Испытания и контроль качества изделий (ИСПЫТАНИЯ АВИАЦИОННЫХ ДВИГАТЕЛЕЙ)
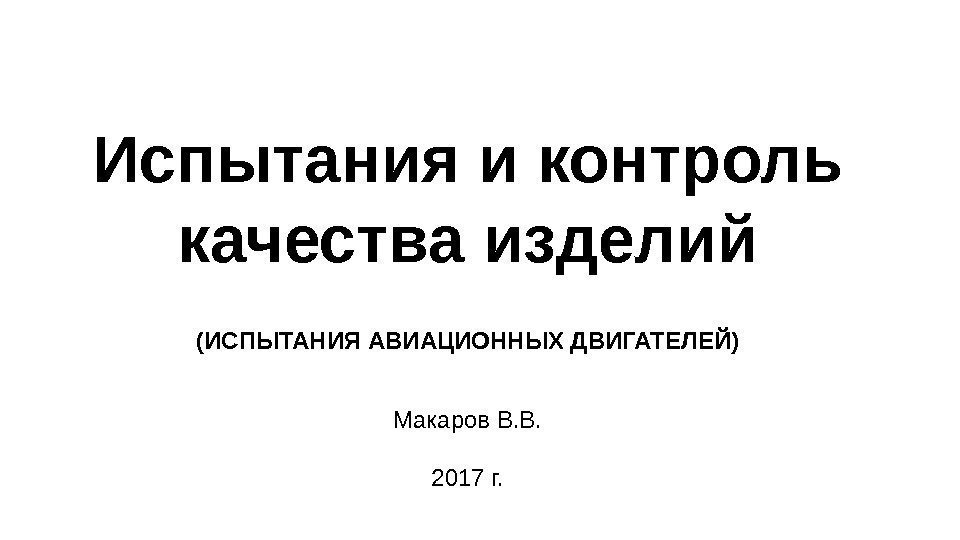
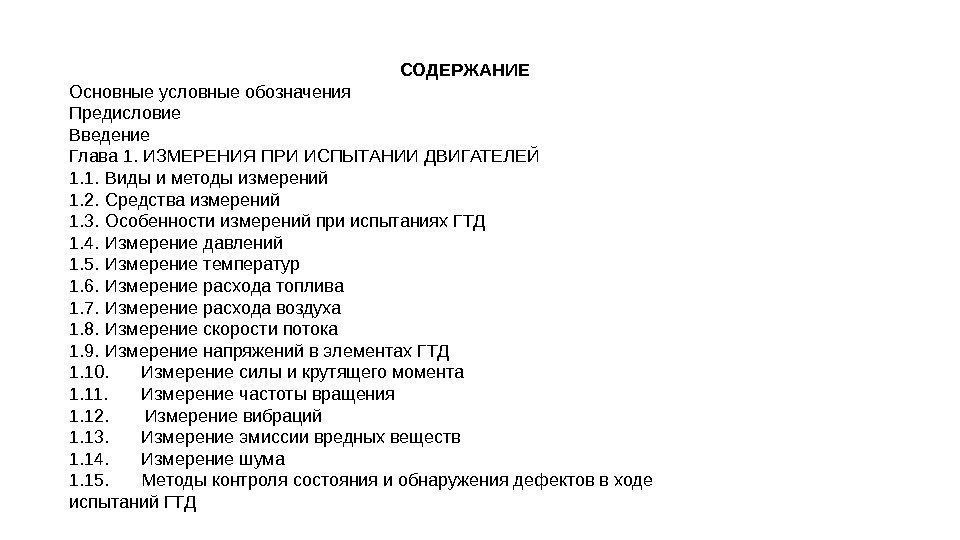
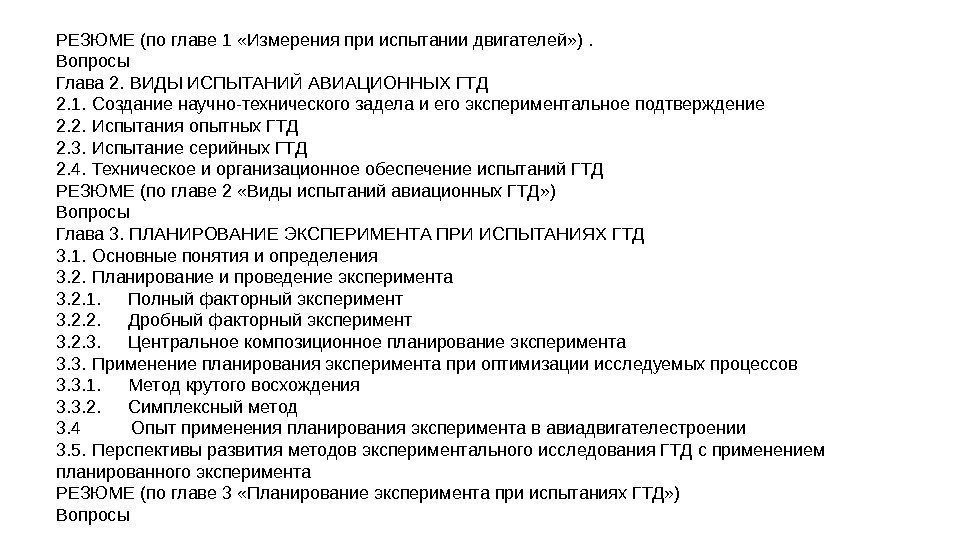
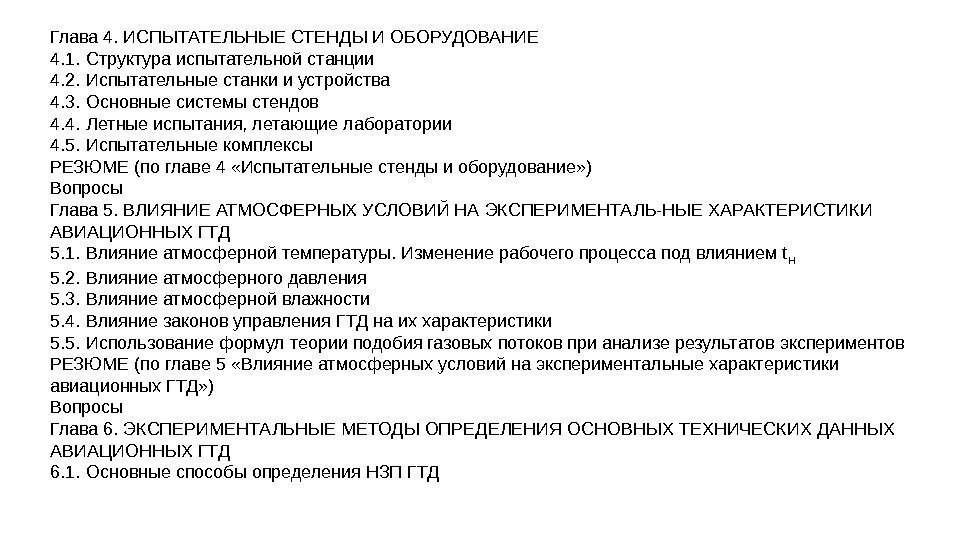
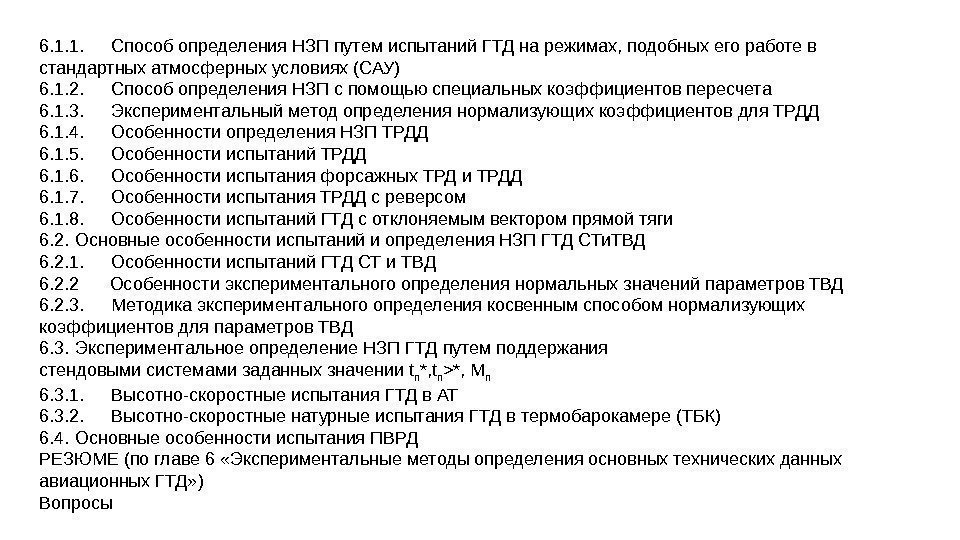
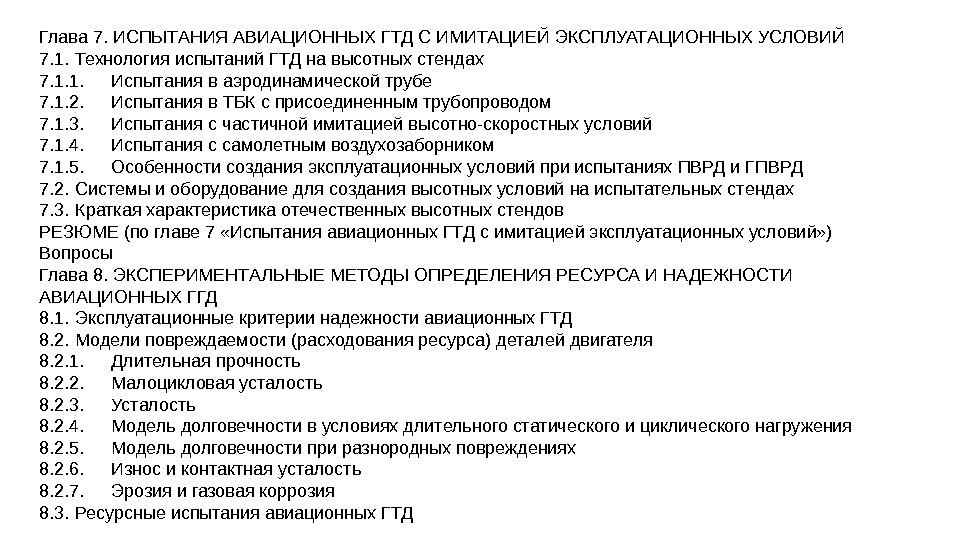
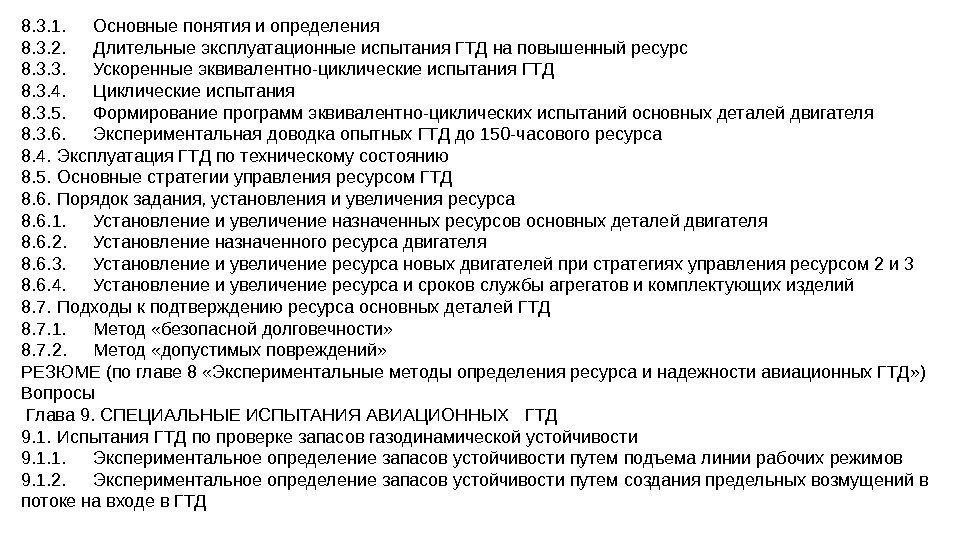
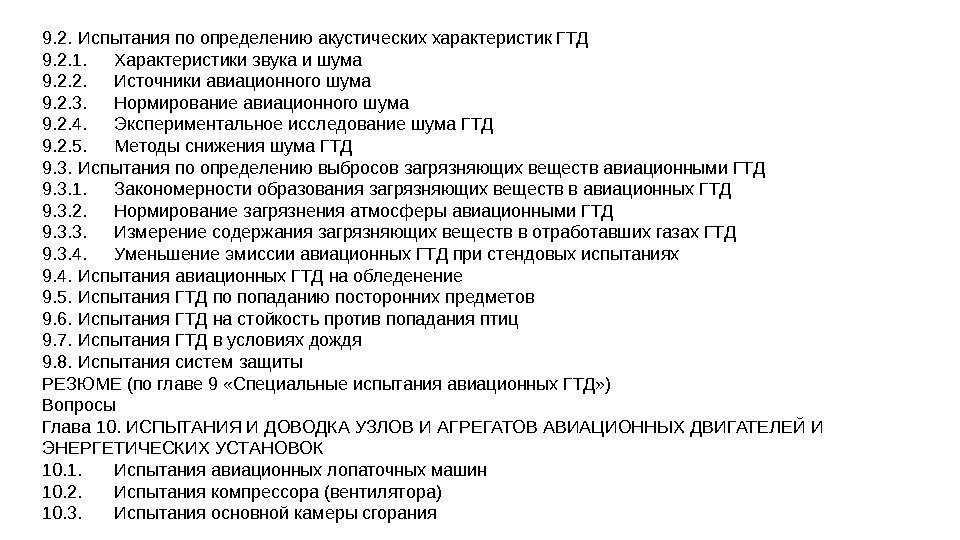
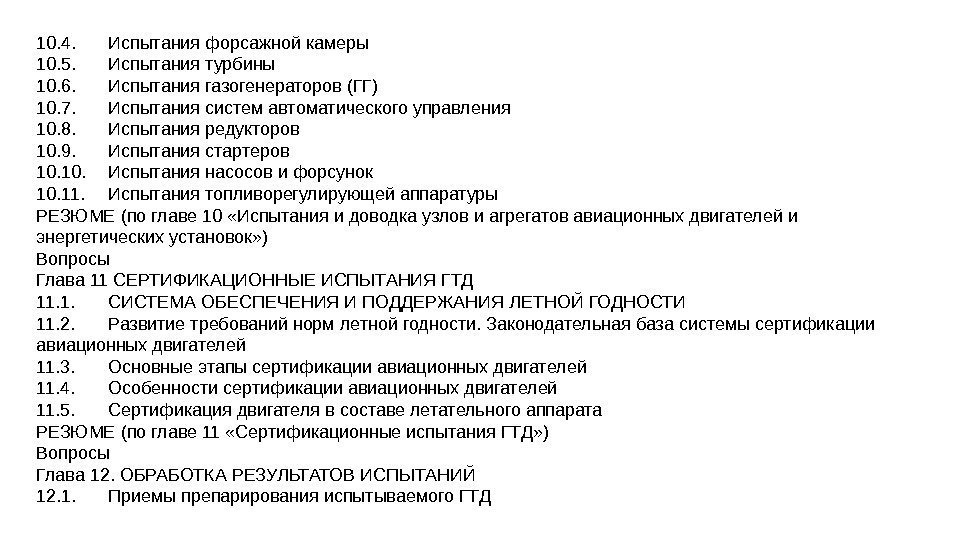
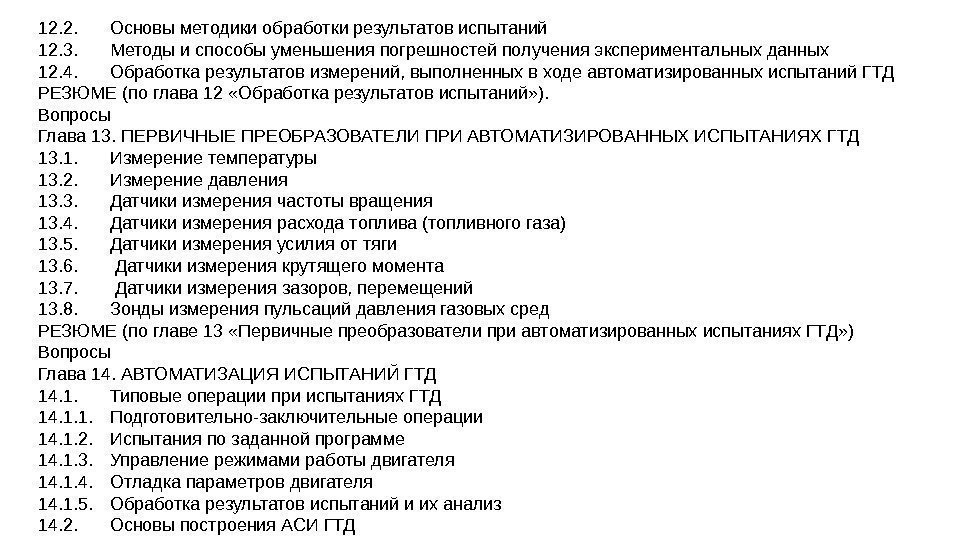
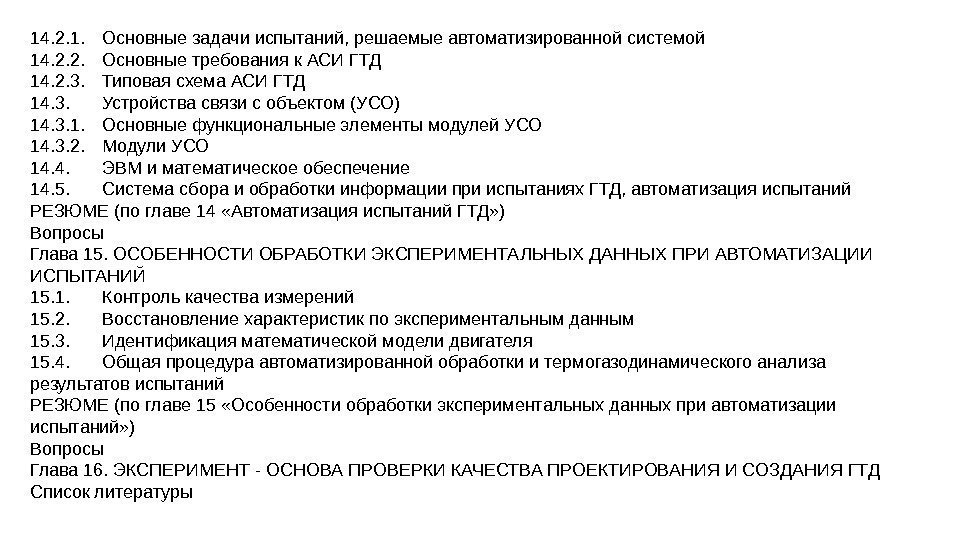
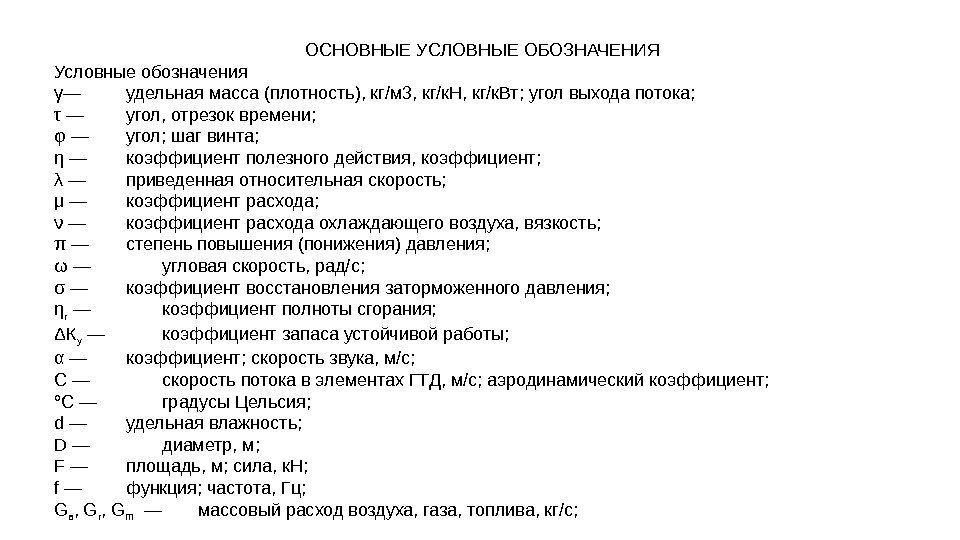
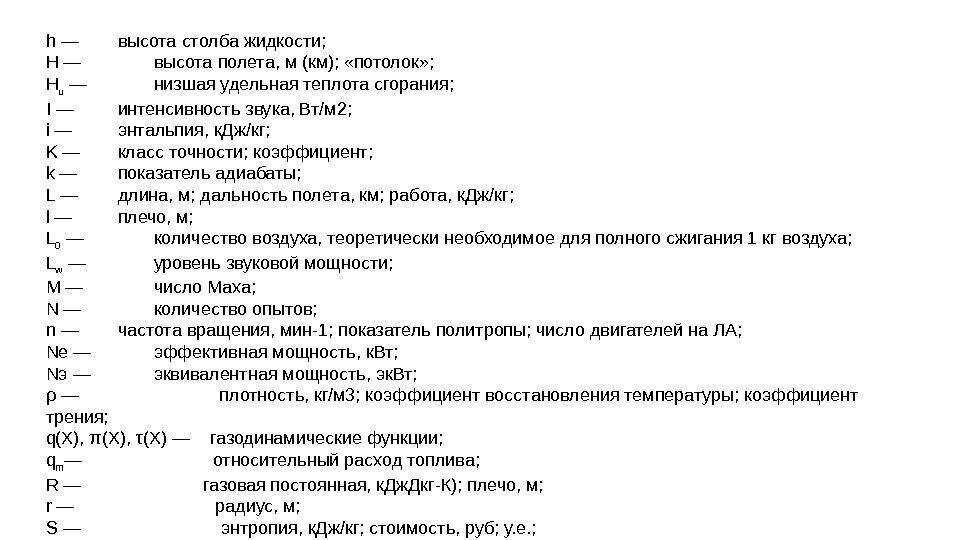

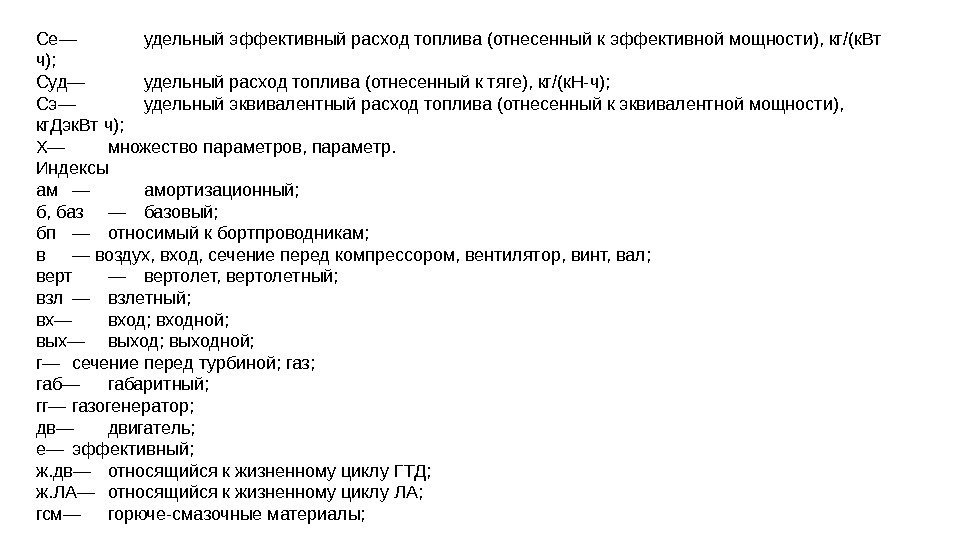
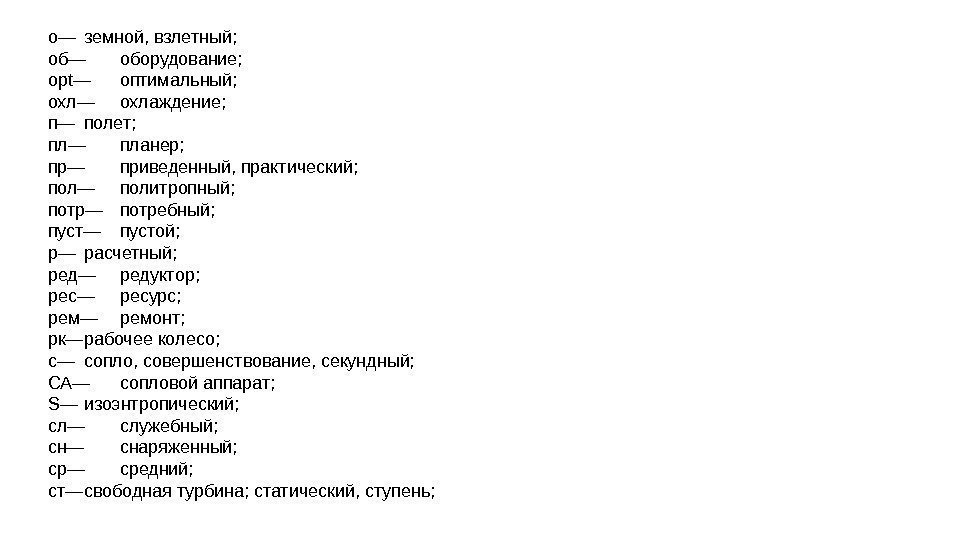
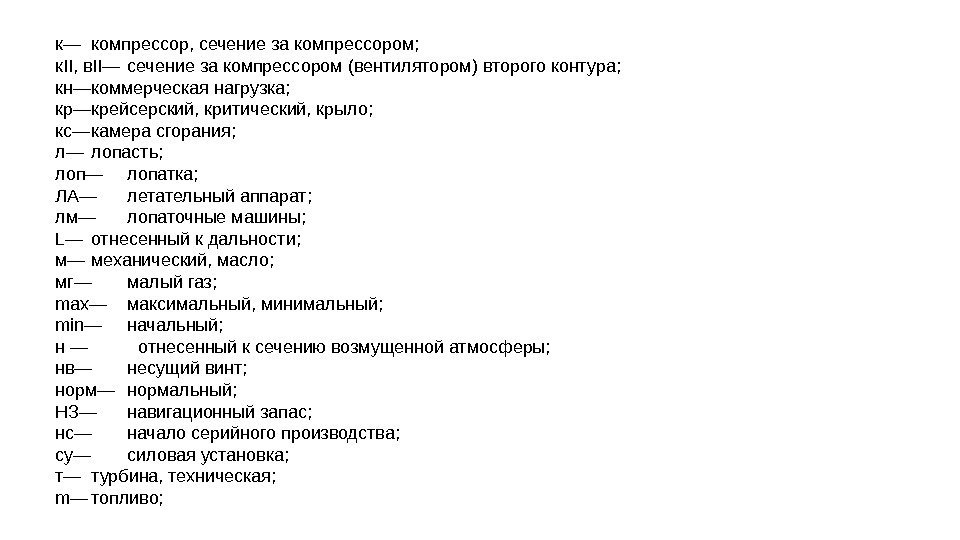
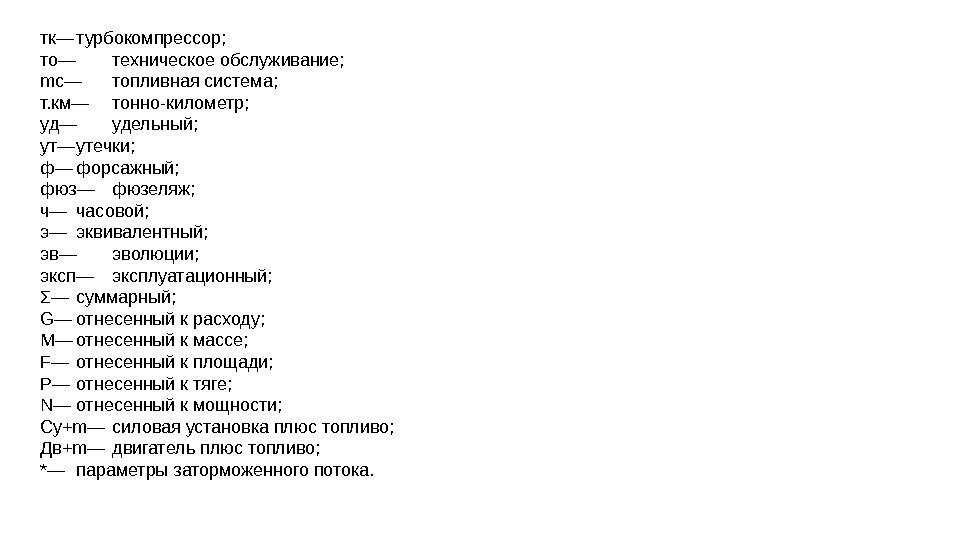
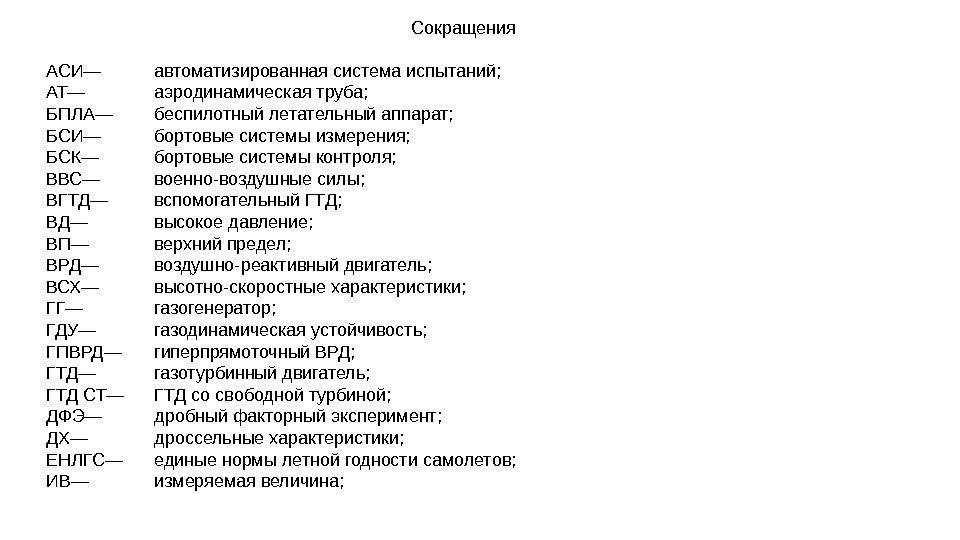
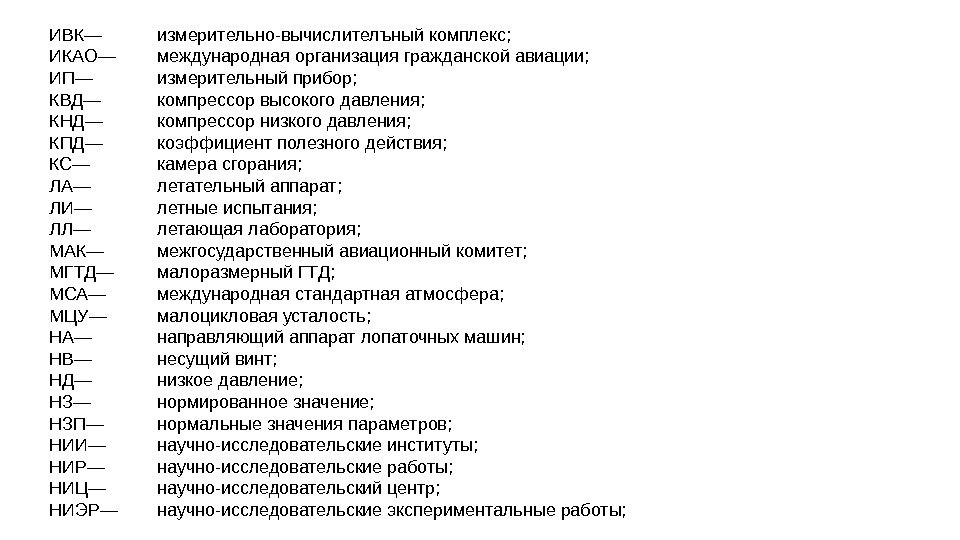
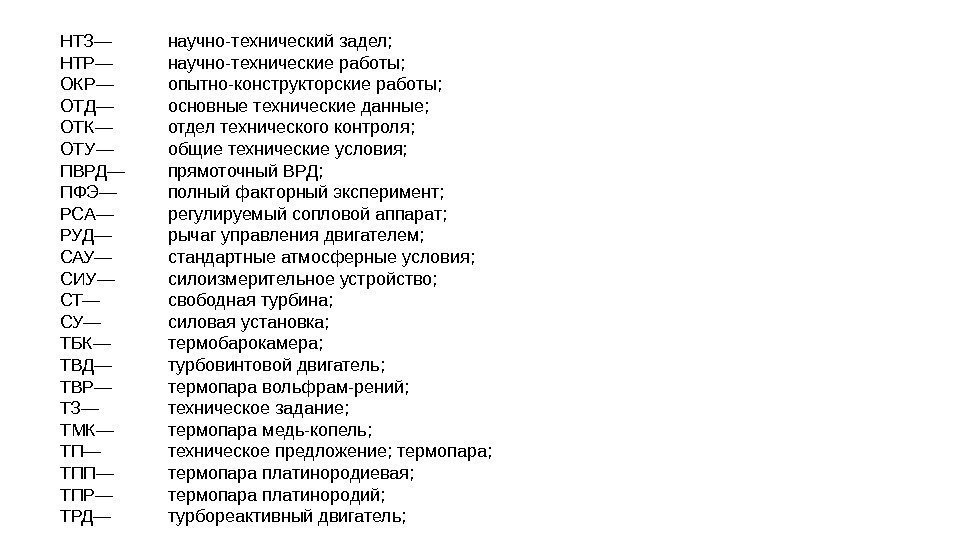
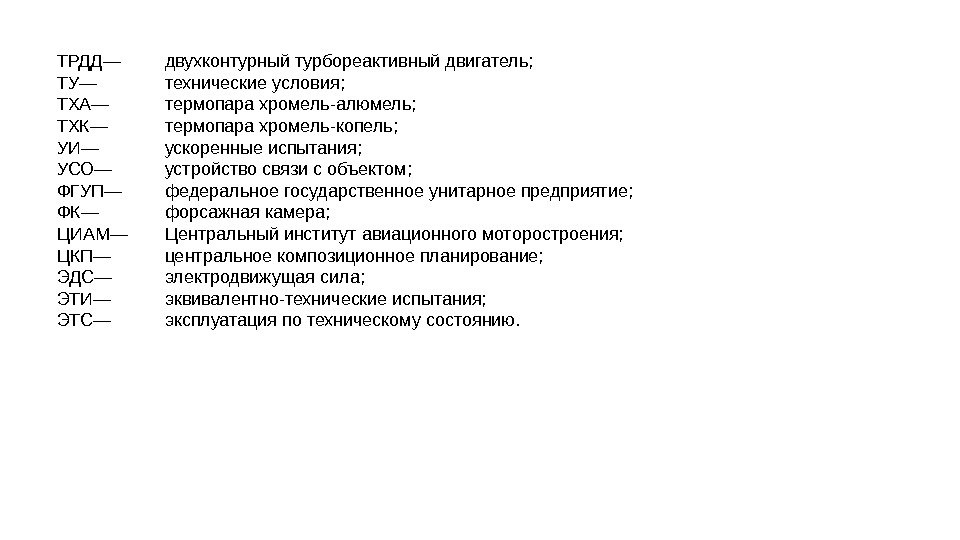
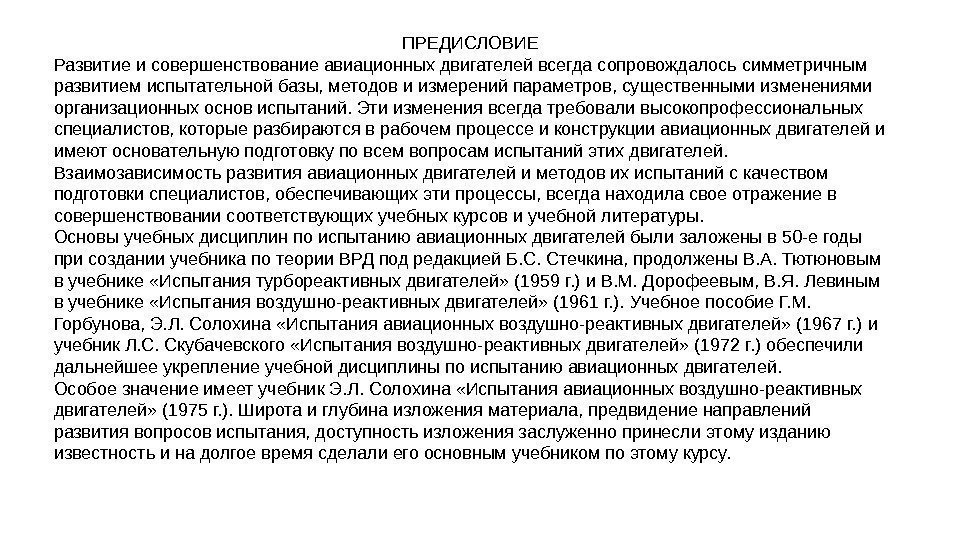
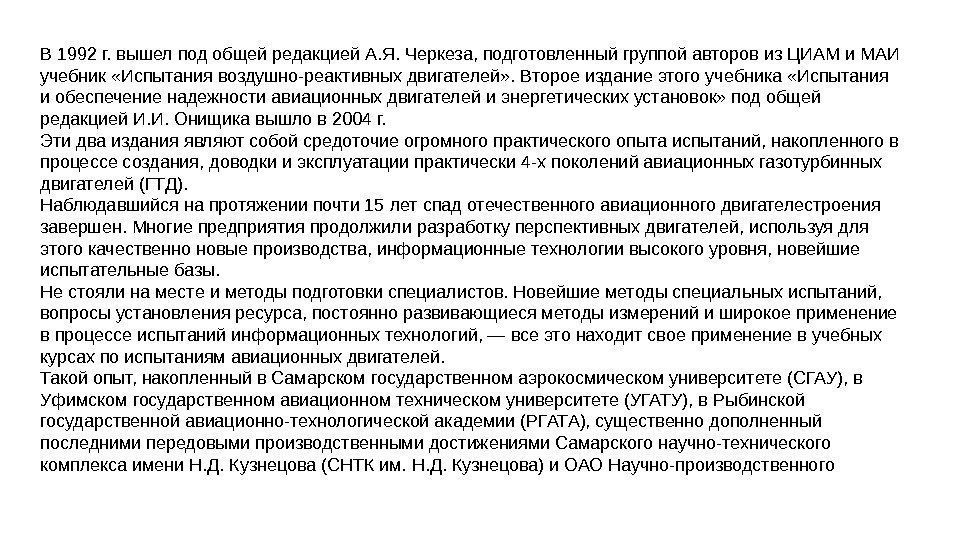
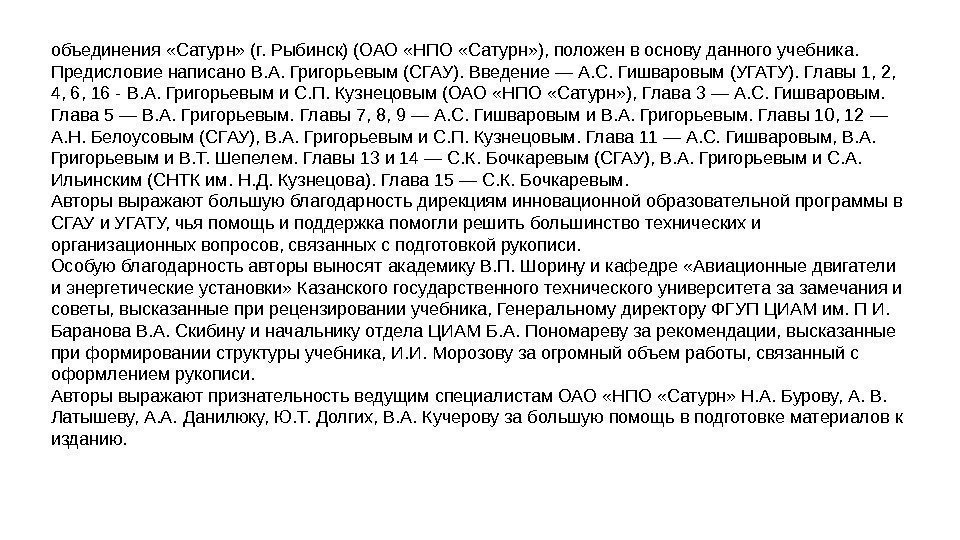
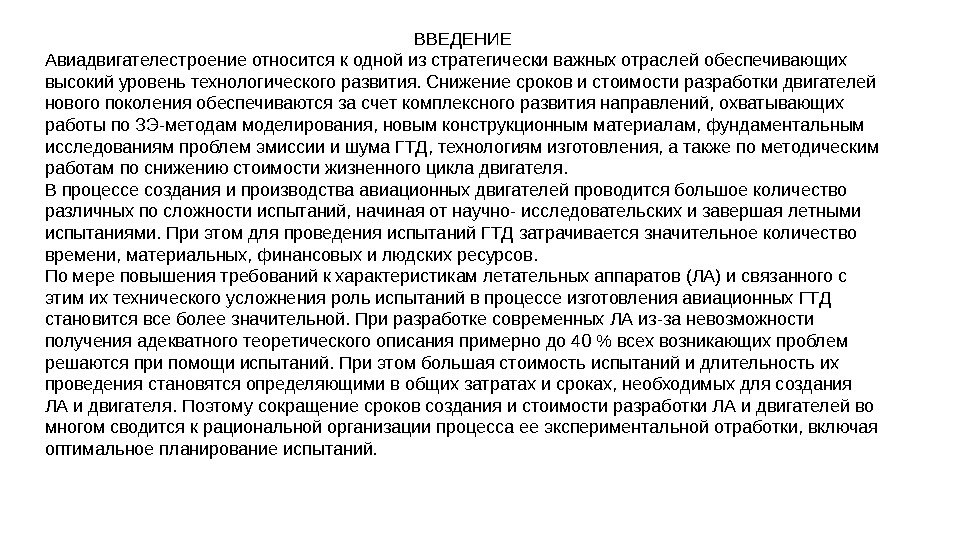
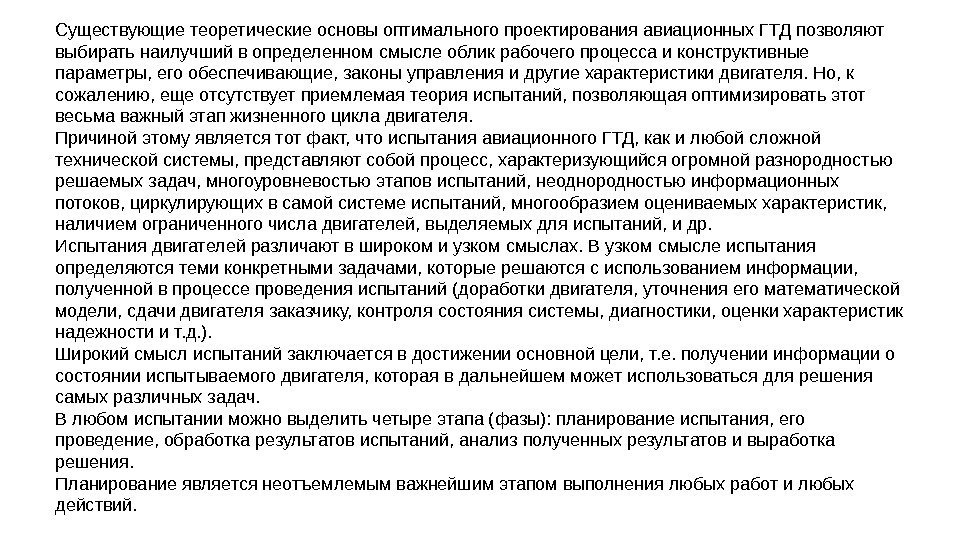
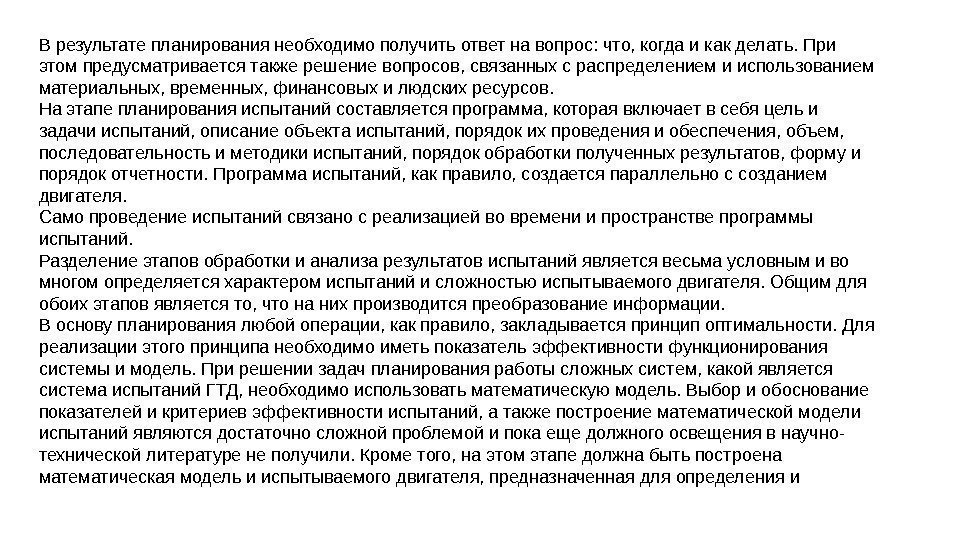
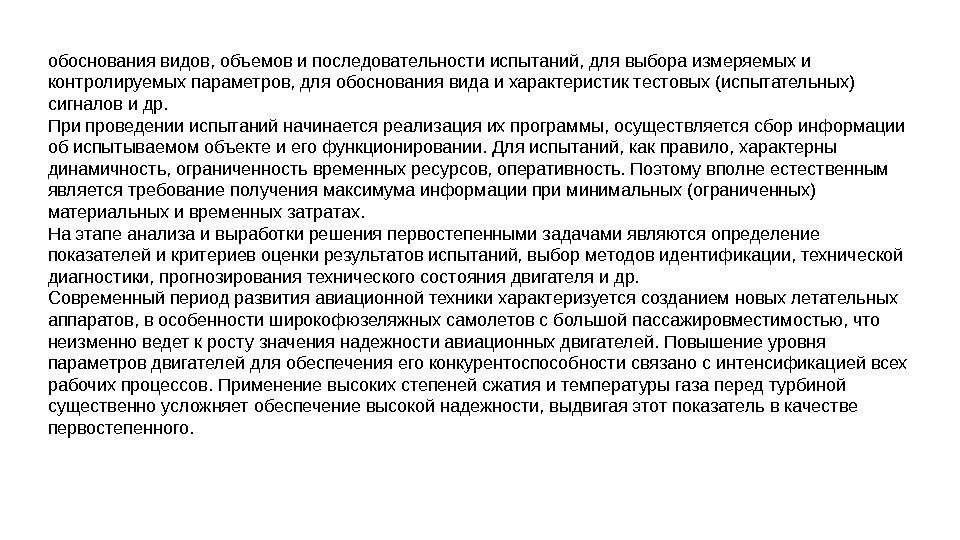
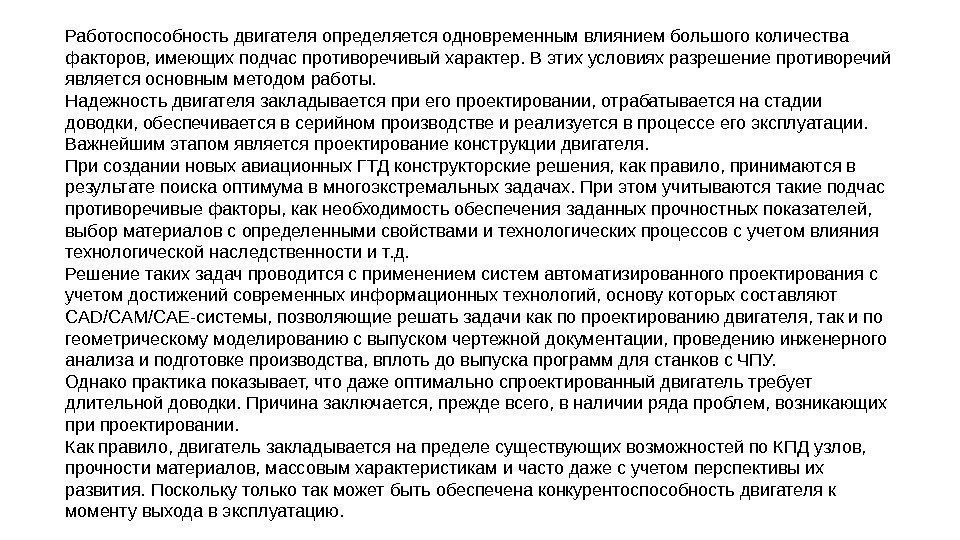
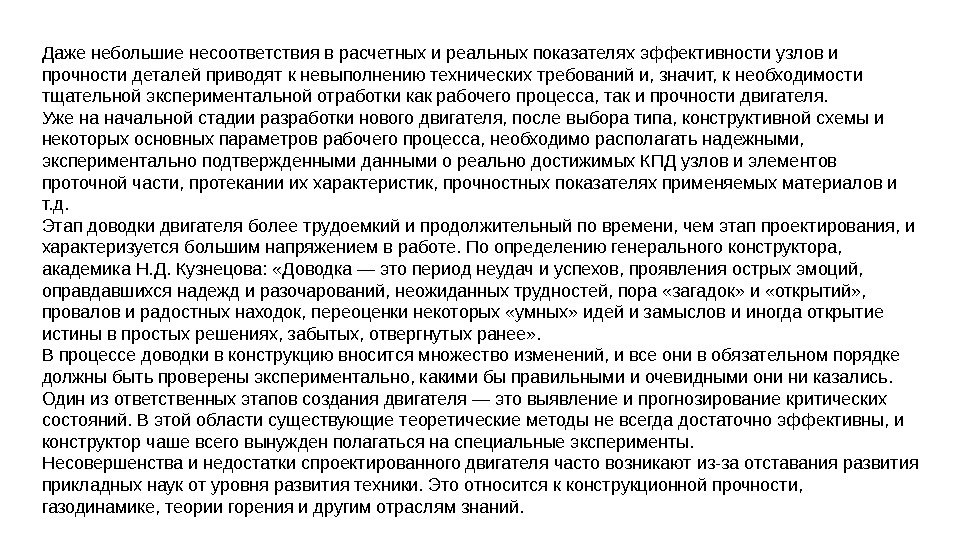
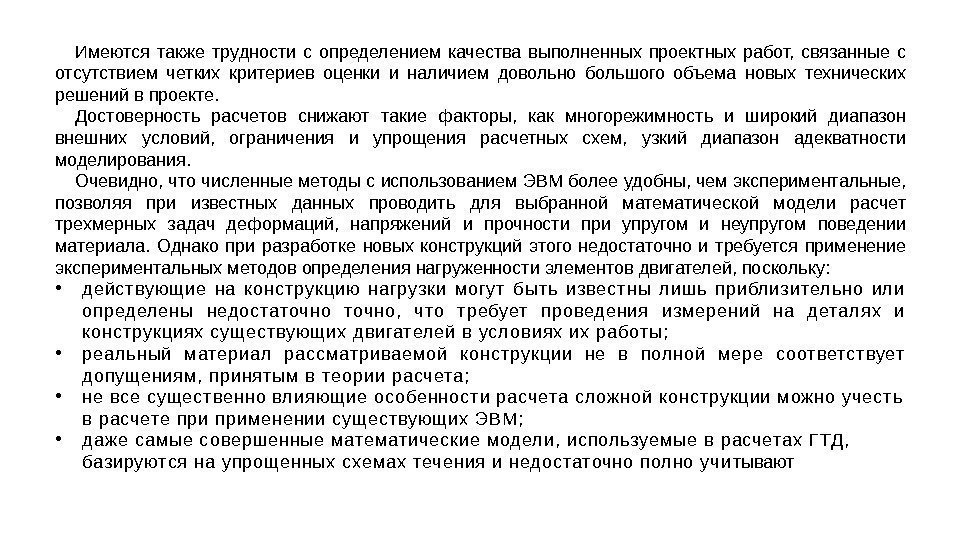
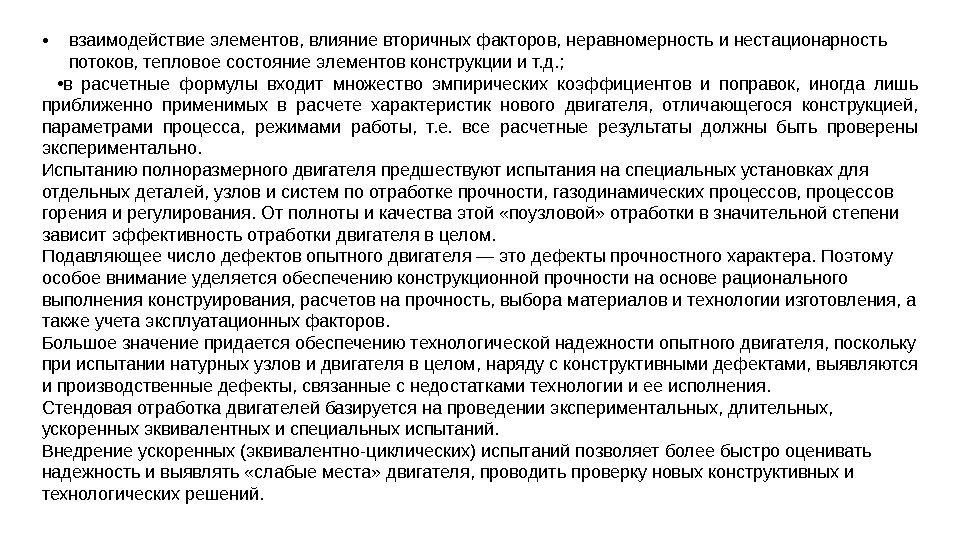
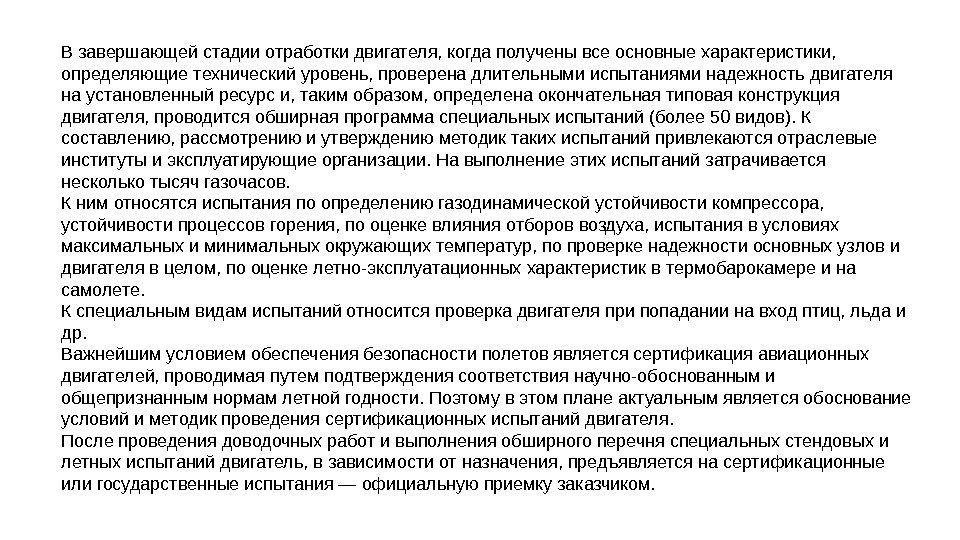
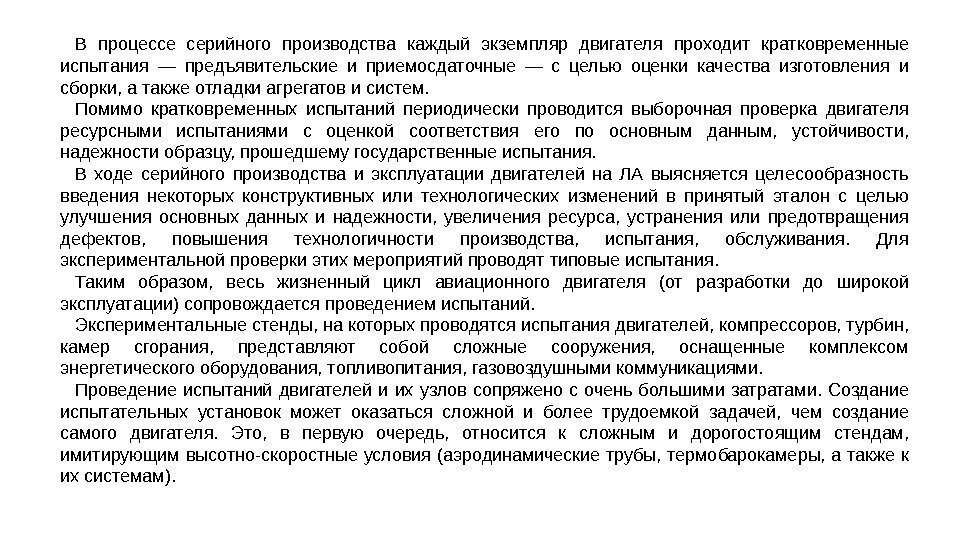
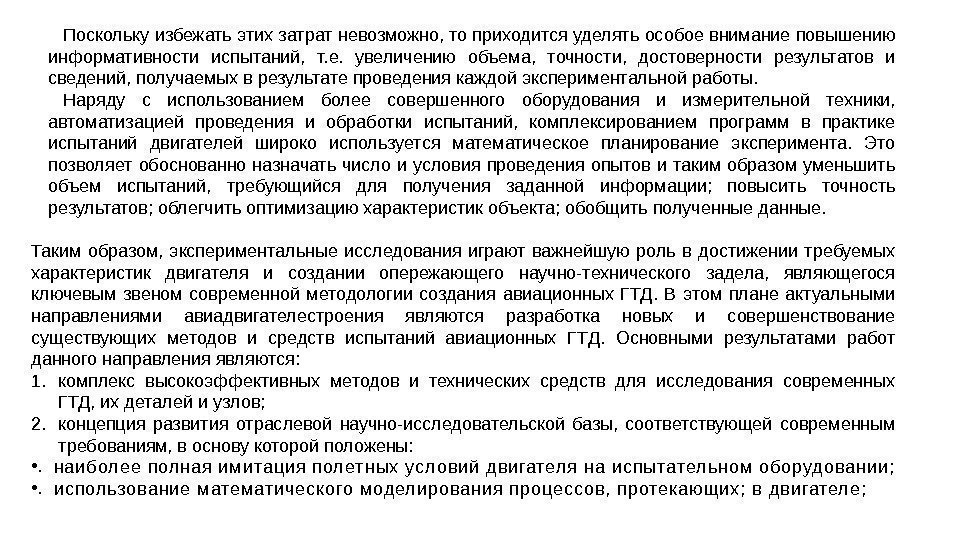
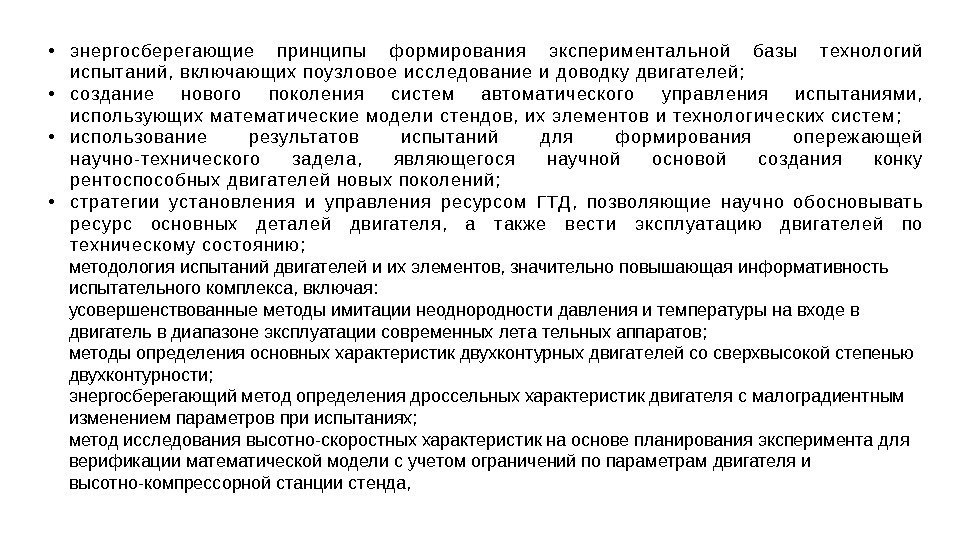
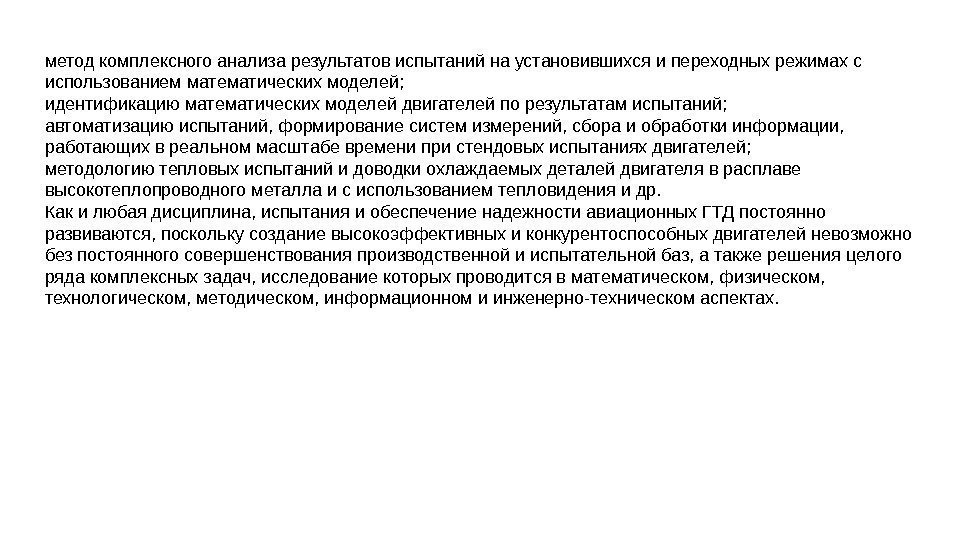
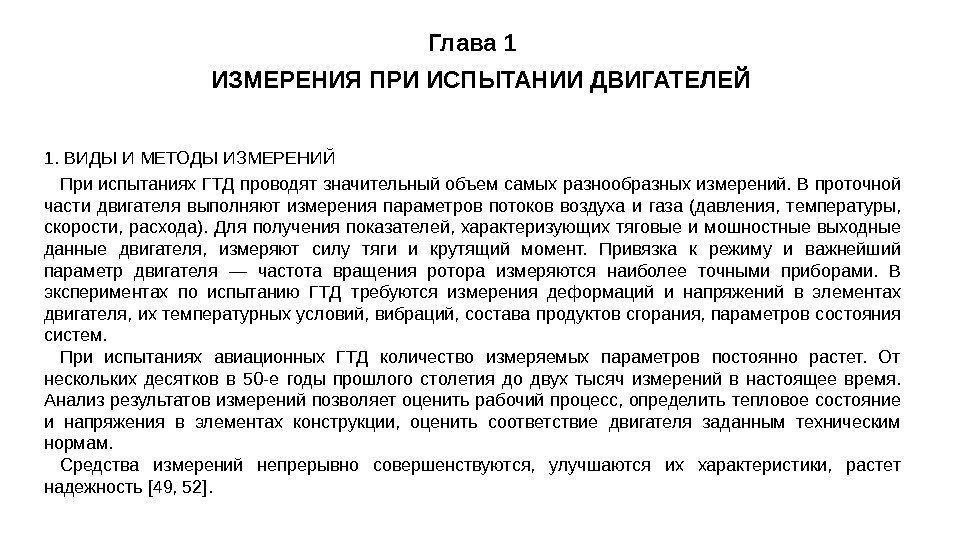
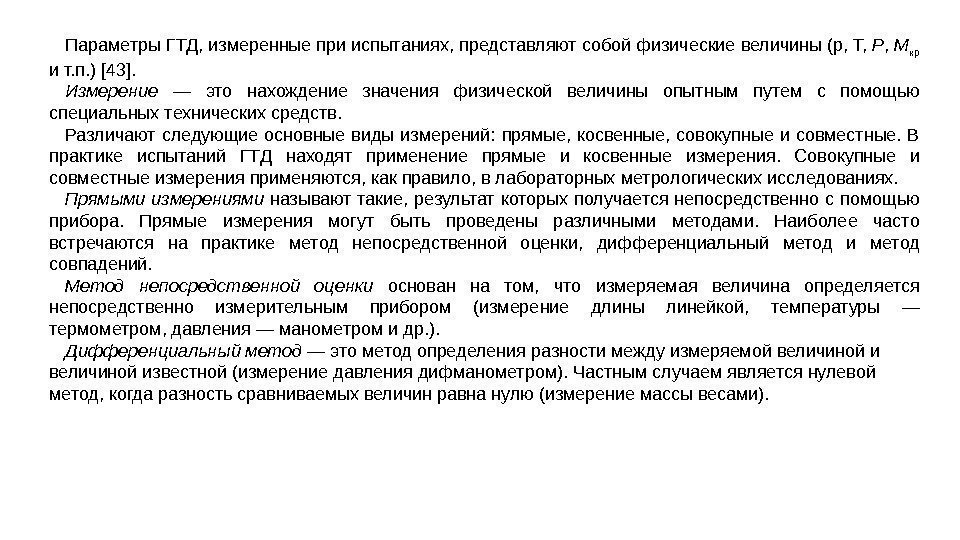
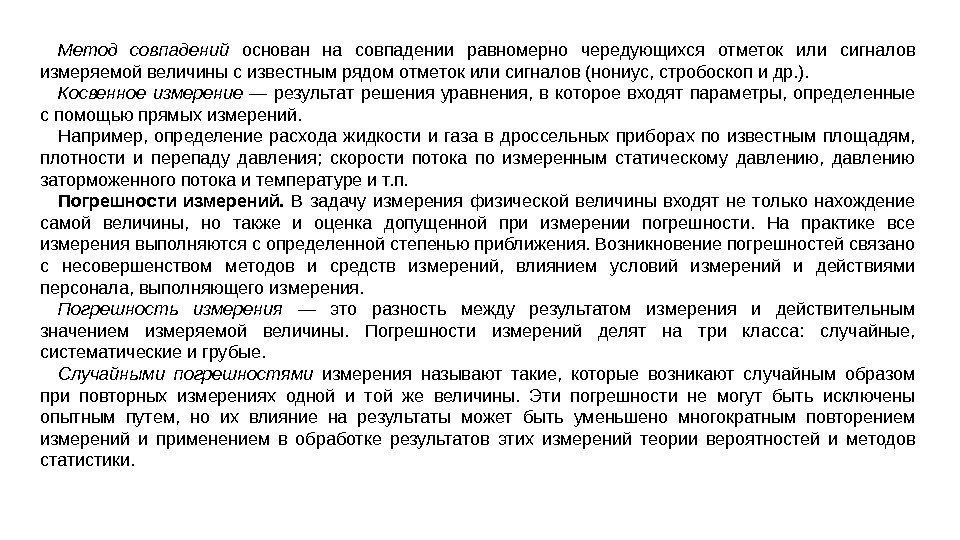
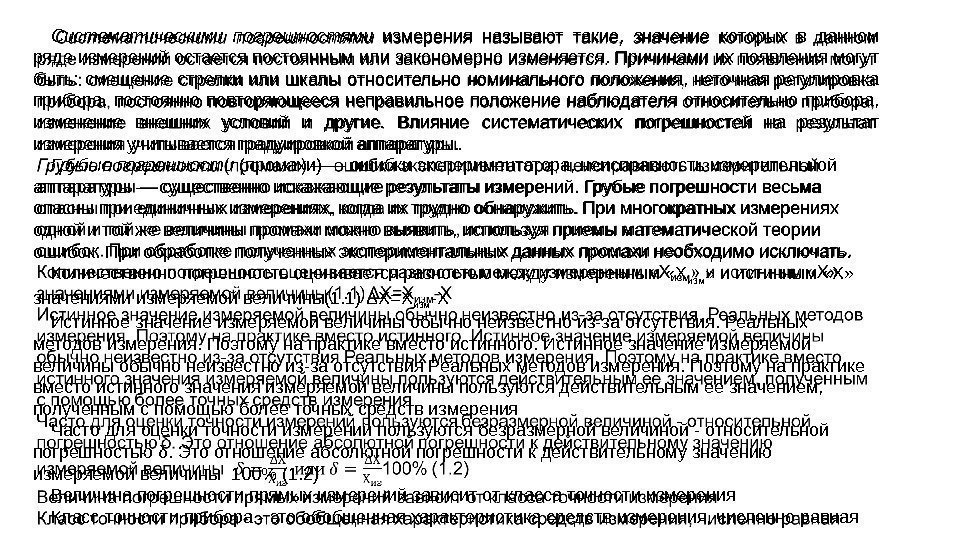
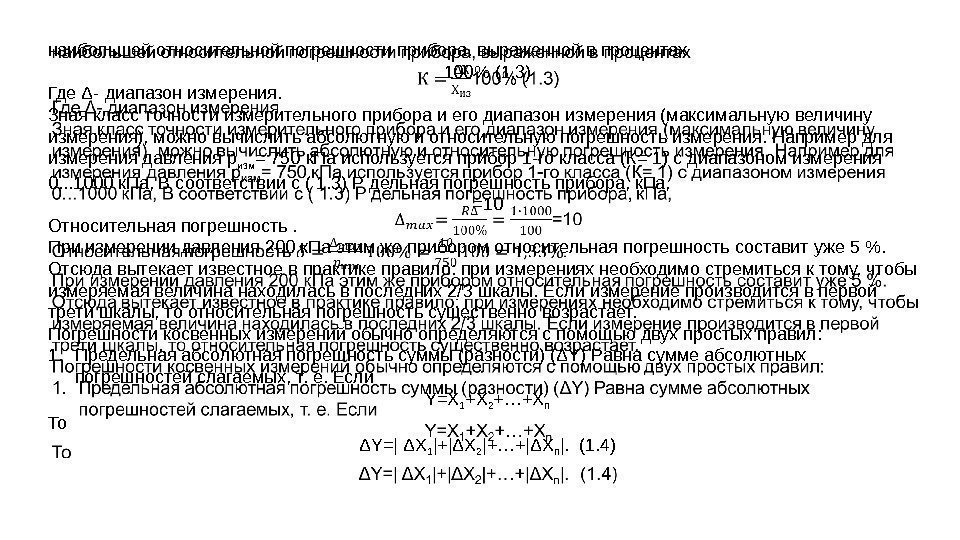
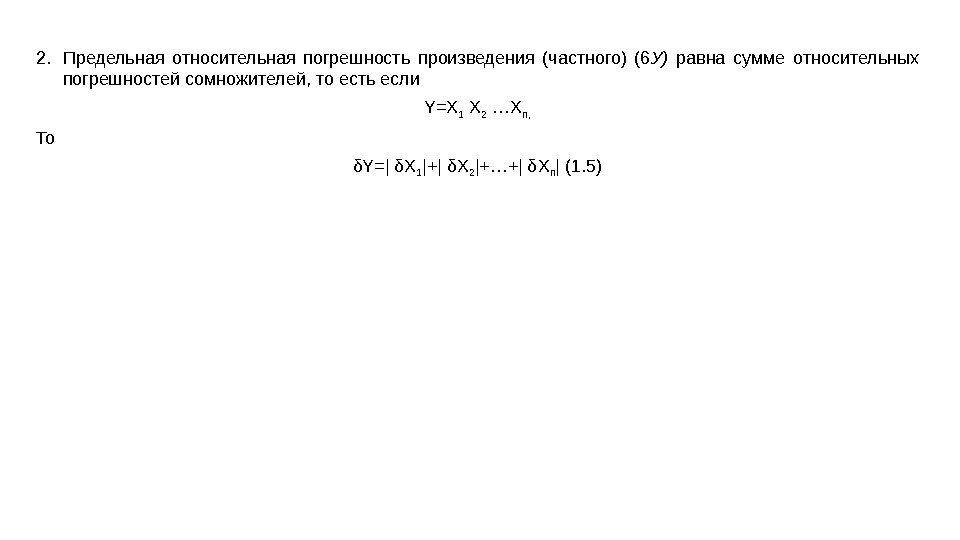
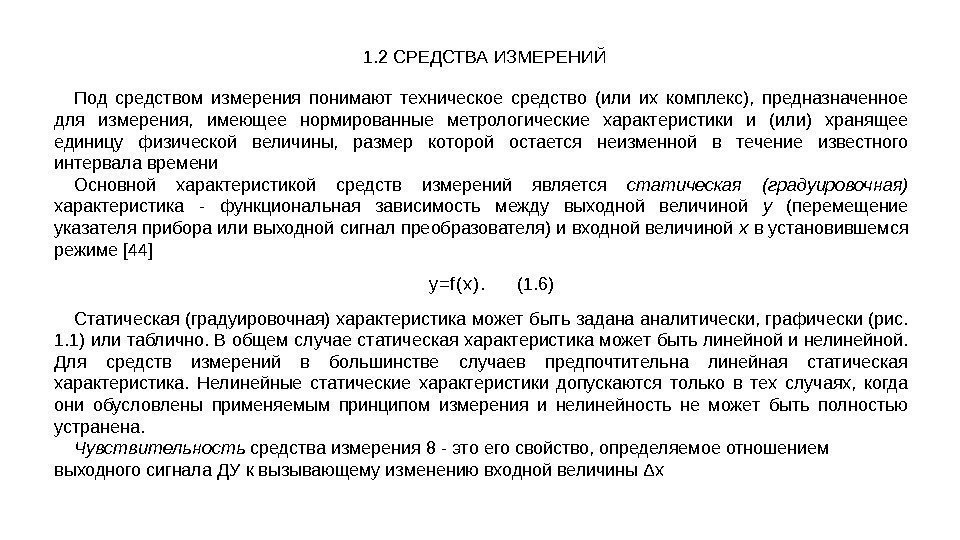
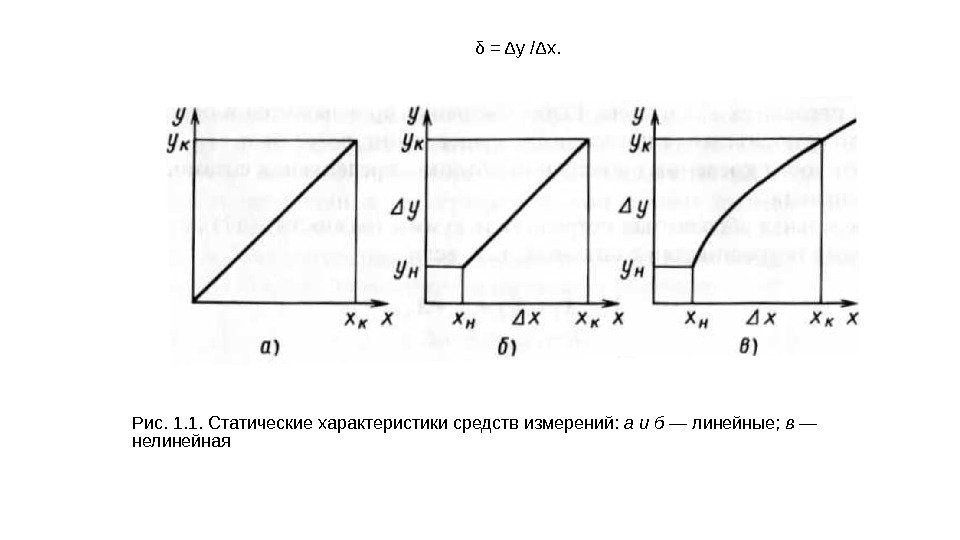
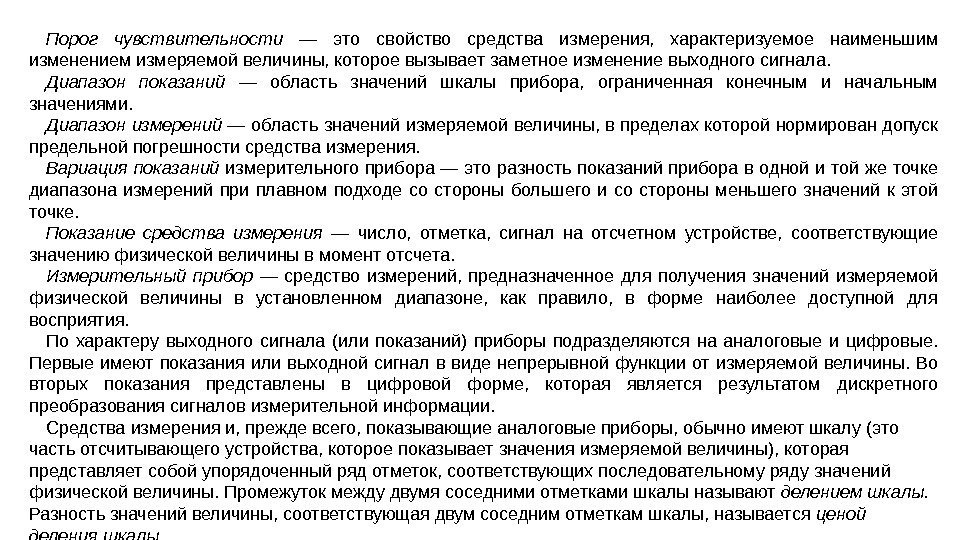
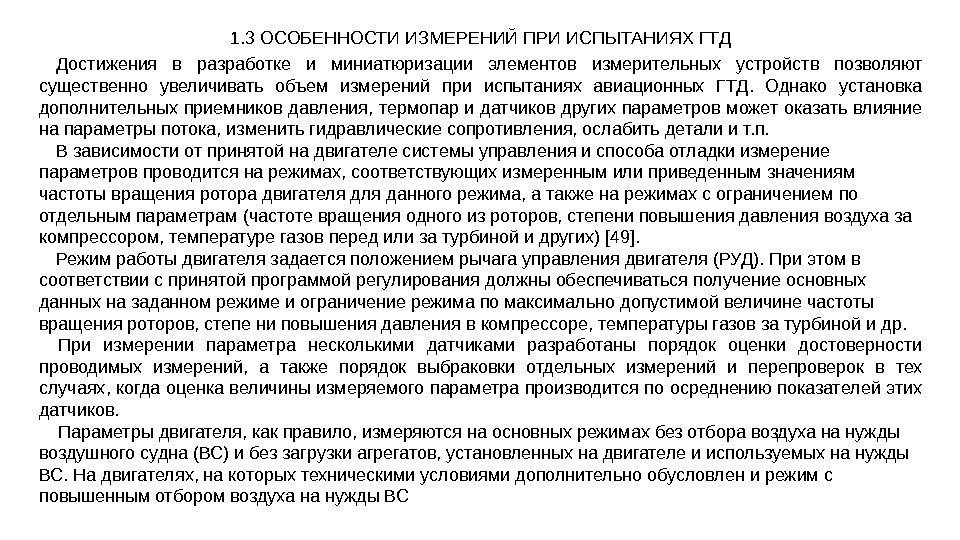
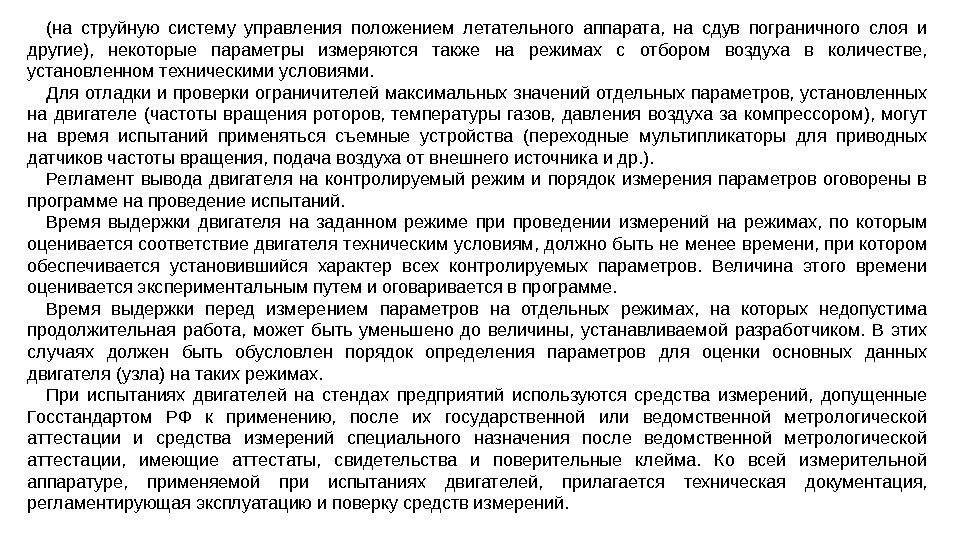
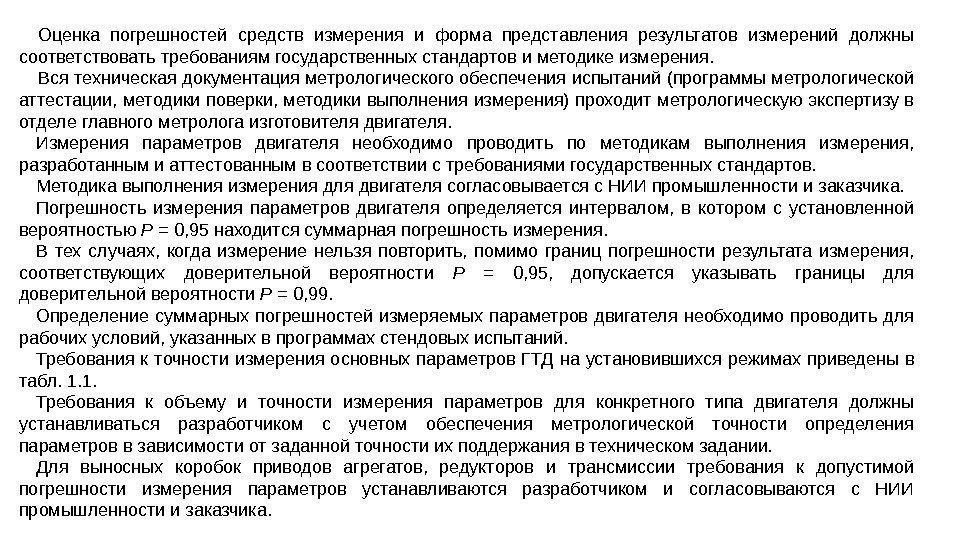
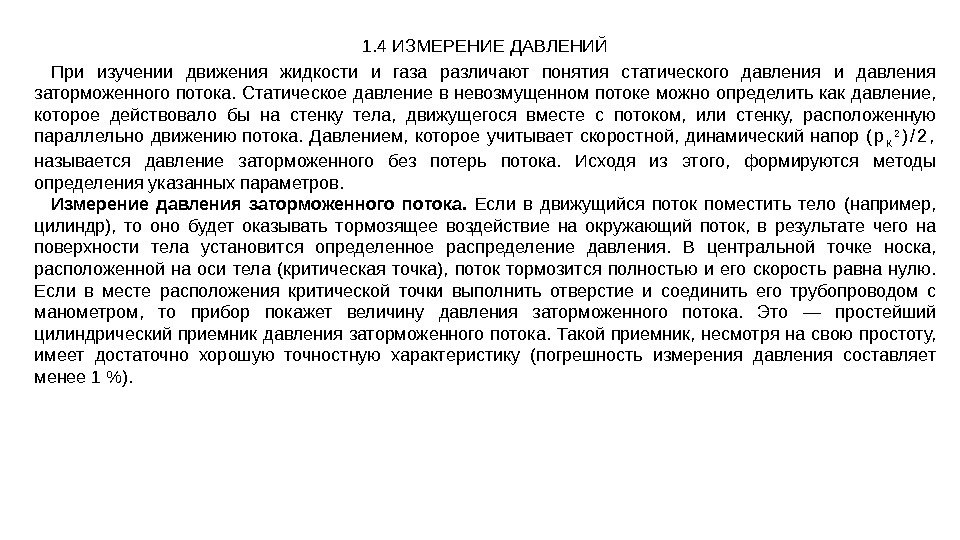
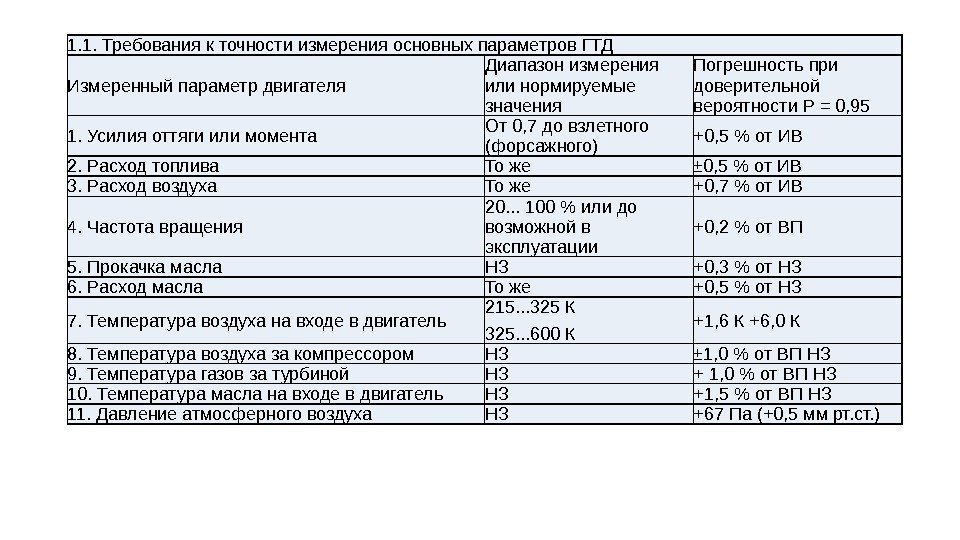
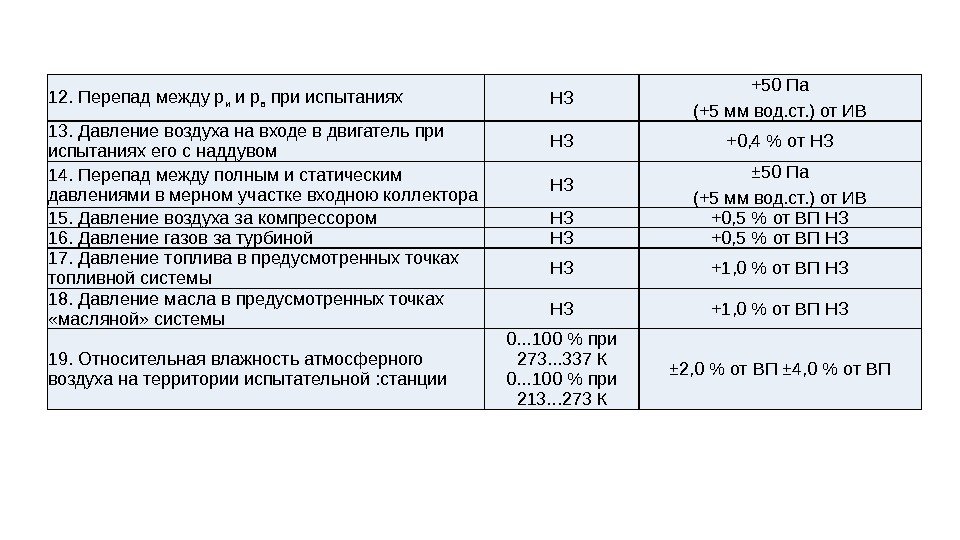
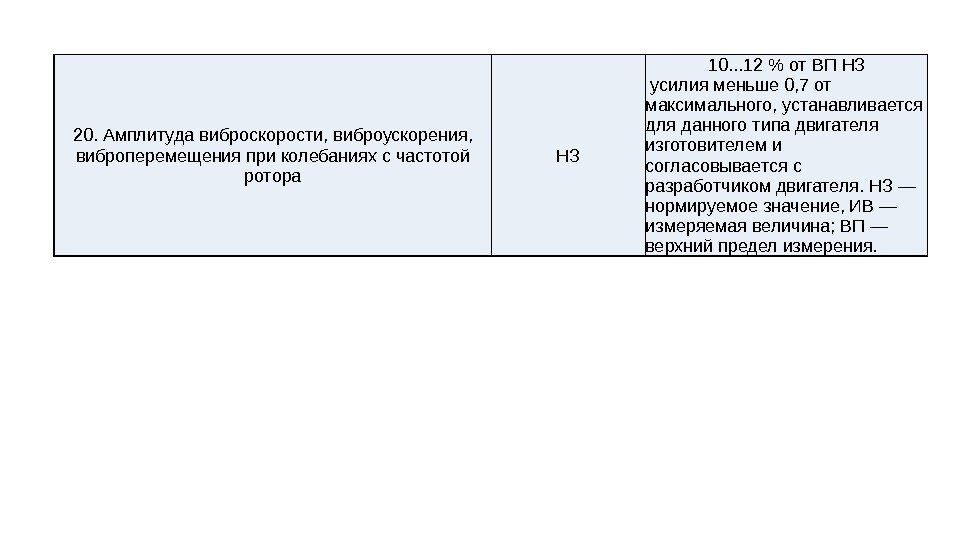
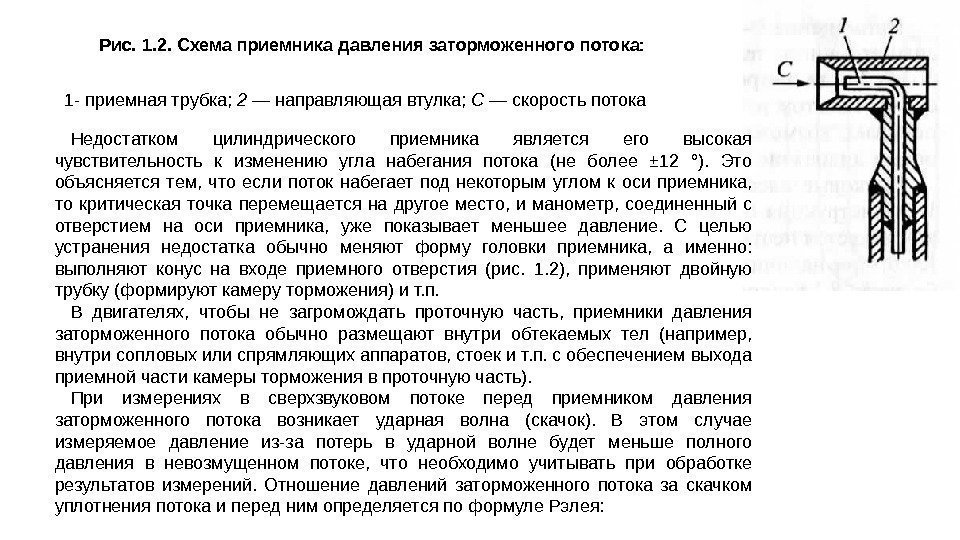
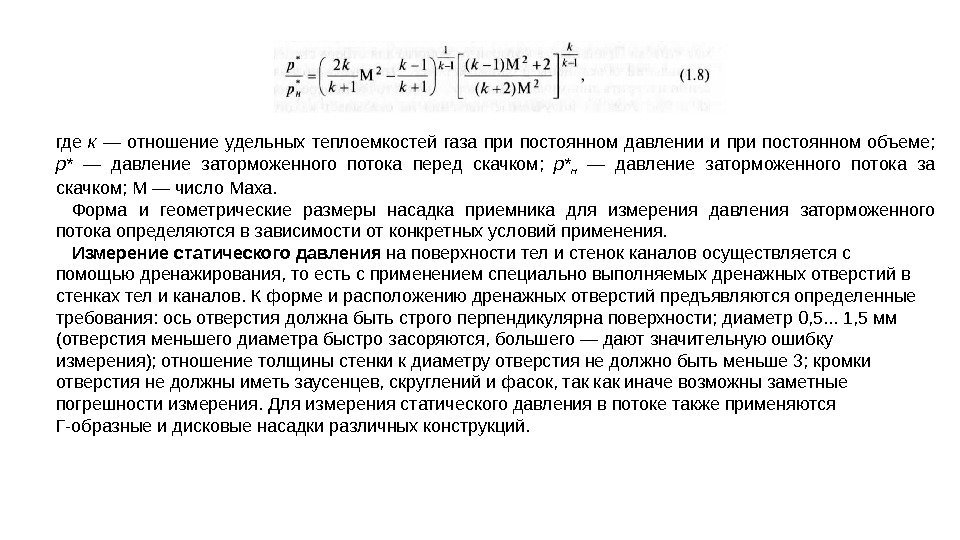
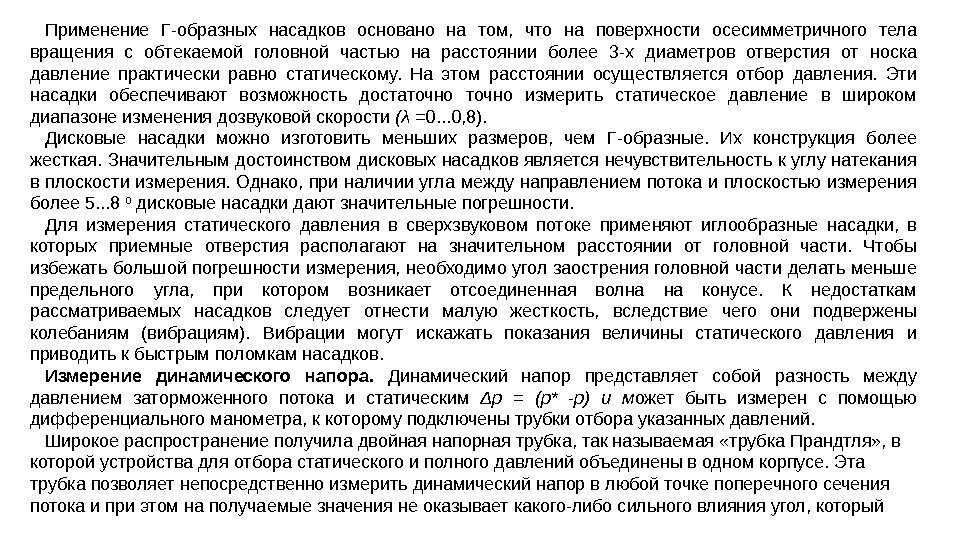
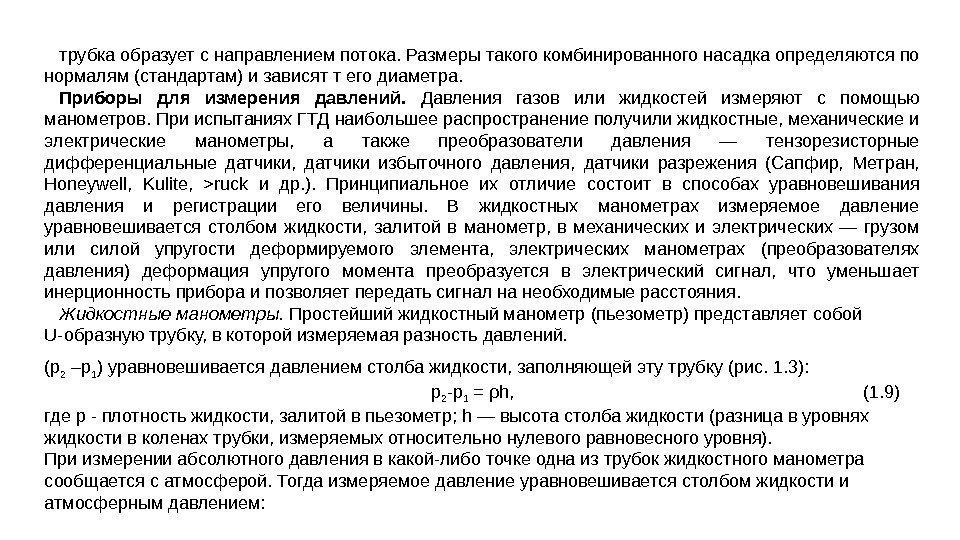
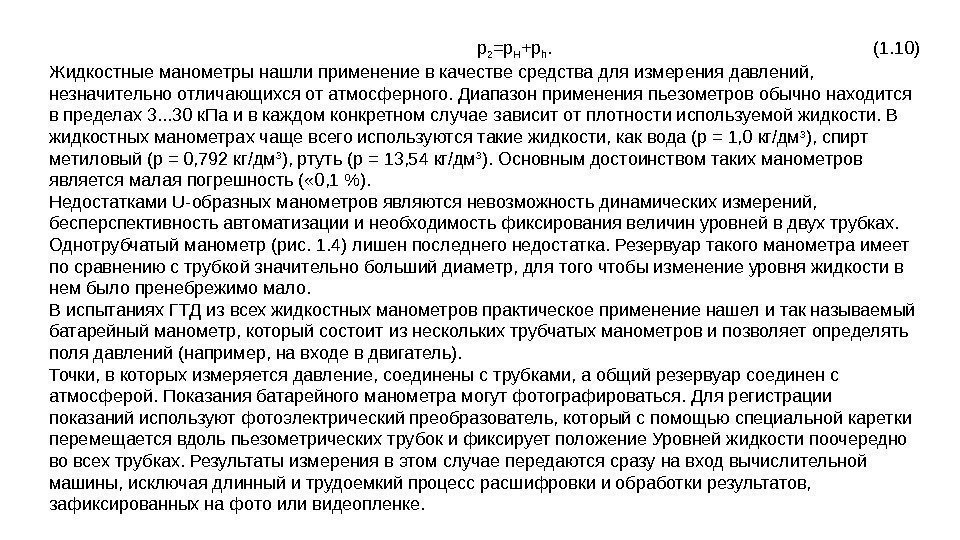
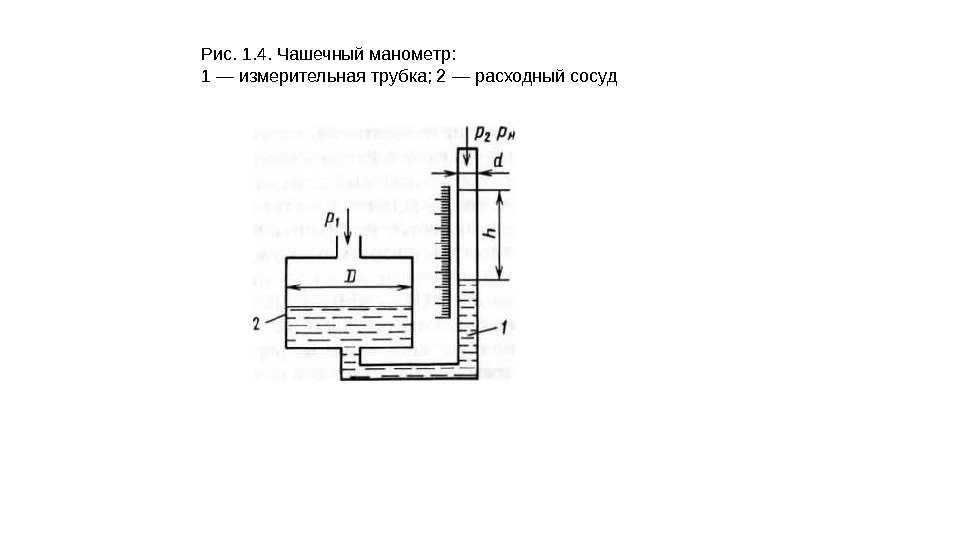
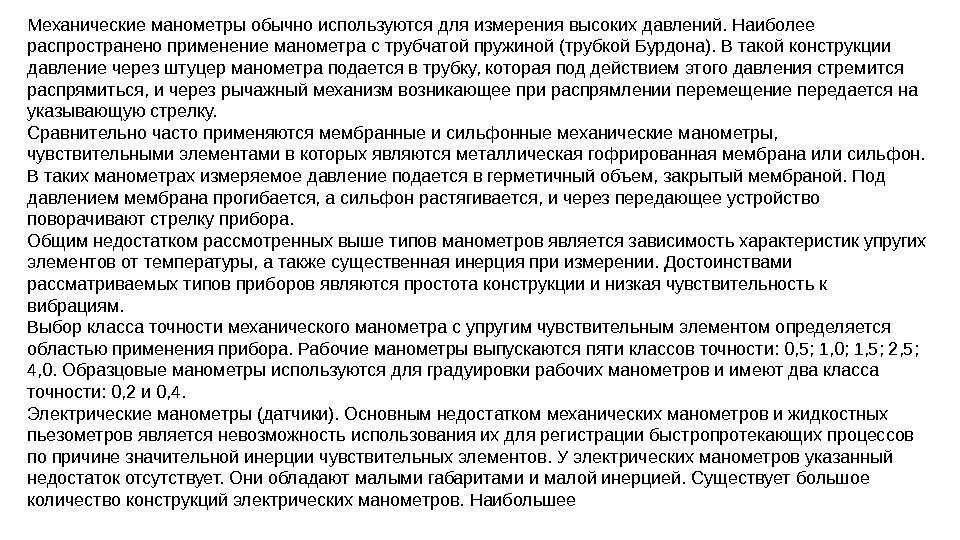
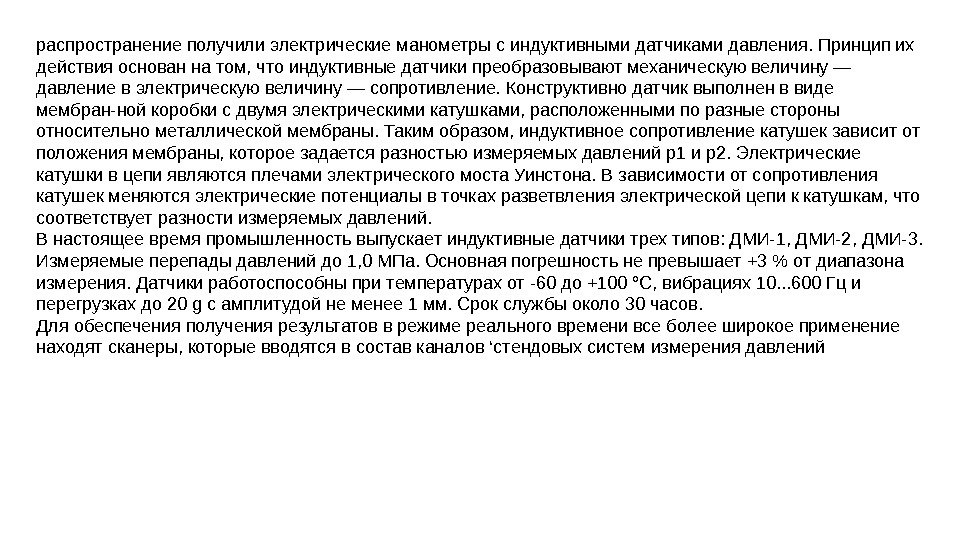
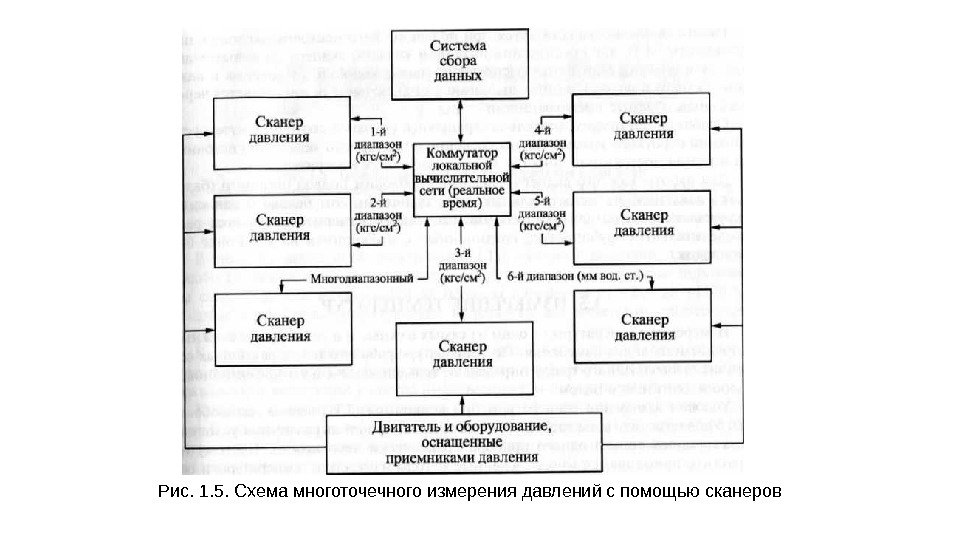
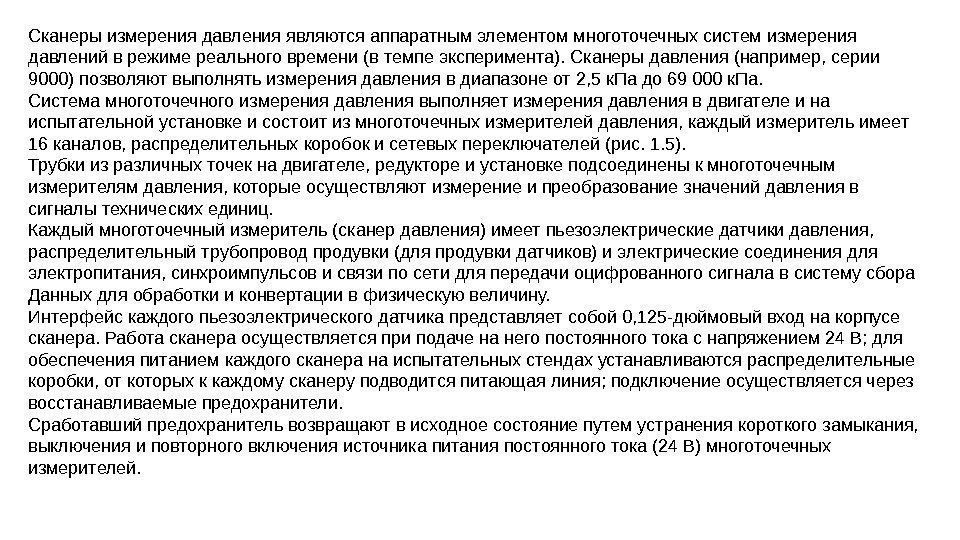
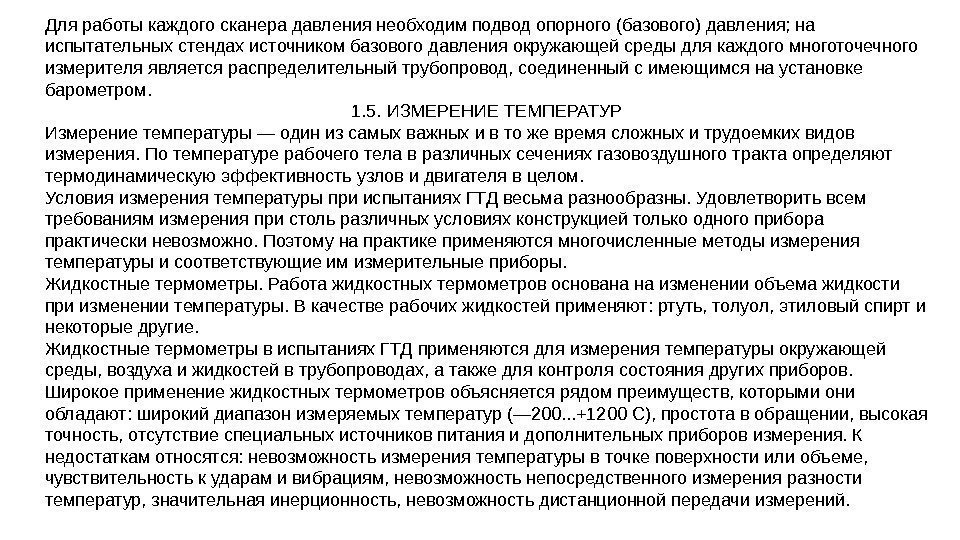
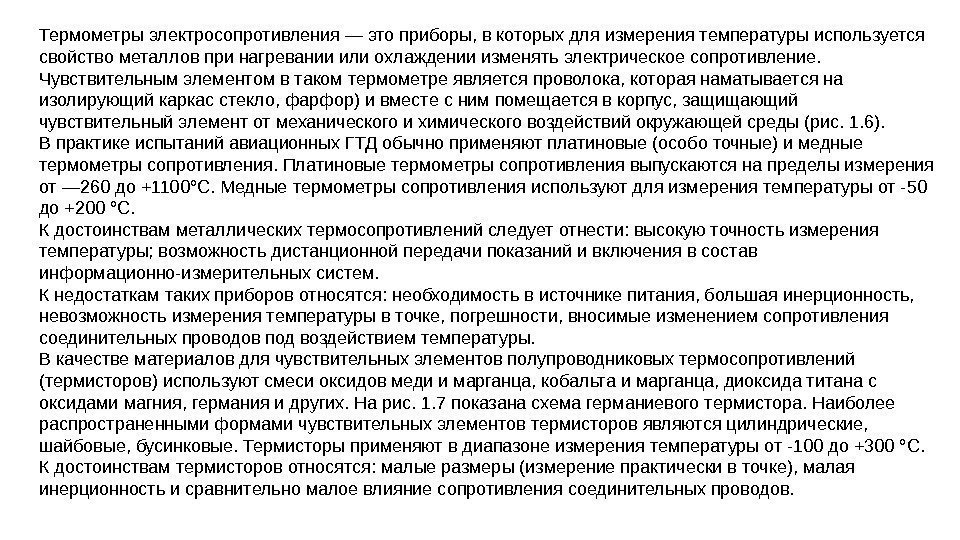
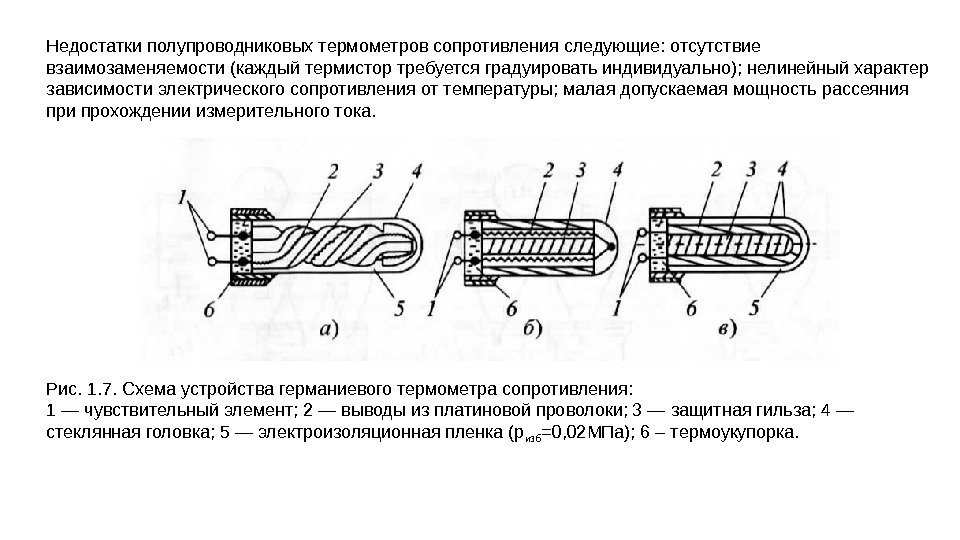
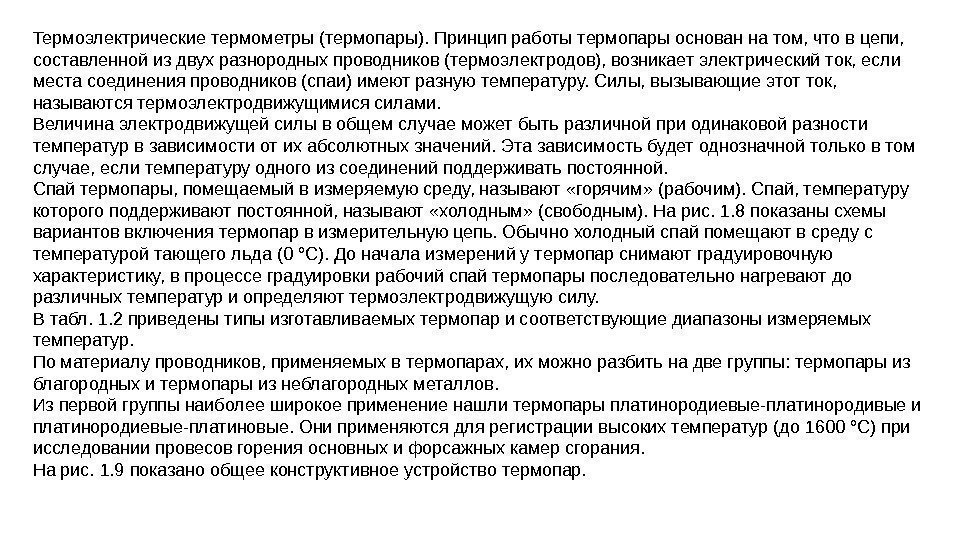
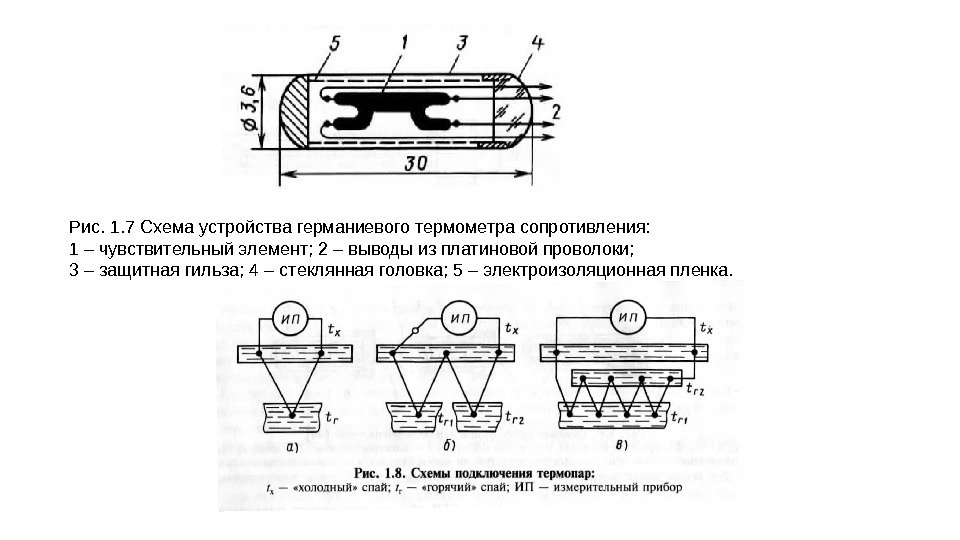
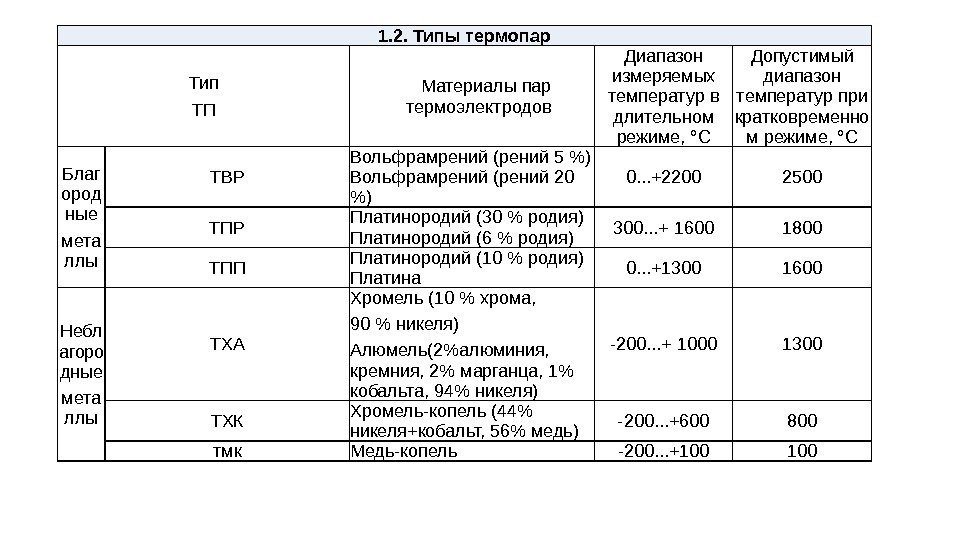
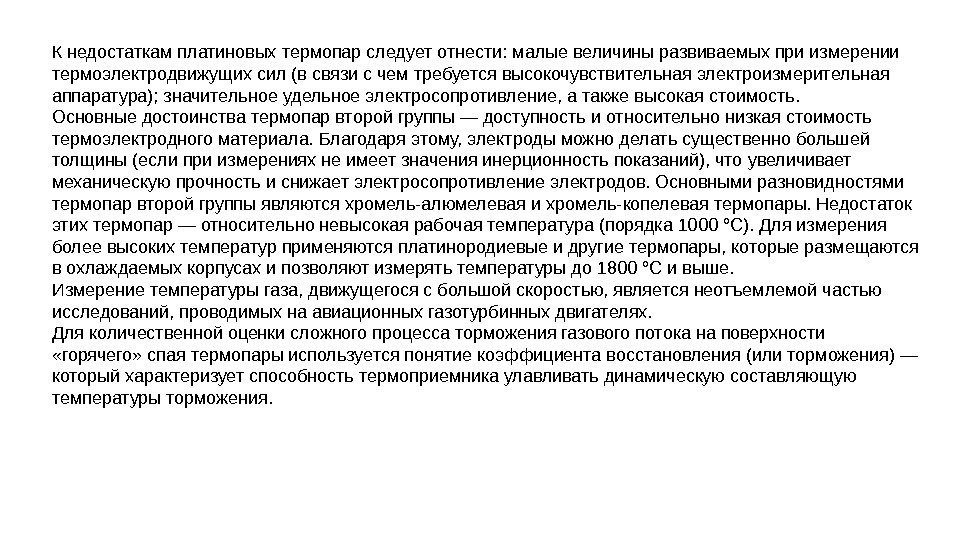
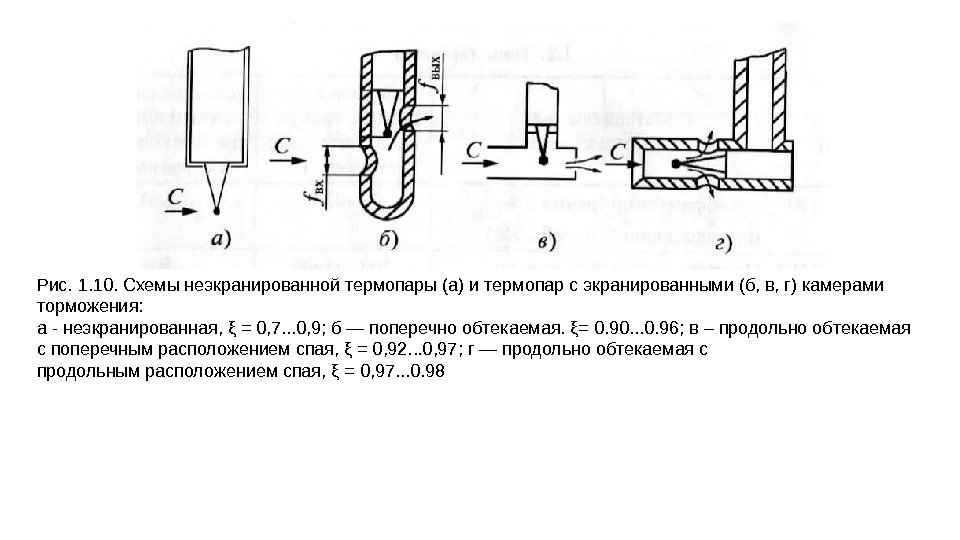
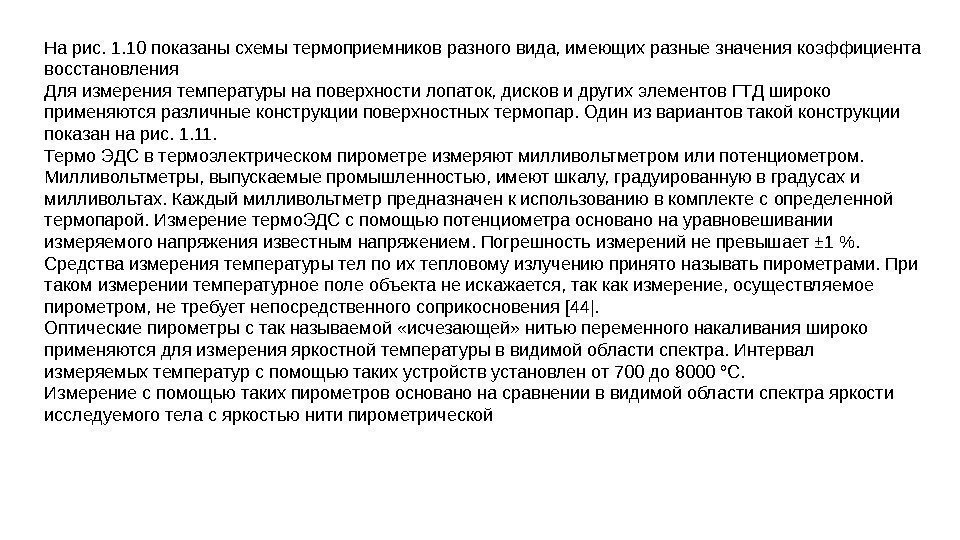
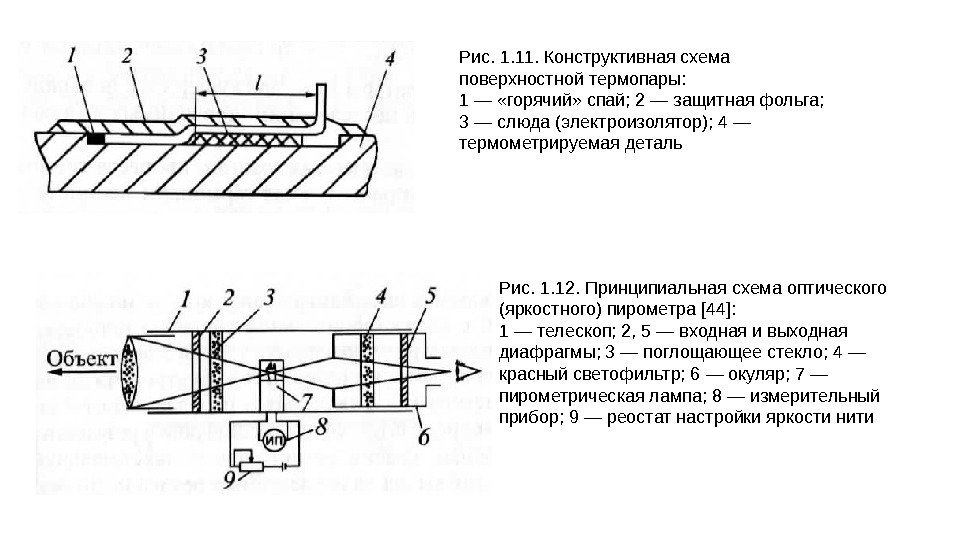
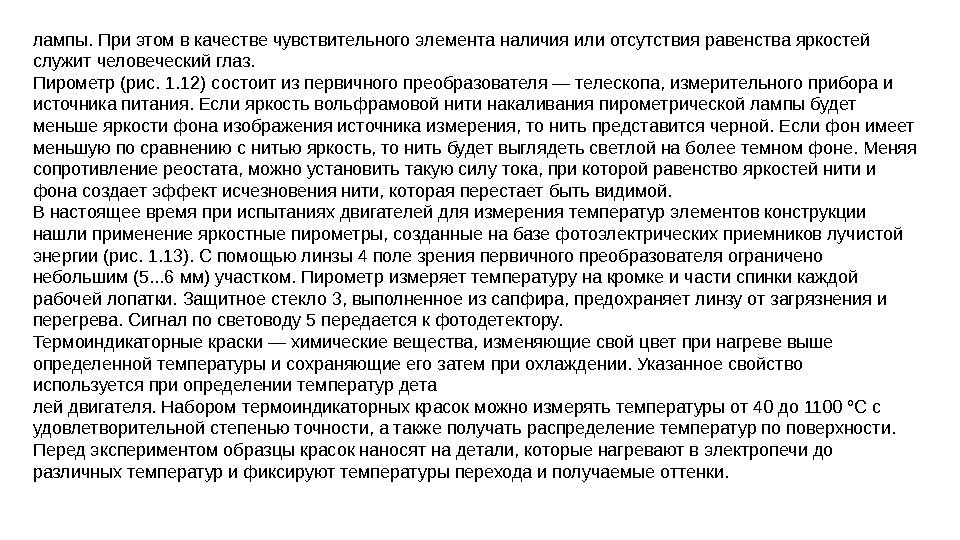
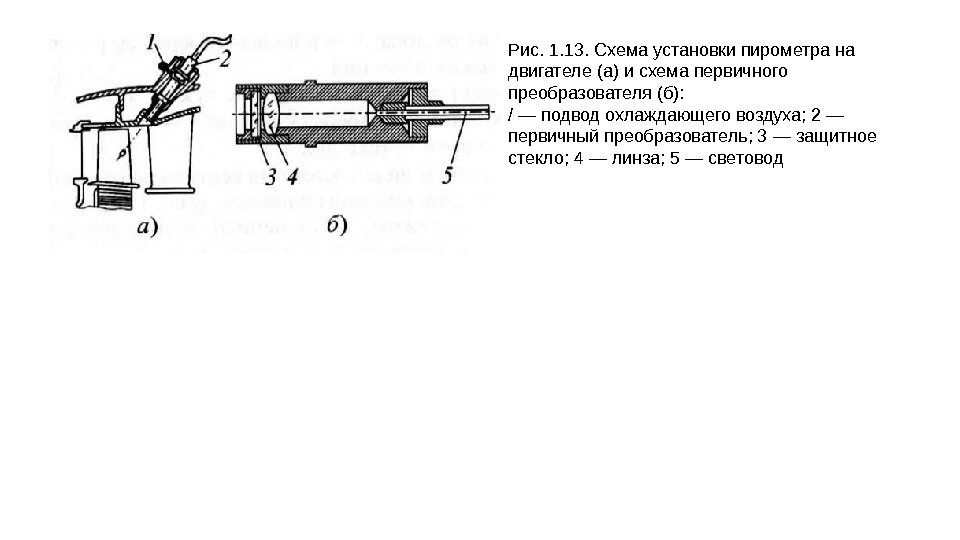
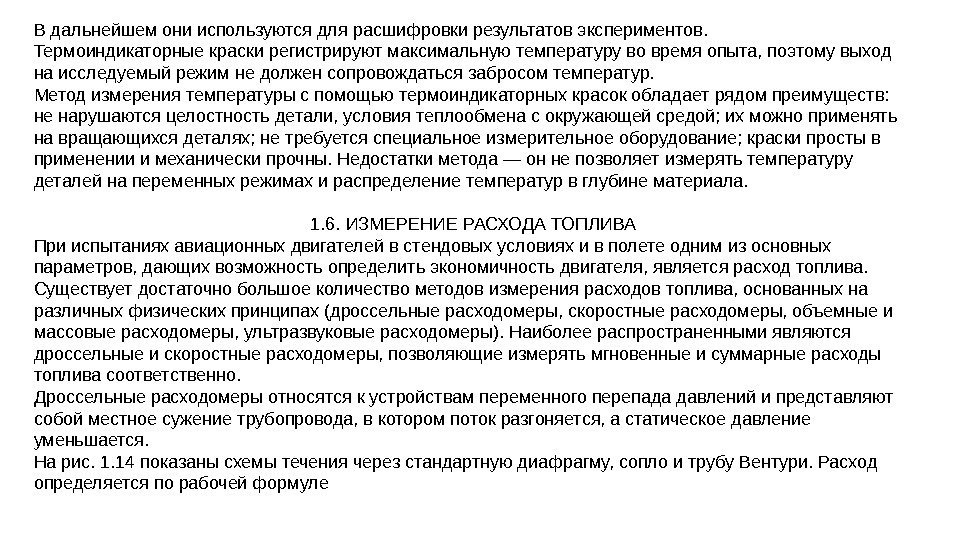
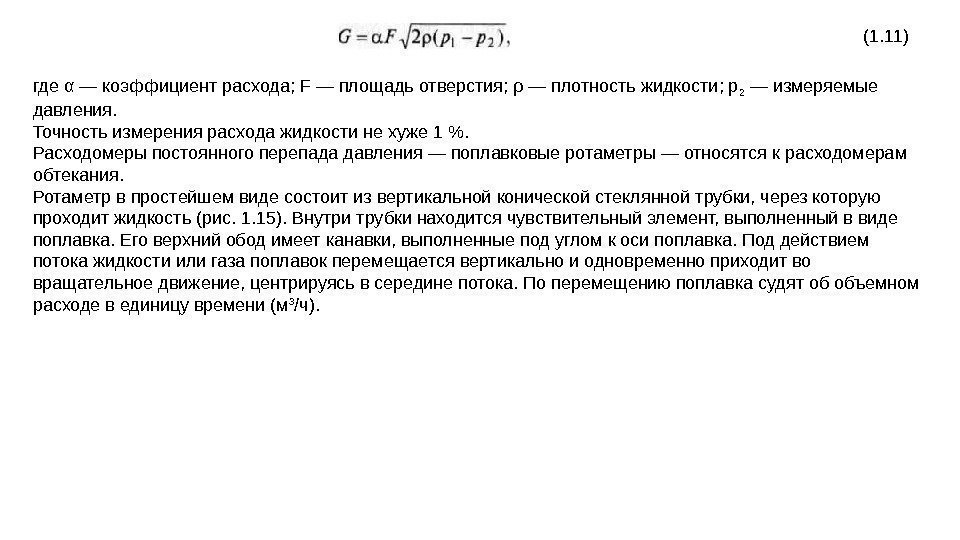
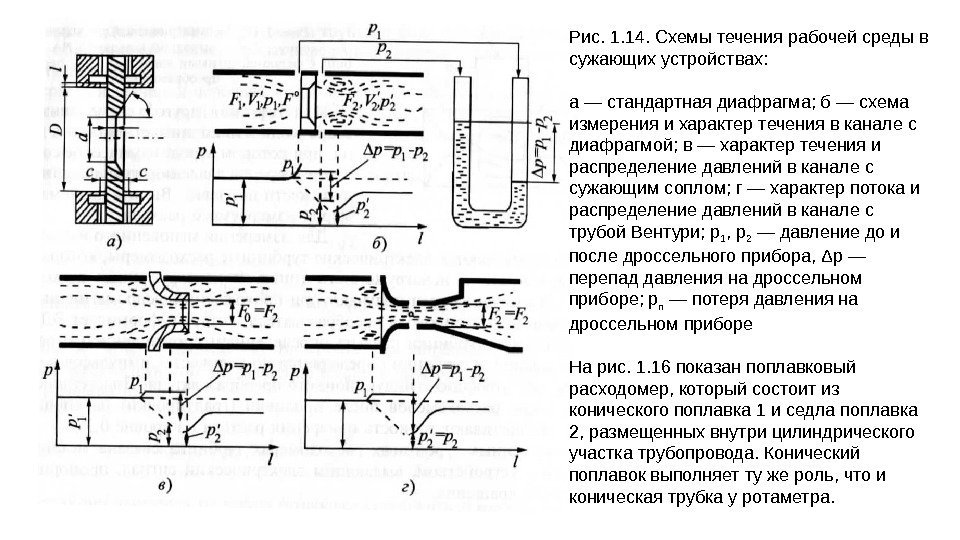
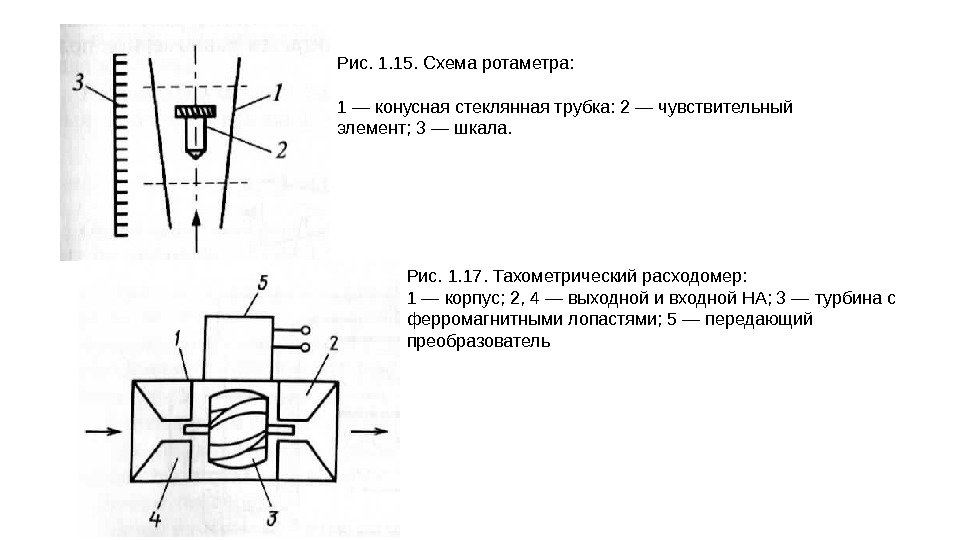
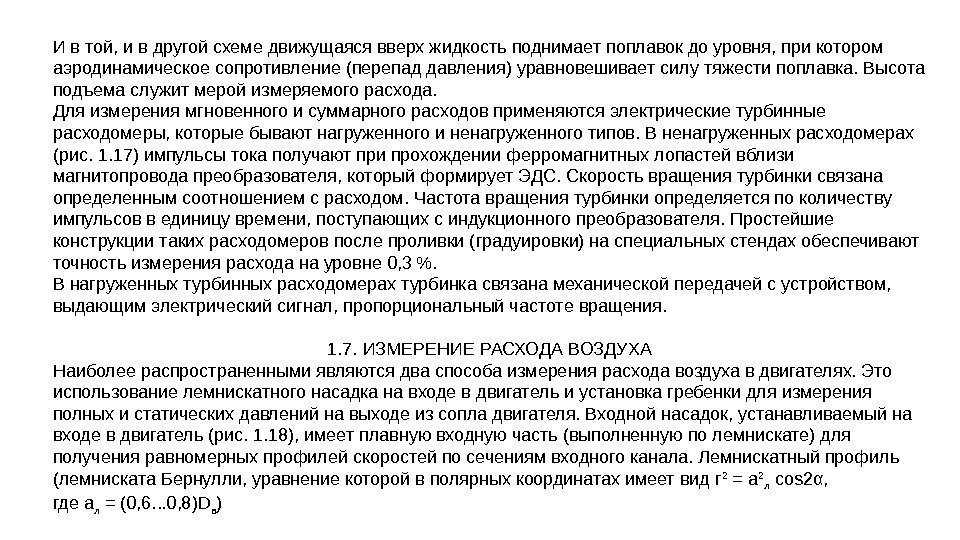
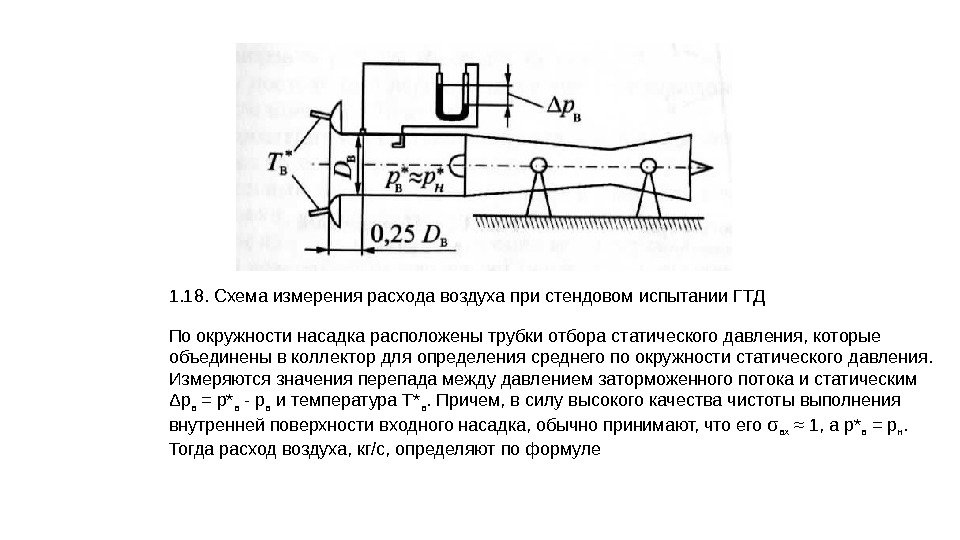
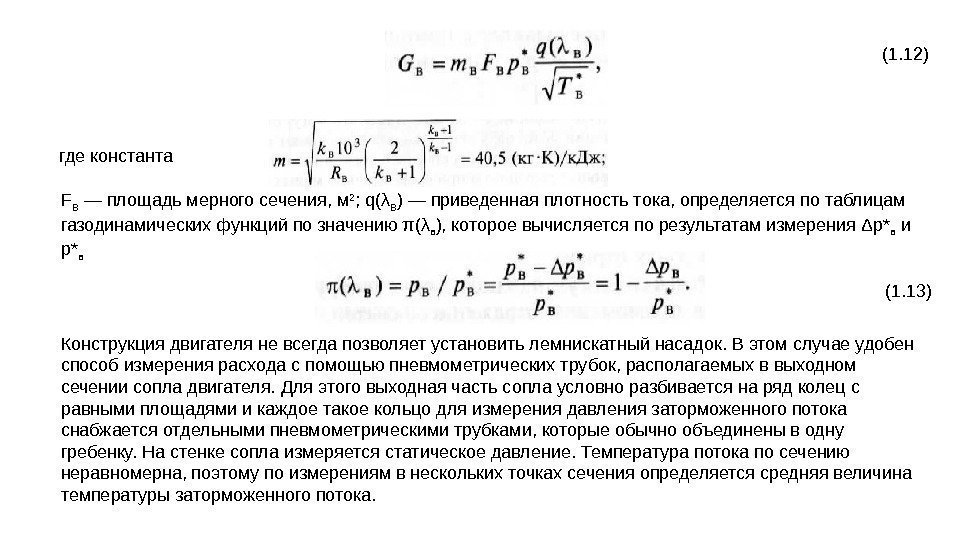
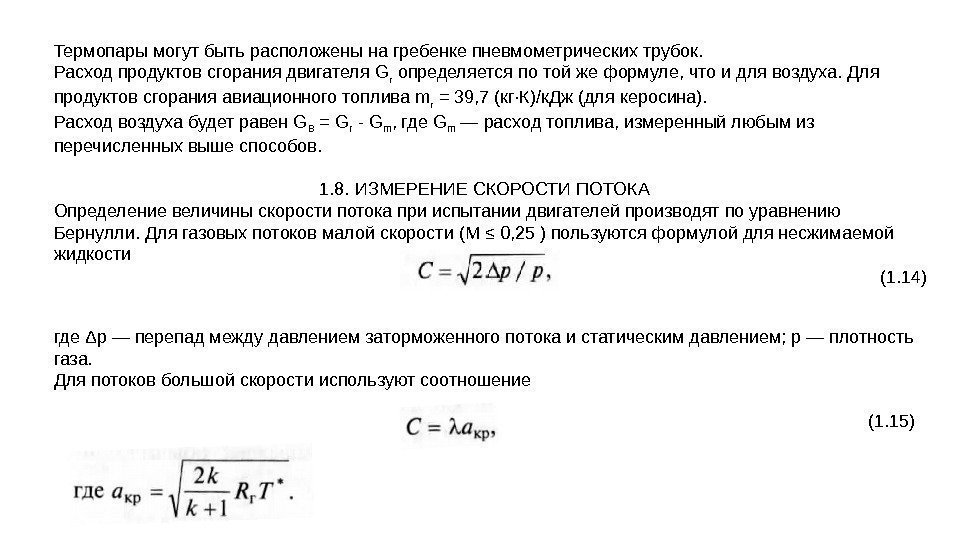
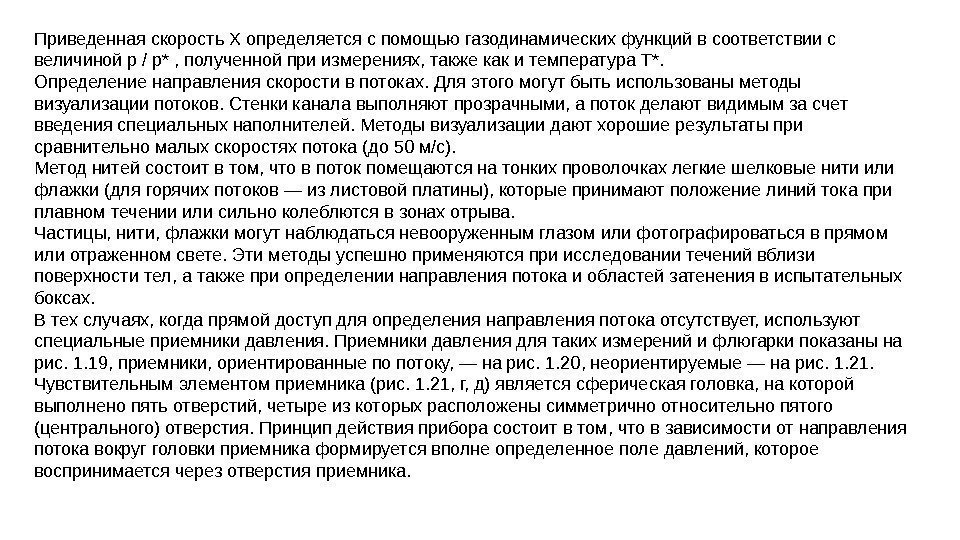
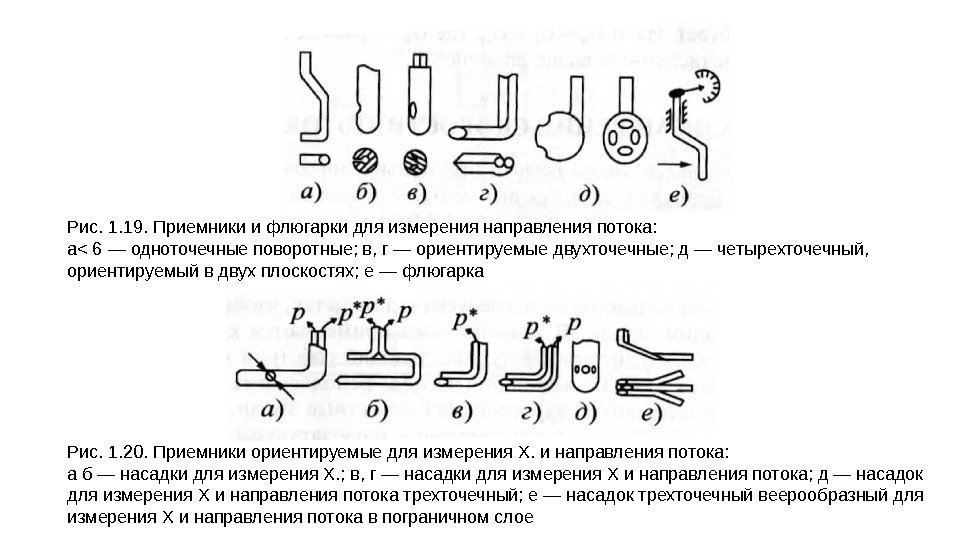
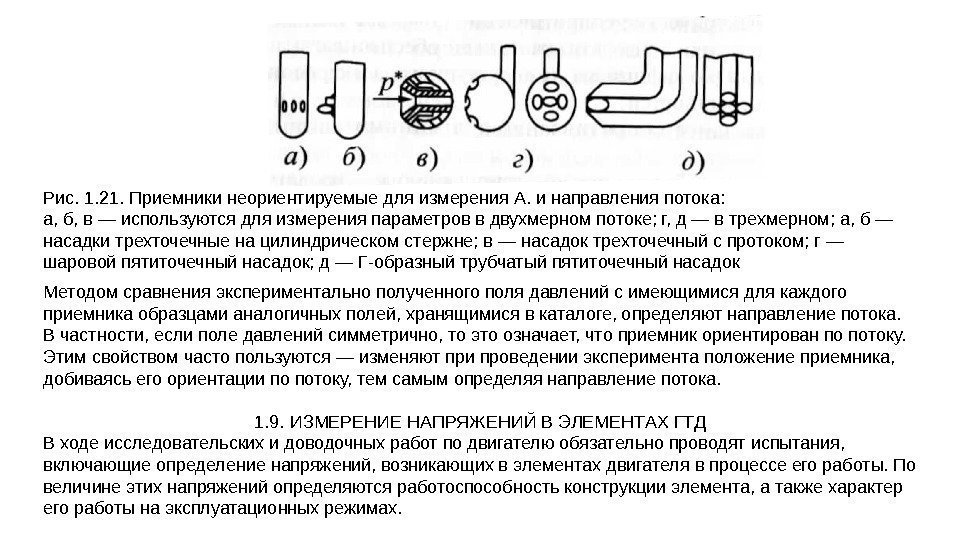
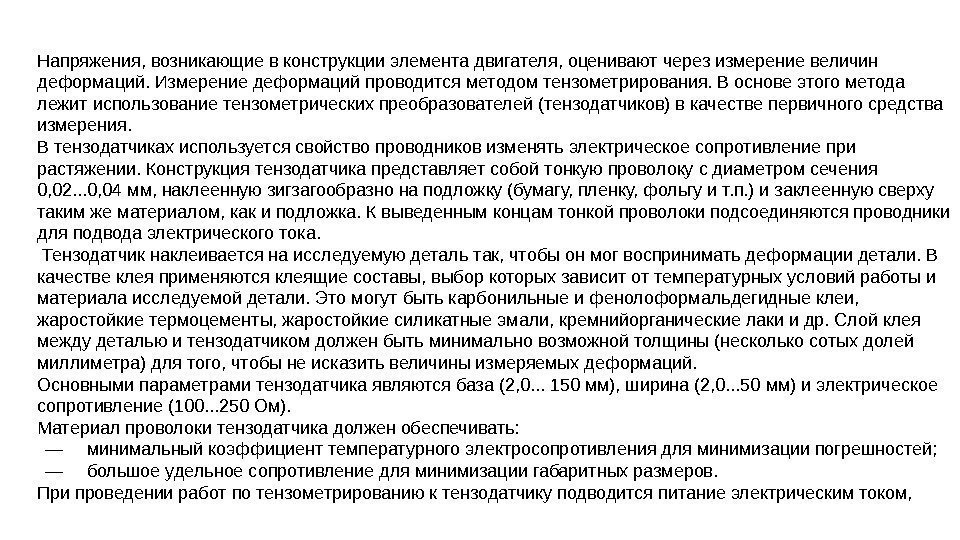
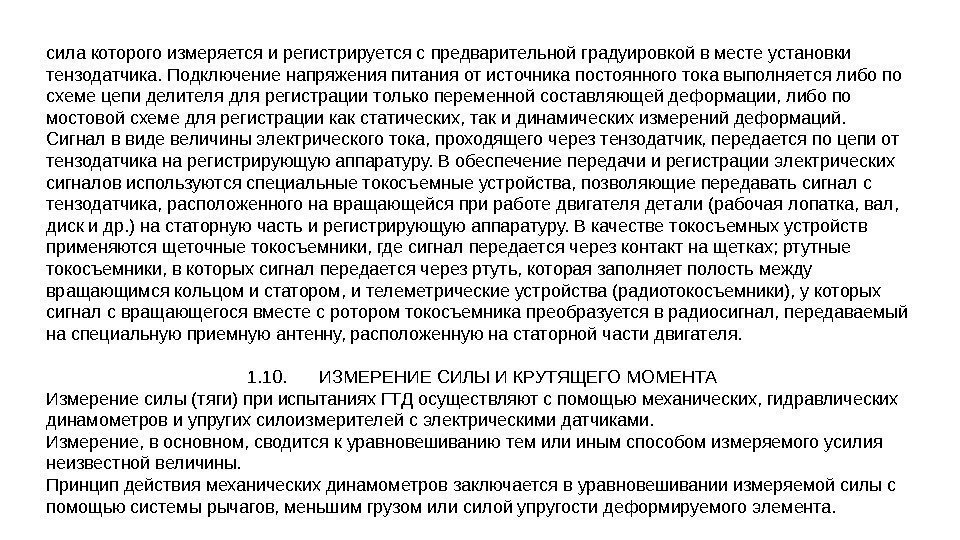
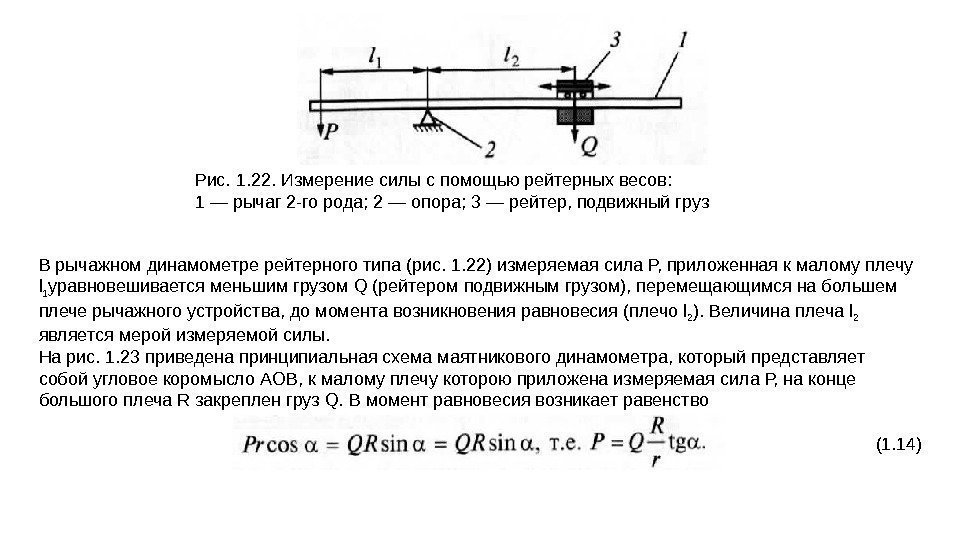
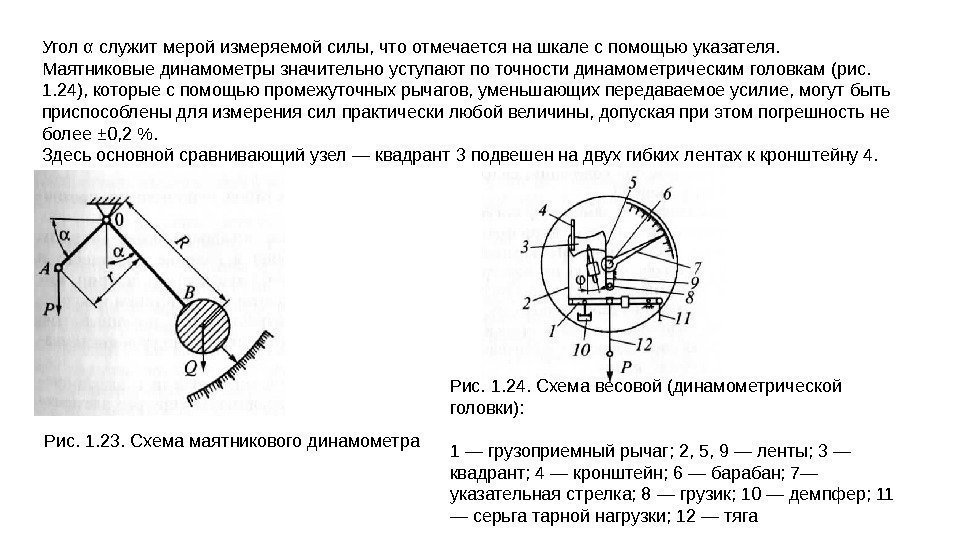
![Рис. 1. 25. Компенсационная диафрагменная месдоза [32]: 1 — поршень: 2 — корпус: 3 Рис. 1. 25. Компенсационная диафрагменная месдоза [32]: 1 — поршень: 2 — корпус: 3](http://present5.com/presentforday2/20170201/mmk_ispytania_i_kontrol_kachestva_izdeliy_2017_images/mmk_ispytania_i_kontrol_kachestva_izdeliy_2017_91.jpg)
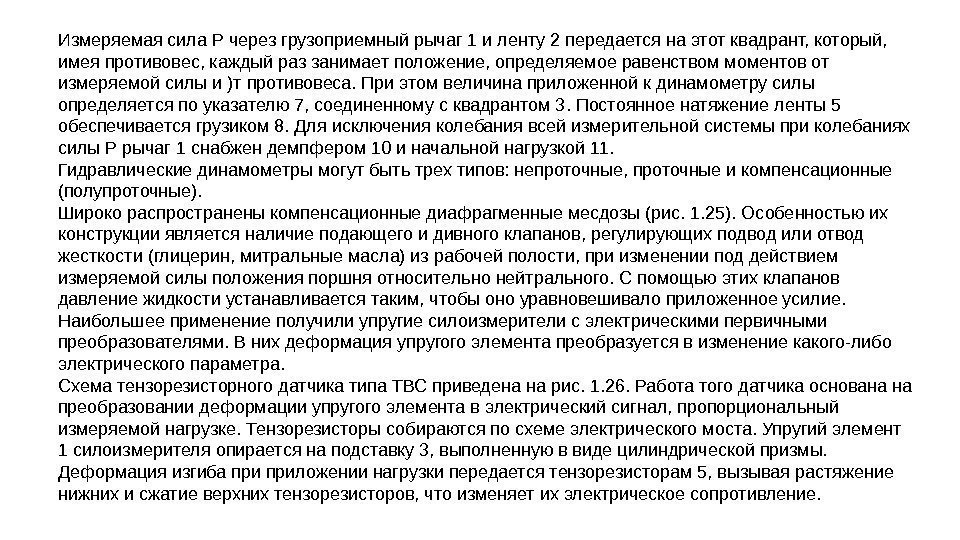
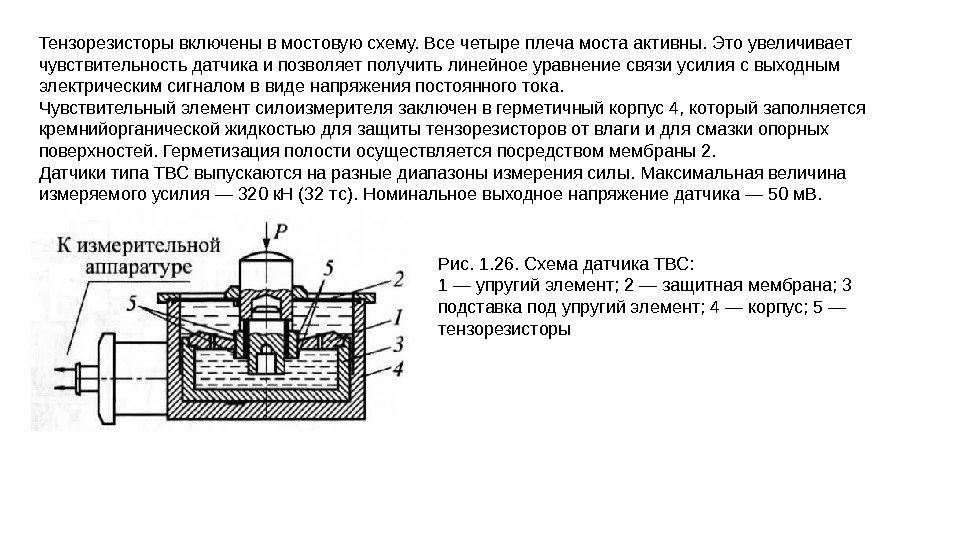
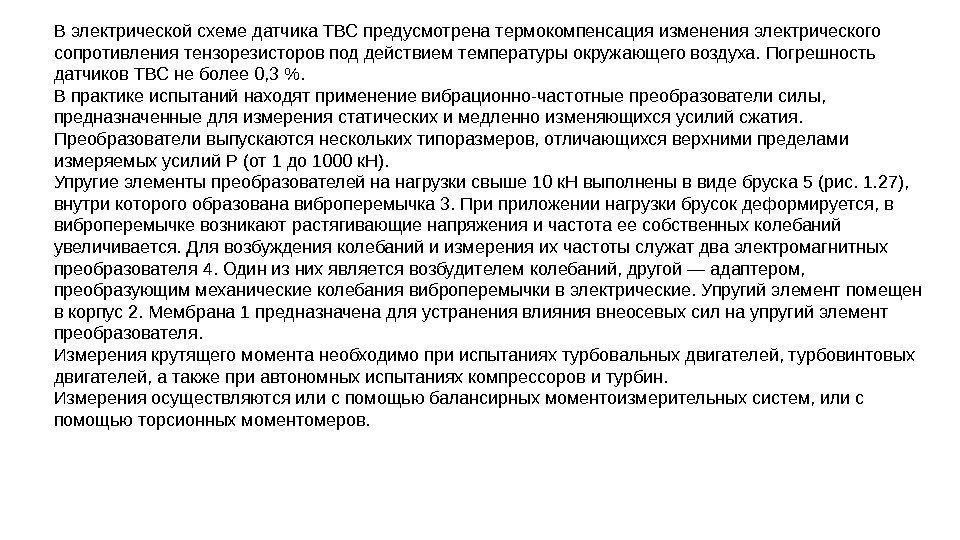
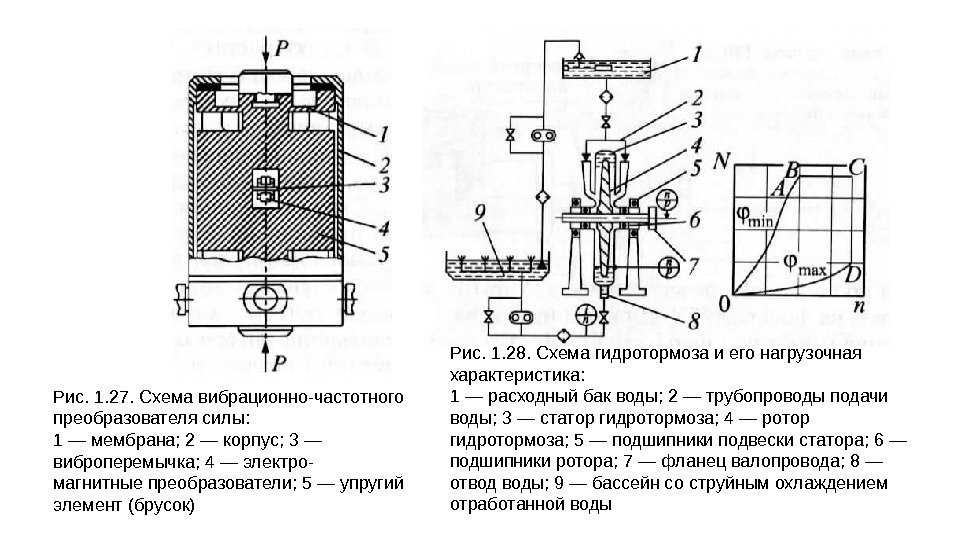
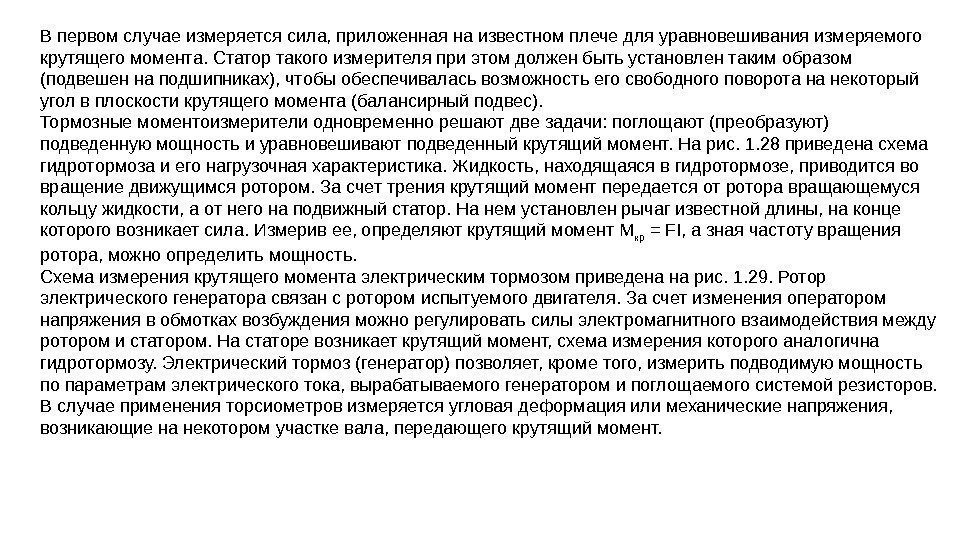
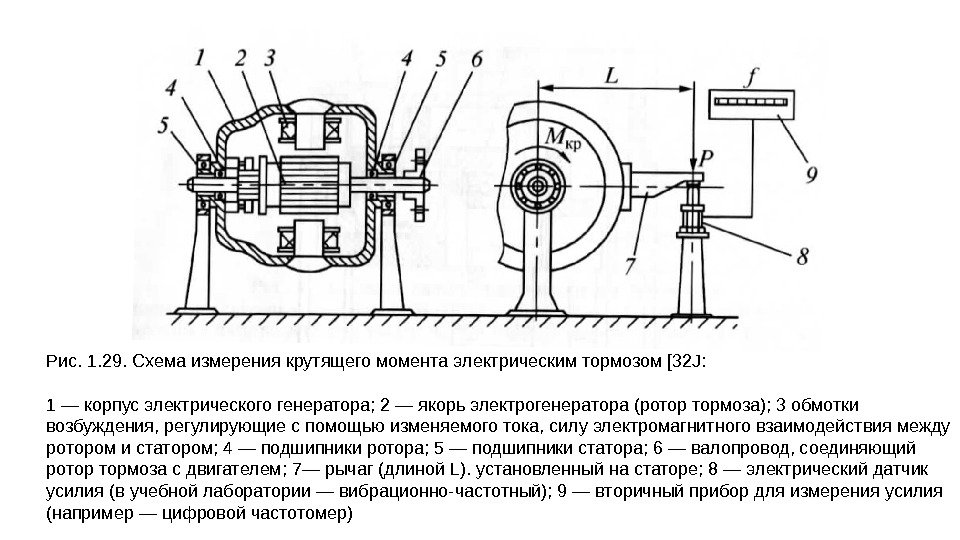
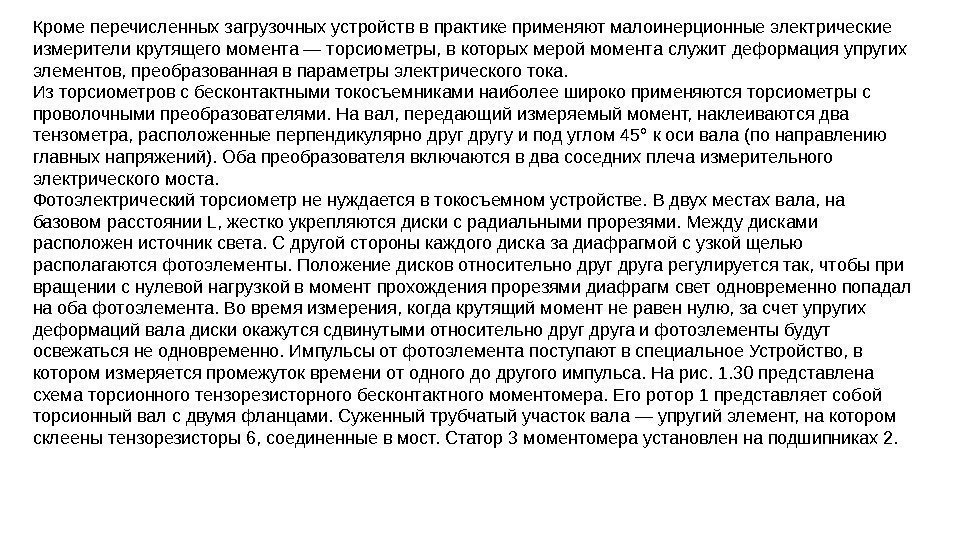
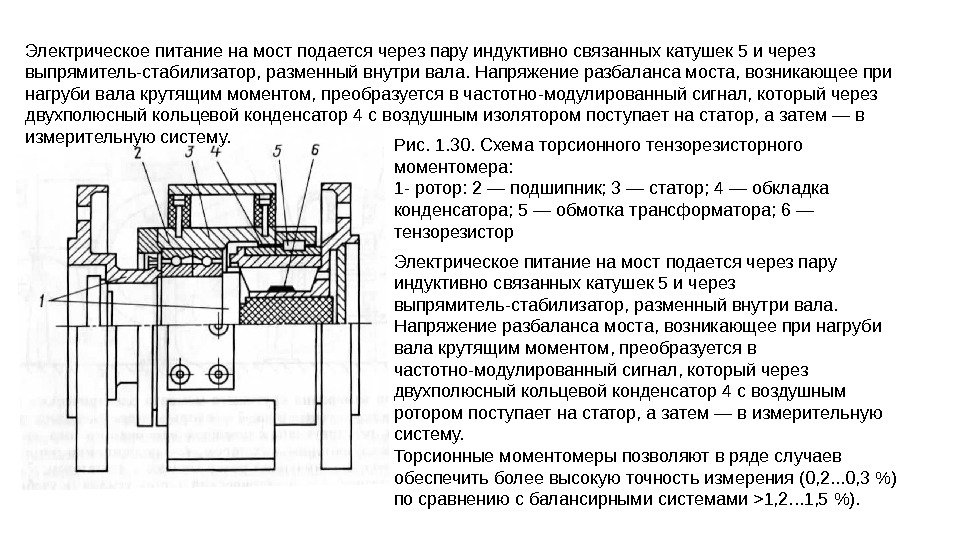
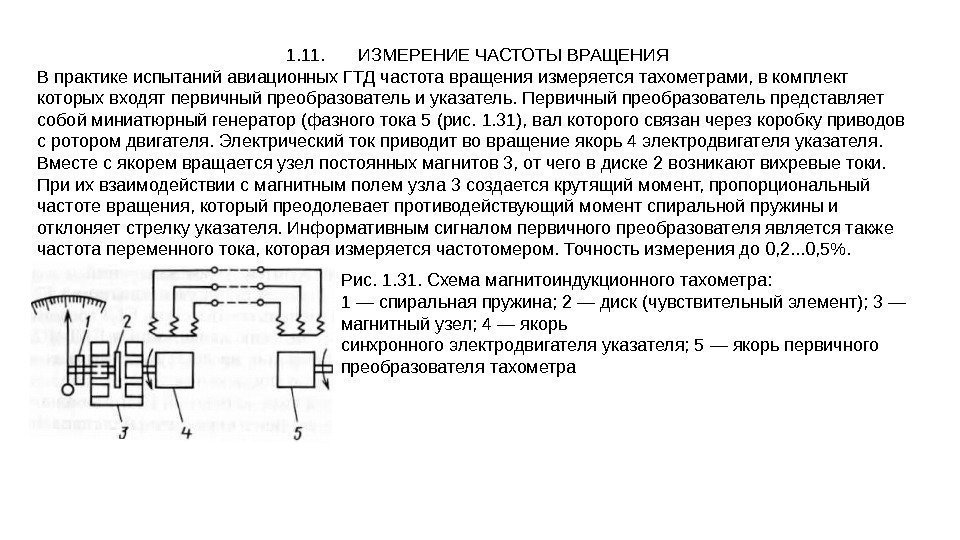
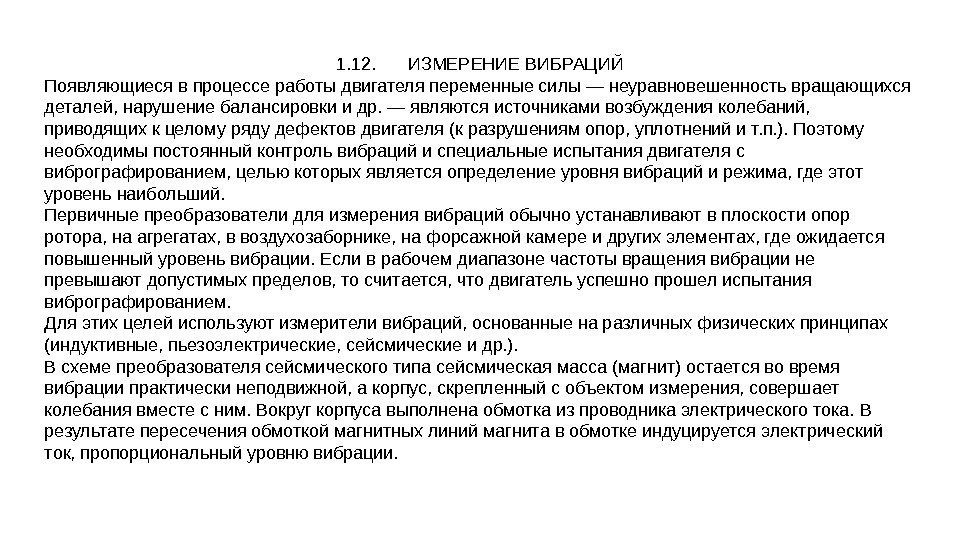
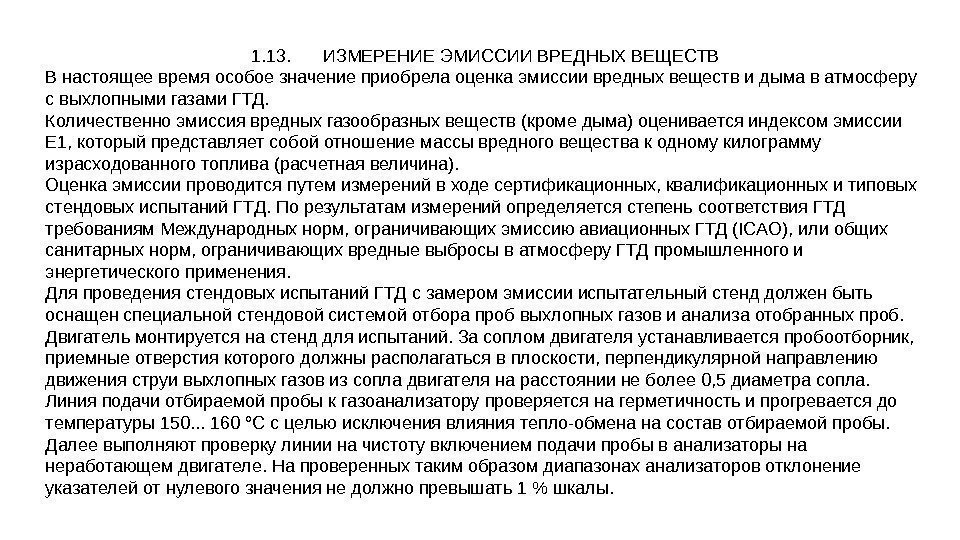
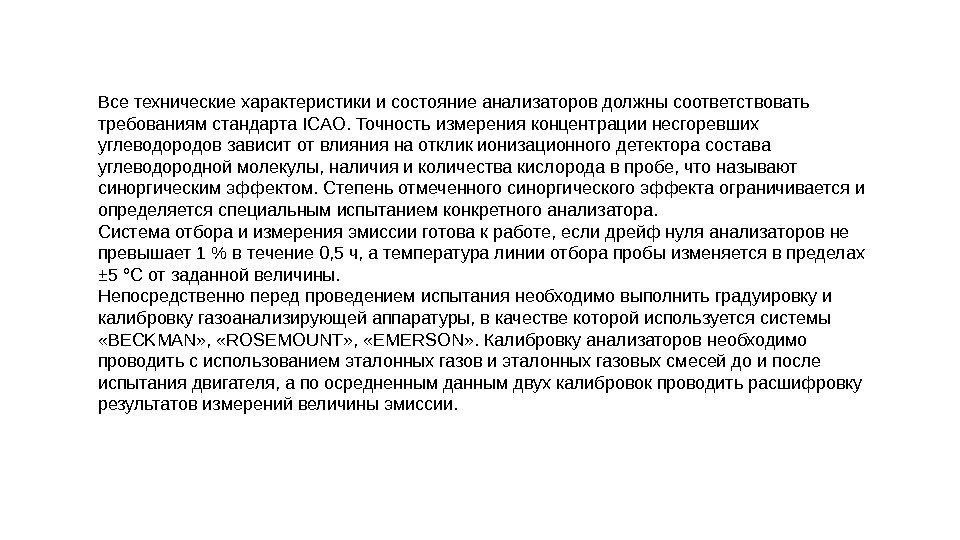
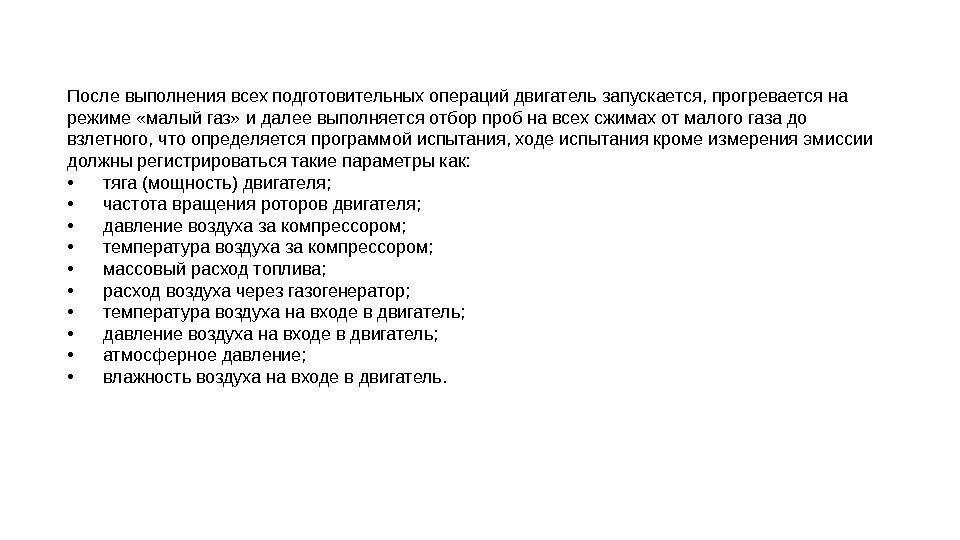
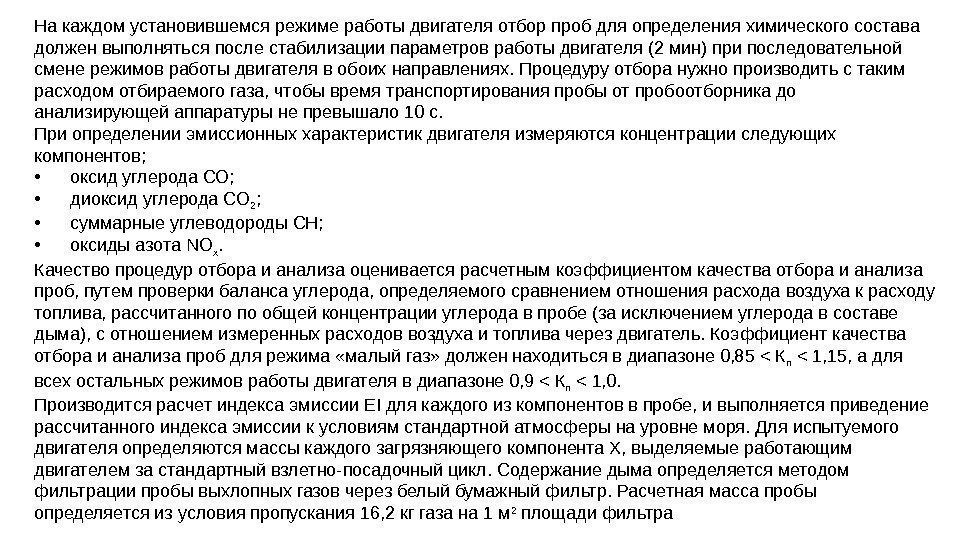
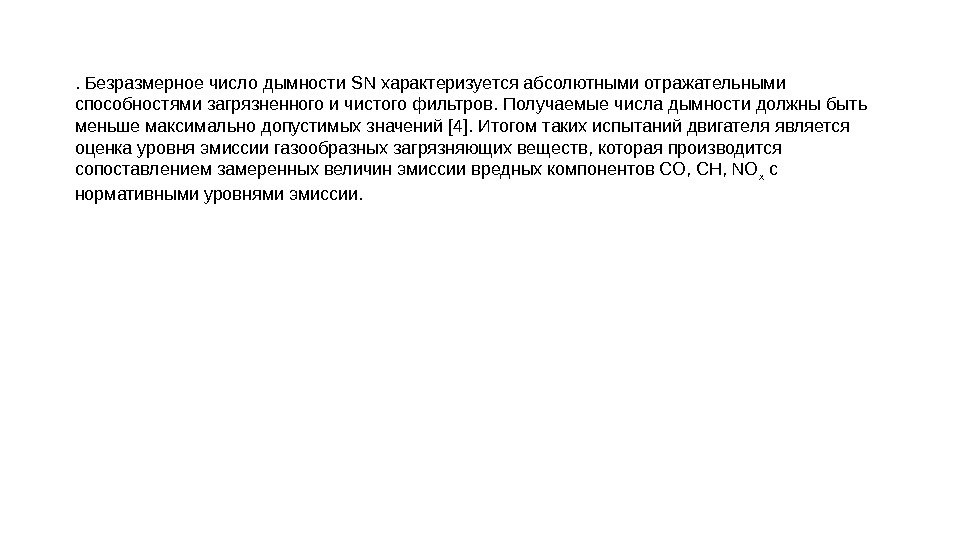
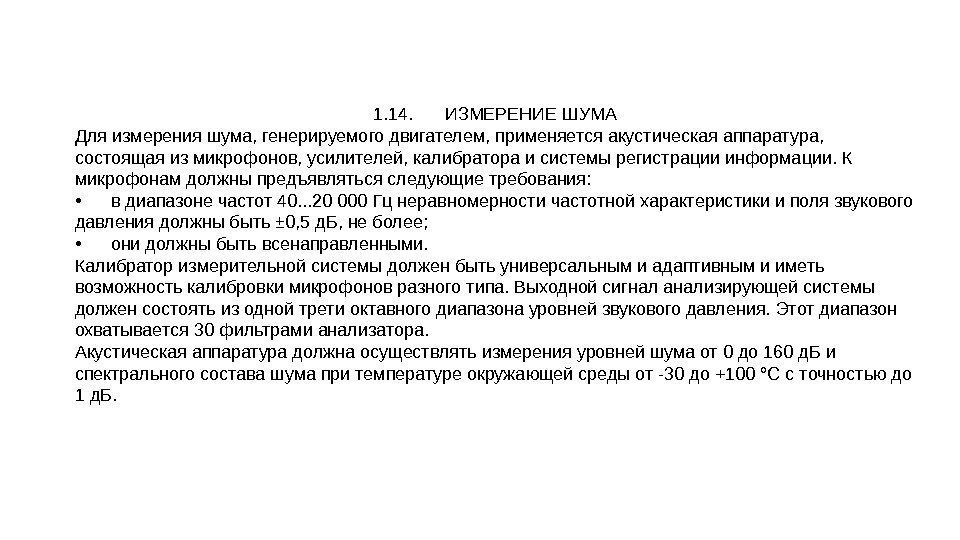
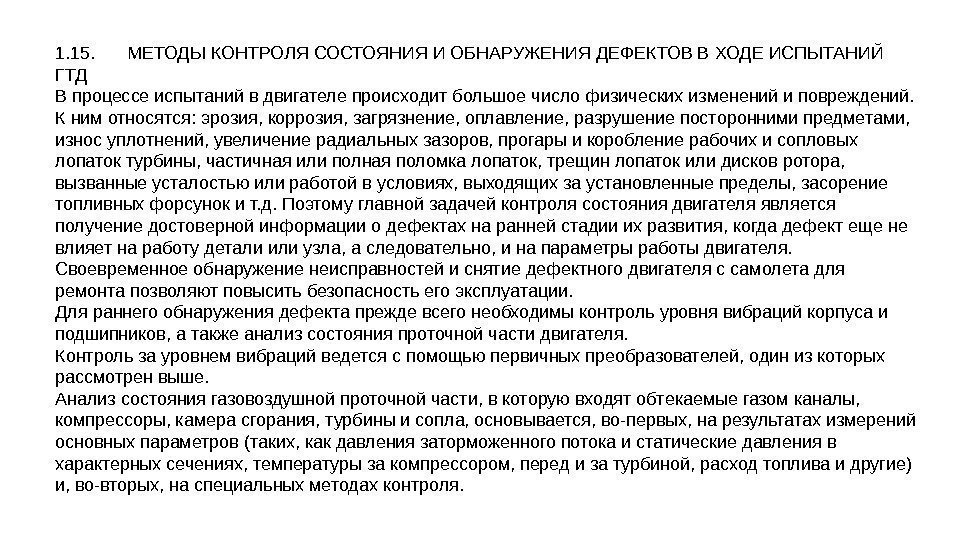
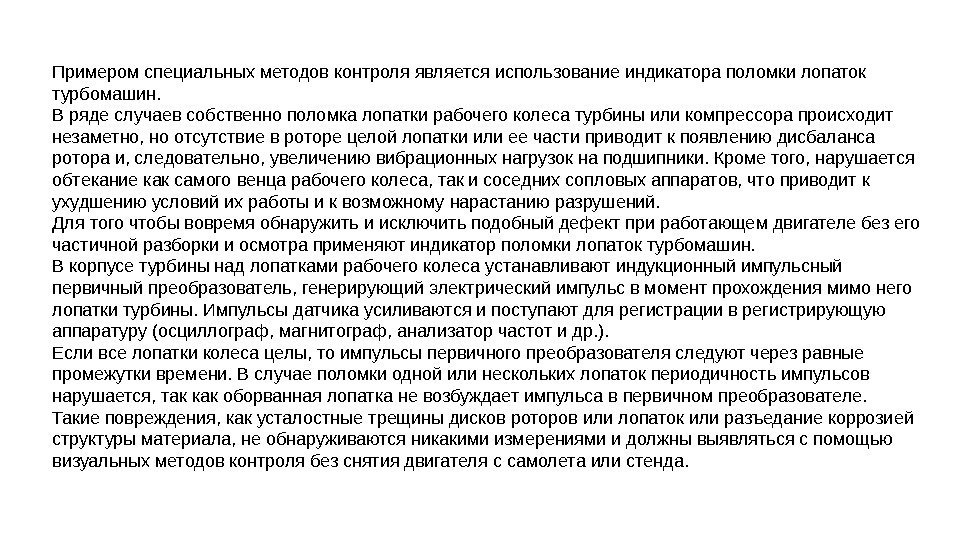
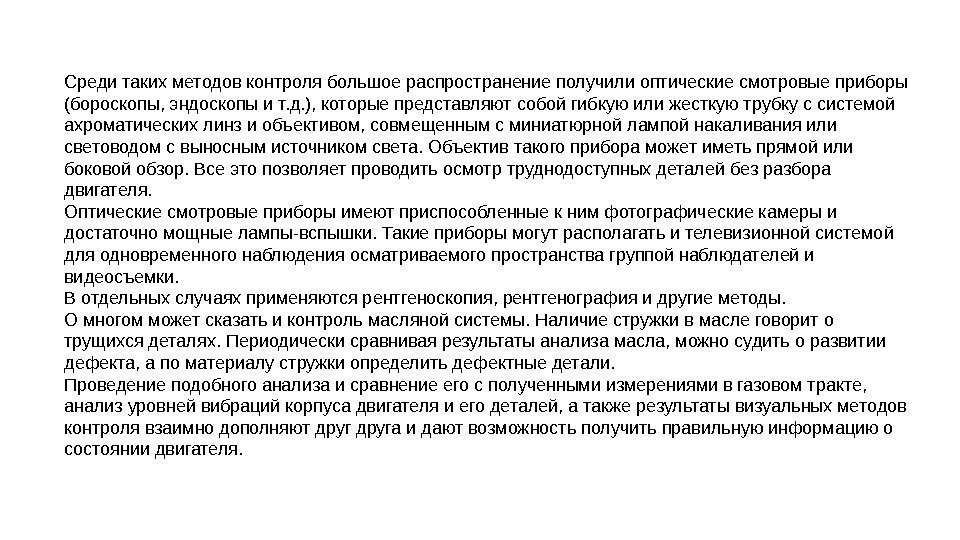
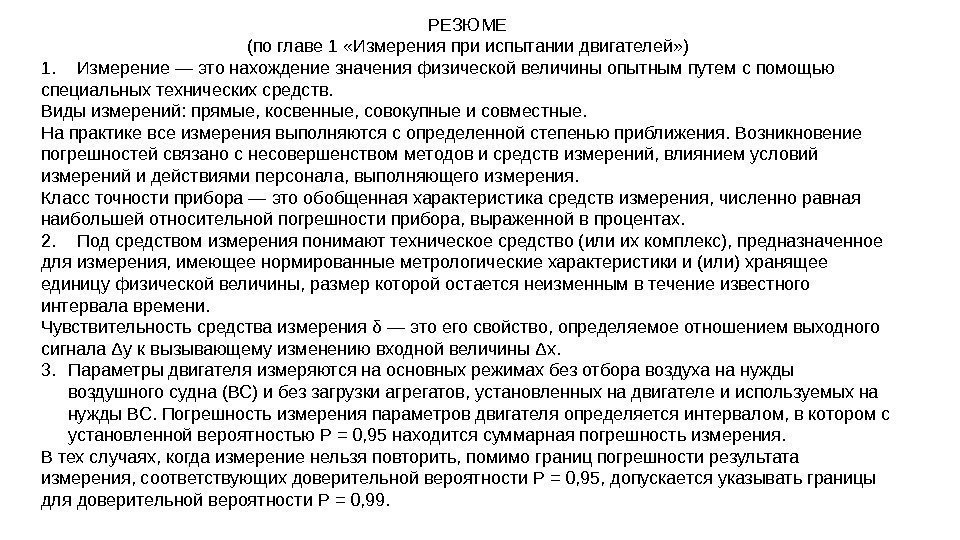
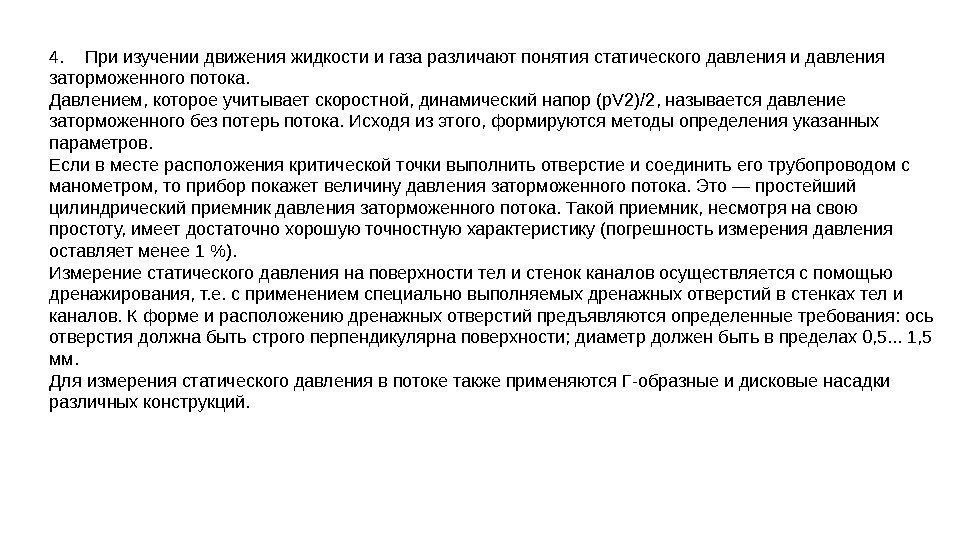
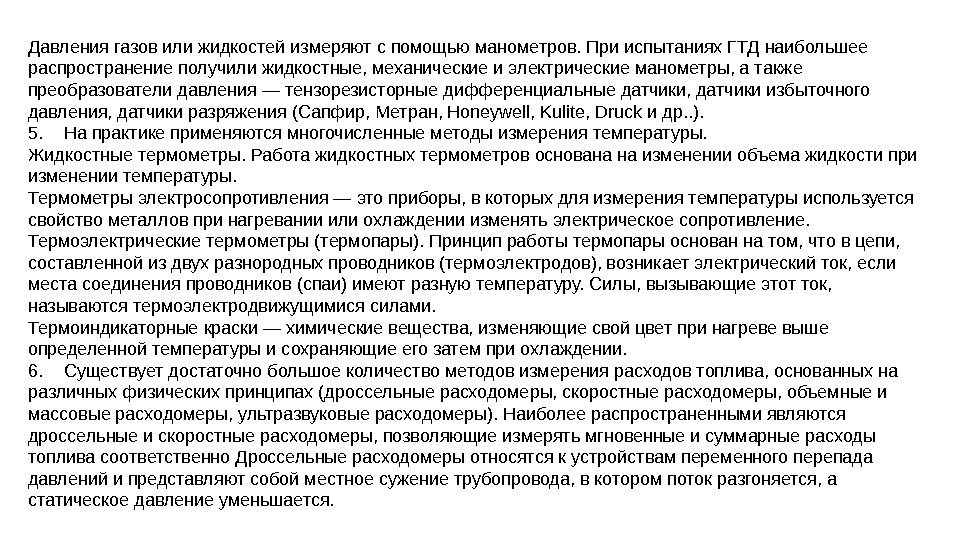
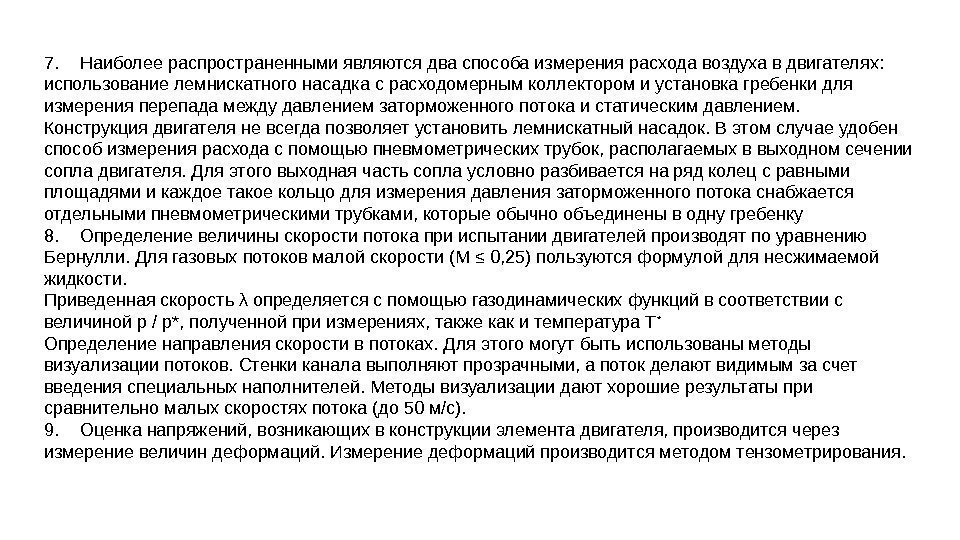
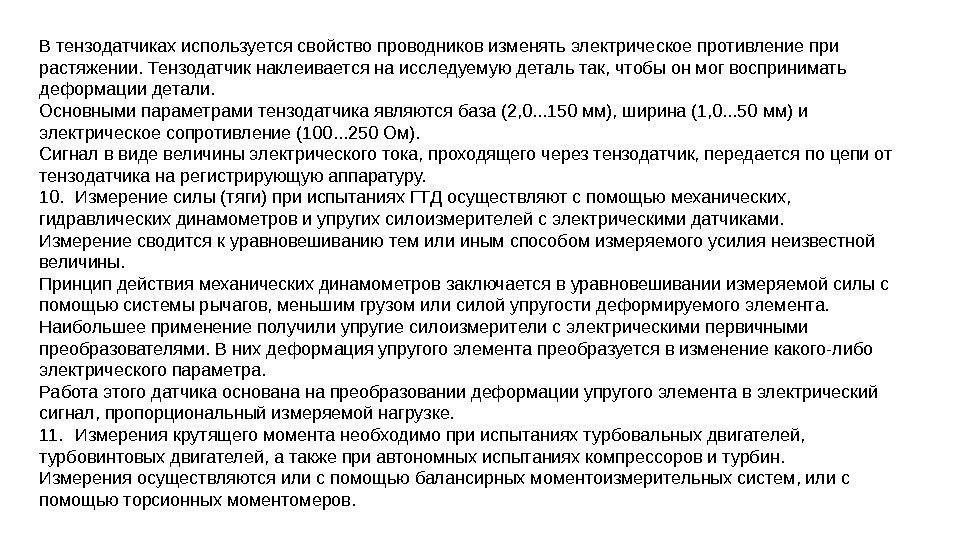
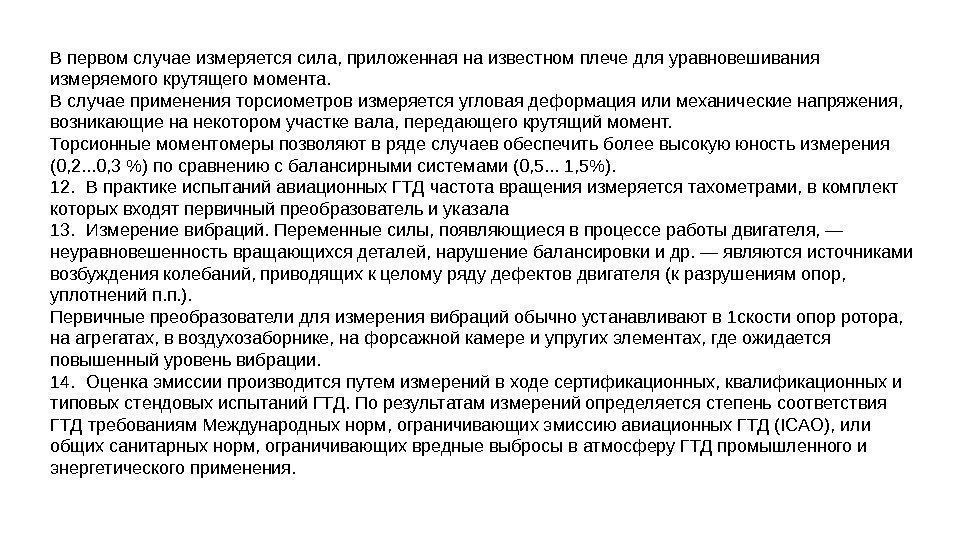
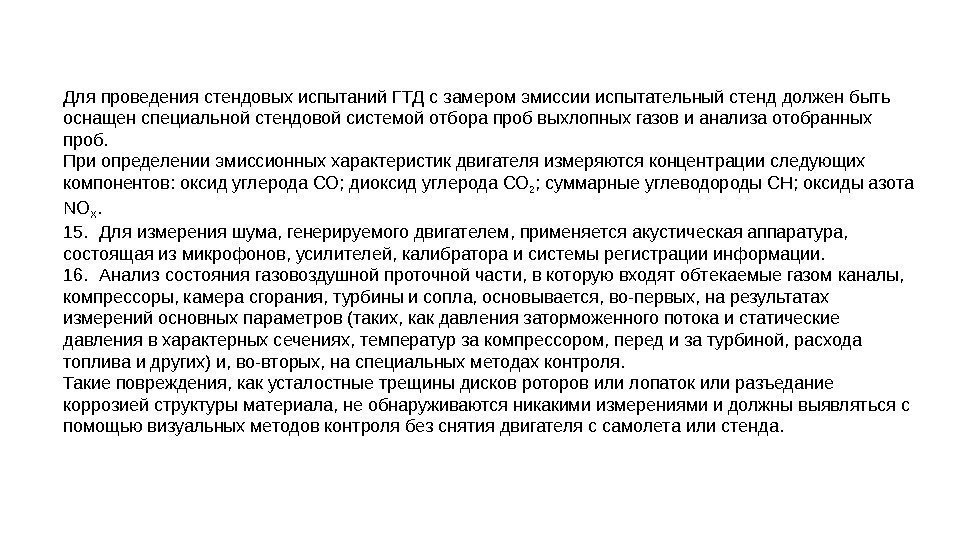
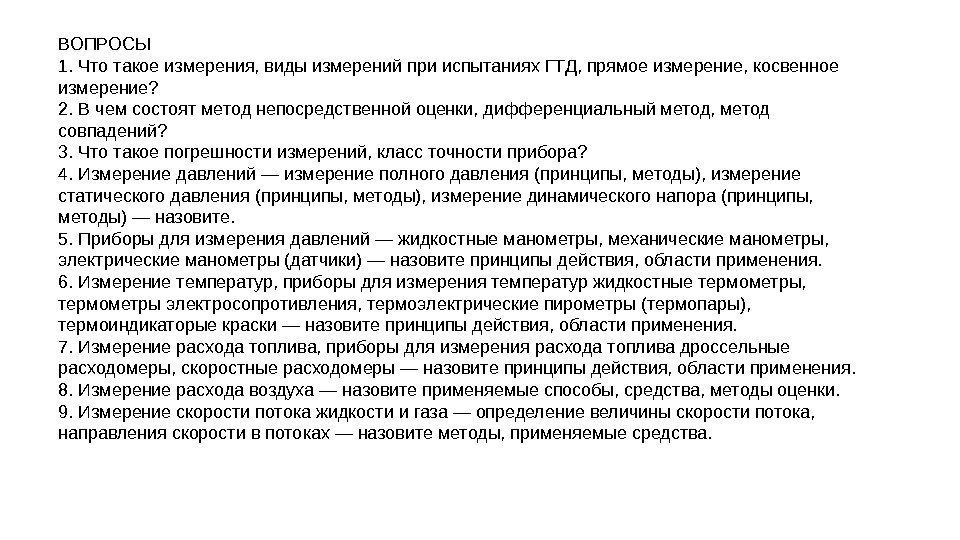
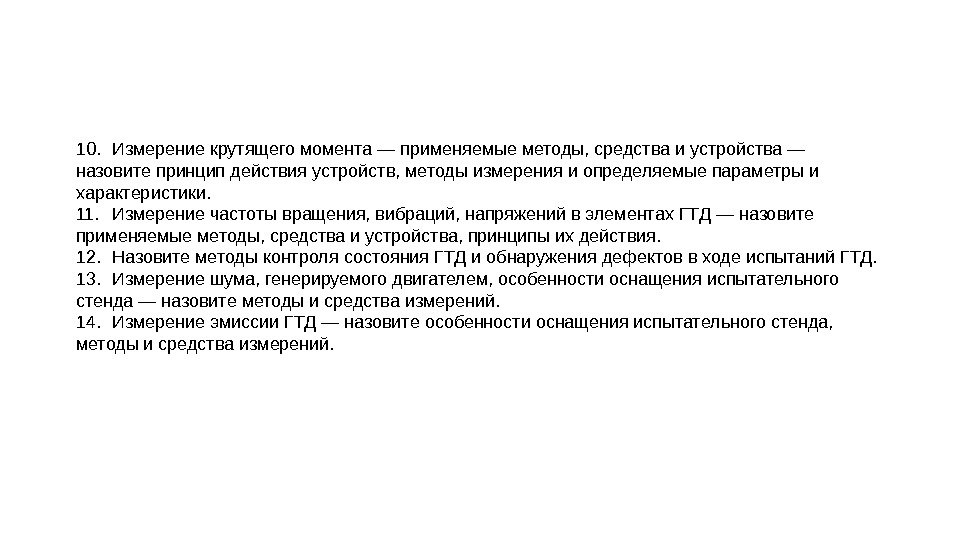
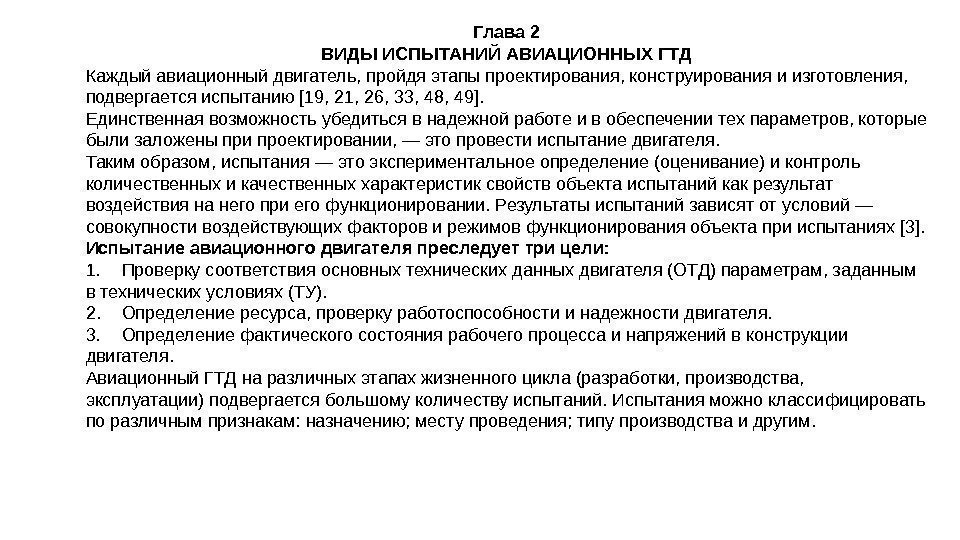
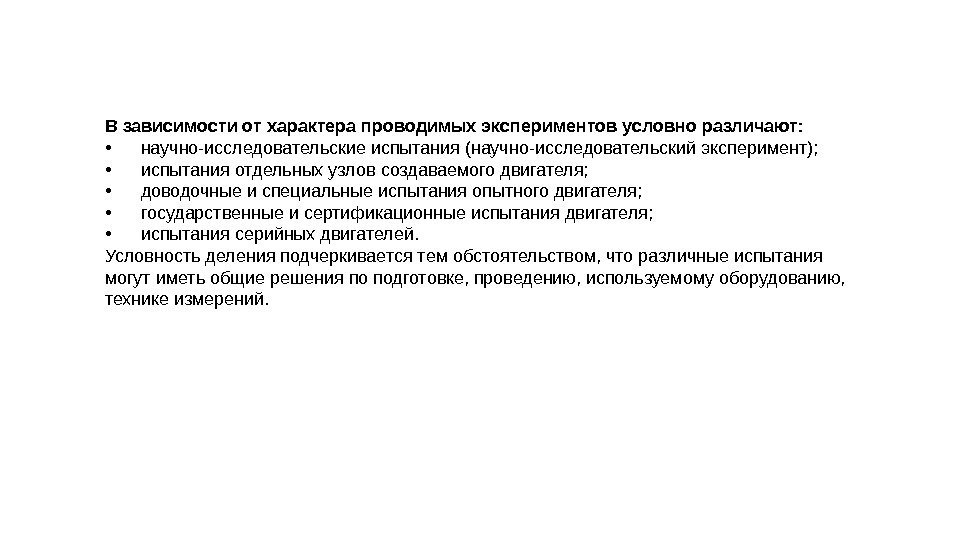
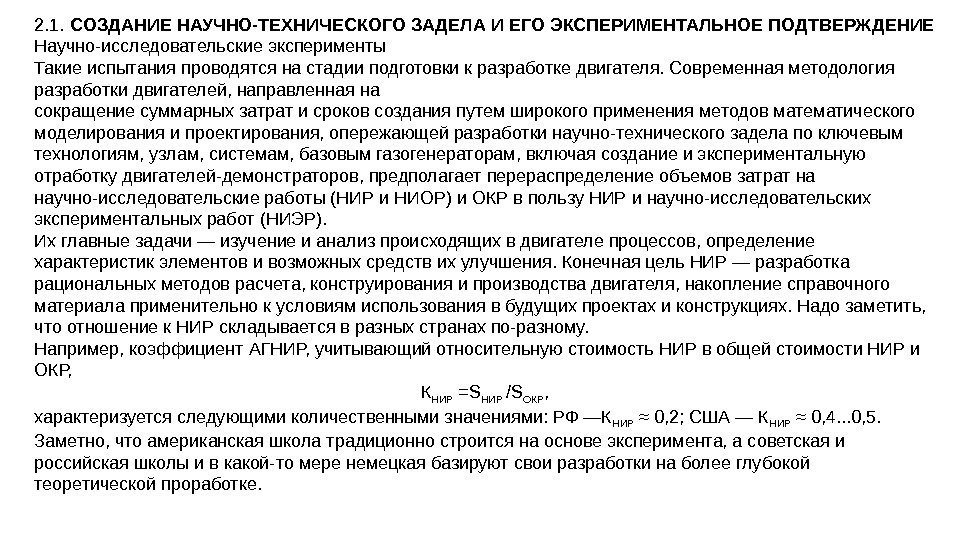
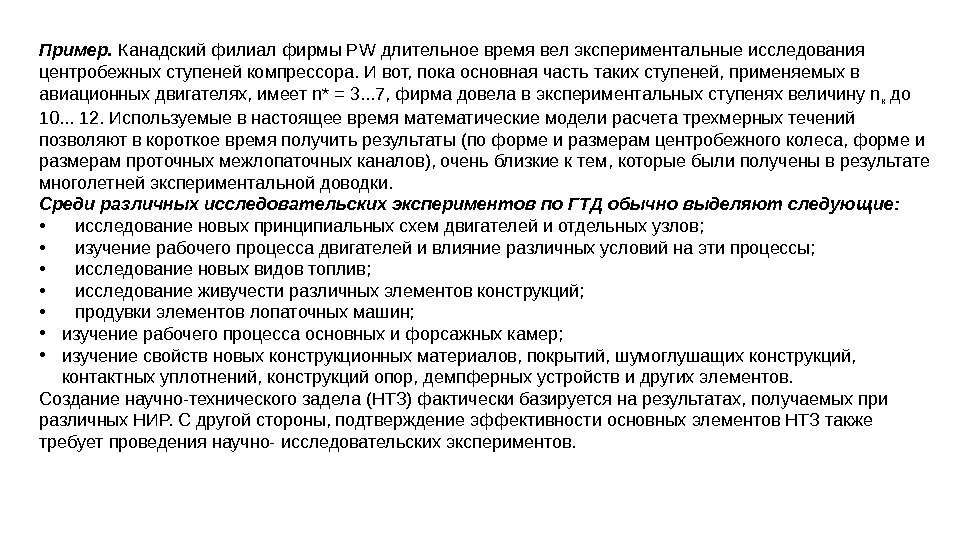
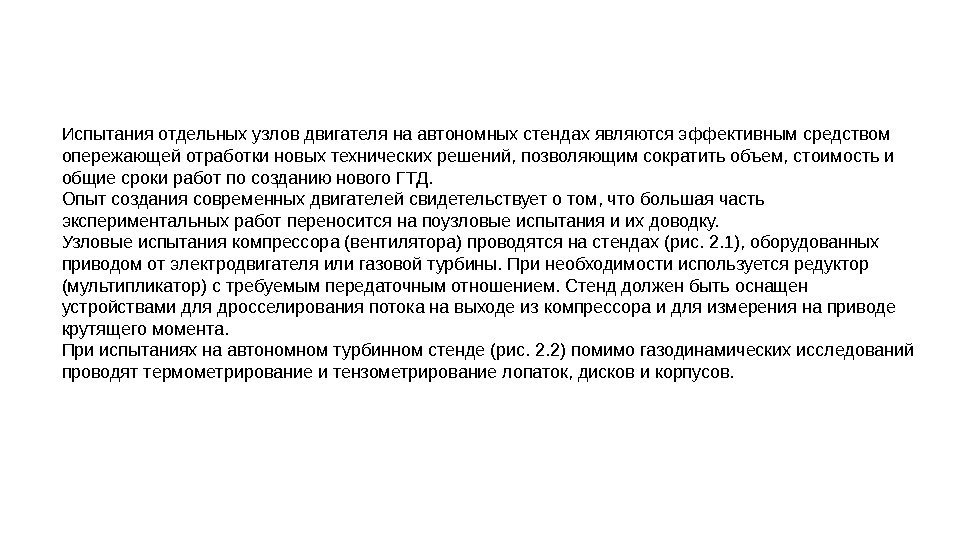
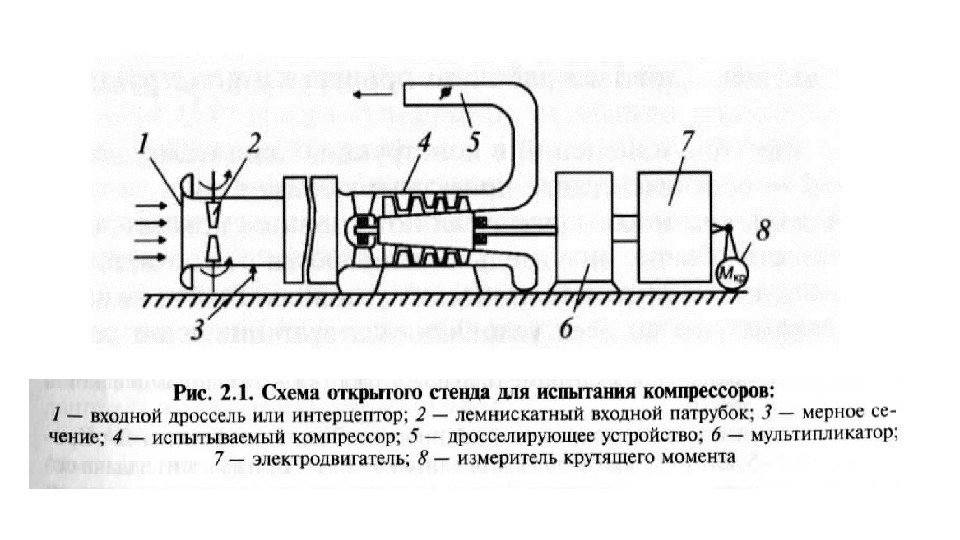

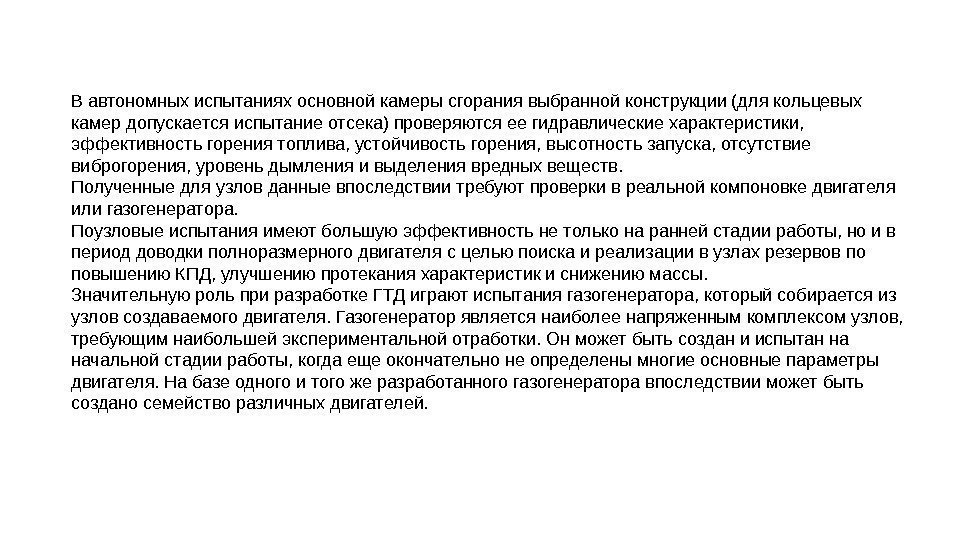
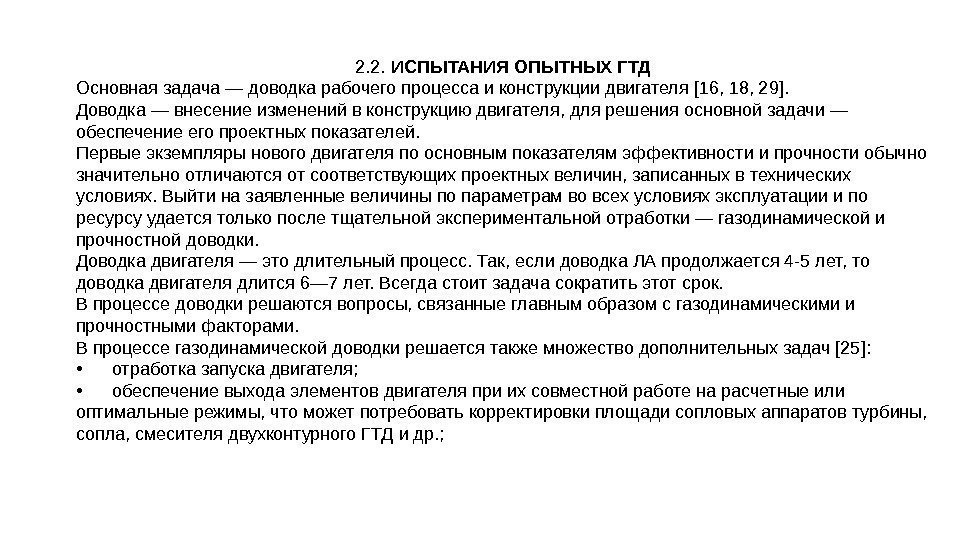
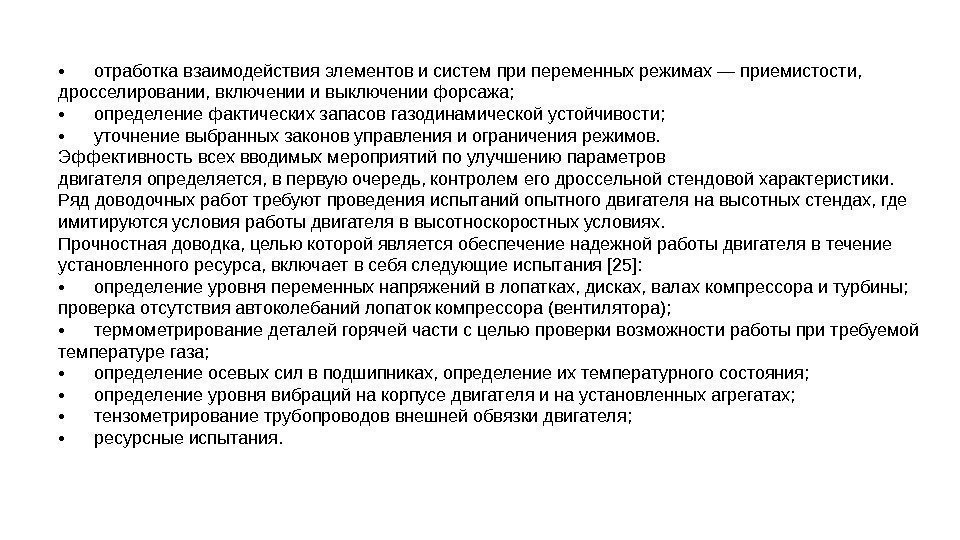
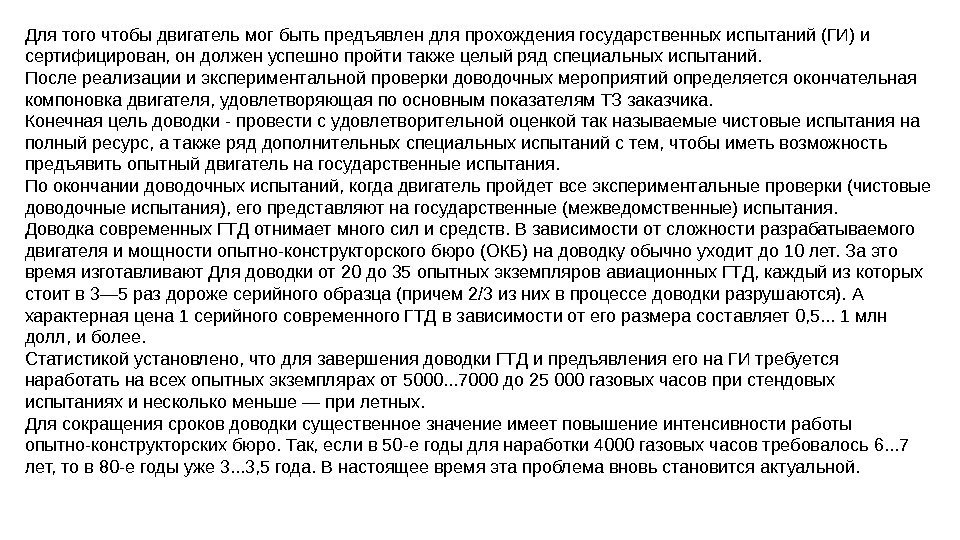
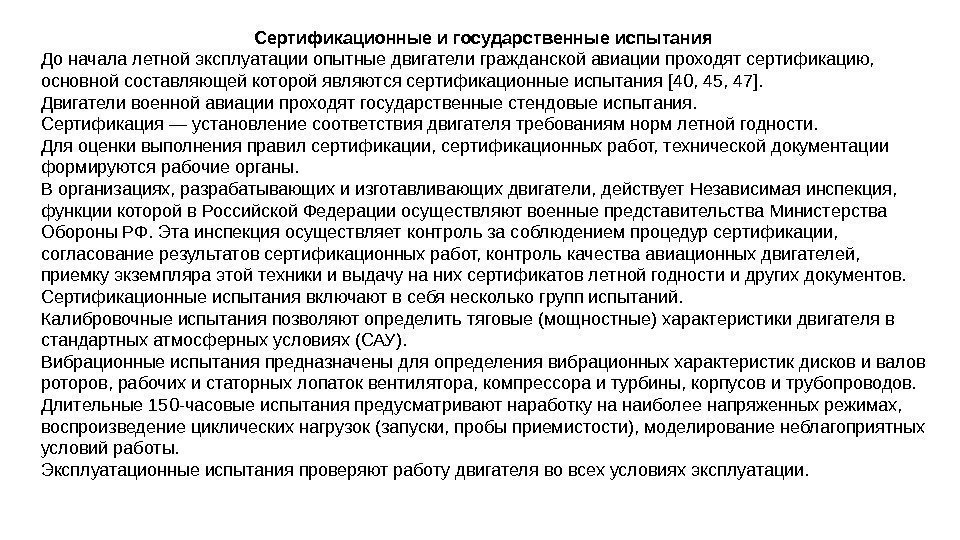
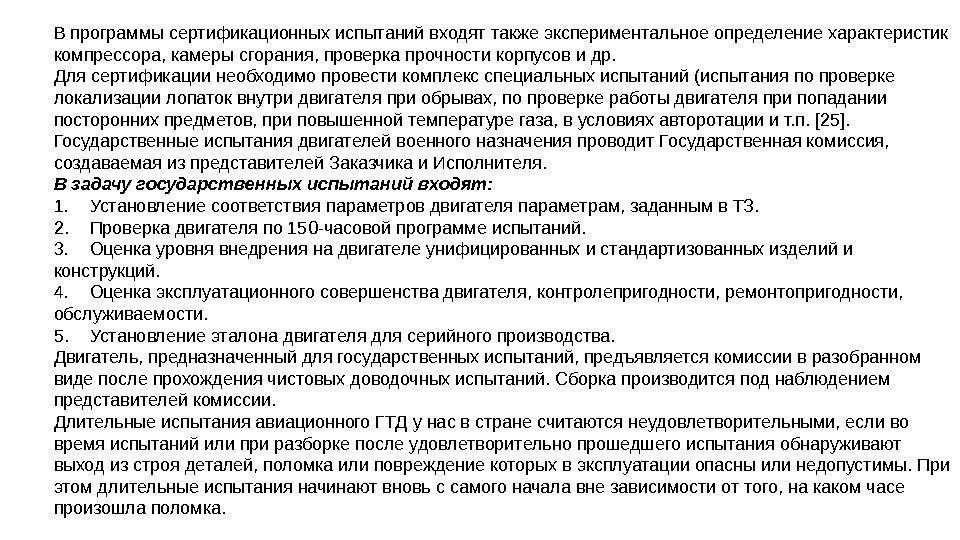
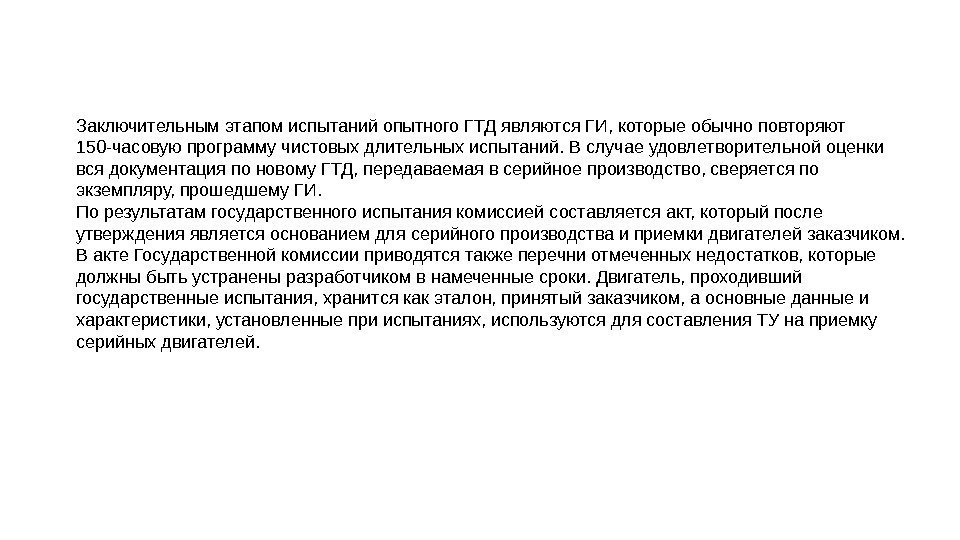
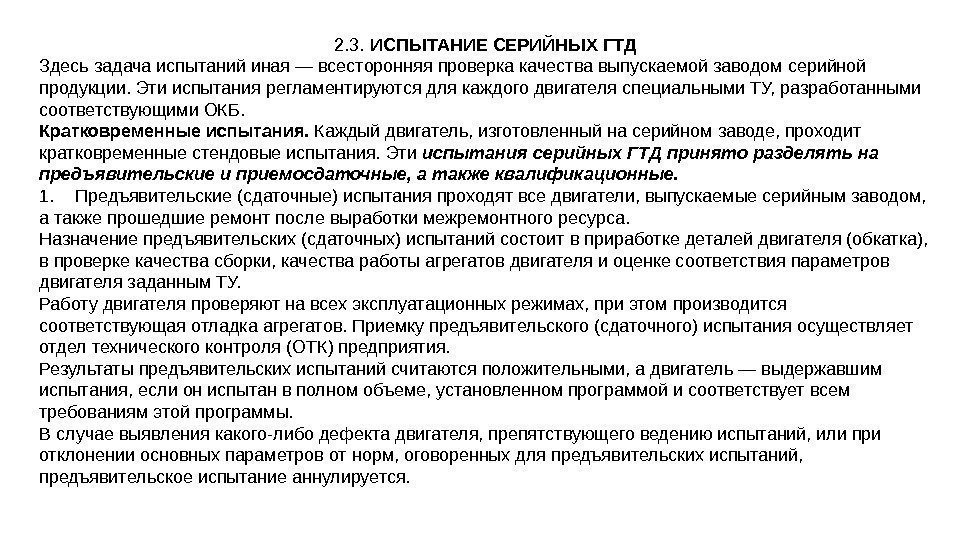
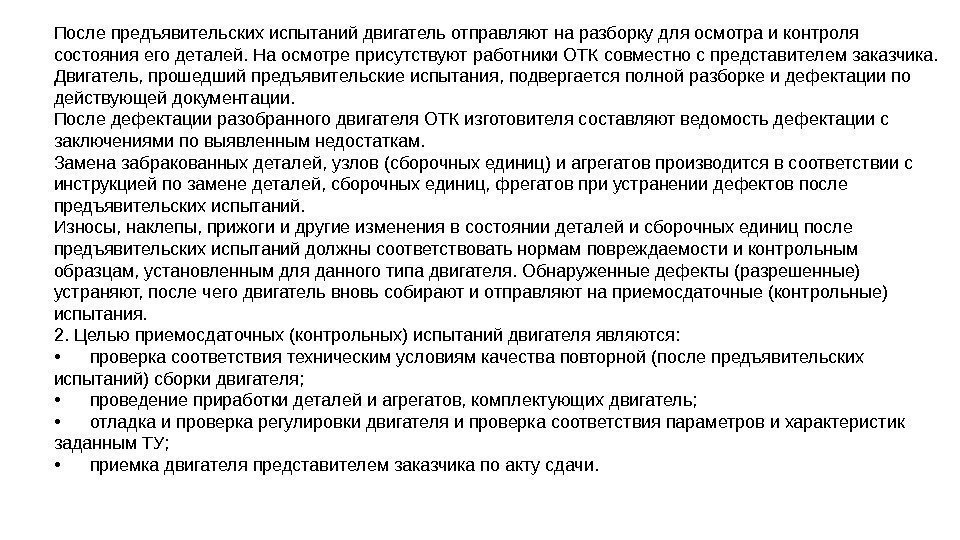
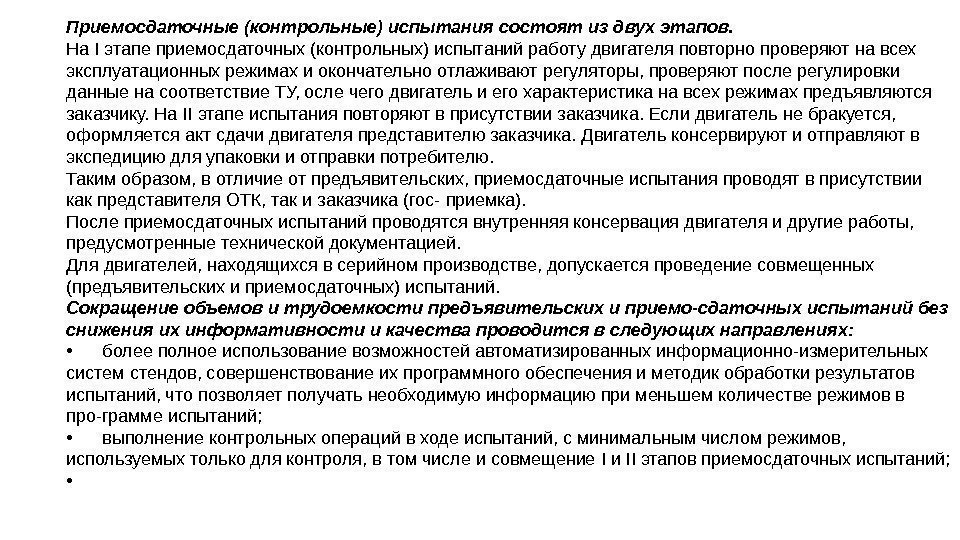
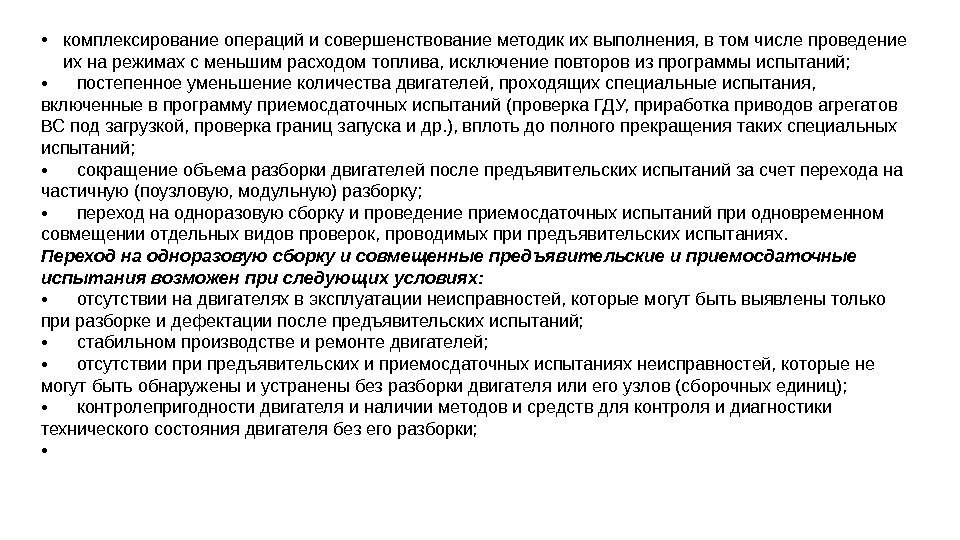
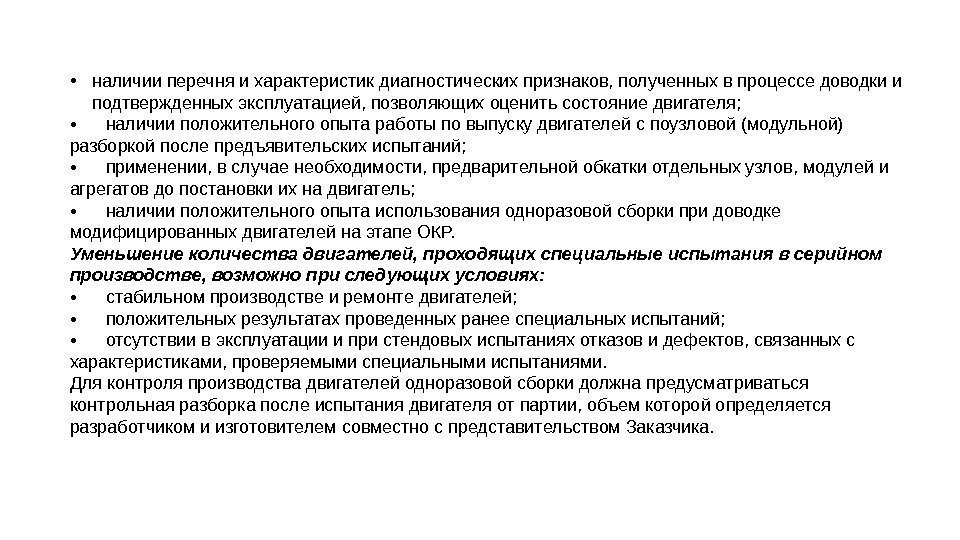
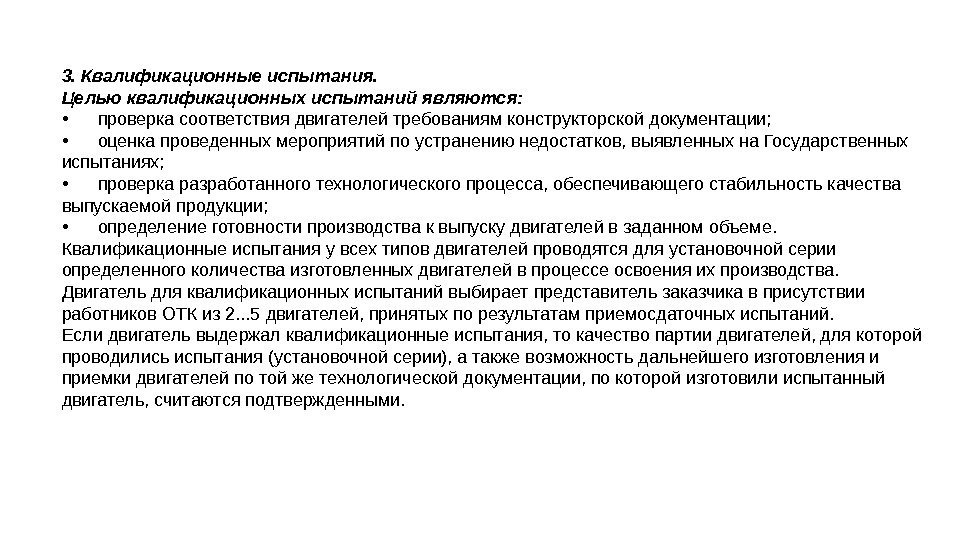
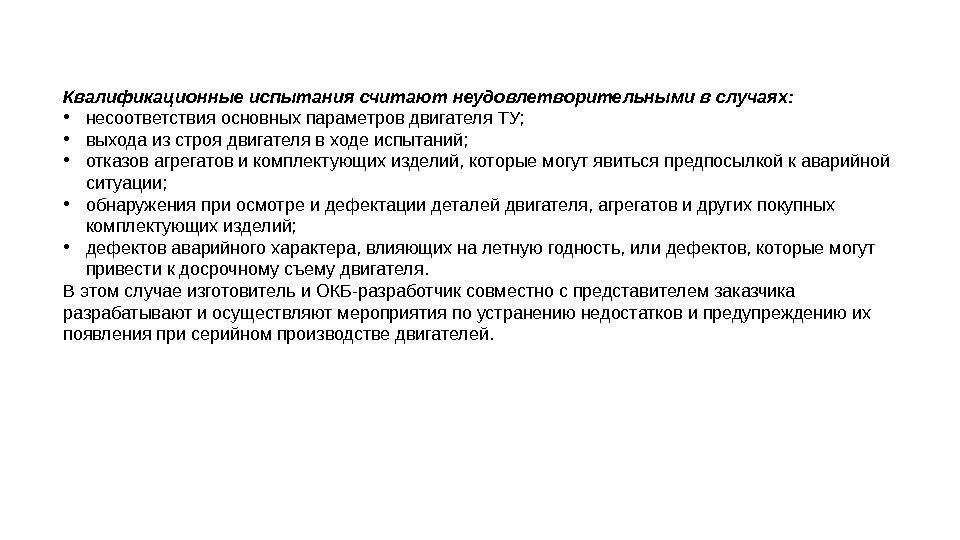
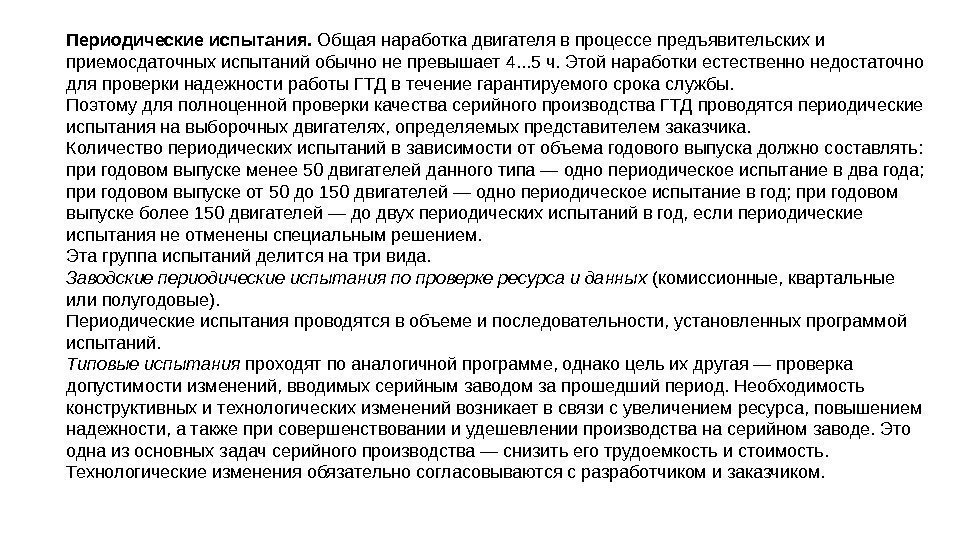
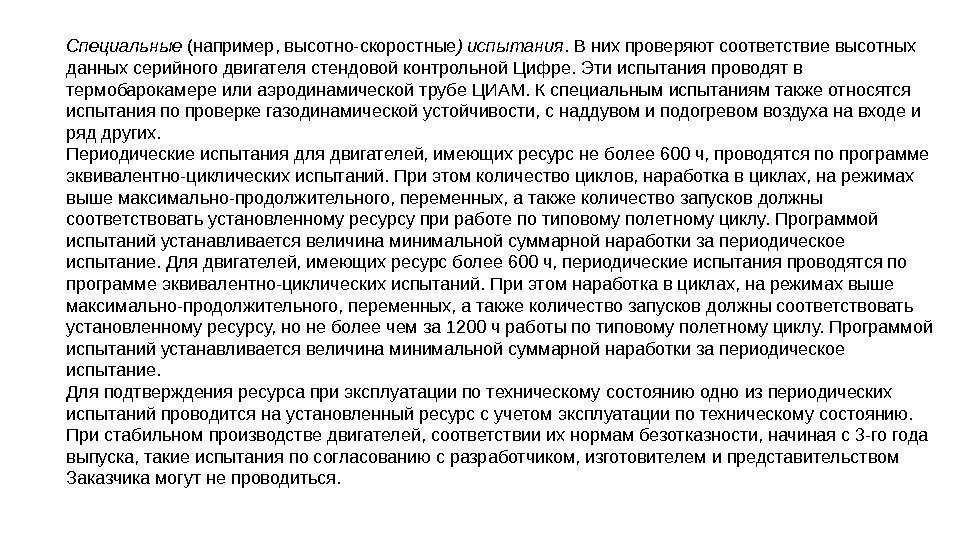
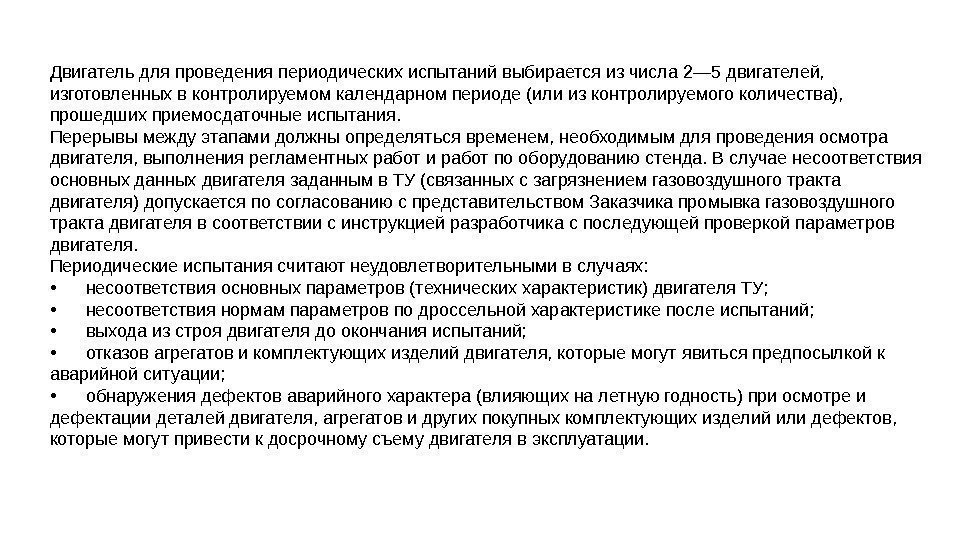
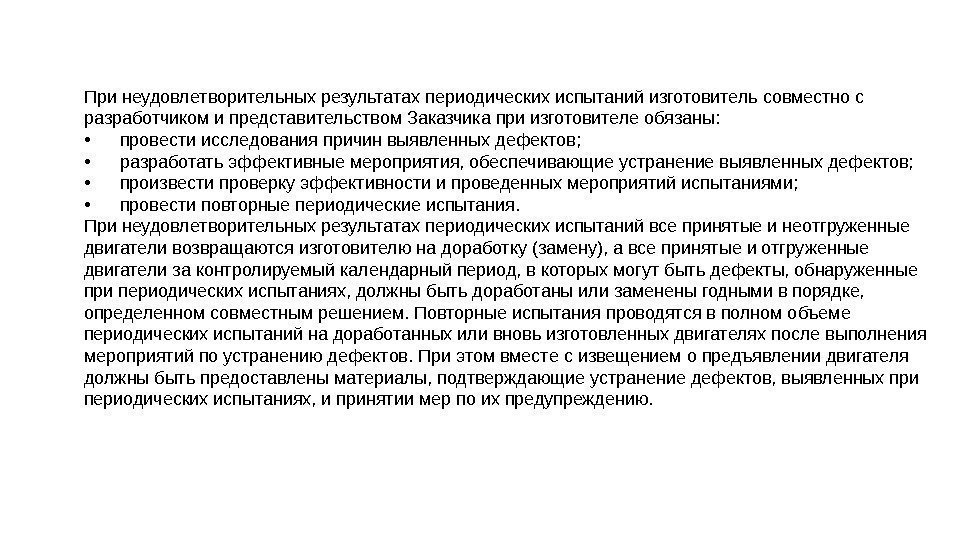
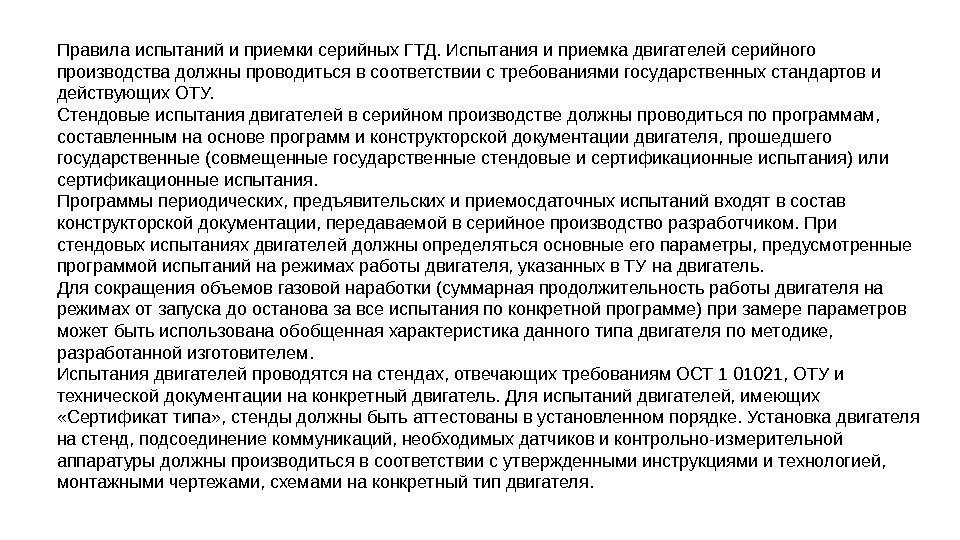
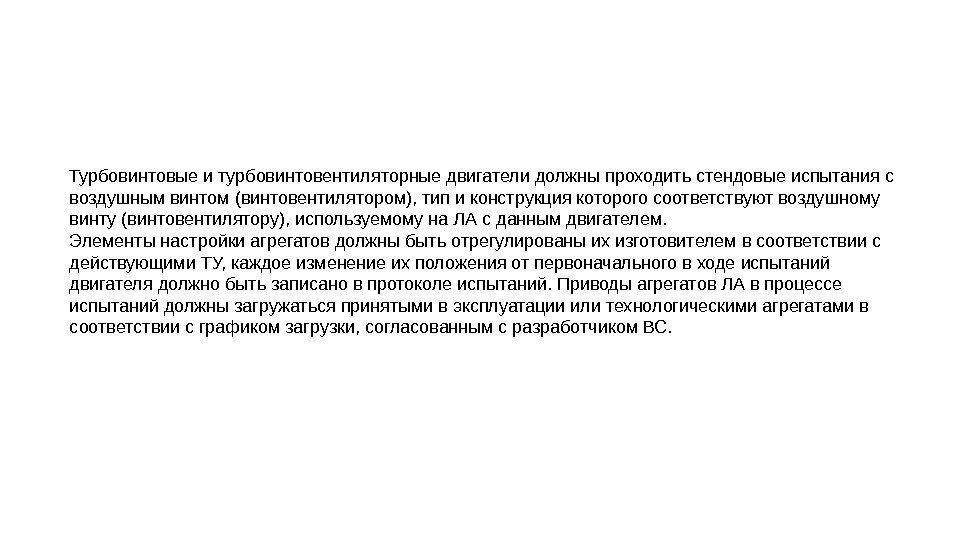
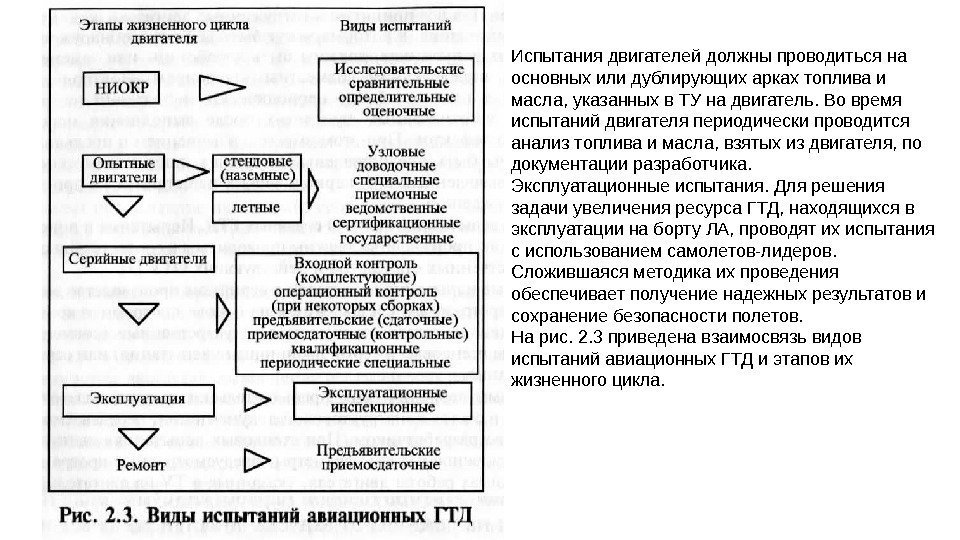
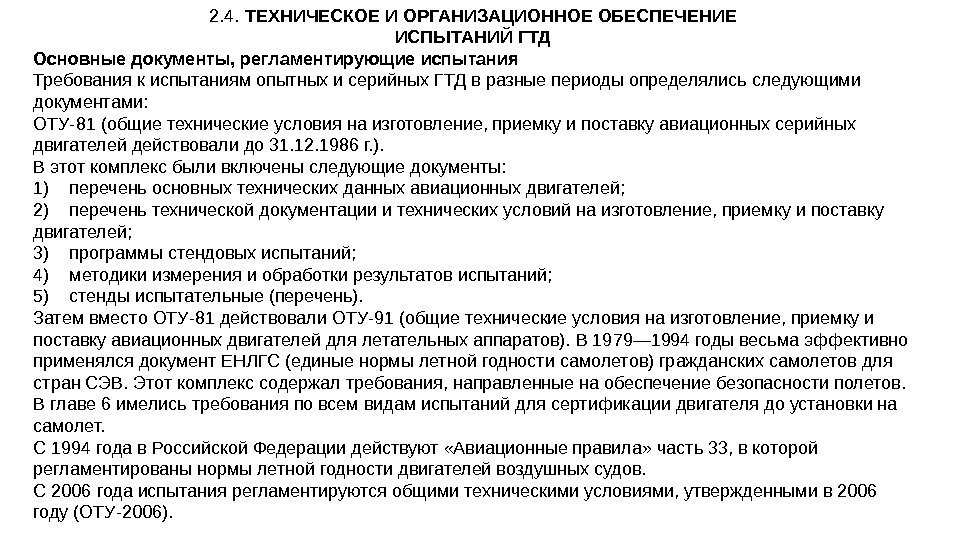
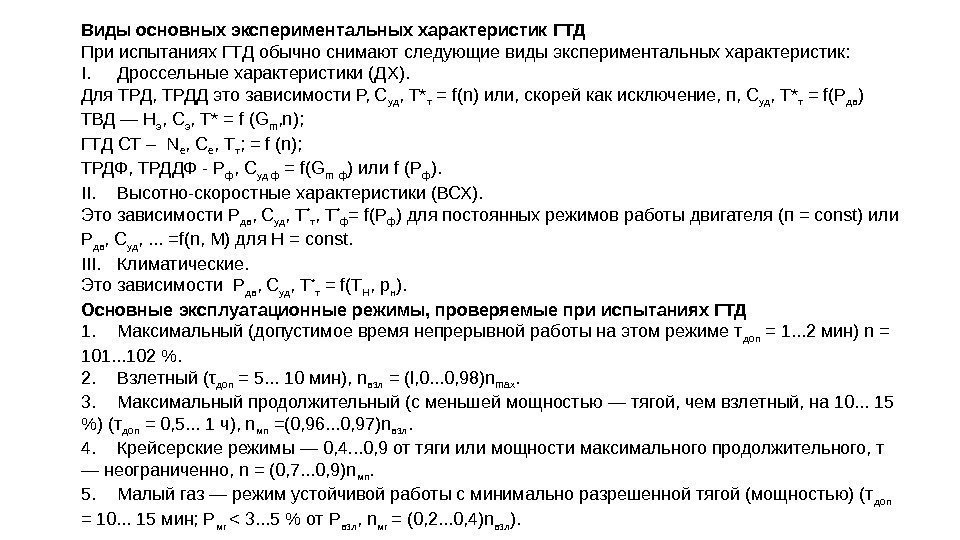
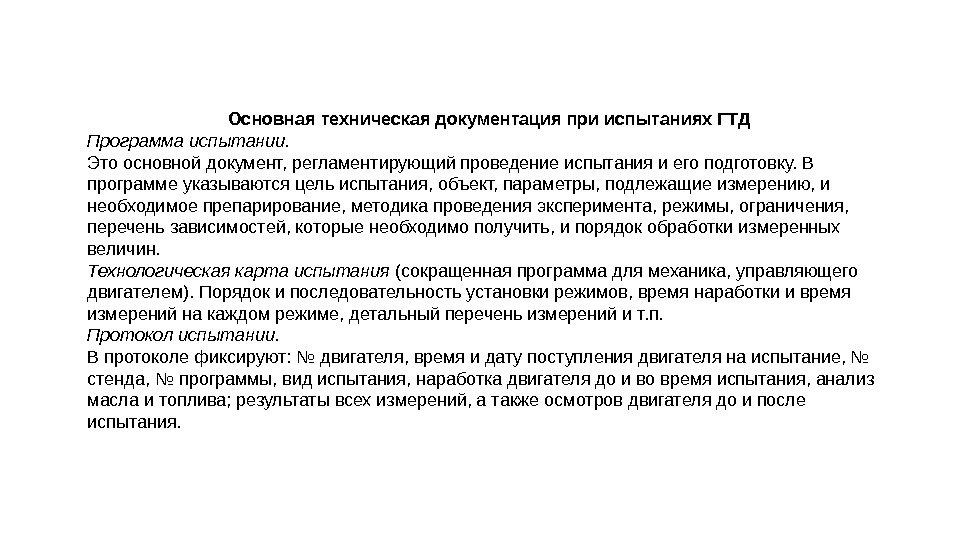
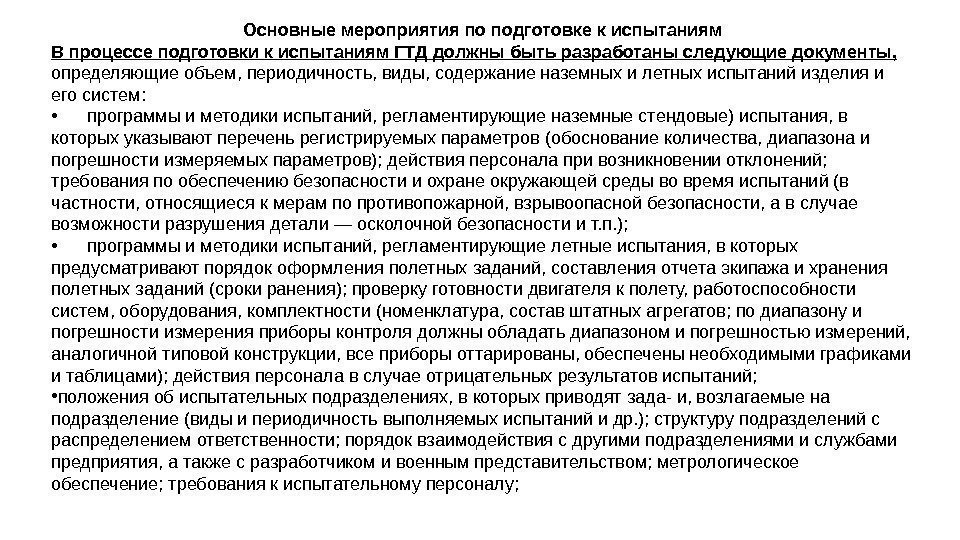
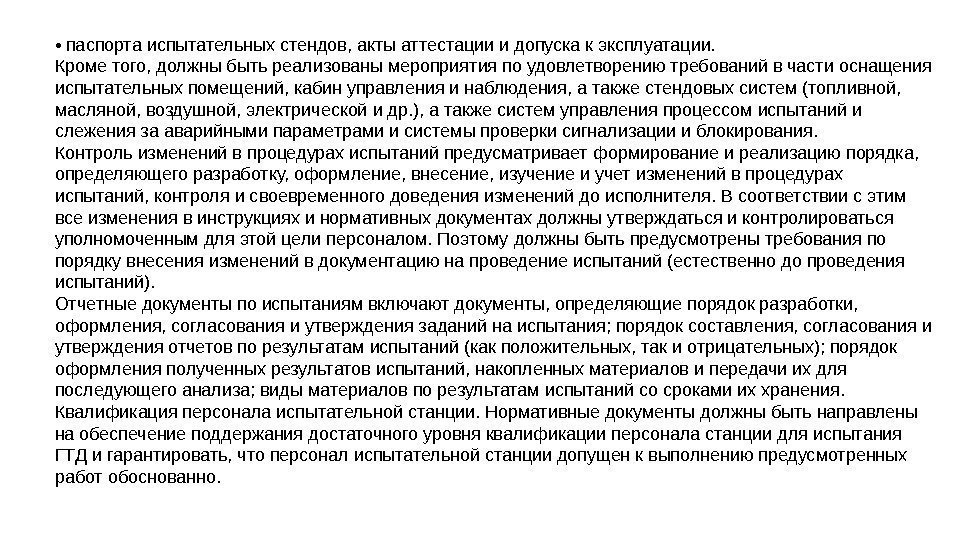
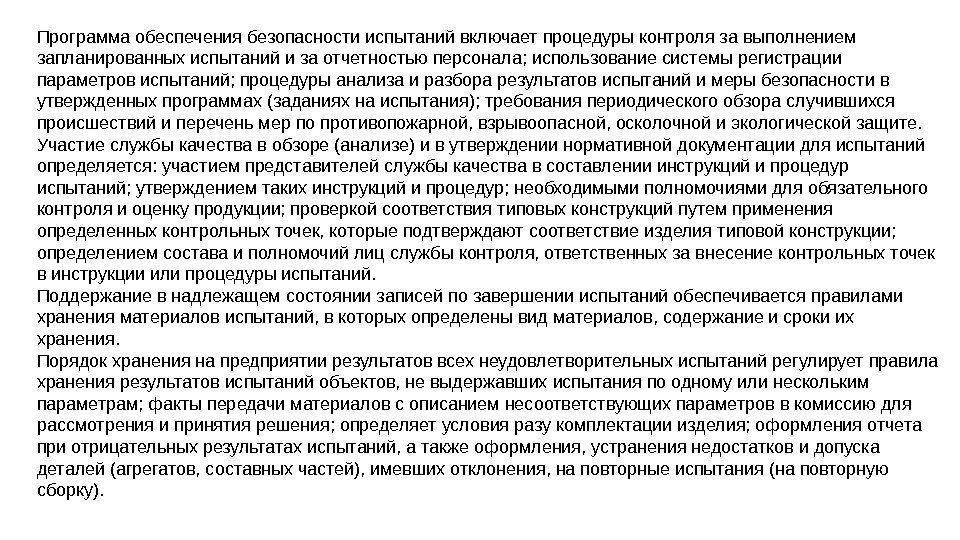
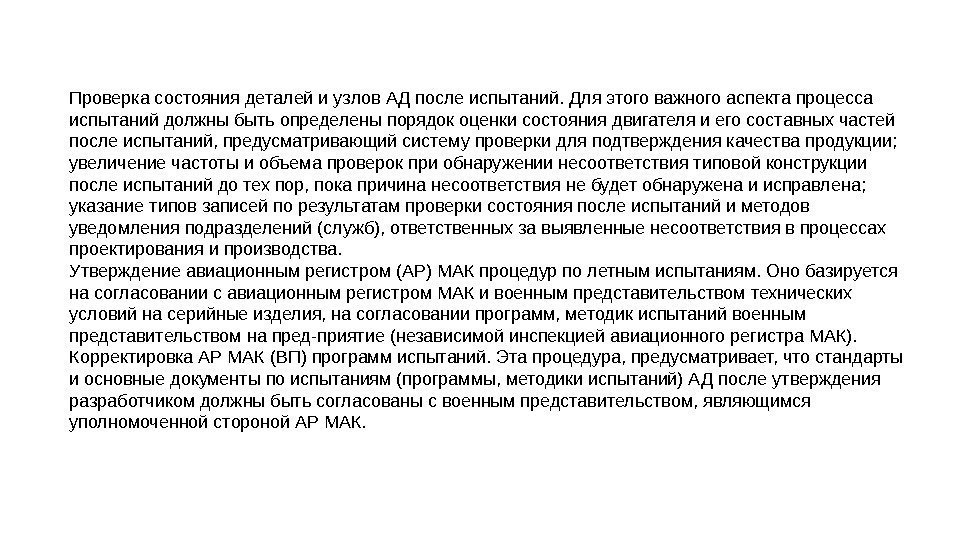
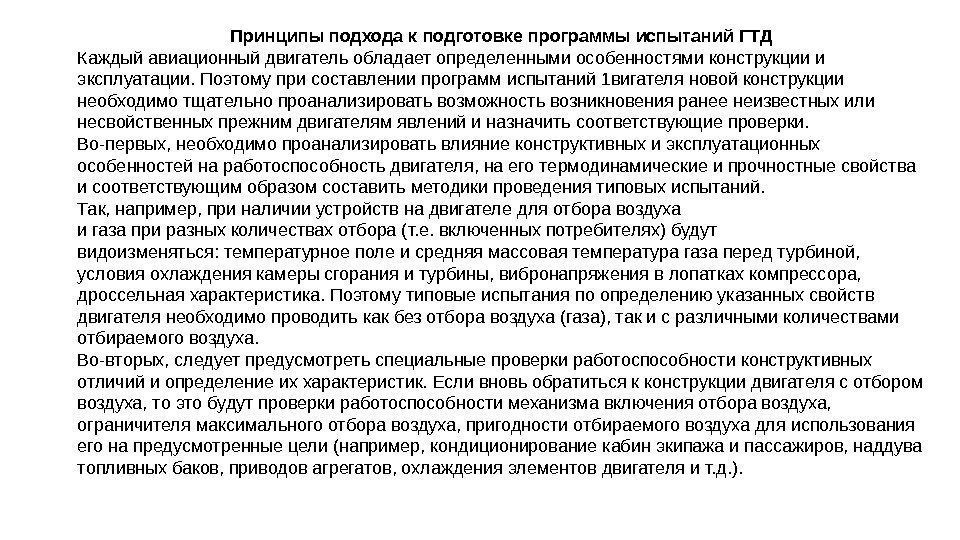
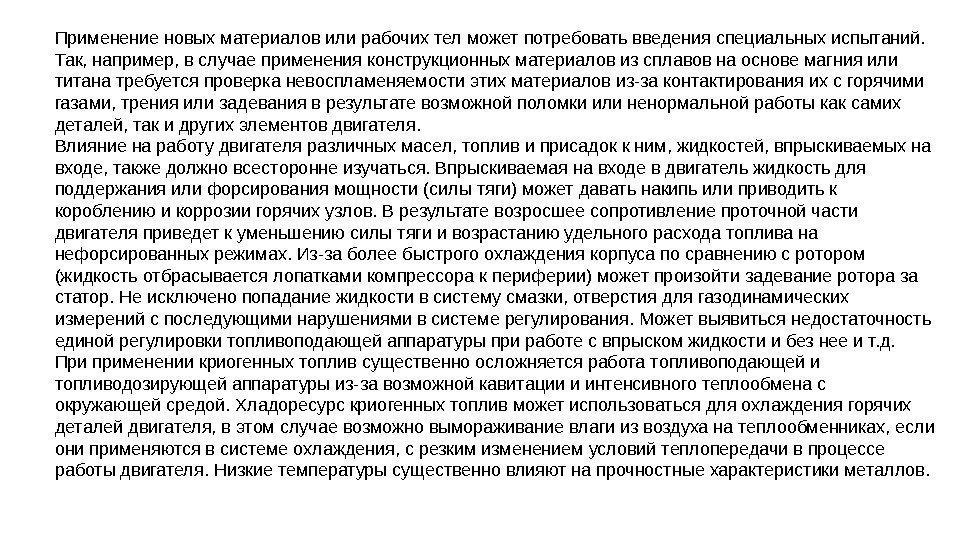
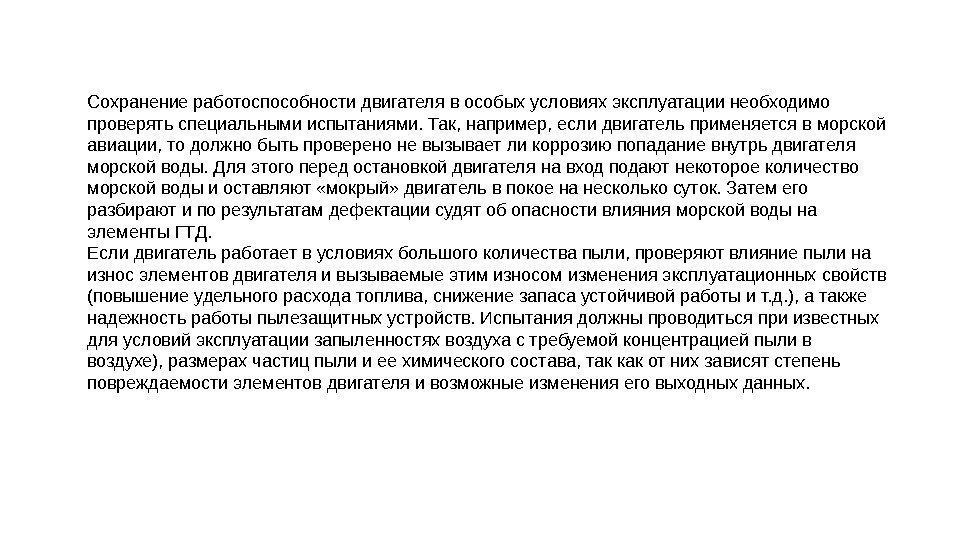
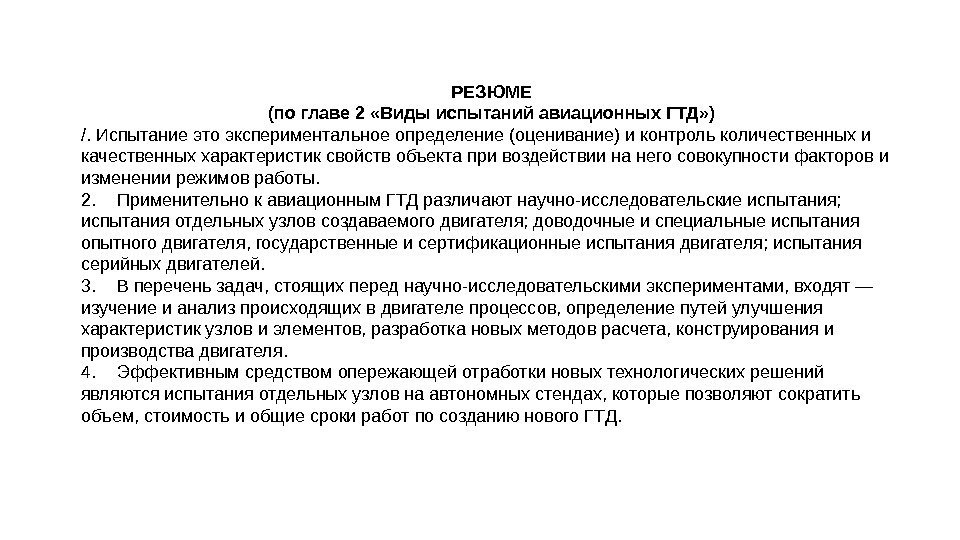
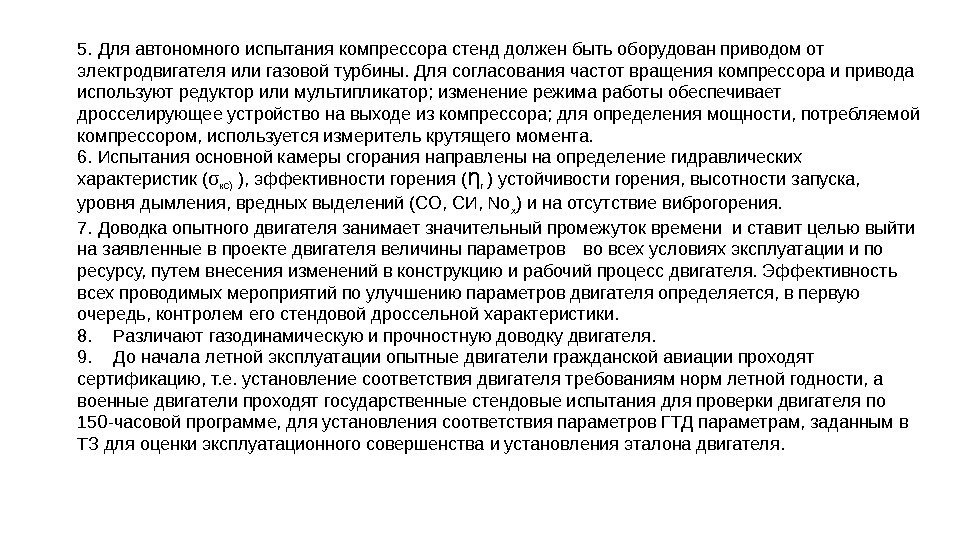
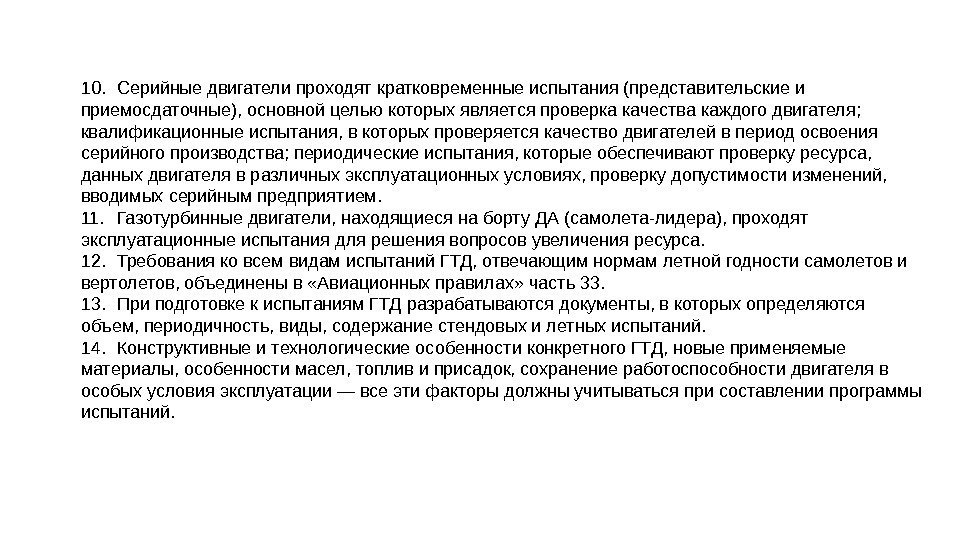
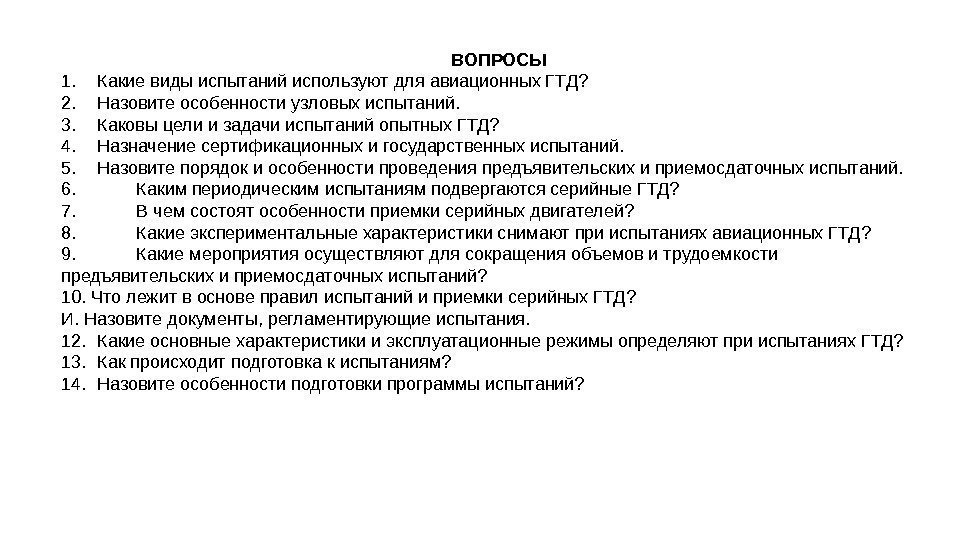
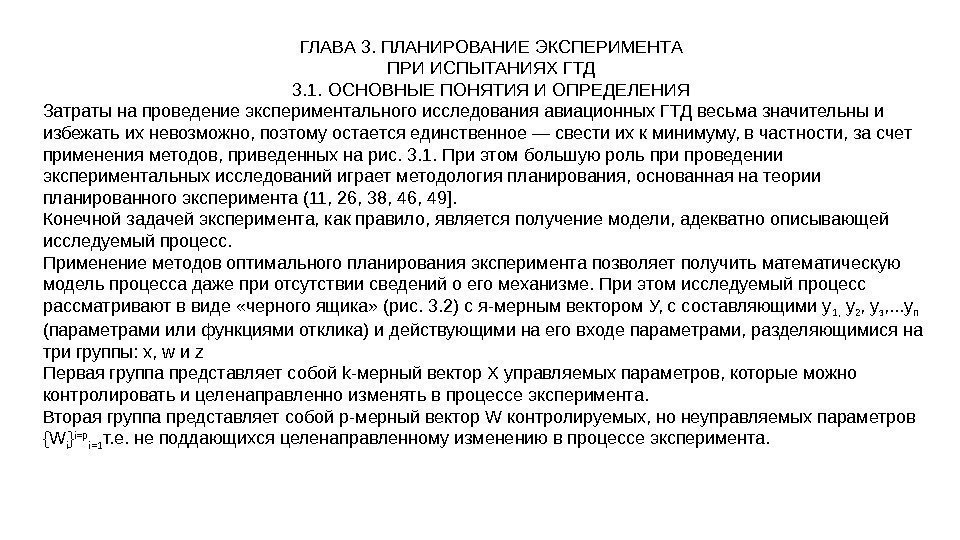
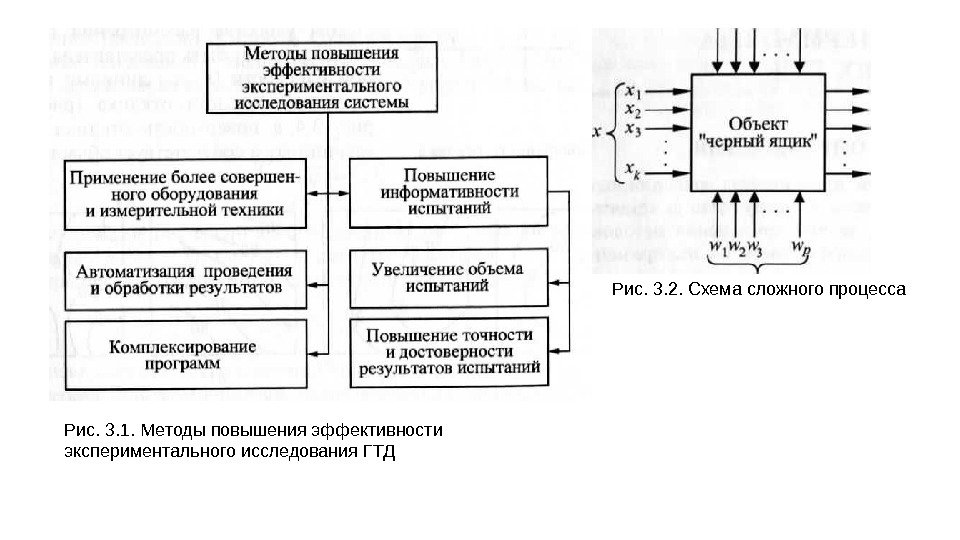
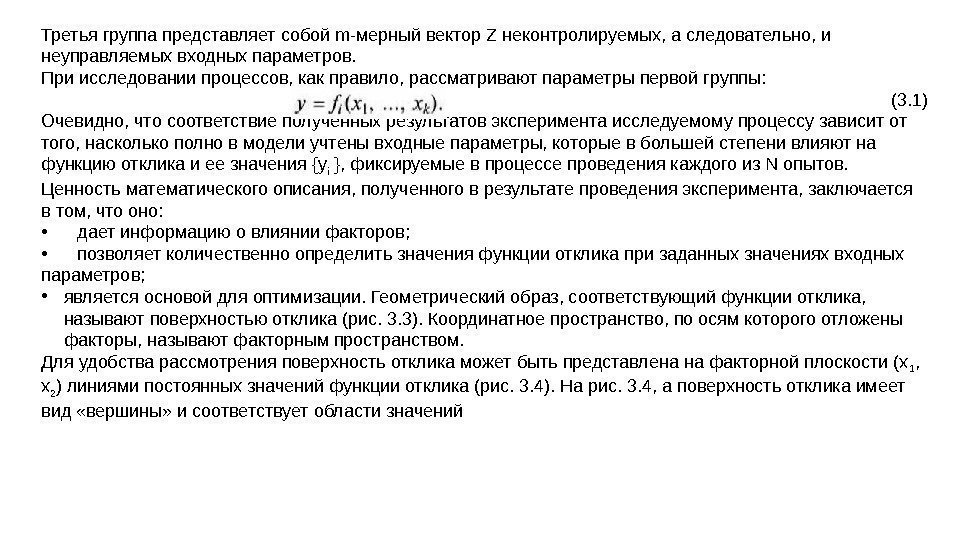
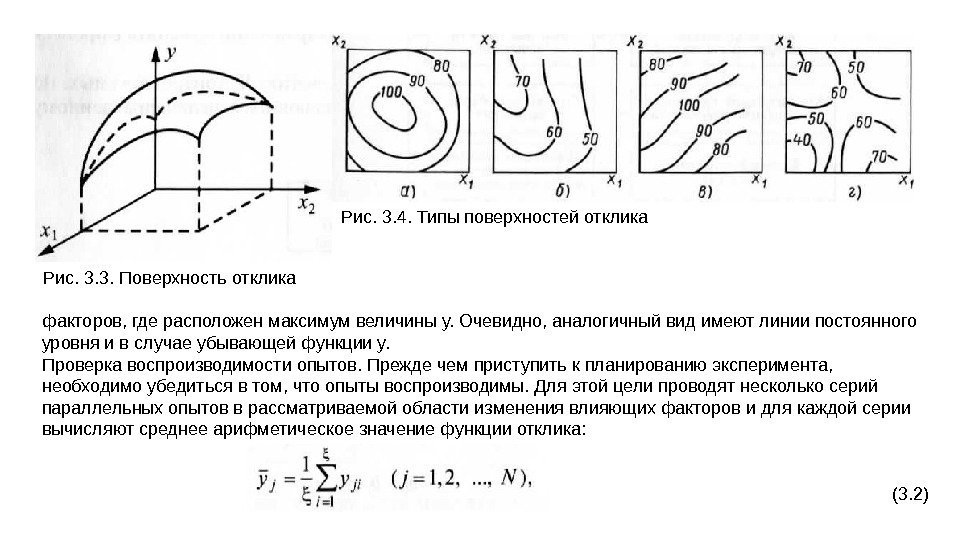
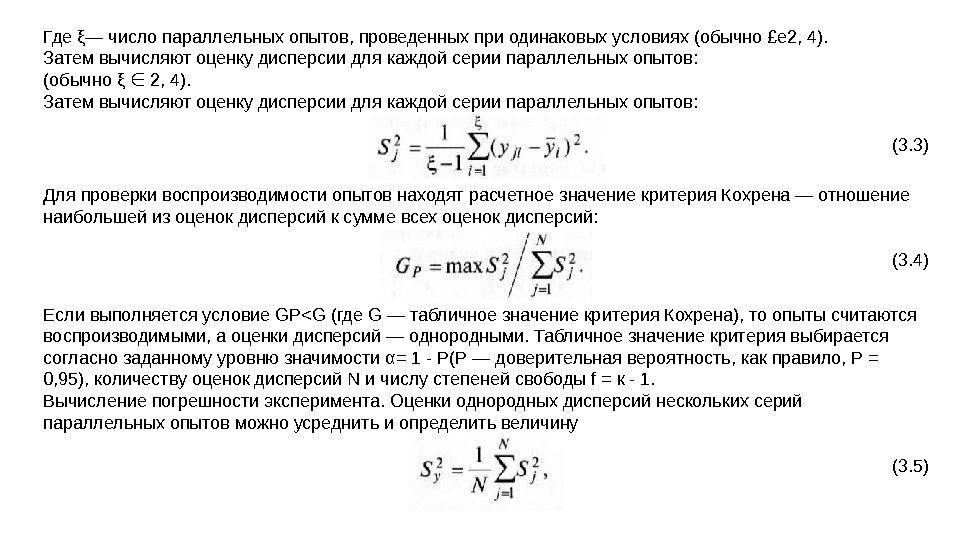
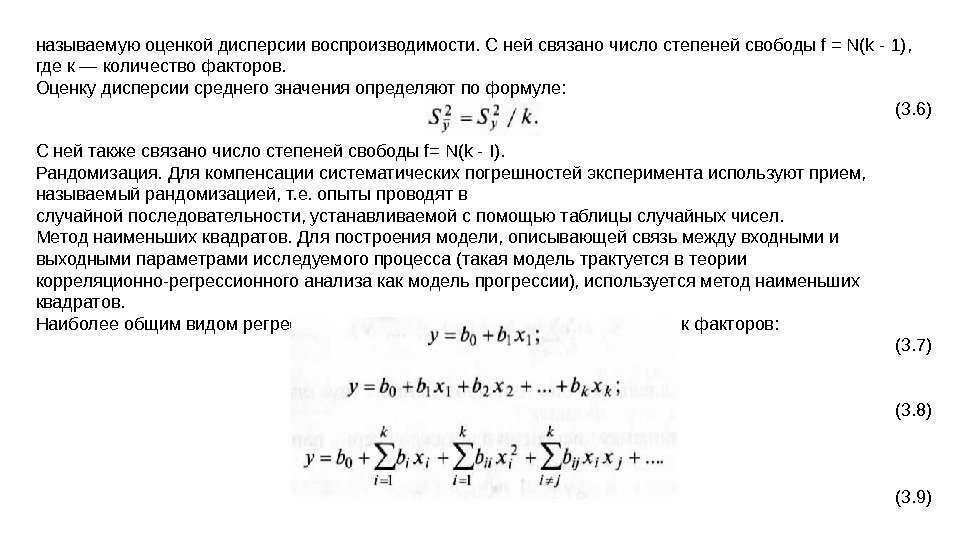
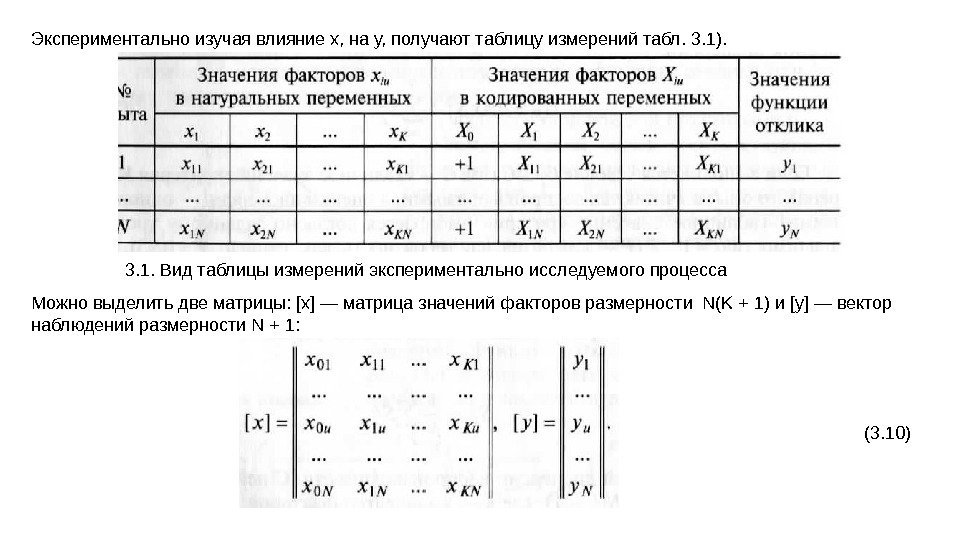
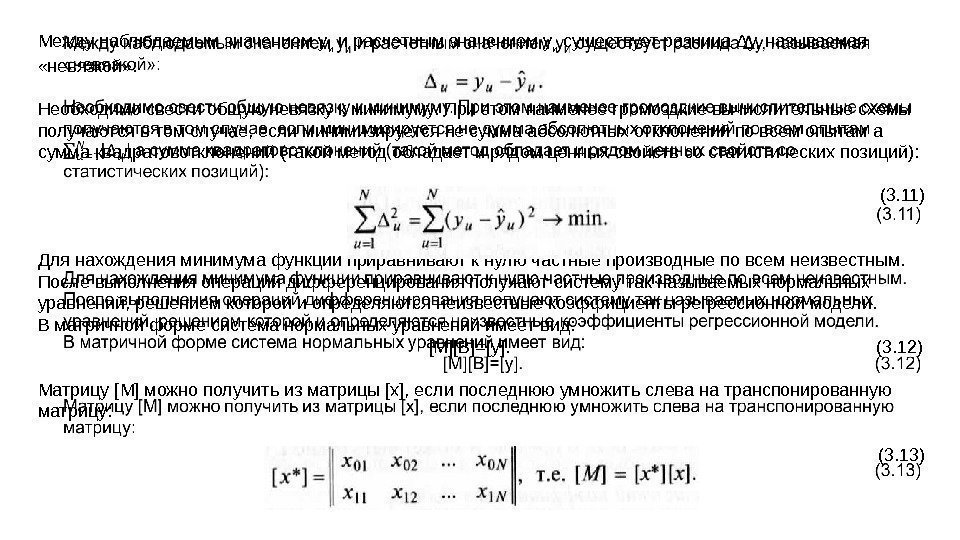
![Аналогичным образом матрица [y M ] получается из матрицы [у]: [y M ]=[x*][y] Аналогичным образом матрица [y M ] получается из матрицы [у]: [y M ]=[x*][y]](http://present5.com/presentforday2/20170201/mmk_ispytania_i_kontrol_kachestva_izdeliy_2017_images/mmk_ispytania_i_kontrol_kachestva_izdeliy_2017_170.jpg)
![Матрица [Д] называется ковариационной или матрицей ошибок. Она имеет первостепенное значение при построении моделей, Матрица [Д] называется ковариационной или матрицей ошибок. Она имеет первостепенное значение при построении моделей,](http://present5.com/presentforday2/20170201/mmk_ispytania_i_kontrol_kachestva_izdeliy_2017_images/mmk_ispytania_i_kontrol_kachestva_izdeliy_2017_171.jpg)
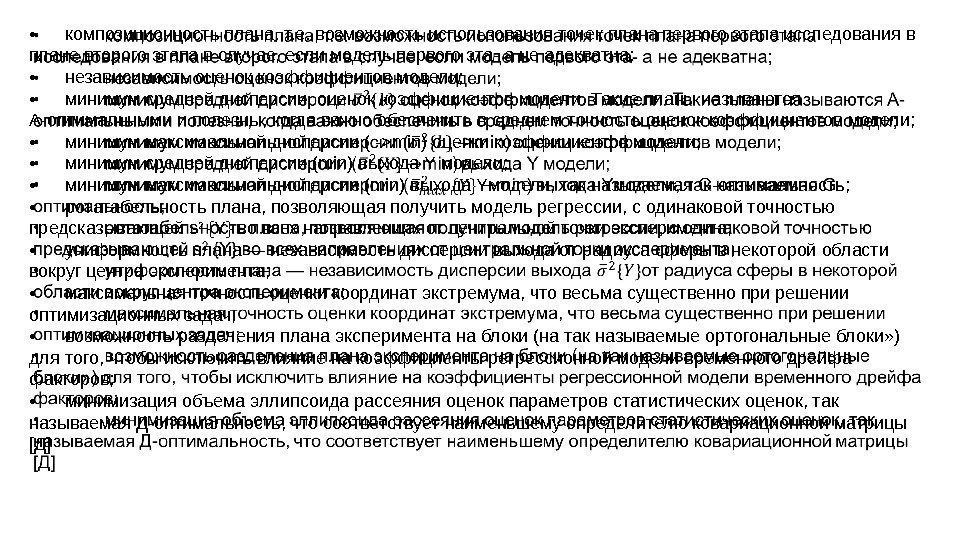
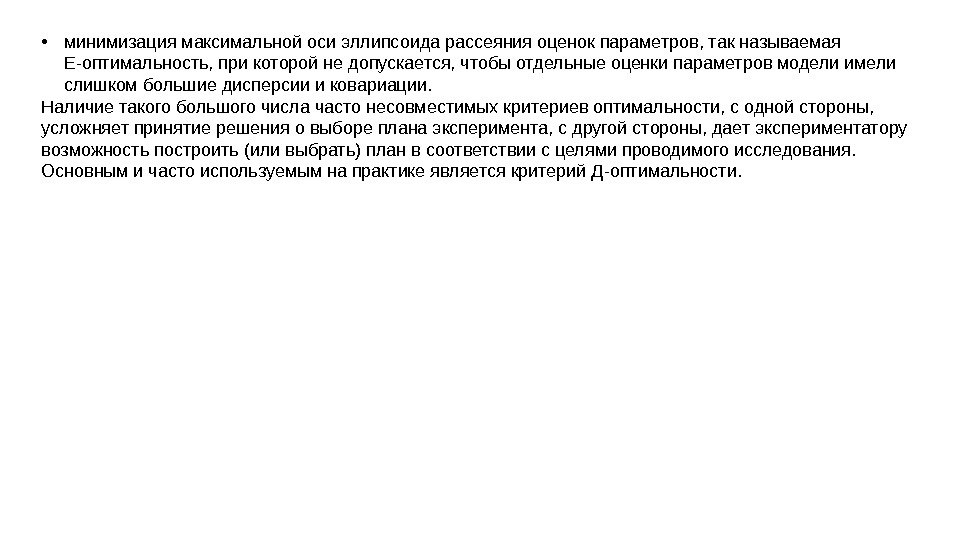
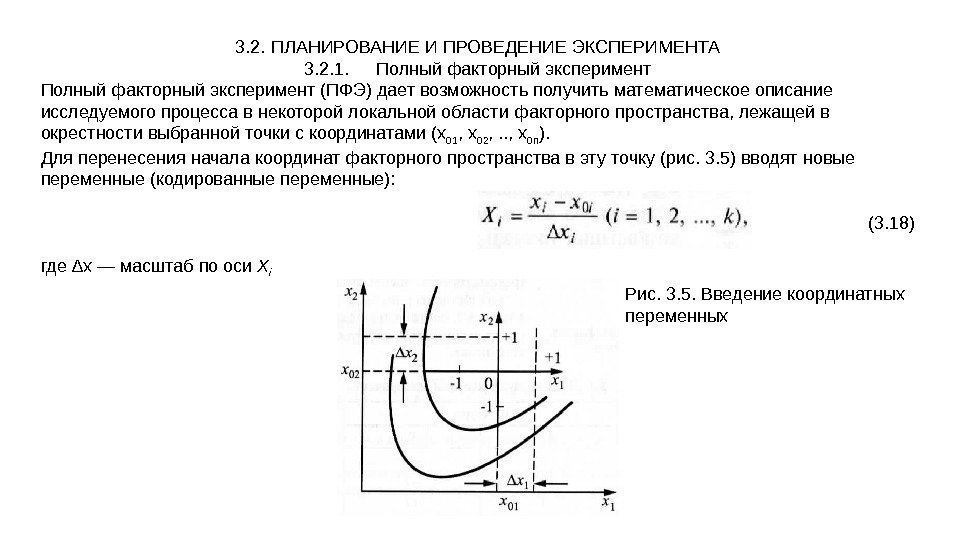
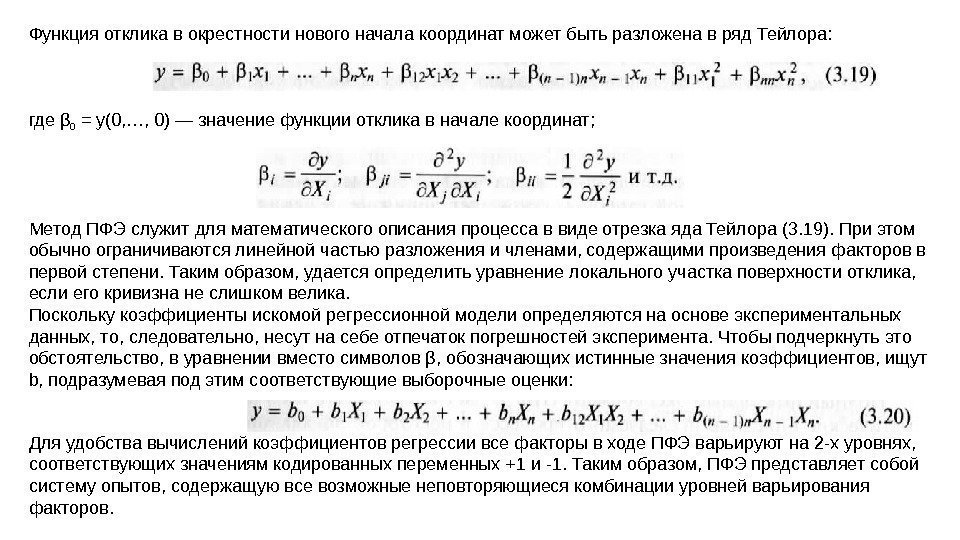
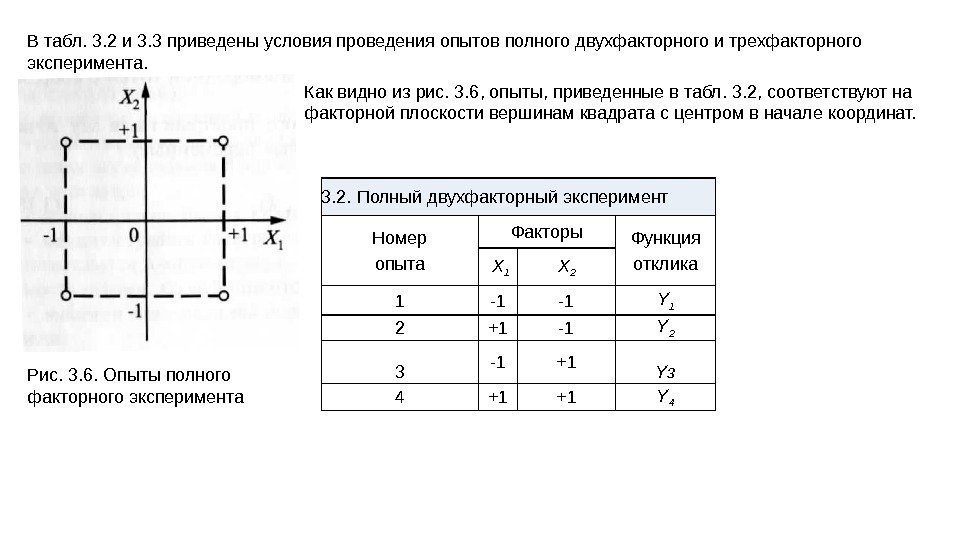
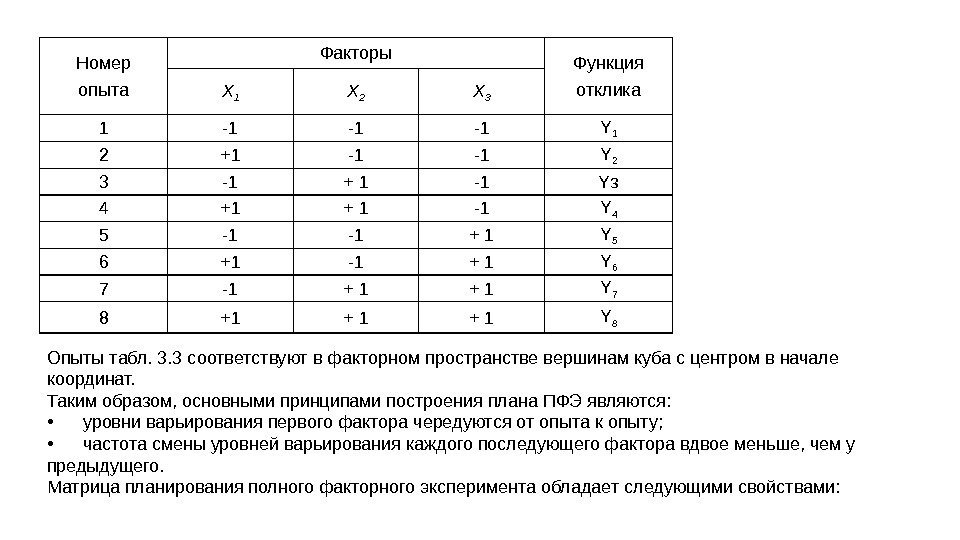
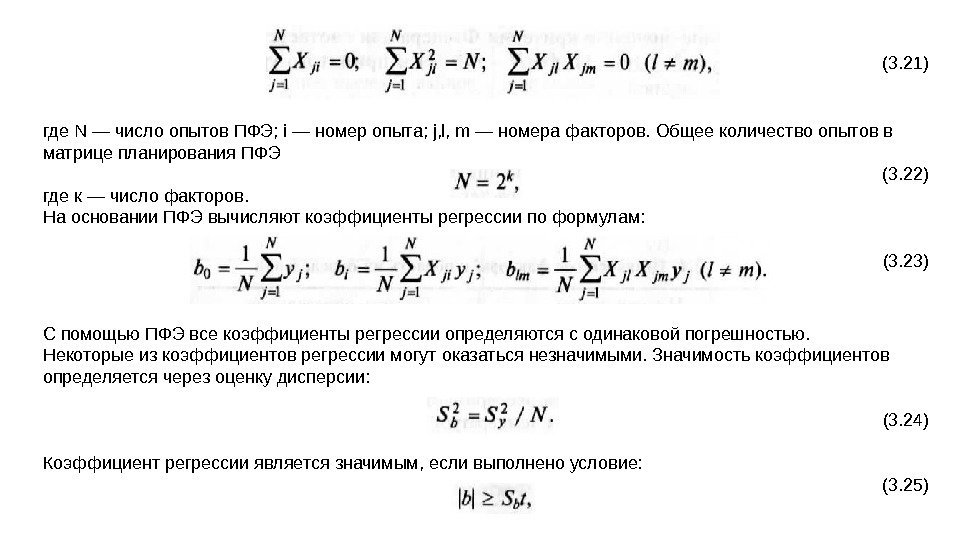
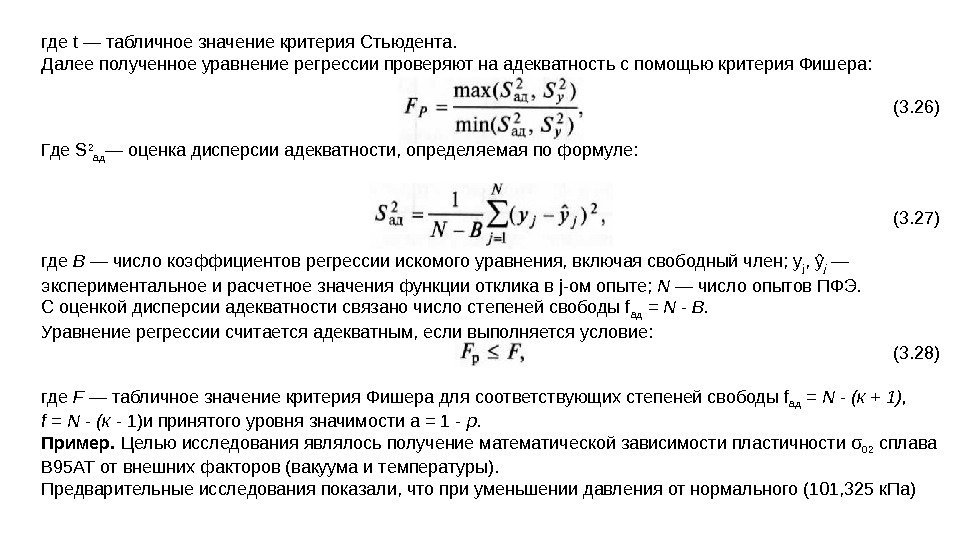
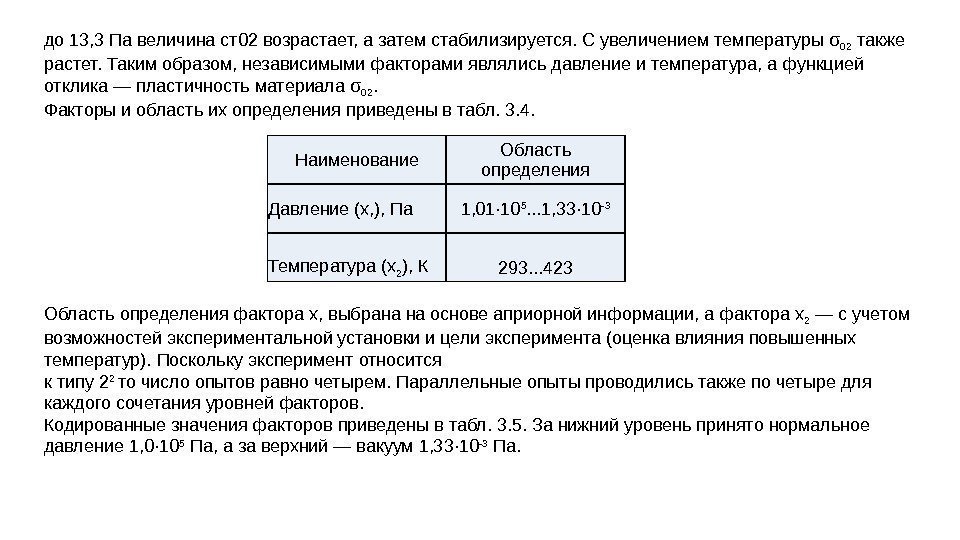
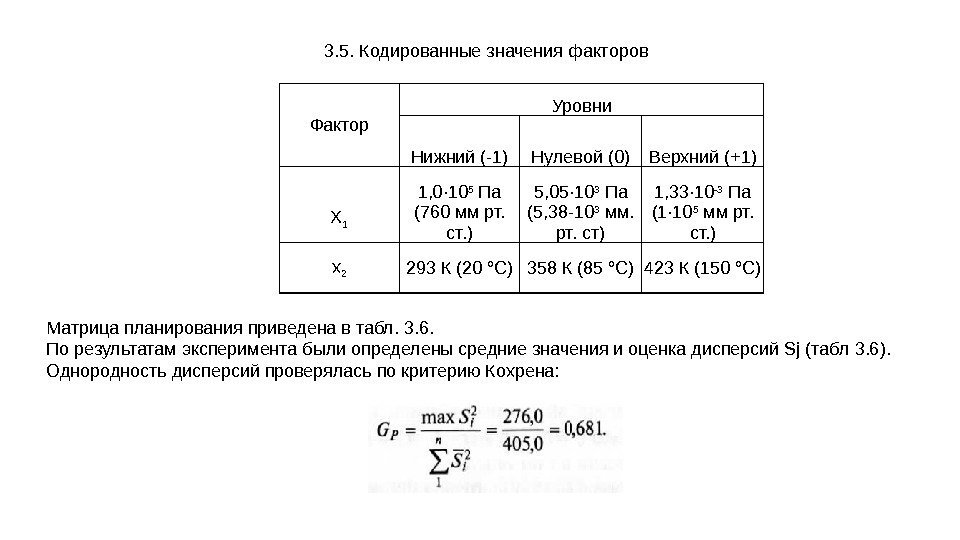
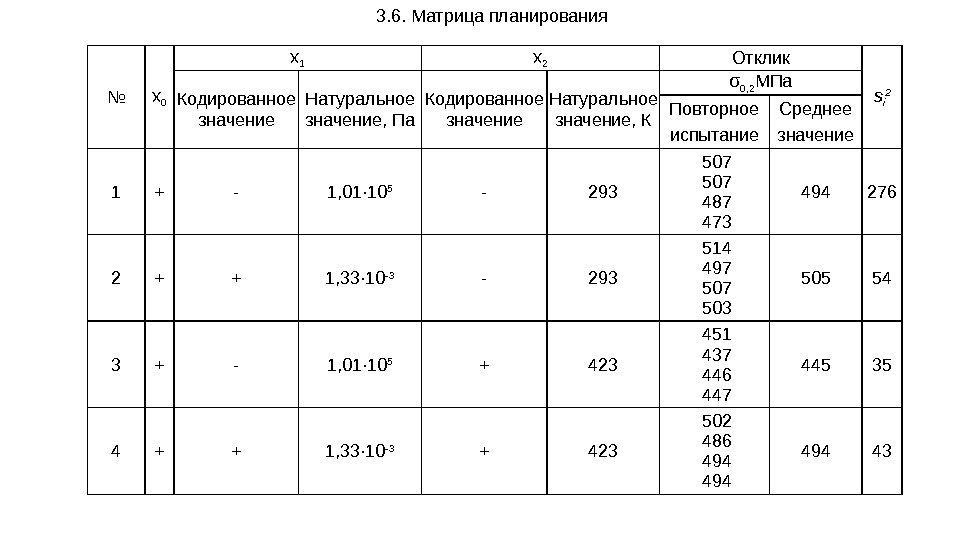
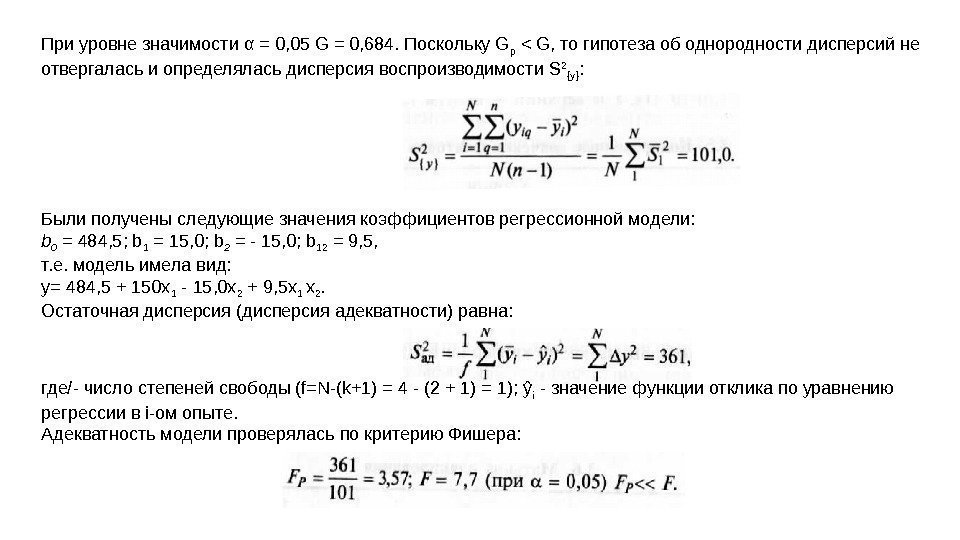
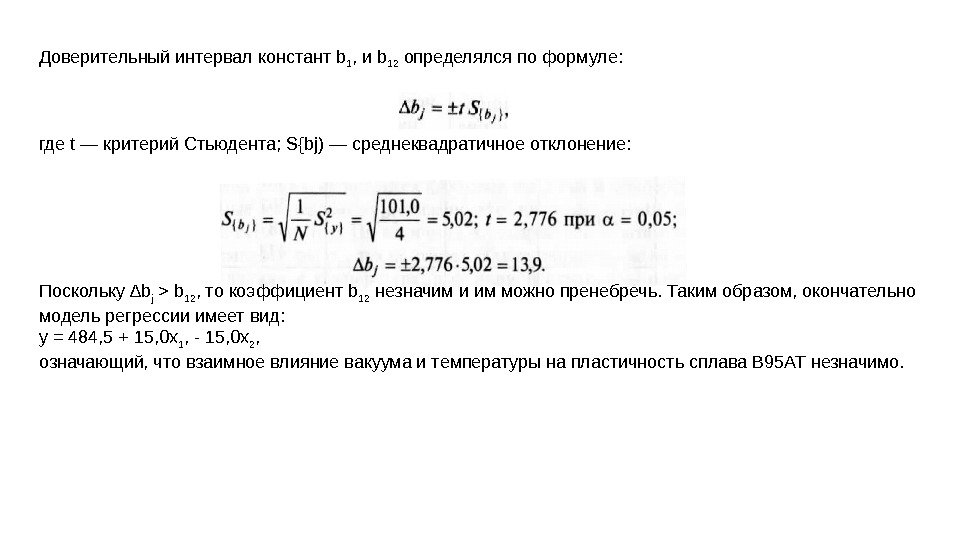
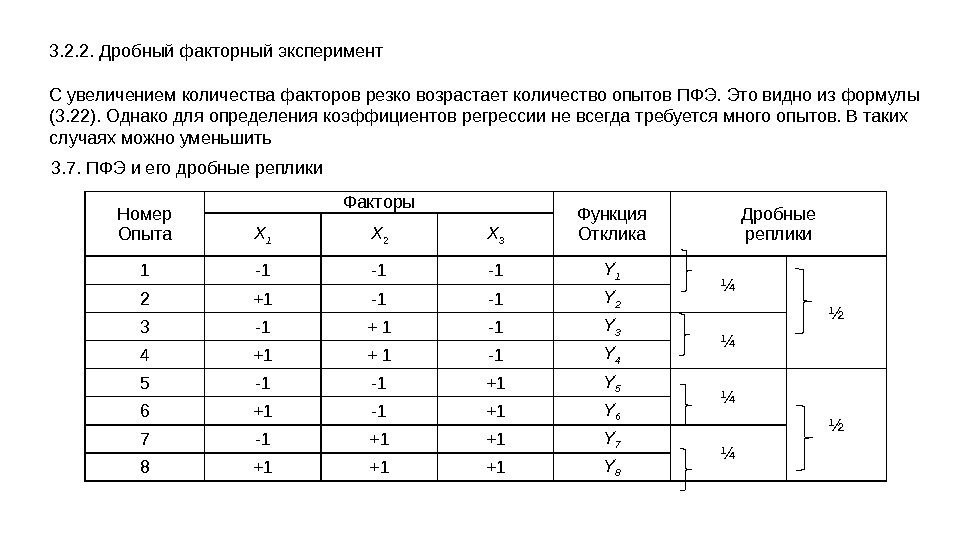
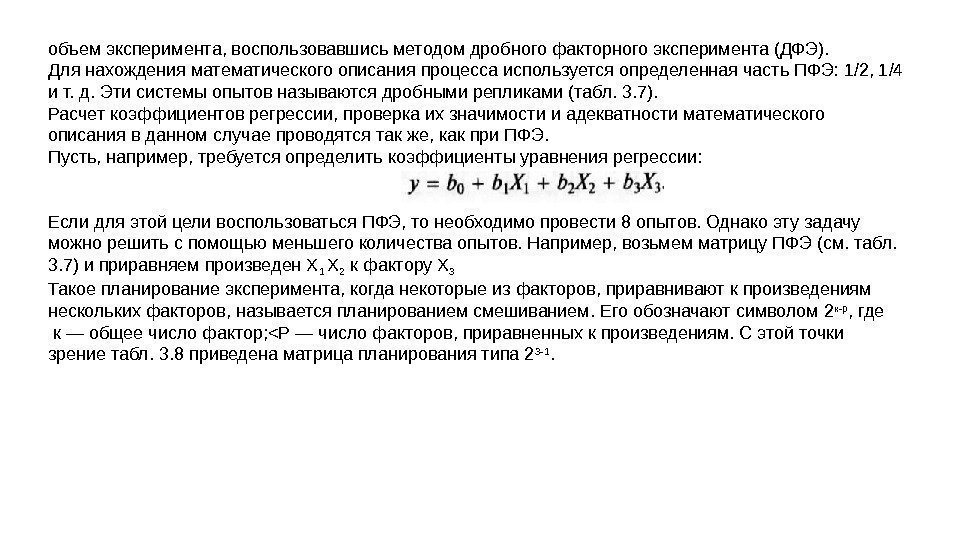
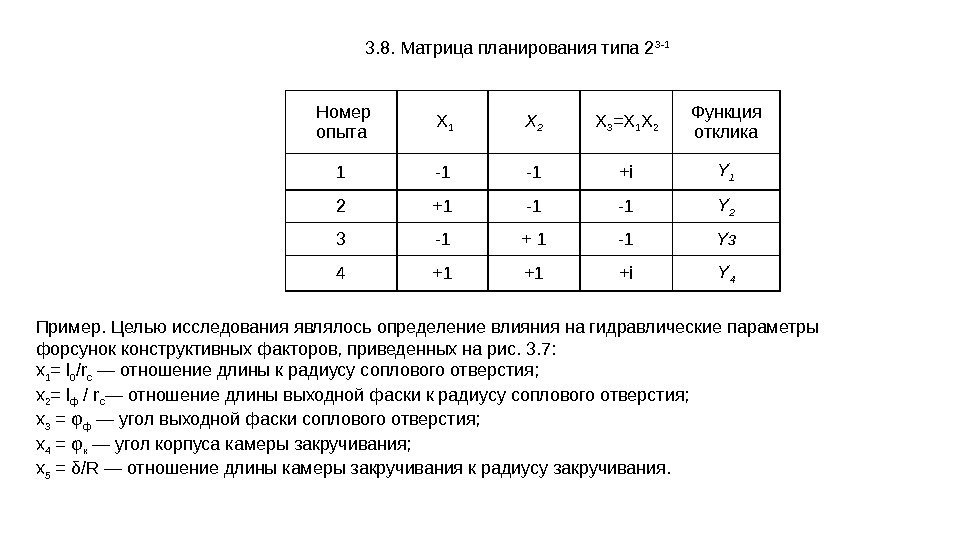
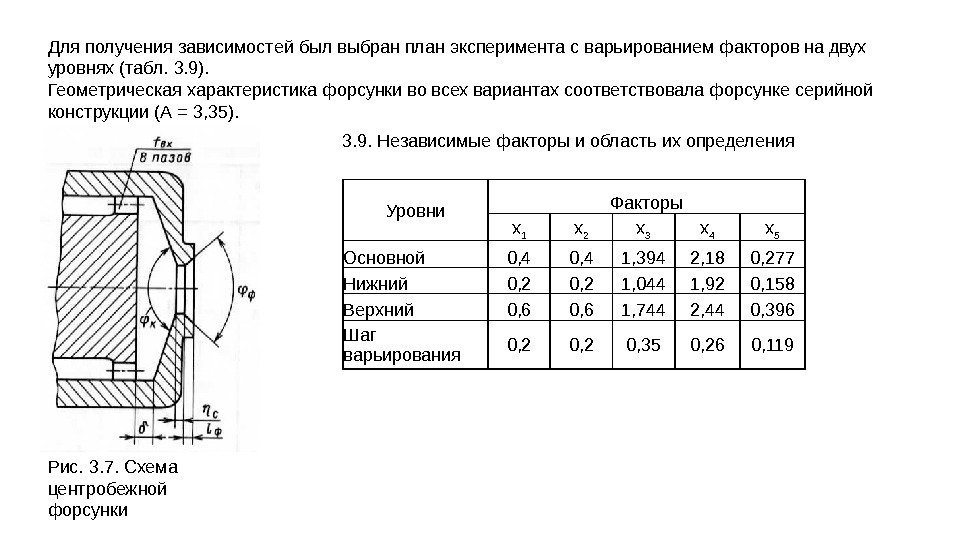
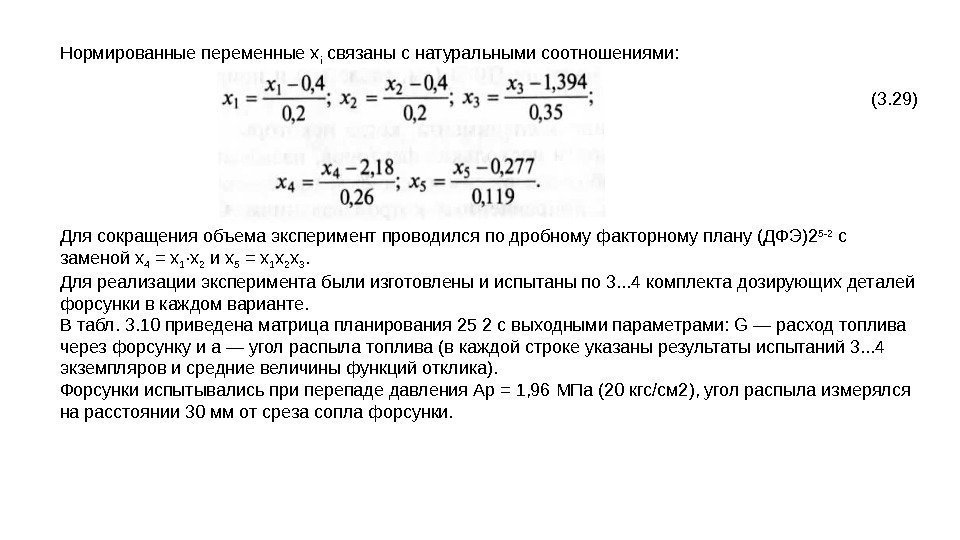
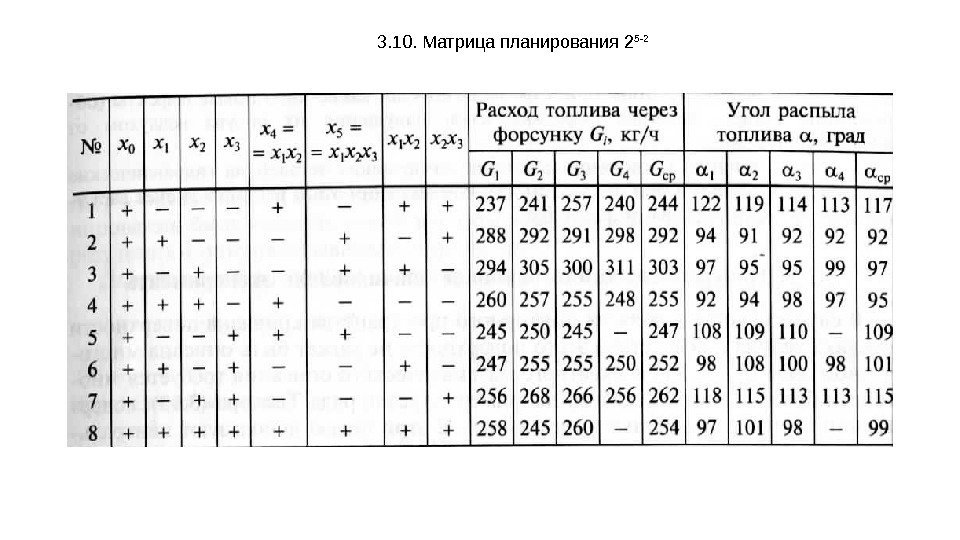
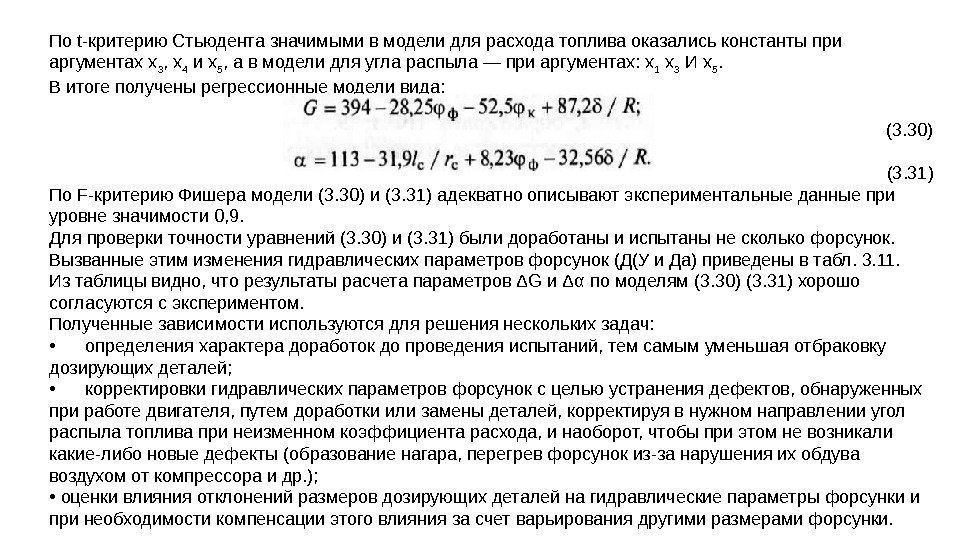
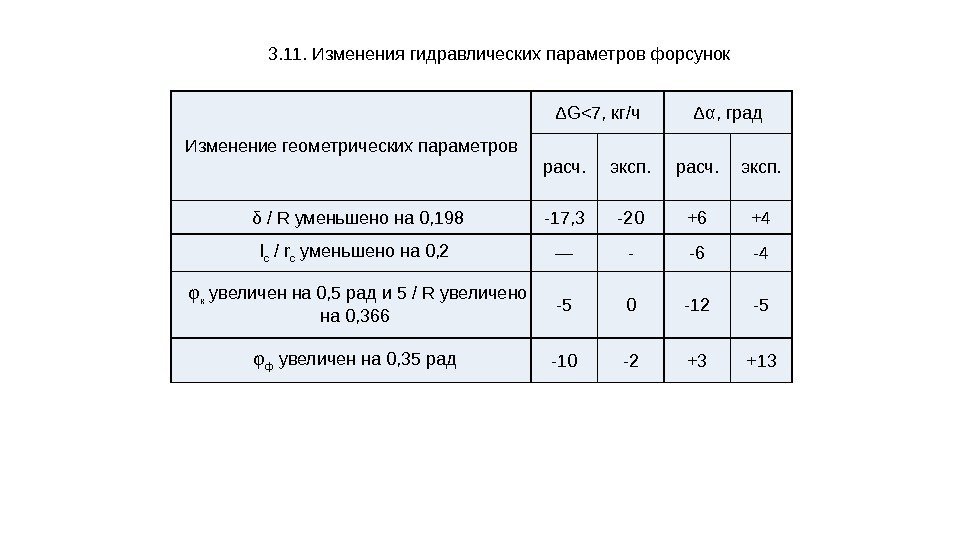
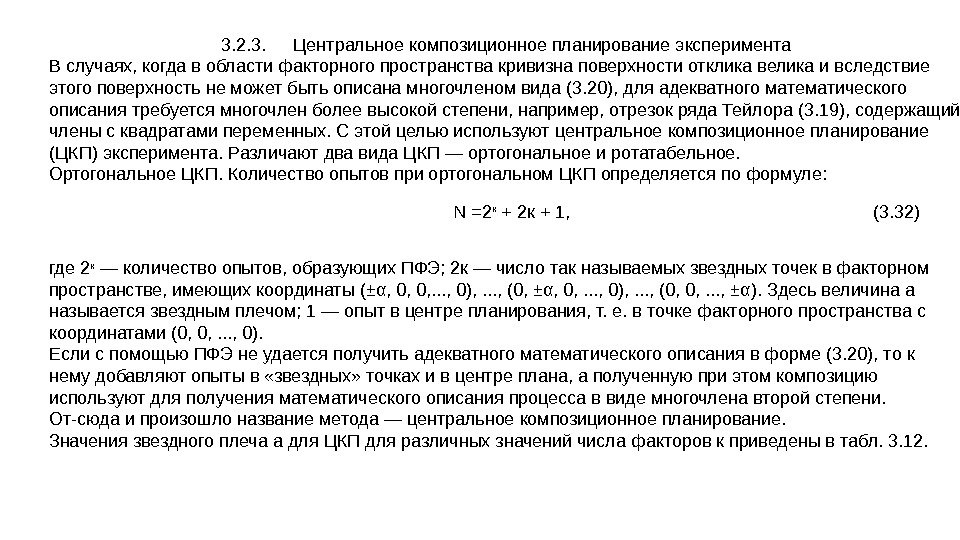
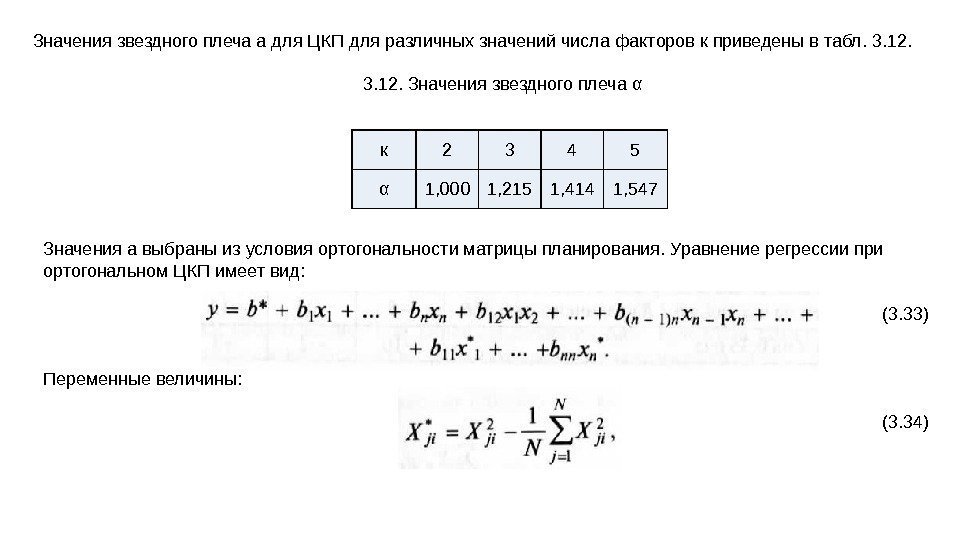
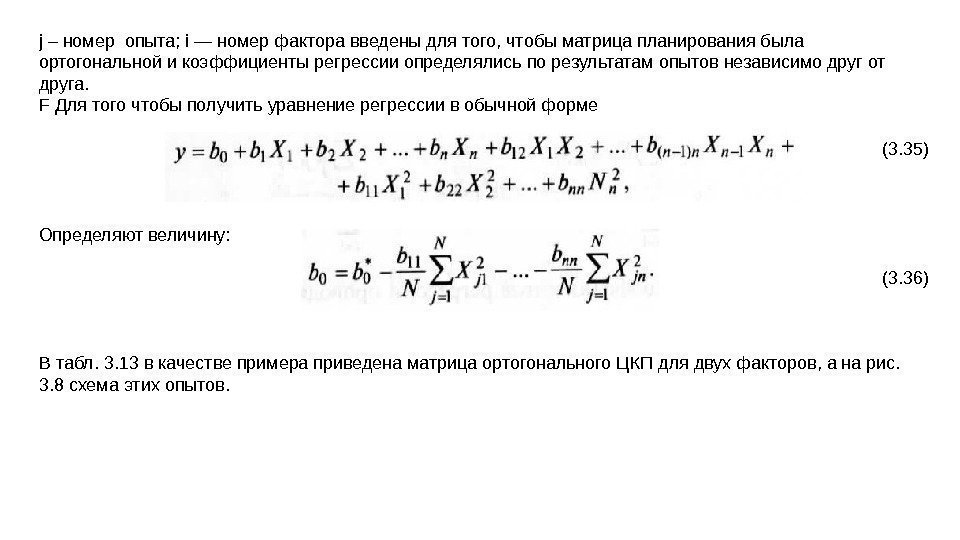
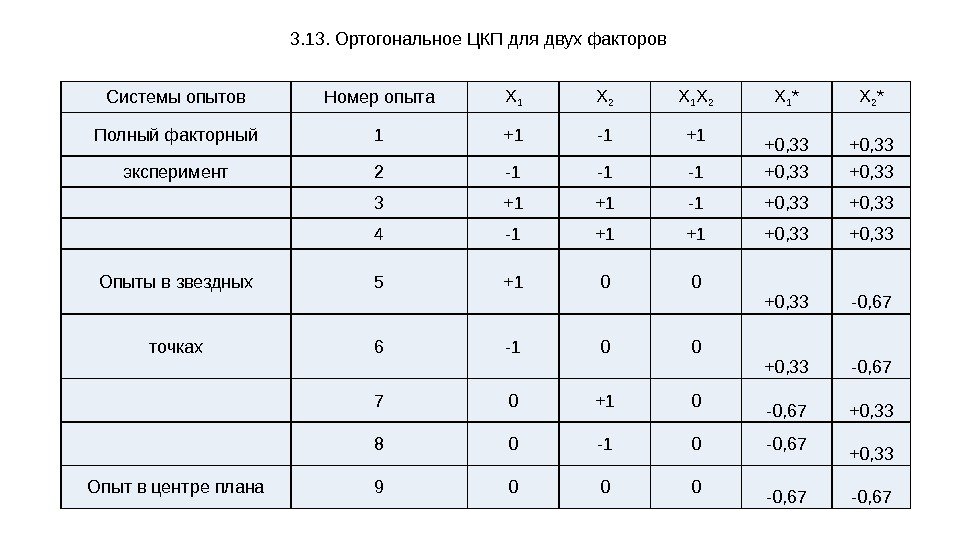
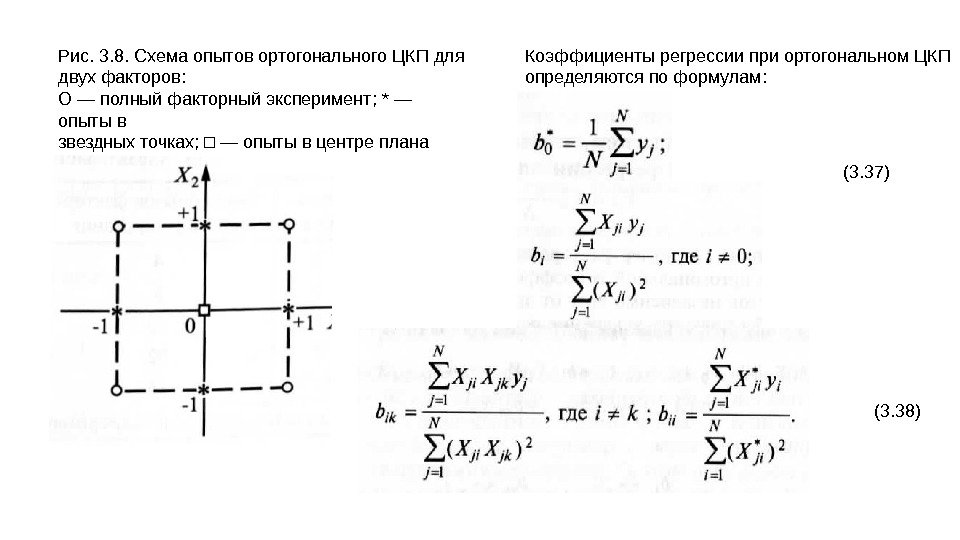
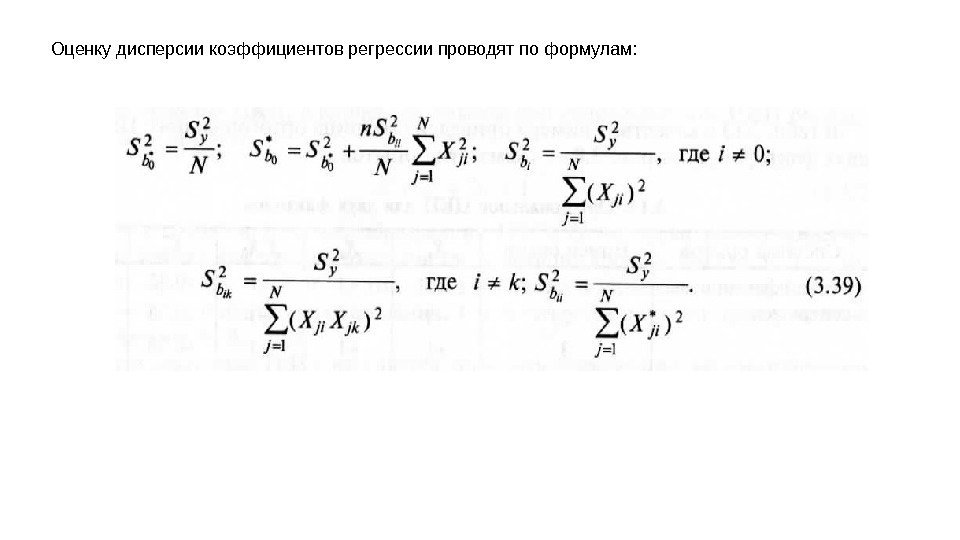
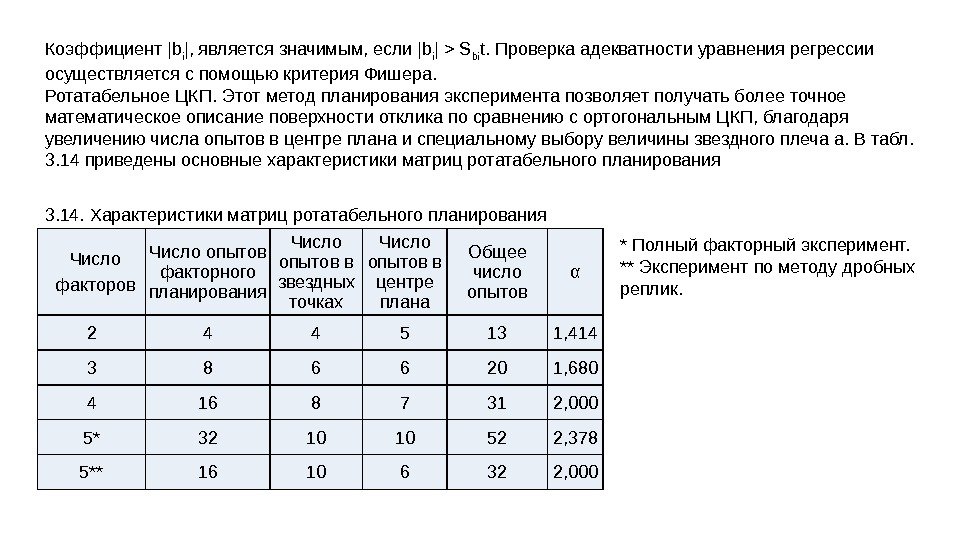
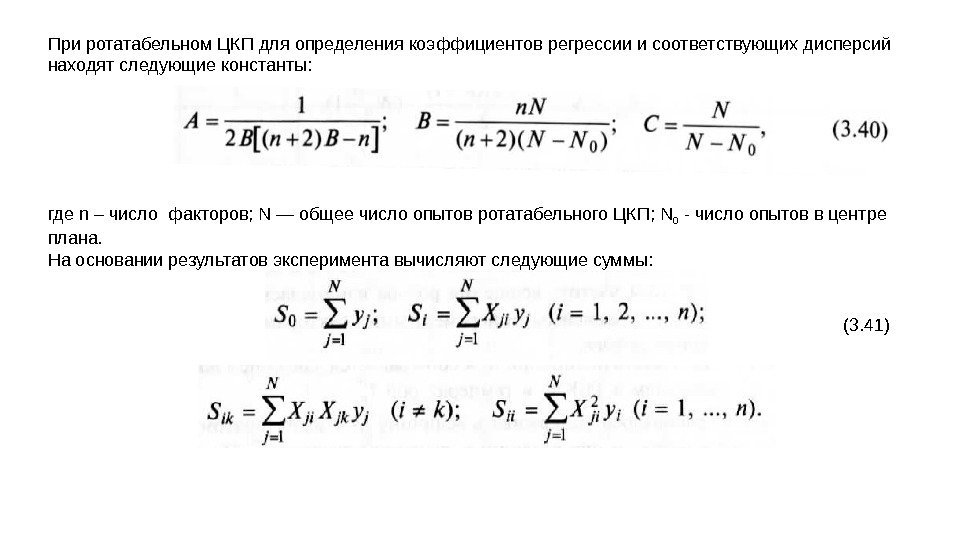
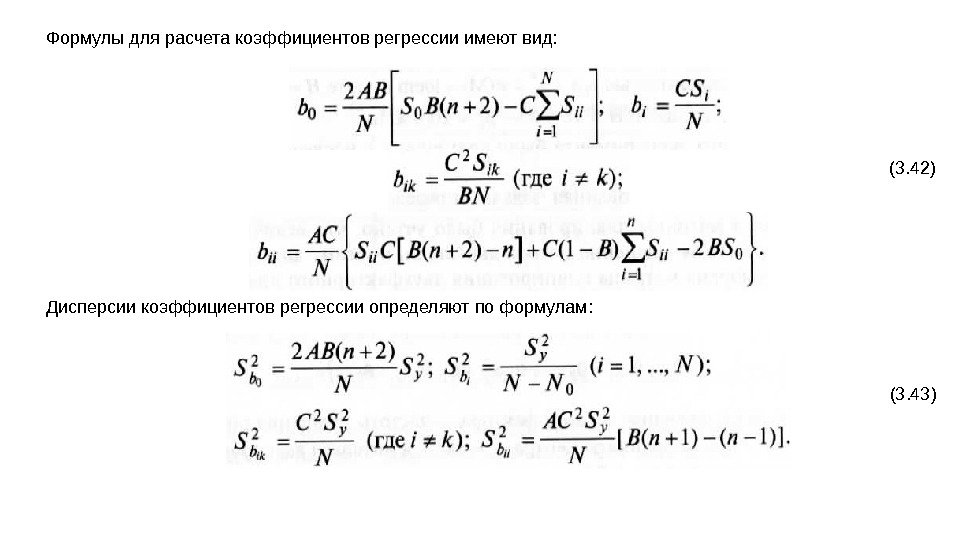
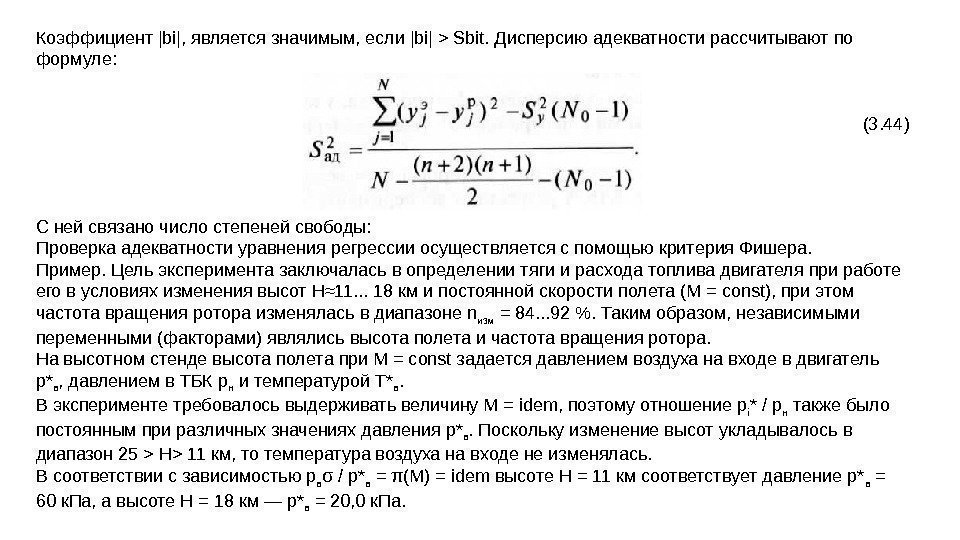
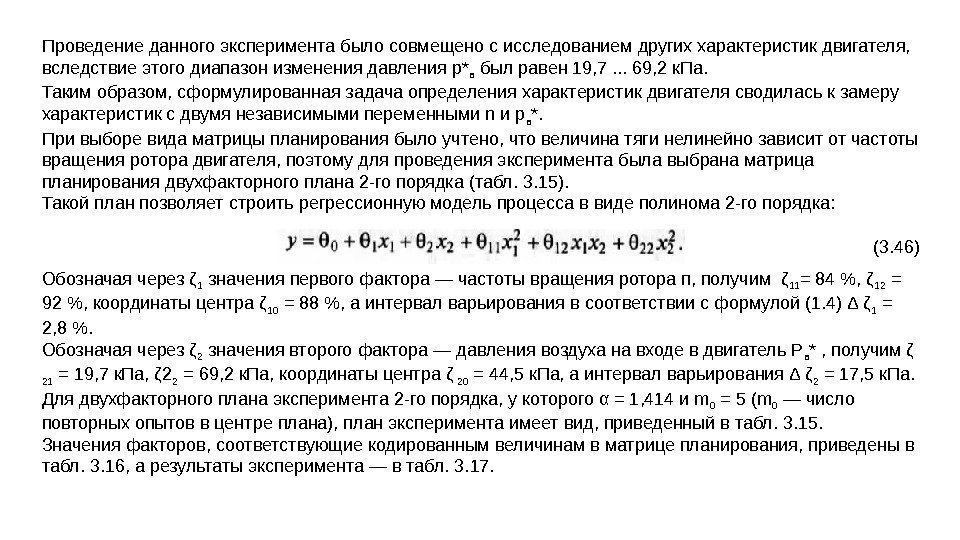
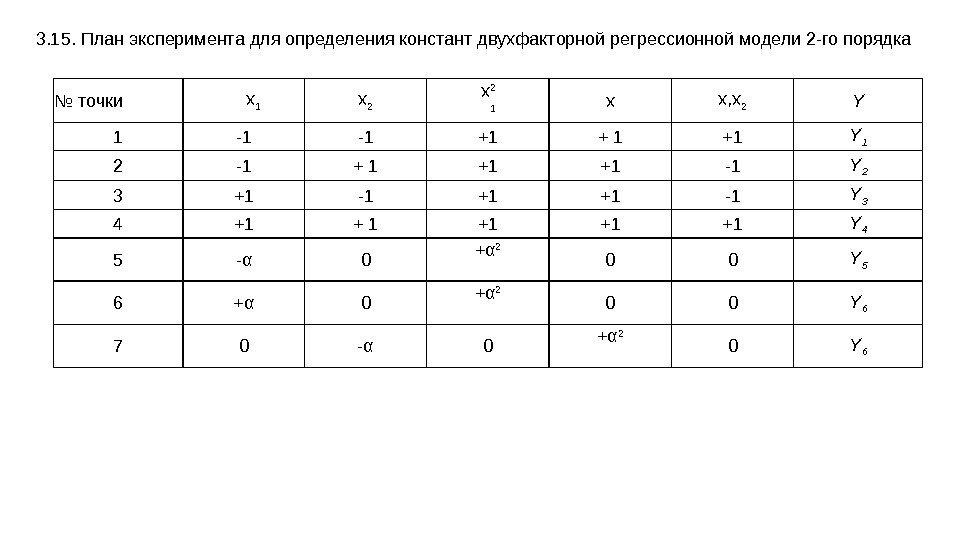
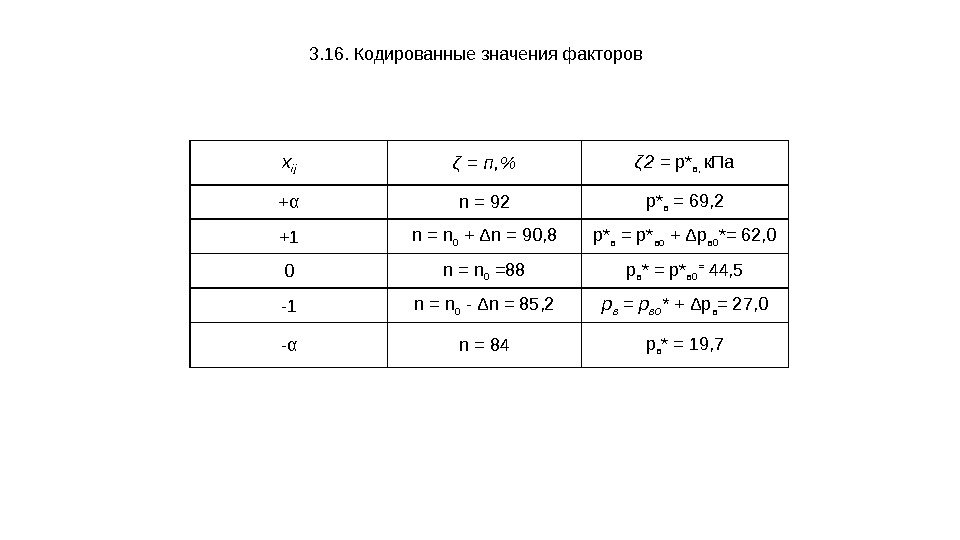
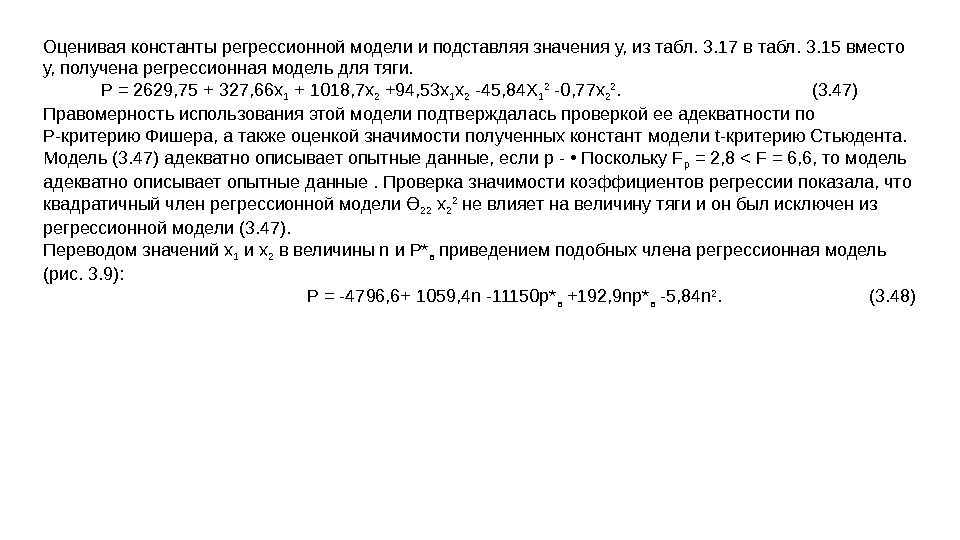
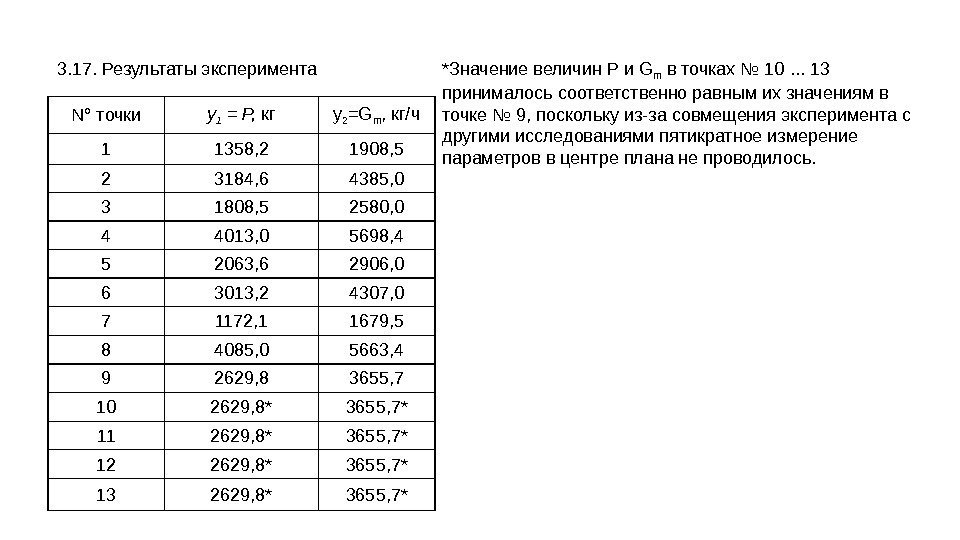
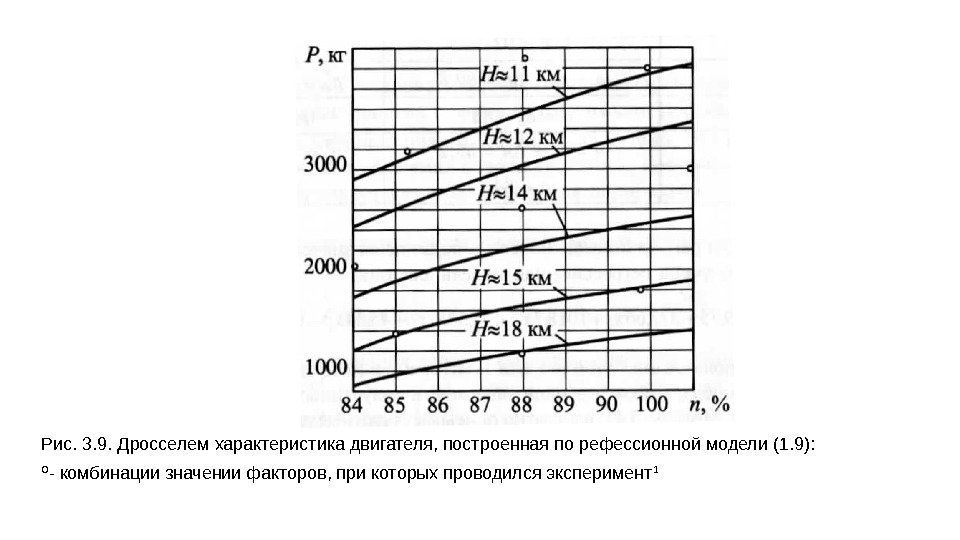
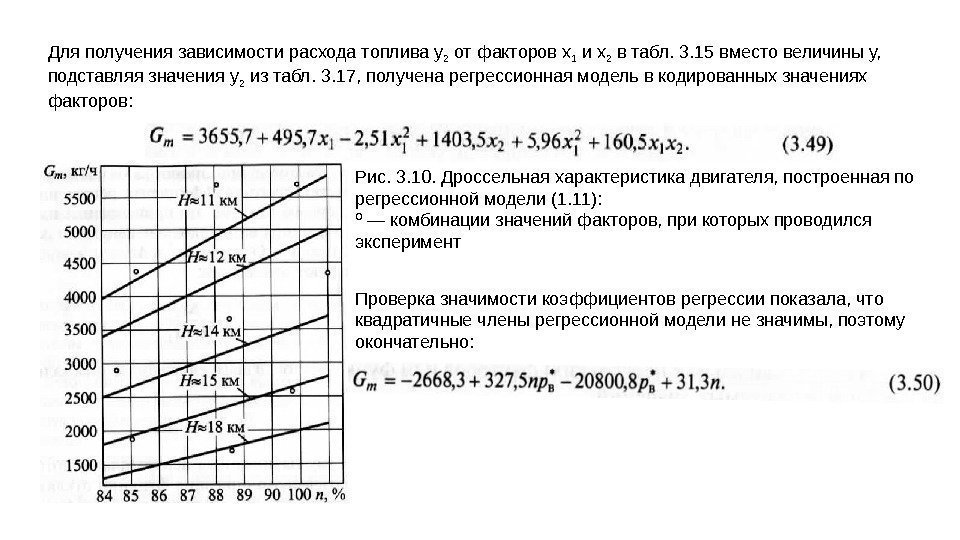
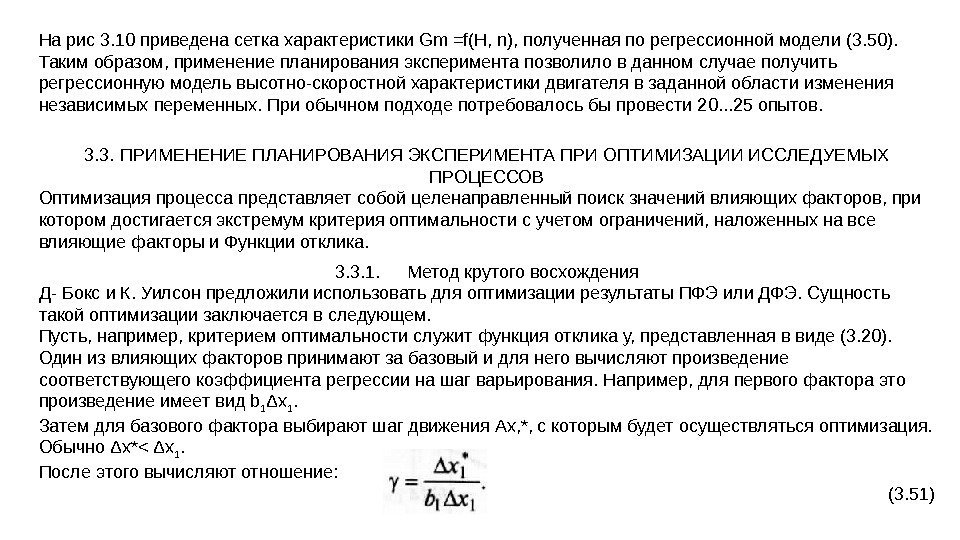
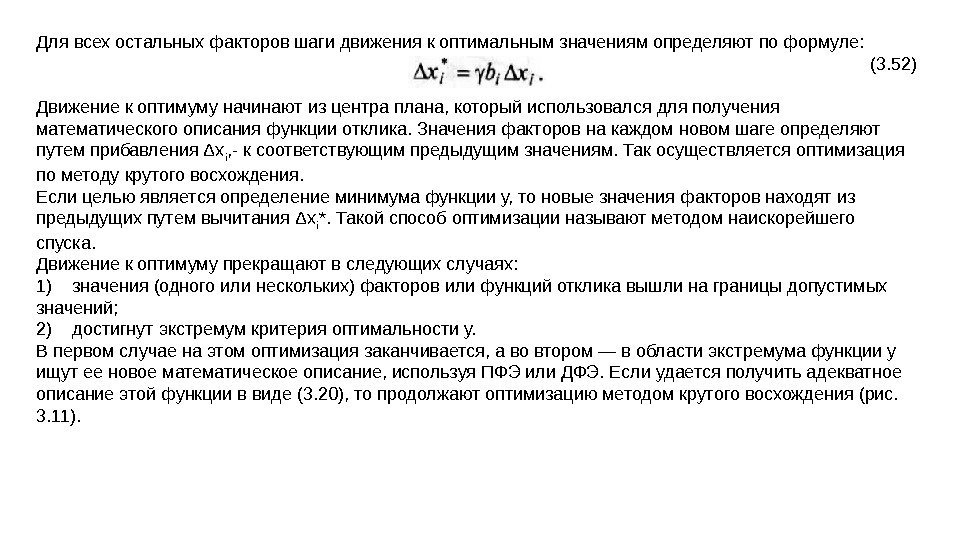
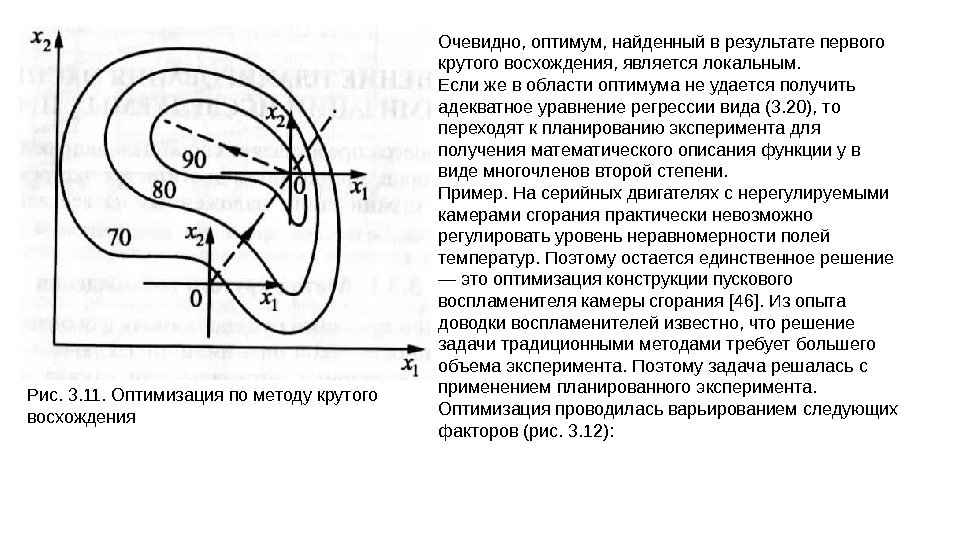
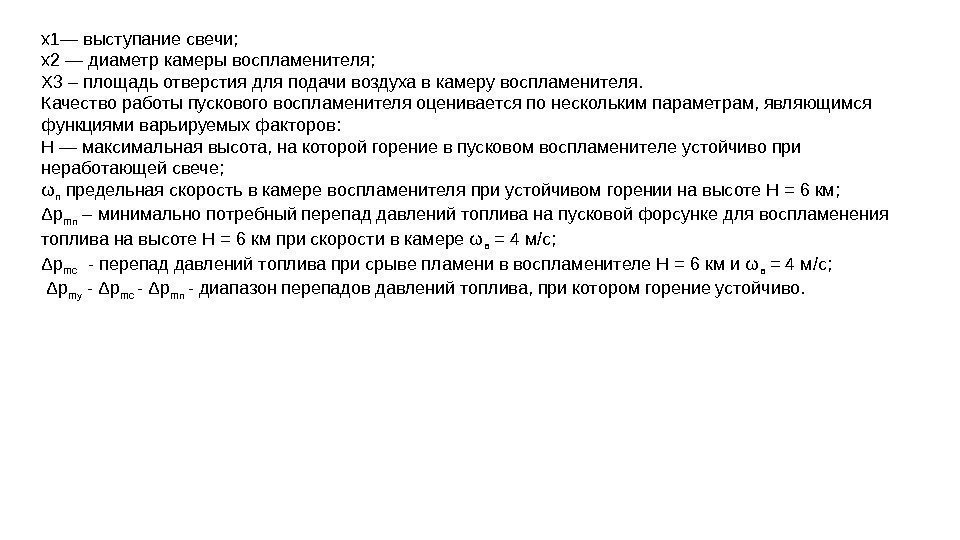
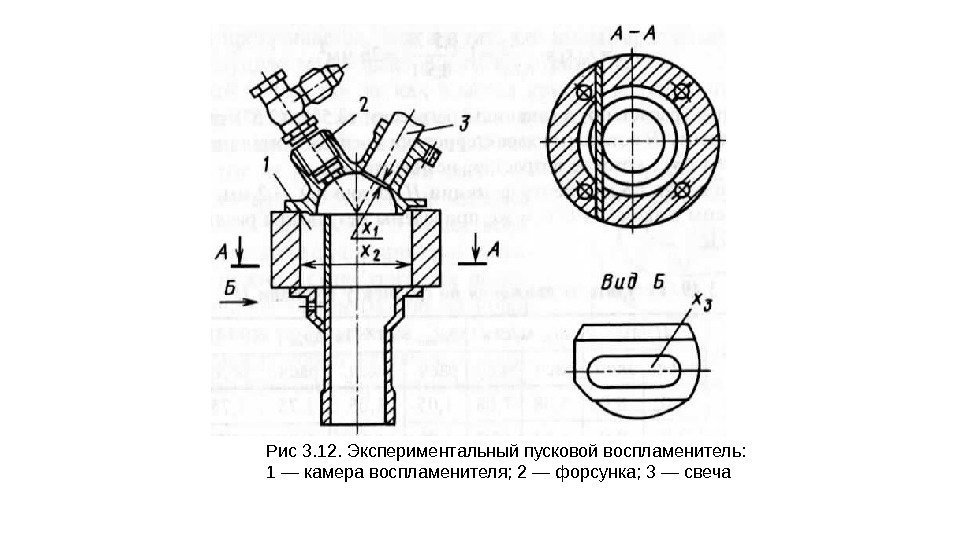
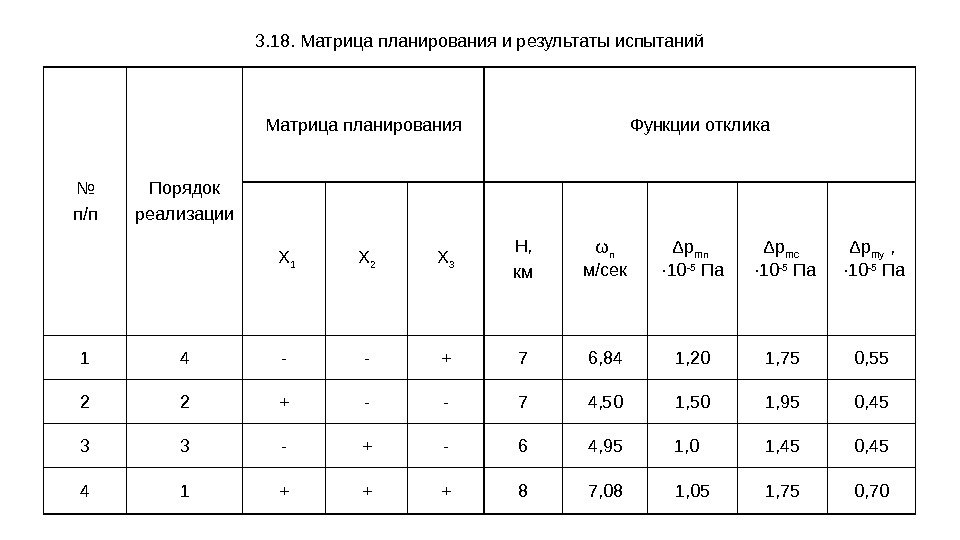
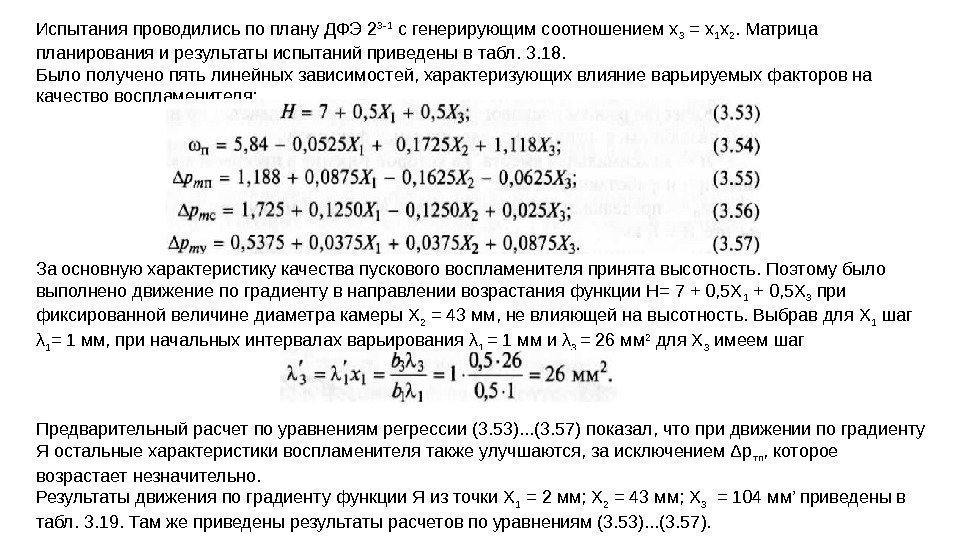
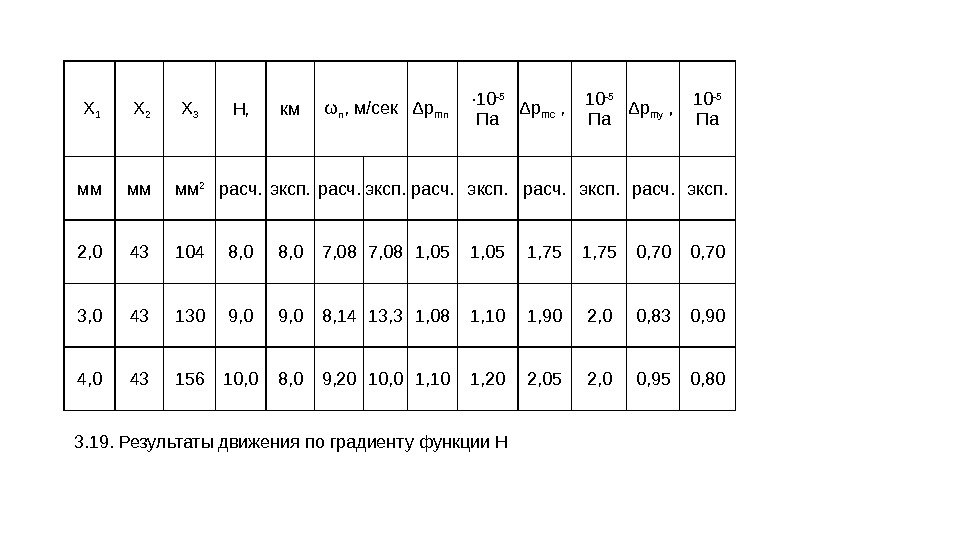
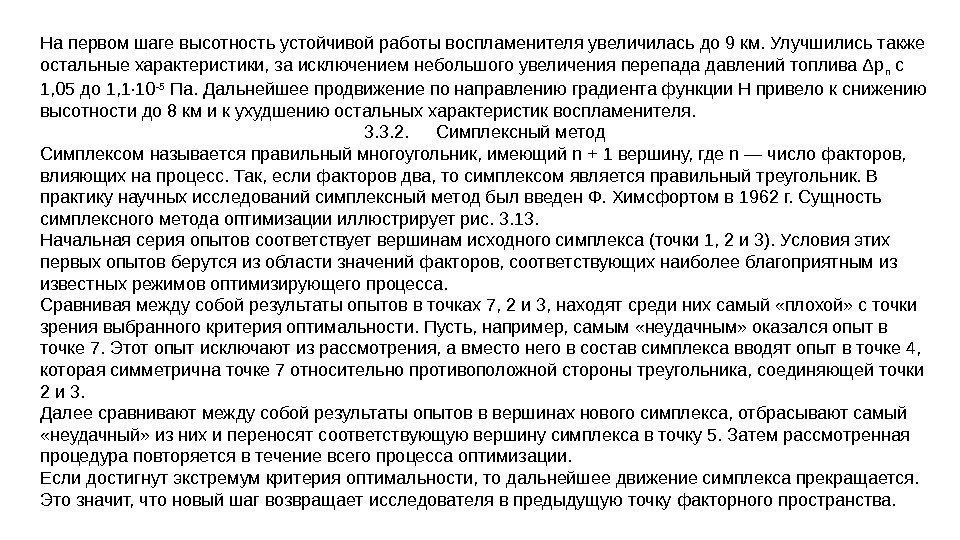
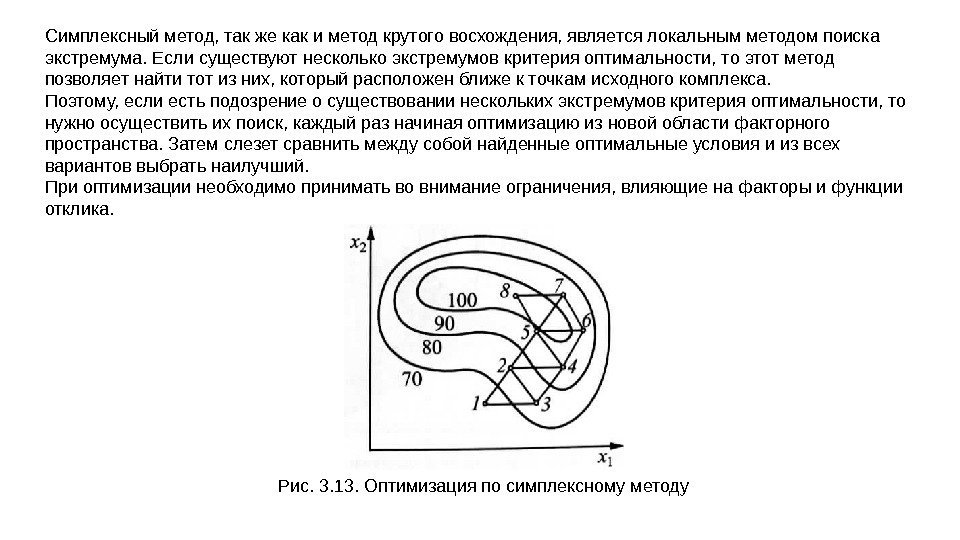
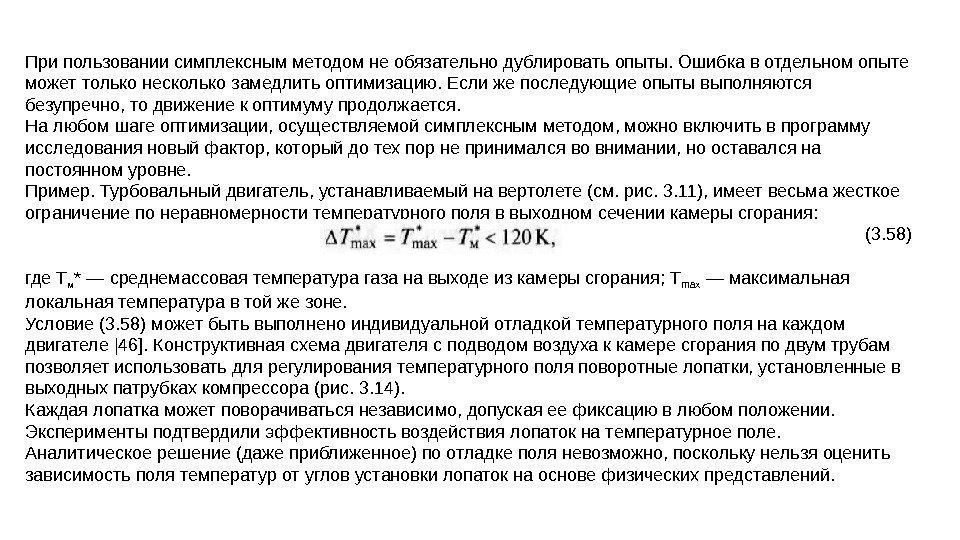
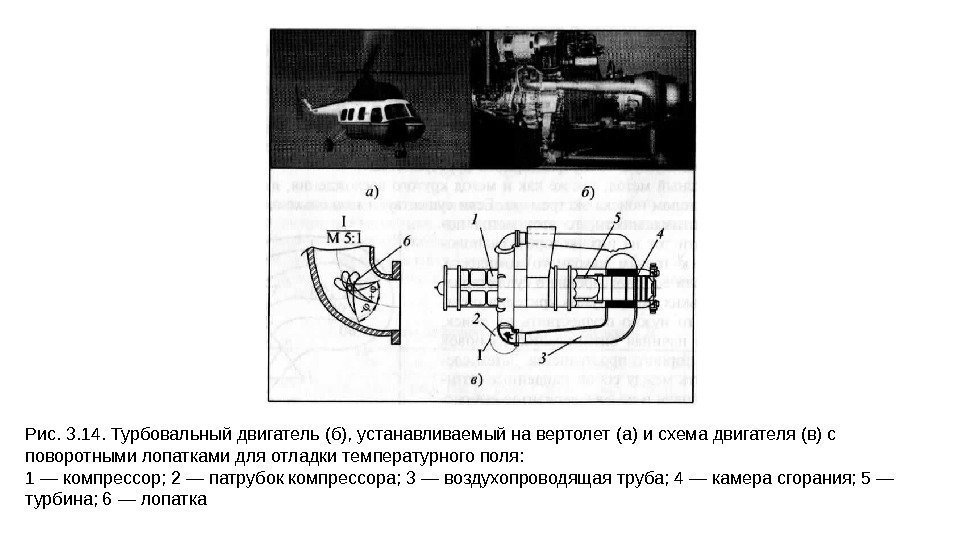
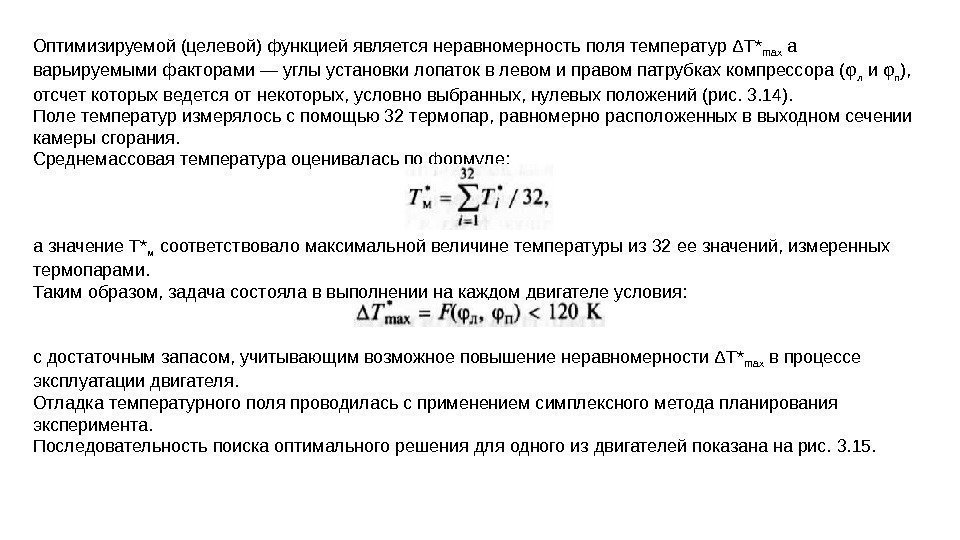
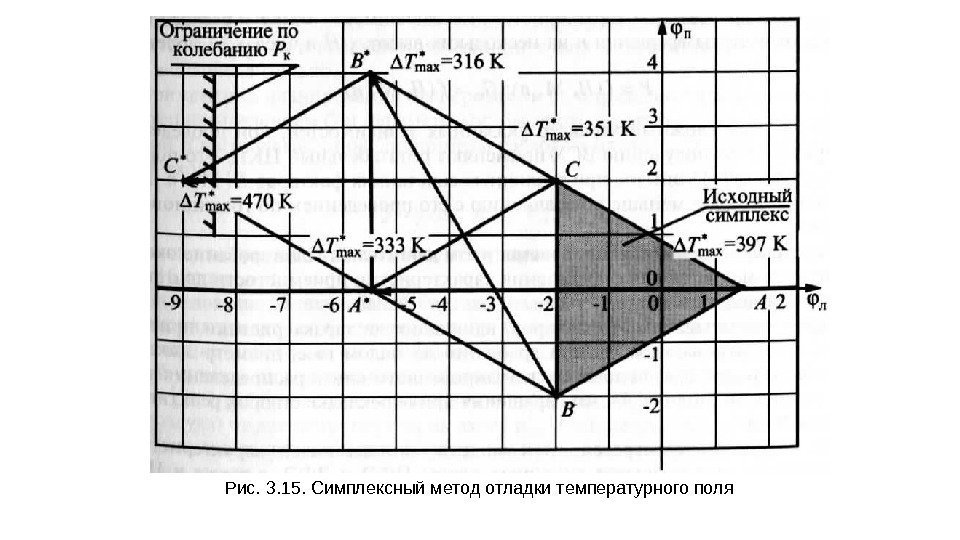
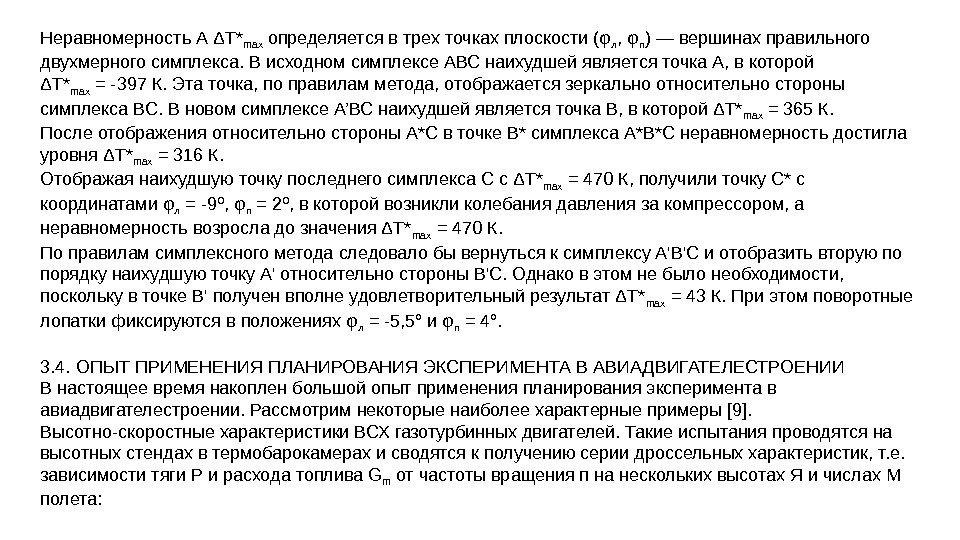
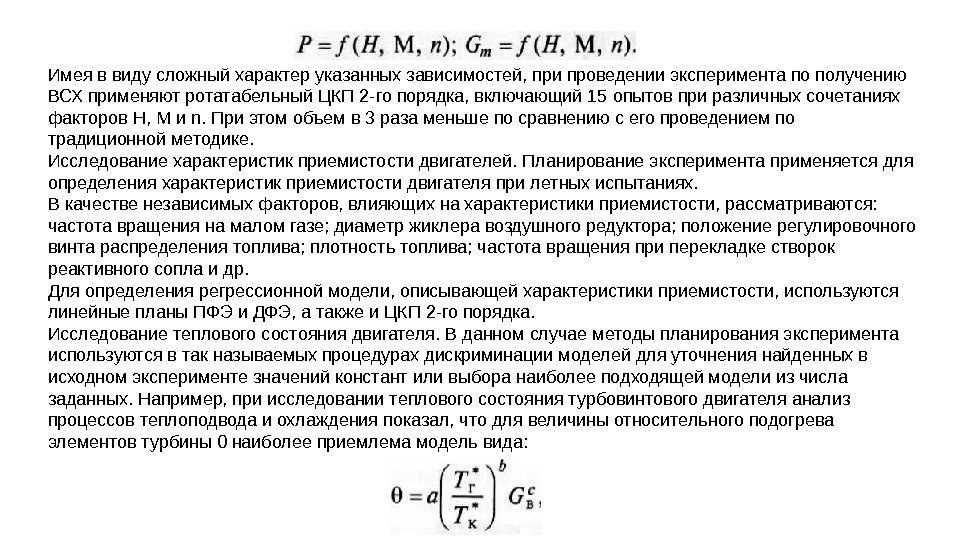
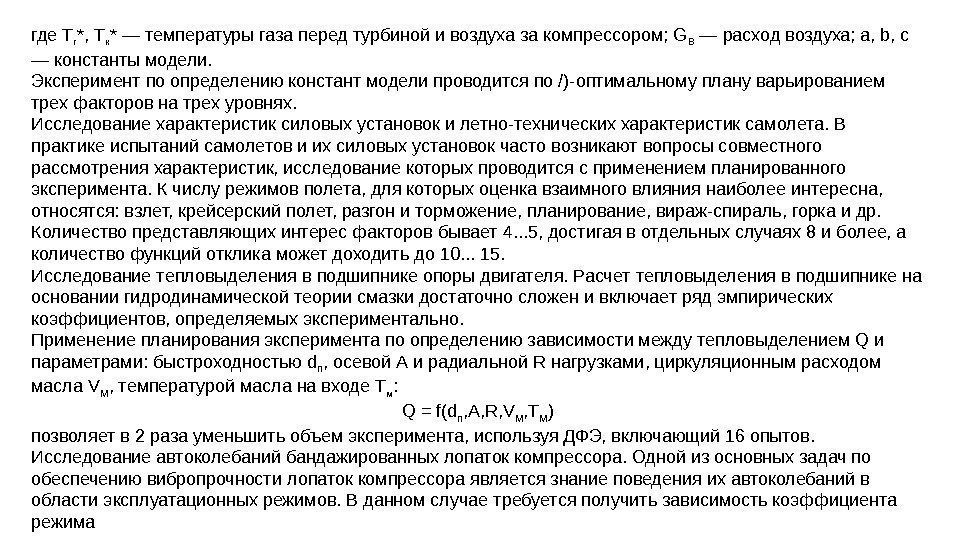
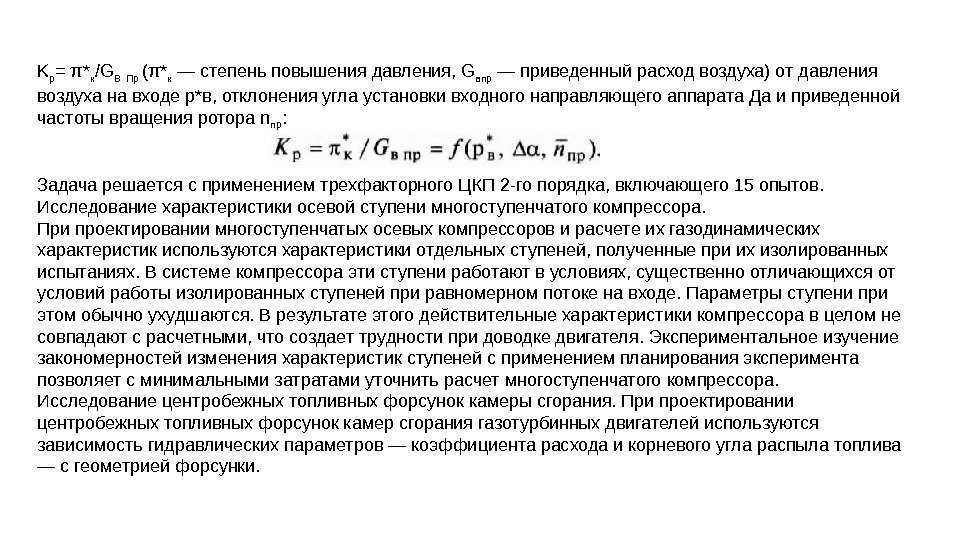
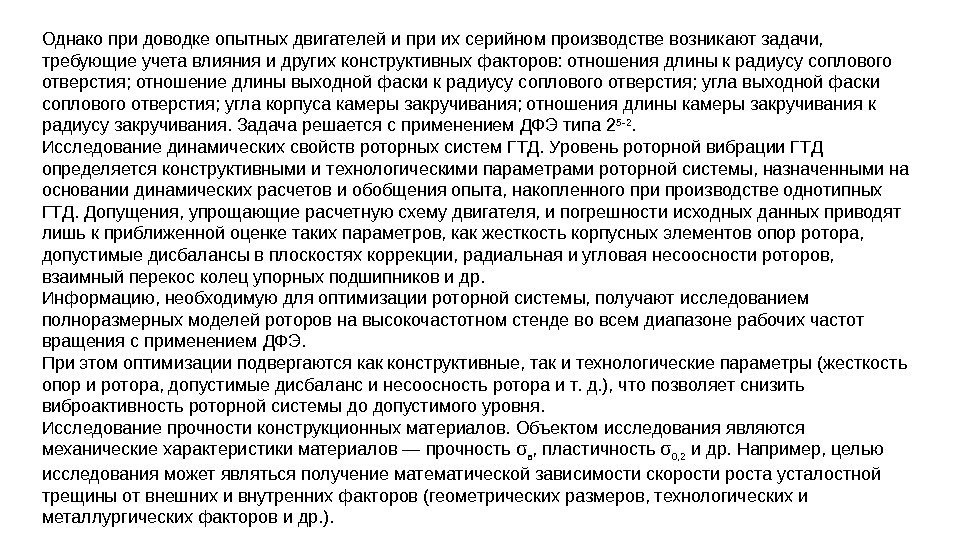
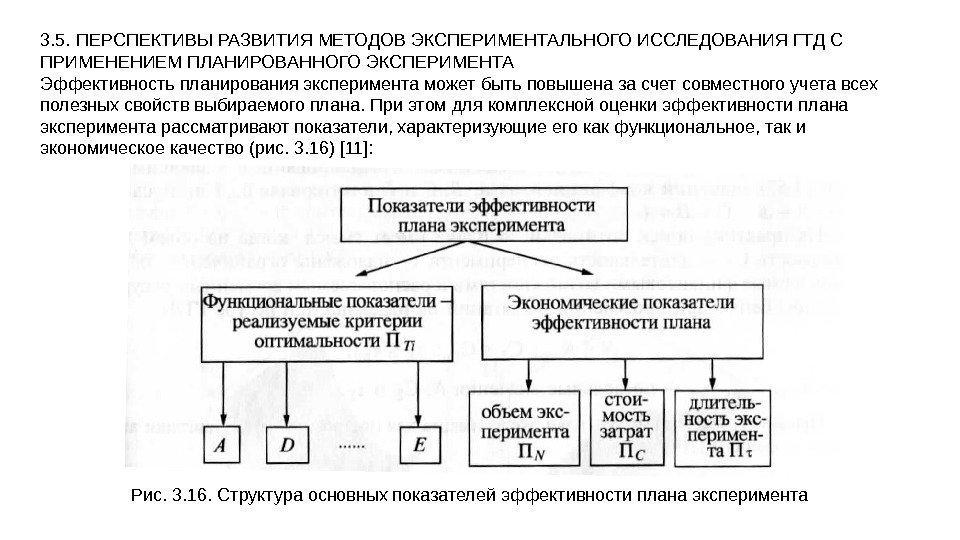

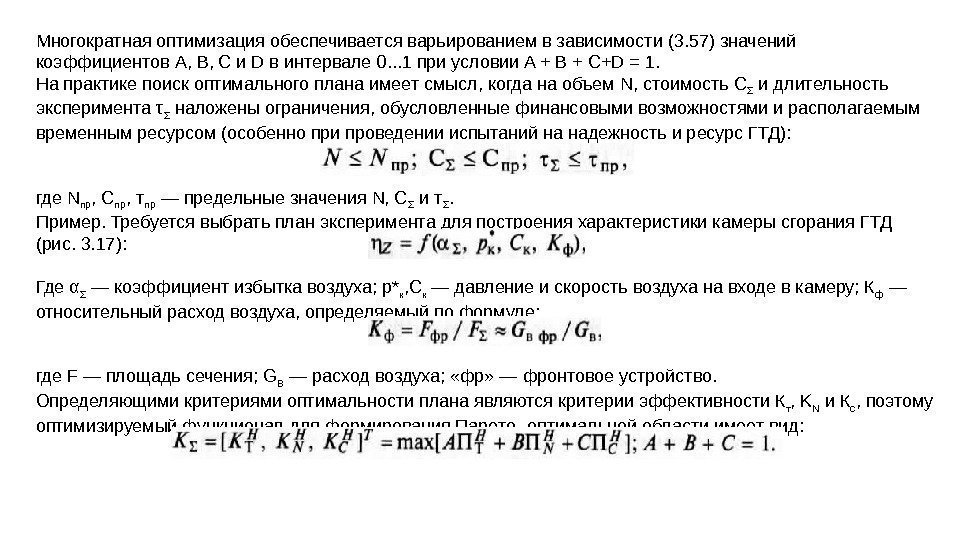
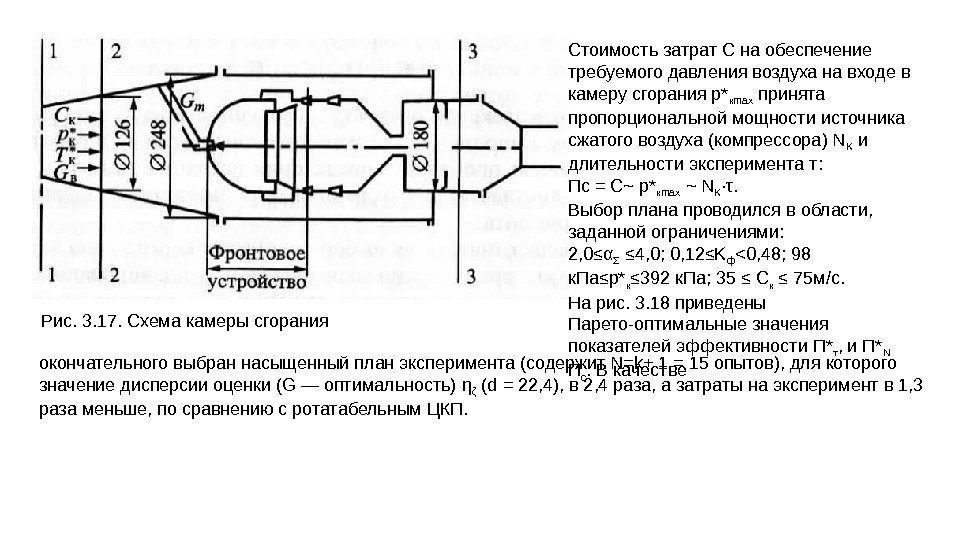
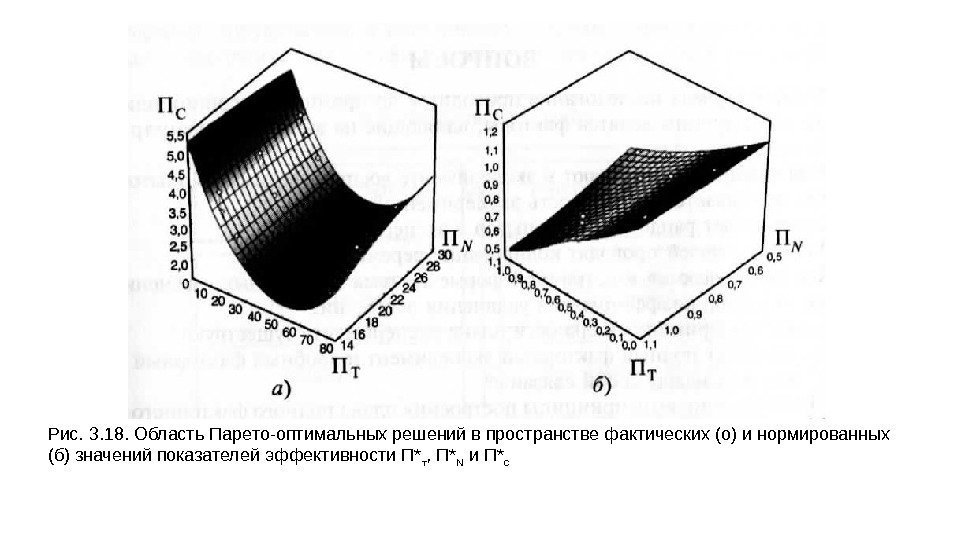
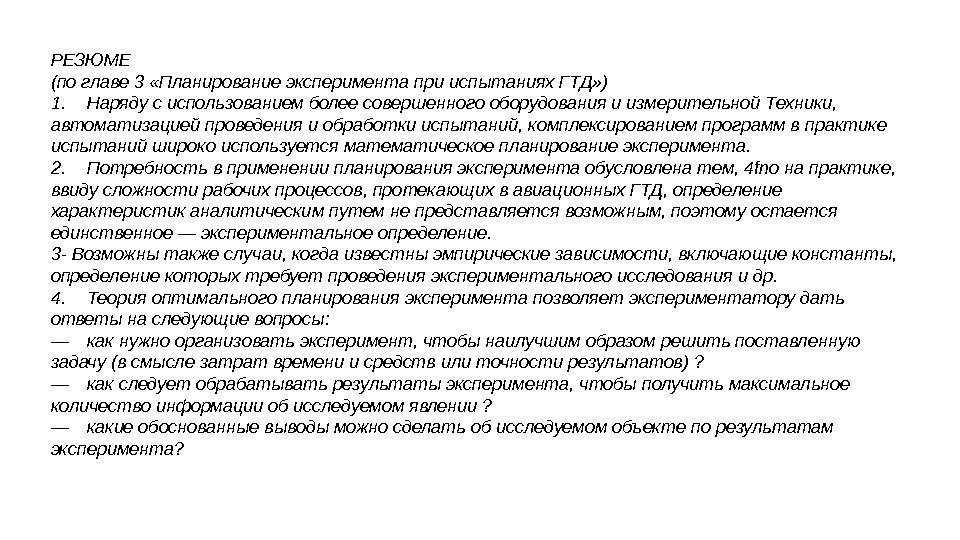
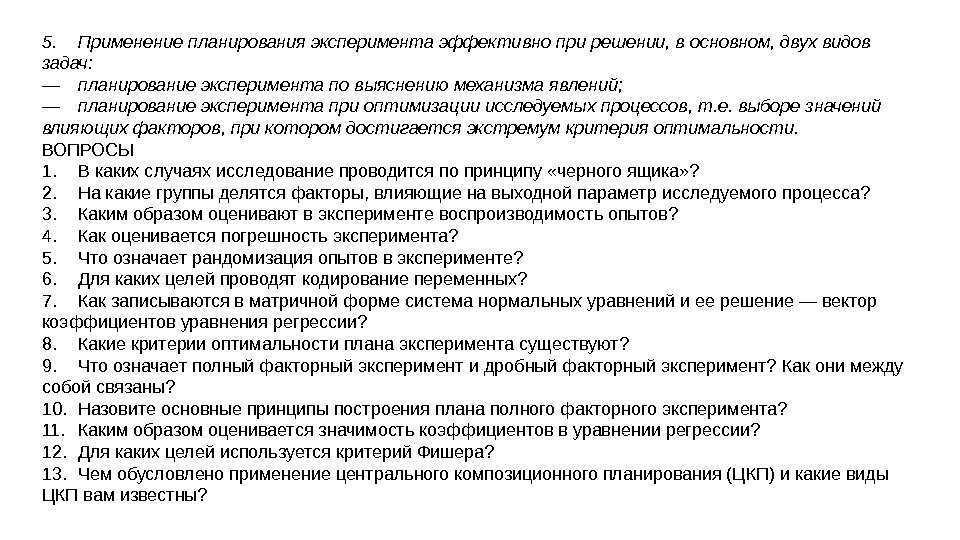
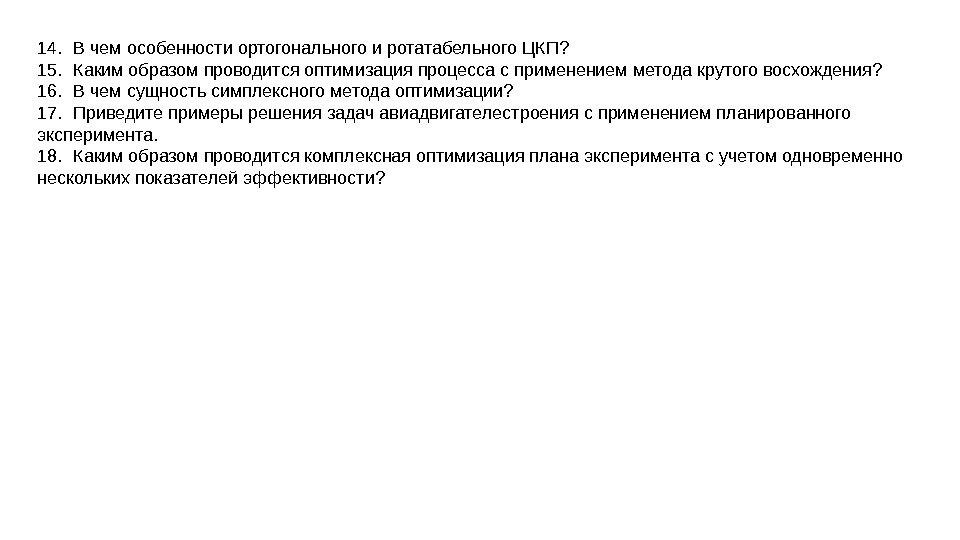
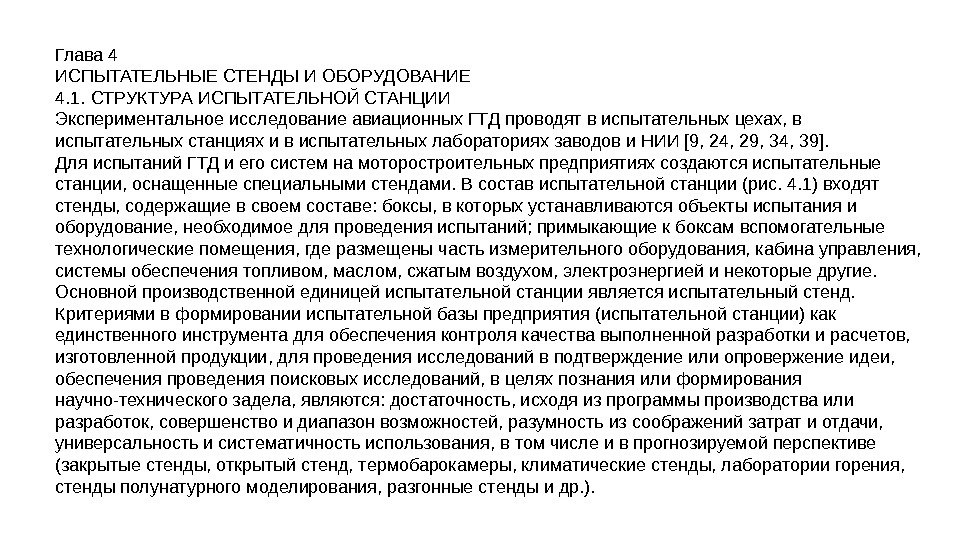
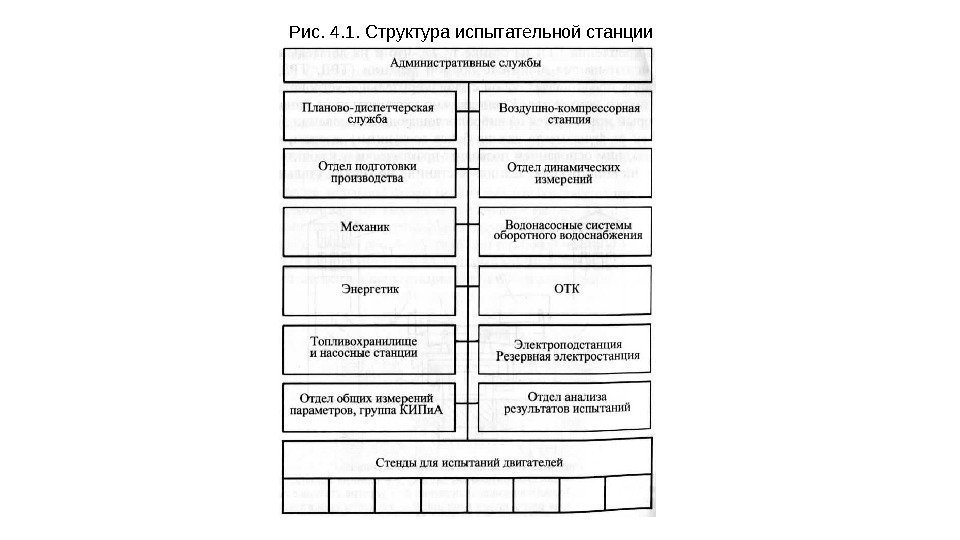
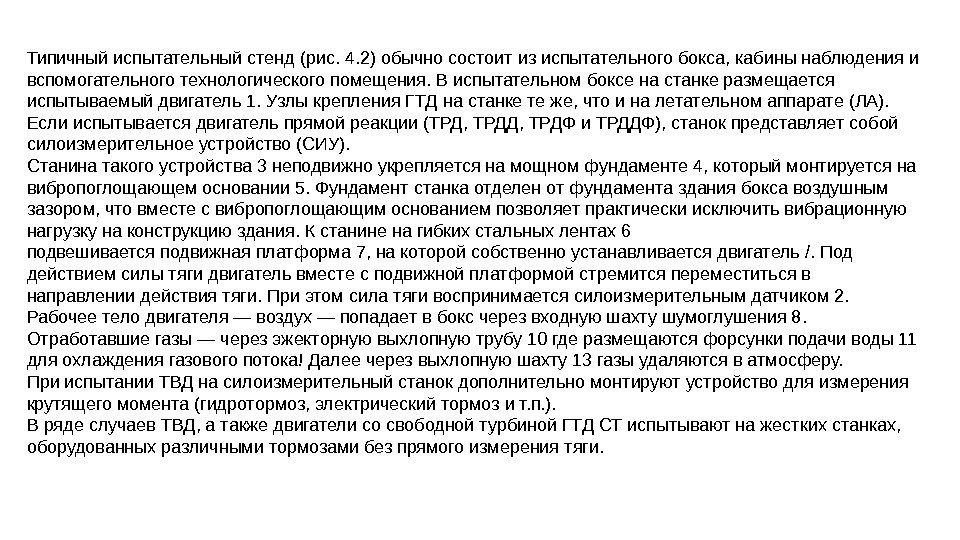
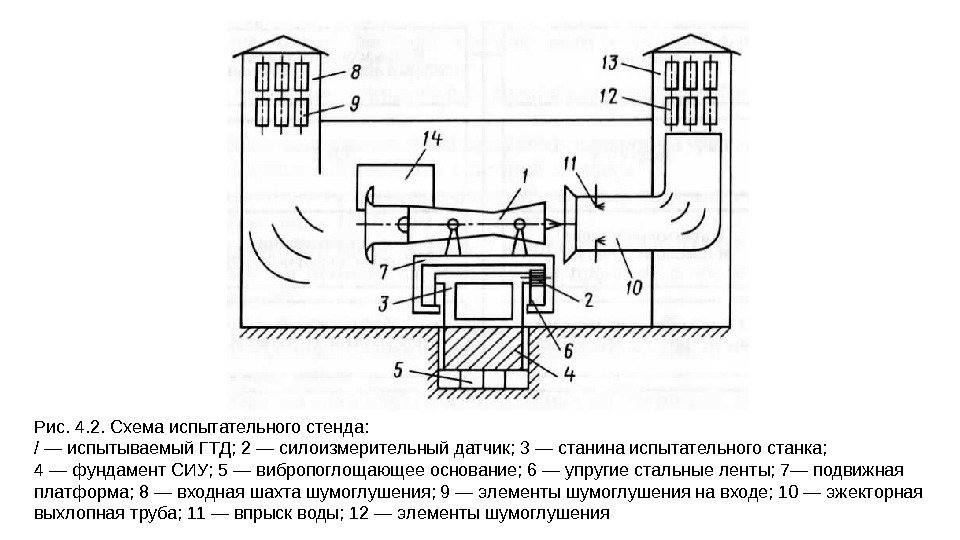
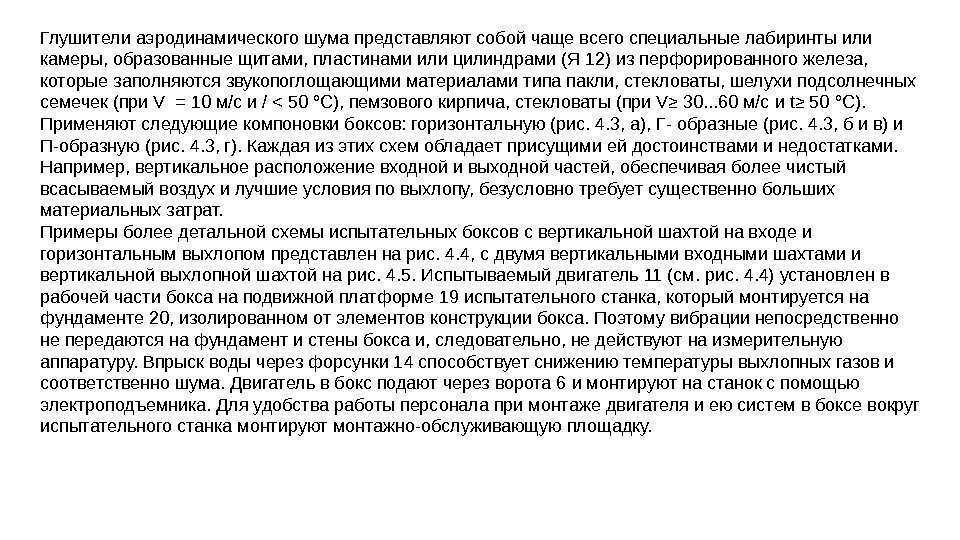
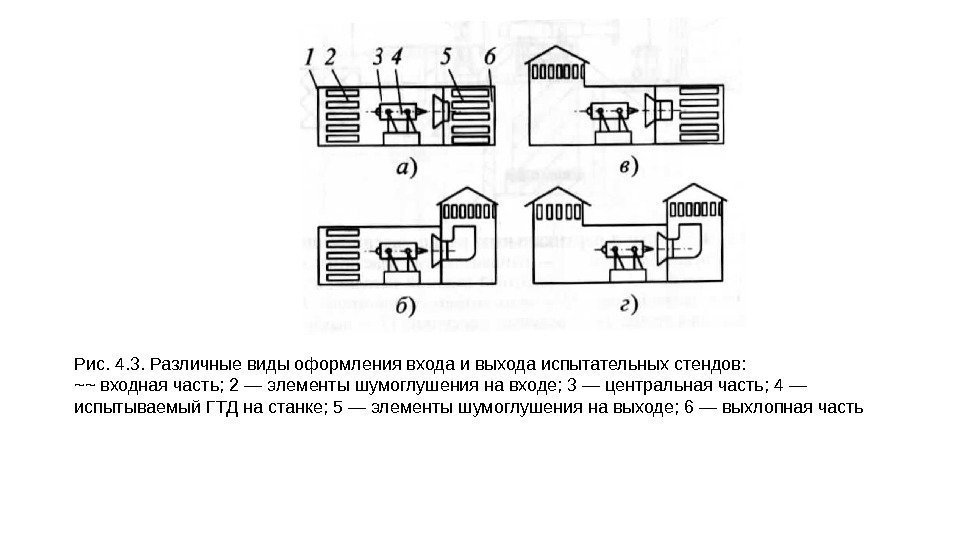
![Рис. 4. 4. Г-образный испытательный бокс [49]: 1 — входная шахта; 2 — глушители Рис. 4. 4. Г-образный испытательный бокс [49]: 1 — входная шахта; 2 — глушители](http://present5.com/presentforday2/20170201/mmk_ispytania_i_kontrol_kachestva_izdeliy_2017_images/mmk_ispytania_i_kontrol_kachestva_izdeliy_2017_243.jpg)
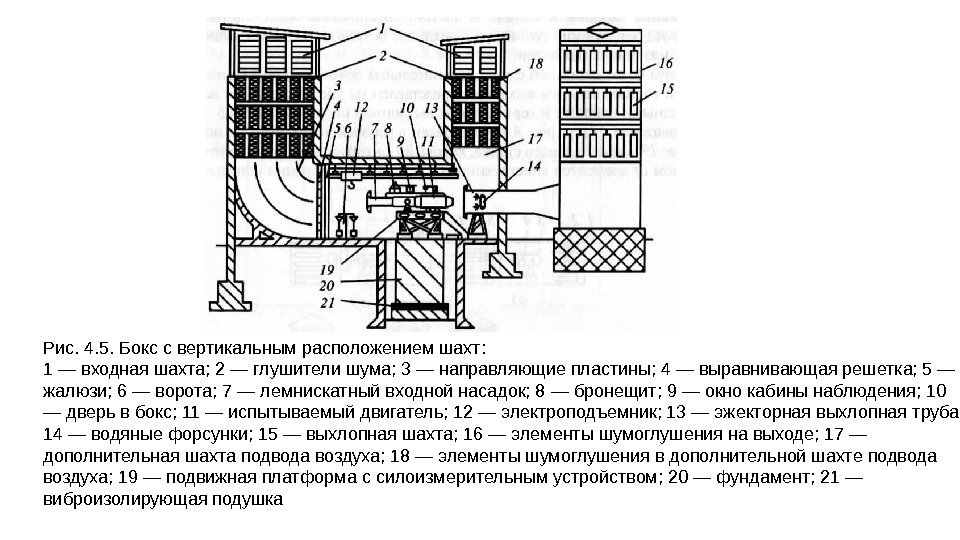
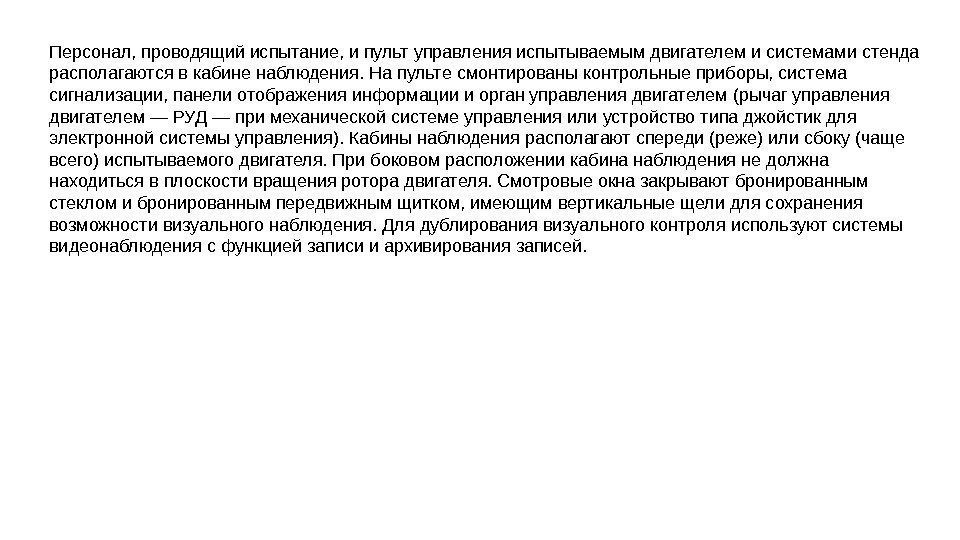
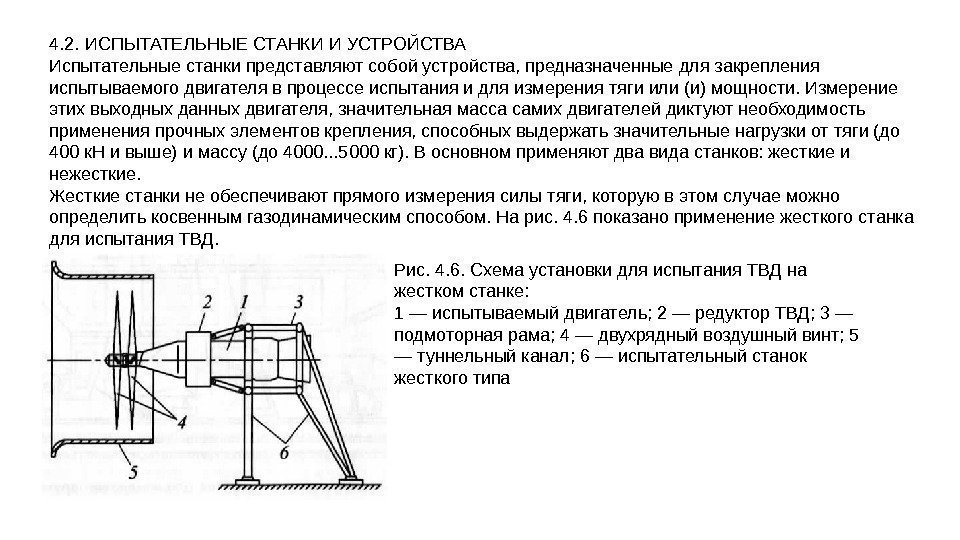
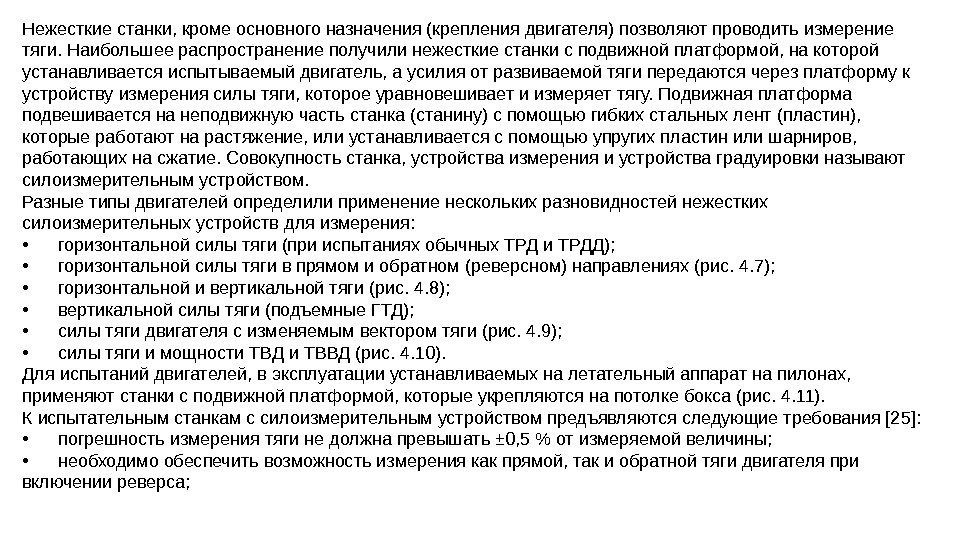
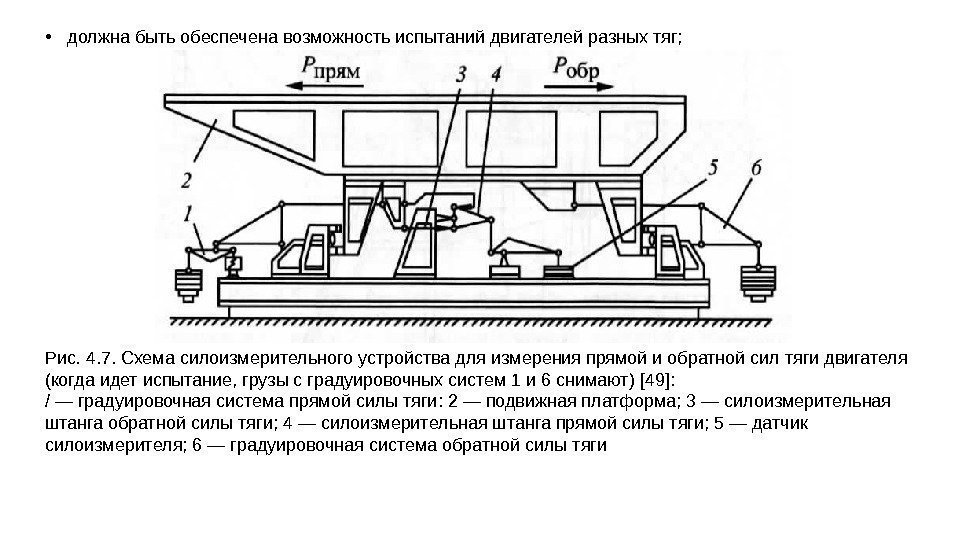
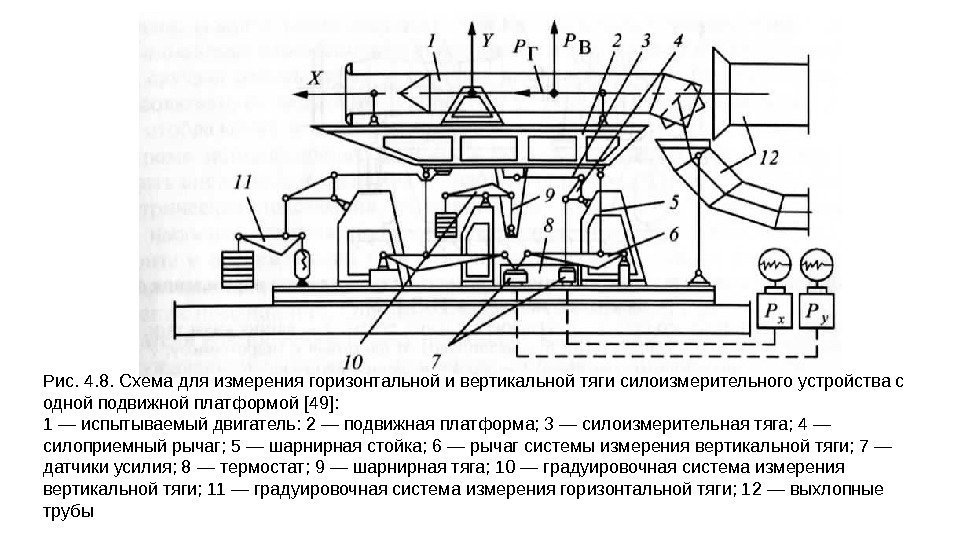
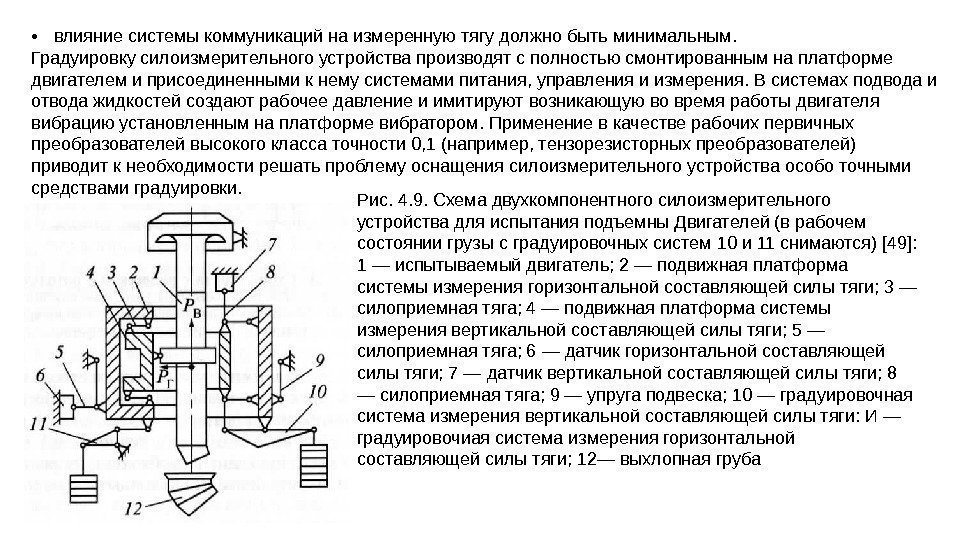
![Рис. 4. 10. Схема испытательного силоизмерительного устройства для определения эквивалентной мощности ТВД [32]: I Рис. 4. 10. Схема испытательного силоизмерительного устройства для определения эквивалентной мощности ТВД [32]: I](http://present5.com/presentforday2/20170201/mmk_ispytania_i_kontrol_kachestva_izdeliy_2017_images/mmk_ispytania_i_kontrol_kachestva_izdeliy_2017_251.jpg)
![Рис. 4. 11. Схема станка с подвеской к потолку [42]: / — испытываемый двигатель; Рис. 4. 11. Схема станка с подвеской к потолку [42]: / — испытываемый двигатель;](http://present5.com/presentforday2/20170201/mmk_ispytania_i_kontrol_kachestva_izdeliy_2017_images/mmk_ispytania_i_kontrol_kachestva_izdeliy_2017_252.jpg)
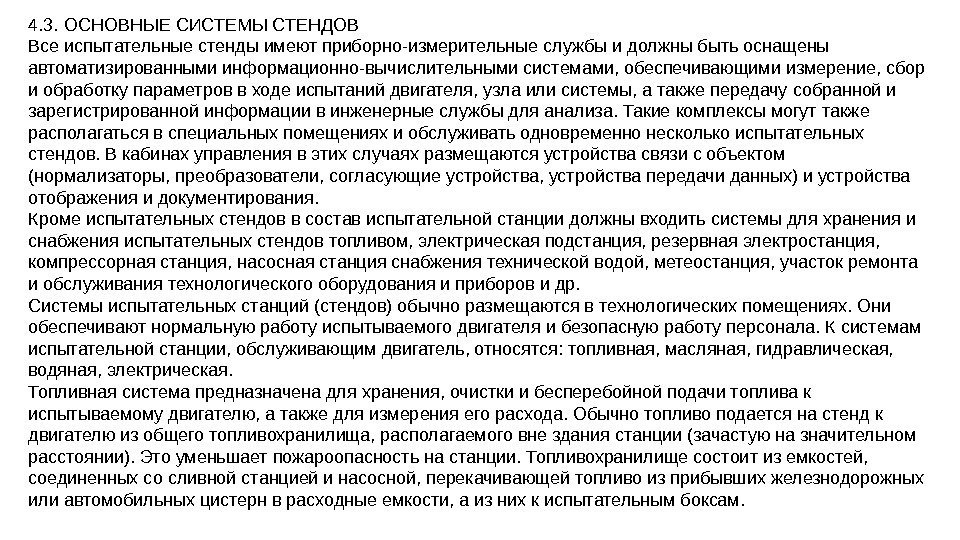
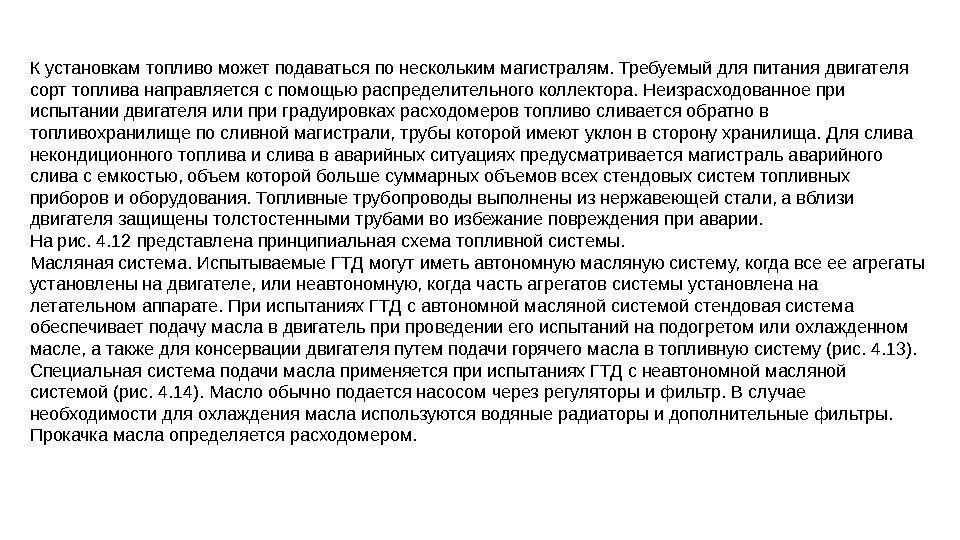
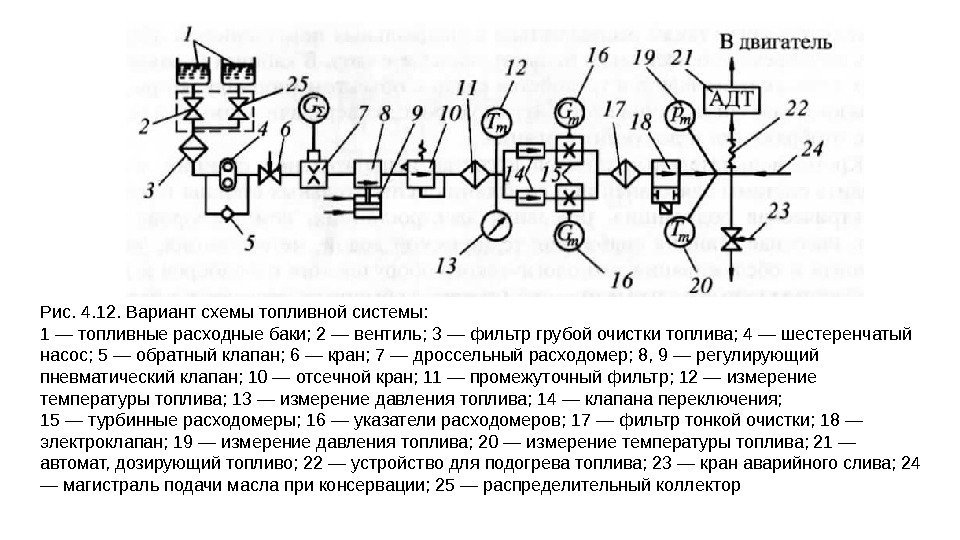
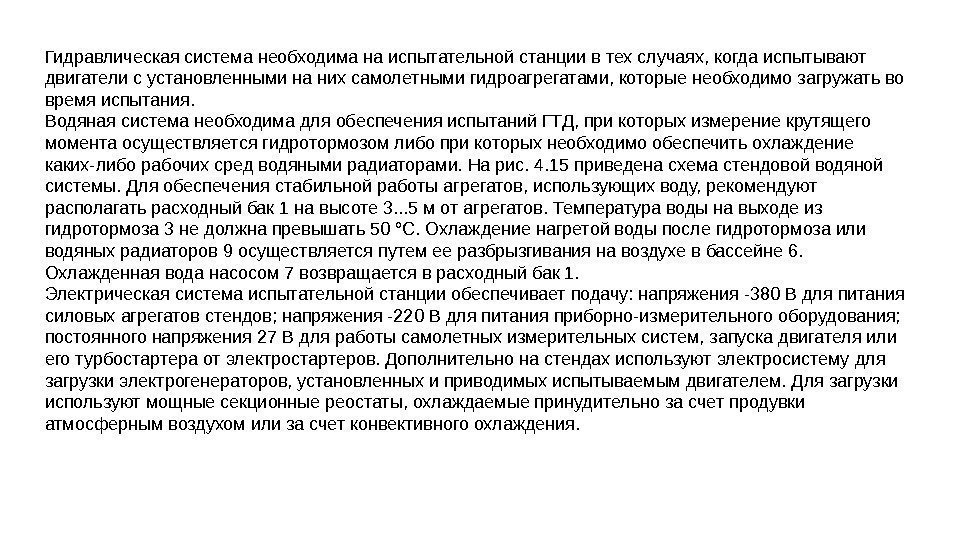
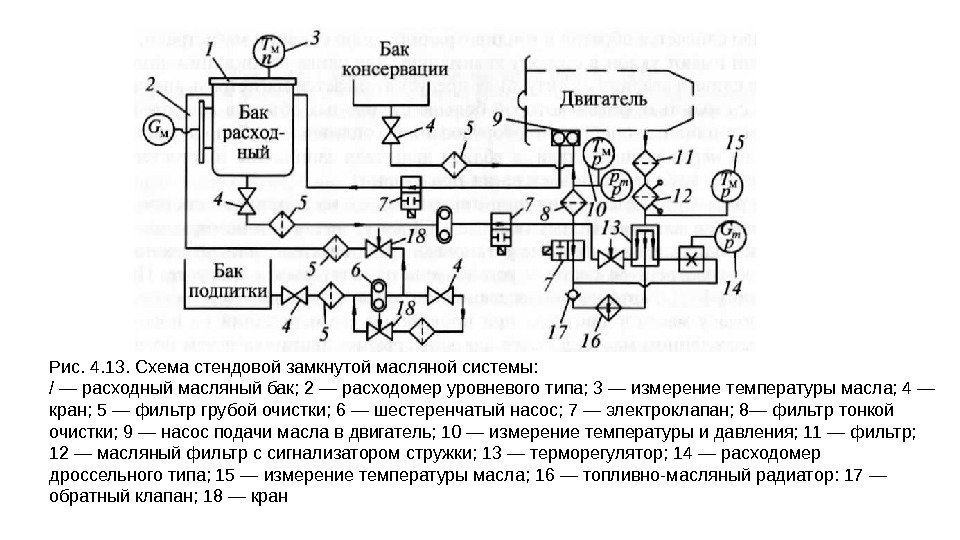
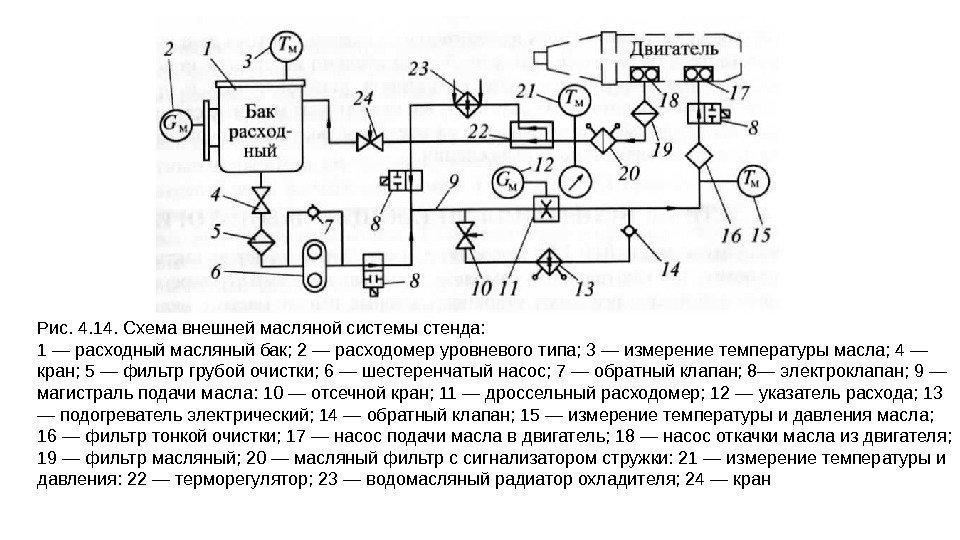
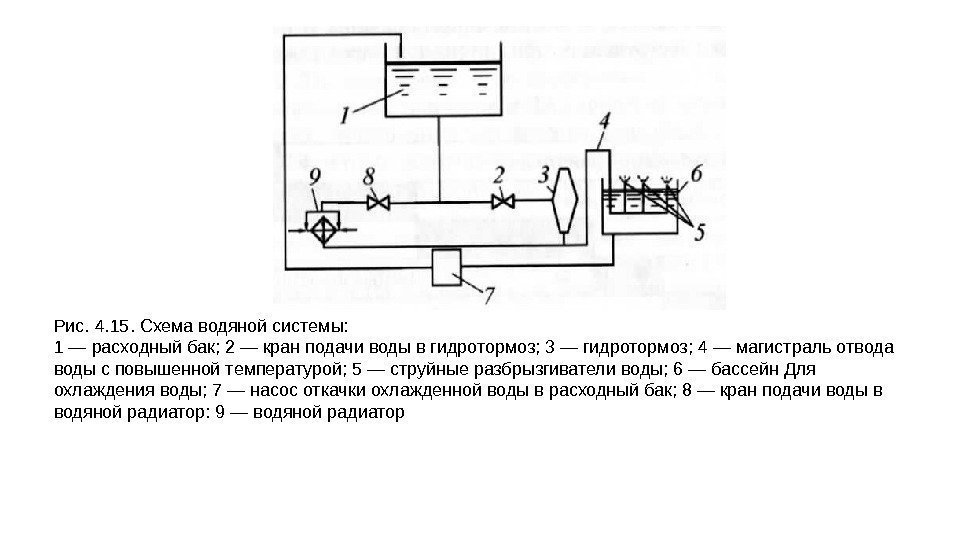
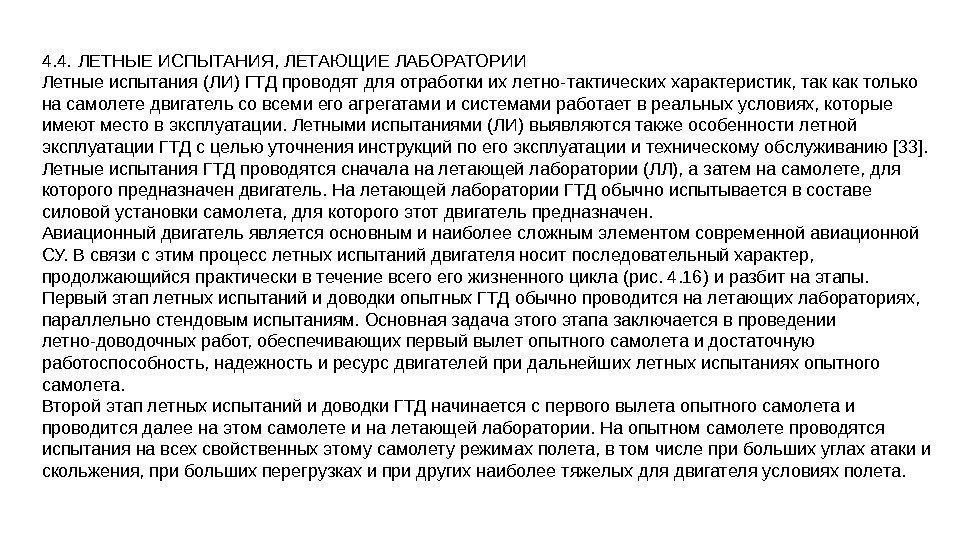
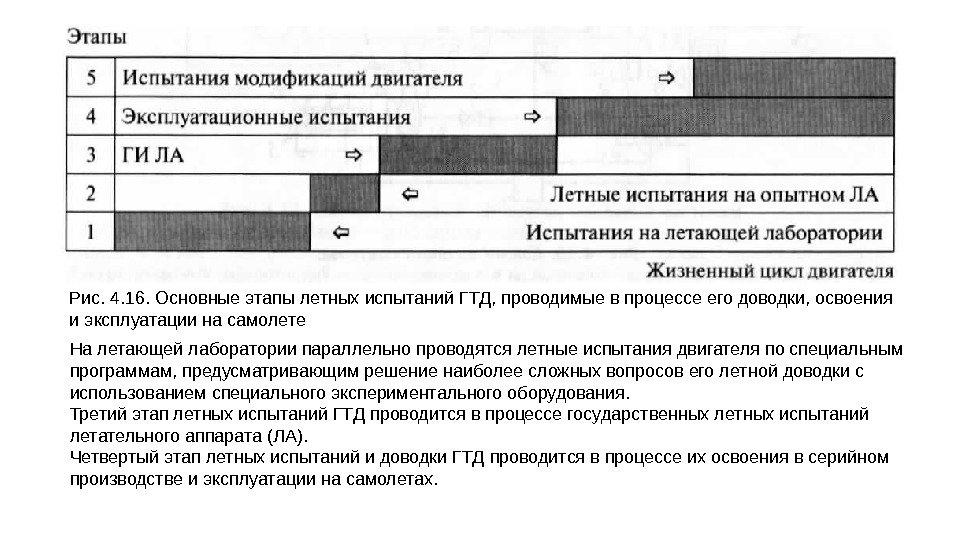
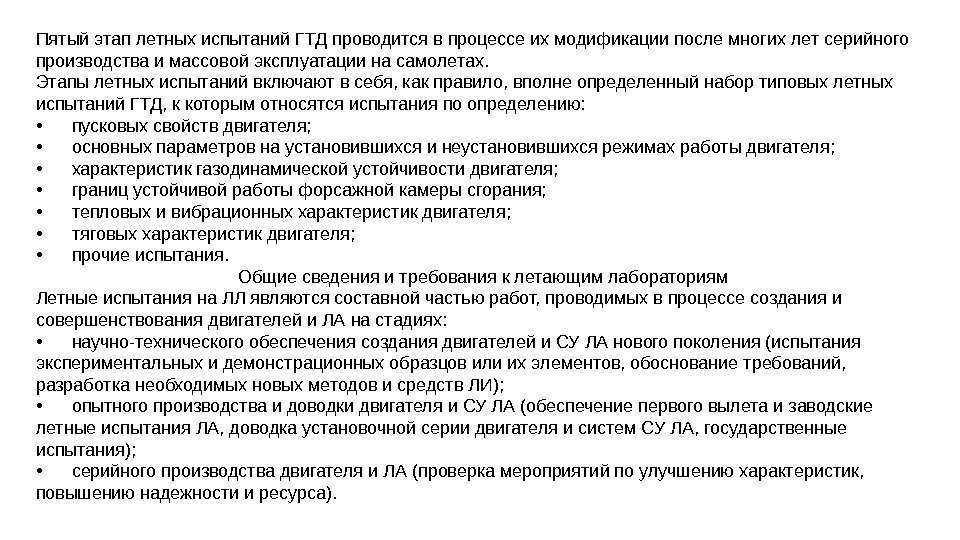
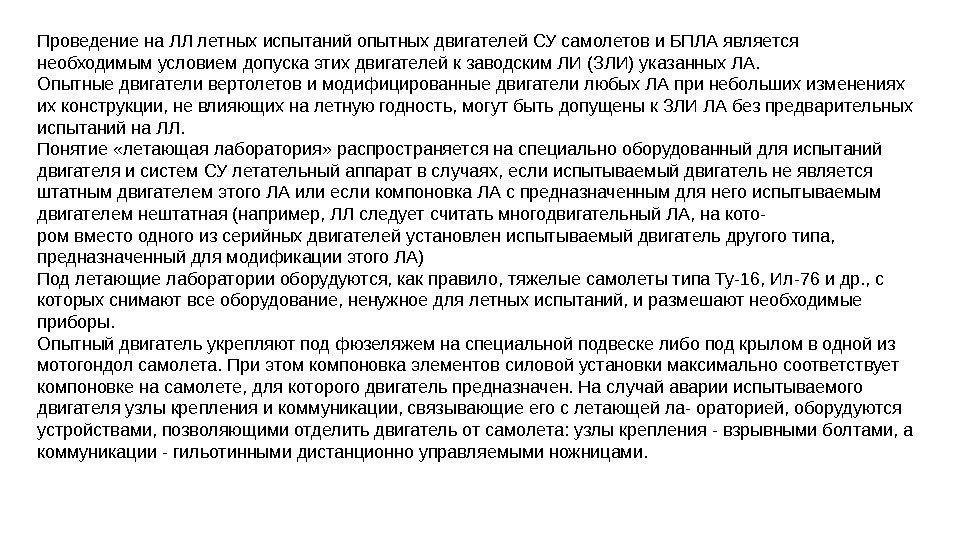
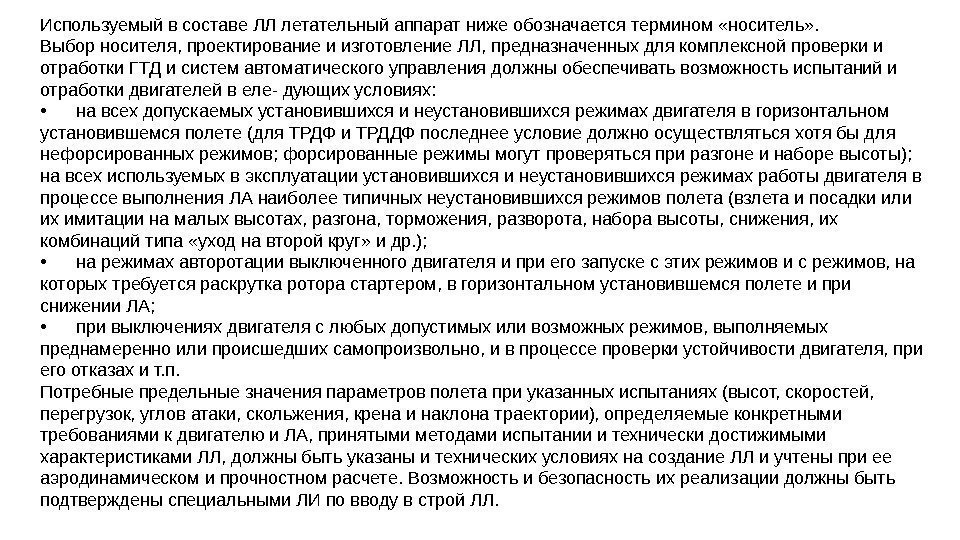
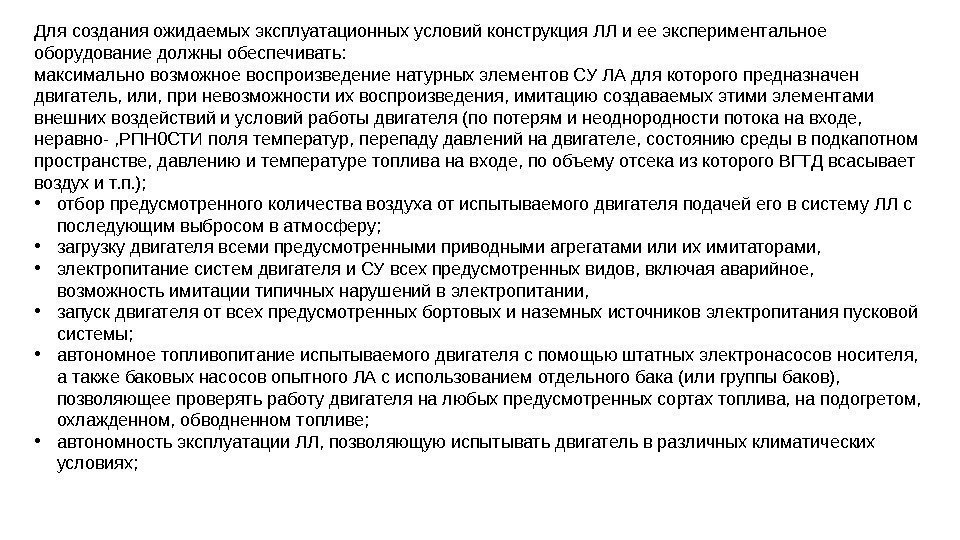
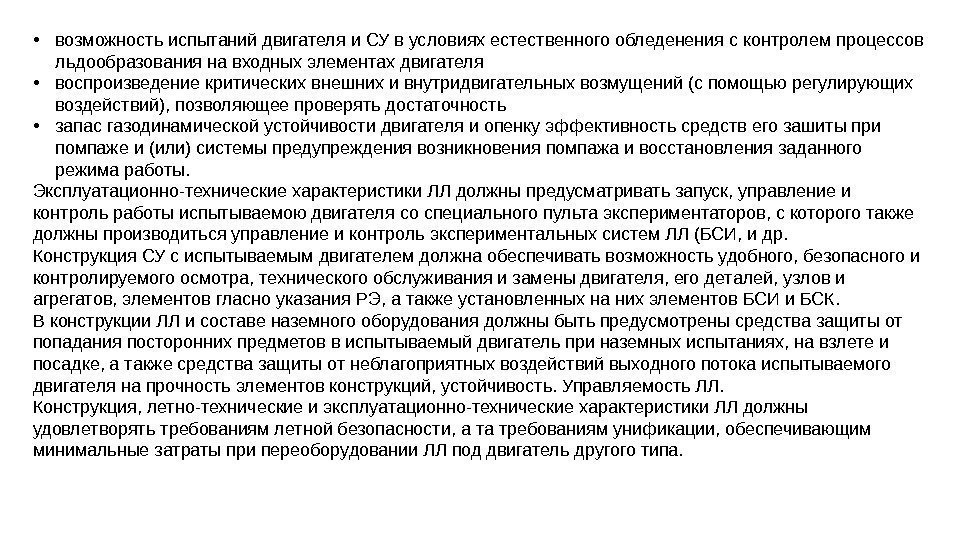
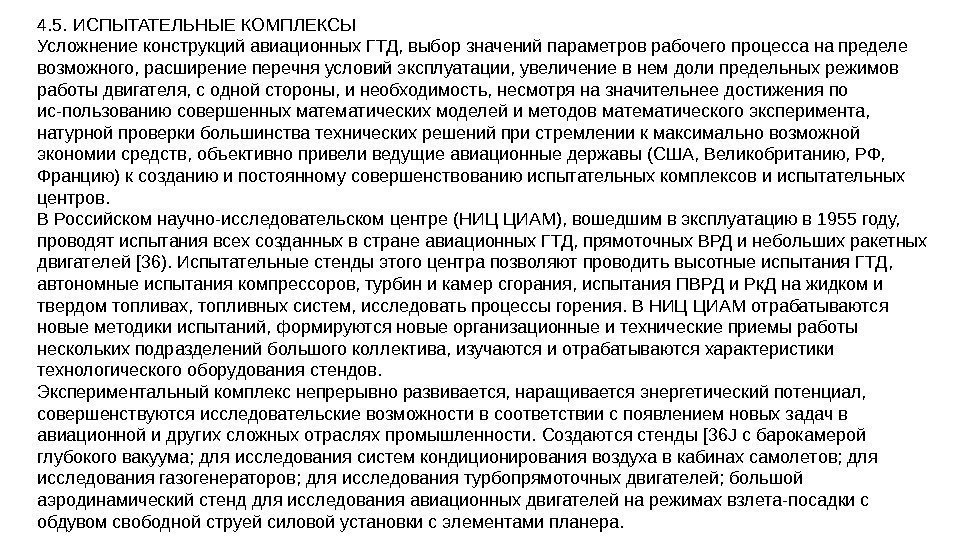
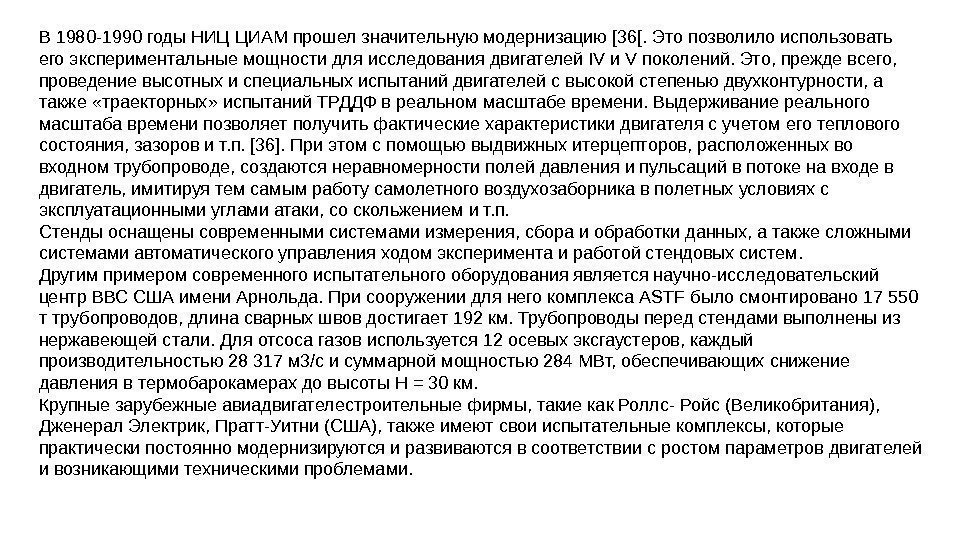
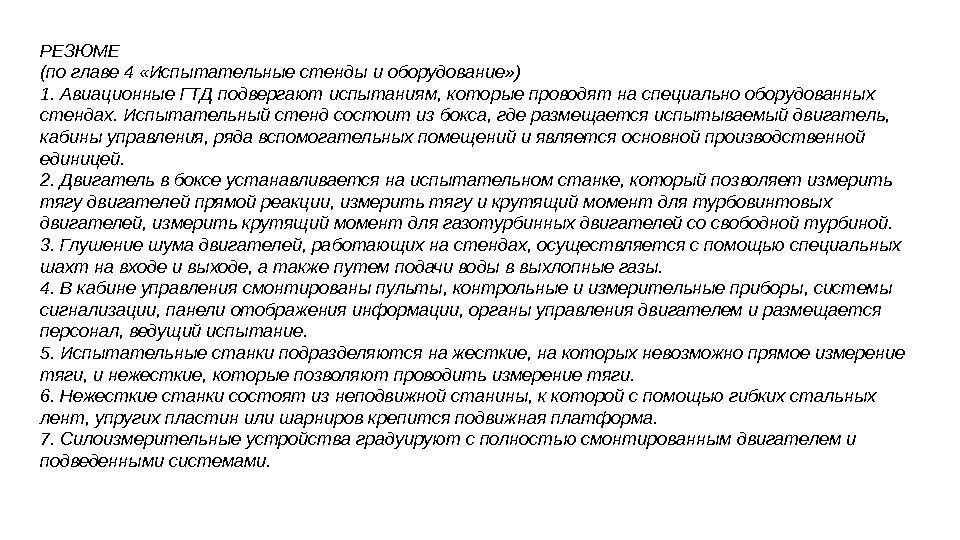
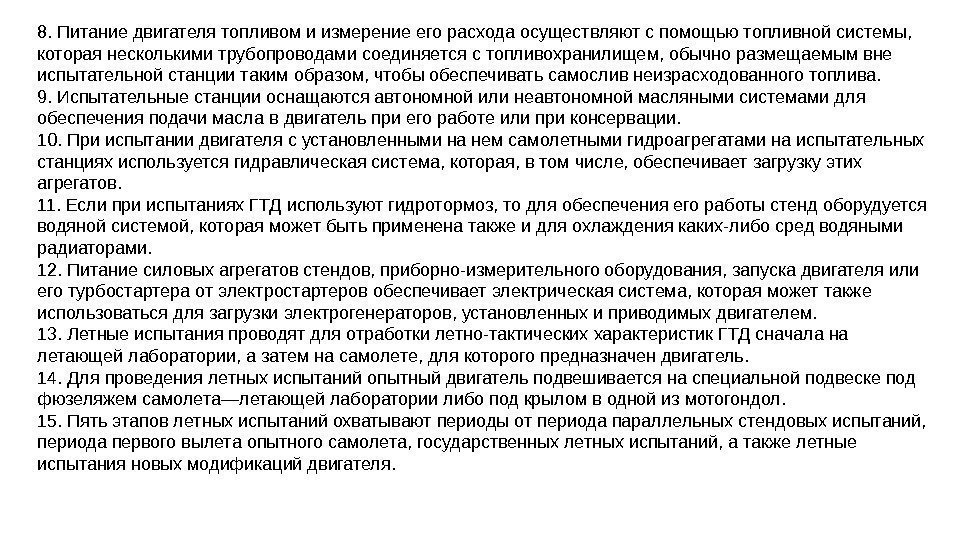
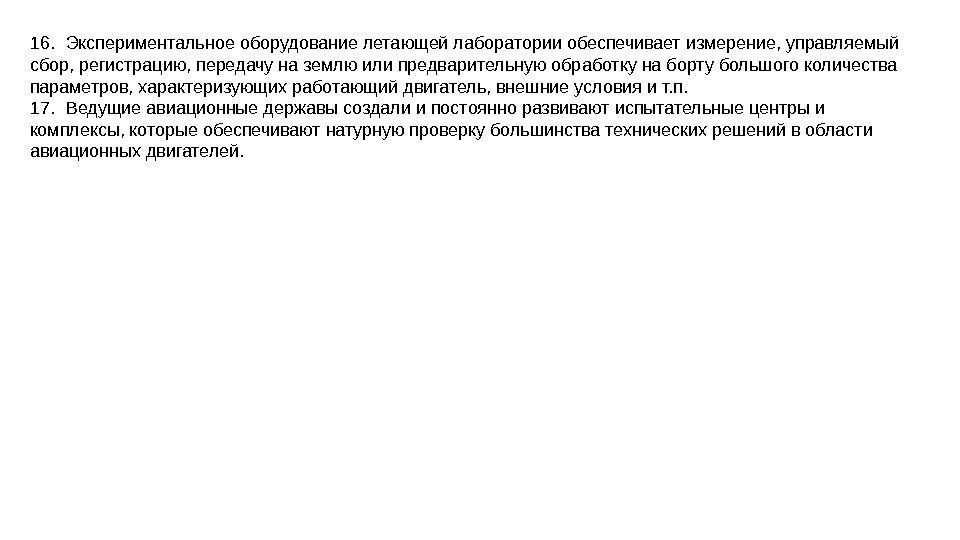
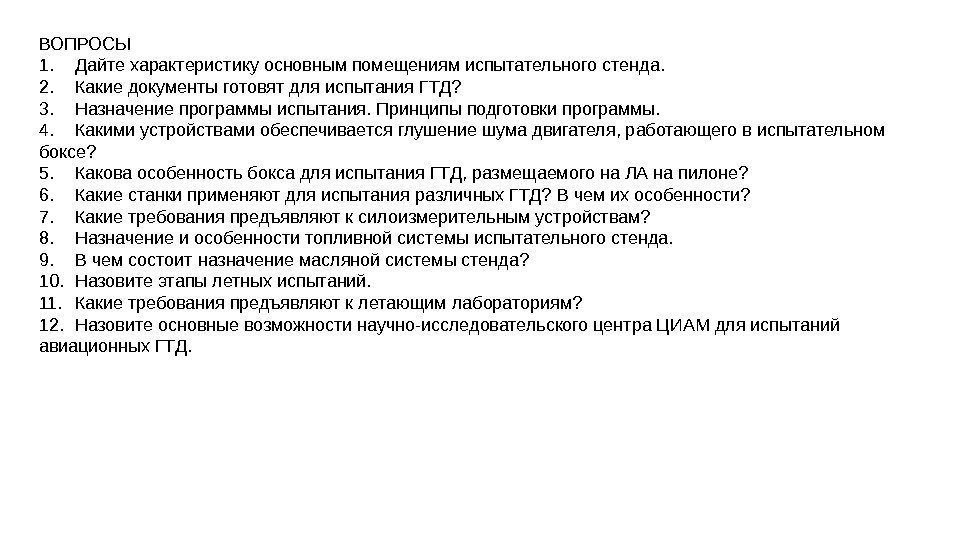
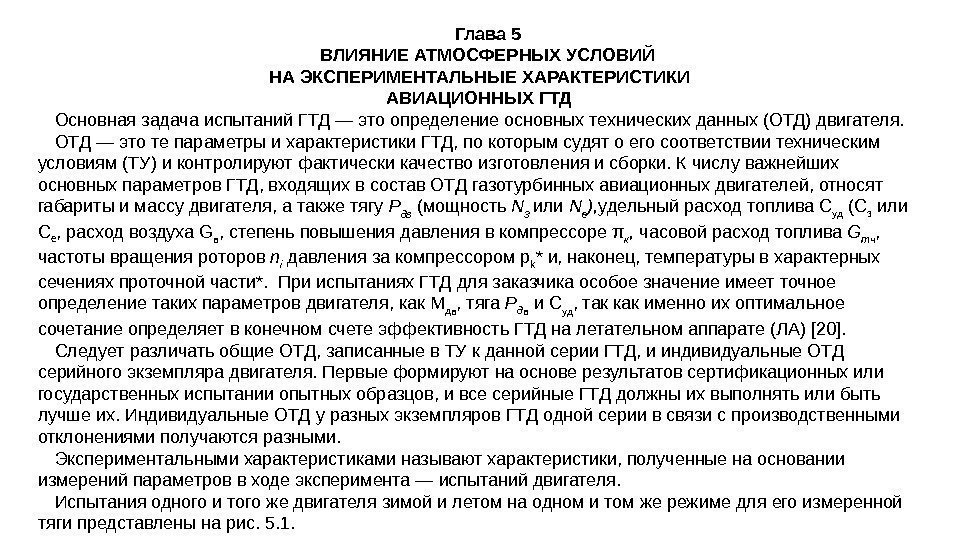
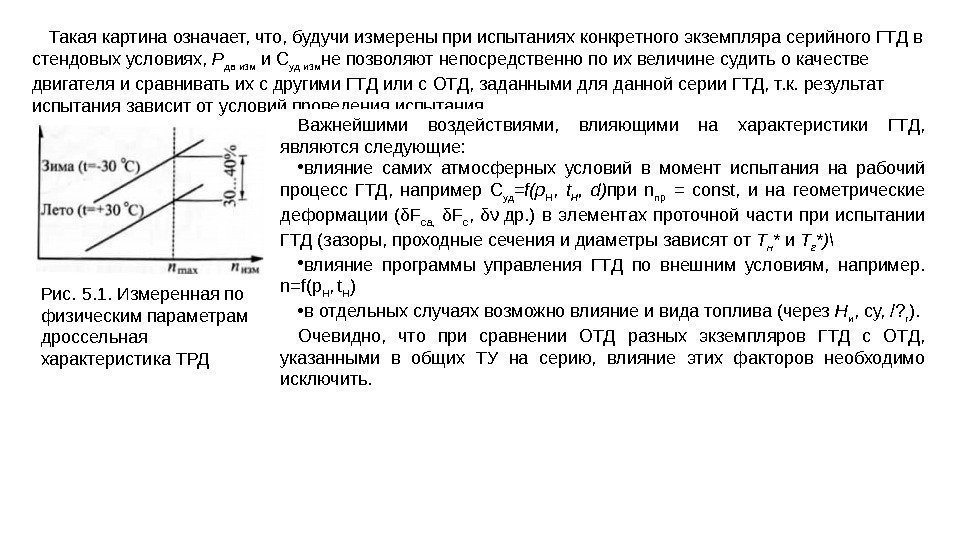
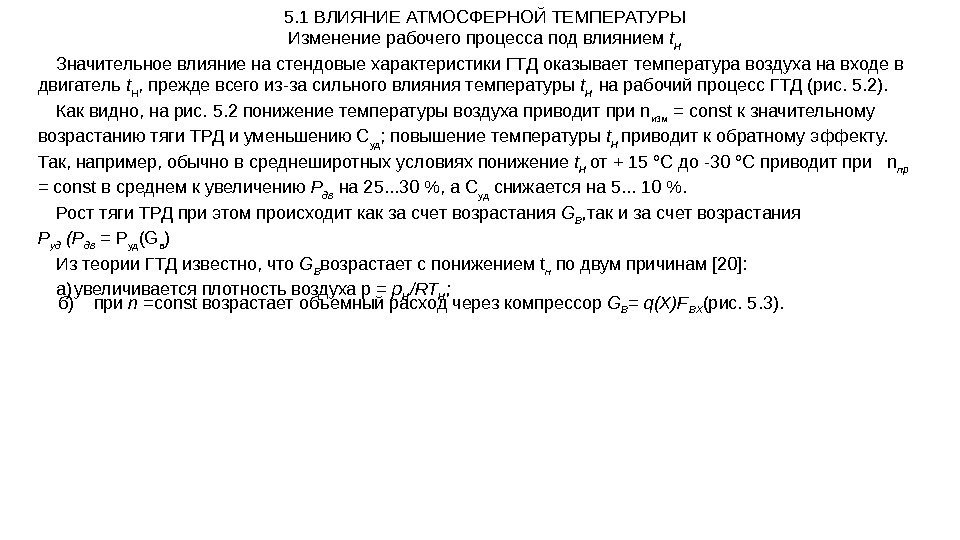
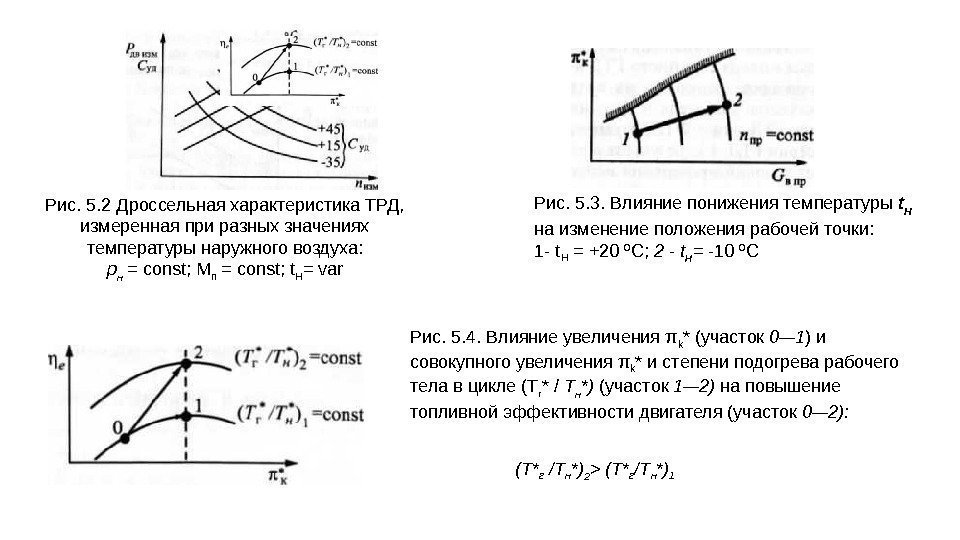
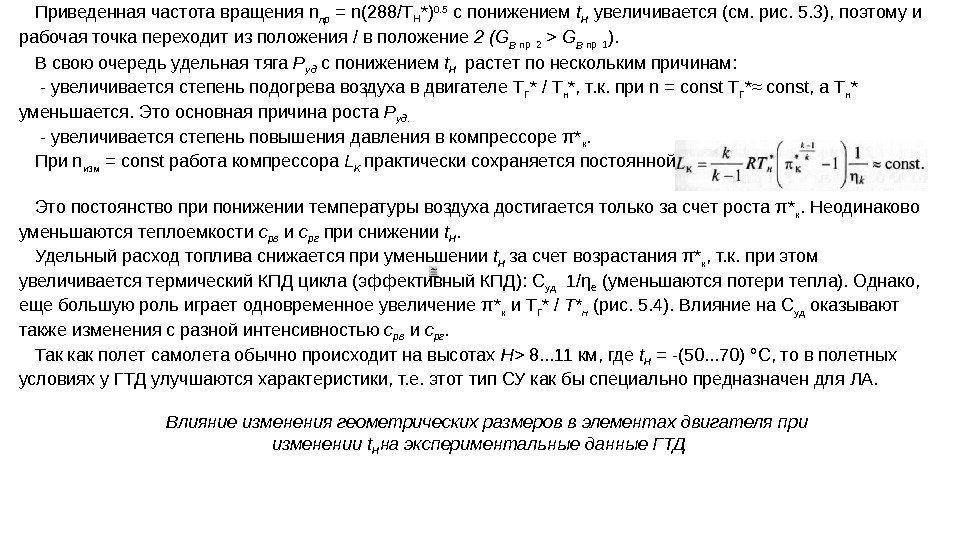
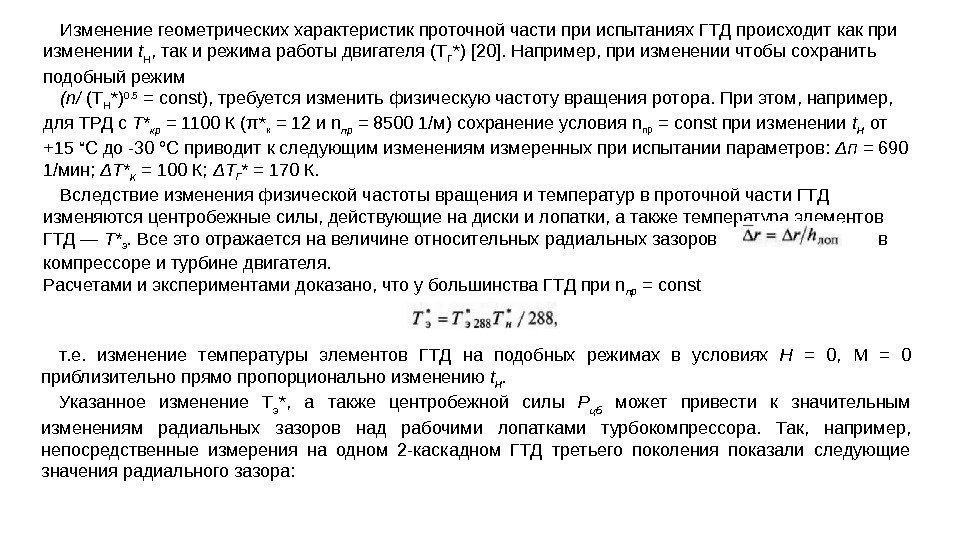
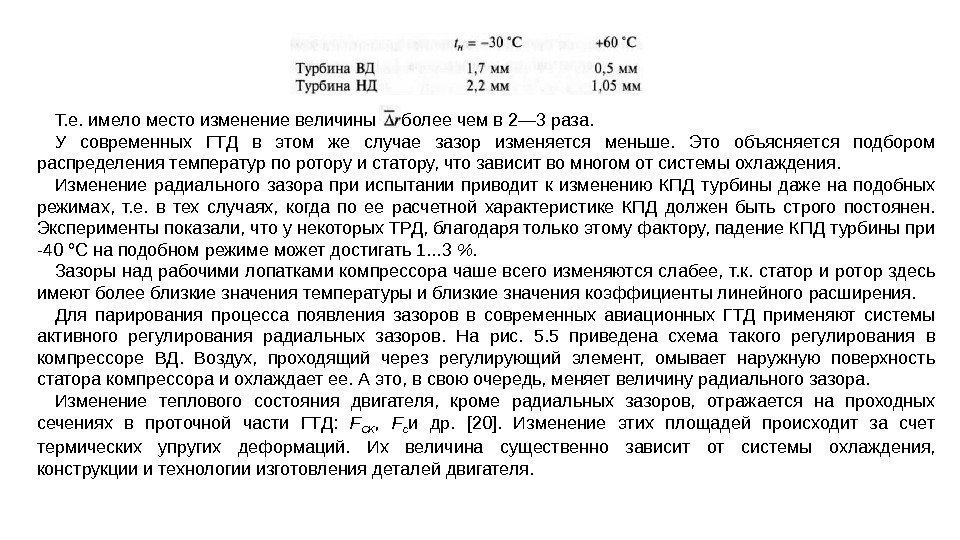
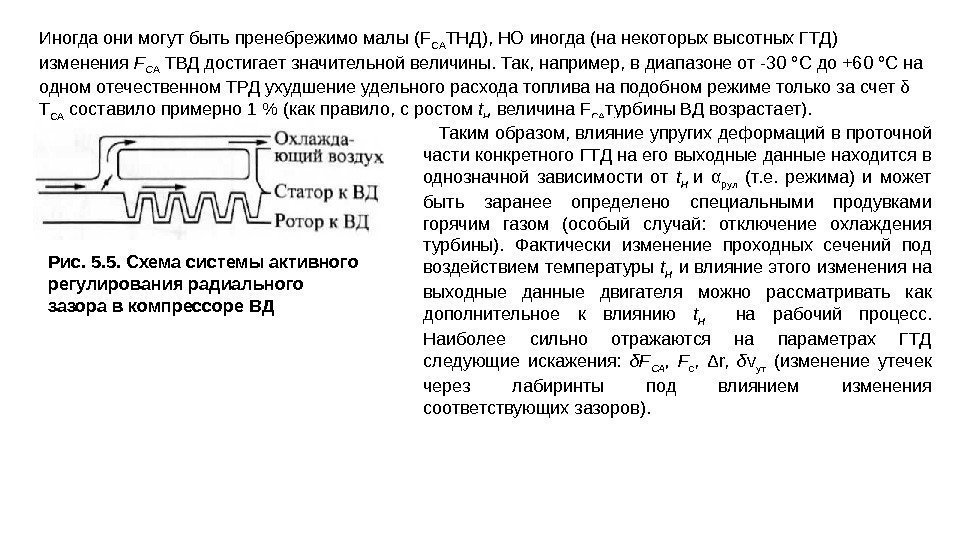
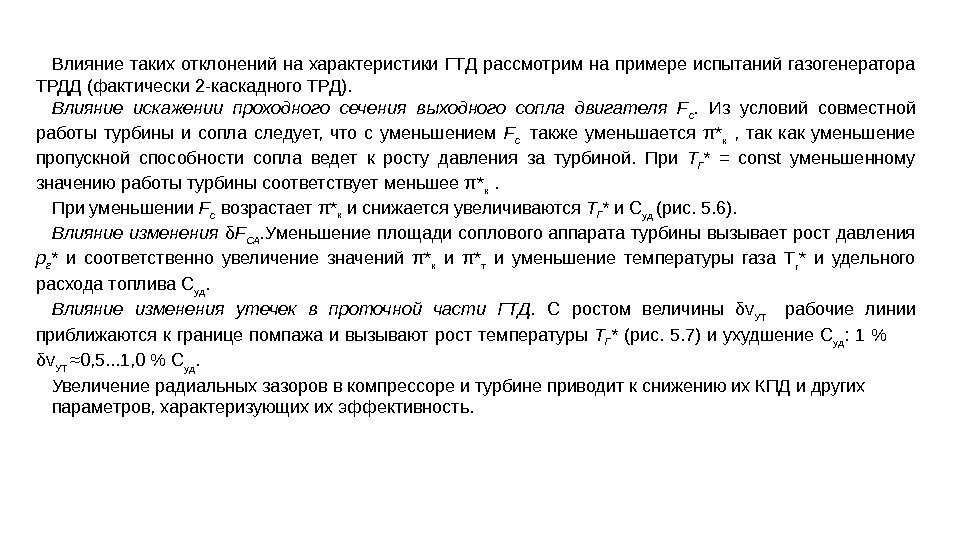
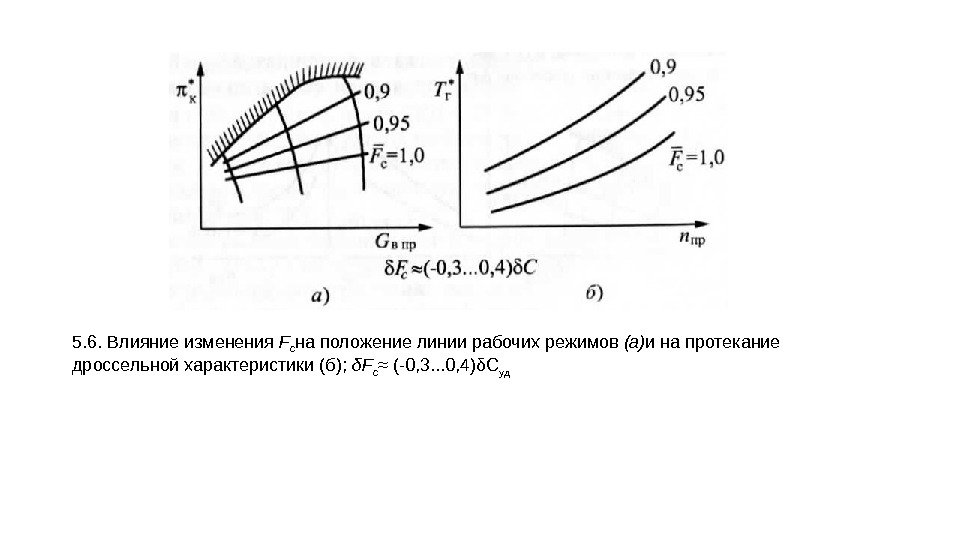
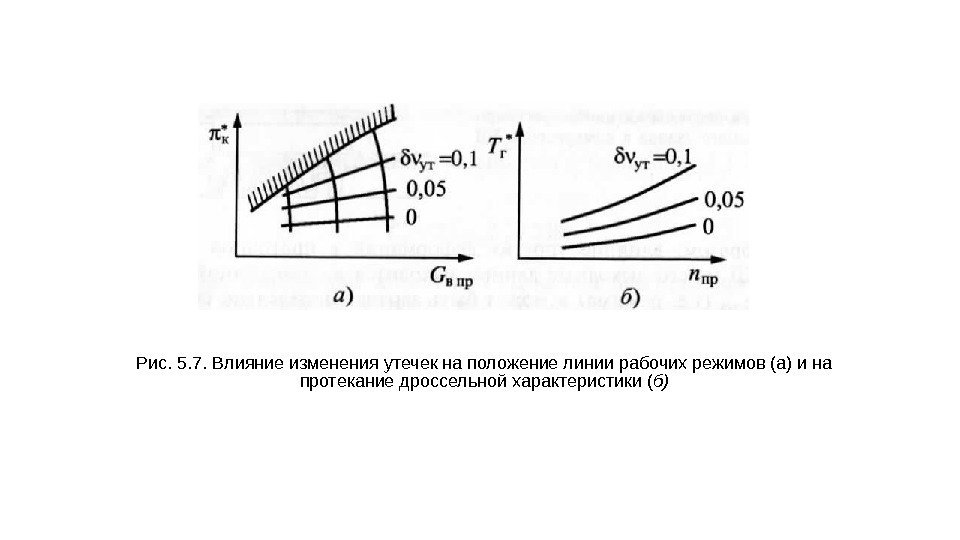
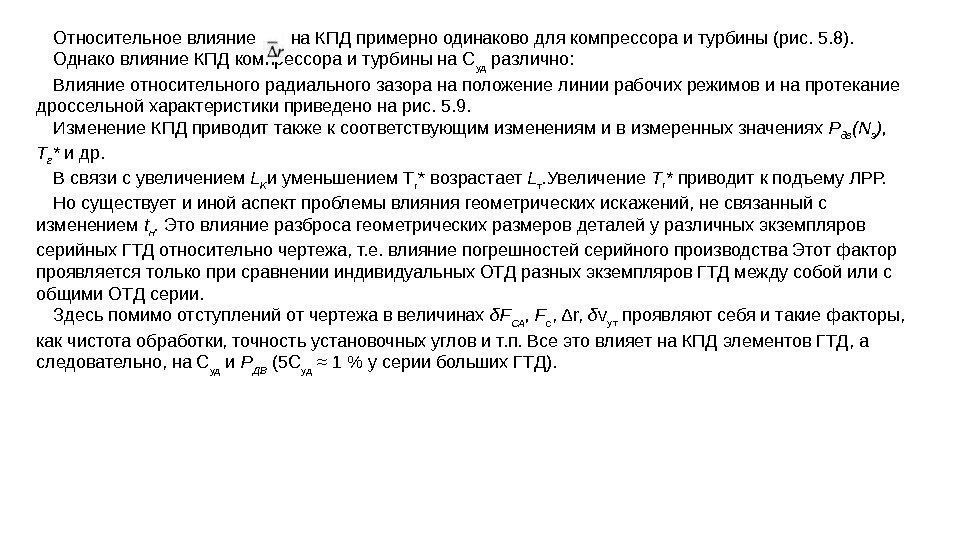
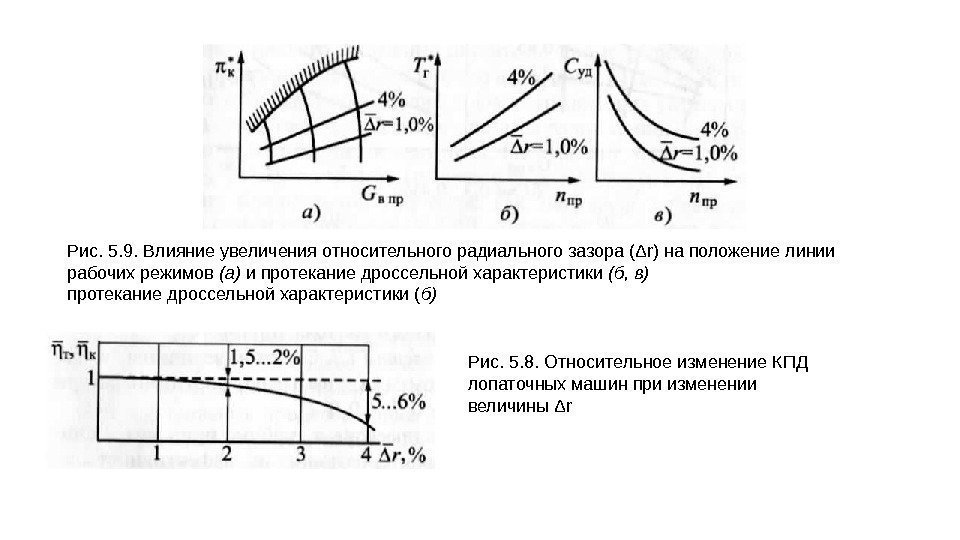
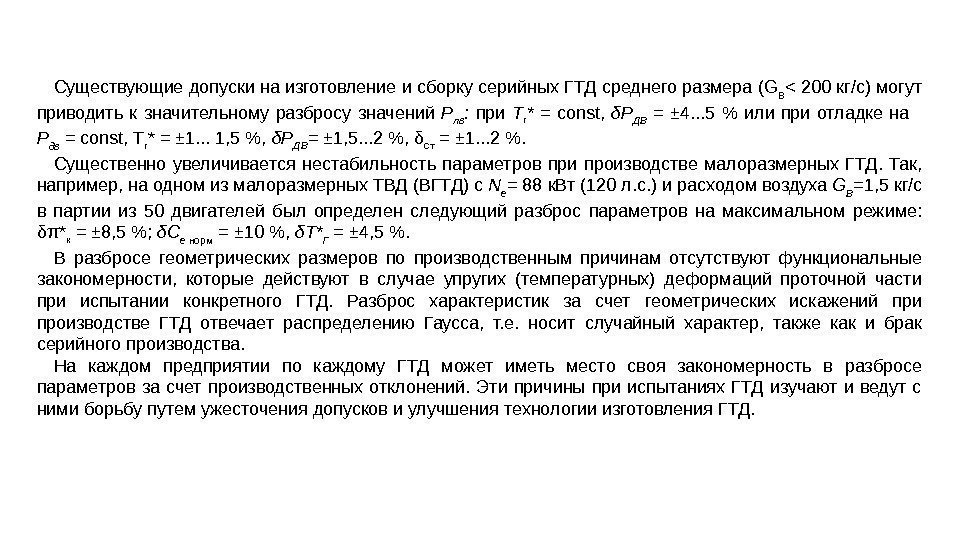
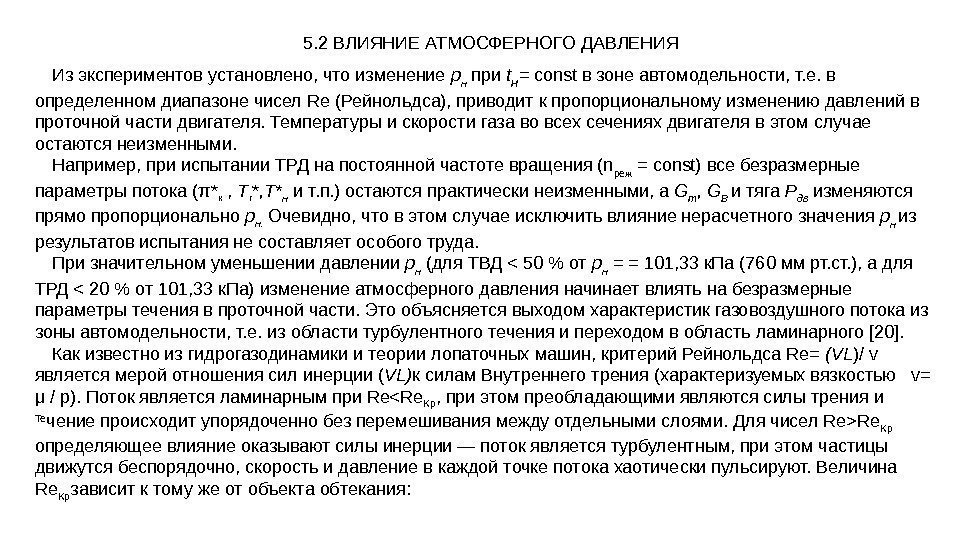
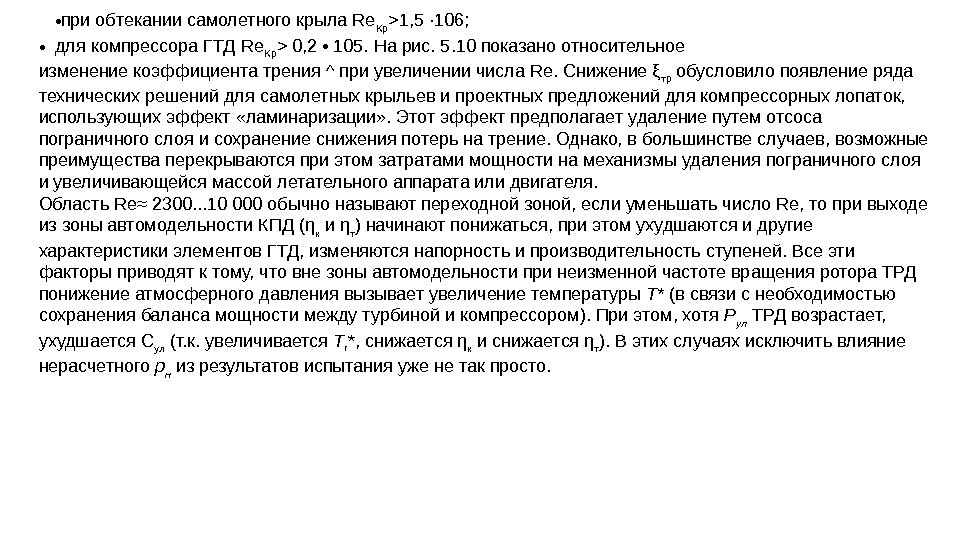
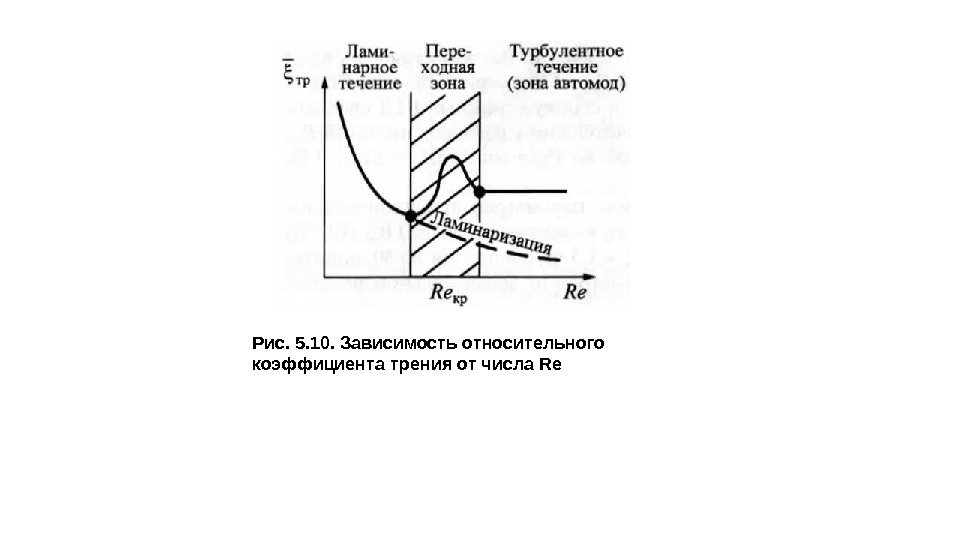
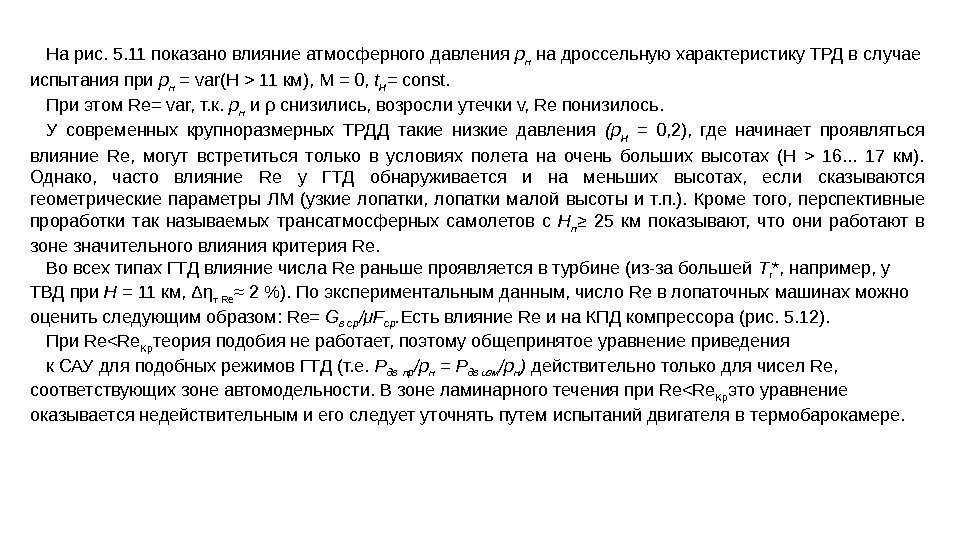
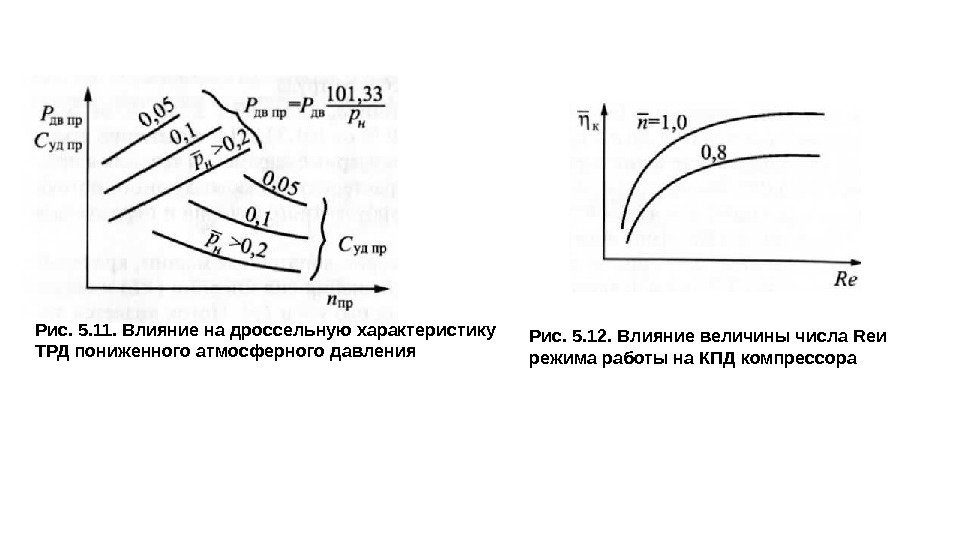
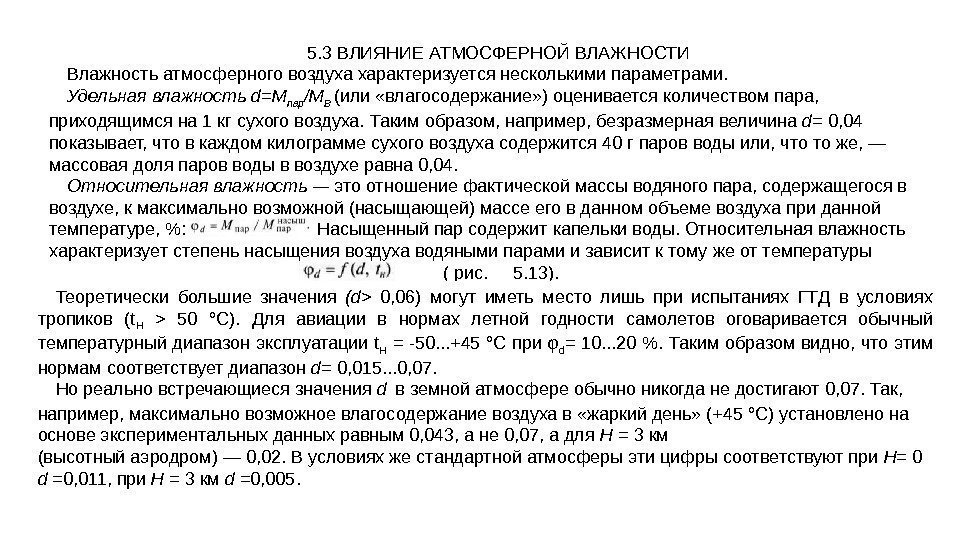
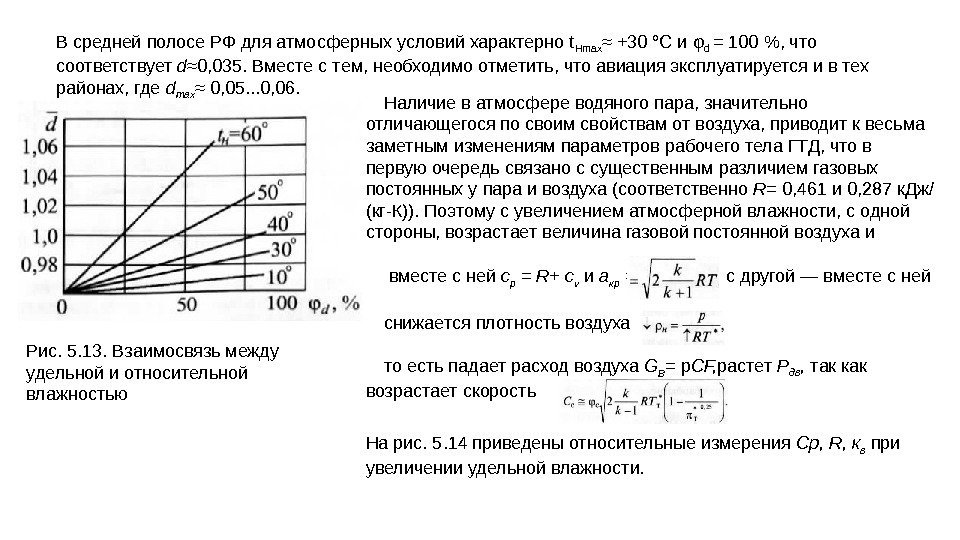
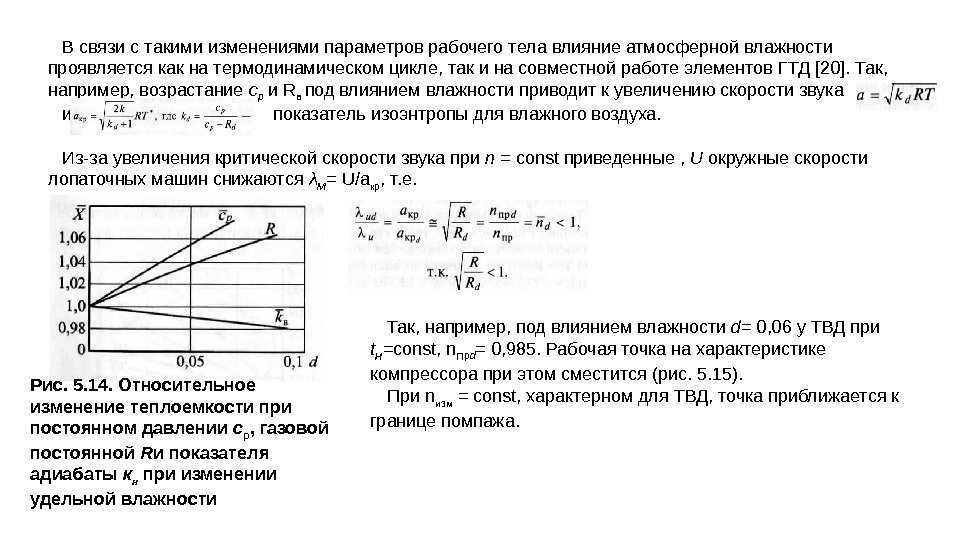
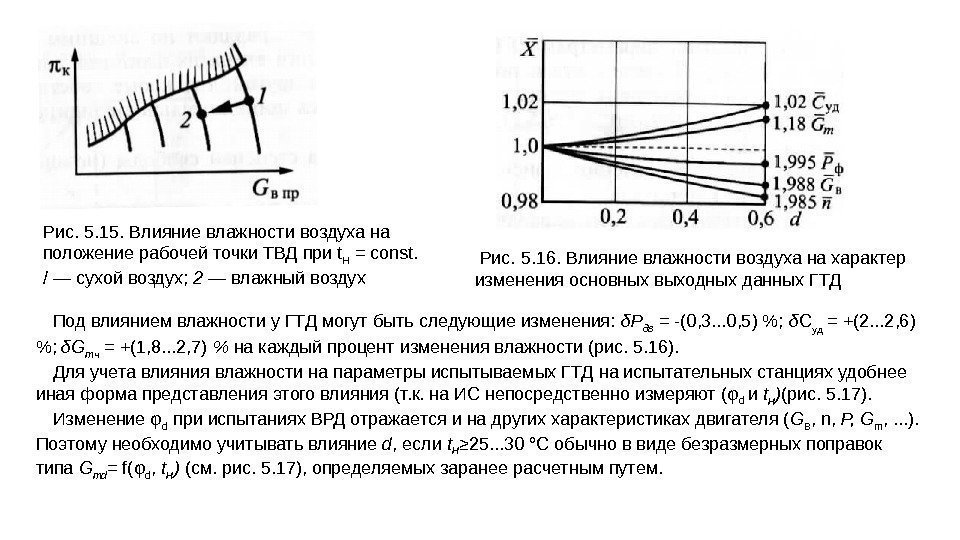
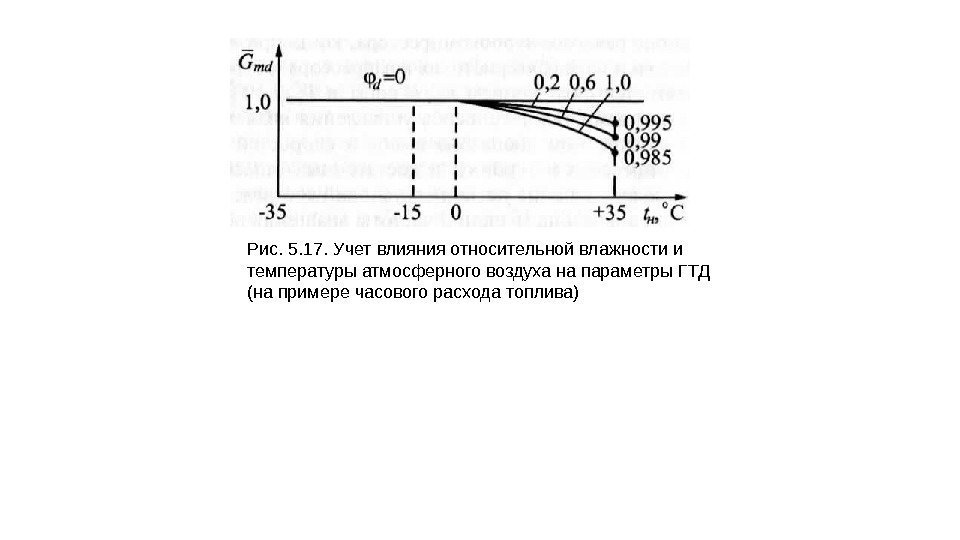
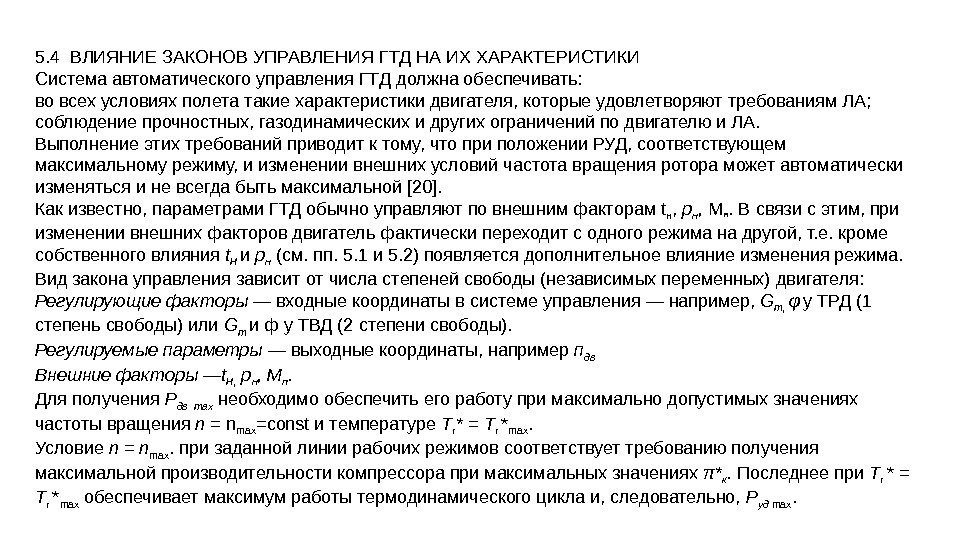
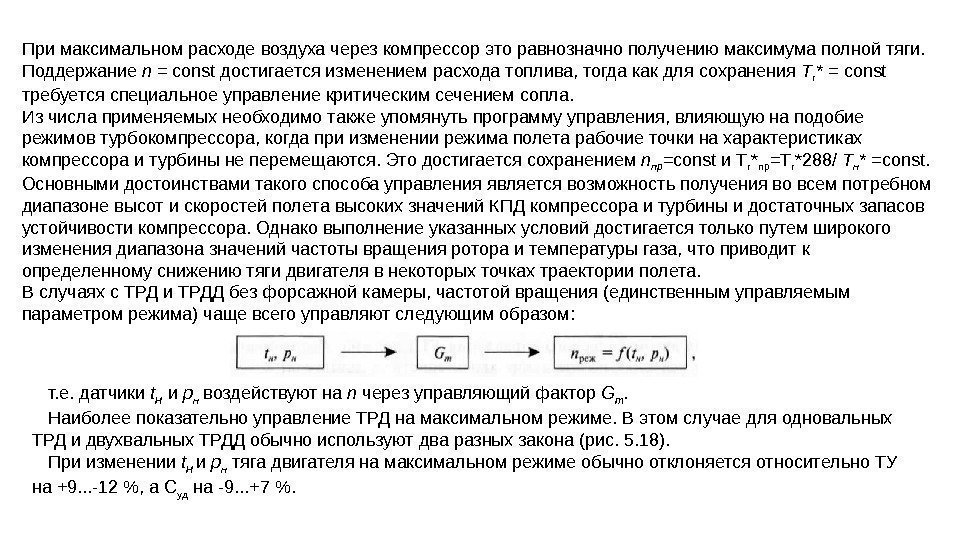
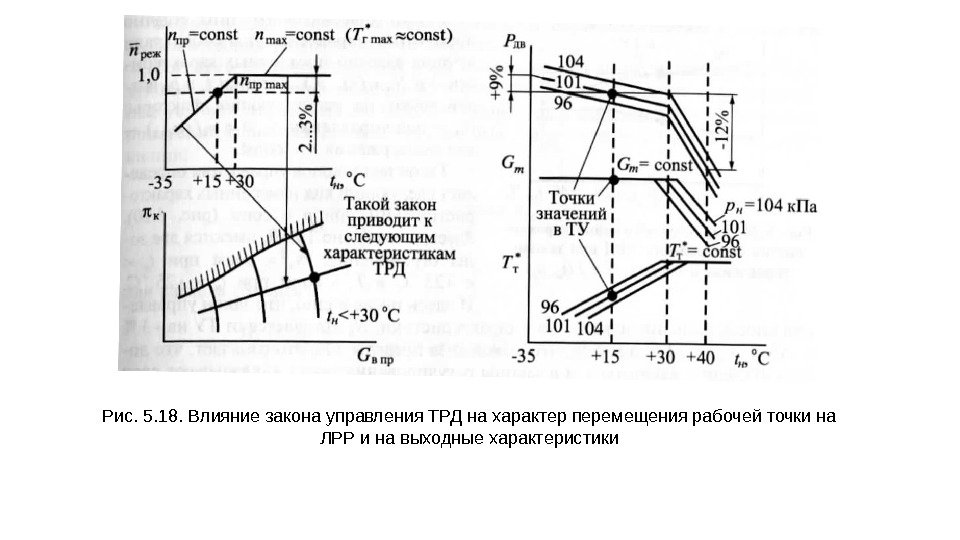
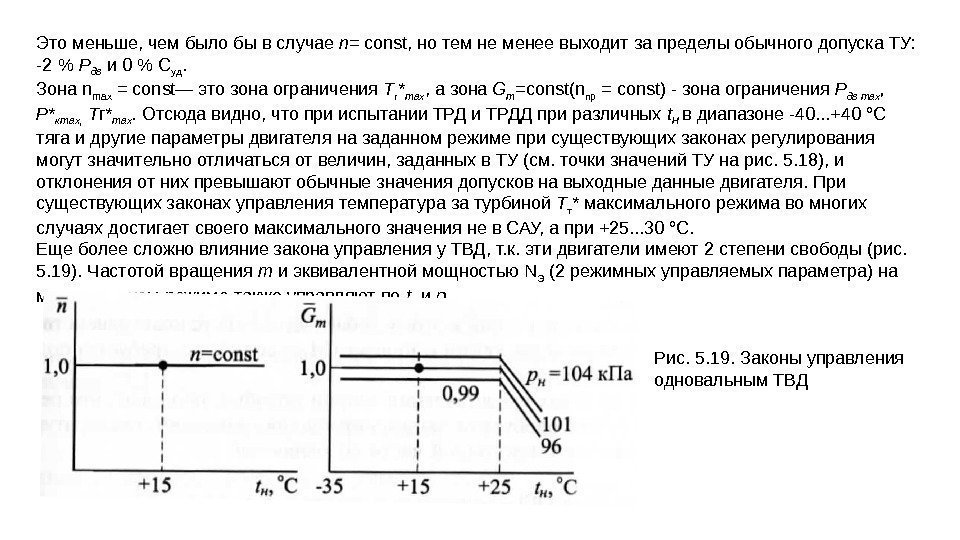
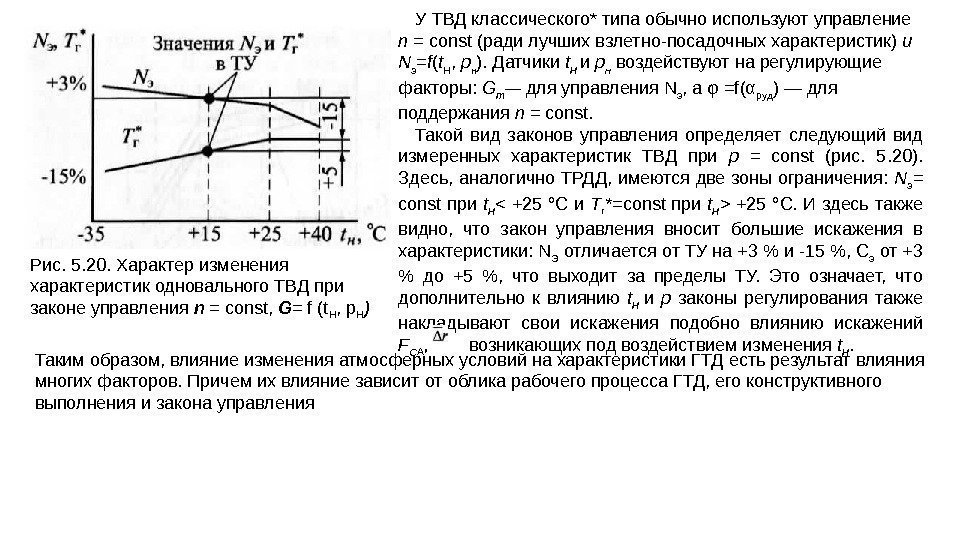
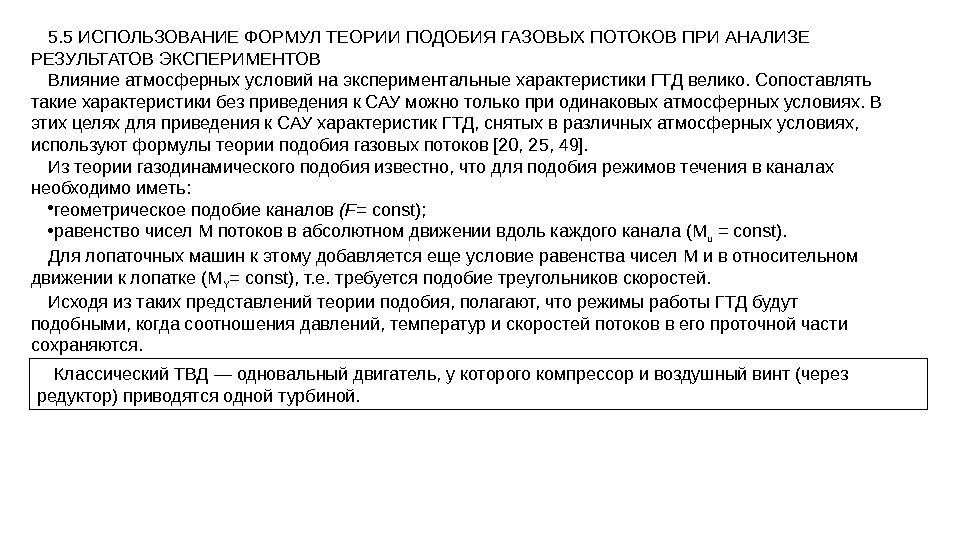
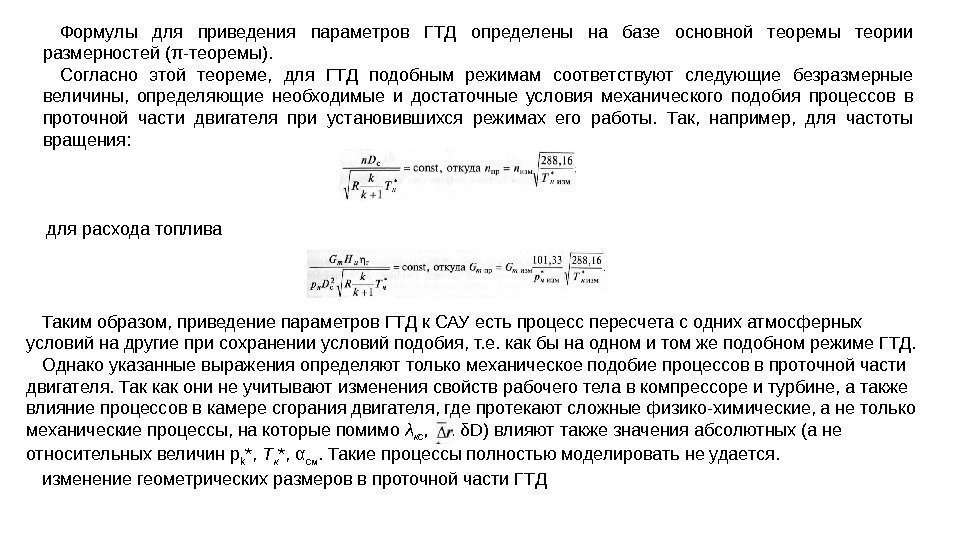
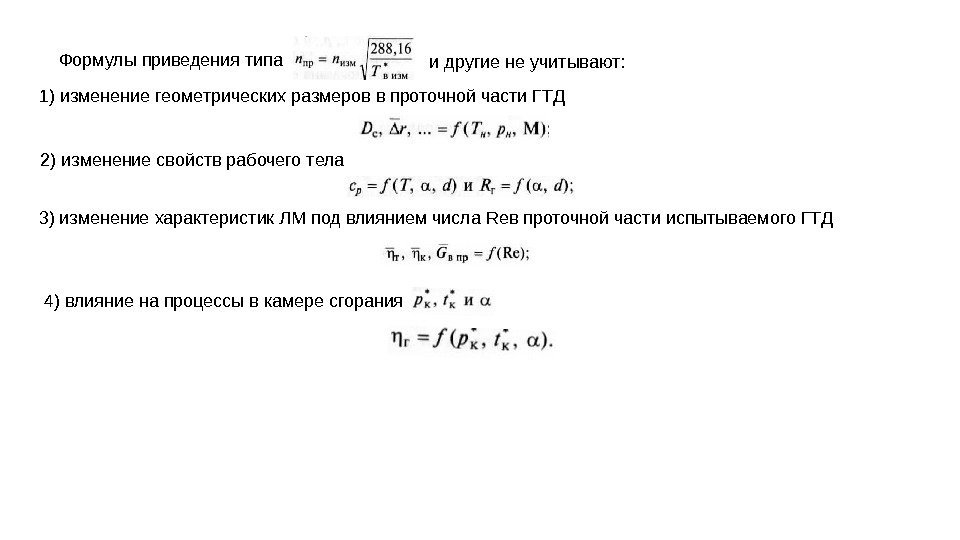
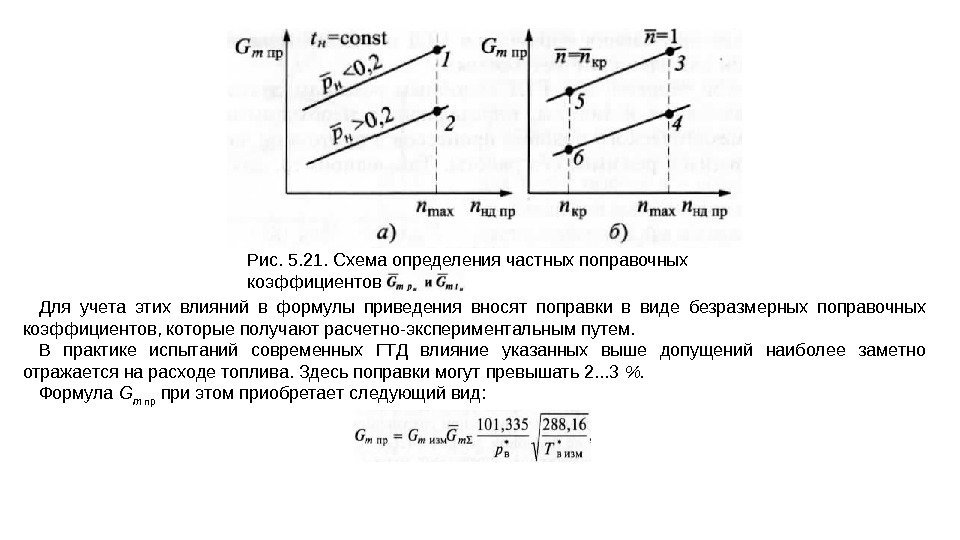
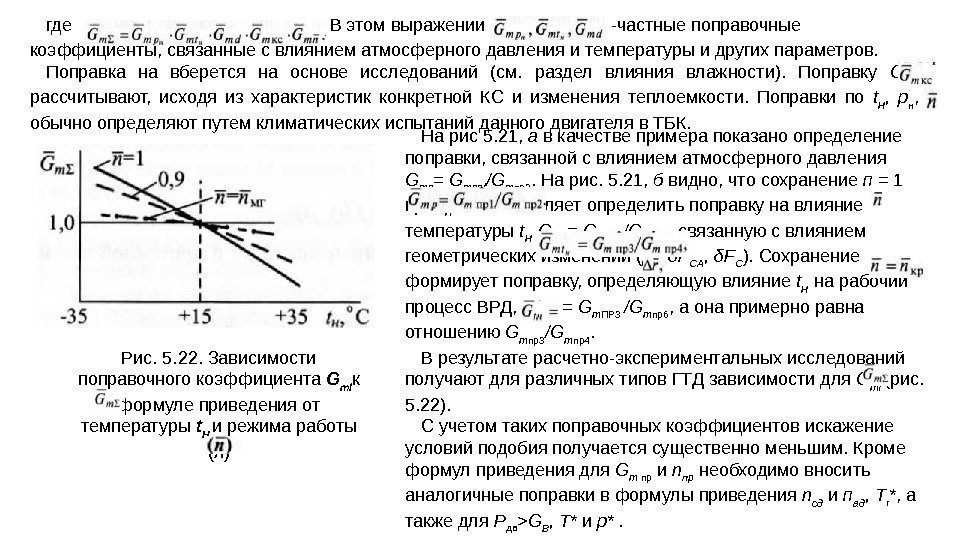
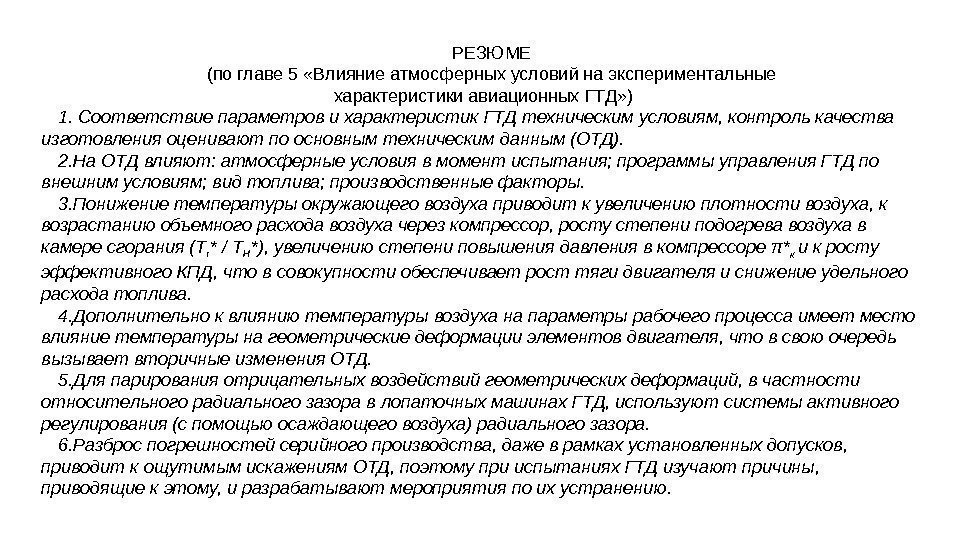
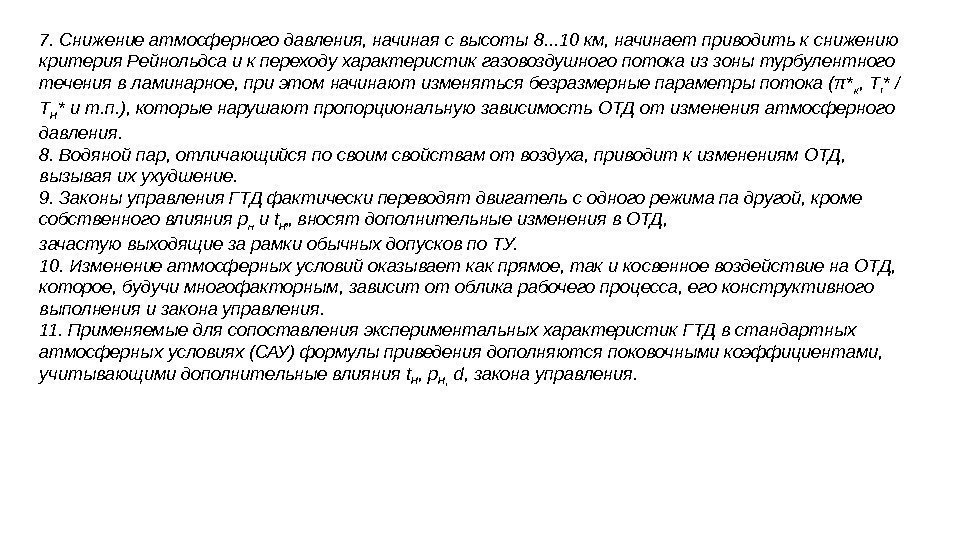
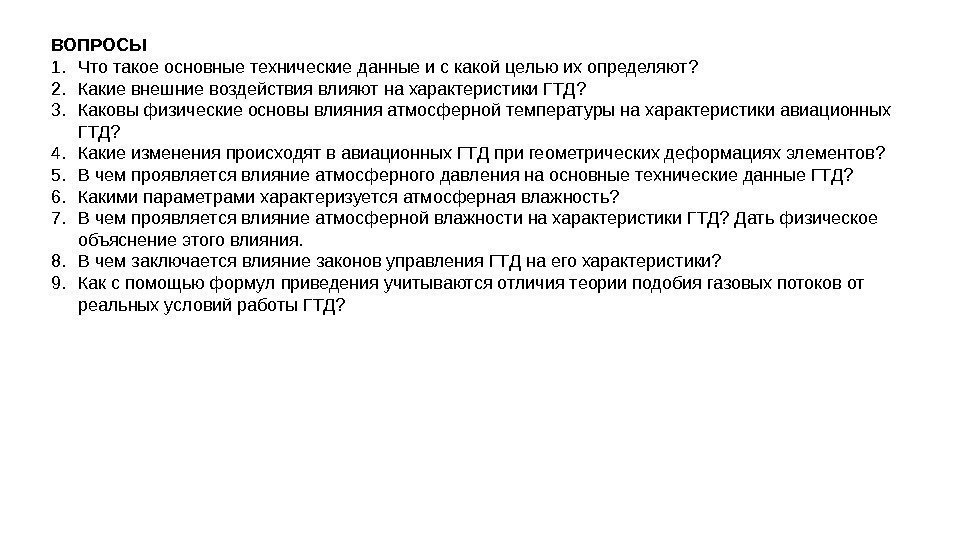
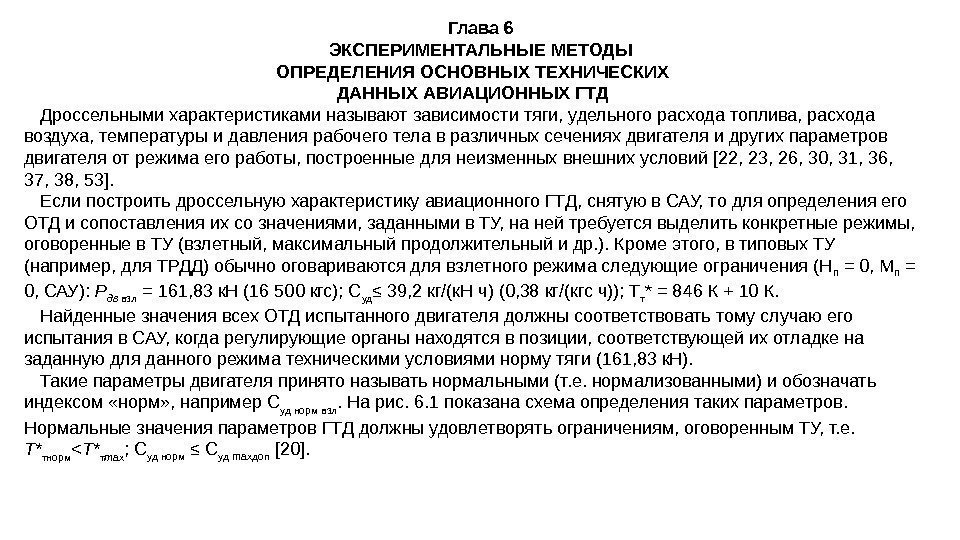
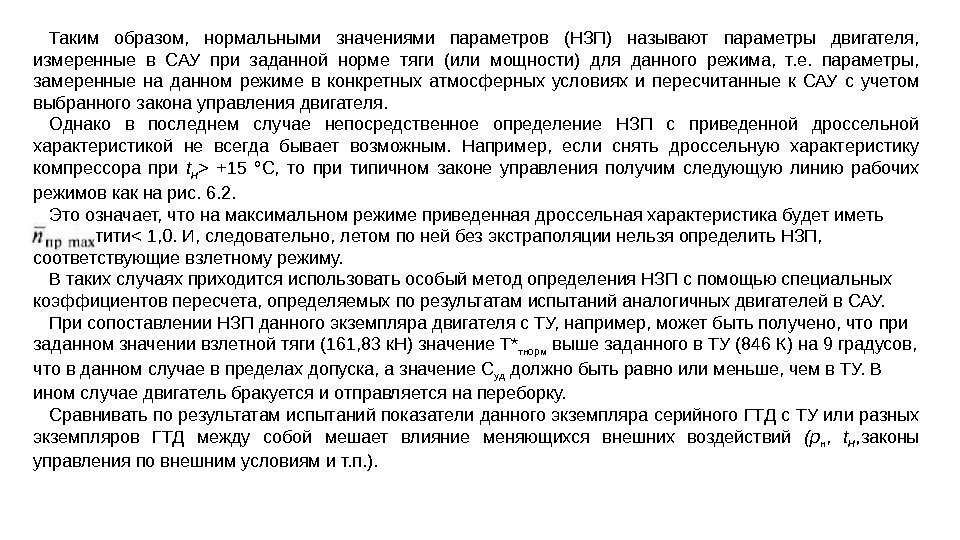
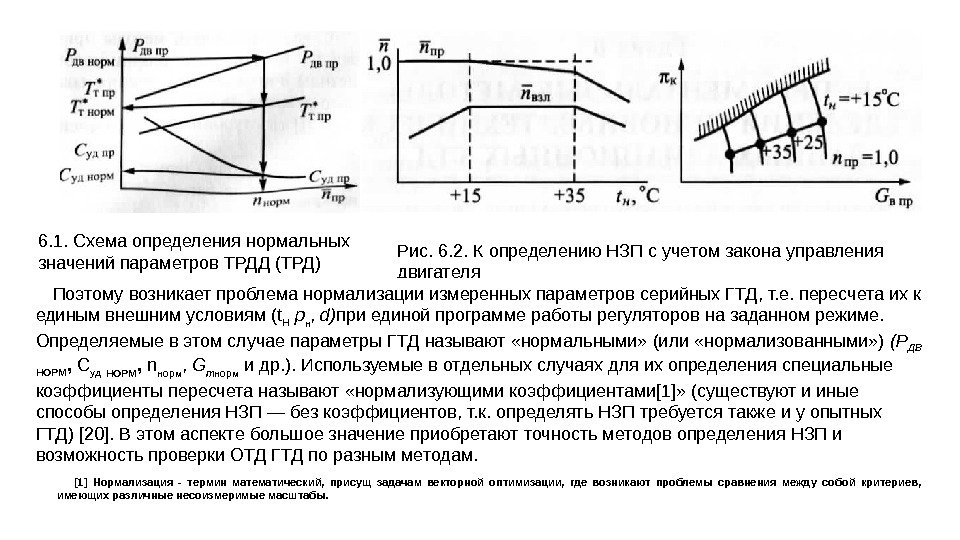
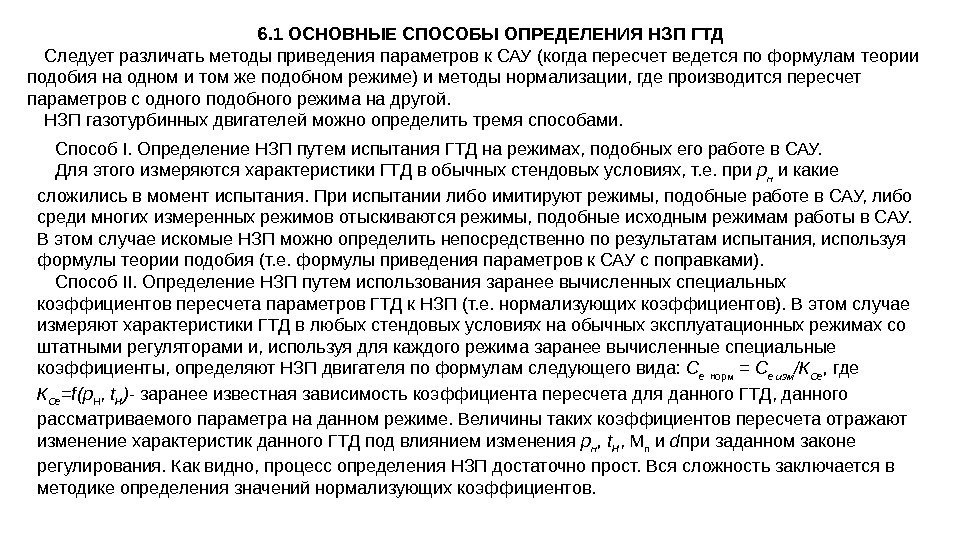
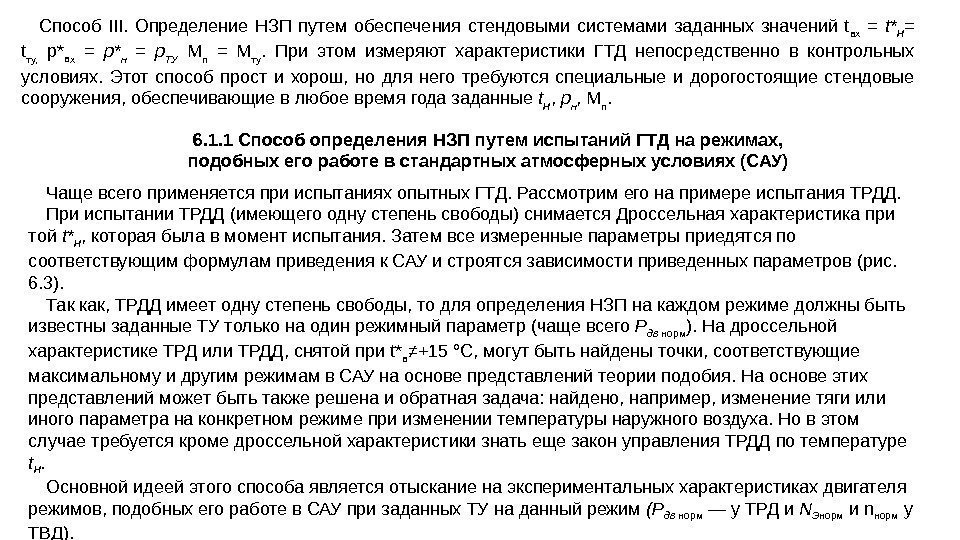
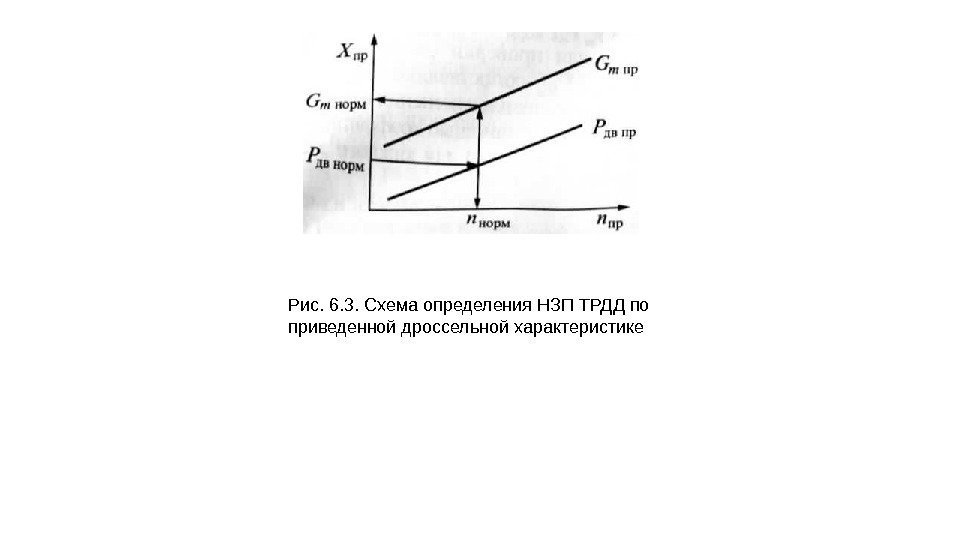
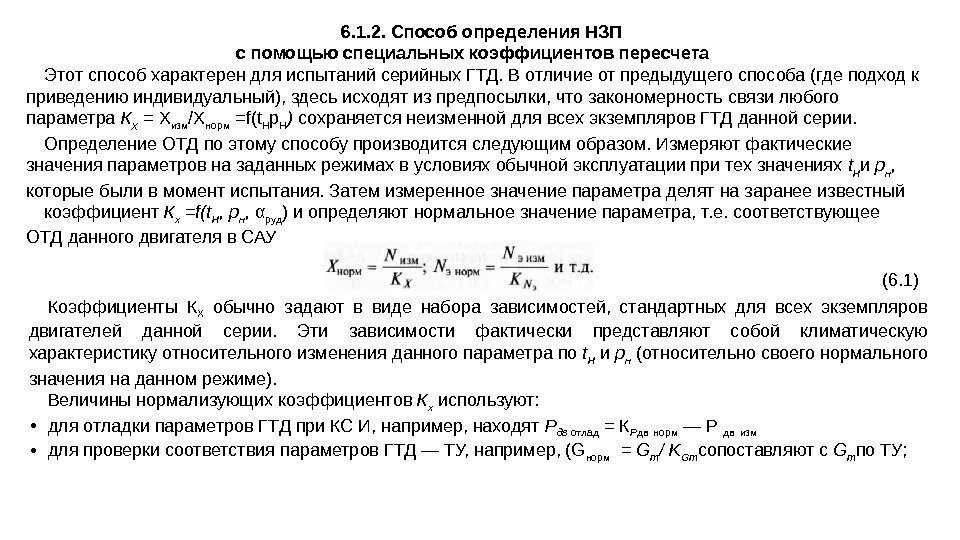
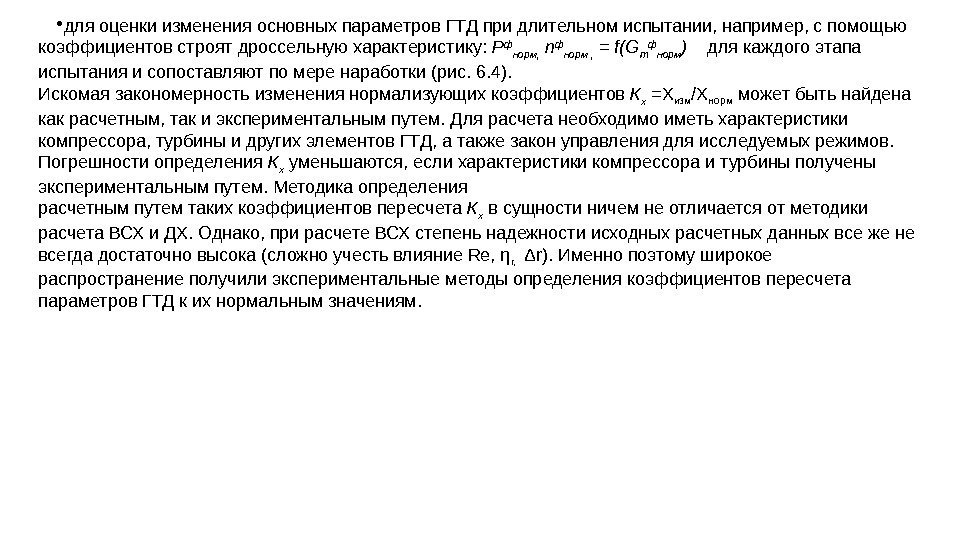
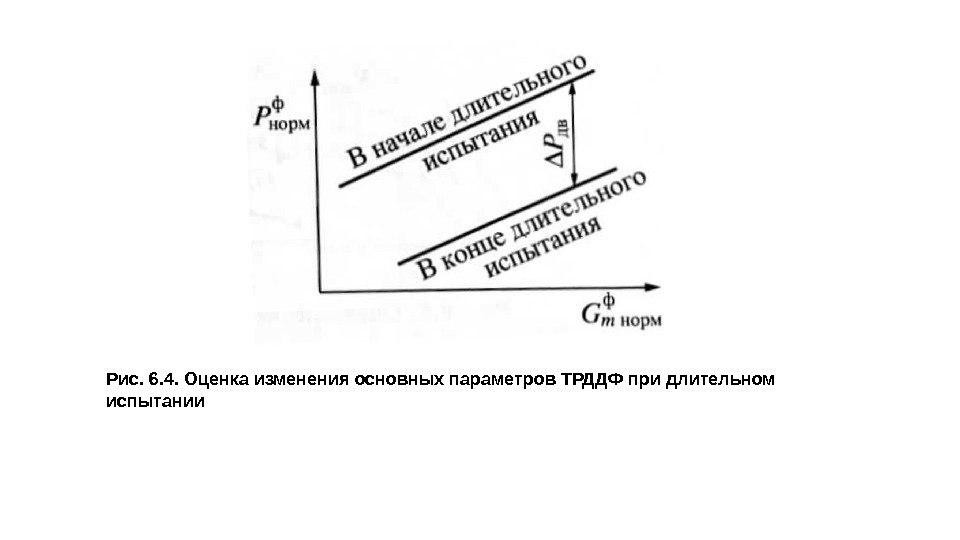
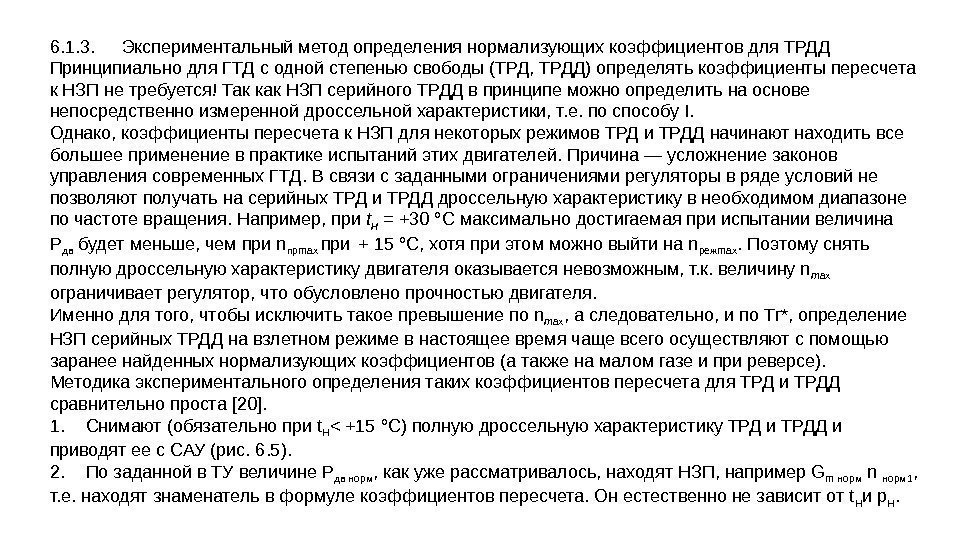
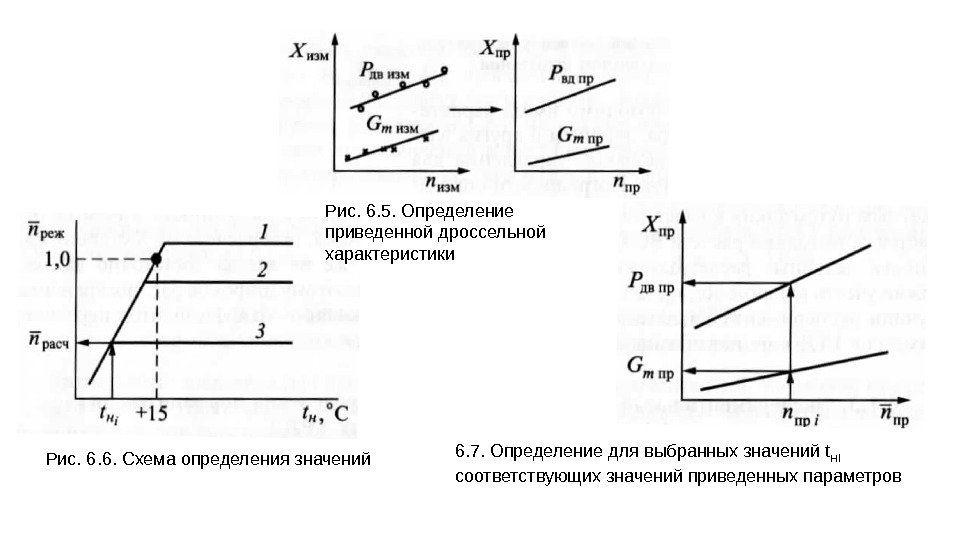
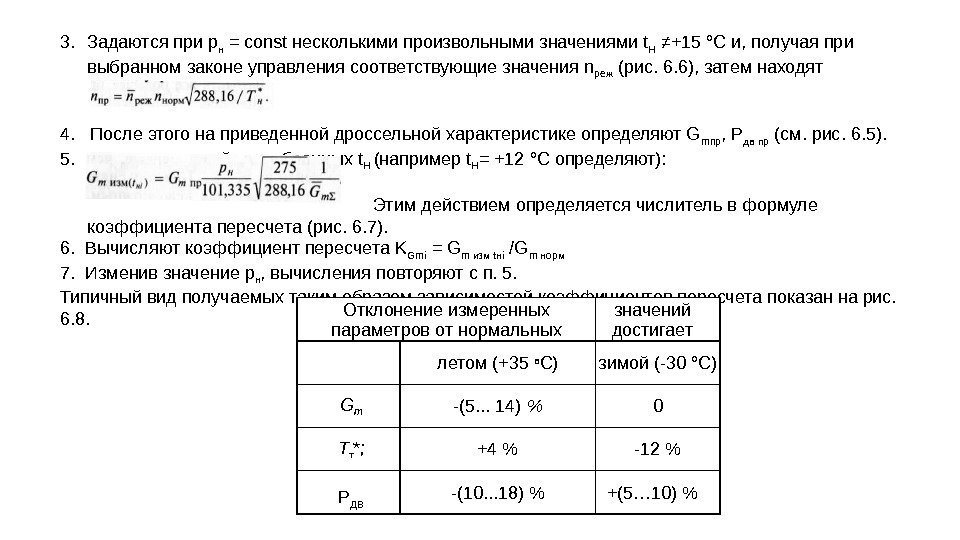
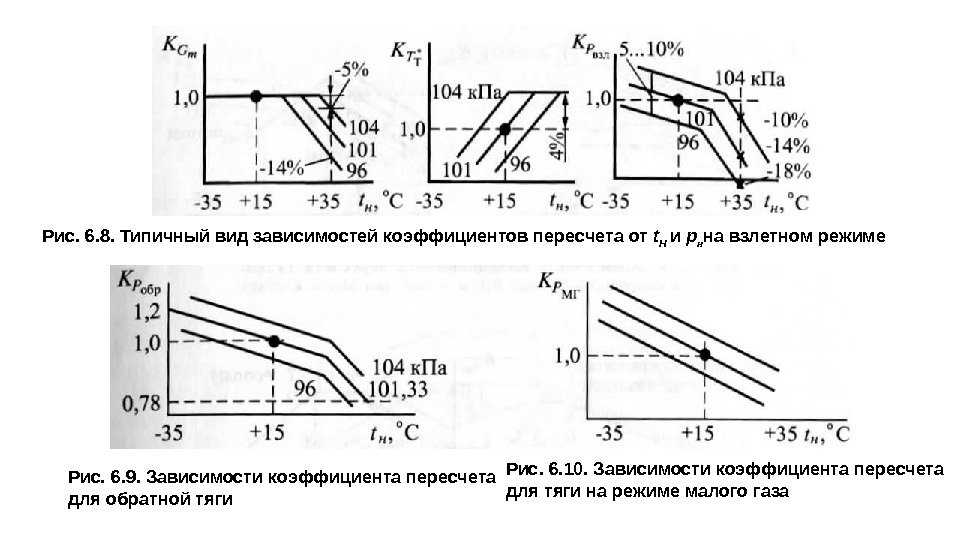
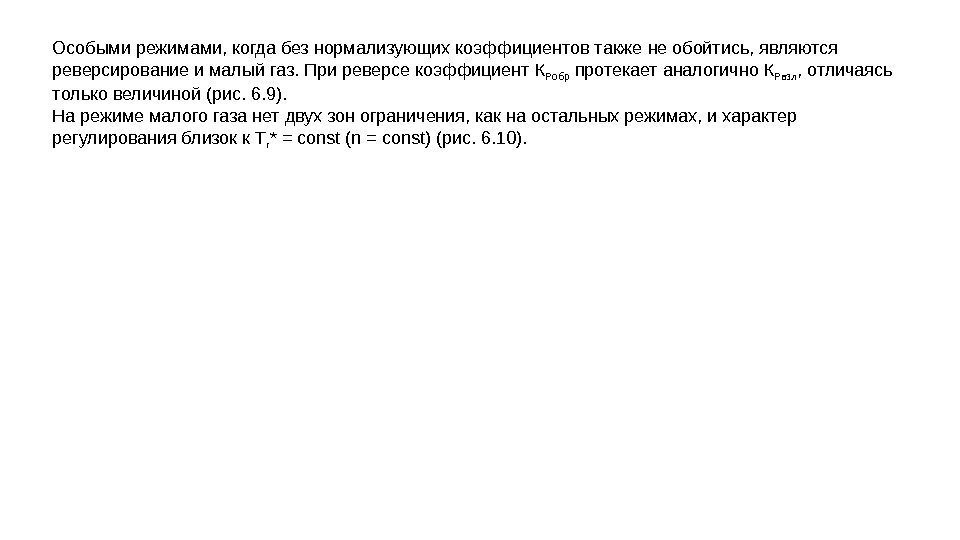
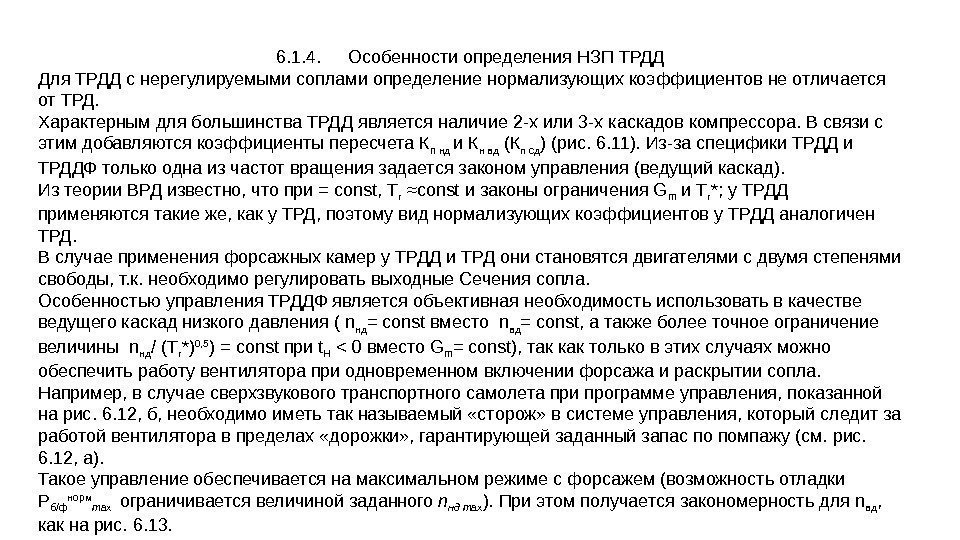
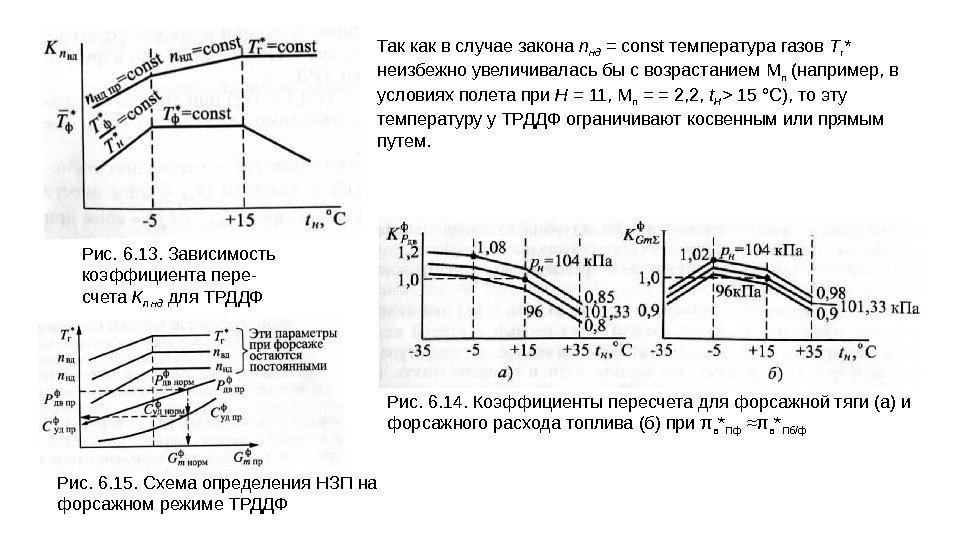
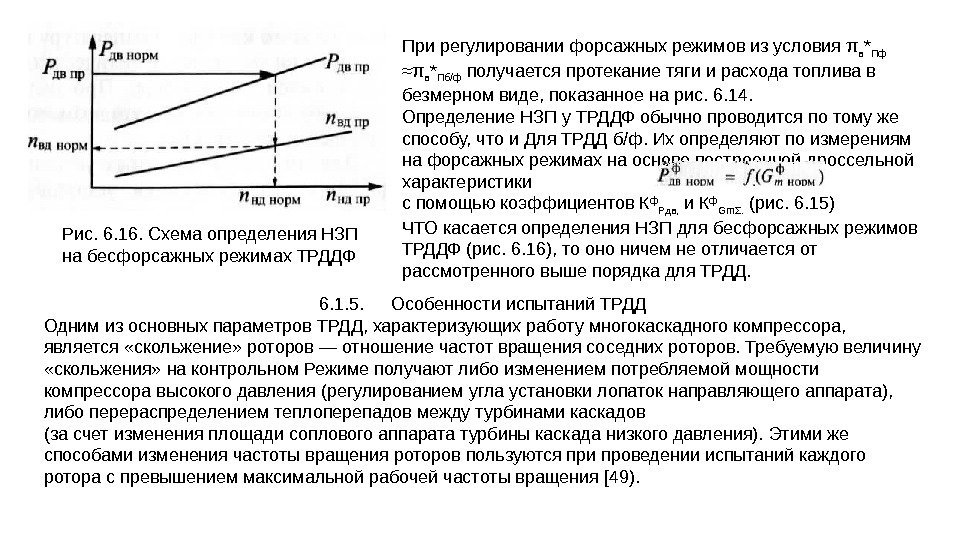
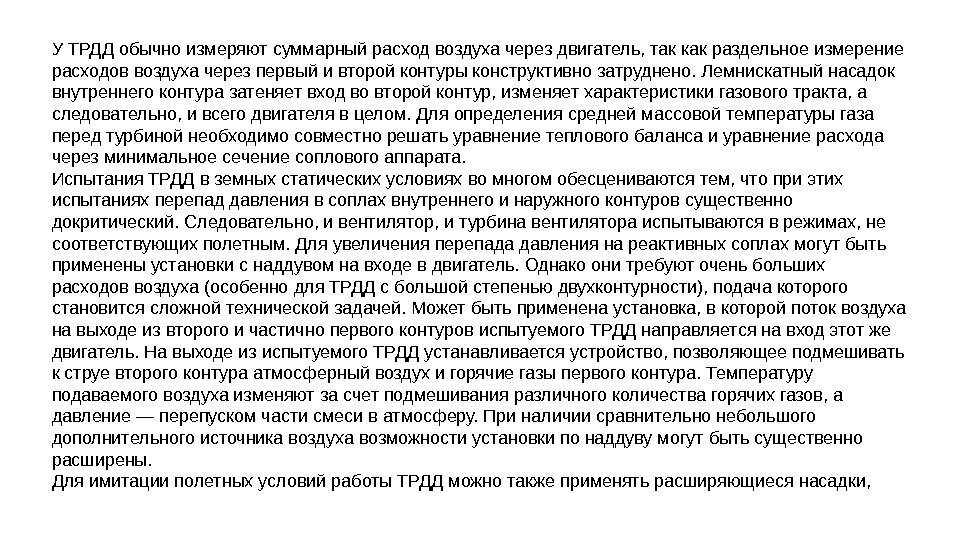
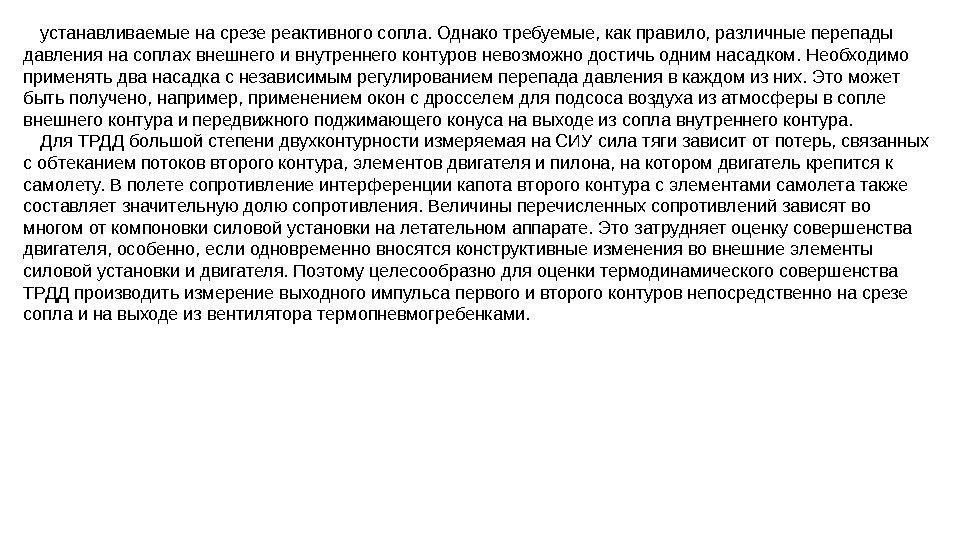
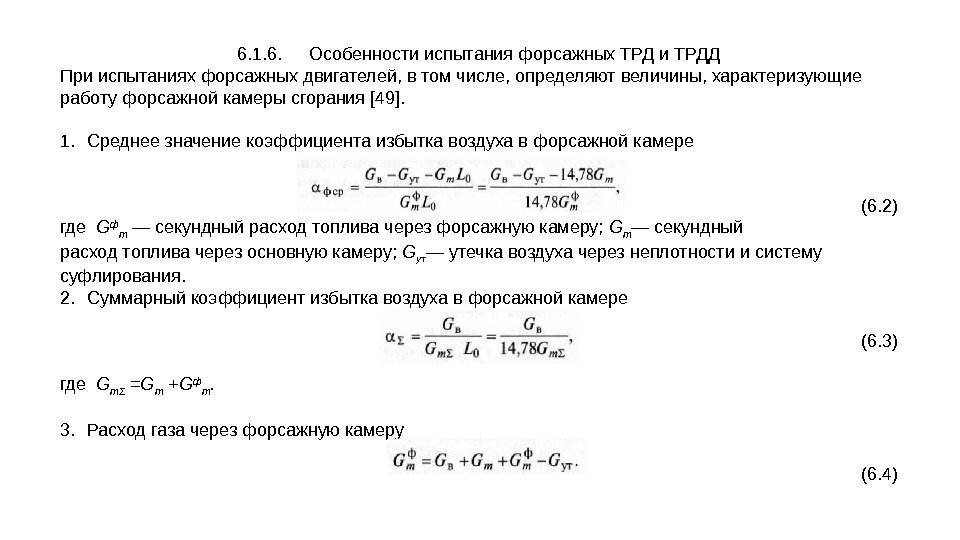
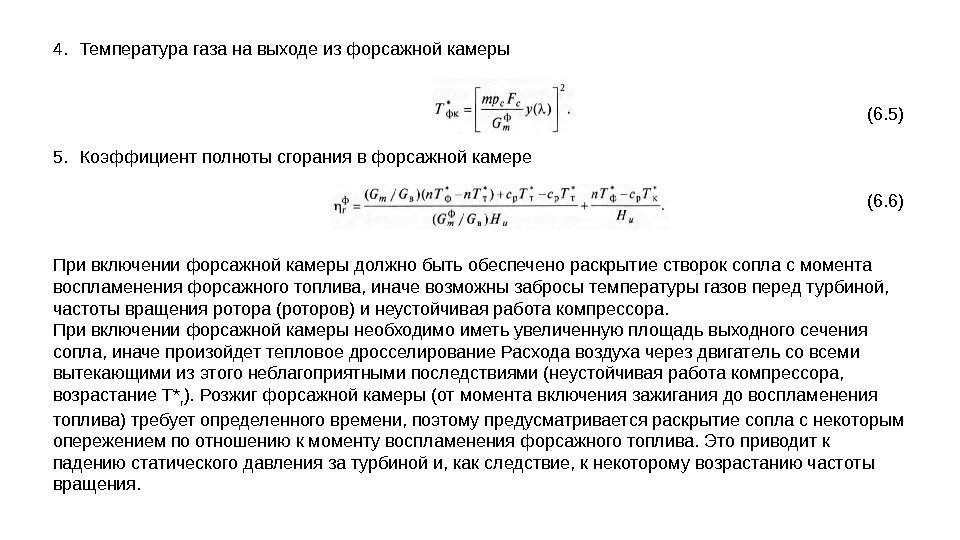
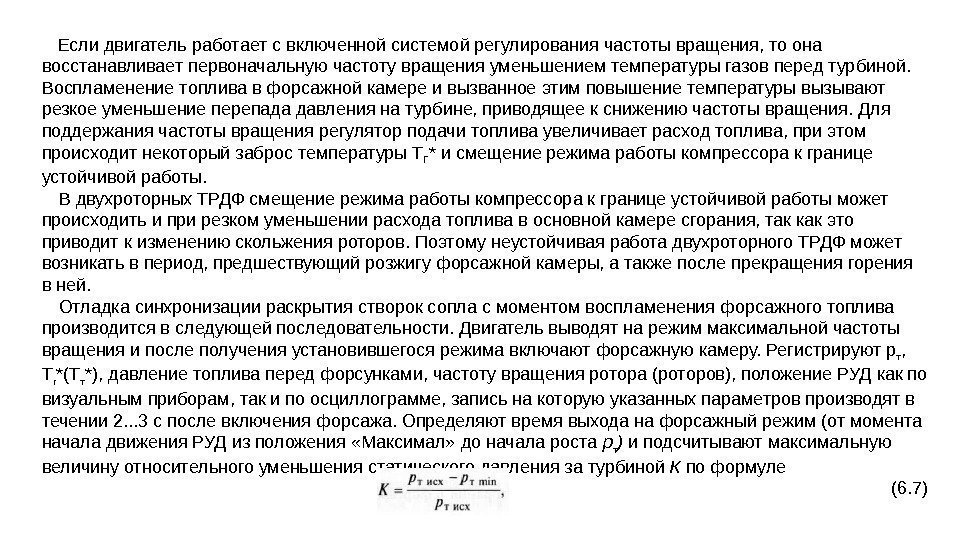
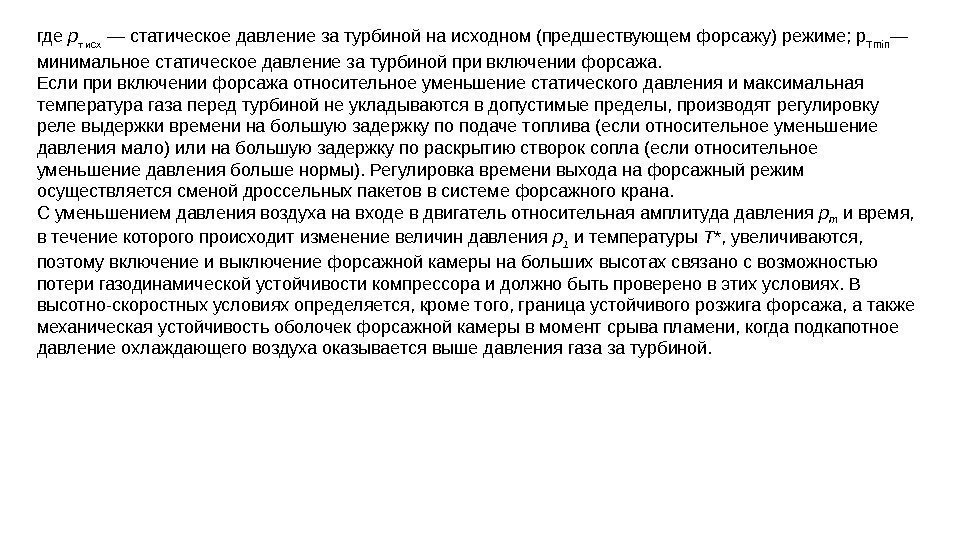
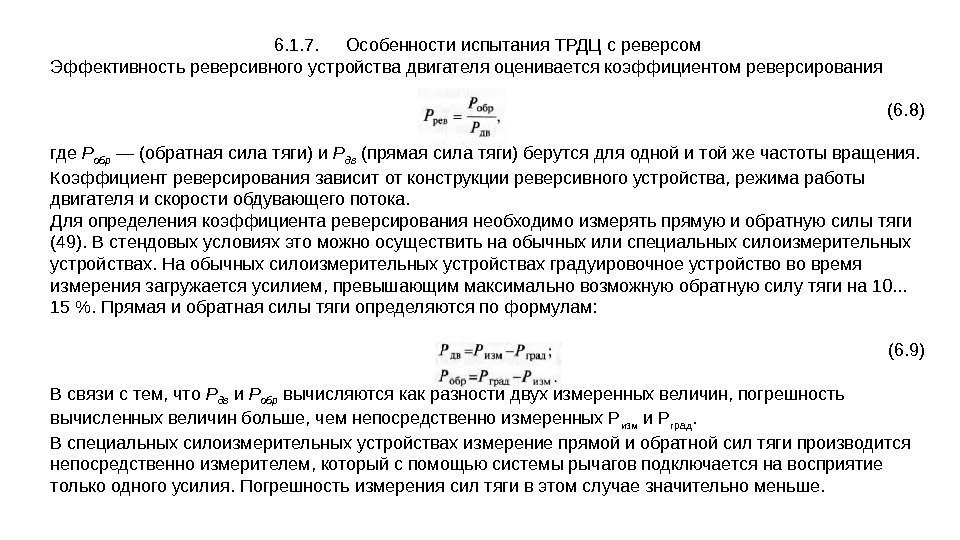
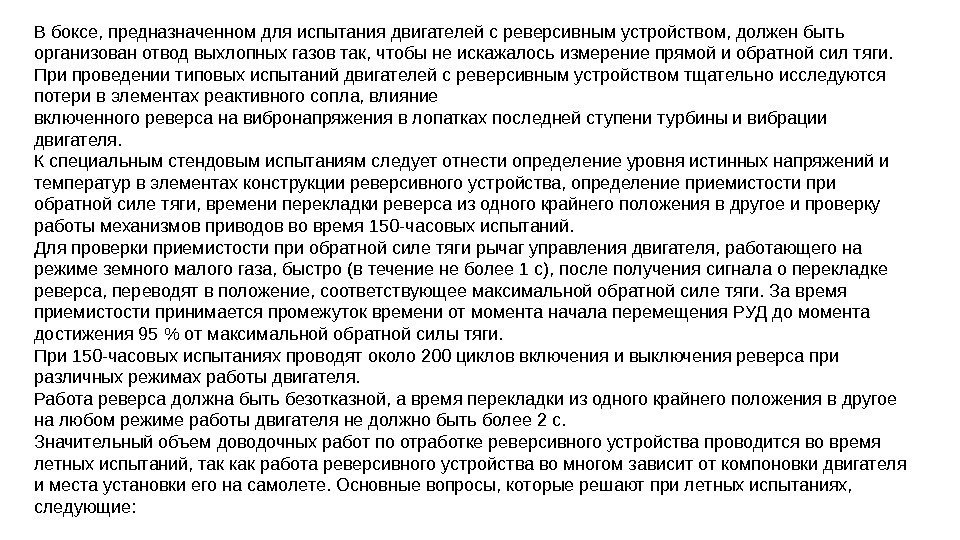
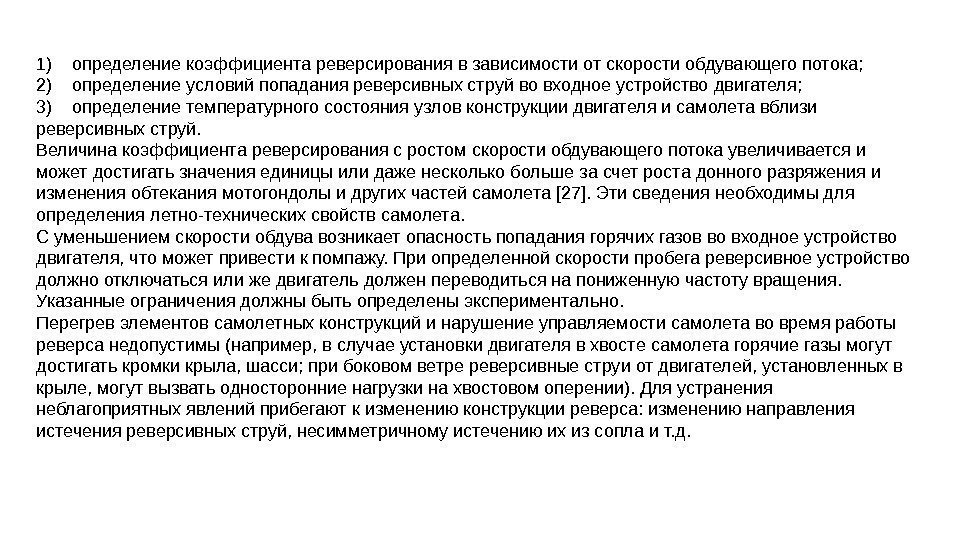
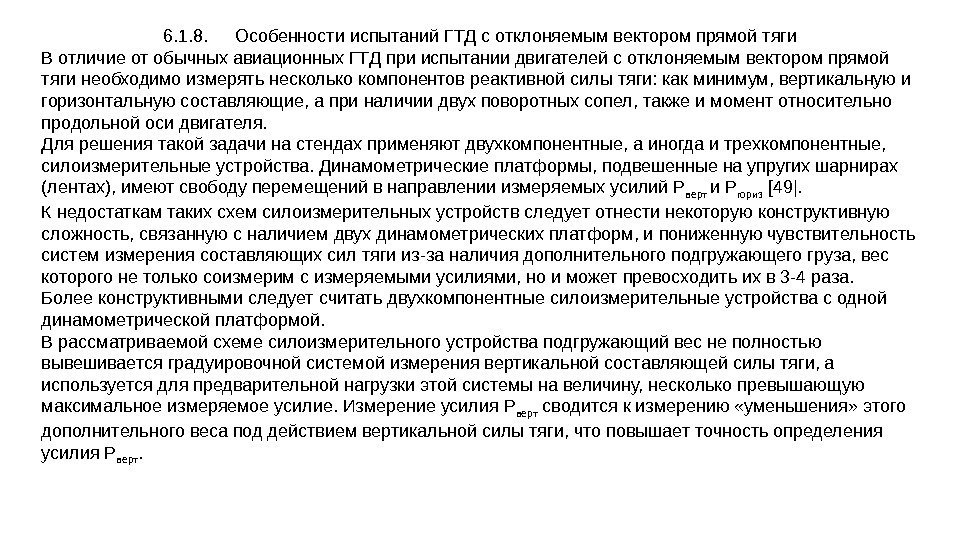
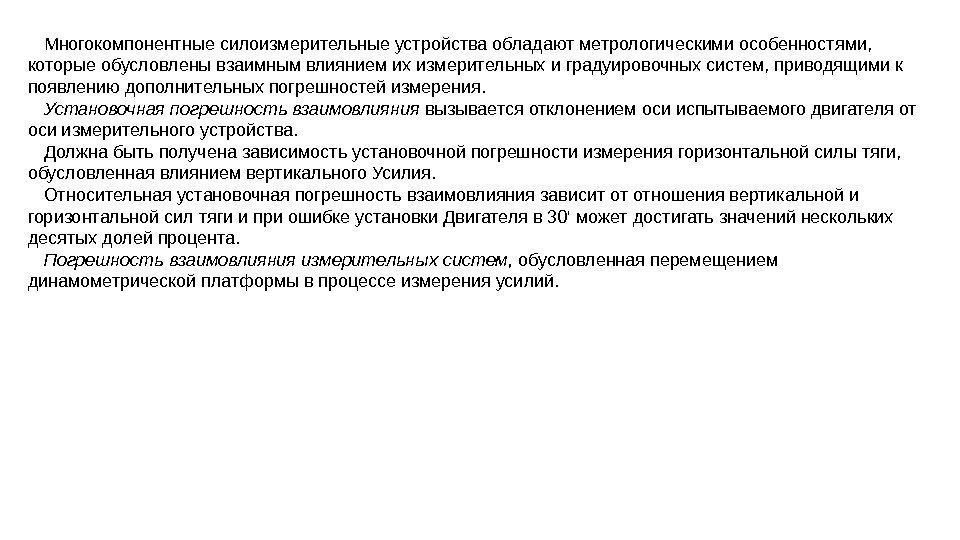
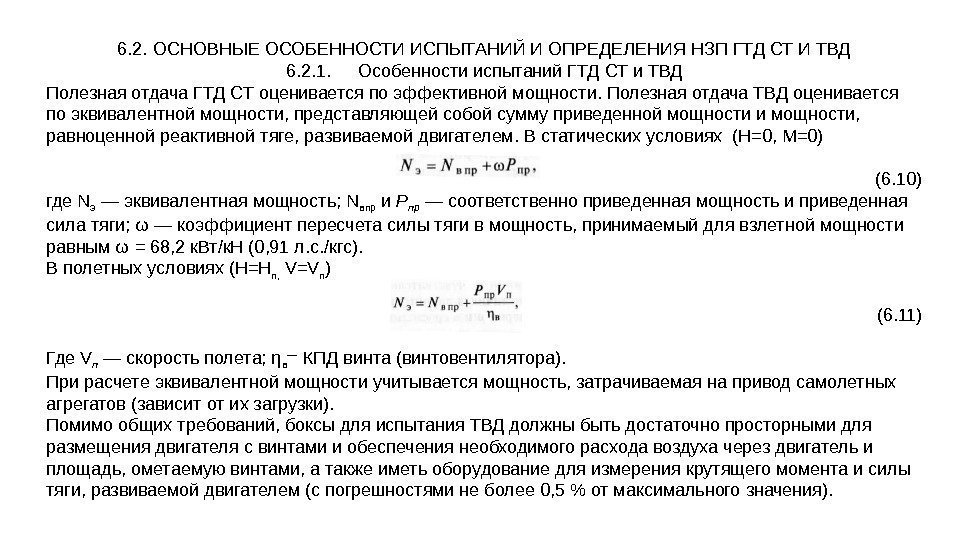
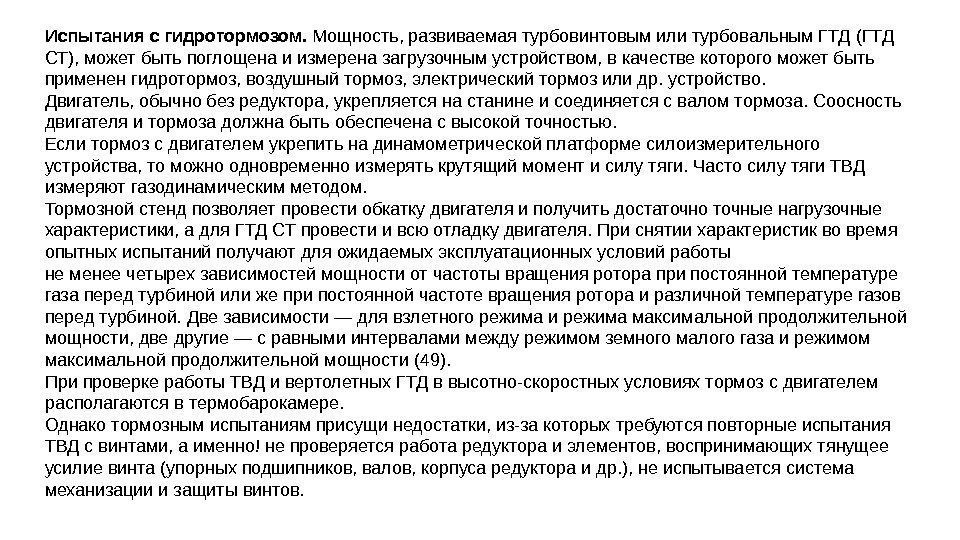
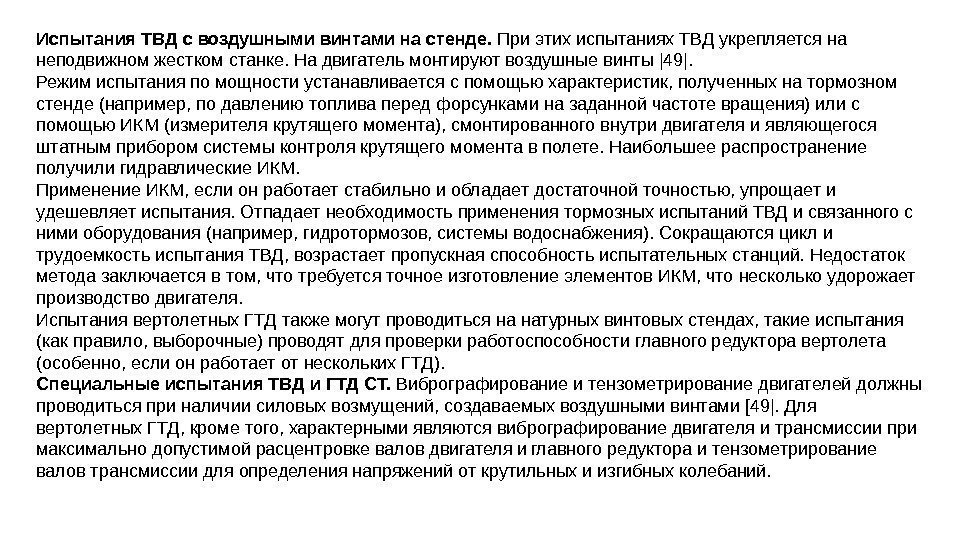
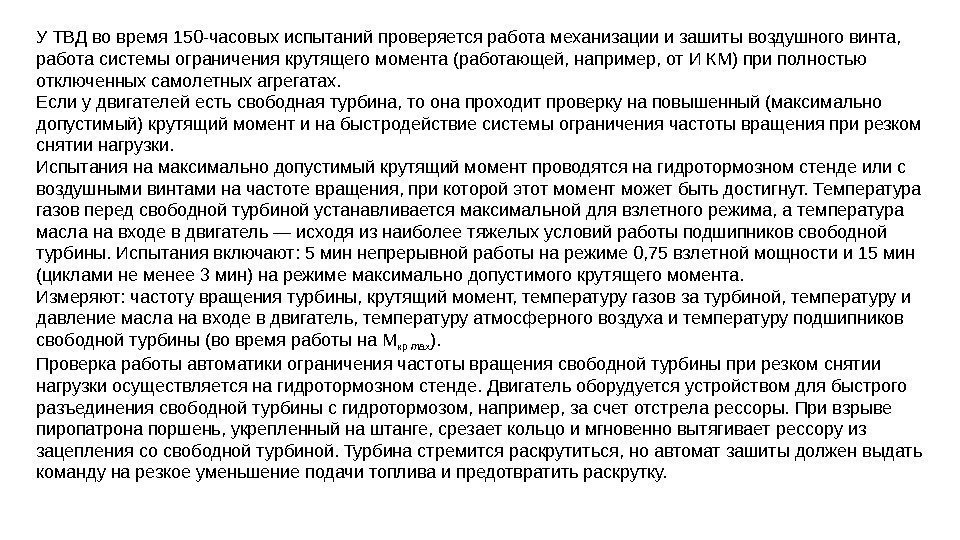
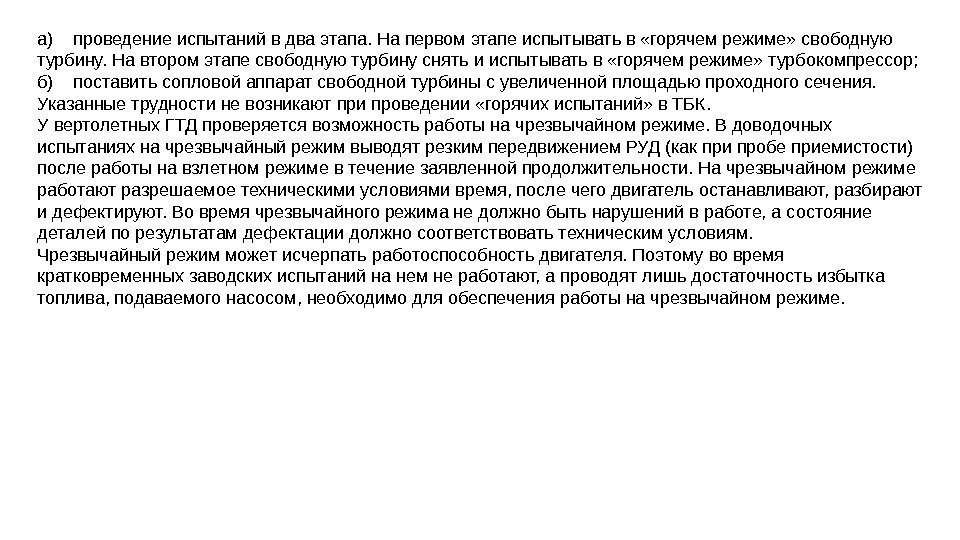
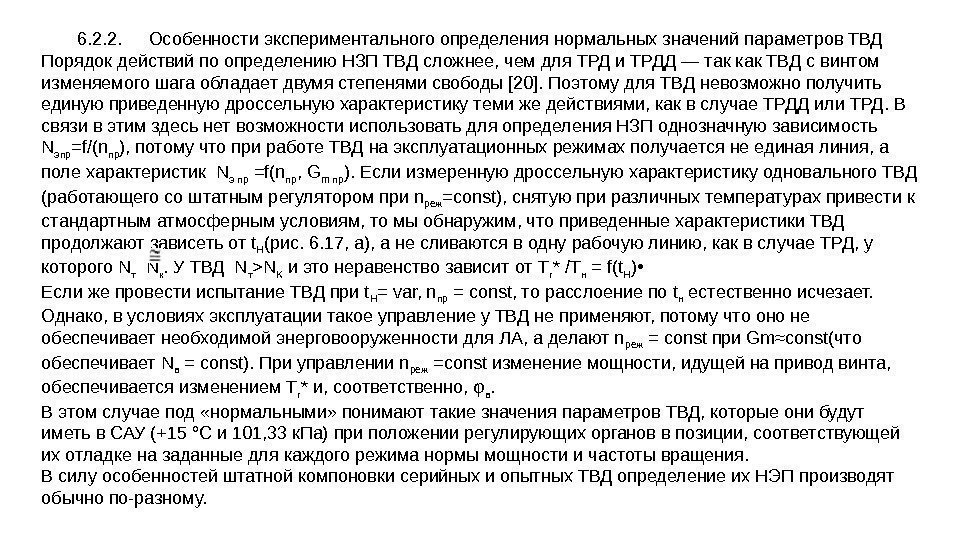
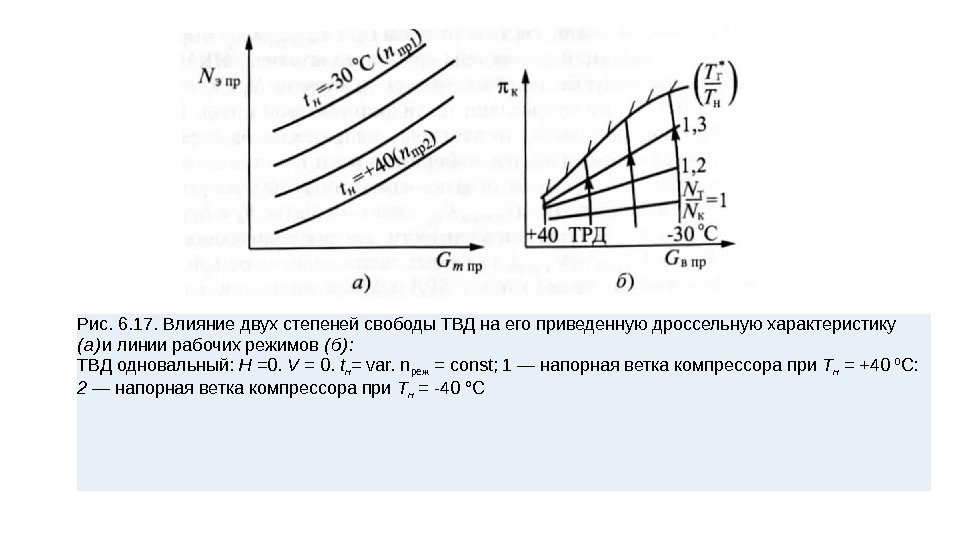
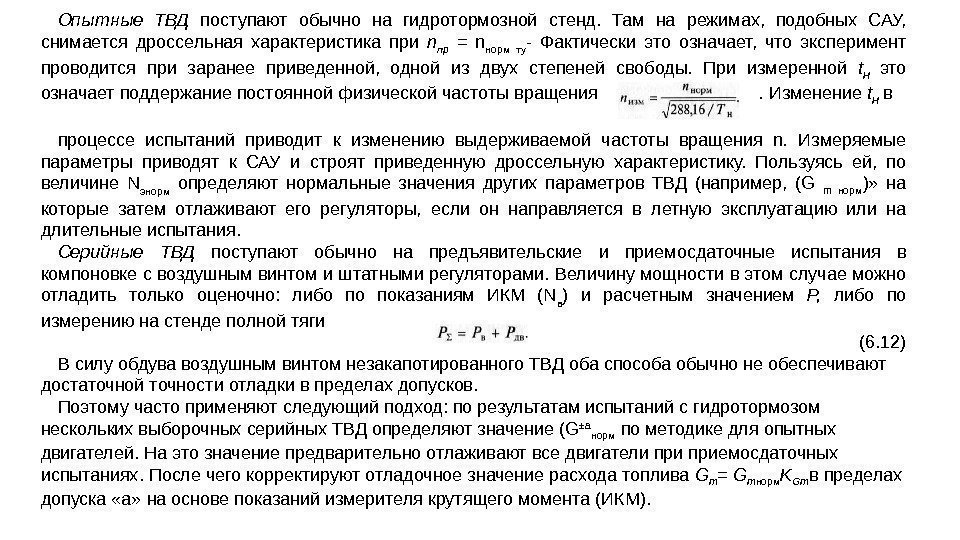
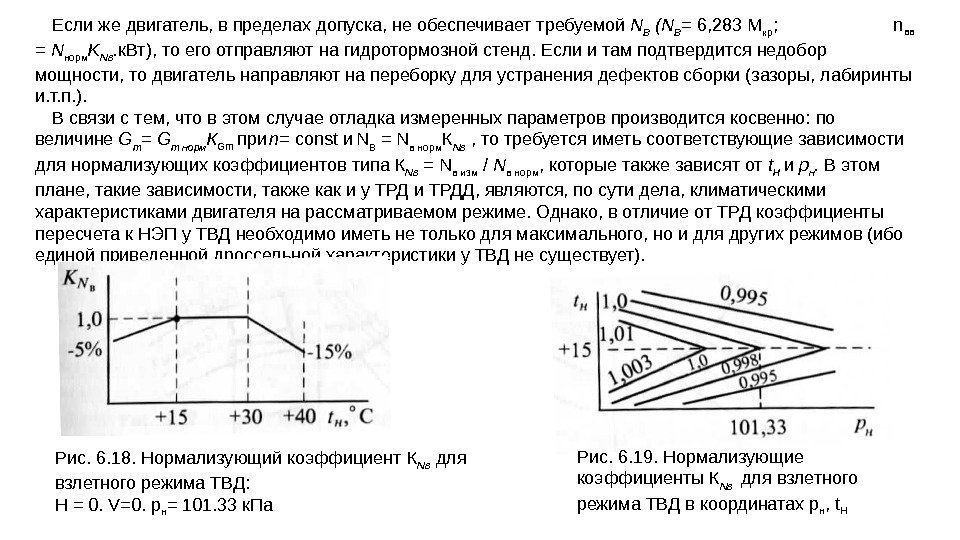
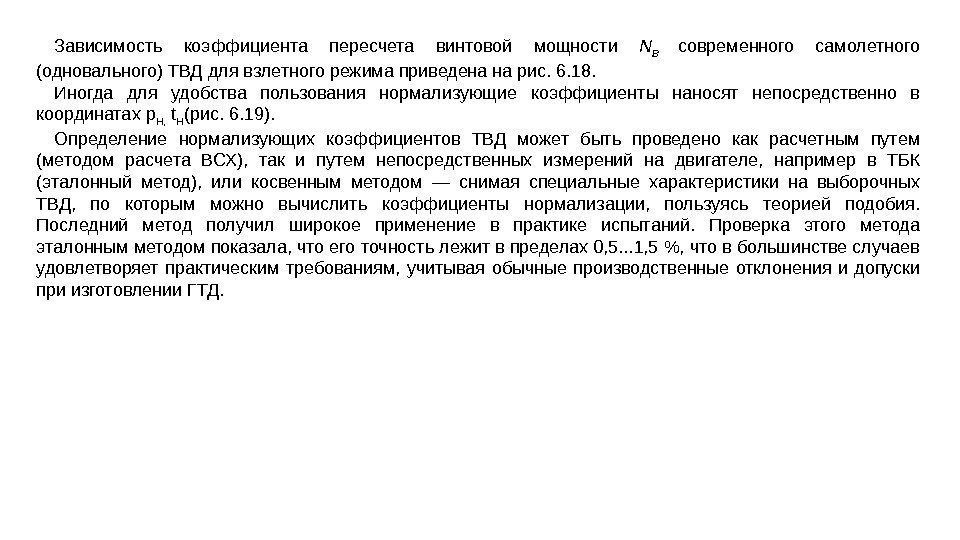
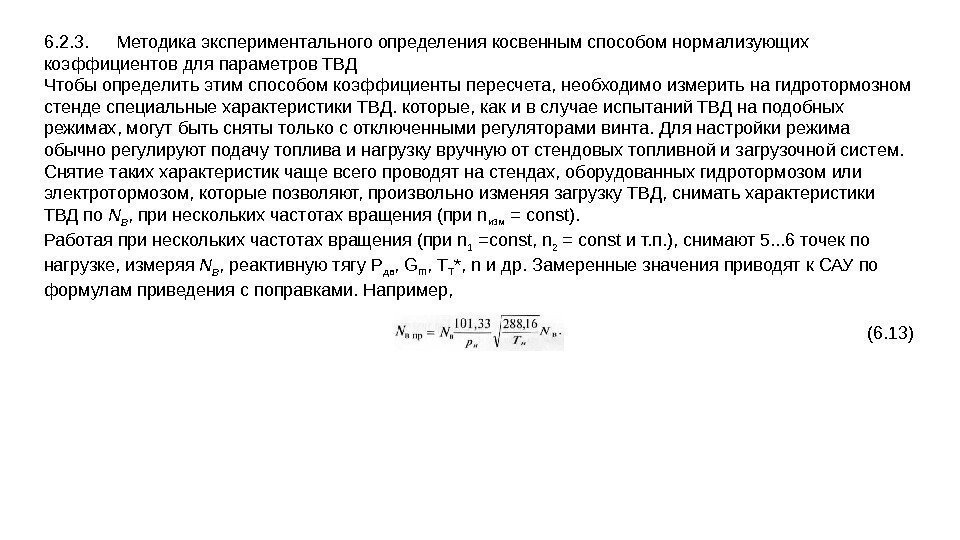
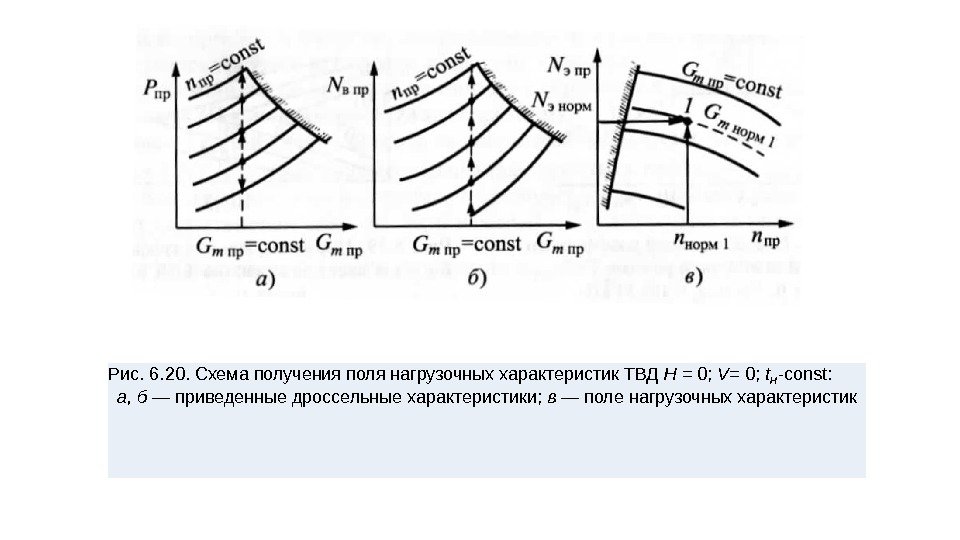
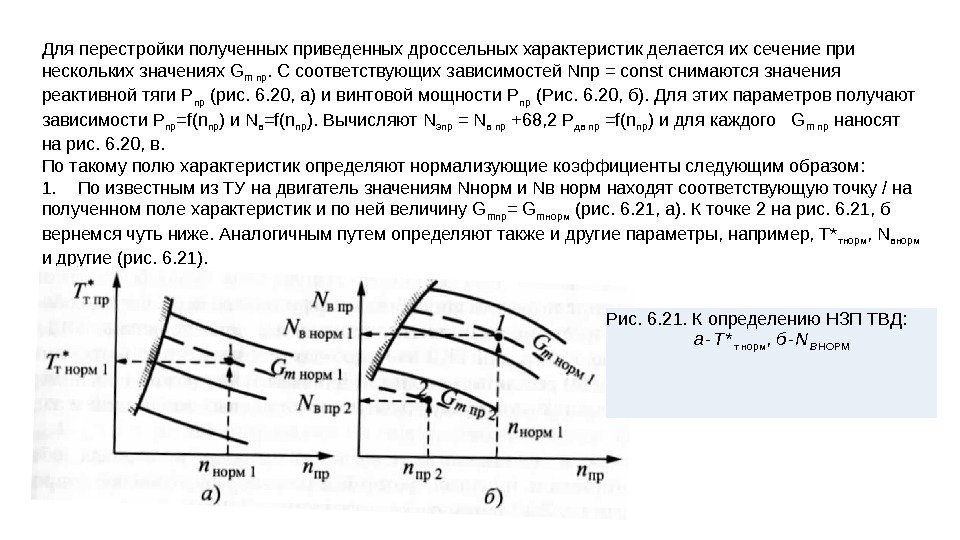
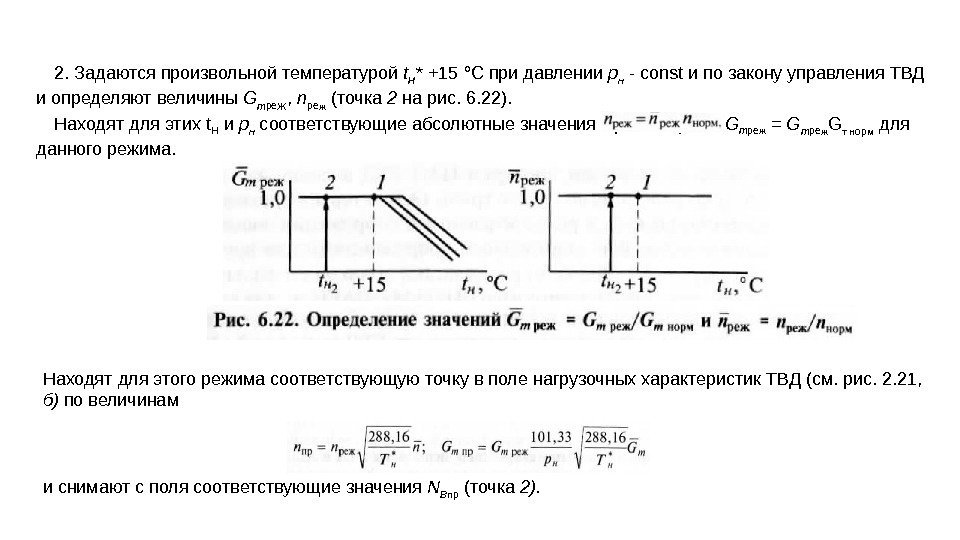
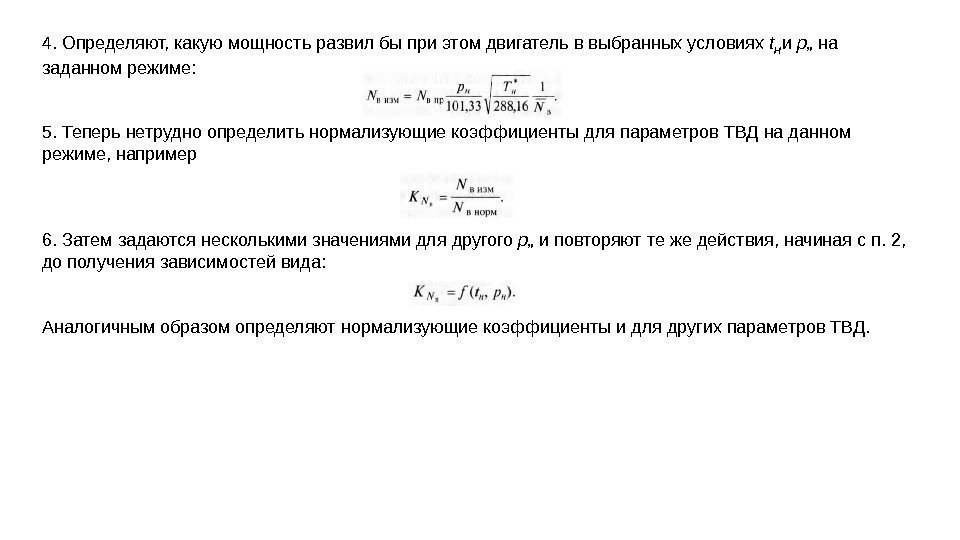
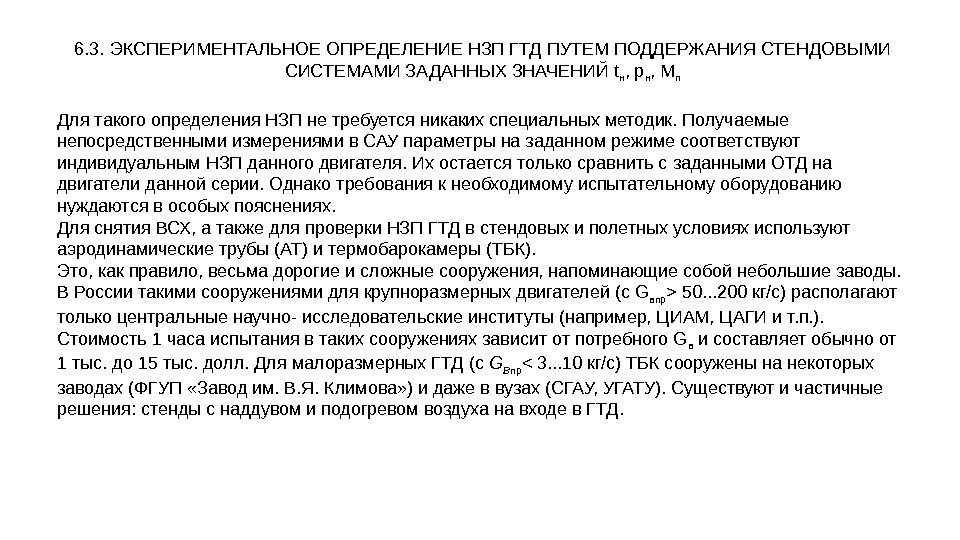
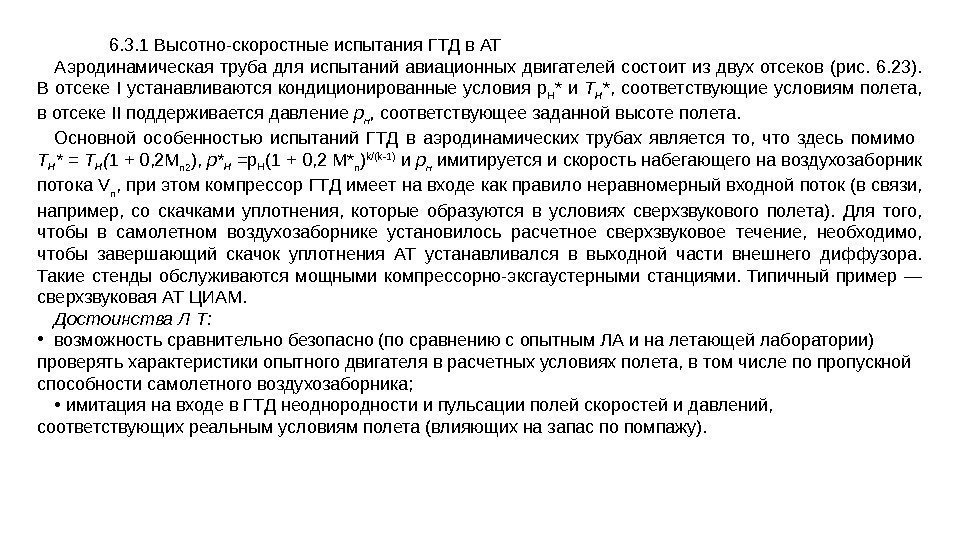
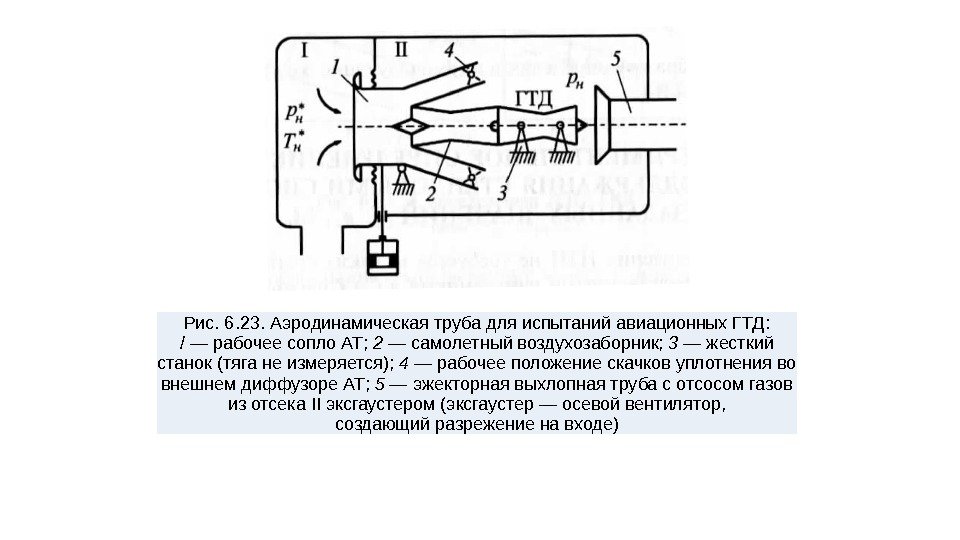
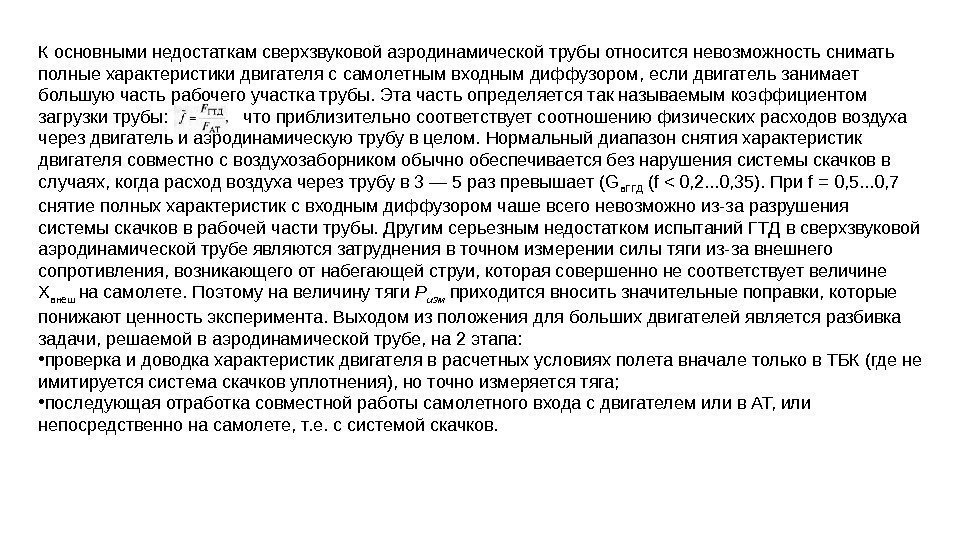
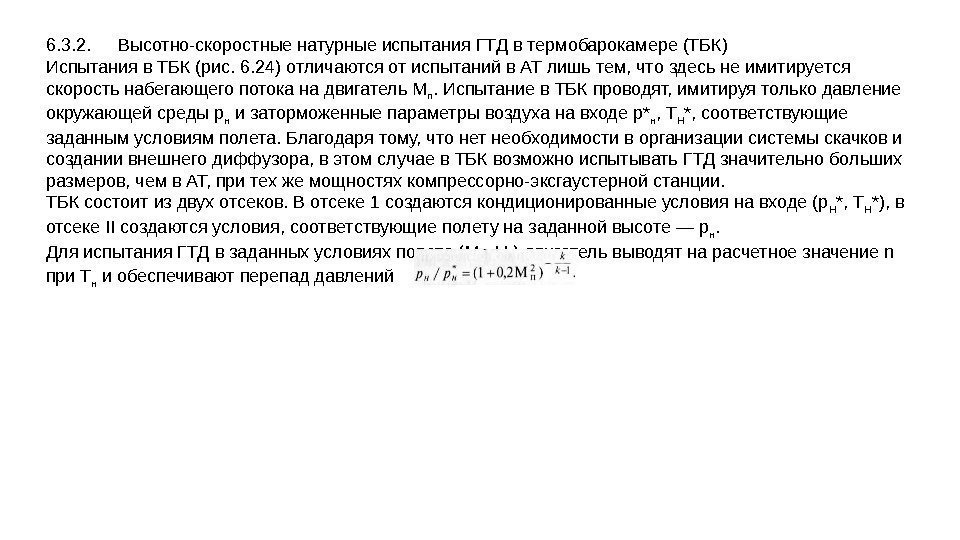
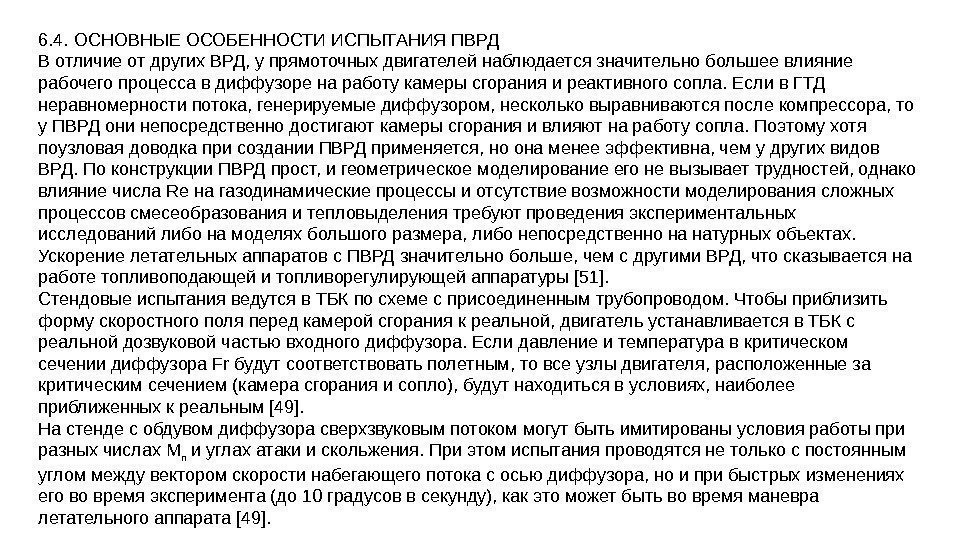
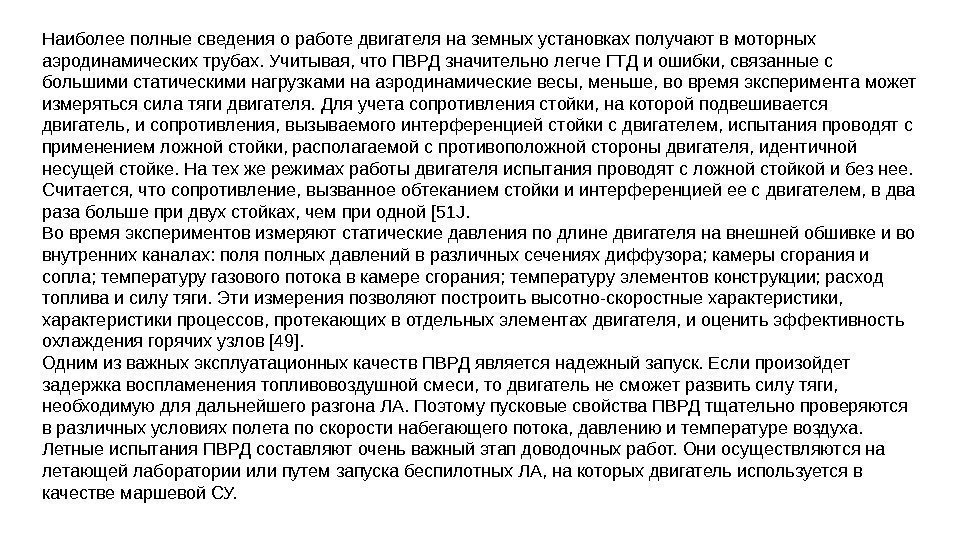
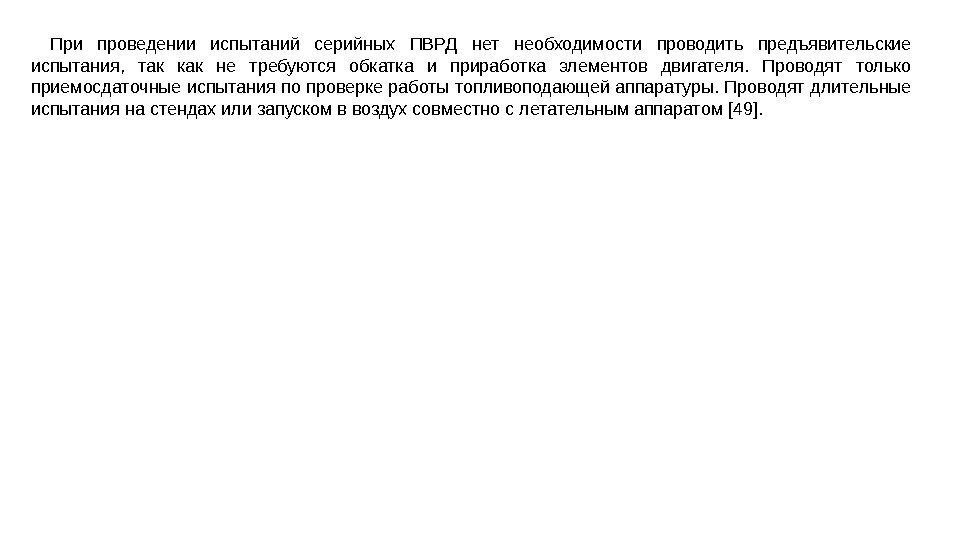
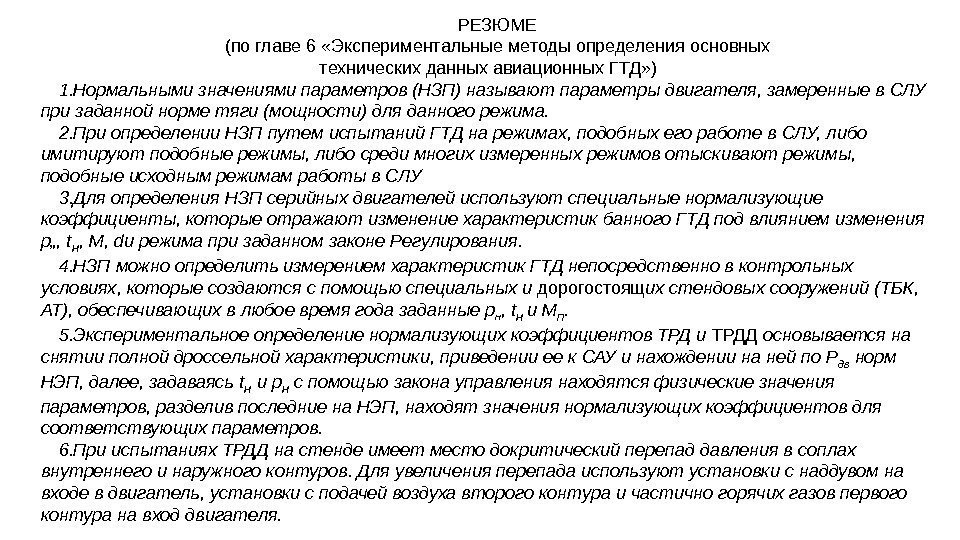
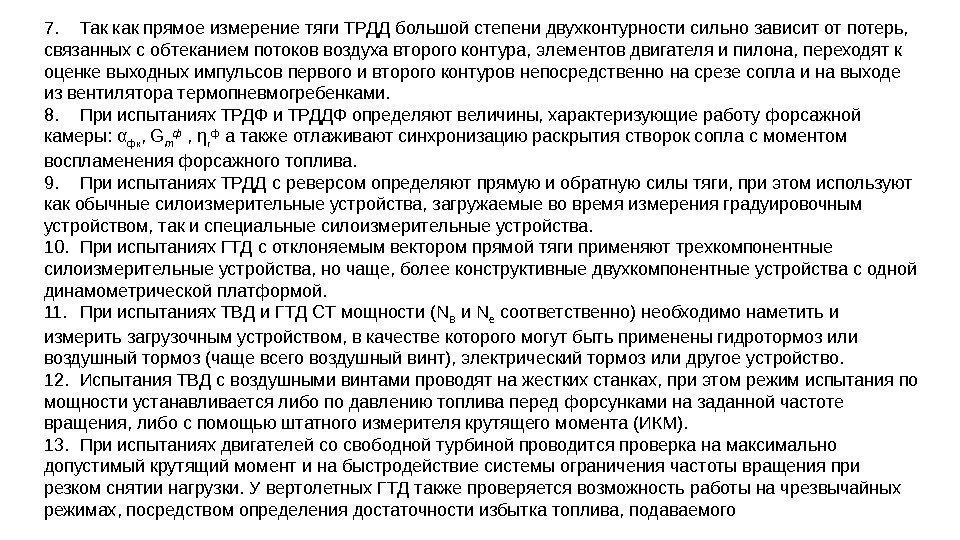
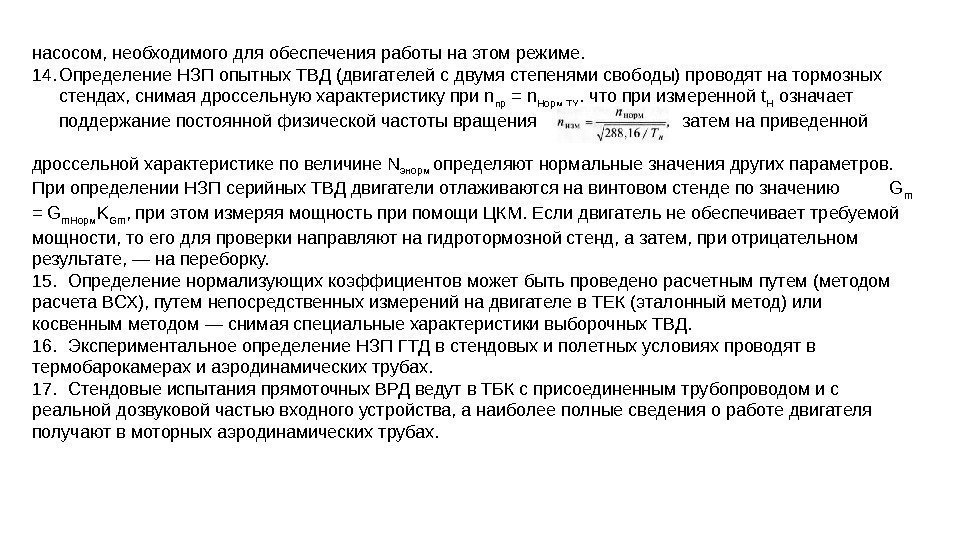
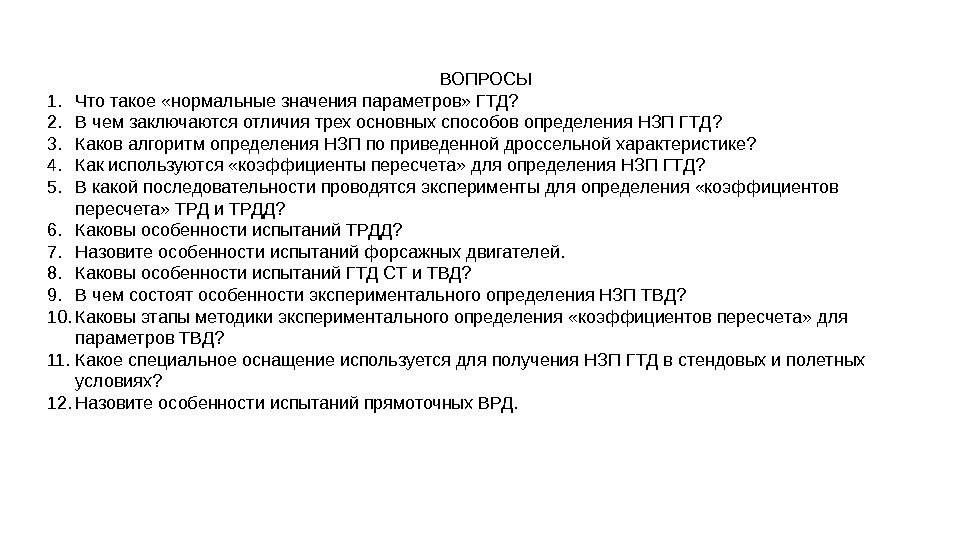
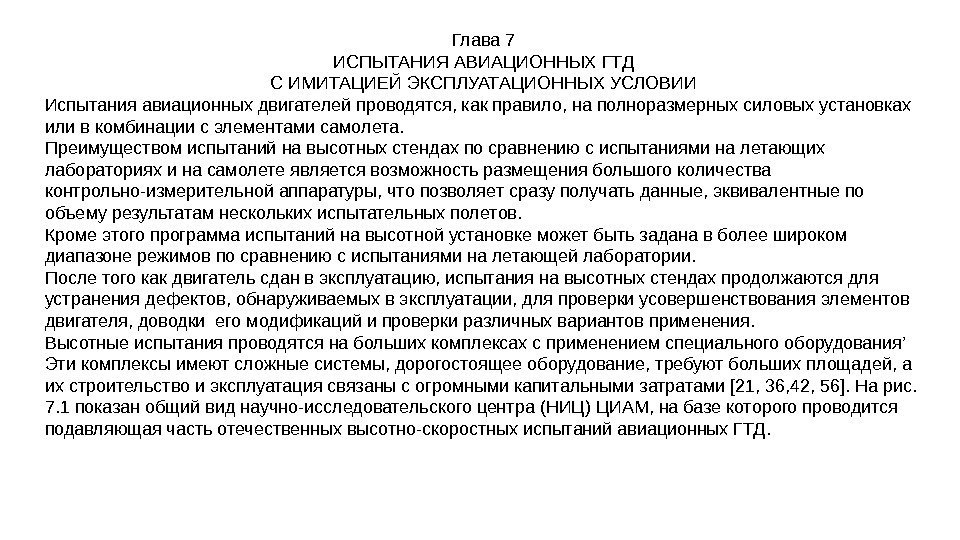
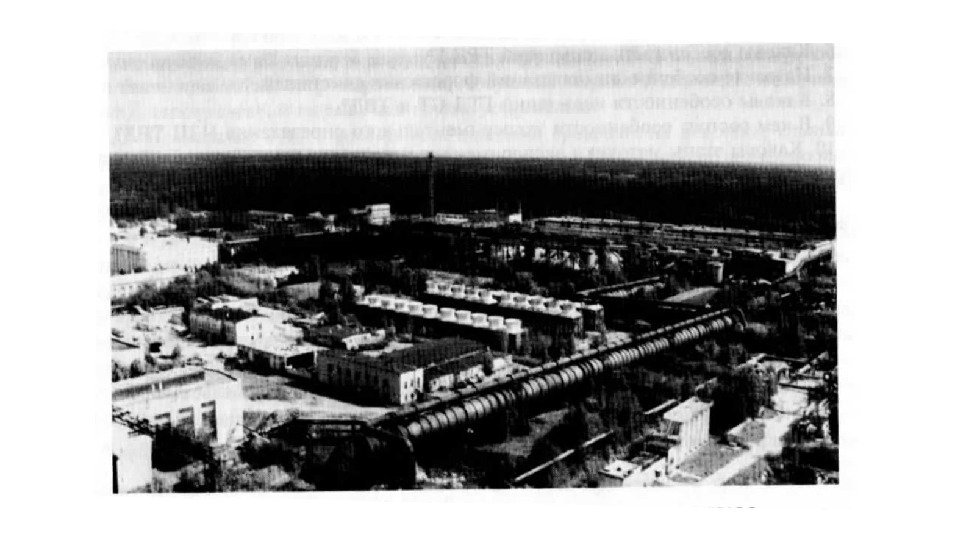
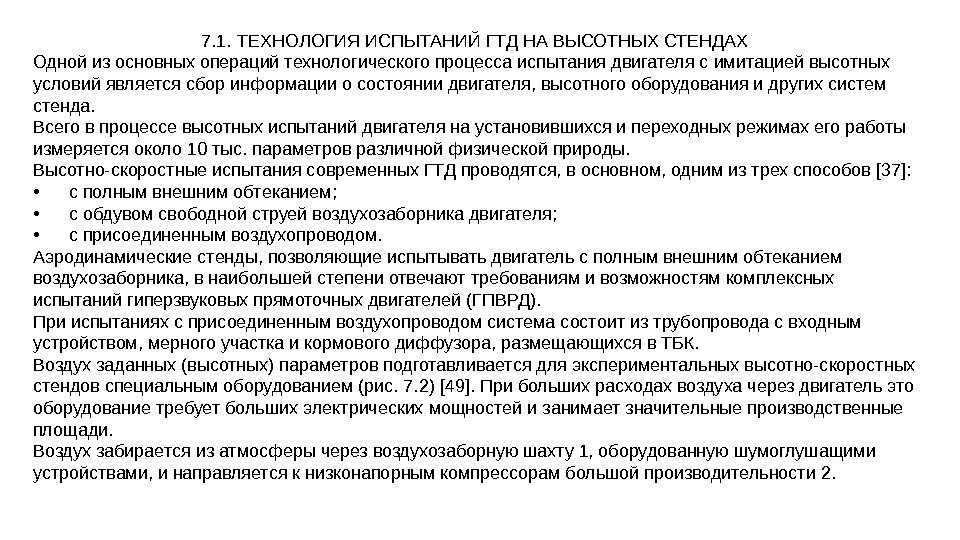
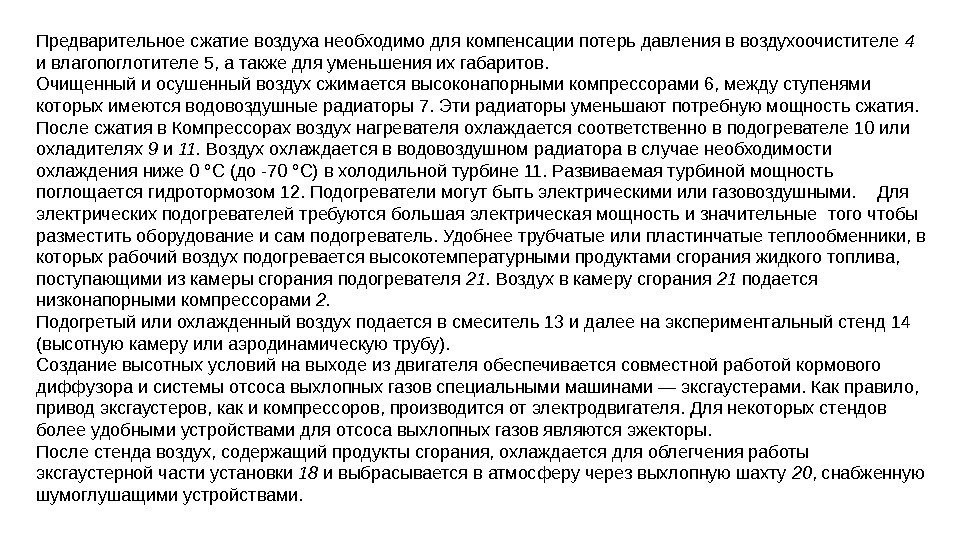
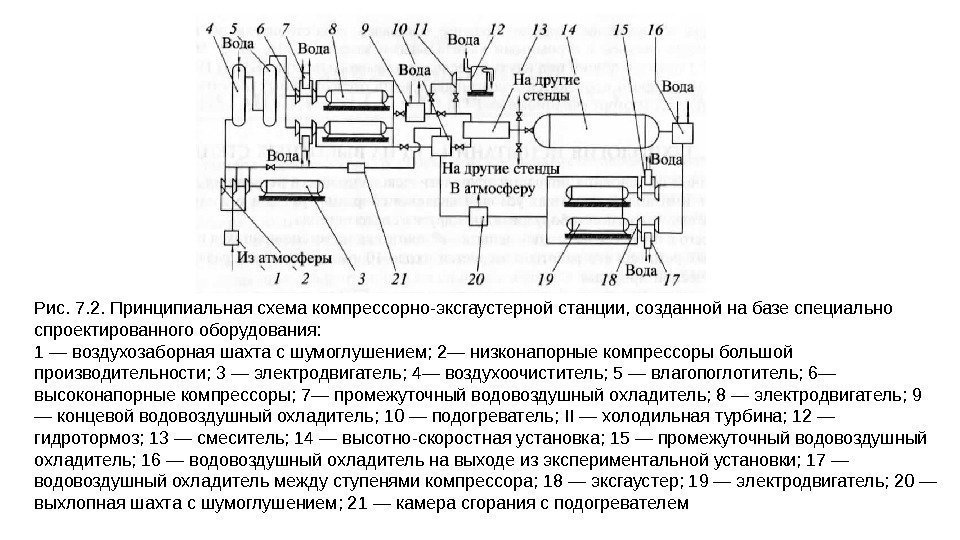
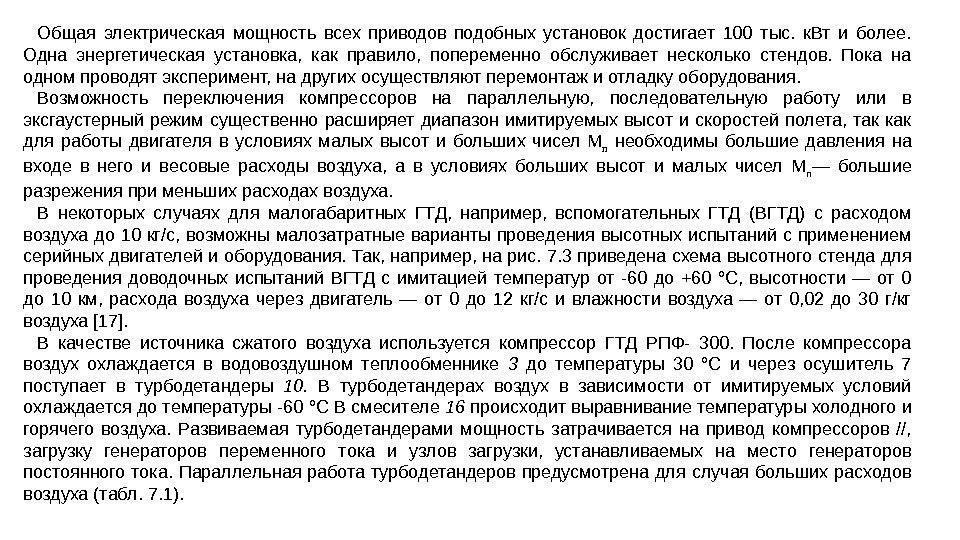
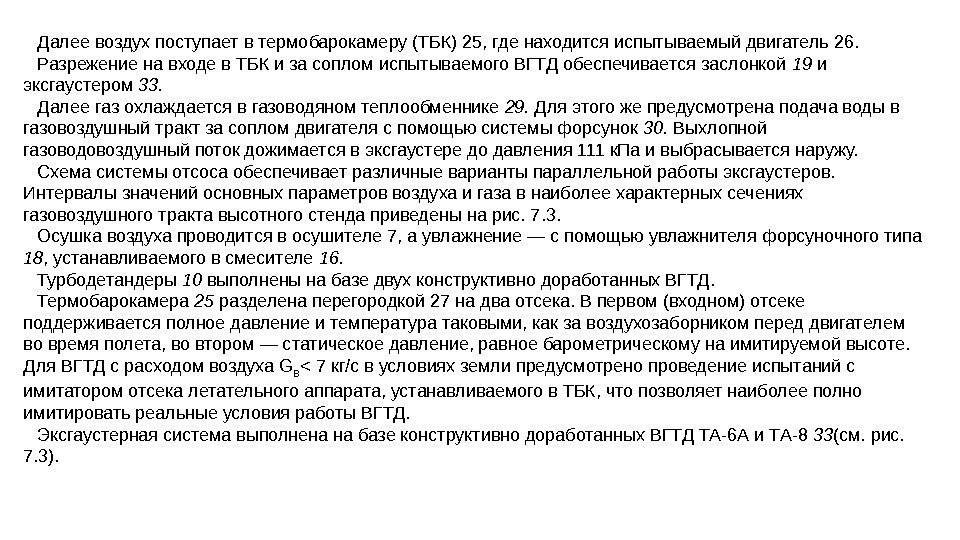
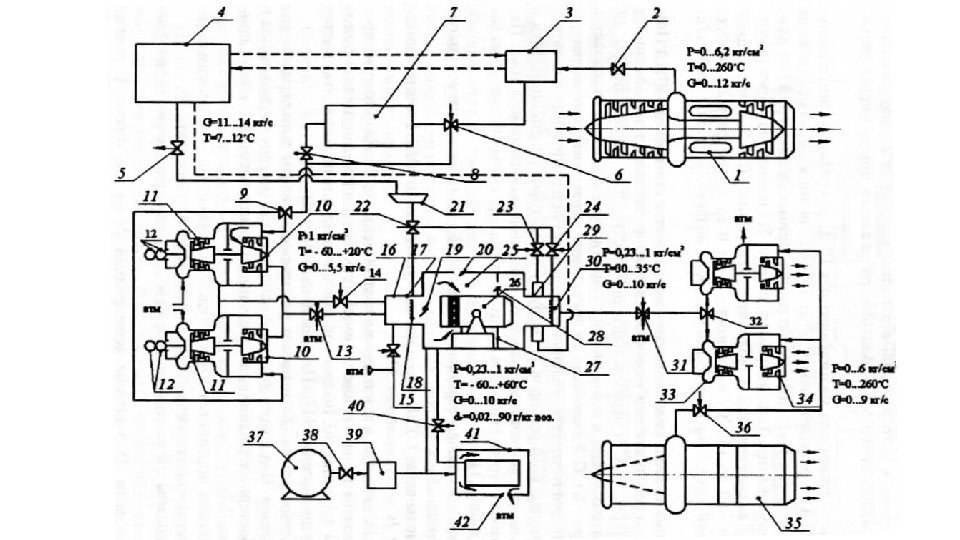
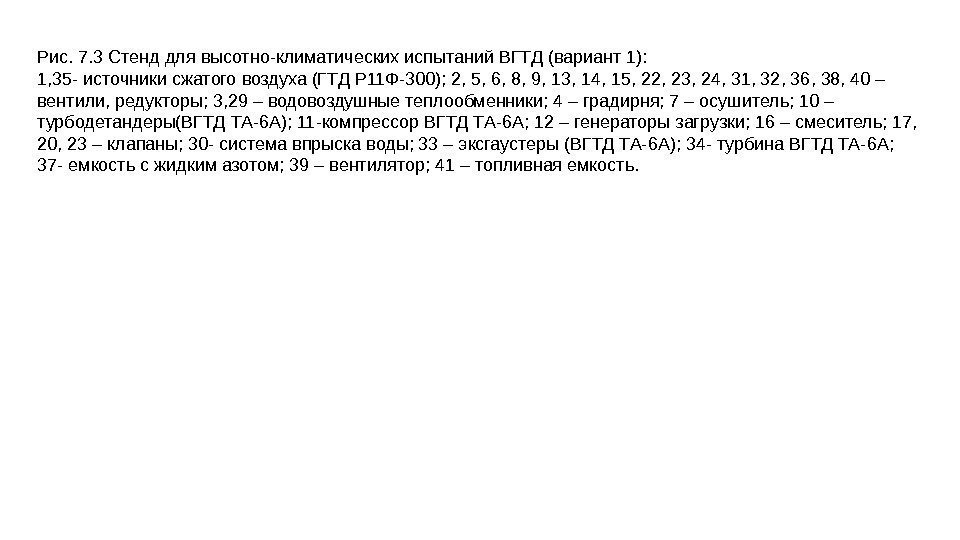
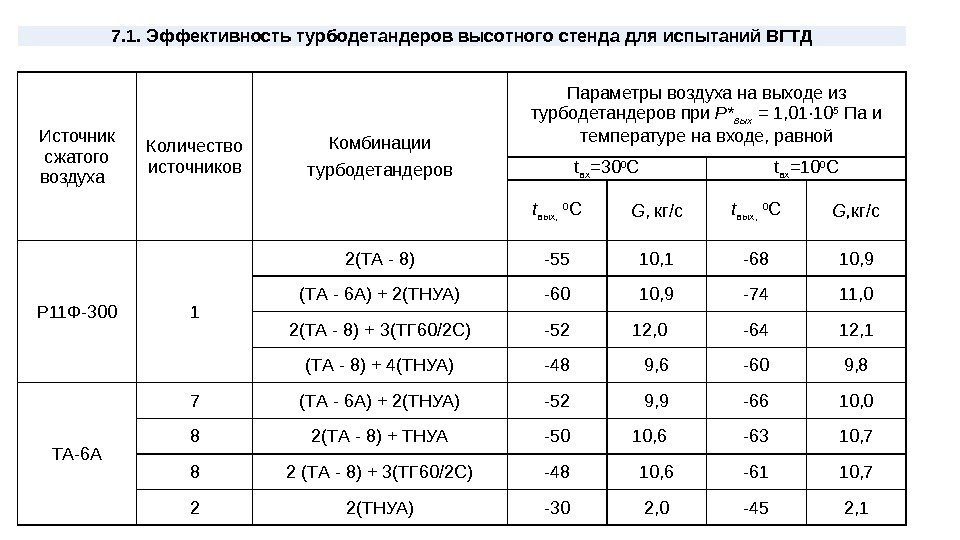
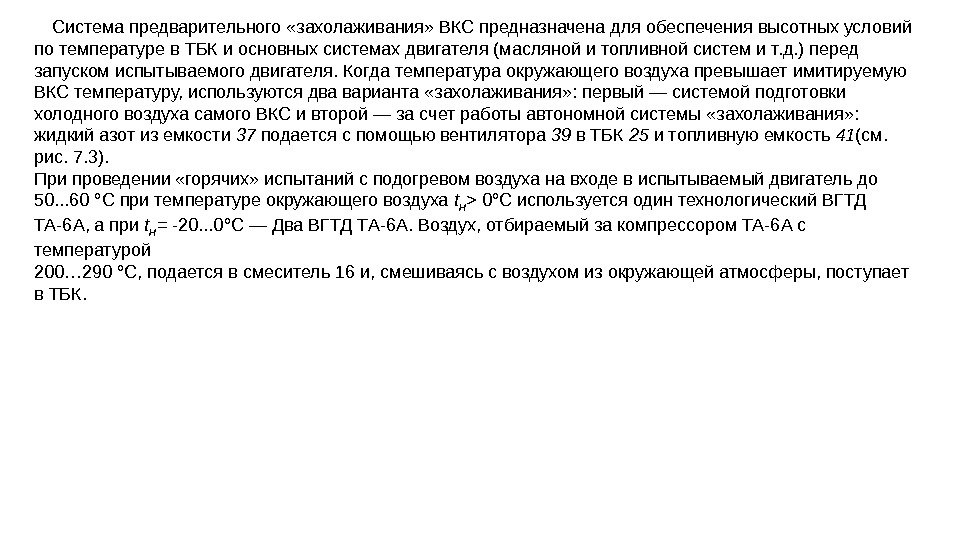
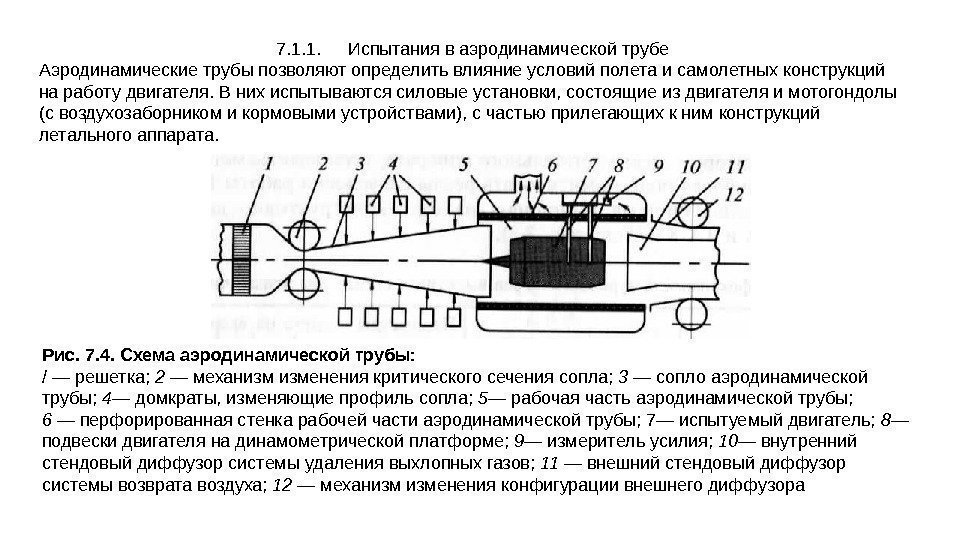
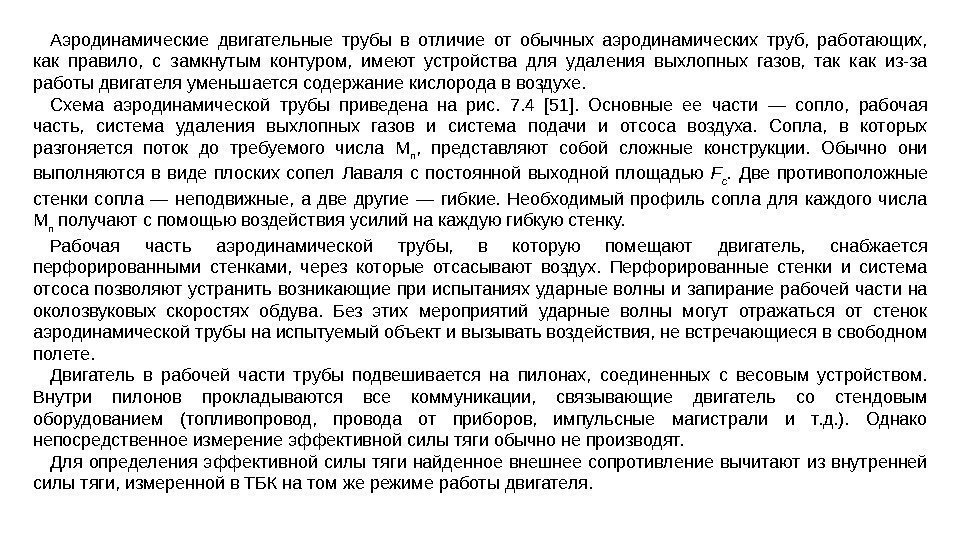
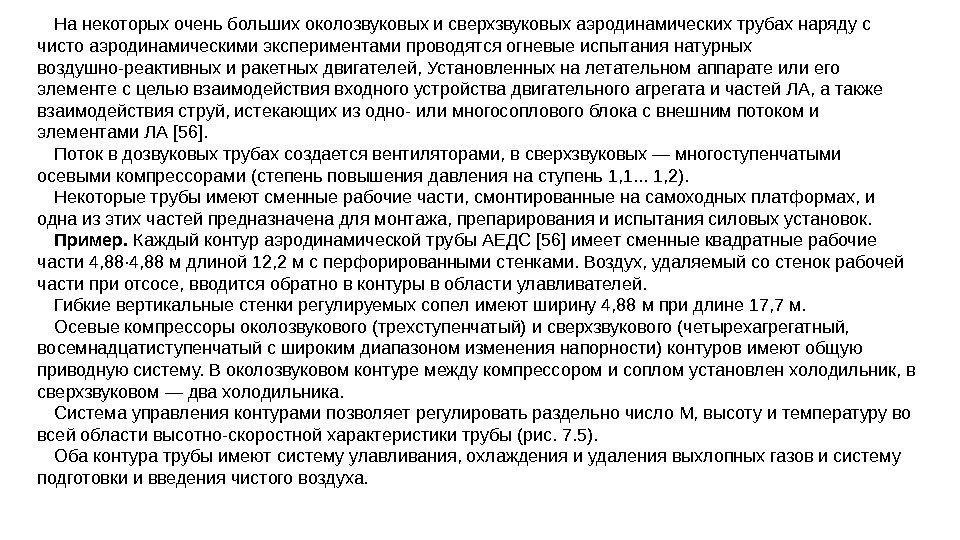
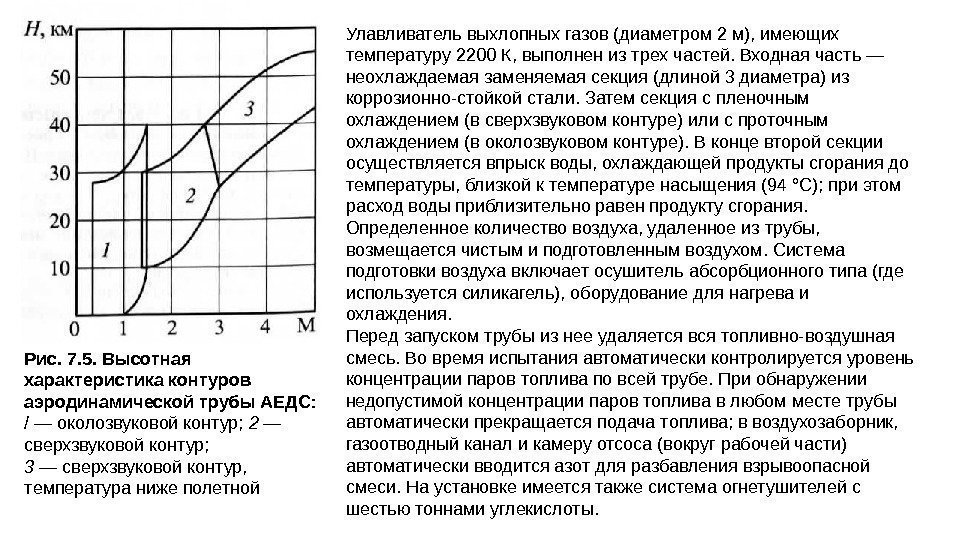
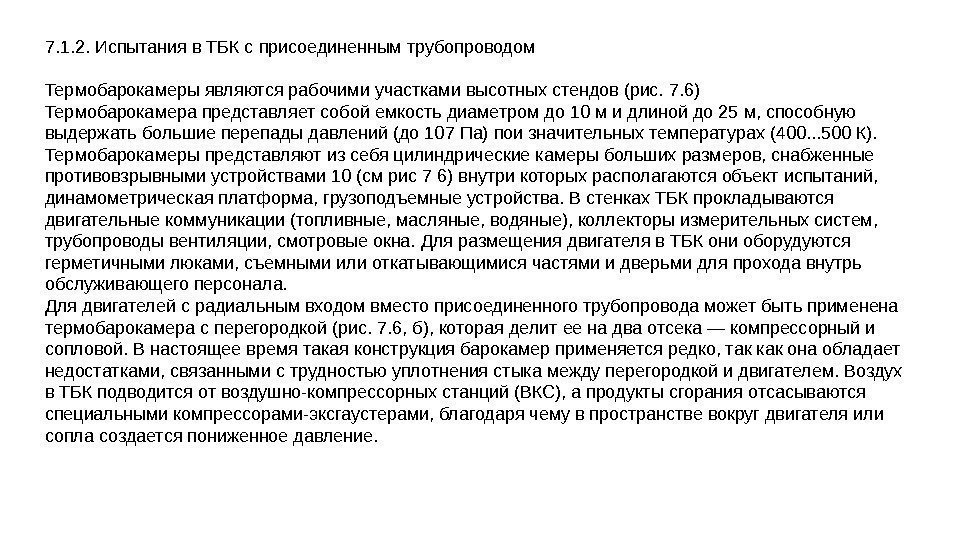
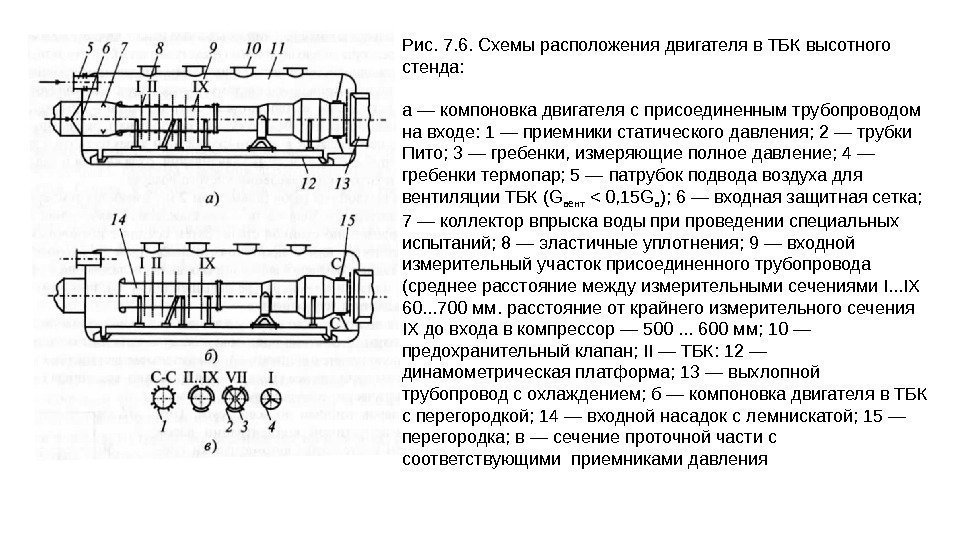
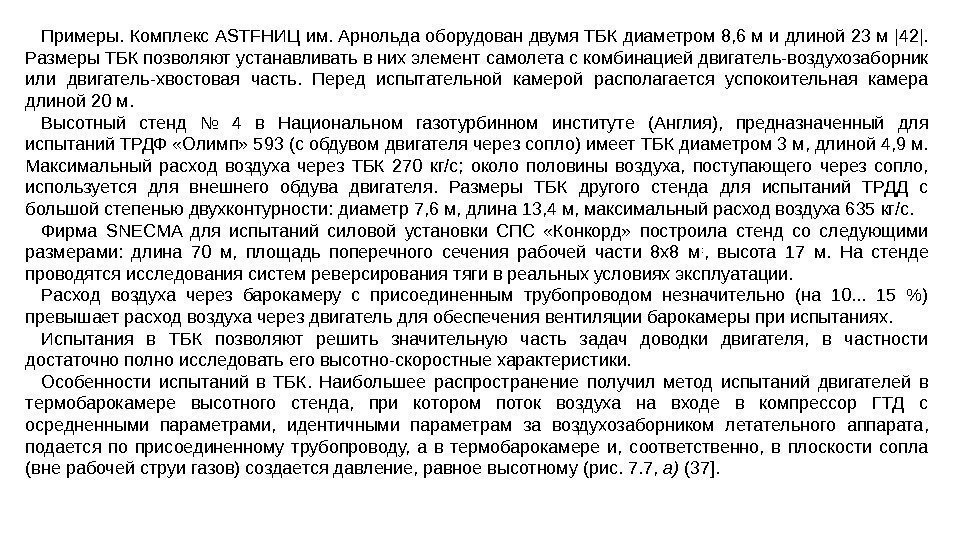
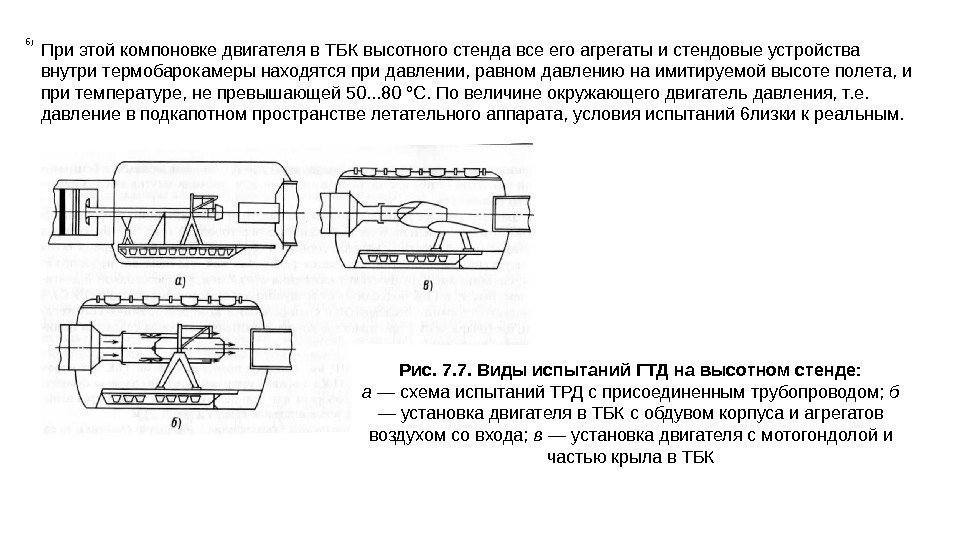
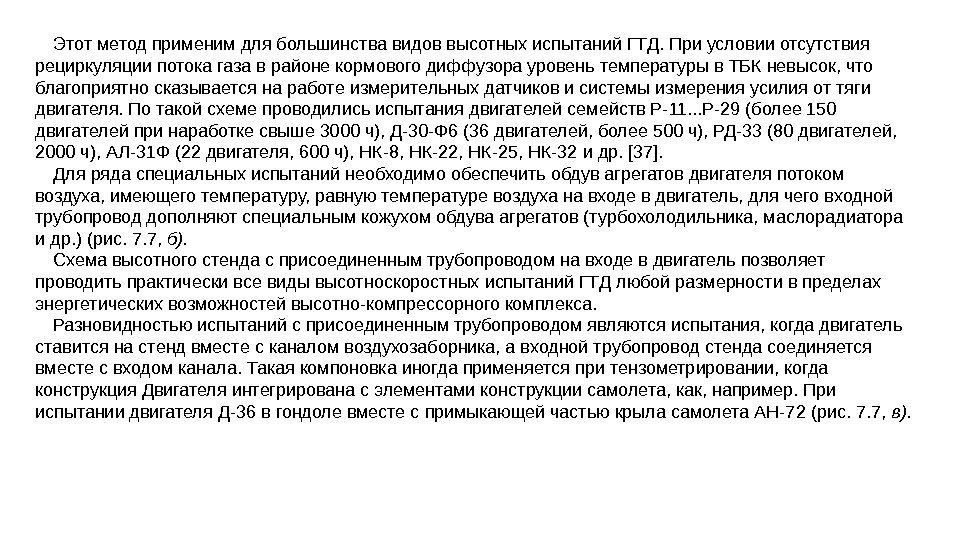
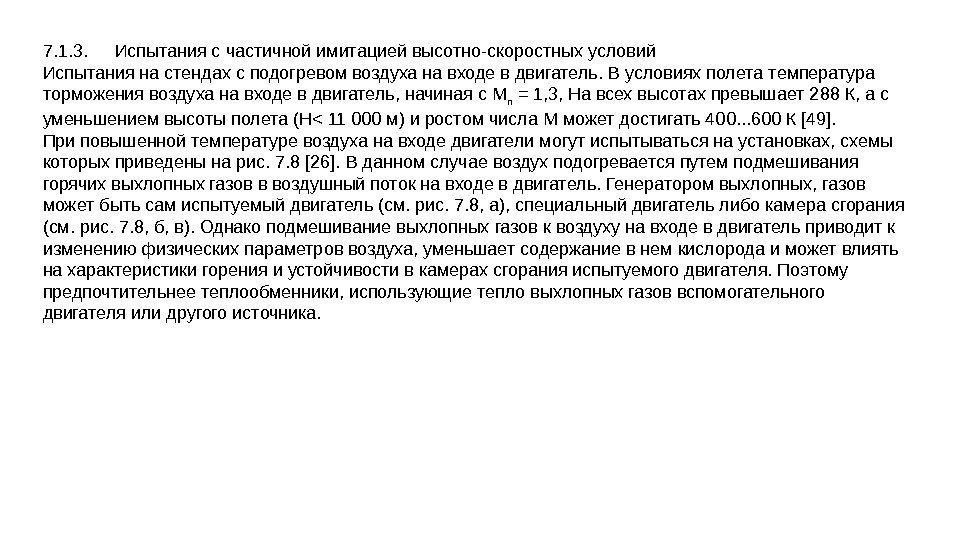
![7. 8. Схемы установок для испытания двигателя с подогревом воздуха на входе [49]: а 7. 8. Схемы установок для испытания двигателя с подогревом воздуха на входе [49]: а](http://present5.com/presentforday2/20170201/mmk_ispytania_i_kontrol_kachestva_izdeliy_2017_images/mmk_ispytania_i_kontrol_kachestva_izdeliy_2017_386.jpg)
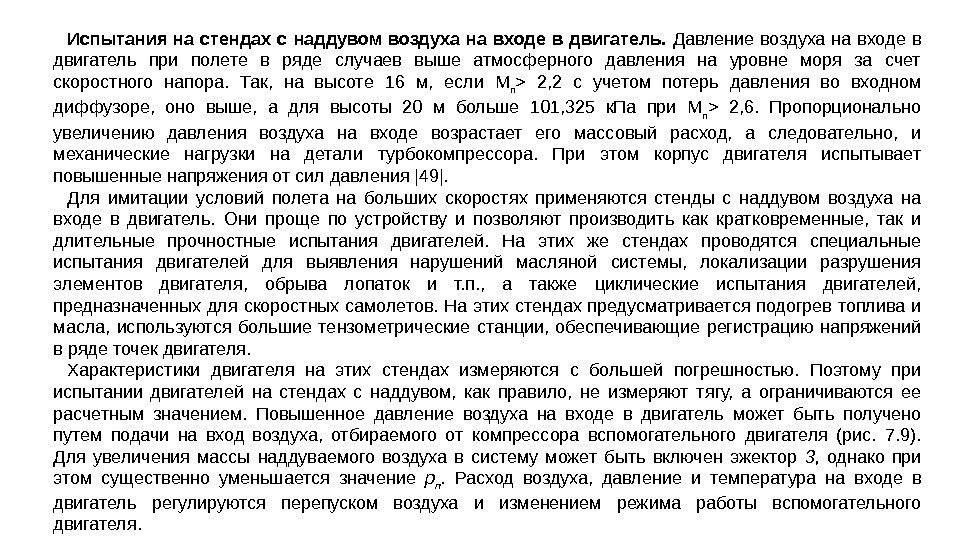
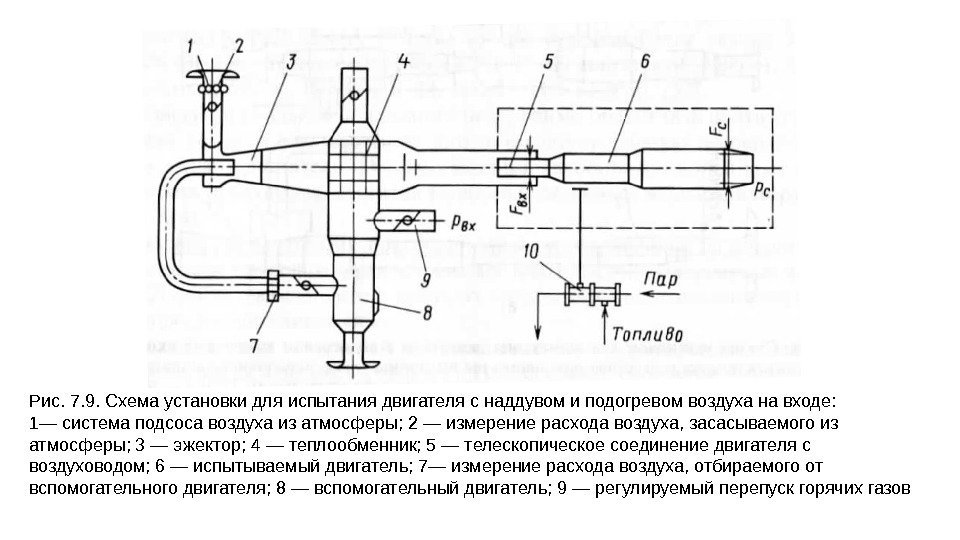
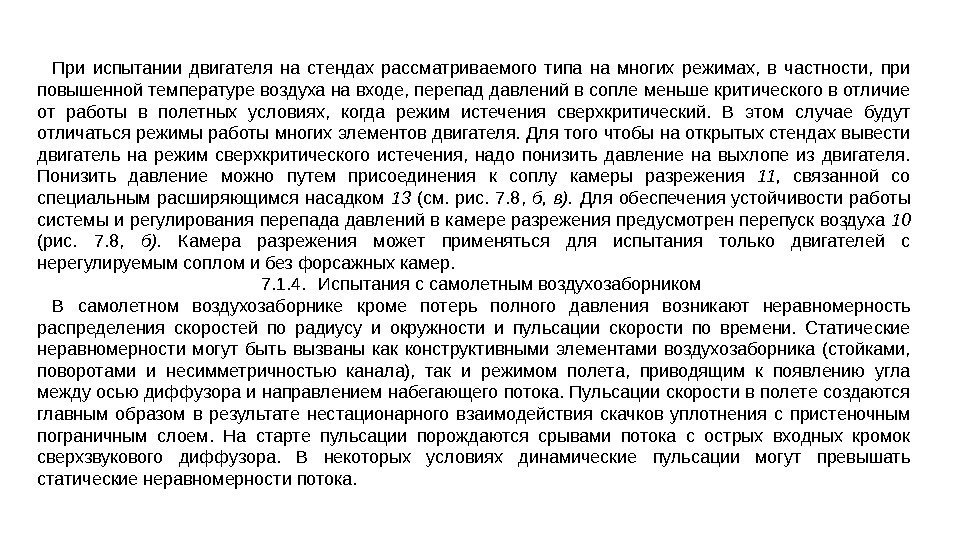
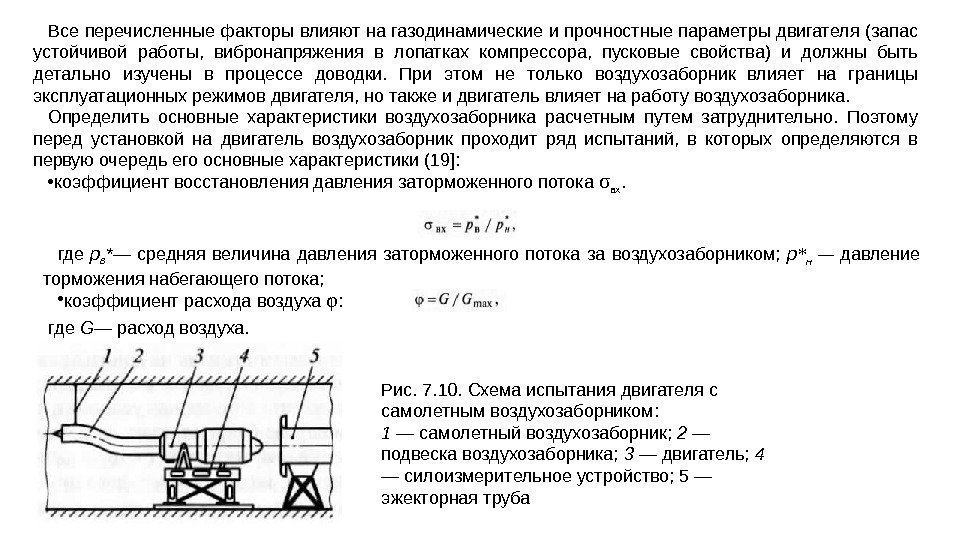
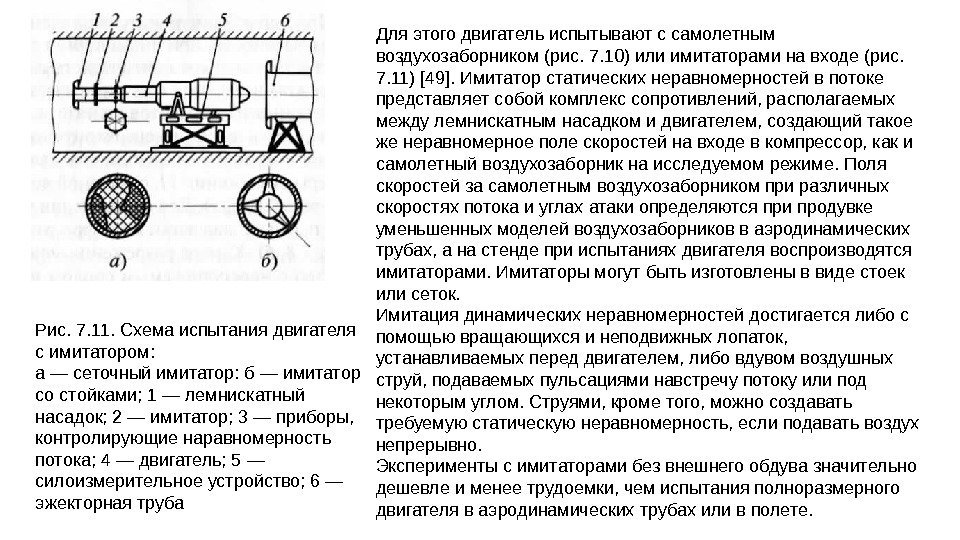
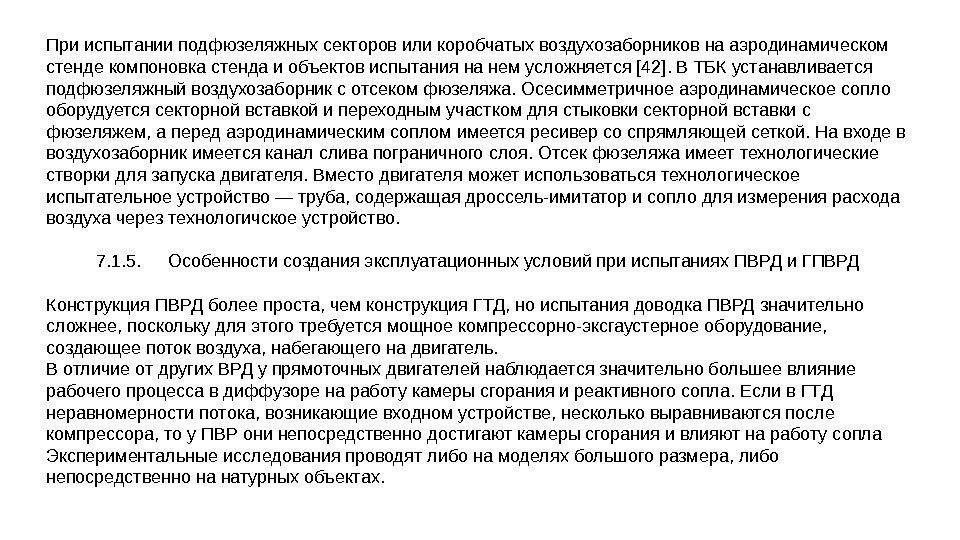
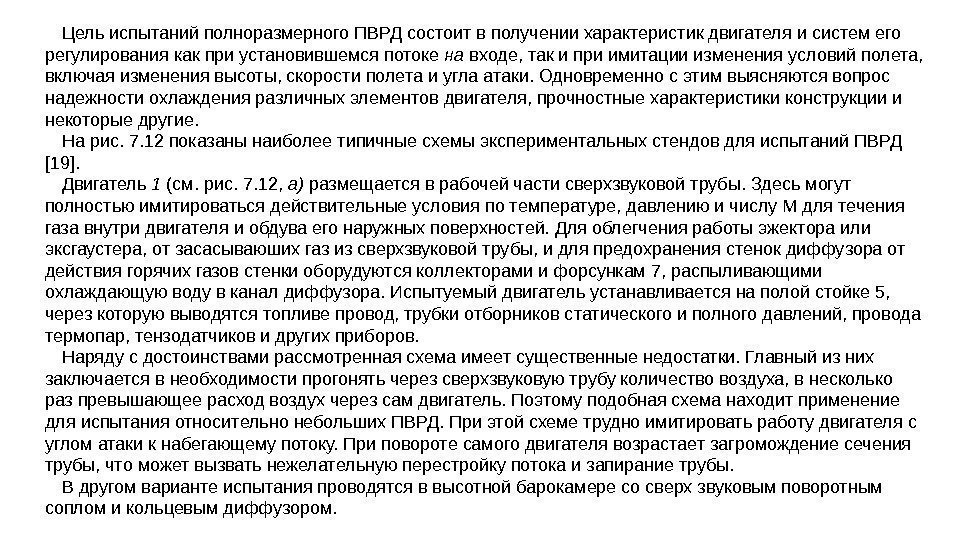
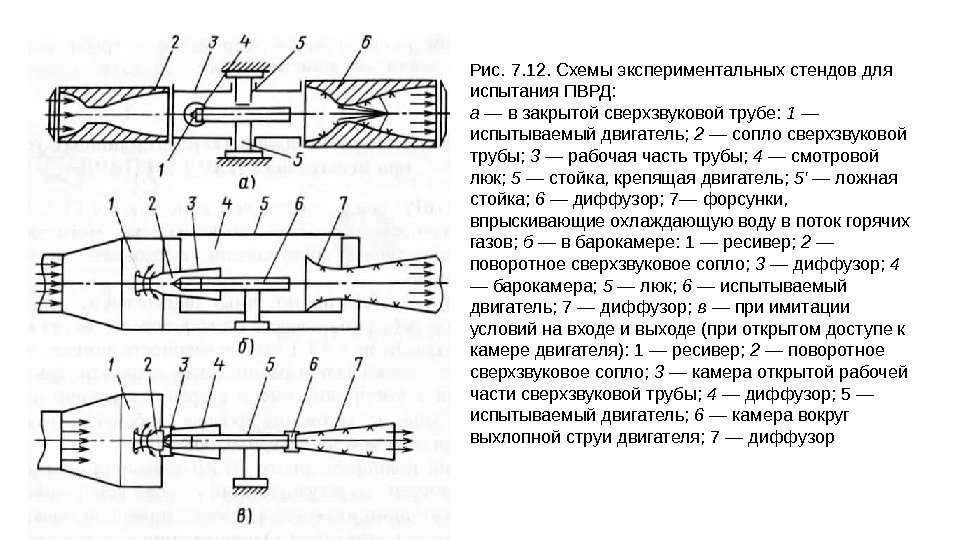
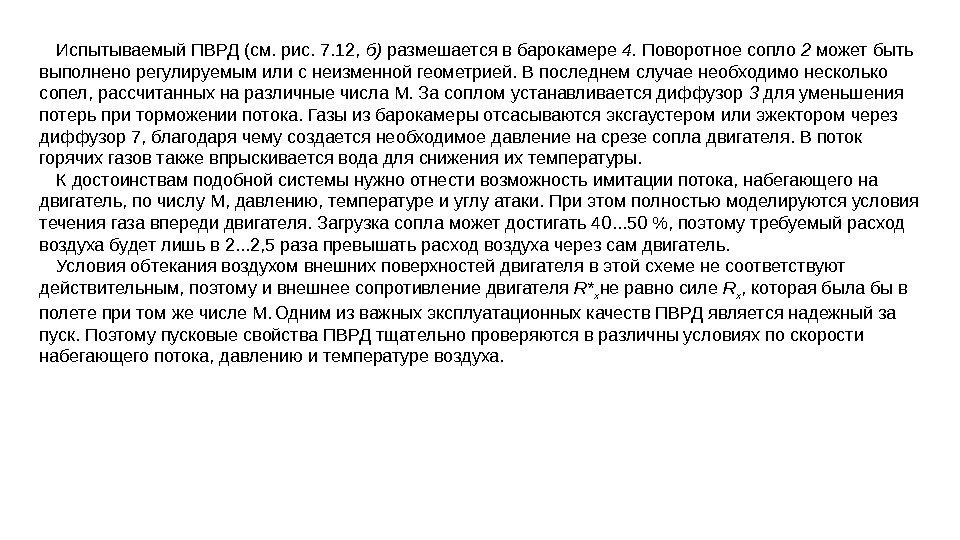
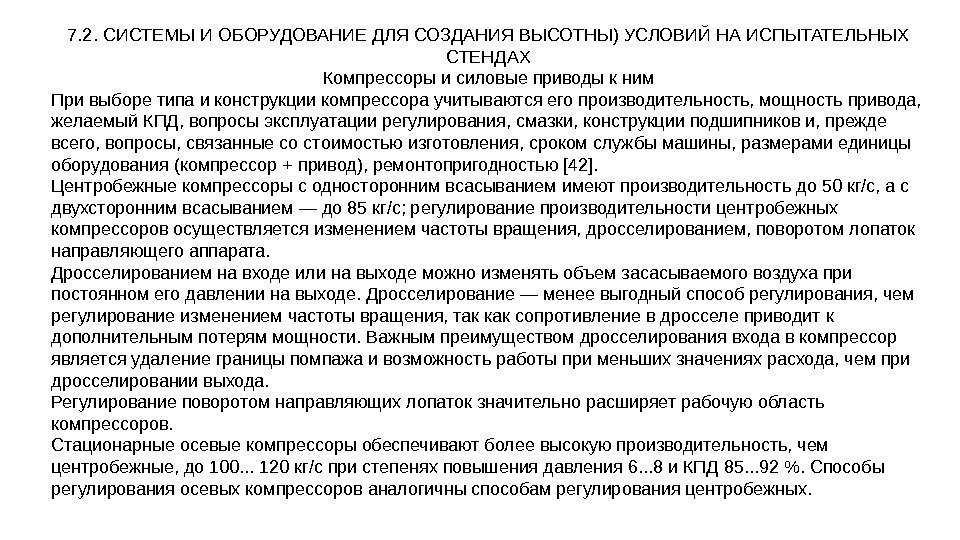
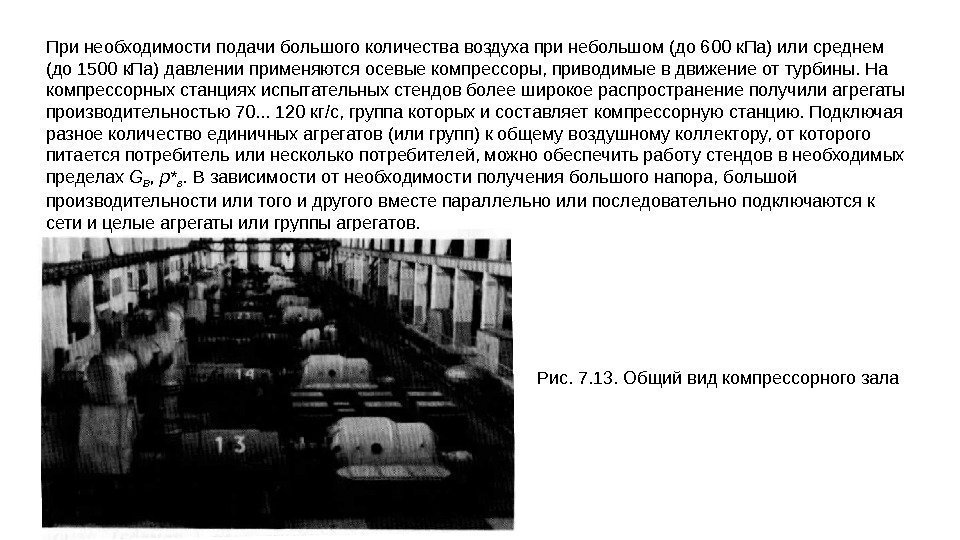
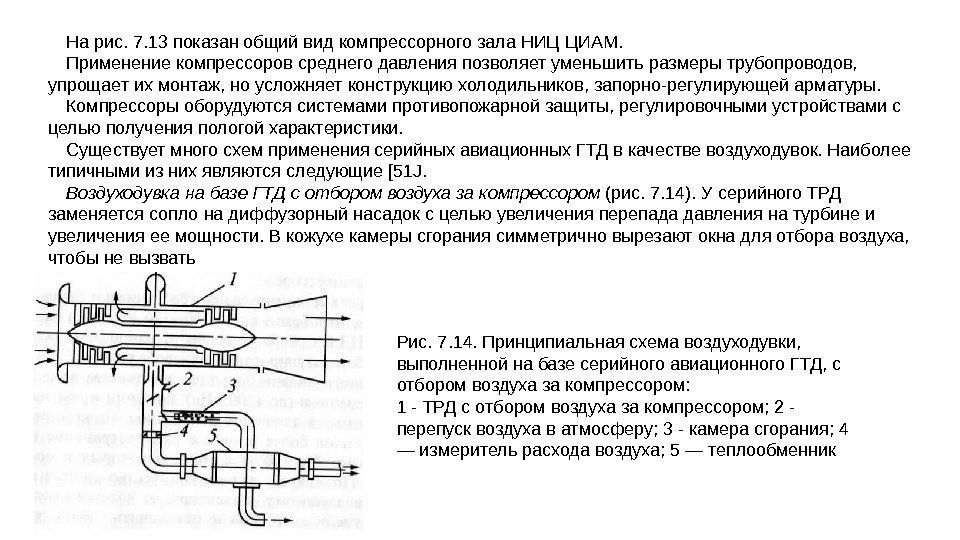
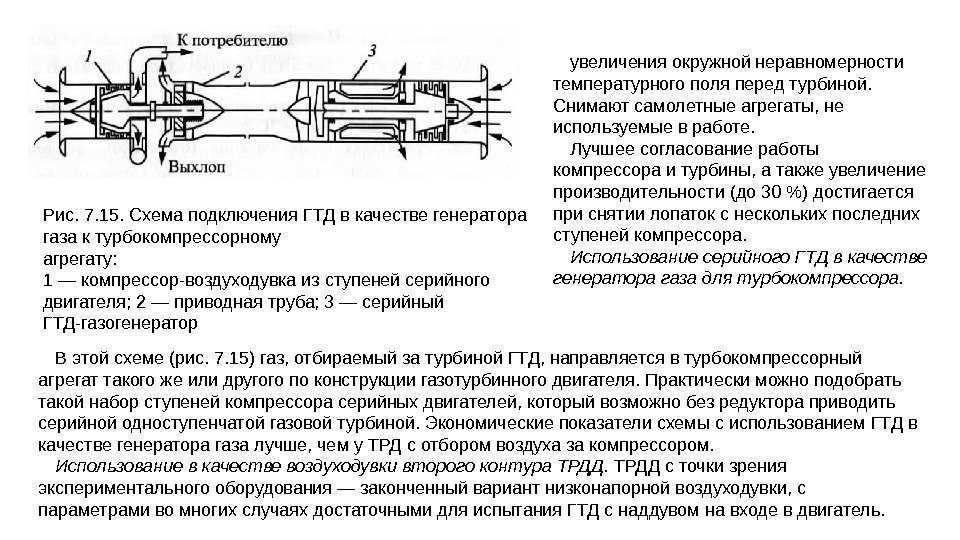
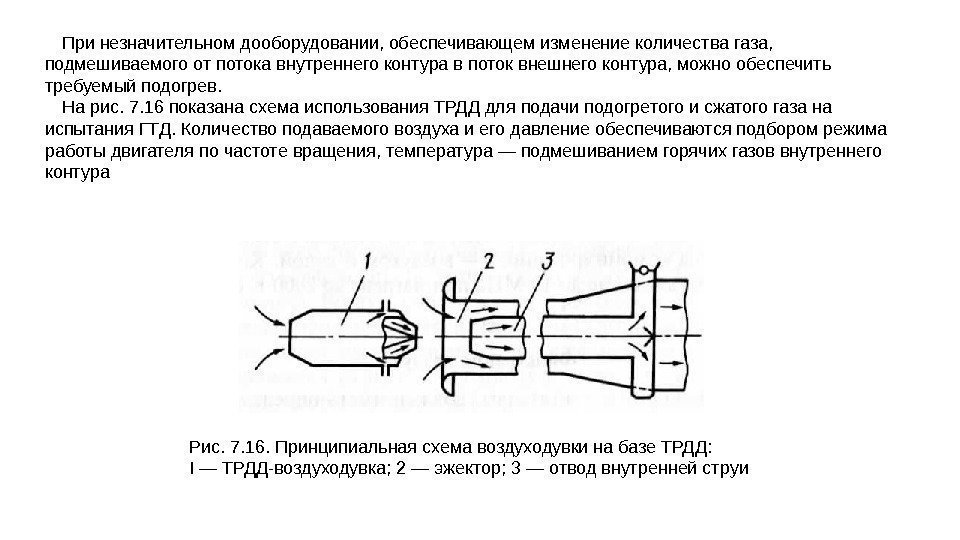
![Подогрев воздуха на входе в двигатель осуществляется одним из следующих способов [37]: • Подогрев воздуха на входе в двигатель осуществляется одним из следующих способов [37]: •](http://present5.com/presentforday2/20170201/mmk_ispytania_i_kontrol_kachestva_izdeliy_2017_images/mmk_ispytania_i_kontrol_kachestva_izdeliy_2017_401.jpg)
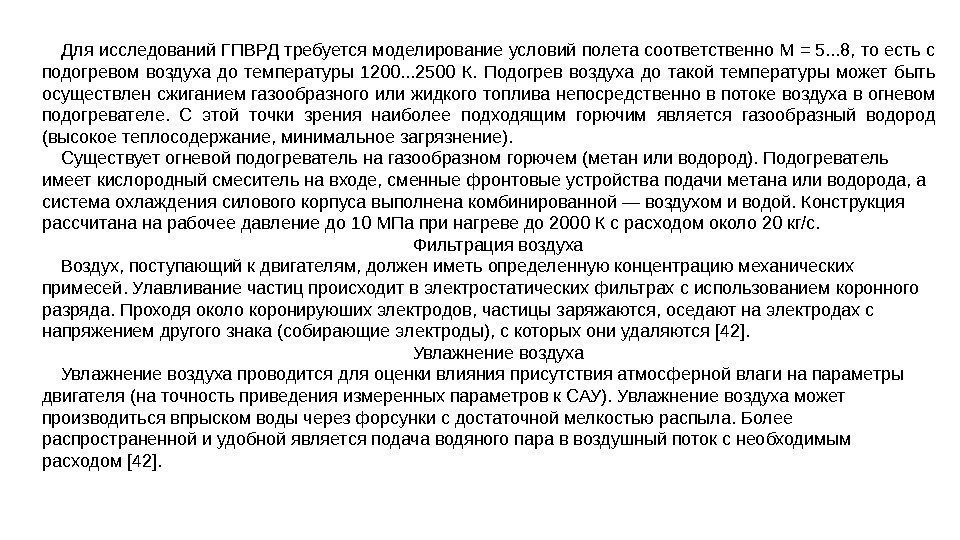
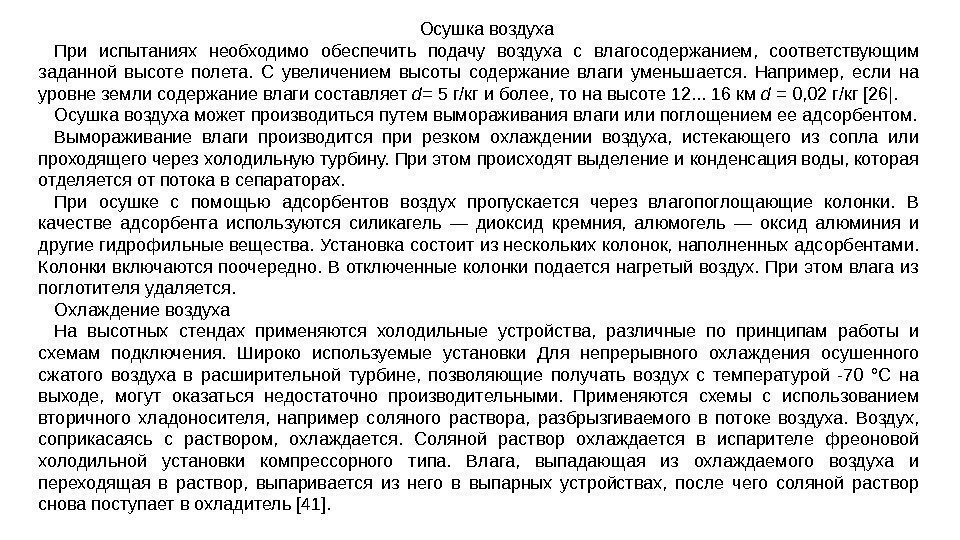
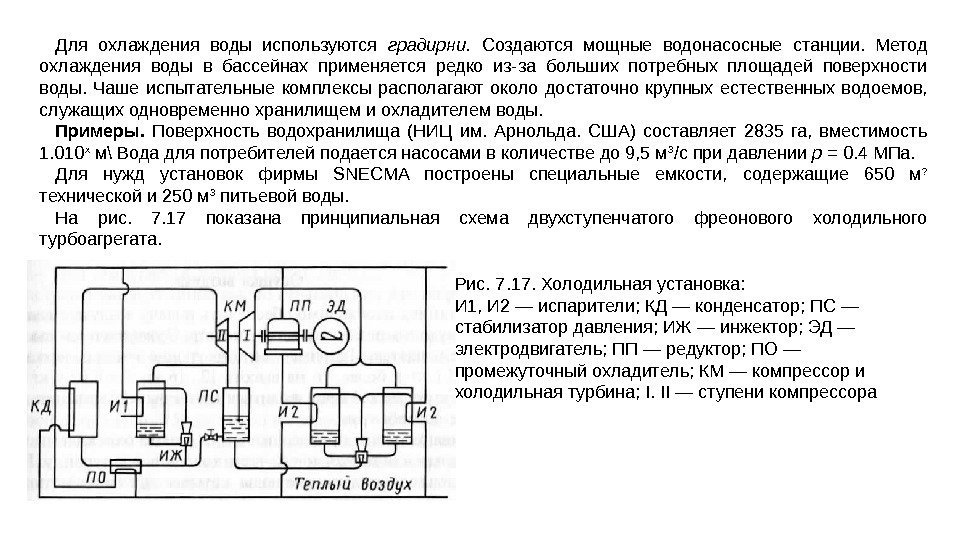
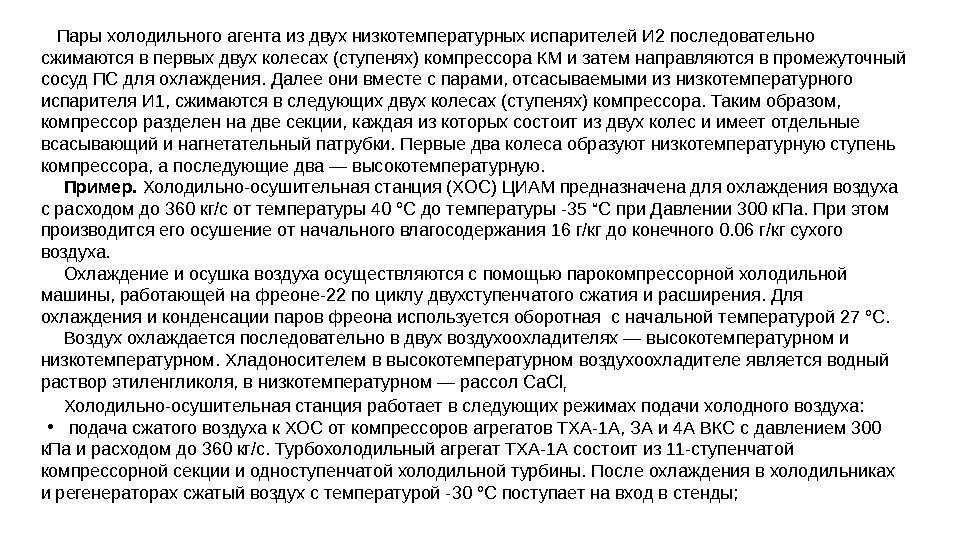
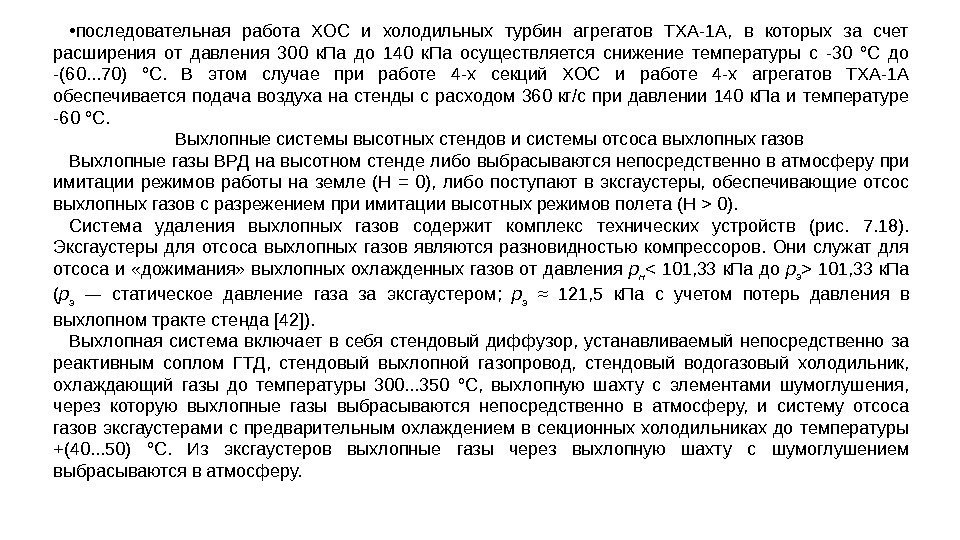
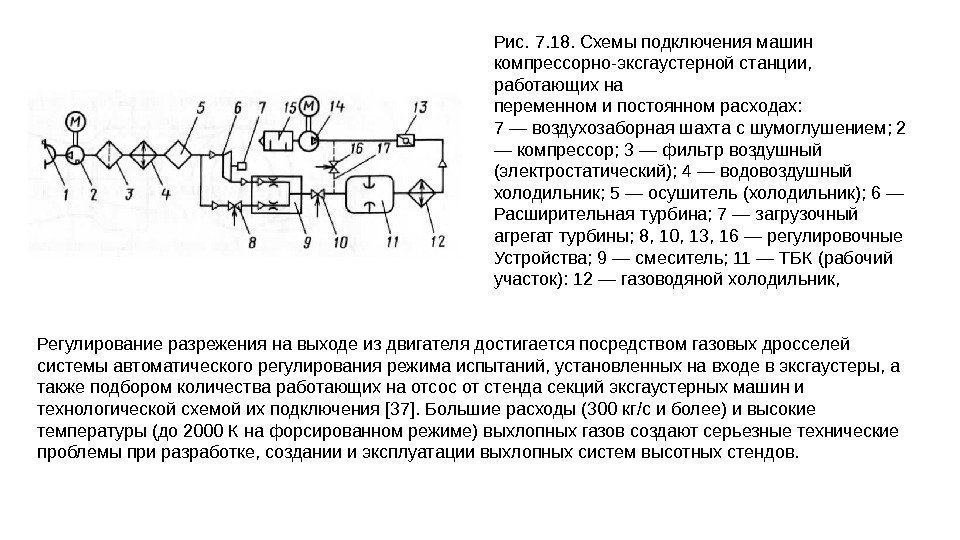
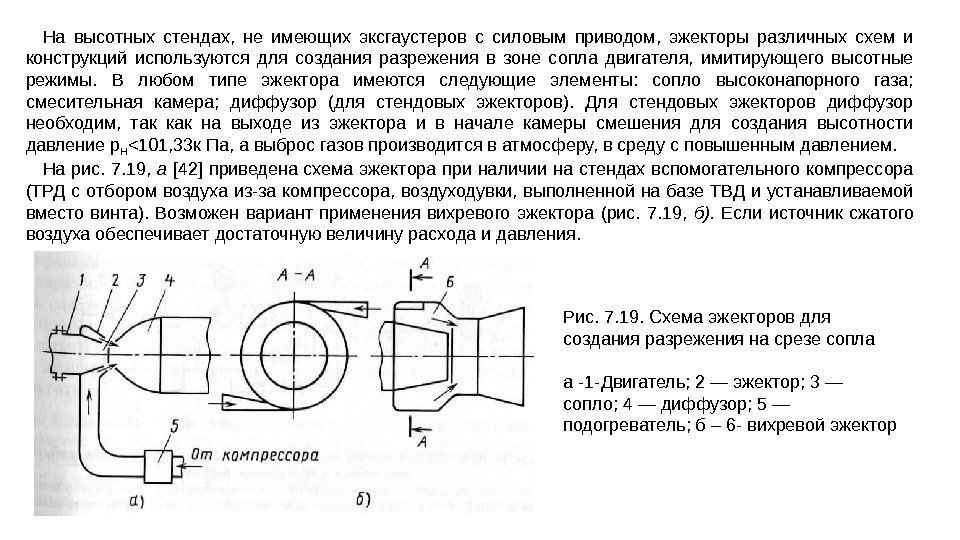
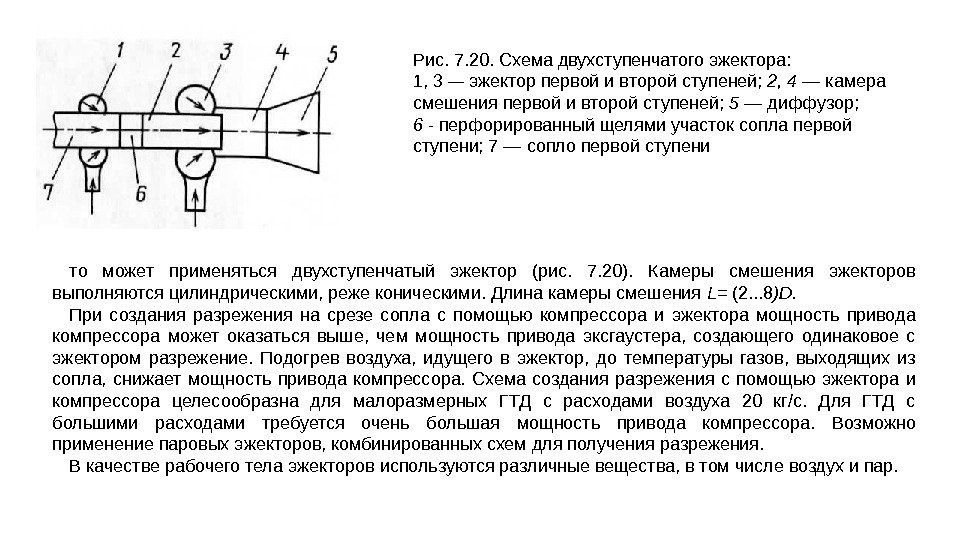
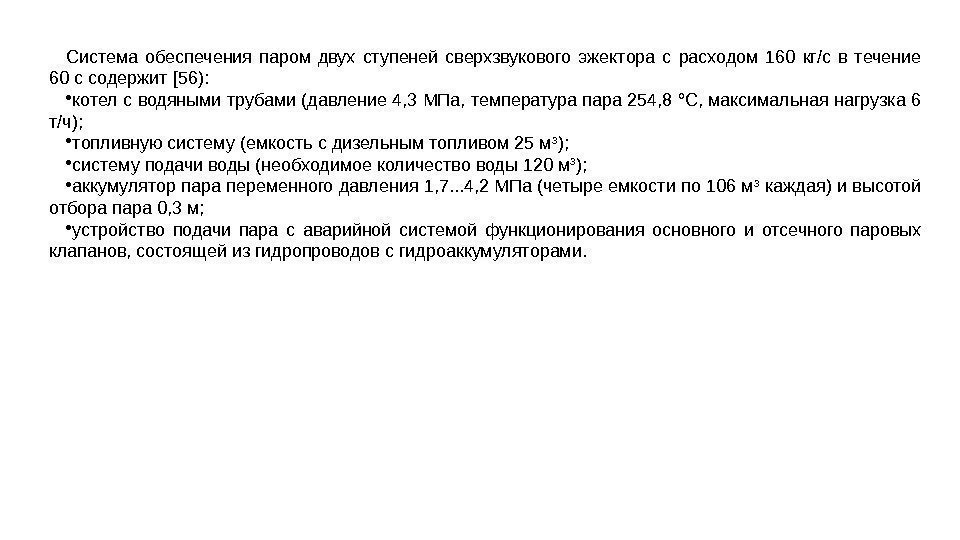
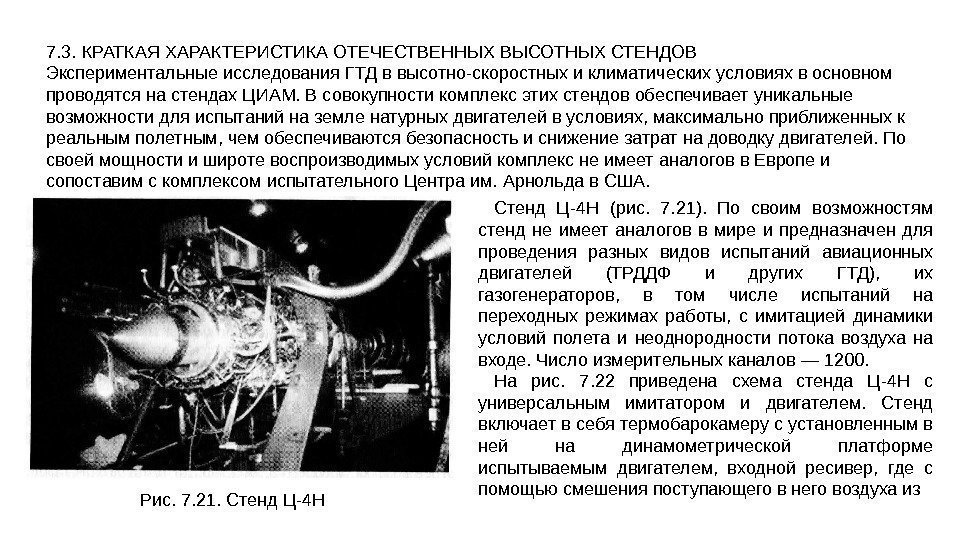
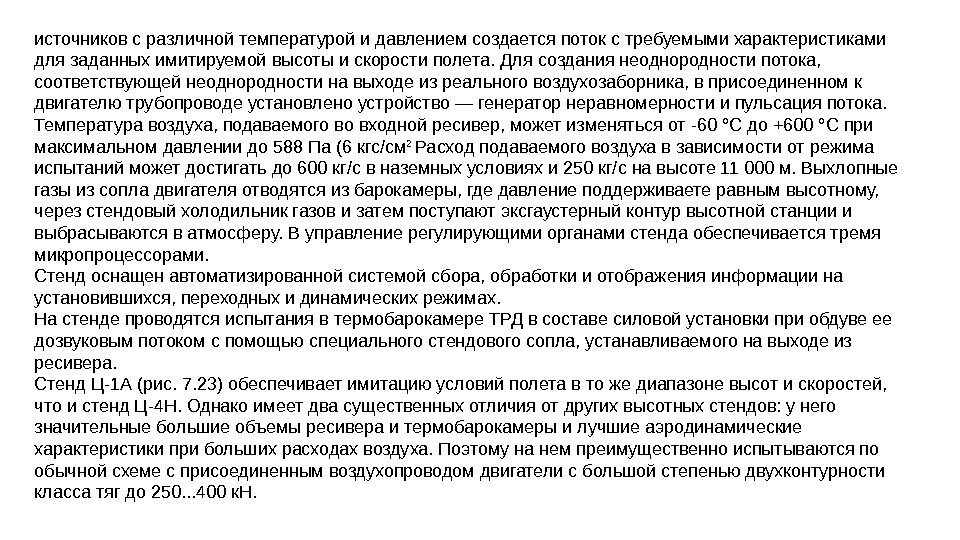
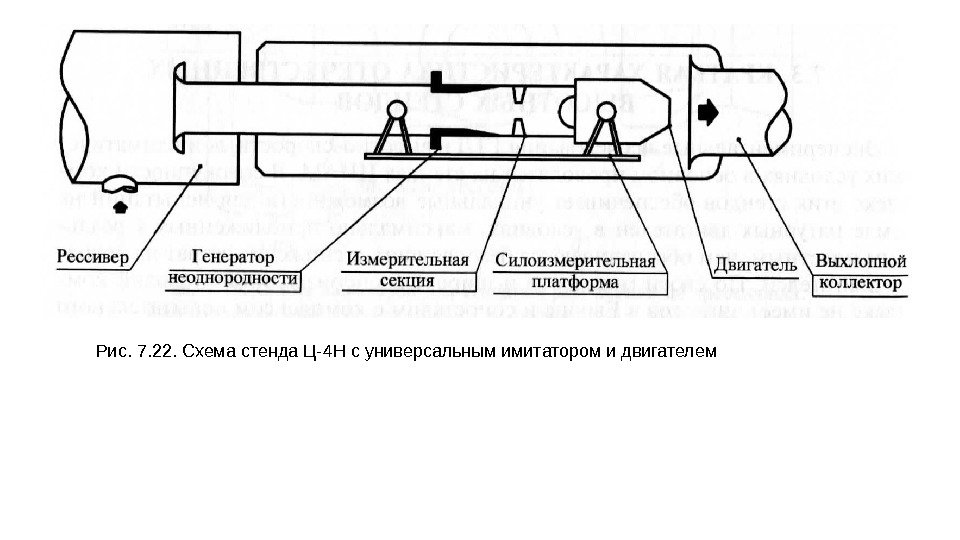
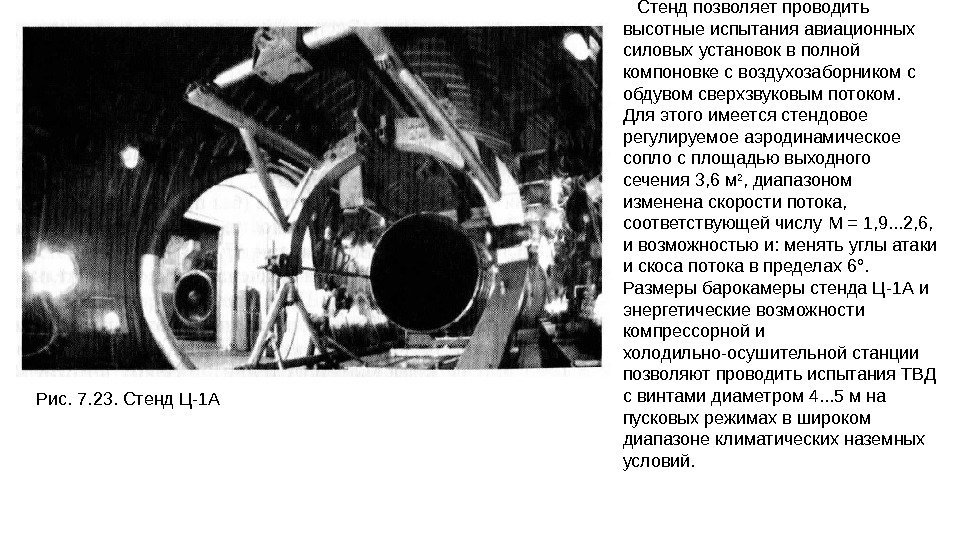
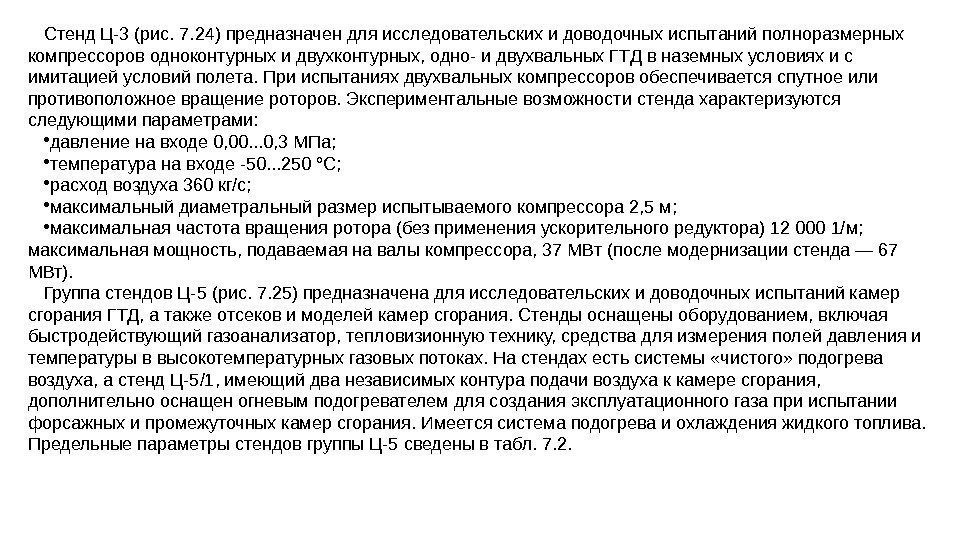
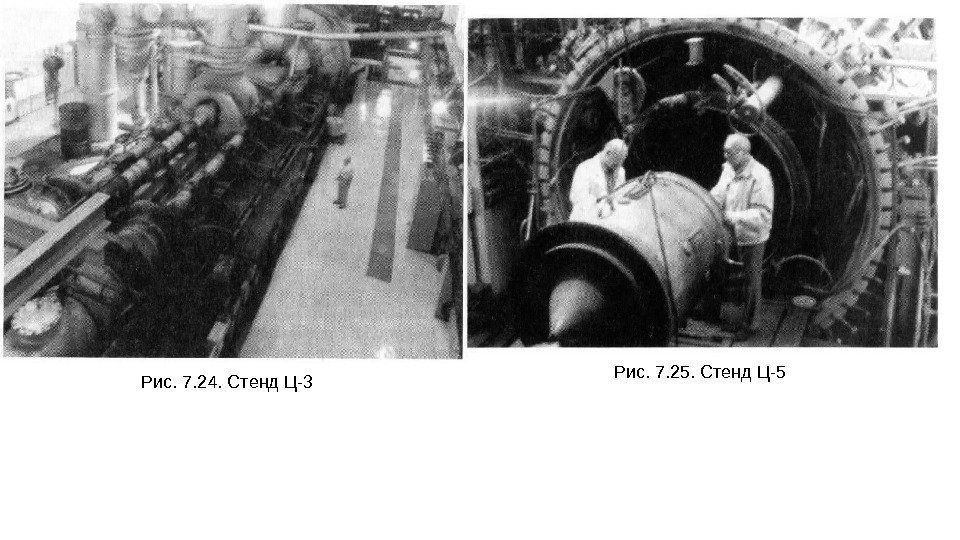
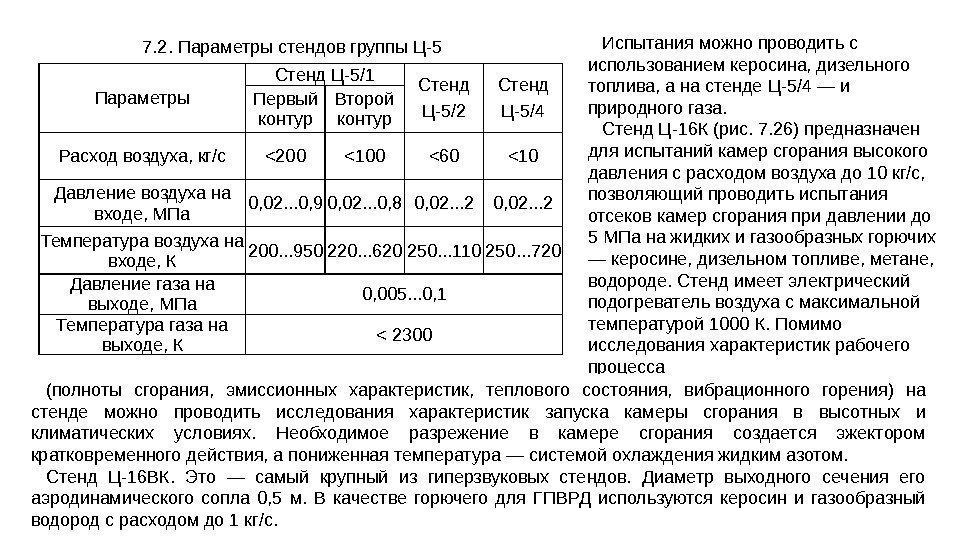
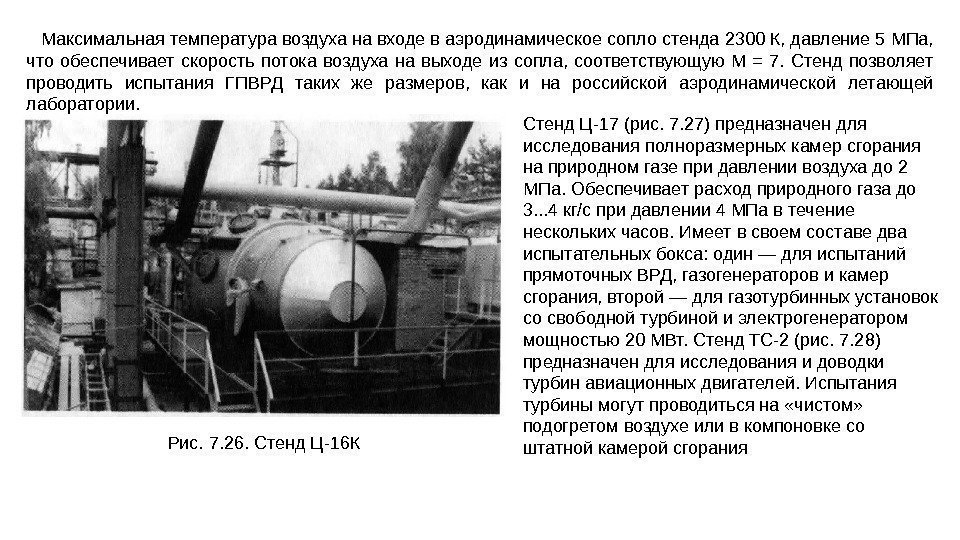

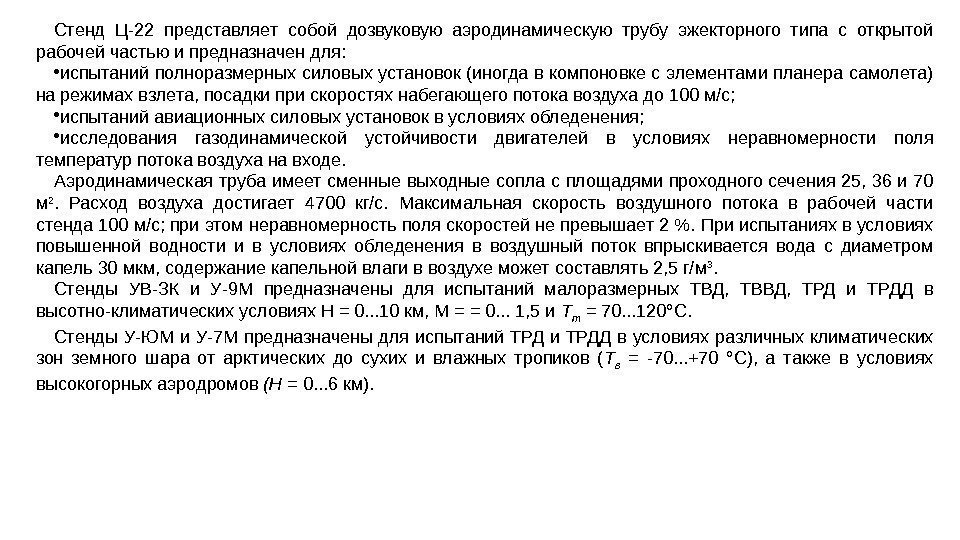
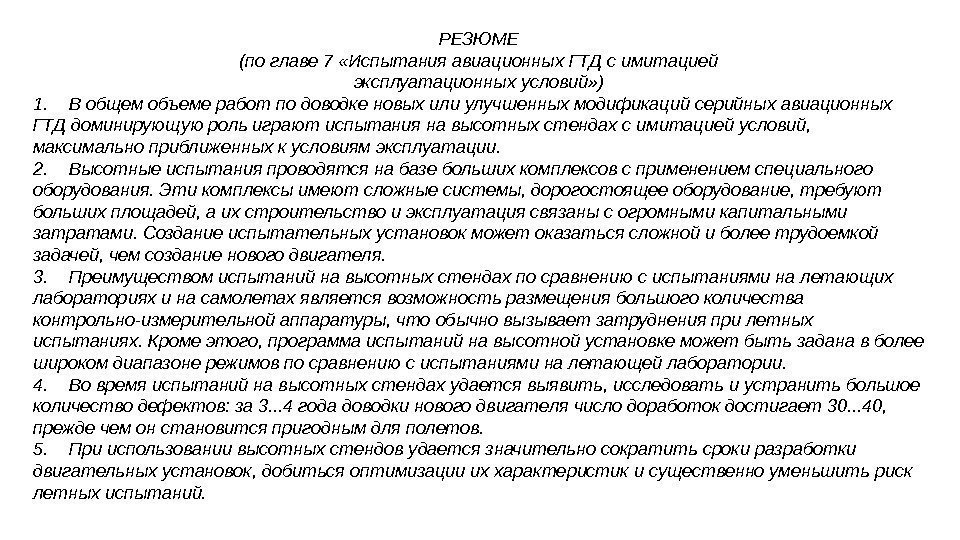
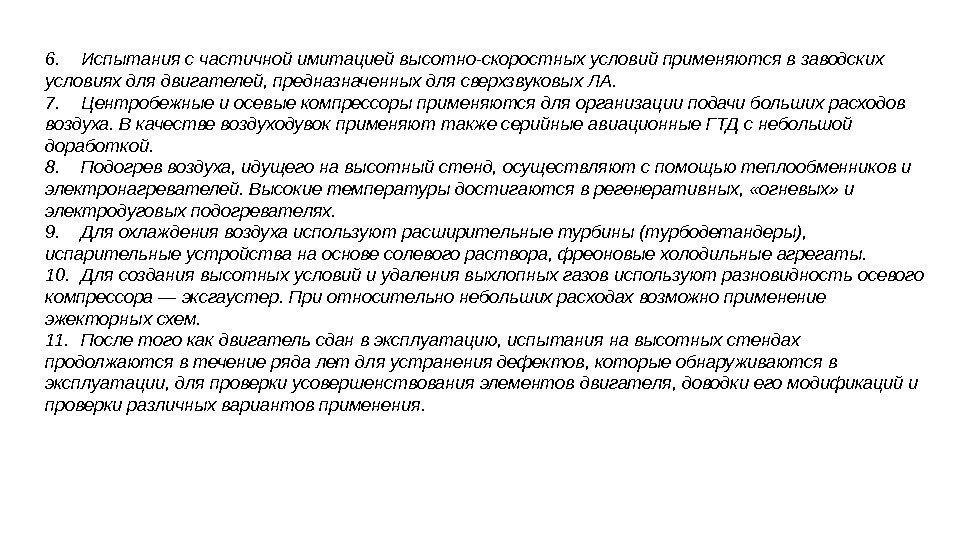
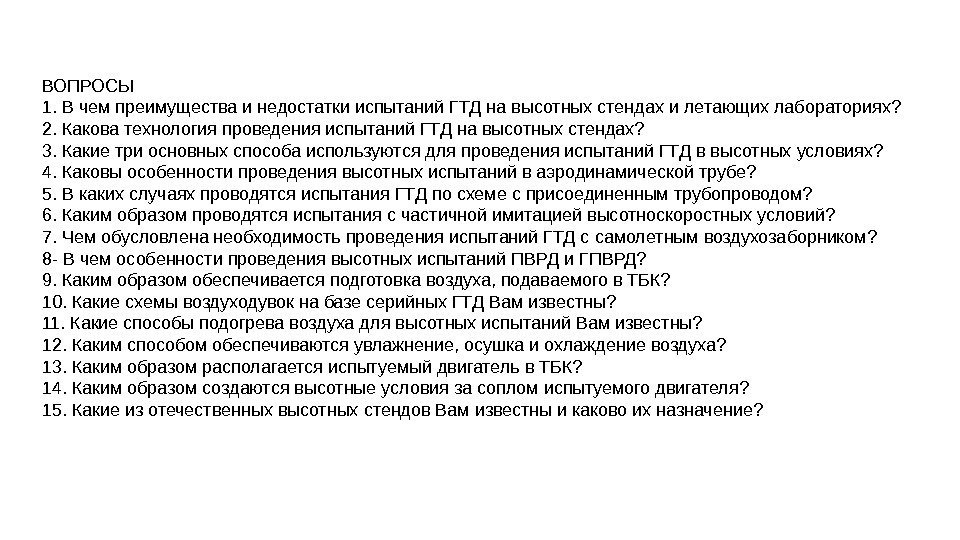
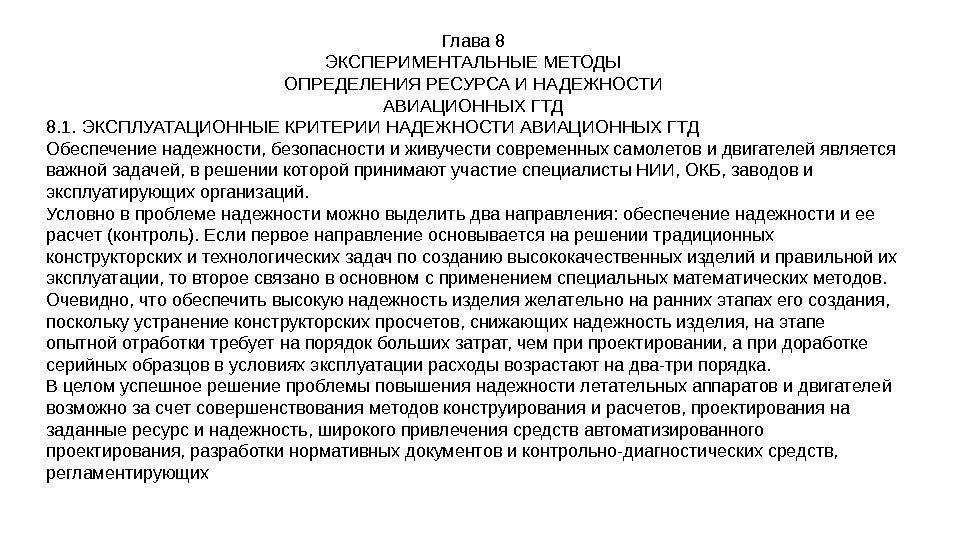
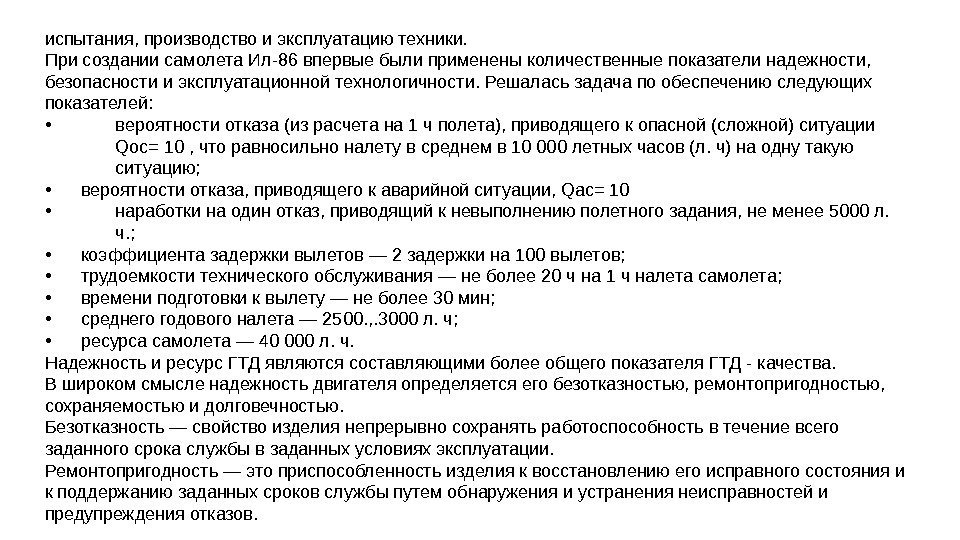
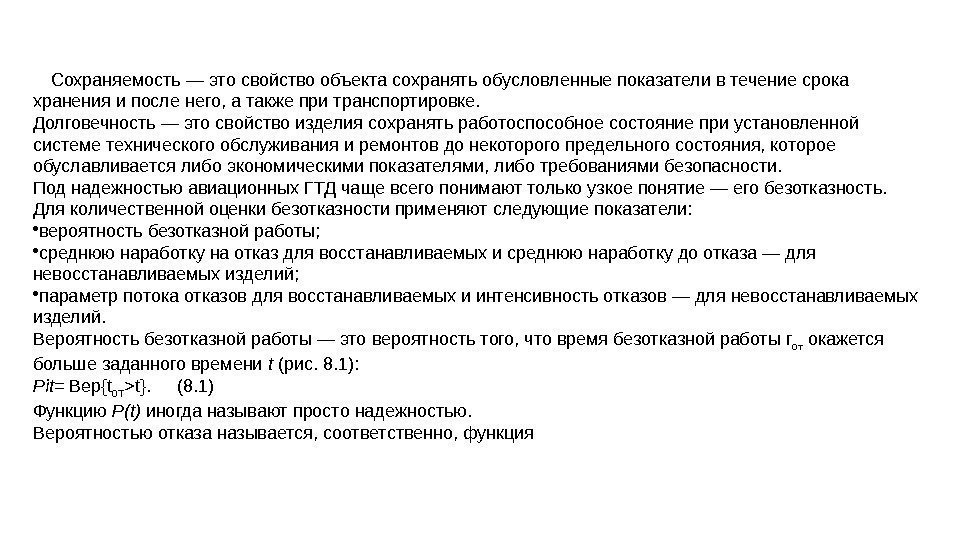
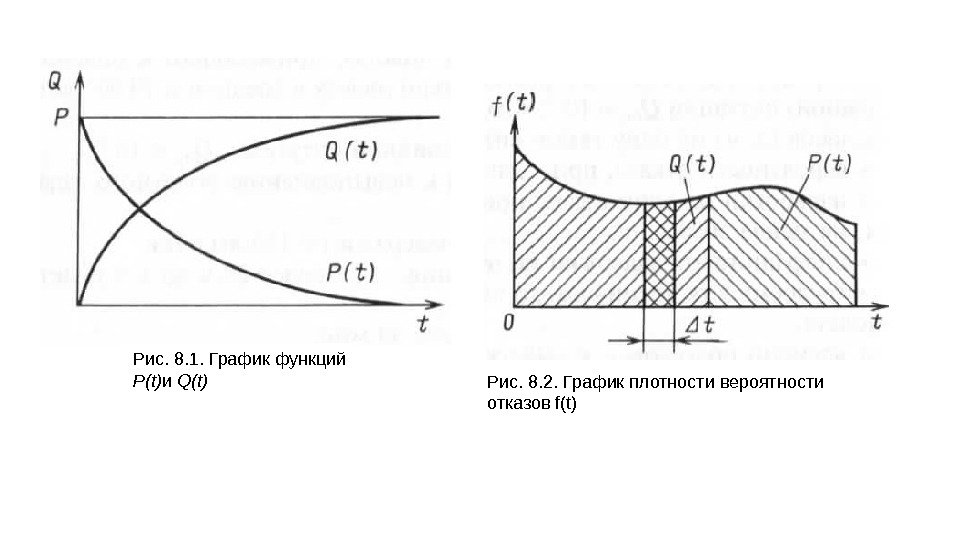
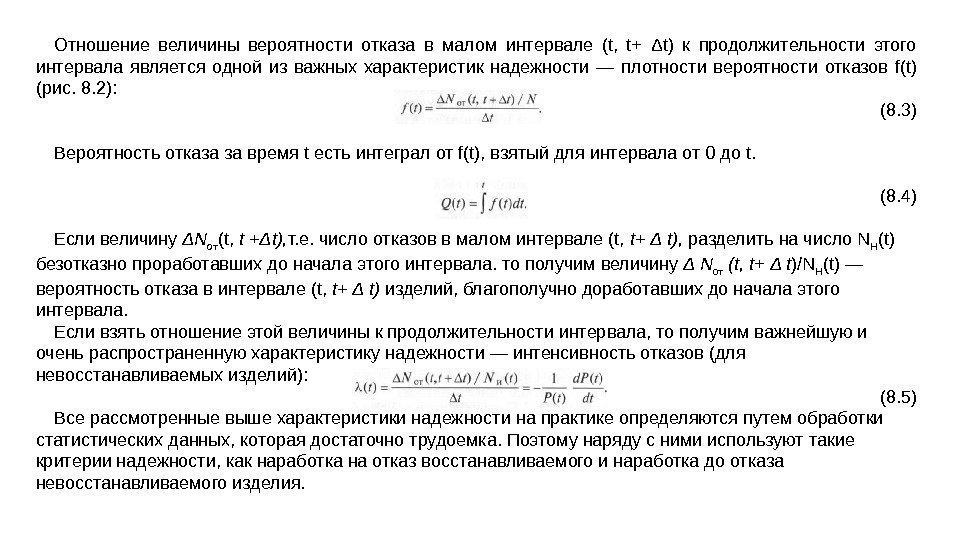
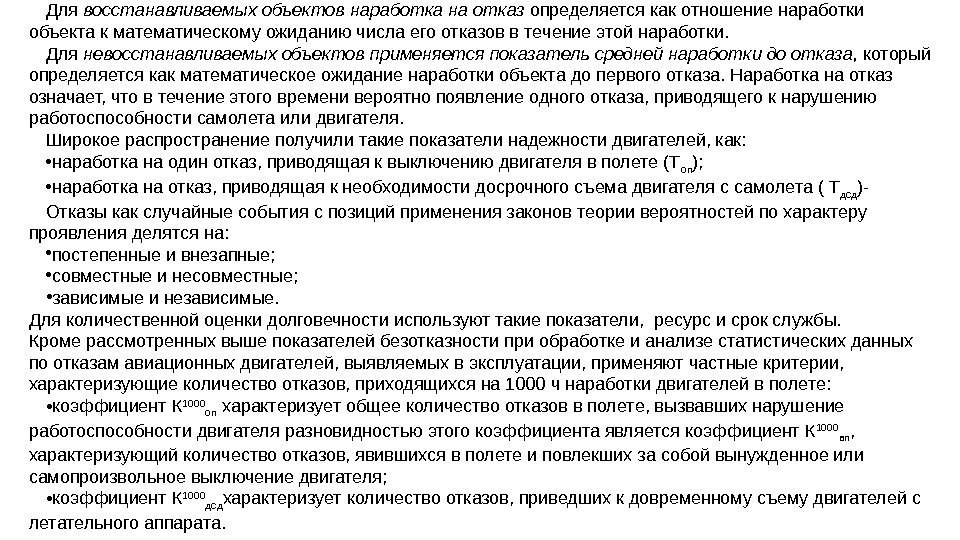
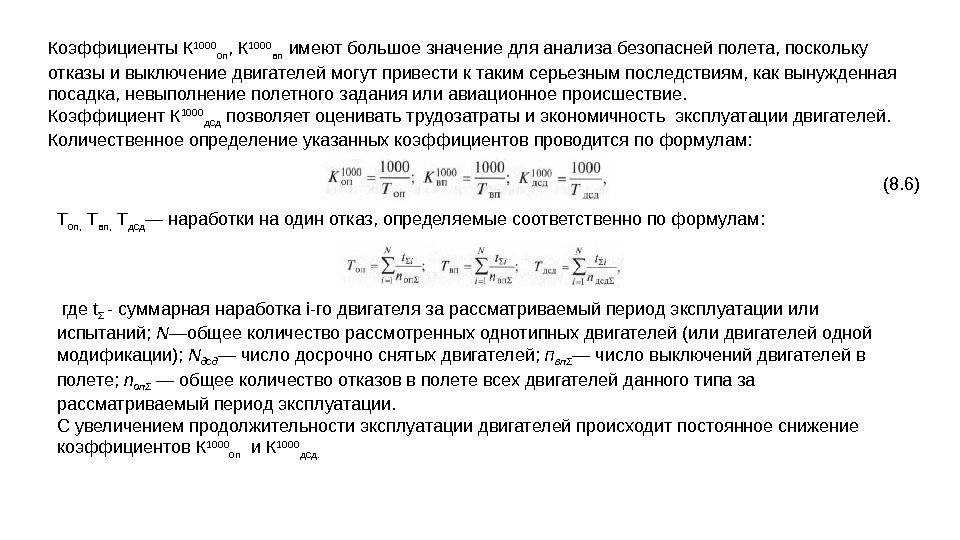

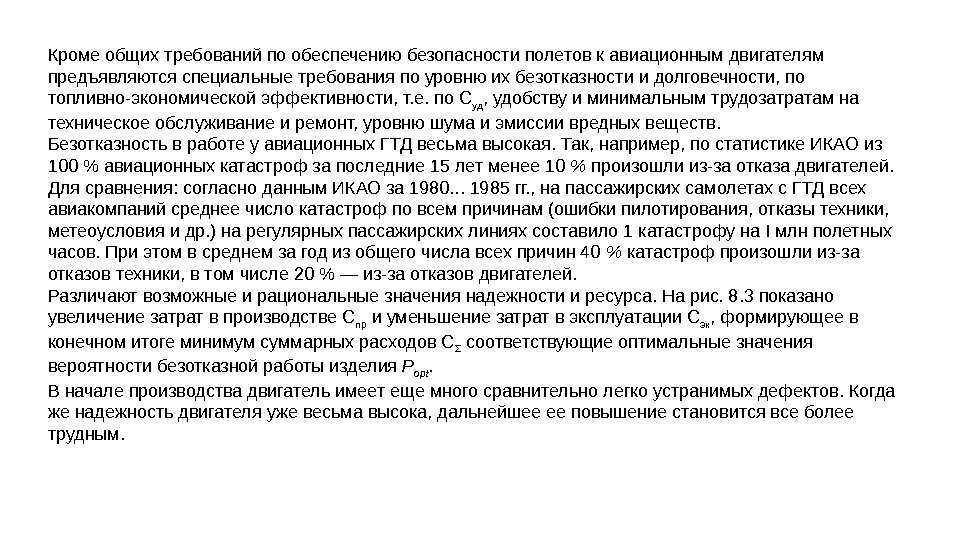
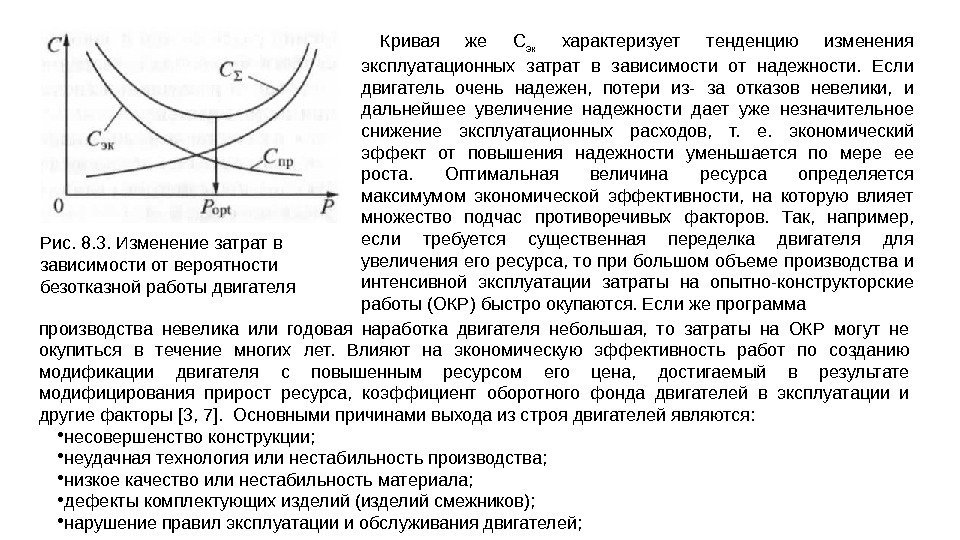
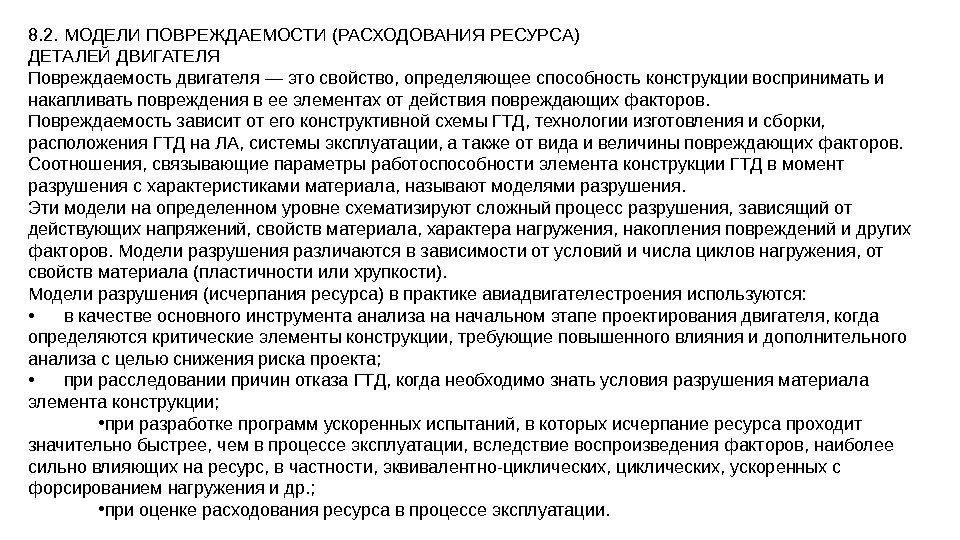
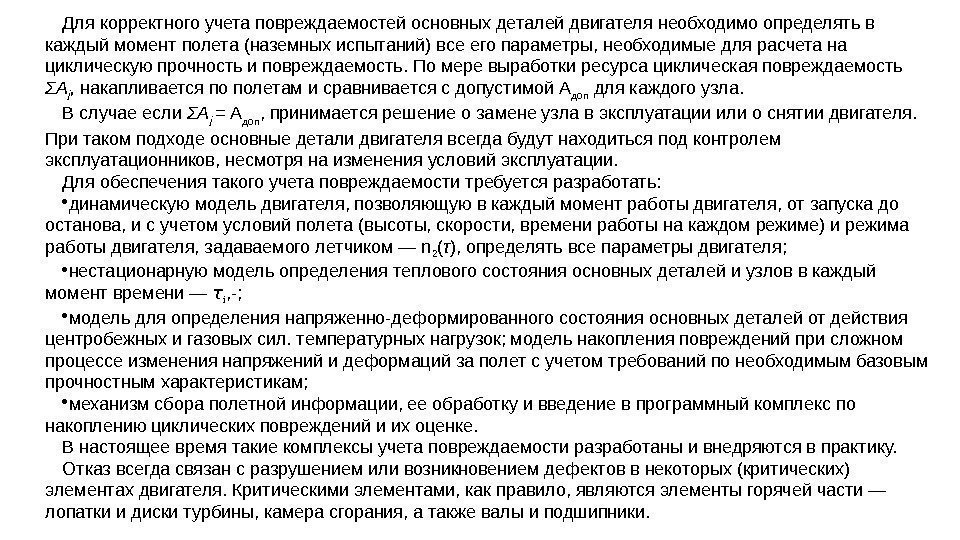
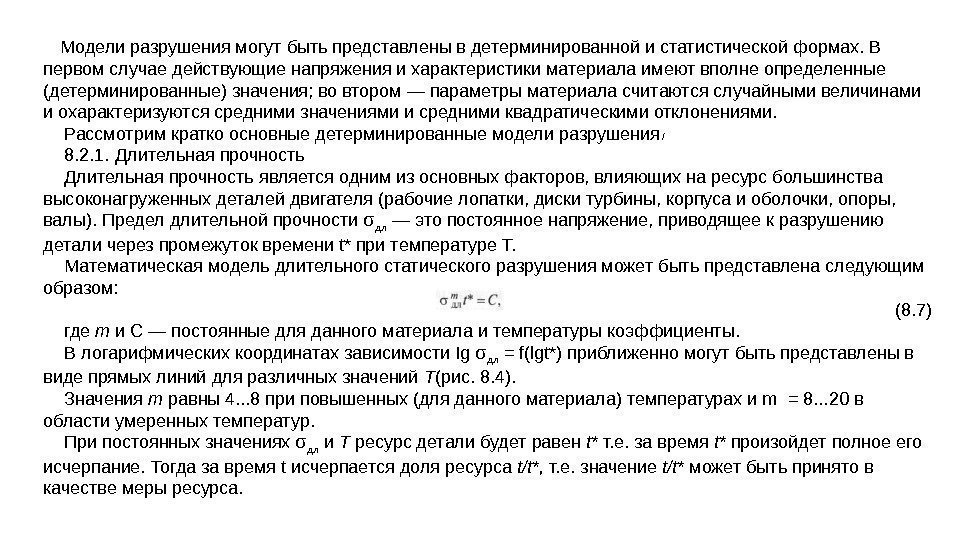
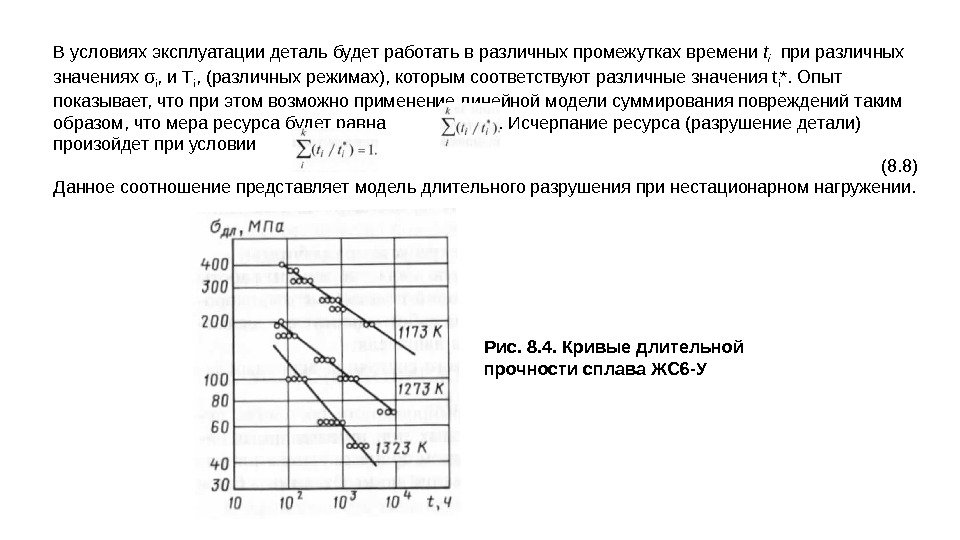
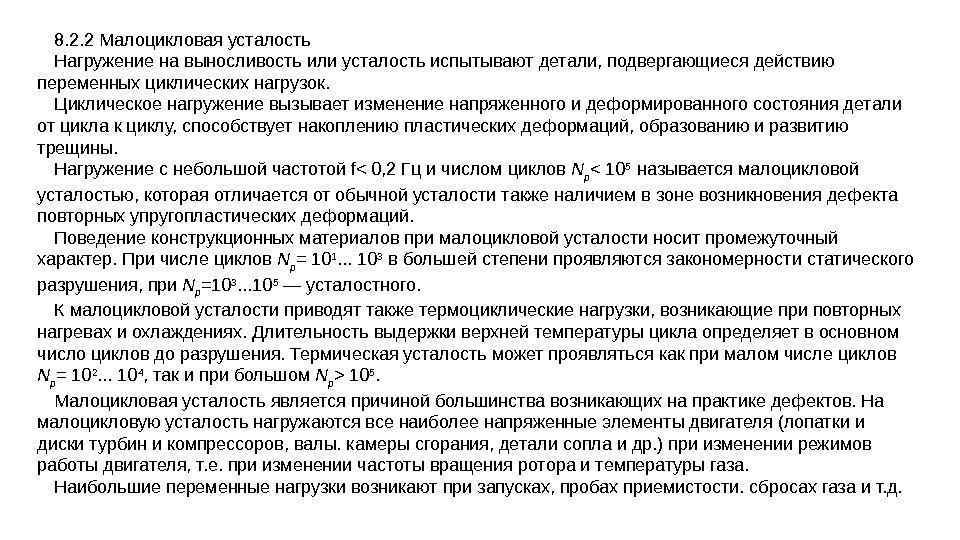
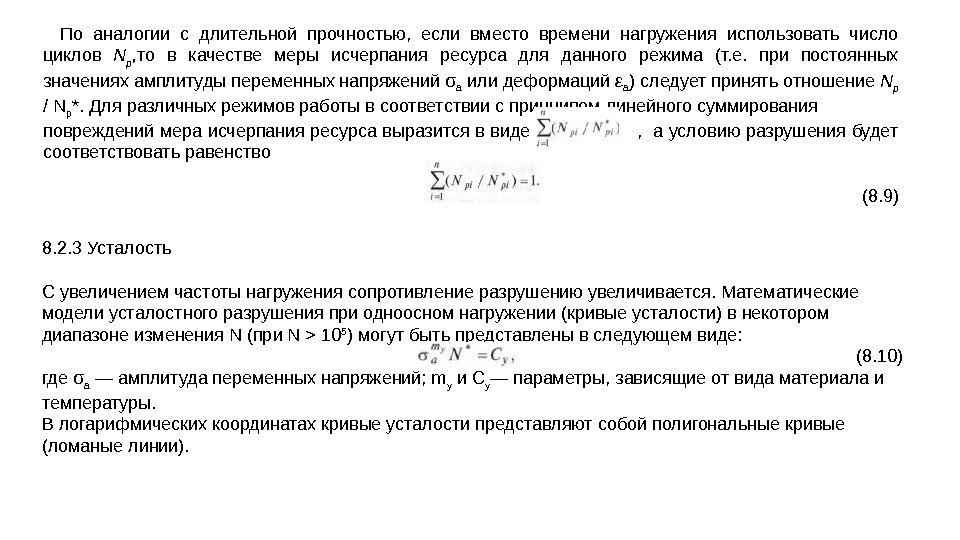
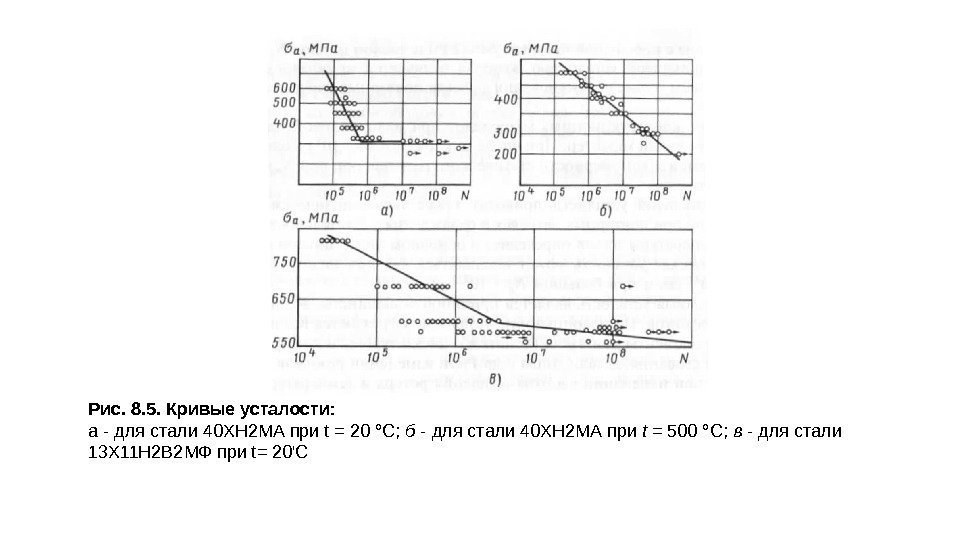
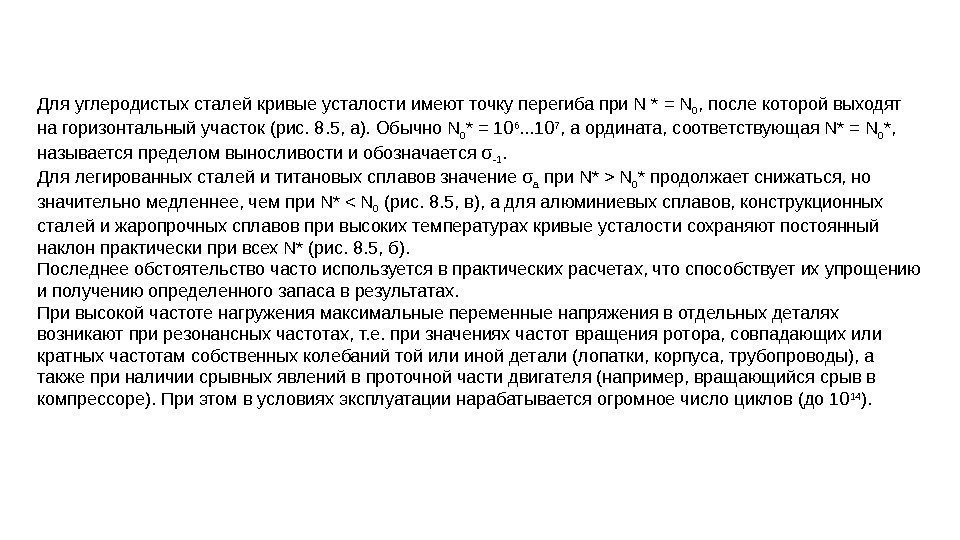
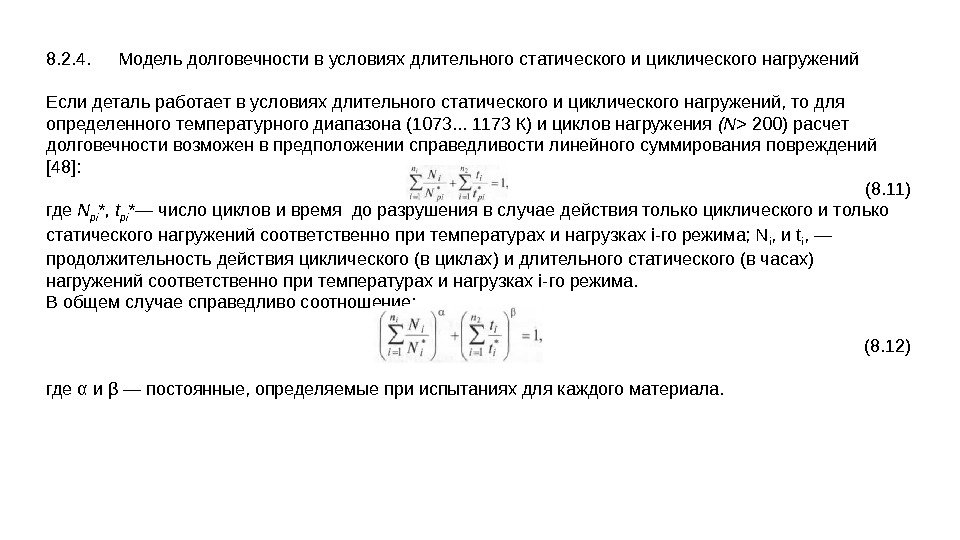
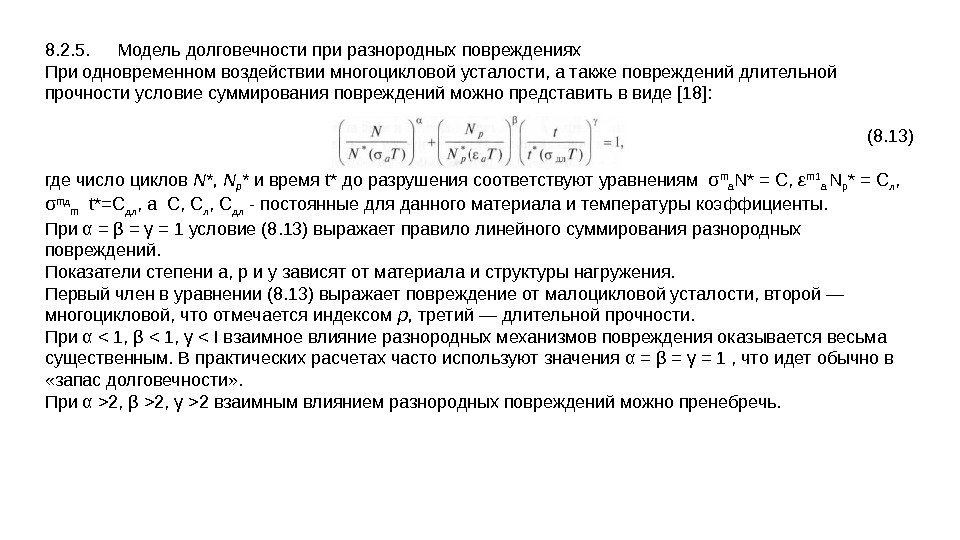
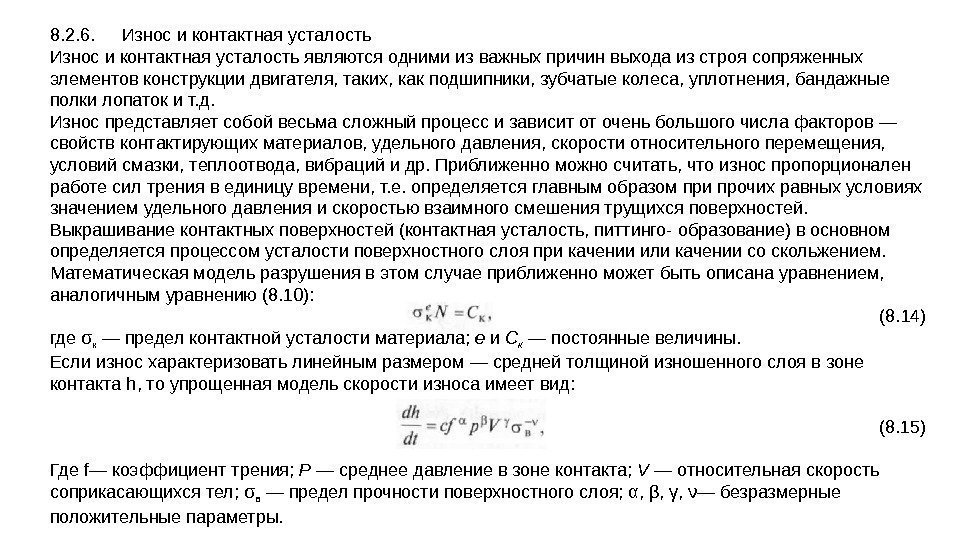

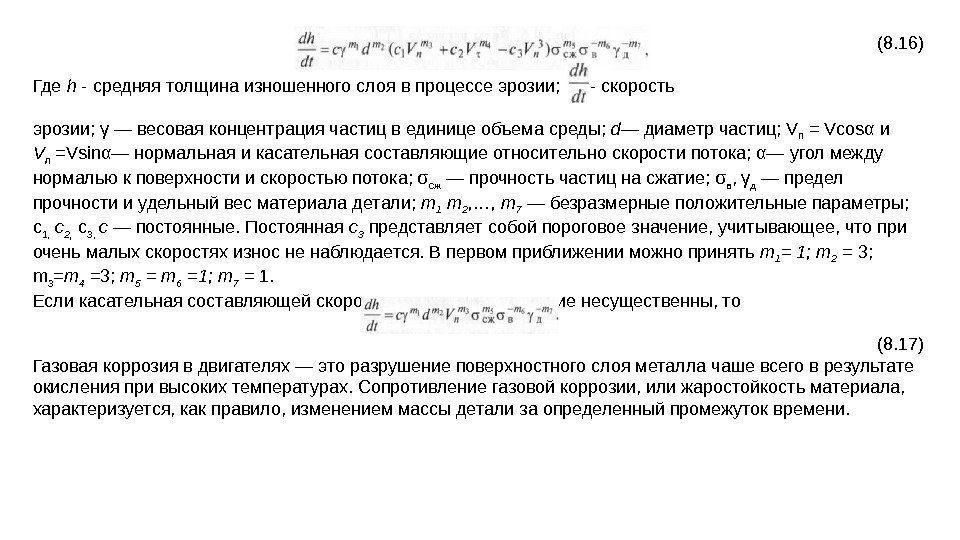
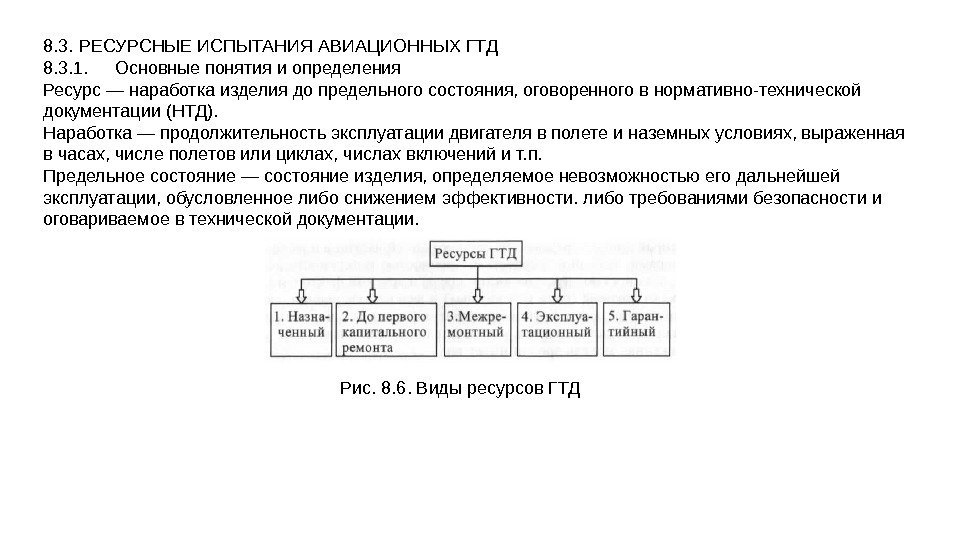
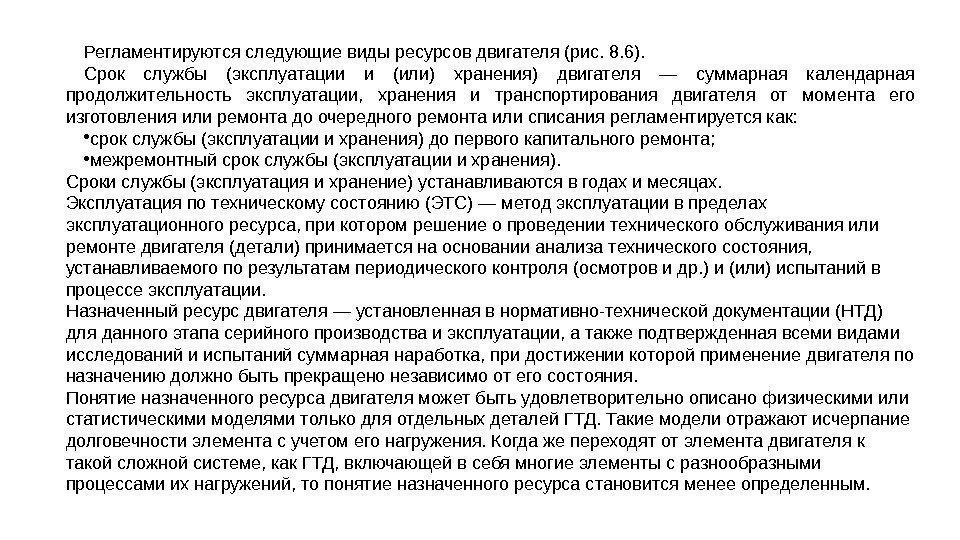
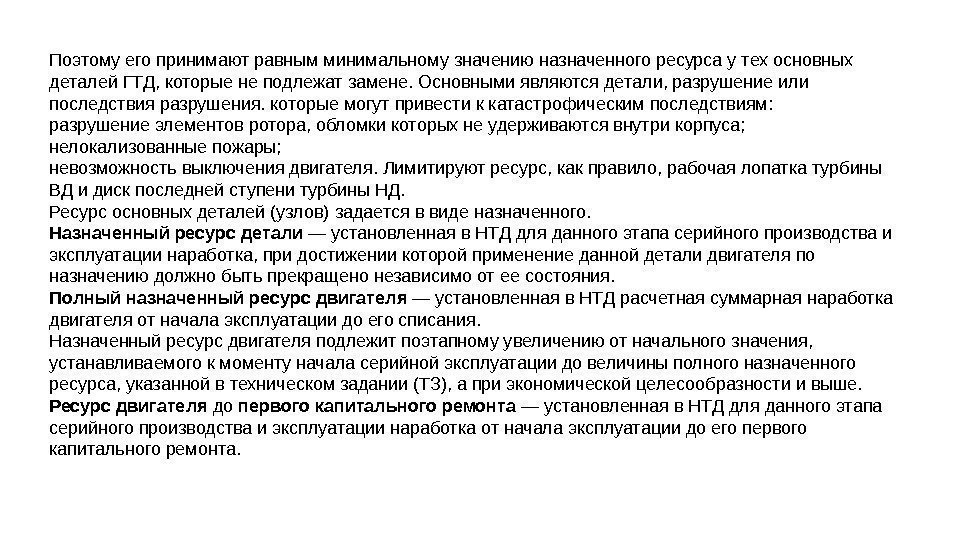
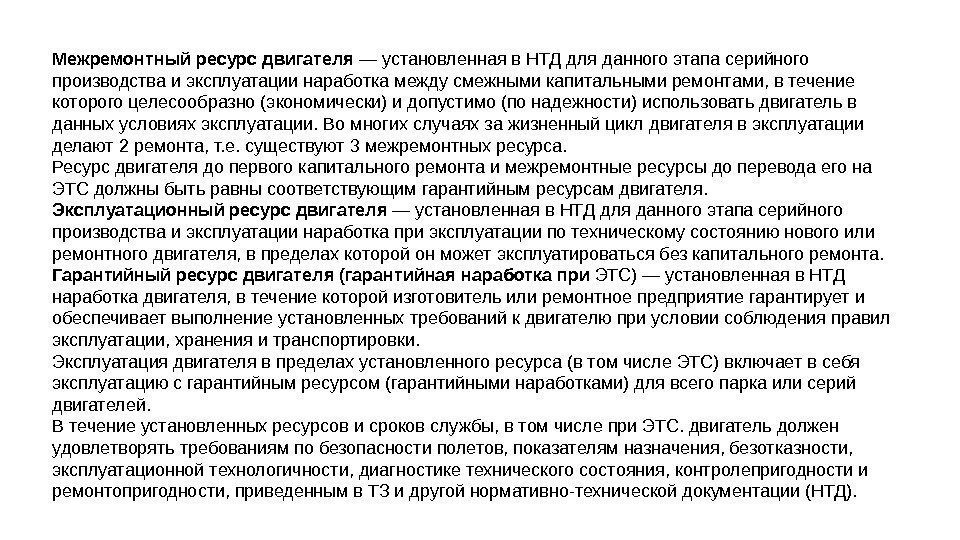
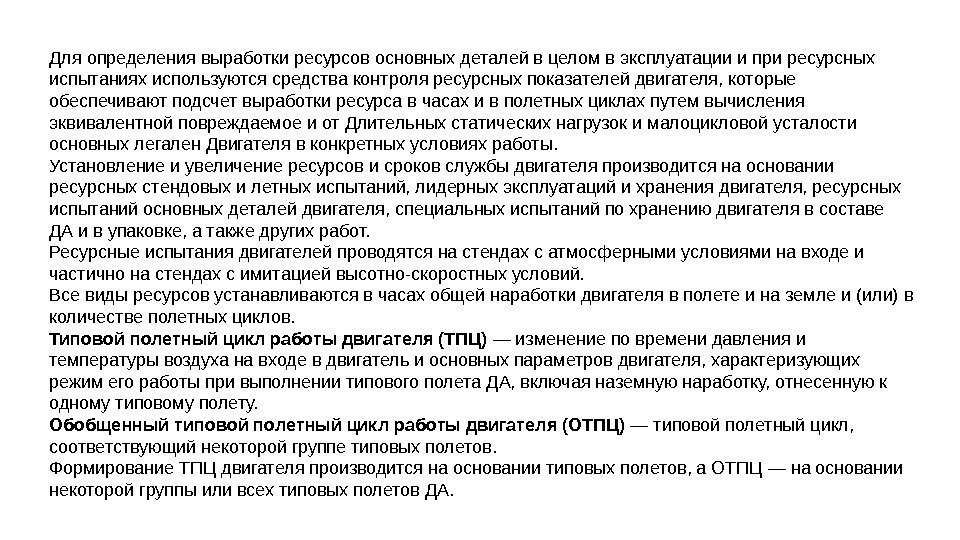
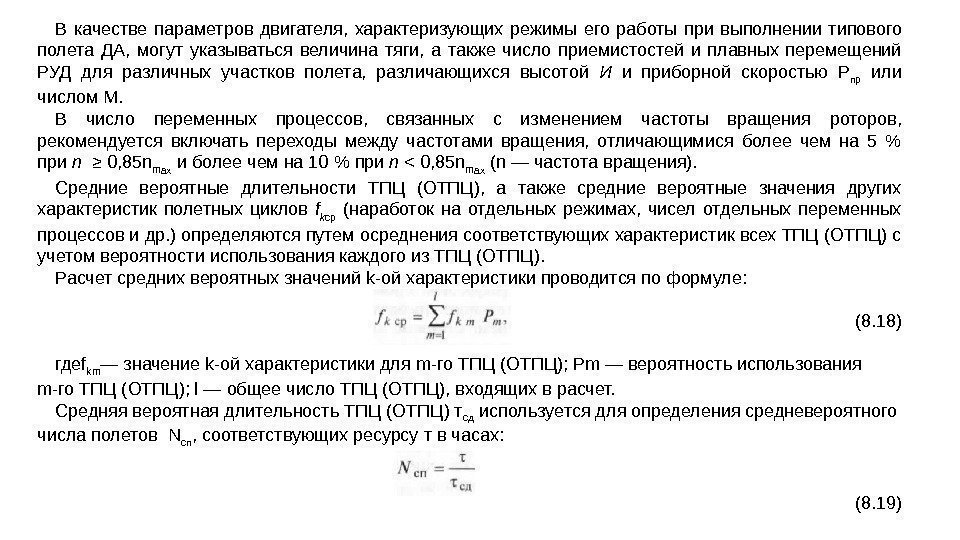
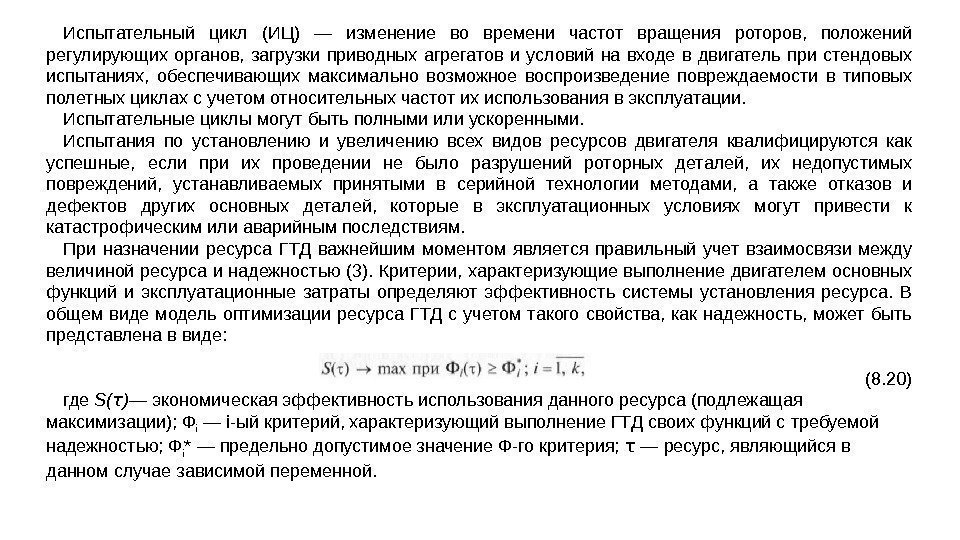
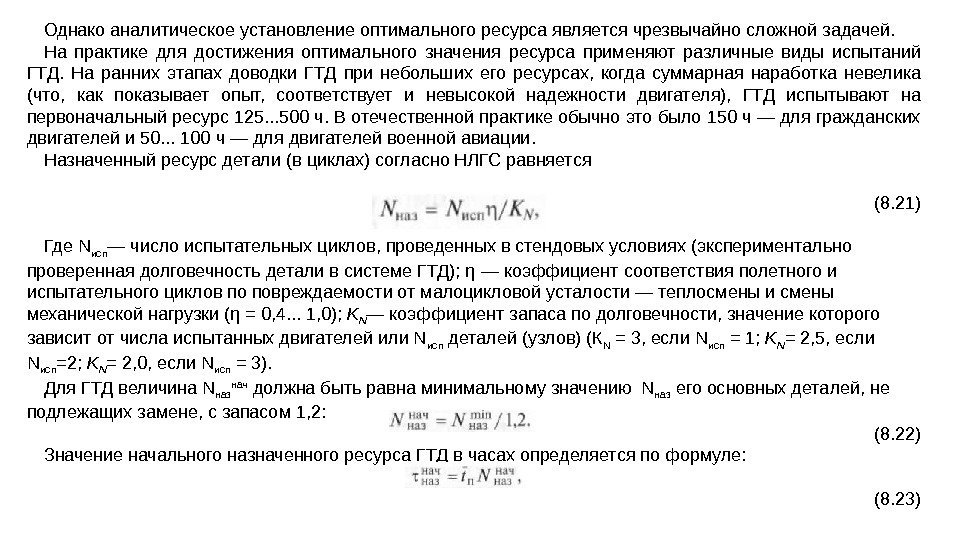
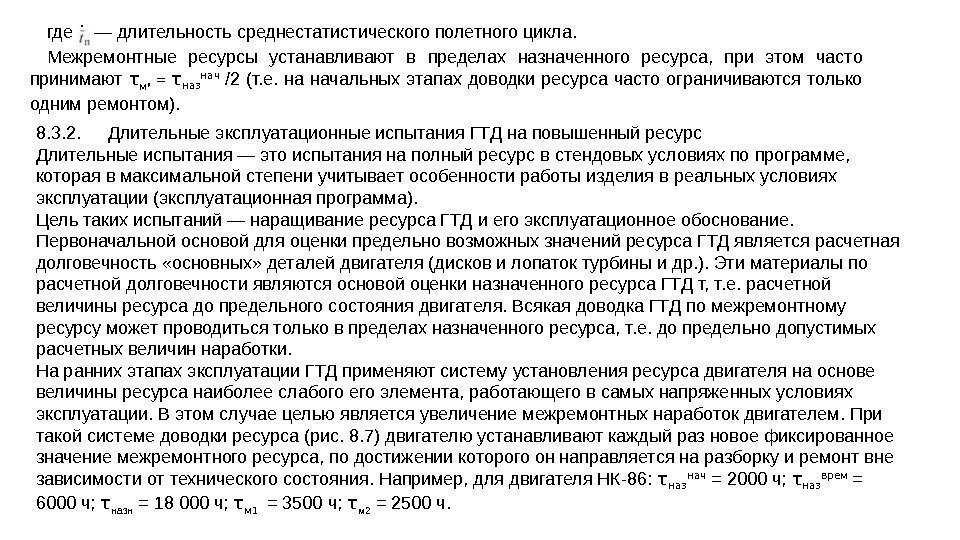
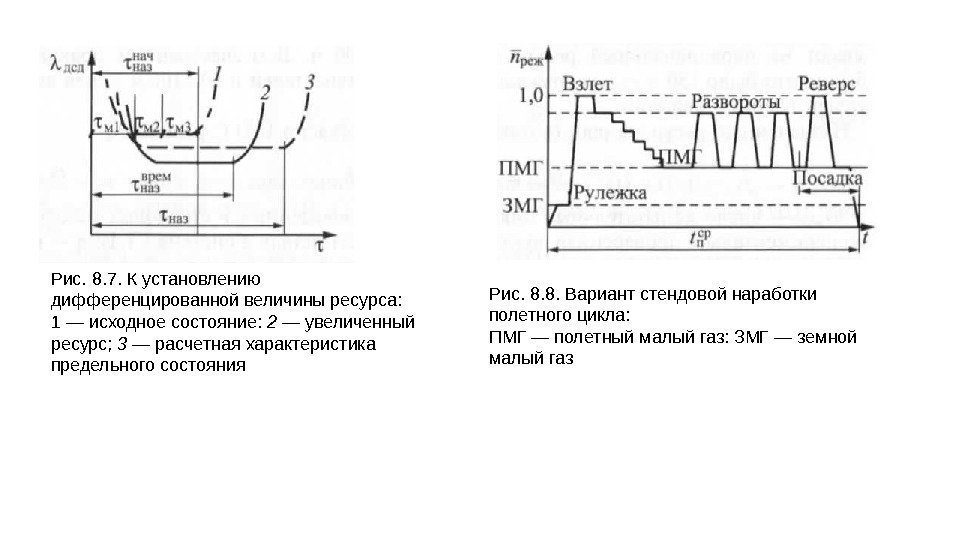
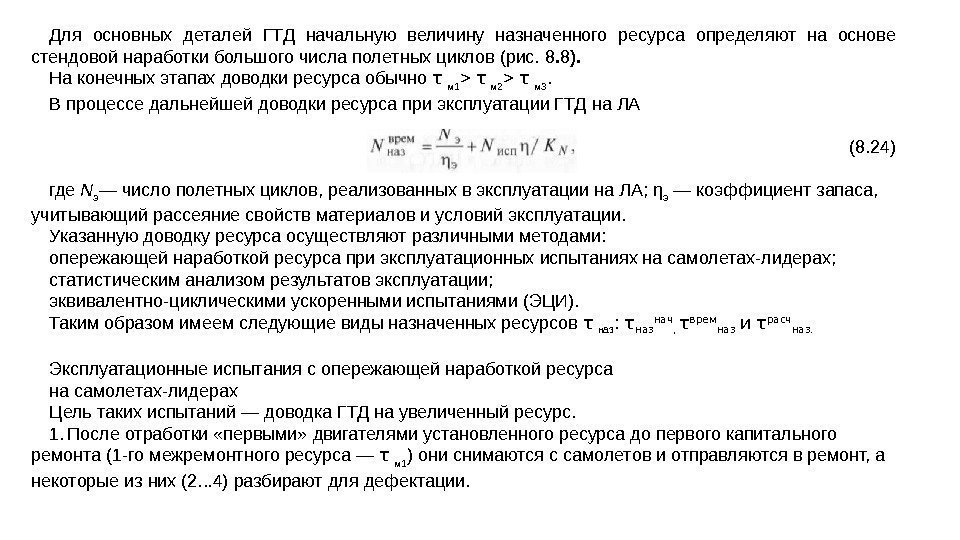
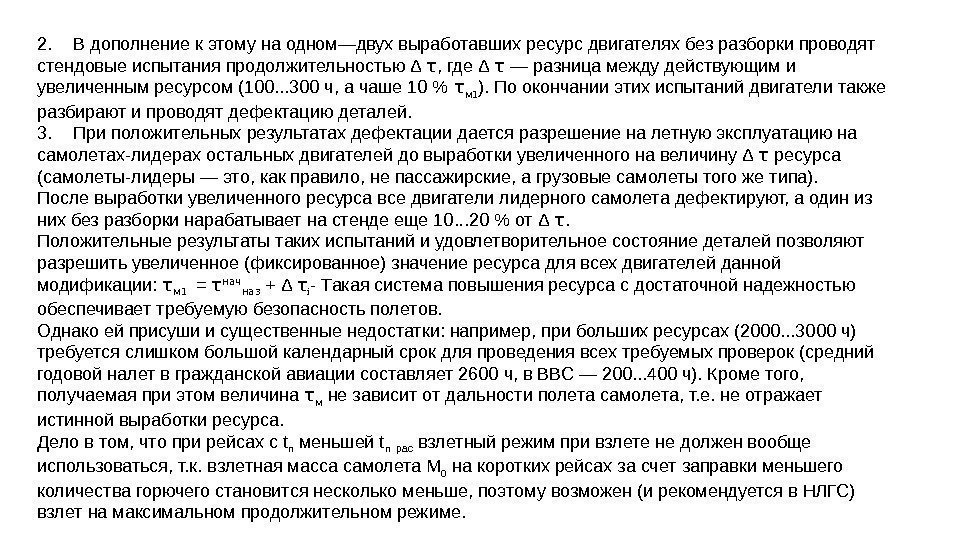
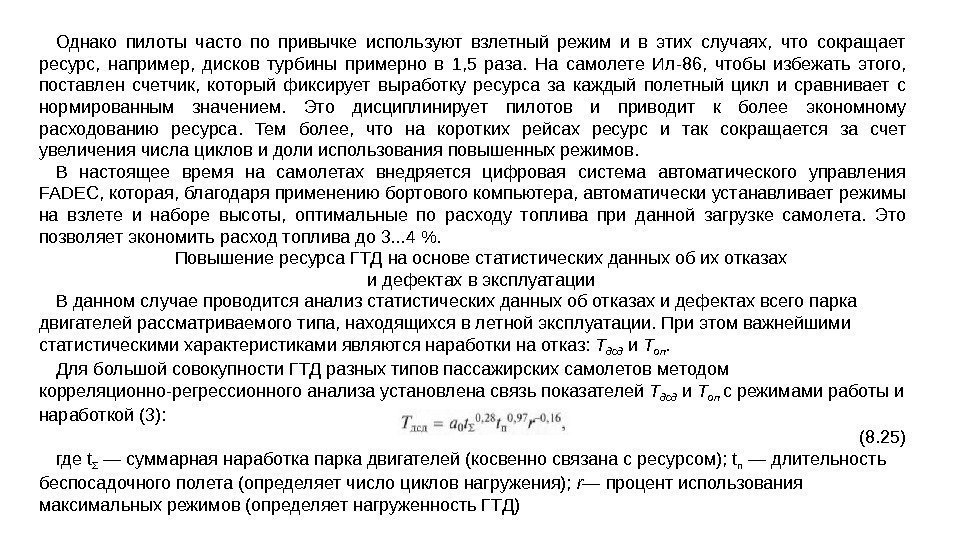
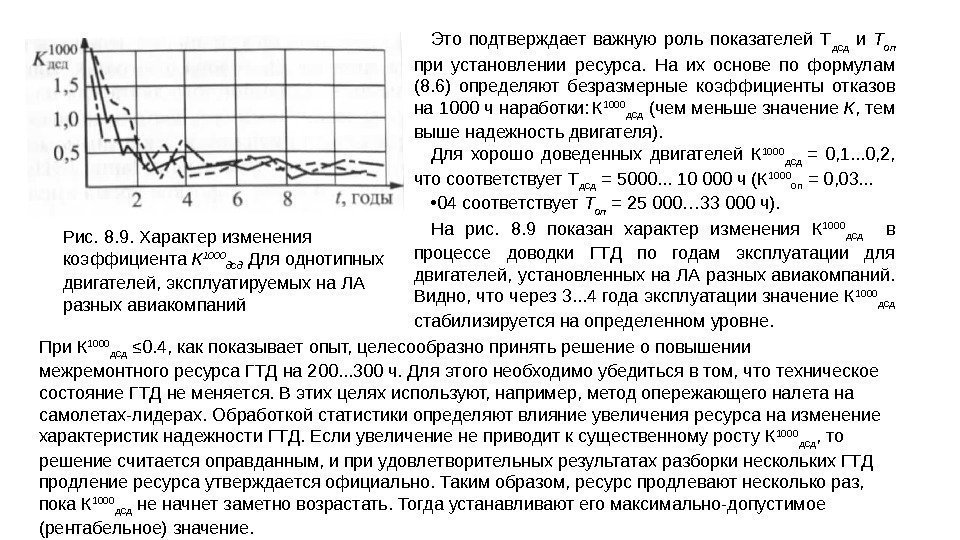
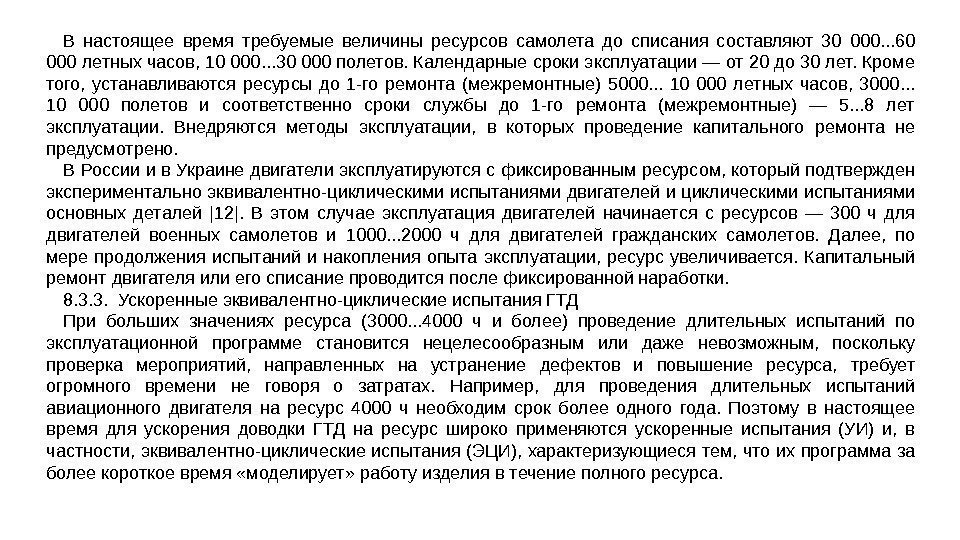

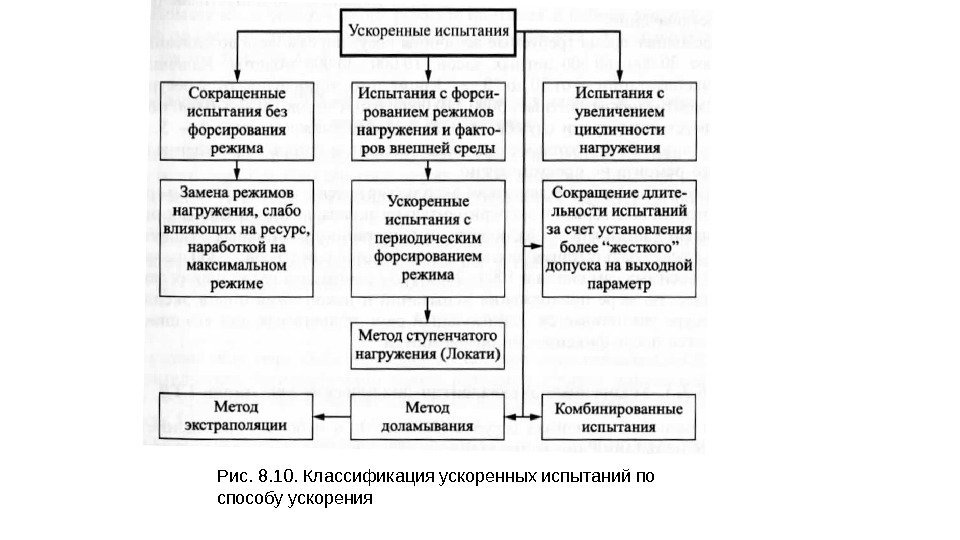
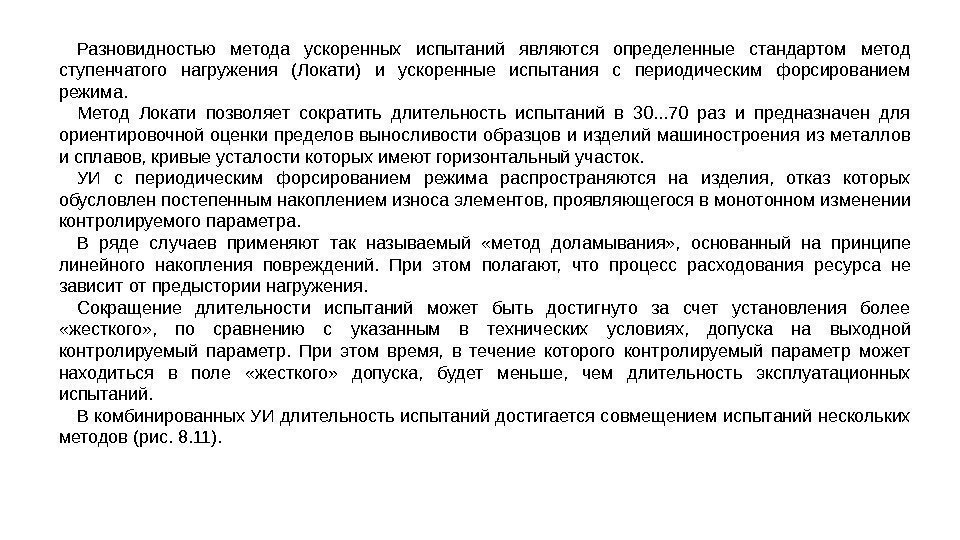
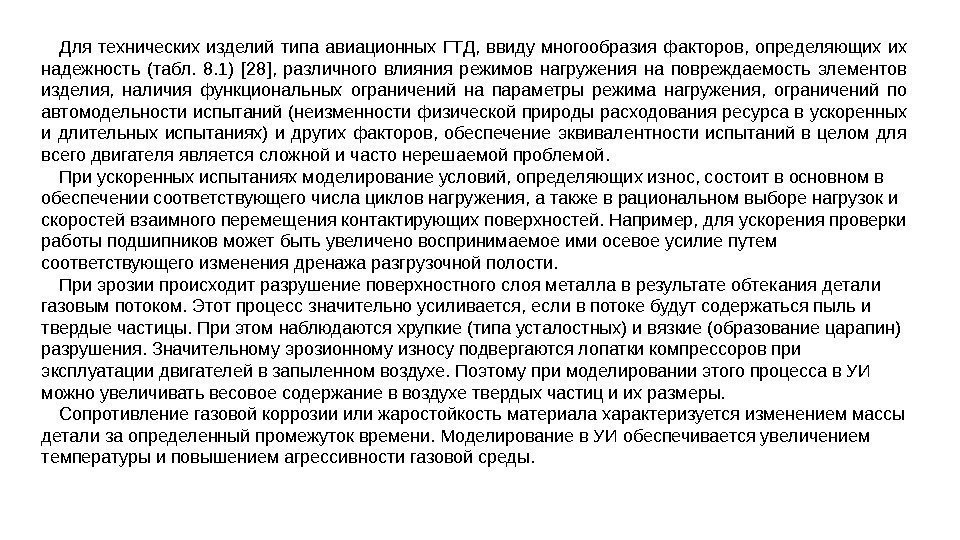
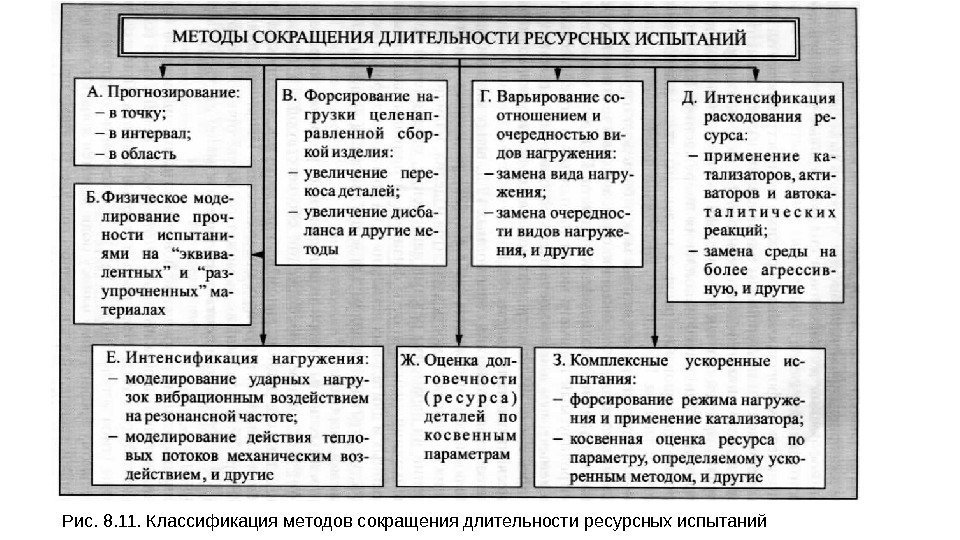
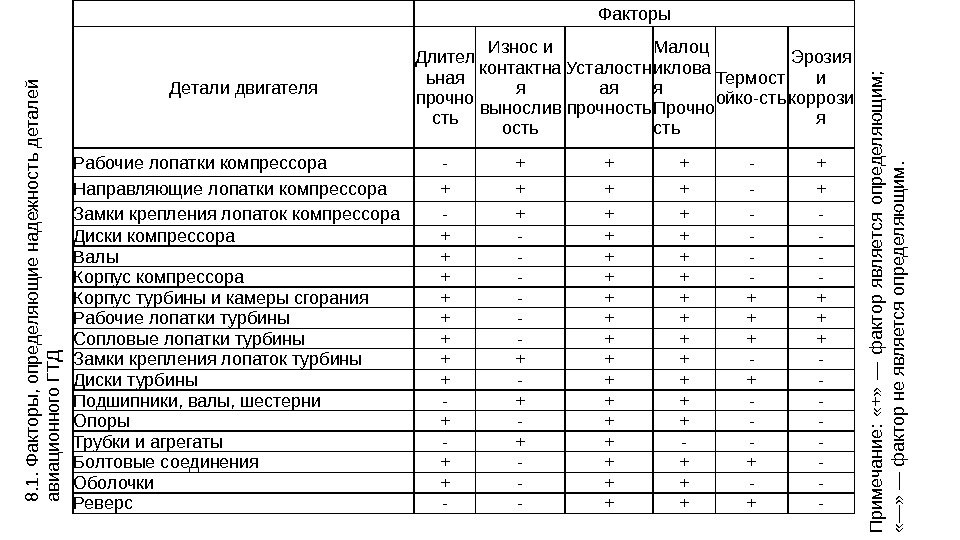
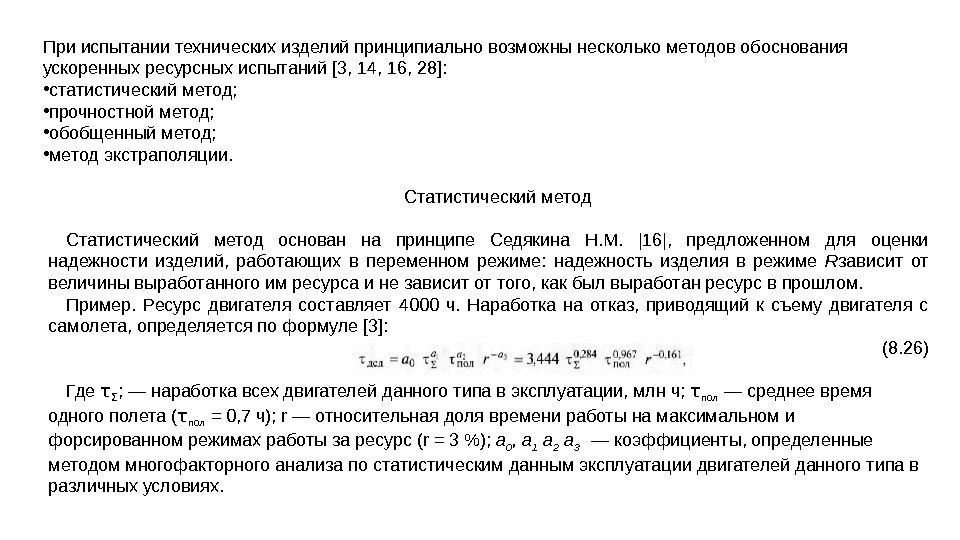
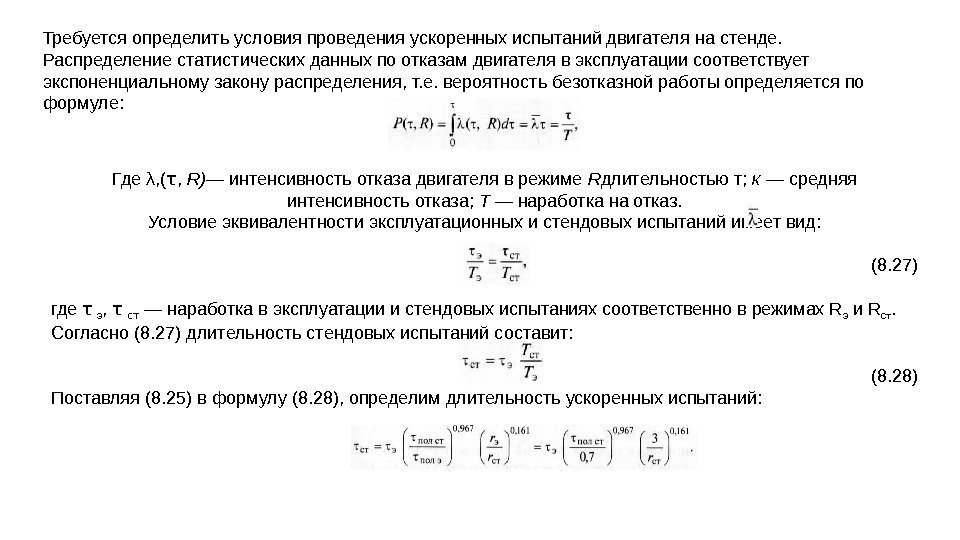
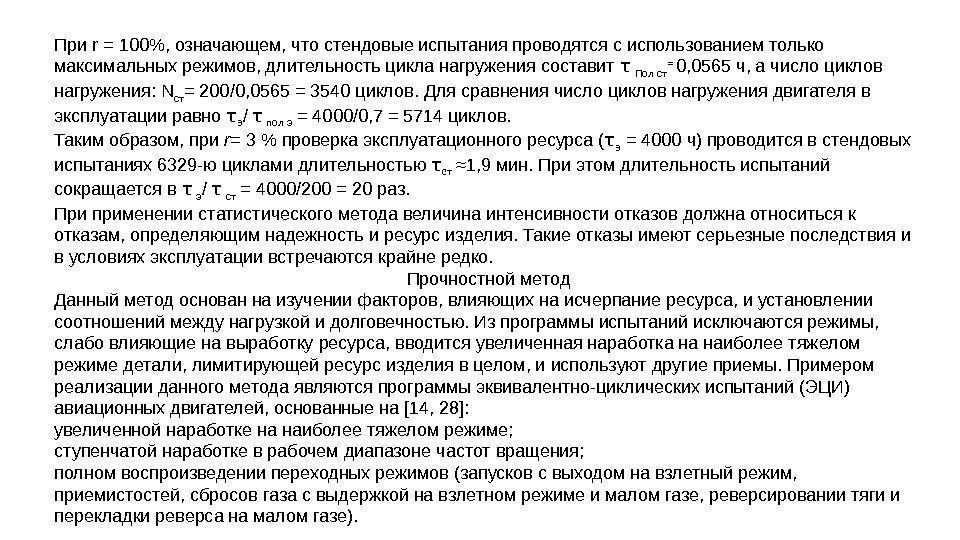
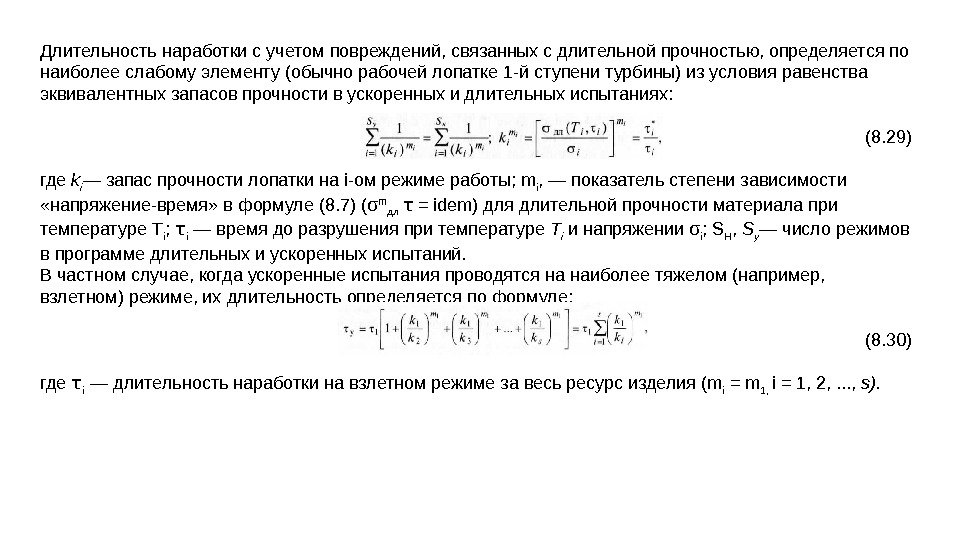
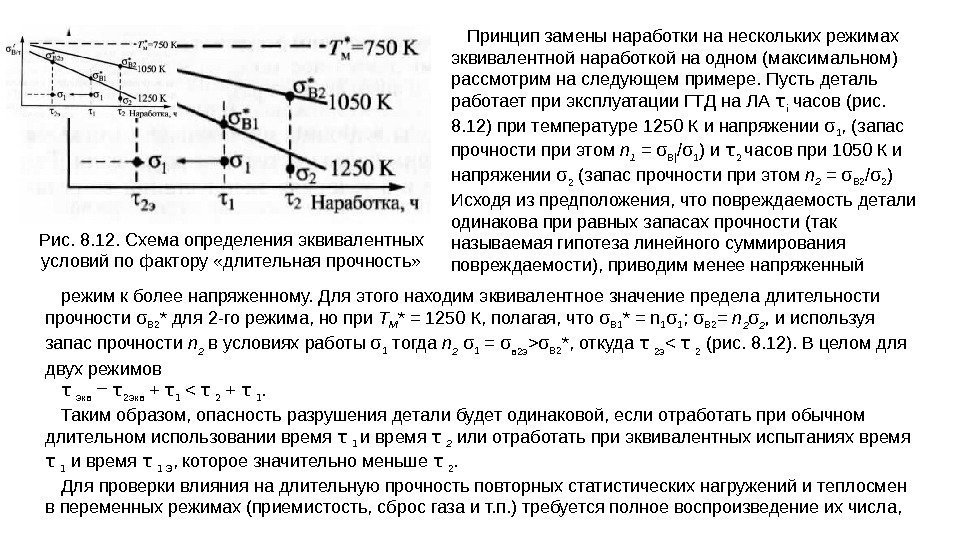
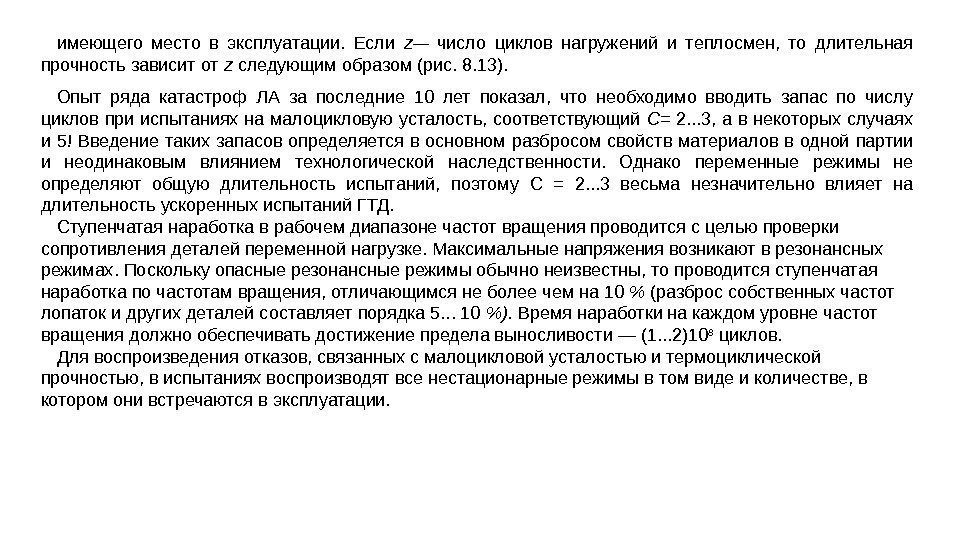
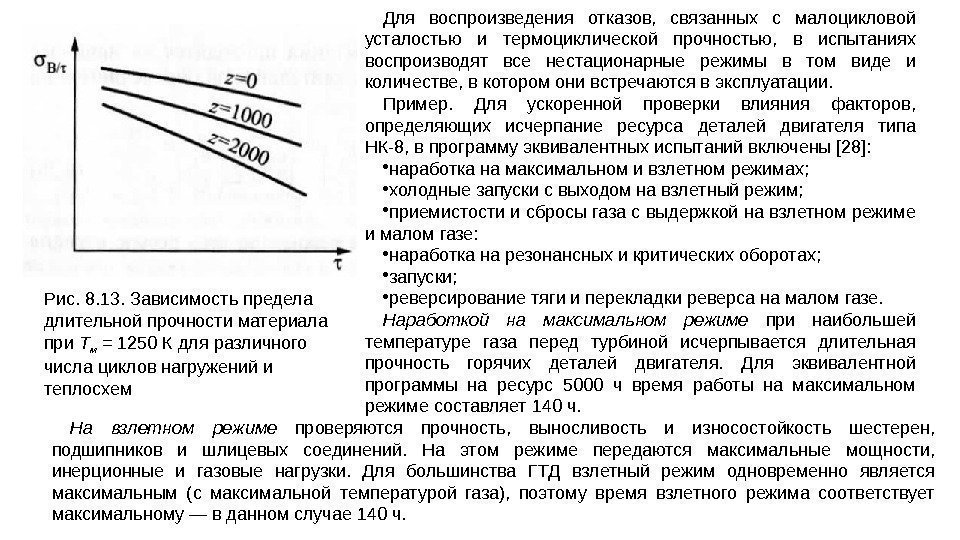
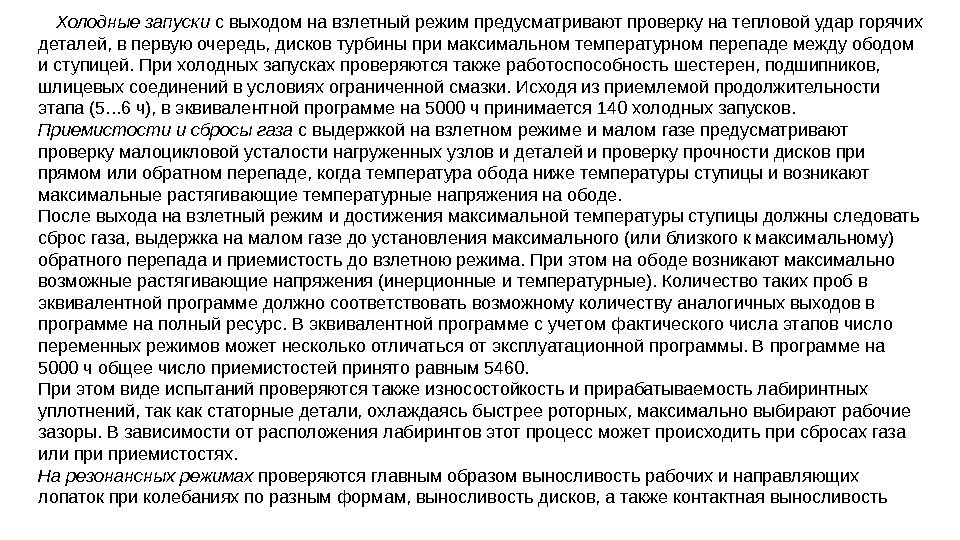
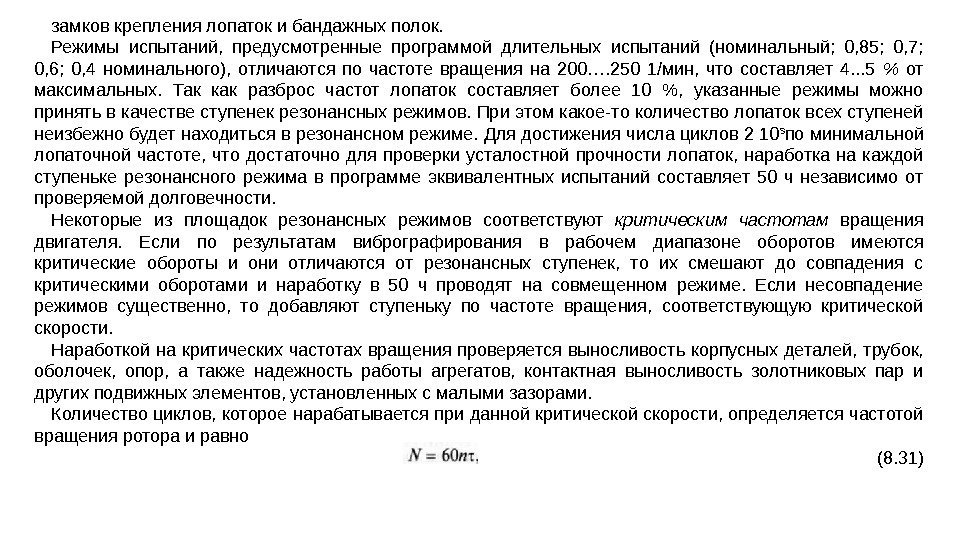
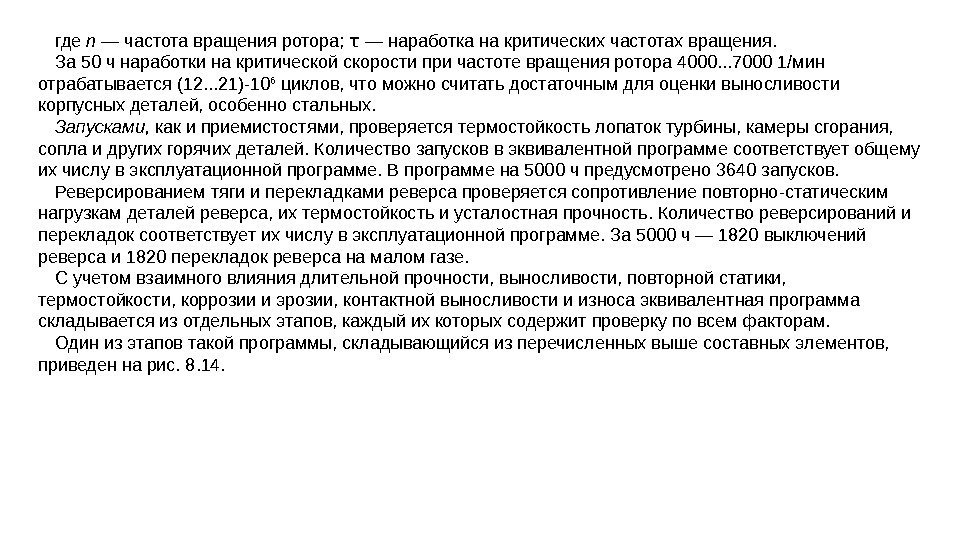
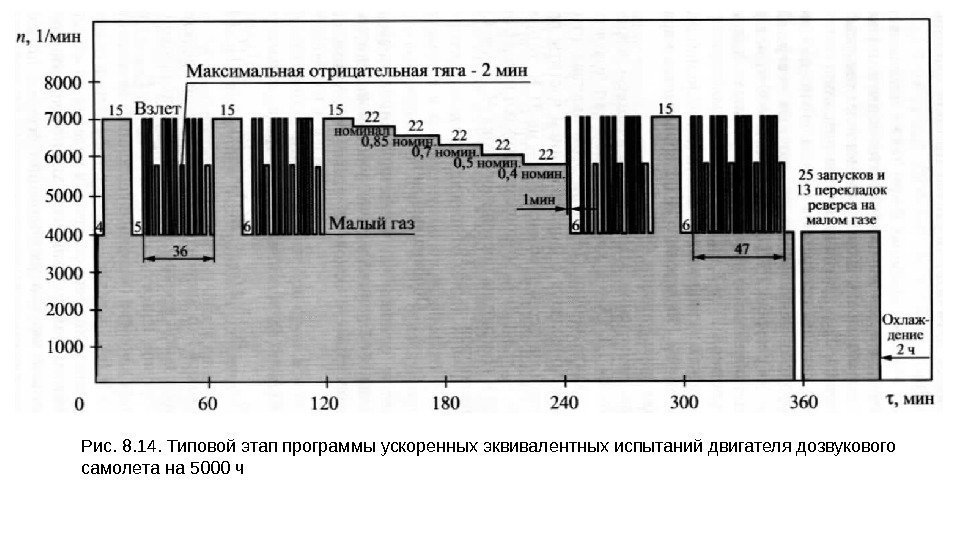
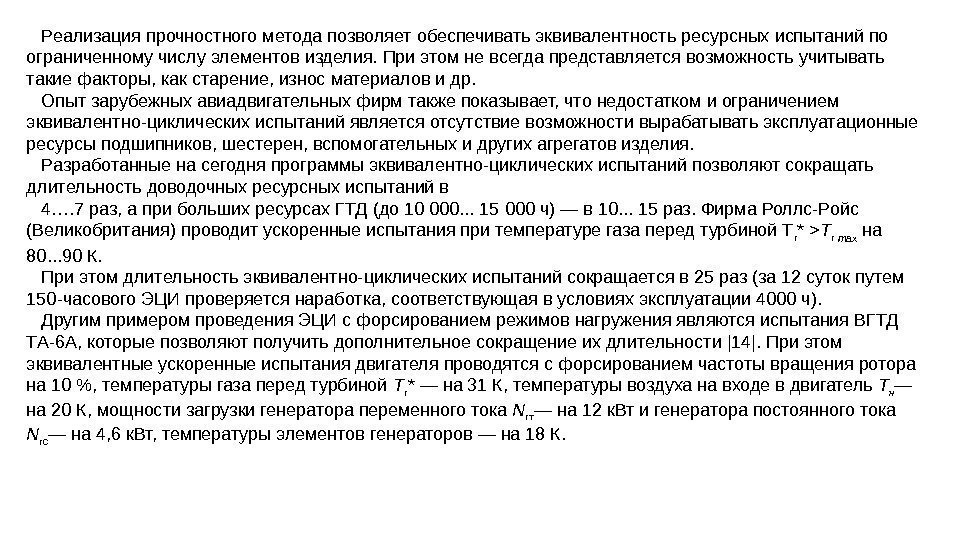
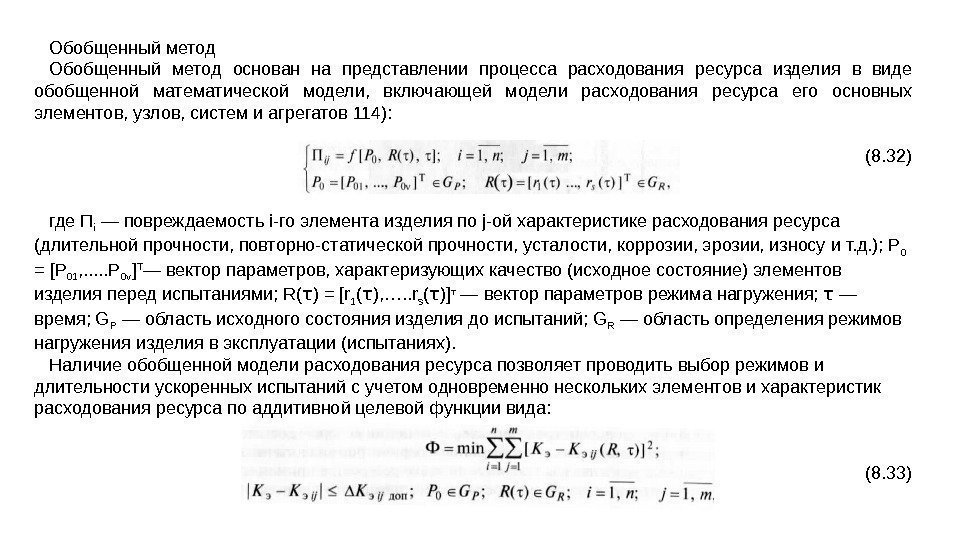
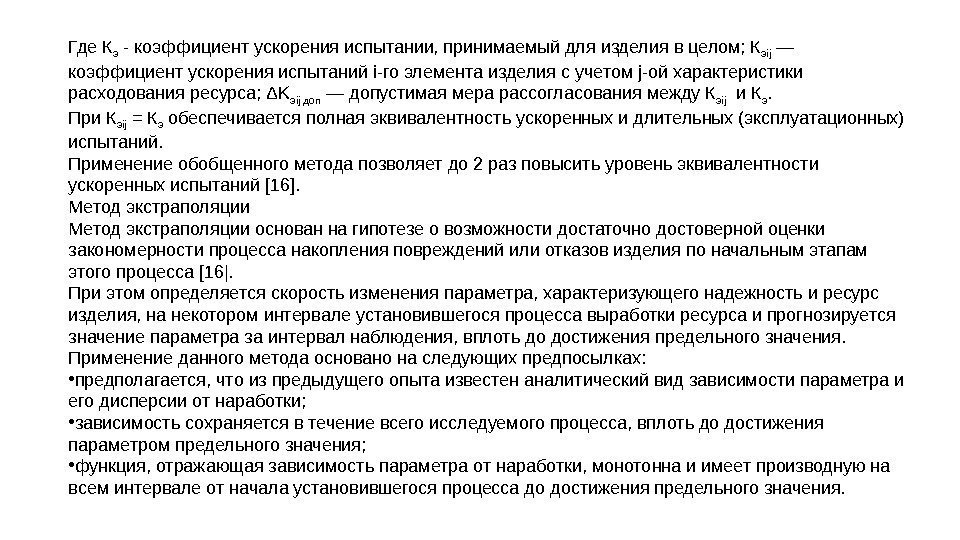
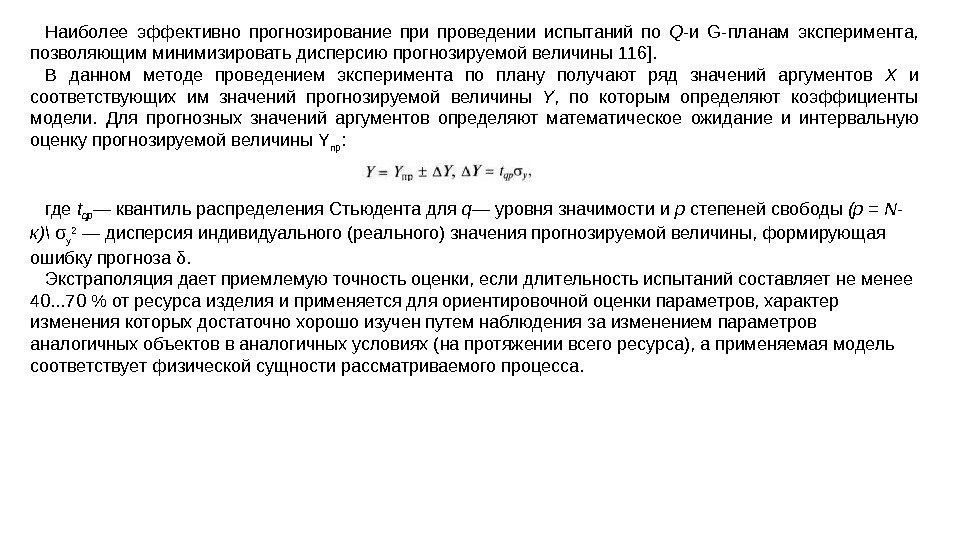
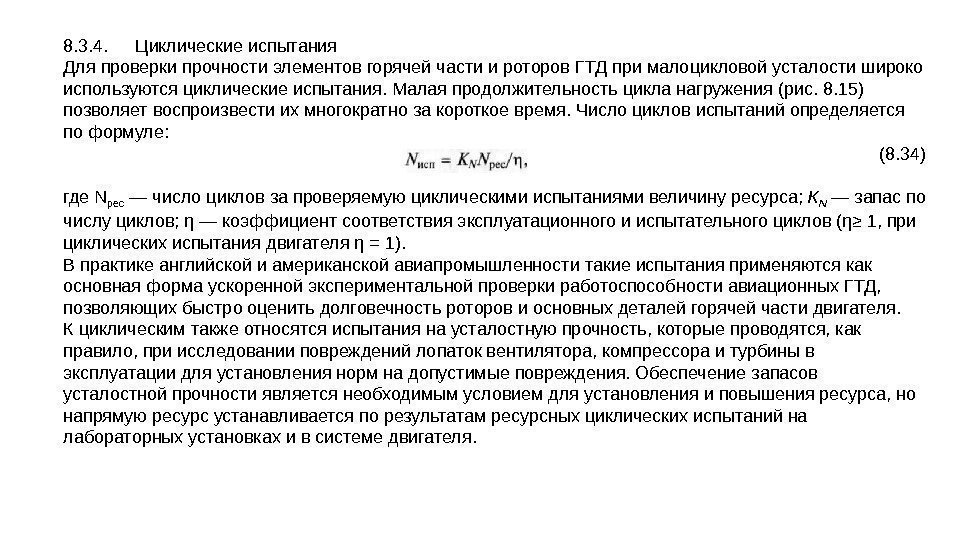
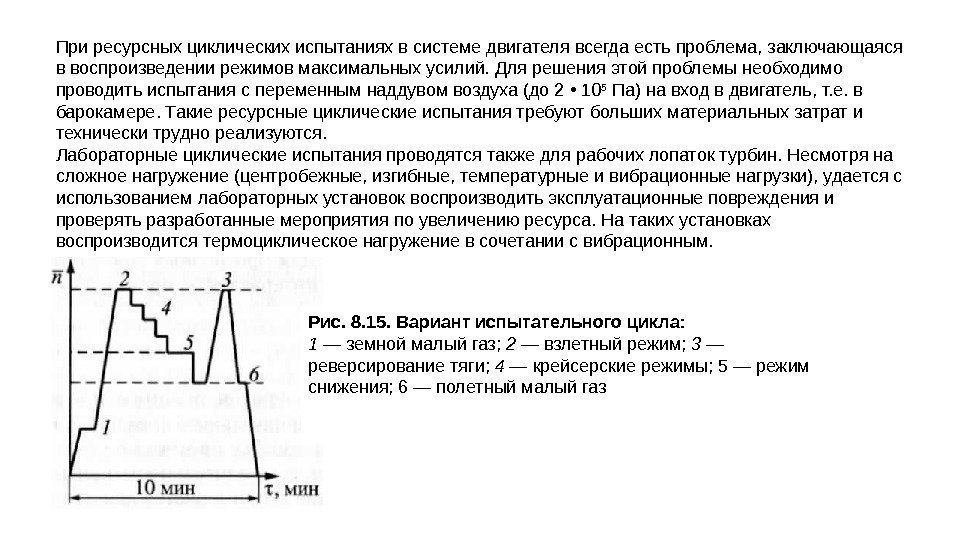
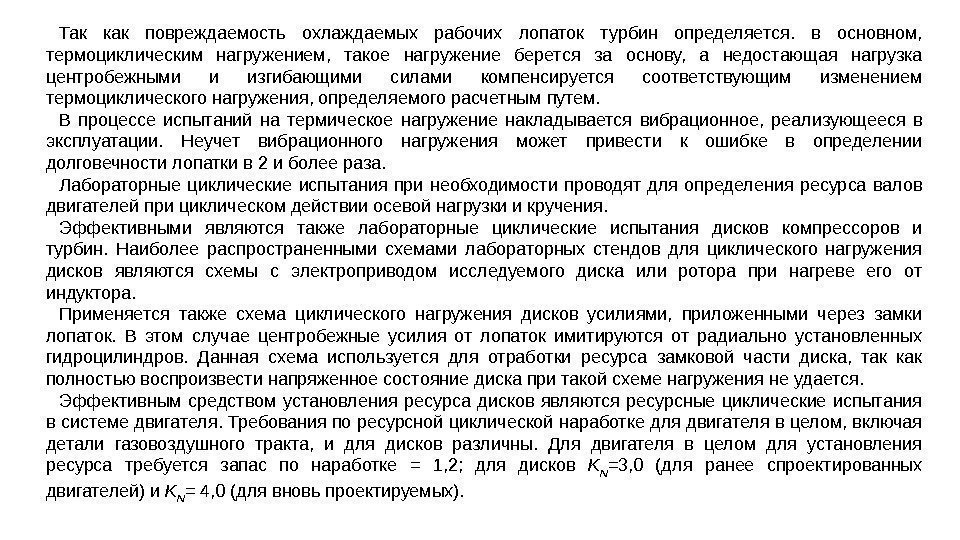
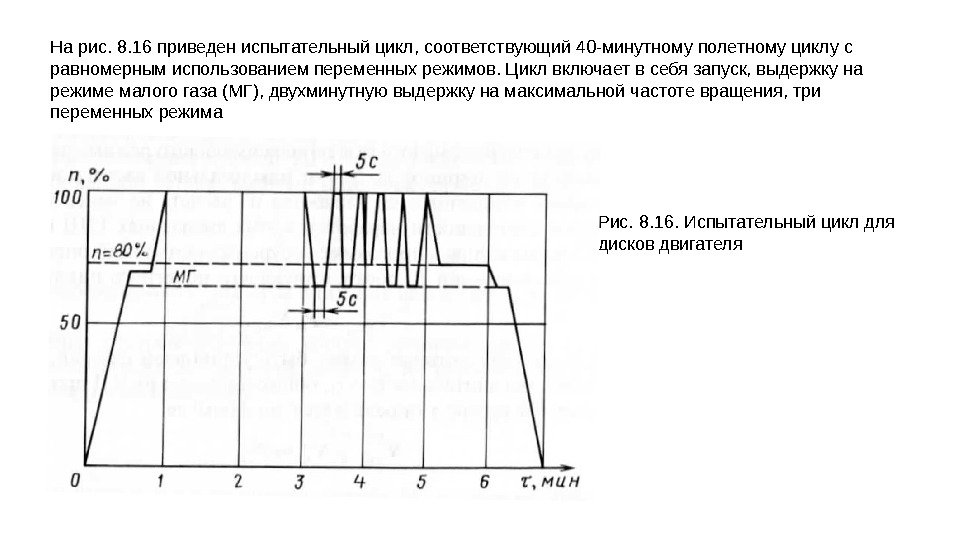
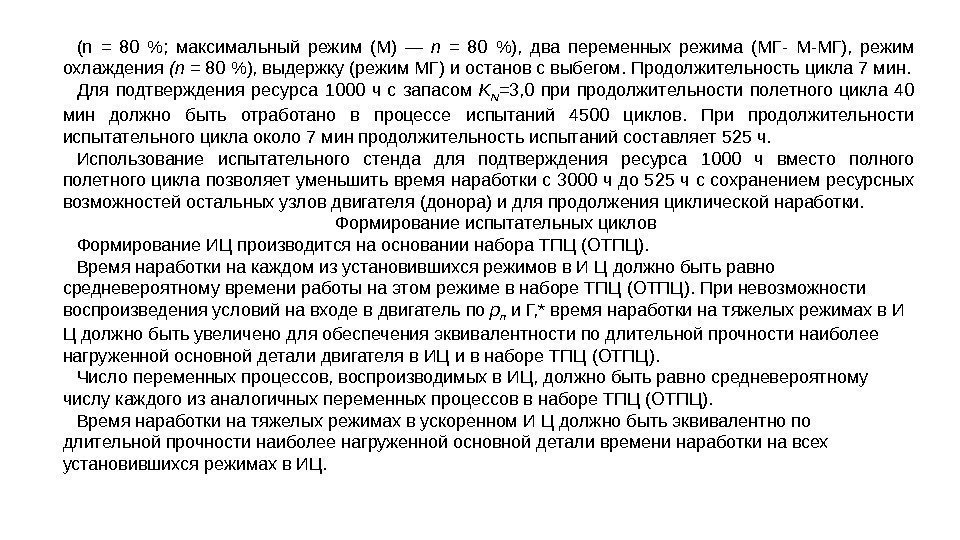
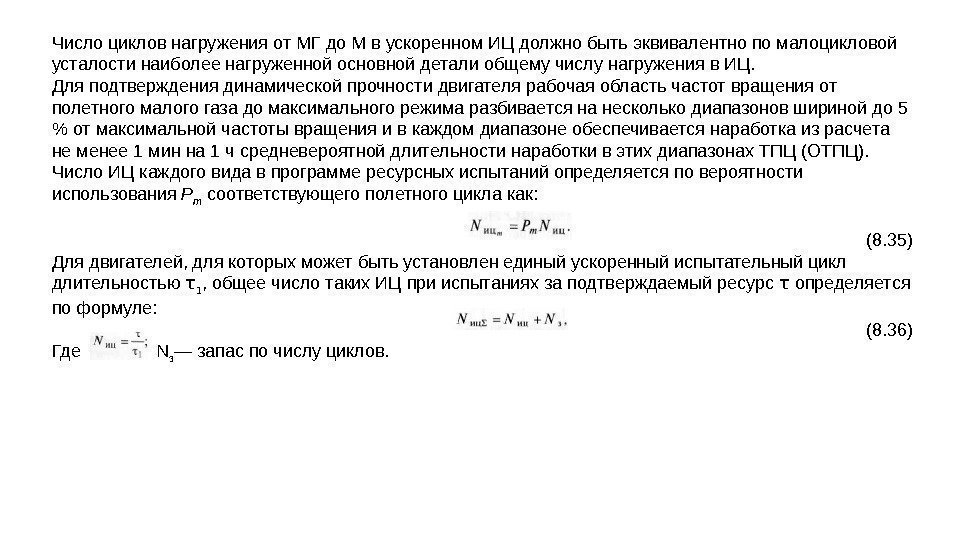
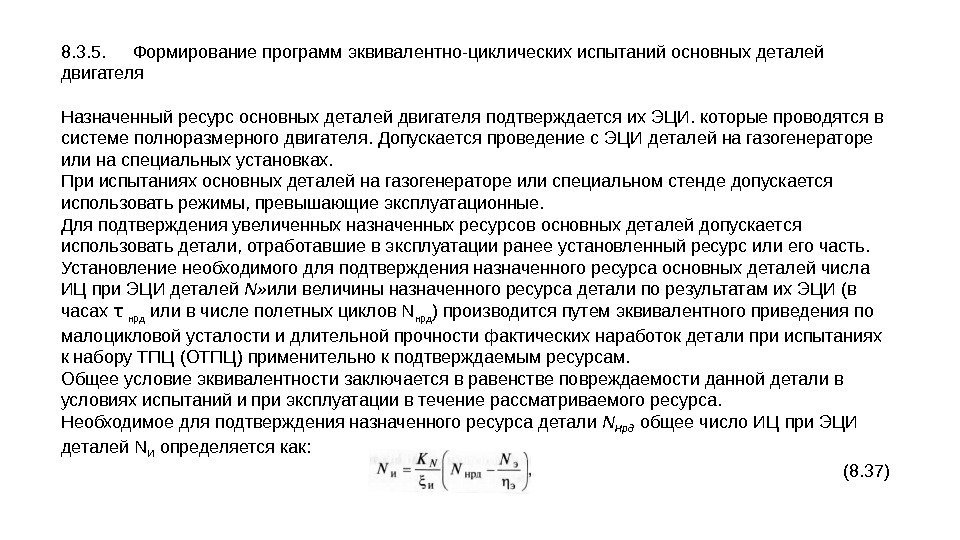
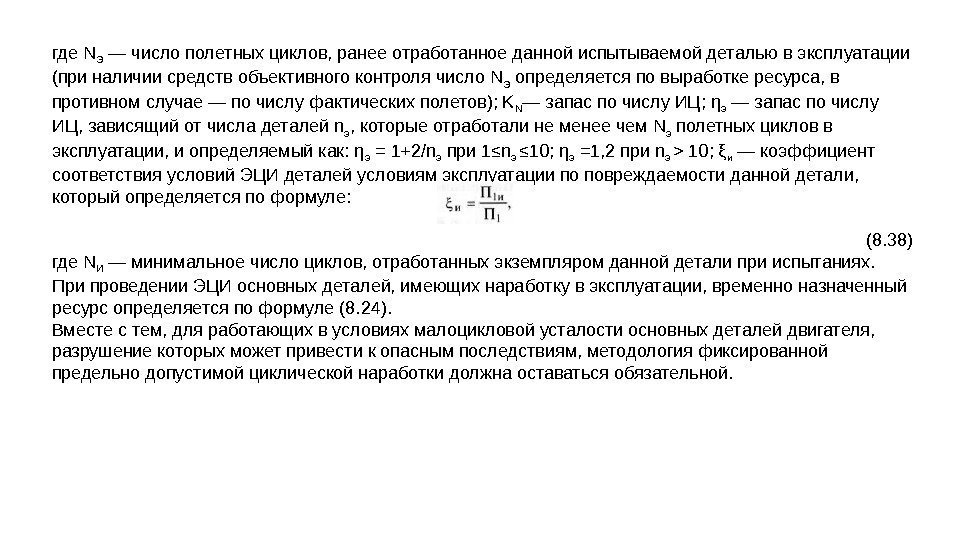
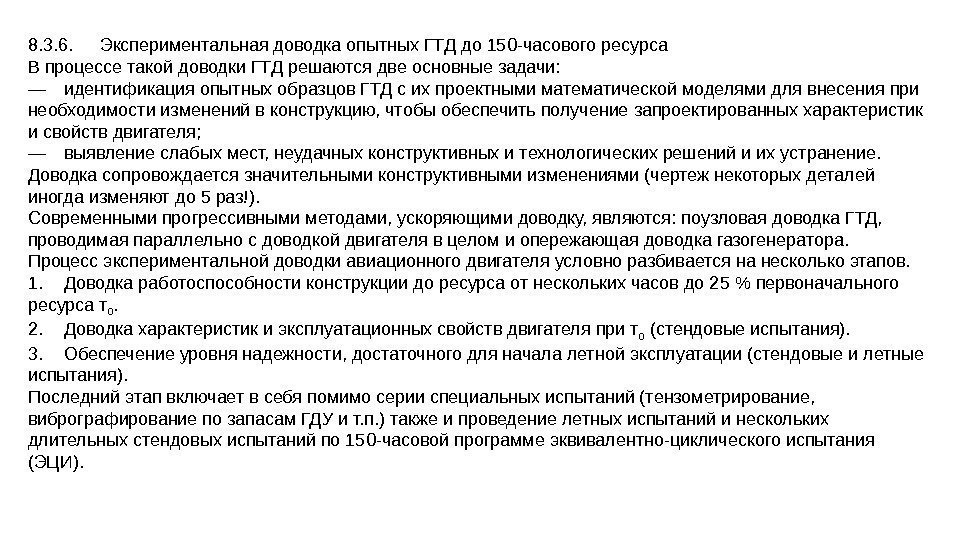
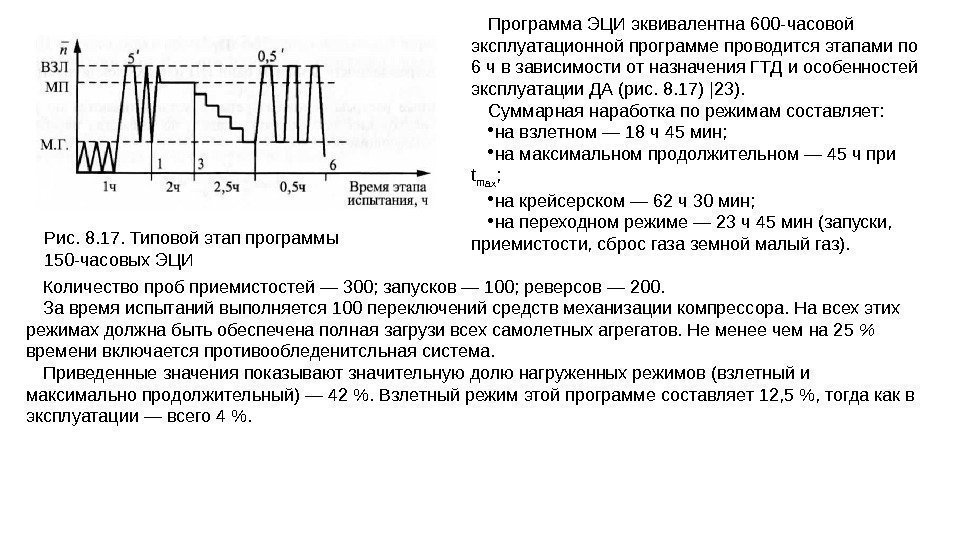
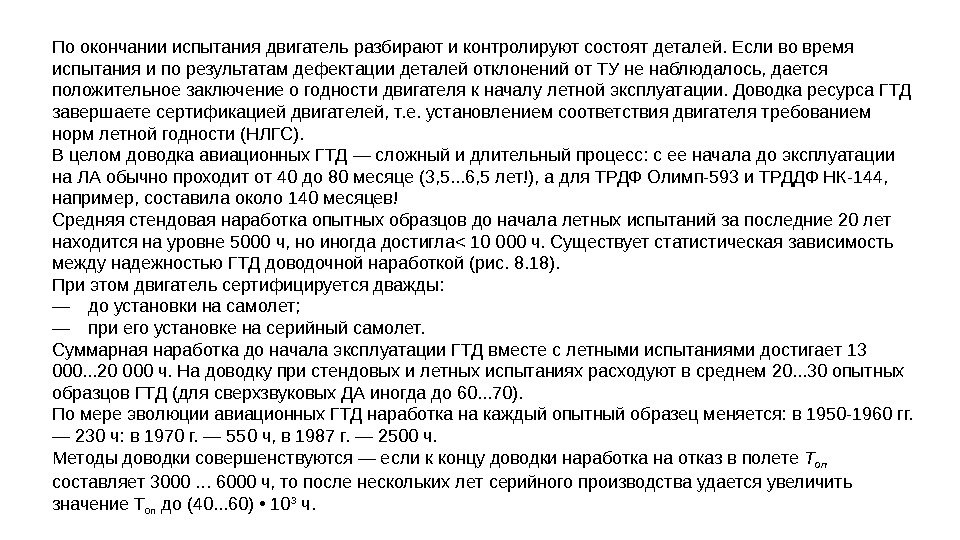
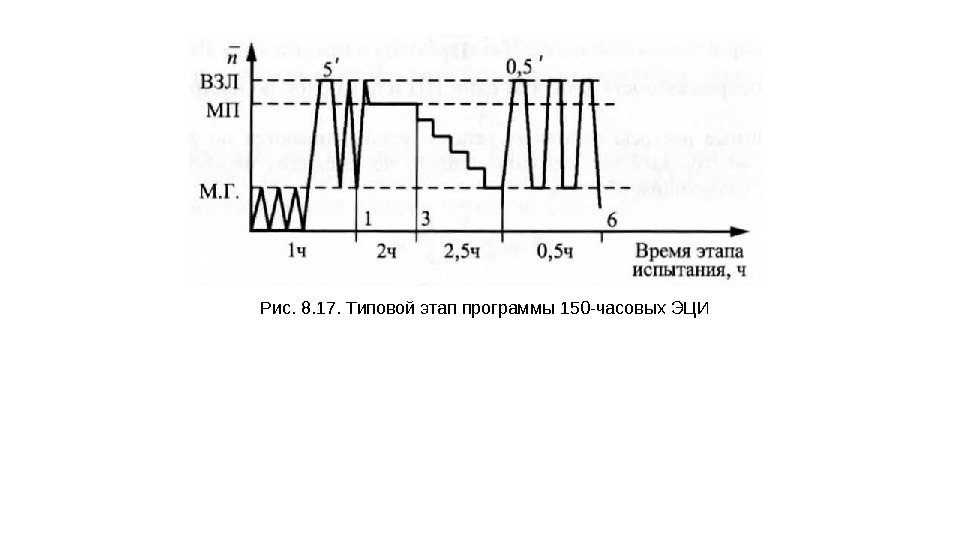
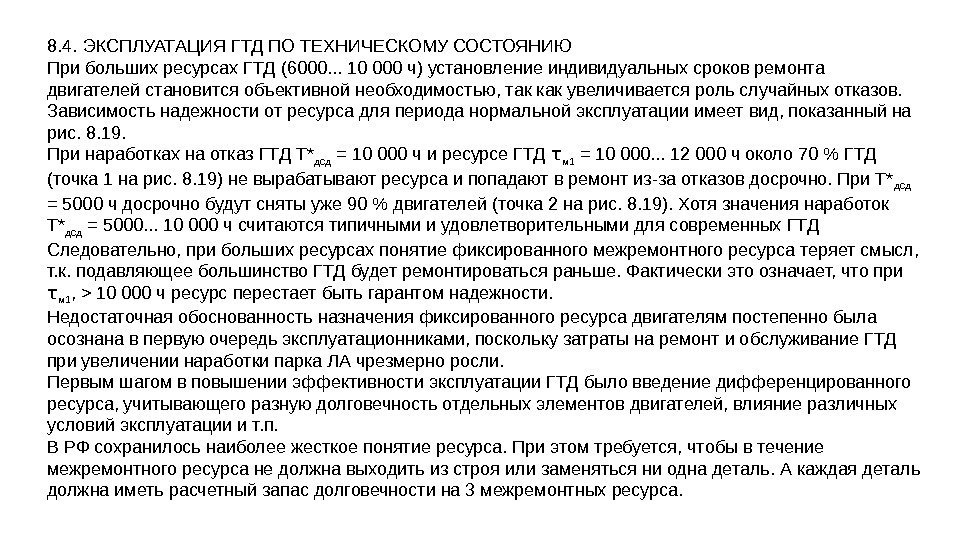
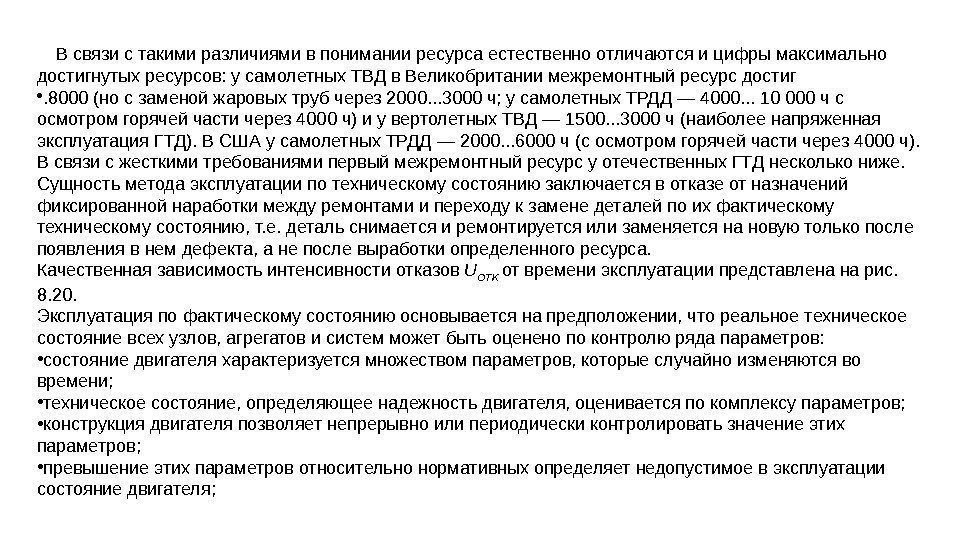
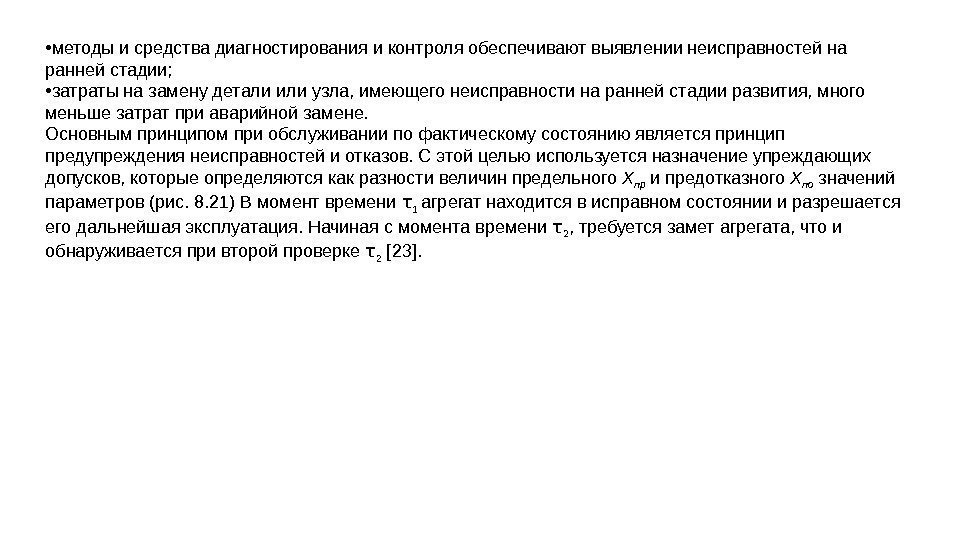
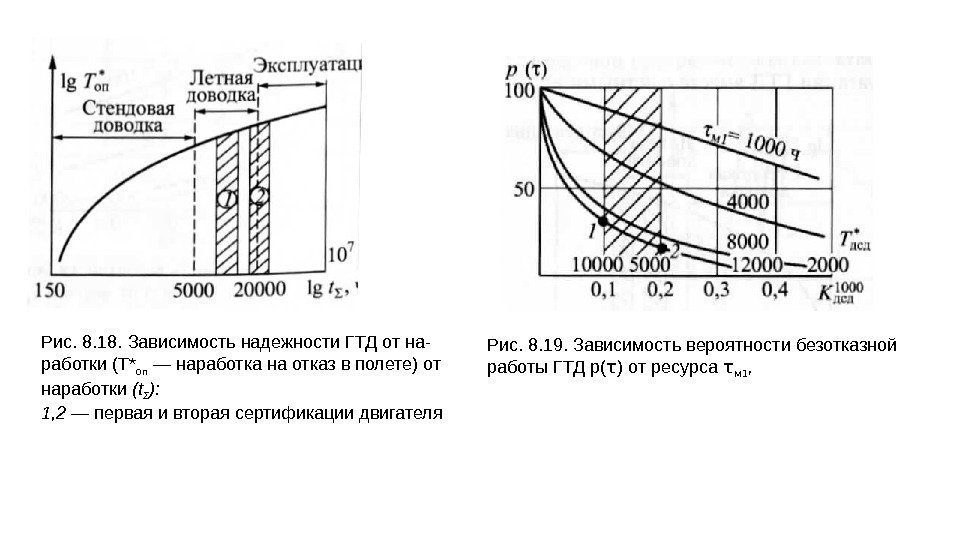
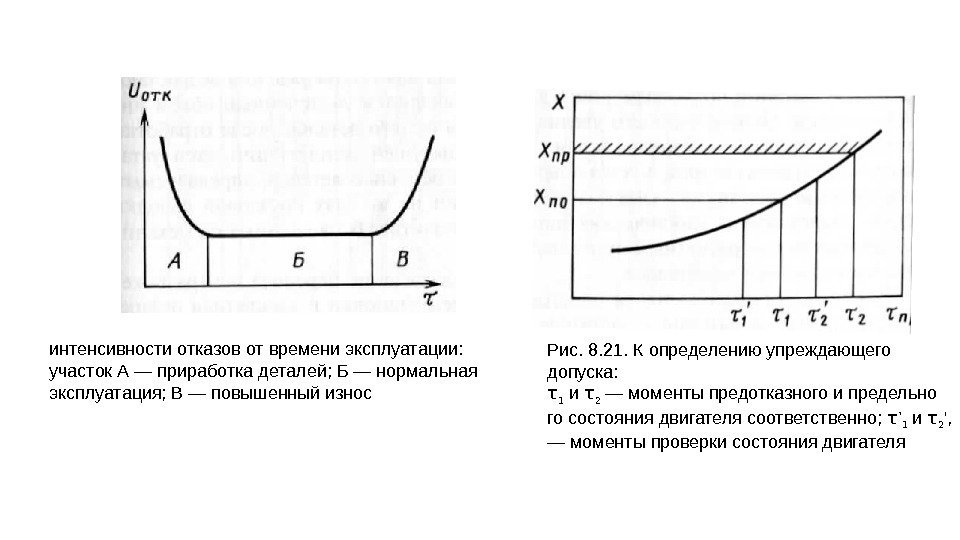
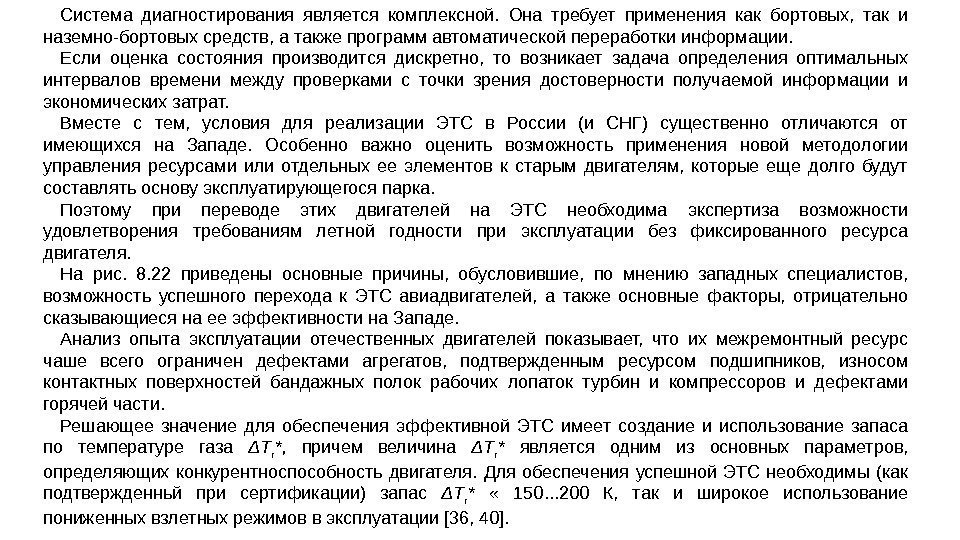
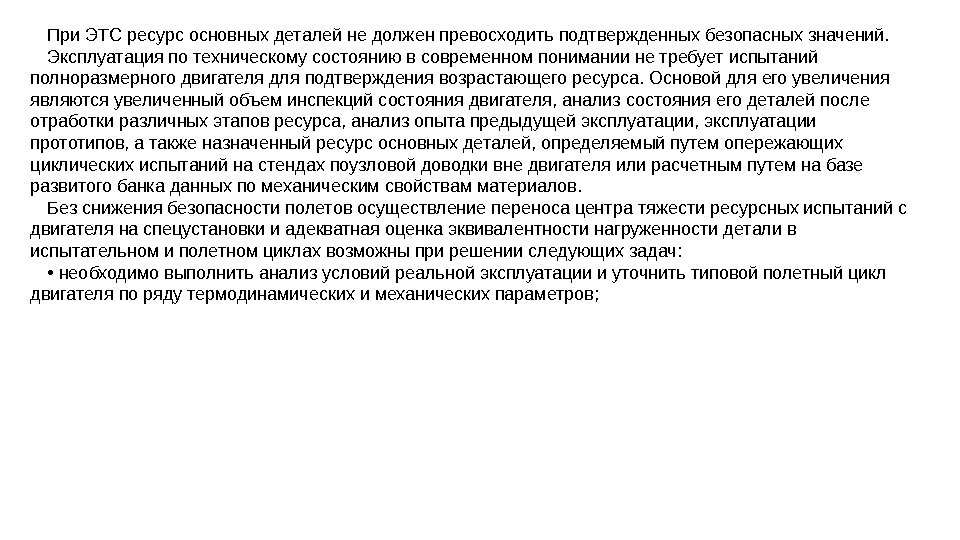
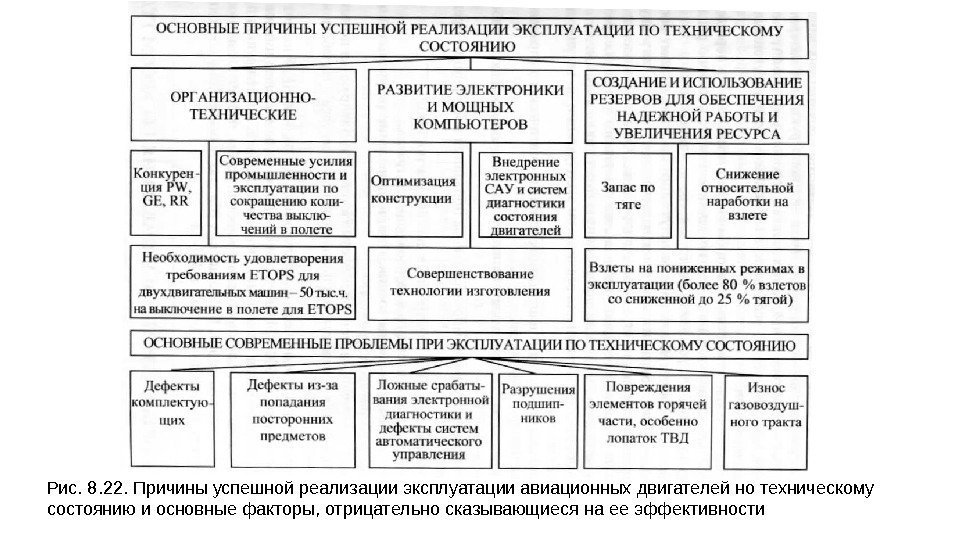
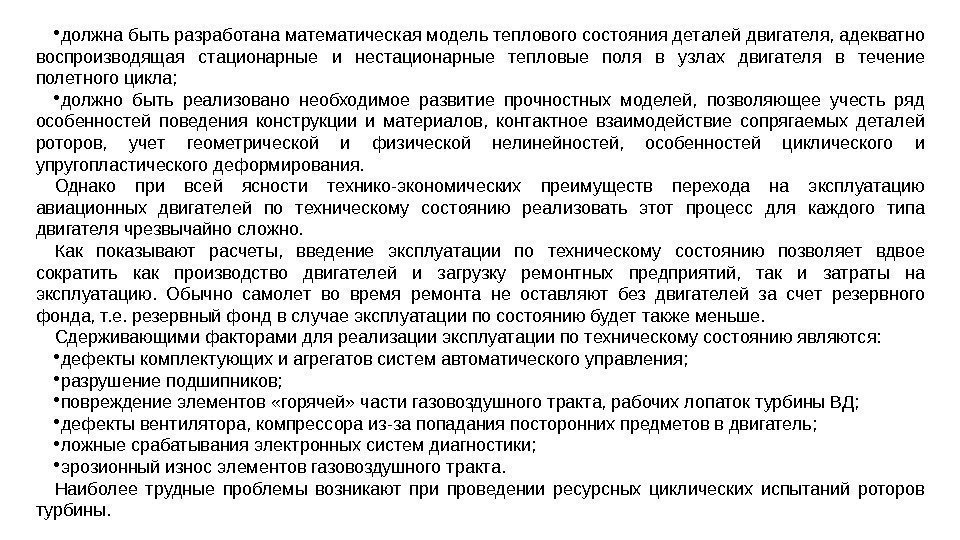
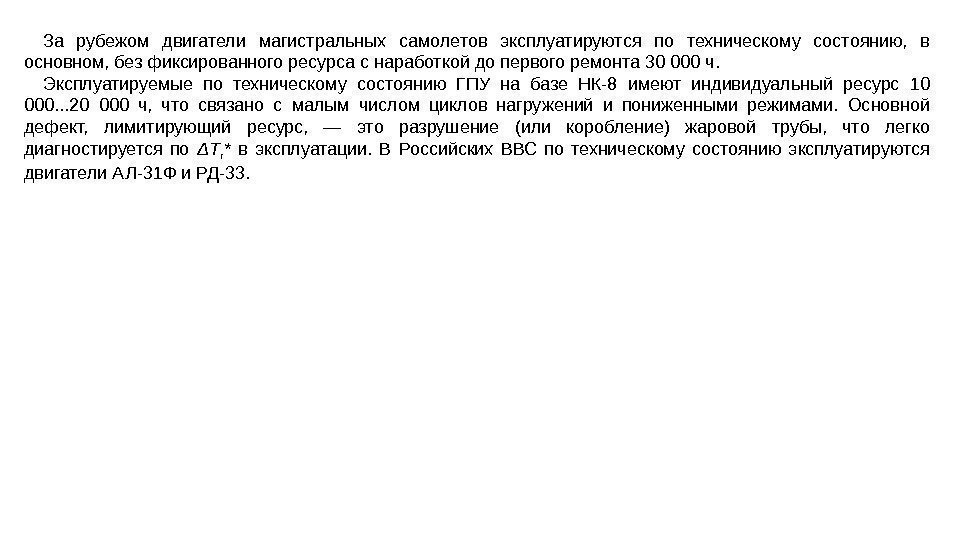
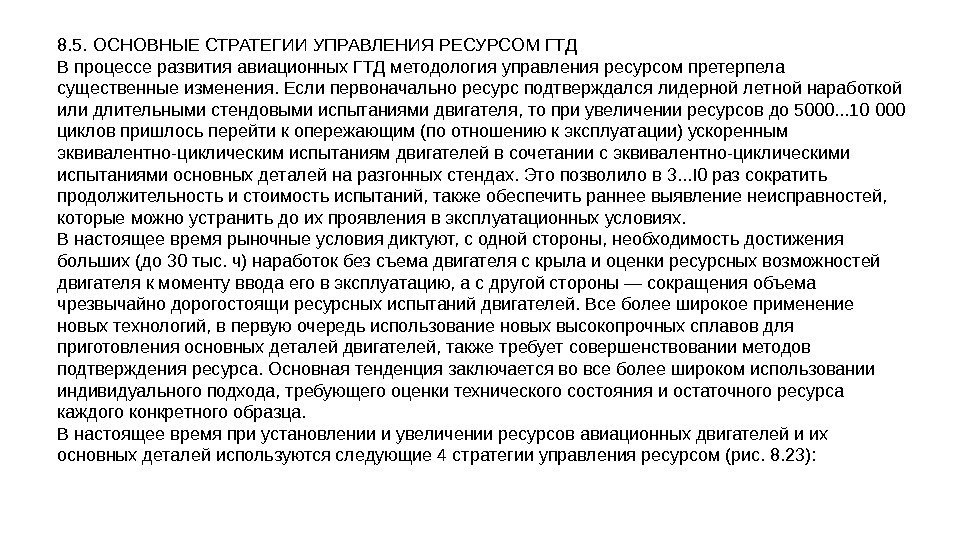
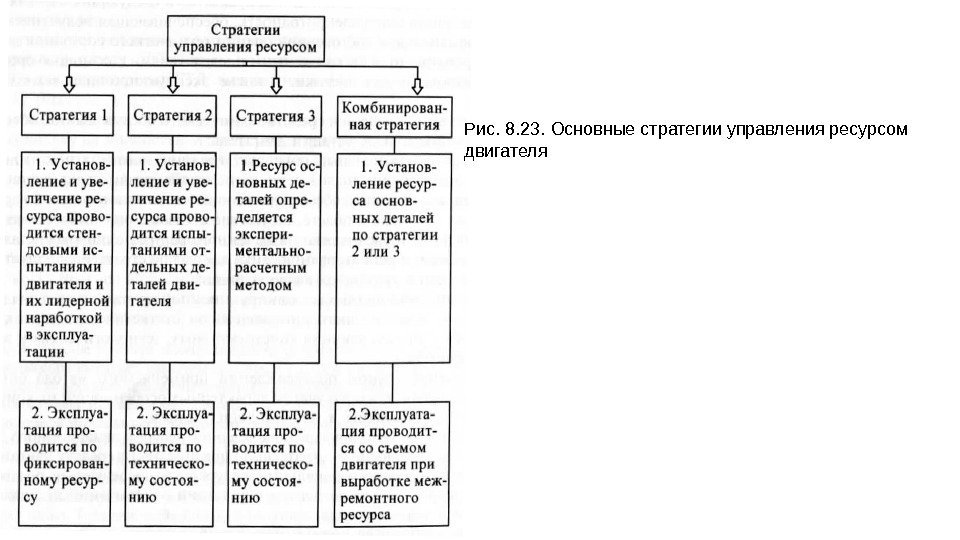
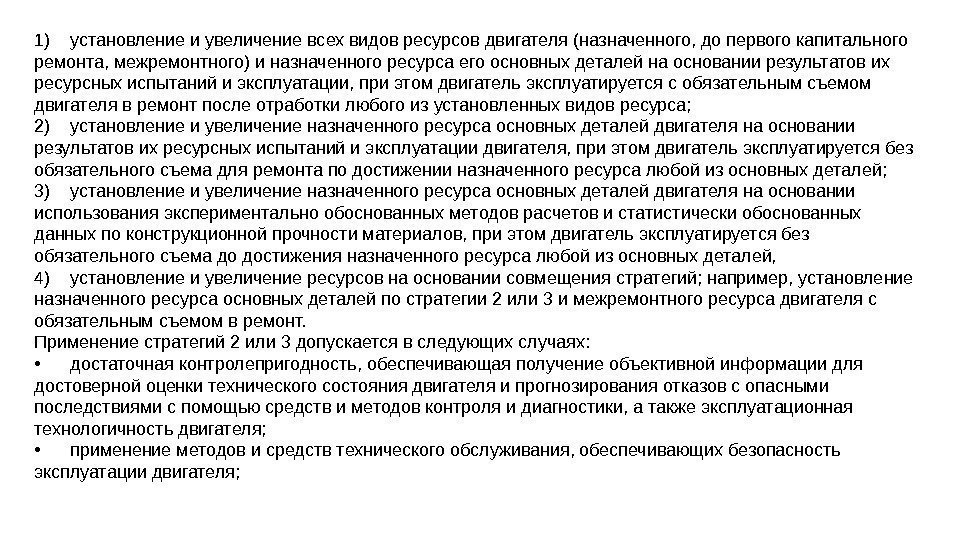
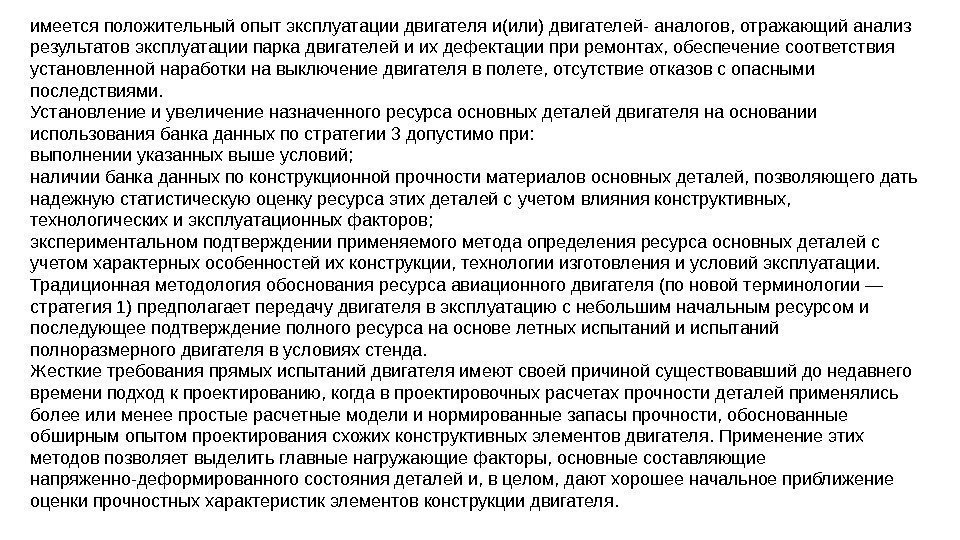
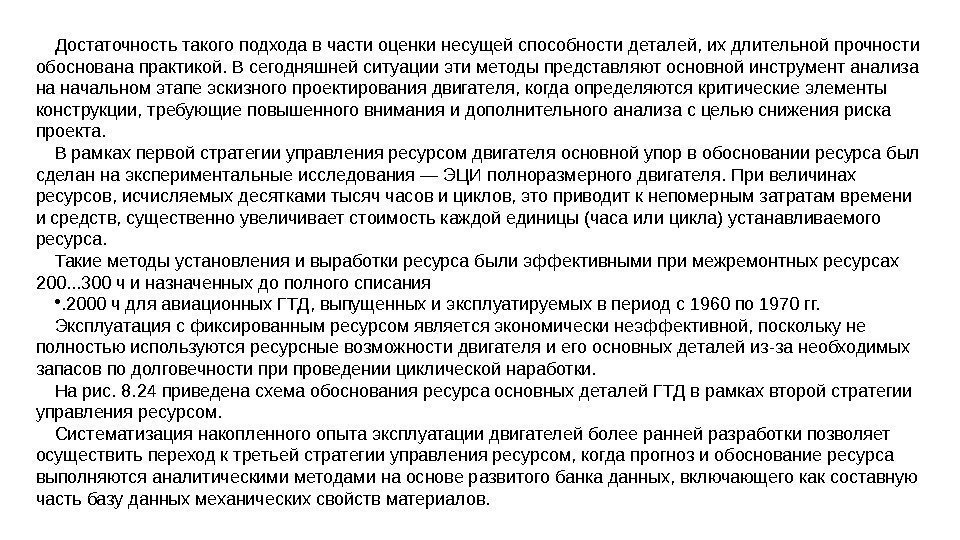
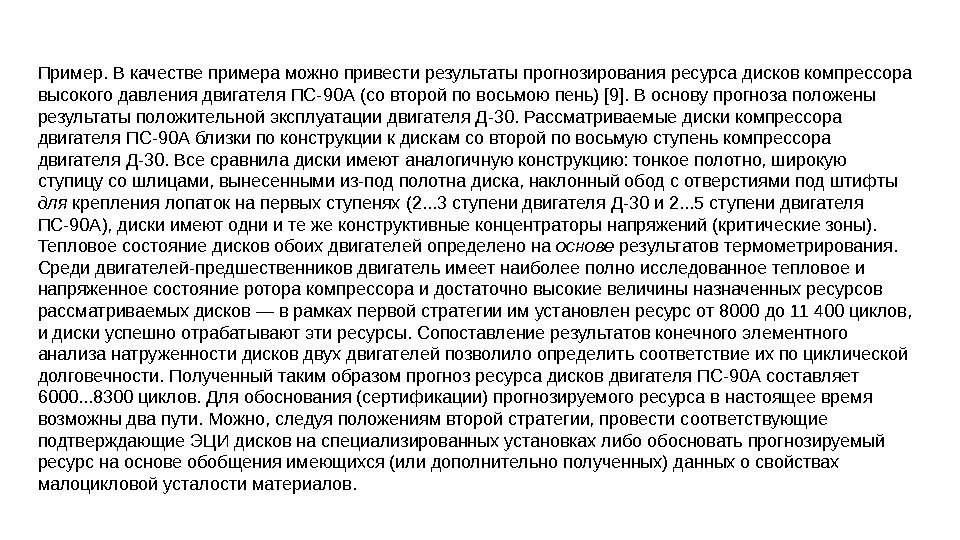
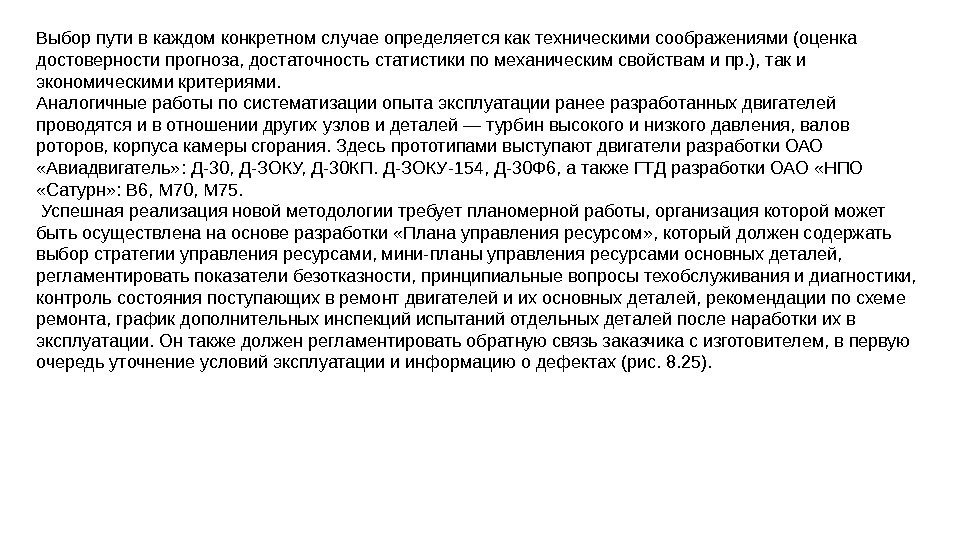
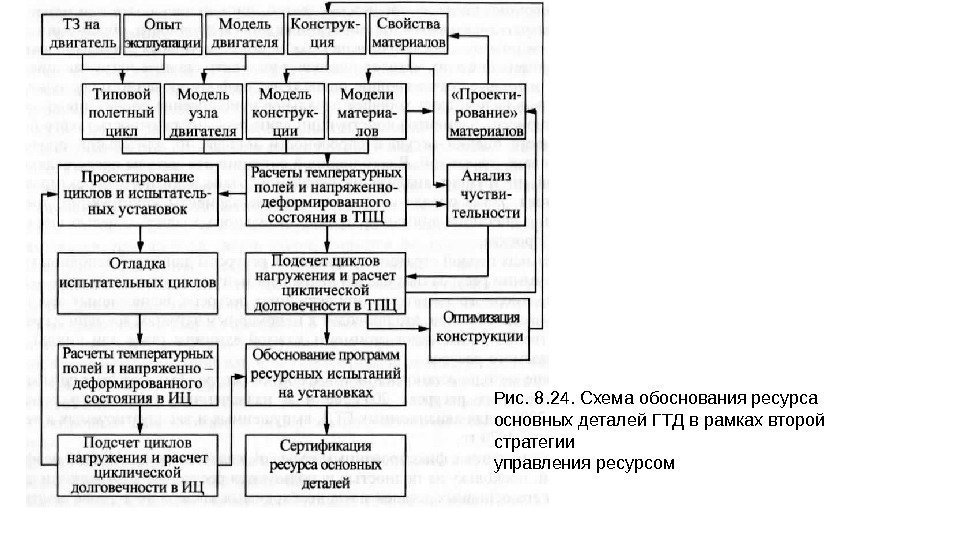
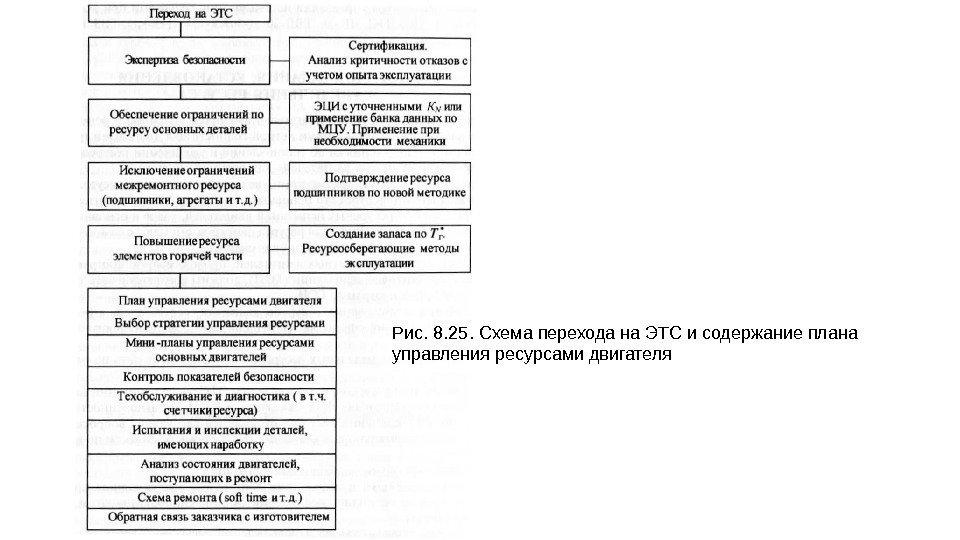
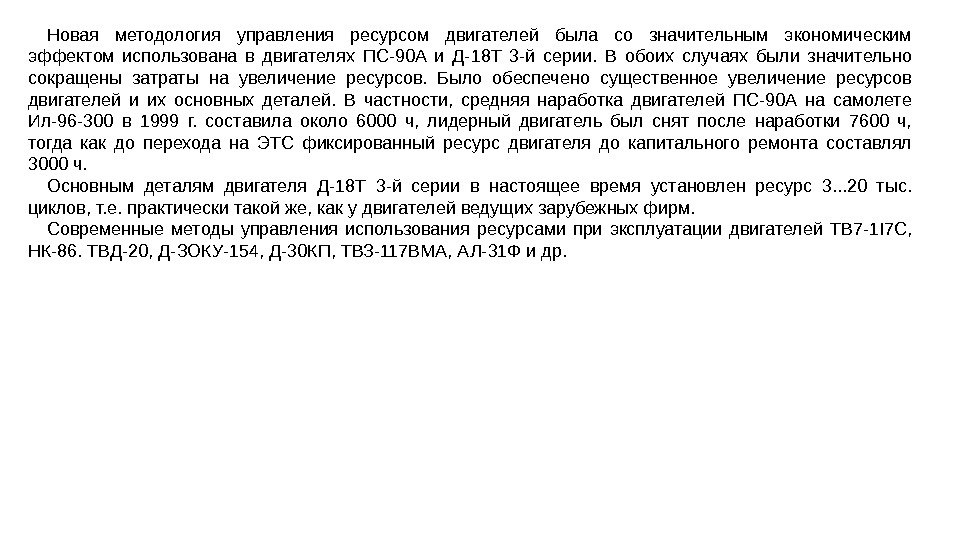
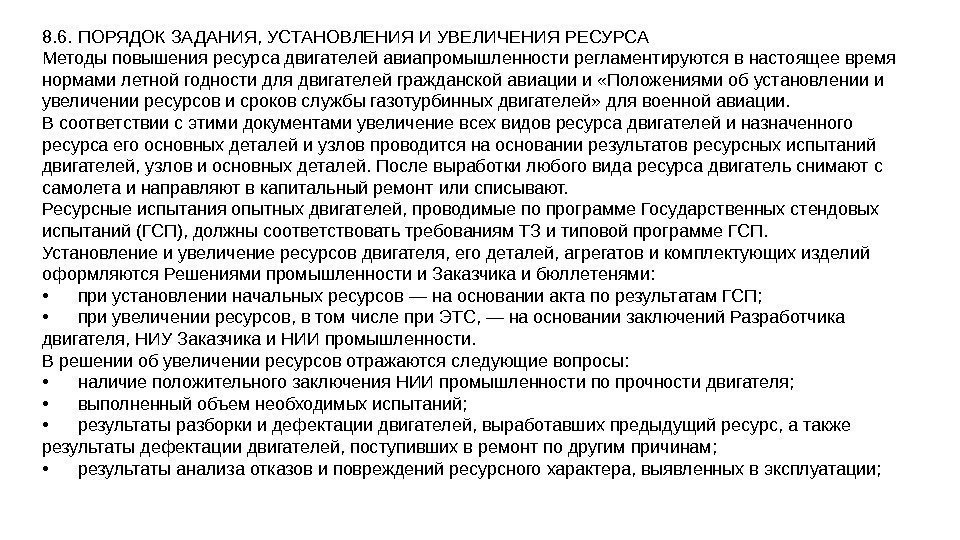

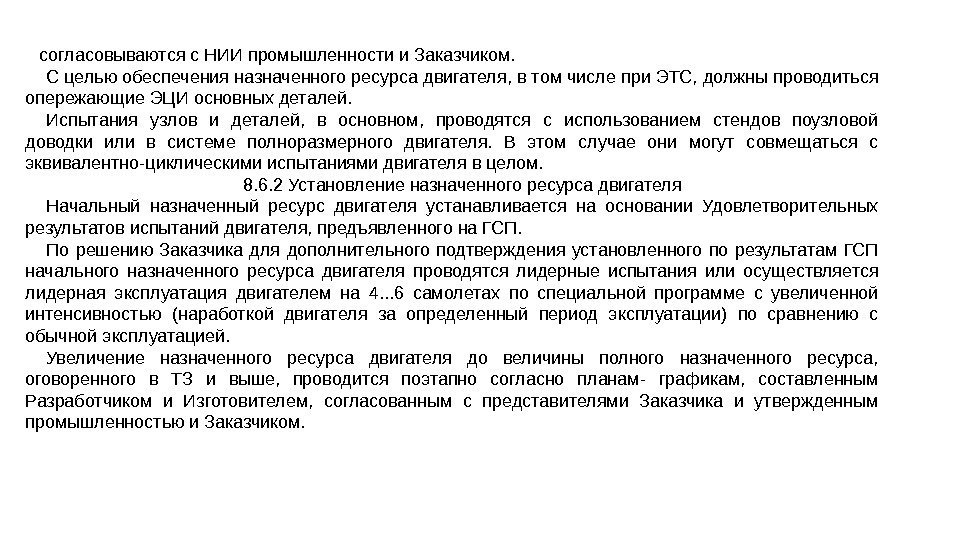
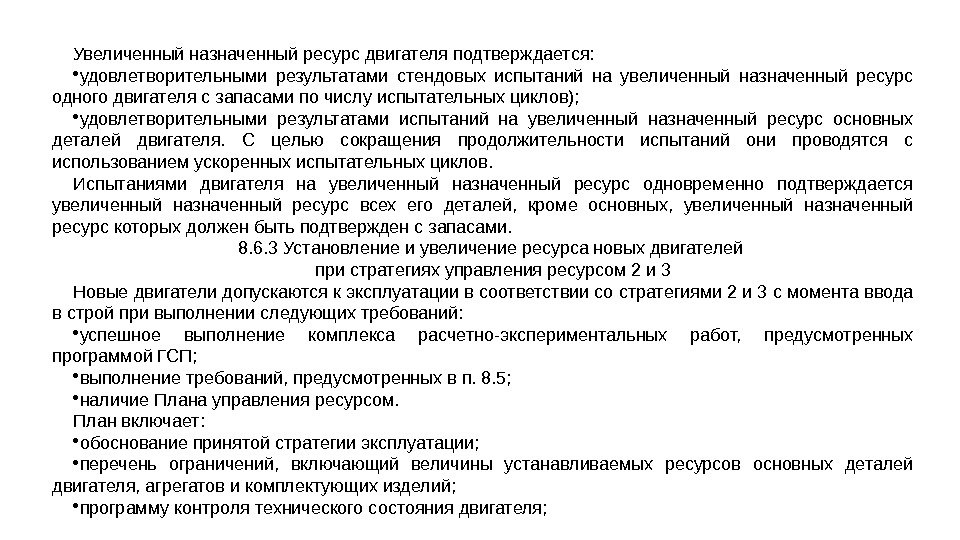
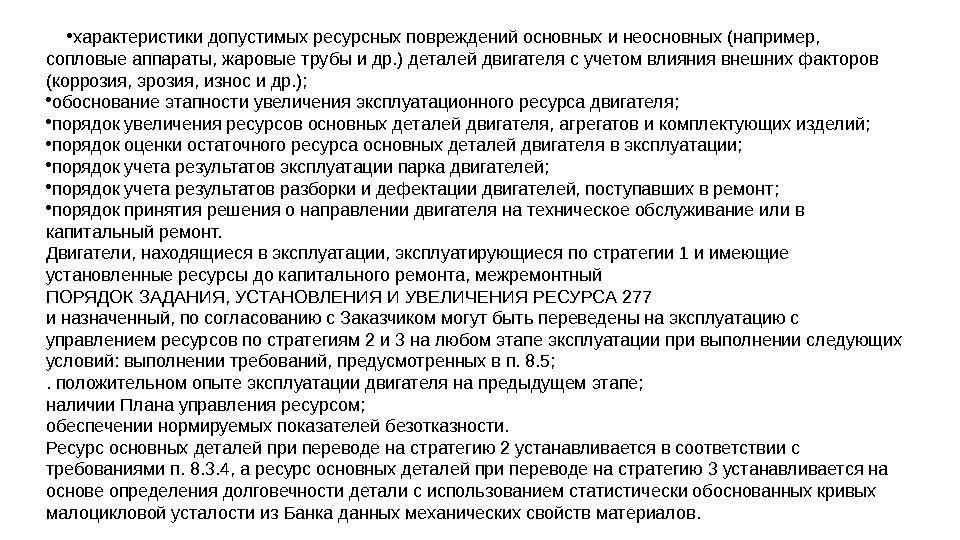
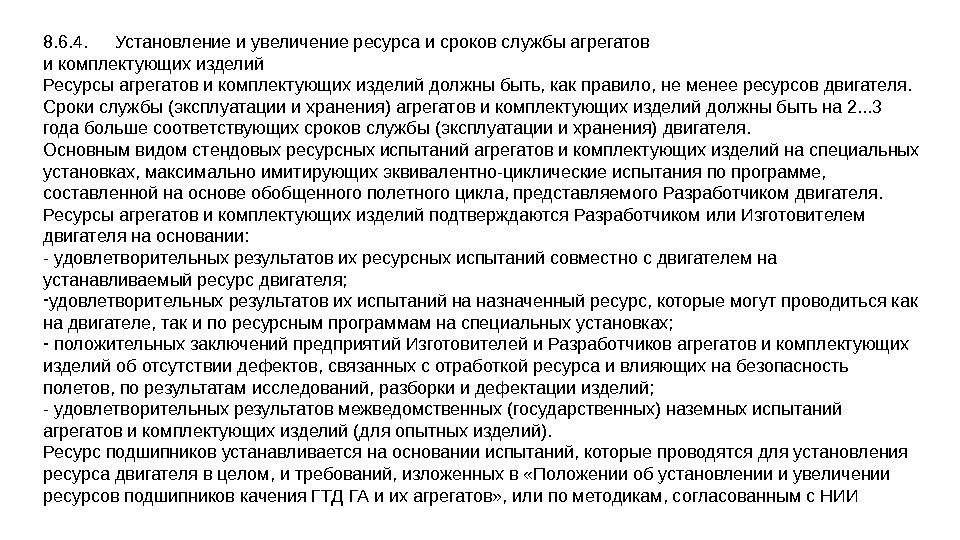
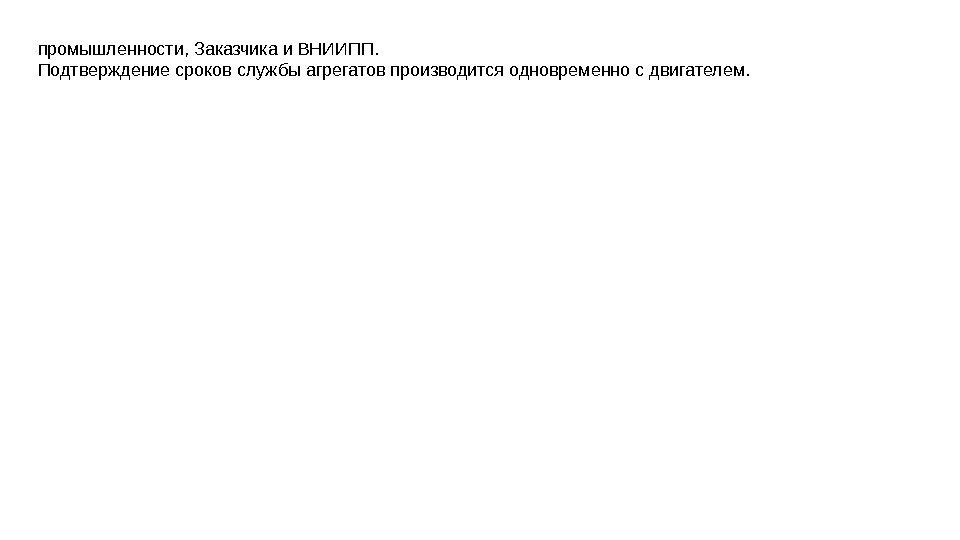
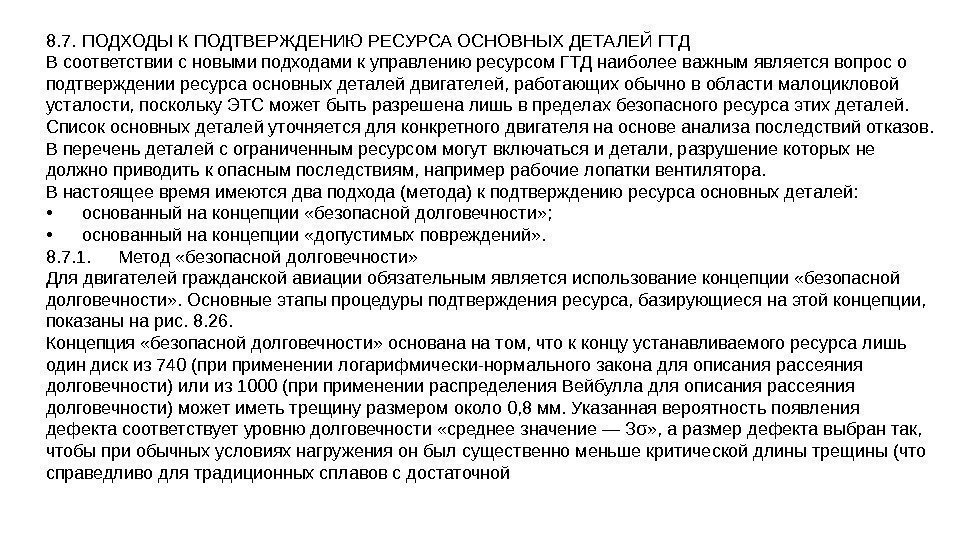
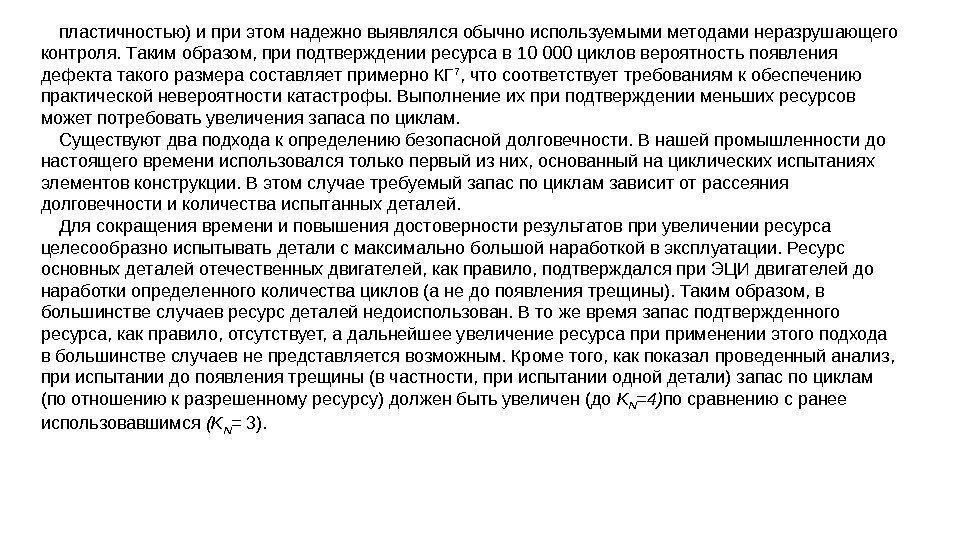
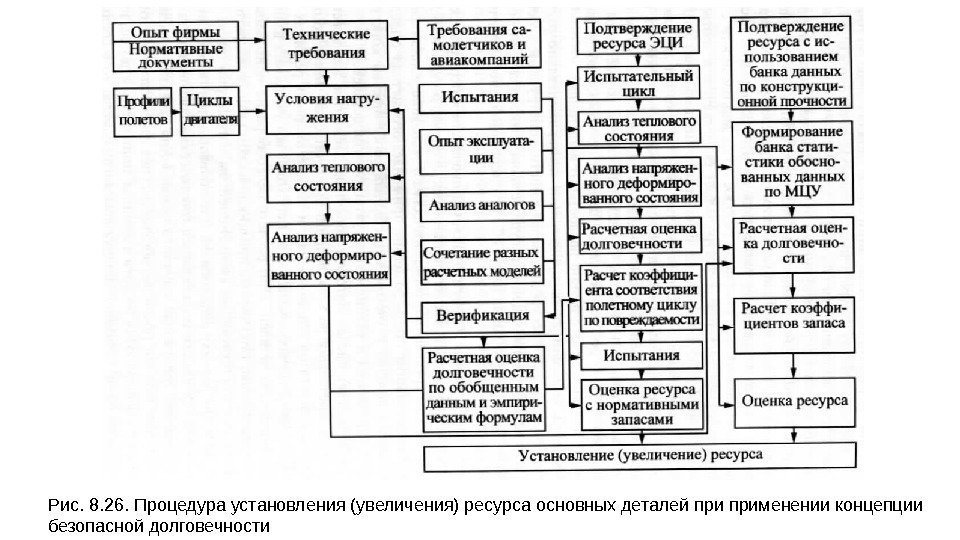
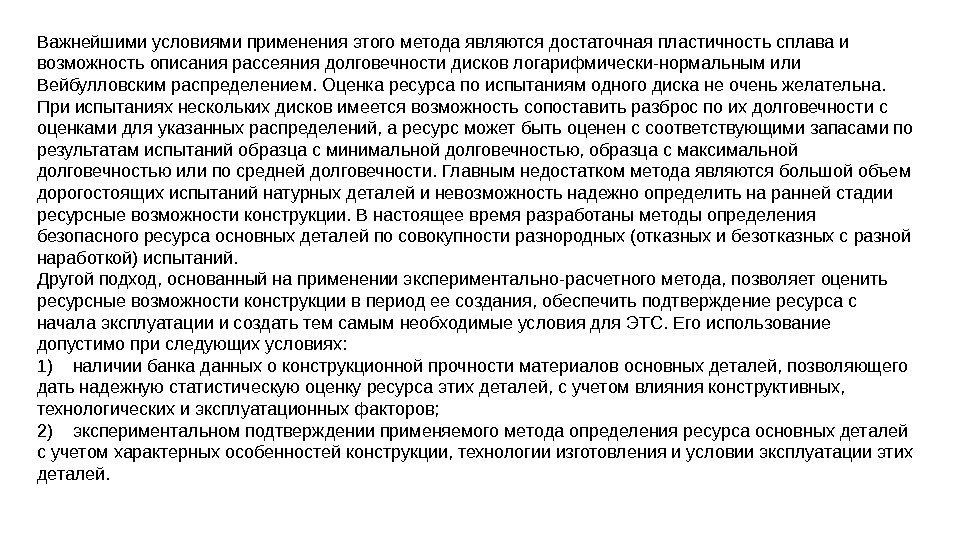
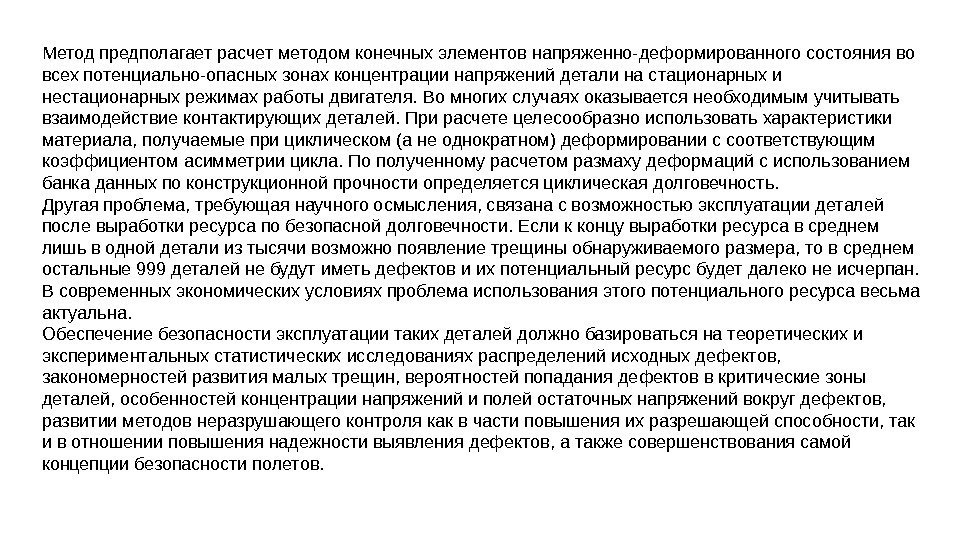
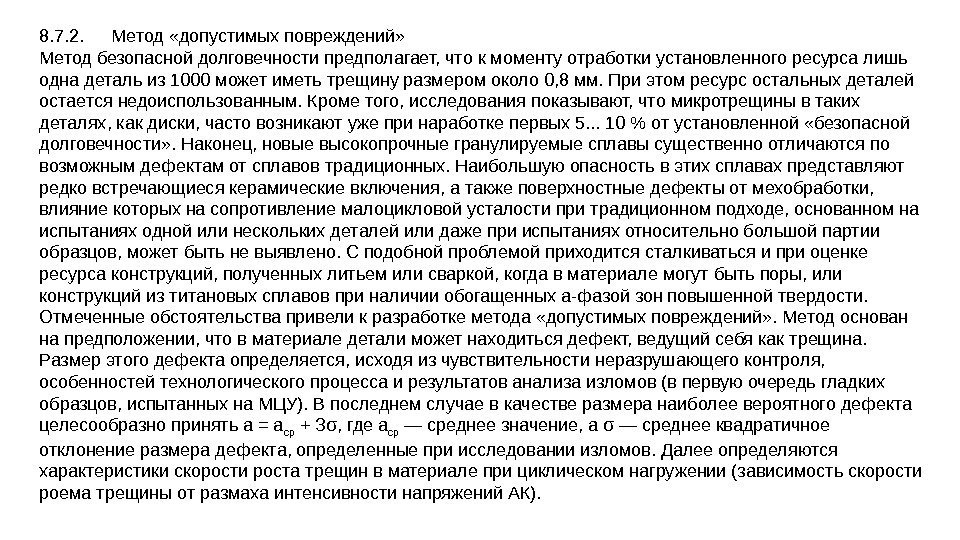
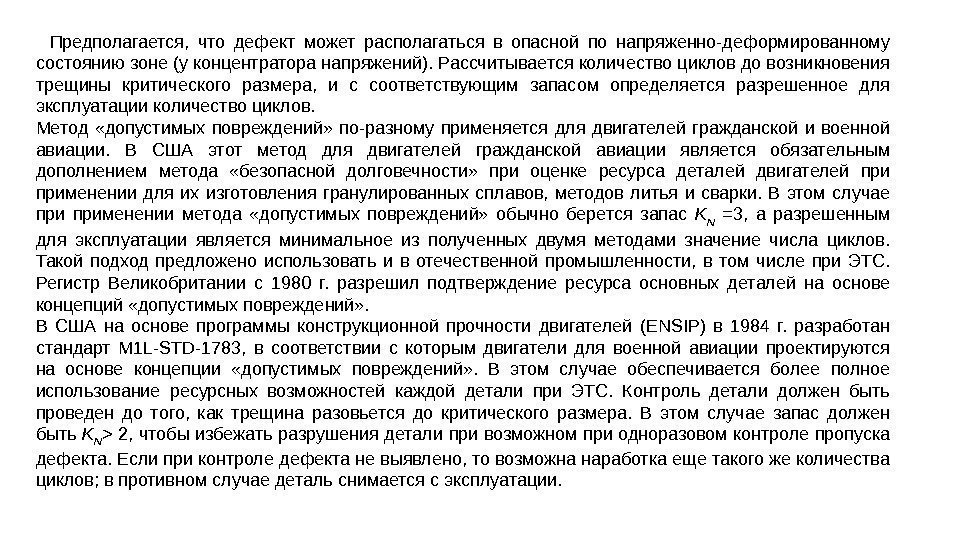
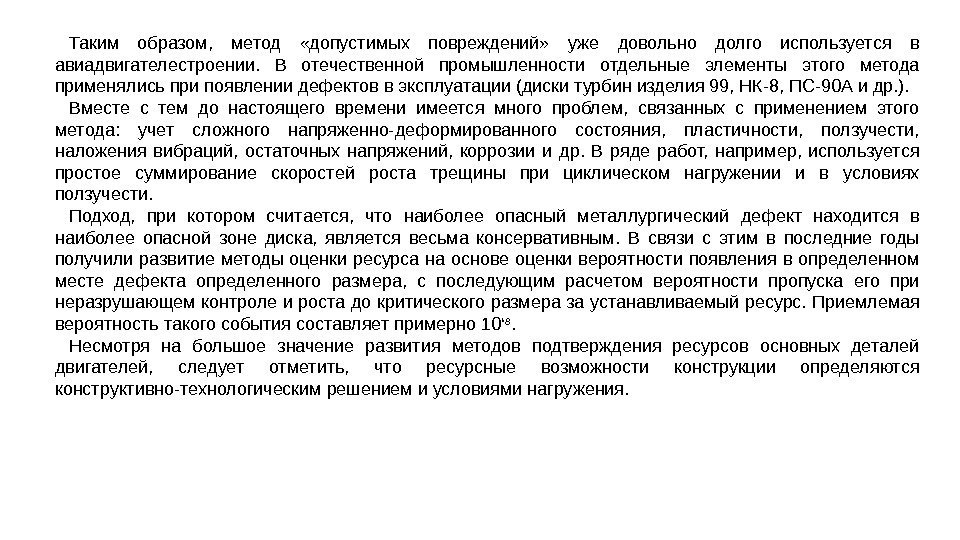
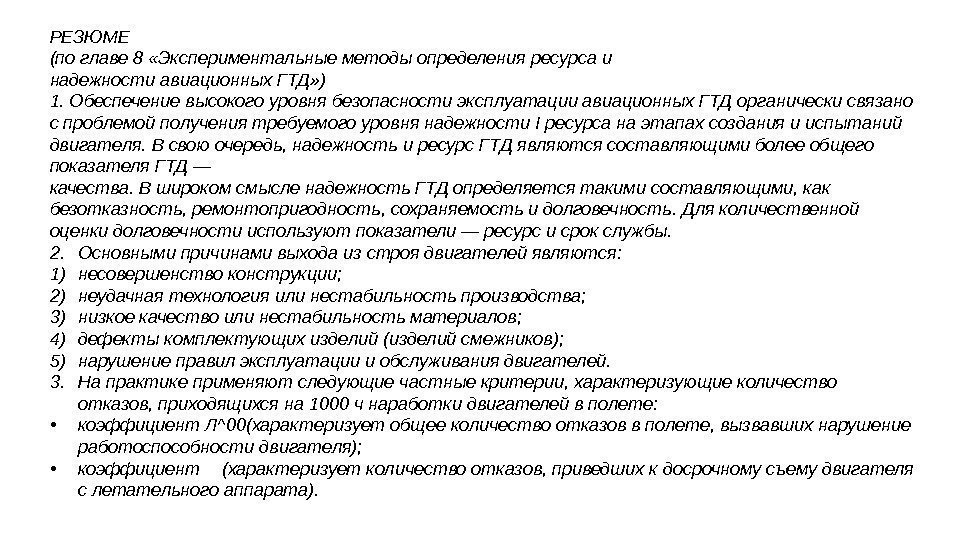
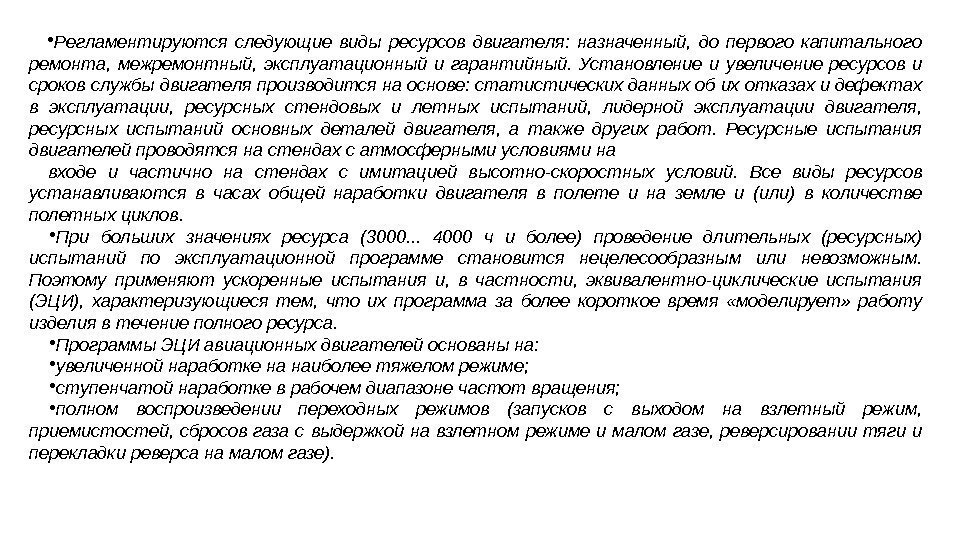
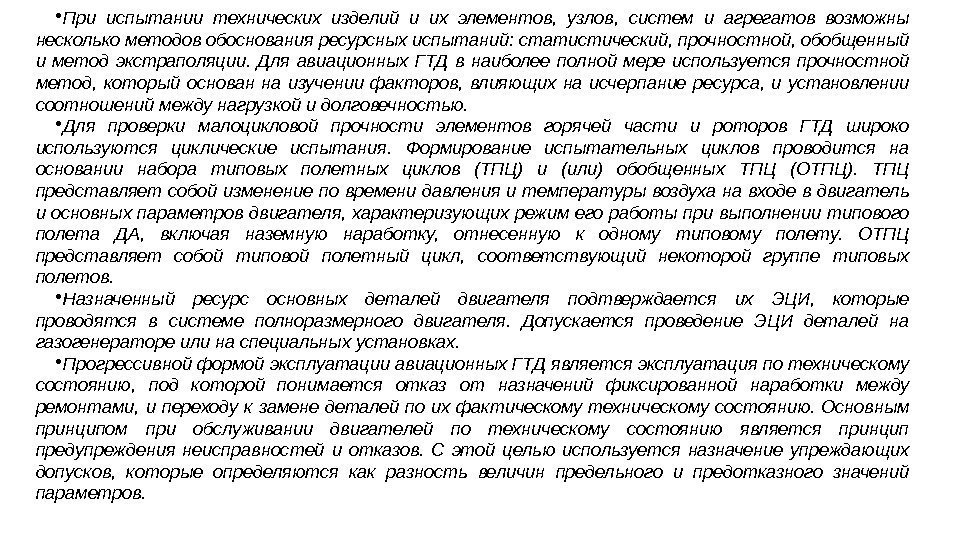
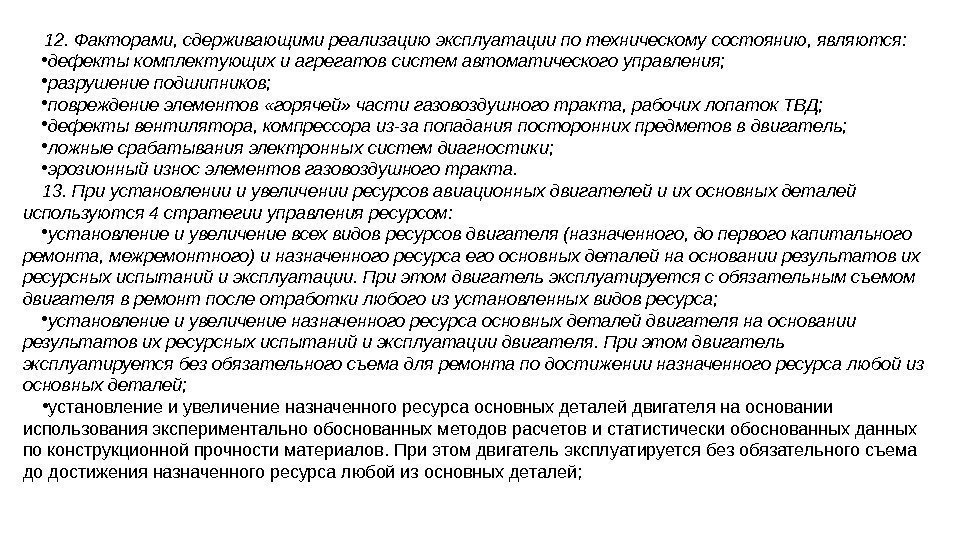
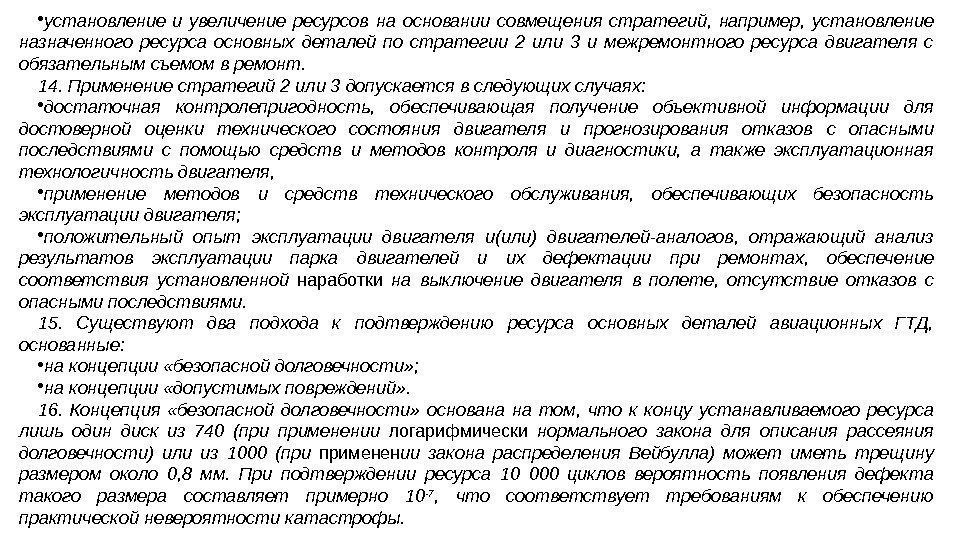
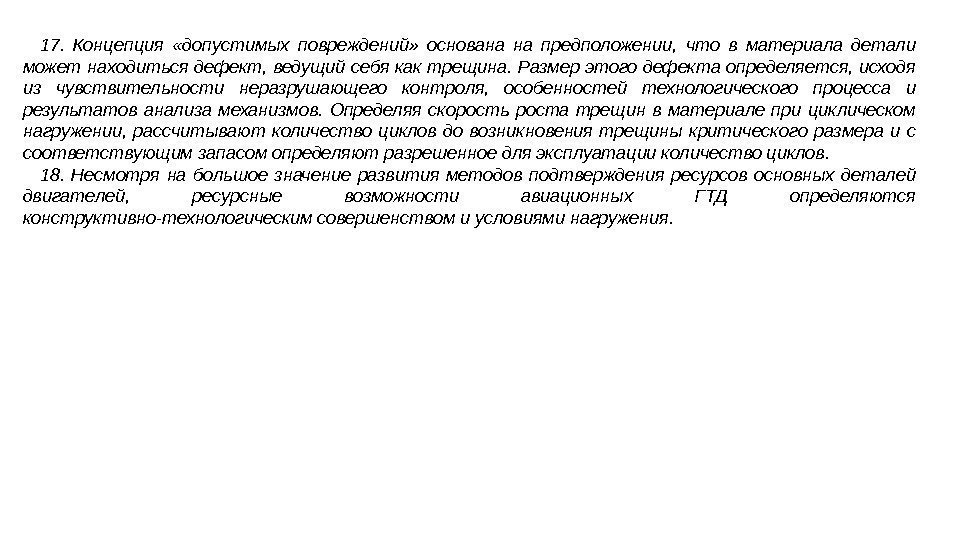
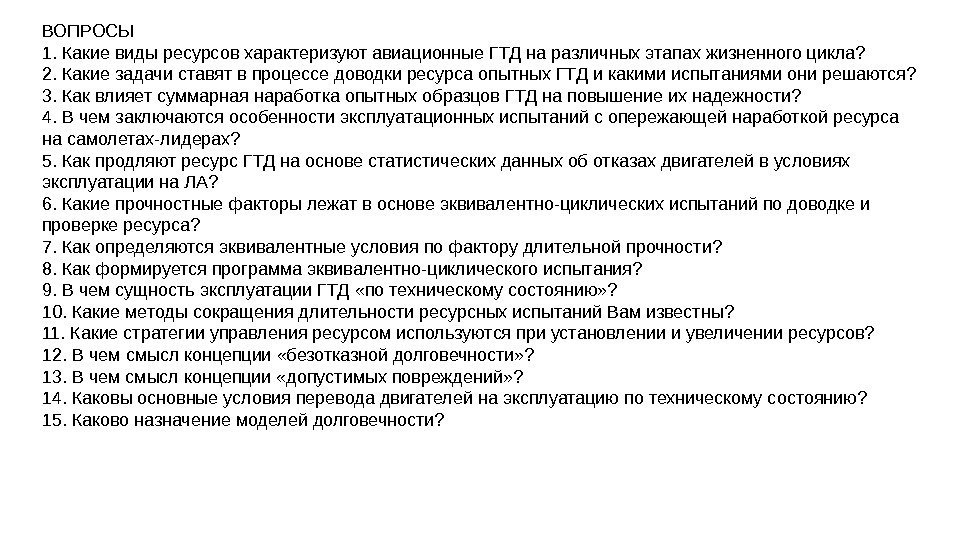
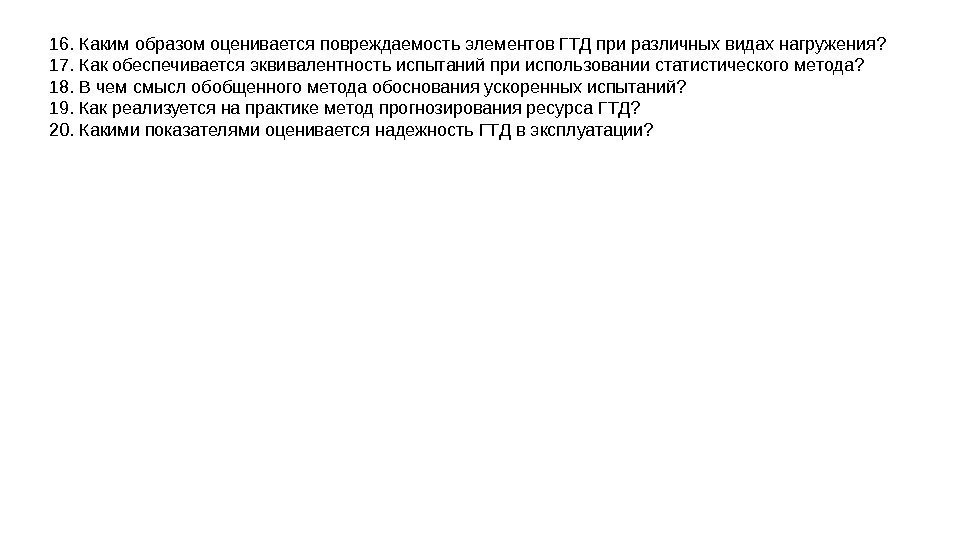
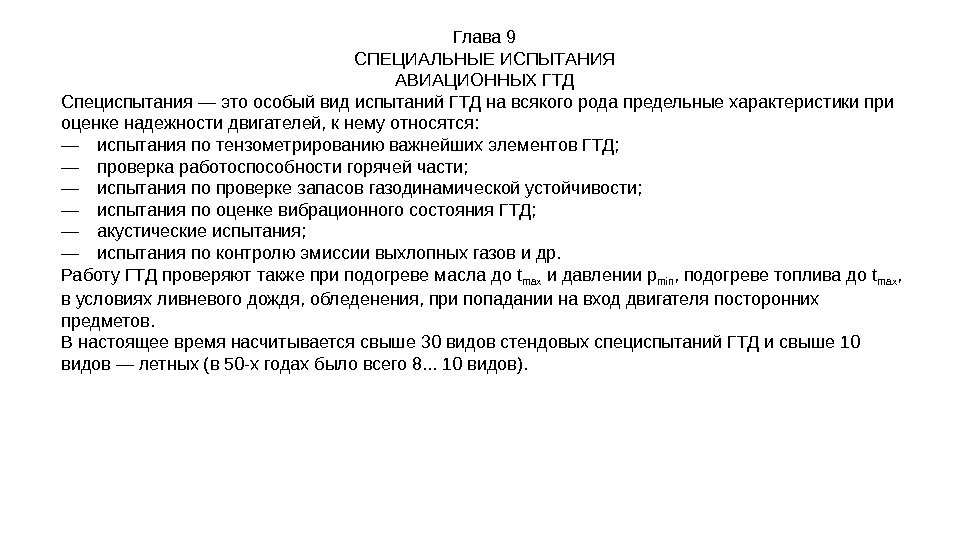
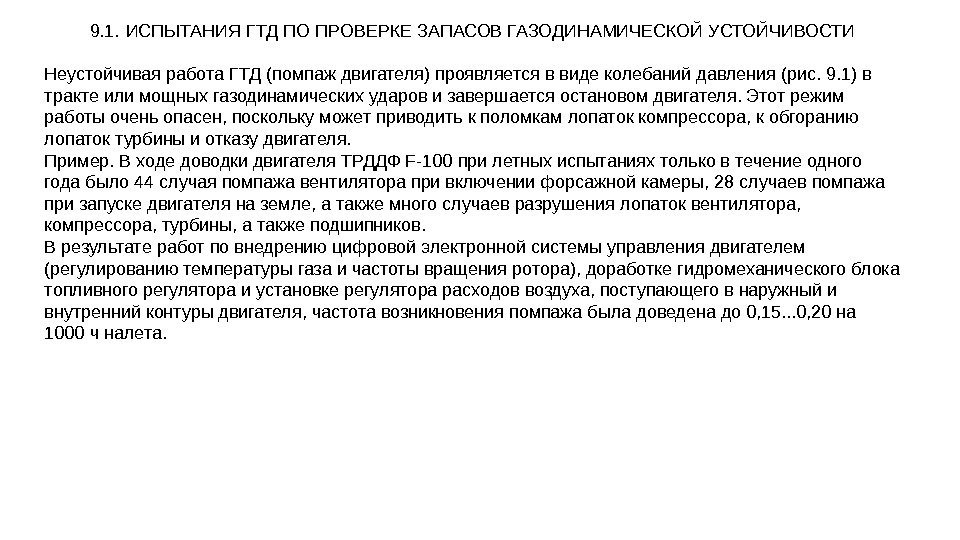
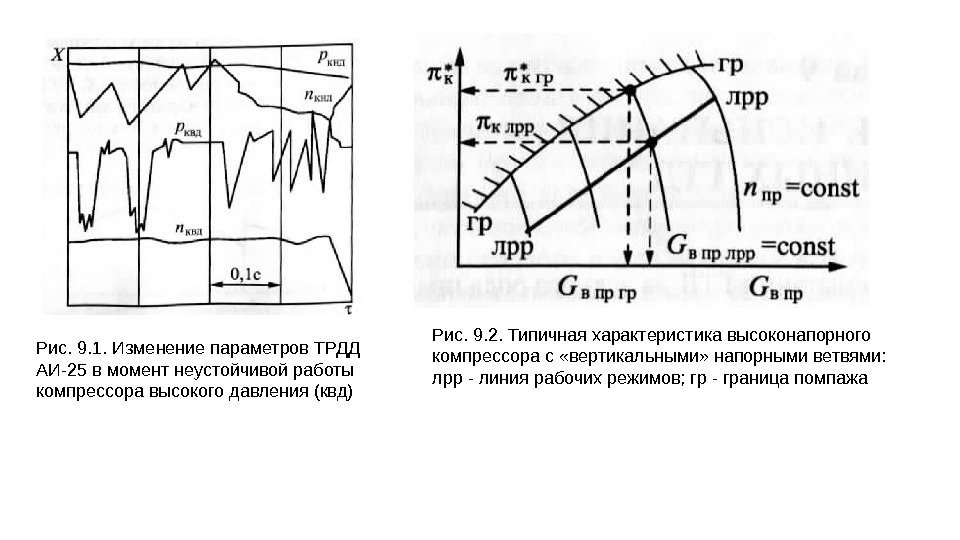
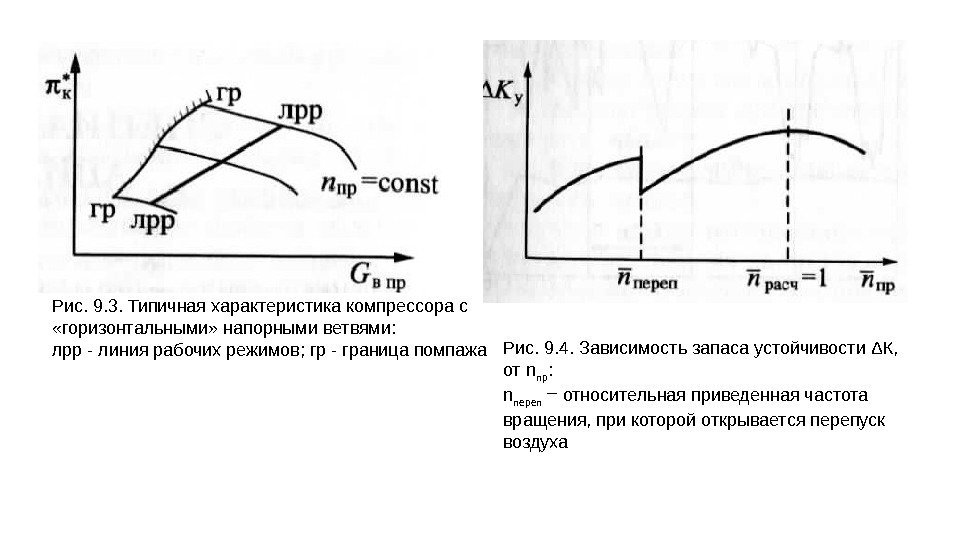
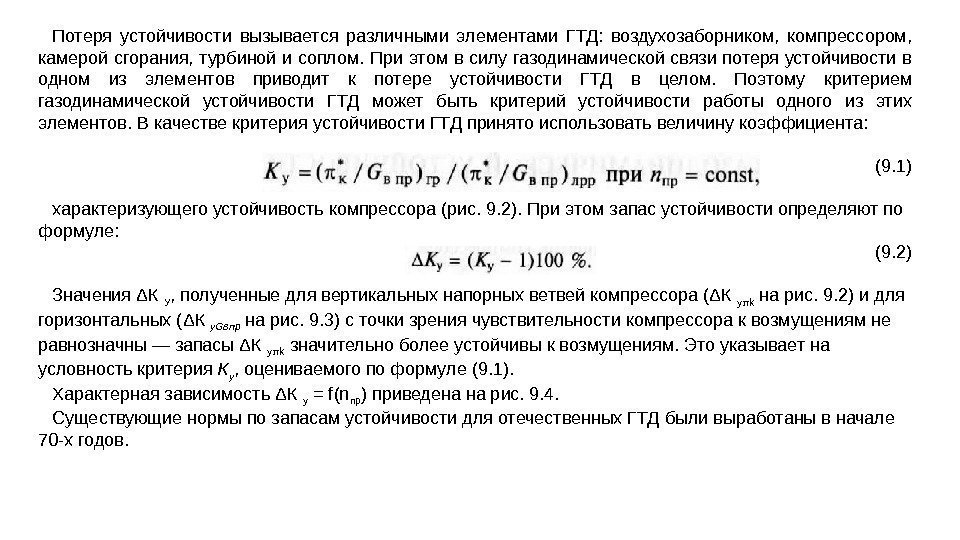
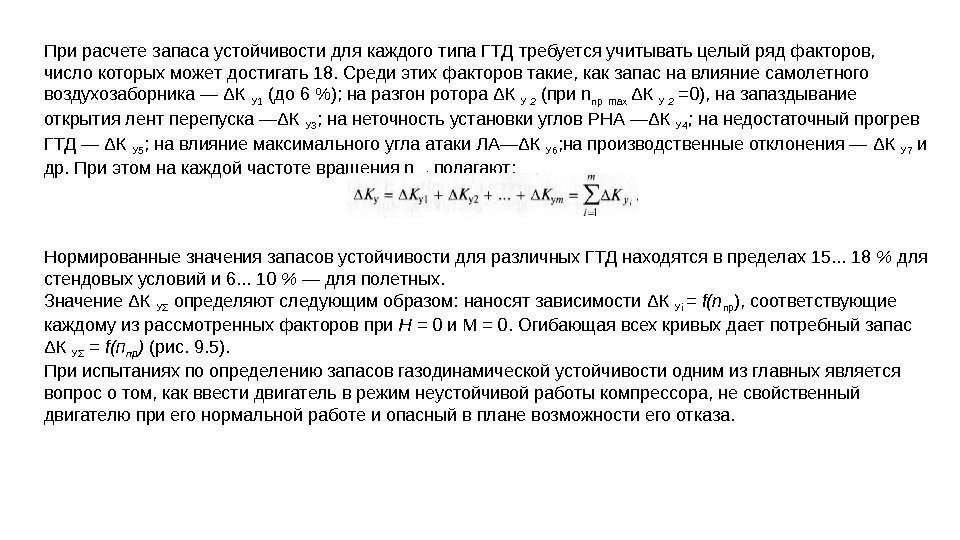
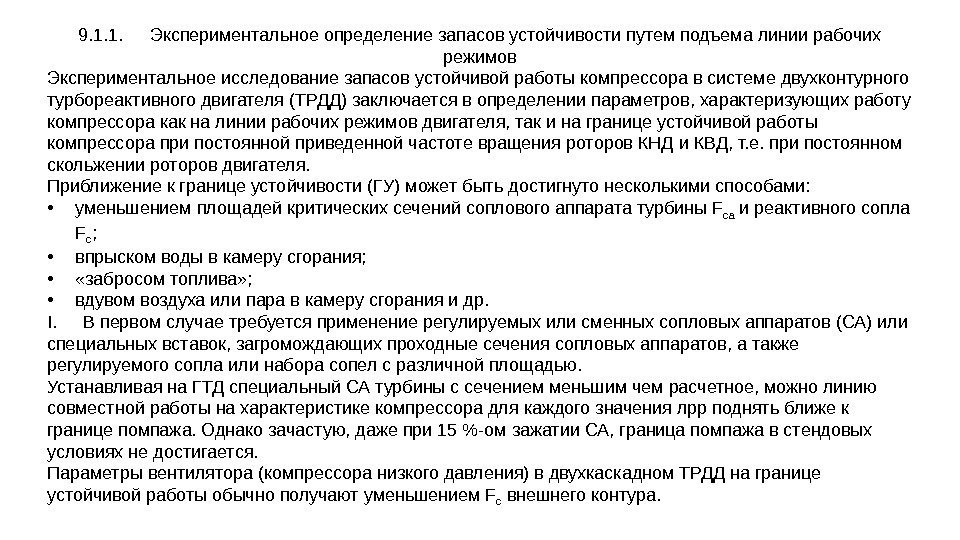
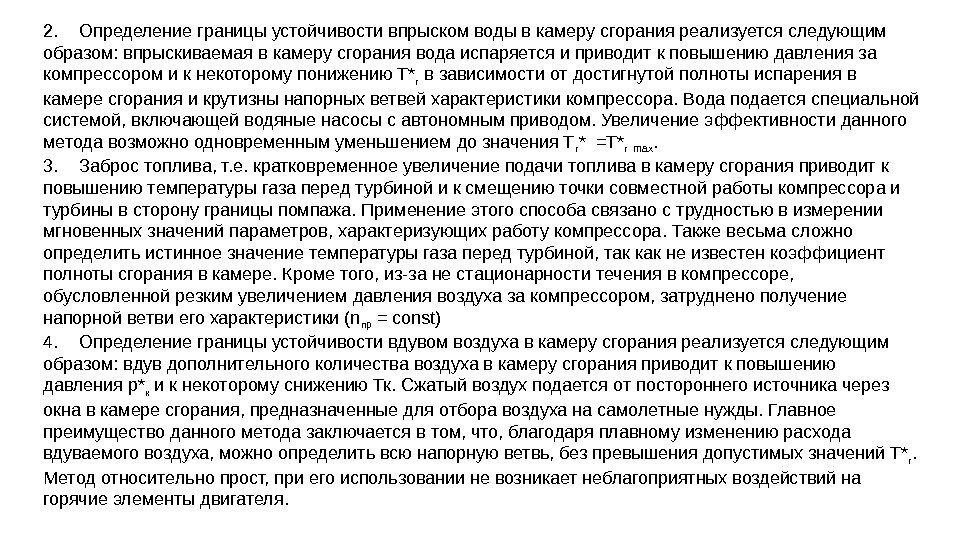
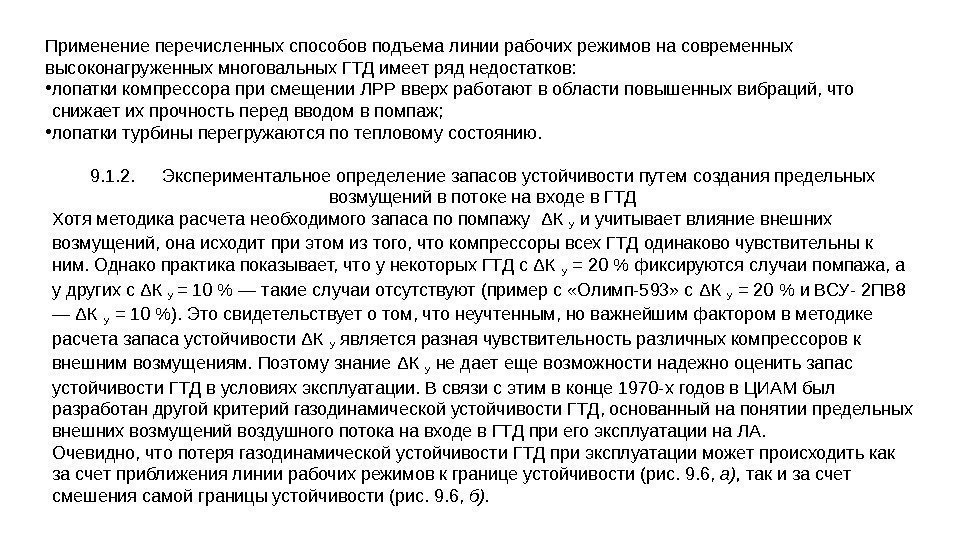
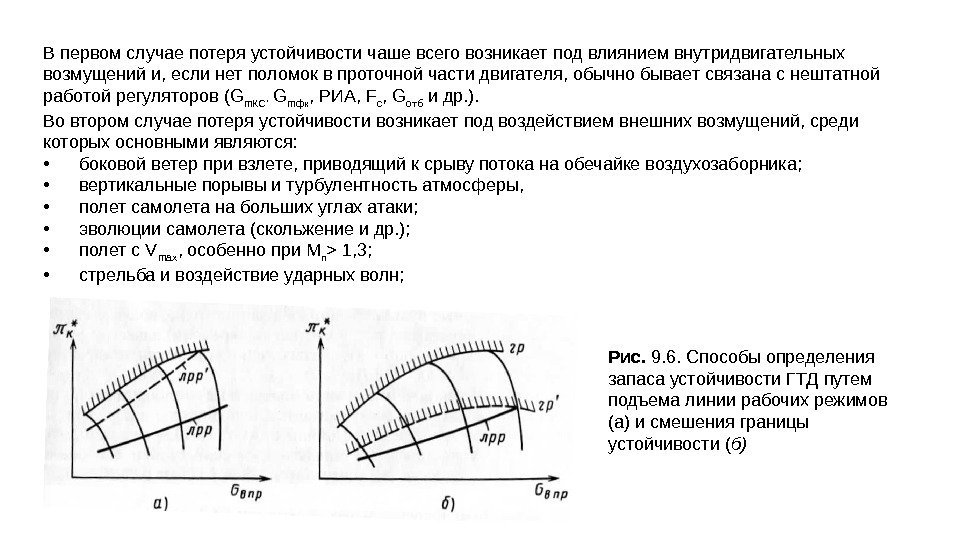
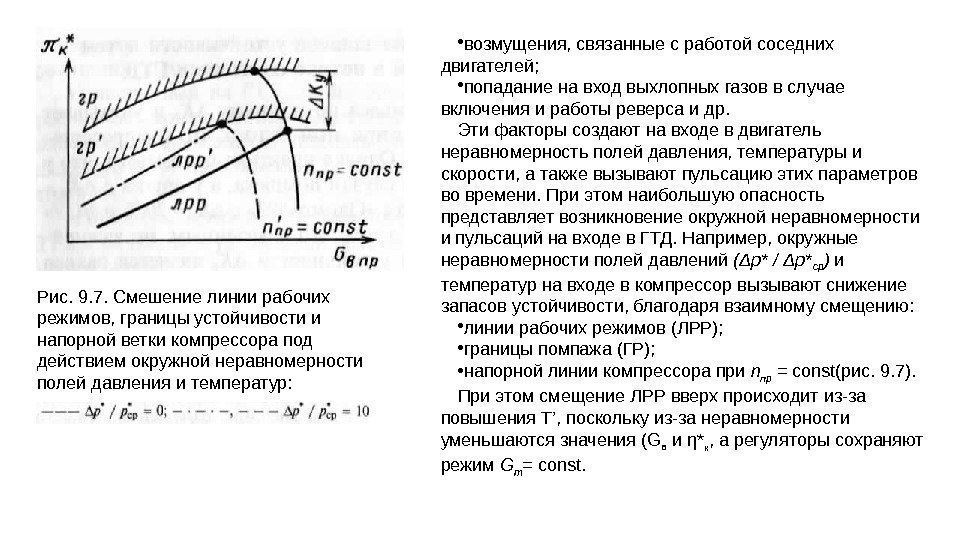
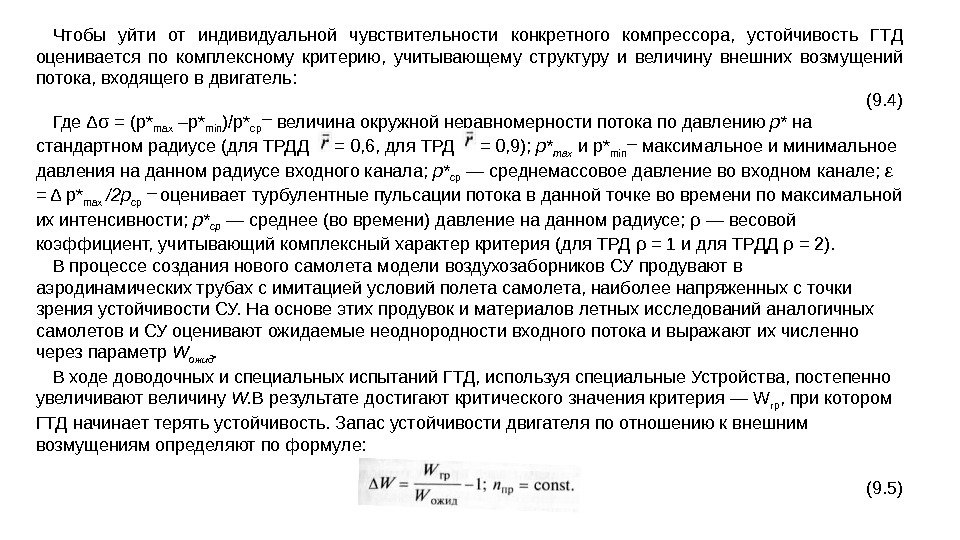
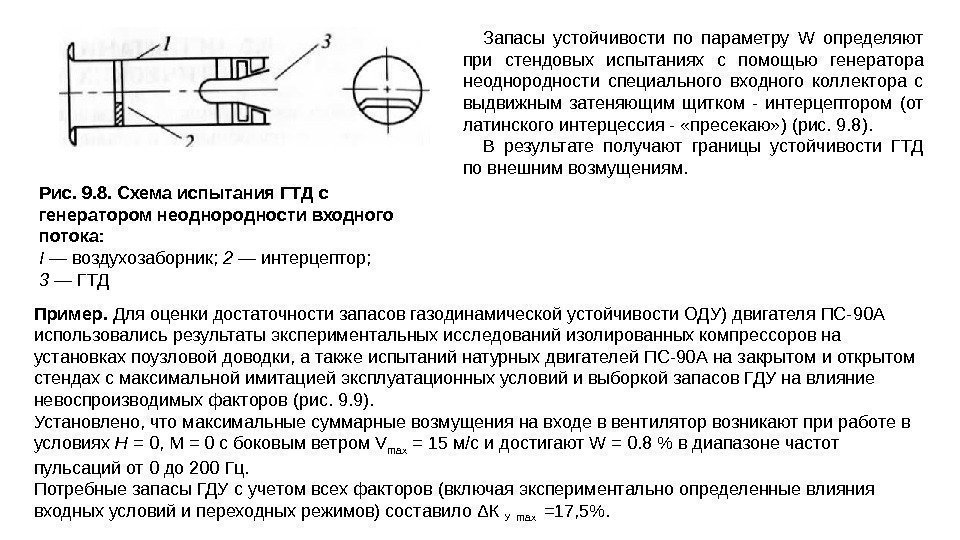
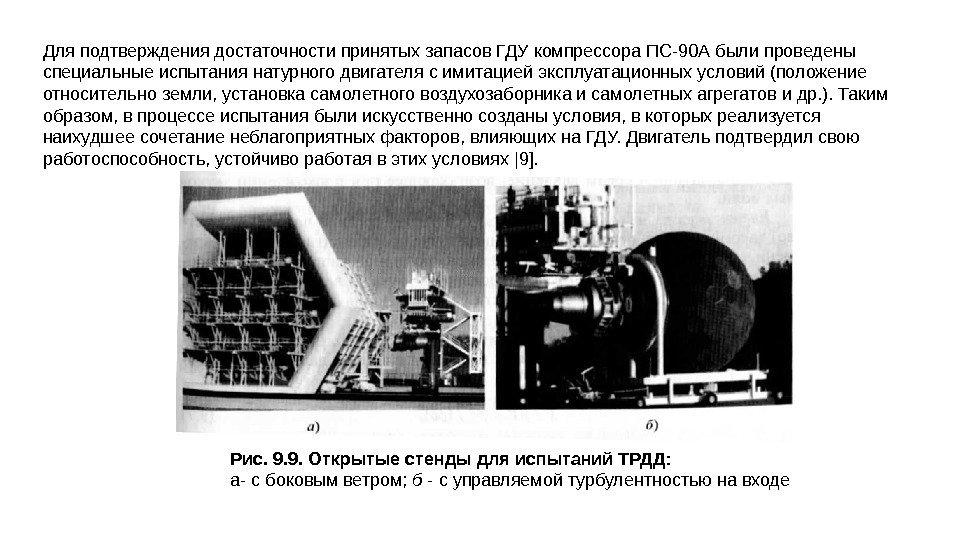
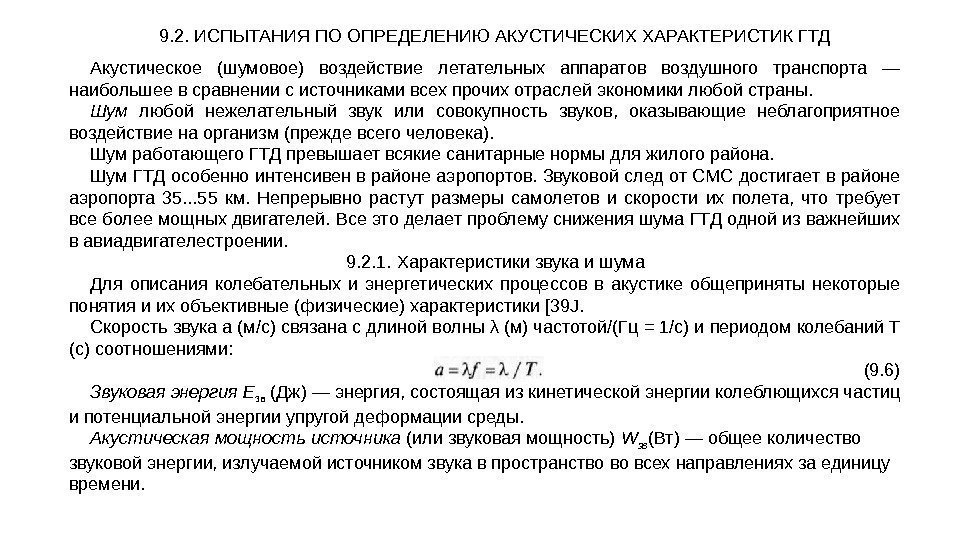
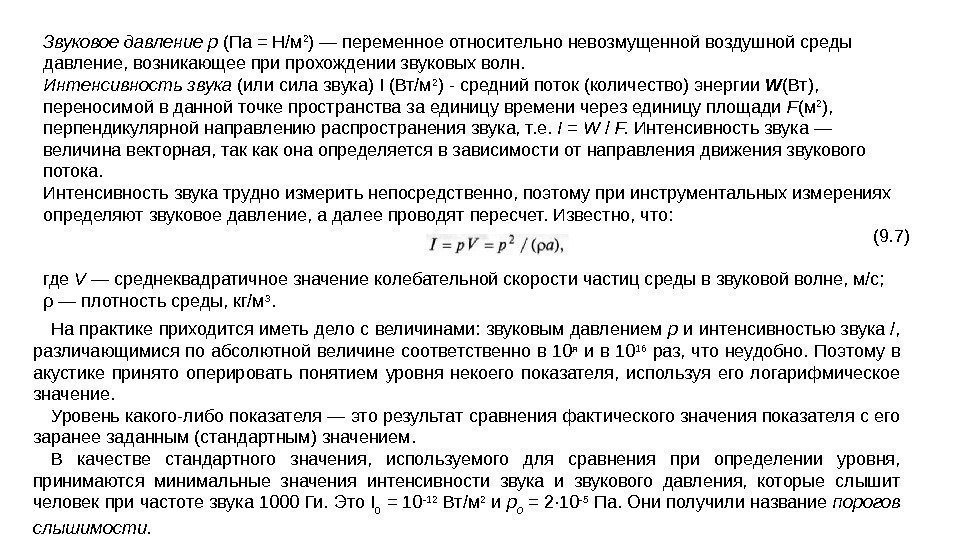

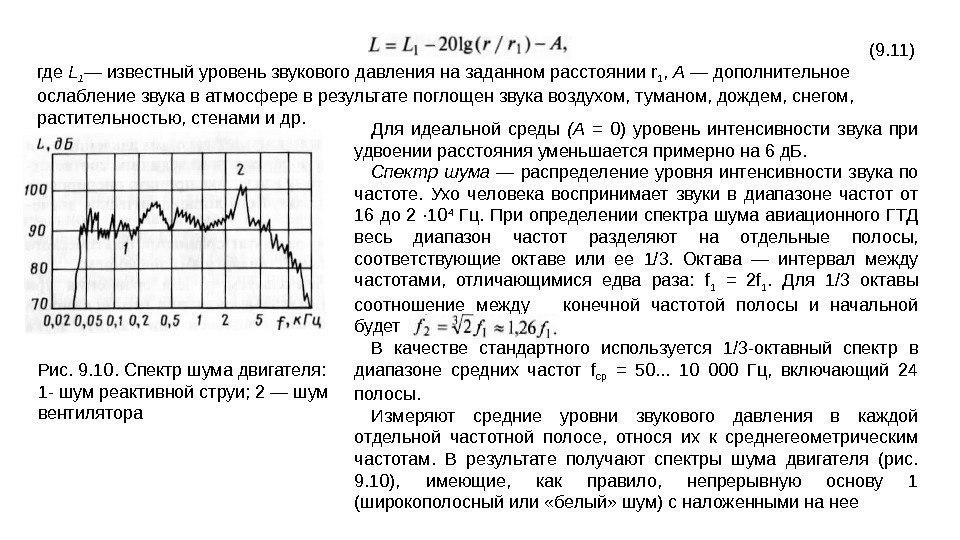
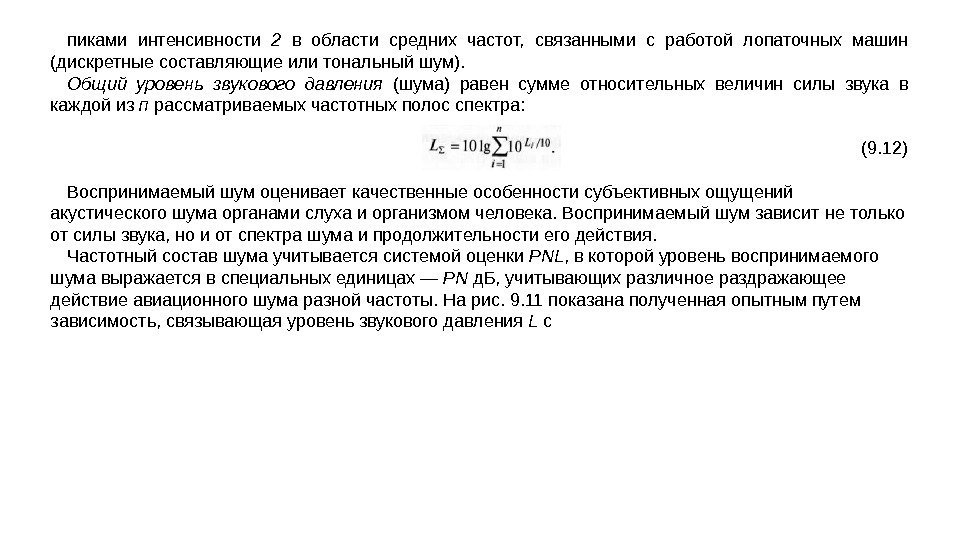
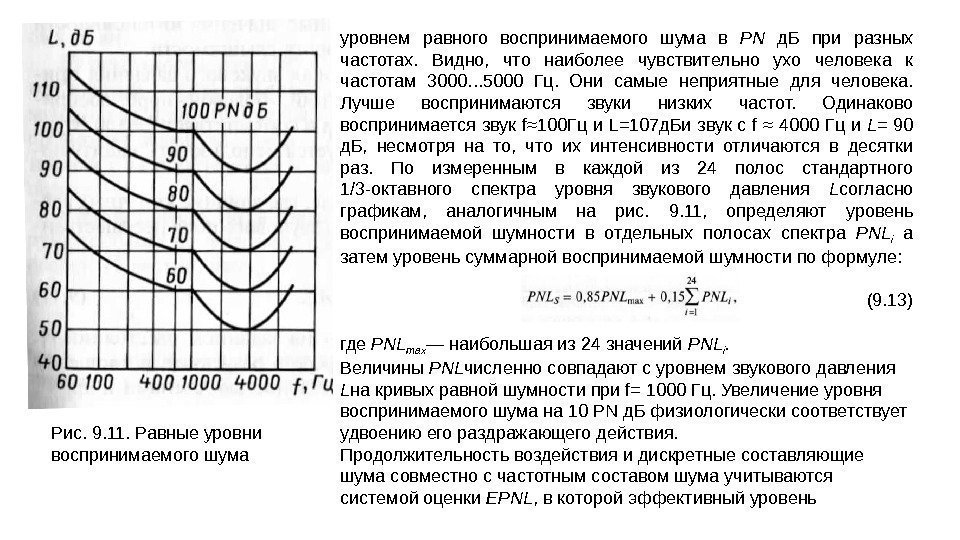
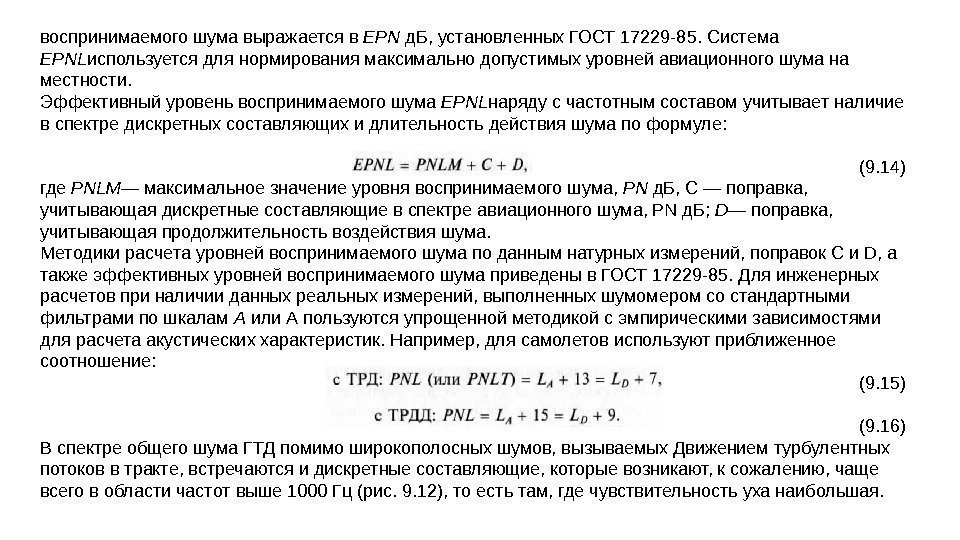
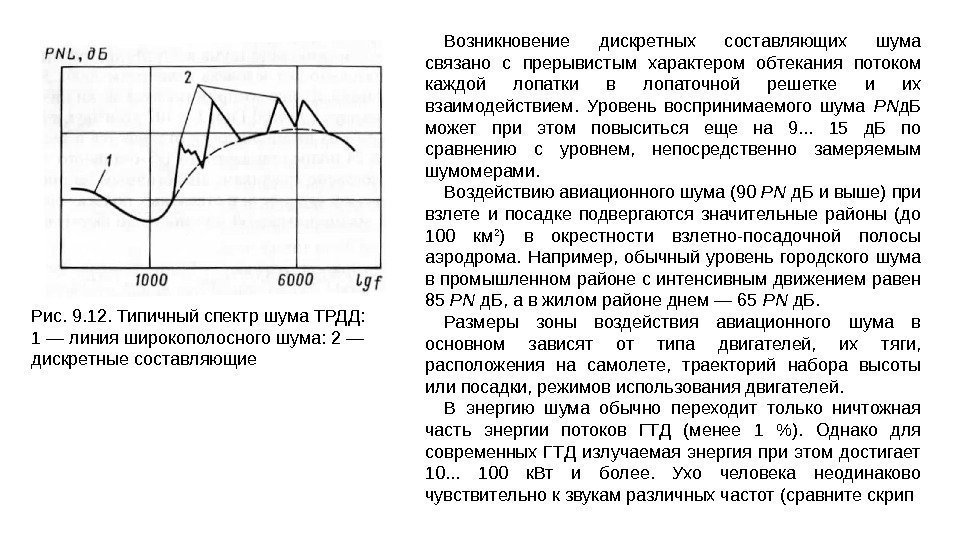
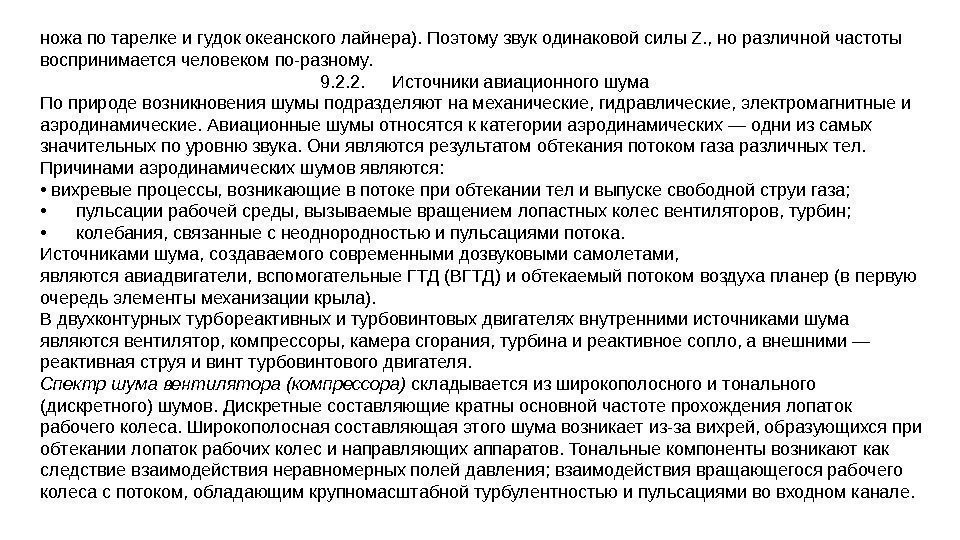
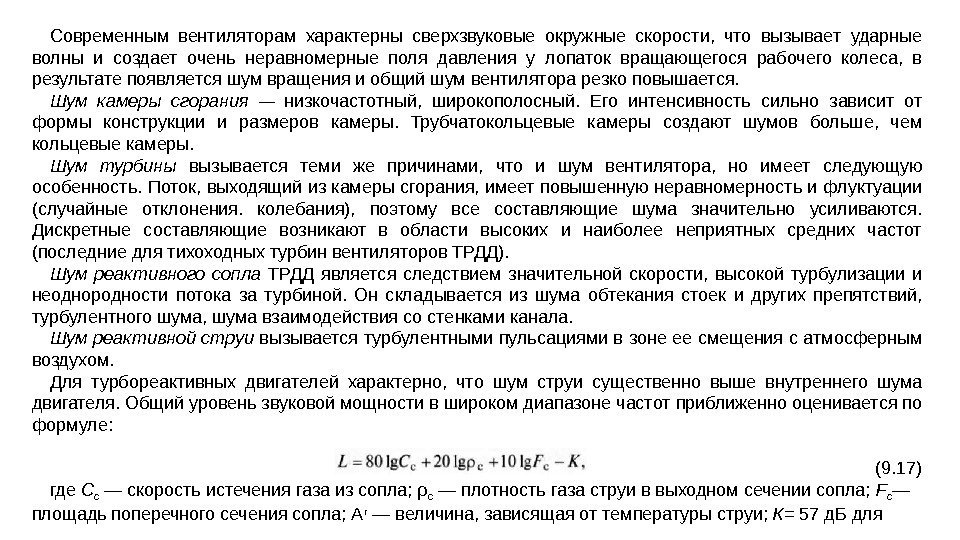
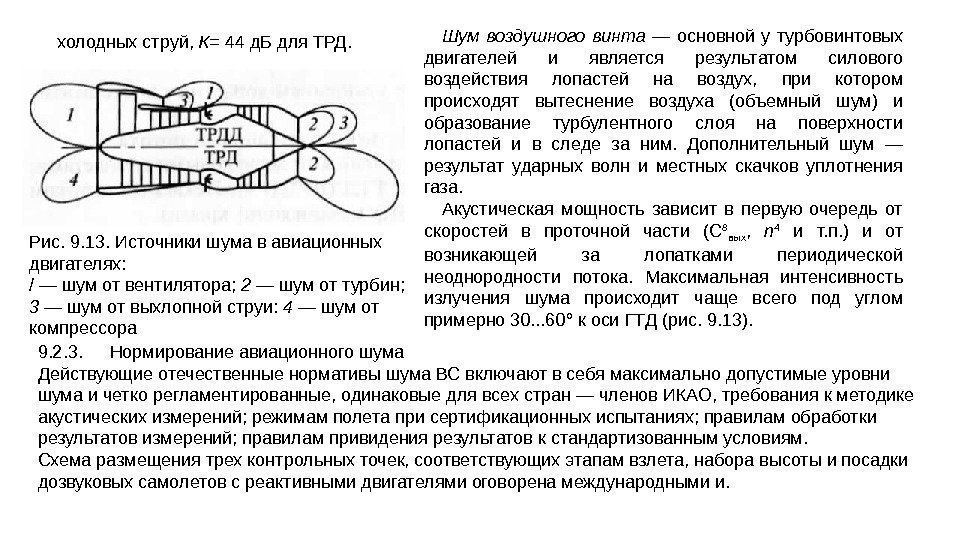
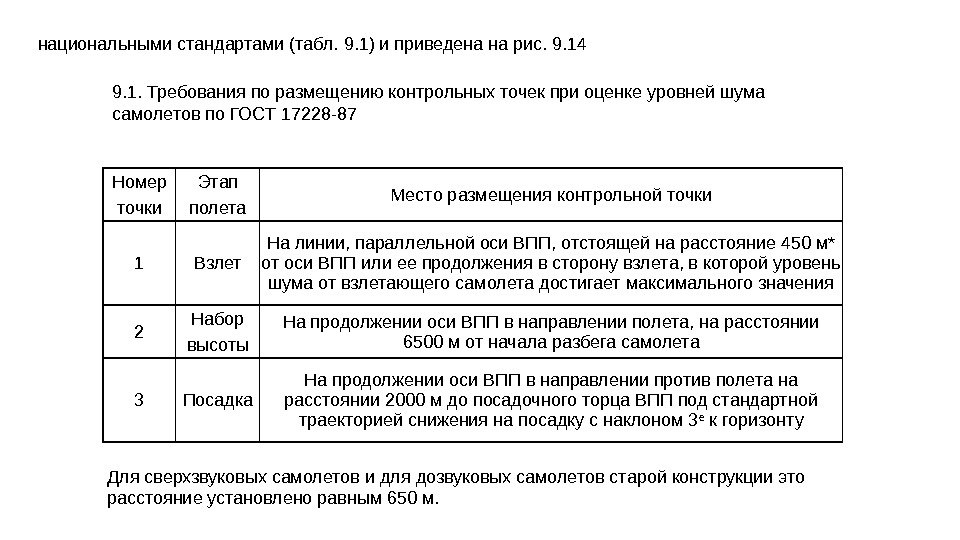
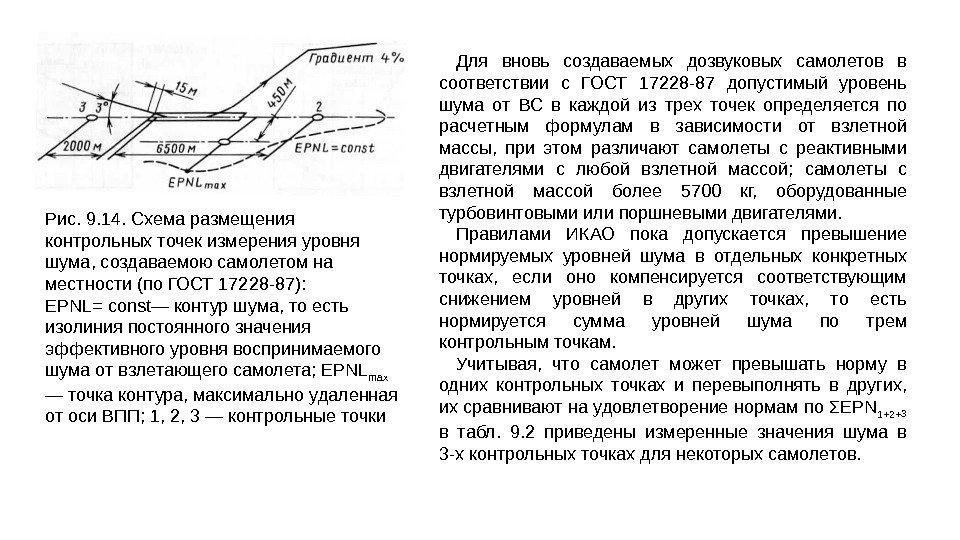
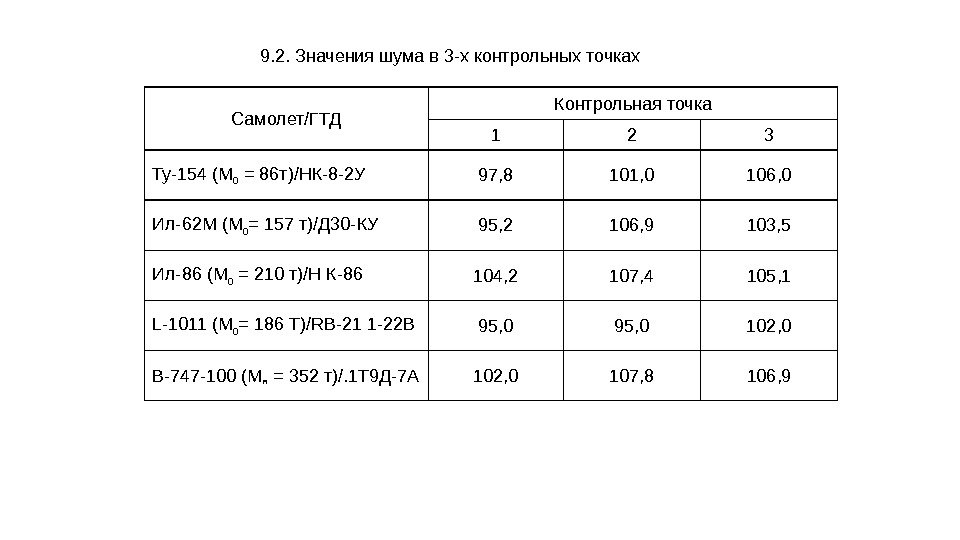
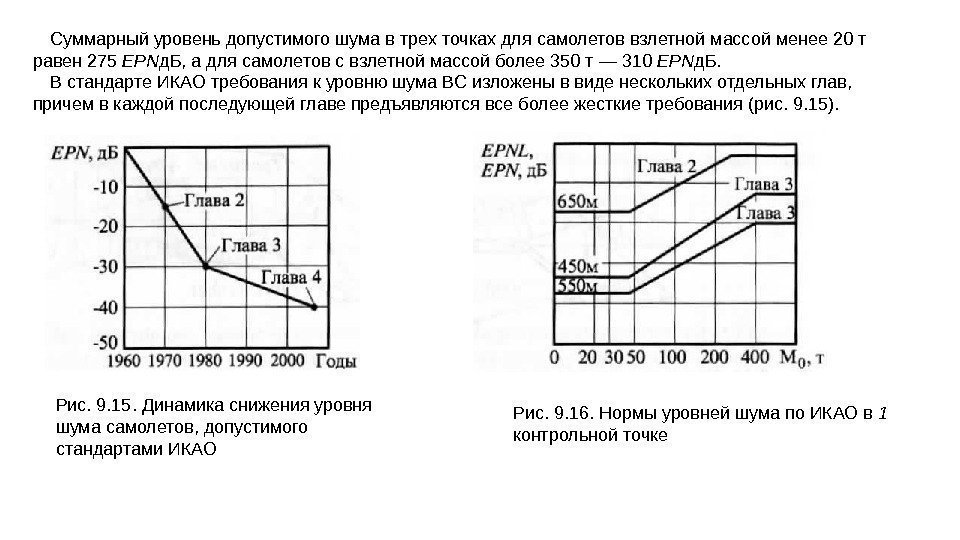
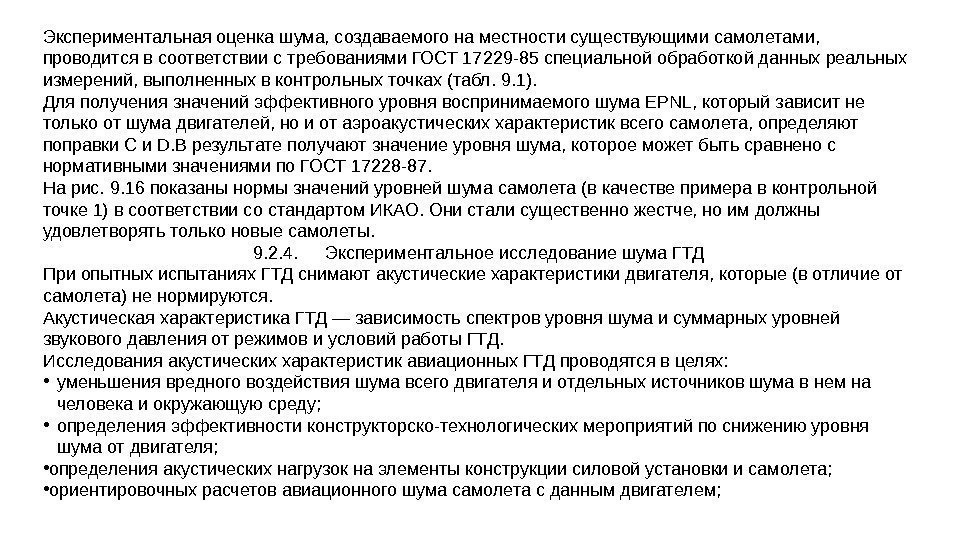

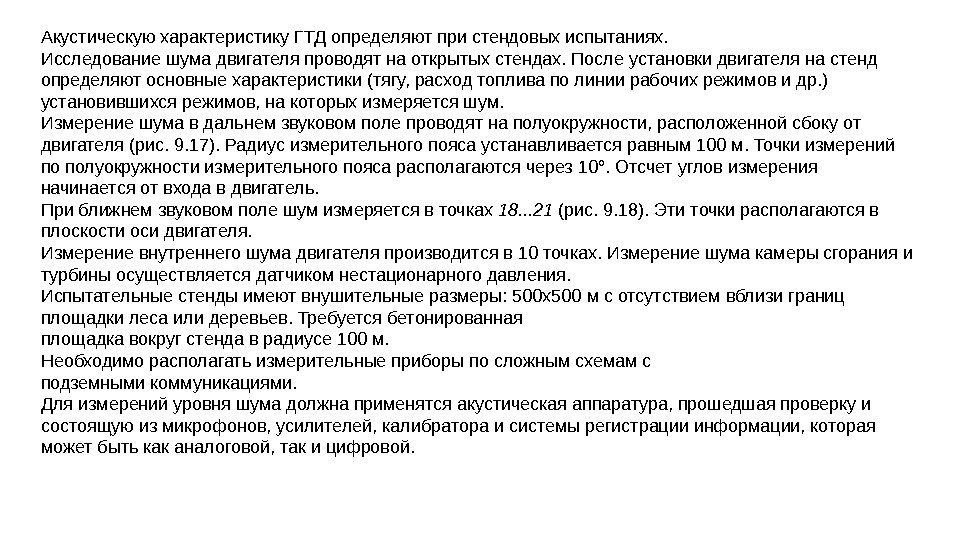
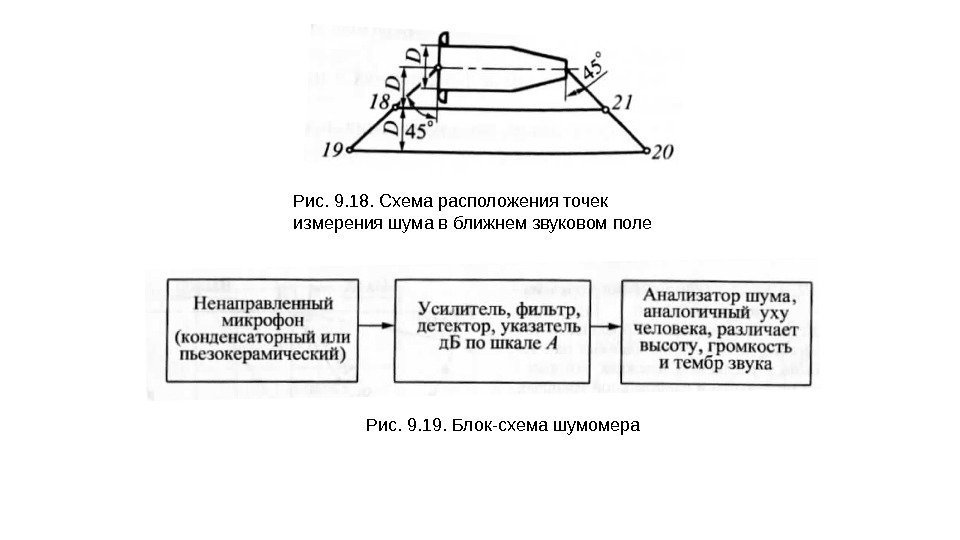
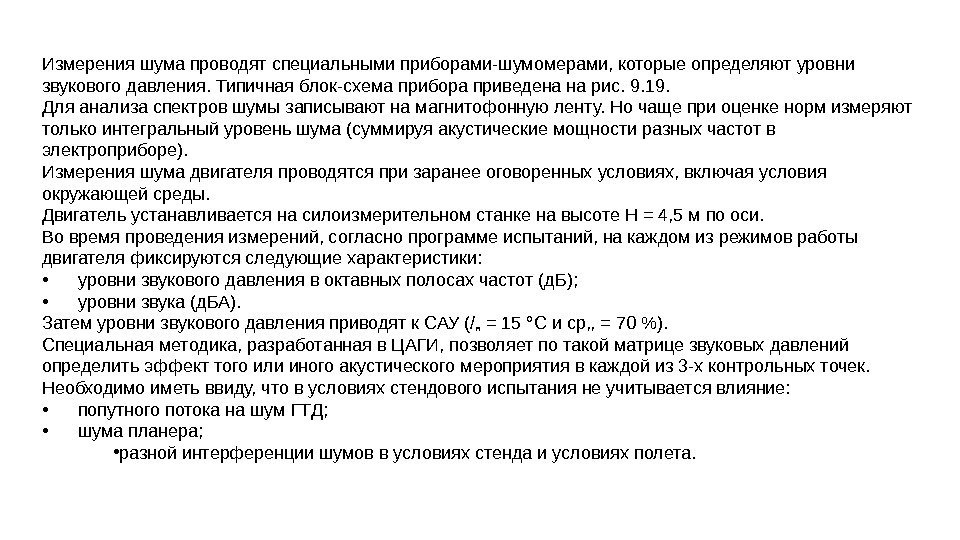
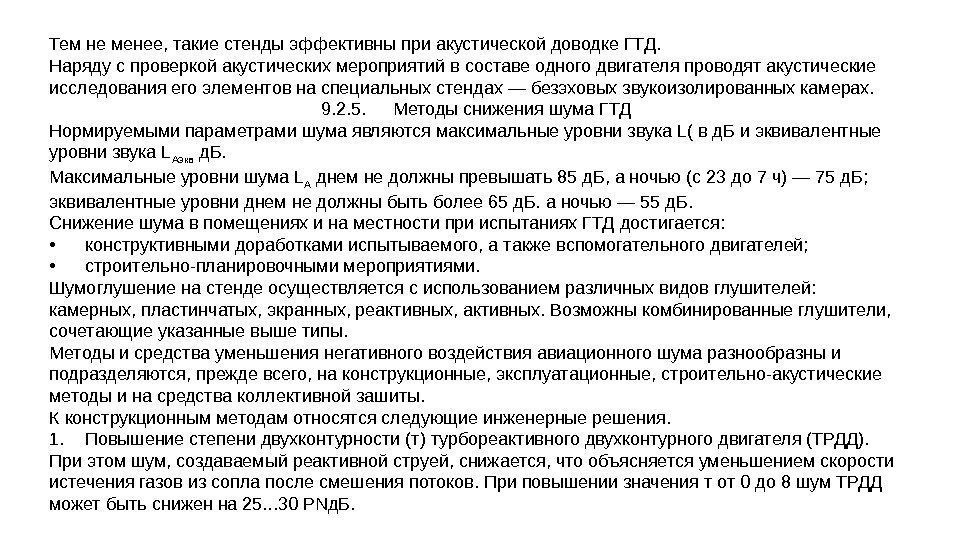
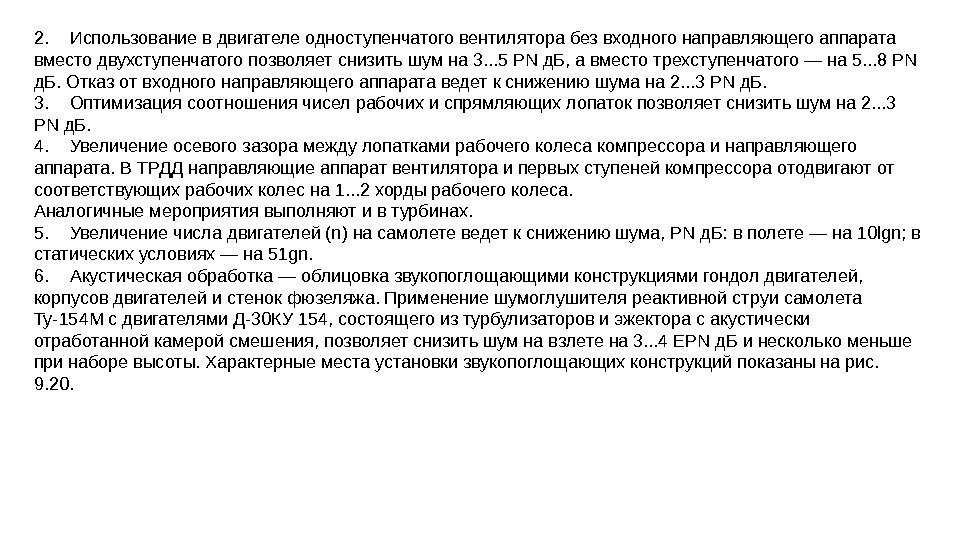
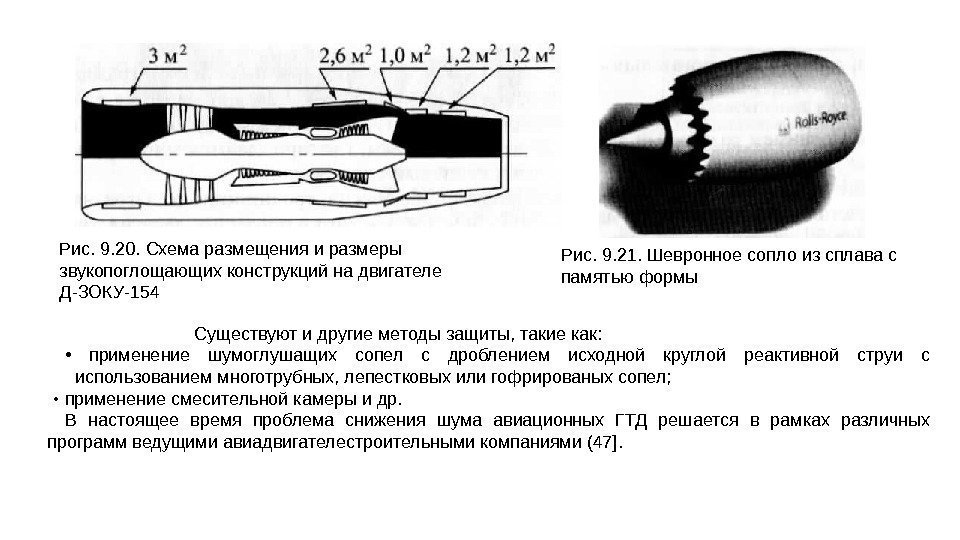
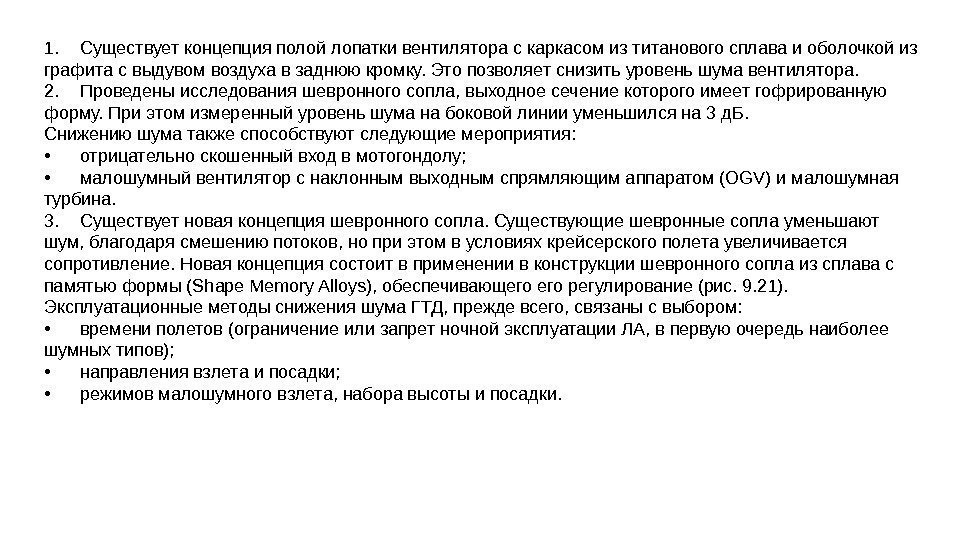
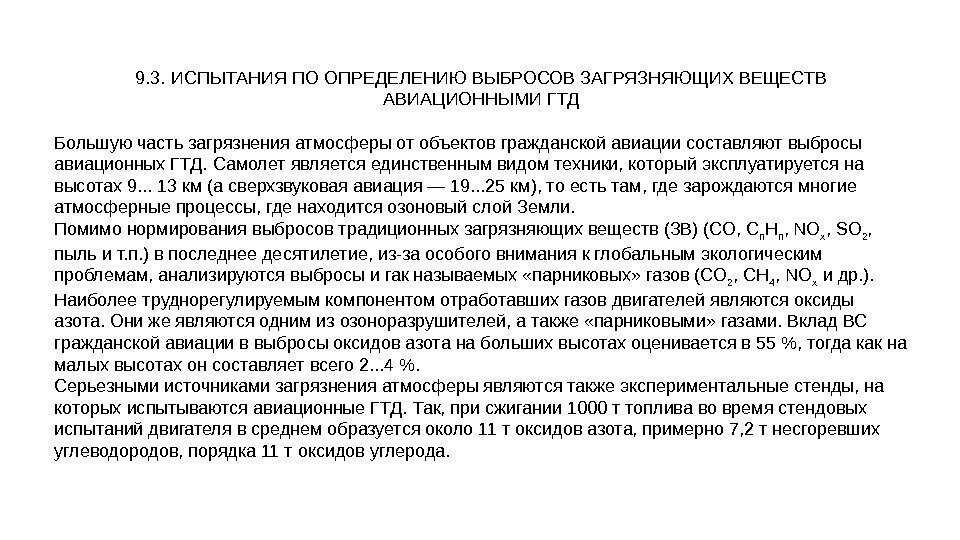
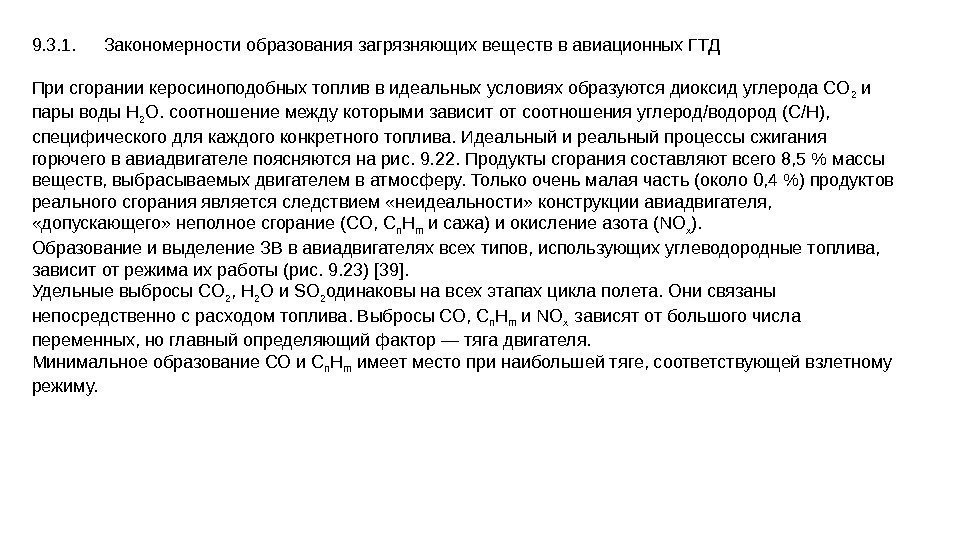
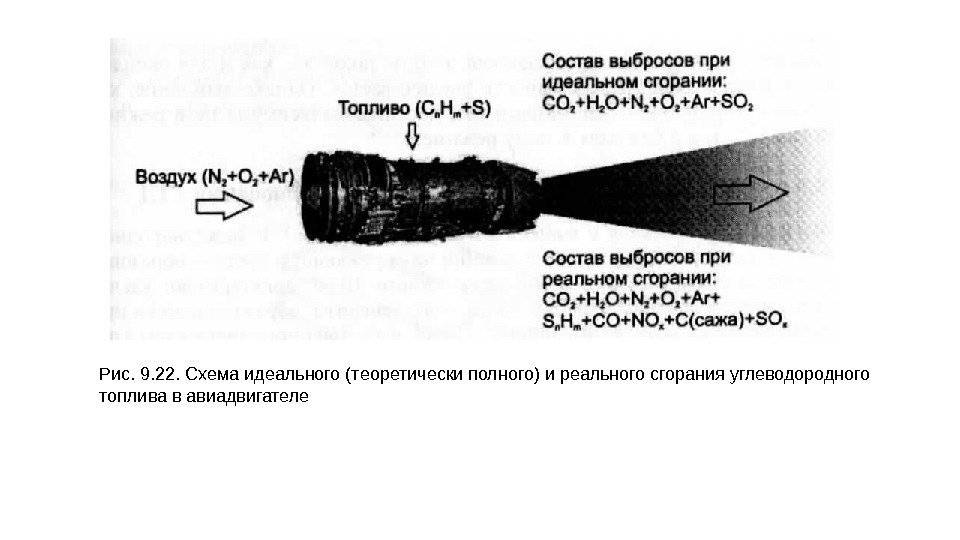
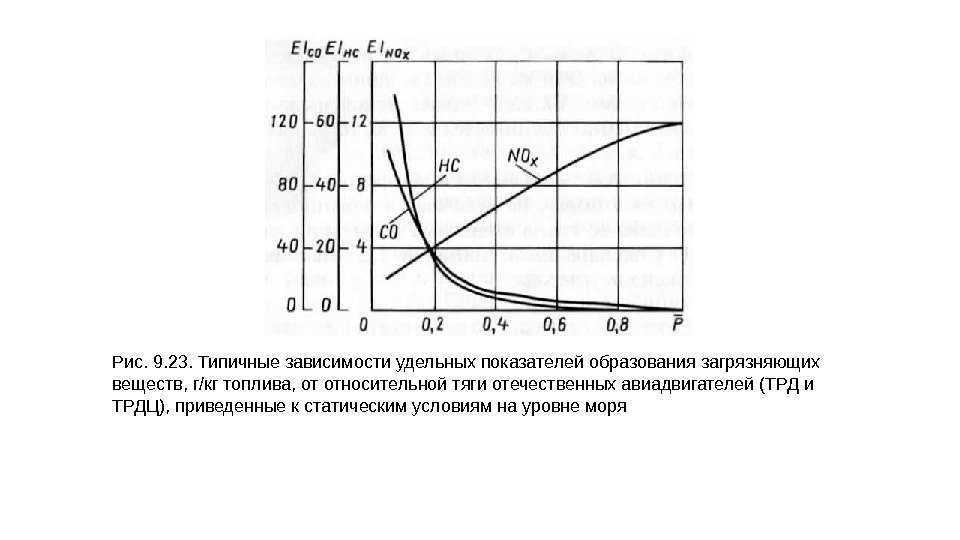
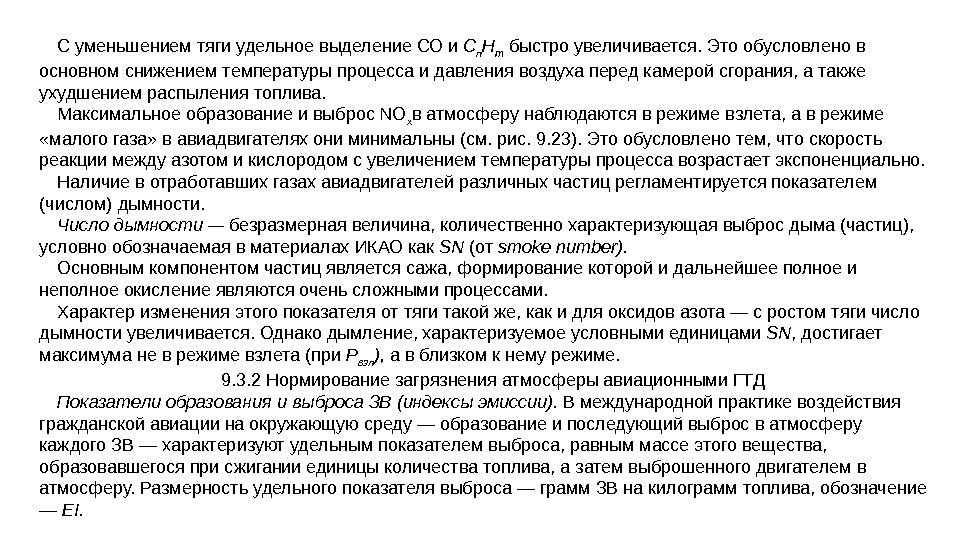
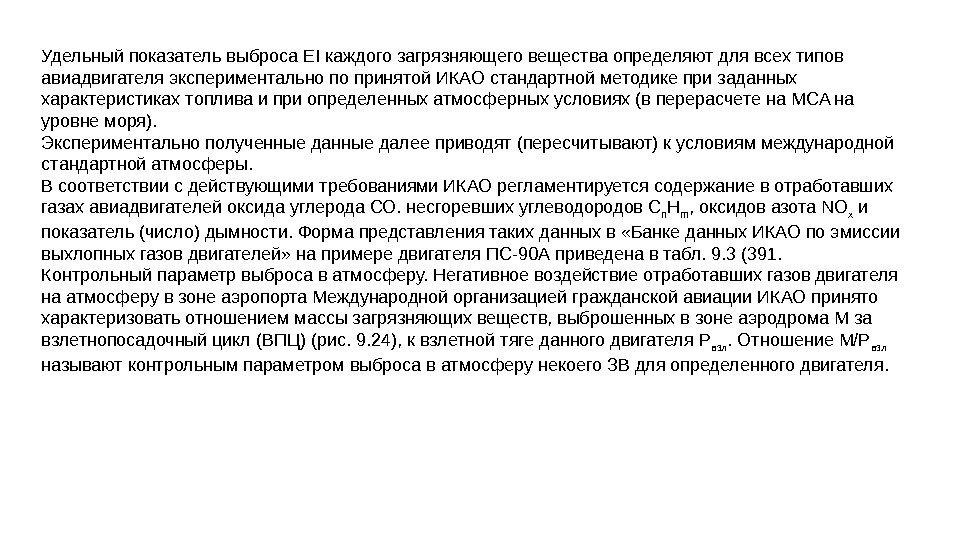
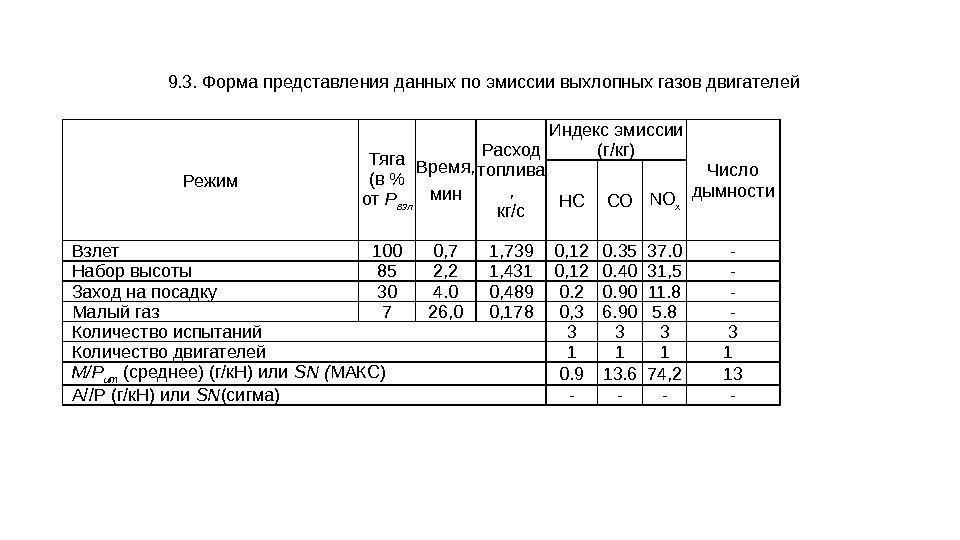
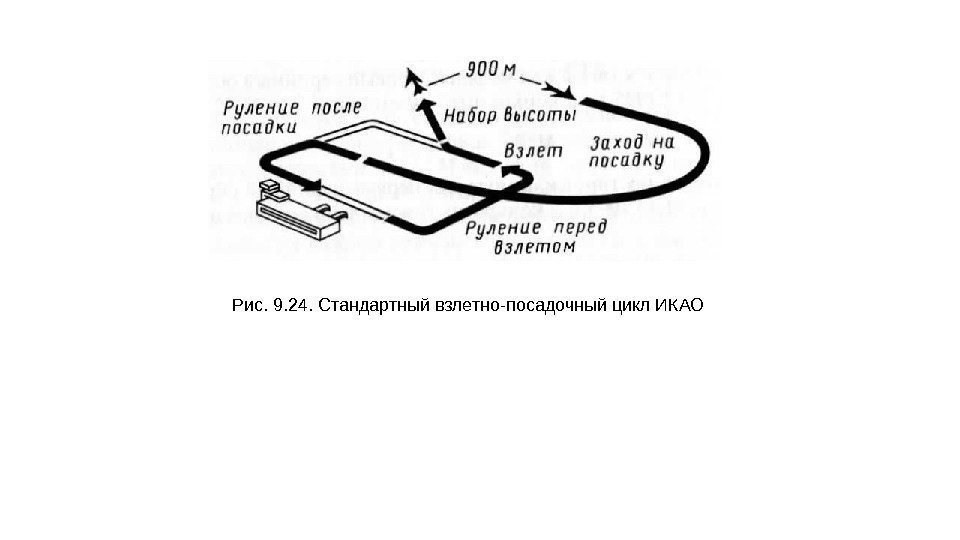
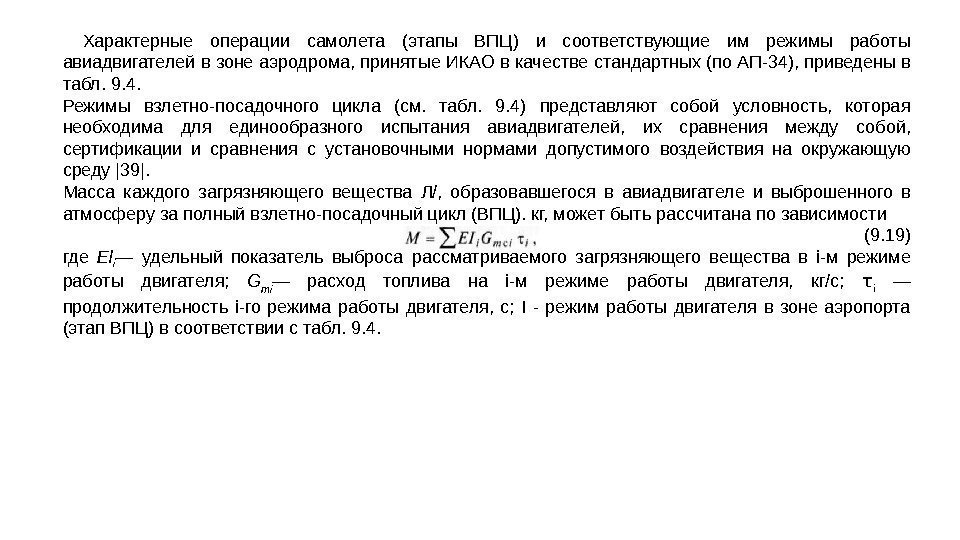
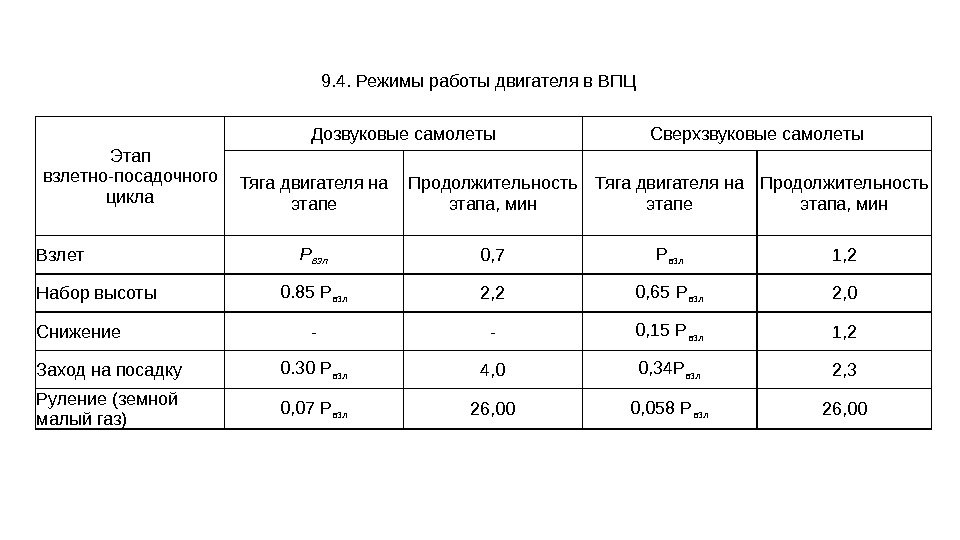
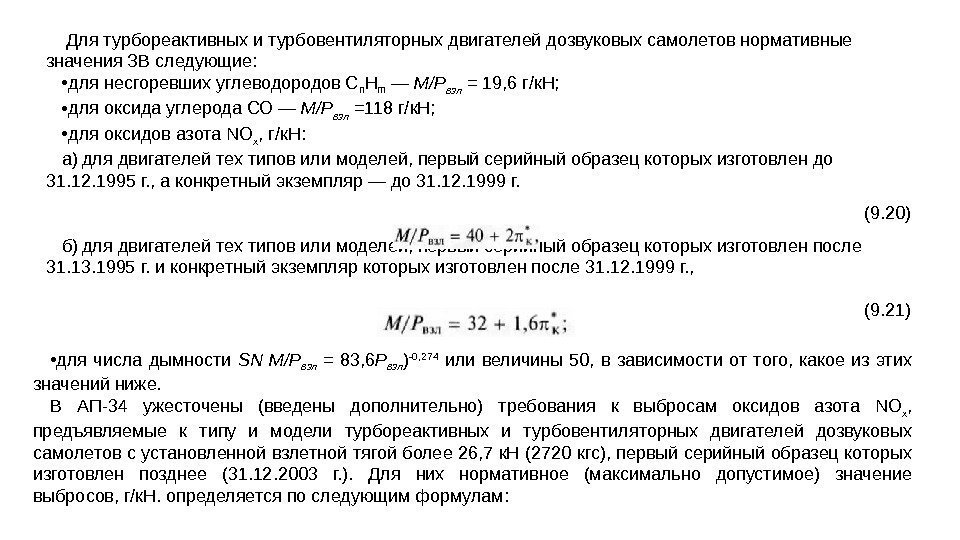
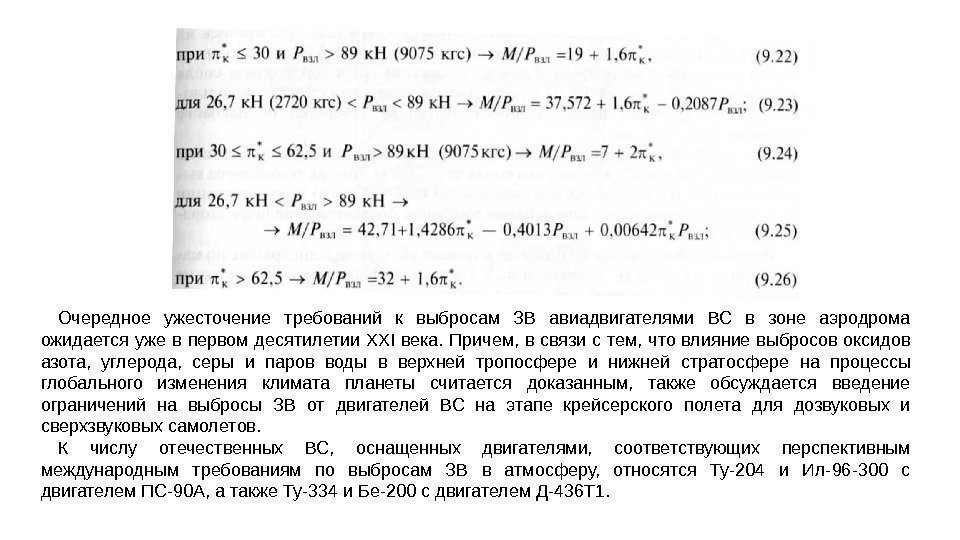
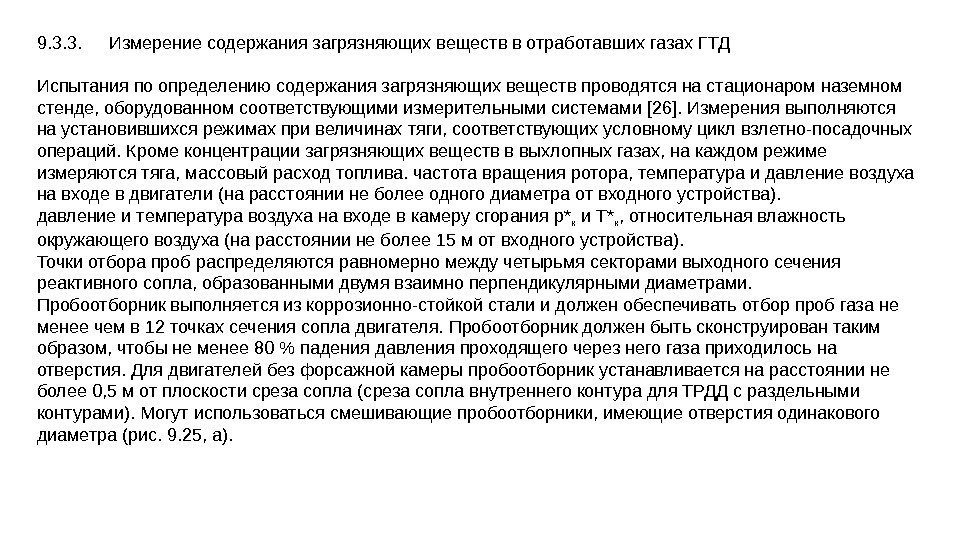
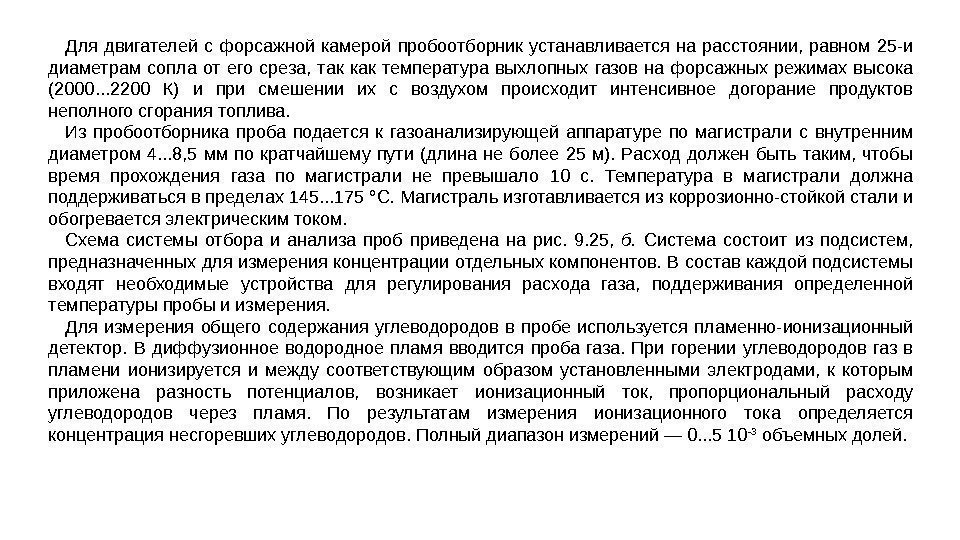
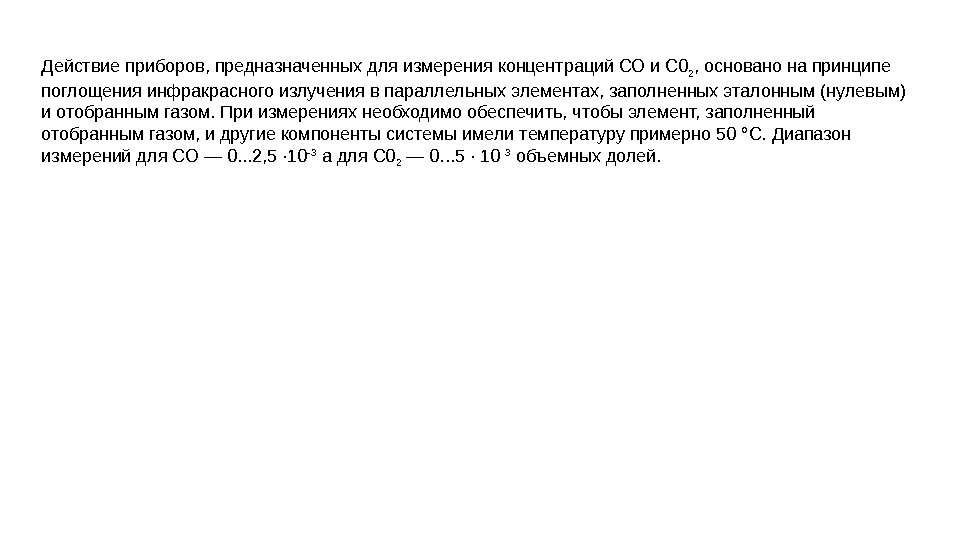
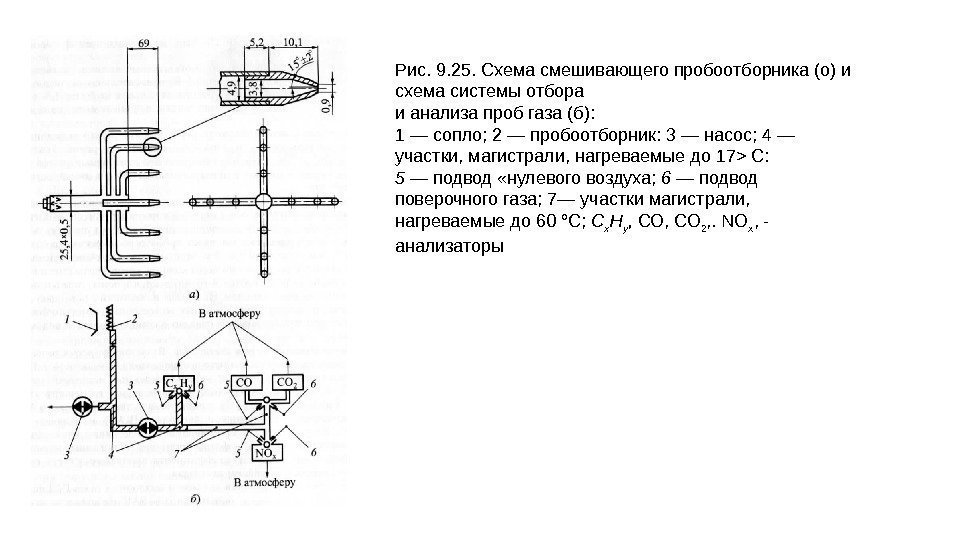
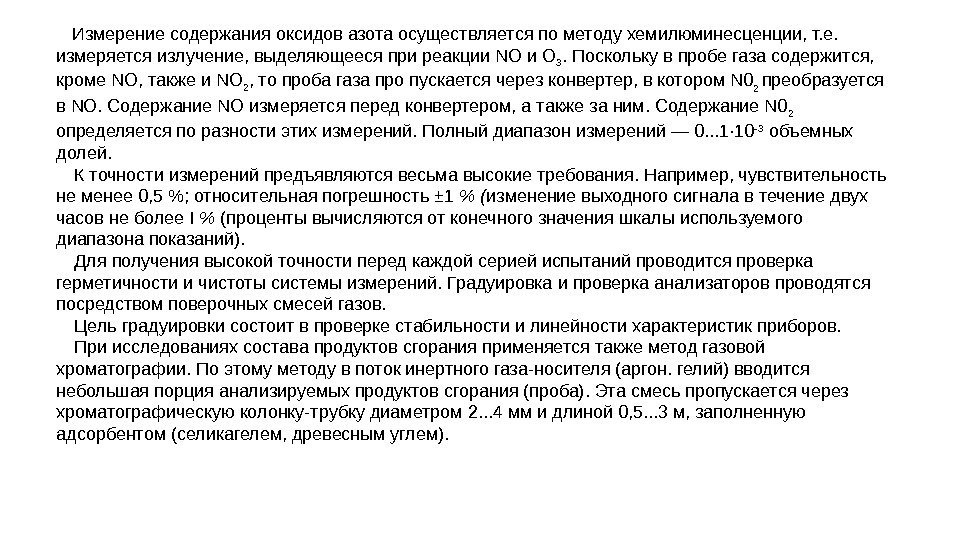
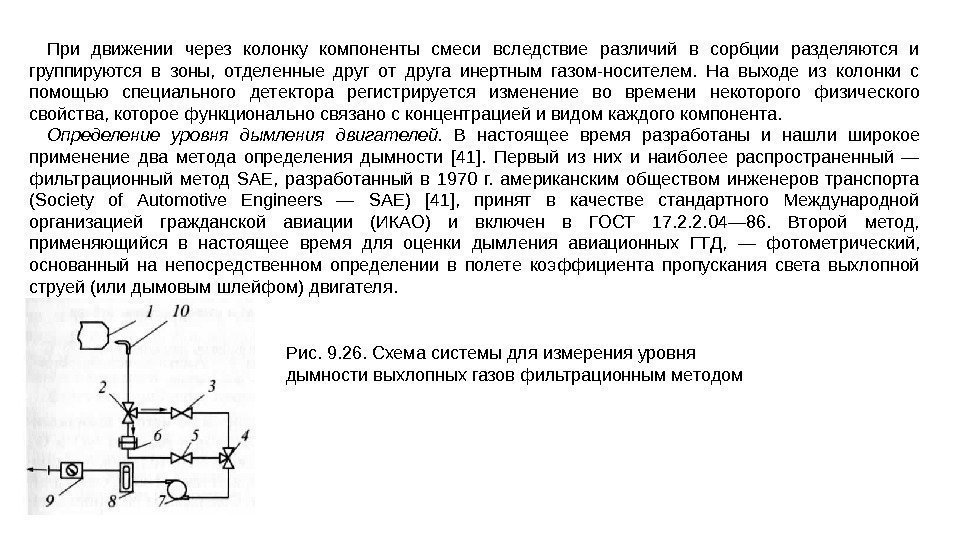
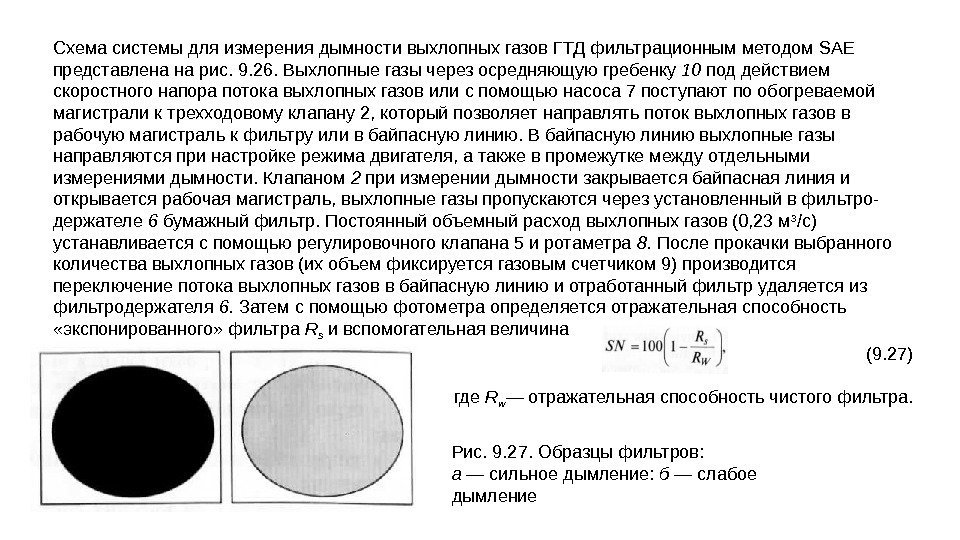
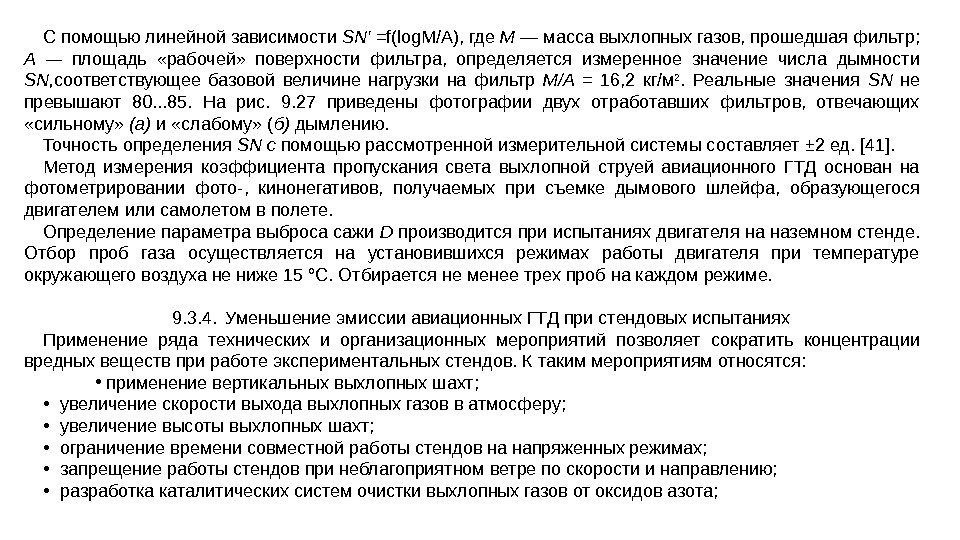
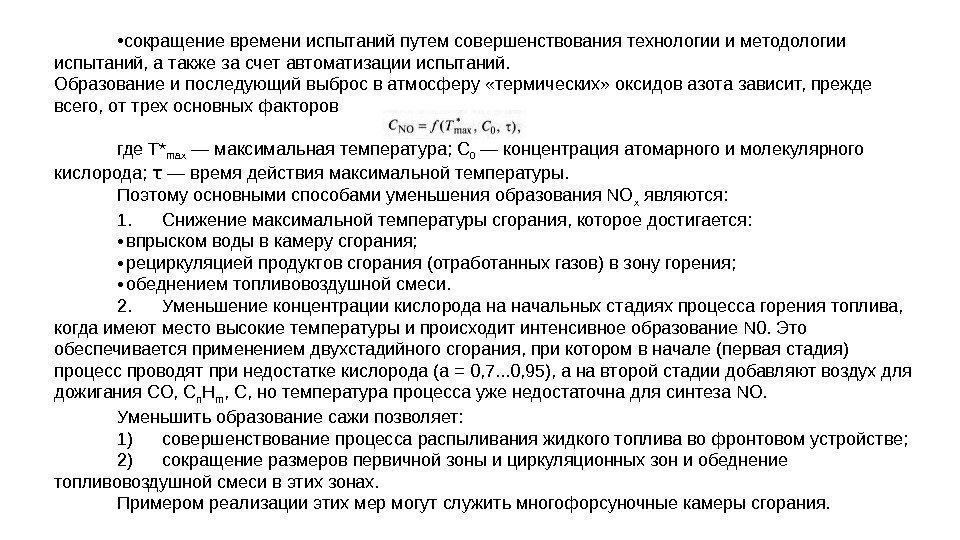
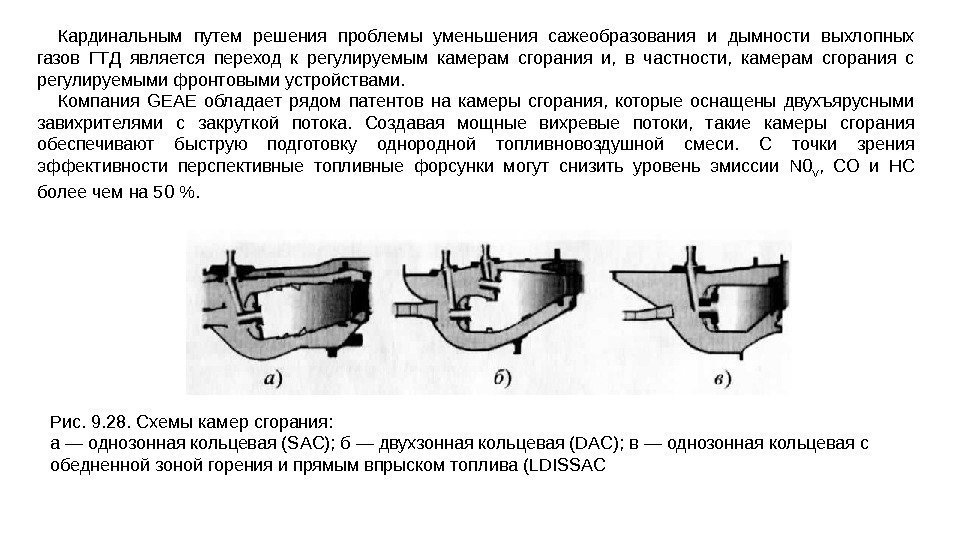
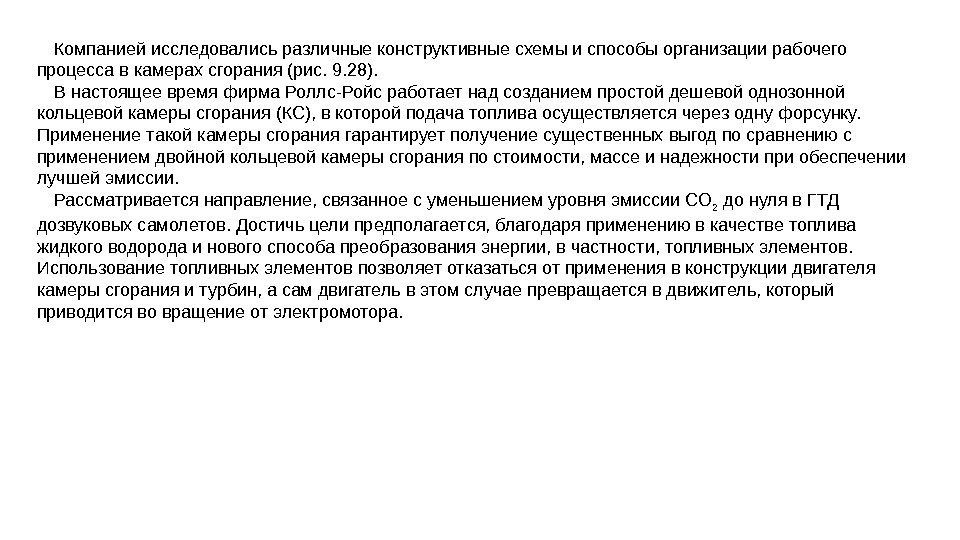
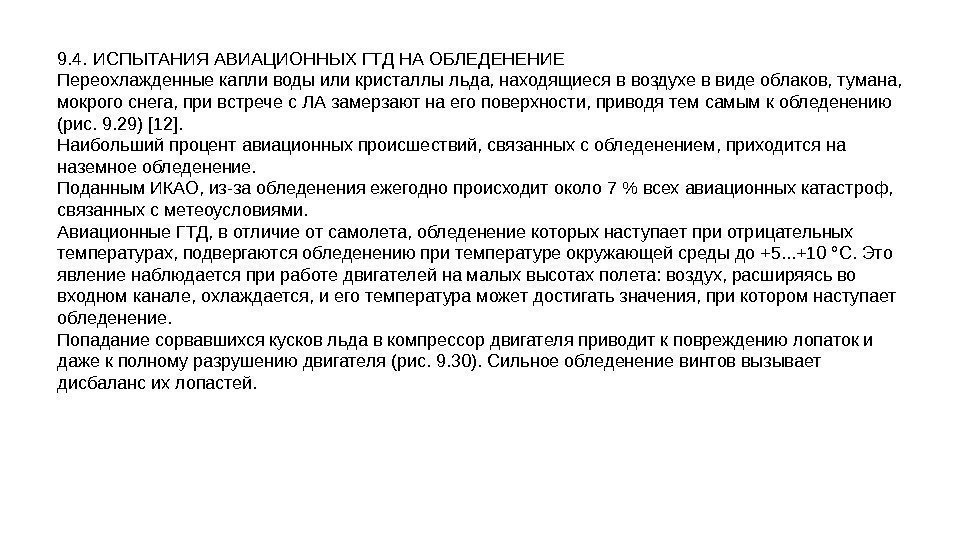
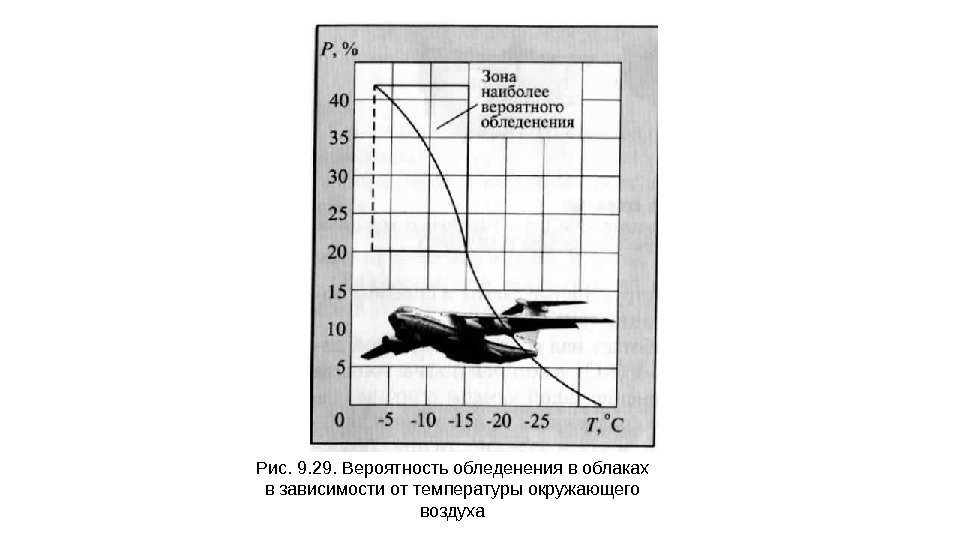
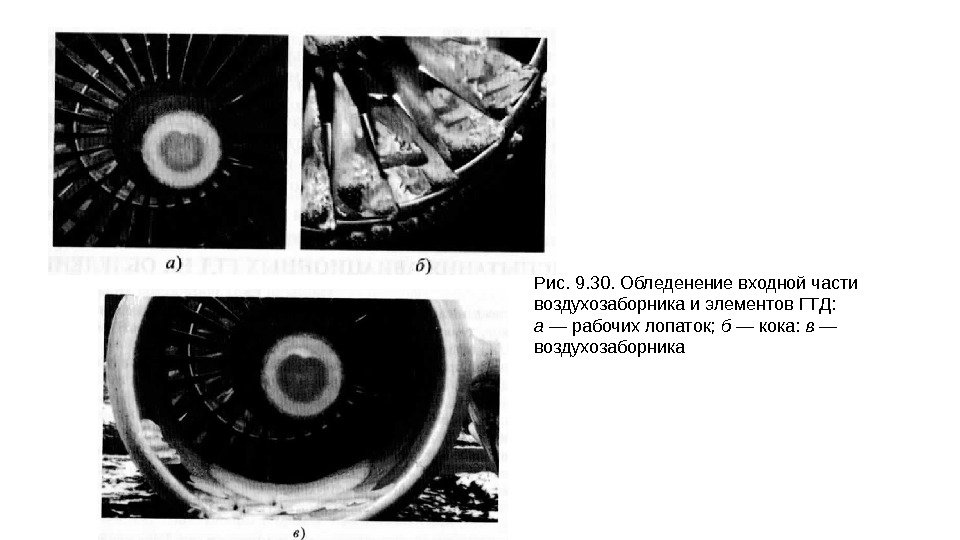
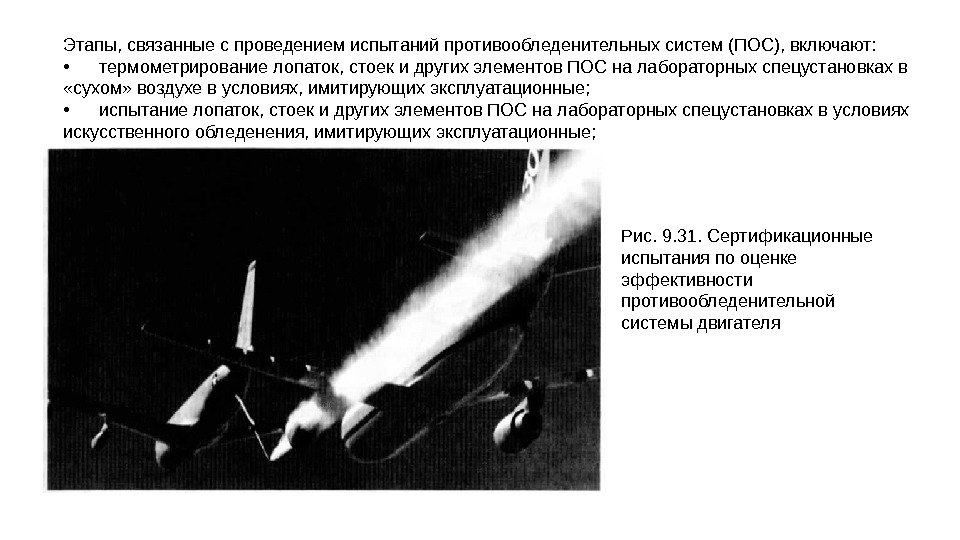
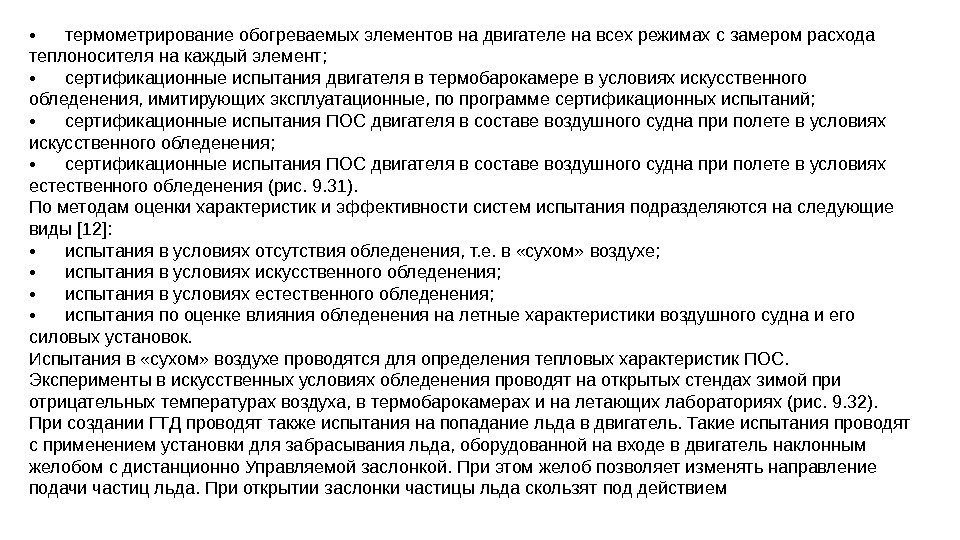
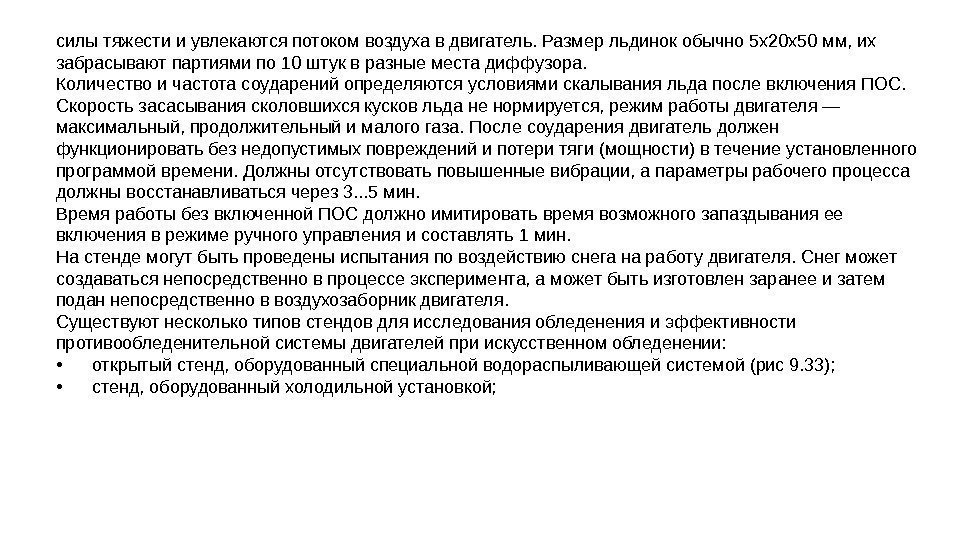
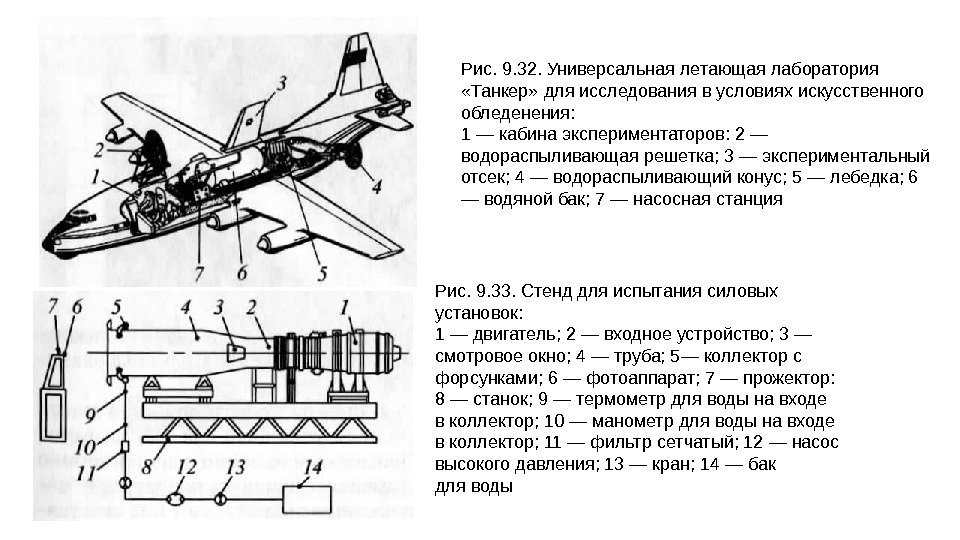
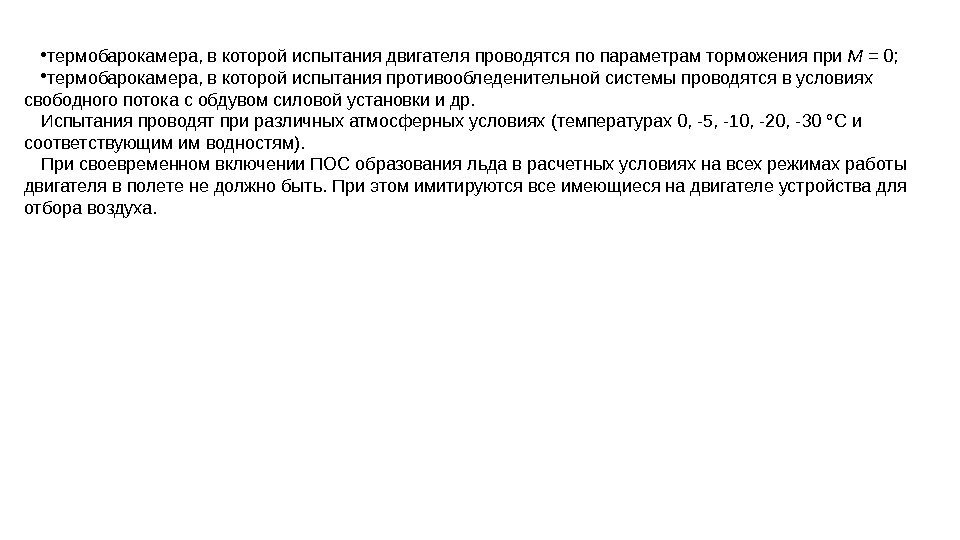
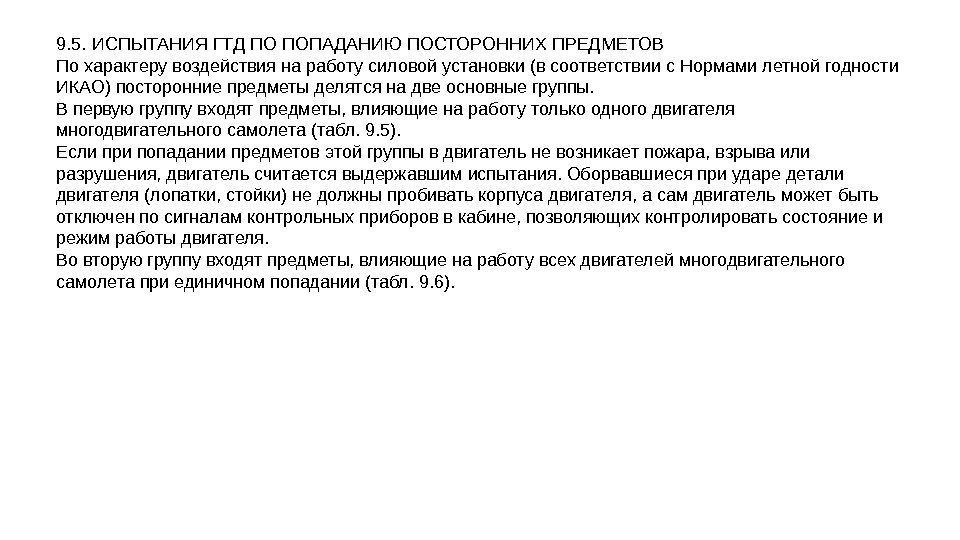
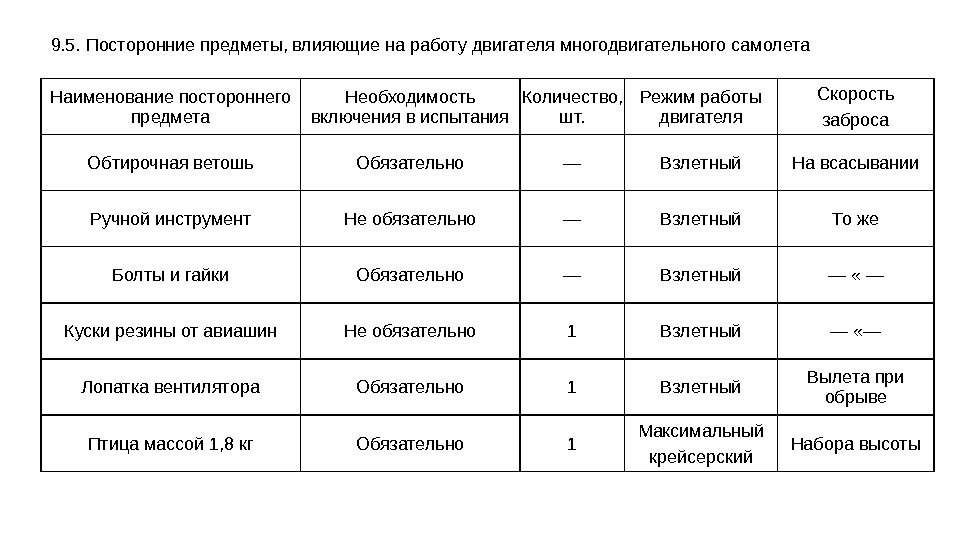
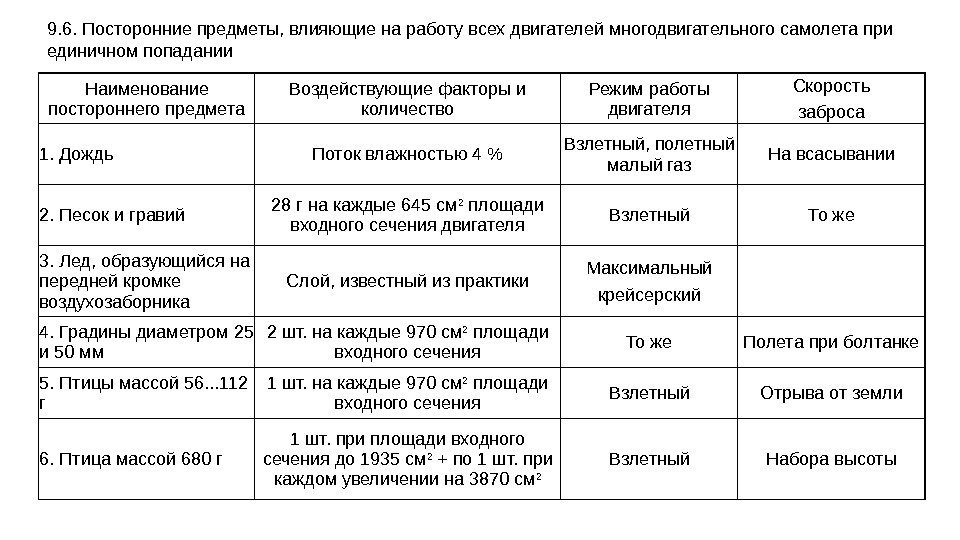
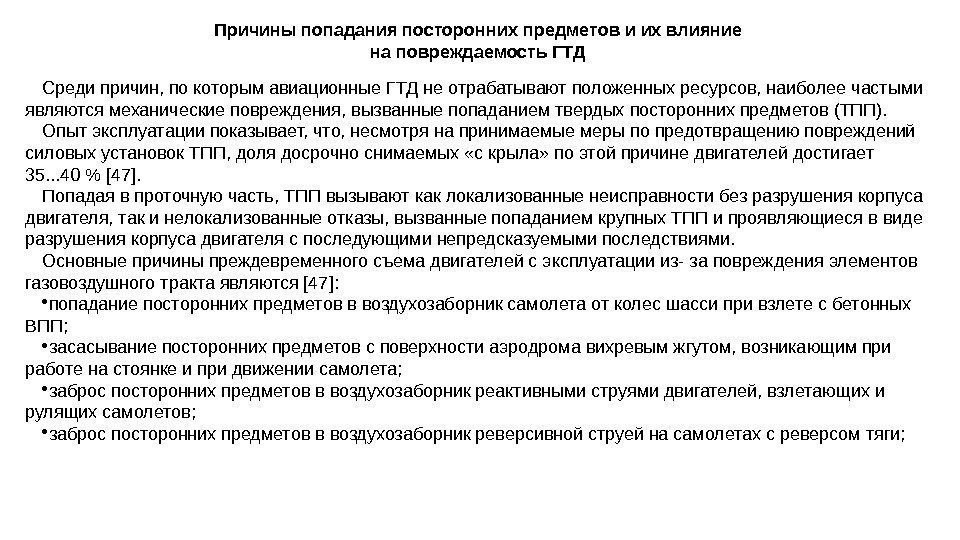
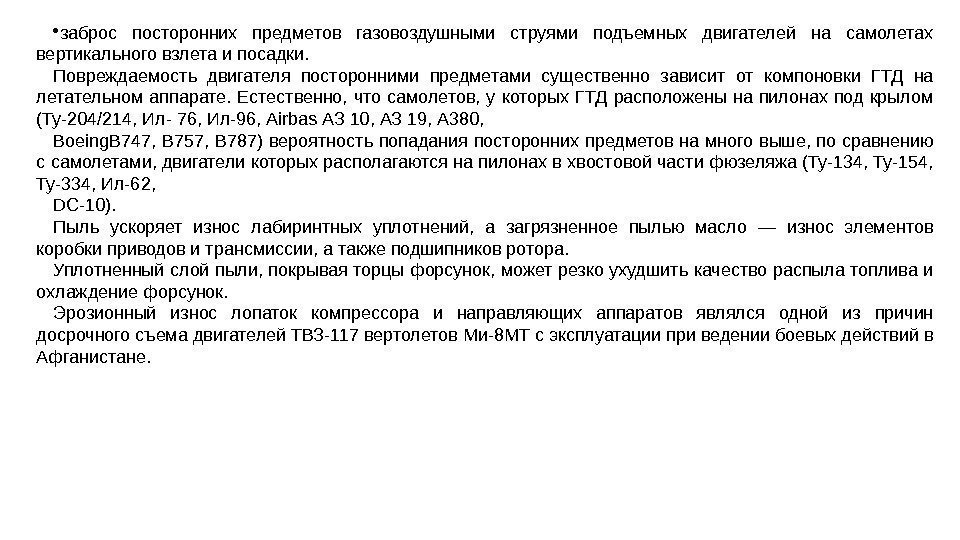
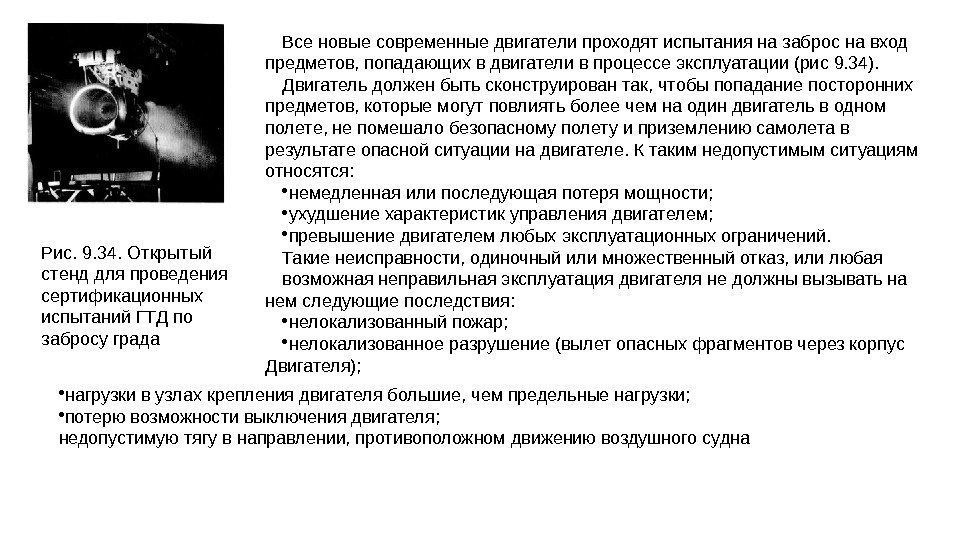
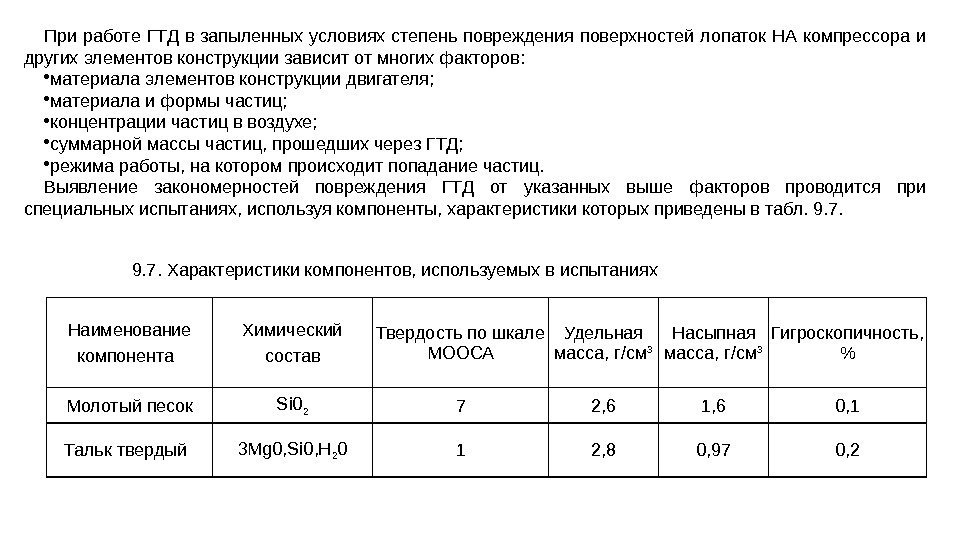
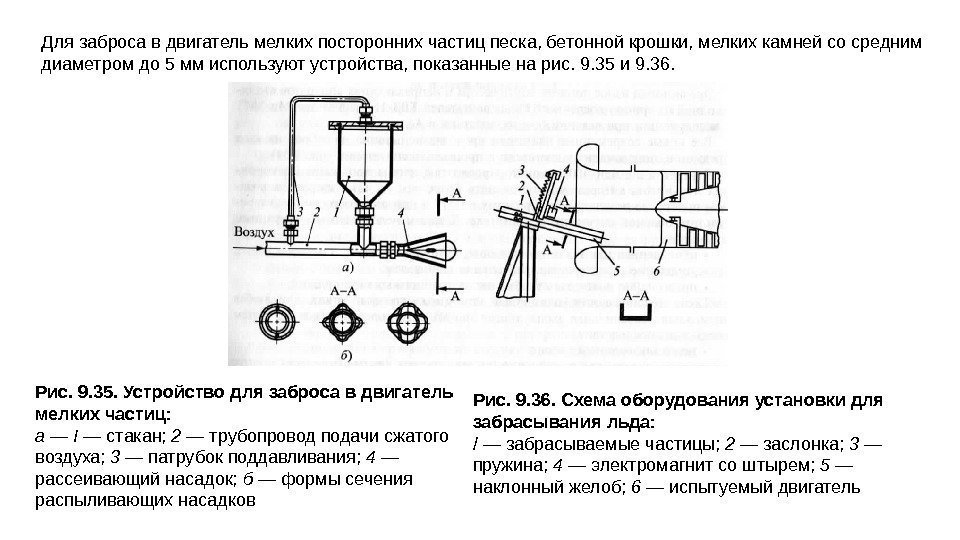
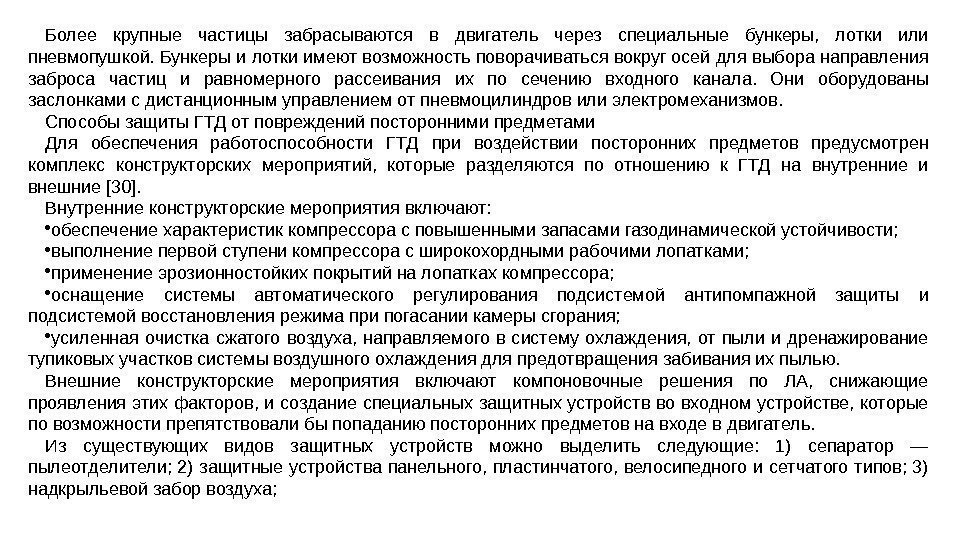
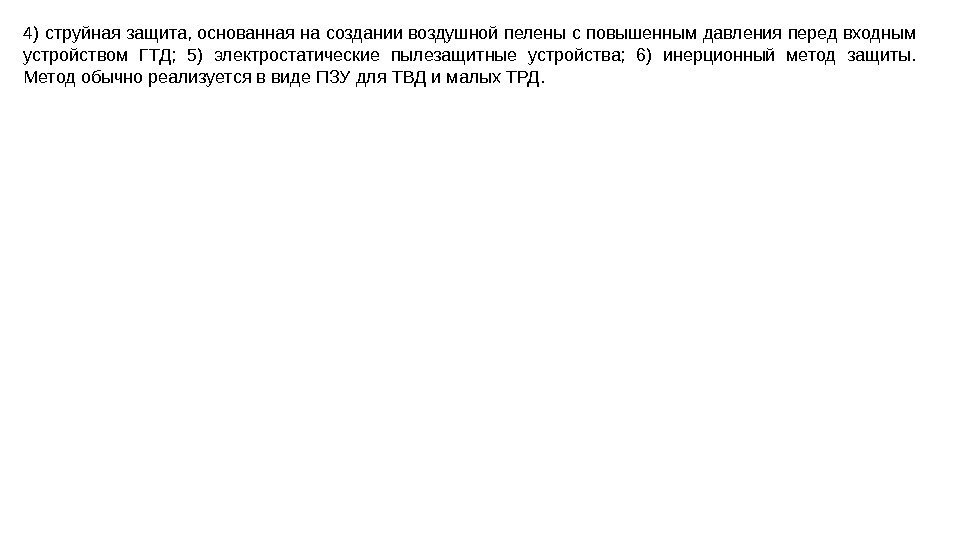
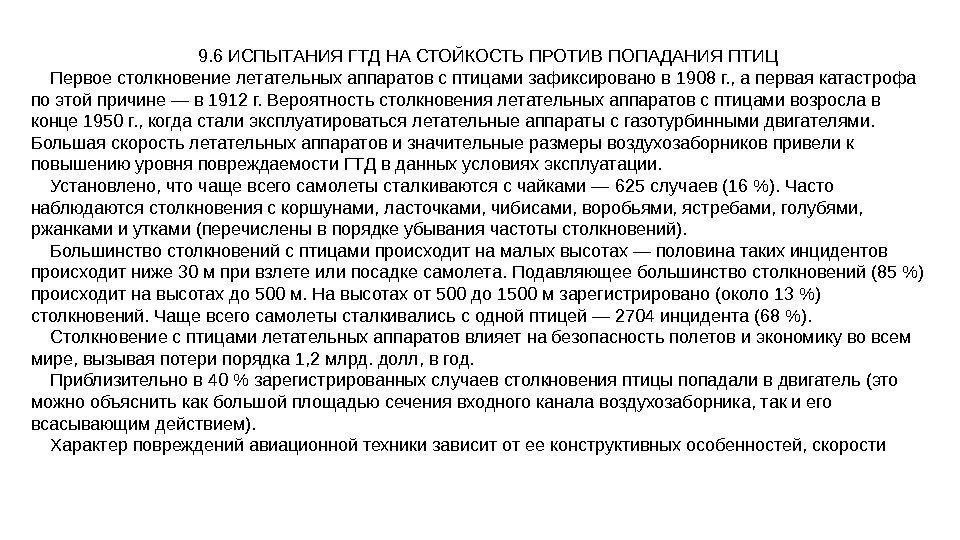
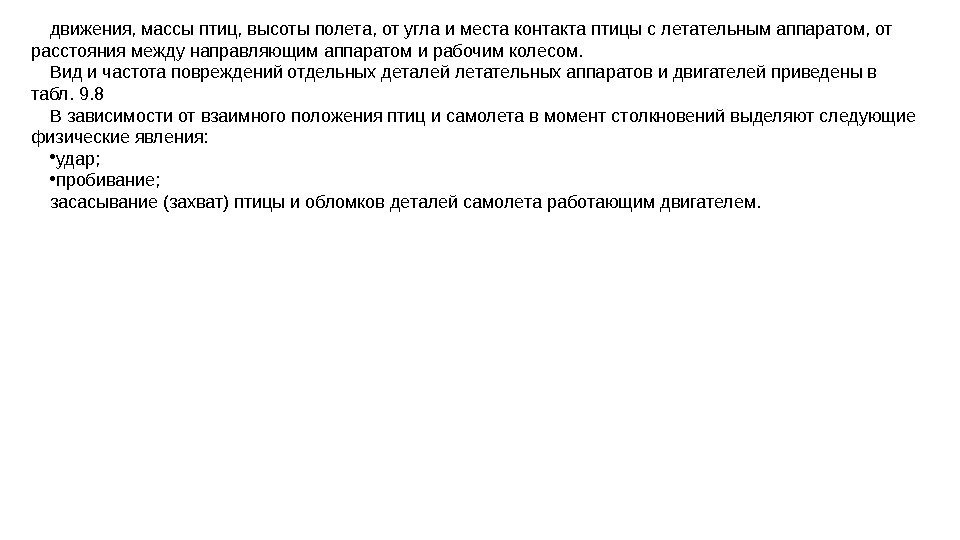

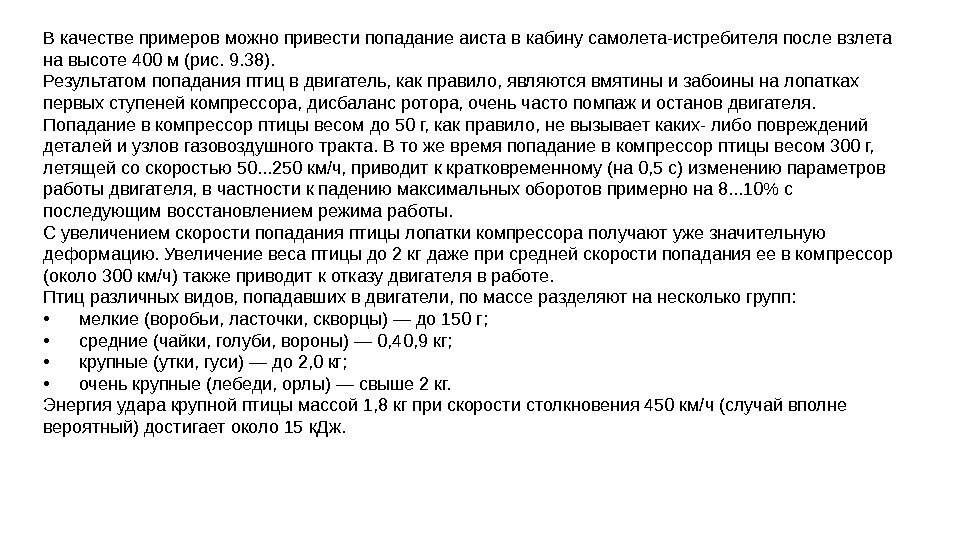
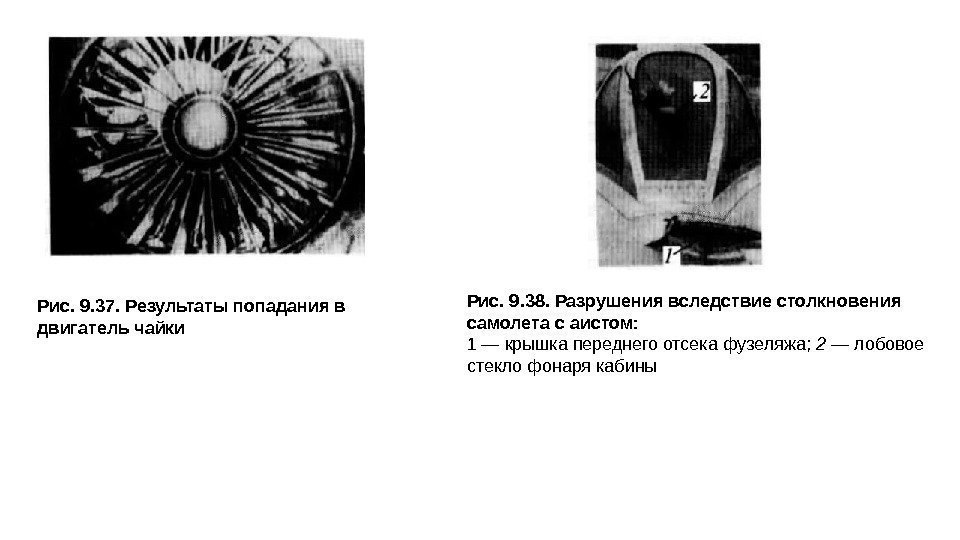
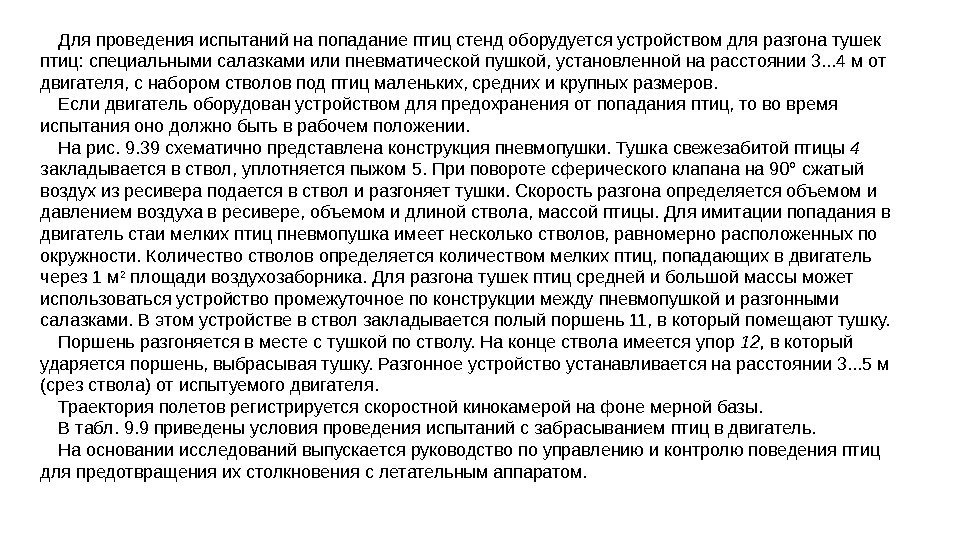
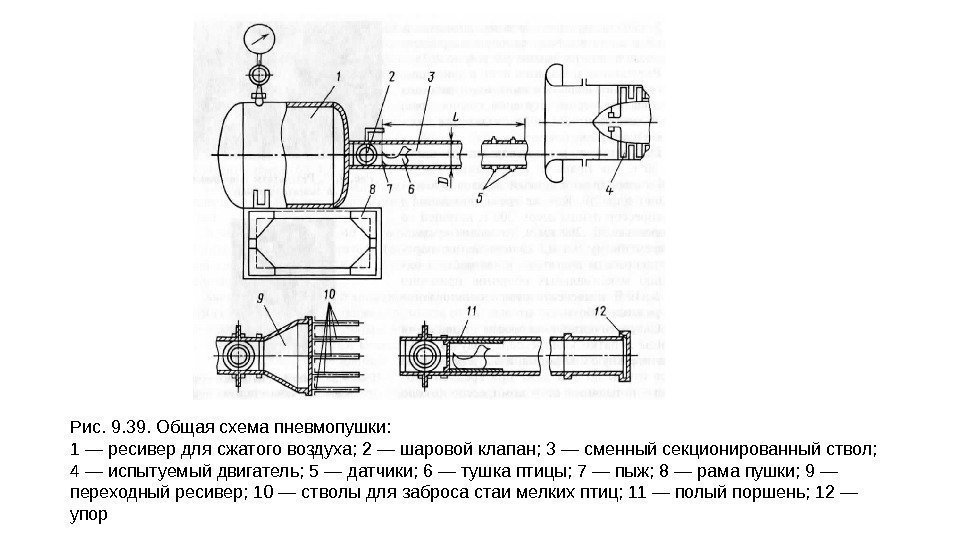
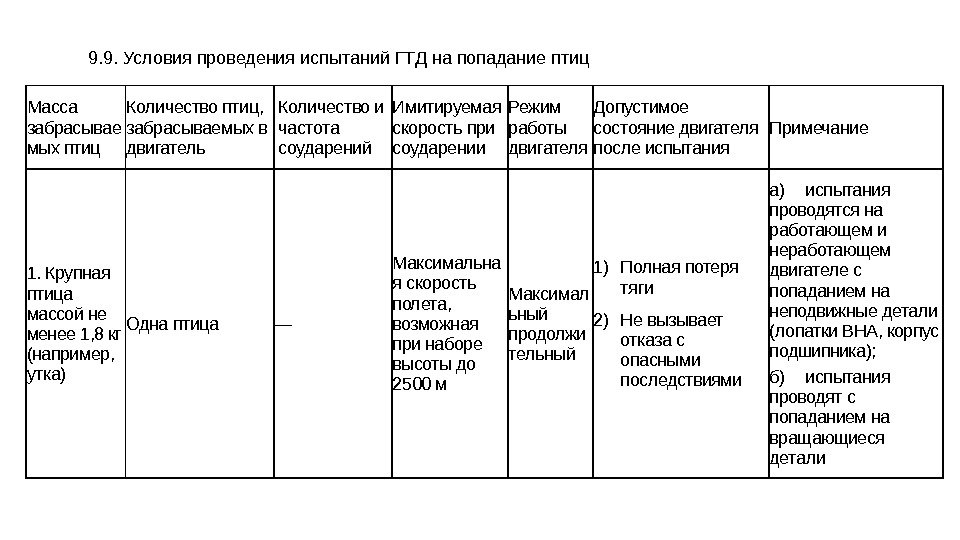
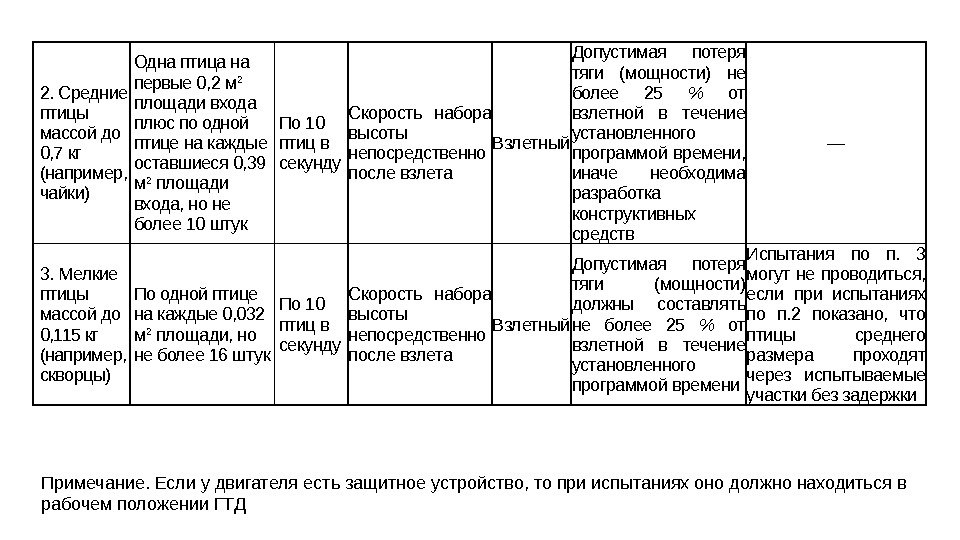
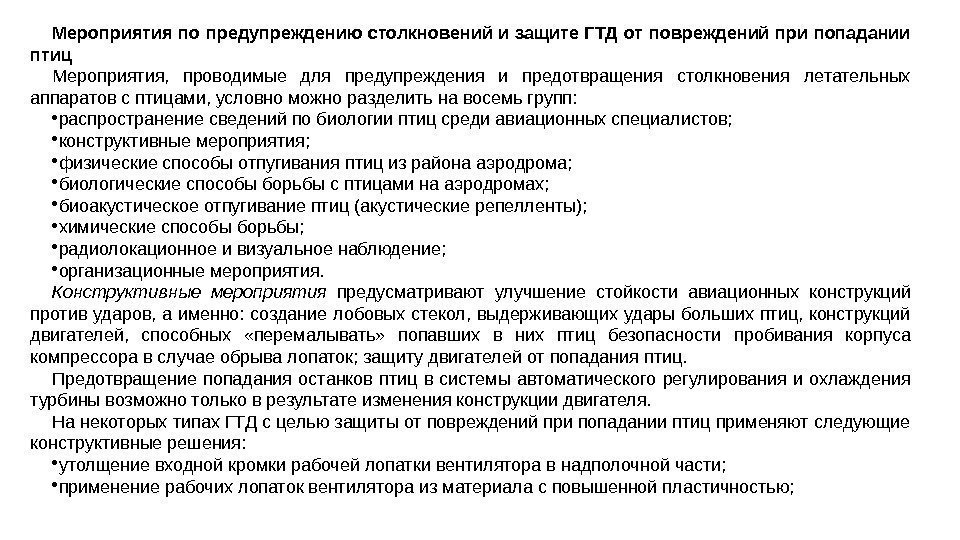
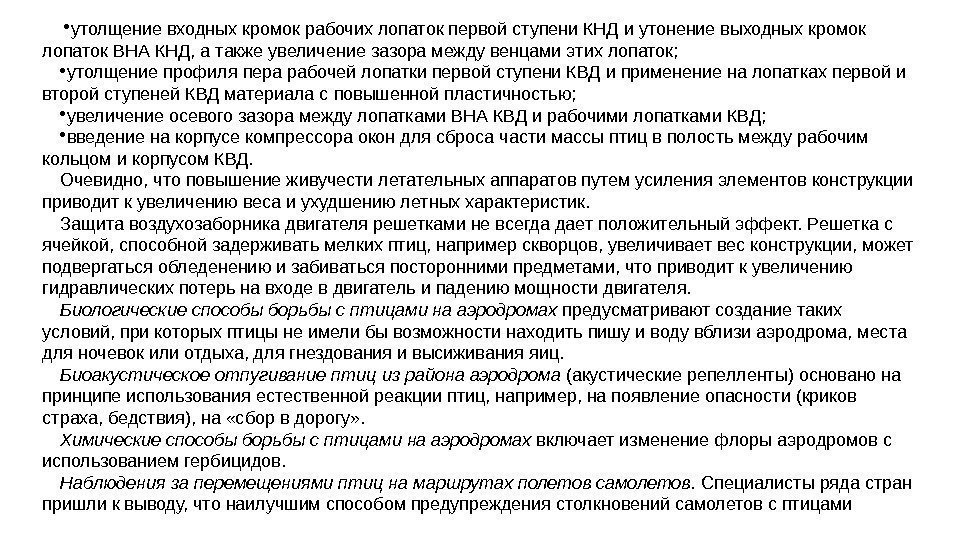
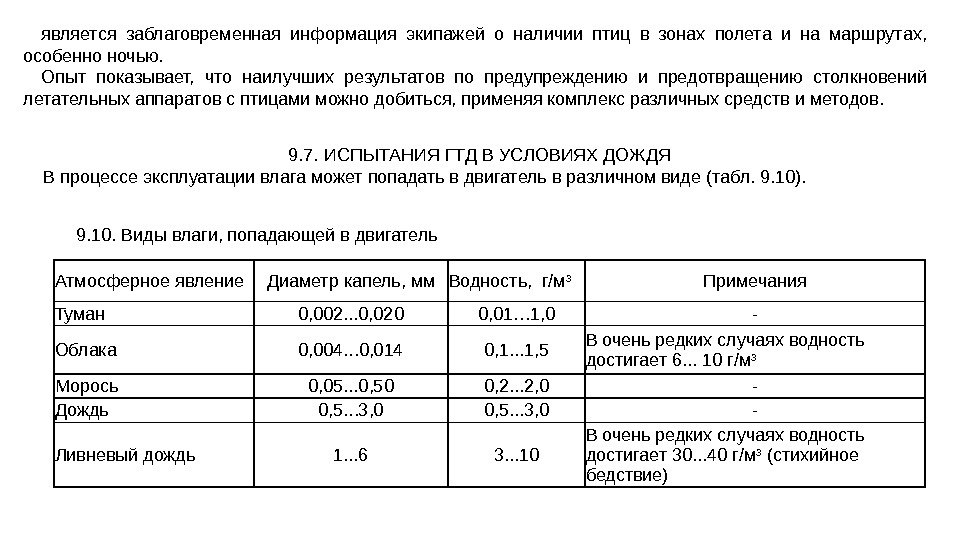
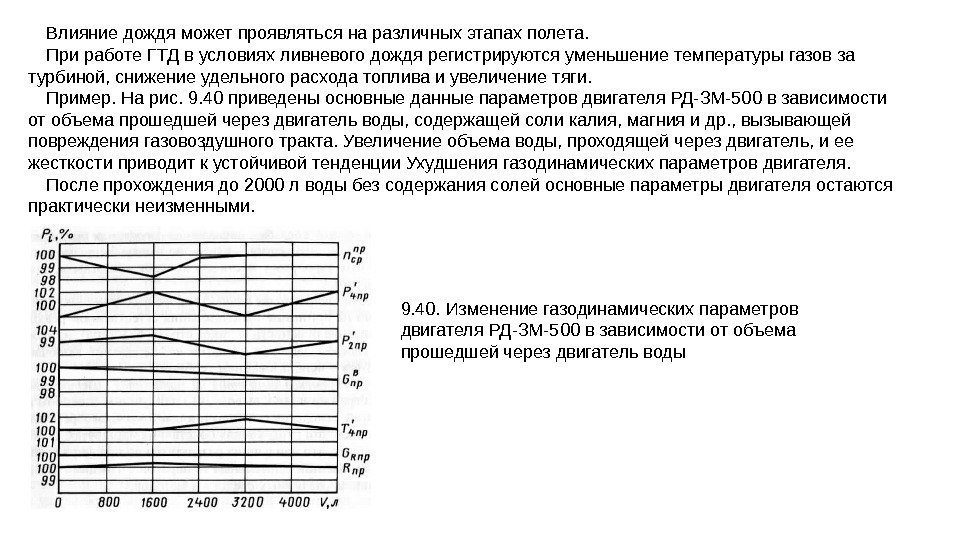
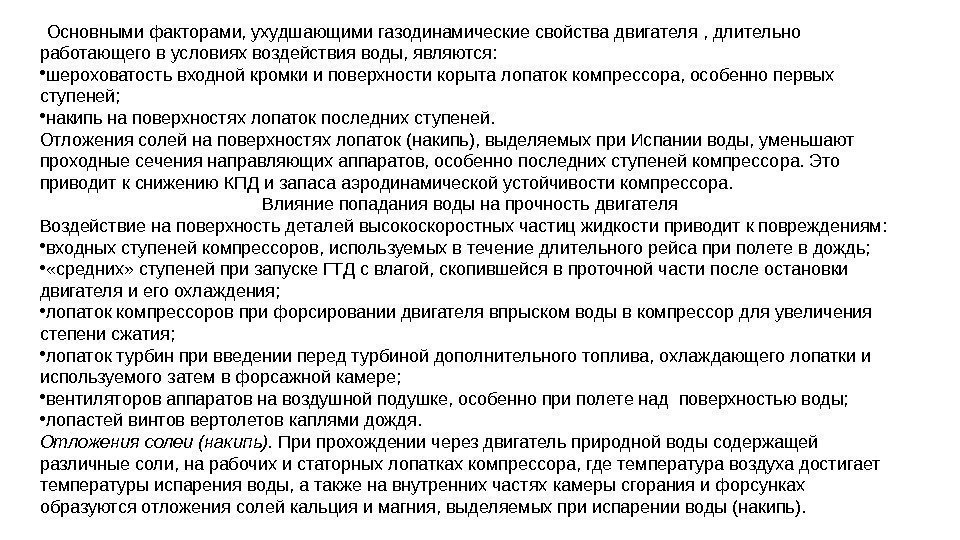
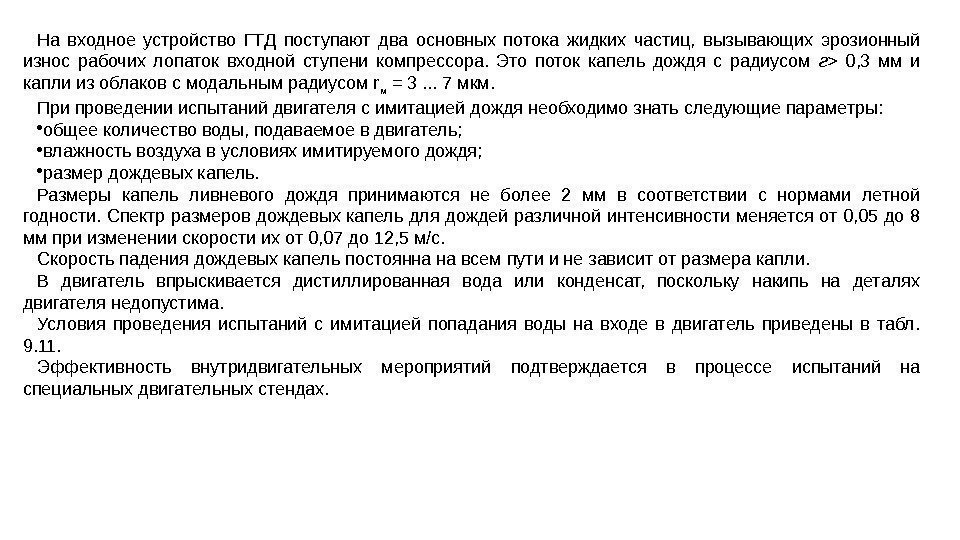
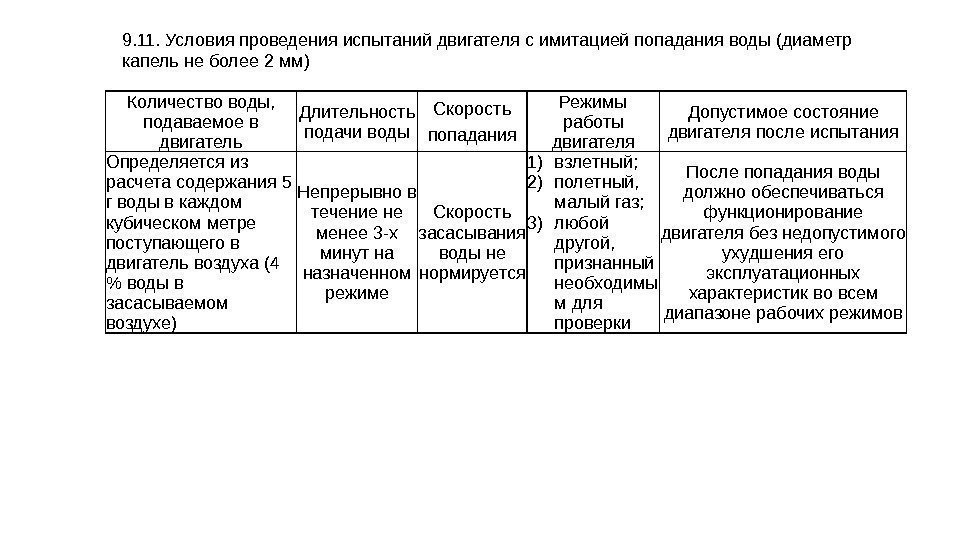
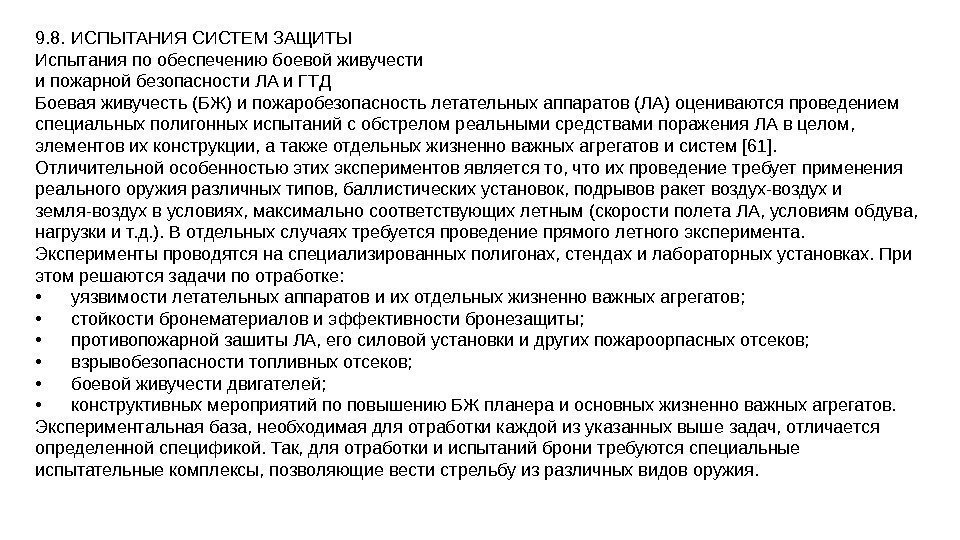
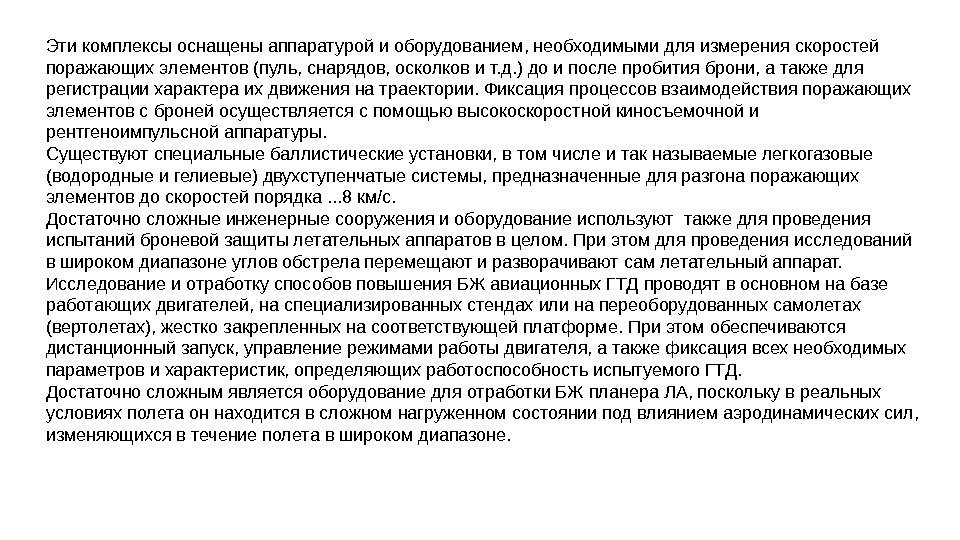
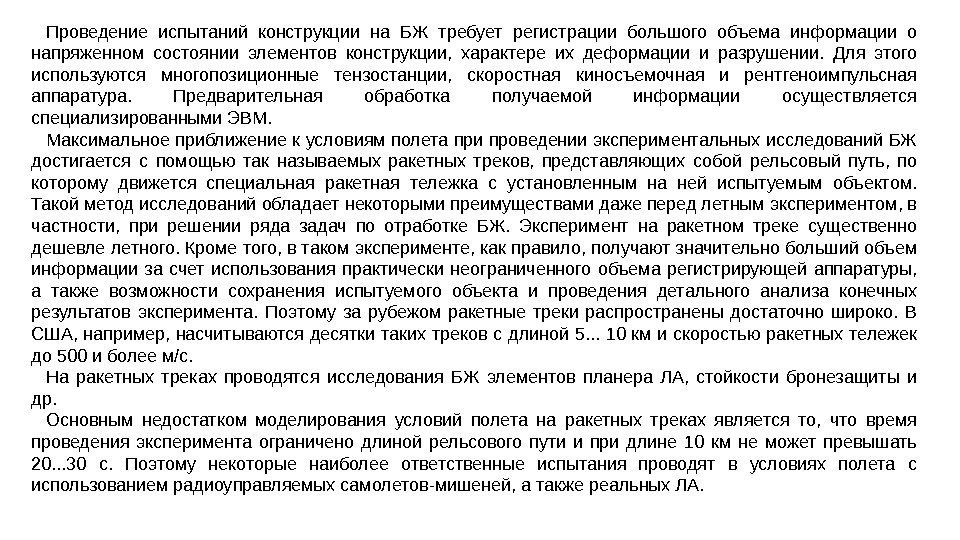
![Боевые повреждения авиационных ГТД Для боевых повреждений элементов конструкции ГТД характерны следующие особенности [48]: Боевые повреждения авиационных ГТД Для боевых повреждений элементов конструкции ГТД характерны следующие особенности [48]:](http://present5.com/presentforday2/20170201/mmk_ispytania_i_kontrol_kachestva_izdeliy_2017_images/mmk_ispytania_i_kontrol_kachestva_izdeliy_2017_636.jpg)
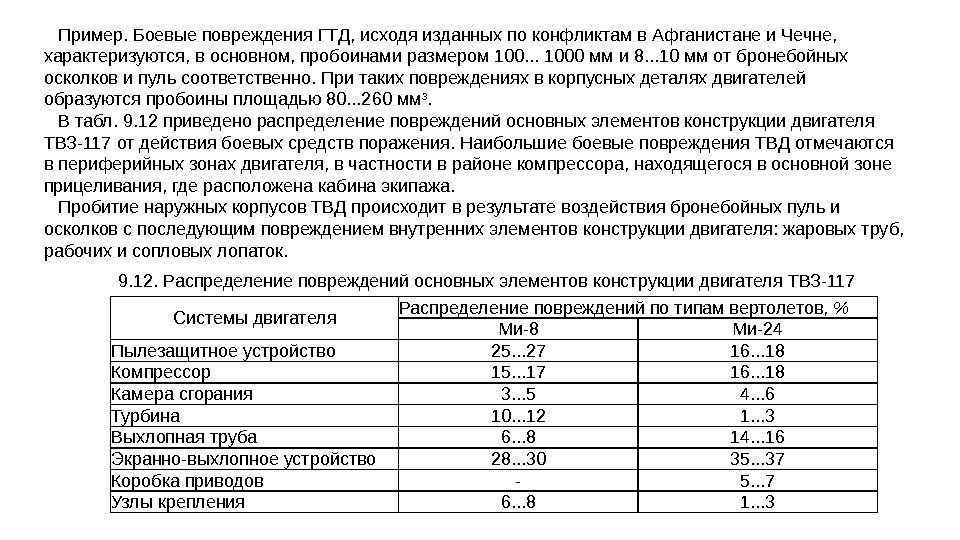
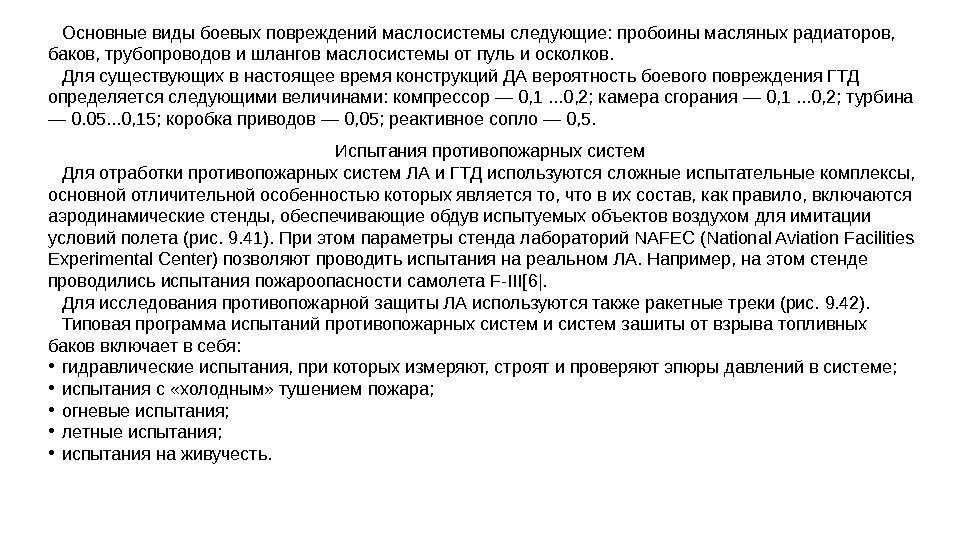
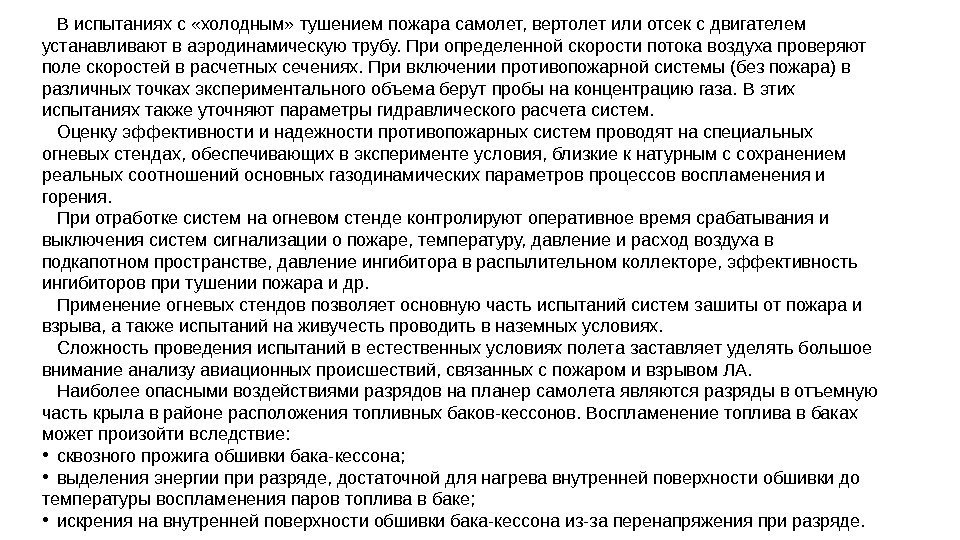
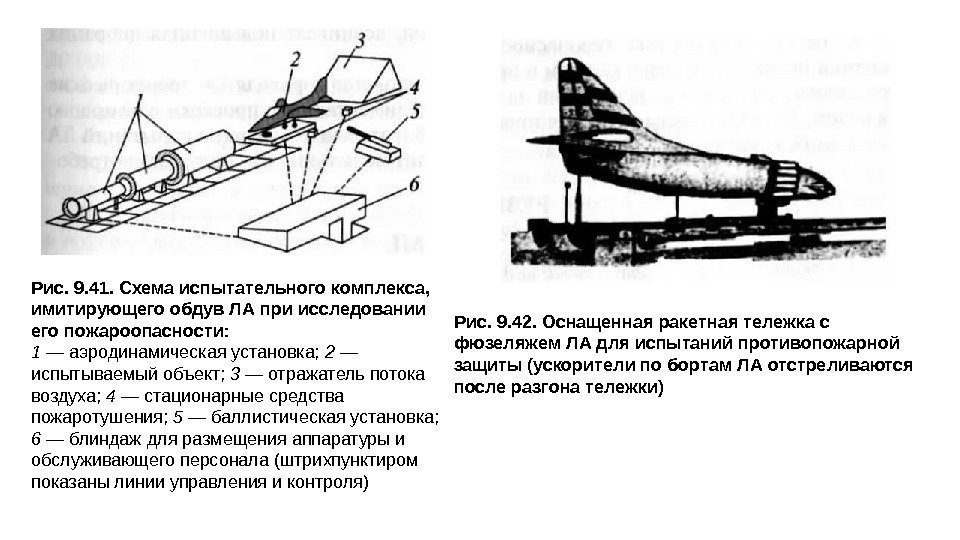

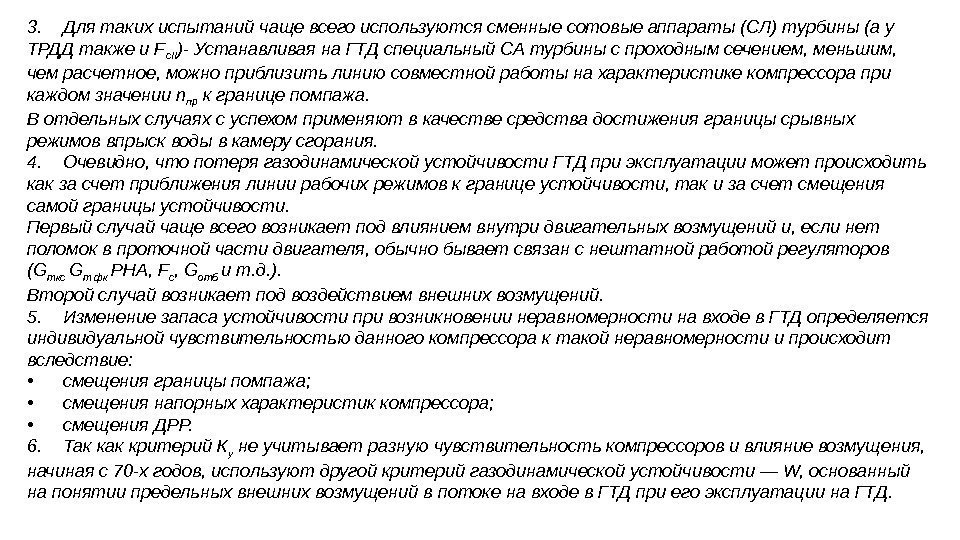
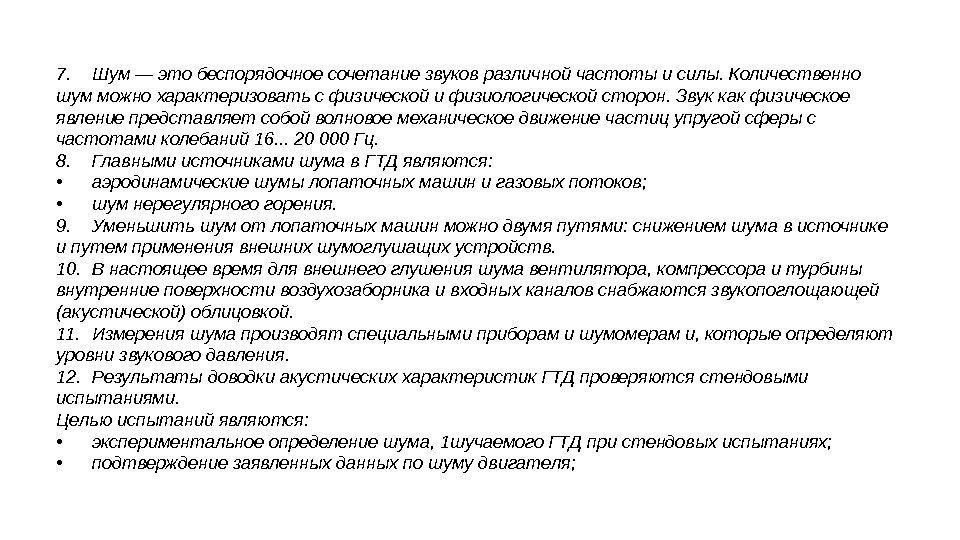
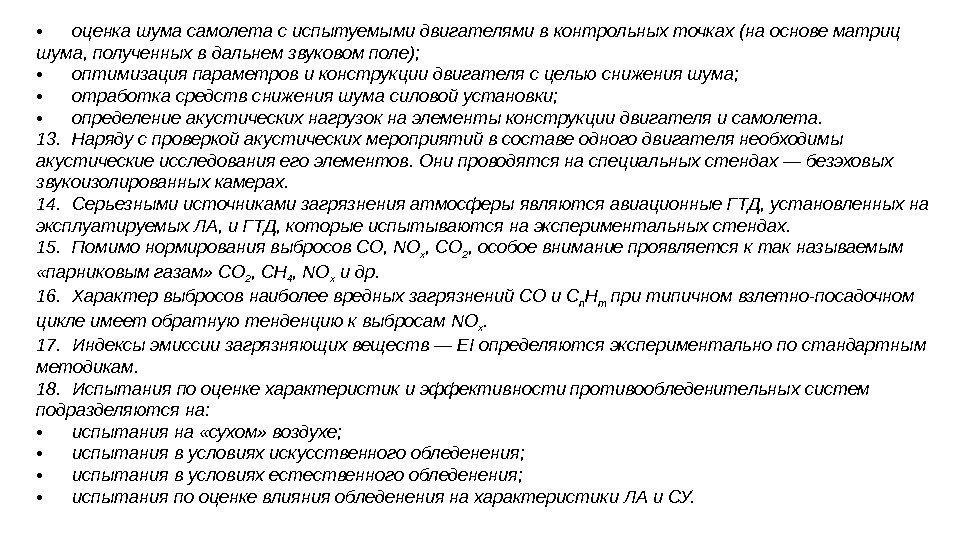
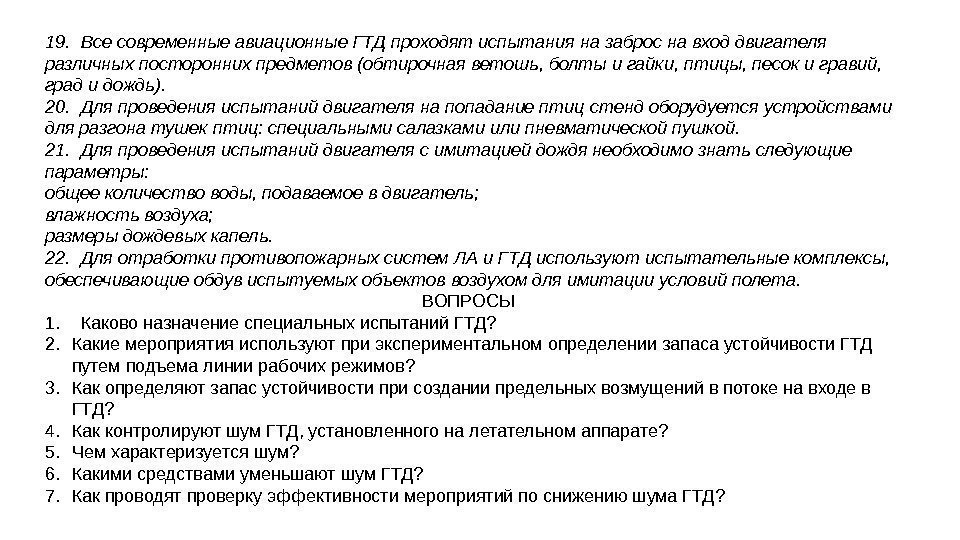
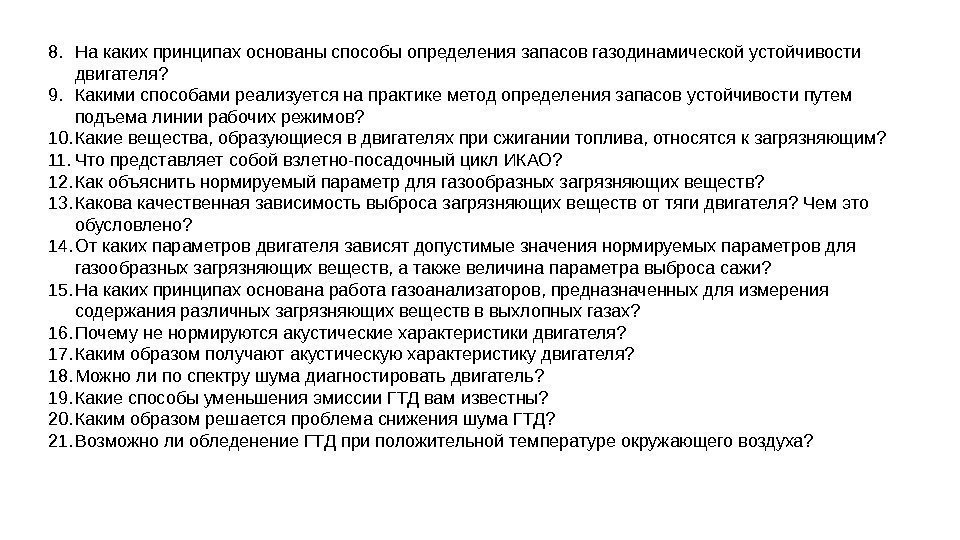
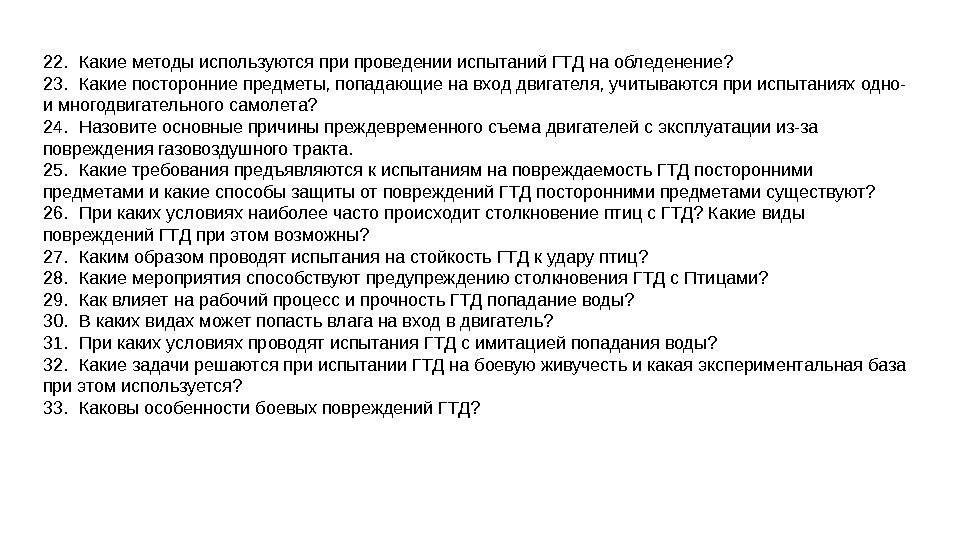
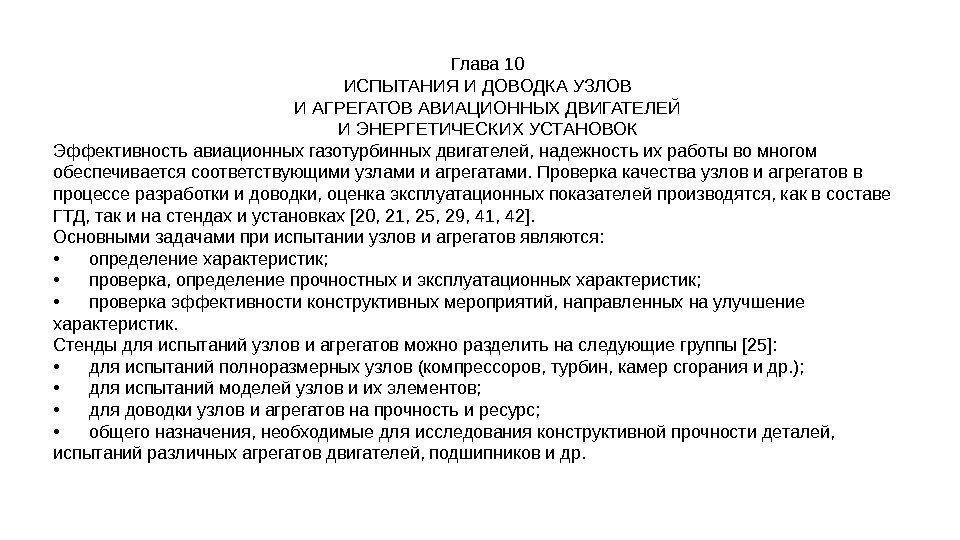
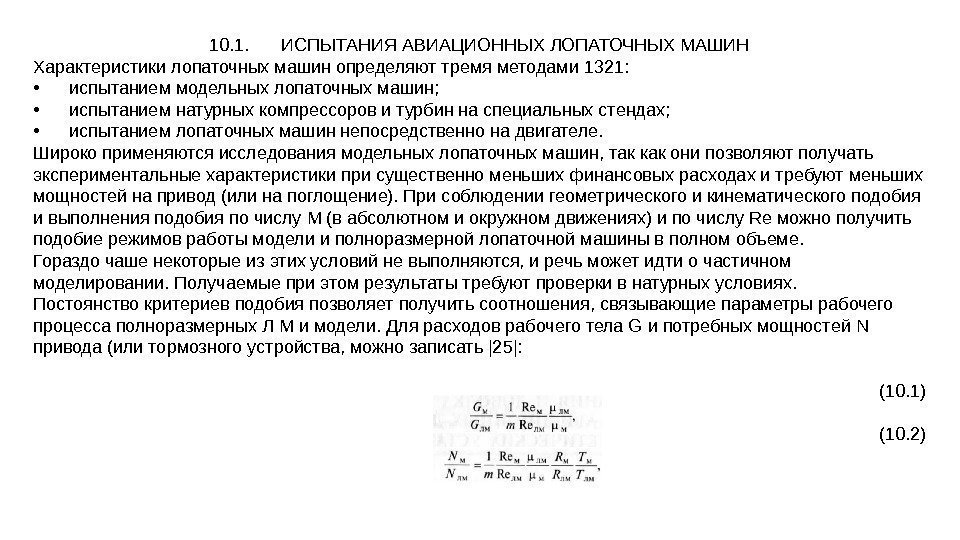
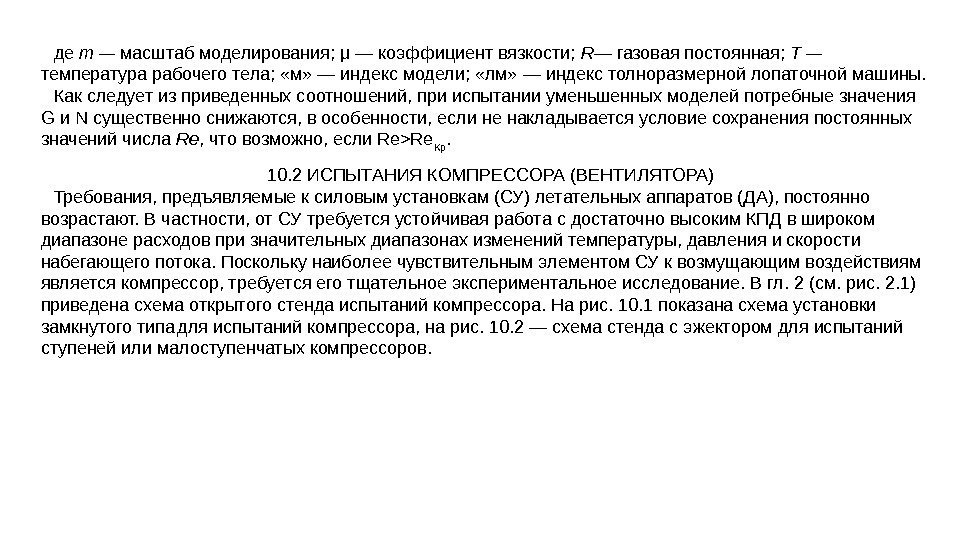
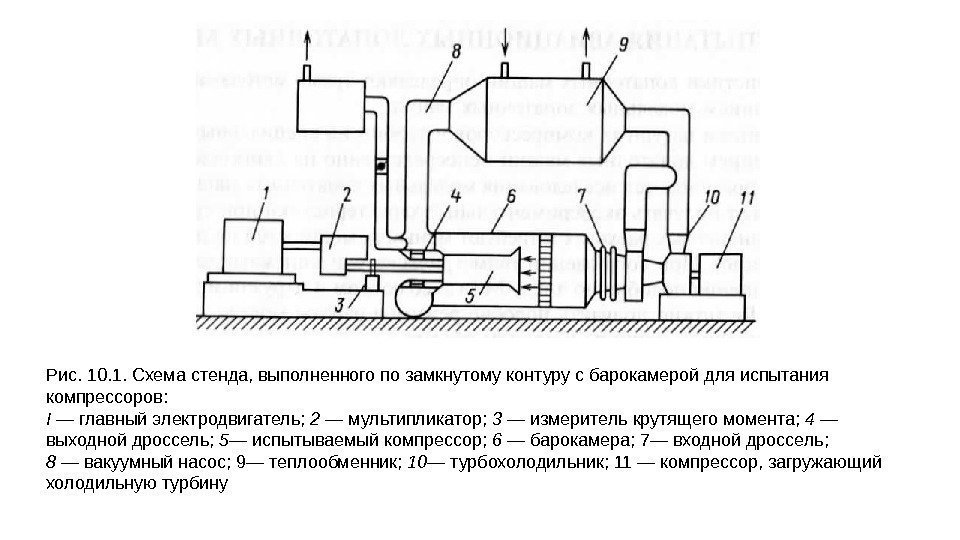
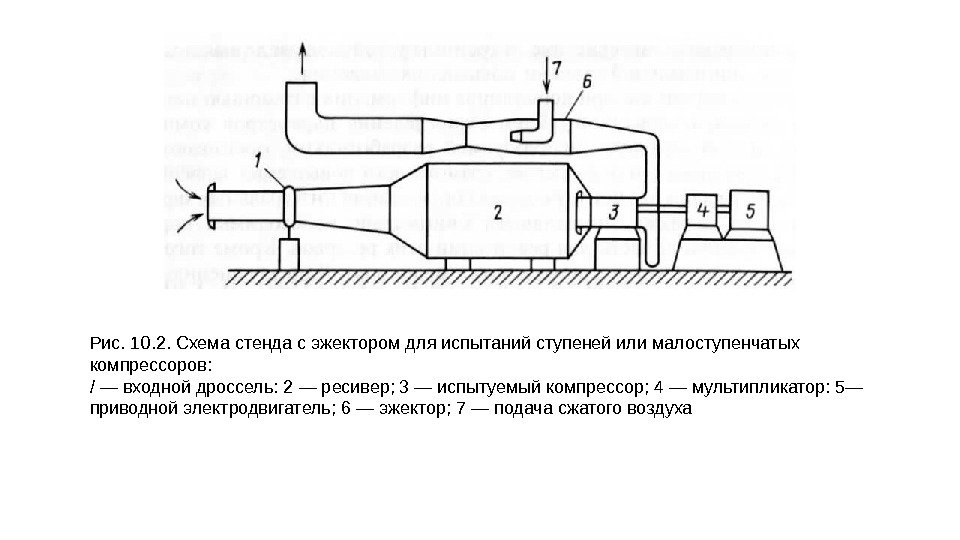
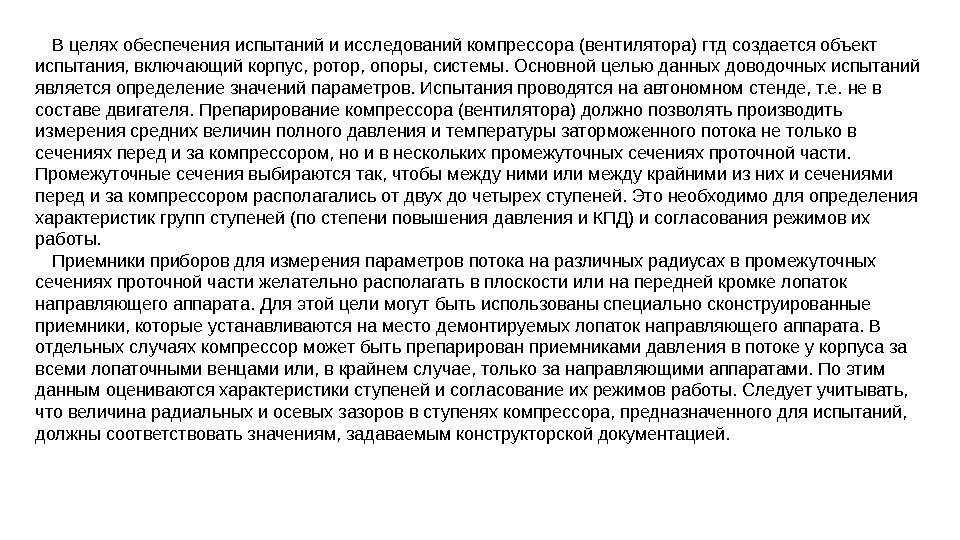
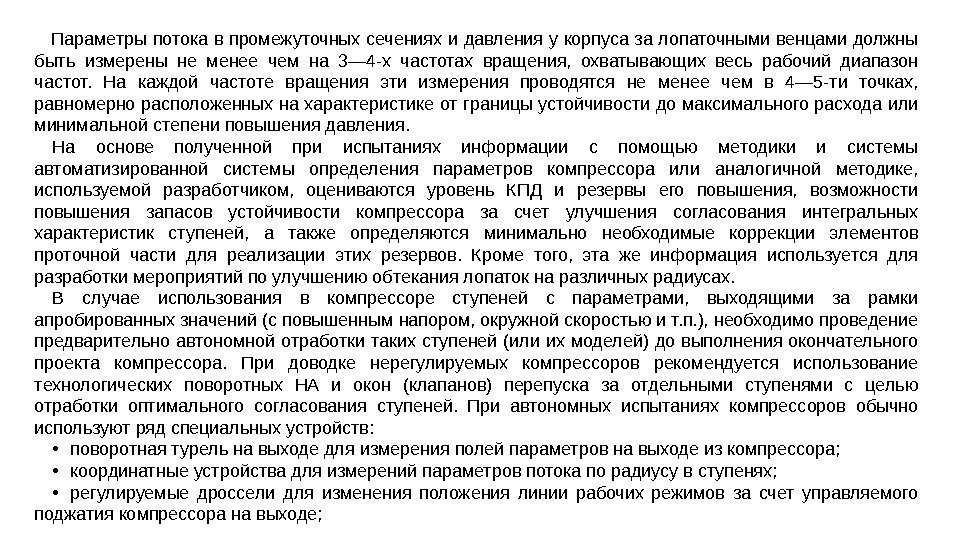
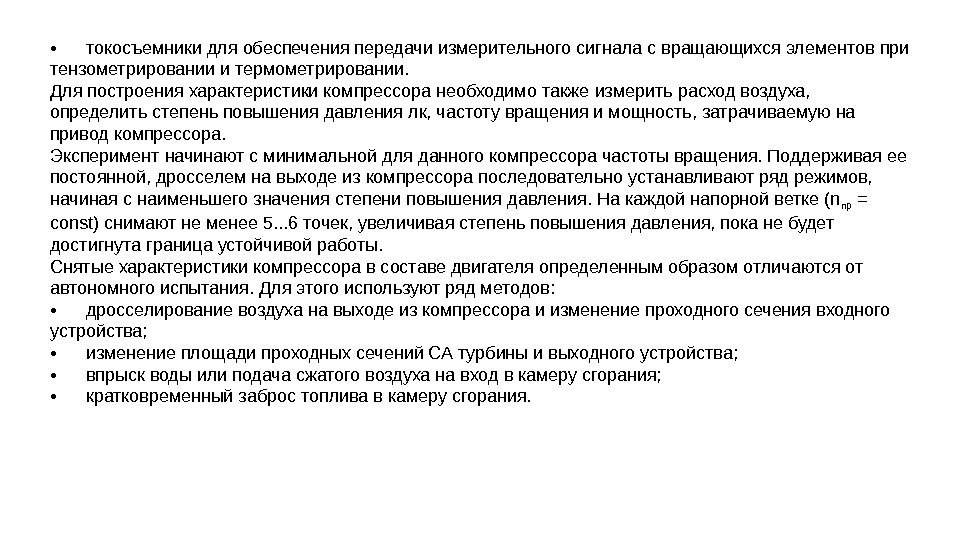
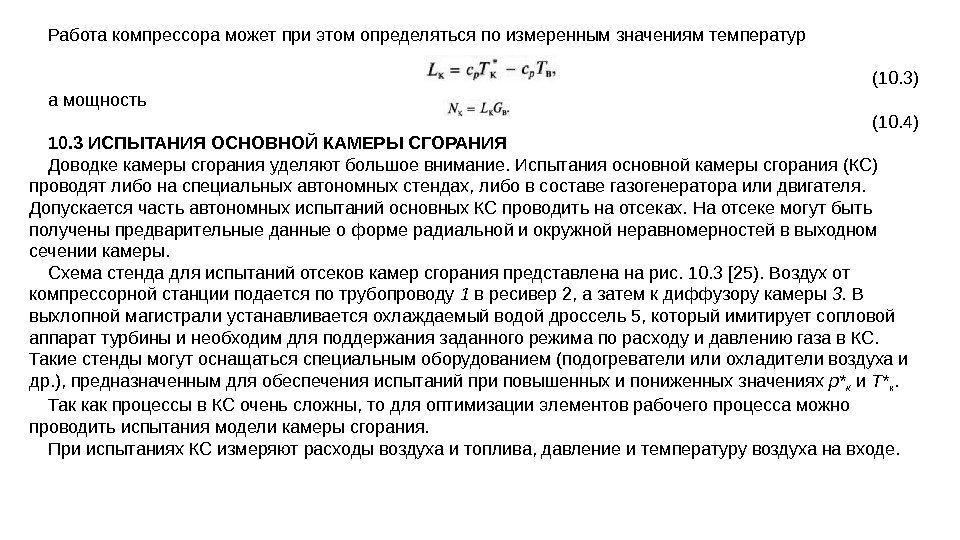
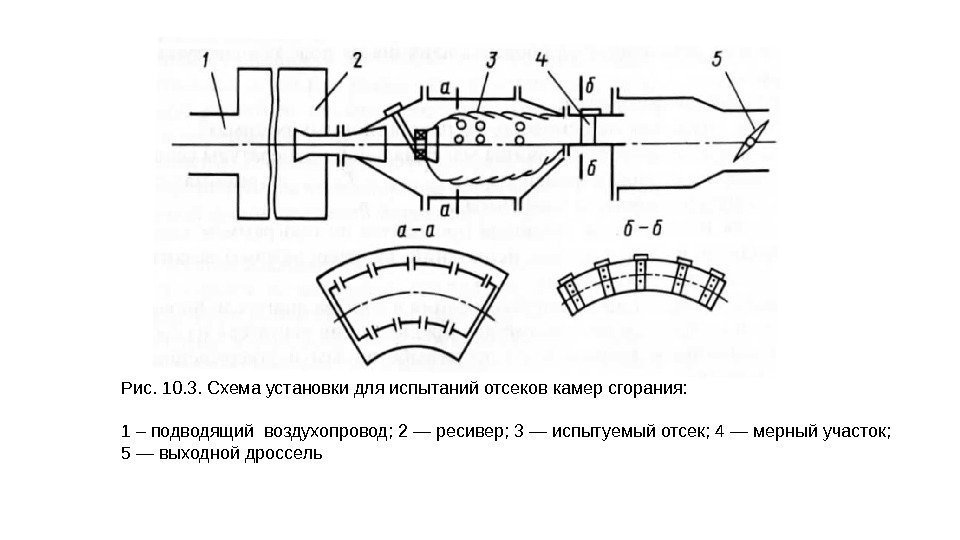
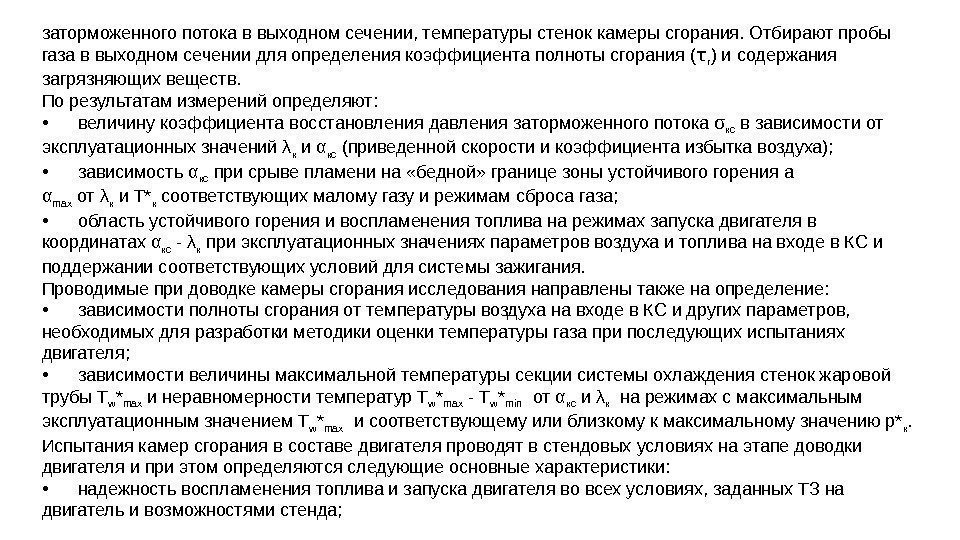
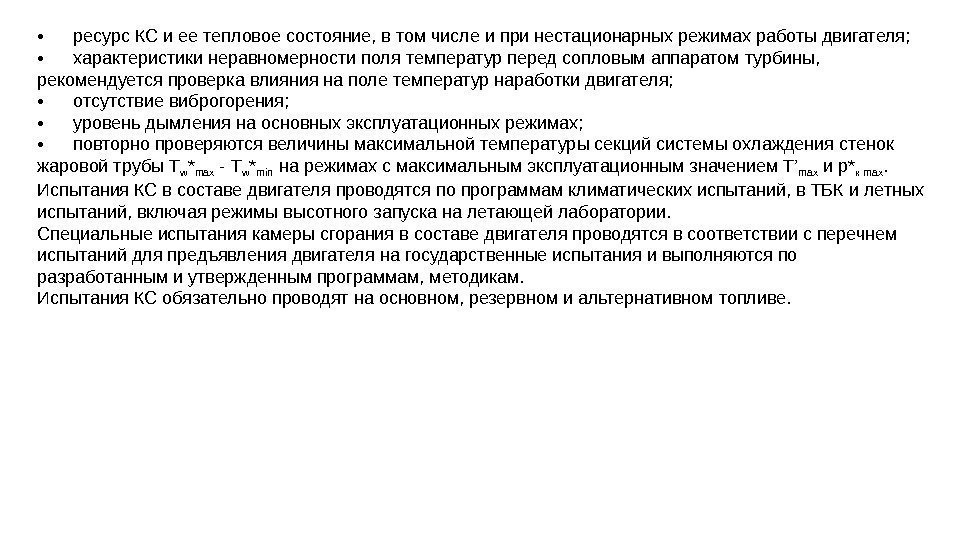
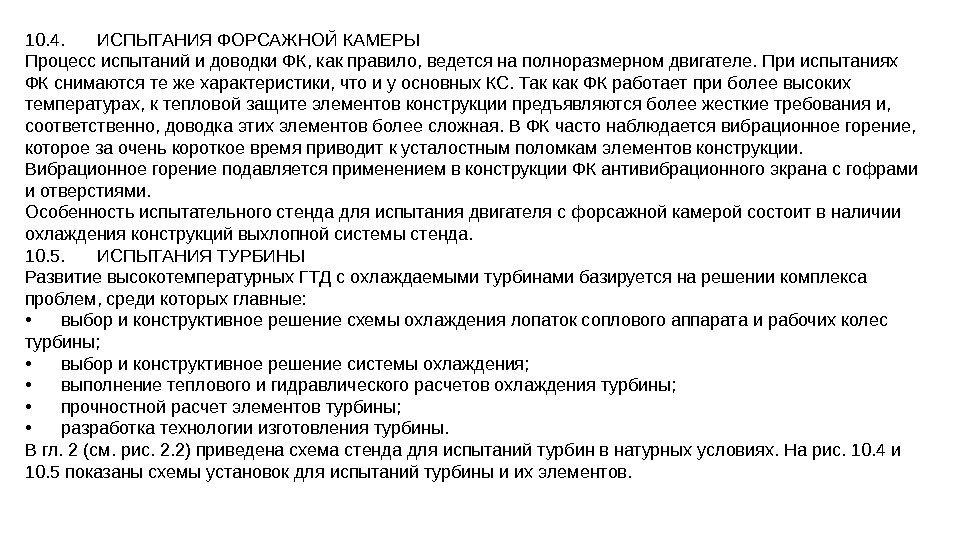
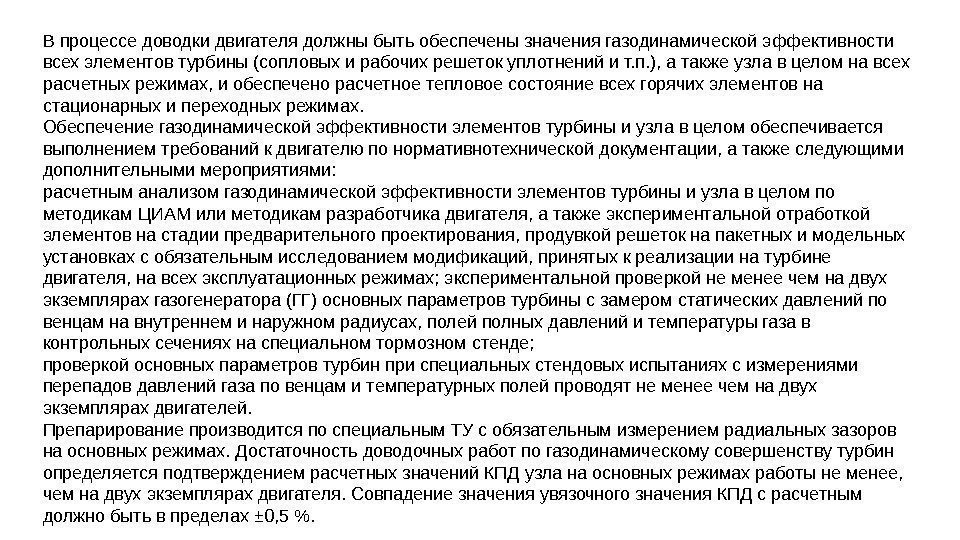
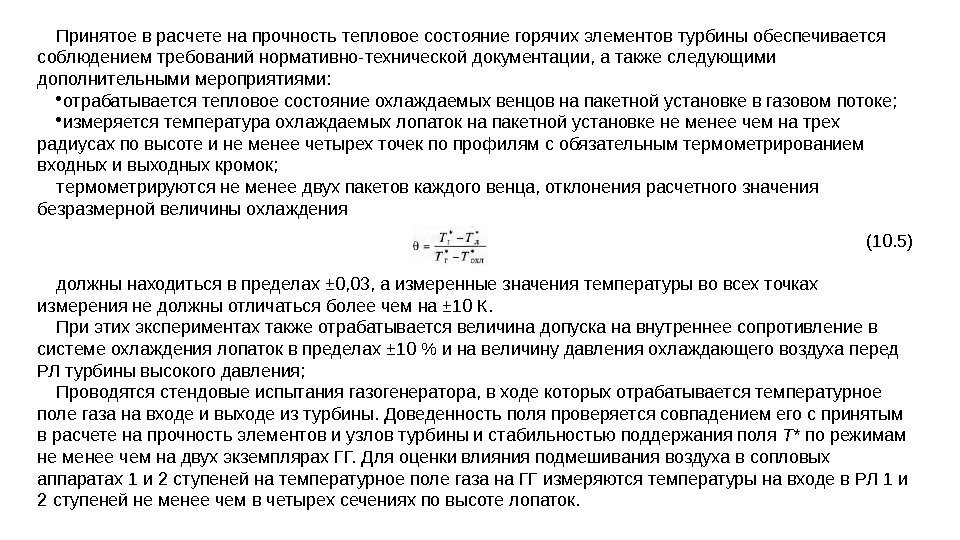
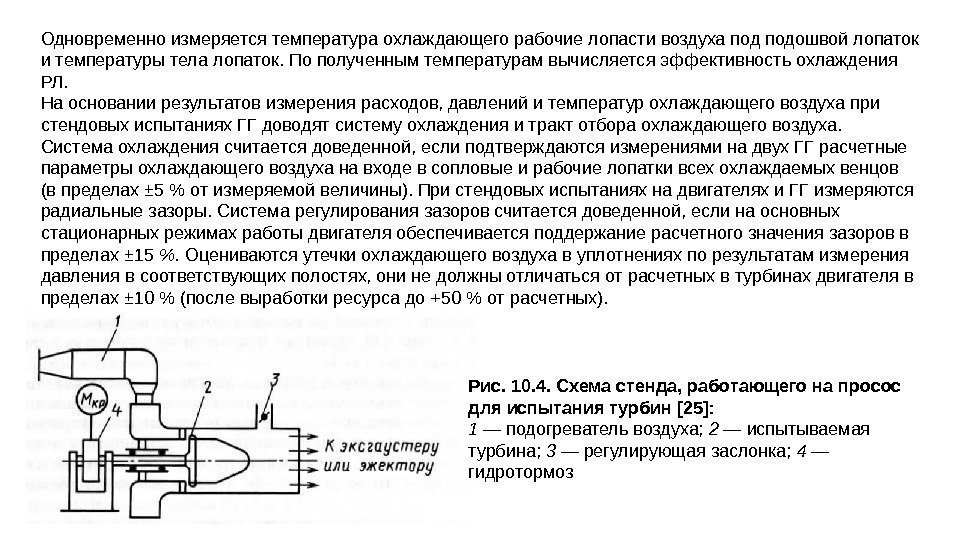
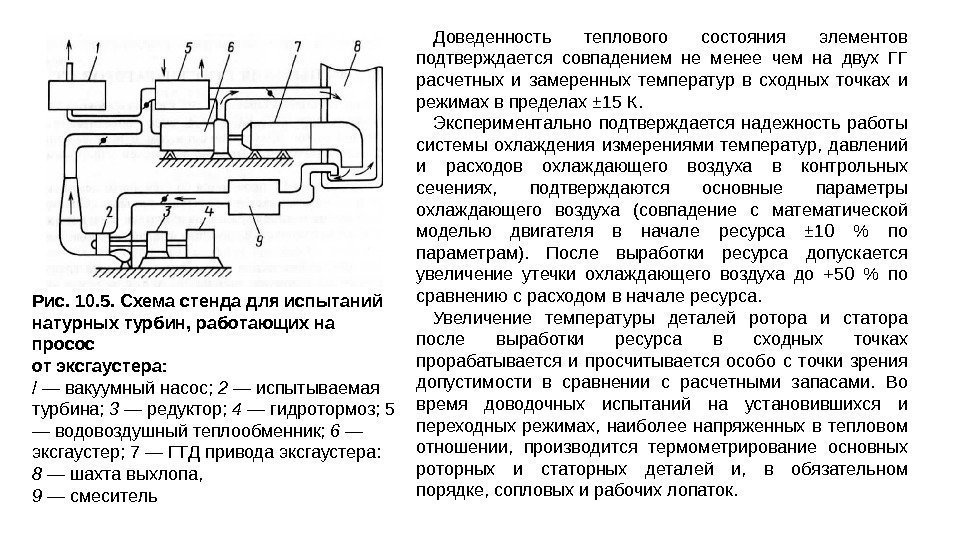
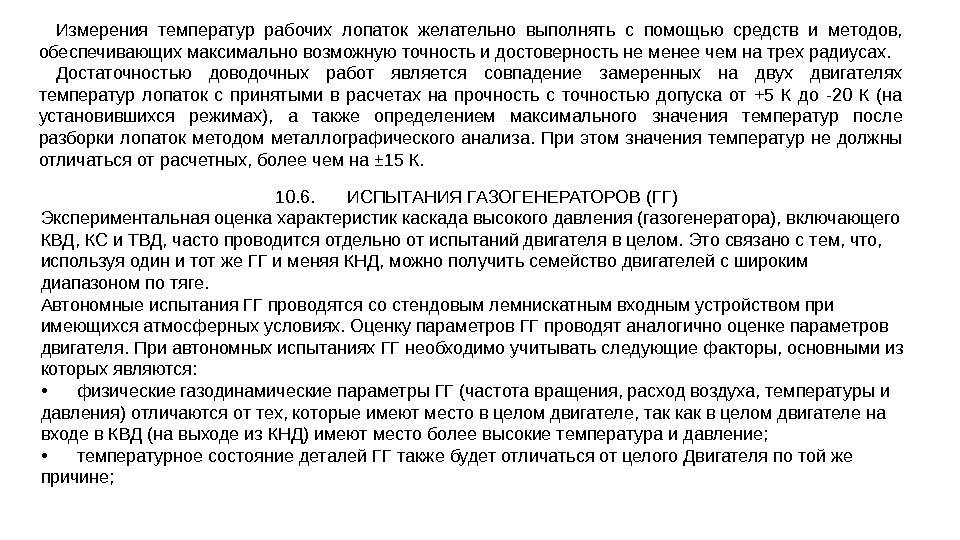
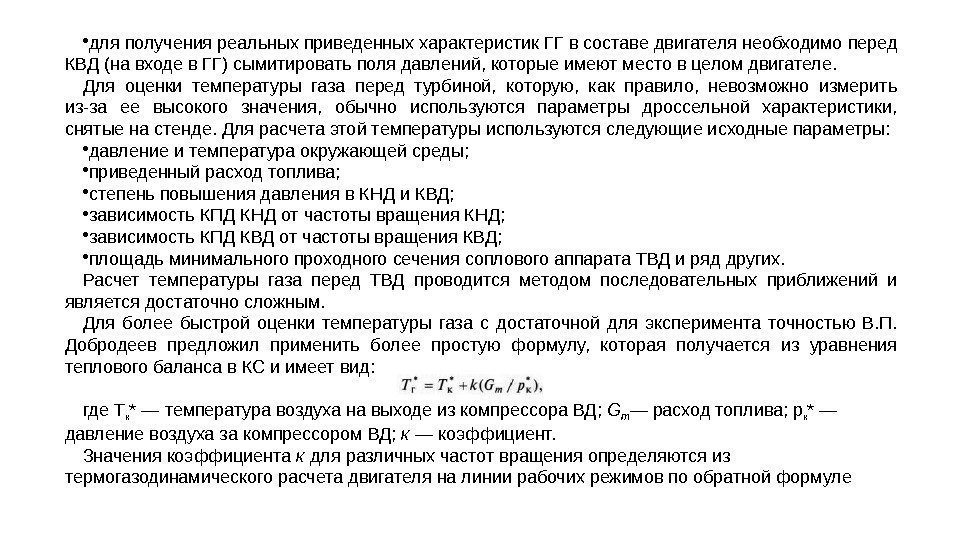
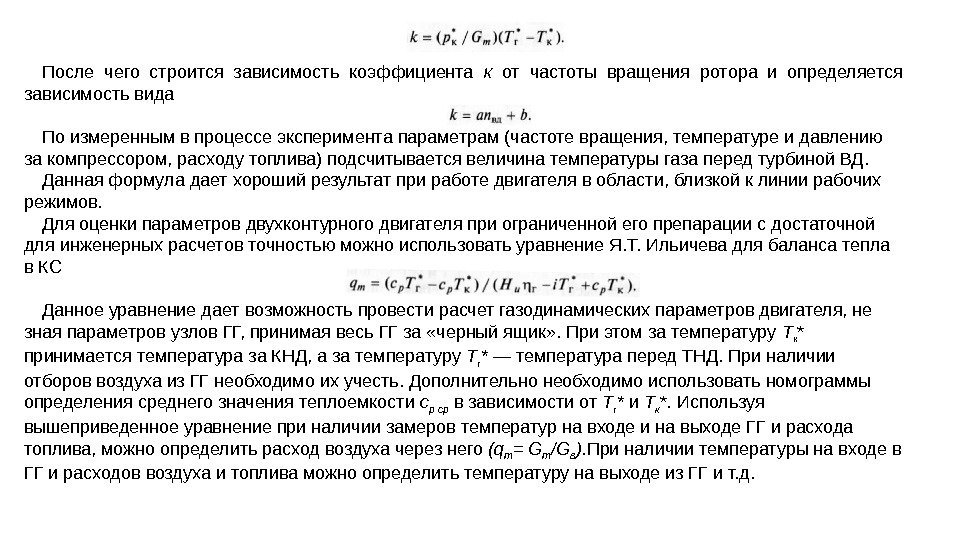
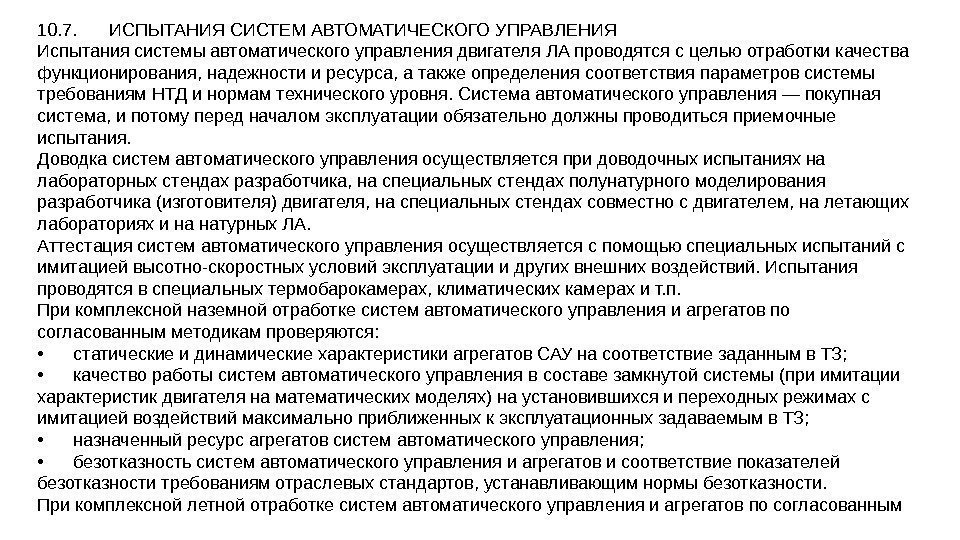
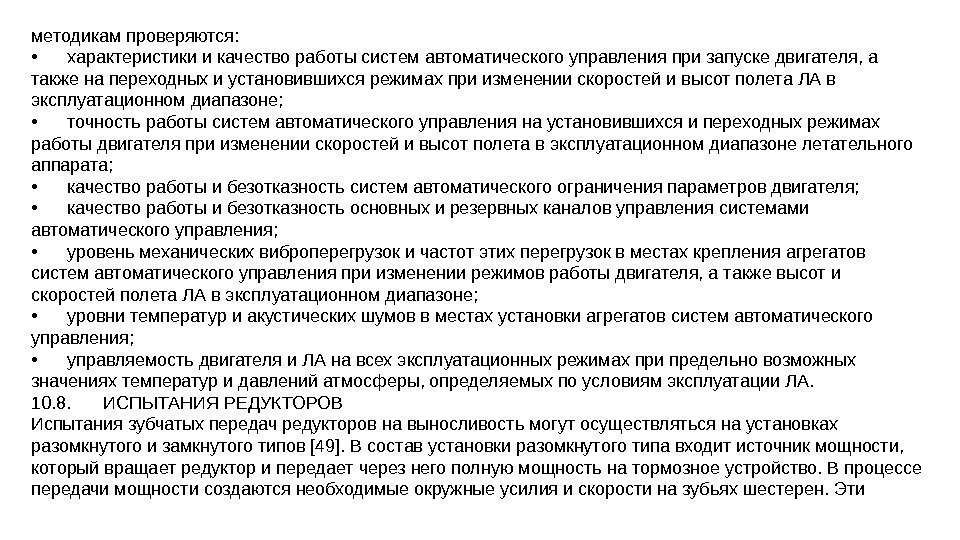
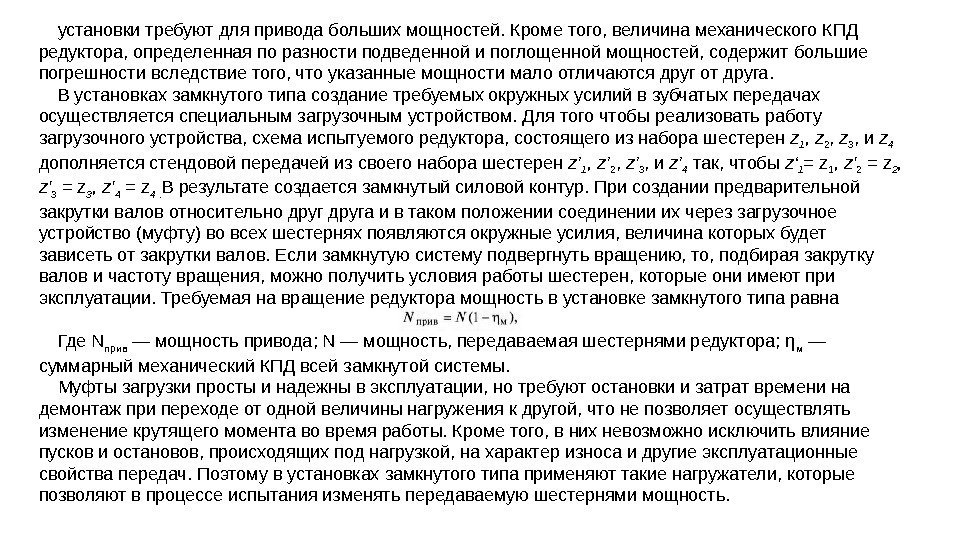
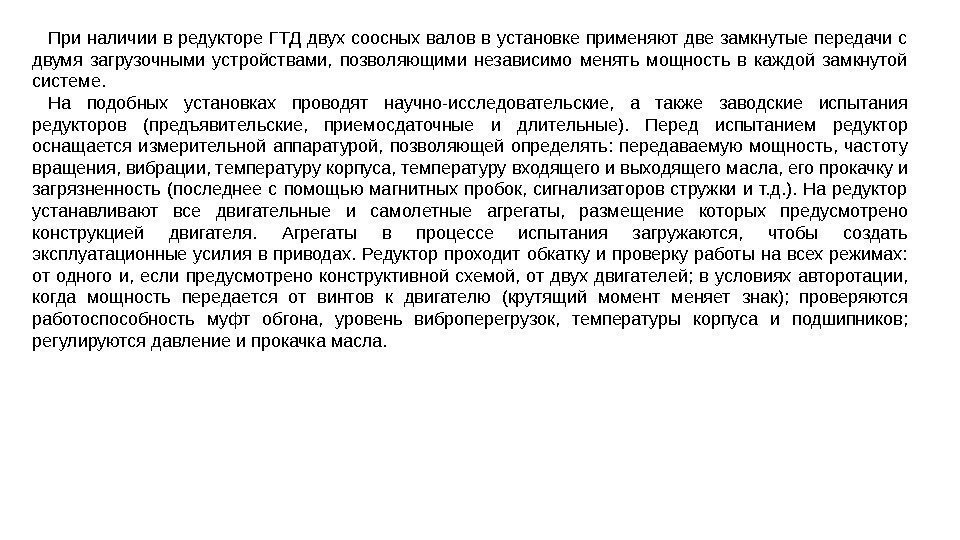
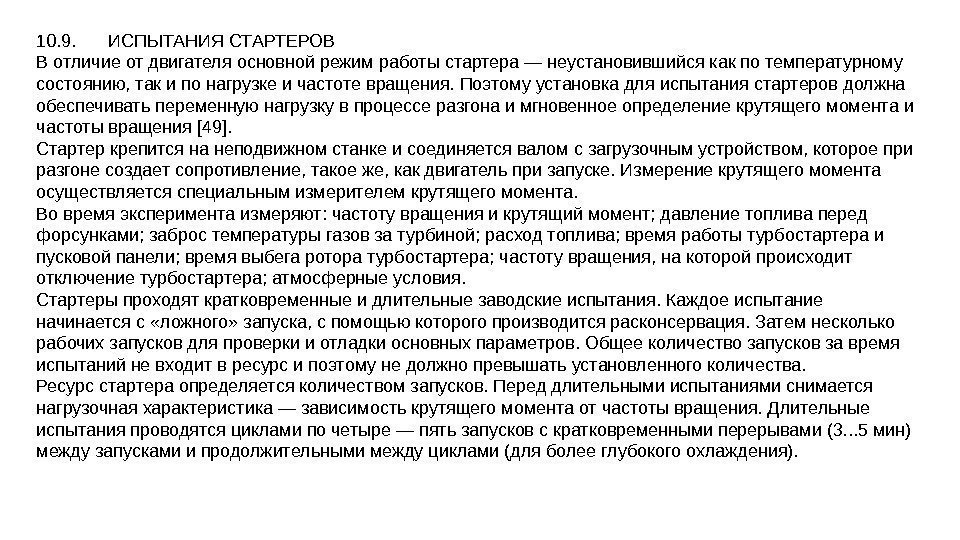
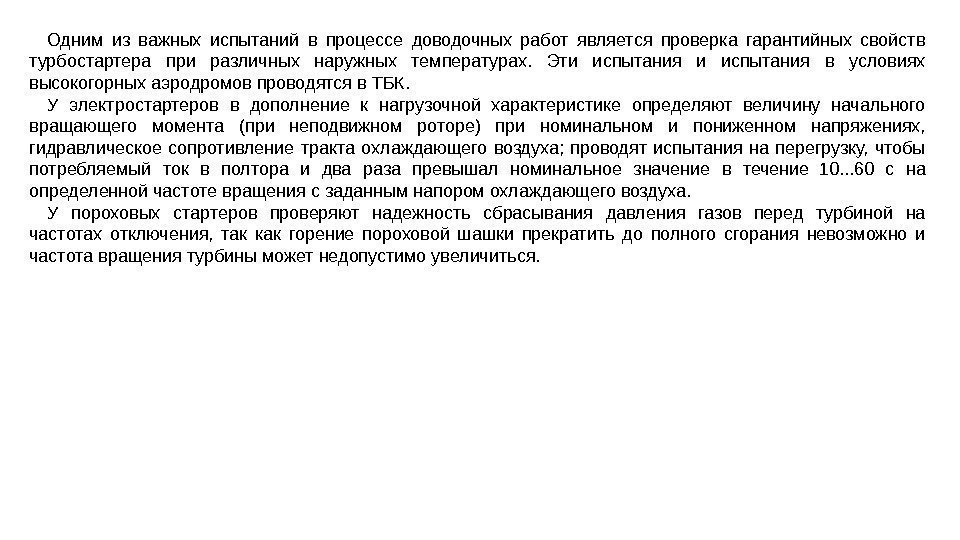
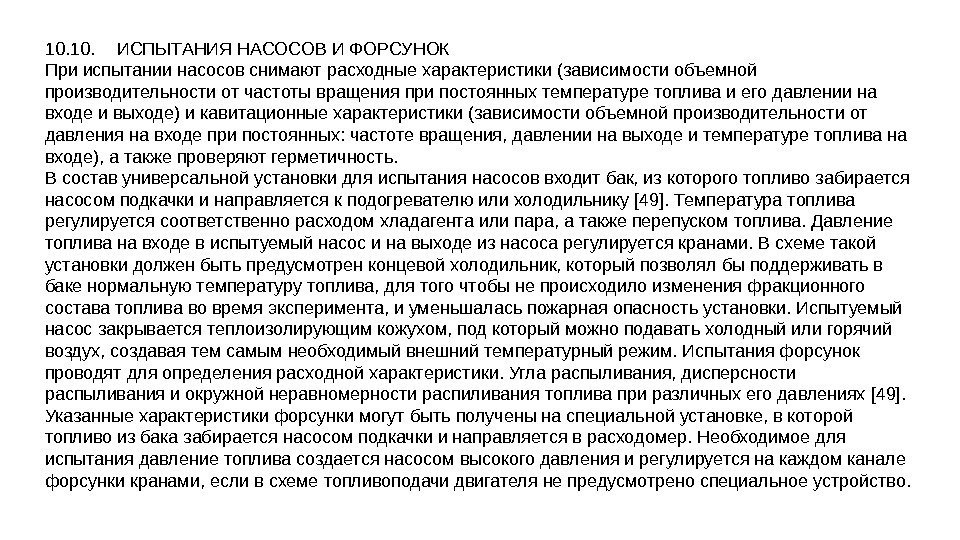
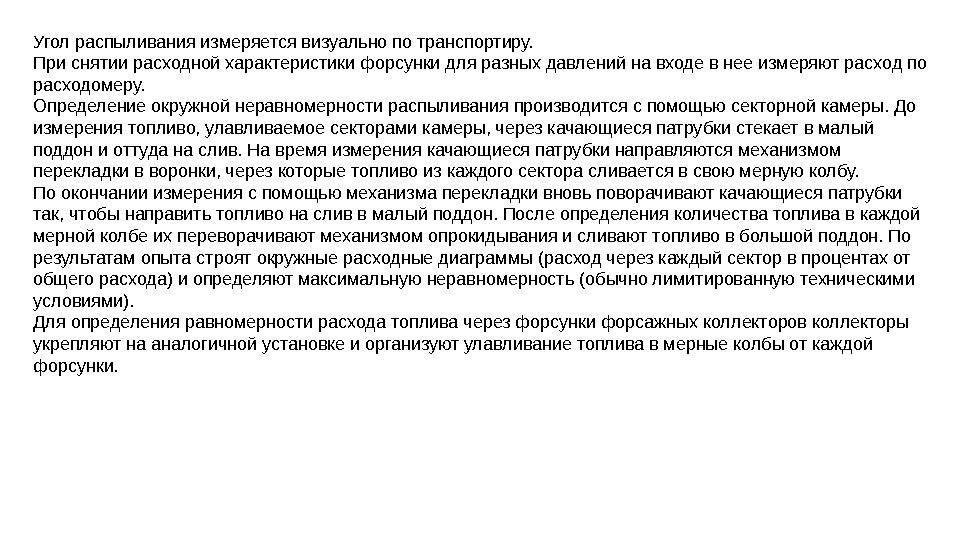
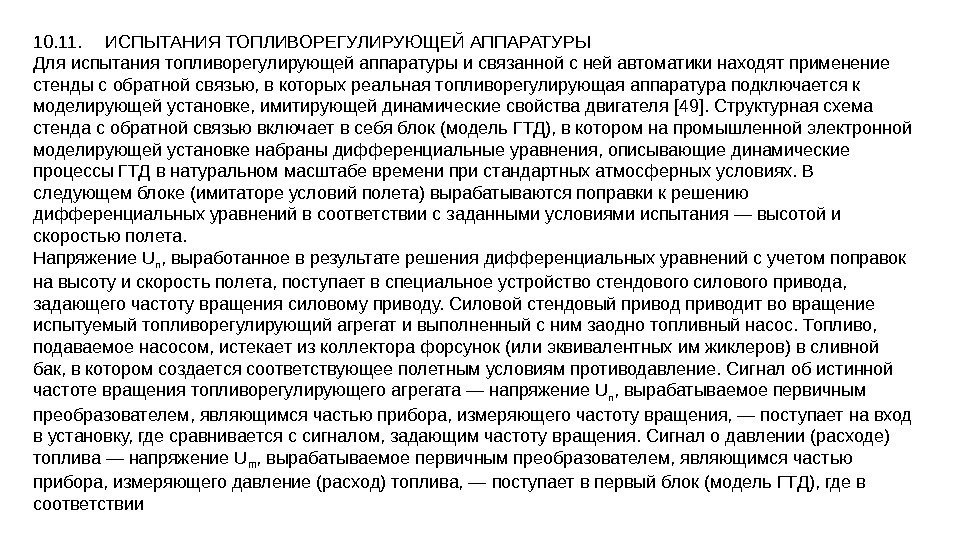

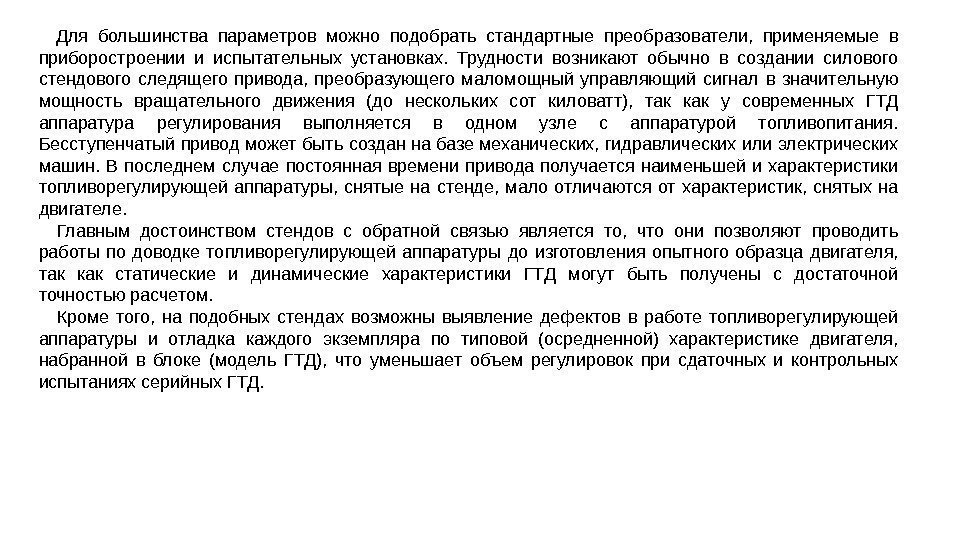
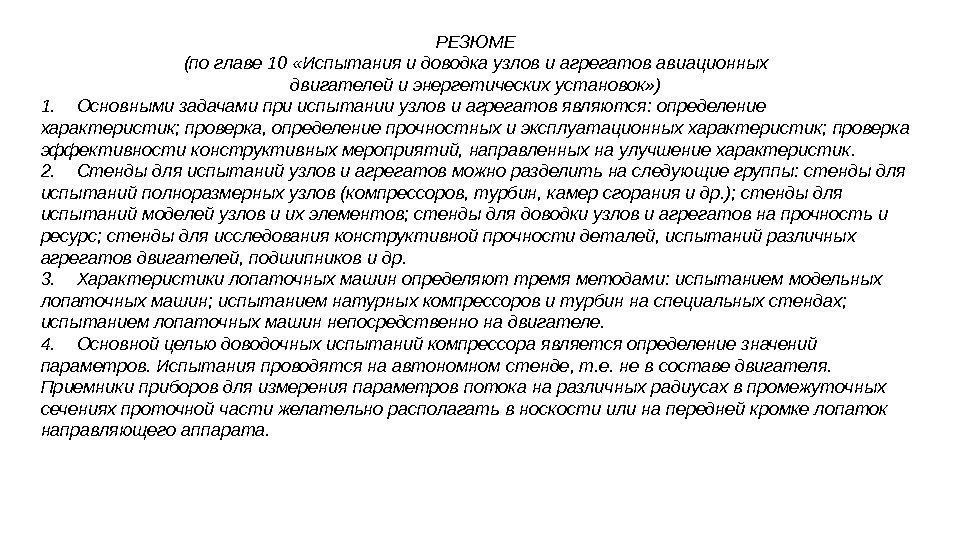
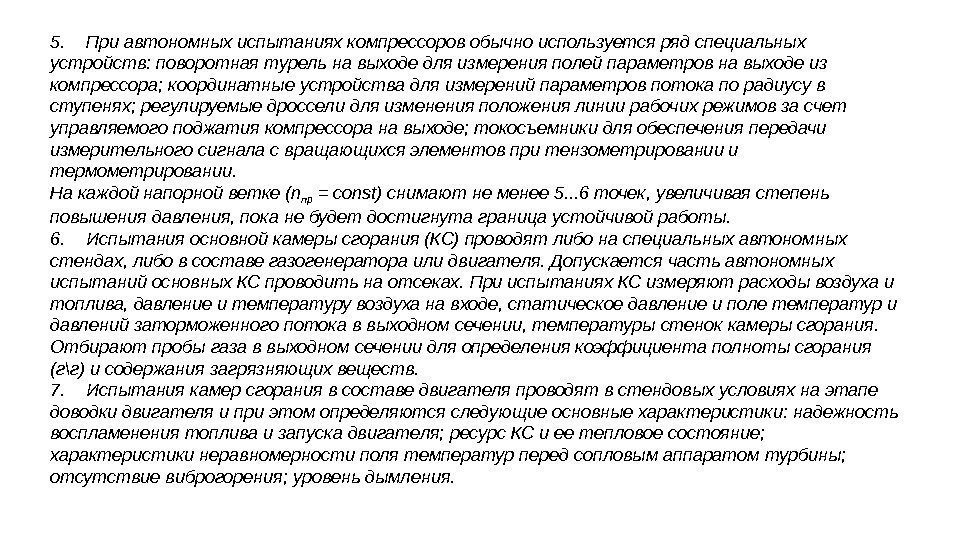
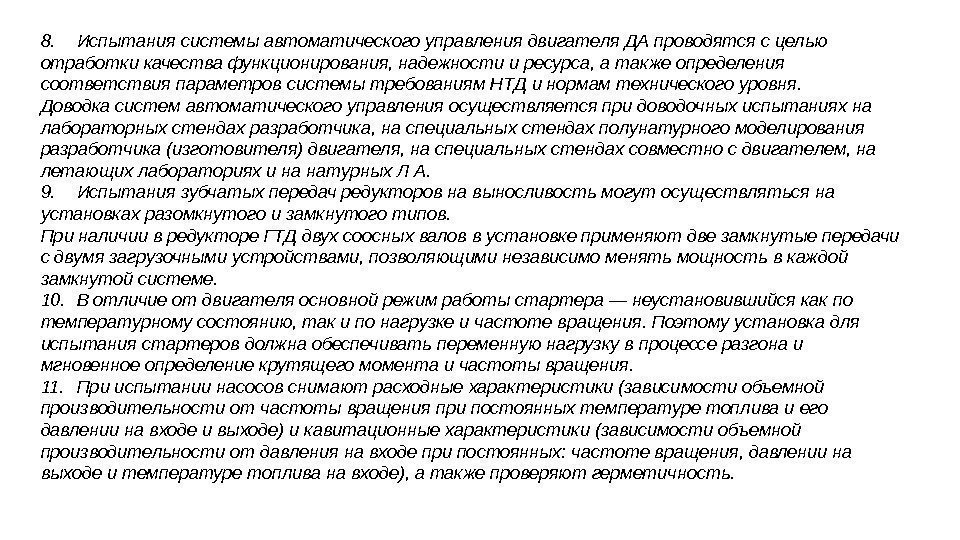
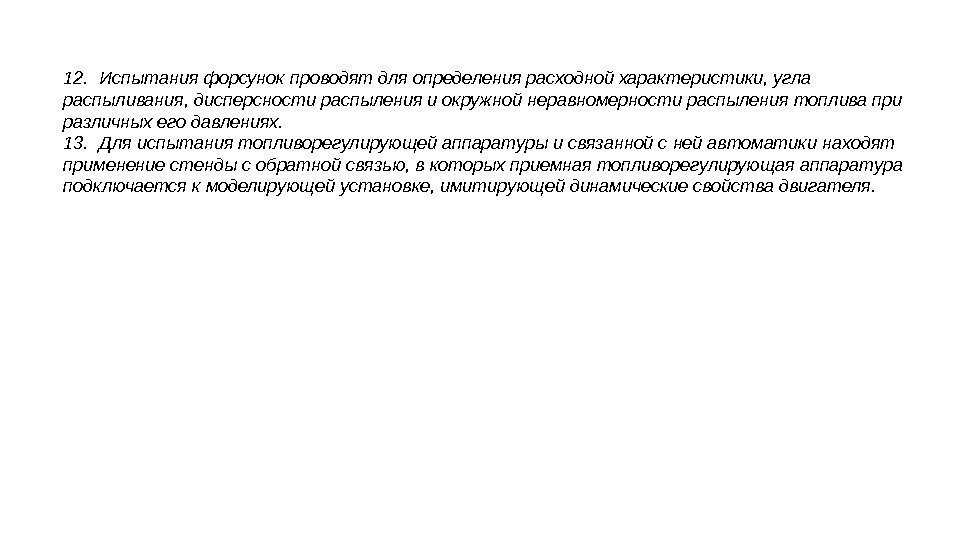
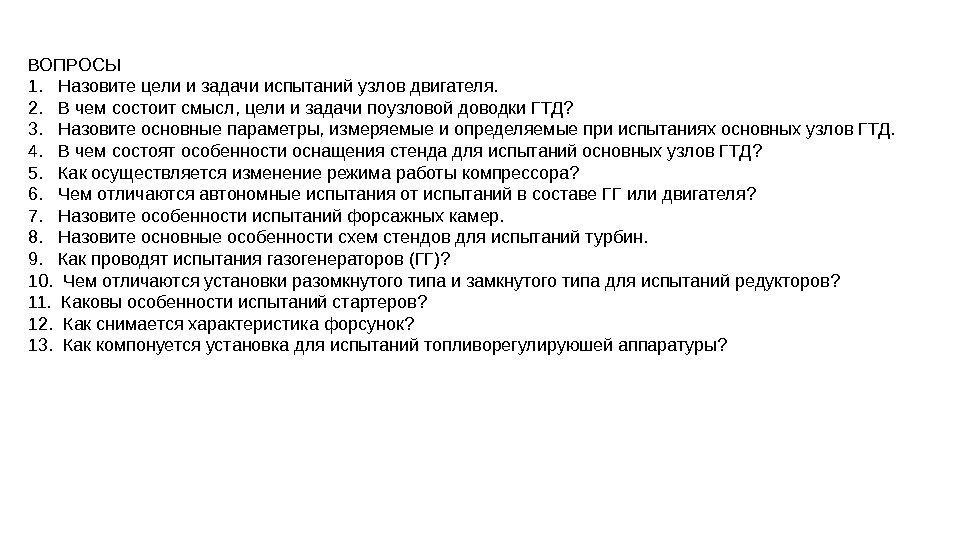
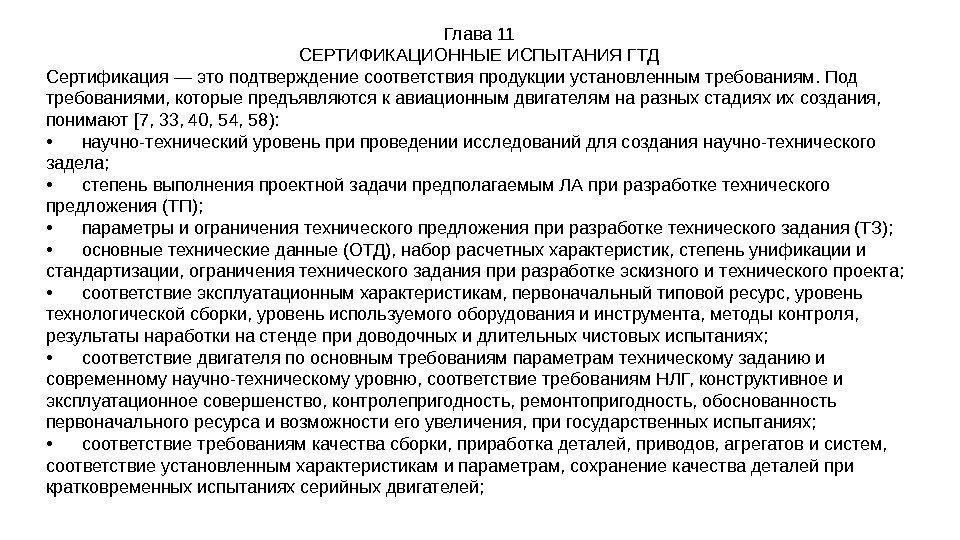
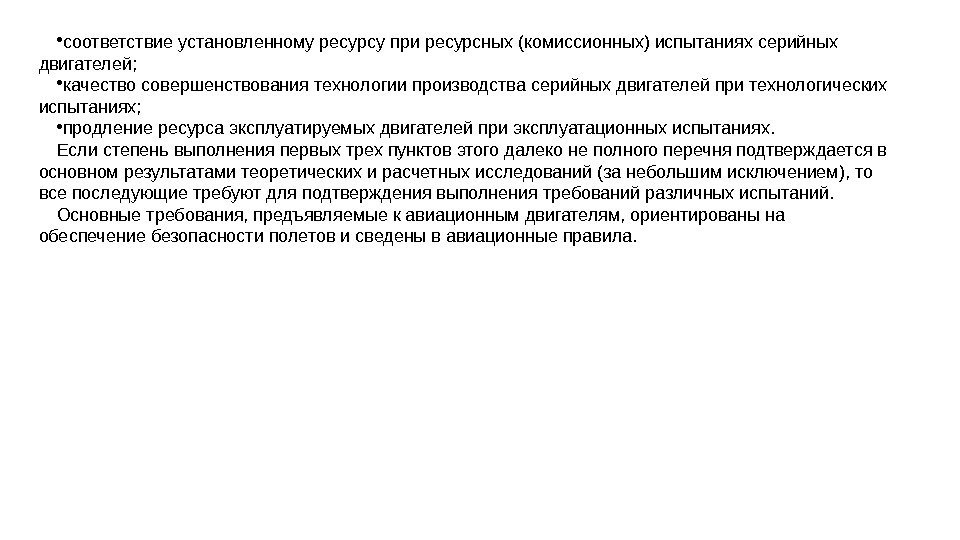
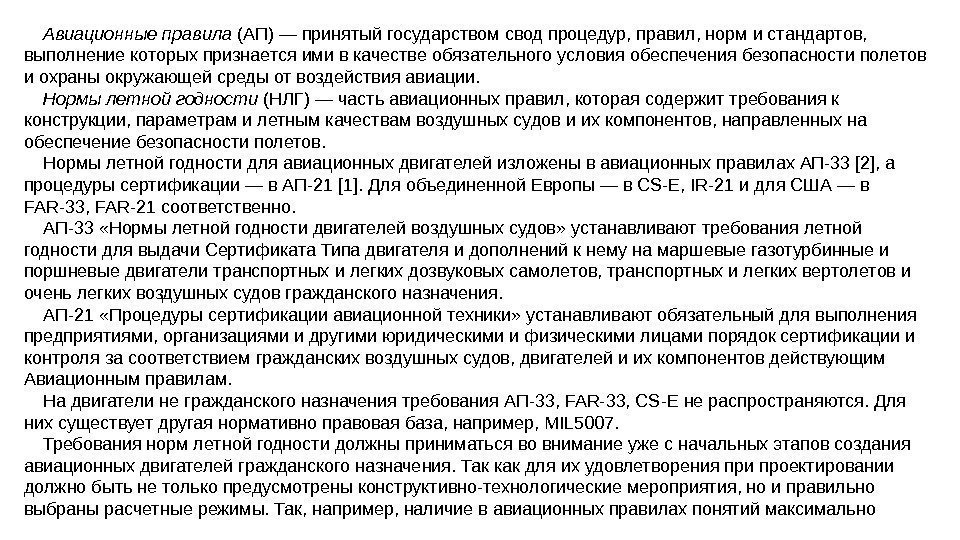
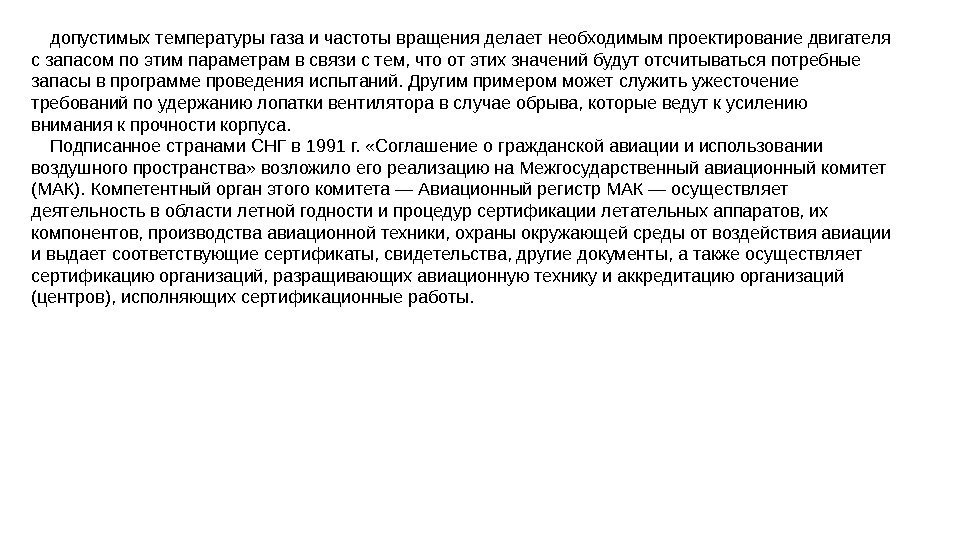
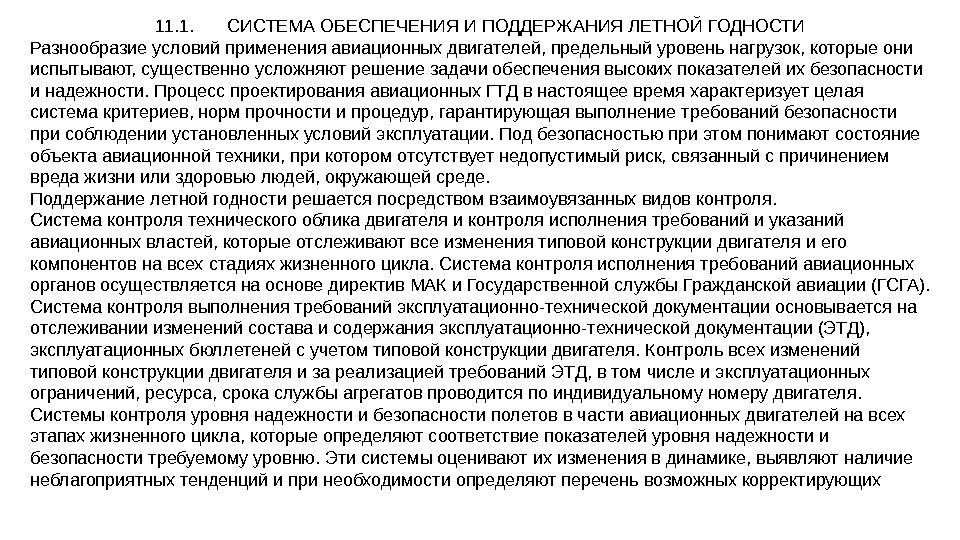
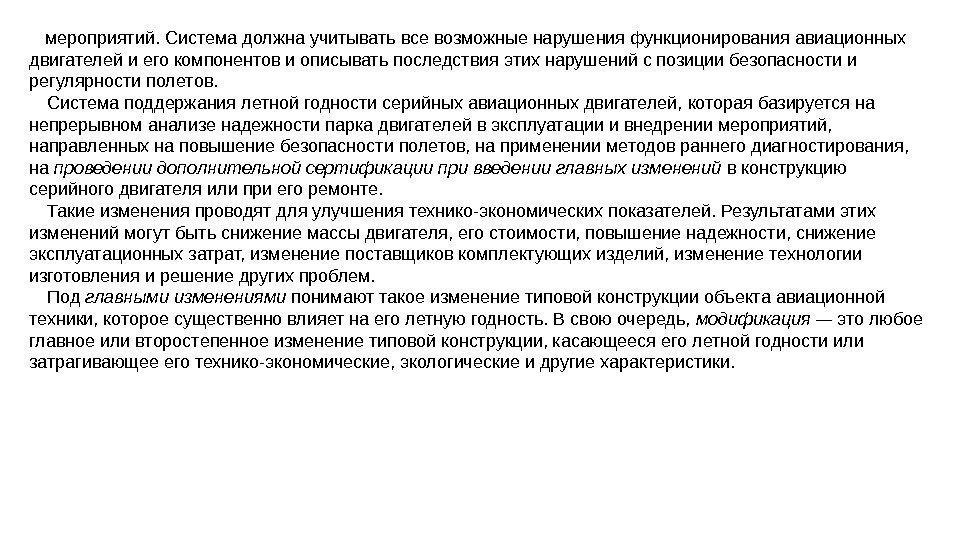
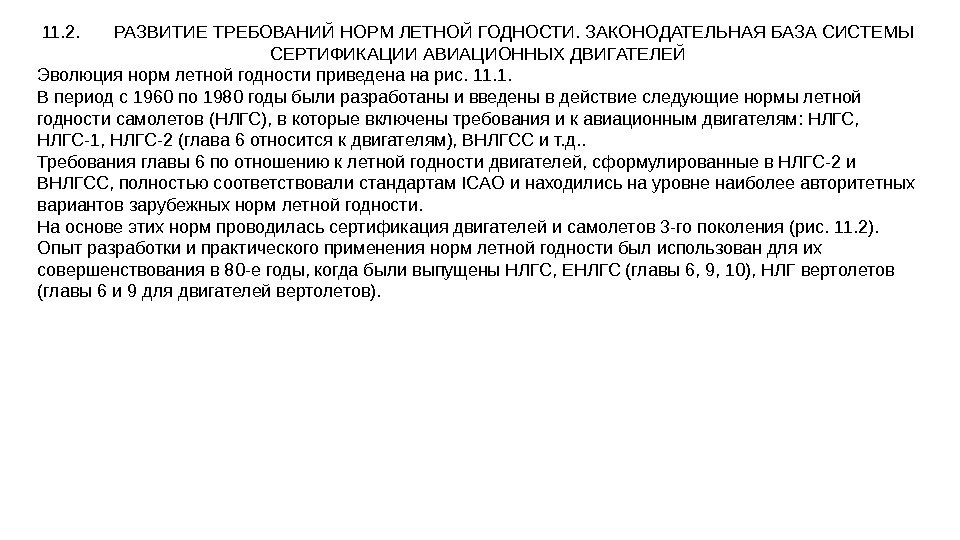
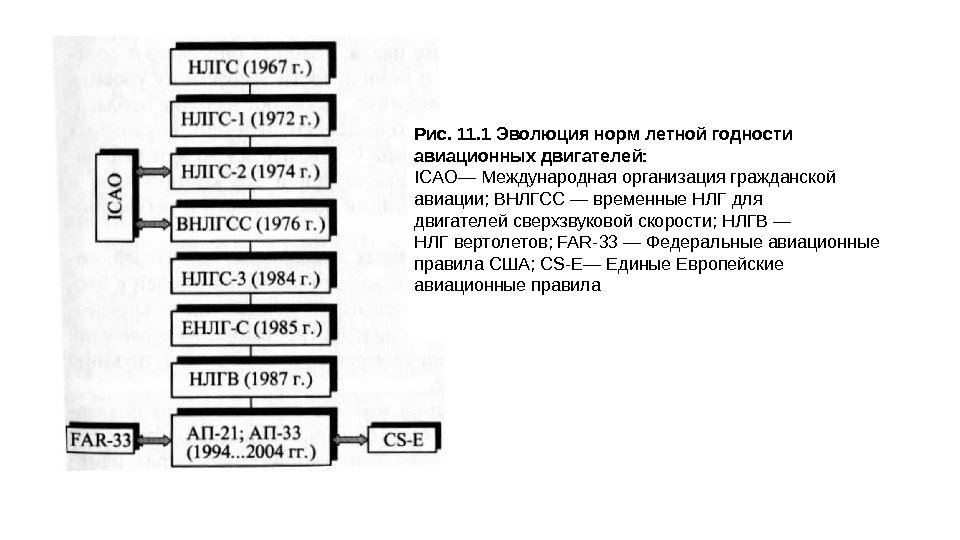
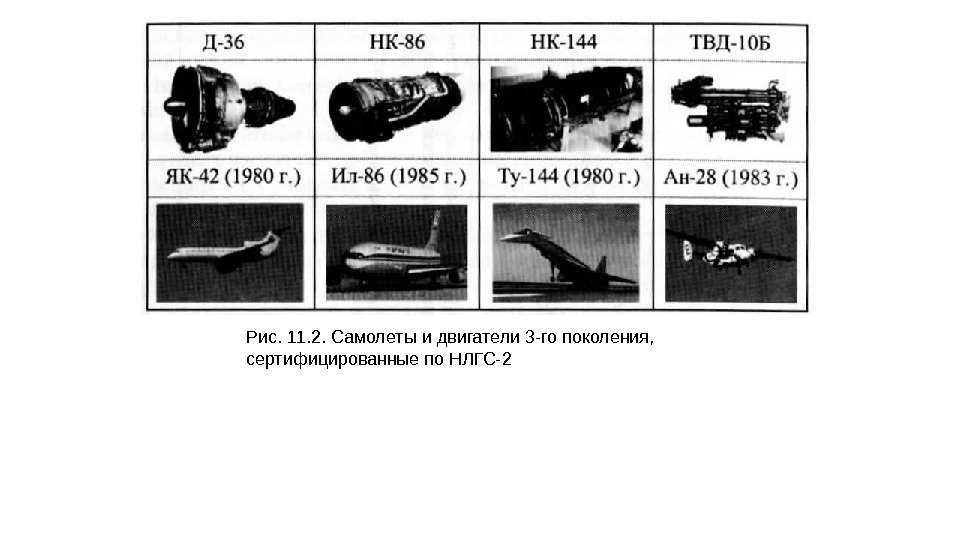
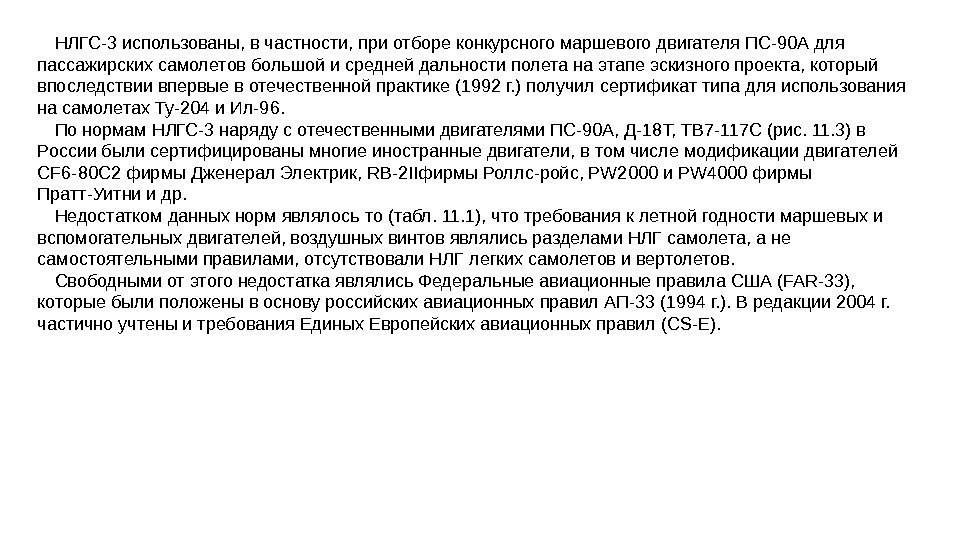
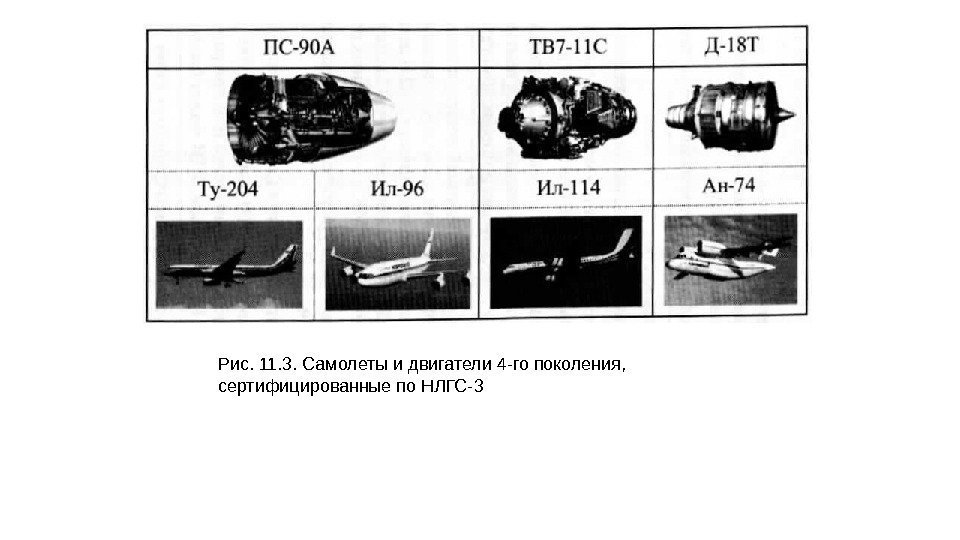
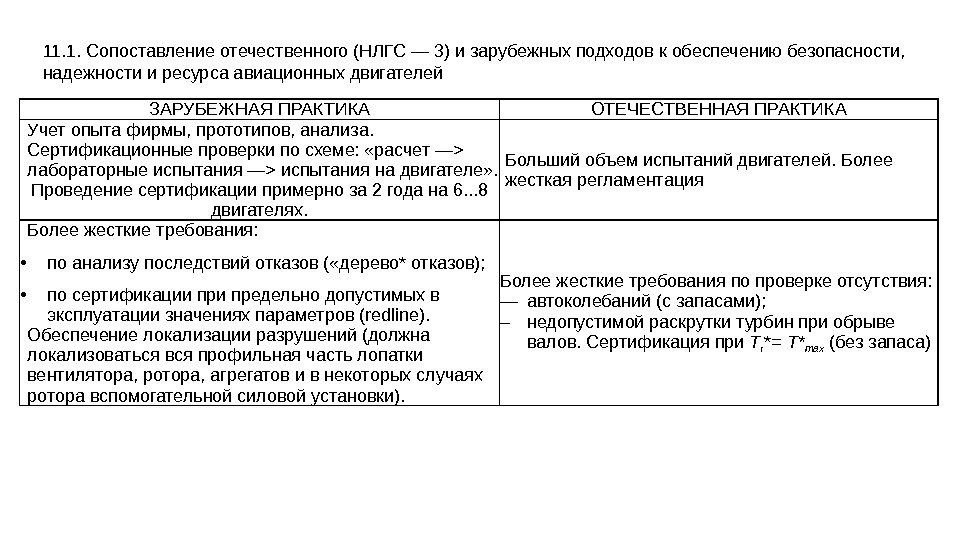
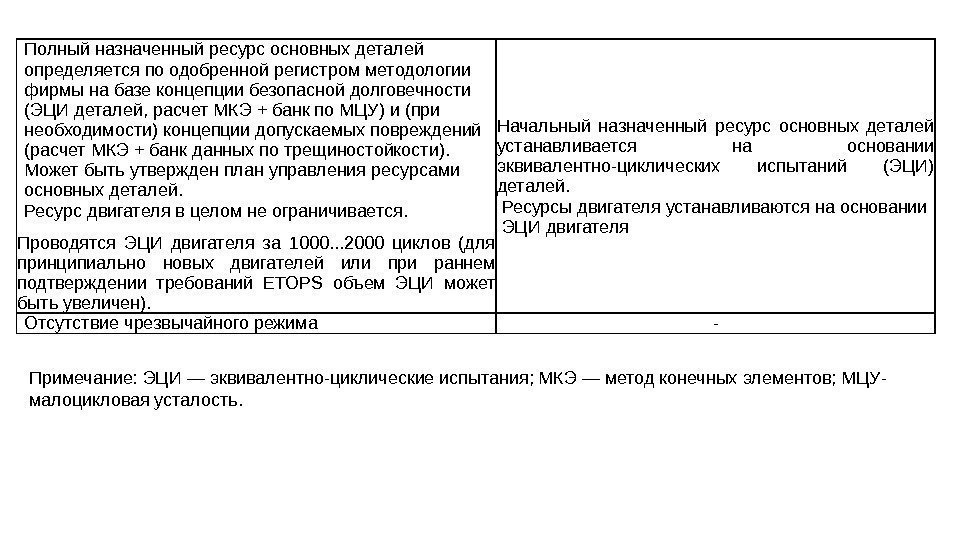
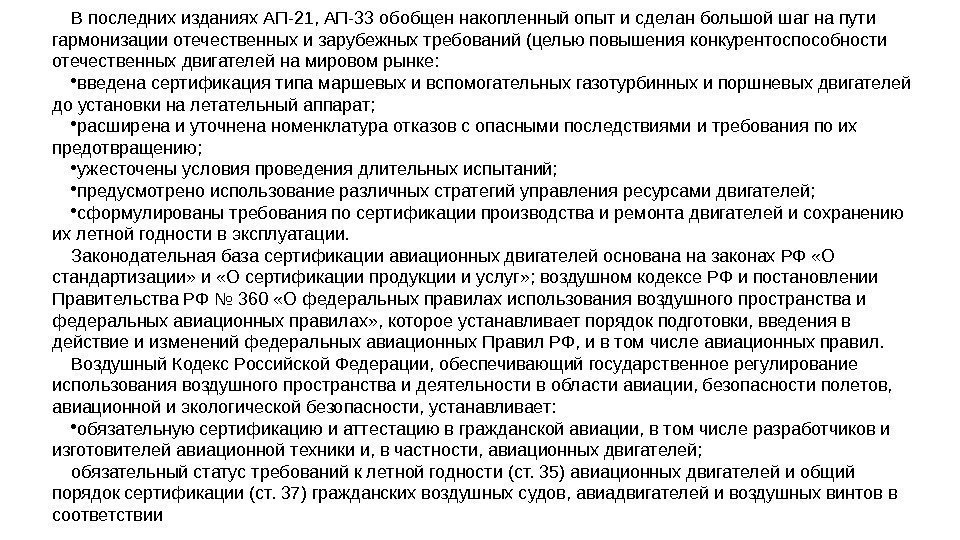
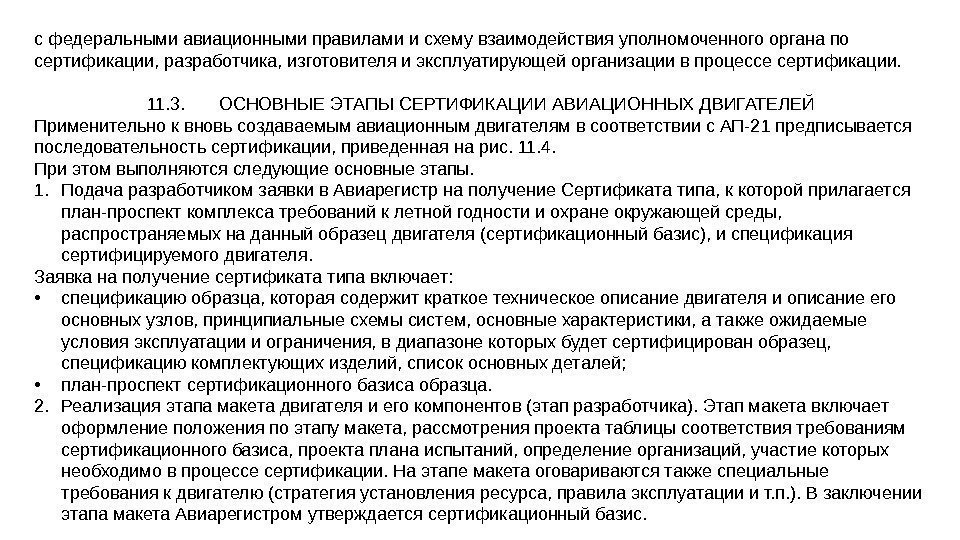
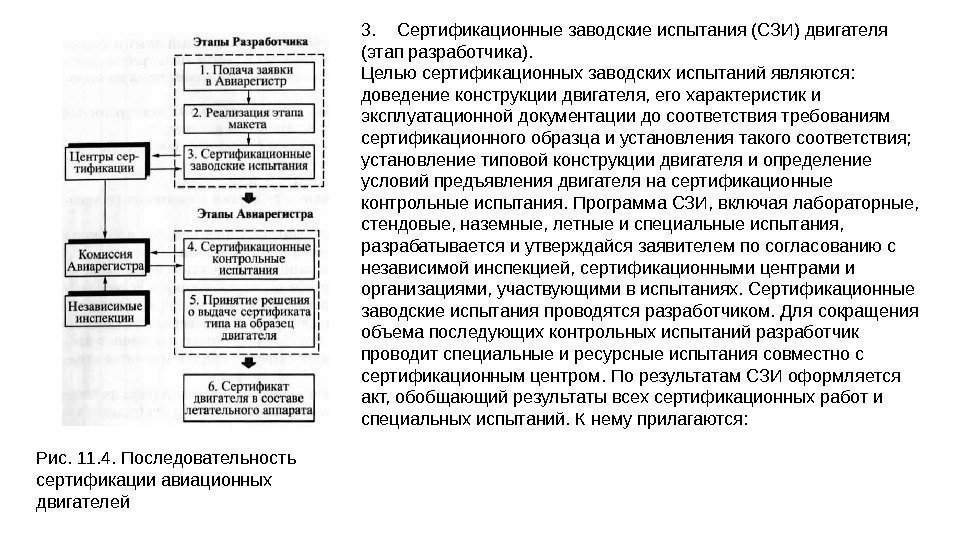
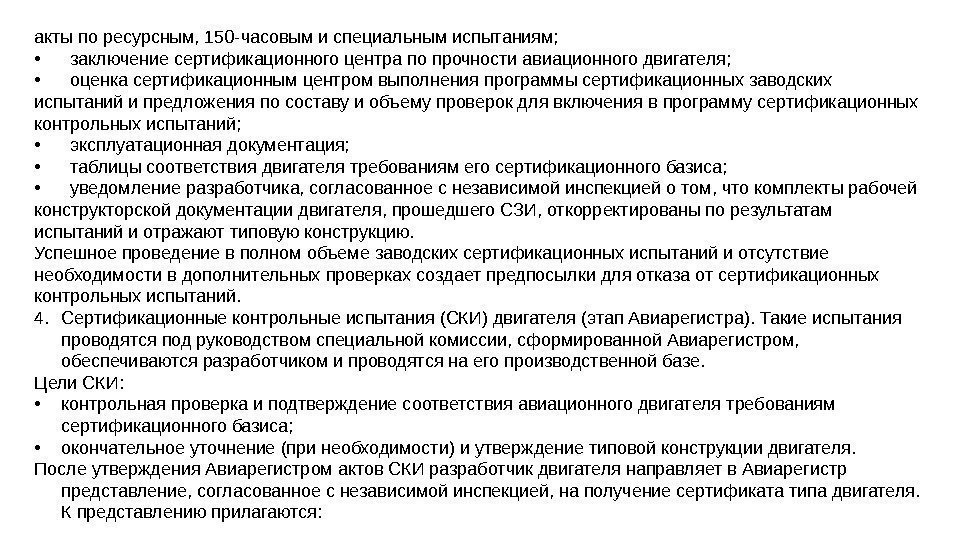
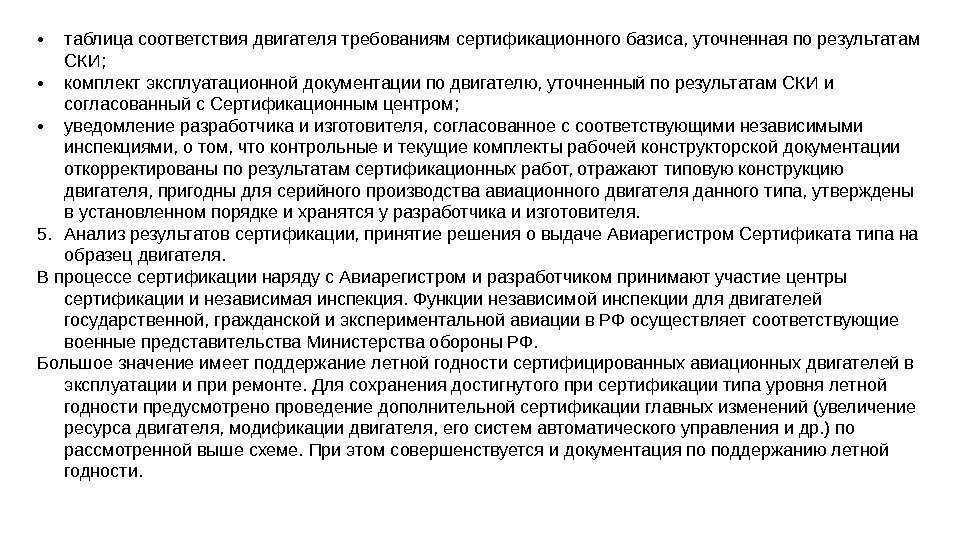
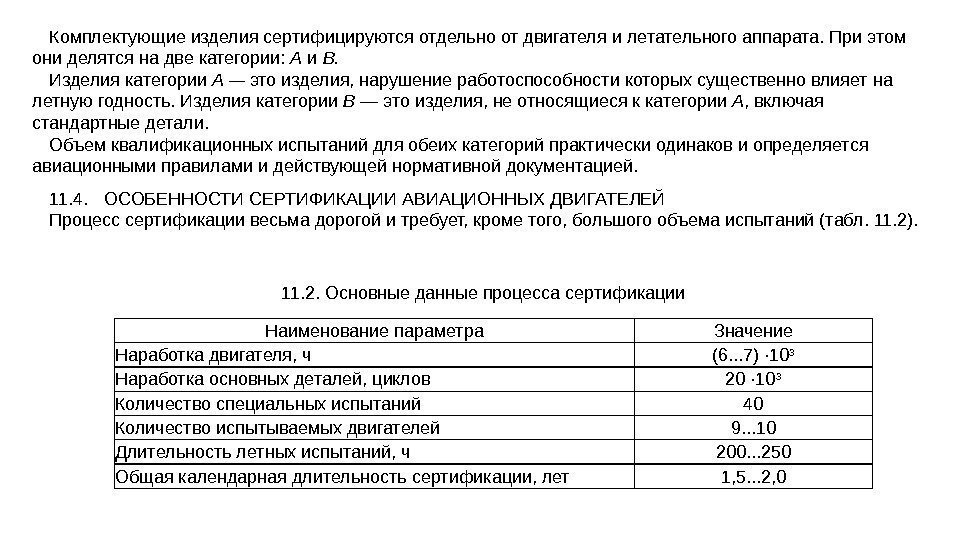
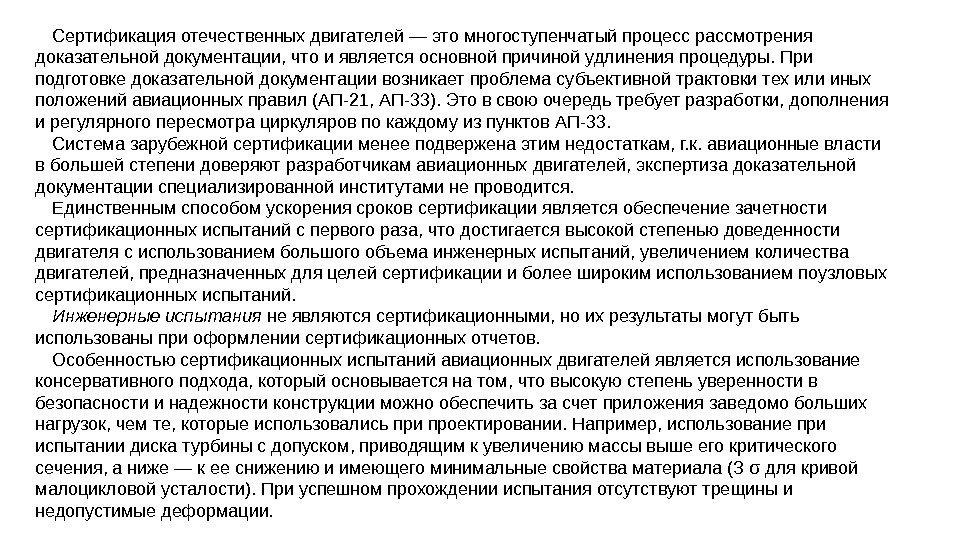
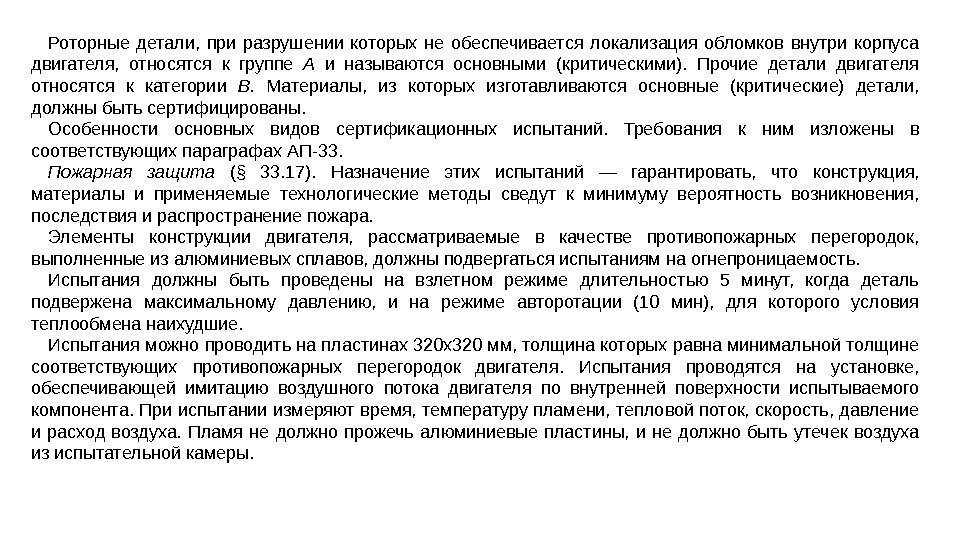
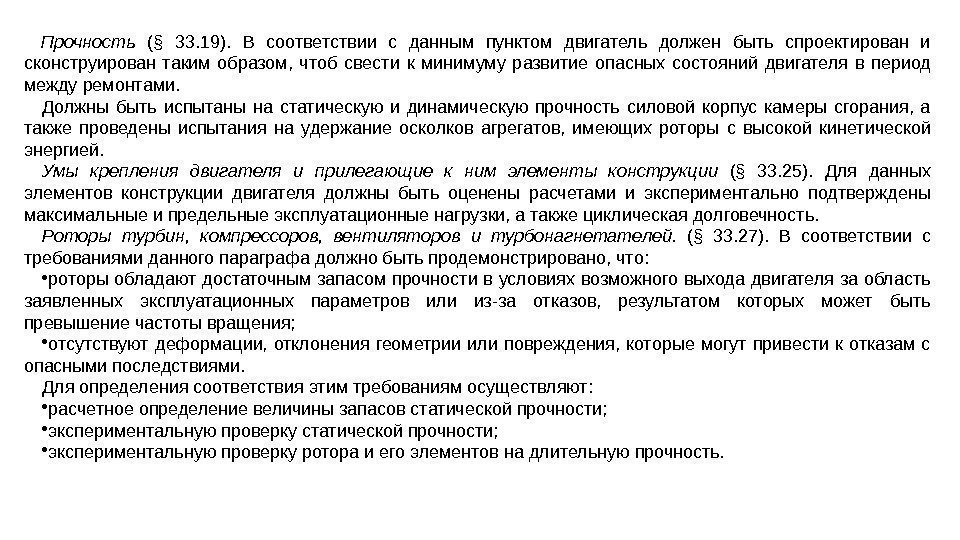
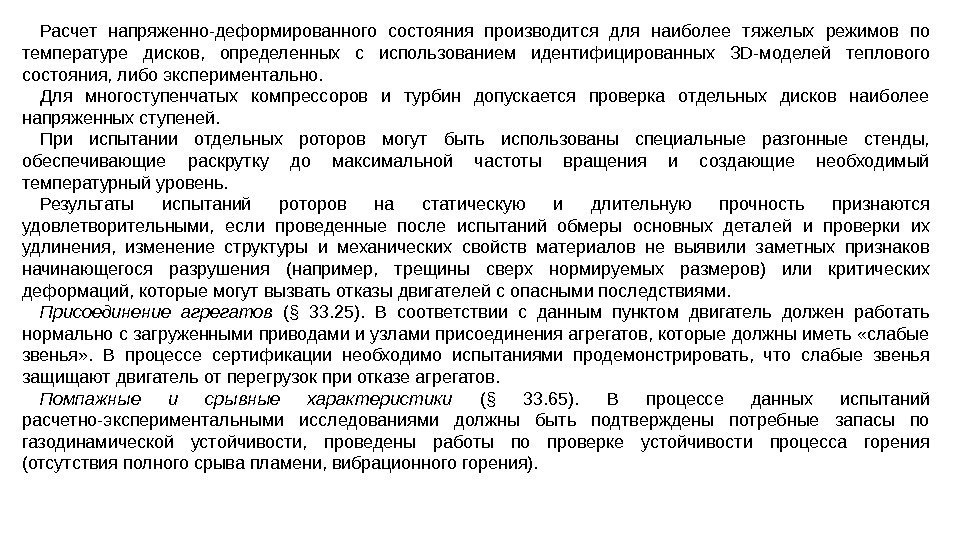
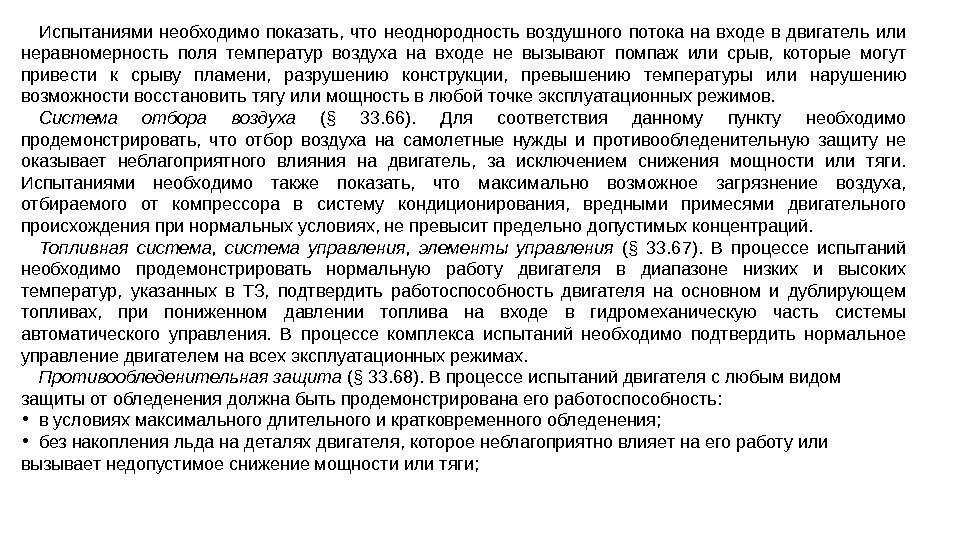
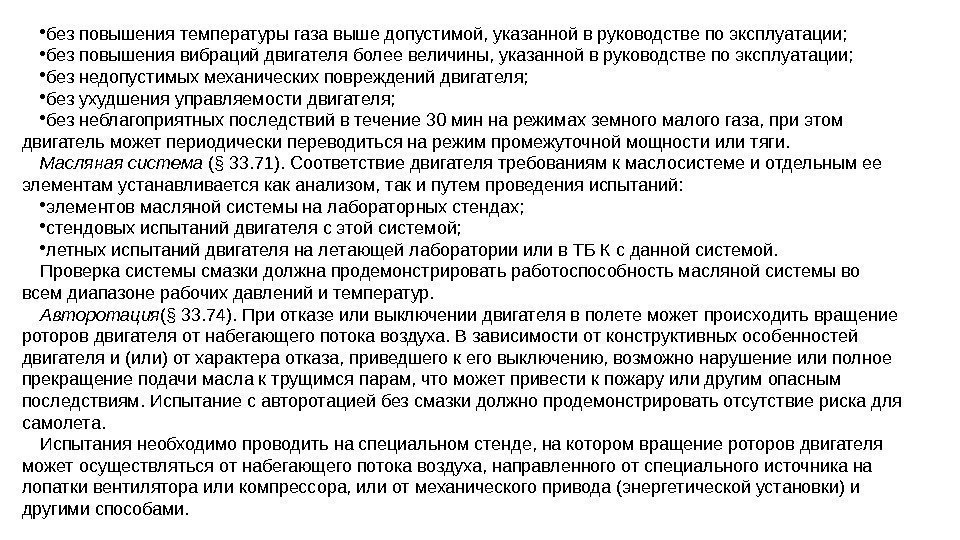
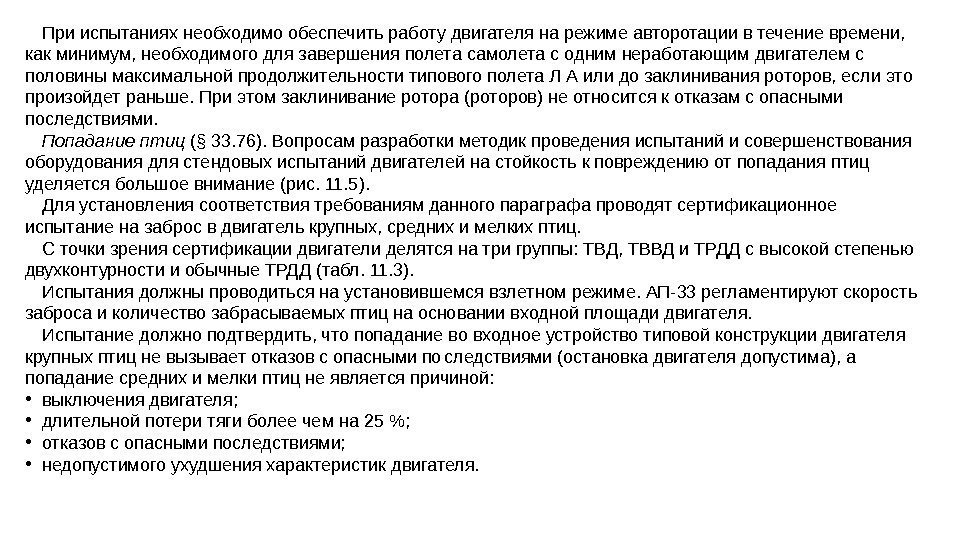
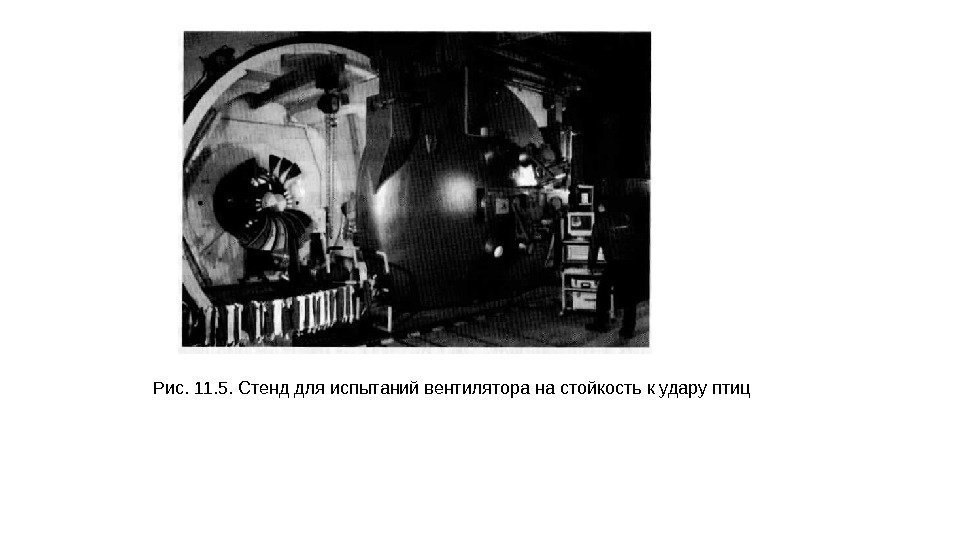
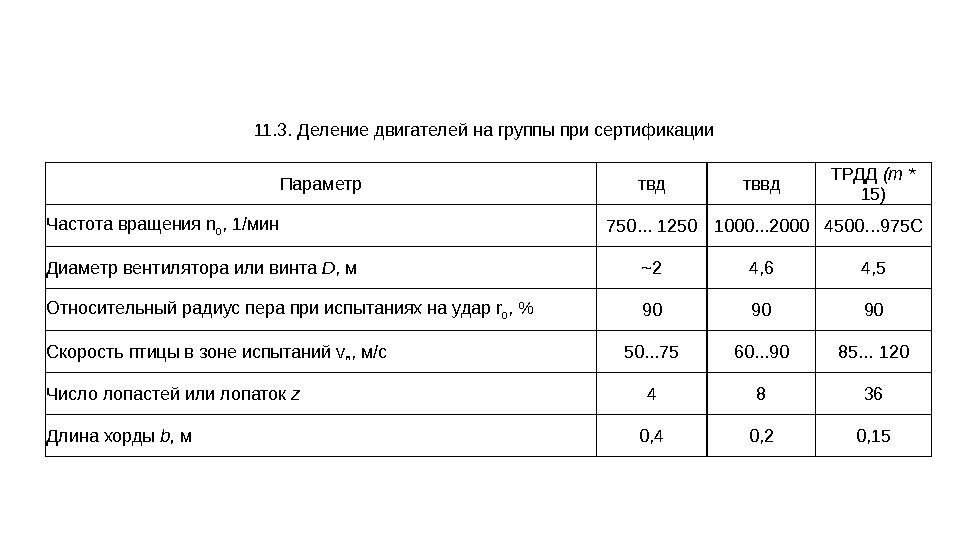
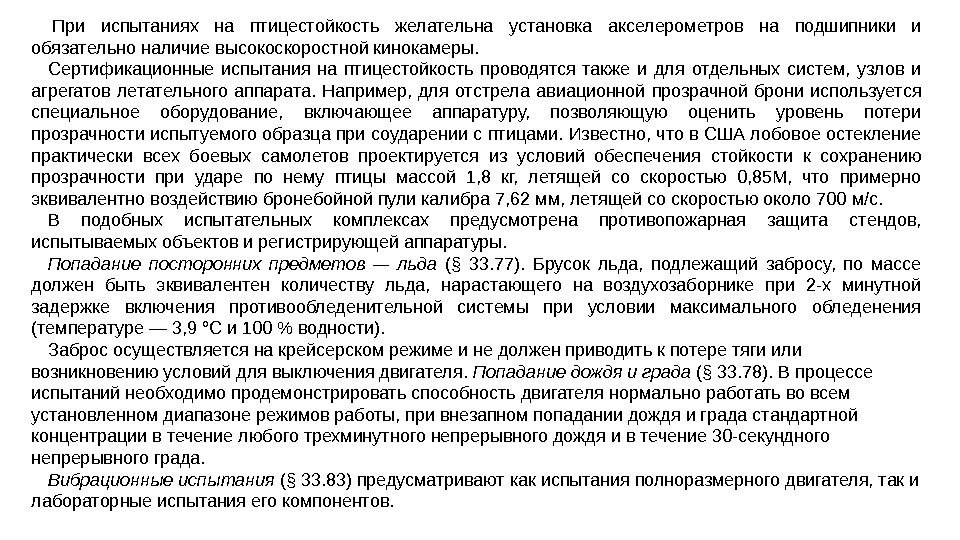
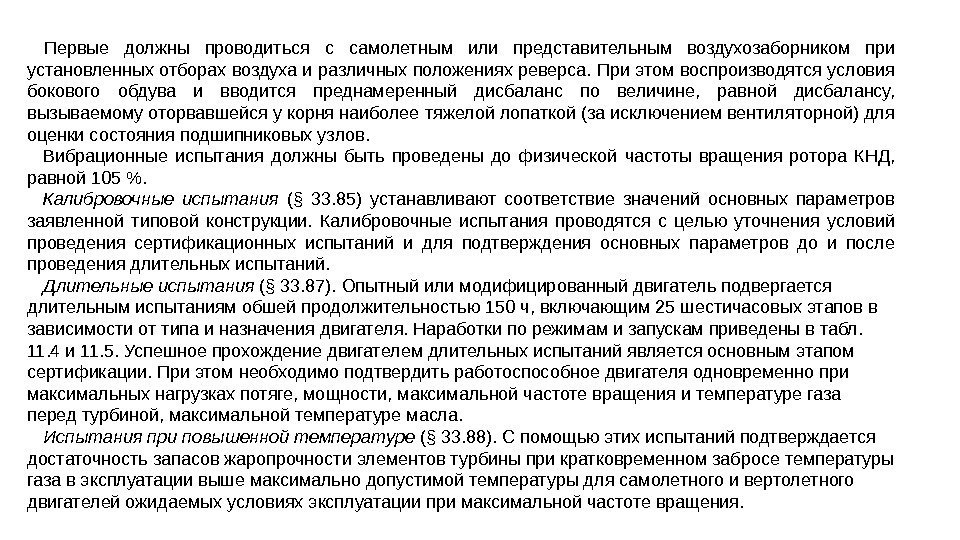
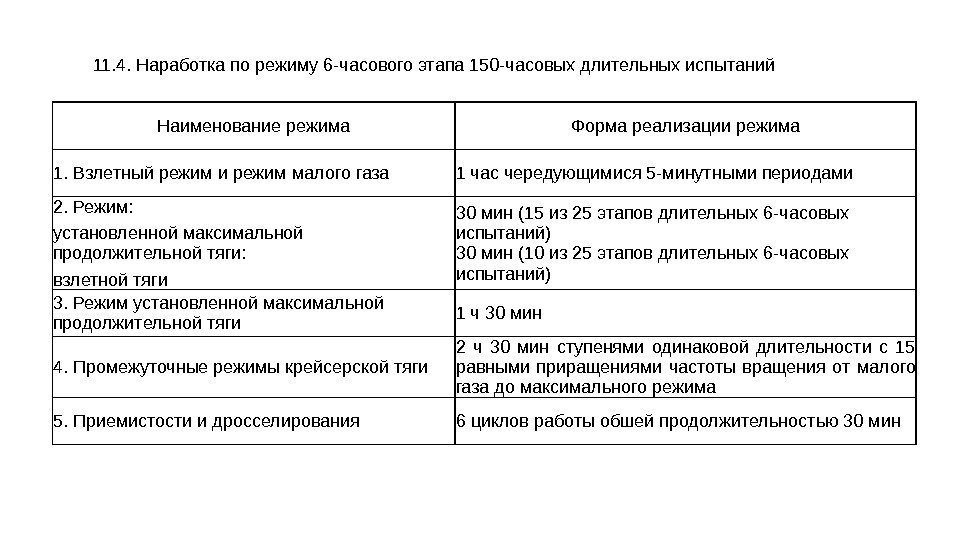

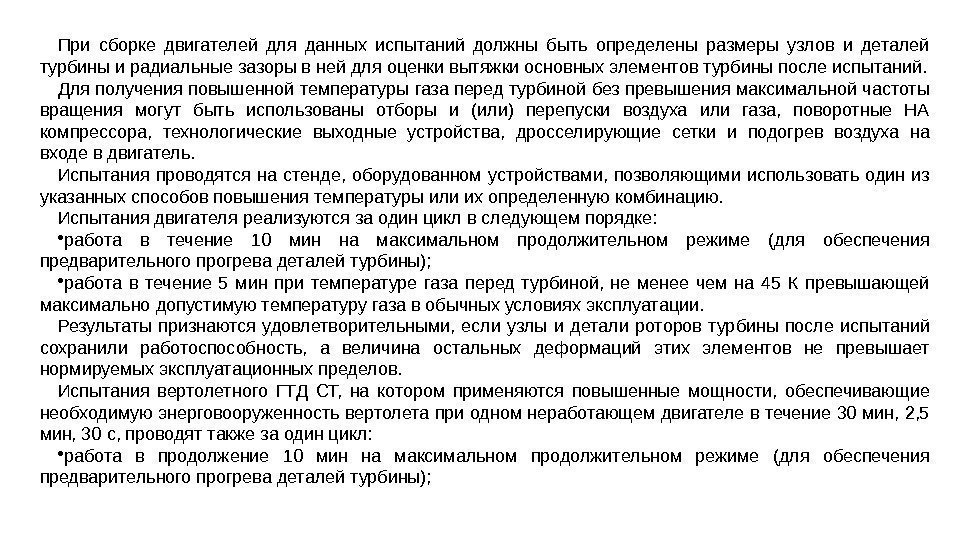
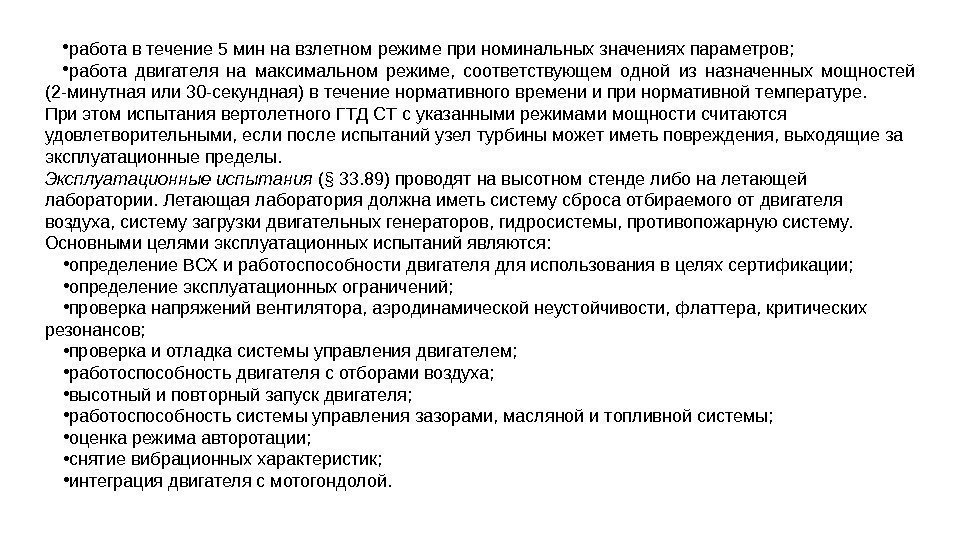
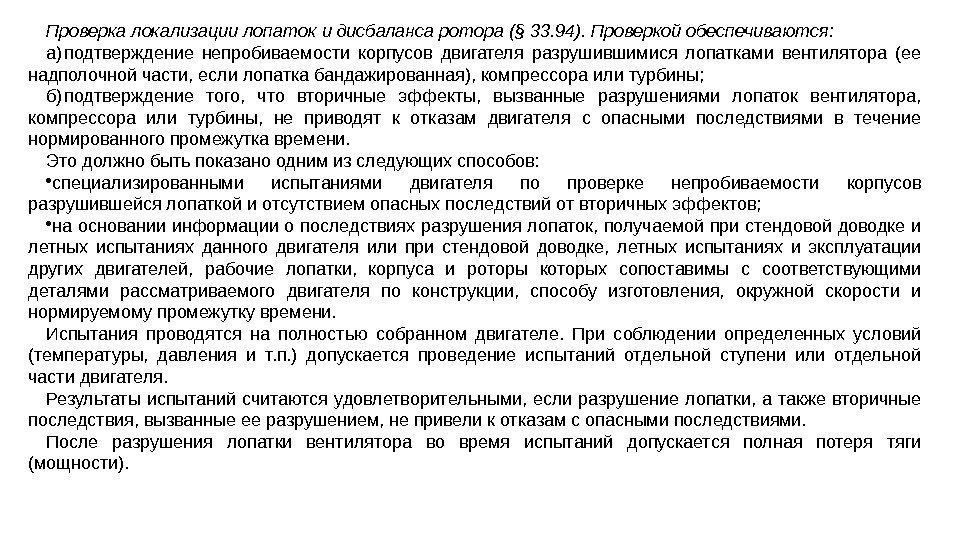
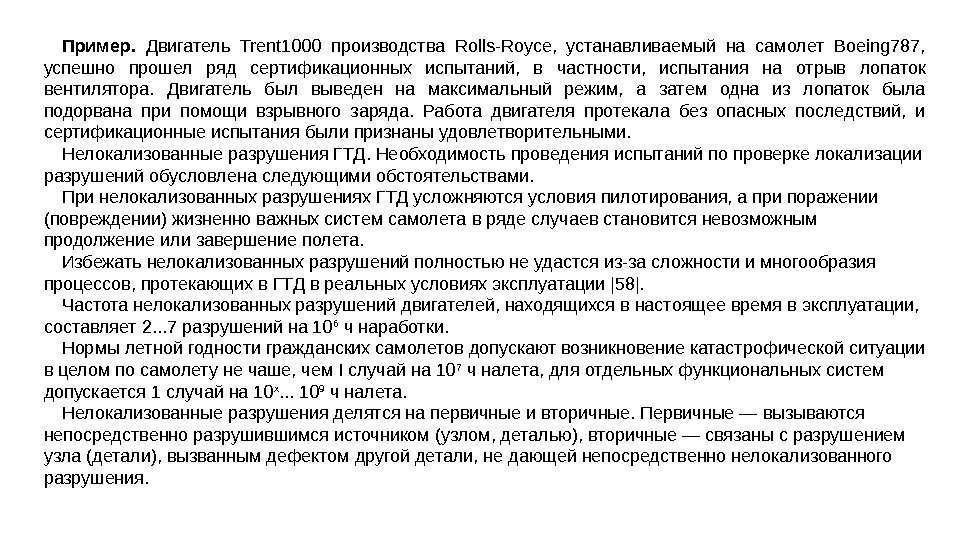
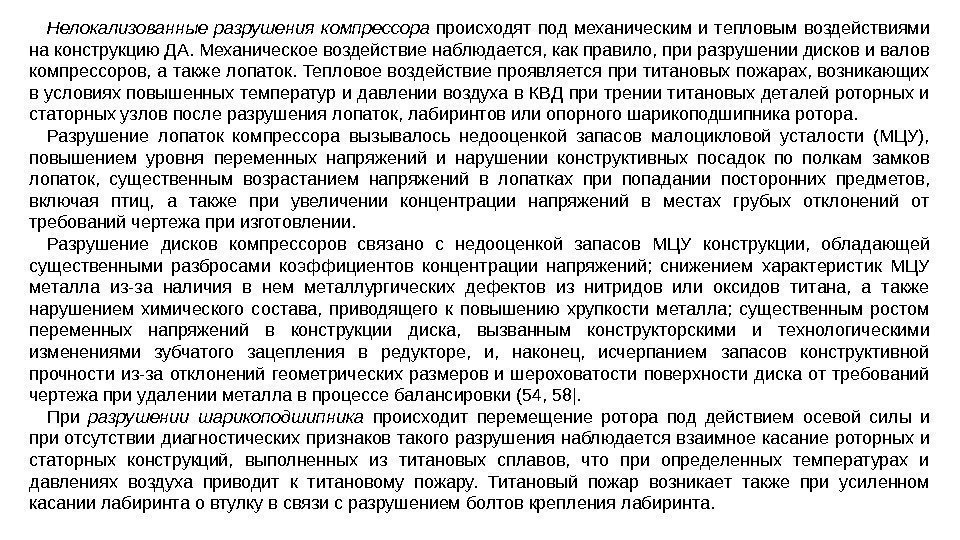
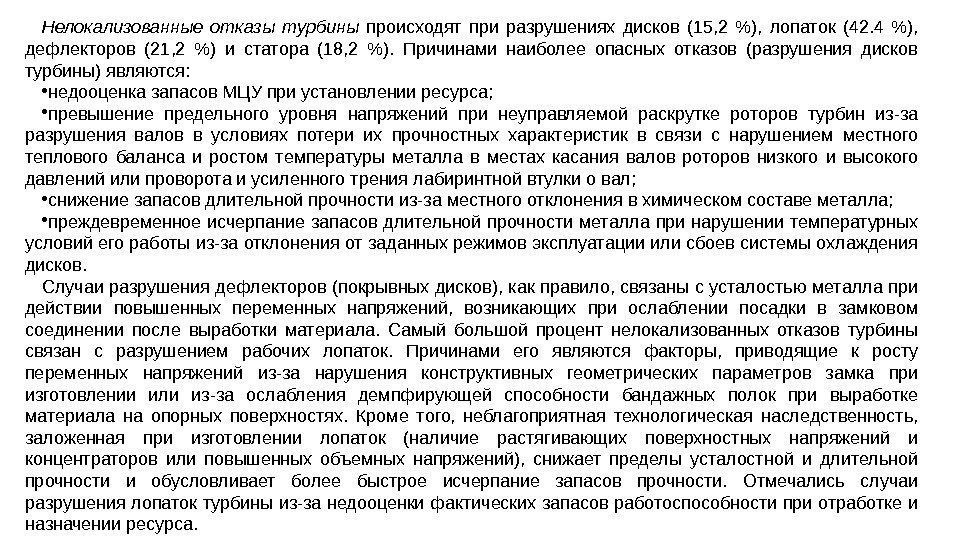
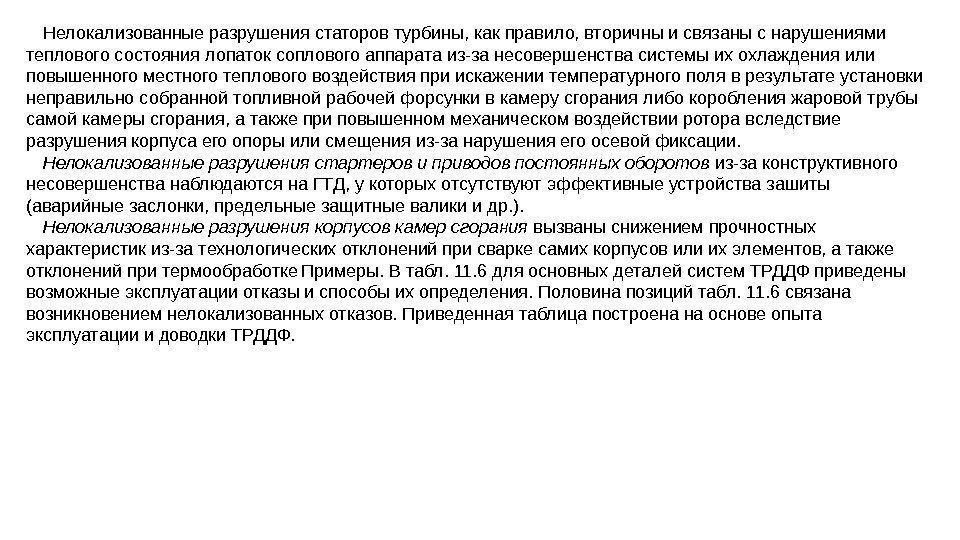
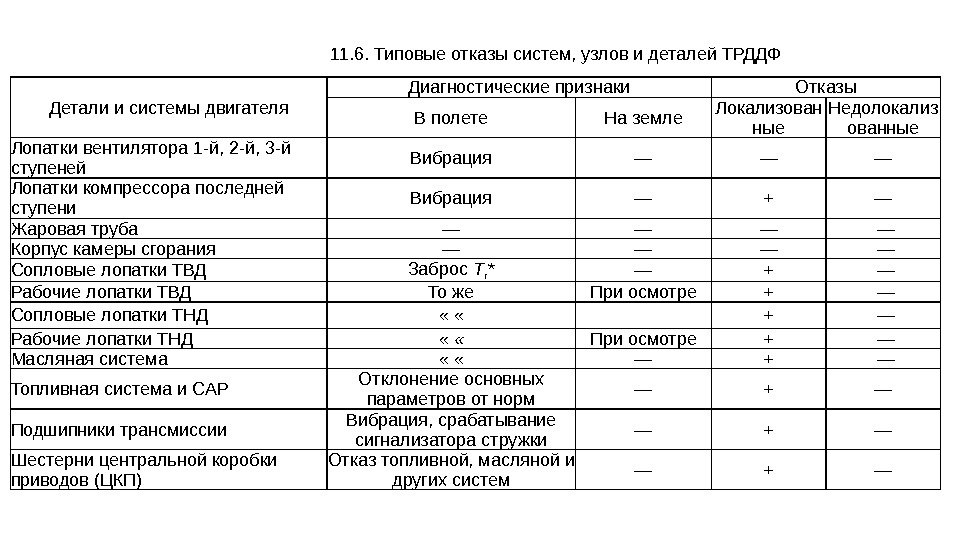
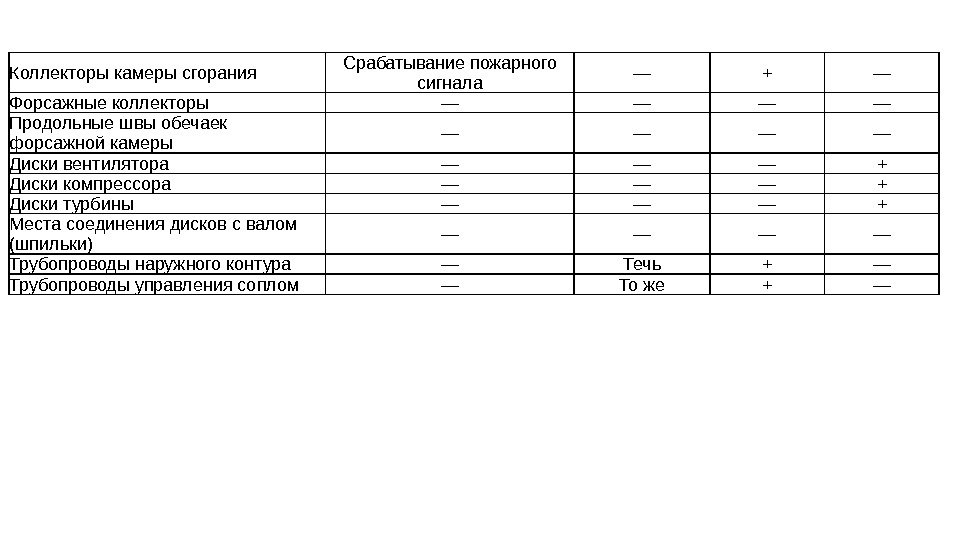
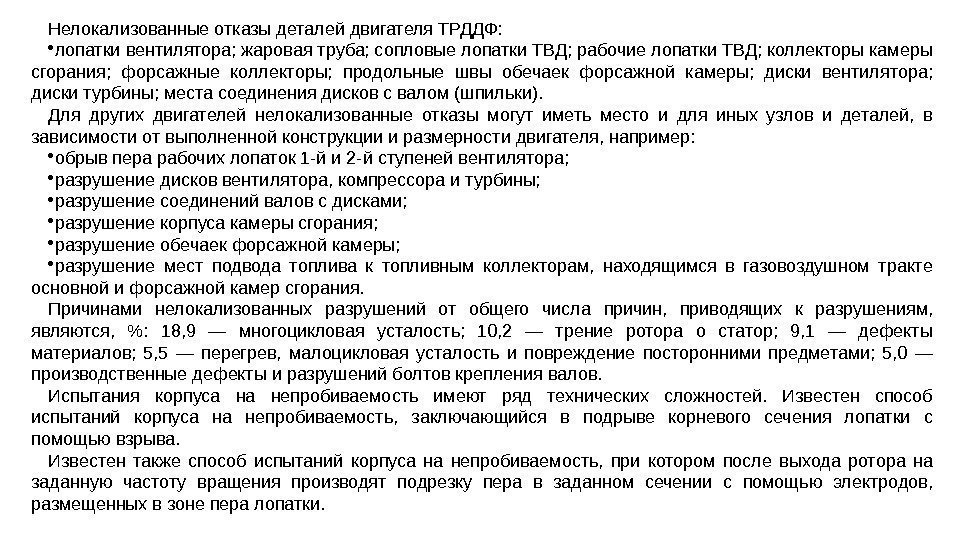
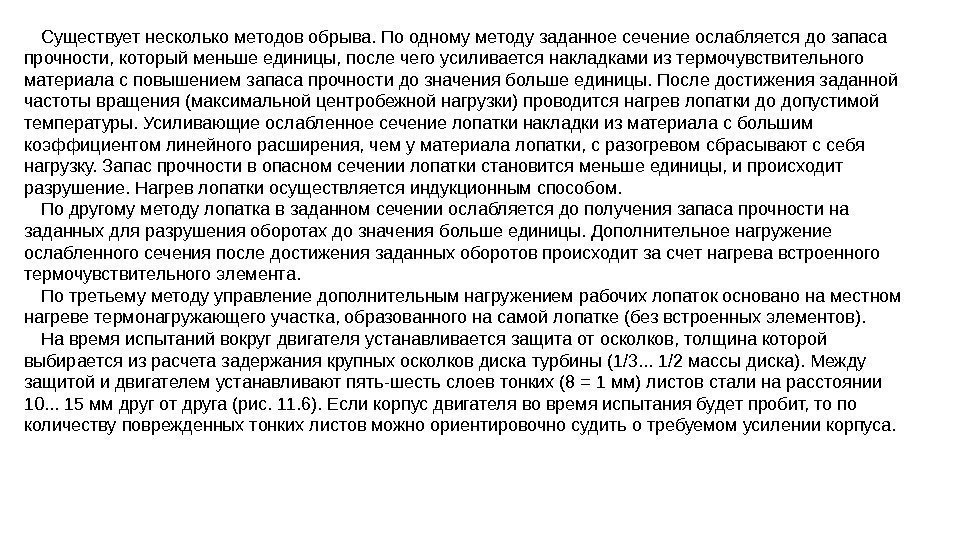
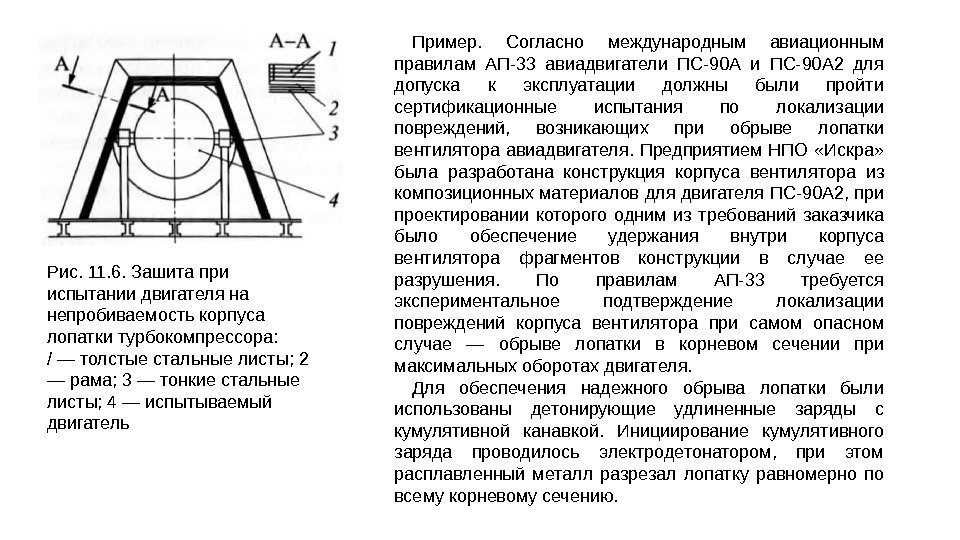
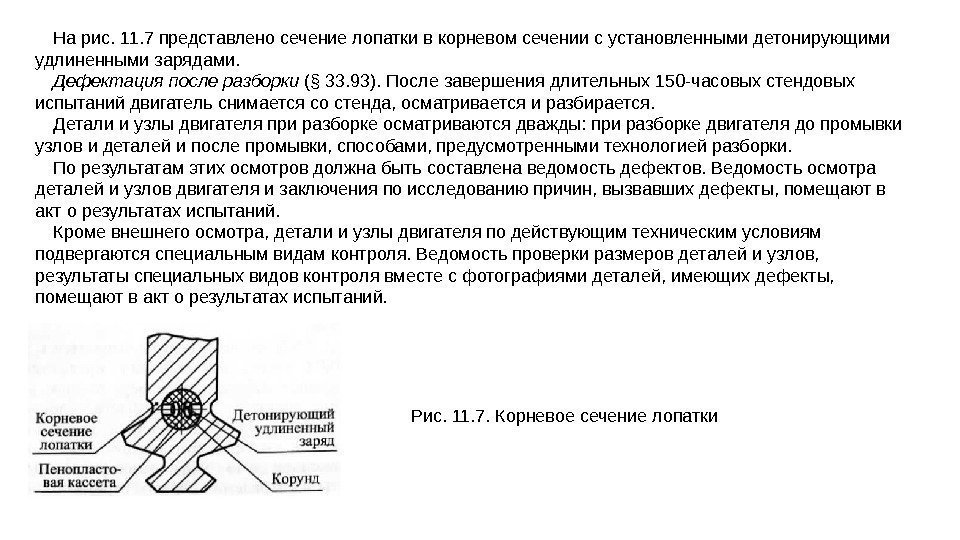
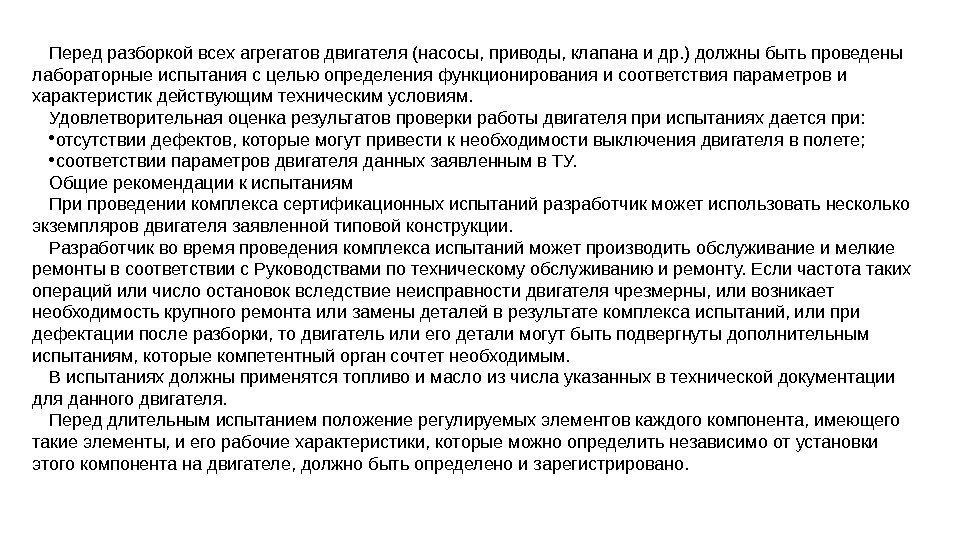
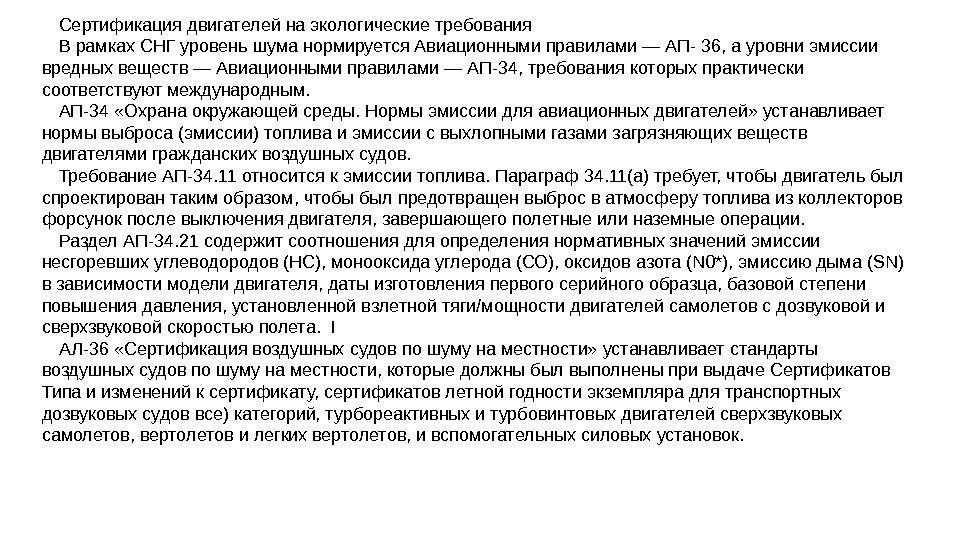
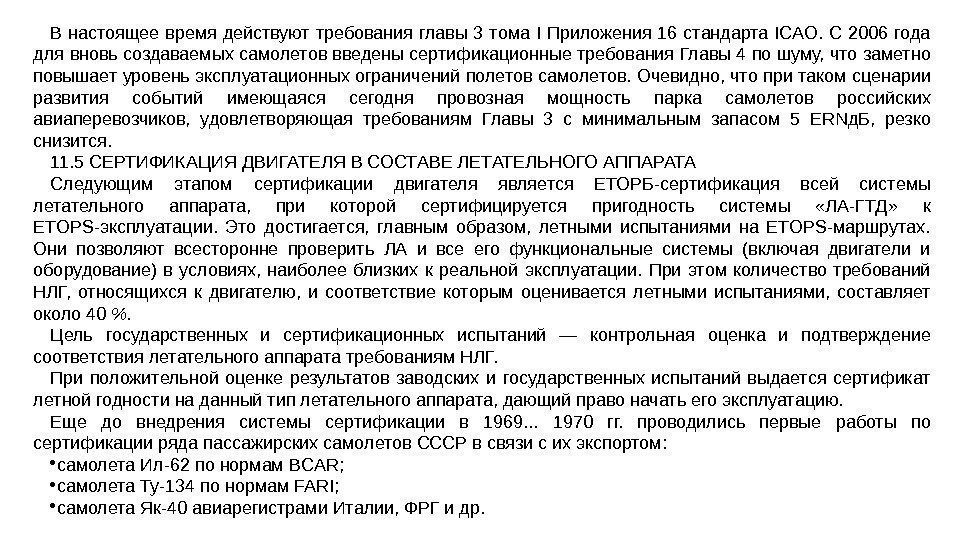


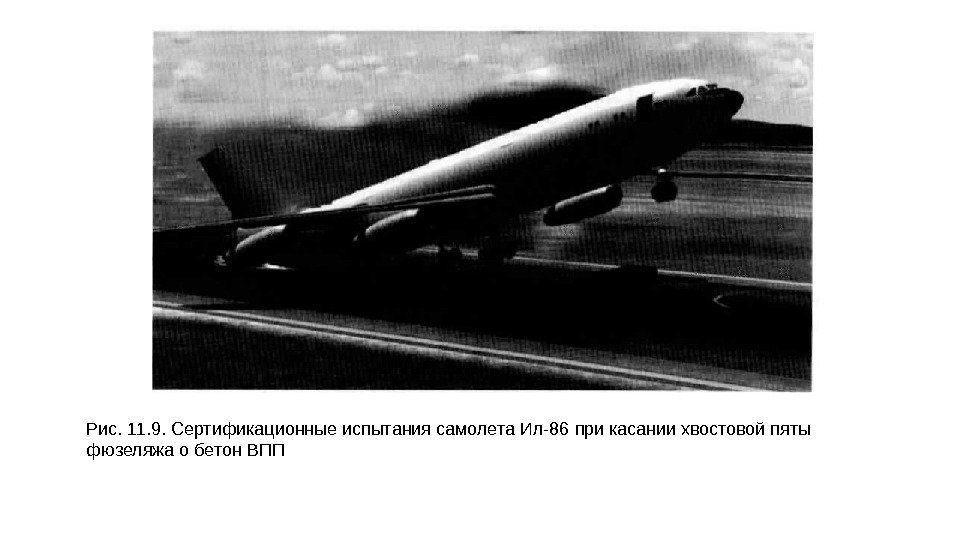
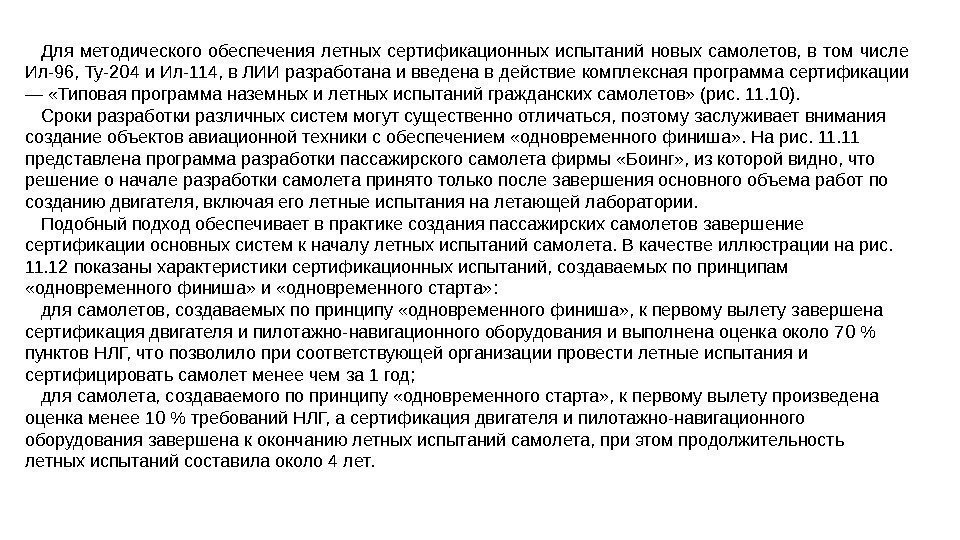
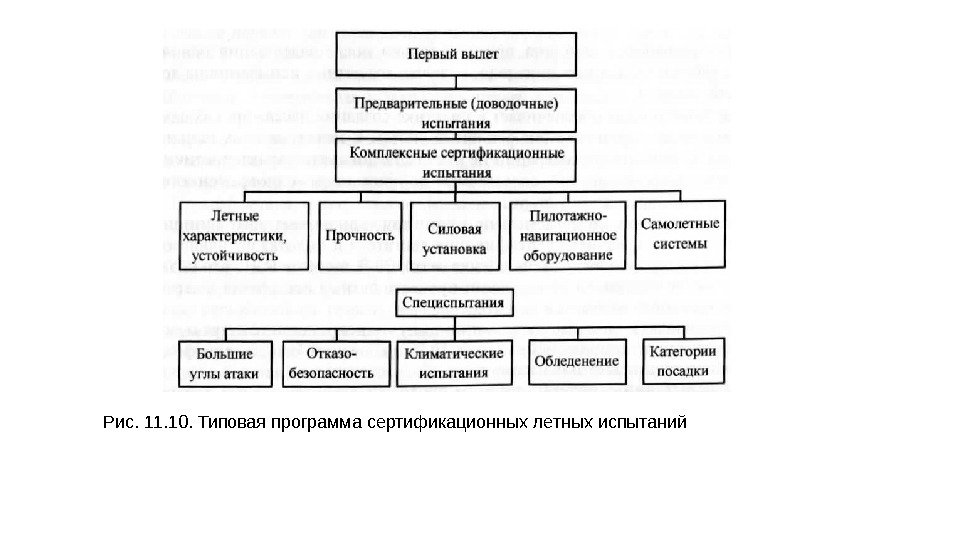
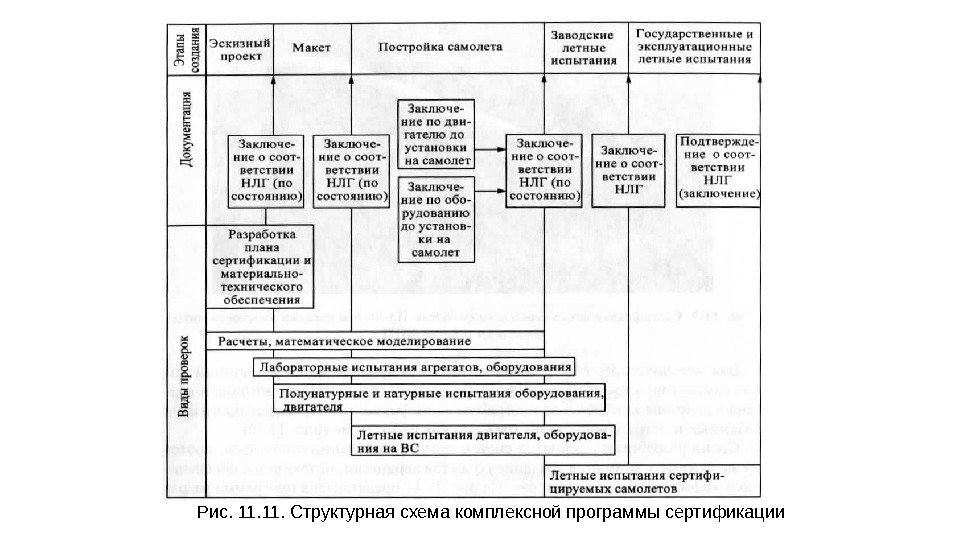
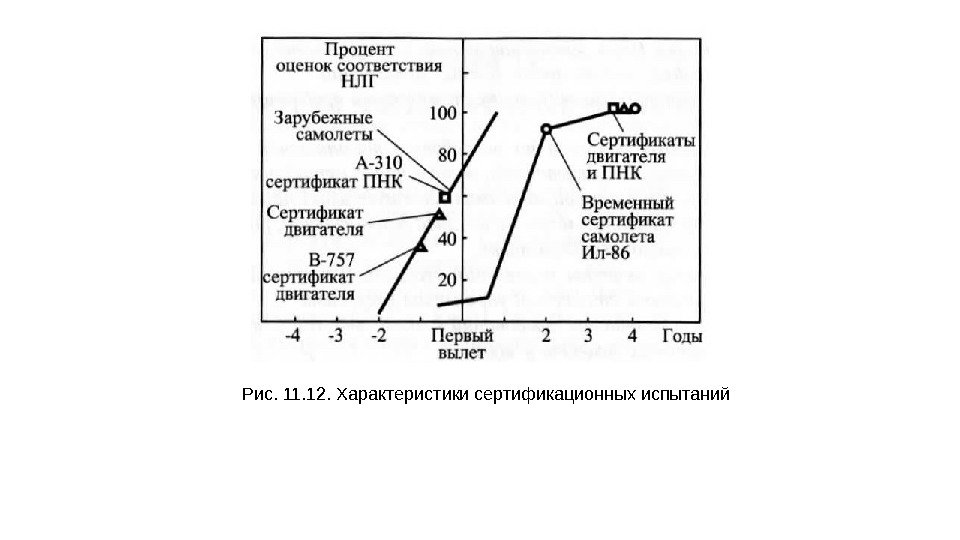
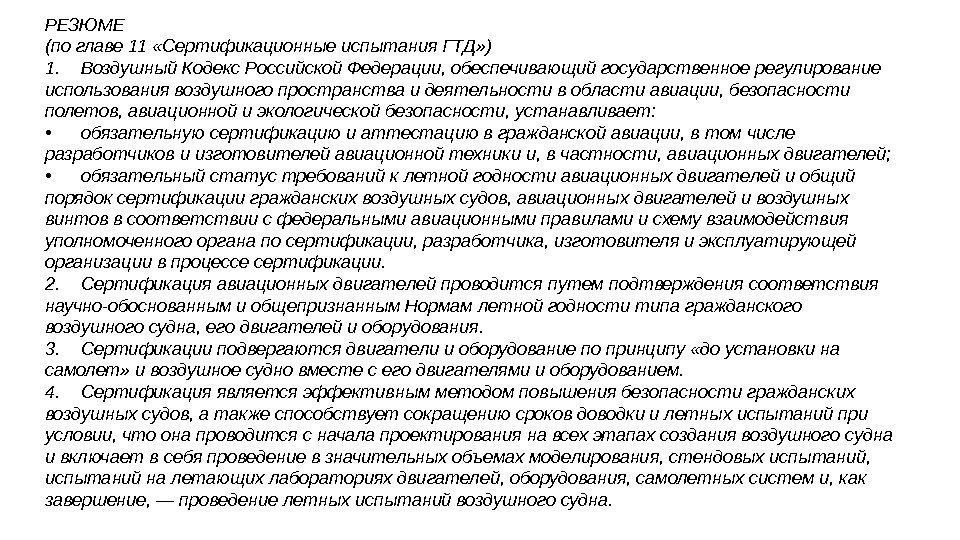
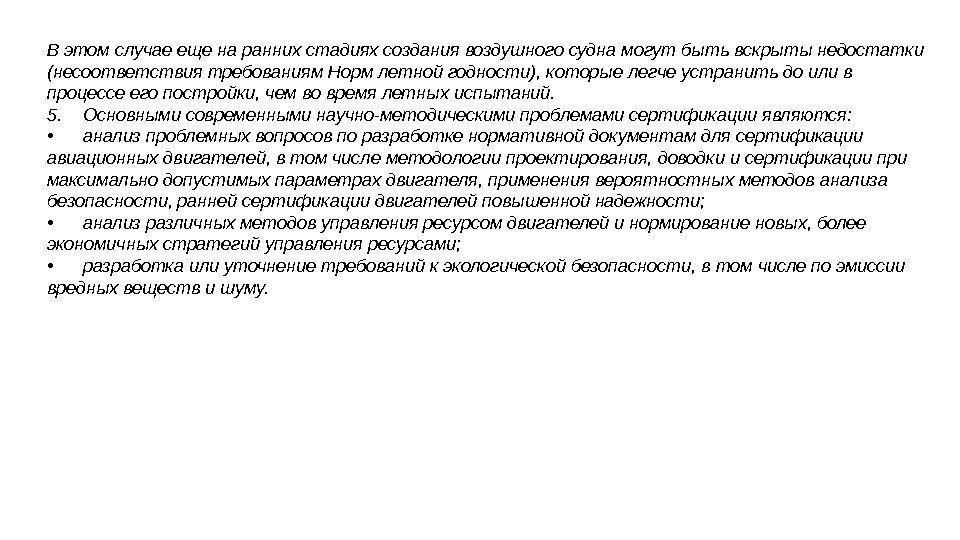
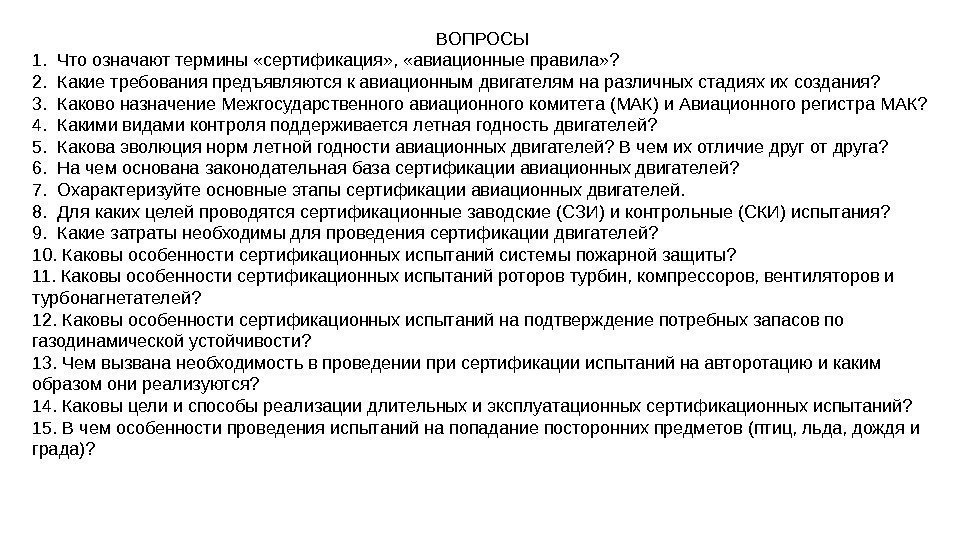
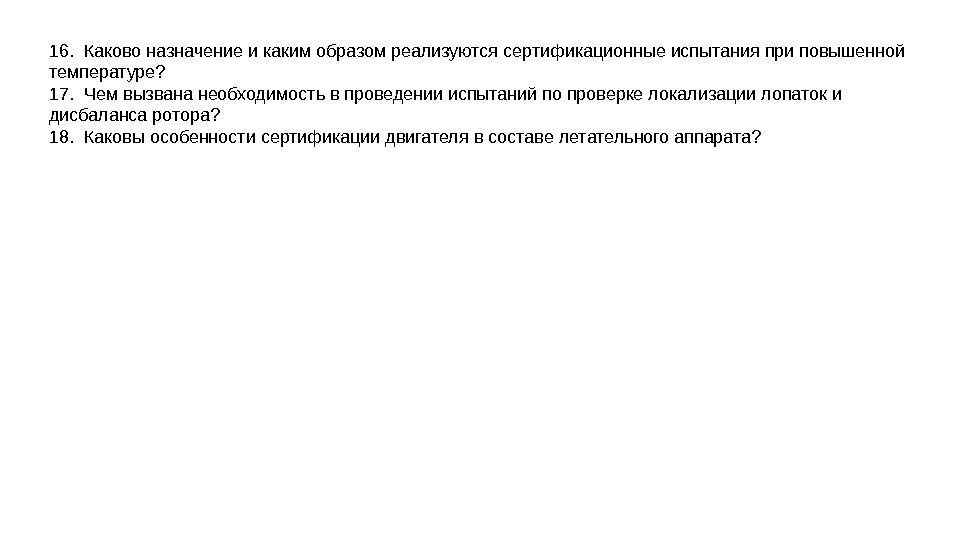
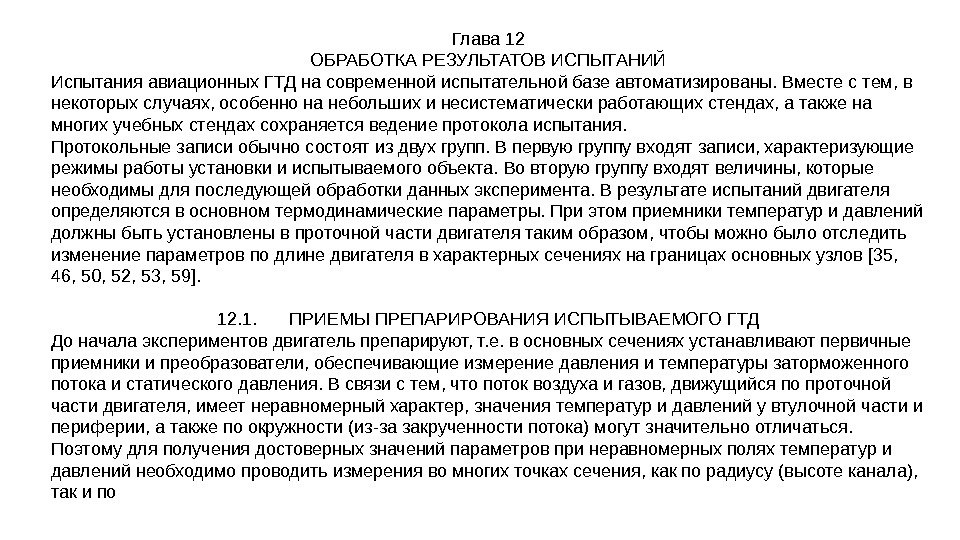
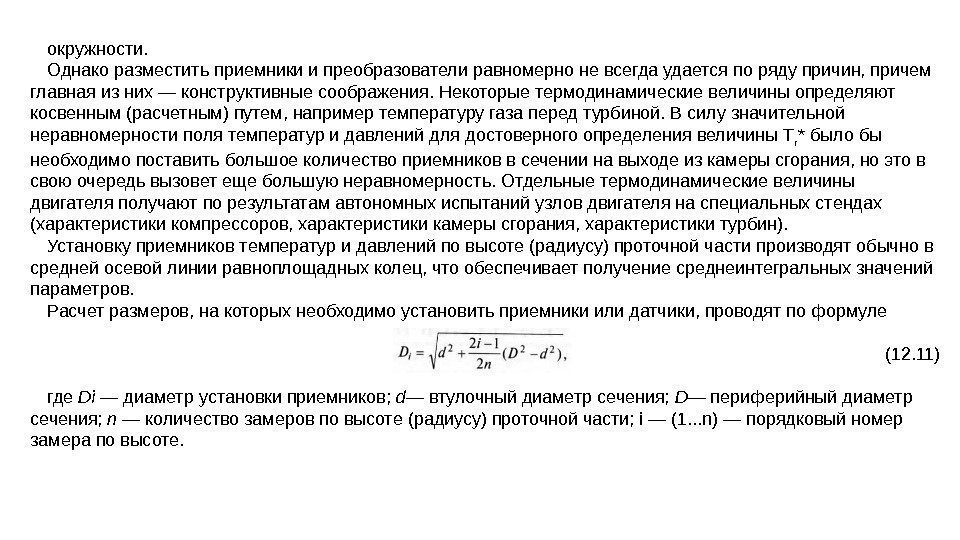
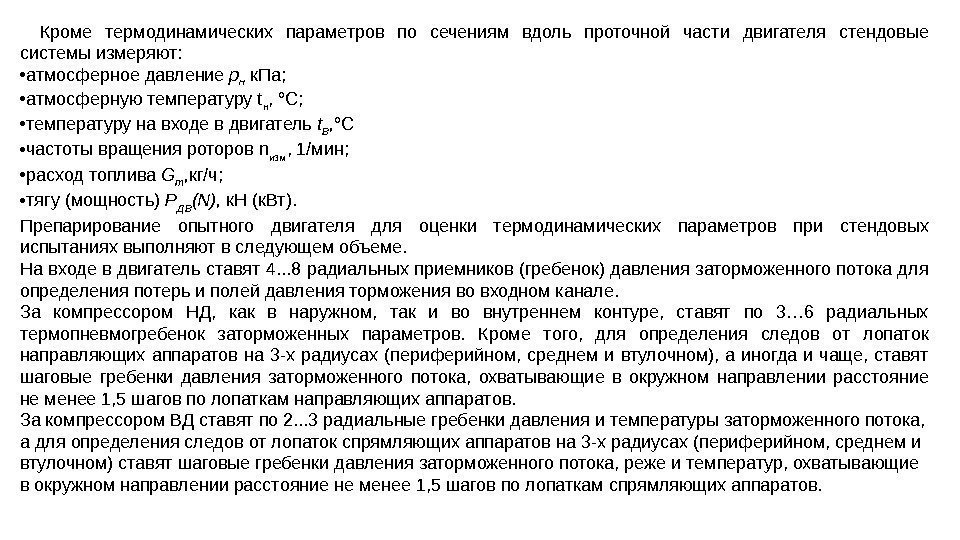

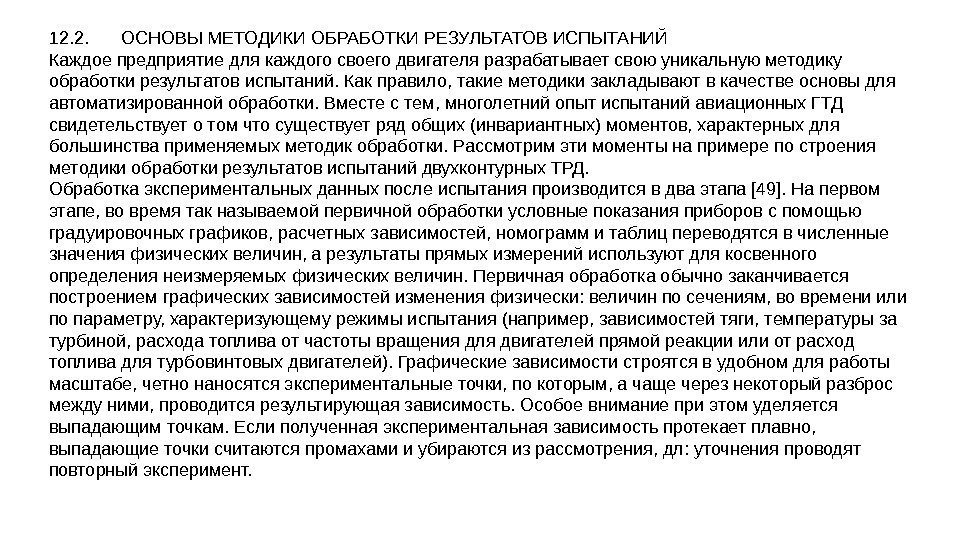
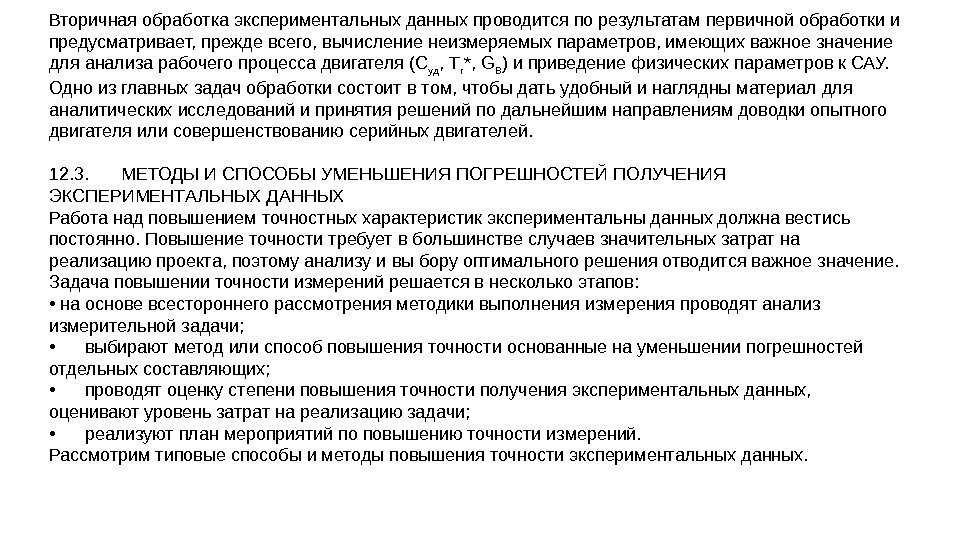
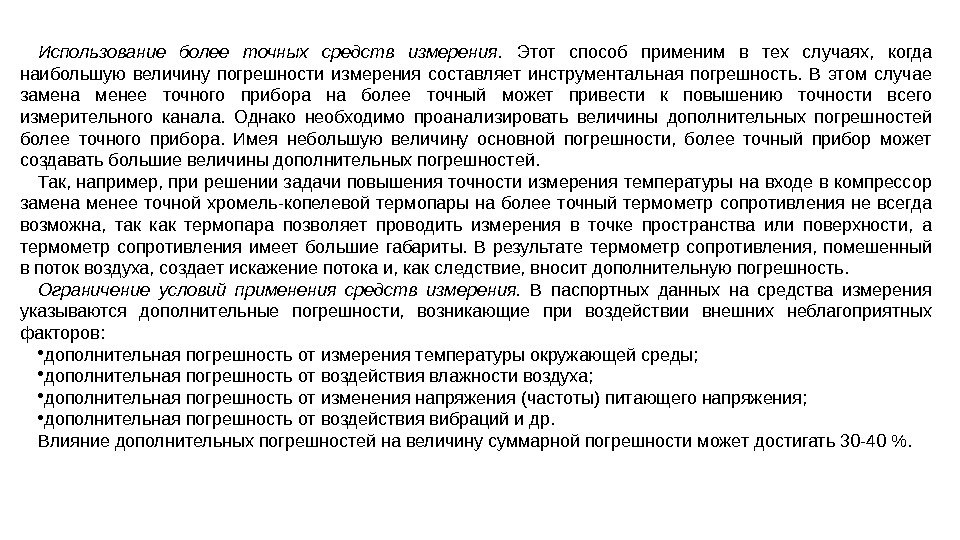
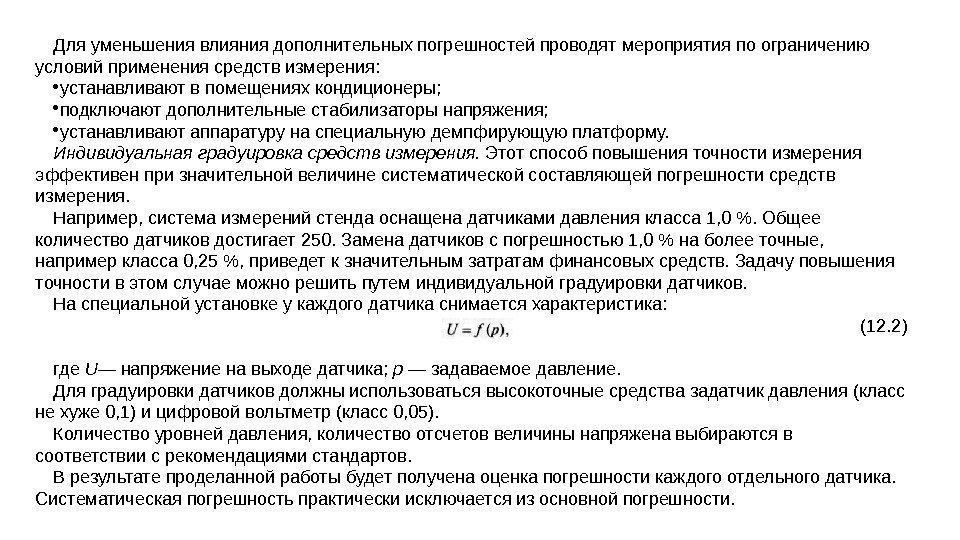
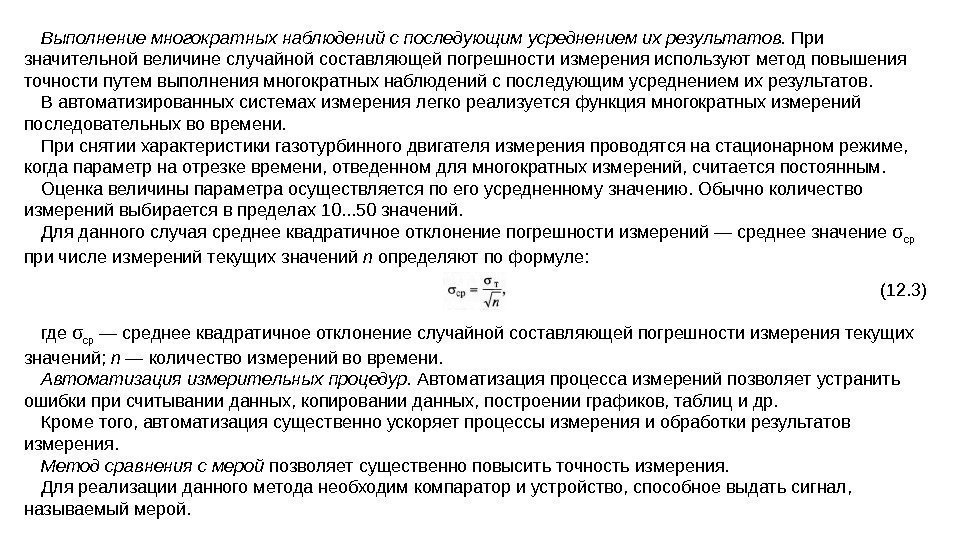
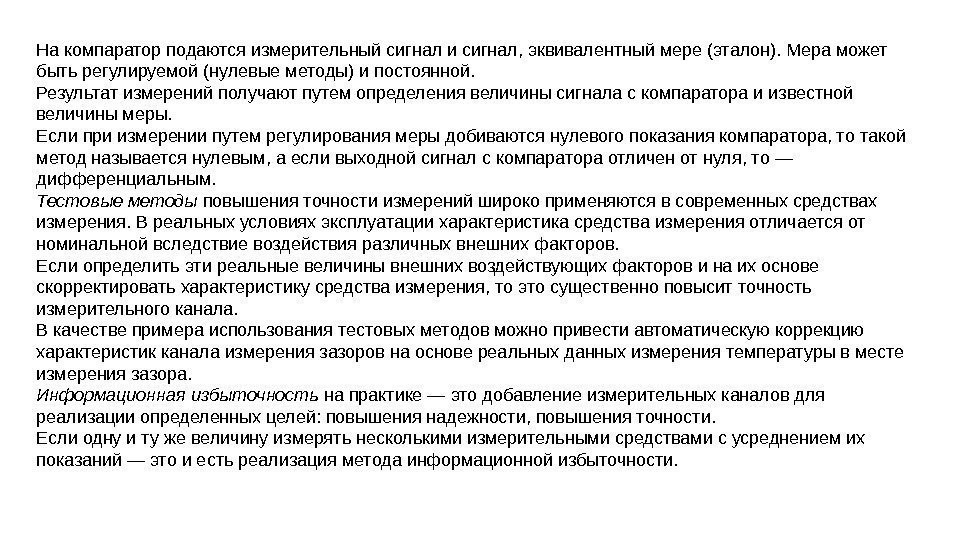

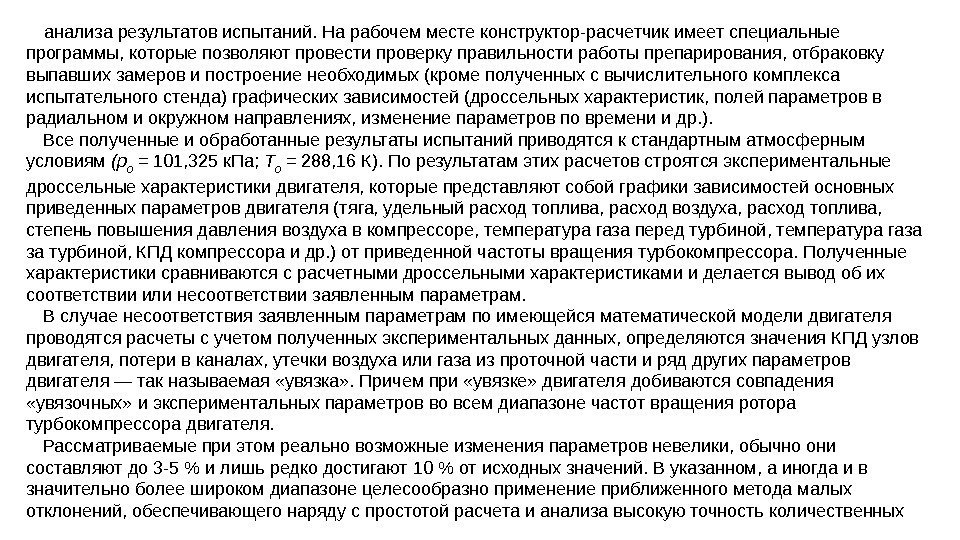
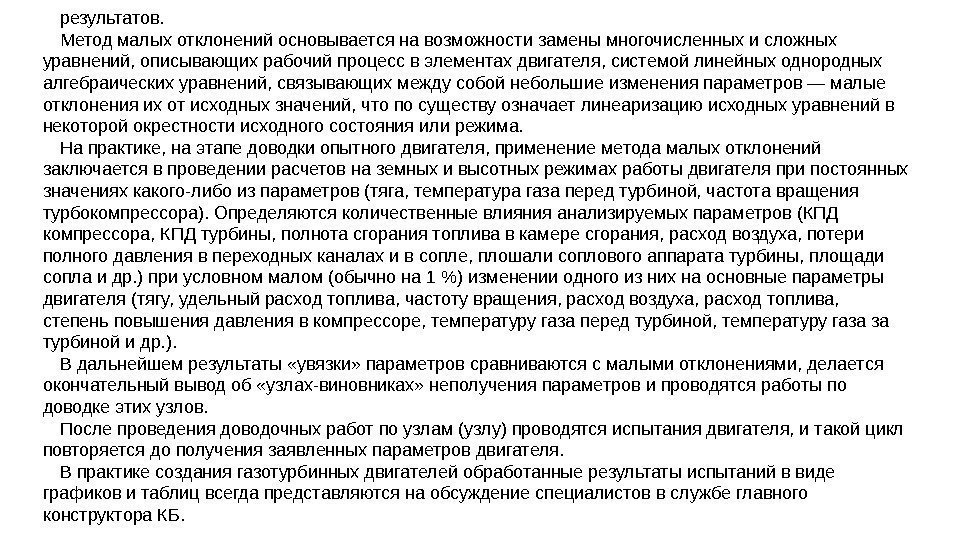
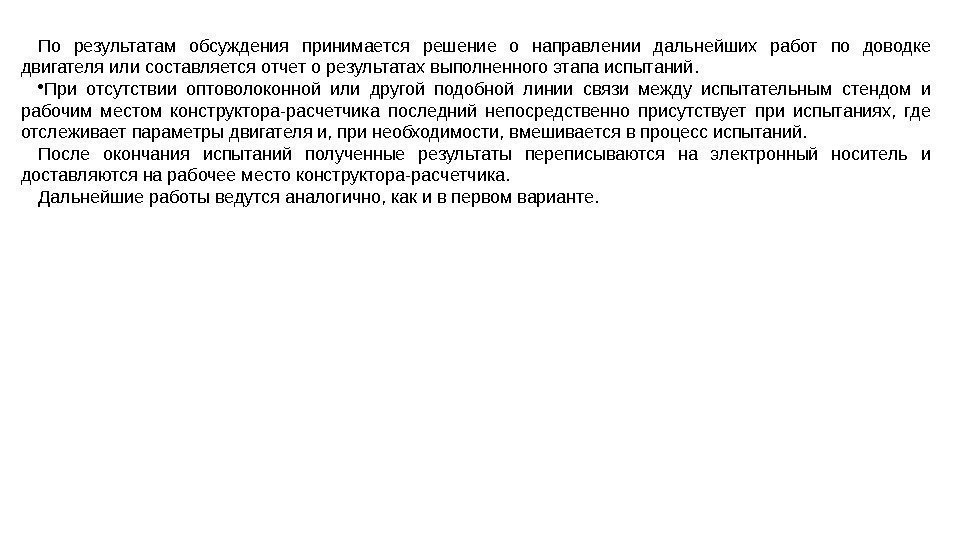
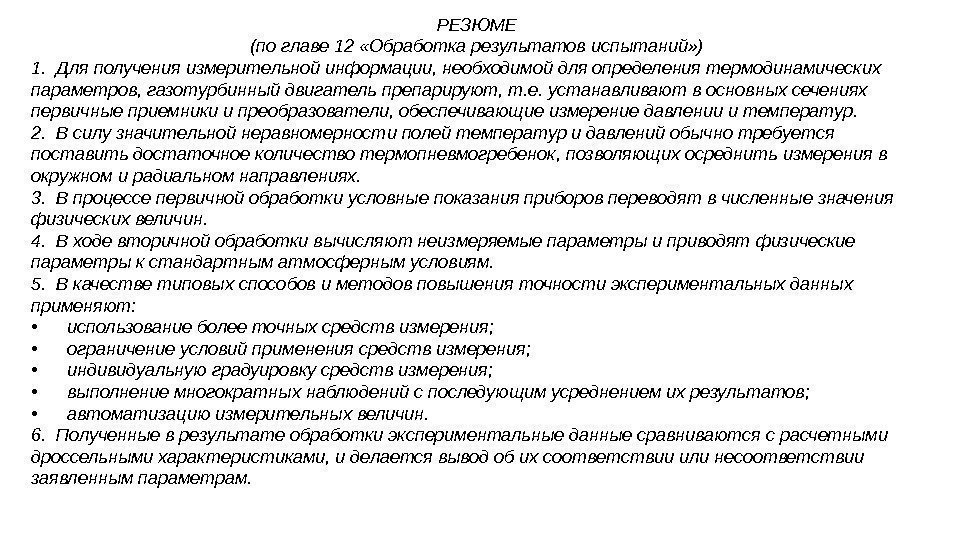
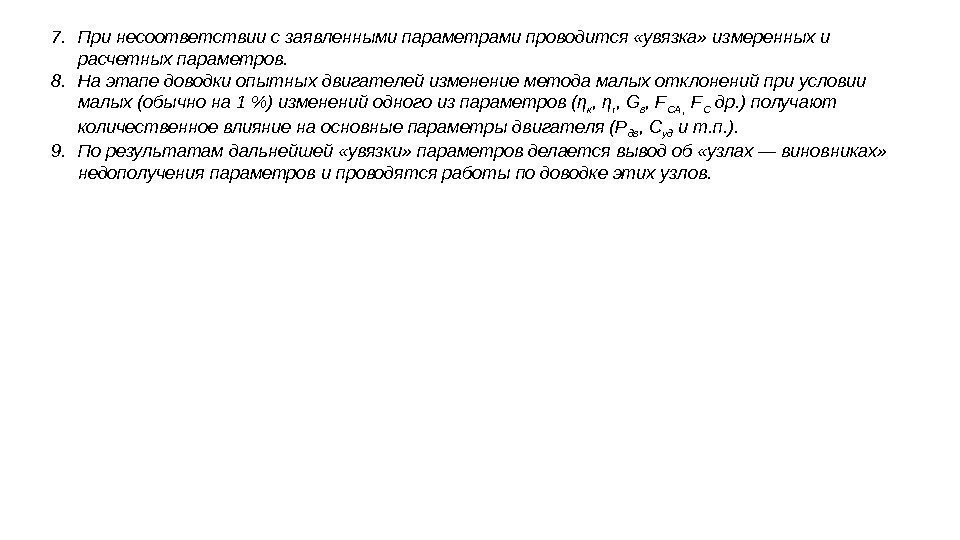
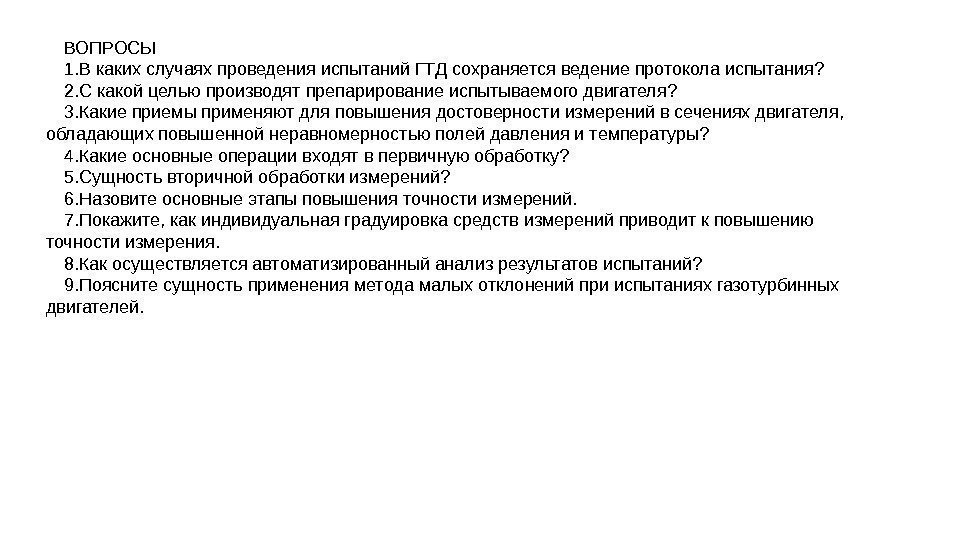
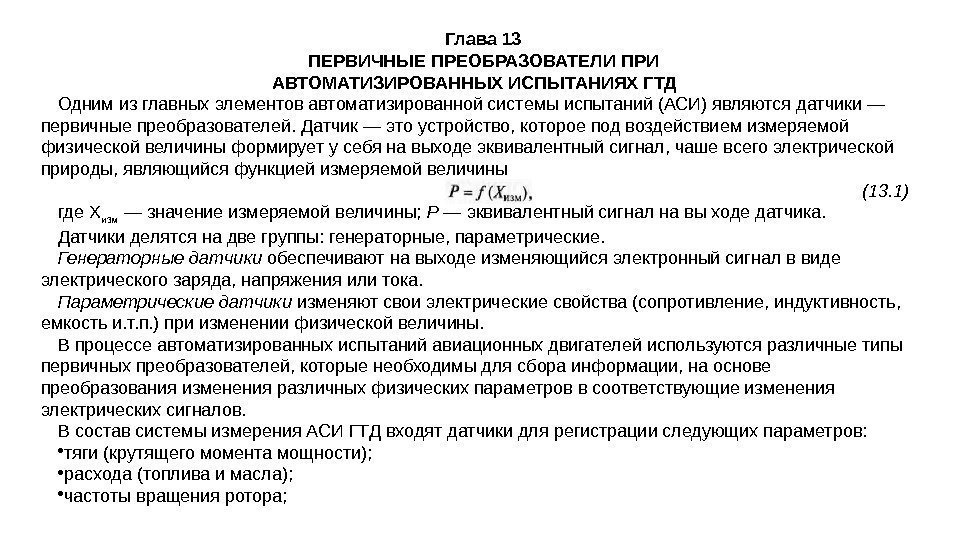

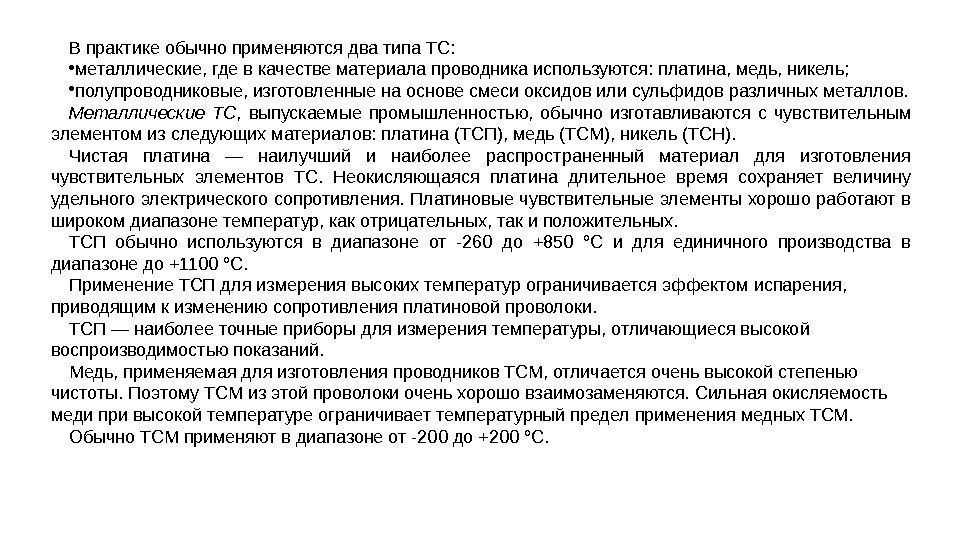
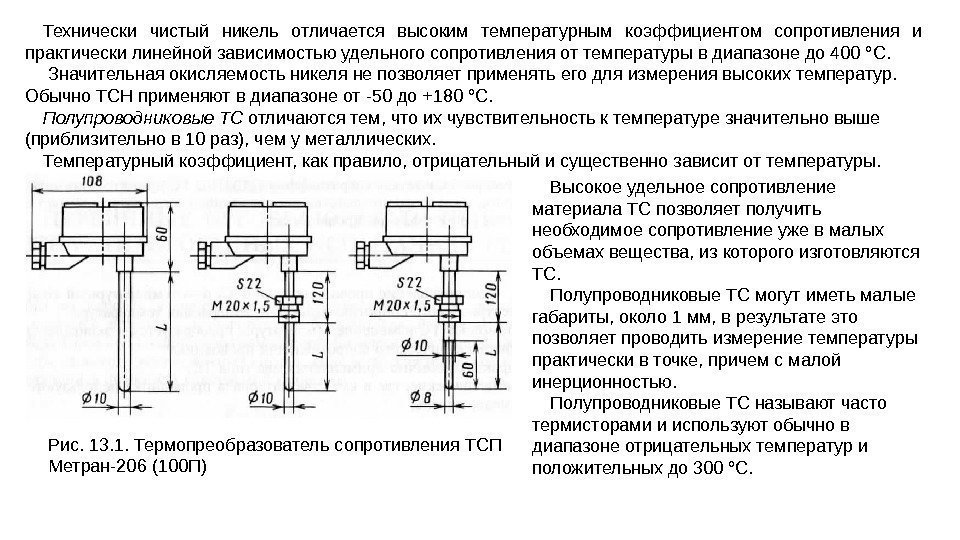
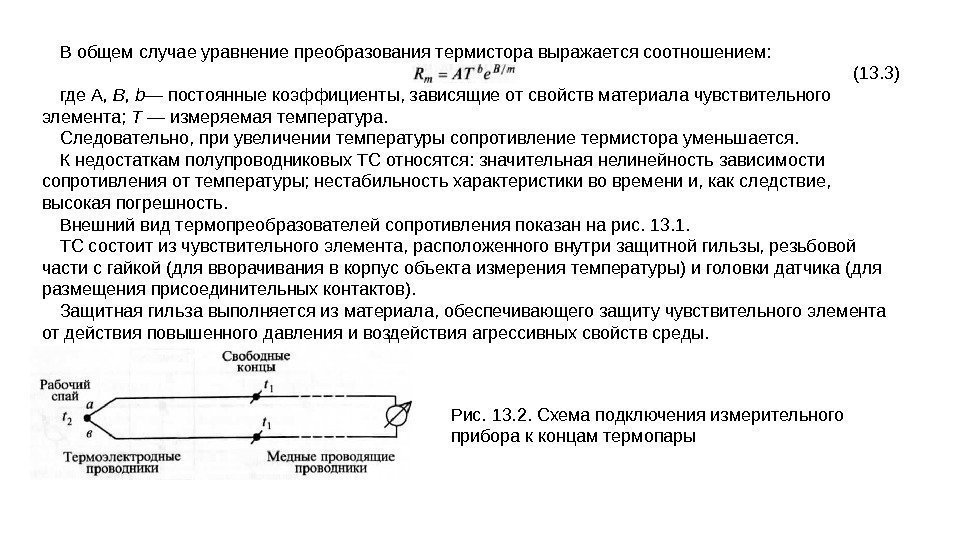
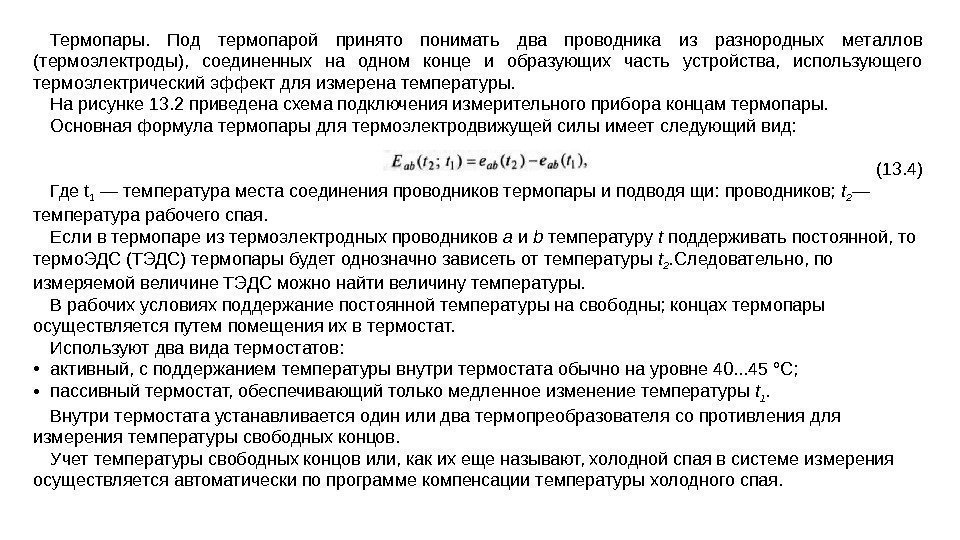
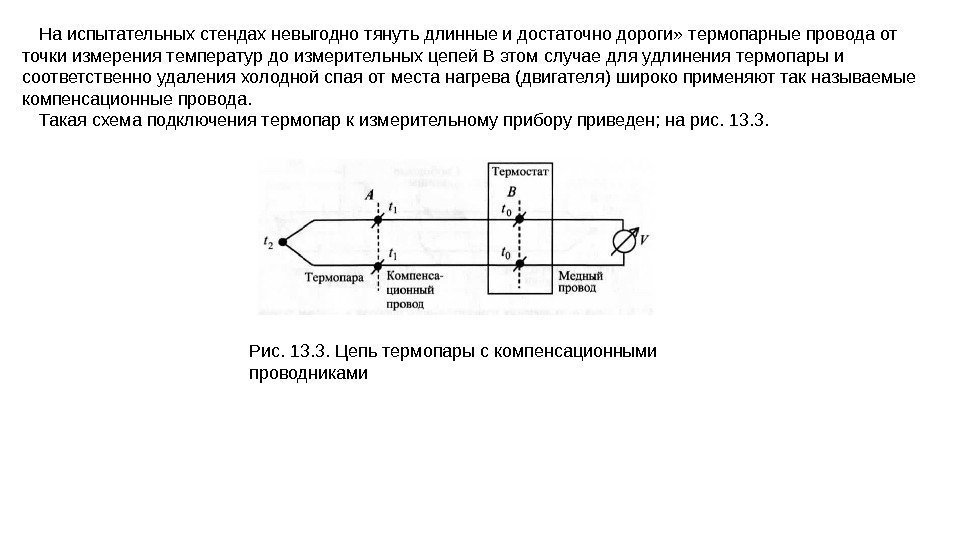
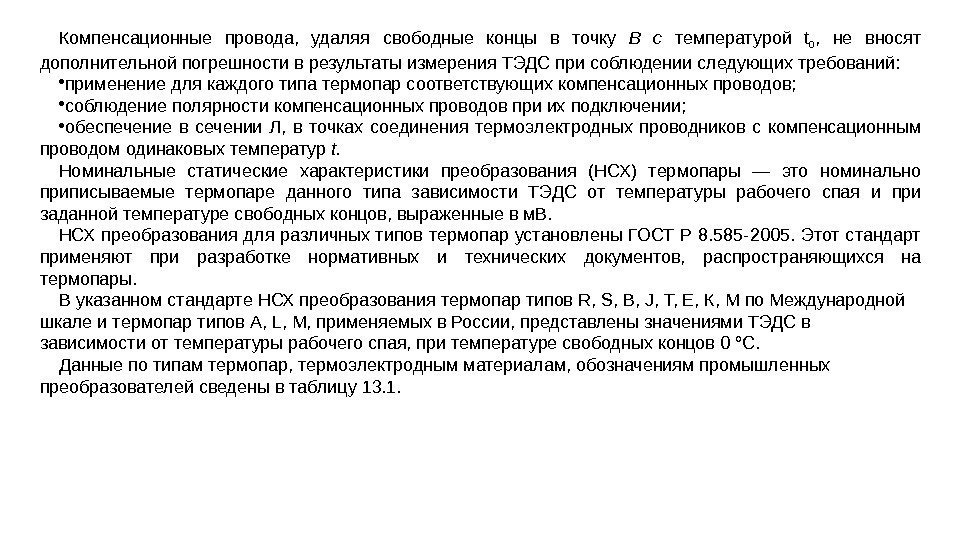
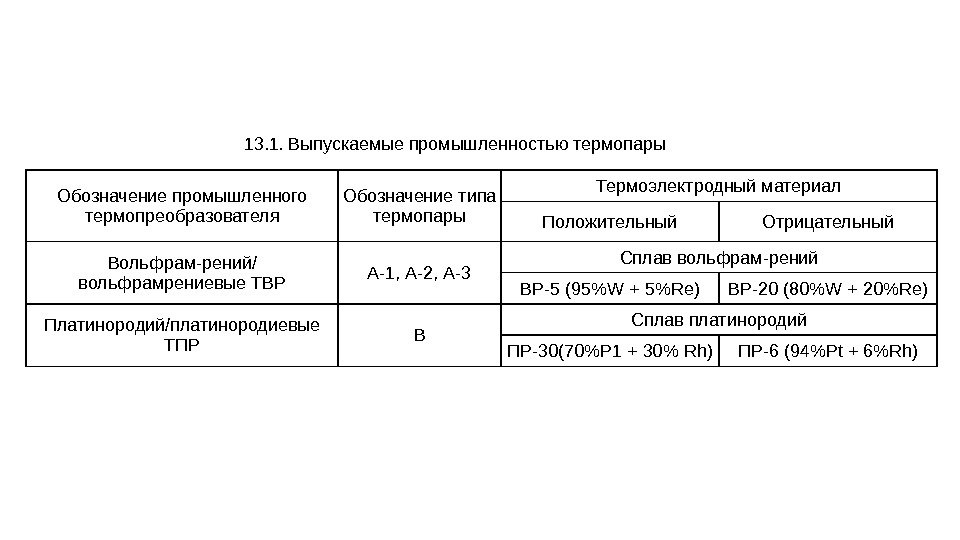
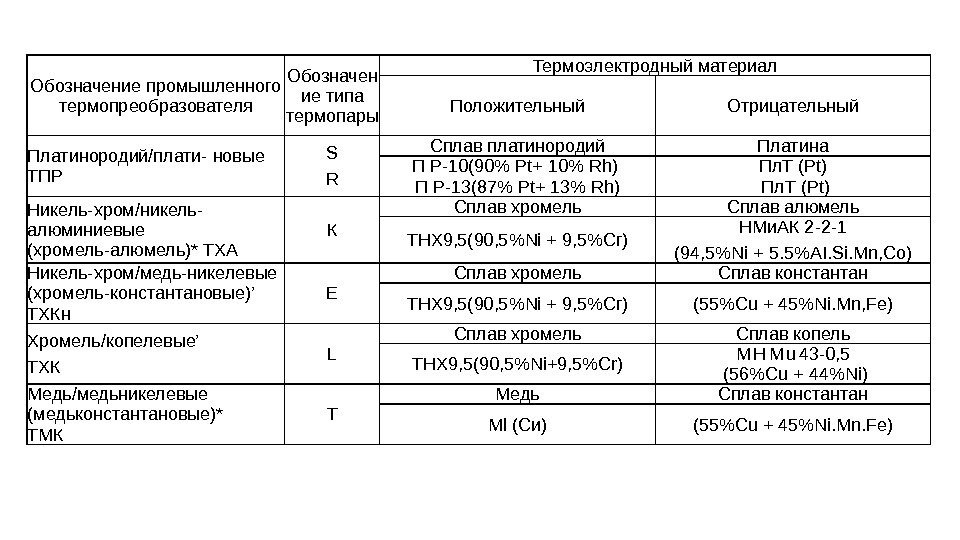
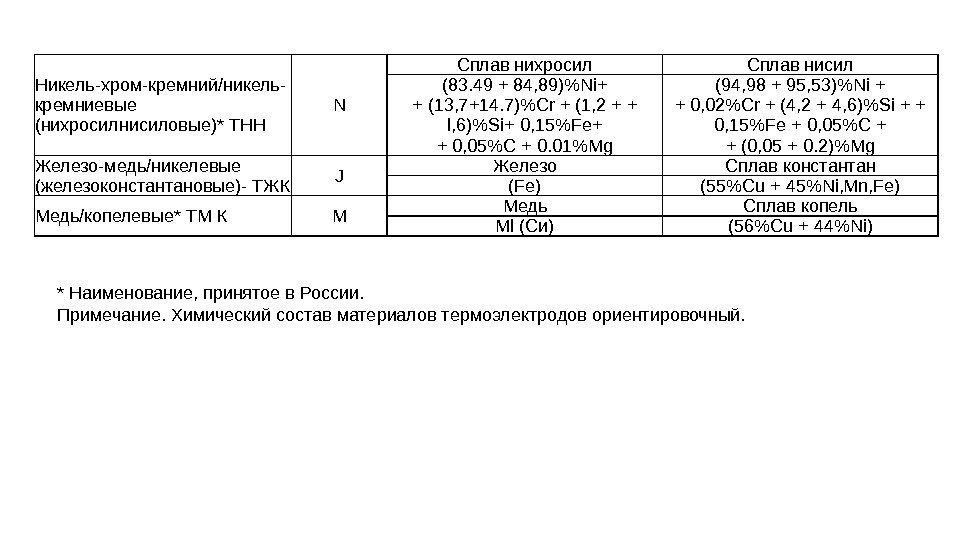
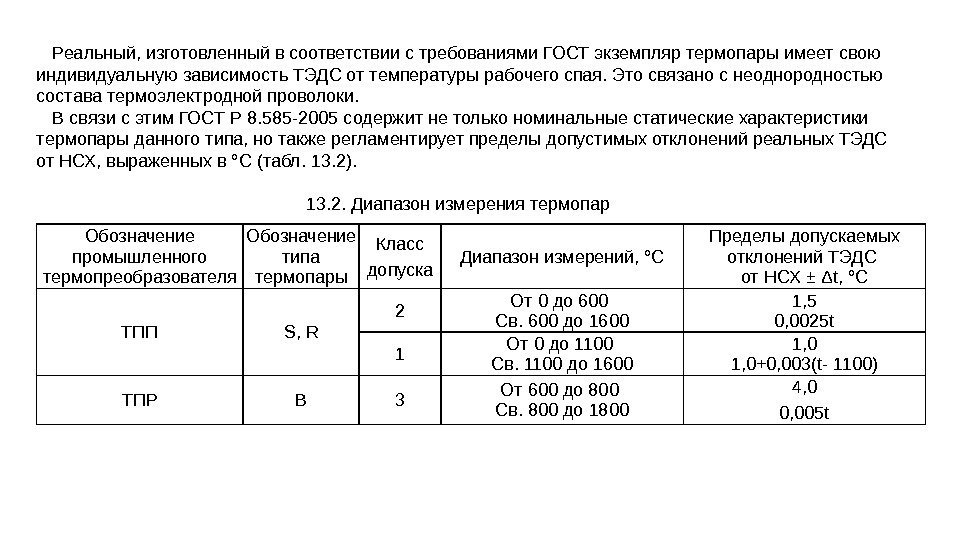
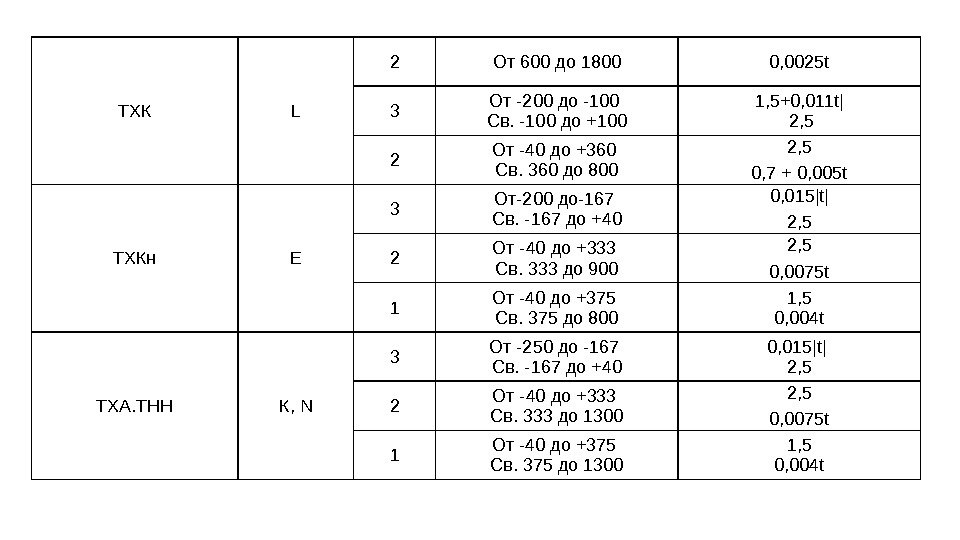
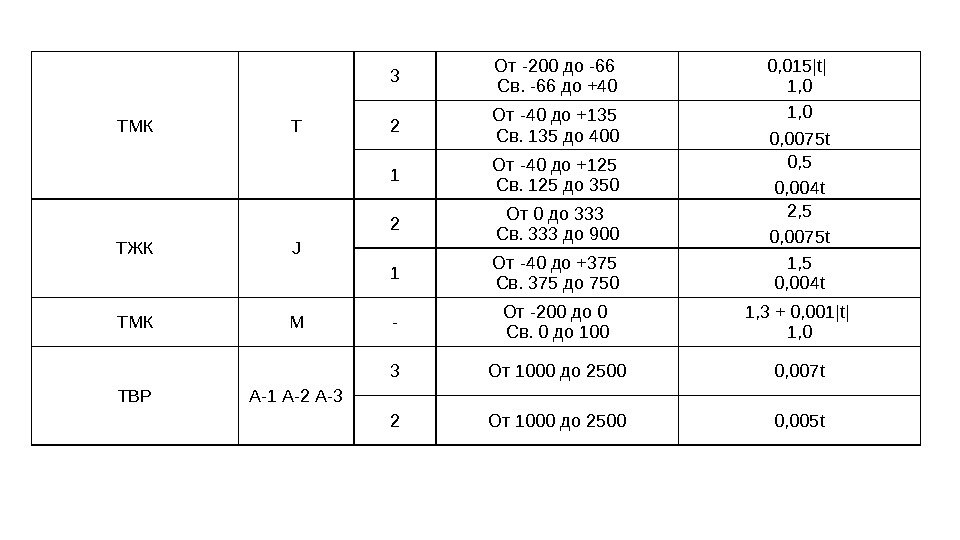
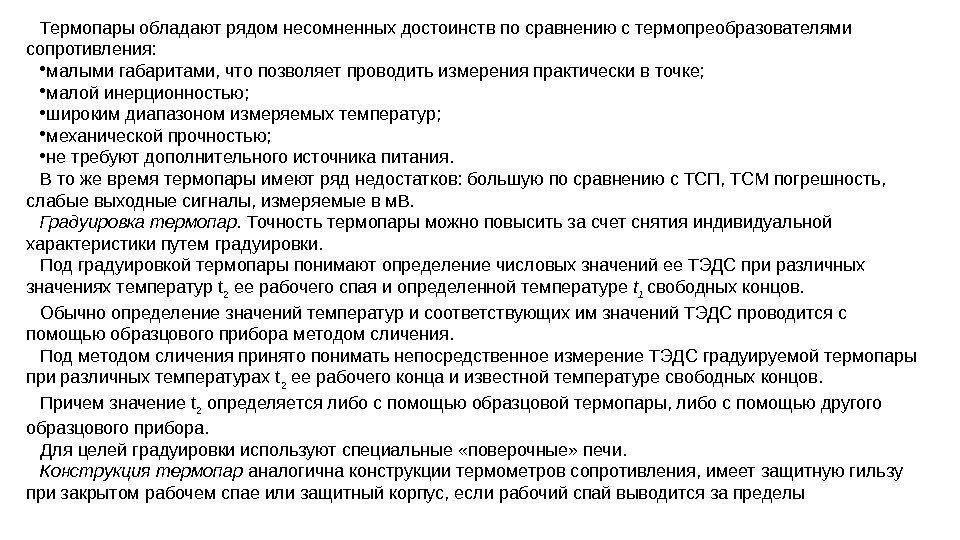
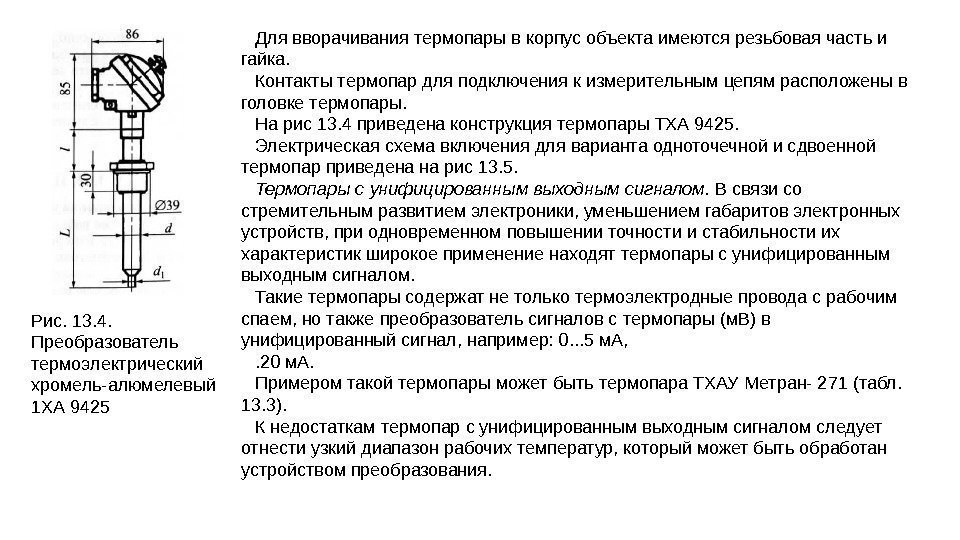
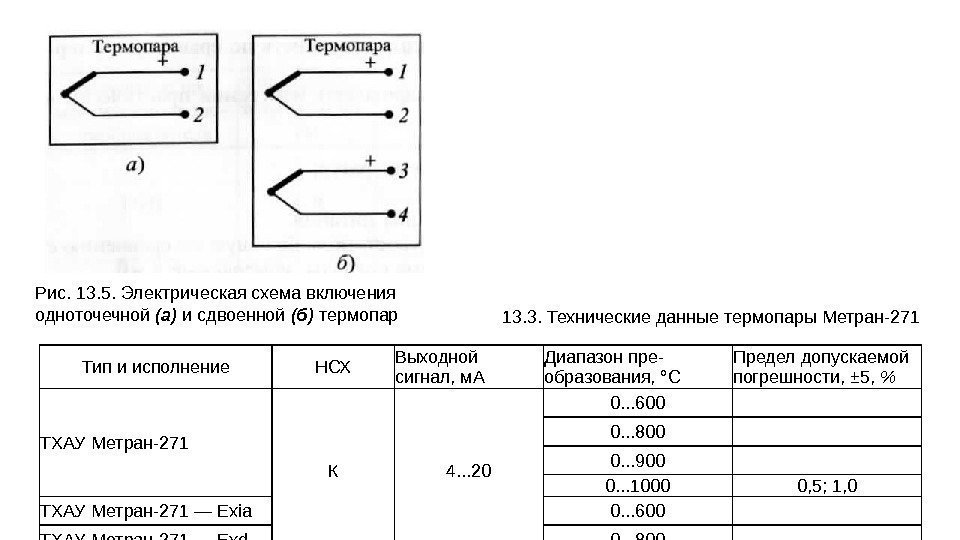
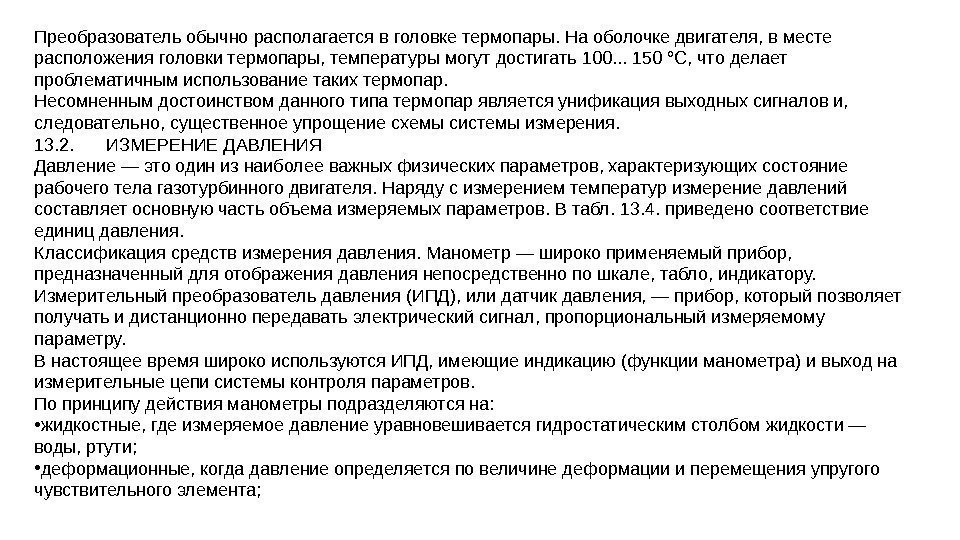
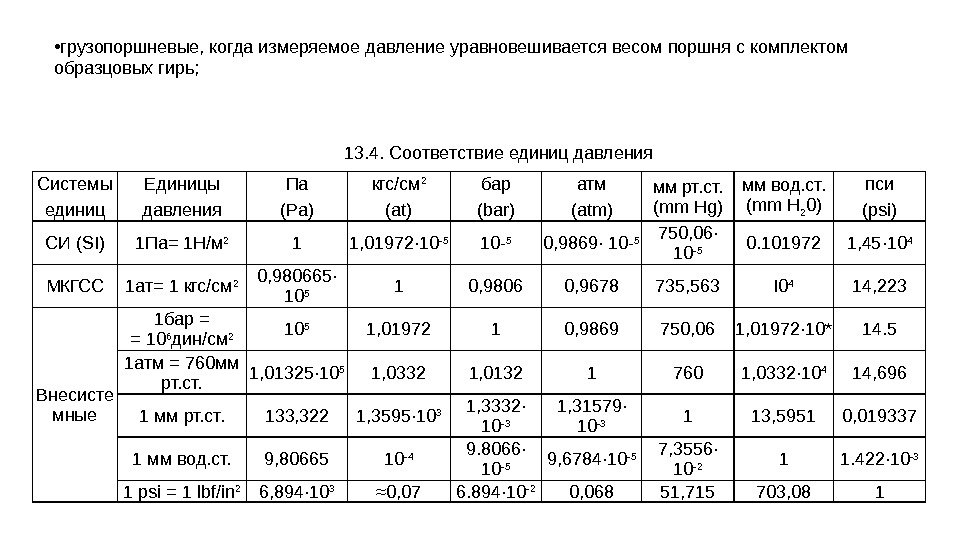
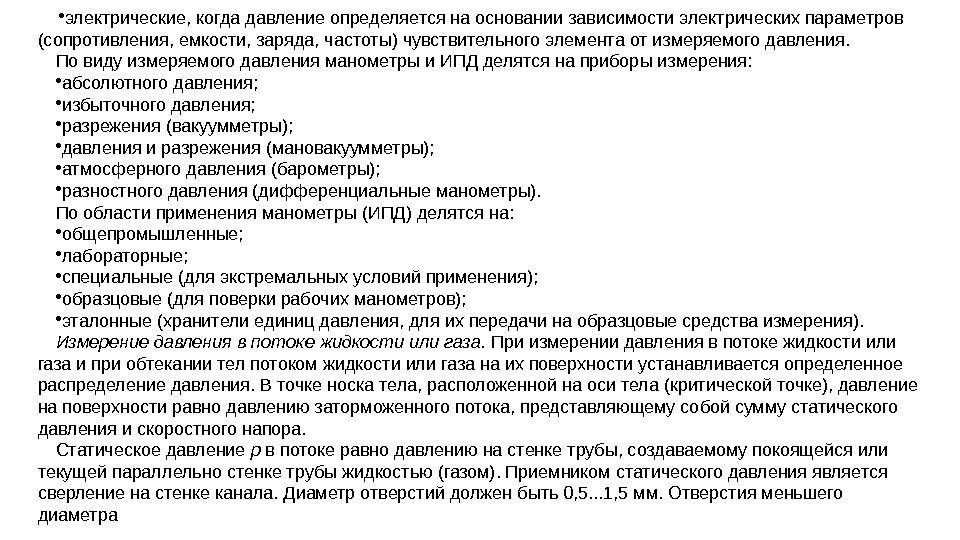
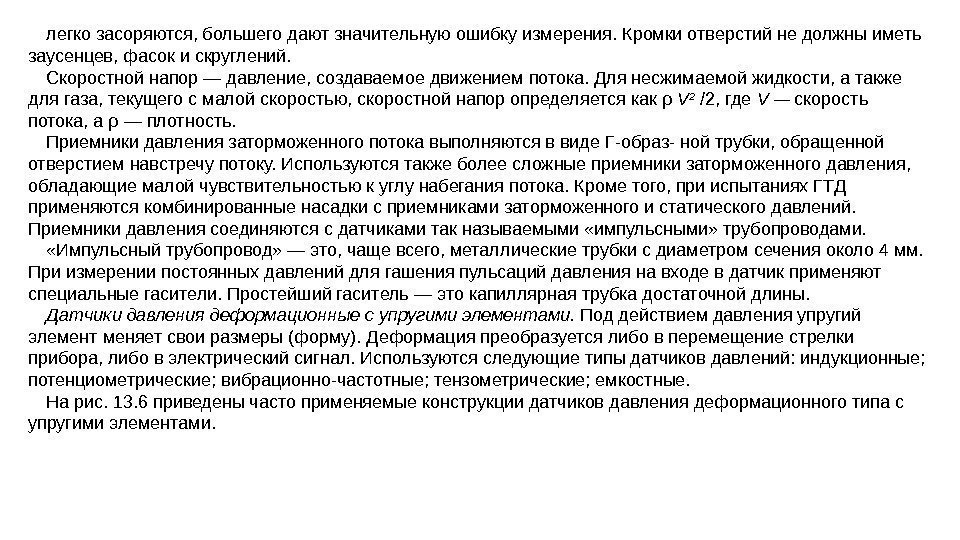
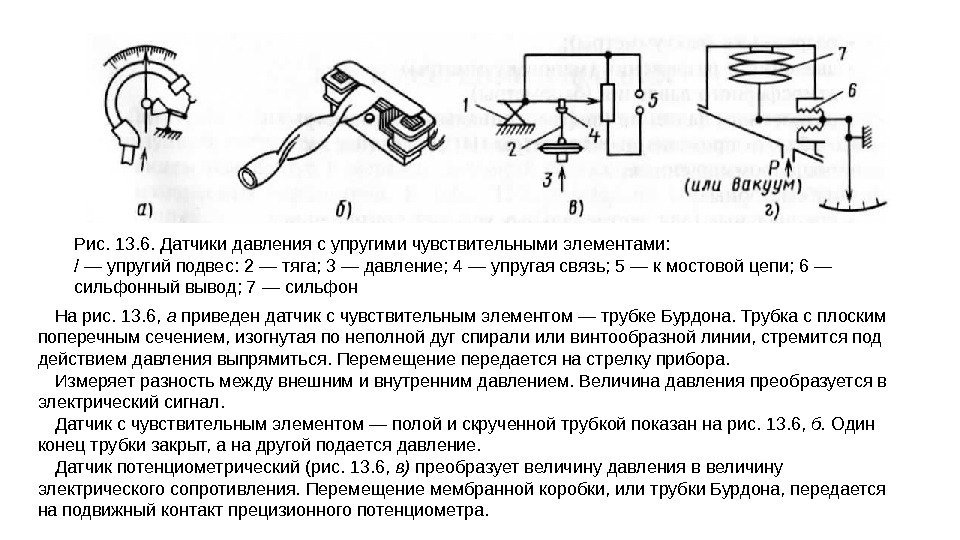
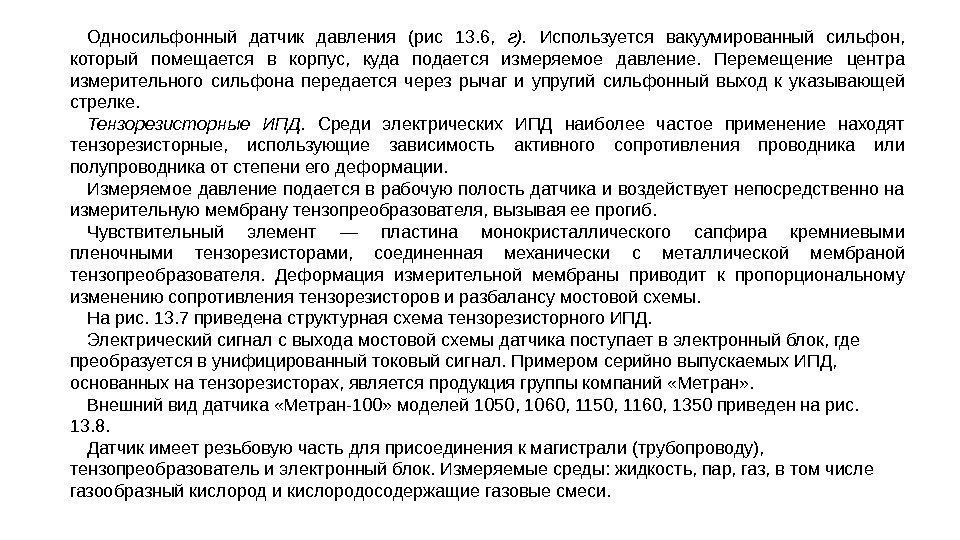
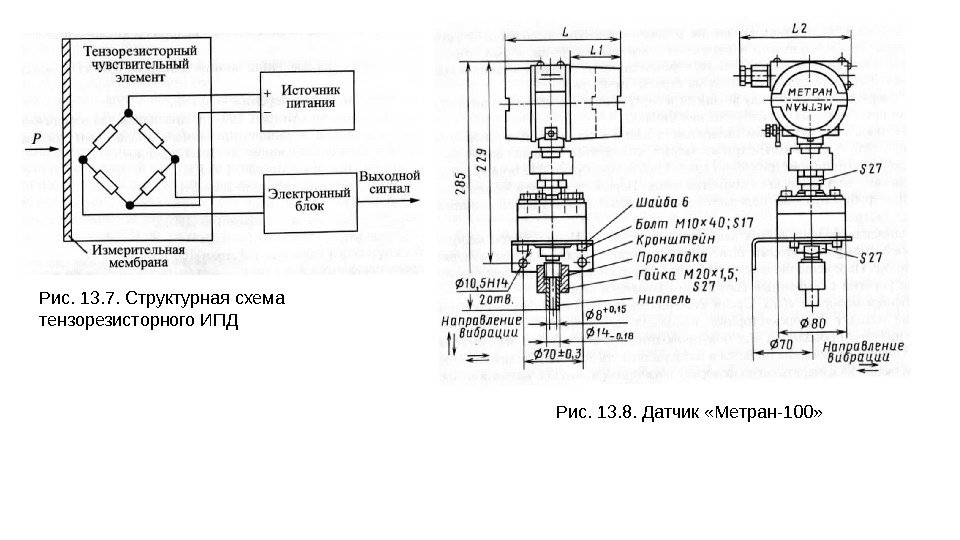
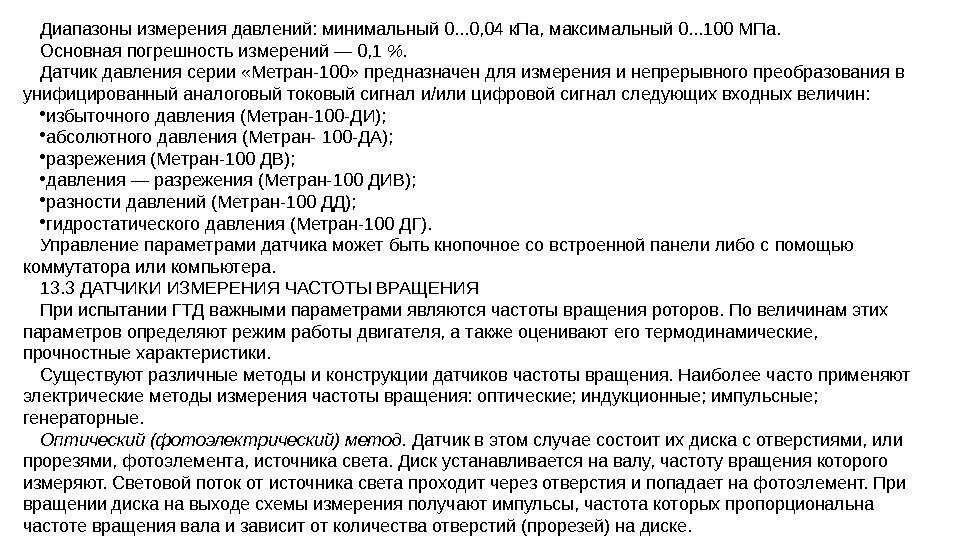
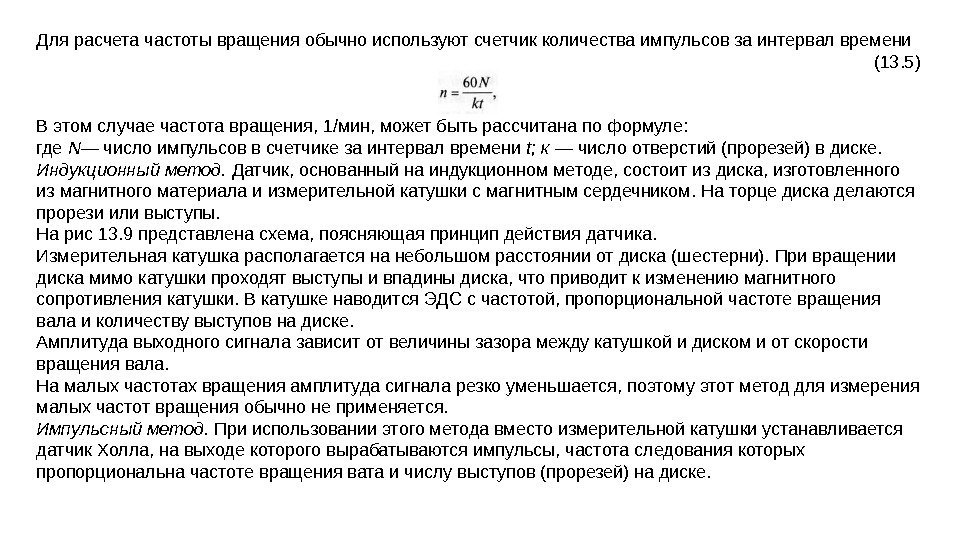
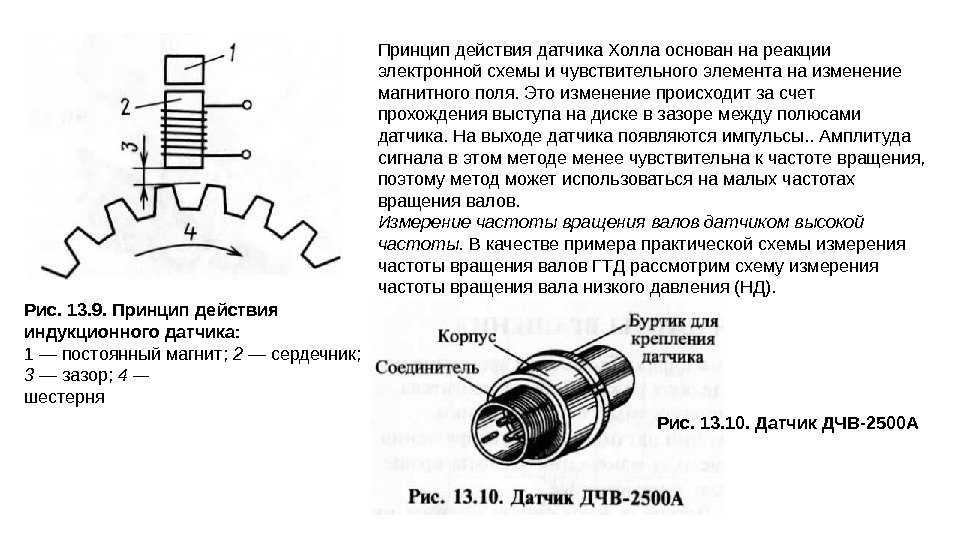
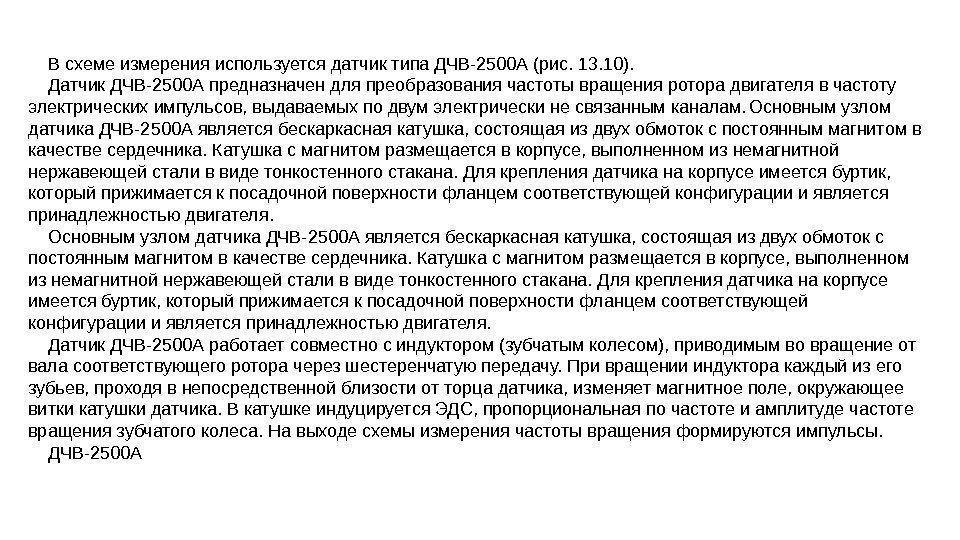
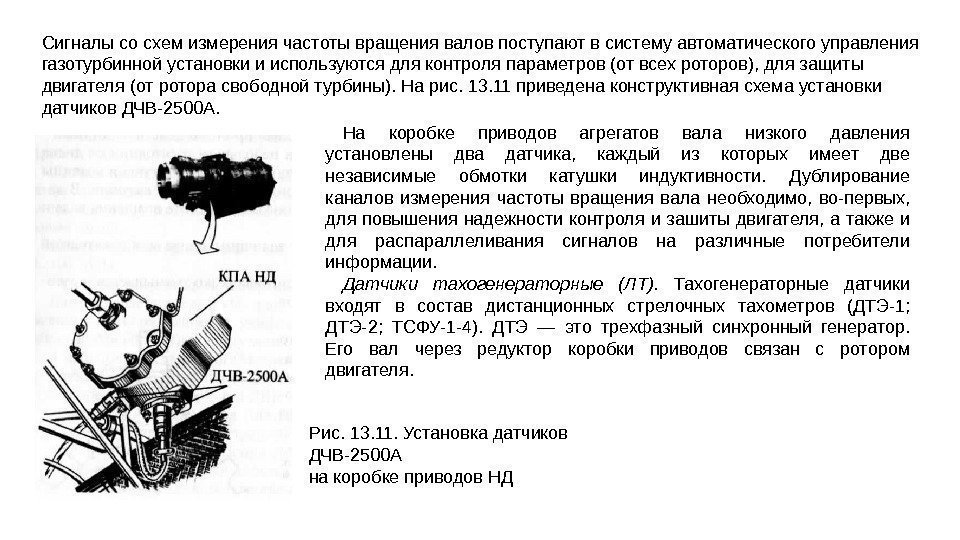
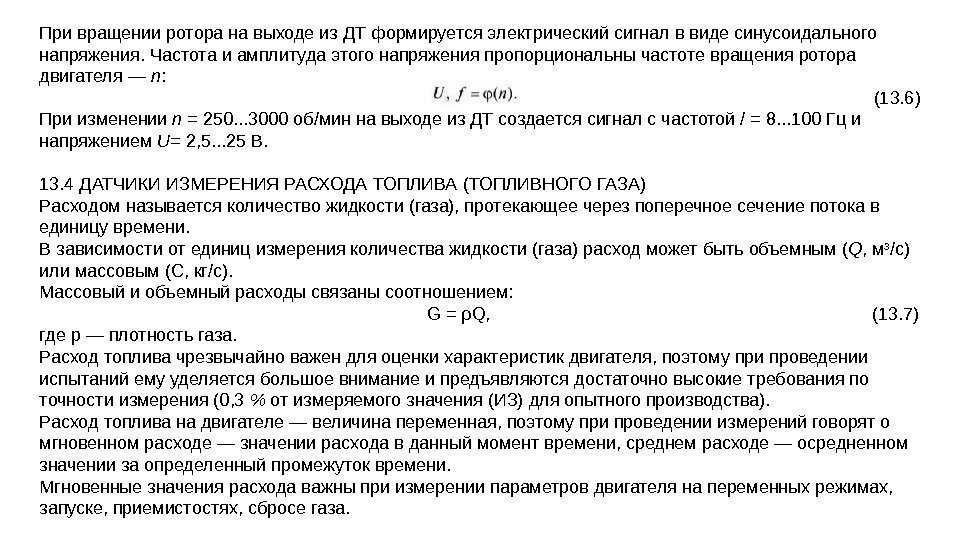
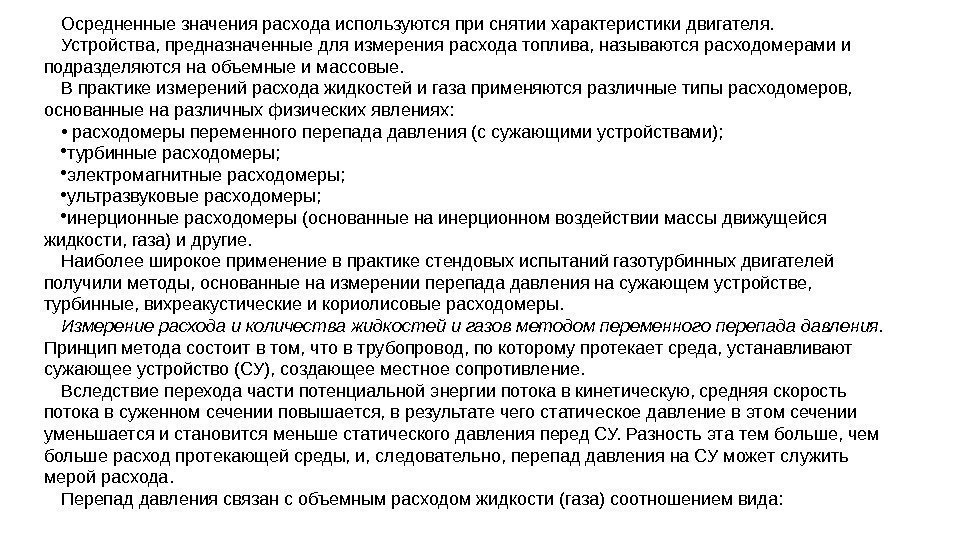
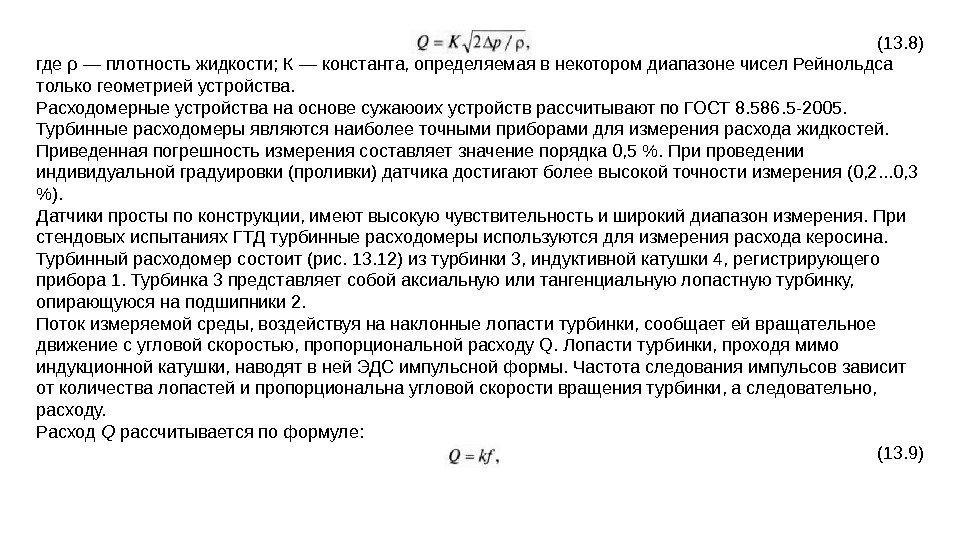
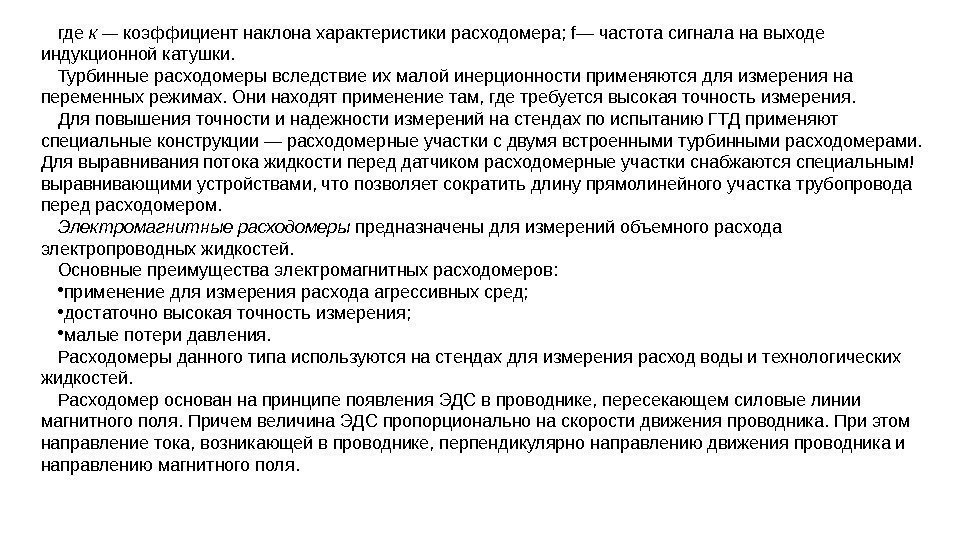
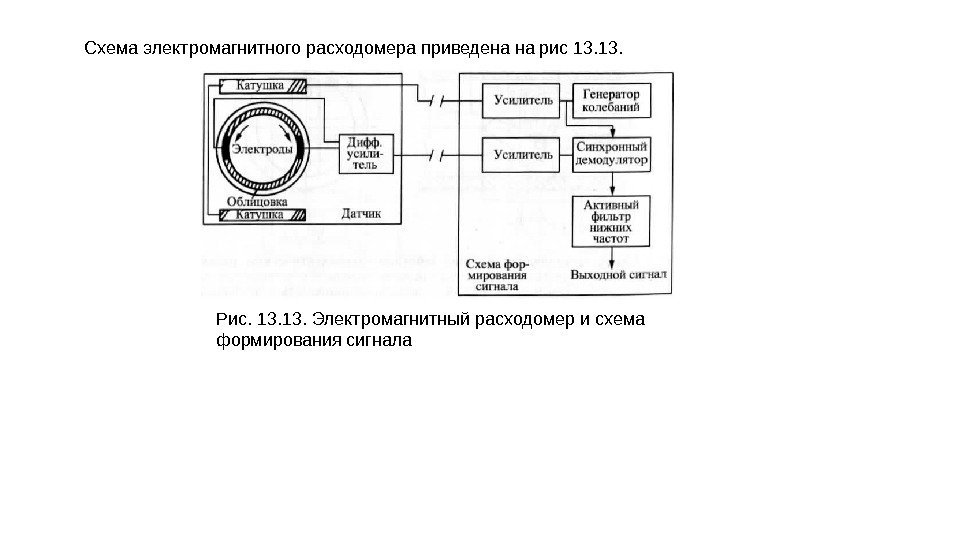
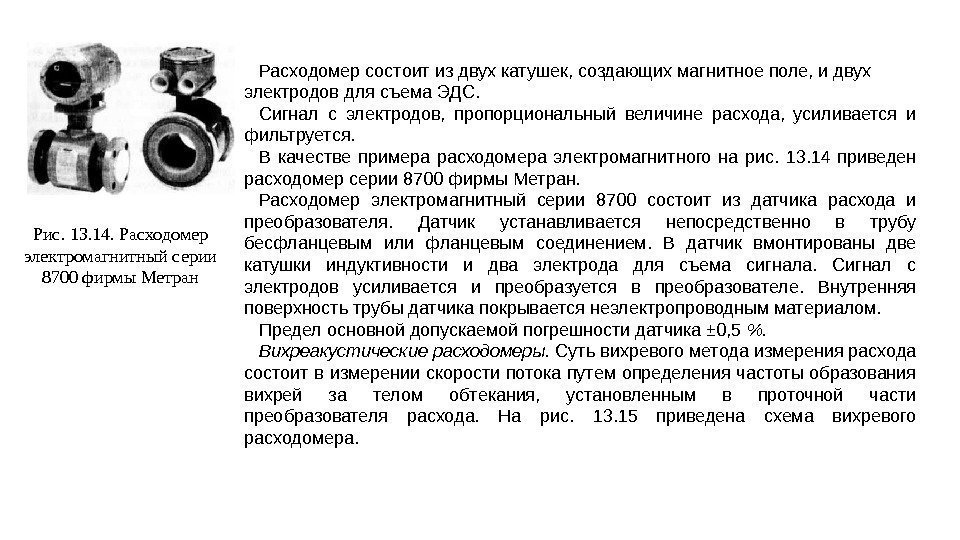
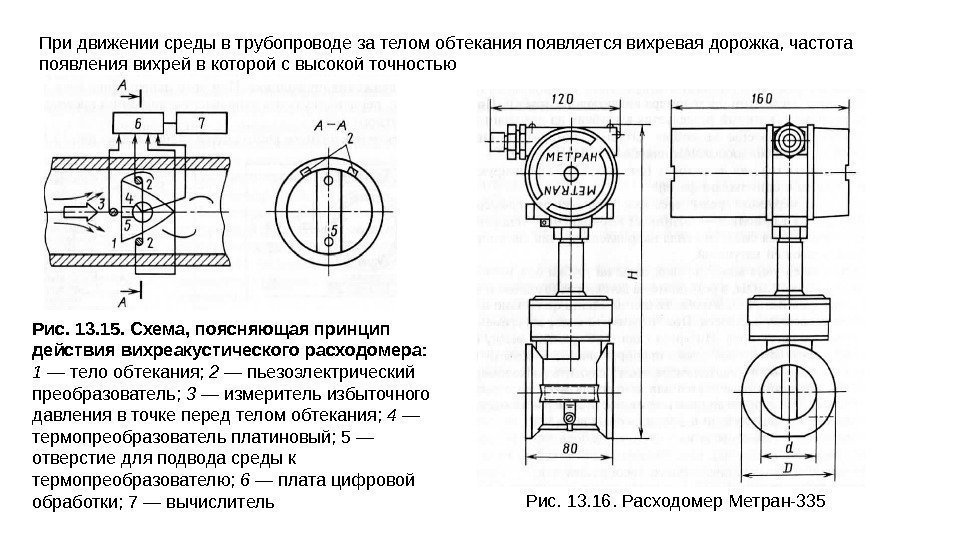
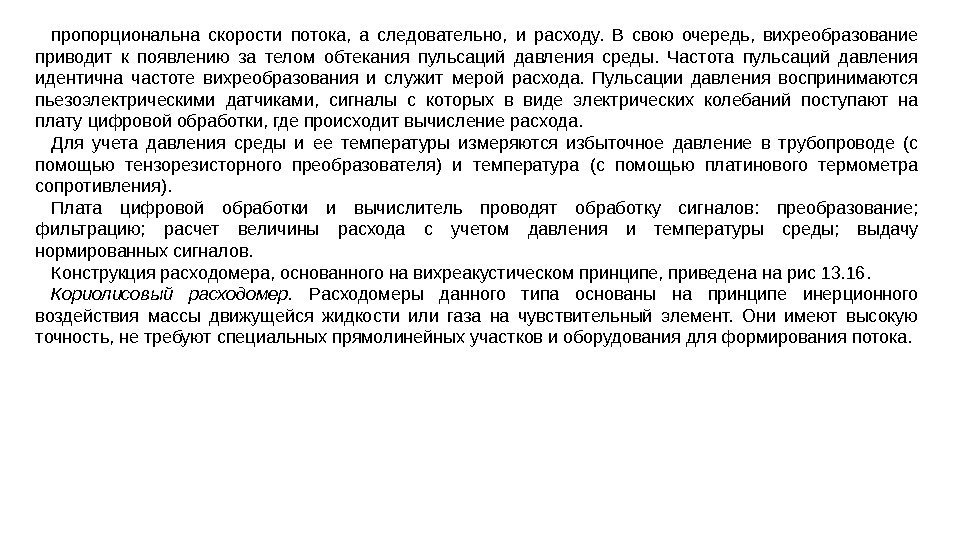
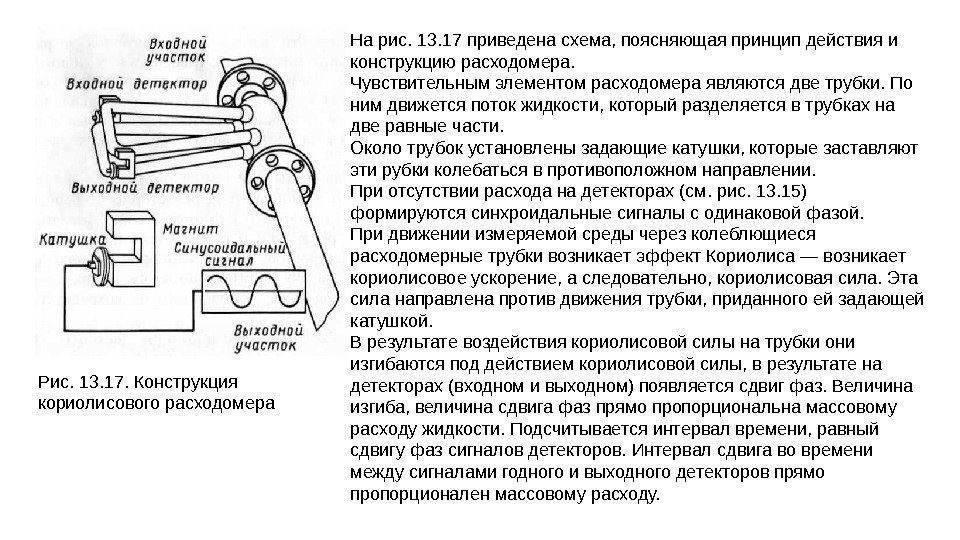
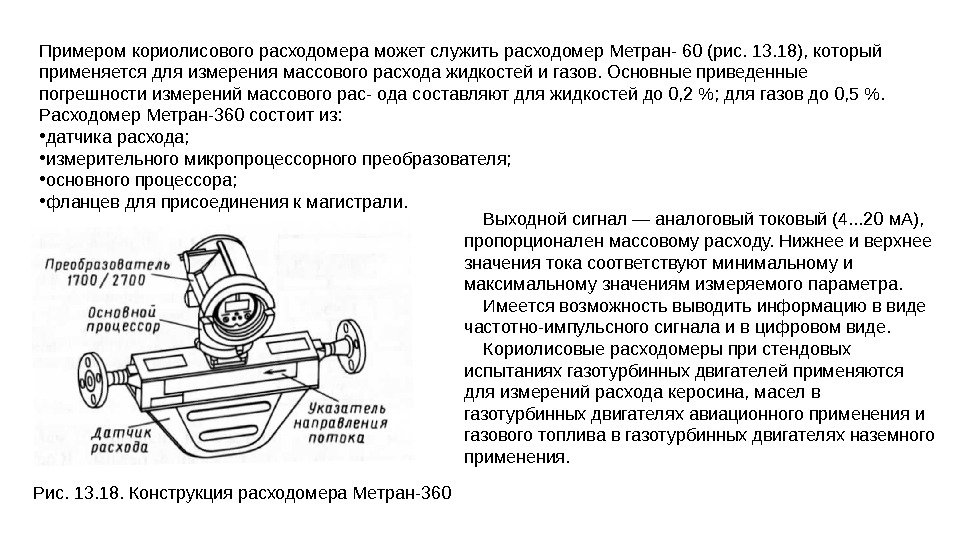
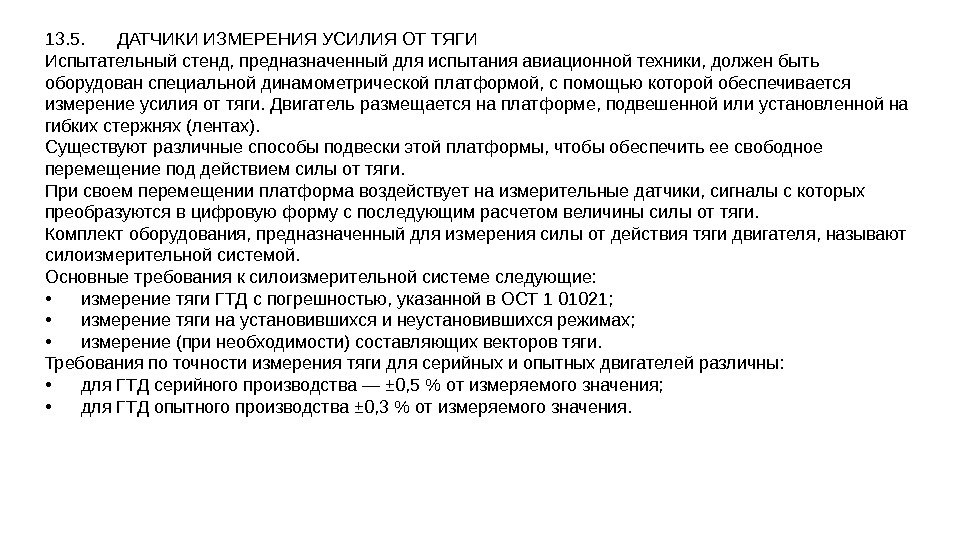
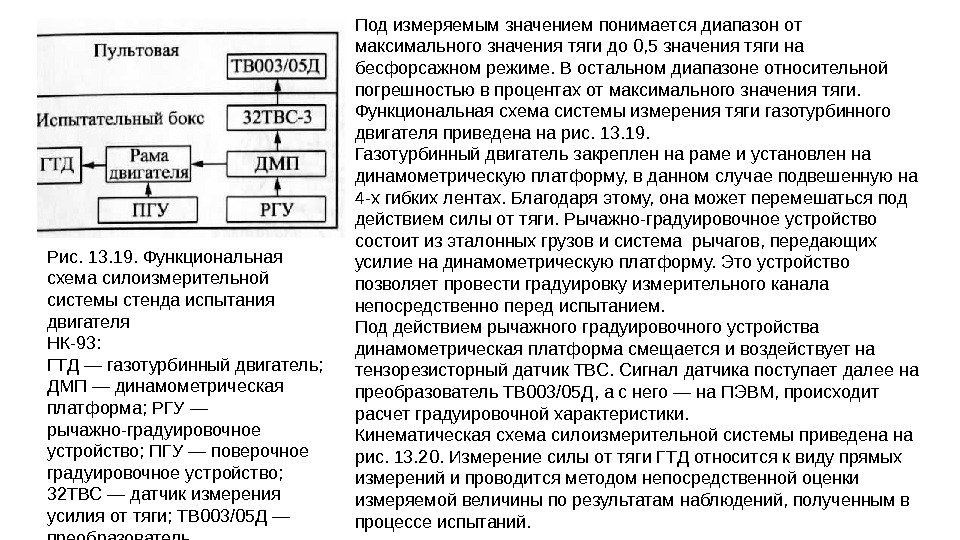
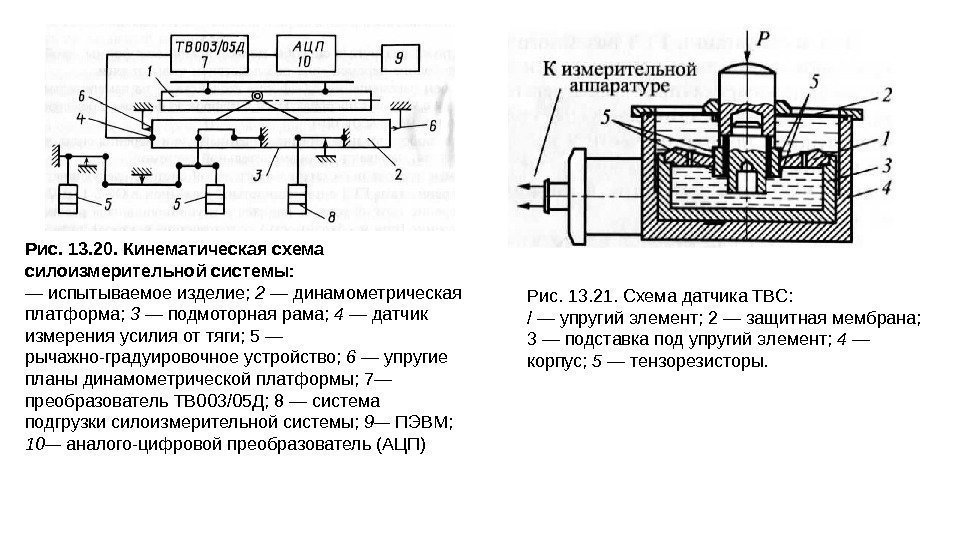
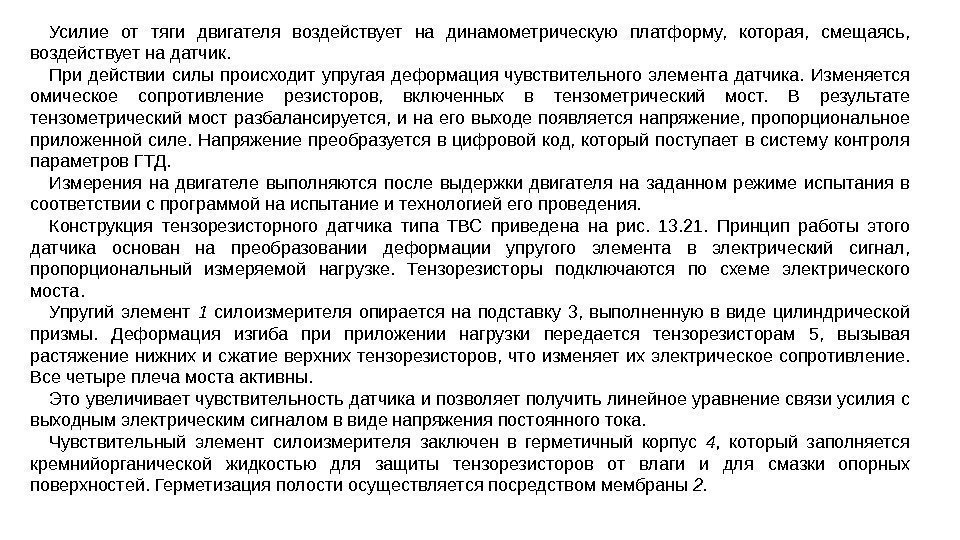
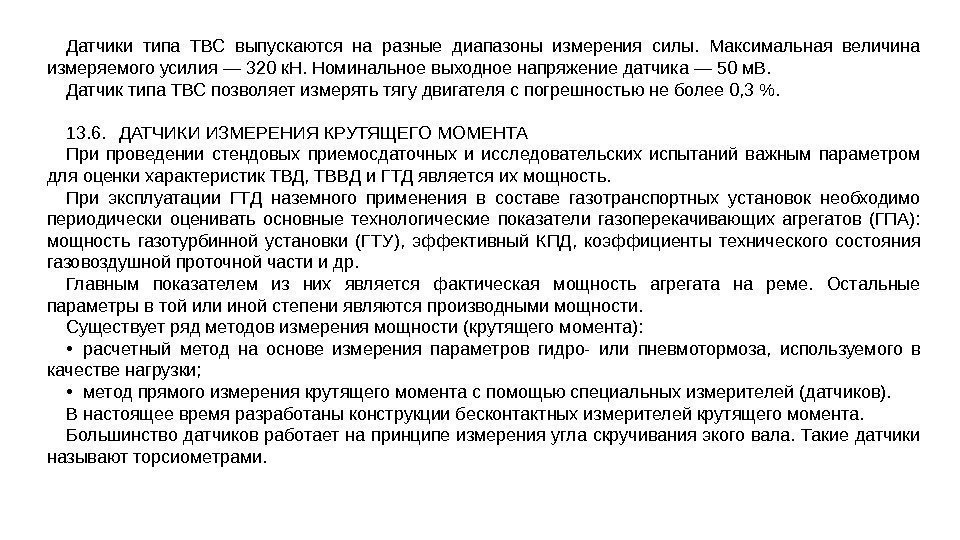
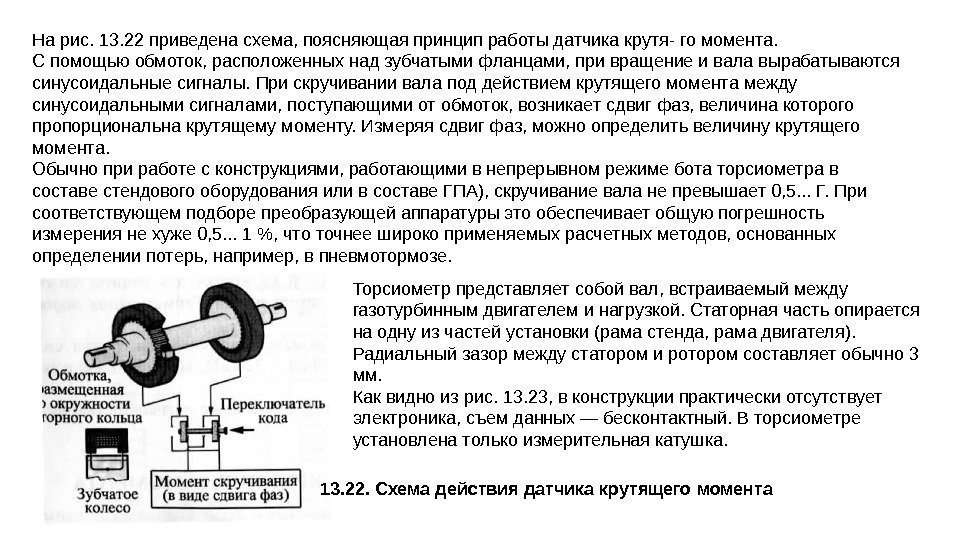
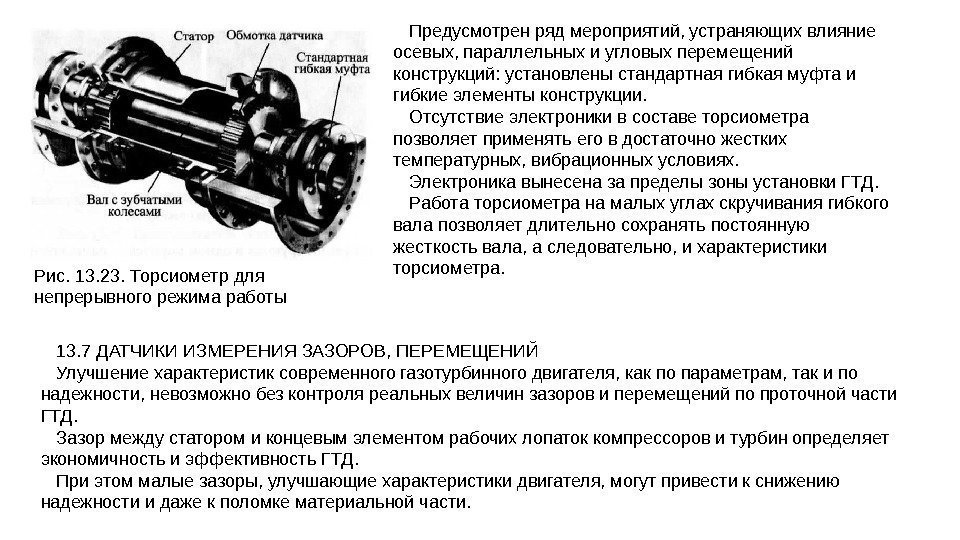
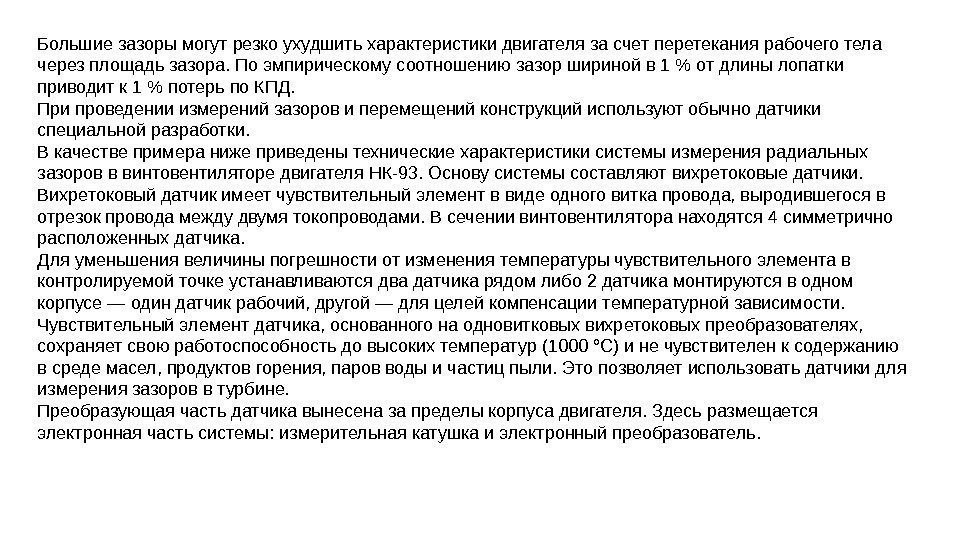
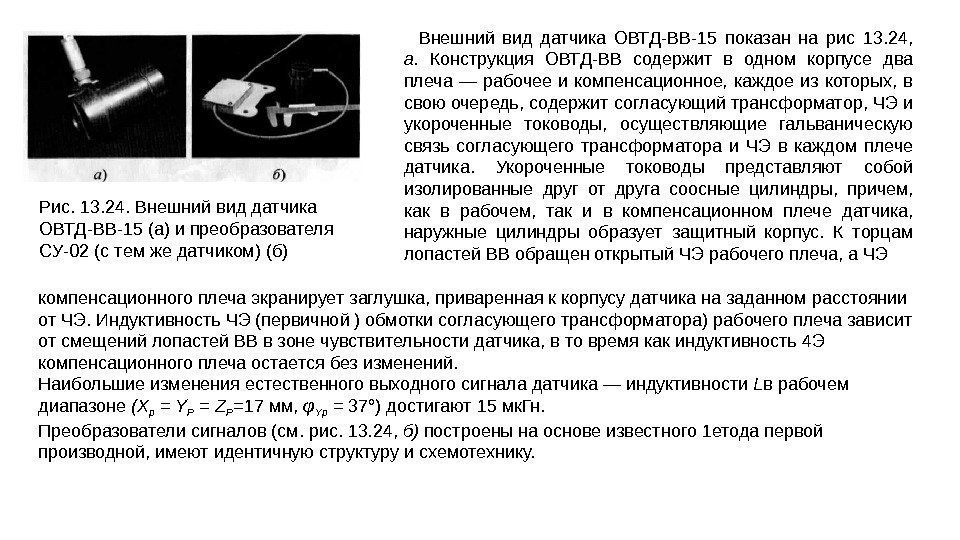
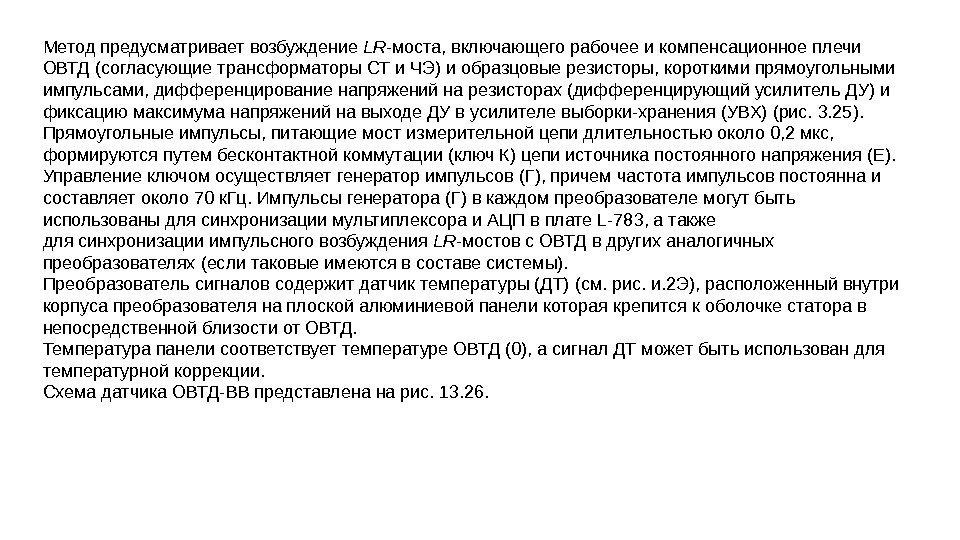
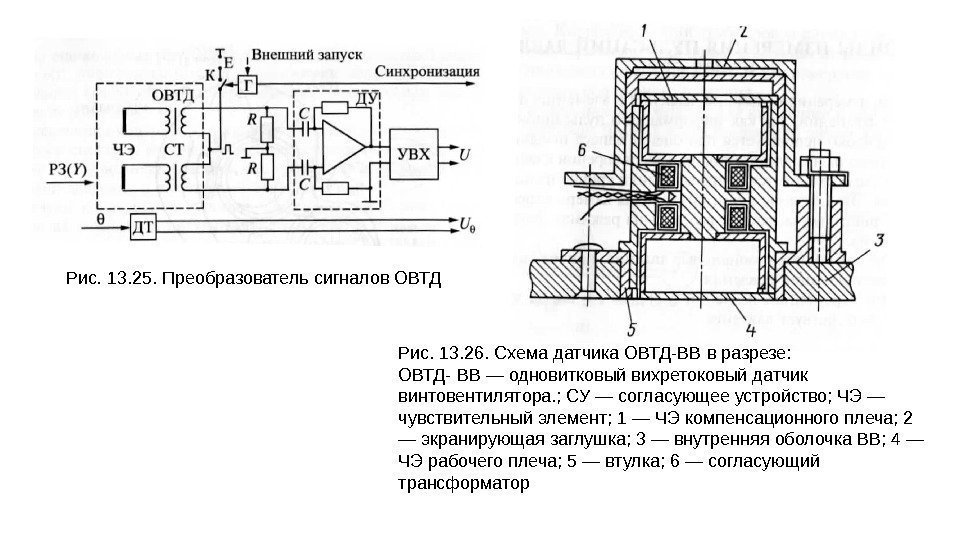
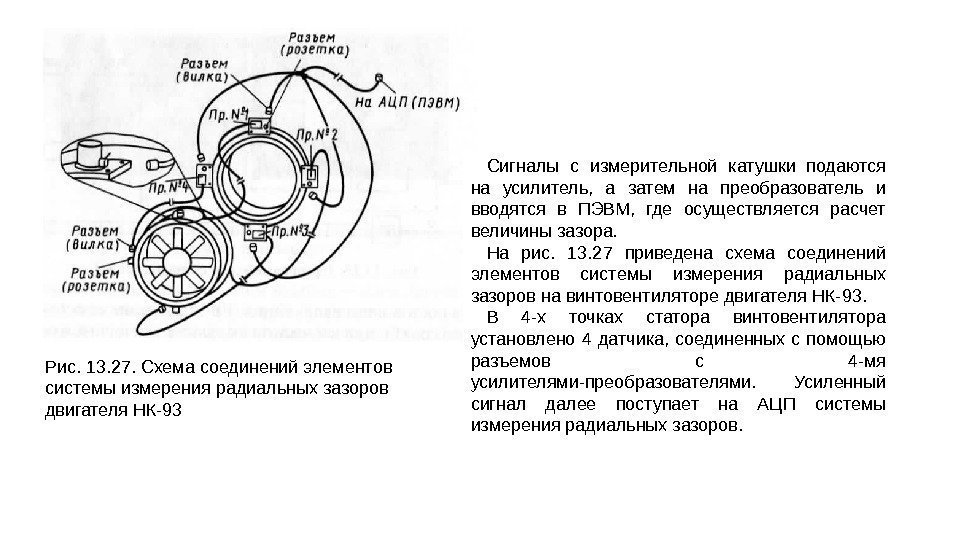
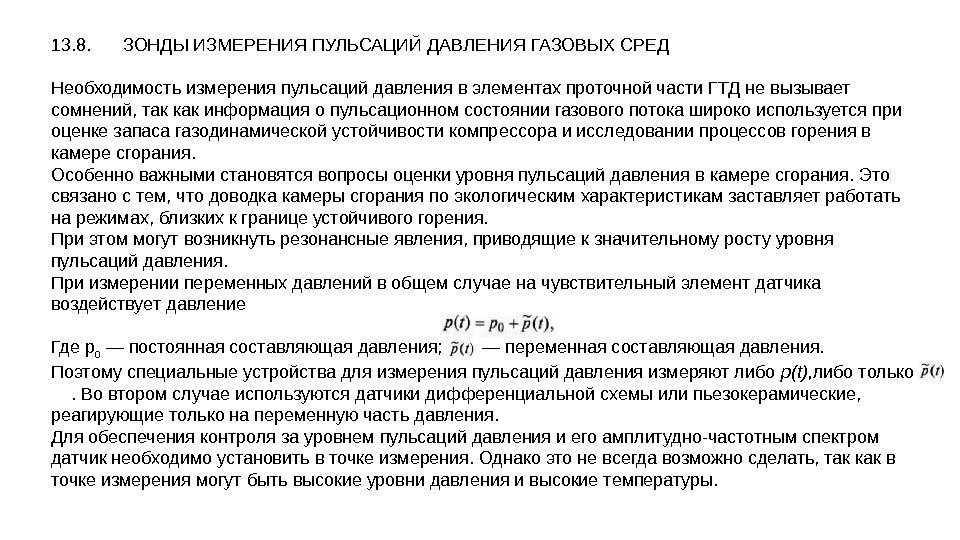
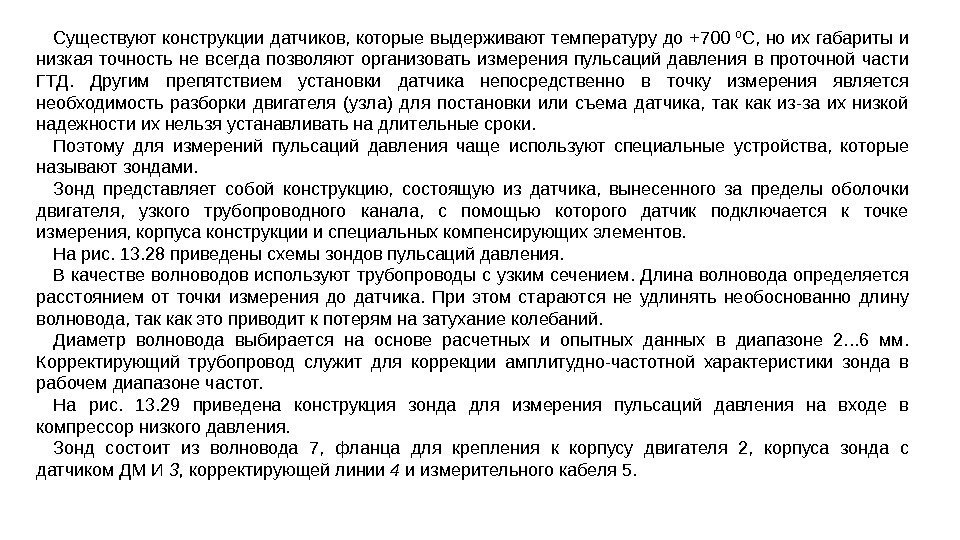
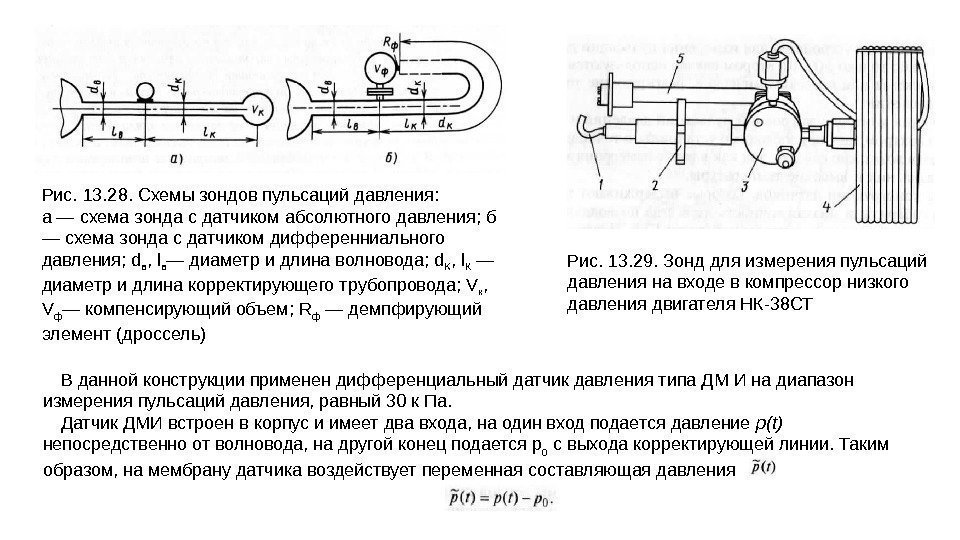
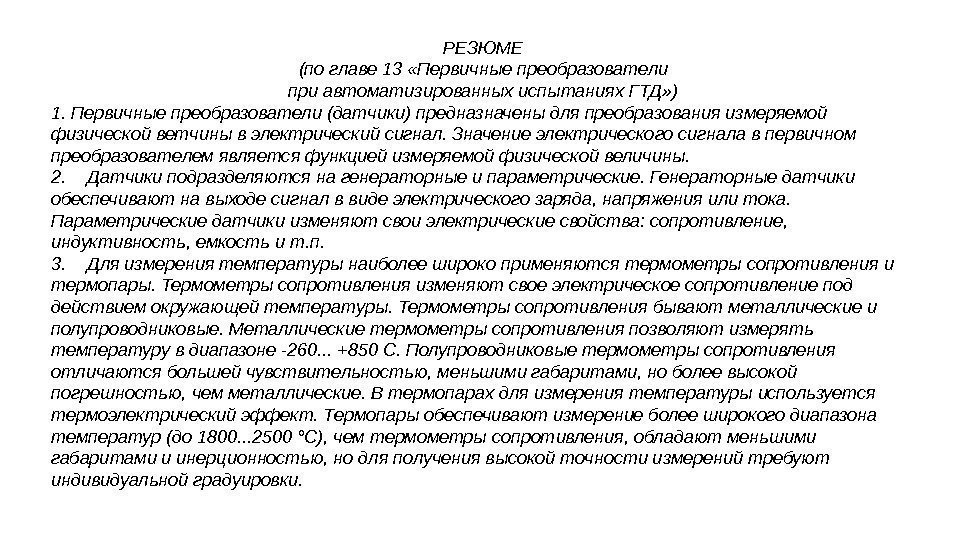
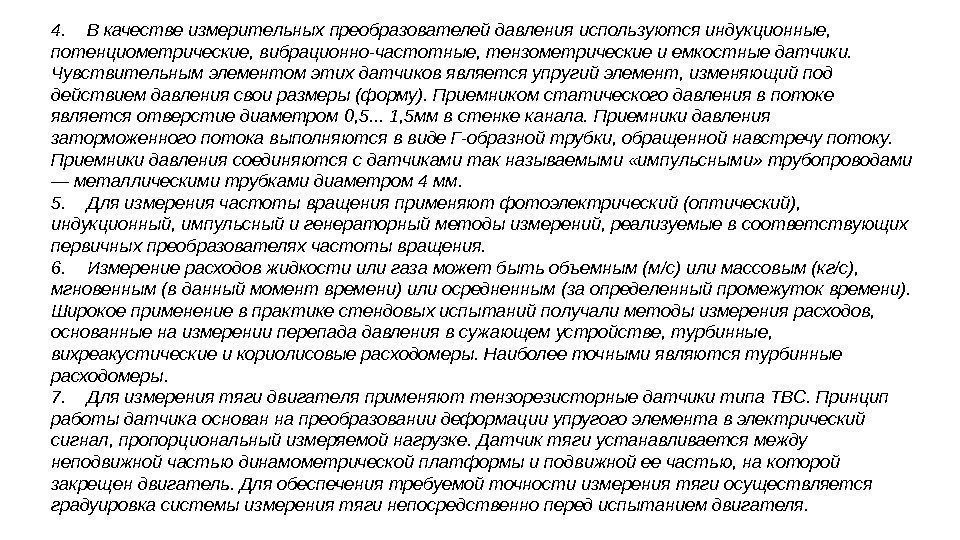
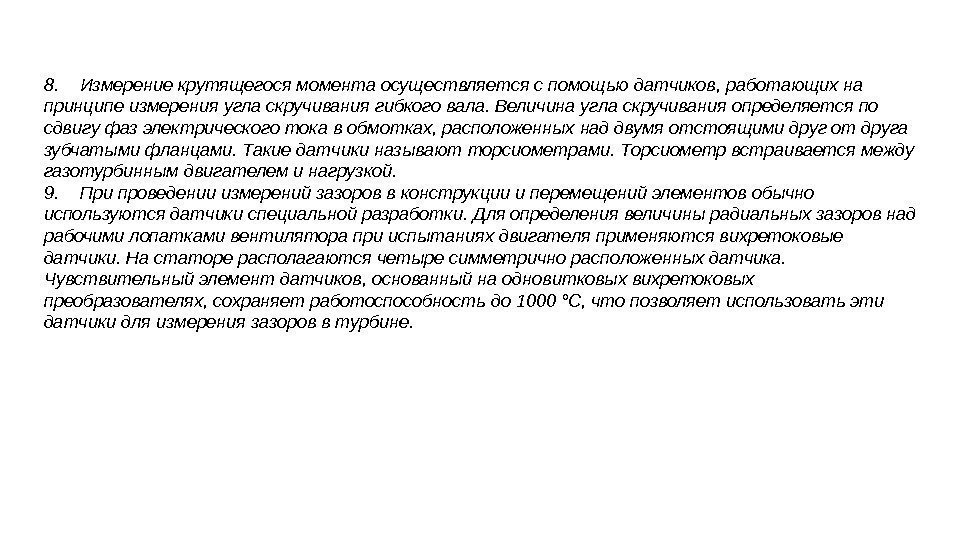
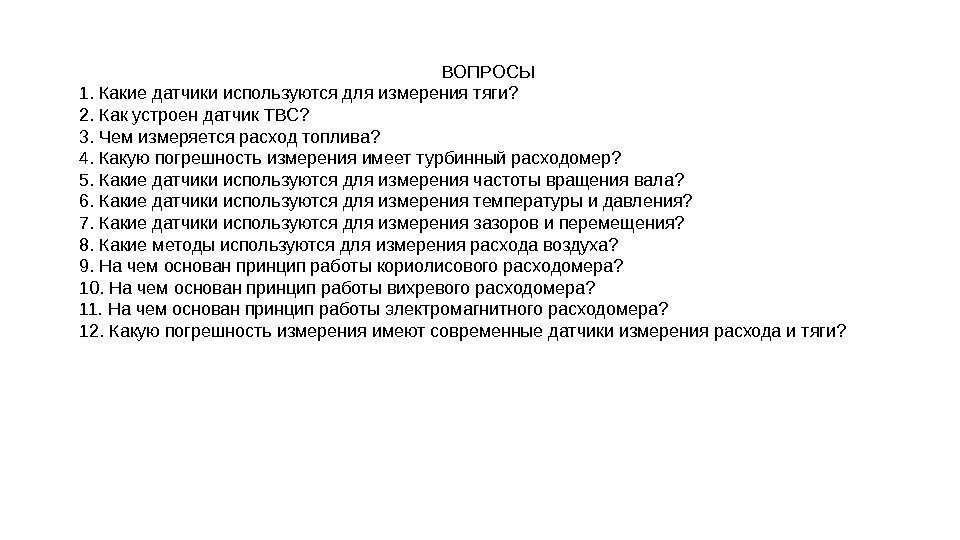
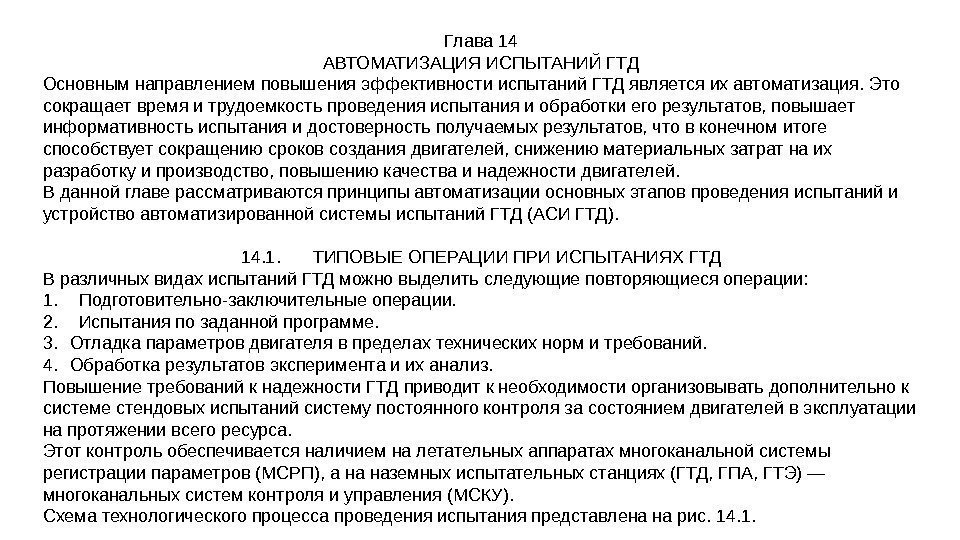
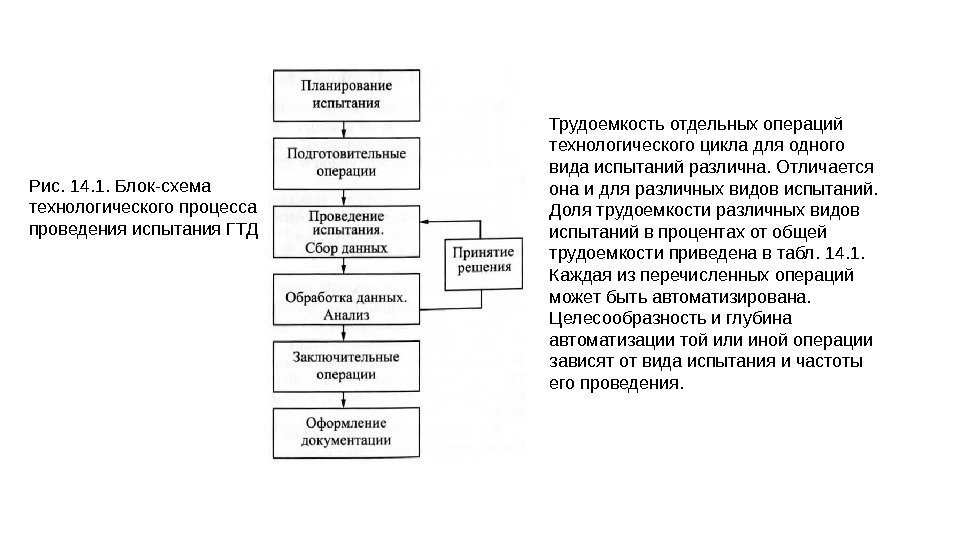
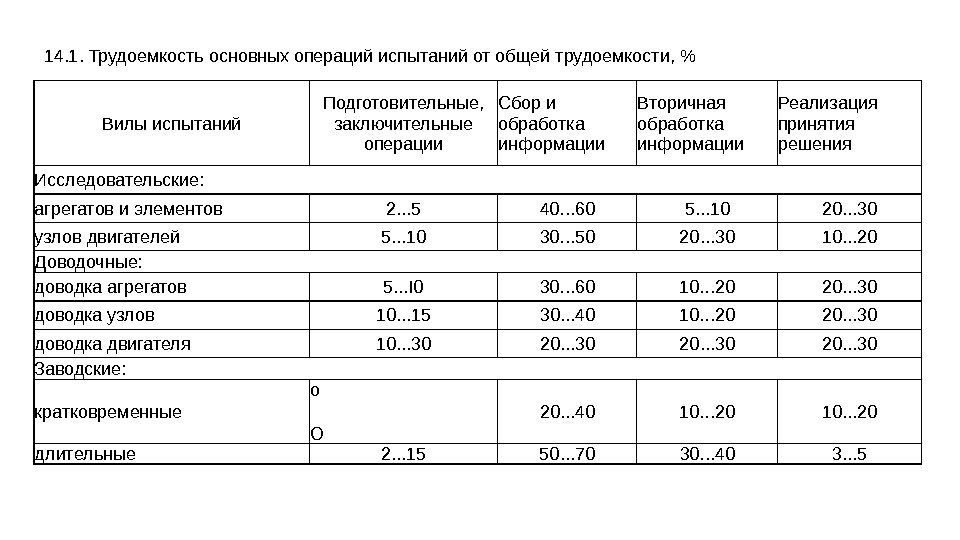
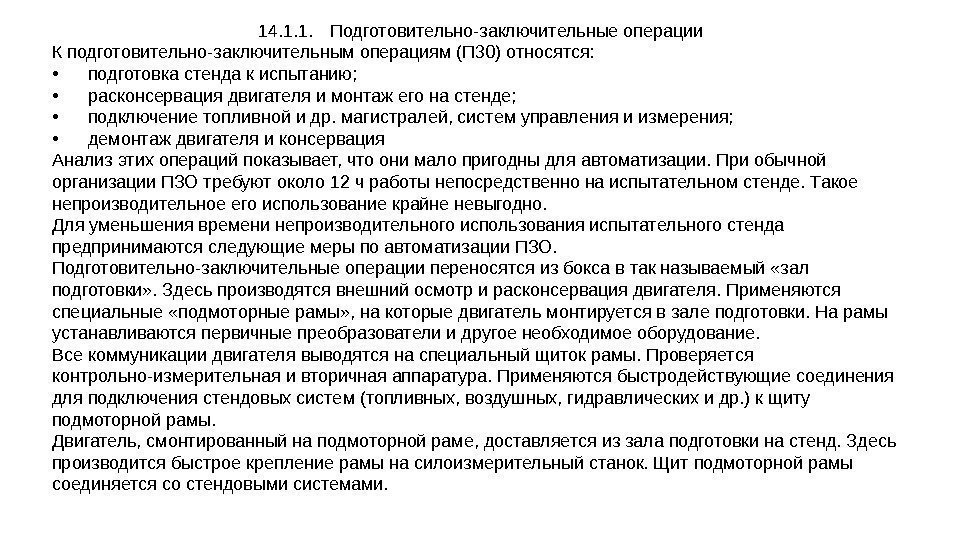
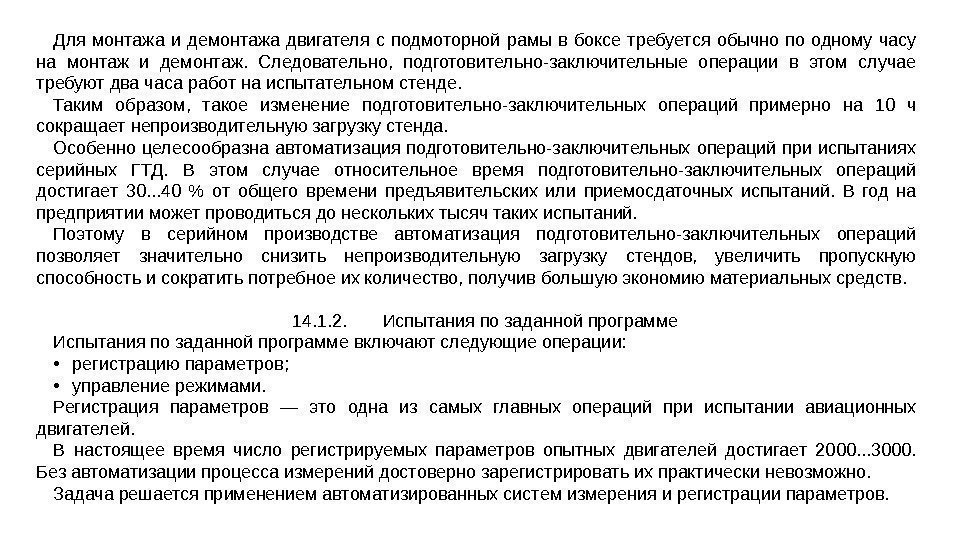
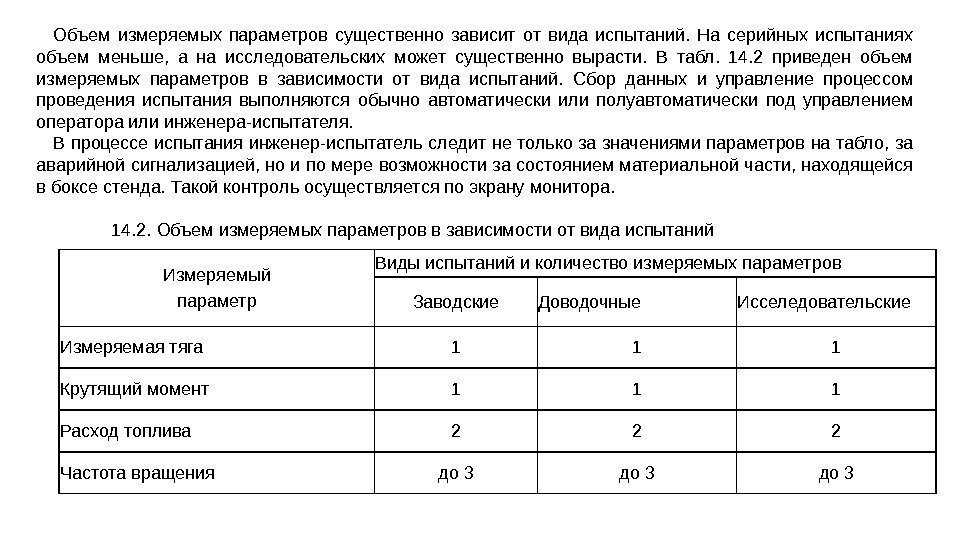
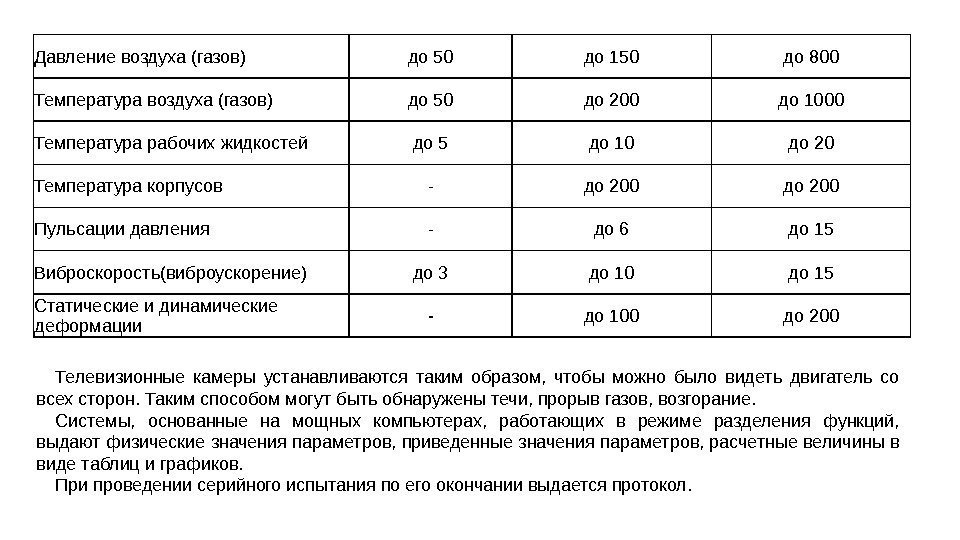
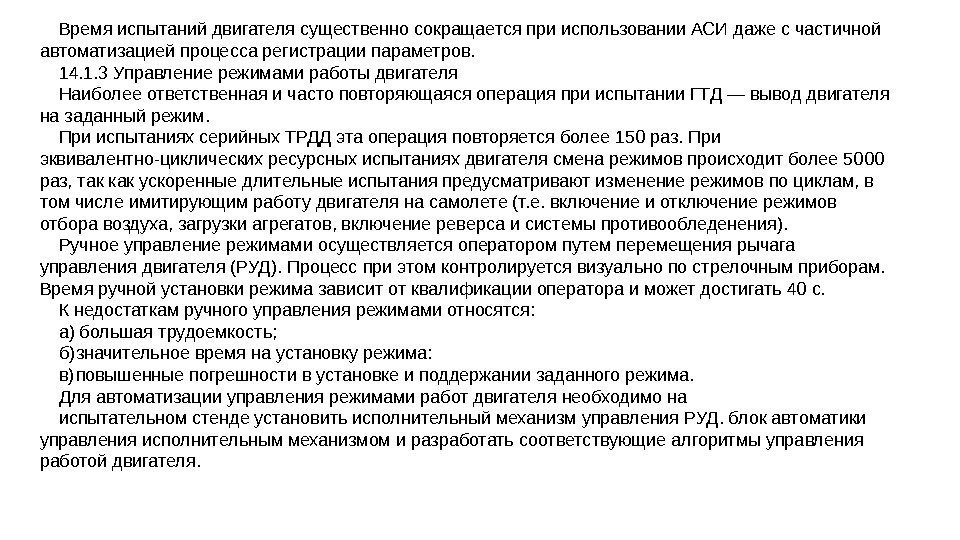
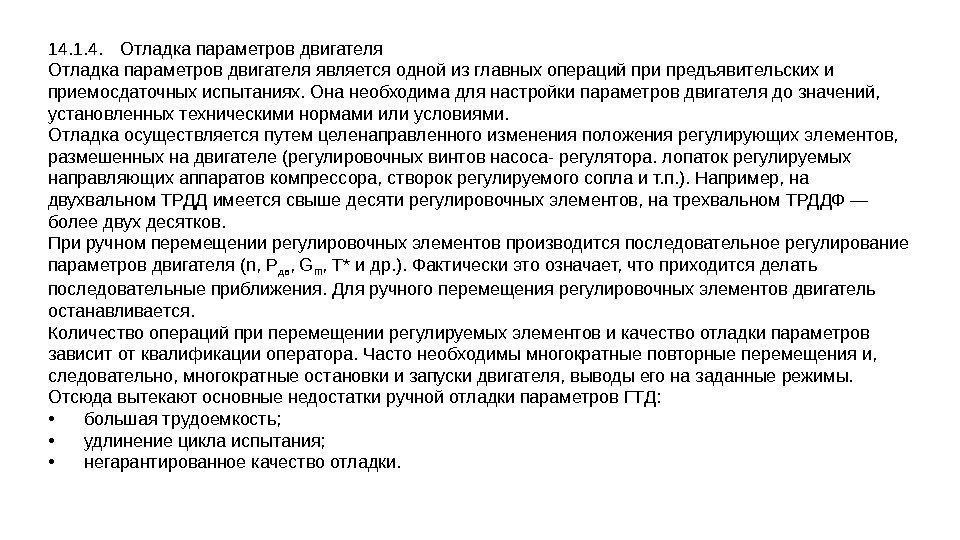
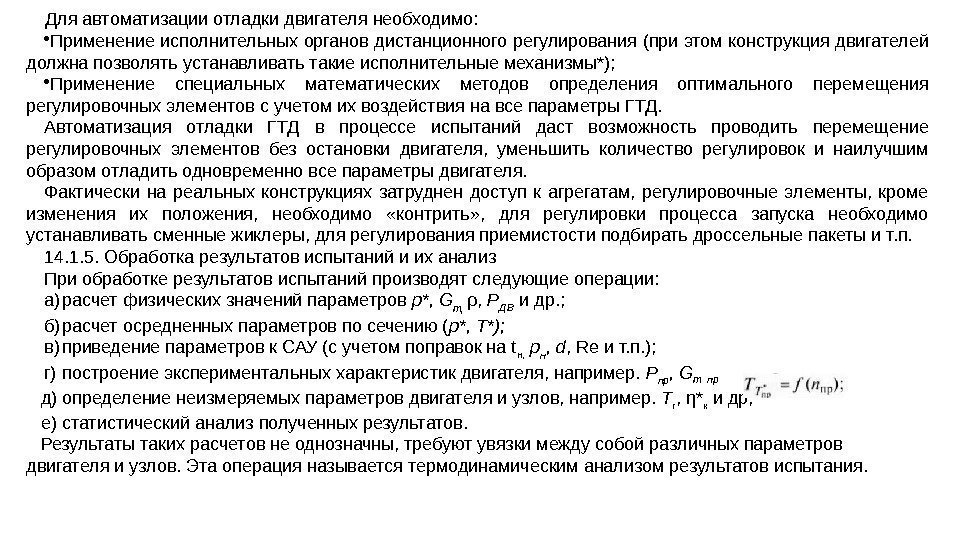
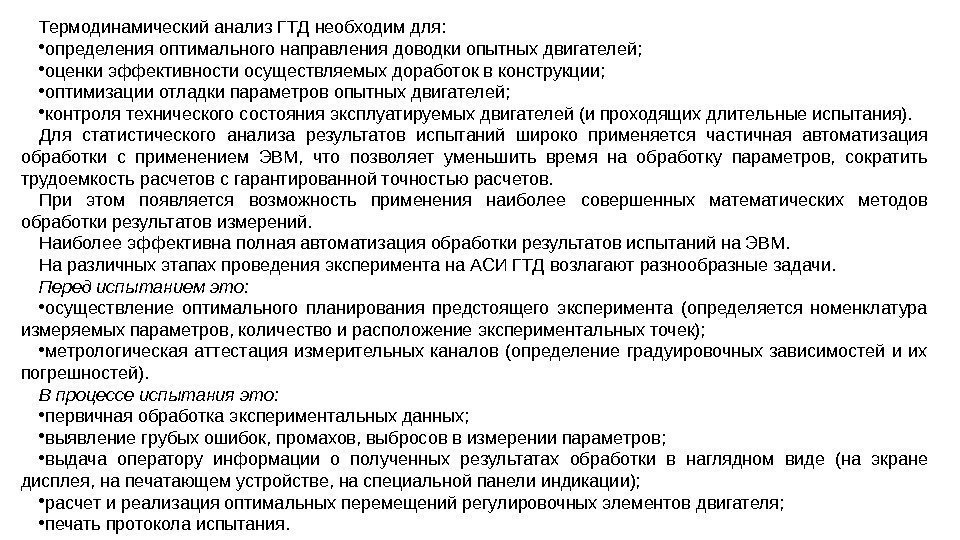
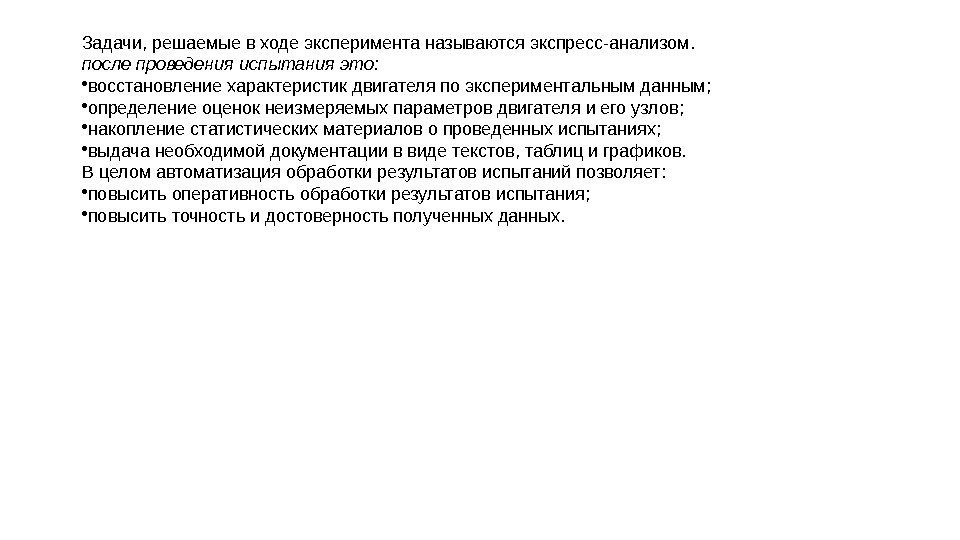
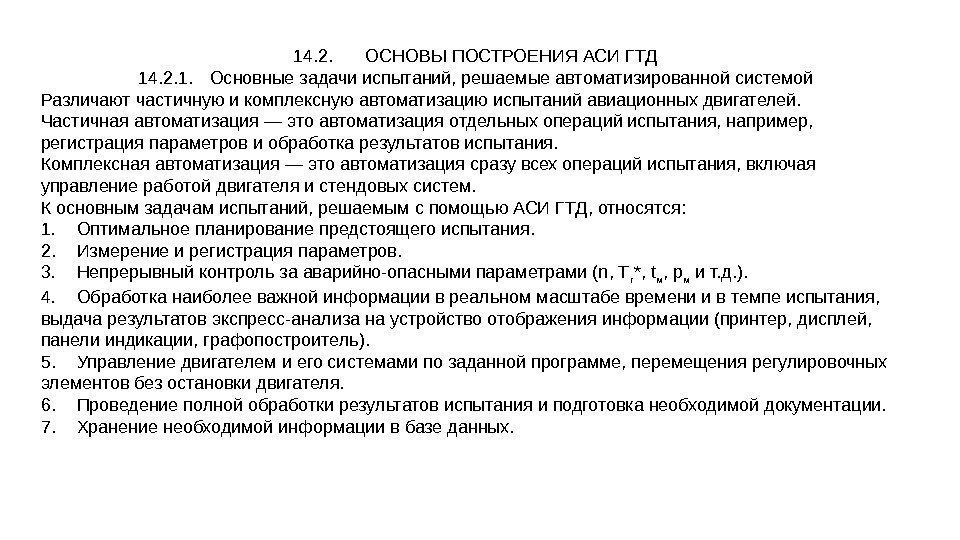
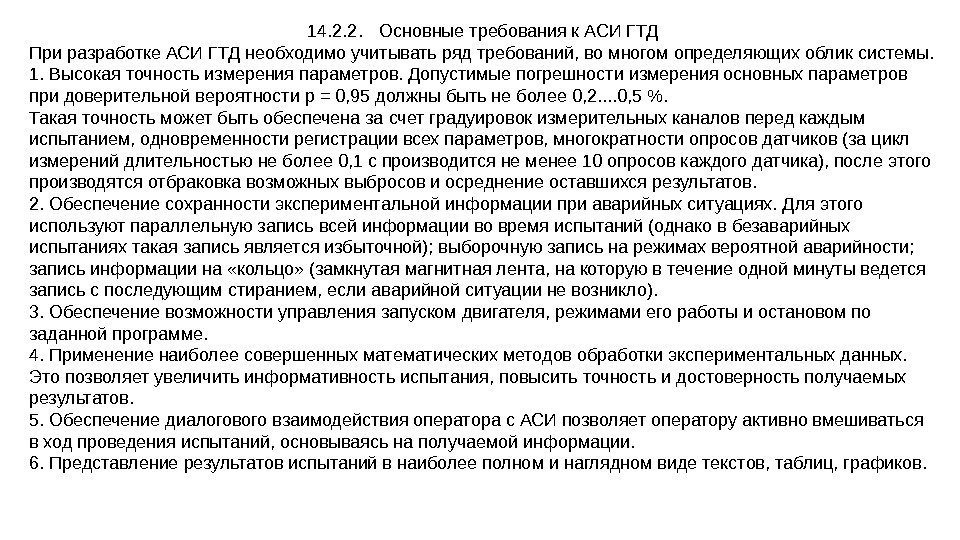
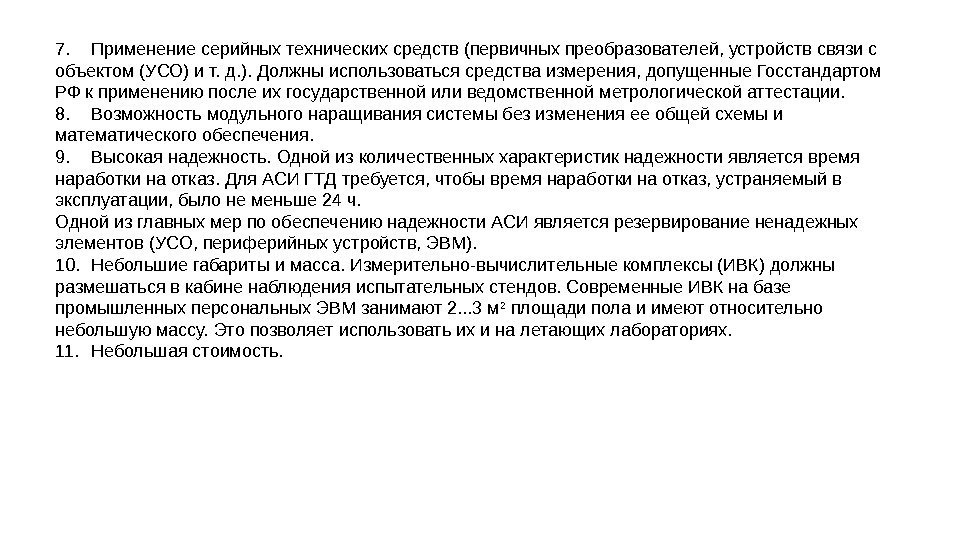
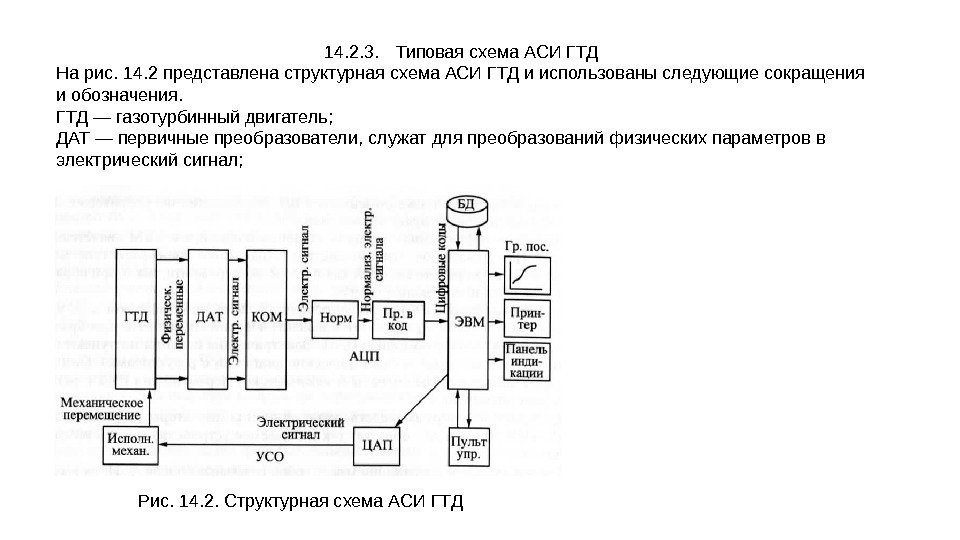
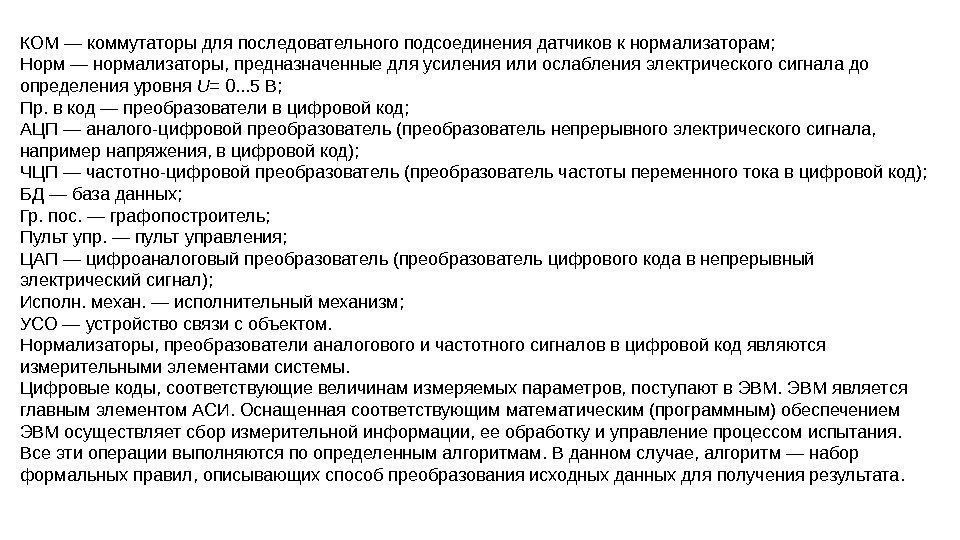
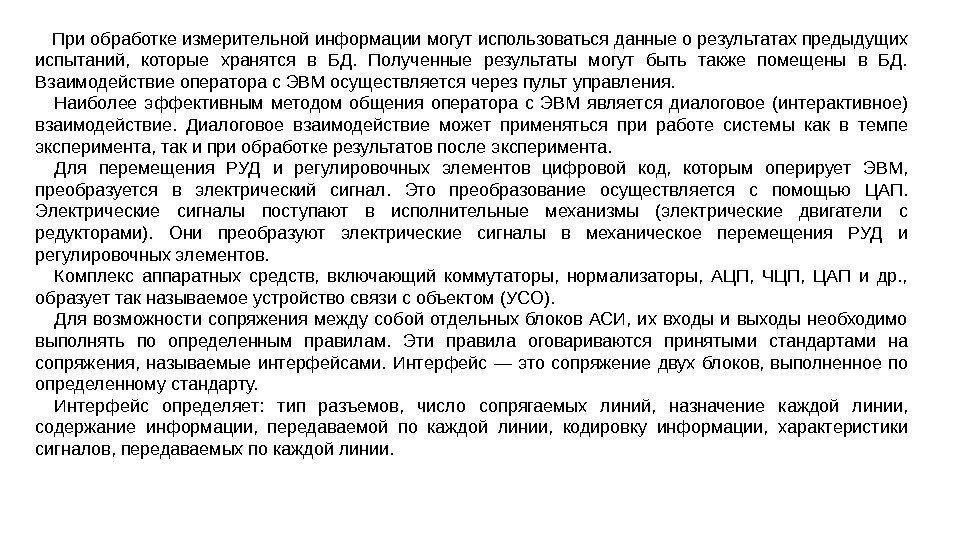
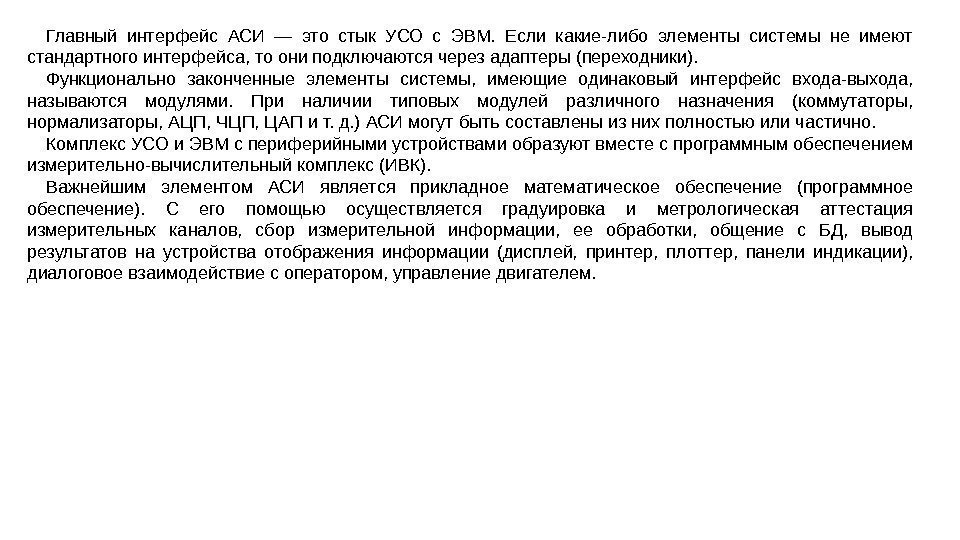
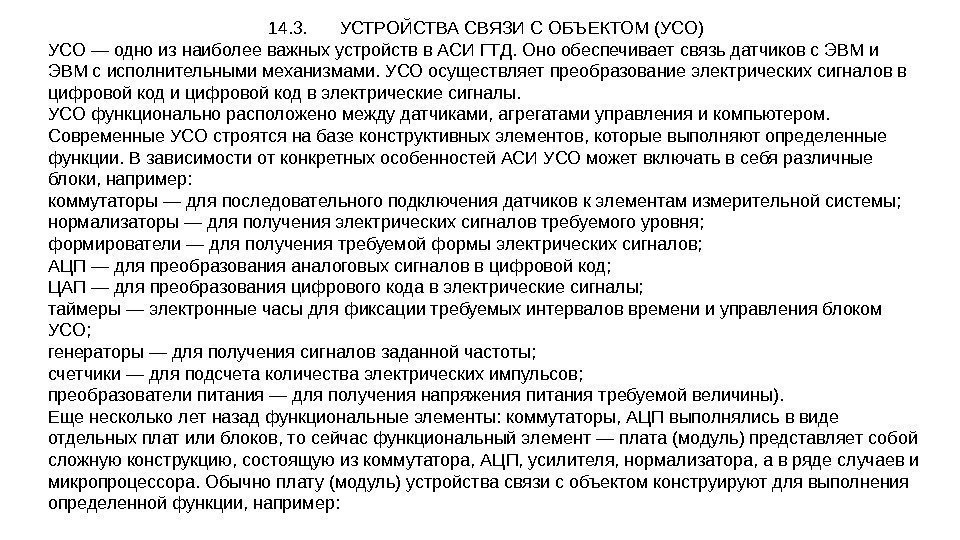
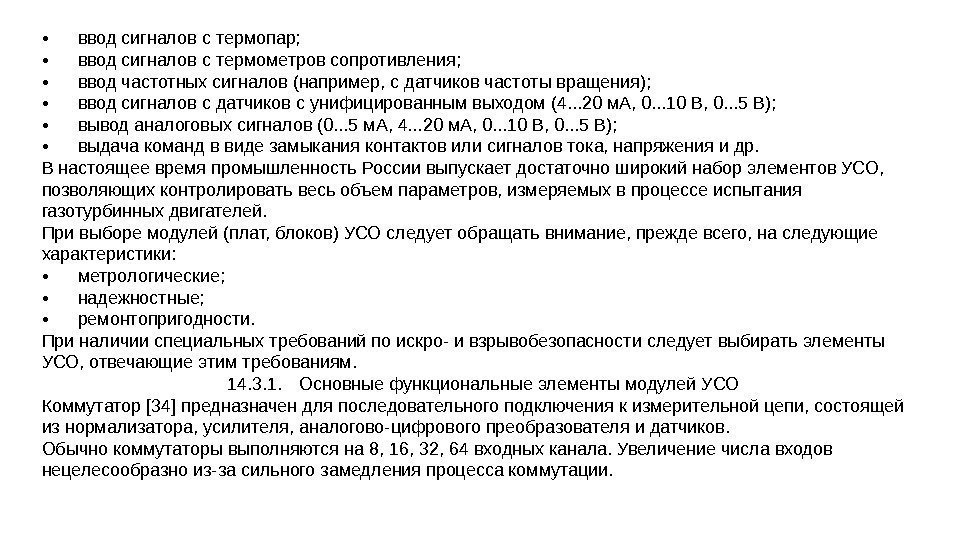
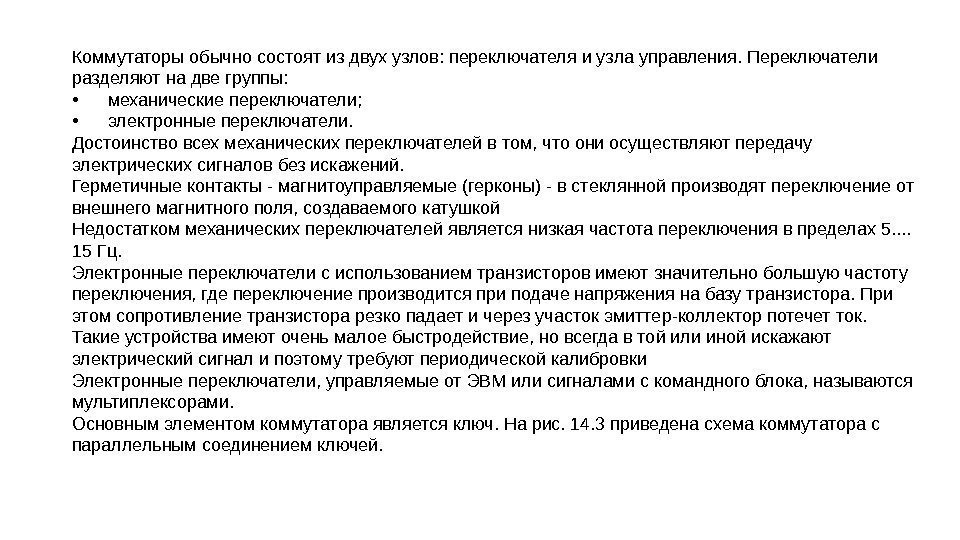
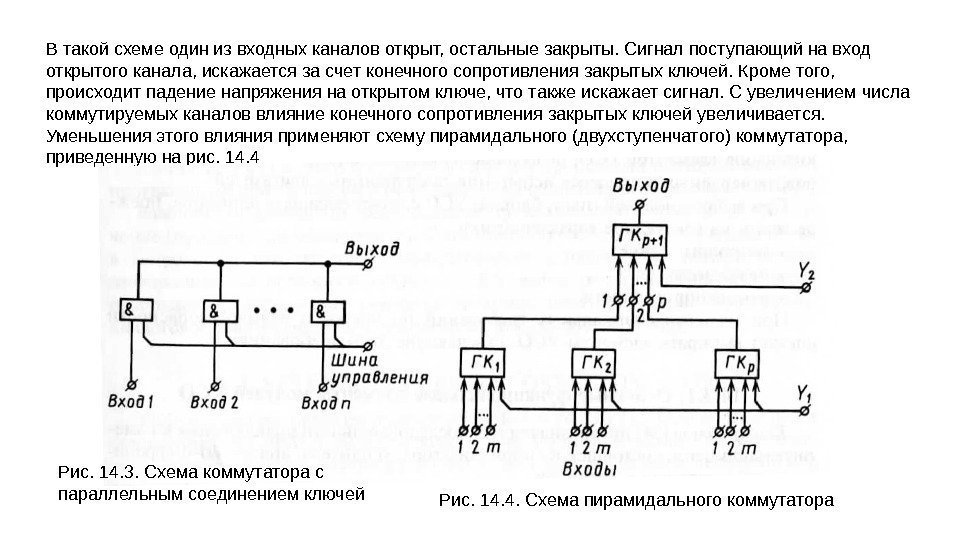
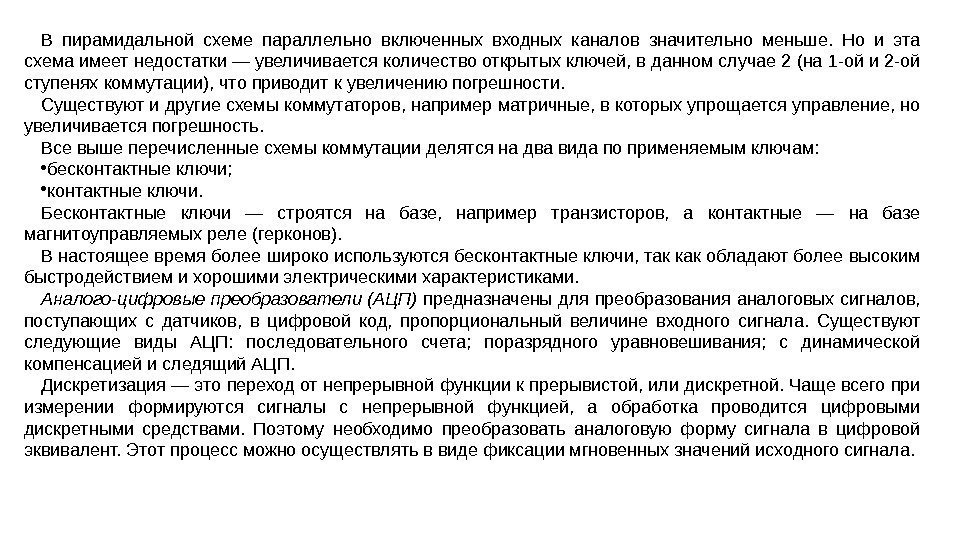
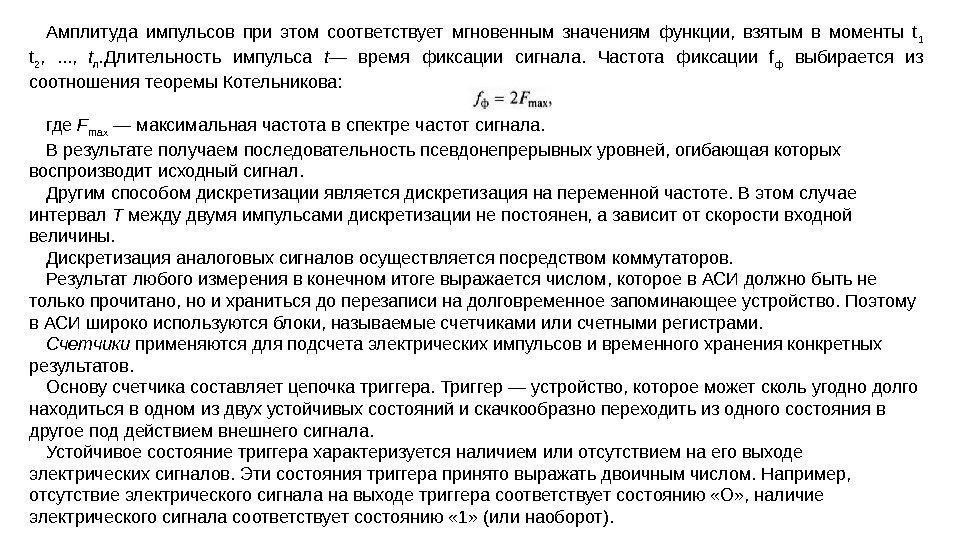
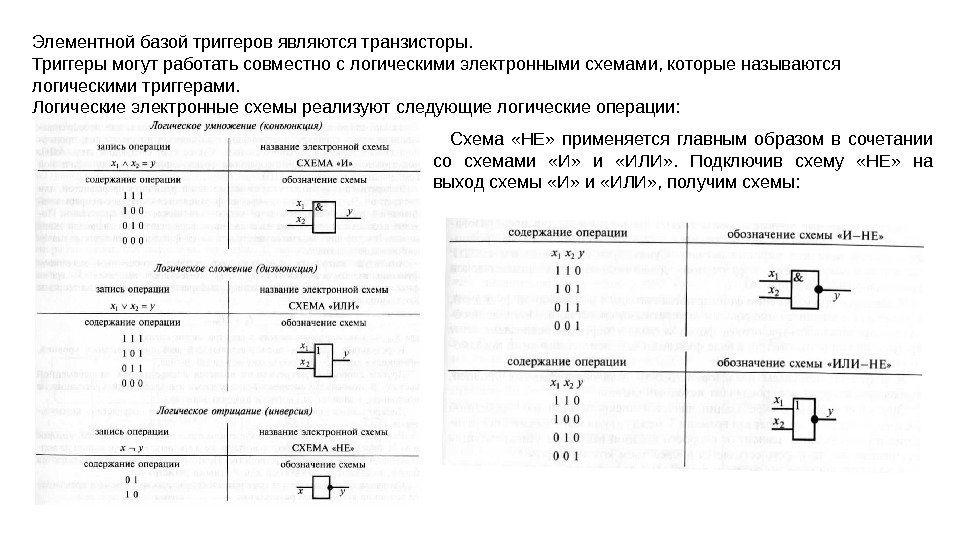
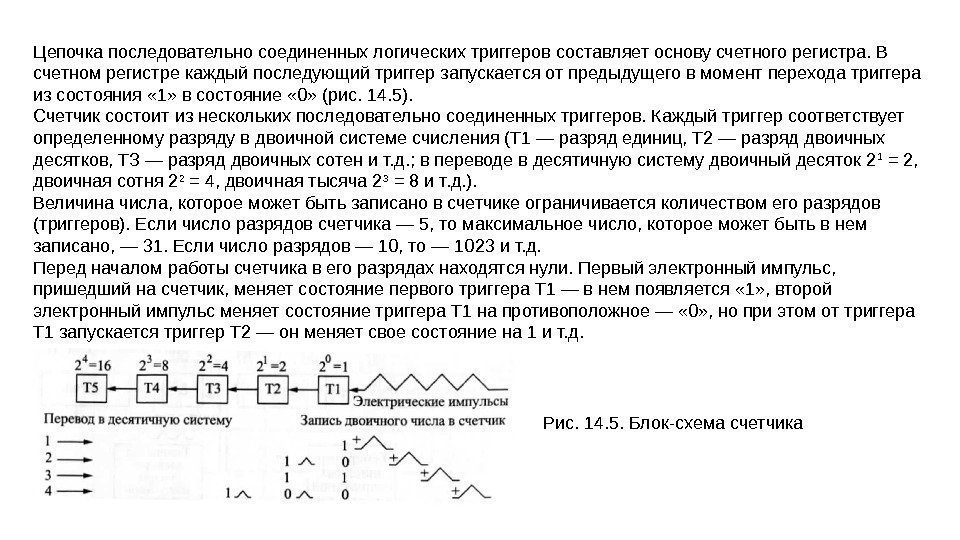
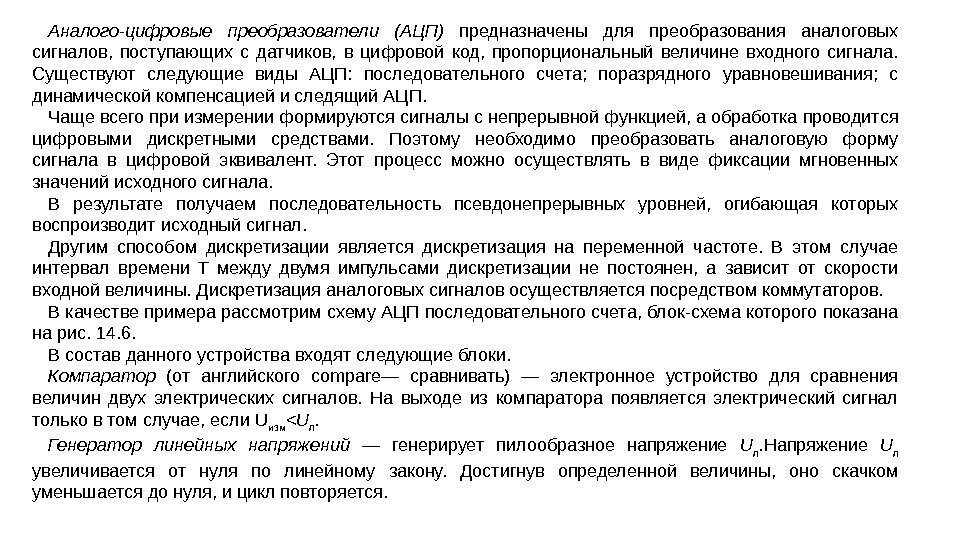
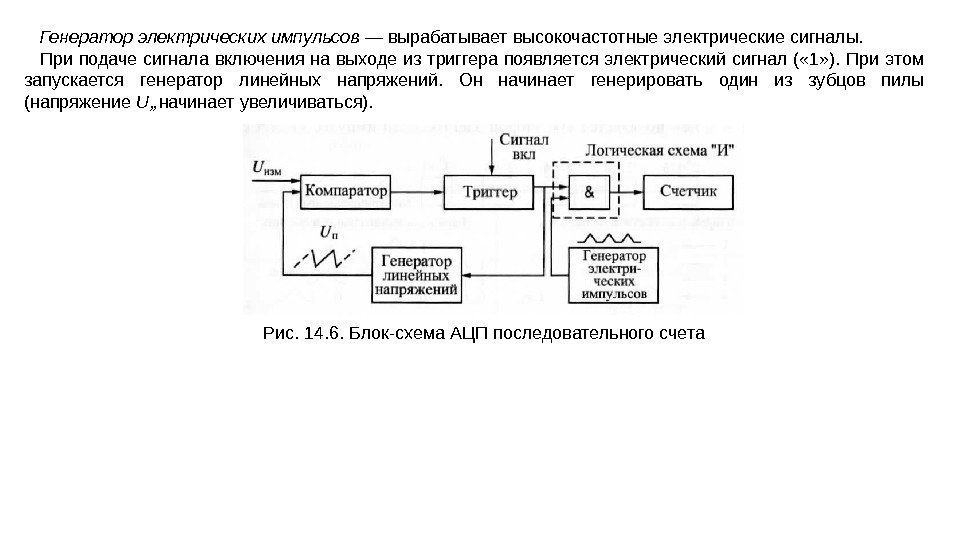
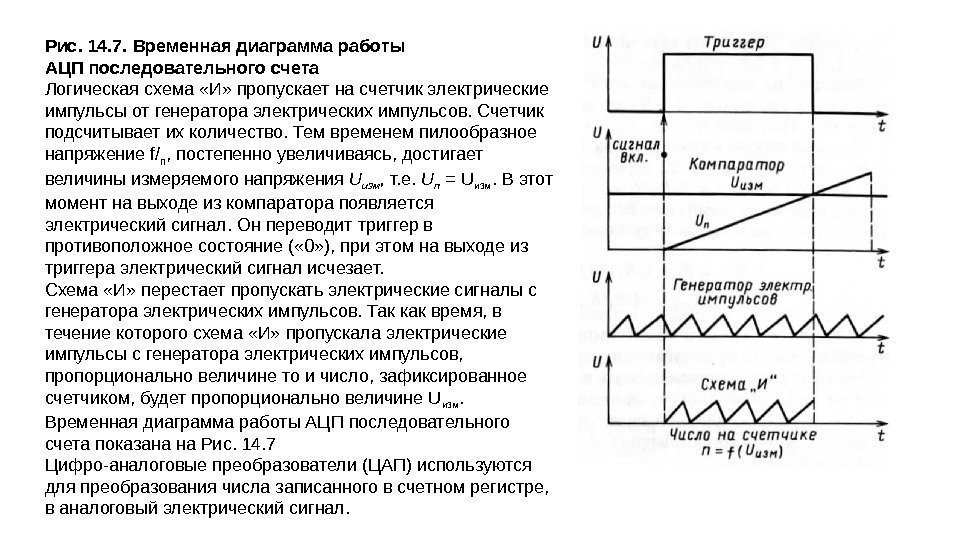
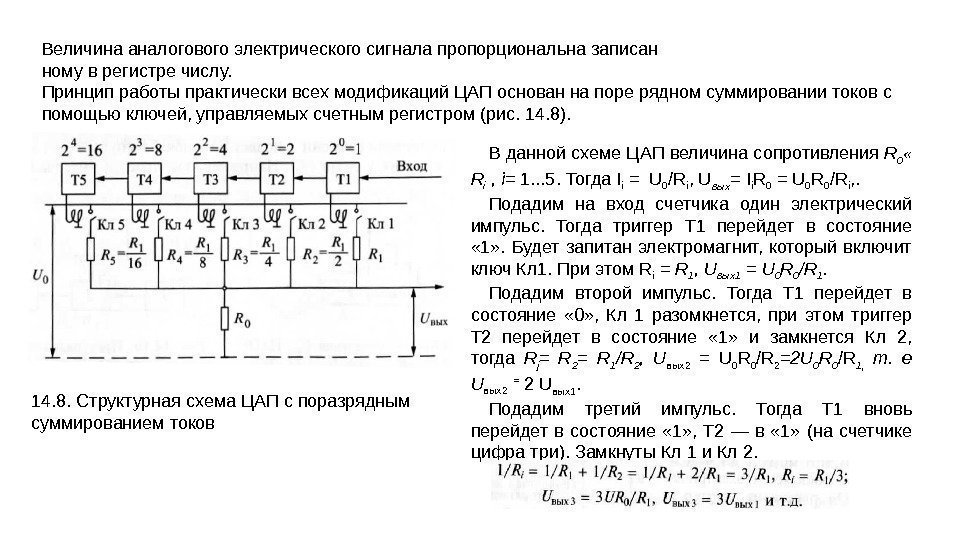

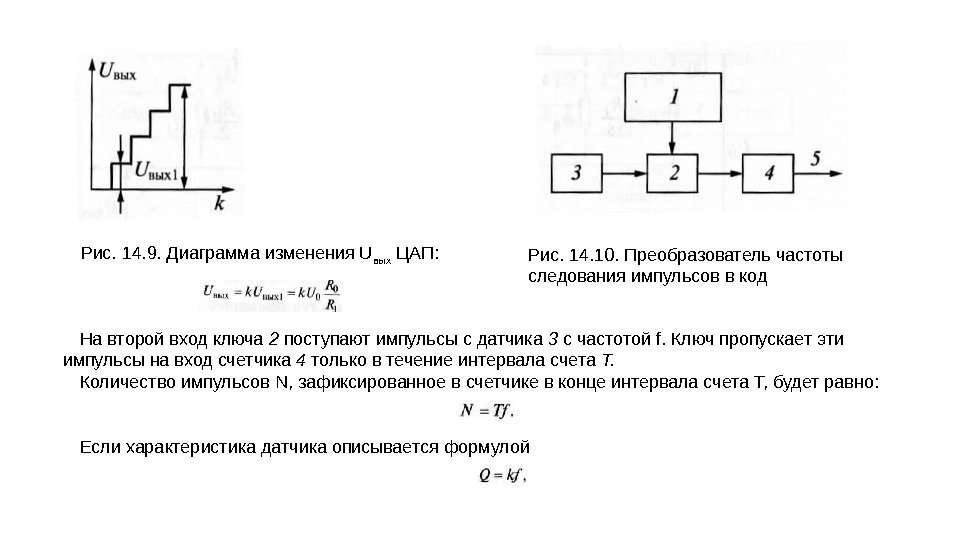
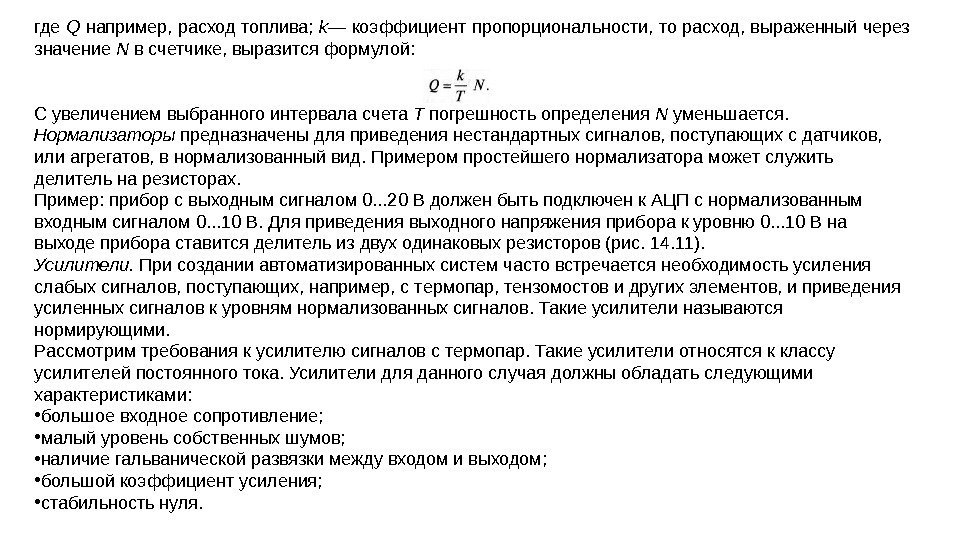
![В качестве предварительного усилителя [5] используют дифференциальный усилитель, выполненный в виде интегральной микросхемы В качестве предварительного усилителя [5] используют дифференциальный усилитель, выполненный в виде интегральной микросхемы](http://present5.com/presentforday2/20170201/mmk_ispytania_i_kontrol_kachestva_izdeliy_2017_images/mmk_ispytania_i_kontrol_kachestva_izdeliy_2017_852.jpg)
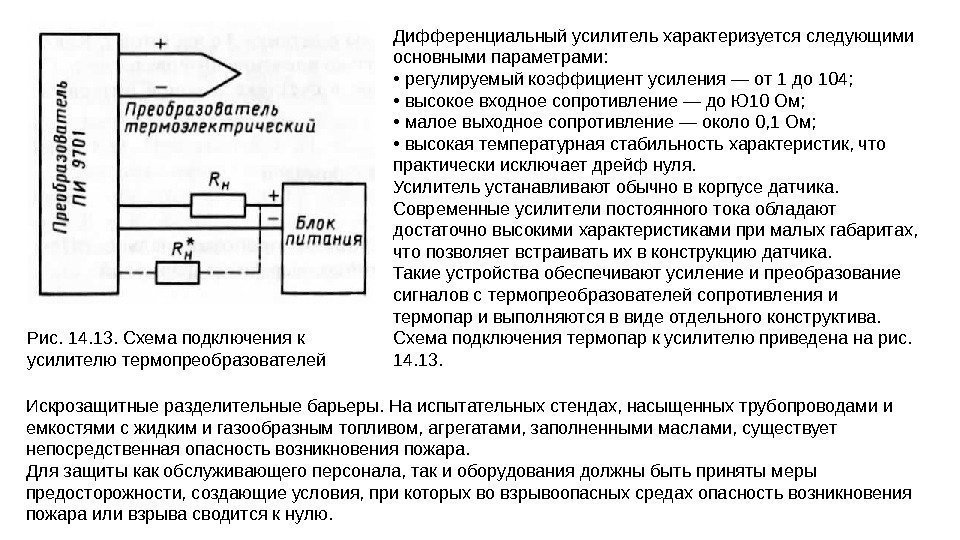
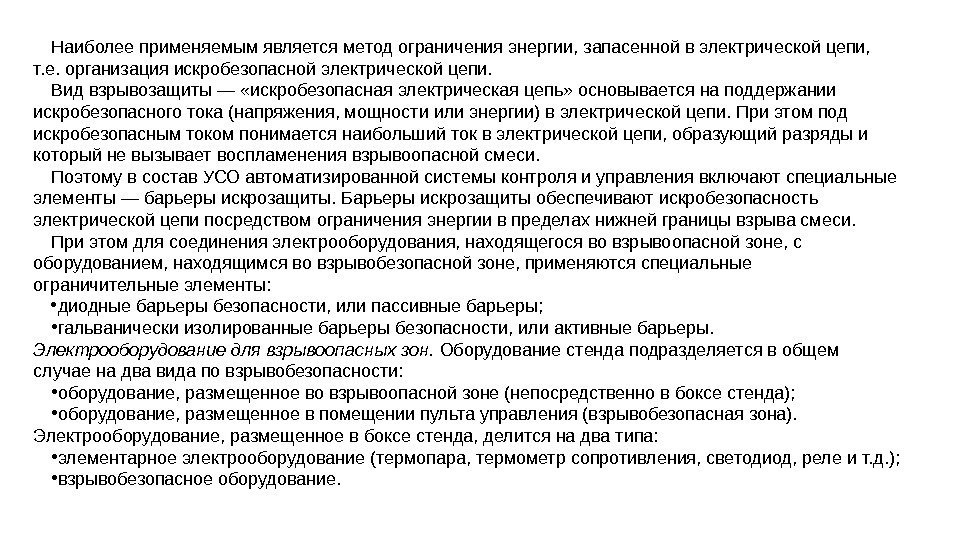
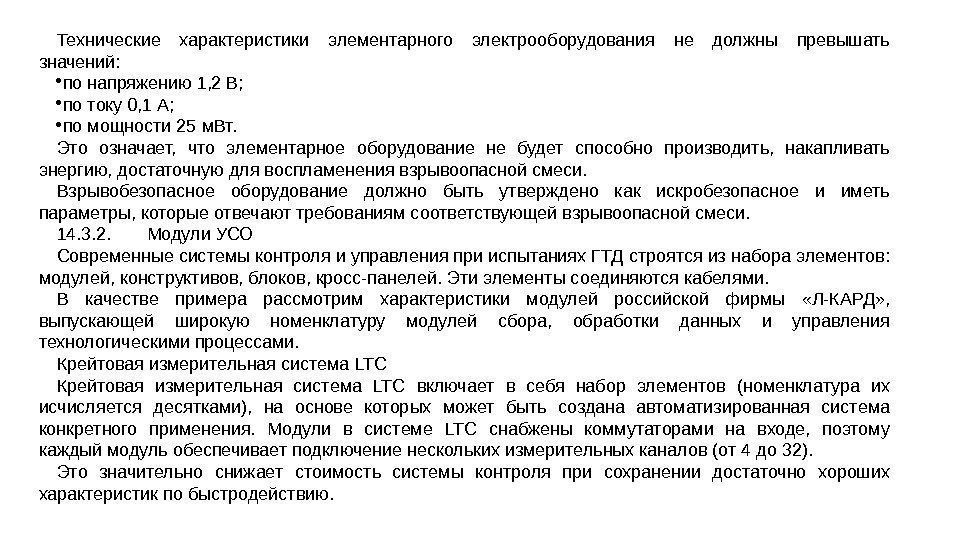
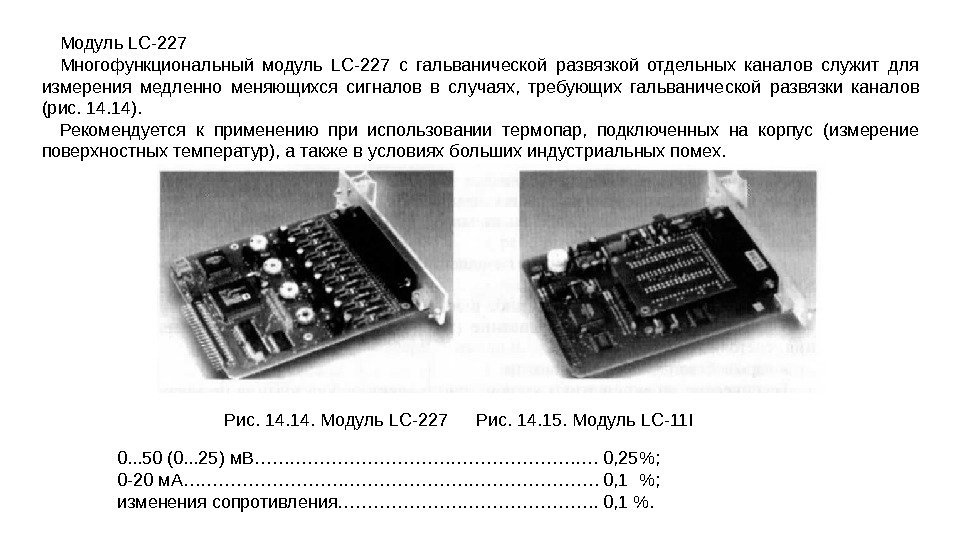
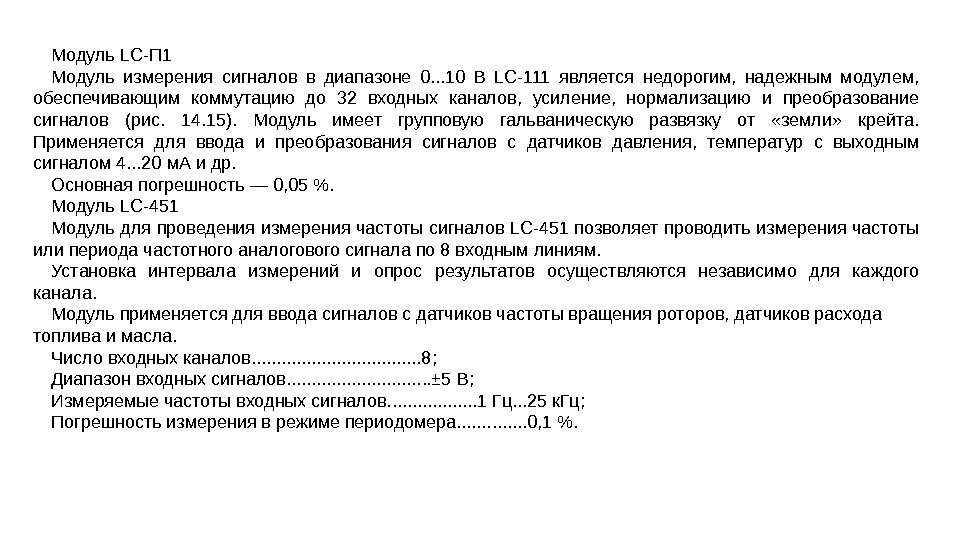
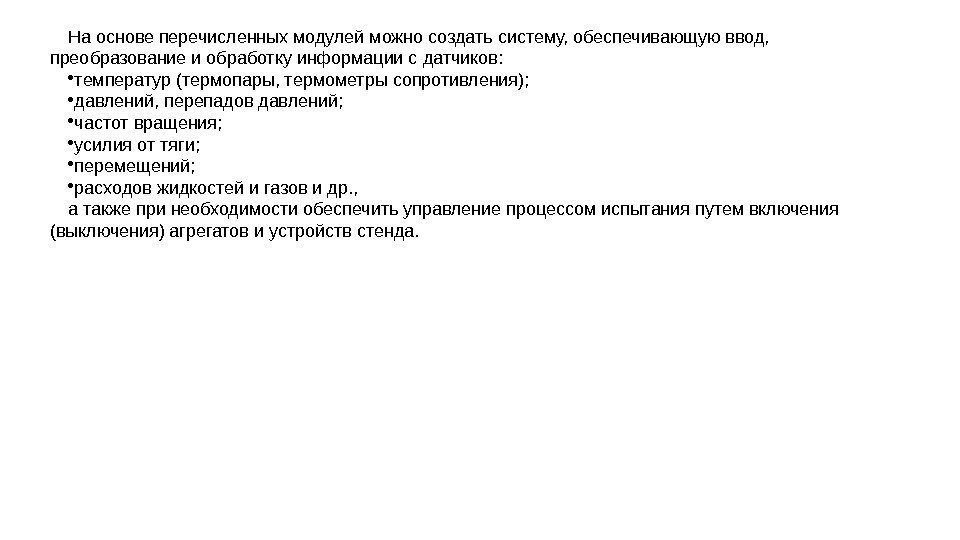
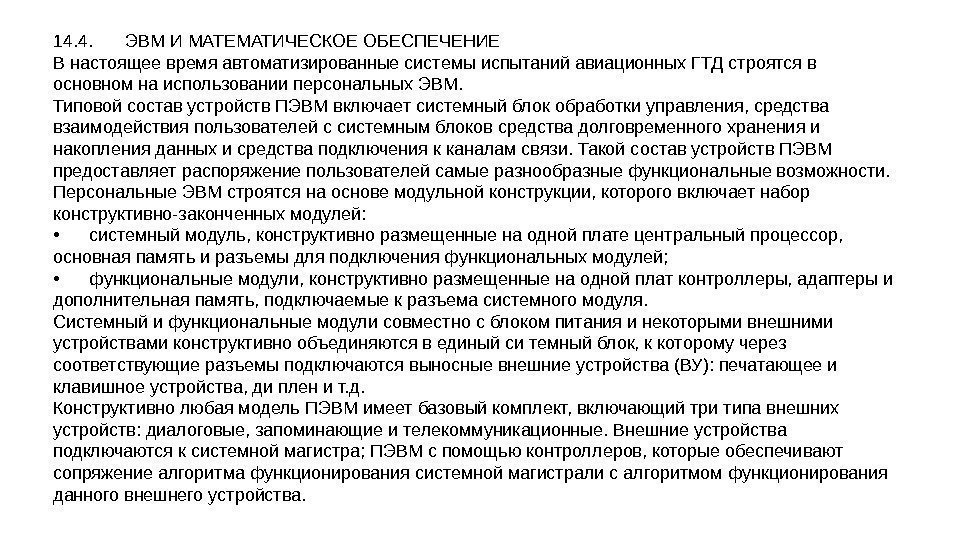
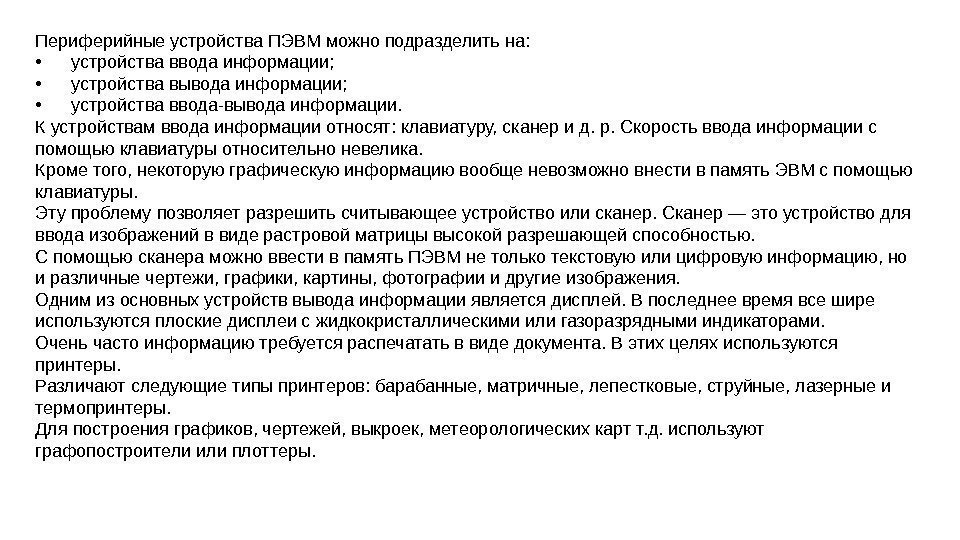
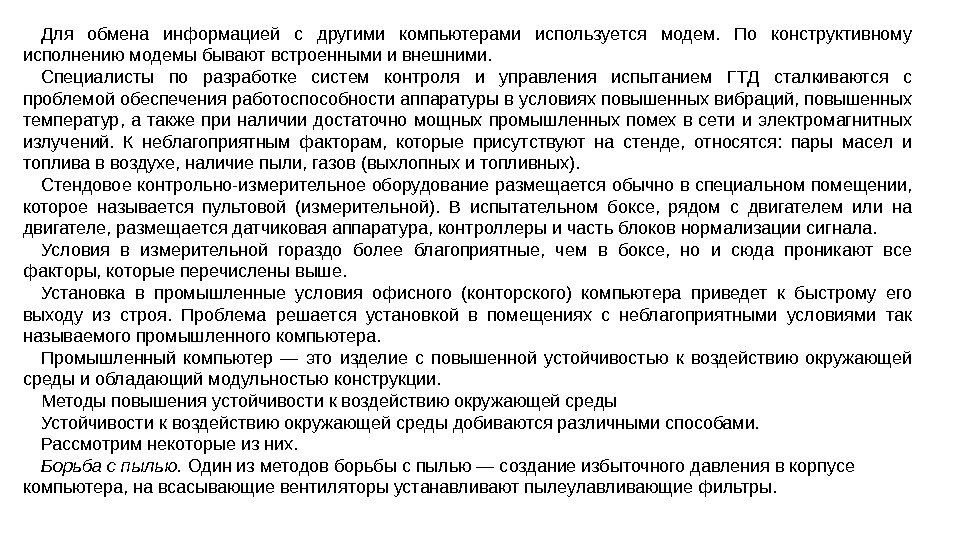
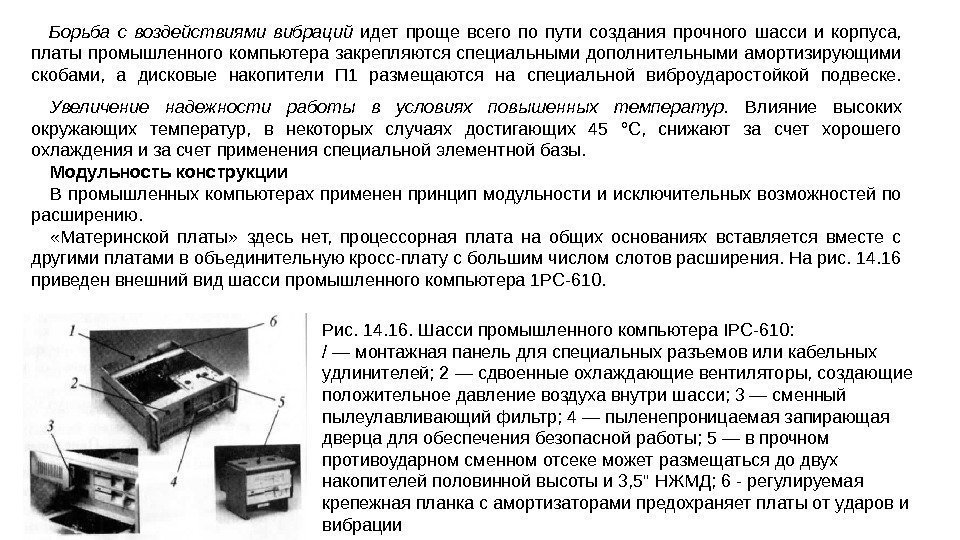
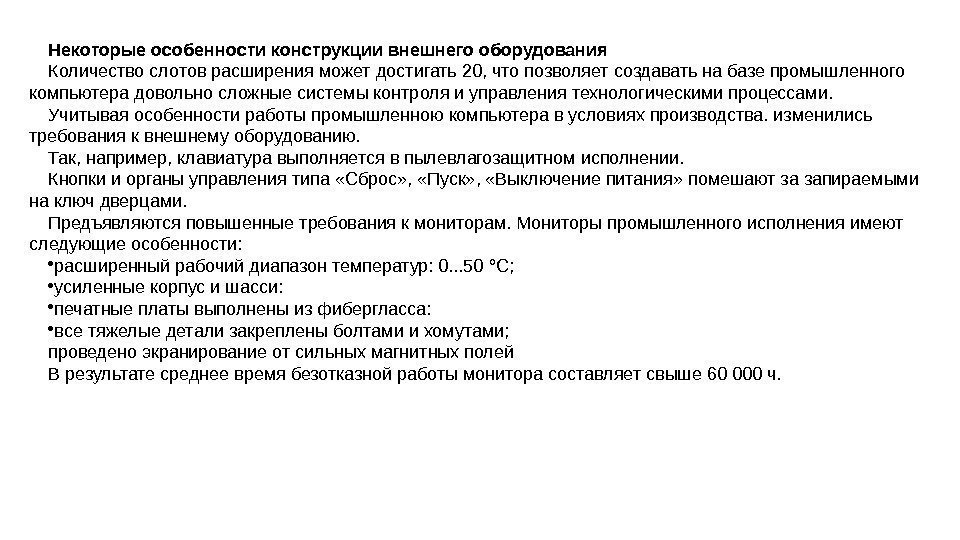
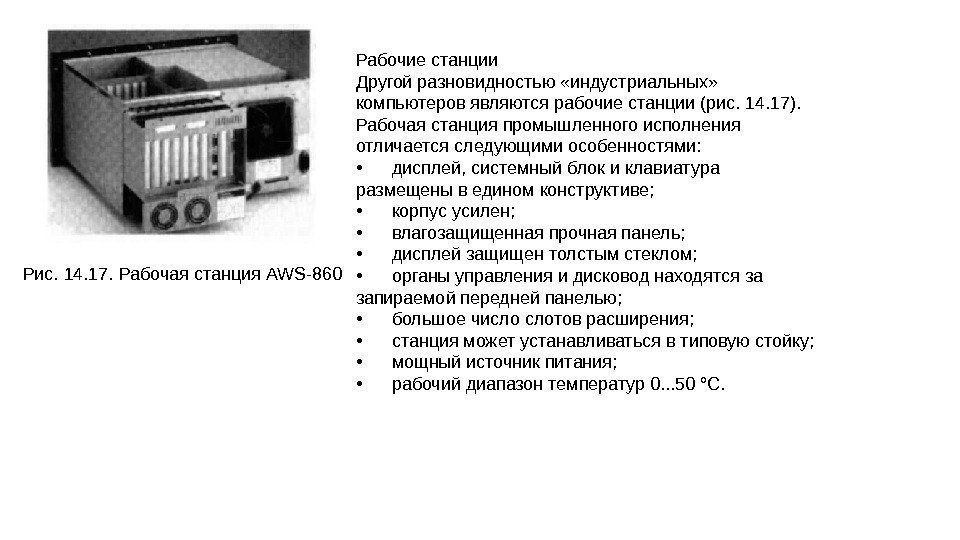
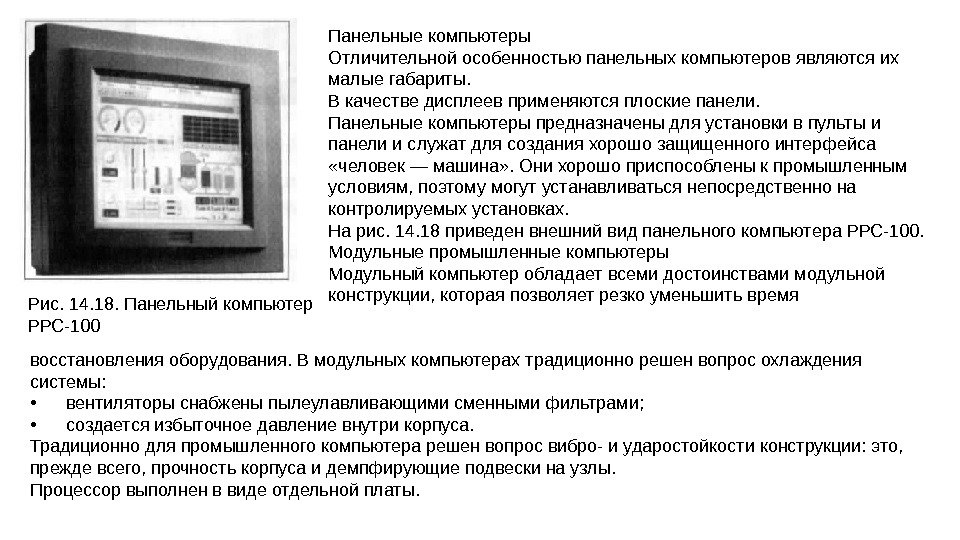
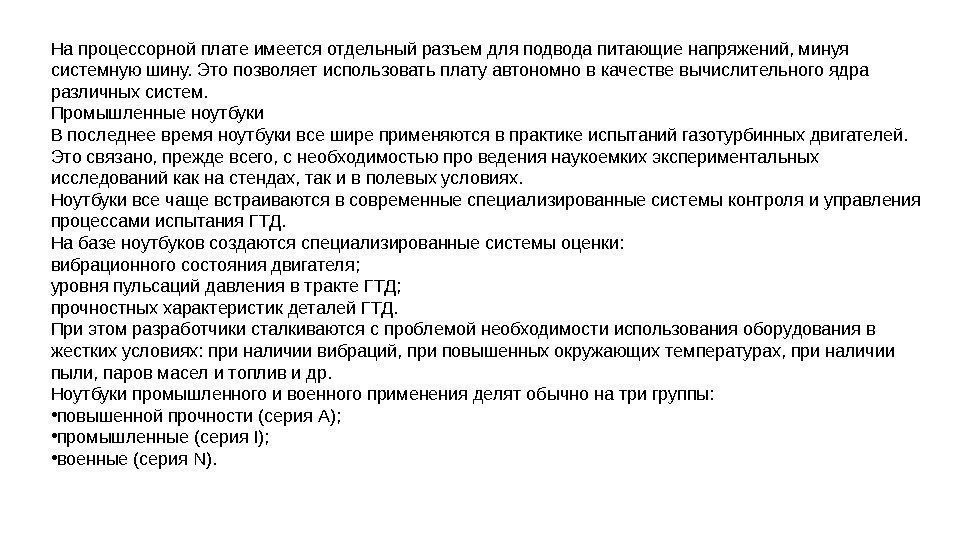
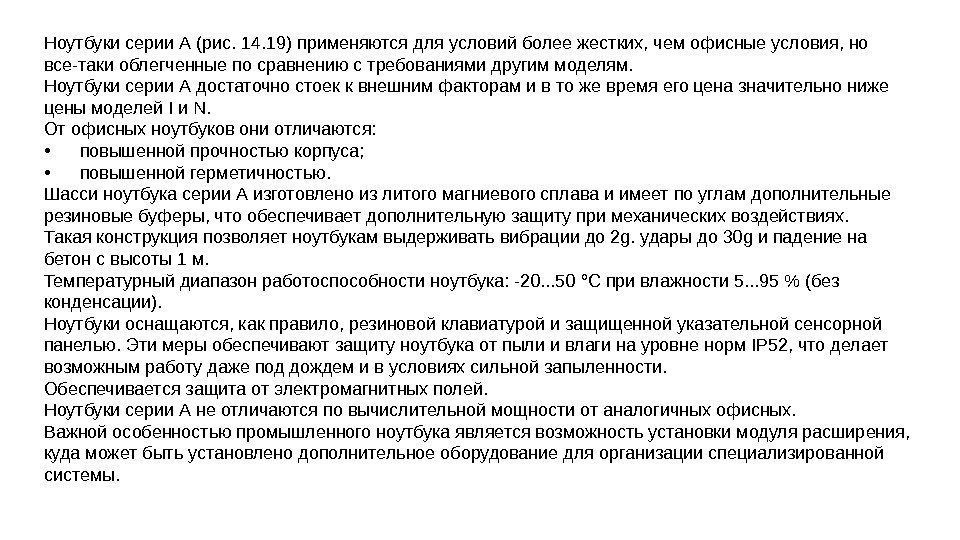
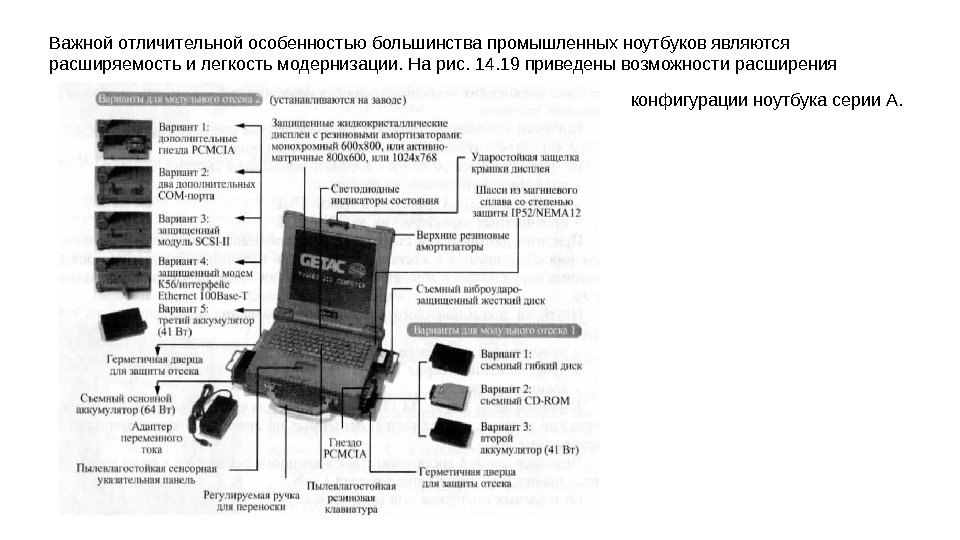
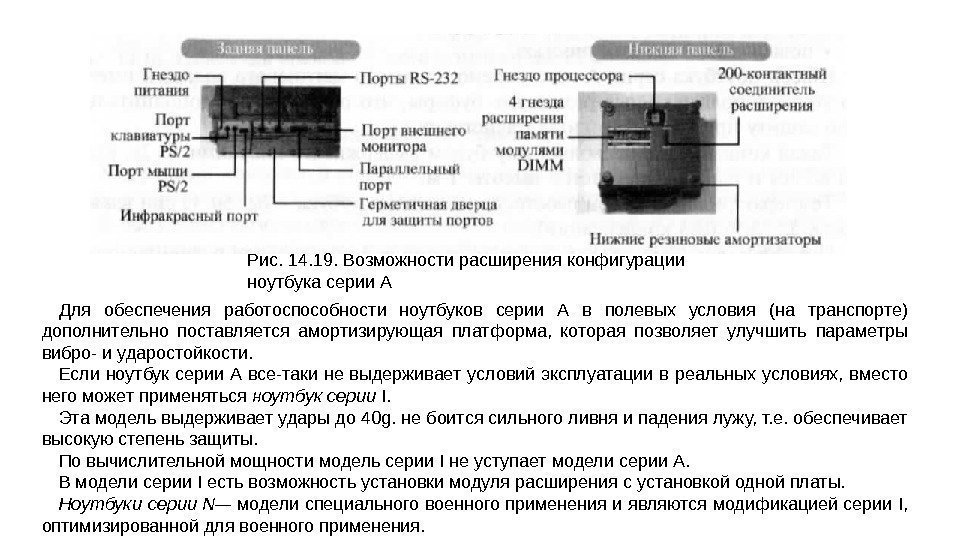
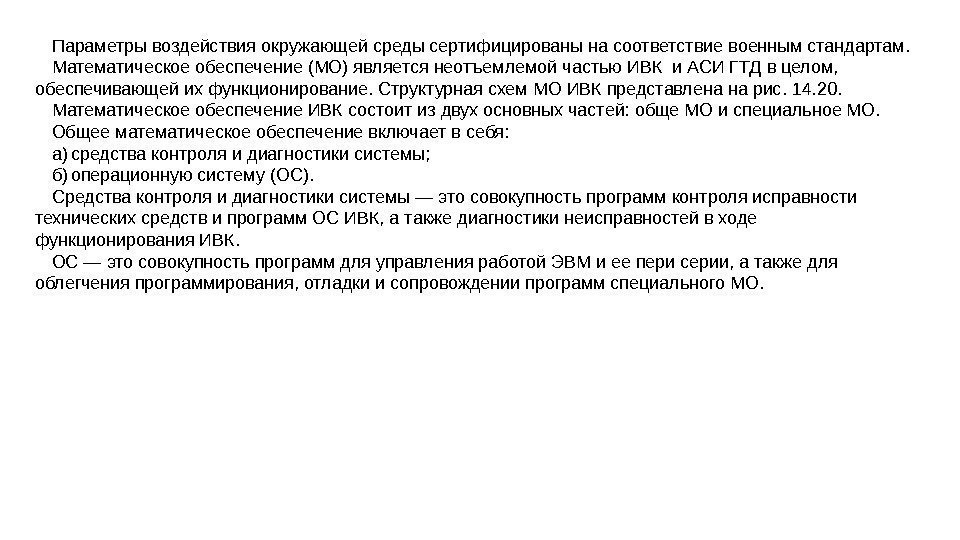
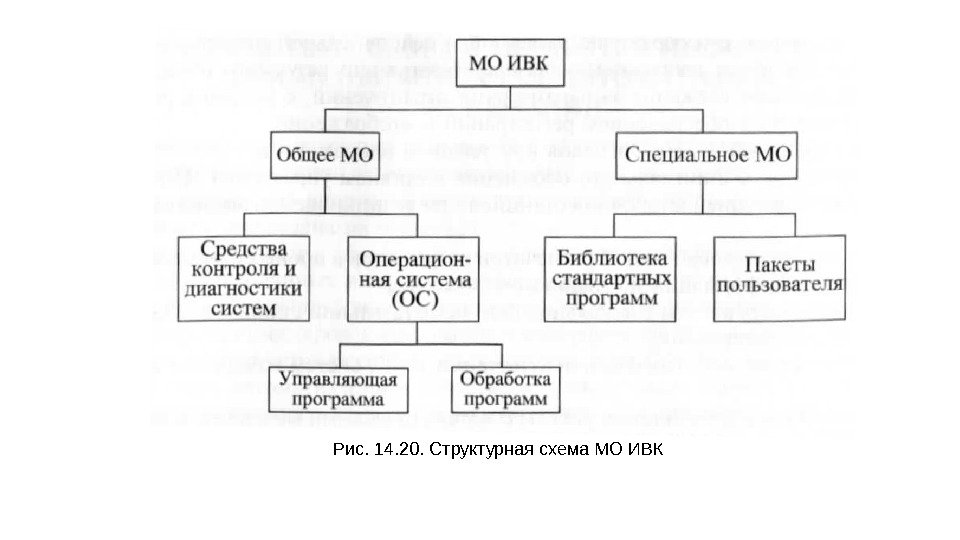
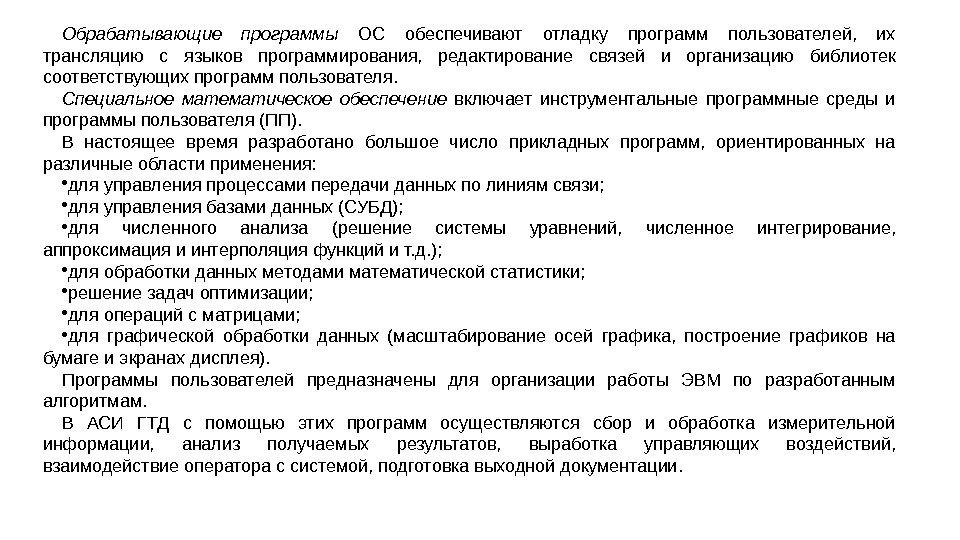
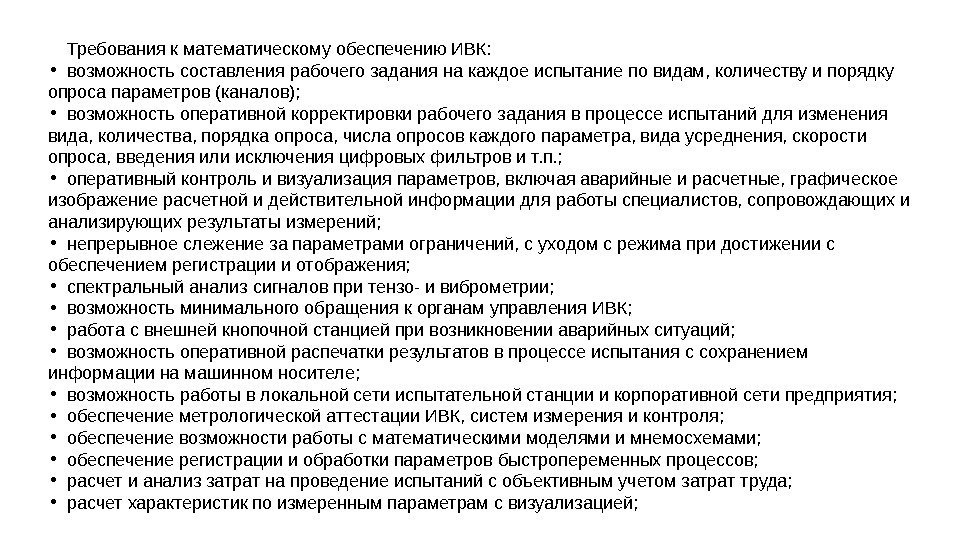
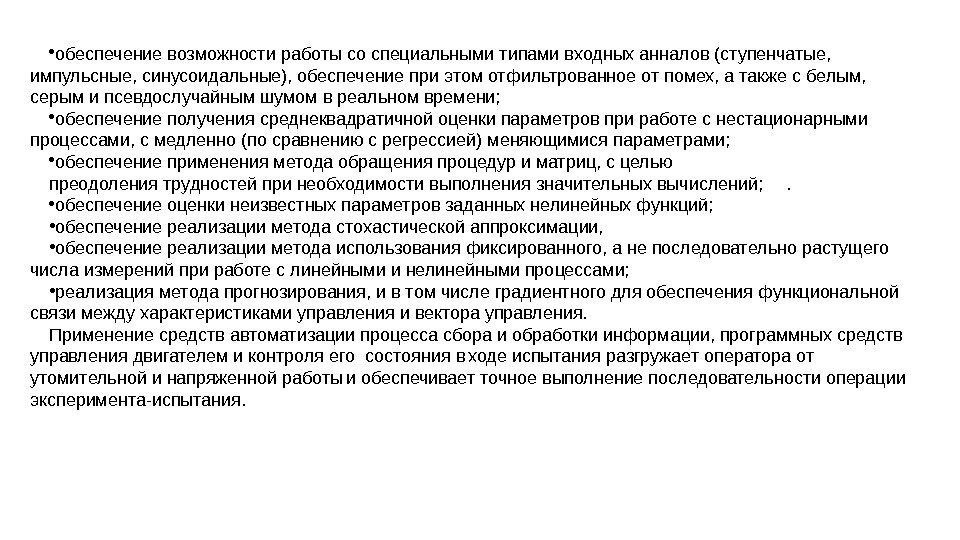
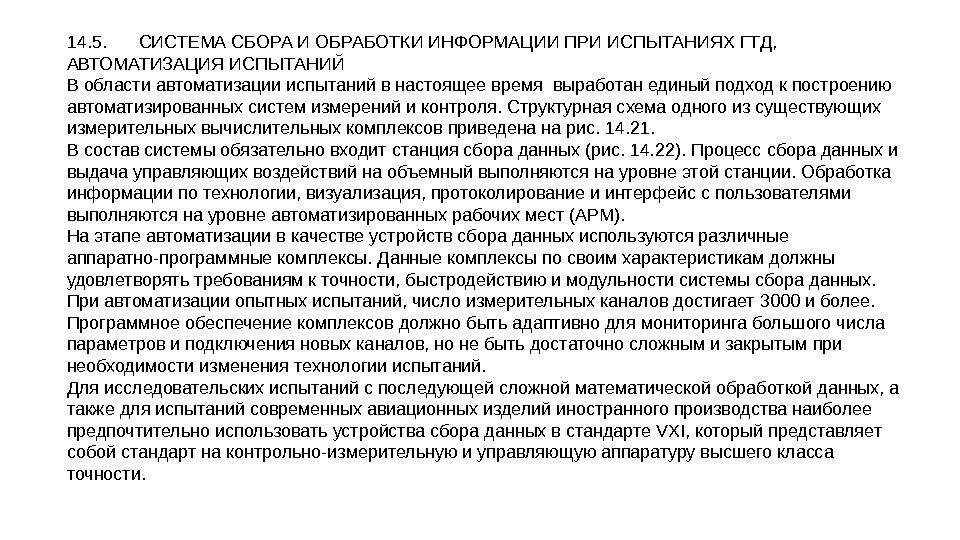
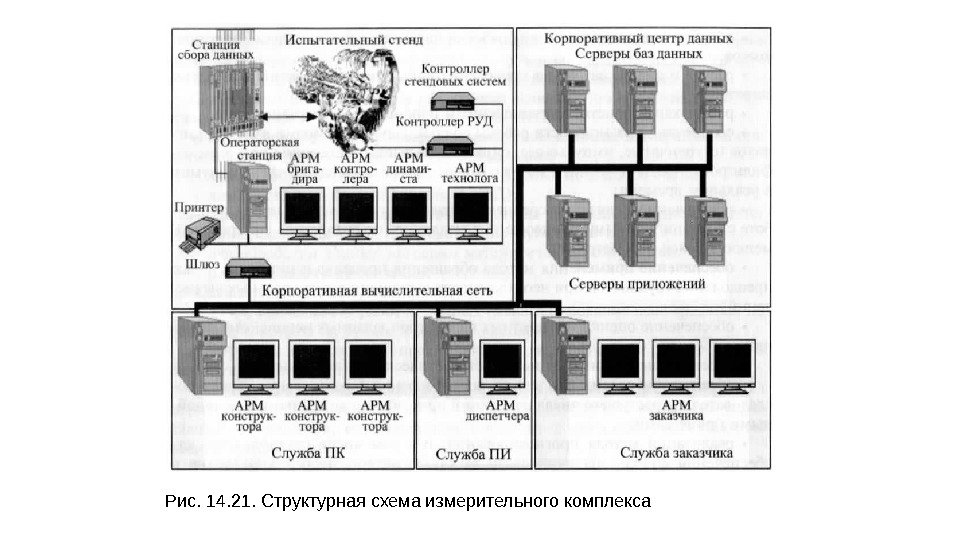

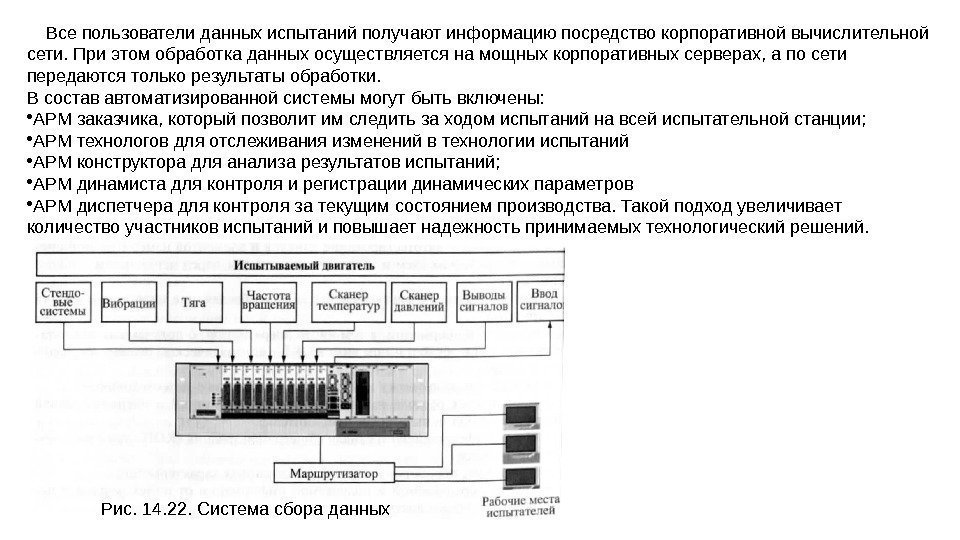
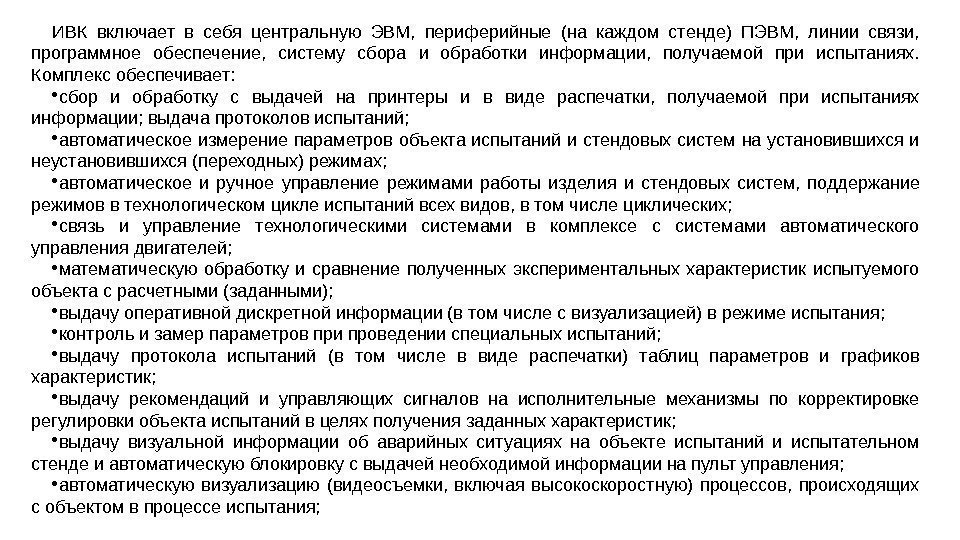
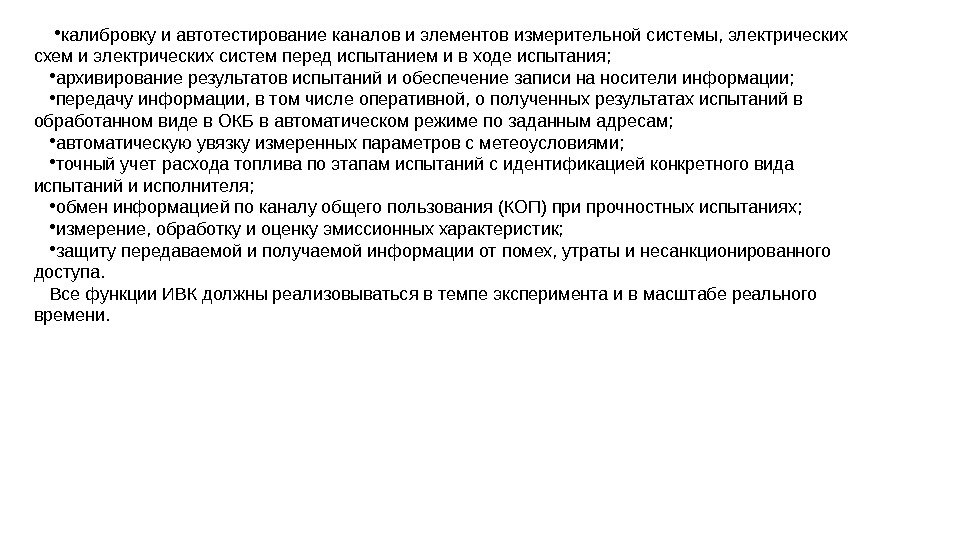
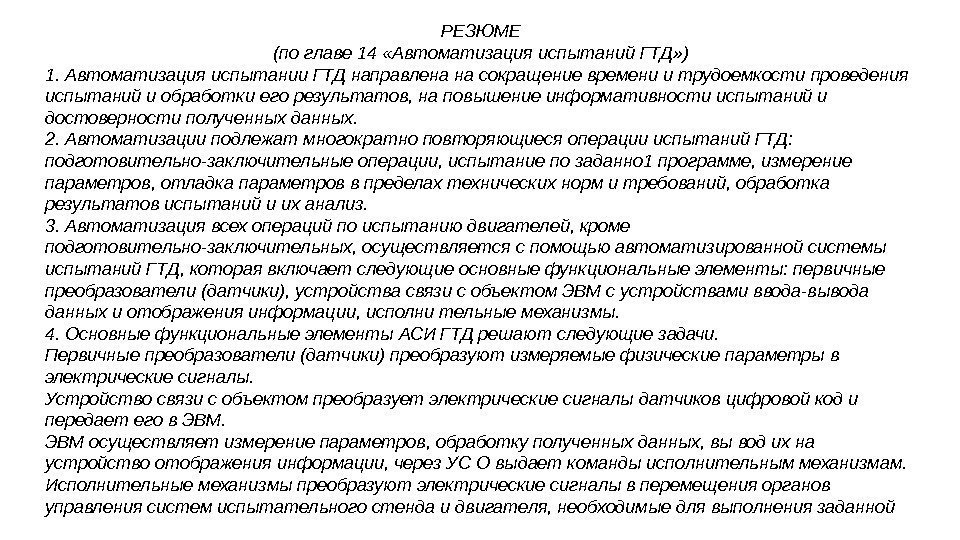
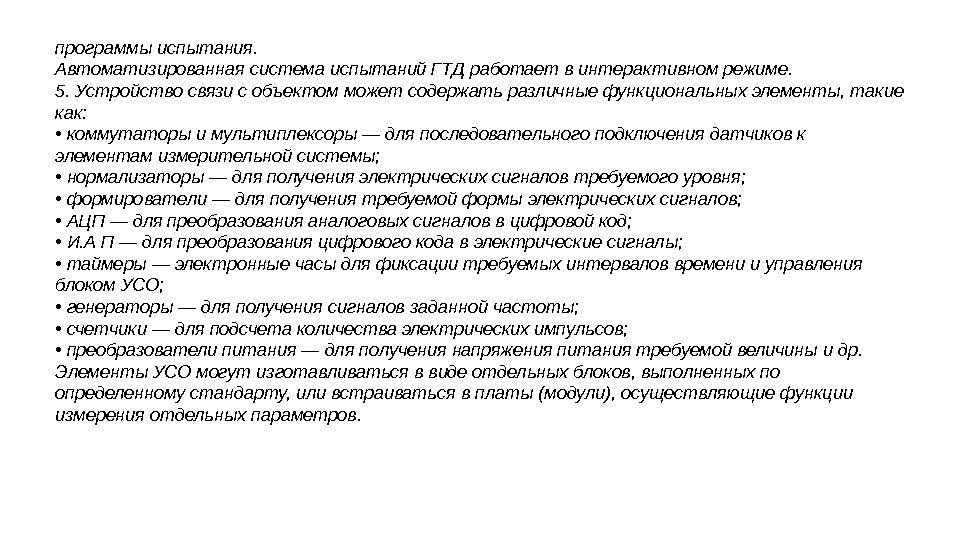
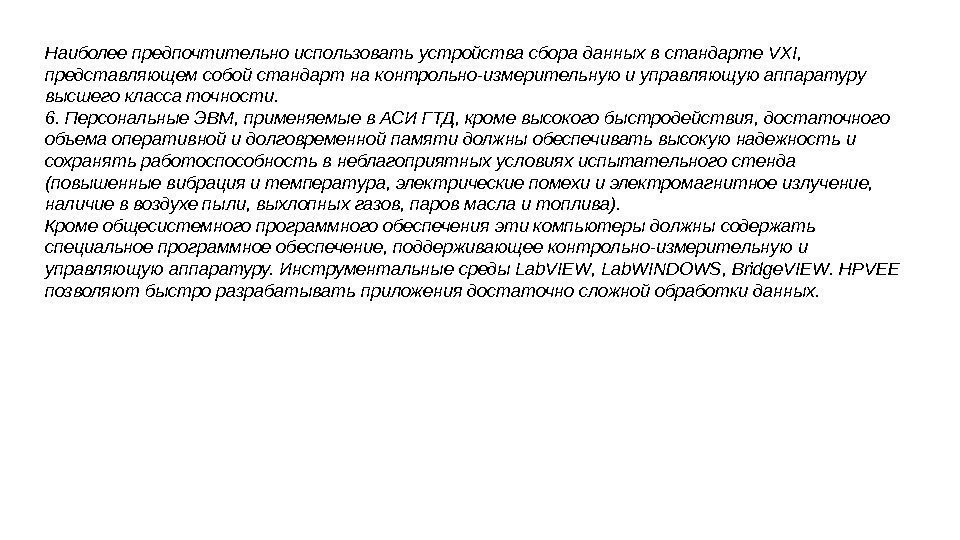
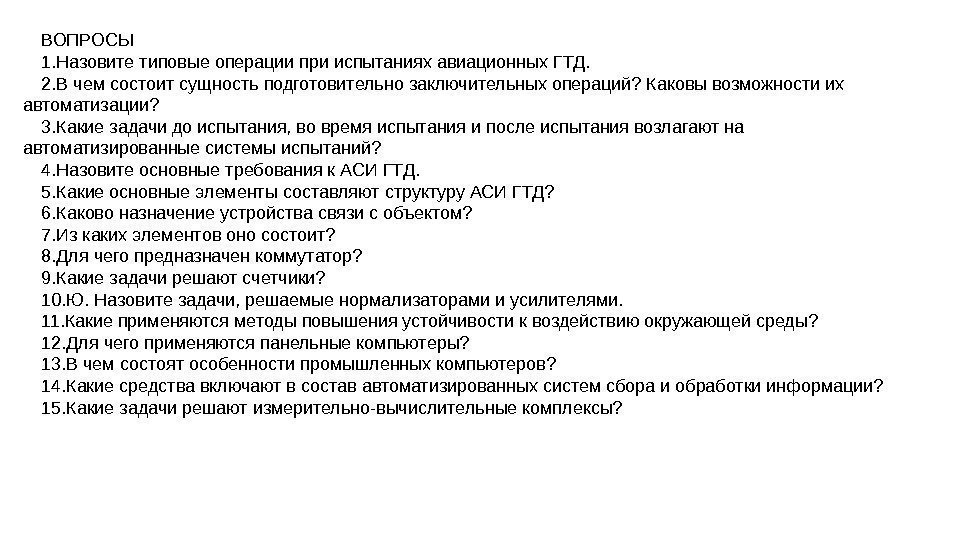
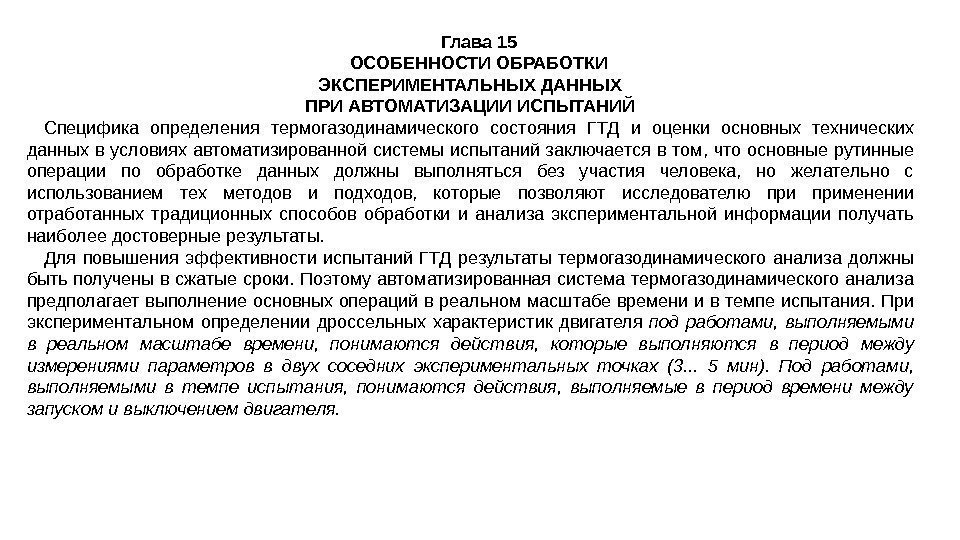
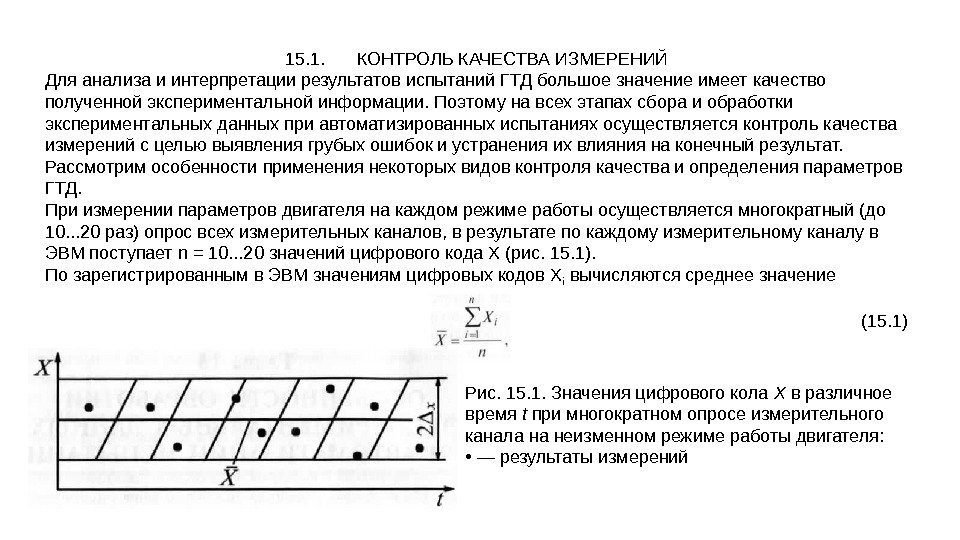
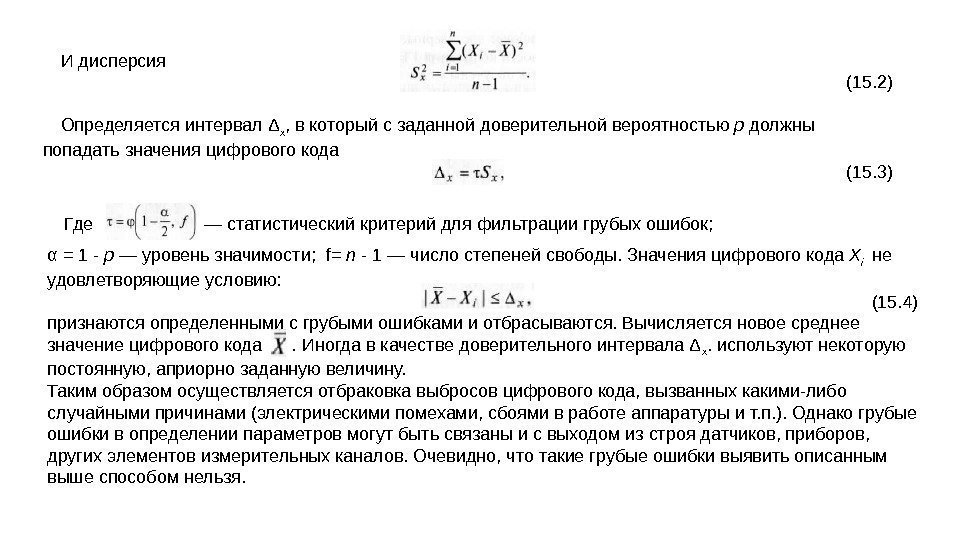
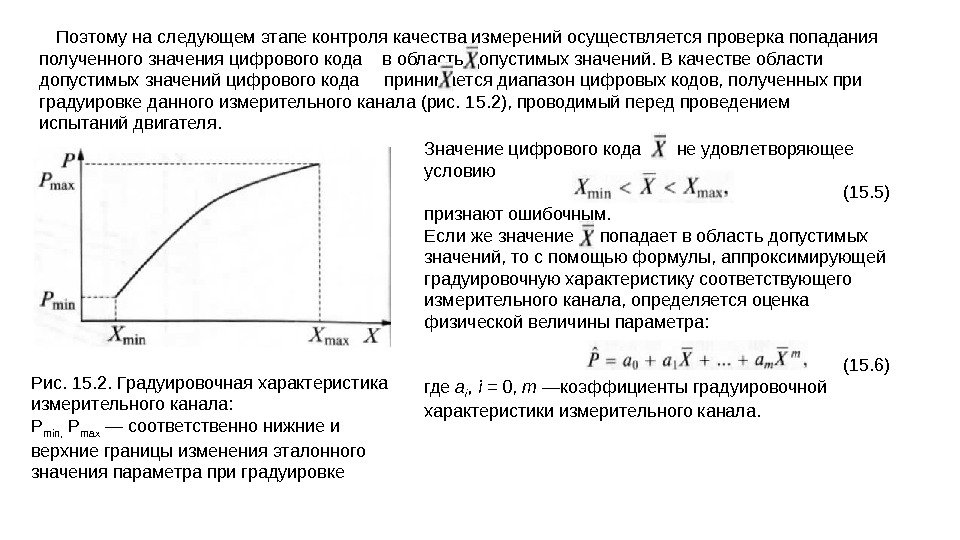
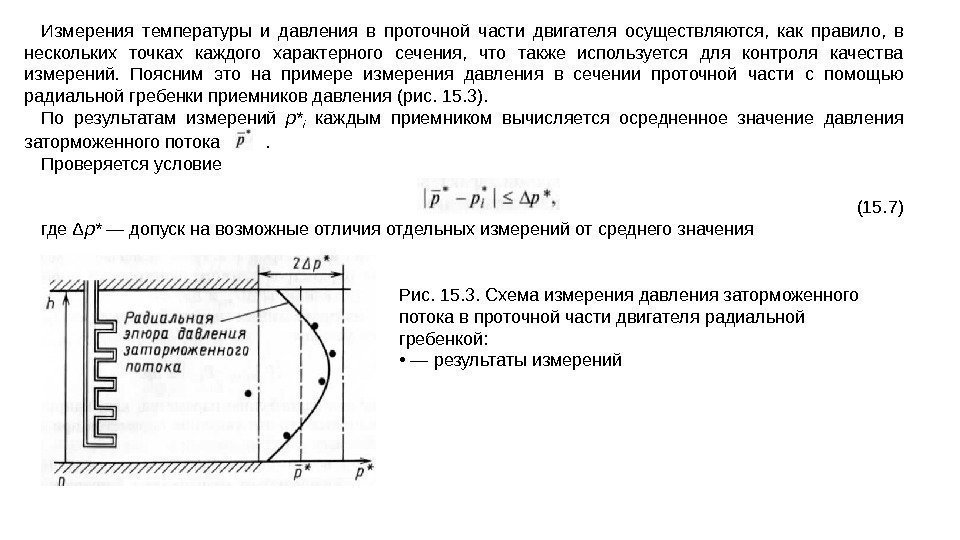
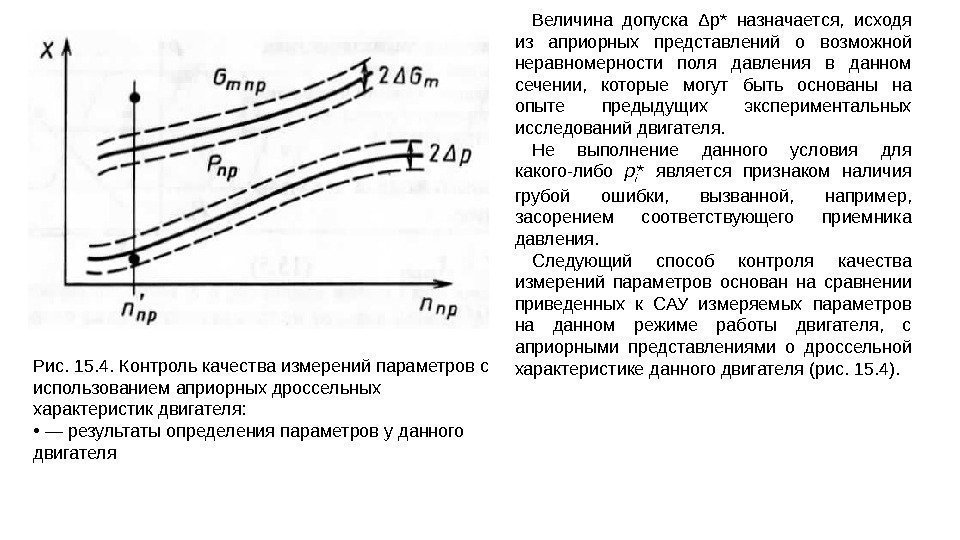
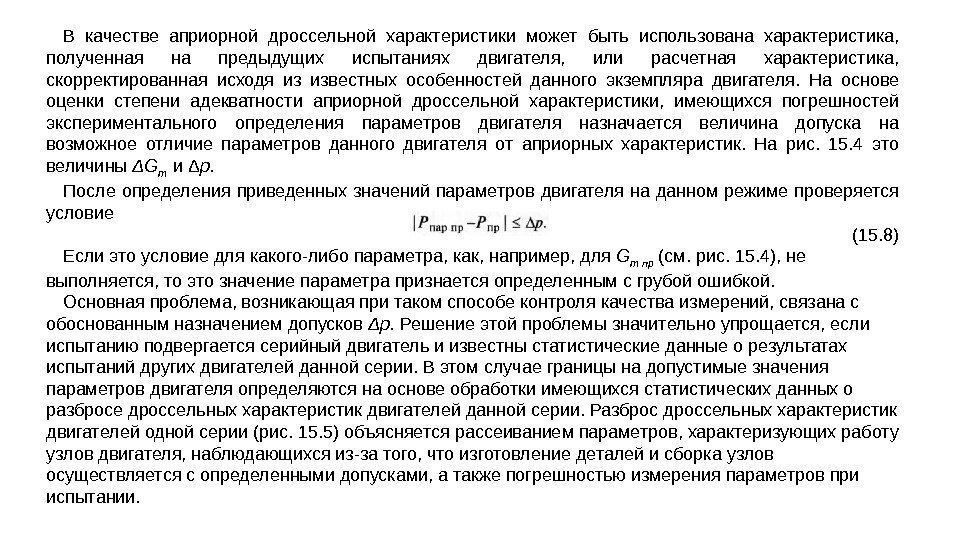
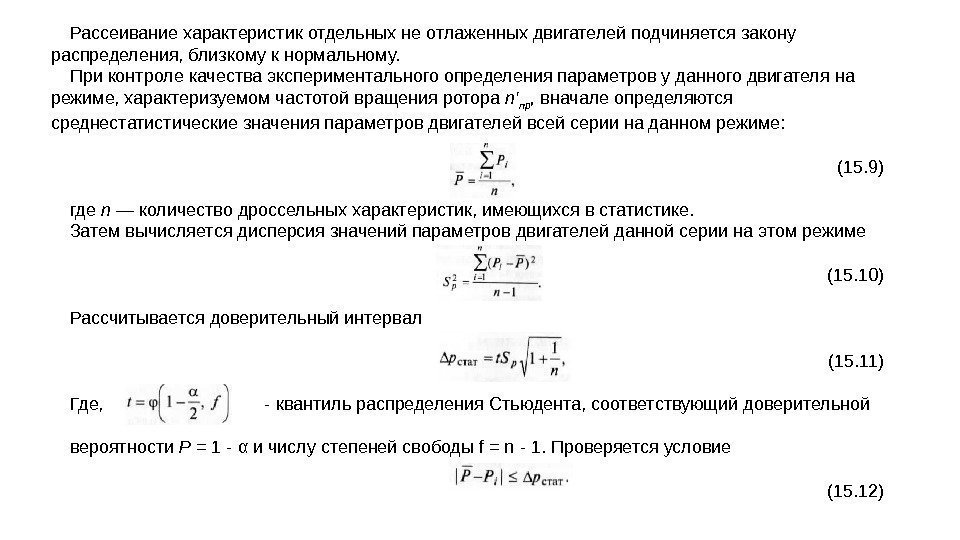
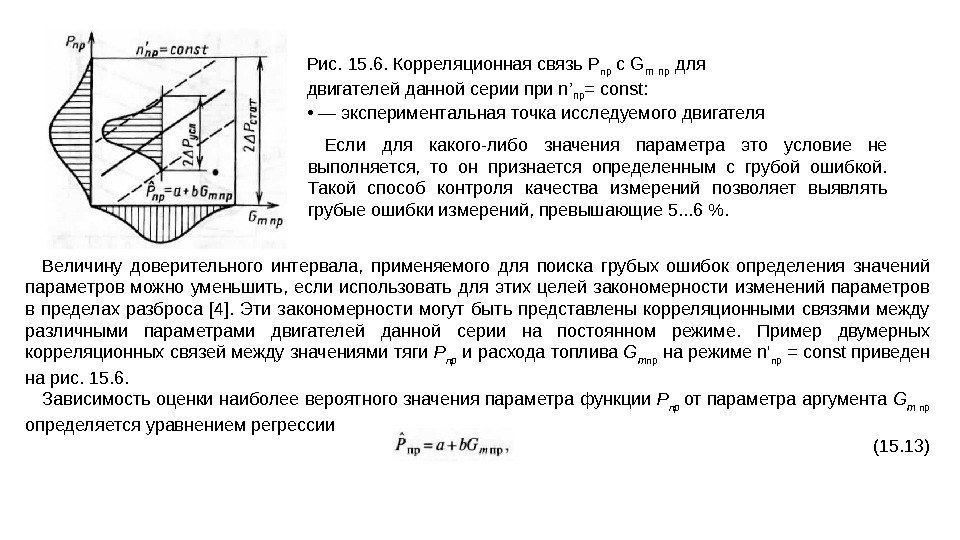
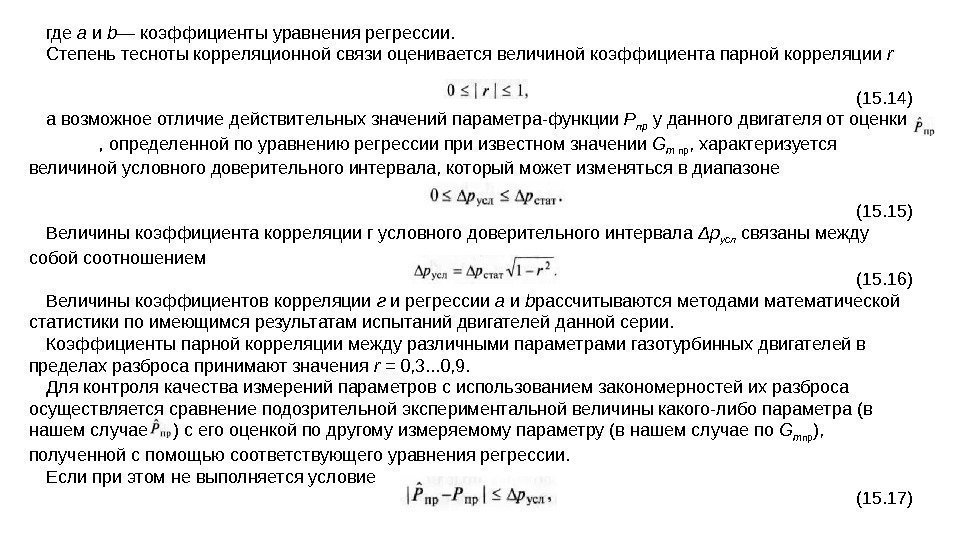
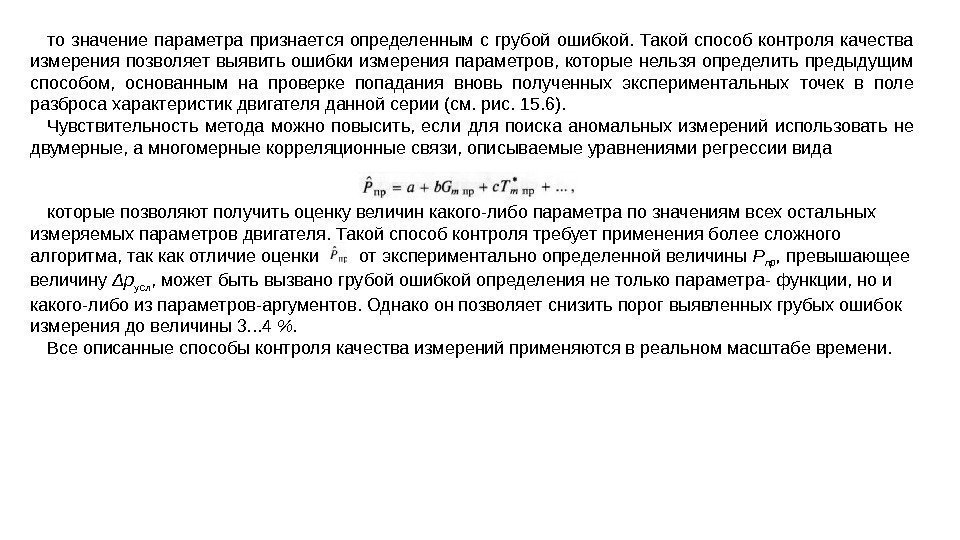
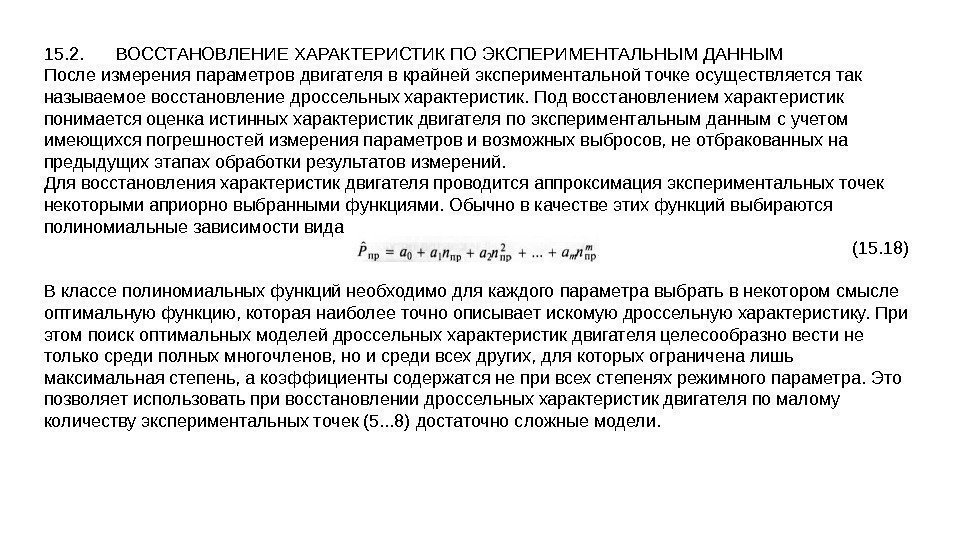
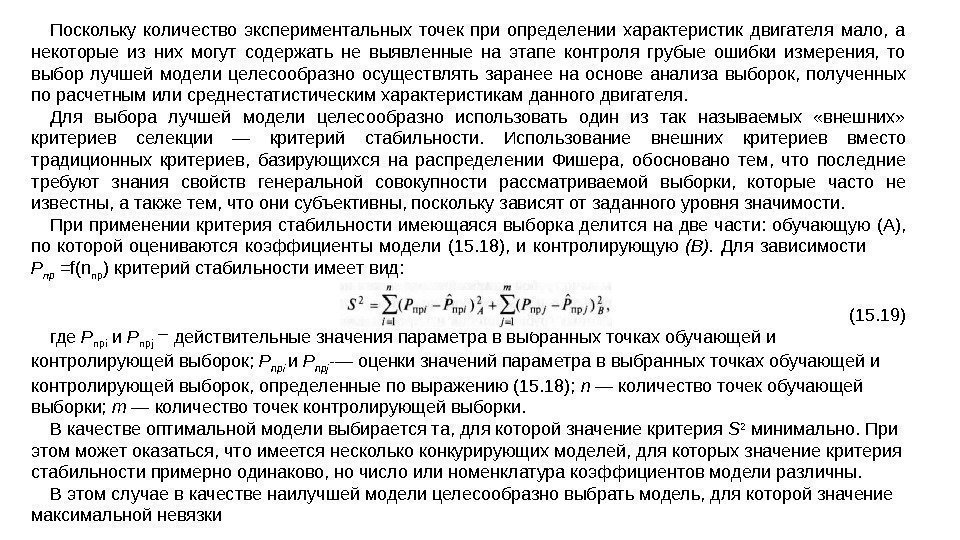
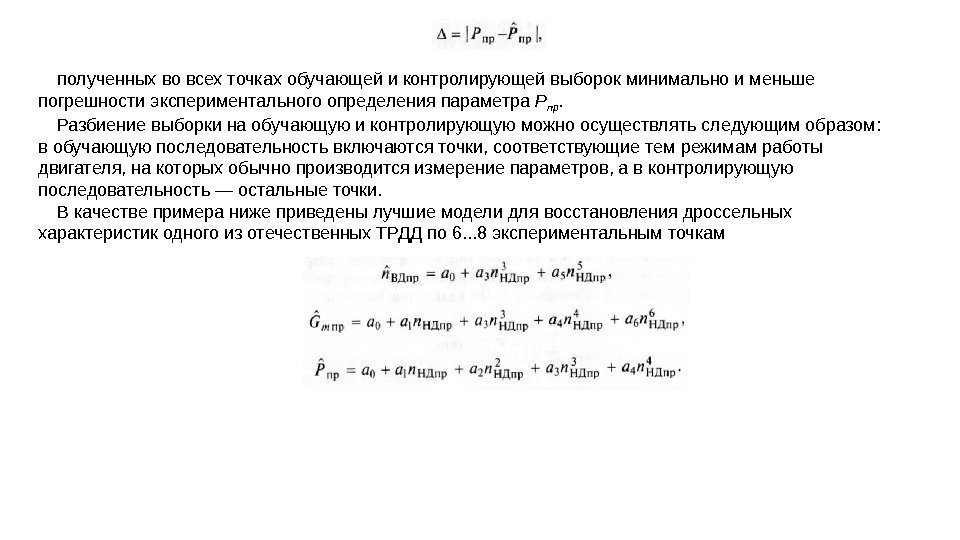
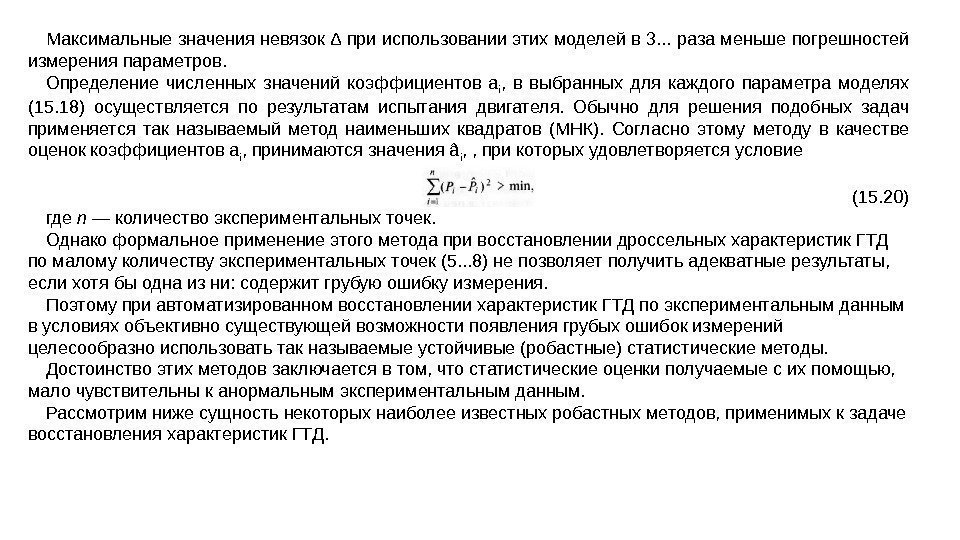
![Метод наименьших модулей [35]. Сущность метода наименьших модулей состоит в аппроксимации погрешностей измерения случайными Метод наименьших модулей [35]. Сущность метода наименьших модулей состоит в аппроксимации погрешностей измерения случайными](http://present5.com/presentforday2/20170201/mmk_ispytania_i_kontrol_kachestva_izdeliy_2017_images/mmk_ispytania_i_kontrol_kachestva_izdeliy_2017_900.jpg)
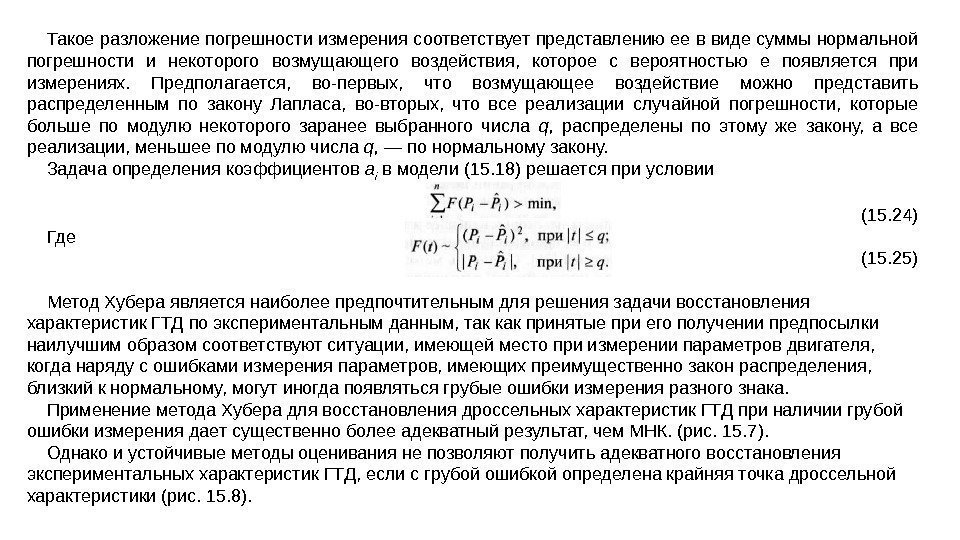
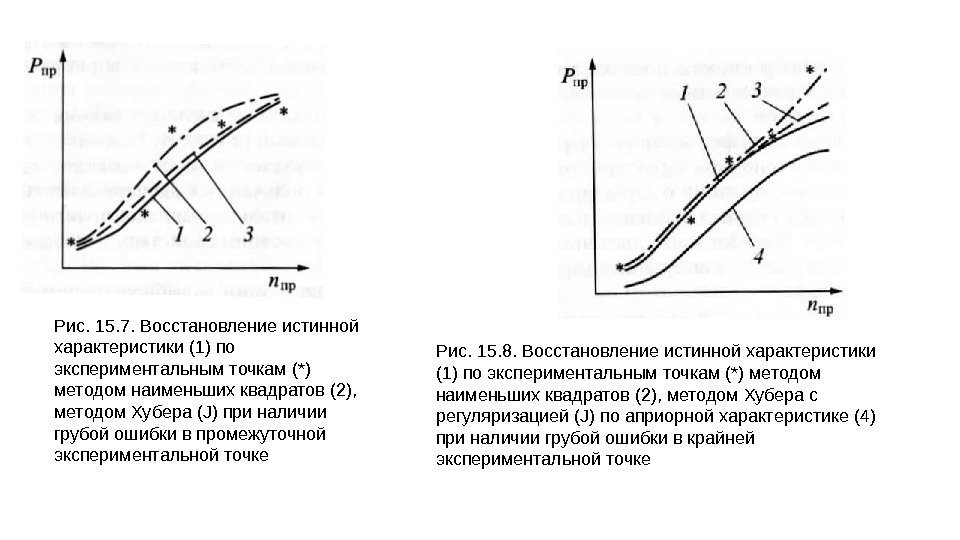
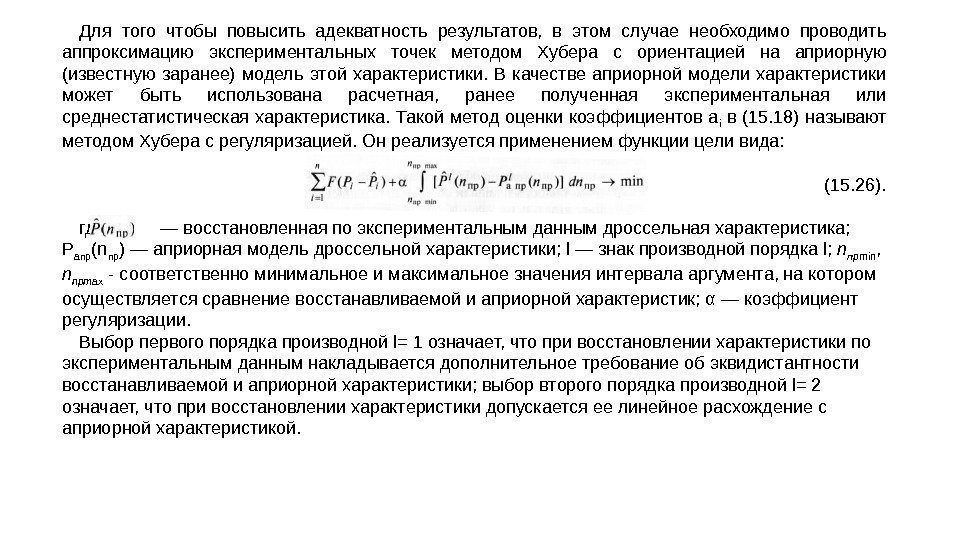
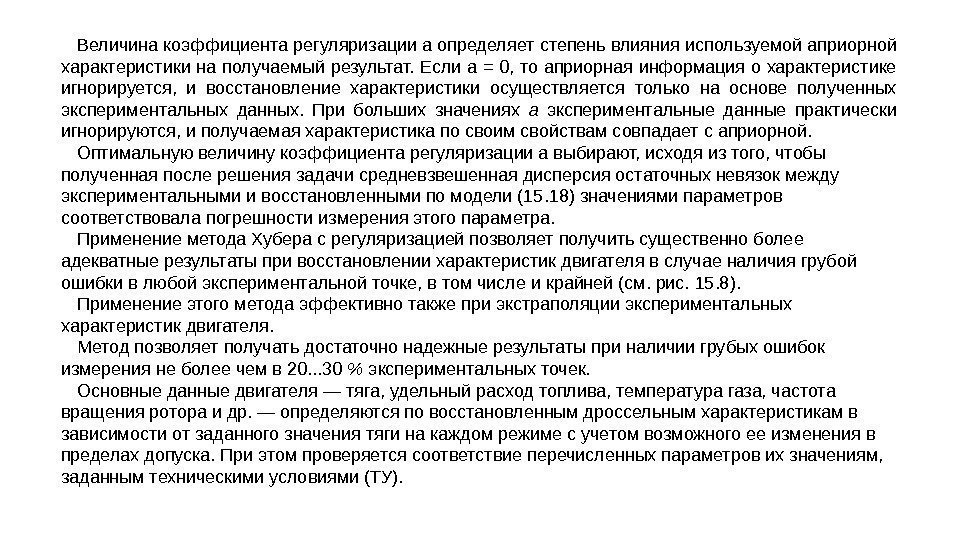
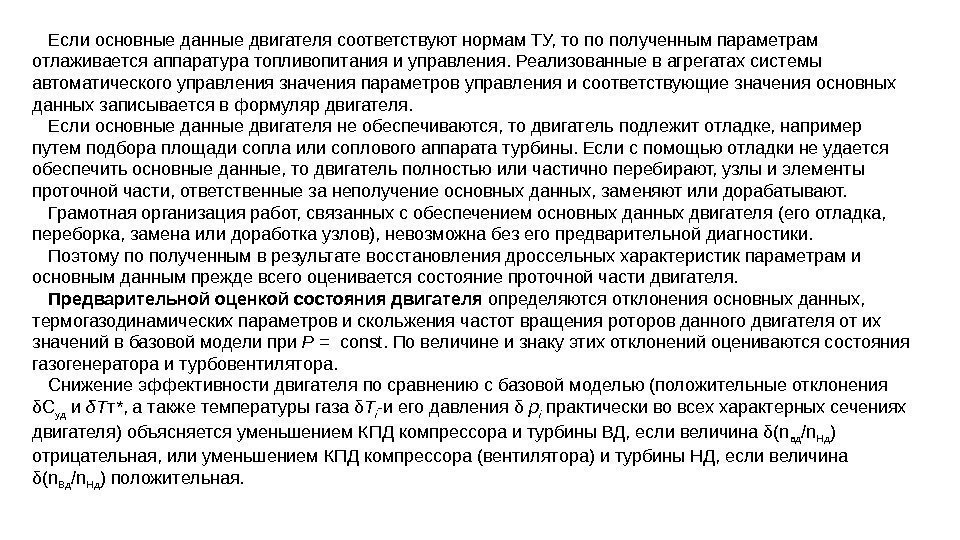
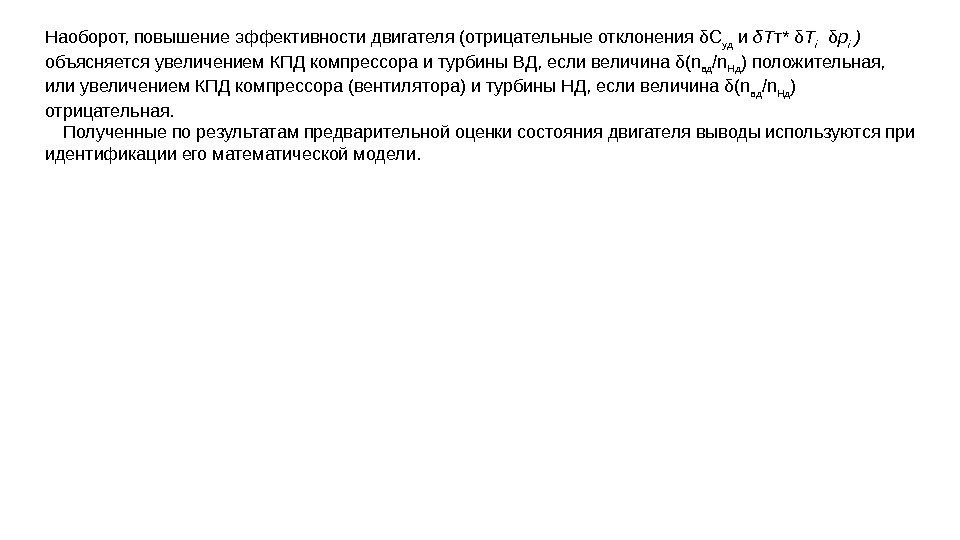
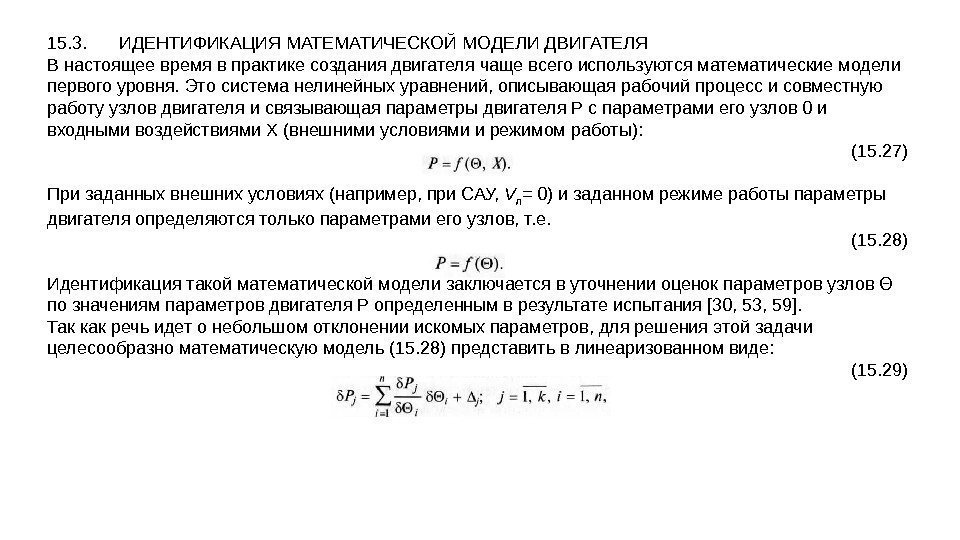
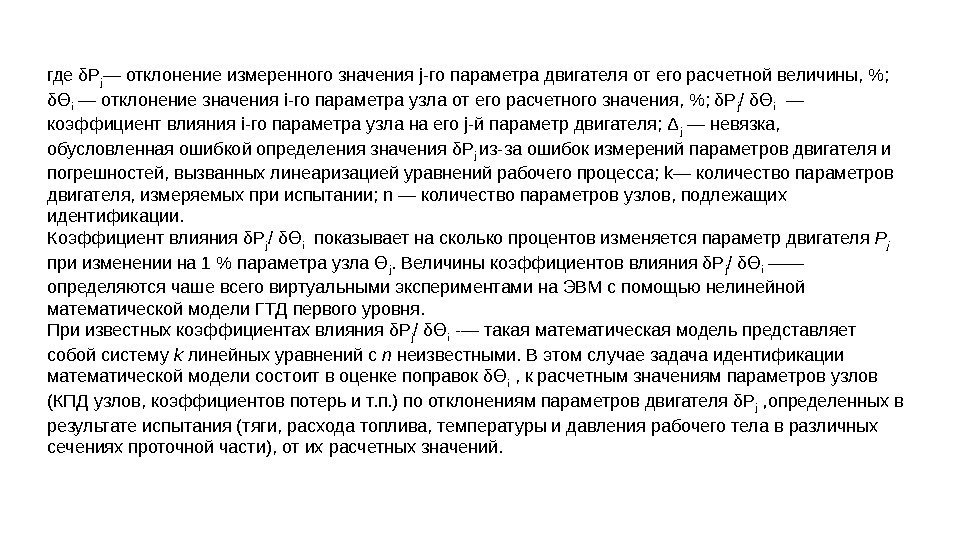
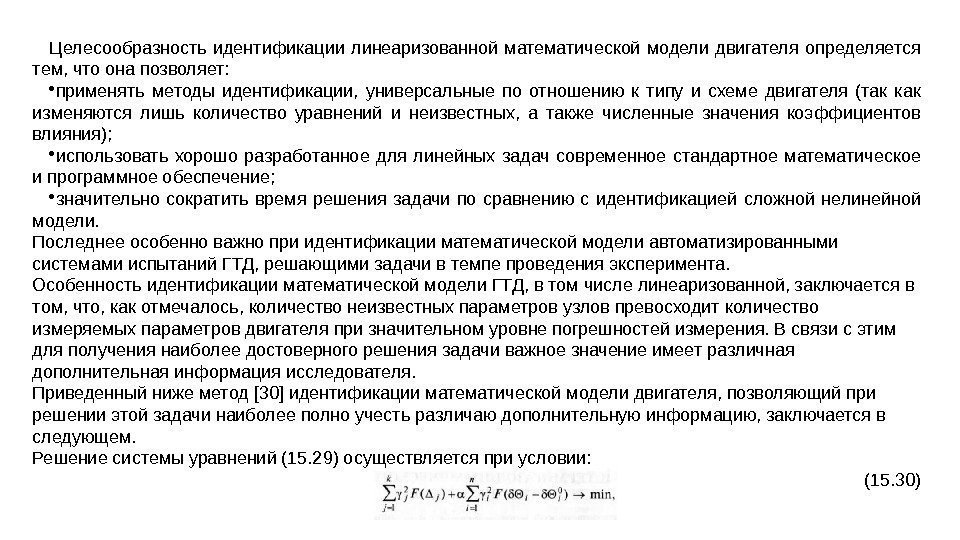
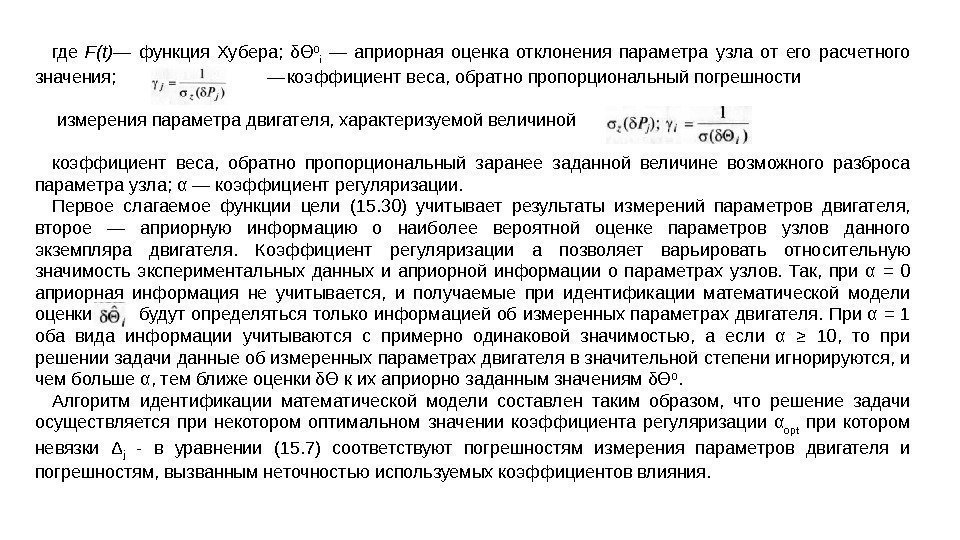
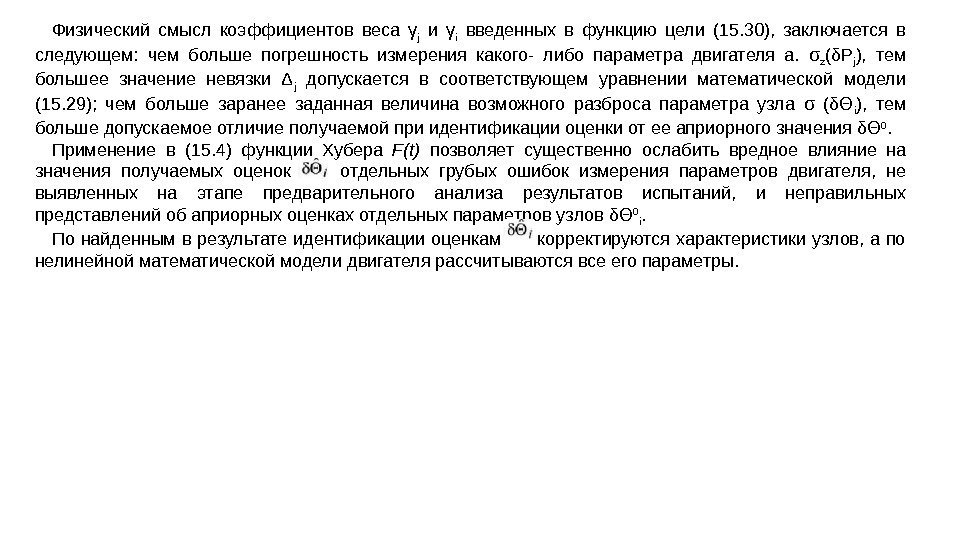
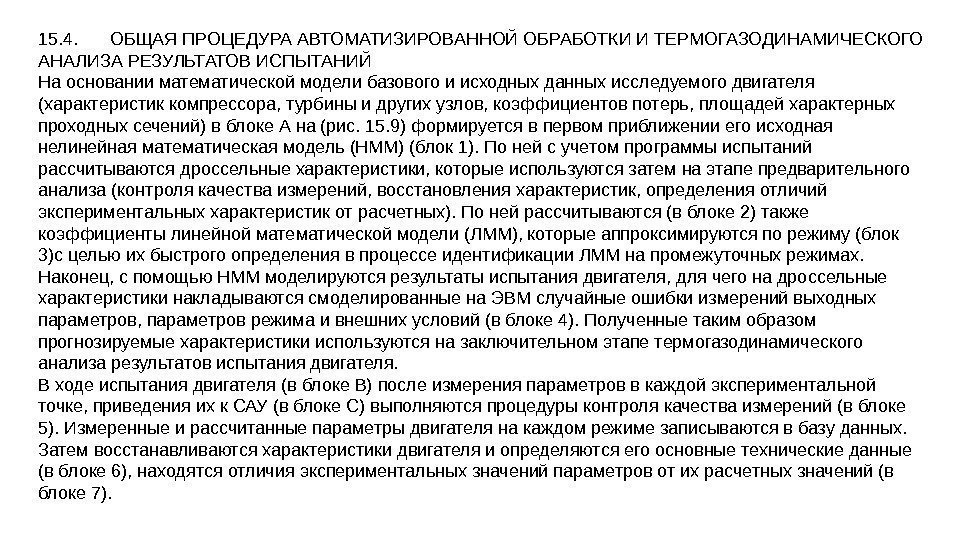
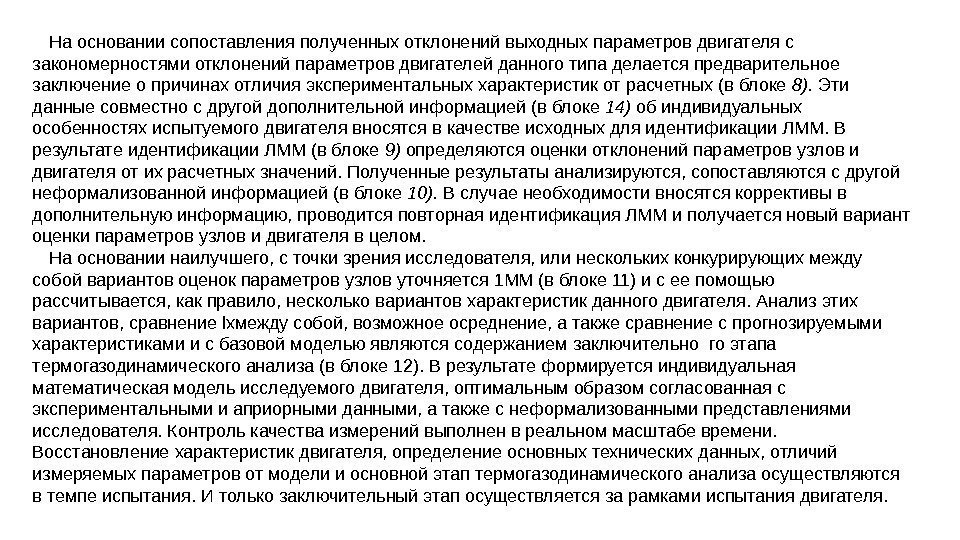
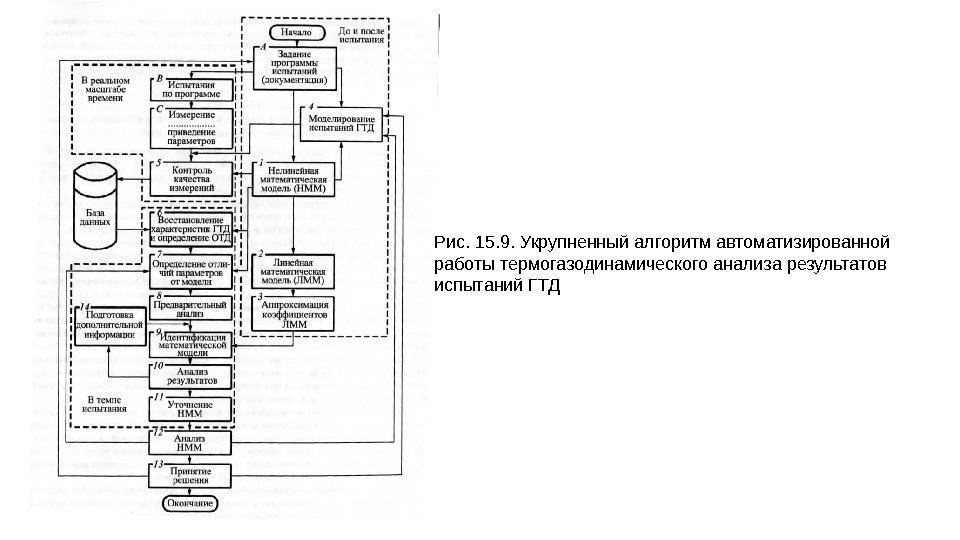
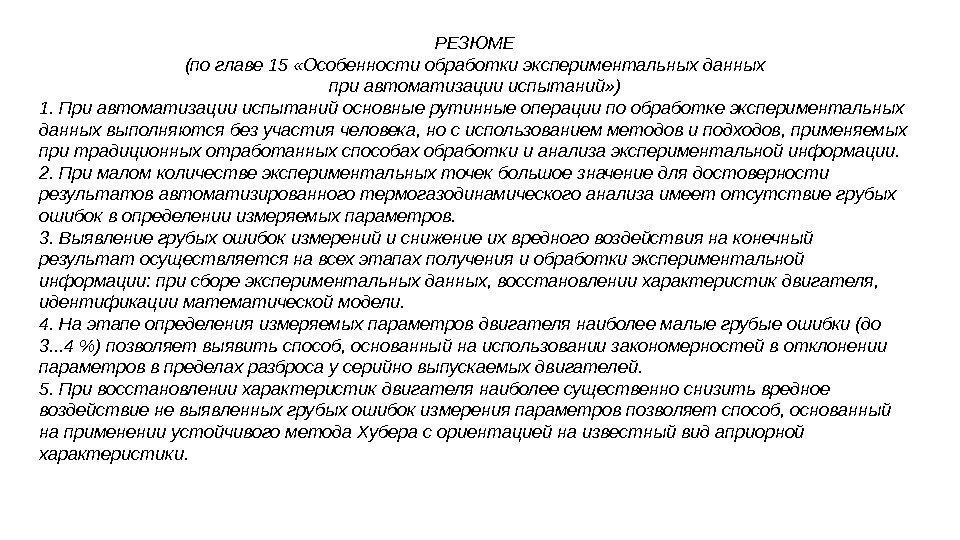
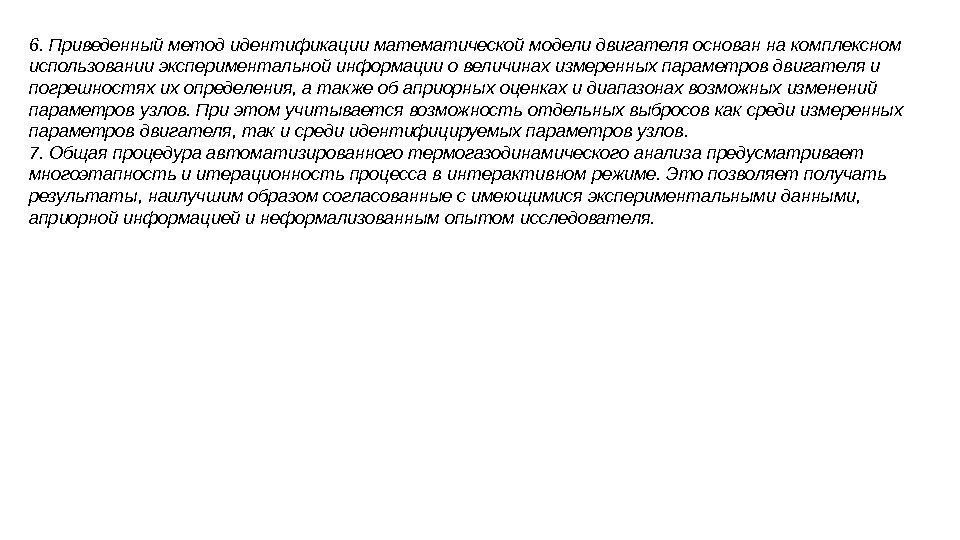
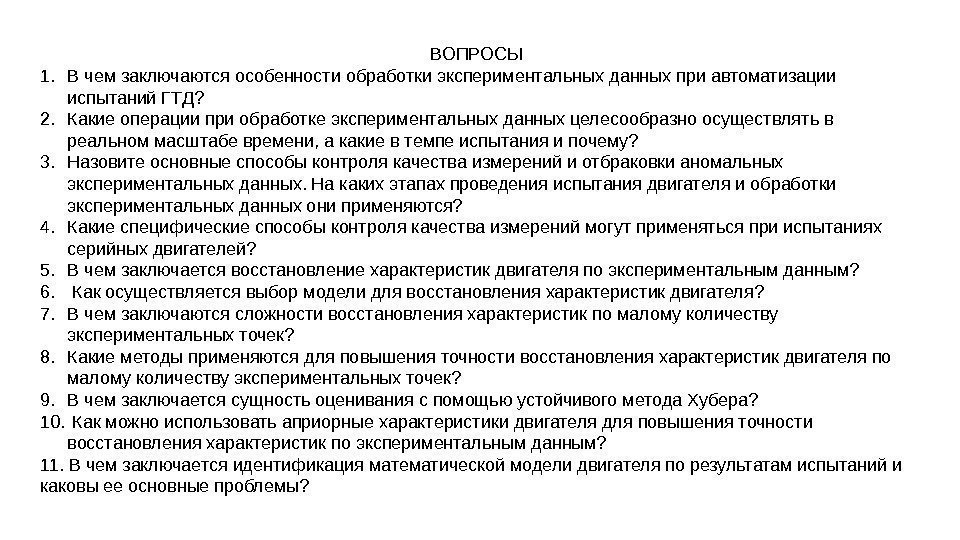
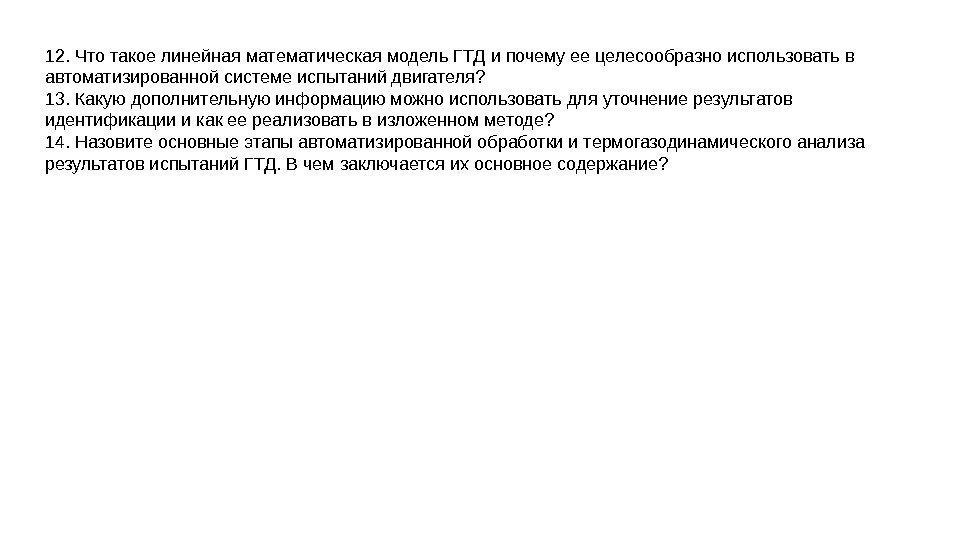
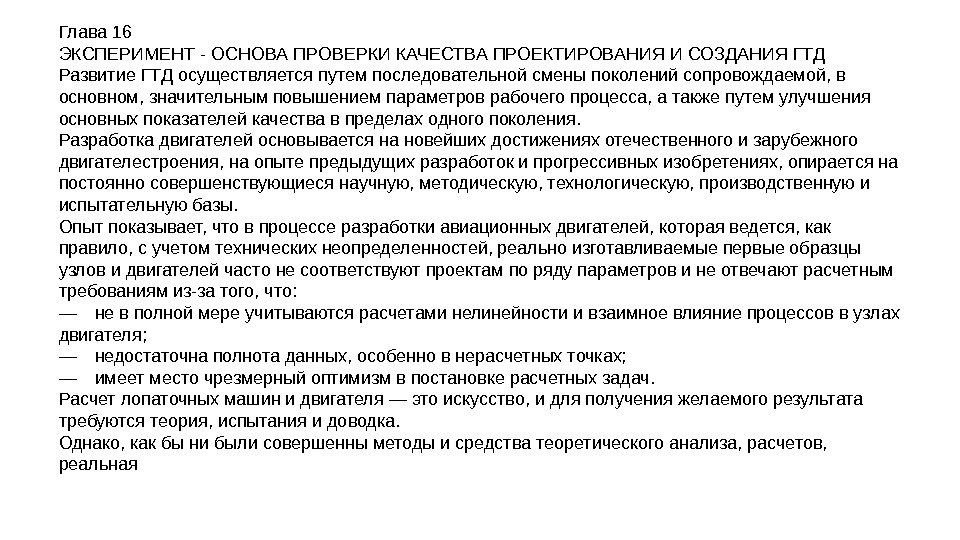
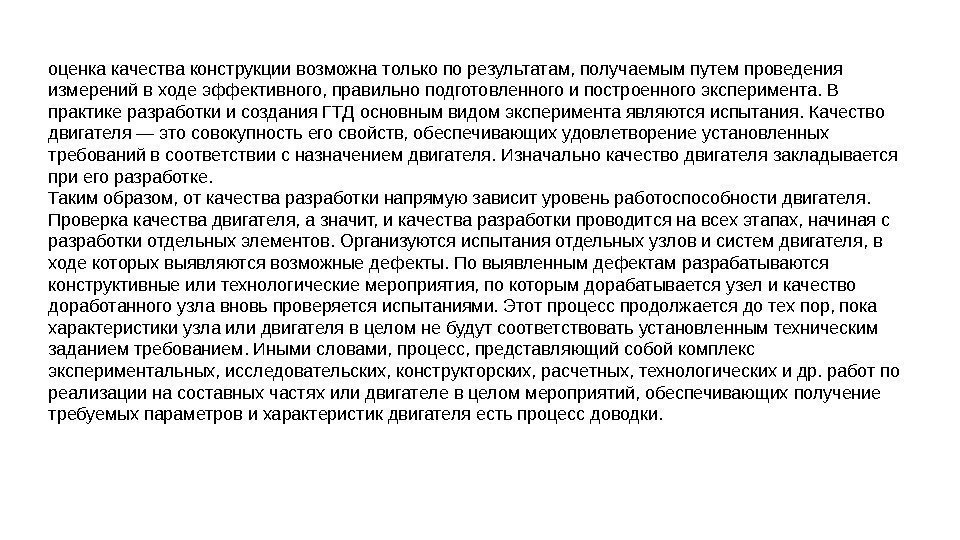
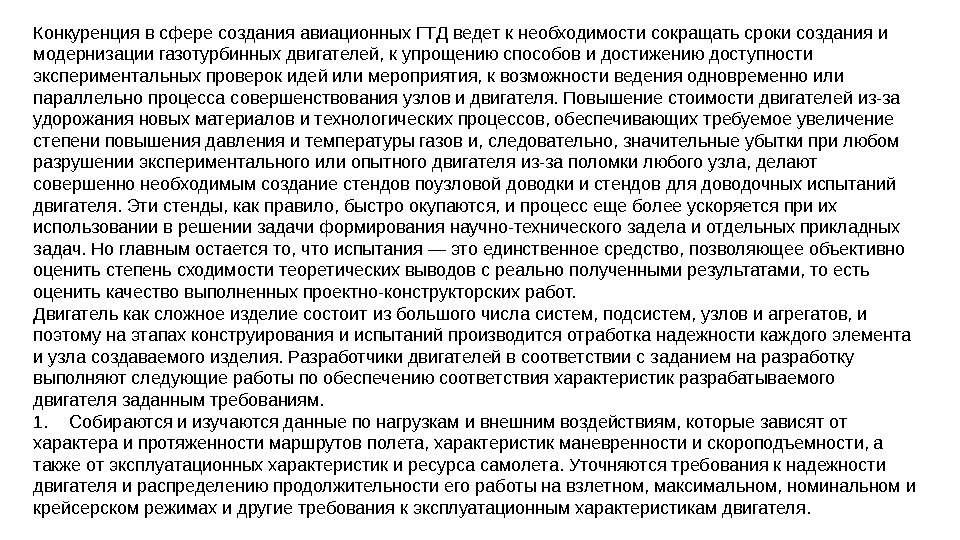
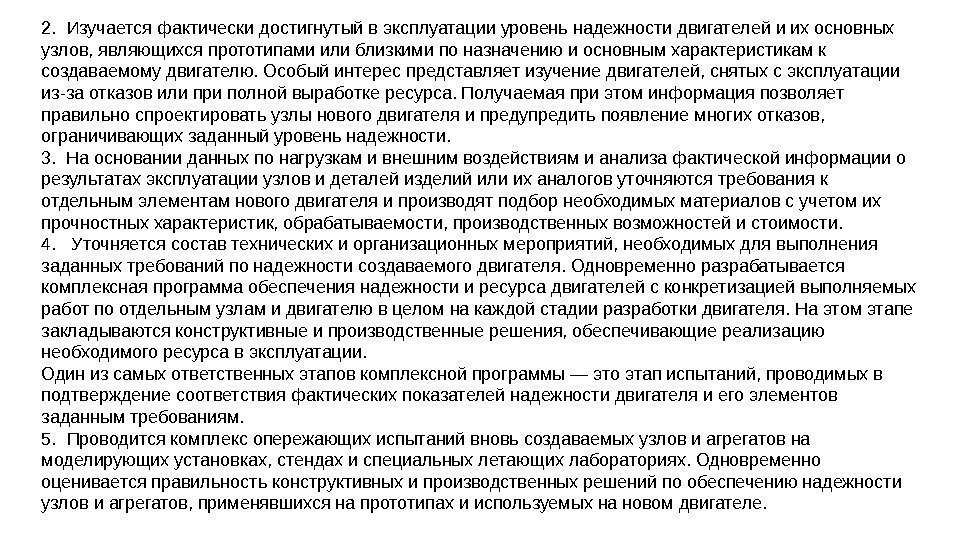
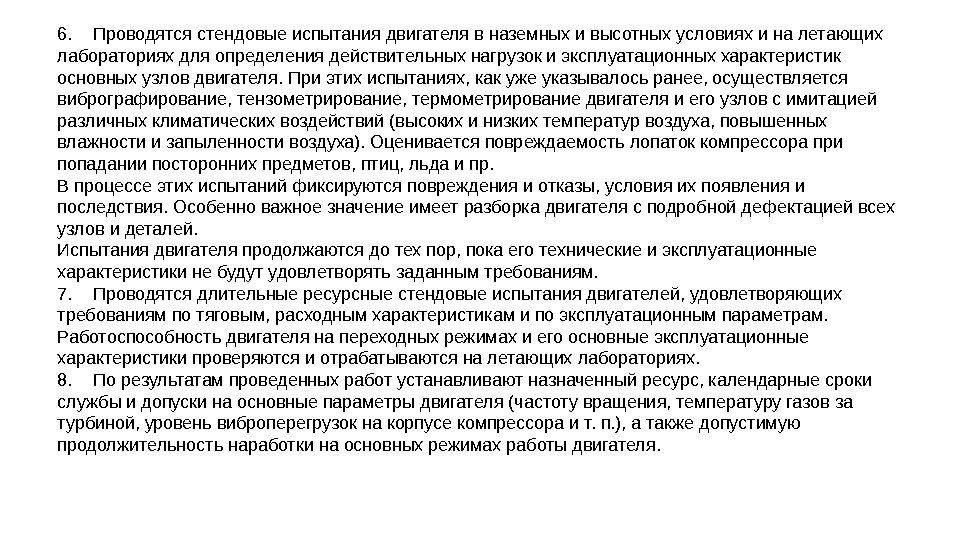
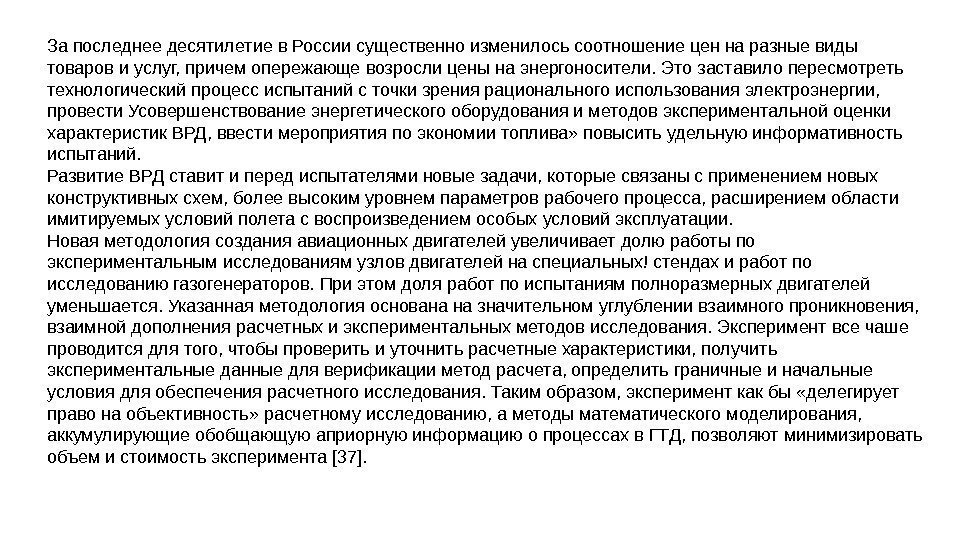
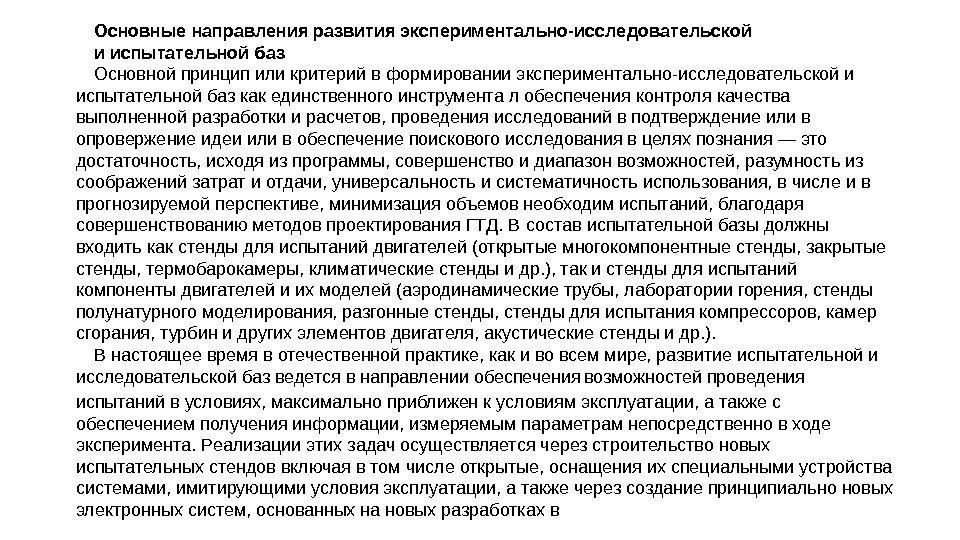
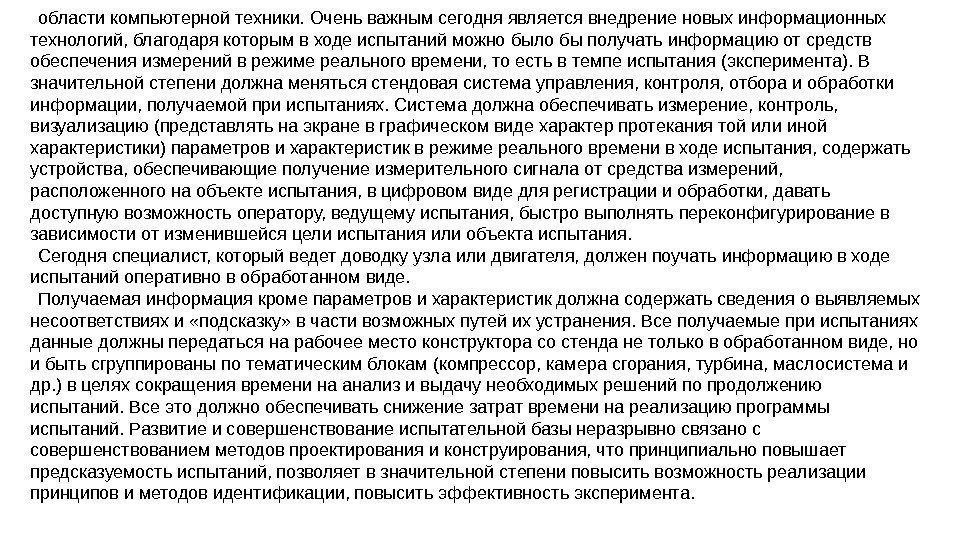
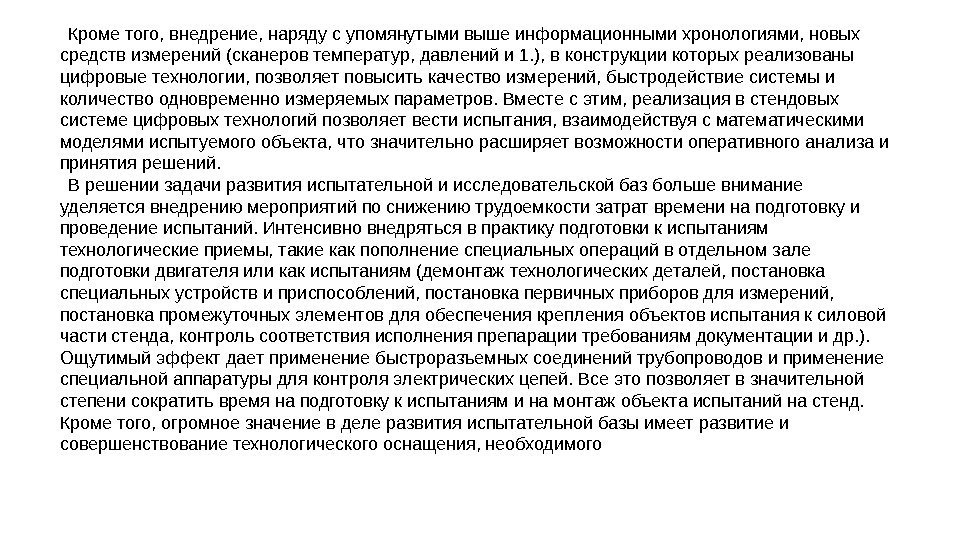
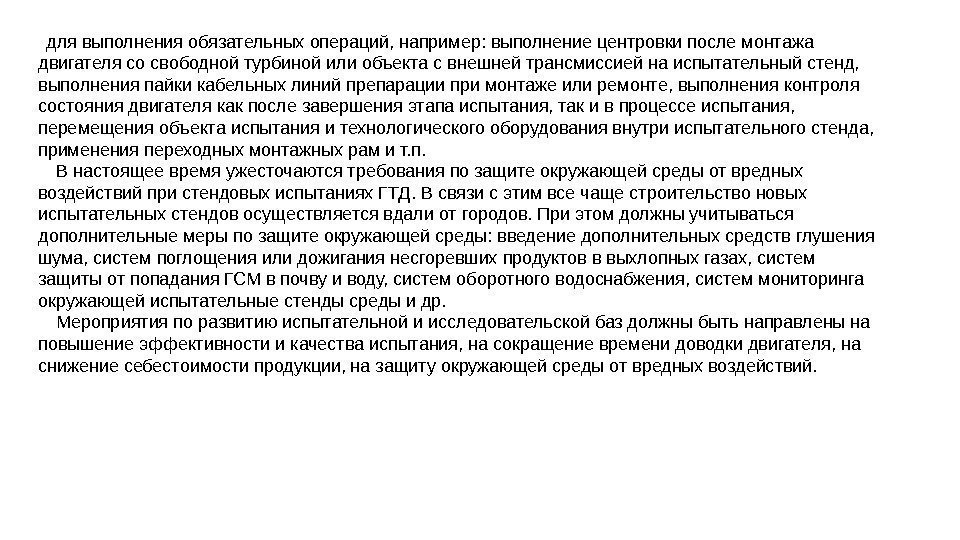
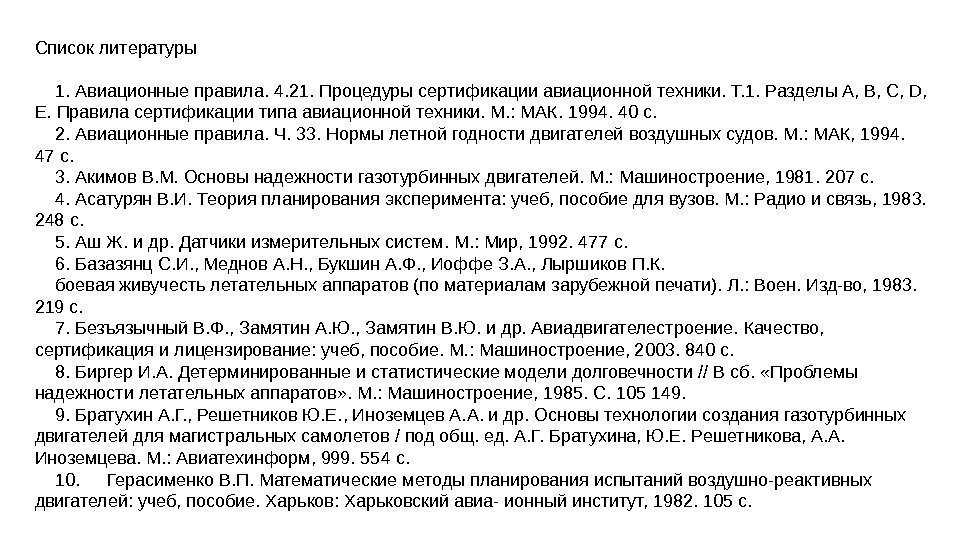
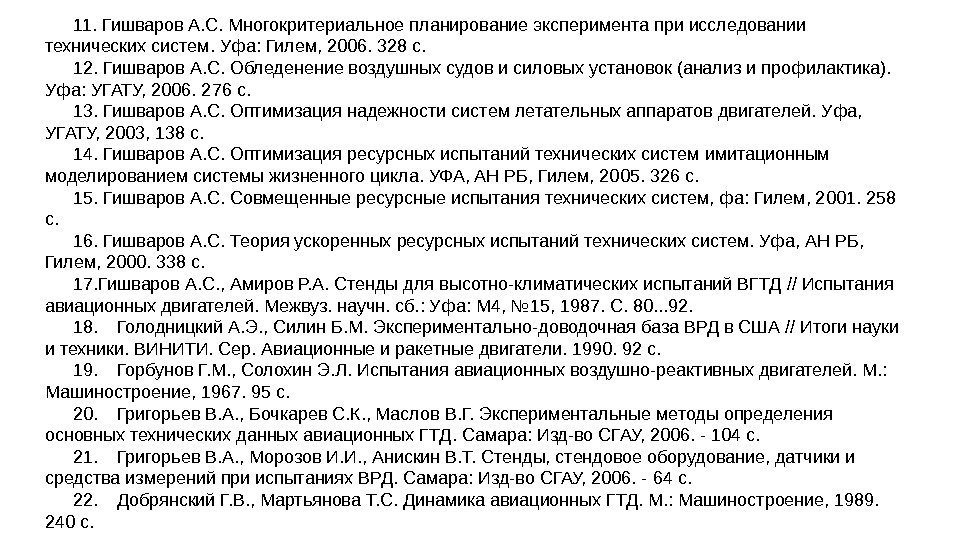
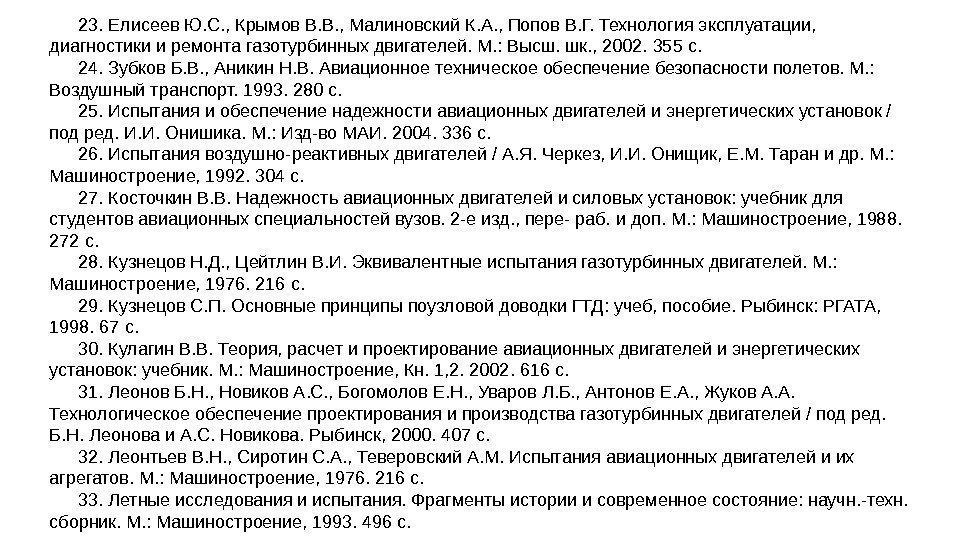
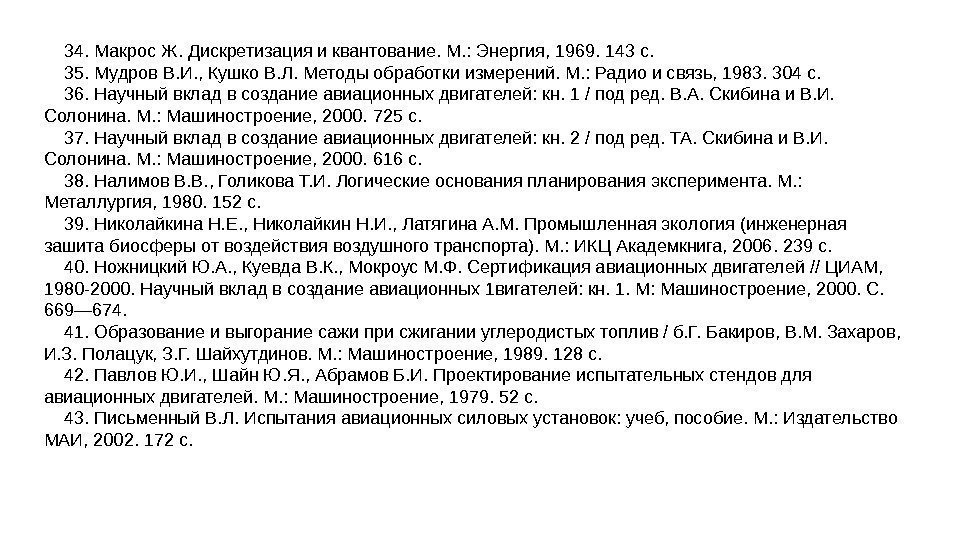
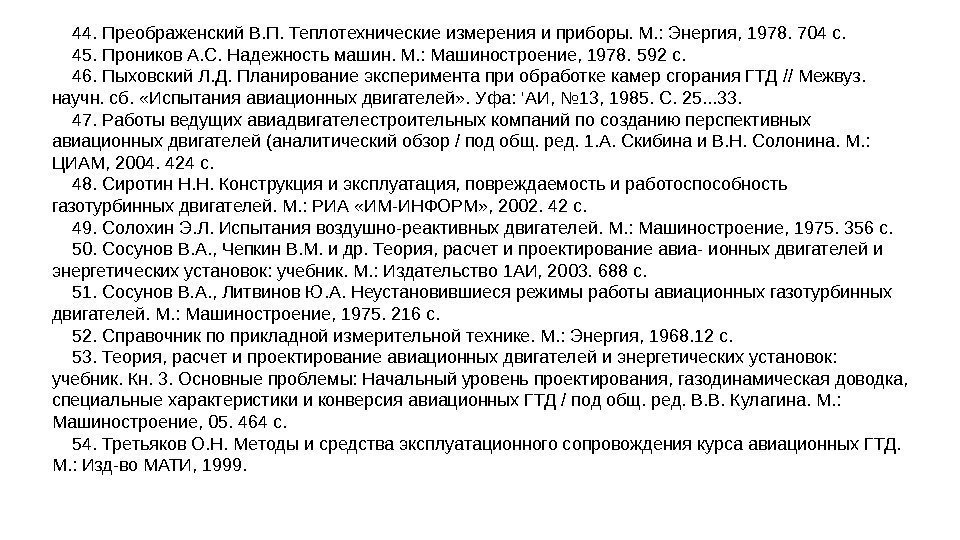
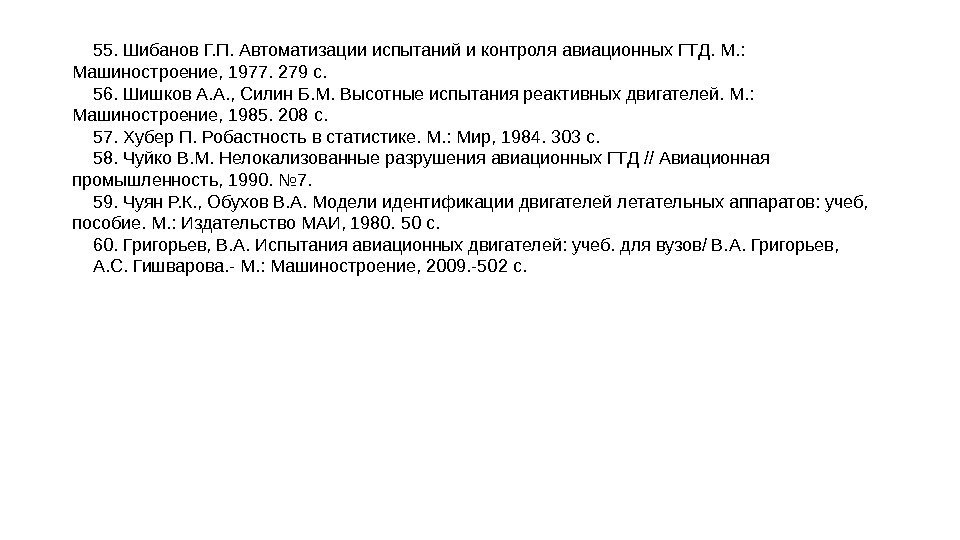

mmk_ispytania_i_kontrol_kachestva_izdeliy_2017.pptx
- Размер: 55.6 Мб
- Автор:
- Количество слайдов: 935
Описание презентации Испытания и контроль качества изделий (ИСПЫТАНИЯ АВИАЦИОННЫХ ДВИГАТЕЛЕЙ) по слайдам
Испытания и контроль качества изделий (ИСПЫТАНИЯ АВИАЦИОННЫХ ДВИГАТЕЛЕЙ) Макаров В. В. 2017 г.
СОДЕРЖАНИЕ Основные условные обозначения Предисловие Введение Глава 1. ИЗМЕРЕНИЯ ПРИ ИСПЫТАНИИ ДВИГАТЕЛЕЙ 1. 1. Виды и методы измерений 1. 2. Средства измерений 1. 3. Особенности измерений при испытаниях ГТД 1. 4. Измерение давлений 1. 5. Измерение температур 1. 6. Измерение расхода топлива 1. 7. Измерение расхода воздуха 1. 8. Измерение скорости потока 1. 9. Измерение напряжений в элементах ГТД 1. 10. Измерение силы и крутящего момента 1. 11. Измерение частоты вращения 1. 12. Измерение вибраций 1. 13. Измерение эмиссии вредных веществ 1. 14. Измерение шума 1. 15. Методы контроля состояния и обнаружения дефектов в ходе испытаний ГТД
РЕЗЮМЕ (по главе 1 «Измерения при испытании двигателей» ). Вопросы Глава 2. ВИДЫ ИСПЫТАНИЙ АВИАЦИОННЫХ ГТД 2. 1. Создание научно-технического задела и его экспериментальное подтверждение 2. 2. Испытания опытных ГТД 2. 3. Испытание серийных ГТД 2. 4. Техническое и организационное обеспечение испытаний ГТД РЕЗЮМЕ (по главе 2 «Виды испытаний авиационных ГТД» ) Вопросы Глава 3. ПЛАНИРОВАНИЕ ЭКСПЕРИМЕНТА ПРИ ИСПЫТАНИЯХ ГТД 3. 1. Основные понятия и определения 3. 2. Планирование и проведение эксперимента 3. 2. 1. Полный факторный эксперимент 3. 2. 2. Дробный факторный эксперимент 3. 2. 3. Центральное композиционное планирование эксперимента 3. 3. Применение планирования эксперимента при оптимизации исследуемых процессов 3. 3. 1. Метод крутого восхождения 3. 3. 2. Симплексный метод 3. 4 Опыт применения планирования эксперимента в авиадвигателестроении 3. 5. Перспективы развития методов экспериментального исследования ГТД с применением планированного эксперимента РЕЗЮМЕ (по главе 3 «Планирование эксперимента при испытаниях ГТД» ) Вопросы
Глава 4. ИСПЫТАТЕЛЬНЫЕ СТЕНДЫ И ОБОРУДОВАНИЕ 4. 1. Структура испытательной станции 4. 2. Испытательные станки и устройства 4. 3. Основные системы стендов 4. 4. Летные испытания, летающие лаборатории 4. 5. Испытательные комплексы РЕЗЮМЕ (по главе 4 «Испытательные стенды и оборудование» ) Вопросы Глава 5. ВЛИЯНИЕ АТМОСФЕРНЫХ УСЛОВИЙ НА ЭКСПЕРИМЕНТАЛЬ-НЫЕ ХАРАКТЕРИСТИКИ АВИАЦИОННЫХ ГТД 5. 1. Влияние атмосферной температуры. Изменение рабочего процесса под влиянием t H 5. 2. Влияние атмосферного давления 5. 3. Влияние атмосферной влажности 5. 4. Влияние законов управления ГТД на их характеристики 5. 5. Использование формул теории подобия газовых потоков при анализе результатов экспериментов РЕЗЮМЕ (по главе 5 «Влияние атмосферных условий на экспериментальные характеристики авиационных ГТД» ) Вопросы Глава 6. ЭКСПЕРИМЕНТАЛЬНЫЕ МЕТОДЫ ОПРЕДЕЛЕНИЯ ОСНОВНЫХ ТЕХНИЧЕСКИХ ДАННЫХ АВИАЦИОННЫХ ГТД 6. 1. Основные способы определения НЗП ГТД
6. 1. 1. Способ определения НЗП путем испытаний ГТД на режимах, подобных его работе в стандартных атмосферных условиях (САУ) 6. 1. 2. Способ определения НЗП с помощью специальных коэффициентов пересчета 6. 1. 3. Экспериментальный метод определения нормализующих коэффициентов для ТРДД 6. 1. 4. Особенности определения НЗП ТРДД 6. 1. 5. Особенности испытаний ТРДД 6. 1. 6. Особенности испытания форсажных ТРД и ТРДД 6. 1. 7. Особенности испытания ТРДД с реверсом 6. 1. 8. Особенности испытаний ГТД с отклоняемым вектором прямой тяги 6. 2. Основные особенности испытаний и определения НЗП ГТД СТи. ТВД 6. 2. 1. Особенности испытаний ГТД СТ и ТВД 6. 2. 2 Особенности экспериментального определения нормальных значений параметров ТВД 6. 2. 3. Методика экспериментального определения косвенным способом нормализующих коэффициентов для параметров ТВД 6. 3. Экспериментальное определение НЗП ГТД путем поддержания стендовыми системами заданных значении t n *, t n >*, М n 6. 3. 1. Высотно-скоростные испытания ГТД в АТ 6. 3. 2. Высотно-скоростные натурные испытания ГТД в термобарокамере (ТБК) 6. 4. Основные особенности испытания ПВРД РЕЗЮМЕ (по главе 6 «Экспериментальные методы определения основных технических данных авиационных ГТД» ) Вопросы
Глава 7. ИСПЫТАНИЯ АВИАЦИОННЫХ ГТД С ИМИТАЦИЕЙ ЭКСПЛУАТАЦИОННЫХ УСЛОВИЙ 7. 1. Технология испытаний ГТД на высотных стендах 7. 1. 1. Испытания в аэродинамической трубе 7. 1. 2. Испытания в ТБК с присоединенным трубопроводом 7. 1. 3. Испытания с частичной имитацией высотно-скоростных условий 7. 1. 4. Испытания с самолетным воздухозаборником 7. 1. 5. Особенности создания эксплуатационных условий при испытаниях ПВРД и ГПВРД 7. 2. Системы и оборудование для создания высотных условий на испытательных стендах 7. 3. Краткая характеристика отечественных высотных стендов РЕЗЮМЕ (по главе 7 «Испытания авиационных ГТД с имитацией эксплуатационных условий» ) Вопросы Глава 8. ЭКСПЕРИМЕНТАЛЬНЫЕ МЕТОДЫ ОПРЕДЕЛЕНИЯ РЕСУРСА И НАДЕЖНОСТИ АВИАЦИОННЫХ ГГД 8. 1. Эксплуатационные критерии надежности авиационных ГТД 8. 2. Модели повреждаемости (расходования ресурса) деталей двигателя 8. 2. 1. Длительная прочность 8. 2. 2. Малоцикловая усталость 8. 2. 3. Усталость 8. 2. 4. Модель долговечности в условиях длительного статического и циклического нагружения 8. 2. 5. Модель долговечности при разнородных повреждениях 8. 2. 6. Износ и контактная усталость 8. 2. 7. Эрозия и газовая коррозия 8. 3. Ресурсные испытания авиационных ГТД
8. 3. 1. Основные понятия и определения 8. 3. 2. Длительные эксплуатационные испытания ГТД на повышенный ресурс 8. 3. 3. Ускоренные эквивалентно-циклические испытания ГТД 8. 3. 4. Циклические испытания 8. 3. 5. Формирование программ эквивалентно-циклических испытаний основных деталей двигателя 8. 3. 6. Экспериментальная доводка опытных ГТД до 150 -часового ресурса 8. 4. Эксплуатация ГТД по техническому состоянию 8. 5. Основные стратегии управления ресурсом ГТД 8. 6. Порядок задания, установления и увеличения ресурса 8. 6. 1. Установление и увеличение назначенных ресурсов основных деталей двигателя 8. 6. 2. Установление назначенного ресурса двигателя 8. 6. 3. Установление и увеличение ресурса новых двигателей при стратегиях управления ресурсом 2 и 3 8. 6. 4. Установление и увеличение ресурса и сроков службы агрегатов и комплектующих изделий 8. 7. Подходы к подтверждению ресурса основных деталей ГТД 8. 7. 1. Метод «безопасной долговечности» 8. 7. 2. Метод «допустимых повреждений» РЕЗЮМЕ (по главе 8 «Экспериментальные методы определения ресурса и надежности авиационных ГТД» ) Вопросы Глава 9. СПЕЦИАЛЬНЫЕ ИСПЫТАНИЯ АВИАЦИОННЫХ ГТД 9. 1. Испытания ГТД по проверке запасов газодинамической устойчивости 9. 1. 1. Экспериментальное определение запасов устойчивости путем подъема линии рабочих режимов 9. 1. 2. Экспериментальное определение запасов устойчивости путем создания предельных возмущений в потоке на входе в ГТД
9. 2. Испытания по определению акустических характеристик ГТД 9. 2. 1. Характеристики звука и шума 9. 2. 2. Источники авиационного шума 9. 2. 3. Нормирование авиационного шума 9. 2. 4. Экспериментальное исследование шума ГТД 9. 2. 5. Методы снижения шума ГТД 9. 3. Испытания по определению выбросов загрязняющих веществ авиационными ГТД 9. 3. 1. Закономерности образования загрязняющих веществ в авиационных ГТД 9. 3. 2. Нормирование загрязнения атмосферы авиационными ГТД 9. 3. 3. Измерение содержания загрязняющих веществ в отработавших газах ГТД 9. 3. 4. Уменьшение эмиссии авиационных ГТД при стендовых испытаниях 9. 4. Испытания авиационных ГТД на обледенение 9. 5. Испытания ГТД по попаданию посторонних предметов 9. 6. Испытания ГТД на стойкость против попадания птиц 9. 7. Испытания ГТД в условиях дождя 9. 8. Испытания систем защиты РЕЗЮМЕ (по главе 9 «Специальные испытания авиационных ГТД» ) Вопросы Глава 10. ИСПЫТАНИЯ И ДОВОДКА УЗЛОВ И АГРЕГАТОВ АВИАЦИОННЫХ ДВИГАТЕЛЕЙ И ЭНЕРГЕТИЧЕСКИХ УСТАНОВОК 10. 1. Испытания авиационных лопаточных машин 10. 2. Испытания компрессора (вентилятора) 10. 3. Испытания основной камеры сгорания
10. 4. Испытания форсажной камеры 10. 5. Испытания турбины 10. 6. Испытания газогенераторов (ГГ) 10. 7. Испытания систем автоматического управления 10. 8. Испытания редукторов 10. 9. Испытания стартеров 10. Испытания насосов и форсунок 10. 11. Испытания топливорегулирующей аппаратуры РЕЗЮМЕ (по главе 10 «Испытания и доводка узлов и агрегатов авиационных двигателей и энергетических установок» ) Вопросы Глава 11 СЕРТИФИКАЦИОННЫЕ ИСПЫТАНИЯ ГТД 11. 1. СИСТЕМА ОБЕСПЕЧЕНИЯ И ПОДДЕРЖАНИЯ ЛЕТНОЙ ГОДНОСТИ 11. 2. Развитие требований норм летной годности. Законодательная база системы сертификации авиационных двигателей 11. 3. Основные этапы сертификации авиационных двигателей 11. 4. Особенности сертификации авиационных двигателей 11. 5. Сертификация двигателя в составе летательного аппарата РЕЗЮМЕ (по главе 11 «Сертификационные испытания ГТД» ) Вопросы Глава 12. ОБРАБОТКА РЕЗУЛЬТАТОВ ИСПЫТАНИЙ 12. 1. Приемы препарирования испытываемого ГТД
12. 2. Основы методики обработки результатов испытаний 12. 3. Методы и способы уменьшения погрешностей получения экспериментальных данных 12. 4. Обработка результатов измерений, выполненных в ходе автоматизированных испытаний ГТД РЕЗЮМЕ (по глава 12 «Обработка результатов испытаний» ). Вопросы Глава 13. ПЕРВИЧНЫЕ ПРЕОБРАЗОВАТЕЛИ ПРИ АВТОМАТИЗИРОВАННЫХ ИСПЫТАНИЯХ ГТД 13. 1. Измерение температуры 13. 2. Измерение давления 13. 3. Датчики измерения частоты вращения 13. 4. Датчики измерения расхода топлива (топливного газа) 13. 5. Датчики измерения усилия от тяги 13. 6. Датчики измерения крутящего момента 13. 7. Датчики измерения зазоров, перемещений 13. 8. Зонды измерения пульсаций давления газовых сред РЕЗЮМЕ (по главе 13 «Первичные преобразователи при автоматизированных испытаниях ГТД» ) Вопросы Глава 14. АВТОМАТИЗАЦИЯ ИСПЫТАНИЙ ГТД 14. 1. Типовые операции при испытаниях ГТД 14. 1. 1. Подготовительно-заключительные операции 14. 1. 2. Испытания по заданной программе 14. 1. 3. Управление режимами работы двигателя 14. 1. 4. Отладка параметров двигателя 14. 1. 5. Обработка результатов испытаний и их анализ 14. 2. Основы построения АСИ ГТД
14. 2. 1. Основные задачи испытаний, решаемые автоматизированной системой 14. 2. 2. Основные требования к АСИ ГТД 14. 2. 3. Типовая схема АСИ ГТД 14. 3. Устройства связи с объектом (УСО) 14. 3. 1. Основные функциональные элементы модулей УСО 14. 3. 2. Модули УСО 14. 4. ЭВМ и математическое обеспечение 14. 5. Система сбора и обработки информации при испытаниях ГТД, автоматизация испытаний РЕЗЮМЕ (по главе 14 «Автоматизация испытаний ГТД» ) Вопросы Глава 15. ОСОБЕННОСТИ ОБРАБОТКИ ЭКСПЕРИМЕНТАЛЬНЫХ ДАННЫХ ПРИ АВТОМАТИЗАЦИИ ИСПЫТАНИЙ 15. 1. Контроль качества измерений 15. 2. Восстановление характеристик по экспериментальным данным 15. 3. Идентификация математической модели двигателя 15. 4. Общая процедура автоматизированной обработки и термогазодинамического анализа результатов испытаний РЕЗЮМЕ (по главе 15 «Особенности обработки экспериментальных данных при автоматизации испытаний» ) Вопросы Глава 16. ЭКСПЕРИМЕНТ — ОСНОВА ПРОВЕРКИ КАЧЕСТВА ПРОЕКТИРОВАНИЯ И СОЗДАНИЯ ГТД Список литературы
ОСНОВНЫЕ УСЛОВНЫЕ ОБОЗНАЧЕНИЯ Условные обозначения γ — удельная масса (плотность), кг/м 3, кг/к. Н, кг/к. Вт; угол выхода потока; τ — угол, отрезок времени; φ — угол; шаг винта; η — коэффициент полезного действия, коэффициент; λ — приведенная относительная скорость; μ — коэффициент расхода; ν — коэффициент расхода охлаждающего воздуха, вязкость; π — степень повышения (понижения) давления; ω — угловая скорость, рад/с; σ — коэффициент восстановления заторможенного давления; η г — коэффициент полноты сгорания; ΔК у — коэффициент запаса устойчивой работы; α — коэффициент; скорость звука, м/с; С — скорость потока в элементах ГТД, м/с; аэродинамический коэффициент; °С — градусы Цельсия; d — удельная влажность; D — диаметр, м; F — площадь, м; сила, к. Н; f — функция; частота, Гц; G в , G г , G m — массовый расход воздуха, газа, топлива, кг/с;
h — высота столба жидкости; H — высота полета, м (км); «потолок» ; H u — низшая удельная теплота сгорания; I — интенсивность звука, Вт/м 2; i — энтальпия, к. Дж/кг; K — класс точности; коэффициент; k — показатель адиабаты; L — длина, м; дальность полета, км; работа, к. Дж/кг; l — плечо, м; L 0 — количество воздуха, теоретически необходимое для полного сжигания 1 кг воздуха; L w — уровень звуковой мощности; M — число Маха; N — количество опытов; n — частота вращения, мин-1; показатель политропы; число двигателей на ЛА; Ne — эффективная мощность, к. Вт; Nэ — эквивалентная мощность, эк. Вт; ρ — плотность, кг/м 3; коэффициент восстановления температуры; коэффициент трения; q(Х), π (Х), τ(Х) — газодинамические функции; q m — относительный расход топлива; R — газовая постоянная, к. Дж. Дкг-К); плечо, м; r — радиус, м; S — энтропия, к. Дж/кг; стоимость, руб; у. е. ;
Т — температура, К\ период времени, год; ч; м; с; межремонтный ресурс, ч; t— время; температура, °С; U— окружная скорость, м/с; V— скорость полета, м/с; W— количество контролируемых параметров; x— оптимизируемый параметр; аргумент функции; координата; y— критерий эффективности; целевая функция; координата; Y— множество функций; ζ— число ступеней; количество ЛА; количество двигателей в партии; количество неконтролируемых параметров; Δ— разность, интервал, предельная погрешность; σ— относительная погрешность, чувствительность средства; —ϴ сила, к. Н; B— коэффициент избытка воздуха; ширина; коэффициент; в— хорда; коэффициент; М— масса, кг; М кр — крутящий момент; П— производительность; Р— сила тяги, к. Н; вероятность; р— давление, к. Па; с— удельная теплоемкость;
Се— удельный эффективный расход топлива (отнесенный к эффективной мощности), кг/(к. Вт ч); Суд— удельный расход топлива (отнесенный к тяге), кг/(к. Н-ч); Сэ— удельный эквивалентный расход топлива (отнесенный к эквивалентной мощности), кг. Дэк. Вт ч); Х— множество параметров, параметр. Индексы ам — амортизационный; б, баз — базовый; бп — относимый к бортпроводникам; в — воздух, вход, сечение перед компрессором, вентилятор, винт, вал; верт — вертолет, вертолетный; взл — взлетный; вх— вход; входной; вых— выход; выходной; г— сечение перед турбиной; газ; габ— габаритный; гг— газогенератор; дв— двигатель; е— эффективный; ж. дв— относящийся к жизненному циклу ГТД; ж. ЛА— относящийся к жизненному циклу ЛА; гсм— горюче-смазочные материалы;
о— земной, взлетный; об— оборудование; opt— оптимальный; охл— охлаждение; п— полет; пл— планер; пр— приведенный, практический; пол— политропный; потр— потребный; пуст— пустой; р— расчетный; ред— редуктор; рес— ресурс; рем— ремонт; рк— рабочее колесо; с— сопло, совершенствование, секундный; СА— сопловой аппарат; S— изоэнтропический; сл— служебный; сн— снаряженный; ср— средний; ст— свободная турбина; статический, ступень;
к— компрессор, сечение за компрессором; к. II, в. II— сечение за компрессором (вентилятором) второго контура; кн— коммерческая нагрузка; кр— крейсерский, критический, крыло; кс— камера сгорания; л— лопасть; лоп— лопатка; ЛА— летательный аппарат; лм— лопаточные машины; L— отнесенный к дальности; м— механический, масло; мг— малый газ; max— максимальный, минимальный; min— начальный; н — отнесенный к сечению возмущенной атмосферы; нв— несущий винт; норм— нормальный; НЗ— навигационный запас; нс— начало серийного производства; су— силовая установка; т— турбина, техническая; m— топливо;
тк— турбокомпрессор; то— техническое обслуживание; mc— топливная система; т. км— тонно-километр; уд— удельный; ут— утечки; ф— форсажный; фюз— фюзеляж; ч— часовой; э— эквивалентный; эв— эволюции; эксп— эксплуатационный; Σ— суммарный; G— отнесенный к расходу; M— отнесенный к массе; F— отнесенный к площади; P— отнесенный к тяге; N— отнесенный к мощности; Су+m— силовая установка плюс топливо; Дв+m— двигатель плюс топливо; *— параметры заторможенного потока.
Сокращения АСИ— автоматизированная система испытаний; АТ— аэродинамическая труба; БПЛА— беспилотный летательный аппарат; БСИ— бортовые системы измерения; БСК— бортовые системы контроля; ВВС— военно-воздушные силы; ВГТД— вспомогательный ГТД; ВД— высокое давление; ВП— верхний предел; ВРД— воздушно-реактивный двигатель; ВСХ— высотно-скоростные характеристики; ГГ— газогенератор; ГДУ— газодинамическая устойчивость; ГПВРД— гиперпрямоточный ВРД; ГТД— газотурбинный двигатель; ГТД СТ— ГТД со свободной турбиной; ДФЭ— дробный факторный эксперимент; ДХ— дроссельные характеристики; ЕНЛГС— единые нормы летной годности самолетов; ИВ— измеряемая величина;
ИВК— измерительно-вычислителъный комплекс; ИКАО— международная организация гражданской авиации; ИП— измерительный прибор; КВД— компрессор высокого давления; КНД— компрессор низкого давления; КПД— коэффициент полезного действия; КС— камера сгорания; ЛА— летательный аппарат; ЛИ— летные испытания; ЛЛ— летающая лаборатория; МАК— межгосударственный авиационный комитет; МГТД— малоразмерный ГТД; МСА— международная стандартная атмосфера; МЦУ— малоцикловая усталость; НА— направляющий аппарат лопаточных машин; НВ— несущий винт; НД— низкое давление; НЗ— нормированное значение; НЗП— нормальные значения параметров; НИИ— научно-исследовательские институты; НИР— научно-исследовательские работы; НИЦ— научно-исследовательский центр; НИЭР— научно-исследовательские экспериментальные работы;
НТЗ— научно-технический задел; НТР— научно-технические работы; ОКР— опытно-конструкторские работы; ОТД— основные технические данные; ОТК— отдел технического контроля; ОТУ— общие технические условия; ПВРД— прямоточный ВРД; ПФЭ— полный факторный эксперимент; РСА— регулируемый сопловой аппарат; РУД— рычаг управления двигателем; САУ— стандартные атмосферные условия; СИУ— силоизмерительное устройство; СТ— свободная турбина; СУ— силовая установка; ТБК— термобарокамера; ТВД— турбовинтовой двигатель; ТВР— термопара вольфрам-рений; ТЗ— техническое задание; ТМК— термопара медь-копель; ТП— техническое предложение; термопара; ТПП— термопара платинородиевая; ТПР— термопара платинородий; ТРД— турбореактивный двигатель;
ТРДД— двухконтурный турбореактивный двигатель; ТУ— технические условия; ТХА— термопара хромель-алюмель; ТХК— термопара хромель-копель; УИ— ускоренные испытания; УСО— устройство связи с объектом; ФГУП— федеральное государственное унитарное предприятие; ФК— форсажная камера; ЦИАМ— Центральный институт авиационного моторостроения; ЦКП— центральное композиционное планирование; ЭДС— электродвижущая сила; ЭТИ— эквивалентно-технические испытания; ЭТС— эксплуатация по техническому состоянию.
ПРЕДИСЛОВИЕ Развитие и совершенствование авиационных двигателей всегда сопровождалось симметричным развитием испытательной базы, методов и измерений параметров, существенными изменениями организационных основ испытаний. Эти изменения всегда требовали высокопрофессиональных специалистов, которые разбираются в рабочем процессе и конструкции авиационных двигателей и имеют основательную подготовку по всем вопросам испытаний этих двигателей. Взаимозависимость развития авиационных двигателей и методов их испытаний с качеством подготовки специалистов, обеспечивающих эти процессы, всегда находила свое отражение в совершенствовании соответствующих учебных курсов и учебной литературы. Основы учебных дисциплин по испытанию авиационных двигателей были заложены в 50 -е годы при создании учебника по теории ВРД под редакцией Б. С. Стечкина, продолжены В. А. Тютюновым в учебнике «Испытания турбореактивных двигателей» (1959 г. ) и В. М. Дорофеевым, В. Я. Левиным в учебнике «Испытания воздушно-реактивных двигателей» (1961 г. ). Учебное пособие Г. М. Горбунова, Э. Л. Солохина «Испытания авиационных воздушно-реактивных двигателей» (1967 г. ) и учебник Л. С. Скубачевского «Испытания воздушно-реактивных двигателей» (1972 г. ) обеспечили дальнейшее укрепление учебной дисциплины по испытанию авиационных двигателей. Особое значение имеет учебник Э. Л. Солохина «Испытания авиационных воздушно-реактивных двигателей» (1975 г. ). Широта и глубина изложения материала, предвидение направлений развития вопросов испытания, доступность изложения заслуженно принесли этому изданию известность и на долгое время сделали его основным учебником по этому курсу.
В 1992 г. вышел под общей редакцией А. Я. Черкеза, подготовленный группой авторов из ЦИАМ и МАИ учебник «Испытания воздушно-реактивных двигателей» . Второе издание этого учебника «Испытания и обеспечение надежности авиационных двигателей и энергетических установок» под общей редакцией И. И. Онищика вышло в 2004 г. Эти два издания являют собой средоточие огромного практического опыта испытаний, накопленного в процессе создания, доводки и эксплуатации практически 4 -х поколений авиационных газотурбинных двигателей (ГТД). Наблюдавшийся на протяжении почти 15 лет спад отечественного авиационного двигателестроения завершен. Многие предприятия продолжили разработку перспективных двигателей, используя для этого качественно новые производства, информационные технологии высокого уровня, новейшие испытательные базы. Не стояли на месте и методы подготовки специалистов. Новейшие методы специальных испытаний, вопросы установления ресурса, постоянно развивающиеся методы измерений и широкое применение в процессе испытаний информационных технологий, — все это находит свое применение в учебных курсах по испытаниям авиационных двигателей. Такой опыт, накопленный в Самарском государственном аэрокосмическом университете (СГАУ), в Уфимском государственном авиационном техническом университете (УГАТУ), в Рыбинской государственной авиационно-технологической академии (РГАТА), существенно дополненный последними передовыми производственными достижениями Самарского научно-технического комплекса имени Н. Д. Кузнецова (СНТК им. Н. Д. Кузнецова) и ОАО Научно-производственного
объединения «Сатурн» (г. Рыбинск) (ОАО «НПО «Сатурн» ), положен в основу данного учебника. Предисловие написано В. А. Григорьевым (СГАУ). Введение — А. С. Гишваровым (УГАТУ). Главы 1, 2, 4, 6, 16 — В. А. Григорьевым и С. П. Кузнецовым (ОАО «НПО «Сатурн» ), Глава 3 — А. С. Гишваровым. Глава 5 — В. А. Григорьевым. Главы 7, 8, 9 — А. С. Гишваровым и В. А. Григорьевым. Главы 10, 12 — А. Н. Белоусовым (СГАУ), В. А. Григорьевым и С. П. Кузнецовым. Глава 11 — А. С. Гишваровым, В. А. Григорьевым и В. Т. Шепелем. Главы 13 и 14 — С. К. Бочкаревым (СГАУ), В. А. Григорьевым и С. А. Ильинским (СНТК им. Н. Д. Кузнецова). Глава 15 — С. К. Бочкаревым. Авторы выражают большую благодарность дирекциям инновационной образовательной программы в СГАУ и УГАТУ, чья помощь и поддержка помогли решить большинство технических и организационных вопросов, связанных с подготовкой рукописи. Особую благодарность авторы выносят академику В. П. Шорину и кафедре «Авиационные двигатели и энергетические установки» Казанского государственного технического университета за замечания и советы, высказанные при рецензировании учебника, Генеральному директору ФГУП ЦИАМ им. П И. Баранова В. А. Скибину и начальнику отдела ЦИАМ Б. А. Пономареву за рекомендации, высказанные при формировании структуры учебника, И. И. Морозову за огромный объем работы, связанный с оформлением рукописи. Авторы выражают признательность ведущим специалистам ОАО «НПО «Сатурн» Н. А. Бурову, А. В. Латышеву, А. А. Данилюку, Ю. Т. Долгих, В. А. Кучерову за большую помощь в подготовке материалов к изданию.
ВВЕДЕНИЕ Авиадвигателестроение относится к одной из стратегически важных отраслей обеспечивающих высокий уровень технологического развития. Снижение сроков и стоимости разработки двигателей нового поколения обеспечиваются за счет комплексного развития направлений, охватывающих работы по ЗЭ-методам моделирования, новым конструкционным материалам, фундаментальным исследованиям проблем эмиссии и шума ГТД, технологиям изготовления, а также по методическим работам по снижению стоимости жизненного цикла двигателя. В процессе создания и производства авиационных двигателей проводится большое количество различных по сложности испытаний, начиная от научно- исследовательских и завершая летными испытаниями. При этом для проведения испытаний ГТД затрачивается значительное количество времени, материальных, финансовых и людских ресурсов. По мере повышения требований к характеристикам летательных аппаратов (ЛА) и связанного с этим их технического усложнения роль испытаний в процессе изготовления авиационных ГТД становится все более значительной. При разработке современных ЛА из-за невозможности получения адекватного теоретического описания примерно до 40 % всех возникающих проблем решаются при помощи испытаний. При этом большая стоимость испытаний и длительность их проведения становятся определяющими в общих затратах и сроках, необходимых для создания ЛА и двигателя. Поэтому сокращение сроков создания и стоимости разработки ЛА и двигателей во многом сводится к рациональной организации процесса ее экспериментальной отработки, включая оптимальное планирование испытаний.
Существующие теоретические основы оптимального проектирования авиационных ГТД позволяют выбирать наилучший в определенном смысле облик рабочего процесса и конструктивные параметры, его обеспечивающие, законы управления и другие характеристики двигателя. Но, к сожалению, еще отсутствует приемлемая теория испытаний, позволяющая оптимизировать этот весьма важный этап жизненного цикла двигателя. Причиной этому является тот факт, что испытания авиационного ГТД, как и любой сложной технической системы, представляют собой процесс, характеризующийся огромной разнородностью решаемых задач, многоуровневостью этапов испытаний, неоднородностью информационных потоков, циркулирующих в самой системе испытаний, многообразием оцениваемых характеристик, наличием ограниченного числа двигателей, выделяемых для испытаний, и др. Испытания двигателей различают в широком и узком смыслах. В узком смысле испытания определяются теми конкретными задачами, которые решаются с использованием информации, полученной в процессе проведения испытаний (доработки двигателя, уточнения его математической модели, сдачи двигателя заказчику, контроля состояния системы, диагностики, оценки характеристик надежности и т. д. ). Широкий смысл испытаний заключается в достижении основной цели, т. е. получении информации о состоянии испытываемого двигателя, которая в дальнейшем может использоваться для решения самых различных задач. В любом испытании можно выделить четыре этапа (фазы): планирование испытания, его проведение, обработка результатов испытаний, анализ полученных результатов и выработка решения. Планирование является неотъемлемым важнейшим этапом выполнения любых работ и любых действий.
В результате планирования необходимо получить ответ на вопрос: что, когда и как делать. При этом предусматривается также решение вопросов, связанных с распределением и использованием материальных, временных, финансовых и людских ресурсов. На этапе планирования испытаний составляется программа, которая включает в себя цель и задачи испытаний, описание объекта испытаний, порядок их проведения и обеспечения, объем, последовательность и методики испытаний, порядок обработки полученных результатов, форму и порядок отчетности. Программа испытаний, как правило, создается параллельно с созданием двигателя. Само проведение испытаний связано с реализацией во времени и пространстве программы испытаний. Разделение этапов обработки и анализа результатов испытаний является весьма условным и во многом определяется характером испытаний и сложностью испытываемого двигателя. Общим для обоих этапов является то, что на них производится преобразование информации. В основу планирования любой операции, как правило, закладывается принцип оптимальности. Для реализации этого принципа необходимо иметь показатель эффективности функционирования системы и модель. При решении задач планирования работы сложных систем, какой является система испытаний ГТД, необходимо использовать математическую модель. Выбор и обоснование показателей и критериев эффективности испытаний, а также построение математической модели испытаний являются достаточно сложной проблемой и пока еще должного освещения в научно- технической литературе не получили. Кроме того, на этом этапе должна быть построена математическая модель и испытываемого двигателя, предназначенная для определения и
обоснования видов, объемов и последовательности испытаний, для выбора измеряемых и контролируемых параметров, для обоснования вида и характеристик тестовых (испытательных) сигналов и др. При проведении испытаний начинается реализация их программы, осуществляется сбор информации об испытываемом объекте и его функционировании. Для испытаний, как правило, характерны динамичность, ограниченность временных ресурсов, оперативность. Поэтому вполне естественным является требование получения максимума информации при минимальных (ограниченных) материальных и временных затратах. На этапе анализа и выработки решения первостепенными задачами являются определение показателей и критериев оценки результатов испытаний, выбор методов идентификации, технической диагностики, прогнозирования технического состояния двигателя и др. Современный период развития авиационной техники характеризуется созданием новых летательных аппаратов, в особенности широкофюзеляжных самолетов с большой пассажировместимостью, что неизменно ведет к росту значения надежности авиационных двигателей. Повышение уровня параметров двигателей для обеспечения его конкурентоспособности связано с интенсификацией всех рабочих процессов. Применение высоких степеней сжатия и температуры газа перед турбиной существенно усложняет обеспечение высокой надежности, выдвигая этот показатель в качестве первостепенного.
Работоспособность двигателя определяется одновременным влиянием большого количества факторов, имеющих подчас противоречивый характер. В этих условиях разрешение противоречий является основным методом работы. Надежность двигателя закладывается при его проектировании, отрабатывается на стадии доводки, обеспечивается в серийном производстве и реализуется в процессе его эксплуатации. Важнейшим этапом является проектирование конструкции двигателя. При создании новых авиационных ГТД конструкторские решения, как правило, принимаются в результате поиска оптимума в многоэкстремальных задачах. При этом учитываются такие подчас противоречивые факторы, как необходимость обеспечения заданных прочностных показателей, выбор материалов с определенными свойствами и технологических процессов с учетом влияния технологической наследственности и т. д. Решение таких задач проводится с применением систем автоматизированного проектирования с учетом достижений современных информационных технологий, основу которых составляют CAD/CAM/CAE-системы, позволяющие решать задачи как по проектированию двигателя, так и по геометрическому моделированию с выпуском чертежной документации, проведению инженерного анализа и подготовке производства, вплоть до выпуска программ для станков с ЧПУ. Однако практика показывает, что даже оптимально спроектированный двигатель требует длительной доводки. Причина заключается, прежде всего, в наличии ряда проблем, возникающих при проектировании. Как правило, двигатель закладывается на пределе существующих возможностей по КПД узлов, прочности материалов, массовым характеристикам и часто даже с учетом перспективы их развития. Поскольку только так может быть обеспечена конкурентоспособность двигателя к моменту выхода в эксплуатацию.
Даже небольшие несоответствия в расчетных и реальных показателях эффективности узлов и прочности деталей приводят к невыполнению технических требований и, значит, к необходимости тщательной экспериментальной отработки как рабочего процесса, так и прочности двигателя. Уже на начальной стадии разработки нового двигателя, после выбора типа, конструктивной схемы и некоторых основных параметров рабочего процесса, необходимо располагать надежными, экспериментально подтвержденными данными о реально достижимых КПД узлов и элементов проточной части, протекании их характеристик, прочностных показателях применяемых материалов и т. д. Этап доводки двигателя более трудоемкий и продолжительный по времени, чем этап проектирования, и характеризуется большим напряжением в работе. По определению генерального конструктора, академика Н. Д. Кузнецова: «Доводка — это период неудач и успехов, проявления острых эмоций, оправдавшихся надежд и разочарований, неожиданных трудностей, пора «загадок» и «открытий» , провалов и радостных находок, переоценки некоторых «умных» идей и замыслов и иногда открытие истины в простых решениях, забытых, отвергнутых ранее» . В процессе доводки в конструкцию вносится множество изменений, и все они в обязательном порядке должны быть проверены экспериментально, какими бы правильными и очевидными они ни казались. Один из ответственных этапов создания двигателя — это выявление и прогнозирование критических состояний. В этой области существующие теоретические методы не всегда достаточно эффективны, и конструктор чаше всего вынужден полагаться на специальные эксперименты. Несовершенства и недостатки спроектированного двигателя часто возникают из-за отставания развития прикладных наук от уровня развития техники. Это относится к конструкционной прочности, газодинамике, теории горения и другим отраслям знаний.
Имеются также трудности с определением качества выполненных проектных работ, связанные с отсутствием четких критериев оценки и наличием довольно большого объема новых технических решений в проекте. Достоверность расчетов снижают такие факторы, как многорежимность и широкий диапазон внешних условий, ограничения и упрощения расчетных схем, узкий диапазон адекватности моделирования. Очевидно, что численные методы с использованием ЭВМ более удобны, чем экспериментальные, позволяя при известных данных проводить для выбранной математической модели расчет трехмерных задач деформаций, напряжений и прочности при упругом и неупругом поведении материала. Однако при разработке новых конструкций этого недостаточно и требуется применение экспериментальных методов определения нагруженности элементов двигателей, поскольку: • д ейс т ву ющ ие на к о нс т ру к цию на г ру з к и м ог у т б ы т ь из ве ст ны л и шь пр ибл и з ит ел ь н о ил и опр ед ел е ны н ед о ст аточ н о т оч но , ч то т ребует про вед е ни я из ме ре ни й на д етал я х и к о нс т ру к ция х су ще с т ву ющ их д в игател е й в ус л ов и я х их ра б от ы ; • ре ал ь ный мат е ри ал р ас с м ат р ива е мой к о нс т ру к ци и не в пол ной мер е с о от вет с т вует д опу ще ния м , пр ин я т ы м в те ор ии р асч ет а ; • не вс е с у ще с т вен но вл и я ющ ие о с обен но ст и р а сч ет а с л ож н ой к он с т ру к ции мож н о у ч е ст ь в р асч ет е при пр им ене ни и с ущес т ву ющ их Э В М; • д аж е с а мые с о вер шен ные мат емат ич е ск и е мод ел и , и с пол ь зуе мы е в р асч ета х Г ТД , баз и ру ют ся на у пр още нны х с хе ма х т еч ен ия и н ед ос т ат оч н о пол но у ч и тывают
• взаимодействие элементов, влияние вторичных факторов, неравномерность и нестационарность потоков, тепловое состояние элементов конструкции и т. д. ; • в расчетные формулы входит множество эмпирических коэффициентов и поправок, иногда лишь приближенно применимых в расчете характеристик нового двигателя, отличающегося конструкцией, параметрами процесса, режимами работы, т. е. все расчетные результаты должны быть проверены экспериментально. Испытанию полноразмерного двигателя предшествуют испытания на специальных установках для отдельных деталей, узлов и систем по отработке прочности, газодинамических процессов, процессов горения и регулирования. От полноты и качества этой «поузловой» отработки в значительной степени зависит эффективность отработки двигателя в целом. Подавляющее число дефектов опытного двигателя — это дефекты прочностного характера. Поэтому особое внимание уделяется обеспечению конструкционной прочности на основе рационального выполнения конструирования, расчетов на прочность, выбора материалов и технологии изготовления, а также учета эксплуатационных факторов. Большое значение придается обеспечению технологической надежности опытного двигателя, поскольку при испытании натурных узлов и двигателя в целом, наряду с конструктивными дефектами, выявляются и производственные дефекты, связанные с недостатками технологии и ее исполнения. Стендовая отработка двигателей базируется на проведении экспериментальных, длительных, ускоренных эквивалентных и специальных испытаний. Внедрение ускоренных (эквивалентно-циклических) испытаний позволяет более быстро оценивать надежность и выявлять «слабые места» двигателя, проводить проверку новых конструктивных и технологических решений.
В завершающей стадии отработки двигателя, когда получены все основные характеристики, определяющие технический уровень, проверена длительными испытаниями надежность двигателя на установленный ресурс и, таким образом, определена окончательная типовая конструкция двигателя, проводится обширная программа специальных испытаний (более 50 видов). К составлению, рассмотрению и утверждению методик таких испытаний привлекаются отраслевые институты и эксплуатирующие организации. На выполнение этих испытаний затрачивается несколько тысяч газочасов. К ним относятся испытания по определению газодинамической устойчивости компрессора, устойчивости процессов горения, по оценке влияния отборов воздуха, испытания в условиях максимальных и минимальных окружающих температур, по проверке надежности основных узлов и двигателя в целом, по оценке летно-эксплуатационных характеристик в термобарокамере и на самолете. К специальным видам испытаний относится проверка двигателя при попадании на вход птиц, льда и др. Важнейшим условием обеспечения безопасности полетов является сертификация авиационных двигателей, проводимая путем подтверждения соответствия научно-обоснованным и общепризнанным нормам летной годности. Поэтому в этом плане актуальным является обоснование условий и методик проведения сертификационных испытаний двигателя. После проведения доводочных работ и выполнения обширного перечня специальных стендовых и летных испытаний двигатель, в зависимости от назначения, предъявляется на сертификационные или государственные испытания — официальную приемку заказчиком.
В процессе серийного производства каждый экземпляр двигателя проходит кратковременные испытания — предъявительские и приемосдаточные — с целью оценки качества изготовления и сборки, а также отладки агрегатов и систем. Помимо кратковременных испытаний периодически проводится выборочная проверка двигателя ресурсными испытаниями с оценкой соответствия его по основным данным, устойчивости, надежности образцу, прошедшему государственные испытания. В ходе серийного производства и эксплуатации двигателей на ЛА выясняется целесообразность введения некоторых конструктивных или технологических изменений в принятый эталон с целью улучшения основных данных и надежности, увеличения ресурса, устранения или предотвращения дефектов, повышения технологичности производства, испытания, обслуживания. Для экспериментальной проверки этих мероприятий проводят типовые испытания. Таким образом, весь жизненный цикл авиационного двигателя (от разработки до широкой эксплуатации) сопровождается проведением испытаний. Экспериментальные стенды, на которых проводятся испытания двигателей, компрессоров, турбин, камер сгорания, представляют собой сложные сооружения, оснащенные комплексом энергетического оборудования, топливопитания, газовоздушными коммуникациями. Проведение испытаний двигателей и их узлов сопряжено с очень большими затратами. Создание испытательных установок может оказаться сложной и более трудоемкой задачей, чем создание самого двигателя. Это, в первую очередь, относится к сложным и дорогостоящим стендам, имитирующим высотно-скоростные условия (аэродинамические трубы, термобарокамеры, а также к их системам).
Поскольку избежать этих затрат невозможно, то приходится уделять особое внимание повышению информативности испытаний, т. е. увеличению объема, точности, достоверности результатов и сведений, получаемых в результате про ведения каждой экспериментальной работы. Наряду с использованием более совершенного оборудования и измерительной техники, автоматизацией проведения и обработки испытаний, комплексированием программ в практике испытаний двигателей широко используется математическое планирование эксперимента. Это позволяет обоснованно назначать число и условия проведения опытов и таким образом уменьшить объем испытаний, требующийся для получения заданной информации; повысить точность результатов; облегчить оптимизацию характеристик объекта; обобщить полученные данные. Таким образом, экспериментальные исследования играют важнейшую роль в достижении требуемых характеристик двигателя и создании опережающего научно-технического задела, являющегося ключевым звеном современной методологии создания авиационных ГТД. В этом плане актуальными направлениями авиадвигателестроения являются разработка новых и совершенствование существующих методов и средств испытаний авиационных ГТД. Основными результатами работ данного направления являются: 1. комплекс высокоэффективных методов и технических средств для исследования современных ГТД, их деталей и узлов; 2. концепция развития отраслевой научно-исследовательской базы, соответствующей современным требованиям, в основу которой положены: • . на иб ол ее пол на я и ми та ция пол ет н ых ус л о в ий д ви гател я н а ис пыт ат ел ь ном о б оруд овани и ; • . ис пол ь зо ва ни е м ат ем ат ич е с к о го м од ел и рован ия проце с с ов , пр оте к аю щи х ; в д в игател е ;
• эне р го с бере га ющ ие пр и нципы ф ор ми ро ва ни я эк с пер им ен та л ь ной баз ы тех нол ог ий ис п ыта ни й, вк л юч аю щи х поу зл ово е и с с л ед о ва ни е и д овод к у д в игател е й; • с озд ан ие но во го пок ол е ни я с и с те м а вто мат ич ес к ого у пра вл е ни я и спы та ни я ми , ис п ол ь зу ю щи х мате м ат и ч е с ки е мод ел и с т ен д о в, их эл е ме нто в и т ех нол о ги ч е с к их с и с те м; • ис п ол ь зо ва ни е р езул ьтато в и с пыт ани й д л я фо р мир ован ия о пе реж ающей нау ч но — тех ни ч е с к ого з а д ел а , я вл я ю щего с я н ау ч но й о с новой с озд ан ия к он к у ре нт ос по с об ных д в игател е й но вы х пок ол ен ий ; • с т рат ег ии ус та новл ен ия и у пр а вл ен ия р ес урс о м Г ТД , поз вол я ющ ие нау ч но о б ос но в ыват ь ре с ур с ос н ов ны х д ет ал е й д ви гател я , а та к ж е вес т и эк с пл уат аци ю д в игат ел ей по т ех н ич ес к о м у с о с то я ни ю; методология испытаний двигателей и их элементов, значительно повышающая информативность испытательного комплекса, включая: усовершенствованные методы имитации неоднородности давления и температуры на входе в двигатель в диапазоне эксплуатации современных лета тельных аппаратов; методы определения основных характеристик двухконтурных двигaтeлeй со сверхвысокой степенью двухконтурности; энергосберегающий метод определения дроссельных характеристик двигателя с малоградиентным изменением параметров при испытаниях; метод исследования высотно-скоростных характеристик на основе планирования эксперимента для верификации математической модели с учетом ограничений по параметрам двигателя и высотно-компрессорной станции стенда,
метод комплексного анализа результатов испытаний на установившихся и переходных режимах с использованием математических моделей; идентификацию математических моделей двигателей по результатам испытаний; автоматизацию испытаний, формирование систем измерений, сбора и обработки информации, работающих в реальном масштабе времени при стендовых испытаниях двигателей; методологию тепловых испытаний и доводки охлаждаемых деталей двигателя в расплаве высокотеплопроводного металла и с использованием тепловидения и др. Как и любая дисциплина, испытания и обеспечение надежности авиационных ГТД постоянно развиваются, поскольку создание высокоэффективных и конкурентоспособных двигателей невозможно без постоянного совершенствования производственной и испытательной баз, а также решения целого ряда комплексных задач, исследование которых проводится в математическом, физическом, технологическом, методическом, информационном и инженерно-техническом аспектах.
Глава 1 ИЗМЕРЕНИЯ ПРИ ИСПЫТАНИИ ДВИГАТЕЛЕЙ 1. ВИДЫ И МЕТОДЫ ИЗМЕРЕНИЙ При испытаниях ГТД проводят значительный объем самых разнообразных измерений. В проточной части двигателя выполняют измерения параметров потоков воздуха и газа (давления, температуры, скорости, расхода). Для получения показателей, характеризующих тяговые и мошностные выходные данные двигателя, измеряют силу тяги и крутящий момент. Привязка к режиму и важнейший параметр двигателя — частота вращения ротора измеряются наиболее точными приборами. В экспериментах по испытанию ГТД требуются измерения деформаций и напряжений в элементах двигателя, их температурных условий, вибраций, состава продуктов сгорания, параметров состояния систем. При испытаниях авиационных ГТД количество измеряемых параметров постоянно растет. От нескольких десятков в 50 -е годы прошлого столетия до двух тысяч измерений в настоящее время. Анализ результатов измерений позволяет оценить рабочий процесс, определить тепловое состояние и напряжения в элементах конструкции, оценить соответствие двигателя заданным техническим нормам. Средства измерений непрерывно совершенствуются, улучшаются их характеристики, растет надежность [49, 52].
Параметры ГТД, измеренные при испытаниях, представляют собой физические величины (р, Т, Р , М кр и т. п. ) [43]. Измерение — это нахождение значения физической величины опытным путем с помощью специальных технических средств. Различают следующие основные виды измерений: прямые, косвенные, совокупные и совместные. В практике испытаний ГТД находят применение прямые и косвенные измерения. Совокупные и совместные измерения применяются, как правило, в лабораторных метрологических исследованиях. Прямыми измерениями называют такие, результат которых получается непосредственно с помощью прибора. Прямые измерения могут быть проведены различными методами. Наиболее часто встречаются на практике метод непосредственной оценки, дифференциальный метод и метод совпадений. Метод непосредственной оценки основан на том, что измеряемая величина определяется непосредственно измерительным прибором (измерение длины линейкой, температуры — термометром, давления — манометром и др. ). Дифференциальный метод — это метод определения разности между измеряе мой величиной известной (измерение давления дифманометром). Частным случаем является нулевой метод, когда разность сравниваемых величин равна нулю (измерение массы весами).
Метод совпадений основан на совпадении равномерно чередующихся отметок или сигналов измеряемой величины с известным рядом отметок или сигналов (нониус, стробоскоп и др. ). Косвенное измерение — результат решения уравнения, в которое входят параметры, определенные с помощью прямых измерений. Например, определение расхода жидкости и газа в дроссельных приборах по известным площадям, плотности и перепаду давления; скорости потока по измеренным статическому давлению, давлению заторможенного потока и температуре и т. п. Погрешности измерений. В задачу измерения физической величины входят не только нахождение самой величины, но также и оценка допущенной при измерении погрешности. На практике все измерения выполняются с определенной степенью приближения. Возникновение погрешностей связано с несовершенством методов и средств измерений, влиянием условий измерений и действиями персонала, выполняющего измерения. Погрешность измерения — это разность между результатом измерения и действительным значением измеряемой величины. Погрешности измерений делят на три класса: случайные, систематические и грубые. Случайными погрешностями измерения называют такие, которые возникают случайным образом при повторных измерениях одной и той же величины. Эти погрешности не могут быть исключены опытным путем, но их влияние на результаты может быть уменьшено многократным повторением измерений и применением в обработке результатов этих измерений теории вероятностей и методов статистики.
Систематическими погрешностями измерения называют такие, значение которых в данном ряде измерений остается постоянным или закономерно изменяется. Причинами их появления могут быть: смещение стрелки или шкалы относительно номинального положения, неточная регулировка при бора, постоянно повторяющееся неправильное положение наблюдателя от носительно прибора, изменение внешних условий и другие. Влияние систе матических погрешностей на результат измерения учитывается градуировкой аппаратуры. Грубые погрешности (промахи) — ошибки экспериментатора, неисправность измерительной аппаратуры — существенно искажающие результаты измере ний. Грубые погрешности весьма опасны при единичных измерениях, когда их трудно обнаружить. При многократных измерениях одной и той же величины промахи можно выявить, используя приемы математической теории ошибок. При обработке полученных экспериментальных данных промахи необходимо исключать. Количественно погрешность оценивается разностью между измеренным «Х изм » и истинным «Х» значениями измеряемой величины(1. 1) ΔХ=Х изм -Х Истинное значение измеряемой величины обычно неизвестно из-за отсутствия. Реальных методов измерения. Поэтому на практике вместо истинного. Истинное значение измеряемой величины обычно неизвестно из-за отсутствия Реальных методов измерения. Поэтому на практике вместо истинного значения измеряемой величины пользуются действительным ее значением, полученным с помощью более точных средств измерения Часто для оценки точности измерений пользуются безразмерной величиной — относительной погрешностью δ. Это отношение абсолютной погрешности к действительному значению измеряемой величины 100% (1. 2) Величина погрешности прямых измерений зависит от класса точности измерения Класс точности прибора — это обобщенная характеристика средств измерения, численно равная
наибольшей относительной погрешности прибора, выраженной в процентах 100% (1. 3) Где Δ- диапазон измерения. Зная класс точности измерительного прибора и его диапазон измерения (максимальную величину измерения), можно вычислить абсолютную и относительную погрешность измерения. Например для измерения давления р изм = 750 к. Па используется прибор 1 -го класса (К= 1) с диапазоном измерения 0. . . 1000 к. Па, В соответствии с ( 1. 3) Р дельная погрешность прибора, к. Па, =10 Относительная погрешность. При измерении давления 200 к. Па этим же прибором относительная погрешность составит уже 5 %. Отсюда вытекает известное в практике правило: при измерениях необходимо стремиться к тому, чтобы измеряемая величина находилась в последних 2/3 шкалы. Если измерение производится в первой трети шкалы, то относительная погрешность существенно возрастает. Погрешности косвенных измерений обычно определяются с помощью двух простых правил: 1. Предельная абсолютная погрешность суммы (разности) (ΔY) Равна сумме абсолютных погрешностей слагаемых, т. е. Если Y=X 1 +X 2 +…+X n То ΔY=| ΔX 1 |+|ΔX 2 |+…+|ΔX n |. (1. 4)
2. Предельная относительная погрешность произведения (частного) (6 У) равна сумме относительных погрешностей сомножителей, то есть если Y=X 1 X 2 …X n, То δY=| δX 1 |+| δX 2 |+…+| δX n | (1. 5)
Под средством измерения понимают техническое средство (или их комплекс), предназначенное для измерения, имеющее нормированные метрологические характеристики и (или) хранящее единицу физической величины, размер которой остается неизменной в течение известного интервала времени Основной характеристикой средств измерений является статическая (градуировочная) характеристика — функциональная зависимость между выходной величиной у (перемещение указателя прибора или выходной сигнал преобразователя) и входной величиной х в установившемся режиме [44] y =f ( х ). (1. 6) Статическая (градуировочная) характеристика может быть задана аналитически, графически (рис. 1. 1) или таблично. В общем случае статическая характеристика может быть линейной и нелинейной. Для средств измерений в большинстве случаев предпочтительна линейная статическая характеристика. Нелинейные статические характеристики допускаются только в тех случаях, когда они обусловлены применяемым принципом измерения и нелинейность не может быть полностью устранена. Чувствительность средства измерения 8 — это его свойство, определяемое отношением выходного сигнала ДУ к вызывающему изменению входной величины Δх 1. 2 СРЕДСТВА ИЗМЕРЕНИЙ
δ = Δу /Δх. Рис. 1. 1. Статические характеристики средств измерений: а и б — линейные; в — нелинейная
Порог чувствительности — это свойство средства измерения, характеризуемое наименьшим изменением измеряемой величины, которое вызывает заметное изменение выходного сигнала. Диапазон показаний — область значений шкалы прибора, ограниченная конечным и начальным значениями. Диапазон измерений — область значений измеряемой величины, в пределах которой нормирован допуск предельной погрешности средства измерения. Вариация показаний измерительного прибора — это разность показаний прибора в одной и той же точке диапазона измерений при плавном подходе со стороны большего и со стороны меньшего значений к этой точке. Показание средства измерения — число, отметка, сигнал на отсчетном устройстве, соответствующие значению физической величины в момент отсчета. Измерительный прибор — средство измерений, предназначенное для получения значений измеряемой физической величины в установленном диапазоне, как правило, в форме наиболее доступной для восприятия. По характеру выходного сигнала (или показаний) приборы подразделяются на аналоговые и цифровые. Первые имеют показания или выходной сигнал в виде непрерывной функции от измеряемой величины. Во вторых показания представлены в цифровой форме, которая является результатом дискретного преобразования сигналов измерительной информации. Средства измерения и, прежде всего, показывающие аналоговые приборы, обычно имеют шкалу (это часть отсчитывающего устройства, которое показывает значения измеряемой величины), которая представляет собой упорядоченный ряд отметок, соответствующих последовательному ряду значений физической величины. Промежуток между двумя соседними отметками шкалы называют делением шкалы. Разность значений величины, соответствующая двум соседним отметкам шкалы, называется ценой деления шкалы
1. 3 ОСОБЕННОСТИ ИЗМЕРЕНИЙ ПРИ ИСПЫТАНИЯХ ГТД Достижения в разработке и миниатюризации элементов измерительных устройств позволяют существенно увеличивать объем измерений при испытаниях авиационных ГТД. Однако установка дополнительных приемников давления, термопар и датчиков других параметров может оказать влияние на параметры потока, изменить гидравлические сопротивления, ослабить детали и т. п. В зависимости от принятой на двигателе системы управления и способа отладки измерение параметров проводится на режимах, соответствующих измеренным или приведенным значениям частоты вращения ротора двигателя данного режима, а также на режимах с ограничением по отдельным параметрам (частоте вращения одного из роторов, степени повышения давления воздуха за компрессором, температуре газов перед или за турбиной и других) [49]. Режим работы двигателя задается положением рычага управления двигателя (РУД). При этом в соответствии с принятой программой регулирования должны обеспечиваться получение основных данных на заданном режиме и ограничение режима по максимально допустимой величине частоты вращения роторов, степе ни повышения давления в компрессоре, температуры газов за турбиной и др. При измерении параметра несколькими датчиками разработаны порядок оценки достоверности проводимых измерений, а также порядок выбраковки отдельных измерений и перепроверок в тех случаях, когда оценка величины измеряемого параметра производится по осреднению показателей этих датчиков. Параметры двигателя, как правило, измеряются на основных режимах без отбора воздуха на нужды воздушного судна (ВС) и без загрузки агрегатов, установленных на двигателе и используемых на нужды ВС. На двигателях, на которых техническими условиями дополнительно обусловлен и режим с повышенным отбором воздуха на нужды ВС
(на струйную систему управления положением летательного аппарата, на сдув пограничного слоя и другие), некоторые параметры измеряются также на режимах с отбором воздуха в количестве, установленном техническими условиями. Для отладки и проверки ограничителей максимальных значений отдельных параметров, установленных на двигателе (частоты вращения роторов, температуры газов, давления воздуха за компрессором), могут на время испытаний применяться съемные устройства (переходные мультипликаторы для приводных датчиков частоты вращения, подача воздуха от внешнего источника и др. ). Регламент вывода двигателя на контролируемый режим и порядок измерения параметров оговорены в программе на проведение испытаний. Время выдержки двигателя на заданном режиме при проведении измерений на режимах, по которым оценивается соответствие двигателя техническим условиям, должно быть не менее времени, при котором обеспечивается установившийся характер всех контролируемых параметров. Величина этого времени оценивается экспериментальным путем и оговаривается в программе. Время выдержки перед измерением параметров на отдельных режимах, на которых недопустима продолжительная работа, может быть уменьшено до ве личины, устанавливаемой разработчиком. В этих случаях должен быть обусловлен порядок определения параметров для оценки основных данных двигателя (узла) на таких режимах. При испытаниях двигателей на стендах предприятий используются средства измерений, допущенные Госстандартом РФ к применению, после их государственной или ведомственной метрологической аттестации и средства измерений специального назначения после ведомственной метрологической аттестации, имеющие аттестаты, свидетельства и поверительные клейма. Ко всей измерительной аппаратуре, применяемой при испытаниях двигателей, прилагается техническая документация, регламентирующая эксплуатацию и поверку средств измерений.
Оценка погрешностей средств измерения и форма представления результатов измерений должны соответствовать требованиям государственных стандартов и методике измерения. Вся техническая документация метрологического обеспечения испытаний (программы метрологической аттестации, методики поверки, методики выполнения измерения) проходит метрологическую экспертизу в отделе главного метролога изготовителя двигателя. Измерения параметров двигателя необходимо проводить по методикам выполнения измерения, разработанным и аттестованным в соответствии с требованиями государственных стандартов. Методика выполнения измерения для двигателя согласовывается с НИИ промышленности и заказчика. Погрешность измерения параметров двигателя определяется интервалом, в котором с установленной вероятностью Р = 0, 95 находится суммарная погрешность измерения. В тех случаях, когда измерение нельзя повторить, помимо границ погрешности результата измерения, соответствующих доверительной вероятности Р = 0, 95, допускается указывать границы для доверительной вероятности Р = 0, 99. Определение суммарных погрешностей измеряемых параметров двигателя необходимо проводить для рабочих условий, указанных в программах стендовых испытаний. Требования к точности измерения основных параметров ГТД на установившихся режимах приведены в табл. 1. 1. Требования к объему и точности измерения параметров для конкретного типа двигателя должны устанавливаться разработчиком с учетом обеспечения метрологической точности определения параметров в зависимости от заданной точности их поддержания в техническом задании. Для выносных коробок приводов агрегатов, редукторов и трансмиссии требования к допустимой погрешности измерения параметров устанавливаются разработчиком и согласовываются с НИИ промышленности и заказчика.
1. 4 ИЗМЕРЕНИЕ ДАВЛЕНИЙ При изучении движения жидкости и газа различают понятия статического давления и давления заторможенного потока. Статическое давление в невозмущенном потоке можно определить как давление, которое действовало бы на стенку тела, движущегося вместе с потоком, или стенку, расположенную параллельно движению потока. Давлением, которое учитывает скоростной, динамический напор ( р К 2 ) / 2 , называется давление заторможенного без потерь потока. Исходя из этого, формируются методы определения указанных параметров. Измерение давления заторможенного потока. Если в движущийся поток поместить тело (например, цилиндр), то оно будет оказывать тормозящее воздействие на окружающий поток, в результате чего на поверхности тела установится определенное распределение давления. В центральной точке носка, расположенной на оси тела (критическая точка), поток тормозится полностью и его скорость равна нулю. Если в месте расположения критической точки выполнить отверстие и соединить его трубопроводом с манометром, то прибор покажет величину давления заторможенного потока. Это — простейший цилиндрический приемник давления заторможенного потока. Такой приемник, несмотря на свою простоту, имеет достаточно хорошую точностную характеристику (погрешность измерения давления составляет менее 1 %).
1. 1. Требования к точности измерения основных параметров ГТД Измеренный параметр двигателя Диапазон измере ния или норми руемые значения Погрешность при до верительной вероятно сти Р = 0, 95 1. Усилия оттяги или момента От 0, 7 до взлетно го (форсажного) +0, 5 % от ИВ 2. Расход топлива То же ± 0, 5 % от ИВ 3. Расход воздуха То же +0, 7 % от ИВ 4. Частота вращения 20. . . 100 % или до возможной в эксплуатации +0, 2 % от ВП 5. Прокачка масла НЗ +0, 3 % от НЗ 6. Расход масла То же +0, 5 % от НЗ 7. Температура воздуха на входе в двигатель 215. . . 325 К 325. . . 600 К +1, 6 К +6, 0 К 8. Температура воздуха за компрессором НЗ ± 1, 0 % от ВП НЗ 9. Температура газов за турбиной НЗ + 1, 0 % от ВП НЗ 10. Температура масла на входе в двигатель НЗ +1, 5 % от ВП НЗ 11. Давление атмосферного воздуха НЗ +67 Па (+0, 5 мм рт. ст. )
12. Перепад между р и и р в при испытаниях НЗ +50 Па (+5 мм вод. ст. ) от ИВ 13. Давление воздуха на входе в двигатель при испытаниях его с наддувом НЗ +0, 4 % от НЗ 14. Перепад между полным и статическим давлениями в мерном участке входною коллектора НЗ ± 50 Па (+5 мм вод. ст. ) от ИВ 15. Давление воздуха за компрессором НЗ +0, 5 % от ВП НЗ 16. Давление газов за турбиной НЗ +0, 5 % от ВП НЗ 17. Давление топлива в предусмотренных точках топливной системы НЗ +1, 0 % от ВП НЗ 18. Давление масла в предусмотренных точках «масляной» системы НЗ +1, 0 % от ВП НЗ 19. Относительная влажность атмосферного воздуха на территории испытательной : станции 0. . . 100 % при 273. . . 337 К 0. . . 100 % при 213. . . 273 К ± 2, 0 % от ВП ± 4, 0 % от ВП
20. Амплитуда виброскорости, виброускорения, виброперемещения при колебаниях с частотой ротора НЗ 10. . . 12 % от ВП НЗ усилия меньше 0, 7 от максимального, устанавливается для данного типа двигателя изготовителем и согласовывается с разработчиком двигателя. НЗ — нормируемое значение, ИВ — измеряемая величина; ВП — верхний предел измерения.
Рис. 1. 2. Схема приемника давления заторможенного потока: 1 — приемная трубка; 2 — направляющая втулка; С — скорость потока Недостатком цилиндрического приемника является его высокая чувствительность к изменению угла набегания потока (не более ± 12 °). Это объясняется тем, что если поток набегает под некоторым углом к оси приемника, то критическая точка перемещается на другое место, и манометр, соединенный с отверстием на оси приемника, уже показывает меньшее давление. С целью устранения недостатка обычно меняют форму головки приемника, а именно: выполняют конус на входе приемного отверстия (рис. 1. 2), применяют двойную трубку (формируют камеру торможения) и т. п. В двигателях, чтобы не загромождать проточную часть, приемники давления заторможенного потока обычно размещают внутри обтекаемых тел (например, внутри сопловых или спрямляющих аппаратов, стоек и т. п. с обеспечением выхода приемной части камеры торможения в проточную часть). При измерениях в сверхзвуковом потоке перед приемником давления заторможенного потока возникает ударная волна (скачок). В этом случае измеряемое давление из-за потерь в ударной волне будет меньше полного давления в невозмущенном потоке, что необходимо учитывать при обработке результатов измерений. Отношение давлений заторможенного потока за скачком уплотнения потока и перед ним определяется по формуле Рэлея:
где к — отношение удельных теплоемкостей газа при постоянном давлении и при постоянном объеме; р* — давление заторможенного потока перед скачком; р* н — давление заторможенного потока за скачком; М — число Маха. Форма и геометрические размеры насадка приемника для измерения давле ния заторможенного потока определяются в зависимости от конкретных условий применения. Измерение статического давления на поверхности тел и стенок каналов осуществляется с помощью дренажирования, то есть с применением специально выполняемых дренажных отверстий в стенках тел и каналов. К форме и расположению дренажных отверстий предъявляются определенные требования: ось отверстия должна быть строго перпендикулярна поверхности; диаметр 0, 5. . . 1, 5 мм (отверстия меньшего диаметра быстро засоряются, большего — дают значительную ошибку измерения); отношение толщины стенки к диаметру отверстия не должно быть меньше 3; кромки отверстия не должны иметь заусенцев, скруглений и фасок, так как иначе возможны заметные погрешности измерения. Для измерения статического давления в потоке также применяются Г-образные и дисковые насадки различных конструкций.
Применение Г-образных насадков основано на том, что на поверхности осесимметричного тела вращения с обтекаемой головной частью на расстоянии более 3 -х диаметров отверстия от носка давление практически равно статическому. На этом расстоянии осуществляется отбор давления. Эти насадки обеспечивают возможность достаточно измерить статическое давление в широком диапазоне изменения дозвуковой скорости (λ =0. . . 0, 8). Дисковые насадки можно изготовить меньших размеров, чем Г-образные. Их конструкция более жесткая. Значительным достоинством дисковых насадков является нечувствительность к углу натекания в плоскости измерения. Од нако, при наличии угла между направлением потока и плоскостью измерения более 5. . . 8 0 дисковые насадки дают значительные погрешности. Для измерения статического давления в сверхзвуковом потоке применяют иглообразные насадки, в которых приемные отверстия располагают на значительном расстоянии от головной части. Чтобы избежать большой погрешности измерения, необходимо угол заострения головной части делать меньше предельного угла, при котором возникает отсоединенная волна на конусе. К недостаткам рассматриваемых насадков следует отнести малую жесткость, вследствие чего они подвержены колебаниям (вибрациям). Вибрации могут иска жать показания величины статического давления и приводить к быстрым поломкам насадков. Измерение динамического напора. Динамический напор представляет собой разность между давлением заторможенного потока и статическим Δр = (р* -р) и м ожет быть измерен с помощью дифференциального манометра, к которому подключены трубки отбора указанных давлений. Широкое распространение получила двойная напорная трубка, так называемая «трубка Прандтля» , в которой устройства для отбора статического и полного давлений объединены в одном корпусе. Эта трубка позволяет непосредственно измерить динамический напор в любой точке поперечного сечения потока и при этом на получаемые значения не оказывает какого-либо сильного влияния угол, который
трубка образует с направлением потока. Размеры такого комбинированного насадка определяются по нормалям (стандартам) и зависят т его диаметра. Приборы для измерения давлений. Давления газов или жидкостей измеряют с помощью манометров. При испытаниях ГТД наибольшее распространение получили жидкостные, механические и электрические манометры, а также преобразователи давления — тензорезисторные дифференциальные датчики, датчики избыточного давления, датчики разрежения (Сапфир, Метран, Honeywell, Kulite, >ruck и др. ). Принципиальное их отличие состоит в способах уравновешивания давления и регистрации его величины. В жидкостных манометрах измеряемое давление уравновешивается столбом жидкости, залитой в манометр, в механических и электрических — грузом или силой упругости деформируемого элемента, электрических манометрах (преобразователях давления) деформация упругого момента преобразуется в электрический сигнал, что уменьшает инерционность прибора и позволяет передать сигнал на необходимые расстояния. Жидкостные манометры. Простейший жидкостный манометр (пьезометр) представляет собой U-образную трубку, в которой измеряемая разность давлений. (р 2 –р 1 ) уравновешивается давлением столба жидкости, заполняющей эту трубку (рис. 1. 3): р 2 -р 1 = ρh, (1. 9) где р — плотность жидкости, залитой в пьезометр; h — высота столба жидкости (разница в уровнях жидкости в коленах трубки, измеряемых относительно нулевого равновесного уровня). При измерении абсолютного давления в какой-либо точке одна из трубок жидкостного манометра сообщается с атмосферой. Тогда измеряемое давление уравновешивается столбом жидкости и атмосферным давлением:
p 2 =p H +p h. (1. 10) Жидкостные манометры нашли применение в качестве средства для измерения давлений, незначительно отличающихся от атмосферного. Диапазон применения пьезометров обычно находится в пределах 3. . . 30 к. Па и в каждом конкретном случае зависит от плотности используемой жидкости. В жидкостных манометрах чаще всего используются такие жидкости, как вода (р = 1, 0 кг/дм 3 ), спирт метиловый (р = 0, 792 кг/дм 3 ), ртуть (р = 13, 54 кг/дм 3 ). Основным достоинством таких манометров является малая погрешность ( « 0, 1 %). Недостатками U-образных манометров являются невозможность динамических измерений, бесперспективность автоматизации и необходимость фиксирования величин уровней в двух трубках. Однотрубчатый манометр (рис. 1. 4) лишен последнего недостатка. Резервуар такого манометра имеет по сравнению с трубкой значительно больший диаметр, для того чтобы изменение уровня жидкости в нем было пренебрежимо мало. В испытаниях ГТД из всех жидкостных манометров практическое применение нашел и так называемый батарейный манометр, который состоит из нескольких трубчатых манометров и позволяет определять поля давлений (например, на входе в двигатель). Точки, в которых измеряется давление, соединены с трубками, а общий резервуар соединен с атмосферой. Показания батарейного манометра могут фотографироваться. Для регистрации показаний используют фотоэлектрический преобразователь, который с помощью специальной каретки перемещается вдоль пьезометрических трубок и фиксирует положение Уровней жидкости поочередно во всех трубках. Результаты измерения в этом случае передаются сразу на вход вычислительной машины, исключая длинный и трудоемкий процесс расшифровки и обработки результатов, зафиксированных на фото или видеопленке.
Рис. 1. 4. Чашечный манометр: 1 — измерительная трубка; 2 — расходный сосуд
Механические манометры обычно используются для измерения высоких давлений. Наиболее распространено применение манометра с трубчатой пружиной (трубкой Бурдона). В такой конструкции давление через штуцер манометра подается в трубку, которая под действием этого давления стремится распрямиться, и через рычажный механизм возникающее при распрямлении перемещение передается на указывающую стрелку. Сравнительно часто применяются мембранные и сильфонные механические манометры, чувствительными элементами в которых являются металлическая гофрированная мембрана или сильфон. В таких манометрах измеряемое давление подается в герметичный объем, закрытый мембраной. Под давлением мембрана прогибается, а сильфон растягивается, и через передающее устройство поворачивают стрелку прибора. Общим недостатком рассмотренных выше типов манометров является зависимость характеристик упругих элементов от температуры, а также существенная инерция при измерении. Достоинствами рассматриваемых типов приборов являются простота конструкции и низкая чувствительность к вибрациям. Выбор класса точности механического манометра с упругим чувствительным элементом определяется областью применения прибора. Рабочие манометры выпускаются пяти классов точности: 0, 5; 1, 0; 1, 5; 2, 5; 4, 0. Образцовые манометры используются для градуировки рабочих манометров и имеют два класса точности: 0, 2 и 0, 4. Электрические манометры (датчики). Основным недостатком механических манометров и жидкостных пьезометров является невозможность использования их для регистрации быстропротекающих процессов по причине значительной инерции чувствительных элементов. У электрических манометров указанный недостаток отсутствует. Они обладают малыми габаритами и малой инерцией. Существует большое количество конструкций электрических манометров. Наибольшее
распространение получили электрические манометры с индуктивными датчиками давления. Принцип их действия основан на том, что индуктивные датчики преобразовывают механическую величину — давление в электрическую величину — сопротивление. Конструктивно датчик выполнен в виде мембран-ной коробки с двумя электрическими катушками, расположенными по разные стороны относительно металлической мембраны. Таким образом, индуктивное сопротивление катушек зависит от положения мембраны, которое задается разностью измеряемых давлений р1 и р2. Электрические катушки в цепи являются плечами электрического моста Уинстона. В зависимости от сопротивления катушек меняются электрические потенциалы в точках разветвления электрической цепи к катушкам, что соответствует разности измеряемых давлений. В настоящее время промышленность выпускает индуктивные датчики трех типов: ДМИ-1, ДМИ-2, ДМИ-3. Измеряемые перепады давлений до 1, 0 МПа. Основная погрешность не превышает +3 % от диапазона измерения. Датчики работоспособны при температурах от -60 до +100 °С, вибрациях 10. . . 600 Гц и перегрузках до 20 g с амплитудой не менее 1 мм. Срок службы около 30 часов. Для обеспечения получения результатов в режиме реального времени все более широкое применение находят сканеры, которые вводятся в состав каналов ‘стендовых систем измерения давлений
Рис. 1. 5. Схема многоточечного измерения давлений с помощью сканеров
Сканеры измерения давления являются аппаратным элементом многоточечных систем измерения давлений в режиме реального времени (в темпе эксперимента). Сканеры давления (например, серии 9000) позволяют выполнять измерения давления в диапазоне от 2, 5 к. Па до 69 000 к. Па. Система многоточечного измерения давления выполняет измерения давления в двигателе и на испытательной установке и состоит из многоточечных измерителей давления, каждый измеритель имеет 16 каналов, распределительных коробок и сетевых переключателей (рис. 1. 5). Трубки из различных точек на двигателе, редукторе и установке подсоединены к многоточечным измерителям давления, которые осуществляют измерение и преобразование значений давления в сигналы технических единиц. Каждый многоточечный измеритель (сканер давления) имеет пьезоэлектрические датчики давления, распределительный трубопровод продувки (для продувки датчиков) и электрические соединения для электропитания, синхроимпульсов и связи по сети для передачи оцифрованного сигнала в систему сбора Данных для обработки и конвертации в физическую величину. Интерфейс каждого пьезоэлектрического датчика представляет собой 0, 125 -дюймовый вход на корпусе сканера. Работа сканера осуществляется при подаче на него постоянного тока с напряжением 24 В; для обеспечения питанием каждого сканера на испытательных стендах устанавливаются распределительные коробки, от которых к каждому сканеру подводится питающая линия; подключение осуществляется через восстанавливаемые предохранители. Сработавший предохранитель возвращают в исходное состояние путем устранения короткого замыкания, выключения и повторного включения источника питания постоянного тока (24 В) многоточечных измерителей.
Для работы каждого сканера давления необходим подвод опорного (базового) давления; на испытательных стендах источником базового давления окружающей среды для каждого многоточечного измерителя является распределительный трубопровод, соединенный с имеющимся на установке барометром. 1. 5. ИЗМЕРЕНИЕ ТЕМПЕРАТУР Измерение температуры — один из самых важных и в то же время сложных и трудоемких видов измерения. По температуре рабочего тела в различных сечениях газовоздушного тракта определяют термодинамическую эффективность узлов и двигателя в целом. Условия измерения температуры при испытаниях ГТД весьма разнообразны. Удовлетворить всем требованиям измерения при столь различных условиях конструкцией только одного прибора практически невозможно. Поэтому на практике применяются многочисленные методы измерения температуры и соответствующие им измерительные приборы. Жидкостные термометры. Работа жидкостных термометров основана на изменении объема жидкости при изменении температуры. В качестве рабочих жидкостей применяют: ртуть, толуол, этиловый спирт и некоторые другие. Жидкостные термометры в испытаниях ГТД применяются для измерения температуры окружающей среды, воздуха и жидкостей в трубопроводах, а также для контроля состояния других приборов. Широкое применение жидкостных термометров объясняется рядом преимуществ, которыми они обладают: широкий диапазон измеряемых температур (— 200. . . +1200 С), простота в обращении, высокая точность, отсутствие специальных источников питания и дополнительных приборов измерения. К недостаткам относятся: невозможность измерения температуры в точке поверхности или объеме, чувствительность к ударам и вибрациям, невозможность непосредственного измерения разности температур, значительная инерционность, невозможность дистанционной передачи измерений.
Термометры электросопротивления — это приборы, в которых для измерения температуры используется свойство металлов при нагревании или охлаждении изменять электрическое сопротивление. Чувствительным элементом в таком термометре является проволока, которая наматывается на изолирующий каркас стекло, фарфор) и вместе с ним помещается в корпус, защищающий чувствительный элемент от механического и химического воздействий окружающей среды (рис. 1. 6). В практике испытаний авиационных ГТД обычно применяют платиновые (особо точные) и медные термометры сопротивления. Платиновые термометры сопротивления выпускаются на пределы измерения от — 260 до +1100°С. Медные термометры сопротивления используют для измерения температуры от -50 до +200 °С. К достоинствам металлических термосопротивлений следует отнести: высокую точность измерения температуры; возможность дистанционной передачи показаний и включения в состав информационно-измерительных систем. К недостаткам таких приборов относятся: необходимость в источнике питания, большая инерционность, невозможность измерения температуры в точке, погрешности, вносимые изменением сопротивления соединительных проводов под воздействием температуры. В качестве материалов для чувствительных элементов полупроводниковых термосопротивлений (термисторов) используют смеси оксидов меди и марганца, кобальта и марганца, диоксида титана с оксидами магния, германия и других. На рис. 1. 7 показана схема германиевого термистора. Наиболее распространенными формами чувствительных элементов термисторов являются цилиндрические, шайбовые, бусинковые. Термисторы применяют в диапазоне измерения температуры от -100 до +300 °С. К достоинствам термисторов относятся: малые размеры (измерение практически в точке), малая инерционность и сравнительно малое влияние сопротивления соединительных проводов.
Недостатки полупроводниковых термометров сопротивления следующие: отсутствие взаимозаменяемости (каждый термистор требуется градуировать индивидуально); нелинейный характер зависимости электрического сопротивления от температуры; малая допускаемая мощность рассеяния при прохождении измерительного тока. Рис. 1. 7. Схема устройства германиевого термометра сопротивления: 1 — чувствительный элемент; 2 — выводы из платиновой проволоки; 3 — защитная гильза; 4 — стеклянная головка; 5 — электроизоляционная пленка (p изб =0, 02 МПа); 6 – термоукупорка.
Термоэлектрические термометры (термопары). Принцип работы термопары основан на том, что в цепи, составленной из двух разнородных проводников (термоэлектродов), возникает электрический ток, если места соединения проводников (спаи) имеют разную температуру. Силы, вызывающие этот ток, называются термоэлектродвижущимися силами. Величина электродвижущей силы в общем случае может быть различной при одинаковой разности температур в зависимости от их абсолютных значений. Эта зависимость будет однозначной только в том случае, если температуру одного из соединений поддерживать постоянной. Спай термопары, помещаемый в измеряемую среду, называют «горячим» (рабочим). Спай, температуру которого поддерживают постоянной, называют «холодным» (свободным). На рис. 1. 8 показаны схемы вариантов включения термопар в измерительную цепь. Обычно холодный спай помещают в среду с температурой тающего льда (0 °С). До начала измерений у термопар снимают градуировочную характеристику, в процессе градуировки рабочий спай термопары последовательно нагревают до различных температур и определяют термоэлектродвижущую силу. В табл. 1. 2 приведены типы изготавливаемых термопар и соответствующие диапазоны измеряемых температур. По материалу проводников, применяемых в термопарах, их можно разбить на две группы: термопары из благородных и термопары из неблагородных металлов. Из первой группы наиболее широкое применение нашли термопары платинородиевые-платинородивые и платинородиевые-платиновые. Они применяются для регистрации высоких температур (до 1600 °С) при исследовании провесов горения основных и форсажных камер сгорания. На рис. 1. 9 показано общее конструктивное устройство термопар.
Рис. 1. 7 Схема устройства германиевого термометра сопротивления: 1 – чувствительный элемент; 2 – выводы из платиновой проволоки; 3 – защитная гильза; 4 – стеклянная головка; 5 – электроизоляционная пленка.
1. 2. Типы термопар Тип ТП Материалы пар термоэлектродов Диапазон изме ряемых темпера тур в длительном режиме, °С Допустимый диа пазон температур при кратковремен но м режиме, °С Благ ород ные мета ллы ТВР Вольфрамрений (рений 5 %) Вольфрамрений (рений 20 %) 0. . . +2200 2500 ТПР Платинородий (30 % родия) Платинородий (6 % родия) 300. . . + 1600 1800 ТПП Платинородий (10 % родия) Платина 0. . . +1300 1600 Небл агоро дные мета ллы ТХА Хромель (10 % хрома, 90 % никеля) Алюмель(2%алюминия, кремния, 2% марганца, 1% кобальта, 94% никеля) -200. . . + 1000 1300 ТХК Хромель-копель (44% никеля+кобальт, 56% медь) -200. . . +600 800 тмк Медь-копель -200. . . +
К недостаткам платиновых термопар следует отнести: малые величины развиваемых при измерении термоэлектродвижущих сил (в связи с чем требуется высокочувствительная электроизмерительная аппаратура); значительное удельное электросопротивление, а также высокая стоимость. Основные достоинства термопар второй группы — доступность и относительно низкая стоимость термоэлектродного материала. Благодаря этому, электроды можно делать существенно большей толщины (если при измерениях не имеет значения инерционность показаний), что увеличивает механическую прочность и снижает электросопротивление электродов. Основными разновидностями термопар второй группы являются хромель-алюмелевая и хромель-копелевая термопары. Недостаток этих термопар — относительно невысокая рабочая температура (порядка 1000 °С). Для измерения более высоких температур применяются платинородиевые и другие термопары, которые размещаются в охлаждаемых корпусах и позволяют измерять температуры до 1800 °С и выше. Измерение температуры газа, движущегося с большой скоростью, является неотъемлемой частью исследований, проводимых на авиационных газотурбинных двигателях. Для количественной оценки сложного процесса торможения газового потока на поверхности «горячего» спая термопары используется понятие коэффициента восстановления (или торможения) — который характеризует способность термоприемника улавливать динамическую составляющую температуры торможения.
Рис. 1. 10. Схемы неэкранированной термопары (а) и термопар с экранированными (б, в, г) камерами торможения: а — неэкранированная, ξ = 0, 7. . . 0, 9; б — поперечно обтекаемая. ξ= 0. 90. . . 0. 96; в – продольно обтекаемая с поперечным расположением спая, ξ = 0, 92. . . 0, 97; г — продольно обтекаемая с продольным расположением спая, ξ = 0, 97. . . 0.
На рис. 1. 10 показаны схемы термоприемников разного вида, имеющих разные значения коэффициента восстановления Для измерения температуры на поверхности лопаток, дисков и других элементов ГТД широко применяются различные конструкции поверхностных термопар. Один из вариантов такой конструкции показан на рис. 1. 11. Термо ЭДС в термоэлектрическом пирометре измеряют милливольтметром или потенциометром. Милливольтметры, выпускаемые промышленностью, имеют шкалу, градуированную в градусах и милливольтах. Каждый милливольтметр предназначен к использованию в комплекте с определенной термопарой. Измерение термо. ЭДС с помощью потенциометра основано на уравновешивании измеряемого напряжения известным напряжением. Погрешность измерений не превышает ± 1 %. Средства измерения температуры тел по их тепловому излучению принято называть пирометрами. При таком измерении температурное поле объекта не искажается, так как измерение, осуществляемое пирометром, не требует непосредственного соприкосновения [44|. Оптические пирометры с так называемой «исчезающей» нитью переменного накаливания широко применяются для измерения яркостной температуры в видимой области спектра. Интервал измеряемых температур с помощью таких устройств установлен от 700 до 8000 °С. Измерение с помощью таких пирометров основано на сравнении в видимой области спектра яркости исследуемого тела с яркостью нити пирометрической
Рис. 1. 11. Конструктивная схема поверхностной термопары: 1 — «горячий» спай; 2 — защитная фольга; 3 — слюда (электроизолятор); 4 — термометрируемая деталь Рис. 1. 12. Принципиальная схема оптического (яркостного) пирометра [44]: 1 — телескоп; 2, 5 — входная и выходная диафрагмы; 3 — поглощающее стекло; 4 — красный светофильтр; 6 — окуляр; 7 — пирометрическая лампа; 8 — измерительный прибор; 9 — реостат настройки яркости нити
лампы. При этом в качестве чувствительного элемента наличия или отсутствия равенства яркостей служит человеческий глаз. Пирометр (рис. 1. 12) состоит из первичного преобразователя — телескопа, измерительного прибора и источника питания. Если яркость вольфрамовой нити накаливания пирометрической лампы будет меньше яркости фона изображения источника измерения, то нить представится черной. Если фон имеет меньшую по сравнению с нитью яркость, то нить будет выглядеть светлой на более темном фоне. Меняя сопротивление реостата, можно установить такую силу тока, при которой равенство яркостей нити и фона создает эффект исчезновения нити, которая перестает быть видимой. В настоящее время при испытаниях двигателей для измерения температур элементов конструкции нашли применение яркостные пирометры, созданные на базе фотоэлектрических приемников лучистой энергии (рис. 1. 13). С помощью линзы 4 поле зрения первичного преобразователя ограничено небольшим (5. . . 6 мм) участком. Пирометр измеряет температуру на кромке и части спинки каждой рабочей лопатки. Защитное стекло 3, выполненное из сапфира, предохраняет линзу от загрязнения и перегрева. Сигнал по световоду 5 передается к фотодетектору. Термоиндикаторные краски — химические вещества, изменяющие свой цвет при нагреве выше определенной температуры и сохраняющие его затем при охлаждении. Указанное свойство используется при определении температур дета лей двигателя. Набором термоиндикаторных красок можно измерять температуры от 40 до 1100 °С с удовлетворительной степенью точности, а также получать распределение температур по поверхности. Перед экспериментом образцы красок наносят на детали, которые нагревают в электропечи до различных температур и фиксируют температуры перехода и получаемые оттенки.
Рис. 1. 13. Схема установки пирометра на двигателе (а) и схема первичного преобразователя (б): / — подвод охлаждающего воздуха; 2 — первичный преобразователь; 3 — защитное стекло; 4 — линза; 5 — световод
В дальнейшем они используются для расшифровки результатов экспериментов. Термоиндикаторные краски регистрируют максимальную температуру во время опыта, поэтому выход на исследуемый режим не должен сопровождаться забросом температур. Метод измерения температуры с помощью термоиндикаторных красок обладает рядом преимуществ: не нарушаются целостность детали, условия теплообмена с окружающей средой; их можно применять на вращающихся деталях; не требуется специальное измерительное оборудование; краски просты в применении и механически прочны. Недостатки метода — он не позволяет измерять температуру деталей на переменных режимах и распределение температур в глубине материала. 1. 6. ИЗМЕРЕНИЕ РАСХОДА ТОПЛИВА При испытаниях авиационных двигателей в стендовых условиях и в полете одним из основных параметров, дающих возможность определить экономичность двигателя, является расход топлива. Существует достаточно большое количество методов измерения расходов топлива, основанных на различных физических принципах (дроссельные расходомеры, скоростные расходомеры, объемные и массовые расходомеры, ультразвуковые расходомеры). Наиболее распространенными являются дроссельные и скоростные расходомеры, позволяющие измерять мгновенные и суммарные расходы топлива соответственно. Дроссельные расходомеры относятся к устройствам переменного перепада давлений и представляют собой местное сужение трубопровода, в котором поток разгоняется, а статическое давление уменьшается. На рис. 1. 14 показаны схемы течения через стандартную диафрагму, сопло и трубу Вентури. Расход определяется по рабочей формуле
(1. 11) где α — коэффициент расхода; F — площадь отверстия; ρ — плотность жидкости; р 2 — измеряемые давления. Точность измерения расхода жидкости не хуже 1 %. Расходомеры постоянного перепада давления — поплавковые ротаметры — относятся к расходомерам обтекания. Ротаметр в простейшем виде состоит из вертикальной конической стеклянной трубки, через которую проходит жидкость (рис. 1. 15). Внутри трубки находится чувствительный элемент, выполненный в виде поплавка. Его верхний обод имеет канавки, выполненные под углом к оси поплавка. Под действием потока жидкости или газа поплавок перемещается вертикально и одновременно приходит во вращательное движение, центрируясь в середине потока. По перемещению поплавка судят об объемном расходе в единицу времени (м 3 /ч).
Рис. 1. 14. Схемы течения рабочей среды в сужающих устройствах: а — стандартная диафрагма; б — схема измерения и характер течения в канале с диафрагмой; в — характер течения и распределение давлений в канале с сужающим соплом; г — характер потока и распределение давлений в канале с трубой Вентури; р 1 , p 2 — давление до и после дроссельного прибора, Δр — перепад давления на дроссельном приборе; р п — потеря давления на дроссельном приборе На рис. 1. 16 показан поплавковый расходомер, который состоит из конического поплавка 1 и седла поплавка 2, размещенных внутри цилиндрического участка трубопровода. Конический поплавок выполняет ту же роль, что и коническая трубка у ротаметра.
Рис. 1. 15. Схема ротаметра: 1 — конусная стеклянная трубка: 2 — чувствительный элемент; 3 — шкала. Рис. 1. 17. Тахометрический расходомер: 1 — корпус; 2, 4 — выходной и входной НА; 3 — турбина с ферромагнитными лопастями; 5 — передающий преобразователь
И в той, и в другой схеме движущаяся вверх жидкость поднимает поплавок до уровня, при котором аэродинамическое сопротивление (перепад давления) уравновешивает силу тяжести поплавка. Высота подъема служит мерой измеряемого расхода. Для измерения мгновенного и суммарного расходов применяются электрические турбинные расходомеры, которые бывают нагруженного и ненагруженного типов. В ненагруженных расходомерах (рис. 1. 17) импульсы тока получают при прохождении ферромагнитных лопастей вблизи магнитопровода преобразователя, который формирует ЭДС. Скорость вращения турбинки связана определенным соотношением с расходом. Частота вращения турбинки определяется по количеству импульсов в единицу времени, поступающих с индукционного преобразователя. Простейшие конструкции таких расходомеров после проливки (градуировки) на специальных стендах обеспечивают точность измерения расхода на уровне 0, 3 %. В нагруженных турбинных расходомерах турбинка связана механической передачей с устройством, выдающим электрический сигнал, пропорциональный частоте вращения. 1. 7. ИЗМЕРЕНИЕ РАСХОДА ВОЗДУХА Наиболее распространенными являются два способа измерения расхода воздуха в двигателях. Это использование лемнискатного насадка на входе в двигатель и установка гребенки для измерения полных и статических давлений на выходе из сопла двигателя. Входной насадок, устанавливаемый на входе в двигатель (рис. 1. 18), имеет плавную входную часть (выполненную по лемнискате) для получения равномерных профилей скоростей по сечениям входного канала. Лемнискатный профиль (лемниската Бернулли, уравнение которой в полярных координатах имеет вид г 2 = а 2 л cos 2α, где а л = (0, 6. . . 0, 8)D в )
1. 18. Схема измерения расхода воздуха при стендовом испытании ГТД По окружности насадка расположены трубки отбора статического давления, которые объединены в коллектор для определения среднего по окружности статического давления. Измеряются значения перепада между давлением заторможенного потока и статическим Δр в = р* в — р в и температура Т* в. Причем, в силу высокого качества чистоты выполнения внутренней поверхности входного насадка, обычно принимают, что его σ вх ≈ 1, а р* в = р н. Тогда расход воздуха, кг/с, определяют по формуле
(1. 12) где константа F B — площадь мерного сечения, м 2 ; q(λ B ) — приведенная плотность тока, определяется по таблицам газодинамических функций по значению π(λ в ), которое вычисляется по результатам измерения Δр* в и р* в (1. 13) Конструкция двигателя не всегда позволяет установить лемнискатный насадок. В этом случае удобен способ измерения расхода с помощью пневмометрических трубок, располагаемых в выходном сечении сопла двигателя. Для этого выходная часть сопла условно разбивается на ряд колец с равными площадями и каждое такое кольцо для измерения давления заторможенного потока снабжается отдельными пневмометрическими трубками, которые обычно объединены в одну гребенку. На стенке сопла измеряется статическое давление. Температура потока по сечению неравномерна, поэтому по измерениям в нескольких точках сечения определяется средняя величина температуры заторможенного потока.
Термопары могут быть расположены на гребенке пневмометрических трубок. Расход продуктов сгорания двигателя G г определяется по той же формуле, что и для воздуха. Для продуктов сгорания авиационного топлива m г = 39, 7 (кг∙К)/к. Дж (для керосина). Расход воздуха будет равен G B = G r — G m , где G m — расход топлива, измеренный любым из перечисленных выше способов. 1. 8. ИЗМЕРЕНИЕ СКОРОСТИ ПОТОКА Определение величины скорости потока при испытании двигателей производят по уравнению Бернулли. Для газовых потоков малой скорости (М ≤ 0, 25 ) пользуются формулой для несжимаемой жидкости (1. 14) где Δр — перепад между давлением заторможенного потока и статическим давлением; р — плотность газа. Для потоков большой скорости используют соотношение (1. 15)
Приведенная скорость X определяется с помощью газодинамических функций в соответствии с величиной р / р* , полученной при измерениях, также как и температура Т*. Определение направления скорости в потоках. Для этого могут быть использованы методы визуализации потоков. Стенки канала выполняют прозрачными, а поток делают видимым за счет введения специальных наполнителей. Методы визуализации дают хорошие результаты при сравнительно малых скоростях потока (до 50 м/с). Метод нитей состоит в том, что в поток помещаются на тонких проволочках легкие шелковые нити или флажки (для горячих потоков — из листовой платины), которые принимают положение линий тока при плавном течении или сильно колеблются в зонах отрыва. Частицы, нити, флажки могут наблюдаться невооруженным глазом или фотографироваться в прямом или отраженном свете. Эти методы успешно применяются при исследовании течений вблизи поверхности тел, а также при определении направления потока и областей затенения в испытательных боксах. В тех случаях, когда прямой доступ для определения направления потока отсутствует, используют специальные приемники давления. Приемники давления для таких измерений и флюгарки показаны на рис. 1. 19, приемники, ориентированные по потоку, — на рис. 1. 20, неориентируемые — на рис. 1. 21. Чувствительным элементом приемника (рис. 1. 21, г, д) является сферическая головка, на которой выполнено пять отверстий, четыре из которых расположены симметрично относительно пятого (центрального) отверстия. Принцип действия прибора состоит в том, что в зависимости от направления потока вокруг головки приемника формируется вполне определенное поле давлений, которое воспринимается через отверстия приемника.
Рис. 1. 19. Приемники и флюгарки для измерения направления потока: а< 6 — одноточечные поворотные; в, г — ориентируемые двухточечные; д — четырехточечный, ориентируемый в двух плоскостях; е — флюгарка Рис. 1. 20. Приемники ориентируемые для измерения X. и направления потока: а б — насадки для измерения X. ; в, г — насадки для измерения X и направления потока; д — насадок для измерения X и направления потока трехточечный; е — насадок трехточечный веерообразный для измерения X и направления потока в пограничном слое
Рис. 1. 21. Приемники неориентируемые для измерения А. и направления потока: а, б, в — используются для измерения параметров в двухмерном потоке; г, д — в трехмерном; а, б — насадки трехточечные на цилиндрическом стержне; в — насадок трехточечный с протоком; г — шаровой пятиточечный насадок; д — Г-образный трубчатый пятиточечный насадок Методом сравнения экспериментально полученного поля давлений с имеющимися для каждого приемника образцами аналогичных полей, хранящимися в каталоге, определяют направление потока. В частности, если поле давлений симметрично, то это означает, что приемник ориентирован по потоку. Этим свойством часто пользуются — изменяют при проведении эксперимента положение приемника, добиваясь его ориентации по потоку, тем самым определяя направление потока. 1. 9. ИЗМЕРЕНИЕ НАПРЯЖЕНИЙ В ЭЛЕМЕНТАХ ГТД В ходе исследовательских и доводочных работ по двигателю обязательно проводят испытания, включающие определение напряжений, возникающих в элементах двигателя в процессе его работы. По величине этих напряжений определяются работоспособность конструкции элемента, а также характер его работы на эксплуатационных режимах.
Напряжения, возникающие в конструкции элемента двигателя, оценивают через измерение величин деформаций. Измерение деформаций проводится методом тензометрирования. В основе этого метода лежит использование тензометрических преобразователей (тензодатчиков) в качестве первичного средства измерения. В тензодатчиках используется свойство проводников изменять электрическое сопротивление при растяжении. Конструкция тензодатчика представляет собой тонкую проволоку с диаметром сечения 0, 02. . . 0, 04 мм, наклеенную зигзагообразно на подложку (бумагу, пленку, фольгу и т. п. ) и заклеенную сверху таким же материалом, как и подложка. К выведенным концам тонкой проволоки подсоединяются проводники для подвода электрического тока. Тензодатчик наклеивается на исследуемую деталь так, чтобы он мог воспринимать деформации детали. В качестве клея применяются клеящие составы, выбор которых зависит от температурных условий работы и материала исследуемой детали. Это могут быть карбонильные и фенолоформальдегидные клеи, жаростойкие термоцементы, жаростойкие силикатные эмали, кремнийорганические лаки и др. Слой клея между деталью и тензодатчиком должен быть минимально возможной толщины (несколько сотых долей миллиметра) для того, чтобы не исказить величины измеряемых деформаций. Основными параметрами тензодатчика являются база (2, 0. . . 150 мм), ширина (2, 0. . . 50 мм) и электрическое сопротивление (100. . . 250 Ом). Материал проволоки тензодатчика должен обеспечивать: — минимальный коэффициент температурного электросопротивления для минимизации погрешностей; — большое удельное сопротивление для минимизации габаритных размеров. При проведении работ по тензометрированию к тензодатчику подводится питание электрическим током,
сила которого измеряется и регистрируется с предварительной градуировкой в месте установки тензодатчика. Подключение напряжения питания от источника постоянного тока выполняется либо по схеме цепи делителя для регистрации только переменной составляющей деформации, либо по мостовой схеме для регистрации как статических, так и динамических измерений деформаций. Сигнал в виде величины электрического тока, проходящего через тензодатчик, передается по цепи от тензодатчика на регистрирующую аппаратуру. В обеспечение передачи и регистрации электрических сигналов используются специальные токосъемные устройства, позволяющие передавать сигнал с тензодатчика, расположенного на вращающейся при работе двигателя детали (рабочая лопатка, вал, диск и др. ) на статорную часть и регистрирующую аппаратуру. В качестве токосъемных устройств применяются щеточные токосъемники, где сигнал передается через контакт на щетках; ртутные токосъемники, в которых сигнал передается через ртуть, которая заполняет полость между вращающимся кольцом и статором, и телеметрические устройства (радиотокосъемники), у которых сигнал с вращающегося вместе с ротором токосъемника преобразуется в радиосигнал, передаваемый на специальную приемную антенну, расположенную на статорной части двигателя. 1. 10. ИЗМЕРЕНИЕ СИЛЫ И КРУТЯЩЕГО МОМЕНТА Измерение силы (тяги) при испытаниях ГТД осуществляют с помощью механических, гидравлических динамометров и упругих силоизмерителей с электрическими датчиками. Измерение, в основном, сводится к уравновешиванию тем или иным способом измеряемого усилия неизвестной величины. Принцип действия механических динамометров заключается в уравновешивании измеряемой силы с помощью системы рычагов, меньшим грузом или силой упругости деформируемого элемента.
Рис. 1. 22. Измерение силы с помощью рейтерных весов: 1 — рычаг 2 -го рода; 2 — опора; 3 — рейтер, подвижный груз В рычажном динамометре рейтерного типа (рис. 1. 22) измеряемая сила Р, приложенная к малому плечу l 1 уравновешивается меньшим грузом Q (рейтером подвижным грузом), перемещающимся на большем плече рычажного устройства, до момента возникновения равновесия (плечо l 2 ). Величина плеча l 2 является мерой измеряемой силы. На рис. 1. 23 приведена принципиальная схема маятникового динамометра, который представляет собой угловое коромысло AОВ, к малому плечу которою приложена измеряемая сила Р, на конце большого плеча R закреплен груз Q. В момент равновесия возникает равенство (1. 14)
Угол α служит мерой измеряемой силы, что отмечается на шкале с помощью указателя. Маятниковые динамометры значительно уступают по точности динамометрическим головкам (рис. 1. 24), которые с помощью промежуточных рычагов, уменьшающих передаваемое усилие, могут быть приспособлены для измерения сил практически любой величины, допуская при этом погрешность не более ± 0, 2 %. Здесь основной сравнивающий узел — квадрант 3 подвешен на двух гибких лентах к кронштейну 4. Рис. 1. 23. Схема маятникового динамометра Рис. 1. 24. Схема весовой (динамометрической головки): 1 — грузоприемный рычаг; 2, 5, 9 — ленты; 3 — квадрант; 4 — кронштейн; 6 — барабан; 7— указательная стрелка; 8 — грузик; 10 — демпфер; 11 — серьга тарной нагрузки; 12 — тяга
Рис. 1. 25. Компенсационная диафрагменная месдоза [32]: 1 — поршень: 2 — корпус: 3 — фланцевое кольцо: 4 — диафрагма; 5 — вставка; 6 — подающий клапан; 7 — сливной клапан; 8 — толкатель; 9— шариковый затвор; 10— расходный баллон; 11 – компенсационный баллон; 12 — маслобак; 13 — приемник давления; 14 — весовая головка
Измеряемая сила Р через грузоприемный рычаг 1 и ленту 2 передается на этот квадрант, который, имея противовес, каждый раз занимает положение, определяемое равенством моментов от измеряемой силы и )т противовеса. При этом величина приложенной к динамометру силы определяется по указателю 7, соединенному с квадрантом 3. Постоянное натяжение ленты 5 обеспечивается грузиком 8. Для исключения колебания всей измерительной системы при колебаниях силы Р рычаг 1 снабжен демпфером 10 и начальной нагрузкой 11. Гидравлические динамометры могут быть трех типов: непроточные, проточные и компенсационные (полупроточные). Широко распространены компенсационные диафрагменные месдозы (рис. 1. 25). Особенностью их конструкции является наличие подающего и дивного клапанов, регулирующих подвод или отвод жесткости (глицерин, митральные масла) из рабочей полости, при изменении под действием измеряемой силы положения поршня относительно нейтрального. С помощью этих клапанов давление жидкости устанавливается таким, чтобы оно уравновешивало приложенное усилие. Наибольшее применение получили упругие силоизмерители с электрическими первичными преобразователями. В них деформация упругого элемента преобразуется в изменение какого-либо электрического параметра. Схема тензорезисторного датчика типа ТВС приведена на рис. 1. 26. Работа того датчика основана на преобразовании деформации упругого элемента в электрический сигнал, пропорциональный измеряемой нагрузке. Тензорезисторы собираются по схеме электрического моста. Упругий элемент 1 силоизмерителя опирается на подставку 3, выполненную в виде цилиндрической призмы. Деформация изгиба приложении нагрузки передается тензорезисторам 5, вызывая растяжение нижних и сжатие верхних тензорезисторов, что изменяет их электрическое сопротивление.
Тензорезисторы включены в мостовую схему. Все четыре плеча моста активны. Это увеличивает чувствительность датчика и позволяет получить линейное уравнение связи усилия с выходным электрическим сигналом в виде напряжения постоянного тока. Чувствительный элемент силоизмерителя заключен в герметичный корпус 4, который заполняется кремнийорганической жидкостью для защиты тензорезисторов от влаги и для смазки опорных поверхностей. Герметизация полости осуществляется посредством мембраны 2. Датчики типа ТВС выпускаются на разные диапазоны измерения силы. Максимальная величина измеряемого усилия — 320 к. Н (32 тс). Номинальное выходное напряжение датчика — 50 м. В. Рис. 1. 26. Схема датчика ТВС: 1 — упругий элемент; 2 — защитная мембрана; 3 подставка под упругий элемент; 4 — корпус; 5 — тензорезисторы
В электрической схеме датчика ТВС предусмотрена термокомпенсация изменения электрического сопротивления тензорезисторов под действием температуры окружающего воздуха. Погрешность датчиков ТВС не более 0, 3 %. В практике испытаний находят применение вибрационно-частотные преобразователи силы, предназначенные для измерения статических и медленно изменяющихся усилий сжатия. Преобразователи выпускаются нескольких типоразмеров, отличающихся верхними пределами измеряемых усилий Р (от 1 до 1000 к. Н). Упругие элементы преобразователей на нагрузки свыше 10 к. Н выполнены в виде бруска 5 (рис. 1. 27), внутри которого образована виброперемычка 3. При приложении нагрузки брусок деформируется, в виброперемычке возникают растягивающие напряжения и частота ее собственных колебаний увеличивается. Для возбуждения колебаний и измерения их частоты служат два электромагнитных преобразователя 4. Один из них является возбудителем колебаний, другой — адаптером, преобразующим механические колебания виброперемычки в электрические. Упругий элемент помещен в корпус 2. Мембрана 1 предназначена для устранения влияния внеосевых сил на упругий элемент преобразователя. Измерения крутящего момента необходимо при испытаниях турбовальных двигателей, турбовинтовых двигателей, а также при автономных испытаниях компрессоров и турбин. Измерения осуществляются или с помощью балансирных моментоизмерительных систем, или с помощью торсионных моментомеров.
Рис. 1. 27. Схема вибрационно-частотного преобразователя силы: 1 — мембрана; 2 — корпус; 3 — виброперемычка; 4 — электро- магнитные преобразователи; 5 — упругий элемент (брусок) Рис. 1. 28. Схема гидротормоза и его нагрузочная характеристика: 1 — расходный бак воды; 2 — трубопроводы подачи воды; 3 — статор гидротормоза; 4 — ротор гидротормоза; 5 — подшипники подвески статора; 6 — подшипники ротора; 7 — фланец валопровода; 8 — отвод воды; 9 — бассейн со струйным охлаждением отработанной воды
В первом случае измеряется сила, приложенная на известном плече для уравновешивания измеряемого крутящего момента. Статор такого измерителя при этом должен быть установлен таким образом (подвешен на подшипниках), чтобы обеспечивалась возможность его свободного поворота на некоторый угол в плоскости крутящего момента (балансирный подвес). Тормозные моментоизмерители одновременно решают две задачи: поглощают (преобразуют) подведенную мощность и уравновешивают подведенный крутящий момент. На рис. 1. 28 приведена схема гидротормоза и его нагрузочная характеристика. Жидкость, находящаяся в гидротормозе, приводится во вращение движущимся ротором. За счет трения крутящий момент передается от ротора вращающемуся кольцу жидкости, а от него на подвижный статор. На нем установлен рычаг известной длины, на конце которого возникает сила. Измерив ее, определяют крутящий момент М кр = FI, а зная частоту вращения ротора, можно определить мощность. Схема измерения крутящего момента электрическим тормозом приведена на рис. 1. 29. Ротор электрического генератора связан с ротором испытуемого двигателя. За счет изменения оператором напряжения в обмотках возбуждения можно регулировать силы электромагнитного взаимодействия между ротором и статором. На статоре возникает крутящий момент, схема измерения которого аналогична гидротормозу. Электрический тормоз (генератор) позволяет, кроме того, измерить подводимую мощность по параметрам электрического тока, вырабатываемого генератором и поглощаемого системой резисторов. В случае применения торсиометров измеряется угловая деформация или механические напряжения, возникающие на некотором участке вала, передающего крутящий момент.
Рис. 1. 29. Схема измерения крутящего момента электрическим тормозом [32 J: 1 — корпус электрического генератора; 2 — якорь электрогенератора (ротор тормоза); 3 обмотки возбуждения, регулирующие с помощью изменяемого тока, силу электромагнитного взаимодействия между ротором и статором; 4 — подшипники ротора; 5 — подшипники статора; 6 — валопровод, соединяющий ротор тормоза с двигателем; 7— рычаг (длиной L). установленный на статоре; 8 — электрический датчик усилия (в учебной лаборатории — вибрационно-частотный); 9 — вторичный прибор для измерения усилия (например — цифровой частотомер)
Кроме перечисленных загрузочных устройств в практике применяют малоинерционные электрические измерители крутящего момента — торсиометры, в которых мерой момента служит деформация упругих элементов, преобразованная в параметры электрического тока. Из торсиометров с бесконтактными токосъемниками наиболее широко применяются торсиометры с проволочными преобразователями. На вал, передающий измеряемый момент, наклеиваются два тензометра, расположенные перпендикулярно другу и под углом 45° к оси вала (по направлению главных напряжений). Оба преобразователя включаются в два соседних плеча измерительного электрического моста. Фотоэлектрический торсиометр не нуждается в токосъемном устройстве. В двух местах вала, на базовом расстоянии L, жестко укрепляются диски с радиальными прорезями. Между дисками расположен источник света. С другой стороны каждого диска за диафрагмой с узкой щелью располагаются фотоэлементы. Положение дисков относительно друга регулируется так, чтобы при вращении с нулевой нагрузкой в момент прохождения прорезями диафрагм свет одновременно попадал на оба фотоэлемента. Во время измерения, когда крутящий момент не равен нулю, за счет упругих деформаций вала диски окажутся сдвинутыми относительно друга и фотоэлементы будут освежаться не одновременно. Импульсы от фотоэлемента поступают в специальное Устройство, в котором измеряется промежуток времени от одного до другого импульса. На рис. 1. 30 представлена схема торсионного тензорезисторного бесконтактного моментомера. Его ротор 1 представляет собой торсионный вал с двумя фланцами. Суженный трубчатый участок вала — упругий элемент, на котором склеены тензорезисторы 6, соединенные в мост. Статор 3 моментомера установлен на подшипниках 2.
Электрическое питание на мост подается через пару индуктивно связанных катушек 5 и через выпрямитель-стабилизатор, разменный внутри вала. Напряжение разбаланса моста, возникающее при нагруби вала крутящим моментом, преобразуется в частотно-модулированный сигнал, который через двухполюсный кольцевой конденсатор 4 с воздушным изолятором поступает на статор, а затем — в измерительную систему. Рис. 1. 30. Схема торсионного тензорезисторного моментомера: 1 — ротор: 2 — подшипник; 3 — статор; 4 — обкладка конденсатора; 5 — обмотка трансформатора; 6 — тензорезистор Электрическое питание на мост подается через пару индуктивно связанных катушек 5 и через выпрямитель-стабилизатор, разменный внутри вала. Напряжение разбаланса моста, возникающее при нагруби вала крутящим моментом, преобразуется в частотно-модулированный сигнал, который через двухполюсный кольцевой конденсатор 4 с воздушным ротором поступает на статор, а затем — в измерительную систему. Торсионные моментомеры позволяют в ряде случаев обеспечить более высокую точность измерения (0, 2. . . 0, 3 %) по сравнению с балансирными системами >1, 2. . . 1, 5 %).
1. 11. ИЗМЕРЕНИЕ ЧАСТОТЫ ВРАЩЕНИЯ В практике испытаний авиационных ГТД частота вращения измеряется тахометрами, в комплект которых входят первичный преобразователь и указатель. Первичный преобразователь представляет собой миниатюрный генератор (фазного тока 5 (рис. 1. 31), вал которого связан через коробку приводов с ротором двигателя. Электрический ток приводит во вращение якорь 4 электродвигателя указателя. Вместе с якорем вращается узел постоянных магнитов 3, от чего в диске 2 возникают вихревые токи. При их взаимодействии с магнитным полем узла 3 создается крутящий момент, пропорциональный частоте вращения, который преодолевает противодействующий момент спиральной пружины и отклоняет стрелку указателя. Информативным сигналом первичного преобразователя является также частота переменного тока, которая измеряется частотомером. Точность измерения до 0, 2. . . 0, 5%. Рис. 1. 31. Схема магнитоиндукционного тахометра: 1 — спиральная пружина; 2 — диск (чувствительный элемент); 3 — магнитный узел; 4 — якорь синхронного электродвигателя указателя; 5 — якорь первичного преобразователя тахометра
1. 12. ИЗМЕРЕНИЕ ВИБРАЦИЙ Появляющиеся в процессе работы двигателя переменные силы — неуравновешенность вращающихся деталей, нарушение балансировки и др. — являются источниками возбуждения колебаний, приводящих к целому ряду дефектов двигателя (к разрушениям опор, уплотнений и т. п. ). Поэтому необходимы постоянный контроль вибраций и специальные испытания двигателя с вибрографированием, целью которых является определение уровня вибраций и режима, где этот уровень наибольший. Первичные преобразователи для измерения вибраций обычно устанавливают в плоскости опор ротора, на агрегатах, в воздухозаборнике, на форсажной камере и других элементах, где ожидается повышенный уровень вибрации. Если в рабочем диапазоне частоты вращения вибрации не превышают допустимых пределов, то считается, что двигатель успешно прошел испытания вибрографированием. Для этих целей используют измерители вибраций, основанные на различных физических принципах (индуктивные, пьезоэлектрические, сейсмические и др. ). В схеме преобразователя сейсмического типа сейсмическая масса (магнит) остается во время вибрации практически неподвижной, а корпус, скрепленный с объектом измерения, совершает колебания вместе с ним. Вокруг корпуса выполнена обмотка из проводника электрического тока. В результате пересечения обмоткой магнитных линий магнита в обмотке индуцируется электрический ток, пропорциональный уровню вибрации.
1. 13. ИЗМЕРЕНИЕ ЭМИССИИ ВРЕДНЫХ ВЕЩЕСТВ В настоящее время особое значение приобрела оценка эмиссии вредных веществ и дыма в атмосферу с выхлопными газами ГТД. Количественно эмиссия вредных газообразных веществ (кроме дыма) оценивается индексом эмиссии Е 1, который представляет собой отношение массы вредного вещества к одному килограмму израсходованного топлива (расчетная величина). Оценка эмиссии проводится путем измерений в ходе сертификационных, квалификационных и типовых стендовых испытаний ГТД. По результатам измерений определяется степень соответствия ГТД требованиям Международных норм, ограничивающих эмиссию авиационных ГТД (ICAO), или общих санитарных норм, ограничивающих вредные выбросы в атмосферу ГТД промышленного и энергетического применения. Для проведения стендовых испытаний ГТД с замером эмиссии испытательный стенд должен быть оснащен специальной стендовой системой отбора проб выхлопных газов и анализа отобранных проб. Двигатель монтируется на стенд для испытаний. За соплом двигателя устанавливается пробоотборник, приемные отверстия которого должны располагаться в плоскости, перпендикулярной направлению движения струи выхлопных газов из сопла двигателя на расстоянии не более 0, 5 диаметра сопла. Линия подачи отбираемой пробы к газоанализатору проверяется на герметичность и прогревается до температуры 150. . . 160 °С с целью исключения влияния тепло-обмена на состав отбираемой пробы. Далее выполняют проверку линии на чистоту включением подачи пробы в анализаторы на неработающем двигателе. На проверенных таким образом диапазонах анализаторов отклонение указателей от нулевого значения не должно превышать 1 % шкалы.
Все технические характеристики и состояние анализаторов должны соответствовать требованиям стандарта ICAO. Точность измерения концентрации несгоревших углеводородов зависит от влияния на отклик ионизационного детектора состава углеводородной молекулы, наличия и количества кислорода в пробе, что называют синоргическим эффектом. Степень отмеченного синоргического эффекта ограничивается и определяется специальным испытанием конкретного анализатора. Система отбора и измерения эмиссии готова к работе, если дрейф нуля анализаторов не превышает 1 % в течение 0, 5 ч, а температура линии отбора пробы изменяется в пределах ± 5 °С от заданной величины. Непосредственно перед проведением испытания необходимо выполнить градуировку и калибровку газоанализирующей аппаратуры, в качестве которой используется системы «BECKMAN» , «ROSEMOUNT» , «EMERSON» . Калибровку анализаторов необходимо проводить с использованием эталонных газов и эталонных газовых смесей до и после испытания двигателя, а по осредненным данным двух калибровок проводить расшифровку результатов измерений величины эмиссии.
После выполнения всех подготовительных операций двигатель запускается, прогревается на режиме «малый газ» и далее выполняется отбор проб на всех сжимах от малого газа до взлетного, что определяется программой испытания, ходе испытания кроме измерения эмиссии должны регистрироваться такие параметры как: • тяга (мощность) двигателя; • частота вращения роторов двигателя; • давление воздуха за компрессором; • температура воздуха за компрессором; • массовый расход топлива; • расход воздуха через газогенератор; • температура воздуха на входе в двигатель; • давление воздуха на входе в двигатель; • атмосферное давление; • влажность воздуха на входе в двигатель.
На каждом установившемся режиме работы двигателя отбор проб для определения химического состава должен выполняться после стабилизации параметров работы двигателя (2 мин) при последовательной смене режимов работы двигателя в обоих направлениях. Процедуру отбора нужно производить с таким расходом отбираемого газа, чтобы время транспортирования пробы от пробоотборника до анализирующей аппаратуры не превышало 10 с. При определении эмиссионных характеристик двигателя измеряются концентрации следующих компонентов; • оксид углерода СО; • диоксид углерода СО 2 ; • суммарные углеводороды СН; • оксиды азота NO x. Качество процедур отбора и анализа оценивается расчетным коэффициентом качества отбора и анализа проб, путем проверки баланса углерода, определяемого сравнением отношения расхода воздуха к расходу топлива, рассчитанного по общей концентрации углерода в пробе (за исключением углерода в составе дыма), с отношением измеренных расходов воздуха и топлива через двигатель. Коэффициент качества отбора и анализа проб для режима «малый газ» должен находиться в диапазоне 0, 85 < К п < 1, 15, а для всех остальных режимов работы двигателя в диапазоне 0, 9 < К п < 1, 0. Производится расчет индекса эмиссии EI для каждого из компонентов в пробе, и выполняется приведение рассчитанного индекса эмиссии к условиям стандартной атмосферы на уровне моря. Для испытуемого двигателя определяются массы каждого загрязняющего компонента X, выделяемые работающим двигателем за стандартный взлетно-посадочный цикл. Содержание дыма определяется методом фильтрации пробы выхлопных газов через белый бумажный фильтр. Расчетная масса пробы определяется из условия пропускания 16, 2 кг газа на 1 м 2 площади фильтра
. Безразмерное число дымности SN характеризуется абсолютными отражательными способностями загрязненного и чистого фильтров. Получаемые числа дымности должны быть меньше максимально допустимых значений [4]. Итогом таких испытаний двигателя является оценка уровня эмиссии газообразных загрязняющих веществ, которая производится сопоставлением замеренных величин эмиссии вредных компонентов СО, СН, NO x с нормативными уровнями эмиссии.
1. 14. ИЗМЕРЕНИЕ ШУМА Для измерения шума, генерируемого двигателем, применяется акустическая аппаратура, состоящая из микрофонов, усилителей, калибратора и системы регистрации информации. К микрофонам должны предъявляться следующие требования: • в диапазоне частот 40. . . 20 000 Гц неравномерности частотной характеристики и поля звукового давления должны быть ± 0, 5 д. Б, не более; • они должны быть всенаправленными. Калибратор измерительной системы должен быть универсальным и адаптивным и иметь возможность калибровки микрофонов разного типа. Выходной сигнал анализирующей системы должен состоять из одной трети октавного диапазона уровней звукового давления. Этот диапазон охватывается 30 фильтрами анализатора. Акустическая аппаратура должна осуществлять измерения уровней шума от 0 до 160 д. Б и спектрального состава шума при температуре окружающей среды от -30 до +100 °С с точностью до 1 д. Б.
1. 15. МЕТОДЫ КОНТРОЛЯ СОСТОЯНИЯ И ОБНАРУЖЕНИЯ ДЕФЕКТОВ В ХОДЕ ИСПЫТАНИЙ ГТД В процессе испытаний в двигателе происходит большое число физических изменений и повреждений. К ним относятся: эрозия, коррозия, загрязнение, оплавление, разрушение посторонними предметами, износ уплотнений, увеличение радиальных зазоров, прогары и коробление рабочих и сопловых лопаток турбины, частичная или полная поломка лопаток, трещин лопаток или дисков ротора, вызванные усталостью или работой в условиях, выходящих за установленные пределы, засорение топливных форсунок и т. д. Поэтому главной задачей контроля состояния двигателя является получение достоверной информации о дефектах на ранней стадии их развития, когда дефект еще не влияет на работу детали или узла, а следовательно, и на параметры работы двигателя. Своевременное обнаружение неисправностей и снятие дефектного двигателя с самолета для ремонта позволяют повысить безопасность его эксплуатации. Для раннего обнаружения дефекта прежде всего необходимы контроль уровня вибраций корпуса и подшипников, а также анализ состояния проточной части двигателя. Контроль за уровнем вибраций ведется с помощью первичных преобразователей, один из которых рассмотрен выше. Анализ состояния газовоздушной проточной части, в которую входят обтекаемые газом каналы, компрессоры, камера сгорания, турбины и сопла, основывается, во-первых, на результатах измерений основных параметров (таких, как давления заторможенного потока и статические давления в характерных сечениях, температуры за компрессором, перед и за турбиной, расход топлива и другие) и, во-вторых, на специальных методах контроля.
Примером специальных методов контроля является использование индикатора поломки лопаток турбомашин. В ряде случаев собственно поломка лопатки рабочего колеса турбины или компрессора происходит незаметно, но отсутствие в роторе целой лопатки или ее части приводит к появлению дисбаланса ротора и, следовательно, увеличению вибрационных нагрузок на подшипники. Кроме того, нарушается обтекание как самого венца рабочего колеса, так и соседних сопловых аппаратов, что приводит к ухудшению условий их работы и к возможному нарастанию разрушений. Для того чтобы вовремя обнаружить и исключить подобный дефект при работающем двигателе без его частичной разборки и осмотра применяют индикатор поломки лопаток турбомашин. В корпусе турбины над лопатками рабочего колеса устанавливают индукционный импульсный первичный преобразователь, генерирующий электрический импульс в момент прохождения мимо него лопатки турбины. Импульсы датчика усиливаются и поступают для регистрации в регистрирующую аппаратуру (осциллограф, магнитограф, анализатор частот и др. ). Если все лопатки колеса целы, то импульсы первичного преобразователя следуют через равные промежутки времени. В случае поломки одной или нескольких лопаток периодичность импульсов нарушается, так как оборванная лопатка не возбуждает импульса в первичном преобразователе. Такие повреждения, как усталостные трещины дисков роторов или лопаток или разъедание коррозией структуры материала, не обнаруживаются никакими измерениями и должны выявляться с помощью визуальных методов контроля без снятия двигателя с самолета или стенда.
Среди таких методов контроля большое распространение получили оптические смотровые приборы (бороскопы, эндоскопы и т. д. ), которые представляют собой гибкую или жесткую трубку с системой ахроматических линз и объективом, совмещенным с миниатюрной лампой накаливания или световодом с выносным источником света. Объектив такого прибора может иметь прямой или боковой обзор. Все это позволяет проводить осмотр труднодоступных деталей без разбора двигателя. Оптические смотровые приборы имеют приспособленные к ним фотографические камеры и достаточно мощные лампы-вспышки. Такие приборы могут располагать и телевизионной системой для одновременного наблюдения осматриваемого пространства группой наблюдателей и видеосъемки. В отдельных случаях применяются рентгеноскопия, рентгенография и другие методы. О многом может сказать и контроль масляной системы. Наличие стружки в масле говорит о трущихся деталях. Периодически сравнивая результаты анализа масла, можно судить о развитии дефекта, а по материалу стружки определить дефектные детали. Проведение подобного анализа и сравнение его с полученными измерениями в газовом тракте, анализ уровней вибраций корпуса двигателя и его деталей, а также результаты визуальных методов контроля взаимно дополняют друга и дают возможность получить правильную информацию о состоянии двигателя.
РЕЗЮМЕ (по главе 1 «Измерения при испытании двигателей» ) 1. Измерение — это нахождение значения физической величины опытным путем с помощью специальных технических средств. Виды измерений: прямые, косвенные, совокупные и совместные. На практике все измерения выполняются с определенной степенью приближения. Возникновение погрешностей связано с несовершенством методов и средств измерений, влиянием условий измерений и действиями персонала, выполняющего измерения. Класс точности прибора — это обобщенная характеристика средств измерения, численно равная наибольшей относительной погрешности прибора, выраженной в процентах. 2. Под средством измерения понимают техническое средство (или их комплекс), предназначенное для измерения, имеющее нормированные метрологические характеристики и (или) хранящее единицу физической величины, размер которой остается неизменным в течение известного интервала времени. Чувствительность средства измерения δ — это его свойство, определяемое отношением выходного сигнала Δу к вызывающему изменению входной величины Δх. 3. Параметры двигателя измеряются на основных режимах без отбора воздуха на нужды воздушного судна (ВС) и без загрузки агрегатов, установленных на двигателе и используемых на нужды ВС. Погрешность измерения параметров двигателя определяется интервалом, в котором с установленной вероятностью Р = 0, 95 находится суммарная погрешность измерения. В тех случаях, когда измерение нельзя повторить, помимо границ погрешности результата измерения, соответствующих доверительной вероятности Р = 0, 95, допускается указывать границы для доверительной вероятности Р = 0, 99.
4. При изучении движения жидкости и газа различают понятия статического давления и давления заторможенного потока. Давлением, которое учитывает скоростной, динамический напор (p. V 2)/2, называется давление заторможенного без потерь потока. Исходя из этого, формируются методы определения указанных параметров. Если в месте расположения критической точки выполнить отверстие и соединить его трубопроводом с манометром, то прибор покажет величину давления заторможенного потока. Это — простейший цилиндрический приемник давления заторможенного потока. Такой приемник, несмотря на свою простоту, имеет достаточно хорошую точностную характеристику (погрешность измерения давления оставляет менее 1 %). Измерение статического давления на поверхности тел и стенок каналов осуществляется с помощью дренажирования, т. е. с применением специально выполняемых дренажных отверстий в стенках тел и каналов. К форме и расположению дренажных отверстий предъявляются определенные требования: ось отверстия должна быть строго перпендикулярна поверхности; диаметр должен быть в пределах 0, 5. . . 1, 5 мм. Для измерения статического давления в потоке также применяются Г-образные и дисковые насадки различных конструкций.
Давления газов или жидкостей измеряют с помощью манометров. При испытаниях ГТД наибольшее распространение получили жидкостные, механические и электрические манометры, а также преобразователи давления — тензорезисторные дифференциальные датчики, датчики избыточного давления, датчики разряжения (Сапфир, Метран, Honeywell, Kulite, Druck и др. . ). 5. На практике применяются многочисленные методы измерения температуры. Жидкостные термометры. Работа жидкостных термометров основана на изменении объема жидкости при изменении температуры. Термометры электросопротивления — это приборы, в которых для измерения температуры используется свойство металлов при нагревании или охлаждении изменять электрическое сопротивление. Термоэлектрические термометры (термопары). Принцип работы термопары основан на том, что в цепи, составленной из двух разнородных проводников (термоэлектродов), возникает электрический ток, если места соединения проводников (спаи) имеют разную температуру. Силы, вызывающие этот ток, называются термоэлектродвижущимися силами. Термоиндикаторные краски — химические вещества, изменяющие свой цвет при нагреве выше определенной температуры и сохраняющие его затем при охлаждении. 6. Существует достаточно большое количество методов измерения расходов топлива, основанных на различных физических принципах (дроссельные расходомеры, скоростные расходомеры, объемные и массовые расходомеры, ультразвуковые расходомеры). Наиболее распространенными являются дроссельные и скоростные расходомеры, позволяющие измерять мгновенные и суммарные расходы топлива соответственно Дроссельные расходомеры относятся к устройствам переменного перепада давлений и представляют собой местное сужение трубопровода, в котором поток разгоняется, а статическое давление уменьшается.
7. Наиболее распространенными являются два способа измерения расхода воздуха в двигателях: использование лемнискатного насадка с расходомерным коллектором и установка гребенки для измерения перепада между давлением заторможенного потока и статическим давлением. Конструкция двигателя не всегда позволяет установить лемнискатный насадок. В этом случае удобен способ измерения расхода с помощью пневмометрических трубок, располагаемых в выходном сечении сопла двигателя. Для этого выходная часть сопла условно разбивается на ряд колец с равными площадями и каждое такое кольцо для измерения давления заторможенного потока снабжается отдельными пневмометрическими трубками, которые обычно объединены в одну гребенку 8. Определение величины скорости потока при испытании двигателей производят по уравнению Бернулли. Для газовых потоков малой скорости (M ≤ 0, 25) пользуются формулой для несжимаемой жидкости. Приведенная скорость λ определяется с помощью газодинамических функций в соответствии с величиной р / р*, полученной при измерениях, также как и температура Т * Определение направления скорости в потоках. Для этого могут быть использованы методы визуализации потоков. Стенки канала выполняют прозрачными, а поток делают видимым за счет введения специальных наполнителей. Методы визуализации дают хорошие результаты при сравнительно малых скоростях потока (до 50 м/с). 9. Оценка напряжений, возникающих в конструкции элемента двигателя, производится через измерение величин деформаций. Измерение деформаций производится методом тензометрирования.
В тензодатчиках используется свойство проводников изменять электрическое противление при растяжении. Тензодатчик наклеивается на исследуемую деталь так, чтобы он мог воспринимать деформации детали. Основными параметрами тензодатчика являются база (2, 0. . . 150 мм), ширина (1, 0. . . 50 мм) и электрическое сопротивление (100. . . 250 Ом). Сигнал в виде величины электрического тока, проходящего через тензодатчик, передается по цепи от тензодатчика на регистрирующую аппаратуру. 10. Измерение силы (тяги) при испытаниях ГТД осуществляют с помощью механических, гидравлических динамометров и упругих силоизмерителей с электрическими датчиками. Измерение сводится к уравновешиванию тем или иным способом измеряемого усилия неизвестной величины. Принцип действия механических динамометров заключается в уравновешивании измеряемой силы с помощью системы рычагов, меньшим грузом или силой упругости деформируемого элемента. Наибольшее применение получили упругие силоизмерители с электрическими первичными преобразователями. В них деформация упругого элемента преобразуется в изменение какого-либо электрического параметра. Работа этого датчика основана на преобразовании деформации упругого элемента в электрический сигнал, пропорциональный измеряемой нагрузке. 11. Измерения крутящего момента необходимо при испытаниях турбовальных двигателей, турбовинтовых двигателей, а также при автономных испытаниях компрессоров и турбин. Измерения осуществляются или с помощью балансирных моментоизмерительных систем, или с помощью торсионных моментомеров.
В первом случае измеряется сила, приложенная на известном плече для уравновешивания измеряемого крутящего момента. В случае применения торсиометров измеряется угловая деформация или механические напряжения, возникающие на некотором участке вала, передающего крутящий момент. Торсионные моментомеры позволяют в ряде случаев обеспечить более высокую юность измерения (0, 2. . . 0, 3 %) по сравнению с балансирными системами (0, 5. . . 1, 5%). 12. В практике испытаний авиационных ГТД частота вращения измеряется тахометрами, в комплект которых входят первичный преобразователь и указала 13. Измерение вибраций. Переменные силы, появляющиеся в процессе работы двигателя, — неуравновешенность вращающихся деталей, нарушение балансировки и др. — являются источниками возбуждения колебаний, приводящих к целому ряду дефектов двигателя (к разрушениям опор, уплотнений п. п. ). Первичные преобразователи для измерения вибраций обычно устанавливают в 1 скости опор ротора, на агрегатах, в воздухозаборнике, на форсажной камере и упругих элементах, где ожидается повышенный уровень вибрации. 14. Оценка эмиссии производится путем измерений в ходе сертификационных, квалификационных и типовых стендовых испытаний ГТД. По результатам измерений определяется степень соответствия ГТД требованиям Международных норм, ограничивающих эмиссию авиационных ГТД (ICAO), или общих санитарных норм, ограничивающих вредные выбросы в атмосферу ГТД промышленного и энергетического применения.
Для проведения стендовых испытаний ГТД с замером эмиссии испытательный стенд должен быть оснащен специальной стендовой системой отбора проб выхлопных газов и анализа отобранных проб. При определении эмиссионных характеристик двигателя измеряются концентрации следующих компонентов: оксид углерода СО; диоксид углерода СО 2 ; суммарные углеводороды СН; оксиды азота NО X. 15. Для измерения шума, генерируемого двигателем, применяется акустическая аппаратура, состоящая из микрофонов, усилителей, калибратора и системы регистрации информации. 16. Анализ состояния газовоздушной проточной части, в которую входят обтекаемые газом каналы, компрессоры, камера сгорания, турбины и сопла, основывается, во-первых, на результатах измерений основных параметров (таких, как давления заторможенного потока и статические давления в характерных сечениях, температур за компрессором, перед и за турбиной, расхода топлива и других) и, во-вторых, на специальных методах контроля. Такие повреждения, как усталостные трещины дисков роторов или лопаток или разъедание коррозией структуры материала, не обнаруживаются никакими измерениями и должны выявляться с помощью визуальных методов контроля без снятия двигателя с самолета или стенда.
ВОПРОСЫ 1. Что такое измерения, виды измерений при испытаниях ГТД, прямое измерение, косвенное измерение? 2. В чем состоят метод непосредственной оценки, дифференциальный метод, метод совпадений? 3. Что такое погрешности измерений, класс точности прибора? 4. Измерение давлений — измерение полного давления (принципы, методы), измерение статического давления (принципы, методы), измерение динамического напора (принципы, методы) — назовите. 5. Приборы для измерения давлений — жидкостные манометры, механические манометры, электрические манометры (датчики) — назовите принципы действия, области применения. 6. Измерение температур, приборы для измерения температур жидкостные термометры, термометры электросопротивления, термоэлектрические пирометры (термопары), термоиндикаторые краски — назовите принципы действия, области применения. 7. Измерение расхода топлива, приборы для измерения расхода топлива дроссельные расходомеры, скоростные расходомеры — назовите принципы действия, области применения. 8. Измерение расхода воздуха — назовите применяемые способы, средства, методы оценки. 9. Измерение скорости потока жидкости и газа — определение величины скорости потока, направления скорости в потоках — назовите методы, применяемые средства.
10. Измерение крутящего момента — применяемые методы, средства и устройства — назовите принцип действия устройств, методы измерения и определяемые параметры и характеристики. 11. Измерение частоты вращения, вибраций, напряжений в элементах ГТД — назовите применяемые методы, средства и устройства, принципы их действия. 12. Назовите методы контроля состояния ГТД и обнаружения дефектов в ходе испытаний ГТД. 13. Измерение шума, генерируемого двигателем, особенности оснащения испытательного стенда — назовите методы и средства измерений. 14. Измерение эмиссии ГТД — назовите особенности оснащения испытательного стенда, методы и средства измерений.
Глава 2 ВИДЫ ИСПЫТАНИЙ АВИАЦИОННЫХ ГТД Каждый авиационный двигатель, пройдя этапы проектирования, конструирования и изготовления, подвергается испытанию [19, 21, 26, 33, 48, 49]. Единственная возможность убедиться в надежной работе и в обеспечении тех параметров, которые были заложены при проектировании, — это провести испытание двигателя. Таким образом, испытания — это экспериментальное определение (оценивание) и контроль количественных и качественных характеристик свойств объекта испытаний как результат воздействия на него при его функционировании. Результаты испытаний зависят от условий — совокупности воздействующих факторов и режимов функционирования объекта при испытаниях [3]. Испытание авиационного двигателя преследует три цели: 1. Проверку соответствия основных технических данных двигателя (ОТД) параметрам, заданным в технических условиях (ТУ). 2. Определение ресурса, проверку работоспособности и надежности двигателя. 3. Определение фактического состояния рабочего процесса и напряжений в конструкции двигателя. Авиационный ГТД на различных этапах жизненного цикла (разработки, производства, эксплуатации) подвергается большому количеству испытаний. Испытания можно классифицировать по различным признакам: назначению; месту проведения; типу производства и другим.
В зависимости от характера проводимых экспериментов условно различают: • научно-исследовательские испытания (научно-исследовательский эксперимент); • испытания отдельных узлов создаваемого двигателя; • доводочные и специальные испытания опытного двигателя; • государственные и сертификационные испытания двигателя; • испытания серийных двигателей. Условность деления подчеркивается тем обстоятельством, что различные испытания могут иметь общие решения по подготовке, проведению, используемому оборудованию, технике измерений.
2. 1. СОЗДАНИЕ НАУЧНО-ТЕХНИЧЕСКОГО ЗАДЕЛА И ЕГО ЭКСПЕРИМЕНТАЛЬНОЕ ПОДТВЕРЖДЕНИЕ Научно-исследовательские эксперименты Такие испытания проводятся на стадии подготовки к разработке двигателя. Современная методология разработки двигателей, направленная на сокращение суммарных затрат и сроков создания путем широкого применения методов математического моделирования и проектирования, опережающей разработки научно-технического задела по ключевым технологиям, узлам, системам, базовым газогенераторам, включая создание и экспериментальную отработку двигателей-демонстраторов, предполагает перераспределение объемов затрат на научно-исследовательские работы (НИР и НИОР) и ОКР в пользу НИР и научно-исследовательских экспериментальных работ (НИЭР). Их главные задачи — изучение и анализ происходящих в двигателе процессов, определение характеристик элементов и возможных средств их улучшения. Конечная цель НИР — разработка рациональных методов расчета, конструирования и производства двигателя, накопление справочного материала применительно к условиям использования в будущих проектах и конструкциях. Надо заметить, что отношение к НИР складывается в разных странах по-разному. Например, коэффициент АГНИР, учитывающий относительную стоимость НИР в общей стоимости НИР и ОКР, К НИР =S НИР /S ОКР , характеризуется следующими количественными значениями: РФ —К НИР ≈ 0, 2; США — К НИР ≈ 0, 4. . . 0, 5. Заметно, что американская школа традиционно строится на основе эксперимента, а советская и российская школы и в какой-то мере немецкая базируют свои разработки на более глубокой теоретической проработке.
Пример. Канадский филиал фирмы PW длительное время вел экспериментальные исследования центробежных ступеней компрессора. И вот, пока основная часть таких ступеней, применяемых в авиационных двигателях, имеет n* = 3. . . 7, фирма довела в экспериментальных ступенях величину n к до 10. . . 12. Используемые в настоящее время математические модели расчета трехмерных течений позволяют в короткое время получить результаты (по форме и размерам центробежного колеса, форме и размерам проточных межлопаточных каналов), очень близкие к тем, которые были получены в результате многолетней экспериментальной доводки. Среди различных исследовательских экспериментов по ГТД обычно выделяют следующие: • исследование новых принципиальных схем двигателей и отдельных узлов; • изучение рабочего процесса двигателей и влияние различных условий на эти процессы; • исследование новых видов топлив; • исследование живучести различных элементов конструкций; • продувки элементов лопаточных машин; • изучение рабочего процесса основных и форсажных камер; • изучение свойств новых конструкционных материалов, покрытий, шумоглушащих конструкций, контактных уплотнений, конструкций опор, демпферных устройств и других элементов. Создание научно-технического задела (НТЗ) фактически базируется на результатах, получаемых при различных НИР. С другой стороны, подтверждение эффективности основных элементов НТЗ также требует проведения научно- исследовательских экспериментов.
Испытания отдельных узлов двигателя на автономных стендах являются эффективным средством опережающей отработки новых технических решений, позволяющим сократить объем, стоимость и общие сроки работ по созданию нового ГТД. Опыт создания современных двигателей свидетельствует о том, что большая часть экспериментальных работ переносится на поузловые испытания и их доводку. Узловые испытания компрессора (вентилятора) проводятся на стендах (рис. 2. 1), оборудованных приводом от электродвигателя или газовой турбины. При необходимости используется редуктор (мультипликатор) с требуемым передаточным отношением. Стенд должен быть оснащен устройствами для дросселирования потока на выходе из компрессора и для измерения на приводе крутящего момента. При испытаниях на автономном турбинном стенде (рис. 2. 2) помимо газодинамических исследований проводят термометрирование и тензометрирование лопаток, дисков и корпусов.
В автономных испытаниях основной камеры сгорания выбранной конструкции (для кольцевых камер допускается испытание отсека) проверяются ее гидравлические характеристики, эффективность горения топлива, устойчивость горения, высотность запуска, отсутствие виброгорения, уровень дымления и выделения вредных веществ. Полученные для узлов данные впоследствии требуют проверки в реальной компоновке двигателя или газогенератора. Поузловые испытания имеют большую эффективность не только на ранней стадии работы, но и в период доводки полноразмерного двигателя с целью поиска и реализации в узлах резервов по повышению КПД, улучшению протекания характеристик и снижению массы. Значительную роль при разработке ГТД играют испытания газогенератора, который собирается из узлов создаваемого двигателя. Газогенератор является наиболее напряженным комплексом узлов, требующим наибольшей экспериментальной отработки. Он может быть создан и испытан на начальной стадии работы, когда еще окончательно не определены многие основные параметры двигателя. На базе одного и того же разработанного газогенератора впоследствии может быть создано семейство различных двигателей.
2. 2. ИСПЫТАНИЯ ОПЫТНЫХ ГТД Основная задача — доводка рабочего процесса и конструкции двигателя [16, 18, 29]. Доводка — внесение изменений в конструкцию двигателя, для решения основной задачи — обеспечение его проектных показателей. Первые экземпляры нового двигателя по основным показателям эффективности и прочности обычно значительно отличаются от соответствующих проектных величин, записанных в технических условиях. Выйти на заявленные величины по параметрам во всех условиях эксплуатации и по ресурсу удается только после тщательной экспериментальной отработки — газодинамической и прочностной доводки. Доводка двигателя — это длительный процесс. Так, если доводка ЛА продолжается 4 -5 лет, то доводка двигателя длится 6— 7 лет. Всегда стоит задача сократить этот срок. В процессе доводки решаются вопросы, связанные главным образом с газодинамическими и прочностными факторами. В процессе газодинамической доводки решается также множество дополнительных задач [25]: • отработка запуска двигателя; • обеспечение выхода элементов двигателя при их совместной работе на расчетные или оптимальные режимы, что может потребовать корректировки площади сопловых аппаратов турбины, сопла, смесителя двухконтурного ГТД и др. ;
• отработка взаимодействия элементов и систем при переменных режимах — приемистости, дросселировании, включении и выключении форсажа; • определение фактических запасов газодинамической устойчивости; • уточнение выбранных законов управления и ограничения режимов. Эффективность всех вводимых мероприятий по улучшению параметров двигателя определяется, в первую очередь, контролем его дроссельной стендовой характеристики. Ряд доводочных работ требуют проведения испытаний опытного двигателя на высотных стендах, где имитируются условия работы двигателя в высотноскоростных условиях. Прочностная доводка, целью которой является обеспечение надежной работы двигателя в течение установленного ресурса, включает в себя следующие испытания [25]: • определение уровня переменных напряжений в лопатках, дисках, валах компрессора и турбины; проверка отсутствия автоколебаний лопаток компрессора (вентилятора); • термометрирование деталей горячей части с целью проверки возможности работы при требуемой температуре газа; • определение осевых сил в подшипниках, определение их температурного состояния; • определение уровня вибраций на корпусе двигателя и на установленных агрегатах; • тензометрирование трубопроводов внешней обвязки двигателя; • ресурсные испытания.
Для того чтобы двигатель мог быть предъявлен для прохождения государственных испытаний (ГИ) и сертифицирован, он должен успешно пройти также целый ряд специальных испытаний. После реализации и экспериментальной проверки доводочных мероприятий определяется окончательная компоновка двигателя, удовлетворяющая по основным показателям ТЗ заказчика. Конечная цель доводки — провести с удовлетворительной оценкой так называемые чистовые испытания на полный ресурс, а также ряд дополнительных специальных испытаний с тем, чтобы иметь возможность предъявить опытный двигатель на государственные испытания. По окончании доводочных испытаний, когда двигатель пройдет все экспериментальные проверки (чистовые доводочные испытания), его представляют на государственные (межведомственные) испытания. Доводка современных ГТД отнимает много сил и средств. В зависимости от сложности разрабатываемого двигателя и мощности опытно-конструкторского бюро (ОКБ) на доводку обычно уходит до 10 лет. За это время изготавливают Для доводки от 20 до 35 опытных экземпляров авиационных ГТД, каждый из которых стоит в 3— 5 раз дороже серийного образца (причем 2/3 из них в процессе доводки разрушаются). А характерная цена 1 серийного современного ГТД в зависимости от его размера составляет 0, 5. . . 1 млн долл, и более. Статистикой установлено, что для завершения доводки ГТД и предъявления его на ГИ требуется наработать на всех опытных экземплярах от 5000. . . 7000 до 25 000 газовых часов при стендовых испытаниях и несколько меньше — при летных. Для сокращения сроков доводки существенное значение имеет повышение интенсивности работы опытно-конструкторских бюро. Так, если в 50 -е годы для наработки 4000 газовых часов требовалось 6. . . 7 лет, то в 80 -е годы уже 3. . . 3, 5 года. В настоящее время эта проблема вновь становится актуальной.
Сертификационные и государственные испытания До начала летной эксплуатации опытные двигатели гражданской авиации проходят сертификацию, основной составляющей которой являются сертификационные испытания [40, 45, 47]. Двигатели военной авиации проходят государственные стендовые испытания. Сертификация — установление соответствия двигателя требованиям норм летной годности. Для оценки выполнения правил сертификации, сертификационных работ, технической документации формируются рабочие органы. В организациях, разрабатывающих и изготавливающих двигатели, действует Независимая инспекция, функции которой в Российской Федерации осуществляют военные представительства Министерства Обороны РФ. Эта инспекция осуществляет контроль за соблюдением процедур сертификации, согласование результатов сертификационных работ, контроль качества авиационных двигателей, приемку экземпляра этой техники и выдачу на них сертификатов летной годности и других документов. Сертификационные испытания включают в себя несколько групп испытаний. Калибровочные испытания позволяют определить тяговые (мощностные) характеристики двигателя в стандартных атмосферных условиях (САУ). Вибрационные испытания предназначены для определения вибрационных характеристик дисков и валов роторов, рабочих и статорных лопаток вентилятора, компрессора и турбины, корпусов и трубопроводов. Длительные 150 -часовые испытания предусматривают наработку на наиболее напряженных режимах, воспроизведение циклических нагрузок (запуски, пробы приемистости), моделирование неблагоприятных условий работы. Эксплуатационные испытания проверяют работу двигателя во всех условиях эксплуатации.
В программы сертификационных испытаний входят также экспериментальное определение характеристик компрессора, камеры сгорания, проверка прочности корпусов и др. Для сертификации необходимо провести комплекс специальных испытаний (испытания по проверке локализации лопаток внутри двигателя при обрывах, по проверке работы двигателя при попадании посторонних предметов, при повышенной температуре газа, в условиях авторотации и т. п. [25]. Государственные испытания двигателей военного назначения проводит Государственная комиссия, создаваемая из представителей Заказчика и Исполнителя. В задачу государственных испытаний входят: 1. Установление соответствия параметров двигателя параметрам, заданным в ТЗ. 2. Проверка двигателя по 150 -часовой программе испытаний. 3. Оценка уровня внедрения на двигателе унифицированных и стандартизованных изделий и конструкций. 4. Оценка эксплуатационного совершенства двигателя, контролепригодности, ремонтопригодности, обслуживаемости. 5. Установление эталона двигателя для серийного производства. Двигатель, предназначенный для государственных испытаний, предъявляется комиссии в разобранном виде после прохождения чистовых доводочных испытаний. Сборка производится под наблюдением представителей комиссии. Длительные испытания авиационного ГТД у нас в стране считаются неудовлетворительными, если во время испытаний или при разборке после удовлетворительно прошедшего испытания обнаруживают выход из строя деталей, поломка или повреждение которых в эксплуатации опасны или недопустимы. При этом длительные испытания начинают вновь с самого начала вне зависимости от того, на каком часе произошла поломка.
Заключительным этапом испытаний опытного ГТД являются ГИ, которые обычно повторяют 150 -часовую программу чистовых длительных испытаний. В случае удовлетворительной оценки вся документация по новому ГТД, передаваемая в серийное производство, сверяется по экземпляру, прошедшему ГИ. По результатам государственного испытания комиссией составляется акт, который после утверждения является основанием для серийного производства и приемки двигателей заказчиком. В акте Государственной комиссии приводятся также перечни отмеченных недостатков, которые должны быть устранены разработчиком в намеченные сроки. Двигатель, проходивший государственные испытания, хранится как эталон, принятый заказчиком, а основные данные и характеристики, установленные при испытаниях, используются для составления ТУ на приемку серийных двигателей.
2. 3. ИСПЫТАНИЕ СЕРИЙНЫХ ГТД Здесь задача испытаний иная — всесторонняя проверка качества выпускаемой заводом серийной продукции. Эти испытания регламентируются для каждого двигателя специальными ТУ, разработанными соответствующими ОКБ. Кратковременные испытания. Каждый двигатель, изготовленный на серийном заводе, проходит кратковременные стендовые испытания. Эти испытания серийных ГТД принято разделять на предъявительские и приемосдаточные, а также квалификационные. 1. Предъявительские (сдаточные) испытания проходят все двигатели, выпускаемые серийным заводом, а также прошедшие ремонт после выработки межремонтного ресурса. Назначение предъявительских (сдаточных) испытаний состоит в приработке деталей двигателя (обкатка), в проверке качества сборки, качества работы агрегатов двигателя и оценке соответствия параметров двигателя заданным ТУ. Работу двигателя проверяют на всех эксплуатационных режимах, при этом производится соответствующая отладка агрегатов. Приемку предъявительского (сдаточного) испытания осуществляет отдел технического контроля (ОТК) предприятия. Результаты предъявительских испытаний считаются положительными, а двигатель — выдержавшим испытания, если он испытан в полном объеме, установленном программой и соответствует всем требованиям этой программы. В случае выявления какого-либо дефекта двигателя, препятствующего ведению испытаний, или при отклонении основных параметров от норм, оговоренных для предъявительских испытаний, предъявительское испытание аннулируется.
После предъявительских испытаний двигатель отправляют на разборку для осмотра и контроля состояния его деталей. На осмотре присутствуют работники ОТК совместно с представителем заказчика. Двигатель, прошедший предъявительские испытания, подвергается полной разборке и дефектации по действующей документации. После дефектации разобранного двигателя ОТК изготовителя составляют ведомость дефектации с заключениями по выявленным недостаткам. Замена забракованных деталей, узлов (сборочных единиц) и агрегатов производится в соответствии с инструкцией по замене деталей, сборочных единиц, фрегатов при устранении дефектов после предъявительских испытаний. Износы, наклепы, прижоги и другие изменения в состоянии деталей и сборочных единиц после предъявительских испытаний должны соответствовать нормам повреждаемости и контрольным образцам, установленным для данного типа двигателя. Обнаруженные дефекты (разрешенные) устраняют, после чего двигатель вновь собирают и отправляют на приемосдаточные (контрольные) испытания. 2. Целью приемосдаточных (контрольных) испытаний двигателя являются: • проверка соответствия техническим условиям качества повторной (после предъявительских испытаний) сборки двигателя; • проведение приработки деталей и агрегатов, комплектующих двигатель; • отладка и проверка регулировки двигателя и проверка соответствия параметров и характеристик заданным ТУ; • приемка двигателя представителем заказчика по акту сдачи.
Приемосдаточные (контрольные) испытания состоят из двух этапов. На I этапе приемосдаточных (контрольных) испытаний работу двигателя повторно проверяют на всех эксплуатационных режимах и окончательно отлаживают регуляторы, проверяют после регулировки данные на соответствие ТУ, осле чего двигатель и его характеристика на всех режимах предъявляются заказчику. На II этапе испытания повторяют в присутствии заказчика. Если двигатель не бракуется, оформляется акт сдачи двигателя представителю заказчика. Двигатель консервируют и отправляют в экспедицию для упаковки и отправки потребителю. Таким образом, в отличие от предъявительских, приемосдаточные испытания проводят в присутствии как представителя ОТК, так и заказчика (гос- приемка). После приемосдаточных испытаний проводятся внутренняя консервация двигателя и другие работы, предусмотренные технической документацией. Для двигателей, находящихся в серийном производстве, допускается проведение совмещенных (предъявительских и приемосдаточных) испытаний. Сокращение объемов и трудоемкости предъявительских и приемо-сдаточных испытаний без снижения их информативности и качества проводится в следующих направлениях: • более полное использование возможностей автоматизированных информационно-измерительных систем стендов, совершенствование их программного обеспечения и методик обработки результатов испытаний, что позволяет получать необходимую информацию при меньшем количестве режимов в про-грамме испытаний; • выполнение контрольных операций в ходе испытаний, с минимальным числом режимов, используемых только для контроля, в том числе и совмещение I и II этапов приемосдаточных испытаний; •
• комплексирование операций и совершенствование методик их выполнения, в том числе проведение их на режимах с меньшим расходом топлива, исключение повторов из программы испытаний; • постепенное уменьшение количества двигателей, проходящих специальные испытания, включенные в программу приемосдаточных испытаний (проверка ГДУ, приработка приводов агрегатов ВС под загрузкой, проверка границ запуска и др. ), вплоть до полного прекращения таких специальных испытаний; • сокращение объема разборки двигателей после предъявительских испытаний за счет перехода на частичную (поузловую, модульную) разборку; • переход на одноразовую сборку и проведение приемосдаточных испытаний при одновременном совмещении отдельных видов проверок, проводимых при предъявительских испытаниях. Переход на одноразовую сборку и совмещенные предъявительские и приемосдаточные испытания возможен при следующих условиях: • отсутствии на двигателях в эксплуатации неисправностей, которые могут быть выявлены только при разборке и дефектации после предъявительских испытаний; • стабильном производстве и ремонте двигателей; • отсутствии предъявительских и приемосдаточных испытаниях неисправностей, которые не могут быть обнаружены и устранены без разборки двигателя или его узлов (сборочных единиц); • контролепригодности двигателя и наличии методов и средств для контроля и диагностики технического состояния двигателя без его разборки; •
• наличии перечня и характеристик диагностических признаков, полученных в процессе доводки и подтвержденных эксплуатацией, позволяющих оценить состояние двигателя; • наличии положительного опыта работы по выпуску двигателей с поузловой (модульной) разборкой после предъявительских испытаний; • применении, в случае необходимости, предварительной обкатки отдельных узлов, модулей и агрегатов до постановки их на двигатель; • наличии положительного опыта использования одноразовой сборки при доводке модифицированных двигателей на этапе ОКР. Уменьшение количества двигателей, проходящих специальные испытания в серийном производстве, возможно при следующих условиях: • стабильном производстве и ремонте двигателей; • положительных результатах проведенных ранее специальных испытаний; • отсутствии в эксплуатации и при стендовых испытаниях отказов и дефектов, связанных с характеристиками, проверяемыми специальными испытаниями. Для контроля производства двигателей одноразовой сборки должна предусматриваться контрольная разборка после испытания двигателя от партии, объем которой определяется разработчиком и изготовителем совместно с представительством Заказчика.
3. Квалификационные испытания. Целью квалификационных испытаний являются: • проверка соответствия двигателей требованиям конструкторской документации; • оценка проведенных мероприятий по устранению недостатков, выявленных на Государственных испытаниях; • проверка разработанного технологического процесса, обеспечивающего стабильность качества выпускаемой продукции; • определение готовности производства к выпуску двигателей в заданном объеме. Квалификационные испытания у всех типов двигателей проводятся для установочной серии определенного количества изготовленных двигателей в процессе освоения их производства. Двигатель для квалификационных испытаний выбирает представитель заказчика в присутствии работников ОТК из 2. . . 5 двигателей, принятых по результатам приемосдаточных испытаний. Если двигатель выдержал квалификационные испытания, то качество партии двигателей, для которой проводились испытания (установочной серии), а также возможность дальнейшего изготовления и приемки двигателей по той же технологической документации, по которой изготовили испытанный двигатель, считаются подтвержденными.
Квалификационные испытания считают неудовлетворительными в случаях: • несоответствия основных параметров двигателя ТУ; • выхода из строя двигателя в ходе испытаний; • отказов агрегатов и комплектующих изделий, которые могут явиться предпосылкой к аварийной ситуации; • обнаружения при осмотре и дефектации деталей двигателя, агрегатов и других покупных комплектующих изделий; • дефектов аварийного характера, влияющих на летную годность, или дефектов, которые могут привести к досрочному съему двигателя. В этом случае изготовитель и ОКБ-разработчик совместно с представителем заказчика разрабатывают и осуществляют мероприятия по устранению недостатков и предупреждению их появления при серийном производстве двигателей.
Периодические испытания. Общая наработка двигателя в процессе предъявительских и приемосдаточных испытаний обычно не превышает 4. . . 5 ч. Этой наработки естественно недостаточно для проверки надежности работы ГТД в течение гарантируемого срока службы. Поэтому для полноценной проверки качества серийного производства ГТД проводятся периодические испытания на выборочных двигателях, определяемых представителем заказчика. Количество периодических испытаний в зависимости от объема годового выпуска должно составлять: при годовом выпуске менее 50 двигателей данного типа — одно периодическое испытание в два года; при годовом выпуске от 50 до 150 двигателей — одно периодическое испытание в год; при годовом выпуске более 150 двигателей — до двух периодических испытаний в год, если периодические испытания не отменены специальным решением. Эта группа испытаний делится на три вида. Заводские периодические испытания по проверке ресурса и данных (комиссионные, квартальные или полугодовые). Периодические испытания проводятся в объеме и последовательности, установленных программой испытаний. Типовые испытания проходят по аналогичной программе, однако цель их другая — проверка допустимости изменений, вводимых серийным заводом за прошедший период. Необходимость конструктивных и технологических изменений возникает в связи с увеличением ресурса, повышением надежности, а также при совершенствовании и удешевлении производства на серийном заводе. Это одна из основных задач серийного производства — снизить его трудоемкость и стоимость. Технологические изменения обязательно согласовываются с разработчиком и заказчиком.
Специальные (например, высотно-скоростные ) испытания. В них проверяют соответствие высотных данных серийного двигателя стендовой контрольной Цифре. Эти испытания проводят в термобарокамере или аэродинамической трубе ЦИАМ. К специальным испытаниям также относятся испытания по проверке газодинамической устойчивости, с наддувом и подогревом воздуха на входе и ряд других. Периодические испытания для двигателей, имеющих ресурс не более 600 ч, проводятся по программе эквивалентно-циклических испытаний. При этом количество циклов, наработка в циклах, на режимах выше максимально-продолжительного, переменных, а также количество запусков должны соответствовать установленному ресурсу при работе по типовому полетному циклу. Программой испытаний устанавливается величина минимальной суммарной наработки за периодическое испытание. Для двигателей, имеющих ресурс более 600 ч, периодические испытания проводятся по программе эквивалентно-циклических испытаний. При этом наработка в циклах, на режимах выше максимально-продолжительного, переменных, а также количество запусков должны соответствовать установленному ресурсу, но не более чем за 1200 ч работы по типовому полетному циклу. Программой испытаний устанавливается величина минимальной суммарной наработки за периодическое испытание. Для подтверждения ресурса при эксплуатации по техническому состоянию одно из периодических испытаний проводится на установленный ресурс с учетом эксплуатации по техническому состоянию. При стабильном производстве двигателей, соответствии их нормам безотказности, начиная с 3 -го года выпуска, такие испытания по согласованию с разработчиком, изготовителем и представительством Заказчика могут не проводиться.
Двигатель для проведения периодических испытаний выбирается из числа 2— 5 двигателей, изготовленных в контролируемом календарном периоде (или из контролируемого количества), прошедших приемосдаточные испытания. Перерывы между этапами должны определяться временем, необходимым для проведения осмотра двигателя, выполнения регламентных работ и работ по оборудованию стенда. В случае несоответствия основных данных двигателя заданным в ТУ (связанных с загрязнением газовоздушного тракта двигателя) допускается по согласованию с представительством Заказчика промывка газовоздушного тракта двигателя в соответствии с инструкцией разработчика с последующей проверкой параметров двигателя. Периодические испытания считают неудовлетворительными в случаях: • несоответствия основных параметров (технических характеристик) двигателя ТУ; • несоответствия нормам параметров по дроссельной характеристике после испытаний; • выхода из строя двигателя до окончания испытаний; • отказов агрегатов и комплектующих изделий двигателя, которые могут явиться предпосылкой к аварийной ситуации; • обнаружения дефектов аварийного характера (влияющих на летную годность) при осмотре и дефектации деталей двигателя, агрегатов и других покупных комплектующих изделий или дефектов, которые могут привести к досрочному съему двигателя в эксплуатации.
При неудовлетворительных результатах периодических испытаний изготовитель совместно с разработчиком и представительством Заказчика при изготовителе обязаны: • провести исследования причин выявленных дефектов; • разработать эффективные мероприятия, обеспечивающие устранение выявленных дефектов; • произвести проверку эффективности и проведенных мероприятий испытаниями; • провести повторные периодические испытания. При неудовлетворительных результатах периодических испытаний все принятые и неотгруженные двигатели возвращаются изготовителю на доработку (замену), а все принятые и отгруженные двигатели за контролируемый календарный период, в которых могут быть дефекты, обнаруженные при периодических испытаниях, должны быть доработаны или заменены годными в порядке, определенном совместным решением. Повторные испытания проводятся в полном объеме периодических испытаний на доработанных или вновь изготовленных двигателях после выполнения мероприятий по устранению дефектов. При этом вместе с извещением о предъявлении двигателя должны быть предоставлены материалы, подтверждающие устранение дефектов, выявленных при периодических испытаниях, и принятии мер по их предупреждению.
Правила испытаний и приемки серийных ГТД. Испытания и приемка двигателей серийного производства должны проводиться в соответствии с требованиями государственных стандартов и действующих ОТУ. Стендовые испытания двигателей в серийном производстве должны проводиться по программам, составленным на основе программ и конструкторской документации двигателя, прошедшего государственные (совмещенные государственные стендовые и сертификационные испытания) или сертификационные испытания. Программы периодических, предъявительских и приемосдаточных испытаний входят в состав конструкторской документации, передаваемой в серийное производство разработчиком. При стендовых испытаниях двигателей должны определяться основные его параметры, предусмотренные программой испытаний на режимах работы двигателя, указанных в ТУ на двигатель. Для сокращения объемов газовой наработки (суммарная продолжительность работы двигателя на режимах от запуска до останова за все испытания по конкретной программе) при замере параметров может быть использована обобщенная характеристика данного типа двигателя по методике, разработанной изготовителем. Испытания двигателей проводятся на стендах, отвечающих требованиям ОСТ 1 01021, ОТУ и технической документации на конкретный двигатель. Для испытаний двигателей, имеющих «Сертификат типа» , стенды должны быть аттестованы в установленном порядке. Установка двигателя на стенд, подсоединение коммуникаций, необходимых датчиков и контрольно-измерительной аппаратуры должны производиться в соответствии с утвержденными инструкциями и технологией, монтажными чертежами, схемами на конкретный тип двигателя.
Турбовинтовые и турбовинтовентиляторные двигатели должны проходить стендовые испытания с воздушным винтом (винтовентилятором), тип и конструкция которого соответствуют воздушному винту (винтовентилятору), используемому на ЛА с данным двигателем. Элементы настройки агрегатов должны быть отрегулированы их изготовителем в соответствии с действующими ТУ, каждое изменение их положения от первоначального в ходе испытаний двигателя должно быть записано в протоколе испытаний. Приводы агрегатов ЛА в процессе испытаний должны загружаться принятыми в эксплуатации или технологическими агрегатами в соответствии с графиком загрузки, согласованным с разработчиком ВС.
Испытания двигателей должны проводиться на основных или дублирующих арках топлива и масла, указанных в ТУ на двигатель. Во время испытаний двигателя периодически проводится анализ топлива и масла, взятых из двигателя, по документации разработчика. Эксплуатационные испытания. Для решения задачи увеличения ресурса ГТД, находящихся в эксплуатации на борту ЛА, проводят их испытания с использованием самолетов-лидеров. Сложившаяся методика их проведения обеспечивает получение надежных результатов и сохранение безопасности полетов. На рис. 2. 3 приведена взаимосвязь видов испытаний авиационных ГТД и этапов их жизненного цикла.
2. 4. ТЕХНИЧЕСКОЕ И ОРГАНИЗАЦИОННОЕ ОБЕСПЕЧЕНИЕ ИСПЫТАНИЙ ГТД Основные документы, регламентирующие испытания Требования к испытаниям опытных и серийных ГТД в разные периоды определялись следующими документами: ОТУ-81 (общие технические условия на изготовление, приемку и поставку авиационных серийных двигателей действовали до 31. 12. 1986 г. ). В этот комплекс были включены следующие документы: 1) перечень основных технических данных авиационных двигателей; 2) перечень технической документации и технических условий на изготовление, приемку и поставку двигателей; 3) программы стендовых испытаний; 4) методики измерения и обработки результатов испытаний; 5) стенды испытательные (перечень). Затем вместо ОТУ-81 действовали ОТУ-91 (общие технические условия на изготовление, приемку и поставку авиационных двигателей для летательных аппаратов). В 1979— 1994 годы весьма эффективно применялся документ ЕНЛГС (единые нормы летной годности самолетов) гражданских самолетов для стран СЭВ. Этот комплекс содержал требования, направленные на обеспечение безопасности полетов. В главе 6 имелись требования по всем видам испытаний для сертификации двигателя до установки на самолет. С 1994 года в Российской Федерации действуют «Авиационные правила» часть 33, в которой регламентированы нормы летной годности двигателей воздушных судов. С 2006 года испытания регламентируются общими техническими условиями, утвержденными в 2006 году (ОТУ-2006).
Виды основных экспериментальных характеристик ГТД При испытаниях ГТД обычно снимают следующие виды экспериментальных характеристик: I. Дроссельные характеристики (ДХ). Для ТРД, ТРДД это зависимости Р, С уд , Т* т = f(n) или, скорей как исключение, п, С уд , Т* т = f(Р дв ) ТВД — Н э , С э , Т* = f (G m , n); ГТД СТ – N e , С е , Т т ; = f (n); ТРДФ, ТРДДФ — Р ф , С уд ф = f(G m ф ) или f (Р ф ). II. Высотно-скоростные характеристики (ВСХ). Это зависимости Р дв , С уд , Т * т , Т * ф = f(Р ф ) для постоянных режимов работы двигателя (п = const) или P дв , С уд , . . . =f(n, М) для Н = const. III. Климатические. Это зависимости Р дв , С уд , Т * т = f(T H , р н ). Основные эксплуатационные режимы, проверяемые при испытаниях ГТД 1. Максимальный (допустимое время непрерывной работы на этом режиме т доп = 1. . . 2 мин) n = 101. . . 102 %. 2. Взлетный (τ доп = 5. . . 10 мин), n взл = (l, 0. . . 0, 98)n max. 3. Максимальный продолжительный (с меньшей мощностью — тягой, чем взлетный, на 10. . . 15 %) (т доп = 0, 5. . . 1 ч), n мп =(0, 96. . . 0, 97)n взл. 4. Крейсерские режимы — 0, 4. . . 0, 9 от тяги или мощности максимального продолжительного, т — неограниченно, n = (0, 7. . . 0, 9)n мп. 5. Малый газ — режим устойчивой работы с минимально разрешенной тягой (мощностью) (т доп = 10. . . 15 мин; Р мг < 3. . . 5 % от Р взл , n мг = (0, 2. . . 0, 4)n взл ).
Основная техническая документация при испытаниях ГТД Программа испытании. Это основной документ, регламентирующий проведение испытания и его подготовку. В программе указываются цель испытания, объект, параметры, подлежащие измерению, и необходимое препарирование, методика проведения эксперимента, режимы, ограничения, перечень зависимостей, которые необходимо получить, и порядок обработки измеренных величин. Технологическая карта испытания (сокращенная программа для механика, управляющего двигателем). Порядок и последовательность установки режимов, время наработки и время измерений на каждом режиме, детальный перечень измерений и т. п. Протокол испытании. В протоколе фиксируют: № двигателя, время и дату поступления двигателя на испытание, № стенда, № программы, вид испытания, наработка двигателя до и во время испытания, анализ масла и топлива; результаты всех измерений, а также осмотров двигателя до и после испытания.
Основные мероприятия по подготовке к испытаниям В процессе подготовки к испытаниям ГТД должны быть разработаны следующие документы, определяющие объем, периодичность, виды, содержание наземных и летных испытаний изделия и его систем: • программы и методики испытаний, регламентирующие наземные стендовые) испытания, в которых указывают перечень регистрируемых параметров (обоснование количества, диапазона и погрешности измеряемых параметров); действия персонала при возникновении отклонений; требования по обеспечению безопасности и охране окружающей среды во время испытаний (в частности, относящиеся к мерам по противопожарной, взрывоопасной безопасности, а в случае возможности разрушения детали — осколочной безопасности и т. п. ); • программы и методики испытаний, регламентирующие летные испытания, в которых предусматривают порядок оформления полетных заданий, составления отчета экипажа и хранения полетных заданий (сроки ранения); проверку готовности двигателя к полету, работоспособности систем, оборудования, комплектности (номенклатура, состав штатных агрегатов; по диапазону и погрешности измерения приборы контроля должны обладать диапазоном и погрешностью измерений, аналогичной типовой конструкции, все приборы оттарированы, обеспечены необходимыми графиками и таблицами); действия персонала в случае отрицательных результатов испытаний; • положения об испытательных подразделениях, в которых приводят зада- и, возлагаемые на подразделение (виды и периодичность выполняемых испытаний и др. ); структуру подразделений с распределением ответственности; порядок взаимодействия с другими подразделениями и службами предприятия, а также с разработчиком и военным представительством; метрологическое обеспечение; требования к испытательному персоналу;
• паспорта испытательных стендов, акты аттестации и допуска к эксплуатации. Кроме того, должны быть реализованы мероприятия по удовлетворению требований в части оснащения испытательных помещений, кабин управления и наблюдения, а также стендовых систем (топливной, масляной, воздушной, электрической и др. ), а также систем управления процессом испытаний и слежения за аварийными параметрами и системы проверки сигнализации и блокирования. Контроль изменений в процедурах испытаний предусматривает формирование и реализацию порядка, определяющего разработку, оформление, внесение, изучение и учет изменений в процедурах испытаний, контроля и своевременного доведения изменений до исполнителя. В соответствии с этим все изменения в инструкциях и нормативных документах должны утверждаться и контролироваться уполномоченным для этой цели персоналом. Поэтому должны быть предусмотрены требования по порядку внесения изменений в документацию на проведение испытаний (естественно до проведения испытаний). Отчетные документы по испытаниям включают документы, определяющие порядок разработки, оформления, согласования и утверждения заданий на испытания; порядок составления, согласования и утверждения отчетов по результатам испытаний (как положительных, так и отрицательных); порядок оформления полученных результатов испытаний, накопленных материалов и передачи их для последующего анализа; виды материалов по результатам испытаний со сроками их хранения. Квалификация персонала испытательной станции. Нормативные документы должны быть направлены на обеспечение поддержания достаточного уровня квалификации персонала станции для испытания ГТД и гарантировать, что персонал испытательной станции допущен к выполнению предусмотренных работ обоснованно.
Программа обеспечения безопасности испытаний включает процедуры контроля за выполнением запланированных испытаний и за отчетностью персонала; использование системы регистрации параметров испытаний; процедуры анализа и разбора результатов испытаний и меры безопасности в утвержденных программах (заданиях на испытания); требования периодического обзора случившихся происшествий и перечень мер по противопожарной, взрывоопасной, осколочной и экологической защите. Участие службы качества в обзоре (анализе) и в утверждении нормативной документации для испытаний определяется: участием представителей службы качества в составлении инструкций и процедур испытаний; утверждением таких инструкций и процедур; необходимыми полномочиями для обязательного контроля и оценку продукции; проверкой соответствия типовых конструкций путем применения определенных контрольных точек, которые подтверждают соответствие изделия типовой конструкции; определением состава и полномочий лиц службы контроля, ответственных за внесение контрольных точек в инструкции или процедуры испытаний. Поддержание в надлежащем состоянии записей по завершении испытаний обеспечивается правилами хранения материалов испытаний, в которых определены вид материалов, содержание и сроки их хранения. Порядок хранения на предприятии результатов всех неудовлетворительных испытаний регулирует правила хранения результатов испытаний объектов, не выдержавших испытания по одному или нескольким параметрам; факты передачи материалов с описанием несоответствующих параметров в комиссию для рассмотрения и принятия решения; определяет условия разу комплектации изделия; оформления отчета при отрицательных результатах испытаний, а также оформления, устранения недостатков и допуска деталей (агрегатов, составных частей), имевших отклонения, на повторные испытания (на повторную сборку).
Проверка состояния деталей и узлов АД после испытаний. Для этого важного аспекта процесса испытаний должны быть определены порядок оценки состояния двигателя и его составных частей после испытаний, предусматривающий систему проверки для подтверждения качества продукции; увеличение частоты и объема проверок при обнаружении несоответствия типовой конструкции после испытаний до тех пор, пока причина несоответствия не будет обнаружена и исправлена; указание типов записей по результатам проверки состояния после испытаний и методов уведомления подразделений (служб), ответственных за выявленные несоответствия в процессах проектирования и производства. Утверждение авиационным регистром (АР) МАК процедур по летным испытаниям. Оно базируется на согласовании с авиационным регистром МАК и военным представительством технических условий на серийные изделия, на согласовании программ, методик испытаний военным представительством на пред-приятие (независимой инспекцией авиационного регистра МАК). Корректировка АР МАК (ВП) программ испытаний. Эта процедура, предусматривает, что стандарты и основные документы по испытаниям (программы, методики испытаний) АД после утверждения разработчиком должны быть согласованы с военным представительством, являющимся уполномоченной стороной АР МАК.
Принципы подхода к подготовке программы испытаний ГТД Каждый авиационный двигатель обладает определенными особенностями конструкции и эксплуатации. Поэтому при составлении программ испытаний 1 вигателя новой конструкции необходимо тщательно проанализировать возможность возникновения ранее неизвестных или несвойственных прежним двигателям явлений и назначить соответствующие проверки. Во-первых, необходимо проанализировать влияние конструктивных и эксплуатационных особенностей на работоспособность двигателя, на его термодинамические и прочностные свойства и соответствующим образом составить методики проведения типовых испытаний. Так, например, при наличии устройств на двигателе для отбора воздуха и газа при разных количествах отбора (т. е. включенных потребителях) будут видоизменяться: температурное поле и средняя массовая температура газа перед турбиной, условия охлаждения камеры сгорания и турбины, вибронапряжения в лопатках компрессора, дроссельная характеристика. Поэтому типовые испытания по определению указанных свойств двигателя необходимо проводить как без отбора воздуха (газа), так и с различными количествами отбираемого воздуха. Во-вторых, следует предусмотреть специальные проверки работоспособно сти конструктивных отличий и определение их характеристик. Если вновь об ратиться к конструкции двигателя с отбором воздуха, то это будут проверки ра ботоспособности механизма включения отбора воздуха, ограничителя макси мального отбора воздуха, пригодности отбираемого воздуха для использования его на предусмотренные цели (например, кондиционирование кабин экипажа и пассажиров, наддува топливных баков, приводов агрегатов, охлаждения эле ментов двигателя и т. д. ).
Применение новых материалов или рабочих тел может потребовать введения специальных испытаний. Так, например, в случае применения конструкционных материалов из сплавов на основе магния или титана требуется проверка невоспламеняемости этих материалов из-за контактирования их с горячими газами, трения или задевания в результате возможной поломки или ненормальной работы как самих деталей, так и других элементов двигателя. Влияние на работу двигателя различных масел, топлив и присадок к ним, жидкостей, впрыскиваемых на входе, также должно всесторонне изучаться. Впрыскиваемая на входе в двигатель жидкость для поддержания или форсирования мощности (силы тяги) может давать накипь или приводить к короблению и коррозии горячих узлов. В результате возросшее сопротивление проточной части двигателя приведет к уменьшению силы тяги и возрастанию удельного расхода топлива на нефорсированных режимах. Из-за более быстрого охлаждения корпуса по сравнению с ротором (жидкость отбрасывается лопатками компрессора к периферии) может произойти задевание ротора за статор. Не исключено попадание жидкости в систему смазки, отверстия для газодинамических измерений с последующими нарушениями в системе регулирования. Может выявиться недостаточность единой регулировки топливоподающей аппаратуры при работе с впрыском жидкости и без нее и т. д. При применении криогенных топлив существенно осложняется работа топливоподающей и топливодозирующей аппаратуры из-за возможной кавитации и интенсивного теплообмена с окружающей средой. Хладоресурс криогенных топлив может использоваться для охлаждения горячих деталей двигателя, в этом случае возможно вымораживание влаги из воздуха на теплообменниках, если они применяются в системе охлаждения, с резким изменением условий теплопередачи в процессе работы двигателя. Низкие температуры существенно влияют на прочностные характеристики металлов.
Сохранение работоспособности двигателя в особых условиях эксплуатации необходимо проверять специальными испытаниями. Так, например, если двигатель применяется в морской авиации, то должно быть проверено не вызывает ли коррозию попадание внутрь двигателя морской воды. Для этого перед остановкой двигателя на вход подают некоторое количество морской воды и оставляют «мокрый» двигатель в покое на несколько суток. Затем его разбирают и по результатам дефектации судят об опасности влияния морской воды на элементы ГТД. Если двигатель работает в условиях большого количества пыли, проверяют влияние пыли на износ элементов двигателя и вызываемые этим износом изменения эксплуатационных свойств (повышение удельного расхода топлива, снижение запаса устойчивой работы и т. д. ), а также надежность работы пылезащитных устройств. Испытания должны проводиться при известных для условий эксплуатации запыленностях воздуха с требуемой концентрацией пыли в воздухе), размерах частиц пыли и ее химического состава, так как от них зависят степень повреждаемости элементов двигателя и возможные изменения его выходных данных.
РЕЗЮМЕ (по главе 2 «Виды испытаний авиационных ГТД» ) /. Испытание это экспериментальное определение (оценивание) и контроль количественных и качественных характеристик свойств объекта при воздействии на него совокупности факторов и изменении режимов работы. 2. Применительно к авиационным ГТД различают научно-исследовательские испытания; испытания отдельных узлов создаваемого двигателя; доводочные и специальные испытания опытного двигателя, государственные и сертификационные испытания двигателя; испытания серийных двигателей. 3. В перечень задач, стоящих перед научно-исследовательскими экспериментами, входят — изучение и анализ происходящих в двигателе процессов, определение путей улучшения характеристик узлов и элементов, разработка новых методов расчета, конструирования и производства двигателя. 4. Эффективным средством опережающей отработки новых технологических решений являются испытания отдельных узлов на автономных стендах, которые позволяют сократить объем, стоимость и общие сроки работ по созданию нового ГТД.
5. Для автономного испытания компрессора стенд должен быть оборудован приводом от электродвигателя или газовой турбины. Для согласования частот вращения компрессора и привода используют редуктор или мультипликатор; изменение режима работы обеспечивает дросселирующее устройство на выходе из компрессора; для определения мощности, потребляемой компрессором, используется измеритель крутящего момента. 6. Испытания основной камеры сгорания направлены на определение гидравлических характеристик (σ кс) ), эффективности горения (Ƞ г ) устойчивости горения, высотности запуска, уровня дымления, вредных выделений (СО, СИ, No х ) и на отсутствие виброгорения. 7. Доводка опытного двигателя занимает значительный промежуток времени и ставит целью выйти на заявленные в проекте двигателя величины параметров во всех условиях эксплуатации и по ресурсу, путем внесения изменений в конструкцию и рабочий процесс двигателя. Эффективность всех проводимых мероприятий по улучшению параметров двигателя определяется, в первую очередь, контролем его стендовой дроссельной характеристики. 8. Различают газодинамическую и прочностную доводку двигателя. 9. До начала летной эксплуатации опытные двигатели гражданской авиации проходят сертификацию, т. е. установление соответствия двигателя требованиям норм летной годности, а военные двигатели проходят государственные стендовые испытания для проверки двигателя по 150 -часовой программе, для установления соответствия параметров ГТД параметрам, заданным в ТЗ для оценки эксплуатационного совершенства и установления эталона двигателя.
10. Серийные двигатели проходят кратковременные испытания (представительские и приемосдаточные), основной целью которых является проверка качества каждого двигателя; квалификационные испытания, в которых проверяется качество двигателей в период освоения серийного производства; периодические испытания, которые обеспечивают проверку ресурса, данных двигателя в различных эксплуатационных условиях, проверку допустимости изменений, вводимых серийным предприятием. 11. Газотурбинные двигатели, находящиеся на борту ДА (самолета-лидера), проходят эксплуатационные испытания для решения вопросов увеличения ресурса. 12. Требования ко всем видам испытаний ГТД, отвечающим нормам летной годности самолетов и вертолетов, объединены в «Авиационных правилах» часть 33. 13. При подготовке к испытаниям ГТД разрабатываются документы, в которых определяются объем, периодичность, виды, содержание стендовых и летных испытаний. 14. Конструктивные и технологические особенности конкретного ГТД, новые применяемые материалы, особенности масел, топлив и присадок, сохранение работоспособности двигателя в особых условия эксплуатации — все эти факторы должны учитываться при составлении программы испытаний.
ВОПРОСЫ 1. Какие виды испытаний используют для авиационных ГТД? 2. Назовите особенности узловых испытаний. 3. Каковы цели и задачи испытаний опытных ГТД? 4. Назначение сертификационных и государственных испытаний. 5. Назовите порядок и особенности проведения предъявительских и приемосдаточных испытаний. 6. Каким периодическим испытаниям подвергаются серийные ГТД? 7. В чем состоят особенности приемки серийных двигателей? 8. Какие экспериментальные характеристики снимают при испытаниях авиационных ГТД? 9. Какие мероприятия осуществляют для сокращения объемов и трудоемкости предъявительских и приемосдаточных испытаний? 10. Что лежит в основе правил испытаний и приемки серийных ГТД? И. Назовите документы, регламентирующие испытания. 12. Какие основные характеристики и эксплуатационные режимы определяют при испытаниях ГТД? 13. Как происходит подготовка к испытаниям? 14. Назовите особенности подготовки программы испытаний?
ГЛАВА 3. ПЛАНИРОВАНИЕ ЭКСПЕРИМЕНТА ПРИ ИСПЫТАНИЯХ ГТД 3. 1. ОСНОВНЫЕ ПОНЯТИЯ И ОПРЕДЕЛЕНИЯ Затраты на проведение экспериментального исследования авиационных ГТД весьма значительны и избежать их невозможно, поэтому остается единственное — свести их к минимуму, в частности, за счет применения методов, приведенных на рис. 3. 1. При этом большую роль при проведении экспериментальных исследований играет методология планирования, основанная на теории планированного эксперимента (11, 26, 38, 46, 49]. Конечной задачей эксперимента, как правило, является получение модели, адекватно описывающей исследуемый процесс. Применение методов оптимального планирования эксперимента позволяет получить математическую модель процесса даже при отсутствии сведений о его механизме. При этом исследуемый процесс рассматривают в виде «черного ящика» (рис. 3. 2) с я-мерным вектором У, с составляющими у 1, у 2 , у з , . . . у n (параметрами или функциями отклика) и действующими на его входе параметрами, разделяющимися на три группы: х, w и z Первая группа представляет собой k-мерный вектор X управляемых параметров, которые можно контролировать и целенаправленно изменять в процессе эксперимента. Вторая группа представляет собой p-мерный вектор W контролируемых, но неуправляемых параметров {W i } i=p i=1 т. е. не поддающихся целенаправленному изменению в процессе эксперимента.
Рис. 3. 1. Методы повышения эффективности экспериментального исследования ГТД Рис. 3. 2. Схема сложного процесса
Третья группа представляет собой m-мерный вектор Z неконтролируемых, а следовательно, и неуправляемых входных параметров. При исследовании процессов, как правило, рассматривают параметры первой группы: (3. 1) Очевидно, что соответствие полученных результатов эксперимента исследуемому процессу зависит от того, насколько полно в модели учтены входные параметры, которые в большей степени влияют на функцию отклика и ее значения {у i }, фиксируемые в процессе проведения каждого из N опытов. Ценность математического описания, полученного в результате проведения эксперимента, заключается в том, что оно: • дает информацию о влиянии факторов; • позволяет количественно определить значения функции отклика при заданных значениях входных параметров; • является основой для оптимизации. Геометрический образ, соответствующий функции отклика, называют поверхностью отклика (рис. 3. 3). Координатное пространство, по осям которого отложены факторы, называют факторным пространством. Для удобства рассмотрения поверхность отклика может быть представлена на факторной плоскости (х 1 , х 2 ) линиями постоянных значений функции отклика (рис. 3. 4). На рис. 3. 4, а поверхность отклика имеет вид «вершины» и соответствует области значений
Рис. 3. 3. Поверхность отклика Рис. 3. 4. Типы поверхностей отклика факторов, где расположен максимум величины у. Очевидно, аналогичный вид имеют линии постоянного уровня и в случае убывающей функции у. Проверка воспроизводимости опытов. Прежде чем приступить к планированию эксперимента, необходимо убедиться в том, что опыты воспроизводимы. Для этой цели проводят несколько серий параллельных опытов в рассматриваемой области изменения влияющих факторов и для каждой серии вычисляют среднее арифметическое значение функции отклика: (3. 2)
Где ξ— число параллельных опытов, проведенных при одинаковых условиях (обычно £е 2, 4). Затем вычисляют оценку дисперсии для каждой серии параллельных опытов: (обычно ξ 2, 4). ∈ Затем вычисляют оценку дисперсии для каждой серии параллельных опытов: (3. 3) Для проверки воспроизводимости опытов находят расчетное значение критерия Кохрена — отношение наибольшей из оценок дисперсий к сумме всех оценок дисперсий: (3. 4) Если выполняется условие GP<G (где G — табличное значение критерия Кохрена), то опыты считаются воспроизводимыми, а оценки дисперсий — однородными. Табличное значение критерия выбирается согласно заданному уровню значимости α= 1 — Р(Р — доверительная вероятность, как правило, Р = 0, 95), количеству оценок дисперсий N и числу степеней свободы f = к — 1. Вычисление погрешности эксперимента. Оценки однородных дисперсий нескольких серий параллельных опытов можно усреднить и определить величину (3. 5)
называемую оценкой дисперсии воспроизводимости. С ней связано число степеней свободы f = N(k — 1), где к — количество факторов. Оценку дисперсии среднего значения определяют по формуле: (3. 6) С ней также связано число степеней свободы f= N(k — I). Рандомизация. Для компенсации систематических погрешностей эксперимента используют прием, называемый рандомизацией, т. е. опыты проводят в случайной последовательности, устанавливаемой с помощью таблицы случайных чисел. Метод наименьших квадратов. Для построения модели, описывающей связь между входными и выходными параметрами исследуемого процесса (такая модель трактуется в теории корреляционно-регрессионного анализа как модель прогрессии), используется метод наименьших квадратов. Наиболее общим видом регрессионной модели является полином степени т к факторов: (3. 7) (3. 8) (3. 9)
Экспериментально изучая влияние х, на у, получают таблицу измерений табл. 3. 1). 3. 1. Вид таблицы измерений экспериментально исследуемого процесса Можно выделить две матрицы: [х] — матрица значений факторов размерности N(K + 1) и [у] — вектор наблюдений размерности N + 1: (3. 10)
Между наблюдаемым значением у и и расчетным значением у и существует разница Δу, называемая «невязкой» : Необходимо свести общую невязку к минимуму. При этом наименее громоздкие вычислительные схемы получаются в том случае, если минимизируется не сумма абсолютных отклонений по всем опытам а сумма квадратовотклонений (такой метод обладает и рядом ценных свойств со статистических позиций): (3. 11) Для нахождения минимума функции приравнивают к нулю частные производные по всем неизвестным. После выполнения операций дифференцирования получают систему так называемых нормальных уравнений, решением которой и определяются неизвестные коэффициенты регрессионной модели. В матричной форме система нормальных уравнений имеет вид: [M][B]=[y]. (3. 12) Матрицу [M] можно получить из матрицы [х], если последнюю умножить слева на транспонированную матрицу: (3. 13)
Аналогичным образом матрица [y M ] получается из матрицы [у]: [y M ]=[x*][y] (3. 14) и система нормальных уравнений для любого числа факторов к записывается в виде: [x*][x][B]=[x*][y]. (3. 15) В матричной форме вышеизложенное определение коэффициентов b i сводится к нахождению вектора-столбца |B] в уравнении (3. 12). Если обе части этого уравнения умножить слева на обратную матрицу |Д| = [х*][х] то будет определен вектор [В], поскольку произведение [Д][х*|[х] дает единичную матрицу [E]: [B]=[Д][x*][y], (3. 16) где [Д] для однофакторной матрицы имеет вид: (3. 17)
Матрица [Д] называется ковариационной или матрицей ошибок. Она имеет первостепенное значение при построении моделей, поскольку ее свойства опpеделяют собой свойства моделей, методы планирования эксперимента и возможности интерпретации результатов моделирования. По ее элементам с ii и с ij определяют коэффициенты моделей b i (3. 7). . . (3. 9) и их важнейшие статистические характеристики. Важным свойством ковариационной матрицы [Д] является то, что она не зависит от вектора наблюдений [у], т. е. от свойств информации, по которой троится модель. Следовательно, свойства матрицы [Д] могут быть исследованы до проведения эксперимента. Поскольку ковариационная матрица [Д] есть обращенная информационная матрица [М] = [Д] -1 а информационная матрица [М] связана с матрицей [х] соотношением [М] = [х*][х], то и матрица [х] может быть исследована и сконструирована некоторым оптимальным (с точки зрения елей исследователя) образом до проведения эксперимента. Исследование коариаиионных матриц [Д] и конструирование на их основе матриц [х] и есть одно из основных направлений оптимального планирования эксперимента. Критерии оптимальности плана эксперимента. Оптимальность планов оценивается по большому количеству критериев, каждый из которых приобретает особую ценность для экспериментатора в зависимости от целей проводимого исследования: • минимизация числа опытов, т. е. близость числа опытов N к числу оцениваемых параметров модели L. В пределе N может быть равно L (так называемый насыщенный план); • простота вычислении коэффициентов модели;
• композиционность плана, т. е. возможность использования точек плана первого этапа исследования в плане второго этапа в случае, если модель первого эта- а не адекватна; • независимость оценок коэффициентов модели; • минимум средней дисперсии оценок коэффициентов модели. Такие планы называются А-оптимальными и полезны, когда важно обеспечить в среднем точность оценок коэффициентов модели; • минимум максимальной дисперсии ( ->min) оценки коэффициентов модели; • минимум средней дисперсии (min) выхода Y модели; • минимум максимальной дисперсии (min) выхода Yмодели, так называемая G-оптимальность; • ротатабельность плана, позволяющая получить модель регрессии, с одинаковой точностью предсказывающей s 2 {Y} во всех направлениях от центральной точки эксперимента; • униформность плана — независимость дисперсии выхода от радиуса сферы в некоторой области вокруг центра эксперимента; • максимальная точность оценки координат экстремума, что весьма существенно при решении оптимизационных задач; • возможность разделения плана эксперимента на блоки (на так называемые ортогональные блоки» ) для того, чтобы исключить влияние на коэффициенты регрессионной модели временного дрейфа факторов; • минимизация объема эллипсоида рассеяния оценок параметров статистических оценок, так называемая Д-оптимальность, что соответствует наименьшему определителю ковариационной матрицы [Д]
• минимизация максимальной оси эллипсоида рассеяния оценок параметров, так называемая Е-оптимальность, при которой не допускается, чтобы отдельные оценки параметров модели имели слишком большие дисперсии и ковариации. Наличие такого большого числа часто несовместимых критериев оптимальности, с одной стороны, усложняет принятие решения о выборе плана эксперимента, с другой стороны, дает экспериментатору возможность построить (или выбрать) план в соответствии с целями проводимого исследования. Основным и часто используемым на практике является критерий Д-оптимальности.
3. 2. ПЛАНИРОВАНИЕ И ПРОВЕДЕНИЕ ЭКСПЕРИМЕНТА 3. 2. 1. Полный факторный эксперимент (ПФЭ) дает возможность получить математическое описание исследуемого процесса в некоторой локальной области факторного пространства, лежащей в окрестности выбранной точки с координатами (x 01 , x 02 , . . , x 0 n ). Для перенесения начала координат факторного пространства в эту точку (рис. 3. 5) вводят новые переменные (кодированные переменные): (3. 18) где ∆x — масштаб по оси Х i Рис. 3. 5. Введение координатных переменных
Функция отклика в окрестности нового начала координат может быть разложена в ряд Тейлора: где β 0 = y(0, …, 0) — значение функции отклика в начале координат; Метод ПФЭ служит для математического описания процесса в виде отрезка яда Тейлора (3. 19). При этом обычно ограничиваются линейной частью разложения и членами, содержащими произведения факторов в первой степени. Таким образом, удается определить уравнение локального участка поверхности отклика, если его кривизна не слишком велика. Поскольку коэффициенты искомой регрессионной модели определяются на основе экспериментальных данных, то, следовательно, несут на себе отпечаток погрешностей эксперимента. Чтобы подчеркнуть это обстоятельство, в уравнении вместо символов β , обозначающих истинные значения коэффициентов, ищут b, подразумевая под этим соответствующие выборочные оценки: Для удобства вычислений коэффициентов регрессии все факторы в ходе ПФЭ варьируют на 2 -х уровнях, соответствующих значениям кодированных переменных +1 и -1. Таким образом, ПФЭ представляет собой систему опытов, содержащую все возможные неповторяющиеся комбинации уровней варьирования факторов.
В табл. 3. 2 и 3. 3 приведены условия проведения опытов полного двухфакторного и трехфакторного эксперимента. Риc. 3. 6. Опыты полного факторного эксперимента Как видно из рис. 3. 6, опыты, приведенные в табл. 3. 2, соответствуют на факторной плоскости вершинам квадрата с центром в начале координат. 3. 2. Полный двухфакторный эксперимент Номер опыта Факторы Функция отклика Х 1 Х 2 1 -1 -1 Y 1 2 +1 -1 Y 2 3 -1 +1 Yз 4 +1 +1 Y
Номер опыта Факторы Функция отклика Х 1 Х 2 Х 3 1 -1 -1 -1 Y 1 2 +1 -1 -1 Y 2 3 -1 + 1 -1 Yз 4 +1 + 1 -1 Y 4 5 -1 -1 + 1 Y 5 6 +1 -1 + 1 Y 6 7 -1 + 1 Y 7 8 +1 + 1 Y 8 Опыты табл. 3. 3 соответствуют в факторном пространстве вершинам куба с центром в начале координат. Таким образом, основными принципами построения плана ПФЭ являются: • уровни варьирования первого фактора чередуются от опыта к опыту; • частота смены уровней варьирования каждого последующего фактора вдвое меньше, чем у предыдущего. Матрица планирования полного факторного эксперимента обладает следующими свойствами:
(3. 21) где N — число опытов ПФЭ; i — номер опыта; j, l, m — номера факторов. Общее количество опытов в матрице планирования ПФЭ (3. 22) где к — число факторов. На основании ПФЭ вычисляют коэффициенты регрессии по формулам: (3. 23) С помощью ПФЭ все коэффициенты регрессии определяются с одинаковой погрешностью. Некоторые из коэффициентов регрессии могут оказаться незначимыми. Значимость коэффициентов определяется через оценку дисперсии: (3. 24) Коэффициент регрессии является значимым, если выполнено условие: (3. 25)
где t — табличное значение критерия Стьюдента. Далее полученное уравнение регрессии проверяют на адекватность с помощью критерия Фишера: (3. 26) Где S 2 ад — оценка дисперсии адекватности, определяемая по формуле: (3. 27) где В — число коэффициентов регрессии искомого уравнения, включая свобод ный член; у j , ŷ j — экспериментальное и расчетное значения функции отклика в j-ом опыте; N — число опытов ПФЭ. С оценкой дисперсии адекватности связано число степеней свободы f ад = N — В. Уравнение регрессии считается адекватным, если выполняется условие: (3. 28) где F — табличное значение критерия Фишера для соответствующих степе ней свободы f ад = N — (к + 1), f = N — (к — 1)и принятого уровня значимо сти а = 1 — р. Пример. Целью исследования являлось получение математической зависимости пла стичности σ 02 сплава В 95 АТ от внешних факторов (вакуума и температуры). Предварительные исследования показали, что при уменьшении давления от нор мального (101, 325 к. Па)
до 13, 3 Па величина ст02 возрастает, а затем стабилизируется. С увеличением температуры σ 02 также растет. Таким образом, независимыми факторами являлись давление и температура, а функцией отклика — пластичность материала σ 02. Факторы и область их определения приведены в табл. 3. 4. Наименование Область определения Давление (х, ), Па 1, 01 ∙ 1 0 5. . . 1, 33 ∙ 10 -3 Температура (х 2 ), К 293. . . 423 Область определения фактора х, выбрана на основе априорной информации, а фактора х 2 — с учетом возможностей экспериментальной установки и цели эксперимента (оценка влияния повышенных температур). Поскольку эксперимент относится к типу 2 2 то число опытов равно четырем. Параллельные опыты проводились также по четыре для каждого сочетания уровней факторов. Кодированные значения факторов приведены в табл. 3. 5. За нижний уровень принято нормальное давление 1, 0 ∙ 10 5 Па, а за верхний — вакуум 1, 33 ∙ 10 -3 Па.
3. 5. Кодированные значения факторов Фактор Уровни Нижний (-1) Нулевой (0) Верхний (+1) Х 1 1, 0 ∙ 1 0 5 Па (760 мм рт. ст. ) 5, 05 ∙ 10 3 Па (5, 38 -10 3 мм. рт. ст) 1, 33 ∙ 10 -3 Па (1 ∙ 10 5 мм рт. ст. ) х 2 293 К (20 °С) 358 К (85 °С) 423 К (150 °С) Матрица планирования приведена в табл. 3. 6. По результатам эксперимента были определены средние значения и оценка дисперсий Sj (табл 3. 6). Однородность дисперсий проверялась по критерию Кохрена:
3. 6. Матрица планирования № х 0 х 1 х 2 Отклик s i 2 Кодированное значение Натуральное значение, Па Кодированное значение Натуральное значение, К σ 0, 2 МПа Повторное испытание Среднее значение 1 + — 1, 01 ∙ 10 5 — 293 507 487 473 494 276 2 + + 1, 33 ∙ 10 -3 — 293 514 497 503 505 54 3 + — 1, 01 ∙ 10 5 + 423 451 437 446 447 445 35 4 + + 1, 33 ∙ 10 -3 +
При уровне значимости α = 0, 05 G = 0, 684. Поскольку G p < G, то гипотеза об однородности дисперсий не отвергалась и определялась дисперсия воспроизводимости S 2 {y} : Были получены следующие значения коэффициентов регрессионной модели: b 0 = 484, 5; b 1 = 15, 0; b 2 = — 15, 0; b 12 = 9, 5, т. е. модель имела вид: y= 484, 5 + 150 х 1 — 15, 0 х 2 + 9, 5 x 1 x 2. Остаточная дисперсия (дисперсия адекватности) равна: где/- число степеней свободы (f=N-(k+1) = 4 — (2 + 1) = 1); ŷ i — значение функции отклика по уравнению регрессии в i-ом опыте. Адекватность модели проверялась по критерию Фишера:
Доверительный интервал констант b 1 , и b 12 определялся по формуле: где t — критерий Стьюдента; S{bj) — среднеквадратичное отклонение: Поскольку ∆ b j > b 12 , то коэффициент b 12 незначим и им можно пренебречь. Таким образом, окончательно модель регрессии имеет вид: у = 484, 5 + 15, 0 х 1 , — 15, 0 х 2 , означающий, что взаимное влияние вакуума и температуры на пластичность сплава В 95 АТ незначимо.
3. 2. 2. Дробный факторный эксперимент С увеличением количества факторов резко возрастает количество опытов ПФЭ. Это видно из формулы (3. 22). Однако для определения коэффициентов регрессии не всегда требуется много опытов. В таких случаях можно уменьшить 3. 7. ПФЭ и его дробные реплики Номер Опыта Факторы Функция Отклика Дробные реплики. X 1 X 2 X 3 1 -1 -1 -1 Y 1 ¼ ½ 2 +1 -1 -1 Y 2 3 -1 + 1 -1 Y 3 ¼ 4 +1 + 1 -1 Y 4 5 -1 -1 +1 Y 5 ¼ ½ 6 +1 -1 +1 Y 6 7 -1 +1 +1 Y 7 ¼ 8 +1 +1 +1 Y
объем эксперимента, воспользовавшись методом дробного факторного эксперимента (ДФЭ). Для нахождения математического описания процесса используется определенная часть ПФЭ: 1/2, 1/4 и т. д. Эти системы опытов называются дробными репликами (табл. 3. 7). Расчет коэффициентов регрессии, проверка их значимости и адекватности математического описания в данном случае проводятся так же, как при ПФЭ. Пусть, например, требуется определить коэффициенты уравнения регрессии: Если для этой цели воспользоваться ПФЭ, то необходимо провести 8 опытов. Однако эту задачу можно решить с помощью меньшего количества опытов. Например, возьмем матрицу ПФЭ (см. табл. 3. 7) и приравняем произведен Х 1 Х 2 к фактору Х 3 Такое планирование эксперимента, когда некоторые из факторов, приравнивают к произведениям нескольких факторов, называется планированием смешиванием. Его обозначают символом 2 к-р , где к — общее число фактор; <Р — число факторов, приравненных к произведениям. С этой точки зрение табл. 3. 8 приведена матрица планирования типа 2 3 -1.
3. 8. Матрица планирования типа 2 3 -1 Номер опыта Х 1 Х 2 Х 3 =Х 1 Х 2 Функция отклика 1 -1 -1 +i Y 1 2 +1 -1 -1 Y 2 3 -1 + 1 -1 Yз 4 +1 +1 +i Y 4 Пример. Целью исследования являлось определение влияния на гидравлические параметры форсунок конструктивных факторов, приведенных на рис. 3. 7: x 1 = l 0 /r c — отношение длины к радиусу соплового отверстия; х 2 = l ф / r c — отношение длины выходной фаски к радиусу соплового отверстия; х 3 = φ ф — угол выходной фаски соплового отверстия; х 4 = φ к — угол корпуса камеры закручивания; x 5 = δ/R — отношение длины камеры закручивания к радиусу закручивания.
Для получения зависимостей был выбран план эксперимента с варьированием факторов на двух уровнях (табл. 3. 9). Геометрическая характеристика форсунки во всех вариантах соответствовала форсунке серийной конструкции (А = 3, 35). Рис. 3. 7. Схема центробежной форсунки 3. 9. Независимые факторы и область их определения Уровни Факторы х 1 х 2 х 3 х 4 х 5 Основной 0, 4 1, 394 2, 18 0, 277 Нижний 0, 2 1, 044 1, 92 0, 158 Верхний 0, 6 1, 744 2, 44 0, 396 Шаг варьирования 0, 2 0, 35 0, 26 0,
Нормированные переменные х i связаны с натуральными соотношениями: (3. 29) Для сокращения объема эксперимент проводился по дробному факторному плану (ДФЭ)2 5 -2 с заменой х 4 = х 1 ∙х 2 и х 5 = х 1 х 2 х 3. Для реализации эксперимента были изготовлены и испытаны по 3. . . 4 комплекта дозирующих деталей форсунки в каждом варианте. В табл. 3. 10 приведена матрица планирования 25 2 с выходными параметрами: G — расход топлива через форсунку и а — угол распыла топлива (в каждой строке указаны результаты испытаний 3. . . 4 экземпляров и средние величины функций отклика). Форсунки испытывались при перепаде давления Ар = 1, 96 МПа (20 кгс/см 2), угол распыла измерялся на расстоянии 30 мм от среза сопла форсунки.
3. 10. Матрица планирования 2 5 —
По t-критерию Стьюдента значимыми в модели для расхода топлива оказались константы при аргументах х 3 , х 4 и х 5 , а в модели для угла распыла — при аргументаx: x 1 x 3 И x 5. В итоге получены регрессионные модели вида: (3. 30) (3. 31) По F-критерию Фишера модели (3. 30) и (3. 31) адекватно описывают экспериментальные данные при уровне значимости 0, 9. Для проверки точности уравнений (3. 30) и (3. 31) были доработаны и испытаны не сколько форсунок. Вызванные этим изменения гидравлических параметров форсунок (Д(У и Да) приведены в табл. 3. 11. Из таблицы видно, что результаты расчета параметров ΔG и Δα по моделям (3. 30) (3. 31) хорошо согласуются с экспериментом. Полученные зависимости используются для решения нескольких задач: • определения характера доработок до проведения испытаний, тем самым уменьшая отбраковку дозирующих деталей; • корректировки гидравлических параметров форсунок с целью устранения дефектов, обнаруженных при работе двигателя, путем доработки или замены деталей, корректируя в нужном направлении угол распыла топлива при неизменном коэффициента расхода, и наоборот, чтобы при этом не возникали какие-либо новые дефекты (образование нагара, перегрев форсунок из-за нарушения их обдува воздухом от компрессора и др. ); • оценки влияния отклонений размеров дозирующих деталей на гидравлические параметры форсунки и при необходимости компенсации этого влияния за счет варьирования другими размерами форсунки.
3. 11. Изменения гидравлических параметров форсунок Изменение геометрических параметров ΔG<7, кг/ч Δα, град расч. эксп. δ / R уменьшено на 0, 198 -17, 3 -20 +6 +4 l с / r с уменьшено на 0, 2 — — -6 -4 φ к увеличен на 0, 5 рад и 5 / R увеличено на 0, 366 -5 0 -12 -5 φ ф увеличен на 0, 35 рад -10 -2 +3 +
3. 2. 3. Центральное композиционное планирование эксперимента В случаях, когда в области факторного пространства кривизна поверхности отклика велика и вследствие этого поверхность не может быть описана многочленом вида (3. 20), для адекватного математического описания требуется многочлен более высокой степени, например, отрезок ряда Тейлора (3. 19), содержащий члены с квадратами переменных. С этой целью используют центральное композиционное планирование (ЦКП) эксперимента. Различают два вида ЦКП — ортогональное и ротатабельное. Ортогональное ЦКП. Количество опытов при ортогональном ЦКП определяется по формуле: N =2 к + 2 к + 1, (3. 32) где 2 к — количество опытов, образующих ПФЭ; 2 к — число так называемых звездных точек в факторном пространстве, имеющих координаты (±α, 0, 0, . . . , 0), . . . , (0, ±α, 0, . . . , 0), . . . , (0, 0, . . . , ±α). Здесь величина а называется звездным плечом; 1 — опыт в центре планирования, т. е. в точке факторного пространства с координатами (0, 0, . . . , 0). Если с помощью ПФЭ не удается получить адекватного математического описания в форме (3. 20), то к нему добавляют опыты в «звездных» точках и в центре плана, а полученную при этом композицию используют для получения математического описания процесса в виде многочлена второй степени. От-сюда и произошло название метода — центральное композиционное планирование. Значения звездного плеча а для ЦКП для различных значений числа факторов к приведены в табл. 3. 12.
3. 12. Значения звездного плеча αЗначения звездного плеча а для ЦКП для различных значений числа факторов к приведены в табл. 3. 12. к 2 3 4 5 α 1, 000 1, 215 1, 414 1, 547 Значения а выбраны из условия ортогональности матрицы планирования. Уравнение регрессии при ортогональном ЦКП имеет вид: (3. 33) Переменные величины: (3. 34)
j – номер опыта; i — номер фактора введены для того, чтобы матрица планирования была ортогональной и коэффициенты регрессии определялись по результатам опытов независимо друг от друга. F Для того чтобы получить уравнение регрессии в обычной форме (3. 35) Определяют величину: (3. 36) В табл. 3. 13 в качестве примера приведена матрица ортогонального ЦКП для двух факторов, а на рис. 3. 8 схема этих опытов.
3. 13. Ортогональное ЦКП для двух факторов Системы опытов Номер опыта Х 1 Х 2 Х 1 * X 2 * Полный факторный 1 +1 -1 +1 +0, 33 эксперимент 2 -1 -1 -1 +0, 33 3 +1 +1 -1 +0, 33 4 -1 +1 +1 +0, 33 Опыты в звездных 5 +1 0 0 +0, 33 -0, 67 точках 6 -1 0 0 +0, 33 -0, 67 7 0 +1 0 -0, 67 +0, 33 8 0 -1 0 -0, 67 +0, 33 Опыт в центре плана 9 0 0 0 -0,
Рис. 3. 8. Схема опытов ортогонального ЦКП для двух факторов: О — полный факторный эксперимент; * — опыты в звездных точках; □ — опыты в центре плана Коэффициенты регрессии при ортогональном ЦКП определяются по формулам: (3. 37) (3. 38)
Оценку дисперсии коэффициентов регрессии проводят по формулам:
Коэффициент |b i |, является значимым, если |b i | > S bi t. Проверка адекватности уравнения регрессии осуществляется с помощью критерия Фишера. Ротатабельное ЦКП. Этот метод планирования эксперимента позволяет получать более точное математическое описание поверхности отклика по сравнению с ортогональным ЦКП, благодаря увеличению числа опытов в центре плана и специальному выбору величины звездного плеча а. В табл. 3. 14 приведены основные характеристики матриц ротатабельного планирования 3. 14. Характеристики матриц ротатабельного планирования Число факторов Число опытов фактор ного планирования Число опытов в звездных точках Число опытов в центре плана Общее число опытов α 2 4 4 5 13 1, 414 3 8 6 6 20 1, 680 4 16 8 7 31 2, 000 5* 32 10 10 52 2, 378 5** 16 10 6 32 2, 000 * Полный факторный эксперимент. ** Эксперимент по методу дробных реплик.
При ротатабельном ЦКП для определения коэффициентов регрессии и соответствующих дисперсий находят следующие константы: где n – число факторов; N — общее число опытов ротатабельного ЦКП; N 0 — число опытов в центре плана. На основании результатов эксперимента вычисляют следующие суммы: (3. 41)
Формулы для расчета коэффициентов регрессии имеют вид: (3. 42) Дисперсии коэффициентов регрессии определяют по формулам: (3. 43)
Коэффициент |bi|, является значимым, если |bi| > Sbit. Дисперсию адекватности рассчитывают по формуле: (3. 44) С ней связано число степеней свободы: Проверка адекватности уравнения регрессии осуществляется с помощью критерия Фишера. Пример. Цель эксперимента заключалась в определении тяги и расхода топлива двигателя при работе его в условиях изменения высот H≈11. . . 18 км и постоянной скорости полета (М = const), при этом частота вращения ротора изменялась в диапазоне n изм = 84. . . 92 %. Таким образом, независимыми переменными (факторами) являлись высота полета и частота вращения ротора. На высотном стенде высота полета при М = const задается давлением воздуха на входе в двигатель р* в , давлением в ТБК р н и температурой Т* в. В эксперименте требовалось выдерживать величину М = idem, поэтому отношение p i * / р н также было постоянным при различных значениях давления р* в. Поскольку изменение высот укладывалось в диапазон 25 > Н> 11 км, то температура воздуха на входе не изменялась. В соответствии с зависимостью р в σ / р* в = π(М) = idem высоте Н = 11 км соответствует давление р* в = 60 к. Па, а высоте Н = 18 км — р* в = 20, 0 к. Па.
Проведение данного эксперимента было совмещено с исследованием других характеристик двигателя, вследствие этого диапазон изменения давления р* в был равен 19, 7. . . 69, 2 к. Па. Таким образом, сформулированная задача определения характеристик двигателя сводилась к замеру характеристик с двумя независимыми переменными n и р в *. При выборе вида матрицы планирования было учтено, что величина тяги нелинейно зависит от частоты вращения ротора двигателя, поэтому для проведения эксперимента была выбрана матрица планирования двухфакторного плана 2 -го порядка (табл. 3. 15). Такой план позволяет строить регрессионную модель процесса в виде полинома 2 -го порядка: (3. 46) Обозначая через ζ 1 значения первого фактора — частоты вращения ротора п, получим ζ 11 = 84 %, ζ 12 = 92 %, координаты центра ζ 10 = 88 %, а интервал варьирования в соответствии с формулой (1. 4) Δ ζ 1 = 2, 8 %. Обозначая через ζ 2 значения второго фактора — давления воздуха на входе в двигатель Р в * , получим ζ 21 = 19, 7 к. Па, ζ 2 2 = 69, 2 к. Па, координаты центра ζ 20 = 44, 5 к. Па, а интервал варьирования Δ ζ 2 = 17, 5 к. Па. Для двухфакторного плана эксперимента 2 -го порядка, у которого α = 1, 414 и m 0 = 5 (m 0 — число повторных опытов в центре плана), план эксперимента имеет вид, приведенный в табл. 3. 15. Значения факторов, соответствующие кодированным величинам в матрице планирования, приведены в табл. 3. 16, а результаты эксперимента — в табл. 3. 17.
3. 15. План эксперимента для определения констант двухфакторной регрессионной модели 2 -го порядка № точки x 1 x 2 х 2 1 x х, х 2 Y 1 -1 -1 +1 + 1 +1 Y 1 2 -1 + 1 +1 +1 -1 Y 2 3 +1 -1 +1 +1 -1 Y 3 4 +1 + 1 +1 +1 +1 Y 4 5 -α 0 +α 2 0 0 Y 5 6 + α 0 + α 2 0 0 Y 6 7 0 -α 0 + α 2 0 Y
3. 16. Кодированные значения факторов х ij ζ = п, % ζ 2 = p* в, к. Па +α n = 92 р* в = 69, 2 +1 n = n 0 + Δn = 90, 8 р* в = р* во + Δр в 0 *= 62, 0 0 n = n 0 =88 р в * = р* в 0 = 44, 5 -1 n = n 0 — Δn = 85, 2 р в = р в 0 * + Δр в = 27, 0 -α n = 84 р в * = 19,
Оценивая константы регрессионной модели и подставляя значения у, из табл. 3. 17 в табл. 3. 15 вместо у, получена регрессионная модель для тяги. Р = 2629, 75 + 327, 66 х 1 + 1018, 7 х 2 +94, 53 х 1 х 2 -45, 84 Х 1 2 -0, 77 х 2 2. (3. 47) Правомерность использования этой модели подтверждалась проверкой ее адекватности по Р-критерию Фишера, а также оценкой значимости полученных констант модели t-критерию Стьюдента. Модель (3. 47) адекватно описывает опытные данные, если р — • Поскольку F p = 2, 8 < F = 6, 6, то модель адекватно описывает опытные данные. Проверка значимости коэффициентов регрессии показала, что квадратичный член регрессионной модели ϴ 22 х 2 2 не влияет на величину тяги и он был исключен из регрессионной модели (3. 47). Переводом значений х 1 и х 2 в величины n и Р* в приведением подобных члена регрессионная модель (рис. 3. 9): Р = -4796, 6+ 1059, 4 n -11150 p* в +192, 9 np* в -5, 84 n 2. (3. 48)
N° точки y 1 = Р, кг y 2 =G m , кг/ч 1 1358, 2 1908, 5 2 3184, 6 4385, 0 3 1808, 5 2580, 0 4 4013, 0 5698, 4 5 2063, 6 2906, 0 6 3013, 2 4307, 0 7 1172, 1 1679, 5 8 4085, 0 5663, 4 9 2629, 8 3655, 7 10 2629, 8* 3655, 7* 11 2629, 8* 3655, 7* 12 2629, 8* 3655, 7* 13 2629, 8* 3655, 7*3. 17. Результаты эксперимента *Значение величин Р и G m в точках № 10. . . 13 принималось соответственно равным их значениям в точке № 9, поскольку из-за совмещения эксперимента с другими исследованиями пятикратное измерение параметров в центре плана не проводилось.
Рис. 3. 9. Дросселем характеристика двигателя, построенная по рефессионной модели (1. 9): ⁰ — комбинации значении факторов, при которых проводился эксперимент
Для получения зависимости расхода топлива у 2 от факторов х 1 и х 2 в табл. 3. 15 вместо величины у, подставляя значения у 2 из табл. 3. 17, получена регрессионная модель в кодированных значениях факторов: Рис. 3. 10. Дроссельная характеристика двигателя, построенная по регрессионной модели (1. 11): — ⁰ комбинации значений факторов, при которых проводился эксперимент Проверка значимости коэффициентов регрессии показала, что квадратичные члены регрессионной модели не значимы, поэтому окончательно:
На рис 3. 10 приведена сетка характеристики Gm =f(H, n), полученная по регрессионной модели (3. 50). Таким образом, применение планирования эксперимента позволило в данном случае получить регрессионную модель высотно-скоростной характеристики двигателя в заданной области изменения независимых переменных. При обычном подходе потребовалось бы провести 20. . . 25 опытов. 3. 3. ПРИМЕНЕНИЕ ПЛАНИРОВАНИЯ ЭКСПЕРИМЕНТА ПРИ ОПТИМИЗАЦИИ ИССЛЕДУЕМЫХ ПРОЦЕССОВ Оптимизация процесса представляет собой целенаправленный поиск значений влияющих факторов, при котором достигается экстремум критерия оптимальности с учетом ограничений, наложенных на все влияющие факторы и Функции отклика. 3. 3. 1. Метод крутого восхождения Д- Бокс и К. Уилсон предложили использовать для оптимизации результаты ПФЭ или ДФЭ. Сущность такой оптимизации заключается в следующем. Пусть, например, критерием оптимальности служит функция отклика у, представленная в виде (3. 20). Один из влияющих факторов принимают за базовый и для него вычисляют произведение соответствующего коэффициента регрессии на шаг варьирования. Например, для первого фактора это произведение имеет вид b 1 Δx 1. Затем для базового фактора выбирают шаг движения Ах, *, с которым будет осуществляться оптимизация. Обычно Δx*< Δx 1. После этого вычисляют отношение: (3. 51)
Для всех остальных факторов шаги движения к оптимальным значениям определяют по формуле: (3. 52) Движение к оптимуму начинают из центра плана, который использовался для получения математического описания функции отклика. Значения факторов на каждом новом шаге определяют путем прибавления Δх i , — к соответствующим предыдущим значениям. Так осуществляется оптимизация по методу крутого восхождения. Если целью является определение минимума функции у, то новые значения факторов находят из предыдущих путем вычитания Δх i *. Такой способ оптимизации называют методом наискорейшего спуска. Движение к оптимуму прекращают в следующих случаях: 1) значения (одного или нескольких) факторов или функций отклика вышли на границы допустимых значений; 2) достигнут экстремум критерия оптимальности у. В первом случае на этом оптимизация заканчивается, а во втором — в области экстремума функции у ищут ее новое математическое описание, используя ПФЭ или ДФЭ. Если удается получить адекватное описание этой функции в виде (3. 20), то продолжают оптимизацию методом крутого восхождения (рис. 3. 11).
Рис. 3. 11. Оптимизация по методу крутого восхождения Очевидно, оптимум, найденный в результате первого крутого восхождения, является локальным. Если же в области оптимума не удается получить адекватное уравнение регрессии вида (3. 20), то переходят к планированию эксперимента для получения математического описания функции у в виде многочленов второй степени. Пример. На серийных двигателях с нерегулируемыми камерами сгорания практически невозможно регулировать уровень неравномерности полей температур. Поэтому остается единственное решение — это оптимизация конструкции пускового воспламенителя камеры сгорания [46]. Из опыта доводки воспламенителей известно, что решение задачи традиционными методами требует большего объема эксперимента. Поэтому задача решалась с применением планированного эксперимента. Оптимизация проводилась варьированием следующих факторов (рис. 3. 12):
х1— выступание свечи; x 2 — диаметр камеры воспламенителя; X 3 – площадь отверстия для подачи воздуха в камеру воспламенителя. Качество работы пускового воспламенителя оценивается по нескольким параметрам, являющимся функциями варьируемых факторов: Н — максимальная высота, на которой горение в пусковом воспламенителе устойчиво при неработающей свече; ω п предельная скорость в камере воспламенителя при устойчивом горении на высоте Н = 6 км; Δp mп – минимально потребный перепад давлений топлива на пусковой форсунке для воспламенения топлива на высоте Н = 6 км при скорости в камере ω в = 4 м/с; Δp mс — перепад давлений топлива при срыве пламени в воспламенителе Н = 6 км и ω в = 4 м/с; Δp mу — Δp mс — Δp mп — диапазон перепадов давлений топлива, при котором горение устойчиво.
Рис 3. 12. Экспериментальный пусковой воспламенитель: 1 — камера воспламенителя; 2 — форсунка; 3 — свеча
№ п/п Порядок реализации Матрица планирования Функции отклика Х 1 Х 2 Х 3 Н, км ω п м/сек Δp mп ∙ 10 -5 Па Δp mс ∙ 10 -5 Па Δp mу , ∙ 10 -5 Па 1 4 — — + 7 6, 84 1, 20 1, 75 0, 55 2 2 + — — 7 4, 50 1, 95 0, 45 3 3 — + — 6 4, 95 1, 0 1, 45 0, 45 4 1 + + + 8 7, 08 1, 05 1, 75 0, 703. 18. Матрица планирования и результаты испытаний
Испытания проводились по плану ДФЭ 2 3 -1 с генерирующим соотношением х 3 = х 1 х 2. Матрица планирования и результаты испытаний приведены в табл. 3. 18. Было получено пять линейных зависимостей, характеризующих влияние варьируемых факторов на качество воспламенителя: За основную характеристику качества пускового воспламенителя принята высотность. Поэтому было выполнено движение по градиенту в направлении возрастания функции Н= 7 + 0, 5 Х 1 + 0, 5 Х 3 при фиксированной величине диаметра камеры Х 2 = 43 мм, не влияющей на высотность. Выбрав для Х 1 шаг λ 1 = 1 мм, при начальных интервалах варьирования λ 1 = 1 мм и λ 3 = 26 мм 2 для Х 3 имеем шаг Предварительный расчет по уравнениям регрессии (3. 53). . . (3. 57) показал, что при движении по градиенту Я остальные характеристики воспламенителя также улучшаются, за исключением Δр тп , которое возрастает незначительно. Результаты движения по градиенту функции Я из точки Х 1 = 2 мм; Х 2 = 43 мм; Х 3 = 104 мм’ приведены в табл. 3. 19. Там же приведены результаты расчетов по уравнениям (3. 53). . . (3. 57).
Х 1 Х 2 Х 3 Н, км ω п , м/сек Δp mп ∙ 10 -5 Па Δp mс , 10 -5 Па Δp mу , 10 -5 Па мм мм мм 2 расч. эксп. 2, 0 43 104 8, 0 7, 08 1, 05 1, 75 0, 70 3, 0 43 130 9, 0 8, 14 13, 3 1, 08 1, 10 1, 90 2, 0 0, 83 0, 90 4, 0 43 156 10, 0 8, 0 9, 20 10, 0 1, 10 1, 20 2, 05 2, 0 0, 95 0, 80 3. 19. Результаты движения по градиенту функции Н
На первом шаге высотность устойчивой работы воспламенителя увеличилась до 9 км. Улучшились также остальные характеристики, за исключением небольшого увеличения перепада давлений топлива Δр п с 1, 05 до 1, 1∙ 10 -5 Па. Дальнейшее продвижение по направлению градиента функции Н привело к снижению высотности до 8 км и к ухудшению остальных характеристик воспламенителя. 3. 3. 2. Симплексный метод Симплексом называется правильный многоугольник, имеющий n + 1 вершину, где n — число факторов, влияющих на процесс. Так, если факторов два, то симплексом является правильный треугольник. В практику научных исследований симплексный метод был введен Ф. Химсфортом в 1962 г. Сущность симплексного метода оптимизации иллюстрирует рис. 3. 13. Начальная серия опытов соответствует вершинам исходного симплекса (точки 1, 2 и 3). Условия этих первых опытов берутся из области значений факторов, соответствующих наиболее благоприятным из известных режимов оптимизирующего процесса. Сравнивая между собой результаты опытов в точках 7, 2 и 3, находят среди них самый «плохой» с точки зрения выбранного критерия оптимальности. Пусть, например, самым «неудачным» оказался опыт в точке 7. Этот опыт исключают из рассмотрения, а вместо него в состав симплекса вводят опыт в точке 4, которая симметрична точке 7 относительно противоположной стороны треугольника, соединяющей точки 2 и 3. Далее сравнивают между собой результаты опытов в вершинах нового симплекса, отбрасывают самый «неудачный» из них и переносят соответствующую вершину симплекса в точку 5. Затем рассмотренная процедура повторяется в течение всего процесса оптимизации. Если достигнут экстремум критерия оптимальности, то дальнейшее движение симплекса прекращается. Это значит, что новый шаг возвращает исследователя в предыдущую точку факторного пространства.
Симплексный метод, так же как и метод крутого восхождения, является локальным методом поиска экстремума. Если существуют несколько экстремумов критерия оптимальности, то этот метод позволяет найти тот из них, который расположен ближе к точкам исходного комплекса. Поэтому, если есть подозрение о существовании нескольких экстремумов критерия оптимальности, то нужно осуществить их поиск, каждый раз начиная оптимизацию из новой области факторного пространства. Затем слезет сравнить между собой найденные оптимальные условия и из всех вариантов выбрать наилучший. При оптимизации необходимо принимать во внимание ограничения, влияющие на факторы и функции отклика. Рис. 3. 13. Оптимизация по симплексному методу
При пользовании симплексным методом не обязательно дублировать опыты. Ошибка в отдельном опыте может только несколько замедлить оптимизацию. Если же последующие опыты выполняются безупречно, то движение к оптимуму продолжается. На любом шаге оптимизации, осуществляемой симплексным методом, можно включить в программу исследования новый фактор, который до тех пор не принимался во внимании, но оставался на постоянном уровне. Пример. Турбовальный двигатель, устанавливаемый на вертолете (см. рис. 3. 11), имеет весьма жесткое ограничение по неравномерности температурного поля в выходном сечении камеры сгорания: (3. 58) где T м * — среднемассовая температура газа на выходе из камеры сгорания; Т max — максимальная локальная температура в той же зоне. Условие (3. 58) может быть выполнено индивидуальной отладкой температурного поля на каждом двигателе |46]. Конструктивная схема двигателя с подводом воздуха к камере сгорания по двум трубам позволяет использовать для регулирования температурного поля поворотные лопатки, установленные в выходных патрубках компрессора (рис. 3. 14). Каждая лопатка может поворачиваться независимо, допуская ее фиксацию в любом положении. Эксперименты подтвердили эффективность воздействия лопаток на температурное поле. Аналитическое решение (даже приближенное) по отладке поля невозможно, поскольку нельзя оценить зависимость поля температур от углов установки лопаток на основе физических представлений.
Рис. 3. 14. Турбовальный двигатель (б), устанавливаемый на вертолет (а) и схема двигателя (в) с поворотными лопатками для отладки температурного поля: 1 — компрессор; 2 — патрубок компрессора; 3 — воздухопроводящая труба; 4 — камера сгорания; 5 — турбина; 6 — лопатка
Оптимизируемой (целевой) функцией является неравномерность поля температур ΔТ* max а варьируемыми факторами — углы установки лопаток в левом и правом патрубках компрессора (φ л и φ п ), отсчет которых ведется от некоторых, условно выбранных, нулевых положений (рис. 3. 14). Поле температур измерялось с помощью 32 термопар, равномерно расположенных в выходном сечении камеры сгорания. Среднемассовая температура оценивалась по формуле: а значение Т* м соответствовало максимальной величине температуры из 32 ее значений, измеренных термопарами. Таким образом, задача состояла в выполнении на каждом двигателе условия: с достаточным запасом, учитывающим возможное повышение неравномерности ΔТ* max в процессе эксплуатации двигателя. Отладка температурного поля проводилась с применением симплексного метода планирования эксперимента. Последовательность поиска оптимального решения для одного из двигателей показана на рис. 3. 15.
Рис. 3. 15. Симплексный метод отладки температурного поля
Неравномерность А ΔТ* max определяется в трех точках плоскости (φ л , φ п ) — вершинах правильного двухмерного симплекса. В исходном симплексе АВС наихудшей является точка А, в которой ΔТ* max = -397 К. Эта точка, по правилам метода, отображается зеркально относительно стороны симплекса ВС. В новом симплексе А’ВС наихудшей является точка В, в которой ΔТ* max = 365 К. После отображения относительно стороны А*С в точке В* симплекса А*В*С неравномерность достигла уровня ΔТ* max = 316 К. Отображая наихудшую точку последнего симплекса С с ΔТ* mах = 470 К, получили точку С* с координатами φ л = -9 , φ⁰ п = 2 , в которой возникли колебания давления за компрессором, а ⁰ неравномерность возросла до значения ΔТ* max = 470 К. По правилам симплексного метода следовало бы вернуться к симплексу А’В’С и отобразить вторую по порядку наихудшую точку А’ относительно стороны В’С. Однако в этом не было необходимости, поскольку в точке В’ получен вполне удовлетворительный результат ΔТ* max = 43 К. При этом поворотные лопатки фиксируются в положениях φ л = -5, 5° и φ п = 4°. 3. 4. ОПЫТ ПРИМЕНЕНИЯ ПЛАНИРОВАНИЯ ЭКСПЕРИМЕНТА В АВИАДВИГАТЕЛЕСТРОЕНИИ В настоящее время накоплен большой опыт применения планирования эксперимента в авиадвигателестроении. Рассмотрим некоторые наиболее характерные примеры [9]. Высотно-скоростные характеристики ВСХ газотурбинных двигателей. Такие испытания проводятся на высотных стендах в термобарокамерах и сводятся к получению серии дроссельных характеристик, т. е. зависимости тяги Р и расхода топлива G m от частоты вращения п на нескольких высотах Я и числах М полета:
Имея в виду сложный характер указанных зависимостей, при проведении эксперимента по получению ВСХ применяют ротатабельный ЦКП 2 -го порядка, включающий 15 опытов при различных сочетаниях факторов H, М и n. При этом объем в 3 раза меньше по сравнению с его проведением по традиционной методике. Исследование характеристик приемистости двигателей. Планирование эксперимента применяется для определения характеристик приемистости двигателя при летных испытаниях. В качестве независимых факторов, влияющих на характеристики приемистости, рассматриваются: частота вращения на малом газе; диаметр жиклера воздушного редуктора; положение регулировочного винта распределения топлива; плотность топлива; частота вращения при перекладке створок реактивного сопла и др. Для определения регрессионной модели, описывающей характеристики приемистости, используются линейные планы ПФЭ и ДФЭ, а также и ЦКП 2 -го порядка. Исследование теплового состояния двигателя. В данном случае методы планирования эксперимента используются в так называемых процедурах дискриминации моделей для уточнения найденных в исходном эксперименте значений констант или выбора наиболее подходящей модели из числа заданных. Например, при исследовании теплового состояния турбовинтового двигателя анализ процессов теплоподвода и охлаждения показал, что для величины относительного подогрева элементов турбины 0 наиболее приемлема модель вида:
где Т г *, Т к * — температуры газа перед турбиной и воздуха за компрессором; G B — расход воздуха; а, b, с — константы модели. Эксперимент по определению констант модели проводится по /)-оптимальному плану варьированием трех факторов на трех уровнях. Исследование характеристик силовых установок и летно-технических характеристик самолета. В практике испытаний самолетов и их силовых установок часто возникают вопросы совместного рассмотрения характеристик, исследование которых проводится с применением планированного эксперимента. К числу режимов полета, для которых оценка взаимного влияния наиболее интересна, относятся: взлет, крейсерский полет, разгон и торможение, планирование, вираж-спираль, горка и др. Количество представляющих интерес факторов бывает 4. . . 5, достигая в отдельных случаях 8 и более, а количество функций отклика может доходить до 10. . . 15. Исследование тепловыделения в подшипнике опоры двигателя. Расчет тепловыделения в подшипнике на основании гидродинамической теории смазки достаточно сложен и включает ряд эмпирических коэффициентов, определяемых экспериментально. Применение планирования эксперимента по определению зависимости между тепловыделением Q и параметрами: быстроходностью d n , осевой А и радиальной R нагрузками, циркуляционным расходом масла V M , температурой масла на входе Т м : Q = f(d n , A, R, V M , T M ) позволяет в 2 раза уменьшить объем эксперимента, используя ДФЭ, включающий 16 опытов. Исследование автоколебаний бандажированных лопаток компрессора. Одной из основных задач по обеспечению вибропрочности лопаток компрессора является знание поведения их автоколебаний в области эксплуатационных режимов. В данном случае требуется получить зависимость коэффициента режима
K p = π* к /G B Пр (π* к — степень повышения давления, G впр — приведенный расход воздуха) от давления воздуха на входе р*в, отклонения угла установки входного направляющего аппарата Да и приведенной частоты вращения ротора n пр : Задача решается с применением трехфакторного ЦКП 2 -го порядка, включающего 15 опытов. Исследование характеристики осевой ступени многоступенчатого компрессора. При проектировании многоступенчатых осевых компрессоров и расчете их газодинамических характеристик используются характеристики отдельных ступеней, полученные при их изолированных испытаниях. В системе компрессора эти ступени работают в условиях, существенно отличающихся от условий работы изолированных ступеней при равномерном потоке на входе. Параметры ступени при этом обычно ухудшаются. В результате этого действительные характеристики компрессора в целом не совпадают с расчетными, что создает трудности при доводке двигателя. Экспериментальное изучение закономерностей изменения характеристик ступеней с применением планирования эксперимента позволяет с минимальными затратами уточнить расчет многоступенчатого компрессора. Исследование центробежных топливных форсунок камеры сгорания. При проектировании центробежных топливных форсунок камер сгорания газотурбинных двигателей используются зависимость гидравлических параметров — коэффициента расхода и корневого угла распыла топлива — с геометрией форсунки.
Однако при доводке опытных двигателей и при их серийном производстве возникают задачи, требующие учета влияния и других конструктивных факторов: отношения длины к радиусу соплового отверстия; отношение длины выходной фаски к радиусу соплового отверстия; угла выходной фаски соплового отверстия; угла корпуса камеры закручивания; отношения длины камеры закручивания к радиусу закручивания. Задача решается с применением ДФЭ типа 2 5 -2. Исследование динамических свойств роторных систем ГТД. Уровень роторной вибрации ГТД определяется конструктивными и технологическими параметрами роторной системы, назначенными на основании динамических расчетов и обобщения опыта, накопленного при производстве однотипных ГТД. Допущения, упрощающие расчетную схему двигателя, и погрешности исходных данных приводят лишь к приближенной оценке таких параметров, как жесткость корпусных элементов опор ротора, допустимые дисбалансы в плоскостях коррекции, радиальная и угловая несоосности роторов, взаимный перекос колец упорных подшипников и др. Информацию, необходимую для оптимизации роторной системы, получают исследованием полноразмерных моделей роторов на высокочастотном стенде во всем диапазоне рабочих частот вращения с применением ДФЭ. При этом оптимизации подвергаются как конструктивные, так и технологические параметры (жесткость опор и ротора, допустимые дисбаланс и несоосность ротора и т. д. ), что позволяет снизить виброактивность роторной системы до допустимого уровня. Исследование прочности конструкционных материалов. Объектом исследования являются механические характеристики материалов — прочность σ в , пластичность σ 0, 2 и др. Например, целью исследования может являться получение математической зависимости скорости роста усталостной трещины от внешних и внутренних факторов (геометрических размеров, технологических и металлургических факторов и др. ).
3. 5. ПЕРСПЕКТИВЫ РАЗВИТИЯ МЕТОДОВ ЭКСПЕРИМЕНТАЛЬНОГО ИССЛЕДОВАНИЯ ГТД С ПРИМЕНЕНИЕМ ПЛАНИРОВАННОГО ЭКСПЕРИМЕНТА Эффективность планирования эксперимента может быть повышена за счет совместного учета всех полезных свойств выбираемого плана. При этом для комплексной оценки эффективности плана эксперимента рассматривают показатели, характеризующие его как функциональное, так и экономическое качество (рис. 3. 16) [11]: Рис. 3. 16. Структура основных показателей эффективности плана эксперимента
• показатель П т , характеризующий точность регрессионной модели, описывающей исследуемый объект (процесс), • показатель ПN, характеризующий объем эксперимента (количество опытов в плане); • показатель Пс, характеризующий стоимость затрат на проведение эксперимента • показатель П τ характеризующий длительность проведения эксперимента. Совместный учет показателей П т , П N П с и П τ , позволяет проводить многокритериальную оптимизацию плана, характеризуемого некоторым обобщенным показателем эффективности Э: Э(П Т , П N , П с , П τ )->opt. (3. 59) При этом комплексная оптимизация плана эксперимента основана на последовательном выполнении следующих основных этапов работ: этап 1 включает процедуру определения исходных данных; этап 2 предназначен для формирования множества Парето-оптимальных планов эксперимента; этап 3 включает процедуру выбора окончательного плана эксперимента. ‘ При многофакторном и многокритериальном планировании отсутствие одного единственного оптимального решения обусловлено противоречивостью критериев эффективности плана эксперимента. Множество Парето-оптимальных планов формируется многократной оптимизацией векторного функционала К Σ , являющегося сверткой нормированных значений показателей эффективности плана эксперимента К т , K N , К С и К т : где А, В, С, D — положительные числа, используемые в методе Парето (А + В + С + D = 1); K i П i H — критерии и нормированные значения показателей эффективности.
Многократная оптимизация обеспечивается варьированием в зависимости (3. 57) значений коэффициентов А, В, С и D в интервале 0. . . 1 при условии A + B + C+D = 1. На практике поиск оптимального плана имеет смысл, когда на объем N, стоимость C Σ и длительность эксперимента τ Σ наложены ограничения, обусловленные финансовыми возможностями и располагаемым временным ресурсом (особенно при проведении испытаний на надежность и ресурс ГТД): где N пр , С пр , т пр — предельные значения N, C Σ и т Σ. Пример. Требуется выбрать план эксперимента для построения характеристики камеры сгорания ГТД (рис. 3. 17): Где α Σ — коэффициент избытка воздуха; р* к , С к — давление и скорость воздуха на входе в камеру; К ф — относительный расход воздуха, определяемый по формуле: где F — площадь сечения; G B — расход воздуха; «фр» — фронтовое устройство. Определяющими критериями оптимальности плана являются критерии эффективности К т , K N и К с , поэтому оптимизируемый функционал для формирования Парето- оптимальной области имеет вид:
Рис. 3. 17. Схема камеры сгорания Стоимость затрат С на обеспечение требуемого давления воздуха на входе в камеру сгорания р* кmах принята пропорциональной мощности источника сжатого воздуха (компрессора) N K и длительности эксперимента т: Пс = С~ р* кmах ~ N K ∙τ. Выбор плана проводился в области, заданной ограничениями: 2, 0≤α Σ ≤ 4, 0; 0, 12≤K ф <0, 48; 98 к. Па≤р* к ≤ 392 к. Па; 35 ≤ С к ≤ 75 м/с. На рис. 3. 18 приведены Парето-оптимальные значения показателей эффективности П* т , и П* N П с. В качествеокончательного выбран насыщенный план эксперимента (содержит N=k+ 1 = 15 опытов), для которого значение дисперсии оценки (G — оптимальность) η ζ (d = 22, 4), в 2, 4 раза, а затраты на эксперимент в 1, 3 раза меньше, по сравнению с ротатабельным ЦКП.
Рис. 3. 18. Область Парето-оптимальных решений в пространстве фактических (о) и нормированных (б) значений показателей эффективности П* т , П* N и П* с
РЕЗЮМЕ (по главе 3 «Планирование эксперимента при испытаниях ГТД» ) 1. Наряду с использованием более совершенного оборудования и измерительной Техники, автоматизацией проведения и обработки испытаний, комплексированием программ в практике испытаний широко используется математическое планирование эксперимента. 2. Потребность в применении планирования эксперимента обусловлена тем, 4 fno на практике, ввиду сложности рабочих процессов, протекающих в авиационных ГТД, определение характеристик аналитическим путем не представляется возможным, поэтому остается единственное — экспериментальное определение. 3 — Возможны также случаи, когда известны эмпирические зависимости, включающие константы, определение которых требует проведения экспериментального исследования и др. 4. Теория оптимального планирования эксперимента позволяет экспериментатору дать ответы на следующие вопросы: — как нужно организовать эксперимент, чтобы наилучшим образом решить поставленную задачу (в смысле затрат времени и средств или точности результатов) ? — как следует обрабатывать результаты эксперимента, чтобы получить максимальное количество информации об исследуемом явлении ? — какие обоснованные выводы можно сделать об исследуемом объекте по результатам эксперимента?
5. Применение планирования эксперимента эффективно при решении, в основном, двух видов задач: — планирование эксперимента по выяснению механизма явлений; — планирование эксперимента при оптимизации исследуемых процессов, т. е. выборе значений влияющих факторов, при котором достигается экстремум критерия оптимальности. ВОПРОСЫ 1. В каких случаях исследование проводится по принципу «черного ящика» ? 2. На какие группы делятся факторы, влияющие на выходной параметр исследуемого процесса? 3. Каким образом оценивают в эксперименте воспроизводимость опытов? 4. Как оценивается погрешность эксперимента? 5. Что означает рандомизация опытов в эксперименте? 6. Для каких целей проводят кодирование переменных? 7. Как записываются в матричной форме система нормальных уравнений и ее решение — вектор коэффициентов уравнения регрессии? 8. Какие критерии оптимальности плана эксперимента существуют? 9. Что означает полный факторный эксперимент и дробный факторный эксперимент? Как они между собой связаны? 10. Назовите основные принципы построения плана полного факторного эксперимента? 11. Каким образом оценивается значимость коэффициентов в уравнении регрессии? 12. Для каких целей используется критерий Фишера? 13. Чем обусловлено применение центрального композиционного планирования (ЦКП) и какие виды ЦКП вам известны?
14. В чем особенности ортогонального и ротатабельного ЦКП? 15. Каким образом проводится оптимизация процесса с применением метода крутого восхождения? 16. В чем сущность симплексного метода оптимизации? 17. Приведите примеры решения задач авиадвигателестроения с применением планированного эксперимента. 18. Каким образом проводится комплексная оптимизация плана эксперимента с учетом одновременно нескольких показателей эффективности?
Глава 4 ИСПЫТАТЕЛЬНЫЕ СТЕНДЫ И ОБОРУДОВАНИЕ 4. 1. СТРУКТУРА ИСПЫТАТЕЛЬНОЙ СТАНЦИИ Экспериментальное исследование авиационных ГТД проводят в испытательных цехах, в испытательных станциях и в испытательных лабораториях заводов и НИИ [9, 24, 29, 34, 39]. Для испытаний ГТД и его систем на моторостроительных предприятиях создаются испытательные станции, оснащенные специальными стендами. В состав испытательной станции (рис. 4. 1) входят стенды, содержащие в своем составе: боксы, в которых устанавливаются объекты испытания и оборудование, необходимое для проведения испытаний; примыкающие к боксам вспомогательные технологические помещения, где размещены часть измерительного оборудования, кабина управления, системы обеспечения топливом, маслом, сжатым воздухом, электроэнергией и некоторые другие. Основной производственной единицей испытательной станции является испытательный стенд. Критериями в формировании испытательной базы предприятия (испытательной станции) как единственного инструмента для обеспечения контроля качества выполненной разработки и расчетов, изготовленной продукции, для проведения исследований в подтверждение или опровержение идеи, обеспечения проведения поисковых исследований, в целях познания или формирования научно-технического задела, являются: достаточность, исходя из программы производства или разработок, совершенство и диапазон возможностей, разумность из соображений затрат и отдачи, универсальность и систематичность использования, в том числе и в прогнозируемой перспективе (закрытые стенды, открытый стенд, термобарокамеры, климатические стенды, лаборатории горения, стенды полунатурного моделирования, разгонные стенды и др. ).
Рис. 4. 1. Структура испытательной станции
Типичный испытательный стенд (рис. 4. 2) обычно состоит из испытательного бокса, кабины наблюдения и вспомогательного технологического помещения. В испытательном боксе на станке размещается испытываемый двигатель 1. Узлы крепления ГТД на станке те же, что и на летательном аппарате (ЛА). Если испытывается двигатель прямой реакции (ТРД, ТРДФ и ТРДДФ), станок представляет собой силоизмерительное устройство (СИУ). Станина такого устройства 3 неподвижно укрепляется на мощном фундаменте 4, который монтируется на вибропоглощающем основании 5. Фундамент станка отделен от фундамента здания бокса воздушным зазором, что вместе с вибропоглощающим основанием позволяет практически исключить вибрационную нагрузку на конструкцию здания. К станине на гибких стальных лентах 6 подвешивается подвижная платформа 7, на которой собственно устанавливается двигатель /. Под действием силы тяги двигатель вместе с подвижной платформой стремится переместиться в направлении действия тяги. При этом сила тяги воспринимается силоизмерительным датчиком 2. Рабочее тело двигателя — воздух — попадает в бокс через входную шахту шумоглушения 8. Отработавшие газы — через эжекторную выхлопную трубу 10 где размещаются форсунки подачи воды 11 для охлаждения газового потока! Далее через выхлопную шахту 13 газы удаляются в атмосферу. При испытании ТВД на силоизмерительный станок дополнительно монтируют устройство для измерения крутящего момента (гидротормоз, электрический тормоз и т. п. ). В ряде случаев ТВД, а также двигатели со свободной турбиной ГТД СТ испытывают на жестких станках, оборудованных различными тормозами без прямого измерения тяги.
Рис. 4. 2. Схема испытательного стенда: / — испытываемый ГТД; 2 — силоизмерительный датчик; 3 — станина испытательного станка; 4 — фундамент СИУ; 5 — вибропоглощающее основание; 6 — упругие стальные ленты; 7— подвижная платформа; 8 — входная шахта шумоглушения; 9 — элементы шумоглушения на входе; 10 — эжекторная выхлопная труба; 11 — впрыск воды; 12 — элементы шумоглушения
Глушители аэродинамического шума представляют собой чаще всего специальные лабиринты или камеры, образованные щитами, пластинами или цилиндрами (Я 12) из перфорированного железа, которые заполняются звукопоглощающими материалами типа пакли, стекловаты, шелухи подсолнечных семечек (при V = 10 м/с и / < 50 °С), пемзового кирпича, стекловаты (при V≥ 30. . . 60 м/с и t≥ 50 °С). Применяют следующие компоновки боксов: горизонтальную (рис. 4. 3, а), Г- образные (рис. 4. 3, б и в) и П-образную (рис. 4. 3, г). Каждая из этих схем обладает присущими ей достоинствами и недостатками. Например, вертикальное расположение входной и выходной частей, обеспечивая более чистый всасываемый воздух и лучшие условия по выхлопу, безусловно требует существенно больших материальных затрат. Примеры более детальной схемы испытательных боксов с вертикальной шахтой на входе и горизонтальным выхлопом представлен на рис. 4. 4, с двумя вертикальными входными шахтами и вертикальной выхлопной шахтой на рис. 4. 5. Испытываемый двигатель 11 (см. рис. 4. 4) установлен в рабочей части бокса на подвижной платформе 19 испытательного станка, который монтируется на фундаменте 20, изолированном от элементов конструкции бокса. Поэтому вибрации непосредственно не передаются на фундамент и стены бокса и, следовательно, не действуют на измерительную аппаратуру. Впрыск воды через форсунки 14 способствует снижению температуры выхлопных газов и соответственно шума. Двигатель в бокс подают через ворота 6 и монтируют на станок с помощью электроподъемника. Для удобства работы персонала при монтаже двигателя и ею систем в боксе вокруг испытательного станка монтируют монтажно-обслуживающую площадку.
Рис. 4. 3. Различные виды оформления входа и выхода испытательных стендов: ~~ входная часть; 2 — элементы шумоглушения на входе; 3 — центральная часть; 4 — испытываемый ГТД на станке; 5 — элементы шумоглушения на выходе; 6 — выхлопная часть
Рис. 4. 4. Г-образный испытательный бокс [49]: 1 — входная шахта; 2 — глушители шума на входе; 3 — направляющие пластины; 4 — выравнивающая решетка; 5 — жалюзи; 6 — ворота; 7 — лемнискатный входной насадок; 8 — бронещит; 9 — окно кабины наблюдения; 10 — дверь в бокс; 11 — испытываемый двигатель; 12 — электроподъемник; 13 — эжекторная выхлопная труба; 14 — водяные форсунки; 15 — шумоглушение на выходе; 16 — отбойная решетка; 17 — защитная сетка; 18 — калорифер; 19 — подвижная платформа с силоизмерительным устройством; 20 — фундамент; 21 — виброизолирующая подушка; 22 — монтажно-обслуживающая площадка
Рис. 4. 5. Бокс с вертикальным расположением шахт: 1 — входная шахта; 2 — глушители шума; 3 — направляющие пластины; 4 — выравнивающая решетка; 5 — жалюзи; 6 — ворота; 7 — лемнискатный входной насадок; 8 — бронещит; 9 — окно кабины наблюдения; 10 — дверь в бокс; 11 — испытываемый двигатель; 12 — электроподъемник; 13 — эжекторная выхлопная труба; 14 — водяные форсунки; 15 — выхлопная шахта; 16 — элементы шумоглушения на выходе; 17 — дополнительная шахта подвода воздуха; 18 — элементы шумоглушения в дополнительной шахте подвода воздуха; 19 — подвижная платформа с силоизмерительным устройством; 20 — фундамент; 21 — виброизолирующая подушка
Персонал, проводящий испытание, и пульт управления испытываемым двигателем и системами стенда располагаются в кабине наблюдения. На пульте смонтированы контрольные приборы, система сигнализации, панели отображения информации и орган управления двигателем (рычаг управления двигателем — РУД — при механической системе управления или устройство типа джойстик для электронной системы управления). Кабины наблюдения располагают спереди (реже) или сбоку (чаще всего) испытываемого двигателя. При боковом расположении кабина наблюдения не должна находиться в плоскости вращения ротора двигателя. Смотровые окна закрывают бронированным стеклом и бронированным передвижным щитком, имеющим вертикальные щели для сохранения возможности визуального наблюдения. Для дублирования визуального контроля используют системы видеонаблюдения с функцией записи и архивирования записей.
4. 2. ИСПЫТАТЕЛЬНЫЕ СТАНКИ И УСТРОЙСТВА Испытательные станки представляют собой устройства, предназначенные для закрепления испытываемого двигателя в процессе испытания и для измерения тяги или (и) мощности. Измерение этих выходных данных двигателя, значительная масса самих двигателей диктуют необходимость применения прочных элементов крепления, способных выдержать значительные нагрузки от тяги (до 400 к. Н и выше) и массу (до 4000. . . 5000 кг). В основном применяют два вида станков: жесткие и нежесткие. Жесткие станки не обеспечивают прямого измерения силы тяги, которую в этом случае можно определить косвенным газодинамическим способом. На рис. 4. 6 показано применение жесткого станка для испытания ТВД. Рис. 4. 6. Схема установки для испытания ТВД на жестком станке: 1 — испытываемый двигатель; 2 — редуктор ТВД; 3 — подмоторная рама; 4 — двухрядный воздушный винт; 5 — туннельный канал; 6 — испытательный станок жесткого типа
Нежесткие станки, кроме основного назначения (крепления двигателя) позволяют проводить измерение тяги. Наибольшее распространение получили нежесткие станки с подвижной платформой, на которой устанавливается испытываемый двигатель, а усилия от развиваемой тяги передаются через платформу к устройству измерения силы тяги, которое уравновешивает и измеряет тягу. Подвижная платформа подвешивается на неподвижную часть станка (станину) с помощью гибких стальных лент (пластин), которые работают на растяжение, или устанавливается с помощью упругих пластин или шарниров, работающих на сжатие. Совокупность станка, устройства измерения и устройства градуировки называют силоизмерительным устройством. Разные типы двигателей определили применение нескольких разновидностей нежестких силоизмерительных устройств для измерения: • горизонтальной силы тяги (при испытаниях обычных ТРД и ТРДД); • горизонтальной силы тяги в прямом и обратном (реверсном) направлениях (рис. 4. 7); • горизонтальной и вертикальной тяги (рис. 4. 8); • вертикальной силы тяги (подъемные ГТД); • силы тяги двигателя с изменяемым вектором тяги (рис. 4. 9); • силы тяги и мощности ТВД и ТВВД (рис. 4. 10). Для испытаний двигателей, в эксплуатации устанавливаемых на летательный аппарат на пилонах, применяют станки с подвижной платформой, которые укрепляются на потолке бокса (рис. 4. 11). К испытательным станкам с силоизмерительным устройством предъявляются следующие требования [25]: • погрешность измерения тяги не должна превышать ± 0, 5 % от измеряемой величины; • необходимо обеспечить возможность измерения как прямой, так и обратной тяги двигателя при включении реверса;
• должна быть обеспечена возможность испытаний двигателей разных тяг; Рис. 4. 7. Схема силоизмерительного устройства для измерения прямой и обратной сил тяги двигателя (когда идет испытание, грузы с градуировочных систем 1 и 6 снимают) [49]: / — градуировочная система прямой силы тяги: 2 — подвижная платформа; 3 — силоизмерительная штанга обратной силы тяги; 4 — силоизмерительная штанга прямой силы тяги; 5 — датчик силоизмерителя; 6 — градуировочная система обратной силы тяги
Рис. 4. 8. Схема для измерения горизонтальной и вертикальной тяги силоизмерительного устройства с одной подвижной платформой [49]: 1 — испытываемый двигатель: 2 — подвижная платформа; 3 — силоизмерительная тяга; 4 — силоприемный рычаг; 5 — шарнирная стойка; 6 — рычаг системы измерения вертикальной тяги; 7 — датчики усилия; 8 — термостат; 9 — шарнирная тяга; 10 — градуировочная система измерения вертикальной тяги; 11 — градуировочная система измерения горизонтальной тяги; 12 — выхлопные трубы
• влияние системы коммуникаций на измеренную тягу должно быть минимальным. Градуировку силоизмерительного устройства производят с полностью смонтированным на платформе двигателем и присоединенными к нему системами питания, управления и измерения. В системах подвода и отвода жидкостей создают рабочее давление и имитируют возникающую во время работы двигателя вибрацию установленным на платформе вибратором. Применение в качестве рабочих первичных преобразователей высокого класса точности 0, 1 (например, тензорезисторных преобразователей) приводит к необходимости решать проблему оснащения силоизмерительного устройства особо точными средствами градуировки. Рис. 4. 9. Схема двухкомпонентного силоизмерительного устройства для испытания подъемны Двигателей (в рабочем состоянии грузы с градуировочных систем 10 и 11 снимаются) [49]: 1 — испытываемый двигатель; 2 — подвижная платформа системы измерения горизонтальной составляющей силы тяги; 3 — силоприемная тяга; 4 — подвижная платформа системы измерения вертикальной составляющей силы тяги; 5 — силоприемная тяга; 6 — датчик горизонтальной составляющей силы тяги; 7 — датчик вертикальной составляющей силы тяги; 8 — силоприемная тяга; 9 — упруга подвеска; 10 — градуировочная система измерения вертикальной составляющей силы тяги: И — градуировочиая система измерения горизонтальной составляющей силы тяги; 12— выхлопная груба
Рис. 4. 10. Схема испытательного силоизмерительного устройства для определения эквивалентной мощности ТВД [32]: I — станина испытательного станка; 2 — гибкие стальные ленты; 3 — датчик силы тяги; 4 — подвижная платформа; 5 — гидротормоз; 6 — валопровод от двигателя к гидротормозу; 7 — испытываемый двигатель; 8 — узлы крепления двигателя
Рис. 4. 11. Схема станка с подвеской к потолку [42]: / — испытываемый двигатель; 2 — быстросъемная рама; 3 — комбинированный упругий шарнир (растяжения-сжатия); 4 — датчик силоизмерителя; 5 — силопередающий упор; 6 — рама станины; 7 — подвижная платформа
4. 3. ОСНОВНЫЕ СИСТЕМЫ СТЕНДОВ Все испытательные стенды имеют приборно-измерительные службы и должны быть оснащены автоматизированными информационно-вычислительными системами, обеспечивающими измерение, сбор и обработку параметров в ходе испытаний двигателя, узла или системы, а также передачу собранной и зарегистрированной информации в инженерные службы для анализа. Такие комплексы могут также располагаться в специальных помещениях и обслуживать одновременно несколько испытательных стендов. В кабинах управления в этих случаях размещаются устройства связи с объектом (нормализаторы, преобразователи, согласующие устройства, устройства передачи данных) и устройства отображения и документирования. Кроме испытательных стендов в состав испытательной станции должны входить системы для хранения и снабжения испытательных стендов топливом, электрическая подстанция, резервная электростанция, компрессорная станция, насосная станция снабжения технической водой, метеостанция, участок ремонта и обслуживания технологического оборудования и приборов и др. Системы испытательных станций (стендов) обычно размещаются в технологических помещениях. Они обеспечивают нормальную работу испытываемого двигателя и безопасную работу персонала. К системам испытательной станции, обслуживающим двигатель, относятся: топливная, масляная, гидравлическая, водяная, электрическая. Топливная система предназначена для хранения, очистки и бесперебойной подачи топлива к испытываемому двигателю, а также для измерения его расхода. Обычно топливо подается на стенд к двигателю из общего топливохранилища, располагаемого вне здания станции (зачастую на значительном расстоянии). Это уменьшает пожароопасность на станции. Топливохранилище состоит из емкостей, соединенных со сливной станцией и насосной, перекачивающей топливо из прибывших железнодорожных или автомобильных цистерн в расходные емкости, а из них к испытательным боксам.
К установкам топливо может подаваться по нескольким магистралям. Требуемый для питания двигателя сорт топлива направляется с помощью распределительного коллектора. Неизрасходованное при испытании двигателя или при градуировках расходомеров топливо сливается обратно в топливохранилище по сливной магистрали, трубы которой имеют уклон в сторону хранилища. Для слива некондиционного топлива и слива в аварийных ситуациях предусматривается магистраль аварийного слива с емкостью, объем которой больше суммарных объемов всех стендовых систем топливных приборов и оборудования. Топливные трубопроводы выполнены из нержавеющей стали, а вблизи двигателя защищены толстостенными трубами во избежание повреждения при аварии. На рис. 4. 12 представлена принципиальная схема топливной системы. Масляная система. Испытываемые ГТД могут иметь автономную масляную систему, когда все ее агрегаты установлены на двигателе, или неавтономную, когда часть агрегатов системы установлена на летательном аппарате. При испытаниях ГТД с автономной масляной системой стендовая система обеспечивает подачу масла в двигатель при проведении его испытаний на подогретом или охлажденном масле, а также для консервации двигателя путем подачи горячего масла в топливную систему (рис. 4. 13). Специальная система подачи масла применяется при испытаниях ГТД с неавтономной масляной системой (рис. 4. 14). Масло обычно подается насосом через регуляторы и фильтр. В случае необходимости для охлаждения масла используются водяные радиаторы и дополнительные фильтры. Прокачка масла определяется расходомером.
Рис. 4. 12. Вариант схемы топливной системы: 1 — топливные расходные баки; 2 — вентиль; 3 — фильтр грубой очистки топлива; 4 — шестеренчатый насос; 5 — обратный клапан; 6 — кран; 7 — дроссельный расходомер; 8, 9 — регулирующий пневматический клапан; 10 — отсечной кран; 11 — промежуточный фильтр; 12 — измерение температуры топлива; 13 — измерение давления топлива; 14 — клапана переключения; 15 — турбинные расходомеры; 16 — указатели расходомеров; 17 — фильтр тонкой очистки; 18 — электроклапан; 19 — измерение давления топлива; 20 — измерение температуры топлива; 21 — автомат, дозирующий топливо; 22 — устройство для подогрева топлива; 23 — кран аварийного слива; 24 — магистраль подачи масла при консервации; 25 — распределительный коллектор
Гидравлическая система необходима на испытательной станции в тех случаях, когда испытывают двигатели с установленными на них самолетными гидроагрегатами, которые необходимо загружать во время испытания. Водяная система необходима для обеспечения испытаний ГТД, при которых измерение крутящего момента осуществляется гидротормозом либо при которых необходимо обеспечить охлаждение каких-либо рабочих сред водяными радиаторами. На рис. 4. 15 приведена схема стендовой водяной системы. Для обеспечения стабильной работы агрегатов, использующих воду, рекомендуют располагать расходный бак 1 на высоте 3. . . 5 м от агрегатов. Температура воды на выходе из гидротормоза 3 не должна превышать 50 °С. Охлаждение нагретой воды после гидротормоза или водяных радиаторов 9 осуществляется путем ее разбрызгивания на воздухе в бассейне 6. Охлажденная вода насосом 7 возвращается в расходный бак 1. Электрическая система испытательной станции обеспечивает подачу: напряжения -380 В для питания силовых агрегатов стендов; напряжения -220 В для питания приборно-измерительного оборудования; постоянного напряжения 27 В для работы самолетных измерительных систем, запуска двигателя или его турбостартера от электростартеров. Дополнительно на стендах используют электросистему для загрузки электрогенераторов, установленных и приводимых испытываемым двигателем. Для загрузки используют мощные секционные реостаты, охлаждаемые принудительно за счет продувки атмосферным воздухом или за счет конвективного охлаждения.
Рис. 4. 13. Схема стендовой замкнутой масляной системы: / — расходный масляный бак; 2 — расходомер уровневого типа; 3 — измерение температуры масла; 4 — кран; 5 — фильтр грубой очистки; 6 — шестеренчатый насос; 7 — электроклапан; 8— фильтр тонкой очистки; 9 — насос подачи масла в двигатель; 10 — измерение температуры и давления; 11 — фильтр; 12 — масляный фильтр с сигнализатором стружки; 13 — терморегулятор; 14 — расходомер дроссельного типа; 15 — измерение температуры масла; 16 — топливно-масляный радиатор: 17 — обратный клапан; 18 — кран
Рис. 4. 14. Схема внешней масляной системы стенда: 1 — расходный масляный бак; 2 — расходомер уровневого типа; 3 — измерение температуры масла; 4 — кран; 5 — фильтр грубой очистки; 6 — шестеренчатый насос; 7 — обратный клапан; 8— электроклапан; 9 — магистраль подачи масла: 10 — отсечной кран; 11 — дроссельный расходомер; 12 — указатель расхода; 13 — подогреватель электрический; 14 — обратный клапан; 15 — измерение температуры и давления масла; 16 — фильтр тонкой очистки; 17 — насос подачи масла в двигатель; 18 — насос откачки масла из двигателя; 19 — фильтр масляный; 20 — масляный фильтр с сигнализатором стружки: 21 — измерение температуры и давления: 22 — терморегулятор; 23 — водомасляный радиатор охладителя; 24 — кран
Рис. 4. 15. Схема водяной системы: 1 — расходный бак; 2 — кран подачи воды в гидротормоз; 3 — гидротормоз; 4 — магистраль отвода воды с повышенной температурой; 5 — струйные разбрызгиватели воды; 6 — бассейн Для охлаждения воды; 7 — насос откачки охлажденной воды в расходный бак; 8 — кран подачи воды в водяной радиатор: 9 — водяной радиатор
4. 4. ЛЕТНЫЕ ИСПЫТАНИЯ, ЛЕТАЮЩИЕ ЛАБОРАТОРИИ Летные испытания (ЛИ) ГТД проводят для отработки их летно-тактических характеристик, так как только на самолете двигатель со всеми его агрегатами и системами работает в реальных условиях, которые имеют место в эксплуатации. Летными испытаниями (ЛИ) выявляются также особенности летной эксплуатации ГТД с целью уточнения инструкций по его эксплуатации и техническому обслуживанию [33]. Летные испытания ГТД проводятся сначала на летающей лаборатории (ЛЛ), а затем на самолете, для которого предназначен двигатель. На летающей лаборатории ГТД обычно испытывается в составе силовой установки самолета, для которого этот двигатель предназначен. Авиационный двигатель является основным и наиболее сложным элементом современной авиационной СУ. В связи с этим процесс летных испытаний двигателя носит последовательный характер, продолжающийся практически в течение всего жизненного цикла (рис. 4. 16) и разбит на этапы. Первый этап летных испытаний и доводки опытных ГТД обычно проводится на летающих лабораториях, параллельно стендовым испытаниям. Основная задача этого этапа заключается в проведении летно-доводочных работ, обеспечивающих первый вылет опытного самолета и достаточную работоспособность, надежность и ресурс двигателей при дальнейших летных испытаниях опытного самолета. Второй этап летных испытаний и доводки ГТД начинается с первого вылета опытного самолета и проводится далее на этом самолете и на летающей лаборатории. На опытном самолете проводятся испытания на всех свойственных этому самолету режимах полета, в том числе при больших углах атаки и скольжения, при больших перегрузках и при других наиболее тяжелых для двигателя условиях полета.
Рис. 4. 16. Основные этапы летных испытаний ГТД, проводимые в процессе его доводки, освоения и эксплуатации на самолете На летающей лаборатории параллельно проводятся летные испытания двигателя по специальным программам, предусматривающим решение наиболее сложных вопросов его летной доводки с использованием специального экспериментального оборудования. Третий этап летных испытаний ГТД проводится в процессе государственных летных испытаний летательного аппарата (ЛА). Четвертый этап летных испытаний и доводки ГТД проводится в процессе их освоения в серийном производстве и эксплуатации на самолетах.
Пятый этап летных испытаний ГТД проводится в процессе их модификации после многих лет серийного производства и массовой эксплуатации на самолетах. Этапы летных испытаний включают в себя, как правило, вполне определенный набор типовых летных испытаний ГТД, к которым относятся испытания по определению: • пусковых свойств двигателя; • основных параметров на установившихся и неустановившихся режимах работы двигателя; • характеристик газодинамической устойчивости двигателя; • границ устойчивой работы форсажной камеры сгорания; • тепловых и вибрационных характеристик двигателя; • тяговых характеристик двигателя; • прочие испытания. Общие сведения и требования к летающим лабораториям Летные испытания на ЛЛ являются составной частью работ, проводимых в процессе создания и совершенствования двигателей и ЛА на стадиях: • научно-технического обеспечения создания двигателей и СУ ЛА нового поколения (испытания экспериментальных и демонстрационных образцов или их элементов, обоснование требований, разработка необходимых новых методов и средств ЛИ); • опытного производства и доводки двигателя и СУ ЛА (обеспечение первого вылета и заводские летные испытания ЛА, доводка установочной серии двигателя и систем СУ ЛА, государственные испытания); • серийного производства двигателя и ЛА (проверка мероприятий по улучшению характеристик, повышению надежности и ресурса).
Проведение на ЛЛ летных испытаний опытных двигателей СУ самолетов и БПЛА является необходимым условием допуска этих двигателей к заводским ЛИ (ЗЛИ) указанных ЛА. Опытные двигатели вертолетов и модифицированные двигатели любых ЛА при небольших изменениях их конструкции, не влияющих на летную годность, могут быть допущены к ЗЛИ ЛА без предварительных испытаний на ЛЛ. Понятие «летающая лаборатория» распространяется на специально оборудованный для испытаний двигателя и систем СУ летательный аппарат в случаях, если испытываемый двигатель не является штатным двигателем этого ЛА или если компоновка ЛА с предназначенным для него испытываемым двигателем нештатная (например, ЛЛ следует считать многодвигательный ЛА, на кото- ром вместо одного из серийных двигателей установлен испытываемый двигатель другого типа, предназначенный для модификации этого ЛА) Под летающие лаборатории оборудуются, как правило, тяжелые самолеты типа Ту-16, Ил-76 и др. , с которых снимают все оборудование, ненужное для летных испытаний, и размешают необходимые приборы. Опытный двигатель укрепляют под фюзеляжем на специальной подвеске либо под крылом в одной из мотогондол самолета. При этом компоновка элементов силовой установки максимально соответствует компоновке на самолете, для которого двигатель предназначен. На случай аварии испытываемого двигателя узлы крепления и коммуникации, связывающие его с летающей ла- ораторией, оборудуются устройствами, позволяющими отделить двигатель от самолета: узлы крепления — взрывными болтами, а коммуникации — гильотинными дистанционно управляемыми ножницами.
Используемый в составе ЛЛ летательный аппарат ниже обозначается термином «носитель» . Выбор носителя, проектирование и изготовление ЛЛ, предназначенных для комплексной проверки и отработки ГТД и систем автоматического управления должны обеспечивать возможность испытаний и отработки двигателей в еле- дующих условиях: • на всех допускаемых установившихся и неустановившихся режимах двигателя в горизонтальном установившемся полете (для ТРДФ и ТРДДФ последнее условие должно осуществляться хотя бы для нефорсированных режимов; форсированные режимы могут проверяться при разгоне и наборе высоты); на всех используемых в эксплуатации установившихся и неустановившихся режимах работы двигателя в процессе выполнения ЛА наиболее типичных неустановившихся режимов полета (взлета и посадки или их имитации на малых высотах, разгона, торможения, разворота, набора высоты, снижения, их комбинаций типа «уход на второй круг» и др. ); • на режимах авторотации выключенного двигателя и при его запуске с этих режимов и с режимов, на которых требуется раскрутка ротора стартером, в горизонтальном установившемся полете и при снижении ЛА; • при выключениях двигателя с любых допустимых или возможных режимов, выполняемых преднамеренно или происшедших самопроизвольно, и в процессе проверки устойчивости двигателя, при его отказах и т. п. Потребные предельные значения параметров полета при указанных испытаниях (высот, скоростей, перегрузок, углов атаки, скольжения, крена и наклона траектории), определяемые конкретными требованиями к двигателю и ЛА, принятыми методами испытании и технически достижимыми характеристиками ЛЛ, должны быть указаны и технических условиях на создание ЛЛ и учтены при ее аэродинамическом и прочностном расчете. Возможность и безопасность их реализации должны быть подтверждены специальными ЛИ по вводу в строй ЛЛ.
Для создания ожидаемых эксплуатационных условий конструкция ЛЛ и ее экспериментальное оборудование должны обеспечивать: максимально возможное воспроизведение натурных элементов СУ ЛА для которого предназначен двигатель, или, при невозможности их воспроизведения, имитацию создаваемых этими элементами внешних воздействий и условий работы двигателя (по потерям и неоднородности потока на входе, неравно- , РПН 0 СТИ поля температур, перепаду давлений на двигателе, состоянию среды в подкапотном пространстве, давлению и температуре топлива на входе, по объему отсека из которого ВГТД всасывает воздух и т. п. ); • отбор предусмотренного количества воздуха от испытываемого двигателя подачей его в систему ЛЛ с последующим выбросом в атмосферу; • загрузку двигателя всеми предусмотренными приводными агрегатами или их имитаторами, • электропитание систем двигателя и СУ всех предусмотренных видов, включая аварийное, возможность имитации типичных нарушений в электропитании, • запуск двигателя от всех предусмотренных бортовых и наземных источников электропитания пусковой системы; • автономное топливопитание испытываемого двигателя с помощью штатных электронасосов носителя, а также баковых насосов опытного ЛА с использованием отдельного бака (или группы баков), позволяющее проверять работу двигателя на любых предусмотренных сортах топлива, на подогретом, охлажденном, обводненном топливе; • автономность эксплуатации ЛЛ, позволяющую испытывать двигатель в различных климатических условиях;
• возможность испытаний двигателя и СУ в условиях естественного обледенения с контролем процессов льдообразования на входных элементах двигателя • воспроизведение критических внешних и внутридвигательных возмущений (с помощью регулирующих воздействий), позволяющее проверять достаточность • запас газодинамической устойчивости двигателя и опенку эффективность средств его зашиты при помпаже и (или) системы предупреждения возникновения помпажа и восстановления заданного режима работы. Эксплуатационно-технические характеристики ЛЛ должны предусматривать запуск, управление и контроль работы испытываемою двигателя со специального пульта экспериментаторов, с которого также должны производиться управление и контроль экспериментальных систем ЛЛ (БСИ, и др. Конструкция СУ с испытываемым двигателем должна обеспечивать возможность удобного, безопасного и контролируемого осмотра, технического обслуживания и замены двигателя, его деталей, узлов и агрегатов, элементов гласно указания РЭ, а также установленных на них элементов БСИ и БСК. В конструкции ЛЛ и составе наземного оборудования должны быть предусмотрены средства защиты от попадания посторонних предметов в испытываемый двигатель при наземных испытаниях, на взлете и посадке, а также средства защиты от неблагоприятных воздействий выходного потока испытываемого двигателя на прочность элементов конструкций, устойчивость. Управляемость ЛЛ. Конструкция, летно-технические и эксплуатационно-технические характеристики ЛЛ должны удовлетворять требованиям летной безопасности, а та требованиям унификации, обеспечивающим минимальные затраты при переоборудовании ЛЛ под двигатель другого типа.
4. 5. ИСПЫТАТЕЛЬНЫЕ КОМПЛЕКСЫ Усложнение конструкций авиационных ГТД, выбор значений параметров рабочего процесса на пределе возможного, расширение перечня условий эксплуатации, увеличение в нем доли предельных режимов работы двигателя, с одной стороны, и необходимость, несмотря на значительнее достижения по ис-пользованию совершенных математических моделей и методов математического эксперимента, натурной проверки большинства технических решений при стремлении к максимально возможной экономии средств, объективно привели ведущие авиационные державы (США, Великобританию, РФ, Францию) к созданию и постоянному совершенствованию испытательных комплексов и испытательных центров. В Российском научно-исследовательском центре (НИЦ ЦИАМ), вошедшим в эксплуатацию в 1955 году, проводят испытания всех созданных в стране авиационных ГТД, прямоточных ВРД и небольших ракетных двигателей [36). Испытательные стенды этого центра позволяют проводить высотные испытания ГТД, автономные испытания компрессоров, турбин и камер сгорания, испытания ПВРД и Рк. Д на жидком и твердом топливах, топливных систем, исследовать процессы горения. В НИЦ ЦИАМ отрабатываются новые методики испытаний, формируются новые организационные и технические приемы работы нескольких подразделений большого коллектива, изучаются и отрабатываются характеристики технологического оборудования стендов. Экспериментальный комплекс непрерывно развивается, наращивается энергетический потенциал, совершенствуются исследовательские возможности в соответствии с появлением новых задач в авиационной и других сложных отраслях промышленности. Создаются стенды [36 J с барокамерой глубокого вакуума; для исследования систем кондиционирования воздуха в кабинах самолетов; для исследования газогенераторов; для исследования турбопрямоточных двигателей; большой аэродинамический стенд для исследования авиационных двигателей на режимах взлета-посадки с обдувом свободной струей силовой установки с элементами планера.
В 1980 -1990 годы НИЦ ЦИАМ прошел значительную модернизацию [36[. Это позволило использовать его экспериментальные мощности для исследования двигателей IV и V поколений. Это, прежде всего, проведение высотных и специальных испытаний двигателей с высокой степенью двухконтурности, а также «траекторных» испытаний ТРДДФ в реальном масштабе времени. Выдерживание реального масштаба времени позволяет получить фактические характеристики двигателя с учетом его теплового состояния, зазоров и т. п. [36]. При этом с помощью выдвижных итерцепторов, расположенных во входном трубопроводе, создаются неравномерности полей давления и пульсаций в потоке на входе в двигатель, имитируя тем самым работу самолетного воздухозаборника в полетных условиях с эксплуатационными углами атаки, со скольжением и т. п. Стенды оснащены современными системами измерения, сбора и обработки данных, а также сложными системами автоматического управления ходом эксперимента и работой стендовых систем. Другим примером современного испытательного оборудования является научно-исследовательский центр ВВС США имени Арнольда. При сооружении для него комплекса ASTF было смонтировано 17 550 т трубопроводов, длина сварных швов достигает 192 км. Трубопроводы перед стендами выполнены из нержавеющей стали. Для отсоса газов используется 12 осевых эксгаустеров, каждый производительностью 28 317 м 3/с и суммарной мощностью 284 МВт, обеспечивающих снижение давления в термобарокамерах до высоты Н = 30 км. Крупные зарубежные авиадвигателестроительные фирмы, такие как Роллс- Ройс (Великобритания), Дженерал Электрик, Пратт-Уитни (США), также имеют свои испытательные комплексы, которые практически постоянно модернизируются и развиваются в соответствии с ростом параметров двигателей и возникающими техническими проблемами.
РЕЗЮМЕ (по главе 4 «Испытательные стенды и оборудование» ) 1. Авиационные ГТД подвергают испытаниям, которые проводят на специально оборудованных стендах. Испытательный стенд состоит из бокса, где размещается испытываемый двигатель, кабины управления, ряда вспомогательных помещений и является основной производственной единицей. 2. Двигатель в боксе устанавливается на испытательном станке, который позволяет измерить тягу двигателей прямой реакции, измерить тягу и крутящий момент для турбовинтовых двигателей, измерить крутящий момент для газотурбинных двигателей со свободной турбиной. 3. Глушение шума двигателей, работающих на стендах, осуществляется с помощью специальных шахт на входе и выходе, а также путем подачи воды в выхлопные газы. 4. В кабине управления смонтированы пульты, контрольные и измерительные приборы, системы сигнализации, панели отображения информации, органы управления двигателем и размещается персонал, ведущий испытание. 5. Испытательные станки подразделяются на жесткие, на которых невозможно прямое измерение тяги, и нежесткие, которые позволяют проводить измерение тяги. 6. Нежесткие станки состоят из неподвижной станины, к которой с помощью гибких стальных лент, упругих пластин или шарниров крепится подвижная платформа. 7. Силоизмерительные устройства градуируют с полностью смонтированным двигателем и подведенными системами.
8. Питание двигателя топливом и измерение его расхода осуществляют с помощью топливной системы, которая несколькими трубопроводами соединяется с топливохранилищем, обычно размещаемым вне испытательной станции таким образом, чтобы обеспечивать самослив неизрасходованного топлива. 9. Испытательные станции оснащаются автономной или неавтономной масляными системами для обеспечения подачи масла в двигатель при его работе или при консервации. 10. При испытании двигателя с установленными на нем самолетными гидроагрегатами на испытательных станциях используется гидравлическая система, которая, в том числе, обеспечивает загрузку этих агрегатов. 11. Если при испытаниях ГТД используют гидротормоз, то для обеспечения его работы стенд оборудуется водяной системой, которая может быть применена также и для охлаждения каких-либо сред водяными радиаторами. 12. Питание силовых агрегатов стендов, приборно-измерительного оборудования, запуска двигателя или его турбостартера от электростартеров обеспечивает электрическая система, которая может также использоваться для загрузки электрогенераторов, установленных и приводимых двигателем. 13. Летные испытания проводят для отработки летно-тактических характеристик ГТД сначала на летающей лаборатории, а затем на самолете, для которого предназначен двигатель. 14. Для проведения летных испытаний опытный двигатель подвешивается на специальной подвеске под фюзеляжем самолета—летающей лаборатории либо под крылом в одной из мотогондол. 15. Пять этапов летных испытаний охватывают периоды от периода параллельных стендовых испытаний, периода первого вылета опытного самолета, государственных летных испытаний, а также летные испытания новых модификаций двигателя.
16. Экспериментальное оборудование летающей лаборатории обеспечивает измерение, управляемый сбор, регистрацию, передачу на землю или предварительную обработку на борту большого количества параметров, характеризующих работающий двигатель, внешние условия и т. п. 17. Ведущие авиационные державы создали и постоянно развивают испытательные центры и комплексы, которые обеспечивают натурную проверку большинства технических решений в области авиационных двигателей.
ВОПРОСЫ 1. Дайте характеристику основным помещениям испытательного стенда. 2. Какие документы готовят для испытания ГТД? 3. Назначение программы испытания. Принципы подготовки программы. 4. Какими устройствами обеспечивается глушение шума двигателя, работающего в испытательном боксе? 5. Какова особенность бокса для испытания ГТД, размещаемого на ЛА на пилоне? 6. Какие станки применяют для испытания различных ГТД? В чем их особенности? 7. Какие требования предъявляют к силоизмерительным устройствам? 8. Назначение и особенности топливной системы испытательного стенда. 9. В чем состоит назначение масляной системы стенда? 10. Назовите этапы летных испытаний. 11. Какие требования предъявляют к летающим лабораториям? 12. Назовите основные возможности научно-исследовательского центра ЦИАМ для испытаний авиационных ГТД.
Глава 5 ВЛИЯНИЕ АТМОСФЕРНЫХ УСЛОВИЙ НА ЭКСПЕРИМЕНТАЛЬНЫЕ ХАРАКТЕРИСТИКИ АВИАЦИОННЫХ ГТД Основная задача испытаний ГТД — это определение основных технических данных (ОТД) двигателя. ОТД — это те параметры и характеристики ГТД, по которым судят о его соответствии техническим условиям (ТУ) и контролируют фактически качество изготовления и сборки. К числу важнейших основных параметров ГТД, входящих в состав ОТД газотурбинных авиационных двигателей, относят габариты и массу двигателя, а также тягу Р дв (мощность N 3 или N e ), удельный расход топлива С уд (С з или С е , расход воздуха G в , степень повышения давления в компрессоре π к , часовой расход топлива G m ч , частоты вращения роторов n i давления за компрессором р k * и, наконец, температуры в характерных сечениях проточной части*. При испытаниях ГТД для заказчика особое значение имеет точное оп ределение таких параметров двигателя, как M д в , тяга Р д в и С уд , так как именно их оптимальное сочетание определяет в конечном счете эффективность ГТД на летательном аппарате (ЛА) [20]. Следует различать общие ОТД, записанные в ТУ к данной серии ГТД, и ин дивидуальные ОТД серийного экземпляра двигателя. Первые формируют на основе результатов сертификационных или государственных испытании опыт ных образцов, и все серийные ГТД должны их выполнять или быть лучше их. Индивидуальные ОТД у разных экземпляров ГТД одной серии в связи с произ водственными отклонениями получаются разными. Экспериментальными характеристиками называют характеристики, полу ченные на основании измерений параметров в ходе эксперимента — испытаний двигателя. Испытания одного и того же двигателя зимой и летом на одном и том же режиме для его измеренной тяги представлены на рис. 5. 1.
Такая картина означает, что, будучи измерены при испытаниях конкретного экземпляра серийного ГТД в стендовых условиях, Р дв изм и С уд изм не позволяют непосредственно по их величине судить о качестве двигателя и сравнивать их с другими ГТД или с ОТД, заданными для данной серии ГТД, т. к. результат испытания зависит от условий проведения испытания. Рис. 5. 1. Измеренная по физическим параметрам дроссельная характеристика ТРД Важнейшими воздействиями, влияющими на характеристики ГТД, являют ся следующие: • влияние самих атмосферных условий в момент испытания на рабочий процесс ГТД, например С уд =f(p H , t H , d) при n пр = const, и на геометрические де формации (δF ca, δF c , δν др. ) в элементах проточной части при испытании ГТД (зазоры, проходные сечения и диаметры зависят от Т н * и Т г *)\ • влияние программы управления ГТД по внешним условиям, например. n=f(p H , t H ) • в отдельных случаях возможно влияние и вида топлива (через Н и , су, /? г ). Очевидно, что при сравнении ОТД разных экземпляров ГТД с ОТД, указан ными в общих ТУ на серию, влияние этих факторов необходимо исключить.
5. 1 ВЛИЯНИЕ АТМОСФЕРНОЙ ТЕМПЕРАТУРЫ Изменение рабочего процесса под влиянием t H Значительное влияние на стендовые характеристики ГТД оказывает темпе ратура воздуха на входе в двигатель t H , прежде всего из-за сильного влияния температуры t H на рабочий процесс ГТД (рис. 5. 2). Как видно, на рис. 5. 2 понижение температуры воздуха приводит при n изм = const к значительному возрастанию тяги ТРД и уменьшению С уд ; повышение температуры t H приводит к обратному эффекту. Так, например, обычно в среднеширотных условиях понижение t H от + 15 °С до -30 °С приводит при n пр = const в среднем к увеличению Р дв на 25. . . 30 %, а С уд снижается на 5. . . 10 %. Рост тяги ТРД при этом происходит как за счет возрастания G B , так и за счет возрастания Р уд (Р дв = Р уд (G в ) Из теории ГТД известно, что G B возрастает с понижением t н по двум причинам [20]: а) увеличивается плотность воздуха р = p H /RT H ; б) при n = const возрастает объемный расход через компрессор G B = q(X)F BX (рис. 5. 3).
Рис. 5. 2 Дроссельная характеристика ТРД, изме ренная при разных значениях температуры наруж ного воздуха: р н = const; М n = const; t H = var Рис. 5. 3. Влияние понижения температуры t Н на изменение положения рабочей точки: 1 — t H = +20 ºС; 2 — t H = -10 ºС Рис. 5. 4. Влияние увеличения π k * (участок 0 — 1 ) и совокупного увеличения π k * и степени подогрева рабочего тела в цикле (T г * / Т н *) (участок 1 — 2) на повышение топливной эффективности двигателя (участок 0 — 2): (Т* г /Т н *) 2 > (Т* г /Т н *)
Приведенная частота вращения n пр = n(288/T H *) 0. 5 с понижением t H увеличивается (см. рис. 5. 3), поэтому и рабочая точка переходит из положения / в положение 2 (G B пр 2 > G B пр 1 ). В свою очередь удельная тяга Р уд с понижением t H растет по нескольким причинам: — увеличивается степень подогрева воздуха в двигателе Т Г * / Т н *, т. к. при n = const Т Г *≈ const, а Т н * уменьшается. Это основная причина роста Р уд. — увеличивается степень повышения давления в компрессоре π* к. При n изм = const работа компрессора L K практически сохраняется постоянной Это постоянство при понижении температуры воздуха достигается только за счет роста π* к. Неодинаково уменьшаются теплоемкости с рв и с рг при снижении t H. Удельный расход топлива снижается при уменьшении t H за счет возрастания π* к , т. к. при этом увеличивается термический КПД цикла (эффективный КПД): С уд 1/η е (уменьшаются потери тепла). Однако, еще большую роль играет одновременное увеличение π* к и Т Г * / Т* н (рис. 5. 4). Влияние на С уд оказывают так же изменения с разной интенсивностью с рв и с рг. Так как полет самолета обычно происходит на высотах Н > 8. . . 11 км, где t H = -(50. . . 70) °С, то в полетных условиях у ГТД улучшаются характеристики, т. е. этот тип СУ как бы специально предназначен для ЛА. Влияние изменения геометрических размеров в элементах двигателя при изменении t H на экспериментальные данные ГТД
Изменение геометрических характеристик проточной части при испытаниях ГТД происходит как при изменении t H , так и режима работы двигателя ( Т Г * ) [20]. Например, при изменении чтобы сохранить подобный режим (n/ (Т H *) 0. 5 = const), требуется изменить физическую частоту вращения ротора. При этом, например, для ТРД с Т* кр = 1100 К ( π* к = 12 и n пр = 8500 1/м) сохранение условия n пр = const при изменении t H от +15 “С до -30 °С приводит к следующим изменениям измеренных при испытании параметров: Δп = 690 1/мин; ΔТ* К = 100 К; ΔТ Г * = 170 К. Вследствие изменения физической частоты вращения и температур в про точной части ГТД изменяются центробежные силы, действующие на диски и лопатки, а также температура элементов ГТД — Т* э. Все это отражается на вели чине относительных радиальных зазоров в компрессоре и турбине двигателя. Расчетами и экспериментами доказано, что у большинства ГТД при n пр = const т. е. изменение температуры элементов ГТД на подобных режимах в условиях Н = 0, М = 0 приблизительно прямо пропорционально изменению t H. Указанное изменение Т э *, а также центробежной силы Р цб может привести к значительным изменениям радиальных зазоров над рабочими лопатками турбокомпрессора. Так, например, непосредственные измерения на одном 2 -каскадном ГТД третьего поколения показали следующие значения радиального зазора:
Т. е. имело место изменение величины более чем в 2— 3 раза. У современных ГТД в этом же случае зазор изменяется меньше. Это объясняется подбором распределения температур по ротору и статору, что зависит во многом от системы охлаждения. Изменение радиального зазора при испытании приводит к изменению КПД турбины даже на подобных режимах, т. е. в тех случаях, когда по ее расчетной характеристике КПД должен быть строго постоянен. Эксперименты показали, что у некоторых ТРД, благодаря только этому фактору, падение КПД турбины при -40 °С на подобном режиме может достигать 1. . . 3 %. Зазоры над рабочими лопатками компрессора чаше всего изменяются слабее, т. к. статор и ротор здесь имеют более близкие значения температуры и близкие значения коэффициенты линейного расширения. Для парирования процесса появления зазоров в современных авиационных ГТД применяют системы активного регулирования радиальных зазоров. На рис. 5. 5 приведена схема такого регулирования в компрессоре ВД. Воздух, проходящий через регулирующий элемент, омывает наружную поверхность статора компрессора и охлаждает ее. А это, в свою очередь, меняет величину радиального зазора. Изменение теплового состояния двигателя, кроме радиальных зазоров, от ражается на проходных сечениях в проточной части ГТД: F CK , F c и др. [20]. Изменение этих площадей происходит за счет термических упругих деформаций. Их величина существенно зависит от системы охлаждения, конструкции и тех нологии изготовления деталей двигателя.
Иногда они могут быть пренебрежимо малы (F CA ТНД), НО иногда (на некоторых высотных ГТД) изменения F С А ТВД достигает значительной величины. Так, например, в диапазоне от -30 °С до +60 °С на одном отечественном ТРД ухудшение удельного расхода топлива на подобном режиме только за счет δ Т СА составило примерно 1 % (как правило, с ростом t H величина F CA турбины ВД возрастает). Рис. 5. 5. Схема системы активного регулирования радиального зазора в компрессоре ВД Таким образом, влияние упругих деформаций в проточной части конкретного ГТД на его выходные данные находится в однозначной зависимости от t H и α рул (т. е. режима) и может быть заранее определено специальными продувками горячим газом (особый случай: отключение охлаждения турбины). Фактически изменение проходных сечений под воздействием температуры t H и влияние этого изменения на выходные данные двигателя можно рассматривать как дополнительное к влиянию t H на рабочий процесс. Наиболее сильно отражаются на параметрах ГТД следующие искажения: δF CA , F c , Δr, δ v ут (изменение утечек через лабиринты под влиянием изменения соответствующих зазоров).
Влияние таких отклонений на характеристики ГТД рассмотрим на примере испытаний газогенератора ТРДД (фактически 2 -каскадного ТРД). Влияние искажении проходного сечения выходного сопла двигателя F c. Из условий совместной работы турбины и сопла следует, что с уменьшением F c также уменьшается π* к , так как уменьшение пропускной способности сопла ведет к росту давления за турбиной. При Т Г * = const уменьшенному значению работы турбины соответствует меньшее π* к . При уменьшении F c возрастает π* к и снижается увеличиваются Т Г * и С уд (рис. 5. 6). Влияние изменения δ F CA. Уменьшение площади соплового аппарата турбины вызывает рост давления р г * и соответственно увеличение значений π* к и π* т и уменьшение температуры газа Т г * и удельного расхода топлива С уд. Влияние изменения утечек в проточной части ГТД. С ростом величины δv УT рабочие линии приближаются к границе помпажа и вызывают рост температуры Т Г * (рис. 5. 7) и ухудшение С уд : 1 % δv УT ≈0, 5. . . 1, 0 % С уд. Увеличение радиальных зазоров в компрессоре и турбине приводит к сни жению их КПД и других параметров, характеризующих их эффективность.
5. 6. Влияние изменения F c на положение линии рабочих режимов (а) и на протекание дроссельной характеристики (б); δF c ≈ (-0, 3. . . 0, 4)δС уд
Рис. 5. 7. Влияние изменения утечек на положение линии рабочих режимов (а) и на протекание дроссельной характеристики ( б)
Относительное влияние на КПД примерно одинаково для компрессора и турбины (рис. 5. 8). Однако влияние КПД компрессора и турбины на С уд различно: Влияние относительного радиального зазора на положение линии рабочих режимов и на протекание дроссельной характеристики приведено на рис. 5. 9. Изменение КПД приводит также к соответствующим изменениям и в измеренных значениях Р дв (N э ), Т г * и др. В связи с увеличением L K и уменьшением Т г * возрастает L т. Увеличение Т г * приводит к подъему ЛРР. Но существует и иной аспект проблемы влияния геометрических искажений, не связанный с изменением t н. Это влияние разброса геометрических раз меров деталей у различных экземпляров серийных ГТД относительно чертежа, т. е. влияние погрешностей серийного производства Этот фактор проявляется только при сравнении индивидуальных ОТД разных экземпляров ГТД между собой или с общими ОТД серии. Здесь помимо отступлений от чертежа в величинах δF CA , F c , Δr, δ v ут проявляют себя и такие факторы, как чистота обработки, точность установочных углов и т. п. Все это влияет на КПД элементов ГТД, а следовательно, на С уд и Р ДВ (5 С уд ≈ 1 % у серии больших ГТД).
Рис. 5. 9. Влияние увеличения относительного радиального зазора (Δr) на положение линии рабочих режимов (а) и протекание дроссельной характеристики (б, в) протекание дроссельной характеристики ( б) Рис. 5. 8. Относительное изменение КПД лопаточных машин при изменении величины Δr
Существующие допуски на изготовление и сборку серийных ГТД среднего размера (G В < 200 кг/с) могут приводить к значительному разбросу значений Р лв : при Т г * = const, δР ДВ = ± 4. . . 5 % или при отладке на Р дв = const, Т г * = ± 1. . . 1, 5 %, δР ДВ = ± 1, 5. . . 2 %, δ ст = ± 1. . . 2 %. Существенно увеличивается нестабильность параметров при производстве малоразмерных ГТД. Так, например, на одном из малоразмерных ТВД (ВГТД) с N e = 88 к. Вт (120 л. с. ) и расходом воздуха G B = 1, 5 кг/с в партии из 50 двигате лей был определен следующий разброс параметров на максимальном режиме: δ π* к = ± 8, 5 %; δС е норм = ± 10 %, δТ* Г = ± 4, 5 %. В разбросе геометрических размеров по производственным причинам отсутствуют функциональные закономерности, которые действуют в случае упругих (температурных) деформаций проточной части при испытании конкретного ГТД. Разброс характеристик за счет геометрических искажений при производстве ГТД отвечает распределению Гаусса, т. е. носит случайный характер, также как и брак серийного производства. На каждом предприятии по каждому ГТД может иметь место своя закономерность в разбросе параметров за счет производственных отклонений. Эти причины при испытаниях ГТД изучают и ведут с ними борьбу путем ужесточения допусков и улучшения технологии изготовления ГТД.
5. 2 ВЛИЯНИЕ АТМОСФЕРНОГО ДАВЛЕНИЯ Из экспериментов установлено, что изменение р н при t H = const в зоне автомодельности, т. е. в определенном диапазоне чисел Re (Рейнольдса), приводит к пропорциональному изменению давлений в проточной части двигателя. Тем пературы и скорости газа во всех сечениях двигателя в этом случае остаются неизменными. Например, при испытании ТРД на постоянной частоте вращения (n реж = const) все безразмерные параметры потока ( π* к , Т г * , Т* н и т. п. ) остаются практически неизменными, a G m , G B и тяга Р дв изменяются прямо пропорционально р н. Очевидно, что в этом случае исключить влияние нерасчетного значения р н из результатов испытания не составляет особого труда. При значительном уменьшении давлении р н (для ТВД < 50 % от р н = = 101, 33 к. Па (760 мм рт. ст. ), а для ТРД < 20 % от 101, 33 к. Па) изменение атмо сферного давления начинает влиять на безразмерные параметры течения в про точной части. Это объясняется выходом характеристик газовоздушного потока из зоны автомодельности, т. е. из области турбулентного течения и переходом в область ламинарного [20]. Как известно из гидрогазодинамики и теории лопаточных машин, критерий Рейнольдса Re= (VL )/ v является мерой отношения сил инерции ( VL) к силам Внутреннего трения (характеризуемых вязкостью v= μ / р). Поток является ламинарным при ReRe Kp определяющее влияние оказывают силы инерции — поток является турбулентным, при этом частицы движутся беспорядоч но, скорость и давление в каждой точке потока хаотически пульсируют. Величина Re Kp зависит к тому же от объекта обтекания:
• при обтекании самолетного крыла Re Kp >1, 5 ∙ 106; • для компрессора ГТД Re Kp > 0, 2 • 105. На рис. 5. 10 показано относительное изменение коэффициента трения ^ при увеличении числа Re. Снижение ξ тр обусловило появление ряда технических ре шений для самолетных крыльев и про ектных предложений для компрессорных лопаток, использующих эффект «ламинаризации» . Этот эффект предполагает удаление путем отсоса пограничного слоя и сохранение снижения потерь на трение. Однако, в большинстве случаев, возможные преимущества перекрываются при этом затратами мощности на механизмы удаления пограничного слоя и увеличивающейся массой летательного аппарата или двигателя. Область Re≈ 2300. . . 10 000 обычно называют переходной зоной, если уменьшать число Re, то при выходе из зоны автомодельности КПД (η к и η т ) начинают понижаться, при этом ухудшаются и другие характеристики эле ментов ГТД, изменяются напорность и производительность ступеней. Все эти факторы приводят к тому, что вне зоны автомодельности при неизмен ной частоте вращения ротора ТРД понижение атмосферного давления вызывает увеличение температуры Т* (в связи с необходимостью сохранения баланса мощности между турбиной и компрессором). При этом, хотя Р ул ТРД возрастает, ухудшается С ул (т. к. увеличивается Т г *, снижается η к и снижается η т ). В этих случаях исключить влияние нерасчетного р н из результатов испытания уже не так просто.
Рис. 5. 10. Зависимость относительного коэффициента трения от числа Re
На рис. 5. 11 показано влияние атмосферного давления р н на дроссельную характеристику ТРД в случае испытания при р н = var(Н > 11 км), М = 0, t H = const. При этом Re= var, т. к. р н и ρ снизились, возросли утечки v, Re понизилось. У современных крупноразмерных ТРДД такие низкие давления (р Н = 0, 2), где начинает проявляться влияние Re, могут встретиться только в условиях полета на очень больших высотах (Н > 16. . . 17 км). Однако, часто влияние Re у ГТД обнаруживается и на меньших высотах, если сказываются геометрические параметры ЛМ (узкие лопатки, лопатки малой высоты и т. п. ). Кроме того, перспективные проработки так называемых трансатмосферных самолетов с Н п ≥ 25 км показывают, что они работают в зоне значительного влияния критерия Re. Во всех типах ГТД влияние числа Re раньше проявляется в турбине (из-за большей Т г *, например, у ТВД при Н = 11 км, Δη т Re ≈ 2 %). По экспериментальным данным, число Re в лопаточных машинах можно оценить следующим образом: Re= G в ср /μF cp. Есть влияние Re и на КПД компрессора (рис. 5. 12). При Re<Re Kp теория подобия не работает, поэтому общепринятое уравнение приведения к САУ для подобных режимов ГТД (т. е. Р дв пр /р н = Р дв изм /р н ) действительно только для чисел Re, соответствующих зоне автомодельности. В зоне ламинар ного течения при Re<Re Kp это уравнение оказывается недействительным и его следует уточнять путем испытаний двигателя в термобарокамере.
Рис. 5. 12. Влияние величины числа Reи режима работы на КПД компрессора. Рис. 5. 11. Влияние на дроссельную ха рактеристику ТРД пониженного атмо сферного давления
5. 3 ВЛИЯНИЕ АТМОСФЕРНОЙ ВЛАЖНОСТИ Влажность атмосферного воздуха характеризуется несколькими пара метрами. Удельная влажность d = M nap /M B (или «влагосодержание» ) оценивается количеством пара, приходящимся на 1 кг сухого воздуха. Таким образом, например, безразмерная величина d = 0, 04 показывает, что в каждом килограмме сухого воздуха содержится 40 г паров воды или, что то же, — массовая доля паров воды в воздухе равна 0, 04. Относительная влажность — это отношение фактической массы водяного па ра, содержащегося в воздухе, к максимально возможной (насыщающей) массе его в данном объеме воздуха при данной температуре, %: . Насыщенный пар содержит капельки воды. Относительная влажность характе ризует степень насыщения воздуха водяными парами и зависит к тому же от температуры ( рис. 5. 13). Теоретически большие значения (d > 0, 06) могут иметь место лишь при ис пытаниях ГТД в условиях тропиков (t H > 50 °С). Для авиации в нормах летной годности самолетов оговаривается обычный температурный диапазон эксплуатации t H = -50. . . +45 °С при φ d = 10. . . 20 %. Таким образом видно, что этим нормам соответствует диапазон d= 0, 015. . . 0, 07. Но реально встречающиеся значения d в земной атмосфере обычно никогда не достигают 0, 07. Так, например, максимально возможное влагосодержание воздуха в «жаркий день» (+45 °С) установлено на основе экспериментальных данных равным 0, 043, а не 0, 07, а для Н = 3 км (высотный аэродром) — 0, 02. В условиях же стандартной атмосферы эти цифры соответствуют при Н= 0 d = 0, 011, при Н = 3 км d = 0, 005.
В средней полосе РФ для атмосферных условий характерно t Hmax ≈ +30 °С и φ d = 100 %, что соответствует d ≈0, 035. Вместе с тем, необходимо отметить, что авиация эксплуатируется и в тех районах, где d max ≈ 0, 05. . . 0, 06. Рис. 5. 13. Взаимосвязь между удельной и относительной влажностью Наличие в атмосфере водяного пара, значительно отличающегося по своим свойствам от воздуха, приводит к весьма заметным изменениям параметров рабочего тела ГТД, что в первую очередь связано с существенным различием газовых постоянных у пара и воздуха (соответственно R = 0, 461 и 0, 287 к. Дж/ (кг-К)). Поэтому с увеличением атмосферной влажности, с одной стороны, возрастает величина газовой постоянной воздуха и вместе с ней с р = R + с v и а кр = с другой — вместе с ней снижается плотность воздуха то есть падает расход воздуха G B = р CF, растет Р дв , так как возрастает скорость На рис. 5. 14 приведены относительные измерения Ср, R, к в при увеличении удельной влажности.
В связи с такими изменениями параметров рабочего тела влияние атмосферной влажности проявляется как на термодинамическом цикле, так и на совместной работе элементов ГТД [20]. Так, например, возрастание с p и R в под влиянием влажности приводит к увеличению скорости звука и показатель изоэнтропы для влажного воздуха. Из-за увеличения критической скорости звука при n = const приведенные , U окружные скорости лопаточных машин снижаются λ M = U/a кр , т. е. Рис. 5. 14. Относительное изменение теплоемкости при постоянном давлении с р , газовой постоянной R и показателя адиабаты к н при изменении удельной влажности Так, например, под влиянием влаж ности d = 0, 06 у ТВД при t H = const, n П р d = 0, 985. Рабочая точка на характеристике компрессора при этом сместится (рис. 5. 15). При n изм = const, характерном для ТВД, точка приближается к границе помпажа.
Рис. 5. 15. Влияние влажности воздуха на по ложение рабочей точки ТВД при t H = const. / — сухой воздух; 2 — влажный воздух Рис. 5. 16. Влияние влажности воздуха на характер изменения основных выходных данных ГТД Под влиянием влажности у ГТД могут быть следующие изменения: δP дв = -(0, 3. . . 0, 5) %; δ С уд = +(2. . . 2, 6) %; δG m ч = +(1, 8. . . 2, 7) % на каждый процент изменения влажности (рис. 5. 16). Для учета влияния влажности на параметры испытываемых ГТД на испытательных станциях удобнее иная форма представления этого влияния (т. к. на ИС непосредственно измеряют (φ d и t H ) (рис. 5. 17). Изменение φ d при испытаниях ВРД отражается и на других характеристиках двигателя ( G B , n, Р, G m , . . . ). Поэтому необходимо учитывать влияние d , если t H ≥ 25. . . 30 °С обычно в виде безразмерных поправок типа G md = f( φ d , t H ) (см. рис. 5. 17), определяемых заранее расчетным путем.
Рис. 5. 17. Учет влияния относительной влажности и температуры атмосферного воздуха на параметры ГТД (на примере часового расхода топлива)
5. 4 ВЛИЯНИЕ ЗАКОНОВ УПРАВЛЕНИЯ ГТД НА ИХ ХАРАКТЕРИСТИКИ Система автоматического управления ГТД должна обеспечивать: во всех условиях полета такие характеристики двигателя, которые удовле творяют требованиям ЛА; соблюдение прочностных, газодинамических и других ограничений по двигателю и ЛА. Выполнение этих требований приводит к тому, что при положении РУД, соответствующем максимальному режиму, и изменении внешних условий часто та вращения ротора может автоматически изменяться и не всегда быть максимальной [20]. Как известно, параметрами ГТД обычно управляют по внешним факторам t н , р н , М„. В связи с этим, при изменении внешних факторов двигатель фактически переходит с одного режима на другой, т. е. кроме собственного влияния t H и р н (см. пп. 5. 1 и 5. 2) появляется дополнительное влияние изменения режима. Вид закона управления зависит от числа степеней свободы (независимых переменных) двигателя: Регулирующие факторы — входные координаты в системе управления — например, G m, φ у ТРД (1 степень свободы) или G m и ф у ТВД (2 степени свободы). Регулируемые параметры — выходные координаты, например п дв Внешние факторы —t H, р н , М п. Для получения Р дв тах необходимо обеспечить его работу при максимально допустимых значениях частоты вращения n = n mах = const и температуре Т г * = Т г * max. Условие n = n max. при заданной линии рабочих режимов соответствует требованию получения максимальной производительности компрессора при макси мальных значениях π* к. Последнее при Т г * = Т г * max обеспечивает максимум работы термодинамического цикла и, следовательно, Р уд mах.
При максимальном расходе воздуха через компрессор это равнозначно получению максимума полной тяги. Поддержание n = const достигается изменением расхода топлива, тогда как для сохранения Т г * = const требуется специальное управление критическим сечением сопла. Из числа применяемых необходимо также упомянуть программу управления, влияющую на подобие режимов турбокомпрессора, когда при изменении режима полета рабочие точки на характеристиках компрессора и турбины не перемещаются. Это достигается сохранением n пр =const и Т г * пр =Т г *288/ Т н * = const. Основными достоинствами такого способа управления является возможность получения во всем потребном диапазоне высот и скоростей полета высоких значений КПД компрессора и турбины и достаточных запасов устойчивости компрессора. Однако выполнение указанных условий достигается только путем широкого изменения диапазона значений частоты вращения ротора и температуры газа, что приводит к определенному снижению тяги двигателя в некото рых точках траектории полета. В случаях с ТРД и ТРДД без форсажной камеры, частотой вращения (единственным управляемым параметром режима) чаще всего управляют следующим образом: т. е. датчики t Н и р н воздействуют на n через управляющий фактор G m. Наиболее показательно управление ТРД на максимальном режиме. В этом случае для одновальных ТРД и двухвальных ТРДД обычно используют два разных закона (рис. 5. 18). При изменении t H и р н тяга двигателя на максимальном режиме обычно отклоняется относительно ТУ на +9. . . -12 %, а С уд на -9. . . +7 %.
Рис. 5. 18. Влияние закона управления ТРД на характер перемещения рабочей точки на ЛРР и на выходные характеристики
Это меньше, чем было бы в случае n = const, но тем не менее выходит за пределы обычного допуска ТУ: -2 % Р дв и 0 % С уд. Зона n mах = const— это зона ограничения Т г * тах , а зона G m = const(n пр = const) — зона ограничения Р дв тах , Р* ктах, Т г * тах. Отсюда видно, что при испытании ТРДД при различных t H в диапазоне -40. . . +40 °С тяга и другие параметры дви гателя на заданном режиме при существующих законах регулирования могут значительно отличаться от величин, заданных в ТУ (см. точки значений ТУ на рис. 5. 18), и отклонения от них превышают обычные значения допусков на вы ходные данные двигателя. При существующих законах управления температура за турбиной T т * максимального режима во многих случаях достигает своего максимального значения не в САУ, а при +25. . . 30 °С. Еще более сложно влияние закона управления у ТВД, т. к. эти двигатели имеют 2 степени свободы (рис. 5. 19). Частотой вращения т и эквивалентной мощностью N Э (2 режимных управляемых параметра) на максимальном режиме также управляют по t H и р н. Рис. 5. 19. Законы управления одновальным ТВД
Рис. 5. 20. Характер изменения характеристик одновального ТВД при законе управления n = const, G = f (t H , p H ) У ТВД классического* типа обычно используют управление n = const (ради лучших взлетно-посадочных характеристик) и N э =f ( t H , р н ). Датчики t H и р н воздействуют на регулирующие факторы: G m — для управления N э , а φ =f(α руд ) — для поддержания n = const. Такой вид законов управления определяет следующий вид измеренных характе ристик ТВД при р = const (рис. 5. 20). Здесь, аналогично ТРДД, имеются две зоны ограничения: N э = const при t H +25 °С. И здесь также видно, что закон управле ния вносит большие искажения в характеристики: N Э отличается от ТУ на +3 % и -15 %, С э от +3 % до +5 %, что выходит за пределы ТУ. Это означает, что до полнительно к влиянию t H и р законы регулирования также накладывают свои искажения подобно влиянию искажений F C А , возникающих под воздействием изменения t H. Таким образом, влияние изменения атмосферных условий на характеристи ки ГТД есть результат влияния многих факторов. Причем их влияние зависит от облика рабочего процесса ГТД, его конструктивного выполнения и закона управления
5. 5 ИСПОЛЬЗОВАНИЕ ФОРМУЛ ТЕОРИИ ПОДОБИЯ ГАЗОВЫХ ПОТОКОВ ПРИ АНАЛИЗЕ РЕЗУЛЬТАТОВ ЭКСПЕРИМЕНТОВ Влияние атмосферных условий на экспериментальные характеристики ГТД велико. Сопоставлять такие характеристики без приведения к САУ можно только при одинаковых атмосферных условиях. В этих целях для приведения к САУ характеристик ГТД, снятых в различных атмосферных условиях, используют формулы теории подобия газовых потоков [20, 25, 49]. Из теории газодинамического подобия известно, что для подобия режимов течения в каналах необходимо иметь: • геометрическое подобие каналов (F = const); • равенство чисел М потоков в абсолютном движении вдоль каждого канала (М u = const). Для лопаточных машин к этому добавляется еще условие равенства чисел М и в относительном движении к лопатке (М Y = const), т. е. требуется подобие треугольников скоростей. Исходя из таких представлений теории подобия, полагают, что режимы работы ГТД будут подобными, когда соотношения давлений, температур и скоро стей потоков в его проточной части сохраняются. Классический ТВД — одновальный двигатель, у которого компрессор и воздушный винт (через редуктор) приводятся одной турбиной.
Формулы для приведения параметров ГТД определены на базе основной теоремы теории размерностей (π-теоремы). Согласно этой теореме, для ГТД подобным режимам соответствуют следующие безразмерные величины, определяющие необходимые и достаточные условия механического подобия процессов в проточной части двигателя при установившихся режимах его работы. Так, например, для частоты вращения: для расхода топлива Таким образом, приведение параметров ГТД к САУ есть процесс пересчета с одних атмосферных условий на другие при сохранении условий подобия, т. е. как бы на одном и том же подобном режиме ГТД. Однако указанные выражения определяют только механическое подобие процессов в проточной части двигателя. Так как они не учитывают изменения свойств рабочего тела в компрессоре и турбине, а также влияние процессов в камере сгорания двигателя, где протекают сложные физико-химические, а не только механические процессы, на которые помимо λ кс , Дг, δD) влияют также значения абсолютных (а не относительных величин p k *, Т к *, α см. Такие процессы полностью моделировать не удается. изменение геометрических размеров в проточной части ГТД
Формулы приведения типа и другие не учитывают: 1) изменение геометрических размеров в проточной части ГТД 2) изменение свойств рабочего тела 3) изменение характеристик ЛМ под влиянием числа Reв проточной части испытываемого ГТД 4) влияние на процессы в камере сгорания
Рис. 5. 21. Схема определения частных поправочных коэффициентов Для учета этих влияний в формулы приведения вносят поправки в виде безразмерных поправочных коэффициентов, которые получают расчетно-экспериментальным путем. В практике испытаний современных ГТД влияние указанных выше допущений наиболее заметно отражается на расходе топлива. Здесь поправки могут превышать 2. . . 3 %. Формула G m пр при этом приобретает следующий вид:
где . В этом выражении — частные поправочные коэффициенты, связанные с влиянием атмосферного давле ния и температуры и других параметров. Поправка на вберется на основе исследований (см. раздел влияния влажно сти). Поправку G m. KC рассчитывают, исходя из характеристик конкретной КС и изменения теплоемкости. Поправки по t H , р н , п обычно определяют путем климатических испытаний данного двигателя в ТБК. На рис 5. 21, а в качестве примера показано определение поправки, связан ной с влиянием атмосферного давления G mp = G mnp[ /G m пр2. На рис. 5. 21, б видно, что сохранение п = 1 при t H = var позволяет определить поправку на влияние температуры t H G m. K = G mnp 3 /G m пр4 , связанную с влиянием геометрических измене ний (Дг, δF CA , δF C ). Сохранение формирует поправку, определяющую влияние t H на рабочий процесс ВРД, G t. H = = G m ПР 3 /G m пр6 , а она примерно равна отношению G m пр3 /G m пр4. В результате расчетно-экспериментальных исследований получают для различ ных типов ГТД зависимости для G ml (рис. 5. 22). С учетом таких поправочных коэффициентов искажение условий подобия получается существенно меньшим. Кроме формул приведения для G m пр и n пр необходимо вносить аналогичные поправки в формулы приведения n сд и п ад , Т г * , а также для Р дв > G B , Т* и р*. Рис. 5. 22. Зависимости поправочного коэффициента G ml к формуле приведения от температуры t H и режима работы (л)
РЕЗЮМЕ (по главе 5 «Влияние атмосферных условий на экспериментальные характеристики авиационных ГТД» ) 1. Соответствие параметров и характеристик ГТД техническим условиям, контроль качества изготовления оценивают по основным техническим данным (ОТД). 2. На ОТД влияют: атмосферные условия в момент испытания; программы управления ГТД по внешним условиям; вид топлива; производственные факторы. 3. Понижение температуры окружающего воздуха приводит к увеличению плотности воздуха, к возрастанию объемного расхода воздуха через компрессор, росту степени подогрева воздуха в камере сгорания ( Т г * / Т H * ), увеличению степени повышения давления в компрессоре π* к и к росту эффективного КПД, что в совокупности обеспечивает рост тяги двигателя и снижение удельного расхода топлива. 4. Дополнительно к влиянию температуры воздуха на параметры рабочего процесса имеет место влияние температуры на геометрические деформации элемен тов двигателя, что в свою очередь вызывает вторичные изменения ОТД. 5. Для парирования отрицательных воздействий геометрических деформаций, в частности относительного радиального зазора в лопаточных машинах ГТД, используют системы активного регулирования (с помощью осаждающего воздуха) радиального зазора. 6. Разброс погрешностей серийного производства, даже в рамках установленных допусков, приводит к ощутимым искажениям ОТД, поэтому при испытаниях ГТД изучают причины, приводящие к этому, и разрабатывают мероприятия по их устранению.
7. Снижение атмосферного давления, начиная с высоты 8. . . 10 км, начинает приводить к снижению критерия Рейнольдса и к переходу характеристик газовоздушного потока из зоны турбулентного течения в ламинарное, при этом начинают изменяться безразмерные параметры потока (π* к , Т г * / Т H * и т. п. ), которые нарушают пропорциональную зависимость ОТД от изменения атмосферного давления. 8. Водяной пар, отличающийся по своим свойствам от воздуха, приводит к изменениям ОТД, вызывая их ухудшение. 9. Законы управления ГТД фактически переводят двигатель с одного режима па другой, кроме собственного влияния р н и t H „ вносят дополнительные изменения в ОТД, зачастую выходящие за рамки обычных допусков по ТУ. 10. Изменение атмосферных условий оказывает как прямое, так и косвенное воздействие на ОТД, которое, будучи многофакторным, зависит от облика рабочего процесса, его конструктивного выполнения и закона управления. 11. Применяемые для сопоставления экспериментальных характеристик ГТД в стандартных атмосферных условиях (САУ) формулы приведения дополняются по ковочными коэффициентами, учитывающими дополнительные влияния t H , р H, d, закона управления.
ВОПРОСЫ 1. Что такое основные технические данные и с какой целью их определяют? 2. Какие внешние воздействия влияют на характеристики ГТД? 3. Каковы физические основы влияния атмосферной температуры на характери стики авиационных ГТД? 4. Какие изменения происходят в авиационных ГТД при геометрических дефор мациях элементов? 5. В чем проявляется влияние атмосферного давления на основные технические данные ГТД? 6. Какими параметрами характеризуется атмосферная влажность? 7. В чем проявляется влияние атмосферной влажности на характеристики ГТД? Дать физическое объяснение этого влияния. 8. В чем заключается влияние законов управления ГТД на его характеристики? 9. Как с помощью формул приведения учитываются отличия теории подобия газовых потоков от реальных условий работы ГТД?
Глава 6 ЭКСПЕРИМЕНТАЛЬНЫЕ МЕТОДЫ ОПРЕДЕЛЕНИЯ ОСНОВНЫХ ТЕХНИЧЕСКИХ ДАННЫХ АВИАЦИОННЫХ ГТД Дроссельными характеристиками называют зависимости тяги, удельного расхода топлива, расхода воздуха, температуры и давления рабочего тела в различных сечениях двигателя и других параметров двигателя от режима его работы, построенные для неизменных внешних условий [22, 23, 26, 30, 31, 36, 37, 38, 53]. Если построить дроссельную характеристику авиационного ГТД, снятую в САУ, то для определения его ОТД и сопоставления их со значениями, заданными в ТУ, на ней требуется выделить конкретные режимы, оговоренные в ТУ (взлетный, максимальный продолжительный и др. ). Кроме этого, в типовых ТУ (например, для ТРДД) обычно оговариваются для взлетного режима следующие ограничения (H n = 0, М n = 0, САУ): Р дв взл = 161, 83 к. Н (16 500 кгс); С уд ≤ 39, 2 кг/(к. Н ч) (0, 38 кг/(кгс ч)); Т т * = 846 К + 10 К. Найденные значения всех ОТД испытанного двигателя должны соответство вать тому случаю его испытания в САУ, когда регулирующие органы находятся в позиции, соответствующей их отладке на заданную для данного режима техническими условиями норму тяги (161, 83 к. Н). Такие параметры двигателя принято называть нормальными (т. е. нормализованными) и обозначать индексом «норм» , например С уд норм взл. На рис. 6. 1 показана схема определения таких параметров. Нормальные значения параметров ГТД должны удовлетворять ограничениям, оговоренным ТУ, т. е. Т* тнорм < Т* т т ах ; С уд норм ≤ С уд maxдоп [20].
Таким образом, нормальными значениями параметров (НЗП) называют параметры двигателя, измеренные в САУ при заданной норме тяги (или мощности) для данного режима, т. е. параметры, замеренные на данном режиме в конкретных атмосферных условиях и пересчитанные к САУ с учетом выбранного закона управления двигателя. Однако в последнем случае непосредственное определение НЗП с приведенной дроссельной характеристикой не всегда бывает возможным. Например, если снять дроссельную характеристику компрессора при t H > +15 °С, то при типичном законе управления получим следующую линию рабочих режимов как на рис. 6. 2. Это означает, что на максимальном режиме приведенная дроссельная характеристика будет иметь ьтитити< 1, 0. И, следо вательно, летом по ней без экстраполяции нельзя определить НЗП, соответствую щие взлетному режиму. В таких случаях приходится использовать особый метод определения НЗП с помощью специальных коэффициентов пересчета, определяемых по результатам испытаний аналогичных двигателей в САУ. При сопоставлении НЗП данного экземпляра двигателя с ТУ, например, может быть получено, что при заданном значении взлетной тяги (161, 83 к. Н) значение Т* тнорм выше заданного в ТУ (846 К) на 9 градусов, что в данном случае в преде лах допуска, а значение С уд должно быть равно или меньше, чем в ТУ. В ином случае двигатель бракуется и отправляется на переборку. Сравнивать по результатам испытаний показатели данного экземпляра серийного ГТД с ТУ или разных экземпляров ГТД между собой мешает влияние меняющихся внешних воздействий (р н , t H , законы управления по внешним условиям и т. п. ).
6. 1. Схема определения нормальных значений параметров ТРДД (ТРД) Рис. 6. 2. К определению НЗП с учетом закона управления двигателя Поэтому возникает проблема нормализации измеренных параметров серийных ГТД, т. е. пересчета их к единым внешним условиям (t H р н , d) при единой программе работы регуляторов на заданном режиме. Опреде ляемые в этом случае параметры ГТД называют «нормальными» (или «норма лизованными» ) (Р ДВ НОРМ , С уд НОРМ , n норм , G m норм и др. ). Используемые в отдель ных случаях для их определения специальные коэффициенты пересчета называют «нормализующими коэффициентами[1]» (существуют и иные способы оп ределения НЗП — без коэффициентов, т. к. определять НЗП требуется также и у опытных ГТД) [20]. В этом аспекте большое значение приобретают точность методов определе ния НЗП и возможность проверки ОТД ГТД по разным методам. [1] Нормализация — термин математический, присущ задачам векторной оптимизации, где возникают проблемы сравнения между собой критериев, имеющих различные несо измеримые масштабы.
6. 1 ОСНОВНЫЕ СПОСОБЫ ОПРЕДЕЛЕНИЯ НЗП ГТД Следует различать методы приведения параметров к САУ (когда пересчет ведется по формулам теории подобия на одном и том же подобном режиме) и методы нормализации, где производится пересчет параметров с одного подоб ного режима на другой. НЗП газотурбинных двигателей можно определить тремя способами. Способ I. Определение НЗП путем испытания ГТД на режимах, подобных его работе в САУ. Для этого измеряются характеристики ГТД в обычных стендовых условиях, т. е. при р н и какие сложились в момент испытания. При испытании либо имитируют режимы, подобные работе в САУ, либо среди многих измеренных режимов отыскиваются режимы, подобные исходным режимам работы в САУ. В этом случае искомые НЗП можно определить непосредственно по результа там испытания, используя формулы теории подобия (т. е. формулы приведения параметров к САУ с поправками). Способ II. Определение НЗП путем использования заранее вычисленных специальных коэффициентов пересчета параметров ГТД к НЗП (т. е. нормализующих коэффициентов). В этом случае измеряют характеристики ГТД в любых стендовых условиях на обычных эксплуатационных режимах со штатными регуляторами и, используя для каждого режима заранее вычис ленные специальные коэффициенты, определяют НЗП двигателя по фор мулам следующего вида: С е н орм = С е изм /К Се , где К Се =f(p H , t H ) — заранее известная зависимость коэффициента пересчета для данного ГТД, данного рассматриваемого параметра на данном режиме. Величины таких коэффи циентов пересчета отражают изменение характеристик данного ГТД под влиянием изменения р н , t H , М п и d при заданном законе регулирования. Как видно, процесс определения НЗП достаточно прост. Вся сложность за ключается в методике определения значений нормализующих коэффициентов.
Способ III. Определение НЗП путем обеспечения стендовыми системами заданных значений t вх = t* H = t ту, р* в х = р* н = р ТУ М п = М ту. При этом измеря ют характеристики ГТД непосредственно в контрольных условиях. Этот способ прост и хорош, но для него требуются специальные и дорогостоящие стендовые сооружения, обеспечивающие в любое время года заданные t H , р н , М п. 6. 1. 1 Способ определения НЗП путем испытаний ГТД на режимах, подобных его работе в стандартных атмосферных условиях (САУ) Чаще всего применяется при испытаниях опытных ГТД. Рассмотрим его на примере испытания ТРДД. При испытании ТРДД (имеющего одну степень свободы) снимается Дроссельная характеристика при той t* H , которая была в момент испытания. Затем все измеренные параметры приедятся по соответствующим формулам приведения к САУ и строятся зависимости приведенных параметров (рис. 6. 3). Так как, ТРДД имеет одну степень свободы, то для определения НЗП на ка ждом режиме должны быть известны заданные ТУ только на один режимный параметр (чаще всего Р дв норм ). На дроссельной характеристике ТРД или ТРДД, снятой при t* в ≠ +15 °С, могут быть найдены точки, соответствующие максимальному и другим режимам в САУ на основе представлений теории подобия. На основе этих представлений может быть также решена и обратная задача: найдено, например, изменение тяги или иного параметра на конкрет ном режиме при изменении температуры наружного воздуха. Но в этом слу чае требуется кроме дроссельной характеристики знать еще закон управления ТРДД по температуре t H. Основной идеей этого способа является отыскание на экспериментальных характеристиках двигателя режимов, подобных его работе в САУ при заданных ТУ на данный режим (Р дв норм — у ТРД и N Э норм и n норм у ТВД).
Рис. 6. 3. Схема определения НЗП ТРДД по приведенной дроссельной характеристике
1 нор м А, к -, N : э норм N. к и т. д. ( 6. 1 )6. 1. 2. Способ определения НЗП с помощью специальных коэффициентов пересчета Этот способ характерен для испытаний серийных ГТД. В отличие от предыдущего способа (где подход к приведению индивидуальный), здесь исходят из предпосылки, что закономерность связи любого параметра К Х = Х изм /Х норм =f(t H p H ) сохраняется неизменной для всех экземпляров ГТД данной серии. Определение ОТД по этому способу производится следующим образом. Измеряют фактические значения параметров на заданных режимах в условиях обычной эксплуатации при тех значениях t H и р н , которые были в момент испытания. Затем измеренное значение параметра делят на заранее известный коэффициент К х =f(t H , р н , α руд ) и определяют нормальное значение параметра, т. е. соответствующее ОТД данного двигателя в САУ (6. 1) Коэффициенты К Х обычно задают в виде набора зависимостей, стандартных для всех экземпляров двигателей данной серии. Эти зависимости фактически представляют собой климатическую характеристику относительного изменения данного параметра по t H и р н (относительно своего нормального значения на данном режиме). Величины нормализующих коэффициентов К х используют: • для отладки параметров ГТД при КС И, например, находят Р дв отлад = К Р дв норм — Р дв изм • для проверки соответствия параметров ГТД — ТУ, например, (G норм = G m / K Gm сопоставляют с G m по ТУ;
• для оценки изменения основных параметров ГТД при длительном испытании, например, с помощью коэффициентов строят дроссельную характеристику: Р ф норм, n ф норм , = f(G т ф норм ) для каждого этапа испытания и сопоставляют по мере наработки (рис. 6. 4). Искомая закономерность изменения нормализующих коэффициентов К х =Х изм /Х норм может быть найдена как расчетным, так и экспериментальным пу тем. Для расчета необходимо иметь характеристики компрессора, турбины и других элементов ГТД, а также закон управления для исследуемых режимов. Погрешности определения К х уменьшаются, если характеристики компрессора и турбины получены экспери ментальным путем. Методика определения расчетным путем таких коэффициентов пересчета К х в сущности ничем не отличается от методики расчета ВСХ и ДХ. Однако, при расчете ВСХ степень на дежности исходных расчетных данных все же не всегда достаточно высока (сложно учесть влияние Re, η г, Δr). Именно поэтому широкое распространение получили экспериментальные методы определения коэффициентов пересчета параметров ГТД к их нормальным значениям.
Рис. 6. 4. Оценка изменения основных параметров ТРДДФ при длительном испытании
6. 1. 3. Экспериментальный метод определения нормализующих коэффициентов для ТРДД Принципиально для ГТД с одной степенью свободы (ТРД, ТРДД) определять коэффициенты пересчета к НЗП не требуется! Так как НЗП серийного ТРДД в принципе можно определить на основе непосредственно измеренной дроссельной характеристики, т. е. по способу I. Однако, коэффициенты пересчета к НЗП для некоторых режимов ТРД и ТРДД начинают находить все большее применение в практике испытаний этих двигателей. Причина — усложнение законов управления современных ГТД. В связи с заданными ограничениями регуляторы в ряде условий не позволяют получать на серийных ТРД и ТРДД дроссельную характеристику в необходимом диапазоне по частоте вращения. Например, при t H = +30 °С максимально достигаемая при испытании величина Р дв будет меньше, чем при n прmax при + 15 °С, хотя при этом можно выйти на n режmаx. Поэтому снять полную дроссельную характеристику двигателя оказывается невозможным, т. к. величину n т ах ограничивает регулятор, что обусловлено прочностью двигателя. Именно для того, чтобы исключить такое превышение по n т ах , а следовательно, и по Тг*, определение НЗП серийных ТРДД на взлетном режиме в настоящее время чаще всего осуществляют с помощью заранее найденных нормализующих коэффициентов (а также на малом газе и при реверсе). Методика экспериментального определения таких коэффициентов пересчета для ТРД и ТРДД сравнительно проста [20]. 1. Снимают (обязательно при t H < +15 °С) полную дроссельную характеристику ТРД и ТРДД и приводят ее с САУ (рис. 6. 5). 2. По заданной в ТУ величине Р дв норм , как уже рассматривалось, находят НЗП, например G m норм n норм 1 , т. е. находят знаменатель в формуле коэффициентов пересчета. Он естественно не зависит от t H и р H.
Рис. 6. 5. Определение приведенной дроссельной характеристики Рис. 6. 6. Схема определения значений 6. 7. Определение для выбранных значений t Hl соответствующих значений приведенных параметров
3. Задаются при р н = const несколькими произвольными значениями t H ≠+15 °С и, получая при выбранном законе управления соответствующие значения n реж (рис. 6. 6), затем находят 4. После этого на приведенной дроссельной характеристике определяют G mnp , P дв пр (см. рис. 6. 5). 5. Далее для одной из выбранных t H (например t H = +12 °С определяют): Этим действием определяется числитель в формуле коэффициента пересчета (рис. 6. 7). 6. Вычисляют коэффициент пересчета K Gmi = G m изм tнi /G m норм 7. Изменив значение р н , вычисления повторяют с п. 5. Типичный вид получаемых таким образом зависимостей коэффициентов пересчета показан на рис. 6. 8. Отклонение измеренных параметров от нормальных значений достигает летом (+35 в С) зимой (-30 °С) G m -(5. . . 14) % 0 Т т * ; +4 % -12 % Р ДВ -(10. . . 18) % +(5… 10) %
Рис. 6. 8. Типичный вид зависимостей коэффициентов пересчета от t H и р н на взлетном режиме Рис. 6. 9. Зависимости коэффициента пересчета для обратной тяги Рис. 6. 10. Зависимости коэффициента пересчета для тяги на режиме малого газа
Особыми режимами, когда без нормализующих коэффициентов также не обойтись, являются реверсирование и малый газ. При реверсе коэффициент К Робр протекает аналогично К Рвзл , отличаясь только величиной (рис. 6. 9). На режиме малого газа нет двух зон ограничения, как на остальных режимах, и характер регулирования близок к Т г * = const (n = const) (рис. 6. 10).
6. 1. 4. Особенности определения НЗП ТРДД Для ТРДД с нерегулируемыми соплами определение нормализующих коэффициентов не отличается от ТРД. Характерным для большинства ТРДД является наличие 2 -х или 3 -х каскадов компрессора. В связи с этим добавляются коэффициенты пересчета К n нд и К н вд (К п сд ) (рис. 6. 11). Из-за специфики ТРДДФ только одна из частот вращения задается законом управления (ведущий каскад). Из теории ВРД известно, что при = const, Т г ≈const и законы ограничения G m и Т г *; у ТРДД применяются такие же, как у ТРД, поэтому вид нормализующих коэффициентов у ТРДД аналогичен ТРД. В случае применения форсажных камер у ТРДД и ТРД они становятся двигателями с двумя степенями свободы, т. к. необходимо регулировать выходные Сечения сопла. Особенностью управления ТРДДФ является объективная необходимость использовать в качестве ведущего каскад низкого давления ( n нд = const вместо n вд = const, а также более точное ограничение величины n нд / (Т г *) 0, 5 ) = const при t H < 0 вместо G m = const), так как только в этих случаях можно обеспечить работу вентилятора при одновременном включении форсажа и раскрытии сопла. Например, в случае сверхзвукового транспортного самолета при программе управления, показанной на рис. 6. 12, б, необходимо иметь так называемый «сторож» в системе управления, который следит за работой вентилятора в пределах «дорожки» , гарантирующей заданный запас по помпажу (см. рис. 6. 12, а). Такое управление обеспечивается на максимальном режиме с форсажем (возможность отладки Р б/ф норм т ах ограничивается величиной заданного n нд т ах ). При этом получается закономерность для n вд , как на рис. 6. 13.
Рис. 6. 13. Зависимость коэффициента пере- счета К n нд для ТРДДФ Так как в случае закона n нд = const температура газов Т г * неизбежно увеличивалась бы с возрастанием М п (например, в условиях полета при Н = 11, М п = = 2, 2, t H > 15 °С), то эту температуру у ТРДДФ ограничивают косвенным или прямым путем. Рис. 6. 14. Коэффициенты пересчета для форсажной тяги (а) и форсажного расхода топлива (б) при π в * Пф ≈π в * Пб/ф Рис. 6. 15. Схема определения НЗП на форсажном режиме ТРДДФ
Рис. 6. 16. Схема определения НЗП на бесфорсажных режимах ТРДДФ При регулировании форсажных режимов из условия π в * Пф ≈π в * Пб/ф получается протекание тяги и расхода топлива в безмерном виде, показанное на рис. 6. 14. Определение НЗП у ТРДДФ обычно проводится по тому же способу, что и Для ТРДД б/ф. Их определяют по измерениям на форсажных режимах на основе построенной дроссельной характеристики с помощью коэффициентов К ф Рдв, и К ф GmΣ. (рис. 6. 15) ЧТО касается определения НЗП для бесфорсажных режимов ТРДДФ (рис. 6. 16), то оно ничем не отличается от рассмотренного выше порядка для ТРДД. 6. 1. 5. Особенности испытаний ТРДД Одним из основных параметров ТРДД, характеризующих работу многокаскадного компрессора, является «скольжение» роторов — отношение частот вращения соседних роторов. Требуемую величину «скольжения» на контрольном Режиме получают либо изменением потребляемой мощности компрессора высокого давления (регулированием угла установки лопаток направляющего аппарата), либо перераспределением теплоперепадов между турбинами каскадов (за счет изменения площади соплового аппарата турбины каскада низкого давления). Этими же способами изменения частоты вращения роторов пользуются при проведении испытаний каждого ротора с превышением максимальной рабочей частоты вращения [49).
У ТРДД обычно измеряют суммарный расход воздуха через двигатель, так как раздельное измерение расходов воздуха через первый и второй контуры конструктивно затруднено. Лемнискатный насадок внутреннего контура затеняет вход во второй контур, изменяет характеристики газового тракта, а следовательно, и всего двигателя в целом. Для определения средней массовой температуры газа перед турбиной необходимо совместно решать уравнение теплового баланса и уравнение расхода через минимальное сечение соплового аппарата. Испытания ТРДД в земных статических условиях во многом обесцениваются тем, что при этих испытаниях перепад давления в соплах внутреннего и наружного контуров существенно докритический. Следовательно, и вентилятор, и турбина вентилятора испытываются в режимах, не соответствующих полетным. Для увеличения перепада давления на реактивных соплах могут быть применены установки с наддувом на входе в двигатель. Однако они требуют очень больших расходов воздуха (особенно для ТРДД с большой степенью двухконтурности), подача которого становится сложной технической задачей. Может быть применена установка, в которой поток воздуха на выходе из второго и частично первого контуров испытуемого ТРДД направляется на вход этот же двигатель. На выходе из испытуемого ТРДД устанавливается устройство, позволяющее подмешивать к струе второго контура атмосферный воздух и горячие газы первого контура. Температуру подаваемого воздуха изменяют за счет подмешивания различного количества горячих газов, а давление — перепуском части смеси в атмосферу. При наличии сравнительно небольшого дополнительного источника воздуха возможности установки по наддуву могут быть существенно расширены. Для имитации полетных условий работы ТРДД можно также применять расширяющиеся насадки,
устанавливаемые на срезе реактивного сопла. Однако требуемые, как правило, различные перепады давления на соплах внешнего и внутреннего контуров невозможно достичь одним насадком. Не обходимо применять два насадка с независимым регулированием перепада давления в каждом из них. Это может быть получено, например, примене нием окон с дросселем для подсоса воздуха из атмосферы в сопле внешнего контура и передвижного поджимающего конуса на выходе из сопла внутрен него контура. Для ТРДД большой степени двухконтурности измеряемая на СИУ сила тяги зависит от потерь, связанных с обтеканием потоков второго контура, элементов двигателя и пилона, на котором двигатель крепится к самолету. В полете сопротивление интерференции капота второго контура с элементами самолета также составляет значительную долю сопротивления. Вели чины перечисленных сопротивлений зависят во многом от компоновки силовой установки на летательном аппарате. Это затрудняет оценку совершенства двигателя, особенно, если одновременно вносятся конструктив ные изменения во внешние элементы силовой установки и двигателя. Поэтому целесообразно для оценки термодинамического совершенства ТРДД производить измерение выходного импульса первого и второго контуров непосредственно на срезе сопла и на выходе из вентилятора термопневмо гребенками.
6. 1. 6. Особенности испытания форсажных ТРД и ТРДД При испытаниях форсажных двигателей, в том числе, определяют величины, характеризующие работу форсажной камеры сгорания [49]. 1. Среднее значение коэффициента избытка воздуха в форсажной камере (6. 2) где G ф т — секундный расход топлива через форсажную камеру; G m — секундный расход топлива через основную камеру; G у т — утечка воздуха через неплотности и систему суфлирования. 2. Суммарный коэффициент избытка воздуха в форсажной камере (6. 3) где G mΣ =G т +G ф т. 3. Расход газа через форсажную камеру (6. 4)
4. Температура газа на выходе из форсажной камеры (6. 5) 5. Коэффициент полноты сгорания в форсажной камере (6. 6) При включении форсажной камеры должно быть обеспечено раскрытие створок сопла с момента воспламенения форсажного топлива, иначе возможны забросы температуры газов перед турбиной, частоты вращения ротора (рото ров) и неустойчивая работа компрессора. При включении форсажной камеры необходимо иметь увеличенную пло щадь выходного сечения сопла, иначе произойдет тепловое дросселирование Расхода воздуха через двигатель со всеми вытекающими из этого неблагоприятными последствиями (неустойчивая работа компрессора, возрастание Т* г ). Розжиг форсажной камеры (от момента включения зажигания до воспламене ния топлива) требует определенного времени, поэтому предусматривается раскрытие сопла с некоторым опережением по отношению к моменту воспламенения форсажного топлива. Это приводит к падению статического давления за турбиной и, как следствие, к некоторому возрастанию частоты вращения.
Если двигатель работает с включенной системой регулирования частоты вращения, то она восстанавливает первоначальную частоту враще ния уменьшением температуры газов перед турбиной. Воспламенение топ лива в форсажной камере и вызванное этим повышение температуры вызывают резкое уменьшение перепада давления на турбине, приводящее к снижению частоты вращения. Для поддержания частоты вращения регулятор подачи топлива увеличивает расход топлива, при этом происходит некоторый заброс температуры Т Г * и смещение режима работы компрессора к гра нице устойчивой работы. В двухроторных ТРДФ смещение режима работы компрессора к границе устойчивой работы может происходить и при резком уменьшении расхода топлива в основной камере сгорания, так как это приводит к изменению скольжения роторов. Поэтому неустойчивая работа двухроторного ТРДФ может возникать в период, предшествующий розжигу форсажной камеры, а также после прекращения горения в ней. Отладка синхронизации раскрытия створок сопла с моментом воспламене ния форсажного топлива производится в следующей последовательности. Двигатель выводят на режим максимальной частоты вращения и после получения установившегося режима включают форсажную камеру. Регистрируют р т , Т г *(Т т *), давление топлива перед форсунками, частоту вращения ротора (роторов), положение РУД как по визуальным приборам, так и по осциллограмме, запись на которую указанных параметров производят в течении 2. . . 3 с после включения форсажа. Определяют время выхода на форсажный режим (от момента начала движения РУД из положения «Максимал» до начала роста р т ) и подсчитывают максимальную величину относительного уменьшения статического давления за турбиной К по формуле (6. 7)
где р т исх — статическое давление за турбиной на исходном (предшествующем форсажу) режиме; p Tmin — минимальное статическое давление за турбиной при включении форсажа. Если при включении форсажа относительное уменьшение статического давления и максимальная температура газа перед турбиной не укладываются в допустимые пределы, производят регулировку реле выдержки времени на большую задержку по подаче топлива (если относительное уменьшение давления мало) или на большую задержку по раскрытию створок сопла (если относительное уменьшение давления больше нормы). Регулировка времени выхода на форсажный режим осуществляется сменой дроссельных пакетов в системе форсажного крана. С уменьшением давления воздуха на входе в двигатель относительная амплитуда давления р т и время, в течение которого происходит изменение величин давления р 1 и температуры Т *, увеличиваются, поэтому включение и выключение форсажной камеры на больших высотах связано с возможно стью потери газодинамической устойчивости компрессора и должно быть проверено в этих условиях. В высотно-скоростных условиях определяется, кроме того, граница устойчивого розжига форсажа, а также механическая устойчивость оболочек форсажной камеры в момент срыва пламени, когда подкапотное давление охлаждающего воздуха оказывается выше давления газа за турбиной.
6. 1. 7. Особенности испытания ТРДЦ с реверсом Эффективность реверсивного устройства двигателя оценивается коэффициентом реверсирования (6. 8) где Р обр — (обратная сила тяги) и Р дв (прямая сила тяги) берутся для одной и той же частоты вращения. Коэффициент реверсирования зависит от конструкции реверсивного уст ройства, режима работы двигателя и скорости обдувающего потока. Для определения коэффициента реверсирования необходимо измерять прямую и обратную силы тяги (49). В стендовых условиях это можно осущест вить на обычных или специальных силоизмерительных устройствах. На обыч ных силоизмерительных устройствах градуировочное устройство во время из мерения загружается усилием, превышающим максимально возможную об ратную силу тяги на 10. . . 15 %. Прямая и обратная силы тяги определяются по формулам: (6. 9) В связи с тем, что Р дв и Р обр вычисляются как разности двух измеренных ве личин, погрешность вычисленных величин больше, чем непосредственно из меренных Р изм и Р град. В специальных силоизмерительных устройствах измерение прямой и обрат ной сил тяги производится непосредственно измерителем, который с помощью системы рычагов подключается на восприятие только одного усилия. Погрешность измерения сил тяги в этом случае значительно меньше.
В боксе, предназначенном для испытания двигателей с реверсивным устройством, должен быть организован отвод выхлопных газов так, чтобы не искажалось измерение прямой и обратной сил тяги. При проведении типовых испытаний двигателей с реверсивным устройством тщательно исследуются потери в элементах реактивного сопла, влияние включенного реверса на вибронапряжения в лопатках последней ступени турбины и вибрации двигателя. К специальным стендовым испытаниям следует отнести определение уровня истинных напряжений и температур в элементах конструкции реверсивного устройства, определение приемистости при обратной силе тяги, времени перекладки реверса из одного крайнего положения в другое и проверку работы механизмов приводов во время 150 -часовых испытаний. Для проверки приемистости при обратной силе тяги рычаг управления двигателя, работающего на режиме земного малого газа, быстро (в течение не более 1 с), после получения сигнала о перекладке реверса, переводят в положение, соответствующее максимальной обратной силе тяги. За время приемистости принимается промежуток времени от момента начала перемещения РУД до момента достижения 95 % от максимальной обратной силы тяги. При 150 -часовых испытаниях проводят около 200 циклов включения и выключения реверса при различных режимах работы двигателя. Работа реверса должна быть безотказной, а время перекладки из одного крайнего положения в другое на любом режиме работы двигателя не должно быть более 2 с. Значительный объем доводочных работ по отработке реверсивного устройства проводится во время летных испытаний, так как работа реверсивного устройства во многом зависит от компоновки двигателя и места установки его на самолете. Основные вопросы, которые решают при летных испытаниях, следующие:
1) определение коэффициента реверсирования в зависимости от скорости обдувающего потока; 2) определение условий попадания реверсивных струй во входное устройство двигателя; 3) определение температурного состояния узлов конструкции двигателя и самолета вблизи реверсивных струй. Величина коэффициента реверсирования с ростом скорости обдувающего потока увеличивается и может достигать значения единицы или даже несколько больше за счет роста донного разряжения и изменения обтекания мотогондолы и других частей самолета [27]. Эти сведения необходимы для определения летно-технических свойств самолета. С уменьшением скорости обдува возникает опасность попадания горячих газов во входное устройство двигателя, что может привести к помпажу. При определенной скорости пробега реверсивное устройство должно отключаться или же двигатель должен переводиться на пониженную частоту вращения. Указанные ограничения должны быть определены экспериментально. Перегрев элементов самолетных конструкций и нарушение управляемости самолета во время работы реверса недопустимы (например, в случае установки двигателя в хвосте самолета горячие газы могут достигать кромки крыла, шасси; при боковом ветре реверсивные струи от двигателей, установленных в крыле, могут вызвать односторонние нагрузки на хвостовом оперении). Для устранения неблагоприятных явлений прибегают к изменению конструкции реверса: изменению направления истечения реверсивных струй, несимметричному истечению их из сопла и т. д.
6. 1. 8. Особенности испытаний ГТД с отклоняемым вектором прямой тяги В отличие от обычных авиационных ГТД при испытании двигателей с отклоняемым вектором прямой тяги необходимо измерять несколько компонентов реактивной силы тяги: как минимум, вертикальную и горизонтальную составляющие, а при наличии двух поворотных сопел, также и момент относительно продольной оси двигателя. Для решения такой задачи на стендах применяют двухкомпонентные, а иногда и трехкомпонентные, силоизмерительные устройства. Динамометрические платформы, подвешенные на упругих шарнирах (лентах), имеют свободу перемещений в направлении измеряемых усилий Р верт и Р гориз [49|. К недостаткам таких схем силоизмерительных устройств следует отнести некоторую конструктивную сложность, связанную с наличием двух динамометрических платформ, и пониженную чувствительность систем измерения составляющих сил тяги из-за наличия дополнительного подгружающего груза, вес которого не только соизмерим с измеряемыми усилиями, но и может превосходить их в 3 -4 раза. Более конструктивными следует считать двухкомпонентные силоизмерительные устройства с одной динамометрической платформой. В рассматриваемой схеме силоизмерительного устройства подгружающий вес не полностью вывешивается градуировочной системой измерения вертикальной составляющей силы тяги, а используется для предварительной нагрузки этой системы на величину, несколько превышающую максимальное измеряемое усилие. Измерение усилия Р верт сводится к измерению «уменьшения» этого дополнительного веса под действием вертикальной силы тяги, что повышает точность определения усилия Р верт.
Многокомпонентные силоизмерительные устройства обладают метрологи ческими особенностями, которые обусловлены взаимным влиянием их изме рительных и градуировочных систем, приводящими к появлению дополнитель ных погрешностей измерения. Установочная погрешность взаимовлияния вызывается отклонением оси ис пытываемого двигателя от оси измерительного устройства. Должна быть получена зависимость установочной погрешности измере ния горизонтальной силы тяги, обусловленная влиянием вертикального Усилия. Относительная установочная погрешность взаимовлияния зависит от от ношения вертикальной и горизонтальной сил тяги и при ошибке установки Двигателя в 30′ может достигать значений нескольких десятых долей про цента. Погрешность взаимовлияния измерительных систем, обусловленная переме щением динамометрической платформы в процессе измерения усилий.
6. 2. ОСНОВНЫЕ ОСОБЕННОСТИ ИСПЫТАНИЙ И ОПРЕДЕЛЕНИЯ НЗП ГТД СТ И ТВД 6. 2. 1. Особенности испытаний ГТД СТ и ТВД Полезная отдача ГТД СТ оценивается по эффективной мощности. Полезная отдача ТВД оценивается по эквивалентной мощности, представляющей собой сумму приведенной мощности и мощности, равноценной реактивной тяге, развиваемой двигателем. В статических условиях (Н=0, М=0) (6. 10) где N э — эквивалентная мощность; N впр и Р пр — соответственно приведен ная мощность и приведенная сила тяги; ω — коэффициент пересчета силы тяги в мощность, принимаемый для взлетной мощности равным ω = 68, 2 к. Вт/к. Н (0, 91 л. с. /кгс). В полетных условиях (Н=Н п, V=V п ) (6. 11) Где V п — скорость полета; η в — КПД винта (винтовентилятора). При расчете эквивалентной мощности учитывается мощность, затрачи ваемая на привод самолетных агрегатов (зависит от их загрузки). Помимо общих требований, боксы для испытания ТВД должны быть доста точно просторными для размещения двигателя с винтами и обеспечения необ ходимого расхода воздуха через двигатель и площадь, ометаемую винтами, а также иметь оборудование для измерения крутящего момента и силы тяги, раз виваемой двигателем (с погрешностями не более 0, 5 % от максимального зна чения).
Испытания с гидротормозом. Мощность, развиваемая турбовинтовым или турбовальным ГТД (ГТД СТ), может быть поглощена и измерена загрузочным устройством, в качестве которого может быть применен гидротормоз, воздушный тормоз, электрический тормоз или др. устройство. Двигатель, обычно без редуктора, укрепляется на станине и соединяется с валом тормоза. Соосность двигателя и тормоза должна быть обеспечена с высокой точностью. Если тормоз с двигателем укрепить на динамометрической платформе силоизмерительного устройства, то можно одновременно измерять крутящий момент и силу тяги. Часто силу тяги ТВД измеряют газодинамическим методом. Тормозной стенд позволяет провести обкатку двигателя и получить достаточно точные нагрузочные характеристики, а для ГТД СТ провести и всю отладку двигателя. При снятии характеристик во время опытных испытаний получают для ожидаемых эксплуатационных условий работы не менее четырех зависимостей мощности от частоты вращения ротора при постоянной температуре газа перед турбиной или же при постоянной частоте вращения ротора и различной температуре газов перед турбиной. Две зависимости — для взлетного режима и режима максимальной продолжительной мощности, две другие — с равными интервалами между режимом земного малого газа и режимом максимальной продолжительной мощности (49). При проверке работы ТВД и вертолетных ГТД в высотно-скоростных условиях тормоз с двигателем располагаются в термобарокамере. Однако тормозным испытаниям присущи недостатки, из-за которых требуются повторные испытания ТВД с винтами, а именно! не проверяется работа редуктора и элементов, воспринимающих тянущее усилие винта (упорных подшипников, валов, корпуса редуктора и др. ), не испытывается система механизации и защиты винтов.
Испытания ТВД с воздушными винтами на стенде. При этих испытаниях ТВД укрепляется на неподвижном жестком станке. На двигатель монтируют воздушные винты |49|. Режим испытания по мощности устанавливается с помощью характеристик, полученных на тормозном стенде (например, по давлению топлива перед форсунками на заданной частоте вращения) или с помощью ИКМ (измерителя крутящего момента), смонтированного внутри двигателя и являющегося штатным прибором системы контроля крутящего момента в полете. Наибольшее распространение получили гидравлические ИКМ. Применение ИКМ, если он работает стабильно и обладает достаточной точностью, упрощает и удешевляет испытания. Отпадает необходимость применения тормозных испытаний ТВД и связанного с ними оборудования (например, гидротормозов, системы водоснабжения). Сокращаются цикл и трудоемкость испытания ТВД, возрастает пропускная способность испытательных станций. Недостаток метода заключается в том, что требуется точное изготовление элементов ИКМ, что несколько удорожает производство двигателя. Испытания вертолетных ГТД также могут проводиться на натурных винтовых стендах, такие испытания (как правило, выборочные) проводят для проверки работоспособности главного редуктора вертолета (особенно, если он работает от нескольких ГТД). Специальные испытания ТВД и ГТД СТ. Вибрографирование и тензометрирование двигателей должны проводиться при наличии силовых возму щений, создаваемых воздушными винтами [49|. Для вертолетных ГТД, кроме того, характерными являются вибрографирование двигателя и трансмиссии при максимально допустимой расцентровке валов двигателя и главного редуктора и тензометрирование валов трансмиссии для опре деления напряжений от крутильных и изгибных колебаний.
У ТВД во время 150 -часовых испытаний проверяется работа механизации и зашиты воздушного винта, работа системы ограничения крутящего момента (работающей, например, от И КМ) при полностью отключенных самолетных агрегатах. Если у двигателей есть свободная турбина, то она проходит проверку на повышенный (максимально допустимый) крутящий момент и на быстродействие системы ограничения частоты вращения при резком снятии нагрузки. Испытания на максимально допустимый крутящий момент проводятся на гидротормозном стенде или с воздушными винтами на частоте вращения, при которой этот момент может быть достигнут. Температура газов перед свободной турбиной устанавливается максимальной для взлетного режима, а температура масла на входе в двигатель — исходя из наиболее тяжелых условий работы подшипников свободной турбины. Испытания включают: 5 мин непрерывной работы на режиме 0, 75 взлетной мощности и 15 мин (циклами не менее 3 мин) на режиме максимально допустимого крутящего момента. Измеряют: частоту вращения турбины, крутящий момент, температуру газов за турбиной, температуру и давление масла на входе в двигатель, температуру атмосферного воздуха и температуру подшипников свободной турбины (во время работы на М кр т ах ). Проверка работы автоматики ограничения частоты вращения свободной турбины при резком снятии нагрузки осуществляется на гидротормозном стенде. Двигатель оборудуется устройством для быстрого разъединения свободной турбины с гидротормозом, например, за счет отстрела рессоры. При взрыве пиропатрона поршень, укрепленный на штанге, срезает кольцо и мгновенно вытягивает рессору из зацепления со свободной турбиной. Турбина стремится раскрутиться, но автомат зашиты должен выдать команду на резкое уменьшение подачи топлива и предотвратить раскрутку.
а) проведение испытаний в два этапа. На первом этапе испытывать в «горячем режиме» свободную турбину. На втором этапе свободную турбину снять и испытывать в «горячем режиме» турбокомпрессор; б) поставить сопловой аппарат свободной турбины с увеличенной площадью проходного сечения. Указанные трудности не возникают при проведении «горячих испытаний» в ТБК. У вертолетных ГТД проверяется возможность работы на чрезвычайном режиме. В доводочных испытаниях на чрезвычайный режим выводят резким передвижением РУД (как при пробе приемистости) после работы на взлетном режиме в течение заявленной продолжительности. На чрезвычайном режиме работают разрешаемое техническими условиями время, после чего двигатель останавливают, разбирают и дефектируют. Во время чрезвычайного режима не должно быть нарушений в работе, а состояние деталей по результатам дефектации должно соответствовать техническим условиям. Чрезвычайный режим может исчерпать работоспособность двигателя. Поэтому во время кратковременных заводских испытаний на нем не работают, а проводят лишь достаточность избытка топлива, подаваемого насосом, необходимо для обеспечения работы на чрезвычайном режиме.
6. 2. 2. Особенности экспериментального определения нормальных значений параметров ТВД Порядок действий по определению НЗП ТВД сложнее, чем для ТРД и ТРДД — так как ТВД с винтом изменяемого шага обладает двумя степенями свободы [20]. Поэтому для ТВД невозможно получить единую приведенную дроссельную характеристику теми же действиями, как в случае ТРДД или ТРД. В связи в этим здесь нет возможности использовать для определения НЗП однозначную зависимость N эпp =f/(n пр ), потому что при работе ТВД на эксплуатационных режимах получается не единая линия, а поле характеристик N э пр =f(n пр , G m пр ). Если измеренную дроссельную характеристику одновального ТВД (работающего со штатным регулятором при n реж =const), снятую при различных температурах привести к стандартным атмосферным условиям, то мы обнаружим, что приведенные характеристики ТВД продолжают зависеть от t H (рис. 6. 17, а), а не сливаются в одну рабочую линию, как в случае ТРД, у которого N т N к. У ТВД N т >N K и это неравенство зависит от Т г * /Т н = f(t H ) • Если же провести испытание ТВД при t H = var, n пр = const, то расслоение по t н естественно исчезает. Однако, в условиях эксплуатации такое управление у ТВД не применяют, потому что оно не обеспечивает необходимой энерговооруженности для ЛА, а делают n реж = const при Gm≈const(что обеспечивает N в = const). При управлении n реж =const изменение мощности, идущей на привод винта, обеспечивается изменением Т г * и, соответственно, φ в. В этом случае под «нормальными» понимают такие значения параметров ТВД, которые они будут иметь в САУ (+15 °С и 101, 33 к. Па) при положении регулирующих органов в позиции, соответствующей их отладке на заданные для каждого режима нормы мощности и частоты вращения. В силу особенностей штатной компоновки серийных и опытных ТВД опре деление их НЭП производят обычно по-разному.
Рис. 6. 17. Влияние двух степеней свободы ТВД на его приведенную дроссельную характеристику ( а ) и линии рабочих режимов ( б) : ТВД одновальный: Н = 0. V = 0. t н = var. n реж = const; 1 — напорная ветка компрессора при Т н = +40 0 С: 2 — напорная ветка компрессора при Т н = -40 °С
Опытные ТВД поступают обычно на гидротормозной стенд. Там на режимах, подобных САУ, снимается дроссельная характеристика при n пр = n норм ту — Фактически это означает, что эксперимент проводится при заранее приведенной, одной из двух степеней свободы. При измеренной t H это означает поддержание постоянной физической частоты вращения . Изменение t H в процессе испытаний приводит к изменению выдерживаемой частоты вращения n. Измеряемые параметры приводят к САУ и строят приведенную дроссельную характеристику. Пользуясь ей, по величине N энорм определяют нормальные значения других параметров ТВД (например, (G m норм )» на которые затем отлаживают его регуляторы, если он направляется в летную эксплуатацию или на дли тельные испытания. Серийные ТВД поступают обычно на предъявительские и приемосдаточные испытания в компоновке с воздушным винтом и штатными регуляторами. Величину мощности в этом случае можно отладить только оценочно: либо по показаниям ИКМ (N в ) и расчетным значением Р, либо по измерению на стенде полной тяги (6. 12) В силу обдува воздушным винтом незакапотированного ТВД оба способа обычно не обеспечивают достаточной точности отладки в пределах до пусков. Поэтому часто применяют следующий подход: по результатам испытаний с гидротормозом нескольких выборочных серийных ТВД определяют значение (G ±a норм по методике для опытных двигателей. На это значение предварительно отлаживают все двигатели приемосдаточных испытаниях. После чего корректируют отладочное значение расхода топлива G m = G m норм K Gm в пределах допуска «а» на основе показаний измерителя крутящего момента (ИКМ).
Если же двигатель, в пределах допуска, не обеспечивает требуемой N B (N B = 6, 283 М кр ; n вв = N норм K Nв. к. Вт), то его отправляют на гидротормозной стенд. Если и там подтвердится недобор мощности, то двигатель направляют на переборку для устранения дефектов сборки (зазоры, лабиринты и. т. п. ). В связи с тем, что в этом случае отладка измеренных параметров произво дится косвенно: по величине G m = G m норм К Gm при n = const и N B = N в норм К Nв , то требуется иметь соответствующие зависимости для нормализующих коэффи циентов типа К Nв = N в изм / N в норм , которые также зависят от t H и р н. В этом плане, такие зависимости, также как и у ТРД и ТРДД, являются, по сути дела, климатическими характеристиками двигателя на рассматриваемом режиме. Однако, в отличие от ТРД коэффициенты пересчета к НЭП у ТВД необходимо иметь не только для максимального, но и для других режимов (ибо единой при веденной дроссельной характеристики у ТВД не существует). Рис. 6. 19. Нормализующие коэффициенты К Nв для взлетного режима ТВД в координатах р н , t НРис. 6. 18. Нормализующий коэффициент К Nв для взлетного режима ТВД: H = 0. V=0. р н = 101. 33 к. Па
Зависимость коэффициента пересчета винтовой мощности N B современного самолетного (одновального) ТВД для взлетного режима приведена на рис. 6. 18. Иногда для удобства пользования нормализующие коэффициенты наносят непосредственно в координатах p H, t H (рис. 6. 19). Определение нормализующих коэффициентов ТВД может быть проведено как расчетным путем (методом расчета ВСХ), так и путем непосредственных измере ний на двигателе, например в ТБК (эталонный метод), или косвенным методом — снимая специальные характеристики на выборочных ТВД, по которым можно вы числить коэффициенты нормализации, пользуясь теорией подобия. Последний метод получил широкое применение в практике испытаний. Проверка этого мето да эталонным методом показала, что его точность лежит в пределах 0, 5. . . 1, 5 %, что в большинстве случаев удовлетворяет практическим требованиям, учитывая обыч ные производственные отклонения и допуски при изготовлении ГТД.
6. 2. 3. Методика экспериментального определения косвенным способом нормализующих коэффициентов для параметров ТВД Чтобы определить этим способом коэффициенты пересчета, необходимо измерить на гидротормозном стенде специальные характеристики ТВД. которые, как и в случае испытаний ТВД на подобных режимах, могут быть сняты только с отключенными регуляторами винта. Для настройки режима обычно регулируют подачу топлива и нагрузку вручную от стендовых топливной и загрузочной систем. Снятие таких характеристик чаще всего проводят на стендах, оборудованных гидротормозом или электротормозом, которые позволяют, произвольно изменяя загрузку ТВД, снимать характеристики ТВД по N B , при нескольких частотах вращения (при n изм = const). Работая при нескольких частотах вращения (при n 1 =const, n 2 = const и т. п. ), снимают 5. . . 6 точек по нагрузке, измеряя N B , реактивную тягу Р дв , G m , Т Т *, n и др. Замеренные значения приводят к САУ по формулам приведения с поправками. Например, (6. 13)
Рис. 6. 20. Схема получения поля нагрузочных характеристик ТВД Н = 0; V= 0; t H — const: а, б — приведенные дроссельные характеристики; в — поле нагрузочных характеристик
Для перестройки полученных приведенных дроссельных характеристик делается их сечение при нескольких значениях G m пр. С соответствующих зависимостей Nпр = const снимаются значения реактивной тяги Р пр (рис. 6. 20, а) и винтовой мощности P пр (Рис. 6. 20, б). Для этих параметров получают зависимости P пр =f(n пр ) и N в =f(n пр ). Вычисляют N эпр = N в пр +68, 2 Р дв пр =f(n пр ) и для каждого G m пр наносят на рис. 6. 20, в. По такому полю характеристик определяют нормализующие коэффициенты следующим образом: 1. По известным из ТУ на двигатель значениям Nнорм и Nв норм находят соответствующую точку / на полученном поле характеристик и по ней величину G mпp = G mнорм (рис. 6. 21, а). К точке 2 на рис. 6. 21, б вернемся чуть ниже. Аналогичным путем определяют также и другие параметры, например, Т* тнорм , N внорм и другие (рис. 6. 21). Рис. 6. 21. К определению НЗП ТВД: a — T * т норм , б — N B НОPМ
2. Задаются произвольной температурой t H * +15 °С при давлении р н — const и по закону управления ТВД и определяют величины G m рe Ж , n рe ж (точка 2 на рис. 6. 22). Находят для этих t H и р н соответствующие абсолютные значения Ярсж — Я рсж G m реж = G m рe ж G т норм для данного режима. Находят для этого режима соответствующую точку в поле нагрузочных характеристик ТВД (см. рис. 2. 21, б) по величинам и снимают с поля соответствующие значения N B пр (точка 2).
4. Определяют, какую мощность развил бы при этом двигатель в выбранных условиях t H и р„ на заданном режиме: 5. Теперь нетрудно определить нормализующие коэффициенты для пара метров ТВД на данном режиме, например 6. Затем задаются несколькими значениями для другого р„ и повторяют те же действия, начиная с п. 2, до получения зависимостей вида: Аналогичным образом определяют нормализующие коэффициенты и для других параметров ТВД.
6. 3. ЭКСПЕРИМЕНТАЛЬНОЕ ОПРЕДЕЛЕНИЕ НЗП ГТД ПУТЕМ ПОДДЕРЖАНИЯ СТЕНДОВЫМИ СИСТЕМАМИ ЗАДАННЫХ ЗНАЧЕНИЙ t н , р н , М п Для такого определения НЗП не требуется никаких специальных методик. Получаемые непосредственными измерениями в САУ параметры на заданном режиме соответствуют индивидуальным НЗП данного двигателя. Их остается только сравнить с заданными ОТД на двигатели данной серии. Однако требования к необходимому испытательному оборудованию нуждаются в особых пояснениях. Для снятия ВСХ, а также для проверки НЗП ГТД в стендовых и полетных условиях используют аэродинамические трубы (АТ) и термобарокамеры (ТБК). Это, как правило, весьма дорогие и сложные сооружения, напоминающие собой небольшие заводы. В России такими сооружениями для крупноразмер ных двигателей (с G впр > 50. . . 200 кг/с) располагают только центральные научно- исследовательские институты (например, ЦИАМ, ЦАГИ и т. п. ). Стоимость 1 часа испытания в таких сооружениях зависит от потребного G в и составляет обычно от 1 тыс. до 15 тыс. долл. Для малоразмерных ГТД (с G B пр < 3. . . 10 кг/с) ТБК сооружены на некоторых заводах (ФГУП «Завод им. В. Я. Климова» ) и да же в вузах (СГАУ, УГАТУ). Существуют и частичные решения: стенды с наддувом и подогревом воздуха на входе в ГТД.
6. 3. 1 Высотно-скоростные испытания ГТД в АТ Аэродинамическая труба для испытаний авиационных двигателей состоит из двух отсеков (рис. 6. 23). В отсеке I устанавливаются кондиционированные условия p H * и Т H *, соответствующие условиям полета, в отсеке II поддерживается давление р н , соответствующее заданной высоте полета. Основной особенностью испытаний ГТД в аэродинамических трубах является то, что здесь помимо Т H * = Т H ( 1 + 0, 2 М п 2 ), р* H =p H (1 + 0, 2 М* п ) k/(k-1) и р н имитируется и скорость набегающего на воздухозаборник потока V п , при этом ком прессор ГТД имеет на входе как правило неравномерный входной поток (в связи, например, со скачками уплотнения, которые образуются в условиях сверх звукового полета). Для того, чтобы в самолетном воздухозаборнике установилось расчетное сверхзвуковое течение, необходимо, чтобы завершающий скачок уплотнения АТ устанавливался в выходной части внешнего диффузора. Такие стенды обслуживаются мощными компрессорно-эксгаустерными станциями. Типичный пример — сверхзвуковая АТ ЦИАМ. Достоинства Л Т: • возможность сравнительно безопасно (по сравнению с опытным ЛА и на летающей лаборатории) проверять характеристики опытного двигателя в расчетных условиях полета, в том числе по пропускной способности самолетного воздухозаборника; • имитация на входе в ГТД неоднородности и пульсации полей скоростей и давлений, соответствующих реальным условиям полета (влияющих на запас по помпажу).
Рис. 6. 23. Аэродинамическая труба для испытаний авиационных ГТД: / — рабочее сопло АТ; 2 — самолетный воздухозаборник; 3 — жесткий станок (тяга не измеря ется); 4 — рабочее положение скачков уплотнения во внешнем диффузоре АТ; 5 — эжекторная выхлопная труба с отсосом газов из отсека II эксгаустером (эксгаустер — осевой вентилятор, создающий разрежение на входе)
К основными недостаткам сверхзвуковой аэродинамической трубы относится невозможность снимать полные характеристики двигателя с самолетным входным диффузором, если двигатель занимает большую часть рабочего участка трубы. Эта часть определяется так называемым коэффициентом загрузки трубы: что приблизительно соответствует соотношению физических расходов воздуха через двигатель и аэродинамическую трубу в целом. Нормальный диапазон снятия характеристик двигателя совместно с воздухозаборником обычно обеспечивается без нарушения системы скачков в случаях, когда расход воздуха через трубу в 3 — 5 раз превышает (G в. ГГД (f < 0, 2. . . 0, 35). При f = 0, 5. . . 0, 7 снятие полных характеристик с входным диффузором чаше всего невозможно из-за разрушения системы скачков в рабочей части трубы. Другим серьезным недостатком испытаний ГТД в сверхзвуковой аэродинамической трубе являются затруднения в точном измерении силы тяги из-за внешнего сопротивления, возникающего от набегающей струи, которая совершенно не соответствует величине X внеш на самолете. Поэтому на величину тяги Р изм приходится вносить значительные поправки, которые понижают ценность эксперимента. Выходом из положения для больших двигателей является раз бивка задачи, решаемой в аэродинамической трубе, на 2 этапа: • проверка и доводка характеристик двигателя в расчетных условиях полета вначале только в ТБК (где не имитируется система скачков уплотнения), но точно измеряется тяга; • последующая отработка совместной работы самолетного входа с двигате лем или в АТ, или непосредственно на самолете, т. е. с системой скачков.
6. 3. 2. Высотно-скоростные натурные испытания ГТД в термобарокамере (ТБК) Испытания в ТБК (рис. 6. 24) отличаются от испытаний в АТ лишь тем, что здесь не имитируется скорость набегающего потока на двигатель М п. Испытание в ТБК проводят, имитируя только давление окружающей среды р н и заторможенные параметры воздуха на входе р* н , Т Н *, соответствующие заданным условиям полета. Благодаря тому, что нет необходимости в организации системы скачков и создании внешнего диффузора, в этом случае в ТБК возможно испытывать ГТД значительно больших размеров, чем в АТ, при тех же мощностях компрессорно-эксгаустерной станции. ТБК состоит из двух отсеков. В отсеке 1 создаются кондиционированные условия на входе (р Н *, Т Н *), в отсеке II создаются условия, соответствующие полету на заданной высоте — р н. Для испытания ГТД в заданных условиях полета (М п , Н п ) двигатель выводят на расчетное значение n при Т н и обеспечивают перепад давлений
6. 4. ОСНОВНЫЕ ОСОБЕННОСТИ ИСПЫТАНИЯ ПВРД В отличие от других ВРД, у прямоточных двигателей наблюдается значительно большее влияние рабочего процесса в диффузоре на работу камеры сгорания и реактивного сопла. Если в ГТД неравномерности потока, генерируемые диффузором, несколько выравниваются после компрессора, то у ПВРД они непосредственно достигают камеры сгорания и влияют на работу сопла. Поэтому хотя поузловая доводка при создании ПВРД применяется, но она менее эффективна, чем у других видов ВРД. По конструкции ПВРД прост, и геометрическое моделирование его не вызывает трудностей, однако влияние числа Re на газодинамические процессы и отсутствие возможности моделирования сложных процессов смесеобразования и тепловыделения требуют проведения экспериментальных исследований либо на моделях большого размера, либо непосредственно на натурных объектах. Ускорение летательных аппаратов с ПВРД значительно больше, чем с другими ВРД, что сказывается на работе топливоподающей и топливорегулирующей аппаратуры [51]. Стендовые испытания ведутся в ТБК по схеме с присоединенным трубопроводом. Чтобы приблизить форму скоростного поля перед камерой сгорания к реальной, двигатель устанавливается в ТБК с реальной дозвуковой частью входного диффузора. Если давление и температура в критическом сечении диффузора Fr будут соответствовать полетным, то все узлы двигателя, расположенные за критическим сечением (камера сгорания и сопло), будут находиться в условиях, наиболее приближенных к реальным [49]. На стенде с обдувом диффузора сверхзвуковым потоком могут быть имитированы условия работы при разных числах М п и углах атаки и скольжения. При этом испытания проводятся не только с постоянным углом между вектором скорости набегающего потока с осью диффузора, но и при быстрых изменениях его во время эксперимента (до 10 градусов в секунду), как это может быть во время маневра летательного аппарата [49].
Наиболее полные сведения о работе двигателя на земных установках получают в моторных аэродинамических трубах. Учитывая, что ПВРД значительно легче ГТД и ошибки, связанные с большими статическими нагрузками на аэродинамические весы, меньше, во время эксперимента может измеряться сила тяги двигателя. Для учета сопротивления стойки, на которой подвешивается двигатель, и сопротивления, вызываемого интерференцией стойки с двигателем, испытания проводят с применением ложной стойки, располагаемой с про тивоположной стороны двигателя, идентичной несущей стойке. На тех же режимах работы двигателя испытания проводят с ложной стойкой и без нее. Считается, что сопротивление, вызванное обтеканием стойки и интерференцией ее с двигателем, в два раза больше при двух стойках, чем при одной [51 J. Во время экспериментов измеряют статические давления по длине двигате ля на внешней обшивке и во внутренних каналах: поля полных давлений в раз личных сечениях диффузора; камеры сгорания и сопла; температуру газового потока в камере сгорания; температуру элементов конструкции; расход топлива и силу тяги. Эти измерения позволяют построить высотно-скоростные характеристики, характеристики процессов, протекающих в отдельных элементах дви гателя, и оценить эффективность охлаждения горячих узлов [49]. Одним из важных эксплуатационных качеств ПВРД является надежный за пуск. Если произойдет задержка воспламенения топливовоздушной смеси, то двигатель не сможет развить силу тяги, необходимую для дальнейшего разгона ЛА. Поэтому пусковые свойства ПВРД тщательно проверяются в различных условиях полета по скорости набегающего потока, давлению и температуре воздуха. Летные испытания ПВРД составляют очень важный этап доводочных работ. Они осуществляются на летающей лаборатории или путем запуска беспилотных ЛА, на которых двигатель используется в качестве маршевой СУ.
При проведении испытаний серийных ПВРД нет необходимости проводить предъявительские испытания, так как не требуются обкатка и приработка эле ментов двигателя. Проводят только приемосдаточные испытания по проверке работы топливоподающей аппаратуры. Проводят длительные испытания на стендах или запуском в воздух совместно с летательным аппаратом [49].
РЕЗЮМЕ (по главе 6 «Экспериментальные методы определения основных технических данных авиационных ГТД» ) 1. Нормальными значениями параметров (НЗП) называют параметры двига теля, замеренные в СЛУ при заданной норме тяги (мощности) для данного режима. 2. При определении НЗП путем испытаний ГТД на режимах, подобных его ра боте в СЛУ, либо имитируют подобные режимы, либо среди многих измеренных ре жимов отыскивают режимы, подобные исходным режимам работы в СЛУ 3. Для определения НЗП серийных двигателей используют специальные нор мализующие коэффициенты, которые отражают изменение характеристик банного ГТД под влиянием изменения р„, t H , М, dи режима при заданном законе Регулирования. 4. НЗП можно определить измерением характеристик ГТД непосредственно в кoнтрольных условиях, которые создаются с помощью специальных и дорогостоящ их стендовых сооружений (ТБК, АТ), обеспечивающих в любое время года заданные р н , t H и М П. 5. Экспериментальное onpeдeлeнue нормализующих коэффициентов ТРД и ТРДД основывается на снятии полной дроссельной характеристики, приведении ее к САУ и нахождении на ней по Р дв норм НЭП, далее, задаваясь t H и р H с помощью закона управления находятся физические значения параметров, разделив последние на НЭП, находят значения нормализующих коэффициентов для соответствующих параметров. 6. При испытаниях ТРДД на стенде имеет место докритический перепад давления в соплах внутреннего и наружного контуров. Для увеличения перепада используют установки с наддувом на входе в двигатель, установки с подачей воздуха второго контура и частично горячих газов первого контура на вход двигателя.
7. Так как прямое измерение тяги ТРДД большой степени двухконтурности сильно зависит от потерь, связанных с обтеканием потоков воздуха второго контура, элементов двигателя и пилона, переходят к оценке выходных импульсов первого и второго контуров непосредственно на срезе сопла и на выходе из вентилятора термопневмогребенками. 8. При испытаниях ТРДФ и ТРДДФ определяют величины, характеризующие работу форсажной камеры: α фк , G т ф , η г ф а также отлаживают синхронизацию раскрытия створок сопла с моментом воспламенения форсажного топлива. 9. При испытаниях ТРДД с реверсом определяют прямую и обратную силы тяги, при этом используют как обычные силоизмерительные устройства, загружаемые во время измерения градуировочным устройством, так и специальные силоизмерительные устройства. 10. При испытаниях ГТД с отклоняемым вектором прямой тяги применяют трехкомпонентные силоизмерительные устройства, но чаще, более конструктивные двухкомпонентные устройства с одной динамометрической платформой. 11. При испытаниях ТВД и ГТД СТ мощности (N B и N e соответственно) необходимо наметить и измерить загрузочным устройством, в качестве которого могут быть применены гидротормоз или воздушный тормоз (чаще всего воздушный винт), электрический тормоз или другое устройство. 12. Испытания ТВД с воздушными винтами проводят на жестких станках, при этом режим испытания по мощности устанавливается либо по давлению топлива перед форсунками на заданной частоте вращения, либо с помощью штатного измерителя крутящего момента (ИКМ). 13. При испытаниях двигателей со свободной турбиной проводится проверка на максимально допустимый крутящий момент и на быстродействие системы ограничения частоты вращения при резком снятии нагрузки. У вертолетных ГТД также проверяется возможность работы на чрезвычайных режимах, посредством определения достаточности избытка топлива, подаваемого
насосом, необходимого для обеспечения работы на этом режиме. 14. Определение НЗП опытных ТВД (двигателей с двумя степенями свободы) проводят на тормозных стендах, снимая дроссельную характеристику при n пр = n Норм ТУ. что пpи измеренной t H означает поддержание постоянной физической частоты вращения затем на приведенной дроссельной характеристике по величине N энорм определяют нормальные значения других параметров. При определении НЗП серийных ТВД двигатели отлаживаются на винтовом стенде по значению G m = G m. Hopм K Gm , при этом измеряя мощность при помощи ЦКМ. Если двигатель не обеспечивает требуемой мощности, то его для проверки направляют на гидротормозной стенд, а затем, при отрицательном результате, — на переборку. 15. Определение нормализующих коэффициентов может быть проведено расчетным путем (методом расчета ВСХ), путем непосредственных измерений на двигателе в ТЕК (эталонный метод) или косвенным методом — снимая специальные характеристики выборочных ТВД. 16. Экспериментальное определение НЗП ГТД в стендовых и полетных условиях проводят в термобарокамерах и аэродинамических трубах. 17. Стендовые испытания прямоточных ВРД ведут в ТБК с присоединенным трубопроводом и с реальной дозвуковой частью входного устройства, а наиболее полные сведения о работе двигателя получают в моторных аэродинамических трубах.
ВОПРОСЫ 1. Что такое «нормальные значения параметров» ГТД? 2. В чем заключаются отличия трех основных способов определения НЗП ГТД? 3. Каков алгоритм определения НЗП по приведенной дроссельной характеристике? 4. Как используются «коэффициенты пересчета» для определения НЗП ГТД? 5. В какой последовательности проводятся эксперименты для определения «коэффициентов пересчета» ТРД и ТРДД? 6. Каковы особенности испытаний ТРДД? 7. Назовите особенности испытаний форсажных двигателей. 8. Каковы особенности испытаний ГТД СТ и ТВД? 9. В чем состоят особенности экспериментального определения НЗП ТВД? 10. Каковы этапы методики экспериментального определения «коэффициентов пересчета» для параметров ТВД? 11. Какое специальное оснащение используется для получения НЗП ГТД в стендовых и полетных условиях? 12. Назовите особенности испытаний прямоточных ВРД.
Глава 7 ИСПЫТАНИЯ АВИАЦИОННЫХ ГТД С ИМИТАЦИЕЙ ЭКСПЛУАТАЦИОННЫХ УСЛОВИИ Испытания авиационных двигателей проводятся, как правило, на полноразмерных силовых установках или в комбинации с элементами самолета. Преимуществом испытаний на высотных стендах по сравнению с испытаниями на летающих лабораториях и на самолете является возможность размещения большого количества контрольно-измерительной аппаратуры, что позволяет сразу получать данные, эквивалентные по объему результатам нескольких испытательных полетов. Кроме этого программа испытаний на высотной установке может быть задана в более широком диапазоне режимов по сравнению с испытаниями на летающей лаборатории. После того как двигатель сдан в эксплуатацию, испытания на высотных стендах продолжаются для устранения дефектов, обнаруживаемых в эксплуатации, для проверки усовершенствования элементов двигателя, доводки его модификаций и проверки различных вариантов применения. Высотные испытания проводятся на больших комплексах с применением специального оборудования’ Эти комплексы имеют сложные системы, дорогостоящее оборудование, требуют больших площадей, а их строительство и эксплуатация связаны с огромными капитальными затратами [21, 36, 42, 56]. На рис. 7. 1 показан общий вид научно-исследовательского центра (НИЦ) ЦИАМ, на базе которого проводится подавляющая часть отечественных высотно-ско ростных испытаний авиационных ГТД.
7. 1. ТЕХНОЛОГИЯ ИСПЫТАНИЙ ГТД НА ВЫСОТНЫХ СТЕНДАХ Одной из основных операций технологического процесса испытания двигателя с имитацией высотных условий является сбор информации о состоянии двигателя, высотного оборудования и других систем стенда. Всего в процессе высотных испытаний двигателя на установившихся и переходных режимах его работы измеряется около 10 тыс. параметров различной физической природы. Высотно-скоростные испытания современных ГТД проводятся, в основном, одним из трех способов [37]: • с полным внешним обтеканием; • с обдувом свободной струей воздухозаборника двигателя; • с присоединенным воздухопроводом. Аэродинамические стенды, позволяющие испытывать двигатель с полным внешним обтеканием воздухозаборника, в наибольшей степени отвечают требованиям и возможностям комплексных испытаний гиперзвуковых прямоточных двигателей (ГПВРД). При испытаниях с присоединенным воздухопроводом система состоит из трубопровода с входным устройством, мерного участка и кормового диффузора, размещающихся в ТБК. Воздух заданных (высотных) параметров подготавливается для экспериментальных высотно-скоростных стендов специальным оборудованием (рис. 7. 2) [49]. При больших расходах воздуха через двигатель это оборудование требует больших электрических мощностей и занимает значительные производственные площади. Воздух забирается из атмосферы через воздухозаборную шахту 1, оборудованную шумоглушащими устройствами, и направляется к низконапорным компрессорам большой производительности 2.
Предварительное сжатие воздуха необходимо для компенсации потерь давления в воздухоочистителе 4 и влагопоглотителе 5, а также для уменьшения их габаритов. Очищенный и осушенный воздух сжимается высоконапорными компрессорами 6, между ступенями которых имеются водовоздушные радиаторы 7. Эти радиаторы уменьшают потребную мощность сжатия. После сжатия в Компрессорах воздух нагревателя охлаждается соответственно в подогревателе 10 или охладителях 9 и 11. Воздух охлаждается в водовоздушном радиатора в случае необходимости охлаждения ниже 0 °С (до -70 °С) в холодильной турбине 11. Развиваемая турбиной мощность поглощается гидротормозом 12. Подогреватели могут быть электрическими или газовоздушными. Для электрических подогревателей требуются большая электрическая мощность и значительные того чтобы разместить оборудование и сам подогреватель. Удобнее трубчатые или пластинчатые теплообменники, в которых рабочий воздух подогревается высокотемпературными продуктами сгорания жидкого топлива, поступающими из камеры сгорания подогревателя 21. Воздух в камеру сгорания 21 подается низконапор ными компрессорами 2. Подогретый или охлажденный воздух подается в смеситель 13 и далее на экспериментальный стенд 14 (высотную камеру или аэродинамическую трубу). Создание высотных условий на выходе из двигателя обеспечивается со вместной работой кормового диффузора и системы отсоса выхлопных газов специальными машинами — эксгаустерами. Как правило, привод эксгаустеров, как и компрессоров, производится от электродвигателя. Для некоторых стендов более удобными устройствами для отсоса выхлопных газов являются эжекторы. После стенда воздух, содержащий продукты сгорания, охлаждается для облегчения работы эксгаустерной части установки 18 и выбрасывается в атмосферу через выхлопную шахту 20 , снабженную шумоглушащими устройст вами.
Рис. 7. 2. Принципиальная схема компрессорно-эксгаустерной станции, созданной на базе специально спроектированного оборудования: 1 — воздухозаборная шахта с шумоглушением; 2— низконапорные компрессоры большой производительности; 3 — электродвигатель; 4— воздухоочиститель; 5 — влагопоглотитель; 6— высоконапорные компрессоры; 7— промежуточный водовоздушный охладитель; 8 — электродвигатель; 9 — концевой водовоздушный охладитель; 10 — подогреватель; II — холодильная турбина; 12 — гидротормоз; 13 — смеситель; 14 — высотно-скоростная установка; 15 — промежуточный водовоздушный охладитель; 16 — водовоздушный охладитель на выходе из экспериментальной установки; 17 — водовоздушный охладитель между ступенями компрессора; 18 — эксгаустер; 19 — электродвигатель; 20 — выхлопная шахта с шумоглушением; 21 — камера сгорания с подогревателем
Общая электрическая мощность всех приводов подобных установок достигает 100 тыс. к. Вт и более. Одна энергетическая установка, как правило, попере менно обслуживает несколько стендов. Пока на одном проводят эксперимент, на других осуществляют перемонтаж и отладку оборудования. Возможность переключения компрессоров на параллельную, последо вательную работу или в эксгаустерный режим существенно расширяет диапазон имитируемых высот и скоростей полета, так как для работы дви гателя в условиях малых высот и больших чисел М п необходимы большие давления на входе в него и весовые расходы воздуха, а в условиях боль ших высот и малых чисел М п — большие разрежения при меньших расходах воздуха. В некоторых случаях для малогабаритных ГТД, например, вспомогатель ных ГТД (ВГТД) с расходом воздуха до 10 кг/с, возможны малозатратные варианты проведения высотных испытаний с применением серийных дви гателей и оборудования. Так, например, на рис. 7. 3 приведена схема высот ного стенда для проведения доводочных испытаний ВГТД с имитацией температур от -60 до +60 °С, высотности — от 0 до 10 км, расхода воздуха через двигатель — от 0 до 12 кг/с и влажности воздуха — от 0, 02 до 30 г/кг воздуха [17]. В качестве источника сжатого воздуха используется компрессор ГТД РПФ- 300. После компрессора воздух охлаждается в водовоздушном теплообменнике 3 до температуры 30 °С и через осушитель 7 поступает в турбодетандеры 10. В турбодетандерах воздух в зависимости от имитируемых условий охлаждается до температуры -60 °С В смесителе 16 происходит выравнивание температуры холодного и горячего воздуха. Развиваемая турбодетандерами мощность затра чивается на привод компрессоров //, загрузку генераторов переменного тока и узлов загрузки, устанавливаемых на место генераторов постоянного тока. Па раллельная работа турбодетандеров предусмотрена для случая больших расходов воздуха (табл. 7. 1).
Далее воздух поступает в термобарокамеру (ТБК) 25, где находится испытываемый двигатель 26. Разрежение на входе в ТБК и за соплом испытываемого ВГТД обеспечивается заслонкой 19 и эксгаустером 33. Далее газ охлаждается в газоводяном теплообменнике 29. Для этого же предусмотрена подача воды в газовоздушный тракт за соплом двигателя с помощью системы форсунок 30. Выхлопной газоводовоздушный поток дожимается в эксгаустере до давления 111 к. Па и выбрасывается наружу. Схема системы отсоса обеспечивает различные варианты параллельной работы эксгаустеров. Интервалы значений основных параметров воздуха и газа в наиболее характерных сечениях газовоздушного тракта высотного стенда приведены на рис. 7. 3. Осушка воздуха проводится в осушителе 7, а увлажнение — с помощью ув лажнителя форсуночного типа 18 , устанавливаемого в смесителе 16. Турбодетандеры 10 выполнены на базе двух конструктивно доработан ных ВГТД. Термобарокамера 25 разделена перегородкой 27 на два отсека. В первом (входном) отсеке поддерживается полное давление и температура таковыми, как за воздухозаборником перед двигателем во время полета, во втором — статическое давление, равное барометрическому на имитируемой высоте. Для ВГТД с расходом воздуха G В < 7 кг/с в условиях земли предусмотрено проведение испы таний с имитатором отсека летательного аппарата, устанавливаемого в ТБК, что позволяет наиболее полно имитировать реальные условия работы ВГТД. Эксгаустерная система выполнена на базе конструктивно доработанных ВГТД ТА-6 А и ТА-8 33 (см. рис. 7. 3).
Рис. 7. 3 Стенд для высотно-климатических испытаний ВГТД (вариант 1): 1, 35 — источники сжатого воздуха (ГТД Р 11 Ф-300); 2, 5, 6, 8, 9, 13, 14, 15, 22, 23, 24, 31, 32, 36, 38, 40 – вентили, редукторы; 3, 29 – водовоздушные теплообменники; 4 – градирня; 7 – осушитель; 10 – турбодетандеры(ВГТД ТА-6 А); 11 -компрессор ВГТД ТА-6 А; 12 – генераторы загрузки; 16 – смеситель; 17, 20, 23 – клапаны; 30 — система впрыска воды; 33 – эксгаустеры (ВГТД ТА-6 А); 34 — турбина ВГТД ТА-6 А; 37 — емкость с жидким азотом; 39 – вентилятор; 41 – топливная емкость.
Источник сжатого воздуха Количе ство ис точников Комбинации турбодетандеров Параметры воздуха на выходе из турбодетандеров при Р* вых = 1, 01∙ 10 5 Па и температуре на входе, равной t вх =30 0 С t вх =10 0 С t вых, 0 С G , кг/с t вых, 0 С G, кг/с Р 11 Ф-300 1 2(ТА — 8) -55 10, 1 -68 10, 9 (ТА — 6 А) + 2(ТНУА) -60 10, 9 -74 11, 0 2(ТА — 8) + 3(ТГ 60/2 С) -52 12, 0 -64 12, 1 (ТА — 8) + 4(ТНУА) -48 9, 6 -60 9, 8 ТА-6 А 7 (ТА — 6 А) + 2(ТНУА) -52 9, 9 -66 10, 0 8 2(ТА — 8) + ТНУА -50 10, 6 -63 10, 7 8 2 (ТА — 8) + 3(ТГ 60/2 С) -48 10, 6 -61 10, 7 2 2(ТНУА) -30 2, 0 -45 2, 17. 1. Эффективность турбодетандеров высотного стенда для испытаний ВГТД
Система предварительного «захолаживания» ВКС предназначена для обес печения высотных условий по температуре в ТБК и основных системах двига теля (масляной и топливной систем и т. д. ) перед запуском испытываемого дви гателя. Когда температура окружающего воздуха превышает имитируемую ВКС температуру, используются два варианта «захолаживания» : первый — системой подготовки холодного воздуха самого ВКС и второй — за счет работы автоном ной системы «захолаживания» : жидкий азот из емкости 37 подается с помощью вентилятора 39 в ТБК 25 и топливную емкость 41 (см. рис. 7. 3). При проведении «горячих» испытаний с подогревом воздуха на входе в ис пытываемый двигатель до 50. . . 60 °С при температуре окружающего воздуха t H > 0°С используется один технологический ВГТД ТА-6 А, а при t H = -20. . . 0°С — Два ВГТД ТА-6 А. Воздух, отбираемый за компрессором ТА-6 А с температурой 200… 290 °С, подается в смеситель 16 и, смешиваясь с воздухом из окружающей атмосферы, поступает в ТБК.
7. 1. 1. Испытания в аэродинамической трубе Аэродинамические трубы позволяют определить влияние условий полета и самолетных конструкций на работу двигателя. В них испытываются силовые установки, состоящие из двигателя и мотогондолы (с воздухозаборником и кормовыми устройствами), с частью прилегающих к ним конструкций летального аппарата. Рис. 7. 4. Схема аэродинамической трубы: / — решетка; 2 — механизм изменения критического сечения сопла; 3 — сопло аэродинамической трубы; 4 — домкраты, изменяющие профиль сопла; 5 — рабочая часть аэродинамической трубы; 6 — перфорированная стенка рабочей части аэродинамической трубы; 7— испытуемый двигатель; 8 — подвески двигателя на динамометрической платформе; 9 — измеритель усилия; 10 — внутрен ний стендовый диффузор системы удаления выхлопных газов; 11 — внешний стендовый диффузор системы возврата воздуха; 12 — механизм изменения конфигурации внешнего диффузора
Аэродинамические двигательные трубы в отличие от обычных аэродинамических труб, работающих, как правило, с замкнутым контуром, имеют устройства для удаления выхлопных газов, так как из-за работы двигателя уменьшается содержание кислорода в воздухе. Схема аэродинамической трубы приведена на рис. 7. 4 [51]. Основные ее части — сопло, рабочая часть, система удаления выхлопных газов и система подачи и отсоса воздуха. Сопла, в которых разгоняется поток до требуемого числа М п , представляют собой сложные конструкции. Обычно они выполняются в виде плоских сопел Лаваля с постоянной выходной площадью F c. Две противоположные стенки сопла — неподвижные, а две другие — гибкие. Необходимый профиль сопла для каждого числа М п получают с помощью воздействия усилий на каждую гибкую стенку. Рабочая часть аэродинамической трубы, в которую помещают двигатель, снабжается перфорированными стенками, через которые отсасывают воздух. Перфорированные стенки и система отсоса позволяют устранить возникающие при испытаниях ударные волны и запирание рабочей части на околозвуковых скоростях обдува. Без этих мероприятий ударные волны могут отражаться от стенок аэродинамической трубы на испытуемый объект и вызывать воздействия, не встречающиеся в свободном полете. Двигатель в рабочей части трубы подвешивается на пилонах, соединенных с весовым устройством. Внутри пилонов прокладываются все коммуникации, связывающие двигатель со стендовым оборудованием (топливопровод, провода от приборов, импульсные магистрали и т. д. ). Однако непосредственное измерение эффективной силы тяги обычно не производят. Для определения эффективной силы тяги найденное внешнее сопротивление вычитают из внутренней силы тяги, измеренной в ТБК на том же режиме работы двигателя.
На некоторых очень больших околозвуковых и сверхзвуковых аэродинами ческих трубах наряду с чисто аэродинамическими экспериментами проводятся огневые испытания натурных воздушно-реактивных и ракетных двигателей, Установленных на летательном аппарате или его элементе с целью взаимодействия входного устройства двигательного агрегата и частей ЛА, а также взаимодействия струй, истекающих из одно- или многосоплового блока с внешним потоком и элементами ЛА [56]. Поток в дозвуковых трубах создается вентиляторами, в сверхзвуковых — многоступенчатыми осевыми компрессорами (степень повышения давления на ступень 1, 1. . . 1, 2). Некоторые трубы имеют сменные рабочие части, смонтированные на само ходных платформах, и одна из этих частей предназначена для монтажа, препа рирования и испытания силовых установок. Пример. Каждый контур аэродинамической трубы АЕДС [56] имеет сменные квадратные рабочие части 4, 88∙ 4, 88 м длиной 12, 2 м с перфорированными стенками. Воздух, удаляемый со стенок рабочей части при отсосе, вводится обратно в контуры в области улавливателей. Гибкие вертикальные стенки регулируемых сопел имеют ширину 4, 88 м при длине 17, 7 м. Осевые компрессоры околозвукового (трехступенчатый) и сверхзвукового (четырехагрегатный, восемнадцатиступенчатый с широким диапазоном изменения напорности) контуров имеют общую приводную систему. В околозвуковом контуре между компрес сором и соплом установлен холодильник, в сверхзвуковом — два холодильника. Система управления контурами позволяет регулировать раздельно число М, высоту и температуру во всей области высотно-скоростной характеристики трубы (рис. 7. 5). Оба контура трубы имеют систему улавливания, охлаждения и удаления выхлопных газов и систему подготовки и введения чистого воздуха.
Улавливатель выхлопных газов (диаметром 2 м), имеющих температуру 2200 К, выполнен из трех частей. Входная часть — неохлаждаемая заменяемая секция (длиной 3 диаметра) из коррозионно-стойкой стали. Затем секция с пленочным охлаждением (в сверхзвуковом контуре) или с проточным охлаждением (в околозвуковом контуре). В конце второй секции осуществляется впрыск воды, охлаждающей продукты сгорания до температуры, близкой к температуре насыщения (94 °С); при этом расход воды приблизительно равен продукту сгорания. Определенное количество воздуха, удаленное из трубы, возмещается чистым и подготовленным воздухом. Система подготовки воздуха включает осушитель абсорбционного типа (где используется силикагель), оборудование для нагрева и охлаждения. Перед запуском трубы из нее удаляется вся топливно-воздушная смесь. Во время испытания автоматически контролируется уровень концентрации паров топлива по всей трубе. При обнаружении недопустимой концентрации паров топлива в любом месте трубы автоматически прекращается подача топлива; в воздухозаборник, газоотводный канал и камеру отсоса (вокруг рабочей части) автоматически вводится азот для разбавления взрывоопасной смеси. На установке имеется также система огнетушителей с шестью тоннами углекислоты. Рис. 7. 5. Высотная характеристика контуров аэродинамической трубы АЕДС: / — околозвуковой контур; 2 — сверхзвуковой контур; 3 — сверхзвуковой контур, температура ниже полетной
7. 1. 2. Испытания в ТБК с присоединенным трубопроводом Термобарокамеры являются рабочими участками высотных стендов (рис. 7. 6) Термобарокамера представляет собой емкость диаметром до 10 м и длиной до 25 м, способную выдержать большие перепады давлений (до 107 Па) пои значительных температурах (400. . . 500 К). Термобарокамеры представляют из себя цилиндрические камеры больших размеров, снабженные противовзрывными устройствами 10 (см рис 7 6) внутри которых располагаются объект испытаний, динамометрическая платформа, грузоподъемные устройства. В стенках ТБК прокладываются двигательные коммуникации (топливные, масляные, водяные), коллекторы измерительных систем, трубопроводы вентиляции, смотровые окна. Для размещения двигателя в ТБК они оборудуются герметичными люками, съемными или откатывающимися частями и дверьми для прохода внутрь обслуживающего персонала. Для двигателей с радиальным входом вместо присоединенного трубопровода может быть применена термобарокамера с перегородкой (рис. 7. 6, б), которая делит ее на два отсека — компрессорный и сопловой. В настоящее время такая конструкция барокамер применяется редко, так как она обладает недостатками, связанными с трудностью уплотнения стыка между перегородкой и двигателем. Воздух в ТБК подводится от воздушно-компрессорных станций (ВКС), а продукты сгорания отсасываются специальными компрессорами-эксгаустерами, благодаря чему в пространстве вокруг двигателя или сопла создается пониженное давление.
Рис. 7. 6. Схемы расположения двигателя в ТБК высотного стенда: а — компоновка двигателя с присоединенным трубопроводом на входе: 1 — приемники статического давления; 2 — трубки Пито; 3 — гребенки, измеряющие полное давление; 4 — гребенки термопар; 5 — патрубок подвода воздуха для вентиляции ТБК (G вент < 0, 15 G в ); 6 — входная защитная сетка; 7 — коллектор впрыска воды при проведении специальных испытаний; 8 — эластичные уплотнения; 9 — входной измерительный участок присоединенного трубопровода (среднее расстояние между измерительными сечениями I. . . IX 60. . . 700 мм. расстояние от крайнего измерительного сечения IX до входа в компрессор — 500. . . 600 мм; 10 — предохранительный клапан; II — ТБК: 12 — динамометрическая платформа; 13 — выхлопной трубопровод с охлаждением; б — компоновка двигателя в ТБК с перегородкой; 14 — входной насадок с лемнискатой; 15 — перегородка; в — сечение проточной части с соответствующими приемниками давления
Примеры. Комплекс ASTFНИЦ им. Арнольда оборудован двумя ТБК диаметром 8, 6 м и длиной 23 м |42|. Размеры ТБК позволяют устанавливать в них элемент самолета с комбинацией двигатель-воздухозаборник или двигатель-хвостовая часть. Перед испытательной камерой располагается успокоительная камера длиной 20 м. Высотный стенд № 4 в Национальном газотурбинном институте (Англия), пред назначенный для испытаний ТРДФ «Олимп» 593 (с обдувом двигателя через сопло) имеет ТБК диаметром 3 м, длиной 4, 9 м. Максимальный расход воздуха через ТБК 270 кг/с; около половины воздуха, поступающего через сопло, используется для внешнего обдува двигателя. Размеры ТБК другого стенда для испытаний ТРДД с большой степенью двухконтурности: диаметр 7, 6 м, длина 13, 4 м, максимальный расход воздуха 635 кг/с. Фирма SNECMA для испытаний силовой установки СПС «Конкорд» построила стенд со следующими размерами: длина 70 м, площадь поперечного сечения рабочей части 8 x 8 м : , высота 17 м. На стенде проводятся исследования систем реверсирования тяги в реальных условиях эксплуатации. Расход воздуха через барокамеру с присоединенным трубопроводом незначительно (на 10. . . 15 %) превышает расход воздуха через двигатель для обеспечения вентиляции барокамеры при испытаниях. Испытания в ТБК позволяют решить значительную часть задач доводки двига теля, в частности достаточно полно исследовать его высотно-скоростные характе ристики. Особенности испытаний в ТБК. Наибольшее распространение получил метод испытаний двигателей в термобарокамере высотного стенда, при котором по ток воздуха на входе в компрессор ГТД с осредненными параметрами, идентич ными параметрам за воздухозаборником летательного аппарата, подается по присоединенному трубопроводу, а в термобарокамере и, соответственно, в плоскости сопла (вне рабочей струи газов) создается давление, равное высотному (рис. 7. 7, а) (37].
При этой компоновке двигателя в ТБК высотного стенда все его агрегаты и стендовые устройства внутри термобарокамеры находятся при давлении, равном давлению на имитируемой высоте полета, и при температуре, не превышающей 50. . . 80 °С. По величине окружающего двигатель давления, т. е. давление в подкапотном пространстве летательного аппарата, условия испытаний 6 лизки к реальным. 6 ) Рис. 7. 7. Виды испытаний ГТД на высотном стенде: а — схема испытаний ТРД с присоединенным трубопроводом; б — установка двигателя в ТБК с обдувом корпуса и агрегатов воздухом со входа; в — установка двигателя с мотогондолой и частью крыла в ТБК
Этот метод применим для большинства видов высотных испытаний ГТД. При условии отсутствия рециркуляции потока газа в районе кормового диффузора уровень температуры в ТБК невысок, что благоприятно сказывается на работе измерительных датчиков и системы измерения усилия от тяги двигателя. По такой схеме проводились испытания двигателей семейств Р-11. . . Р-29 (более 150 двигателей при наработке свыше 3000 ч), Д-30 -Ф 6 (36 двигателей, более 500 ч), РД-33 (80 двигателей, 2000 ч), АЛ-31 Ф (22 двигателя, 600 ч), НК-8, НК-22, НК-25, НК-32 и др. [37]. Для ряда специальных испытаний необходимо обеспечить обдув агрегатов двигателя потоком воздуха, имеющего температуру, равную температуре воздуха на входе в двигатель, для чего входной трубопровод дополняют специальным кожухом обдува агрегатов (турбохолодильника, маслорадиатора и др. ) (рис. 7. 7, б). Схема высотного стенда с присоединенным трубопроводом на входе в двига тель позволяет проводить практически все виды высотноскоростных испыта ний ГТД любой размерности в пределах энергетических возможностей высотно-компрессорного комплекса. Разновидностью испытаний с присоединенным трубопроводом являются испытания, когда двигатель ставится на стенд вместе с каналом воздухозаборника, а входной трубопровод стенда соединяется вместе с входом канала. Такая компоновка иногда применяется при тензометрировании, когда конструкция Двигателя интегрирована с элементами конструкции самолета, как, например. При испытании двигателя Д-36 в гондоле вместе с примыкающей частью крыла самолета АН-72 (рис. 7. 7, в).
7. 1. 3. Испытания с частичной имитацией высотно-скоростных условий Испытания на стендах с подогревом воздуха на входе в двигатель. В условиях полета температура торможения воздуха на входе в двигатель, начиная с М п = 1, 3, На всех высотах превышает 288 К, а с уменьшением высоты полета (Н< 11 000 м) и ростом числа М может достигать 400. . . 600 К [49]. При повышенной температуре воздуха на входе двигатели могут испытываться на установках, схемы которых приведены на рис. 7. 8 [26]. В данном случае воздух подогревается путем подмешивания горячих выхлопных газов в воздушный поток на входе в двигатель. Генератором выхлопных, газов может быть сам испытуемый двигатель (см. рис. 7. 8, а), специальный двигатель либо камера сгорания (см. рис. 7. 8, б, в). Однако подмешивание выхлопных газов к воздуху на входе в двигатель приводит к изменению физических параметров воздуха, уменьшает содержание в нем кислорода и может влиять на характеристики горения и устойчивости в камерах сгорания испытуемого двигателя. Поэтому предпочтительнее теплообменники, использующие тепло выхлопных газов вспомогательного двигателя или другого источника.
7. 8. Схемы установок для испытания двигателя с подогревом воздуха на входе [49]: а — подогрев воздуха вследствие подмешивания выхлопных газов испытуемого двигателя; б — подогрев воздуха путем подмешивания выхлопных газов вспомогательного ТРД; в — подогрев воздуха вследствие сгорания топлива в специальной камере сгорания; 1 — насос; 2 — вспомогательный двигатель; 3 — система подсоса воздуха из атмосферы; 4 — эжектор: 5 — перепуск газов в атмосферу; 6 — система подачи горячего воздуха на обогрев внешней поверхности двигателя; 7 — сопло Витошинского; 8 — капот; 9 — испытуемый двигатель; 10 — система подсоса воздуха в камеру разрежения; 11 — камера разрежения; 12 — специальная камера сгорания; 13 — насадок разрежения
Испытания на стендах с наддувом воздуха на входе в двигатель. Давление воздуха на входе в двигатель при полете в ряде случаев выше атмосферного давления на уровне моря за счет скоростного напора. Так, на высоте 16 м, если М п > 2, 2 с учетом потерь давления во входном диффузоре, оно выше, а для высоты 20 м больше 101, 325 к. Па при М п > 2, 6. Пропорционально увеличению давления воздуха на входе возрастает его массовый расход, а следовательно, и механические нагрузки на детали турбокомпрессора. При этом корпус двигателя испытывает повышенные напряжения от сил давления |49|. Для имитации условий полета на больших скоростях применяются стенды с наддувом воздуха на входе в двигатель. Они проще по устройству и позволяют производить как кратковременные, так и длительные прочностные испытания двигателей. На этих же стендах проводятся специальные испытания двигателей для выявления нарушений масляной системы, локализации разрушения элемен тов двигателя, обрыва лопаток и т. п. , а также циклические испытания двигателей, предназначенных для скоростных самолетов. На этих стендах предусматривается подогрев топлива и масла, используются большие тензометрические станции, обеспечивающие регистрацию напряжений в ряде точек двигателя. Характеристики двигателя на этих стендах измеряются с большей погрешностью. Поэтому при испытании двигателей на стендах с наддувом, как прави ло, не измеряют тягу, а ограничиваются ее расчетным значением. Повышенное давление воздуха на входе в двигатель может быть получено пу тем подачи на вход воздуха, отбираемого от компрессора вспомогательного двигателя (рис. 7. 9). Для увеличения массы наддуваемого воздуха в систему может быть включен эжектор 3, однако при этом существенно уменьшается значение р п. Расход воздуха, давление и температура на входе в двигатель регулируются пе репуском воздуха и изменением режима работы вспомогательного двигателя.
Рис. 7. 9. Схема установки для испытания двигателя с наддувом и подогревом воздуха на входе: 1— система подсоса воздуха из атмосферы; 2 — измерение расхода воздуха, засасываемого из атмосферы; 3 — эжектор; 4 — теплообменник; 5 — телескопическое соединение двигателя с воздуховодом; 6 — испытываемый двигатель; 7— измерение расхода воздуха, отбираемого oт вспомогательного двигателя; 8 — вспомогательный двигатель; 9 — регулируемый перепуск горячих газов
При испытании двигателя на стендах рассматриваемого типа на многих режимах, в частности, при повышенной температуре воздуха на входе, перепад давлений в сопле меньше критического в отличие от работы в полетных условиях, когда режим истечения сверхкритический. В этом случае будут отличаться режимы работы многих элементов двигателя. Для того чтобы на открытых стендах вывести двигатель на режим сверхкритического истечения, надо понизить давление на выхлопе из двигателя. Понизить давление можно путем присоединения к соплу камеры разрежения 11, связанной со специальным расширяющимся насадком 13 (см. рис. 7. 8, б, в). Для обеспечения устойчивости работы системы и регулирования перепада давлений в камере разрежения предусмотрен перепуск воздуха 10 (рис. 7. 8, б). Камера разрежения может применяться для испытания только двигателей с нерегулируемым соплом и без форсажных камер. 7. 1. 4. Испытания с самолетным воздухозаборником В самолетном воздухозаборнике кроме потерь полного давления возникают неравномерность распределения скоростей по радиусу и окружности и пульсации скорости по времени. Статические неравномерности могут быть вызваны как конструктивными элементами воздухозаборника (стойками, поворотами и несимметричностью канала), так и режимом полета, приводящим к появлению угла между осью диффузора и направлением набегающего потока. Пульсации скорости в полете создаются главным образом в результате нестационарного взаимодействия скачков уплотнения с пристеночным пограничным слоем. На старте пульсации порождаются срывами потока с острых входных кромок сверхзвукового диффузора. В некоторых условиях динамические пульсации могут превышать статические неравномерности потока.
Все перечисленные факторы влияют на газодинамические и прочностные параметры двигателя (запас устойчивой работы, вибронапряжения в лопатках компрессора, пусковые свойства) и должны быть детально изучены в процессе доводки. При этом не только воздухозаборник влияет на границы эксплуатационных режимов двигателя, но также и двигатель влияет на работу воздухозаборника. Определить основные характеристики воздухозаборника расчетным путем затруднительно. Поэтому перед установкой на двигатель воздухозаборник проходит ряд испытаний, в которых определяются в первую очередь его основные характеристики (19]: • коэффициент восстановления давления заторможенного потока σ вх. где p в * — средняя величина давления заторможенного потока за воздухозаборником; р * н — давление торможения набегающего потока; • коэффициент расхода воздуха φ: где G — расход воздуха. Рис. 7. 10. Схема испытания двигателя с самолетным воздухозаборником: 1 — самолетный воздухозаборник; 2 — под веска воздухозаборника; 3 — двигатель; 4 — силоизмерительное устройство; 5 — эжекторная труба
Рис. 7. 11. Схема испытания двигателя с имитатором: а — сеточный имитатор: б — имитатор со стойками; 1 — лемнискатный насадок; 2 — имитатор; 3 — приборы, контролирующие наравномерность потока; 4 — двигатель; 5 — силоизмерительное устройство; 6 — эжекторная труба Для этого двигатель испытывают с самолетным воздухозаборником (рис. 7. 10) или имитаторами на входе (рис. 7. 11) [49]. Имитатор статических неравно мерностей в потоке представляет собой комплекс сопротивлений, распо лагаемых между лемнискатным насадком и двигателем, создающий такое же неравномерное поле скоростей на входе в компрессор, как и самолетный воздухозаборник на исследуемом режиме. Поля скоростей за самолетным воздухозаборником при различных скоростях потока и углах атаки определяются при продувке уменьшенных моделей воздухозаборников в аэродинамических трубах, а на стенде при испытаниях двигателя воспроизводятся имитаторами. Имитаторы могут быть изготовлены в виде стоек или сеток. Имитация динамических неравномерностей достигается либо с помощью вращающихся и неподвижных лопаток, устанавливаемых перед двигателем, либо вдувом воздушных струй, подаваемых пульсациями навстречу потоку или под некоторым углом. Струями, кроме того, можно создавать требуемую статическую неравномерность, если подавать воздух непрерывно. Эксперименты с имитаторами без внешнего обдува значительно дешевле и менее трудоемки, чем испытания полноразмерного двигателя в аэродинамических трубах или в полете.
При испытании подфюзеляжных секторов или коробчатых воздухозаборников на аэродинамическом стенде компоновка стенда и объектов испытания на нем усложняется [42]. В ТБК устанавливается подфюзеляжный воздухозаборник с отсеком фюзеляжа. Осесимметричное аэродинамическое сопло оборудуется секторной вставкой и переходным участком для стыковки секторной вставки с фюзеляжем, а перед аэродинамическим соплом имеется ресивер со спрямляющей сеткой. На входе в воздухозаборник име ется канал слива пограничного слоя. Отсек фюзеляжа имеет технологиче ские створки для запуска двигателя. Вместо двигателя может использоваться технологическое испытательное устройство — труба, содержащая дроссель-имитатор и сопло для измерения расхода воздуха через технологичское устройство. 7. 1. 5. Особенности создания эксплуатационных условий при испытаниях ПВРД и ГПВРД Конструкция ПВРД более проста, чем конструкция ГТД, но испытания доводка ПВРД значительно сложнее, поскольку для этого требуется мощное компрессорно-эксгаустерное оборудование, создающее поток воздуха, набегающего на двигатель. В отличие от других ВРД у прямоточных двигателей наблюдается значительно большее влияние рабочего процесса в диффузоре на работу камеры сгорания и реактивного сопла. Если в ГТД неравномерности потока, возникающие входном устройстве, несколько выравниваются после компрессора, то у ПВР они непосредственно достигают камеры сгорания и влияют на работу сопла Экспериментальные исследования проводят либо на моделях большого размера, либо непосредственно на натурных объектах.
Цель испытаний полноразмерного ПВРД состоит в получении характеристик двигателя и систем его регулирования как при установившемся потоке на входе, так и при имитации изменения условий полета, включая изменения высоты, скорости полета и угла атаки. Одновременно с этим выясняются вопрос надежности охлаждения различных элементов двигателя, прочностные xapaктеристики конструкции и некоторые другие. На рис. 7. 12 показаны наиболее типичные схемы экспериментальных стендов для испытаний ПВРД [19]. Двигатель 1 (см. рис. 7. 12, а) размещается в рабочей части сверхзвуковой трубы. Здесь могут полностью имитироваться действительные условия по тeмпературе, давлению и числу М для течения газа внутри двигателя и обдува его наружных поверхностей. Для облегчения работы эжектора или эксгаустера, от засасываюших газ из сверхзвуковой трубы, и для предохранения стенок диффузора от действия горячих газов стенки оборудуются коллекторами и форсункам 7, распыливающими охлаждающую воду в канал диффузора. Испытуемый двигатель устанавливается на полой стойке 5, через которую выводятся топливе провод, трубки отборников статического и полного давлений, провода термопар, тензодатчиков и других приборов. Наряду с достоинствами рассмотренная схема имеет существенные недостатки. Главный из них заключается в необходимости прогонять через сверхзвуковую трубу количество воздуха, в несколько раз превышающее расход воздух через сам двигатель. Поэтому подобная схема находит применение для испытания относительно небольших ПВРД. При этой схеме трудно имитировать работу двигателя с углом атаки к набегающему потоку. При повороте самого двигателя возрастает загромождение сечения трубы, что может вызвать нежелательную перестройку потока и запирание трубы. В другом варианте испытания проводятся в высотной барокамере со сверх звуковым поворотным соплом и кольцевым диффузором.
Рис. 7. 12. Схемы экспериментальных стендов для испытания ПВРД: а — в закрытой сверхзвуковой трубе: 1 — испытываемый двигатель; 2 — сопло сверхзвуковой тру бы; 3 — рабочая часть трубы; 4 — смотровой люк; 5 — стойка, крепящая двигатель; 5′ — ложная стойка; 6 — диффузор; 7— форсунки, впрыскивающие охлаждающую воду в поток горячих газов; б — в барокамере: 1 — ресивер; 2 — поворотное сверхзвуковое сопло; 3 — диффузор; 4 — барока мера; 5 — люк; 6 — испытываемый двигатель; 7 — диффузор; в — при имитации условий на входе и выходе (при открытом доступе к камере двигателя): 1 — ресивер; 2 — поворотное сверхзвуковое сопло; 3 — камера открытой рабочей части сверхзвуковой трубы; 4 — диффузор; 5 — испытывае мый двигатель; 6 — камера вокруг выхлопной струи двигателя; 7 — диффузор
Испытываемый ПВРД (см. рис. 7. 12, б) размешается в барокамере 4. Поворотное сопло 2 может быть выполнено регулируемым или с неизменной геометрией. В последнем случае необходимо несколько сопел, рассчитанных на различные числа М. За соплом устанавливается диффузор 3 для уменьшения потерь при торможении потока. Газы из барокамеры отсасываются эксгаустером или эжектором через диффузор 7, благодаря чему создается необходимое давление на срезе сопла двигателя. В поток горячих газов также впрыскивается вода для снижения их температуры. К достоинствам подобной системы нужно отнести возможность имитации потока, набегающего на двигатель, по числу М, давлению, температуре и углу атаки. При этом полностью моделируются условия течения газа впереди двигателя. Загрузка сопла может достигать 40. . . 50 %, поэтому требуемый расход воздуха будет лишь в 2. . . 2, 5 раза превышать расход воздуха через сам двигатель. Условия обтекания воздухом внешних поверхностей двигателя в этой схеме не соответствуют действительным, поэтому и внешнее сопротивление двигателя R* x не равно силе R x , которая была бы в полете при том же числе М. Одним из важных эксплуатационных качеств ПВРД является надежный за пуск. Поэтому пусковые свойства ПВРД тщательно проверяются в различны условиях по скорости набегающего потока, давлению и температуре воздуха.
7. 2. СИСТЕМЫ И ОБОРУДОВАНИЕ ДЛЯ СОЗДАНИЯ ВЫСОТНЫ) УСЛОВИЙ НА ИСПЫТАТЕЛЬНЫХ СТЕНДАХ Компрессоры и силовые приводы к ним При выборе типа и конструкции компрессора учитываются его производительность, мощность привода, желаемый КПД, вопросы эксплуатации регулирования, смазки, конструкции подшипников и, прежде всего, вопросы, связанные со стоимостью изготовления, сроком службы машины, размерами единицы оборудования (компрессор + привод), ремонтопригодностью [42]. Центробежные компрессоры с односторонним всасыванием имеют производительность до 50 кг/с, а с двухсторонним всасыванием — до 85 кг/с; регулирование производительности центробежных компрессоров осуществляется изменением частоты вращения, дросселированием, поворотом лопаток направляющего аппарата. Дросселированием на входе или на выходе можно изменять объем засасываемого воздуха при постоянном его давлении на выходе. Дросселирование — менее выгодный способ регулирования, чем регулирование изменением частоты вращения, так как сопротивление в дросселе приводит к дополнительным потерям мощности. Важным преимуществом дросселирования входа в компрессор является удаление границы помпажа и возможность работы при меньших значениях расхода, чем при дросселировании выхода. Регулирование поворотом направляющих лопаток значительно расширяет рабочую область компрессоров. Стационарные осевые компрессоры обеспечивают более высокую производительность, чем центробежные, до 100. . . 120 кг/с при степенях повышения давления 6. . . 8 и КПД 85. . . 92 %. Способы регулирования осевых компрессоров аналогичны способам регулирования центробежных.
При необходимости подачи большого количества воздуха при небольшом (до 600 к. Па) или среднем (до 1500 к. Па) давлении применяются осевые компрессоры, приводимые в движение от турбины. На компрессорных станциях испытательных стендов более широкое распространение получили агрегаты производительностью 70. . . 120 кг/с, группа которых и составляет компрессорную станцию. Подключая разное количество единичных агрегатов (или групп) к общему воздушному коллектору, от которого питается потребитель или несколько потребителей, можно обеспечить работу стендов в необходимых пределах G B , р* в. В зависимости от необходимости получения большого напора, большой производительности или того и другого вместе параллельно или последовательно подключаются к сети и целые агрегаты или группы агрегатов. Рис. 7. 13. Общий вид компрессорного зала
На рис. 7. 13 показан общий вид компрессорного зала НИЦ ЦИАМ. Применение компрессоров среднего давления позволяет уменьшить размеры трубопроводов, упрощает их монтаж, но усложняет конструкцию холодильников, запорно-регулирующей арматуры. Компрессоры оборудуются системами противопожарной защиты, регулировочными устройствами с целью получения пологой характеристики. Существует много схем применения серийных авиационных ГТД в качестве воздуходувок. Наиболее типичными из них являются следующие [51 J. Воздуходувка на базе ГТД с отбором воздуха за компрессором (рис. 7. 14). У серийного ТРД заменяется сопло на диффузорный насадок с целью увеличения перепада давления на турбине и увеличения ее мощности. В кожухе камеры сгорания симметрично вырезают окна для отбора воздуха, чтобы не вызвать Рис. 7. 14. Принципиальная схема воздуходувки, выполненной на базе серийного авиационного ГТД, с отбором воздуха за компрессором: 1 — ТРД с отбором воздуха за компрессором; 2 — перепуск воздуха в атмосферу; 3 — камера сгорания; 4 — измеритель расхода воздуха; 5 — теплообменник
Рис. 7. 15. Схема подключения ГТД в качестве генератора газа к турбокомпрессорному агрегату: 1 — компрессор-воздуходувка из ступеней серийного двигателя; 2 — приводная труба; 3 — серийный ГТД-газогенератор увеличения окружной неравномерности температурного поля перед турбиной. Снимают самолетные агрегаты, не используемые в работе. Лучшее согласование работы компрессора и турбины, а также увеличение производительности (до 30 %) достигается при снятии лопаток с нескольких последних ступеней компрессора. Использование серийного ГТД в качестве генератора газа для турбокомпрессо ра. В этой схеме (рис. 7. 15) газ, отбираемый за турбиной ГТД, направляется в турбокомпрессорный агрегат такого же или другого по конструкции газотур бинного двигателя. Практически можно подобрать такой набор ступеней ком прессора серийных двигателей, который возможно без редуктора приводить се рийной одноступенчатой газовой турбиной. Экономические показатели схемы с использованием ГТД в качестве генератора газа лучше, чем у ТРД с отбором воздуха за компрессором. Использование в качестве воздуходувки второго контура ТРДД с точки зрения экспериментального оборудования — законченный вариант низкона порной воздуходувки, с параметрами во многих случаях достаточными для ис пытания ГТД с наддувом на входе в двигатель.
При незначительном дооборудо вании, обеспечивающем изменение количества газа, подмешиваемого от пото ка внутреннего контура в поток внешнего контура, можно обеспечить требуемый подогрев. На рис. 7. 16 показана схема использования ТРДД для подачи подогретого и сжатого газа на испытания ГТД. Количество подаваемого воздуха и его давление обеспечиваются подбором режима работы двигателя по частоте вращения, температура — подмешиванием горячих газов внутреннего контура Рис. 7. 16. Принципиальная схема воздуходувки на базе ТРДД: I — ТРДД-воздуходувка; 2 — эжектор; 3 — отвод внутренней струи
Подогрев воздуха на входе в двигатель осуществляется одним из следующих способов [37]: • в воздухоподогревателях рекуперативного типа (теплообменниках). Предельная температура нагрева t т ах ≈600°С; • в электроподогревателях сопротивления (омических) до температуры t т ах ≈ 800°С; • в регенеративных подогревателях (кауперах) до температуры W* 2000°С; • в «огневых» подогревателях непосредственным сжиганием топлива в потоке до температуры t т ах ≈ 2000. . . 2200°С; • в электродуговых подогревателях постоянного или переменного тока — плазмотронах — при температуре нагрева более 2200 °С. Электроподогреватели этих типов имеют ограничения как по расходу, так и по давлению воздуха. Для установок кратковременного действия могут использоваться и другие способы нагрева — адиабатического сжатия, электроразрядный, в ударной волне и др. Работа подогревателей в условиях испытательного стенда характеризуется высокой цикличностью (100. . . 150 запусков из холодного состояния в год), изменениями режима работы в течение одного цикла испытаний, что существенно ужесточает температурно-напряженное состояние элементов конструкции. Электроподогреватели сопротивления малоинерционны, выгодно отличаются своей компактностью, обеспечивают чистый (без загрязнения потока) нагрев воздуха. Существует многомодульная система электроподогрева воздуха на стенде Ц-5 -4 ЦИАМ: подогрев от 0 до 700 °С, электрическая мощность 20 МВт с диапазоном регулирования (5. . . 10 %) N max.
Для исследований ГПВРД требуется моделирование условий полета соответственно М = 5. . . 8, то есть с подогревом воздуха до температуры 1200. . . 2500 К. Подогрев воздуха до такой температуры может быть осуществлен сжиганием газообразного или жидкого топлива непосредственно в потоке воздуха в огневом подогревателе. С этой точки зрения наиболее подходящим горючим является газообразный водород (высокое теплосодержание, минимальное загрязнение). Существует огневой подогреватель на газообразном горючем (метан или водород). Подогреватель имеет кислородный смеситель на входе, сменные фронтовые устройства подачи метана или водорода, а система охлаждения силового корпуса выполнена комбинированной — воздухом и водой. Конструкция рассчитана на рабочее давление до 10 МПа при нагреве до 2000 К с расходом около 20 кг/с. Фильтрация воздуха Воздух, поступающий к двигателям, должен иметь определенную концентрацию механических примесей. Улавливание частиц происходит в электростатических фильтрах с использованием коронного разряда. Проходя около коронируюших электродов, частицы заряжаются, оседают на электродах с напряжением другого знака (собирающие электроды), с которых они удаляются [42]. Увлажнение воздуха проводится для оценки влияния присутствия атмосферной влаги на параметры двигателя (на точность приведения измеренных параметров к САУ). Увлажнение воздуха может производиться впрыском воды через форсунки с достаточной мелкостью распыла. Более распространенной и удобной является подача водяного пара в воздушный поток с необходимым расходом [42].
Осушка воздуха При испытаниях необходимо обеспечить подачу воздуха с влагосодержанием, соответствующим заданной высоте полета. С увеличением высоты содержание влаги уменьшается. Например, если на уровне земли содержание влаги составляет d = 5 г/кг и более, то на высоте 12. . . 16 км d = 0, 02 г/кг [26|. Осушка воздуха может производиться путем вымораживания влаги или поглощением ее адсорбентом. Вымораживание влаги производится при резком охлаждении воздуха, истекающего из сопла или проходящего через холодильную турбину. При этом происходят выделение и конденсация воды, которая отделяется от потока в сепараторах. При осушке с помощью адсорбентов воздух пропускается через влагопоглощающие колонки. В качестве адсорбента используются силикагель — диоксид кремния, алюмогель — оксид алюминия и другие гидрофильные вещества. Установка состоит из нескольких колонок, наполненных адсорбентами. Колонки включаются поочередно. В отключенные колонки подается нагретый воздух. При этом влага из поглотителя удаляется. Охлаждение воздуха На высотных стендах применяются холодильные устройства, различные по принципам работы и схемам подключения. Широко используемые установки Для непрерывного охлаждения осушенного сжатого воздуха в расширительной турбине, позволяющие получать воздух с температурой -70 °С на выходе, могут оказаться недостаточно производительными. Применяются схемы с использованием вторичного хладоносителя, например соляного раствора, разбрызгиваемого в потоке воздуха. Воздух, соприкасаясь с раствором, охлаждается. Соляной раствор охлаждается в испарителе фреоновой холодильной установки компрессорного типа. Влага, выпадающая из охлаждаемого воздуха и переходящая в раствор, выпаривается из него в выпарных устройствах, после чего соляной раствор снова поступает в охладитель [41].
Для охлаждения воды используются градирни. Создаются мощные водонасосные станции. Метод охлаждения воды в бассейнах применяется редко из-за больших потребных площадей поверхности воды. Чаше испытательные комплексы располагают около достаточно крупных естественных водоемов, служа щих одновременно хранилищем и охладителем воды. Примеры. Поверхность водохранилища (НИЦ им. Арнольда. США) составляет 2835 га, вместимость 1. 010 х м\ Вода для потребителей подается насосами в количестве до 9, 5 м 3 /с при давлении р = 0. 4 МПа. Для нужд установок фирмы SNECMA построены специальные емкости, содержащие 650 м ? технической и 250 м 3 питьевой воды. На рис. 7. 17 показана принципиальная схема двухступенчатого фреонового холодильного турбоагрегата. Рис. 7. 17. Холодильная установка: И 1, И 2 — испарители; КД — конденсатор; ПС — стабилизатор давления; ИЖ — инжектор; ЭД — электродвигатель; ПП — редуктор; ПО — промежуточный охладитель; КМ — компрессор и холодильная турбина; I. II — ступени компрессора
Пары холодильного агента из двух низкотемпературных испарителей И 2 последовательно сжимаются в первых двух колесах (ступенях) компрессора КМ и затем направляются в промежуточный сосуд ПС для охлаждения. Далее они вместе с парами, отсасываемыми из низкотемпературного испарителя И 1, сжи маются в следующих двух колесах (ступенях) компрессора. Таким образом, компрессор разделен на две секции, каждая из которых состоит из двух колес и имеет отдельные всасывающий и нагнетательный патрубки. Первые два колеса образуют низкотемпературную ступень компрессора, а последующие два — высокотемпературную. Пример. Холодильно-осушительная станция (ХОС) ЦИАМ предназначена для охлаждения воздуха с расходом до 360 кг/с от температуры 40 °С до температуры -35 “С при Давлении 300 к. Па. При этом производится его осушение от начального влагосодержания 16 г/кг до конечного 0. 06 г/кг сухого воздуха. Охлаждение и осушка воздуха осуществляются с помощью парокомпрессорной холодильной машины, работающей на фреоне-22 по циклу двухступенчатого сжатия и расширения. Для охлаждения и конденсации паров фреона используется оборотная с начальной температурой 27 °С. Воздух охлаждается последовательно в двух воздухоохладителях — высокотемпературном и низкотемпературном. Хладоносителем в высокотемпературном воздухо охладителе является водный раствор этиленгликоля, в низкотемпературном — рассол Са. Сl г Холодильно-осушительная станция работает в следующих режимах подачи холодного воздуха: • подача сжатого воздуха к ХОС от компрессоров агрегатов ТХА-1 А, ЗА и 4 А ВКС с давлением 300 к. Па и расходом до 360 кг/с. Турбохолодильный агрегат ТХА-1 А со стоит из 11 -ступенчатой компрессорной секции и одноступенчатой холодильной турбины. После охлаждения в холодильниках и регенераторах сжатый воздух с температурой -30 °С поступает на вход в стенды;
• последовательная работа ХОС и холодильных турбин агрегатов ТХА-1 А, в которых за счет расширения от давления 300 к. Па до 140 к. Па осуществляется снижение температуры с -30 °С до -(60. . . 70) °С. В этом случае при работе 4 -х секций ХОС и работе 4 -х агрегатов ТХА-1 А обеспечивается подача воздуха на стенды с расходом 360 кг/с при давлении 140 к. Па и температуре -60 °С. Выхлопные системы высотных стендов и системы отсоса выхлопных газов Выхлопные газы ВРД на высотном стенде либо выбрасываются непосредственно в атмосферу при имитации режимов работы на земле (Н = 0), либо посту пают в эксгаустеры, обеспечивающие отсос выхлопных газов с разрежением при имитации высотных режимов полета (Н > 0). Система удаления выхлопных газов содержит комплекс технических устройств (рис. 7. 18). Эксгаустеры для отсоса выхлопных газов являются разновидностью компрессоров. Они служат для отсоса и «дожимания» выхлопных охлажденных газов от давления р н 101, 33 к. Па ( р э — статическое давление газа за эксгаустером; р э ≈ 121, 5 к. Па с учетом потерь давления в выхлопном тракте стенда [42]). Выхлопная система включает в себя стендовый диффузор, устанавливаемый непосредственно за реактивным соплом ГТД, стендовый выхлопной га зопровод, стендовый водогазовый холодильник, охлаждающий газы до температуры 300. . . 350 °С, выхлопную шахту с элементами шумоглушения, через которую выхлопные газы выбрасываются непосредственно в атмосферу, и систему отсоса газов эксгаустерами с предварительным охлаждением в секционных холодильниках до температуры +(40. . . 50) °С. Из эксгаустеров выхлопные газы через выхлопную шахту с шумоглушением выбрасываются в атмосферу.
Регулирование разрежения на выходе из двигателя достигается посредством газовых дросселей системы автоматического регулирования режима испытаний, установленных на входе в эксгаустеры, а также подбором количества работающих на отсос от стенда секций эксгаустерных машин и технологической схемой их подключения [37]. Большие расходы (300 кг/с и более) и высокие температуры (до 2000 К на форсированном режиме) выхлопных газов создают серьезные технические проблемы при разработке, создании и эксплуатации выхлопных систем высотных стендов. Рис. 7. 18. Схемы подключения машин компрессорно-эксгаустерной станции, работающих на переменном и постоянном расходах: 7 — воздухозаборная шахта с шумоглушением; 2 — компрессор; 3 — фильтр воздушный (электростатический); 4 — водовоздушный холодильник; 5 — осушитель (холодильник); 6 — Расширительная турбина; 7 — загрузочный агрегат турбины; 8, 10, 13, 16 — регулировочные Устройства; 9 — смеситель; 11 — ТБК (рабочий участок): 12 — газоводяной холодильник,
На высотных стендах, не имеющих эксгаустеров с силовым приводом, эжекторы различных схем и конструкций используются для создания разрежения в зоне сопла двигателя, имитирующего высотные режимы. В любом типе эжектора имеются следующие элементы: сопло высоконапорного газа; смесительная камера; диффузор (для стендовых эжекторов). Для стендовых эжекторов диффузор необходим, так как на выходе из эжектора и в начале камеры смешения для создания высотности давление р Н <101, 33 к Па, а выброс газов производится в атмосферу, в среду с повышенным давлением. На рис. 7. 19, а [42] приведена схема эжектора при наличии на стендах вспомогательного компрессора (ТРД с отбором воздуха из-за компрессора, воздуходувки, выполненной на базе ТВД и устанавливаемой вместо винта). Возможен вариант применения вихревого эжектора (рис. 7. 19, б). Если источник сжатого воздуха обеспечивает достаточную величину расхода и давления. Рис. 7. 19. Схема эжекторов для создания разрежения на срезе сопла а -1 -Двигатель; 2 — эжектор; 3 — сопло; 4 — диффузор; 5 — подогреватель; б – 6 — вихревой эжектор
Рис. 7. 20. Схема двухступенчатого эжектора: 1, 3 — эжектор первой и второй ступеней; 2, 4 — камера смешения первой и второй ступеней; 5 — диффузор; 6 — перфорированный щелями участок сопла первой ступени; 7 — сопло первой ступени то может применяться двухступенчатый эжектор (рис. 7. 20). Камеры смешения эжекторов выполняются цилиндрическими, реже коническими. Длина камеры смешения L = (2. . . 8 )D. При создания разрежения на срезе сопла с помощью компрессора и эжектора мощность привода компрессора может оказаться выше, чем мощность привода эксгаустера, создающего одинаковое с эжектором разрежение. Подогрев воздуха, идущего в эжектор, до температуры газов, выходящих из сопла, снижает мощность привода компрессора. Схема создания разрежения с помощью эжектора и компрессора целесообразна для малоразмерных ГТД с расходами воздуха 20 кг/с. Для ГТД с большими расходами требуется очень большая мощность привода компрессора. Возможно применение паровых эжекторов, комбинированных схем для получения разрежения. В качестве рабочего тела эжекторов используются различные вещества, в том числе воздух и пар.
Система обеспечения паром двух ступеней сверхзвукового эжектора с расходом 160 кг/с в течение 60 с содержит [56): • котел с водяными трубами (давление 4, 3 МПа, температура пара 254, 8 °С, максимальная нагрузка 6 т/ч); • топливную систему (емкость с дизельным топливом 25 м 3 ); • систему подачи воды (необходимое количество воды 120 м 3 ); • аккумулятор пара переменного давления 1, 7. . . 4, 2 МПа (четыре емкости по 106 м 3 каждая) и высотой отбора пара 0, 3 м; • устройство подачи пара с аварийной системой функционирования основ ного и отсечного паровых клапанов, состоящей из гидропроводов с гидроаккумуляторами.
7. 3. КРАТКАЯ ХАРАКТЕРИСТИКА ОТЕЧЕСТВЕННЫХ ВЫСОТНЫХ СТЕНДОВ Экспериментальные исследования ГТД в высотно-скоростных и климатических условиях в основном проводятся на стендах ЦИАМ. В совокупности комплекс этих стендов обеспечивает уникальные возможности для испытаний на земле натурных двигателей в условиях, максимально приближенных к реальным полетным, чем обеспечиваются безопасность и снижение затрат на доводку двигателей. По своей мощности и широте воспроизводимых условий комплекс не имеет аналогов в Европе и сопоставим с комплексом испытательного Центра им. Арнольда в США. Рис. 7. 21. Стенд Ц-4 Н (рис. 7. 21). По своим возможностям стенд не имеет аналогов в мире и предназначен для проведения разных видов испытаний авиационных двигателей (ТРДДФ и других ГТД), их газогенераторов, в том числе испытаний на переходных режимах работы, с имитацией динамики условий полета и неоднородности потока воздуха на входе. Число измерительных каналов — 1200. На рис. 7. 22 приведена схема стенда Ц-4 Н с универсальным имитатором и двигателем. Стенд включает в себя термобарокамеру с установленным в ней на динамометрической платформе испытываемым двигателем, входной ресивер, где с помощью смешения поступающего в него воздуха из
источников с различной температурой и давлением создается поток с требуемыми характеристиками для заданных имитируемой высоты и скорости полета. Для создания неоднородности потока, соответствующей неоднородности на выходе из реального воздухозаборника, в присоединенном к двигателю трубопроводе установлено устройство — генератор неравномерности и пульсация потока. Температура воздуха, подаваемого во входной ресивер, может изменяться от -60 °С до +600 °С при максимальном давлении до 588 Па (6 кгс/см 2 Расход подаваемого воздуха в зависимости от режима испытаний может достигать до 600 кг/с в наземных условиях и 250 кг/с на высоте 11 000 м. Выхлопные газы из сопла двигателя отводятся из барокамеры, где давление поддерживаете равным высотному, через стендовый холодильник газов и затем поступают эксгаустерный контур высотной станции и выбрасываются в атмосферу. В управление регулирующими органами стенда обеспечивается тремя микропроцессорами. Стенд оснащен автоматизированной системой сбора, обработки и отображения информации на установившихся, переходных и динамических режимах. На стенде проводятся испытания в термобарокамере ТРД в составе силовой установки при обдуве ее дозвуковым потоком с помощью специального стендового сопла, устанавливаемого на выходе из ресивера. Стенд Ц-1 А (рис. 7. 23) обеспечивает имитацию условий полета в то же диапазоне высот и скоростей, что и стенд Ц-4 Н. Однако имеет два cущественных отличия от других высотных стендов: у него значительные большие объемы ресивера и термобарокамеры и лучшие аэродинамические характеристики при больших расходах воздуха. Поэтому на нем преимущественно испытываются по обычной схеме с присоединенным воздухопроводом двигатели с большой степенью двухконтурности класса тяг до 250. . . 400 к. Н.
Рис. 7. 22. Схема стенда Ц-4 Н с универсальным имитатором и двигателем
Рис. 7. 23. Стенд Ц-1 А Стенд позволяет проводить высотные испытания авиационных силовых установок в полной компоновке с воздухозаборником с обдувом сверхзвуковым потоком. Для этого имеется стендовое регулируемое аэродинамическое сопло с площадью выходного сечения 3, 6 м 2 , диапазоном изменена скорости потока, соответствующей числу М = 1, 9. . . 2, 6, и возможностью и: менять углы атаки и скоса потока в пределах 6°. Размеры барокамеры стенда Ц-1 А и энергетические возможности компрессорной и холодильно-осушительной станции позволяют проводить испытания ТВД с винтами диаметром 4. . . 5 м на пусковых режимах в широком диапазоне климатических наземных условий.
Стенд Ц-3 (рис. 7. 24) предназначен для исследовательских и доводочных испытаний полноразмерных компрессоров одноконтурных и двухконтурных, одно- и двухвальных ГТД в наземных условиях и с имитацией условий полета. При испытаниях двухвальных компрессоров обеспечивается спутное или про тивоположное вращение роторов. Экспериментальные возможности стенда характеризуются следующими параметрами: • давление на входе 0, 00. . . 0, 3 МПа; • температура на входе -50. . . 250 °С; • расход воздуха 360 кг/с; • максимальный диаметральный размер испытываемого компрессора 2, 5 м; • максимальная частота вращения ротора (без применения ускорительного редуктора) 12 000 1/м; максимальная мощность, подаваемая на валы компрессора, 37 МВт (после модернизации стенда — 67 МВт). Группа стендов Ц-5 (рис. 7. 25) предназначена для исследовательских и доводочных испытаний камер сгорания ГТД, а также отсеков и моделей камер сгорания. Стенды оснащены оборудованием, включая быстродействующий газоанализатор, тепловизионную технику, средства для измерения полей давления и температуры в высокотемпературных газовых потоках. На стендах есть системы «чистого» подогрева воздуха, а стенд Ц-5/1, имеющий два независимых контура подачи воздуха к камере сгорания, дополнительно оснащен огневым подогревателем для создания эксплуатационного газа при испытании форсажных и промежуточных камер сгорания. Имеется система подогрева и охлаждения жидкого топлива. Предельные параметры стендов группы Ц-5 сведены в табл. 7. 2.
Рис. 7. 24. Стенд Ц-3 Рис. 7. 25. Стенд Ц-
Параметры Стенд Ц-5/1 Стенд Ц-5/2 Стенд Ц-5/4 Первый контур Второй контур Расход воздуха, кг/с <200 <100 <60 <10 Давление воздуха на входе, МПа 0, 02. . . 0, 9 0, 02. . . 0, 8 0, 02. . . 2 Температура воздуха на входе, К 200. . . 950 220. . . 620 250. . . 110 250. . . 720 Давление газа на выходе, МПа 0, 005. . . 0, 1 Температура газа на выходе, К < 23007. 2. Параметры стендов группы Ц-5 Испытания можно проводить с использованием керосина, дизельного топлива, а на стенде Ц-5/4 — и природного газа. Стенд Ц-16 К (рис. 7. 26) предназначен для испытаний камер сгорания высокого давления с расходом воздуха до 10 кг/с, позволяющий проводить испытания отсеков камер сгорания при давлении до 5 МПа на жидких и газообразных горючих — керосине, дизельном топливе, метане, водороде. Стенд имеет электрический подогреватель воздуха с максимальной температурой 1000 К. Помимо исследования характеристик рабочего процесса (полноты сгорания, эмиссионных характеристик, теплового состояния, вибрационного горения) на стенде можно проводить исследования характеристик запуска камеры сгорания в высотных и климатических условиях. Необходимое разрежение в камере сгорания создается эжектором кратковременного действия, а пониженная температура — системой охлаждения жидким азотом. Стенд Ц-16 ВК. Это — самый крупный из гиперзвуковых стендов. Диаметр выходного сечения его аэродинамического сопла 0, 5 м. В качестве горючего для ГПВРД используются керосин и газообразный водород с расходом до 1 кг/с.
Максимальная температура воздуха на входе в аэродинамическое сопло стенда 2300 К, давление 5 МПа, что обеспечивает скорость потока воздуха на выходе из сопла, соответствующую М = 7. Стенд позволяет проводить испыта ния ГПВРД таких же размеров, как и на российской аэродинамической летающей лаборатории. Рис. 7. 26. Стенд Ц-16 К Стенд Ц-17 (рис. 7. 27) предназначен для исследования полноразмерных камер сгорания на природном газе при давлении воздуха до 2 МПа. Обеспечивает расход природного газа до 3. . . 4 кг/с при давлении 4 МПа в течение нескольких часов. Имеет в своем составе два испытательных бокса: один — для испытаний прямоточных ВРД, газогенераторов и камер сгорания, второй — для газотурбинных установок со свободной турбиной и электрогенератором мощностью 20 МВт. Стенд ТС-2 (рис. 7. 28) предназначен для исследования и доводки турбин авиационных двигателей. Испытания турбины могут проводиться на «чистом» подогретом воздухе или в компоновке со штатной камерой сгорания
Рис. 7. 27. Стенд Ц-17 Рис. 7. 28. Стенд ТС-2 (рис. 7. 28) предназначен для исследования и доводки турбин авиационных двигателей. Испытания турбины могут проводиться на «чистом» подогретом воздухе или в компоновке со штатной камерой сгорания. Стенд ха рактеризуется следующими параметрами: • максимальное давление воздуха на входе 2, 2 МПа; температура воздуха на входе (при «чистом» подогреве) до 900 К; • расход воздуха на внешний обдув модели 5 кг/с; • давление воздуха на входе в модель 1 МПа.
Стенд Ц-22 представляет собой дозвуковую аэродинамическую трубу эжекторного типа с открытой рабочей частью и предназначен для: • испытаний полноразмерных силовых установок (иногда в компоновке с элементами планера самолета) на режимах взлета, посадки при скоростях набегающего потока воздуха до 100 м/с; • испытаний авиационных силовых установок в условиях обледенения; • исследования газодинамической устойчивости двигателей в условиях неравномерности поля температур потока воздуха на входе. Аэродинамическая труба имеет сменные выходные сопла с площадями проходного сечения 25, 36 и 70 м 2. Расход воздуха достигает 4700 кг/с. Максимальная скорость воздушного потока в рабочей части стенда 100 м/с; при этом неравномерность поля скоростей не превышает 2 %. При испытаниях в условиях повышенной водности и в условиях обледенения в воздушный поток впрыскивается вода с диаметром капель 30 мкм, содержание капельной влаги в воздухе может составлять 2, 5 г/м 3. Стенды УВ-ЗК и У-9 М предназначены для испытаний малоразмерных ТВД, ТВВД, ТРД и ТРДД в высотно-климатических условиях Н = 0. . . 10 км, М = = 0. . . 1, 5 и Т т = 70. . . 120°С. Стенды У-ЮМ и У-7 М предназначены для испытаний ТРД и ТРДД в условиях различных климатических зон земного шара от арктических до сухих и влажных тропиков ( Т в = -70. . . +70 °С), а также в условиях высокогорных аэро дромов (Н = 0. . . 6 км).
РЕЗЮМЕ (по главе 7 «Испытания авиационных ГТД с имитацией эксплуатационных условий» ) 1. В общем объеме работ по доводке новых или улучшенных модификаций серийных авиационных ГТД доминирующую роль играют испытания на высотных стендах с имитацией условий, максимально приближенных к условиям эксплуатации. 2. Высотные испытания проводятся на базе больших комплексов с применением специального оборудования. Эти комплексы имеют сложные системы, дорогостоящее оборудование, требуют больших площадей, а их строительство и эксплуатация связаны с огромными капитальными затратами. Создание испытательных установок может оказаться сложной и более трудоемкой задачей, чем создание нового двигателя. 3. Преимуществом испытаний на высотных стендах по сравнению с испытаниями на летающих лабораториях и на самолетах является возможность размещения большого количества контрольно-измерительной аппаратуры, что обычно вызывает затруднения при летных испытаниях. Кроме этого, программа испытаний на высотной установке может быть задана в более широком диапазоне режимов по сравнению с испытаниями на летающей лаборатории. 4. Во время испытаний на высотных стендах удается выявить, исследовать и устранить большое количество дефектов: за 3. . . 4 года доводки нового двигателя число доработок достигает 30. . . 40, прежде чем он становится пригодным для полетов. 5. При использовании высотных стендов удается значительно сократить сроки разработки двигательных установок, добиться оптимизации их характеристик и существенно уменьшить риск летных испытаний.
6. Испытания с частичной имитацией высотно-скоростных условий применяются в заводских условиях для двигателей, предназначенных для сверхзвуковых ЛА. 7. Центробежные и осевые компрессоры применяются для организации подачи больших расходов воздуха. В качестве воздуходувок применяют также серийные авиационные ГТД с небольшой доработкой. 8. Подогрев воздуха, идущего на высотный стенд, осуществляют с помощью теплообменников и электронагревателей. Высокие температуры достигаются в регенеративных, «огневых» и электродуговых подогревателях. 9. Для охлаждения воздуха используют расширительные турбины (турбодетандеры), испарительные устройства на основе солевого раствора, фреоновые холодильные агрегаты. 10. Для создания высотных условий и удаления выхлопных газов используют разновидность осевого компрессора — эксгаустер. При относительно небольших расходах возможно применение эжекторных схем. 11. После того как двигатель сдан в эксплуатацию, испытания на высотных стендах продолжаются в течение ряда лет для устранения дефектов, которые обнаруживаются в эксплуатации, для проверки усовершенствования элементов двигателя, доводки его модификаций и проверки различных вариантов применения.
ВОПРОСЫ 1. В чем преимущества и недостатки испытаний ГТД на высотных стендах и летающих лабораториях? 2. Какова технология проведения испытаний ГТД на высотных стендах? 3. Какие три основных способа используются для проведения испытаний ГТД в высотных условиях? 4. Каковы особенности проведения высотных испытаний в аэродинамической трубе? 5. В каких случаях проводятся испытания ГТД по схеме с присоединенным трубопроводом? 6. Каким образом проводятся испытания с частичной имитацией высотноскоростных условий? 7. Чем обусловлена необходимость проведения испытаний ГТД с самолетным воздухозаборником? 8 — В чем особенности проведения высотных испытаний ПВРД и ГПВРД? 9. Каким образом обеспечивается подготовка воздуха, подаваемого в ТБК? 10. Какие схемы воздуходувок на базе серийных ГТД Вам известны? 11. Какие способы подогрева воздуха для высотных испытаний Вам известны? 12. Каким способом обеспечиваются увлажнение, осушка и охлаждение воздуха? 13. Каким образом располагается испытуемый двигатель в ТБК? 14. Каким образом создаются высотные условия за соплом испытуемого двигателя? 15. Какие из отечественных высотных стендов Вам известны и каково их назначение?
Глава 8 ЭКСПЕРИМЕНТАЛЬНЫЕ МЕТОДЫ ОПРЕДЕЛЕНИЯ РЕСУРСА И НАДЕЖНОСТИ АВИАЦИОННЫХ ГТД 8. 1. ЭКСПЛУАТАЦИОННЫЕ КРИТЕРИИ НАДЕЖНОСТИ АВИАЦИОННЫХ ГТД Обеспечение надежности, безопасности и живучести современных самолетов и двигателей является важной задачей, в решении которой принимают участие специалисты НИИ, ОКБ, заводов и эксплуатирующих организаций. Условно в проблеме надежности можно выделить два направления: обеспечение надежности и ее расчет (контроль). Если первое направление основывается на решении традиционных конструкторских и технологических задач по созданию высококачественных изделий и правильной их эксплуатации, то второе связано в основном с применением специальных математических методов. Очевидно, что обеспечить высокую надежность изделия желательно на ранних этапах его создания, поскольку устранение конструкторских просчетов, снижающих надежность изделия, на этапе опытной отработки требует на порядок больших затрат, чем при проектировании, а при доработке серийных образцов в условиях эксплуатации расходы возрастают на два-три порядка. В целом успешное решение проблемы повышения надежности летательных аппаратов и двигателей возможно за счет совершенствования методов конструирования и расчетов, проектирования на заданные ресурс и надежность, широкого привлечения средств автоматизированного проектирования, разработки нормативных документов и контрольно-диагностических средств, регламентирующих
испытания, производство и эксплуатацию техники. При создании самолета Ил-86 впервые были применены количественные показатели надежности, безопасности и эксплуатационной технологичности. Решалась задача по обеспечению следующих показателей: • вероятности отказа (из расчета на 1 ч полета), приводящего к опасной (сложной) ситуации Qoc= 10 , что равносильно налету в среднем в 10 000 летных часов (л. ч) на одну такую ситуацию; • вероятности отказа, приводящего к аварийной ситуации, Qac= 10 • наработки на один отказ, приводящий к невыполнению полетного задания, не менее 5000 л. ч. ; • коэффициента задержки вылетов — 2 задержки на 100 вылетов; • трудоемкости технического обслуживания — не более 20 ч на 1 ч налета самолета; • времени подготовки к вылету — не более 30 мин; • среднего годового налета — 2500. , . 3000 л. ч; • ресурса самолета — 40 000 л. ч. Надежность и ресурс ГТД являются составляющими более общего показателя ГТД — качества. В широком смысле надежность двигателя определяется его безотказностью, ремонтопригодностью, сохраняемостью и долговечностью. Безотказность — свойство изделия непрерывно сохранять работоспособность в течение всего заданного срока службы в заданных условиях эксплуатации. Ремонтопригодность — это приспособленность изделия к восстановлению его исправного состояния и к поддержанию заданных сроков службы путем обнаружения и устранения неисправностей и предупреждения отказов.
Сохраняемость — это свойство объекта сохранять обусловленные показатели в течение срока хранения и после него, а также при транспортировке. Долговечность — это свойство изделия сохранять работоспособное состояние при установленной системе технического обслуживания и ремонтов до некоторого предельного состояния, которое обуславливается либо экономическими показателями, либо требованиями безопасности. Под надежностью авиационных ГТД чаще всего понимают только узкое понятие — его безотказность. Для количественной оценки безотказности применяют следующие показатели: • вероятность безотказной работы; • среднюю наработку на отказ для восстанавливаемых и среднюю наработку до отказа — для невосстанавливаемых изделий; • параметр потока отказов для восстанавливаемых и интенсивность отказов — для невосстанавливаемых изделий. Вероятность безотказной работы — это вероятность того, что время безотказной работы г от окажется больше заданного времени t (рис. 8. 1): Pit = Bep{t 0 T >t}. (8. 1) Функцию P(t) иногда называют просто надежностью. Вероятностью отказа называется, соответственно, функция
Рис. 8. 1. График функций P(t) и Q(t) Рис. 8. 2. График плотности вероятности отказов f(t)
Отношение величины вероятности отказа в малом интервале (t, t+ Δt) к продолжительности этого интервала является одной из важных характеристик надежности — плотности вероятности отказов f(t) (рис. 8. 2): (8. 3) Вероятность отказа за время t есть интеграл от f(t), взятый для интервала от 0 до t. (8. 4) Если величину ΔN o т (t, t +Δt), т. е. число отказов в малом интервале (t, t+ Δ t), разделить на число N H (t) безотказно проработавших до начала этого интервала. то получим величину Δ N oт (t, t + Δ t )/N H (t) — вероятность отказа в интервале (t, t+ Δ t) изделий, благополучно доработавших до начала этого интервала. Если взять отношение этой величины к продолжительности интервала, то получим важнейшую и очень распространенную характеристику надежности — интенсивность отказов (для невосстанавливаемых изделий): (8. 5) Все рассмотренные выше характеристики надежности на практике определяются путем обработки статистических данных, которая достаточно трудоемка. Поэтому наряду с ними используют такие критерии надежности, как наработка на отказ восстанавливаемого и наработка до отказа невосстанавливаемого изделия.
Для восстанавливаемых объектов наработка на отказ определяется как отно шение наработки объекта к математическому ожиданию числа его отказов в те чение этой наработки. Для невосстанавливаемых объектов применяется показатель средней наработки до отказа, который определяется как математическое ожидание наработки объекта до первого отказа. Наработка на отказ означает, что в течение этого времени вероятно появление одного отказа, приводящего к нарушению работоспособности самолета или двигателя. Широкое распространение получили такие показатели надежности двигателей, как: • наработка на один отказ, приводящая к выключению двигателя в полете (Т оп ); • наработка на отказ, приводящая к необходимости досрочного съема двигателя с самолета ( Т дсд )- Отказы как случайные события с позиций применения законов теории вероятностей по характеру проявления делятся на: • постепенные и внезапные; • совместные и несовместные; • зависимые и независимые. Для количественной оценки долговечности используют такие показатели, ресурс и срок службы. Кроме рассмотренных выше показателей безотказности при обработке и анализе статистических данных по отказам авиационных двигателей, выявляемых в эксплуатации, применяют частные критерии, характеризующие количество отказов, приходящихся на 1000 ч наработки двигателей в полете: • коэффициент К 1000 оп характеризует общее количество отказов в полете, вызвавших нарушение работоспособности двигателя разновидностью этого коэффициента является коэффициент К 1000 вп , характеризующий количество отказов, явившихся в полете и повлекших за собой вынужденное или самопроизвольное выключение двигателя; • коэффициент К 1000 дсд характеризует количество отказов, приведших к довременному съему двигателей с летательного аппарата.
Коэффициенты К 1000 оп , К 1000 вп имеют большое значение для анализа безопасней полета, поскольку отказы и выключение двигателей могут привести к таким серьезным последствиям, как вынужденная посадка, невыполнение полетного задания или авиационное происшествие. Коэффициент К 1000 дсд позволяет оценивать трудозатраты и экономичность эксплуатации двигателей. Количественное определение указанных коэффициентов проводится по формулам: (8. 6) Т оп, Т вп, Т дсд — наработки на один отказ, определяемые соответственно по формулам: где t Σ — суммарная наработка i-го двигателя за рассматриваемый период эксплуатации или испытаний; N— общее количество рассмотренных однотипных двигателей (или двигателей одной модификации); N дсд — число досрочно снятых двигателей; п впΣ — число выключений двигателей в полете; n опΣ — общее количество отказов в полете всех двигателей данного типа за рассматриваемый период эксплуатации. С увеличением продолжительности эксплуатации двигателей происходит постоянное снижение коэффициентов К 1000 оп и К 1000 дсд.
Для практического использования результатов количественной оценки надежности принята следующая классификация отказов авиационных двигателей: • конструктивный отказ (отказ, обусловленный ошибками или недостатка при конструировании или несовершенством конструкции); • производственно-технологический отказ (отказ, обусловленный нарушениями (недостатками) принятого производственно-технологического процесса и его несовершенством); конструктивно-производственный отказ (отказ, вызванный как ошибками при конструировании, так и нарушениями (или несовершенством) производственно-технологического процесса); эксплуатационный отказ (отказ, вызванный нарушением правил эксплуатации и технического обслуживания). Кроме того, отказы могут наступать из-за плохого качества материала, попадания в двигатель посторонних предметов, низкого качества поставляемых агрегатов и покупных деталей. К числу недопустимых отказов, которые приводят к катастрофическим последствиям, относятся: • разрушение элементов роторов, обломки которых не удерживаются внутри корпуса (нелокализованные разрушения); • отказы, вызывающие повышенное содержание вредных примесей в воздухе, отбираемом для жизнеобеспечения экипажа; • нелокализованные пожары; • отказы, приводящие к возникновению отрицательной тяги; • отказы, исключающие возможность выключения двигателя.
Кроме общих требований по обеспечению безопасности полетов к авиаци онным двигателям предъявляются специальные требования по уровню их безотказности и долговечности, по топливно-экономической эффективности, т. е. по С уд , удобству и минимальным трудозатратам на техническое обслуживание и ремонт, уровню шума и эмиссии вредных веществ. Безотказность в работе у авиационных ГТД весьма высокая. Так, например, по статистике ИКАО из 100 % авиационных катастроф за последние 15 лет ме нее 10 % произошли из-за отказа двигателей. Для сравнения: согласно данным ИКАО за 1980. . . 1985 гг. , на пассажирских самолетах с ГТД всех авиакомпаний среднее число катастроф по всем причинам (ошибки пилотирования, отказы техники, метеоусловия и др. ) на регулярных пассажирских линиях составило 1 катастрофу на I млн полетных часов. При этом в среднем за год из общего числа всех причин 40 % катастроф произошли из-за отказов техники, в том числе 20 % — из-за отказов двигателей. Различают возможные и рациональные значения надежности и ресурса. На рис. 8. 3 показано увеличение затрат в производстве С пр и уменьшение затрат в эксплуатации С эк , формирующее в конечном итоге минимум суммарных расходов C Σ соответствующие оптимальные значения вероятности безотказной работы изделия Р орt. В начале производства двигатель имеет еще много сравнительно легко устранимых дефектов. Когда же надежность двигателя уже весьма высока, дальнейшее ее повышение становится все более трудным.
Рис. 8. 3. Изменение затрат в зависимости от вероятности безотказной работы двигателя Кривая же С эк характеризует тенденцию изменения эксплуатационных за трат в зависимости от надежности. Если двигатель очень надежен, потери из- за отказов невелики, и дальнейшее увеличение надежности дает уже незначительное снижение эксплуатационных расходов, т. е. экономический эффект от повышения надежности уменьшается по мере ее роста. Оптимальная величина ресурса определяется максимумом экономической эффективности, на которую влияет множество подчас противоречивых факторов. Так, например, если требуется существенная переделка двигателя для увеличения его ресурса, то при большом объеме производства и интенсивной эксплуатации затраты на опытно-конструкторские работы (ОКР) быстро окупаются. Если же программа производства невелика или годовая наработка двигателя небольшая, то затраты на ОКР могут не окупиться в течение многих лет. Влияют на экономическую эффективность работ по созданию модификации двигателя с повышенным ресурсом его цена, достигаемый в результате модифицирования прирост ресурса, коэффициент оборотного фонда двигателей в эксплуатации и другие факторы [3, 7]. Основными причинами выхода из строя двигателей являются: • несовершенство конструкции; • неудачная технология или нестабильность производства; • низкое качество или нестабильность материала; • дефекты комплектующих изделий (изделий смежников); • нарушение правил эксплуатации и обслуживания двигателей;
8. 2. МОДЕЛИ ПОВРЕЖДАЕМОСТИ (РАСХОДОВАНИЯ РЕСУРСА) ДЕТАЛЕЙ ДВИГАТЕЛЯ Повреждаемость двигателя — это свойство, определяющее способность конструкции воспринимать и накапливать повреждения в ее элементах от действия повреждающих факторов. Повреждаемость зависит от его конструктивной схемы ГТД, технологии изготовления и сборки, расположения ГТД на ЛА, системы эксплуатации, а также от вида и величины повреждающих факторов. Соотношения, связывающие параметры работоспособности элемента конструкции ГТД в момент разрушения с характеристиками материала, называют моделями разрушения. Эти модели на определенном уровне схематизируют сложный процесс разрушения, зависящий от действующих напряжений, свойств материала, характера нагружения, накопления повреждений и других факторов. Модели разрушения различаются в зависимости от условий и числа циклов нагружения, от свойств материала (пластичности или хрупкости). Модели разрушения (исчерпания ресурса) в практике авиадвигателестроения используются: • в качестве основного инструмента анализа на начальном этапе проектирования двигателя, когда определяются критические элементы конструкции, требующие повышенного влияния и дополнительного анализа с целью снижения риска проекта; • при расследовании причин отказа ГТД, когда необходимо знать условия разрушения материала элемента конструкции; • при разработке программ ускоренных испытаний, в которых исчерпание ресурса проходит значительно быстрее, чем в процессе эксплуатации, вследствие воспроизведения факторов, наиболее сильно влияющих на ресурс, в част ности, эквивалентно-циклических, ускоренных с форсированием нагружения и др. ; • при оценке расходования ресурса в процессе эксплуатации.
Для корректного учета повреждаемостей основных деталей двигателя необходимо определять в каждый момент полета (наземных испытаний) все его параметры, необходимые для расчета на циклическую прочность и повреждаемость. По мере выработки ресурса циклическая повреждаемость ΣА j , накапливается по полетам и сравнивается с допустимой А доп для каждого узла. В случае если ΣА j = А доп , принимается решение о замене узла в эксплуатации или о снятии двигателя. При таком подходе основные детали двигателя всегда будут находиться под контролем эксплуатационников, несмотря на изменения условий эксплуатации. Для обеспечения такого учета повреждаемости требуется разработать: • динамическую модель двигателя, позволяющую в каждый момент работы двигателя, от запуска до останова, и с учетом условий полета (высоты, скорости, времени работы на каждом режиме) и режима работы двигателя, задаваемого летчиком — n 2 ( τ ), определять все параметры двигателя; • нестационарную модель определения теплового состояния основных деталей и узлов в каждый момент времени — τ i , -; • модель для определения напряженно-деформированного состояния основных деталей от действия центробежных и газовых сил. температурных нагрузок; модель накопления повреждений при сложном процессе изменения напряжений и деформаций за полет с учетом требований по необходимым базовым прочностным характеристикам; • механизм сбора полетной информации, ее обработку и введение в программный комплекс по накоплению циклических повреждений и их оценке. В настоящее время такие комплексы учета повреждаемости разработаны и внедряются в практику. Отказ всегда связан с разрушением или возникновением дефектов в некоторых (критических) элементах двигателя. Критическими элементами, как правило, являются элементы горячей части — лопатки и диски турбины, камера сгорания, а также валы и подшипники.
Модели разрушения могут быть представлены в детерминированной и статистической формах. В первом случае действующие напряжения и характеристики материала имеют вполне определенные (детерминированные) значения; во втором — параметры материала считаются случайными величинами и охарактеризуются средними значениями и средними квадратическими отклоне ниями. Рассмотрим кратко основные детерминированные модели разрушения / 8. 2. 1. Длительная прочность является одним из основных факторов, влияющих на ресурс большинства высоконагруженных деталей двигателя (рабочие лопатки, диски турбины, корпуса и оболочки, опоры, валы). Предел длительной прочности σ дл — это постоянное напряжение, приводящее к разрушению детали через промежуток времени t* при температуре Т. Математическая модель длительного статического разрушения может быть представлена следующим образом: (8. 7) где m и С — постоянные для данного материала и температуры коэффициенты. В логарифмических координатах зависимости Ig σ дл = f(lgt*) приближенно могут быть представлены в виде прямых линий для различных значений Т (рис. 8. 4). Значения m равны 4. . . 8 при повышенных (для данного материала) температурах и m = 8. . . 20 в области умеренных температур. При постоянных значениях σ дл и Т ресурс детали будет равен t* т. е. за время t* произойдет полное его исчерпание. Тогда за время t исчерпается доля ресурса t/t*, т. е. значение t/t* может быть принято в качестве меры ресурса.
В условиях эксплуатации деталь будет работать в различных промежутках времени t i при различных значениях σ i , и T i , (различных режимах), которым соответствуют различные значения t i *. Опыт показывает, что при этом возможно применение линейной модели суммирования повреждений таким образом, что мера ресурса будет равна £(f, /1 ]). Исчерпание ресурса (разрушение детали) произойдет при условии (8. 8) Данное соотношение представляет модель длительного разрушения при нестационарном нагружении. Рис. 8. 4. Кривые длительной прочности сплава ЖС 6 -У
8. 2. 2 Малоцикловая усталость Нагружение на выносливость или усталость испытывают детали, подвергающиеся действию переменных циклических нагрузок. Циклическое нагружение вызывает изменение напряженного и деформированного состояния детали от цикла к циклу, способствует накоплению пластических деформаций, образованию и развитию трещины. Нагружение с небольшой частотой f< 0, 2 Гц и числом циклов N p 10 5. Малоцикловая усталость является причиной большинства возникающих на практике дефектов. На малоцикловую усталость нагружаются все наиболее напряженные элементы двигателя (лопатки и диски турбин и компрессоров, валы. камеры сгорания, детали сопла и др. ) при изменении режимов работы двигателя, т. е. при изменении частоты вращения ротора и температуры газа. Наибольшие переменные нагрузки возникают при запусках, пробах приеми стости. сбросах газа и т. д.
По аналогии с длительной прочностью, если вместо времени нагружения использовать число циклов N p , то в качестве меры исчерпания ресурса для данного режима (т. е. при постоянных значениях амплитуды переменных напряжений σ a или деформаций ε a ) следует принять отношение N р / N p *. Для различных режимов работы в соответствии с принципом линейного суммирования повреждений мера исчерпания ресурса выразится в виде , а условию разрушения будет соответствовать равенство (8. 9) 8. 2. 3 Усталость С увеличением частоты нагружения сопротивление разрушению увеличивается. Математические модели усталостного разрушения при одноосном нагружении (кривые усталости) в некотором диапазоне изменения N (при N > 10 5 ) могут быть представлены в следующем виде: (8. 10) где σ а — амплитуда переменных напряжений; m у и С у — параметры, зависящие от вида материала и температуры. В логарифмических координатах кривые усталости представляют собой полигональные кривые (ломаные линии).
Рис. 8. 5. Кривые усталости: a — для стали 40 ХН 2 МА при t = 20 °С; б — для стали 40 ХН 2 МА при t = 500 °С; в — для стали 13 X 11 Н 2 В 2 МФ при t= 20’С
Для углеродистых сталей кривые усталости имеют точку перегиба при N * = N 0 , после которой выходят на горизонтальный участок (рис. 8. 5, а). Обычно N 0 * = 10 6. . . 10 7 , а ордината, соответствующая N* = N 0 *, называется пределом выносливости и обозначается σ -1. Для легированных сталей и титановых сплавов значение σ а при N* > N 0 * продолжает снижаться, но значительно медленнее, чем при N* < N 0 (рис. 8. 5, в), а для алюминиевых сплавов, конструкционных сталей и жаропрочных сплавов при высоких температурах кривые усталости сохраняют постоянный наклон практически при всех N* (рис. 8. 5, б). Последнее обстоятельство часто используется в практических расчетах, что способствует их упрощению и получению определенного запаса в результатах. При высокой частоте нагружения максимальные переменные напряжения в отдельных деталях возникают при резонансных частотах, т. е. при значениях частот вращения ротора, совпадающих или кратных частотам собственных колебаний той или иной детали (лопатки, корпуса, трубопроводы), а также при наличии срывных явлений в проточной части двигателя (например, вращающийся срыв в компрессоре). При этом в условиях эксплуатации нарабатывается огромное число циклов (до 10 14 ).
8. 2. 4. Модель долговечности в условиях длительного статического и циклического нагружений Если деталь работает в условиях длительного статического и циклического нагружений, то для определенного температурного диапазона (1073. . . 1173 К) и циклов нагружения (N> 200) расчет долговечности возможен в предположении справедливости линейного суммирования повреждений [48]: (8. 11) где N pi *, t pi *— число циклов и время до разрушения в случае действия только циклического и только статического нагружений соответственно при темпера турах и нагрузках i-го режима; N i , и t i , — продолжительность действия циклического (в циклах) и длительного статического (в часах) нагружений соответст венно при температурах и нагрузках i-го режима. В общем случае справедливо соотношение: (8. 12) где α и β — постоянные, определяемые при испытаниях для каждого материала.
8. 2. 5. Модель долговечности при разнородных повреждениях При одновременном воздействии многоцикловой усталости, а также повреждений длительной прочности условие суммирования повреждений можно представить в виде [18]: (8. 13) где число циклов N*, N p * и время t* до разрушения соответствуют уравнениям σ m a N* = С, ε m 1 a N p * = С л , σ mд m t*=С дл , а С, С л , С дл — постоянные для данного материала и температуры коэффициенты. При α = β = γ = 1 условие (8. 13) выражает правило линейного суммирования разнородных повреждений. Показатели степени а, р и у зависят от материала и структуры нагружения. Первый член в уравнении (8. 13) выражает повреждение от малоцикловой ус талости, второй — многоцикловой, что отмечается индексом р, третий — длительной прочности. При α < 1, β < 1, γ 2, β >2, γ >2 взаимным влиянием разнородных повреждений можно пренебречь.
8. 2. 6. Износ и контактная усталость являются одними из важных причин выхода из строя сопряженных элементов конструкции двигателя, таких, как подшипники, зубчатые колеса, уплотнения, бандажные полки лопаток и т. д. Износ представляет собой весьма сложный процесс и зависит от очень большого числа факторов — свойств контактирующих материалов, удельного давления, скорости относительного перемещения, условий смазки, теплоотвода, вибраций и др. Приближенно можно считать, что износ пропорционален работе сил трения в единицу времени, т. е. определяется главным образом при прочих равных условиях значением удельного давления и скоростью взаимного смешения трущихся поверхностей. Выкрашивание контактных поверхностей (контактная усталость, питтинго- образование) в основном определяется процессом усталости поверхностного слоя при качении или качении со скольжением. Математическая модель разрушения в этом случае приближенно может быть описана уравнением, аналогичным уравнению (8. 10): (8. 14) где σ к — предел контактной усталости материала; е и С к — постоянные ве личины. Если износ характеризовать линейным размером — средней толщиной из ношенного слоя в зоне контакта h, то упрощенная модель скорости износа имеет вид: (8. 15) Где f— коэффициент трения; Р — среднее давление в зоне контакта; V — отно сительная скорость соприкасающихся тел; σ в — предел прочности поверхност ного слоя; α, β, γ, ν— безразмерные положительные параметры.
Постоянная с зависит от типа соединения, в котором происходит износ, от материалов трущейся пары, свойств окружающей среды, типа смазки, наличия абразивных частиц и других факторов, от выбора единиц измерения h, p, V , σ в. Максимальная относительная скорость в соединениях (условно неподвижных) определяется формулой V =δω, где δ(t) =δcos(ωt) δ — амплитуда относительного смещения; ω — круговая частота изменения взаимного расположения элементов. При условии α=β=γ=ν=1 следует, что скорость износа при прочих равных условиях пропорциональна работе сил трения (в единицу времени). В общем случае все параметры модели износа могут быть определены на основании экспериментальных данных. 8. 2. 7. Эрозия и газовая коррозия При эрозии происходит разрушение поверхностного слоя металла в результате обтекания детали газовым потоком. Этот процесс значительно усиливается, если в потоке будут содержаться пыль и твердые частицы. При этом наблюдаются хрупкие (типа усталостных) и вязкие (образование царапин) разрушения. Значительному эрозионному износу подвергаются лопатки компрессоров при эксплуатации двигателей в запыленном воздухе. Эрозионный износ определяется концентрацией частиц в потоке, их скоростью. размерами, массой и твердостью, прочностью поверхности детали, температурой, влажностью, агрессивностью среды и другими факторами. При эрозии возникают хрупкие (типа усталостных) и вязкие разрушения, связанные с процессами типа резания. Хрупкие разрушения связаны с нормальной составляющей скорости частиц, вязкие — с касательной составляющей. Приближенная модель эрозии имеет вид:
(8. 16) Где h — средняя толщина изношенного слоя в процессе эрозии; — скорость эрозии; γ — весовая концентрация частиц в единице объема среды; d— диаметр частиц; V n = Vcosα и V n = Vsinα— нормальная и касательная составляющие от носительно скорости потока; α— угол между нормалью к поверхности и скоростью потока; σ сж — прочность частиц на сжатие; σ в , γ д — предел прочности и удельный вес материала детали; т 1 т 2 , …, т 7 — безразмерные положительные параметры; с 1, с 2, с 3, с — постоянные. Постоянная с 3 представляет собой пороговое значение, учитывающее, что при очень малых скоростях износ не наблюдается. В первом приближении можно принять т 1 = 1; т 2 = 3; m 3 = т 4 =3; т 5 = т 6 =1; т 7 = 1. Если касательная составляющей скорости и пороговое значение несущест венны, то (8. 17) Газовая коррозия в двигателях — это разрушение поверхностного слоя ме талла чаше всего в результате окисления при высоких температурах. Сопротив ление газовой коррозии, или жаростойкость материала, характеризуется, как правило, изменением массы детали за определенный промежуток времени.
8. 3. РЕСУРСНЫЕ ИСПЫТАНИЯ АВИАЦИОННЫХ ГТД 8. 3. 1. Основные понятия и определения Ресурс — наработка изделия до предельного состояния, оговоренного в нормативно-технической документации (НТД). Наработка — продолжительность эксплуатации двигателя в полете и наземных условиях, выраженная в часах, числе полетов или циклах, числах включений и т. п. Предельное состояние — состояние изделия, определяемое невозможностью его дальнейшей эксплуатации, обусловленное либо снижением эффективности. либо требованиями безопасности и оговариваемое в технической документации. Рис. 8. 6. Виды ресурсов ГТД
Регламентируются следующие виды ресурсов двигателя (рис. 8. 6). Срок службы (эксплуатации и (или) хранения) двигателя — суммарная календарная продолжительность эксплуатации, хранения и транспортирования двигателя от момента его изготовления или ремонта до очередного ремонта или списания регламентируется как: • срок службы (эксплуатации и хранения) до первого капитального ремонта; • межремонтный срок службы (эксплуатации и хранения). Сроки службы (эксплуатация и хранение) устанавливаются в годах и месяцах. Эксплуатация по техническому состоянию (ЭТС) — метод эксплуатации в пределах эксплуатационного ресурса, при котором решение о проведении технического обслуживания или ремонте двигателя (детали) принимается на основании анализа технического состояния, устанавливаемого по результатам периодического контроля (осмотров и др. ) и (или) испытаний в процессе эксплуатации. Назначенный ресурс двигателя — установленная в нормативно-технической документации (НТД) для данного этапа серийного производства и эксплуатации, а также подтвержденная всеми видами исследований и испытаний суммарная наработка, при достижении которой применение двигателя по назначению должно быть прекращено независимо от его состояния. Понятие назначенного ресурса двигателя может быть удовлетворительно описано физическими или статистическими моделями только для отдельных деталей ГТД. Такие модели отражают исчерпание долговечности элемента с учетом его нагружения. Когда же переходят от элемента двигателя к такой сложной системе, как ГТД, включающей в себя многие элементы с разнообразными процессами их нагружений, то понятие назначенного ресурса становится менее определенным.
Поэтому его принимают равным минимальному значению назначенного ресурса у тех основных деталей ГТД, которые не подлежат замене. Основными являются детали, разрушение или последствия разрушения. которые могут привести к катастрофическим последствиям: разрушение элементов ротора, обломки которых не удерживаются внутри корпуса; нелокализованные пожары; невозможность выключения двигателя. Лимитируют ресурс, как правило, рабочая лопатка турбины ВД и диск последней ступени турбины НД. Ресурс основных деталей (узлов) задается в виде назначенного. Назначенный ресурс детали — установленная в НТД для данного этапа серийного производства и эксплуатации наработка, при достижении которой применение данной детали двигателя по назначению должно быть прекращено независимо от ее состояния. Полный назначенный ресурс двигателя — установленная в НТД расчетная суммарная наработка двигателя от начала эксплуатации до его списания. Назначенный ресурс двигателя подлежит поэтапному увеличению от на чального значения, устанавливаемого к моменту начала серийной эксплуатации до величины полного назначенного ресурса, указанной в техническом задании (ТЗ), а при экономической целесообразности и выше. Ресурс двигателя до первого капитального ремонта — установленная в НТД для данного этапа серийного производства и эксплуатации наработка от начала эксплуатации до его первого капитального ремонта.
Межремонтный ресурс двигателя — установленная в НТД для данного этапа серийного производства и эксплуатации наработка между смежными капитальными ремонтами, в течение которого целесообразно (экономически) и допустимо (по надежности) использовать двигатель в данных условиях эксплуатации. Во многих случаях за жизненный цикл двигателя в эксплуатации делают 2 ремонта, т. е. существуют 3 межремонтных ресурса. Ресурс двигателя до первого капитального ремонта и межремонтные ресур сы до перевода его на ЭТС должны быть равны соответствующим гарантийным ресурсам двигателя. Эксплуатационный ресурс двигателя — установленная в НТД для данного этапа серийного производства и эксплуатации наработка при эксплуатации по техническому состоянию нового или ремонтного двигателя, в пределах которой он может эксплуатироваться без капитального ремонта. Гарантийный ресурс двигателя (гарантийная наработка при ЭТС) — установленная в НТД наработка двигателя, в течение которой изготовитель или ре монтное предприятие гарантирует и обеспечивает выполнение установленных требований к двигателю при условии соблюдения правил эксплуатации, хранения и транспортировки. Эксплуатация двигателя в пределах установленного ресурса (в том числе ЭТС) включает в себя эксплуатацию с гарантийным ресурсом (гарантийными наработками) для всего парка или серий двигателей. В течение установленных ресурсов и сроков службы, в том числе при ЭТС. двигатель должен удовлетворять требованиям по безопасности полетов, показателям назначения, безотказности, эксплуатационной технологичности, диагностике технического состояния, контролепригодности и ремонтопригодности, приведенным в ТЗ и другой нормативно-технической документации (НТД).
Для определения выработки ресурсов основных деталей в целом в эксплуатации и при ресурсных испытаниях используются средства контроля ресурсных показателей двигателя, которые обеспечивают подсчет выработки ресурса в часах и в полетных циклах путем вычисления эквивалентной повреждаемое и от Длительных статических нагрузок и малоцикловой усталости основных легален Двигателя в конкретных условиях работы. Установление и увеличение ресурсов и сроков службы двигателя производится на основании ресурсных стендовых и летных испытаний, лидерных эксплуатаций и хранения двигателя, ресурсных испытаний основных деталей двигателя, специальных испытаний по хранению двигателя в составе ДА и в упаковке, а также других работ. Ресурсные испытания двигателей проводятся на стендах с атмосферными условиями на входе и частично на стендах с имитацией высотно-скоростных условий. Все виды ресурсов устанавливаются в часах общей наработки двигателя в полете и на земле и (или) в количестве полетных циклов. Типовой полетный цикл работы двигателя (ТПЦ) — изменение по времени давления и температуры воздуха на входе в двигатель и основных параметров двигателя, характеризующих режим его работы при выполнении типового полета ДА, включая наземную наработку, отнесенную к одному типовому полету. Обобщенный типовой полетный цикл работы двигателя (ОТПЦ) — типовой полетный цикл, соответствующий некоторой группе типовых полетов. Формирование ТПЦ двигателя производится на основании типовых поле тов, а ОТПЦ — на основании некоторой группы или всех типовых полетов ДА.
В качестве параметров двигателя, характеризующих режимы его работы при выполнении типового полета ДА, могут указываться величина тяги, а также число приемистостей и плавных перемещений РУД для различных участков полета, различающихся высотой И и приборной скоростью Р пр или числом М. В число переменных процессов, связанных с изменением частоты вращения роторов, рекомендуется включать переходы между частотами вращения, отличающимися более чем на 5 % при n ≥ 0, 85 n m ах и более чем на 10 % при n < 0, 85 n m ах (n — частота вращения). Средние вероятные длительности ТПЦ (ОТПЦ), а также средние вероятные значения других характеристик полетных циклов f k ср (наработок на отдельных режимах, чисел отдельных переменных процессов и др. ) определяются путем осреднения соответствующих характеристик всех ТПЦ (ОТПЦ) с учетом вероятности использования каждого из ТПЦ (ОТПЦ). Расчет средних вероятных значений k-ой характеристики проводится по формуле: (8. 18) гдеf km — значение k-ой характеристики для m-го ТПЦ (ОТПЦ); Рm — вероятность использования m-го ТПЦ (ОТПЦ); l — общее число ТПЦ (ОТПЦ), входящих в расчет. Средняя вероятная длительность ТПЦ (ОТПЦ) т сд используется для определения средневероятного числа полетов N cп , соответствующих ресурсу т в часах: (8. 19)
Испытательный цикл (ИЦ) — изменение во времени частот вращения роторов, положений регулирующих органов, загрузки приводных агрегатов и условий на входе в двигатель при стендовых испытаниях, обеспечивающих максимально возможное воспроизведение повреждаемости в типовых по летных циклах с учетом относительных частот их использования в эксплуатации. Испытательные циклы могут быть полными или ускоренными. Испытания по установлению и увеличению всех видов ресурсов двигателя квалифицируются как успешные, если при их проведении не было разрушений роторных деталей, их недопустимых повреждений, устанавливаемых принятыми в серийной технологии методами, а также отказов и дефектов других основных деталей, которые в эксплуатационных условиях могут привести к катастрофическим или аварийным последствиям. При назначении ресурса ГТД важнейшим моментом является правильный учет взаимосвязи между величиной ресурса и надежностью (3). Критерии, характеризующие выполнение двигателем основных функций и эксплуатационные затраты определяют эффективность системы установления ресурса. В общем виде модель оптимизации ресурса ГТД с учетом такого свойства, как надежность, может быть представлена в виде: (8. 20) где S( τ ) — экономическая эффективность использования данного ресурса (подлежащая максимизации); Ф i — i-ый критерий, характеризующий выполнение ГТД своих функций с требуемой надежностью; Ф i * — предельно допустимое значение Ф-го критерия; τ — ресурс, являющийся в данном случае зависимой переменной.
Однако аналитическое установление оптимального ресурса является чрезвычайно сложной задачей. На практике для достижения оптимального значения ресурса применяют различные виды испытаний ГТД. На ранних этапах доводки ГТД при небольших его ресурсах, когда суммарная наработка невелика (что, как пока зывает опыт, соответствует и невысокой надежности двигателя), ГТД испытывают на первоначальный ресурс 125. . . 500 ч. В отечественной практике обычно это было 150 ч — для гражданских двигателей и 50. . . 100 ч — для дви гателей военной авиации. Назначенный ресурс детали (в циклах) согласно НЛГС равняется (8. 21) Где N исп — число испытательных циклов, проведенных в стендовых условиях (экспериментально проверенная долговечность детали в системе ГТД); η — ко эффициент соответствия полетного и испытательного циклов по повреждаемо сти от малоцикловой усталости — теплосмены и смены механической нагрузки (η = 0, 4. . . 1, 0); K N — коэффициент запаса по долговечности, значение которого зависит от числа испытанных двигателей или N исп деталей (узлов) (К N = 3, если N исп = 1; K N = 2, 5, если N исп =2; K N = 2, 0, если N исп = 3). Для ГТД величина N наз нач должна быть равна минимальному значению N наз его основных деталей, не подлежащих замене, с запасом 1, 2: (8. 22) Значение начального назначенного ресурса ГТД в часах определяется по формуле: (8. 23)
где / п — длительность среднестатистического полетного цикла. Межремонтные ресурсы устанавливают в пределах назначенного ресурса, при этом часто принимают τ м , = τ наз нач /2 (т. е. на начальных этапах доводки ресурса часто ограничиваются только одним ремонтом). 8. 3. 2. Длительные эксплуатационные испытания ГТД на повышенный ресурс Длительные испытания — это испытания на полный ресурс в стендовых условиях по программе, которая в максимальной степени учитывает особенности работы изделия в реальных условиях эксплуатации (эксплуатационная программа). Цель таких испытаний — наращивание ресурса ГТД и его эксплуатационное обоснование. Первоначальной основой для оценки предельно возможных значений ресурса ГТД является расчетная долговечность «основных» деталей двигателя (дисков и лопаток турбины и др. ). Эти материалы по расчетной долговечности являются основой оценки назначенного ресурса ГТД т, т. е. расчетной величины ресурса до предельного состояния двигателя. Всякая доводка ГТД по межремонтному ресурсу может проводиться только в пределах назначенного ресурса, т. е. до предельно допустимых расчетных величин наработки. На ранних этапах эксплуатации ГТД применяют систему установления ресурса двигателя на основе величины ресурса наиболее слабого его элемента, работающего в самых напряженных условиях эксплуатации. В этом случае целью является увеличение межремонтных наработок двигателем. При такой системе доводки ресурса (рис. 8. 7) двигателю устанавливают каждый раз новое фикси рованное значение межремонтного ресурса, по достижении которого он на правляется на разборку и ремонт вне зависимости от технического состояния. Например, для двигателя НК-86: τ наз нач = 2000 ч; τ наз врем = 6000 ч; τ назн = 18 000 ч; τ 1 м = 3500 ч; τ м 2 = 2500 ч.
Рис. 8. 7. К установлению дифференциро ванной величины ресурса: 1 — исходное состояние: 2 — увеличенный ресурс; 3 — расчетная характеристика предельного состояния Рис. 8. 8. Вариант стендовой наработки полетного цикла: ПМГ — полетный малый газ: ЗМГ — земной малый газ
Для основных деталей ГТД начальную величину назначенного ресурса определяют на основе стендовой наработки большого числа полетных циклов (рис. 8. 8 ). На конечных этапах доводки ресурса обычно τ м 1 > τ м 2 > τ м 3. В процессе дальнейшей доводки ресурса при эксплуатации ГТД на ЛА (8. 24) где N э — число полетных циклов, реализованных в эксплуатации на ЛА; η э — коэффициент запаса, учитывающий рассеяние свойств материалов и условий эксплуатации. Указанную доводку ресурса осуществляют различными методами: опережающей наработкой ресурса при эксплуатационных испытаниях на самолетах-лидерах; статистическим анализом результатов эксплуатации; эквивалентно-циклическими ускоренными испытаниями (ЭЦИ). Таким образом имеем следующие виды назначенных ресурсов τ наз : τ наз нач , τ врем наз и τ расч. наз Эксплуатационные испытания с опережающей наработкой ресурса на самолетах-лидерах Цель таких испытаний — доводка ГТД на увеличенный ресурс. 1. После отработки «первыми» двигателями установленного ресурса до первого капитального ремонта (1 -го межремонтного ресурса — τ м 1 ) они снимаются с самолетов и отправляются в ремонт, а некоторые из них (2. . . 4) разбирают для дефектации.
2. В дополнение к этому на одном—двух выработавших ресурс двигателях без разборки проводят стендовые испытания продолжительностью Δ τ , где Δ τ — разница между действующим и увеличенным ресурсом (100. . . 300 ч, а чаше 10 % τ 1 м ). По окончании этих испытаний двигатели также разбирают и проводят дефектацию деталей. 3. При положительных результатах дефектации дается разрешение на летную эксплуатацию на самолетах-лидерах остальных двигателей до выработки увеличенного на величину Δ τ ресурса (самолеты-лидеры — это, как правило, не пассажирские, а грузовые самолеты того же типа). После выработки увеличенного ресурса все двигатели лидерного самолета дефектируют, а один из них без разборки нарабатывает на стенде еще 10. . . 20 % от Δ τ. Положительные результаты таких испытаний и удовлетворительное состояние деталей позволяют разрешить увеличенное (фиксированное) значение ресурса для всех двигателей данной модификации: τ 1 м = τ нач наз + Δ τ i — Такая система повышения ресурса с достаточной надежностью обеспечивает требуемую безопасность полетов. Однако ей присуши и существенные недостатки: например, при больших ресурсах (2000. . . 3000 ч) требуется слишком большой календарный срок для проведения всех требуемых проверок (средний годовой налет в гражданской авиации составляет 2600 ч, в ВВС — 200. . . 400 ч). Кроме того, получаемая при этом величина τ м не зависит от дальности полета самолета, т. е. не отражает истинной выработки ресурса. Дело в том, что при рейсах с t п меньшей t п рас взлетный режим при взлете не должен вообще использоваться, т. к. взлетная масса самолета М 0 на коротких рейсах за счет заправки меньшего количества горючего становится несколько меньше, поэтому возможен (и рекомендуется в НЛГС) взлет на максимальном продолжительном режиме.
Однако пилоты часто по привычке используют взлетный режим и в этих случаях, что сокращает ресурс, например, дисков турбины примерно в 1, 5 раза. На самолете Ил-86, чтобы избежать этого, поставлен счетчик, который фиксирует выработку ресурса за каждый полетный цикл и сравнивает с нормированным значением. Это дисциплинирует пилотов и приводит к более экономному расходованию ресурса. Тем более, что на коротких рейсах ресурс и так сокращается за счет увеличения числа циклов и доли использования повышенных режимов. В настоящее время на самолетах внедряется цифровая система автоматического управления FADEC, которая, благодаря применению бортового компьютера, автоматически устанавливает режимы на взлете и наборе высоты, оптимальные по расходу топлива при данной загрузке самолета. Это позволяет эко номить расход топлива до 3. . . 4 %. Повышение ресурса ГТД на основе статистических данных об их отказах и дефектах в эксплуатации В данном случае проводится анализ статистических данных об отказах и дефектах всего парка двигателей рассматриваемого типа, находящихся в летной эксплуатации. При этом важнейшими статистическими характеристиками являются наработки на отказ: Т дсд и Т оп. Для большой совокупности ГТД разных типов пассажирских самолетов методом корреляционно-регрессионного анализа установлена связь показателей Т дсд и Т оп с режимами работы и наработкой (3): (8. 25) где t Σ — суммарная наработка парка двигателей (косвенно связана с ресурсом); t п — длительность беспосадочного полета (определяет число циклов нагружения); r— процент использования максимальных режимов (определяет нагруженность ГТД)
Рис. 8. 9. Характер изменения коэффициен та К 1000 дсд Для однотипных двигателей, экс плуатируемых на ЛА разных авиакомпаний Это подтверждает важную роль показателей Т дсд и Т оп при установлении ресурса. На их основе по формулам (8. 6) определяют безразмерные коэффициенты отказов на 1000 ч наработки: К 1000 дсд (чем меньше значение К , тем выше надежность двигателя). Для хорошо доведенных двигателей К 1000 дсд = 0, 1. . . 0, 2, что соответствует Т дсд = 5000. . . 10 000 ч (К 1000 оп = 0, 03. . . • 04 соответствует Т оп = 25 000… 33 000 ч). На рис. 8. 9 показан характер изменения К 1000 дсд в процессе доводки ГТД по годам эксплуатации для двигателей, установленных на ЛА разных авиаком паний. Видно, что через 3. . . 4 года эксплуатации значение К 1000 дсд стабилизируется на определенном уровне. При К 1000 дсд ≤ 0. 4, как показывает опыт, целесообразно принять решение о повышении межремонтного ресурса ГТД на 200. . . 300 ч. Для этого необходимо убедиться в том, что техническое состояние ГТД не меняется. В этих целях используют, например, метод опережающего налета на самолетах-лидерах. Обработкой статистики определяют влияние увеличения ресурса на изменение характеристик надежности ГТД. Если увеличение не приводит к существенному росту К 1000 дсд , то решение считается оправданным, и при удовлетворительных результатах разборки нескольких ГТД продление ресурса утверждается официально. Таким образом, ресурс продлевают несколько раз, пока К 1000 дсд не начнет заметно возрастать. Тогда устанавливают его максимально-допустимое (рентабельное) значение.
В настоящее время требуемые величины ресурсов самолета до списания составляют 30 000. . . 60 000 летных часов, 10 000. . . 30 000 полетов. Календарные сроки эксплуатации — от 20 до 30 лет. Кроме того, устанавливаются ресурсы до 1 -го ремонта (межремонтные) 5000. . . 10 000 летных часов, 3000. . . 10 000 полетов и соответственно сроки службы до 1 -го ремонта (межремонтные) — 5. . . 8 лет эксплуатации. Внедряются методы эксплуатации, в которых проведение капитального ремонта не предусмотрено. В России и в Украине двигатели эксплуатируются с фиксированным ресурсом, который подтвержден экспериментально эквивалентно-циклическими испытаниями двигателей и циклическими испытаниями основных деталей |12|. В этом случае эксплуатация двигателей начинается с ресурсов — 300 ч для двигателей военных самолетов и 1000. . . 2000 ч для двигателей гражданских самолетов. Далее, по мере продолжения испытаний и накопления опыта эксплуатации, ресурс увеличивается. Капитальный ремонт двигателя или его списание проводится после фиксированной наработки. 8. 3. 3. Ускоренные эквивалентно-циклические испытания ГТД При больших значениях ресурса (3000. . . 4000 ч и более) проведение длительных испытаний по эксплуатационной программе становится нецелесообразным или даже невозможным, поскольку проверка мероприятий, направленных на устранение дефектов и повышение ресурса, требует огромного времени не говоря о затратах. Например, для проведения длительных испытаний авиационного двигателя на ресурс 4000 ч необходим срок более одного года. Поэтому в настоящее время для ускорения доводки ГТД на ресурс широко применяются ускоренные испытания (УИ) и, в частности, эквивалентно-циклические испытания (ЭЦИ), характеризующиеся тем, что их программа за более короткое время «моделирует» работу изделия в течение полного ресурса.
Роль УИ возрастает при переходе изделий на эксплуатацию «по техническому состоянию» , поскольку для перехода на такой метод эксплуатации одним из основных требований является обеспечение высокого технического ресурса изделия, подтвержденного специальными, длительными и эквивалентными ускоренными испытаниями [28). В общем случае выбор конкретного метода УИ зависит от многих факторов: сложности и степени ответственности конструкции, ее стоимости, степени изученности процессов расходования ресурса, возможностей испытательного оборудования, вида задач, решаемых при испытании, и других факторов [15, 16, 45] На практике применяются УИ, разделяемые по способу ускорения (рис. 8. 10) [ 16]. Основным ускоряющим фактором при проведении ускоренных испытаний технических изделий является температура, под влиянием которой меняется механическая прочность материалов, падает напряжение разрыва, увеличивается износ, ускоряется старение и т. д.
Рис. 8. 10. Классификация ускоренных испытаний по способу ускорения
Разновидностью метода ускоренных испытаний являются определенные стандартом метод ступенчатого нагружения (Локати) и ускоренные испытания с периодическим форсированием режима. Метод Локати позволяет сократить длительность испытаний в 30. . . 70 раз и предназначен для ориентировочной оценки пределов выносливости образцов и изделий машиностроения из металлов и сплавов, кривые усталости которых имеют горизонтальный участок. УИ с периодическим форсированием режима распространяются на изделия, отказ которых обусловлен постепенным накоплением износа элементов, проявляющегося в монотонном изменении контролируемого параметра. В ряде случаев применяют так называемый «метод доламывания» , основанный на принципе линейного накопления повреждений. При этом полагают, что процесс расходования ресурса не зависит от предыстории нагружения. Сокращение длительности испытаний может быть достигнуто за счет установления более «жесткого» , по сравнению с указанным в технических условиях, допуска на выходной контролируемый параметр. При этом время, в течение которого контролируемый параметр может находиться в поле «жесткого» допуска, будет меньше, чем длительность эксплуатационных испытаний. В комбинированных УИ длительность испытаний достигается совмещением испытаний нескольких методов (рис. 8. 11).
Для технических изделий типа авиационных ГТД, ввиду многообразия факторов, определяющих их надежность (табл. 8. 1) [28], различного влияния режимов нагружения на повреждаемость элементов изделия, наличия функциональных ограничений на параметры режима нагружения, ограничений по автомодельности испытаний (неизменности физической природы расходования ресурса в ускоренных и длительных испытаниях) и других факторов, обеспечение эквивалентности испытаний в целом для всего двигателя является сложной и часто нерешаемой проблемой. При ускоренных испытаниях моделирование условий, определяющих износ, состоит в основном в обеспечении соответствующего числа циклов нагружения, а также в рациональном выборе нагрузок и скоростей взаимного перемещения контактирующих поверхностей. Например, для ускорения проверки работы подшипников может быть увеличено воспринимаемое ими осевое усилие путем соответствующего изменения дренажа разгрузочной полости. При эрозии происходит разрушение поверхностного слоя металла в результате обтекания детали газовым потоком. Этот процесс значительно усиливается, если в потоке будут содержаться пыль и твердые частицы. При этом наблюдаются хрупкие (типа усталостных) и вязкие (образование царапин) разрушения. Значительному эрозионному износу подвергаются лопатки компрессоров при эксплуатации двигателей в запыленном воздухе. Поэтому при моделировании этого процесса в УИ можно увеличивать весовое содержание в воздухе твердых частиц и их размеры. Сопротивление газовой коррозии или жаростойкость материала характеризуется изменением массы детали за определенный промежуток времени. Моделирование в УИ обеспечивается увеличением температуры и повышением агрессивности газовой среды.
Рис. 8. 11. Классификация методов сокращения длительности ресурсных испытаний
Факторы Детали двигателя Длител ьная проч но сть Износ и контактна я вынослив ость Усталост н ая проч ность Малоц иклова я Прочно сть Термост ойко-сть Эрозия и кор рози я Рабочие лопатки ком прессора — + + + — + Направляющие лопатки компрессора + + — + Замки крепления лопа ток компрессора — + + + — — Диски компрессора + — + + — — Валы + — + + — — Корпус компрессора + — + + — — Корпус турбины и каме ры сгорания + — + + Рабочие лопатки турбины + — + + Сопловые лопатки тур бины + — + + Замки крепления лопа ток турбины + + — — Диски турбины + — + + + — Подшипники, валы, шес терни — + + + — — Опоры + — + + — — Трубки и агрегаты — + + — — — Болтовые соединения + — + + + — Оболочки + — + + — — Реверс — — + + + -П рим ечание: «+ » — ф актор явл яется опред ел яю щ им ; « — » — ф актор не явл яется оп ред ел яю щ им. 8. 1. Ф акторы , опред ел яю щ ие над еж ность д етал ей авиац ионного ГТ Д
Статистический метод основан на принципе Седякина Н. М. |16|, предло женном для оценки надежности изделий, работающих в переменном режиме: надежность изделия в режиме R зависит от величины выработанного им ресурса и не зависит от того, как был выработан ресурс в прошлом. Пример. Ресурс двигателя составляет 4000 ч. Наработка на отказ, приводящий к съему двигателя с самолета, определяется по формуле [3]: (8. 26) Где τ Σ ; — наработка всех двигателей данного типа в эксплуатации, млн ч; τ пол — среднее время одного полета ( τ пол = 0, 7 ч); r — относительная доля времени работы на максимальном и форсированном режимах работы за ресурс (r = 3 %); а 0 , а 1 а 2 а 3 — коэффици енты, определенные методом многофакторного анализа по статистическим данным эксплуатации двигателей данного типа в различных условиях. При испытании технических изделий принципиально возможны несколько методов обоснования ускоренных ресурсных испытаний [3, 14, 16, 28]: • статистический метод; • прочностной метод; • обобщенный метод; • метод экстраполяции.
Требуется определить условия проведения ускоренных испытаний двигателя на стенде. Распределение статистических данных по отказам двигателя в эксплуатации соответствует экспоненциальному закону распределения, т. е. вероятность безотказной работы определяется по формуле: Где λ, ( τ , R) — интенсивность отказа двигателя в режиме R длительностью т; к — средняя интенсивность отказа; Т — наработка на отказ. Условие эквивалентности эксплуатационных и стендовых испытаний имеет вид: (8. 27) где τ э , τ ст — наработка в эксплуатации и стендовых испытаниях соответственно в режи мах R э и R ст. Согласно (8. 27) длительность стендовых испытаний составит: (8. 28) Поставляя (8. 25) в формулу (8. 28), определим длительность ускоренных испытаний:
При r = 100%, означающем, что стендовые испытания проводятся с использованием только максимальных режимов, длительность цикла нагружения составит τ Пол ст = 0, 0565 ч, а число циклов нагружения: N ст = 200/0, 0565 = 3540 циклов. Для сравнения число циклов нагружения двигателя в эксплуатации равно τ э / τ пол э = 4000/0, 7 = 5714 циклов. Таким образом, при r= 3 % проверка эксплуатационного ресурса ( τ э = 4000 ч) проводится в стендовых испытаниях 6329 -ю циклами длительностью τ c т ≈1, 9 мин. При этом длительность испытаний сокращается в τ э / τ ст = 4000/200 = 20 раз. При применении статистического метода величина интенсивности отказов должна относиться к отказам, определяющим надежность и ресурс изделия. Такие отказы имеют серьезные последствия и в условиях эксплуатации встречаются крайне редко. Прочностной метод Данный метод основан на изучении факторов, влияющих на исчерпание ресурса, и установлении соотношений между нагрузкой и долговечностью. Из программы испытаний исключаются режимы, слабо влияющие на выработку ресурса, вводится увеличенная наработка на наиболее тяжелом режиме детали, лимитирующей ресурс изделия в целом, и используют другие приемы. Примером реализации данного метода являются программы эквивалентно-циклических испытаний (ЭЦИ) авиационных двигателей, основанные на [14, 28]: увеличенной наработке на наиболее тяжелом режиме; ступенчатой наработке в рабочем диапазоне частот вращения; полном воспроизведении переходных режимов (запусков с выходом на взлетный режим, приемистостей, сбросов газа с выдержкой на взлетном режиме и малом газе, реверсировании тяги и перекладки реверса на малом газе).
Длительность наработки с учетом повреждений, связанных с длительной прочностью, определяется по наиболее слабому элементу (обычно рабочей ло патке 1 -й ступени турбины) из условия равенства эквивалентных запасов проч ности в ускоренных и длительных испытаниях: (8. 29) где k i — запас прочности лопатки на i-ом режиме работы; m i , — показатель степени зависимости «напряжение-время» в формуле (8. 7) (σ m дл τ = idem) для дли тельной прочности материала при температуре T i ; τ i — время до разрушения при температуре Т i и напряжении σ i ; S H , S y — число режимов в программе длительных и ускоренных испытаний. В частном случае, когда ускоренные испытания проводятся на наиболее тяжелом (например, взлетном) режиме, их длительность определяется по формуле: (8. 30) где τ i — длительность наработки на взлетном режиме за весь ресурс изделия (m i = m 1, i = 1, 2, . . . , s).
Рис. 8. 12. Схема определения эквивалентных условий по фактору «длительная прочность» Принцип замены наработки на нескольких режимах эквивалентной наработкой на одном (максимальном) рассмотрим на следующем примере. Пусть деталь работает при эксплуатации ГТД на ЛА τ i часов (рис. 8. 12) при температуре 1250 К и напряжении σ 1 , (запас прочности при этом n 1 = σ B| /σ 1 ) и τ 2 часов при 1050 К и напряжении σ 2 (запас прочности при этом n 2 = σ B 2 / σ 2 ) Исходя из предположения, что повреждаемость детали одинакова при равных запасах прочности (так называемая гипотеза линейного суммирования повреждаемости), приводим менее напряженный режим к более напряженному. Для этого находим эквивалентное значение предела длительности прочности σ B 2 * для 2 -го режима, но при Т M * = 1250 К, полагая, что σ B 1 * = n 1 σ 1 ; σ B 2 = n 2 σ 2 , и используя запас прочности n 2 в условиях работы σ 1 тогда n 2 σ 1 = σ в 2 э >σ B 2 *, откуда τ 2 э < τ 2 (рис. 8. 12). В целом для двух режимов τ экв — τ 2 экв + τ 1 < τ 2 + τ 1. Таким образом, опасность разрушения детали будет одинаковой, если отработать при обычном длительном использовании время τ 1 и время τ 2 или отработать при эквивалентных испытаниях время τ 1 и время τ 1 Э , которое значительно меньше τ 2. Для проверки влияния на длительную прочность повторных статистических нагружений и теплосмен в переменных режимах (приемистость, сброс газа и т. п. ) требуется полное воспроизведение их числа,
имеющего место в эксплуатации. Если z — число циклов нагружений и теплосмен, то длительная прочность зависит от z следующим образом (рис. 8. 13). Опыт ряда катастроф ЛА за последние 10 лет показал, что необходимо вводить запас по числу циклов при испытаниях на малоцикловую усталость, соответствующий С= 2. . . 3, а в некоторых случаях и 5! Введение таких запасов определяется в основном разбросом свойств материалов в одной партии и неодинаковым влиянием технологической наследственности. Однако переменные режимы не определяют общую длительность испытаний, поэтому С = 2. . . 3 весьма незначительно влияет на длительность ускоренных испытаний ГТД. Ступенчатая наработка в рабочем диапазоне частот вращения проводится с целью проверки сопротивления деталей переменной нагрузке. Максимальные напряжения возникают в резонансных режимах. Поскольку опасные резонансные режимы обычно неизвестны, то проводится ступенчатая наработка по частотам вращения, отличающимся не более чем на 10 % (разброс собственных частот лопаток и других деталей составляет порядка 5. . . 10 %). Время наработки на каждом уровне частот вращения должно обеспечивать достижение предела выносливости — (1. . . 2)10 8 циклов. Для воспроизведения отказов, связанных с малоцикловой усталостью и термоциклической прочностью, в испытаниях воспроизводят все нестационарные режимы в том виде и количестве, в котором они встречаются в эксплуатации.
Рис. 8. 13. Зависимость предела длительной прочности материала при Т м = 1250 К для различного числа циклов нагружений и теплосхем Для воспроизведения отказов, связанных с малоцикловой усталостью и термоциклической прочностью, в испытаниях воспроизводят все нестационарные режимы в том виде и количестве, в котором они встречаются в эксплуатации. Пример. Для ускоренной проверки влияния факторов, определяющих исчерпание ресурса деталей двигателя типа НК-8, в программу эквивалентных испытаний включены [28]: • наработка на максимальном и взлетном режимах; • холодные запуски с выходом на взлетный режим; • приемистости и сбросы газа с выдержкой на взлетном режиме и малом газе: • наработка на резонансных и критических оборотах; • запуски; • реверсирование тяги и перекладки реверса на малом газе. Наработкой на максимальном режиме при наибольшей температуре газа перед турбиной исчерпывается длительная прочность горячих деталей двигателя. Для эквивалентной программы на ресурс 5000 ч время работы на максимальном режиме составляет 140 ч. На взлетном режиме проверяются прочность, выносливость и износостойкость шестерен, подшипников и шлицевых соединений. На этом режиме передаются максималь ные мощности, инерционные и газовые нагрузки. Для большинства ГТД взлетный режим одновременно является максимальным (с максимальной температурой газа), по этому время взлетного режима соответствует максимальному — в данном случае 140 ч.
Холодные запуски с выходом на взлетный режим предусматривают проверку на тепловой удар горячих деталей, в первую очередь, дисков турбины при максимальном тем пературном перепаде между ободом и ступицей. При холодных запусках проверяются также работоспособность шестерен, подшипников, шлицевых соединений в условиях ограниченной смазки. Исходя из приемлемой продолжительности этапа (5. . . 6 ч), в эк вивалентной программе на 5000 ч принимается 140 холодных запусков. Приемистости и сбросы газа с выдержкой на взлетном режиме и малом газе преду сматривают проверку малоцикловой усталости нагруженных узлов и деталей и проверку прочности дисков при прямом или обратном перепаде, когда температура обода ниже температуры ступицы и возникают максимальные растягивающие температурные напряжения на ободе. После выхода на взлетный режим и достижения максимальной температуры ступицы должны следовать сброс газа, выдержка на малом газе до установления максимального (или близкого к максимальному) обратного перепада и приемистость до взлетною режима. При этом на ободе возникают максимально возможные растягивающие напряжения (инерционные и температурные). Количество таких проб в эквивалентной программе должно соответствовать возможному количеству аналогичных выходов в программе на полный ресурс. В эквивалентной программе с учетом фактического числа этапов число переменных режимов может несколько отличаться от эксплуатационной программы. В программе на 5000 ч общее число приемистостей принято равным 5460. При этом виде испытаний проверяются также износостойкость и прирабатываемость лабиринтных уплотнений, так как статорные детали, охлаждаясь быстрее роторных, максимально выбирают рабочие зазоры. В зависимости от расположения лабирин тов этот процесс может происходить при сбросах газа или приемистостях. На резонансных режимах проверяются главным образом выносливость рабочих и на правляющих лопаток при колебаниях по разным формам, выносливость дисков, а так же контактная выносливость
замков крепления лопаток и бандажных полок. Режимы испытаний, предусмотренные программой длительных испытаний (номинальный; 0, 85; 0, 7; 0, 6; 0, 4 номинального), отличаются по частоте вращения на 200…. 250 1/мин, что составляет 4. . . 5 % от максимальных. Так как разброс частот лопаток составляет более 10 %, указанные режимы можно принять в качестве ступенек резонансных режимов. При этом какое-то количество лопаток всех ступеней неизбежно будет находиться в резонансном режиме. Для достижения числа циклов 2 10 s по минимальной лопаточной частоте, что достаточно для проверки усталостной прочности лопаток, наработка на каждой ступеньке резонансного режима в программе эквивалентных испытаний составляет 50 ч независимо от проверяемой долговечности. Некоторые из площадок резонансных режимов соответствуют критическим частотам вращения двигателя. Если по результатам вибрографирования в рабочем диапазоне оборотов имеются критические обороты и они отличаются от резонансных ступенек, то их смешают до совпадения с критическими оборотами и наработку в 50 ч проводят на совмещенном режиме. Если несовпадение режимов существенно, то добавляют ступеньку по частоте вращения, соответствующую критической скорости. Наработкой на критических частотах вращения проверяется выносливость корпусных деталей, трубок, оболочек, опор, а также надежность работы агрегатов, контактная выносливость золотниковых пар и других подвижных элементов, установленных с малыми зазорами. Количество циклов, которое нарабатывается при данной критической скорости, оп ределяется частотой вращения ротора и равно (8. 31)
где n — частота вращения ротора; τ — наработка на критических частотах вращения. За 50 ч наработки на критической скорости при частоте вращения ротора 4000. . . 7000 1/мин отрабатывается (12. . . 21)-10 6 циклов, что можно считать достаточным для оценки выносливости корпусных деталей, особенно стальных. Запусками, как и приемистостями, проверяется термостойкость лопаток турбины, камеры сгорания, сопла и других горячих деталей. Количество запусков в эквивалентной программе соответствует общему их числу в эксплуатационной программе. В программе на 5000 ч предусмотрено 3640 запусков. Реверсированием тяги и перекладками реверса проверяется сопротивление повторно-статическим нагрузкам деталей реверса, их термостойкость и усталостная прочность. Количество реверсирований и перекладок соответствует их числу в эксплуатационной программе. За 5000 ч — 1820 выключений реверса и 1820 перекладок реверса на малом газе. С учетом взаимного влияния длительной прочности, выносливости, повторной статики, термостойкости, коррозии и эрозии, контактной выносливости и износа эквивалентная программа складывается из отдельных этапов, каждый их которых содержит проверку по всем факторам. Один из этапов такой программы, складывающийся из перечисленных выше составных элементов, приведен на рис. 8. 14.
Рис. 8. 14. Типовой этап программы ускоренных эквивалентных испытаний двигателя дозвукового самолета на 5000 ч
Реализация прочностного метода позволяет обеспечивать эквивалентность ресурсных испытаний по ограниченному числу элементов изделия. При этом не всегда представляется возможность учитывать такие факторы, как старение, износ материалов и др. Опыт зарубежных авиадвигательных фирм также показывает, что недостатком и ограничением эквивалентно-циклических испытаний является отсутствие возможности вырабатывать эксплуатационные ресурсы подшипников, шестерен, вспомогательных и других агрегатов изделия. Разработанные на сегодня программы эквивалентно-циклических испытаний позволяют сокращать длительность доводочных ресурсных испытаний в 4…. 7 раз, а при больших ресурсах ГТД (до 10 000. . . 15 000 ч) — в 10. . . 15 раз. Фирма Роллс-Ройс (Великобритания) проводит ускоренные испытания при температуре газа перед турбиной Т г * > Т г т ах на 80. . . 90 К. При этом длительность эквивалентно-циклических испытаний сокращается в 25 раз (за 12 суток путем 150 -часового ЭЦИ проверяется наработка, соответствующая в условиях эксплуатации 4000 ч). Другим примером проведения ЭЦИ с форсированием режимов нагружения являются испытания ВГТД ТА-6 А, которые позволяют получить дополнительное сокращение их длительности |14|. При этом эквивалентные ускоренные испытания двигателя проводятся с форсированием частоты вращения ротора на 10 %, температуры газа перед турбиной Т г * — на 31 К, температуры воздуха на входе в двигатель Т н — на 20 К, мощности загрузки генератора переменного тока N гт — на 12 к. Вт и генератора постоянного тока N гс — на 4, 6 к. Вт, температуры элементов генераторов — на 18 К.
Обобщенный метод основан на представлении процесса расходования ресурса изделия в виде обобщенной математической модели, включающей мо дели расходования ресурса его основных элементов, узлов, систем и агрега тов 114): (8. 32) где П i — повреждаемость i-го элемента изделия по j-ой характеристике расходования ресурса (длительной прочности, повторно-статической прочности, усталости, коррозии, эрозии, износу и т. д. ); Р 0 = [P 01 , . . . P 0 v ] T — вектор параметров, характеризующих качество (исходное состояние) элементов изделия перед испытаниями; R( τ ) = [r 1 ( τ ), …. . r s ( τ )] т — вектор параметров режима нагружения; τ — время; G P — область исходного состояния изделия до испытаний; G R — область определения режимов нагружения изделия в эксплуатации (испытаниях). Наличие обобщенной модели расходования ресурса позволяет проводить выбор режимов и длительности ускоренных испытаний с учетом одновременно нескольких элементов и характеристик расходования ресурса по аддитивной целевой функции вида: (8. 33)
Где К э — коэффициент ускорения испытании, принимаемый для изделия в целом; К эij — коэффициент ускорения испытаний i-го элемента изделия с учетом j-ой характеристики расходования ресурса; ΔK эij доп — допустимая мера рассогласования между К эij и К э. При К эij = К э обеспечивается полная эквивалентность ускоренных и длительных (эксплуатационных) испытаний. Применение обобщенного метода позволяет до 2 раз повысить уровень эквивалентности ускоренных испытаний [16]. Метод экстраполяции основан на гипотезе о возможности достаточно досто верной оценки закономерности процесса накопления повреждений или отказов изделия по начальным этапам этого процесса [16|. При этом определяется скорость изменения параметра, характеризующего надежность и ресурс изделия, на некотором интервале установившегося процесса выработки ресурса и прогнозируется значение параметра за интервал наблюдения, вплоть до достижения предельного значения. Применение данного метода основано на следующих предпосылках: • предполагается, что из предыдущего опыта известен аналитический вид зависимости параметра и его дисперсии от наработки; • зависимость сохраняется в течение всего исследуемого процесса, вплоть до достижения параметром предельного значения; • функция, отражающая зависимость параметра от наработки, монотонна и имеет производную на всем интервале от начала установившегося процесса до достижения предельного значения.
Наиболее эффективно прогнозирование при проведении испытаний по Q- и G-планам эксперимента, позволяющим минимизировать дисперсию прогнозируемой величины 116]. В данном методе проведением эксперимента по плану получают ряд значений аргументов X и соответствующих им значений прогнозируемой величины Y , по которым определяют коэффициенты модели. Для прогнозных значений аргументов определяют математическое ожидание и интервальную оценку прогнозируемой величины Y пр : где t qp — квантиль распределения Стьюдента для q— уровня значимости и р степеней свободы (р = N- к)\ σ y 2 — дисперсия индивидуального (реального) значения прогнозируемой величины, формирующая ошибку прогноза δ. Экстраполяция дает приемлемую точность оценки, если длительность испытаний составляет не менее 40. . . 70 % от ресурса изделия и применяется для ориентировочной оценки параметров, характер изменения которых достаточно хорошо изучен путем наблюдения за изменением параметров аналогичных объектов в аналогичных условиях (на протяжении всего ресурса), а применяемая модель соответствует физической сущности рассматриваемого процесса.
8. 3. 4. Циклические испытания Для проверки прочности элементов горячей части и роторов ГТД при малоцикловой усталости широко используются циклические испытания. Малая продолжительность цикла нагружения (рис. 8. 15) позволяет воспроизвести их многократно за короткое время. Число циклов испытаний определяется по формуле: (8. 34) где N рес — число циклов за проверяемую циклическими испытаниями величину ресурса; К N — запас по числу циклов; η — коэффициент соответствия эксплуатационного и испытательного циклов (η≥ 1, при циклических испытания двигателя η = 1). В практике английской и американской авиапромышленности такие испытания применяются как основная форма ускоренной экспериментальной проверки работоспособности авиационных ГТД, позволяющих быстро оценить долговечность роторов и основных деталей горячей части двигателя. К циклическим также относятся испытания на усталостную прочность, которые проводятся, как правило, при исследовании повреждений лопаток вентилятора, компрессора и турбины в эксплуатации для установления норм на допустимые повреждения. Обеспечение запасов усталостной прочности является необходимым условием для установления и повышения ресурса, но напрямую ресурс устанавливается по результатам ресурсных циклических испытаний на лабораторных установках и в системе двигателя.
При ресурсных циклических испытаниях в системе двигателя всегда есть проблема, заключающаяся в воспроизведении режимов максимальных усилий. Для решения этой проблемы необходимо проводить испытания с переменным наддувом воздуха (до 2 • 10 5 Па) на вход в двигатель, т. е. в барокамере. Такие ресурсные циклические испытания требуют больших материальных затрат и тех нически трудно реализуются. Лабораторные циклические испытания проводятся также для рабочих лопаток турбин. Несмотря на сложное нагружение (центробежные, изгибные, температурные и вибрационные нагрузки), удается с использованием лабораторных установок воспроизводить эксплуатационные повреждения и проверять разработанные мероприятия по увеличению ресурса. На таких установках воспроизводится термоциклическое нагружение в сочетании с вибрационным. Рис. 8. 15. Вариант испытательного цикла: 1 — земной малый газ; 2 — взлетный режим; 3 — реверсирование тяги; 4 — крейсерские режимы; 5 — режим снижения; 6 — полетный малый газ
Так как повреждаемость охлаждаемых рабочих лопаток турбин определяется. в основном, термоциклическим нагружением, такое нагружение берется за основу, а недостающая нагрузка центробежными и изгибающими силами компенсируется соответствующим изменением термоциклического нагружения, определяемого расчетным путем. В процессе испытаний на термическое нагружение накладывается вибрационное, реализующееся в эксплуатации. Неучет вибрационного нагружения может привести к ошибке в определении долговечности лопатки в 2 и более раза. Лабораторные циклические испытания при необходимости проводят для определения ресурса валов двигателей при циклическом действии осевой нагрузки и кручения. Эффективными являются также лабораторные циклические испытания дисков компрессоров и турбин. Наиболее распространенными схемами лабораторных стендов для циклического нагружения дисков являются схемы с электроприводом исследуемого диска или ротора при нагреве его от индуктора. Применяется также схема циклического нагружения дисков усилиями, приложенными через замки лопаток. В этом случае центробежные усилия от лопаток имитируются от радиально установленных гидроцилиндров. Данная схема используется для отработки ресурса замковой части диска, так как полностью воспроизвести напряженное состояние диска при такой схеме нагружения не удается. Эффективным средством установления ресурса дисков являются ресурсные циклические испытания в системе двигателя. Требования по ресурсной циклической наработке для двигателя в целом, включая детали газовоздушного тракта, и для дисков различны. Для двигателя в целом для установления ресурса требуется запас по наработке = 1, 2; для дисков K N = 3, 0 (для ранее спроектированных двигателей) и K N = 4, 0 (для вновь проектируемых).
На рис. 8. 16 приведен испытательный цикл, соответствующий 40 -минутному полетному циклу с равномерным использованием переменных режимов. Цикл включает в себя запуск, выдержку на режиме малого газа (МГ), двухминутную выдержку на максимальной частоте вращения, три переменных режима Рис. 8. 16. Испытательный цикл для дисков двигателя
(n = 80 %; максимальный режим (М) — n = 80 %), два переменных режима (МГ- М-МГ), режим охлаждения (n = 80 %), выдержку (режим МГ) и останов с выбегом. Продолжительность цикла 7 мин. Для подтверждения ресурса 1000 ч с запасом K N = 3, 0 при продолжительно сти полетного цикла 40 мин должно быть отработано в процессе испытаний 4500 циклов. При продолжительности испытательного цикла около 7 мин продолжительность испытаний составляет 525 ч. Использование испытательного стенда для подтверждения ресурса 1000 ч вместо полного полетного цикла позволяет уменьшить время наработки с 3000 ч до 525 ч с сохранением ресурсных возможностей остальных узлов двигателя (донора) и для продолжения циклической наработки. Формирование испытательных циклов Формирование ИЦ производится на основании набора ТПЦ (ОТПЦ). Время наработки на каждом из установившихся режимов в И Ц должно быть равно средневероятному времени работы на этом режиме в наборе ТПЦ (ОТПЦ). При невозможности воспроизведения условий на входе в двигатель по р п и Г, * время наработки на тяжелых режимах в И Ц должно быть увеличено для обеспечения эквивалентности по длительной прочности наиболее нагруженной основной детали двигателя в ИЦ и в наборе ТПЦ (ОТПЦ). Число переменных процессов, воспроизводимых в ИЦ, должно быть равно средневероятному числу каждого из аналогичных переменных процессов в на боре ТПЦ (ОТПЦ). Время наработки на тяжелых режимах в ускоренном И Ц должно быть экви валентно по длительной прочности наиболее нагруженной основной детали времени наработки на всех установившихся режимах в ИЦ.
Число циклов нагружения от МГ до М в ускоренном ИЦ должно быть эквивалентно по малоцикловой усталости наиболее нагруженной основной детали общему числу нагружения в ИЦ. Для подтверждения динамической прочности двигателя рабочая область частот вращения от полетного малого газа до максимального режима разбивается на несколько диапазонов шириной до 5 % от максимальной частоты вращения и в каждом диапазоне обеспечивается наработка из расчета не менее 1 мин на 1 ч средневероятной длительности наработки в этих диапазонах ТПЦ (ОТПЦ). Число ИЦ каждого вида в программе ресурсных испытаний определяется по вероятности использования Р т соответствующего полетного цикла как: (8. 35) Для двигателей, для которых может быть установлен единый ускоренный испытательный цикл длительностью τ 1 , общее число таких ИЦ при испытаниях за подтверждаемый ресурс τ определяется по формуле: (8. 36) Где N з — запас по числу циклов.
8. 3. 5. Формирование программ эквивалентно-циклических испытаний основных деталей двигателя Назначенный ресурс основных деталей двигателя подтверждается их ЭЦИ. которые проводятся в системе полноразмерного двигателя. Допускается прове дение с ЭЦИ деталей на газогенераторе или на специальных установках. При испытаниях основных деталей на газогенераторе или специальном стенде допускается использовать режимы, превышающие эксплуатационные. Для подтверждения увеличенных назначенных ресурсов основных деталей допускается использовать детали, отработавшие в эксплуатации ранее установленный ресурс или его часть. Установление необходимого для подтверждения назначенного ресурса основных деталей числа ИЦ при ЭЦИ деталей N» или величины назначенного ресурса детали по результатам их ЭЦИ (в часах τ нрд или в числе полетных циклов N нрд ) производится путем эквивалентного приведения по малоцикловой усталости и длительной прочности фактических наработок детали при испытаниях к набору ТПЦ (ОТПЦ) применительно к подтверждаемым ресурсам. Общее условие эквивалентности заключается в равенстве повреждаемости данной детали в условиях испытаний и при эксплуатации в течение рассматриваемого ресурса. Необходимое для подтверждения назначенного ресурса детали N Hpд общее число ИЦ при ЭЦИ деталей N И определяется как: (8. 37)
где N Э — число полетных циклов, ранее отработанное данной испытываемой деталью в эксплуатации (при наличии средств объективного контроля число N Э определяется по выработке ресурса, в противном случае — по числу фактических полетов); K N — запас по числу ИЦ; η э — запас по числу ИЦ, зависящий от числа деталей n э , которые отработали не менее чем N э полетных циклов в эксплуатации, и определяемый как: η э = 1+2/n э при 1≤n э ≤ 10; η э =1, 2 при n э > 10; ξ и — коэффициент соответствия условий ЭЦИ деталей условиям эксплуатации по повреждаемости данной детали, который определяется по формуле: (8. 38) где N И — минимальное число циклов, отработанных экземпляром данной де тали при испытаниях. При проведении ЭЦИ основных деталей, имеющих наработку в эксплуата ции, временно назначенный ресурс определяется по формуле (8. 24). Вместе с тем, для работающих в условиях малоцикловой усталости основных деталей двигателя, разрушение которых может привести к опасным последст виям, методология фиксированной предельно допустимой циклической нара ботки должна оставаться обязательной.
8. 3. 6. Экспериментальная доводка опытных ГТД до 150 -часового ресурса В процессе такой доводки ГТД решаются две основные задачи: — идентификация опытных образцов ГТД с их проектными математической моделями для внесения при необходимости изменений в конструкцию, чтобы обеспечить получение запроектированных характеристик и свойств двигателя; — выявление слабых мест, неудачных конструктивных и технологических решений и их устранение. Доводка сопровождается значительными конструктивными изменениями (чертеж некоторых деталей иногда изменяют до 5 раз!). Современными прогрессивными методами, ускоряющими доводку, являются: поузловая доводка ГТД, проводимая параллельно с доводкой двигателя в целом и опережающая доводка газогенератора. Процесс экспериментальной доводки авиационного двигателя условно разбивается на несколько этапов. 1. Доводка работоспособности конструкции до ресурса от нескольких часов до 25 % первоначального ресурса т 0. 2. Доводка характеристик и эксплуатационных свойств двигателя при т 0 (стендовые испытания). 3. Обеспечение уровня надежности, достаточного для начала летной эксплуатации (стендовые и летные испытания). Последний этап включает в себя помимо серии специальных испытаний (тензометрирование, вибрографирование по запасам ГДУ и т. п. ) также и проведение летных испытаний и нескольких длительных стендовых испытаний по 150 -часовой программе эквивалентно-циклического испытания (ЭЦИ).
Рис. 8. 17. Типовой этап программы 150 -часовых ЭЦИ Программа ЭЦИ эквивалентна 600 -часовой эксплуатационной программе проводится этапами по 6 ч в зависимости от назначения ГТД и особенностей эксплуатации ДА (рис. 8. 17) |23). Суммарная наработка по режимам составляет: • на взлетном — 18 ч 45 мин; • на максимальном продолжительном — 45 ч при t m ах ; • на крейсерском — 62 ч 30 мин; • на переходном режиме — 23 ч 45 мин (запуски, приемистости, сброс газа земной малый газ). Количество проб приемистостей — 300; запусков — 100; реверсов — 200. За время испытаний выполняется 100 переключений средств механизации компрессора. На всех этих режимах должна быть обеспечена полная загрузи всех самолетных агрегатов. Не менее чем на 25 % времени включается противообледенитсльная система. Приведенные значения показывают значительную долю нагруженных режимов (взлетный и максимально продолжительный) — 42 %. Взлетный режим этой программе составляет 12, 5 %, тогда как в эксплуатации — всего 4 %.
По окончании испытания двигатель разбирают и контролируют состоят деталей. Если во время испытания и по результатам дефектации деталей отклонений от ТУ не наблюдалось, дается положительное заключение о годности двигателя к началу летной эксплуатации. Доводка ресурса ГТД завершаете сертификацией двигателей, т. е. установлением соответствия двигателя требованием норм летной годности (НЛГС). В целом доводка авиационных ГТД — сложный и длительный процесс: с ее начала до эксплуатации на ЛА обычно проходит от 40 до 80 месяце (3, 5. . . 6, 5 лет!), а для ТРДФ Олимп-593 и ТРДДФ НК-144, например, составила около 140 месяцев! Средняя стендовая наработка опытных образцов до начала летных испытаний за последние 20 лет находится на уровне 5000 ч, но иногда достигла< 10 000 ч. Существует статистическая зависимость между надежностью ГТД доводочной наработкой (рис. 8. 18). При этом двигатель сертифицируется дважды: — до установки на самолет; — при его установке на серийный самолет. Суммарная наработка до начала эксплуатации ГТД вместе с летными испытаниями достигает 13 000. . . 20 000 ч. На доводку при стендовых и летных испытаниях расходуют в среднем 20. . . 30 опытных образцов ГТД (для сверхзвуковых ДА иногда до 60. . . 70). По мере эволюции авиационных ГТД наработка на каждый опытный обра зец меняется: в 1950 -1960 гг. — 230 ч: в 1970 г. — 550 ч, в 1987 г. — 2500 ч. Методы доводки совершенствуются — если к концу доводки наработка на отказ в полете Т оп составляет 3000. . . 6000 ч, то после нескольких лет серийного производства удается увеличить значение Т оп до (40. . . 60) • 10 3 ч.
Рис. 8. 17. Типовой этап программы 150 -часовых ЭЦИ
8. 4. ЭКСПЛУАТАЦИЯ ГТД ПО ТЕХНИЧЕСКОМУ СОСТОЯНИЮ При больших ресурсах ГТД (6000. . . 10 000 ч) установление индивидуальных сроков ремонта двигателей становится объективной необходимостью, так как увеличивается роль случайных отказов. Зависимость надежности от ресурса для периода нормальной эксплуатации имеет вид, показанный на рис. 8. 19. При наработках на отказ ГТД Т* дсд = 10 000 ч и ресурсе ГТД τ м 1 = 10 000. . . 12 000 ч около 70 % ГТД (точка 1 на рис. 8. 19) не вырабатывают ресурса и попадают в ремонт из-за отказов досрочно. При Т* дсд = 5000 ч досрочно будут сняты уже 90 % двигателей (точка 2 на рис. 8. 19). Хотя значения наработок Т* дсд = 5000. . . 10 000 ч считаются типичными и удовлетворительными для современных ГТД Следовательно, при больших ресурсах понятие фиксированного межремонтного ресурса теряет смысл, т. к. подавляющее большинство ГТД будет ремонтироваться раньше. Фактически это означает, что при τ м 1 , > 10 000 ч ресурс перестает быть гарантом надежности. Недостаточная обоснованность назначения фиксированного ресурса двигателям постепенно была осознана в первую очередь эксплуатационниками, поскольку затраты на ремонт и обслуживание ГТД при увеличении наработки парка ЛА чрезмерно росли. Первым шагом в повышении эффективности эксплуатации ГТД было введение дифференцированного ресурса, учитывающего разную долговечность отдельных элементов двигателей, влияние различных условий эксплуатации и т. п. В РФ сохранилось наиболее жесткое понятие ресурса. При этом требуется, чтобы в течение межремонтного ресурса не должна выходить из строя или заменяться ни одна деталь. А каждая деталь должна иметь расчетный запас долговечности на 3 межремонтных ресурса.
В связи с такими различиями в пони мании ресурса естественно отличаются и цифры максимально достигнутых ресурсов: у самолетных ТВД в Великобритании межремонтный ресурс достиг • . 8000 (но с заменой жаровых труб через 2000. . . 3000 ч; у самолетных ТРДД — 4000. . . 10 000 ч с осмотром горячей части через 4000 ч) и у вертолетных ТВД — 1500. . . 3000 ч (наиболее напряженная эксплуатация ГТД). В США у самолетных ТРДД — 2000. . . 6000 ч (с осмотром горячей части через 4000 ч). В связи с жесткими требованиями первый межремонтный ресурс у отечественных ГТД несколько ниже. Сущность метода эксплуатации по техническому состоянию заключается в отказе от назначений фиксированной наработки между ремонтами и переходу к замене деталей по их фактическому техническому состоянию, т. е. деталь снимается и ремонтируется или заменяется на новую только после появления в нем дефекта, а не после выработки определенного ресурса. Качественная зависимость интенсивности отказов U OTK от времени эксплуатации представлена на рис. 8. 20. Эксплуатация по фактическому состоянию основывается на предположении, что реальное техническое состояние всех узлов, агрегатов и систем может быть оценено по контролю ряда параметров: • состояние двигателя характеризуется множеством параметров, которые случайно изменяются во времени; • техническое состояние, определяющее надежность двигателя, оценивается по комплексу параметров; • конструкция двигателя позволяет непрерывно или периодически контролировать значение этих параметров; • превышение этих параметров относительно нормативных определяет недопустимое в эксплуатации состояние двигателя;
• методы и средства диагностирования и контроля обеспечивают выявлении неисправностей на ранней стадии; • затраты на замену детали или узла, имеющего неисправности на ранней стадии развития, много меньше затрат при аварийной замене. Основным принципом при обслуживании по фактическому состоянию является принцип предупреждения неисправностей и отказов. С этой целью исполь зуется назначение упреждающих допусков, которые определяются как разности величин предельного Х пр и предотказного Х по значений параметров (рис. 8. 21) В момент времени τ 1 агрегат находится в исправном состоянии и разрешается его дальнейшая эксплуатация. Начиная с момента времени τ 2 , требуется замет агрегата, что и обнаруживается при второй проверке τ 2 [23].
Рис. 8. 18. Зависимость надежности ГТД от на- работки (Т* оп — наработка на отказ в полете) от наработки (t Σ ): 1, 2 — первая и вторая сертификации двигателя Рис. 8. 19. Зависимость вероятности безотказной работы ГТД p( τ ) от ресурса τ 1 м ,
интенсивности отказов от времени экс плуатации: участок А — приработка деталей; Б — нормаль ная эксплуатация; В — повышенный износ Рис. 8. 21. К определению упреждающего допуска: τ 1 и τ 2 — моменты предотказного и предельно го состояния двигателя соответственно; ’τ 1 и τ 2 ‘, — моменты проверки состояния двигателя
Система диагностирования является комплексной. Она требует применения как бортовых, так и наземно-бортовых средств, а также программ автоматической переработки информации. Если оценка состояния производится дискретно, то возникает задача определения оптимальных интервалов времени между проверками с точки зрения достоверности получаемой информации и экономических затрат. Вместе с тем, условия для реализации ЭТС в России (и СНГ) существенно отличаются от имеющихся на Западе. Особенно важно оценить возможность применения новой методологии управления ресурсами или отдельных ее элементов к старым двигателям, которые еще долго будут составлять основу эксплуатирующегося парка. Поэтому при переводе этих двигателей на ЭТС необходима экспертиза возможности удовлетворения требованиям летной годности при эксплуатации без фиксированного ресурса двигателя. На рис. 8. 22 приведены основные причины, обусловившие, по мнению западных специалистов, возможность успешного перехода к ЭТС авиадвигателей, а также основные факторы, отрицательно сказывающиеся на ее эффективности на Западе. Анализ опыта эксплуатации отечественных двигателей показывает, что их межремонтный ресурс чаше всего ограничен дефектами агрегатов, подтвержденным ресурсом подшипников, износом контактных поверхностей бандажных полок рабочих лопаток турбин и компрессоров и дефектами горячей части. Решающее значение для обеспечения эффективной ЭТС имеет создание и использование запаса по температуре газа ΔТ г *, причем величина ΔТ г * является одним из основных параметров, определяющих конкурентноспособность двигателя. Для обеспечения успешной ЭТС необходимы (как подтвержденньй при сертификации) запас ΔТ г * « 150. . . 200 К, так и широкое использование пони женных взлетных режимов в эксплуатации [36, 40].
При ЭТС ресурс основных деталей не должен превосходить подтвержденных безопасных значений. Эксплуатация по техническому состоянию в современном понимании не требует испытаний полноразмерного двигателя для подтверждения возрастающего ресурса. Основой для его увеличения являются увеличенный объем инспекций состояния двигателя, анализ состояния его деталей после отработки различных этапов ресурса, анализ опыта предыдущей эксплуатации, эксплуатации прототипов, а также назначенный ресурс основных деталей, определяемый путем опережающих циклических испытаний на стендах поузловой доводки вне двигателя или расчетным путем на базе развитого банка данных по механи ческим свойствам материалов. Без снижения безопасности полетов осуществление переноса центра тяжести ресурсных испытаний с двигателя на спецустановки и адекватная оценка эквивалентности нагруженности детали в испытательном и полетном циклах возможны при решении следующих задач: • необходимо выполнить анализ условий реальной эксплуатации и уточнить типовой полетный цикл двигателя по ряду термодинамических и механических параметров;
Рис. 8. 22. Причины успешной реализации эксплуатации авиационных двигателей но техническому состоянию и основные факто ры, отрицательно сказывающиеся на ее эффективности
• должна быть разработана математическая модель теплового состояния деталей двигателя, адекватно воспроизводящая стационарные и нестационарные тепловые поля в узлах двигателя в течение полетного цикла; • должно быть реализовано необходимое развитие прочностных моделей, позволяющее учесть ряд особенностей поведения конструкции и материалов, контактное взаимодействие сопрягаемых деталей роторов, учет геометрической и физической нелинейностей, особенностей циклического и упругопластиче ского деформирования. Однако при всей ясности технико-экономических преимуществ перехода на эксплуатацию авиационных двигателей по техническому состоянию реализовать этот процесс для каждого типа двигателя чрезвычайно сложно. Как показывают расчеты, введение эксплуатации по техническому состоянию позволяет вдвое сократить как производство двигателей и загрузку ремонтных предприятий, так и затраты на эксплуатацию. Обычно самолет во время ремонта не оставляют без двигателей за счет резервного фонда, т. е. резервный фонд в случае эксплуатации по состоянию будет также меньше. Сдерживающими факторами для реализации эксплуатации по техническому состоянию являются: • дефекты комплектующих и агрегатов систем автоматического управления; • разрушение подшипников; • повреждение элементов «горячей» части газовоздушного тракта, рабочих лопаток турбины ВД; • дефекты вентилятора, компрессора из-за попадания посторонних предметов в двигатель; • ложные срабатывания электронных систем диагностики; • эрозионный износ элементов газовоздушного тракта. Наиболее трудные проблемы возникают при проведении ресурсных циклических испытаний роторов турбины.
За рубежом двигатели магистральных самолетов эксплуатируются по техни ческому состоянию, в основном, без фиксированного ресурса с наработкой до первого ремонта 30 000 ч. Эксплуатируемые по техническому состоянию ГПУ на базе НК-8 имеют ин дивидуальный ресурс 10 000. . . 20 000 ч, что связано с малым числом циклов на гружений и пониженными режимами. Основной дефект, лимитирующий ре сурс, — это разрушение (или коробление) жаровой трубы, что легко диагности руется по ΔТ г * в эксплуатации. В Российских ВВС по техническому состоянию эксплуатируются двигатели АЛ-31 Ф и РД-33.
8. 5. ОСНОВНЫЕ СТРАТЕГИИ УПРАВЛЕНИЯ РЕСУРСОМ ГТД В процессе развития авиационных ГТД методология управления ресурсом претерпела существенные изменения. Если первоначально ресурс подтверждался лидерной летной наработкой или длительными стендовыми испытаниями двигателя, то при увеличении ресурсов до 5000. . . 10 000 циклов пришлось перейти к опережающим (по отношению к эксплуатации) ускоренным эквивалентно-циклическим испытаниям двигателей в сочетании с эквивалентно-циклическими испытаниями основных деталей на разгонных стендах. Это позволило в 3. . . I 0 раз сократить продолжительность и стоимость испытаний, также обеспечить раннее выявление неисправностей, которые можно устранить до их проявления в эксплуатационных условиях. В настоящее время рыночные условия диктуют, с одной стороны, необходимость достижения больших (до 30 тыс. ч) наработок без съема двигателя с крыла и оценки ресурсных возможностей двигателя к моменту ввода его в эксплуатацию, а с другой стороны — сокращения объема чрезвычайно дорогостоящи ресурсных испытаний двигателей. Все более широкое применение новых технологий, в первую очередь использование новых высокопрочных сплавов для приготовления основных деталей двигателей, также требует совершенствовании методов подтверждения ресурса. Основная тенденция заключается во все более широком использовании индивидуального подхода, требующего оценки технического состояния и остаточного ресурса каждого конкретного образца. В настоящее время при установлении и увеличении ресурсов авиационных двигателей и их основных деталей используются следующие 4 стратегии yпpaвления ресурсом (рис. 8. 23):
Рис. 8. 23. Основные стратегии управления ресурсом двигателя
1) установление и увеличение всех видов ресурсов двигателя (назначенного, до первого капитального ремонта, межремонтного) и назначенного ресурса его основных деталей на основании результатов их ресурсных испытаний и эксплуатации, при этом двигатель эксплуатируется с обязательным съемом двигателя в ремонт после отработки любого из установленных видов ресурса; 2) установление и увеличение назначенного ресурса основных деталей двигателя на основании результатов их ресурсных испытаний и эксплуатации двигателя, при этом двигатель эксплуатируется без обязательного съема для ремонта по достижении назначенного ресурса любой из основных деталей; 3) установление и увеличение назначенного ресурса основных деталей двигателя на основании использования экспериментально обоснованных методов расчетов и статистически обоснованных данных по конструкционной прочности материалов, при этом двигатель эксплуатируется без обязательного съема до достижения назначенного ресурса любой из основных деталей, 4) установление и увеличение ресурсов на основании совмещения стратегий; например, установление назначенного ресурса основных деталей по стратегии 2 или 3 и межремонтного ресурса двигателя с обязательным съемом в ремонт. Применение стратегий 2 или 3 допускается в следующих случаях: • достаточная контролепригодность, обеспечивающая получение объективной информации для достоверной оценки технического состояния двигателя и прогнозирования отказов с опасными последствиями с помощью средств и методов контроля и диагностики, а также эксплуатационная технологичность двигателя; • применение методов и средств технического обслуживания, обеспечивающих безопасность эксплуатации двигателя;
имеется положительный опыт эксплуатации двигателя и(или) двигателей- аналогов, отражающий анализ результатов эксплуатации парка двигателей и их дефектации при ремонтах, обеспечение соответствия установленной наработки на выключение двигателя в полете, отсутствие отказов с опасными последствиями. Установление и увеличение назначенного ресурса основных деталей двига теля на основании использования банка данных по стратегии 3 допустимо при: выполнении указанных выше условий; наличии банка данных по конструкционной прочности материалов основ ных деталей, позволяющего дать надежную статистическую оценку ресурса этих деталей с учетом влияния конструктивных, технологических и эксплуатационных факторов; экспериментальном подтверждении применяемого метода определения ресурса основных деталей с учетом характерных особенностей их конструкции, технологии изготовления и условий эксплуатации. Традиционная методология обоснования ресурса авиационного двигателя (по новой терминологии — стратегия 1) предполагает передачу двигателя в эксплуатацию с небольшим начальным ресурсом и последующее подтверждение полного ресурса на основе летных испытаний и испытаний полноразмерного двигателя в условиях стенда. Жесткие требования прямых испытаний двигателя имеют своей причиной существовавший до недавнего времени подход к проектированию, когда в проектировочных расчетах прочности деталей применялись более или менее простые расчетные модели и нормированные запасы прочности, обоснованные об ширным опытом проектирования схожих конструктивных элементов двигателя. Применение этих методов позволяет выделить главные нагружающие факторы, основные составляющие напряженно-деформированного состояния деталей и, в целом, дают хорошее начальное приближение оценки прочностных характеристик элементов конструкции двигателя.
Достаточность такого подхо да в части оценки несущей способности деталей, их длительной прочности обоснована практикой. В сегодняшней ситуации эти методы представляют основной инструмент анализа на начальном этапе эскизного проектирования двигателя, когда определяются критические элементы конструкции, требующие повышенного внимания и дополнительного анализа с целью снижения риска проекта. В рамках первой стратегии управления ресурсом двигателя основной упор в обосновании ресурса был сделан на экспериментальные исследования — ЭЦИ полноразмерного двигателя. При величинах ресурсов, исчисляемых десятками тысяч часов и циклов, это приводит к непомерным затратам времени и средств, существенно увеличивает стоимость каждой единицы (часа или цикла) устанавливаемого ресурса. Такие методы установления и выработки ресурса были эффективными при межремонтных ресурсах 200. . . 300 ч и назначенных до полного списания • . 2000 ч для авиационных ГТД, выпущенных и эксплуатируемых в период с 1960 по 1970 гг. Эксплуатация с фиксированным ресурсом является экономически неэффективной, поскольку не полностью используются ресурсные возможности двигателя и его основных деталей из-за необходимых запасов по долговечности проведении циклической наработки. На рис. 8. 24 приведена схема обоснования ресурса основных деталей ГТД в рамках второй стратегии управления ресурсом. Систематизация накопленного опыта эксплуатации двигателей более ранней разработки позволяет осуществить переход к третьей стратегии управления ресурсом, когда прогноз и обоснование ресурса выполняются аналитическими методами на основе развитого банка данных, включающего как составную часть базу данных механических свойств материалов.
Пример. В качестве примера можно привести результаты прогнозирования ресурса дисков компрессора высокого давления двигателя ПС-90 А (со второй по восьмою пень) [9]. В основу прогноза положены результаты положительной эксплуатации двигателя Д-30. Рассматриваемые диски компрессора двигателя ПС-90 А близки по конструкции к дискам со второй по восьмую ступень компрессора двигателя Д-30. Все сравнила диски имеют аналогичную конструкцию: тонкое полотно, широкую ступицу со шлицами, вынесенными из-под полотна диска, наклонный обод с отверстиями под штифты для крепления лопаток на первых ступенях (2. . . 3 ступени двигателя Д-30 и 2. . . 5 ступени двигателя ПС-90 А), диски имеют одни и те же конструктивные концентраторы напряжений (критические зоны). Тепловое состояние дисков обоих двигателей определено на основе результатов термометрирования. Среди двигателей-предшественников двигатель имеет наиболее полно исследованное тепловое и напряженное состояние ротора компрессора и достаточно высокие величины назначенных ресурсов рассматриваемых дисков — в рамках первой стратегии им установлен ресурс от 8000 до 11 400 циклов, и диски успешно отрабатывают эти ресурсы. Сопоставление результатов конечного элементного анализа натруженности дисков двух двигателей позволило определить соответствие их по циклической долговечности. Полученный таким образом прогноз ресурса дисков двигателя ПС-90 А составляет 6000. . . 8300 циклов. Для обоснования (сертификации) прогнозируемого ресурса в настоящее время возможны два пути. Можно, следуя положениям второй стратегии, провести соответствующие подтверждающие ЭЦИ дисков на специализированных установках либо обосновать прогнозируемый ресурс на основе обобщения имеющихся (или дополнительно полученных) данных о свойствах малоцикловой усталости материалов.
Выбор пути в каждом конкретном случае определяется как техническими соображениями (оценка достоверности прогноза, достаточность статистики по механическим свойствам и пр. ), так и экономическими критериями. Аналогичные работы по систематизации опыта эксплуатации ранее разработанных двигателей проводятся и в отношении других узлов и деталей — турбин высокого и низкого давления, валов роторов, корпуса камеры сгорания. Здесь прототипами выступают двигатели разработки ОАО «Авиадвигатель» : Д-30, Д-ЗОКУ, Д-30 КП. Д-ЗОКУ-154, Д-30 Ф 6, а также ГТД разработки ОАО «НПО «Сатурн» : В 6, М 70, М 75. Успешная реализация новой методологии требует планомерной работы, организация которой может быть осуществлена на основе разработки «Плана yпpaвления ресурсом» , который должен содержать выбор стратегии управления ресурсами, мини-планы управления ресурсами основных деталей, регламентировать показатели безотказности, принципиальные вопросы техобслуживания и диагностики, контроль состояния поступающих в ремонт двигателей и их основных деталей, рекомендации по схеме ремонта, график дополнительных инспекций испытаний отдельных деталей после наработки их в эксплуатации. Он также должен регламентировать обратную связь заказчика с изготовителем, в первую очередь уточнение условий эксплуатации и информацию о дефектах (рис. 8. 25).
Рис. 8. 24. Схема обоснования ресурса основных деталей ГТД в рамках второй стратегии управления ресурсом
Рис. 8. 25. Схема перехода на ЭТС и содержание плана управления ресурсами двигателя
Новая методология управления ресурсом двигателей была со значительным экономическим эффектом использована в двигателях ПС-90 А и Д-18 Т 3 -й се рии. В обоих случаях были значительно сокращены затраты на увеличение ре сурсов. Было обеспечено существенное увеличение ресурсов двигателей и их основных деталей. В частности, средняя наработка двигателей ПС-90 А на са молете Ил-96 -300 в 1999 г. составила около 6000 ч, лидерный двигатель был снят после наработки 7600 ч, тогда как до перехода на ЭТС фиксированный ре сурс двигателя до капитального ремонта составлял 3000 ч. Основным деталям двигателя Д-18 Т 3 -й серии в настоящее время установ лен ресурс 3. . . 20 тыс. циклов, т. е. практически такой же, как у двигателей веду щих зарубежных фирм. Современные методы управления использования ресурсами при эксплуата ции двигателей TB 7 -1 I 7 C, НК-86. ТВД-20, Д-ЗОКУ-154, Д-30 КП, ТВЗ-117 ВМА, АЛ-31 Ф и др.
8. 6. ПОРЯДОК ЗАДАНИЯ, УСТАНОВЛЕНИЯ И УВЕЛИЧЕНИЯ РЕСУРСА Методы повышения ресурса двигателей авиапромышленности регламентируются в настоящее время нормами летной годности для двигателей гражданской авиации и «Положениями об установлении и увеличении ресурсов и сроков службы газотурбинных двигателей» для военной авиации. В соответствии с этими документами увеличение всех видов ресурса двигателей и назначенного ресурса его основных деталей и узлов проводится на основании результатов ресурсных испытаний двигателей, узлов и основных деталей. После выработки любого вида ресурса двигатель снимают с самолета и направляют в капитальный ремонт или списывают. Ресурсные испытания опытных двигателей, проводимые по программе Государственных стендовых испытаний (ГСП), должны соответствовать требованиям ТЗ и типовой программе ГСП. Установление и увеличение ресурсов двигателя, его деталей, агрегатов и комплектующих изделий оформляются Решениями промышленности и Заказчика и бюллетенями: • при установлении начальных ресурсов — на основании акта по результатам ГСП; • при увеличении ресурсов, в том числе при ЭТС, — на основании заключений Разработчика двигателя, НИУ Заказчика и НИИ промышленности. В решении об увеличении ресурсов отражаются следующие вопросы: • наличие положительного заключения НИИ промышленности по прочности двигателя; • выполненный объем необходимых испытаний; • результаты разборки и дефектации двигателей, выработавших предыдущий ресурс, а также результаты дефектации двигателей, поступивших в ремонт по другим причинам; • результаты анализа отказов и повреждений ресурсного характера, выявленных в эксплуатации;
• соответствие показателей безотказности нормированным значениям; • конструктивные особенности двигателя увеличенного ресурса; • анализ эффективности мероприятий по устранению конструктивно-производственных дефектов; • достаточность методов и средств диагностики технического состояния в эксплуатации. 8. 6. 1. Установление и увеличение назначенных ресурсов основных деталей двигателя К основным деталям относятся детали двигателя, отказы которых вследствие недостаточной их долговечности могут привести к возникновению аварийной или катастрофической ситуации для ЛА (детали роторов вентилятора, компрессоров и турбин; валы; жаровые трубы; основные и форсажные камеры; корпуса, работающие под давлением; трубопроводы масляной, топливной и гидравлической систем; элементы подвески двигателя и другие детали, работоспособность которых, в основном, определяется исчерпанием малоцикловой долговечности). Для однодвигательных ЛА к основным деталям, кроме того, относятся все детали, отказы которых приводят к неустранимому в полете выключению двигателя, потере тяги ниже критического уровня или недопустимому изменению направления тяги. Начальные назначенные ресурсы основных деталей двигателя подтверждаются ресурсными испытаниями на специальных установках с учетом коэффициентов соответствия испытательного цикла детали и ТПЦ и нормированных запасов по числу испытательных циклов детали. Коэффициенты соответствия учитывают различие в условиях повреждаемости данной детали по малоцикловой усталости и длительной прочности в испытательном и полетном циклах. Методики и математические модели подсчета повреждаемости формируются Разработчиком и
согласовываются с НИИ промышленности и Заказчиком. С целью обеспечения назначенного ресурса двигателя, в том числе при ЭТС, должны проводиться опережающие ЭЦИ основных деталей. Испытания узлов и деталей, в основном, проводятся с использованием стендов поузловой доводки или в системе полноразмерного двигателя. В этом случае они могут совмещаться с эквивалентно-циклическими испытаниями двигателя в целом. 8. 6. 2 Установление назначенного ресурса двигателя Начальный назначенный ресурс двигателя устанавливается на основании Удовлетворительных результатов испытаний двигателя, предъявленного на ГСП. По решению Заказчика для дополнительного подтверждения установленно го по результатам ГСП начального назначенного ресурса двигателя проводятся лидерные испытания или осуществляется лидерная эксплуатация двигателем на 4. . . 6 самолетах по специальной программе с увеличенной интенсивностью (наработкой двигателя за определенный период эксплуатации) по сравнению с обычной эксплуатацией. Увеличение назначенного ресурса двигателя до величины полного назначен ного ресурса, оговоренного в ТЗ и выше, проводится поэтапно согласно планам- графикам, составленным Разработчиком и Изготовителем, согласованным с представителями Заказчика и утвержденным промышленностью и Заказчиком.
Увеличенный назначенный ресурс двигателя подтверждается: • удовлетворительными результатами стендовых испытаний на увеличенный назначенный ресурс одного двигателя с запасами по числу испытательных циклов); • удовлетворительными результатами испытаний на увеличенный назначенный ресурс основных деталей двигателя. С целью сокращения продолжительности испытаний они проводятся с использованием ускоренных испытательных циклов. Испытаниями двигателя на увеличенный назначенный ресурс одновременно подтверждается увеличенный назначенный ресурс всех его деталей, кроме основных, увеличенный назначенный ресурс которых должен быть подтвержден с запасами. 8. 6. 3 Установление и увеличение ресурса новых двигателей при стратегиях управления ресурсом 2 и 3 Новые двигатели допускаются к эксплуатации в соответствии со стратегиями 2 и 3 с момента ввода в строй при выполнении следующих требований: • успешное выполнение комплекса расчетно-экспериментальных работ, предусмотренных программой ГСП; • выполнение требований, предусмотренных в п. 8. 5; • наличие Плана управления ресурсом. План включает: • обоснование принятой стратегии эксплуатации; • перечень ограничений, включающий величины устанавливаемых ресурсов основных деталей двигателя, агрегатов и комплектующих изделий; • программу контроля технического состояния двигателя;
• характеристики допустимых ресурсных повреждений основных и неосновных (например, сопловые аппараты, жаровые трубы и др. ) деталей двигателя с учетом влияния внешних факторов (коррозия, эрозия, износ и др. ); • обоснование этапности увеличения эксплуатационного ресурса двигателя; • порядок увеличения ресурсов основных деталей двигателя, агрегатов и комплектующих изделий; • порядок оценки остаточного ресурса основных деталей двигателя в эксплуатации; • порядок учета результатов эксплуатации парка двигателей; • порядок учета результатов разборки и дефектации двигателей, поступавших в ремонт; • порядок принятия решения о направлении двигателя на техническое обслуживание или в капитальный ремонт. Двигатели, находящиеся в эксплуатации, эксплуатирующиеся по стратегии 1 и имеющие установленные ресурсы до капитального ремонта, межремонтный ПОРЯДОК ЗАДАНИЯ, УСТАНОВЛЕНИЯ И УВЕЛИЧЕНИЯ РЕСУРСА 277 и назначенный, по согласованию с Заказчиком могут быть переведены на эксплуатацию с управлением ресурсов по стратегиям 2 и 3 на любом этапе эксплуатации при выполнении следующих условий: выполнении требований, предусмотренных в п. 8. 5; . положительном опыте эксплуатации двигателя на предыдущем этапе; наличии Плана управления ресурсом; обеспечении нормируемых показателей безотказности. Ресурс основных деталей при переводе на стратегию 2 устанавливается в соответствии с требованиями п. 8. 3. 4, а ресурс основных деталей при переводе на стратегию 3 устанавливается на основе определения долговечности детали с использованием статистически обоснованных кривых малоцикловой усталости из Банка данных механических свойств материалов.
8. 6. 4. Установление и увеличение ресурса и сроков службы агрегатов и комплектующих изделий Ресурсы агрегатов и комплектующих изделий должны быть, как правило, не менее ресурсов двигателя. Сроки службы (эксплуатации и хранения) агрегатов и комплектующих изделий должны быть на 2. . . 3 года больше соответствующих сроков службы (эксплуатации и хранения) двигателя. Основным видом стендовых ресурсных испытаний агрегатов и комплектующих изделий на специальных установках, максимально имитирующих эквивалентно-циклические испытания по программе, составленной на основе обобщенного полетного цикла, представляемого Разработчиком двигателя. Ресурсы агрегатов и комплектующих изделий подтверждаются Разработчиком или Изготовителем двигателя на основании: — удовлетворительных результатов их ресурсных испытаний совместно с двигателем на устанавливаемый ресурс двигателя; — удовлетворительных результатов их испытаний на назначенный ресурс, которые могут проводиться как на двигателе, так и по ресурсным программам на специальных установках; — положительных заключений предприятий Изготовителей и Разработчиков агрегатов и комплектующих изделий об отсутствии дефектов, связанных с отработкой ресурса и влияющих на безопасность полетов, по результатам исследований, разборки и дефектации изделий; — удовлетворительных результатов межведомственных (государственных) наземных испытаний агрегатов и комплектующих изделий (для опытных изделий). Ресурс подшипников устанавливается на основании испытаний, которые проводятся для установления ресурса двигателя в целом, и требований, изложенных в «Положении об установлении и увеличении ресурсов подшипников качения ГТД ГА и их агрегатов» , или по методикам, согласованным с НИИ
промышленности, Заказчика и ВНИИПП. Подтверждение сроков службы агрегатов производится одновременно с двигателем.
8. 7. ПОДХОДЫ К ПОДТВЕРЖДЕНИЮ РЕСУРСА ОСНОВНЫХ ДЕТАЛЕЙ ГТД В соответствии с новыми подходами к управлению ресурсом ГТД наиболее важным является вопрос о подтверждении ресурса основных деталей двигателей, работающих обычно в области малоцикловой усталости, поскольку ЭТС может быть разрешена лишь в пределах безопасного ресурса этих деталей. Список основных деталей уточняется для конкретного двигателя на основе анализа последствий отказов. В перечень деталей с ограниченным ресурсом могут включаться и детали, разрушение которых не должно приводить к опасным последствиям, например рабочие лопатки вентилятора. В настоящее время имеются два подхода (метода) к подтверждению ресурса основных деталей: • основанный на концепции «безопасной долговечности» ; • основанный на концепции «допустимых повреждений» . 8. 7. 1. Метод «безопасной долговечности» Для двигателей гражданской авиации обязательным является использование концепции «безопасной долговечности» . Основные этапы процедуры подтверждения ресурса, базирующиеся на этой концепции, показаны на рис. 8. 26. Концепция «безопасной долговечности» основана на том, что к концу устанавливаемого ресурса лишь один диск из 740 (при применении логарифмически-нормального закона для описания рассеяния долговечности) или из 1000 (при применении распределения Вейбулла для описания рассеяния долговечности) может иметь трещину размером около 0, 8 мм. Указанная вероятность появления дефекта соответствует уровню долговечности «среднее значение — Зσ» , a размер дефекта выбран так, чтобы при обычных условиях нагружения он был существенно меньше критической длины трещины (что справедливо для традиционных сплавов с достаточной
пластичностью) и при этом надежно выявлялся обычно используемыми методами неразрушающего контроля. Таким образом, при подтверждении ресурса в 10 000 циклов вероятность появления дефекта такого размера составляет примерно КГ 7 , что соответствует требованиям к обеспечению практической невероятности катастрофы. Выполнение их при подтверждении меньших ресурсов может потребовать увеличения запаса по циклам. Существуют два подхода к определению безопасной долговечности. В нашей промышленности до настоящего времени использовался только первый из них, основанный на циклических испытаниях элементов конструкции. В этом случае требуемый запас по циклам зависит от рассеяния долговечности и количества испытанных деталей. Для сокращения времени и повышения достоверности результатов при увеличении ресурса целесообразно испытывать детали с максимально большой наработкой в эксплуатации. Ресурс основных деталей отечественных двигателей, как правило, подтверждался при ЭЦИ двигателей до наработки определенного количества циклов (а не до появления трещины). Таким образом, в большинстве случаев ресурс деталей недоиспользован. В то же время запас подтвержден ного ресурса, как правило, отсутствует, а дальнейшее увеличение ресурса применении этого подхода в большинстве случаев не представляется возможным. Кроме того, как показал проведенный анализ, при испытании до появления трещины (в частности, при испытании одной детали) запас по циклам (по отношению к разрешенному ресурсу) должен быть увеличен (до K N =4) по сравнению с ранее использовавшимся (K N = 3).
Рис. 8. 26. Процедура установления (увеличения) ресурса основных деталей применении концепции безопасной долговечности
Важнейшими условиями применения этого метода являются достаточная пластичность сплава и возможность описания рассеяния долговечности дисков логарифмически-нормальным или Вейбулловским распределением. Оценка ресурса по испытаниям одного диска не очень желательна. При испытаниях нескольких дисков имеется возможность сопоставить разброс по их долговечности с оценками для указанных распределений, а ресурс может быть оценен с соответствующими запасами по результатам испытаний образца с минимальной долговечностью, образца с максимальной долговечностью или по средней долговечности. Главным недостатком метода являются большой объем дорогостоящих испытаний натурных деталей и невозможность надежно определить на ранней стадии ресурсные возможности конструкции. В настоящее время разработаны методы определения безопасного ресурса основных деталей по совокупности разнородных (отказных и безотказных с разной наработкой) испытаний. Другой подход, основанный на применении экспериментально-расчетного метода, позволяет оценить ресурсные возможности конструкции в период ее создания, обеспечить подтверждение ресурса с начала эксплуатации и создать тем самым необходимые условия для ЭТС. Его использование допустимо при следующих условиях: 1) наличии банка данных о конструкционной прочности материалов основных деталей, позволяющего дать надежную статистическую оценку ресурса этих деталей, с учетом влияния конструктивных, технологических и эксплуатационных факторов; 2) экспериментальном подтверждении применяемого метода определения ресурса основных деталей с учетом характерных особенностей конструкции, технологии изготовления и условии эксплуатации этих деталей.
Метод предполагает расчет методом конечных элементов напряженно-деформированного состояния во всех потенциально-опасных зонах концентрации напряжений детали на стационарных и нестационарных режимах работы двигателя. Во многих случаях оказывается необходимым учитывать взаимодействие контактирующих деталей. При расчете целесообразно использовать характеристики материала, получаемые при циклическом (а не однократном) деформировании с соответствующим коэффициентом асимметрии цикла. По полученному расчетом размаху деформаций с использованием банка данных по конструкционной прочности определяется циклическая долговечность. Другая проблема, требующая научного осмысления, связана с возможностью эксплуатации деталей после выработки ресурса по безопасной долговечности. Если к концу выработки ресурса в среднем лишь в одной детали из тысячи возможно появление трещины обнаруживаемого размера, то в среднем остальные 999 деталей не будут иметь дефектов и их потенциальный ресурс будет далеко не исчерпан. В современных экономических условиях проблема использования этого потенциального ресурса весьма актуальна. Обеспечение безопасности эксплуатации таких деталей должно базироваться на теоретических и экспериментальных статистических исследованиях распределений исходных дефектов, закономерностей развития малых трещин, вероятностей попадания дефектов в критические зоны деталей, особенностей концентрации напряжений и полей остаточных напряжений вокруг дефектов, развитии методов неразрушающего контроля как в части повышения их разрешающей способности, так и в отношении повышения надежности выявления дефектов, а также совершенствования самой концепции безопасности полетов.
8. 7. 2. Метод «допустимых повреждений» Метод безопасной долговечности предполагает, что к моменту отработки установленного ресурса лишь одна деталь из 1000 может иметь трещину размером около 0, 8 мм. При этом ресурс остальных деталей остается недоиспользованным. Кроме того, исследования показывают, что микротрещины в таких деталях, как диски, часто возникают уже при наработке первых 5. . . 10 % от установленной «безопасной долговечности» . Наконец, новые высокопрочные гранулируемые сплавы существенно отличаются по возможным дефектам от сплавов традиционных. Наибольшую опасность в этих сплавах представляют редко встречающиеся керамические включения, а также поверхностные дефекты от мехобработки, влияние которых на сопротивление малоцикловой усталости при традиционном подходе, основанном на испытаниях одной или нескольких деталей или даже при испытаниях относительно большой партии образцов, может быть не выявлено. С подобной проблемой приходится сталкиваться и при оценке ресурса конструкций, полученных литьем или сваркой, когда в материале могут быть поры, или конструкций из титановых сплавов при наличии обогащенных a-фазой зон повышенной твердости. Отмеченные обстоятельства привели к разработке метода «допустимых повреждений» . Метод основан на предположении, что в материале детали может находиться дефект, ведущий себя как трещина. Размер этого дефекта определяется, исходя из чувствительности неразрушающего контроля, особенностей технологического процесса и результатов анализа изломов (в первую очередь гладких образцов, испытанных на МЦУ). В последнем случае в качестве размера наиболее вероятного дефекта целесообразно принять а = а ср + Зσ, где а ср — среднее значение, а σ — среднее квадратичное отклонение размера дефекта, определенные при исследовании изломов. Далее определяются характеристики скорости роста трещин в материале при циклическом нагружении (зависимость скорости роема трещины от размаха интенсивности напряжений АК).
Предполагается, что дефект может располагаться в опасной по напряженно-деформированному состоя нию зоне (у концентратора напряжений). Рассчитывается количество циклов до возникновения трещины критического размера, и с соответствующим запасом определяется разрешенное для эксплуатации количество циклов. Метод «допустимых повреждений» по-разному применяется для двигателей гражданской и военной авиации. В США этот метод для двигателей гражданской авиации является обязательным дополнением метода «безопасной долго вечности» при оценке ресурса деталей двигателей применении для их изготовления гранулированных сплавов, методов литья и сварки. В этом случае применении метода «допустимых повреждений» обычно берется запас K N = 3, а разрешенным для эксплуатации является минимальное из полученных двумя методами значение числа циклов. Такой подход предложено использовать и в отечественной промышленности, в том числе при ЭТС. Регистр Великобрита нии с 1980 г. разрешил подтверждение ресурса основных деталей на основе концепций «допустимых повреждений» . В США на основе программы конструкционной прочности двигателей (ENSIP) в 1984 г. разработан стандарт M 1 L-STD-1783, в соответствии с кото рым двигатели для военной авиации проектируются на основе концепции «до пустимых повреждений» . В этом случае обеспечивается более полное использование ресурсных возможностей каждой детали при ЭТС. Контроль детали должен быть проведен до того, как трещина разовьется до критического размера. В этом случае запас должен быть K N > 2, чтобы избежать разрушения детали при возможном при одноразовом контроле пропуска дефекта. Если при контроле дефекта не выявлено, то возможна наработка еще такого же количества циклов; в противном случае деталь снимается с эксплуатации.
Таким образом, метод «допустимых повреждений» уже довольно долго используется в авиадвигателестроении. В отечественной промышленности от дельные элементы этого метода применялись при появлении дефектов в эксплуатации (диски турбин изделия 99, НК-8, ПС-90 А и др. ). Вместе с тем до настоящего времени имеется много проблем, связанных с при менением этого метода: учет сложного напряженно-деформированного состояния, пластичности, ползучести, наложения вибраций, остаточных напряжений, коррозии и др. В ряде работ, например, используется простое суммирование скоростей роста трещины при циклическом нагружении и в условиях ползучести. Подход, при котором считается, что наиболее опасный металлургический дефект находится в наиболее опасной зоне диска, является весьма консервативным. В связи с этим в последние годы получили развитие методы оценки ресурса на основе оценки вероятности появления в определенном месте дефекта определенного размера, с последующим расчетом вероятности пропуска его при неразрушающем контроле и роста до критического размера за устанавливаемый ресурс. Приемлемая вероятность такого события составляет примерно 10‘ 8. Несмотря на большое значение развития методов подтверждения ресурсов основных деталей двигателей, следует отметить, что ресурсные возможности конструкции определяются конструктивно-технологическим решением и условиями нагружения.
РЕЗЮМЕ (по главе 8 «Экспериментальные методы определения ресурса и надежности авиационных ГТД» ) 1. Обеспечение высокого уровня безопасности эксплуатации авиационных ГТД органически связано с проблемой получения требуемого уровня надежности I ресурса на этапах создания и испытаний двигателя. В свою очередь, надежность и ресурс ГТД являются составляющими более общего показателя ГТД — качества. В широком смысле надежность ГТД определяется такими составляющими, как безотказность, ремонтопригодность, сохраняемость и долговечность. Для количественной оценки долговечности используют показатели — ресурс и срок службы. 2. Основными причинами выхода из строя двигателей являются: 1) несовершенство конструкции; 2) неудачная технология или нестабильность производства; 3) низкое качество или нестабильность материалов; 4) дефекты комплектующих изделий (изделий смежников); 5) нарушение правил эксплуатации и обслуживания двигателей. 3. На практике применяют следующие частные критерии, характеризующие количество отказов, приходящихся на 1000 ч наработки двигателей в полете: • коэффициент Л^00(характеризует общее количество отказов в полете, вызвавших нарушение работоспособности двигателя); • коэффициент (характеризует количество отказов, приведших к досрочному съему двигателя с летательного аппарата).
• Регламентируются следующие виды ресурсов двигателя: назначенный, до первого капитального ремонта, межремонтный, эксплуатационный и гарантийный. Установление и увеличение ресурсов и сроков службы двигателя производится на основе: статистических данных об их отказах и дефектах в эксплуатации, ресурсных стендовых и летных испытаний, лидерной эксплуатации двигателя, ресурсных испытаний основных деталей двигателя, а также других работ. Ресурсные испытания двигателей проводятся на стендах с атмосферными условиями на входе и частично на стендах с имитацией высотно-скоростных условий. Все виды ресурсов устанавливаются в часах общей наработки двигателя в полете и на земле и (или) в количестве полетных циклов. • При больших значениях ресурса (3000. . . 4000 ч и более) проведение длительных (ресурсных) испытаний по эксплуатационной программе становится нецелесооб разным или невозможным. Поэтому применяют ускоренные испытания и, в частности, эквивалентно-циклические испытания (ЭЦИ), характеризующиеся тем, что их программа за более короткое время «моделирует» работу изделия в течение полного ресурса. • Программы ЭЦИ авиационных двигателей основаны на: • увеличенной наработке на наиболее тяжелом режиме; • ступенчатой наработке в рабочем диапазоне частот вращения; • полном воспроизведении переходных режимов (запусков с выходом на взлет ный режим, приемистостей, сбросов газа с выдержкой на взлетном режиме и ма лом газе, реверсировании тяги и перекладки реверса на малом газе).
• При испытании технических изделий и их элементов, узлов, систем и агрегатов возможны несколько методов обоснования ресурсных испытаний: статистический, прочностной, обобщенный и метод экстраполяции. Для авиационных ГТД в наиболее полной мере используется прочностной метод, который основан на изучении факторов, влияющих на исчерпание ресурса, и установлении соотношений между нагрузкой и долговечностью. • Для проверки малоцикловой прочности элементов горячей части и роторов ГТД широко используются циклические испытания. Формирование испытательных циклов проводится на основании набора типовых полетных циклов (ТПЦ) и (или) обобщенных ТПЦ (ОТПЦ). ТПЦ представляет собой изменение по времени давления и температуры воздуха на входе в двигатель и основных параметров двигателя, характеризующих режим его работы при выполнении типового полета ДА, включая наземную наработку, отнесенную к одному типовому полету. ОТПЦ представляет собой типовой полетный цикл, соответствующий некоторой группе типовых полетов. • Назначенный ресурс основных деталей двигателя подтверждается их ЭЦИ, которые проводятся в системе полноразмерного двигателя. Допускается проведение ЭЦИ деталей на газогенераторе или на специальных установках. • Прогрессивной формой эксплуатации авиационных ГТД является эксплуатация по техническому состоянию, под которой понимается отказ от назначений фиксированной наработки между ремонтами, и переходу к замене деталей по их фактическому техническому состоянию. Основным принципом при обслуживании двигателей по техническому состоянию является принцип предупреждения неисправностей и отказов. С этой целью используется назначение упреждающих допусков, которые определяются как разность величин предельного и предотказного значений параметров.
12. Факторами, сдерживающими реализацию эксплуатации по техническому состоянию, являются: • дефекты комплектующих и агрегатов систем автоматического управления; • разрушение подшипников; • повреждение элементов «горячей» части газовоздушного тракта, рабочих лопаток ТВД; • дефекты вентилятора, компрессора из-за попадания посторонних предметов в двигатель; • ложные срабатывания электронных систем диагностики; • эрозионный износ элементов газовоздушного тракта. 13. При установлении и увеличении ресурсов авиационных двигателей и их основных деталей используются 4 стратегии управления ресурсом: • установление и увеличение всех видов ресурсов двигателя (назначенного, до первого капитального ремонта, межремонтного) и назначенного ресурса его основных деталей на основании результатов их ресурсных испытаний и эксплуатации. При этом двигатель эксплуатируется с обязательным съемом двигателя в ремонт после отработки любого из установленных видов ресурса; • установление и увеличение назначенного ресурса основных деталей двигателя на основании результатов их ресурсных испытаний и эксплуатации двигателя. При этом двигатель эксплуатируется без обязательного съема для ремонта по достижении назначенного ресурса любой из основных деталей; • установление и увеличение назначенного ресурса основных деталей двигателя на основании использования экспериментально обоснованных методов расчетов и статистически обоснованных данных по конструкционной прочности материалов. При этом двигатель эксплуатируется без обязательного съема до достижения на значенного ресурса любой из основных деталей;
• установление и увеличение ресурсов на основании совмещения стратегий, на пример, установление назначенного ресурса основных деталей по стратегии 2 или 3 и межремонтного ресурса двигателя с обязательным съемом в ремонт. 14. Применение стратегий 2 или 3 допускается в следующих случаях: • достаточная контролепригодность, обеспечивающая получение объективной информации для достоверной оценки технического состояния двигателя и прогно зирования отказов с опасными последствиями с помощью средств и методов кон троля и диагностики, а также эксплуатационная технологичность двигателя, • применение методов и средств технического обслуживания, обеспечивающих безопасность эксплуатации двигателя; • положительный опыт эксплуатации двигателя и(или) двигателей-анало гов, отражающий анализ результатов эксплуатации парка двигателей и их дефектации при ремонтах, обеспечение соответствия установленной наработки на выключение двигателя в полете, отсутствие отказов с опасными последст виями. 15. Существуют два подхода к подтверждению ресурса основных деталей авиа ционных ГТД, основанные: • на концепции «безопасной долговечности» ; • на концепции «допустимых повреждений» . 16. Концепция «безопасной долговечности» основана на том, что к концу уста навливаемого ресурса лишь один диск из 740 (при применении логарифмически нормального закона для описания рассеяния долговечности) или из 1000 (при применен ии закона распределения Вейбулла) может иметь трещину размером около 0, 8 мм. При подтверждении ресурса 10 000 циклов вероятность появления дефекта такого размера составляет примерно 10 -7 , что соответствует требованиям к обеспечению практической невероятности катастрофы.
17. Концепция «допустимых повреждений» основана на предположении, что в материала детали может находиться дефект, ведущий себя как трещина. Размер этого дефекта определяется, исходя из чувствительности неразрушающего кон троля, особенностей технологического процесса и результатов анализа механизмов. Определяя скорость роста трещин в материале при циклическом нагружении, рассчитывают количество циклов до возникновения трещины критического размера и с соответствующим запасом определяют разрешенное для эксплуатации количе ство циклов. 18. Несмотря на большое значение развития методов подтверждения ресур сов основных деталей двигателей, ресурсные возможности авиационных ГТД определяются конструктивно-технологическим совершенством и условиями нагружения.
ВОПРОСЫ 1. Какие виды ресурсов характеризуют авиационные ГТД на различных этапах жизненного цикла? 2. Какие задачи ставят в процессе доводки ресурса опытных ГТД и какими испытаниями они решаются? 3. Как влияет суммарная наработка опытных образцов ГТД на повышение их надежности? 4. В чем заключаются особенности эксплуатационных испытаний с опережающей наработкой ресурса на самолетах-лидерах? 5. Как продляют ресурс ГТД на основе статистических данных об отказах двигателей в условиях эксплуатации на ЛА? 6. Какие прочностные факторы лежат в основе эквивалентно-циклических испытаний по доводке и проверке ресурса? 7. Как определяются эквивалентные условия по фактору длительной прочности? 8. Как формируется программа эквивалентно-циклического испытания? 9. В чем сущность эксплуатации ГТД «по техническому состоянию» ? 10. Какие методы сокращения длительности ресурсных испытаний Вам известны? 11. Какие стратегии управления ресурсом используются при установлении и увеличении ресурсов? 12. В чем смысл концепции «безотказной долговечности» ? 13. В чем смысл концепции «допустимых повреждений» ? 14. Каковы основные условия перевода двигателей на эксплуатацию по техническому состоянию? 15. Каково назначение моделей долговечности?
16. Каким образом оценивается повреждаемость элементов ГТД при различных видах нагружения? 17. Как обеспечивается эквивалентность испытаний при использовании статистического метода? 18. В чем смысл обобщенного метода обоснования ускоренных испытаний? 19. Как реализуется на практике метод прогнозирования ресурса ГТД? 20. Какими показателями оценивается надежность ГТД в эксплуатации?
Глава 9 СПЕЦИАЛЬНЫЕ ИСПЫТАНИЯ АВИАЦИОННЫХ ГТД Специспытания — это особый вид испытаний ГТД на всякого рода предельные характеристики при оценке надежности двигателей, к нему относятся: — испытания по тензометрированию важнейших элементов ГТД; — проверка работоспособности горячей части; — испытания по проверке запасов газодинамической устойчивости; — испытания по оценке вибрационного состояния ГТД; — акустические испытания; — испытания по контролю эмиссии выхлопных газов и др. Работу ГТД проверяют также при подогреве масла до t mах и давлении p min , подогреве топлива до t mах , в условиях ливневого дождя, обледенения, при попадании на вход двигателя посторонних предметов. В настоящее время насчитывается свыше 30 видов стендовых специспытаний ГТД и свыше 10 видов — летных (в 50 -х годах было всего 8. . . 10 видов).
9. 1. ИСПЫТАНИЯ ГТД ПО ПРОВЕРКЕ ЗАПАСОВ ГАЗОДИНАМИЧЕСКОЙ УСТОЙЧИВОСТИ Неустойчивая работа ГТД (помпаж двигателя) проявляется в виде колебаний давления (рис. 9. 1) в тракте или мощных газодинамических ударов и завершается остановом двигателя. Этот режим работы очень опасен, поскольку может приводить к поломкам лопаток компрессора, к обгоранию лопаток турбины и отказу двигателя. Пример. В ходе доводки двигателя ТРДДФ F-100 при летных испытаниях только в течение одного года было 44 случая помпажа вентилятора при включении форсажной камеры, 28 случаев помпажа при запуске двигателя на земле, а также много случаев разрушения лопаток вентилятора, компрессора, турбины, а также подшипников. В результате работ по внедрению цифровой электронной системы управления двигателем (регулированию температуры газа и частоты вращения ротора), доработке гидромеханического блока топливного регулятора и установке регулятора расходов воздуха, поступающего в наружный и внутренний контуры двигателя, частота возникновения помпажа была доведена до 0, 15. . . 0, 20 на 1000 ч налета.
Рис. 9. 1. Изменение параметров ТРДД АИ-25 в момент неустойчивой работы компрессора высокого давления (квд) Рис. 9. 2. Типичная характеристика высоконапорного компрессора с «вертикальными» напорными ветвями: лрр — линия рабочих режимов; гр — граница помпажа
Рис. 9. 3. Типичная характеристика компрессора с «горизонтальными» напорными ветвями: лрр — линия рабочих режимов; гр — граница помпажа Рис. 9. 4. Зависимость запаса устойчивости ΔК, от n пр : n пeреп — относительная приведенная частота вращения, при которой открывается перепуск воздуха
Потеря устойчивости вызывается различными элементами ГТД: воздухозаборником, компрессором, камерой сгорания, турбиной и соплом. При этом в силу газодинамической связи потеря устойчивости в одном из элементов при водит к потере устойчивости ГТД в целом. Поэтому критерием газодинамической устойчивости ГТД может быть критерий устойчивости работы одного из этих элементов. В качестве критерия устойчивости ГТД принято использовать величину коэффициента: (9. 1) характеризующего устойчивость компрессора (рис. 9. 2). При этом запас устойчивости определяют по формуле: (9. 2) Значения ΔК У , полученные для вертикальных напорных ветвей компрессора ( ΔК уπk на рис. 9. 2) и для горизонтальных ( ΔК у. Gвпр на рис. 9. 3) с точки зрения чувствительности компрессора к возмущениям не равнозначны — запасы ΔК уπk значительно более устойчивы к возмущениям. Это указывает на условность критерия К у , оцениваемого по формуле (9. 1). Характерная зависимость ΔК у = f(n пр ) приведена на рис. 9. 4. Существующие нормы по запасам устойчивости для отечественных ГТД были выработаны в начале 70 -х годов.
При расчете запаса устойчивости для каждого типа ГТД требуется учитывать целый ряд факторов, число которых может достигать 18. Среди этих факторов такие, как запас на влияние самолетного воздухозаборника — ΔК У 1 (до 6 %); на разгон ротора ΔК У 2 (при n пр max ΔК У 2 =0), на запаздывание открытия лент перепуска — ΔК У 3 ; на неточность установки углов РНА — ΔК У 4 ; на недостаточный прогрев ГТД — ΔК У 5 ; на влияние максимального угла атаки ЛA— ΔК У 6 ; на производственные отклонения — ΔК У 7 и др. При этом на каждой частоте вращения n прi полагают: Нормированные значения запасов устойчивости для различных ГТД находятся в пределах 15. . . 18 % для стендовых условий и 6. . . 10 % — для полетных. Значение ΔК УΣ определяют следующим образом: наносят зависимости ΔК Уi = f(n пр ), соответствующие каждому из рассмотренных факторов при Н = 0 и М = 0. Огибающая всех кривых дает потребный запас ΔК УΣ = f(п пр ) (рис. 9. 5). При испытаниях по определению запасов газодинамической устойчивости одним из главных является вопрос о том, как ввести двигатель в режим неустойчивой работы компрессора, не свойственный двигателю при его нормальной работе и опасный в плане возможности его отказа.
9. 1. 1. Экспериментальное определение запасов устойчивости путем подъема линии рабочих режимов Экспериментальное исследование запасов устойчивой работы компрессора в системе двухконтурного турбореактивного двигателя (ТРДД) заключается в определении параметров, характеризующих работу компрессора как на линии рабочих режимов двигателя, так и на границе устойчивой работы компрессора при постоянной приведенной частоте вращения роторов КНД и КВД, т. е. при постоянном скольжении роторов двигателя. Приближение к границе устойчивости (ГУ) может быть достигнуто несколькими способами: • уменьшением площадей критических сечений соплового аппарата турбины F ca и реактивного сопла F c ; • впрыском воды в камеру сгорания; • «забросом топлива» ; • вдувом воздуха или пара в камеру сгорания и др. I. В первом случае требуется применение регулируемых или сменных сопловых аппаратов (СА) или специальных вставок, загромождающих проходные сечения сопловых аппаратов, а также регулируемого сопла или набора сопел с различной площадью. Устанавливая на ГТД специальный СА турбины с сечением меньшим чем расчетное, можно линию совместной работы на характеристике компрессора для каждого значения лрр поднять ближе к границе помпажа. Однако зачастую, даже при 15 %-ом зажатии СА, граница помпажа в стендовых условиях не достигается. Параметры вентилятора (компрессора низкого давления) в двухкаскадном ТРДД на границе устойчивой работы обычно получают уменьшением F c внешнего контура.
2. Определение границы устойчивости впрыском воды в камеру сгорания реализуется следующим образом: впрыскиваемая в камеру сгорания вода испаряется и приводит к повышению давления за компрессором и к некоторому понижению Т* г в зависимости от достигнутой полноты испарения в камере сгорания и крутизны напорных ветвей характеристики компрессора. Вода подается специальной системой, включающей водяные насосы с автономным приводом. Увеличение эффективности данного метода возможно одновременным уменьшением до значения T г * =T* г mах. 3. Заброс топлива, т. е. кратковременное увеличение подачи топлива в камеру сгорания приводит к повышению температуры газа перед турбиной и к смещению точки совместной работы компрессора и турбины в сторону границы помпажа. Применение этого способа связано с трудностью в измерении мгновенных значений параметров, характеризующих работу компрессора. Также весьма сложно определить истинное значение температуры газа перед турбиной, так как не известен коэффициент полноты сгорания в камере. Кроме того, из-за не стационарности течения в компрессоре, обусловленной резким увеличением давления воздуха за компрессором, затруднено получение напорной ветви его характеристики (n пр = const) 4. Определение границы устойчивости вдувом воздуха в камеру сгорания реализуется следующим образом: вдув дополнительного количества воздуха в камеру сгорания приводит к повышению давления р* к и к некоторому снижению Тк. Сжатый воздух подается от постороннего источника через окна в камере сгорания, предназначенные для отбора воздуха на самолетные нужды. Главное преимущество данного метода заключается в том, что, благодаря плавному изменению расхода вдуваемого воздуха, можно определить всю напорную ветвь, без превышения допустимых значений Т* г. Метод относительно прост, при его использовании не возникает неблагоприятных воздействий на горячие элементы двигателя.
Применение перечисленных способов подъема линии рабочих режимов на современных высоконагруженных многовальных ГТД имеет ряд недостатков: • лопатки компрессора при смещении ЛРР вверх работают в области повышенных вибраций, что снижает их прочность перед вводом в помпаж; • лопатки турбины перегружаются по тепловому состоянию. 9. 1. 2. Экспериментальное определение запасов устойчивости путем создания предельных возмущений в потоке на входе в ГТД Хотя методика расчета необходимого запаса по помпажу ΔК У и учитывает влияние внешних возмущений, она исходит при этом из того, что компрессоры всех ГТД одинаково чувствительны к ним. Однако практика показывает, что у некоторых ГТД с ΔК У = 20 % фиксируются случаи помпажа, а у других с ΔК У = 10 % — такие случаи отсутствуют (пример с «Олимп-593» с ΔК У = 20 % и ВСУ- 2 ПВ 8 — ΔК У = 10 %). Это свидетельствует о том, что неучтенным, но важнейшим фактором в методике расчета запаса устойчивости ΔК У является разная чувствительность различных компрессоров к внешним возмущениям. Поэтому знание ΔК У не дает еще возможности надежно оценить запас устойчивости ГТД в условиях эксплуатации. В связи с этим в конце 1970 -х годов в ЦИАМ был разработан другой критерий газодинамической устойчивости ГТД, основанный на понятии предельных внешних возмущений воздушного потока на входе в ГТД при его эксплуатации на ЛА. Очевидно, что потеря газодинамической устойчивости ГТД при эксплуатации может происходить как за счет приближения линии рабочих режимов к границе устойчивости (рис. 9. 6, а), так и за счет смешения самой границы устойчивости (рис. 9. 6, б).
В первом случае потеря устойчивости чаше всего возникает под влиянием внутридвигательных возмущений и, если нет поломок в проточной части двигателя, обычно бывает связана с нештатной работой регуляторов (G m. КС’ G mфк , РИА, F c , G отб и др. ). Во втором случае потеря устойчивости возникает под воздействием внешних возмущений, среди которых основными являются: • боковой ветер при взлете, приводящий к срыву потока на обечайке воздухозаборника; • вертикальные порывы и турбулентность атмосферы, • полет самолета на больших углах атаки; • эволюции самолета (скольжение и др. ); • полет с V mах , особенно при М п > 1, 3; • стрельба и воздействие ударных волн; Рис. 9. 6. Способы определения запаса устойчивости ГТД путем подъема линии рабочих режимов (a) и смешения границы устойчивости ( б)
Рис. 9. 7. Смешение линии рабочих режимов, границы устойчивости и напорной ветки компрессора под действием окружной неравномерности полей давления и температур: • возмущения, связанные с работой соседних двигателей; • попадание на вход выхлопных газов в случае включения и работы реверса и др. Эти факторы создают на входе в двигатель неравномерность полей давления, температуры и скорости, а также вызывают пульсацию этих параметров во времени. При этом наибольшую опасность представляет возникновение окружной неравномерности и пульсаций на входе в ГТД. Например, окружные неравномерности полей давлений (Δр* / Δр* ср ) и температур на входе в компрессор вызывают снижение запасов устойчивости, благодаря взаимному смещению: • линии рабочих режимов (ЛРР); • границы помпажа (ГР); • напорной линии компрессора при n пр = const(рис. 9. 7). При этом смещение ЛРР вверх происходит из-за повышения T’, поскольку из-за неравномерности уменьшаются значения (G в и η* к , а регуляторы сохраняют режим G m = const.
Чтобы уйти от индивидуальной чувствительности конкретного компрессора, устойчивость ГТД оценивается по комплексному критерию, учитывающему структуру и величину внешних возмущений потока, входящего в двигатель: (9. 4) Где Δσ = (p* max –p* min )/p* cp — величина окружной неравномерности потока по давлению р* на стандартном радиусе (для ТРДД = 0, 6, для ТРД = 0, 9); р* тах и p* min — максимальное и минимальное давления на данном радиусе входного ка нала; р* с р — среднемассовое давление во входном канале; ε = Δ p* max /2 p с р — оценивает турбулентные пульсации потока в данной точке во времени по максимальной их интенсивности; р* ср — среднее (во времени) давление на данном радиусе; ρ — весовой коэффициент, учитывающий комплексный характер критерия (для ТРД ρ = 1 и для ТРДД ρ = 2). В процессе создания нового самолета модели воздухозаборников СУ продувают в аэродинамических трубах с имитацией условий полета самолета, наиболее напряженных с точки зрения устойчивости СУ. На основе этих продувок и материалов летных исследований аналогичных самолетов и СУ оценивают ожидаемые неоднородности входного потока и выражают их численно через параметр W ожид. В ходе доводочных и специальных испытаний ГТД, используя специальные Устройства, постепенно увеличивают величину W. В результате достигают критического значения критерия — W гр , при котором ГТД начинает терять устойчивость. Запас устойчивости двигателя по отношению к внешним возмущениям определяют по формуле: (9. 5)
Рис. 9. 8. Схема испытания ГТД с генера тором неоднородности входного потока: I — воздухозаборник; 2 — интерцептор; 3 — ГТД Пример. Для оценки достаточности запасов газодинамической устойчивости ОДУ) двигателя ПС-90 А использовались результаты экспериментальных исследований изо лированных компрессоров на установках поузловой доводки, а также испытаний натурных двигателей ПС-90 А на закрытом и открытом стендах с максимальной имитацией эксплуатационных условий и выборкой запасов ГДУ на влияние невоспроизводимых факторов (рис. 9. 9). Установлено, что максимальные суммарные возмущения на входе в вентилятор воз никают при работе в условиях Н = 0, М = 0 с боковым ветром V max = 15 м/с и достигают W = 0. 8 % в диапазоне частот пульсаций от 0 до 200 Гц. Потребные запасы ГДУ с учетом всех факторов (включая экспериментально определенные влияния входных условий и переходных режимов) составило ΔК У max =17, 5%. Запасы устойчивости по параметру W определяют при стендовых испытаниях с помощью генератора неоднородности специального входного коллектора с выдвижным затеняющим щитком — интерцептором (от латинского интерцессия — «пресекаю» ) (рис. 9. 8). В результате получают границы устойчивости ГТД по внешним возмущениям.
Для подтверждения достаточности принятых запасов ГДУ компрессора ПС-90 А были проведены специальные испытания натурного двигателя с имитацией эксплуатационных условий (положение относительно земли, установка самолетного воздухозаборника и самолетных агрегатов и др. ). Таким образом, в процессе испытания были искусственно созданы условия, в которых реализуется наихудшее сочетание неблагоприятных факторов, влияющих на ГДУ. Двигатель подтвердил свою работоспособность, устойчиво работая в этих условиях |9]. Рис. 9. 9. Открытые стенды для испытаний ТРДД: a- с боковым ветром; б — с управляемой турбулентностью на входе
9. 2. ИСПЫТАНИЯ ПО ОПРЕДЕЛЕНИЮ АКУСТИЧЕСКИХ ХАРАКТЕРИСТИК ГТД Акустическое (шумовое) воздействие летательных аппаратов воздушного транспорта — наибольшее в сравнении с источниками всех прочих отраслей экономики любой страны. Шум любой нежелательный звук или совокупность звуков, оказывающие неблагоприятное воздействие на организм (прежде всего человека). Шум работающего ГТД превышает всякие санитарные нормы для жилого района. Шум ГТД особенно интенсивен в районе аэропортов. Звуковой след от СМС достигает в районе аэропорта 35. . . 55 км. Непрерывно растут размеры самолетов и скорости их полета, что требует все более мощных двигателей. Все это делает проблему снижения шума ГТД одной из важнейших в авиадвигателестроении. 9. 2. 1. Характеристики звука и шума Для описания колебательных и энергетических процессов в акустике общеприняты некоторые понятия и их объективные (физические) характеристики [39 J. Скорость звука а (м/с) связана с длиной волны λ (м) частотой/(Гц = 1/с) и периодом колебаний Т (с) соотношениями: (9. 6) Звуковая энергия Е зв (Дж) — энергия, состоящая из кинетической энергии колеблющихся частиц и потенциальной энергии упругой деформации среды. Акустическая мощность источника (или звуковая мощность) W зв (Вт) — общее количество звуковой энергии, излучаемой источником звука в пространст во во всех направлениях за единицу времени.
Звуковое давление р (Па = Н/м 2 ) — переменное относительно невозмущенной воздушной среды давление, возникающее при прохождении звуковых волн. Интенсивность звука (или сила звука) I (Вт/м 2 ) — средний поток (количество) энергии W (Вт), переносимой в данной точке пространства за единицу времени через единицу площади F (м 2 ), перпендикулярной направлению распространения звука, т. е. I = W / F. Интенсивность звука — величина векторная, так как она определяется в зависимости от направления движения звукового потока. Интенсивность звука трудно измерить непосредственно, поэтому при инструментальных измерениях определяют звуковое давление, а далее проводят пересчет. Известно, что: (9. 7) где V — среднеквадратичное значение колебательной скорости частиц среды в звуковой волне, м/с; ρ — плотность среды, кг/м 3. На практике приходится иметь дело с величинами: звуковым давлением р и интенсивностью звука /, различающимися по абсолютной величине соответст венно в 10 я и в 10 16 раз, что неудобно. Поэтому в акустике принято оперировать понятием уровня некоего показателя, используя его логарифмическое значение. Уровень какого-либо показателя — это результат сравнения фактического значения показателя с его заранее заданным (стандартным) значением. В качестве стандартного значения, используемого для сравнения при определении уровня, принимаются минимальные значения интенсивности звука и звукового давления, которые слышит человек при частоте звука 1000 Ги. Это I 0 = 10 -12 Вт/м 2 и р 0 = 2∙ 10 -5 Па. Они получили название порогов слышимости.
Уровень звуковой мощности в децибелах: (9. 8) Где W — полная звуковая мощность источника, Вт; W 0 = 10 -12 Вт — условная величина, принятая для сравнения и являющаяся наименьшим пороговым значением. Звуковое давление в соответствии с (9. 7) определяется по формуле: (9. 9) где ρ и а — плотность атмосферного воздуха и скорость звука в нем. Приборы, применяемые при акустических измерениях, воспринимают звуковое давление и измеряют его в определенных полосах частот, выделяемых с помощью частотных фильтров. Уровень звукового давления (уровень интенсивности звука) в децибелах определяется по формуле: (9. 10) где I 0 =10 -12 Вт/м 2 и р 0 = 2 • 10 -5 Па — минимальные значения интенсивности звука и звукового давления, соответствующие порогу слышимости. Из формулы (9. 10) видно, что увеличение уровня звукового давления примерно на 3 д. Б означает удвоение силы звука. Верхний, «болевой» порог восприятия звука ухом человека зависит от частоты звука и соответствует / ≈ 100 Bт/м или L ≈ 140 д. Б. При шуме более 80 д. Б рекомендуется использовать защиту органов слуха. Распространение звука в дальнем звуковом поле, где влияние конечных размеров и форм излучателя звука на характеристики звукового поля несущественно, определяется соотношением:
Рис. 9. 10. Спектр шума двигателя: 1 — шум реактивной струи; 2 — шум вентилятора (9. 11) где L 1 — известный уровень звукового давления на заданном расстоянии r 1 , А — дополнительное ослабление звука в атмосфере в результате поглощен звука воздухом, туманом, дождем, снегом, растительностью, стенами и др. Для идеальной среды (А = 0) уро вень интенсивности звука при удвое нии расстояния уменьшается примерно на 6 д. Б. Спектр шума — распределение уров ня интенсивности звука по частоте. Ухо человека воспринимает звуки в диапа зоне частот от 16 до 2 ∙ 10 4 Гц. При определении спектра шума авиационного ГТД весь диапазон частот разделяют на отдельные полосы, соответствующие октаве или ее 1/3. Октава — интервал между частотами, отличающимися едва раза: f 1 = 2 f 1. Для 1/3 октавы соотношение между конечной частотой полосы и начальной будет В качестве стандартного используется 1/3 -октавный спектр в диапазоне средних частот f cр = 50. . . 10 000 Гц, включающий 24 полосы. Измеряют средние уровни звукового давления в каждой отдельной частотной полосе, относя их к среднегеометрическим частотам. В результате получают спектры шума двигателя (рис. 9. 10), имеющие, как правило, непрерывную основу 1 (широкополосный или «белый» шум) с наложенными на нее
пиками интенсивности 2 в области средних частот, связанными с работой лопаточных машин (дискретные составляющие или тональный шум). Общий уровень звукового давления (шума) равен сумме относительных величин силы звука в каждой из п рассматриваемых частотных полос спектра: (9. 12) Воспринимаемый шум оценивает качественные особенности субъективных ощущений акустического шума органами слуха и организмом человека. Восприни маемый шум зависит не только от силы звука, но и от спектра шума и продолжительности его действия. Частотный состав шума учитывается системой оценки PNL , в которой уровень воспринимаемого шума выражается в специальных единицах — PN д. Б, учитывающих различное раздражающее действие авиационного шума разной частоты. На рис. 9. 11 показана полученная опытным путем зависимость, связывающая уровень звукового давления L с
Рис. 9. 11. Равные уровни воспринимаемого шума уровнем равного воспринимаемого шума в PN д. Б при разных частотах. Видно, что наиболее чувствительно ухо человека к частотам 3000. . . 5000 Гц. Они самые неприятные для человека. Лучше воспринимаются звуки низких частот. Одина ково воспринимается звук f≈100 Гц и L=107 д. Би звук с f ≈ 4000 Гц и L = 90 д. Б, несмотря на то, что их интенсивности отличаются в десятки раз. По изме ренным в каждой из 24 полос стандартного 1/3 -октавного спектра уровня зву кового давления L согласно графикам, аналогичным на рис. 9. 11, определяют уровень воспринимаемой шумности в отдельных полосах спектра PNL i а затем уровень суммарной воспринимаемой шумности по формуле: (9. 13) где PNL max — наибольшая из 24 значений PNL i. Величины PNL численно совпадают с уровнем звукового давления L на кри вых равной шумности при f= 1000 Гц. Увеличение уровня воспринимаемого шума на 10 РN д. Б физиологически соответствует удвоению его раздражающего действия. Продолжительность воздействия и дискретные составляющие шума совме стно с частотным составом шума учитываются системой оценки EPNL , в кото рой эффективный уровень
воспринимаемого шума выражается в EPN д. Б, установленных ГОСТ 17229 -85. Система EPNL используется для нормирования максимально допустимых уровней авиационного шума на местности. Эффективный уровень воспринимаемого шума EPNL наряду с частотным составом учитывает наличие в спектре дискретных составляющих и длительность действия шума по формуле: (9. 14) где PNLM — максимальное значение уровня воспринимаемого шума, PN д. Б, С — поправка, учитывающая дискретные составляющие в спектре авиационного шума, РN д. Б; D — поправка, учитывающая продолжительность воздействия шума. Методики расчета уровней воспринимаемого шума по данным натурных измерений, поправок С и D, а также эффективных уровней воспринимаемого шу ма приведены в ГОСТ 17229 -85. Для инженерных расчетов при наличии данных реальных измерений, выполненных шумомером со стандартными фильтрами по шкалам А или А пользуются упрощенной методикой с эмпирическими зависимостями для расчета акустических характеристик. Например, для самолетов используют приближенное соотношение: (9. 15) (9. 16) В спектре общего шума ГТД помимо широкополосных шумов, вызываемых Движением турбулентных потоков в тракте, встречаются и дискретные составляющие, которые возникают, к сожалению, чаще всего в области частот выше 1000 Гц (рис. 9. 12), то есть там, где чувствительность уха наибольшая.
Рис. 9. 12. Типичный спектр шума ТРДД: 1 — линия широкополосного шума: 2 — дискретные составляющие Возникновение дискретных составляющих шума связано с прерывистым характером обтекания потоком каждой лопатки в лопаточной решетке и их взаимодействием. Уровень воспринимаемого шума PN д. Б может при этом повы ситься еще на 9. . . 15 д. Б по сравнению с уровнем, непосредственно замеряемым шумомерами. Воздействию авиационного шума (90 PN д. Б и выше) при взлете и посадке подвергаются значительные районы (до 100 км 2 ) в окрестности взлетно-посадочной полосы аэродрома. Например, обычный уровень городского шума в промышленном районе с интенсивным движением равен 85 PN д. Б, а в жилом районе днем — 65 PN д. Б. Размеры зоны воздействия авиационного шума в основном зависят от типа двигателей, их тяги, расположения на самолете, траекторий набора высоты или посадки, режимов использования двигателей. В энергию шума обычно переходит только ничтожная часть энергии пото ков ГТД (менее 1 %). Однако для современных ГТД излучаемая энергия при этом достигает 10. . . 100 к. Вт и более. Ухо человека неодинаково чувствительно к звукам различных частот (сравните скрип
ножа по тарелке и гудок океанского лайнера). Поэтому звук одинаковой силы Z. , но различной частоты воспринимается человеком по-разному. 9. 2. 2. Источники авиационного шума По природе возникновения шумы подразделяют на механические, гидравлические, электромагнитные и аэродинамические. Авиационные шумы относятся к категории аэродинамических — одни из самых значительных по уровню звука. Они являются результатом обтекания потоком газа различных тел. Причинами аэродинамических шумов являются: • вихревые процессы, возникающие в потоке при обтекании тел и выпуске свободной струи газа; • пульсации рабочей среды, вызываемые вращением лопастных колес вентиляторов, турбин; • колебания, связанные с неоднородностью и пульсациями потока. Источниками шума, создаваемого современными дозвуковыми самолетами, являются авиадвигатели, вспомогательные ГТД (ВГТД) и обтекаемый потоком воздуха планер (в первую очередь элементы механизации крыла). В двухконтурных турбореактивных и турбовинтовых двигателях внутренними источниками шума являются вентилятор, компрессоры, камера сгорания, турбина и реактивное сопло, а внешними — реактивная струя и винт турбовинтового двигателя. Спектр шума вентилятора (компрессора) складывается из широкополосного и тонального (дискретного) шумов. Дискретные составляющие кратны основной частоте прохождения лопаток рабочего колеса. Широкополосная составляющая этого шума возникает из-за вихрей, образующихся при обтекании лопаток рабочих колес и направляющих аппаратов. Тональные компоненты возникают как следствие взаимодействия неравномерных полей давления; взаимодействия вращающегося рабочего колеса с потоком, обладающим крупномасштабной турбулентностью и пульсациями во входном канале.
Современным вентиляторам характерны сверхзвуковые окружные скорости, что вызывает ударные волны и создает очень неравномерные поля давления у лопаток вращающегося рабочего колеса, в результате появляется шум вращения и общий шум вентилятора резко повышается. Шум камеры сгорания — низкочастотный, широкополосный. Его интенсивность сильно зависит от формы конструкции и размеров камеры. Трубчато кольцевые камеры создают шумов больше, чем кольцевые камеры. Шум турбины вызывается теми же причинами, что и шум вентилятора, но имеет следующую особенность. Поток, выходящий из камеры сгорания, имеет повышенную неравномерность и флуктуации (случайные отклонения. колебания), поэтому все составляющие шума значительно усиливаются. Дискретные составляющие возникают в области высоких и наиболее неприятных средних частот (последние для тихоходных турбин вентиляторов ТРДД). Шум реактивного сопла ТРДД является следствием значительной скорости, высокой турбулизации и неоднородности потока за турбиной. Он складывается из шума обтекания стоек и других препятствий, турбулентного шума, шума взаимодействия со стенками канала. Шум реактивной струи вызывается турбулентными пульсациями в зоне ее смещения с атмосферным воздухом. Для турбореактивных двигателей характерно, что шум струи существенно выше внутреннего шума двигателя. Общий уровень звуковой мощности в ши роком диапазоне частот приближенно оценивается по формуле: (9. 17) где С с — скорость истечения газа из сопла; ρ с — плотность газа струи в выход ном сечении сопла; F c — площадь поперечного сечения сопла; А г — величина, зависящая от температуры струи; К= 57 д. Б для
холодных струй, К= 44 д. Б для ТРД. Рис. 9. 13. Источники шума в авиационных двигателях: / — шум от вентилятора; 2 — шум от турбин; 3 — шум от выхлопной струи: 4 — шум от компрессора Шум воздушного винта — основной у турбовинтовых двигателей и является результатом силового воздействия лопастей на воздух, при котором происходят вытеснение воздуха (объемный шум) и образование турбулентного слоя на поверхности лопастей и в следе за ним. Дополнительный шум — результат ударных волн и местных скачков уплотнения газа. Акустическая мощность зависит в первую очередь от скоростей в проточной части (С 8 вых , n 4 и т. п. ) и от возникающей за лопатками периодической неодно родности потока. Максимальная интенсивность излучения шума происходит чаще всего под углом примерно 30. . . 60° к оси ГТД (рис. 9. 13). 9. 2. 3. Нормирование авиационного шума Действующие отечественные нормативы шума ВС включают в себя максимально допустимые уровни шума и четко регламентированные, одинаковые для всех стран — членов ИКАО, требования к методике акустических измерений; режимам полета при сертификационных испытаниях; правилам обработки результатов измерений; правилам привидения результатов к стандартизованным условиям. Схема размещения трех контрольных точек, соответствующих этапам взлета, набора высоты и посадки дозвуковых самолетов с реактивными двигателями оговорена международными и.
национальными стандартами (табл. 9. 1) и приведена на рис. 9. 14 Номер точки Этап полета Место размещения контрольной точки 1 Взлет На линии, параллельной оси ВПП, отстоящей на расстояние 450 м* от оси ВПП или ее продолжения в сторону взлета, в которой уро вень шума от взлетающего самолета достигает максимального зна чения 2 Набор высоты На продолжении оси ВПП в направлении полета, на расстоянии 6500 м от начала разбега самолета 3 Посадка На продолжении оси ВПП в направлении против полета на рас стоянии 2000 м до посадочного торца ВПП под стандартной траек торией снижения на посадку с наклоном 3 е к горизонту Для сверхзвуковых самолетов и для дозвуковых самолетов старой конструкции это расстояние установлено равным 650 м. 9. 1. Требования по размещению контрольных точек при оценке уровней шума самолетов по ГОСТ 17228 —
Рис. 9. 14. Схема размещения контрольных точек измерения уровня шума, создаваемою самолетом на местности (по ГОСТ 17228 -87): EPNL= const— контур шума, то есть изолиния постоянного значения эффективного уровня воспринимаемого шума от взлетающего самолета; EPNL max — точка контура, максимально удаленная от оси ВПП; 1, 2, 3 — контрольные точки Для вновь создаваемых дозвуковых самолетов в соответствии с ГОСТ 17228 -87 допустимый уровень шума от ВС в каждой из трех точек определяется по расчетным формулам в зависимости от взлетной массы, при этом различают самолеты с реактивными двигателями с любой взлетной массой; самолеты с взлетной массой более 5700 кг, оборудованные турбовинтовыми или поршневыми двигателями. Правилами ИКАО пока допускается превышение нормируемых уровней шума в отдельных конкретных точках, если оно компенсируется соответствующим снижением уровней в других точках, то есть нормируется сумма уровней шума по трем контрольным точкам. Учитывая, что самолет может превышать норму в одних контрольных точках и перевыполнять в других, их сравнивают на удовлетворение нормам по ΣEPN 1+2+ 3 в табл. 9. 2 приведены измеренные значения шума в 3 -х контрольных точках для некоторых самолетов.
Самолет/ГТД Контрольная точка 1 2 3 Ту-154 (М 0 = 86 т)/НК-8 -2 У 97, 8 101, 0 106, 0 Ил-62 М (М 0 = 157 т)/Д 30 -КУ 95, 2 106, 9 103, 5 Ил-86 (М 0 = 210 т)/Н К-86 104, 2 107, 4 105, 1 L-1011 (М 0 = 186 T)/RB-21 1 -22 В 95, 0 102, 0 В-747 -100 (М„ = 352 т)/. 1 Т 9 Д-7 А 102, 0 107, 8 106, 99. 2. Значения шума в 3 -х контрольных точках
Суммарный уровень допустимого шума в трех точках для самолетов взлетной массой менее 20 т равен 275 EPN д. Б, а для самолетов с взлетной массой бо лее 350 т — 310 EPN д. Б. В стандарте ИКАО требования к уровню шума ВС изложены в виде нескольких отдельных глав, причем в каждой последующей главе предъявляются все более жесткие требования (рис. 9. 15). Рис. 9. 15. Динамика снижения уровня шума самолетов, допустимого стандартами ИКАО Рис. 9. 16. Нормы уровней шума по ИКАО в 1 контрольной точке
Экспериментальная оценка шума, создаваемого на местности существующими самолетами, проводится в соответствии с требованиями ГОСТ 17229 -85 специальной обработкой данных реальных измерений, выполненных в контрольных точках (табл. 9. 1). Для получения значений эффективного уровня воспринимаемого шума EPNL, который зависит не только от шума двигателей, но и от аэроакустических характеристик всего самолета, определяют поправки С и D. В результате получают значение уровня шума, которое может быть сравнено с нормативными значениями по ГОСТ 17228 -87. На рис. 9. 16 показаны нормы значений уровней шума самолета (в качестве примера в контрольной точке 1) в соответствии со стандартом ИКАО. Они стали существенно жестче, но им должны удовлетворять только новые самолеты. 9. 2. 4. Экспериментальное исследование шума ГТД При опытных испытаниях ГТД снимают акустические характеристики двигателя, которые (в отличие от самолета) не нормируются. Акустическая характеристика ГТД — зависимость спектров уровня шума и суммарных уровней звукового давления от режимов и условий работы ГТД. Исследования акустических характеристик авиационных ГТД проводятся в целях: • уменьшения вредного воздействия шума всего двигателя и отдельных источников шума в нем на человека и окружающую среду; • определения эффективности конструкторско-технологических мероприятий по снижению уровня шума от двигателя; • определения акустических нагрузок на элементы конструкции силовой установки и самолета; • ориентировочных расчетов авиационного шума самолета с данным двигателем;
• разработки эксплуатационных приемов уменьшения авиационного шума (трассы минимального шума, предпочтительной по шуму ВПП, многосегментной глиссады, аэродромного глушителя шума при наземной проверке двигателей и др. ); • диагностики двигателя и его узлов, поскольку появление неисправностей в системах двигателя ведет к появлению новых источников аэродина мического шума и, следовательно, к изменению спектра шума при работе двигателя. Рис. 9. 17. Схема расположения точек измерения шума: 10. . . 18 — подвижные микрофоны на телескопических мачтах, установленных на дистанционно управляемых тележках, которые движутся по рельсам в специальной траншее; 9 — неподвижный микрофон на телескопической мачте высотой до оси двигателя 0, 5 м
Акустическую характеристику ГТД определяют при стендовых испытаниях. Исследование шума двигателя проводят на открытых стендах. После установки двигателя на стенд определяют основные характеристики (тягу, расход топлива по линии рабочих режимов и др. ) установившихся режимов, на которых измеряется шум. Измерение шума в дальнем звуковом поле проводят на полуокружности, расположенной сбоку от двигателя (рис. 9. 17). Радиус измерительного пояса устанавливается равным 100 м. Точки измерений по полуокружности измерительного пояса располагаются через 10°. Отсчет углов измерения начинается от входа в двигатель. При ближнем звуковом поле шум измеряется в точках 18. . . 21 (рис. 9. 18). Эти точки располагаются в плоскости оси двигателя. Измерение внутреннего шума двигателя производится в 10 точках. Измерение шума камеры сгорания и турбины осуществляется датчиком нестационарного давления. Испытательные стенды имеют внушительные размеры: 500 x 500 м с отсутствием вблизи границ площадки леса или деревьев. Требуется бетонированная площадка вокруг стенда в радиусе 100 м. Необходимо располагать измерительные приборы по сложным схемам с подземными коммуникациями. Для измерений уровня шума должна применятся акустическая аппаратура, прошедшая проверку и состоящую из микрофонов, усилителей, калибратора и системы регистрации информации, которая может быть как аналоговой, так и цифровой.
Рис. 9. 18. Схема расположения точек измерения шума в ближнем звуковом поле Рис. 9. 19. Блок-схема шумомера
Измерения шума проводят специальными приборами-шумомерами, которые определяют уровни звукового давления. Типичная блок-схема прибора приведена на рис. 9. 19. Для анализа спектров шумы записывают на магнитофонную ленту. Но чаще при оценке норм измеряют только интегральный уровень шума (суммируя акустические мощности разных частот в электроприборе). Измерения шума двигателя проводятся при заранее оговоренных условиях, включая условия окружающей среды. Двигатель устанавливается на силоизмерительном станке на высоте Н = 4, 5 м по оси. Во время проведения измерений, согласно программе испытаний, на каждом из режимов работы двигателя фиксируются следующие характеристики: • уровни звукового давления в октавных полосах частот (д. Б); • уровни звука (д. БА). Затем уровни звукового давления приводят к САУ (/„ = 15 °С и ср, , = 70 %). Специальная методика, разработанная в ЦАГИ, позволяет по такой матрице звуковых давлений определить эффект того или иного акустического мероприятия в каждой из 3 -х контрольных точек. Необходимо иметь ввиду, что в условиях стендового испытания не учитывается влияние: • попутного потока на шум ГТД; • шума планера; • разной интерференции шумов в условиях стенда и условиях полета.
Тем не менее, такие стенды эффективны при акустической доводке ГТД. Наряду с проверкой акустических мероприятий в составе одного двигателя проводят акустические исследования его элементов на специальных стендах — безэховых звукоизолированных камерах. 9. 2. 5. Методы снижения шума ГТД Нормируемыми параметрами шума являются максимальные уровни звука L( в д. Б и эквивалентные уровни звука L Aэкв д. Б. Максимальные уровни шума L A днем не должны превышать 85 д. Б, а ночью (с 23 до 7 ч) — 75 д. Б; эквивалентные уровни днем не должны быть более 65 д. Б. а ночью — 55 д. Б. Снижение шума в помещениях и на местности при испытаниях ГТД достигается: • конструктивными доработками испытываемого, а также вспомогательного двигателей; • строительно-планировочными мероприятиями. Шумоглушение на стенде осуществляется с использованием различных видов глушителей: камерных, пластинчатых, экранных, реактивных, активных. Возможны комбинированные глушители, сочетающие указанные выше типы. Методы и средства уменьшения негативного воздействия авиационного шума разнообразны и подразделяются, прежде всего, на конструкционные, эксплуатационные, строительно-акустические методы и на средства коллективной зашиты. К конструкционным методам относятся следующие инженерные решения. 1. Повышение степени двухконтурности (т) турбореактивного двухконтурного двигателя (ТРДД). При этом шум, создаваемый реактивной струей, снижается, что объясняется уменьшением скорости истечения газов из сопла после смешения потоков. При повышении значения т от 0 до 8 шум ТРДД может быть снижен на 25. . . 30 PNд. Б.
2. Использование в двигателе одноступенчатого вентилятора без входного направляющего аппарата вместо двухступенчатого позволяет снизить шум на 3. . . 5 РN д. Б, а вместо трехступенчатого — на 5. . . 8 PN д. Б. Отказ от входного направляющего аппарата ведет к снижению шума на 2. . . 3 PN д. Б. 3. Оптимизация соотношения чисел рабочих и спрямляющих лопаток позволяет снизить шум на 2. . . 3 PN д. Б. 4. Увеличение осевого зазора между лопатками рабочего колеса компрессора и направляющего аппарата. В ТРДД направляющие аппарат вентилятора и первых ступеней компрессора отодвигают от соответствующих рабочих колес на 1. . . 2 хорды рабочего колеса. Аналогичные мероприятия выполняют и в турбинах. 5. Увеличение числа двигателей (n) на самолете ведет к снижению шума, PN д. Б: в полете — на 10 lgn; в статических условиях — на 51 gn. 6. Акустическая обработка — облицовка звукопоглощающими конструкциями гондол двигателей, корпусов двигателей и стенок фюзеляжа. Применение шумоглушителя реактивной струи самолета Ту-154 М с двигателями Д-30 КУ 154, состоящего из турбулизаторов и эжектора с акустически отработанной камерой смешения, позволяет снизить шум на взлете на 3. . . 4 EPN д. Б и несколько меньше при наборе высоты. Характерные места установки звукопоглощающих конструкций показаны на рис. 9. 20.
Рис. 9. 20. Схема размещения и размеры звукопоглощающих конструкций на двигателе Д-ЗОКУ-154 Рис. 9. 21. Шевронное сопло из сплава с памятью формы Существуют и другие методы защиты, такие как: • применение шумоглушащих сопел с дроблением исходной круглой реактивной струи с использованием многотрубных, лепестковых или гофрированых сопел; • применение смесительной камеры и др. В настоящее время проблема снижения шума авиационных ГТД решается в рамках различных программ ведущими авиадвигателестроительными компаниями (47].
1. Существует концепция полой лопатки вентилятора с каркасом из титанового сплава и оболочкой из графита с выдувом воздуха в заднюю кромку. Это позволяет снизить уровень шума вентилятора. 2. Проведены исследования шевронного сопла, выходное сечение которого имеет гофрированную форму. При этом измеренный уровень шума на боковой линии уменьшился на 3 д. Б. Снижению шума также способствуют следующие мероприятия: • отрицательно скошенный вход в мотогондолу; • малошумный вентилятор с наклонным выходным спрямляющим аппаратом (OGV) и малошумная турбина. 3. Существует новая концепция шевронного сопла. Существующие шевронные сопла уменьшают шум, благодаря смешению потоков, но при этом в условиях крейсерского полета увеличивается сопротивление. Новая концепция состоит в применении в конструкции шевронного сопла из сплава с памятью формы (Shape Memory Alloys), обеспечивающего регулирование (рис. 9. 21). Эксплуатационные методы снижения шума ГТД, прежде всего, связаны с выбором: • времени полетов (ограничение или запрет ночной эксплуатации ЛА, в первую очередь наиболее шумных типов); • направления взлета и посадки; • режимов малошумного взлета, набора высоты и посадки.
9. 3. ИСПЫТАНИЯ ПО ОПРЕДЕЛЕНИЮ ВЫБРОСОВ ЗАГРЯЗНЯЮЩИХ ВЕЩЕСТВ АВИАЦИОННЫМИ ГТД Большую часть загрязнения атмосферы от объектов гражданской авиации составляют выбросы авиационных ГТД. Самолет является единственным видом техники, который эксплуатируется на высотах 9. . . 13 км (а сверхзвуковая авиация — 19. . . 25 км), то есть там, где зарождаются многие атмосферные процессы, где находится озоновый слой Земли. Помимо нормирования выбросов традиционных загрязняющих веществ (ЗВ) (СО, С n Н n , NO x , SO 2 , пыль и т. п. ) в последнее десятилетие, из-за особого внимания к глобальным экологическим проблемам, анализируются выбросы и гак называемых «парниковых» газов (СO 2 , СН 4 , NO x и др. ). Наиболее труднорегулируемым компонентом отработавших газов двигателей являются оксиды азота. Они же являются одним из озоноразрушителей, а также «парниковыми» газами. Вклад ВС гражданской авиации в выбросы оксидов азота на больших высотах оценивается в 55 %, тогда как на малых высотах он составляет всего 2. . . 4 %. Серьезными источниками загрязнения атмосферы являются также экспериментальные стенды, на которых испытываются авиационные ГТД. Так, при сжигании 1000 т топлива во время стендовых испытаний двигателя в среднем образуется около 11 т оксидов азота, примерно 7, 2 т несгоревших углеводородов, порядка 11 т оксидов углерода.
9. 3. 1. Закономерности образования загрязняющих веществ в авиационных ГТД При сгорании керосиноподобных топлив в идеальных условиях образуются диоксид углерода СO 2 и пары воды Н 2 O. соотношение между которыми зависит от соотношения углерод/водород (С/Н), специфического для каждого конкретного топлива. Идеальный и реальный процессы сжигания горючего в авиадвигателе поясняются на рис. 9. 22. Продукты сгорания составляют всего 8, 5 % массы веществ, выбрасываемых двигателем в атмосферу. Только очень малая часть (около 0, 4 %) продуктов реального сгорания является следствием «неидеальности» конструкции авиадвигателя, «допускающего» неполное сгорание (СО, С n Н m и сажа) и окисление азота (NO x ). Образование и выделение ЗВ в авиадвигателях всех типов, использующих углеводородные топлива, зависит от режима их работы (рис. 9. 23) [39]. Удельные выбросы СO 2 , Н 2 O и SO 2 одинаковы на всех этапах цикла полета. Они связаны непосредственно с расходом топлива. Выбросы СО, С n Н m и NO x зависят от большого числа переменных, но главный определяющий фактор — тяга двигателя. Минимальное образование СО и С n Н m имеет место при наибольшей тяге, соответствующей взлетному режиму.
Рис. 9. 22. Схема идеального (теоретически полного) и реального сгорания углеводородного топлива в авиадвигателе
Рис. 9. 23. Типичные зависимости удельных показателей образования загрязняющих веществ, г/кг топлива, от относительной тяги отечественных авиадвигателей (ТРД и ТРДЦ), приведенные к статическим условиям на уровне моря
С уменьшением тяги удельное выделение СО и С п H т быстро увеличивается. Это обусловлено в основном снижением температуры процесса и давления воз духа перед камерой сгорания, а также ухудшением распыления топлива. Максимальное образование и выброс NO x в атмосферу наблюдаются в режиме взлета, а в режиме «малого газа» в авиадвигателях они минимальны (см. рис. 9. 23). Это обусловлено тем, что скорость реакции между азотом и кислородом с увеличением температуры процесса возрастает экспоненциально. Наличие в отработавших газах авиадвигателей различных частиц регламентируется показателем (числом) дымности. Число дымности — безразмерная величина, количественно характеризующая выброс дыма (частиц), условно обозначаемая в материалах ИКАО как SN (от smoke number). Основным компонентом частиц является сажа, формирование которой и дальнейшее полное и неполное окисление являются очень сложными процессами. Характер изменения этого показателя от тяги такой же, как и для оксидов азота — с ростом тяги число дымности увеличивается. Однако дымление, характеризуемое условными единицами SN , достигает максимума не в режиме взлета (при Р взл ), а в близком к нему режиме. 9. 3. 2 Нормирование загрязнения атмосферы авиационными ГТД Показатели образования и выброса ЗВ (индексы эмиссии). В международной практике воздействия гражданской авиации на окружающую среду — образование и последующий выброс в атмосферу каждого ЗВ — характеризуют удельным показателем выброса, равным массе этого вещества, образовавшегося при сжигании единицы количества топлива, а затем выброшенного двигателем в атмосферу. Размерность удельного показателя выброса — грамм ЗВ на килограмм топлива, обозначение — EI.
Удельный показатель выброса ЕI каждого загрязняющего вещества определяют для всех типов авиадвигателя экспериментально по принятой ИКАО стандартной методике при заданных характеристиках топлива и при определенных атмосферных условиях (в перерасчете на MCA на уровне моря). Экспериментально полученные далее приводят (пересчитывают) к условиям международной стандартной атмосферы. В соответствии с действующими требованиями ИКАО регламентируется содержание в отработавших газах авиадвигателей оксида углерода СО. несгоревших углеводородов С n Н m , оксидов азота NO x и показатель (число) дымности. Форма представления таких данных в «Банке данных ИКАО по эмиссии выхлопных газов двигателей» на примере двигателя ПС-90 А приведена в табл. 9. 3 (391. Контрольный параметр выброса в атмосферу. Негативное воздействие отработавших газов двигателя на атмосферу в зоне аэропорта Международной организацией гражданской авиации ИКАО принято характеризовать отношением массы загрязняющих веществ, выброшенных в зоне аэродрома М за взлетнопосадочный цикл (ВПЦ) (рис. 9. 24), к взлетной тяге данного двигателя Р взл. Отношение М/Р взл называют контрольным параметром выброса в атмосферу некоего ЗВ для определенного двигателя.
Режим Тяга (в % от P взл Время, мин Расход топлива , кг/с Индекс эмиссии (г/кг) Число дымности НС СО NO х Взлет 100 0, 7 1, 739 0, 12 0. 35 37. 0 — Набор высоты 85 2, 2 1, 431 0, 12 0. 40 31, 5 — Заход на посадку 30 4. 0 0, 489 0. 2 0. 90 11. 8 — Малый газ 7 26, 0 0, 178 0, 3 6. 90 5. 8 — Количество испытаний 3 3 Количество двигателей 1 1 М/Р ит (среднее) (г/к. Н) или SN ( МАКС) 0. 9 13. 6 74, 2 13 А//Р (г/к. Н) или SN (сигма) — -9. 3. Форма представления данных по эмиссии выхлопных газов двигателей
Рис. 9. 24. Стандартный взлетно-посадочный цикл ИКАО
Характерные операции самолета (этапы ВПЦ) и соответствующие им режимы работы авиадвигателей в зоне аэродрома, принятые ИКАО в качестве стандартных (по АП-34), приведены в табл. 9. 4. Режимы взлетно-посадочного цикла (см. табл. 9. 4) представляют собой условность, которая необходима для единообразного испытания авиадвигателей, их сравнения между собой, сертификации и сравнения с установочными нормами допустимого воздействия на окружающую среду |39|. Масса каждого загрязняющего вещества Л/, образовавшегося в авиадвигателе и выброшенного в атмосферу за полный взлетно-посадочный цикл (ВПЦ). кг, может быть рассчитана по зависимости (9. 19) где El i — удельный показатель выброса рассматриваемого загрязняющего вещества в i-м режиме работы двигателя; G mi — расход топлива на i-м режиме работы двигателя, кг/с; τ i — продолжительность i-го режима работы двигате ля, с; I — режим работы двигателя в зоне аэропорта (этап ВПЦ) в соответствии с табл. 9. 4.
Этап взлетно-посадочного цикла Дозвуковые самолеты Сверхзвуковые самолеты Тяга двигателя на этапе Продолжительность этапа, мин Взлет Р взл 0, 7 Р взл 1, 2 Набор высоты 0. 85 Р взл 2, 2 0, 65 Р взл 2, 0 Снижение — — 0, 15 Р взл 1, 2 Заход на посадку 0. 30 Р взл 4, 0 0, 34 Р взл 2, 3 Руление (земной малый газ) 0, 07 Р взл 26, 00 0, 058 Р взл 26, 009. 4. Режимы работы двигателя в ВПЦ
Для турбореактивных и турбовентиляторных двигателей дозвуковых самолетов нормативные значения ЗВ следующие: • для несгоревших углеводородов С n Н m — М/Р взл = 19, 6 г/к. Н; • для оксида углерода СО — М/Р взл =118 г/к. Н; • для оксидов азота NO х , г/к. Н: а) для двигателей тех типов или моделей, первый серийный образец которых изготовлен до 31. 12. 1995 г. , а конкретный экземпляр — до 31. 12. 1999 г. (9. 20) б) для двигателей тех типов или моделей, первый серийный образец которых изготовлен после 31. 13. 1995 г. и конкретный экземпляр которых изготовлен после 31. 12. 1999 г. , (9. 21) • для числа дымности SN М/Р взл = 83, 6 Р взл ) -0, 274 или величины 50, в зависимости от того, какое из этих значений ниже. В АП-34 ужесточены (введены дополнительно) требования к выбросам оксидов азота NO х , предъявляемые к типу и модели турбореактивных и турбовентиляторных двигателей дозвуковых самолетов с установленной взлетной тягой более 26, 7 к. Н (2720 кгс), первый серийный образец кото рых изготовлен позднее (31. 12. 2003 г. ). Для них нормативное (максимально допустимое) значение выбросов, г/к. Н. определяется по следующим формулам:
Очередное ужесточение требований к выбросам ЗВ авиадвигателями ВС в зоне аэродрома ожидается уже в первом десятилетии XXI века. Причем, в связи с тем, что влияние выбросов оксидов азота, углерода, серы и паров воды в верхней тропосфере и нижней стратосфере на процессы глобального изменения климата планеты считается доказанным, также обсуждается введение ограничений на выбросы ЗВ от двигателей ВС на этапе крейсерского полета для дозвуковых и сверхзвуковых самолетов. К числу отечественных ВС, оснащенных двигателями, соответствующих перспективным международным требованиям по выбросам ЗВ в атмосферу, относятся Ту-204 и Ил-96 -300 с двигателем ПС-90 А, а также Ту-334 и Бе-200 с двигателем Д-436 Т 1.
9. 3. 3. Измерение содержания загрязняющих веществ в отработавших газах ГТД Испытания по определению содержания загрязняющих веществ проводятся на стационаром наземном стенде, оборудованном соответствующими измерительными системами [26]. Измерения выполняются на установившихся режимах при величинах тяги, соответствующих условному цикл взлетно-посадочных операций. Кроме концентрации загрязняющих веществ в выхлопных газах, на каждом режиме измеряются тяга, массовый расход топлива. частота вращения ротора, температура и давление воздуха на входе в двигатели (на расстоянии не более одного диаметра от входного устройства). давление и температура воздуха на входе в камеру сгорания р* к и Т* к , относительная влажность окружающего воздуха (на расстоянии не более 15 м от входного устройства). Точки отбора проб распределяются равномерно между четырьмя секторами выходного сечения реактивного сопла, образованными двумя взаимно перпендикулярными диаметрами. Пробоотборник выполняется из коррозионно-стойкой стали и должен обеспечивать отбор проб газа не менее чем в 12 точках сечения сопла двигателя. Пробоотборник должен быть сконструирован таким образом, чтобы не менее 80 % падения давления проходящего через него газа приходилось на отверстия. Для двигателей без форсажной камеры пробоотборник устанавливается на расстоянии не более 0, 5 м от плоскости среза сопла (среза сопла внутреннего контура для ТРДД с раздельными контурами). Могут использоваться смешивающие пробоотборники, имеющие отверстия одинакового диаметра (рис. 9. 25, а).
Для двигателей с форсажной камерой пробоотборник устанавливается на расстоянии, равном 25 -и диаметрам сопла от его среза, так как температура выхлопных газов на форсажных режимах высока (2000. . . 2200 К) и при смешении их с воздухом происходит интенсивное догорание продуктов неполного сгорания топлива. Из пробоотборника проба подается к газоанализирующей аппаратуре по магистрали с внутренним диаметром 4. . . 8, 5 мм по кратчайшему пути (длина не более 25 м). Расход должен быть таким, чтобы время прохождения газа по магистрали не превышало 10 с. Температура в магистрали должна поддерживаться в пределах 145. . . 175 °С. Магистраль изготавливается из коррозионно-стойкой стали и обогревается электрическим током. Схема системы отбора и анализа проб приведена на рис. 9. 25, б. Система состоит из подсистем, предназначенных для измерения концентрации отдельных компонентов. В состав каждой подсистемы входят необходимые устройства для регулирования расхода газа, поддерживания определенной температуры пробы и измерения. Для измерения общего содержания углеводородов в пробе используется пламенно-ионизационный детектор. В диффузионное водородное пламя вводится проба газа. При горении углеводородов газ в пламени ионизируется и между соответствующим образом установленными электродами, к которым приложена разность потенциалов, возникает ионизационный ток, пропорциональный расходу углеводородов через пламя. По результатам измерения ионизационного тока определяется концентрация несгоревших углеводородов. Полный диапазон измерений — 0. . . 5 10 -3 объемных долей.
Действие приборов, предназначенных для измерения концентраций СО и С 0 2 , основано на принципе поглощения инфракрасного излучения в параллельных элементах, заполненных эталонным (нулевым) и отобранным газом. При измерениях необходимо обеспечить, чтобы элемент, заполненный отобранным газом, и другие компоненты системы имели температуру примерно 50 °С. Диапазон измерений для СО — 0. . . 2, 5 ∙ 10 -3 а для С 0 2 — 0. . . 5 ∙ 10 3 объемных долей.
Рис. 9. 25. Схема смешивающего пробоотборника (о) и схема системы отбора и анализа проб газа (б): 1 — сопло; 2 — пробоотборник: 3 — насос; 4 — участки, магистрали, нагреваемые до 17> С: 5 — подвод «нулевого воздуха; 6 — подвод поверочного газа; 7— участки магистрали, нагреваемые до 60 °С; С х Н у , СО, СО 2 , . NО х , — анализаторы
Измерение содержания оксидов азота осуществляется по методу хемилюминесценции, т. е. измеряется излучение, выделяющееся при реакции NO и О 3. Поскольку в пробе газа содержится, кроме NO, также и NO 2 , то проба газа про пускается через конвертер, в котором N 0 2 преобразуется в NO. Содержание NO измеряется перед конвертером, а также за ним. Содержание N 0 2 определяется по разности этих измерений. Полный диапазон измерений — 0. . . 1∙ 10 -3 объ емных долей. К точности измерений предъявляются весьма высокие требования. Например, чувствительность не менее 0, 5 %; относительная погрешность ± 1 % ( изменение выходного сигнала в течение двух часов не более I % (проценты вычисляются от конечного значения шкалы используемого диапазона показаний). Для получения высокой точности перед каждой серией испытаний проводится проверка герметичности и чистоты системы измерений. Градуировка и проверка анализаторов проводятся посредством поверочных смесей газов. Цель градуировки состоит в проверке стабильности и линейности характеристик приборов. При исследованиях состава продуктов сгорания применяется также метод газовой хроматографии. По этому методу в поток инертного газа-носителя (аргон. гелий) вводится небольшая порция анализируемых продуктов сгорания (проба). Эта смесь пропускается через хроматографическую колонку-трубку диаметром 2. . . 4 мм и длиной 0, 5. . . 3 м, заполненную адсорбентом (селикагелем, древесным углем).
При движении через колонку компоненты смеси вследствие различий в сорбции разделяются и группируются в зоны, отделенные друг от друга инертным газом-носителем. На выходе из колонки с помощью специального детектора регистрируется изменение во времени некоторого физического свойства, которое функционально связано с концентрацией и видом каждого компонента. Определение уровня дымления двигателей. В настоящее время разработаны и нашли широкое применение два метода определения дымности [41]. Первый из них и наиболее распространенный — фильтрационный метод SAE, разработан ный в 1970 г. американским обществом инженеров транспорта (Society of Automotive Engineers — SAE) [41], принят в качестве стандартного Международной организацией гражданской авиации (ИКАО) и включен в ГОСТ 17. 2. 2. 04— 86. Второй метод, применяющийся в настоящее время для оценки дымления авиационных ГТД, — фотометрический, основанный на непосредственном определении в полете коэффициента пропускания света выхлопной струей (или дымовым шлейфом) двигателя. Рис. 9. 26. Схема системы для измерения уровня дымности выхлопных газов фильтрационным методом
Схема системы для измерения дымности выхлопных газов ГТД фильтрационным методом SAE представлена на рис. 9. 26. Выхлопные газы через осредняющую гребенку 10 под действием скоростного напора потока выхлопных газов или с помощью насоса 7 поступают по обогреваемой магистрали к трехходовому клапану 2, который позволяет направлять поток выхлопных газов в рабочую магистраль к фильтру или в байпасную линию. В байпасную линию выхлопные газы направляются при настройке режима двигателя, а также в промежутке между отдельными измерениями дымности. Клапаном 2 при измерении дымности закрывается байпасная линия и открывается рабочая магистраль, выхлопные газы пропускаются через установленный в фильтро- держателе 6 бумажный фильтр. Постоянный объемный расход выхлопных газов (0, 23 м 3 /с) устанавливается с помощью регулировочного клапана 5 и ротаметра 8. После прокачки выбранного количества выхлопных газов (их объем фиксируется газовым счетчиком 9) производится переключение потока выхлопных газов в байпасную линию и отработанный фильтр удаляется из фильтродержателя 6. Затем с помощью фотометра определяется отражательная способность «экспонированного» фильтра R s и вспомогательная величина (9. 27) где R w — отражательная способность чистого фильтра. Рис. 9. 27. Образцы фильтров: а — сильное дымление: б — слабое дымление
С помощью линейной зависимости SN’ =f(log. M/A), где М — масса выхлоп ных газов, прошедшая фильтр; А — площадь «рабочей» поверхности фильтра, определяется измеренное значение числа дымности SN, соответствующее базовой величине нагрузки на фильтр М/А = 16, 2 кг/м 2. Реальные значения SN не превышают 80. . . 85. На рис. 9. 27 приведены фотографии двух отработавших фильтров, отвечающих «сильному» (а) и «слабому» ( б) дымлению. Точность определения SN с помощью рассмотренной измерительной системы составляет ± 2 ед. [41]. Метод измерения коэффициента пропускания света выхлопной струей авиационного ГТД основан на фотометрировании фото-, кинонегативов, получаемых при съемке дымового шлейфа, образующегося двигателем или самолетом в полете. Определение параметра выброса сажи D производится при испытаниях двигателя на наземном стенде. Отбор проб газа осуществляется на установившихся режимах работы двигателя при температуре окружающего воздуха не ниже 15 °С. Отбирается не менее трех проб на каждом режиме. 9. 3. 4. Уменьшение эмиссии авиационных ГТД при стендовых испытаниях Применение ряда технических и организационных мероприятий позволяет сократить концентрации вредных веществ при работе экспериментальных стендов. К таким мероприятиям относятся: • применение вертикальных выхлопных шахт; • увеличение скорости выхода выхлопных газов в атмосферу; • увеличение высоты выхлопных шахт; • ограничение времени совместной работы стендов на напряженных режимах; • запрещение работы стендов при неблагоприятном ветре по скорости и направлению; • разработка каталитических систем очистки выхлопных газов от оксидов азота;
• сокращение времени испытаний путем совершенствования технологии и методологии испытаний, а также за счет автоматизации испытаний. Образование и последующий выброс в атмосферу «термических» оксидов азота зависит, прежде всего, от трех основных факторов где Т* mах — максимальная температура; С 0 — концентрация атомарного и молекулярного кислорода; τ — время действия максимальной температуры. Поэтому основными способами уменьшения образования NO x являются: 1. Снижение максимальной температуры сгорания, которое достигается: • впрыском воды в камеру сгорания; • рециркуляцией продуктов сгорания (отработанных газов) в зону горения; • обеднением топливовоздушной смеси. 2. Уменьшение концентрации кислорода на начальных стадиях процесса горения топлива, когда имеют место высокие температуры и происходит интенсивное образование N 0. Это обеспечивается применением двухстадийного сгорания, при котором в начале (первая стадия) процесс проводят при недостатке кислорода (а = 0, 7. . . 0, 95), а на второй стадии добавляют воздух для дожигания СО, С n Н m , С, но температура процесса уже недостаточна для синтеза NO. Уменьшить образование сажи позволяет: 1) совершенствование процесса распыливания жидкого топлива во фронтовом устройстве; 2) сокращение размеров первичной зоны и циркуляционных зон и обеднение топливовоздушной смеси в этих зонах. Примером реализации этих мер могут служить многофорсуночные камеры сгорания.
Кардинальным путем решения проблемы уменьшения сажеобразования и дымности выхлопных газов ГТД является переход к регулируемым камерам сгорания и, в частности, камерам сгорания с регулируемыми фронтовыми устройствами. Компания GEAE обладает рядом патентов на камеры сгорания, которые оснащены двухъярусными завихрителями с закруткой потока. Создавая мощные вихревые потоки, такие камеры сгорания обеспечивают быструю подготовку однородной топливновоздушной смеси. С точки зрения эффективности перспективные топливные форсунки могут снизить уровень эмиссии N 0 V , СО и НС более чем на 50 %. Рис. 9. 28. Схемы камер сгорания: а — однозонная кольцевая (SAC); б — двухзонная кольцевая (DAC); в — однозонная кольцевая с обедненной зоной горения и прямым впрыском топлива (LDISS
Компанией исследовались различные конструктивные схемы и способы организации рабочего процесса в камерах сгорания (рис. 9. 28). В настоящее время фирма Роллс-Ройс работает над созданием простой дешевой однозонной кольцевой камеры сгорания (КС), в которой подача топлива осуществляется через одну форсунку. Применение такой камеры сгорания га рантирует получение существенных выгод по сравнению с применением двойной кольцевой камеры сгорания по стоимости, массе и надежности при обеспечении лучшей эмиссии. Рассматривается направление, связанное с уменьшением уровня эмиссии СO 2 до нуля в ГТД дозвуковых самолетов. Достичь цели предполагается, благодаря применению в качестве топлива жидкого водорода и нового способа преобразования энергии, в частности, топливных элементов. Использование топливных элементов позволяет отказаться от применения в конструкции двигателя камеры сгорания и турбин, а сам двигатель в этом случае превращается в движитель, который приводится во вращение от электромотора.
9. 4. ИСПЫТАНИЯ АВИАЦИОННЫХ ГТД НА ОБЛЕДЕНЕНИЕ Переохлажденные капли воды или кристаллы льда, находящиеся в воздухе в виде облаков, тумана, мокрого снега, при встрече с ЛА замерзают на его поверхности, приводя тем самым к обледенению (рис. 9. 29) [12]. Наибольший процент авиационных происшествий, связанных с обледенением, приходится на наземное обледенение. Поданным ИКАО, из-за обледенения ежегодно происходит около 7 % всех авиационных катастроф, связанных с метеоусловиями. Авиационные ГТД, в отличие от самолета, обледенение которых наступает при отрицательных температурах, подвергаются обледенению при температуре окружающей среды до +5. . . +10 °С. Это явление наблюдается при работе двигателей на малых высотах полета: воздух, расширяясь во входном канале, охлаждается, и его температура может достигать значения, при котором наступает обледенение. Попадание сорвавшихся кусков льда в компрессор двигателя приводит к повреждению лопаток и даже к полному разрушению двигателя (рис. 9. 30). Сильное обледенение винтов вызывает дисбаланс их лопастей.
Рис. 9. 29. Вероятность обледенения в облаках в зависимости от температуры окружающего воздуха
Рис. 9. 30. Обледенение входной части воздухозаборника и элементов ГТД: а — рабочих лопаток; б — кока: в — воздухозаборника
Этапы, связанные с проведением испытаний противообледенительных систем (ПОС), включают: • термометрирование лопаток, стоек и других элементов ПОС на лабораторных спецустановках в «сухом» воздухе в условиях, имитирующих эксплуатационные; • испытание лопаток, стоек и других элементов ПОС на лабораторных спецустановках в условиях искусственного обледенения, имитирующих эксплуатационные; Рис. 9. 31. Сертификационные испытания по оценке эффективности противообледенительной системы двигателя
• термометрирование обогреваемых элементов на двигателе на всех режимах с замером расхода теплоносителя на каждый элемент; • сертификационные испытания двигателя в термобарокамере в условиях искусственного обледенения, имитирующих эксплуатационные, по программе сертификационных испытаний; • сертификационные испытания ПОС двигателя в составе воздушного судна при полете в условиях искусственного обледенения; • сертификационные испытания ПОС двигателя в составе воздушного судна при полете в условиях естественного обледенения (рис. 9. 31). По методам оценки характеристик и эффективности систем испытания подразделяются на следующие виды [12]: • испытания в условиях отсутствия обледенения, т. е. в «сухом» воздухе; • испытания в условиях искусственного обледенения; • испытания в условиях естественного обледенения; • испытания по оценке влияния обледенения на летные характеристики воздушного судна и его силовых установок. Испытания в «сухом» воздухе проводятся для определения тепловых характеристик ПОС. Эксперименты в искусственных условиях обледенения проводят на открытых стендах зимой при отрицательных температурах воздуха, в термобарокамерах и на летающих лабораториях (рис. 9. 32). При создании ГТД проводят также испытания на попадание льда в двигатель. Такие испытания проводят с применением установки для забрасывания льда, оборудованной на входе в двигатель наклонным желобом с дистанционно Управляемой заслонкой. При этом желоб позволяет изменять направление подачи частиц льда. При открытии заслонки частицы льда скользят под действием
силы тяжести и увлекаются потоком воздуха в двигатель. Размер льдинок обычно 5 x 20 x 50 мм, их забрасывают партиями по 10 штук в разные места диффузора. Количество и частота соударений определяются условиями скалывания льда после включения ПОС. Скорость засасывания сколовшихся кусков льда не нормируется, режим работы двигателя — максимальный, продолжительный и малого газа. После соударения двигатель должен функционировать без недопустимых повреждений и потери тяги (мощности) в течение установленного программой времени. Должны отсутствовать повышенные вибрации, а параметры рабочего процесса должны восстанавливаться через 3. . . 5 мин. Время работы без включенной ПОС должно имитировать время возможного запаздывания ее включения в режиме ручного управления и составлять 1 мин. На стенде могут быть проведены испытания по воздействию снега на работу двигателя. Снег может создаваться непосредственно в процессе эксперимента, а может быть изготовлен заранее и затем подан непосредственно в воздухозаборник двигателя. Существуют несколько типов стендов для исследования обледенения и эффективности противообледенительной системы двигателей при искусственном обледенении: • открытый стенд, оборудованный специальной водораспыливающей системой (рис 9. 33); • стенд, оборудованный холодильной установкой;
Рис. 9. 32. Универсальная летающая лаборатория «Танкер» для исследования в условиях искусственного обледенения: 1 — кабина экспериментаторов: 2 — водораспыливающая решетка; 3 — экспериментальный отсек; 4 — водораспыливающий конус; 5 — лебедка; 6 — водяной бак; 7 — насосная станция Рис. 9. 33. Стенд для испытания силовых установок: 1 — двигатель; 2 — входное устройство; 3 — смотровое окно; 4 — труба; 5— коллектор с форсунками; 6 — фотоаппарат; 7 — прожектор: 8 — станок; 9 — термометр для воды на входе в коллектор; 10 — манометр для воды на входе в коллектор; 11 — фильтр сетчатый; 12 — насос высокого давления; 13 — кран; 14 — бак для воды
• термобарокамера, в которой испытания двигателя проводятся по параметрам торможения при М = 0; • термобарокамера, в которой испытания противообледенительной системы проводятся в условиях свободного потока с обдувом силовой установки и др. Испытания проводят при различных атмосферных условиях (температурах 0, -5, -10, -20, -30 °С и соответствующим им водностям). При своевременном включении ПОС образования льда в расчетных условиях на всех режимах работы двигателя в полете не должно быть. При этом имитируются все имеющиеся на двигателе устройства для отбора воздуха.
9. 5. ИСПЫТАНИЯ ГТД ПО ПОПАДАНИЮ ПОСТОРОННИХ ПРЕДМЕТОВ По характеру воздействия на работу силовой установки (в соответствии с Нормами летной годности ИКАО) посторонние предметы делятся на две основные группы. В первую группу входят предметы, влияющие на работу только одного двигателя многодвигательного самолета (табл. 9. 5). Если при попадании предметов этой группы в двигатель не возникает пожара, взрыва или разрушения, двигатель считается выдержавшим испытания. Оборвавшиеся при ударе детали двигателя (лопатки, стойки) не должны пробивать корпуса двигателя, а сам двигатель может быть отключен по сигналам контрольных приборов в кабине, позволяющих контролировать состояние и режим работы двигателя. Во вторую группу входят предметы, влияющие на работу всех двигателей многодвигательного самолета при единичном попадании (табл. 9. 6).
Наименование постороннего предмета Необходимость включения в испытания Количество, шт. Режим работы двигателя Скорость заброса Обтирочная ветошь Обязательно — Взлетный На всасывании Ручной инструмент Не обязательно — Взлетный То же Болты и гайки Обязательно — Взлетный — « — Куски резины от авиашин Не обязательно 1 Взлетный — «— Лопатка вентилятора Обязательно 1 Взлетный Вылета при обрыве Птица массой 1, 8 кг Обязательно 1 Максимальный крейсерский Набора высоты9. 5. Посторонние предметы, влияющие на работу двигателя многодвигательного самолета
Наименование постороннего предмета Воздействующие факторы и количество Режим работы двигателя Скорость заброса 1. Дождь Поток влажностью 4 % Взлетный, полет ный малый газ На всасывании 2. Песок и гравий 28 г на каждые 645 см 2 площа ди входного сечения двигателя Взлетный То же 3. Лед, образующий ся на передней кромке воздухозаборника Слой, известный из практики Максимальный крейсерский 4. Градины диаметром 25 и 50 мм 2 шт. на каждые 970 см 2 площа ди входного сечения То же Полета при бол танке 5. Птицы массой 56. . . 112 г 1 шт. на каждые 970 см 2 площа ди входного сечения Взлетный Отрыва от земли 6. Птица массой 680 г 1 шт. при площади входного се чения до 1935 см 2 + по 1 шт. при каждом увеличении на 3870 см 2 Взлетный Набора высоты9. 6. Посторонние предметы, влияющие на работу всех двигателей многодвигательного самолета при единичном попадании
Причины попадания посторонних предметов и их влияние на повреждаемость ГТД Среди причин, по которым авиационные ГТД не отрабатывают положенных ресурсов, наиболее частыми являются механические повреждения, вызванные попаданием твердых посторонних предметов (ТПП). Опыт эксплуатации показывает, что, несмотря на принимаемые меры по предотвращению повреждений силовых установок ТПП, доля досрочно сни маемых «с крыла» по этой причине двигателей достигает 35. . . 40 % [47]. Попадая в проточную часть, ТПП вызывают как локализованные неисправности без разрушения корпуса двигателя, так и нелокализованные отказы, вызванные попаданием крупных ТПП и проявляющиеся в виде разрушения корпуса двигателя с последующими непредсказуемыми последствиями. Основные причины преждевременного съема двигателей с эксплуатации из- за повреждения элементов газовоздушного тракта являются [47]: • попадание посторонних предметов в воздухозаборник самолета от колес шасси при взлете с бетонных ВПП; • засасывание посторонних предметов с поверхности аэродрома вихревым жгутом, возникающим при работе на стоянке и при движении самолета; • заброс посторонних предметов в воздухозаборник реактивными струями двигателей, взлетающих и рулящих самолетов; • заброс посторонних предметов в воздухозаборник реверсивной струей на самолетах с реверсом тяги;
• заброс посторонних предметов га зовоздушными струями подъемных двигателей на самолетах вертикального взлета и посадки. Повреждаемость двигателя посто ронними предметами существенно зависит от компоновки ГТД на летательном аппарате. Естественно, что самолетов, у которых ГТД расположены на пилонах под крылом (Ту-204/214, Ил- 76, Ил-96, Airbas АЗ 10, АЗ 19, А 380, Boeing. В 747, В 757, В 787) вероятность попадания посторонних предметов на много выше, по сравнению с самолетами, двигатели которых располагаются на пилонах в хвостовой части фюзеляжа (Ту-134, Ту-154, Ту-334, Ил-62, DC-10). Пыль ускоряет износ лабиринтных уплотнений, а загрязненное пылью масло — износ элементов коробки приводов и трансмиссии, а также подшипников ротора. Уплотненный слой пыли, покрывая торцы форсунок, может резко ухудшить качество распыла топлива и охлаждение форсунок. Эрозионный износ лопаток компрессора и направляющих аппаратов являлся одной из причин досрочного съема двигателей ТВЗ-117 вертолетов Ми-8 МТ с эксплуатации при ведении боевых действий в Афганистане.
Рис. 9. 34. Открытый стенд для проведения сертификационных испытаний ГТД по забросу града Все новые современные двигатели проходят испытания на заброс на вход предметов, попадающих в двигатели в процессе эксплуатации (рис 9. 34). Двигатель должен быть сконструирован так, чтобы попадание посторонних предметов, которые могут повлиять более чем на один двигатель в одном полете, не помешало безопасному полету и приземлению самолета в результате опасной ситуации на двигателе. К таким недопустимым ситуациям относятся: • немедленная или последующая потеря мощности; • ухудшение характеристик управления двигателем; • превышение двигателем любых эксплуатационных ограничений. Такие неисправности, одиночный или множественный отказ, или любая возможная неправильная эксплуатация двигателя не должны вызывать на нем следующие последствия: • нелокализованный пожар; • нелокализованное разрушение (вылет опасных фрагментов через корпус Двигателя); • нагрузки в узлах крепления двигателя большие, чем предельные нагрузки; • потерю возможности выключения двигателя; недопустимую тягу в направлении, противоположном движению воздушного судна
При работе ГТД в запыленных условиях степень повреждения поверхностей лопаток НА компрессора и других элементов конструкции зависит от многих факторов: • материала элементов конструкции двигателя; • материала и формы частиц; • концентрации частиц в воздухе; • суммарной массы частиц, прошедших через ГТД; • режима работы, на котором происходит попадание частиц. Выявление закономерностей повреждения ГТД от указанных выше факторов проводится при специальных испытаниях, используя компоненты, характеристики которых приведены в табл. 9. 7. Наименование компонента Химический состав Твердость по шкале МООСА Удельная масса, г/см 3 Насыпная масса, г/см 3 Гигроскопичность, % Молотый песок Si 0 2 7 2, 6 1, 6 0, 1 Тальк твердый 3 Mg 0, Si 0, H 2 0 1 2, 8 0, 97 0, 29. 7. Характеристики компонентов, используемых в испытаниях
Для заброса в двигатель мелких посторонних частиц песка, бетонной крошки, мелких камней со средним диаметром до 5 мм используют устройства, показанные на рис. 9. 35 и 9. 36. Рис. 9. 35. Устройство для заброса в двигатель мелких частиц: а — I — стакан; 2 — трубопровод подачи сжатого воздуха; 3 — патрубок поддавливания; 4 — рассеивающий насадок; б — формы сечения распыливающих насадков Рис. 9. 36. Схема оборудования установки для забрасывания льда: / — забрасываемые частицы; 2 — заслонка; 3 — пружина; 4 — электромагнит со штырем; 5 — наклонный желоб; 6 — испытуемый двигатель
Более крупные частицы забрасываются в двигатель через специальные бункеры, лотки или пневмопушкой. Бункеры и лотки имеют возможность поворачиваться вокруг осей для выбора направления заброса частиц и рав номерного рассеивания их по сечению входного канала. Они оборудованы заслонками с дистанционным управлением от пневмоцилиндров или электромеханизмов. Способы защиты ГТД от повреждений посторонними предметами Для обеспечения работоспособности ГТД при воздействии посторонних предметов предусмотрен комплекс конструкторских мероприятий, которые разделяются по отношению к ГТД на внутренние и внешние [30]. Внутренние конструкторские мероприятия включают: • обеспечение характеристик компрессора с повышенными запасами газо динамической устойчивости; • выполнение первой ступени компрессора с широкохордными рабочими лопатками; • применение эрозионностойких покрытий на лопатках компрессора; • оснащение системы автоматического регулирования подсистемой антипомпажной защиты и подсистемой восстановления режима при погасании камеры сгорания; • усиленная очистка сжатого воздуха, направляемого в систему охлаждения, от пыли и дренажирование тупиковых участков системы воздушного охлаждения для предотвращения забивания их пылью. Внешние конструкторские мероприятия включают компоновочные реше ния по ЛА, снижающие проявления этих факторов, и создание специальных защитных устройств во входном устройстве, которые по возможности препятствовали бы попаданию посторонних предметов на входе в двигатель. Из существующих видов защитных устройств можно выделить следующие: 1) сепаратор — пылеотделители; 2) защитные устройства панельного, пластинчатого, велосипедного и сетчатого типов; 3) надкрыльевой забор воздуха;
4) струйная защита, основанная на создании воздушной пелены с повышенным давления перед входным устройством ГТД; 5) электростатические пылезащитные устройства; 6) инерционный метод защиты. Метод обычно реализуется в виде ПЗУ для ТВД и малых ТРД.
9. 6 ИСПЫТАНИЯ ГТД НА СТОЙКОСТЬ ПРОТИВ ПОПАДАНИЯ ПТИЦ Первое столкновение летательных аппаратов с птицами зафиксировано в 1908 г. , а первая катастрофа по этой причине — в 1912 г. Вероятность столкновения летательных аппаратов с птицами возросла в конце 1950 г. , когда стали эксплуатироваться летательные аппараты с газотурбинными двигателями. Большая скорость летательных аппаратов и значительные размеры воздухоза борников привели к повышению уровня повреждаемости ГТД в данных условиях эксплуатации. Установлено, что чаще всего самолеты сталкиваются с чайками — 625 случа ев (16 %). Часто наблюдаются столкновения с коршунами, ласточками, чибисами, воробьями, ястребами, голубями, ржанками и утками (перечислены в порядке убывания частоты столкновений). Большинство столкновений с птицами происходит на малых высотах — половина таких инцидентов происходит ниже 30 м при взлете или посадке самолета. Подавляющее большинство столкновений (85 %) происходит на высотах до 500 м. На высотах от 500 до 1500 м зарегистрировано (около 13 %) столкновений. Чаще всего самолеты сталкивались с одной птицей — 2704 инцидента (68 %). Столкновение с птицами летательных аппаратов влияет на безопасность полетов и экономику во всем мире, вызывая потери порядка 1, 2 млрд. долл, в год. Приблизительно в 40 % зарегистрированных случаев столкновения птицы попадали в двигатель (это можно объяснить как большой площадью сечения входного канала воздухозаборника, так и его всасывающим действием). Характер повреждений авиационной техники зависит от ее конструктивных особенностей, скорости
движения, массы птиц, высоты полета, от угла и места контакта птицы с летательным аппаратом, от расстояния между направляющим аппаратом и рабочим колесом. Вид и частота повреждений отдельных деталей летательных аппаратов и двигателей приведены в табл. 9. 8 В зависимости от взаимного положения птиц и самолета в момент столкновений выделяют следующие физические явления: • удар; • пробивание; засасывание (захват) птицы и обломков деталей самолета работающим двигателем.
Вид повреждения Частота повреждения, % Деформация и повреждение лопаток компрессора (рис. 9. 37) 85, 6 Забоины и вырыв материала на входных кромках лопаток компрессора 5, 6 Вмятины на стойках входного направляющего аппарата 3, 2 Обрыв лопаток компрессора 1, 6 Помпаж двигателя 0, 8 Посторонний шум в двигателе 0, 8 Оплавление лопаток турбины и разрушение конуса сопла 0, 8 Заклинивание ротора двигателя 0, 8 Флюгирование винта ТВД 0, 89. 8. Вид и частота повреждений деталей летательного аппарата и двигателя
В качестве примеров можно привести попадание аиста в кабину самолета-истребителя после взлета на высоте 400 м (рис. 9. 38). Результатом попадания птиц в двигатель, как правило, являются вмятины и забоины на лопатках первых ступеней компрессора, дисбаланс ротора, очень часто помпаж и останов двигателя. Попадание в компрессор птицы весом до 50 г, как правило, не вызывает каких- либо повреждений деталей и узлов газовоздушного тракта. В то же время попадание в компрессор птицы весом 300 г, летящей со скоростью 50. . . 250 км/ч, приводит к кратковременному (на 0, 5 с) изменению параметров работы двигателя, в частности к падению максимальных оборотов примерно на 8. . . 10% с последующим восстановлением режима работы. С увеличением скорости попадания птицы лопатки компрессора получают уже значительную деформацию. Увеличение веса птицы до 2 кг даже при средней скорости попадания ее в компрессор (около 300 км/ч) также приводит к отказу двигателя в работе. Птиц различных видов, попадавших в двигатели, по массе разделяют на несколько групп: • мелкие (воробьи, ласточки, скворцы) — до 150 г; • средние (чайки, голуби, вороны) — 0, 4 0, 9 кг; • крупные (утки, гуси) — до 2, 0 кг; • очень крупные (лебеди, орлы) — свыше 2 кг. Энергия удара крупной птицы массой 1, 8 кг при скорости столкновения 450 км/ч (случай вполне вероятный) достигает около 15 к. Дж.
Рис. 9. 37. Результаты попадания в двигатель чайки Рис. 9. 38. Разрушения вследствие столкновения самолета с аистом: 1 — крышка переднего отсека фузеляжа; 2 — лобовое стекло фонаря кабины
Для проведения испытаний на попадание птиц стенд оборудуется устройством для разгона тушек птиц: специальными салазками или пневматической пушкой, установленной на расстоянии 3. . . 4 м от двигателя, с набором стволов под птиц маленьких, средних и крупных размеров. Если двигатель оборудован устройством для предохранения от попадания птиц, то во время испытания оно должно быть в рабочем положении. На рис. 9. 39 схематично представлена конструкция пневмопушки. Тушка свежезабитой птицы 4 закладывается в ствол, уплотняется пыжом 5. При повороте сферического клапана на 90° сжатый воздух из ресивера подается в ствол и разгоняет тушки. Скорость разгона определяется объемом и давлением воздуха в ресивере, объемом и длиной ствола, массой птицы. Для имитации попадания в двигатель стаи мелких птиц пневмопушка имеет несколько стволов, равно мерно расположенных по окружности. Количестволов определяется количеством мелких птиц, попадающих в двигатель через 1 м 2 площади воздухозаборника. Для разгона тушек птиц средней и большой массы может использо ваться устройство промежуточное по конструкции между пневмопушкой и разгонными салазками. В этом устройстве в ствол закладывается полый поршень 11, в который помещают тушку. Поршень разгоняется в месте с тушкой по стволу. На конце ствола имеет ся упор 12, в который ударяется поршень, выбрасывая тушку. Разгонное устройство устанавливается на расстоянии 3. . . 5 м (срез ствола) от испытуемого двигателя. Траектория полетов регистрируется скоростной кинокамерой на фоне мерной базы. В табл. 9. 9 приведены условия проведения испытаний с забрасыванием птиц в двигатель. На основании исследований выпускается руководство по управлению и контролю поведения птиц для предотвращения их столкновения с летательным аппаратом.
Рис. 9. 39. Общая схема пневмопушки: 1 — ресивер для сжатого воздуха; 2 — шаровой клапан; 3 — сменный секционированный ствол; 4 — испытуемый двигатель; 5 — датчики; 6 — тушка птицы; 7 — пыж; 8 — рама пушки; 9 — переходный ресивер; 10 — стволы для заброса стаи мелких птиц; 11 — полый поршень; 12 — упор
Масса забрасывае мых птиц Количество птиц, забрасываемых в двигатель Количество и частота соударений Имитируемая скорость при соударении Режим работы двигателя Допустимое состояние двигателя после испытания Примечание 1. Крупная птица мас сой не ме нее 1, 8 кг (например, утка) Одна птица — Максималь на я скорость полета, воз можная при наборе высо ты до 2500 м Максимал ь ный продол жи тельный 1) Полная потеря тяги 2) Не вызывает отказа с опасными последст виями а) испытания проводят ся на работающем и не работающем двигателе с попаданием на непод вижные детали (лопатки ВНА, корпус подшип ника); б) испытания проводят с попаданием на вращаю щиеся детали 9. 9. Условия проведения испытаний ГТД на попадание птиц
2. Средние птицы мас сой до 0, 7 кг (например, чайки) Одна птица на пер вые 0, 2 м 2 площади входа плюс по од ной птице на каж дые оставшиеся 0, 39 м 2 площади входа, но не более 10 штук По 10 птиц в секунду Скорость набора высоты непосредственно после взлета Взлетный Допустимая потеря тя ги (мощности) не бо лее 25 % от взлетной в течение установленно го программой време ни, иначе необходима разработка конструк тивных средств — 3. Мелкие птицы мас сой до 0, 115 кг (на пример, скворцы) По одной птице на каждые 0, 032 м 2 площади, но не бо лее 16 штук По 10 птиц в секунду Скорость набора высоты непосредственно после взлета Взлетный Допустимая потеря тя ги (мощности) долж ны составлять не более 25 % от взлетной в те чение установленного программой времени Испытания по п. 3 могут не проводиться, если при испытаниях по п. 2 пока зано, что птицы среднего размера проходят через испытываемые участки без задержки Примечание. Если у двигателя есть защитное устройство, то при испытаниях оно должно находиться в рабочем положении ГТД
Мероприятия по предупреждению столкновений и защите ГТД от повреждений при попадании птиц Мероприятия, проводимые для предупреждения и предотвращения столкнове ния летательных аппаратов с птицами, условно можно разделить на восемь групп: • распространение сведений по биологии птиц среди авиационных специа листов; • конструктивные мероприятия; • физические способы отпугивания птиц из района аэродрома; • биологические способы борьбы с птицами на аэродромах; • биоакустическое отпугивание птиц (акустические репелленты); • химические способы борьбы; • радиолокационное и визуальное наблюдение; • организационные мероприятия. Конструктивные мероприятия предусматривают улучшение стойкости авиационных конструкций против ударов, а именно: создание лобовых стекол, выдерживающих удары больших птиц, конструкций двигателей, способных «перемалывать» попавших в них птиц безопасности пробивания корпуса компрессора в случае обрыва лопаток; защиту двигателей от попадания птиц. Предотвращение попадания останков птиц в системы автоматического регулирования и охлаждения турбины возможно только в результате изменения конструкции двигателя. На некоторых типах ГТД с целью защиты от повреждений при попадании птиц применяют следующие конструктивные решения: • утолщение входной кромки рабочей лопатки вентилятора в надполочной части; • применение рабочих лопаток вентилятора из материала с повышенной пластичностью;
• утолщение входных кромок рабочих лопаток первой ступени КНД и утонение выходных кромок лопаток ВНА КНД, а также увеличение зазора между венцами этих лопаток; • утолщение профиля пера рабочей лопатки первой ступени КВД и приме нение на лопатках первой и второй ступеней КВД материала с повышенной пластичностью; • увеличение осевого зазора между лопатками ВНА КВД и рабочими лопатками КВД; • введение на корпусе компрессора окон для сброса части массы птиц в полость между рабочим кольцом и корпусом КВД. Очевидно, что повышение живучести летательных аппаратов путем усиления элементов конструкции приводит к увеличению веса и ухудшению летных характеристик. Защита воздухозаборника двигателя решетками не всегда дает положительный эффект. Решетка с ячейкой, способной задерживать мелких птиц, например скворцов, увеличивает вес конструкции, может подвергаться обледенению и забиваться посторонними предметами, что приводит к увеличению гидравлических потерь на входе в двигатель и падению мощности двигателя. Биологические способы борьбы с птицами на аэродромах предусматривают создание таких условий, при которых птицы не имели бы возможности находить пишу и воду вблизи аэродрома, места для ночевок или отдыха, для гнездования и высиживания яиц. Биоакустическое отпугивание птиц из района аэродрома (акустические репелленты) основано на принципе использования естественной реакции птиц, например, на появление опасности (криков страха, бедствия), на «сбор в дорогу» . Химические способы борьбы с птицами на аэродромах включает изменение флоры аэродромов с использованием гербицидов. Наблюдения за перемещениями птиц на маршрутах полетов самолетов. Спе циалисты ряда стран пришли к выводу, что наилучшим способом предупреждения столкновений самолетов с птицами
является заблаговременная информация экипажей о наличии птиц в зонах полета и на маршрутах, особенно ночью. Опыт показывает, что наилучших результатов по предупреждению и предотвращению столкновений летательных аппаратов с птицами можно добиться, применяя комплекс различных средств и методов. 9. 7. ИСПЫТАНИЯ ГТД В УСЛОВИЯХ ДОЖДЯ В процессе эксплуатации влага может попадать в двигатель в различном виде (табл. 9. 10). Атмосферное явление Диаметр капель, мм Водность, г/м 3 Примечания Туман 0, 002. . . 0, 020 0, 01… 1, 0 — Облака 0, 004. . . 0, 014 0, 1. . . 1, 5 В очень редких случаях водность достигает 6. . . 10 г/м 3 Морось 0, 05. . . 0, 50 0, 2. . . 2, 0 — Дождь 0, 5. . . 3, 0 — Ливневый дождь 1. . . 6 3. . . 10 В очень редких случаях водность достигает 30. . . 40 г/м 3 (стихийное бедствие)9. 10. Виды влаги, попадающей в двигатель
Влияние дождя может проявляться на различных этапах полета. При работе ГТД в условиях ливневого дождя регистрируются уменьшение температуры газов за турбиной, снижение удельного расхода топлива и увеличение тяги. Пример. На рис. 9. 40 приведены основные данные параметров двигателя РД-ЗМ-500 в зависимости от объема прошедшей через двигатель воды, содержащей соли калия, магния и др. , вызывающей повреждения газовоздушного тракта. Увеличение объема во ды, проходящей через двигатель, и ее жесткости приводит к устойчивой тенденции Ухудшения газодинамических параметров двигателя. После прохождения до 2000 л воды без содержания солей основные параметры двигателя остаются практически неизменными. 9. 40. Изменение газодинамических параметров двигателя РД-ЗМ-500 в зависимости от объема прошедшей через двигатель воды
Основными факторами, ухудшающими газодинамические свойства двигателя , длительно работающего в условиях воздействия воды, являются: • шероховатость входной кромки и поверхности корыта лопаток компрессора, особенно первых ступеней; • накипь на поверхностях лопаток последних ступеней. Отложения солей на поверхностях лопаток (накипь), выделяемых при Испании воды, уменьшают проходные сечения направляющих аппаратов, особенно последних ступеней компрессора. Это приводит к снижению КПД и запаса аэродинамической устойчивости компрессора. Влияние попадания воды на прочность двигателя Воздействие на поверхность деталей высокоскоростных частиц жидкости приводит к повреждениям: • входных ступеней компрессоров, используемых в течение длительного рейса при полете в дождь; • «средних» ступеней при запуске ГТД с влагой, скопившейся в проточной части после остановки двигателя и его охлаждения; • лопаток компрессоров при форсировании двигателя впрыском воды в компрессор для увеличения степени сжатия; • лопаток турбин при введении перед турбиной дополнительного топлива, охлаждающего лопатки и используемого затем в форсажной камере; • вентиляторов аппаратов на воздушной подушке, особенно при полете над поверхностью воды; • лопастей винтов вертолетов каплями дождя. Отложения солеи (накипь). При прохождении через двигатель природной воды содержащей различные соли, на рабочих и статорных лопатках компрессо ра, где температура воздуха достигает температуры испарения воды, а также на внутренних частях камеры сгорания и форсунках образуются отложения солей кальция и магния, выделяемых при испарении воды (накипь).
На входное устройство ГТД поступают два основных потока жидких частиц, вызывающих эрозионный износ рабочих лопаток входной ступени компрессо ра. Это поток капель дождя с радиусом г > 0, 3 мм и капли из облаков с модальным радиусом r м = 3. . . 7 мкм. При проведении испытаний двигателя с имитацией дождя необходимо знать следующие параметры: • общее количество воды, подаваемое в двигатель; • влажность воздуха в условиях имитируемого дождя; • размер дождевых капель. Размеры капель ливневого дождя принимаются не более 2 мм в соответствии с нормами летной годности. Спектр размеров дождевых капель для дождей различной интенсивности меняется от 0, 05 до 8 мм при изменении скорости их от 0, 07 до 12, 5 м/с. Скорость падения дождевых капель постоянна на всем пути и не зависит от размера капли. В двигатель впрыскивается дистиллированная вода или конденсат, поскольку накипь на деталях двигателя недопустима. Условия проведения испытаний с имитацией попадания воды на входе в двигатель приведены в табл. 9. 11. Эффективность внутридвигательных мероприятий подтверждается в процессе испытаний на специальных двигательных стендах.
Количество воды, подаваемое в двигатель Длительность подачи воды Скорость попадания Режимы работы двигателя Допустимое состояние двигателя после испытания Определяется из расчета содержания 5 г воды в каждом кубическом метре поступающего в двигатель воздуха (4 % воды в засасываемом воздухе) Непрерывно в течение не менее 3 -х минут на назначенном режиме Скорость засасывания воды не нормируется 1) взлетный; 2) полетный, малый газ; 3) любой другой, признанный необходимы м для проверки После попадания воды должно обеспечиваться функционирование двигателя без недопустимого ухудшения его эксплуатационных характеристик во всем диапазоне рабочих режимов 9. 11. Условия проведения испытаний двигателя с имитацией попадания воды (диаметр капель не более 2 мм)
9. 8. ИСПЫТАНИЯ СИСТЕМ ЗАЩИТЫ Испытания по обеспечению боевой живучести и пожарной безопасности ЛА и ГТД Боевая живучесть (БЖ) и пожаробезопасность летательных аппаратов (ЛА) оцениваются проведением специальных полигонных испытаний с обстрелом реальными средствами поражения ЛА в целом, элементов их конструкции, а также отдельных жизненно важных агрегатов и систем [61]. Отличительной особенностью этих экспериментов является то, что их проведение требует применения реального оружия различных типов, баллистических установок, подрывов ракет воздух-воздух и земля-воздух в условиях, максимально соответствующих летным (скорости полета ЛА, условиям обдува, нагрузки и т. д. ). В отдельных случаях требуется проведение прямого летного эксперимента. Эксперименты проводятся на специализированных полигонах, стендах и лабораторных установках. При этом решаются задачи по отработке: • уязвимости летательных аппаратов и их отдельных жизненно важных агрегатов; • стойкости бронематериалов и эффективности бронезащиты; • противопожарной зашиты ЛА, его силовой установки и других пожароорпасных отсеков; • взрывобезопасности топливных отсеков; • боевой живучести двигателей; • конструктивных мероприятий по повышению БЖ планера и основных жизненно важных агрегатов. Экспериментальная база, необходимая для отработки каждой из указанных выше задач, отличается определенной спецификой. Так, для отработки и испытаний брони требуются специальные испытательные комплексы, позволяющие вести стрельбу из различных видов оружия.
Эти комплексы оснащены аппаратурой и оборудованием, необходимыми для измерения скоростей поражающих элементов (пуль, снарядов, осколков и т. д. ) до и после пробития брони, а также для регистрации характера их движения на траектории. Фиксация процессов взаимодействия поражающих элементов с броней осуществляется с помощью высокоскоростной киносъемочной и рентгеноимпульсной аппаратуры. Существуют специальные баллистические установки, в том числе и так называемые легкогазовые (водородные и гелиевые) двухступенчатые системы, предназначенные для разгона поражающих элементов до скоростей порядка. . . 8 км/с. Достаточно сложные инженерные сооружения и оборудование используют также для проведения испытаний броневой защиты летательных аппаратов в целом. При этом для проведения исследований в широком диапазоне углов обстрела перемещают и разворачивают сам летательный аппарат. Исследование и отработку способов повышения БЖ авиационных ГТД проводят в основном на базе работающих двигателей, на специализированных стендах или на переоборудованных самолетах (вертолетах), жестко закрепленных на соответствующей платформе. При этом обеспечиваются дистанционный запуск, управление режимами работы двигателя, а также фиксация всех необходимых параметров и характеристик, определяющих работоспособность испытуемого ГТД. Достаточно сложным является оборудование для отработки БЖ планера ЛА, поскольку в реальных условиях полета он находится в сложном нагруженном состоянии под влиянием аэродинамических сил, изменяющихся в течение полета в широком диапазоне.
Проведение испытаний конструкции на БЖ требует регистрации большого объема информации о напряженном состоянии элементов конструкции, характере их деформации и разрушении. Для этого используются многопозиционные тензостанции, скоростная киносъемочная и рентгеноимпульсная аппара тура. Предварительная обработка получаемой информации осуществляется специализированными ЭВМ. Максимальное приближение к условиям полета при проведении экспериментальных исследований БЖ достигается с помощью так называемых ракетных треков, представляющих собой рельсовый путь, по которому движется специальная ракетная тележка с установленным на ней испытуемым объектом. Такой метод исследований обладает некоторыми преимуществами даже перед летным экспериментом, в частности, при решении ряда задач по отработке БЖ. Эксперимент на ракетном треке существенно дешевле летного. Кроме того, в таком эксперименте, как правило, получают значительно больший объем информации за счет использования практически неограниченного объема регистрирующей аппаратуры, а также возможности сохранения испытуемого объекта и проведения детального анализа конечных результатов эксперимента. Поэто му за рубежом ракетные треки распространены достаточно широко. В США, например, насчитываются десятки таких треков с длиной 5. . . 10 км и скоростью ракетных тележек до 500 и более м/с. На ракетных треках проводятся исследования БЖ элементов планера ЛА, стойкости бронезащиты и др. Основным недостатком моделирования условий полета на ракетных треках является то, что время проведения эксперимента ограничено длиной рельсового пути и при длине 10 км не может превышать 20. . . 30 с. Поэтому некоторые наиболее ответственные испытания проводят в условиях полета с использованием радиоуправляемых самолетов-мишеней, а также реальных ЛА.
Боевые повреждения авиационных ГТД Для боевых повреждений элементов конструкции ГТД характерны следующие особенности [48]: • большая хрупкость в изломах; • значительное упрочнение материала вблизи мест разрушения; • изменение величины твердости по направлению от края излома по экспоненциальному закону затухания ударной волны. При воздействии средств поражения на конструкцию ГТД возможны разные механизмы повреждения. 1. Множественное растрескивание. Такое разрушение характерно для материалов, обладающих более высокой прочностью при сжатии, чем при растяжении. 2. Выкрашивание. Этот вид повреждения внешне похож на множественное растрескивание и обусловлен развитием больших деформаций при локальной гетерогенности и анизотропии материала. 3. Общее разрушение — возникает в результате воздействия ударной волны, создающей напряжения, превышающие предел прочности материала. 4. Выбивание материала в зоне удара — возникает в результате соударения средства поражения с деталью. 5. Пробой с адиабатическим сдвигом — характеризуется выбиванием пробки и образованием узких, ярко выраженных сдвиговых полос. Работа пластической деформации практически полностью превращается в тепло. Локальное повышение температуры может достигать 100 °С. 6. Пробой с образованием лепестков на тыльной поверхности детали. Такое разрушение обусловлено действием высоких радиальных и окружных растягивающих напряжений после прохождения начальной ударной волны. Пробой с образованием лепестков сопровождается возникновением большого изгибающего момента и интенсивным пластическим деформированием.
Пример. Боевые повреждения ГТД, исходя изданных по конфликтам в Афганистане и Чечне, характеризуются, в основном, пробоинами размером 100. . . 1000 мм и 8. . . 10 мм от бронебойных осколков и пуль соответственно. При таких повреждениях в корпусных деталях двигателей образуются пробоины площадью 80. . . 260 мм 3. В табл. 9. 12 приведено распределение повреждений основных элементов конструк ции двигателя ТВЗ-117 от действия боевых средств поражения. Наибольшие боевые по вреждения ТВД отмечаются в периферийных зонах двигателя, в частности в районе компрессора, находящегося в основной зоне прицеливания, где расположена кабина экипажа. Пробитие наружных корпусов ТВД происходит в результате воздействия бронебойных пуль и осколков с последующим повреждением внутренних элементов конструкции двигателя: жаровых труб, рабочих и сопловых лопаток. Системы двигателя Распределение повреждений по типам вертолетов, % Ми-8 Ми-24 Пылезащитное устройство 25. . . 27 16. . . 18 Компрессор 15. . . 17 16. . . 18 Камера сгорания 3. . . 5 4. . . 6 Турбина 10. . . 12 1. . . 3 Выхлопная труба 6. . . 8 14. . . 16 Экранно-выхлопное устройство 28. . . 30 35. . . 37 Коробка приводов — 5. . . 7 Узлы крепления 6. . . 8 1. . . 39. 12. Распределение повреждений основных элементов конструкции двигателя ТВЗ-
Основные виды боевых повреждений маслосистемы следующие: пробоины масля ных радиаторов, баков, трубопроводов и шлангов маслосистемы от пуль и осколков. Для существующих в настоящее время конструкций ДА вероятность боевого повреждения ГТД определяется следующими величинами: компрессор — 0, 1. . . 0, 2; камера сгорания — 0, 1. . . 0, 2; турбина — 0. 05. . . 0, 15; коробка приводов — 0, 05; реактивное сопло — 0, 5. Испытания противопожарных систем Для отработки противопожарных систем ЛА и ГТД используются сложные испытательные комплексы, основной отличительной особенностью которых является то, что в их состав, как правило, включаются аэродинамические стен ды, обеспечивающие обдув испытуемых объектов воздухом для имитации усло вий полета (рис. 9. 41). При этом параметры стенда лабораторий NAFEC (National Aviation Facilities Experimental Center) позволяют проводить испыта ния на реальном ЛА. Например, на этом стенде проводились испытания пожароопасности самолета F-III[6|. Для исследования противопожарной защиты ЛА используются также ракет ные треки (рис. 9. 42). Типовая программа испытаний противопожарных систем и систем зашиты от взрыва топливных баков включает в себя: • гидравлические испытания, при которых измеряют, строят и проверяют эпюры давлений в системе; • испытания с «холодным» тушением пожара; • огневые испытания; • летные испытания; • испытания на живучесть.
В испытаниях с «холодным» тушением пожара самолет, вертолет или отсек с двигателем устанавливают в аэродинамическую трубу. При определенной скорости потока воздуха проверяют поле скоростей в расчетных сечениях. При включении противопожарной системы (без пожара) в различных точках экспериментального объема берут пробы на концентрацию газа. В этих испытаниях также уточняют параметры гидравлического расчета систем. Оценку эффективности и надежности противопожарных систем проводят на специальных огневых стендах, обеспечивающих в эксперименте условия, близ кие к натурным с сохранением реальных соотношений основных газодинамических параметров процессов воспламенения и горения. При отработке систем на огневом стенде контролируют оперативное время срабатывания и выключения систем сигнализации о пожаре, температуру, давление и расход воздуха в подкапотном пространстве, давление ингибитора в распылительном коллекторе, эффективность ингибиторов при тушении пожара и др. Применение огневых стендов позволяет основную часть испытаний систем зашиты от пожара и взрыва, а также испытаний на живучесть проводить в наземных условиях. Сложность проведения испытаний в естественных условиях полета заставляет уделять большое внимание анализу авиационных происшествий, связанных с пожаром и взрывом ЛА. Наиболее опасными воздействиями разрядов на планер самолета являются разряды в отъемную часть крыла в районе расположения топливных баков-кес сонов. Воспламенение топлива в баках может произойти вследствие: • сквозного прожига обшивки бака-кессона; • выделения энергии при разряде, достаточной для нагрева внутренней поверхности обшивки до температуры воспламенения паров топлива в баке; • искрения на внутренней поверхности обшивки бака-кессона из-за перенапряжения при разряде.
Рис. 9. 41. Схема испытательного комплекса, имитирующего обдув ЛА при исследовании его пожароопасности: 1 — аэродинамическая установка; 2 — испытываемый объект; 3 — отражатель потока воздуха; 4 — стационарные средства пожаро тушения; 5 — баллистическая установка; 6 — блиндаж для размещения аппаратуры и обслуживающего персонала (штрихпунктиром показаны линии управления и контроля) Рис. 9. 42. Оснащенная ракетная тележка с фюзеляжем ЛА для испытаний противопо жарной защиты (ускорители по бортам ЛА отстреливаются после разгона тележки)
Как правило, отказы авиационных ГТД связаны не с прямым попаданием разряда в двигатель, а с возмущениями, вызванными разрядом в воздушном потоке в зоне перед двигателем, то есть с воздействием ударной волны от разряда. Это приводит к срывным явлениям на лопатках компрессора и газодинамической неустойчивости работы двигателя (помпажу). При этом наблюдается падение частоты вращения ротора двигателя, увеличивается расход топлива, растет температура газа за турбиной, возникает повышенная вибрация двигателя. С целью обеспечения безопасности полетов проводятся теоретические оценки последствий удара молнии и экспериментальные проверки с помощью различных стендов — от испытаний на избирательность удара до испытаний ЛА в целом. Вся гражданская авиация проходит испытания на соответствие требованиям безопасности. РЕЗЮМЕ (по главе 9 «Специальные испытания авиационных ГТД» ) 1. Специспытания — это особый вид испытаний ГТД на всякого рода предель ные характеристики при оценке надежности двигателей. 2. При специспытании по определению запаса газодинамической устойчиво сти главным методическим вопросом является вопрос о том, как ввести двига тель в режим неустойчивой работы компрессора, т. е. режим, несвойственный двигателю при нормальной работе и опасный в смысле возможности выхода его из строя.
3. Для таких испытаний чаще всего используются сменные сотовые аппараты (СЛ) турбины (а у ТРДД также и F c. II )- Устанавливая на ГТД специальный СА турбины с проходным сечением, меньшим, чем расчетное, можно приблизить линию совместной работы на характеристике компрессора при каждом значении n пр к границе помпажа. В отдельных случаях с успехом применяют в качестве средства достижения границы срывных режимов впрыск воды в камеру сгорания. 4. Очевидно, что потеря газодинамической устойчивости ГТД при эксплуатации может происходить как за счет приближения линии рабочих режимов к границе устойчивости, так и за счет смещения самой границы устойчивости. Первый случай чаще всего возникает под влиянием внутри двигательных возмущений и, если нет поломок в проточной части двигателя, обычно бывает связан с нештатной работой регуляторов (G mкс G m фк PHA, F c , G отб и т. д. ). Второй случай возникает под воздействием внешних возмущений. 5. Изменение запаса устойчивости при возникновении неравномерности на входе в ГТД определяется индивидуальной чувствительностью данного компрессора к такой неравномерности и происходит вследствие: • смещения границы помпажа; • смещения напорных характеристик компрессора; • смещения ДРР. 6. Так критерий К у не учитывает разную чувствительность компрессоров и влияние возмущения, начиная с 70 -х годов, используют другой критерий газодинамической устойчивости — W, основанный на понятии предельных внешних возмущений в потоке на входе в ГТД при его эксплуатации на ГТД.
7. Шум — это беспорядочное сочетание звуков различной частоты и силы. Количественно шум можно характеризовать с физической и физиологической сторон. Звук как физическое явление представляет собой волновое механическое движение частиц упругой сферы с частотами колебаний 16. . . 20 000 Гц. 8. Главными источниками шума в ГТД являются: • аэродинамические шумы лопаточных машин и газовых потоков; • шум нерегулярного горения. 9. Уменьшить шум от лопаточных машин можно двумя путями: снижением шума в источнике и путем применения внешних шумоглушащих устройств. 10. В настоящее время для внешнего глушения шума вентилятора, компрессора и турбины внутренние поверхности воздухозаборника и входных каналов снабжаются звукопоглощающей (акустической) облицовкой. 11. Измерения шума производят специальными приборам и шумомерам и, которые определяют уровни звукового давления. 12. Результаты доводки акустических характеристик ГТД проверяются стендовыми испытаниями. Целью испытаний являются: • экспериментальное определение шума, 1 шучаемого ГТД при стендовых испытаниях; • подтверждение заявленных данных по шуму двигателя;
• оценка шума самолета с испытуемыми двигателями в контрольных точках (на основе матриц шума, полученных в дальнем звуковом поле); • оптимизация параметров и конструкции двигателя с целью снижения шума; • отработка средств снижения шума силовой установки; • определение акустических нагрузок на элементы конструкции двигателя и самолета. 13. Наряду с проверкой акустических мероприятий в составе одного двигателя необходимы акустические исследования его элементов. Они проводятся на специaльныx стендах — безэховых звукоизолированных камерах. 14. Серьезными источниками загрязнения атмосферы являются авиационные ГТД, установленных на эксплуатируемых ЛА, и ГТД, которые испытываются на экспериментальных стендах. 15. Помимо нормирования выбросов СО, NO х , СО 2 , особое внимание проявляется к так называемым «парниковым газам» СО 2 , СН 4 , NO х и др. 16. Характер выбросов наиболее вредных загрязнений СО и С n Н m при типичном взлетно-посадочном цикле имеет обратную тенденцию к выбросам NO x. 17. Индексы эмиссии загрязняющих веществ — EI определяются экспериментально по стандартным методикам. 18. Испытания по оценке характеристик и эффективности противообледенительных систем подразделяются на: • испытания на «сухом» воздухе; • испытания в условиях искусственного обледенения; • испытания в условиях естественного обледенения; • испытания по оценке влияния обледенения на характеристики ЛА и СУ.
19. Все современные авиационные ГТД проходят испытания на заброс на вход двигателя различных посторонних предметов (обтирочная ветошь, болты и гайки, птицы, песок и гравий, град и дождь). 20. Для проведения испытаний двигателя на попадание птиц стенд оборудуется устройствами для разгона тушек птиц: специальными салазками или пневматической пушкой. 21. Для проведения испытаний двигателя с имитацией дождя необходимо знать следующие параметры: общее количество воды, подаваемое в двигатель; влажность воздуха; размеры дождевых капель. 22. Для отработки противопожарных систем ЛА и ГТД используют испытательные комплексы, обеспечивающие обдув испытуемых объектов воздухом для имитации условий полета. ВОПРОСЫ 1. Каково назначение специальных испытаний ГТД? 2. Какие мероприятия используют при экспериментальном определении запаса устойчивости ГТД путем подъема линии рабочих режимов? 3. Как определяют запас устойчивости при создании предельных возмущений в потоке на входе в ГТД? 4. Как контролируют шум ГТД, установленного на летательном аппарате? 5. Чем характеризуется шум? 6. Какими средствами уменьшают шум ГТД? 7. Как проводят проверку эффективности мероприятий по снижению шума ГТД?
8. На каких принципах основаны способы определения запасов газодинамической устойчивости двигателя? 9. Какими способами реализуется на практике метод определения запасов устойчивости путем подъема линии рабочих режимов? 10. Какие вещества, образующиеся в двигателях при сжигании топлива, относятся к загрязняющим? 11. Что представляет собой взлетно-посадочный цикл ИКАО? 12. Как объяснить нормируемый параметр для газообразных загрязняющих веществ? 13. Какова качественная зависимость выброса загрязняющих веществ от тяги двигателя? Чем это обусловлено? 14. От каких параметров двигателя зависят допустимые значения нормируемых параметров для газообразных загрязняющих веществ, а также величина параметра выброса сажи? 15. На каких принципах основана работа газоанализаторов, предназначенных для измерения содержания различных загрязняющих веществ в выхлопных газах? 16. Почему не нормируются акустические характеристики двигателя? 17. Каким образом получают акустическую характеристику двигателя? 18. Можно ли по спектру шума диагностировать двигатель? 19. Какие способы уменьшения эмиссии ГТД вам известны? 20. Каким образом решается проблема снижения шума ГТД? 21. Возможно ли обледенение ГТД при положительной температуре окружающего воздуха?
22. Какие методы используются при проведении испытаний ГТД на обледенение? 23. Какие посторонние предметы, попадающие на вход двигателя, учитываются при испытаниях одно- и многодвигательного самолета? 24. Назовите основные причины преждевременного съема двигателей с эксплуатации из-за повреждения газовоздушного тракта. 25. Какие требования предъявляются к испытаниям на повреждаемость ГТД посторонними предметами и какие способы защиты от повреждений ГТД посторонними предметами существуют? 26. При каких условиях наиболее часто происходит столкновение птиц с ГТД? Какие виды повреждений ГТД при этом возможны? 27. Каким образом проводят испытания на стойкость ГТД к удару птиц? 28. Какие мероприятия способствуют предупреждению столкновения ГТД с Птицами? 29. Как влияет на рабочий процесс и прочность ГТД попадание воды? 30. В каких видах может попасть влага на вход в двигатель? 31. При каких условиях проводят испытания ГТД с имитацией попадания воды? 32. Какие задачи решаются при испытании ГТД на боевую живучесть и какая экспериментальная база при этом используется? 33. Каковы особенности боевых повреждений ГТД?
Глава 10 ИСПЫТАНИЯ И ДОВОДКА УЗЛОВ И АГРЕГАТОВ АВИАЦИОННЫХ ДВИГАТЕЛЕЙ И ЭНЕРГЕТИЧЕСКИХ УСТАНОВОК Эффективность авиационных газотурбинных двигателей, надежность их работы во многом обеспечивается соответствующими узлами и агрегатами. Проверка качества узлов и агрегатов в процессе разработки и доводки, оценка эксплуатационных показателей производятся, как в составе ГТД, так и на стендах и установках [20, 21, 25, 29, 41, 42]. Основными задачами при испытании узлов и агрегатов являются: • определение характеристик; • проверка, определение прочностных и эксплуатационных характеристик; • проверка эффективности конструктивных мероприятий, направленных на улучшение характеристик. Стенды для испытаний узлов и агрегатов можно разделить на следующие группы [25]: • для испытаний полноразмерных узлов (компрессоров, турбин, камер сгорания и др. ); • для испытаний моделей узлов и их элементов; • для доводки узлов и агрегатов на прочность и ресурс; • общего назначения, необходимые для исследования конструктивной прочности деталей, испытаний различных агрегатов двигателей, подшипников и др.
10. 1. ИСПЫТАНИЯ АВИАЦИОННЫХ ЛОПАТОЧНЫХ МАШИН Характеристики лопаточных машин определяют тремя методами 1321: • испытанием модельных лопаточных машин; • испытанием натурных компрессоров и турбин на специальных стендах; • испытанием лопаточных машин непосредственно на двигателе. Широко применяются исследования модельных лопаточных машин, так как они позволяют получать экспериментальные характеристики при существенно меньших финансовых расходах и требуют меньших мощностей на привод (или на поглощение). При соблюдении геометрического и кинематического подобия и выполнения подобия по числу М (в абсолютном и окружном движениях) и по числу Re можно получить подобие режимов работы модели и полноразмерной лопаточной машины в полном объеме. Гораздо чаше некоторые из этих условий не выполняются, и речь может идти о частичном моделировании. Получаемые при этом результаты требуют проверки в натурных условиях. Постоянство критериев подобия позволяет получить соотношения, связывающие параметры рабочего процесса полноразмерных Л М и модели. Для расходов рабочего тела G и потребных мощностей N привода (или тормозного устройства, можно записать |25|: (10. 1) (10. 2)
де т — масштаб моделирования; μ — коэффициент вязкости; R — газовая постоянная; Т — температура рабочего тела; «м» — индекс модели; «лм» — индекс толноразмерной лопаточной машины. Как следует из приведенных соотношений, при испытании уменьшенных моделей потребные значения G и N существенно снижаются, в особенности, если не накладывается условие сохранения постоянных значений числа Re , что возможно, если Re>Re Kp. 10. 2 ИСПЫТАНИЯ КОМПРЕССОРА (ВЕНТИЛЯТОРА) Требования, предъявляемые к силовым установкам (СУ) летательных аппаратов (ДА), постоянно возрастают. В частности, от СУ требуется устойчивая работа с достаточно высоким КПД в широком диапазоне расходов при значительных диапазонах изменений температуры, давления и скорости набегающего потока. Поскольку наиболее чувствительным элементом СУ к возмущающим воздействиям является компрессор, требуется его тщательное экспериментальное исследование. В гл. 2 (см. рис. 2. 1) приведена схема открытого стенда испытаний компрессора. На рис. 10. 1 показана схема установки замкнутого типа для испытаний компрессора, на рис. 10. 2 — схема стенда с эжектором для испытаний ступеней или малоступенчатых компрессоров.
Рис. 10. 1. Схема стенда, выполненного по замкнутому контуру с барокамерой для испы тания компрессоров: I — главный электродвигатель; 2 — мультипликатор; 3 — измеритель крутящего момента; 4 — выходной дроссель; 5 — испытываемый компрессор; 6 — барокамера; 7— входной дроссель; 8 — вакуумный насос; 9— теплообменник; 10 — турбохолодильник; 11 — компрессор, загружающий холодильную турбину
Рис. 10. 2. Схема стенда с эжектором для испытаний ступеней или малоступенчатых компрессоров: / — входной дроссель: 2 — ресивер; 3 — испытуемый компрессор; 4 — мультипликатор: 5— приводной электродвигатель; 6 — эжектор; 7 — подача сжатого воздуха
В целях обеспечения испытаний и исследований компрессора (вентилятора) гтд создается объект испытания, включающий корпус, ротор, опоры, системы. Основной целью данных доводочных испытаний является определение значений параметров. Испытания проводятся на автономном стенде, т. е. не в составе двигателя. Препарирование компрессора (вентилятора) должно позволять производить измерения средних величин полного давле ния и температуры заторможенного потока не только в сечениях перед и за компрессором, но и в нескольких промежуточных сечениях проточной части. Промежуточные сечения выбираются так, чтобы между ними или между крайними из них и сечениями перед и за компрессором располагались от двух до четырех ступеней. Это необходимо для определения характеристик групп ступеней (по степени повышения давления и КПД) и согласования режимов их работы. Приемники приборов для измерения параметров потока на различных радиусах в промежуточных сечениях проточной части желательно располагать в плоскости или на передней кромке лопаток направляющего аппарата. Для этой цели могут быть использованы специально сконструированные приемники, которые устанавливаются на место демонтируемых лопаток направляющего аппарата. В отдельных случаях компрессор может быть препарирован приемниками давления в потоке у корпуса за всеми лопаточными венцами или, в крайнем случае, только за направляющими аппаратами. По этим данным оцениваются характеристики ступеней и согласование их режимов работы. Следует учитывать, что величина радиальных и осевых зазоров в ступенях компрессо ра, предназначенного для испытаний, должны соответствовать значениям, задаваемым конструкторской документацией.
Параметры потока в промежуточных сечениях и давления у корпуса за лопаточными венцами должны быть измерены не менее чем на 3— 4 -х частотах вращения, охватывающих весь рабочий диапазон частот. На каждой частоте вращения эти измерения проводятся не менее чем в 4— 5 -ти точках, равномерно расположенных на характеристике от границы устойчивости до максимального расхода или минимальной степени повышения давления. На основе полученной при испытаниях информации с помощью методики и системы автоматизированной системы определения параметров компрессора или аналогичной методике, используемой разработчиком, оцениваются уровень КПД и резервы его повышения, возможности повышения запасов устойчивости компрессора за счет улучшения согласования интегральных характеристик ступеней, а также определяются минимально необходимые коррекции элементов проточной части для реализации этих резервов. Кроме того, эта же информация используется для разработки мероприятий по улучшению обтекания лопаток на различных радиусах. В случае использования в компрессоре ступеней с параметрами, выходящими за рамки апробированных значений (с повышенным напором, окружной скоростью и т. п. ), необходимо проведение предварительно автономной отработки таких ступеней (или их моделей) до выполнения окончательного проекта компрессора. При доводке нерегулируемых компрессоров рекомендуется использование технологических поворотных НА и окон (клапанов) перепуска за отдельными ступенями с целью отработки оптимального согласования ступеней. При автономных испытаниях компрессоров обычно используют ряд специальных устройств: • поворотная турель на выходе для измерения полей параметров на выходе из компрессора; • координатные устройства для измерений параметров потока по радиусу в ступенях; • регулируемые дроссели для изменения положения линии рабочих режимов за счет управляемого поджатия компрессора на выходе;
• токосъемники для обеспечения передачи измерительного сигнала с вращающихся элементов при тензометрировании и термометрировании. Для построения характеристики компрессора необходимо также измерить расход воздуха, определить степень повышения давления лк, частоту вращения и мощность, затрачиваемую на привод компрессора. Эксперимент начинают с минимальной для данного компрессора частоты вращения. Поддерживая ее постоянной, дросселем на выходе из компрессора последовательно устанавливают ряд режимов, начиная с наименьшего значения степени повышения давления. На каждой напорной ветке (n пр = const) снимают не менее 5. . . 6 точек, увеличивая степень повышения давления, пока не будет достигнута граница устойчивой работы. Снятые характеристики компрессора в составе двигателя определенным образом отличаются от автономного испытания. Для этого используют ряд методов: • дросселирование воздуха на выходе из компрессора и изменение проходного сечения входного устройства; • изменение площади проходных сечений СА турбины и выходного устройства; • впрыск воды или подача сжатого воздуха на вход в камеру сгорания; • кратковременный заброс топлива в камеру сгорания.
Работа компрессора может при этом определяться по измеренным значени ям температур (10. 3) а мощность (10. 4) 10. 3 ИСПЫТАНИЯ ОСНОВНОЙ КАМЕРЫ СГОРАНИЯ Доводке камеры сгорания уделяют большое внимание. Испытания основной камеры сгорания (КС) проводят либо на специальных автономных стендах, либо в составе газогенератора или двигателя. Допускается часть автономных испытаний основных КС проводить на отсеках. На отсеке могут быть получены предварительные данные о форме радиальной и окружной неравномерностей в выходном сечении камеры. Схема стенда для испытаний отсеков камер сгорания представлена на рис. 10. 3 [25). Воздух от компрессорной станции подается по трубопроводу 1 в ресивер 2, а затем к диффузору камеры 3. В выхлопной магистрали устанавливается охлаждаемый водой дроссель 5, который имитирует сопловой аппарат турбины и необходим для поддержания заданного режима по расходу и давлению газа в КС. Такие стенды могут оснащаться специальным оборудованием (подогреватели или охладители воздуха и др. ), предназначенным для обеспечения испытаний при повышенных и пониженных значениях р* к и Т* к. Так как процессы в КС очень сложны, то для оптимизации элементов рабочего процесса можно проводить испытания модели камеры сгорания. При испытаниях КС измеряют расходы воздуха и топлива, давление и температуру воздуха на входе.
Рис. 10. 3. Схема установки для испытаний отсеков камер сгорания: 1 – подводящий воздухопровод; 2 — ресивер; 3 — испытуемый отсек; 4 — мерный участок; 5 — выходной дроссель
заторможенного потока в выходном сечении, температуры стенок камеры сгорания. Отбирают пробы газа в выходном сечении для определения коэффициента полноты сгорания ( τ г ) и содержания загрязняющих веществ. По результатам измерений определяют: • величину коэффициента восстановления давления заторможенного потока σ кс в зависимости от эксплуатационных значений λ к и α кс (приведенной скорости и коэффициента избытка воздуха); • зависимость α кс при срыве пламени на «бедной» границе зоны устойчивого горения а α mах от λ к и Т* к соответствующих малому газу и режимам сброса газа; • область устойчивого горения и воспламенения топлива на режимах запуска двигателя в координатах α кс — λ к при эксплуатационных значениях параметров воздуха и топлива на входе в КС и поддержании соответствующих условий для системы зажигания. Проводимые при доводке камеры сгорания исследования направлены также на определение: • зависимости полноты сгорания от температуры воздуха на входе в КС и других параметров, необходимых для разработки методики оценки температуры газа при последующих испытаниях двигателя; • зависимости величины максимальной температуры секции системы охлаждения стенок жаровой трубы Т w * mах и неравномерности температур Т w * mах — Т w * min от α кс и λ к на режимах с максимальным эксплуатационным значением Т w * mах и соответствующему или близкому к максимальному значению р* к. Испытания камер сгорания в составе двигателя проводят в стендовых условиях на этапе доводки двигателя и при этом определяются следующие основные характеристики: • надежность воспламенения топлива и запуска двигателя во всех условиях, заданных ТЗ на двигатель и возможностями стенда;
• ресурс КС и ее тепловое состояние, в том числе и при нестационарных режимах работы двигателя; • характеристики неравномерности поля температур перед сопловым аппаратом турбины, рекомендуется проверка влияния на поле температур наработки двигателя; • отсутствие виброгорения; • уровень дымления на основных эксплуатационных режимах; • повторно проверяются величины максимальной температуры секций системы охлаждения стенок жаровой трубы Т w * mах — Т w * min на режимах с максимальным эксплуатационным значением Т’ max и р* к mах. Испытания КС в составе двигателя проводятся по программам климатических испытаний, в ТБК и летных испытаний, включая режимы высотного запуска на летающей лаборатории. Специальные испытания камеры сгорания в составе двигателя проводятся в соответствии с перечнем испытаний для предъявления двигателя на государственные испытания и выполняются по разработанным и утвержденным программам, методикам. Испытания КС обязательно проводят на основном, резервном и альтернативном топливе.
10. 4. ИСПЫТАНИЯ ФОРСАЖНОЙ КАМЕРЫ Процесс испытаний и доводки ФК, как правило, ведется на полноразмерном двигателе. При испытаниях ФК снимаются те же характеристики, что и у основных КС. Так как ФК работает при более высоких температурах, к тепловой защите элементов конструкции предъявляются более жесткие требования и, соответственно, доводка этих элементов более сложная. В ФК часто наблюдается вибрационное горение, которое за очень короткое время приводит к усталостным поломкам элементов конструкции. Вибрационное горение подавляется применением в конструкции ФК антивибрационного экрана с гофрами и отверстиями. Особенность испытательного стенда для испытания двигателя с форсажной камерой состоит в наличии охлаждения конструкций выхлопной системы стенда. 10. 5. ИСПЫТАНИЯ ТУРБИНЫ Развитие высокотемпературных ГТД с охлаждаемыми турбинами базируется на решении комплекса проблем, среди которых главные: • выбор и конструктивное решение схемы охлаждения лопаток соплового аппарата и рабочих колес турбины; • выбор и конструктивное решение системы охлаждения; • выполнение теплового и гидравлического расчетов охлаждения турбины; • прочностной расчет элементов турбины; • разработка технологии изготовления турбины. В гл. 2 (см. рис. 2. 2) приведена схема стенда для испытаний турбин в натурных условиях. На рис. 10. 4 и 10. 5 показаны схемы установок для испытаний турбины и их элементов.
В процессе доводки двигателя должны быть обеспечены значения газодинамической эффективности всех элементов турбины (сопловых и рабочих решеток уплотнений и т. п. ), а также узла в целом на всех расчетных режимах, и обеспечено расчетное тепловое состояние всех горячих элементов на стационарных и переходных режимах. Обеспечение газодинамической эффективности элементов турбины и узла в целом обеспечивается выполнением требований к двигателю по нормативно технической документации, а также следующими дополнительными мероприятиями: расчетным анализом газодинамической эффективности элементов турбины и узла в целом по методикам ЦИАМ или методикам разработчика двигателя, а также экспериментальной отработкой элементов на стадии предварительного проектирования, продувкой решеток на пакетных и модельных установках с обязательным исследованием модификаций, принятых к реализации на турбине двигателя, на всех эксплуатационных режимах; экспериментальной проверкой не менее чем на двух экземплярах газогенератора (ГГ) основных параметров турбины с замером статических давлений по венцам на внутреннем и наружном радиусах, полей полных давлений и температуры газа в контрольных сечениях на специальном тормозном стенде; проверкой основных параметров турбин при специальных стендовых испытаниях с измерениями перепадов давлений газа по венцам и температурных полей проводят не менее чем на двух экземплярах двигателей. Препарирование производится по специальным ТУ с обязательным измерением радиальных зазоров на основных режимах. Достаточность доводочных работ по газодинамическому совершенству турбин определяется подтверждением расчетных значений КПД узла на основных режимах работы не менее, чем на двух экземплярах двигателя. Совпадение значения увязочного значения КПД с расчетным должно быть в пределах ± 0, 5 %.
Принятое в расчете на прочность тепловое состояние горячих элементов турбины обеспечивается соблюдением требований нормативно-технической документации, а также следующими дополнительными мероприятиями: • отрабатывается тепловое состояние охлаждаемых венцов на пакетной установке в газовом потоке; • измеряется температура охлаждаемых лопаток на пакетной установке не менее чем на трех радиусах по высоте и не менее четырех точек по профилям с обязательным термометрированием входных и выходных кромок; термометрируются не менее двух пакетов каждого венца, отклонения расчетного значения безразмерной величины охлаждения (10. 5) должны находиться в пределах ± 0, 03, а измеренные значения температуры во всех точках измерения не должны отличаться более чем на ± 10 К. При этих экспериментах также отрабатывается величина допуска на внутреннее сопротивление в системе охлаждения лопаток в пределах ± 10 % и на величину давления охлаждающего воздуха перед РЛ турбины высокого давления; Проводятся стендовые испытания газогенератора, в ходе которых отрабатывается температурное поле газа на входе и выходе из турбины. Доведенность поля проверяется совпадением его с принятым в расчете на прочность элементов и узлов турбины и стабильностью поддержания поля Т* по режимам не менее чем на двух экземплярах ГГ. Для оценки влияния подмешивания воздуха в сопловых аппаратах 1 и 2 ступеней на температурное поле газа на ГГ измеряются температуры на входе в РЛ 1 и 2 ступеней не менее чем в четырех сечениях по высоте лопаток.
Одновременно измеряется температура охлаждающего рабочие лопасти воздуха подошвой лопаток и температуры тела лопаток. По полученным температурам вычисляется эффективность охлаждения РЛ. На основании результатов измерения расходов, давлений и температур охлаждающего воздуха при стендовых испытаниях ГГ доводят систему ох лаждения и тракт отбора охлаждающего воздуха. Система охлаждения считается доведенной, если подтверждаются измерениями на двух ГГ расчетные параметры охлаждающего воздуха на входе в сопловые и рабочие ло патки всех охлаждаемых венцов (в пределах ± 5 % от измеряемой величи ны). При стендовых испытаниях на двигателях и ГГ измеряются радиальные зазоры. Система регулирования зазоров считается доведенной, если на основных стационарных режимах работы двигателя обеспечивается поддержание расчетного значения зазоров в пределах ± 15 %. Оцениваются утечки охлаждающего воздуха в уплотнениях по результатам измерения давления в соответствующих полостях, они не должны отличаться от расчетных в турбинах двигателя в пределах ± 10 % (после выработки ресурса до +50 % от расчетных). Рис. 10. 4. Схема стенда, работающего на просос для испытания турбин [25]: 1 — подогреватель воздуха; 2 — испытываемая турбина; 3 — регулирующая заслонка; 4 — гидротормоз
Рис. 10. 5. Схема стенда для испытаний натурных турбин, работающих на просос от эксгаустера: / — вакуумный насос; 2 — испытываемая турбина; 3 — редуктор; 4 — гидротормоз; 5 — водовоздушный теплообменник; 6 — эксгаустер; 7 — ГТД привода эксгаустера: 8 — шахта выхлопа, 9 — смеситель Доведенность теплового состояния элементов подтверждается совпадением не менее чем на двух ГГ расчетных и замеренных температур в сходных точках и режимах в пределах ± 15 К. Экспериментально подтверждается надежность работы системы охлажде ния измерениями температур, давлений и расходов охлаждающего воздуха в контрольных сечениях, подтверждаются основные параметры охлаждающего воздуха (совпадение с математической моделью двигателя в начале ресурса ± 10 % по параметрам). После выработки ресурса допускается увеличение утечки охлаждающего воздуха до +50 % по сравнению с расходом в начале ресурса. Увеличение температуры деталей ротора и статора после выработки ресурса в сходных точках прорабатывается и просчитывается особо с точки зрения допустимости в сравнении с расчетными запасами. Во время дово дочных испытаний на установившихся и переходных режимах, наиболее напряженных в тепловом отношении, производится термометрирование основных роторных и статорных деталей и, в обязательном порядке, сопловых и рабочих лопаток.
Измерения температур рабочих лопаток желательно выполнять с помощью средств и методов, обеспечивающих максимально возможную точность и достоверность не менее чем на трех радиусах. Достаточностью доводочных работ является совпадение замеренных на двух двигателях температур лопаток с принятыми в расчетах на прочность с точностью допуска от +5 К до -20 К (на установившихся режимах), а также определением максимального значения температур после разборки лопаток методом металлографического анализа. При этом значения температур не должны отличаться от расчетных, более чем на ± 15 К. 10. 6. ИСПЫТАНИЯ ГАЗОГЕНЕРАТОРОВ (ГГ) Экспериментальная оценка характеристик каскада высокого давления (газогенератора), включающего КВД, КС и ТВД, часто проводится отдельно от испытаний двигателя в целом. Это связано с тем, что, используя один и тот же ГГ и меняя КНД, можно получить семейство двигателей с широким диапазоном по тяге. Автономные испытания ГГ проводятся со стендовым лемнискатным входным устройством при имеющихся атмосферных условиях. Оценку параметров ГГ проводят аналогично оценке параметров двигателя. При автономных испытаниях ГГ необходимо учитывать следующие факторы, основными из которых являются: • физические газодинамические параметры ГГ (частота вращения, расход воздуха, температуры и давления) отличаются от тех, которые имеют место в целом двигателе, так как в целом двигателе на входе в КВД (на выходе из КНД) имеют место более высокие температура и давление; • температурное состояние деталей ГГ также будет отличаться от целого Двигателя по той же причине;
• для получения реальных приведенных характеристик ГГ в составе двигателя необходимо перед КВД (на входе в ГГ) сымитировать поля давлений, которые имеют место в целом двигателе. Для оценки температуры газа перед турбиной, которую, как правило, невозможно измерить из-за ее высокого значения, обычно используются параметры дроссельной характеристики, снятые на стенде. Для расчета этой температуры используются следующие исходные параметры: • давление и температура окружающей среды; • приведенный расход топлива; • степень повышения давления в КНД и КВД; • зависимость КПД КНД от частоты вращения КНД; • зависимость КПД КВД от частоты вращения КВД; • площадь минимального проходного сечения соплового аппарата ТВД и ряд других. Расчет температуры газа перед ТВД проводится методом последовательных приближений и является достаточно сложным. Для более быстрой оценки температуры газа с достаточной для эксперимента точностью В. П. Добродеев предложил применить более простую формулу, которая получается из уравнения теплового баланса в КС и имеет вид: где Т к * — температура воздуха на выходе из компрессора ВД; G m — расход топлива; р к * — давление воздуха за компрессором ВД; к — коэффициент. Значения коэффициента к для различных частот вращения определяются из термогазодинамического расчета двигателя на линии рабочих режимов по обратной формуле
После чего строится зависимость коэффициента к от частоты вращения ротора и определяется зависимость вида По измеренным в процессе эксперимента параметрам (частоте вращения, температуре и давлению за компрессором, расходу топлива) подсчитывается величина температуры газа перед турбиной ВД. Данная формула дает хороший результат при работе двигателя в области, близкой к линии рабочих режимов. Для оценки параметров двухконтурного двигателя при ограниченной его препарации с достаточной для инженерных расчетов точностью можно исполь зовать уравнение Я. Т. Ильичева для баланса тепла в КС Данное уравнение дает возможность провести расчет газодинамических па раметров двигателя, не зная параметров узлов ГГ, принимая весь ГГ за «черный ящик» . При этом за температуру Т к * принимается температура за КНД, а за тем пературу Т г * — температура перед ТНД. При наличии отборов воздуха из ГГ необходимо их учесть. Дополнительно необходимо использовать номограммы оп ределения среднего значения теплоемкости с р ср в зависимости от Т г * и Т к *. Ис пользуя вышеприведенное уравнение при наличии замеров температур на входе и на выходе ГГ и расхода топлива, можно определить расход воздуха через него (q m = G m /G в ). При наличии температуры на входе в ГГ и расходов воздуха и топлива можно определить температуру на выходе из ГГ и т. д.
10. 7. ИСПЫТАНИЯ СИСТЕМ АВТОМАТИЧЕСКОГО УПРАВЛЕНИЯ Испытания системы автоматического управления двигателя ЛА проводятся с целью отработки качества функционирования, надежности и ресурса, а также определения соответствия параметров системы требованиям НТД и нормам технического уровня. Система автоматического управления — покупная система, и потому перед началом эксплуатации обязательно должны проводиться приемочные испытания. Доводка систем автоматического управления осуществляется при доводочных испытаниях на лабораторных стендах разработчика, на специальных стендах полунатурного моделирования разработчика (изготовителя) двигателя, на специальных стендах совместно с двигателем, на летающих лабораториях и на натурных ЛА. Аттестация систем автоматического управления осуществляется с помощью специальных испытаний с имитацией высотно-скоростных условий эксплуатации и других внешних воздействий. Испытания проводятся в специальных термобарокамерах, климатических камерах и т. п. При комплексной наземной отработке систем автоматического управления и агрегатов по согласованным методикам проверяются: • статические и динамические характеристики агрегатов САУ на соответствие заданным в ТЗ; • качество работы систем автоматического управления в составе замкнутой системы (при имитации характеристик двигателя на математических моделях) на установившихся и переходных режимах с имитацией воздействий максимально приближенных к эксплуатационных задаваемым в ТЗ; • назначенный ресурс агрегатов систем автоматического управления; • безотказность систем автоматического управления и агрегатов и соответствие показателей безотказности требованиям отраслевых стандартов, устанавливающим нормы безотказности. При комплексной летной отработке систем автоматического управления и агрегатов по согласованным
методикам проверяются: • характеристики и качество работы систем автоматического управления при запуске двигателя, а также на переходных и установившихся режимах при изменении скоростей и высот полета ЛА в эксплуатационном диапазоне; • точность работы систем автоматического управления на установившихся и переходных режимах работы двигателя при изменении скоростей и высот полета в эксплуатационном диапазоне летательного аппарата; • качество работы и безотказность систем автоматического ограничения параметров двигателя; • качество работы и безотказность основных и резервных каналов управления системами автоматического управления; • уровень механических виброперегрузок и частот этих перегрузок в местах крепления агрегатов систем автоматического управления при изменении режимов работы двигателя, а также высот и скоростей полета ЛА в эксплуатационном диапазоне; • уровни температур и акустических шумов в местах установки агрегатов систем автоматического управления; • управляемость двигателя и ЛА на всех эксплуатационных режимах при предельно возможных значениях температур и давлений атмосферы, определяемых по условиям эксплуатации ЛА. 10. 8. ИСПЫТАНИЯ РЕДУКТОРОВ Испытания зубчатых передач редукторов на выносливость могут осуществляться на установках разомкнутого и замкнутого типов [49]. В состав установки разомкнутого типа входит источник мощности, который вращает редуктор и передает через него полную мощность на тормозное устройство. В процессе передачи мощности создаются необходимые окружные усилия и скорости на зубьях шестерен. Эти
установки требуют для привода больших мощностей. Кроме того, величина механического КПД редуктора, определенная по разности подведенной и поглощенной мощностей, содержит большие погрешности вследствие того, что указанные мощности мало отличаются друг от друга. В установках замкнутого типа создание требуемых окружных усилий в зубчатых передачах осуществляется специальным загрузочным устройством. Для того чтобы реализовать работу загрузочного устройства, схема испытуемого ре дуктора, состоящего из набора шестерен z 1 , z 2 , z 3 , и z 4 дополняется стендовой передачей из своего набора шестерен z’ 1 , z’ 2 , z’ 3 , и z’ 4 так, чтобы z‘ 1 = z 1 , z’ 2 = z 2 , z’ 3 = z 3 , z’ 4 = z 4. В результате создается замкнутый силовой контур. При создании предварительной закрутки валов относительно друга и в таком поло жении соединении их через загрузочное устройство (муфту) во всех шестернях появляются окружные усилия, величина которых будет зависеть от закрутки ва лов. Если замкнутую систему подвергнуть вращению, то, подбирая закрутку ва лов и частоту вращения, можно получить условия работы шестерен, которые они имеют при эксплуатации. Требуемая на вращение редуктора мощность в установке замкнутого типа равна Где N прив — мощность привода; N — мощность, передаваемая шестернями ре дуктора; η м — суммарный механический КПД всей замкнутой системы. Муфты загрузки просты и надежны в эксплуатации, но требуют остановки и затрат времени на демонтаж при переходе от одной величины нагружения к другой, что не позволяет осуществлять изменение крутящего момента во время работы. Кроме того, в них невозможно исключить влияние пусков и остановов, происходящих под нагрузкой, на характер износа и другие эксплуатационные свойства передач. Поэтому в установках замкнутого типа применяют такие нагружатели, которые позволяют в процессе испытания изменять передаваемую шестернями мощность.
При наличии в редукторе ГТД двух соосных валов в установке применяют две замкнутые передачи с двумя загрузочными устройствами, позволяющими независимо менять мощность в каждой замкнутой системе. На подобных установках проводят научно-исследовательские, а также заводские испытания редукторов (предъявительские, приемосдаточные и длительные). Перед испытанием редуктор оснащается измерительной аппаратурой, позволяющей определять: передаваемую мощность, частоту вращения, вибрации, температуру корпуса, температуру входящего и выходящего масла, его прокачку и загрязненность (последнее с помощью магнитных пробок, сигнали заторов стружки и т. д. ). На редуктор устанавливают все двигательные и самолетные агрегаты, размещение которых предусмотрено конструкцией двигателя. Агрегаты в процессе испытания загружаются, чтобы создать эксплуатационные усилия в приводах. Редуктор проходит обкатку и проверку работы на всех режимах: от одного и, если предусмотрено конструктивной схемой, от двух двига телей; в условиях авторотации, когда мощность передается от винтов к двигателю (крутящий момент меняет знак); проверяются работоспособность муфт обгона, уровень виброперегрузок, температуры корпуса и подшипников; регулируются давление и прокачка масла.
10. 9. ИСПЫТАНИЯ СТАРТЕРОВ В отличие от двигателя основной режим работы стартера — неустановившийся как по температурному состоянию, так и по нагрузке и частоте вращения. Поэтому установка для испытания стартеров должна обеспечивать переменную нагрузку в процессе разгона и мгновенное определение крутящего момента и частоты вращения [49]. Стартер крепится на неподвижном станке и соединяется валом с загрузочным устройством, которое при разгоне создает сопротивление, такое же, как двигатель при запуске. Измерение крутящего момента осуществляется специальным измерителем крутящего момента. Во время эксперимента измеряют: частоту вращения и крутящий момент; давление топлива перед форсунками; заброс температуры газов за турбиной; расход топлива; время работы турбостартера и пусковой панели; время выбега ротора турбостартера; частоту вращения, на которой происходит отключение турбостартера; атмосферные условия. Стартеры проходят кратковременные и длительные заводские испытания. Каждое испытание начинается с «ложного» запуска, с помощью которого производится расконсервация. Затем несколько рабочих запусков для проверки и отладки основных параметров. Общее количество запусков за время испытаний не входит в ресурс и поэтому не должно превышать установленного количества. Ресурс стартера определяется количеством запусков. Перед длительными испытаниями снимается нагрузочная характеристика — зависимость крутяще го момента от частоты вращения. Длительные испытания проводятся циклами по четыре — пять запусков с кратковременными перерывами (3. . . 5 мин) меж ду запусками и продолжительными между циклами (для более глубокого охлаждения).
Одним из важных испытаний в процессе доводочных работ является проверка гарантийных свойств турбостартера при различных наружных температурах. Эти испытания в условиях высокогорных аэродромов проводятся в ТБК. У электростартеров в дополнение к нагрузочной характеристике определяют величину начального вращающего момента (при неподвижном роторе) при номинальном и пониженном напряжениях, гидравлическое сопротивление тракта охлаждающего воздуха; проводят испытания на перегрузку, чтобы потребляемый ток в полтора и два раза превышал номинальное значение в течение 10. . . 60 с на определенной частоте вращения с заданным напором охлаждающего воздуха. У пороховых стартеров проверяют надежность сбрасывания давления газов перед турбиной на частотах отключения, так как горение пороховой шашки прекратить до полного сгорания невозможно и частота вращения турбины может недопустимо увеличиться.
10. ИСПЫТАНИЯ НАСОСОВ И ФОРСУНОК При испытании насосов снимают расходные характеристики (зависимости объемной производительности от частоты вращения при постоянных температуре топлива и его давлении на входе и выходе) и кавитационные характеристики (зависимости объемной производительности от давления на входе при постоянных: частоте вращения, давлении на выходе и температуре топлива на входе), а также проверяют герметичность. В состав универсальной установки для испытания насосов входит бак, из которого топливо забирается насосом подкачки и направляется к подогревателю или холодильнику [49]. Температура топлива регулируется соответственно расходом хладагента или пара, а также перепуском топлива. Давление топлива на входе в испытуемый насос и на выходе из насоса регулируется кранами. В схеме такой установки должен быть предусмотрен концевой холодильник, который позволял бы поддерживать в баке нормальную температуру топлива, для того чтобы не происходило изменения фракционного состава топлива во время эксперимента, и уменьшалась пожарная опасность установки. Испытуемый насос закрывается теплоизолирующим кожухом, под который можно подавать холодный или горячий воздух, создавая тем самым необходимый внешний температурный режим. Испытания форсунок проводят для определения расходной характеристики. Угла распыливания, дисперсности распыливания и окружной неравномерности распиливания топлива при различных его давлениях [49]. Указанные характе ристики форсунки могут быть получены на специальной установке, в которой топливо из бака забирается насосом подкачки и направляется в расходомер. Необходимое для испытания давление топлива создается насосом высокого давления и регулируется на каждом канале форсунки кранами, если в схеме топливоподачи двигателя не предусмотрено специальное устройство.
Угол распыливания измеряется визуально по транспортиру. При снятии расходной характеристики форсунки для разных давлений на входе в нее измеряют расход по расходомеру. Определение окружной неравномерности распыливания производится с помощью секторной камеры. До измерения топливо, улавливаемое секторами камеры, через качающиеся патрубки стекает в малый поддон и оттуда на слив. На время измерения качающиеся патрубки направляются механизмом перекладки в воронки, через которые топливо из каждого сектора сливается в свою мерную колбу. По окончании измерения с помощью механизма перекладки вновь поворачивают качающиеся патрубки так, чтобы направить топливо на слив в малый поддон. После определения количества топлива в каждой мерной колбе их переворачивают механизмом опрокидывания и сливают топливо в большой поддон. По результатам опыта строят окружные расходные диаграммы (расход через каждый сектор в процентах от общего расхода) и определяют максимальную неравномерность (обычно лимитированную техническими условиями). Для определения равномерности расхода топлива через форсунки форсажных коллекторов коллекторы укрепляют на аналогичной установке и организу ют улавливание топлива в мерные колбы от каждой форсунки.
10. 11. ИСПЫТАНИЯ ТОПЛИВОРЕГУЛИРУЮЩЕЙ АППАРАТУРЫ Для испытания топливорегулирующей аппаратуры и связанной с ней автоматики находят применение стенды с обратной связью, в которых реальная топливорегулирующая аппаратура подключается к моделирующей установке, имитирующей динамические свойства двигателя [49]. Структурная схема стенда с обратной связью включает в себя блок (модель ГТД), в котором на промышленной электронной моделирующей установке набраны дифференциальные уравнения, описывающие динамические процессы ГТД в натуральном масштабе времени при стандартных атмосферных условиях. В следующем блоке (имитаторе условий полета) вырабатываются поправки к решению дифференциальных уравнений в соответствии с заданными условиями испытания — высотой и скоростью полета. Напряжение U п , выработанное в результате решения дифференциальных уравнений с учетом поправок на высоту и скорость полета, поступает в специальное устройство стендового силового привода, задающего частоту вращения силовому приводу. Силовой стендовый приводит во вращение испытуемый топливорегулирующий агрегат и выполненный с ним заодно топливный насос. Топливо, подаваемое насосом, истекает из коллектора форсунок (или эквивалентных им жиклеров) в сливной бак, в котором создается соответствующее полетным условиям противодавление. Сигнал об истинной частоте вращения топливорегулирующего агрегата — напряжение U п , вырабатываемое первичным преобразователем, являющимся частью прибора, измеряющего частоту вращения, — поступает на вход в установку, где сравнивается с сигналом, задающим частоту вращения. Сигнал о давлении (расходе) топлива — напряжение U m , вырабатываемое первичным преобразователем, являющимся частью прибора, измеряющего давление (расход) топлива, — поступает в первый блок (модель ГТД), где в соответствии
со статической характеристикой, заложенной в нее, вырабатывается сигнал о необходимой частоте вращения топливорегулирующего агрегата. В установившемся режиме сигналы на требуемые величины расхода топлива и частоты вращения соответствуют действительным. При приложении управляющего возмущения сектором газа или другим способом (например, через блок имитации условий полета) соответствие нарушается и под воздействием управляющих сигналов возникает переходный процесс в работе топливного агрегата, который протекает так же, как у реального ГТД. В конструкции испытуемого агрегата могут быть устройства, управляющие системами регулирования сопла, направляющими аппаратами компрессора и др. В этом случае топливорегулирующий агрегат соединяется системами с исполнительными механизмами, сигналы о положении которых U F , U α и т. д. направляются в блок (модель ГТД). Модель ГТД вырабатывает также сигналы, соответствующие работе сигнализаторов ограничителей по π* к , р* к , Т г *, π* т и других. С помощью этих сигналов осуществляется дополнительное воздействие на работу испытуемого агрегата. Поскольку между механическими процессами, проходящими в топливорегулирующей аппаратуре, и работой электронно-моделирующего блока должна быть непрерывная связь, требуются специальные устройства, преобразующие температуру, давление, угловые и линейные перемещения, а также другие параметры в электрические сигналы и наоборот. Устройства эти должны быть быстродействующими и обладать минимальными статическими и динамическими погрешностями.
Для большинства параметров можно подобрать стандартные преобразователи, применяемые в приборостроении и испытательных установках. Трудности возникают обычно в создании силового стендового следящего привода, преобразующего маломощный управляющий сигнал в значительную мощность вращательного движения (до нескольких сот киловатт), так как у современных ГТД аппаратура регулирования выполняется в одном узле с аппаратурой топливопитания. Бесступенчатый привод может быть создан на базе механических, гидравлических или электрических машин. В последнем случае постоянная времени привода получается наименьшей и характеристики топливорегулирующей аппаратуры, снятые на стенде, мало отличаются от характеристик, снятых на двигателе. Главным достоинством стендов с обратной связью является то, что они позволяют проводить работы по доводке топливорегулирующей аппаратуры до изготовления опытного образца двигателя, так как статические и динамические характеристики ГТД могут быть получены с достаточной точностью расчетом. Кроме того, на подобных стендах возможны выявление дефектов в работе топливорегулирующей аппаратуры и отладка каждого экземпляра по типовой (осредненной) характеристике двигателя, набранной в блоке (модель ГТД), что уменьшает объем регулировок при сдаточных и контрольных испытаниях серийных ГТД.
РЕЗЮМЕ (по главе 10 «Испытания и доводка узлов и агрегатов авиационных двигателей и энергетических установок» ) 1. Основными задачами при испытании узлов и агрегатов являются: определение характеристик; проверка, определение прочностных и эксплуатационных характеристик; проверка эффективности конструктивных мероприятий, направленных на улучшение характеристик. 2. Стенды для испытаний узлов и агрегатов можно разделить на следующие группы: стенды для испытаний полноразмерных узлов (компрессоров, турбин, камер сгорания и др. ); стенды для испытаний моделей узлов и их элементов; стенды для доводки узлов и агрегатов на прочность и ресурс; стенды для исследования конструктивной прочности деталей, испытаний различных агрегатов двигателей, подшипников и др. 3. Характеристики лопаточных машин определяют тремя методами: испытанием модельных лопаточных машин; испытанием натурных компрессоров и турбин на специальных стендах; испытанием лопаточных машин непосредственно на двигателе. 4. Основной целью доводочных испытаний компрессора является определение значений параметров. Испытания проводятся на автономном стенде, т. е. не в составе двигателя. Приемники приборов для измерения параметров потока на различных радиусах в промежуточных сечениях проточной части желательно располагать в носкости или на передней кромке лопаток направляющего аппарата.
5. При автономных испытаниях компрессоров обычно используется ряд специальных устройств: поворотная турель на выходе для измерения полей параметров на выходе из компрессора; координатные устройства для измерений параметров потока по радиусу в ступенях; регулируемые дроссели для изменения положения линии рабочих режимов за счет управляемого поджатия компрессора на выходе; токосъемники для обеспечения передачи измерительного сигнала с вращающихся элементов при тензометрировании и термометрировании. На каждой напорной ветке (n пр = const) снимают не менее 5. . . 6 точек, увеличивая степень повышения давления, пока не будет достигнута граница устойчивой работы. 6. Испытания основной камеры сгорания (КС) проводят либо на специальных автономных стендах, либо в составе газогенератора или двигателя. Допускается часть автономных испытаний основных КС проводить на отсеках. При испытаниях КС измеряют расходы воздуха и топлива, давление и температуру воздуха на входе, статическое давление и поле температур и давлений заторможенного потока в выходном сечении, температуры стенок камеры сгорания. Отбирают пробы газа в выходном сечении для определения коэффициента полноты сгорания (г\г) и содержания загрязняющих веществ. 7. Испытания камер сгорания в составе двигателя проводят в стендовых условиях на этапе доводки двигателя и при этом определяются следующие основные характеристики: надежность воспламенения топлива и запуска двигателя; ресурс КС и ее тепловое состояние; характеристики неравномерности поля температур перед сопловым аппаратом турбины; отсутствие виброгорения; уровень дымления.
8. Испытания системы автоматического управления двигателя ДА проводятся с целью отработки качества функционирования, надежности и ресурса, а также определения соответствия параметров системы требованиям НТД и нормам технического уровня. Доводка систем автоматического управления осуществляется при доводочных испытаниях на лабораторных стендах разработчика, на специальных стендах полунатурного моделирования разработчика (изготовителя) двигателя, на специальных стендах совместно с двигателем, на летающих лабораториях и на натурных Л А. 9. Испытания зубчатых передач редукторов на выносливость могут осуществляться на установках разомкнутого и замкнутого типов. При наличии в редукторе ГТД двух соосных валов в установке применяют две замкнутые передачи с двумя загрузочными устройствами, позволяющими независимо менять мощность в каждой замкнутой системе. 10. В отличие от двигателя основной режим работы стартера — неустановившийся как по температурному состоянию, так и по нагрузке и частоте вращения. Поэтому установка для испытания стартеров должна обеспечивать переменную нагрузку в процессе разгона и мгновенное определение крутящего момента и частоты вращения. 11. При испытании насосов снимают расходные характеристики (зависимости объемной производительности от частоты вращения при постоянных температуре топлива и его давлении на входе и выходе) и кавитационные характеристики (зависимости объемной производительности от давления на входе при постоянных: частоте вращения, давлении на выходе и температуре топлива на входе), а также проверяют герметичность.
12. Испытания форсунок проводят для определения расходной характеристики, угла распыливания, дисперсности распыления и окружной неравномерности распыления топлива при различных его давлениях. 13. Для испытания топливорегулирующей аппаратуры и связанной с ней автоматики находят применение стенды с обратной связью, в которых приемная топливорегулирующая аппаратура подключается к моделирующей установке, имитирующей динамические свойства двигателя.
ВОПРОСЫ 1. Назовите цели и задачи испытаний узлов двигателя. 2. В чем состоит смысл, цели и задачи поузловой доводки ГТД? 3. Назовите основные параметры, измеряемые и определяемые при испытаниях основных узлов ГТД. 4. В чем состоят особенности оснащения стенда для испытаний основных узлов ГТД? 5. Как осуществляется изменение режима работы компрессора? 6. Чем отличаются автономные испытания от испытаний в составе ГГ или двигателя? 7. Назовите особенности испытаний форсажных камер. 8. Назовите основные особенности схем стендов для испытаний турбин. 9. Как проводят испытания газогенераторов (ГГ)? 10. Чем отличаются установки разомкнутого типа и замкнутого типа для испытаний редукторов? 11. Каковы особенности испытаний стартеров? 12. Как снимается характеристика форсунок? 13. Как компонуется установка для испытаний топливорегулируюшей аппаратуры?
Глава 11 СЕРТИФИКАЦИОННЫЕ ИСПЫТАНИЯ ГТД Сертификация — это подтверждение соответствия продукции установленным требованиям. Под требованиями, которые предъявляются к авиационным двигателям на разных стадиях их создания, понимают [7, 33, 40, 54, 58): • научно-технический уровень при проведении исследований для создания научно-технического задела; • степень выполнения проектной задачи предполагаемым ЛА при разработке технического предложения (ТП); • параметры и ограничения технического предложения при разработке технического задания (ТЗ); • основные технические данные (ОТД), набор расчетных характеристик, степень унификации и стандартизации, ограничения технического задания при разработке эскизного и технического проекта; • соответствие эксплуатационным характеристикам, первоначальный типовой ресурс, уровень технологической сборки, уровень используемого оборудования и инструмента, методы контроля, результаты наработки на стенде при доводочных и длительных чистовых испытаниях; • соответствие двигателя по основным требованиям параметрам техническому заданию и современному научно-техническому уровню, соответствие требованиям НЛГ, конструктивное и эксплуатационное совершенство, контролепригодность, ремонтопригодность, обоснованность первоначального ресурса и возможности его увеличения, при государственных испытаниях; • соответствие требованиям качества сборки, приработка деталей, приводов, агрегатов и систем, соответствие установленным характеристикам и параметрам, сохранение качества деталей при кратковременных испытаниях серийных двигателей;
• соответствие установленному ресурсу при ресурсных (комиссионных) испытаниях серийных двигателей; • качество совершенствования технологии производства серийных двигателей при технологических испытаниях; • продление ресурса эксплуатируемых двигателей при эксплуатационных испытаниях. Если степень выполнения первых трех пунктов этого далеко не полного перечня подтверждается в основном результатами теоретических и расчетных исследований (за небольшим исключением), то все последующие требуют для подтверждения выполнения требований различных испытаний. Основные требования, предъявляемые к авиационным двигателям, ориентированы на обеспечение безопасности полетов и сведены в авиационные правила.
Авиационные правила (АП) — принятый государством свод процедур, правил, норм и стандартов, выполнение которых признается ими в качестве обязательного условия обеспечения безопасности полетов и охраны окружающей среды от воздействия авиации. Нормы летной годности (НЛГ) — часть авиационных правил, которая содержит требования к конструкции, параметрам и летным качествам воздушных судов и их компонентов, направленных на обеспечение безопасности полетов. Нормы летной годности для авиационных двигателей изложены в авиационных правилах АП-33 [2], а процедуры сертификации — в АП-21 [1]. Для объединенной Европы — в CS-E, IR-21 и для США — в FAR-33, FAR-21 соответственно. АП-33 «Нормы летной годности двигателей воздушных судов» устанавливают требования летной годности для выдачи Сертификата Типа двигателя и дополнений к нему на маршевые газотурбинные и поршневые двигатели транспортных и легких дозвуковых самолетов, транспортных и легких вертолетов и очень легких воздушных судов гражданского назначения. АП-21 «Процедуры сертификации авиационной техники» устанавливают обязательный для выполнения предприятиями, организациями и другими юридическими и физическими лицами порядок сертификации и контроля за соответствием гражданских воздушных судов, двигателей и их компонентов действующим Авиационным правилам. На двигатели не гражданского назначения требования АП-33, FAR-33, CS-E не распространяются. Для них существует другая нормативно правовая база, например, MIL 5007. Требования норм летной годности должны приниматься во внимание уже с начальных этапов создания авиационных двигателей гражданского назначения. Так как для их удовлетворения при проектировании должно быть не только предусмотрены конструктивно-технологические мероприятия, но и правильно выбраны расчетные режимы. Так, например, наличие в авиационных правилах понятий максимально
допустимых температуры газа и частоты вращения делает необходимым проектирование двигателя с запасом по этим параметрам в связи с тем, что от этих значений будут отсчитываться потребные запасы в программе проведения испытаний. Другим примером может служить ужесточение требований по удержанию ло патки вентилятора в случае обрыва, которые ведут к усилению внимания к прочности корпуса. Подписанное странами СНГ в 1991 г. «Соглашение о гражданской авиации и использовании воздушного пространства» возложило его реализацию на Межгосударственный авиационный комитет (МАК). Компетентный орган этого комитета — Авиационный регистр МАК — осуществляет деятельность в области летной годности и процедур сертификации летательных аппаратов, их компонентов, производства авиационной техники, охраны окружающей среды от воздействия авиации и выдает соответствующие сертификаты, свидетельства, другие документы, а также осуществляет сертификацию организаций, разращивающих авиационную технику и аккредитацию организаций (центров), исполняющих сертификационные работы.
11. 1. СИСТЕМА ОБЕСПЕЧЕНИЯ И ПОДДЕРЖАНИЯ ЛЕТНОЙ ГОДНОСТИ Разнообразие условий применения авиационных двигателей, предельный уровень нагрузок, которые они испытывают, существенно усложняют решение задачи обеспечения высоких показателей их безопасности и надежности. Процесс проектирования авиационных ГТД в настоящее время характеризует целая система критериев, норм прочности и процедур, гарантирующая выполнение требований безопасности при соблюдении установленных условий эксплуатации. Под безопасностью при этом понимают состояние объекта авиационной техники, при котором отсутствует недопустимый риск, связанный с причинением вреда жизни или здоровью людей, окружающей среде. Поддержание летной годности решается посредством взаимоувязанных видов контроля. Система контроля технического облика двигателя и контроля исполнения требований и указаний авиационных властей, которые отслеживают все изменения типовой конструкции двигателя и его компонентов на всех стадиях жизненного цикла. Система контроля исполнения требований авиационных органов осуществляется на основе директив МАК и Государственной службы Гражданской авиации (ГСГА). Система контроля выполнения требований эксплуатационно-технической документации основывается на отслеживании изменений состава и содержания эксплуатационно-технической документации (ЭТД), эксплуатационных бюллетеней с учетом типовой конструкции двигателя. Контроль всех изменений типовой конструкции двигателя и за реализацией требований ЭТД, в том числе и эксплуатационных ограничений, ресурса, срока службы агрегатов проводится по индивидуальному номеру двигателя. Системы контроля уровня надежности и безопасности полетов в части авиационных двигателей на всех этапах жизненного цикла, которые определяют соответствие показателей уровня надежности и безопасности требуемому уровню. Эти системы оценивают их изменения в динамике, выявляют наличие неблагоприятных тенденций и при необходимости определяют перечень возможных корректирующих
мероприятий. Система должна учитывать все возможные нарушения функционирования авиационных двигателей и его компонентов и описывать последствия этих нарушений с позиции безопасности и регулярно сти полетов. Система поддержания летной годности серийных авиационных двигателей, которая базируется на непрерывном анализе надежности парка двигателей в эксплуатации и внедрении мероприятий, направленных на повышение безопасно сти полетов, на применении методов раннего диагностирования, на проведении дополнительной сертификации при введении главных изменений в конструкцию серийного двигателя или при его ремонте. Такие изменения проводят для улучшения технико-экономических показателей. Результатами этих изменений могут быть снижение массы двигателя, его стоимости, повышение надежности, снижение эксплуатационных затрат, изменение поставщиков комплектующих изделий, изменение технологии изготовления и решение других проблем. Под главными изменениями понимают такое изменение типовой конструкции объекта авиационной техники, которое существенно влияет на его летную годность. В свою очередь, модификация — это любое главное или второстепенное изменение типовой конструкции, касающееся его летной годности или затрагивающее его технико-экономические, экологические и другие характеристики.
11. 2. РАЗВИТИЕ ТРЕБОВАНИЙ НОРМ ЛЕТНОЙ ГОДНОСТИ. ЗАКОНОДАТЕЛЬНАЯ БАЗА СИСТЕМЫ СЕРТИФИКАЦИИ АВИАЦИОННЫХ ДВИГАТЕЛЕЙ Эволюция норм летной годности приведена на рис. 11. 1. В период с 1960 по 1980 годы были разработаны и введены в действие следующие нормы летной годности самолетов (НЛГС), в которые включены требования и к авиационным двигателям: НЛГС, НЛГС-1, НЛГС-2 (глава 6 относится к двигателям), ВНЛГСС и т. д. . Требования главы 6 по отношению к летной годности двигателей, сформулированные в НЛГС-2 и ВНЛГСС, полностью соответствовали стандартам ICAO и находились на уровне наиболее авторитетных вариантов зарубежных норм летной годности. На основе этих норм проводилась сертификация двигателей и самолетов 3 -го поколения (рис. 11. 2). Опыт разработки и практического применения норм летной годности был использован для их совершенствования в 80 -е годы, когда были выпущены НЛГС, ЕНЛГС (главы 6, 9, 10), НЛГ вертолетов (главы 6 и 9 для двигателей вертолетов).
Рис. 11. 1 Эволюция норм летной годности авиационных двигателей: ICAO— Международная организация гражданской авиации; ВНЛГСС — временные НЛГ для двигателей сверхзвуковой скорости; НЛГВ — НЛГ вертолетов; FAR-33 — Федеральные авиационные правила США; CS-E— Единые Европейские авиационные правила
Рис. 11. 2. Самолеты и двигатели 3 -го поколения, сертифицированные по НЛГС-
НЛГС-3 использованы, в частности, при отборе конкурсного маршевого двигателя ПС-90 А для пассажирских самолетов большой и средней дальности полета на этапе эскизного проекта, который впоследствии впервые в отечественной практике (1992 г. ) получил сертификат типа для использования на самолетах Ту-204 и Ил-96. По нормам НЛГС-3 наряду с отечественными двигателями ПС-90 А, Д-18 Т, ТВ 7 -117 С (рис. 11. 3) в России были сертифицированы многие иностранные двигатели, в том числе модификации двигателей CF 6 -80 C 2 фирмы Дженерал Электрик, RB-2 IIфирмы Роллс-ройс, PW 2000 и PW 4000 фирмы Пратт-Уитни и др. Недостатком данных норм являлось то (табл. 11. 1), что требования к летной годности маршевых и вспомогательных двигателей, воздушных винтов являлись разделами НЛГ самолета, а не самостоятельными правилами, отсутствовали НЛГ легких самолетов и вертолетов. Свободными от этого недостатка являлись Федеральные авиационные правила США (FAR-33), которые были положены в основу российских авиационных правил АП-33 (1994 г. ). В редакции 2004 г. частично учтены и требования Единых Европейских авиационных правил (CS-E).
Рис. 11. 3. Самолеты и двигатели 4 -го поколения, сертифицированные по НЛГС-
ЗАРУБЕЖНАЯ ПРАКТИКА ОТЕЧЕСТВЕННАЯ ПРАКТИКА Учет опыта фирмы, прототипов, анализа. Сертификационные проверки по схеме: «расчет —> лабораторные испытания —> испытания на двигателе» . Проведение сертификации примерно за 2 года на 6. . . 8 двигателях. Больший объем испытаний двигателей. Более жесткая регламентация Более жесткие требования: • по анализу последствий отказов ( «дерево* отказов); • по сертификации предельно допустимых в эксплуатации значениях параметров (redline). Обеспечение локализации разрушений (должна локализоваться вся профильная часть лопатки вентилятора, ротора, агрегатов и в некоторых случаях ротора вспомогательной силовой установки). Более жесткие требования по проверке отсутствия: — автоколебаний (с запасами); недопустимой раскрутки турбин при обрыве валов. Сертификация при Т г *= Т* max (без запаса)11. 1. Сопоставление отечественного (НЛГС — 3) и зарубежных подходов к обеспечению безопасности, надежности и ресурса авиационных двигателей
Полный назначенный ресурс основных деталей определяется по одобренной регистром методологии фирмы на базе концепции безопасной долговечности (ЭЦИ деталей, расчет МКЭ + банк по МЦУ) и (при необходимости) концепции допускаемых повреж дений (расчет МКЭ + банк данных по трещиностойкости). Может быть утвержден план управления ресурсами основных де талей. Ресурс двигателя в целом не ограничивается. Проводятся ЭЦИ двигателя за 1000. . . 2000 циклов (для принципи ально новых двигателей или при раннем подтверждении требова ний ETOPS объем ЭЦИ может быть увеличен). Начальный назначенный ресурс основных деталей устанав ливается на основании эквивалентно-циклических испыта ний (ЭЦИ) деталей. Ресурсы двигателя устанавливаются на основании ЭЦИ двигателя Отсутствие чрезвычайного режима — Примечание: ЭЦИ — эквивалентно-циклические испытания; МКЭ — метод конечных элементов; МЦУ- малоцикловая усталость.
В последних изданиях АП-21, АП-33 обобщен накопленный опыт и сделан большой шаг на пути гармонизации отечественных и зарубежных требований (целью повышения конкурентоспособности отечественных двигателей на мировом рынке: • введена сертификация типа маршевых и вспомогательных газотурбинных и поршневых двигателей до установки на летательный аппарат; • расширена и уточнена номенклатура отказов с опасными последствиями и требования по их предотвращению; • ужесточены условия проведения длительных испытаний; • предусмотрено использование различных стратегий управления ресурсами двигателей; • сформулированы требования по сертификации производства и ремонта двигателей и сохранению их летной годности в эксплуатации. Законодательная база сертификации авиационных двигателей основана на законах РФ «О стандартизации» и «О сертификации продукции и услуг» ; воздушном кодексе РФ и постановлении Правительства РФ № 360 «О федеральных правилах использования воздушного пространства и федеральных авиационных правилах» , которое устанавливает порядок подготовки, введения в действие и изменений федеральных авиационных Правил РФ, и в том числе авиационных правил. Воздушный Кодекс Российской Федерации, обеспечивающий государственное регулирование использования воздушного пространства и деятельности в области авиации, безопасности полетов, авиационной и экологической безопасности, устанавливает: • обязательную сертификацию и аттестацию в гражданской авиации, в том числе разработчиков и изготовителей авиационной техники и, в частности, авиационных двигателей; обязательный статус требований к летной годности (ст. 35) авиационных двигателей и общий порядок сертификации (ст. 37) гражданских воздушных судов, авиадвигателей и воздушных винтов в соответствии
с федеральными авиационными правилами и схему взаимодействия уполномоченного органа по сертификации, разработчика, изготовителя и эксплуатирующей организации в процессе сертификации. 11. 3. ОСНОВНЫЕ ЭТАПЫ СЕРТИФИКАЦИИ АВИАЦИОННЫХ ДВИГАТЕЛЕЙ Применительно к вновь создаваемым авиационным двигателям в соответствии с АП-21 предписывается последовательность сертификации, приведенная на рис. 11. 4. При этом выполняются следующие основные этапы. 1. Подача разработчиком заявки в Авиарегистр на получение Сертификата типа, к которой прилагается план-проспект комплекса требований к летной годности и охране окружающей среды, распространяемых на данный образец двигателя (сертификационный базис), и спецификация сертифицируемого двигателя. Заявка на получение сертификата типа включает: • спецификацию образца, которая содержит краткое техническое описание двигателя и описание его основных узлов, принципиальные схемы систем, основные характеристики, а также ожидаемые условия эксплуатации и ограничения, в диапазоне которых будет сертифицирован образец, спецификацию комплектующих изделий, список основных деталей; • план-проспект сертификационного базиса образца. 2. Реализация этапа макета двигателя и его компонентов (этап разработчика). Этап макета включает оформление положения по этапу макета, рассмотрения проекта таблицы соответствия требованиям сертификационного базиса, проекта плана испытаний, определение организаций, участие которых необходимо в процессе сертификации. На этапе макета оговариваются также специальные требования к двигателю (стратегия установления ресурса, правила эксплуатации и т. п. ). В заключении этапа макета Авиарегистром утверждается сертификационный базис.
Рис. 11. 4. Последовательность сертификации авиационных двигателей 3. Сертификационные заводские испытания (СЗИ) двигателя (этап разработчика). Целью сертификационных заводских испытаний являются: доведение конструкции двигателя, его характеристик и эксплуатационной документации до соответствия требованиям сертификационного образца и установления такого соответствия; установление типовой конструкции двигателя и определение условий предъявления двигателя на сертификационные контрольные испытания. Программа СЗИ, включая лабораторные, стендовые, наземные, летные и специальные испытания, разрабатывается и утверждайся заявителем по согласованию с независимой инспекцией, сертификационными центрами и организациями, участвующими в испытаниях. Сертификационные заводские испытания проводятся разработчиком. Для сокращения объема последующих контрольных испытаний разработчик проводит специальные и ресурсные испытания совместно с сертификационным центром. По результатам СЗИ оформляется акт, обобщающий результаты всех сертификационных работ и специальных испытаний. К нему прилагаются:
акты по ресурсным, 150 -часовым и специальным испытаниям; • заключение сертификационного центра по прочности авиационного двигателя; • оценка сертификационным центром выполнения программы сертификационных заводских испытаний и предложения по составу и объему проверок для включения в программу сертификационных контрольных испытаний; • эксплуатационная документация; • таблицы соответствия двигателя требованиям его сертификационного базиса; • уведомление разработчика, согласованное с независимой инспекцией о том, что комплекты рабочей конструкторской документации двигателя, прошедшего СЗИ, откорректированы по результатам испытаний и отражают типовую конструкцию. Успешное проведение в полном объеме заводских сертификационных испытаний и отсутствие необходимости в дополнительных проверках создает предпосылки для отказа от сертификационных контрольных испытаний. 4. Сертификационные контрольные испытания (СКИ) двигателя (этап Авиарегистра). Такие испытания проводятся под руководством специальной комиссии, сформированной Авиарегистром, обеспечиваются разработчиком и проводятся на его производственной базе. Цели СКИ: • контрольная проверка и подтверждение соответствия авиационного двигателя требованиям сертификационного базиса; • окончательное уточнение (при необходимости) и утверждение типовой конструкции двигателя. После утверждения Авиарегистром актов СКИ разработчик двигателя направляет в Авиарегистр представление, согласованное с независимой инспекцией, на получение сертификата типа двигателя. К представлению прилагаются:
• таблица соответствия двигателя требованиям сертификационного базиса, уточненная по результатам СКИ; • комплект эксплуатационной документации по двигателю, уточненный по результатам СКИ и согласованный с Сертификационным центром; • уведомление разработчика и изготовителя, согласованное с соответствующими независимыми инспекциями, о том, что контрольные и текущие комплекты рабочей конструкторской документации откорректированы по результатам сертификационных работ, отражают типовую конструкцию двигателя, пригодны для серийного производства авиационного двигателя данного типа, утверждены в установленном порядке и хранятся у разработчика и изготовителя. 5. Анализ результатов сертификации, принятие решения о выдаче Авиарегистром Сертификата типа на образец двигателя. В процессе сертификации наряду с Авиарегистром и разработчиком принимают участие центры сертификации и независимая инспекция. Функции независимой инспекции для двигателей государственной, гражданской и экспериментальной авиации в РФ осуществляет соответствующие военные представительства Министерства обороны РФ. Большое значение имеет поддержание летной годности сертифицированных авиационных двигателей в эксплуатации и при ремонте. Для сохранения достигнутого при сертификации типа уровня летной годности предусмотрено проведение дополнительной сертификации главных изменений (увеличение ресурса двигателя, модификации двигателя, его систем автоматического управления и др. ) по рассмотренной выше схеме. При этом совершенствуется и документация по поддержанию летной годности.
Комплектующие изделия сертифицируются отдельно от двигателя и лета тельного аппарата. При этом они делятся на две категории: А и В. Изделия категории А — это изделия, нарушение работоспособности которых существенно влияет на летную годность. Изделия категории В — это изделия, не относящиеся к категории А , включая стандартные детали. Объем квалификационных испытаний для обеих категорий практически одинаков и определяется авиационными правилами и действующей норматив ной документацией. 11. 4. ОСОБЕННОСТИ СЕРТИФИКАЦИИ АВИАЦИОННЫХ ДВИГАТЕЛЕЙ Процесс сертификации весьма дорогой и требует, кроме того, большого объема испытаний (табл. 11. 2). Наименование параметра Значение Наработка двигателя, ч (6. . . 7) ∙ 10 3 Наработка основных деталей, циклов 20 ∙ 10 3 Количество специальных испытаний 40 Количество испытываемых двигателей 9. . . 10 Длительность летных испытаний, ч 200. . . 250 Общая календарная длительность сертификации, лет 1, 5. . . 2, 011. 2. Основные данные процесса сертификации
Сертификация отечественных двигателей — это многоступенчатый процесс рассмотрения доказательной документации, что и является основной причиной удлинения процедуры. При подготовке доказательной документации возникает проблема субъективной трактовки тех или иных положений авиационных правил (АП-21, АП-33). Это в свою очередь требует разработки, дополнения и регулярного пересмотра циркуляров по каждому из пунктов АП-33. Система зарубежной сертификации менее подвержена этим недостаткам, г. к. авиационные власти в большей степени доверяют разработчикам авиационных двигателей, экспертиза доказательной документации специализированной институтами не проводится. Единственным способом ускорения сроков сертификации является обеспечение зачетности сертификационных испытаний с первого раза, что достигается высокой степенью доведенности двигателя с использованием большого объема инженерных испытаний, увеличением количества двигателей, предназначенных для целей сертификации и более широким использованием поузловых сертификационных испытаний. Инженерные испытания не являются сертификационными, но их результаты могут быть использованы при оформлении сертификационных отчетов. Особенностью сертификационных испытаний авиационных двигателей является использование консервативного подхода, который основывается на том, что высокую степень уверенности в безопасности и надежности конструкции можно обеспечить за счет приложения заведомо больших нагрузок, чем те, которые использовались при проектировании. Например, использование при испытании диска турбины с допуском, приводящим к увеличению массы выше его критического сечения, а ниже — к ее снижению и имеющего минимальные свойства материала (З σ для кривой малоцикловой усталости). При успешном прохождении испытания отсутствуют трещины и недопустимые деформации.
Роторные детали, при разрушении которых не обеспечивается локализация обломков внутри корпуса двигателя, относятся к группе А и называются основными (критическими). Прочие детали двигателя относятся к категории В. Материалы, из которых изготавливаются основные (критические) детали, должны быть сертифицированы. Особенности основных видов сертификационных испытаний. Требования к ним изложены в соответствующих параграфах АП-33. Пожарная защита (§ 33. 17). Назначение этих испытаний — гарантировать, что конструкция, материалы и применяемые технологические методы сведут к минимуму вероятность возникновения, последствия и распространение пожара. Элементы конструкции двигателя, рассматриваемые в качестве противопожарных перегородок, выполненные из алюминиевых сплавов, должны подвергаться испытаниям на огнепроницаемость. Испытания должны быть проведены на взлетном режиме длительностью 5 минут, когда деталь подвержена максимальному давлению, и на режиме авто ротации (10 мин), для которого условия теплообмена наихудшие. Испытания можно проводить на пластинах 320 x 320 мм, толщина которых равна минимальной толщине соответствующих противопожарных перегородок двигателя. Испытания проводятся на установке, обеспечивающей имитацию воздушного потока двигателя по внутренней поверхности испытываемого компонента. При испытании измеряют время, температуру пламени, тепловой поток, скорость, давление и расход воздуха. Пламя не должно прожечь алюминиевые пластины, и не должно быть утечек воздуха из испытательной камеры.
Прочность (§ 33. 19). В соответствии с данным пунктом двигатель должен быть спроектирован и сконструирован таким образом, чтоб свести к минимуму развитие опасных состояний двигателя в период между ремонтами. Должны быть испытаны на статическую и динамическую прочность силовой корпус камеры сгорания, а также проведены испытания на удержание осколков агрегатов, имеющих роторы с высокой кинетической энергией. Умы крепления двигателя и прилегающие к ним элементы конструкции (§ 33. 25). Для данных элементов конструкции двигателя должны быть оценены расчетами и экспериментально подтверждены максимальные и предельные эксплуатационные нагрузки, а также циклическая долговечность. Роторы турбин, компрессоров, вентиляторов и турбонагнетателей. (§ 33. 27). В соответствии с требованиями данного параграфа должно быть продемонстрировано, что: • роторы обладают достаточным запасом прочности в условиях возмож ного выхода двигателя за область заявленных эксплуатационных параметров или из-за отказов, результатом которых может быть превышение частоты вращения; • отсутствуют деформации, отклонения геометрии или повреждения, которые могут привести к отказам с опасными последствиями. Для определения соответствия этим требованиям осуществляют: • расчетное определение величины запасов статической прочности; • экспериментальную проверку ротора и его элементов на длительную прочность.
Расчет напряженно-деформированного состояния производится для наиболее тяжелых режимов по температуре дисков, определенных с использовани ем идентифицированных ЗD-моделей теплового состояния, либо экспериментально. Для многоступенчатых компрессоров и турбин допускается проверка отдельных дисков наиболее напряженных ступеней. При испытании отдельных роторов могут быть использованы специальные разгонные стенды, обеспечивающие раскрутку до максимальной частоты вращения и создающие необходимый температурный уровень. Результаты испытаний роторов на статическую и длительную прочность признаются удовлетворительными, если проведенные после испытаний обмеры основных деталей и проверки их удлинения, изменение структуры и механических свойств материалов не выявили заметных признаков начинающегося разрушения (например, трещины сверх нормируемых размеров) или критических деформаций, которые могут вызвать отказы двигателей с опасными последствиями. Присоединение агрегатов (§ 33. 25). В соответствии с данным пунктом двигатель должен работать нормально с загруженными приводами и узлами присоединения агрегатов, которые должны иметь «слабые звенья» . В процессе сертификации необходимо испытаниями продемонстрировать, что слабые звенья за щищают двигатель от перегрузок при отказе агрегатов. Помпажные и срывные характеристики (§ 33. 65). В процессе данных испытаний расчетно-экспериментальными исследованиями должны быть подтверждены потребные запасы по газодинамической устойчивости, проведены работы по проверке устойчивости процесса горения (отсутствия полного срыва пламени, вибрационного горения).
Испытаниями необходимо показать, что неоднородность воздушного потока на входе в двигатель или неравномерность поля температур воздуха на входе не вызывают помпаж или срыв, которые могут привести к срыву пламени, разрушению конструкции, превышению температуры или нарушению воз можности восстановить тягу или мощность в любой точке эксплуатационных режимов. Система отбора воздуха (§ 33. 66). Для соответствия данному пункту необхо димо продемонстрировать, что отбор воздуха на самолетные нужды и противообледенительную защиту не оказывает неблагоприятного влияния на двигатель, за исключением снижения мощности или тяги. Испытаниями необходимо также показать, что максимально возможное загрязнение воздуха, отбираемого от компрессора в систему кондиционирования, вредными примесями двигательного происхождения при нормальных условиях, не превысит предельно допустимых концентраций. Топливная система, система управления, элементы управления (§ 33. 67). В процессе испытаний необходимо продемонстрировать нормальную работу двигателя в диапазоне низких и высоких температур, указанных в ТЗ, подтвердить работоспособность двигателя на основном и дублирующем топливах, при пониженном давлении топлива на входе в гидромеханическую часть системы автоматического управления. В процессе комплекса испытаний необходимо подтвердить нормальное управление двигателем на всех эксплуатационных режимах. Противообледенительная защита (§ 33. 68). В процессе испытаний двигателя с любым видом защиты от обледенения должна быть продемонстрирована его работоспособность: • в условиях максимального длительного и кратковременного обледенения; • без накопления льда на деталях двигателя, которое неблагоприятно влияет на его работу или вызывает недопустимое снижение мощности или тяги;
• без повышения температуры газа выше допустимой, указанной в руководстве по эксплуатации; • без повышения вибраций двигателя более величины, указанной в руководстве по эксплуатации; • без недопустимых механических повреждений двигателя; • без ухудшения управляемости двигателя; • без неблагоприятных последствий в течение 30 мин на режимах земного малого газа, при этом двигатель может периодически переводиться на режим промежуточной мощности или тяги. Масляная система (§ 33. 71). Соответствие двигателя требованиям к маслосистеме и отдельным ее элементам устанавливается как анализом, так и путем проведения испытаний: • элементов масляной системы на лабораторных стендах; • стендовых испытаний двигателя с этой системой; • летных испытаний двигателя на летающей лаборатории или в ТБ К с данной системой. Проверка системы смазки должна продемонстрировать работоспособность масляной системы во всем диапазоне рабочих давлений и температур. Авторотация (§ 33. 74). При отказе или выключении двигателя в полете может происходить вращение роторов двигателя от набегающего потока воздуха. В зависимости от конструктивных особенностей двигателя и (или) от характера отказа, приведшего к его выключению, возможно нарушение или полное пре кращение подачи масла к трущимся парам, что может привести к пожару или другим опасным последствиям. Испытание с авторотацией без смазки должно продемонстрировать отсутствие риска для самолета. Испытания необходимо проводить на специальном стенде, на котором вращение роторов двигателя может осуществляться от набегающего потока воздуха, направленного от специального источника на лопатки вентилятора или компрессора, или от механического привода (энергетической установки) и другими способами.
При испытаниях необходимо обеспечить работу двигателя на режиме авторотации в течение времени, как минимум, необходимого для завершения полета самолета с одним неработающим двигателем с половины максимальной продолжительности типового полета Л А или до заклинивания роторов, если это произойдет раньше. При этом заклинивание ротора (роторов) не относится к отказам с опасными последствиями. Попадание птиц (§ 33. 76). Вопросам разработки методик проведения испытаний и совершенствования оборудования для стендовых испытаний двигателей на стойкость к повреждению от попадания птиц уделяется большое внимание (рис. 11. 5). Для установления соответствия требованиям данного параграфа проводят сертификационное испытание на заброс в двигатель крупных, средних и мелких птиц. С точки зрения сертификации двигатели делятся на три группы: ТВД, ТВВД и ТРДД с высокой степенью двухконтурности и обычные ТРДД (табл. 11. 3). Испытания должны проводиться на установившемся взлетном режиме. АП-33 регламентируют скорость заброса и количество забрасываемых птиц на основании входной площади двигателя. Испытание должно подтвердить, что попадание во входное устройство типовой конструкции двигателя крупных птиц не вызывает отказов с опасными по следствиями (остановка двигателя допустима), а попадание средних и мелки птиц не является причиной: • выключения двигателя; • длительной потери тяги более чем на 25 %; • отказов с опасными последствиями; • недопустимого ухудшения характеристик двигателя.
Рис. 11. 5. Стенд для испытаний вентилятора на стойкость к удару птиц
Параметр твд тввд ТРДД (т * 15) Частота вращения n 0 , 1/мин 750. . . 1250 1000. . . 2000 4500. . . 975 С Диаметр вентилятора или винта D , м ~2 4, 6 4, 5 Относительный радиус пера при испытаниях на удар r 0 , % 90 90 90 Скорость птицы в зоне испытаний v„, м/с 50. . . 75 60. . . 90 85. . . 120 Число лопастей или лопаток z 4 8 36 Длина хорды b, м 0, 4 0, 2 0, 1511. 3. Деление двигателей на группы при сертификации
При испытаниях на птицестойкость желательна установка акселерометров на подшипники и обязательно наличие высокоскоростной кинокамеры. Сертификационные испытания на птицестойкость проводятся также и для отдельных систем, узлов и агрегатов летательного аппарата. Например, для отстрела авиационной прозрачной брони используется специальное оборудование, включающее аппаратуру, позволяющую оценить уровень потери прозрачности испытуемого образца при соударении с птицами. Известно, что в США лобовое остекление практически всех боевых самолетов проектируется из условий обеспечения стойкости к сохранению прозрачности при ударе по нему птицы массой 1, 8 кг, летящей со скоростью 0, 85 М, что примерно эквивалентно воздействию бронебойной пули калибра 7, 62 мм, летящей со скоростью около 700 м/с. В подобных испытательных комплексах предусмотрена противопожарная защита стендов, испытываемых объектов и регистрирующей аппаратуры. Попадание посторонних предметов — льда (§ 33. 77). Брусок льда, подлежа щий забросу, по массе должен быть эквивалентен количеству льда, нарастаю щего на воздухозаборнике при 2 -х минутной задержке включения противообледенительной системы при условии максимального обледенения (температу ре — 3, 9 °С и 100 % водности). Заброс осуществляется на крейсерском режиме и не должен приводить к потере тяги или возникновению условий для выключения двигателя. Попадание дождя и града (§ 33. 78). В процессе испытаний необходимо продемонстрировать способность двигателя нормально работать во всем установленном диапазоне режимов работы, при внезапном попадании дождя и града стандартной концентрации в течение любого трехминутного непрерывного дождя и в течение 30 -секундного непрерывного града. Вибрационные испытания (§ 33. 83) предусматривают как испытания полноразмерного двигателя, так и лабораторные испытания его компонентов.
Первые должны проводиться с самолетным или представительным воздухозаборником при установленных отборах воздуха и различных положениях реверса. При этом воспроизводятся условия бокового обдува и вводится преднамеренный дисбаланс по величине, равной дисбалансу, вызываемому оторвавшейся у корня наиболее тяжелой лопаткой (за исключением вентиляторной) для оценки состояния подшипниковых узлов. Вибрационные испытания должны быть проведены до физической частоты вращения ротора КНД, равной 105 %. Калибровочные испытания (§ 33. 85) устанавливают соответствие значений основных параметров заявленной типовой конструкции. Калибровочные испытания проводятся с целью уточнения условий проведения сертификационных испытаний и для подтверждения основных параметров до и после проведения длительных испытаний. Длительные испытания (§ 33. 87). Опытный или модифицированный двигатель подвергается длительным испытаниям обшей продолжительностью 150 ч, включающим 25 шестичасовых этапов в зависимости от типа и назначения двигателя. Наработки по режимам и запускам приведены в табл. 11. 4 и 11. 5. Успешное прохождение двигателем длительных испытаний является основным этапом сертификации. При этом необходимо подтвердить работоспособное двигателя одновременно при максимальных нагрузках потяге, мощности, максимальной частоте вращения и температуре газа перед турбиной, максимальной температуре масла. Испытания при повышенной температуре (§ 33. 88). С помощью этих испытаний подтверждается достаточность запасов жаропрочности элементов турбины при кратковременном забросе температуры газа в эксплуатации выше максимально допустимой температуры для самолетного и вертолетного двигателей ожидаемых условиях эксплуатации при максимальной частоте вращения.
Наименование режима Форма реализации режима 1. Взлетный режим и режим малого газа 1 час чередующимися 5 -минутными периодами 2. Режим: установленной максимальной продолжительной тяги: взлетной тяги 30 мин (15 из 25 этапов длительных 6 -часовых испытаний) 30 мин (10 из 25 этапов длительных 6 -часо вых испытаний) 3. Режим установленной максимальной продолжительной тяги 1 ч 30 мин 4. Промежуточные режимы крейсер ской тяги 2 ч 30 мин ступенями одинаковой длительности с 15 равными приращениями частоты вращения от малого газа до максимального режима 5. Приемистости и дросселирования 6 циклов работы обшей продолжительностью 30 мин 11. 4. Наработка по режиму 6 -часового этапа 150 -часовых длительных испытаний
Общее количество запусков, из которых: 100 осуществляемых не ранее чем через 2 ч после выключения двигателей; 25 ложных; 10 повторных не позже, чем через 15 мин после выключения двигателя; 10 после длительных 150 -часовых испытаний 5511. 5. Распределение запусков за период 150 -часовых испытаний
При сборке двигателей для данных испытаний должны быть определены размеры узлов и деталей турбины и радиальные зазоры в ней для оценки вы тяжки основных элементов турбины после испытаний. Для получения повышенной температуры газа перед турбиной без превышения максимальной частоты вращения могут быть использованы отборы и (или) перепуски воздуха или газа, поворотные НА компрессора, технологические выходные устройства, дросселирующие сетки и подогрев воздуха на входе в двигатель. Испытания проводятся на стенде, оборудованном устройствами, позволяющими использовать один из указанных способов повышения температуры или их определенную комбинацию. Испытания двигателя реализуются за один цикл в следующем порядке: • работа в течение 10 мин на максимальном продолжительном режиме (для обеспечения предварительного прогрева деталей турбины); • работа в течение 5 мин при температуре газа перед турбиной, не менее чем на 45 К превышающей максимально допустимую температуру газа в обычных условиях эксплуатации. Результаты признаются удовлетворительными, если узлы и детали роторов турбины после испытаний сохранили работоспособность, а величина остальных деформаций этих элементов не превышает нормируемых эксплуатационных пределов. Испытания вертолетного ГТД СТ, на котором применяются повышенные мощности, обеспечивающие необходимую энерговооруженность вертолета при одном неработающем двигателе в течение 30 мин, 2, 5 мин, 30 с, проводят также за один цикл: • работа в продолжение 10 мин на максимальном продолжительном режиме (для обеспечения предварительного прогрева деталей турбины);
• работа в течение 5 мин на взлетном режиме при номинальных значениях параметров; • работа двигателя на максимальном режиме, соответствующем одной из назначенных мощностей (2 -минутная или 30 -секундная) в течение нормативного времени и при нормативной температуре. При этом испытания вертолетного ГТД СТ с указанными режимами мощности считаются удовлетворительными, если после испытаний узел турбины может иметь повреждения, выходящие за эксплуатационные пределы. Эксплуатационные испытания (§ 33. 89) проводят на высотном стенде либо на летающей лаборатории. Летающая лаборатория должна иметь систему сброса отбираемого от двигателя воздуха, систему загрузки двигательных генераторов, гидросистемы, противопожарную систему. Основными целями эксплуатационных испытаний являются: • определение ВСХ и работоспособности двигателя для использования в целях сертификации; • определение эксплуатационных ограничений; • проверка напряжений вентилятора, аэродинамической неустойчивости, флаттера, критических резонансов; • проверка и отладка системы управления двигателем; • работоспособность двигателя с отборами воздуха; • высотный и повторный запуск двигателя; • работоспособность системы управления зазорами, масляной и топливной системы; • оценка режима авторотации; • снятие вибрационных характеристик; • интеграция двигателя с мотогондолой.
Проверка локализации лопаток и дисбаланса ротора (§ 33. 94). Проверкой обеспечиваются: а) подтверждение непробиваемости корпусов двигателя разрушившимися лопатками вентилятора (ее надполочной части, если лопатка бандажированная), компрессора или турбины; б) подтверждение того, что вторичные эффекты, вызванные разрушениями лопаток вентилятора, компрессора или турбины, не приводят к отказам двигателя с опасными последствиями в течение нормированного промежутка времени. Это должно быть показано одним из следующих способов: • специализированными испытаниями двигателя по проверке непробиваемости корпусов разрушившейся лопаткой и отсутствием опасных последствий от вторичных эффектов; • на основании информации о последствиях разрушения лопаток, получаемой при стендовой доводке и летных испытаниях данного двигателя или при стендовой доводке, летных испытаниях и эксплуатации других двигателей, рабочие лопатки, корпуса и роторы которых сопоставимы с соответствующими деталями рассматриваемого двигателя по конструкции, способу изготовления, окружной скорости и нормируемому промежутку времени. Испытания проводятся на полностью собранном двигателе. При соблюдении определенных условий (температуры, давления и т. п. ) допускается проведение испытаний отдельной ступени или отдельной части двигателя. Результаты испытаний считаются удовлетворительными, если разрушение лопатки, а также вторичные последствия, вызванные ее разрушением, не привели к отказам с опасными последствиями. После разрушения лопатки вентилятора во время испытаний допускается полная потеря тяги (мощности).
Пример. Двигатель Trent 1000 производства Rolls-Royce, устанавливаемый на самолет Boeing 787, успешно прошел ряд сертификационных испытаний, в частности, испытания на отрыв лопаток вентилятора. Двигатель был выведен на максимальный режим, а затем одна из лопаток была подорвана при помощи взрывного заряда. Работа двигателя протекала без опасных последствий, и сертификационные испытания были признаны удовлетворительными. Нелокализованные разрушения ГТД. Необходимость проведения испытаний по проверке локализации разрушений обусловлена следующими обстоятельствами. При нелокализованных разрушениях ГТД усложняются условия пилотиро вания, а при поражении (повреждении) жизненно важных систем самолета в ряде случаев становится невозможным продолжение или завершение полета. Избежать нелокализованных разрушений полностью не удастся из-за сложности и многообразия процессов, протекающих в ГТД в реальных условиях эксплуатации |58|. Частота нелокализованных разрушений двигателей, находящихся в настоящее время в эксплуатации, составляет 2. . . 7 разрушений на 10 6 ч наработки. Нормы летной годности гражданских самолетов допускают возникновение катастрофической ситуации в целом по самолету не чаше, чем I случай на 10 7 ч налета, для отдельных функциональных систем допускается 1 случай на 10 х. . . 10 9 ч налета. Нелокализованные разрушения делятся на первичные и вторичные. Первичные — вызываются непосредственно разрушившимся источником (узлом, деталью), вторичные — связаны с разрушением узла (детали), вызванным дефектом другой детали, не дающей непосредственно нелокализованного разрушения.
Нелокализованные разрушения компрессора происходят под механическим и тепловым воздействиями на конструкцию ДА. Механическое воздействие наблюдается, как правило, при разрушении дисков и валов компрессоров, а также лопаток. Тепловое воздействие проявляется при титановых пожарах, возникающих в условиях повышенных температур и давлении воздуха в КВД при трении титановых деталей роторных и статорных узлов после разрушения лопаток, лабиринтов или опорного шарикоподшипника ротора. Разрушение лопаток компрессора вызывалось недооценкой запасов мало цикловой усталости (МЦУ), повышением уровня переменных напряжений и нарушении конструктивных посадок по полкам замков лопаток, существенным возрастанием напряжений в лопатках при попадании посторонних предметов, включая птиц, а также при увеличении концентрации напряжений в местах грубых отклонений от требований чертежа при изготовлении. Разрушение дисков компрессоров связано с недооценкой запасов МЦУ конструкции, обладающей существенными разбросами коэффициентов концентрации напряжений; снижением характеристик МЦУ металла из-за наличия в нем металлургических дефектов из нитридов или оксидов титана, а также нарушением химического состава, приводящего к повышению хрупкости металла; существенным ростом переменных напряжений в конструкции диска, вызванным конструкторскими и технологическими изменениями зубчатого зацепления в редукторе, и, наконец, исчерпанием запасов конструктивной прочности из-за отклонений геометрических размеров и шероховатости поверхности диска от требований чертежа при удалении металла в процессе балансировки (54, 58|. При разрушении шарикоподшипника происходит перемещение ротора под действием осевой силы и при отсутствии диагностических признаков такого разрушения наблюдается взаимное касание роторных и статорных конструкций, выполненных из титановых сплавов, что при определенных температурах и давлениях воздуха приводит к титановому пожару. Титановый пожар возникает также при усиленном касании лабиринта о втулку в связи с разрушением болтов крепления лабиринта.
Нелокализованные отказы турбины происходят при разрушениях дисков (15, 2 %), лопаток (42. 4 %), дефлекторов (21, 2 %) и статора (18, 2 %). Причинами наиболее опасных отказов (разрушения дисков турбины) являются: • недооценка запасов МЦУ при установлении ресурса; • превышение предельного уровня напряжений при неуправляемой раскрутке роторов турбин из-за разрушения валов в условиях потери их прочностных характеристик в связи с нарушением местного теплового баланса и ростом температуры металла в местах касания валов роторов низкого и высокого давлений или проворота и усиленного трения лабиринтной втулки о вал; • снижение запасов длительной прочности из-за местного отклонения в химическом составе металла; • преждевременное исчерпание запасов длительной прочности металла при нарушении температурных условий его работы из-за отклонения от заданных режимов эксплуатации или сбоев системы охлаждения дисков. Случаи разрушения дефлекторов (покрывных дисков), как правило, связаны с усталостью металла при действии повышенных переменных напряжений, возникающих при ослаблении посадки в замковом соединении после выработки материала. Самый большой процент нелокализованных отказов турбины связан с разрушением рабочих лопаток. Причинами его являются факторы, приводящие к росту переменных напряжений из-за нарушения конструктивных геометрических параметров замка при изготовлении или из-за ослабления демпфирующей способности бандажных полок при выработке материала на опорных поверхностях. Кроме того, неблагоприятная технологическая наследственность, заложенная при изготовлении лопаток (наличие растягивающих поверхностных напряжений и концентраторов или повышенных объемных напряжений), снижает пределы уста лостной и длительной прочности и обусловливает более быстрое исчерпание запасов прочности. Отмечались случаи разрушения лопаток турбины из-за недооценки фактических запасов работоспособности при отработке и назначении ресурса.
Нелокализованные разрушения статоров турбины, как правило, вторичны и связаны с нарушениями теплового состояния лопаток соплового аппарата из-за несовершенства системы их охлаждения или повышенного местного теплового воздействия при искажении температурного поля в результате установки неправильно собранной топливной рабочей форсунки в камеру сгорания либо коробления жаровой трубы самой камеры сгорания, а также при повышенном механическом воздействии ротора вследствие разрушения корпуса его опоры или смещения из-за нарушения его осевой фиксации. Нелокализованные разрушения стартеров и приводов постоянных оборотов из-за конструктивного несовершенства наблюдаются на ГТД, у которых отсутствуют эффективные устройства зашиты (аварийные заслонки, предельные защитные валики и др. ). Нелокализованные разрушения корпусов камер сгорания вызваны снижением прочностных характеристик из-за технологических отклонений при сварке самих корпусов или их элементов, а также отклонений при термообработке Примеры. В табл. 11. 6 для основных деталей систем ТРДДФ приведены возможные эксплуатации отказы и способы их определения. Половина позиций табл. 11. 6 связана возникновением нелокализованных отказов. Приведенная таблица построена на основе опыта эксплуатации и доводки ТРДДФ.
Детали и системы двигателя Диагностические признаки Отказы В полете На земле Локали зован ные Недолокализ ованные Лопатки вентилятора 1 -й, 2 -й, 3 -й ступеней Вибрация — — — Лопатки компрессора по следней ступени Вибрация — + — Жаровая труба — — Корпус камеры сгорания — — Сопловые лопатки ТВД Заброс Т г * — + — Рабочие лопатки ТВД То же При осмотре + — Сопловые лопатки ТНД « « + — Рабочие лопатки ТНД « « При осмотре + — Масляная система « « — + — Топливная система и САР Отклонение основных параметров от норм — + — Подшипники трансмиссии Вибрация, срабатывание сигнализатора стружки — + — Шестерни центральной ко робки приводов (ЦКП) Отказ топливной, мас ляной и других систем — + — 11. 6. Типовые отказы систем, узлов и деталей ТРДДФ
Коллекторы камеры сгорания Срабатывание пожар ного сигнала — + — Форсажные коллекторы — — Продольные швы обечаек форсажной камеры — — Диски вентилятора — — — + Диски компрессора — — — + Диски турбины — — — + Места соединения дисков с ва лом (шпильки) — — Трубопроводы наружного кон тура — Течь + — Трубопроводы управления со плом — То же + —
Нелокализованные отказы деталей двигателя ТРДДФ: • лопатки вентилятора; жаровая труба; сопловые лопатки ТВД; рабочие лопатки ТВД; коллекторы камеры сгорания; форсажные коллекторы; продольные швы обечаек форсажной камеры; диски вентилятора; диски турбины; места соединения дисков с ва лом (шпильки). Для других двигателей нелокализованные отказы могут иметь место и для иных узлов и деталей, в зависимости от выполненной конструкции и размерности двигателя, например: • обрыв пера рабочих лопаток 1 -й и 2 -й ступеней вентилятора; • разрушение дисков вентилятора, компрессора и турбины; • разрушение соединений валов с дисками; • разрушение корпуса камеры сгорания; • разрушение обечаек форсажной камеры; • разрушение мест подвода топлива к топливным коллекторам, находящимся в газовоздушном тракте основной и форсажной камер сгорания. Причинами нелокализованных разрушений от общего числа причин, приводящих к разрушениям, являются, %: 18, 9 — многоцикловая усталость; 10, 2 — трение ротора о статор; 9, 1 — дефекты материалов; 5, 5 — перегрев, малоцикловая усталость и повреждение посторонними предметами; 5, 0 — производственные дефекты и разрушений болтов крепления валов. Испытания корпуса на непробиваемость имеют ряд технических сложно стей. Известен способ испытаний корпуса на непробиваемость, заключающийся в подрыве корневого сечения лопатки с помощью взрыва. Известен также способ испытаний корпуса на непробиваемость, при кото ром после выхода ротора на заданную частоту вращения производят подрезку пера в заданном сечении с помощью электродов, размещенных в зоне пера лопатки.
Существует несколько методов обрыва. По одному методу заданное сечение ослабляется до запаса прочности, который меньше единицы, после чего усиливается накладками из термочувствительного материала с повышением запаса прочности до значения больше единицы. После достижения заданной частоты вращения (максимальной центробежной нагрузки) проводится нагрев лопатки до допустимой температуры. Усиливающие ослабленное сечение лопатки накладки из материала с большим коэффициентом линейного расширения, чем у материала лопатки, с разогревом сбрасывают с себя нагрузку. Запас прочности в опасном сечении лопатки становится меньше единицы, и происходит разрушение. Нагрев лопатки осуществляется индукционным способом. По другому методу лопатка в заданном сечении ослабляется до получения запаса прочности на заданных для разрушения оборотах до значения больше единицы. Дополнительное нагружение ослабленного сечения после достижения заданных оборотов происходит за счет нагрева встроенного термочувствительного элемента. По третьему методу управление дополнительным нагружением рабочих лопаток основано на местном нагреве термонагружающего участка, образованного на самой лопатке (без встроенных элементов). На время испытаний вокруг двигателя устанавливается защита от осколков, толщина которой выбирается из расчета задержания крупных осколков диска турбины (1/3. . . 1/2 массы диска). Между защитой и двигателем устанавливают пять-шесть слоев тонких (8 = 1 мм) листов стали на расстоянии 10. . . 15 мм друг от друга (рис. 11. 6). Если корпус двигателя во время испытания будет пробит, то по количеству поврежденных тонких листов можно ориентировочно судить о требуемом усилении корпуса.
Рис. 11. 6. Зашита при испытании двигателя на непробиваемость корпуса лопатки турбокомпрессора: / — толстые стальные листы; 2 — рама; 3 — тонкие стальные листы; 4 — испытываемый двигатель Пример. Согласно международным авиационным правилам АП-33 авиадвигатели ПС-90 А 2 для допуска к эксплуатации должны были пройти сертификационные испытания по локализации повреждений, возникающих при обрыве лопатки вентилятора авиадвигателя. Предприятием НПО «Искра» была разработана конструкция корпуса вентилятора из композиционных материалов для двигателя ПС-90 А 2, при проектировании которого одним из требований заказчика было обеспечение удержания внутри корпуса вентилятора фрагментов конструкции в случае ее разрушения. По правилам АП-33 требуется экспериментальное подтверждение локализации повреждений корпуса вентилятора при самом опасном случае — обрыве лопатки в корневом сечении при максимальных оборотах двигателя. Для обеспечения надежного обрыва лопатки были использованы детонирующие удлиненные заряды с кумулятивной канавкой. Инициирование кумулятивного заряда проводилось электродетонатором, при этом расплавленный металл разрезал лопатку равномерно по всему корневому сечению.
На рис. 11. 7 представлено сечение лопатки в корневом сечении с установленными детонирующими удлиненными зарядами. Дефектация после разборки (§ 33. 93). После завершения длительных 150 -часовых стендовых испытаний двигатель снимается со стенда, осматривается и разбирается. Детали и узлы двигателя при разборке осматриваются дважды: при разборке двигателя до промывки узлов и деталей и после промывки, способами, предусмотренными технологией разборки. По результатам этих осмотров должна быть составлена ведомость дефектов. Ведомость осмотра деталей и узлов двигателя и заключения по исследованию причин, вызвавших дефекты, помещают в акт о результатах испытаний. Кроме внешнего осмотра, детали и узлы двигателя по действующим техническим условиям подвергаются специальным видам контроля. Ведомость проверки размеров деталей и узлов, результаты специальных видов контроля вместе с фотографиями деталей, имеющих дефекты, помещают в акт о результатах испытаний. Рис. 11. 7. Корневое сечение лопатки
Перед разборкой всех агрегатов двигателя (насосы, приводы, клапана и др. ) должны быть проведены лабораторные испытания с целью определения функционирования и соответствия параметров и характеристик действующим техническим условиям. Удовлетворительная оценка результатов проверки работы двигателя при испытаниях дается при: • отсутствии дефектов, которые могут привести к необходимости выключения двигателя в полете; • соответствии параметров двигателя данных заявленным в ТУ. Общие рекомендации к испытаниям При проведении комплекса сертификационных испытаний разработчик может использовать несколько экземпляров двигателя заявленной типовой конструкции. Разработчик во время проведения комплекса испытаний может производить обслуживание и мелкие ремонты в соответствии с Руководствами по техническому обслуживанию и ремонту. Если частота таких операций или число остановок вследствие неисправности двигателя чрезмерны, или возникает необходимость крупного ремонта или замены деталей в результате комплекса испытаний, или при дефектации после разборки, то двигатель или его детали могут быть подвергнуты дополнительным испытаниям, которые компетентный орган сочтет необходимым. В испытаниях должны применятся топливо и масло из числа указанных в технической документации для данного двигателя. Перед длительным испытанием положение регулируемых элементов каждого компонента, имеющего такие элементы, и его рабочие характеристики, которые можно определить независимо от установки этого компонента на двигателе, должно быть определено и зарегистрировано.
Сертификация двигателей на экологические требования В рамках СНГ уровень шума нормируется Авиационными правилами — АП- 36, а уровни эмиссии вредных веществ — Авиационными правилами — АП-34, требования которых практически соответствуют международным. АП-34 «Охрана окружающей среды. Нормы эмиссии для авиационных двигателей» устанавливает нормы выброса (эмиссии) топлива и эмиссии с выхлопными газами загрязняющих веществ двигателями гражданских воздушных судов. Требование АП-34. 11 относится к эмиссии топлива. Параграф 34. 11(a) требует, чтобы двигатель был спроектирован таким образом, чтобы был предотвращен выброс в атмосферу топлива из коллекторов форсунок после выключения двигателя, завершающего полетные или наземные операции. Раздел АП-34. 21 содержит соотношения для определения нормативных значений эмиссии несгоревших углеводородов (НС), монооксида углерода (СО), оксидов азота (N 0*), эмиссию дыма (SN) в зависимости модели двигателя, даты изготовления первого серийного образца, базовой степени повышения давления, установленной взлетной тяги/мощности двигателей самолетов с дозвуковой и сверхзвуковой скоростью полета. I АЛ-36 «Сертификация воздушных судов по шуму на местности» устанавливает стандарты воздушных судов по шуму на местности, которые должны был выполнены при выдаче Сертификатов Типа и изменений к сертификату, сертификатов летной годности экземпляра для транспортных дозвуковых судов все) категорий, турбореактивных и турбовинтовых двигателей сверхзвуковых самолетов, вертолетов и легких вертолетов, и вспомогательных силовых установок.
В настоящее время действуют требования главы 3 тома I Приложения 16 стандарта ICAO. С 2006 года для вновь создаваемых самолетов введены сер тификационные требования Главы 4 по шуму, что заметно повышает уровень эксплуатационных ограничений полетов самолетов. Очевидно, что при таком сценарии развития событий имеющаяся сегодня провозная мощность парка са молетов российских авиаперевозчиков, удовлетворяющая требованиям Главы 3 с минимальным запасом 5 ERNд. Б, резко снизится. 11. 5 СЕРТИФИКАЦИЯ ДВИГАТЕЛЯ В СОСТАВЕ ЛЕТАТЕЛЬНОГО АППАРАТА Следующим этапом сертификации двигателя является ЕТОРБ-сертификация всей системы летательного аппарата, при которой сертифицируется пригодность системы «ЛА-ГТД» к ETOPS-эксплуатации. Это достигается, главным образом, летными испытаниями на ETOPS-маршрутах. Они позволяют всесторонне проверить ЛА и все его функциональные системы (включая двигатели и оборудование) в условиях, наиболее близких к реальной эксплуатации. При этом количество требований НЛГ, относящихся к двигателю, и соответствие которым оценивается летными испытаниями, составляет около 40 %. Цель государственных и сертификационных испытаний — контрольная оценка и подтверждение соответствия летательного аппарата требованиям НЛГ. При положительной оценке результатов заводских и государственных испытаний выдается сертификат летной годности на данный тип летательного аппарата, дающий право начать его эксплуатацию. Еще до внедрения системы сертификации в 1969. . . 1970 гг. проводились первые работы по сертификации ряда пассажирских самолетов СССР в связи с их экспортом: • самолета Ил-62 по нормам BCAR; • самолета Ту-134 по нормам FARI; • самолета Як-40 авиарегистрами Италии, ФРГ и др.
Отечественная система сертификации была разработана Госавиарегистром СССР, созданным в 1973 г. Для организации планомерной работы по сертификации обычно уже на этапе эскизного проектирования разрабатывается программа сертификации (рис. 11. 8), которая охватывает все виды сертификационных работ. ETOPS (Extended range operations witht woairlines) — полет увеличенной дальности на Л А с двумя двигателями. Рис. 11. 8. Программа создания самолета
Программа состоит из отдельных этапов, включающих эскизный проект, макет самолета, постройку самолета, заводские, государственные и эксплуатационные испытания самолета. Характер указанных этапов определяет содержание работ по обеспечению и контролю соответствия требованиям НЛГ. Многие примеры свидетельствуют о том, что характер требований норм и система сертификации существенно, а иногда и коренным образом, меняют содержание испытаний или их анализ. Пример. В Нормах летной годности детально отработаны идеология и требования, направленные на обеспечение безопасности взлета и посадки. Нормами установлено, что скорость подъема носового колеса назначается с 5 %-ным запасом от минимальной скорости отрыва V тin o т р , которая должна быть продемонстрирована при выполнении взлета. Для самолета Ил-86 значение V тin o т р ограничено касанием хвостовой части (пяты) фюзеляжа. В связи с этим программа сертификационных испытаний включала достаточно сложный эксперимент, который ранее не проводился. На рис. 11. 9 показан процесс взлета с демонстрацией V тin o т р самолета Ил-86 при касании хвостовой пяты фюзеляжа бетона взлетно-посадочной полосы (ВПП) (33|.
Рис. 11. 9. Сертификационные испытания самолета Ил-86 при касании хвостовой пяты фюзеляжа о бетон ВПП
Для методического обеспечения летных сертификационных испытаний новых самолетов, в том числе Ил-96, Ту-204 и Ил-114, в ЛИИ разработана и введена в действие комплексная программа сертификации — «Типовая программа наземных и летных испытаний гражданских самолетов» (рис. 11. 10). Сроки разработки различных систем могут существенно отличаться, поэтому заслуживает внимания создание объектов авиационной техники с обеспечением «одновременного финиша» . На рис. 11 представлена программа разработки пассажирского самолета фирмы «Боинг» , из которой видно, что решение о начале разработки самолета принято только после завершения основного объема работ по созданию двигателя, включая его летные испытания на летающей лаборатории. Подобный подход обеспечивает в практике создания пассажирских самолетов завершение сертификации основных систем к началу летных испытаний самолета. В качестве иллюстрации на рис. 11. 12 показаны характеристики сертификационных испытаний, создаваемых по принципам «одновременного финиша» и «одновременного старта» : для самолетов, создаваемых по принципу «одновременного финиша» , к первому вылету завершена сертификация двигателя и пилотажно-навигационного оборудования и выполнена оценка около 70 % пунктов НЛГ, что позволило при соответствующей организации провести летные испытания и сертифицировать самолет менее чем за 1 год; для самолета, создаваемого по принципу «одновременного старта» , к первому вылету произведена оценка менее 10 % требований НЛГ, а сертификация двигателя и пилотажно-навигационного оборудования завершена к окончанию летных испытаний самолета, при этом продолжительность летных испытаний составила около 4 лет.
Рис. 11. 10. Типовая программа сертификационных летных испытаний
Рис. 11. Структурная схема комплексной программы сертификации
Рис. 11. 12. Характеристики сертификационных испытаний
РЕЗЮМЕ (по главе 11 «Сертификационные испытания ГТД» ) 1. Воздушный Кодекс Российской Федерации, обеспечивающий государственное регулирование использования воздушного пространства и деятельности в области авиации, безопасности полетов, авиационной и экологической безопасности, устанавливает: • обязательную сертификацию и аттестацию в гражданской авиации, в том числе разработчиков и изготовителей авиационной техники и, в частности, авиационных двигателей; • обязательный статус требований к летной годности авиационных двигателей и общий порядок сертификации гражданских воздушных судов, авиационных двигателей и воздушных винтов в соответствии с федеральными авиационными правилами и схему взаимодействия уполномоченного органа по сертификации, разработчика, изготовителя и эксплуатирующей организации в процессе сертификации. 2. Сертификация авиационных двигателей проводится путем подтверждения соответствия научно-обоснованным и общепризнанным Нормам летной годности типа гражданского воздушного судна, его двигателей и оборудования. 3. Сертификации подвергаются двигатели и оборудование по принципу «до установки на самолет» и воздушное судно вместе с его двигателями и оборудованием. 4. Сертификация является эффективным методом повышения безопасности гражданских воздушных судов, а также способствует сокращению сроков доводки и летных испытаний при условии, что она проводится с начала проектирования на всех этапах создания воздушного судна и включает в себя проведение в значительных объемах моделирования, стендовых испытаний, испытаний на летающих лабораториях двигателей, оборудования, самолетных систем и, как завершение, — проведение летных испытаний воздушного судна.
В этом случае еще на ранних стадиях создания воздушного судна могут быть вскрыты недостатки (несоответствия требованиям Норм летной годности), которые легче устранить до или в процессе его постройки, чем во время летных испытаний. 5. Основными современными научно-методическими проблемами сертификации являются: • анализ проблемных вопросов по разработке нормативной документам для сертификации авиационных двигателей, в том числе методологии проектирования, доводки и сертификации при максимально допустимых параметрах двигателя, применения вероятностных методов анализа безопасности, ранней сертификации двигателей повышенной надежности; • анализ различных методов управления ресурсом двигателей и нормирование новых, более экономичных стратегий управления ресурсами; • разработка или уточнение требований к экологической безопасности, в том числе по эмиссии вредных веществ и шуму.
ВОПРОСЫ 1. Что означают термины «сертификация» , «авиационные правила» ? 2. Какие требования предъявляются к авиационным двигателям на различных стадиях их создания? 3. Каково назначение Межгосударственного авиационного комитета (МАК) и Авиационного регистра МАК? 4. Какими видами контроля поддерживается летная годность двигателей? 5. Какова эволюция норм летной годности авиационных двигателей? В чем их отличие друг от друга? 6. На чем основана законодательная база сертификации авиационных двигателей? 7. Охарактеризуйте основные этапы сертификации авиационных двигателей. 8. Для каких целей проводятся сертификационные заводские (СЗИ) и контрольные (СКИ) испытания? 9. Какие затраты необходимы для проведения сертификации двигателей? 10. Каковы особенности сертификационных испытаний системы пожарной защиты? 11. Каковы особенности сертификационных испытаний роторов турбин, компрессоров, вентиляторов и турбонагнетателей? 12. Каковы особенности сертификационных испытаний на подтверждение потребных запасов по газодинамической устойчивости? 13. Чем вызвана необходимость в проведении при сертификации испытаний на авторотацию и каким образом они реализуются? 14. Каковы цели и способы реализации длительных и эксплуатационных сертификационных испытаний? 15. В чем особенности проведения испытаний на попадание посторонних предметов (птиц, льда, дождя и града)?
16. Каково назначение и каким образом реализуются сертификационные испытания при повышенной температуре? 17. Чем вызвана необходимость в проведении испытаний по проверке локализации лопаток и дисбаланса ротора? 18. Каковы особенности сертификации двигателя в составе летательного аппарата?
Глава 12 ОБРАБОТКА РЕЗУЛЬТАТОВ ИСПЫТАНИЙ Испытания авиационных ГТД на современной испытательной базе автоматизированы. Вместе с тем, в некоторых случаях, особенно на небольших и несистематически работающих стендах, а также на многих учебных стендах сохраняется ведение протокола испытания. Протокольные записи обычно состоят из двух групп. В первую группу входят записи, характеризующие режимы работы установки и испытываемого объекта. Во вторую группу входят величины, которые необходимы для последующей обработки данных эксперимента. В результате испытаний двигателя определяются в основном термодинамические параметры. При этом приемники температур и давлений должны быть установлены в проточной части двигателя таким образом, чтобы можно было отследить изменение параметров по длине двигателя в характерных сечениях на границах основных узлов [35, 46, 50, 52, 53, 59]. 12. 1. ПРИЕМЫ ПРЕПАРИРОВАНИЯ ИСПЫТЫВАЕМОГО ГТД До начала экспериментов двигатель препарируют, т. е. в основных сечениях устанавливают первичные приемники и преобразователи, обеспечивающие измерение давления и температуры заторможенного потока и статического давления. В связи с тем, что поток воздуха и газов, движущийся по проточной части двигателя, имеет неравномерный характер, значения температур и давлений у втулочной части и периферии, а также по окружности (из-за закрученности потока) могут значительно отличаться. Поэтому для получения достоверных значений параметров при неравномерных полях температур и давлений необходимо проводить измерения во многих точках сечения, как по радиусу (высоте канала), так и по
окружности. Однако разместить приемники и преобразователи равномерно не всегда удается по ряду причин, причем главная из них — конструктивные соображения. Некоторые термодинамические величины определяют косвенным (расчетным) путем, например температуру газа перед турбиной. В силу значительной неравномерности поля температур и давлений для достоверного определения величины Т г * было бы необходимо поставить большое количество приемников в сечении на выходе из камеры сгорания, но это в свою очередь вызовет еще большую неравномерность. Отдельные термодинамические величины двигателя по лучают по результатам автономных испытаний узлов двигателя на специальных стендах (характеристики компрессоров, характеристики камеры сгорания, характеристики турбин). Установку приемников температур и давлений по высоте (радиусу) проточной части производят обычно в средней осевой линии равноплощадных колец, что обеспечивает получение среднеинтегральных значений параметров. Расчет размеров, на которых необходимо установить приемники или датчики, проводят по формуле (12. 11) где Di — диаметр установки приемников; d — втулочный диаметр сечения; D — периферийный диаметр сечения; n — количество замеров по высоте (радиусу) проточной части; i — (1. . . n) — порядковый номер замера по высоте.
Кроме термодинамических параметров по сечениям вдоль проточной части двигателя стендовые системы измеряют: • атмосферное давление р н к. Па; • атмосферную температуру t н , °С; • температуру на входе в двигатель t B , °С • частоты вращения роторов n изм , 1/мин; • расход топлива G m , кг/ч; • тягу (мощность) Р ДВ (N), к. Н (к. Вт). Препарирование опытного двигателя для оценки термодинамических параметров при стендовых испытаниях выполняют в следующем объеме. На входе в двигатель ставят 4. . . 8 радиальных приемников (гребенок) давления заторможенного потока для определения потерь и полей давления тормо жения во входном канале. За компрессором НД, как в наружном, так и во внутреннем контуре, ставят по 3… 6 радиальных термопневмогребенок заторможенных параметров. Кроме того, для определения следов от лопаток направляющих аппаратов на 3 -х радиусах (периферийном, среднем и втулочном), а иногда и чаще, ставят шаговые гребенки давления заторможенного потока, охватывающие в окружном направлении расстояние не менее 1, 5 шагов по лопаткам направляющих аппаратов. За компрессором ВД ставят по 2. . . 3 радиальные гребенки давления и температуры заторможенного потока, а для определения следов от лопаток спрям ляющих аппаратов на 3 -х радиусах (периферийном, среднем и втулочном) ставят шаговые гребенки давления заторможенного потока, реже и температур, охватывающие в окружном направлении расстояние не менее 1, 5 шагов по лопаткам спрямляющих аппаратов.
За камерой сгорания препарирование обычно не делают, а параметры (Т г *, р г *) определяются расчетным путем. За турбиной НД ставят от 3 до 12 радиальных гребенок давления и температуры заторможенного потока. Если имеется камера смешения, то ставят по окружности на стенках наружного и внутреннего контуров в сечении на входе в камеру смешения. На срезе реактивного сопла ставят по 2. . . 3 радиальных термопневмогребенок параметров заторможенного потока для определения качества смешения потоков наружного и внутренних контуров. При раздельном выхлопе на выходе из сопла 2 -го контура ставят 2. . . 3 радиальных гребенки давления заторможенного потока для определения потерь р* во 2 -м контуре.
12. 2. ОСНОВЫ МЕТОДИКИ ОБРАБОТКИ РЕЗУЛЬТАТОВ ИСПЫТАНИЙ Каждое предприятие для каждого своего двигателя разрабатывает свою уникальную методику обработки результатов испытаний. Как правило, такие методики закладывают в качестве основы для автоматизированной обработки. Вместе с тем, многолетний опыт испытаний авиационных ГТД свидетельствует о том что существует ряд общих (инвариантных) моментов, характерных для большинства применяемых методик обработки. Рассмотрим эти моменты на примере по строения методики обработки результатов испытаний двухконтурных ТРД. Обработка экспериментальных данных после испытания производится в два этапа [49]. На первом этапе, во время так называемой первичной обработки условные показания приборов с помощью градуировочных графиков, расчетных зависимостей, номограмм и таблиц переводятся в численные значения физических величин, а результаты прямых измерений используют для косвенного определения неизмеряемых физических величин. Первичная обработка обычно заканчивается построением графических зависимостей изменения физически: величин по сечениям, во времени или по параметру, характеризующему режимы испытания (например, зависимостей тяги, температуры за турбиной, расхода топлива от частоты вращения для двигателей прямой реакции или от расход топлива для турбовинтовых двигателей). Графические зависимости строятся в удобном для работы масштабе, четно наносятся экспериментальные точки, по которым, а чаще через некоторый разброс между ними, проводится результирующая зависимость. Особое внимание при этом уделяется выпадающим точкам. Если полученная экспериментальная зависимость протекает плавно, выпадающие точки считаются промахами и убираются из рассмотрения, дл: уточнения проводят повторный эксперимент.
Вторичная обработка экспериментальных данных проводится по результатам первичной обработки и предусматривает, прежде всего, вычисление неизмеряемых параметров, имеющих важное значение для анализа рабочего процесса двигателя (С уд , Т г *, G В ) и приведение физических параметров к САУ. Одно из главных задач обработки состоит в том, чтобы дать удобный и наглядны материал для аналитических исследований и принятия решений по дальнейшим направлениям доводки опытного двигателя или совершенствованию серийных двигателей. 12. 3. МЕТОДЫ И СПОСОБЫ УМЕНЬШЕНИЯ ПОГРЕШНОСТЕЙ ПОЛУЧЕНИЯ ЭКСПЕРИМЕНТАЛЬНЫХ ДАННЫХ Работа над повышением точностных характеристик экспериментальны данных должна вестись постоянно. Повышение точности требует в большинстве случаев значительных затрат на реализацию проекта, поэтому анализу и вы бору оптимального решения отводится важное значение. Задача повышении точности измерений решается в несколько этапов: • на основе всестороннего рассмотрения методики выполнения измерения проводят анализ измерительной задачи; • выбирают метод или способ повышения точности основанные на уменьшении погрешностей отдельных составляющих; • проводят оценку степени повышения точности получения экспериментальных данных, оценивают уровень затрат на реализацию задачи; • реализуют план мероприятий по повышению точности измерений. Рассмотрим типовые способы и методы повышения точности экспериментальных данных.
Использование более точных средств измерения. Этот способ применим в тех случаях, когда наибольшую величину погрешности измерения составляет инструментальная погрешность. В этом случае замена менее точного прибора на бо лее точный может привести к повышению точности всего измерительного канала. Однако необходимо проанализировать величины дополнительных погрешностей более точного прибора. Имея небольшую величину основной по грешности, более точный прибор может создавать большие величины дополнительных погрешностей. Так, например, при решении задачи повышения точности измерения температуры на входе в компрессор замена менее точной хромель-копелевой термо пары на более точный термометр сопротивления не всегда возможна, так как термопара позволяет проводить измерения в точке пространства или поверхности, а термометр сопротивления имеет большие габариты. В результате термометр сопротивления, помешенный в поток воздуха, создает искажение потока и, как следствие, вносит дополнительную погрешность. Ограничение условий применения средств измерения. В паспортных данных на средства измерения указываются дополнительные погрешности, возникающие при воздействии внешних неблагоприятных факторов: • дополнительная погрешность от измерения температуры окружающей среды; • дополнительная погрешность от воздействия влажности воздуха; • дополнительная погрешность от изменения напряжения (частоты) питающего напряжения; • дополнительная погрешность от воздействия вибраций и др. Влияние дополнительных погрешностей на величину суммарной погрешности может достигать 30 -40 %.
Для уменьшения влияния дополнительных погрешностей проводят мероприятия по ограничению условий применения средств измерения: • устанавливают в помещениях кондиционеры; • подключают дополнительные стабилизаторы напряжения; • устанавливают аппаратуру на специальную демпфирующую платформу. Индивидуальная градуировка средств измерения. Этот способ повышения точности измерения эффективен при значительной величине систематической составляющей погрешности средств измерения. Например, система измерений стенда оснащена датчиками давления класса 1, 0 %. Общее количество датчиков достигает 250. Замена датчиков с погрешно стью 1, 0 % на более точные, например класса 0, 25 %, приведет к значительным затратам финансовых средств. Задачу повышения точности в этом случае можно решить путем индивидуальной градуировки датчиков. На специальной установке у каждого датчика снимается характеристика: (12. 2) где U — напряжение на выходе датчика; р — задаваемое давление. Для градуировки датчиков должны использоваться высокоточные средства задатчик давления (класс не хуже 0, 1) и цифровой вольтметр (класс 0, 05). Количество уровней давления, количество отсчетов величины напряжена выбираются в соответствии с рекомендациями стандартов. В результате проделанной работы будет получена оценка погрешности каждого отдельного датчика. Систематическая погрешность практически исключается из основной погрешности.
Выполнение многократных наблюдений с последующим усреднением их результатов. При значительной величине случайной составляющей погрешности измерения используют метод повышения точности путем выполнения многократных наблюдений с последующим усреднением их результатов. В автоматизированных системах измерения легко реализуется функция многократных измерений последовательных во времени. При снятии характеристики газотурбинного двигателя измерения проводятся на стационарном режиме, когда параметр на отрезке времени, отведенном для многократных измерений, считается постоянным. Оценка величины параметра осуществляется по его усредненному значению. Обычно количество измерений выбирается в пределах 10. . . 50 зна чений. Для данного случая среднее квадратичное отклонение погрешности измерений — среднее значение σ ср при числе измерений текущих значений n опре деляют по формуле: (12. 3) где σ ср — среднее квадратичное отклонение случайной составляющей погреш ности измерения текущих значений; n — количество измерений во времени. Автоматизация измерительных процедур. Автоматизация процесса измерений позволяет устранить ошибки при считывании данных, копировании данных, построении графиков, таблиц и др. Кроме того, автоматизация существенно ускоряет процессы измерения и обработки результатов измерения. Метод сравнения с мерой позволяет существенно повысить точность измерения. Для реализации данного метода необходим компаратор и устройство, способное выдать сигнал, называемый мерой.
На компаратор подаются измерительный сигнал и сигнал, эквивалентный мере (эталон). Мера может быть регулируемой (нулевые методы) и постоянной. Результат измерений получают путем определения величины сигнала с компаратора и известной величины меры. Если при измерении путем регулирования меры добиваются нулевого показания компаратора, то такой метод называется нулевым, а если выходной сигнал с компаратора отличен от нуля, то — дифференциальным. Тестовые методы повышения точности измерений широко применяются в современных средствах измерения. В реальных условиях эксплуатации характеристика средства измерения отличается от номинальной вследствие воздействия различных внешних факторов. Если определить эти реальные величины внешних воздействующих факторов и на их основе скорректировать характеристику средства измерения, то это существенно повысит точность измерительного канала. В качестве примера использования тестовых методов можно привести автоматическую коррекцию характеристик канала измерения зазоров на основе реальных данных измерения температуры в месте измерения зазора. Информационная избыточность на практике — это добавление измерительных каналов для реализации определенных целей: повышения надежности, повышения точности. Если одну и ту же величину измерять несколькими измерительными средствами с усреднением их показаний — это и есть реализация метода информационной избыточности.
При проведении испытаний газотурбинных двигателей для определения величины давления, температуры в сечении используют специальные многоточечные устройства — приемники ( «гребенки» ). Так, например, давление на входе в компрессор измеряется 30 датчиками. Это позволяет, во-первых, решить проблему оценки поля давлений в сечении, с другой стороны, при оценке характеристики двигателя существенно повысить точность измерения параметра за счет определения давления в сечении как среднего значения по показанию 30 датчиков. 12. 4. ОБРАБОТКА РЕЗУЛЬТАТОВ ИЗМЕРЕНИЙ, ВЫПОЛНЕННЫХ В ХОДЕ АВТОМАТИЗИРОВАННЫХ ИСПЫТАНИЙ ГТД В зависимости от технического оснащения предприятия вычислительной техникой, необходимого оборудования и специалистов возможны следующие последовательности работы с измерительной информацией. 1. Между испытательным стендом и рабочим местом конструктора-расчетчика существует оптоволоконная или другая подобная связь, с помощью которой конструктор-расчетчик на экране своего компьютера имеет возможность наблюдать в темпе эксперимента все параметры двигателя и их изменение и, при необходимости, вмешиваться в процесс испытаний. Одновременно программными средствами ИВК испытательного стенда ведется первичная обработка параметров двигателя и приведение их к стандартным атмосферным условиям. Первичная и обработанная информация накапливается в базе данных на сервере. После окончания испытаний необходимая информация извлекается с сервера на персональный компьютер конструктора-расчетчика для более глубокого
анализа результатов испытаний. На рабочем месте конструктор-расчетчик имеет специальные программы, которые позволяют провести проверку правильности работы препарирования, отбраковку выпавших замеров и построение необходимых (кроме полученных с вычислительного комплекса испытательного стенда) графических зависимостей (дроссельных характеристик, полей параметров в радиальном и окружном направлениях, изменение параметров по времени и др. ). Все полученные и обработанные результаты испытаний приводятся к стандартным атмосферным условиям (р 0 = 101, 325 к. Па; Т 0 = 288, 16 К). По результатам этих расчетов строятся экспериментальные дроссельные характеристики двигателя, которые представляют собой графики зависимостей основных при веденных параметров двигателя (тяга, удельный расход топлива, расход воздуха, расход топлива, степень повышения давления воздуха в компрессоре, температура газа перед турбиной, температура газа за турбиной, КПД компрессо ра и др. ) от приведенной частоты вращения турбокомпрессора. Полученные характеристики сравниваются с расчетными дроссельными характеристиками и делается вывод об их соответствии или несоответствии заявленным параметрам. В случае несоответствия заявленным параметрам по имеющейся математической модели двигателя проводятся расчеты с учетом полученных экспериментальных данных, определяются значения КПД узлов двигателя, потери в каналах, утечки воздуха или газа из проточной части и ряд других параметров двигателя — так называемая «увязка» . Причем при «увязке» двигателя добиваются совпадения «увязочных» и экспериментальных параметров во всем диапазоне частот вращения ротора турбокомпрессора двигателя. Рассматриваемые при этом реально возможные изменения параметров невелики, обычно они составляют до 3 -5 % и лишь редко достигают 10 % от исходных значений. В указанном, а иногда и в значительно более широком диапазоне целесообразно применение приближенного метода малых отклонений, обеспечивающего наряду с простотой расчета и анализа высокую точность количественных
результатов. Метод малых отклонений основывается на возможности замены многочисленных и сложных уравнений, описывающих рабочий процесс в элементах двигателя, системой линейных однородных алгебраических уравнений, связывающих между собой небольшие изменения параметров — малые отклонения их от исходных значений, что по существу означает линеаризацию исходных уравнений в некоторой окрестности исходного состояния или режима. На практике, на этапе доводки опытного двигателя, применение метода малых отклонений заключается в проведении расчетов на земных и высотных режимах работы двигателя при постоянных значениях какого-либо из параметров (тяга, температура газа перед турбиной, частота вращения турбокомпрессора). Определяются количественные влияния анализируемых параметров (КПД компрессора, КПД турбины, полнота сгорания топлива в камере сгорания, расход воздуха, потери полного давления в переходных каналах и в сопле, плошали соплового аппарата турбины, площади сопла и др. ) при условном малом (обычно на 1 %) изменении одного из них на основные параметры двигателя (тягу, удельный расход топлива, частоту вращения, расход воздуха, расход топлива, степень повышения давления в компрессоре, температуру газа перед турбиной, температуру газа за турбиной и др. ). В дальнейшем результаты «увязки» параметров сравниваются с малыми отклонениями, делается окончательный вывод об «узлах-виновниках» неполучения параметров и проводятся работы по доводке этих узлов. После проведения доводочных работ по узлам (узлу) проводятся испытания двигателя, и такой цикл повторяется до получения заявленных параметров двигателя. В практике создания газотурбинных двигателей обработанные результаты испытаний в виде графиков и таблиц всегда представляются на обсуждение специалистов в службе главного конструктора КБ.
По результатам обсуждения принимается решение о направлении дальнейших работ по доводке двигателя или составляется отчет о результатах выполненного этапа испытаний. • При отсутствии оптоволоконной или другой подобной линии связи между испытательным стендом и рабочим местом конструктора-расчетчика последний непосредственно присутствует при испытаниях, где отслеживает параметры двигателя и, при необходимости, вмешивается в процесс испытаний. После окончания испытаний полученные результаты переписываются на электронный носитель и доставляются на рабочее место конструктора-расчетчика. Дальнейшие работы ведутся аналогично, как и в первом варианте.
РЕЗЮМЕ (по главе 12 «Обработка результатов испытаний» ) 1. Для получения измерительной информации, необходимой для определения термодинамических параметров, газотурбинный двигатель препарируют, т. е. устанавливают в основных сечениях первичные приемники и преобразователи, обеспечивающие измерение давлении и температур. 2. В силу значительной неравномерности полей температур и давлений обычно требуется поставить достаточное количество термопневмогребенок, позволяющих осреднить измерения в окружном и радиальном направлениях. 3. В процессе первичной обработки условные показания приборов переводят в численные значения физических величин. 4. В ходе вторичной обработки вычисляют неизмеряемые параметры и приводят физические параметры к стандартным атмосферным условиям. 5. В качестве типовых способов и методов повышения точности экспериментальных данных применяют: • использование более точных средств измерения; • ограничение условий применения средств измерения; • индивидуальную градуировку средств измерения; • выполнение многократных наблюдений с последующим усреднением их результатов; • автоматизацию измерительных величин. 6. Полученные в результате обработки экспериментальные данные сравниваются с расчетными дроссельными характеристиками, и делается вывод об их соответствии или несоответствии заявленным параметрам.
7. При несоответствии с заявленными параметрами проводится «увязка» измеренных и расчетных параметров. 8. На этапе доводки опытных двигателей изменение метода малых отклонений при условии малых (обычно на 1 %) изменений одного из параметров (η к , η г , G в , F СА , F C др. ) получают количественное влияние на основные параметры двигателя (Р дв , С уд и т. п. ). 9. По результатам дальнейшей «увязки» параметров делается вывод об «узлах — виновниках» недополучения параметров и проводятся работы по доводке этих узлов.
ВОПРОСЫ 1. В каких случаях проведения испытаний ГТД сохраняется ведение протокола испытания? 2. С какой целью производят препарирование испытываемого двигателя? 3. Какие приемы применяют для повышения достоверности измерений в сече ниях двигателя, обладающих повышенной неравномерностью полей давления и температуры? 4. Какие основные операции входят в первичную обработку? 5. Сущность вторичной обработки измерений? 6. Назовите основные этапы повышения точности измерений. 7. Покажите, как индивидуальная градуировка средств измерений приводит к повышению точности измерения. 8. Как осуществляется автоматизированный анализ результатов испытаний? 9. Поясните сущность применения метода малых отклонений при испытаниях газотурбинных двигателей.
Глава 13 ПЕРВИЧНЫЕ ПРЕОБРАЗОВАТЕЛИ ПРИ АВТОМАТИЗИРОВАННЫХ ИСПЫТАНИЯХ ГТД Одним из главных элементов автоматизированной системы испытаний (АСИ) являются датчики — первичные преобразователей. Датчик — это уст ройство, которое под воздействием измеряемой физической величины формирует у себя на выходе эквивалентный сигнал, чаше всего электрической природы, являющийся функцией измеряемой величины (13. 1) где Х изм — значение измеряемой величины; Р — эквивалентный сигнал на вы ходе датчика. Датчики делятся на две группы: генераторные, параметрические. Генераторные датчики обеспечивают на выходе изменяющийся электронный сигнал в виде электрического заряда, напряжения или тока. Параметрические датчики изменяют свои электрические свойства (сопротивление, индуктивность, емкость и. т. п. ) при изменении физической величины. В процессе автоматизированных испытаний авиационных двигателей используются различные типы первичных преобразователей, которые необходимы для сбора информации, на основе преобразования изменения различных физических параметров в соответствующие изменения электрических сигналов. В состав системы измерения АСИ ГТД входят датчики для регистрации следующих параметров: • тяги (крутящего момента мощности); • расхода (топлива и масла); • частоты вращения ротора;
• угловых перемещений (а РУД, регулировочных элементов); • давлений и температур (до 90 % от общего количества датчиков, применяемых при испытаниях ГТД); • напряжений в деталях; • виброускорений. Кроме того, при проведении исследований ГТД применяются специальные иды датчиков для измерения: • зазоров и перемещений; • пульсирующих давлений; • углов поворота и др. 13. 1 ИЗМЕРЕНИЕ ТЕМПЕРАТУРЫ Для измерения температуры ГТД наиболее широко применяются термометры электрического сопротивления и термопары. Термопреобразователи сопротивления (ТС). Под ТС принято понимать термо приемник, у которого под действием окружающей температуры меняется элек трическое сопротивление проводника: (13. 2) где (ω 0 — сопротивление проводника при 0 °С; α — температурный коэффициент электрического сопротивления; Т — измеряемая температура. С помощью ТС изменение температуры преобразуется в эквивалентное изменение электрического сопротивления проводника.
В практике обычно применяются два типа ТС: • металлические, где в качестве материала проводника используются: платина, медь, никель; • полупроводниковые, изготовленные на основе смеси оксидов или сульфидов различных металлов. Металлические ТС , выпускаемые промышленностью, обычно изготавлива ются с чувствительным элементом из следующих материалов: платина (ТСП), медь (ТСМ), никель (ТСН). Чистая платина — наилучший и наиболее распространенный материал для изготовления чувствительных элементов ТС. Неокисляющаяся платина дли тельное время сохраняет величину удельного электрического сопротивления. Платиновые чувствительные элементы хорошо работают в широком диапазоне температур, как отрицательных, так и положительных. ТСП обычно используются в диапазоне от -260 до +850 °С и для единичного производства в диапазоне до +1100 °С. Применение ТСП для измерения высоких температур ограничивается эф фектом испарения, приводящим к изменению сопротивления платиновой проволоки. ТСП — наиболее точные приборы для измерения температуры, отличаю щиеся высокой воспроизводимостью показаний. Медь, применяемая для изготовления проводников ТСМ, отличается очень высокой степенью чистоты. Поэтому ТСМ из этой проволоки очень хорошо взаимозаменяются. Сильная окисляемость меди при высокой температуре ог раничивает температурный предел применения медных ТСМ. Обычно ТСМ применяют в диапазоне от -200 до +200 °С.
Технически чистый никель отличается высоким температурным коэффициентом сопротивления и практически линейной зависимостью удельного сопротивления от температуры в диапазоне до 400 °С. Значительная окисляемость никеля не позволяет применять его для измерения высоких температур. Обычно ТСН применяют в диапазоне от -50 до +180 °С. Полупроводниковые ТС отличаются тем, что их чувствительность к температуре значительно выше (приблизительно в 10 раз), чем у металлических. Температурный коэффициент, как правило, отрицательный и существенно зависит от температуры. Рис. 13. 1. Термопреобразователь сопротивления ТСП Метран-206 (100 П) Высокое удельное сопротивление материала ТС позволяет получить необходимое сопротивление уже в малых объемах вещества, из которого изготовляются ТС. Полупроводниковые ТС могут иметь малые габариты, около 1 мм, в результате это позволяет проводить измерение температуры практически в точке, причем с малой инерционностью. Полупроводниковые ТС называют часто термисторами и используют обычно в диапазоне отрицательных температур и положительных до 300 °С.
В общем случае уравнение преобразования термистора выражается соотношением: (13. 3) где A , В, b — постоянные коэффициенты, зависящие от свойств материала чувствительного элемента; Т — измеряемая температура. Следовательно, при увеличении температуры сопротивление термистора уменьшается. К недостаткам полупроводниковых ТС относятся: значительная нелинейность зависимости сопротивления от температуры; нестабильность характеристики во времени и, как следствие, высокая погрешность. Внешний вид термопреобразователей сопротивления показан на рис. 13. 1. ТС состоит из чувствительного элемента, расположенного внутри защитной гильзы, резьбовой части с гайкой (для вворачивания в корпус объекта измере ния температуры) и головки датчика (для размещения присоединительных контактов). Защитная гильза выполняется из материала, обеспечивающего защиту чувствительного элемента от действия повышенного давления и воздействия агрессивных свойств среды. Рис. 13. 2. Схема подключения измерительного прибора к концам термопары
Термопары. Под термопарой принято понимать два проводника из разнородных металлов (термоэлектроды), соединенных на одном конце и образующих часть устройства, использующего термоэлектрический эффект для измерена температуры. На рисунке 13. 2 приведена схема подключения измерительного прибора концам термопары. Основная формула термопары для термоэлектродвижущей силы имеет следующий вид: (13. 4) Где t 1 — температура места соединения проводников термопары и подводя щи: проводников; t 2 — температура рабочего спая. Если в термопаре из термоэлектродных проводников a и b температуру t поддерживать постоянной, то термо. ЭДС (ТЭДС) термопары будет однозначно зависеть от температуры t 2. Следовательно, по измеряемой величине ТЭДС можно найти величину температуры. В рабочих условиях поддержание постоянной температуры на свободны; концах термопары осуществляется путем помещения их в термостат. Используют два вида термостатов: • активный, с поддержанием температуры внутри термостата обычно на уровне 40. . . 45 °С; • пассивный термостат, обеспечивающий только медленное изменение температуры t 1. Внутри термостата устанавливается один или два термопреобразователя со противления для измерения температуры свободных концов. Учет температуры свободных концов или, как их еще называют, холодной спая в системе измерения осуществляется автоматически по программе компенсации температуры холодного спая.
На испытательных стендах невыгодно тянуть длинные и достаточно дороги» термопарные провода от точки измерения температур до измерительных цепей В этом случае для удлинения термопары и соответственно удаления холодной спая от места нагрева (двигателя) широко применяют так называемые компенсационные провода. Такая схема подключения термопар к измерительному прибору приведен; на рис. 13. 3. Рис. 13. 3. Цепь термопары с компенсационными проводниками
Компенсационные провода, удаляя свободные концы в точку В с температурой t 0 , не вносят дополнительной погрешности в результаты измерения ТЭДС при соблюдении следующих требований: • применение для каждого типа термопар соответствующих компенсацион ных проводов; • соблюдение полярности компенсационных проводов при их подклю чении; • обеспечение в сечении Л, в точках соединения термоэлектродных провод ников с компенсационным проводом одинаковых температур t. Номинальные статические характеристики преобразования (НСХ) термопары — это номинально приписываемые термопаре данного типа зависимости ТЭДС от температуры рабочего спая и при заданной температуре свободных концов, выраженные в м. В. НСХ преобразования для различных типов термопар установлены ГОСТ Р 8. 585 -2005. Этот стандарт применяют при разработке нормативных и технических документов, распространяющихся на термопары. В указанном стандарте НСХ преобразования термопар типов R, S, В, J, Т, Е, К, М по Международной шкале и термопар типов A, L, М, применяемых в России, представлены значениями ТЭДС в зависимости от температуры рабочего спая, при температуре свободных концов 0 °С. Данные по типам термопар, термоэлектродным материалам, обозначениям промышленных преобразователей сведены в таблицу 13. 1.
Обозначение промышленного термопреобразователя Обозначение типа термопары Термоэлектродный материал Положительный Отрицательный Вольфрам-рений/ вольфрамрениевые ТВР А-1, А-2, А-3 Сплав вольфрам-рений BP-5 (95%W + 5%Re) BP-20 (80%W + 20%Re) Платинородий/платинородиевые ТПР В Сплав платинородий ПР-30(70%Р 1 + 30% Rh) ПР-6 (94%Pt + 6%Rh)13. 1. Выпускаемые промышленностью термопары
Обозначение промышленного термопреобразователя Обозначен ие типа термопары Термоэлектродный материал Положительный Отрицательный Платинородий/плати- новые ТПР S R Сплав платинородий Платина П Р-10(90% Pt+ 10% Rh) П Р-13(87% Pt+ 13% Rh) Пл. Т (Pt) Никель-хром/никель- алюминиевые (хромель-алюмель)* ТХА К Сплав хромель Сплав алюмель THX 9, 5(90, 5%Ni + 9, 5%Сг) НМи. АК 2 -2 -1 (94, 5%Ni + 5. 5%AI. Si. Mn, Co) Никель-хром/медь-никелевые (хромель-константановые)’ ТХКн Е Сплав хромель Сплав константан THX 9, 5(90, 5%Ni + 9, 5%Сг) (55%Cu + 45%Ni. Mn, Fe) Хромель/копелевые’ ТХК L Сплав хромель Сплав копель THX 9, 5(90, 5%Ni+9, 5%Cr) M H M u 43 -0, 5 (56%Cu + 44%Ni) Медь/медьникелевые (медьконстантановые)* ТМК Т Медь Сплав константан Ml (Си) (55%Cu + 45%Ni. Mn. Fe)
Никель-хром-кремний/никель- кремниевые (нихросилнисиловые)* ТНН N Сплав нихросил Сплав нисил (83. 49 + 84, 89)%Ni+ + (13, 7+14. 7)%Сr + (1, 2 + + l, 6)%Si+ 0, 15%Fe+ + 0, 05%С + 0. 01%Mg (94, 98 + 95, 53)%Ni + + 0, 02%Cr + (4, 2 + 4, 6)%Si + + 0, 15%Fe + 0, 05%C + + (0, 05 + 0. 2)%Mg Железо-медь/никелевые (железоконстантановые)- ТЖК J Железо Сплав константан (Fe) (55%Cu + 45%Ni, Mn, Fe) Медь/копелевые* ТМ К М Медь Сплав копель Ml (Си) (56%Cu + 44%Ni) * Наименование, принятое в России. Примечание. Химический состав материалов термоэлектродов ориентировочный.
Реальный, изготовленный в соответствии с требованиями ГОСТ экземпляр термопары имеет свою индивидуальную зависимость ТЭДС от температуры рабочего спая. Это связано с неоднородностью состава термоэлектродной проволоки. В связи с этим ГОСТ Р 8. 585 -2005 содержит не только номинальные статические характеристики термопары данного типа, но также регламентирует пределы допустимых отклонений реальных ТЭДС от НСХ, выраженных в °С (табл. 13. 2). Обозначение промышленного термопреобразователя Обозначение типа термопары Класс допуска Диапазон измерений, °С Пределы допускаемых отклонений ТЭДС от НСХ ± Δt, °С ТПП S, R 2 От 0 до 600 Св. 600 до 1600 1, 5 0, 0025 t 1 От 0 до 1100 Св. 1100 до 1600 1, 0+0, 003(t- 1100) ТПР В 3 От 600 до 800 Св. 800 до 1800 4, 0 0, 005 t 13. 2. Диапазон измерения термопар
ТХК L 2 От 600 до 1800 0, 0025 t 3 От -200 до -100 Св. -100 до +100 1, 5+0, 011 t| 2, 5 2 От -40 до +360 Св. 360 до 800 2, 5 0, 7 + 0, 005 t ТХКн Е 3 От-200 до-167 Св. -167 до +40 0, 015|t| 2, 5 2 От -40 до +333 Св. 333 до 900 2, 5 0, 0075 t 1 От -40 до +375 Св. 375 до 800 1, 5 0, 004 t ТХА. ТНН К, N 3 От -250 до -167 Св. -167 до +40 0, 015|t| 2, 5 2 От -40 до +333 Св. 333 до 1300 2, 5 0, 0075 t 1 От -40 до +375 Св. 375 до 1300 1, 5 0, 004 t
ТМК Т 3 От -200 до -66 Св. -66 до +40 0, 015|t| 1, 0 2 От -40 до +135 Св. 135 до 400 1, 0 0, 0075 t 1 От -40 до +125 Св. 125 до 350 0, 5 0, 004 t ТЖК J 2 От 0 до 333 Св. 333 до 900 2, 5 0, 0075 t 1 От -40 до +375 Св. 375 до 750 1, 5 0, 004 t ТМК M — От -200 до 0 Св. 0 до 100 1, 3 + 0, 001|t| 1, 0 ТВР А-1 А-2 А-3 3 От 1000 до 2500 0, 007 t 2 От 1000 до 2500 0, 005 t
Термопары обладают рядом несомненных достоинств по сравнению с термопреобразователями сопротивления: • малыми габаритами, что позволяет проводить измерения практически в точке; • малой инерционностью; • широким диапазоном измеряемых температур; • механической прочностью; • не требуют дополнительного источника питания. В то же время термопары имеют ряд недостатков: большую по сравнению с ТСП, ТСМ погрешность, слабые выходные сигналы, измеряемые в м. В. Градуировка термопар. Точность термопары можно повысить за счет снятия индивидуальной характеристики путем градуировки. Под градуировкой термопары понимают определение числовых значений ее ТЭДС при различных значениях температур t 2 ее рабочего спая и определенной температуре t 1 свободных концов. Обычно определение значений температур и соответствующих им значений ТЭДС проводится с помощью образцового прибора методом сличения. Под методом сличения принято понимать непосредственное измерение ТЭДС градуируемой термопары при различных температурах t 2 ее рабочего конца и из вестной температуре свободных концов. Причем значение t 2 определяется либо с помощью образцовой термопары, либо с помощью другого образцового прибора. Для целей градуировки используют специальные «поверочные» печи. Конструкция термопар аналогична конструкции термометров сопротивления, имеет защитную гильзу при закрытом рабочем спае или защитный корпус, если рабочий спай выводится за пределы
Рис. 13. 4. Преобразователь термоэлектрический хромель-алюмелевый 1 ХА 9425 Для вворачивания термопары в кор пус объекта имеются резьбовая часть и гайка. Контакты термопар для подключе ния к измерительным цепям расположены в головке термопары. На рис 13. 4 приведена конструк ция термопары ТХА 9425. Электрическая схема включения для варианта одноточечной и сдвоенной термопар приведена на рис 13. 5. Термопары с унифицированным выход ным сигналом. В связи со стремительным развитием электроники, уменьшением габаритов электронных устройств, при одновременном повышении точности и стабильности их характеристик широкое применение находят термопары с унифицированным выходным сигналом. Такие термопары содержат не только термоэлектродные провода с рабочим спаем, но также преобразователь сигналов с термопары (м. В) в унифицированный сигнал, например: 0. . . 5 м. А, . 20 м. А. Примером такой термопары может быть термопара ТХАУ Метран- 271 (табл. 13. 3). К недостаткам термопар с унифицированным выходным сигналом следует отнести узкий диапазон рабочих температур, который может быть обработан устройством преобразования.
Рис. 13. 5. Электрическая схема включения одноточечной (а) и сдвоенной (б) термопар Тип и исполнение НСХ Выходной сигнал, м. А Диапазон пре- образования, °С Предел допускаемой погрешности, ± 5, % ТХАУ Метран-271 К 4. . . 20 0. . . 600 0. . . 800 0. . . 900 0. . . 1000 0, 5; 1, 0 ТХАУ Метран-271 — Exia 0. . . 600 ТХАУ Метран-271 — Exd 0. . . 80013. 3. Технические данные термопары Метран-
Преобразователь обычно располагается в головке термопары. На оболочке двигателя, в месте расположения головки термопары, температуры могут достигать 100. . . 150 °С, что делает проблематичным использование таких термопар. Несомненным достоинством данного типа термопар является унификация выходных сигналов и, следовательно, существенное упрощение схемы системы измерения. 13. 2. ИЗМЕРЕНИЕ ДАВЛЕНИЯ Давление — это один из наиболее важных физических параметров, характеризующих состояние рабочего тела газотурбинного двигателя. Наряду с измерением температур измерение давлений составляет основную часть объема измеряемых параметров. В табл. 13. 4. приведено соответствие единиц давления. Классификация средств измерения давления. Манометр — широко применяемый прибор, предназначенный для отображения давления непосредственно по шкале, табло, индикатору. Измерительный преобразователь давления (ИПД), или датчик давления, — прибор, который позволяет получать и дистанционно передавать электриче ский сигнал, пропорциональный измеряемому параметру. В настоящее время широко используются ИПД, имеющие индикацию (функ ции манометра) и выход на измерительные цепи системы контроля параметров. По принципу действия манометры подразделяются на: • жидкостные, где измеряемое давление уравновешивается гидростатиче ским столбом жидкости — воды, ртути; • деформационные, когда давление определяется по величине деформации и перемещения упругого чувствительного элемента;
• грузопоршневые, когда измеряемое давление уравновешивается весом поршня с комплектом образцовых гирь; Системы единиц Единицы давления Па (Ра) кгс/см 2 (at) бар (bar) атм (atm) мм рт. ст. (mm Hg) мм вод. ст. (mm Н 2 0) пси (psi) СИ (SI) 1 Па= 1 Н/м 2 1 1, 01972∙ 10 -5 10 — 5 0, 9869∙ 10 — 5 750, 06∙ 10 -5 0. 101972 1, 45∙ 10 4 МКГСС 1 ат= 1 кгс/см 2 0, 980665∙ 10 5 1 0, 9806 0, 9678 735, 563 I 0 4 14, 223 Внесисте мные 1 бар = = 10 6 дин/см 2 10 5 1, 01972 1 0, 9869 750, 06 1, 01972∙ 10* 14. 5 1 атм = 760 мм рт. ст. 1, 01325∙ 10 5 1, 0332 1, 0132 1 760 1, 0332∙ 10 4 14, 696 1 мм рт. ст. 133, 322 1, 3595∙ 10 3 1, 3332∙ 10 -3 1, 31579∙ 10 -3 1 13, 5951 0, 019337 1 мм вод. ст. 9, 80665 10 -4 9. 8066∙ 10 -5 9, 6784∙ 10 -5 7, 3556∙ 10 -2 1 1. 422∙ 10 -3 1 psi = 1 lbf/in 2 6, 894∙ 10 3 ≈ 0, 07 6. 894∙ 10 -2 0, 068 51, 715 703, 08 113. 4. Соответствие единиц давления
• электрические, когда давление определяется на основании зависимости электрических параметров (сопротивления, емкости, заряда, частоты) чувствительного элемента от измеряемого давления. По виду измеряемого давления манометры и ИПД делятся на приборы измерения: • абсолютного давления; • избыточного давления; • разрежения (вакуумметры); • давления и разрежения (мановакуумметры); • атмосферного давления (барометры); • разностного давления (дифференциальные манометры). По области применения манометры (ИПД) делятся на: • общепромышленные; • лабораторные; • специальные (для экстремальных условий применения); • образцовые (для поверки рабочих манометров); • эталонные (хранители единиц давления, для их передачи на образцовые средства измерения). Измерение давления в потоке жидкости или газа. При измерении давления в потоке жидкости или газа и при обтекании тел потоком жидкости или газа на их поверхности устанавливается определенное распределение давления. В точке носка тела, расположенной на оси тела (критической точке), давление на по верхности равно давлению заторможенного потока, представляющему собой сумму статического давления и скоростного напора. Статическое давление р в потоке равно давлению на стенке трубы, создаваемому покоящейся или текущей параллельно стенке трубы жидкостью (газом). Приемником статического давления является сверление на стенке канала. Диа метр отверстий должен быть 0, 5. . . 1, 5 мм. Отверстия меньшего диаметра
легко засоряются, большего дают значительную ошибку измерения. Кромки отверстий не должны иметь заусенцев, фасок и скруглений. Скоростной напор — давление, создаваемое движением потока. Для несжимаемой жидкости, а также для газа, текущего с малой скоростью, скоростной напор определяется как ρ V 2 /2, где V — скорость потока, а ρ — плотность. Приемники давления заторможенного потока выполняются в виде Г-образ- ной трубки, обращенной отверстием навстречу потоку. Используются также более сложные приемники заторможенного давления, обладающие малой чувствительностью к углу набегания потока. Кроме того, при испытаниях ГТД применяются комбинированные насадки с приемниками заторможенного и статического давлений. Приемники давления соединяются с датчиками так на зываемыми «импульсными» трубопроводами. «Импульсный трубопровод» — это, чаще всего, металлические трубки с диаметром сечения около 4 мм. При измерении постоянных давлений для гашения пульсаций давления на входе в датчик применяют специальные гасители. Простейший гаситель — это капиллярная трубка достаточной длины. Датчики давления деформационные с упругими элементами. Под действием давления упругий элемент меняет свои размеры (форму). Деформация преобразуется либо в перемещение стрелки прибора, либо в электрический сигнал. Используются следующие типы датчиков давлений: индукционные; потенциометрические; вибрационно-частотные; тензометрические; емкостные. На рис. 13. 6 приведены часто применяемые конструкции датчиков давления деформационного типа с упругими элементами.
Рис. 13. 6. Датчики давления с упругими чувствительными элементами: / — упругий подвес: 2 — тяга; 3 — давление; 4 — упругая связь; 5 — к мостовой цепи; 6 — сильфонный вывод; 7 — сильфон На рис. 13. 6, а приведен датчик с чувствительным элементом — трубке Бурдона. Трубка с плоским поперечным сечением, изогнутая по неполной дуг спирали или винтообразной линии, стремится под действием давления выпрямиться. Перемещение передается на стрелку прибора. Измеряет разность между внешним и внутренним давлением. Величина давления преобразуется в электрический сигнал. Датчик с чувствительным элементом — полой и скрученной трубкой показан на рис. 13. 6, б. Один конец трубки закрыт, а на другой подается давление. Датчик потенциометрический (рис. 13. 6, в) преобразует величину давления в величину электрического сопротивления. Перемещение мембранной коробки, или трубки Бурдона, передается на подвижный контакт прецизионного потенциометра.
Односильфонный датчик давления (рис 13. 6, г). Используется вакуумированный сильфон, который помещается в корпус, куда подается измеряемое давление. Перемещение центра измерительного сильфона передается через рычаг и упругий сильфонный выход к указывающей стрелке. Тензорезисторные ИПД. Среди электрических ИПД наиболее частое применение находят тензорезисторные, использующие зависимость активного сопротивления проводника или полупроводника от степени его деформации. Измеряемое давление подается в рабочую полость датчика и воздействует непосредственно на измерительную мембрану тензопреобразователя, вызывая ее прогиб. Чувствительный элемент — пластина монокристаллического сапфира кремниевыми пленочными тензорезисторами, соединенная механически с металлической мембраной тензопреобразователя. Деформация измерительной мембраны приводит к пропорциональному изменению сопротивления тензорезисторов и разбалансу мостовой схемы. На рис. 13. 7 приведена структурная схема тензорезисторного ИПД. Электрический сигнал с выхода мостовой схемы датчика поступает в электронный блок, где преобразуется в унифицированный токовый сигнал. Примером серийно выпускаемых ИПД, основанных на тензорезисторах, является продукция группы компаний «Метран» . Внешний вид датчика «Метран-100» моделей 1050, 1060, 1150, 1160, 1350 приведен на рис. 13. 8. Датчик имеет резьбовую часть для присоединения к магистрали (трубопро воду), тензопреобразователь и электронный блок. Измеряемые среды: жидкость, пар, газ, в том числе газообразный кислород и кислородосодержащие газовые смеси.
Рис. 13. 7. Структурная схема тензорезисторного ИПД Рис. 13. 8. Датчик «Метран-100»
Диапазоны измерения давлений: минимальный 0. . . 0, 04 к. Па, максимальный 0. . . 100 МПа. Основная погрешность измерений — 0, 1 %. Датчик давления серии «Метран-100» предназначен для измерения и непрерывного преобразования в унифицированный аналоговый токовый сигнал и/или цифровой сигнал следующих входных величин: • избыточного давления (Метран-100 -ДИ); • абсолютного давления (Метран- 100 -ДА); • разрежения (Метран-100 ДВ); • давления — разрежения (Метран-100 ДИВ); • разности давлений (Метран-100 ДД); • гидростатического давления (Метран-100 ДГ). Управление параметрами датчика может быть кнопочное со встроенной панели либо с помощью коммутатора или компьютера. 13. 3 ДАТЧИКИ ИЗМЕРЕНИЯ ЧАСТОТЫ ВРАЩЕНИЯ При испытании ГТД важными параметрами являются частоты вращения роторов. По величинам этих параметров определяют режим работы двигателя, а также оценивают его термодинамические, прочностные характеристики. Существуют различные методы и конструкции датчиков частоты вращения. Наиболее часто применяют электрические методы измерения частоты вращения: оптические; индукционные; импульсные; генераторные. Оптический (фотоэлектрический) метод. Датчик в этом случае состоит их диска с отверстиями, или прорезями, фотоэлемента, источника света. Диск устанавливается на валу, частоту вращения которого измеряют. Световой поток от источника света проходит через отверстия и попадает на фотоэлемент. При вращении диска на выходе схемы измерения получают импульсы, частота которых пропорциональна частоте вращения вала и зависит от количества отверстий (прорезей) на диске.
Для расчета частоты вращения обычно используют счетчик количества импульсов за интервал времени (13. 5) В этом случае частота вращения, 1/мин, может быть рассчитана по формуле: где N — число импульсов в счетчике за интервал времени t; к — число отверстий (прорезей) в диске. Индукционный метод. Датчик, основанный на индукционном методе, состоит из диска, изготовленного из магнитного материала и измерительной катушки с магнитным сердечником. На торце диска делаются прорези или выступы. На рис 13. 9 представлена схема, поясняющая принцип действия датчика. Измерительная катушка располагается на небольшом расстоянии от диска (шестерни). При вращении диска мимо катушки проходят выступы и впадины диска, что приводит к изменению магнитного сопротивления катушки. В катушке наводится ЭДС с частотой, пропорциональной частоте вращения вала и количеству выступов на диске. Амплитуда выходного сигнала зависит от величины зазора между катушкой и диском и от скорости вращения вала. На малых частотах вращения амплитуда сигнала резко уменьшается, поэтому этот метод для измерения малых частот вращения обычно не применяется. Импульсный метод. При использовании этого метода вместо измерительной катушки устанавливается датчик Холла, на выходе которого вырабатываются импульсы, частота следования которых пропорциональна частоте вращения вата и числу выступов (прорезей) на диске.
Рис. 13. 9. Принцип действия индукционного датчика: 1 — постоянный магнит; 2 — сердечник; 3 — зазор; 4 — шестерня Принцип действия датчика Холла основан на реакции электронной схемы и чув ствительного элемента на изменение магнитного поля. Это изменение происходит за счет прохождения выступа на диске в зазоре между полюсами датчика. На выходе датчика появляются импульсы. . Амплитуда сигнала в этом методе менее чувствительна к частоте вращения, поэтому метод может использоваться на малых частотах вращения валов. Измерение частоты вращения валов датчиком высокой частоты. В качестве примера практической схемы измерения частоты вращения валов ГТД рассмотрим схему измерения частоты вращения вала низкого давления (НД). Рис. 13. 10. Датчик ДЧВ-2500 А
В схеме измерения используется датчик типа ДЧВ-2500 А (рис. 13. 10). Датчик ДЧВ-2500 А предназначен для преобразования частоты вращения ротора двигателя в частоту электрических импульсов, выдаваемых по двум электрически не связанным каналам. Основным узлом датчика ДЧВ-2500 А является бескаркасная катушка, состоящая из двух обмоток с постоянным магнитом в качестве сердечника. Катушка с магнитом размещается в корпусе, выполненном из немагнитной нержавеющей стали в виде тонкостенного стакана. Для крепления датчика на корпусе имеется буртик, который прижимается к посадочной поверхности фланцем соответствующей конфигурации и является принадлежностью двигателя. Основным узлом датчика ДЧВ-2500 А является бескаркасная катушка, состоящая из двух обмоток с постоянным магнитом в качестве сердечника. Катушка с магнитом размещается в корпусе, выполненном из немагнитной нержавеющей стали в виде тонкостенного стакана. Для крепления датчика на корпусе имеется буртик, который прижимается к посадочной поверхности фланцем соответствующей конфигурации и является принадлежностью двигателя. Датчик ДЧВ-2500 А работает совместно с индуктором (зубчатым колесом), приводимым во вращение от вала соответствующего ротора через шестеренчатую передачу. При вращении индуктора каждый из его зубьев, проходя в непосредственной близости от торца датчика, изменяет магнитное поле, окружающее витки катушки датчика. В катушке индуцируется ЭДС, пропорциональная по частоте и амплитуде частоте вращения зубчатого колеса. На выходе схемы измерения частоты вращения формируются импульсы. ДЧВ-2500 А
Сигналы со схем измерения частоты вращения валов поступают в систему автоматического управления газотурбинной установки и используются для кон троля параметров (от всех роторов), для защиты двигателя (от ротора свободной турбины). На рис. 13. 11 приведена конструктивная схема установки датчиков ДЧВ-2500 А. Рис. 13. 11. Установка датчиков ДЧВ-2500 А на коробке приводов НД На коробке приводов агрегатов вала низкого давления установлены два датчика, каждый из которых имеет две независимые обмотки катушки индуктивности. Дублирование каналов измерения частоты вращения вала необходимо, во-первых, для повышения надежности контроля и зашиты двигателя, а также и для распараллеливания сигналов на различные потребители информации. Датчики тахогенераторные (ЛТ). Тахогенераторные датчики входят в состав дистанционных стрелочных тахометров (ДТЭ-1; ДТЭ-2; ТСФУ-1 -4). ДТЭ — это трехфазный синхронный генератор. Его вал через редуктор коробки приводов связан с ротором двигателя.
При вращении ротора на выходе из ДТ формируется электрический сигнал в виде синусоидального напряжения. Частота и амплитуда этого напряжения пропорциональны частоте вращения ротора двигателя — n : (13. 6) При изменении n = 250. . . 3000 об/мин на выходе из ДТ создается сигнал с частотой / = 8. . . 100 Гц и напряжением U= 2, 5. . . 25 В. 13. 4 ДАТЧИКИ ИЗМЕРЕНИЯ РАСХОДА ТОПЛИВА (ТОПЛИВНОГО ГАЗА) Расходом называется количество жидкости (газа), протекающее через попе речное сечение потока в единицу времени. В зависимости от единиц измерения количества жидкости (газа) расход мо жет быть объемным ( Q , м 3 /с) или массовым (С, кг/с). Массовый и объемный расходы связаны соотношением: G = ρQ, (13. 7) где р — плотность газа. Расход топлива чрезвычайно важен для оценки характеристик двигателя, поэтому при проведении испытаний ему уделяется большое внимание и предъ являются достаточно высокие требования по точности измерения (0, 3 % от из меряемого значения (ИЗ) для опытного производства). Расход топлива на двигателе — величина переменная, поэтому при проведе нии измерений говорят о мгновенном расходе — значении расхода в данный момент времени, среднем расходе — осредненном значении за определенный промежуток времени. Мгновенные значения расхода важны при измерении параметров двигателя на переменных режимах, запуске, приемистостях, сбросе газа.
Осредненные значения расхода используются при снятии характеристики двигателя. Устройства, предназначенные для измерения расхода топлива, называются расходомерами и подразделяются на объемные и массовые. В практике измерений расхода жидкостей и газа применяются различные типы расходомеров, основанные на различных физических явлениях: • расходомеры переменного перепада давления (с сужающими устройствами); • турбинные расходомеры; • электромагнитные расходомеры; • ультразвуковые расходомеры; • инерционные расходомеры (основанные на инерционном воздействии массы движущейся жидкости, газа) и другие. Наиболее широкое применение в практике стендовых испытаний газотур бинных двигателей получили методы, основанные на измерении перепада дав ления на сужающем устройстве, турбинные, вихреакустические и кориолисовые расходомеры. Измерение расхода и количества жидкостей и газов методом переменного пере пада давления. Принцип метода состоит в том, что в трубопровод, по которому протекает среда, устанавливают сужающее устройство (СУ), создающее местное сопротивление. Вследствие перехода части потенциальной энергии потока в кинетическую, средняя скорость потока в суженном сечении повышается, в результате чего статическое давление в этом сечении уменьшается и становится меньше статического давления перед СУ. Разность эта тем больше, чем больше расход протекающей среды, и, следовательно, перепад давления на СУ может служить мерой расхода. Перепад давления связан с объемным расходом жидкости (газа) соотношением вида:
(13. 8) где ρ — плотность жидкости; К — константа, определяемая в некотором диапазоне чисел Рейнольдса только геометрией устройства. Расходомерные устройства на основе сужаюoих устройств рассчитывают по ГОСТ 8. 586. 5 -2005. Турбинные расходомеры являются наиболее точными приборами для измерения расхода жидкостей. Приведенная погрешность измерения составляет значение порядка 0, 5 %. При проведении индивидуальной градуировки (проливки) датчика достигают более высокой точности измерения (0, 2. . . 0, 3 %). Датчики просты по конструкции, имеют высокую чувствительность и широкий диапазон измерения. При стендовых испытаниях ГТД турбинные расходомеры используются для измерения расхода керосина. Турбинный расходомер состоит (рис. 13. 12) из турбинки 3, индуктивной катушки 4, регистрирующего прибора 1. Турбинка 3 представляет собой аксиальную или тангенциальную лопастную турбинку, опирающуюся на подшипники 2. Поток измеряемой среды, воздействуя на наклонные лопасти турбинки, сообщает ей вращательное движение с угловой скоростью, пропорциональной расходу Q. Лопасти турбинки, проходя мимо индукционной катушки, наводят в ней ЭДС импульсной формы. Частота следования импульсов за висит от количества лопастей и пропорциональна угловой скорости вращения турбинки, а следовательно, расходу. Расход Q рассчитывается по формуле: (13. 9)
где к — коэффициент наклона характеристики расходомера; f— частота сигнала на выходе индукционной катушки. Турбинные расходомеры вследствие их малой инерционности применяются для измерения на переменных режимах. Они находят применение там, где требуется высокая точность измерения. Для повышения точности и надежности измерений на стендах по испыта нию ГТД применяют специальные конструкции — расходомерные участки с двумя встроенными турбинными расходомерами. Для выравнивания потока жидкости перед датчиком расходомерные участки снабжаются специальным! выравнивающими устройствами, что позволяет сократить длину прямолиней ного участка трубопровода перед расходомером. Электромагнитные расходомеры предназначены для измерений объемного расхода электропроводных жидкостей. Основные преимущества электромагнитных расходомеров: • применение для измерения расхода агрессивных сред; • достаточно высокая точность измерения; • малые потери давления. Расходомеры данного типа используются на стендах для измерения расход воды и технологических жидкостей. Расходомер основан на принципе появления ЭДС в проводнике, пересекающем силовые линии магнитного поля. Причем величина ЭДС пропорционально на скорости движения проводника. При этом направление тока, возникающей в проводнике, перпендикулярно направлению движения проводника и направлению магнитного поля.
Схема электромагнитного расходомера приведена на рис 13. Рис. 13. Электромагнитный расходомер и схема формирования сигнала
Расходомер состоит из двух катушек, создающих магнитное поле, и двух элек тродов для съема ЭДС. Сигнал с электродов, пропорциональный величине расхода, усиливается и фильтруется. В качестве примера расходомера электромагнитного на рис. 13. 14 приведен расходомер серии 8700 фирмы Метран. Расходомер электромагнитный се рии 8700 состоит из датчика расхода и преобразователя. Датчик устанавливается непосредственно в трубу бесфланцевым или фланцевым соединением. В датчик вмонтированы две катушки индуктивности и два электрода для съема сигнала. Сигнал с электродов усиливается и преобразуется в преобразователе. Внутренняя поверхность трубы датчика покрывается неэлектропроводным материалом. Предел основной допускаемой погрешности датчика ± 0, 5 %. Вихреакустические расходомеры. Суть вихревого метода измерения расхода состоит в измерении скорости потока путем определения частоты образования вихрей за телом обтекания, установленным в проточной части преобразователя расхода. На рис. 13. 15 приведена схема вихревого расходомера. Рис. 13. 14. Расходомер электромагнитный серии 8700 фирмы Метран
При движении среды в трубопроводе за телом обтекания появляется вихревая дорожка, частота появления вихрей в которой с высокой точностью Рис. 13. 15. Схема, поясняющая принцип действия вихреакустического расходомера: 1 — тело обтекания; 2 — пьезоэлектрический преобразователь; 3 — измеритель избыточного давления в точке перед телом обтекания; 4 — термопреобразователь платиновый; 5 — отверстие для подвода среды к термопреобразователю; 6 — плата цифровой обработки; 7 — вычислитель Рис. 13. 16. Расходомер Метран-
пропорциональна скорости потока, а следовательно, и расходу. В свою очередь, вихреобразование приводит к появлению за телом обтекания пульсаций давления среды. Частота пульсаций давления идентична частоте вихреобразования и служит мерой расхода. Пульсации давления воспринимаются пьезоэлектрическими датчиками, сигналы с которых в виде электрических колебаний поступают на плату цифровой обработки, где происходит вычисление расхода. Для учета давления среды и ее температуры измеряются избыточное давление в трубопроводе (с помощью тензорезисторного преобразователя) и температура (с помощью платинового термометра сопротивления). Плата цифровой обработки и вычислитель проводят обработку сигналов: преобразование; фильтрацию; расчет величины расхода с учетом давления и температуры среды; выдачу нормированных сигналов. Конструкция расходомера, основанного на вихреакустическом принципе, приведена на рис 13. 16. Кориолисовый расходомер. Расходомеры данного типа основаны на принципе инерционного воздействия массы движущейся жидкости или газа на чувствительный элемент. Они имеют высокую точность, не требуют специальных прямолинейных участков и оборудования для формирования потока.
Рис. 13. 17. Конструкция кориолисового расходомера На рис. 13. 17 приведена схема, поясняющая принцип действия и конструкцию расходомера. Чувствительным элементом расходомера являются две трубки. По ним движется поток жидкости, который разделяется в трубках на две равные части. Около трубок установлены задающие катушки, которые заставляют эти рубки колебаться в противоположном направлении. При отсутствии расхода на детекторах (см. рис. 13. 15) формируются синхроидальные сигналы с одинаковой фазой. При движении измеряемой среды через колеблющиеся расходомерные трубки возникает эффект Кориолиса — возникает кориолисовое ускорение, а следовательно, кориолисовая сила. Эта сила направлена против движения трубки, приданного ей задающей катушкой. В результате воздействия кориолисовой силы на трубки они изгибаются под действием кориолисовой силы, в результате на детекторах (входном и выходном) появляется сдвиг фаз. Величина изгиба, величина сдвига фаз прямо пропорциональна массовому расходу жидкости. Подсчитывается интервал времени, равный сдвигу фаз сигналов детекторов. Интервал сдвига во времени между сигналами годного и выходного детекторов прямо пропорционален массовому расходу.
Примером кориолисового расходомера может служить расходомер Метран- 60 (рис. 13. 18), который применяется для измерения массового расхода жидкостей и газов. Основные приведенные погрешности измерений массового рас- ода составляют для жидкостей до 0, 2 %; для газов до 0, 5 %. Расходомер Метран-360 состоит из: • датчика расхода; • измерительного микропроцессорного преобразователя; • основного процессора; • фланцев для присоединения к магистрали. Рис. 13. 18. Конструкция расходомера Метран-360 Выходной сигнал — аналоговый токовый (4. . . 20 м. А), пропорционален массовому расходу. Нижнее и верхнее значения тока соответствуют минимальному и максимальному значениям измеряемого параметра. Имеется возможность выводить информацию в виде частотно-импульсного сигнала и в цифровом виде. Кориолисовые расходомеры при стендовых испытаниях газотурбинных двигателей применяются для измерений расхода керосина, масел в газотурбинных двигателях авиационного применения и газового топлива в газотурбинных двигателях наземного применения.
13. 5. ДАТЧИКИ ИЗМЕРЕНИЯ УСИЛИЯ ОТ ТЯГИ Испытательный стенд, предназначенный для испытания авиационной техники, должен быть оборудован специальной динамометрической платформой, с помощью которой обеспечивается измерение усилия от тяги. Двигатель размещается на платформе, подвешенной или установленной на гибких стержнях (лентах). Существуют различные способы подвески этой платформы, чтобы обеспечить ее свободное перемещение под действием силы от тяги. При своем перемещении платформа воздействует на измерительные датчики, сигналы с которых преобразуются в цифровую форму с последующим расчетом величины силы от тяги. Комплект оборудования, предназначенный для измерения силы от действия тяги двигателя, называют силоизмерительной системой. Основные требования к силоизмерительной системе следующие: • измерение тяги ГТД с погрешностью, указанной в ОСТ 1 01021; • измерение тяги на установившихся и неустановившихся режимах; • измерение (при необходимости) составляющих векторов тяги. Требования по точности измерения тяги для серийных и опытных двигателей различны: • для ГТД серийного производства — ± 0, 5 % от измеряемого значения; • для ГТД опытного производства ± 0, 3 % от измеряемого значения.
Рис. 13. 19. Функциональная схема силоизмерительной системы стенда испытания двигателя НК-93: ГТД — газотурбинный двигатель; ДМП — динамометрическая платформа; РГУ — рычажно-градуировочное устройство; ПГУ — поверочное градуировочное устройство; 32 ТВС — датчик измерения усилия от тяги; ТВ 003/05 Д — преобразователь Под измеряемым значением понимается диапазон от максимального значения тяги до 0, 5 значения тяги на бесфорсажном режиме. В остальном диапазоне относительной погрешностью в процентах от максимального значения тяги. Функциональная схема системы измерения тяги газотурбинного двигателя приведена на рис. 13. 19. Газотурбинный двигатель закреплен на раме и установлен на динамометрическую платформу, в данном случае подвешенную на 4 -х гибких лентах. Благодаря этому, она может перемешаться под действием силы от тяги. Рычажно-градуировочное устройство состоит из эталонных грузов и система рычагов, передающих усилие на динамометрическую платформу. Это устройство позволяет провести градуировку измерительного канала непосредственно перед испытанием. Под действием рычажного градуировочного устройства динамометрическая платформа смещается и воздействует на тензорезисторный датчик ТВС. Сигнал датчика поступает далее на преобразователь ТВ 003/05 Д, а с него — на ПЭВМ, происходит расчет градуировочной характеристики. Кинематическая схема силоизмерительной системы приведена на рис. 13. 20. Измерение силы от тяги ГТД относится к виду прямых измерений и проводится методом непосредственной оценки измеряемой величины по результатам наблюдений, полученным в процессе испытаний.
Рис. 13. 20. Кинематическая схема силоизмерительной системы: — испытываемое изделие; 2 — динамометрическая платформа; 3 — подмоторная рама; 4 — датчик измерения усилия от тяги; 5 — рычажно-градуировочное устройство; 6 — упругие планы динамометрической платформы; 7— преобразователь ТВ 003/05 Д; 8 — система подгрузки силоизмерительной системы; 9 — ПЭВМ; 10 — аналого-цифровой преобразователь (АЦП) Рис. 13. 21. Схема датчика ТВС: / — упругий элемент; 2 — защитная мембрана; 3 — подставка под упругий элемент; 4 — корпус; 5 — тензорезисторы.
Усилие от тяги двигателя воздействует на динамометрическую платформу, которая, смещаясь, воздействует на датчик. При действии силы происходит упругая деформация чувствительного элемента датчика. Изменяется омическое сопротивление резисторов, включенных в тензометрический мост. В результате тензометрический мост разбалансируется, и на его выходе появляется напряжение, пропорциональное приложенной силе. Напряжение преобразуется в цифровой код, который поступает в систему контроля параметров ГТД. Измерения на двигателе выполняются после выдержки двигателя на заданном режиме испытания в соответствии с программой на испытание и технологией его проведения. Конструкция тензорезисторного датчика типа ТВС приведена на рис. 13. 21. Принцип работы этого датчика основан на преобразовании деформации упругого элемента в электрический сигнал, пропорциональный измеряемой нагрузке. Тензорезисторы подключаются по схеме электрического моста. Упругий элемент 1 силоизмерителя опирается на подставку 3, выполненную в виде цилиндрической призмы. Деформация изгиба приложении нагрузки передается тензорезисторам 5, вызывая растяжение нижних и сжатие верхних тензорезисторов, что изменяет их электрическое сопротивление. Все четыре плеча моста активны. Это увеличивает чувствительность датчика и позволяет получить линейное уравнение связи усилия с выходным электрическим сигналом в виде напряжения постоянного тока. Чувствительный элемент силоизмерителя заключен в герметичный корпус 4, который заполняется кремнийорганической жидкостью для защиты тензорезисторов от влаги и для смазки опорных поверхностей. Герметизация полости осуществляется посредством мембраны 2.
Датчики типа ТВС выпускаются на разные диапазоны измерения силы. Максимальная величина измеряемого усилия — 320 к. Н. Номинальное выход ное напряжение датчика — 50 м. В. Датчик типа ТВС позволяет измерять тягу двигателя с погрешностью не бо лее 0, 3 %. 13. 6. ДАТЧИКИ ИЗМЕРЕНИЯ КРУТЯЩЕГО МОМЕНТА При проведении стендовых приемосдаточных и исследовательских испытаний важным параметром для оценки характеристик ТВД, ТВВД и ГТД является их мощность. При эксплуатации ГТД наземного применения в составе газотранспортных установок необходимо периодически оценивать основные технологические показатели газоперекачивающих агрегатов (ГПА): мощность газотурбинной установки (ГТУ), эффективный КПД, коэффициенты технического состояния газовоздушной проточной части и др. Главным показателем из них является фактическая мощность агрегата на реме. Остальные параметры в той или иной степени являются производными мощности. Существует ряд методов измерения мощности (крутящего момента): • расчетный метод на основе измерения параметров гидро- или пневмотормоза, используемого в качестве нагрузки; • метод прямого измерения крутящего момента с помощью специальных измерителей (датчиков). В настоящее время разработаны конструкции бесконтактных измерителей крутящего момента. Большинство датчиков работает на принципе измерения угла скручивания экого вала. Такие датчики называют торсиометрами.
На рис. 13. 22 приведена схема, поясняющая принцип работы датчика крутя- го момента. С помощью обмоток, расположенных над зубчатыми фланцами, при вращение и вала вырабатываются синусоидальные сигналы. При скручивании вала под действием крутящего момента между синусоидальными сигналами, поступающими от обмоток, возникает сдвиг фаз, величина которого пропорциональна крутящему моменту. Измеряя сдвиг фаз, можно определить величину крутящего момента. Обычно при работе с конструкциями, работающими в непрерывном режиме бота торсиометра в составе стендового оборудования или в составе ГПА), скручивание вала не превышает 0, 5. . . Г. При соответствующем подборе преобразующей аппаратуры это обеспечивает общую погрешность измерения не хуже 0, 5. . . 1 %, что точнее широко применяемых расчетных методов, основанных определении потерь, например, в пневмотормозе. 13. 22. Схема действия датчика кру тящего момента Торсиометр представляет собой вал, встраиваемый между газотурбинным двигателем и нагрузкой. Статорная часть опирается на одну из частей установки (рама стенда, рама двигателя). Радиальный зазор между статором и ротором составляет обычно 3 мм. Как видно из рис. 13. 23, в конструкции практически отсутствует электроника, съем данных — бесконтактный. В торсиометре установлена только измерительная катушка.
Рис. 13. 23. Торсиометр для непрерывного режима работы Предусмотрен ряд мероприятий, устраняющих влияние осевых, параллельных и угловых перемещений конструкций: установлены стандартная гиб кая муфта и гибкие элементы конструкции. Отсутствие электроники в составе торсиометра позволяет применять его в достаточно жестких температурных, вибрационных условиях. Электроника вынесена за пределы зоны установки ГТД. Работа торсиометра на малых углах скручивания гибкого вала позволяет длительно сохранять постоянную жесткость вала, а следовательно, и характери стики торсиометра. 13. 7 ДАТЧИКИ ИЗМЕРЕНИЯ ЗАЗОРОВ, ПЕРЕМЕЩЕНИЙ Улучшение характеристик современного газотурбинного двигателя, как по параметрам, так и по надежности, невозможно без контроля реальных величин зазоров и перемещений по проточной части ГТД. Зазор между статором и концевым элементом рабочих лопаток компрессо ров и турбин определяет экономичность и эффективность ГТД. При этом малые зазоры, улучшающие характеристики двигателя, могут при вести к снижению надежности и даже к поломке материальной части.
Большие зазоры могут резко ухудшить характеристики двигателя за счет перетекания рабочего тела через площадь зазора. По эмпирическому соотношению зазор шириной в 1 % от длины лопатки приводит к 1 % потерь по КПД. При проведении измерений зазоров и перемещений конструкций используют обычно датчики специальной разработки. В качестве примера ниже приведены технические характеристики системы измерения радиальных зазоров в винтовентиляторе двигателя НК-93. Основу системы составляют вихретоковые датчики. Вихретоковый датчик имеет чувствительный элемент в виде одного витка провода, выродившегося в отрезок провода между двумя токопроводами. В сечении винтовентилятора находятся 4 симметрично расположенных датчика. Для уменьшения величины погрешности от изменения температуры чувст вительного элемента в контролируемой точке устанавливаются два датчика рядом либо 2 датчика монтируются в одном корпусе — один датчик рабочий, другой — для целей компенсации температурной зависимости. Чувствительный элемент датчика, основанного на одновитковых вихретоковых преобразователях, сохраняет свою работоспособность до высоких температур (1000 °С) и не чувствителен к содержанию в среде масел, продуктов горения, паров воды и частиц пыли. Это позволяет использовать датчики для измерения зазоров в турбине. Преобразующая часть датчика вынесена за пределы корпуса двигателя. Здесь размещается электронная часть системы: измерительная катушка и электронный преобразователь.
Рис. 13. 24. Внешний вид датчика ОВТД-ВВ-15 (а) и преобразователя СУ-02 (с тем же датчиком) (б) Внешний вид датчика ОВТД-ВВ-15 показан на рис 13. 24, а. Конструкция ОВТД-ВВ содержит в одном корпусе два плеча — рабочее и компенсационное, каждое из которых, в свою очередь, содержит согласующий трансформатор, ЧЭ и укороченные тоководы, осуществляющие гальваническую связь согласующе го трансформатора и ЧЭ в каждом плече датчика. Укороченные тоководы пред ставляют собой изолированные друг от друга соосные цилиндры, причем, как в рабочем, так и в компенсационном плече датчика, наружные цилиндры образует защитный корпус. К торцам лопастей ВВ обращен открытый ЧЭ рабочего плеча, а ЧЭ компенсационного плеча экранирует заглушка, приваренная к корпусу датчика на заданном расстоянии от ЧЭ. Индуктивность ЧЭ (первичной ) обмотки согласующего трансформатора) рабочего плеча зависит от смещений лопастей ВВ в зоне чувствительности датчика, в то время как индуктивность 4 Э компенсационного плеча остается без изменений. Наибольшие изменения естественного выходного сигнала датчика — индуктивности L в рабочем диапазоне (Х р = Y P = Z P = 17 мм, φ Yр = 37°) достигают 15 мк. Гн. Преобразователи сигналов (см. рис. 13. 24, б) построены на основе известного 1 етода первой производной, имеют идентичную структуру и схемотехнику.
Метод предусматривает возбуждение LR- моста, включающего рабочее и компенсационное плечи ОВТД (согласующие трансформаторы СТ и ЧЭ) и образцовые резисторы, короткими прямоугольными импульсами, дифференцирование напряжений на резисторах (дифференцирующий усилитель ДУ) и фиксацию максимума напряжений на выходе ДУ в усилителе выборки-хранения (УВХ) (рис. 3. 25). Прямоугольные импульсы, питающие мост измерительной цепи длительностью около 0, 2 мкс, формируются путем бесконтактной коммутации (ключ К) цепи источника постоянного напряжения (Е). Управление ключом осуществляет генератор импульсов (Г), причем частота импульсов постоянна и составляет около 70 к. Гц. Импульсы генератора (Г) в каждом преобразователе могут быть использованы для синхронизации мультиплексора и АЦП в плате L-783, а также для синхронизации импульсного возбуждения LR -мостов с ОВТД в других ана логичных преобразователях (если таковые имеются в составе системы). Преобразователь сигналов содержит датчик температуры (ДТ) (см. рис. и. 2 Э), расположенный внутри корпуса преобразователя на плоской алюминиевой пане ли которая крепится к оболочке статора в непосредственной близости от ОВТД. Температура панели соответствует температуре ОВТД (0), а сигнал ДТ может быть использован для температурной коррекции. Схема датчика ОВТД-ВВ представлена на рис. 13. 26.
Рис. 13. 25. Преобразователь сигналов ОВТД Рис. 13. 26. Схема датчика ОВТД-ВВ в разрезе: ОВТД- ВВ — одновитковый вихретоковый датчик винтовентилятора. ; СУ — согласующее устройство; ЧЭ — чувствительный элемент; 1 — ЧЭ компенсационного плеча; 2 — экранирующая заглушка; 3 — внутренняя оболочка ВВ; 4 — ЧЭ рабочего плеча; 5 — втулка; 6 — согласующий трансформатор
Рис. 13. 27. Схема соединений элементов системы измерения радиальных зазоров двигателя НК-93 Сигналы с измерительной катушки подаются на усилитель, а затем на преобразователь и вводятся в ПЭВМ, где осуществляется расчет величины зазора. На рис. 13. 27 приведена схема соединений элементов системы измерения радиальных зазоров на винтовентиляторе двигателя НК-93. В 4 -х точках статора винтовентилятора установлено 4 датчика, соединенных с помощью разъемов с 4 -мя усилителями-преобразователями. Усиленный сигнал далее поступает на АЦП системы измерения радиальных зазоров.
13. 8. ЗОНДЫ ИЗМЕРЕНИЯ ПУЛЬСАЦИЙ ДАВЛЕНИЯ ГАЗОВЫХ СРЕД Необходимость измерения пульсаций давления в элементах проточной части ГТД не вызывает сомнений, так как информация о пульсационном состоянии газового потока широко используется при оценке запаса газодинамической устойчивости компрессора и исследовании процессов горения в камере сгорания. Особенно важными становятся вопросы оценки уровня пульсаций давления в камере сгорания. Это связано с тем, что доводка камеры сгорания по экологическим характеристикам заставляет работать на режимах, близких к границе устойчивого горения. При этом могут возникнуть резонансные явления, приводящие к значительному росту уровня пульсаций давления. При измерении переменных давлений в общем случае на чувствительный элемент датчика воздействует давление Где р 0 — постоянная составляющая давления; — переменная составляющая давления. Поэтому специальные устройства для измерения пульсаций давления измеряют либо p(t), либо только . Во втором случае используются датчики дифференциальной схемы или пьезокерамические, реагирующие только на переменную часть давления. Для обеспечения контроля за уровнем пульсаций давления и его амплитудно-частотным спектром датчик необходимо установить в точке измерения. Однако это не всегда возможно сделать, так как в точке измерения могут быть высокие уровни давления и высокие температуры.
Существуют конструкции датчиков, которые выдерживают температуру до +700 0 С, но их габариты и низкая точность не всегда позволяют организовать измерения пульсаций давления в проточной части ГТД. Другим препятствием установки датчика непосредственно в точку измерения является необходимость разборки двигателя (узла) для постановки или съема датчика, так как из-за их низкой надежности их нельзя устанавливать на длительные сроки. Поэтому для измерений пульсаций давления чаще используют специальные устройства, которые называют зондами. Зонд представляет собой конструкцию, состоящую из датчика, вынесенного за пределы оболочки двигателя, узкого трубопроводного канала, с помощью которого датчик подключается к точке измерения, корпуса конструкции и спе циальных компенсирующих элементов. На рис. 13. 28 приведены схемы зондов пульсаций давления. В качестве волноводов используют трубопроводы с узким сечением. Длина волновода определяется расстоянием от точки измерения до датчика. При этом стараются не удлинять необоснованно длину волновода, так как это приводит к потерям на затухание колебаний. Диаметр волновода выбирается на основе расчетных и опытных данных в диапазоне 2. . . 6 мм. Корректирующий трубопровод служит для коррекции ам плитудно-частотной характеристики зонда в рабочем диапазоне частот. На рис. 13. 29 приведена конструкция зонда для измерения пульсаций давле ния на входе в компрессор низкого давления. Зонд состоит из волновода 7, фланца для крепления к корпусу двигателя 2, корпуса зонда с датчиком ДМ И 3, корректирующей линии 4 и измерительного кабеля 5.
Рис. 13. 28. Схемы зондов пульсаций давления: а — схема зонда с датчиком абсолютного давления; б — схема зонда с датчиком дифференниального давления; d в , l в — диаметр и длина волновода; d K , l К — диаметр и длина корректирующего трубопровода; V к , V ф — компенсирующий объем; R ф — демпфирующий элемент (дроссель) Рис. 13. 29. Зонд для измерения пульсаций давления на входе в компрессор низкого дав ления двигателя НК-38 СТ В данной конструкции применен дифференциальный датчик давления типа ДМ И на диапазон измерения пульсаций давления, равный 30 к Па. Датчик ДМИ встроен в корпус и имеет два входа, на один вход подается дав ление p(t) непосредственно от волновода, на другой конец подается p 0 с выхода корректирующей линии. Таким образом, на мембрану датчика воздействует пе ременная составляющая давления :
РЕЗЮМЕ (по главе 13 «Первичные преобразователи при автоматизированных испытаниях ГТД» ) 1. Первичные преобразователи (датчики) предназначены для преобразования измеряемой физической ветчины в электрический сигнал. Значение электрического сигнала в первичном преобразователем является функцией измеряемой физической величины. 2. Датчики подразделяются на генераторные и параметрические. Генераторные датчики обеспечивают на выходе сигнал в виде электрического заряда, напряжения или тока. Параметрические датчики изменяют свои электрические свойства: сопротивление, индуктивность, емкость и т. п. 3. Для измерения температуры наиболее широко применяются термометры сопротивления и термопары. Термометры сопротивления изменяют свое электрическое сопротивление под действием окружающей температуры. Термометры сопротивления бывают металлические и полупроводниковые. Металлические термометры сопротивления позволяют измерять температуру в диапазоне -260. . . +850 С. Полупроводниковые термометры сопротивления отличаются большей чувствительностью, меньшими габаритами, но более высокой погрешностью, чем металлические. В термопарах для измерения температуры используется термоэлектрический эффект. Термопары обеспечивают измерение более широкого диапазона температур (до 1800. . . 2500 °С), чем термометры сопротивления, обладают меньшими габаритами и инерционностью, но для получения высокой точности измерений требуют индивидуальной градуировки.
4. В качестве измерительных преобразователей давления используются индукционные, потенциометрические, вибрационно-частотные, тензометрические и емкостные датчики. Чувствительным элементом этих датчиков является упругий элемент, изменяющий под действием давления свои размеры (форму). Приемником статического давления в потоке является отверстие диаметром 0, 5. . . 1, 5 мм в стенке канала. Приемники давления заторможенного потока выполняются в виде Г-образной трубки, обращенной навстречу потоку. Приемники давления соединяются с датчиками так называемыми «импульсными» трубопроводами — металлическими трубками диаметром 4 мм. 5. Для измерения частоты вращения применяют фотоэлектрический (оптический), индукционный, импульсный и генераторный методы измерений, реализуемые в соответствующих первичных преобразователях частоты вращения. 6. Измерение расходов жидкости или газа может быть объемным (м/с) или массовым (кг/с), мгновенным (в данный момент времени) или осредненным (за определенный промежуток времени). Широкое применение в практике стендовых испытаний получали методы измерения расходов, основанные на измерении перепада давления в сужающем устройстве, турбинные, вихреакустические и кориолисовые расходомеры. Наиболее точными являются турбинные расходомеры. 7. Для измерения тяги двигателя применяют тензорезисторные датчики типа ТВС. Принцип работы датчика основан на преобразовании деформации упругого элемента в электрический сигнал, пропорциональный измеряемой нагрузке. Датчик тяги устанавливается между неподвижной частью динамометрической платформы и подвижной ее частью, на которой закрещен двигатель. Для обеспечения требуемой точности измерения тяги осуществляется градуировка системы измерения тяги непосредственно перед испытанием двигателя.
8. Измерение крутящегося момента осуществляется с помощью датчиков, работающих на принципе измерения угла скручивания гибкого вала. Величина угла скручивания определяется по сдвигу фаз электрического тока в обмотках, расположенных над двумя отстоящими друг от друга зубчатыми фланцами. Такие датчики называют торсиометрами. Торсиометр встраивается между газотурбинным двигателем и нагрузкой. 9. При проведении измерений зазоров в конструкции и перемещений элементов обычно используются датчики специальной разработки. Для определения величины радиальных зазоров над рабочими лопатками вентилятора при испытаниях двигателя применяются вихретоковые датчики. На статоре располагаются четыре симметрично расположенных датчика. Чувствительный элемент датчиков, основанный на одновитковых вихретоковых преобразователях, сохраняет работоспособность до 1000 °С, что позволяет использовать эти датчики для измерения зазоров в турбине.
ВОПРОСЫ 1. Какие датчики используются для измерения тяги? 2. Как устроен датчик ТВС? 3. Чем измеряется расход топлива? 4. Какую погрешность измерения имеет турбинный расходомер? 5. Какие датчики используются для измерения частоты вращения вала? 6. Какие датчики используются для измерения температуры и давления? 7. Какие датчики используются для измерения зазоров и перемещения? 8. Какие методы используются для измерения расхода воздуха? 9. На чем основан принцип работы кориолисового расходомера? 10. На чем основан принцип работы вихревого расходомера? 11. На чем основан принцип работы электромагнитного расходомера? 12. Какую погрешность измерения имеют современные датчики измерения расхода и тяги?
Глава 14 АВТОМАТИЗАЦИЯ ИСПЫТАНИЙ ГТД Основным направлением повышения эффективности испытаний ГТД является их автоматизация. Это сокращает время и трудоемкость проведения испытания и обработки его результатов, повышает информативность испытания и достоверность получаемых результатов, что в конечном итоге способствует сокращению сроков создания двигателей, снижению материальных затрат на их разработку и производство, повышению качества и надежности двигателей. В данной главе рассматриваются принципы автоматизации основных этапов проведения испытаний и устройство автоматизированной системы испытаний ГТД (АСИ ГТД). 14. 1. ТИПОВЫЕ ОПЕРАЦИИ ПРИ ИСПЫТАНИЯХ ГТД В различных видах испытаний ГТД можно выделить следующие повторяющиеся операции: 1. Подготовительно-заключительные операции. 2. Испытания по заданной программе. 3. Отладка параметров двигателя в пределах технических норм и требований. 4. Обработка результатов эксперимента и их анализ. Повышение требований к надежности ГТД приводит к необходимости организовывать дополнительно к системе стендовых испытаний систему постоянного контроля за состоянием двигателей в эксплуатации на протяжении всего ресурса. Этот контроль обеспечивается наличием на летательных аппаратах многоканальной системы регистрации параметров (МСРП), а на наземных испытательных станциях (ГТД, ГПА, ГТЭ) — многоканальных систем контроля и управления (МСКУ). Схема технологического процесса проведения испытания представлена на рис. 14. 1.
Рис. 14. 1. Блок-схема технологического процесса проведения испытания ГТД Трудоемкость отдельных операций технологического цикла для одного вида испытаний различна. Отличается она и для различных видов испытаний. Доля трудоемкости различных видов испытаний в процентах от общей трудоемкости приведена в табл. 14. 1. Каждая из перечисленных операций может быть автоматизирована. Целесообразность и глубина автоматизации той или иной операции зависят от вида испытания и частоты его проведения.
Вилы испытаний Подготовитель ные, заключи тельные операции Сбор и обработка информации Вторичная обработка информации Реализация принятия решения Исследовательские: агрегатов и элементов 2. . . 5 40. . . 60 5. . . 10 20. . . 30 узлов двигателей 5. . . 10 30. . . 50 20. . . 30 10. . . 20 Доводочные: доводка агрегатов 5. . . I 0 30. . . 60 10. . . 20 20. . . 30 доводка узлов 10. . . 15 30. . . 40 10. . . 20 20. . . 30 доводка двигателя 10. . . 30 20. . . 30 Заводские: кратковременные о О 20. . . 40 10. . . 20 длительные 2. . . 15 50. . . 70 30. . . 40 3. . . 514. 1. Трудоемкость основных операций испытаний от общей трудоемкости, %
14. 1. 1. Подготовительно-заключительные операции К подготовительно-заключительным операциям (П 30) относятся: • подготовка стенда к испытанию; • расконсервация двигателя и монтаж его на стенде; • подключение топливной и др. магистралей, систем управления и измерения; • демонтаж двигателя и консервация Анализ этих операций показывает, что они мало пригодны для автоматизации. При обычной организации ПЗО требуют около 12 ч работы непосредственно на испытательном стенде. Такое непроизводительное его использование крайне невыгодно. Для уменьшения времени непроизводительного использования испытательного стенда предпринимаются следующие меры по автоматизации ПЗО. Подготовительно-заключительные операции переносятся из бокса в так называемый «зал подготовки» . Здесь производятся внешний осмотр и расконсервация двигателя. Применяются специальные «подмоторные рамы» , на которые двигатель монтируется в зале подготовки. На рамы устанавливаются первичные преобразователи и другое необходимое оборудование. Все коммуникации двигателя выводятся на специальный щиток рамы. Проверяется контрольно-измерительная и вторичная аппаратура. Применяются быстродействующие соединения для подключения стендовых систем (топливных, воздушных, гидравлических и др. ) к щиту подмоторной рамы. Двигатель, смонтированный на подмоторной раме, доставляется из зала подготовки на стенд. Здесь производится быстрое крепление рамы на силоизмерительный станок. Щит подмоторной рамы соединяется со стендовыми системами.
Для монтажа и демонтажа двигателя с подмоторной рамы в боксе требуется обычно по одному часу на монтаж и демонтаж. Следовательно, подготовительно-заключительные операции в этом случае требуют два часа работ на испытательном стенде. Таким образом, такое изменение подготовительно-заключительных операций примерно на 10 ч сокращает непроизводительную загрузку стенда. Особенно целесообразна автоматизация подготовительно-заключительных операций при испытаниях серийных ГТД. В этом случае относительное время подготовительно-заключительных операций достигает 30. . . 40 % от общего времени предъявительских или приемосдаточных испытаний. В год на предприятии может проводиться до нескольких тысяч таких испытаний. Поэтому в серийном производстве автоматизация подготовительно-заключительных операций позволяет значительно снизить непроизводительную загрузку стендов, увеличить пропускную способность и сократить потребное их количество, получив большую экономию материальных средств. 14. 1. 2. Испытания по заданной программе включают следующие операции: • регистрацию параметров; • управление режимами. Регистрация параметров — это одна из самых главных операций при испытании авиационных двигателей. В настоящее время число регистрируемых параметров опытных двигателей достигает 2000. . . 3000. Без автоматизации процесса измерений достоверно зарегистрировать их практически невозможно. Задача решается применением автоматизированных систем измерения и регистрации параметров.
Объем измеряемых параметров существенно зависит от вида испытаний. На серийных испытаниях объем меньше, а на исследовательских может существенно вырасти. В табл. 14. 2 приведен объем измеряемых параметров в зависимости от вида испытаний. Сбор данных и управление процессом проведения испытания выполняются обычно автоматически или полуавтоматически под управлением оператора или инженера-испытателя. В процессе испытания инженер-испытатель следит не только за значениями параметров на табло, за аварийной сигнализацией, но и по мере возможности за состоянием материальной части, находящейся в боксе стенда. Такой контроль осуществляется по экрану монитора. Измеряемый параметр Виды испытаний и количество измеряемых параметров Заводские Доводочные Исселедовательские Измеряемая тяга 1 1 1 Крутящий момент 1 1 1 Расход топлива 2 2 2 Частота вращения до 314. 2. Объем измеряемых параметров в зависимости от вида испытаний
Давление воздуха (газов) до 50 до 150 до 800 Температура воздуха (газов) до 50 до 200 до 1000 Температура рабочих жидкостей до 5 до 10 до 20 Температура корпусов — до 200 Пульсации давления — до 6 до 15 Виброскорость(виброускорение) до 3 до 10 до 15 Статические и динамические деформации — до 100 до 200 Телевизионные камеры устанавливаются таким образом, чтобы можно было видеть двигатель со всех сторон. Таким способом могут быть обнаружены течи, прорыв газов, возгорание. Системы, основанные на мощных компьютерах, работающих в режиме разделения функций, выдают физические значения параметров, приведенные значения параметров, расчетные величины в виде таблиц и графиков. При проведении серийного испытания по его окончании выдается протокол.
Время испытаний двигателя существенно сокращается при использовании АСИ даже с частичной автоматизацией процесса регистрации параметров. 14. 1. 3 Управление режимами работы двигателя Наиболее ответственная и часто повторяющаяся операция при испытании ГТД — вывод двигателя на заданный режим. При испытаниях серийных ТРДД эта операция повторяется более 150 раз. При эквивалентно-циклических ресурсных испытаниях двигателя смена режимов происходит более 5000 раз, так как ускоренные длительные испытания предусматривают изменение режимов по циклам, в том числе имитирующим работу двигателя на самолете (т. е. включение и отключение режимов отбора воздуха, за грузки агрегатов, включение реверса и системы противообледенения). Ручное управление режимами осуществляется оператором путем перемеще ния рычага управления двигателя (РУД). Процесс при этом контролируется визуально по стрелочным приборам. Время ручной установки режима зависит от квалификации оператора и может достигать 40 с. К недостаткам ручного управления режимами относятся: а) большая трудоемкость; б) значительное время на установку режима: в) повышенные погрешности в установке и поддержании заданного режима. Для автоматизации управления режимами работ двигателя необходимо на испытательном стенде установить исполнительный механизм управления РУД. блок автоматики управления исполнительным механизмом и разработать соответствующие алгоритмы управления работой двигателя.
14. 1. 4. Отладка параметров двигателя является одной из главных операций при предъявительских и приемосдаточных испытаниях. Она необходима для настройки параметров двигателя до значений, установленных техническими нормами или условиями. Отладка осуществляется путем целенаправленного изменения положения регулирующих элементов, размешенных на двигателе (регулировочных винтов насоса- регулятора. лопаток регулируемых направляющих аппаратов компрессора, створок регулируемого сопла и т. п. ). Например, на двухвальном ТРДД имеется свыше десяти регулировочных элементов, на трехвальном ТРДДФ — более двух десятков. При ручном перемещении регулировочных элементов производится последовательное регулирование параметров двигателя (n, P дв , G m , Т* и др. ). Фактически это означает, что приходится делать последовательные приближения. Для ручного перемещения регулировочных элементов двигатель останавливается. Количество операций при перемещении регулируемых элементов и качество отладки параметров зависит от квалификации оператора. Часто необходимы многократные повторные перемещения и, следовательно, многократные остановки и запуски двигателя, выводы его на заданные режимы. Отсюда вытекают основные недостатки ручной отладки параметров ГТД: • большая трудоемкость; • удлинение цикла испытания; • негарантированное качество отладки.
Для автоматизации отладки двигателя необходимо: • Применение исполнительных органов дистанционного регулирования (при этом конструкция двигателей должна позволять устанавливать такие исполнительные механизмы*); • Применение специальных математических методов определения опти мального перемещения регулировочных элементов с учетом их воздействия на все параметры ГТД. Автоматизация отладки ГТД в процессе испытаний даст возможность проводить перемещение регулировочных элементов без остановки двигателя, уменьшить количество регулировок и наилучшим образом отладить одновременно все параметры двигателя. Фактически на реальных конструкциях затруднен доступ к агрегатам, регулировочные элементы, кроме изменения их положения, необходимо «контрить» , для регулировки процесса запуска необходимо устанавливать сменные жиклеры, для регулирования приемистости подбирать дроссельные пакеты и т. п. 14. 1. 5. Обработка результатов испытаний и их анализ При обработке результатов испытаний производят следующие операции: а) расчет физических значений параметров р*, G m, ρ , P ДB и др. ; б) расчет осредненных параметров по сечению ( р*, Т*); в) приведение параметров к САУ (с учетом поправок на t н, р н , d , Re и т. п. ); г) построение экспериментальных характеристик двигателя, например. Р пр , G m пр д) определение неизмеряемых параметров двигателя и узлов, например. Т г , η* к и др, е) статистический анализ полученных результатов. Результаты таких расчетов не однозначны, требуют увязки между собой различных параметров двигателя и узлов. Эта операция называется термодинами ческим анализом результатов испытания.
Термодинамический анализ ГТД необходим для: • определения оптимального направления доводки опытных двигателей; • оценки эффективности осуществляемых доработок в конструкции; • оптимизации отладки параметров опытных двигателей; • контроля технического состояния эксплуатируемых двигателей (и проходящих длительные испытания). Для статистического анализа результатов испытаний широко применяется частичная автоматизация обработки с применением ЭВМ, что позволяет уменьшить время на обработку параметров, сократить трудоемкость расчетов с гарантированной точностью расчетов. При этом появляется возможность применения наиболее совершенных математических методов обработки результатов измерений. Наиболее эффективна полная автоматизация обработки результатов испытаний на ЭВМ. На различных этапах проведения эксперимента на АСИ ГТД возлагают раз нообразные задачи. Перед испытанием это: • осуществление оптимального планирования предстоящего эксперимента (определяется номенклатура измеряемых параметров, количество и расположение экспериментальных точек); • метрологическая аттестация измерительных каналов (определение градуировочных зависимостей и их погрешностей). В процессе испытания это: • первичная обработка экспериментальных данных; • выявление грубых ошибок, промахов, выбросов в измерении пара метров; • выдача оператору информации о полученных результатах обработки в наглядном виде (на экране дисплея, на печатающем устройстве, на специальной панели индикации); • расчет и реализация оптимальных перемещений регулировочных элементов двигателя; • печать протокола испытания.
Задачи, решаемые в ходе эксперимента называются экспресс-анализом. после проведения испытания это: • восстановление характеристик двигателя по экспериментальным данным; • определение оценок неизмеряемых параметров двигателя и его узлов; • накопление статистических материалов о проведенных испытаниях; • выдача необходимой документации в виде текстов, таблиц и графиков. В целом автоматизация обработки результатов испытаний позволяет: • повысить оперативность обработки результатов испытания; • повысить точность и достоверность полученных данных.
14. 2. ОСНОВЫ ПОСТРОЕНИЯ АСИ ГТД 14. 2. 1. Основные задачи испытаний, решаемые автоматизированной системой Различают частичную и комплексную автоматизацию испытаний авиационных двигателей. Частичная автоматизация — это автоматизация отдельных операций испытания, например, регистрация параметров и обработка результатов испытания. Комплексная автоматизация — это автоматизация сразу всех операций испытания, включая управление работой двигателя и стендовых систем. К основным задачам испытаний, решаемым с помощью АСИ ГТД, относятся: 1. Оптимальное планирование предстоящего испытания. 2. Измерение и регистрация параметров. 3. Непрерывный контроль за аварийно-опасными параметрами (n, Т г *, t м , p м и т. д. ). 4. Обработка наиболее важной информации в реальном масштабе времени и в темпе испытания, выдача результатов экспресс-анализа на устройство отображения информации (принтер, дисплей, панели индикации, графопостроитель). 5. Управление двигателем и его системами по заданной программе, перемещения регулировочных элементов без остановки двигателя. 6. Проведение полной обработки результатов испытания и подготовка необходимой документации. 7. Хранение необходимой информации в базе данных.
14. 2. 2. Основные требования к АСИ ГТД При разработке АСИ ГТД необходимо учитывать ряд требований, во многом определяющих облик cистемы. 1. Высокая точность измерения параметров. Допустимые погрешности измерения основных параметров при доверительной вероятности р = 0, 95 должны быть не более 0, 2. . 0, 5 %. Такая точность может быть обеспечена за счет градуировок измерительных каналов перед каждым испытанием, одновременности регистрации всех параметров, многократности опросов датчиков (за цикл измерений длительностью не более 0, 1 с производится не менее 10 опросов каждого датчика), после этого производятся отбраковка возможных выбросов и осреднение оставшихся результатов. 2. Обеспечение сохранности экспериментальной информации при аварийных ситуациях. Для этого используют параллельную запись всей информации во время испытаний (однако в безаварийных испытаниях такая запись является избыточной); выборочную запись на режимах вероятной аварийности; запись информации на «кольцо» (замкнутая магнитная лента, на которую в течение одной минуты ведется запись с последующим стиранием, если аварийной ситуации не возникло). 3. Обеспечение возможности управления запуском двигателя, режимами его работы и остановом по заданной программе. 4. Применение наиболее совершенных математических методов обработки экспериментальных данных. Это позволяет увеличить информативность испытания, повысить точность и достоверность получаемых результатов. 5. Обеспечение диалогового взаимодействия оператора с АСИ позволяет оператору активно вмешиваться в ход проведения испытаний, основываясь на получаемой информации. 6. Представление результатов испытаний в наиболее полном и наглядном виде текстов, таблиц, графиков.
7. Применение серийных технических средств (первичных преобразователей, устройств связи с объектом (УСО) и т. д. ). Должны использоваться средства измерения, допущенные Госстандартом РФ к применению после их государственной или ведомственной метрологической аттестации. 8. Возможность модульного наращивания системы без изменения ее общей схемы и математического обеспечения. 9. Высокая надежность. Одной из количественных характеристик надежности является время наработки на отказ. Для АСИ ГТД требуется, чтобы время наработки на отказ, устраняемый в эксплуатации, было не меньше 24 ч. Одной из главных мер по обеспечению надежности АСИ является резервирование ненадежных элементов (УСО, периферийных устройств, ЭВМ). 10. Небольшие габариты и масса. Измерительно-вычислительные комплексы (ИВК) должны размешаться в кабине наблюдения испытательных стендов. Современные ИВК на базе промышленных персональных ЭВМ занимают 2. . . 3 м 2 площади пола и имеют относительно небольшую массу. Это позволяет использовать их и на летающих лабораториях. 11. Небольшая стоимость.
14. 2. 3. Типовая схема АСИ ГТД На рис. 14. 2 представлена структурная схема АСИ ГТД и использованы следующие сокращения и обозначения. ГТД — газотурбинный двигатель; ДАТ — первичные преобразователи, служат для преобразований физических параметров в электрический сигнал; Рис. 14. 2. Структурная схема АСИ ГТД
КОМ — коммутаторы для последовательного подсоединения датчиков к нормализаторам; Норм — нормализаторы, предназначенные для усиления или ослабления электрического сигнала до определения уровня U = 0. . . 5 В; Пр. в код — преобразователи в цифровой код; АЦП — аналого-цифровой преобразователь (преобразователь непрерывного электрического сигнала, например напряжения, в цифровой код); ЧЦП — частотно-цифровой преобразователь (преобразователь частоты переменного тока в цифровой код); БД — база данных; Гр. пос. — графопостроитель; Пульт упр. — пульт управления; ЦАП — цифроаналоговый преобразователь (преобразователь цифрового ко да в непрерывный электрический сигнал); Исполн. механ. — исполнительный механизм; УСО — устройство связи с объектом. Нормализаторы, преобразователи аналогового и частотного сигналов в цифровой код являются измерительными элементами системы. Цифровые коды, соответствующие величинам измеряемых параметров, поступают в ЭВМ является главным элементом АСИ. Оснащенная соответствующим математическим (программным) обеспечением ЭВМ осуществляет сбор измерительной информации, ее обработку и управление процессом испытания. Все эти операции выполняются по определенным алгоритмам. В данном случае, алгоритм — набор формальных правил, описывающих способ преобразования исходных данных для получения результата.
При обработке измерительной информации могут использоваться данные о результатах предыдущих испытаний, которые хранятся в БД. Полученные результаты могут быть также помещены в БД. Взаимодействие оператора с ЭВМ осуществляется через пульт управления. Наиболее эффективным методом общения оператора с ЭВМ является диа логовое (интерактивное) взаимодействие. Диалоговое взаимодействие может применяться при работе системы как в темпе эксперимента, так и при обработке результатов после эксперимента. Для перемещения РУД и регулировочных элементов цифровой код, кото рым оперирует ЭВМ, преобразуется в электрический сигнал. Это преобразование осуществляется с помощью ЦАП. Электрические сигналы поступают в исполнительные механизмы (электрические двигатели с редукторами). Они преобразуют электрические сигналы в механическое перемещения РУД и регулировочных элементов. Комплекс аппаратных средств, включающий коммутаторы, нормализаторы, АЦП, ЧЦП, ЦАП и др. , образует так называемое устройство связи с объектом (УСО). Для возможности сопряжения между собой отдельных блоков АСИ, их входы и выходы необходимо выполнять по определенным правилам. Эти правила оговариваются принятыми стандартами на сопряжения, называемые интерфейсами. Интерфейс — это сопряжение двух блоков, выполненное по определенному стандарту. Интерфейс определяет: тип разъемов, число сопрягаемых линий, назначение каждой линии, содержание информации, передаваемой по каждой линии, коди ровку информации, характеристики сигналов, передаваемых по каждой линии.
Главный интерфейс АСИ — это стык УСО с ЭВМ. Если какие-либо элементы системы не имеют стандартного интерфейса, то они подключаются через адаптеры (переходники). Функционально законченные элементы системы, имеющие одинаковый интерфейс входа-выхода, называются модулями. При наличии типовых модулей различного назначения (коммутаторы, нормализаторы, АЦП, ЧЦП, ЦАП и т. д. ) АСИ могут быть составлены из них полностью или частично. Комплекс УСО и ЭВМ с периферийными устройствами образуют вместе с программным обеспечением измерительно-вычислительный комплекс (ИВК). Важнейшим элементом АСИ является прикладное математическое обеспечение (программное обеспечение). С его помощью осуществляется градуировка и метрологическая аттестация измерительных каналов, сбор измерительной информации, ее обработки, общение с БД, вывод результатов на устройства отображения информации (дисплей, принтер, плоттер, панели индикации), диалоговое взаимодействие с оператором, управление двигателем.
14. 3. УСТРОЙСТВА СВЯЗИ С ОБЪЕКТОМ (УСО) УСО — одно из наиболее важных устройств в АСИ ГТД. Оно обеспечивает связь датчиков с ЭВМ и ЭВМ с исполнительными механизмами. УСО осуществляет преобразование электрических сигналов в цифровой код и цифровой код в электрические сигналы. УСО функционально расположено между датчиками, агрегатами управления и компьютером. Современные УСО строятся на базе конструктивных элементов, которые выполняют определенные функции. В зависимости от конкретных особенностей АСИ УСО может включать в себя различные блоки, например: коммутаторы — для последовательного подключения датчиков к элементам измерительной системы; нормализаторы — для получения электрических сигналов требуемого уровня; формирователи — для получения требуемой формы электрических сигналов; АЦП — для преобразования аналоговых сигналов в цифровой код; ЦАП — для преобразования цифрового кода в электрические сигналы; таймеры — электронные часы для фиксации требуемых интервалов времени и управления блоком УСО; генераторы — для получения сигналов заданной частоты; счетчики — для подсчета количества электрических импульсов; преобразователи питания — для получения напряжения питания требуемой величины). Еще несколько лет назад функциональные элементы: коммутаторы, АЦП выполнялись в виде отдельных плат или блоков, то сейчас функциональный элемент — плата (модуль) представляет собой сложную конструкцию, состоящую из коммутатора, АЦП, усилителя, нормализатора, а в ряде случаев и микропроцессора. Обычно плату (модуль) устройства связи с объектом конструируют для выполнения определенной функции, например:
• ввод сигналов с термопар; • ввод сигналов с термометров сопротивления; • ввод частотных сигналов (например, с датчиков частоты вращения); • ввод сигналов с датчиков с унифицированным выходом (4. . . 20 м. А, 0. . . 10 В, 0. . . 5 В); • вывод аналоговых сигналов (0. . . 5 м. А, 4. . . 20 м. А, 0. . . 10 В, 0. . . 5 В); • выдача команд в виде замыкания контактов или сигналов тока, напряжения и др. В настоящее время промышленность России выпускает достаточно широкий набор элементов УСО, позволяющих контролировать весь объем параметров, измеряемых в процессе испытания газотурбинных двигателей. При выборе модулей (плат, блоков) УСО следует обращать внимание, прежде всего, на следующие характеристики: • метрологические; • надежностные; • ремонтопригодности. При наличии специальных требований по искро- и взрывобезопасности следует выбирать элементы УСО, отвечающие этим требованиям. 14. 3. 1. Основные функциональные элементы модулей УСО Коммутатор [34] предназначен для последовательного подключения к измерительной цепи, состоящей из нормализатора, усилителя, аналогово-цифрового преобразователя и датчиков. Обычно коммутаторы выполняются на 8, 16, 32, 64 входных канала. Увеличение числа входов нецелесообразно из-за сильного замедления процесса коммутации.
Коммутаторы обычно состоят из двух узлов: переключателя и узла управления. Переключатели разделяют на две группы: • механические переключатели; • электронные переключатели. Достоинство всех механических переключателей в том, что они осуществляют передачу электрических сигналов без искажений. Герметичные контакты — магнитоуправляемые (герконы) — в стеклянной производят переключение от внешнего магнитного поля, создаваемого катушкой Недостатком механических переключателей является низкая частота переключения в пределах 5. . 15 Гц. Электронные переключатели с использованием транзисторов имеют значительно большую частоту переключения, где переключение производится при подаче напряжения на базу транзистора. При этом сопротивление транзистора резко падает и через участок эмиттер-коллектор потечет ток. Такие устройства имеют очень малое быстродействие, но всегда в той или иной искажают электрический сигнал и поэтому требуют периодической калибровки Электронные переключатели, управляемые от ЭВМ или сигналами с командного блока, называются мультиплексорами. Основным элементом коммутатора является ключ. На рис. 14. 3 приведена схема коммутатора с параллельным соединением ключей.
В такой схеме один из входных каналов открыт, остальные закрыты. Сигнал поступающий на вход открытого канала, искажается за счет конечного сопротивления закрытых ключей. Кроме того, происходит падение напряжения на открытом ключе, что также искажает сигнал. С увеличением числа коммутируемых каналов влияние конечного сопротивления закрытых ключей увеличивается. Уменьшения этого влияния применяют схему пирамидального (двухступенчатого) коммутатора, приведенную на рис. 14. 4 Рис. 14. 3. Схема коммутатора с параллельным соединением ключей Рис. 14. 4. Схема пирамидального коммутатора
В пирамидальной схеме параллельно включенных входных каналов значительно меньше. Но и эта схема имеет недостатки — увеличивается количество открытых ключей, в данном случае 2 (на 1 -ой и 2 -ой ступенях коммутации), что приводит к увеличению погрешности. Существуют и другие схемы коммутаторов, например матричные, в которых упрощается управление, но увеличивается погрешность. Все выше перечисленные схемы коммутации делятся на два вида по применяемым ключам: • бесконтактные ключи; • контактные ключи. Бесконтактные ключи — строятся на базе, например транзисторов, а контактные — на базе магнитоуправляемых реле (герконов). В настоящее время более широко используются бесконтактные ключи, так как обладают более высоким быстродействием и хорошими электрическими характеристиками. Аналого-цифровые преобразователи (АЦП) предназначены для преобразования аналоговых сигналов, поступающих с датчиков, в цифровой код, пропорциональный величине входного сигнала. Существуют следующие виды АЦП: последовательного счета; поразрядного уравновешивания; с динамической компенсацией и следящий АЦП. Дискретизация — это переход от непрерывной функции к прерывистой, или дискретной. Чаще всего при измерении формируются сигналы с непрерывной функцией, а обработка проводится цифровыми дискретными средствами. Поэтому необходимо преобразовать аналоговую форму сигнала в цифровой эквивалент. Этот процесс можно осуществлять в виде фиксации мгновенных значений исходного сигнала.
Амплитуда импульсов при этом соответствует мгновенным значениям функции, взятым в моменты t 1 t 2 , . . . , t n. Длительность импульса t — время фиксации сигнала. Частота фиксации f ф выбирается из соотношения теоремы Котельникова: где F mах — максимальная частота в спектре частот сигнала. В результате получаем последовательность псевдонепрерывных уровней, огибающая которых воспроизводит исходный сигнал. Другим способом дискретизации является дискретизация на переменной частоте. В этом случае интервал Т между двумя импульсами дискретизации не постоянен, а зависит от скорости входной величины. Дискретизация аналоговых сигналов осуществляется посредством коммутаторов. Результат любого измерения в конечном итоге выражается числом, которое в АСИ должно быть не только прочитано, но и храниться до перезаписи на долговременное запоминающее устройство. Поэтому в АСИ широко используются блоки, называемые счетчиками или счетными регистрами. Счетчики применяются для подсчета электрических импульсов и временного хранения конкретных результатов. Основу счетчика составляет цепочка триггера. Триггер — устройство, которое может сколь угодно долго находиться в одном из двух устойчивых состоя ний и скачкообразно переходить из одного состояния в другое под действием внешнего сигнала. Устойчивое состояние триггера характеризуется наличием или отсутствием на его выходе электрических сигналов. Эти состояния триггера принято выра жать двоичным числом. Например, отсутствие электрического сигнала на выходе триггера соответствует состоянию «О» , наличие электрического сигнала соответствует состоянию « 1» (или наоборот).
Элементной базой триггеров являются транзисторы. Триггеры могут работать совместно с логическими электронными схемами, которые называются логическими триггерами. Логические электронные схемы реализуют следующие логические опера ции: Схема «НЕ» применяется главным образом в сочетании со схемами «И» и «ИЛИ» . Подключив схему «НЕ» на выход схемы «И» и «ИЛИ» , получим схемы:
Цепочка последовательно соединенных логических триггеров составляет основу счетного регистра. В счетном регистре каждый последующий триггер запускается от предыдущего в момент перехода триггера из состояния « 1» в состояние « 0» (рис. 14. 5). Счетчик состоит из нескольких последовательно соединенных триггеров. Каждый триггер соответствует определенному разряду в двоичной системе счисления (Т 1 — разряд единиц, Т 2 — разряд двоичных десятков, ТЗ — разряд двоичных сотен и т. д. ; в переводе в десятичную систему двоичный десяток 2 1 = 2, двоичная сотня 2 2 = 4, двоичная тысяча 2 3 = 8 и т. д. ). Величина числа, которое может быть записано в счетчике ограничивается количеством его разрядов (триггеров). Если число разрядов счетчика — 5, то максимальное число, которое может быть в нем записано, — 31. Если число разрядов — 10, то — 1023 и т. д. Перед началом работы счетчика в его разрядах находятся нули. Первый электронный импульс, пришедший на счетчик, меняет состояние первого триггера Т 1 — в нем появляется « 1» , второй электронный импульс меняет состояние триггера Т 1 на противоположное — « 0» , но при этом от триггера Т 1 запус кается триггер Т 2 — он меняет свое состояние на 1 и т. д. Рис. 14. 5. Блок-схема счетчика
Аналого-цифровые преобразователи (АЦП) предназначены для преобразования аналоговых сигналов, поступающих с датчиков, в цифровой код, пропорциональный величине входного сигнала. Существуют следующие виды АЦП: последовательного счета; поразрядного уравновешивания; с динамической компенсацией и следящий АЦП. Чаще всего при измерении формируются сигналы с непрерывной функцией, а обработка проводится цифровыми дискретными средствами. Поэтому необходимо преобразовать аналоговую форму сигнала в цифровой эквивалент. Этот процесс можно осуществлять в виде фиксации мгновенных значений исходного сигнала. В результате получаем последовательность псевдонепрерывных уровней, огибающая которых воспроизводит исходный сигнал. Другим способом дискретизации является дискретизация на переменной частоте. В этом случае интервал времени Т между двумя импульсами дискрети зации не постоянен, а зависит от скорости входной величины. Дискретизация аналоговых сигналов осуществляется посредством коммутаторов. В качестве примера рассмотрим схему АЦП последовательного счета, блок-схема которого показана на рис. 14. 6. В состав данного устройства входят следующие блоки. Компаратор (от английского compare— сравнивать) — электронное устройство для сравнения величин двух электрических сигналов. На выходе из компа ратора появляется электрический сигнал только в том случае, если U изм < U n. Генератор линейных напряжений — генерирует пилообразное напряжение U n. Напряжение U n увеличивается от нуля по линейному закону. Достигнув определенной величины, оно скачком уменьшается до нуля, и цикл повторяется.
Генератор электрических импульсов — вырабатывает высокочастотные электрические сигналы. При подаче сигнала включения на выходе из триггера появляется электрический сигнал ( « 1» ). При этом запускается генератор линейных напряжений. Он начинает генерировать один из зубцов пилы (напряжение U „ начинает увеличиваться). Рис. 14. 6. Блок-схема АЦП последовательного счета
Рис. 14. 7. Временная диаграмма работы АЦП последовательного счета Логическая схема «И» пропускает на счетчик электрические импульсы от генератора электрических импульсов. Счетчик подсчитывает их количество. Тем временем пилообразное напряжение f/ n , постепенно увеличиваясь, достигает ве личины измеряемого напряжения U изм , т. е. U п = U изм. В этот момент на выходе из компаратора появляется электрический сигнал. Он переводит триггер в противоположное состояние ( « 0» ), при этом на выходе из триггера электрический сигнал исчезает. Схема «И» перестает пропускать электрические сигналы с генератора электрических импульсов. Так как время, в течение которого схема «И» пропускала электрические импульсы с генератора электрических импульсов, пропорционально величине то и число, зафиксированное счетчиком, будет пропорционально величине U изм. Временная диаграмма работы АЦП последовательного счета показана на Рис. 14. 7 Цифро-аналоговые преобразователи (ЦАП) используются для преобразования числа записанного в счетном регистре, в аналоговый электрический сигнал.
Величина аналогового электрического сигнала пропорциональна записан ному в регистре числу. Принцип работы практически всех модификаций ЦАП основан на поре рядном суммировании токов с помощью ключей, управляемых счетным регистром (рис. 14. 8). 14. 8. Структурная схема ЦАП с поразрядным суммированием токов В данной схеме ЦАП величина сопротивления R 0 « R i , i= 1. . . 5. Тогда I i = U 0 /R i , U вых = I i R 0 = U 0 R 0 / R i , . Подадим на вход счетчика один электрический импульс. Тогда триггер Т 1 перейдет в состояние « 1» . Будет запитан электромагнит, который включит ключ Кл 1. При этом R i = R 1 , U вых1 = U 0 R 0 /R 1. Подадим второй импульс. Тогда Т 1 перейдет в состояние « 0» , Кл 1 разомк нется, при этом триггер Т 2 перейдет в состояние « 1» и замкнется Кл 2, тогда R j = R 2 = R 1 /R 2 , U вых2 = U 0 R 0 /R 2 = 2 U 0 R 0 /R 1, т. е U вых2 = 2 U вых1. Подадим третий импульс. Тогда Т 1 вновь перейдет в состояние « 1» , Т 2 — в « 1» (на счетчике цифра три). Замкнуты Кл 1 и Кл 2.
При приходе каждого нового импульса (увеличили на единицу записанного в регистре числа) U вых ступенчато увеличивается на величину U вых1 = U 0 R 0 /R. Таким образом напряжение на выходе ЦАП оказывается пропорциональным числу k, записанному в счетном регистре (рис. 14. 9). Для получения линейной характеристики преобразования числа k в U вых необходимо, чтобы сопротивления R i находились в пропорции, указанной на блок-схеме ЦАП. Подбор этих сопротивлений упрощается на базе одинаковых значений сопротивлений R i по схеме R 2 =R 1 /2; R 3 = R 0 /4 и т. д. за счет параллельного их включения. Преобразователь частоты следования импульсов в код. При испытании ГТД ряд датчиков, используемых для измерения параметров, вследствие их принципа действия имеет на выходе последовательность импульсов, частота следования которых пропорциональна физической величине. К таким параметрам двигателя относятся, прежде всего: • частоты вращения роторов двигателя; • расходы жидкостей (расходомер турбинного типа). Для преобразования последовательности импульсов в код применяют специальные схемы. На рис. 14. 10 приведена блок-схема такого преобразователя. Задатчик интервала времени 1 подает на ключ 2 импульс, соответствующий выбранному интервалу счета (Г). Например, выбирается интервал счета 1 с.
Рис. 14. 9. Диаграмма изменения U вых ЦАП: Рис. 14. 10. Преобразователь частоты следования импульсов в код На второй вход ключа 2 поступают импульсы с датчика 3 с частотой f. Ключ пропускает эти импульсы на вход счетчика 4 только в течение интервала счета Т. Количество импульсов N, зафиксированное в счетчике в конце интервала счета T, будет равно: Если характеристика датчика описывается формулой
где Q например, расход топлива; k — коэффициент пропорциональности, то расход, выраженный через значение N в счетчике, выразится формулой: С увеличением выбранного интервала счета Т погрешность определения N уменьшается. Нормализаторы предназначены для приведения нестандартных сигналов, поступающих с датчиков, или агрегатов, в нормализованный вид. Примером простейшего нормализатора может служить делитель на резисторах. Пример: прибор с выходным сигналом 0. . . 20 В должен быть подключен к АЦП с нор мализованным входным сигналом 0. . . 10 В. Для приведения выходного напряжения прибора к уровню 0. . . 10 В на выходе прибора ставится делитель из двух одинаковых резисторов (рис. 14. 11). Усилители. При создании автоматизированных систем часто встречается необходимость усиления слабых сигналов, поступающих, например, с термопар, тензомостов и других элементов, и приведения усиленных сигналов к уровням нормализованных сигналов. Такие усилители называются нормирующими. Рассмотрим требования к усилителю сигналов с термопар. Такие усилители относятся к классу усилителей постоянного тока. Усилители для данного случая должны обладать следующими характеристиками: • большое входное сопротивление; • малый уровень собственных шумов; • наличие гальванической развязки между входом и выходом; • большой коэффициент усиления; • стабильность нуля.
В качестве предварительного усилителя [5] используют дифференциальный усилитель, выполненный в виде интегральной микросхемы (рис. 14. 12). Рис. 14. 12. Схема подключения усилителя к мосту Уитстона. Рис. 14. 11. Схема делителя напряжения
Рис. 14. 13. Схема подключения к усилителю термопреобразователей Дифференциальный усилитель характеризуется следующими основными параметрами: • регулируемый коэффициент усиления — от 1 до 104; • высокое входное сопротивление — до Ю 10 Ом; • малое выходное сопротивление — около 0, 1 Ом; • высокая температурная стабильность характеристик, что практически исключает дрейф нуля. Усилитель устанавливают обычно в корпусе датчика. Современные усилители постоянного тока обладают достаточно высокими характеристиками при малых габаритах, что позволяет встраивать их в конструкцию датчика. Такие устройства обеспечивают усиление и преобразование сигналов с термопреобразователей сопротивления и термопар и выполняются в виде отдельного конструктива. Схема подключения термопар к усилителю приведена на рис. 14. 13. Искрозащитные разделительные барьеры. На испытательных стендах, насыщенных трубопроводами и емкостями с жидким и газообразным топливом, агрегатами, заполненными маслами, существует непосредственная опасность возникновения пожара. Для защиты как обслуживающего персонала, так и оборудования должны быть приняты меры предосторожности, создающие условия, при которых во взрывоопасных средах опасность возникновения пожара или взрыва сводится к нулю.
Наиболее применяемым является метод ограничения энергии, запасенной в электрической цепи, т. е. организация искробезопасной электрической цепи. Вид взрывозащиты — «искробезопасная электрическая цепь» основывается на поддержании искробезопасного тока (напряжения, мощности или энергии) в электрической цепи. При этом под искробезопасным током понимается наи больший ток в электрической цепи, образующий разряды и который не вызы вает воспламенения взрывоопасной смеси. Поэтому в состав УСО автоматизированной системы контроля и управления включают специальные элементы — барьеры искрозащиты. Барьеры искрозащиты обеспечивают искробезопасность электрической цепи посредством огра ничения энергии в пределах нижней границы взрыва смеси. При этом для соединения электрооборудования, находящегося во взрыво опасной зоне, с оборудованием, находящимся во взрывобезопасной зоне, при меняются специальные ограничительные элементы: • диодные барьеры безопасности, или пассивные барьеры; • гальванически изолированные барьеры безопасности, или активные барьеры. Электрооборудование для взрывоопасных зон. Оборудование стенда подразделяется в общем случае на два вида по взрывобезопасности: • оборудование, размещенное во взрывоопасной зоне (непосредственно в боксе стенда); • оборудование, размещенное в помещении пульта управления (взрывобе зопасная зона). Электрооборудование, размещенное в боксе стенда, делится на два типа: • элементарное электрооборудование (термопара, термометр сопротивле ния, светодиод, реле и т. д. ); • взрывобезопасное оборудование.
Технические характеристики элементарного электрооборудования не долж ны превышать значений: • по напряжению 1, 2 В; • по току 0, 1 А; • по мощности 25 м. Вт. Это означает, что элементарное оборудование не будет способно производить, накапливать энергию, достаточную для воспламенения взрывоопасной смеси. Взрывобезопасное оборудование должно быть утверждено как искробезопасное и иметь параметры, которые отвечают требованиям соответствующей взрывоопасной смеси. 14. 3. 2. Модули УСО Современные системы контроля и управления при испытаниях ГТД строятся из набора элементов: модулей, конструктивов, блоков, кросс-панелей. Эти элементы соединяются кабелями. В качестве примера рассмотрим характеристики модулей российской фирмы «Л-КАРД» , выпускающей широкую номенклатуру модулей сбора, обработки данных и управления технологическими процессами. Крейтовая измерительная система LTC включает в себя набор элементов (номенклатура их исчисляется десятками), на основе которых может быть создана автоматизированная система конкретного применения. Модули в системе LTC снабжены коммутаторами на входе, поэтому каждый модуль обеспечивает подключение нескольких измерительных каналов (от 4 до 32). Это значительно снижает стоимость системы контроля при сохранении достаточно хороших характеристик по быстродействию.
Модуль LC-227 Многофункциональный модуль LC-227 с гальванической развязкой отдельных каналов служит для измерения медленно меняющихся сигналов в случаях, требующих гальванической развязки каналов (рис. 14). Рекомендуется к применению при использовании термопар, подключенных на корпус (измерение поверхностных температур), а также в условиях больших индустриальных помех. Рис. 14. Модуль LC-227 Рис. 14. 15. Модуль LC-11 I 0. . . 50 (0. . . 25) м. В…………………………. 0, 25 %; 0 -20 м. А………………………………. 0, 1 %; изменения сопротивления…………………. . 0, 1 %.
Модуль LC-П 1 Модуль измерения сигналов в диапазоне 0. . . 10 В LC-111 является недорогим, надежным модулем, обеспечивающим коммутацию до 32 входных каналов, усиление, нормализацию и преобразование сигналов (рис. 14. 15). Модуль имеет групповую гальваническую развязку от «земли» крейта. Применяется для ввода и преобразования сигналов с датчиков давления, температур с выходным сигналом 4. . . 20 м. А и др. Основная погрешность — 0, 05 %. Модуль LC-451 Модуль для проведения измерения частоты сигналов LC-451 позволяет проводить измерения частоты или периода частотного аналогового сигнала по 8 входным линиям. Установка интервала измерений и опрос результатов осуществляются независимо для каждого канала. Модуль применяется для ввода сигналов с датчиков частоты вращения рото ров, датчиков расхода топлива и масла. Число входных каналов. . . . 8; Диапазон входных сигналов. . . . ± 5 В; Измеряемые частоты входных сигналов. . . . 1 Гц. . . 25 к. Гц; Погрешность измерения в режиме периодомера. . . 0, 1 %.
На основе перечисленных модулей можно создать систему, обеспечивающую ввод, преобразование и обработку информации с датчиков: • температур (термопары, термометры сопротивления); • давлений, перепадов давлений; • частот вращения; • усилия от тяги; • перемещений; • расходов жидкостей и газов и др. , а также при необходимости обеспечить управление процессом испытания путем включения (выключения) агрегатов и устройств стенда.
14. 4. ЭВМ И МАТЕМАТИЧЕСКОЕ ОБЕСПЕЧЕНИЕ В настоящее время автоматизированные системы испытаний авиационных ГТД строятся в основном на использовании персональных ЭВМ. Типовой состав устройств ПЭВМ включает системный блок обработки управления, средства взаимодействия пользователей с системным блоков средства долговременного хранения и накопления данных и средства подключения к каналам связи. Такой состав устройств ПЭВМ предоставляет распоряжение пользователей самые разнообразные функциональные возможности. Персональные ЭВМ строятся на основе модульной конструкции, которого включает набор конструктивно-законченных модулей: • системный модуль, конструктивно размещенные на одной плате центральный процессор, основная память и разъемы для подключения функциональных модулей; • функциональные модули, конструктивно размещенные на одной плат контроллеры, адаптеры и дополнительная память, подключаемые к разъема системного модуля. Системный и функциональные модули совместно с блоком питания и некоторыми внешними устройствами конструктивно объединяются в единый си темный блок, к которому через соответствующие разъемы подключаются выносные внешние устройства (ВУ): печатающее и клавишное устройства, ди плен и т. д. Конструктивно любая модель ПЭВМ имеет базовый комплект, включающий три типа внешних устройств: диалоговые, запоминающие и телекоммуникационные. Внешние устройства подключаются к системной магистра; ПЭВМ с помощью контроллеров, которые обеспечивают сопряжение алгоритма функционирования системной магистрали с алгоритмом функционирования данного внешнего устройства.
Периферийные устройства ПЭВМ можно подразделить на: • устройства ввода информации; • устройства вывода информации; • устройства ввода-вывода информации. К устройствам ввода информации относят: клавиатуру, сканер и д. р. Скорость ввода информации с помощью клавиатуры относительно невелика. Кроме того, некоторую графическую информацию вообще невозможно внести в память ЭВМ с помощью клавиатуры. Эту проблему позволяет разрешить считывающее устройство или сканер. Сканер — это устройство для ввода изображений в виде растровой матрицы высокой разрешающей способностью. С помощью сканера можно ввести в память ПЭВМ не только текстовую или цифровую информацию, но и различные чертежи, графики, картины, фотогра фии и другие изображения. Одним из основных устройств вывода информации является дисплей. В по следнее время все шире используются плоские дисплеи с жидкокристалличе скими или газоразрядными индикаторами. Очень часто информацию требуется распечатать в виде документа. В этих целях используются принтеры. Различают следующие типы принтеров: барабанные, матричные, лепестко вые, струйные, лазерные и термопринтеры. Для построения графиков, чертежей, выкроек, метеорологических карт т. д. используют графопостроители или плоттеры.
Для обмена информацией с другими компьютерами используется модем. По конструктивному исполнению модемы бывают встроенными и внешними. Специалисты по разработке систем контроля и управления испытанием ГТД сталкиваются с проблемой обеспечения работоспособности аппаратуры в условиях повышенных вибраций, повышенных температур, а также при наличии достаточно мощных промышленных помех в сети и электромагнитных излучений. К неблагоприятным факторам, которые присутствуют на стенде, относятся: пары масел и топлива в воздухе, наличие пыли, газов (выхлопных и топливных). Стендовое контрольно-измерительное оборудование размещается обычно в специальном помещении, которое называется пультовой (измерительной). В испытательном боксе, рядом с двигателем или на двигателе, размещается датчиковая аппаратура, контроллеры и часть блоков нормализации сигнала. Условия в измерительной гораздо более благоприятные, чем в боксе, но и сюда проникают все факторы, которые перечислены выше. Установка в промышленные условия офисного (конторского) компьютера приведет к быстрому его выходу из строя. Проблема решается установкой в по мещениях с неблагоприятными условиями так называемого промышленного компьютера. Промышленный компьютер — это изделие с повышенной устойчивостью к воздействию окружающей среды и обладающий модульностью конструкции. Методы повышения устойчивости к воздействию окружающей среды Устойчивости к воздействию окружающей среды добиваются различными способами. Рассмотрим некоторые из них. Борьба с пылью. Один из методов борьбы с пылью — создание избыточного давления в корпусе компьютера, на всасывающие вентиляторы устанавливают пылеулавливающие фильтры.
Борьба с воздействиями вибраций идет проще всего по пути создания прочного шасси и корпуса, платы промышленного компьютера закрепляются специальными дополнительными амортизирующими скобами, а дисковые накопители П 1 размещаются на специальной виброударостойкой подвеске. Увеличение надежности работы в условиях повышенных температур. Влияние высоких окружающих температур, в некоторых случаях достигающих 45 °С, снижают за счет хорошего охлаждения и за счет применения специальной элементной базы. Модульность конструкции В промышленных компьютерах применен принцип модульности и исклю чительных возможностей по расширению. «Материнской платы» здесь нет, процессорная плата на общих основаниях вставляется вместе с другими платами в объединительную кросс-плату с большим числом слотов расширения. На рис. 14. 16 приведен внешний вид шасси промышленного компьютера 1 РС-610. Рис. 14. 16. Шасси промышленного компьютера IPC-610: / — монтажная панель для специальных разъемов или кабельных удлинителей; 2 — сдвоенные охлаждающие вентиляторы, создающие положительное давление воздуха внутри шасси; 3 — сменный пылеулавливающий фильтр; 4 — пыленепроницаемая запирающая дверца для обеспечения безопасной работы; 5 — в прочном противоударном сменном отсеке может размещаться до двух накопителей половинной высоты и 3, 5″ НЖМД; 6 — регулируемая крепежная планка с амортизаторами предохраняет платы от ударов и вибрации
Некоторые особенности конструкции внешнего оборудования Количество слотов расширения может достигать 20, что позволяет создавать на базе промышленного компьютера довольно сложные системы контроля и управления технологическими процессами. Учитывая особенности работы промышленною компьютера в условиях производства. изменились требования к внешнему оборудованию. Так, например, клавиатура выполняется в пылевлагозащитном исполнении. Кнопки и органы управления типа «Сброс» , «Пуск» , «Выключение питания» помешают за запираемыми на ключ дверцами. Предъявляются повышенные требования к мониторам. Мониторы промыш ленного исполнения имеют следующие особенности: • расширенный рабочий диапазон температур: 0. . . 50 °С; • усиленные корпус и шасси: • печатные платы выполнены из фибергласса: • все тяжелые детали закреплены болтами и хомутами; проведено экранирование от сильных магнитных полей В результате среднее время безотказной работы монитора составляет свыше 60 000 ч.
Рабочие станции Другой разновидностью «индустриальных» компьютеров являются рабочие станции (рис. 14. 17). Рабочая станция промышленного исполнения отличается следующими особенностями: • дисплей, системный блок и клавиатура размещены в едином конструктиве; • корпус усилен; • влагозащищенная прочная панель; • дисплей защищен толстым стеклом; • органы управления и дисковод находятся за запираемой передней панелью; • большое число слотов расширения; • станция может устанавливаться в типовую стойку; • мощный источник питания; • рабочий диапазон температур 0. . . 50 °С. Рис. 14. 17. Рабочая станция AWS-
Рис. 14. 18. Панельный компьютер РРС-100 Панельные компьютеры Отличительной особенностью панельных компьютеров являются их малые габариты. В качестве дисплеев применяются плоские панели. Панельные компьютеры предназначены для установки в пульты и панели и служат для создания хорошо защищенного интерфейса «человек — машина» . Они хорошо приспособлены к промышленным условиям, поэтому могут устанавливаться непосредственно на контролируемых установках. На рис. 14. 18 приведен внешний вид панельного компьютера РРС-100. Модульные промышленные компьютеры Модульный компьютер обладает всеми достоинствами модульной конструкции, которая позволяет резко уменьшить время восстановления оборудования. В модульных компьютерах традиционно решен вопрос охлаждения системы: • вентиляторы снабжены пылеулавливающими сменными фильтрами; • создается избыточное давление внутри корпуса. Традиционно для промышленного компьютера решен вопрос вибро- и ударостойкости конструкции: это, прежде всего, прочность корпуса и демпфирующие подвески на узлы. Процессор выполнен в виде отдельной платы.
На процессорной плате имеется отдельный разъем для подвода питающие напряжений, минуя системную шину. Это позволяет использовать плату автономно в качестве вычислительного ядра различных систем. Промышленные ноутбуки В последнее время ноутбуки все шире применяются в практике испытаний газотурбинных двигателей. Это связано, прежде всего, с необходимостью про ведения наукоемких экспериментальных исследований как на стендах, так и в полевых условиях. Ноутбуки все чаще встраиваются в современные специализированные системы контроля и управления процессами испытания ГТД. На базе ноутбуков создаются специализированные системы оценки: вибрационного состояния двигателя; уровня пульсаций давления в тракте ГТД; прочностных характеристик деталей ГТД. При этом разработчики сталкиваются с проблемой необходимости использования оборудования в жестких условиях: при наличии вибраций, при повышенных окружающих температурах, при наличии пыли, паров масел и топлив и др. Ноутбуки промышленного и военного применения делят обычно на три группы: • повышенной прочности (серия А); • промышленные (серия I); • военные (серия N).
Ноутбуки серии А (рис. 14. 19) применяются для условий более жестких, чем офисные условия, но все-таки облегченные по сравнению с требованиями другим моделям. Ноутбуки серии А достаточно стоек к внешним факторам и в то же время его цена значительно ниже цены моделей I и N. От офисных ноутбуков они отличаются: • повышенной прочностью корпуса; • повышенной герметичностью. Шасси ноутбука серии А изготовлено из литого магниевого сплава и имеет по углам дополнительные резиновые буферы, что обеспечивает дополнительную защиту при механических воздействиях. Такая конструкция позволяет ноутбукам выдерживать вибрации до 2 g. удары до 30 g и падение на бетон с высоты 1 м. Температурный диапазон работоспособности ноутбука: -20. . . 50 °С при влажности 5. . . 95 % (без конденсации). Ноутбуки оснащаются, как правило, резиновой клавиатурой и защищенной указательной сенсорной панелью. Эти меры обеспечивают защиту ноутбука от пыли и влаги на уровне норм IP 52, что делает возможным работу даже под дождем и в условиях сильной запыленности. Обеспечивается защита от электромагнитных полей. Ноутбуки серии А не отличаются по вычислительной мощности от аналогичных офисных. Важной особенностью промышленного ноутбука является возможность установки модуля расширения, куда может быть установлено дополнительное оборудование для организации специализированной системы.
Важной отличительной особенностью большинства промышленных ноутбуков являются расширяемость и легкость модернизации. На рис. 14. 19 приведены возможности расширения конфигурации ноутбука серии А.
Рис. 14. 19. Возможности расширения конфигурации ноутбука серии А Для обеспечения работоспособности ноутбуков серии А в полевых условия (на транспорте) дополнительно поставляется амортизирующая платформа, которая позволяет улучшить параметры вибро- и ударостойкости. Если ноутбук серии А все-таки не выдерживает условий эксплуатации в реальных условиях, вместо него может применяться ноутбук серии I. Эта модель выдерживает удары до 40 g. не боится сильного ливня и падения лужу, т. е. обеспечивает высокую степень защиты. По вычислительной мощности модель серии I не уступает модели серии А. В модели серии I есть возможность установки модуля расширения с установкой одной платы. Ноутбуки серии N — модели специального военного применения и являются модификацией серии I, оптимизированной для военного применения.
Параметры воздействия окружающей среды сертифицированы на соответствие военным стандартам. Математическое обеспечение (МО) является неотъемлемой частью ИВК и АСИ ГТД в целом, обеспечивающей их функционирование. Структурная схем МО ИВК представлена на рис. 14. 20. Математическое обеспечение ИВК состоит из двух основных частей: обще МО и специальное МО. Общее математическое обеспечение включает в себя: а) средства контроля и диагностики системы; б) операционную систему (ОС). Средства контроля и диагностики системы — это совокупность программ контроля исправности технических средств и программ ОС ИВК, а также диагностики неисправностей в ходе функционирования ИВК. ОС — это совокупность программ для управления работой ЭВМ и ее пери серии, а также для облегчения программирования, отладки и сопровождении программ специального МО.
Рис. 14. 20. Структурная схема МО ИВК
Обрабатывающие программы ОС обеспечивают отладку программ пользователей, их трансляцию с языков программирования, редактирование связей и организацию библиотек соответствующих программ пользователя. Специальное математическое обеспечение включает инструментальные программные среды и программы пользователя (ПП). В настоящее время разработано большое число прикладных программ, ориентированных на различные области применения: • для управления процессами передачи данных по линиям связи; • для управления базами данных (СУБД); • для численного анализа (решение системы уравнений, численное интегрирование, аппроксимация и интерполяция функций и т. д. ); • для обработки данных методами математической статистики; • решение задач оптимизации; • для операций с матрицами; • для графической обработки данных (масштабирование осей графика, построение графиков на бумаге и экранах дисплея). Программы пользователей предназначены для организации работы ЭВМ по разработанным алгоритмам. В АСИ ГТД с помощью этих программ осуществляются сбор и обработка измерительной информации, анализ получаемых результатов, выработка управляющих воздействий, взаимодействие оператора с системой, подготовка выходной документации.
Требования к математическому обеспечению ИВК: • возможность составления рабочего задания на каждое испытание по ви дам, количеству и порядку опроса параметров (каналов); • возможность оперативной корректировки рабочего задания в процессе испытаний для изменения вида, количества, порядка опроса, числа опросов ка ждого параметра, вида усреднения, скорости опроса, введения или исключения цифровых фильтров и т. п. ; • оперативный контроль и визуализация параметров, включая аварийные и рас четные, графическое изображение расчетной и действительной информации для работы специалистов, сопровождающих и анализирующих результаты измерений; • непрерывное слежение за параметрами ограничений, с уходом с режима при достижении с обеспечением регистрации и отображения; • спектральный анализ сигналов при тензо- и виброметрии; • возможность минимального обращения к органам управления ИВК; • работа с внешней кнопочной станцией при возникновении аварийных си туаций; • возможность оперативной распечатки результатов в процессе испытания с сохранением информации на машинном носителе; • возможность работы в локальной сети испытательной станции и корпора тивной сети предприятия; • обеспечение метрологической аттестации ИВК, систем измерения и кон троля; • обеспечение возможности работы с математическими моделями и мнемо схемами; • обеспечение регистрации и обработки параметров быстропеременных процессов; • расчет и анализ затрат на проведение испытаний с объективным учетом затрат труда; • расчет характеристик по измеренным параметрам с визуализацией;
• обеспечение возможности работы со специальными типами входных анналов (ступенчатые, импульсные, синусоидальные), обеспечение при этом отфильтрованное от помех, а также с белым, серым и псевдослучайным шумом в реальном времени; • обеспечение получения среднеквадратичной оценки параметров при работе с нестационарными процессами, с медленно (по сравнению с регрессией) меняющимися параметрами; • обеспечение применения метода обращения процедур и матриц, с целью преодоления трудностей при необходимости выполнения значительных вычислений; . • обеспечение оценки неизвестных параметров заданных нелинейных функций; • обеспечение реализации метода стохастической аппроксимации, • обеспечение реализации метода использования фиксированного, а не последовательно растущего числа измерений при работе с линейными и нелинейными процессами; • реализация метода прогнозирования, и в том числе градиентного для обеспечения функциональной связи между характеристиками управления и вектора управления. Применение средств автоматизации процесса сбора и обработки информации, программных средств управления двигателем и контроля его состояния в ходе испытания разгружает оператора от утомительной и напряженной работы и обеспечивает точное выполнение последовательности операции эксперимента-испытания.
14. 5. СИСТЕМА СБОРА И ОБРАБОТКИ ИНФОРМАЦИИ ПРИ ИСПЫТАНИЯХ ГТД, АВТОМАТИЗАЦИЯ ИСПЫТАНИЙ В области автоматизации испытаний в настоящее время выработан единый подход к построению автоматизированных систем измерений и контроля. Структурная схема одного из существующих измерительных вычислительных комплексов приведена на рис. 14. 21. В состав системы обязательно входит станция сбора данных (рис. 14. 22). Процесс сбора данных и выдача управляющих воздействий на объемный выполняются на уровне этой станции. Обработка информации по технологии, визуализация, протоколирование и интерфейс с пользователями выполняются на уровне автоматизированных рабочих мест (АРМ). На этапе автоматизации в качестве устройств сбора данных используются различные аппаратно-программные комплексы. Данные комплексы по своим характеристикам должны удовлетворять требованиям к точности, быстродействию и модульности системы сбора данных. При автоматизации опытных испытаний, число измерительных каналов достигает 3000 и более. Программное обеспечение комплексов должно быть адаптивно для мониторинга большого числа параметров и подключения новых каналов, но не быть достаточно сложным и закрытым при необходимости изменения технологии испытаний. Для исследовательских испытаний с последующей сложной математической обработкой данных, а также для испытаний современных авиационных изделий иностранного производства наиболее предпочтительно использовать устройства сбора данных в стандарте VXI, который представляет собой стандарт на контрольно-измерительную и управляющую аппаратуру высшего класса точности.
Рис. 14. 21. Структурная схема измерительного комплекса
Программное обеспечение, поддерживающее аппаратуру в этом стандарте, имеет высокую степень унификации. Прогрессивные инструментальные среды Lab. VIEW, Lab. WINDOWS. Bridge. VIEW, HPVEEпозволяют быстро разрабаты вать приложения сложной обработки данных на уровне технолога и расчетчика. АРМ бригадира-испытателя также является обязательным в составе автома тизированной системы. Именно на нем ведется управление техпроцессом испытаний. В составе системы может присутствовать АРМ контролера. Основное назначение — проверка соответствия параметров двигателя требуемым нормам со стороны бюро технического контроля. АРМ бригадира и контролера на холятся непосредственно на испытательном стенде и получают информация в реальном темпе испытаний с устройства сбора данных через сетевой интерфейс. Результаты испытаний в режиме реального времени поступают в едины корпоративный центр данных. Хранение результатов в едином центре обеспечивает: • гарантированное сохранение данных в соответствии с жесткими правилами отказоустойчивости и катастрофоустойчивости; • гарантированную защиту данных от несанкционированного использования, изменения и уничтожения; • авторизованный доступ к данным различным категориям пользователей • высокую скорость работы приложений (программ анализа данных) с использованием технологии «клиент — сервер» ; • работу всех пользователей с единым электронным документом.
Все пользователи данных испытаний получают информацию посредство корпоративной вычислительной сети. При этом обработка данных осуществляется на мощных корпоративных серверах, а по сети передаются только результаты обработки. В состав автоматизированной системы могут быть включены: • АРМ заказчика, который позволит им следить за ходом испытаний на всей испытательной станции; • АРМ технологов для отслеживания изменений в технологии испытаний • АРМ конструктора для анализа результатов испытаний; • АРМ динамиста для контроля и регистрации динамических параметров • АРМ диспетчера для контроля за текущим состоянием производства. Такой подход увеличивает количество участников испытаний и повышает надежность принимаемых технологический решений. Рис. 14. 22. Система сбора данных
ИВК включает в себя центральную ЭВМ, периферийные (на каждом стенде) ПЭВМ, линии связи, программное обеспечение, систему сбора и обработки информации, получаемой при испытаниях. Комплекс обеспечивает: • сбор и обработку с выдачей на принтеры и в виде распечатки, получаемой при испытаниях информации; выдача протоколов испытаний; • автоматическое измерение параметров объекта испытаний и стендовых систем на установившихся и неустановившихся (переходных) режимах; • автоматическое и ручное управление режимами работы изделия и стендовых систем, поддержание режимов в технологическом цикле испытаний всех видов, в том числе циклических; • связь и управление технологическими системами в комплексе с системами автоматического управления двигателей; • математическую обработку и сравнение полученных экспериментальных характеристик испытуемого объекта с расчетными (заданными); • выдачу оперативной дискретной информации (в том числе с визуализацией) в режиме испытания; • контроль и замер параметров при проведении специальных испытаний; • выдачу протокола испытаний (в том числе в виде распечатки) таблиц параметров и графиков характеристик; • выдачу рекомендаций и управляющих сигналов на исполнительные механизмы по корректировке регулировки объекта испытаний в целях получения заданных характеристик; • выдачу визуальной информации об аварийных ситуациях на объекте испытаний и испытательном стенде и автоматическую блокировку с выдачей необходимой информации на пульт управления; • автоматическую визуализацию (видеосъемки, включая высокоскоростную) процессов, происходящих с объектом в процессе испытания;
• калибровку и автотестирование каналов и элементов измерительной системы, электрических схем и электрических систем перед испытанием и в ходе испытания; • архивирование результатов испытаний и обеспечение записи на носители информации; • передачу информации, в том числе оперативной, о полученных результатах испытаний в обработанном виде в ОКБ в автоматическом режиме по заданным адресам; • автоматическую увязку измеренных параметров с метеоусловиями; • точный учет расхода топлива по этапам испытаний с идентификацией конкретного вида испытаний и исполнителя; • обмен информацией по каналу общего пользования (КОП) при прочностных испытаниях; • измерение, обработку и оценку эмиссионных характеристик; • защиту передаваемой и получаемой информации от помех, утраты и несанкционированного доступа. Все функции ИВК должны реализовываться в темпе эксперимента и в масштабе реального времени.
РЕЗЮМЕ (по главе 14 «Автоматизация испытаний ГТД» ) 1. Автоматизация испытании ГТД направлена на сокращение времени и трудоемкости проведения испытаний и обработки его результатов, на повышение информативности испытаний и достоверности полученных данных. 2. Автоматизации подлежат многократно повторяющиеся операции испытаний ГТД: подготовительно-заключительные операции, испытание по заданно 1 программе, измерение параметров, отладка параметров в пределах технических норм и требований, обработка результатов испытаний и их анализ. 3. Автоматизация всех операций по испытанию двигателей, кроме подготовительно-заключительных, осуществляется с помощью автоматизированной системы испытаний ГТД, которая включает следующие основные функциональные элементы: первичные преобразователи (датчики), устройства связи с объектом ЭВМ с устройствами ввода-вывода данных и отображения информации, исполни тельные механизмы. 4. Основные функциональные элементы АСИ ГТД решают следующие задачи. Первичные преобразователи (датчики) преобразуют измеряемые физические параметры в электрические сигналы. Устройство связи с объектом преобразует электрические сигналы датчиков цифровой код и передает его в ЭВМ осуществляет измерение параметров, обработку полученных данных, вы вод их на устройство отображения информации, через УС О выдает команды исполнительным механизмам. Исполнительные механизмы преобразуют электрические сигналы в перемещения органов управления систем испытательного стенда и двигателя, необходимые для выполнения заданной
программы испытания. Автоматизированная система испытаний ГТД работает в интерактивном режиме. 5. Устройство связи с объектом может содержать различные функциональных элементы, такие как: • коммутаторы и мультиплексоры — для последовательного подключения датчиков к элементам измерительной системы; • нормализаторы — для получения электрических сигналов требуемого уровня; • формирователи — для получения требуемой формы электрических сигналов; • АЦП — для преобразования аналоговых сигналов в цифровой код; • И. А П — для преобразования цифрового кода в электрические сигналы; • таймеры — электронные часы для фиксации требуемых интервалов времени и управления блоком УСО; • генераторы — для получения сигналов заданной частоты; • счетчики — для подсчета количества электрических импульсов; • преобразователи питания — для получения напряжения питания требуемой величины и др. Элементы УСО могут изготавливаться в виде отдельных блоков, выполненных по определенному стандарту, или встраиваться в платы (модули), осуществляющие функции измерения отдельных параметров.
Наиболее предпочтительно использовать устройства сбора данных в стандарте VXI, представляющем собой стандарт на контрольно-измерительную и управляющую аппаратуру высшего класса точности. 6. Персональные ЭВМ, применяемые в АСИ ГТД, кроме высокого быстродействия, достаточного объема оперативной и долговременной памяти должны обеспечивать высокую надежность и сохранять работоспособность в неблагоприятных условиях испытательного стенда (повышенные вибрация и температура, электрические помехи и электромагнитное излучение, наличие в воздухе пыли, выхлопных газов, паров масла и топлива). Кроме общесистемного программного обеспечения эти компьютеры должны содержать специальное программное обеспечение, поддерживающее контрольно-измерительную и управляющую аппаратуру. Инструментальные среды Lab. VIEW, Lab. WINDOWS, Bridge. VIEW. HPVEE позволяют быстро разрабатывать приложения достаточно сложной обработки данных.
ВОПРОСЫ 1. Назовите типовые операции при испытаниях авиационных ГТД. 2. В чем состоит сущность подготовительно заключительных операций? Каковы возможности их автоматизации? 3. Какие задачи до испытания, во время испытания и после испытания возлага ют на автоматизированные системы испытаний? 4. Назовите основные требования к АСИ ГТД. 5. Какие основные элементы составляют структуру АСИ ГТД? 6. Каково назначение устройства связи с объектом? 7. Из каких элементов оно состоит? 8. Для чего предназначен коммутатор? 9. Какие задачи решают счетчики? 10. Ю. Назовите задачи, решаемые нормализаторами и усилителями. 11. Какие применяются методы повышения устойчивости к воздействию окру жающей среды? 12. Для чего применяются панельные компьютеры? 13. В чем состоят особенности промышленных компьютеров? 14. Какие средства включают в состав автоматизированных систем сбора и обра ботки информации? 15. Какие задачи решают измерительно-вычислительные комплексы?
Глава 15 ОСОБЕННОСТИ ОБРАБОТКИ ЭКСПЕРИМЕНТАЛЬНЫХ ДАННЫХ ПРИ АВТОМАТИЗАЦИИ ИСПЫТАНИЙ Специфика определения термогазодинамического состояния ГТД и оценки основных технических данных в условиях автоматизированной системы испы таний заключается в том, что основные рутинные операции по обработке дан ных должны выполняться без участия человека, но желательно с использовани ем тех методов и подходов, которые позволяют исследователю применении отработанных традиционных способов обработки и анализа эксперименталь ной информации получать наиболее достоверные результаты. Для повышения эффективности испытаний ГТД результаты термогазодина мического анализа должны быть получены в сжатые сроки. Поэтому автомати зированная система термогазодинамического анализа предполагает выполне ние основных операций в реальном масштабе времени и в темпе испытания. При экспериментальном определении дроссельных характеристик двигателя под работами, выполняемыми в реальном масштабе времени, понимаются дейст вия, которые выполняются в период между измерениями параметров в двух сосед них экспериментальных точках (3. . . 5 мин). Под работами, выполняемыми в темпе испытания, понимаются действия, выполняемые в период времени между запус ком и выключением двигателя.
15. 1. КОНТРОЛЬ КАЧЕСТВА ИЗМЕРЕНИЙ Для анализа и интерпретации результатов испытаний ГТД большое значение имеет качество полученной экспериментальной информации. Поэтому на всех этапах сбора и обработки экспериментальных данных при автоматизированных испытаниях осуществляется контроль качества измерений с целью выявления грубых ошибок и устранения их влияния на конечный результат. Рассмотрим особенности применения некоторых видов контроля качества и определения параметров ГТД. При измерении параметров двигателя на каждом режиме работы осуществляется многократный (до 10. . . 20 раз) опрос всех измерительных каналов, в результате по каждому измерительному каналу в ЭВМ поступает n = 10. . . 20 значений цифрового кода X (рис. 15. 1). По зарегистрированным в ЭВМ значениям цифровых кодов Х i вычисляются среднее значение (15. 1) Рис. 15. 1. Значения цифрового кола X в различное время t при многократном опросе из мерительного канала на неизменном режиме работы двигателя: • — результаты измерений
α = 1 — р — уровень значимости; f= n — 1 — число степеней свободы. Значения цифрового кода X i не удовлетворяющие условию: (15. 4) признаются определенными с грубыми ошибками и отбрасываются. Вычисляется новое среднее значение цифрового кода . Иногда в качестве доверитель ного интервала Δ x. используют некоторую постоянную, априорно заданную ве личину. Таким образом осуществляется отбраковка выбросов цифрового кода, вызванных какими-либо случайными причинами (электрическими помехами, сбоями в работе аппаратуры и т. п. ). Однако грубые ошибки в определении параметров могут быть связаны и с выходом из строя датчиков, приборов, других элементов измерительных каналов. Очевидно, что такие грубые ошибки выявить описанным выше способом нельзя. И дисперсия (15. 2) Определяется интервал Δ х , в который с заданной доверительной вероятностью р должны попадать значения цифрового кода (15. 3) Где — статистический критерий для фильтрации грубых ошибок;
Поэтому на следующем этапе контроля качества измерений осуществляется проверка попадания полученного значения цифрового кода в область допустимых значений. В качестве области допустимых значений цифрового кода принимается диапазон цифровых кодов, полученных при градуировке данного измерительного канала (рис. 15. 2), проводимый перед проведением испытаний двигателя. Рис. 15. 2. Градуировочная характеристика измерительного канала: P min, Р mах — соответственно нижние и верхние границы изменения эталонного значения параметра при градуировке Значение цифрового кода не удовлетворяющее условию (15. 5) признают ошибочным. Если же значение попадает в область допустимых значений, то с помощью формулы, аппроксимирующей градуировочную характеристику соответствующего измерительного канала, определяется оценка физической величины параметра: (15. 6) где a i , i = 0, m — коэффициенты градуировочной характеристики измерительно го канала.
Измерения температуры и давления в проточной части двигателя осуществ ляются, как правило, в нескольких точках каждого характерного сечения, что также используется для контроля качества измерений. Поясним это на примере измерения давления в сечении проточной части с помощью радиальной гребенки приемников давления (рис. 15. 3). По результатам измерений р* i каждым приемником вычисляется осредненное значение давления заторможенного потока . Проверяется условие (15. 7) где Δ р* — допуск на возможные отличия отдельных измерений от среднего зна чения Рис. 15. 3. Схема измерения давления заторможенного потока в проточной части двигателя радиальной гребенкой: • — результаты измерений
Рис. 15. 4. Контроль качества измерений параметров с использованием априорных дроссельных характеристик двигателя: • — результаты определения параметров у данного двигателя Величина допуска Δр* назначается, исходя из априорных представлений о возможной неравномерности поля давления в данном сечении, которые могут быть основаны на опыте предыдущих экспериментальных исследований двигателя. Не выполнение данного условия для какого-либо р i * является признаком наличия грубой ошибки, вызванной, например, засорением соответствующего приемника давления. Следующий способ контроля качества измерений параметров основан на сравнении приведенных к САУ измеряемых параметров на данном режиме работы двигателя, с априорными представлениями о дроссельной характеристике данного двигателя (рис. 15. 4).
В качестве априорной дроссельной характеристики может быть использова на характеристика, полученная на предыдущих испытаниях двигателя, или расчетная характеристика, скорректированная исходя из известных особенностей данного экземпляра двигателя. На основе оценки степени адекватности априорной дроссельной характеристики, имеющихся погрешностей экспериментального определения параметров двигателя назначается величина допуска на возможное отличие параметров данного двигателя от априорных характеристик. На рис. 15. 4 это величины ΔG m и Δ р. После определения приведенных значений параметров двигателя на данном режиме проверяется условие (15. 8) Если это условие для какого-либо параметра, как, например, для G m пр (см. рис. 15. 4), не выполняется, то это значение параметра признается определенным с грубой ошибкой. Основная проблема, возникающая при таком способе контроля качества измерений, связана с обоснованным назначением допусков Δр. Решение этой проблемы значительно упрощается, если испытанию подвергается серийный двигатель и известны статистические данные о результатах испытаний других двигателей данной серии. В этом случае границы на допустимые значения параметров двигателя определяются на основе обработки имеющихся статистических данных о разбросе дроссельных характеристик двигателей данной серии. Разброс дроссельных характеристик двигателей одной серии (рис. 15. 5) объясняется рассеиванием параметров, характеризующих работу узлов двигателя, наблюдающихся из-за того, что изготовление деталей и сборка узлов осуществляется с определенными допусками, а также погрешностью измерения параметров при испытании.
Рассеивание характеристик отдельных не отлаженных двигателей подчиня ется закону распределения, близкому к нормальному. При контроле качества экспериментального определения параметров у дан ного двигателя на режиме, характеризуемом частотой вращения ротора n’ пр , вначале определяются среднестатистические значения параметров двигателей всей серии на данном режиме: (15. 9) где n — количество дроссельных характеристик, имеющихся в статистике. Затем вычисляется дисперсия значений параметров двигателей данной се рии на этом режиме (15. 10) Рассчитывается доверительный интервал (15. 11) Где, — квантиль распределения Стьюдента, соответствующий доверительной вероятности Р = 1 — α и числу степеней свободы f = n — 1. Проверяется условие (15. 12)
Рис. 15. 6. Корреляционная связь Р пр с G m np для двигателей данной серии при n’ np = const: • — экспериментальная точка исследуемого двигателя Если для какого-либо значения параметра это условие не выполняется, то он признает ся определенным с грубой ошибкой. Такой способ контроля качества измерений позво ляет выявлять грубые ошибки измерений, превышающие 5. . . 6 %. Величину доверительного интервала, при меняемого для поиска грубых ошибок опре деления значений параметров можно умень шить, если использовать для этих целей закономерности изменений парамет ров в пределах разброса [4]. Эти закономерности могут быть представлены кор реляционными связями между различными параметрами двигателей данной серии на постоянном режиме. Пример двумерных корреляционных связей ме жду значениями тяги Р пр и расхода топлива G m пр на режиме n’ пр = const приве ден на рис. 15. 6. Зависимость оценки наиболее вероятного значения параметра функции Р пр от параметра аргумента G m пр определяется уравнением регрессии (15. 13)
где а и b — коэффициенты уравнения регрессии. Степень тесноты корреляционной связи оценивается величиной коэффициента парной корреляции r (15. 14) а возможное отличие действительных значений параметра-функции Р пр у данного двигателя от оценки , определенной по уравнению регрессии при из вестном значении G m пр , характеризуется величиной условного доверительного интервала, который может изменяться в диапазоне (15. 15) Величины коэффициента корреляции г условного доверительного интервала Δр усл связаны между собой соотношением (15. 16) Величины коэффициентов корреляции г и регрессии а и b рассчитываются методами математической статистики по имеющимся результатам испытаний двигателей данной серии. Коэффициенты парной корреляции между различными параметрами га зотурбинных двигателей в пределах разброса принимают значения r = 0, 3. . . 0, 9. Для контроля качества измерений параметров с использованием закономер ностей их разброса осуществляется сравнение подозрительной эксперимен тальной величины какого-либо параметра (в нашем случае ) с его оценкой по другому измеряемому параметру (в нашем случае по G m пр ), полученной с по мощью соответствующего уравнения регрессии. Если при этом не выполняется условие (15. 17)
то значение параметра признается определенным с грубой ошибкой. Такой способ контроля качества измерения позволяет выявить ошибки измерения параметров, которые нельзя определить предыдущим способом, основанным на проверке попадания вновь полученных экспериментальных точек в поле разброса характеристик двигателя данной серии (см. рис. 15. 6). Чувствительность метода можно повысить, если для поиска аномальных измерений использовать не двумерные, а многомерные корреляционные связи, описываемые уравнениями регрессии вида которые позволяют получить оценку величин какого-либо параметра по значениям всех остальных измеряемых параметров двигателя. Такой способ контро ля требует применения более сложного алгоритма, так как отличие оценки от экспериментально определенной величины Р пр , превышающее величину Δр усл , может быть вызвано грубой ошибкой определения не только параметра- функции, но и какого-либо из параметров-аргументов. Однако он позволяет снизить порог выявленных грубых ошибок измерения до величины 3. . . 4 %. Все описанные способы контроля качества измерений применяются в реальном масштабе времени.
15. 2. ВОССТАНОВЛЕНИЕ ХАРАКТЕРИСТИК ПО ЭКСПЕРИМЕНТАЛЬНЫМ ДАННЫМ После измерения параметров двигателя в крайней экспериментальной точке осуществляется так называемое восстановление дроссельных характеристик. Под восстановлением характеристик понимается оценка истинных характеристик двигателя по экспериментальным данным с учетом имеющихся погрешностей измерения параметров и возможных выбросов, не отбракованных на предыдущих этапах обработки результатов измерений. Для восстановления характеристик двигателя проводится аппроксимация экспериментальных точек некоторыми априорно выбранными функциями. Обычно в качестве этих функций выбираются полиномиальные зависимости вида (15. 18) В классе полиномиальных функций необходимо для каждого параметра вы брать в некотором смысле оптимальную функцию, которая наиболее точно описывает искомую дроссельную характеристику. При этом поиск оптимальных моделей дроссельных характеристик двигателя целесообразно вести не только среди полных многочленов, но и среди всех других, для которых ограничена лишь максимальная степень, а коэффициенты содержатся не при всех степенях режимного параметра. Это позволяет использовать при восстановлении дроссельных характеристик двигателя по малому количеству экспериментальных точек (5. . . 8) достаточно сложные модели.
Поскольку количество экспериментальных точек при определении характеристик двигателя мало, а некоторые из них могут содержать не выявленные на этапе контроля грубые ошибки измерения, то выбор лучшей модели целесообразно осуществлять заранее на основе анализа выборок, полученных по расчетным или среднестатистическим характеристикам данного двигателя. Для выбора лучшей модели целесообразно использовать один из так называемых «внешних» критериев селекции — критерий стабильности. Использование внешних критериев вместо традиционных критериев, базирующихся на распределении Фишера, обосновано тем, что последние требуют знания свойств генеральной совокупности рассматриваемой выборки, которые часто не известны, а также тем, что они субъективны, поскольку зависят от заданного уровня значимости. При применении критерия стабильности имеющаяся выборка делится на две части: обучающую (A), по которой оцениваются коэффициенты модели (15. 18), и контролирующую (В). Для зависимости Р пр =f(n пр ) критерий стабильности имеет вид: (15. 19) где Р прi и Р прj — действительные значения параметра в выбранных точках обу чающей и контролирующей выборок; P npi и P npj — — оценки значений параметра в выбранных точках обучающей и контролирующей выборок, определенные по выражению (15. 18); n — количество точек обучающей выборки; т — количество точек контролирующей выборки. В качестве оптимальной модели выбирается та, для которой значение критерия S 2 минимально. При этом может оказаться, что имеется несколько конкурирующих моделей, для которых значение критерия стабильности примерно одинаково, но число или номенклатура коэффициентов модели различны. В этом случае в качестве наилучшей модели целесообразно выбрать модель, для которой значение максимальной невязки
полученных во всех точках обучающей и контролирующей выборок минималь но и меньше погрешности экспериментального определения параметра Р пр. Разбиение выборки на обучающую и контролирующую можно осуществлять следующим образом: в обучающую последовательность включаются точки, соответствующие тем режимам работы двигателя, на которых обычно производится измерение параметров, а в контролирующую последовательность — остальные точки. В качестве примера ниже приведены лучшие модели для восстановления дроссельных характеристик одного из отечественных ТРДД по 6. . . 8 экспериментальным точкам
Максимальные значения невязок Δ при использовании этих моделей в 3. . . раза меньше погрешностей измерения параметров. Определение численных значений коэффициентов a i , в выбранных для каждого параметра моделях (15. 18) осуществляется по результатам испытания двигателя. Обычно для решения подобных задач применяется так называемый метод наименьших квадратов (МНК). Согласно этому методу в качестве оценок коэффициентов a i , принимаются значения â i , , при которых удовлетворяется условие (15. 20) где n — количество экспериментальных точек. Однако формальное применение этого метода при восстановлении дроссельных характеристик ГТД по малому количеству экспериментальных точек (5. . . 8) не позволяет получить адекватные результаты, если хотя бы одна из ни: содержит грубую ошибку измерения. Поэтому при автоматизированном восстановлении характеристик ГТД по экспериментальным данным в условиях объективно существующей возможности появления грубых ошибок измерений целесообразно использовать так называемые устойчивые (робастные) статистические методы. Достоинство этих методов заключается в том, что статистические оценки получаемые с их помощью, мало чувствительны к анормальным экспериментальным данным. Рассмотрим ниже сущность некоторых наиболее известных робастных методов, применимых к задаче восстановления характеристик ГТД.
Метод наименьших модулей [35]. Сущность метода наименьших модулей состоит в аппроксимации погрешностей измерения случайными величина ми, распределенными по закону Лапласа. Такую аппроксимацию целесообразно применять в тех случаях, когда измеряемые величины, кроме ошибок измерения, распределенных нормально, имеют ошибки описания (ошибок модели), которые соизмеримы с погрешностью измерения, или когда о случайной погрешности известно лишь то, что она обладает ограниченной дисперсией. Задача определения коэффициентов а i в модели (15. 18) решается, исходя из условия: (15. 21) Метод Форсайта. Этот метод является попыткой найти компромисс между методом наименьших квадратов и методом наименьших модулей. При его применении коэффициенты полинома (15. 18) находятся из условия: (15. 22) где 1 ≤ r ≤ 2. Метод Хубера [57]. Он основан на том, что случайные погрешности измерения аппроксимируются случайными величинами, имеющими следующую функцию распределения: (15. 23) где N(t) — функция нормального распределения; G(t) — функция симметричного «загрязняющего» распределения; ε — малое положительное число.
Такое разложение погрешности измерения соответствует представлению ее в виде суммы нормальной погрешности и некоторого возмущающего воздействия, которое с вероятностью е появляется при измерениях. Предполагается, во-первых, что возмущающее воздействие можно представить распределенным по закону Лапласа, во-вторых, что все реализации случайной погрешности, которые больше по модулю некоторого заранее выбранного числа q, распределены по этому же закону, а все реализации, меньшее по модулю числа q, — по нормальному закону. Задача определения коэффициентов а i в модели (15. 18) решается при ус ловии (15. 24) Где (15. 25) Метод Хубера является наиболее предпочтительным для решения задачи восстановления характеристик ГТД по экспериментальным данным, так как принятые при его получении предпосылки наилучшим образом соответствуют ситуации, имеющей место при измерении параметров двигателя, когда наряду с ошибками измерения параметров, имеющих преимущественно закон распределения, близкий к нормальному, могут иногда появляться грубые ошибки изме рения разного знака. Применение метода Хубера для восстановления дроссельных характеристик ГТД при наличии грубой ошибки измерения дает существенно более адекват ный результат, чем МНК. (рис. 15. 7). Однако и устойчивые методы оценивания не позволяют получить адекватного восстановления экспериментальных характеристик ГТД, если с грубой ошибкой определена крайняя точка дроссельной характеристики (рис. 15. 8).
Рис. 15. 7. Восстановление истинной характеристики (1) по экспериментальным точкам (*) методом наименьших квадратов (2), методом Хубера (J) при наличии грубой ошибки в промежуточной экспериментальной точке Рис. 15. 8. Восстановление истинной характеристики (1) по экспериментальным точкам (*) методом наименьших квадратов (2), методом Хубера с регуляризацией (J) по априорной характеристике (4) при наличии грубой ошибки в крайней экспериментальной точке
Для того чтобы повысить адекватность результатов, в этом случае необходи мо проводить аппроксимацию экспериментальных точек методом Хубера с ориентацией на априорную (известную заранее) модель этой характеристики. В качестве априорной модели характеристики может быть использована рас четная, ранее полученная экспериментальная или среднестатистическая харак теристика. Такой метод оценки коэффициентов a i в (15. 18) называют методом Хубера с регуляризацией. Он реализуется применением функции цели вида: (15. 26). где — восстановленная по экспериментальным данным дроссельная ха рактеристика; P апр (n пр ) — априорная модель дроссельной характеристики; l — знак производной порядка l; n пр min , n npm ах — соответственно минимальное и максимальное значения интервала аргумента, на котором осуществляется срав нение восстанавливаемой и априорной характеристик; α — коэффициент регуляризации. Выбор первого порядка производной l= 1 означает, что при восстановлении характеристики по экспериментальным данным накладывается дополнительное требование об эквидистантности восстанавливаемой и априорной характеристики; выбор второго порядка производной l= 2 означает, что при восстановлении характеристики допускается ее линейное расхождение с априорной характеристикой.
Величина коэффициента регуляризации а определяет степень влияния используемой априорной характеристики на получаемый результат. Если а = 0, то априорная информация о характеристике игнорируется, и восстановление характеристики осуществляется только на основе полученных экспериментальных данных. При больших значениях а экспериментальные данные практически игнорируются, и получаемая характеристика по своим свойствам совпадает с априорной. Оптимальную величину коэффициента регуляризации а выбирают, исходя из того, чтобы полученная после решения задачи средневзвешенная дисперсия остаточных невязок между экспериментальными и восстановленными по модели (15. 18) значениями параметров соответствовала погрешности измерения этого параметра. Применение метода Хубера с регуляризацией позволяет получить существенно более адекватные результаты при восстановлении характеристик двигателя в случае наличия грубой ошибки в любой экспериментальной точке, в том числе и крайней (см. рис. 15. 8). Применение этого метода эффективно также при экстраполяции экспериментальных характеристик двигателя. Метод позволяет получать достаточно надежные результаты при наличии грубых ошибок измерения не более чем в 20. . . 30 % экспериментальных точек. Основные данные двигателя — тяга, удельный расход топлива, температура газа, частота вращения ротора и др. — определяются по восстановленным дроссельным характеристикам в зависимости от заданного значения тяги на каждом режиме с учетом возможного ее изменения в пределах допуска. При этом проверяется соответствие перечисленных параметров их значениям, заданным техническими условиями (ТУ).
Если основные данные двигателя соответствуют нормам ТУ, то по получен ным параметрам отлаживается аппаратура топливопитания и управления. Реализованные в агрегатах системы автоматического управления значения параметров управления и соответствующие значения основных данных записыва ется в формуляр двигателя. Если основные данные двигателя не обеспечиваются, то двигатель подлежит отладке, например путем подбора площади сопла или соплового аппарата тур бины. Если с помощью отладки не удается обеспечить основные данные, то двигатель полностью или частично перебирают, узлы и элементы проточной части, ответственные за неполучение основных данных, заменяют или дорабатывают. Грамотная организация работ, связанных с обеспечением основных данных двигателя (его отладка, переборка, замена или доработка узлов), невозможна без его предварительной диагностики. Поэтому по полученным в результате восстановления дроссельных характеристик параметрам и основным данным прежде всего оценивается состояние проточной части двигателя. Предварительной оценкой состояния двигателя определяются отклонения ос новных данных, термогазодинамических параметров и скольжения частот вра щения роторов данного двигателя от их значений в базовой модели при Р = const. По величине и знаку этих отклонений оцениваются состояния газоге нератора и турбовентилятора. Снижение эффективности двигателя по сравнению с базовой моделью (по ложительные отклонения δС уд и δТ т * , а также температуры газа δ Т i — и его давле ния δ р i практически во всех характерных сечениях двигателя) объясняется уменьшением КПД компрессора и турбины ВД, если величина δ(n вд /n Нд ) отри цательная, или уменьшением КПД компрессора (вентилятора) и турбины НД, если величина δ(n Вд /n Нд ) положительная.
Наоборот, повышение эффективности двигателя (отрицательные отклонения δС уд и δТ т * δ Т i δ р i ) объясняется увеличением КПД компрессора и турбины ВД, если величина δ(n вд /n Нд ) положительная, или увеличением КПД компрессо ра (вентилятора) и турбины НД, если величина δ(n вд /n Нд ) отрицательная. Полученные по результатам предварительной оценки состояния двигателя выводы используются при идентификации его математической модели.
15. 3. ИДЕНТИФИКАЦИЯ МАТЕМАТИЧЕСКОЙ МОДЕЛИ ДВИГАТЕЛЯ В настоящее время в практике создания двигателя чаще всего используются математические модели первого уровня. Это система нелинейных уравнений, описывающая рабочий процесс и совместную работу узлов двигателя и связывающая параметры двигателя Р с параметрами его узлов 0 и входными воздействиями X (внешними условиями и режимом работы): (15. 27) При заданных внешних условиях (например, при САУ, V n = 0) и заданном режиме работы параметры двигателя определяются только параметрами его уз лов, т. е. (15. 28) Идентификация такой математической модели заключается в уточнении оценок параметров узлов Θ по значениям параметров двигателя P определен ным в результате испытания [30, 53, 59]. Так как речь идет о небольшом отклонении искомых параметров, для реше ния этой задачи целесообразно математическую модель (15. 28) представить в линеаризованном виде: (15. 29)
где δP j — отклонение измеренного значения j-го параметра двигателя от его расчетной величины, %; δΘ i — отклонение значения i-го параметра узла от его расчетного значения, %; δP j / δΘ i — коэффициент влияния i-го параметра узла на его j-й параметр двигателя; Δ j — невязка, обусловленная ошибкой определения значения δP j из-за ошибок измерений параметров двигателя и погрешностей, вызванных линеаризацией уравнений рабочего процесса; k— количество параметров двигателя, измеряемых при испытании; n — количество параметров узлов, подлежащих идентификации. Коэффициент влияния δP j / δΘ i показывает на сколько процентов изменяется параметр двигателя P j при изменении на 1 % параметра узла Θ j. Величины коэффициентов влияния δP j / δΘ i —— определяются чаше всего виртуальными экспериментами на ЭВМ с помощью нелинейной математической модели ГТД первого уровня. При известных коэффициентах влияния δP j / δΘ i -— такая математическая модель представляет собой систему k линейных уравнений с n неизвестными. В этом случае задача идентификации математической модели состоит в оценке попра вок δΘ i , к расчетным значениям параметров узлов (КПД узлов, коэффициентов потерь и т. п. ) по отклонениям параметров двигателя δP j , определенных в ре зультате испытания (тяги, расхода топлива, температуры и давления рабочего тела в различных сечениях проточной части), от их расчетных значений.
Целесообразность идентификации линеаризованной математической модели двигателя определяется тем, что она позволяет: • применять методы идентификации, универсальные по отношению к типу и схеме двигателя (так как изменяются лишь количество уравнений и неизвестных, а также численные значения коэффициентов влияния); • использовать хорошо разработанное для линейных задач современное стандартное математическое и программное обеспечение; • значительно сократить время решения задачи по сравнению с идентификацией сложной нелинейной модели. Последнее особенно важно при идентификации математической модели автоматизированными системами испытаний ГТД, решающими задачи в темпе проведения эксперимента. Особенность идентификации математической модели ГТД, в том числе линеаризованной, заключается в том, что, как отмечалось, количество неизвестных параметров узлов превосходит количество измеряемых параметров двигателя при значительном уровне погрешностей измерения. В связи с этим для получения наиболее достоверного решения задачи важное значение имеет различная дополнительная информация исследователя. Приведенный ниже метод [30] идентификации математической модели двигателя, позволяющий при решении этой задачи наиболее полно учесть различ аю дополнительную информацию, заключается в следующем. Решение системы уравнений (15. 29) осуществляется при условии: (15. 30)
где F(t) — функция Хубера; δΘ 0 i — априорная оценка отклонения параметра узла от его расчетного значения; — коэффициент веса, обратно пропорциональный погрешности измерения параметра двигателя, характеризуе мой величиной коэффициент веса, обратно пропорциональный заранее заданной величине возможного разброса параметра узла; α — коэффициент регуляризации. Первое слагаемое функции цели (15. 30) учитывает результаты измерений параметров двигателя, второе — априорную информацию о наиболее вероятной оценке параметров узлов данного экземпляра двигателя. Коэффициент регуляризации а позволяет варьировать относительную значимость экспериментальных данных и априорной информации о параметрах узлов. Так, при α = 0 априорная информация не учитывается, и получаемые при идентификации математической модели оценки будут определяться только информацией об измеренных параметрах двигателя. При α = 1 оба вида информации учитываются с примерно одинаковой значимостью, а если α ≥ 10, то при решении задачи данные об измеренных параметрах двигателя в значительной степени игнорируются, и чем больше α, тем ближе оценки δΘ к их априорно заданным значениям δΘ 0. Алгоритм идентификации математической модели составлен таким образом, что решение задачи осуществляется при некотором оптимальном значении коэффициента регуляризации α орt при котором невязки Δ j — в уравнении (15. 7) соответствуют погрешностям измерения параметров двигателя и погреш ностям, вызванным неточностью используемых коэффициентов влияния.
Физический смысл коэффициентов веса γ j и γ i введенных в функцию цели (15. 30), заключается в следующем: чем больше погрешность измерения какого- либо параметра двигателя а. σ z (δP j ), тем большее значение невязки Δ j допускается в соответствующем уравнении математической модели (15. 29); чем больше заранее заданная величина возможного разброса параметра узла σ (δΘ i ), тем больше допускаемое отличие получаемой при идентификации оценки от ее ап риорного значения δΘ 0. Применение в (15. 4) функции Хубера F(t) позволяет существенно ослабить вредное влияние на значения получаемых оценок отдельных грубых оши бок измерения параметров двигателя, не выявленных на этапе предварительно го анализа результатов испытаний, и неправильных представлений об априор ных оценках отдельных параметров узлов δΘ 0 i. По найденным в результате идентификации оценкам корректируются характеристики узлов, а по нелинейной математической модели двигателя рассчитываются все его параметры.
15. 4. ОБЩАЯ ПРОЦЕДУРА АВТОМАТИЗИРОВАННОЙ ОБРАБОТКИ И ТЕРМОГАЗОДИНАМИЧЕСКОГО АНАЛИЗА РЕЗУЛЬТАТОВ ИСПЫТАНИЙ На основании математической модели базового и исходных данных исследуемого двигателя (характеристик компрессора, турбины и других узлов, коэффициентов потерь, площадей характерных проходных сечений) в блоке А на (рис. 15. 9) формируется в первом приближении его исходная нелинейная математическая модель (НММ) (блок 1). По ней с учетом программы испытаний рассчитываются дроссельные характеристики, которые используются затем на этапе предварительного анализа (контроля качества измерений, восстановления характеристик, определения отличий экспериментальных характеристик от расчетных). По ней рассчитываются (в блоке 2) также коэффициенты линейной математической модели (ЛММ), которые аппроксимируются по режиму (блок 3)с целью их быстрого определения в процессе идентификации ЛММ на промежуточных режимах. Наконец, с помощью НММ моделируются результаты испытания двигателя, для чего на дроссельные характеристики накладываются смоделированные на ЭВМ случайные ошибки измерений выходных параметров, параметров режима и внешних условий (в блоке 4). Полученные таким образом прогнозируемые характеристики используются на заключительном этапе термогазодинамического анализа результатов испытания двигателя. В ходе испытания двигателя (в блоке В) после измерения параметров в каждой экспериментальной точке, приведения их к САУ (в блоке С) выполняются процедуры контроля качества измерений (в блоке 5). Измеренные и рассчитанные параметры двигателя на каждом режиме записываются в базу данных. Затем восстанавливаются характеристики двигателя и определяются его основные технические данные (в блоке 6), находятся отличия экспериментальных значений параметров от их расчетных значений (в блоке 7).
На основании сопоставления полученных отклонений выходных парамет ров двигателя с закономерностями отклонений параметров двигателей данного типа делается предварительное заключение о причинах отличия эксперимен тальных характеристик от расчетных (в блоке 8). Эти данные совместно с дру гой дополнительной информацией (в блоке 14) об индивидуальных особенно стях испытуемого двигателя вносятся в качестве исходных для идентификации ЛММ. В результате идентификации ЛММ (в блоке 9) определяются оценки от клонений параметров узлов и двигателя от их расчетных значений. Полученные результаты анализируются, сопоставляются с другой неформализованной ин формацией (в блоке 10). В случае необходимости вносятся коррективы в дополнительную информацию, проводится повторная идентификация ЛММ и получается новый вариант оценки параметров узлов и двигателя в целом. На основании наилучшего, с точки зрения исследователя, или нескольких конкурирующих между собой вариантов оценок параметров узлов уточняется 1 ММ (в блоке 11) и с ее помощью рассчитывается, как правило, несколько вариантов характеристик данного двигателя. Анализ этих вариантов, сравнение lxмежду собой, возможное осреднение, а также сравнение с прогнозируемыми характеристиками и с базовой моделью являются содержанием заключительно го этапа термогазодинамического анализа (в блоке 12). В результате формируется индивидуальная математическая модель исследуемого двигателя, оптимальным образом согласованная с экспериментальными и априорными данными, а также с неформализованными представлениями исследователя. Контроль качества измерений выполнен в реальном масштабе времени. Восстановление характеристик двигателя, определение основных технических данных, отличий измеряемых параметров от модели и основной этап термога зодинамического анализа осуществляются в темпе испытания. И только заклю чительный этап осуществляется за рамками испытания двигателя.
Рис. 15. 9. Укрупненный алгоритм автоматизированной работы термогазодинамического анализа результатов испытаний ГТД
РЕЗЮМЕ (по главе 15 «Особенности обработки экспериментальных данных при автоматизации испытаний» ) 1. При автоматизации испытаний основные рутинные операции по обработке экспериментальных данных выполняются без участия человека, но с использованием методов и подходов, применяемых при традиционных отработанных способах обработки и анализа экспериментальной информации. 2. При малом количестве экспериментальных точек большое значение для достоверности результатов автоматизированного термогазодинамического анализа имеет отсутствие грубых ошибок в определении измеряемых параметров. 3. Выявление грубых ошибок измерений и снижение их вредного воздействия на конечный результат осуществляется на всех этапах получения и обработки экспериментальной информации: при сборе экспериментальных данных, восстановлении характеристик двигателя, идентификации математической модели. 4. На этапе определения измеряемых параметров двигателя наиболее малые грубые ошибки (до 3. . . 4 %) позволяет выявить способ, основанный на использовании закономерностей в отклонении параметров в пределах разброса у серийно выпускаемых двигателей. 5. При восстановлении характеристик двигателя наиболее существенно снизить вредное воздействие не выявленных грубых ошибок измерения параметров позволяет способ, основанный на применении устойчивого метода Хубера с ориентацией на известный вид априорной характеристики.
6. Приведенный метод идентификации математической модели двигателя основан на комплексном использовании экспериментальной информации о величинах измеренных параметров двигателя и погрешностях их определения, а также об априорных оценках и диапазонах возможных изменений параметров узлов. При этом учитывается возможность отдельных выбросов как среди измеренных параметров двигателя, так и среди идентифицируемых параметров узлов. 7. Общая процедура автоматизированного термогазодинамического анализа предусматривает многоэтапность и итерационность процесса в интерактивном режиме. Это позволяет получать результаты, наилучшим образом согласованные с имеющимися экспериментальными данными, априорной информацией и неформа лизованным опытом исследователя.
ВОПРОСЫ 1. В чем заключаются особенности обработки экспериментальных данных при автоматизации испытаний ГТД? 2. Какие операции при обработке экспериментальных данных целесообразно осуществлять в реальном масштабе времени, а какие в темпе испытания и почему? 3. Назовите основные способы контроля качества измерений и отбраковки аномальных экспериментальных данных. На каких этапах проведения испытания двигателя и обработки экспериментальных данных они применяются? 4. Какие специфические способы контроля качества измерений могут применяться при испытаниях серийных двигателей? 5. В чем заключается восстановление характеристик двигателя по экспериментальным данным? 6. Как осуществляется выбор модели для восстановления характеристик двигателя? 7. В чем заключаются сложности восстановления характеристик по малому количеству экспериментальных точек? 8. Какие методы применяются для повышения точности восстановления характеристик двигателя по малому количеству экспериментальных точек? 9. В чем заключается сущность оценивания с помощью устойчивого метода Хубера? 10. Как можно использовать априорные характеристики двигателя для повышения точности восстановления характеристик по экспериментальным данным? 11. В чем заключается идентификация математической модели двигателя по результатам испытаний и каковы ее основные проблемы?
12. Что такое линейная математическая модель ГТД и почему ее целесообразно использовать в автоматизированной системе испытаний двигателя? 13. Какую дополнительную информацию можно использовать для уточнение результатов идентификации и как ее реализовать в изложенном методе? 14. Назовите основные этапы автоматизированной обработки и термогазодинамического анализа результатов испытаний ГТД. В чем заключается их основное содержание?
Глава 16 ЭКСПЕРИМЕНТ — ОСНОВА ПРОВЕРКИ КАЧЕСТВА ПРОЕКТИРОВАНИЯ И СОЗДАНИЯ ГТД Развитие ГТД осуществляется путем последовательной смены поколений сопровождаемой, в основном, значительным повышением параметров рабочего процесса, а также путем улучшения основных показателей качества в пределах одного поколения. Разработка двигателей основывается на новейших достижениях отечественного и зарубежного двигателестроения, на опыте предыдущих разработок и прогрессивных изобретениях, опирается на постоянно совершенствующиеся научную, методическую, технологическую, производственную и испытательную базы. Опыт показывает, что в процессе разработки авиационных двигателей, которая ведется, как правило, с учетом технических неопределенностей, реально изготавливаемые первые образцы узлов и двигателей часто не соответствуют проектам по ряду параметров и не отвечают расчетным требованиям из-за того, что: — не в полной мере учитываются расчетами нелинейности и взаимное влияние процессов в узлах двигателя; — недостаточна полнота данных, особенно в нерасчетных точках; — имеет место чрезмерный оптимизм в постановке расчетных задач. Расчет лопаточных машин и двигателя — это искусство, и для получения желаемого результата требуются теория, испытания и доводка. Однако, как бы ни были совершенны методы и средства теоретического анализа, расчетов, реальная
оценка качества конструкции возможна только по результатам, получаемым путем проведения измерений в ходе эффективного, правильно подготовленного и построенного эксперимента. В практике разработки и создания ГТД основным видом эксперимента являются испытания. Качество двигателя — это совокупность его свойств, обеспечивающих удовлетворение установленных требований в соответствии с назначением двигателя. Изначально качество двигателя закладывается при его разработке. Таким образом, от качества разработки напрямую зависит уровень работоспособности двигателя. Проверка качества двигателя, а значит, и качества разработки проводится на всех этапах, начиная с разработки отдельных элементов. Организуются испытания отдельных узлов и систем двигателя, в ходе которых выявляются возможные дефекты. По выявленным дефектам разрабатываются конструктивные или технологические мероприятия, по которым дорабатывается узел и качество доработанного узла вновь проверяется испытаниями. Этот процесс продолжается до тех пор, пока характеристики узла или двигателя в целом не будут соответствовать установленным техническим заданием требованием. Иными словами, процесс, представляющий собой комплекс экспериментальных, исследовательских, конструкторских, расчетных, технологических и др. работ по реализации на составных частях или двигателе в целом меро приятий, обеспечивающих получение требуемых параметров и характеристик двигателя есть процесс доводки.
Конкуренция в сфере создания авиационных ГТД ведет к необходимости сокращать сроки создания и модернизации газотурбинных двигателей, к упрощению способов и достижению доступности экспериментальных проверок идей или мероприятия, к возможности ведения одновременно или параллельно процесса совершенствования узлов и двигателя. Повышение стоимости двигателей из-за удорожания новых материалов и технологических процессов, обеспечивающих требуемое увеличение степени повышения давления и температуры газов и, следовательно, значительные убытки при любом разрушении экспериментального или опытного двигателя из-за поломки любого узла, делают совершенно необходимым создание стендов поузловой доводки и стендов для доводочных испытаний двигателя. Эти стенды, как правило, быстро окупаются, и процесс еще более ускоряется при их использовании в решении задачи формирования научно-технического задела и отдельных прикладных задач. Но главным остается то, что испытания — это единственное средство, позволяющее объективно оценить степень сходимости теоретических выводов с реально полученными результатами, то есть оценить качество выполненных проектно-конструкторских работ. Двигатель как сложное изделие состоит из большого числа систем, подсистем, узлов и агрегатов, и поэтому на этапах конструирования и испытаний производится отработка надежности каждого элемента и узла создаваемого изделия. Разработчики двигателей в соответствии с заданием на разработку выполняют следующие работы по обеспечению соответствия характеристик разрабатываемого двигателя заданным требованиям. 1. Собираются и изучаются данные по нагрузкам и внешним воздействиям, которые зависят от характера и протяженности маршрутов полета, характеристик маневренности и скороподъемности, а также от эксплуатационных характеристик и ресурса самолета. Уточняются требования к надежности двигателя и распределению продолжительности его работы на взлетном, максимальном, номинальном и крейсерском режимах и другие требования к эксплуатационным характеристикам двигателя.
2. Изучается фактически достигнутый в эксплуатации уровень надежности двигателей и их основных узлов, являющихся прототипами или близкими по назначению и основным характеристикам к создаваемому двигателю. Особый интерес представляет изучение двигателей, снятых с эксплуатации из-за отказов или при полной выработке ресурса. Получаемая при этом информация позволяет правильно спроектировать узлы нового двигателя и предупредить появление многих отказов, ограничивающих заданный уровень надежности. 3. На основании данных по нагрузкам и внешним воздействиям и анализа фактической информации о результатах эксплуатации узлов и деталей изделий или их аналогов уточняются требования к отдельным элементам нового двигателя и производят подбор необходимых материалов с учетом их прочностных характеристик, обрабатываемости, производственных возможностей и стоимости. 4. Уточняется состав технических и организационных мероприятий, необходимых для выполнения заданных требований по надежности создаваемого двигателя. Одновременно разрабатывается комплексная программа обеспечения надежности и ресурса двигателей с конкретизацией выполняемых работ по отдельным узлам и двигателю в целом на каждой стадии разработки двигателя. На этом этапе закладываются конструктивные и производственные решения, обеспечивающие реализацию необходимого ресурса в эксплуатации. Один из самых ответственных этапов комплексной программы — это этап испытаний, проводимых в подтверждение соответствия фактических показателей надежности двигателя и его элементов заданным требованиям. 5. Проводится комплекс опережающих испытаний вновь создаваемых узлов и агрегатов на моделирующих установках, стендах и специальных летающих лабораториях. Одновременно оценивается правильность конструктивных и производственных решений по обеспечению надежности узлов и агрегатов, применявшихся на прототипах и используемых на новом двигателе.
6. Проводятся стендовые испытания двигателя в наземных и высотных условиях и на летающих лабораториях для определения действительных нагрузок и эксплуатационных характеристик основных узлов двигателя. При этих испытаниях, как уже указывалось ранее, осуществляется вибрографирование, тензометрирование, термометрирование двигателя и его узлов с имитацией различных климатических воздействий (высоких и низких температур воздуха, повышенных влажности и запыленности воздуха). Оценивается повреждаемость лопаток компрессора при попадании посторонних предметов, птиц, льда и пр. В процессе этих испытаний фиксируются повреждения и отказы, условия их появления и последствия. Особенно важное значение имеет разборка двигателя с подробной дефектацией всех узлов и деталей. Испытания двигателя продолжаются до тех пор, пока его технические и эксплуатационные характеристики не будут удовлетворять заданным требованиям. 7. Проводятся длительные ресурсные стендовые испытания двигателей, удовлетворяющих требованиям по тяговым, расходным характеристикам и по эксплуатационным параметрам. Работоспособность двигателя на переходных режимах и его основные эксплуатационные характеристики проверяются и отрабатываются на летающих лабораториях. 8. По результатам проведенных работ устанавливают назначенный ресурс, календарные сроки службы и допуски на основные параметры двигателя (частоту вращения, температуру газов за турбиной, уровень виброперегрузок на корпусе компрессора и т. п. ), а также допустимую продолжительность наработки на основных режимах работы двигателя.
За последнее десятилетие в России существенно изменилось соотношение цен на разные виды товаров и услуг, причем опережающе возросли цены на энергоносители. Это заставило пересмотреть технологический процесс испытаний с точки зрения рационального использования электроэнергии, провести Усовершенствование энергетического оборудования и методов экспериментальной оценки характеристик ВРД, ввести мероприятия по экономии топлива» повысить удельную информативность испытаний. Развитие ВРД ставит и перед испытателями новые задачи, которые связаны с применением новых конструктивных схем, более высоким уровнем параметров рабочего процесса, расширением области имитируемых условий полета с воспроизведением особых условий эксплуатации. Новая методология создания авиационных двигателей увеличивает долю работы по экспериментальным исследованиям узлов двигателей на специальных! стендах и работ по исследованию газогенераторов. При этом доля работ по испытаниям полноразмерных двигателей уменьшается. Указанная методология основана на значительном углублении взаимного проникновения, взаимной дополнения расчетных и экспериментальных методов исследования. Эксперимент все чаше проводится для того, чтобы проверить и уточнить расчетные характеристики, получить экспериментальные данные для верификации метод расчета, определить граничные и начальные условия для обеспечения расчетного исследования. Таким образом, эксперимент как бы «делегирует право на объективность» расчетному исследованию, а методы математического моделирования, аккумулирующие обобщающую априорную информацию о пpoцессах в ГТД, позволяют минимизировать объем и стоимость эксперимента [37].
Основные направления развития экспериментально-исследовательской и испытательной баз Основной принцип или критерий в формировании экспериментально-исследовательской и испытательной баз как единственного инструмента л обеспечения контроля качества выполненной разработки и расчетов, проведения исследований в подтверждение или в опровержение идеи или в обеспечение поискового исследования в целях познания — это достаточность, исходя из программы, совершенство и диапазон возможностей, разумность из соображений затрат и отдачи, универсальность и систематичность использования, в числе и в прогнозируемой перспективе, минимизация объемов необходим испытаний, благодаря совершенствованию методов проектирования ГТД. В сос тав испытательной базы должны входить как стенды для испытаний двигателей (открытые многокомпонентные стенды, закрытые стенды, термобарокамеры, климатические стенды и др. ), так и стенды для испытаний компоненты двигателей и их моделей (аэродинамические трубы, лаборатории горения, стенды полунатурного моделирования, разгонные стенды, стенды для испытания компрессоров, камер сгорания, турбин и других элементов двигателя, акустические стенды и др. ). В настоящее время в отечественной практике, как и во всем мире, развитие испытательной и исследовательской баз ведется в направлении обеспечения возможностей проведения испытаний в условиях, максимально приближен к условиям эксплуатации, а также с обеспечением получения информации, измеряемым параметрам непосредственно в ходе эксперимента. Реализации этих задач осуществляется через строительство новых испытательных стендов включая в том числе открытые, оснащения их специальными устройства системами, имитирующими условия эксплуатации, а также через создание принципиально новых электронных систем, основанных на новых разработках в
области компьютерной техники. Очень важным сегодня является внедрение новых информационных технологий, благодаря которым в ходе испытаний можно было бы получать информацию от средств обеспечения измерений в режиме реального времени, то есть в темпе испытания (эксперимента). В значительной степени должна меняться стендовая система управления, контроля, отбора и обработки информации, получаемой при испытаниях. Система должна обеспечивать измерение, контроль, визуализацию (представлять на экране в графическом виде характер протекания той или иной характеристики) параметров и характеристик в режиме реального времени в ходе испытания, содержать устройства, обеспечивающие получение измерительного сигнала от средства измерений, расположенного на объекте испытания, в цифровом виде для регистрации и обработки, давать доступную возможность оператору, ведущему испытания, быстро выполнять переконфигурирование в зависимости от изменившейся цели испытания или объекта испытания. Сегодня специалист, который ведет доводку узла или двигателя, должен поучать информацию в ходе испытаний оперативно в обработанном виде. Получаемая информация кроме параметров и характеристик должна содержать сведения о выявляемых несоответствиях и «подсказку» в части возможных путей их устранения. Все получаемые при испытаниях данные должны передаться на рабочее место конструктора со стенда не только в обработанном виде, но и быть сгруппированы по тематическим блокам (компрессор, камера сгорания, турбина, маслосистема и др. ) в целях сокращения времени на анализ и выдачу необходимых решений по продолжению испытаний. Все это должно обеспечивать снижение затрат времени на реализацию программы испытаний. Развитие и совершенствование испытательной базы неразрывно связано с совершенствованием методов проектирования и конструирования, что принципиально повышает предсказуемость испытаний, позволяет в значительной степени повысить возможность реализации принципов и методов идентификации, повысить эффективность эксперимента.
Кроме того, внедрение, наряду с упомянутыми выше информационными хронологиями, новых средств измерений (сканеров температур, давлений и 1. ), в конструкции которых реализованы цифровые технологии, позволяет повысить качество измерений, быстродействие системы и количество одновременно измеряемых параметров. Вместе с этим, реализация в стендовых системе цифровых технологий позволяет вести испытания, взаимодействуя с математическими моделями испытуемого объекта, что значительно расширяет возможности оперативного анализа и принятия решений. В решении задачи развития испытательной и исследовательской баз больше внимание уделяется внедрению мероприятий по снижению трудоемкости затрат времени на подготовку и проведение испытаний. Интенсивно внедряться в практику подготовки к испытаниям технологические приемы, такие как пополнение специальных операций в отдельном зале подготовки двигателя или кaк испытаниям (демонтаж технологических деталей, постановка специальных устройств и приспособлений, постановка первичных приборов для измерений, постановка промежуточных элементов для обеспечения крепления объектов испытания к силовой части стенда, контроль соответствия исполнения препарации требованиям документации и др. ). Ощутимый эффект дает применение быстроразъемных соединений трубопроводов и применение специальной аппаратуры для контроля электрических цепей. Все это позволяет в значительной степени сократить время на подготовку к испытаниям и на монтаж объекта испытаний на стенд. Кроме того, огромное значение в деле развития испытательной базы имеет развитие и совершенствование технологического оснащения, необходимого
для выполнения обязательных операций, например: выполнение центровки после монтажа двигателя со свободной турбиной или объекта с внешней трансмиссией на испытательный стенд, выполнения пайки кабельных линий препарации при монтаже или ремонте, выполнения контроля состояния двигателя как после завершения этапа испытания, так и в процессе испытания, перемещения объекта испытания и технологического оборудования внутри испытательного стенда, применения переходных монтажных рам и т. п. В настоящее время ужесточаются требования по защите окружающей среды от вредных воздействий при стендовых испытаниях ГТД. В связи с этим все чаще строительство новых испытательных стендов осуществляется вдали от городов. При этом должны учитываться дополнительные меры по защите окружаю щей среды: введение дополнительных средств глушения шума, систем поглощения или дожигания несгоревших продуктов в выхлопных газах, систем защиты от попадания ГСМ в почву и воду, систем оборотного водоснабжения, систем мониторинга окружающей испытательные стенды среды и др. Мероприятия по развитию испытательной и исследовательской баз должны быть направлены на повышение эффективности и качества испытания, на сокращение времени доводки двигателя, на снижение себестоимости продукции, на защиту окружающей среды от вредных воздействий.
Список литературы 1. Авиационные правила. 4. 21. Процедуры сертификации авиационной техники. Т. 1. Разделы А, В, С, D, Е. Правила сертификации типа авиационной техники. М. : МАК. 1994. 40 с. 2. Авиационные правила. Ч. 33. Нормы летной годности двигателей воздушных судов. М. : МАК, 1994. 47 с. 3. Акимов В. М. Основы надежности газотурбинных двигателей. М. : Машиностроение, 1981. 207 с. 4. Асатурян В. И. Теория планирования эксперимента: учеб, пособие для вузов. М. : Радио и связь, 1983. 248 с. 5. Аш Ж. и др. Датчики измерительных систем. М. : Мир, 1992. 477 с. 6. Базазянц С. И. , Меднов А. Н. , Букшин А. Ф. , Иоффе З. А. , Лыршиков П. К. боевая живучесть летательных аппаратов (по материалам зарубежной печати). Л. : Воен. Изд-во, 1983. 219 с. 7. Безъязычный В. Ф. , Замятин А. Ю. , Замятин В. Ю. и др. Авиадвигателестроение. Качество, сертификация и лицензирование: учеб, пособие. М. : Машиностроение, 2003. 840 с. 8. Биргер И. А. Детерминированные и статистические модели долговечности // В сб. «Проблемы надежности летательных аппаратов» . М. : Машиностроение, 1985. С. 105 149. 9. Братухин А. Г. , Решетников Ю. Е. , Иноземцев А. А. и др. Основы технологии создания газотурбинных двигателей для магистральных самолетов / под общ. ед. А. Г. Братухина, Ю. Е. Решетникова, А. А. Иноземцева. М. : Авиатехинформ, 999. 554 с. 10. Герасименко В. П. Математические методы планирования испытаний воздушно-реактивных двигателей: учеб, пособие. Харьков: Харьковский авиа- ионный институт, 1982. 105 с.
11. Гишваров А. С. Многокритериальное планирование эксперимента при исследовании технических систем. Уфа: Гилем, 2006. 328 с. 12. Гишваров А. С. Обледенение воздушных судов и силовых установок (анализ и профилактика). Уфа: УГАТУ, 2006. 276 с. 13. Гишваров А. С. Оптимизация надежности систем летательных аппаратов двигателей. Уфа, УГАТУ, 2003, 138 с. 14. Гишваров А. С. Оптимизация ресурсных испытаний технических систем имитационным моделированием системы жизненного цикла. УФА, АН РБ, Гилем, 2005. 326 с. 15. Гишваров А. С. Совмещенные ресурсные испытания технических систем, фа: Гилем, 2001. 258 с. 16. Гишваров А. С. Теория ускоренных ресурсных испытаний технических систем. Уфа, АН РБ, Гилем, 2000. 338 с. 17. Гишваров А. С. , Амиров Р. А. Стенды для высотно-климатических испытаний ВГТД // Испытания авиационных двигателей. Межвуз. научн. сб. : Уфа: М 4, № 15, 1987. С. 80. . . 92. 18. Голодницкий А. Э. , Силин Б. М. Экспериментально-доводочная база ВРД в США // Итоги науки и техники. ВИНИТИ. Сер. Авиационные и ракетные двигатели. 1990. 92 с. 19. Горбунов Г. М. , Солохин Э. Л. Испытания авиационных воздушно-реактивных двигателей. М. : Машиностроение, 1967. 95 с. 20. Григорьев В. А. , Бочкарев С. К. , Маслов В. Г. Экспериментальные методы определения основных технических данных авиационных ГТД. Самара: Изд-во СГАУ, 2006. — 104 с. 21. Григорьев В. А. , Морозов И. И. , Анискин В. Т. Стенды, стендовое оборудование, датчики и средства измерений при испытаниях ВРД. Самара: Изд-во СГАУ, 2006. — 64 с. 22. Добрянский Г. В. , Мартьянова Т. С. Динамика авиационных ГТД. М. : Машиностроение, 1989. 240 с.
23. Елисеев Ю. С. , Крымов В. В. , Малиновский К. А. , Попов В. Г. Технология эксплуатации, диагностики и ремонта газотурбинных двигателей. М. : Высш. шк. , 2002. 355 с. 24. Зубков Б. В. , Аникин Н. В. Авиационное техническое обеспечение безопасности полетов. М. : Воздушный транспорт. 1993. 280 с. 25. Испытания и обеспечение надежности авиационных двигателей и энергетических установок / под ред. И. И. Онишика. М. : Изд-во МАИ. 2004. 336 с. 26. Испытания воздушно-реактивных двигателей / А. Я. Черкез, И. И. Онищик, Е. М. Таран и др. М. : Машиностроение, 1992. 304 с. 27. Косточкин В. В. Надежность авиационных двигателей и силовых установок: учебник для студентов авиационных специальностей вузов. 2 -е изд. , пере- раб. и доп. М. : Машиностроение, 1988. 272 с. 28. Кузнецов Н. Д. , Цейтлин В. И. Эквивалентные испытания газотурбинных двигателей. М. : Машиностроение, 1976. 216 с. 29. Кузнецов С. П. Основные принципы поузловой доводки ГТД: учеб, пособие. Рыбинск: РГАТА, 1998. 67 с. 30. Кулагин В. В. Теория, расчет и проектирование авиационных двигателей и энергетических установок: учебник. М. : Машиностроение, Кн. 1, 2. 2002. 616 с. 31. Леонов Б. Н. , Новиков А. С. , Богомолов Е. Н. , Уваров Л. Б. , Антонов Е. А. , Жуков А. А. Технологическое обеспечение проектирования и производства газотурбинных двигателей / под ред. Б. Н. Леонова и А. С. Новикова. Рыбинск, 2000. 407 с. 32. Леонтьев В. Н. , Сиротин С. А. , Теверовский А. М. Испытания авиационных двигателей и их агрегатов. М. : Машиностроение, 1976. 216 с. 33. Летные исследования и испытания. Фрагменты истории и современное состояние: научн. -техн. сборник. М. : Машиностроение, 1993. 496 с.
34. Макрос Ж. Дискретизация и квантование. М. : Энергия, 1969. 143 с. 35. Мудров В. И. , Кушко В. Л. Методы обработки измерений. М. : Радио и связь, 1983. 304 с. 36. Научный вклад в создание авиационных двигателей: кн. 1 / под ред. В. А. Скибина и В. И. Солонина. М. : Машиностроение, 2000. 725 с. 37. Научный вклад в создание авиационных двигателей: кн. 2 / под ред. ТА. Скибина и В. И. Солонина. М. : Машиностроение, 2000. 616 с. 38. Налимов В. В. , Голикова Т. И. Логические основания планирования эксперимента. М. : Металлургия, 1980. 152 с. 39. Николайкина Н. Е. , Николайкин Н. И. , Латягина А. М. Промышленная экология (инженерная зашита биосферы от воздействия воздушного транспорта). М. : ИКЦ Академкнига, 2006. 239 с. 40. Ножницкий Ю. А. , Куевда В. К. , Мокроус М. Ф. Сертификация авиационных двигателей // ЦИАМ, 1980 -2000. Научный вклад в создание авиационных 1 вигателей: кн. 1. М: Машиностроение, 2000. С. 669— 674. 41. Образование и выгорание сажи при сжигании углеродистых топлив / б. Г. Бакиров, В. М. Захаров, И. З. Полацук, З. Г. Шайхутдинов. М. : Машиностроение, 1989. 128 с. 42. Павлов Ю. И. , Шайн Ю. Я. , Абрамов Б. И. Проектирование испытательных стендов для авиационных двигателей. М. : Машиностроение, 1979. 52 с. 43. Письменный В. Л. Испытания авиационных силовых установок: учеб, пособие. М. : Издательство МАИ, 2002. 172 с.
44. Преображенский В. П. Теплотехнические измерения и приборы. М. : Энергия, 1978. 704 с. 45. Проников А. С. Надежность машин. М. : Машиностроение, 1978. 592 с. 46. Пыховский Л. Д. Планирование эксперимента при обработке камер сгорания ГТД // Межвуз. научн. сб. «Испытания авиационных двигателей» . Уфа: ‘АИ, № 13, 1985. С. 25. . . 33. 47. Работы ведущих авиадвигателестроительных компаний по созданию перспективных авиационных двигателей (аналитический обзор / под общ. ред. 1. А. Скибина и В. Н. Солонина. М. : ЦИАМ, 2004. 424 с. 48. Сиротин Н. Н. Конструкция и эксплуатация, повреждаемость и работоспособность газотурбинных двигателей. М. : РИА «ИМ-ИНФОРМ» , 2002. 42 с. 49. Солохин Э. Л. Испытания воздушно-реактивных двигателей. М. : Машиностроение, 1975. 356 с. 50. Сосунов В. А. , Чепкин В. М. и др. Теория, расчет и проектирование авиа- ионных двигателей и энергетических установок: учебник. М. : Издательство 1 АИ, 2003. 688 с. 51. Сосунов В. А. , Литвинов Ю. А. Неустановившиеся режимы работы авиационных газотурбинных двигателей. М. : Машиностроение, 1975. 216 с. 52. Справочник по прикладной измерительной технике. М. : Энергия, 1968. 12 с. 53. Теория, расчет и проектирование авиационных двигателей и энергетических установок: учебник. Кн. 3. Основные проблемы: Начальный уровень проектирования, газодинамическая доводка, специальные характеристики и конверсия авиационных ГТД / под общ. ред. В. В. Кулагина. М. : Машиностроение, 05. 464 с. 54. Третьяков О. Н. Методы и средства эксплуатационного сопровождения курса авиационных ГТД. М. : Изд-во МАТИ, 1999.
55. Шибанов Г. П. Автоматизации испытаний и контроля авиационных ГТД. М. : Машиностроение, 1977. 279 с. 56. Шишков А. А. , Силин Б. М. Высотные испытания реактивных двигателей. М. : Машиностроение, 1985. 208 с. 57. Хубер П. Робастность в статистике. М. : Мир, 1984. 303 с. 58. Чуйко В. М. Нелокализованные разрушения авиационных ГТД // Авиационная промышленность, 1990. № 7. 59. Чуян Р. К. , Обухов В. А. Модели идентификации двигателей летательных аппаратов: учеб, пособие. М. : Издательство МАИ, 1980. 50 с. 60. Григорьев, В. А. Испытания авиационных двигателей: учеб. для вузов/ В. А. Григорьев, А. С. Гишварова. — М. : Машиностроение, 2009. -502 с.