Слайд 1 Основные технологические процессы получения ВМ Вопросы:
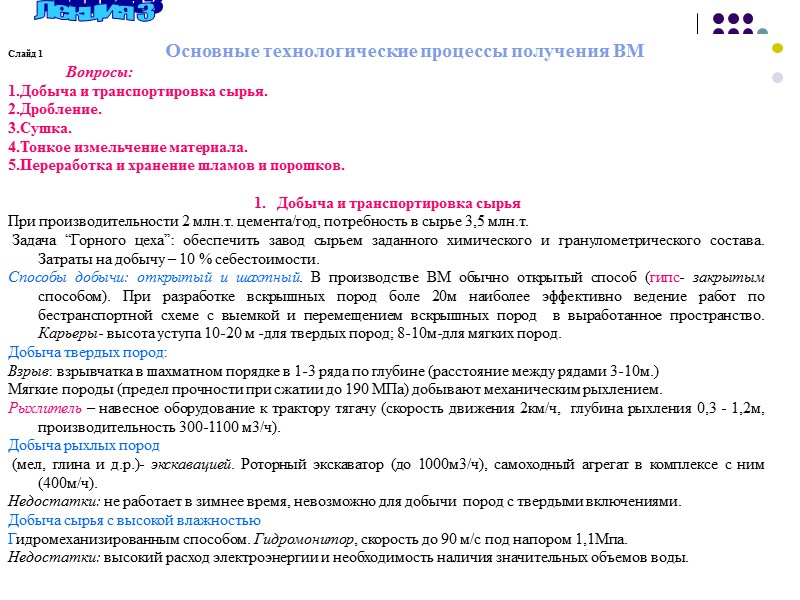
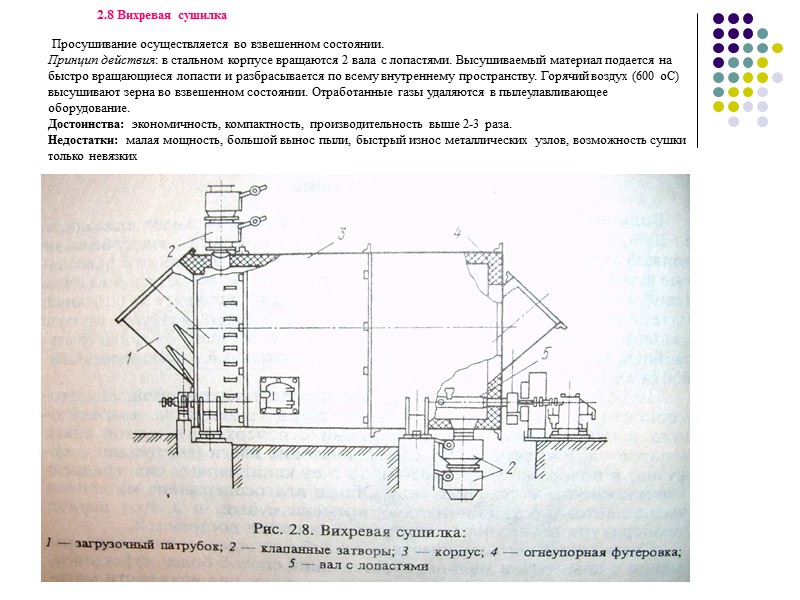
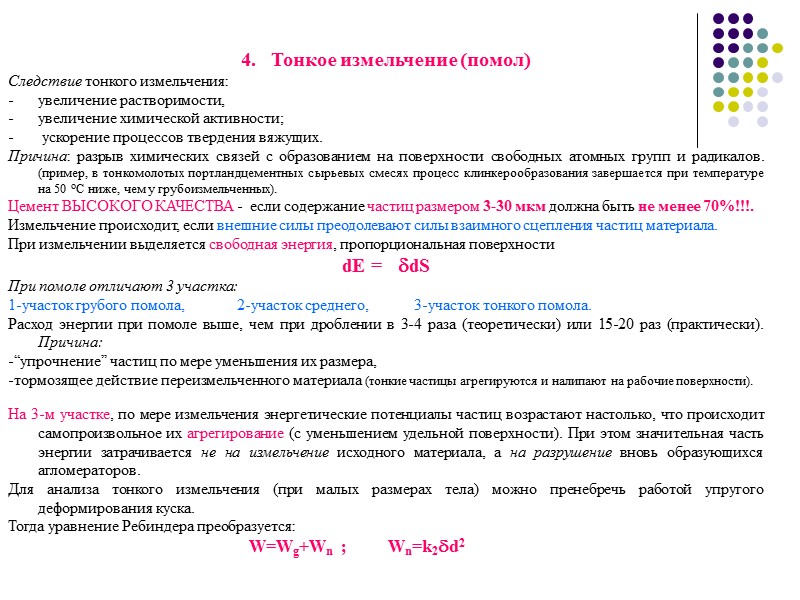
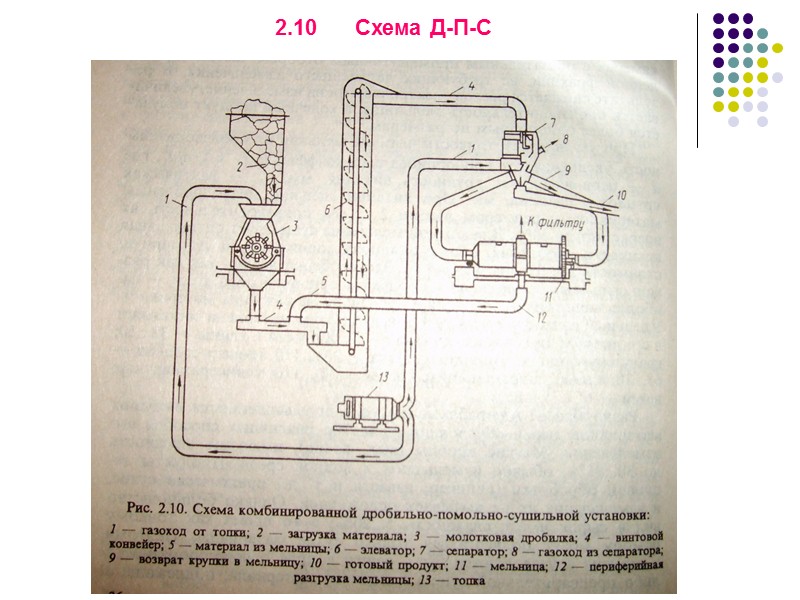
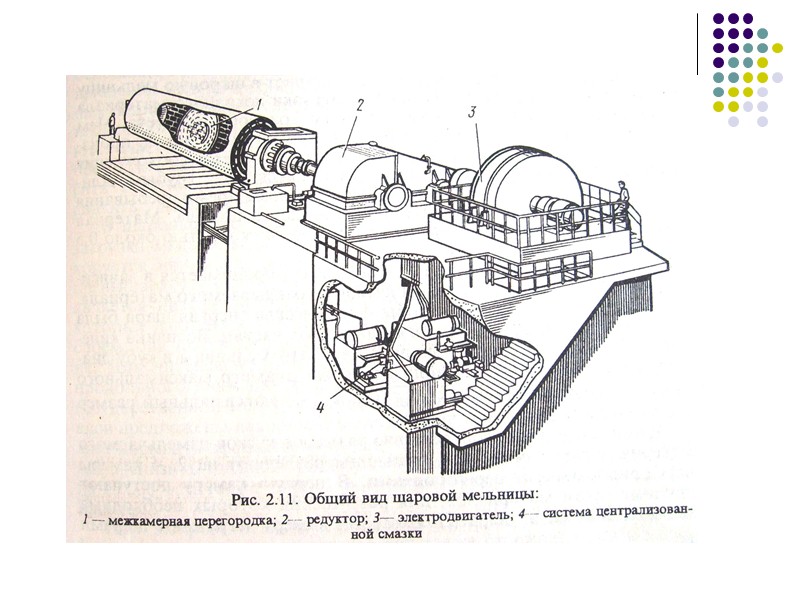
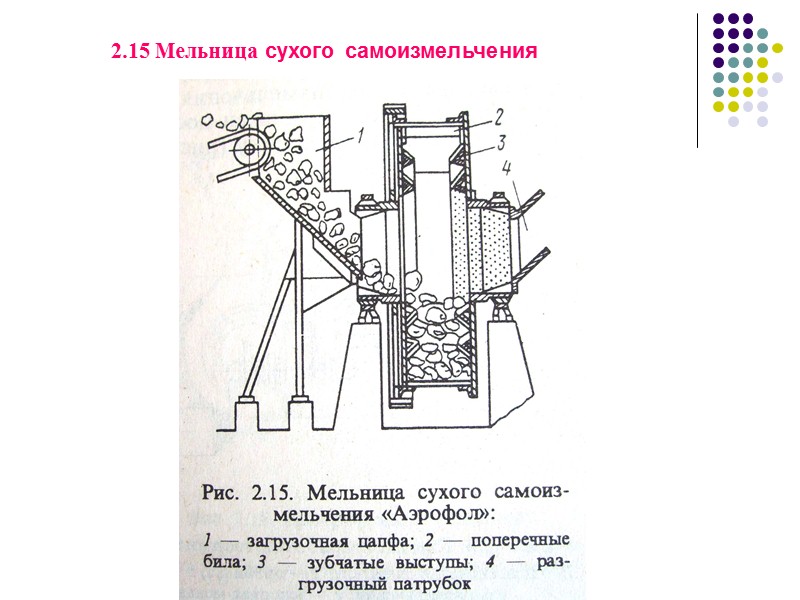
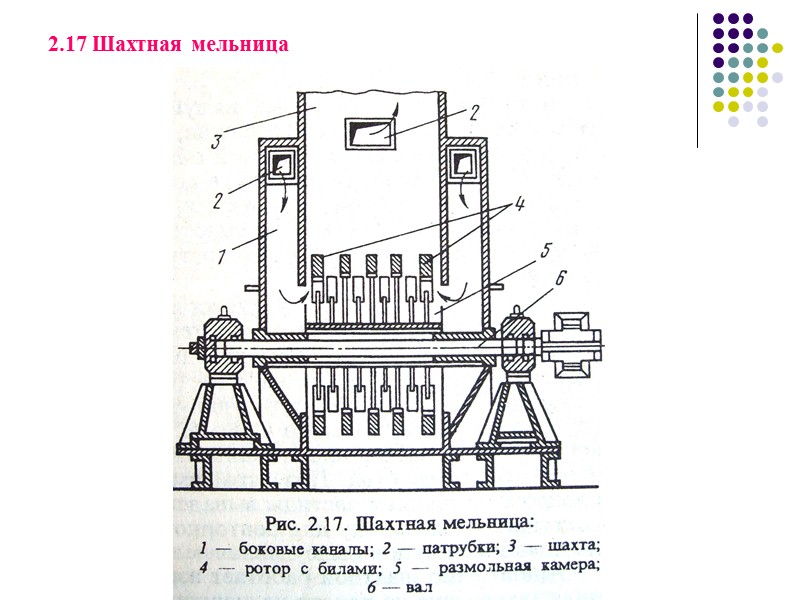
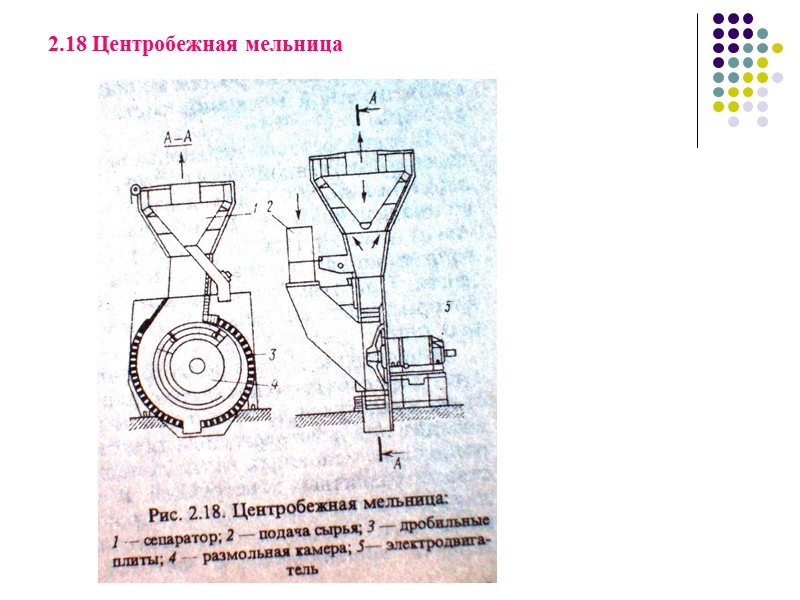
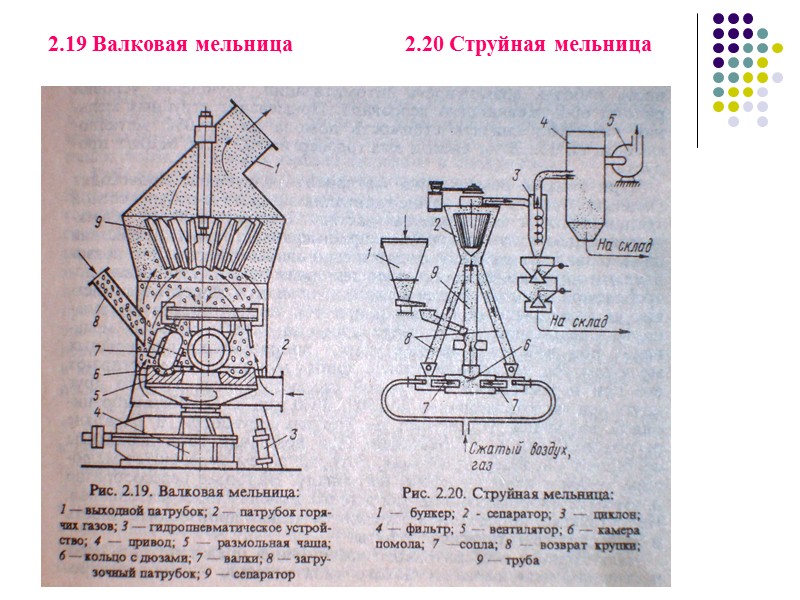
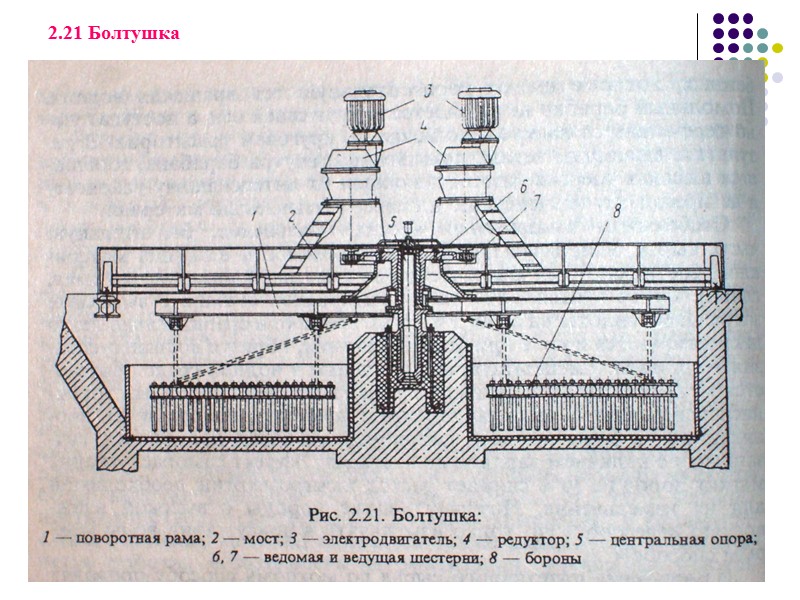
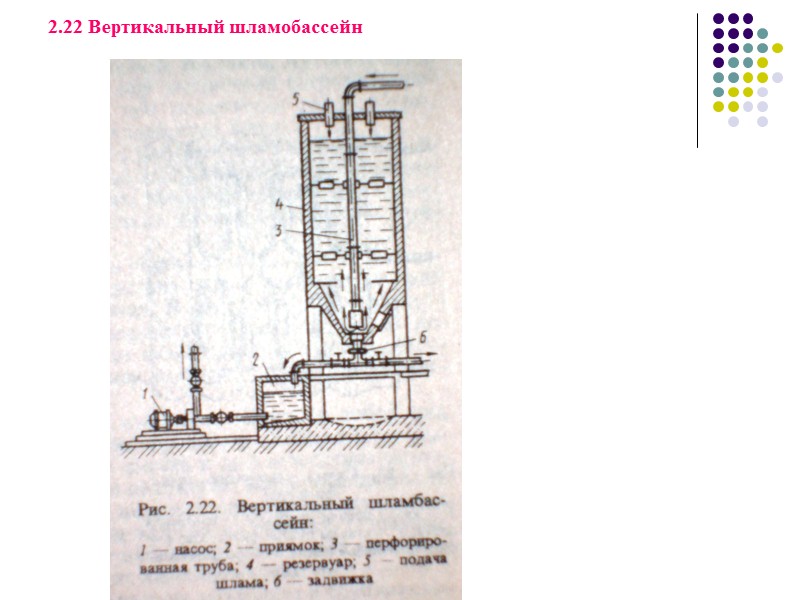
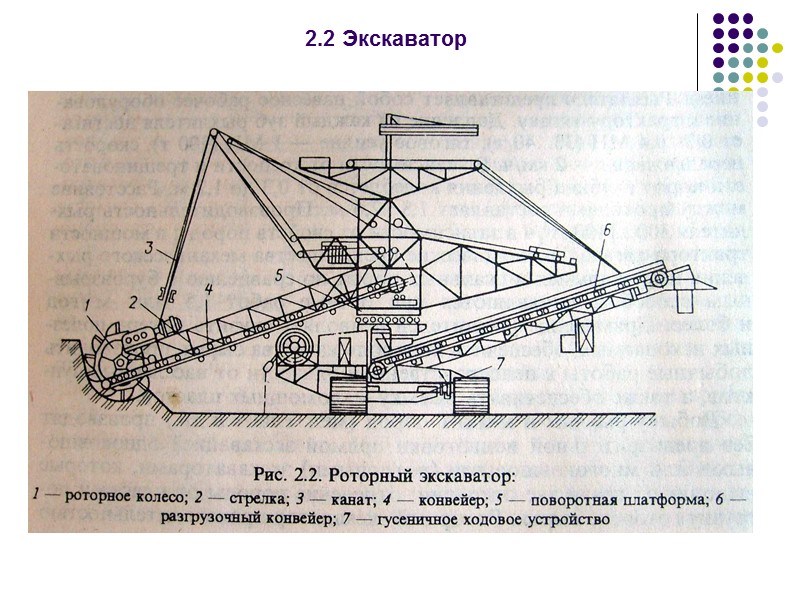
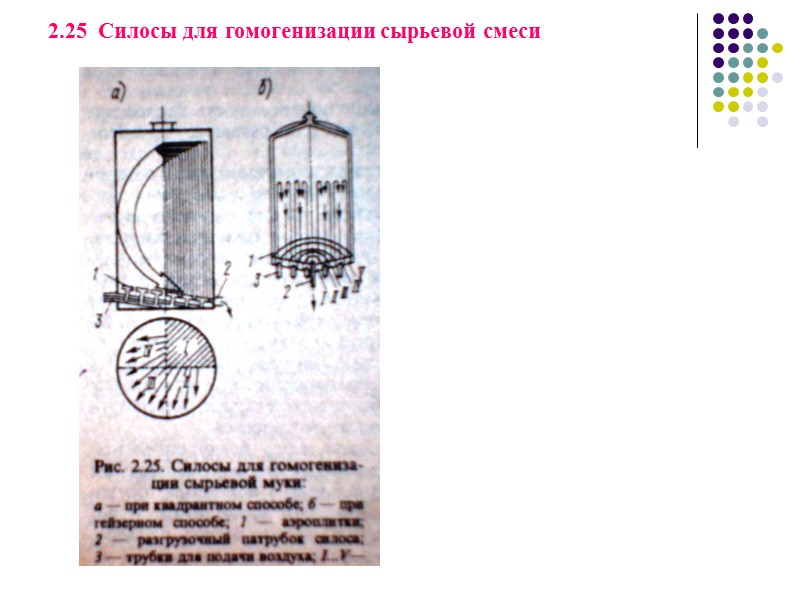
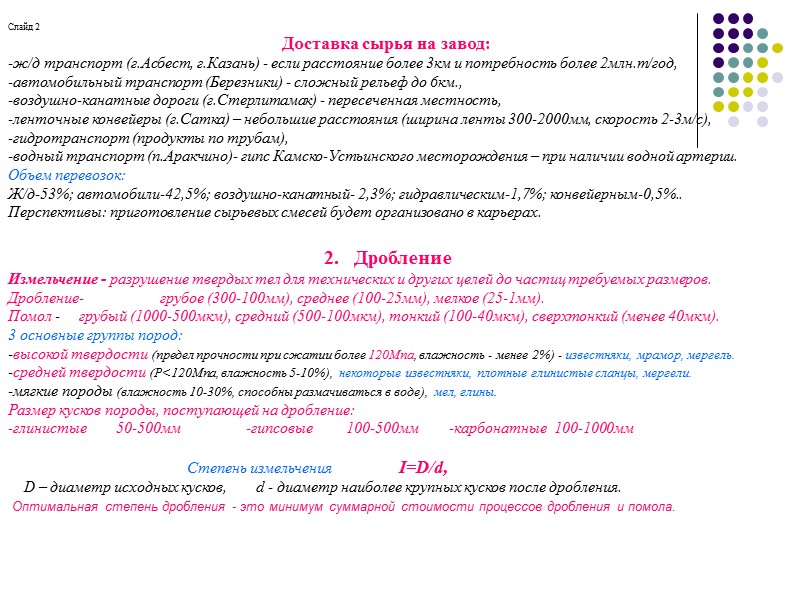
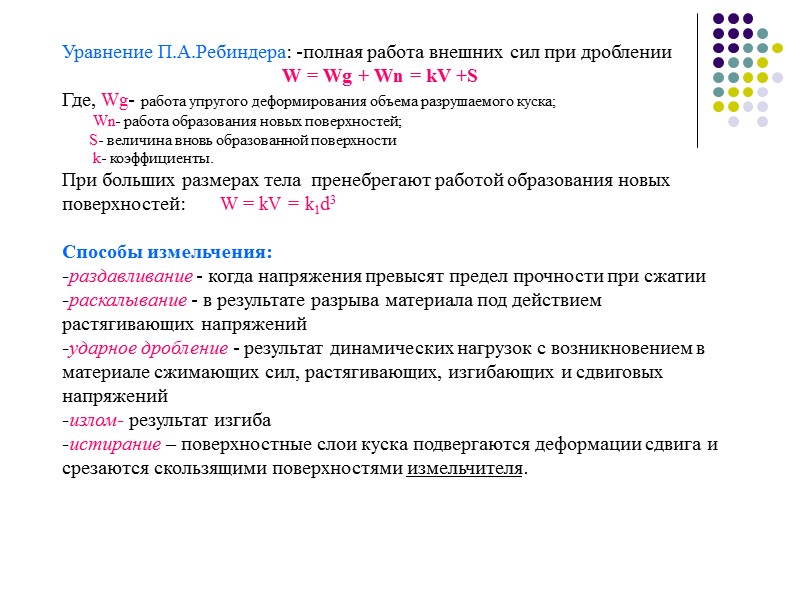
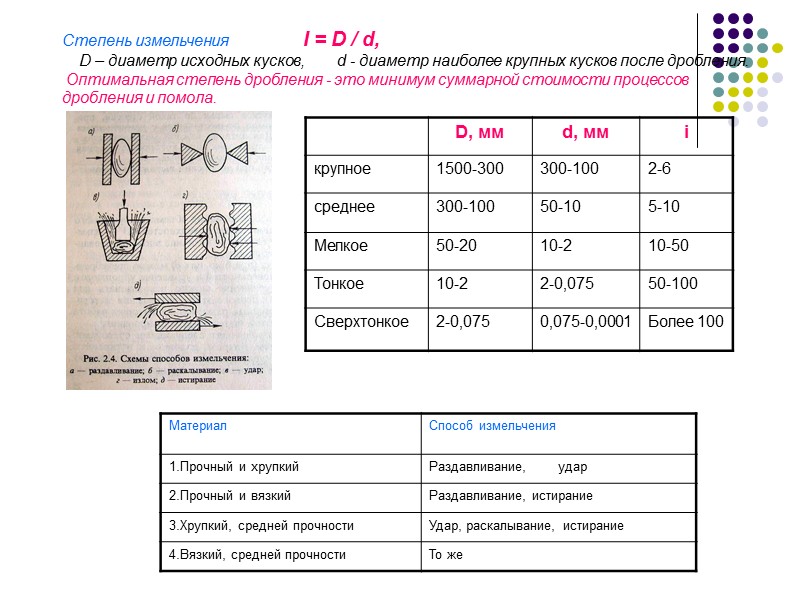
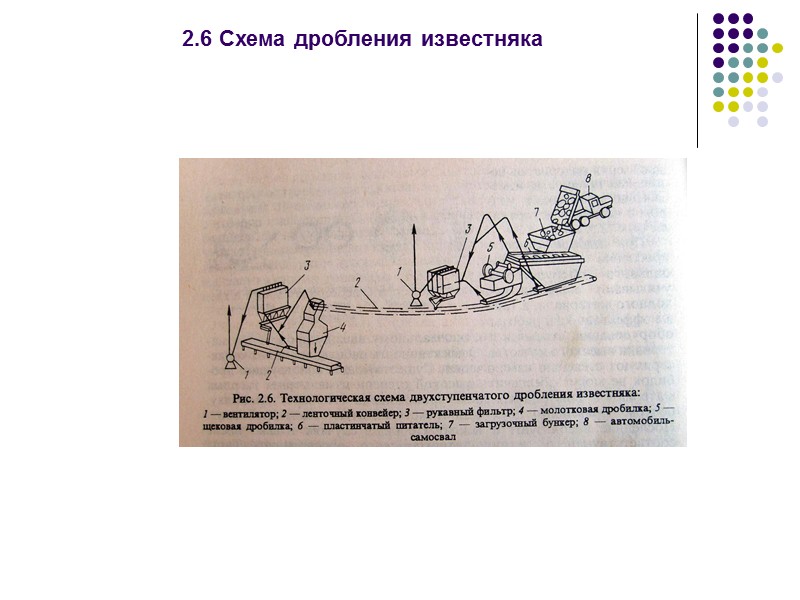
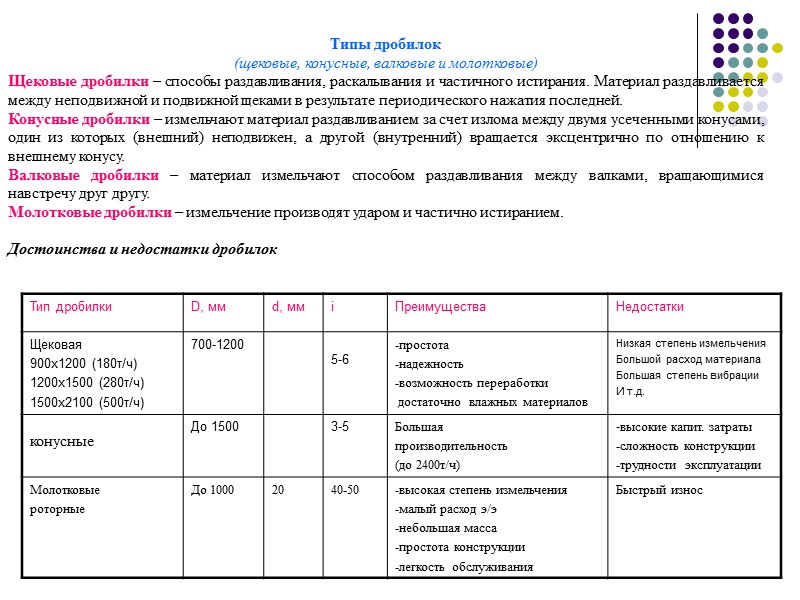
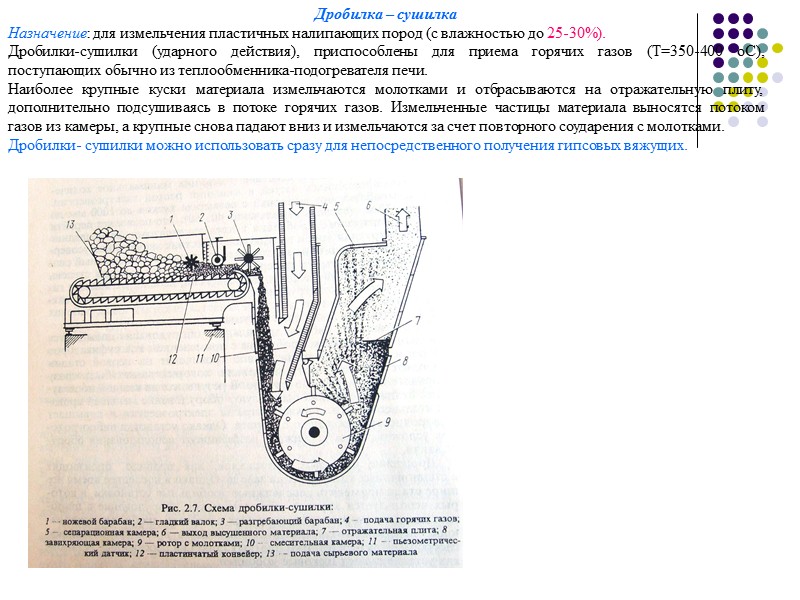
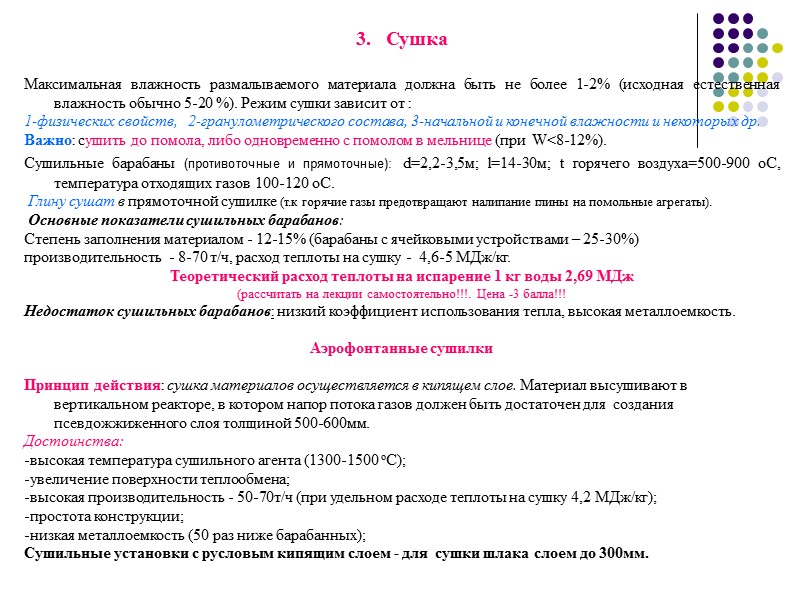

30-l-3_dobycha_syryya.ppt_huzya
- Количество слайдов: 20
Слайд 1 Основные технологические процессы получения ВМ Вопросы: 1.Добыча и транспортировка сырья. 2.Дробление. 3.Сушка. 4.Тонкое измельчение материала. 5.Переработка и хранение шламов и порошков. 1. Добыча и транспортировка сырья При производительности 2 млн.т. цемента/год, потребность в сырье 3,5 млн.т. Задача “Горного цеха”: обеспечить завод сырьем заданного химического и гранулометрического состава. Затраты на добычу – 10 % себестоимости. Способы добычи: открытый и шахтный. В производстве ВМ обычно открытый способ (гипс- закрытым способом). При разработке вскрышных пород боле 20м наиболее эффективно ведение работ по бестранспортной схеме с выемкой и перемещением вскрышных пород в выработанное пространство. Карьеры- высота уступа 10-20 м -для твердых пород; 8-10м-для мягких пород. Добыча твердых пород: Взрыв: взрывчатка в шахматном порядке в 1-3 ряда по глубине (расстояние между рядами 3-10м.) Мягкие породы (предел прочности при сжатии до 190 МПа) добывают механическим рыхлением. Рыхлитель – навесное оборудование к трактору тягачу (скорость движения 2км/ч, глубина рыхления 0,3 - 1,2м, производительность 300-1100 м3/ч). Добыча рыхлых пород (мел, глина и д.р.)- экскавацией. Роторный экскаватор (до 1000м3/ч), самоходный агрегат в комплексе с ним (400м/ч). Недостатки: не работает в зимнее время, невозможно для добычи пород с твердыми включениями. Добыча сырья с высокой влажностью Гидромеханизированным способом. Гидромонитор, скорость до 90 м/с под напором 1,1Мпа. Недостатки: высокий расход электроэнергии и необходимость наличия значительных объемов воды. Лекция 3
2.2 Экскаватор
Слайд 2 Доставка сырья на завод: -ж/д транспорт (г.Асбест, г.Казань) - если расстояние более 3км и потребность более 2млн.т/год, -автомобильный транспорт (Березники) - сложный рельеф до 6км., -воздушно-канатные дороги (г.Стерлитамак) - пересеченная местность, -ленточные конвейеры (г.Сатка) – небольшие расстояния (ширина ленты 300-2000мм, скорость 2-3м/с), -гидротранспорт (продукты по трубам), -водный транспорт (п.Аракчино)- гипс Камско-Устьинского месторождения – при наличии водной артерии. Объем перевозок: Ж/д-53%; автомобили-42,5%; воздушно-канатный- 2,3%; гидравлическим-1,7%; конвейерным-0,5%.. Перспективы: приготовление сырьевых смесей будет организовано в карьерах. 2. Дробление Измельчение - разрушение твердых тел для технических и других целей до частиц требуемых размеров. Дробление- грубое (300-100мм), среднее (100-25мм), мелкое (25-1мм). Помол - грубый (1000-500мкм), средний (500-100мкм), тонкий (100-40мкм), сверхтонкий (менее 40мкм). 3 основные группы пород: -высокой твердости (предел прочности при сжатии более 120Мпа, влажность - менее 2%) - известняки, мрамор, мергель. -средней твердости (Р<120Мпа, влажность 5-10%), некоторые известняки, плотные глинистые сланцы, мергели. -мягкие породы (влажность 10-30%, способны размачиваться в воде), мел, глины. Размер кусков породы, поступающей на дробление: -глинистые 50-500мм -гипсовые 100-500мм -карбонатные 100-1000мм Степень измельчения I=D/d, D – диаметр исходных кусков, d - диаметр наиболее крупных кусков после дробления. Оптимальная степень дробления - это минимум суммарной стоимости процессов дробления и помола.
Уравнение П.А.Ребиндера: -полная работа внешних сил при дроблении W = Wg + Wn = kV +S Где, Wg- работа упругого деформирования объема разрушаемого куска; Wn- работа образования новых поверхностей; S- величина вновь образованной поверхности k- коэффициенты. При больших размерах тела пренебрегают работой образования новых поверхностей: W = kV = k1d3 Способы измельчения: -раздавливание - когда напряжения превысят предел прочности при сжатии -раскалывание - в результате разрыва материала под действием растягивающих напряжений -ударное дробление - результат динамических нагрузок с возникновением в материале сжимающих сил, растягивающих, изгибающих и сдвиговых напряжений -излом- результат изгиба -истирание – поверхностные слои куска подвергаются деформации сдвига и срезаются скользящими поверхностями измельчителя.
Степень измельчения I = D / d, D – диаметр исходных кусков, d - диаметр наиболее крупных кусков после дробления. Оптимальная степень дробления - это минимум суммарной стоимости процессов дробления и помола.
2.6 Схема дробления известняка
Типы дробилок (щековые, конусные, валковые и молотковые) Щековые дробилки – способы раздавливания, раскалывания и частичного истирания. Материал раздавливается между неподвижной и подвижной щеками в результате периодического нажатия последней. Конусные дробилки – измельчают материал раздавливанием за счет излома между двумя усеченными конусами, один из которых (внешний) неподвижен, а другой (внутренний) вращается эксцентрично по отношению к внешнему конусу. Валковые дробилки – материал измельчают способом раздавливания между валками, вращающимися навстречу друг другу. Молотковые дробилки – измельчение производят ударом и частично истиранием. Достоинства и недостатки дробилок
Дробилка – сушилка Назначение: для измельчения пластичных налипающих пород (с влажностью до 25-30%). Дробилки-сушилки (ударного действия), приспособлены для приема горячих газов (Т=350-400 оС), поступающих обычно из теплообменника-подогревателя печи. Наиболее крупные куски материала измельчаются молотками и отбрасываются на отражательную плиту, дополнительно подсушиваясь в потоке горячих газов. Измельченные частицы материала выносятся потоком газов из камеры, а крупные снова падают вниз и измельчаются за счет повторного соударения с молотками. Дробилки- сушилки можно использовать сразу для непосредственного получения гипсовых вяжущих.
Сушка Максимальная влажность размалываемого материала должна быть не более 1-2% (исходная естественная влажность обычно 5-20 %). Режим сушки зависит от : 1-физических свойств, 2-гранулометрического состава, 3-начальной и конечной влажности и некоторых др. Важно: cушить до помола, либо одновременно с помолом в мельнице (при W<8-12%). Сушильные барабаны (противоточные и прямоточные): d=2,2-3,5м; l=14-30м; t горячего воздуха=500-900 оС, температура отходящих газов 100-120 оС. Глину сушат в прямоточной сушилке (т.к горячие газы предотвращают налипание глины на помольные агрегаты). Основные показатели сушильных барабанов: Степень заполнения материалом - 12-15% (барабаны с ячейковыми устройствами – 25-30%) производительность - 8-70 т/ч, расход теплоты на сушку - 4,6-5 МДж/кг. Теоретический расход теплоты на испарение 1 кг воды 2,69 МДж (рассчитать на лекции самостоятельно!!!. Цена -3 балла!!! Недостаток сушильных барабанов: низкий коэффициент использования тепла, высокая металлоемкость. Аэрофонтанные сушилки Принцип действия: сушка материалов осуществляется в кипящем слое. Материал высушивают в вертикальном реакторе, в котором напор потока газов должен быть достаточен для создания псевдожжиженного слоя толщиной 500-600мм. Достоинства: -высокая температура сушильного агента (1300-1500 оС); -увеличение поверхности теплообмена; -высокая производительность - 50-70т/ч (при удельном расходе теплоты на сушку 4,2 МДж/кг); -простота конструкции; -низкая металлоемкость (50 раз ниже барабанных); Сушильные установки с русловым кипящим слоем - для сушки шлака слоем до 300мм.
2.8 Вихревая сушилка Просушивание осуществляется во взвешенном состоянии. Принцип действия: в стальном корпусе вращаются 2 вала с лопастями. Высушиваемый материал подается на быстро вращающиеся лопасти и разбрасывается по всему внутреннему пространству. Горячий воздух (600 оС) высушивают зерна во взвешенном состоянии. Отработанные газы удаляются в пылеулавливающее оборудование. Достоинства: экономичность, компактность, производительность выше 2-3 раза. Недостатки: малая мощность, большой вынос пыли, быстрый износ металлических узлов, возможность сушки только невязких
4. Тонкое измельчение (помол) Следствие тонкого измельчения: увеличение растворимости, увеличение химической активности; ускорение процессов твердения вяжущих. Причина: разрыв химических связей с образованием на поверхности свободных атомных групп и радикалов. (пример, в тонкомолотых портландцементных сырьевых смесях процесс клинкерообразования завершается при температуре на 50 оС ниже, чем у грубоизмельченных). Цемент ВЫСОКОГО КАЧЕСТВА - если содержание частиц размером 3-30 мкм должна быть не менее 70%!!!. Измельчение происходит, если внешние силы преодолевают силы взаимного сцепления частиц материала. При измельчении выделяется свободная энергия, пропорциональная поверхности dE = dS При помоле отличают 3 участка: 1-участок грубого помола, 2-участок среднего, 3-участок тонкого помола. Расход энергии при помоле выше, чем при дроблении в 3-4 раза (теоретически) или 15-20 раз (практически). Причина: -“упрочнение” частиц по мере уменьшения их размера, -тормозящее действие переизмельченного материала (тонкие частицы агрегируются и налипают на рабочие поверхности). На 3-м участке, по мере измельчения энергетические потенциалы частиц возрастают настолько, что происходит самопроизвольное их агрегирование (с уменьшением удельной поверхности). При этом значительная часть энергии затрачивается не на измельчение исходного материала, а на разрушение вновь образующихся агломераторов. Для анализа тонкого измельчения (при малых размерах тела) можно пренебречь работой упругого деформирования куска. Тогда уравнение Ребиндера преобразуется: W=Wg+Wn ; Wn=k2d2
2.10 Схема Д-П-С
2.15 Мельница сухого самоизмельчения
2.17 Шахтная мельница
2.18 Центробежная мельница
2.19 Валковая мельница 2.20 Струйная мельница
2.21 Болтушка
2.22 Вертикальный шламобассейн
2.25 Силосы для гомогенизации сырьевой смеси