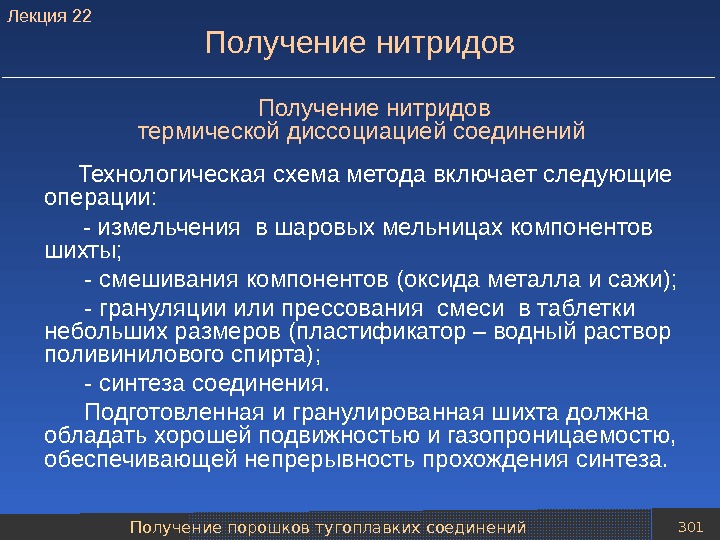
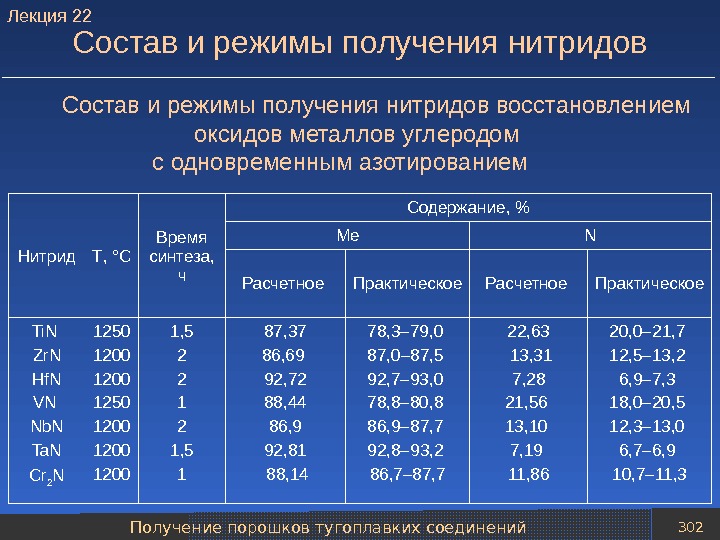
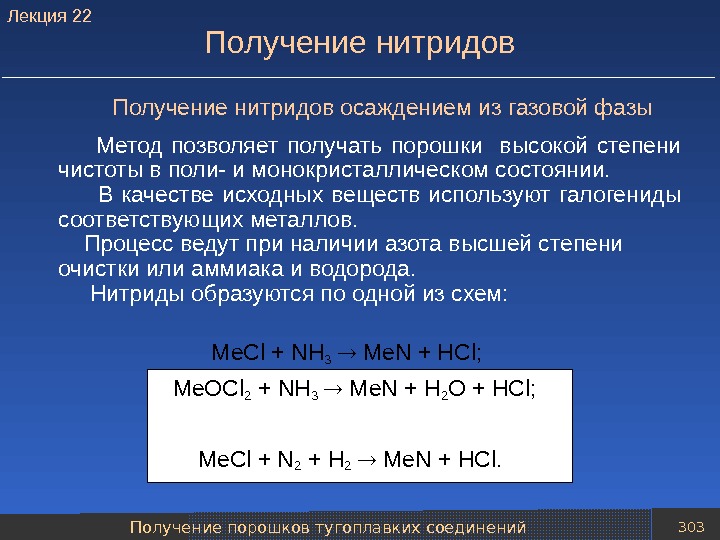
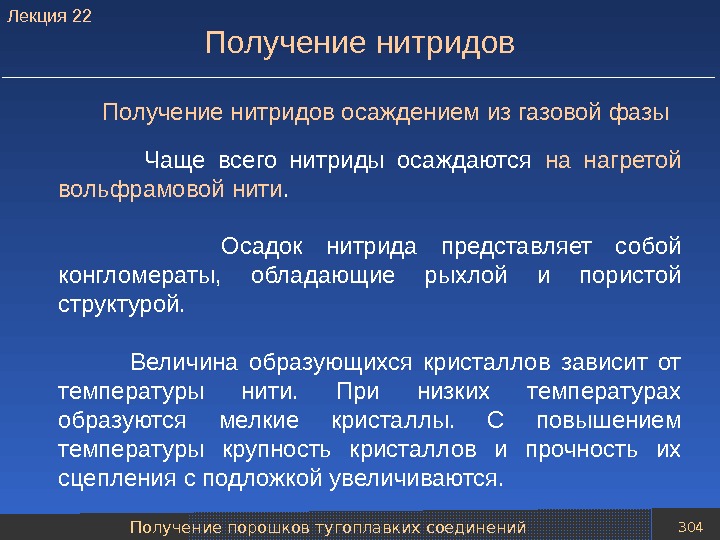
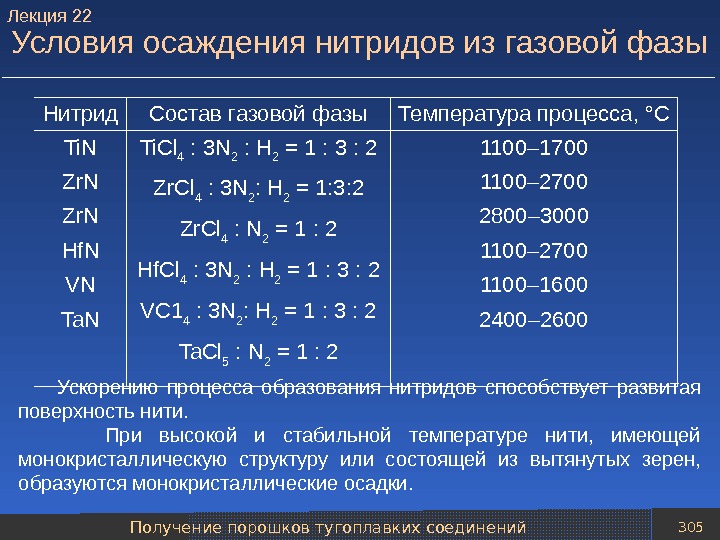
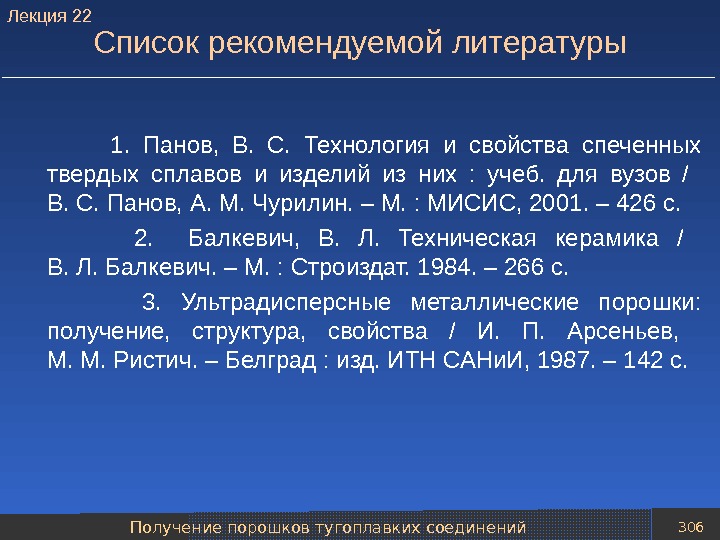
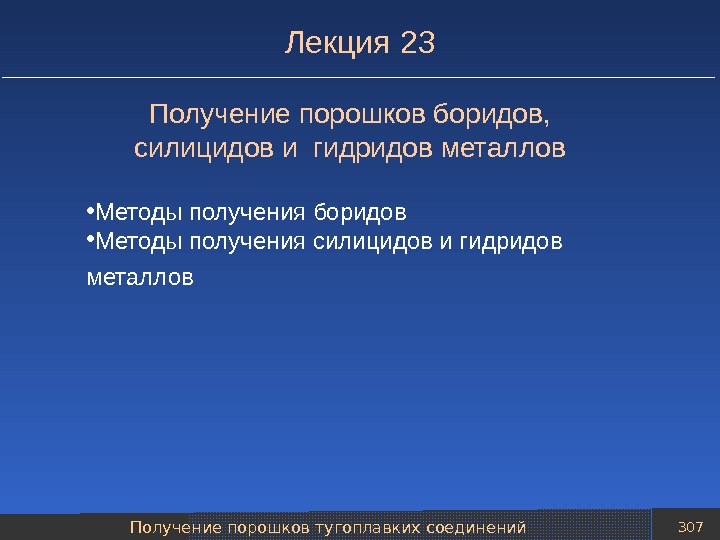
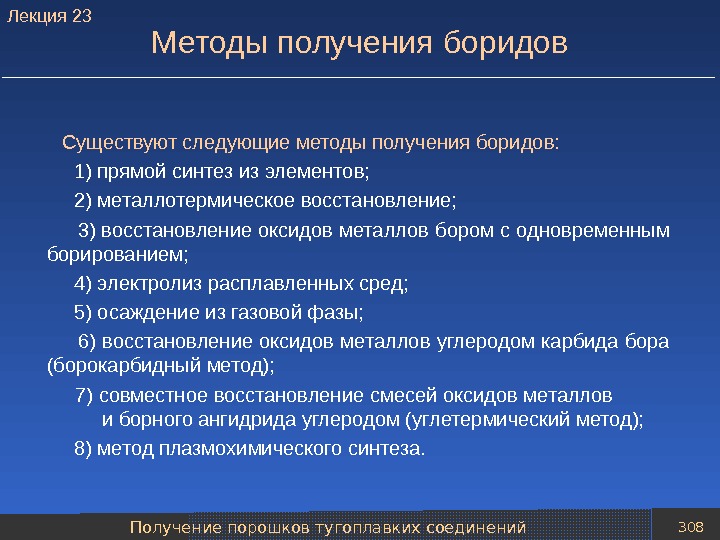
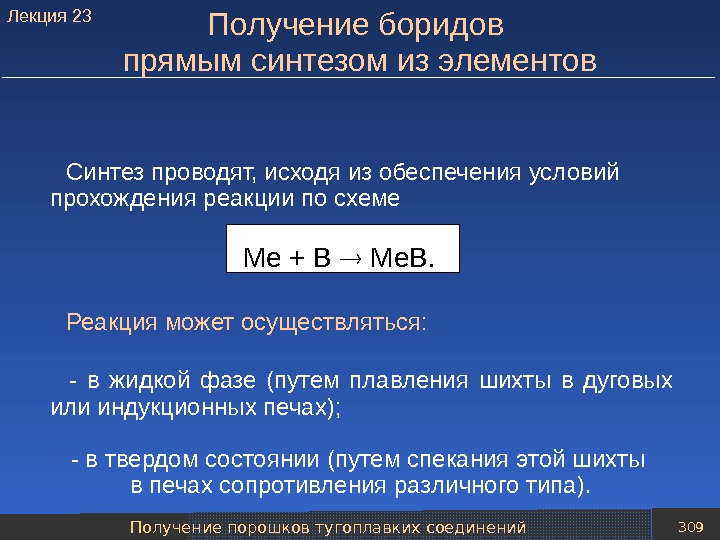
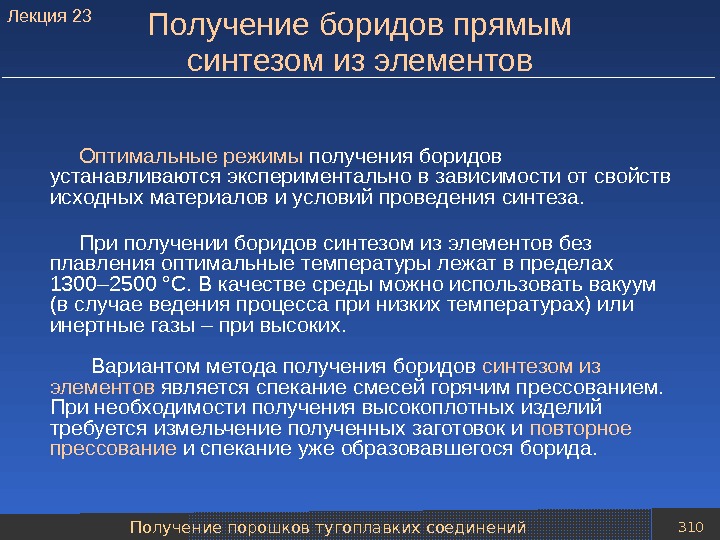
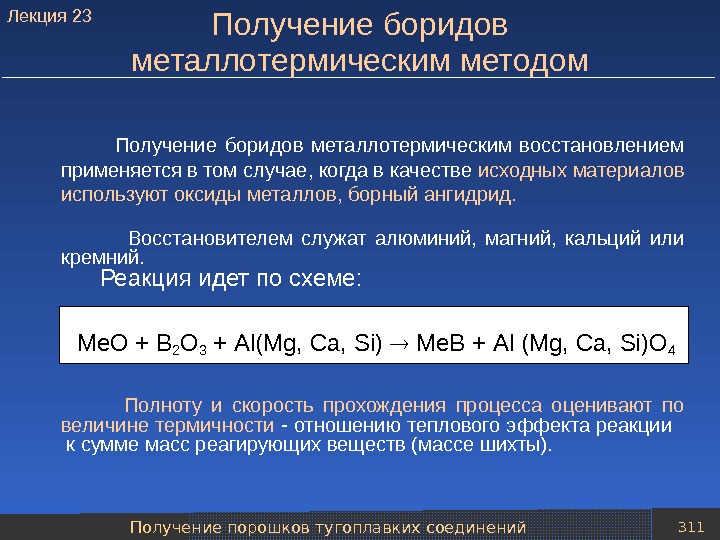
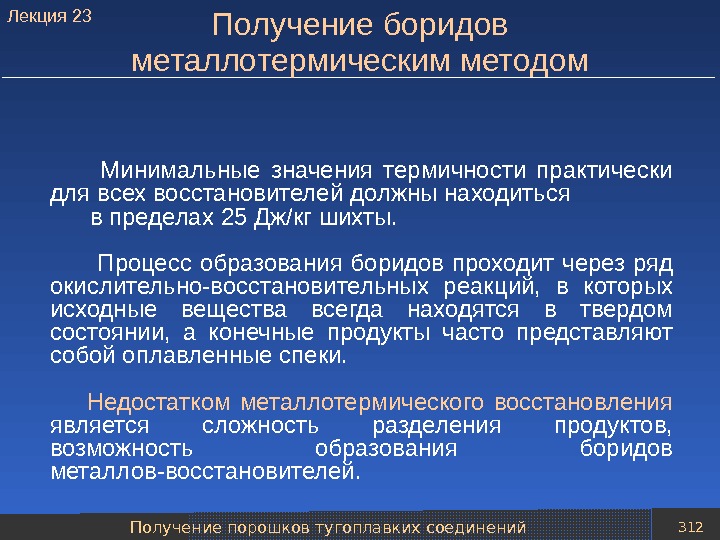
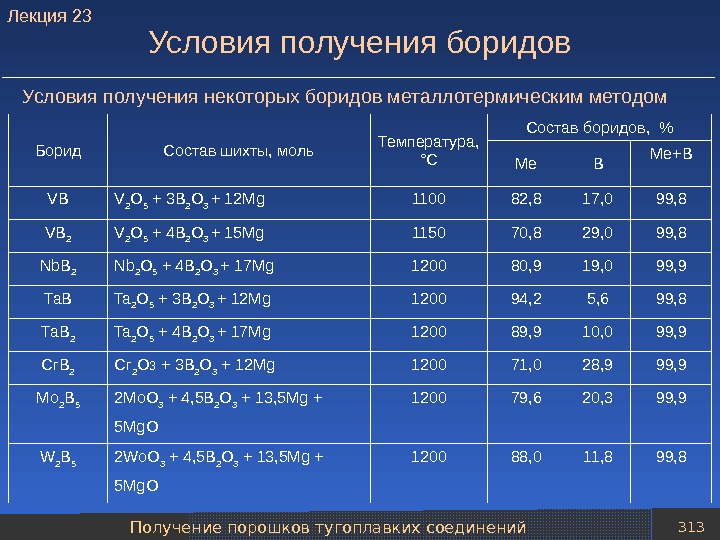
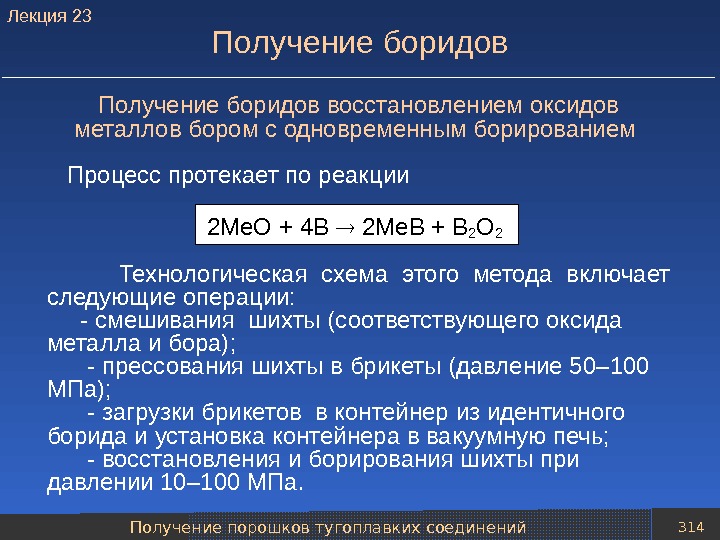
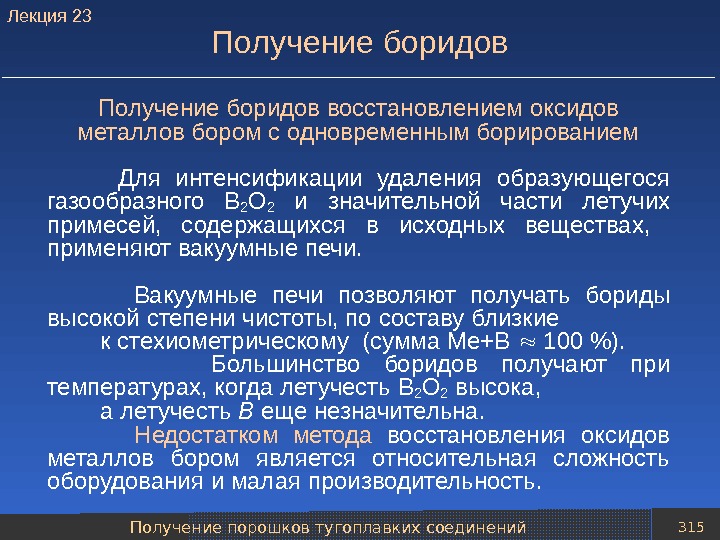
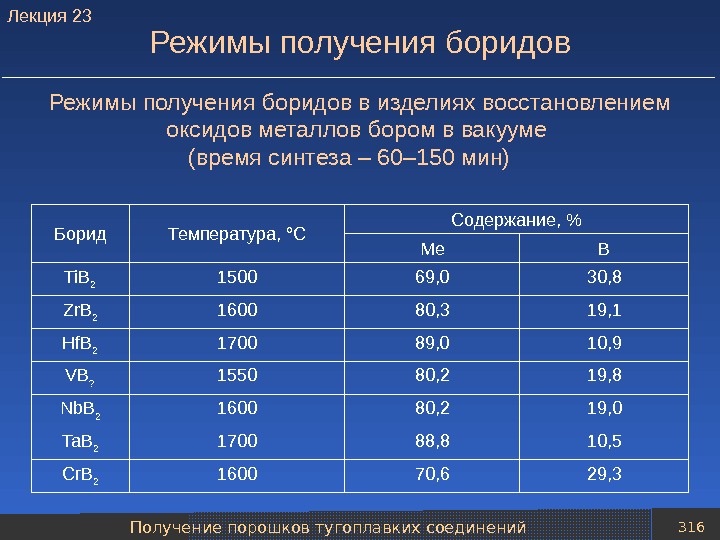
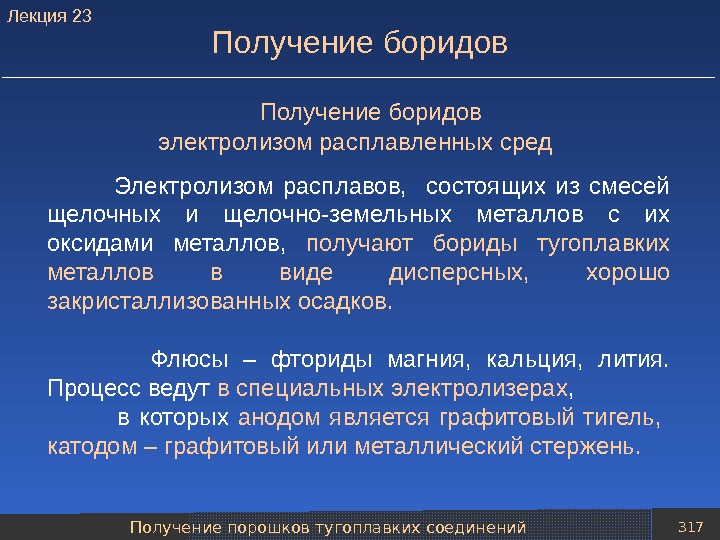

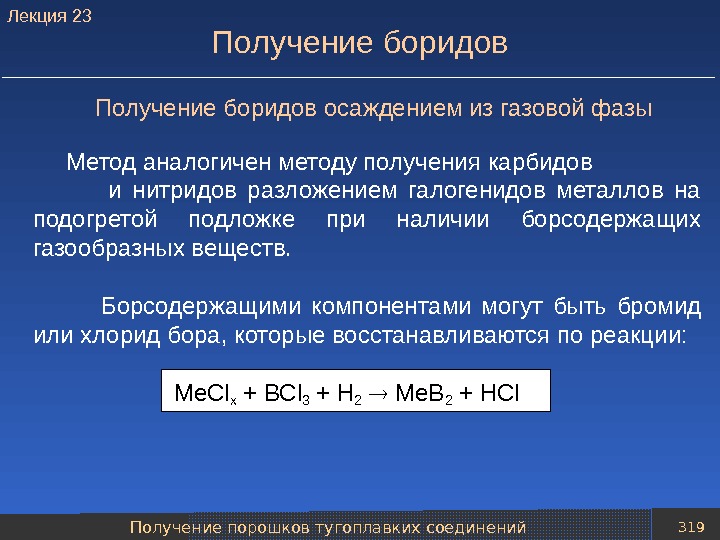
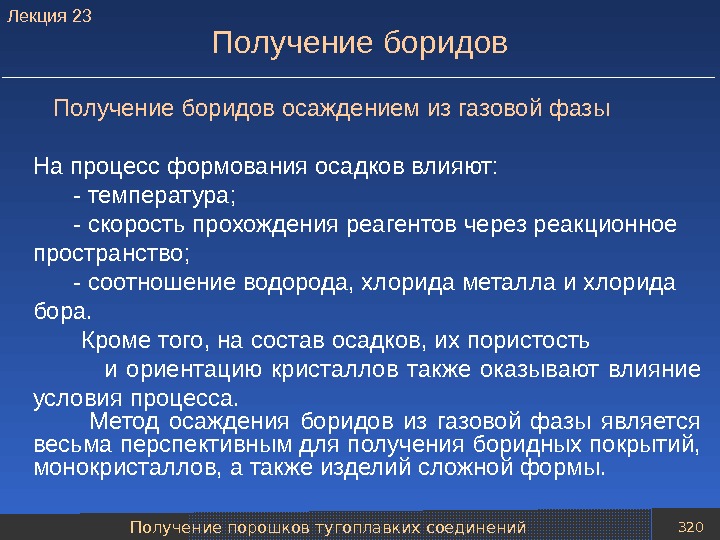
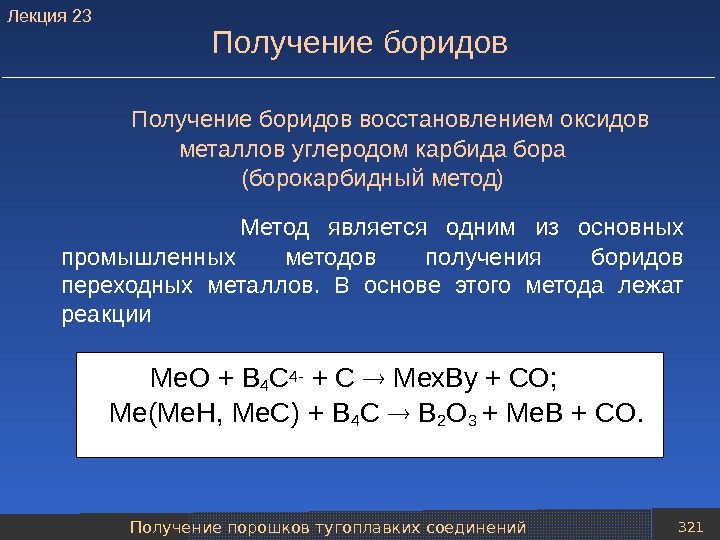
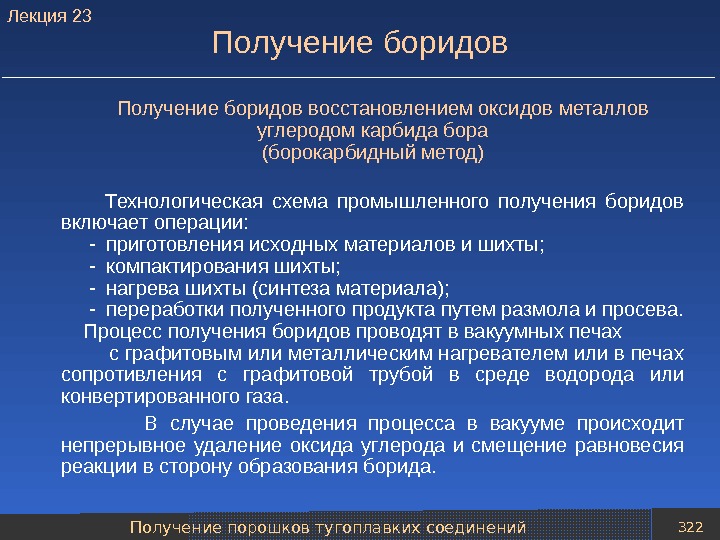
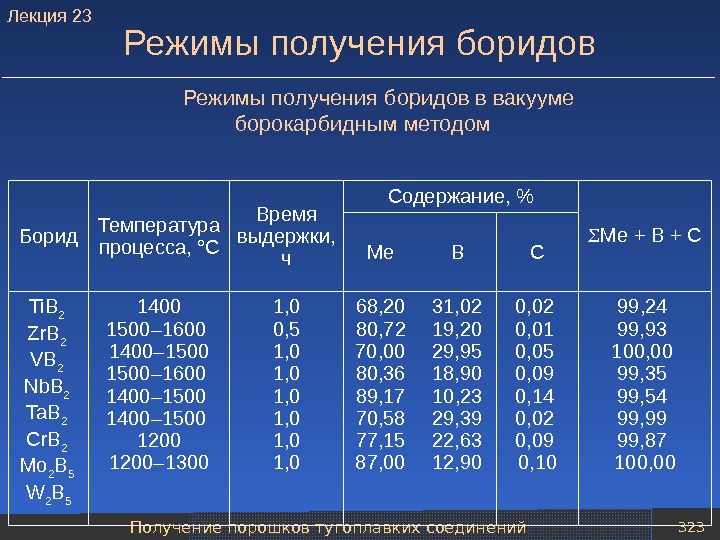
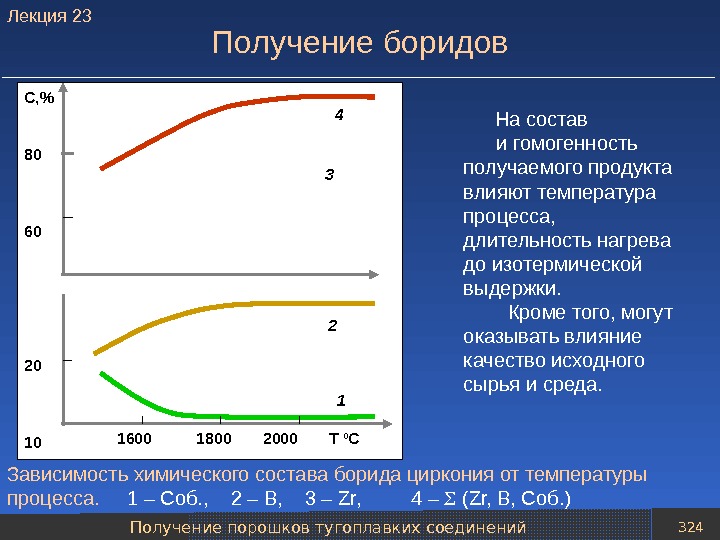

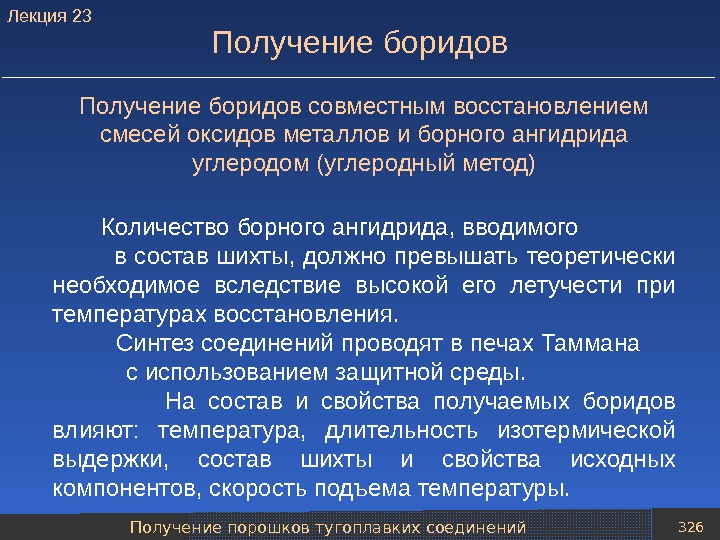
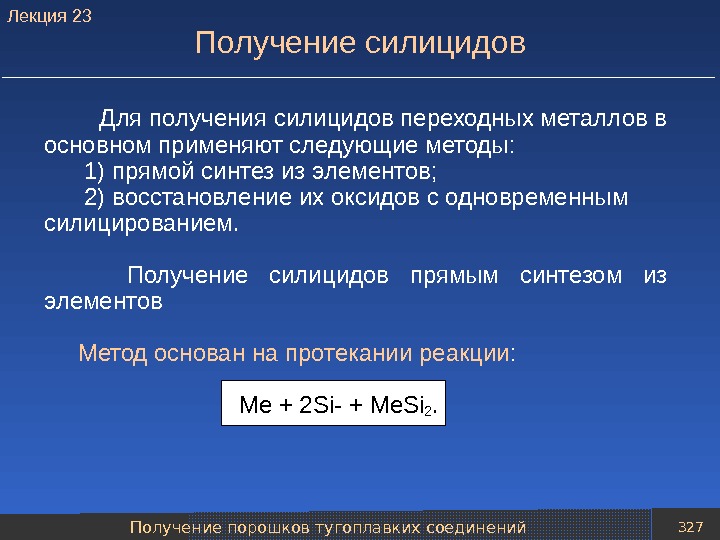
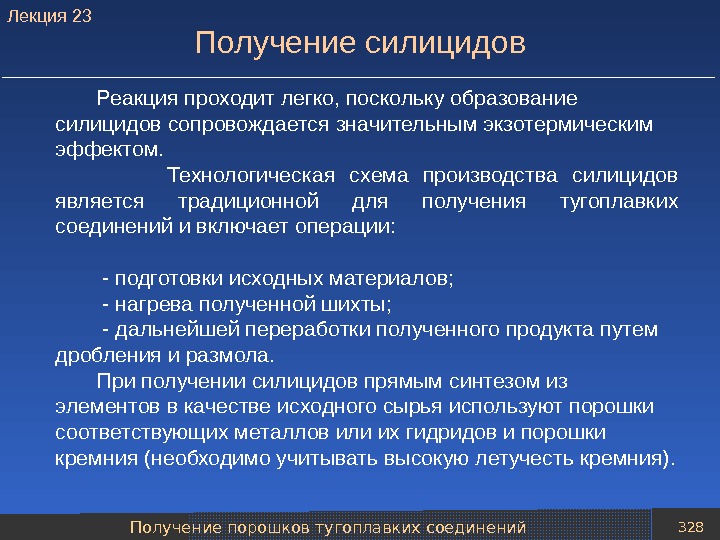
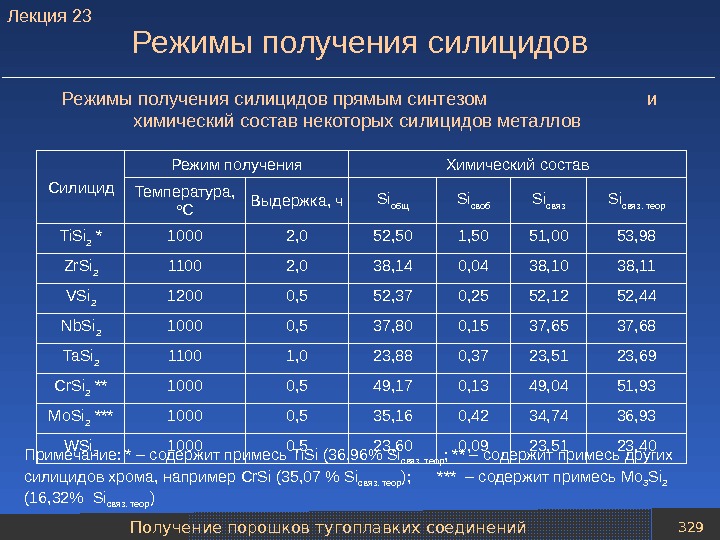

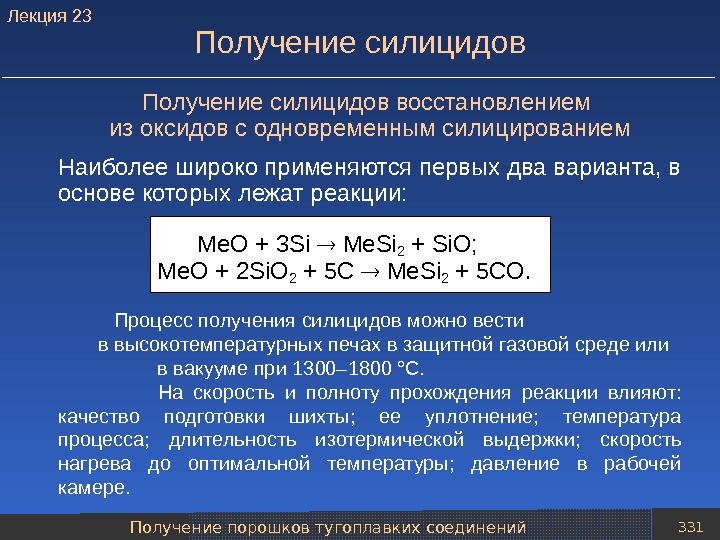
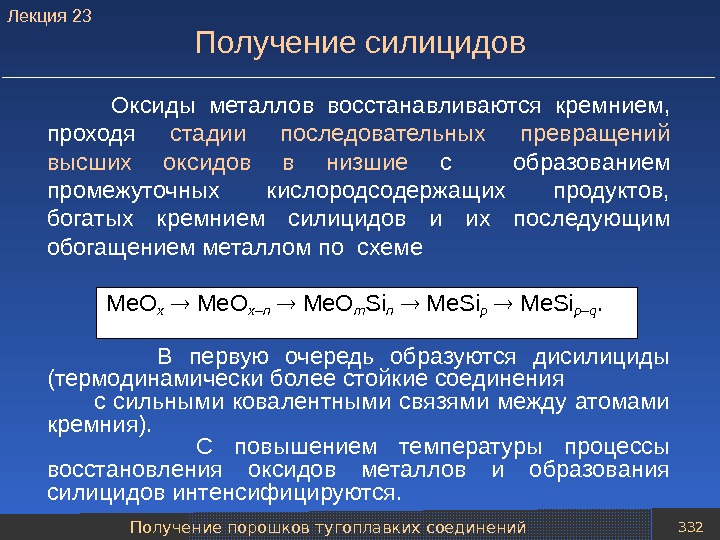
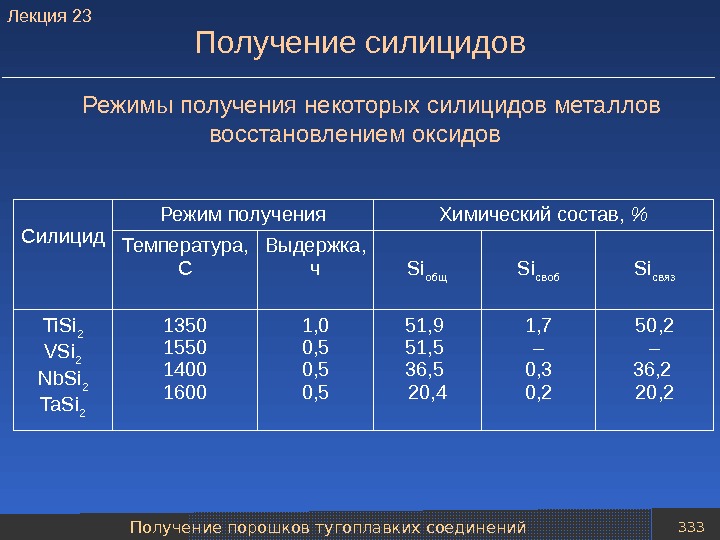

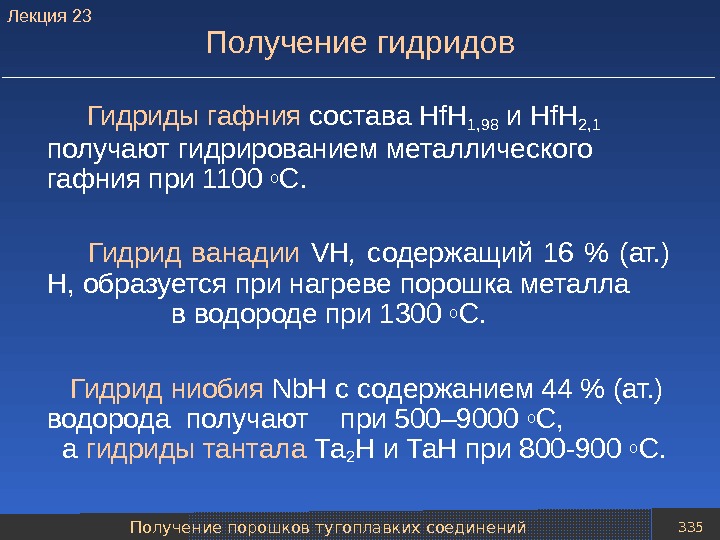
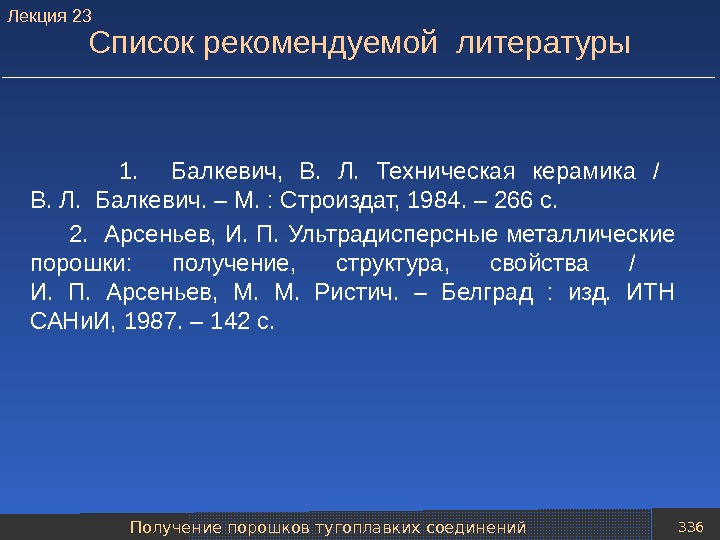
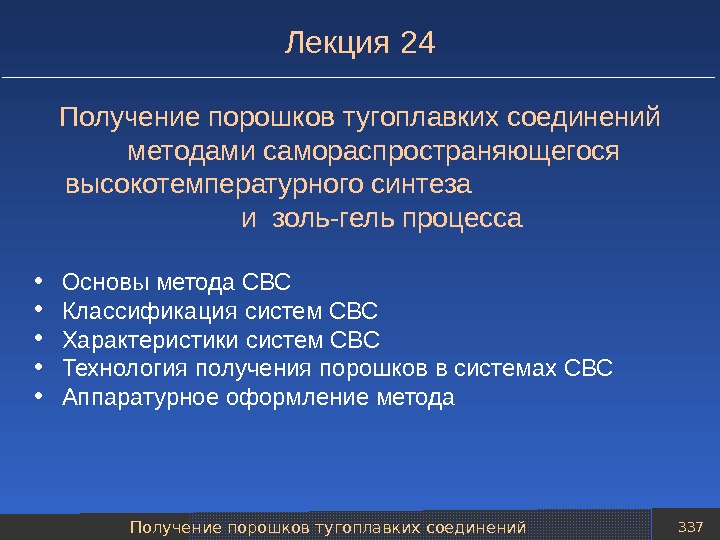
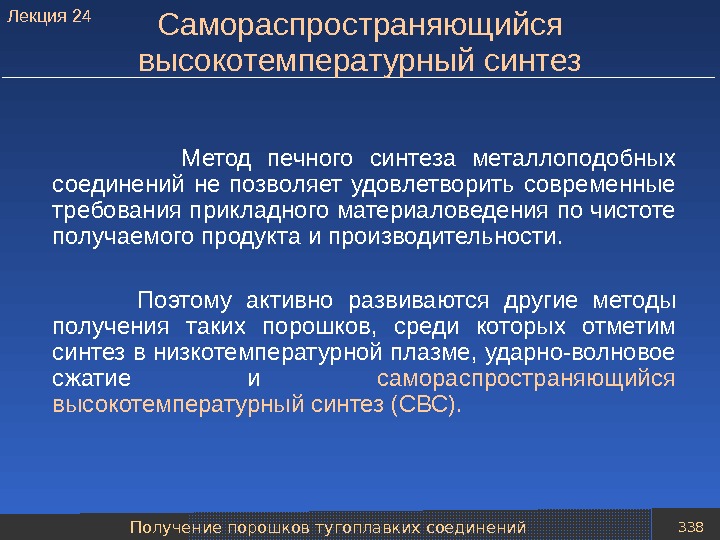
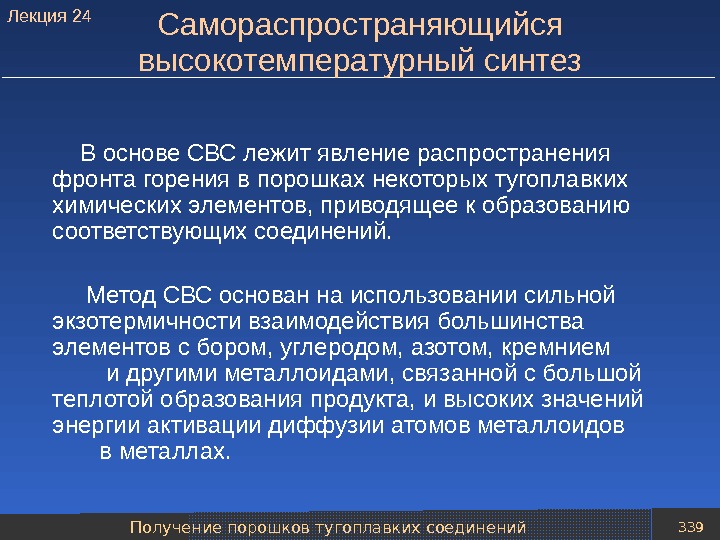
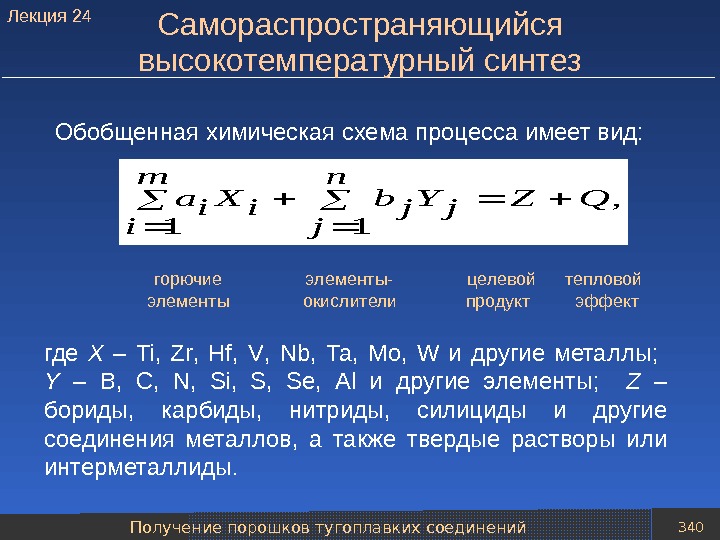
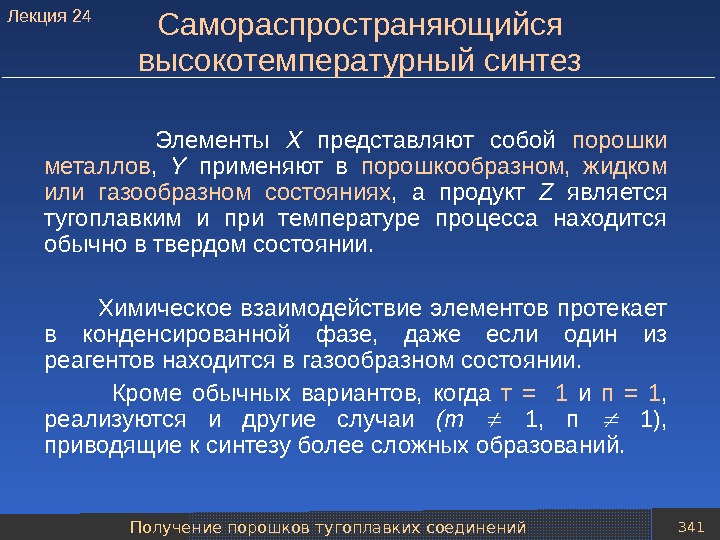
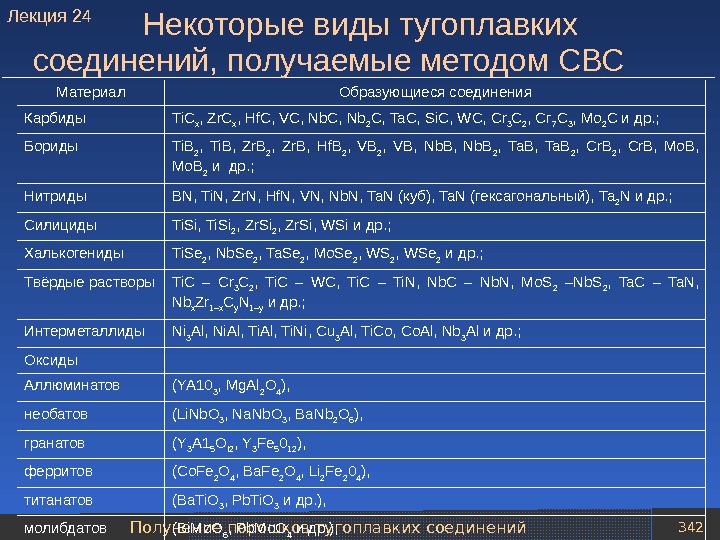
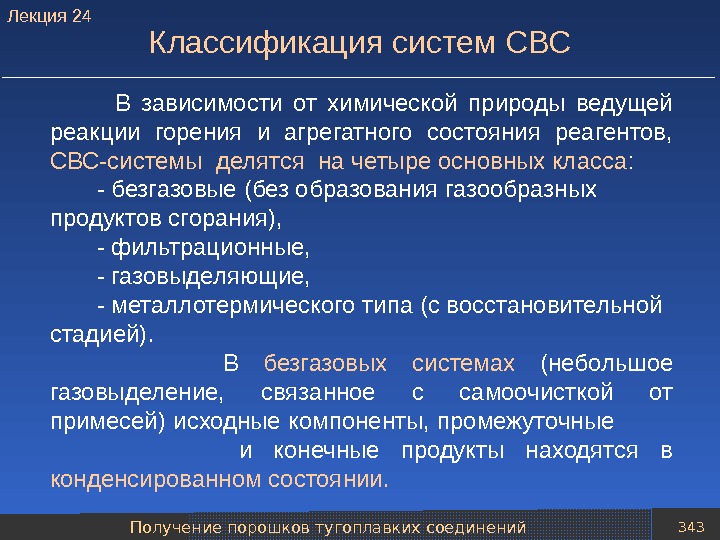
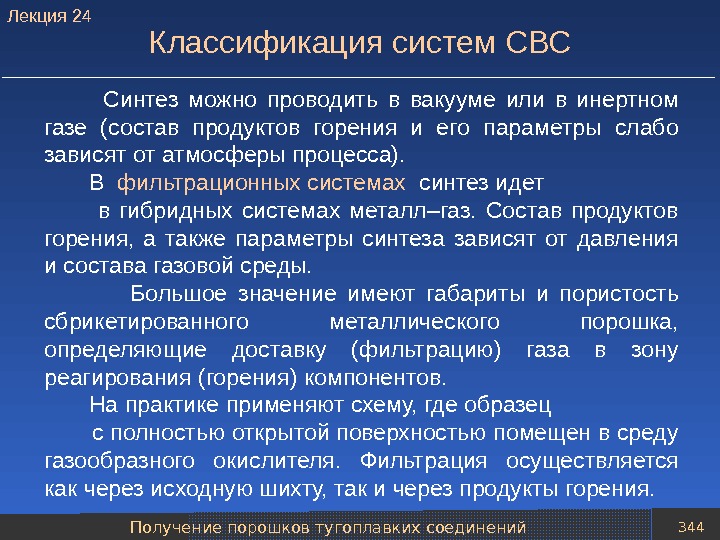


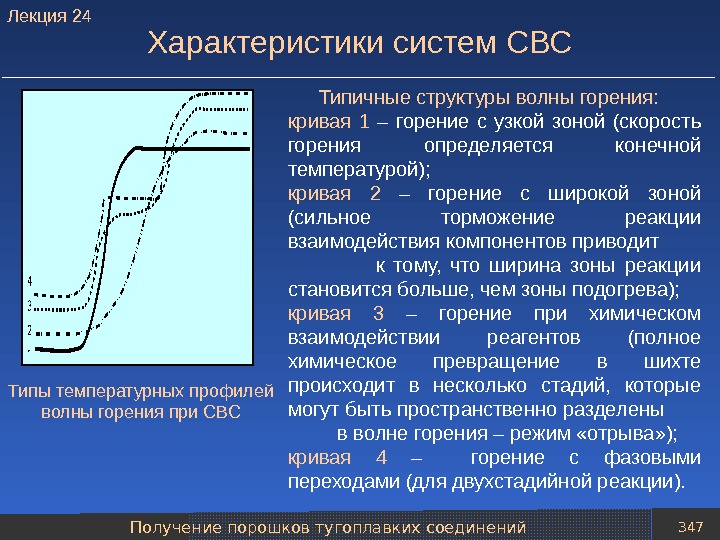
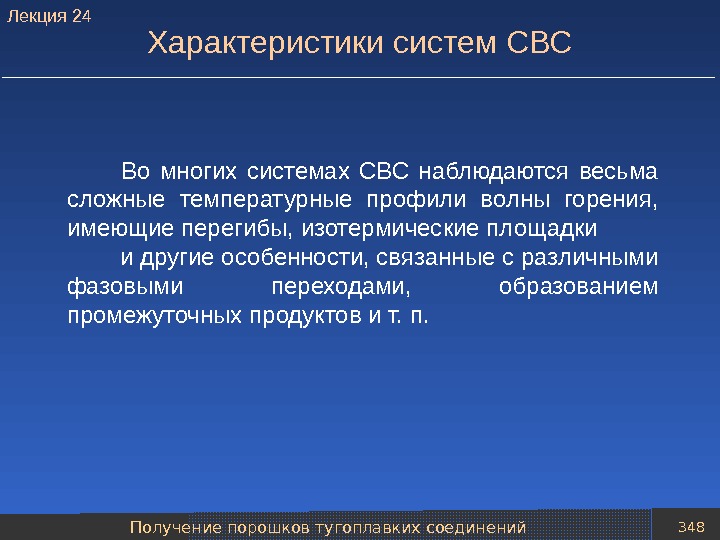
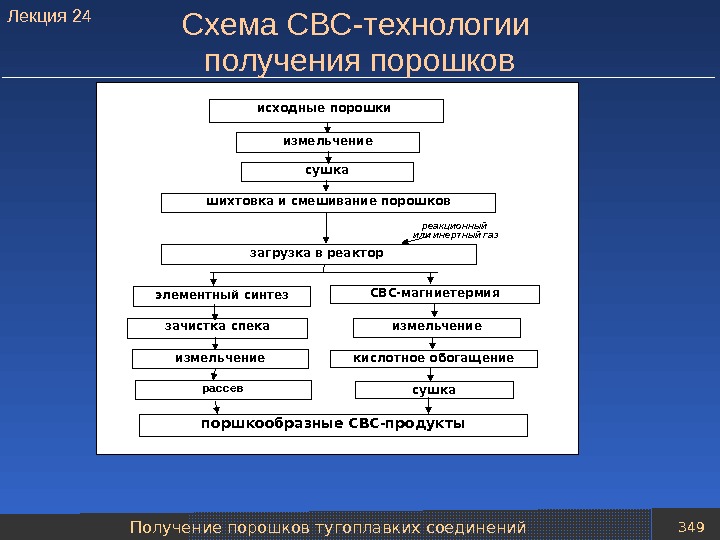
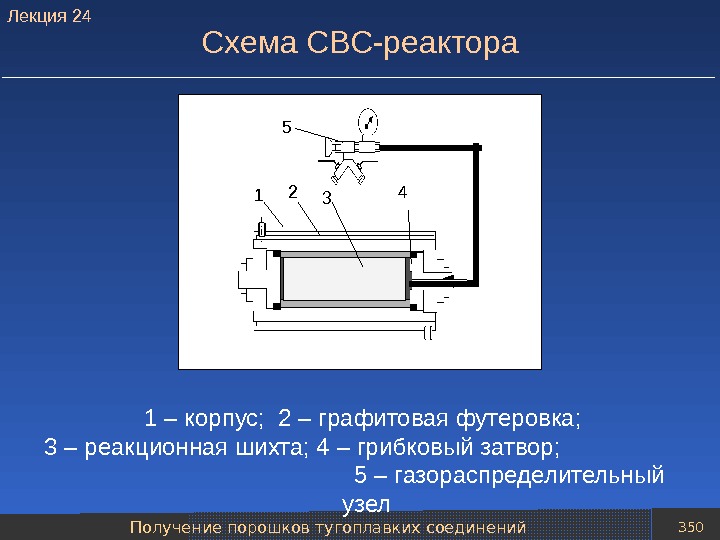
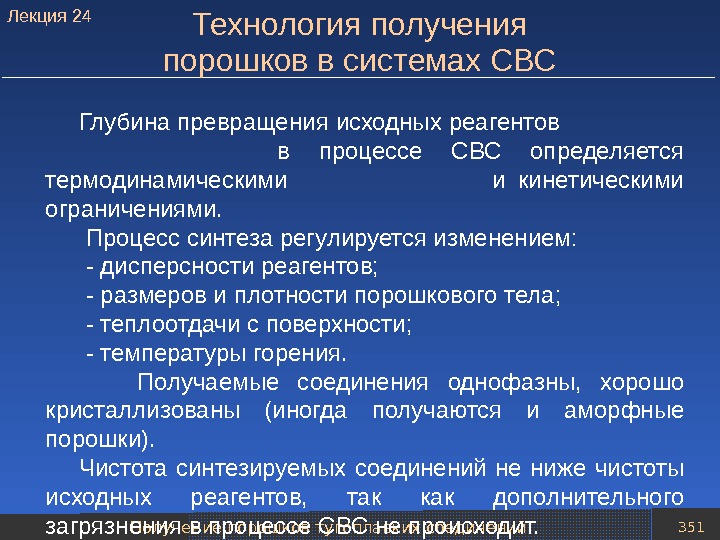
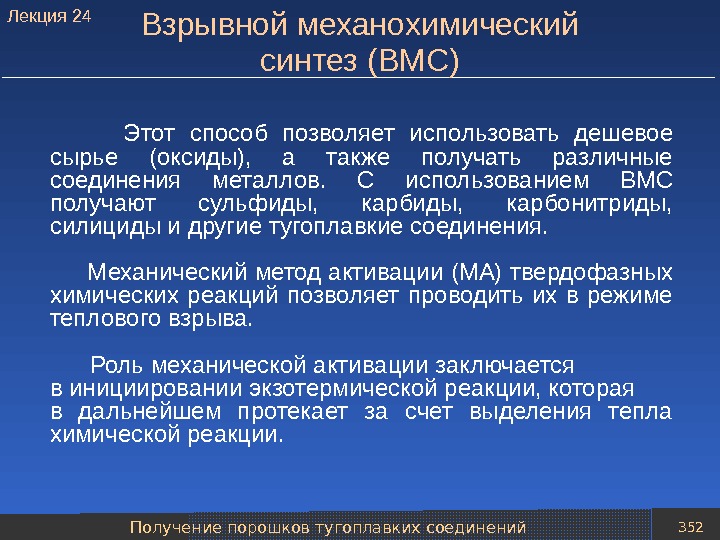
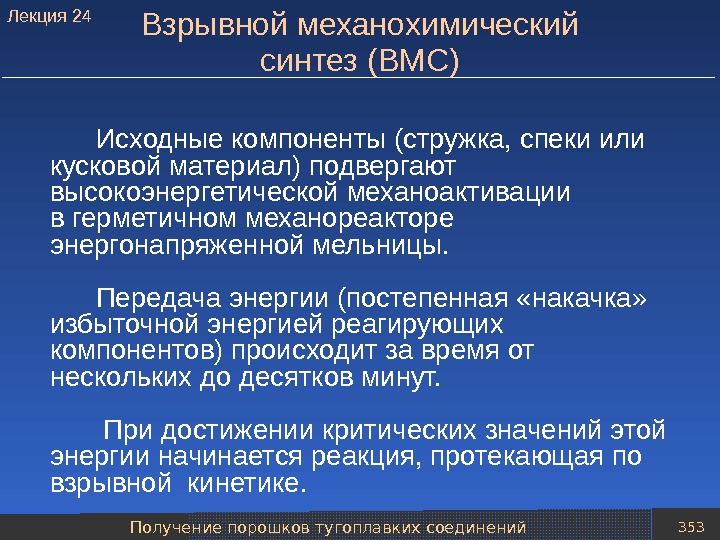
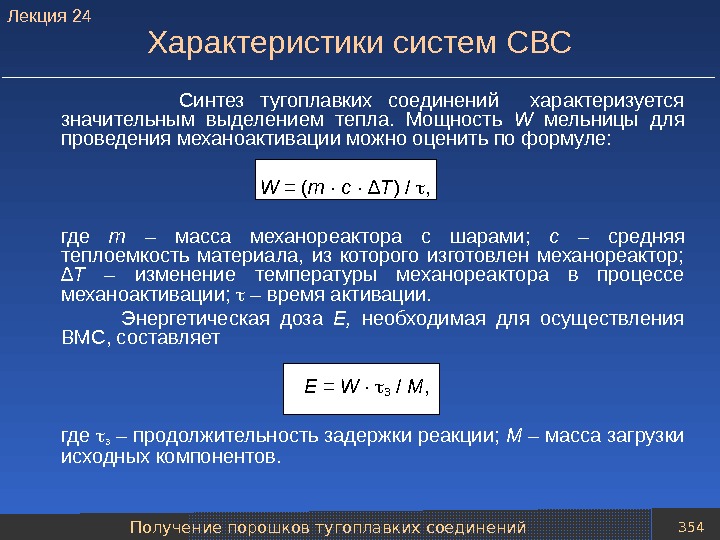
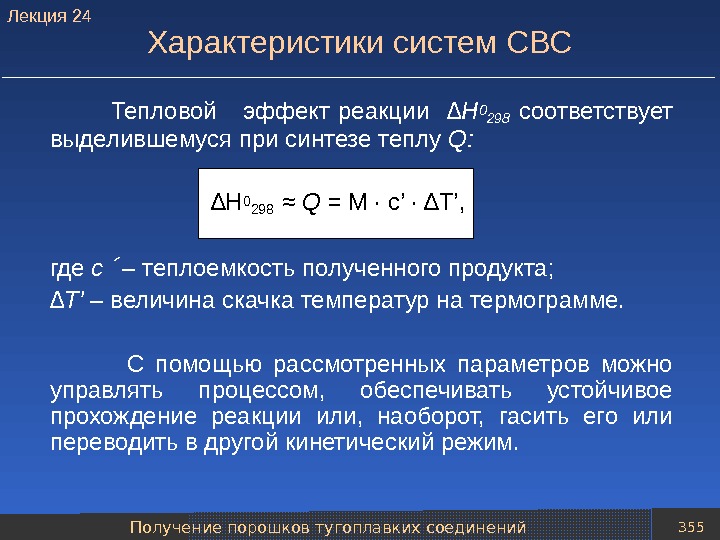
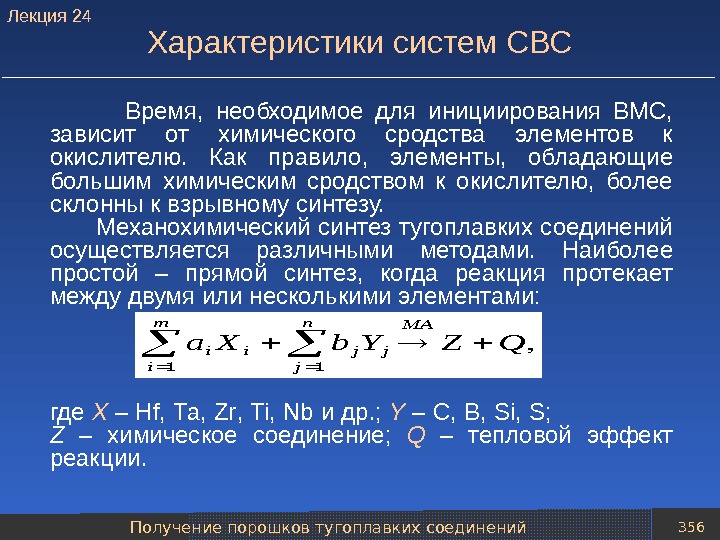
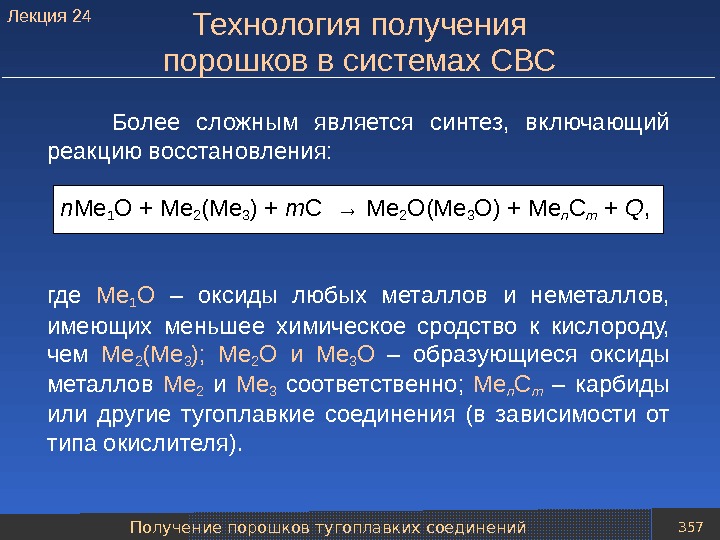

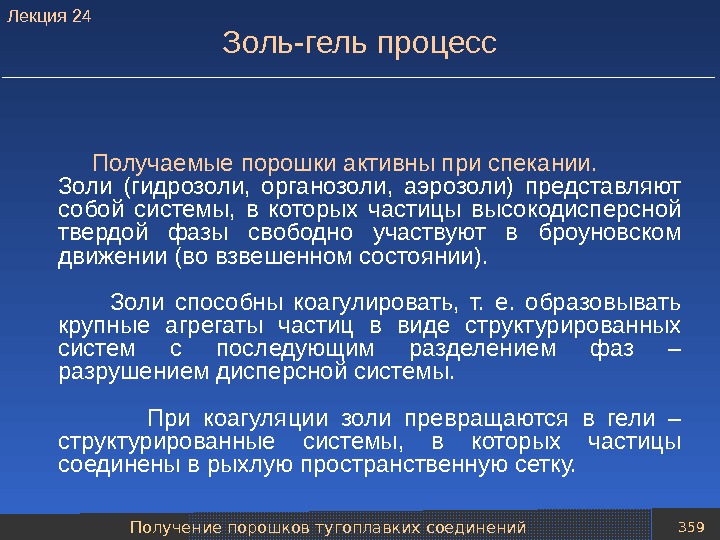
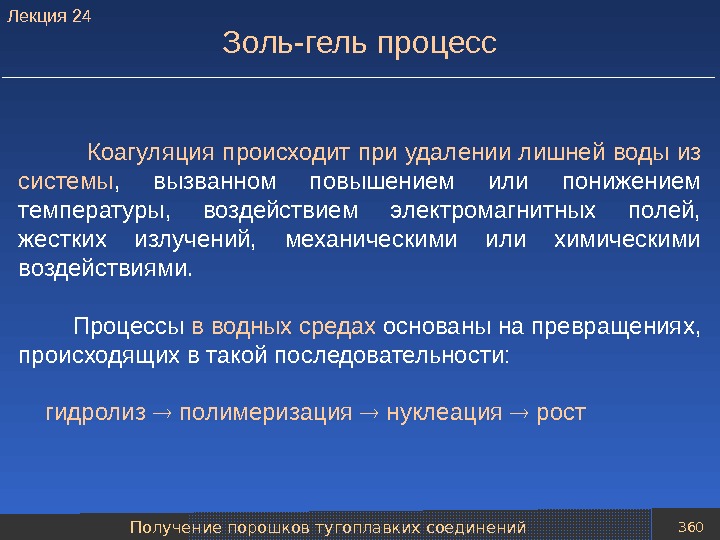
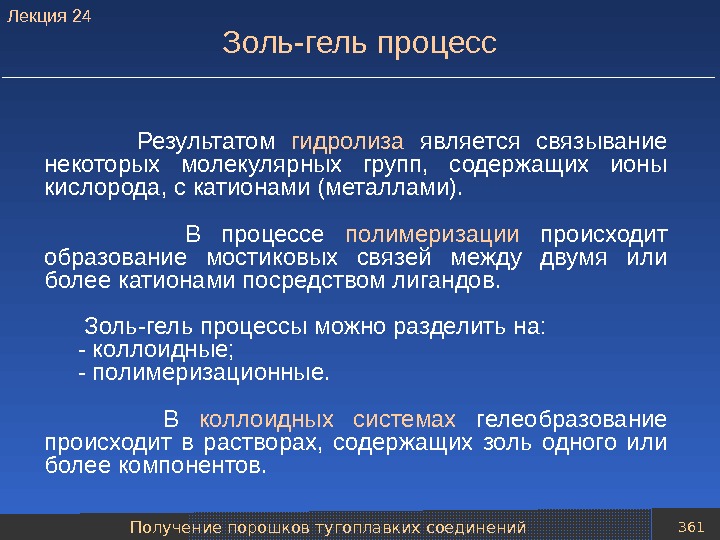
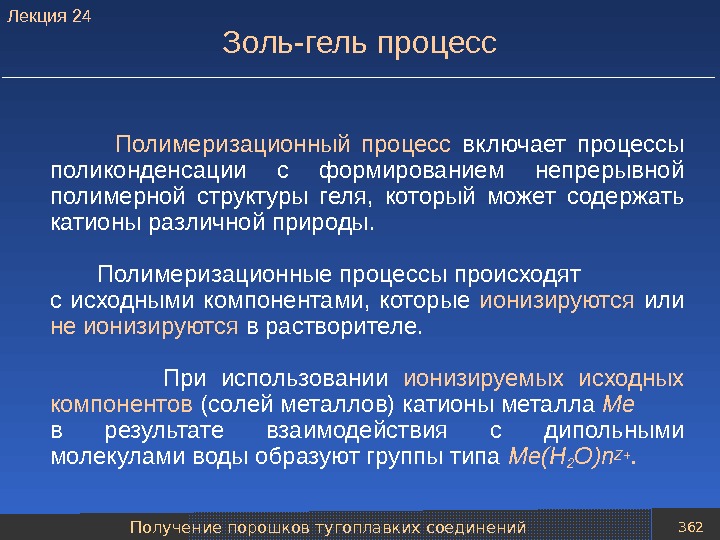

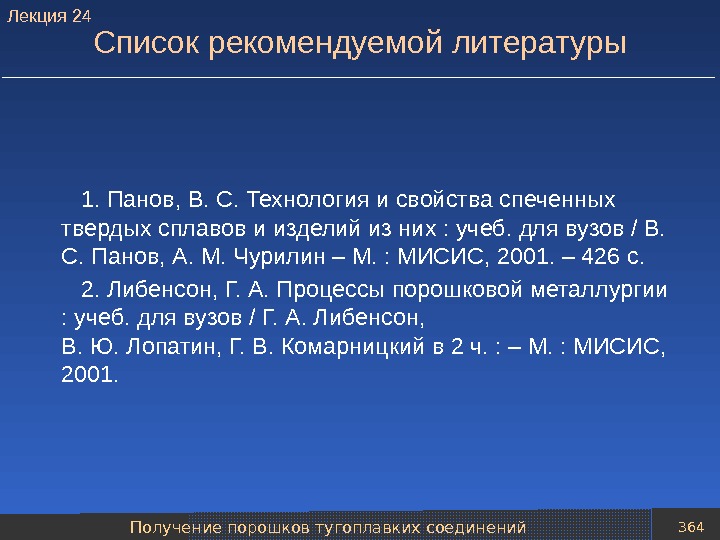
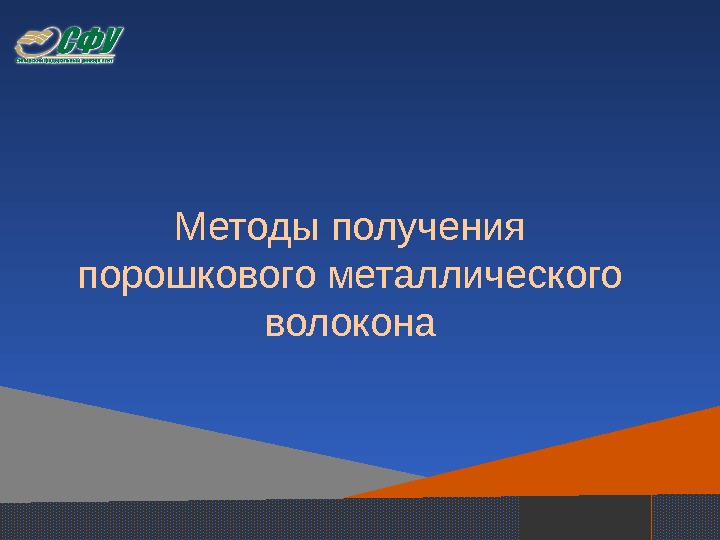
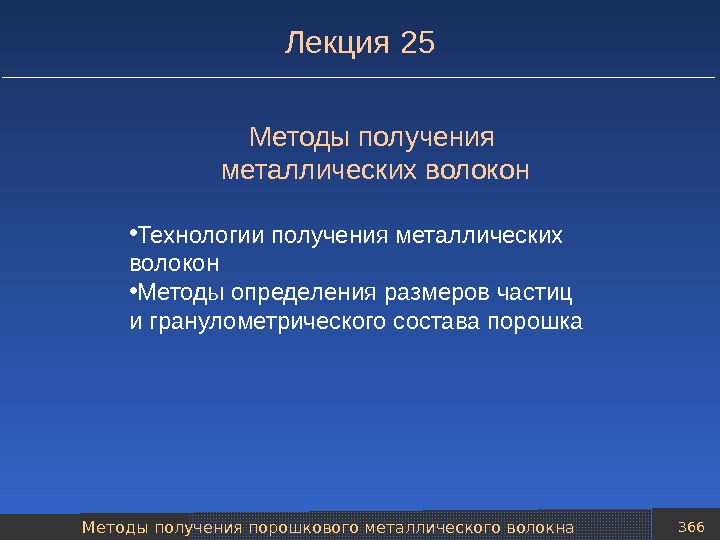
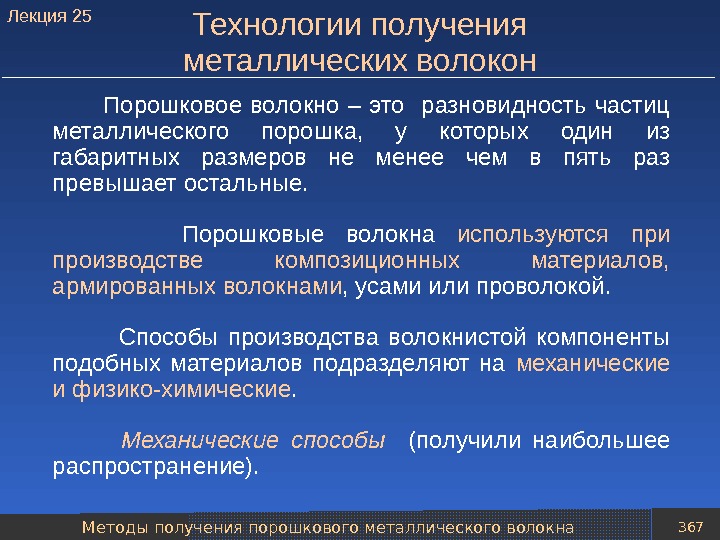

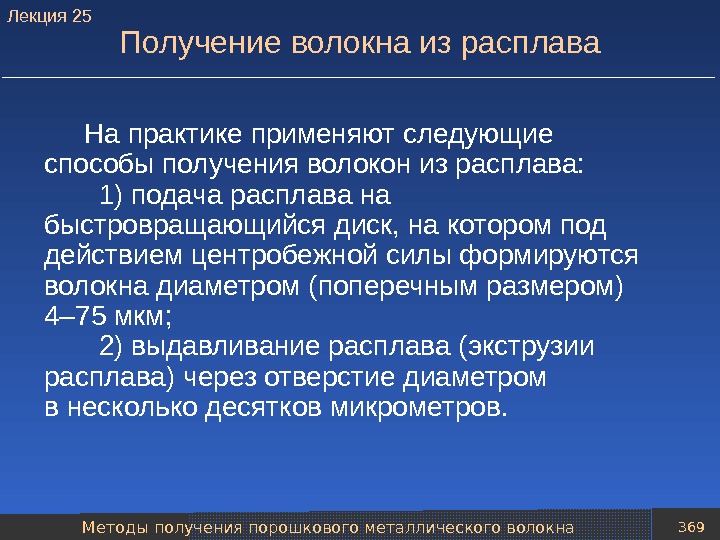
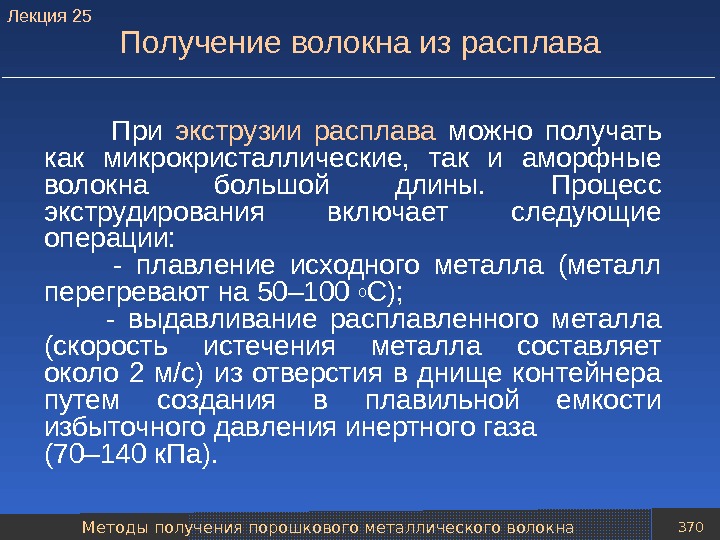
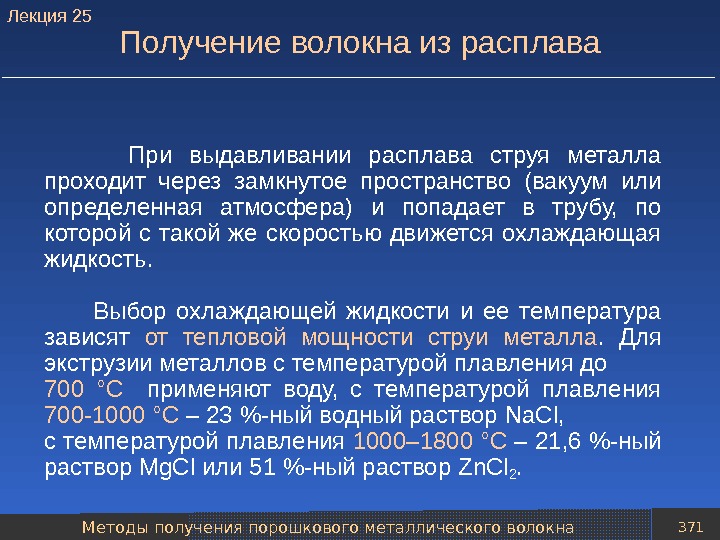
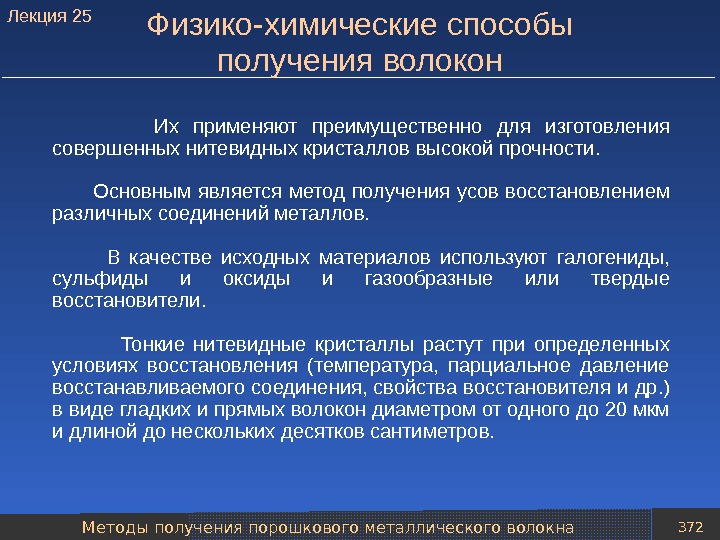
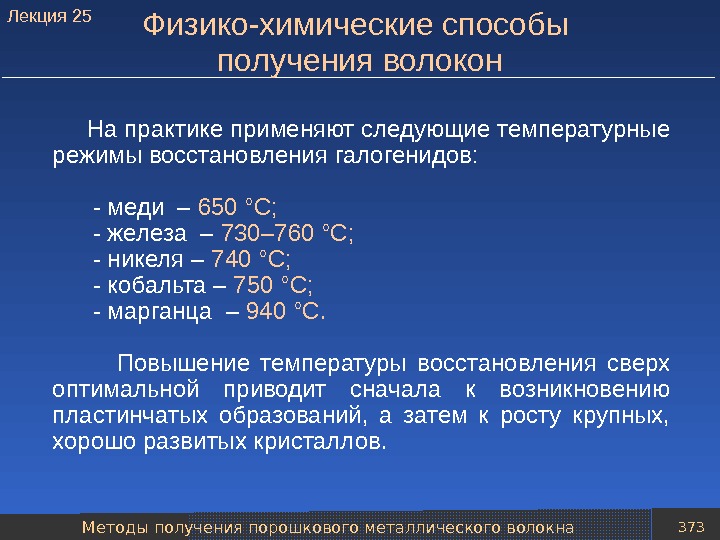
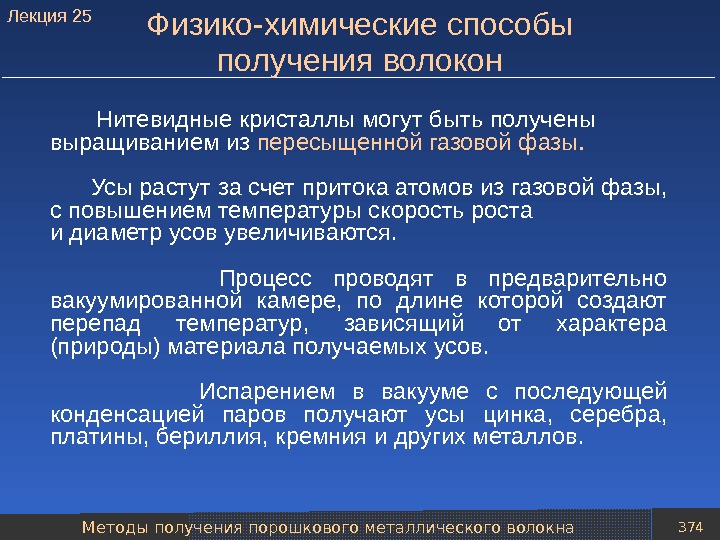
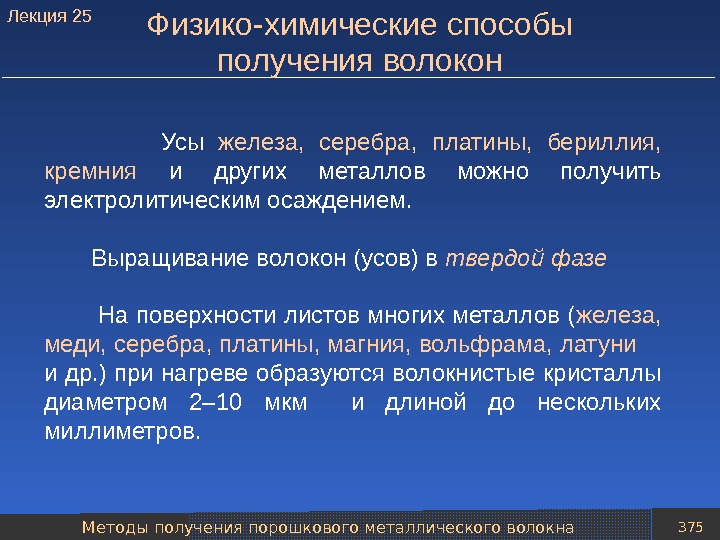
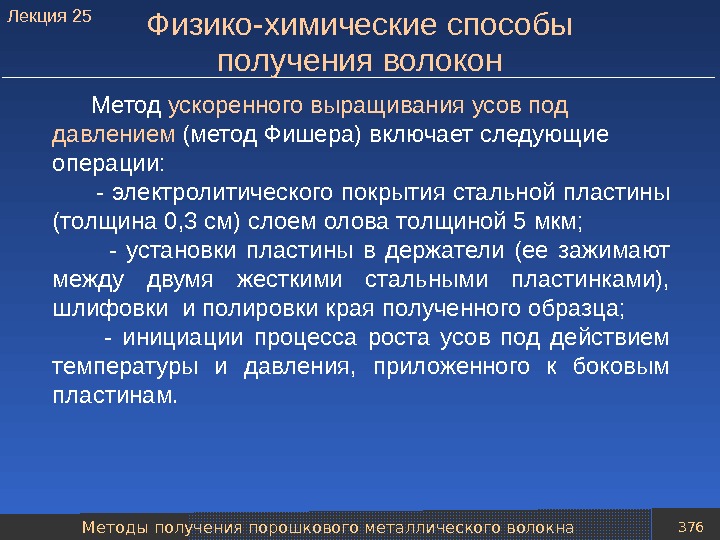

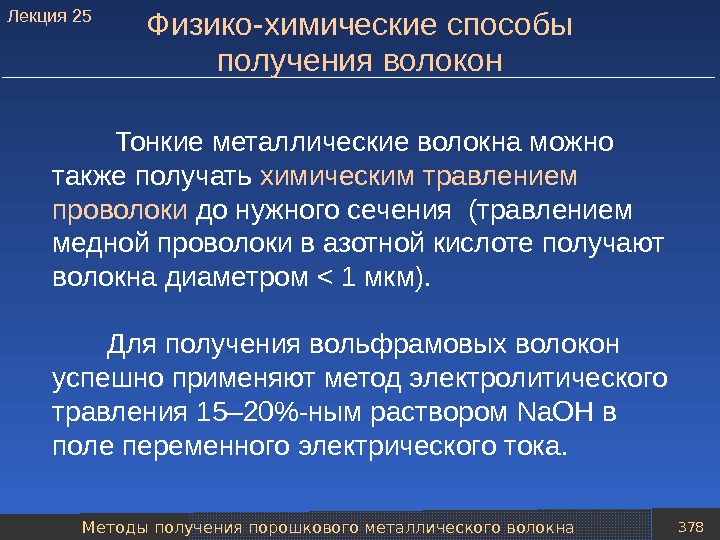
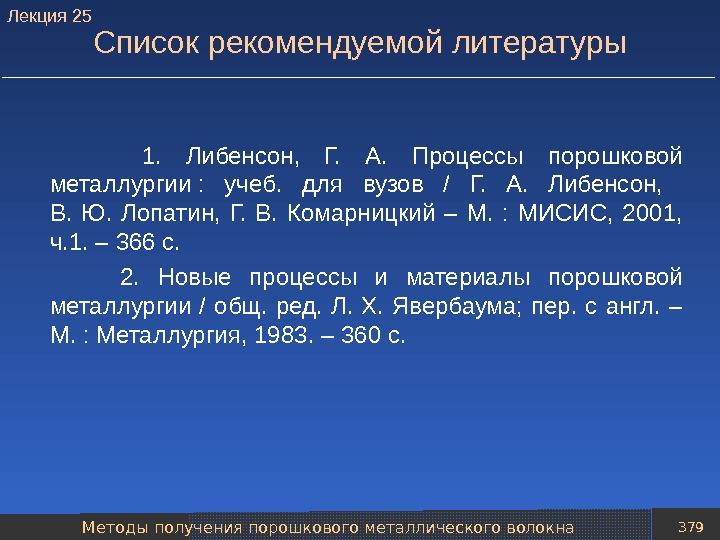
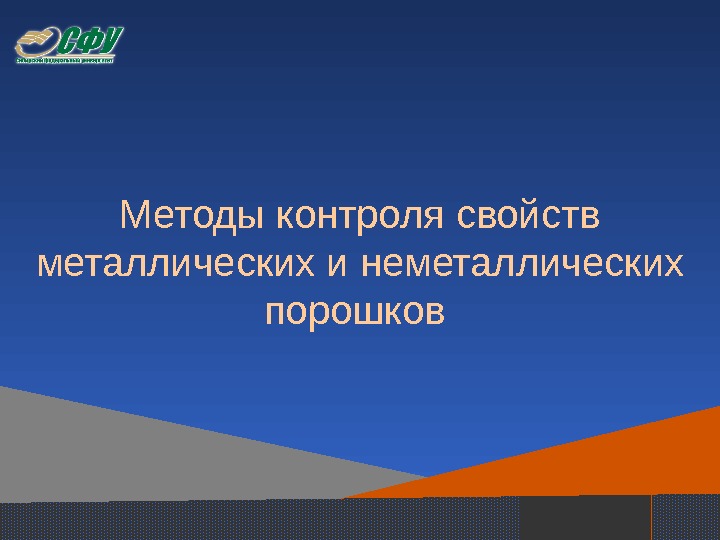
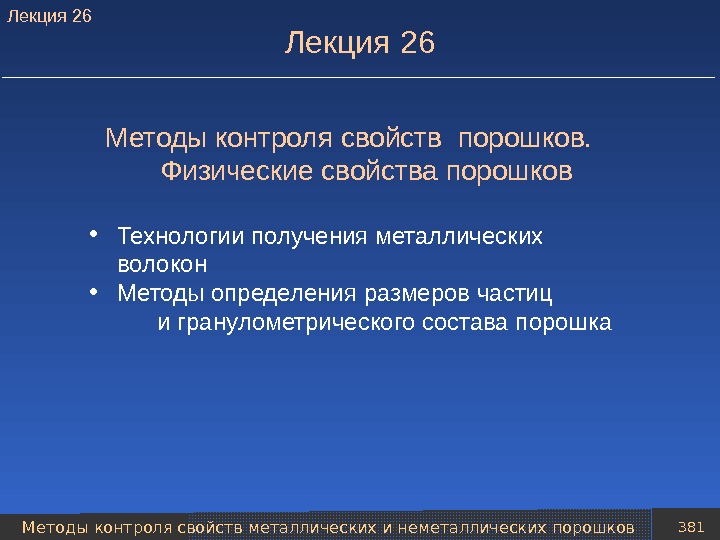
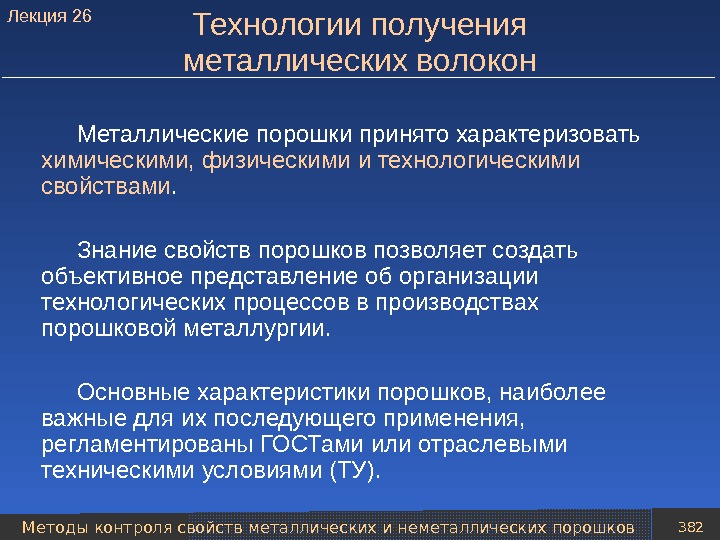
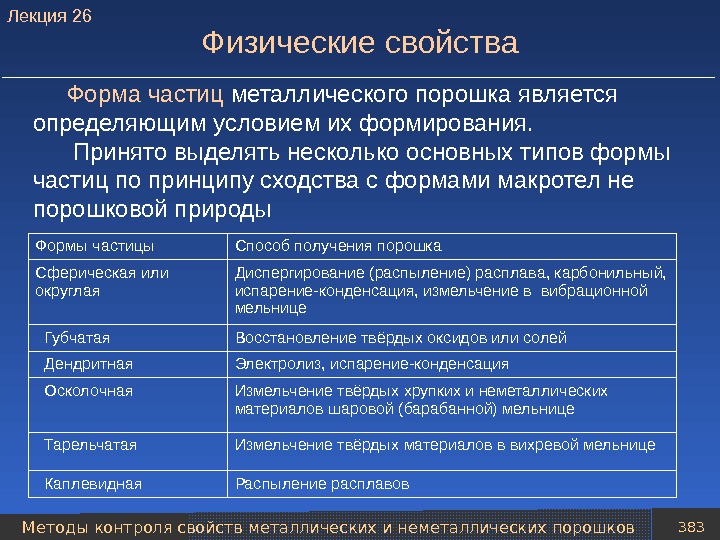

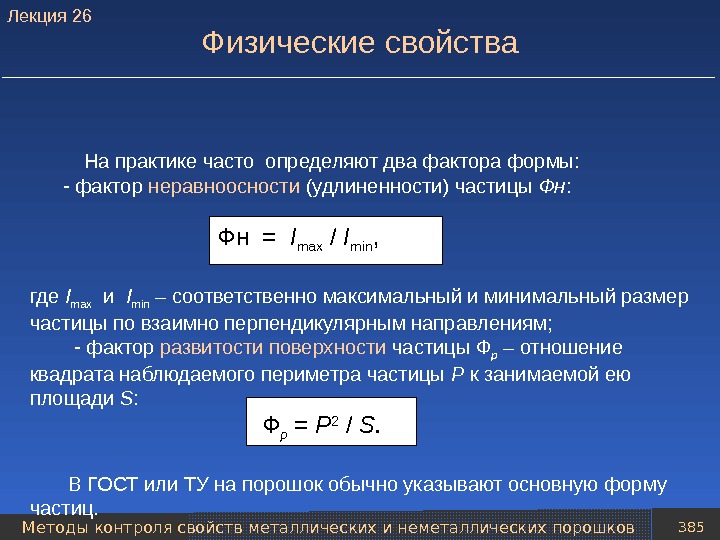
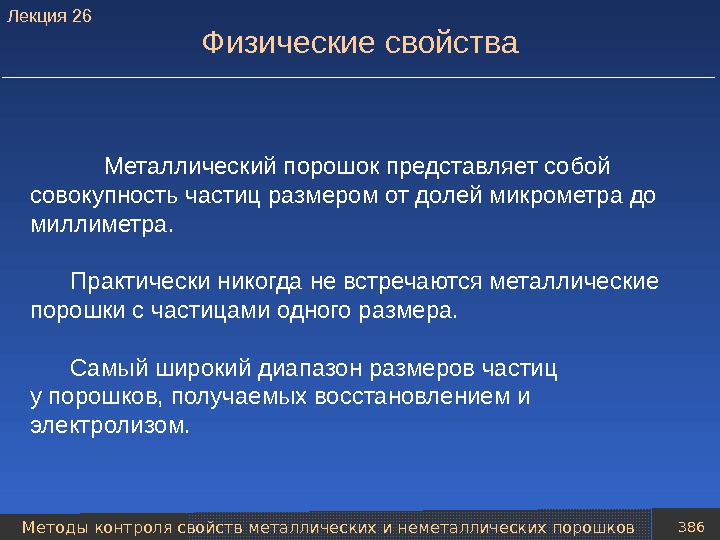
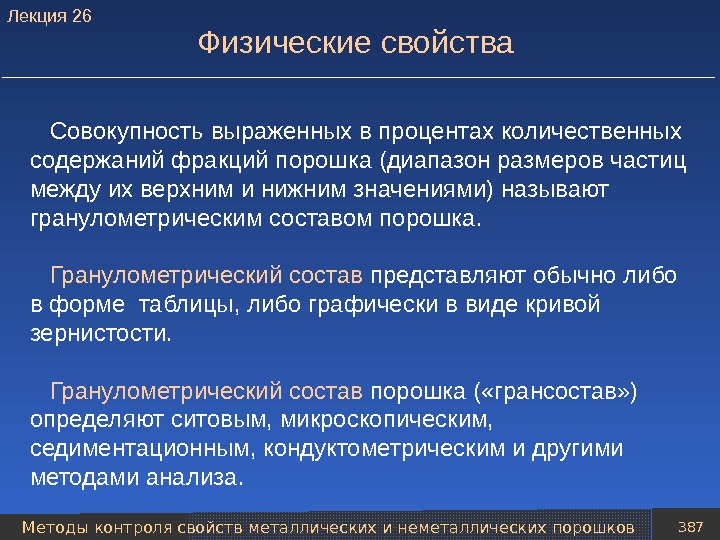
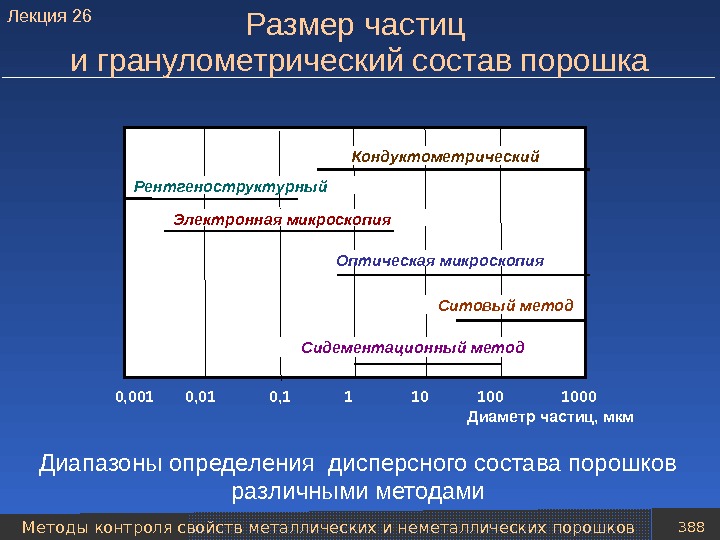
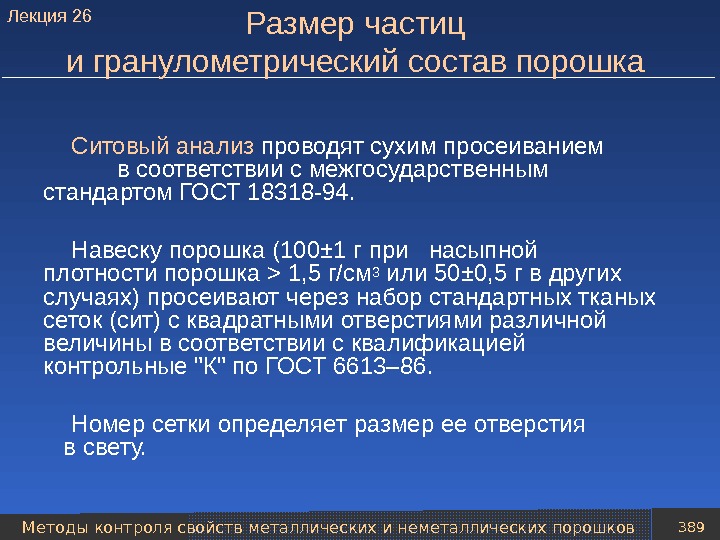
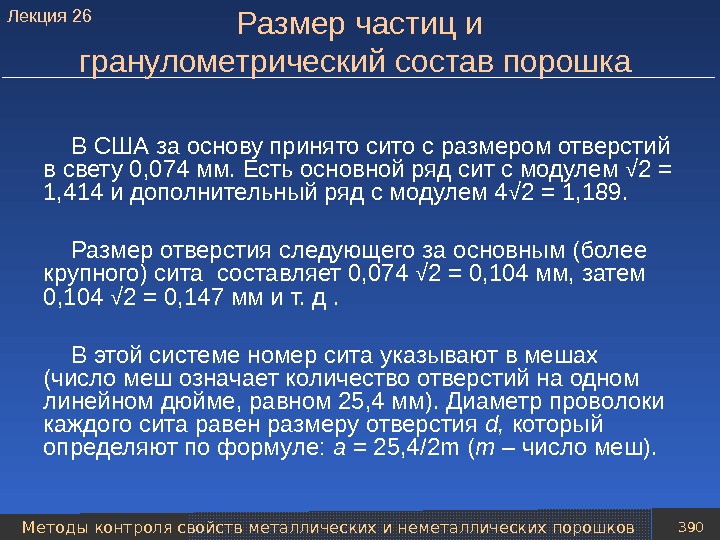
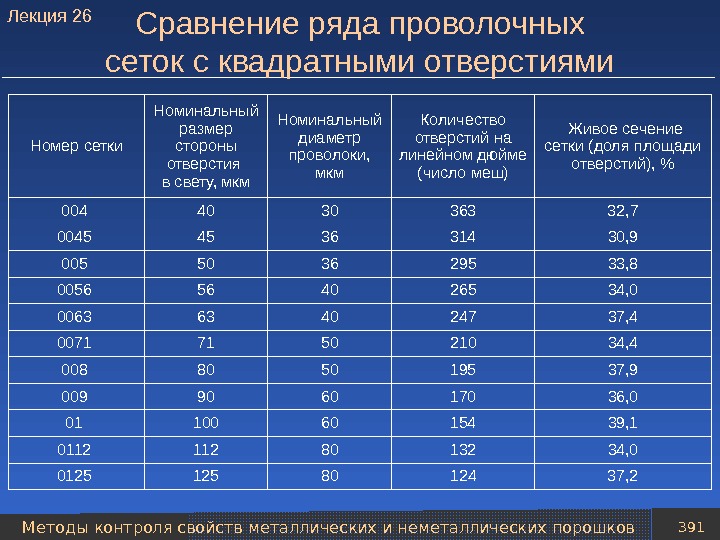
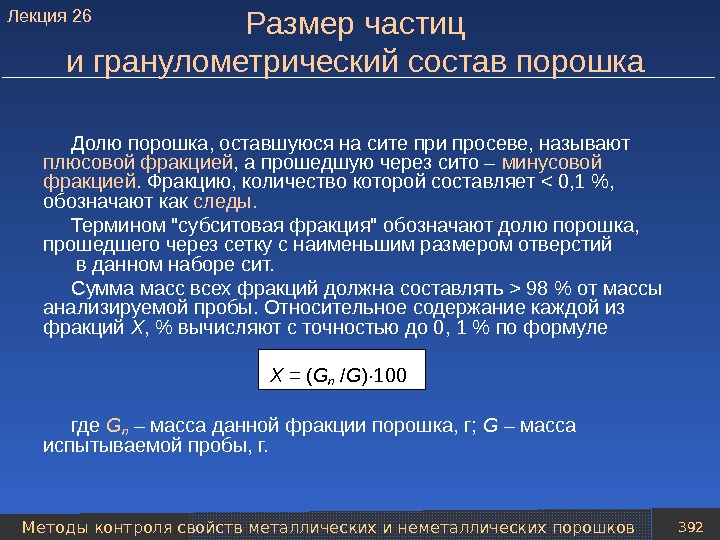
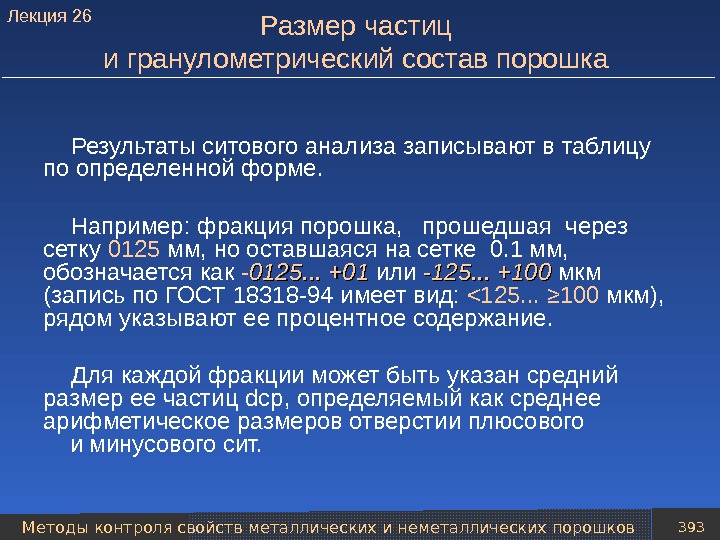
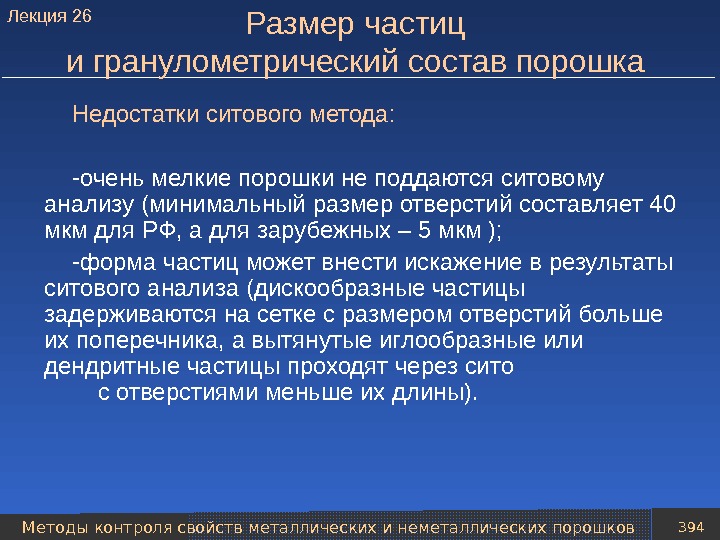
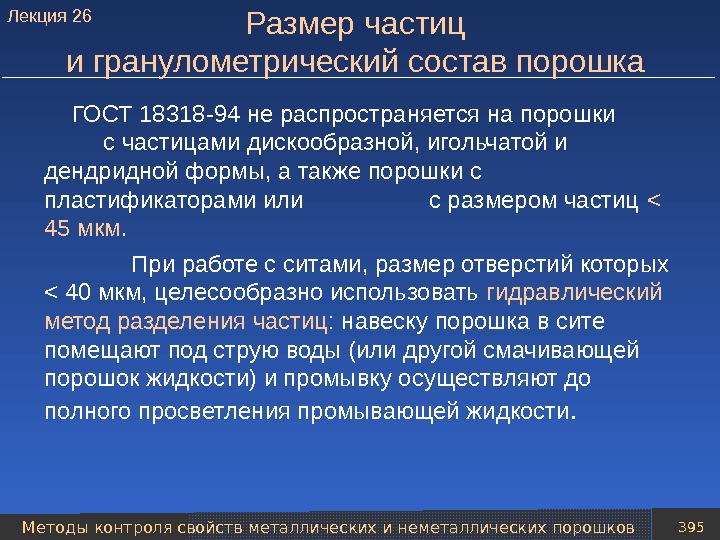
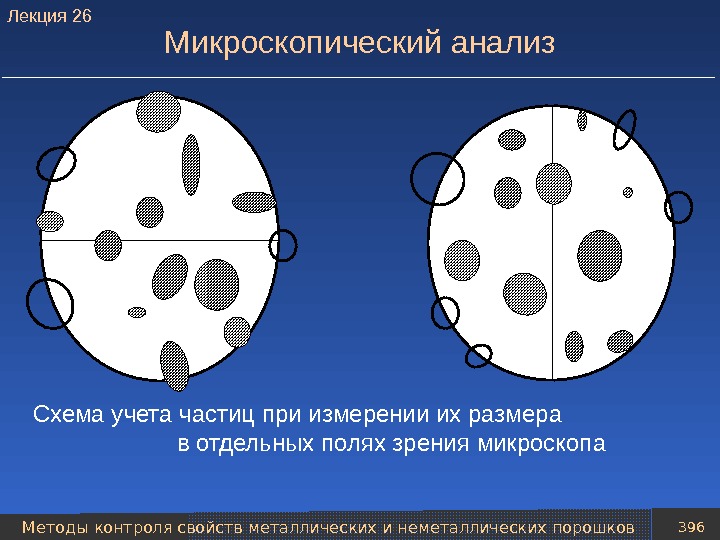

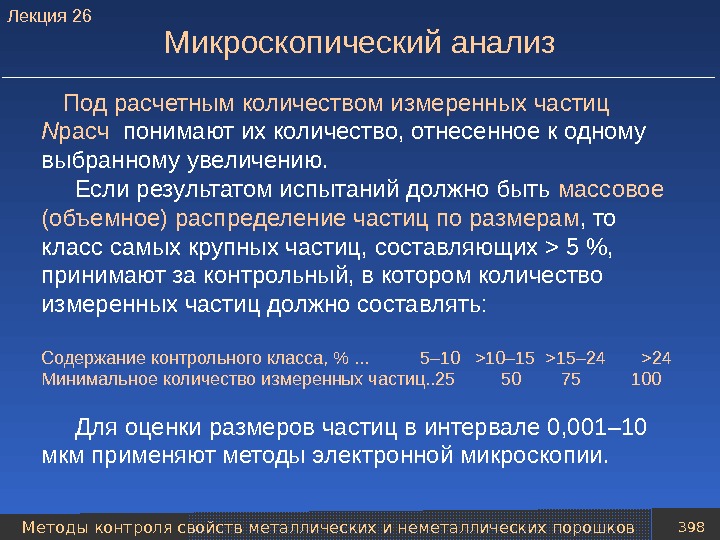
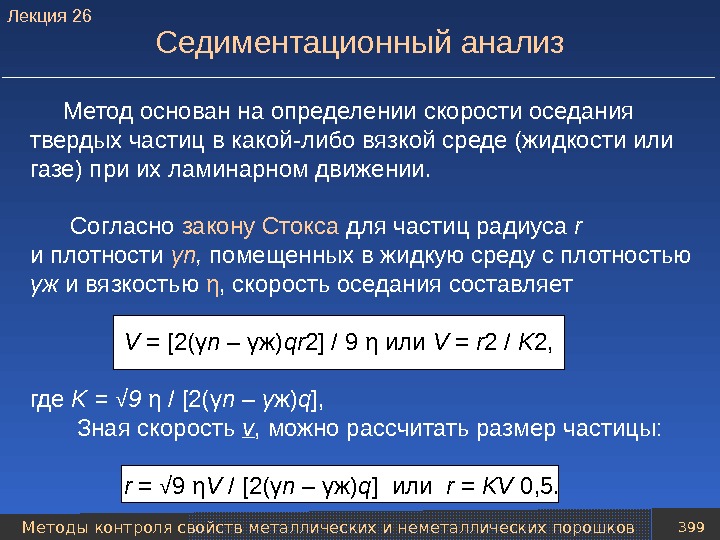
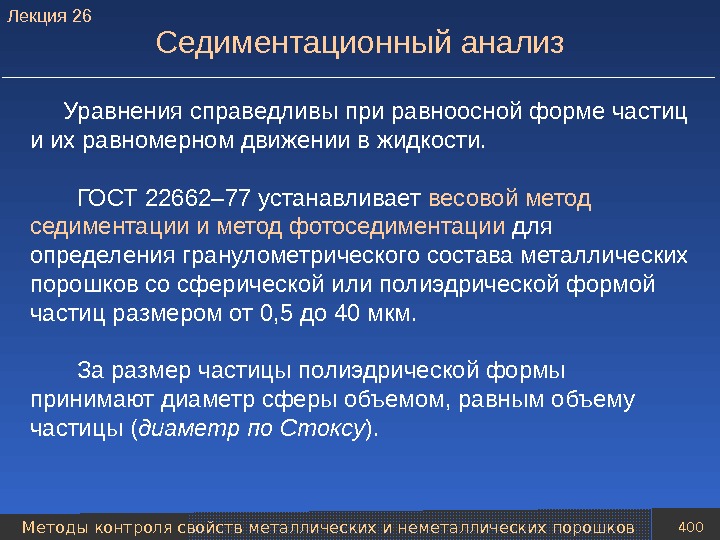
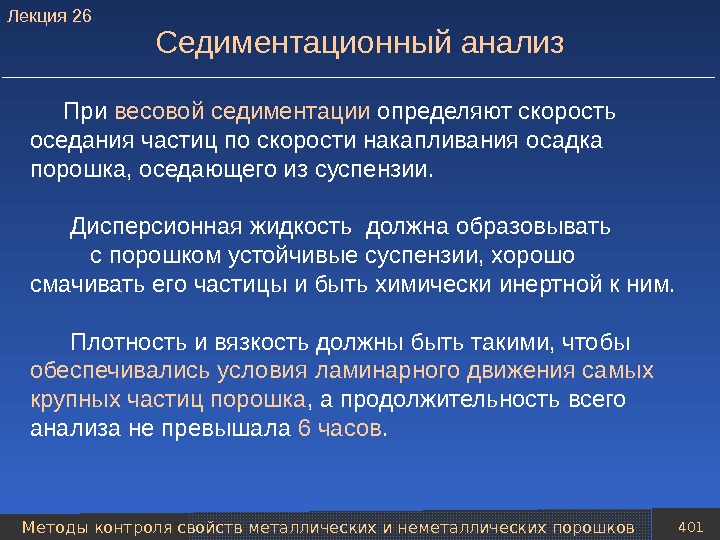
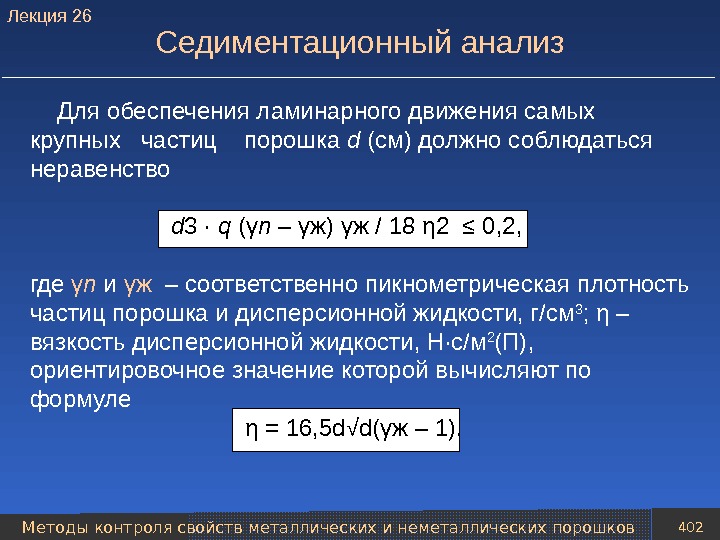
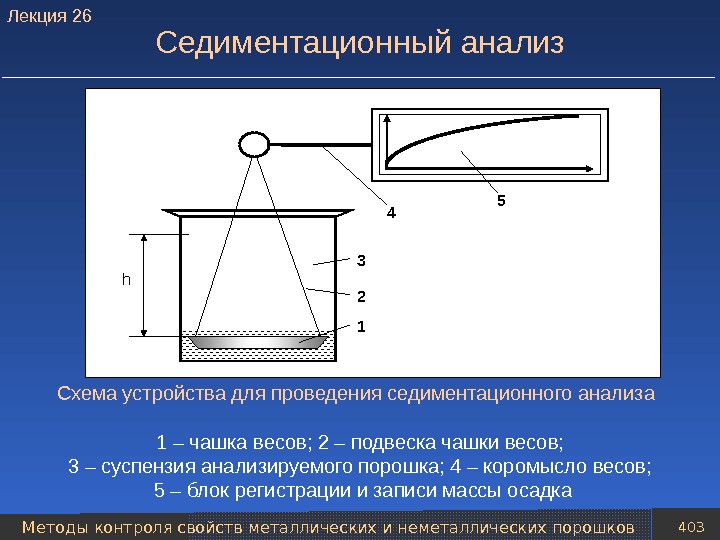
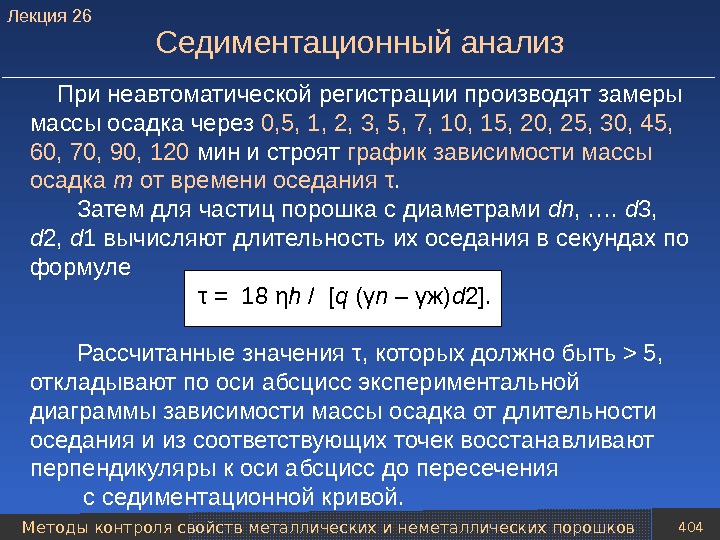

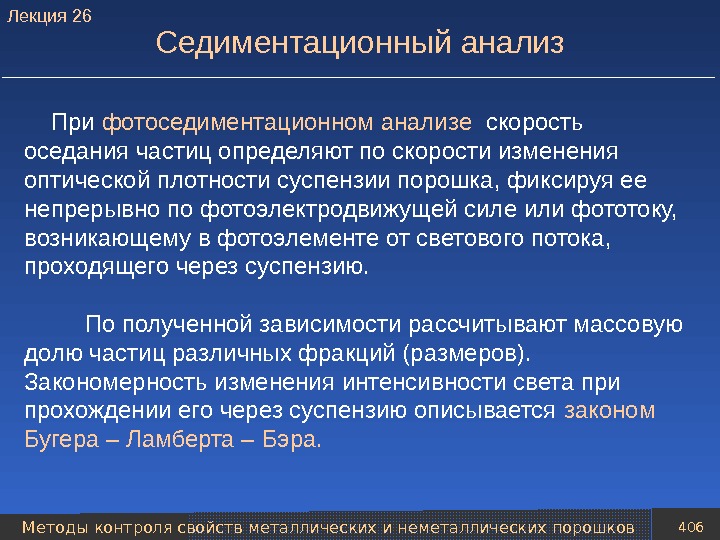
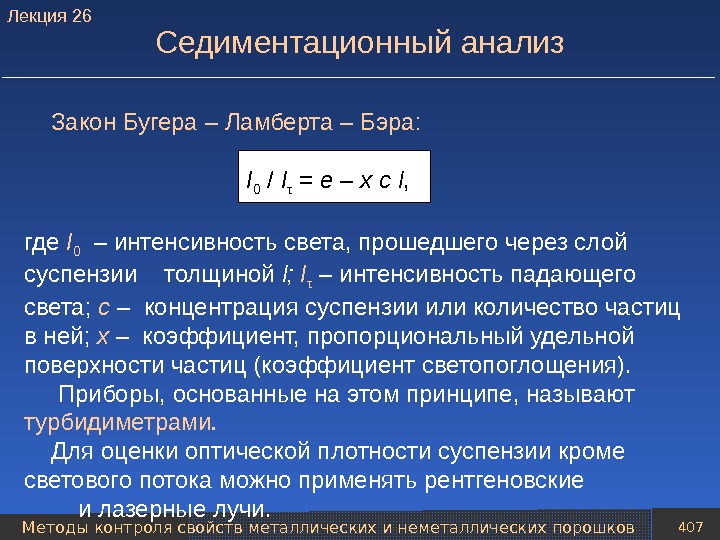
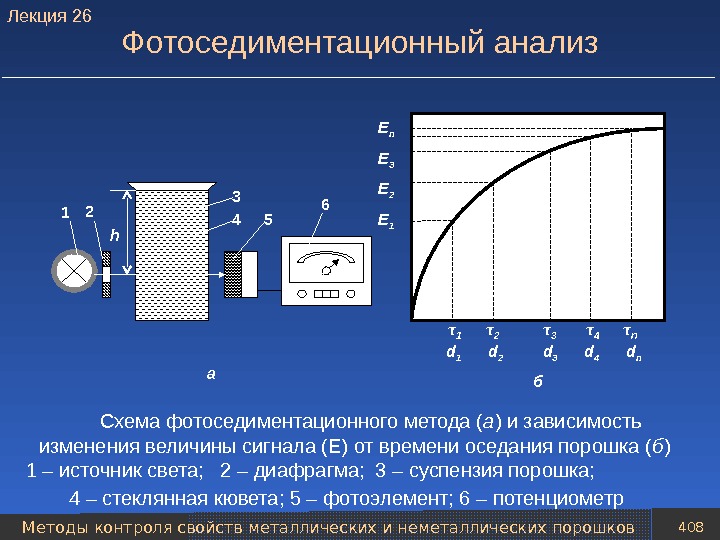
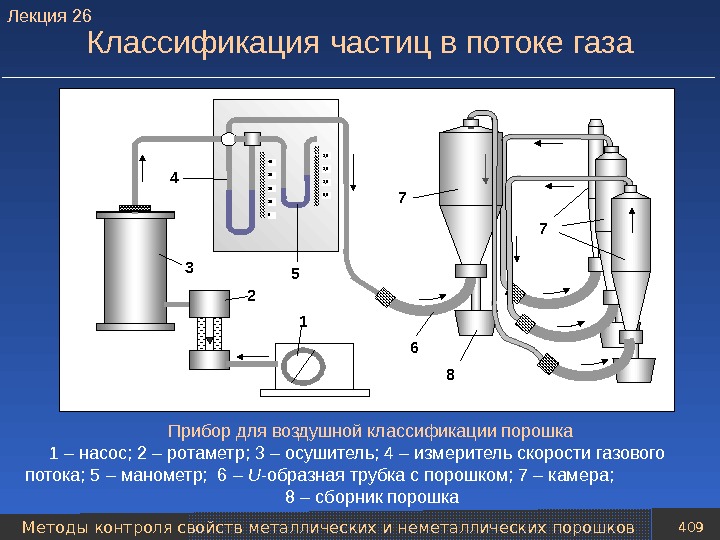

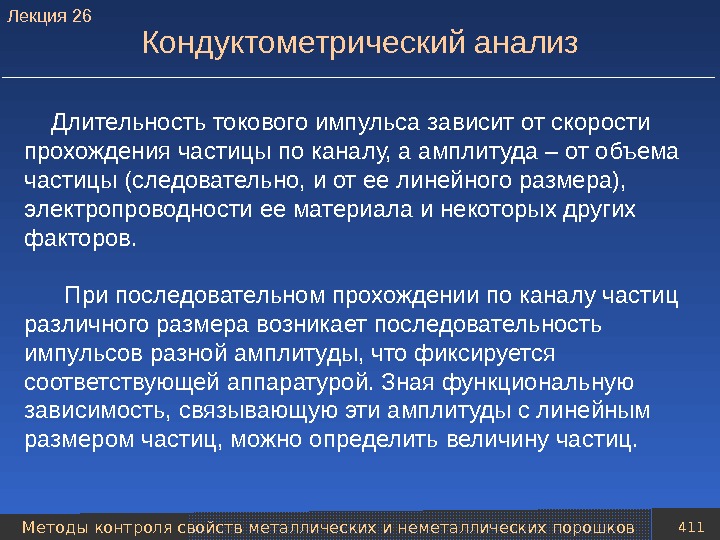
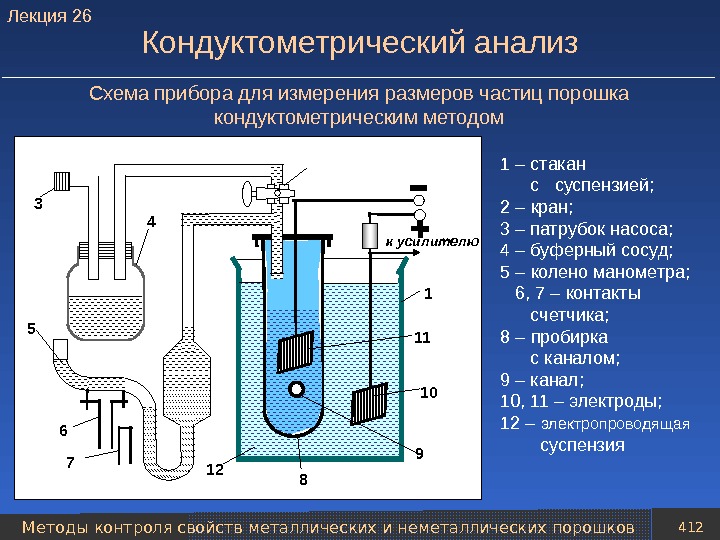
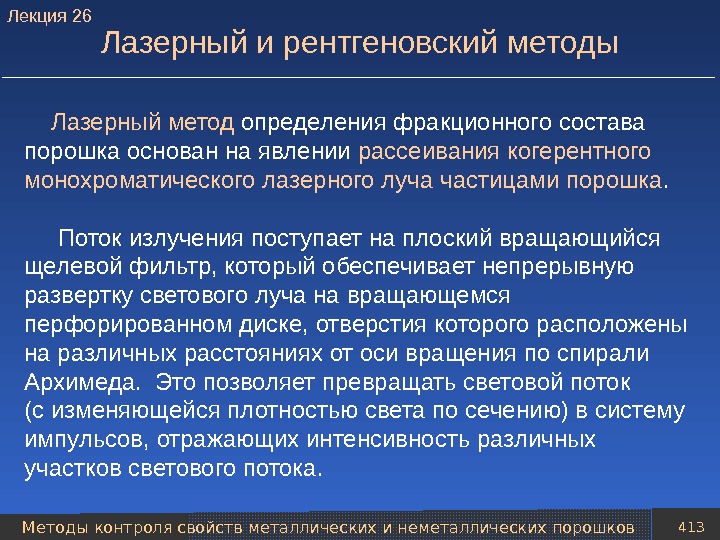
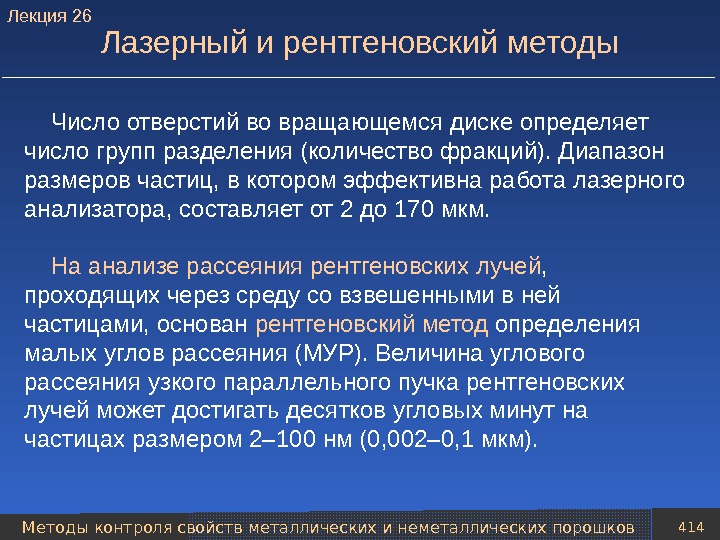
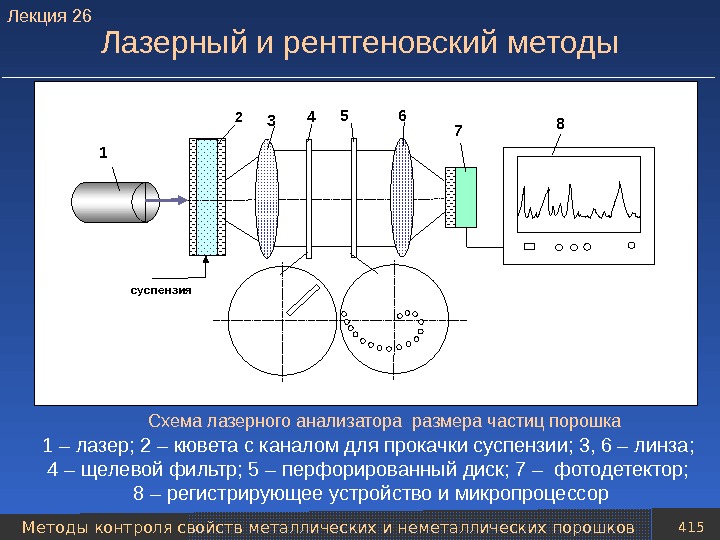
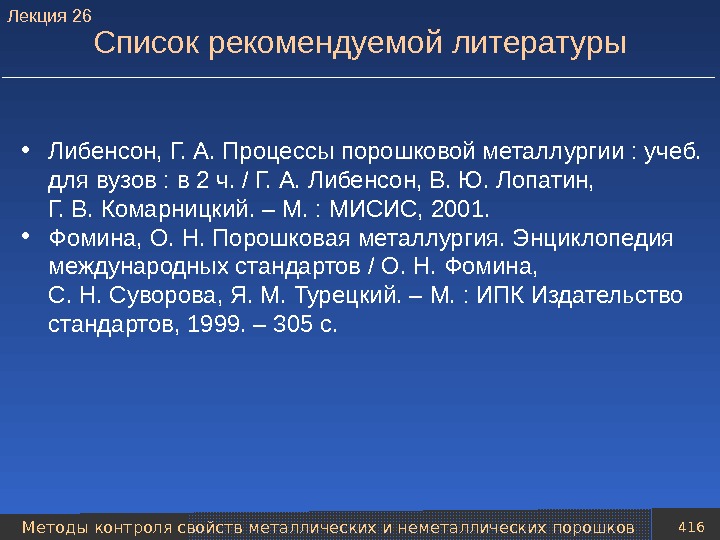
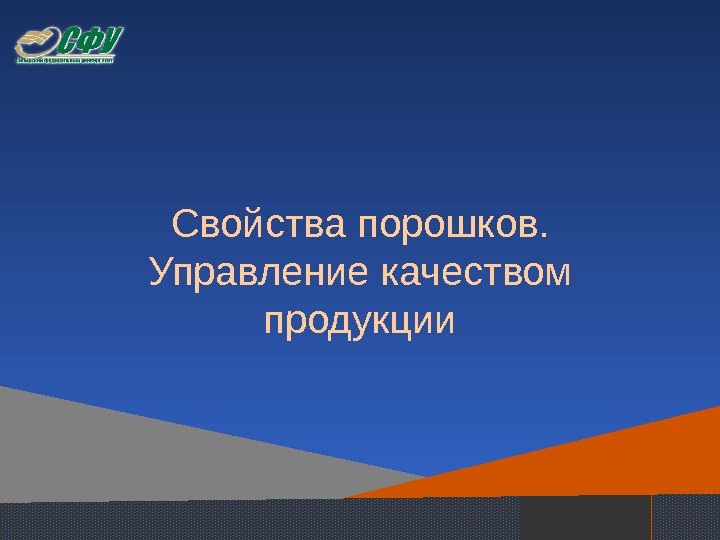
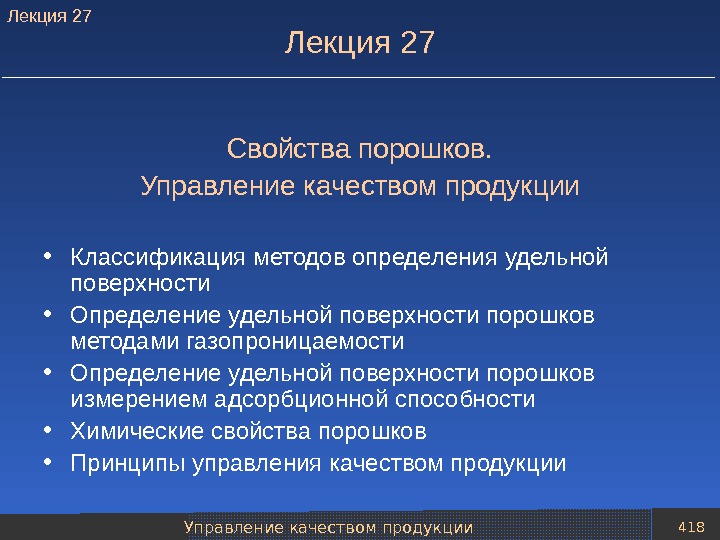

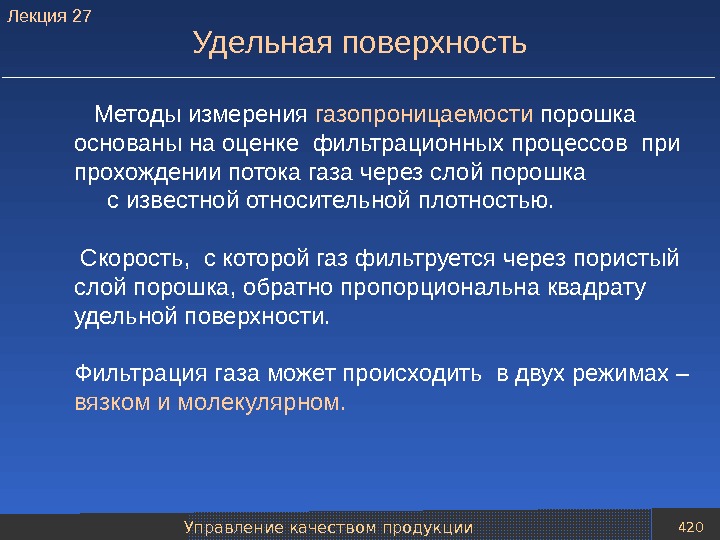
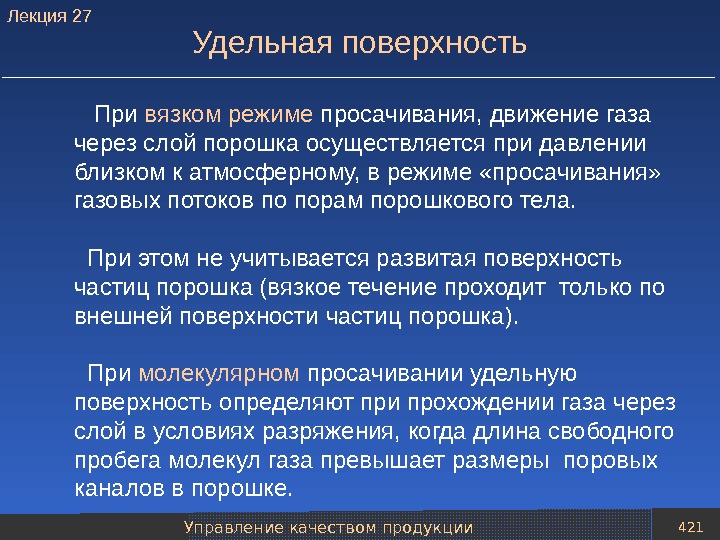
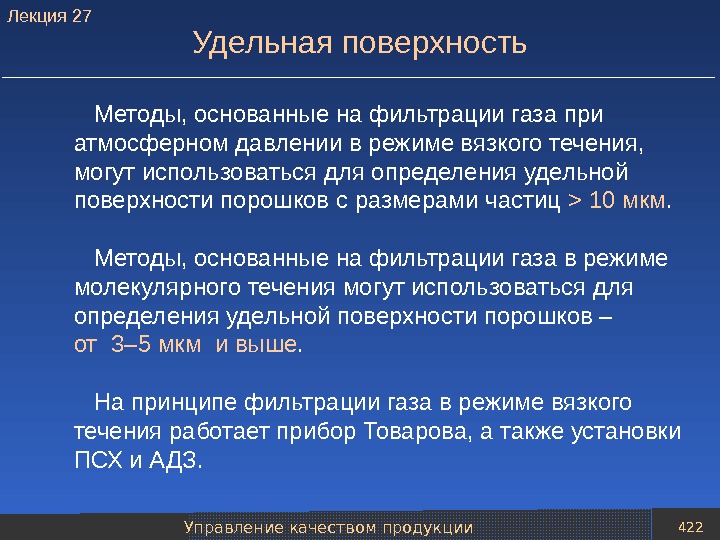

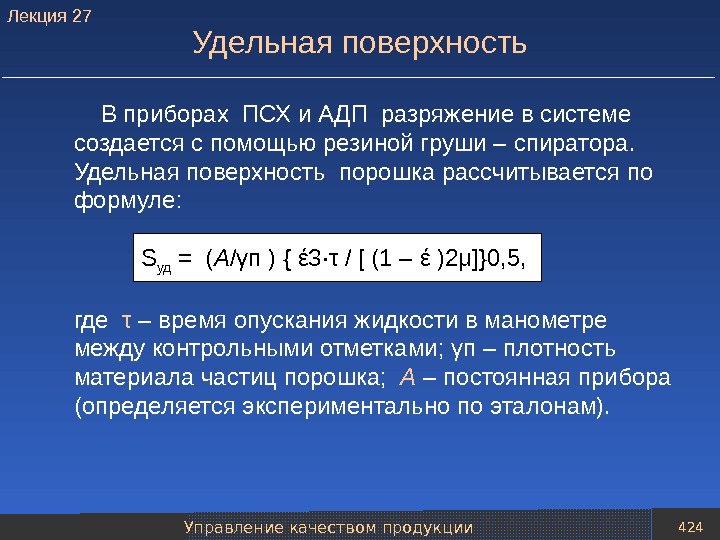

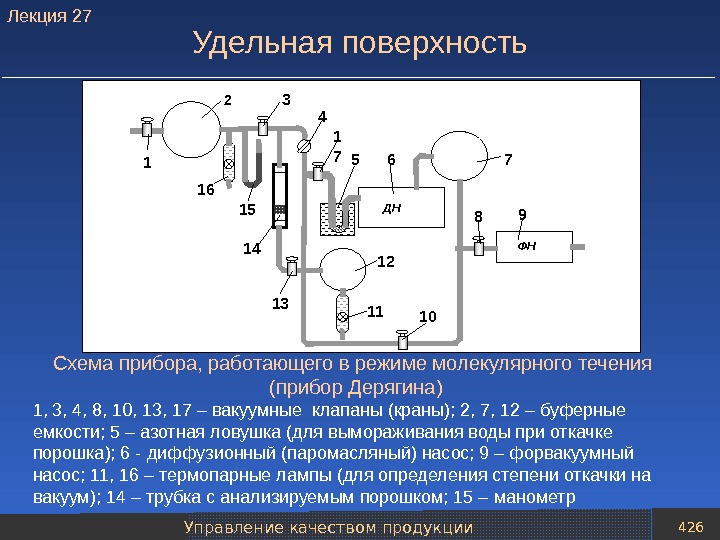
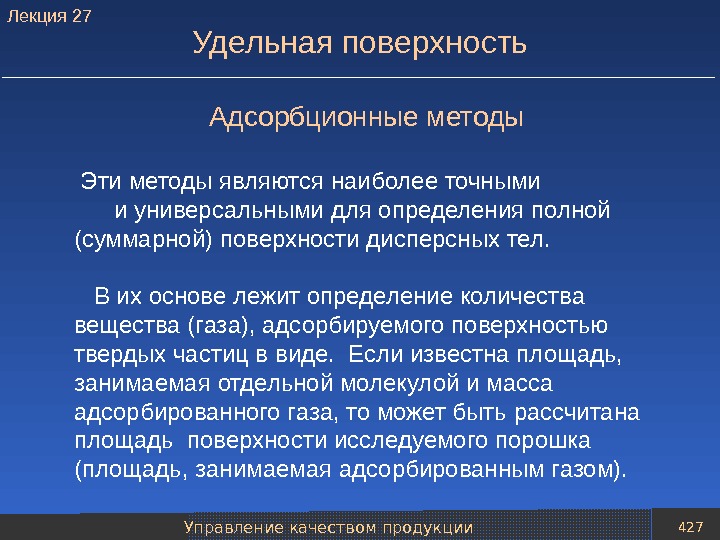
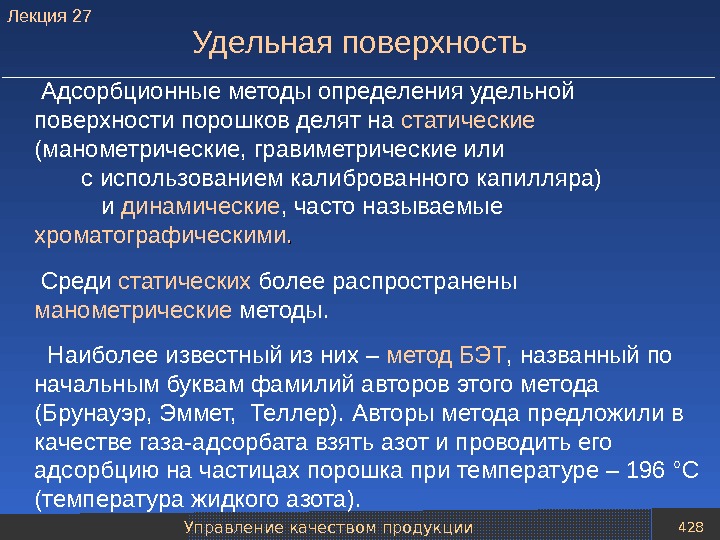
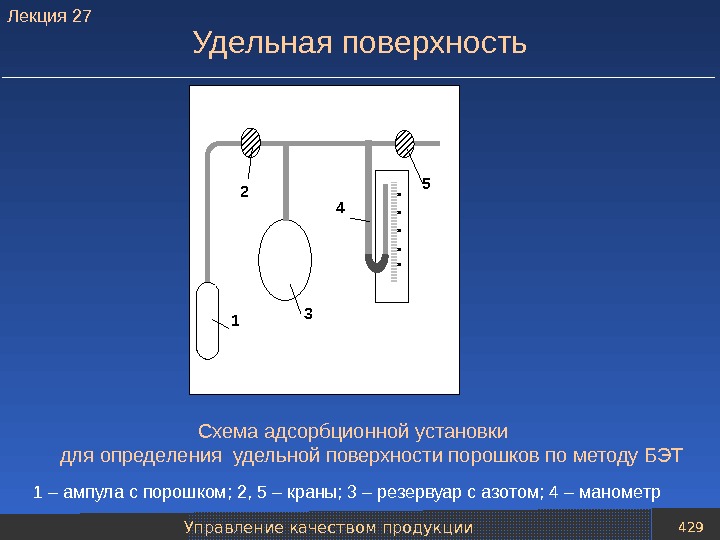
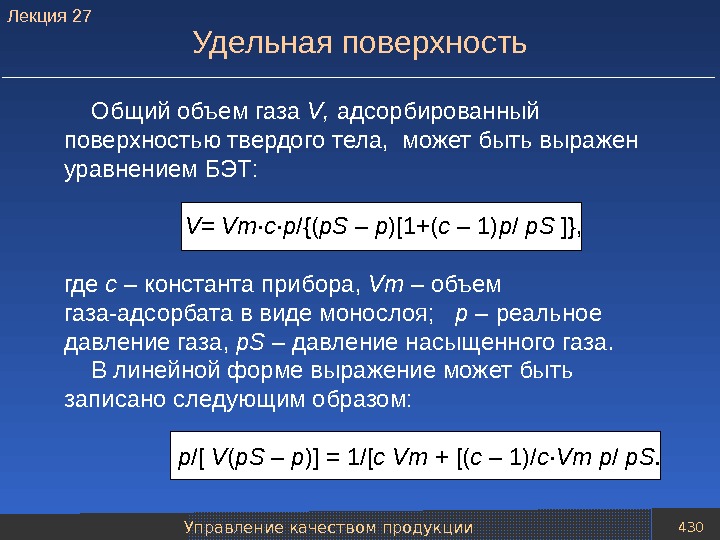
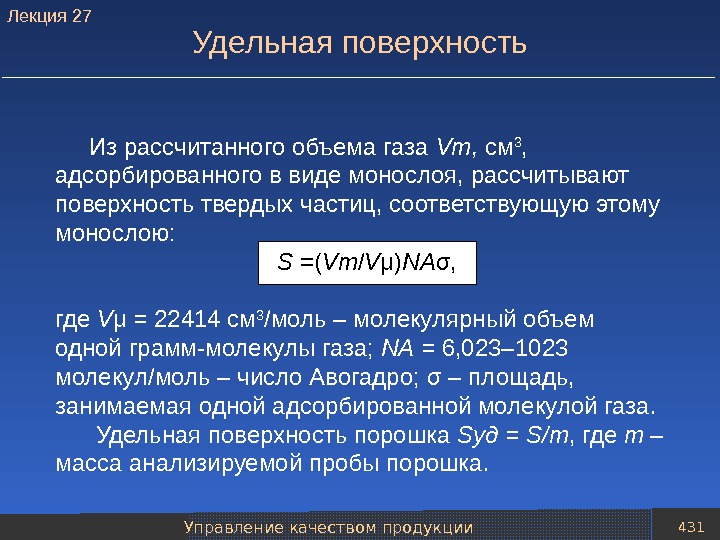
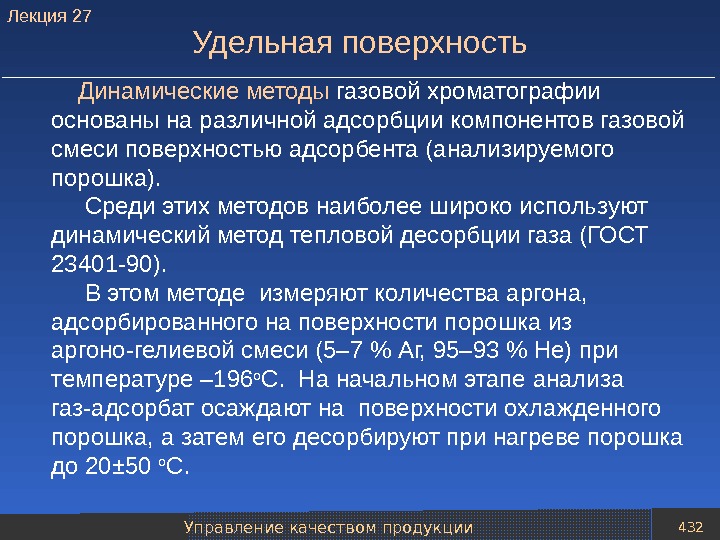
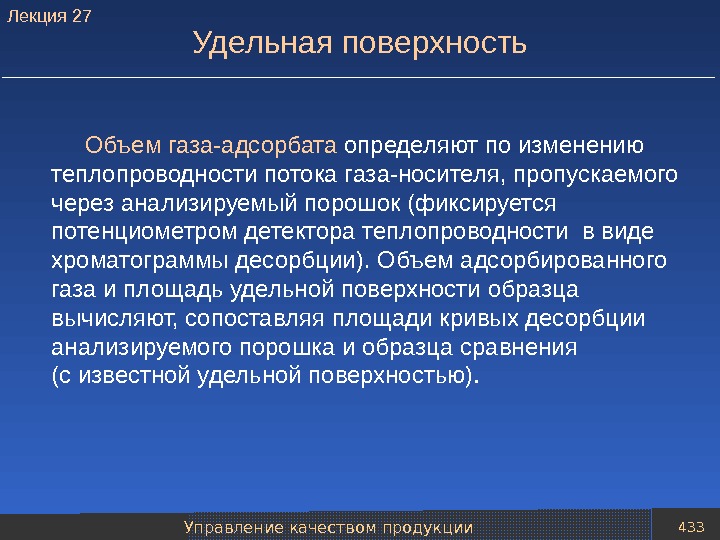

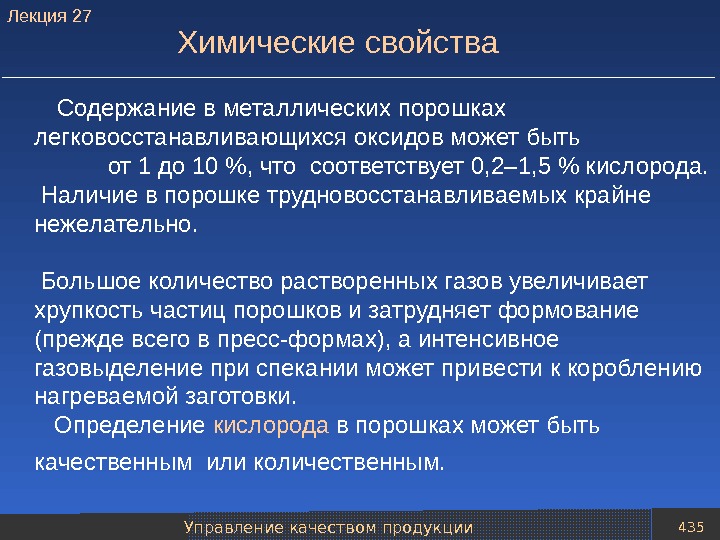

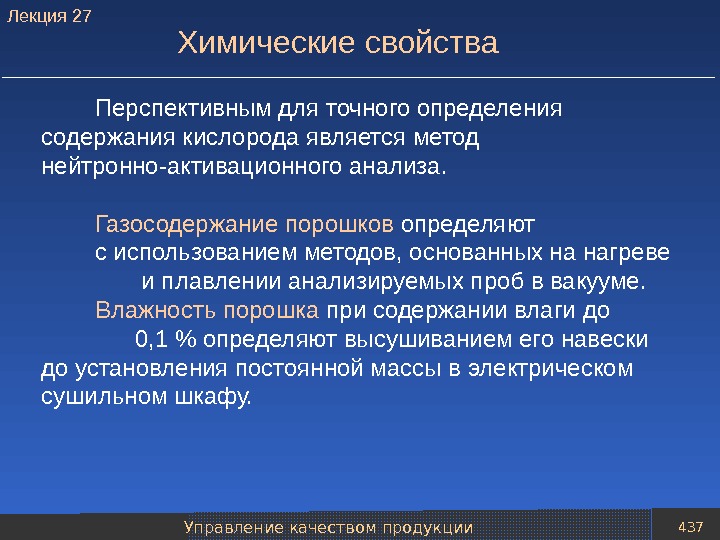

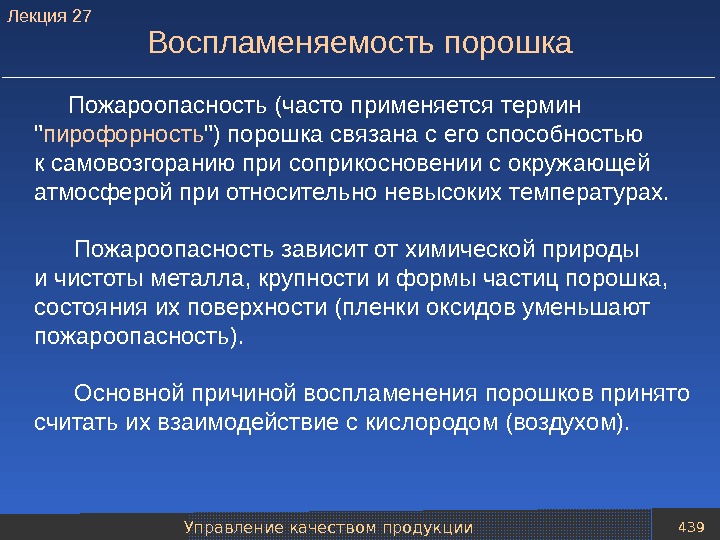
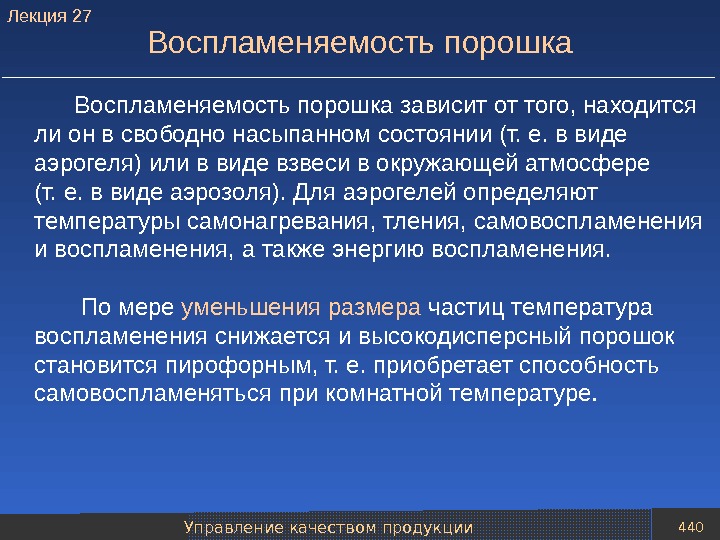
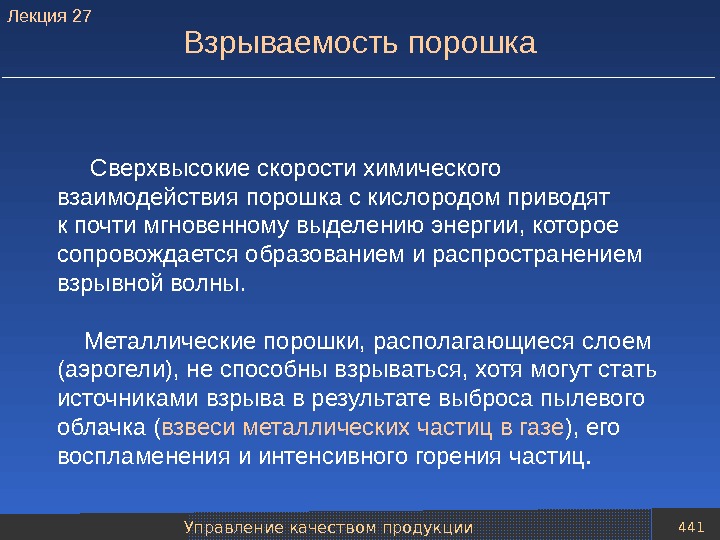
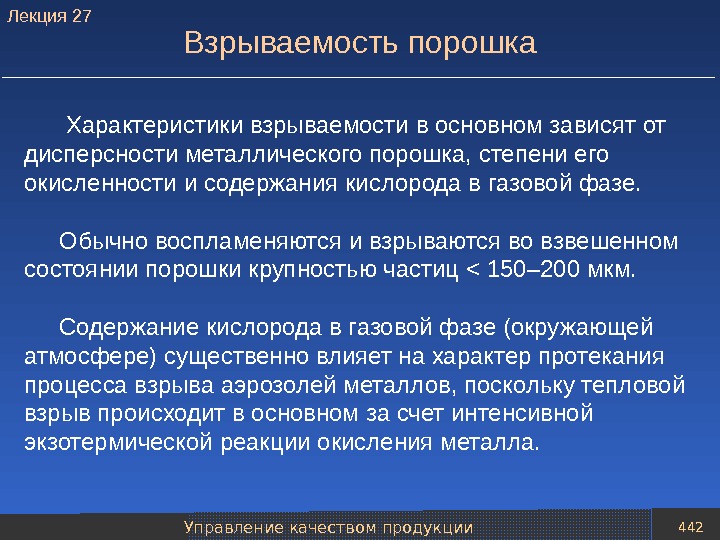
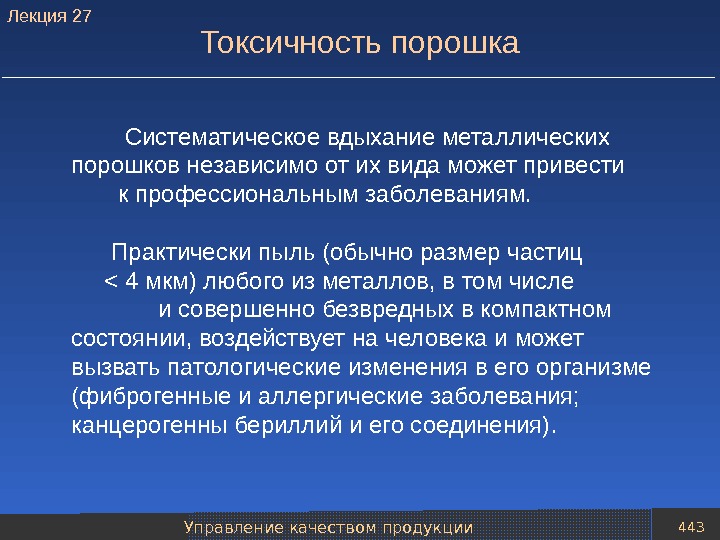
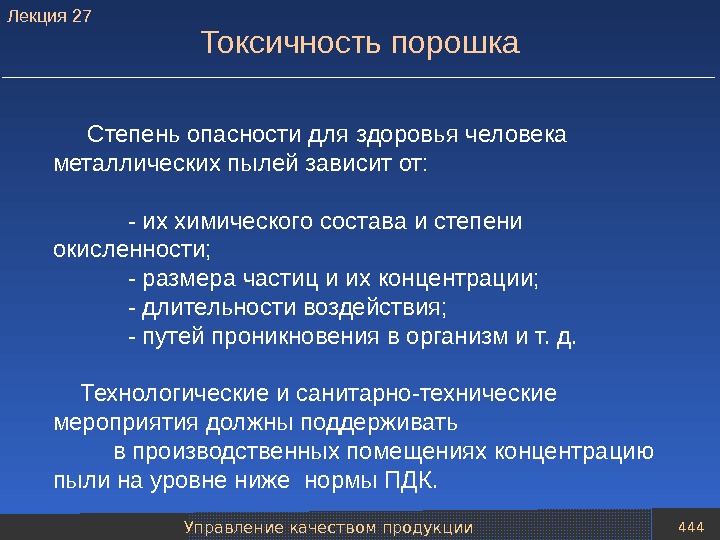
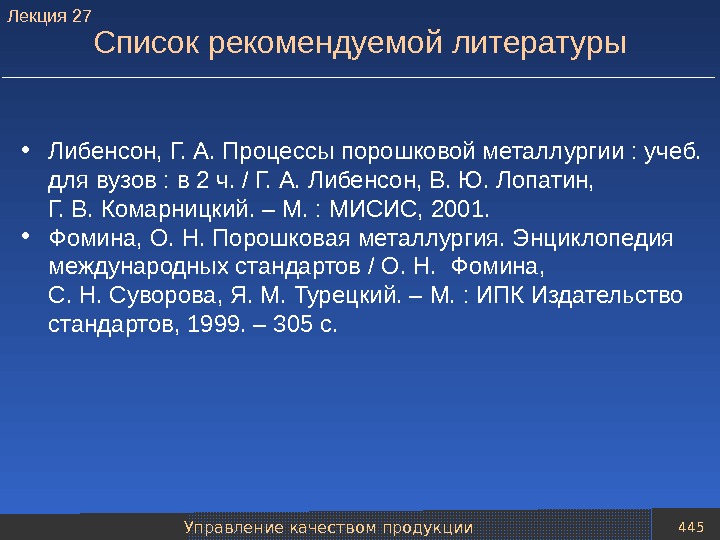
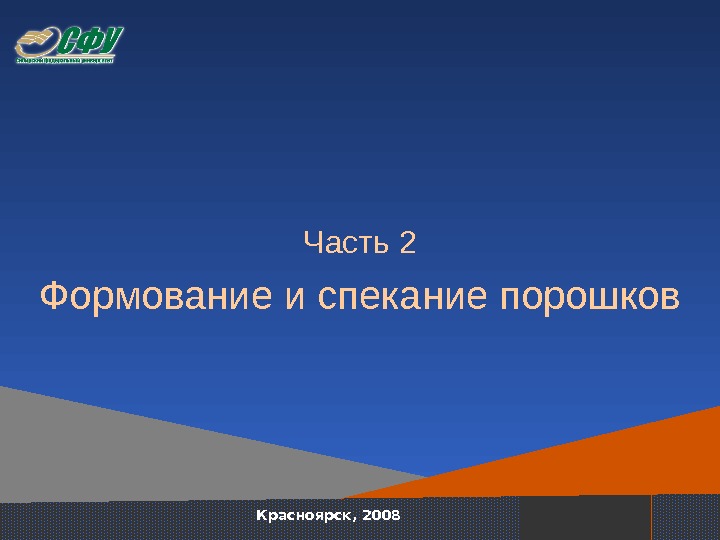
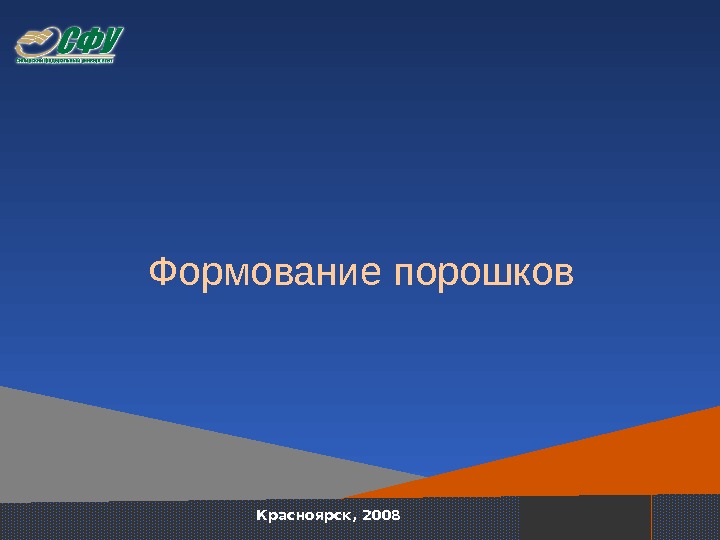
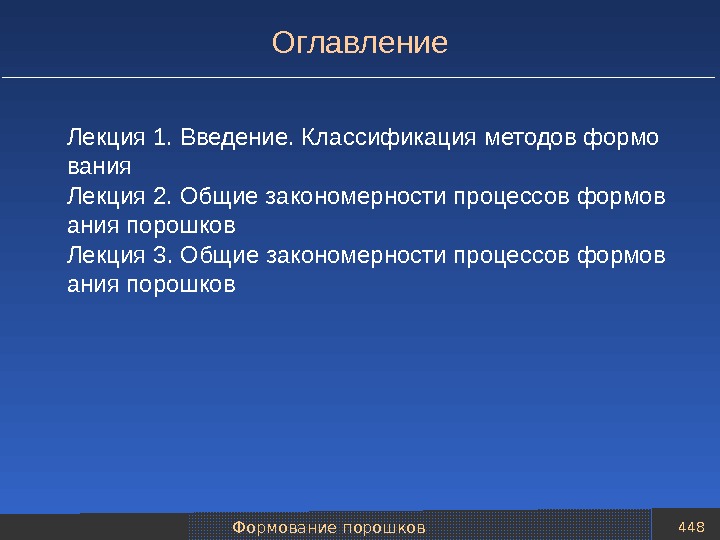

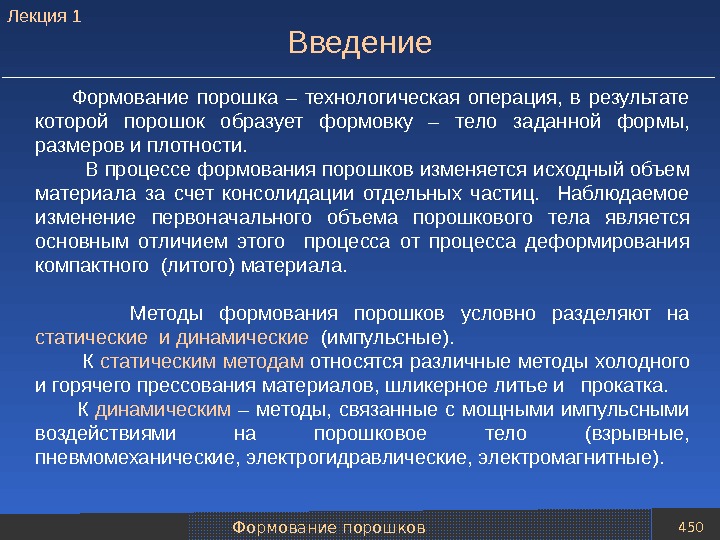

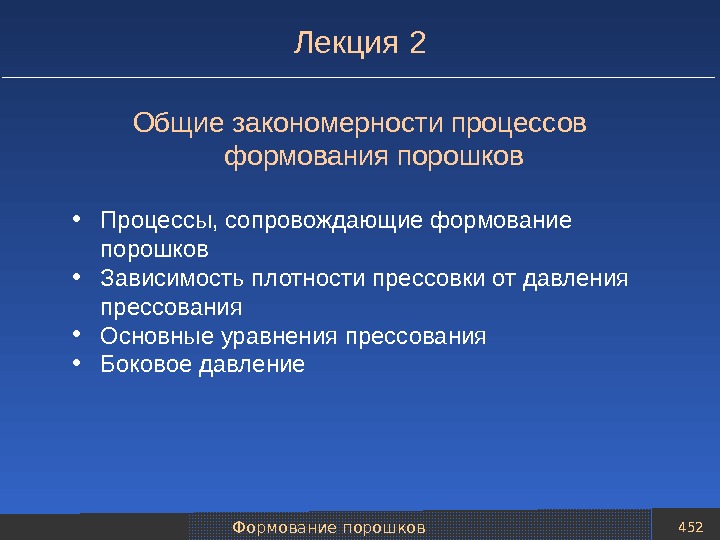
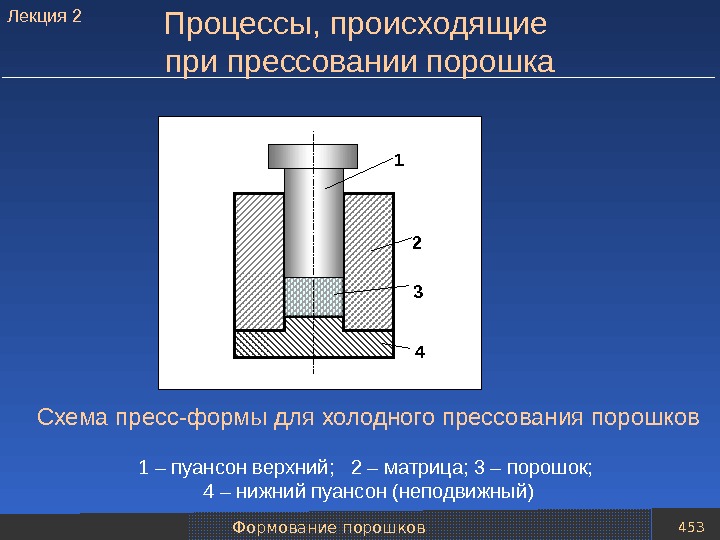
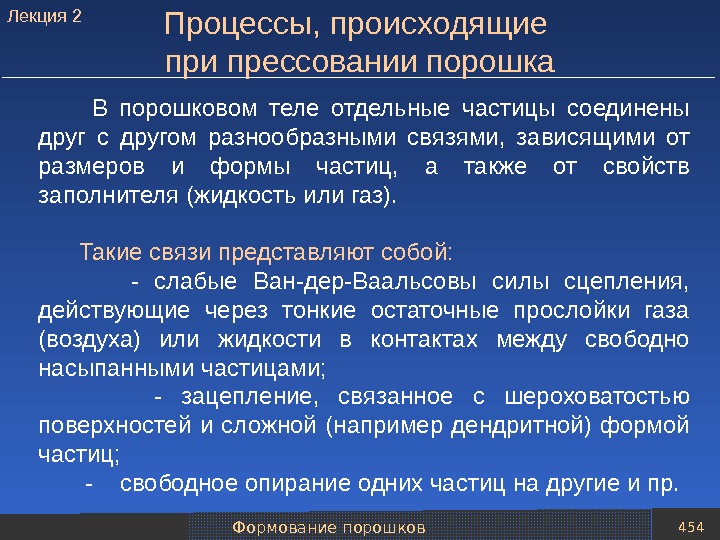

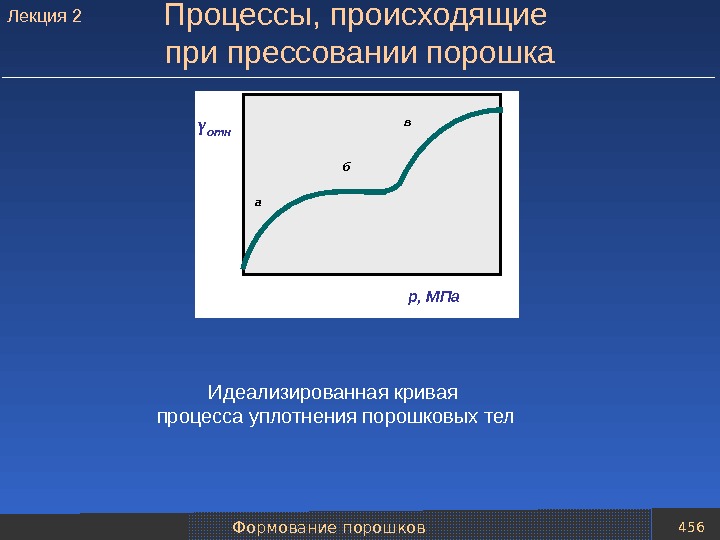
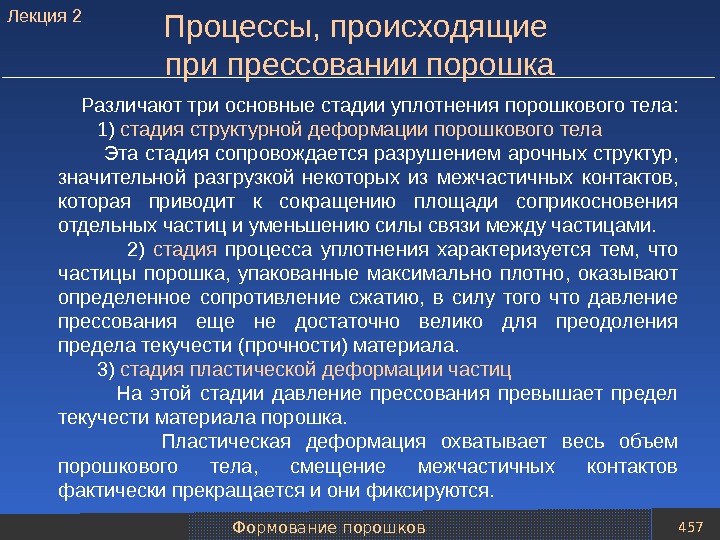
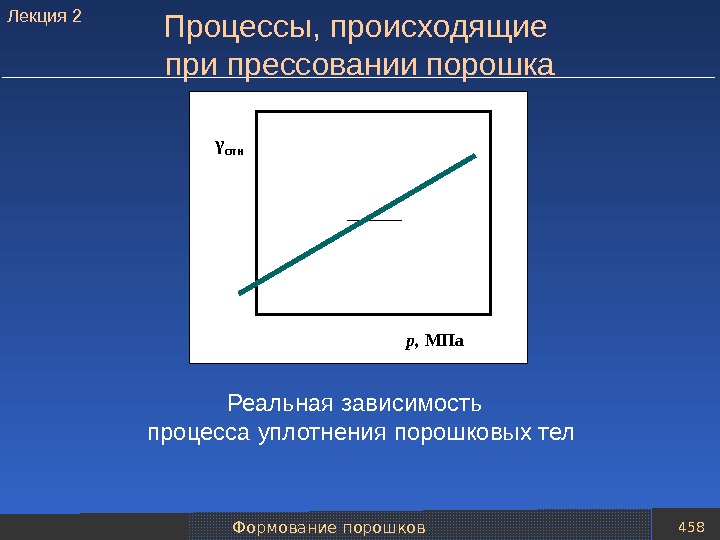
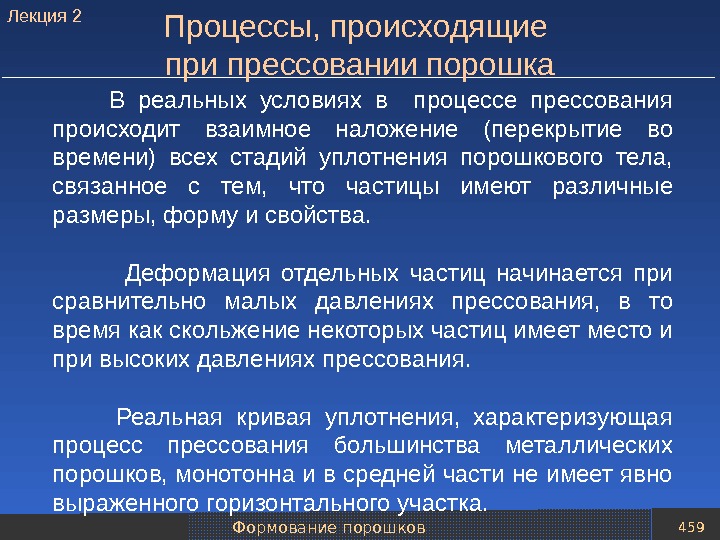
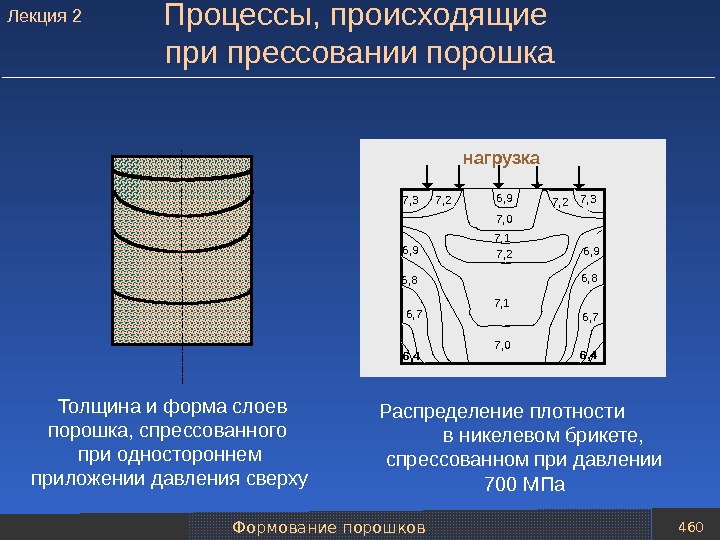

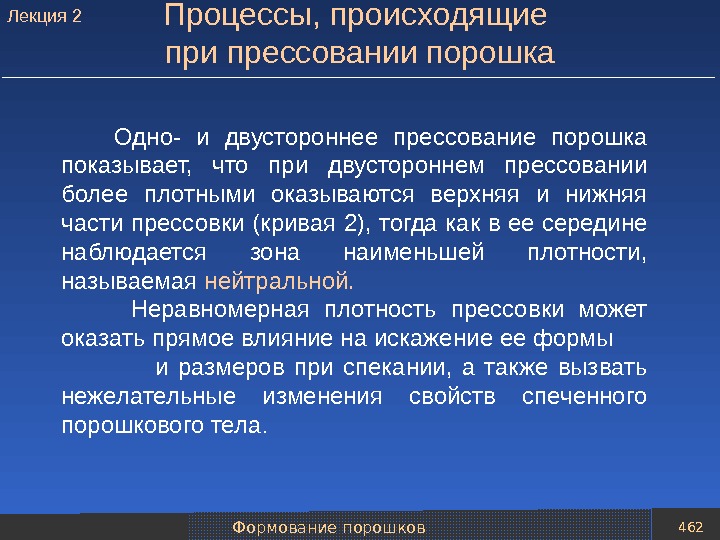
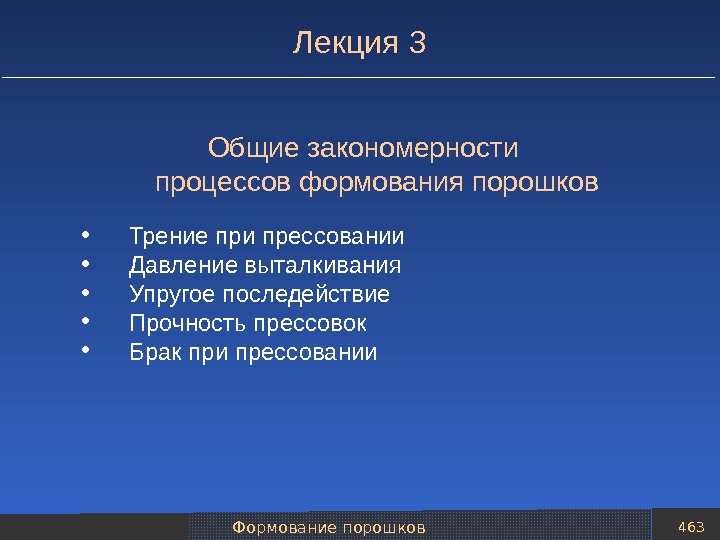
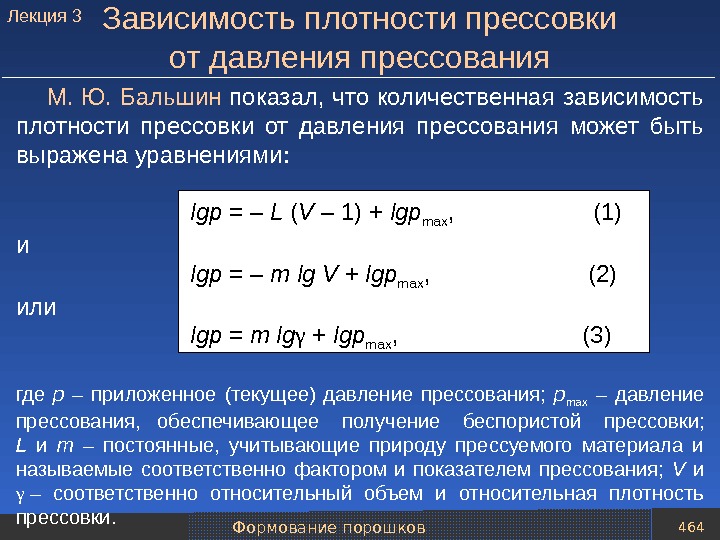
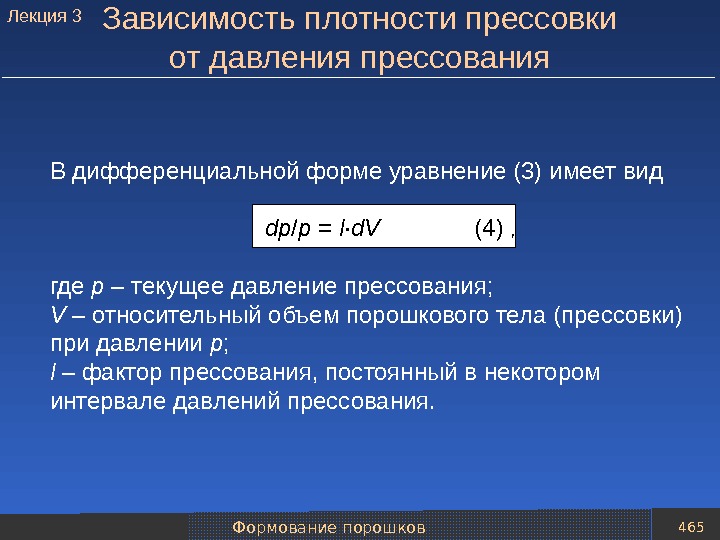
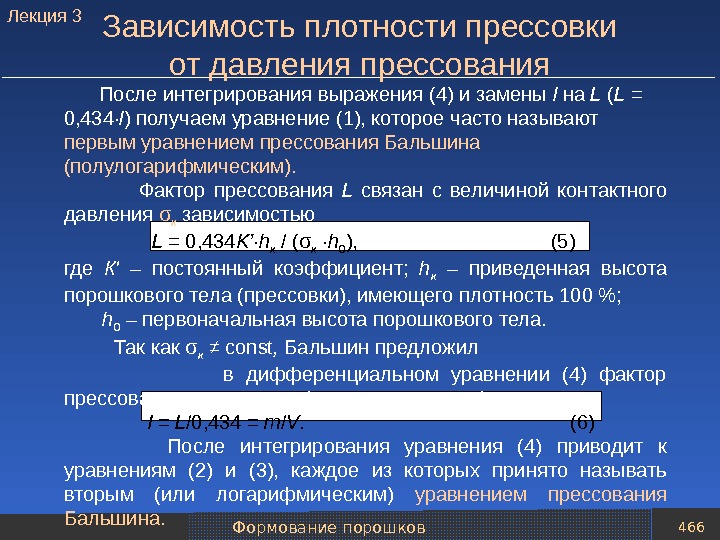
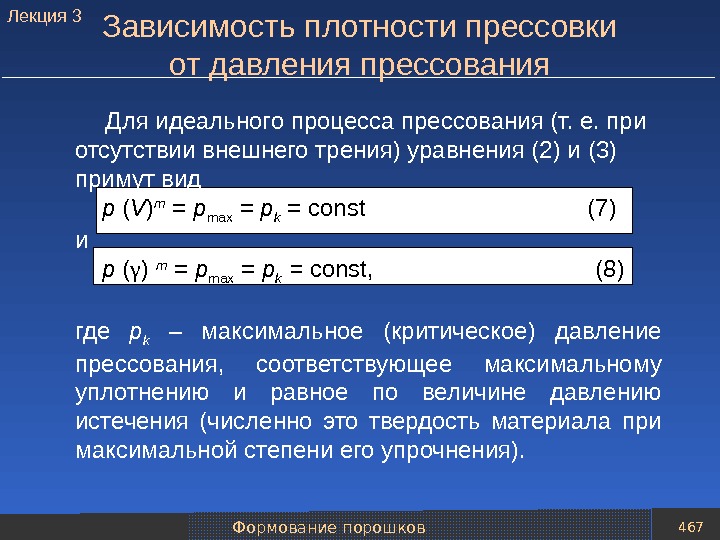
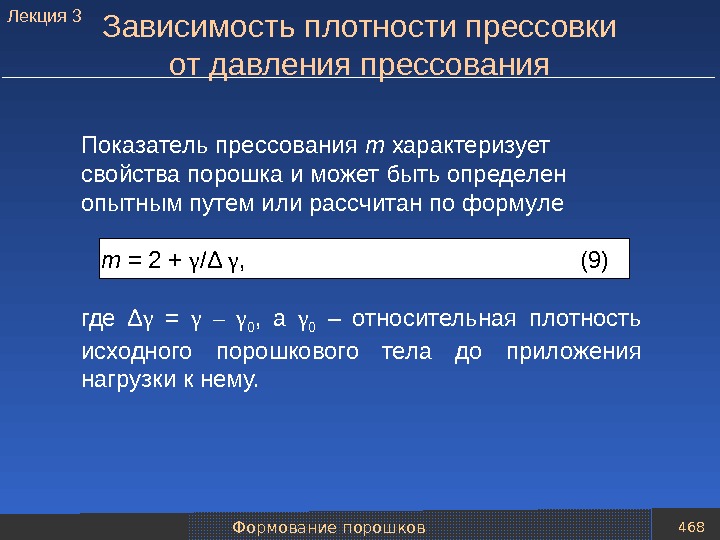
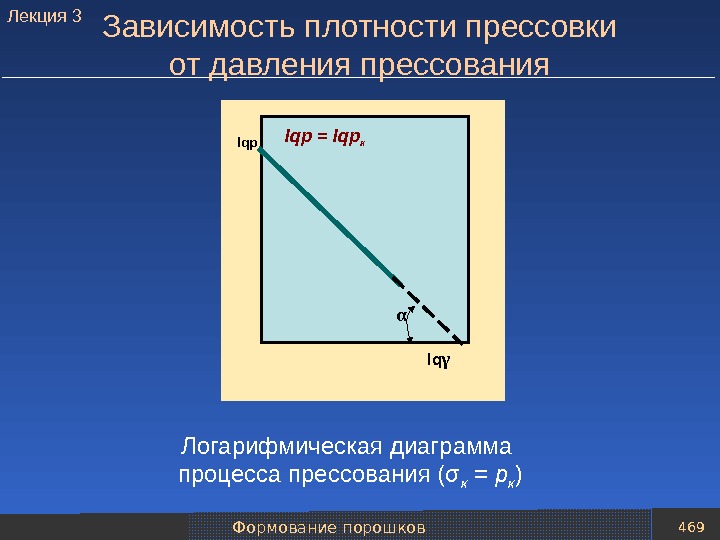
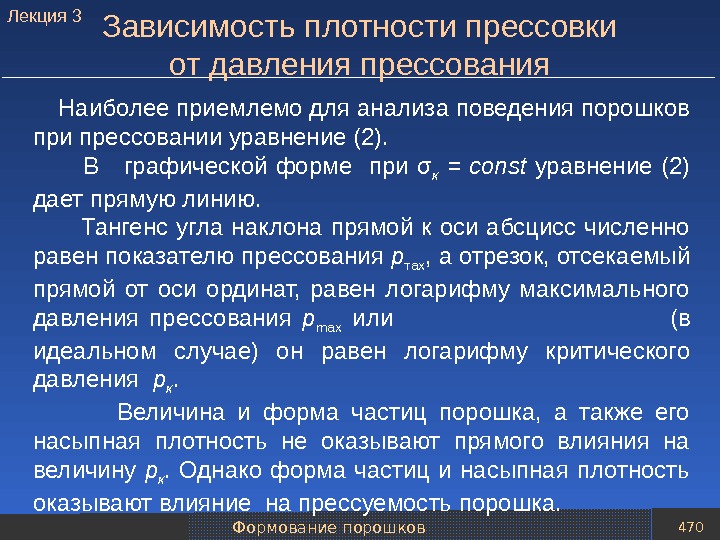
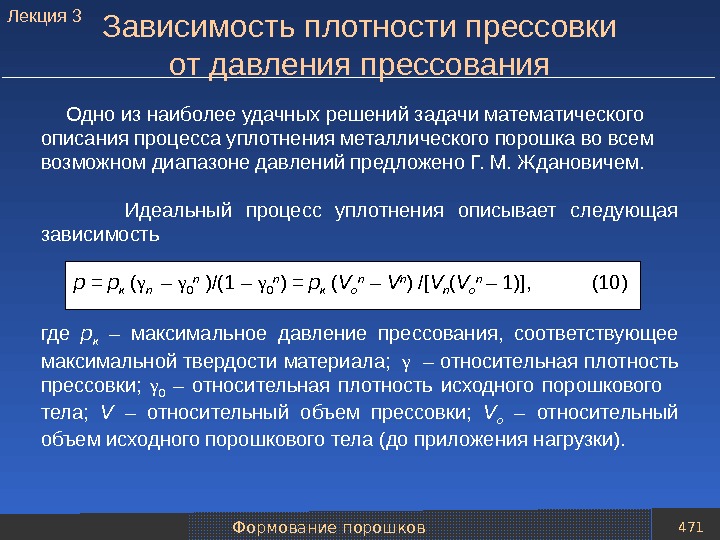
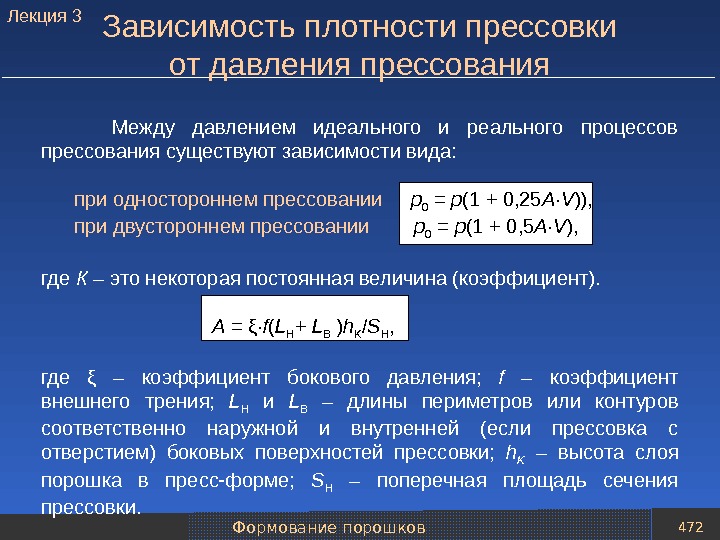


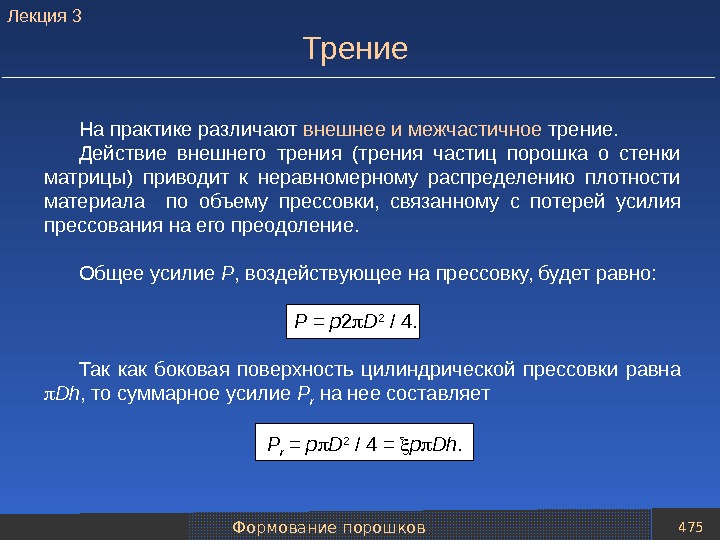
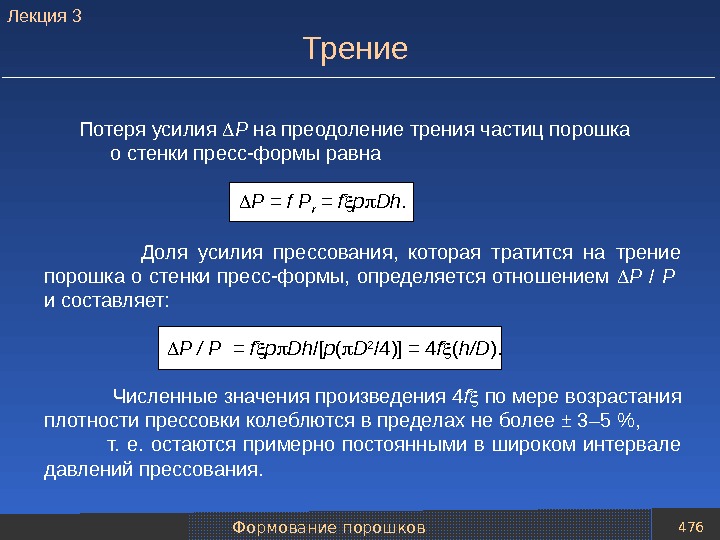
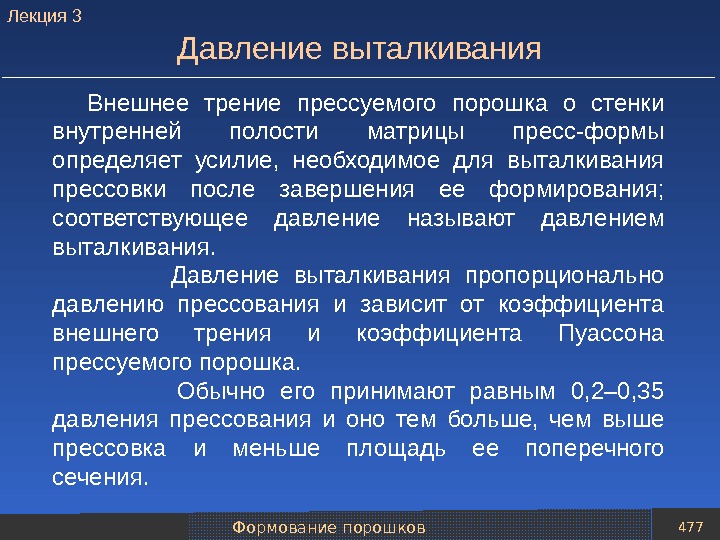
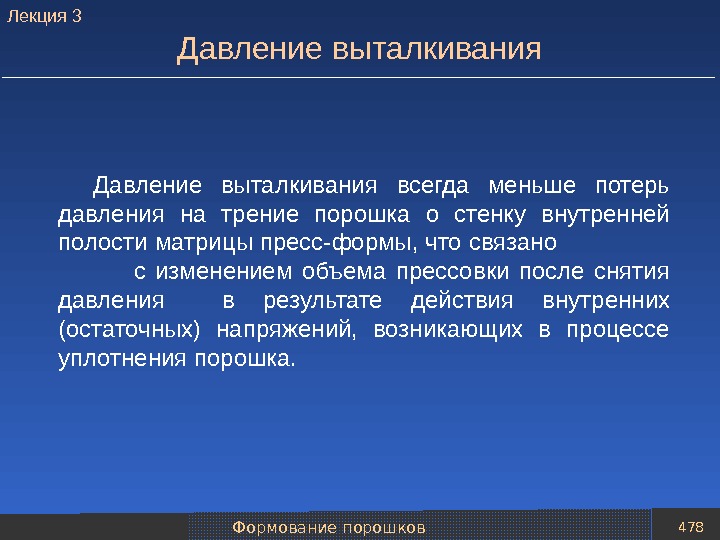
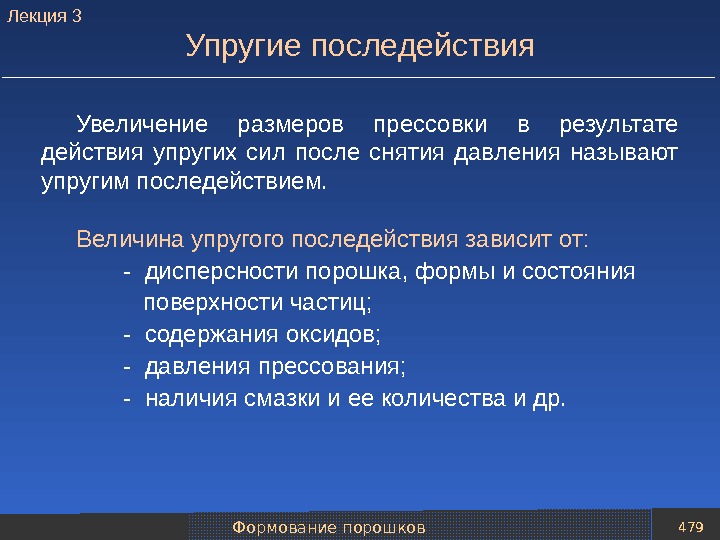
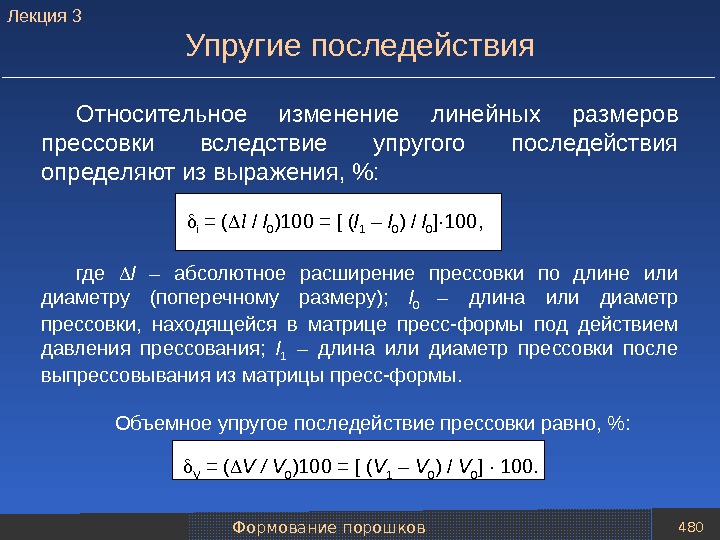

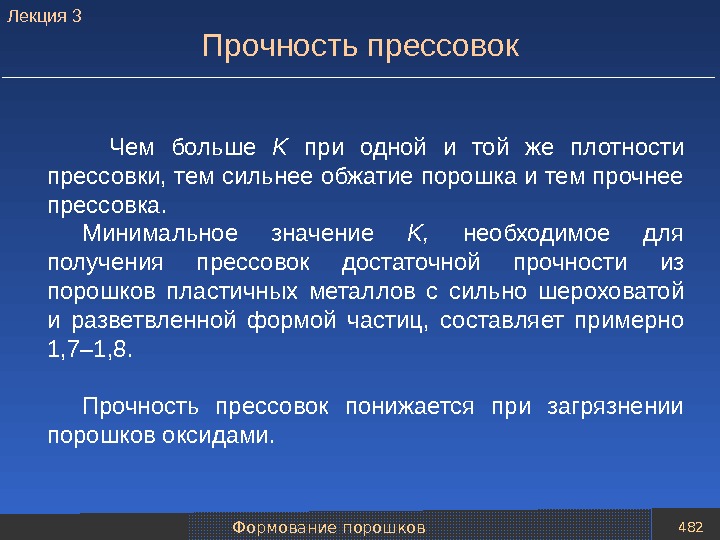
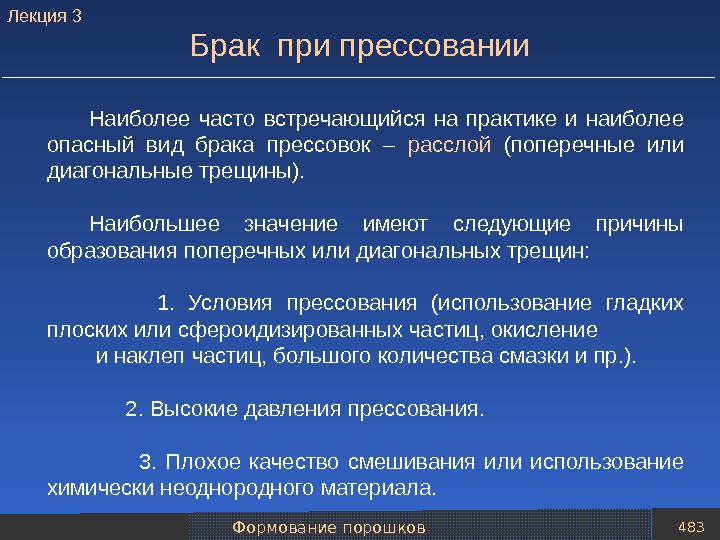
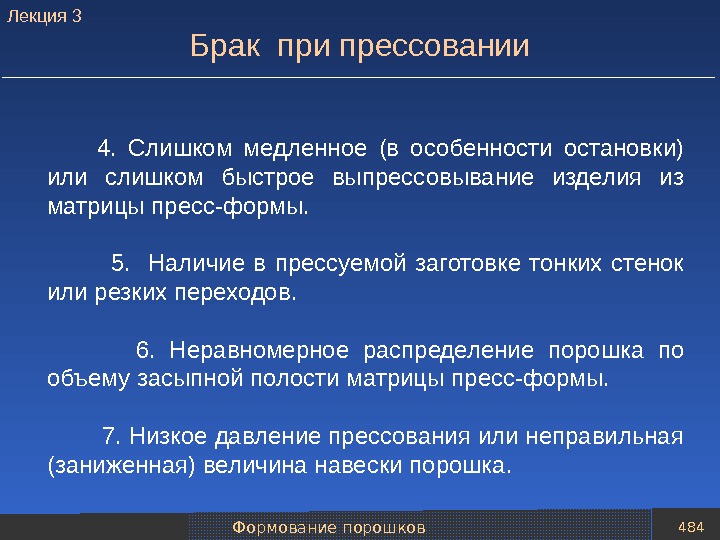
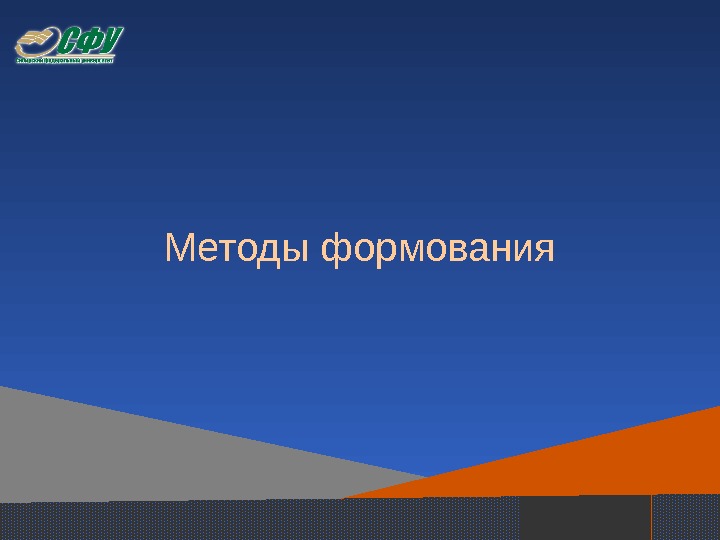

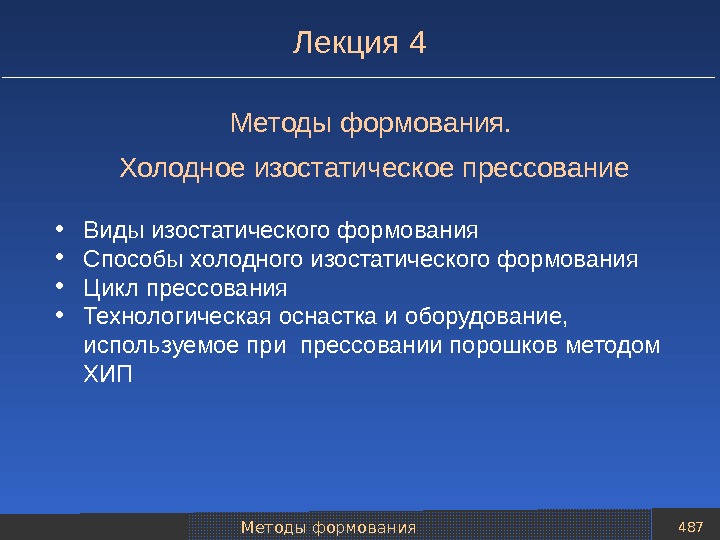
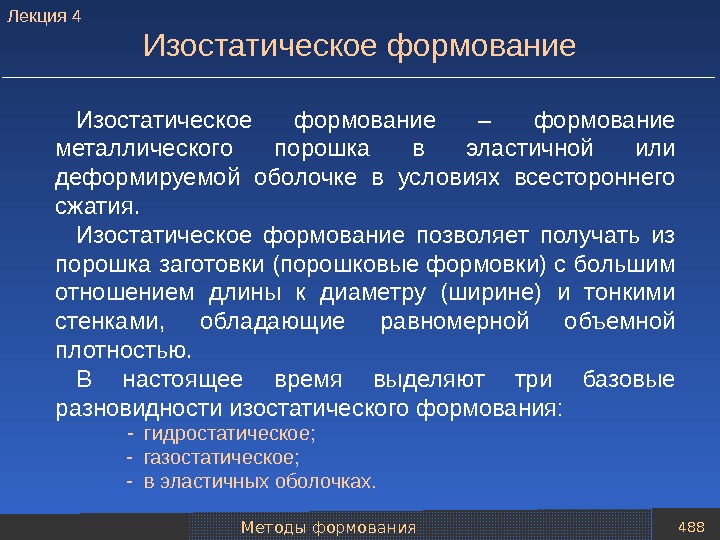

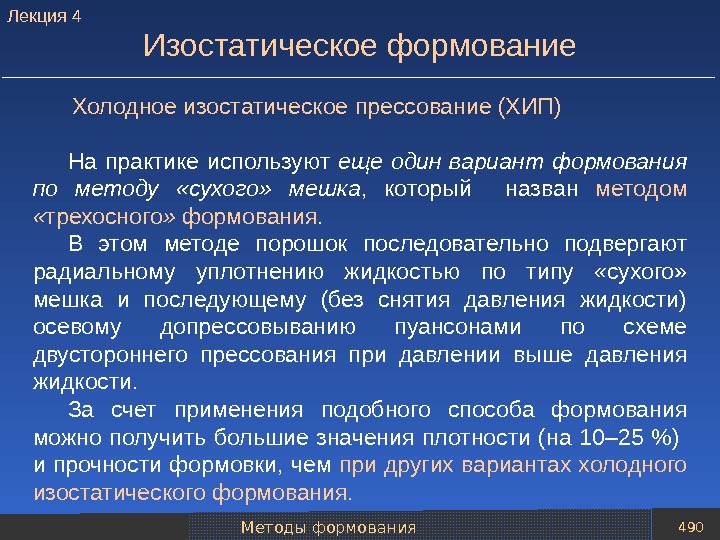
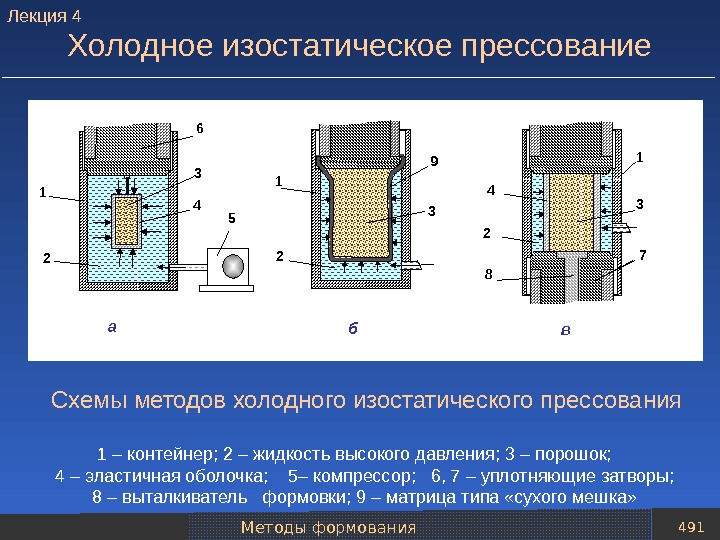
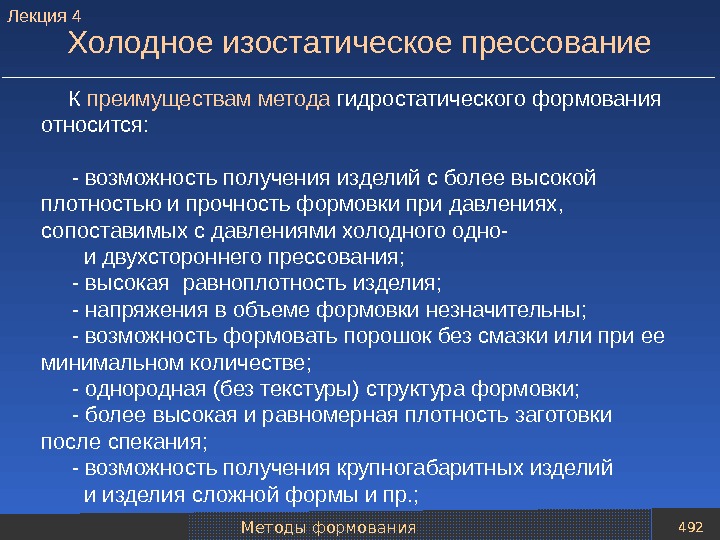
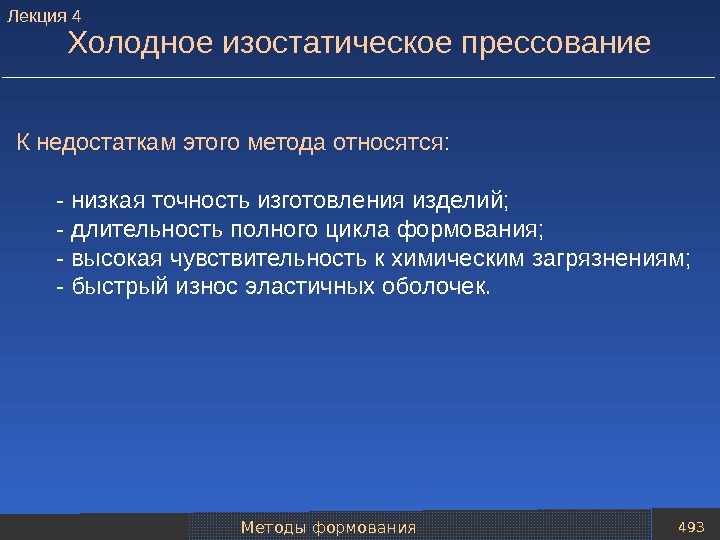
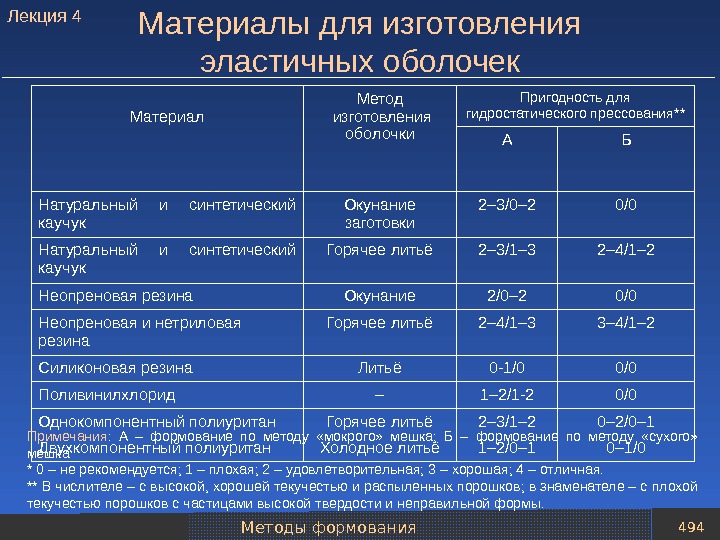
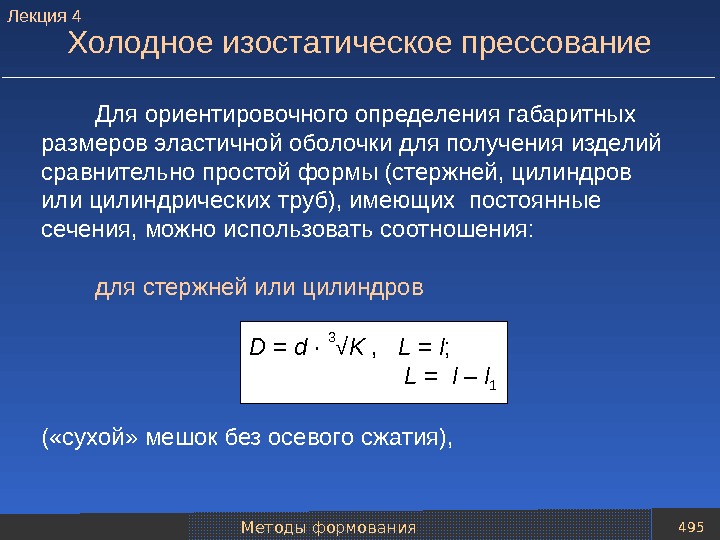

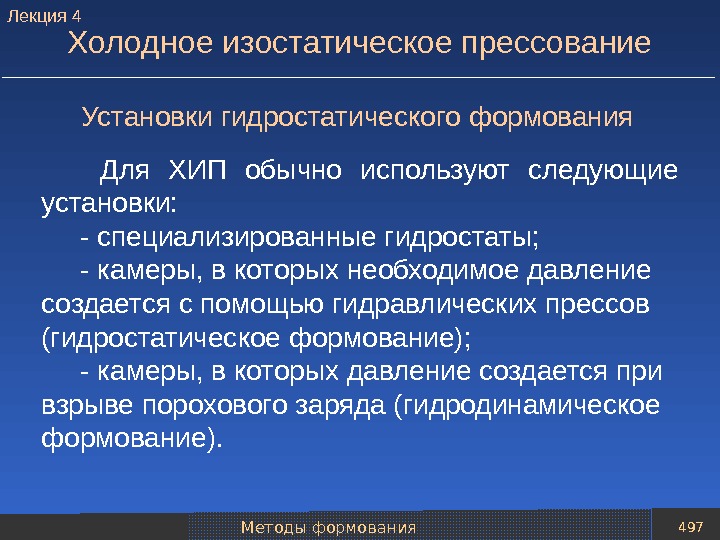
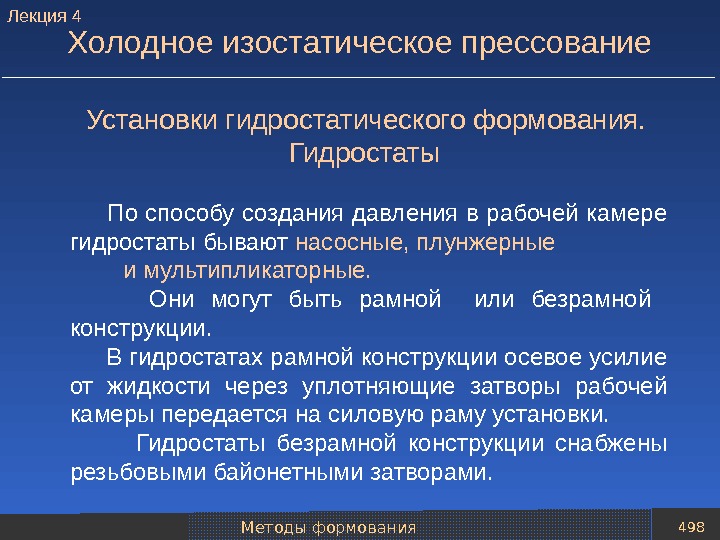
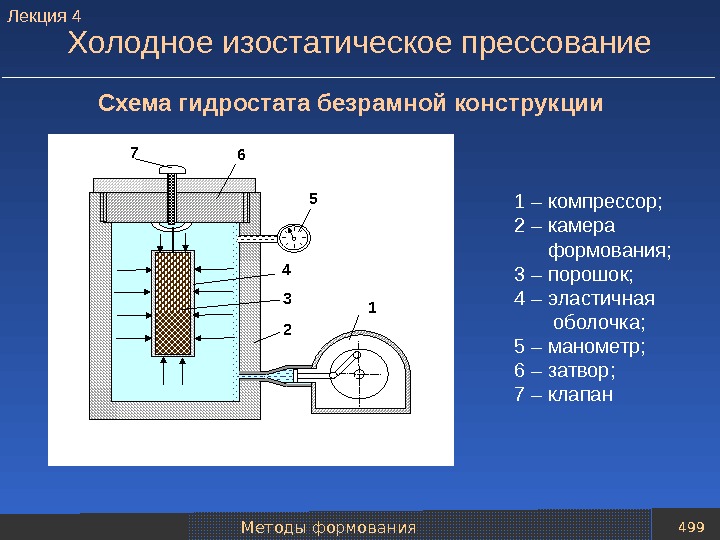
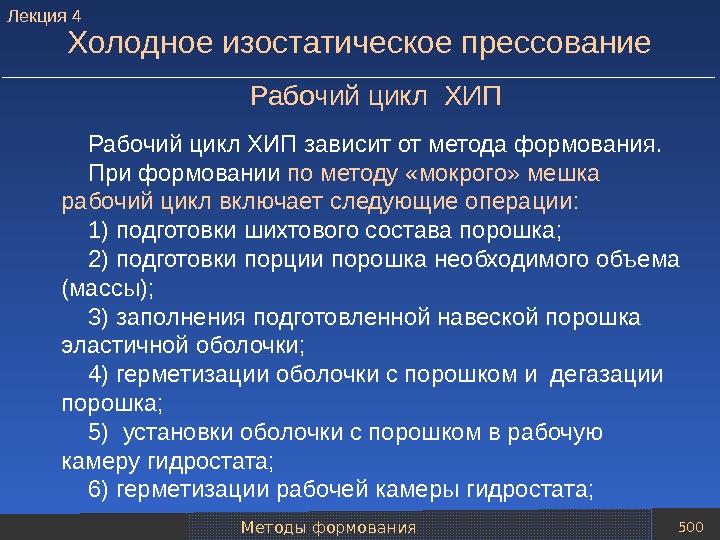
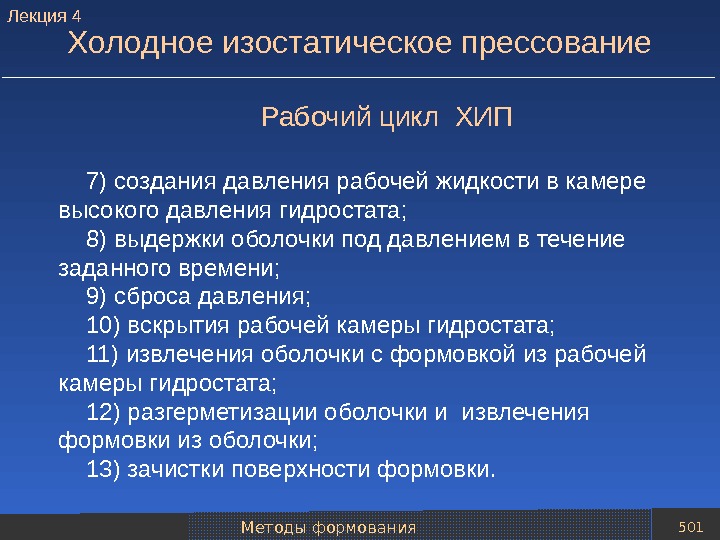
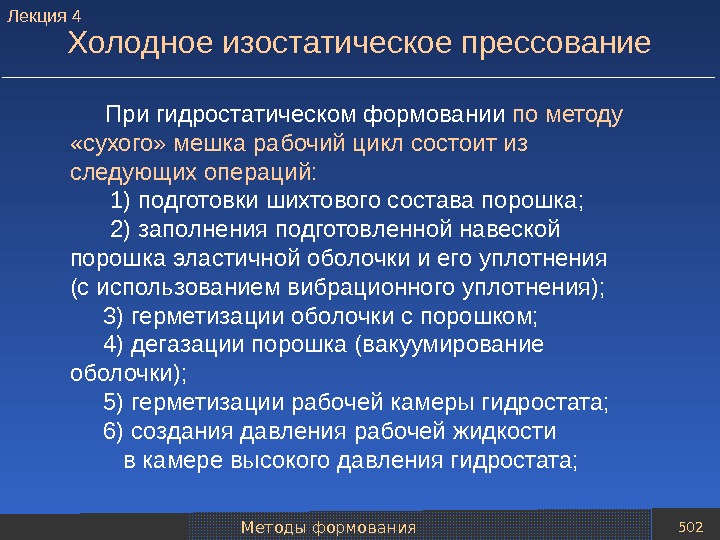
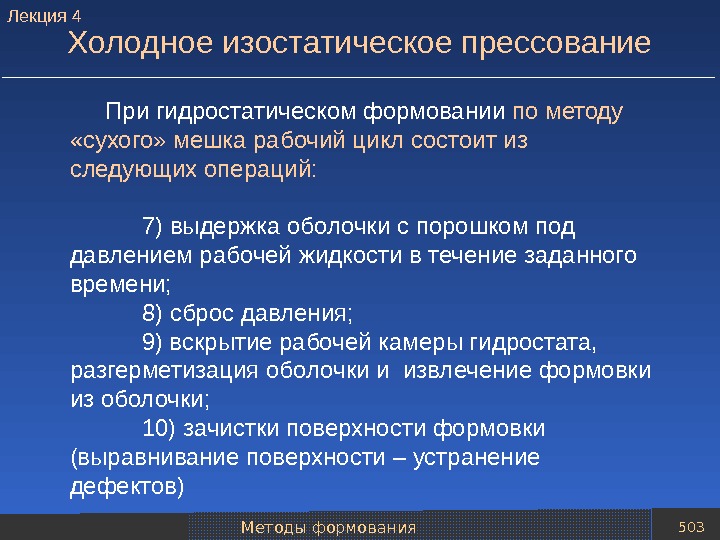
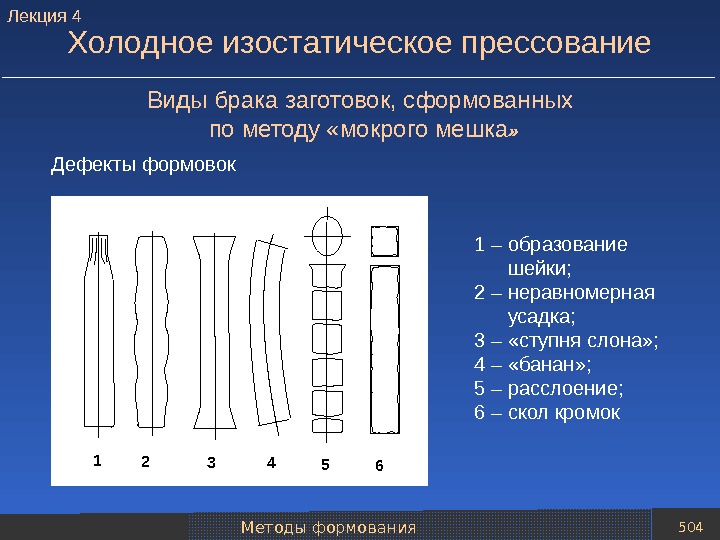
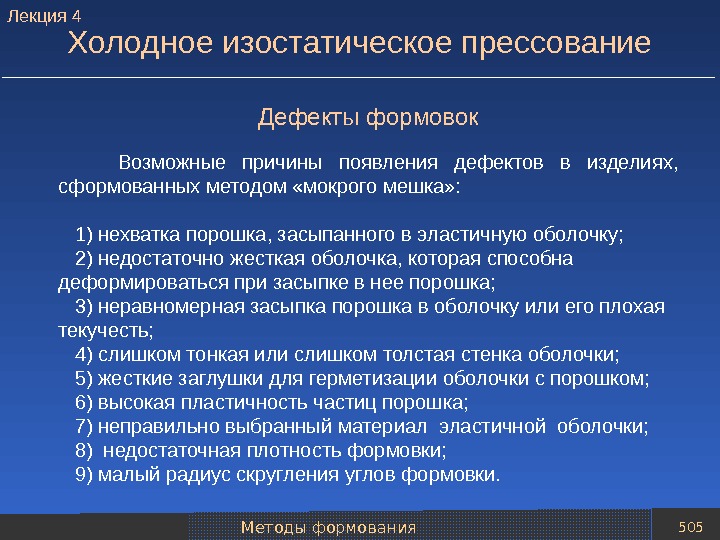
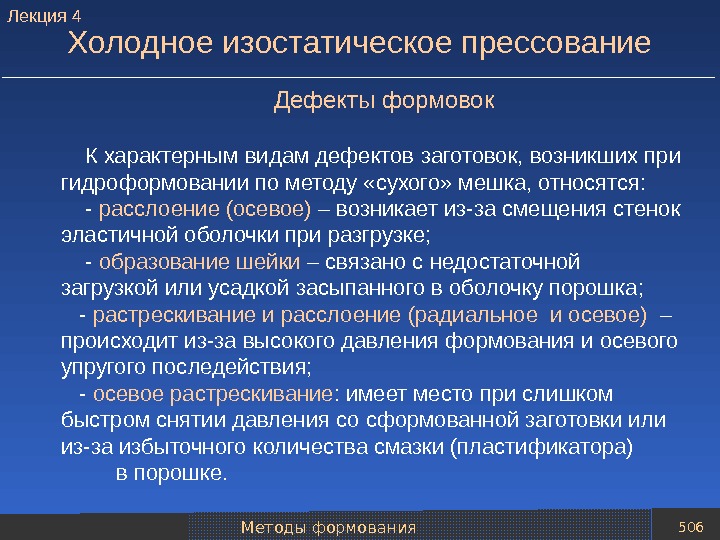
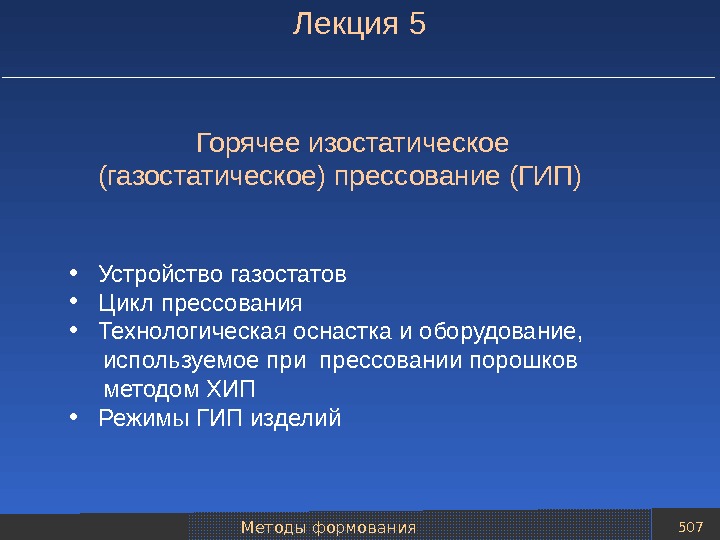
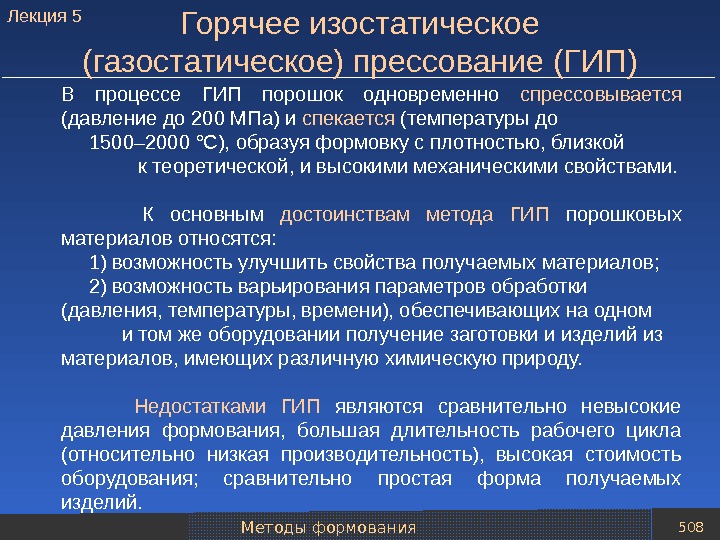
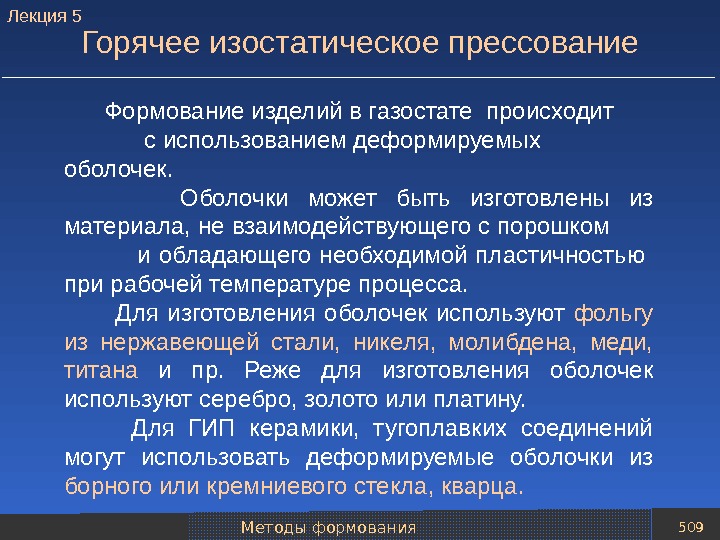
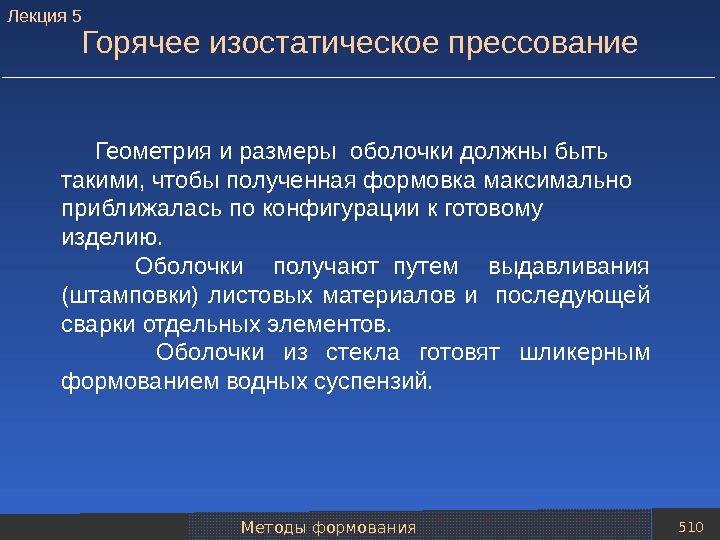
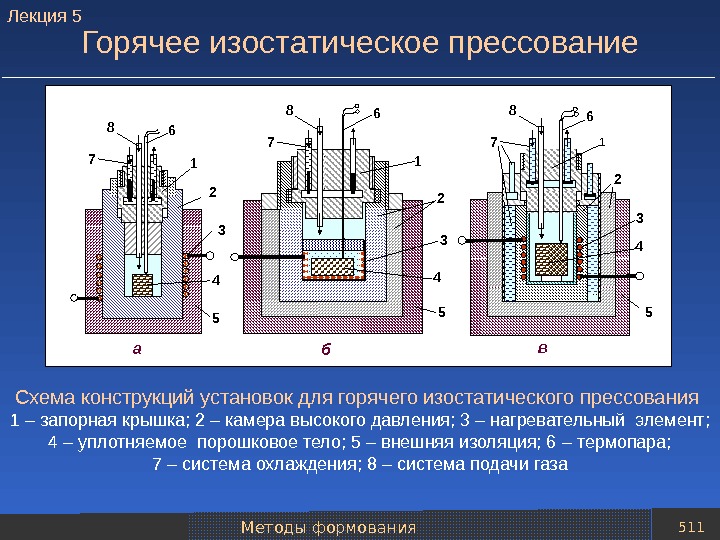
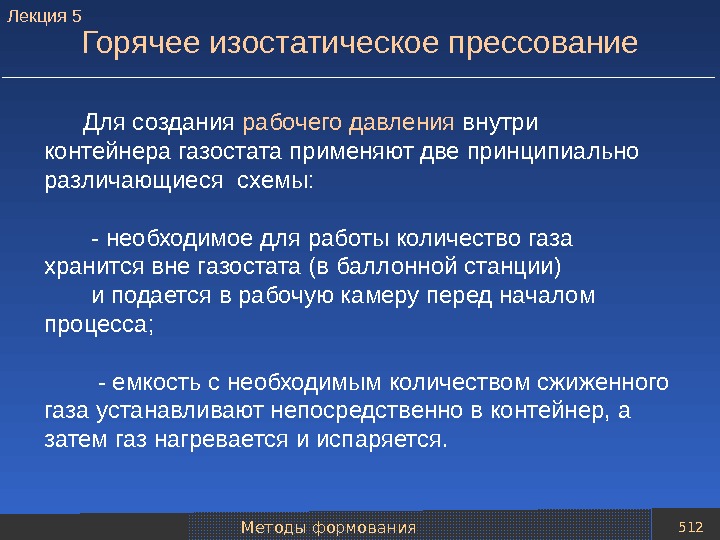




























































































































































































































































presentation_poroshk_met-giya_766_slaydov.ppt
- Размер: 8.4 Mегабайта
- Количество слайдов: 763
Описание презентации Презентация presentation Порошк мет-гия 766 слайдов по слайдам
Оглавление Часть 1. Получение порошков Часть 2. Формование и спекание порошков
Часть 1 Получение порошков
Оглавление • Введение. История развития порошковой металлург ии. Классификация методов получения порошков • Восстановители и защитные среды • Охрана труда и окружающей среды • Механические методы получения порошков • Физико-химические методы получения порошков • Получение порошков тугоплавких соединений • Методы получения порошкового металлического вол окна • Методы контроля свойств металлических и неметаллических порошков • Управление качеством продукции
Введение. История развития порошковой металлургии Классификация методов получения порошков
Введение. История развития порошковой металлургии 5 Лекция 1 Введение. История развития порошковой металлургии. Классификация методов получения порошков • История развития порошковой металлургии • Вклад русских ученых в развитие технологий порошковой металлургии • Перспективы развития отрасли • Классификация методов получения порошков • Размерность порошков
Введение. История развития порошковой металлургии 6 Введение в курс Еще в бронзовом веке люди умели получать и применять некоторые виды порошков, а также применять горячую ковку порошковой массы. Вплоть до XIX века изделия из железа не могли получать литьем, так как не было способов создания необходимых температур. Губчатое железо В распоряжении металлургов в основном были температуры 1000 – 1100 0 С, развивающиеся при горении древесины. Все решил кричный метод, в основе которого лежала переработка «болотной руды» и последующая ковка полученной губчатой заготовки в нагретом состоянии. Лекция
Введение. История развития порошковой металлургии 7 Введение в курс Для уменьшения пористости губку, состоящую из отдельных частиц, многократно нагревали в печи и проковывали. Исследования археологов показывают, что в 950 – 1000 гг. в Киевской Руси, Рязани и Новгороде из железной крины изготовляли различные предметы быта, оружие и др. Научные основы порошковой металлургии разработал в 1752 – 1763 гг. М. В. Ломоносов , который рассматривал процессы получения порошкового свинца, способы перевода различных материалов в порошкообразное состояние. Им было дано понятие спекания как операции перевода «порошкообразного тела , которому по желанию придана известная форма, в каменистое вещество» . Лекция
Введение. История развития порошковой металлургии 8 Введение в курс П. Г. Соболевский В 1827 г. на торжественном собрании Ученого комитета по горной и соляной части (г. С. -Петербург) 21 марта 1827 г. выступил П. Г. Соболевский (1782 – 1841 гг. ), сообщивший о создании им нового способа получения различных изделий из порошка платины. П. Г. Соболевским были продемонстрированы медали, жетоны, чаши, тигли, бруски массой до 2, 4 кг, различные украшения и пр. , полученные путем прессования предварительно сформованной и нагретой до “белого каления” заготовки из губчатой платины. Лекция
Введение. История развития порошковой металлургии 9 Введение в курс П. Г. C оболевский отмечает в своем докладе, что “от одного удара кружок платины вовсе изменяет вид свой; зернистое сложение его становится плотным и оный делается совершенно ковким. После обжатия кружки проковываются в полоски или прутки желаемого вида обыкновенным образом» . Платиновые монеты, отчеканенные в России в 1828 – 1845 гг. Лекция
Введение. История развития порошковой металлургии 10 Введение в курс По способу , разработанному П. Г. Соболевским , с 1828 г. налажена массовая чеканка платиновых монет достоинством 3, 6 и 12 руб. на серебро, продолжавшаяся до 1845 г. (всего за 18 лет было выпущено монет на сумму более четырех миллионов рублей), которая и стала первым промышленным применением порошковой металлургии. После смерти П. Г. Соболевского чеканка платиновых монет была прекращена. Возрождение порошковой металлургии в конце XIX–XX вв. было связано с необходимостью удовлетворения потребностей быстро развивавшейся электротехники. Лекция
Введение. История развития порошковой металлургии 11 Введение в курс Электроламповой промышленности требовались тугоплавкие материалы для нитей ламп накаливания, электромашиностроению были необходимы меднографитовые щетки и т. п. В 1900 г. наш соотечественник А. Н. Ладыгин на Всемирной Парижской выставке демонстрировал электрическую лампочку с телом накала из вольфрамовой проволоки, полученной методом порошковой металлургии. Лекция
Введение. История развития порошковой металлургии 12 Введение в курс Решение этих и других трудных технических задач послужило мощным толчком к налаживанию производства порошковых изделий: самосмазывающихся подшипников, твердых сплавов, магнитных, электроконтактных и конструкционных материалов, а также многих других видов продукции. В 1947 году двадцатью пятью странами создана Международная организация по стандартизации ( International Organization for Standardization – ISO ). Задачи, которые решают международные стандарты: • облегчение международного товарооборота; • расширение сотрудничества в области интеллектуальной, научной, технической и экономической деятельности. Лекция
Введение. История развития порошковой металлургии 13 Введение в курс В настоящее время насчитывается уже более 100 участников – стран мира этой организации. В составе ISO в 1966 году создан технический комитет 119, занимающийся стандартизацией в области порошковой металлургии (ИСО/ТК 119 «Порошковая металлургия» ). Россия входит в состав 13 активных членов технического комитета. В настоящее время в РФ действует ГОСТ 17359 -82 «Порошковая металлургия. Термины и определения» , разработанный на основе Международного стандарта ИСО 3252. Лекция
Классификация методов получения порошков 14 Определение Металлический порошок – совокупность частиц металла, сплава или металлоподобного соединения размерами до одного миллиметра, находящихся во взаимном контакте и не связанных между собой. Общепринятым является условное деление методов получения порошков на физико-химические и механические. Лекция
Классификация методов получения порошков 15 К физико-химическим методам относят технологические процессы производства порошков, связанные с глубокими физико-химическими превращениями исходного сырья. В результате получаемый порошок по химическому составу и структуре существенно отличается от исходного материала. Механические методы обеспечивают превращение исходного материала в порошок без существенного изменения его химического состава. Лекция
Классификация методов получения порошков 16 Методы промышленного производства металлических порошков Методы получения порошков Характеристика метода Получаемые порошки Механические методы получения порошков 1. Дробление и размол твердых материалов Измельчение стружки, обрезков и компактных материалов проводят в шаровых, вихревых, молотковых и других мельницах, КПД которых сравнительно невелик Железо, медь, марганец, латунь, бронза, хром, алюминий, стали 2. Диспергирова-ние расплава Струю расплавленного металла диспергируют механическим способом (воздействием центробежных сил и др. ) или действуя на нее потоком энергоносителя (газа или жидкости) Алюминий, свинец, цинк, бронза, латунь, железо, чугун, сталь. Лекция
Классификация методов получения порошков 17 Продолжение таблицы Методы получения порошков Характеристика метода Получаемые порошки Механические методы получения порошков 3. Обработка твердых (компактных) металлов резанием Получают крупные порошки. При станочной обработке литых металлов или сплавов подбирают такой режим резания, который обеспечивает образование частиц, а не стружки Сталь, латунь, бронза, магний. Лекция
Классификация методов получения порошков 18 Продолжение таблицы Методы получения порошков Характеристика метода Получаемые порошки Физико-химические методы получения порошков Химическое восстановление: 1. 1. Оксидов и других твердых соединений металлов Один из наиболее распространенных и экономичных способов. Восстановителями служат газы (водород, конвертированный природный газ и др. ), твердый углерод (кокс, сажа и др. ) и металлы (натрий, кальций и др. ). Исходным сырьем – окисленные руды, рудные концентраты, отходы и побочные продукты металлургического производства (например, прокатная окалина), а также различные химические соединения металлов Железо, медь, никель, кобальт, вольфрам, молибден, титан, тантал, цирконий, уран, сплавы, а также соединения с неметаллами (карбиды, бориды и др. )Лекция
Классификация методов получения порошков 19 Продолжение таблицы Методы получения порошков Характеристика метода Получаемые порошки Физико-химические методы получения порошков 1. 2. Различных соединений металлов из водных растворов Один из самых экономичных способов, позволяющий получать высококачественные металлические порошки. Восстановитель – водород или оксид углерода. Исходное сырье – сернокислые или аммиачные растворы солей соответствующих металлов Медь, никель, кобальт, серебро, золото 1. 3. Газообразных соединений различных металлов Газообразные соединения металлов восстанавливают водородом в реакторе кипящего слоя или в плазме Вольфрам, молибден, никель. Лекция
Классификация методов получения порошков 20 Продолжение таблицы Методы получения порошков Характеристика метода Получаемые порошки Физико-химические методы получения порошков 2. Электролиз водных растворов или расплавленных солей различных металлов На катоде под действием электрического тока осаждают из водных растворов или расплавов солей чистые порошки практически любых металлов Медь, никель, железо, серебро; тантал, титан, цирконий, железо 3. Диссоциация карбонилов Разлагают нагреванием соединение металла с СО типа Меа(СО) c. Применяют в промышленности для производства высококачественных дисперсных порошков Железо, никель, кобальт, вольфрам, молибден. Лекция
Классификация методов получения порошков 21 Продолжение таблицы Методы получения порошков Характеристика метода Получаемые порошки Физико-химические методы получения порошков 4. Термодиффузионное насыщение Чередующиеся слои или смесь порошков разнородных металлов нагревают до температуры, обеспечивающей их активное взаимодействие Латунь, сплавы на основе хрома, легированные стали 5. Испарение –конденсация Для получения порошка металл испаряют и затем конденсируют его пары на холодной поверхности Металлы с невысокой температурой испарения 6. Межкристаллитная коррозия В компактном (литом) металле или сплаве при помощи химического травителя разрушают межкристаллитные прослойки Коррозионно-стой кие и хромоникелевые стали. Лекция
Классификация методов получения порошков 22 В зависимости от размеров частиц порошки подразделяют на следующие группы: — нано — (размер частиц < 0, 01 мкм); — ультра — (размер частиц 0, 01– 0, 1 мкм); — высокодисперсные (размер частиц 0, 1– 10 мкм); — мелкие (размер частиц 10– 40 мкм); — средние (размер частиц 40– 250 мкм); — крупные (размер частиц 250– 1000 мкм). К механическим методам получения порошков относится и грануляция расплава (образование крупных частиц порошка происходит при сливании расплавленного металла в жидкость). Лекция
Классификация методов получения порошков 23 1. Либенсон, Г. А. Процессы порошковой металлургии : в 2 ч. : учеб. для вузов / Г. А. Либенсон, В. Ю. Лопатин, Г. В. Комарницкий. – М. : МИСИС, 2001. 2. Федорченко, И. М. Порошковая металлургия. Материалы, технологии, свойства, области применения: справочник / И. Францевич, И. Д. Родомысльский и др. – Киев : Наукова думка, 1985. – 624 с. 3. Фомина, О. Н. Порошковая металлургия. Энциклопедия международных стандартов / С. Н. Суворова, Я. М. Турецкий – М. : ИПК Изд-во стандартов, 1999. – 305 с. Список рекомендуемой литературы. Лекция
Восстановители и защитные среды Красноярск,
Оглавление Лекция 2. Восстановители и защитные среды Лекция 3. Восстановители и защитные среды Красноярск,
Восстановители и защитные среды 26 Лекция 2 Восстановители и защитные среды • Классификация восстановителей и защитных сред • Характеристики твердых и газообразных восстановителей (защитных сред) • Методы получения газообразных сред • Газообразные среды сложного состава
Восстановители и защитные среды 27 Классификация восстановителей и защитных сред Защитные среды подразделяются на: — газовые; — сыпучие; — комбинированные (состоящие из твердых засыпок и защитного газа): — вакуум. Жидкие защитные среды – расплавы солей металлов шлаков, стекол, легкоплавких окислов. Твердые защитные засыпки состоят из порошков химически активных металлов (их соединений) и напонлителя (прокаленного глинозема с добавкой углерода в виде сажи, древесного угля). Лекция
Восстановители и защитные среды 28 Классификация восстановителей и защитных сред По составу газовые защитные среды разделяются на системы: 1. Н 2 – Н 2 О; 2. H 2 —Н 2 О— N 2 ; 3. СО—СО 2 — N 2 ; 4. СО—СО 2 — H 2 О— N ; 5. СО—СО 2 —Н 2 О—СН 4 — N 2 ; 6. Азот, инертные газы (аргон, гелий), вакуум. Лекция
Восстановители и защитные среды 29 Характеристики твердых и газообразных восстановителей (защитных сред) Условие равновесия, при котором соотношение металла и его оксидов с течением времени остается неизменным, характеризуется константами равновесия: К 1 = РН 2 /РН 2 О ; К 2 = РСО /РСО 2. Лекция
Восстановители и защитные среды 30 Характеристики твердых и газообразных восстановителей (защитных сред). По условиям взаимодействия с восстановительными газами Н 2 , СО, Н 2 +СО металлы можно разделить на группы : 1. Медь, никель, кобальт, молибден, вольфрам и железо. Восстановление оксидов х возможно при использовании любой из газовых сред. 2. Хром, марганец, кремний и ванадий. Восстановление оксидов возможно только водородом. 3. Алюминий, бериллий, титан, цирконий. Восстановление оксидов возможно только остро осушенным водородом в присутствии геттеров. Лекция
Восстановители и защитные среды 31 Способы получения восстановителей 1 8 7 4 54 3 2 К газгольдеру 6 1 – колонна–генератор водорода; 2 – подогреватель пара; 3 – теплообменник; 4 – клапаны подачи первичного водяного пара; 5 – отделение генерации водорода, заполненное железосодержащим порошковым материалом; 6 – скруббер; 7 – клапан регулировки давления подогретого пара; 8 – насос. Схема установки для производства водорода железоконтактным методом. Лекция
Восстановители и защитные среды 32 Способы получения газовых сред сложного состава Тип среды Исходное соединение Способ получения среды Н 2 –Н 2 О– N 2 Диссоциированный аммиак Разложение в диссоциаторе Частичное сжигание при вз = 0, 7– 0, 9 и сушка силикагелем или цеолитом СО–СО 2 Генераторный газ, полученный из древесного угля при температуре 1000 °С и осушенный силикагелем или цеолитом СО–СО 2 –Н 2 О– N 2 Эндотермический газ Экзотермический газ Доменный газ Конвертированный природный газ Неполное сжигание ( вз = 0, 25 – 0, 30) природного газа или пропана Неполное сжигание ( вз = 0, 6) углеводородов, охлаждение, очистка от СО 2 , сушка силикагелем или цеолитом Очистка от СО 2 , сушка силикагелем или цеолитом Высокотемпературная парогазовая конверсия (1100 °С при СН 4 : Н 2 О=1: 1) СО–СО 2 –Н 2 О–СН 4 – N 2 Науглероживающий газ Неполное сжигание ( вз = 0, 4) углеводородов с последующей добавкой природного газа. Лекция
Восстановители и защитные среды 33 Схема рабочей зоны установки выработки конвертированного природного газа 1 – тепловая изоляция рабочей зоны печи; 2 – реактор; 3 – шамотный муфель-сердечник с никелевым катализатором; 4 – топочные зазоры для нагрева реактора; 5 – перфорированная труба для подачи парогазовой смеси в муфель; 6 – труба для транспортировки восстановителя 3 1 5 6 2 Парогазовая смесь 4 Лекция
Восстановители и защитные среды 34 Схема установки для получения эндогаза (установка ЭН-60) 1 – камера сероочистки; 2 – манометр; 3 – холодильник; 4 – ротаметр; 5 – регулятор давления; 6 – смесительный клапан; 7 – газогенератор; 8 – катализатор; 9 – холодильник; 10 – газодувка; 11 – заслонка; 12 – гидрозатвор; 13 – клапаны; 14 – нагревательный элемент Реакции горения газа : первая стадия СН 4 + 2 О 2 = СО 2 + 2 Н 2 О + Q , вторая стадия СН 4 + СО 2 = 2 СО + 2 Н 2 – Q СН 4 + Н 2 О = СО + Н 2 – Q 1 2 43 5 1 6 7 8 1110 9 К печи 1213 1414 Лекция
Восстановители и защитные среды 35 Лекция 3 Восстановители и защитные среды • Классификация жидких защитных сред и восстановителей • Сыпучие защитные среды • Применение на практике жидких и сыпучих защитных сред • Печи для получения порошков и спекания изделий • Методы очистки и осушки газовых сред
Восстановители и защитные среды 36 Конструкция контейнеров с плавким затвором а – контейнер с верхним затвором без карманов, б – контейнер с верхним затвором карманного типа: 1 – гранулы материала плавкого затвора; 2 – контейнер; 3 – обрабатываемые детали; 4 – карман; 5 – песок; 6 – верхняя крышка контейнера; 7 – асбестовая прокладка; 8 – засыпка 1 23 45 ба 8 8 7 6 Лекция
Восстановители и защитные среды 37 Очистка газа от кислорода, СО 2 , HCN и других примесей с помощью этаноламина: CO 2 + 2 RNH 2 + H 2 O (RNH 3 ) 2 CO 3 , CO 2 + (RNH 3 )2 CO 2 + H 2 O 2 RNH 3 HCO 3 , где R – группа ОН–СН 2. Для тонкой очистки защитных газовых сред используют химические, адсорбционные, диффузионные, ректификационные и каталитические методы. Очистка и осушка защитных газовых сред. Лекция
Восстановители и защитные среды 38 Химические методы: — очистка газов с помощью гидрата оксида железа; — силикагеля, алюмогеля; — геттеров (металлической меди, кальция). Адсорбционные методы основаны на способности твердых поверхностей (активные угли, активный оксид алюминия, силикагели, кристаллические алюмосиликаты (цеолиты)) сорбировать газы. Ректификация основана на различии состава пара над жидкостью в равновесном состоянии и состава жидкой фазы. Диффузионные методы очистки основаны на проницаемости металлических пористых перегородок для атомных газов и непроницаемости для молекулярных газов. Очистка и осушка защитных газовых сред. Лекция
Восстановители и защитные среды 39 1. Федорченко, И. М. Порошковая металлургия. Материалы, технологии, свойства, области применения : справ. / И. И. Францевич, И. Д. Родомысльский и др. – Киев : Наукова думка, 1985. – 624 с. 2. Кипарисов, С. Оборудование предприятий порошковой металлургии / О. В. Падалко. – М. : Металлургия, 1988. – 448 с. Список рекомендуемой литературы. Лекция
Охрана труда и окружающей среды Красноярск,
Охрана труда и окружающей среды 41 Лекция 4 Охрана труда и окружающей среды в порошковой металлургии • Основные операции технологического цикла порошковой металлургии • Виды воздействия на персонал производств порошковой металлургии. Факторы воздействия и их проявление • Пожаро- и взрывоопасность порошков • Мероприятия по охране труда и защите персонала производств порошковой металлургии от вредных и опасных воздействий
Охрана труда и окружающей среды 421. 1. Размол исходных материалов и полученной губки в производстве порошков методом восстановления. 2. 2. Распыление расплавленных металлов в порошок; смешивание и рассев металлических и неметаллических порошков. 3. 3. Электролиз растворов при получении порошков методом электролиза и при нанесении гальванических покрытий. 4. 4. Формование изделий методами прессования, прокатки и другими. 5. 5. Спекание изделий в газовых защитных средах. 6. 6. Термическая и механическая обработка изделий (резанием, шлифованием, калиброванием). 7. 7. Пропитка пористых изделий. Основные операции технологий порошковой металлургии Лекция
Охрана труда и окружающей среды 43 Производство изделий методами порошковой металлургии по степени вредности и безопасности относится к категории В. Для обеспечения безопасной работы в производствах порошковой металлургии применяются меры по охране труда и технике безопасности, существующие в металлургическом и химическом производстве, в гальванических и механических цехах, а также правила, специально разработанные для технологических процессов порошковой металлургии. Основные операции технологий порошковой металлургии Лекция
Охрана труда и окружающей среды 44 Содержание пыли на рабочих местах при изготовлении изделий методами порошковой металлургии, мг/м 3 Виды воздействия на персонал Операции Изделия на основе железа Изделия на основе меди Просев порошка железа 10, 2 – Просев порошка графита Загрузка вибросита вручную и просев материала (без укрытия) 15, 8 166, 6 Просев бронзографитовой смеси в укрытии – 11, 3 Прессование железографитовых изделий на полуавтоматических прессах То же на гидравлических прессах 0, 32 2, 7 – – Ручная дозировка железографитовой смеси 19, 5 – Загрузка бункера полуавтоматического пресса – 58, 9 Прессование изделий: — на полуавтомате — вручную – – 69, 5 86, 3 Шлифовка изделий: — влажная — сухая – – 16, 6 584, 6 Лекция
Охрана труда и окружающей среды 45 Значения предельно допустимых концентраций. Виды воздействия на персонал Вещество ПДК, мг/м 3 Медь 0, 5 Дисульфид молибдена 10, 0 Оксид меди 0, 1 Аммиак 0, 02 Медь с добавками графита до 30 %, олова до 10 %, никеля до 30 % 0, 5 Бензин 0, 3 Марганец (в пересчете на М n 0 4 ) 0, 3 Оксид углерода 0, 02 Железо восстановленное с содержанием до 3 % графита 6, 0 Серная кислота 0, 001 Оксид железа 6, 0 Спирт этиловый 1, 0 Свинец 0, 01 Цианистый водород и соли синильной кислоты (в пересчете на НС N ) 0, 0003 Оксид алюминия 2, 0 Аммиак 0, 02 Карбид бора 2, 0 Бензол 0, 05 Карбид кремния 5, 0 Оксид азота (в пересчете на N 2 O 5 ) 0, 05 Нитрид бора 6, 0 Сернистый газ 0, 02— 0, 04 Сероводород 0, 01 Лекция
Охрана труда и окружающей среды 46 Пожароопасность и взрывоопасность процессов порошковой металлургии обусловлена применением тонкодисперсных порошков, легковоспламеняющихся и хорошо горящих основных и вспомогательных материалов (водород, диссоциированный аммиак, конвертированный природный газ). Пирофорность порошков (способность при определенных условиях воспламеняться под действием внутренних экзотермических процессов) и их взрываемость зависят от природы порошка, его дисперсности, химического состава формы частиц и пр. Пожаро- и взрывоопасность. Лекция
Охрана труда и окружающей среды 47 Воспламеняемость и взрываемость металлических порошков зависит от: 1) содержания наиболее активной примеси; 2) степени окисленности; 3) размера частиц; 4) удельной поверхности частиц. Пожаро- и взрывоопасность. Лекция
Охрана труда и окружающей среды 48 Пожаро- и взрывоопасность Показатели пирофорности и взрываемости металлических порошков Материал D ч , мкм Порошок в слое Взвешенная в воздухе пыль Т св, °С Т в, °С НКПВ, г/м 3 Железо восстановленное <50 475 350 300 66 Кремний <74 790 …. 770 100 Ферромарганец <74 240 …. 450 130 Олово <53 430 …. 630 190 Свинец <53 270 …. 710 …. Медь <44 …. …. 700 …. Лекция
Охрана труда и окружающей среды 49 Мероприятия по охране труда Наличие специфических факторов опасного воздействия на организм человека требует проведения в производстве мероприятий санитарно-технического и технологического порядка, предупреждающих выделение пыли, газов и испарений и доведение их концентрации до допустимых норм: — использование менее токсичных материалов; — герметичной аппаратуры; — применение эффективных систем пылеулавливания; — замена сухих способов производства мокрыми; — применение средств индивидуальной защиты работающих (масок, респираторов, перчаток, одежды). Радикальным решением проблемы обеспечения безопасности труда является автоматизация операций, представляющих опасность для здоровья рабочего. Лекция
Охрана труда и окружающей среды 50 1. Федорченко, И. М. Порошковая металлургия. Материалы, технологии, свойства, области применения : справ. / И. Францевич, И. Д. Родомысльский и др. – Киев : Наукова думка, 1985. – 624 с. Список рекомендуемой литературы. Лекция
Механические методы получения порошков Красноярск,
Механические методы получения порошков 52 Оглавление Лекция 5. Механические методы получения порошков Лекция 6. Измельчение материалов в шаровых мельниц ах Лекция 7. Получение механолигированных порошков Лекция 8. Получение порошков металлов и неметаллов ультразвуковым измельчением в жидких средах Лекция 9. Диспергирование расплавов
Механические методы получения порошков 53 Лекция 5 Механические методы получения порошков • Закономерности процессов разрушения твердых материалов • Методы предварительного измельчения крупных кусковых материалов • Измельчение материалов в молотковых мельницах • Получение порошков методом резания
Механические методы получения порошков 54 Измельчение материалов в молотковых мельницах 1 3 4 2 5 6 7 8 9 1 – электродвигатель; 2 – муфта; 3 – губка; 4 – загрузочный бункер; 5 – загрузочный люк с защелкой; 6 – корпус мельницы; 7 – била; 8 – металлическая решетка с ситовым полотном; 9 – порошок. Молотковая мельница. Лекция
Механические методы получения порошков 55 Получение порошков резанием 1 2 3 4 5 1 – барабан кратцмашины; 2 – царапающая лента; 3 – слиток металла; 4 – держатель слитка металла; 5 – металлический порошок. Схема установки для получения порошка магния с использованием кратцмашины. Лекция
Механические методы получения порошков 56 1. Либенсон, Г. А. Процессы порошковой металлургии : в 2 ч. : учеб. для вузов / Г. А. Либенсон, В. Ю. Лопатин, Г. В. Комарницкий. – М. : МИСИС, 2001, 2. Кипарисов, С. Оборудование предприятий порошковой металлургии / С. С. Кипарисов, О. В. Падалко. – М. : Металлургия, 1988. – 448 с. 3. Агранат, Б. А. Ультразвук в порошковой металлургии / Б. А. Агранат, А. П. Гудович. – М. : Металлургия, 1986. – 186 с. Список рекомендуемой литературы. Лекция
Механические методы получения порошков 57 Лекция 6 Измельчение материалов в шаровых мельницах • Устройство и основные элементы шаровых мельниц. Классификация мельниц • Режимы измельчения материалов • Понятие «критической скорости» вращения барабана мельницы • Факторы, определяющие степень измельчения • Режимы измельчения • Управление процессом измельчения
Механические методы получения порошков 58 Классификация шаровых мельниц Соотношение между дробящим и истирающим действием размольных тел определяется отношением диаметра барабана ( D ) к его длине ( L ). В мельницах одинакового объема при D : L > 3 преобладает дробящее действие размольных тел, при D : L 3 – истирающее. В практике порошковой металлургии используют шаровые мельницы: — с периодической загрузкой и разгрузкой; — с центральной разгрузкой измельченного материала; — с торцевой разгрузкой через диафрагму; — с периферической разгрузкой через щели в барабане и окружающее его цилиндрическое сито. Лекция
Механические методы получения порошков 59 Классификация шаровых мельниц а б в г д а , в – мельницы с центральной загрузкой барабана через цапфу; б – мельница с торцевой загрузкой (цилиндроконическая мельница); г – мельница с периферической загрузкой и выгрузкой материала через сита Схемы шаровых мельниц. Лекция
Механические методы получения порошков 60 Решающее влияние на интенсивность и механизм размола оказывают: — скорость вращения барабана мельницы; — число и размер размольных тел; — масса измельчаемого материала: — продолжительность размола; — среда размола. Критическая скорость вращения барабана. Лекция
Механические методы получения порошков 61 Скорость, при которой наблюдаются размольные тела под действием центробежных сил будут вращаться вместе с барабаном. Подобный режим работы называют критической скоростью вращения ( n кр ). n кр = 42, 4/ D , где D – диаметр барабана мельницы, м. При измельчении материалов применяют два основных режима работы шаровых мельниц: — режим интенсивного измельчения, при котором на материал действуют в основном раздавливающие и ударные усилия; — режим перекатывания, при котором на материал действуют истирающие и раздавливающие усилия. Критическая скорость вращения барабана. Лекция
Механические методы получения порошков 62 Факторы определяющие степень измельчения а – режим скольжения при n ≤ 0, 2 n кр ; б – режим перекатывания при n ≤ 0, 4– 06 n кр ; в – режим интенсивного измельчения (водопадный режим) при n ≤ 0, 75– 0, 85 n кр ; г – движение шаров при n ≥ n кра б в г. Схема движения шаров в барабане шаровой мельницы при различной скорости его вращения Лекция
Механические методы получения порошков 63 1. Либенсон, Г. А. Процессы порошковой металлургии : в 2 ч. : учеб. для вузов / Г. А. Либенсон, В. Ю. Лопатин, Г. В. Комарницкий. – М. : МИСИС, 2001. 2. Кипарисов, С. С. Оборудование предприятий порошковой металлургии – М. : Металлургия, 1988. – 448 с. 3. Новые процессы и материалы порошковой металлургии / ред. Л. Х. Явербаума ; пер. с англ. – М. : Металлургия, 1983. – 360 с. 4. Андриевский, Р. А. Введение в порошковую металлургию : учеб. пособие для вузов / Р. А. Андриевский. – Фрунзе : Илим, 1988. – 174 с. Список рекомендуемой литературы. Лекция
Механические методы получения порошков 64 Лекция 7 Получение механолигированных порошков • Технология получения механолигированных порошков • Измельчение материалов в аттриторах • Измельчение материалов в вибрационных и вихревых мельницах • Измельчение материалов в планетарных центробежных и гироскопических мельницах
Механические методы получения порошков 65 Измельчение материалов в аттриторах Схема аттритора 1 – корпус мельницы (размольная емкость); 2 – водоохлаждаемые стенки корпуса мельницы; 3 – вал мешалки аттритора; 4 – измельчаемый материал; 5 – размольные тела; 6 – лопасти мешалки 2 3 14 65 Вода. Лекция
Механические методы получения порошков 66 Измельчение материалов в вибромельницах 1 3 4 2 5 1 6 7 1 – электродвигатель; 2 – соединительная муфта; 3 – корпус мельницы; 4 – загрузочный люк; 5 – размольные тела; 6 – дебалансный вал; 7 – амортизаторы (пружины) Схема вибрационной мельницы. Лекция
Механические методы получения порошков 67 Измельчение материалов в планетарных мельницах 1 3 2 14 5 Схема планетарной центробежной мельницы 1 – редуктор; 2 – опорный стол; 3 – корпус-шкив с механизмом привода барабанов; 4 – барабан с размольными телами; обоймы для установки барабанов. Лекция
Механические методы получения порошков 68 Измельчение материалов в вихревых мельницах 1 – рабочая камера мельницы; 2 – бункер для загрузки измельчаемого материала; 3 – приемная камера; 4 – пропеллеры; 5 – отсадочная камера; 6 – насос для подачи газа в рабочую камеру: 7 – порошок; 8 – емкость для выгрузки порошка из отсадочной камеры2 3 46 5 7 8 1 Схема вихревой мельницы. Лекция
Механические методы получения порошков 69 1. Либенсон, Г. А. Процессы порошковой металлургии : в 2 ч. : учеб. для вузов / Г. А. Либенсон, В. Ю. Лопатин, Г. В. Комарницкий. – М. : МИСИС, 2001. 2. Кипарисов, С. С. Оборудование предприятий порошковой металлургии / С. С. Кипарисов. – М. : Металлургия, 1988. – 448 с. 3. Якименко, В. Б. Железные порошки. Технология, состав, структура, свойства, экономика / В. Б. Якименко, В. Я. Буланов, В. В. Рукин и др. – М. : Наука, 1982. – 264 с. Список рекомендуемой литературы. Лекция
Механические методы получения порошков 70 Лекция 8 Получение порошков металлов и неметаллов ультразвуковым измельчением в жидких средах • Ультразвук и его взаимодействие с жидкостями • Условия кавитирования газовых пузырьков. Режимы ультразвукового диспергирования • Механизмы разрушения материалов под действием кавитационных процессов • Факторы, определяющие эффективность процесса измельчения материалов ультразвуком • Аппаратурное оформление процесса • Измельчение материалов в аппаратах магнитного индукционного вращателя
Механические методы получения порошков 71 Ультразвук и его взаимодействие с жидкостями Ультразвук представляет собой упругие колебания и волны, частота которых лежит в пределах от 10 до нескольких десятков ГГц (низкочастотные колебания – 15– 100 к. Гц, средних частот – 100 к. Гц – 10 МГц, высокочастотные – 10 МГц – 1 ГГц; свыше 1 ГГц – гиперзвук). Лекция
Механические методы получения порошков 72 Ультразвук и его взаимодействие с жидкостями Кавитационные процессы наступают лишь для тех пузырьков, начальный радиус которых R 0 больше некоторого критического радиуса R кр , но меньше резонансного R рез R рез > R 0 > R кр. При R 0 < R кр пузырьки не участвуют в кавитации (при данной частоте колебаний). При R 0 R рез пузырьки вытесняются на поверхность жидкости. Значение R кр определяют из выражения R кр = 1, 33 / (0, 7 P a + P p – P o ), где – коэффициент поверхностного натяжения жидкости; P a – звуковое давление; P p – упругость пара жидкости; P o – статическое давление в объеме жидкости. Лекция
Механические методы получения порошков 73 Аппаратурное оформление процесса Схемы ультразвуковых установок а – установка с рабочей ванной конической формы: 1 – излучатель магнитострикционного преобразователя; 2 – корпус ванны; 3 – суспензия порошка; 4 – патрубки для подачи и удаления охлаждающей жидкости; 5 – патрубок для подачи газа; 6 – манометр; 7 – вентиль для подачи суспензии; 8 – патрубок для удаления суспензии измельченного порошка 10 20 30 5 4050 60 0 1 6 3 824 7 5 газ а. Лекция
Механические методы получения порошков 74 Аппаратурное оформление процесса Схемы ультразвуковых установок б – установка с ванной цилиндрической формы: 1 – излучатель магнитострикционного преобразователя; 2 – сменный стакан; 3 – суспензия порошка; 4 – душирующее устройство; 5 – съемная крышка; 6 – патрубки для подачи и удаления охлаждающей жидкости; 7 – патрубок для подачи газа 36 1 4 25 7 б. Лекция
Механические методы получения порошков 75 1. Либенсон, Г. А. Процессы порошковой металлургии. В 2 ч. : учеб. для вузов / Г. А. Либенсон, В. Ю. Лопатин, Г. В. Комарницкий. – М. : МИСИС, 2001. 2. Роман, О. В. Справочник по порошковой металлургии: порошки, материалы, процессы / О. В. Роман, И. П. Габриэлов. – Минск : Беларусь, 1988. – 175 с. 3. Агранат, Б. А. Ультразвук в порошковой металлургии / Б. А. Агранат, А. П. Гудович. – М. : Металлургия, 1986. – 186 с. Список рекомендуемой литературы. Лекция
Механические методы получения порошков 76 Лекция 9 Диспергирование расплавов • Физико-химические и механические процессы при диспергировании расплавов • Факторы, определяющие процесс измельчения расплавов энергоносителями • Типовые технологические схемы распыления расплавов • Классификация методов диспергирования расплавов
Механические методы получения порошков 77 Процессы при диспергировании расплавов Распад струи жидкости под действием газового потока можно описать с помощью следующей критериальной функции: d / D = f ( W е , L р , M , N ), где d – средний диаметр частиц-капель; D – диаметр струи расплава; W е – критерий Вебера (характеризует соотношение сил инерции и поверхностного натяжения); L р – критерий Лапласа; M и N – критерии, характеризующие соотношение плотности и вязкости газа-энергоносителя и расплава. Лекция
Механические методы получения порошков 78 Процессы при диспергировании расплавов W е = V 2 г г D 0 / ; L р = 2 ж / ( ж D 0 ); M = V 2 г г / ( ж V 2 ж ) ; N = г / ж , где V г и V ж – скорости газового потока и расплава; г и ж – плотности газа и расплава; г и ж – вязкости газа и расплава; – поверхностная энергия ; D 0 – диаметр первоначальной пряди расплава. Размер образующихся частиц порошка можно оценить эмпирической формулой: d = (585/Δ V )( ж / ж ) 0, 5 + 597 ( ж / ж ж ) 0, 45 (1000 G ж / G г ), где ж , G ж – соответственно поверхностная энергия, плотность, вязкость и удельный расход расплава; G г – удельный расход газа-энергоносителя; Δ V – относительная скорость газового потока. Лекция
Механические методы получения порошков 79 Технологические схемы распыления расплавов Методы распыления металлического расплава различаются: 1) по виду энергии, затрачиваемой на его создание, 2) виду силового воздействия на расплав при диспергировании, 3) по типу среды используемой при создании и диспергировании расплава. Типовая технологическая схема распыления расплавов газом (аргоном, азотом, воздухом) или жидкостью (чаще всего водой) включает следующие основные операции: — подготовки расплава; — транспортировки расплава к установке распыления и диспергирования расплава; — классификации частиц полученного порошка; — усреднения состава нескольких партий порошка; — упаковки порошка. Лекция
Механические методы получения порошков 80 Типовые технологические схемы распыления расплавов Типовая технологическая схема распыления расплава воздухом в воду 1 – печь; 2 – емкость для расплава металла; 3 – установка распыления; 4 – насос для перекачки пульпы порошка; 5 – гидроциклон; 6 – фильтр; 7 – вращающаяся сушильная печь; 8 – бункер для хранения высушенного порошка; 9 – двойной конусообразный смеситель; 10 – печь для восстановления порошка (печь с шагающим подом); 11 – молотковая мельница; 12 – классификатор; 13 – смеситель (для усреднения порошка); 14 – бункеры для хранения порошка перед упаковкой 1 2 4 5 6 7 83 9 10 11 12 14 13 Лекция
Механические методы получения порошков 81 Типовые технологические схемы распыления расплавов Типовая технологическая схема распыления расплава водой в воду 1 – печь; 2 – емкость для расплава металла; 3 – установка распыления; 4 – насос; 5 – гидроциклон; 6 – сушильная печь; 7 – мельница; 8, 13 – классификатор; 9, 12 – магнитный сепаратор; 10 – печь для восстановления порошка (конвейерная); 11 – молотковая мельница; 14 – бункеры для хранения порошка; 15 – весы; 16 – смеситель; 17 – бункер для хранения порошка перед упаковкой 1 2 4 5 6 7 83 9 10 11 12 13 14 16 17 15 Лекция
Механические методы получения порошков 82 Классификация методов диспергирования расплавов Все методы диспергирования расплавов условно можно разделить на несколько групп: — методы центробежного распыления; — методы ультразвукового распыления; — методы распыления потоками энергоносителей; — бесконтактные методы распыления; — высокоскоростные методы распыления. Лекция
Механические методы получения порошков 83 1. Либенсон, Г. А. , Процессы порошковой металлургии : учеб. для вузов : в 2 ч. / Г. А. Либенсон, В. Ю. Лопатин, Г. В. Комарницкий. – М. : МИСИС, 2001. 2. Силаев А. Ф. Диспергирование жидких металлов и сплавов / А. Ф. Силаев, Б. Д Фишман. – М. : Металлургия, 1983. – 144 с. Список рекомендуемой литературы. Лекция
Физико-химические методы получения порошков Красноярск,
Физико-химические методы получения порошков 85 Оглавление Лекция 10. Методы диспергирования расплавов Лекция 11. Восстановление химических соединений ме таллов Лекция 12. Получение порошков железа восстановлени ем химических соединений Лекция 13. Получение порошков вольфрама восстановлением оксидов водородом и углеродом Лекция 14. Получение порошков молибдена, титана и циркония восстановлением химических соедине ний Лекция 15. Получение порошков тантала, ниобия, меди, кобальта, никеля и легированных сплавов
Физико-химические методы получения порошков 86 Оглавление Лекция 16. Восстановление химических соединений мета ллов из растворов солей и газообразных соединений ме таллов Лекция 17. Общие закономерности процессов производс тва порошков электролизом Лекция 18. Получение порошков электролизом водных р астворов Лекция 19. Получение порошков электролизом расплавл енных сред Лекция 20. Получение порошков металлов методом терм ической диссоциации карбонилов Лекция 21. Получение порошков методом межкристалли тной коррозии, испарения-конденсации, термодиффузн ого насыщения
Физико-химические методы получения порошков 87 Лекция 10 Методы диспергирования расплавов • Центробежное распыление расплавов • Ультразвуковое распыление расплавов • Диспергирование расплавов потоками энергоносителей • Бесконтактные методы распыления расплавов • Высокоскоростные методы затвердения расплавов
Физико-химические методы получения порошков 88 Центробежное распыление расплавов Схемы установок для центробежного распыления расплавов металлов а – способ вращающегося электрода: 1 – противоэлектрод; 2 – быстровращающийся электрод; 3 – пленка расплавленного металла б – способ вращающегося диска: 1 – водоохлаждаемый диск; 2 – пленка металла; 3 – тигель с расплавом металла. А К Вода. Капли-частицы3 2 13 1 2 а б. Лекция
Физико-химические методы получения порошков 89 Ультразвуковое диспергирование расплавов Схемы ультразвукового диспергирования расплавов металлов а – установка с вынесенным излучателем: 1 – система подачи газа; 2 – печь; 3 – графитовый стакан; 4 – расплав металла; 5 – твердосплавное сопло; 6 – излучатель ультразвуковых колебаний; 7 – нагревательное излучателя; 8 – камера распыления газ 1 2 3 645 78 Газ а. Лекция
Физико-химические методы получения порошков 90 Ультразвуковое диспергирование расплавов Схемы ультразвукового диспергирования расплавов металлов б – установка с излучателем, проходящим через емкость с расплавом: 1 – концентратор колебаний; 2 – нагревательное устройство; 3 – контейнер с расплавом; 4 – излучатель Газ Расплав металла Вода 1 3 2 4 б. Лекция
Физико-химические методы получения порошков 91 Диспергирование расплавов энергоносителями Схема с вертикальным расположением форсуночного устройства: 1 – металлоприемник; 2 – струя расплава; 3 – форсуночное устройство; 4 – кольцевое сопло Лаваля Газ 4 2 31 Лекция 10 Схемы распыления расплава воздействием струи газа
Физико-химические методы получения порошков 92 Диспергирование расплавов энергоносителями Схема многоструйного форсуночного элемента трубчатого типа: 1 – металлоприемник; 2 – трубопроводы; 3 – отверстия для выхода газа; 4 – струя расплава; 5 – струи газа Газ 3 42 1 2 5 Лекция 10 Схемы распыления расплава воздействием струи газа
Физико-химические методы получения порошков 93 Бесконтактные методы диспергирования Схемы бесконтактных методов распыления расплава а – пропускание тока по струе расплава: 1 – тигель; 2 – электроды; 3 – индуктор; 4 – расплав; 5 – камера; 6 – сборник порошка 2 3 41 5 6 2 а. Лекция
Физико-химические методы получения порошков 94 Бесконтактные методы диспергирования Схемы бесконтактных методов распыления расплава б – при наложении электромагнитного поля на струю; в – при наложении электромагнитного поля на расплав: 1 – металлоприемник; 2 – электромагнитная катушка; 3 – струя расплава 2 3 1 б в 1 3 2 Лекция
Физико-химические методы получения порошков 95 Диспергирование энергоносителями Схемы распылительных установок а – прямоточная установка: 1 – металлоприемник с форсункой; 2, 8 – верхний и нижний затворы; 3 – камера распыления; 4 – теплообменник; 5 – газовый охладитель; 6 – манометр; 7 – сборник порошка; 9 – дроссель; 10 – компрессор; 11 – ресивер; 12, 13 – фильтры грубой и тонкой очистки 1 2 4 3 5 6 7 8 910 11 12 13 а. Лекция
Физико-химические методы получения порошков 96 Диспергирование энергоносителями Схемы распылительных установок б – установка, работающая на выброс: 1 – металлоприемник и форсунка; 2, 7 – верхний и нижний затворы; 3 – обратный клапан; 4 – камера распыления; 5 – разделитель; 6 – камера охлаждения; 8 – сборник порошка; 9 – газоподогреватель; 10 – газовый редуктор; 11 – ресивер; 12 – компрессор 1 9 122 3 4 5 6 7 8 10 11 б. Лекция
Физико-химические методы получения порошков 971. Либенсон, Г. А. Процессы порошковой металлургии : учеб. для вузов в 2 ч. / Г. А. Либенсон, В. Ю. Лопатин, Г. В. Комарницкий. – М. : МИСИС, 2001. 2. Силаев, А. Ф. Диспергирование жидких металлов и сплавов / А. Ф. Силаев, Б. Д. Фишман. – М. : Металлургия, 1983. – 144 с. 3. Васильев, В. А. Высокоскоростное затвердение расплавов / В. А. Васильев, Б. С. Митин, И. Н. Пашков и др. – М. : СП ИНТЕРИНЖИНИРИНГ, 1998. – 267 с. Список рекомендуемой литературы. Лекция
Физико-химические методы получения порошков 98 Лекция 11 Восстановление химических соединений металлов • Общие закономерности процессов восстановления • Металлотермическое восстановление • Кинетика процесса восстановления • Механизм восстановления химических соединений металлов • Получение порошков железа восстановлением оксидов углеродом • Способы получения порошков железа восстановлением оксидов углеродом
Физико-химические методы получения порошков 99 Общие закономерности процессов восстановления Под восстановлением в порошковой металлургии понимают процесс получения металла из его химического соединения путем отнятия неметаллической составляющей (кислорода, солевого остатка и др. ) при помощи какого-либо вещества, называемого восстановителем. Всякий процесс восстановления одновременно является и процессом окисления : когда исходное химическое соединение металла теряет неметаллическую составляющую (восстанавливается), восстановитель вступает с ней во взаимодействие (окисляется). Лекция
Физико-химические методы получения порошков 100 Общие закономерности процессов восстановления В общем случае простейшую реакцию восстановления можно представить как Ме. А + X Ме + ХА ± Q , где Ме – металл, порошок которого хотят получать; А – неметаллическая составляющая (кислород, хлор, фтор, солевой остаток и др. ) восстанавливаемого соединения Ме. А ; X – восстановитель; Q – тепловой эффект реакции. Восстановитель – это вещество, которое при заданной температуре процесса обладает большим химическим сродством к неметаллической составляющей восстанавливаемого соединения, чем металл, входящий в это соединение. Лекция
Физико-химические методы получения порошков 101 Общие закономерности процессов восстановления Для оценки возможности протекания реакции восстановления сравнивают величины, характеризующие прочность химических связей в соединениях Ме. А и ХА. Количественной мерой этих величин (принято говорить «мерой химического сродства» ) служит величина свободной энергии Гиббса Q 0 T , высвобождающейся при образовании соответствующего химического соединения: чем больше высвобождается энергии, тем прочнее химическое соединение. Лекция
В простейшем виде для стандартных условий (компоненты находятся в чистом виде, давление газа в реакционном пространстве равно атмосферному) выражение для Q 0 T реакции имеет вид Q 0 T = Q 0 XA – Q 0 Me. A = – R T ln. K P , где Q 0 XA , Q 0 Me. A – стандартные свободные энергии образования соединений ХА и Ме. А при температуре Т , K P – константа равновесия реакции; R – газовая постоянная; Т – температура проведения процесса восстановления. Когда реакция идет с участием газообразных веществ, для ее развития в нужном направлении наряду с температурой важно отношение их парциальных давлений. Физико-химические методы получения порошков 102 Общие закономерности процессов восстановления. Лекция
Физико-химические методы получения порошков 103 Общие закономерности процессов восстановления Механизм восстановления химических соединений металлов твердыми или газообразными восстановителями основан на адсорбционно-автокаталитической теории. Процесс превращения происходит в следующей последовательности: 1) внешняя диффузия молекул газообразного восстановителя к поверхности восстанавливаемого соединения и физическая адсорбция молекул на этой поверхности, 2) активирование адсорбированных молекул за счет усиления действия на них силового поля кристаллической решетки. Лекция
Физико-химические методы получения порошков 104 Общие закономерности процессов восстановления 3) отдача адсорбированными атомами электронов в решетку восстанавливаемого соединения, в результате чего образуются нейтральные атомы металла (на поверхности восстанавливаемого соединения), ионы восстановителя и ионы неметаллической составляющей восстанавливаемого соединения, 4) отрыв неметаллических ионов от поверхности восстанавливаемого соединения и их переход на более выгодные (с энергетической позиций) места в молекуле восстановителя, 5) десорбция нейтральных (энергетически пассивных) молекул соединения восстановителя с поверхности раздела фаз и их диффузия вглубь газообразного слоя восстановителя под давлением активных молекул. Лекция
Физико-химические методы получения порошков 105 Получение порошков железа восстановлением углеродом Сырьем для получения порошков служат оксиды железа, рудные концентраты или его хлористые соединения. В соответствии с диаграммой состояния системы “железо– кислород” существуют три оксида железа: Fe 2 O 3 или гематит (30, 06 % О), Fe 3 O 4 или магнетит (27, 64 % О) и Fe. O , который должен содержать 22, 27 % кислорода. Однако в реальных условиях последнего соединения не существует, в связи с тем, что на диаграмме состояния Fe–O в данной области присутствует соединение с широкой областью гомогенности на основе Fe. O, обогащенное кислородом. Его название – “вюстит”, а общая формула Fe х O. При температуре ниже 572 о С вюстит неустойчив и распадается на железо и Fe 3 O 4 . Лекция
Физико-химические методы получения порошков 106 Получение порошков железа восстановлением углеродом Наиболее распространенным сырьем являются окисленные руды железа или прокатная окалина. В высокообогащенном рудном концентрате железо находится в виде гематита, магнетита, лимонита ( HFe. O 22 ) ) и сидерита ( Fe. CO 33 ). ). Лекция
Физико-химические методы получения порошков 107 Получение порошков железа восстановлением углеродом Получение порошков железа и его сплавов Реакция восстановления оксидов железа твердым углеродом протекает по следующему механизму: Fe 2 O 3 + C = 2 Fe 3 O 4 + 2 CO (1) 6 Fe 2 O 3 + C = 4 Fe 3 O 4 + CO 2 (2) х Fe 3 O 4 + C = 2 Fe х O + CO 2 (3) 2 Fe 3 O 4 + C = 6 Fe х O + CO 2 (4) Fe х O + C = х Fe + С O 2 (5) 2 Fe х O + C = 2 х Fe 3 O 4 + 2 CO (6) Fe 3 O 4 + 4 C = 3 Fe + 4 CO (7) 2 Fe 3 O 4 + 3 C = 3 Fe + 2 CO 2 (8)Лекция
Физико-химические методы получения порошков 108 Получение порошков железа восстановлением углеродом Практическое восстановление оксидов железа на всех последующих этапах процесса обеспечивает СО, образующийся при окислении углерода: С + О 2 = СО 2 С + СО 2 = 2 СО _______ 2 С + О 2 = 2 СОЛекция
Физико-химические методы получения порошков 109 Получение порошков железа восстановлением углеродом Получение порошков железа и его сплавов Реакции, протекающие с участием газовой, выглядят следующим образом: 2 Fe 2 O 3 + C О = 2 Fe 3 O 4 + CO 2 + Q (9) х Fe 3 O 4 + C О = 3 Fe х O + CO 2 – Q (10) Fe х O + C О = х Fe + С O 2 + Q (11) Все приведенные реакции являются суммарными, идущими с образованием окислов углерода: Ме. О + СО = Ме + СО 2 С + СО 2 = 2 СО _______ Ме. О + С = Ме + СО 2 Лекция
Физико-химические методы получения порошков 110 Получение порошков железа восстановлением углеродом Р=1 атм Fe. O (вюстит) 2 3 430 СО, % 60 400 1200100080060090 СО 2 , % Т, 0 С 10 40 701 1 – С + СО 2 = 2 СО 2 – Fe. O + CO = Fe + CO 2 3 – Fe 3 O 4 + CO = Fe. O + CO 2 4 – Fe 2 O 3 + CO = Fe 3 O 4 + CO 2 Кривые равновесия реакций восстановления оксидов железа окислом углерода. Лекция
Физико-химические методы получения порошков 111 Способы получения порошков железа Основные технологические варианты получения порошков железа с использованием в качестве восстановителя углерода: — восстановление твердым углеродом; — восстановление сажистым железом; — комбинированное восстановление; — содовый способ. Лекция
Физико-химические методы получения порошков 112 Способы получения порошков железа В качестве восстановителя используют молотый графит, кокс, термощлыб. Состав шихты в тигле: 60– 69 % оксидного сырья, 25– 33 % термошлыба или кокса, 6– 7 % известняка. Температура восстановления 1175– 1200 о С, время 30– 40 ч. Общее время пребывания тиглей в проходной тоннельной печи может составлять до 90 часов Тигель Восстановитель Восстанавливаемое соединение Восстановление твердым углеродом. Лекция
Физико-химические методы получения порошков 113 Способы получения порошков железа Восстановление сажистым железом Сажистое железо получают путем термокаталитического разложения углеводородных газов в порах железной губки при температуре 700– 900 о С. Оптимальное содержание углерода в сажистом железе составляет от 20 до 50 %. Основная масса углерода в сажистом железе находится в свободном состоянии в виде отдельных субмикронных частиц сажи. Введение сажистого железа в восстанавливаемую шихту позволяет ускорить процесс восстановления и уменьшить температуру восстановления на 100– 200 о С. Это связано с тем, что присутствие в зоне реакции сажистого железа приводит к образованию на начальном этапе восстановления большого количества центров активации процесса (зародышей металлической фазы), действующих каталитически. Лекция
Физико-химические методы получения порошков 114 Способы получения порошков железа Комбинированное восстановление а б Схема размещения брикетированной шихты в муфеле шахтной печи при использовании простых ( а ) и кольцевых ( б ) перфорированных стаканов. Лекция
Физико-химические методы получения порошков 115 Способы получения порошков железа Содовый способ Сущность содового способа заключается в совмещении процесса восстановления и химического рафинирования железосодержащего сырья кальцинированной содой ( Na 2 CO 3 ). Процесс восстановления осуществляют при нагреве шихты из смеси оксида железа, углерода и соды до температуры выше 700 о С. . Лекция
Физико-химические методы получения порошков 116 Способы получения порошков железа Содовый способ Примеси, содержащиеся в шихте (кислородные соединения кальция, кремния, марганца, мышьяка, фосфора и пр. ), образуют растворимые в воде и разбавленных кислотах соединения на основе натрия ( Na 2 O , Al 2 O 3 , 2 Si. O 2 , Na 2 Si. O 3 , Na 3 P О 4 и пр. ). Соду берут с четырех– пятикратным избытком от необходимого на связывание примесей. Сода при восстановлении действует каталитически, ускоряя газификацию углерода и кристаллохимические превращения в восстанавливаемом материале. Лекция
Физико-химические методы получения порошков 117 1. Либенсон, Г. А. Процессы порошковой металлургии : учебник для вузов в 2 ч. / Г. А. Либенсон, В. Ю. Лопатин, Г. В. Комарницкий – М. : МИСИС, 2001. 2. Якименко, В. Б. Железные порошки. Технология, состав, структура, свойства, экономика / В. Б. Якименко, В. Я. Буланов, В. В. Рукин и др. – М. : Наука, 1982. – 264 с. 3. Роман, О. В. Актуальные проблемы порошковой металлургии / О. В. Роман, В. С. Аруначалам, И. М. Федоренко и др. – М. : Металлургия, 1990. 231 с. Список рекомендуемой литературы. Лекция
Физико-химические методы получения порошков 118 Лекция 12 Получение порошков железа восстановлением химических соединений • Методы восстановления оксидов железа водородом • Хлоридный способ получения порошков железа • Металлотермические методы получения порошков железа
Физико-химические методы получения порошков 119 Методы восстановления железа водородом Процесс восстановления Fe 2 O 3 до железа происходит по трехступенчатой ( выше 572 о С ) Fe 2 O 3 Fe 3 O 4 Fe x O Fe или двухступенчатой ( ниже 572 о С ) Fe 2 O 3 Fe 3 O 4 Fe схемам: 3 Fe 2 O 3 + H 2 = 2 Fe 3 O 4 + H 2 O + Q x. Fe 3 O 4 + H 2 = 3 Fe x O + H 2 O – Q Fe x O + H 2 = x. Fe + H 2 O – Q Fe 3 O 4 + 4 H 2 = 3 Fe + 4 H 2 O – Q Лекция
Физико-химические методы получения порошков 120 Методы восстановления железа водородом На практике используют несколько основных вариантов процесса восстановления оксида железа водородом: — восстановление в стационарном слое; — восстановление во вращающейся печи; — восстановление в кипящем слое. Лекция
Физико-химические методы получения порошков 121 Методы восстановления железа водородом С Н 2 , % 80 3 60 4 40 1 20 СD 2 A 1 B a 300 1 T, 0 C 500 700 900 1100 Кривые равновесия реакции восстановления оксидов железа водородом. Лекция
Физико-химические методы получения порошков 122 Хлоридный способ Fe + 2 HCl = Fe. Cl 2 + H 2 – Q Аппаратурно-технологическая схема получения железного порошка хлоридным способом 1 – емкость с раствором соляной кислоты; 2 – реактор с кислотостойкой футеровкой; 3 – отстойник; 4 – фильтр; 5 – упариватель; 6 – кристаллизатор; 7 – центрифуга; 8 – сушильная камера; 9 – пресс для брикетирования кристаллов хлористого железа; 10 – восстановительная печь; 11 – пылеуловитель; 12 – скруббер; 13 – осушитель; 14 – компрессор; 15 – очиститель для улавливания HCl и H 2 SЖелезо- содержащи е сырье Пары воды Железный порошок. Влажный водород Раствор НCl. Выделившийся при растворении сырья водород 1 2 3 4 6 5 7 98 1413 12 11 1015 15 Раствор НCl Вода. Лекция
Физико-химические методы получения порошков 123 Карбидотермический метод Железные порошки высокой чистоты получают восстановлением прокатной окалины или богатой окисленной железной руды карбидом кальция Fe 2 O 3 + ЗСа = 2 Fe + ЗСа. О Fe 2 O 3 + ЗС = 2 Fe + ЗСОЛекция
Физико-химические методы получения порошков 124 Гидридно-кальциевый метод Порошки сталей и сплавов сложного состава получают совместным восстановлением смеси оксидов (или смеси оксидов и металлических порошков) гидридом кальция. где n – порядковый номер (от 1 до k ) компонента шихты (оксида) и соответствующего ему металла в готовом продукте (порошке сплава); k – максимальное число оксидов в шихте; a n – число атомов металла в молекуле соответствующего оксида (от 1 до 3); b n – число атомов кислорода в молекуле соответствующего оксида (от 1 до 5, для компонента, вводимого в виде металлического порошка, b n = 0); А n – количество грамм-молекул в соответствии с заданным составом сплава 2 2 1 1 1 ( ) (Ca. H ) (Ca. O) (H ) , n nk k k n n n a b n n n n A Me O A b A b A a Me Лекция
Физико-химические методы получения порошков 125 Список рекомендуемой литературы. Лекция 12 1. Либенсон, Г. А. Процессы порошковой металлургии : учебник для вузов в 2 ч. / Г. А. Либенсон, В. Ю. Лопатин, Г. В. Комарницкий. – М. : МИСИС, 2001. 2. Якименко, В. Б. Железные порошки. Технология, состав, структура, свойства, экономика / В. Б. Якименко, В. Я. Буланов, В. В. Рукин и др. – М. : Наука, 1982. – 264 с. 3. Роман, О. В. Актуальные проблемы порошковой металлургии / О. В. Роман, В. С. Аруначалам, И. М. Федоренко и др. – М. : Металлургия, 1990. 231 с.
Физико-химические методы получения порошков 126 Лекция 13 Получение порошков вольфрама восстановлением оксидов водорода и углерода • Взаимодействие в системе вольфрам-кислород. Оксиды вольфрама • Кристаллические модификации вольфрама • Механизм образования частиц вольфрамового порошка • Режимы получения крупно- и мелкодисперсных частиц вольфрама
Физико-химические методы получения порошков 127 Взаимодействие в системе вольфрам – кислород Исходным материалом для получения порошков вольфрама служит вольфрамовый ангидрид, восстановители – водород или твердый углерод (сажа). В системе W – O имеется четыре оксида вольфрама: — WO 3 ( -оксид с областью гомогенности WO 3 – WO 2, 96 ) желтого цвета; — WO 2, 9 или W 20 O 58 ( -оксид с областью гомогенности WO 2, 9 – WO 2, 83 ) синего цвета; — WO 2, 72 или W 18 O 49 ( -оксид с областью гомогенности WO 2, 72 – WO 2, 66 ) фиолетового цвета; — WO 2 ( -оксид с областью гомогенности WO 2, 03 – WO 2 ) темно-коричневого цвета. Лекция
Физико-химические методы получения порошков 128 Взаимодействие в системе вольфрам – кислород Оксид вольфрама WO 3 имеет три кристаллические модификации: — моноклинную, устойчивую ниже 720 °С; — тетрагональную, устойчивую в интервале 720– 1100 °С; — кубическую, устойчивую выше 1100 °С. При 800– 850 °С WO 3 возгоняется в форме полимерных молекул W 3 O 9. Оксид вольфрама WO 2, 9 нестабилен ниже 484 °С и диспропорционирует с образованием WO 2 и WO 3 , а WO 2, 72 нестабилен ниже 585 °С. Лекция
Физико-химические методы получения порошков 129 Восстановление вольфрамового ангидрида водородом Суммарная реакция восстановления WO 3 + 3 H 2 = W + 3 H 2 O проходит через ряд последовательных превращений WO 3 – WO 2, 9 – WO 2, 72 – WO 2 – W Механизм образования зерен WO 2 и, соответственно, W разной величины связан с двумя группами явлений: — переноса вещества через газовую фазу; — кристаллохимическими (структурными) превращениями в твердых фазах. Лекция
Физико-химические методы получения порошков 130 Восстановление вольфрамового ангидрида водородом Получению крупных порошков вольфрама способствуют следующие технологические факторы: 1) высокая температура восстановления в быстрое ее повышение по длине печи; 2) высокий слой WO 3 в лодочке; 3) повышенная влажность водорода; 4) малая скорость подачи водорода; 5) большая скорость продвижения лодочек с WO 3 через печное пространство. Лекция
Физико-химические методы получения порошков 131 Восстановление вольфрамового ангидрида водородом Метод восстановления WO 3 сажей применим лишь в том случае, если в вольфраме допустима примесь углерода. Суммарная реакция восстановления имеет вид: WO 3 + ЗС = W +3 СО Восстановление протекает с участием газообразного СО. Для получения мелкозернистого вольфрама в исходную шихту вводят небольшой избыток сажи с целью исключения спекания и роста частиц вольфрама при 1500 °С и выше. Лекция
Физико-химические методы получения порошков 132 Восстановление вольфрамового ангидрида водородом Высокодисперсные частицы сажи являющихся являются центрами восстановления. При получении крупнозернистых порошков вольфрама в шихту не вводят избыточного количества сажи и процесс восстановления ведут при более высокой температуре (1700– 1800 °С). Восстановление вольфрамового ангидрида углеродом проводят в угольно-трубчатых печах. Лекция
Физико-химические методы получения порошков 133 1. Либенсон, Г. А. Процессы порошковой металлургии : учебник для вузов в 2 ч. / Г. А. Либенсон, В. Ю. Лопатин, Г. В. Комарницкий. – М. : МИСИС, 2001. 2. Федорченко И. М. Порошковая металлургия. Материалы, технологии, свойства, области применения: Справочник / И. М. Федорченко, И. И. Францевич, И. Д. Родомысльский и др. – Киев: Наукова думка, 1985. – 624 с. Список рекомендуемой литературы. Лекция
Физико-химические методы получения порошков 134 Лекция 14 Получение порошков молибдена, титана и циркония восстановлением химических соединений • Технология получения порошков молибдена • Методы получения порошков титана • Методы получения порошков циркония
Физико-химические методы получения порошков 135 Получение порошков молибдена Исходным материалом служит чистый триоксид молибдена Мо. О 3 , получаемый прокаливанием при 450– 500 о С парамолибдата аммония (3( NH 4)2 O · 7 Mo. O 3 · 4 H 2 O ) в муфельных печах или печах с вращающейся трубой. Процесс образования триоксида молибдена из парамолибдата протекает по следующей схеме: ( NH 4 )6 Mo 7 O 24 4 H 2 O 90– 100 о С ( NH 4 )6 Mo 7 O 24 200 о С ( NH 4) 2 Mo 4 O 13 280– 450 о С Mo 7 O 24 Промышленный способ производства порошка молибдена предусматривает восстановление Мо. О 3 хорошо осушенным водородом по схеме Мо. О 3 –Мо. О 2 –Мо. Лекция
Физико-химические методы получения порошков 136 Получение порошков титана Для получения порошков титана используют следующие методы: — восстановление диоксида титана кальцием; — восстановление диоксида титана гидридом кальция; — восстановление хлорида титана натрием или магнием. Лекция
. Так как сродство титана к кислороду высоко, что предопределяет необходимость применения наиболее активного восстановителя – кальция, который должен быть химически чистым прежде всего по азоту (допустимое содержание не более 0, 15 %). Восстановление проходит по суммарной реакции Т i О 2 + 2 Са = Т i + 2 Са. О + Q. Восстановление диоксида титана гидридом кальция. Суммарную реакцию восстановления диоксида титана гидридом кальция можно записать Т i О 2 + 2 Са. Н 2 = Т i + 2 Са. О + 2 Н 2. Физико-химические методы получения порошков 137 Восстановление диоксида титана кальцием. Лекция
Физико-химические методы получения порошков 138 Получение порошков титана Восстановление хлорида титана натрием или магнием. Более экономичным является процесс восстановления Т i С 1 4 магнием ( процесс Крапля ). Реакционное взаимодействие протекает по суммарной реакции: Т i С 1 4 + 2 М g = 2 М g С 1 2 + Т i + Q. Можно заменить магний его легкоплавким (температура плавления около 500 о С) эвтектическим сплавом c кальцием (82 % М g , 18 % Са ). Лекция
Физико-химические методы получения порошков 139 Получение порошков циркония Восстановление диоксида циркония кальцием или его гидридом Zr. O 2 + 2 Са = Zr + 2 Са. О Для снижения содержания кислорода кальций берут с избытком 50– 100 % и применяют длительные выдержки при восстановлении. Восстановление проводят при 900– 1000 0 С в атмосфере сухого водорода. Для регулирования зернистости получающегося порошка циркония в шихту можно добавлять хлористый кальций. При хранении порошка циркония необходимо соблюдать особую осторожность из-за его чрезвычайно высокой пирофорности : емкость с порошком целесообразно заполнить дистиллированной водой. Лекция
Физико-химические методы получения порошков 140 Получение порошков циркония Восстановление фтороцирконата калия натрием Восстановление проводят при 15– 20%-ном избытке натрия в герметичных стальных реакторах в вакууме или в аргоне при 800– 900 о С Фтороцирконат калия (К 2 Z г F 6 ) не гигроскопичен и устойчив на воздухе. Цирконий, полученный этим методом, предназначен для непосредственного использования в пиротехнике или в качестве геттера в электровакуумной технике. Лекция
Физико-химические методы получения порошков 141 1. Зиликман, А. Н. Металлургия редких металлов / А. Н. Зиликман, Б. Г. Коршунов – М. : Металлургия, 1991. – 432 с. 2 . Либенсон, Г. А. Процессы порошковой металлургии : учебник для вузов в 2 ч. / Г. А. Либенсон, В. Ю. Лопатин, Г. В. Комарницкий. – М. : МИСИС, 2001. 3. Федорченко, И. М. Порошковая металлургия. Материалы, технологии, свойства, области применения: Справочник / И. М. Федорченко, И. И. Францевич, И. Д. Родомысльский и др. – Киев : Наукова думка, 1985. – 624 с. Список рекомендуемой литературы. Лекция
Физико-химические методы получения порошков 142 Получение порошков тантала, ниобия, меди, кобальта, никеля и легированных сплавов • Методы получения порошков тантала и необия • Методы получения порошков меди, кобальта и никеля • Получение легированных порошков Лекция
Физико-химические методы получения порошков 143 Получение порошков тантала Восстановление фторотанталата калия натрием Этот метод является одним из наиболее распространенных промышленных методов получения порошка тантала. Реакция восстановления K 2 Ta. F 7 + 5 N а = Та + 5 Na. F + 2 К F Шихту K 2 Ta. F 7 + 5 N а , загруженную в тигель, подогревают через стенку в одном месте до 450– 500 о С. Начавшаяся реакция быстро распространится по всему объему материала. Качество порошка тантала улучшают путем выдержки ректора с шихтой в печи (по завершении процесса) при 1000 о С. Лекция
Восстановление хлорида тантала магнием Технология подобного процесса основана на реакции 2 Та. С 1 5 + 5 М g = 2 Та + 5 М g С l 2 + Q. Реактор (тигель) со смесью Та. С l 5 , магниевой стружки и флюса (хлориды натрия и калия) загружают в шахтную печь, разогретую до 750 о С. Физико-химические методы получения порошков 144 Получение порошков тантала. Лекция
Физико-химические методы получения порошков 145 Получение порошков ниобия Восстановление фторониобата калия натрием K 2 Nb. F 7 + 5 N а = Nb + 2 К F + 5 N а F. Процесс восстановления включает следующие операции: — послойной загрузки шихты в стальной тигель (при 15– 20%-ном избытке натрия) и засыпки шихты слоем хлористого натрия; — загрузки тигля в разогретую до 600 °С шахтную печь и выдержки тигля в течение 1– 1, 5 ч при 900– 1000 о С; — отмывки полученного порошка водой (сначала холодной, а затем горячей) разбавленной азотной или соляной кислотой (для удаления железа, частично титана и других примесей); — отмывки порошка 2, 5%-ной холодной плавиковой кислотой (для уменьшения содержания оксида ниобия). Лекция
Физико-химические методы получения порошков 146 Получение порошков ниобия Восстановление хлорида ниобия магнием Технология подобного процесса основана на реакции 2 Nb С l 5 + 5 М g = 2 Nb + 5 М g С 1 2 + Q. Лекция
Физико-химические методы получения порошков 147 Получение порошков меди Порошок меди может быть получен твердофазным взаимодействием ее кислородсодержащих соединений или солей с реагентом-восстановителем. Сырьем служат окалина или высший оксид меди С u О, восстановители – газ (водород, конвертированный природный газ, диссоциированный аммиак) либо твердый углерод (графит, древесный уголь). Основными компонентами окалины являются металлическая (70– 75 %) и оксидная (30– 25 %) фазы. Содержание влаги до 4– 4, 5 %, технических масел – до 1– 1, 5 %. Лекция
Физико-химические методы получения порошков 148 Получение порошков меди Оксиды меди восстанавливают водородом при 300– 400 о С и выше по автокаталитической реакции Cu. O + H 2 = Cu + H 2 O. Перед восстановлением окалину обжигают в окислительной атмосфере при 250– 300 о С (возможен обжиг при 550– 600 о С) и размалывают до крупности < 100 мкм. Восстановление проводят при 550– 650 о С водородом или конвертированным природным газом. Известен способ получения порошка меди комбинированным восстановлением окалины газообразным и твердым (графит) восстановителями. Лекция
Оксид кобальта Со 2 О 3 или Со 3 О 4 восстанавливают водородом в трубчатых или муфельных электропечах при 500– 700 о С в течение 3– 5 ч: Со 2 О 3 + H 2 = Со + H 2 O или Со 3 О 4 + H 2 = Со + H 2 O Мягкие, легко рассыпающиеся брикеты при растирании и просеве на вибросите через сетку 004 превращаются в порошок с частицами размером 1– 5 мкм, насыпной плотностью <0, 75 г/см 3 и содержанием кислорода 0, 7 %. Физико-химические методы получения порошков 149 Получение порошков кобальта. Лекция
Физико-химические методы получения порошков 150 Получение порошков никеля Оксид никеля Ni. O восстанавливают водородом или водородсодержащим газом при 700– 750 о С в течение 1– 2 ч по реакции Ni О + Н 2 = Ni + Н 2 О. Полученный спек (никелевую губку) дробят и рассевают на фракции. Полученный порошок никеля содержит небольшое количество кобальта (около 0, 5 %). Суммарное содержание Ni. Ni и Со в порошке не менее 99, 5 %. Лекция
Физико-химические методы получения порошков 151 1. Зиликман, А. Н. Металлургия редких металлов / А. Н. Зиликман, Б. Г. Коршунов – М. : Металлургия, 1991. – 432 с. 2 . Либенсон, Г. А. Процессы порошковой металлургии : учебник для вузов в 2 ч. / Г. А. Либенсон, В. Ю. Лопатин, Г. В. Комарницкий. – М. : МИСИС, 2001. 3. Федорченко, И. М. Порошковая металлургия. Материалы, технологии, свойства, области применения : справочник / И. М. Федорченко, И. И. Францевич, И. Д. Родомысльский и др. – Киев : Наукова думка, 1985. – 624 с. Список рекомендуемой литературы. Лекция
Физико-химические методы получения порошков 152 Лекция 16 Восстановление химических соединений металлов из растворов солей и газообразных соединений металлов • Получение порошков автоклавным способом • Получение порошков цементацией растворов солей • Получение порошков в кипящем слое • Получение порошков в плазме
Физико-химические методы получения порошков 153 Получение порошков автоклавным способом Автоклавная технология используется для производства порошков никеля, меди и кобальта: соответствующий металл, вытесняемый в растворе из его соединения водородом под давлением, осаждается в виде твердых частиц на дно камеры реактора. Реакция восстановления катиона металла Ме Z + + ( z /2) Н 2 = Ме 0 + z Н + возможна, если потенциал водорода H 2 меньше (электроотрицательнее), чем электродный потенциал металла Me . Лекция
Физико-химические методы получения порошков 154 Получение порошков автоклавным способом В момент равновесия H 2 , становится равным Me , накапливание массы образующегося в автоклаве осадка металла прекращается. Водород переходит в раствор, содержащий катионы Ме Z + , по реакции ионизации 0, 5 Н 2 = Н + + e. C двигать потенциал водорода в отрицательную сторону можно, повышая р. Н и (или) увеличивая давление водорода в автоклаве. Более эффективно изменять р. Н, повышение которого на единицу эквивалентно изменению давления водорода в 100 раз. Лекция
Физико-химические методы получения порошков 155 Получение порошков автоклавным способом Получение порошка меди Медь может быть выделена восстановлением водородом как из кислых, так и щелочных растворов. В качестве исходного используют раствор сульфата меди или медноаммиачной комплексной соли Восстановление проводят при суммарном давлении газа в автоклаве 2, 4– 3, 5 или 3, 5– 4, 5 МПа ( p H 2 до 1, 5– 2, 5 МПа) и температуре 140– 170 или 180– 200 о С соответственно. Для восстановления отмытых осадков металлургического производства применяют горизонтальные автоклавы с паровой рубашкой с несколькими вертикальными мешалками. Вводя в раствор некоторое количество мелкого порошка меди либо частицы полиакриламида (0, 1– 0, 5 г на 1 л раствора), регулируют размеры частиц получаемого порошка в пределах от 2– 3 до 15– 20 мкм. Лекция
Физико-химические методы получения порошков 156 Получение порошков автоклавным способом Получение порошков никеля и кобальта Полное выделение никеля и кобальта возможно лишь при р. Н > 4, в связи с чем водородное восстановление ведут из растворов, содержащих аммиачные комплексы Ni ( N Н 3 ) 2 2+ или Со( NH 3 ) 2 2+ и ( NH 4 ) 2 SO 4 (для предотвращения гидролиза аммиакатов). Для ускорения реакции зародышеобразования в раствор вводят затравку (мелкие порошки никеля или кобальта). Лекция
Физико-химические методы получения порошков 157 Получение порошков автоклавным способом Получение порошков никеля и кобальта При восстановлении наблюдается следующая последовательность стадии этого процесса: 1) растворение водорода в водном растворе (быстрая стадия); 2) транспорт водорода к поверхности твердой частички затравки (зависит от интенсивности перемешивания); 3) активированная адсорбция водорода на поверхности частички металла-затравки (быстрая стадия); 4) реакция восстановления сорбированных комплексных ионов металла водородом на поверхности твердой частички затравки (медленная стадия); 5) отвод растворимых продуктов реакции в объем раствора (быстрая стадия). Лекция
Физико-химические методы получения порошков 158 Получение порошков цементацией Цементация – электрохимический процесс, который часто называют контактным восстановлением или внутренним электролизом. По своей сути процесс сходен с гальваническим процессом: металл с более отрицательным потенциалом вытесняет из раствора металл с более положительным потенциалом, переходя при этом в раствор. Лекция
Физико-химические методы получения порошков 159 Получение порошков цементацией Электрохимическую реакцию между металлом- цементатором и ионами вытесняемого металла в общем виде можно записать следующим образом: где: ZZ 11 и и ZZ 22 – заряды ионов или валентности вытесняемого металла и металла-цементатора. Для прохождения реакции слева направо вытесняющий металл должен иметь более отрицательный, чем у вытесняемого металла, электродный потенциал. Z 1+ 0 0 Z 2+ 2 1 1 1 2 Z Me +Z Me ®Z Me +Z Me. Лекция
Физико-химические методы получения порошков 160 Получение порошков цементацией Стандартные электродные потенциалы и равновесные соотношения активностей катионов для некоторых пар двухвалентных металлов Металл Φ 0 , В Ме 1 Ме 2 Zn Cu – 0, 763 +0, 320 1, 0 · 10 – 33 Fe Cu – 0, 440 +0, 340 1, 3 · 10 – 27 Ni Cu – 0, 230 + 0, 340 2, 0 · 10 – 20 Zn Ni – 0, 763 +0, 230 5, 0 · 10 – 19 Cu Hq + 0, 340 + 0, 798 1, 6 · 10 – 16 Zn Cd – 0, 796 – 0, 402 3, 2 · 10 – 13 Zn Fe – 0, 796 – 0, 440 8, 0 · 10 – 122 2 1 1/ ZZ Me. Лекция
Физико-химические методы получения порошков 161 Получение порошков цементацией Растворение и осаждение металла из раствора регулируется двумя противоположно действующими факторами: — электролитической упругостью растворения; — осмотическим давлением ионов раствора. Разность этих двух величин определяет значение и величину стандартного электродного потенциала. Время. С корость Схема процесса цементации ( а ) и зависимость скорости цементации от времени ( б )а бẽ Meze. Me. Z 1 1 11 Meze. Me. Z 222 2 Me 2 Лекция
Физико-химические методы получения порошков 162 Получение порошков цементацией Цементация металла из его раствора определяется двумя последовательными процессами: 1) доставкой ионов вытесняемого металла к катодной поверхности металла-цементатора через двойной и диффузионный слой; 2) электрохимическим превращением на границе электрод– раствор, протекающим через несколько промежуточных стадий. Факторы, оказывающие влияние на результат реакции: 1. Цементирующий материал должен образовывать растворимое соединение с анионом, который связан с замещаемым металлом. 2. Металл-цементатор должен находиться в избытке. 3. Раствор должен циркулировать. 4. Повышение температуры не только улучшает условия диффузии, но и снижает энергию активации реакции. Лекция
Физико-химические методы получения порошков 163 Получение порошков в кипящем слое Порошки металлов высокой чистоты можно получить из низкокипящих хлоридов и фторидов вольфрама, молибдена, рения, ниобия или тантала по реакции Ме. Гх + 0, 5 х. Н 2 = Ме + х. НГ, где Г – хлор или фтор. Технологическая схема процесса включает операции: 1) введения в реактор затравочного порошка; 2) подачи газа-восстановителя (смеси аргона и водорода); 3) разогрева реактора; 4) подачи из испарителя паров галогенида; 5) удаления из реактора крупных частиц порошка. Лекция
Физико-химические методы получения порошков 164 Получение порошков в плазме Плазма – это нейтральный газ, содержащий значительное количество положительных и отрицательных ионов и свободных электронов. Плазмохимические методы объединяют возможности быстрого протекания процессов восстановления и закалки продуктов реакции. Они применяются для получения высокодисперсных порошков металлов или их соединений (карбидов, нитридов и др. ). В качестве восстановителя используют водород, углеводороды или конвертированный природный газ, который получают плазменной конверсией углеводородного сырья. Низкотемпературную (4000– 10000 °С) плазму создают путем электродугового разряда высокой интенсивности в среде газа (азот, аргон) или смеси газов. Лекция
Физико-химические методы получения порошков 165 Список рекомендуемой литературы. Лекция 16 1. Зиликман, А. Н. Металлургия редких металлов / А. Н. Зиликман, Б. Г. Коршунов – М. : Металлургия, 1991. – 432 с. 2 . Либенсон, Г. А. Процессы порошковой металлургии : учебник для вузов в 2 ч. / Г. А. Либенсон, В. Ю. Лопатин, Г. В. Комарницкий. – М. : МИСИС, 2001. 3. Федорченко, И. М. Порошковая металлургия. Материалы, технологии, свойства, области применения: Справочник / И. М. Федорченко, И. И. Францевич, И. Д. Родомысльский и др. – Киев : Наукова думка, 1985. – 624 с.
Физико-химические методы получения порошков 166 Лекция 17 Общие закономерности процессов производства порошков электролизом • Общие закономерности процесса электролиза • Выход по току • Факторы, определяющие свойства порошков • Классификация электролитических порошков
Физико-химические методы получения порошков 167 Общие закономерности процессов электролиза Определение: Электролитический металлический порошок – металлический порошок, полученный электролизом растворов или расплавов соединений металлов. В соответствии с величиной напряжения, требуемого для выделения на катоде, металлы образуют ряд напряжений ( цинк, железо, олово, медь, серебро, золото и т. д. ). Чем левее находится металл в ряду напряжений, тем он более электроотрицателен или менее благороден, более активен (по отношению к кислороду кислотам, щелочам и пр. ) и тем большее напряжение требуется для его выделения на катоде. Лекция
Физико-химические методы получения порошков 168 Общие закономерности процессов электролиза В соответствии с законом Фарадея, количество катодного осадка, выделившегося при электролизе, пропорционально силе тока, времени его прохождения через электролит и электрохимическому эквиваленту (т. е. количеству металла, выделяемого за один ампер/час). Электролиз представляет собой своеобразный процесс восстановления, осуществляемый не с помощью восстановителей, а за счет использования энергии электрического тока. Лекция
Физико-химические методы получения порошков 169 Преимущества электролиза: — универсальность; — высокая чистота получаемых металлических порошков; — хорошие технологические свойства порошков. Недостатки электролиза: — большая энергоемкость; — низкая производительность; — необходимость утилизации большого количества отходов производства. Общие закономерности процессов электролиза. Лекция
Физико-химические методы получения порошков 170 Выход по току Реально получаемое количество осадка всегда меньше, чем рассчитанное. Это связано с тем, что: — в процессе электролиза происходит разрядка на катоде ионов нескольких элементов; — частично растворяется выделенный металл: — наблюдается утечка тока через дефекты электроизоляции и пр. Лекция
Физико-химические методы получения порошков 171 Выход по току Для оценки степени несовпадения расчетных и реально полученных количеств осадка используют такой показатель как выход по току, %: А = ( q п / q т )· 100, где q п – масса вещества (осадка), реально выделившаяся при прохождении определенного количества электричества через электролит; q т – масса вещества (осадка), которая должна была бы выделиться. Лекция
Физико-химические методы получения порошков 172 Факторы, определяющие свойства порошков На свойства получаемых порошков оказывают влияние следующие факторы технологического процесса: 1. Плотность тока связывает силу тока с суммарной рабочей поверхностью катодов (катодная плотность тока) или анодов (анодная плотность тока): i = I / S. Лекция
Физико-химические методы получения порошков 173 Факторы, определяющие свойства порошков Выделение металла на катоде начинается в центрах первичной кристаллизации. При большей плотности тока в ванне на единице площади катода разряжается больше ионов, т. е. на катоде создается больше первичных центров кристаллизации. 2. Концентрация ионов выделяемого металла Повышение концентрации выделяемых ионов (при низкой плотности тока) создает благоприятные условия для активного питания сравнительно небольшого количества центров, в результате чего формируется плотный осадок. Лекция
Физико-химические методы получения порошков 174 Факторы, определяющие свойства порошков 3. Температура электролита Повышение температуры увеличивает скорость перемещения ионов и ускоряет их диффузионную подвижность, что компенсирует обеднение приэлектродной области электролита катионами и способствует укрупнению порошков. Одновременно с этим возрастает и интенсивность химического взаимодействия выделяемого металла с электролитом и приводит к ухудшению условий труда (из-за испарения электролита). Электролиз ведут при температуре : — водных растворов – не выше 60 °С; — электролиз расплавов – при температуре, выше температуры плавления электролита, но ниже температуры плавления выделяемого металла. Лекция
Физико-химические методы получения порошков 175 Факторы, определяющие свойства порошков 4. Кислотность электролита Повышение содержания в электролите ионов водорода может привести к их бурному выделению на катоде. Это способствует разрыхлению (измельчению) порошка, но приводит к существенному уменьшению выхода по току и возрастанию расхода энергии. Повышенная кислотность электролита приводит к растворению части металла, выделившегося на катоде. Лекция
Физико-химические методы получения порошков 176 Факторы, определяющие свойства порошков 5. Межэлектродное расстояние Увеличение расстояния между электродами приводит к: — увеличению электросопротивления электролита; — падению силы тока на ванне; — уменьшению его катодной плотности. Это способствует получению более крупных порошков, снижению относительного количества растворяющегося в электролите катодного осадка и увеличению выхода по току. При чрезмерном увеличении межэлектродного расстояния приводит к перегреву электролита и уменьшению выхода по току (растворяется часть катодного осадка). При слишком малом расстоянии между электродами может произойти короткое замыкание , выделение порошка на катоде прекратится, хотя сила тока в ней будет такой же, как и в нормально работающей ванне. Лекция
Физико-химические методы получения порошков 177 Факторы, определяющие свойства порошков 6. Длительность наращивания слоя порошка на катоде В процессе роста частиц порошка значительно увеличивается их суммарная поверхность (особенно у рыхлых осадков). Это приводит к увеличению суммарной поверхности катодов и снижению плотности тока. На катоде образуются более крупные частицы или губка. Несвоевременное удаление порошка может привести к короткому замыканию. Лекция
Физико-химические методы получения порошков 178 Факторы, определяющие свойства порошков 7. Циркуляция электролита В процессе электролиза может произойти частичное расслаивание электролита вследствие различной плотности его составляющих (при электролизе расплавов), обеднение (обогащение) прикатодного (прианодного) пространства катионами (анионами), а также изменение заданной температуры раствора (расплава). Для предотвращения этих нежелательных явлений проводят выравнивание концентрации электролита с помощью системы непрерывной замкнутой циркуляции. Для этого за один час работы электролизера проводят примерно 6– 8 -кратный обмен электролита. Лекция
Физико-химические методы получения порошков 179 Факторы, определяющие свойства порошков 8. Наличие газообразных и органических примесей В электролите присутствует растворенный кислород, пероксид водорода, а также другие окислители, вызывающие окисление поверхности катода. В результате окисления поверхность катода становится более развитой , что способствует образованию рыхлых осадков. Присутствие в электролите органических примесей и поверхностно-активных веществ препятствует росту частиц, что приводит к получению более рыхлых осадков. Лекция
Физико-химические методы получения порошков 180 Классификация электролитических порошков В зависимости от условий электролиза на катоде получают: 1) твердые хрупкие осадки (в виде плотных слоев, чешуек, кристаллов); 2) губчатые мягкие осадки; 3) рыхлые (черные) осадки. Плотные осадки представляют собой слоистые сростки крупных, хорошо сцепленных кристаллов. Губчатые мягкие осадки представляют собой скопления отдельных мелких кристалликов, легко поддающихся разрушению при растирании. Рыхлые осадки являются высокодисперсными порошками, получающимися в готовом виде непосредственно в процессе электролиза. Лекция
Физико-химические методы получения порошков 181 1. Зиликман, А. Н. Металлургия редких металлов / А. Н. Зиликман, Б. Г. Коршунов – М. : Металлургия, 1991. – 432 с. 2 . Либенсон, Г. А. Процессы порошковой металлургии : учебник для вузов в 2 ч. / Г. А. Либенсон, В. Ю. Лопатин, Г. В. Комарницкий. – М. : МИСИС, 2001. Список рекомендуемой литературы. Лекция
Физико-химические методы получения порошков 182 Лекция 18 Получение порошков электролизом водных растворов • Получение порошков меди • Получение порошков никеля и серебра • Получение порошков железа • Получение порошков сплавов • Получение порошков из производственных растворов металлургических предприятий
Физико-химические методы получения порошков 183 Получение порошков меди Диаграмма зависимости размеров частиц порошка от плотности тока и концентрации раствора для меди I – область образования рыхлых осадков; II – область образования губчатых осадков; III – область образования плотных осадков IIII IIЛекция
Физико-химические методы получения порошков 184 Получение медного порошка Схема получения медного порошка 1 – плавильная печь; 2 – узел корректировки состава электролита; 3 – электролизная ванна; 4 – узел промывки, стабилизации и обезвоживания порошка; 5 – установка подготовки стабилизирующего раствора; 6, 9, 12 – бункеры-накопители порошка; 7–сушка порошка; 8 – элеватор; 10 – измельчение порошка; 11 – классификатор порошка; 13 – смеситель (усреднитель) порошка; 14 – упаковка порошка; 15, 16 – ловушки (фильтры); 17 – узел регенерации электролита Катодная медь. Серная кислота Вода Электролит Аноды Отработанный электролит Анодные остатки Крепкий раствор Слабый раствор. На станцию нейтрализации Продукты сгорания природного газа Стабилизир. раствор. Вода Стабилизатор Вода Высевки 2 17 3 1 6 7 15 5 16 4 12 11109 8 14 13 Лекция
Физико-химические методы получения порошков 1854 5 3 6 74 8 б 1 2 3 а. Получение медного порошка Разрез ванны электролизера ящичного типа ( а ) и бункерного типа ( б ) 1 – карман для приема электролита; 2 – промежуточная шина; 3 – анод; 4 – катод; 5 – карман для подачи электролита; 6 – лоток для выпуска электролита; 7 – корпус электролизера; 8 – устройство для выгрузки порошка Лекция
Физико-химические методы получения порошков 186 Получение медного порошка Выравнивание концентрации ионов по объему электролизной ванны и удаление «избытка» ионов меди осуществляют с помощью системы непрерывной замкнутой циркуляции и регенерации раствора (за один час происходит примерно десятикратный обмен раствора). Одновременно с циркуляцией осуществляют регенерацию электролита. Для обеспечения постоянства заданного состава проводят корректировку электролита , включая в систему сблокированных ванн специальные регенеративные ванны с нерастворимыми анодами свинцовыми ( Pb , Pb + 1 % Ag , Pb + 6 % Sb ). Лекция
Физико-химические методы получения порошков 187 Получение медного порошка Общее (суммарное) требуемое количество регенеративных ванн и можно подсчитать по формуле n = ( C Cu 2+ ) V /1, 1858 I B t , где C Cu 2+ – прирост концентрации меди в электролите за время электролиза (ч), г/л; V – суммарный объем электролита во всех ваннах работающих электролизеров, л; I – сила тока, проходящего через электролит, А; B t – катодный коэффициент полезного использования тока (в долях единицы). Лекция
Физико-химические методы получения порошков 188 Получение никелевого порошка Электролит – аммиачные растворы сернокислого никеля (исходным материалом является Ni. S 0 4 – 7 H 2 0). Электролит содержит: — 5– 15 г/л никеля ( Ni 2+ ); — 75– 80 г/л сульфата аммония; — 2– 3 г/л серной кислоты; — 40– 50 г/л хлористого аммония; — до 200 г/л хлористого натрия. Лекция
Физико-химические методы получения порошков 189 Получение никелевого порошка Снижение концентрации сернокислого никеля в электролите приводит к уменьшению среднего размера частиц порошка никеля. Хлористый натрий обеспечивает высокую электропроводность раствора. Хлористый аммоний в электролите играет роль буферной добавки, поддерживающей требуемое значение р. Н. Ионы аммония являются комплексообразователями, связывающими ионы никеля в комплексный ион Ni [ NH 3 ] 2 2+. Это позволяет устранить явление гидролиза сернокислого никеля у катода. Лекция
Физико-химические методы получения порошков 190 Получение порошков сплавов Препятствие : изменения состава электролита в процессе электролиза. Перспективным является проведение электролиза с несколькими растворимыми анодами из индивидуальных компонентов, входящих в состав сплава. При получении двухкомпонентного железокобальтового порошка используют три анода: — растворимого железного; — растворимого кобальтового; — нерастворимого свинцового. Нерастворимый анод используется в сочетании с дополнительным электродом из железной сетки. Катод – никелевый или из нержавеющей стали. Электролит представляет собой смешанный подкисленный H 2 S О 4 до р. Н 2– 2, 5 раствор сульфатов железа Fe. S О 4 и кобальта Co. S О 4. На катоде совместно разряжаются ионы железа, кобальта и водорода. Лекция
Физико-химические методы получения порошков 191 Получение серебряного порошка Порошок получают электролизом раствора азотнокислого серебра Ag. N 0 3. Используют электролит состава: — 10– 15 г/л азотной кислоты; — 40 г/л азотнокислого серебра (25 г/л Ag +) с температурой 35– 40 °С. Плотность тока на ванне электролизера составляет 1400– 1500 А/м 2 , напряжение на ванне 2– 2, 8 В. Анод – листовое серебро, катод алюминиевый. По ГОСТ 9724– 61 производят порошки марок ПС 1 и ПС 2 с содержанием серебра > 99, 9 %. Влажность порошка не должна превышать 0, 08 %. Лекция
Физико-химические методы получения порошков 192 Получение порошков железа В ряду напряжений железо располагается левее водорода и в кислых электролитах на катоде интенсивно выделяется водород. В электролите может образовываться Fe ( OH ) 3 , загрязняющий катодный осадок и нарушающий непрерывность процесса электролиза. Электролит: — сернокислый раствор сульфата железа с добавкой хлористого натрия; — солянокислый раствор хлорида железа с добавкой хлористого аммония; — смесь растворов. Растворимые аноды изготавливают из чугунного лома, обрезков железных листов стружки (содержание углерода < 0, 6 %). Катоды изготавливают из нержавеющей (коррозионно-стойкой) стали. Лекция
Физико-химические методы получения порошков 193 Получение порошков из производственных растворов Ионы цветных металлов содержат: — растворы от выщелачивания руд и отвалов рудников; — растворы травильного производства; — растворы химической переработки продуктов. Препятствия: — наличие органических загрязнений; — низкая концентрация большинства растворов. Необходимость очистки связана с законодательными ограничениями по суммарному содержанию ионов металлов в сточных водах. Ионы цветных металлов, содержащихся в стоках, обладают комплексом токсических действий на человека, живую природу и микроорганизмы. Лекция
Физико-химические методы получения порошков 194 Получение порошков из сточных вод металлургического производства Актуальна задача разработки и внедрения новых способов извлечения: — золота из растворов флотации и гидрометаллургии золотоносных руд; — серебра из растворов от обработки кино-, фотоматериалов; — элементов из отработанных гальванических растворов; — меди, цинка, кадмия, никеля, кобальта, марганца, олова, свинца, ртути из травильных растворов и сточных вод металлургических производств. Перспективными являются новые электролитические способы извлечения металлов с применением высокоповерхностных электродов. Лекция
Физико-химические методы получения порошков 195 1. Зиликман, А. Н. Металлургия редких металлов / А. Н. Зиликман, Б. Г. Коршунов – М. : Металлургия, 1991. – 432 с. 2 . Либенсон, Г. А. Процессы порошковой металлургии : учебник для вузов в 2 ч. / Г. А. Либенсон, В. Ю. Лопатин, Г. В. Комарницкий. – М. : МИСИС, 2001. 3. Ничипоренко, О. С. Порошки меди и ее сплавов / О. С. Ничипоренко, А. В. Помосов, С. С. Набойченко – М. : Металлургия, 1988. – 206 с. Список рекомендуемой литературы. Лекция
Физико-химические методы получения порошков 196 Лекция 19 Получение порошков электролизом расплавленных сред • Факторы, определяющие процесс электролиза расплавленных солей • Получение порошка тантала и ниобия • Получение порошка титана и циркония • Получение порошков железа
Физико-химические методы получения порошков 197 Факторы, определяющие процесс электролиза расплавленных солей Большинство металлических порошков из расплавов получают с использованием хлоридов, фторидов или смеси этих соединений. В герметичных электролизерах создают инертную газовую атмосферу (чаще всего аргон) или вакуум. Структура катодных осадков зависит от условий их осаждения: — состав электролита; — степень его чистоты; — материал и состояние поверхности катода. При наличии ничтожных следов влаги осадки выделяются в виде губки, а при содержании в электролите небольших количеств примесей железа или марганца образуются осадки в виде черного порошка. Лекция
Физико-химические методы получения порошков 198 Факторы, определяющие процесс электролиза расплавленных солей На выход по току влияют состав и температура электролита, плотность тока, расстояние между электродами и другие факторы. Состав электролита. Причина отклонения выхода по току от расчетной – растворимость металла в электролите с последующим окислением анодными продуктами. Снизить растворимость можно при введении солей с более электроотрицательными катионами по сравнению с выделяющимся на катоде металлом. Лекция
Физико-химические методы получения порошков 199 Факторы, определяющие процесс электролиза расплавленных солей Напряжение разложения различных химических соединений металлов при сравнимых концентрациях: E Т = – G T / n. F , где Е Т – напряжение разложения данного соединения металла ; G T – свободная энергия образования соединения металла; n – число электрических зарядов выделяемого металла, входящего в данное соединение; F – число Фарадея. Лекция
Физико-химические методы получения порошков 200 Факторы, определяющие процесс электролиза расплавленных солей Температура электролита Электролиз ведут при температурах, превышающих температуру плавления компонентов электролита, но ниже температуры плавления выделяемого на катоде металла. С повышением температуры электролита и, соответственно, металла на катоде выход по току снижается, так как возрастает интенсивность химического взаимодействия катодного осадка с солевым расплавом. Лекция
Физико-химические методы получения порошков 201 Факторы, определяющие процесс электролиза расплавленных солей Оптимальной является температура, при которой в наименьшей степени протекают вторичные и побочные процессы, снижающие выход по току, при сохранении постоянными других физико-химических свойств электролита. Для снижения температуры плавления электролита в него вводят добавки солей (обычно хлористые и фтористые соединения щелочных и щелочноземельных металлов), у которых катионы электроотрицательнее выделяемого металла. Лекция
Физико-химические методы получения порошков 202 Факторы, определяющие процесс электролиза расплавленных солей Плотность тока Выход по току растет с увеличением плотности тока. Оптимальное значение плотности тока будет соответствовать наибольшему выходу по току, при котором уменьшение потерь выделяемого металла вследствие его вторичного растворения в электролите не будет сопровождаться сильным повышением разряда катионов металла с более электроотрицательным потенциалом. Лекция
Физико-химические методы получения порошков 203 Факторы, определяющие процесс электролиза расплавленных солей Однако слишком высокая плотность тока увеличивает падение напряжения в слое электролита и повышает расход электроэнергии. С увеличением катодной плотности тока соответственно возрастает и анодная плотность тока, что приводит к проявлению анодного эффекта , протеканию побочных процессов – выделения на катоде наряду с основным металлом другого, более электроотрицательного металла. Лекция
Физико-химические методы получения порошков 204 Факторы, определяющие процесс электролиза расплавленных солей Межэлектродное расстояние С увеличением межэлектродного расстояния: — затрудняется перенос растворенного металла от катода к аноду; — уменьшается градиент концентрации растворенного металла; — уменьшается скорость циркуляции электролита при большем объеме расплава. Следствие: абсолютные потери металла уменьшаются, а выход по току возрастает. При чрезмерном увеличении межэлектродного расстояния возрастает затрата электрической энергии (возможен перегрев электролита, что отрицательно влияет на выход по току). Лекция
Физико-химические методы получения порошков 205 Факторы, определяющие процесс электролиза расплавленных солей Анодный эффект – явление резкого возрастания напряжения на ванне с одновременным падением силы тока и появлением характерных искровых разрядов на аноде. При возникновении анодного эффекта электролит отделяется от поверхности анода прослойкой выделяющегося на нем газа, т. е. наблюдается ухудшение смачиваемости анода электролитом. Повышению критической силы тока, вызывающей анодный эффект, способствует наличие в электролите концентрации поверхностно-активных веществ , повышающих смачивание анода электролитом (хлоридов щелочных металлов или растворимых оксидов). Лекция
Физико-химические методы получения порошков 206 Получение порошка тантала Порошок тантала в промышленных масштабах получают с 1922 г. (США). Электролит – оксифторидный или оксифторидно-хлоридный солевой расплав, состоящий из фторотанталата калия K 2 Ta. F 7 хлористого и/или фтористого калия (натрия), в котором растворен пентаоксид тантала. Лекция
Физико-химические методы получения порошков 207 Получение порошка тантала В расплаве K 2 Ta. F 7 + КС 1 + KF происходит взаимодействие: K 2 Ta. F 7 + KF = K 3 Ta. F 8 и K 2 Ta. F , + КС 1 = K 3 Ta. F 7 Cl , в связи с чем в электролите нет свободного K 2 Ta. F 7. После добавления к расплаву Та 2 О 5 идет реакция его растворения: 3 K 3 Ta. F 8 + Та 2 О 5 + 6 KF = 5 K 3 Ta. OF 4 , или K 3 Ta. F 8 + 2 Та 2 О 5 + 12 KF = 5 K 3 Ta О 2 F 4. Лекция
Физико-химические методы получения порошков 208 Получение порошков тантала В оксифторидно-хлоридных электролитах существуют ионы К + , CI – , F – , Ta. F 8 3– , Ta О F 6 3– (при содержании в электролите Та 2 О 5 5 % Ta 2 О 5 ), Ta. F 7 Cl 3– и др. , в том числе Та 5+ . На катоде идет разрядка ионов Та 5+ : Та 5 + 5 → Та (Таẽ 5+ + 2 → Таẽ 3+ + 3 → Та). ẽ Схема анодного процесса : Ta. OF 6 3– – 2 = ẽ Ta. F 5 + F – + 0, 5 О 2 ( О 2 – – 2 → 0, 5 Оẽ 2 ); Ta. F 5 + 3 F – = Ta. F 3– ; 0, 5 О 2 + С = СО (О 2 + С = СО 2 ). Лекция
Физико-химические методы получения порошков 209 Получение порошков тантала Ионы Ta. F 8 3– , реагируя с вводимым в расплав Та 2 О 5 , образуют ионы Ta. OF 6 3–. Состав отходящих газов, %: ~ 95 СО 2 , 5– 7 СО, 0, 3 О. Электролизу в конечном счете подвергается Та 2 О 5 , вводимый в расплав. Лекция
Физико-химические методы получения порошков 210 Получение порошков тантала Для получения тантала, используют электролит состава, %: 3– 3, 5 Та 2 О 5 , 25– 30 K 2 Ta. F 7 , 66, 5– 72 Na. Cl + KCl. Температура плавления электролита – 600 °С (это позволяет вести электролиз при 700 °С). При обеднении электролита по Та 2 О 5 до 1, 5– 2 % возможно проявление анодного эффекта. В электролит периодически добавляют Та 2 О 5 , а также производят его корректировку и по другим компонентам. Применяют электролизеры двух типов: — графитовый тигель (анод) и металлический стержень (катод), опускаемый в центр тигля; — металлический тигель (катод) и анод в виде графитового стержня или полой перфорированной трубки в центре тигля. Лекция
Физико-химические методы получения порошков 211 Получение порошков тантала Электролиз проводят при напряжении 2, 5– 7 В и плотности тока на катоде 3000– 5000 А/м 2 , а на аноде 12000– 16000 А/м 2. Частицы танталового порошка оказываются вкраплены в застывший электролит, который защищает тантал от окисления при остывании. Размер частиц порошка составляет 30– 120 мкм. Лекция
Физико-химические методы получения порошков 212 Получение порошков тантала Для отделения порошка тантала от электролита: — катодный продукт дробят в шаровой мельнице, работающей в замкнутом цикле с воздушным сепаратором; — отмывают порошок тантала от остатков электролита на концентрационных столах в струе воды; — обрабатывают в фарфоровых реакторах горячей смесью соляной и азотной кислот (с целью отмывки примесей молибдена или железа); — промывают водой и сушат. При помоле сухая смесь составных частей электролита отделяется и может быть использована для загрузки в ванну для проведения электролиза. Лекция
Физико-химические методы получения порошков 213 Получение порошков тантала Хлоридный способ В расплав ( Na. Cl + Na. F , Na. Cl + KCl + KF ) с температурой 750– 950 ° C вводят жидкий или парообразный пентахлорид тантала (в расчете на содержание < 10 % Та). Напряжение на ванне 6– 8 В, катодная плотность тока 27000 А/м 2 , анодная плотность тока 2000 А/м 2. Лекция
Физико-химические методы получения порошков 214 Получение порошков тантала Хлоридный способ Метод рафинирования тантала (известен с 1906 г. ) в хлоридно-фторидных и фторидных расплавах, содержащих K 2 Ta. F 7 , ( K 2 Ta. F 7 20 %, Na. Cl 50– 60 %, Na. F 15– 30 %). При электрорафинировании (температура 840– 940 °С, катодная плотность тока 8000 А/м 2 ) происходит очистка тантала от большинства примесей, присутствующих в анодном материале. Содержание железа снижается в 10– 50 раз, кислорода и углерода в 10– 100 раз, вольфрама и молибдена в 104– 105 раз; затруднена лишь очистка от ниобия. Выход по току достигает 85 %. Лекция
Физико-химические методы получения порошков 215 Получение порошков ниобия Применяют два типа электролитов: K 2 Nb. F 7 – KCl – KF – Nb 2 О 5 и K 2 Nb. F 7 – KCl – Na. Cl (используемый для получения или рафинирования ниобия). В расплаве первого электролита (до введения Nb 2 О 5 ) происходит взаимодействие по реакциям K 2 Nb. F 7 + KF = K 3 Nb. F 8 K 2 Nb. F 7 + KCl = K 3 Nb. F 7 Cl Лекция
Физико-химические методы получения порошков 216 Получение порошков ниобия При добавлении пентаоксида ниобия в присутствии избытка KF происходит реакция K 2 Nb. F 7 + 13 KF + 2 Nb 2 О 5 = 5 K 3 Nb 0 2 F 4. В электролите присутствуют комплексные ниобийсодержащие ионы вида Nb. F 8 3– , Nb. F 7 2– , Nb. OF 4 3–. В электролите для рафинирования ниобия соединение K 3 Nb. F 7 Cl диссоциирует на К + , CI – и Nb. F 7 2–. Лекция
Физико-химические методы получения порошков 217 Получение порошков ниобия Электролиз оксифторидных расплавов : — очищенные соли расплавляют в никелевом тигле (катоде); — в расплав вводят Nb 2 О 5. Анод – графитовый стержень, температура электролита около 750 о С; напряжение на ванне 2, 5 В, катодная плотность тока 5000– 6000 А/м 2 , выход по току не превышает 30 %. Получаемый осадок крупнозернист и загрязнен низшими оксидами ниобия. Чистые порошки получают электролизом в хлоридных ( Na. Cl + KC 1) и хлоридно-фторидных ( Na. Cl + Na. F , KC 1 + Na. Cl + + KF и др. ) расплавов с питанием ванны Nb. Cl 5 (2– 3 % Nb в электролите). Лекция
Физико-химические методы получения порошков 218 Получение порошков ниобия Температура электролита 680– 720 °С, катодная плотность тока 10000– 20000 А/м 2. Выход по току не превышает 60 %. Электрорафинированием в электролите K 2 Nb. F 7 , + KC 1 + Na. Cl при 700– 750 °С и катодной плотности тока 1000– 8000 А/м 2 получают порошок ниобия, содержание примесей в котором понижено: по железу на 1– 3, по кремнию на 1– 1, 5, по углероду на 1– 1, 5 и по кислороду на 1 порядок. Лекция
Физико-химические методы получения порошков 219 Получение порошков титана Получение порошка титана электролизом с растворимым анодом из различных титансодержащих материалов развивается и конкурирует с методами металлотермии. Значение процесса получения порошков титана с применением электролиза особенно важно в связи с необходимостью переработки титановых отходов. Стоимость титана в отходах металлургического производства в несколько раз ниже стоимости Ti. Cl 4 , Ti О 2 и сравнима со стоимостью титана в шлаках. Большинство титановых отходов содержит до 4 % механических примесей. Предварительно обезжиренный, промытый и измельченный материал подвергают электрорафинированию. Лекция
Физико-химические методы получения порошков 220 Получение порошков титана Технологическая схема получения порошков титана электролитическим рафинированием его отходов Na. Cl KCl Ti. Cl 4 Прокалка Смешивание Плавка Отходы Ti Отработанный электролит магниевого производства Сушка Очистка Приготовление низших хлоридов. Ar Электролитическое рафинирование Катодный осадок Дробление Классификация фракций Фильтрация Выщелачивание H 2 OHCl Рассев ≥ 0, 18 мм Сушка ≥ 0, 1 мм На выплавку серийных сплавов Затаривание Утилизация Кислые стоки <0, 63 мм ≥ 0, 18 мм <0, 18 мм. Лекция
Физико-химические методы получения порошков 221 Получение порошков титана Технологическая схема производства порошка титана электролитическим рафинированием его отходов включает следующие операции. — подготовки компонентов электролита, их плавления и загрузки в электролизер; — электролитического рафинирования; — удаления и дробления катодного осадка; — выщелачивания остатков электролита; — классификации и сушки полученных порошков. Растворимый анод выполняют из сыпучих (дробленых или измельченных до крупности 5– 40 мм) либо измельченных и сбрикетированных титансодержащих материалов. В качестве солевой основы электролита выбирают системы типа КС l + Na. Cl , KCl + Na. Cl + Mg. Cl 2 или KCl + Na. Cl + Li. Cl. Лекция
Физико-химические методы получения порошков 222 Получение порошков титана Электролиз ведут при температуре 800– 850 °С в атмосфере аргона. При анодном растворении титан переходит в электролит в виде ионов Ti 2+ и Ti 3+ (средняя валентность титана в электролите 2, 2– 2, 3). Катод — из жаростойкой стали. Напряжение на ванне около 6 В. Начальная катодная плотность тока 5000– 15000 А/м 2. Лекция
Физико-химические методы получения порошков 223 Получение порошков титана Анодная плотность тока в 4– 8 раз меньше катодной. Катодный осадок срезают специальным ножом, измельчают до < 5 мм, отделяют от электролита кислотным выщелачиванием, промывают, размалывают, классифицируют и сушат при 65 о С. Выход по току достигает 90 %, а расход (суммарный) электроэнергии составляет 10– 11 к. Втч/кг. Углерод находится в свободном состоянии на поверхности электролита или в анодном остатке в виде карбида. Азот содержится в анодном остатке в виде нитрида или выделяется с анодными газами. Кремний удаляется с газами в виде Si. Cl 4. Лекция
Физико-химические методы получения порошков 224 Получение порошков титана Электрорафинирование сплавов на основе титана проводится при тех же условиях электролиза, что и рафинирование отходов титана. Отделение титана от металлических примесей основано на различии их электродных потенциалов. Лекция
Физико-химические методы получения порошков 225 Получение порошков титана Значения стандартных потенциалов титана и основных легирующих металлов по отношению к серебряному электроду в хлоридных расплавах Na. Cl + KC 1: Mn/Mn 2+ Zr/Zr 2+ Ti/Ti 2+ Al/Al 2+ V/V 2+ Cr/Cr 2+ Fe/Fe 2+ – 1, 41 – 1, 36 – 1, 24 – 1, 08 – 0, 97 – 0, 88 На степень очистки влияют поляризация, которая определяется: — перепадом концентраций ионов титана в порах растущего шламового слоя; — уменьшение концентрации титана в поверхностных слоях анода; — экранирование анода шламовым слоем. Лекция
Физико-химические методы получения порошков 226 Получение порошков циркония Электролиз проводят в расплаве Na. Cl или КС l , содержащем K 2 Zr. F 6. В электролизере у катода протекают реакции Zr. F 6 2– → Zr 6 + 6 F – , Zr 6 + → ẽ Zr 3+ + → ẽ Zr 2+ + 2 → ẽ Zr. У анода разряжаются ионы фтора, который реагирует с ионами натрия или калия: 4 F – + 4 KCl(4 Na. Cl) – 4 ẽ = 4 KF(4 Na. F) + 2 Cl 2 ↑. Лекция
Физико-химические методы получения порошков 227 Получение порошков циркония В ванне электролизера постепенно накапливается фторид калия или натрия. Катодная плотность тока для электролита состава 25– 30 % К 2 Zr. F 6 + 75 – 70 % КС l соответствует 35000– 45000 А/м 2. Катодный осадок (около 30 % порошка циркония с размером частиц 50– 200 мкм ) удаляют с катода, дробят и обрабатывают водой, подкисленной соляной кислотой, промывают и сушат в вакууме при 50– 60 °С. Лекция
Физико-химические методы получения порошков 228 Получение порошков железа Электролизом расплавленных сред получают порошки железа исключительно высокой чистоты. Для электровыделения железа используют растворимые аноды из губчатого железа (< 95 % Fe ), чугуна (< 90 % Fe ) или рудно-угольных окатышей ( Fe 3 0 4 + С). Электролитом служат расплавы КС l + Na. Cl или КС l + Na. Cl + Mg. Cl 2 , в которых растворен Fe. Cl 2 в количестве до 12– 14 %. Лекция
Физико-химические методы получения порошков 229 Получение порошков железа Электролит готовят плавлением при 800– 850 °С в аргоне смеси Na. Cl (22 %), КС l (30– 31 %), Mg. Cl 2 (33– 36 % ), и безводного Fe. Cl 3 и порошок чистого железа (для перевода Fe. Cl 3 в Fe. Cl 4 ). Электролиз ведут в атмосфере азота при 750– 900 °С. Катод – железный , напряжение на электролизере 6 В, катодная плотность тока < 50000 А/м 2 , анодная плотность тока на порядок меньше катодной. Процесс наращивания катодного осадка ведут циклически с остановкой через 1– 2 ч для его съема. Выход по току 80– 90 %. Лекция
Физико-химические методы получения порошков 230 Список рекомендуемой литературы. Лекция 19 1. Зиликман, А. Н. Металлургия редких металлов / А. Н. Зиликман, Б. Г. Коршунов – М. : Металлургия, 1991. – 432 с. 2 . Либенсон, Г. А. Процессы порошковой металлургии : учебник для вузов в 2 ч. / Г. А. Либенсон, В. Ю. Лопатин, Г. В. Комарницкий. – М. : МИСИС, 2001. 3. Ничипоренко, О. С. Порошки меди и ее сплавов / О. С. Ничипоренко, А. В. Помосов, С. С. Набойченко – М. : Металлургия, 1988. – 206 с.
Физико-химические методы получения порошков 231 Лекция 20 Получение порошков металлов методом термической диссоциации карбонилов • Технология карбонил-процесса • Строение карбонилов • Классификация карбонилов • Технологии получения карбонильных порошков • Аппаратурное оформление процесса
Физико-химические методы получения порошков 232 Технология карбонил-процесса Определение. Карбонильный металлический порошок – металлический порошок, полученный разложением карбонильных соединений металлов. Карбонилами металлов называют химические соединения металлов с группами (лигандами) СО. Схематически карбонильный метод (карбонил-процесс) может быть представлен транспортной химической реакцией: Ме а Б в + с. СО → [в. Б] + Ме а (СО) с → а. Ме + с. Со, где Me – переходный металл V – VIII групп периодической системы; Б – балластные вещества (кислород, солевой остаток, примеси и т. п. ); а, в, с – коэффициенты, численные значения которых зависят от природы Me. Лекция
Физико-химические методы получения порошков 233 Технология карбонил-процесса Технологически карбонил-процесс основывается на обратимой реакции: а. Ме + с. СО ↔ Ме а (СО) с Процесс образования карбонила Ме а (СО) с оказывается тесно связанным с диффузионными процессами: — с диффузией СО из газовой фазы к поверхности твердого тела; — с диффузией молекул образующегося карбонила из глубины твердого тела к его поверхности, а затем в газовую фазу. Лекция
Физико-химические методы получения порошков 234 Технология карбонил-процесса Диффузия СО в глубь твердого материала распространяется сплошным фронтом , параллельным внешней поверхности твердого материала. Скорость реакции образования карбонила Ме а (СО) с значительно превосходит скорость диффузии СО к реакционной поверхности, которая и лимитирует общий ход процесса. На образование карбонила металла большое влияние оказывают: — температурные условия процесса; — наличие веществ, тормозящих или ускоряющих реакцию. Лекция
Физико-химические методы получения порошков 235 Строение карбонилов Карбонилы металлов могут быть моно- и полиядерными. В карбонилах металлов, являющихся координационными соединениями, группа СО как донор электронов занимает одно координационное место и присоединяется через атом углерода непосредственно к металлу координативной одинарной связью. Химическая связь в карбонилах металлов обусловливается сближением атомов металла с атомами углерода лигандов СО. Для описания строения истинных карбонилов Н. Сиджвик предложил использовать понятие эффективного атомного номера. ЭАН — число электронов в конфигурации атома инертного газа, замыкающего тот ряд периодической системы элементов, в котором помещается соответствующий металл, образующий карбонил. Разность между ЭАН и атомным номером металла показывает количество электронов, которое необходимо приобрести металлу-акцептору у лигандов СО (доноров). Лекция
Физико-химические методы получения порошков 236 Строение карбонилов В карбонилах металлов возможно существование четырех типов связей: 1) координационно-ковалентная связь Me –СО, при которой атом С отдает металлу электронную пару (σ-связь) и дополнительно связывается с металлом обратной π-связью с участием d -электронов металла; 2) ковалентная связь Me – Me в биметаллических карбонилах, при которой каждый атом металла поставляет для связи один электрон; 3) ковалентная σ-связь между металлом и СО , при которой атом С служит мостиком между двумя атомами металла, образуя связь с каждым из них; 4) в карбонилах типа Ме 6 (СО) 16 имеется связь Me –СО, при которой СО служит мостиком между тремя атомами металла (эти карбонилы не подчиняются правилу ЭАН). Лекция
Физико-химические методы получения порошков 237 Классификация карбонилов По структурному признаку карбонилы металлов можно разделить на одноядерные и многоядерные: 1) одноядерные – с одним атомом металла в молекуле, например Fe ( CO ) 5 , Ni ( CO ) 4 , Me ( CO ) 6 и др. ; 2) многоядерные (с общей формулой Ме а (СО) с ): — монометаллические – с двумя или более одинаковыми атомами металла в молекуле (например Со 2 (СО) 8 , Fe 2 ( CO ) 9 , Fe 3 ( CO ) 12 и др. ); — полиметаллические – с двумя или более разными атомами металлов в молекуле (например Mn 2 Fe ( CO ) 14 , Fe. Ru ( CO ) 12 , Mn. Re. Fe ( CO ) 14 и др. ); — смешанные – с атомами металлов и неметаллов, например CFe 5 ( CO ) 15 , CRu 6 ( CO ) 17 , SCo ( CO ) 9 и др. Лекция
Физико-химические методы получения порошков 238 Технология получения карбонильного порошка При термическом воздействии на карбонилы электроны стремятся занять исходное положение, атом металла из возбужденного состояния стремится перейти в нейтральное, что делает карбонилы исключительно удобными исходными объектами для получения металлов путем термической диссоциации по схеме Ме а (СО) с → а. Ме + с. СО. Термическая диссоциация карбонилов наступает еще до достижения ими температуры кипения. Это объясняется особым характером взаимодействия между металлами-комплексообразователями и лигандами СО: при нагреве у карбонилов имеет место локальное вытягивание электронных орбит у отдельных лигандов СО. Лекция
Физико-химические методы получения порошков 239 Технология получения карбонильных порошков Формирование частиц карбонильного порошка включает два основных процесса: — распад молекул карбонила; — кристаллизации парообразного металла. Распад молекул карбонила приводит к появлению появление атомов металла и газообразных молекул СО. Процесс кристаллизации включает три этапа: 1) образования зародышей; 2) развития зародышей (до размера 4– 20 нм); 3) формирования металлических частиц. На скорость образования зародышей и формирования металлических кристаллов влияют: — степень разрежения в аппарате; — плотность паров образующегося металла; — температура. Лекция
Физико-химические методы получения порошков 240 Технология получения карбонильных порошков В промышленных масштабах карбонил-процесс используют для производства никеля, железа, кобальта, вольфрама, хрома, молибдена и некоторых металлов платиновой группы. Наибольшее практическое значение в настоящее время карбонильный метод имеет для получения порошков никеля и железа , карбонилы которых Ni ( CO ) 4 и Fe ( CO ) 5 были получены соответственно в 1888 г. и в 1891 г. Лекция
Физико-химические методы получения порошков 241 Технология получения карбонильных порошков В 1902 г. в Англии (г. Клайдах, Южный Уэльс) началось промышленное производство карбонильного никеля (метод Монда), при котором синтез и термическое разложение карбонила ведут при давлении, близком к атмосферному, и температурах 50– 60 °С и 200– 250 °С соответственно. Исходным сырьем в процессе служит медно-никелевый штейн ( Cu. S – Ni. S – Fe. S ), а конечный продукт – карбонильный никель Монда – представляет собой сростки частиц (гранулы) диаметром 5– 10 мм, содержание никеля в которых 99, 5– 99, 8 %. Лекция
Физико-химические методы получения порошков 242 Технология получения карбонильных порошков Схема получения порошка карбонильного никеля 1 – газгольдер с СО; 2 – компрессор; 3 – ресивер; 4 – колонна синтеза карбонила; 5 – циркуляционный насос; 6 – холодильник; 7 – сборник сконденсированного карбонила; 8 – сборник сырого карбонила; 9 – ректификационная колонна; 10 – сборник-испаритель готового карбонила; 11 – разложитель (диссоциатор) карбонила 1 23 4 5 6 7 109 8 11 Лекция
Физико-химические методы получения порошков 243 Технология получения карбонильных порошков Производство порошков карбонильного железа в СССР начато с конца 30 -х годов прошлого столетия. Синтез карбонила Fe ( CO ) 5 ведут с использованием в качестве сырьевых материалов губчатого железа, штейна, железой руды, скрапа, стружки. Процесс получения карбонила включает следующие операции: — подготовку исходного сырья (измельчение до кусков 10– 25 мм); — загрузку сырья в колонну синтеза (рассчитан на рабочее давление до 20 МПа); — опрессовку системы сжатым азотом; — сброс азота в атмосферу; — заполнение колонны оксидом углерода до давления 5– 10 МПа; — включение системы циркуляции реакционного газа через слой загруженного в колонну железосодержащего сырья; — синтез карбонильного соединения. Лекция
Физико-химические методы получения порошков 244 Аппаратурное оформление процесса Конструкция испарителей а – испаритель с наружной рубашкой; б – испаритель с внутренним змеевиком. 1 – патрубок для ввода карбонила; 2 – патрубок для вывода продувочного газа; 3 – обогреваемая рубашка; 4 – обогреваемый змеевик 1 1 2 2 4 3 а б. Лекция
Физико-химические методы получения порошков 245 Аппаратурное оформление процесса Схема промышленного аппарата разложения карбонила с газовым обогревом Ǿ 1000 h 1 t 5 t 4 t 1 t 2 t 3 ввод газа h 2 h 1 =5000 мм h 1 =1000 мм вывод газа Стандартный режим разложения пентакарбонила железа: — температура верхней зоны аппарата разложения (0, 8 его высоты) t 5 = 295– 300 °С, — средней зоны (0, 6 его высоты) t 3 = 305– 310 °С, — нижней зоны (0, 3 высоты) t 2 = 310– 345 °С. «Падающий» режим (градиент температур 12– 15 °С); Конвекционный режим ( t 5 = t 2 = 270– 280 °С, t 3 = 280– 290 °С). При «падающем» температурном режиме получают более чистые порошки. Лекция
Физико-химические методы получения порошков 246 Аппаратурное оформление процесса Схема получения карбонильных порошков вольфрама и молибдена 1 – подогреватель водорода; 2 – сублиматор; 3 – теплообменник; 4 – аппарат разложения; 5 – фильтр; 6 – приемник порошка; 7 – баллон с азотом; 8 – фильтр; 9 – колонна с медной стружкой; 10 – холодильник; 11 – осушитель; 12 – баллон с водородом; 13 – катализатор 1 2 3 4 5 67 8 9 10 11 12 13 11 8 Лекция
Физико-химические методы получения порошков 247 1. Сыркин, В. Г. Карбонильные металлы / В. Г. Сыркин. – М. : Металлургия, 1978. – 256 с. 2 . Либенсон, Г. А. Процессы порошковой металлургии : учебник для вузов в 2 ч. / Г. А. Либенсон, В. Ю. Лопатин, Г. В. Комарницкий. – М. : МИСИС, 2001. Список рекомендуемой литературы. Лекция
Физико-химические методы получения порошков 248 Лекция 21 Получение порошков методом межкристаллитной коррозии, испарения-конденсации, термодиффузного насыщения • Метод межкристаллитной коррозии. • Метод испарения–конденсации • Метод термодиффузного насыщения
Физико-химические методы получения порошков 249 Метод термодиффузного насыщения Методом термодиффузного насыщения порошка или губки (основы) получают порошки сталей и сплавов, легированных элементами, оксиды которых трудновосстановимы. На практике применяют два основных способа насыщения: — из твердых засыпок; — из точечных источников. Лекция
Физико-химические методы получения порошков 250 Метод термодиффузного насыщения При применении способа твердых засыпок источник насыщения (порошок легирующего металла, хлористого аммония ( NH 4 Cl ) и наполнителя) равномерно располагается вокруг насыщаемого порошка (губки) металла чередующимися с ним слоями. Недостатками способа являются : — неравномерное распределение насыщающего металла по всей толщине порошка-основы; — трудное регулирование состава получаемого порошка, недостаточно полное использование металла из насыщающей засыпки. Лекция
Физико-химические методы получения порошков 251 Способ насыщения из точечных источников более эффективен и позволяет получать порошки сплава однородного состава. Способ предусматривает: — приготовление смеси из порошков металла-основы и легирующего металла; — введения в подготовленную смесь хлористого аммония; — нагрев подготовленной шихты в течение определенного времени. Метод термодиффузного насыщения. Лекция
Физико-химические методы получения порошков 252 Иногда вместо порошка легирующего металла в шихту вводят его оксид и углерод. В этом случае легирующий элемент образуется в процессе нагрева шихты в результате протекания соответствующей реакции восстановления. Получение порошков, содержащих три и более металлических компонента, может быть реализовано в два этапа: 1 -й этап – совместное восстановление смеси легковосстановимых оксидов металлов; 2 -й этап – насыщение частиц получаемого сплава трудновосстановимыми элементами. Метод термодиффузного насыщения. Лекция
Физико-химические методы получения порошков 253 Метод термодиффузного насыщения Получение порошка стали Х 30 Исходные материалы: железный порошок (0, 063– 0, 16 мм), порошок хрома (< 0, 1 мм), аммоний хлористый и двууглекислый. Процесс термодиффузного насыщения железного порошка включает операции: — смешивания шихты (54, 2 % Fe , 29, 2 % Сг, 2, 5 % NH 4 C 1 и 14, 1 % NH 4 HC О 3 ) в лопастном смесителе; — загрузки шихты в контейнер ; — герметизации слоя шихты (засыпают песком, поверх которого помещают плавкий затвор из плавленого и измельченного натросиликатного порошка); Лекция
Физико-химические методы получения порошков 254 Метод термодиффузного насыщения Получение порошка стали Х 30 — диффузионного насыщения при 1100– 1220 °С (4– 5 ч) в атмосфере остроосушенного конвертированного природного газа или водорода; — дробления и размола губки в молотковых и шаровых мельницах; — рассева на вибросите (фракцию > 0, 25 мм направляют на доизмельчение); — отмывки порошка от остаточных хлоридов; — сушки порошка железа. Лекция
Физико-химические методы получения порошков 255 Метод термодиффузного насыщения Получение порошка эвтектоидной углеродистой стали Смесь на основе восстановленного порошка железа с 2 % сажи и 0, 5 % Ва. СО 3 , загружают в поддон с неплотно закрывающейся крышкой и нагревают в защитной среде при 1030 °С в течение 4 ч. В процессе термической обработки углерод взаимодействует с Ва. СО 3 по реакции С + Ва. СО 3 = Ва + СО 2 + СО Образовавшийся газ обволакивает частицы порошка и науглероживает их. Лекция
Физико-химические методы получения порошков 256 Метод термодиффузного насыщения Получение порошка сплавов Fe – Ni Прокатную окалину (содержание Fe общ около 74, 5 %) с размером частиц < 0, 1 мм смешивают с углекислым никелем основным и сажей. Шихту выдерживают при 1100 °С в течение 4 ч в водороде или конвертированном природном газе. Полученную губку с содержанием никеля до 25 % размалывают. Порошок железоникелевого сплава можно использовать для диффузионного насыщения другими легирующими элементами (хромом, вольфрамом). Лекция
Физико-химические методы получения порошков 257 Метод термодиффузного насыщения Составы шихт и режим диффузионного насыщения (Т = 1100 °С, время – 5 ч) для получения порошков коррозионно-стойких сталей Марка порошка Состав исходной шихты, % Химический состав порошка, % Порошок сплава Fe – Ni Cr NH 4 Cl * NH 4 HCO 3 * Cr Ni C Х 18 Н 9 76(10, 5 % Ni ) 24 3 12 18 , 1 9, 0 0, 11 Х 18 Н 15 76(10, 5 % Ni ) 24 3 12 19, 9 16, 4 0, 10 Х 23 Н 18 76(10, 5 % Ni ) 30 3 12 24, 6 17, 7 0, 17 Примечание: * – сверх 100 % массы металлических порошков. Лекция
Физико-химические методы получения порошков 258 Метод межкристаллитной коррозии В основе этого метода лежит разрушение (растворение) межкристаллитных прослоек в сплавах специально подобранными растворами-травителями. Исходным материалом для получения порошка служат отходы металлообработки (стружка, обрезки листов и лент и т. п. ). Порошки, полученные методом межкристаллитной коррозии, используются при производстве фильтров и конструкционных материалов. Лекция
Физико-химические методы получения порошков 259 Метод межкристаллитной коррозии В случае использования в качестве исходного сырья сплавов из двух или более металлов, растворимых один в другом в жидком состоянии и обладающих полной взаимной нерастворимостью (или ограниченной растворимостью) в твердом состоянии, один из металлов удаляется из сплава, а другой остается в виде порошка. Чувствительность к межкристаллитной коррозии может быть повышена соответствующей термической обработкой сплавов. Лекция
Физико-химические методы получения порошков 260 Метод межкристаллитной коррозии а б в г а – исходная структура сплава; б – структура сплава после термообработки; в – образец в травителе (начальная стадия разрушения межкристаллитных прослоек); г – порошок сплава (межкристаллитные прослойки полностью разрушены)Лекция
Физико-химические методы получения порошков 261 Метод «Испарение–конденсация» Этот метод предусматривает: — перевод компактного или жидкого металла в парообразное состояние (первая фаза процесса, связанная с испарением вещества); — конденсацию образовавшихся паров (вторая фаза процесса) на поверхностях, температура которых ниже точки плавления осаждаемого металла. В обычных условиях над любой поверхностью наблюдается определенное давление паров вещества, соответствующее равновесию, при котором скорость испарения с поверхности равна скорости конденсации паров на ней. Если же заставить пары вещества конденсироваться (осаждаться) на какой-либо другой поверхности (например, более холодной по сравнению с первой), то равновесие нарушится и будет происходить непрерывное испарение вещества. Лекция
Физико-химические методы получения порошков 262 Метод «испарение – конденсация» Конденсация металлического пара в виде дисперсной фазы возможна, если соблюдаются следующие условия: 1. Имеется высокое пересыщение пара, которое вызывает одновременное и множественное возникновение зародышевых центров конденсированной фазы, благодаря чему обедняется паром газовая среда, замедляется рост частиц и система сохраняет дисперсное состояние формируемых частиц. 2. В конденсирующемся паре присутствует нейтральный газ. Лекция
Физико-химические методы получения порошков 263 Метод «испарение – конденсация» Нейтральный газ служит средой, препятствующей коагуляционному и диффузионному росту частиц. Давление нейтрального газа может колебаться от 10 – 3 до 10 2 к. Па. Процесс конденсации металлического пара в порошок может протекать на охлажденной поверхности – гетерофазно, а в объеме – гомофазно и гетерофазно. Условной границей между гомо- и гетерофазным процессом является интервал пересыщений пара (10 4 – 10 8 ) относительно равновесного состояния. Ниже величины 10 4 порошок образуется только на поверхности, выше 10 6 – в объеме. Лекция
Физико-химические методы получения порошков 264 Метод «испарение – конденсация» Гетерофазный процесс образования порошка представляет собой массовый рост кристаллических частиц, зарождение которых происходит на макроскопических дефектах поверхности. Формирование частиц протекает в несколько этапов: — формирования на охлаждаемой подложке сплошной тонкой пленки; — роста кристаллов общим фронтом перпендикулярно подложке; — приобретения растущими кристаллами выраженной огранки (в виде пирамид или призм размером 10– 20 мкм); — прорастания частиц друг в друга. Лекция
Физико-химические методы получения порошков 265 Метод «испарение – конденсация» Гомофазный процесс инициируется пересыщением пара, в результате чего происходит гомо- и гетерофазное образование зародышей частиц порошка. Они растут слиянием в газовом потоке (коагуляционным путем). Форма и структура частиц зависят от тепло- и массопереноса в газовой среде. Когда температура газовой среды выше 0, 7 Т пл металла, по механизму «пар – жидкость – твердое» образуются частицы сферической формы. При температуре ниже 0, 77 Т пл металла образуются (по механизму «пар – кристалл» ) частицы с выраженной огранкой в виде призм, пирамид и сложных изометрических кристаллов по схеме «пар – кристалл» . Лекция
Физико-химические методы получения порошков 266 Метод «испарение – конденсация» Смешанный процесс (гомо-, гетерофазный) В этом процессе новая фаза появляется в объеме зоны конденсации, а рост частиц происходит после осаждения их на холодной поверхности. Для порошков, получаемых в результате смешанного процесса, характерно наличие частиц смешанных форм и структур: гранных, сферических поли- и монокристаллического строения. Лекция
Физико-химические методы получения порошков 267 Метод «испарение – конденсация» Смешанный процесс (гомо-, гетерофазный) Метод «испарение – конденсации» целесообразно использовать при получении порошков металлов с большим или заметным давлением паров при сравнительно низких температурах (цинк, магний, кадмий, бериллий и др. ). Размер частиц получаемого порошка колеблется от 10– 20 мкм до < 0, 1 мкм. Чистота частиц – высокая (наблюдается поверхностное окисление). Лекция
Физико-химические методы получения порошков 268 1. Акименко, В. Б. Металлургия железных и легированных порошков / В. Б. Акименко, В. Я. Буланов, Г. Залазицкий. – М. : Металлургия, 1992. – 256 с. 2 . Либенсон, Г. А. Процессы порошковой металлургии : учебник для вузов в 2 ч. / Г. А. Либенсон, В. Ю. Лопатин, Г. В. Комарницкий. – М. : МИСИС, 2001. Список рекомендуемой литературы. Лекция
Получение порошков тугоплавких соединений
Получение порошков тугоплавких соединений 270 Оглавление Лекция 22. Методы получения порошков тугоплавких со единений. Получение порошков карбидов и нитридов м еталлов Лекция 23. Получение порошков боридов, силицидов и гидридов металлов Лекция 24. Получение порошков тугоплавких соединени й методами самораспространяющегося высокотемператур ного синтеза и золь-гель процесса
Получение порошков тугоплавких соединений 271 Лекция 22 Методы получения порошков тугоплавких соединений Получение порошков карбидов и нитридов металлов • Структура тугоплавких соединений • Методы получения карбидов металлов • Методы получения нитридов металлов. Лекция
Получение порошков тугоплавких соединений 272 Структура тугоплавких соединений Металлоподобные тугоплавкие соединения различных металлов с водородом ( гидриды ), углеродом ( карбиды ), азотом ( нитриды ), бором (бориды) и кремнием ( силициды ) обладают высокими температурой плавления, твердостью, модулем упругости и химической стойкостью, металлическими свойствами (блеск, термические и электрические свойства близки к свойствам металлов) и способностью к сверхпроводимости. Наибольшее практическое значение имеют карбиды, бориды, нитриды и силициды тугоплавких металлов IV – VI групп периодической системы Менделеева ( Ti , Zr , Hf , V , Nb , Та, Mo , W и др. ). Лекция
Получение порошков тугоплавких соединений 273 Структура тугоплавких соединений Структура тугоплавких соединений зависит от соотношения атомных радиусов металла r Me и неметалла (металлоида) r х. По правилу Хэгга , при r Me / r х 1, 7) образуется структура, очень похожая на ту, которой обладает соответствующий металл, но с неметаллическими атомами, расположенными в междоузлиях кристаллической решетки (так называемые фазы внедрения), а при r Me / r х > 0, 59 возникает хотя и металлическая фаза, но с более сложной кристаллической решеткой. Лекция
Получение порошков тугоплавких соединений 274 Атомные радиусы и их соотношения для некоторых металлов и металлоидов Металл и его атомный радиус, нм Металлоиды* и соотношения атомных радиусов металлоида и металла В С N Н Ti 0, 147 0, 59 0, 52 0, 48 0, 20 V 0, 134 0, 65 0, 57 0, 53 0, 22 Сг 0, 136 0, 64 0, 57 0, 52 0, 22 Zr 0, 160 0, 54 0, 48 0, 44 0, 19 Nb 0, 146 0, 60 0, 53 0, 49 0, 20 Mo 0, 139 0, 63 0, 55 0, 51 0, 22 Hf 0, 158 0, 55 0, 49 0, 45 0, 19 Та 0, 146 0, 60 0, 53 0, 49 0, 20 W 0, 139 0, 63 0, 55 0, 51 0, 22 Примечание. * – для В, С, N , Н — атомные радиусы соответственно 0, 087; 0, 077; 0, 071; 0, 030 нм. Кремний , атомный радиус которого 0, 117 нм, образует с переходными металлами растворы типа замещения, а не внедрения. Лекция
Получение порошков тугоплавких соединений 275 Методы получения карбидов металлов В зависимости от требований, предъявляемых к карбидам в отношении состава, содержания примесей, стоимости, применяют тот или иной метод их получения. К основным методам получения карбидов относятся: — прямой синтез из элементов; — восстановление оксидов металлов углеродом с одновременной карбидизацией; — плазмохимический метод; — осаждение из газовой фазы; — электролиз расплавленных сред. Исторически первым был способ получения карбидов из смесей соответствующих металлов с углем. Лекция
Получение порошков тугоплавких соединений 276 Классификация методов получения карбидов металлов В среде восстановительного газа В вакууме Спекание методом горячего прессования В расплаве При температуре ниже Т пл В восстановительной среде В вакууме. Исходные материалы Осаждение из газовой фазы. Восстановление оксидов Электролиз расплавленных сред. Прямой синтез из элементов. Плавление компонентов шихты Нагрев при температуре ниже температуры плавления Плазмохимический синтез Восстановление оксидов углеродом Восстановление оксидов углеродсодержащими газами Взаимодействие металлов или их оксидов с углеродсодержащими газами Взаимодействие галогенидов с углеродсодержащими газами Разложение карбонилов в среде водорода. Лекция
Получение порошков тугоплавких соединений 277 Получение карбидов прямым синтезом из элементов Технологическая схема производства карбидов синтезом из элементов или восстановлением – карбидизацией Металл Оксид Углерод Смешивание Брикетирование Синтез Размол Просев (классификация) Упаковка порошка. Годная фракция Крупная фракция. Лекция
Получение порошков тугоплавких соединений 278 Получение карбидов прямым синтезом из элементов Проведение процессов синтеза карбидов при температурах ниже оптимальных приводит к замедлению процесса диффузии углерода и тем самым к увеличению длительности карбидизации. Превышение температуры синтеза приводит к спеканию образующихся частиц карбида, что затрудняет их дальнейшее измельчение. При производстве карбидов технической чистоты процесс ведут в защитной среде, в качестве которой можно использовать водород, конвертированный газ, реже – диссоциированный аммиак или аргон. Лекция
Получение порошков тугоплавких соединений 279 Методы получения карбидов металлов Термодинамическая характеристика реакций образования некоторых карбидов прямым синтезом из элементов Реакция ΔG ° 298 , к. Дж/моль СО ΔG ° Т , к. Дж/моль СО Температурный интервал , К Т i. O 2 + ЗС → Ti. C + 2 CO Zr 0 2 + ЗС → Zr. C + 2 CO Н f О 2 + ЗС → Hf. C + 2 CO V 2 0 3 + 5 С → 2 VC + ЗСО Nb 2 0 5 + 7 C → 2 Nb. C + 5 CO Ta 2 0 5 + 7 С → 2 Та. С + 5 CO З Cr 2 0 3 + 13 C → Сг 3 С 2 + 9 CO 181, 4 281, 0 286, 7 243, 4 136, 2 159, 8 91, 3 221, 9– 0, 136 Т 330, 8– 0, 167 Т 339, 1– 0, 176 Т 324, 5– 0, 272 Т 180, 0– 0, 147 Т 203, 1– 0142 Т 141, 1– 0, 167 Т 1700– 2000– 2200 1200– 1800 1300– 2000 1500– 2000 1000– 1800 Лекция
Получение порошков тугоплавких соединений 280 Методы получения карбидов металлов Получение карбидов методом восстановления оксидов металлов углеродом с одновременной карбидизацией Получение карбидов восстановлением оксидов соответствующих металлов углеродом с одновременной карбидизацией по сравнению с прямым синтезом являются более экономичными. В качестве исходного сырья используют: — оксиды металлов; — сажу; — чистый графит. На процессы восстановления и карбидизации существенно влияет природа оксидов. Лекция
Получение порошков тугоплавких соединений 281 Технологическая схема получения карбидов металлов Технологическая схема включает следующие операции: — сушки или прокаливания сажи или графита с целью удаления влаги и легколетучих примесей (наличие влаги при карбидизации приводит к обезуглероживанию получаемого продукта); — смешивания исходных материалов в шаровой мельнице (углерод берут с 5– 10 % избытком с целью восполнения его потерь при частичном выгорании); — брикетирования шихты или плотной упаковки в графитовые патроны; — синтеза материала в вакуумные печи с графитовым нагревателем или печи Таммана (в среде водорода, осушенного и очищенного от примесей азота). Лекция
Получение порошков тугоплавких соединений 282 Методы получения карбидов металлов Получение карбидов методом восстановления оксидов металлов углеродом с одновременной карбидизацией С св, % 18 14 10 1 2 3 В , ч1 2 3 Зависимость содержания связанного углерода в продуктах восстановления Ti. O 2 при температуре 1900 о С в среде водорода при использовании в качестве восстановителей сажи ( 1 ), газовой сажи ( 2 ) и ламповой сажи ( 3 ). Лекция
Получение порошков тугоплавких соединений 283 Методы получения карбидов металлов Получение карбидов методом восстановления оксидов металлов углеродом с одновременной карбидизацией Существенное влияние на скорость и полноту протекания процесса получения карбидов оказывает сорт восстановителя и его свойства. Из используемых в качестве восстановителей ацетиленовой сажи, графита, каменноугольного пека и продуктов его коксования наилучшие результаты получаются применении пека. Это обусловлено тем, что при пиролизе углеводородов, содержащихся в пеке, идет активное образование частиц сажи. Лекция
Получение порошков тугоплавких соединений 284 Методы получения карбидов металлов Химический состав карбидов, полученных методом восстановления оксидов металлов углеродом с одновременной карбидизацией * Карбид Условия получения Химический состав , % Нагрев температура , °С Выдержка, ч Me C общ C своб C связ. теор Ti. C Zr. C Nb. C Та. С Быстрый 1, 5 ч Быстрый 3, 2 ч Быстрый 1100– 1180 1450– 1500 1000 1500 1700 1800 1600– 1700 0, 5 2, 5 1, 2 0, 5 3, 5 4, 0 1, 0 80, 15 80, 20 88, 35 88, 40 93, 7 19, 85 19, 79 11, 68 11, 63 11, 65 11, 60 6, 31 0, 59 0, 49 0, 13 0, 11 0, 16 0, 10 19, 26 19, 30 11, 52 11, 54 11, 44 6, 21 20, 05 11, 64 11, 45 6, 22 Примечание: * – восстановления оксидов в вакууме. Лекция
Получение порошков тугоплавких соединений 285 Методы получения карбидов металлов Получение карбидов плазмохимическим методом Плазмохимический метод является перспективным для получения порошков тугоплавких соединений с размером частиц менее одного микрометра. Осуществляется этот метод в условиях низкотемпературной плазмы, характеризующейся температурами порядка 5000– 10000 К. В качестве исходных веществ используют металлы, их оксиды, галогениды, а также углеродсодержащее сырье в виде различных углеводородов, других органических соединений и в некоторых случаях углерод в виде графита. Процесс можно осуществлять в дуговых, высокочастотных, сверхвысокочастотных плазмотронах и установках тлеющего разряда. Лекция
Получение порошков тугоплавких соединений 286 Методы получения карбидов металлов Получение карбидов плазмохимическим методом При температурах низкотемпературной плазмы все ее компоненты переходят в активное состояние, в результате чего взаимодействие между ними происходит с повышенной активностью и высокими скоростями образования целевых продуктов. Высокие температуры синтеза позволяют переводить компоненты в паровую фазу, где и происходит их взаимодействие. Последующее быстрое охлаждение парогазовой смеси приводит к образованию ультрадисперсных или аморфных частиц. Благодаря высокой концентрации энергии химические реакции в плазменном потоке протекают практически мгновенно, что обеспечивает высокую производительность метода. Наиболее удобно получать карбиды в дуговом плазмотроне с использованием расходуемых электродов, изготовленных из смеси металла и углерода. Лекция
Получение порошков тугоплавких соединений 287 Методы получения карбидов металлов Получение карбидов осаждением из газовой фазы Этот метод получения карбидов используется при производстве порошков карбидов высокой чистоты, готовых изделий (особенно сложной конфигурации), монокристаллов или плотных покрытий практически на любых подложках. Метод осаждения карбидов из газовой фазы основан на химических и физических взаимодействиях, возникающих при высоких температурах и протекающих преимущественно на границах раздела фаз и вблизи поверхности твердого тела. Лекция
Получение порошков тугоплавких соединений 288 Получение карбидов осаждением из газовой фазы Применительно к получению карбидов процесс осуществляется по схеме Me. Clx + Cn Нm + Н 2 Ме. С + НС 1 + Н 2. В соответствии с этой схемой восстановителем является водород. Углерод, образующийся в результате разложения углеводорода, связывает металл, выделяющийся вследствие восстановления паров хлорида металла водородом, в карбид. Лекция
Получение порошков тугоплавких соединений 289 Получение карбидов осаждением из газовой фазы При получении карбидов электролизом источником металла являются их оксиды, а поставщиком углерода служат карбонаты щелочных металлов. Для увеличения растворимости оксидов процесс ведут в расплавах метабората натрия и хлоридов или фторидов натрия или калия. Лекция
Получение порошков тугоплавких соединений 290 Получение карбидов осаждением из газовой фазы Например: карбида вольфрама получают из электролита следующего состава Na 2 O B 2 O 3 + 2 Na 2 CO 3 + 4, 5 Li. F + (0, 12 – 0, 16) WO 3 . Процесс ведут при силе тока 20 А, напряжении 3 В и температуре 800 °С. В процессе электролиза из карбонатов выделяется углерод, который, соединяясь с металлом, образует соответствующий карбид. Осадок выделяется на графитовом катоде. При проведении электролиза возникают трудности, обусловленные малой стойкостью карбонатов при высокой температуре и низкой растворимостью оксидов карбидообразующих металлов. Поэтому метод электролиза расплавленных сред не находит промышленного применения и используется в основном в исследовательской практике. Лекция
Получение порошков тугоплавких соединений 291 Получение порошков нитридов Основными методами получения нитридов являются: 1) азотирование металлов или их гидридов азотом или аммиаком; 2) метод плазмохимического синтеза; 3) восстановление оксидов металлов твердым восстановителем (углеродом) в среде азота (аммиака); 4) осаждение нитридов из газовой фазы. Лекция
Получение порошков тугоплавких соединений 292 Азотирование металлов (гидридов металлов) Процесс осуществляется под воздействием азота, аммиака или какого-либо другого азотсодержащего газа на порошки металлов или их гидридов в муфельных проходных печах при температуре 800– 1200 °С при непрерывной подаче газа. Существенно влияют на процесс получения нитридов размеры частиц используемых металлических порошков. В зависимости от характеристик исходных порошков длительность процесса составляет 1– 2 ч. Лекция
Получение порошков тугоплавких соединений 293 Азотирование металлов (гидридов металлов) В основе процесса азотирования лежит механизм диффузии азота в глубь металла с образованием на начальных стадиях твердых растворов. Для повышения подвижности атомов азота в поверхностных слоях рекомендуется ступенчато повышать температуру процесса или вести процесс при повышенных давлениях азота (до 20– 25 МПа). Преимущество метода азотирования под давлением – возможность получения нитридов металлов, которые не взаимодействуют с азотом при атмосферном давлении (молибден, вольфрам). Лекция
Получение порошков тугоплавких соединений 294 Азотирование металлов (гидридов металлов) Применение в качестве исходных материалов гидридов металлов имеет ряд преимуществ: — они являются более хрупкими, чем металлы, и легко поддаются измельчению; — выделяющийся при разложении гидридов водород восстанавливает оксидные пленки, повышая тем самым активность металла. Недостатком применения гидридов является замедление процесса азотирования на начальных стадиях. Применение азота для азотирования предпочтительнее, чем аммиака. Образующийся при диссоциации аммиака водород при температуре 400– 600 °С может образовывать гидриды, для разложения которых при более высоких температурах требуется дополнительная затрата энергии. Лекция
Получение порошков тугоплавких соединений 295 Условия синтеза и состав нитридов, полученных азотированием металлов Нитрид Условия синтеза Содержание , % Т , °С Время синтеза , ч Me N Расчетное Практическое Ti. N Zr. N Hf. N VN W 3 N Nb 2 N Ta. N Cr 2 N Mo 2 N* W 2 N 1200 1400 1200 900 1200– 1 300 700 500 2– 6 1– 2 2– 4 1– 2 3– 4 1 1– 2 0, 5– 1 1– 2 6 4 0, 1– 1 77, 35 86, 69– 92, 78 78, 50 90, 70 86, 90 92, 80 92, 88 78, 30 88, 13 – – 77, 5 86, 8 92, 7– 93, 0 78, 2 90, 6 86, 9 97, 82 92, 6 78, 6 88, 0 – – 22, 65 13, 31 7, 28 21, 50 9, 30 13, 10 3, 02 7, 19 21, 70 11, 87 – – 22, 2 13, 2 11, 8 6, 9– 7, 3 20, 3 8, 6 13, 10 6, 6 7, 3 21, 0 11, 95 – –Лекция
Получение порошков тугоплавких соединений 296 Метод плазмохимического синтеза В качестве исходных веществ используются порошки металлов, их галогениды, оксиды, которые вводят либо непосредственно в зону разряда, либо в высокотемпературную струю плазмы вне зоны разряда. Азот, являясь плазмообразующим газом, выступает одновременно в роли одного из компонентов реакции образования нитридов. Среди газов плазмообразователей ( Ar , He , H 2 , N 2 , O 2 ) азот обладает наибольшей удельной теплотой сгорания в том интервале температур, который поддерживают при плазмохимическом синтезе. Лекция
Получение порошков тугоплавких соединений 297 Метод плазмохимического синтеза Наиболее высокопроизводительным является использование в качестве исходных материалов галогенидов металлов, в частности хлоридов. При введении хлоридов в плазменную струю они разлагаются, образуя мельчайшие частицы металлов или их пары. Нитриды образуются из газовой фазы при взаимодействии паров металла с азотом. Размеры образующихся частиц продукта равняются десяткам нанометров. Например, при взаимодействии тетрахлорида титана с азотной плазмой можно получить нитрид титана, состав которого близок к стехиометрическому размер частиц около 30 нм, а удельная поверхность – 45 м 2 /г. Лекция
Получение нитридов восстановлением оксидов металлов твердым восстановителем в среде азота В основе процесса лежит реакция Ме. О + Ме(Х) + N 2 Ме N + Me. O ( XO ), где Me – металл-восстановитель; X – неметаллический восстановитель (углерод, кремний, бор). Получение порошков тугоплавких соединений 298 Получение нитридов. Лекция
Получение порошков тугоплавких соединений 299 Получение нитридов Получение нитридов восстановлением оксидов металлов твердым восстановителем в среде азота Чаще всего в качестве восстановителя используют углерод, что приводит, наряду с образованием нитридов, к образованию карбидов восстанавливаемых металлов, которые образуют непрерывный ряд твердых растворов. Данный метод применяют в основном для получения нитридов технической чистоты (нитридов титана, циркония, ванадия, ниобия и гафния). Для уменьшения содержания углерода в получаемом продукте процесс ведут при максимально возможных низких температурах, что снижает вероятность образования карбидов. Лекция
Получение порошков тугоплавких соединений 300 Получение нитридов Получение нитридов термической диссоциацией соединений В основе метода лежит принцип последовательного протекания реакций восстановления и азотирования исходного материала. Получаемые этим методом нитриды по составу близки к расчетным. Процесс получения порошка нитрида связан с реакцией восстановления оксида соответствующего металла и последующего взаимодействия образовавшейся металлической фазы с азотом. Лекция
Получение порошков тугоплавких соединений 301 Получение нитридов Получение нитридов термической диссоциацией соединений Технологическая схема метода включает следующие операции: — измельчения в шаровых мельницах компонентов шихты; — смешивания компонентов (оксида металла и сажи); — грануляции или прессования смеси в таблетки небольших размеров (пластификатор – водный раствор поливинилового спирта); — синтеза соединения. Подготовленная и гранулированная шихта должна обладать хорошей подвижностью и газопроницаемостю, обеспечивающей непрерывность прохождения синтеза. Лекция
Получение порошков тугоплавких соединений 302 Состав и режимы получения нитридов восстановлением оксидов металлов углеродом с одновременным азотированием Нитрид Т , °C Время синтеза , ч Содержание, % Me N Расчетное Практическое Ti. N Zr. N Hf. N VN Nb. N Ta. N Cr 2 N 1250 1200 1200 1, 5 2 2 1, 5 1 87, 37 86, 69 92, 72 88, 44 86, 9 92, 81 88, 14 78, 3– 79, 0 87, 0– 87, 5 92, 7– 93, 0 78, 8– 80, 8 86, 9– 87, 7 92, 8– 93, 2 86, 7– 87, 7 22, 63 13, 31 7, 28 21, 56 13, 10 7, 19 11, 86 20, 0– 21, 7 12, 5– 13, 2 6, 9– 7, 3 18, 0– 20, 5 12, 3– 13, 0 6, 7– 6, 9 10, 7– 11, 3 Лекция
Получение порошков тугоплавких соединений 303 Получение нитридов осаждением из газовой фазы Метод позволяет получать порошки высокой степени чистоты в поли- и монокристаллическом состоянии. В качестве исходных веществ используют галогениды соответствующих металлов. Процесс ведут при наличии азота высшей степени очистки или аммиака и водорода. Нитриды образуются по одной из схем: Ме Cl + NH 3 Me. N + НС l ; Me. OCl 2 + NH 3 Me. N + Н 2 О + НС l ; Me. Cl + N 2 + H 2 Me. N + HCl. Лекция
Получение порошков тугоплавких соединений 304 Получение нитридов осаждением из газовой фазы Чаще всего нитриды осаждаются на нагретой вольфрамовой нити. Осадок нитрида представляет собой конгломераты, обладающие рыхлой и пористой структурой. Величина образующихся кристаллов зависит от температуры нити. При низких температурах образуются мелкие кристаллы. С повышением температуры крупность кристаллов и прочность их сцепления с подложкой увеличиваются. Лекция
Получение порошков тугоплавких соединений 305 Условия осаждения нитридов из газовой фазы Нитрид Состав газовой фазы Температура процесса , °C Ti. N Zr. N Hf. N VN Ta. N Ti. Cl 4 : 3 N 2 : Н 2 = 1 : 3 : 2 Zr. Cl 4 : 3 N 2 : Н 2 = 1: 3: 2 Zr. Cl 4 : N 2 = 1 : 2 Hf. Cl 4 : 3 N 2 : H 2 = 1 : 3 : 2 VC 1 4 : 3 N 2 : H 2 = 1 : 3 : 2 Ta. Cl 5 : N 2 = 1 : 2 1100– 1700 1100– 2700 2800– 3000 1100– 2700 1100– 1600 2400– 2600 Ускорению процесса образования нитридов способствует развитая поверхность нити. При высокой и стабильной температуре нити, имеющей монокристаллическую структуру или состоящей из вытянутых зерен, образуются монокристаллические осадки. Лекция
Получение порошков тугоплавких соединений 306 Список рекомендуемой литературы 1. Панов, В. С. Технология и свойства спеченных твердых сплавов и изделий из них : учеб. для вузов / В. С. Панов, А. М. Чурилин. – М. : МИСИС, 2001. – 426 с. 2. Балкевич, В. Л. Техническая керамика / В. Л. Балкевич. – М. : Строиздат. 1984. – 266 с. 3. Ультрадисперсные металлические порошки: получение, структура, свойства / И. П. Арсеньев, М. М. Ристич. – Белград : изд. ИТН САНи. И, 1987. – 142 с. Лекция
Получение порошков тугоплавких соединений 307 Лекция 23 Получение порошков боридов, силицидов и гидридов металлов • Методы получения боридов • Методы получения силицидов и гидридов металлов
Получение порошков тугоплавких соединений 308 Методы получения боридов Существуют следующие методы получения боридов: 1) прямой синтез из элементов; 2) металлотермическое восстановление; 3) восстановление оксидов металлов бором с одновременным борированием; 4) электролиз расплавленных сред; 5) осаждение из газовой фазы; 6) восстановление оксидов металлов углеродом карбида бора (борокарбидный метод); 7) совместное восстановление смесей оксидов металлов и борного ангидрида углеродом (углетермический метод); 8) метод плазмохимического синтеза. Лекция
Получение порошков тугоплавких соединений 309 Получение боридов прямым синтезом из элементов Синтез проводят, исходя из обеспечения условий прохождения реакции по схеме Me + В Ме. В. Реакция может осуществляться: — в жидкой фазе (путем плавления шихты в дуговых или индукционных печах); — в твердом состоянии (путем спекания этой шихты в печах сопротивления различного типа). Лекция
Получение порошков тугоплавких соединений 310 Получение боридов прямым синтезом из элементов Оптимальные режимы получения боридов устанавливаются экспериментально в зависимости от свойств исходных материалов и условий проведения синтеза. При получении боридов синтезом из элементов без плавления оптимальные температуры лежат в пределах 1300– 2500 °С. В качестве среды можно использовать вакуум (в случае ведения процесса при низких температурах) или инертные газы – при высоких. Вариантом метода получения боридов синтезом из элементов является спекание смесей горячим прессованием. При необходимости получения высокоплотных изделий требуется измельчение полученных заготовок и повторное прессование и спекание уже образовавшегося борида. Лекция
Получение боридов металлотермическим восстановлением применяется в том случае, когда в качестве исходных материалов используют оксиды металлов, борный ангидрид. Восстановителем служат алюминий, магний, кальций или кремний. Реакция идет по схеме: Ме. О + В 2 О 3 + Al ( Mg , Ca , Si ) Ме. В + Al ( Mg , Ca , Si ) O 4 Полноту и скорость прохождения процесса оценивают по величине термичности — отношению теплового эффекта реакции к сумме масс реагирующих веществ (массе шихты). Получение порошков тугоплавких соединений 311 Получение боридов металлотермическим методом. Лекция
Получение порошков тугоплавких соединений 312 Получение боридов металлотермическим методом Минимальные значения термичности практически для всех восстановителей должны находиться в пределах 25 Дж/кг шихты. Процесс образования боридов проходит через ряд окислительно-восстановительных реакций, в которых исходные вещества всегда находятся в твердом состоянии, а конечные продукты часто представляют собой оплавленные спеки. Недостатком металлотермического восстановления является сложность разделения продуктов, возможность образования боридов металлов-восстановителей. Лекция
Получение порошков тугоплавких соединений 313 Условия получения боридов Условия получения некоторых боридов металлотермическим методом Борид Состав шихты, моль Температура , ° C Состав боридов , % Me В Ме + В VB V 2 O 5 + 3 B 2 O 3 + 12 Mg 1100 82, 8 17, 0 99, 8 VB 2 V 2 O 5 + 4 B 2 O 3 + 15 Mg 1150 70, 8 29, 0 99, 8 Nb. B 2 Nb 2 O 5 + 4 B 2 O 3 + 17 Mg 1200 80, 9 19, 0 99, 9 Та. В Ta 2 O 5 + 3 B 2 O 3 + 12 Mg 1200 94, 2 5, 6 99, 8 Та. В 2 Ta 2 O 5 + 4 B 2 O 3 + 17 Mg 1200 89, 9 10, 0 99, 9 Сг. В 2 Сг 2 Оз + 3 B 2 O 3 + 12 Mg 1200 71, 0 28, 9 99, 9 Мо 2 В 5 2 Mo. O 3 + 4, 5 B 2 O 3 + 13, 5 Mg + 5 Mg. O 1200 79, 6 20, 3 99, 9 W 2 B 5 2 Wo. O 3 + 4, 5 B 2 O 3 + 13, 5 Mg + 5 Mg. O 1200 88, 0 11, 8 99, 8 Лекция
Получение порошков тугоплавких соединений 314 Получение боридов восстановлением оксидов металлов бором с одновременным борированием Процесс протекает по реакции 2 Ме. О + 4 В 2 Ме. В + В 2 О 2 Технологическая схема этого метода включает следующие операции: — смешивания шихты (соответствующего оксида металла и бора); — прессования шихты в брикеты (давление 50– 100 МПа); — загрузки брикетов в контейнер из идентичного борида и установка контейнера в вакуумную печь; — восстановления и борирования шихты при давлении 10– 100 МПа. Лекция
Получение порошков тугоплавких соединений 315 Получение боридов восстановлением оксидов металлов бором с одновременным борированием Для интенсификации удаления образующегося газообразного В 2 О 2 и значительной части летучих примесей, содержащихся в исходных веществах, применяют вакуумные печи. Вакуумные печи позволяют получать бориды высокой степени чистоты, по составу близкие к стехиометрическому (сумма Ме+В 100 %). Большинство боридов получают при температурах, когда летучесть В 2 О 2 высока, а летучесть В еще незначительна. Недостатком метода восстановления оксидов металлов бором является относительная сложность оборудования и малая производительность. Лекция
Получение порошков тугоплавких соединений 316 Режимы получения боридов в изделиях восстановлением оксидов металлов бором в вакууме (время синтеза – 60– 150 мин) Борид Температура , ° С Содержание , % Me В Ti. B 2 1500 69, 0 30, 8 Zr. B 2 1600 80, 3 19, 1 Hf. B 2 1700 89, 0 10, 9 VB ? 1550 80, 2 19, 8 Nb. B 2 1600 80, 2 19, 0 Ta. B 2 1700 88, 8 10, 5 Сг. В 2 1600 70, 6 29, 3 Лекция
Получение порошков тугоплавких соединений 317 Получение боридов Получение боридов электролизом расплавленных сред Электролизом расплавов, состоящих из смесей щелочных и щелочно-земельных металлов с их оксидами металлов, получают бориды тугоплавких металлов в виде дисперсных, хорошо закристаллизованных осадков. Флюсы – фториды магния, кальция, лития. Процесс ведут в специальных электролизерах , в которых анодом является графитовый тигель, катодом – графитовый или металлический стержень. Лекция
Получение порошков тугоплавких соединений 318 Получение боридов Получение боридов электролизом расплавленных сред Сущность процесса состоит в том, что при электролизе на катоде выделяется элементарный бор , образующийся в результате протекания реакции восстановления ангидрида бора щелочным металлом, возникающим в результате электролиза: 2 В 2 О 3 + 3 Na. BO 2 + В. Наряду с этим протекает процесс восстановления оксида тугоплавкого металла и взаимодействие восстановленного металла с бором, в результате чего образуется борид. Химический состав получаемых при электролизе боридов можно регулировать, изменяя состав содержимого ванны. При этом наибольшее влияние оказывает количество оксидов металлов. Лекция
Получение порошков тугоплавких соединений 319 Получение боридов Получение боридов осаждением из газовой фазы Метод аналогичен методу получения карбидов и нитридов разложением галогенидов металлов на подогретой подложке при наличии борсодержащих газообразных веществ. Борсодержащими компонентами могут быть бромид или хлорид бора, которые восстанавливаются по реакции: Ме. С lх + ВС l 3 + Н 2 Ме. В 2 + НС l Лекция
Получение порошков тугоплавких соединений 320 Получение боридов Получение боридов осаждением из газовой фазы На процесс формования осадков влияют: — температура; — скорость прохождения реагентов через реакционное пространство; — соотношение водорода, хлорида металла и хлорида бора. Кроме того, на состав осадков, их пористость и ориентацию кристаллов также оказывают влияние условия процесса. Метод осаждения боридов из газовой фазы является весьма перспективным для получения боридных покрытий, монокристаллов, а также изделий сложной формы. Лекция
Получение порошков тугоплавких соединений 321 Получение боридов Получение боридов восстановлением оксидов металлов углеродом карбида бора (борокарбидный метод) Метод является одним из основных промышленных методов получения боридов переходных металлов. В основе этого метода лежат реакции Ме. О + В 4 С 4 — + С Мех. Ву + СО; Ме(Ме. Н, Ме. С) + В 4 С В 2 О 3 + Ме. В + CO. Лекция
Получение порошков тугоплавких соединений 322 Получение боридов Получение боридов восстановлением оксидов металлов углеродом карбида бора (борокарбидный метод) Технологическая схема промышленного получения боридов включает операции: — приготовления исходных материалов и шихты; — компактирования шихты; — нагрева шихты (синтеза материала); — переработки полученного продукта путем размола и просева. Процесс получения боридов проводят в вакуумных печах с графитовым или металлическим нагревателем или в печах сопротивления с графитовой трубой в среде водорода или конвертированного газа. В случае проведения процесса в вакууме происходит непрерывное удаление оксида углерода и смещение равновесия реакции в сторону образования борида. Лекция
Получение порошков тугоплавких соединений 323 Режимы получения боридов Режимы получения боридов в вакууме борокарбидным методом Борид Температура процесса , °С Время выдержки , ч Содержание , % Ме + В + С Me B C Ti. B 2 Zr. B 2 VB 2 Nb. B 2 Ta. B 2 Cr. B 2 Мо 2 В 5 W 2 B 5 1400 1500– 1600 1400– 1500 1200– 1300 1, 0 0, 5 1, 0 1, 0 68, 20 80, 72 70, 00 80, 36 89, 17 70, 58 77, 15 87, 00 31, 02 19, 20 29, 95 18, 90 10, 23 29, 39 22, 63 12, 90 0, 02 0, 01 0, 05 0, 09 0, 14 0, 02 0, 09 0, 10 99, 24 99, 93 100, 00 99, 35 99, 54 99, 99 99, 87 100, 00 Лекция
Получение порошков тугоплавких соединений 324 Получение боридов 123 4 C, % 80 60 20 10 1600 1800 2000 Т 0 С На состав и гомогенность получаемого продукта влияют температура процесса, длительность нагрева до изотермической выдержки. Кроме того, могут оказывать влияние качество исходного сырья и среда. Зависимость химического состава борида циркония от температуры процесса. 1 – Соб. , 2 – В, 3 – Zr, 4 – (Zr, B, Соб. )Лекция
Получение порошков тугоплавких соединений 325 Получение боридов совместным восстановлением смесей оксидов металлов и борного ангидрида углеродом (углеродный метод) Метод является одним из основных при производстве боридов в промышленных масштабах. Он отличается от борокарбидного тем, что в качестве исходного сырья могут быть использованы более дешевые материалы (оксиды, борный ангидрид). Ме. О + В 2 О 3 + С Ме х В у + СО Технологическая схема этого метода включает следующие операции: — подготовки исходных компонентов; — смешивания компонентов; — загрузки шихты в печь и проведения синтеза. Лекция
Получение порошков тугоплавких соединений 326 Получение боридов совместным восстановлением смесей оксидов металлов и борного ангидрида углеродом (углеродный метод) Количество борного ангидрида, вводимого в состав шихты, должно превышать теоретически необходимое вследствие высокой его летучести при температурах восстановления. Синтез соединений проводят в печах Таммана с использованием защитной среды. На состав и свойства получаемых боридов влияют: температура, длительность изотермической выдержки, состав шихты и свойства исходных компонентов, скорость подъема температуры. Лекция
Получение порошков тугоплавких соединений 327 Получение силицидов Для получения силицидов переходных металлов в основном применяют следующие методы: 1) прямой синтез из элементов; 2) восстановление их оксидов с одновременным силицированием. Получение силицидов прямым синтезом из элементов Метод основан на протекании реакции : Me + 2 Si — + Me. Si 2. Лекция
Получение порошков тугоплавких соединений 328 Получение силицидов Реакция проходит легко, поскольку образование силицидов сопровождается значительным экзотермическим эффектом. Технологическая схема производства силицидов является традиционной для получения тугоплавких соединений и включает операции: — подготовки исходных материалов; — нагрева полученной шихты; — дальнейшей переработки полученного продукта путем дробления и размола. При получении силицидов прямым синтезом из элементов в качестве исходного сырья используют порошки соответствующих металлов или их гидридов и порошки кремния (необходимо учитывать высокую летучесть кремния). Лекция
Получение порошков тугоплавких соединений 329 Режимы получения силицидов прямым синтезом и химический состав некоторых силицидов металлов Силицид Режим получения Химический состав Температура , о С Выдержка , ч Si o 6 щ Si своб Si связ. теор Ti. Si 2 * 1000 2, 0 52, 50 1, 50 51, 00 53, 98 Zr. Si 2 1100 2, 0 38, 14 0, 04 38, 10 38, 11 VSi 2 1200 0, 5 52, 37 0, 25 52, 12 52, 44 Nb. Si 2 1000 0, 5 37, 80 0, 15 37, 68 Ta. Si 2 1100 1, 0 23, 88 0, 37 23, 51 23, 69 Cr. Si 2 ** 1000 0, 5 49, 17 0, 13 49, 04 51, 93 Mo. Si 2 *** 1000 0, 5 35, 16 0, 42 34, 74 36, 93 WSi 2 1000 0, 5 23, 60 0, 09 23, 51 23, 40 Примечание: * – содержит примесь Ti. Si (36, 96% Si связ. теор ; ** – содержит примесь других силицидов хрома, например Cr. Si (35, 07 % Si связ. теор ); *** – содержит примесь Mo 3 Si 2 (16, 32% Si связ. теор )Лекция
Получение порошков тугоплавких соединений 330 Получение силицидов восстановлением из оксидов с одновременным силицированием При получении силицидов металлов этим методом можно использовать несколько вариантов: 1) восстановление оксидов металлов кремнием; 2) совместное восстановление оксидов металлов и кремния углеродом; 3) восстановление оксидов металлов карбидом кремния; 4) совместное восстановление оксида кремния, силикатов с оксидами металлов углеродом. Лекция
Получение порошков тугоплавких соединений 331 Получение силицидов восстановлением из оксидов с одновременным силицированием Наиболее широко применяются первых два варианта, в основе которых лежат реакции: Ме. О + 3 Si Me. Si 2 + Si. O; Me. O + 2 Si. O 2 + 5 C Me. Si 2 + 5 CO. Процесс получения силицидов можно вести в высокотемпературных печах в защитной газовой среде или в вакууме при 1300– 1800 °С. На скорость и полноту прохождения реакции влияют: качество подготовки шихты; ее уплотнение; температура процесса; длительность изотермической выдержки; скорость нагрева до оптимальной температуры; давление в рабочей камере. Лекция
Получение порошков тугоплавких соединений 332 Получение силицидов Оксиды металлов восстанавливаются кремнием, проходя стадии последовательных превращений высших оксидов в низшие с образованием промежуточных кислородсодержащих продуктов, богатых кремнием силицидов и их последующим обогащением металлом по схеме Ме. О х Me О x – n Me. O m Si n Me. Si p – q. В первую очередь образуются дисилициды (термодинамически более стойкие соединения с сильными ковалентными связями между атомами кремния). С повышением температуры процессы восстановления оксидов металлов и образования силицидов интенсифицируются. Лекция
Получение порошков тугоплавких соединений 333 Получение силицидов Режимы получения некоторых силицидов металлов восстановлением оксидов Силицид Режим получения Химический состав , % Температура , С Выдержка , ч Si общ Si своб Si связ Ti. Si 2 VSi 2 Nb. Si 2 Ta. Si 2 1350 1550 1400 1600 1, 0 0, 5 51, 9 51, 5 36, 5 20, 4 1, 7 – 0, 3 0, 2 50, 2 – 36, 2 20, 2 Лекция
Получение порошков тугоплавких соединений 334 Получение гидридов Порошки гидридов получают в основном прямым синтезом из элементов. Гидрид титана Ti. H 2 готовят обычно гидрированием при 900 0 С титановой губки, полученной магниетермическим восстановлением Ti. Cl 4. После наводораживания губку (гидрид титана) измельчают. Гидриды циркония получают обработкой его порошка водородом при 400– 800 о С. Гидрид, приготовленный при 400 о С, представляет собой Zr. H 2 , а полученный при 800 о С соответствует формуле Zr. H , поэтому обычно продукт гидрирования представляет собой смесь этих гидридов; оба гидрида получают в виде порошков с размером частиц < 40 мкм. Лекция
Получение порошков тугоплавких соединений 335 Получение гидридов Гидриды гафния состава Hf. H 1, 98 и Hf Н 2, 1 получают гидрированием металлического гафния при 1100 о С. Гидрид ванадии VH , содержащий 16 % (ат. ) Н, образуется при нагреве порошка металла в водороде при 1300 о С. Гидрид ниобия Nb. H с содержанием 44 % (ат. ) водорода получают при 500– 9000 о С, а гидриды тантала Та 2 Н и Та. Н при 800 -900 о С. Лекция
Получение порошков тугоплавких соединений 336 Список рекомендуемой литературы 1. Балкевич, В. Л. Техническая керамика / В. Л. Балкевич. – М. : Строиздат, 1984. – 266 с. 2. Арсеньев, И. П. Ультрадисперсные металлические порошки: получение, структура, свойства / И. П. Арсеньев, М. Ристич. – Белград : изд. ИТН САНи. И, 1987. – 142 с. Лекция
Получение порошков тугоплавких соединений 337 Лекция 24 Получение порошков тугоплавких соединений методами самораспространяющегося высокотемпературного синтеза и золь-гель процесса • Основы метода СВС • Классификация систем СВС • Характеристики систем СВС • Технология получения порошков в системах СВС • Аппаратурное оформление метода
Получение порошков тугоплавких соединений 338 Самораспространяющийся высокотемпературный синтез Метод печного синтеза металлоподобных соединений не позволяет удовлетворить современные требования прикладного материаловедения по чистоте получаемого продукта и производительности. Поэтому активно развиваются другие методы получения таких порошков, среди которых отметим синтез в низкотемпературной плазме, ударно-волновое сжатие и самораспространяющийся высокотемпературный синтез (СВС). Лекция
Получение порошков тугоплавких соединений 339 Самораспространяющийся высокотемпературный синтез В основе СВС лежит явление распространения фронта горения в порошках некоторых тугоплавких химических элементов, приводящее к образованию соответствующих соединений. Метод СВС основан на использовании сильной экзотермичности взаимодействия большинства элементов с бором, углеродом, азотом, кремнием и другими металлоидами, связанной с большой теплотой образования продукта, и высоких значений энергии активации диффузии атомов металлоидов в металлах. Лекция
Получение порошков тугоплавких соединений 340 Самораспространяющийся высокотемпературный синтез Обобщенная химическая схема процесса имеет вид: горючие элементы- целевой тепловой элементы окислители продукт эффект где X – Ti , Zr , Hf , V , Nb , Та, Mo , W и другие металлы; Y – В, С, N , Si , Se , Al и другие элементы; Z – бориды, карбиды, нитриды, силициды и другие соединения металлов, а также твердые растворы или интерметаллиды. , 11 QZ n j j. Yjb m i i. Xia Лекция
Получение порошков тугоплавких соединений 341 Самораспространяющийся высокотемпературный синтез Элементы X представляют собой порошки металлов , Y применяют в порошкообразном, жидком или газообразном состояниях , а продукт Z является тугоплавким и при температуре процесса находится обычно в твердом состоянии. Химическое взаимодействие элементов протекает в конденсированной фазе, даже если один из реагентов находится в газообразном состоянии. Кроме обычных вариантов, когда т = 1 и п = 1 , реализуются и другие случаи (т 1, п 1), приводящие к синтезу более сложных образований. Лекция
Получение порошков тугоплавких соединений 342 Некоторые виды тугоплавких соединений, получаемые методом СВС Материал Образующиеся соединения Карбиды Ti. C x , Zr. C x , Hf. C , VC , Nb 2 C , Ta. C , Si. C , WC , Cr 3 C 2 , Сг 7 С 3 , Мо 2 С и др. ; Бориды Ti. B 2 , Ti. B , Zr. B 2 , Zr. B , Hf. B 2 , VB , Nb. B 2 , Ta. B 2 , Cr. B , Mo. B 2 и др. ; Нитриды BN , Ti. N , Zr. N , Hf. N , VN , Nb. N , Ta. N (куб), Ta. N (гексагональный), Ta 2 N и др. ; Силициды Ti. Si , Ti. Si 2 , Zr. Si , WSi и др. ; Халькогениды Ti. Se 2 , Nb. Se 2 , Ta. Se 2 , Mo. Se 2 , WSe 2 и др. ; Твёрдые растворы Ti. C – Cr 3 C 2 , Ti. C – WC, Ti. C – Ti. N, Nb. C – Nb. N, Mo. S 2 –Nb. S 2 , Ta. C – Ta. N, Nb х Zr 1–x С y N 1–y и др. ; Интерметаллиды Ni 3 Al, Ni. Al, Ti. Ni, Cu 3 Al, Ti. Co, Co. Al, Nb 3 Al и др. ; Оксиды Аллюминатов (YA 10 3 , Mg. Al 2 O 4 ), необатов (Li. Nb. O 3 , Na. Nb. O 3 , Ba. Nb 2 O 6 ), гранатов (Y 3 A 1 5 O I 2 , Y 3 Fe 5 0 12 ), ферритов (Co. Fe 2 O 4 , Ba. Fe 2 O 4 , Li 2 Fe 2 0 4 ), титанатов (Ba. Ti. O 3 , Pb. Ti. O 3 и др. ), молибдатов (Bi. Mo. O 6 , Pb. Mo. O 4 и др. ); Лекция
Получение порошков тугоплавких соединений 343 Классификация систем СВС В зависимости от химической природы ведущей реакции горения и агрегатного состояния реагентов, СВС-системы делятся на четыре основных класса : — безгазовые (без образования газообразных продуктов сгорания), — фильтрационные, — газовыделяющие, — металлотермического типа (с восстановительной стадией). В безгазовых системах (небольшое газовыделение, связанное с самоочисткой от примесей) исходные компоненты, промежуточные и конечные продукты находятся в конденсированном состоянии. Лекция
Получение порошков тугоплавких соединений 344 Классификация систем СВС Синтез можно проводить в вакууме или в инертном газе (состав продуктов горения и его параметры слабо зависят от атмосферы процесса). В фильтрационных системах синтез идет в гибридных системах металл–газ. Состав продуктов горения, а также параметры синтеза зависят от давления и состава газовой среды. Большое значение имеют габариты и пористость сбрикетированного металлического порошка, определяющие доставку (фильтрацию) газа в зону реагирования (горения) компонентов. На практике применяют схему, где образец с полностью открытой поверхностью помещен в среду газообразного окислителя. Фильтрация осуществляется как через исходную шихту, так и через продукты горения. Лекция
Получение порошков тугоплавких соединений 345 Классификация систем СВС Газовыделяющими являются системы с легколетучими компонентами (серой, фосфором, селеном и др. ) и сжиженным газом (жидким азотом). Синтез ведут в герметичных емкостях, полностью заполненных твердыми компонентами, так как при их испарении они не покидают реакционный объем, а заполняют лишь поровое пространство. В системах металлотермического типа горение имеет две принципиально различные химические стадии: — восстановление оксидов; — взаимодействие образовавшихся элементов между собой и с добавками, вводимыми в шихту. Лекция
Получение порошков тугоплавких соединений 346 Классификация систем СВС Газовыделяющие СВС-процессы могут быть магниетермическими или алюмотермическими. В общем случае распространение волны горения является одним из возможных режимов, в котором могут протекать экзотермические реакции. Исходная смесь реагентов отделена сравнительно узкой зоной горения от продуктов реакции. Начальная температура шихты низкая (например, комнатная), а температура в зоне реакции ( температура горения ) может достигать 3000– 4000 К. В стационарных условиях зона горения перемещается в сторону исходной шихты с высокой скоростью (до 105 – 106 К/с), называемой нормальной скоростью горения. Лекция
Получение порошков тугоплавких соединений 347 Характеристики систем СВС Типичные структуры волны горения: кривая 1 – горение с узкой зоной (скорость горения определяется конечной температурой); кривая 2 – горение с широкой зоной (сильное торможение реакции взаимодействия компонентов приводит к тому, что ширина зоны реакции становится больше, чем зоны подогрева); кривая 3 – горение при химическом взаимодействии реагентов (полное химическое превращение в шихте происходит в несколько стадий, которые могут быть пространственно разделены в волне горения – режим «отрыва» ); кривая 4 – горение с фазовыми переходами (для двухстадийной реакции). Типы температурных профилей волны горения при СВСЛекция
Получение порошков тугоплавких соединений 348 Характеристики систем СВС Во многих системах СВС наблюдаются весьма сложные температурные профили волны горения, имеющие перегибы, изотермические площадки и другие особенности, связанные с различными фазовыми переходами, образованием промежуточных продуктов и т. п. Лекция
Получение порошков тугоплавких соединений 349 Схема СВС-технологии получения порошков исходные порошки измельчение сушка шихтовка и смешивание порошков загрузка в реактор реакционный или инертный газ зачистка спека измельчение кислотное обогащение рассев сушка поршкообразные СВС-продуктыэлементный синтез СВС-магниетермия. Лекция
Получение порошков тугоплавких соединений 350 Схема СВС-реактора 1 – корпус; 2 – графитовая футеровка; 3 – реакционная шихта; 4 – грибковый затвор; 5 – газораспределительный узел 4 1 2 35 Лекция
Получение порошков тугоплавких соединений 351 Технология получения порошков в системах СВС Глубина превращения исходных реагентов в процессе СВС определяется термодинамическими и кинетическими ограничениями. Процесс синтеза регулируется изменением: — дисперсности реагентов; — размеров и плотности порошкового тела; — теплоотдачи с поверхности; — температуры горения. Получаемые соединения однофазны, хорошо кристаллизованы (иногда получаются и аморфные порошки). Чистота синтезируемых соединений не ниже чистоты исходных реагентов, так как дополнительного загрязнения в процессе СВС не происходит. Лекция
Получение порошков тугоплавких соединений 352 Взрывной механохимический синтез (ВМС) Этот способ позволяет использовать дешевое сырье (оксиды), а также получать различные соединения металлов. С использованием ВМС получают сульфиды, карбонитриды, силициды и другие тугоплавкие соединения. Механический метод активации (МА) твердофазных химических реакций позволяет проводить их в режиме теплового взрыва. Роль механической активации заключается в инициировании экзотермической реакции, которая в дальнейшем протекает за счет выделения тепла химической реакции. Лекция
Получение порошков тугоплавких соединений 353 Взрывной механохимический синтез (ВМС) Исходные компоненты (стружка, спеки или кусковой материал) подвергают высокоэнергетической механоактивации в герметичном механореакторе энергонапряженной мельницы. Передача энергии (постепенная «накачка» избыточной энергией реагирующих компонентов) происходит за время от нескольких до десятков минут. При достижении критических значений этой энергии начинается реакция, протекающая по взрывной кинетике. Лекция
Получение порошков тугоплавких соединений 354 Характеристики систем СВС Синтез тугоплавких соединений характеризуется значительным выделением тепла. Мощность W мельницы для проведения механоактивации можно оценить по формуле: W = ( m · c · ∆T ) / , где т – масса механореактора с шарами; с – средняя теплоемкость материала, из которого изготовлен механореактор; ∆ T – изменение температуры механореактора в процессе механоактивации; – время активации. Энергетическая доза Е, необходимая для осуществления ВМС, составляет E = W · 3 / M , где з – продолжительность задержки реакции; М – масса загрузки исходных компонентов. Лекция
Получение порошков тугоплавких соединений 355 Характеристики систем СВС Тепловой эффект реакции ∆Н 0298 соответствует выделившемуся при синтезе теплу Q : ∆ Н 0298 ≈ Q = M · c’ · ∆T’ , где с – теплоемкость полученного продукта; ∆ T ‘ – величина скачка температур на термограмме. С помощью рассмотренных параметров можно управлять процессом, обеспечивать устойчивое прохождение реакции или, наоборот, гасить его или переводить в другой кинетический режим. Лекция
Получение порошков тугоплавких соединений 356 Характеристики систем СВС Время, необходимое для инициирования ВМС, зависит от химического сродства элементов к окислителю. Как правило, элементы, обладающие большим химическим сродством к окислителю, более склонны к взрывному синтезу. Механохимический синтез тугоплавких соединений осуществляется различными методами. Наиболее простой – прямой синтез, когда реакция протекает между двумя или несколькими элементами: где X – Hf , Та, Zr , Ti , Nb и др. ; Y – С, В, Si , S ; Z – химическое соединение; Q – тепловой эффект реакции. , 11 QZYb. Xa MAn j jj m i ii Лекция
Получение порошков тугоплавких соединений 357 Технология получения порошков в системах СВС Более сложным является синтез, включающий реакцию восстановления: n Me 1 О + Me 2 (Me 3 ) + m C → Me 2 O(Me 3 O) + Me n C m + Q , где Ме 1 О – оксиды любых металлов и неметаллов, имеющих меньшее химическое сродство к кислороду, чем Ме 2 (Ме 3 ); Ме 2 О и Ме 3 О – образующиеся оксиды металлов Ме 2 и Ме 3 соответственно; Ме n С т – карбиды или другие тугоплавкие соединения (в зависимости от типа окислителя). Лекция
Получение порошков тугоплавких соединений 358 Золь-гель процесс В основе этого процесса лежит образование гидроксидов металлов в результате химического превращения высокодисперсных систем ( золей ) в рыхлые аморфные структуры ( гели ). Золь-гель методом изготавливают порошки Ba. Ti. O 3 , Zr. O 2 , Ti. O 2 , WO 3 , Sr. Ti. O 3 , Y 2 O 3 , Al 2 O 3 , Si. O 2 , Si 3 N 4 , оксидные микросферы диаметром от 10 до 2000 мкм, волокна, композиционные материалы, содержащие в матрице дисперсные металлические частицы. Лекция
Получение порошков тугоплавких соединений 359 Золь-гель процесс Получаемые порошки активны при спекании. Золи (гидрозоли, органозоли, аэрозоли) представляют собой системы, в которых частицы высокодисперсной твердой фазы свободно участвуют в броуновском движении (во взвешенном состоянии). Золи способны коагулировать, т. е. образовывать крупные агрегаты частиц в виде структурированных систем с последующим разделением фаз – разрушением дисперсной системы. При коагуляции золи превращаются в гели – структурированные системы, в которых частицы соединены в рыхлую пространственную сетку. Лекция
Получение порошков тугоплавких соединений 360 Золь-гель процесс Коагуляция происходит при удалении лишней воды из системы , вызванном повышением или понижением температуры, воздействием электромагнитных полей, жестких излучений, механическими или химическими воздействиями. Процессы в водных средах основаны на превращениях, происходящих в такой последовательности: гидролиз полимеризация нуклеация рост Лекция
Получение порошков тугоплавких соединений 361 Золь-гель процесс Результатом гидролиза является связывание некоторых молекулярных групп, содержащих ионы кислорода, с катионами (металлами). В процессе полимеризации происходит образование мостиковых связей между двумя или более катионами посредством лигандов. Золь-гель процессы можно разделить на: — коллоидные; — полимеризационные. В коллоидных системах гелеобразование происходит в растворах, содержащих золь одного или более компонентов. Лекция
Получение порошков тугоплавких соединений 362 Золь-гель процесс Полимеризационный процесс включает процессы поликонденсации с формированием непрерывной полимерной структуры геля, который может содержать катионы различной природы. Полимеризационные процессы происходят с исходными компонентами, которые ионизируются или не ионизируются в растворителе. При использовании ионизируемых исходных компонентов (солей металлов) катионы металла Me в результате взаимодействия с дипольными молекулами воды образуют группы типа Ме(Н 2 О) n. Z+. Лекция
Получение порошков тугоплавких соединений 363 Золь-гель процесс При взаимодействии образовавшихся положительно заряженных групп с соответствующими анионами образуются новые группы, катионы которых могут быть связаны лигандами, включающими: — О 2– (кислородные мостики); — ОН – (гидроксильные мостики); — Н 2 О (водные мостики); — анионами А –. Процесс полимеризации зависит от р. Н среды, температуры (образование комплексов часто ускоряется с повышением температуры), концентрации катионов металлов и природы анионов. Лекция
Получение порошков тугоплавких соединений 364 Список рекомендуемой литературы 1. Панов, В. С. Технология и свойства спеченных твердых сплавов и изделий из них : учеб. для вузов / В. С. Панов, А. М. Чурилин – М. : МИСИС, 2001. – 426 с. 2. Либенсон, Г. А. Процессы порошковой металлургии : учеб. для вузов / Г. А. Либенсон, В. Ю. Лопатин, Г. В. Комарницкий в 2 ч. : – М. : МИСИС, 2001. Лекция
Методы получения порошкового металлического волокона
Методы получения порошкового металлического волокна 366 Лекция 25 Методы получения металлических волокон • Технологии получения металлических волокон • Методы определения размеров частиц и гранулометрического состава порошка
Методы получения порошкового металлического волокна 367 Технологии получения металлических волокон Порошковое волокно – это разновидность частиц металлического порошка, у которых один из габаритных размеров не менее чем в пять раз превышает остальные. Порошковые волокна используются при производстве композиционных материалов, армированных волокнами , усами или проволокой. Способы производства волокнистой компоненты подобных материалов подразделяют на механические и физико-химические. Механические способы (получили наибольшее распространение). Лекция
Методы получения порошкового металлического волокна 368 Технологии получения металлических волокон На практике тонкую проволоку и/или металлическую стружку ( «шерсть» ) металла или сплава получают: — протяжкой тонкой проволоки через фильеры или путем шабрения и шевингования на станках; — из расплава (подачей расплава на быстровращающийся диск, экструзией (фонтанированием) расплава, вытяжкой из расплава, методами ВЗР, продавливанием смеси порошка исходного материала со связующим через тонкие отверстия). Как правило, полученные волокна режут на куски определенной (мерной) длины, а затем их обезжиривают в трихлорэтилене, пероксиде натрия или гидроксиде аммония. Лекция
Методы получения порошкового металлического волокна 369 Получение волокна из расплава На практике применяют следующие способы получения волокон из расплава: 1) подача расплава на быстровращающийся диск, на котором под действием центробежной силы формируются волокна диаметром (поперечным размером) 4– 75 мкм; 2) выдавливание расплава (экструзии расплава) через отверстие диаметром в несколько десятков микрометров. Лекция
Методы получения порошкового металлического волокна 370 Получение волокна из расплава При экструзии расплава можно получать как микрокристаллические, так и аморфные волокна большой длины. Процесс экструдирования включает следующие операции: — плавление исходного металла (металл перегревают на 50– 100 о С); — выдавливание расплавленного металла (скорость истечения металла составляет около 2 м/с) из отверстия в днище контейнера путем создания в плавильной емкости избыточного давления инертного газа (70– 140 к. Па). Лекция
Методы получения порошкового металлического волокна 371 Получение волокна из расплава При выдавливании расплава струя металла проходит через замкнутое пространство (вакуум или определенная атмосфера) и попадает в трубу, по которой с такой же скоростью движется охлаждающая жидкость. Выбор охлаждающей жидкости и ее температура зависят от тепловой мощности струи металла. Для экструзии металлов с температурой плавления до 700 °С применяют воду, с температурой плавления 700 -1000 °С – 23 %-ный водный раствор Na. Cl , с температурой плавления 1000– 1800 °С – 21, 6 %-ный раствор Mg. Cl или 51 %-ный раствор Zn. Cl 2. Лекция
Методы получения порошкового металлического волокна 372 Физико-химические способы получения волокон Их применяют преимущественно для изготовления совершенных нитевидных кристаллов высокой прочности. Основным является метод получения усов восстановлением различных соединений металлов. В качестве исходных материалов используют галогениды, сульфиды и оксиды и газообразные или твердые восстановители. Тонкие нитевидные кристаллы растут при определенных условиях восстановления (температура, парциальное давление восстанавливаемого соединения, свойства восстановителя и др. ) в виде гладких и прямых волокон диаметром от одного до 20 мкм и длиной до нескольких десятков сантиметров. Лекция
Методы получения порошкового металлического волокна 373 Физико-химические способы получения волокон На практике применяют следующие температурные режимы восстановления галогенидов: — меди – 650 °С; — железа – 730– 760 °С; — никеля – 740 °С; — кобальта – 750 °С; — марганца – 940 °С. Повышение температуры восстановления сверх оптимальной приводит сначала к возникновению пластинчатых образований, а затем к росту крупных, хорошо развитых кристаллов. Лекция
Методы получения порошкового металлического волокна 374 Физико-химические способы получения волокон Нитевидные кристаллы могут быть получены выращиванием из пересыщенной газовой фазы. Усы растут за счет притока атомов из газовой фазы, с повышением температуры скорость роста и диаметр усов увеличиваются. Процесс проводят в предварительно вакуумированной камере, по длине которой создают перепад температур, зависящий от характера (природы) материала получаемых усов. Испарением в вакууме с последующей конденсацией паров получают усы цинка, серебра, платины, бериллия, кремния и других металлов. Лекция
Методы получения порошкового металлического волокна 375 Физико-химические способы получения волокон Усы железа, серебра, платины, бериллия, кремния и других металлов можно получить электролитическим осаждением. Выращивание волокон (усов) в твердой фазе На поверхности листов многих металлов ( железа, меди, серебра, платины, магния, вольфрама, латуни и др. ) при нагреве образуются волокнистые кристаллы диаметром 2– 10 мкм и длиной до нескольких миллиметров. Лекция
Методы получения порошкового металлического волокна 376 Физико-химические способы получения волокон Метод ускоренного выращивания усов под давлением (метод Фишера) включает следующие операции: — электролитического покрытия стальной пластины (толщина 0, 3 см) слоем олова толщиной 5 мкм; — установки пластины в держатели (ее зажимают между двумя жесткими стальными пластинками), шлифовки и полировки края полученного образца; — инициации процесса роста усов под действием температуры и давления, приложенного к боковым пластинам. Лекция
Методы получения порошкового металлического волокна 377 Физико-химические способы получения волокон Под действием давления, приложенного к стальным пластинкам, на полированных краях слоя олова происходит ускоренный рост усов, достигающих длины 5 мм (диаметр – около 5 мкм) при 215 °С. После удаления усов с поверхности их рост начинается снова на прежних местах, что указывает на наличие фиксированных источников (центров) роста усов. Лекция
Методы получения порошкового металлического волокна 378 Физико-химические способы получения волокон Тонкие металлические волокна можно также получать химическим травлением проволоки до нужного сечения (травлением медной проволоки в азотной кислоте получают волокна диаметром < 1 мкм). Для получения вольфрамовых волокон успешно применяют метод электролитического травления 15– 20%-ным раствором Na. OH в поле переменного электрического тока. Лекция
Методы получения порошкового металлического волокна 379 Список рекомендуемой литературы 1. Либенсон, Г. А. Процессы порошковой металлургии : учеб. для вузов / Г. А. Либенсон, В. Ю. Лопатин, Г. В. Комарницкий – М. : МИСИС, 2001, ч. 1. – 366 с. 2. Новые процессы и материалы порошковой металлургии / общ. ред. Л. Х. Явербаума; пер. с англ. – М. : Металлургия, 1983. – 360 с. Лекция
Методы контроля свойств металлических и неметаллических порошков
Методы контроля свойств металлических и неметаллических порошков 381 Лекция 26 Методы контроля свойств порошков. Физические свойства порошков • Технологии получения металлических волокон • Методы определения размеров частиц и гранулометрического состава порошка. Лекция
Методы контроля свойств металлических и неметаллических порошков 382 Технологии получения металлических волокон Металлические порошки принято характеризовать химическими, физическими и технологическими свойствами. Знание свойств порошков позволяет создать объективное представление об организации технологических процессов в производствах порошковой металлургии. Основные характеристики порошков, наиболее важные для их последующего применения, регламентированы ГОСТами или отраслевыми техническими условиями (ТУ). Лекция
Методы контроля свойств металлических и неметаллических порошков 383 Физические свойства Форма частиц металлического порошка является определяющим условием их формирования. Принято выделять несколько основных типов формы частиц по принципу сходства с формами макротел не порошковой природы Формы частицы Способ получения порошка Сферическая или округлая Диспергирование (распыление) расплава, карбонильный, испарение-конденсация, измельчение в вибрационной мельнице Губчатая Восстановление твёрдых оксидов или солей Дендритная Электролиз, испарение-конденсация Осколочная Измельчение твёрдых хрупких и неметаллических материалов шаровой (барабанной) мельнице Тарельчатая Измельчение твёрдых материалов в вихревой мельнице Каплевидная Распыление расплавов. Лекция
Методы контроля свойств металлических и неметаллических порошков 384 Физические свойства Являясь величиной качественной, форма частиц во многом объективно характеризует порошок, определяя его поведение в процессе формования и спекания. Форма частиц влияет на многие свойства порошковых материалов: плотность, прочность, проницаемость и др. , а также на их однородность. Критерии формы частиц , основанные на безразмерных соотношениях между основными геометрическими параметрами, называются факторами или коэффициентами формы. Лекция
Методы контроля свойств металлических и неметаллических порошков 385 Физические свойства На практике часто определяют два фактора формы: — фактор неравноосности (удлиненности) частицы Фн : Фн = I max / I min , где I max и I min – соответственно максимальный и минимальный размер частицы по взаимно перпендикулярным направлениям; — фактор развитости поверхности частицы Ф р – отношение квадрата наблюдаемого периметра частицы Р к занимаемой ею площади S : Ф р = P 2 / S. В ГОСТ или ТУ на порошок обычно указывают основную форму частиц. Лекция
Методы контроля свойств металлических и неметаллических порошков 386 Физические свойства Металлический порошок представляет собой совокупность частиц размером от долей микрометра до миллиметра. Практически никогда не встречаются металлические порошки с частицами одного размера. Самый широкий диапазон размеров частиц у порошков, получаемых восстановлением и электролизом. Лекция
Методы контроля свойств металлических и неметаллических порошков 387 Физические свойства Совокупность выраженных в процентах количественных содержаний фракций порошка (диапазон размеров частиц между их верхним и нижним значениями) называют гранулометрическим составом порошка. Гранулометрический состав представляют обычно либо в форме таблицы, либо графически в виде кривой зернистости. Гранулометрический состав порошка ( «грансостав» ) определяют ситовым, микроскопическим, седиментационным, кондуктометрическим и другими методами анализа. Лекция
Методы контроля свойств металлических и неметаллических порошков 388 Размер частиц и гранулометрический состав порошка Кондуктометрический Рентгеноструктурный Электронная микроскопия Оптическая микроскопия Ситовый метод Сидементационный метод 0, 001 0, 1 1 1000 Диаметр частиц, мкм Диапазоны определения дисперсного состава порошков различными методами Лекция
Методы контроля свойств металлических и неметаллических порошков 389 Размер частиц и гранулометрический состав порошка Ситовый анализ проводят сухим просеиванием в соответствии с межгосударственным стандартом ГОСТ 18318 -94. Навеску порошка (100± 1 г при насыпной плотности порошка > 1, 5 г/см 3 или 50± 0, 5 г в других случаях) просеивают через набор стандартных тканых сеток (сит) с квадратными отверстиями различной величины в соответствии с квалификацией контрольные «К» по ГОСТ 6613– 86. Номер сетки определяет размер ее отверстия в свету. Лекция
Методы контроля свойств металлических и неметаллических порошков 390 Размер частиц и гранулометрический состав порошка В США за основу принято сито с размером отверстий в свету 0, 074 мм. Есть основной ряд сит с модулем √ 2 = 1, 414 и дополнительный ряд с модулем 4√ 2 = 1, 189. Размер отверстия следующего за основным (более крупного) сита составляет 0, 074 √ 2 = 0, 104 мм, затем 0, 104 √ 2 = 0, 147 мм и т. д. В этой системе номер сита указывают в мешах (число меш означает количество отверстий на одном линейном дюйме, равном 25, 4 мм). Диаметр проволоки каждого сита равен размеру отверстия d , который определяют по формуле: а = 25, 4/2 m ( т – число меш). Лекция
Методы контроля свойств металлических и неметаллических порошков 391 Сравнение ряда проволочных сеток с квадратными отверстиями Номер сетки Номинальный размер стороны отверстия в свету, мкм Номинальный диаметр проволоки, мкм Количество отверстий на линейном дюйме (число меш) Живое сечение сетки (доля площади отверстий), % 004 40 30 363 32, 7 0045 45 36 314 30, 9 005 50 36 295 33, 8 0056 56 40 265 34, 0 0063 63 40 247 37, 4 0071 71 50 210 34, 4 008 80 50 195 37, 9 009 90 60 170 36, 0 01 100 60 154 39, 1 0112 80 132 34, 0 0125 80 124 37, 2 Лекция
Методы контроля свойств металлических и неметаллических порошков 392 Размер частиц и гранулометрический состав порошка Долю порошка, оставшуюся на сите при просеве, называют плюсовой фракцией , а прошедшую через сито – минусовой фракцией. Фракцию, количество которой составляет 98 % от массы анализируемой пробы. Относительное содержание каждой из фракций X , % вычисляют с точностью до 0, 1 % по формуле X = ( G n / G )· 100 где G n – масса данной фракции порошка, г; G – масса испытываемой пробы, г. Лекция
Методы контроля свойств металлических и неметаллических порошков 393 Размер частиц и гранулометрический состав порошка Результаты ситового анализа записывают в таблицу по определенной форме. Например: фракция порошка, прошедшая через сетку 0125 мм, но оставшаяся на сетке 0. 1 мм, обозначается как — 0125. . . +01 или -125. . . +100 мкм (запись по ГОСТ 18318 -94 имеет вид: <125. . . ≥ 100 мкм), рядом указывают ее процентное содержание. Для каждой фракции может быть указан средний размер ее частиц d ср, определяемый как среднее арифметическое размеров отверстии плюсового и минусового сит. Лекция
Методы контроля свойств металлических и неметаллических порошков 394 Размер частиц и гранулометрический состав порошка Недостатки ситового метода: — очень мелкие порошки не поддаются ситовому анализу (минимальный размер отверстий составляет 40 мкм для РФ, а для зарубежных – 5 мкм ); — форма частиц может внести искажение в результаты ситового анализа (дискообразные частицы задерживаются на сетке с размером отверстий больше их поперечника, а вытянутые иглообразные или дендритные частицы проходят через сито с отверстиями меньше их длины). Лекция
Методы контроля свойств металлических и неметаллических порошков 395 Размер частиц и гранулометрический состав порошка ГОСТ 18318 -94 не распространяется на порошки с частицами дискообразной, игольчатой и дендридной формы, а также порошки с пластификаторами или с размером частиц < 45 мкм. При работе с ситами, размер отверстий которых < 40 мкм, целесообразно использовать гидравлический метод разделения частиц : навеску порошка в сите помещают под струю воды (или другой смачивающей порошок жидкости) и промывку осуществляют до полного просветления промывающей жидкости. Лекция
Методы контроля свойств металлических и неметаллических порошков 396 Микроскопический анализ Схема учета частиц при измерении их размера в отдельных полях зрения микроскопа. Лекция
Методы контроля свойств металлических и неметаллических порошков 397 Микроскопический анализ Количество измеренных частиц или их расчетное количество должно быть > 625 (при выполнении этого условия ошибка измерения < 2 %). Интервал размеров частиц разбивают не менее чем на 6 частей (классов); частицы, размер которых соответствует нижнему пределу класса, относят к классу более мелкому. Количественное распределение частиц по размерам получают, относя количество измеренных частиц 1 -го класса к общему количеству измеренных частиц или к их общему расчетному количеству (если измерения проводили при двух или трех различных увеличениях). Лекция
Методы контроля свойств металлических и неметаллических порошков 398 Микроскопический анализ Под расчетным количеством измеренных частиц N расч понимают их количество, отнесенное к одному выбранному увеличению. Если результатом испытаний должно быть массовое (объемное) распределение частиц по размерам , то класс самых крупных частиц, составляющих > 5 %, принимают за контрольный, в котором количество измеренных частиц должно составлять: Содержание контрольного класса, %. . . 5– 10 >10– 15 >15– 24 >24 Минимальное количество измеренных частиц. . 25 50 75 100 Для оценки размеров частиц в интервале 0, 001– 10 мкм применяют методы электронной микроскопии. Лекция
Методы контроля свойств металлических и неметаллических порошков 399 Седиментационный анализ Метод основан на определении скорости оседания твердых частиц в какой-либо вязкой среде (жидкости или газе) при их ламинарном движении. Согласно закону Стокса для частиц радиуса r и плотности γ n , помещенных в жидкую среду с плотностью γ ж и вязкостью η , скорость оседания составляет V = [2( γ n – γ ж) qr 2] / 9 η или V = r 2 / K 2, где K = √ 9 η / [2( γ n – γ ж) q ], Зная скорость v , можно рассчитать размер частицы: r = √ 9 η V / [2( γ n – γ ж) q ] или r = KV 0, 5. Лекция
Методы контроля свойств металлических и неметаллических порошков 400 Седиментационный анализ Уравнения справедливы при равноосной форме частиц и их равномерном движении в жидкости. ГОСТ 22662– 77 устанавливает весовой метод седиментации и метод фотоседиментации для определения гранулометрического состава металлических порошков со сферической или полиэдрической формой частиц размером от 0, 5 до 40 мкм. За размер частицы полиэдрической формы принимают диаметр сферы объемом, равным объему частицы ( диаметр по Стоксу ). Лекция
Методы контроля свойств металлических и неметаллических порошков 401 Седиментационный анализ При весовой седиментации определяют скорость оседания частиц по скорости накапливания осадка порошка, оседающего из суспензии. Дисперсионная жидкость должна образовывать с порошком устойчивые суспензии, хорошо смачивать его частицы и быть химически инертной к ним. Плотность и вязкость должны быть такими, чтобы обеспечивались условия ламинарного движения самых крупных частиц порошка , а продолжительность всего анализа не превышала 6 часов. Лекция
Методы контроля свойств металлических и неметаллических порошков 402 Седиментационный анализ Для обеспечения ламинарного движения самых крупных частиц порошка d (см) должно соблюдаться неравенство d 3 · q ( γ n – γ ж) γ ж / 18 η 2 ≤ 0, 2, где γ n и γ ж – соответственно пикнометрическая плотность частиц порошка и дисперсионной жидкости, г/см 3 ; η – вязкость дисперсионной жидкости, Н · с/м 2 ( П), ориентировочное значение которой вычисляют по формуле η = 16, 5 d √ d ( γ ж – 1). Лекция
Методы контроля свойств металлических и неметаллических порошков 403 Седиментационный анализ Схема устройства для проведения седиментационного анализа 1 – чашка весов; 2 – подвеска чашки весов; 3 – суспензия анализируемого порошка; 4 – коромысло весов; 5 – блок регистрации и записи массы осадка 4 3 5 2 1 h. Лекция
Методы контроля свойств металлических и неметаллических порошков 404 Седиментационный анализ При неавтоматической регистрации производят замеры массы осадка через 0, 5, 1, 2, 3, 5, 7, 10, 15, 20, 25, 30, 45, 60, 70, 90, 120 мин и строят график зависимости массы осадка m от времени оседания τ. Затем для частиц порошка с диаметрами dn , …. d 3, d 2, d 1 вычисляют длительность их оседания в секундах по формуле τ = 18 η h / [ q ( γ n – γ ж) d 2]. Рассчитанные значения τ , которых должно быть > 5, откладывают по оси абсцисс экспериментальной диаграммы зависимости массы осадка от длительности оседания и из соответствующих точек восстанавливают перпендикуляры к оси абсцисс до пересечения с седиментационной кривой. Лекция
Методы контроля свойств металлических и неметаллических порошков 405 Седиментационный анализ Зависимость накопления массы порошка т от длительности его оседания в анализируемой суспензии 0 τ 1 τ 2 τ 3 τ 4 τ n d 1 d 2 d 3 d 4 d n m m 1 m 3 m 2 Лекция
Методы контроля свойств металлических и неметаллических порошков 406 Седиментационный анализ При фотоседиментационном анализе скорость оседания частиц определяют по скорости изменения оптической плотности суспензии порошка, фиксируя ее непрерывно по фотоэлектродвижущей силе или фототоку, возникающему в фотоэлементе от светового потока, проходящего через суспензию. По полученной зависимости рассчитывают массовую долю частиц различных фракций (размеров). Закономерность изменения интенсивности света при прохождении его через суспензию описывается законом Бугера – Ламберта – Бэра. Лекция
Методы контроля свойств металлических и неметаллических порошков 407 Седиментационный анализ Закон Бугера – Ламберта – Бэра: I 0 / I τ = e – x c l , , где I 0 – интенсивность света, прошедшего через слой суспензии толщиной l ; I τ – интенсивность падающего света; с – концентрация суспензии или количество частиц в ней; х – коэффициент, пропорциональный удельной поверхности частиц (коэффициент светопоглощения). Приборы, основанные на этом принципе, называют турбидиметрами. Для оценки оптической плотности суспензии кроме светового потока можно применять рентгеновские и лазерные лучи. Лекция
Методы контроля свойств металлических и неметаллических порошков 408 Фотоседиментационный анализ Схема фотоседиментационного метода ( а ) и зависимость изменения величины сигнала (Е) от времени оседания порошка ( б ) 1 – источник света; 2 – диафрагма; 3 – суспензия порошка; 4 – стеклянная кювета; 5 – фотоэлемент; 6 – потенциометр 1 2 5 63 h 4 τ 1 τ 2 τ 3 τ 4 τ n d 1 d 2 d 3 d 4 d n Е 1 Е 2 Е 3 Е n а б. Лекция
Методы контроля свойств металлических и неметаллических порошков 409 Классификация частиц в потоке газа Прибор для воздушной классификации порошка 1 – насос; 2 – ротаметр; 3 – осушитель; 4 – измеритель скорости газового потока; 5 – манометр; 6 – U -образная трубка с порошком; 7 – камера; 8 – сборник порошка 40 30 20 10 5 1, 0 0, 52, 0 1234 5 7 7 86 Лекция
Методы контроля свойств металлических и неметаллических порошков 410 Кондуктометрический анализ Метод импульсной кондуктометрии предусматривает определение фракционного состава порошка в электрическом поле. Если электропроводящую суспензию перекачивать из одного объема в другой (в каждом из объемов помещены металлические электроды) через короткий канал очень малого диаметра, то при прохождении частицы через этот канал объем электролита в межэлектродной области изменится и на короткое время резко изменится электросопротивление в канале, что вызовет токовый импульс в цепи нагрузки. Лекция
Методы контроля свойств металлических и неметаллических порошков 411 Кондуктометрический анализ Длительность токового импульса зависит от скорости прохождения частицы по каналу, а амплитуда – от объема частицы (следовательно, и от ее линейного размера), электропроводности ее материала и некоторых других факторов. При последовательном прохождении по каналу частиц различного размера возникает последовательность импульсов разной амплитуды, что фиксируется соответствующей аппаратурой. Зная функциональную зависимость, связывающую эти амплитуды с линейным размером частиц, можно определить величину частиц. Лекция
Методы контроля свойств металлических и неметаллических порошков 412 Кондуктометрический анализ 1 – стакан с суспензией; 2 – кран; 3 – патрубок насоса; 4 – буферный сосуд; 5 – колено манометра; 6, 7 – контакты счетчика; 8 – пробирка с каналом; 9 – канал; 10, 11 – электроды; 12 – электропроводящая суспензияк усилителю 14 11 10 9 8765 3 12 Схема прибора для измерения размеров частиц порошка кондуктометрическим методом. Лекция
Методы контроля свойств металлических и неметаллических порошков 413 Лазерный и рентгеновский методы Лазерный метод определения фракционного состава порошка основан на явлении рассеивания когерентного монохроматического лазерного луча частицами порошка. Поток излучения поступает на плоский вращающийся щелевой фильтр, который обеспечивает непрерывную развертку светового луча на вращающемся перфорированном диске, отверстия которого расположены на различных расстояниях от оси вращения по спирали Архимеда. Это позволяет превращать световой поток (с изменяющейся плотностью света по сечению) в систему импульсов, отражающих интенсивность различных участков светового потока. Лекция
Методы контроля свойств металлических и неметаллических порошков 414 Лазерный и рентгеновский методы Число отверстий во вращающемся диске определяет число групп разделения (количество фракций). Диапазон размеров частиц, в котором эффективна работа лазерного анализатора, составляет от 2 до 170 мкм. На анализе рассеяния рентгеновских лучей , проходящих через среду со взвешенными в ней частицами, основан рентгеновский метод определения малых углов рассеяния (МУР). Величина углового рассеяния узкого параллельного пучка рентгеновских лучей может достигать десятков угловых минут на частицах размером 2– 100 нм (0, 002– 0, 1 мкм). Лекция
Методы контроля свойств металлических и неметаллических порошков 415 Лазерный и рентгеновский методы Схема лазерного анализатора размера частиц порошка 1 – лазер; 2 – кювета с каналом для прокачки суспензии; 3, 6 – линза; 4 – щелевой фильтр; 5 – перфорированный диск; 7 – фотодетектор; 8 – регистрирующее устройство и микропроцессор1 8 7 суспензия 2 3 6 5 4 Лекция
Методы контроля свойств металлических и неметаллических порошков 416 Список рекомендуемой литературы • Либенсон, Г. А. Процессы порошковой металлургии : учеб. для вузов : в 2 ч. / Г. А. Либенсон, В. Ю. Лопатин, Г. В. Комарницкий. – М. : МИСИС, 2001. • Фомина, О. Н. Порошковая металлургия. Энциклопедия международных стандартов / О. Н. Фомина, С. Н. Суворова, Я. М. Турецкий. – М. : ИПК Издательство стандартов, 1999. – 305 с. Лекция
Свойства порошков. Управление качеством продукции
Управление качеством продукции 418 Лекция 27 Свойства порошков. Управление качеством продукции • Классификация методов определения удельной поверхности • Определение удельной поверхности порошков методами газопроницаемости • Определение удельной поверхности порошков измерением адсорбционной способности • Химические свойства порошков • Принципы управления качеством продукции. Лекция
Управление качеством продукции 419 Удельная поверхность Удельная поверхность порошка представляет собой сумму наружных поверхностей всех частиц, составляющих единицу его массы или объема. Для большинства порошков металлов и неметаллов характерна поверхность от 0, 01 до 1 м 2 /г. Для отдельных порошков (нано- и ультрадисперсных) удельная поверхность составляет 15– 25 м 2 /г. Удельная поверхность зависит не только от размеров порошка, но и от степени развитости (шероховатости) поверхности. Наиболее часто для определения удельной поверхности используют методы, основанные на измерении газопроницаемости или адсорбционной способности порошка. Лекция
Управление качеством продукции 420 Удельная поверхность Методы измерения газопроницаемости порошка основаны на оценке фильтрационных процессов при прохождении потока газа через слой порошка с известной относительной плотностью. Скорость, с которой газ фильтруется через пористый слой порошка, обратно пропорциональна квадрату удельной поверхности. Фильтрация газа может происходить в двух режимах – вязком и молекулярном. Лекция
Управление качеством продукции 421 Удельная поверхность При вязком режиме просачивания, движение газа через слой порошка осуществляется при давлении близком к атмосферному, в режиме «просачивания» газовых потоков по порам порошкового тела. При этом не учитывается развитая поверхность частиц порошка (вязкое течение проходит только по внешней поверхности частиц порошка). При молекулярном просачивании удельную поверхность определяют при прохождении газа через слой в условиях разряжения, когда длина свободного пробега молекул газа превышает размеры поровых каналов в порошке. Лекция
Управление качеством продукции 422 Удельная поверхность Методы, основанные на фильтрации газа при атмосферном давлении в режиме вязкого течения, могут использоваться для определения удельной поверхности порошков с размерами частиц > 10 мкм. Методы, основанные на фильтрации газа в режиме молекулярного течения могут использоваться для определения удельной поверхности порошков – от 3– 5 мкм и выше. На принципе фильтрации газа в режиме вязкого течения работает прибор Товарова, а также установки ПСХ и АДЗ. Лекция
Управление качеством продукции 423 Удельная поверхность В приборе Товарова пробу засыпают в гильзу и уплотняют, замеряя высоту слоя порошка. Открывая кран сосуда Мариотта, создают постоянный уровень разряжения в нижней части гильзы с порошком. Перепад давлений (степень разряжения) определяют с помощью манометра. Удельную поверхность порошка рассчитывают по формуле: S уд = {14 έ 1, 5 / [ γ п (1 – έ )]}·( F· Δ p· τ / h· μ ·V )0, 5, где F – площадь сечения гильзы с порошком; μ – вязкость воздуха; V – объем воздуха, прошедшего за время τ через слой порошка высотой h ; γ п – плотность материала частиц порошка; έ = ( Wγ п – m )/( Wγ п) – коэффициент пористости порошка массой m в слое объемом W ; Δ p – величина перепада давления, зафиксированная с помощью манометра. Лекция
Управление качеством продукции 424 Удельная поверхность В приборах ПСХ и АДП разряжение в системе создается с помощью резиной груши – спиратора. Удельная поверхность порошка рассчитывается по формуле: S уд = ( А / γ п ) { έ 3 · τ / [ (1 – έ )2 μ ]}0, 5, где τ – время опускания жидкости в манометре между контрольными отметками; γ п – плотность материала частиц порошка; А – постоянная прибора (определяется экспериментально по эталонам). Лекция
Управление качеством продукции 425 Удельная поверхность Схема прибора Товарова 1 – гильза для порошка; 2 – плунжер; 3 – слой порошка; 4 – сосуд Мариотта; 5 – кран сосуда Мариотта; 6 – стакан для стока воды; 7 – манометр 5 64 7 3 2 1 1 Лекция
Управление качеством продукции 426 Удельная поверхность Схема прибора, работающего в режиме молекулярного течения (прибор Дерягина) 1, 3, 4, 8, 10, 13, 17 – вакуумные клапаны (краны); 2, 7, 12 – буферные емкости; 5 – азотная ловушка (для вымораживания воды при откачке порошка); 6 — диффузионный (паромасляный) насос; 9 – форвакуумный насос; 11, 16 – термопарные лампы (для определения степени откачки на вакуум); 14 – трубка с анализируемым порошком; 15 – манометр ДН ФН 1 2 3 16 15 14 13 11 124 8 97 5 1061 7 Лекция
Управление качеством продукции 427 Удельная поверхность Адсорбционные методы Эти методы являются наиболее точными и универсальными для определения полной (суммарной) поверхности дисперсных тел. В их основе лежит определение количества вещества (газа), адсорбируемого поверхностью твердых частиц в виде. Если известна площадь, занимаемая отдельной молекулой и масса адсорбированного газа, то может быть рассчитана площадь поверхности исследуемого порошка (площадь, занимаемая адсорбированным газом). Лекция
Управление качеством продукции 428 Удельная поверхность Адсорбционные методы определения удельной поверхности порошков делят на статические (манометрические, гравиметрические или с использованием калиброванного капилляра) и динамические , часто называемые хроматографическими. . Среди статических более распространены манометрические методы. Наиболее известный из них – метод БЭТ , названный по начальным буквам фамилий авторов этого метода (Брунауэр, Эммет, Теллер). Авторы метода предложили в качестве газа-адсорбата взять азот и проводить его адсорбцию на частицах порошка при температуре – 196 °С (температура жидкого азота). Лекция
Управление качеством продукции 429 Удельная поверхность Схема адсорбционной установки для определения удельной поверхности порошков по методу БЭТ 1 – ампула с порошком; 2, 5 – краны; 3 – резервуар с азотом; 4 – манометр 35 152025302 1 5 4 3 Лекция
Управление качеством продукции 430 Удельная поверхность. Лекция 27 Общий объем газа V , адсорбированный поверхностью твердого тела, может быть выражен уравнением БЭТ: V = Vm·c·p /{( р S – р )[1+( с – 1) р / р S ]}, где с – константа прибора, Vm – объем газа-адсорбата в виде монослоя; р – реальное давление газа, p. S – давление насыщенного газа. В линейной форме выражение может быть записано следующим образом: р /[ V ( р S – р )] = 1/[ с Vm + [( c – 1)/ c·Vm p / р S.
Управление качеством продукции 431 Удельная поверхность Из рассчитанного объема газа Vm , см 3 , адсорбированного в виде монослоя, рассчитывают поверхность твердых частиц, соответствующую этому монослою: S =( Vm / V μ ) NA σ , где V μ = 22414 см 3 /моль – молекулярный объем одной грамм-молекулы газа; NA = 6, 023– 1023 молекул/моль – число Авогадро; σ – площадь, занимаемая одной адсорбированной молекулой газа. Удельная поверхность порошка S уд = S / m , где т – масса анализируемой пробы порошка. Лекция
Управление качеством продукции 432 Удельная поверхность Динамические методы газовой хроматографии основаны на различной адсорбции компонентов газовой смеси поверхностью адсорбента (анализируемого порошка). Среди этих методов наиболее широко используют динамический метод тепловой десорбции газа (ГОСТ 23401 -90). В этом методе измеряют количества аргона, адсорбированного на поверхности порошка из аргоно-гелиевой смеси (5– 7 % Аг, 95– 93 % Не) при температуре – 196 о С. На начальном этапе анализа газ-адсорбат осаждают на поверхности охлажденного порошка, а затем его десорбируют при нагреве порошка до 20± 50 о С. Лекция
Управление качеством продукции 433 Удельная поверхность Объем газа-адсорбата определяют по изменению теплопроводности потока газа-носителя, пропускаемого через анализируемый порошок (фиксируется потенциометром детектора теплопроводности в виде хроматограммы десорбции). Объем адсорбированного газа и площадь удельной поверхности образца вычисляют, сопоставляя площади кривых десорбции анализируемого порошка и образца сравнения (с известной удельной поверхностью). Лекция
Управление качеством продукции 434 Химические свойства Пригодность порошка для изготовления из него материалов и изделий зависит от содержания основного металла, примесей, различных механических загрязнений и газов. Химический состав порошка зависит от метода его производства , а также от степени чистоты исходных материалов. Химический анализ производят по методикам в соответствии с ГОСТами или утвержденной в установленном порядке нормативно-технической документацией; большинство таких методик аналогично применяемым для анализа состава литых металлов и сплавов. Лекция
Управление качеством продукции 435 Химические свойства Содержание в металлических порошках легковосстанавливающихся оксидов может быть от 1 до 10 %, что соответствует 0, 2– 1, 5 % кислорода. Наличие в порошке трудновосстанавливаемых крайне нежелательно. Большое количество растворенных газов увеличивает хрупкость частиц порошков и затрудняет формование (прежде всего в пресс-формах), а интенсивное газовыделение при спекании может привести к короблению нагреваемой заготовки. Определение кислорода в порошках может быть качественным или количественным. Лекция
Управление качеством продукции 436 Химические свойства При качественном определении кислорода (по ГОСТ 18897– 73) определяют потерю массы порции порошка при ее прокаливании в атмосфере сухого водорода или оценивают пикнометрическую плотность частиц порошка. При количественном определении содержания кислорода навеску анализируемого порошка восстанавливают чистым и хорошо осушенным водородом, улавливая образующиеся пары воды пентаоксидом фосфора, оксидом кальция или каким-нибудь другим активным влагопоглотителем. Количество кислорода рассчитывают по привесу соответствующего поглотителя. Лекция
Управление качеством продукции 437 Химические свойства Перспективным для точного определения содержания кислорода является метод нейтронно-активационного анализа. Газосодержание порошков определяют с использованием методов, основанных на нагреве и плавлении анализируемых проб в вакууме. Влажность порошка при содержании влаги до 0, 1 % определяют высушиванием его навески до установления постоянной массы в электрическом сушильном шкафу. Лекция
Навеску порошка помещают в предварительно высушенный стаканчик, закрывают его крышкой и взвешивают. Прошок в стаканчике нагревают при 100– 105 о С в течение 2 ч, охлаждают и взвешивают, после чего сушку повторяют в течение 0, 5 ч, контролируя ее качество. Содержание влаги ( X , %) определяют по формуле X = [( m 2 – m 3 ) / m 1] 100, где m 1, m 2, m 3 – соответственно навеска порошка, масса стаканчика с порошком до и после испытания. Полученные значения X округляют до 0, 01 %. Содержание в порошке влаги от 0, 05 до 0, 5 % определяют в соответствии с ГОСТ 18317– 73 методом, основанным на отгонке инертным газом при 200 °С из металлического порошка воды и ее взаимодействии с реактивом Фишера при электрометрическом титрировании. Управление качеством продукции 438 Химические свойства Лекция
Управление качеством продукции 439 Воспламеняемость порошка Пожароопасность (часто применяется термин » пирофорность «) порошка связана с его способностью к самовозгоранию при соприкосновении с окружающей атмосферой при относительно невысоких температурах. Пожароопасность зависит от химической природы и чистоты металла, крупности и формы частиц порошка, состояния их поверхности (пленки оксидов уменьшают пожароопасность). Основной причиной воспламенения порошков принято считать их взаимодействие с кислородом (воздухом). Лекция
Управление качеством продукции 440 Воспламеняемость порошка зависит от того, находится ли он в свободно насыпанном состоянии (т. е. в виде аэрогеля) или в виде взвеси в окружающей атмосфере (т. е. в виде аэрозоля). Для аэрогелей определяют температуры самонагревания, тления, самовоспламенения и воспламенения, а также энергию воспламенения. По мере уменьшения размера частиц температура воспламенения снижается и высокодисперсный порошок становится пирофорным, т. е. приобретает способность самовоспламеняться при комнатной температуре. Лекция
Управление качеством продукции 441 Взрываемость порошка Сверхвысокие скорости химического взаимодействия порошка с кислородом приводят к почти мгновенному выделению энергии, которое сопровождается образованием и распространением взрывной волны. Металлические порошки, располагающиеся слоем (аэрогели), не способны взрываться, хотя могут стать источниками взрыва в результате выброса пылевого облачка ( взвеси металлических частиц в газе ), его воспламенения и интенсивного горения частиц. Лекция
Управление качеством продукции 442 Взрываемость порошка Характеристики взрываемости в основном зависят от дисперсности металлического порошка, степени его окисленности и содержания кислорода в газовой фазе. Обычно воспламеняются и взрываются во взвешенном состоянии порошки крупностью частиц < 150– 200 мкм. Содержание кислорода в газовой фазе (окружающей атмосфере) существенно влияет на характер протекания процесса взрыва аэрозолей металлов, поскольку тепловой взрыв происходит в основном за счет интенсивной экзотермической реакции окисления металла. Лекция
Управление качеством продукции 443 Токсичность порошка Систематическое вдыхание металлических порошков независимо от их вида может привести к профессиональным заболеваниям. Практически пыль (обычно размер частиц < 4 мкм) любого из металлов, в том числе и совершенно безвредных в компактном состоянии, воздействует на человека и может вызвать патологические изменения в его организме (фиброгенные и аллергические заболевания; канцерогенны бериллий и его соединения). Лекция
Управление качеством продукции 444 Токсичность порошка Степень опасности для здоровья человека металлических пылей зависит от: — их химического состава и степени окисленности; — размера частиц и их концентрации; — длительности воздействия; — путей проникновения в организм и т. д. Технологические и санитарно-технические мероприятия должны поддерживать в производственных помещениях концентрацию пыли на уровне ниже нормы ПДК. Лекция
Управление качеством продукции 445 Список рекомендуемой литературы. Лекция 27 • Либенсон, Г. А. Процессы порошковой металлургии : учеб. для вузов : в 2 ч. / Г. А. Либенсон, В. Ю. Лопатин, Г. В. Комарницкий. – М. : МИСИС, 2001. • Фомина, О. Н. Порошковая металлургия. Энциклопедия международных стандартов / О. Н. Фомина, С. Н. Суворова, Я. М. Турецкий. – М. : ИПК Издательство стандартов, 1999. – 305 с.
Красноярск, 2008 Часть 2 Формование и спекание порошков
Красноярск, 2008 Формование порошков
Формование порошков 448 Оглавление Лекция 1. Введение. Классификация методов формо вания Лекция 2. Общие закономерности процессов формов ания порошков Лекция 3. Общие закономерности процессов формов ания порошков
Формование порошков 449 Лекция 1 Введение. Классификация методов формования • Операции подготовки порошков к формованию
Формование порошков 450 Формование порошка – технологическая операция, в результате которой порошок образует формовку – тело заданной формы, размеров и плотности. В процессе формования порошков изменяется исходный объем материала за счет консолидации отдельных частиц. Наблюдаемое изменение первоначального объема порошкового тела является основным отличием этого процесса от процесса деформирования компактного (литого) материала. Методы формования порошков условно разделяют на статические и динамические (импульсные). К статическим методам относятся различные методы холодного и горячего прессования материалов, шликерное литье и прокатка. К динамическим – методы, связанные с мощными импульсными воздействиями на порошковое тело (взрывные, пневмомеханические, электрогидравлические, электромагнитные). Введение. Лекция
Формование порошков 451 Методы формования металлических порошков Статическое формование Динамическое (импульсное ) формование Холодное прессование Прокатка. Изостатическое формование Шликерное формование Инжекционное формование. Мундштучное формование. Одностороннее Двустороннее Гидростатическое Газостатическое В эластичных втулках Горизонтальная Вертикальная Наклонная Радиусная В пористых формах Электрофоретическое Термопластичных шликеров Вибрационное формование Взврывное Электромагнитное Электрогидравл ическое Пневмомеханич еское Бризантными взрывными веществами Порохами. Классификация методов формования порошков. Лекция
Формование порошков 452 Лекция 2 Общие закономерности процессов формования порошков • Процессы, сопровождающие формование порошков • Зависимость плотности прессовки от давления прессования • Основные уравнения прессования • Боковое давление
Формование порошков 4531 2 3 4 Схема пресс-формы для холодного прессования порошков 1 – пуансон верхний; 2 – матрица; 3 – порошок; 4 – нижний пуансон (неподвижный)Процессы, происходящие при прессовании порошка. Лекция
Формование порошков 454 В порошковом теле отдельные частицы соединены друг с другом разнообразными связями, зависящими от размеров и формы частиц, а также от свойств заполнителя (жидкость или газ). Такие связи представляют собой: — слабые Ван-дер-Ваальсовы силы сцепления, действующие через тонкие остаточные прослойки газа (воздуха) или жидкости в контактах между свободно насыпанными частицами; — зацепление, связанное с шероховатостью поверхностей и сложной (например дендритной) формой частиц; — свободное опирание одних частиц на другие и пр. Процессы, происходящие при прессовании порошка. Лекция
Формование порошков 455 Модель уплотнения порошка в процессе прессования а – свободнонасыпанный порошок; б – уплотненный порошок (частицы заполнили крупные пустоты) а б. Процессы, происходящие при прессовании порошка. Лекция
Формование порошков 456 р, МПаγ отн в б а Идеализированная кривая процесса уплотнения порошковых тел Процессы, происходящие при прессовании порошка. Лекция
Формование порошков 457 Различают три основные стадии уплотнения порошкового тела: 1) стадия структурной деформации порошкового тела Эта стадия сопровождается разрушением арочных структур, значительной разгрузкой некоторых из межчастичных контактов, которая приводит к сокращению площади соприкосновения отдельных частиц и уменьшению силы связи между частицами. 2) стадия процесса уплотнения характеризуется тем, что частицы порошка, упакованные максимально плотно, оказывают определенное сопротивление сжатию, в силу того что давление прессования еще не достаточно велико для преодоления предела текучести (прочности) материала. 3) стадия пластической деформации частиц На этой стадии давление прессования превышает предел текучести материала порошка. Пластическая деформация охватывает весь объем порошкового тела, смещение межчастичных контактов фактически прекращается и они фиксируются. Процессы, происходящие при прессовании порошка. Лекция
Формование порошков 458 р, МПаγ отн. Процессы, происходящие при прессовании порошка Реальная зависимость процесса уплотнения порошковых тел. Лекция
Формование порошков 459 В реальных условиях в процессе прессования происходит взаимное наложение (перекрытие во времени) всех стадий уплотнения порошкового тела, связанное с тем, что частицы имеют различные размеры, форму и свойства. Деформация отдельных частиц начинается при сравнительно малых давлениях прессования, в то время как скольжение некоторых частиц имеет место и при высоких давлениях прессования. Реальная кривая уплотнения, характеризующая процесс прессования большинства металлических порошков, монотонна и в средней части не имеет явно выраженного горизонтального участка. Процессы, происходящие при прессовании порошка. Лекция
Формование порошков 460 Толщина и форма слоев порошка, спрессованного при одностороннем приложении давления сверху 6, 9 6, 8 6, 7 6, 47, 3 7, 2 7, 0 7, 27, 1 7, 07, 1 нагрузка Распределение плотности в никелевом брикете, спрессованном при давлении 700 МПа. Процессы, происходящие при прессовании порошка. Лекция
Формование порошков 461 Изменение плотности по высоте прессовки 1 – одностороннее прессование; 2 – двустороннее прессование h, мм γ , г/см 312 Процессы, происходящие при прессовании порошка. Лекция
Формование порошков 462 Одно- и двустороннее прессование порошка показывает, что при двустороннем прессовании более плотными оказываются верхняя и нижняя части прессовки (кривая 2), тогда как в ее середине наблюдается зона наименьшей плотности, называемая нейтральной. Неравномерная плотность прессовки может оказать прямое влияние на искажение ее формы и размеров при спекании, а также вызвать нежелательные изменения свойств спеченного порошкового тела. Процессы, происходящие при прессовании порошка. Лекция
Формование порошков 463 Общие закономерности процессов формования порошков • Трение при прессовании • Давление выталкивания • Упругое последействие • Прочность прессовок • Брак при прессовании Лекция
Формование порошков 464 М. Ю. Бальшин показал, что количественная зависимость плотности прессовки от давления прессования может быть выражена уравнениями : lgp = – L ( V – 1) + lgp max , (1) и lgp = – m lg V + lgp max , (2) или lgp = m lg γ + lgp max , (3) где p – приложенное (текущее) давление прессования; p max – давление прессования, обеспечивающее получение беспористой прессовки; L и m – постоянные, учитывающие природу прессуемого материала и называемые соответственно фактором и показателем прессования; V и γ – соответственно относительный объем и относительная плотность прессовки. Зависимость плотности прессовки от давления прессования. Лекция
Формование порошков 465 В дифференциальной форме уравнение (3) имеет вид dp / p = l · d. V ( 4 ) , где р – текущее давление прессования; V – относительный объем порошкового тела (прессовки) при давлении р ; l – фактор прессования, постоянный в некотором интервале давлений прессования. Зависимость плотности прессовки от давления прессования. Лекция
Формование порошков 466 После интегрирования выражения ( 4 ) и замены l на L ( L = 0, 434· l ) получаем уравнение ( 1 ), которое часто называют первым уравнением прессования Бальшина (полулогарифмическим). Фактор прессования L связан с величиной контактного давления σ к зависимостью L = 0, 434 K ’· h к / (σ к · h 0 ), ( 5 ) где К’ – постоянный коэффициент; h к – приведенная высота порошкового тела (прессовки), имеющего плотность 100 %; h 0 – первоначальная высота порошкового тела. Так как σ к ≠ const , Бальшин предложил в дифференциальном уравнении (4) фактор прессования l выразить в виде функции I = L /0, 434 = m / V. (6) После интегрирования уравнения (4) приводит к уравнениям (2) и (3), каждое из которых принято называть вторым (или логарифмическим) уравнением прессования Бальшина. Зависимость плотности прессовки от давления прессования. Лекция
Формование порошков 467 Для идеального процесса прессования (т. е. при отсутствии внешнего трения) уравнения (2) и (3) примут вид p ( V ) m = p max = p k = const ( 7 ) и p ( γ ) m = p max = p k = const , ( 8 ) где p k – максимальное (критическое) давление прессования, соответствующее максимальному уплотнению и равное по величине давлению истечения (численно это твердость материала при максимальной степени его упрочнения). Зависимость плотности прессовки от давления прессования. Лекция
Формование порошков 468 Показатель прессования т характеризует свойства порошка и может быть определен опытным путем или рассчитан по формуле m = 2 + γ / Δ γ , (9) где Δ γ = γ – γ 0 , а γ 0 – относительная плотность исходного порошкового тела до приложения нагрузки к нему. Зависимость плотности прессовки от давления прессования. Лекция
Формование порошков 469 lq γlqp = lqp к α Логарифмическая диаграмма процесса прессования (σ к = p к )Зависимость плотности прессовки от давления прессования. Лекция
Формование порошков 470 Наиболее приемлемо для анализа поведения порошков при прессовании уравнение (2). В графической форме при σ к = const уравнение (2) дает прямую линию. Тангенс угла наклона прямой к оси абсцисс численно равен показателю прессования р тах , а отрезок, отсекаемый прямой от оси ординат, равен логарифму максимального давления прессования р m ах или ( в идеальном случае ) он равен логарифму критического давления р к. Величина и форма частиц порошка, а также его насыпная плотность не оказывают прямого влияния на величину р к. Однако форма частиц и насыпная плотность оказывают влияние на прессуемость порошка. Зависимость плотности прессовки от давления прессования. Лекция
Формование порошков 471 Одно из наиболее удачных решений задачи математического описания процесса уплотнения металлического порошка во всем возможном диапазоне давлений предложено Г. М. Ждановичем. Идеальный процесс уплотнения описывает следующая зависимость p = p к ( γ n – γ 0 n )/(1 – γ 0 n ) = p к ( V о n – V n ) /[ V n ( V о n – 1)], (10) где p к – максимальное давление прессования, соответствующее максимальной твердости материала; γ – относительная плотность прессовки; γ 0 – относительная плотность исходного порошкового тела; V – относительный объем прессовки; V о – относительный объем исходного порошкового тела (до приложения нагрузки). Зависимость плотности прессовки от давления прессования. Лекция
Формование порошков 472 Между давлением идеального и реального процессов прессования существуют зависимости вида: при одностороннем прессовании p 0 = p (1 + 0, 25 А· V )), при двустороннем прессовании p 0 = p (1 + 0, 5 А· V ), где К – это некоторая постоянная величина (коэффициент). А = ξ · f ( L H + L B ) h K / S H , где ξ – коэффициент бокового давления; f – коэффициент внешнего трения; L H и L B – длины периметров или контуров соответственно наружной и внутренней (если прессовка с отверстием) боковых поверхностей прессовки; h K – высота слоя порошка в пресс-форме; S H – поперечная площадь сечения прессовки. Зависимость плотности прессовки от давления прессования. Лекция
Формование порошков 473 Частицы порошка движутся не только в направлении приложенной нагрузки, но и перемещаются в радиальном направлении, создавая давление на внутреннюю стенку матрицы. Давление, которое возникает при подобном взаимодействии порошка и пресс-формы называется боковым. В связи с этим важной характеристикой является так называемый коэффициент бокового давления ξ (отношение бокового давления р б к общему давлению прессования р ): ξ = р б / p ≤ 1. Значение в области высоких плотностей порошкового тела составляет 0, 2– 0, 5. Чем пластичнее материал порошка, тем больше значение коэффициента Пуассона ( ξ = /(1 – ) ), тем больше . Боковое давление Лекция
Формование порошков 474 Коэффициент бокового давления растет с увеличением плотности прессовки, но для разных материалов по-разному: чем пластичнее металл, тем в большей степени величина связана с давлением прессования. Боковое давление уменьшается по высоте прессовок, так как внешнее трение снижает давление прессования, приложенное к порошку в пресс-форме. Боковое давление Лекция
Формование порошков 475 На практике различают внешнее и межчастичное трение. Действие внешнего трения (трения частиц порошка о стенки матрицы) приводит к неравномерному распределению плотности материала по объему прессовки, связанному с потерей усилия прессования на его преодоление. Общее усилие Р , воздействующее на прессовку, будет равно: Р = р 2 D 2 / 4. Так как боковая поверхность цилиндрической прессовки равна Dh , то суммарное усилие Р r на нее составляет Р r = p D 2 / 4 = p Dh. Трение Лекция
Формование порошков 476 Потеря усилия P на преодоление трения частиц порошка о стенки пресс-формы равна P = f Р r = f p Dh. Доля усилия прессования, которая тратится на трение порошка о стенки пресс-формы, определяется отношением P / Р и составляет: P / Р = f p Dh /[ p ( D 2 /4)] = 4 f ( h/D ). Численные значения произведения 4 f по мере возрастания плотности прессовки колеблются в пределах не более ± 3– 5 %, т. е. остаются примерно постоянными в широком интервале давлений прессования. Трение Лекция
Формование порошков 477 Внешнее трение прессуемого порошка о стенки внутренней полости матрицы пресс-формы определяет усилие, необходимое для выталкивания прессовки после завершения ее формирования; соответствующее давление называют давлением выталкивания. Давление выталкивания пропорционально давлению прессования и зависит от коэффициента внешнего трения и коэффициента Пуассона прессуемого порошка. Обычно его принимают равным 0, 2– 0, 35 давления прессования и оно тем больше, чем выше прессовка и меньше площадь ее поперечного сечения. Давление выталкивания. Лекция
Формование порошков 478 Давление выталкивания всегда меньше потерь давления на трение порошка о стенку внутренней полости матрицы пресс-формы, что связано с изменением объема прессовки после снятия давления в результате действия внутренних (остаточных) напряжений, возникающих в процессе уплотнения порошка. Давление выталкивания. Лекция
Формование порошков 479 Увеличение размеров прессовки в результате действия упругих сил после снятия давления называют упругим последействием. Величина упругого последействия зависит от: — дисперсности порошка, формы и состояния поверхности частиц; — содержания оксидов; — давления прессования; — наличия смазки и ее количества и др. Упругие последействия. Лекция
Формование порошков 480 Относительное изменение линейных размеров прессовки вследствие упругого последействия определяют из выражения, %: i = ( l / l 0 )100 = [ ( l 1 – l 0 ) / l 0 ] · 100, где l – абсолютное расширение прессовки по длине или диаметру (поперечному размеру); l 0 – длина или диаметр прессовки, находящейся в матрице пресс-формы под действием давления прессования; l 1 – длина или диаметр прессовки после выпрессовывания из матрицы пресс-формы. Объемное упругое последействие прессовки равно, %: V = ( V / V 0 )100 = [ ( V 1 – V 0 ) / V 0 ] · 100. Упругие последействия. Лекция
Формование порошков 481 Прочность прессовок определяется как механическим зацеплением, так и микросхватыванием отдельных участков (неровностей) частиц порошка. В зависимости от природы порошка, его физических и химических свойств действие тех или иных сил будет проявляться в большей или меньшей степени. Прочность прессовки при сжатии в направлении прессования всегда больше прочности в перпендикулярном к нему направлении. На прочность прессовки значительное влияние оказывают коэффициент обжатия K = γ п / γ нас (где γ п – плотность прессовки при данном давлении прессования). Прочность прессовок. Лекция
Формование порошков 482 Чем больше K при одной и той же плотности прессовки, тем сильнее обжатие порошка и тем прочнее прессовка. Минимальное значение K , необходимое для получения прессовок достаточной прочности из порошков пластичных металлов с сильно шероховатой и разветвленной формой частиц, составляет примерно 1, 7– 1, 8. Прочность прессовок понижается при загрязнении порошков оксидами. Прочность прессовок. Лекция
Формование порошков 483 Наиболее часто встречающийся на практике и наиболее опасный вид брака прессовок – расслой (поперечные или диагональные трещины). Наибольшее значение имеют следующие причины образования поперечных или диагональных трещин: 1. Условия прессования (использование гладких плоских или сфероидизированных частиц, окисление и наклеп частиц, большого количества смазки и пр. ). 2. Высокие давления прессования. 3. Плохое качество смешивания или использование химически неоднородного материала. Брак при прессовании. Лекция
Формование порошков 484 4. Слишком медленное (в особенности остановки) или слишком быстрое выпрессовывание изделия из матрицы пресс-формы. 5. Наличие в прессуемой заготовке тонких стенок или резких переходов. 6. Неравномерное распределение порошка по объему засыпной полости матрицы пресс-формы. 7. Низкое давление прессования или неправильная (заниженная) величина навески порошка. Брак при прессовании. Лекция
Методы формования
Методы формования 486 Оглавление Лекция 4. Методы формования. Холодное изостатическое пре ссование Лекция 5. Горячее изостатическое (газостатическое) прессова ние (ГИП) Лекция 6. Прессование в эластичных оболочках. Шликерно е формование во впитывающие формы Лекция 7. Шликерное формование в неадсорбирующие формы, литье из термопластичных шликеров, электрофоретическое литье шликеров Лекция 8. Мундштучное и инжекционное формование порошк ов Лекция 9. Вибрационное формование порошков Лекция 10. Импульсное формование Лекция 11. Получение изделий методом прокатки порошков Лекция 12. Прокатка порошка. Горячее прессование
Методы формования 487 Методы формования. Холодное изостатическое прессование • Виды изостатического формования • Способы холодного изостатического формования • Цикл прессования • Технологическая оснастка и оборудование, используемое при прессовании порошков методом ХИП Лекция
Методы формования 488 Изостатическое формование – формование металлического порошка в эластичной или деформируемой оболочке в условиях всестороннего сжатия. Изостатическое формование позволяет получать из порошка заготовки (порошковые формовки) с большим отношением длины к диаметру (ширине) и тонкими стенками, обладающие равномерной объемной плотностью. В настоящее время выделяют три базовые разновидности изостатического формования: — гидростатическое; — газостатическое; — в эластичных оболочках. Изостатическое формование. Лекция
Методы формования 489 Холодное изостатическое прессование (ХИП) Методом ХИП (метод гидростатического формования) получают цилиндры, трубы, шары и другие изделия сложной формы с массой до нескольких сотен килограмм. Известны две разновидности гидростатического формования: — методом «встроенной или фиксированной матрицы» (метод «сухого мешка» ), — радиального уплотнения методом «сухого» мешка. Изостатическое формование. Лекция
Методы формования 490 Холодное изостатическое прессование (ХИП) На практике используют еще один вариант формования по методу «сухого» мешка , который назван методом « трехосного » формования. В этом методе порошок последовательно подвергают радиальному уплотнению жидкостью по типу «сухого» мешка и последующему (без снятия давления жидкости) осевому допрессовыванию пуансонами по схеме двустороннего прессования при давлении выше давления жидкости. За счет применения подобного способа формования можно получить большие значения плотности (на 10– 25 %) и прочности формовки, чем при других вариантах холодного изостатического формования. Изостатическое формование. Лекция
Методы формования 4911 2 3 4 5 1 96 2 3 72 31 8 а 4 б в Схемы методов холодного изостатического прессования 1 – контейнер; 2 – жидкость высокого давления; 3 – порошок; 4 – эластичная оболочка; 5– компрессор; 6, 7 – уплотняющие затворы; 8 – выталкиватель формовки; 9 – матрица типа «сухого мешка» Холодное изостатическое прессование. Лекция
Методы формования 492 К преимуществам метода гидростатического формования относится: — возможность получения изделий с более высокой плотностью и прочность формовки при давлениях, сопоставимых с давлениями холодного одно- и двухстороннего прессования; — высокая равноплотность изделия; — напряжения в объеме формовки незначительны; — возможность формовать порошок без смазки или при ее минимальном количестве; — однородная (без текстуры) структура формовки; — более высокая и равномерная плотность заготовки после спекания; — возможность получения крупногабаритных изделий и изделия сложной формы и пр. ; Холодное изостатическое прессование. Лекция
Методы формования 493 К недостаткам этого метода относятся : — низкая точность изготовления изделий; — длительность полного цикла формования; — высокая чувствительность к химическим загрязнениям; — быстрый износ эластичных оболочек. Холодное изостатическое прессование. Лекция
Методы формования 494 Материал Метод изготовления оболочки Пригодность для гидростатического прессования ** А Б Натуральный и синтетический каучук Окунание заготовки 2– 3/0– 2 0/0 Натуральный и синтетический каучук Горячее литьё 2– 3/1– 3 2– 4/1– 2 Неопреновая резина Окунание 2/0– 2 0/0 Неопреновая и нетриловая резина Горячее литьё 2– 4/1– 3 3– 4/1– 2 Силиконовая резина Литьё 0 -1/0 0/0 Поливинилхлорид – 1– 2/1 -2 0/0 Однокомпонентный полиуритан Горячее литьё 2– 3/1– 2 0– 2/0– 1 Двухкомпонентный полиуритан Холодное литьё 1– 2/0– 1/0 Примечания : А – формование по методу «мокрого» мешка; Б – формование по методу «сухого» мешка * 0 – не рекомендуется; 1 – плохая; 2 – удовлетворительная; 3 – хорошая; 4 – отличная. ** В числителе – с высокой, хорошей текучестью и распыленных порошков; в знаменателе – с плохой текучестью порошков с частицами высокой твердости и неправильной формы. Материалы для изготовления эластичных оболочек. Лекция
Методы формования 495 Для ориентировочного определения габаритных размеров эластичной оболочки для получения изделий сравнительно простой формы (стержней, цилиндров или цилиндрических труб), имеющих постоянные сечения, можно использовать соотношения: для стержней или цилиндров D = d · 3 √ K , L = l ; L = l – l 1 ( «сухой» мешок без осевого сжатия), Холодное изостатическое прессование. Лекция
Методы формования 496 для цилиндрических труб с открытыми торцами (заглушки при формовании жестко закреплены) D = √ K ( d 2 – b 2 ) + b 2 , d 1 = b — d 2 , где D – внутренний диаметр эластичной оболочки; d – диаметр формовки; b – внутренний диаметр трубной формовки; d 1 – диаметр центрального стержня для формования трубной заготовки; d 2 – усадка по диаметру трубной формовки; L – длина рабочей зоны эластичной оболочки; l – длина формовки; l 1 — осевая усадка формовки; K – коэффициент уплотнения (обжатия) порошка, K = γ п / γ нас ( γ п – плотность формовки при соответствующем рабочем давлении; γ нас – насыпная плотность порошка). Холодное изостатическое прессование. Лекция
Методы формования 497 Установки гидростатического формования Для ХИП обычно используют следующие установки: — специализированные гидростаты; — камеры, в которых необходимое давление создается с помощью гидравлических прессов (гидростатическое формование); — камеры, в которых давление создается при взрыве порохового заряда (гидродинамическое формование). Холодное изостатическое прессование. Лекция
Методы формования 498 Установки гидростатического формования. Гидростаты По способу создания давления в рабочей камере гидростаты бывают насосные, плунжерные и мультипликаторные. Они могут быть рамной или безрамной конструкции. В гидростатах рамной конструкции осевое усилие от жидкости через уплотняющие затворы рабочей камеры передается на силовую раму установки. Гидростаты безрамной конструкции снабжены резьбовыми байонетными затворами. Холодное изостатическое прессование. Лекция
Методы формования 4996 5 4 3 1 7 2 1 – компрессор; 2 – камера формования; 3 – порошок; 4 – эластичная оболочка; 5 – манометр; 6 – затвор; 7 – клапан. Холодное изостатическое прессование Схема гидростата безрамной конструкции Лекция
Методы формования 500 Холодное изостатическое прессование Рабочий цикл ХИП зависит от метода формования. При формовании по методу «мокрого» мешка рабочий цикл включает следующие операции : 1) подготовки шихтового состава порошка; 2) подготовки порции порошка необходимого объема (массы); 3) заполнения подготовленной навеской порошка эластичной оболочки; 4) герметизации оболочки с порошком и дегазации порошка; 5) установки оболочки с порошком в рабочую камеру гидростата; 6) герметизации рабочей камеры гидростата; Лекция
Методы формования 501 Холодное изостатическое прессование Рабочий цикл ХИП 7) создания давления рабочей жидкости в камере высокого давления гидростата; 8) выдержки оболочки под давлением в течение заданного времени; 9) сброса давления; 10) вскрытия рабочей камеры гидростата; 11) извлечения оболочки с формовкой из рабочей камеры гидростата; 12) разгерметизации оболочки и извлечения формовки из оболочки; 13) зачистки поверхности формовки. Лекция
Методы формования 502 Холодное изостатическое прессование При гидростатическом формовании по методу «сухого» мешка рабочий цикл состоит из следующих операций: 1) подготовки шихтового состава порошка; 2) заполнения подготовленной навеской порошка эластичной оболочки и его уплотнения (с использованием вибрационного уплотнения); 3) герметизации оболочки с порошком; 4) дегазации порошка (вакуумирование оболочки); 5) герметизации рабочей камеры гидростата; 6) создания давления рабочей жидкости в камере высокого давления гидростата; Лекция
Методы формования 503 Холодное изостатическое прессование При гидростатическом формовании по методу «сухого» мешка рабочий цикл состоит из следующих операций: 7) выдержка оболочки с порошком под давлением рабочей жидкости в течение заданного времени; 8) сброс давления; 9) вскрытие рабочей камеры гидростата, разгерметизация оболочки и извлечение формовки из оболочки; 10) зачистки поверхности формовки (выравнивание поверхности – устранение дефектов) Лекция
Методы формования 504 Виды брака заготовок, сформованных по методу «мокрого мешка » Дефекты формовок 1 2 3 4 5 6 1 – образование шейки; 2 – неравномерная усадка; 3 – «ступня слона» ; 4 – «банан» ; 5 – расслоение; 6 – скол кромок. Холодное изостатическое прессование. Лекция
Методы формования 505 Холодное изостатическое прессование Дефекты формовок Возможные причины появления дефектов в изделиях, сформованных методом «мокрого мешка» : 1) нехватка порошка, засыпанного в эластичную оболочку; 2) недостаточно жесткая оболочка, которая способна деформироваться при засыпке в нее порошка; 3) неравномерная засыпка порошка в оболочку или его плохая текучесть; 4) слишком тонкая или слишком толстая стенка оболочки; 5) жесткие заглушки для герметизации оболочки с порошком; 6) высокая пластичность частиц порошка; 7) неправильно выбранный материал эластичной оболочки; 8) недостаточная плотность формовки; 9) малый радиус скругления углов формовки. Лекция
Методы формования 506 Холодное изостатическое прессование Дефекты формовок К характерным видам дефектов заготовок, возникших при гидроформовании по методу «сухого» мешка, относятся: — расслоение (осевое) – возникает из-за смещения стенок эластичной оболочки при разгрузке; — образование шейки – связано с недостаточной загрузкой или усадкой засыпанного в оболочку порошка; — растрескивание и расслоение (радиальное и осевое) – происходит из-за высокого давления формования и осевого упругого последействия; — осевое растрескивание : имеет место при слишком быстром снятии давления со сформованной заготовки или из-за избыточного количества смазки (пластификатора) в порошке. Лекция
Методы формования 507 Горячее изостатическое (газостатическое) прессование (ГИП) • Устройство газостатов • Цикл прессования • Технологическая оснастка и оборудование, используемое при прессовании порошков методом ХИП • Режимы ГИП изделий Лекция
Методы формования 508 В процессе ГИП порошок одновременно спрессовывается (давление до 200 МПа) и спекается (температуры до 1500– 2000 °С), образуя формовку с плотностью, близкой к теоретической, и высокими механическими свойствами. К основным достоинствам метода ГИП порошковых материалов относятся: 1) возможность улучшить свойства получаемых материалов; 2) возможность варьирования параметров обработки (давления, температуры, времени), обеспечивающих на одном и том же оборудовании получение заготовки и изделий из материалов, имеющих различную химическую природу. Недостатками ГИП являются сравнительно невысокие давления формования, большая длительность рабочего цикла (относительно низкая производительность), высокая стоимость оборудования; сравнительно простая форма получаемых изделий. Горячее изостатическое (газостатическое) прессование (ГИП)Лекция
Методы формования 509 Горячее изостатическое прессование Формование изделий в газостате происходит с использованием деформируемых оболочек. Оболочки может быть изготовлены из материала, не взаимодействующего с порошком и обладающего необходимой пластичностью при рабочей температуре процесса. Для изготовления оболочек используют фольгу из нержавеющей стали, никеля, молибдена, меди, титана и пр. Реже для изготовления оболочек используют серебро, золото или платину. Для ГИП керамики, тугоплавких соединений могут использовать деформируемые оболочки из борного или кремниевого стекла, кварца. Лекция
Методы формования 510 Горячее изостатическое прессование Геометрия и размеры оболочки должны быть такими, чтобы полученная формовка максимально приближалась по конфигурации к готовому изделию. Оболочки получают путем выдавливания (штамповки) листовых материалов и последующей сварки отдельных элементов. Оболочки из стекла готовят шликерным формованием водных суспензий. Лекция
Методы формования 511 Горячее изостатическое прессование Схема конструкций установок для горячего изостатического прессования 1 – запорная крышка; 2 – камера высокого давления; 3 – нагревательный элемент; 4 – уплотняемое порошковое тело; 5 – внешняя изоляция; 6 – термопара; 7 – система охлаждения; 8 – система подачи газа 3 7 8 6 1 2 3 547 8 6 1 2 54 3 а б в. Лекция
Методы формования 512 Для создания рабочего давления внутри контейнера газостата применяют две принципиально различающиеся схемы: — необходимое для работы количество газа хранится вне газостата (в баллонной станции) и подается в рабочую камеру перед началом процесса; — емкость с необходимым количеством сжиженного газа устанавливают непосредственно в контейнер, а затем газ нагревается и испаряется. Горячее изостатическое прессование. Лекция
Методы формования 513 Устройства для перекачивания газообразной рабочей среды могут быть механические (компрессоры поршневые и мембранные, мультипликаторы, насосы) и термические (термические компрессоры и криогенные термокомпрессоры). Для перекачивания рабочей среды в сжиженном состоянии используют насосы и криогенные термокомпрессоры. Эти устройства для перекачивания рабочей среды могут быть многоступенчатыми и одноступенчатыми (дожимающими). Горячее изостатическое прессование. Лекция
Методы формования 514 Горячее изостатическое прессование Рабочий цикл формования порошка , в газостате включает в себя следующие основные операции: • сборку садки (расчет навески, отмеривание и загрузка порошка в деформируемую оболочку, вибрирование и вакуумирование ее) и установку на заготовках термопар; • загрузку садки в рабочую камеру газостата, вакуумирование рабочего пространства и промывку рабочим газом; • создание в рабочем пространстве газостата необходимых по технологии давления и температуры. Лекция
Методы формования 515 Горячее изостатическое прессование Рабочий цикл формования порошка в газостате включает в себя следующие основные операции: • выдержку садки при рабочих режимах формования; • охлаждение садки и выпуск рабочего газа; • выгрузку садки и освобождение сформованного изделия от оболочки. Порошок перед уплотнением подвергают дегазации для удаления большей части газа, адсорбированного поверхностью частиц, и вибрированию для более плотной упаковки частиц. Лекция
Методы формования 516 Горячее изостатическое прессование В зависимости от технологических требований к конкретному изделию и особенностей конструкции используемого газостата возможны четыре схемы проведения процесса газостатического формования порошка: — с предварительным подъемом давления газовыми компрессорами и последующим разогревом рабочего пространства при выключенном компрессоре; — с одновременным подъемом давления и температуры; — с предварительным разогревом рабочего пространства; — с постоянной температурой в рабочем пространстве и предварительным разогревом оболочек с порошковым телом. Лекция
Методы формования 517 Материал Давление, МПа Температура, °С Время выдержки, ч Относительная плотность Бериллий 69– 105 700– 1100 0, 5– 3 1 Вольфрам 110 70– 140 1550 1370– 1700 1 1– 5 0, 98 1 Тантал 77– 155 1425 0, 4– 0. 5 Диоксид урана 115– 150 700– 1050 3 0, 999 Диборид циркония 100 1350 – 1 Нержавеющая сталь 84 1200 0, 3 0, 98 Инструментальная сталь 100 1 0, 998 100 1150 0, 5 0, 99– 1 Карбид вольфрама 70– 105 1600– 1760 – 1 Нитрид бора 105 1500 0, 1 – Оксид алюминия 70– 140 1150– 1370 0, 5– 0, 3 0, 96– 0, 99 Ферриты 70– 105 1095– 1370 1– 3 –Параметры ГИП некоторых материалов. Лекция
Методы формования 518 Прессование в эластичных оболочках. Шликерное формование во впитывающие формы • Формование порошков в эластичных оболочках • Классификация методов шликерного литья изделий • Шликерное литье во впитывающие формы Лекция
Методы формования 519 Формование в толстостенных эластичных оболочках (втулках) Схема прессования в оболочке а – в момент приложения давления; б – после прессования. 1 – верхний пуансон; 2 – матрица пресс-формы; 3 – резиновая пробка; 4 – порошок; 5 – эластичная оболочка (втулка); 6 – нижний пуансон; 7 – формовка 1 2 3 4 5 6 7 а б. Лекция
Методы формования 520 Формование в толстостенных эластичных оболочках (втулках) В этом методе толстостенную (толщина стенки 10– 20 мм) эластичную оболочку с порошком помещают в матрицу пресс-формы и подвергают прессованию. Пригодны для изготовления оболочек (втулок) парафин, воск (при формовании единичных заготовок), водный раствор желатина с добавками глицерина, эпоксидные смолы и резиновые массы. Лекция
Методы формования 521 Шликерное формование Шликер – устойчивая суспензия металлического или неметаллического порошка в жидкой среде. Шликерное формование – формование путем заполнения шликером пористой формы, обеспечивающей удаление жидкости из шликера. Приведенное определение относится только к шликерному формованию в пористых адсорбирующих и неадсорбирующих формах. Лекция
Методы формования 522 Шликерное формование Разновидностью шликерного формования являются: — формование термопластичных шликеров — электрофоретический метод. Шликерное формование позволяет получать: — изделия сложных форм; — мало- и крупногабаритные изделия; — полые изделия с равномерной толщиной стенок; — изделия точных размеров с высокой чистотой поверхности. Недостатками шликерного формования являются: длительность процесса; необходимость изготовления и хранения больших количеств адсорбирующих форм; потребность в мощном сушильном оборудовании. Лекция
Методы формования 523 Основными (реологическими) свойствами шликеров, определяющими качество получаемых из него заготовок, являются: — текучесть; — седиментационная и агрегативная устойчивость при высоком содержании твердой фазы; — способность заполнять форму. Текучесть шликера – величина, обратная вязкости, характеризует его способность литься, заполнять форму, набирать массу заготовки. Устойчивость шликера – это способность не расслаиваться в течение длительного времени. Шликерное формование. Лекция
Методы формования 524 Седиментационная устойчивость определяется скоростью оседания твердых частиц под действием силы тяжести и зависит в основном от размера частиц и их концентрации в шликере. Агрегативная устойчивость связана со склонностью мелких частиц к агрегатированию (слипанию под действием электростатических сил). Шликерное формование. Лекция
Методы формования 525 Шликерное формование Дисперсность частиц твердой фазы шликера определяет его устойчивость, вязкость и влияет на плотность получаемых заготовок. Жидкая фаза для приготовления шликера должна иметь низкое давление пара, низкие воспламеняемость и токсичность, малую вязкость и не должна активно химически взаимодействовать с твердой фазой. Наиболее часто в качестве основы для получения шликера используют воду (литье в пористые адсорбирующие или неадсорбирующие формы) или парафин (термопластичный шликер). Лекция
Методы формования 526 Шликерное формование Парафины являются предельно насыщенными соединениями углерода с водородом с общей формулой С n Н 2 n +2 и представляет собой продукты переменного состава. Плотность парафинов при 100 о С изменяется от 0, 71 до 0, 77 г/см 3 , температура плавления – от 54 до 49 о С, а вязкость от 1 до 8 Па. Кроме технических парафинов могут использовать церезины и полиэтилен. Лекция
Методы формования 527 Технологический процесс формования предусматривает выполнение следующих операций: — изготовление пористой формы; — приготовление шликера (подготовки дисперсной фазы, дисперсионной среды и их смешивания); — формования заготовки и извлечения из формы; — сушки заготовки; — обжига (спекания) заготовки. Наиболее часто для изготовления впитывающих форм используют гипс ( Ca. S 0 4 · 2 H 2 0), который в обезвоженном состоянии активно поглощает воду. Шликерное формование в пористых адсорбирующих формах. Лекция
Методы формования 528 Процесс изготовления форм из гипса включает следующие операции: — измельчения и сушки гипса при температуре 140– 175 о С до состава Ca. SO 4 · 0, 5 H 2 O ; — подготовки кремообразной смеси гипса с водой; — получения формы для отливки изделия путем заливки смеси в разъемную матрицу с помещенной в нее моделью будущего изделия. Шликерное формование в пористых адсорбирующих формах. Лекция
Методы формования 529 Шликерное формование в пористых адсорбирующих формах Подготовка дисперсной фазы шликера включает операцию получения порошков такой дисперсности, которая обеспечивает максимальную плотность их упаковки без ухудшения технологических свойств шликера. Необходимо стремиться к оптимизации дисперсной (твердой) фазы шликера. Грубые (крупные) порошки дают неустойчивые шликеры и заготовки пониженной прочности. Тонкодисперсные порошки обеспечивают шликеру высокую седиментационную устойчивость и достаточную прочность заготовкам, но скорость набора массы заготовки и ее плотность понижены, что приводит к короблению изделия при усадке и проявлению анизотропии свойств после обжига (спекания). Лекция
Методы формования 530 Шликерное формование в пористых адсорбирующих формах Приготовление шликера (содержание твердой фазы около 50– 70 %) осуществляют одностадийным или двустадийным способом, а также способом предельного насыщения с добавкой зернистого наполнителя. По одностадийному способу предварительно раздробленный материал подвергают мокрому размолу в дисперсионной среде. При двустадийном способе вначале проводят сухой помол материала, а затем смешивают полученный порошок с жидкостью. Лекция
Методы формования 531 Шликерное формование в пористых адсорбирующих формах При подготовке шликера по способу введения зернистого наполнителя на стадии перемешивания твердой фазы с дисперсионной средой к шликеру добавляют крупнозернистый порошок (зернистый наполнитель). Шликер, полученный этим способом применяется для получения крупногабаритных и толстостенных изделий. Лекция
Методы формования 532 Шликерное формование в пористых адсорбирующих формах Формование заготовок осуществляют наливным или сливным способами. Наливной способ используется для получения цельных (не полых) или толстостенных изделий. Шликер наливают в форму в несколько этапов, поддерживая постоянным уровень ее заполнения. Толстостенные изделия получают путем установки в матрицу стержней различного профиля, которые способствуют получению в изделии внутренних полостей правильной формы. Лекция
Методы формования 533 Шликерное формование в пористых адсорбирующих формах Сливной способ отличается от наливного тем, что после заливки шликера в форму ему дают некоторое время «отстояться» , а затем не успевший осесть на стенки формы шликер удаляют из нее, либо переворачивая форму, либо отсасывая шликер с помощью насоса, либо сливая его через отверстие в основании формы. При использовании этого способа на стенке формы образуется слой порошка определенной толщины. Лекция
Методы формования 534 Схема формирования стенки изделия из шликера (стрелками указаны направления потоков жидкости) I IIIII 1 – пористая форма; 2 – стенка отливки; 3 – шликер1 2 3 Шликерное формование в пористых адсорбирующих формах. Лекция
Методы формования 535 Шликерное формование в пористых адсорбирующих формах Время набора массы формирующейся заготовки на стенке формы обычно составляет от 1 до 60 мин. Для повышения скорости диффузии воды в форме, а также скорости отбора влаги из шликера применяют обдув наружной поверхности гипсовой формы теплым воздухом. Для улучшения процесса формования шликер подогревают до 50– 60 °С или вакуумируют. В производственных условиях формование осуществляют на стендах или автоматах. Для придания отлитым изделиям необходимой прочности и облегчения последующего извлечения заготовки отлитые изделия подсушивают в форме (усадка отлитого изделия до 1 %). После извлечения заготовку оправляют (удаляют «прибыльную» часть, зачищают неровности, отдельные сколы) и сушат при температуре 110– 150 о С на воздухе в сушильных шкафах или сушилках. Лекция
Методы формования 536 Шликерное формование в пористых адсорбирующих формах Причины растрескивания заготовок: — неравномерная скорость высыхания; — прилипание к стенкам формы; — недостаточная прочность заготовки; — негомогенность шликера и его тиксотропия (создает неравномерность свойств по толщине стенки). Относительная плотность заготовок составляет 60– 80 % от теоретической. Связь между отдельными частицами обусловлена контактными явлениями и зацеплением. Обжиг или спекание высушенных заготовок проводят в печах по режимам, зависящим от материала заготовки. Для получения пустотелых изделий (тел вращения) из металлических порошков или сечки используют центробежное формование изделий. Лекция
Методы формования 537 Лекция 7 Шликерное формование в неадсорбирующие формы, литье из термопластичных шликеров, электрофоретическое литье шликеров • Литье шликеров в неадсорбирующие формы • Литье из термопластичных шликеров • Электрофоретическое литье
Методы формования 538 Подобный вариант шликерного литья осуществляют различными способами: 1) формованием под вакуумом в перфорированных металлических формах (отверстия диаметром 0, 7– 1, 1 мм, суммарной площадью 30– 40 %). Изнутри стенки формы покрывают слоем бумажной массы, а снаружи создают разрежение около 20– 25 г. Па, которое и обеспечивает отвод жидкости из шликера; 2) формованием под давлением (порядка нескольких мегапаскалей) в разъемных формах со стенками из пористого материала (спеченный стеклянный порошок, пластик), за которыми находятся полости для отвода выдавливающейся из шликера жидкости. Шликерное формование в пористых неадсорбирующих формах. Лекция
Методы формования 539 Подобный вариант шликерного литья осуществляют различными способами: 3) вымораживанием жидкости (неадсорбирующую форму со шликером помещают в смесь бензина и твердой углекислоты с температурой – 40 о С, с последующей «сушкой» (сублимацией) замороженного изделия в вакуумной камере). Шликерное формование в пористых неадсорбирующих формах. Лекция
Методы формования 540 Формование термопластичных шликеров Технологическая схема процесса получения изделий по этому способу включает следующие операции: — подготовки дисперсной фазы (измельчения неметаллических тугоплавких материалов (карбидов, боридов, нитридов и пр. )); — подготовки термопластической связки (подготовка навески необходимого объема); — приготовления шликера (смешивания термопластичной связки с дисперсной фазой); — подготовки форм к заполнению шликером и формованию (отливки) заготовки; — заполнение шликером формы и отвердения отливки; — удаления связки и спекания. Лекция
Методы формования 541 Формование термопластичных шликеров Схема установки для литья изделий из термопластичного шликера 7 8 1 3 4 2 6 9 5 1 – резервуар; 2 – матрица (форма); 3 – отливка; 4 – трубка подачи жидкого шликера в форму; 5 – шликер; 6 – нагревательный элемент; 7 – отверстие для заливки шликера в резервуар; 8 – мешалка; 9 – компрессор. Лекция
Методы формования 542 Формование термопластичных шликеров Температурная кривая удаления связки и припекания изделия 400 200 Время, ч6008001000 Т, о С 1 2 3 4 1 – зона плавления связки; 2 – зона удаления связки из изделия и частичного испарения легколетучих органических фракций; 3 – зона выжигания остатков связки; 4 – зона припекания. Лекция
Методы формования 543 Электрофоретическое формование Этот способ применяют преимущественно для получения тонкостенных и крупногабаритных изделий сравнительно простой конфигурации из керамических шликеров. Изделия получают при пропускании тока (анодная плотность 0, 0015– 0, 03 А/см 2 , напряжение 2– 4 В) через водный шликер. Для осаждения шликера применяют тонкостенные медные формы, которые выполняют анода. Стержневой катод находится в центре формы-анода. Объемная масса получаемых заготовок выше, чем у заготовок, полученных в гипсовых формах или формованием термопластичных шликеров. Время формования заготовки зачастую не превышает нескольких минут. Лекция
Методы формования 544 Лекция 8 Мундштучное и инжекционное формование порошков • Закономерности процесса мундштучного формования порошков. • Выбор условий формования порошков и использованием метода мундштучного формования. • Инжекционное формование порошков.
Методы формования 545 Мундштучное формование – формование металлического порошка путем продавливания его через отверстие. Форма отверстия определяет форму и размеры поперечного сечения изделия. Мундштучным формованием готовят прутки, трубы, сверла, профили и другие длинномерные изделия. Достоинством этого метода является возможность получения изделий с равномерной плотностью. Мундштучное формование. Лекция
Методы формования 546 Уменьшить трение порошка о внутреннюю поверхность матрицы и мундштука можно, нанеся на эти поверхности (или вводя в порошок) смазки или пластификаторы (парафин, раствор каучука в бензине, раствор бакелита в спирте, раствор поливинилового спирта в воде, масла, графит и пр. ). Выбор той или иной смазки зависит от свойств материала и ее влияния на процесс спекания изделий. Количество вводимой в состав порошка смазки обычно не превышает 6– 10 % (по массе). Мундштучное формование. Лекция
Методы формования 547 Схема пресс-формы для мундштучного формования : 1 2 3 64 51 1 2 64 5 Р 37 8 9 ба а – простых изделий; б – изделий (труб, профилей с постоянным сечением) 1 – пуансон; 2 – матрица; 3 – держатель мундштука; 4 – мундштук; 5 – порошок; 6 – сформованное изделие; 7 – плунжер пресса; 8 – звездочка; 9 – ввинченная в звездочку игла. Мундштучное формование. Лекция
Методы формования 548 Давление мундштучного формования при постоянной степени обжатия минимально при выдавливании материала через мундштук с углом конуса 90°. Обычно это давление составляет несколько сотен мегапаскалей. Степень обжатия материала при выдавливании через очко должна составлять не менее 90 %. Степень обжатия можно рассчитать по формуле K =[( S – s )/ s ]100 %, где S – площадь сечения матрицы пресс-формы; s – площадь сечения выходного отверстия (очка) мундштука Мундштучное формование. Лекция
Методы формования 549 При уплотнении порошка в матрице, предшествующем его истечению из очка, образуются отдельные слои материала, отличающиеся по напряженному состоянию и плотности. Поэтому процесс мундштучного формования включает операцию предварительного уплотнения порошка (подпрессовки), которая обеспечивает равномерное напряженное состояние по объему порошка. Мундштучное формование. Лекция
Методы формования 550 Схема движения порошка при мундштучном прессовании Наличие разности сечений контейнера и очка матрицы, сил внешнего трения приводит к тому, что частицы двигаются в направлении, поперечном направлению приложения усилий 1 2 3 45 6 1 – пуансон; 2 – матрица; 3 – держатель мундштука; 4 – мундштук; 5 – порошок; 6 – «застойные» зоны. Мундштучное формование. Лекция
Методы формования 551 Мундштучное формование без пластификатора возможно, если выдавливать нагретые металлы или сплавы. При относительно низких температурах (до 600 о С) заготовку или порошок обычно нагревают вместе с матрицей. Такие металлы, как бериллий, цирконий, титан, вольфрам при горячей обработке могут интенсивно окисляться. Поэтому при их нагреве и формовании необходимо применять защитные среды. В некоторых случаях для защиты заготовок или порошков применяют защитные оболочки. Оболочки могут быть стеклянные, графитовые и металлические (медь, латуни, низкоуглеродистая сталь или биметалл). Мундштучное формование. Лекция
Методы формования 552 Металлические оболочки предохраняют получаемые заготовки от окисления до момента их полного охлаждения и служат смазками, улучшающими процесс истечения. После завершения формования оболочки чаще всего удаляют с заготовки механическим путем, хотя возможно также их удаление травлением в растворах, не действующих на порошковый материал. Мундштучное формование. Лекция
Методы формования 553 Инжекционное формование Этот метод можно рассматривать как разновидность метода литья пластифицированных шликеров. Преимущества инжекционного формования связаны: — с возможностью получения заготовок (деталей) сложной формы, с очень точными размерами и высоким качеством поверхности; — с малой продолжительностю рабочего цикла (около 1, 5– 2 мин. ), что обеспечивает массовое производство заготовок; — высокой степенью автоматизации производства. Методом инжекционного формования обычно изготавливают детали массой от 0, 1 до 150 г. (размеры мелких изделий около 0, 75– 5 мм). Лекция
Методы формования 554 Инжекционное формование Порошки для инжекционного формования должны: — иметь достаточно низкую свободную поверхностную энергию (чтобы хорошо смешиваться со связующим); — быть достаточно мелкими (чтобы хорошо спекаться). Этим требованиям соответствуют сферические порошки. Обычно содержание твердых частиц в смеси с пластификатором составляет от 40 до 90 % по объему в зависимости от их размера и формы. Лекция
Методы формования 555 Технологическая схема производства изделий с использованием метода инжекционного формования включает следующие операции: — подготовки шихты (смешивания твердой фазы с пластификатором); — гранулирования шихты; — формования изделий; — удаления связующего компонента и спекания материала. Инжекционное формование. Лекция
Методы формования 556 В качестве связующего компонента при инжекционном формовании могут использовать пластификаторы и термопластичные материалы (полистирол, полиэтилен, акриловую смолу, парафин, стеарин, диэтилфталат, эфиры жирных кислот и др. ), а также смазки (стеариновую кислоту, стеарат цинка, минеральное масло и др. ). Для проведения инжекционного формования используют, как правило, литьевые машины для производства изделий из пластмасс. Смесь порошка с термопластичным связующим ( «пластизоль » ) получают путем плавления гранул материала. Плотность получаемых заготовок обычно около 70 % от теоретической. Инжекционное формование. Лекция
Методы формования 557 Лекция 9 Вибрационное формование порошков • Основы метода виброформования • Способы и схемы вибрационного формования • Режимы виброформования • Установки для виброформования
Методы формования 558 Вибрационное формование Применение вибрации при засыпке и утряске порошка в пресс-форме или в процессе уплотнения позволяет значительно уменьшить давление прессования и повысить равноплотность получаемых прессовок сложной формы. При вибропресовании порошок приобретает свойства, подобные свойствам жидкости. Положительное воздействие вибрации на процесс уплотнения порошка связано с преобразованием исходной структуры и улучшением взаимоподвижности части. В результате воздействия на порошок вибрации достигается высокая плотность частиц (90 % и выше от теоретически возможной). Наиболее эффективно вибрация проявляется при уплотнении порошков, представляющих собой набор фракций частиц различного размера. Лекция
Методы формования 559 Модель пространственной укладки сферических частиц порошка трех фракций Для получения наиболее плотной укладки размер частиц каждой, последующей за крупной, фракции должен быть в 5– 10 раз меньше размера предыдущей фракции. Количество этой более мелкой фракции можно оценить равенством Андреазена: q = ( d / D ) 0, 5 , где q – количество более мелкой фракции (следующей за более крупной); d – размер частиц этой (более мелкой) фракции; D – размер частиц предшествующей (более крупной) фракции. Вибрационное формование. Лекция
Методы формования 560 Способы вибрационного формования различают по следующим основным признакам: — по характеру динамического воздействия на прессуемый порошок (вибрационное и виброударное формование); — по соотношению между статической и динамической составляющими усилия прессования (силами трения, препятствующими перемещению частиц, и вибрационными силами, способствующими преодолению сил трения); — по характеру процесса : дискретное (прерывистое) вибрационное формование в закрытом пресс-инструменте); непрерывное вибрационное формование (в установках шликерного формования, прокатки порошка и др. ); — по схеме (циклограмме) процесса. Вибрационное формование. Лекция
Методы формования 561 Вибрационное формование На практике используют следующие схемы получения заготовок: — с предварительным вибрационным уплотнением и последующим статическим прессованием; — с вибрационным воздействием на порошок в течение всего процесса прессования (без выдержки под давлением); — с вибрационным или виброударным воздействием на порошок в течение всего цикла прессования. При вибрационном формовании возможны различные варианты процесса: — холодное или горячее прессование; — прессование без смазки или со смазкой; — прессование с вакуумированием порошка и т. п. Лекция
Методы формования 562 Вибрационное формование Пресс-инструмент для осуществления прессования различается: — по способу передачи энергии вибрации порошку (соединения элементов формы с вибратором); — по жесткости опоры матрицы (неподвижная или «плавающая» ); — по жесткости систем передачи статического усилия прессования на верхний пуансон (жесткая и упругая); — по принципу соединения вибратора с пресс-инструментом (жесткое соединение вибратора с пуансонами и матрицей, упругое соединение вибратора с матрицей); — по количеству прессующих пуансонов (с одним, и двумя). Лекция
Методы формования 563 Вибрационное формование р’ ор’ о а б гв д Схемы пресс-инструмента для вибрационного прессования (двунаправленной стрелкой помечен вибрирующий элемент)Лекция
Методы формования 564 При выборе схемы пресс-инструмента для вибрационного прессования стремятся к тому, чтобы энергия вибрации передавалась от вибратора к порошку через возможно более жесткую систему и преимущественно поглощалась им. Вибратор может быть: — гидравлический; — пневматический; — электромагнитный; — магнитнострикционный; — электромеханический (дебалансный, двухвальный дебалансный направленного действия и др. ). В производственных процессах чаще применяют электромеханические вибраторы с динамическим возбуждением колебаний, позволяющие получать значительные величины возмущающих сил при простой конструкции. Более эффективны схемы с вибрирующей матрицей и подвижными пуансонами. Вибрационное формование. Лекция
Методы формования 565 Вибрационное формование При уплотнении больших масс порошка большую роль играют собственная частота колебаний слоя частиц и силы связи между ними. Частоту вибрирования нужно выбирать исходя из резонансной частоты или вибрирующей системы, или уплотняемой массы порошка. Режим вибрирования принято характеризовать частотой колебаний W (количество колебаний тела за одну минуту), ускорением а (см/с 2 ) и амплитудой А (см), которые связаны между собой выражением: А = a / ( π · W /30) 2. Лекция
Методы формования 566 Вибрационное формование При одинаковой амплитуде колебаний плотность укладки частиц порошка возрастает с повышением частоты вибрирования. Для небольших объемов порошка с частицами размером > 100 мкм эффективнее частоты от 6000 до 12000 колебаний в 1 мин, с частицами размером 1– 100 мкм – порядка 12000– 18000 колебаний в 1 мин, с частицами размером < 1 мкм – более 18000 колебаний в 1 мин. Для порошков хрупких материалов необходимо выбирать более высокую частоту и меньшую амплитуду вибрирования. Лекция
Методы формования 567 Лекция 10 Импульсное формование • Методы взрывного формования • Электрогидравлическое формование порошков • Электромагнитное формование • Пневмомеханическое формование
Методы формования 568 Импульсное формование металлического порошка или порошковой формовки, при котором уплотнение производится ударными волнами в интервале времени, не превышающем 1 секунды. Определяющий и характерный признак импульсного формования – высокие скорости приложения нагрузки (5– 10 м/с и выше). Время уплотнения порошка составляет сотые, тысячные или даже стотысячные доли секунды. Лекция
Методы формования 569 Импульсное формование Преимуществами импульсного формования порошков перед традиционными методами является: — возможность создания чрезвычайно высоких давлений; — возможность получения больших плотностей формовки (до 100 %); — возможность сращивания слоев разнородных материалов. Различают следующие виды импульсного формования: — взрывное; — электрогидравлическое; — электромагнитное; — пневмомеханическое. Лекция
Методы формования 570 Взрывное формование Взрыв – очень быстрое выделение энергии, связанное с внезапным изменением агрегатного состояния вещества (переходом из твердого состояния в газообразное). Взрыв, как правило, сопровождается образованием ударной волны. Источником взрыва может являться химическая энергия. Химический взрыв характеризуется крайне быстрым самораспространяющимся превращением некоторых механических смесей различных элементов с выделением теплоты и газообразных продуктов; такие вещества или смеси называют взрывчатыми веществами (ВВ). В методах взрывного формования применяют заряды метательных (порохов) и бризантных взрывчатых веществ. Лекция
Методы формования 571 При применении метательных ВВ возможны различные варианты создания нагрузки на порошковое тело: — передача энергии взрыва через подвижное, твердое тела: ударник–поршень (дистанционный метод); — непосредственное воздействие ударной волны (контактный метод); — передача давления через жидкую среду (дистанционный метод). Ствольные системы (пороховые копры) позволяют разгонять снаряд (ударник) до скорости 20– 600 м/с. Взрывное формование. Лекция
Методы формования 572 Гидродинамические машины способны создавать давление формования до 500– 1500 МПа. В ствольных системах давление пороховых газов передается в рабочую камеру через разделительный поршень, который обеспечивает уплотнение порошка находящегося в рабочей жидкости (смесь воды и эмульсола). Максимальное давление в рабочей камере составляет около 600 МПа, длительность действия импульса давления обычно не более 5 · 10 – 2 с. Продолжительность рабочего цикла не более 2– 4 минут. Взрывное формование. Лекция
Методы формования 573 Метод гидродинамического формования можно использовать для изготовления крупногабаритных фильтров из порошков титана и нержавеющей стали, заготовок из вольфрама и молибдена, имеющих равномерную объемную плотность. Кроме того, этот метод можно использовать для получения изделий из порошков оксидов, нитридов и других материалов. Характер уплотнения порошков в методах взрывного формования аналогичен имеющему место при гидростатическом формовании, но плотность получаемых формовок оказывается несколько ниже. Взрывное формование. Лекция
Методы формования 574 При одинаковой плотности формовок прочность на сжатие и ударная вязкость заготовок после взрывного формования повышены на 20– 30 % за счет разрушения поверхностных оксидных пленок и образования чисто металлических связей. Контактные методы взрывного формования более эффективны при использовании в качестве энергоносителя заряда бризантных ВВ. Взрывное формование. Лекция
Методы формования 575 Взрывное формование Взрывное превращение в этом случае происходит в форме детонации — цепной экзотермической реакции, распространяющейся по ВВ с постоянной и наибольшей для данных условий скоростью, называемой скоростью детонации. Величина скорости детонации для большинства промышленных ВВ составляет 3000– 8000 м/с. Температура продуктов взрыва достигает 3000– 5000 К, плотность их возрастает примерно на 30 % по сравнению с исходной, а пиковое давление за фронтом детонации достигает 3– 28 ГПа. Время действия импульсных давлений при взрыве заряда бризантных ВВ не превышает обычно 5– 9 · 10 – 6 с. Лекция
Методы формования 576 Взрывное формование Микроструктура брикетов из сферического медного порошка (фракция от – 300 до +160 мкм), полученных при статическом нагружении ( а ) и скорости детонации ВВ 3500 ( б ) и 7000 м/с ( в )Лекция
Методы формования 577 Импульсное формование Электрогидравлическое формование При искровом разряде между электродами, погруженными в жидкость, образуется токопроводящий канал , частично заполненный ионизированным газом. Первоначальное сечение канала мало, а энергия в нем нарастает со скоростью 10 4 м/с, и процесс приобретает характер взрыва. Под влиянием быстрого расширения искрового канала в жидкости возникает ударная волна, скорость распространения которой значительно превышает скорость расширения искрового канала, и через 0, 5– 1, 5 мкс фронт ударной волны отрывается от расширяющегося канала. Лекция
Методы формования 578 Импульсное формование Электрогидравлическое формование Превращение электрической энергии в механическую в жидкой среде можно осуществить двумя основными методами: — разрядом конденсатора через зазор между двумя электродами, погруженными в жидкость; — разрядом через проводник, перекрывающий зазор между электродами, погруженными в жидкость. Лекция
Методы формования 579 Импульсное формование Электромагнитное формование Метод основан на использовании для уплотнения порошков энергии мощного импульсного магнитного поля (при напряженности поля 300 к. Э развивается давление порядка 400 МПа). В этом методе деформирование электропроводящего порошкового тела обеспечивают силы, создаваемые взаимодействием инициируемых в нем вихревых токов с током, проходящим через индуктор магнитной катушки. Для получения магнитных импульсов различной конфигурации применяют плоские, спиральные, соленоидные и другие индукторы. Лекция
Методы формования 580 Импульсное формование Электромагнитное формование Выделение накопленной в конденсаторе энергии происходит очень быстро (10– 30 мкс) и некоторая ее часть тратится на нагрев обрабатываемого порошкового тела. Эффективность магнитно-импульсного формования зависит от удельного электросопротивления материала частиц порошка (наиболее подходящими для деформирования являются металлы с высокой электропроводностью, имеющие удельное сопротивление < 15 мк · Ом/см). Лекция
Методы формования 581 Пневмомеханическое формование Для уплотнения порошкового тела используют энергию, выделяющуюся при адиабатическом расширении сильно сжатого газа (воздух, азот и др. ). Типовая установка двустороннего ударного прессования имеет гидравлические и пневматические цилиндры. Гидравлический цилиндр является вспомогательным и служит для восстановления энергии сжатого газа, израсходованного при ударе. Номинальное давление газа в пневмоцилиндре до 12 МПа, номинальное усилие гидроцилиндра 30 к. Н. Импульсное формование. Лекция
Методы формования 582 Пневмомеханическое формование На практике применяются машины, в которых перемещение поршня обеспечивается за счет воспламенения (в камере сгорания) впрыскиваемого топлива. Поршень камеры сгорания соединен с пуансоном пресс-формы. После воспламенения топлива давление в камере сгорания увеличивается в 5– 7 раз и поршень пресс-формы начинает перемещаться, уплотняя порошок. Импульсное формование. Лекция
Методы формования 583 Лекция 11 Получение изделий методом прокатки порошков • Виды прокатки • Параметры прокатки • Уплотнение порошкового тела при прокатке • Виды брака при прокатке
Методы формования 584 Прокатка порошка – это метод получения заготовок (изделий) из металлического порошка путем его обработки с использованием валков прокатного стана. Прокатку порошков применяют для получения заготовок конструкционных материалов (полосы, ленты и профили), а также для производства фильтров, электрохимических электродов и других пористых изделий. Прокатка порошка обеспечивает высокую производительность, возможность получения тонких с большой поверхностью заготовок, обладающих изотропностью свойств и равномерной плотностью. Лекция
Методы формования 585 Прокатка порошка Себестоимость тонкой ленты, прокатанной из порошка, в 2 раза ниже, чем при прокатке слитков. Коренным отличием прокатки порошков от процесса прокатки компактных металлов является изменение свойств прокатанного материала по сравнению со свойствами исходного (переход от сыпучего к жесткому пористому телу). Лекция
Методы формования 586 а б в г д е ж з Способы прокатки порошка а, в – вертикальная; г, д – горизонтальная; е – наклонная (30– 60°); ж, з – радиусная Прокатка порошка. Лекция
Методы формования 5871 γα Н 2 3 4 5α 1 α р α п α сж. Н Зоны и угловые параметры прокатки порошка 1 -я зона (угол α н может быть > 90°) – зона подачи порошка; 2 -я зона (угол α 1 ) – граничная зона (перед зоной уплотнения порошка); 3 -я зона ( α р ~15°) – зона первичного уплотнения порошка (α р – центральный угол, на длине дуги которого под силовым воздействием валков происходит формирование проката из порошка); 4 -я зона (угол α п ) – зона спрессовывания (переход порошка от сыпучего состояния к жесткому пористому); 5 -я зона – зона, в которой окружная скорость валков равна скорости движения проката Прокатка порошка. Лекция
Методы формования 588 а б Характер движения слоев порошка при вертикальной прокатке ( а – Н/ D ≤ 0, 5; б — H/D ≥ 1)Прокатка порошка. Лекция
Методы формования 589 Прокатка порошка Схема перемещения порошка при горизонтальной прокатке При горизонтальной прокатке на порошок действуют два усилия: — радиальное усилие, создающее давление прокатки и уплотняющее порошок; — усилие, стремящееся вытолкнуть порошок из очага деформации в направлении продольной оси валков. Лекция
Методы формования 590 Скорость прокатки обычно составляет от 1 – 3 до 20 – 25 м/мин. В процессе прокатки порошок уплотняется от γ нас или γ тр до плотности проката γ п. Отношение γ п к этим плотностям порошка называют соответственно степенью уплотнения Ζ и коэффициентом уплотнения Ζ уп : Ζ = γ п / γ нас , Ζ уп = γ п / γ утр Прокатка порошка. Лекция
Методы формования 591 Уравнение прокатки порошков основано на применении универсального закона постоянства массы, имеющий вид: γ п = γ нас (1 + α р. прив R / h п ), где α р. прив – приведенный или условный угол прокатки порошка при коэффициенте вытяжки λ = 1, рассчитываемый по известным γ нас и R (радиусу валков) и определяемым экспериментально γ п и h п (толщине проката). Коэффициент вытяжки определяется как отношение объема порошка зоны уплотнения α сж к объему порошка в самом начале этой зоны α р. Прокатка порошка. Лекция
Методы формования 592 Можно выделить три стадии уплотнения порошка при прокатке , которые фактически совпадают со структурной деформацией при прессовании порошка в пресс-форме: — первая стадия уплотнения – перераспределение частиц порошка (удаление арок, проникновение мелких частиц в поры между крупными); — вторая стадия – уменьшение объемов пор за счет увеличения контактных поверхностей; — третья стадия – объемная деформация частиц. Для построения диаграмм уплотняемости порошков при прокатке можно использовать эмпирическое уравнение: γ п = γ утр + р max /( m + n · p max ), где т и n – коэффициенты, зависящие от материала порошка. Прокатка порошка. Лекция
Методы формования 593 Экспериментально установлено, что пористость по толщине порошкового проката распределяется неравномерно. В лентах (полосах) малой толщины (1, 6– 2, 5 мм) пористость непрерывно уменьшается по мере удаления от поверхности к центру сечения. Разница между пористостью у поверхности проката и в центре уменьшается с увеличением его средней плотности и уменьшением толщины. В лентах с толщиной > 2, 5 мм в центральном слое пористость приблизительно постоянна, а в приповерхностных слоях пористость уменьшается по мере удаления от внешней поверхности. Прокатка порошка. Лекция
Методы формования 594 Это обусловлено неравномерностью напряженно-деформированного состояния порошкового тела в очаге уплотнения, так как в поверхностных слоях проката наблюдаются растягивающие напряжения. Неравномерностью напряженно-деформированного состояния является также расслоение проката на две или три (при прокатке толстых полос) части. Прокатка порошка. Лекция
Методы формования 595 Прокатка порошка. Горячее прессование • Плотность проката • Схемы подачи порошка при прокатке • Оборудование для горизонтальной прокатки порошков • Технологические линии прокатки порошков • Горячее прессование Лекция
Методы формования 596 Прокатка порошка а гв б Схемы устройств для регулирования уровня порошка в бункере прокатного стана. Лекция
Методы формования 597 Прокатка порошка Для получения из порошков ленты заданной пористости и толщины применяют специальные устройства, регулирующие уровень порошка или толщину его захвата в зоне деформации. Порошок изолируется от рабочей поверхности валков с помощью: — специальных накладок; — путем изменения ширины щели между передвигающимися или поворотными заслонками; — вертикальной пластины; — величиной щели в дне бункера. Лекция
Методы формования 598 Прокатка порошка Приспособление для принудительной подачи порошка в валки 1 – валки; 2 – камера с порошком; 3 – шнек; 4 – бункер; 5 – шкив двигателя; 6 – клиноременная передача; 7 – двигатель1 2 3 4 76 5 Лекция
Методы формования 599 Прокатка порошка 1 – лента конвейера; 2 – бункер с порошком; 3 – дозирующие устройство; 4 – верхний валок с бортиком; 5, 6 – прижимные ролики; 7 – нижний валок; 8 – устройство для натяжения ленты конвейера 1 32 4 5 6 7 8 Схема устройства для подачи порошка в волки с помощью конвейера. Лекция
Методы формования 600 Прокатка порошка Порошки прокатывают как в холодном, так и в нагретом состоянии. Температурные границы деформаций определяются в зависимости от температуры плавления металла ( Т пл ): — область холодной деформации 0– 0, 25 Т пл ; — область между холодной и горячей деформацией 0, 25– 0, 5 Т пл ; — область горячей деформации 0, 5– 1, 0 Т пл. При горячей прокатке станы снабжают устройствами для нагрева порошка перед процессом прокатки, а сам порошок часто помещают в камеру с защитным газом (во избежание окисления при нагреве). Лекция
Методы формования 601 Прокатка порошка Технологические линии получения проката из металлических порошков включают: — прокатные станы; — печи для спекания материала; — устройства для правки проката; — устройства для намотки проката; — холодильники лент и полос. Лекция
Методы формования 602 Прокатка порошка Пористый прокат Беспористый прокат2 5 24 3 61 4 47 46 76 1 11 33 34 4 1 – валки; 2 – камерная печь; 3 – устройства для намотки проката; 4 – проходная печь; 5 – листовой прокат; 6 – валки для уплотняющей прокатки; 7 – водоохлаждаемые валки Схемы технологических линий для получения проката из металлических порошков. Лекция
Методы формования 603 Горячее прессование – прессование металлического порошка или порошковой формовки при температуре, превышающей температуру рекристаллизации основного компонента. Горячее прессование представляет собой совмещение процессов прессования и спекания и проводится при температурах 0, 5– 0, 95 Т пл основного (матричного) компонента порошкового материала. Этот метод позволяет практически реализовать наблюдаемое при повышении температуры увеличение текучести материала и получать фактически беспористые порошковые изделия. Лекция
Методы формования 604 Горячее прессование Существенным достоинством горячего прессования является максимально быстрое уплотнение порошкового тела и получение заготовок (изделий) с минимальной пористостью при сравнительно малых давлениях прессования. Изменение плотности порошкового тела при горячем прессовании связано с пластической деформацией, нестационарным и стационарным диффузионным крипом. Лекция
Методы формования 605 Различают следующие способы нагрева порошка при горячем прессовании: — прямым пропусканием тока через порошок или пресс-форму; — индукционным нагревом порошка, пресс-формы или промежуточного экрана; — импульсным током высокого напряжения. Наиболее распространенным материалом для изготовления пресс-форм является графит (в том числе силицированный). При температурах до 900– 1000 о С для изготовления пресс-форм используют жаропрочные сплавы. Горячее прессование. Лекция
Методы формования 606 Ограниченное применение имеют пресс-формы из тугоплавких оксидов, силикатов и других химических соединений. Для предотвращения взаимодействия прессуемого материала с материалом пресс-формы внутреннюю рабочую поверхность форм покрывают инертными составами (жидким стеклом, эмалью, нитридом бора и др. ) или защищают металлической фольгой. Важную роль при прессовании играют режимы приложения и снятия нагрузки. Горячее прессование. Лекция
Методы формования 607 Технологический режим прессования целесообразно разбивать на два этапа: — нагрев порошка до некоторой температуры (обычно половина требуемой для изотермической выдержки); — приложение к порошку нагрузки с быстрым нагревом прессуемой массы. Пресс-форма с изделием после ее охлаждения до 500– 600 о С (гидравлический пресс) или до 150– 200 о С (вакуумный пресс) удаляется из него, изделие извлекается и зачищается на шлифовальном станке. Для горячего прессования порошков используют следующие прессы: — рычажно-механические; — гидравлические; — пневматические Горячее прессование. Лекция
Методы формования 608 Схема рычажно-механического пресса для горячего прессования 1 – медные водоохлаждаемые контакты; 2 – графитовая пресс–форма; 3 – центральная втулка; 4 – верхний пуансон; 5 – направляющая втулка; 6 – токоподводы; 7 – изолирующая подкладка ; 8, 9 – опорные стойки; 10 – рычаг; 11 – прессуемый порошок; 12 – подвеска; 13 – груз 1 234 8 5 9 7 12 10 611 13 Горячее прессование. Лекция
Методы формования 609 Особым случаем горячего прессования является электроразрядное или электроимпульсное (искровое) спекание. На прессуемый материал наряду с движущими силами, характерными для обычного горячего прессования, действуют электромеханические силы и проявляются эффекты, порождаемые током. В зависимости от электросопротивления прессуемого материала, массы прилегающего к контакту вещества, его теплоемкости и теплопроводности, силы проходящего через данный контакт тока, приконтактное вещество (металл, сплав или металлоподобное соединение) может оставаться в твердом состоянии или частично расплавиться. Процесс электроразрядного спекания включает, как правило, две стадии: 1) прессования при плотности тока 3– 10 А/см 3 и давлении < 10 МПа; 2) прессования при плотности тока порядка до 5– 8 к. А/см 3 и более высоким давлением (до 30 МПа). Горячее прессование. Лекция
Методы формования 610 Горячее прессование Установка электроразрядного спекания с электромагнитным измерителем-дозатором засыпаемого порошка: 1 2 4 514 13 12 9 11 10 3 + 86 7 1 – устройство для создания механического давления; 2, 12 – электроды-пуансоны; 3 – трубопровод; 4, 5 – измерительные электроды; 6 – порошок; 7 – бункер; 8 – источник питания электроцепи; 9 – устройство для съема сигналов от электродов 4, 5; 10 – усилитель; 11 – источник тока спекания; 13 – матрица пресс-формы; 14 – рабочая полость матрицы. Лекция
Спекание порошков
Спекание порошков 612 Оглавление Лекция 13. Твердофазное спекание материалов Лекция 14. Механизмы массопереноса при твердофазном спекани и Лекция 15. Ползучесть кристаллических тел Лекция 16. Укрупнение частиц при спекании. Уплотнение порошков ого тела Лекция 17. Влияние технологических факторов на процесс спекан ия однокомпонентных систем. Спекание многокомпонентных систем Лекция 18. Твердофазное спекание многокомпонентных систем Лекция 19. Жидкофазное спекание Лекция 20. Жидкофазное спекание и инфильтрация порошковых фо рмовок. Брак при спекании
Спекание порошков 613 Лекция 13 Твердофазное спекание материалов • Стадии процесса спекания • Спекание однокомпонентных систем • Движущие силы процесса спекания. Лекция
Спекание порошков 614 Классификация процессов спекания Спекание систем Однокомпонентных Многокомпонентных Твердофазное С взаимной растворимостью С ограниченной растворимостью С нерастворимыми компонентами С эвтектикой С перитектикой Жидкофазное С исчезающей жидкой фазой С не исчезающей жидкой фазой. Лекция
Спекание порошков 615 Движущие силы процесса спекания • Однокомпонентные системы – наличие свободной поверхностной энергии Гиббса • Многокомпонентные системы – неоднородность химического состава. Лекция
Спекание порошков 616 Твердофазное спекание Твердофазное спекание – это спекание порошкового тела без образования жидкой фазы. Твердофазное спекание применяется для получения изделий на основе одно- или многокомпонентных систем, поведение которых при нагреве во многом зависит от природы и химической чистоты соответствующих компонентов. Лекция
Спекание порошков 617 Спекание однокомпонентных систем Нагрев порошкового тела вызывает в нем определенные структурные изменения, среди которых можно выделить несколько основных стадий процесса спекания. Подобные изменения связаны с объективными причинами ( движущими силами процесса спекания ), от которых зависит перемещение вещества в нагреваемом порошковом теле, т. е. механизм массопереноса. Лекция
Спекание порошков 618 Стадии процесса спекания Для спекаемого порошкового тела характерны некоторые геометрические элементы, определяемые понятиями «шейка» , «межчастичный контакт» , «изометрическая пора» и др. При описании структуры спекаемого материала выделяют три принципиально отличных состояния порошкового тела, каждое из которых соответствует определенной стадии процесса спекания: — стадия припекания порошинок (частиц) к другу, сопровождающееся увеличением площади контакта между ними; — стадия образования фазы вещества (частицы) и фазы «пустоты» (поры); — стадия образования замкнутых (изолированных) пор. Лекция
Спекание порошков 619 Для более детального рассмотрения процессов , сопровождающих нагрев порошковых тел, часто выделяют шесть стадий спекания: 1) возникновение и развитие связей между частицами; 2) образование и рост «шеек» на месте межчастичных контактов; 3) закрытие сквозной пористости (образование изолированных пор); 4) сфероидизация изолированных пор; 5) уплотнение порошкового тела за счет усадки изолированных пор; 6) укрупнение (коалесценция) изолированных пор. Спекание однокомпонентных систем. Лекция
Спекание порошков 620 Развитие связей между частицами начинается сразу с нагревом порошкового тела, т. е. на самом раннем этапе спекания. Рост контактов и образование «шеек» – естественное продолжение процесса межчастичного взаимодействия. Этот процесс сопровождается переносом вещества в область межчастичного контакта и повышением прочности порошкового тела. Спекаемое тело по структуре приближается к состоянию, которое соответствует двум фазам – вещества и пустоты. Спекание однокомпонентных систем. Лекция
Спекание порошков 621 Закрытие сквозной пористости является результатом продолжающегося роста «шеек» и приводит к появлению изолированных групп пор или даже отдельных пор. При этом общий (суммарный) объем пор в порошковом теле уменьшается, происходит повышение его плотности, сопровождающееся усадкой. Сфероидизация пор , как и предыдущая стадия, связана с ростом «шеек» : вещество с различных участков поверхности пор перемещается в область межчастичного контакта, а сами поры (как изолированные, так и сообщающиеся) округляются, приобретая сферичность. Спекание однокомпонентных систем. Лекция
Спекание порошков 622 Спекание однокомпонентных систем Усадка изолированных пор – одна из стадий спекания, требующая высоких температур и большого времени изотермическом выдержки (например, несколько сотен часов). Укрупнение (коалесценция) пор заключается в росте крупных пор за счет уменьшения размеров и исчезновения мелких, изолированных пор. Общая пористость при этом сохраняется неизменной , а число пор уменьшается при увеличении их среднего размера. Уплотнение порошкового тела на этой стадии спекания не происходит. Лекция
Спекание порошков 623 Существуют два основных подхода, дающих представления о движущих силах процесса спекания: 1) основан на том, что процесс превращения порошкового тела в плотное рассматривается как аналог химической реакции, которую можно характеризовать термодинамическим уравнением понижения свободной энергии Δ E. Δ E = Δ H – T Δ S , где Δ H и Δ S – изменение теплосодержания и энтропии системы соответственно; 2) основан на том, что поверхностная энергия эквивалентна поверхностному натяжению, т. е. силе, стремящейся уменьшить площадь поверхности и понизить избыток энергии, связанный с величиной поверхности. Движущие силы спекания. Лекция
Спекание порошков 624 Движущие силы спекания Для описания поведения дисперсной порошковой массы при спекании применяют классические термодинамические уравнения капиллярности, связывающие поверхностное натяжение, кривизну поверхности и внутреннее давление. Механическое равновесие на границе двух фаз, разделенных неплоской поверхностью, можно оценить уравнением Лапласа. Искривление поверхности означает изменение поверхностной энергии, так как происходит изменение площади поверхности. Лекция
Спекание порошков 625 Движущие силы спекания С искривленной поверхностью раздела фаз связана сила или поверхностное (межфазное) давление Δр, являющееся разностью давлений р 1 и р 2 на границе раздела со стороны соответствующих фаз: Δ р = р 1 – р 2 = 0. Равновесие фаз не предполагает равенства давлений со стороны каждой из фаз и будет наблюдаться, когда в них будут равны температуры ( Т 1 = Т 2 = Т ) и химические потенциалы: μ 1 ( р 1 , Т ) = μ 2 ( р 2 , Т ) = μ при V 1 + V 2 = const , где V 1 и V 2 – объемы сосуществующих фаз; μ 1 и μ 2 – химические потенциалы фаз. Лекция
Спекание порошков 626 Термодинамический потенциал системы с учетом граничной энергии имеет вид: Φ = – p 1 V 1 – p 2 V 2 + α 1, 2 S , где α 1, 2 – удельная поверхностная энергия на границе раздела фаз; S – площадь этой поверхности раздела. Давление Δ р можно найти из условия минимума термодинамического потенциала (при d Ф = 0 и V 1 + V 2 = const ): Δр = р 1 – р 2 = α 1, 2 ( d. S / d. V ). (1) Движущие силы спекания. Лекция
Спекание порошков 627 Движущие силы спекания. Лекция 13 Учитывая, что для каждой точки поверхности межфазной границы справедливо выражение d. S / d. V = (1 / R 1 ) + (1 / R 2 ), где R 1 и R 2 – главные радиусы кривизны поверхности, уравнение (1) можно записать как: Δр = р 1 – р 2 = α 1, 2 ( d. S / d. V ) = α 1, 2 [(1/ R 1 ) + (1/ R 2 )] = γ [(1/ R 1 ) + (1/ R 2 ) (2) где γ – поверхностное натяжение, которое для температур спекания примерно соответствует α 1, 2 т. е. γ ≈ α 1, 2. Частный случай уравнения (2) для сферической поверхности, когда R 1 = R 2 = R : Δр = 2 α 1, 2 / R = 2 γ / R
Спекание порошков 628 Модель спекания двух частиц а – радиус частицы; ρ – радиус «шейки» ; х – радиус сечения образующегося контакта; у – половина отрезка, на который сближаются частицы Движущие силы спекания. Лекция
Спекание порошков 629 Равновесие на внешней поверхности «шейки» : р т = р п — γ [(1/ρ) – (1/ х )], (3) где р т – давление (напряжение) в твердом теле (частице); р п – давление со стороны поры. Так как х « а , а ρ « х, уравнение (3) принимает вид р т = р п – γ /ρ. Величина γ / ρ представляет собой растягивающее напряжение, стремящееся сдвинуть край «шейки» в сторону поры, а р п есть давление со стороны поры, препятствующее расширению «шейки» . Движущие силы спекания. Лекция
Спекание порошков 630 Движущие силы спекания Механическое равновесие межфазных давлений для изолированной сферической поры радиуса r можно выразить, как р т = р п – 2 γ / r , где величина 2 γ / r представляет собой напряжение, стремящееся уменьшить поверхность поры путем уменьшения ее размера. В случае 2 γ / r>р п усадка поры возможна, и ее движущей силой является величина – р Т , которую можно рассматривать как сжимающее напряжение, действующее на межфазную границу со стороны твердого тела в области, окружающей пору. Лекция
Спекание порошков 631 Движущие силы спекания Кривизна поверхности частицы и «шейки» определяет существование еще двух движущих сил спекания: — отличного от равновесного давления пара над твердым веществом; — неравновесной концентрации вакансий вблизи изогнутой поверхности шейки. Лекция
Спекание порошков 632 Движущие силы спекания Отклонение от равновесного давления паров вещества над вогнутой поверхностью «шейки» и выпуклой поверхностью частицы можно выразить уравнениями: (4) (5) где р – давление пара вещества над изогнутой поверхностью; р а – давление пара вещества над плоской поверхностью; V 0 – объем атома или молекулы вещества частицы в твердом состоянии; R — газовая постоянная. ), /1ρ/1( γ 0 0 0 x RT V p pp , γ 20 0 0 RTa V p pp Лекция
Спекание порошков 633 Движущие силы спекания Зная, что величина 1/ х , которая много меньше 1/ρ, уравнение (4) принимает вид (6) 0 0 0γ. ρ p p V p RT Лекция
Спекание порошков 634 Формулы (4)–(6) не содержат массы частиц и, следовательно, могут быть применимы к частицам, масса которых равна нулю, т. е. к узловым вакансиям в кристаллической решетке вещества или к порам. Б. Я. Пинес для оценки отклонения концентрации вакансий от равновесной из-за кривизны межфазной границы предложил использовать уравнения: для «шейки» (7) для поверхности частицы (8) где С – концентрация вакансий вблизи «шейки» или выпуклой поверхности частицы; С 0 – равновесная концентрация вакансий; k – постоянная Больцмана). , ρ γ 0 0 0 k. T V C CC , γ 2 0 0 0 k. Ta V C CC Движущие силы спекания. Лекция
Спекание порошков 635 Движущие силы спекания Диффузионный транспортный механизм может быть связан еще с одной движущей силой, определяемой неравновесностью концентраций вакансий вблизи изолированной сферической поры радиуса r: В твердом веществе вблизи рассматриваемой поры концентрация вакансий выше равновесной и тем больше, чем меньше размер поры. Следовательно, между областями спекаемого порошкового тела, удаленными от поверхностей мелких сферических пор, и этими поверхностями, а также между соседними порами разного размера также существуют градиенты концентраций вакансий, определяющие направление диффузионного переноса вещества. k. Tr V C CC 0 0 0γ Лекция
Градиент концентраций вакансий может быть также связан с тем, что внутри частиц межзеренные (межкристаллитные) границы находятся под напряжением и концентрация вакансий вблизи них отличается от равновесной: C = C 0 exp ( σ · V 0 / k·T ), где σ – напряжение, действующее на межзеренной (межкристаллитной) границе (положительное в случае растягивающего и отрицательное в случае сжимающего усилия). Возникающий градиент концентраций вакансий между границами зерен, находящимися под разными по величине или знаку напряжениями, представляет собой движущую силу механизма переноса вещества, связанного с процессом диффузионной ползучести. Спекание порошков 636 Движущие силы спекания. Лекция
Спекание порошков 637 Лекция 14 Механизмы массопереноса при твердофазном спекании • Классификация механизмов массопереноса • Механизм «Испарение-конденсация» • Массоперенос при поверхностной диффузии • Объемная диффузия вещества • Вязкое течение вещества при спекании
Спекание порошков 638 В порошковом теле при его спекании возможны следующие механизмы транспорта вещества: — перенос через газовую фазу (испарения-конденсации); — поверхностная диффузия; — объемная диффузия; — вязкое течение; — течение, вызываемое внешними нагрузками (вязкое течение под давлением). Механизмы массопереноса. Лекция
Спекание порошков 639 Механизмы массопереноса Схемы различных механизмов спекания частиц, контактирующих в точке х 2 ~τ; Δ l≠ 0 х 5 ~τ; Δ l =0 х 5 ~τ; Δ l ≠ 0 х 7 ~τ; Δ l =0 х 5 ~τ; Δ l =0 х 4 ~τ; Δ l ≠ 0 а вб г е д ( Δ l – величина, на которую изменяется расстояние между частицами; х n – изменение радиуса межчастичного контакта за время τ изотермической выдержки) а – вязкое течение; б – объемная диффузия, не приводящая к усадке; в – объемная диффузия при наличии стока в области контакта; г – поверхностная диффузия; д – перенос вещества через газовую фазу; е – припекание под действием внешней нагрузки Лекция
Спекание порошков 640 Объемная диффузия Формулирование и развитие основных представлений о механизме диффузионного блуждания атомов в кристаллической решетке связано с работами Я. И. Френкеля: перемещение атомов в кристаллической решетке есть последовательное замещение ими вакансий, причем коэффициент диффузии атомов D связан с равновесной концентрацией вакансий С 0 и коэффициентом их диффузии D ‘ выражением D = C 0 D ‘. С учетом величин C 0 = e – E в / k. T и D ‘ = D 0 e – E а/ k. T , D = D 0 e –( E в + Е а )/ k T = D 0 e –E о / k. T , где Е 0 – энергия активации диффузии. Величина энергии образования вакансий Е в для большинства металлов составляет порядка 1/3 от энергии активации диффузии Е 0. Наличие избыточных вакансий ( С > С 0 ) приводит к увеличению коэффициента диффузии и, как правило, к понижению ее энергии активации Е 0. Лекция
Спекание порошков 641 Для описания диффузионных потоков атомов имеются два уравнения Фика : m = – DS (ð C /ð x ) (9) и ðС/ð t = D (ð 2 C /ð x 2 ), где m – количество вещества, диффундирующее в единицу времени через площадь S при градиенте концентрации вакансий ð С /ð х. Знак «минус» в уравнении (9) означает, что диффузия атомов происходит в сторону убывания их концентрации). Объемная диффузия. Лекция
Спекание порошков 642 Навстречу потоку атомов движется равный им по величине (но не массе!) поток вакансий. Принято рассматривать несколько механизмов движения вакансий , которые характеризуются различными источниками и стоками вакансий. Объемная диффузия. Лекция
Спекание порошков 643 Объемная диффузия Источники и стоки избыточных вакансий Случай Источник избыточных вакансии Стоки для избыточных вакансий Эффекты от диффузии атомов 1 Вогнутые поверхности «шеек» Выпуклые поверхности частиц Рост «шеек», сфероидизация пор 2 Вогнутые поверхности «шеек» Границы зерен Рост «шеек», сфероидизация и усадка пор 3* Вогнутые поверхности «шеек» Дислокации Рост «шеек», сфероидизация и усадка пор 4 Поверхность сферических пор Поверхности более крупных пор Укрупнение (коалесценция) пор 5 Поверхность сферических пор Границы зерен Укрупнение и усадка пор 6 Поверхность сферических пор Дислокации Укрупнение и усадка пор 7* Дислокации Границы зерен Укрупнение и усадка пор 8* Дислокации Поверхности частиц Рост «шеек», сфероидизация пор 9 Границы зерен Рост «шеек», усадка пор. Лекция
Спекание порошков 644 Объемная диффузия Анализируя возможные пути диффузии, можно сделать вывод о том, что существенную роль при спекании по механизму объемной диффузии имеют границы зерен. Принято считать, что с точки зрения массопереноса по механизму объемной диффузии наиболее важными являются случаи 1, 2, 4 и 5. Структуры контактных областей, возникающих припекании медных проволок а – поликристаллическая проволока, б – монокристаллическая проволока. Лекция
Спекание порошков 645 Объемная диффузия Изучение структуры контактных областей, возникающих при взаимном припекании медной проволоки, показало, что рост площади контактного перешейка сопровождается сближением центров контактирующих проволок лишь в случае наличия в нем межзеренной границы. Лекция
Спекание порошков 646 Б. Я. Пинес предложил выражение, оценивающее время τ п полного исчезновения ( «диффузионного» зарастания) изолированной сферической поры начального радиуса r 0 , находящейся в объеме вещества, где нет других источников вакансий, а их стоком является его внешняя габаритная поверхность: τ п = ( k. T /6 γ DV 0 ) r 0 3. В любой момент времени изотермической выдержки τ при спекании такая изолированная сферическая пора будет иметь радиус r , равный r 3 = r 0 3 – (6 γ DV 0 / k. T ) · τ. Объемная диффузия. Лекция
Спекание порошков 647 Я. И. Френкель сформулировал и количественно решил две задачи, связанные с реализацией при спекании порошкового тела механизма массопереноса путем вязкого течения: о заплывании изолированной поры и о слиянии двух соприкасающихся порошинок (сфер). Фундаментальное положение его теоретических представлений – аналогия между вязким течением аморфных (происходящим по механизму непороговой ползучести путем кооперативного перемещения атомов) и кристаллических тел (также является процессом непороговой ползучести, но перемещение атомов не является процессом кооперативным). Вязкое течение. Лекция
Спекание порошков 648 Вязкое течение кристаллических тел есть результат независимых элементарных актов (скачкообразных перемещений атомов) под влиянием капиллярного давления, вызванного кривизной поверхности частиц или различием напряжений в объеме порошкового тела по величине или знаку. Вязкое течение. Лекция
Для полного слияния двух контактирующих сфер ( x = a 0 ) необходимо время τ п , равное τ п = (2/3 · а 0 ) · (ή / γ ) , где а 0 – начальный размер сферы; ή – коэффициент вязкости вещества при данном состоянии структуры. Для полного заплывания изолированной сферической поры начального радиуса r 0 , который больше размера зерна или блока, где она расположена, необходимо время τ п , равное τ п = (4/3 а 0 ) (ή/ γ ). Радиус r такой поры в процессе изотермической выдержки τ равен r = r 0 – (3/4)( γ /ή) τ. Вязкое течение под давлением – течение вещества, вызываемое внешними нагрузками (связано с деформацией частиц). Спекание порошков 649 Вязкое течение. Лекция
Спекание порошков 650 Лекция 15 Ползучесть кристаллических тел • Механизмы непороговой и пороговой ползучести • Признаки механизмов ползучести • Проявление ползучести в спекаемом теле • Диффузионно-вязкое течение по механизмам Набарро – Херринга – Лифшица и диффузионно-аккомодационному механизму
Спекание порошков 651 Ползучесть кристаллических тел Я. Е. Гегузин, излагая физическую природу явлений, сопровождающих нагрев порошкового тела, сформулировал следующее определение: «Спекание – диффузионная ползучесть под воздействием сил поверхностного натяжения» . Спекание порошкового тела, содержащего соприкасающиеся порошинки и пустоту (поры), сопровождается ползучестью вещества (материала) этого тела. Модель механизма ползучести Лекция
Спекание порошков 652 Механизмы ползучести (деформирования) кристаллического тела в области высоких температур спекания могут быть различными. Выделяют непороговые механизмы , определяющие деформирование при сколь угодно малых напряжениях, и пороговые механизмы , проявляющие себя при напряжениях, превосходящих некоторое предельное. При непороговом механизме деформирования кристаллическое тело ведет себя подобно ньютоновской жидкости (отличие – коэффициент текучести его вещества зависит от структурного состояния тела и может изменяться во времени). При превышении σ Т возбуждаются пороговые механизмы , при которых ползучесть может являться следствием перемещения дислокаций , которые преодолевают различные препятствия (дислокационные стенки, микровключения и пр. ). Ползучесть кристаллических тел. Лекция
Спекание порошков 653 Общим признаком всех механизмов непороговой ползучести является направленный диффузионный поток вакансий (или, что то же самое, поток атомов в противоположном направлении), который возникает в пределах каждого из элементов структуры из-за градиента концентраций вакансий. Диффузионные потоки в пределах отдельного зерна не создают потока в масштабах всего порошкового тела. Р Схема деформирования поликристаллического образца вследствие диффузионно-вязкого преобразования формы зерен Ползучесть кристаллических тел. Лекция
Спекание порошков 654 В настоящее время при описании деформирования порошковых тел рассматривают два основных механизма ползучести: 1) механизм Набарро – Херринга – Лифшица (относится к идеализированному кристаллическому телу), в котором самосогласованное изменение формы зерен приводит к направленному перемещению их центров тяжести, без нарушения первоначальных контактов зерна с соседними зернами; 2) диффузионно-аккомодационный механизм течения поликристаллических структур, согласно которому деформация каждого зерна может нарушать их соседство (механизм Эшби-Фералла). Для осуществления аккомодации зерен необходим диффузионный перенос массы объемом порядка 14 %. Ползучесть кристаллических тел. Лекция
Спекание порошков 655 Ползучесть кристаллических тел Последовательность этапов преобразования формы соседних зерен по механизму диффузионной подстройки Лекция
Спекание порошков 656 Последовательные этапы ( I – V ) изменения взаимного расположения зерен с участием в процессе межзеренной граничной пористости B DA E C F 1 2 3 4 B B BAA D D BD DE F C 3 1 42 I II IV VПолзучесть кристаллических тел. Лекция
Спекание порошков 657 Пороговая ползучесть кристаллических тел связана с проявлением механизмов, действующих при напряжениях, превосходящих величину напряжений необходимых для преодоления препятствий, сдерживающих движение дислокаций. Торможение дислокаций может быть связано с их взаимодействием друг с другом или обусловлено различными локализованными дефектами (стопорами), расположенными в плоскости движения дислокации. К таким дефектам относят: — точечные дефекты и их скопления; — включения посторонней фазы (например оксидов на поверхности частиц); — дислокации в других системах скольжения, пересекающих плоскость, в которой движется рассматриваемая дислокация. Ползучесть кристаллических тел. Лекция
Спекание порошков 658 На ползучесть кристаллических тел при спекании существенное влияние оказывает дефектность их структуры. Деформация порошкового тела обнаруживается уже в процессе нагрева до температуры изотермического режима. Ползучесть, которая проявляется на этом этапе спекания порошкового тела, называется неустановившейся ползучестью (скорость процесса убывает со временем). Ползучесть кристаллических тел. Лекция
Спекание порошков 659 Величина неустановившейся ползучести может быть значительной, если в исходном состоянии структура порошкового тела существенно искажена и его нагрев осуществляют под нагрузкой. Ползучесть, происходящая при нагреве порошкового тела, зависит от режима нагрева, который влияет также на кинетику ползучести в наступившем изотермическом режиме. Ползучесть кристаллических тел. Лекция
Спекание порошков 660 Лекция 16 Укрупнение частиц при спекании. Уплотнение порошкового тела • Рекристаллизация порошкового тела при спекании • Объемные изменения при спекании • Стадии уплотнения • Зональное обособление при усадке
Спекание порошков 661 Рекристаллизация частиц Рекристаллизация – рост (укрупнение) частиц в процессе нагрева порошковых тел. Крупные частицы образуются за счет переноса вещества при общей границе с частицы меньшего размера на частицу большего размера, который происходит путем перемещения атомов через межчастичные границы в сторону частиц с меньшей величиной свободной энергии и поперек контактных участков. Движущая сила рекристаллизации обусловлена стремлением системы перейти в более равновесное состояние с меньшей суммарной поверхностью границ. Разница свободных энергий частиц по обе стороны границы между ними определяет направление движения границы к центру ее кривизны. Лекция
Спекание порошков 662 Рекристаллизация частиц Схема роста частиц в порошковом теле при рекристаллизации Лекция
Спекание порошков 663 Рекристаллизация частиц Установлена закономерность, согласно которой кристаллы, имеющие больше шести граней, будут расти до некоторого предельного размера. Если граней у кристалла меньше шести, то он будет уменьшаться в размере до полного исчезновения. Кристаллы с шестью и более гранями в сечении образуют вогнутые границы, а если граней меньше шести, то их поверхности выпуклы. Скорость роста частиц обратно пропорциональна радиусу кривизны границы и может быть описана выражением d – d 0 = K · τ 0, 5 , где d 0 – линейный размер частицы до начала роста; d – линейный размер частицы, выросший за время τ ; K – коэффициент, учитывающий природу материала. Лекция
Спекание порошков 664 Рекристаллизация в пористых порошковых телах начинается при температуре 0, 3– 0, 4 Т пл и при 0, 75– 0, 85 Т пл она протекает интенсивно, завершая формирование структуры спекаемого изделия. Процесс рекристаллизации идет одновременно с усадкой и другими явлениями, имеет с ними косвенную связь и в значительной степени зависит от них. Рост частиц вызывает лишь перемещение и перераспределение вещества в пределах объема пористого порошкового тела, но не приводит к сокращению объема пор и уплотнению спекаемого изделия. Рекристаллизация частиц. Лекция
Спекание порошков 665 В связи с тормозящим влиянием посторонних включений, находящихся по границам частиц (пор, пленок на поверхности порошинок, межкристаллитного вещества и т. п. ), рост частиц продолжается до некоторого их среднего размера. В результате спекания плотность порошкового тела в подавляющем большинстве случаев возрастает и происходит уменьшение его размеров (линейная усадка) и объема (объемная усадка) как следствие «зарастания» пор, приводящего к сокращению их числа и суммарного объема. Рекристаллизация частиц. Лекция
Спекание порошков 666 Уплотнение порошкового тела Процесс усадки можно разделить на три последовательные стадии. Ранняя стадия. Скорость смещения и объемного деформирования частиц высока. Промежуточная стадия. Пористая матрица из частиц ведет себя как вязкая среда, и ее уплотнение равномерно по всему объему (при равномерном распределении пор). Поздняя стадия. Порошковое тело содержит отдельные изолированные поры, которые залечиваются (зарастают) в результате диффузионного растворения в матричном веществе с выходом вакансий на внешнюю (габаритную) поверхность спекаемой заготовки. Лекция
Спекание порошков 667 Одной из характерных особенностей усадки нагреваемого порошкового тела является замедление ее скорости при изотермической выдержке. В. А. Ивенсен показал, что отношение скоростей сокращения объема пор в два произвольно взятые момента времени τ 1 и τ 2 для данного изотермического спекания равно ( d. V / d τ ) 1 /( d. V / d τ ) 2 = ( V 1 / V 2 ) n , где V 1 и V 2 – суммарные объемы пор в моменты времени τ 1 и τ 2 ; n – показатель, характеризующий интенсивность торможения усадки. Уплотнение порошкового тела. Лекция
Спекание порошков 668 Из этого выражения вытекает уравнение кинетики изменения пористости: V = V н ( q· m· τ + 1 ) – 1/ m , где V – объем пор после выдержки в течение времени τ ; V н – начальный объем пор; m – константа, характеризующая интенсивность снижения скорости сокращения объема пор во время спекания, равная m = n – 1; q – константа, имеющая значение скорости относительного сокращения единицы объема пор в момент начала изотермического спекания, равная q = – ( d. V / d τ ) н /(1/ V н ) и имеющая размерность «время – 1 » . Уплотнение порошкового тела. Лекция
Спекание порошков 669 Уплотнение порошкового тела 1 2 3 4 5 τ , ч 1 53 0 1 Усадк а, %Рост, % Линейная усадка брикетов железа, спрессованных при разных давлениях (МПа): 1 – 400; 2 – 600; 3 – 800; 4 – 1000 1 4 3 2 Рост, % Усадка, %Лекция
Спекание порошков 670 Усадка при изотермическом спекании при ступенчатом подъеме температуры (по В. А. Ивенсену): а – 600 о С; б – 740 о С; в – 880 о С Δ V/V H 0 1 2 3 4 5 6 Время, чба в 0, 8 0, 4 Уплотнение порошкового тела. Лекция
Спекание порошков 671 Уплотнение порошкового тела На кинетику уплотнения влияют: — стабилизация кристаллической структуры (уменьшает величину усадки); — увеличение плотности нагреваемого порошкового тела (сопровождается повышением микроскопической вязкости). Влияние дефектов называют структурным фактором (по М. Ю. Бальшину), а увеличение плотности пористого порошкового – геометрическим фактором (по В. А. Ивенсену). Неоднородное объемное распределение пор по размерам является причиной явления локализации уплотнения, называемого зональным обособлением усадки при спекании. Процесс зонального обособления усадки может привести к росту наиболее крупных межгрупповых пор при одновременном уменьшении наиболее мелких внутригрупповых пор и к повышению газопроницаемости отдельных участков спеченного материала по сравнению с исходной у порошковых формовок. Лекция
Спекание порошков 672 Лекция 17 Влияние технологических факторов на процесс спекания однокомпонентных систем. Спекание многокомпонентных систем • Факторы, определяющие процесс спекания порошкового тела; • активирование процессов спекания однокомпонентных систем; • виды твердофазного спекания многокомпонентных систем.
Спекание порошков 673 Влияние технологических факторов на процесс спекания На процесс спекания оказывают влияние следующие технологические факторы • Свойства исходных порошков • Давление формования • Температура спекания • Продолжительность спекания • Атмосфера спекания Лекция
Спекание порошков 674 Свойства исходных порошков В общем случае на изменение плотности и свойств порошковых формовок при спекании влияют: — величина частиц; — состояние поверхности частиц; — степень несовершенства кристаллического строения частиц; — химический состав порошка и др. Структура изделий, спеченных из высокодисперсных порошков , отличается наличием большого числа крупных зерен, выросших в процессе спекания. Усадка при спекании уменьшается, если исходный порошок или формовку из него подвергнуть отжигу, при котором происходит сглаживание рельефа поверхности частиц, их срастание и устранение несовершенств кристаллического строения. Лекция
Спекание порошков 675 Его влияние на результаты спекания проявляется главным образом через следующие факторы: — изменение общей площади контактов и плотности порошковой формовки; — упругие и пластические свойства материала частиц порошка; — деформацию или разрушение поверхностных слоев частиц порошка; — захлопывание в изолированных порах порошковой формовки воздуха и других газов. С увеличением исходной плотности формовок их объемная и линейные усадки при спекании уменьшаются. Давление формования. Лекция
Спекание порошков 676 Если плотность формовки неодинакова по высоте, то после спекания можно часто наблюдать «талию» . Однако при спекании мелкозернистых порошков происходит «выравнивание» пористости. Усадки при спекании прессовок в направлении приложения давления и в поперечном направлении, как правило, не совпадают. Увеличение давления формования приводит к повышению всех показателей физических и механических свойств спеченных изделий. Давление формования. Лекция
Спекание порошков 677 Влияние технологических факторов на процесс спекания Температура спекания, о СО т носит ельная плот ност ь, %4 3 1 2 Влияние температуры спекания на относительную плотность: 1 – свободно насыпанный порошок; 2 – порошок, спрессованный при малых давлениях; 3 – порошок, спрессованный при высоких давлениях; 4 – порошок, спрессованный при очень высоких давлениях. Лекция
Спекание порошков 678 Плотность порошковых изделий возрастает с повышением температуры спекания тем быстрее, чем ниже было давление формования заготовки из порошка. На процесс спекания значительное влияние оказывает скорость подъема температуры. При быстром подъеме температуры в крупногабаритных порошковых формовках могут наблюдаться местные обособления усадки из-за местных различий в температуре, что в конечном счете может привести к искажению их формы. Температура спекания. Лекция
Спекание порошков 679 Прочность, как и плотность, обычно повышается с ростом температуры спекания. Показатели пластичности порошковых материалов увеличиваются с повышением температуры изотермической выдержки при спекании даже при падении их плотности и прочности (если это имело место). Температура спекания. Лекция
Спекание порошков 680 Выдержка порошковой формовки при заданной температуре спекания вызывает сначала резкий, а затем более медленный рост ее плотности и других свойств. Максимальная прочность достигается за довольно короткое время изотермической выдержки и при дальнейшем спекании она остается на том же уровне или даже несколько снижается. Продолжительность спекания. Лекция
Спекание порошков 681 На практике выдержка при спекании варьируется в довольно широких пределах (от нескольких десятков минут до нескольких десятков часов) и зависит от: — состава материала; — исходной и требуемой плотности порошковой формовки; — размера формовки; — типа и состава защитной среды; — конструкции печи и т. д. Продолжительность спекания. Лекция
Спекание порошков 682 Атмосфера спекания Сравнение результатов спекания порошковых тел, проводимого в различных средах, показывает, что при спекании в восстановительной среде достигается их большая плотность, чем при спекании в нейтральной среде. Очень полно и быстро проходит спекание в вакууме, которое по сравнению со спеканием в нейтральной среде в большинстве случаев начинается при более низких температурах и дает повышенную плотность получаемого порошкового изделия. Лекция
Спекание порошков 683 Атмосфера спекания Практика спекания показывает, что характер влияния газовых сред на уплотнение разных порошковых материалов может быть существенно различным и не все наблюдаемые изменения скорости усадки поддаются рациональному объяснению. Лекция
Спекание порошков 684 Атмосфера спекания Можно выделить четыре наиболее характерных механизма влияния атмосферы спекания на уплотнение порошковых материалов: 1) адсорбционное воздействие на величину энергии поверхности пор и уровень действующих капиллярных сил; 2) травящее воздействие, повышающее шероховатость поверхности пор; 3) торможение уплотнения, вызванное образованием пленки нелетучего соединения в результате химического взаимодействия вещества частиц порошка с компонентами газовой среды. 4) возможность различного поведения газовых сред, оказавшихся внутри изолированных пор, возникших в порошковом теле в процессе спекания. Лекция
Спекание порошков 685 Активирование процессов спекания Активированное спекание – это процесс спекания порошковой формовки при воздействии химических и физических факторов, вызывающих интенсификацию спекания. Активирование спекания связано с более эффективным осуществлением транспортных механизмов массопереноса путем: — изменения состояния поверхности или контакта между частицами порошка; — понижения энергии активации действующего транспортного механизма; — изменения типа транспортного механизма; — изменения транспортного пути. Лекция
Спекание порошков 686 Активирование процессов спекания Методы активирования спекания подразделяют на две основные группы: — химические , основанные на использовании окислительно-восстановительных реакций, процессов диссоциации химических соединений, химического транспорта спекаемого вещества и др. ; — физические , связанные с интенсивным измельчением порошка, воздействием на него облучением, циклическим изменением температуры при спекании (циклическое спекание), наложением магнитного поля на нагреваемую формовку и др. Лекция
Спекание порошков 687 Химические методы активирования спекания можно классифицировать: — по составу активаторов, их источникам (из газовой фазы, засыпки или примесей в спекаемом материале); — по этапу введения (до спекания или в его процессе); — по поведению (активаторы остаются в спеченном изделии или нет). К химическим способам активирования спекания относится изменение его атмосферы. Активировать процесс спекания можно и введя в состав порошка небольшое количество твердых примесных веществ – порошков металлов или неметаллов (в случае спекания керамики). Активирование процессов спекания. Лекция
Спекание порошков 688 Активирование процессов спекания Требования к подобным активирующим добавкам: 1. Температура плавления добавки должна быть ниже, чем основного порошка. 2. Вещество добавки должно быть поверхностно-активным по отношению к основному металлу. Это достигается применении в качестве добавки переходных металлов (оксидов переходных металлов – в случае спекания керамики). При получении керамики в состав материала может вводиться от нескольких десятых до нескольких процентов добавок. В случае использования в качестве добавок чистых металлов основной металл должен хорошо растворяться и диффундировать в добавляемом, а добавляемый металл не должен растворяться в основном. Лекция
Спекание порошков 689 Активирование процессов спекания Физические методы активирования спекания связаны прежде всего с увеличением дисперсности порошка и повышением дефектности кристаллической решетки вещества его частиц. Интенсивное измельчение частиц увеличивает их суммарную поверхность, повышая запас избыточной энергии порошка, и увеличивает толщину «нарушенного слоя» . Это способствует действию такого механизма массопереноса, как «поверхностная диффузия» . При спекании частиц, размер которых меньше нескольких десятых микрометра , возможно снижение температуры спекания на 150– 200 о С. Лекция
Спекание порошков 690 Лекция 18 Твердофазное спекание многокомпонентных систем • Виды твердофазного спекания многокомпонентных систем • Спекание систем с полной взаимной растворимостью компонентов • Спекание систем с ограниченной растворимостью компонентов • Спекание систем с нерастворимыми (невзаимодействующими) компонентами
Спекание порошков 691 Порошковые материалы, используемые в различных отраслях техники, в подавляющем большинстве случаев представляют собой многокомпонентные системы, образование в которых необходимого состава происходит непосредственно при спекании. Главная отличительная черта таких материалов — наличие неравенства концентрацией компонентов в различных микрообъемах исходного порошкового тела (градиент химического состава). Спекание многокомпонентных систем. Лекция
Спекание порошков 692 Процесс спекания разнородных частиц включает процессы: — самодиффузии (обусловливает перенос массы в область контактного перешейка); — гетеродиффузии (обеспечивает выравнивание концентраций компонентов в пределах порошкового тела). Гетеродиффузия (формирующая межфазные поверхности) приводит к торможению уплотнения порошкового тела при нагреве. Физические и механические свойства спеченных порошковых тел зависят от полноты гетеродиффузии. Спекание многокомпонентных систем. Лекция
Спекание порошков 693 Гетеродиффузии благоприятствуют следующие факторы: — использование при спекании дисперсных порошков; — хорошее качество смешивания компонентов; — повышение температуры спекания; — удаление адсорбированных газов и пленок оксидов; — увеличение исходной плотности формовок и пр. Спекание многокомпонентных систем. Лекция
Спекание порошков 694 Процессы, сопровождающие нагрев многокомпонентной системы, в значительной мере определяются характером соответствующих диаграмм состояния. Принято различать следующие виды твердофазного спекания многокомпонентных систем: — спекание компонентов, обладающих полной (неограниченной) взаимной растворимостью; — спекание компонентов, обладающих ограниченной взаимной растворимостью; — спекание компонентов, взаимно нерастворимых (невзаимодействующих). Спекание многокомпонентных систем. Лекция
Спекание порошков 695 Системы с полной взаимной растворимостью компонентов В процессе спекания подобных систем существует несколько фаз (частицы исходных металлов и твердые растворы переменной концентрации), которые в конце спекания образуют одну фазу (твердый раствор). Временная зависимость сокращения объема пор при спекании в условиях развития гетеродиффузии отличается от зависимости, присущей однофазному порошковому телу. Усадка многокомпонентного порошкового тела при нагреве, как правило, меньше аддитивной. Это объясняется более низкой подвижностью атомов в твердых растворах и невозможностью получить при смешивании исходных компонентов абсолютно однородную смесь. Лекция
Спекание порошков 696 Системы с эвтектикой В двухфазной области подобных систем кривая усадки имеет ярко выраженный максимум, соответствует примерно 50 %-ному содержанию разнородных фаз, т. е. их наибольшей межфазной поверхности и, следовательно, максимальному диффузионному межфазному взаимодействию. Снижение усадки в области твердых растворов связано с обычным снижением диффузионной подвижности в них атомов. В эвтектических системах при практическом отсутствии (или чрезвычайно малой) растворимости между фазами нет зависимости усадки от величины межфазной поверхности. Системы с ограниченной растворимостью компонентов. Лекция
Спекание порошков 697 Системы с перитектикой В таких системах усадка в двухфазной области имеет четко выраженный минимум из-за увеличения объема порошкового тела при спекании. По этой причине диффузионное межфазное взаимодействие в двухфазных перитектических системах осуществляется очень слабо. В этом случае создаются условия для беспрепятственного проявления эффекта Френкеля именно в области средних концентраций компонентов порошковых систем. Системы с ограниченной растворимостью компонентов. Лекция
Спекание порошков 698 Спекание многокомпонентных систем Системы с ограниченной растворимостью компонентов Системы с химическими соединениями Взаимодействие компонентов смеси порошков с образованием в процессе спекания химических соединений или интерметаллидов обычно существенно усложняет вид концентрационной зависимости усадки и ход кривых может быть самым различным. Специфичной разновидностью такого спекания многокомпонентных систем является так называемое реакционное спекание , когда при нагреве порошковой формовки совмещают процессы собственно спекания и образования химического соединения. Лекция
Спекание порошков 699 Системы с нерастворимыми (невзаимодействующими) компонентами Б. Я. Пинес сформулировал термодинамическое условие припекания двух частиц разнородных невзаимодействующих компонентов: α АБ < / α А + α Б /, (1) т. е. поверхностная энергия образовавшейся межфазной границы АВ должна быть меньше, чем сумма поверхностных энергий частиц А и В (в противном случае порошковое тело спекаться не будет). Спекание многокомпонентных систем. Лекция
Спекание порошков 700 Механизм и кинетика припекания оказываются существенно различными для двух возможных случаев при соблюдении условия (1): α АБ / α А – α Б / (3) В случае, когда выполняется соотношение (2), происходит покрытие поверхности частицы вещества с большей поверхностной энергией веществом с меньшей поверхностной энергией А Б а в б г Схематическое изображение этапов ( а – г ) припекания частиц. Спекание многокомпонентных систем. Лекция
Спекание порошков 701 Лекция 19 Жидкофазное спекание • Особенности процессов жидкофазного спекания порошков • Стадии жидкофазного спекания • Спекание с жидкой фазой, присутствующей до конца спекания
Спекание порошков 702 Жидкофазное спекание – спекание порошкового тела при температуре, обеспечивающей образование жидкой фазы Термодинамическим условием эффективного жидкофазного спекания является стремление многокомпонентной системы к минимуму свободной поверхностной энергии и химического потенциала, как и при твердофазном спекании. В отличие от твердофазного при жидкофазном спекании из-за большей подвижности системы «жидкое – твердое» наглядно проявляется действие основных движущих сил объемного уплотнения порошкового тела – сил капиллярного стягивания. Жидкофазное спекание. Лекция
Спекание порошков 703 В присутствии жидкой фазы при определенных условиях облегчается развитие сил сцепления между отдельными частицами порошка и может сформироваться малопористая (П < 1 %) структура. При жидкофазном спекании в порошковом теле возникает своего рода капиллярная система (размеры частиц порошка соизмеримы с поперечными размерами поровых каналов), состоящая из твердой, жидкой и газообразной фаз. В связи с этим большое значение приобретает смачивание твердых частиц жидкой фазой, мерой которого является величина краевого угла смачивания θ. Жидкофазное спекание. Лекция
Спекание порошков 704 Величина краевого угла смачивания θ определяется взаимодействием фаз на границе раздела cos θ = ( σ т – σ т–ж ) / σ ж , где σ т , σ т–ж , σ ж – соответственно поверхностные энергии на границах раздела твердое тело – газ, твердое тело – жидкость и жидкость – газ. α Т-Ж α Тα Ж θ α ТРψα Т-Ж Равновесие жидкой капли на твердой поверхности Жидкофазное спекание. Лекция
Спекание порошков 705 Термодинамическим условием смачивания является уменьшение свободной энергии системы при превращении границ раздела твердое тело – газ и жидкость – газ в границу раздела твердое тело – жидкость, т. е. работа адгезии должна быть положительна. При полном смачивании θ = 0°, при полном несмачивании θ = 180°. При θ 90° смачивание плохое и образовавшаяся жидкая фаза тормозит спекание, препятствуя уплотнению порошкового тела. Смачивание улучшается при уменьшении σ т–ж. Изменение величины σ т–ж может быть следствием изменения величин σ т и σ ж. При увеличении времени контакта жидкое – твердое и температуры θ уменьшается и смачивание улучшается. Жидкофазное спекание. Лекция
Спекание порошков 706 Различают следующие типы жидкофазного спекания порошкового тела: — спекание с жидкой фазой присутствующей до конца изотермической выдержки; — спекание с жидкой фазой, исчезающей в процессе нагрева порошкового тела или на этапе изотермической выдержки. Специфической разновидность первого типа процесса жидкофазного спекания, которую называют инфильтрацией порошковой формовки. При любом типе спекания объем образующейся при нагреве жидкой фазы должен составлять от 3– 5 до 50 % (оптимальное количество – 25– 35 %). Жидкофазное спекание. Лекция
Спекание порошков 707 Основные особенности, характерные для спекания в присутствии жидкой фазы: 1. Образование жидкой фазы при спекании, как правило, сопровождается интенсификацией усадки. 2. Увеличение усадки зависит от физико-химических характеристик компонентов, количества жидкой фазы, размера частиц тугоплавкой составляющей и начальной пористости брикетов. 3. Значительную роль при спекании играет величина исходной пористости. 4. В некоторых случаях жидкая фаза присутствует лишь в течение ограниченного времени и спекание осуществляется в основном в твердой фазе. Жидкофазное спекание. Лекция
Спекание порошков 708 Основные особенности, характерные для спекания в присутствии жидкой фазы: 5. Жидкофазным спеканием можно получать специальные структуры, обладающие особенными механическими свойствами 6. Жидкофазное спекание позволяет получить высокопористые порошковые материалы и изделия с размерами, практически равными размерам исходных прессовок. Жидкофазное спекание. Лекция
Спекание порошков 709 Жидкофазное спекание включает три основные стадии: 1) перемещения твердых частиц до состояния плотной укладки под влиянием сил поверхностного натяжения смачивающей их жидкости, 2) уплотнения материала в результате перекристаллизации твердой фазы через жидкую (при условии растворимости твердой фазы в жидкой), 3) срастания частиц тугоплавкого компонента в жесткий каркас ( «скелет» ). Уплотнение частиц при перекристаллизации происходит еще и потому, что одновременно с ростом зерен изменяется и форма частиц. Стадии жидкофазного спекания. Лекция
Спекание порошков 710 Жидкофазное спекание 1 2 3∆ П Т Кривая усадки при жидкофазном спекании 1 – жидкое течение; 2 – растворение и осаждение; 3 – твердофазное спекание. Лекция
Спекание порошков 711 Различают три возможных механизма уплотнения, развивающихся в присутствии жидкой фазы: — жидкофазное течение (механическая перегруппировка), т. е. перемещение частиц под действием капиллярных сил; — растворение-осаждение (перекристаллизация или химическая перегруппировка частиц тугоплавкой фазы), т. е. перенос через жидкость растворенного в ней вещества тугоплавкой фазы с поверхности частиц меньшего размера на поверхность частиц большего размера; — твердофазное спекание , т. е. срастание частиц тугоплавкой фазы (образование жесткого каркаса или «скелета» ). Жидкофазное спекание. Лекция
Спекание порошков 712 Жидкофазное спекание Процесс перекристаллизации включает не менее трех элементарных процессов: 1) растворение вещества мелких частиц, т. е. переход атомов с поверхности этих частиц в раствор (процесс, часто называемый реакцией на межфазной поверхности); 2) диффузию растворенных атомов в жидкости между поверхностями мелких и крупных частиц; 3) отложение растворенного вещества на поверхности крупных частиц. Рост зерен по этому механизму подчиняется той же временной зависимости, что и рост зерна при собирательной рекристаллизации. d n – d 0 n = K τ , где d n и d 0 n – текущая и начальная средняя величина зерна (частицы) соответственно; τ – время спекания; K – константа. Показатель степени n зависит от того, какой элементарный акт определяет скорость всего процесса (если это первый этап, то n = 2, если второй – n = 3 ). Лекция
Спекание порошков 713 Спекание с жидкой фазой, присутствующей до конца спекания При таком спекании в процессе изотермической выдержки жидкая фаза постоянно присутствует в порошковом теле. При полной смачиваемости и заметной растворимости тугоплавкой фазы в жидкой уплотнение достигается уже в первые несколько (1– 10) минут изотермической выдержки и сравнительно небольшом [10– 20 % (объемн. )] количестве жидкой фазы. Жидкофазное спекание. Лекция
Спекание порошков 714 Спекание с жидкой фазой, присутствующей до конца спекания Стадия механической перегруппировки частиц характеризуется дезинтеграцией поликристаллических частиц (наблюдается при плавлении легкоплавкой фазы) и интенсивным перемещением частиц. Химическая перегруппировка вначале приводит к коалесценции и росту более крупных частиц за счет более мелких, а затем и к окончательному уплотнению системы. Жидкофазное спекание. Лекция
Спекание порошков 7151 2 3 4 56 78 910 11 512 1 1 1 2 2 3 3 3 4 4 76 8 9 8 10 11 12 10 6 10 8 Схема усадки при жидкофазном спекании порошковой системы. Жидкофазное спекание. Лекция
Спекание порошков 716 Спекание с жидкой фазой, исчезающей в процессе спекания При спекании систем с жидкой фазой, исчезающей в процессе изотермической выдержки (с образованием твердого раствора или тугоплавкого соединения), спекание является жидкофазным и частицы тугоплавкого компонента А могут стягиваться силами поверхностного натяжения до тех пор, пока существует жидкая фаза. В определенных условиях при жидкофазном спекании имеет место объемный рост порошкового тела, который может быть связан с преимущественной диффузией жидкой фазы в частицы тугоплавкого компонента, что приводит к росту частиц тугоплавкого компонента и увеличению размеров пор. Жидкофазное спекание. Лекция
Спекание порошков 717 Спекание с жидкой фазой, исчезающей в процессе спекания Увеличение пористости можно оценить следующим аналитическим выражением: П = П 0 + С (1 – П 0 ), где П 0 , П – пористость порошкового тела до и после спекания соответственно; С – объемная концентрация легкоплавкой добавки (доли единицы). Жидкофазное спекание. Лекция
Спекание порошков 718 Лекция 20 Жидкофазное спекание и инфильтрация порошковых формовок. Брак при спекании • Спекание порошковых тел с жидкой фазой, исчезающей в процессе спекания • Инфильтрация порошковых формовок • Брак при спекании и меры по его предупреждению
Спекание порошков 719 Инфильтрация порошковой формовки Инфильтрация ( «пропитка» ) – это процесс заполнения порошковой формовки расплавленным металлом или сплавом. Скорость инфильтрации составляет десятые доли миллиметра в секунду, а толщина слоя зависит от свойств расплава и длительности его контакта с твердым каркасом: h = (1/ π ) ( σ ж · cos θ · r э · τ / η ж ) 0, 5 , где r э – эффективный радиус поровых каналов; η ж – вязкость расплава. Лекция
Спекание порошков 720 Инфильтрация порошковой формовки Термодинамическое условие инфильтрации можно выразить следующим образом: σ ж · cos θ > 0. Поскольку σ ж всегда больше нуля, то основным условием осуществления инфильтрации является то, что угол смачивания θ должен быть < 90°. Лекция
Спекание порошков 721 Браки при спекании При спекании появляется не только брак, вызванный нарушением технологии, но и выявляется брак предыдущих операций. Виды брака спеченных изделий: • скрытый расслой • коробление и искажение формы • пережог • недопекание • окисление • корочка • вспучивание • выпотевание • диффузионная пористость • обезуглероживание • сажистый налет • сульфидная пленка • разъедание и шероховатость поверхности. Лекция
Обработка порошковых изделий
Обработка порошковых изделий 723 Оглавление Лекция 21. Обработка спеченных порошковых изделий Лекция 22. Обработка порошковых изделий
Обработка порошковых изделий 724 Лекция 21 Обработка спеченных порошковых изделий • Виды обработки порошковых изделий • Методы термической обработки порошковых изделий • Химико-термическая обработка порошковых изделий
Обработка порошковых изделий 725 Виды обработки порошковых изделий Повысить свойства порошковых материалов можно изменением их структуры, используя различные виды термической, химико-термической, термомеханической и дисперсионно-упрочняющей обработки, защитой от коррозии и механической обработкой для придания изделиям требуемых размеров и формы. Обладая большей суммарной поверхностью , пористые изделия при нагревании более склонны к обезуглероживанию, окислению и т. д. , поэтому при их обработке необходимо применять либо более быстрый нагрев , при котором за счет меньшего времени теплового воздействия химическое взаимодействие затрагивает меньшие объемы, либо осуществлять нагрев в защитных атмосферах или в засыпках. Лекция
Обработка порошковых изделий 726 Виды обработки порошковых изделий Наличие в порошковых материалах пор, заполненных газом, снижает тепло- и температуропроводность изделий. В связи с этим характеристики процессов термической обработки будут отличаться от аналогичных показателей для беспористых изделий. Лекция
Обработка порошковых изделий 727 Методы термической обработки порошковых изделий Термическая обработка делится на: — предварительную (различные виды отжига и нормализация); — окончательную (закалка с отпуском). Предварительная обработка проводится как на порошках, так и на сформованных, спеченных и откалиброванных заготовках с целью улучшения их структуры, технологических и механических свойств (снижения твердости, улучшения обрабатываемости резанием, уменьшения и полного снятия остаточных напряжений). Лекция
Обработка порошковых изделий 728 Методы термической обработки порошковых изделий Окончательной обработке обычно подвергают готовые изделия с целью улучшения или формирования заданной структуры и придания необходимых свойств. Для порошковых материалов с гетерогенной структурой важное значение имеет диффузионный отжиг. Закалка порошковых изделий кроме повышения механических свойств еще и позволяет улучшить физико-химических свойства: магнитные, антикоррозионные и т. д. для беспористых изделий. Лекция
Обработка порошковых изделий 729 Химико-термическая обработка (ХТО) заключается в нагреве и выдержке металлов и сплавов при высокой температуре в активных газовых, жидких или твердых средах. Она обеспечивает изменение свойств поверхности порошковых изделий при диффузионном насыщении частиц материала-основы каким-либо легирующим элементом. При ХТО на поверхности может происходить залечивание пор, играющее большую роль для повышения всего комплекса свойств при сохранении массы и размеров изделий. Лекция
Обработка порошковых изделий 730 Химико-термическая обработка В случае высокоплотных порошковых материалов можно совмещать ХТО со спеканием или нагревом перед каким-либо видом горячего формообразования. После некоторых видов ХТО проводят термическую обработку, улучшающую свойства сердцевины и поверхности изделия. В некоторых случаях ХТО предшествует ТО. Лекция
Обработка порошковых изделий 731 Химико-термическая обработка В качестве рабочих сред при ХТО применяют твердые, жидкие и газообразные вещества. Наиболее эффективными являются газовые среды, обеспечивающие максимально быстрый подвод насыщающего элемента к поверхности. В жидких средах насыщение происходит: — либо вследствие прямого контакта расплава с поверхностью обрабатываемого изделия; — либо за счет газов или элементов в атомарном виде, выделяющихся в результате протекающих в расплаве реакции или электролиза. Лекция
Обработка порошковых изделий 732 Химико-термическая обработка Насыщение в твердых средах характеризуется малой скоростью. Часто для ускорения процесса к твердым средам добавляют активаторы типа NH 4 Cl , NH 4 Br , Ba. CO 3 и др. , с помощью которых формируется активная газовая фаза, принимающая участие в образовании соответствующего насыщенного слоя. Лекция
Обработка порошковых изделий 733 Лекция 22 Обработка порошковых изделий • Термомеханическая обработка порошковых изделий • Дисперсионно-упрочняющая термическая обработка • Противокоррозионная обработка изделий из порошков • Механическая обработка
Обработка порошковых изделий 734 Термомеханическая обработка (ТМО) изделий, заключающаяся в сочетании термической обработки с пластической деформацией. Применяемые схемы ТМО представляют собой варианты трех основных процессов: — высокотемпературной (ВТМО); — низкотемпературной (НТМО); — предварительной термомеханической обработки (ПТМО). Термомеханическая обработка. Лекция
Обработка порошковых изделий 735 При ВТМО деформацию материала с большой степенью обжатия (до 80– 90 %) осуществляют прокаткой, экструзией, штамповкой и т. д. НТМО в основном применяют только для обработки легированных сталей с большой устойчивостью переохлажденного аустенита. При ПТМО деформация и нагрев под закалку разделены во времени: материал вначале подвергают механической деформации в холодном состоянии, а затем закалке и отпуску. Термомеханическая обработка. Лекция
Обработка порошковых изделий 736 Дисперсионно-упрочняющая термическая обработка ДУТО возможна для материалов, компоненты которых при температуре спекания имеют ограниченную взаимную растворимость, уменьшающуюся при снижении температуры в процессе охлаждения после изотермической выдержки. ДУТО складывается из двух этапов: 1) закалки с температур выше линии предельной растворимости компонентов на диаграмме состояния (быстрое охлаждение при закалке в этом случае фиксирует при комнатной температуре пересыщенный неустойчивый твердый раствор); 2) старения сплавов, при котором происходит распад пересыщенного твердого раствора, полученного в результате закалки, и выделения избыточной фазы в виде очень мелкодисперсных частиц химического соединения или твердого раствора. Лекция
Обработка порошковых изделий 737 Защита от коррозии С целью защиты поверхности порошковых изделий от коррозии на нее наносят различные химические или электролитические покрытия: химическое никелирование, фосфатирование, электрохимическое никелирование, меднение, цинкование, хромирование и др. Для предотвращения внутренней коррозии из-за попадания в поровые каналы химических растворов , используемых при создании защитного покрытия, пористые порошковые изделия предварительно пропитывают различными веществами (смолами, битумными лаками, различными химически стойкими веществами). Лекция
Обработка порошковых изделий 738 Защита от коррозии Одним из лучших материалов для заполнения порошкового тела перед покрытием его поверхности защитным слоем является гидрофобная кремнийорганическая жидкость (ГКЖ-94), растворяющаяся в бензине или четыреххлористом углероде. Лекция
Обработка порошковых изделий 739 Защита от коррозии В последние годы для закрытия поверхностных пор применяют так называемых анаэробные (т. е. способные полимеризоваться в отсутствие кислорода воздуха) герметики. В их состав входят: — полимеризационно-активное соединение-ингибитор (основа композиции); — инициатор; — модифицирующие добавки. Лекция
Обработка порошковых изделий 740 Защита от коррозии При попадании их в поровые каналы (при отсутствии воздуха) происходит полимеризация смолы, ее затвердевание и сцепление с металлической поверхностью. Заполнение пор существенно улучшает некоторые механические свойства порошковых изделий и повышает чистоту обработки их поверхности. Лекция
Обработка порошковых изделий 741 Механическая обработка Одно из важных преимуществ порошковой металлургии – получение изделий, не требующих дополнительной механической обработки. Однако в ряде случаев целесообразно изготовлять из порошка заготовки сравнительно простой формы, получение которых не требует применения сложной и дорогой оснастки для формования, а последующее усложнение их формы и повышение точности размеров обеспечивать после спекания калиброванием и обработкой резанием. Лекция
Обработка порошковых изделий 742 Механическая обработка На практике применяют следующие виды механической обработки изделий: — калибрование; — резание (точение, сверление и развертывание отверстий); — шлифование. Лекция
Структура и свойства порошковых изделий
Структура и свойства порошковых изделий 744 Оглавление Лекция 23. Структура и свойства порошковых изделий Лекция 24. Свойства порошковых изделий Лекция 25. Методы определения механических характеристик порошковых тел. Заключение
Структура и свойства порошковых изделий 745 Лекция 23 Структура и свойства порошковых изделий • Особенности строения порошковых тел • Группы свойств • Взаимосвязь параметров и свойств материалов • Особенности структуры порошковых изделий
Структура и свойства порошковых изделий 746 Свойства порошковых изделий и методы их контроля Очень многие свойства порошкового тела зависят не только от его относительной плотности, но и от безразмерного контактного (критического) сечения к , характеризующего долю объема пористого тела, в которой концентрируются направленные процессы. Это связано с тем, что пористое тело в самом общем виде является двухфазной объемной конструкцией, состоящей из твердой фазы и пор. Лекция
Структура и свойства порошковых изделий 747 Свойства порошковых изделий и методы их контроля Для пористого тела характерны следующие особенности: 1) передача энергии и напряжений через пористое тело полностью концентрируется в твердой фазе только в активной части его объема; 2) свойства фазы «пустоты» , заполняющей поры, по сравнению со свойствами твердой фазы исчезающе малы, и ими можно пренебречь; 3) если твердая фаза сама состоит из нескольких разнородных компонентов, априорная (т. е. до проведения эксперимента) оценка свойств порошкового тела значительно усложняется, так как возможна преимущественная концентрация энергии и напряжений в одном из компонентов (главным образом в его активной части). Лекция
Структура и свойства порошковых изделий 748 Свойства порошковых изделий и методы их контроля Зависимость относительного свойства порошкового тела X от относительной плотности ρ отн приведена выражается как χ ~ ρ m отн , где т принимает значения от 0 до. Лекция
Структура и свойства порошковых изделий 749 Свойства порошковых изделий и методы их контроля Обычно выделяют четыре группы свойств: 1) не зависящие от пористости (т = 0) – микротвердость, температура плавления и коэффициент термического расширения материала частиц; 2) аддитивные характеристики (т = 1), зависящие только от количества материала, – теплоемкость, магнитная восприимчивость; 3) свойства типа проводимости (т = 1, 5– 2) – электро- и теплопроводность, модуль упругости, диэлектрическая и начальная магнитная проницаемость; 4) структурно-чувствительные свойства (т = 3– 10) – прочность, пластичность, максимальная магнитная проницаемость, ударная вязкость и др. Лекция
Структура и свойства порошковых изделий 750 Свойства порошковых изделий и методы их контроля В общем виде между различными параметрами и свойствами одного и того же образца существует количественная взаимосвязь: к / ρ отн = ( l / l к )-2, к = E / E K , где l – истинный путь процесса в пористом теле; l к – условный (номинальный) путь процесса в пористом теле; Е и Е к – модуль упругости пористого и беспористого тела соответственно. Оценка свойств порошковых материалов или изделий показывает, что их величина при заданной плотности определяется не только статистическими, но и физико-технологическими факторами. Лекция
Структура и свойства порошковых изделий 751 Свойства порошковых изделий и методы их контроля 0, 25 0, 50 0, 755χ 0, 5 ρ отн 2 4 3 1 Зависимость относительного свойства χ порошкового тела от ρ отн 1 – свойства, не зависящие от пористости; 2 – аддитивные характеристики; 3 – свойства типа проводимости; 4 – структурно-чувствительные характеристики. Лекция
Структура и свойства порошковых изделий 752 Структура порошковых изделий На свойства порошковых материалов (изделий), решающим образом определяющие область их применения, существенное влияние оказывают макро- и микроструктура, формирование которых происходит при отсутствии расплавления основы либо только в твердой фазе, либо при наличии ограниченного объема жидкой фазы. Лекция
Структура и свойства порошковых изделий 753 Структура порошковых изделий Поэтому для таких материалов структурообразование зависит: — от условий получения и свойств металлических порошков; — состава порошковой шихты; — метода формования; — температуры; — скорости нагрева и времени спекания; — скорости охлаждения после спекания; — состава защитной среды; — последующей термической обработки и пр. Лекция
Структура и свойства порошковых изделий 754 Структура порошковых изделий Сочетание в порошковом материале твердых составляющих и пор требует особых мер при изготовлении шлифов и подготовке их поверхности. Искажение формы и размеров пор в плоскости шлифа а – пластическая деформация кромки поры; б – искажение (разрушение) контура поры; в – попадание продуктов шлифовки в пору и образование из нее нескольких мелких пор; г – увеличение контура поры с округлением ее краев: 1 – действительный размер; 2 – контур поры, видимый на шлифе. Лекция
Структура и свойства порошковых изделий 755 Лекция 24 Свойства порошковых изделий • Физические свойства порошковых изделий • Механические свойства
Структура и свойства порошковых изделий 756 Физические свойства порошковых изделий Плотность и пористость изделий Определение плотности и пористости сформованных и спеченных изделий (кроме твердосплавных) регламентировано ГОСТ 18898 -89 и предусматривает применение расчетного и гидростатического методов. Для твердых сплавов плотность определяют по ГОСТ 20018– 74 гидростатическим методом, а пористость – по ГОСТ 9391– 80 металлографическим. Лекция
Структура и свойства порошковых изделий 757 Физические свойства порошковых изделий Плотность и пористость изделий Плотность и пористость сформованных и спеченных изделий определяют расчетным или гидростатическим методом. Пористость твердосплавных изделий можно определить металлографическим методом. Подготовленные образцы не должны иметь следов шлифования, полирования или выкрашивания структурных составляющих. Шлиф изготовляют по поперечному сечению (излому) целого изделия или части его площадью < 2 см 2. Лекция
Структура и свойства порошковых изделий 758 Физические свойства порошковых изделий Электрические, тепловые и магнитные свойства Электро- и теплопроводность порошковых материалов зависят от их пористости и структуры. Эти свойства повышаются пропорционально плотности и асимптотически приближаются к соответствующему значению для компактного металла или сплава того же химического состава. Лекция
Структура и свойства порошковых изделий 759 Физические свойства порошковых изделий Электрические, тепловые и магнитные свойства Связь между теплопроводностью и электрической проводимостью металлов и сплавов определяется числом Лоренца: L = λρ э / T , где λ – теплопроводность, Вт/(м. К); ρ э – электропроводность, Ом м. Для большинства металлов и сплавов L находится в пределах от 2, 110– 8 до 2, 810– 8 Вт Ом/К 2 при комнатной температуре. Лекция
Структура и свойства порошковых изделий 760 Лекция 25 Методы определения механических характеристик порошковых тел. Заключение • Эксплуатационная пригодность порошковых тел и методы ее определения • Определение твердости порошковых тел • Заключение
Структура и свойства порошковых изделий 761 Аналитические зависимости прочности от пористости Автор Выражение Значение констант и применимость выражения Бальшин σ = σ к (1 – П) m m = 3– 6 Красовский σ = σ к (1 – П / П н ) m П н – пористость порошка в состоянии свободной насыпки Рышкевич σ = σ к ехр(– b П) b = 4– 7 Щербань σ = σ к (1 – П 2 )ехр(– b П) Трощенко и Красовский σ = σ к ( 1– 1, 5 П) / (1– 1, 5 β П) β = 2 П< 0, 66 Хейнес σ = σ к (1–П) / (1– b П) b = 5 для стали Вейл σ = σ к (1–П) / (1 + АП) А – параметр Харвей σ = σ к ( l – k ) 3 / [( k 3 + ( l – k ) 3 ] k = [3 П/(4π)] 1/3 Герман σ = K (1–П) m σ к / D m = 4– 7; П = 0, 1– 0, 4; D = 4– 6 мкм. Механические свойства. Лекция
Структура и свойства порошковых изделий 762 Вид образцов для испытаний порошковых материалов на растяжение 32, 0 5, 7± 0, 02 81, 0± 0, 5 89, 7± 0, 5 8, 7± 0, 2 R 4, 35 R 25, 0 Вариант 1 Вариант 2 5, 7± 0, 25 81, 0± 0, 5 89, 7± 0, 590 0 Механические свойства. Лекция
Структура и свойства порошковых изделий 763 Механические свойства Ǿ 0, 25 W 1, 25 W B= W/2± 0, 25 Wa. W ± 0, 25 0, 6 W 0, 55 W 1, 2 W B= W/2± 0, 25 W W± 0, 25 H≥ 4, 4 W а б. Образцы для испытаний на вязкость разрушения а – при изгибе; б – при внецентровом растяжении. Лекция